Table of Contents
UNITED STATES
SECURITIES AND EXCHANGE COMMISSION
Washington, D.C. 20549
FORM 10-K
(Mark One)
x | | Annual report pursuant to Section 13 or 15(d) of the Securities Exchange Act of 1934 for the fiscal year ended December 31, 2008, |
| | |
| | or |
| | |
o | | Transition report pursuant to Section 13 or 15(d) of the Securities Exchange Act of 1934. |
MERIT MEDICAL SYSTEMS, INC.
(Exact name of registrant as specified in its charter)
Utah | | 0-18592 | | 87-0447695 |
(State or other jurisdiction | | (Commission File No.) | | (IRS Employer |
of incorporation) | | | | Identification No.) |
1600 West Merit Parkway
South Jordan, Utah 84095
(Address of principal executive offices, including zip code)
Registrant’s telephone number, including area code: (801) 253-1600
Securities registered pursuant to Section 12(b) of the Act: Common Stock, No Par Value
Securities registered pursuant to Section 12(g) of the Act: None
Indicate by check mark if the registrant is a well-known seasoned issuer, as defined in Rule 405 of the Securities Act. Yes o No x
Indicate by check mark if the registrant is not required to file reports pursuant to Section 13 or Section 15(d) of the Act. Yes o No x
Indicate by check mark whether the registrant (1) has filed all reports required to be filed by Section 13 or 15(d) of the Securities Exchange Act of 1934 during the preceding 12 months (or for such shorter period that the registrant was required to file such reports), and (2) has been subject to such filing requirements for the past 90 days. Yes x Noo
Indicate by check mark if disclosure of delinquent filers pursuant to Item 405 of Regulation S-K is not contained herein, and will not be contained, to the best of the registrant’s knowledge, in definitive proxy or information statements incorporated by reference in Part III of this Form 10-K or any amendment to this Form 10-K. x
Indicate by check mark whether the registrant is a large accelerated filer, an accelerated filer or a non-accelerated filer, or a smaller reporting company. See the definitions of “large accelerated filer,” “accelerated filer,” and “smaller reporting company” in Rule 12b-2 of the Exchange Act.
Large accelerated filer o | | Accelerated filer x |
Non-accelerated filer o (Do not check if a smaller reporting company) | | Smaller reporting company o |
Indicate by check mark whether the registrant is a shell company (as defined in Rule 12b-2 of the Exchange Act). Yes o Nox
The aggregate market value of the registrant’s common stock held by non-affiliates of the registrant, on June 30, 2008, which is the last day of the registrant’s most recently completed second fiscal quarter (based upon the closing sale price of the registrant’s common stock on the NASDAQ National Market System on June 30, 2008), was approximately $380 million. Shares of common stock held by each officer and director of the registrant and by each person who may be deemed to be an affiliate have been excluded.
As of February 27, 2009, the registrant had 28,093,295 shares of the registrant’s common stock outstanding.
Table of Contents
DOCUMENTS INCORPORATED BY REFERENCE
Portions of the following document are incorporated by reference in Part III of this Report: the registrant’s definitive proxy statement relating to the Annual Meeting of Shareholders scheduled for May 20, 2009.
Table of Contents
PART I
Unless otherwise indicated in this report, “Merit”, “we,” “us,” “our,” and similar terms refer to Merit Medical Systems, Inc. and our consolidated subsidiaries
.
DISCLOSURE REGARDING FORWARD-LOOKING STATEMENTS
This report includes “forward-looking statements” within the meaning of Section 27A of the Securities Act of 1933, as amended (the “Securities Act”), and Section 21E of the Securities Exchange Act of 1934, as amended (the “Exchange Act”). All statements other than statements of historical fact are “forward-looking statements” for purposes of these provisions, including any projections of earnings, revenues or other financial items, any statements of the plans and objectives of management for future operations, any statements concerning proposed new products or services, any statements regarding future economic conditions or performance, and any statements of assumptions underlying any of the foregoing. All forward-looking statements included in this report are made as of the date hereof and are based on information available to us as of such date. We assume no obligation to update any forward-looking statement. In some cases, forward-looking statements can be identified by the use of terminology such as “may,” “will,” “expects,” “plans,” “anticipates,” “intends,” “believes,” “estimates,” “potential,” or “continue,” or the negative thereof or other comparable terminology. Although we believe that the expectations reflected in the forward-looking statements contained herein are reasonable, there can be no assurance that such expectations or any of the forward-looking statements will prove to be correct, and actual results could differ materially from those projected or assumed in the forward-looking statements. Future financial condition and results of operations, as well as any forward-looking statements, are subject to inherent risks and uncertainties, including risks relating to the closing of the proposed Alveolus, Inc. (“Alveolus”) and Biosearch Medical Products, Inc., a wholly-owned subsidiary of Hydromer, Inc. (“Biosearch”) transactions and the possibility that conditions to closing those transactions may not be satisfied or that either or both of those transactions may not be completed; unanticipated consequences of Merit’s proposed acquisition of the Alveolus and Biosearch assets; challenges associated with Merit’s efforts to pursue new market opportunities, including opportunities in the gastroenterology and pulmonary markets; infringement of Merit’s technology or the assertion that Merit’s technology infringes the rights of other parties; product recalls and product liability claims; infringement of our technology or the assertion that our technology infringes the rights of other parties; product recalls and product liability claims; downturn of the national economy and its effect on our revenues, collections and supplier relations; termination of supplier relationships, or failure of suppliers to perform; inability to successfully manage growth through acquisitions; delays in obtaining regulatory approvals, or the failure to maintain such approvals; concentration of our revenues among a few products and procedures; development of new products and technologies that could render our products obsolete; market acceptance of new products; delayed introduction of products; price and product competition; availability of labor and materials; cost increases; fluctuations in and obsolescence of inventory; volatility of the market price of our common stock; foreign currency fluctuations; changes in key personnel; work stoppage or transportation risks; modification or limitation of governmental or private insurance reimbursement; changes in health care markets related to health care reform initiatives; failure to comply with environmental laws and regulations and other factors referenced in our press releases and reports filed with the Securities and Exchange Commission (the “SEC”). All subsequent forward-looking statements attributable to us or persons acting on our behalf are expressly qualified in their entirety by these cautionary statements. Additional factors that may have a direct bearing on our operating results are described under Item 1A. “Risk Factors” beginning on page 8.
Item 1. Business.
GENERAL
Merit Medical Systems, Inc. was formed in 1987 by several members of our current management to produce high-quality, single-use medical products. Our initial focus was on creating products to be used by doctors in diagnosing and treating cardiovascular disease. Our products are designed to enable physicians and other health care professionals to perform interventional and diagnostic procedures safely and effectively. Early in our development, we were able to introduce innovative new products and capture significant market share because of our expertise in product design, our proprietary technology, and our skills in injection and insert molding. Later, we developed an innovative line of angioplasty inflation products that included electronic sensing and display features. Angioplasty and stent placement are procedures used to clear out blockages and blood clots in arteries by inserting and inflating a small balloon in the clogged arteries. We market these devices, along with a group of sensor-based products designed to be used by hospital personnel in various diagnostic and interventional catheterization procedures. Recently, we have expanded our product offerings to include angiographic catheters, dialysis catheters, micro catheters and micro access products, guide wires, needles, safety products, therapeutic infusion catheters and accessories, drainage catheters and accessories, sheath introducers, pressure infusion bags, syringes, safety scalpels, kits, and procedure trays. Additionally, we have sought to improve our line of core products.
