Item 2. Management’s Discussion and Analysis of Financial Condition and Results of Operations.
Forward-looking and Cautionary Statements
Some of the information contained in this quarterly report on Form 10-Q may constitute “forward-looking statements” within the meaning of the “safe-harbor” provisions of the Private Securities Litigation Reform Act of 1995. When we use words such as “believe,” “hope,” “expect,” “are likely,” “project” and similar expressions, we do so to identify forward-looking statements. Such statements are based on our then current expectations and are subject to a number of risks and uncertainties that could cause actual results to differ materially from those addressed in the forward-looking statements. Risk factors that may cause such a difference are summarized on pages 24-26 and are incorporated herein.
Executive Summary
First-quarter 2006 net income was $8.2 million (21 cents per share) compared with $5.6 million (14 cents per share) in the first quarter of 2005. Gains on the sale of assets and other items and losses related to plant shutdowns, assets impairments and restructurings are described in Note 2 on page 6. The business segment review begins on page 16.
First-quarter operating profit from ongoing operations in Film Products rose 34% to $15.6 million from $11.6 million in the first quarter of 2005. The increase in operating profit over last year’s first quarter was primarily due to continued growth in the sale of surface protection films, elastic materials and new apertured topsheets. Profits also benefited from an increase in selling prices to cover higher resin costs incurred during the fourth quarter of 2005. Operating profit from ongoing operations in Film Products was $8.2 million in the fourth quarter of 2005, and was adversely affected by record-level, hurricane-related increases in resin prices.
Film Products has index-based pass-through raw material agreements for the majority of its business. However, under certain agreements, changes in resin prices are not passed through for an average period of 90 days. Average quarterly prices of low-density polyethylene resin in the U.S. decreased 8 cents per pound in the first quarter of 2006 after increasing 21 cents per pound or 32% in the fourth quarter of 2005 (see the chart on page 20). Since 2002, U.S. low-density polyethylene resin prices have more than doubled. Resin prices in Europe, Asia and South America have also increased significantly during that time.
We estimate that the lag in the pass-through to customers of changes in resin prices had a positive impact on first-quarter 2006 results of $2 million compared with a negative impact on fourth-quarter 2005 results of $5.5 million (net of the favorable effect of a decline in inventories accounted for under the last-in first-out method). There was no significant resin pass-through lag in the first quarter of 2005.
We expect customer inventory adjustments to have a negative impact on sales and profits in Film Products in the second quarter of 2006.
Film Products continues to expand capacity to support growth in new products. Capital expenditures were $11.4 million in the first quarter of 2006 and are expected to be $45 million for the year. Approximately half of capital expenditures in 2006 relates to expanding the production capacity for surface protection films. Other planned capital expenditures include capacity additions for elastic materials and a new information system, which is currently being rolled out in U.S locations. Depreciation expense was $7.7 million in the first quarter of 2006 compared with $6.1 million in the first quarter of last year, and is projected to increase by $5 million to $31 million for the year.
12
First-quarter operating profit from ongoing operations in Aluminum Extrusions increased to $4.9 million, up 63% from $3.0 million in the first quarter of 2005. The increase in operating profit was mainly due to higher volume, which was up 9.1% to 63.7 million pounds versus 58.4 million pounds in the first quarter of 2005. Growth in shipments continued to be driven by demand for extrusions used in commercial construction and hurricane protection products. Bookings remain solid. Higher selling prices helped to offset the negative impact of higher energy costs of $1.7 million (primarily natural gas) and appreciation of the Canadian Dollar of $300,000. Aluminum Extrusions has hedges in place for a portion of its anticipated natural gas needs through the end of the year.
First-quarter capital expenditures in Aluminum Extrusions were $1.7 million and are expected to be approximately $10 million for the year.
Net pension expense was $675,000 in the first quarter of 2006, an increase of $1.5 million (2 cents per share after taxes) from the net pension income of $793,000 recognized in the first quarter of 2005. We expect net pension expense of $2.8 million in 2006, an unfavorable change of $5.4 million (9 cents per share after taxes) versus 2005. Most of this increase in pension expense relates to a pension plan that is reflected in “Corporate expenses, net” in the operating profit by segment table on page 16. We expect required contributions to our pension plans to be about $800,000 for the year ending December 31, 2006.
During the first quarter of 2006, the company adopted Statement of Financial Accounting Standards No. 123(R),Share-Based Payment (“SFAS 123(R)”), which requires all stock-based compensation to be expensed and accounted for using a fair value-based method. The adoption of SFAS No. 123(R) and the granting of stock options on March 7, 2006 resulted in a first-quarter 2006 pretax charge of $211,000. The company expects to recognize stock option-based compensation costs under the new standard of approximately $1.1 million in 2006 (2 cents per share after taxes).
Net capitalization and other credit measures are provided in the liquidity and capital resources section beginning on page 17.