1
Table of Contents
We offer a broad line of innovative, disposable products designed to assist physicians in diagnosing disease and intervening in the areas of radiology and cardiology. During 2008, our sales of new and existing products increased both in the United States and in foreign markets. We intend to create new products based on our sensor-based technologies, plastics molding, catheter, guide wire, and electronic capabilities, and to develop products for diagnostic and interventional procedures in additional markets. Our sales of stand-alone products, in combination with custom kits, have increased as we have expanded our product lines. In 2008, our U.S. domestic sales force made approximately 41% of our sales directly to U.S. hospitals and approximately 14% of sales through other channels such as U.S. customs packagers and distributors. Original equipment manufacturers, or “OEM,” companies accounted for approximately 17% of our 2008 sales. Approximately 32% of our sales in 2008 were made in international markets (of which OEM international sales accounted for approximately 4%).
During the first quarter of 2008, we entered into an asset purchase and supply agreement with Micrus Endovascular Corporation, a Delaware corporation (“Micrus”), wherein we purchased three catheter platforms, inventories, customer lists and developed technology.
In the third quarter of 2008, we entered into an agreement with Milamy Partners LLC, a Maine corporation (“Milamy”), to terminate exclusive license rights with McKnight Investments, LLC (“McKnight”) and substitute Merit as the exclusive licensee of Milamy’s KanguruWeb® technology. During 2007, we entered into a distribution agreement with Milamy, wherein we purchased the exclusive, worldwide right to distribute Milamy’s KanguruWeb® Abdominal Retraction System in vascular lab markets.
In the fourth quarter of 2008, we entered into an asset purchase agreement with Tran PA-C, Inc., a Florida corporation (“Tran PA-C”), to purchase their catheter extraction products. In connection with this agreement, we purchased inventories, property and equipment, customer lists and developed technology.
Merit Medical Systems, Inc. was organized in July 1987 as a Utah corporation. We also conduct our operations through a number of domestic and foreign subsidiaries. Our principal offices are located at 1600 West Merit Parkway, South Jordan, Utah, 84095, and our telephone number is (801) 253-1600. See Item 2. “Properties.” We maintain an Internet website at www.merit.com.
PRODUCTS
We develop, manufacture and market products that offer a high level of quality, value, and safety to our customers, as well as the patients they serve. In response to feedback from health care professionals, we have built an extensive product offering in the market for interventional cardiology and interventional radiology procedures. In addition, we are making our mark in the areas of dialysis and interventional nephrology, pain management (discography), vein therapy, and other areas of the health care industry.
The competitive advantages of our products are enhanced by our twenty-plus years of experience in the health care industry; our experienced direct sales force and distributors; our ability to combine and customize devices, kits, and trays at the request of our customers; and our dedication to offering “stick to stitch” solutions in the markets we serve worldwide.
Interventional Cardiology and Radiology Products
Interventional cardiology is a branch of the medical specialty of cardiology that deals specifically with the catheter-based diagnosis and treatment of heart diseases. A large number of procedures can be performed by catheterization, and more commonly, involve the insertion of a sheath into the femoral, radial, or brachial artery. Fluoroscopy (X-ray) and computed tomography (CT) are most often used to visualize the vessels and chambers of the heart during these diagnostic and interventional procedures. Percutaneous Coronary Interventions (“PCI”) are used to treat coronary atherosclerosis and the resulting narrowing of the arteries of the heart. Interventional Radiology is related to the minimally invasive treatment of disease in other (peripheral) vessels and organs of the body and Percutaneous Peripheral Intervention (“PPI”) is used to treat similar disease conditions outside the heart.
Inflation Devices. During PCI and PPI procedures, balloons and/or stents are placed within the vasculature. The balloons must be carefully placed, inflated, and deflated within the vessel in order to achieve optimal results without injury to the patient. For almost two decades, we have offered an extensive, innovative line of inflation devices. Products like our IntelliSystem® and Monarch® (state of the art digital inflation systems), as well as the Basix™ COMPAK inflation device, offer the clinician a wide range of features and prices—along with the quality and ergonomic superiority for which we are known. We estimate that we currently supply more than 50% of the worldwide inflation device market.
2
Table of Contents
Hemostasis Valves. We have developed a complete line of technically sophisticated, clinically acclaimed hemostasis valves (also known as Touhy-Borst adaptors) and angioplasty accessories. These valves connect to catheters and allow passage of additional guide wires, balloon catheters, and other devices into the vasculature while reducing the amount of blood loss during the procedures. We believe we currently supply more than 40% of the worldwide market for these devices.
Vascular Access Products. We offer a broad line of devices used to gain and maintain vascular access while protecting the clinician from accidental cuts and needle-sticks during the procedure. These effective and useful devices and kits include the Futura® Safety Scalpel and an improved line of angiography needles (Merit Advance®), as well as the SecureLoc™ Angiographic Needle. In addition, we offer an extensive line of sheath introducers (Prelude®) and mini access kits (MAK™, MAK-NV™ and S-MAK™), which are designed to allow the clinician smooth, less traumatic, and convenient access to the patient’s vasculature.
Diagnostic Catheters, Guide Wires, and Torque Devices. We offer diagnostic catheters and guide wires for use during both cardiology and radiology angiographic procedures. In 2007, we introduced our new IMPRESS® line of diagnostic radiology catheters and in 2008 we expanded the product line to include specialty catheters for use in additional procedures such as fistulagrams where a shorter angiographic catheter is easier to use. These catheters offer interventional radiologists superior performance during a variety of angiography procedures. In addition, our diagnostic guide wires are used to traverse vascular anatomy and aid in placing catheters and other devices. Our pre-coated, high performance InQwire® guide wires are lubricious and are available in a wide range of configurations to meet clinicians’ diagnostic needs. The Merit H2O® hydrophilic guide wire provides enhanced maneuverability through tortuous anatomy. We also offer a line of torque devices (guide wire steering tools) that can be used on both standard and hydrophilic guide wires—in both large and small diameters — and are often included as a component in our angioplasty packs. In 2007, we released our new SeaDragon™ torque device which is designed for use with hydrophilic guide wires.
Angiography and Angioplasty Accessories. Since our introduction of the CCS™ disposable coronary control syringe line in 1988, we have continued to develop innovative, problem-solving devices; accessories; kits; and procedure trays for use during minimally invasive diagnosis and treatment of coronary artery and peripheral disease. Additionally, we offer an extensive line of kits containing manifolds, syringes, tubing, and disposable pressure transducers (MeriTrans®) for measurement of pressures within the vessels and chambers of the heart. We also provide devices, kits, and procedure trays used to effectively and safely manage fluids, contrast media, and waste during angiography and interventional procedures. For example, in 2007, we introduced a new line of CT-Transfer Sets to address the growing CT angiography market.
Safety and Waste Management Systems. We offer a variety of safety-related products and kits. Our ShortStop® and ShortStop Advantage® temporary sharps holders address the potential safety issues associated with accidental needle sticks. Our extensive line of color-coded Medallion® specialty syringes and the PAL™ medication labeling system (which complies with the Joint Commission on Accreditation of Healthcare Organization’s (“JCAHO”) latest patient safety initiatives) help prevent mix-ups in administering medication. We also offer waste management products to avoid accidental exposure to contaminated fluids. These include our OSHA-compliant waste disposal basins, including the BackStop®, BackStop Plus™, MiniStop™, MiniStop+™ and DugOut®. These products have been designed to complement other Merit devices and are included in many of our kits and procedure trays in order to make the clinical setting safer for both clinicians and the patients.
Obesity-Related Products. Patient obesity presents an ever-growing challenge to clinicians and patients during vascular access, angiography, and interventional procedures. Our KanguruWeb® abdominal retraction device addresses this issue. This device allows easier vessel access to clinicians while maintaining patient comfort and dignity during interventional cardiology and radiology procedures. In addition, we offer longer angiography and anesthesia needles, as well as mini access kits for improved vascular access of obese patients.
Specialty Procedure Products
In addition to the procedures and devices detailed above, interventional radiology (also referred to as the special procedures or specials lab) performs a variety of additional minimally invasive diagnostic and interventional procedures. We offer a variety of devices and accessories used during these procedures.
Drainage Catheters and Accessories. We have a complete line of catheters for nephrostomy, abscess, and other drainage procedures. Our ReSolve® non-locking and locking drainage catheter line was expanded in 2006, 2007 and 2008. These catheters’ unique, convenient locking mechanisms are appreciated by clinicians and patients who often comment on the enhanced comfort that the catheter provides them. We also offer a range of catheter fixation devices including the Revolution™ catheter fixation device which was designed to be cost effective, save time, and enhance patient comfort. In addition, we provide a wide selection of accessories that complement our drainage catheters,
3
Table of Contents
including tubing sets and drainage bags. In 2007, we expanded our Drainage Depot™ product line to include the new FZ Drainage Depot Bag™ with soft cloth backing which is more comfortable for patients than traditional bags. In 2008, we introduced the MAK-NV™ Introducer System (mini access introducer system for non-vascular applications). This popular device was designed for easy visualization and quick access into the drainage area. For enhanced visibility, the device features an echo enhanced needle and radiopaque marker tip on the introducer.
Paracentesis and Pericardiocentesis Catheters. Paracentesis is a procedure to remove fluid that has accumulated in the abdominal cavity (peritoneal fluid). Merit’s One-StepTM centesis catheter and our Safety Paracentesis Procedure Tray, are designed to provide clinicians with a safe, convenient, and cost-effective alternative for paracentesis procedures. Pericardiocentesis is a procedure in which fluid is aspirated from the pericardium (the sac enveloping the heart). In 2007, we introduced a new, large (8.3F) outer diameter pericardiocentesis catheter. Our Pericardiocentesis Kit is designed as an organized, ready-to-use, convenient tray to assist the clinician in draining fluid quickly from the pericardial sac. In 2008, the One-Step™ product line was improved and expanded to include a slip-version of the device that we believe will make our products more competitive in the paracentesis market.
Therapeutic Infusion Catheters. We offer a complete line of therapeutic thrombolytic infusion systems featuring the Fountain® Infusion Systems and the Mistique® Infusion Catheters. These technically-advanced catheters are used to treat thrombus (blood clot) formation in the peripheral vessels of the body.
Products for Dialysis and Interventional Nephrology. In 2007, we acquired the ProGuide™ Chronic Dialysis Catheter product line from Datascope Corporation. The ProGuide™ is considered a “workhorse” catheter for long-term dialysis and provides a platform for additional Merit products in the dialysis and interventional nephrology market. For example, the new Prelude® Short Sheath provides vascular access to dialysis grafts, along with our extensive line of micro access devices such as the MAK™/S-MAK™ line of mini access kits. We also offer a wide range of guide wires, diagnostic catheters, therapeutic infusion systems, and safety products that are used during dialysis-related procedures. In 2008, we acquired the Transcatheter Extractor® from Tran PA-C. This novel device is used to remove tunneled chronic dialysis catheters from dialysis patients. Also in 2008, we continued to add to our offering of unique products for the dialysis and interventional nephrology market. The Slip-Not® Suture Retention Device provides a unique and effective method for securing a purse-string suture that controls bleeding after an arteriovenous (“AV”) fistula intervention. In addition, we introduced the new Impress® 30cm angiographic catheters, so we can now offer our customers almost everything they need for completing AV fistula interventions.
Discography Products. Discography is a technique used to determine whether a disc is the source of pain in patients with back or neck pain. During discography, contrast medium is injected into the disc and the patient’s response to the injection is noted. Due, in large part, to their quality and accuracy, our digital inflation devices (IntelliSystem® and Monarch®) are used in many pain management clinics.
MARKETING AND SALES
Target Market/Industry. Our target markets include diagnostic and interventional cardiology, interventional radiology, vascular surgery, interventional nephrology, cardiothoracic surgery and pain management (discography and kyphoplasty).
According to government statistics, coronary and peripheral vascular disease continues to be a leading health problem in the United States. Treatment options range from dietary changes to surgery, depending on the nature of the specific disease or disorder. Endovascular techniques, including angioplasty, stenting, and endoluminal stent grafts, continue to represent important therapeutic options for the treatment of vascular disease. We derive a large percentage of our revenues from sales of products used during percutaneous (through the skin) diagnostic and interventional procedures such as angiography, angioplasty, and stent placement, and we intend to pursue additional sales growth by building on our existing market position in both catheter technology and accessory products.
In addition to products used in the treatment of coronary and peripheral vascular disease, we continue our efforts to develop and distribute other devices used in the major markets we serve. For example, we have developed and are distributing products used for percutaneous abscess drainage. Prior to the widespread use of CT or ultrasound imaging, major surgery was necessary to drain internal fluid collections. Now percutaneous drainage is frequently prescribed as the treatment of choice for many types of fluid collections. Our family of drainage catheters and associated accessory devices are used by physicians in the interventional radiology, vascular surgery, and cardiothoracic surgery markets for the percutaneous drainage of abscess fluid in the biliary system and the urinary tract.
We also service the growing interventional nephrology market. Dialysis, or cleaning of the blood, is necessary in conditions such as acute renal failure, chronic renal failure and end-stage renal disease, or ESRD. The kidneys remove excess water and chemical wastes from blood, permitting clean blood to return to the circulatory system. When the
4
Table of Contents
kidneys malfunction, waste substances are not properly excreted, creating an abnormal buildup of wastes in the bloodstream. Dialysis machines are used to treat this condition. Dialysis catheters, which connect the patient to the dialysis machine, are used at various stages in the treatment of dialysis patients. In the past few years, we have added both catheters and accessories to our dialysis-related product offering.
In general, we serve in are characterized by rapid change resulting from technological advances and scientific discoveries. We plan to continue to develop and launch innovative products to support these clinical trends.
Market Strategy. Our marketing strategy is focused on identifying and introducing a continual flow of highly profitable differentiated products that meet customer needs. In order to stay abreast of customer needs, we seek suggestions from hospital personnel working with our products in cardiology and radiology applications. Suggestions for new products and product improvements may come from engineers, sales people, physicians and technicians who perform the clinical procedures.
When we determine that a product suggestion demonstrates a sustainable competitive advantage, meets customer needs, fits strategically and technologically with our business, and has a good potential financial return, we generally assemble a “project team” comprised of individuals from our sales, marketing, engineering, manufacturing, legal, and quality assurance departments. This team works to identify the customer requirements, integrate the design, compile necessary documentation and testing, and prepare the product for market introduction. We believe that one of our marketing strengths is our capacity to rapidly conceive, design, develop, and introduce new products.
U. S. Sales. Sales of our products in the United States accounted for 68%, 68% and 72% of our total sales for the years ended December 31, 2008, 2007 and 2006, respectively. Our direct sales force currently consists of a Vice President of Sales, nine regional sales managers and 72 direct sales representatives and clinical specialists located in major metropolitan areas throughout the United States. We consider training to be a critical factor in the success of our direct sales force. Our sales people are trained by our personnel at our facilities, by a senior sales person in their respective territories, at regular national and regional sales meetings, by consulting cardiologists and by observation of procedures in catheterization laboratories.