Critical Accounting Policies
In the ordinary course of business, we make a number of estimates and assumptions relating to the reporting of results of operations and financial position in the preparation of financial statements in conformity with generally accepted accounting principles. We believe the estimates, assumptions and judgments described in the section “Management’s Discussion and Analysis of Financial Condition and Results of Operations – Critical Accounting Policies” of our Annual Report on Form 10-K for the year ended December 31, 2005, have the greatest potential impact on our financial statements, so we consider these to be our critical accounting policies. These policies include our accounting for impairment of long-lived assets and goodwill, pension benefits and income taxes. These policies require management to exercise judgments that are often difficult, subjective and complex due to the necessity of estimating the effect of matters that are inherently uncertain. Actual results could differ significantly from those estimates under different assumptions and conditions. We believe the consistent application of these policies enables us to provide readers of our financial statements with useful and reliable information about our operating results and financial condition. There has been no significant change in these policies. See Note 2 on page 6 for losses related to plant shutdowns, assets impairments and restructurings occurring during 2006 and the comparable period in 2005.
Results of Operations
First Quarter 2006 Compared with First Quarter 2005
Overall, sales in the first quarter of 2006 increased by 15.1% compared with 2005. Net sales (sales less freight) increased 8.2% in Film Products primarily due to growth in higher value-added
13
products, including surface protection, elastic and apertured materials, and higher selling prices, which were driven by higher raw material costs. Net sales increased 22.9% in Aluminum Extrusions due to higher volume (up 9.1%) and selling prices. For more information on net sales and volume, see the business segment review beginning on page 16.
Gross profit (sales minus cost of goods sold and freight) as a percentage of sales increased to 13.0% in the first quarter of 2006 from 12.2% in 2005. At Film Products, an overall higher gross profit margin was driven primarily by growth in higher value-added products, including surface protection, elastic and apertured materials. Margins also benefited from an increase in selling prices to cover higher resin costs incurred in the fourth quarter of 2005. At Aluminum Extrusions, gross profit increased but the gross profit margin percentage declined primarily due to higher selling prices to cover higher aluminum and higher energy costs.
As a percentage of sales, selling, general and administrative (“SG&A”) expenses decreased to 6.1% in the first quarter of 2006 compared with 7.3% in 2005 due primarily to higher sales and the divestiture of substantially all of our interest in AFBS, Inc. (formerly known as Therics, Inc.) at the end of the second quarter of 2005.
R&D expenses declined to $1.8 million in the first quarter of 2006 from $2.8 million in 2005 primarily due to the divestiture of substantially all of our interest in AFBS.
Plant shutdowns, asset impairments and restructurings in the first quarter of 2006 shown in the segment operating profit table on page 16 include:
| |
• | A pretax charge of $404,000 related to the planned shutdown of the films manufacturing facility in LaGrange, Georgia, including asset impairment charges of $130,000 and severance (56 people) and other costs of $274,000; |
| |
• | Pretax charges of $1 million for asset impairments relating to machinery & equipment in Film Products; and |
| |
• | Pretax charges of $268,000 for severance and other employee-related costs in connection with restructurings in Film Products ($159,000) and Aluminum Extrusions ($109,000). |
Plant shutdowns, asset impairments and restructurings in the first quarter of 2005 shown in the segment operating profit table on page 16 include:
| |
• | A pretax gain of $1.6 million related to the shutdown of the films manufacturing facility in New Bern, North Carolina, including a $1.8 million gain on the sale of the facility (included in “Other income (expense), net” in the consolidated statements of income), partially offset by shutdown-related expenses of $198,000; |
| |
• | A pretax charge of $1 million for process reengineering costs associated with the implementation of a new information system in Film Products (included in “Costs of goods sold” in the consolidated statements of income); |
| |
• | Pretax charges of $418,000 related to severance and other employee-related costs associated with restructurings in Film Products ($250,000) and Aluminum Extrusions ($168,000); |
| |
• | A pretax charge of $470,000 related to the shutdown of the aluminum extrusions facility in Aurora, Ontario; |
| |
• | A net pretax gain of $120,000 primarily related to the partial reversal to income of certain severance and employee-related accruals associated with the restructuring of the research and development operations in Film Products (of this amount, $199,000 in pretax charges for employee relocation and recruitment is included in “Selling, general and administrative” in the consolidated statements of income); and |
| |
• | Pretax charges of $100,000 for accelerated depreciation related to restructurings in Film Products. |
14
In the first quarter of 2006, a pretax gain on the sale of public equity securities of $56,000 (proceeds also of $56,000) is included in “Other income (expense), net” in the consolidated statements of income and “Gain on the sale of corporate assets” in the operating profit by segment table on page 16. In the first quarter of 2005, a pretax gain for interest receivable on tax refund claims of $508,000 is included in “Other income (expense), net” in the consolidated statements of income and “Corporate expenses, net” in the operating profit by segment table on page 16. For more information on costs and expenses, see the business segment review beginning on page 16.