International Sales. Approximately 144 independent dealer organizations distribute our products worldwide, including territories in Europe, Africa, the Middle East, Asia, South and Central America, and Canada. We have appointed a Vice President for International Sales, based in South Jordan, Utah, who oversees Asia, South and Central America, Australia and Canada. We also have a Vice President of European Sales who oversees Europe, the Middle East and Africa from our facility located in Maastricht, The Netherlands. Approximately 24 direct sales representatives and country managers presently sell our products in Germany, France, the United Kingdom, Belgium, The Netherlands, Denmark, Sweden, Ireland and Austria. In 2008, our international sales grew approximately 12% over our total sales for the year ended December 31, 2007 and accounted for approximately 32% of total sales. With the recent and planned additions to our product lines, we believe that our international sales will continue to increase.
We require our international dealers to inventory products and sell directly to customers within defined sales territories. Each of our products must be approved for sale under the laws of the country in which it is sold. International dealers are responsible for compliance with all applicable laws and regulations in their respective countries.
OEM Sales. We currently have an OEM division that sells molded components, sub-assembled goods, and bulk non-sterile goods, which may be combined with other components and/or goods from other companies and then sold under a Merit or non-Merit label. We engage in both international and domestic OEM sales.
CUSTOMERS
We serve hospital and clinic-based cardiologists, radiologists, anesthesiologists, physiatrists (pain management physicians), neurologists, nephrologists, vascular surgeons, technicians, and nurses, all of whom influence the purchasing decisions for our products. Hospitals and acute care facilities in the United States purchase our products through our direct sales force, distributors, OEM partners, custom packagers and packers who assemble and combine our products in custom kits and packs. Outside the United States, hospitals and acute care facilities purchase our products through our direct sales force, or in the absence of a sales force, through independent distributors or OEM partners.
In 2008, our U.S. domestic sales force made approximately 41% of our sales directly to U.S. hospitals, and they made approximately 14% of our sales through other channels such as U.S. custom packagers and distributors. Approximately 45% of our sales were made by our direct European sales force, international distributors, and our OEM sales force. Sales to our single largest customer, an OEM partner, accounted for approximately 7% of total sales during the year ended December 31, 2008. We generally manufacture products for other medical device companies through our
5
Table of Contents
OEM division. During the year ended December 31, 2008, OEM sales represented approximately 17% of our total revenue.
RESEARCH AND DEVELOPMENT
In 2008, we continued to innovate in the treatment of cardiovascular disease by offering our customers a number of new products. We broadened our Prelude® Sheath Introducer line by developing a number of radial artery access sheaths and valves. The Prelude® Short Sheath line was designed to meet customer expectations for dialysis graft access. The MAK NV™ is a new product line developed to offer non-vascular access for our drainage products. Two other novel products were created to add convenience for the clinician. The Slip-Not® is a device for securing purse string sutures following procedures involving dialysis grafts. Also, the Grandstand™ is a temporary sharps holder which adds safety and innovation to our sharps container line.
Research and development expenses were approximately $9.2 million, $8.7 million, and $8.6 million in 2008, 2007, and 2006, respectively. Our future growth continues to be fueled with multiple product ideas guided by our Chief Executive Officer and our sales and marketing teams, as well as by collaboration with physicians with whom we have longstanding relationships. We have research and development facilities in South Jordan, Utah; Angleton, Texas; Galway, Ireland; and Venlo, The Netherlands. We are also expanding our research and development efforts to include a variety of European technological sources.
MANUFACTURING
We manufacture many of our products utilizing our proprietary technology and our expertise in plastic injection and insert molding. We generally contract with third parties for the tooling of molds, but we design and own all of our molds. We utilize our experience in injection and insert molding technologies in the manufacture of most of the custom components used in our products.
We either assemble the electronic monitors and sensors used in our IntelliSystem® and Monarch® inflation devices from standard electronic components or we purchase them from suppliers. Merit Sensor Systems, Inc., a wholly-owned subsidiary of Merit Medical Systems, Inc., develops and markets silicon sensors. It is presently supplying all of the sensors we utilize in our digital inflation devices.
Our products are manufactured at several factories, including facilities located in South Jordan and Murray, Utah; Galway, Ireland; Venlo, The Netherlands; Angleton, Texas and Chester, Virginia. Our manufacturing capabilities are being expanded into a contract manufacturing facility in Mexico. See Item 2. “Properties.”
We have distribution centers located in South Jordan, Utah; Angleton, Texas; Chester, Virginia and Maastricht, The Netherlands.
We believe that our variety of suppliers for raw materials and components necessary for the manufacture of our products, as well as our long-term relationships with such suppliers, promote stability in our manufacturing process. Historically, we have not been materially affected by interruptions with such suppliers. Furthermore, we seek to develop back-up suppliers for materials and components in the event of supply interruptions.
COMPETITION
We compete in several global markets, including diagnostic and interventional cardiology, interventional radiology, vascular surgery, interventional nephrology, cardiothoracic surgery and pain management. These markets encompass a large number of suppliers of varying sizes.
In the interventional cardiology and radiology markets, we compete with large international, multi-divisional medical supply companies such as Cordis Corporation (Johnson & Johnson), Boston Scientific Corporation, Medtronic, C.R. Bard, and Terumo. Medium-size companies we compete with include Cook, Arrow, AngioDynamics, Vascular Solutions, and ICU Medical. Many of our competitors have substantially greater financial, technical, and marketing resources than we do.
The principal competitive factors in the markets in which our products are sold are quality, price/value, device feature, customer service, breadth of line, and customer relationships. We believe that our products have achieved market acceptance due to the quality of materials and workmanship of our products, innovative design, our willingness to customize to fit customer needs, and our prompt attention to customer requests. Our products are priced competitively, but generally not below prices for competing products. One of our primary competitive strengths is our
6
Table of Contents
relative stability in the marketplace; a comprehensive, broad line of ancillary products; and our history of introducing a variety of new products and product line extensions to the market on a regular basis.
Based on available industry data, with respect to the number of procedures performed, we believe we are the leading provider of digital inflation technology in the world. In addition, we are the world market leader for inflation devices, hemostasis devices, and torque devices. Together with Navilyst Medical, Inc. (formerly Boston Scientific, NAMIC) we are one of two market leaders in the United States for control syringes, waste-disposal systems, tubing, and manifold kits. We believe the recent and planned additions to our product lines will enable us to compete even more effectively in both the U.S. and international markets. There is no assurance; however, that we will be able to maintain our existing competitive advantages or compete successfully in the future.
We derive a substantial majority of our revenues from sales of products used in diagnostic angiography and interventional cardiology and radiology stent procedures. Medical professionals are starting to use new diagnostic methods and interventional procedures and devices, as well as drugs for the treatment and prevention of cardiovascular disease. These new methods, procedures and devices may render some of our products obsolete or limit the markets for our products. However, with the advent of vascular stents and other procedures, we have experienced continued growth in sales of our products.
PATENTS, LICENSES, TRADEMARKS AND COPYRIGHTS
We consider our proprietary technology to be important in the development and manufacture of our products. We seek to protect our technology through a combination of patents, trademarks, trade secrets, copyrights, confidentiality agreements and non-compete agreements. We generally seek patent protection of our technology in the United States and certain foreign countries where such protection appears to be advantageous.
As of December 31, 2008, we owned 84 U.S. patents and had licenses to 13 U.S. patents. Additionally, we either owned or had exclusive rights to 51 pending U.S. patent applications. Internationally, we owned 22 patents, and either owned or had exclusive rights to 20 pending patent applications, all of which are foreign counterparts of the U.S. cases.
We believe that our patents and pending patent applications are materially important to our business, but we do not believe that our business is dependent upon securing such patents. We also operate under licenses from other owners of certain patents, patent applications, technology, trade secrets, know-how, copyrights and trademarks. We believe, however, that no single patent, patent application, technology, trade secret, know-how, copyright, trademark, or license is material in relation to our business as a whole.
Certain minor U.S. patents related to the locking mechanism in our inflation devices expired in 2008 and other patent rights are scheduled to expire thereafter. We expect that related patents will continue to be valuable, in part because of proprietary innovations made since the issuance of our first patent. In 1992, we were granted a license to use patented technology which we incorporated into our inflation devices. In return, we paid a 5.75% ongoing royalty to the licensee, not to exceed $450,000 annually. Royalties paid for such license in each of 2008, 2007 and 2006 were $450,000. The license agreement terminated in August 2008, upon the last expiration date of the licensed patents; however, we continue to use the technology in many of our devices.
We have also registered or applied for registration of several trade names or trademarks. See “Products” above. We have received 134 U.S. and foreign trademark registrations, and other U.S. and foreign trademark applications are currently pending. We have registered copyrights relating to certain software used in our electronic inflation devices.
REGULATION
The U.S. Congress has passed the Federal Food, Drug, and Cosmetic Act (the “Food, Drug and Cosmetic Act”). Under the Food, Drug and Cosmetic Act, and through its own rules, the U.S. Food and Drug Administration (“FDA”) regulates the development, testing, packaging, labeling, and marketing of medical devices and manufacturing procedures relating to these devices. In general, the FDA requires that manufacturers adhere to certain standards designed to ensure the safety and effectiveness of medical devices. We employ a Chief Regulatory Officer and a Vice President of Quality Systems who are responsible for compliance with all applicable FDA regulations.
The FDA’s Quality Systems Regulations define the requirements for our manufacturing processes, require the maintenance of certain records, and provide for unscheduled inspections of our facilities. We must also comply with certain requirements of state, local, and foreign governments in the manufacture and marketing of the Company’s products.
7
Table of Contents
New medical devices may also be subject to either the Section 510(k) Pre-Market Notification regulations or the Pre-Market Approval (“PMA”) regulations promulgated by the FDA and similar regulatory requirements in foreign countries. New products in either category require extensive documentation, careful engineering, and manufacturing controls to ensure quality. Products needing PMA approval require extensive pre-clinical and clinical testing and approval by the FDA prior to marketing. Products subject to Section 510(k) of the Food Drug and Cosmetic Act require FDA clearance prior to marketing. To date, our products have required only compliance with Section 510(k). Most of our products are subject to foreign regulatory approvals before they may be marketed abroad. We place the “CE” mark on devices sold in Europe. The CE mark represents that a product has met EU health, safety, and environmental requirements. We have received ISO 13485 certification for our facilities in Utah, Texas, Virginia and Ireland. We have also received ISO 9001:2000 certification for our Merit Sensor Systems facility in South Jordan, Utah.
EMPLOYEES
As of December 31, 2008, we employed 1,654 people, including 1,255 in manufacturing; 176 in sales and marketing; 123 in engineering, research and development; and 100 in administration.
Many of our present employees are highly skilled. Our failure or success will depend, in part, upon our ability to retain such employees. We believe that an adequate supply of skilled employees is available. We have, from time-to-time, experienced rapid turnover among our entry-level assembly workers, as well as occasional shortages of such workers, resulting in increased labor costs and administrative expenses related to hiring and training replacement and new entry-level employees. Our key employees are bound by agreements or policies of confidentiality. None of our employees are represented by a union or other collective bargaining group. We believe that our relations with our employees are generally good.
AVAILABLE INFORMATION
We file annual, quarterly and current reports and other information with the SEC. These materials can be inspected and copied at the SEC’s Public Reference Room at 100 F Street, N.E., Washington, D.C. 20549. Copies of these materials may also be obtained by mail at prescribed rates from the SEC’s Public Reference Room at the above address. Information about the Public Reference Room can be obtained by calling the SEC at 1-800-SEC-0330. The SEC also maintains an Internet site that contains reports, proxy and information statements, and other information regarding issuers that file electronically with the SEC. The address of the SEC’s Internet website is www.sec.gov.
We make available, free of charge, on our Internet website, located at www.merit.com, our most recent Annual Report on Form 10-K, our most recent Quarterly Report on Form 10-Q, any current reports on Form 8-K filed since our most recent Annual Report on Form 10-K, and any amendments to such reports as soon as reasonably practicable following the electronic filing of such report with the SEC. In addition, we provide electronic or paper copies of such filings free of charge upon request.
FINANCIAL INFORMATION ABOUT FOREIGN AND DOMESTIC OPERATIONS AND EXPORT SALES
For financial information relating to our foreign and domestic sales, transfers between geographic areas, net income and identifiable assets, see Note 11 to our consolidated financial statements set forth in Item 8 of this report.
Item 1A. Risk Factors.
Our business, operations, and financial condition are subject to certain risks and uncertainties. Should one or more of these risks or uncertainties materialize, or should any underlying assumptions prove incorrect, our actual results will vary, and may vary materially from those anticipated, estimated, projected or expected. Among the key factors that may have a direct bearing on our business, operations, or financial condition are the factors identified below:
We may be unable to protect our proprietary technology or may infringe on the proprietary technology of others.
We have obtained U.S. patents and filed additional U.S. and foreign patent applications; however, there can be no assurance that any patents we hold or for which we have applied will provide us with any significant competitive advantages, that third parties will not challenge our patents, or that patents owned by others will not have an adverse effect on our ability to conduct business. We could incur substantial costs in preventing patent infringement, in curbing the unauthorized use of our proprietary technology by others, or in defending against similar claims of others. Since we rely on trade secrets and proprietary know-how to maintain our competitive position, there can be no assurance that others may not independently develop similar or superior technologies.
8
Table of Contents
We operate in an increasingly competitive medical technology marketplace. There has also been substantial litigation regarding patent and other intellectual property rights in the medical device industry. Our activities may require us to defend against claims and actions alleging infringement of the intellectual rights of others. If a court rules against us in any patent litigation, any of several negative outcomes could occur: we could be subject to significant liabilities, we could be forced to seek licenses from third parties, or we could be prevented from marketing certain products. Any of these outcomes could have a material adverse effect on our financial condition and operating results.
Our ability to remain competitive is dependent, in part, upon our ability to prevent other companies from using our proprietary technology incorporated into our products. We seek to protect our technology through a combination of patents, trademarks, and trade secrets, as well as licenses, proprietary know-how and confidentiality agreements. We may be unable, however, to prevent others from using our proprietary information, or continue to use such information our self, for numerous reasons, including the following, any of which could have a material adverse effect on the Company’s business, operations, or financial condition:
· Our issued patents may not be sufficiently broad to prevent others from copying our proprietary technologies;
· Our issued patents may be challenged by third parties and deemed to be overbroad or unenforceable;
· Our products may infringe on the patents or other intellectual property rights of other parties, requiring us to alter or discontinue our manufacture or sale of such products;
· Costs associated with seeking enforcement of our patents against infringement, or defending our self against allegations of infringement, may be significant;
· Our pending patent applications may not be granted for various reasons, including over breadth or conflict with an existing patent; and
· Other persons may independently develop, or have developed, similar or superior technologies.
Economic and industry conditions constantly change, and negative economic conditions in the United States and other countries could materially and adversely affect our business and results of operations.
Our business and our results of operation are affected by many changing economic and other conditions beyond our control. Actual or potential changes in international, national, regional and local economic, business and financial conditions, including recession and inflation, may negatively affect consumer preferences, perceptions, spending patterns or demographic trends, any of which could adversely affect our business and results of operations. We may also experience higher bad-debt rates and slower receivable collection rates in our dealings with our customers. In addition, recent disruptions in the credit markets have resulted in greater volatility, less liquidity, widening of credit spreads, and decreased availability of financing. As a result of these factors, there can be no assurance that financing will be available to us on acceptable terms, if at all. An inability to obtain necessary additional financing on acceptable terms may have an adverse impact on us and on our ability to grow our business.