Interest income, which is included in “Other income (expense), net” in the consolidated statements of income, was $222,000 in the first quarter of 2006 and $98,000 in 2005. Interest expense increased to $1.4 million in the first quarter of 2006 compared with $963,000 in 2005. Average debt outstanding and interest rates were as follows:
| | | | | | | |
|
|
|
|
| | Three Months Ended March 31 | |
| |
| |
(In Millions) | | | 2006 | | | 2005 | |
|
|
|
|
|
|
|
|
Floating-rate debt with interest charged on a | | | | | | | |
rollover basis at one-month LIBOR: | | | | | | | |
Average outstanding debt balance | | $ | 109.6 | | $ | 106.6 | |
Average interest rate | | | 5.4 | % | | 3.8 | % |
Fixed-rate and other debt: | | | | | | | |
Average outstanding debt balance | | $ | 5.7 | | $ | 5.9 | |
Average interest rate | | | 6.7 | % | | 5.1 | % |
|
|
|
|
|
|
|
|
Total debt: | | | | | | | |
Average outstanding debt balance | | $ | 115.3 | | $ | 112.5 | |
Average interest rate | | | 5.5 | % | | 3.9 | % |
|
|
|
|
|
|
|
|
The effective tax rate was 39.6% in the first quarter of 2006 versus 39.8% in 2005.
15
Business Segment Review
The following tables present Tredegar’s net sales and operating profit by segment for the three months ended March 31, 2006 and 2005:
Tredegar Corporation
Net Sales and Operating Profit by Segment
(In Thousands)
(Unaudited)
| | | | | | | |
| | Three Months Ended March 31 | |
| |
| |
| | 2006 | | 2005 | |
| |
| |
| |
Net Sales | | | | | | | |
Film Products | | $ | 126,331 | | $ | 116,711 | |
Aluminum Extrusions | | | 135,159 | | | 109,966 | |
AFBS (formerly Therics) | | | — | | | 137 | |
| |
|
| |
|
| |
Total net sales | | | 261,490 | | | 226,814 | |
Add back freight | | | 6,474 | | | 5,943 | |
| |
|
| |
|
| |
Sales as shown in the Consolidated Statements of Income | | $ | 267,964 | | $ | 232,757 | |
| |
|
| |
|
| |
| | | | | | | |
Operating Profit | | | | | | | |
Film Products: | | | | | | | |
Ongoing operations | | $ | 15,577 | | $ | 11,578 | |
Plant shutdowns, asset impairments and restructurings, net of gain on sale of assets | | | (1,583 | ) | | 369 | |
| | | | | | | |
Aluminum Extrusions: | | | | | | | |
Ongoing operations | | | 4,866 | | | 2,997 | |
Plant shutdowns, asset impairments and restructurings | | | (109 | ) | | (638 | ) |
| | | | | | | |
AFBS (formerly Therics): | | | | | | | |
Ongoing operations | | | — | | | (1,823 | ) |
Loss on investment in Therics, LLC | | | (25 | ) | | — | |
| |
|
| |
|
| |
Total | | | 18,726 | | | 12,483 | |
Interest income | | | 222 | | | 98 | |
Interest expense | | | 1,432 | | | 963 | |
Gain on sale of corporate assets | | | 56 | | | — | |
Stock option-based compensation costs | | | 211 | | | — | |
Corporate expenses, net | | | 3,759 | | | 2,396 | |
| |
|
| |
|
| |
Income before income taxes | | | 13,602 | | | 9,222 | |
Income taxes | | | 5,387 | | | 3,672 | |
| |
|
| |
|
| |
Net income | | $ | 8,215 | | $ | 5,550 | |
| |
|
| |
|
| |
16
Net sales (sales less freight) and operating profit from ongoing operations are the measures of sales and operating profit used by the chief operating decision maker of each segment for purposes of assessing performance.
Film Products
Net sales in Film Products increased 8.2% in the first quarter of 2006 compared with the first quarter of 2005 primarily due to growth in the sale of higher value-added products, including surface protection, elastic and apertured materials, and higher selling prices, which were driven by higher raw material costs. Volume was 64.5 million pounds in the first quarter of 2006 compared with 67.4 million pounds in 2005. Volume declines were mainly due to competitive pressures on certain mature products used in baby diapers and adult incontinence products. See the executive summary on page 12 for discussion of operating profit and planned capital expenditures.
Aluminum Extrusions
First-quarter 2006 net sales in Aluminum Extrusions were up 22.9% due to higher volume (up 9.1%) and selling prices. Volume was 63.7 million pounds in the first quarter of 2006 compared with 58.4 million pounds in 2005. Growth in shipments continued to be driven by demand for extrusions used in commercial construction and hurricane protection products. See the executive summary on page 12 for discussion of operating profit and planned capital expenditures.
AFBS
On June 30, 2005, substantially all of the assets of AFBS, Inc., a wholly-owned subsidiary of Tredegar (formerly known as Therics, Inc.), were sold or assigned to a newly-created limited liability company, Therics, LLC, controlled and managed by an individual not affiliated with Tredegar. AFBS received a 17.5% equity interest in Therics, LLC, valued at $170,000 and a 3.5% interest in Theken Spine, LLC, valued at $800,000, along with potential future payments based on the sale of certain products by Therics, LLC. AFBS retained substantially all of its liabilities in the transaction, which included customary indemnification provisions for pre-transaction liabilities. Tredegar has no obligation or intent to fund any future losses that may occur at Therics, LLC or Theken Spine, LLC. The ownership interest in Therics, LLC is accounted for under the equity method of accounting with losses limited to its initial carrying value of $170,000. The ownership interest in Theken Spine, LLC is accounted for under the cost method, with an impairment loss recognized and a new cost basis established for any write-down to estimated fair value, if necessary. The potential future payments due from Therics, LLC based on the sale of certain products will be recognized as income when earned.