Termination or interruption of relationships with our suppliers, or failure of such suppliers to perform, could disrupt our business.
We rely on raw materials, component parts, finished products, and services supplied by outside third parties in connection with our business. For example, substantially all of our products are sterilized by only a few different entities. In addition, some of our products are manufactured or assembled by third parties. If a supplier of significant raw materials, component parts, finished goods, or services were to terminate its relationship with us, or otherwise cease supplying raw materials, component parts, finished goods, or services consistent with past practice, our ability to meet our obligations to our end customers may be disrupted. A disruption with respect to numerous products, or with respect to a few significant products, could have a material adverse effect on our business, operations or financial condition.
Our products may be subject to recall or product liability claims.
Our products are used in connection with invasive procedures and in other medical contexts in which it is important that those products function with precision and accuracy. If our products do not function as designed, or are designed improperly, we may choose to or be forced by regulatory agencies to withdraw such products from the market. In addition, if medical personnel or their patients suffer injury as a result of any failure of our products to function as designed, or an inappropriate design, we could be subject to lawsuits seeking significant compensatory and punitive
9
Table of Contents
damages. Any product recall or lawsuit seeking significant monetary damages may have a material adverse effect on our business, operations or financial condition.
We generally offer a limited warranty for product returns which are due to defects in quality and workmanship. We attempt to estimate our potential liability for future product returns and establish reserves on our financial statements in amounts that we believe will be sufficient to address our warranty obligations; however, our actual liability for product returns may significantly exceed the amount of our reserves. If we underestimate our potential liability for future product returns, or if unanticipated events result in returns or warranty obligations that exceed our historical experience, our financial condition and operating results could be materially and adversely affected.
We may be unable to successfully manage growth, particularly if accomplished through acquisitions.
Successful implementation of our business strategy will require that we effectively manage any associated growth. To manage growth effectively, our management will need to continue to implement changes in certain aspects of our business, to improve our information systems and operations to respond to increased demand, to attract and retain qualified personnel, and to develop, train, and manage an increasing number of management-level and other employees. Growth could place an increasing strain on our management, financial, product design, marketing, distribution and other resources, and we could experience operating difficulties. Any failure to manage growth effectively could have a material adverse effect on our business, operations or financial condition.
To the extent that we grow through acquisition, we will face the additional challenges of integrating our current operations, culture, information management systems and other characteristics with that of the acquired entity. We may incur significant expenses in connection with negotiating and consummating one or more transactions, and we may inherit certain liabilities in connection with each acquisition. In addition, we may not realize competitive advantages, synergies or other benefits anticipated in connection with such acquisition(s). If we do not adequately identify targets for, or manage issues related to, our future acquisitions, such acquisitions may have a negative adverse effect on our business and financial results.
A significant adverse change in, or failure to comply with, governing regulations could adversely affect our business.
Substantially all of our products are “devices,” as defined in the Federal Food, Drug and Cosmetic Act, and the manufacture, distribution, record keeping, labeling and advertisement of our products are subject to regulation by the FDA in the United States and its equivalent regulatory agencies in various foreign countries in which our products are manufactured, distributed, labeled, offered or sold. Further, we are subject to continual review and periodic inspections at our current facilities with respect to the FDA’s Quality System Regulations and similar requirements of foreign countries. In addition, we are subject to certain export control restrictions governed by the U.S. Department of the Treasury and may be governed by other regulatory agencies in various foreign countries to which our products are exported. Although we believe we are currently in material compliance with these requirements, any failure on our part to comply with all applicable current and future regulations could adversely affect our business, operations, or financial condition.
A significant portion of our revenues are derived from a few products, procedures and/or customers.
A significant portion of our revenues are attributable to sales of our inflation devices. During the year ended December 31, 2008, sales of our inflation devices (including inflation devices sold in custom kits and through OEM channels) accounted for approximately 27% of our total revenues. Sales of our inflation devices to a single OEM customer, representing our largest customer, were approximately 6% of our total inflation device sales for the year ended December 31, 2008. Any material decline in market demand, or change in OEM supplier preference, for our inflation devices could have an adverse effect on our business, operations or financial condition.
In addition, the products that have accounted for a majority of our historical revenues are designed for use in connection with a few related medical procedures, including angioplasty, stent placement procedures, and spinal procedures. If subsequent developments in medical technology or drug therapy make such procedures obsolete, or alter the methodology of such procedures so as to eliminate the usefulness of our products, we may experience a material decrease in demand for our products and experience deteriorating financial performance.
We may be unable to compete in our markets, particularly if there is a significant change in relevant practices and technology.
The market for each of our products is highly competitive. We face competition from many companies which are larger, better established and have greater financial, technical and other resources and greater market presence than
10
Table of Contents
we do. Such resources and market presence may enable our competition to more effectively market competing products or to market competing products at reduced prices in order to gain market share.
In addition, our ability to compete successfully is dependent, in part, upon our response to changes in technology and to our efforts to develop and market new products which achieve significant market acceptance. Competing companies with substantially greater resources than us are actively engaged in research and development of new methods, treatments, drugs, and procedures to treat or prevent cardiovascular disease that could limit the market for our products and eventually make some of our products obsolete. A reduction in the demand for a significant number of our products, or a few key products, could have a material adverse effect on our business, operations or financial condition.
The market price of our common stock has been, and may continue to be, volatile.
The market price of our common stock has been, and may continue to be, volatile for various reasons, including the following, which could have a material adverse effect on our business, operations or financial condition:
· Our announcement of new products or technical innovations, or similar announcements by our competitors;
· Development of new procedures that use, or do not use, our technology;
· Quarter-to-quarter variances in our financial results;
· Claims involving potential infringement of patents and other intellectual property rights;
· Analysts’ and other projections or recommendations regarding our common stock or medical technology stocks generally;
· Any restatement of our financial statements or any investigation of us by the SEC, the FDA or another domestic or foreign regulatory authority; and
· A decline, or rise, of stock prices in the capital markets generally.
Fluctuations in Euro and GBP exchange rates may negatively impact our financial results.
Fluctuations in the rate of exchange between the Euro and GBP relative to the value of the U.S. Dollar could have a negative impact on our margins and financial results. For example, during 2008, the exchange rate between the Euro and the U.S. Dollar resulted in an increase in our gross revenues of approximately $1.3 million and 0.10% in our gross profit.
For the year ended December 31, 2008, approximately $25.6 million, or 11%, of our sales, were denominated in Euros and GBP. If the rate of exchange between the Euro and the GBP declines, against the U.S. Dollar, we may not be able to increase the prices we charge our European customers for products whose prices are denominated in Euros and GBP. Furthermore, we may be unable or elect not to enter into hedging transactions which could mitigate the effect of declining exchange rates. As a result, if the rate of exchange between Euros and GBP declines, against the U.S. Dollar, our financial results may be negatively impacted.
We are dependent upon key personnel.
Our success is dependent on key management personnel, including Fred P. Lampropoulos, our Chairman of the Board, President and Chief Executive Officer. Mr. Lampropoulos is not subject to any agreement prohibiting his departure, and we do not maintain key man life insurance on his life. The loss of Mr. Lampropoulos, or of certain other key management personnel, could have a materially adverse effect our business and operations. Our success also depends on, among other factors, the successful recruitment and retention of key operating, manufacturing, sales and other personnel.
We are subject to work stoppage, transportation and related risks.
We manufacture products at various locations in the United States and international locations, and sell our products worldwide. We depend on third-party transportation companies to deliver supplies necessary to manufacture our products from vendors to our various facilities and to move our products to customers, operating divisions, and other subsidiaries located worldwide. Our manufacturing operations, and the operations of the transportation companies on
11
Table of Contents
which we depend, may be adversely affected by natural disasters or significant human events, such as a war, terrorist attack, riot, strike, slowdown or similar event. Any disruption in our manufacturing or transportation could materially adversely affect our ability to meet customer demands or our operations.