Liquidity and Capital Resources
Changes in operating assets and liabilities from December 31, 2005 to March 31, 2006 are summarized below:
| | | |
| • | Accounts receivable increased significantly by $33.1 million (28%). |
|
| | – | Accounts receivable in Film Products increased by $12.4 million due to higher sales. Days sales outstanding (“DSO”) was 51 at March 31, 2006, consistent with historical levels (DSO at December 31, 2005 was low at 45). |
|
| | – | Accounts receivable in Aluminum Extrusions increased by $22.5 million due to higher sales. DSO was about 45 at March 31, 2006, consistent with historical levels. |
|
| • | Inventories decreased by $1.9 million (3.1%). |
|
| | – | Inventory days were 48 in Film Products consistent with December 31, 2005. Inventory days in Aluminum Extrusions dropped to 25 from a historical average of around 30 due to strong sales in March. |
17
| |
• | Net property, plant and equipment were up $2.2 million (less than 1%) due primarily to capital expenditures of $13.1 million compared with depreciation of $10.7 million. |
| |
• | Accounts payable increased significantly by $21.6 million (35%) due to higher sales and aluminum costs, and remains in the 30-day range in both business units. |
Cash provided by operating activities was $17.5 million in the first three months of 2006 compared with $4.5 million in 2005. The increase is due primarily to improved operating results and lower incremental working capital investment.
Cash used in investing activities was $13.2 million in the first three months of 2006 compared with $15.6 million in 2005 due primarily to lower capital expenditures.
Capital expenditures in the first three months of 2006 primarily included the normal replacement of machinery and equipment and continued expansion of capacity for surface protection films and elastic materials and a new information system in Film Products. Capital expenditures for all of 2006 are expected to be approximately $45 million in Film Products and about $10 million in Aluminum Extrusions.
Net capitalization and indebtedness as defined under our revolving credit agreement as of March 31, 2006 are as follows:
| | | | |
|
Net Capitalization and Indebtedness as of March 31, 2006 (In Thousands) |
|
Net capitalization: | | | | |
Cash and cash equivalents | | $ | 30,138 | |
Debt: | | | | |
$300 million revolving credit agreement maturing December 15, 2010 | | | 111,000 | |
Other debt | | | 5,402 | |
| |
|
| |
Total debt | | | 116,402 | |
| |
|
| |
Debt net of cash and cash equivalents | | | 86,264 | |
Shareholders’ equity | | | 493,552 | |
| |
|
| |
Net capitalization | | $ | 579,816 | |
| |
|
| |
Indebtedness as defined in revolving credit agreement: | | | | |
Total debt | | $ | 116,402 | |
Face value of letters of credit | | | 6,259 | |
| |
|
| |
Indebtedness | | $ | 122,661 | |
|
Under the revolving credit agreement, borrowings are permitted up to $300 million, and $171 million was available to borrow at March 31, 2006. The credit spread and commitment fees charged on the unused amount under the revolving credit agreement at various indebtedness-to-adjusted EBITDA levels are as follows:
| | | |
|
Pricing Under Revolving Credit Agreement (Basis Points) |
|
|
|
|
Indebtedness-to-Adjusted EBITDA Ratio | Credit Spread Over LIBOR | | Commitment Fee |
|
|
|
|
> 2.50x but <= 3x | 125 | | 25 |
> 1.75x but <= 2.50x | 100 | | 20 |
> 1x but <=1.75x | 87.5 | | 17.5 |
<= 1x | 75 | | 15 |
|
|
|
|
18
At March 31, 2006, the interest rate on debt under the revolving credit agreement was priced at one-month LIBOR plus the applicable credit spread of 87.5 basis points.
The computations of adjusted EBITDA, adjusted EBIT, the leverage ratio and interest coverage ratio as defined in the revolving credit agreement are presented below along with the related most restrictive covenants. Adjusted EBITDA and adjusted EBIT as defined in the revolving credit agreement are not intended to represent cash flow from operations as defined by GAAP and should not be considered as either an alternative to net income or to cash flow.
| | | | |
|
Computations of Adjusted EBITDA, Adjusted EBIT, Leverage Ratio and Interest Coverage Ratio as Defined in Revolving Credit Agreement Along with Related Most Restrictive Covenants As of March 31, 2006 (In Thousands) |
|
|
|
|
|
Computations of adjusted EBITDA and adjusted EBIT as defined in revolving credit agreement for the twelve months ended March 31, 2006: | | | | |
Net income | | $ | 18,894 | |
Plus: | | | | |
After-tax losses related to discontinued operations | | | — | |
Total income tax expense for continuing operations | | | 11,688 | |
Interest expense | | | 5,042 | |
Charges related to stock option grants and awards accounted for under the fair value-based method | | | 211 | |
Losses related to the application of the equity method of accounting | | | 170 | |
Depreciation and amortization expense for continuing operations | | | 40,248 | |
All non-cash losses and expenses, plus cash losses and expenses not to exceed $10,000, for continuing operations that are classified as unusual, extraordinary or which are related to plant shutdowns, asset impairments and/or restructurings (cash-related of $8,410) | | | 23,326 | |
Minus: | | | | |
After-tax income related to discontinued operations | | | — | |
Total income tax benefits for continuing operations | | | — | |
Interest income | | | (710 | ) |
All non-cash gains and income, plus cash gains and income not to exceed $10,000, for continuing operations that are classified as unusual, extraordinary or which are related to plant shutdowns, asset impairments and/or restructurings (cash-related of $2,414) | | | (2,414 | ) |
Plus or minus, as applicable, pro forma EBITDA adjustments associated with acquisitions and asset dispositions | | | 1,458 | |
| |
|
| |
Adjusted EBITDA as defined in revolving credit agreement | | | 97,913 | |
Less: Depreciation and amortization expense for continuing operations (including pro forma for acquisitions and asset dispositions) | | | (40,062 | ) |
| |
|
| |
Adjusted EBIT as defined in revolving credit agreement | | $ | 57,851 | |
| |
|
| |
Shareholders’ equity at March 31, 2006 | | $ | 493,552 | |
Computations of leverage and interest coverage ratios as defined in revolving credit agreement: | | | | |
Leverage ratio (indebtedness-to-adjusted EBITDA) | | | 1.25 | x |
Interest coverage ratio (adjusted EBIT-to-interest expense) | | | 11.47 | x |
Most restrictive covenants as defined in revolving credit agreement: | | | | |
Maximum permitted aggregate amount of dividends that can be paid by Tredegar during the term of the revolving credit agreement ($100,000 plus 50% of net income generated after October 1, 2005) | | $ | 104,553 | |
Minimum adjusted shareholders’ equity permitted ($351,918 plus 50% of net income generated after October 1, 2005) | | $ | 356,471 | |
Maximum leverage ratio permitted: | | | | |
Ongoing | | | 3.00 | x |
Pro forma for acquisitions | | | 2.50 | x |
Minimum interest coverage ratio permitted | | | 2.50 | x |
|
|
|
|
|
19
We believe that as of March 31, 2006, we were, and currently we are, in compliance with all of our debt covenants. Noncompliance with any one or more of the debt covenants may have an adverse effect on financial condition or liquidity in the event such noncompliance cannot be cured or should we be unable to obtain a waiver from the lenders. Renegotiation of the covenant through an amendment to the revolving credit agreement may effectively cure the noncompliance, but may have an effect on financial condition or liquidity depending upon how the covenant is renegotiated.
We believe that the borrowing availability under our revolving credit agreement, our current cash balances and our cash flow from operations will be sufficient to satisfy our working capital, capital expenditure and dividend requirements for the foreseeable future.
Item 3. Quantitative and Qualitative Disclosures About Market Risk.
Tredegar has exposure to the volatility of interest rates, polyethylene and polypropylene resin prices, aluminum ingot and scrap prices, energy prices, foreign currencies and emerging markets. See the section on liquidity and capital resources beginning on page 17 regarding the revolving credit agreement and interest rate exposures.
Changes in resin prices, and the timing of those changes, could have a significant impact on profit margins in Film Products. Profit margins in Aluminum Extrusions are sensitive to fluctuations in aluminum ingot and scrap prices as well as energy costs. There is no assurance of our ability to pass through higher raw material and energy costs to our customers.
Average quarterly prices of low density polyethylene resin (a primary raw material for Film Products) are shown in the chart below.
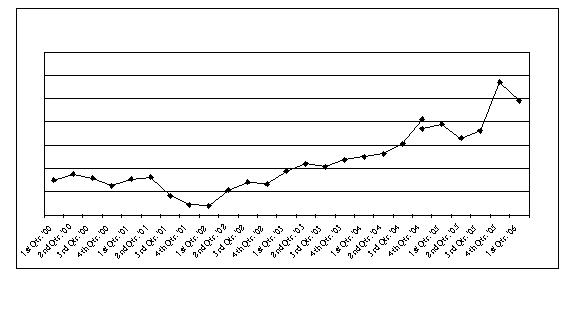
Source: Quarterly averages computed by Tredegar using monthly data provided by Chemical Data Inc. (“CDI”). In January 2005, CDI reflected a 4 cents per pound non-market adjustment based on their estimate of the growth of discounts over the 2000 to 2003 period. The 4th quarter 2004 average rate of 67 cents per pound is shown on a pro forma basis as if the non-market adjustment was made in October 2004.
Quarterly Average U.S. Large Buyer Price for Low Density Polyethylene Resin
(Cents Per Pound)
45
48
46
43
45
46
38
35
34
41
44
43
49
52
51
54
55
56
61
71
67
69
63
66
79
87
Resin prices in Europe, Asia and South America have exhibited similar trends. The price of resin is driven by several factors including supply and demand and the prices of oil, ethylene and natural gas. To address fluctuating resin prices, we have indexed pass-through or cost-sharing agreements covering about 65% of our sales, but many have a 90-day lag. Most new customer contracts contain resin pass-through arrangements.