Limits on reimbursement imposed by governmental and other programs may adversely affect our business.
The cost of a significant portion of medical care is funded by governmental, social security or other insurance programs. Limits on reimbursement imposed by such programs may adversely affect the ability of hospitals and others to purchase our products. In addition, limitations on reimbursement for procedures which utilize our products could adversely affect sales.
Operations at our manufacturing facilities may be negatively impacted by certain factors, including severe weather conditions and the impact of natural disasters.
Our operations can be affected by many factors beyond our control, including severe weather conditions and the impact of natural disasters, including hurricanes and tornados. These conditions can cause substantial damage to facilities, interrupt production and disrupt our ability to deliver products to our customers.
Our operations in Angleton, Texas have been suspended due to hurricanes in recent years. In September 2008 we shut down our operations in Angleton in anticipation of Hurricane Ike and production was restored shortly thereafter. While we incurred minimal damage to our facility, we experienced greater financial damage as a result of the production disruption. Although our insurance covered some of the losses associated with the event, future natural disasters could increase the cost of insurance. We cannot be certain that any losses from business interruption or property damages, along with the increases in insurance costs, will not have a material adverse effect on our results of operations or financial condition.
Our failure to comply with applicable environmental laws and regulations could affect our business and results of operations.
One of our wholly-owned subsidiaries, Merit Sensor Systems, Inc. (“Merit Sensor Systems”), manufactures and assembles certain products that require the use of hazardous materials that are subject to various federal, state and local laws and regulations governing the protection of the environment. While the cost of compliance with such laws and regulations has not had a material adverse effect on our results of operations historically, compliance with future regulations may require additional capital investments in pollution control equipment or changes in the way Merit Sensor Systems makes its products. Additionally, because Merit Sensor Systems uses hazardous and other regulated materials in its manufacturing processes, we are subject to certain risks of liabilities and claims resulting from any accidental releases. While we believe the precautions and infrastructure Merit Sensor Systems has put in place are sufficient, any accidental release may have an adverse affect on our business and results of operations.
Item 1B. | Unresolved Staff Comments. |
| |
| None. |
We own approximately 23 acres of real property situated in the city of South Jordan, Utah, surrounding an additional ten acres of leased real property on which our principal office and manufacturing facility is located which totals approximately 200,000 square feet. We sold the ten-acre site to an unrelated developer in order to facilitate construction of the facility and entered into a 25-year lease agreement (beginning in 1995) to finance the facility. Monthly lease payments attributable to the ten-acre parcel are approximately $138,000. We also hold an option to purchase the facility, exercisable at market value after 25 years. During 2004, we acquired an additional four acres of property south of and adjacent to our main property in South Jordan. During 2005, we acquired an additional seven acres of property just west of our current facility in South Jordan. We believe the acquisition of these additional properties will potentially enable us to expand our operations in the future as property surrounding our existing facilities is limited due to increased development.
At the end of 2004, we completed construction of an approximately 47,000 square foot manufacturing facility in South Jordan, Utah. This facility is used for research, development and pilot production clean rooms and for production of sensors. In the fourth quarter of 2007, our wholly-owned subsidiary, Merit Sensor Systems, Inc., relocated to our South Jordan campus for the anticipated purpose of long-term improvements in costs, quality, efficiency and capacity.
12
Table of Contents
We completed an approximately 140,000 square foot manufacturing facility located in South Jordan, Utah in September 2005. This facility is used for injection and insert molding production, as an automated finished goods warehouse, and as the locale for management information system employees. The new facilities in South Jordan are designed to increase our clean room production capacity and administrative office space to meet current and projected demand that we anticipate we will experience over the next several years.
We own a building of approximately 65,000 square feet with approximately three acres of land, in Galway, County Galway, Republic of Ireland, which serves as our principal office and manufacturing facility for our European operations. The facility houses a research and development team, which developed our diagnostic guide wire, and is working to develop other new products. We also manufacture other products at the Galway facility.
We lease a manufacturing facility of approximately 52,000 square feet located in Murray, Utah. The Murray facility is used for production of several of our products. The leases related to seven of the units at the Murray facility expired in 2007. Given the expiration of these leases, we currently use the seven units on a month-to-month basis. The aggregate lease payments on these Murray facilities are approximately $29,000 per month.
We own approximately 19 acres of land and an approximately 75,000 square foot building in Angleton, Texas. The facility is used for the production of catheter-related products.
We own approximately 12 acres of land and an approximately 100,000 square foot building in Chester, Virginia. The facility is used for production of custom procedure trays used in the medical industry.
We relocated our MCTec operations to a leased manufacturing facility of approximately 10,000 square feet located in Venlo, The Netherlands. The facility is used for the coating of wires and tubing for medical devices. The lease will expire in January 2011. The current monthly lease payment is approximately $7,000.
In May 2008, we completed construction of a new European headquarters in Beek, The Netherlands. The new 31,000 square foot facility is designed to provide for anticipated growth in our European operations.
We believe that our existing and proposed facilities will generally be adequate for our present and future anticipated levels of operations.
Item 3. | Legal Proceedings. |
In the course of conducting our business operations, we are, from time to time, involved in litigation and other disputes. Our management does not currently anticipate that any pending litigation or dispute against us will have a materially adverse effect on our business, operations or financial condition.
Item 4. | Submission of Matters to a Vote of Security Holders. |
No matters were submitted to a vote of our security holders during the fourth quarter of the year ended December 31, 2008.
13
Table of Contents
PART II
Item 5. | Market for Registrant’s Common Equity, Related Stockholder Matters and Issuer Purchases of Equity Securities. |
MARKET PRICE FOR THE COMMON STOCK
Our common stock (the “Common Stock”) is traded on the NASDAQ National Market System under the symbol “MMSI.” The following table sets forth high and low sale prices for the Common Stock for the periods indicated.
For the year ended December 31, 2008 | | High | | Low | |
First Quarter | | $ | 17.41 | | $ | 13.71 | |
Second Quarter | | $ | 16.97 | | $ | 14.00 | |
Third Quarter | | $ | 21.36 | | $ | 14.18 | |
Fourth Quarter | | $ | 19.99 | | $ | 12.35 | |
For the year ended December 31, 2007 | | High | | Low | |
First Quarter | | $ | 15.74 | | $ | 11.90 | |
Second Quarter | | $ | 13.41 | | $ | 10.89 | |
Third Quarter | | $ | 13.38 | | $ | 11.25 | |
Fourth Quarter | | $ | 16.50 | | $ | 12.36 | |
OUTSTANDING SHARES AND NUMBER OF SHAREHOLDERS
As of February 27, 2009, the number of shares of Common Stock outstanding was 28,093,295 held by approximately 167 shareholders of record, not including shareholders whose shares are held in securities position listings.
DIVIDENDS
We have never declared or paid cash dividends on the Common Stock. We presently intend to retain any future earnings for use in our business and, therefore, do not anticipate paying any dividends on the Common Stock in the foreseeable future. In addition, our revolving line of credit contains covenants prohibiting the declaration and distribution of a cash dividend at any time prior to the termination of such line of credit.
14
Table of Contents
PERFORMANCE GRAPH
The following graph compares the performance of the Common Stock with the performance of the NASDAQ Stock Market (U.S. Companies) and NASDAQ Stocks (SIC 3840-3849 U.S. Companies - Surgical, Medical and Dental Instruments and Supplies) for a five-year period by measuring the changes in Common Stock prices from December 31, 2003 to December 31, 2008.