20
In the normal course of business, we enter into fixed-price forward sales contracts with certain customers for the sale of fixed quantities of aluminum extrusions at scheduled intervals. In order to hedge our exposure to aluminum price volatility (see the chart below) under these fixed-price arrangements, which generally have a duration of not more than 12 months, we enter into a combination of forward purchase commitments and futures contracts to acquire or hedge aluminum, based on the scheduled deliveries.

Source: Quarterly averages computed by Tredegar using daily closing data provided by Bloomberg.
Quarterly Average Price of Aluminum
(U.S. Midwest Spot Price - Cents Per Pound)
79
72
76
73
75
72
67
64
66
66
64
66
68
67
70
73
80
83
91
94
88
87
99
115
85
In Aluminum Extrusions, we hedge from time-to-time a portion of our exposure to natural gas price volatility (see the chart below) by entering into fixed-price forward purchase contracts with our natural gas suppliers. As of March 31, 2006, the Company had fixed prices through its natural gas suppliers for a portion of its usage through the end of the year. We estimate that, in an unhedged situation, every $1 per mmBtu per month change in the market price of natural gas has a $150,000 impact on the monthly operating profit of Aluminum Extrusions.
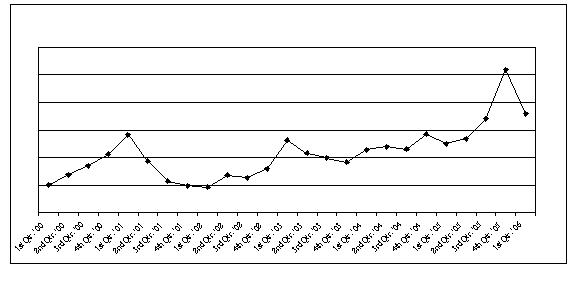
Source: Quarterly averages computed by Tredegar using monthly NYMEX settlement prices.
Quarterly Average Price of Natural Gas
(NYMEX Settlement Prices - $ Per mmBtu)
2.52
3.47
4.27
5.29
7.08
4.67
2.88
2.45
2.32
3.40
3.18
3.98
6.59
5.40
4.97
4.58
5.69
5.99
5.76
6.27
6.73
12.97
8.49
8.98
7.11
21
We sell to customers in foreign markets through our foreign operations and through exports from our U.S. plants. The percentage of sales from manufacturing operations related to foreign markets for the first three months of 2006 and 2005 are as follows:
| | | | | | | | | | | | | |
| |
Percentage of Net Sales from Manufacturing | |
Operations Related to Foreign Markets* | |
| |
| | Three Months Ended March 31 | |
| |
| |
| | 2006 | | 2005 | |
| |
| |
| |
| | Exports | | Foreign | | Exports | | Foreign | |
| | From U.S. | | Operations | | From U.S. | | Operations | |
| |
| |
| |
| |
| |
| | | | | | | | | |
Canada | | | 4 | % | | 15 | % | | 4 | % | | 14 | % |
Europe | | | 1 | | | 12 | | | 1 | | | 14 | |
Latin America | | | — | | | 2 | | | 1 | | | 2 | |
Asia | | | 5 | | | 3 | | | 5 | | | 3 | |
| |
Total | | | 10 | % | | 32 | % | | 11 | % | | 33 | % |
|
* Based on consolidated net sales from manufacturing operations (excludes AFBS). |
We attempt to match the pricing and cost of our products in the same currency (except in Canada where about 75% of our sales of aluminum extrusions are U.S. Dollar-based) and generally view the volatility of foreign currencies (see trends for the Euro, Canadian Dollar and Hungarian Forint in the chart below) and emerging markets, and the corresponding impact on earnings and cash flow, as part of the overall risk of operating in a global environment. Exports from the U.S. are generally denominated in U.S. Dollars. Our foreign currency exposure on income from foreign operations relates to the Canadian Dollar, the Euro, the Hungarian Forint, the Chinese Yuan and the Brazilian Real.
The relatively high percentage of U.S. Dollar-priced sales in Canada is partly due to the shifting of a large portion of the customers previously served by the aluminum extrusions plant in El Campo, Texas, in 2001. The resulting mismatch between the currency denomination of sales and costs causes lower U.S. Dollar translated profits when the Canadian Dollar appreciates since our costs are higher in U.S. Dollar equivalent terms while sales are mostly unaffected (the opposite effect occurs when the Canadian Dollar depreciates in value relative to the U.S. Dollar). We estimate that the appreciation of the Canadian Dollar relative to the U.S. Dollar had an adverse impact on operating profit of about $300,000 in the first quarter of 2006 compared with 2005. In Film Products, where we have been able to better match the currency of our sales and costs, we estimate that the depreciation of foreign currencies (primarily the Euro and Hungarian Forint and to a lesser extent the Chinese Yuan and Brazilian Real) relative to the U.S. Dollar had a negative impact on operating profit of about $300,000 in the first quarter of 2006 compared with 2005.
22
We continue to review the loading of our aluminum extrusions plants in North America to optimize production mix and minimize cost in light of the increase in the U.S. Dollar equivalent cost structure of our plants in Canada.

Source: Quarterly averages computed by Tredegar using daily closing data provided by Bloomberg.
Quarterly Average Exchange Rates of Euro, Hungarian Forint and Canadian
Dollar Relative to the U.S. Dollar
0.40
0.60
0.80
1.00
1.20
1.40
0.0020
0.0025
0.0030
0.0035
0.0040
0.0045
0.0050
0.0055
0.0060
Quarterly Average of U.S. Dollar Equivalent of 1 Euro (Left Axis)
Quarterly Average of U.S. Dollar Equivalent of 1 Canadian Dollar (Left Axis)
Quarterly Average of U.S. Dollar Equivalent of 1 Hungarian Forint (Right Axis)
Item 4. Controls and Procedures.
Pursuant to Rule 13a-15(b) under the Securities Exchange Act of 1934, we carried out an evaluation, with the participation of our management, including our principal executive officer and principal financial officer, of the effectiveness of our disclosure controls and procedures (as defined under Rule 13a-15(e) under the Securities Exchange Act of 1934) as of the end of the period covered by this report. Based upon that evaluation, our principal executive officer and principal financial officer concluded that our disclosure controls and procedures are effective to ensure that information required to be disclosed by us in the reports that we file or submit under the Exchange Act, is recorded, processed, summarized and reported, within the time periods specified in the SEC’s rules and forms, and that such information is accumulated and communicated to our management, including our principal executive officer and principal financial officer, as appropriate, to allow timely decisions regarding required disclosure.
There has been no change in our internal control over financial reporting during the quarter ended March 31, 2006, that has materially affected, or is reasonably likely to materially affect, our internal control over financial reporting, except that during the first quarter of 2006, we installed a new information system in Film Products at several U.S. locations and expect to complete installation at Film Products’ remaining U.S. locations by the end of 2006.
23
PART II – OTHER INFORMATION
Item 1. Legal Proceedings.
On June 23, 2005, the United States Environmental Protection Agency, Region 4 (“EPA”), issued an Administrative Order (Docket No. CAA-04-2005-1838, the “Order”) under the Clean Air Act (as amended from time to time, the “Act”) alleging certain violations by Aluminum Extrusions’ Carthage, Tennessee facility of the refrigerant management regulations promulgated pursuant to the Act. The Order alleged that the violations occurred primarily in 2002 and 2003.
The Order required Aluminum Extrusions to either replace the cooling system at issue or retrofit it with an EPA approved non-ozone depleting substance. The Order further required Aluminum Extrusions to comply with certain applicable provisions of the Act and to provide certified documentation verifying compliance with the Order. Aluminum Extrusions was required to comply with all terms of the Order within 180 days from issuance.
Aluminum Extrusions fulfilled all obligations imposed by the Order during 2005, and reported that fact in a letter to EPA dated October 25, 2005. Although Aluminum Extrusions has not admitted any violations to the EPA pursuant to the Order, Aluminum Extrusions elected to replace the affected cooling system and incurred related replacement costs of approximately $110,000.
Pursuant to a Consent Agreement and Final Order (“CAFO”) that is expected to become effective during the second quarter of 2006, Aluminum Extrusions agreed to (i) pay a civil penalty of $30,422 and (ii) undertake a supplemental environmental project (“SEP”) in an amount of at least $208,170 (“Minimum SEP Expenditure”). The CAFO requires that the SEP be fully implemented within one year of the CAFO’s effective date. Management believes that the SEP will be completed in a satisfactory and timely manner and that actual SEP expenditures will exceed the Minimum SEP Expenditure. If, however, Aluminum Extrusions fails to complete the SEP satisfactorily or fails to spend at least the Minimum SEP Expenditure, Aluminum Extrusions could be responsible under the CAFO for additional penalties of up to $91,000.
Item 1A. Risk Factors.
There are a number of risks and uncertainties that can have a material effect on the operating results of our businesses and our financial condition. These risk factors include, but are not limited to, the following:
General
| |
• | Our future performance is influenced by costs incurred by our operating companies including, for example, the cost of energy and raw materials.These costs include, without limitation, the cost of resin (the raw material on which Film Products primarily depends), aluminum (the raw material on which Aluminum Extrusions primarily depends) natural gas (the principal fuel necessary for Aluminum Extrusions’ plants to operate), electricity and diesel fuel. Resin, aluminum and natural gas prices have risen significantly, and may continue to do so in the future. Tredegar attempts to mitigate the effects of increased costs through price increases and contractual pass-through provisions, but there are no assurances that higher prices can effectively be passed through to our customers or that we will be able to offset fully or on a timely basis the effects of higher raw material costs through price increases or pass-through arrangements. Further, there is no assurance that cost control efforts will be sufficient to offset any additional future declines in revenue or increases in energy, raw material or other costs. |
| |
• | Our substantial international operations subject us to risks of doing business in foreign countries, which could adversely affect our business, financial condition and results of operations. Risks |
24
| |
| inherent in international operations include the following, by way of example: changes in general economic conditions, potential difficulty enforcing agreements and intellectual property rights, restrictions on foreign trade or investment, fluctuations in exchange rates, imposition of additional taxes on our foreign income, nationalization of private enterprises and unexpected adverse changes in foreign laws and regulatory requirements. |
Film Products
| |
• | Film Products is highly dependent on sales associated with one customer, The Procter & Gamble Company (“P&G”). P&G comprised approximately 25% of Tredegar’s net sales in 2005, 27% in 2004 and 29% in 2003. The loss or significant reduction of sales associated with P&G would have a material adverse effect on our business. Other P&G-related factors that could adversely affect our business include, by way of example, (i) failure by P&G to achieve success or maintain share in markets in which P&G sells products containing our materials, (ii) operational decisions by P&G that result in component substitution, inventory reductions and similar changes and (iii) delays in P&G rolling out products utilizing new technologies developed by Tredegar. While we have undertaken efforts to expand our customer base, there can be no assurance that such efforts will be successful, or that they will offset any delay or loss of sales and profits associated with P&G. |
| |
• | Growth of Film Products depends on our ability to develop and deliver new products at competitive prices, especially in the personal care market. Personal care products are now being made with a variety of new materials, replacing traditional backsheet and other components. While we have substantial technical resources, there can be no assurance that our new products can be brought to market successfully, or if brought to market successfully, at the same level of profitability and market share of replaced films. A shift in customer preferences away from our technologies, our inability to develop and deliver new profitable products, or delayed acceptance of our new products in domestic or foreign markets, could have a material adverse effect on our business. In the long term, growth will depend on our ability to provide innovative materials at or below existing material costs, including lowering equipment and other capital costs. |
| |
• | Film Products operates in a field where our significant customers and competitors have substantial intellectual property portfolios. The continued success of this business depends on our ability not only to protect our own technologies and trade secrets, but also to develop and sell new products that do not infringe upon existing patents or threaten existing customer relationships. Although we are not currently involved in any patent litigation, an unfavorable outcome of any such action could have a significant adverse impact on Film Products. |
| |
• | As Film Products expands its personal care business, we have greater credit risk that is inherent in broadening our customer base. |
Aluminum Extrusions
| |
• | Sales volume and profitability of Aluminum Extrusions is cyclical and highly dependent on economic conditions of end-use markets in the United States and Canada, particularly in the construction, distribution and transportation industries. Our market segments are also subject to seasonal slowdowns during the winter months. Because of the high degree of operating leverage inherent in our operations (generally constant fixed costs until full capacity utilization is achieved), the percentage drop in operating profits in a cyclical downturn will likely exceed the percentage drop in volume. Any benefits associated with cost reductions and productivity improvements may not be sufficient to offset the adverse effects on profitability from pricing and margin pressure and higher bad debts that usually accompany a downturn. In addition, higher energy costs and the appreciation of the U.S. Dollar equivalent value of the Canadian Dollar can further reduce profits unless offset by price increases or cost reductions and productivity improvements. |
25
| |
| In 2004, operating profit from ongoing operations in Aluminum Extrusions increased to $22.6 million from $15.1 million in 2003. The $7.5 million or 50% increase in operating profit on 6.7% volume growth during this period was primarily due to operating leverage and pricing improvements. In 2005, operating profit from ongoing operations in Aluminum Extrusions decreased to $19.3 million (down $3.3 million from 2004 or 14.7%) despite higher selling prices and 1.2% volume growth due to higher energy costs (adverse impact estimated of approximately $7 million) and appreciation of the Canadian Dollar (adverse impact estimated of about $3.5 million). |
| |
• | The markets for our products are highly competitive with product quality, service, delivery performance and price being the principal competitive factors. Aluminum Extrusions has around 1,800 customers in a variety of end-use markets within the broad categories of building and construction, distribution, transportation, machinery and equipment, electrical and consumer durables. No single customer exceeds 4% of Aluminum Extrusion’s net sales. Due to the diverse customer mix across many end-use markets, we believe the industry generally tracks the real growth of the overall economy (historical cross-cycle volume growth has been in the 3% range). |
| |
| During improving economic conditions, excess industry capacity is absorbed and pricing pressure becomes less of a factor in many of our end-use markets. Conversely, during an economic slowdown, excess industry capacity often drives increased pricing pressure in many end-use markets as competitors protect their position with key customers. Because the business is susceptible to these changing economic conditions, Aluminum Extrusions targets complex, customized, service-intensive business with more challenging requirements which is competitively more defensible compared to higher volume, standard extrusion applications. |
| |
| Foreign imports, primarily from China, represent a growing portion of the North American aluminum extrusion market. Foreign competition to date has been primarily large volume, standard extrusion profiles that impact some of our less strategic end-use markets. Market share erosion in other end-use markets remains possible. |
| |
| There can be no assurance that we will be able to maintain current margins and profitability. Our continued success and prospects depend on our ability to retain existing customers and participate in overall industry cross-cycle growth. |
Item 5. Other Information.
None.
Item 6. Exhibits.
Exhibit Nos.
26
SIGNATURES
Pursuant to the requirements of the Securities Exchange Act of 1934, the Registrant has duly caused this report to be signed on its behalf by the undersigned thereunto duly authorized.
| | | |
| | Tredegar Corporation |
| | (Registrant) |
| | |
Date: May 5, 2006 | | /s/ D. Andrew Edwards |
| |
| |
| | D. Andrew Edwards |
| | Vice President, Chief Financial Officer and |
| | Treasurer |
| | (Principal Financial and Accounting Officer) |
27