Comparison of 5 Year Cumulative Total Return
Among Merit Medical System, Inc., NASDAQ Stock Market (U.S.)
and NASDAQ Stocks (SIC 3840-3849)
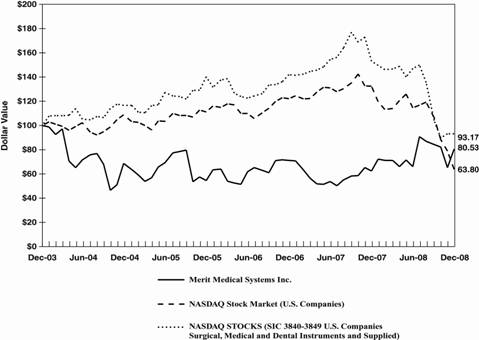
| | 12/2003 | | 12/2004 | | 12/2005 | | 12/2006 | | 12/2007 | | 12/2008 | |
Merit Medical System Inc. | | $ | 100 | | $ | 69 | | $ | 55 | | $ | 71 | | $ | 62 | | $ | 81 | |
NASDAQ Stock Market (U.S. Companies) | | | 100 | | | 109 | | | 111 | | | 122 | | | 132 | | | 64 | |
NASDAQ Stocks (SIC 3840-3849 U.S. Companies) | | | 100 | | | 116 | | | 134 | | | 138 | | | 177 | | | 92 | |
The stock performance graph assumes for comparison that the value of the Common Stock and of each index was $100 on December 31, 2003 and that all dividends were reinvested. Past performance is not necessarily an indicator of future results.
15
Table of Contents
SECURITIES AUTHORIZED FOR ISSUANCE UNDER EQUITY COMPENSATION PLANS
The following table contains information regarding our equity compensation plans as of December 31, 2008 (in thousands):
| | Number of securities to be issued upon exercise of outstanding options, warrants and rights | | Weighted-average exercise price of outstanding options, warrants and rights | | Number of securities remaining available for future issuance under equity compensation plans (excluding securities reflected in column (a)) | |
Plan category | | (a) | | (b) | | (c) | |
Equity compensation Plans approved by security holders | | 3,833 | (1),(3) | $ | 12.12 | | 1,044 | (2),(3) |
Equity compensation Plans not approved by security holders | | 51 | (4) | $ | 10.13 | | | |
Total | | 3,884 | | $ | 12.10 | | 1,044 | |
(1) Consists of 3,832,953 shares of Common Stock subject to the options granted under the Merit Medical Systems, Inc. 2006 Long-Term Incentive Plan.
(2) Consists of 360,395 shares available to be issued under the Merit Medical Systems, Inc. Qualified and Non-Qualified Employee Stock Purchase Plan and 684,619 shares available to be issued under the Merit Medical Systems, Inc. 2006 Long-Term Incentive Plan.
(3) See Note 10 to our consolidated financial statements set forth in Item 8 of this report for additional information regarding these plans.
(4) Consists of warrants issued in the acquisition of MedSource Packaging Concepts LLC (“MedSource”) in 2004.
16
Table of Contents
Item 6. | Selected Financial Data (in thousands). |
| | Years Ended December 31, | |
| | 2008 | | 2007 | | 2006 | | 2005 | | 2004 | |
OPERATING DATA: | | | | | | | | | | | |
Net Sales | | $ | 227,143 | | $ | 207,768 | | $ | 190,674 | | $ | 166,585 | | $ | 151,398 | |
Cost of Sales | | 133,872 | | 127,977 | | 117,596 | | 97,493 | | 83,908 | |
Gross Profit | | 93,271 | | 79,791 | | 73,078 | | 69,092 | | 67,490 | |
| | | | | | | | | | | |
Operating Expenses: | | | | | | | | | | | |
Selling, general and administrative | | 53,127 | | 48,133 | | 45,486 | | 38,579 | | 35,071 | |
Research and development | | 9,160 | | 8,688 | | 8,582 | | 6,992 | | 5,079 | |
| | | | | | | | | | | |
Total operating expenses | | 62,287 | | 56,821 | | 54,068 | | 45,571 | | 40,150 | |
| | | | | | | | | | | |
Income From Operations | | 30,984 | | 22,970 | | 19,010 | | 23,521 | | 27,340 | |
| | | | | | | | | | | |
Other Income (Expense): | | | | | | | | | | | |
Litigation settlement | | | | | | | | | | 100 | |
Interest income | | 781 | | 393 | | 250 | | 491 | | 556 | |
Interest expense | | (17 | ) | (3 | ) | (12 | ) | (18 | ) | (6 | ) |
Other income (expense) | | 97 | | 39 | | (64 | ) | (94 | ) | 16 | |
Other income—net | | 861 | | 429 | | 174 | | 379 | | 666 | |
| | | | | | | | | | | |
Income before income taxes | | 31,845 | | 23,399 | | 19,184 | | 23,900 | | 28,006 | |
| | | | | | | | | | | |
Income Tax Expense | | 11,118 | | 7,811 | | 6,883 | | 8,122 | | 10,074 | |
| | | | | | | | | | | |
Net Income | | $ | 20,727 | | $ | 15,588 | | $ | 12,301 | | $ | 15,778 | | $ | 17,932 | |
| | | | | | | | | | | |
Earnings Per Common Share: | | | | | | | | | | | |
Diluted | | $ | 0.73 | | $ | 0.55 | | $ | 0.44 | | $ | 0.57 | | $ | 0.65 | |
| | | | | | | | | | | |
Average Common Shares: | | | | | | | | | | | |
Diluted | | 28,550 | | 28,204 | | 28,245 | | 27,847 | | 27,691 | |
| | | | | | | | | | | |
BALANCE SHEET DATA: | | | | | | | | | | | |
Working capital | | $ | 84,283 | | $ | 60,194 | | $ | 54,972 | | $ | 43,693 | | $ | 54,944 | |
Total assets | | 231,776 | | 200,420 | | 182,668 | | 162,247 | | 139,877 | |
Long-term debt | | 0 | | 0 | | 0 | | 2 | | 5 | |
Stockholders’ equity | | $ | 194,305 | | $ | 164,368 | | $ | 151,212 | | $ | 132,484 | | $ | 111,052 | |
During the quarter ended December 31 2006, we determined it was not likely that we would pursue the product associated with the intellectual property and assets acquired from Sub-Q, Inc. (“Sub-Q”) due to other priorities and opportunities. Therefore, we recorded an impairment charge of approximately $929,000, during the quarter primarily relating to intellectual property assets acquired from Sub-Q in March 2005.
During the quarter ended December 31, 2005, we adopted Statement of Financial Accounting Standards (“SFAS”) No. 151, Inventory Costs, and recorded additional expenses to cost of sales of $415,000, research and development expense of $83,000 and selling, general and administrative expense of $37,000.
During the year ended December 31, 2004, we accrued severance costs totaling approximately $663,000 related to the employment termination of certain executive employees.
17
Table of Contents
Item 7. | Management’s Discussion and Analysis of Financial Condition and Results of Operations. |
OVERVIEW
Despite difficult worldwide economic conditions during 2008, we reported record sales and earnings for the twelve months ended December 31, 2008. This improvement, compared to our 2007 results, was largely the result of a 9% increase in sales, a substantial improvement in gross margins of 270 basis points, and relatively flat operating expenses as a percentage of sales, and was partially offset by an increase in our effective tax rate of 150 basis points. All of these improvements produced record earnings of $20.7 million, up 33% from the prior year. During 2009, we plan to implement new automation and manufacturing cost saving improvements related to logistics and product labeling, and introduce new products through organic growth and acquisitions, which we believe will increase our average product margins. Also, we plan to identify a location outside the U.S. to locate a manufacturing site in an effort to reduce our product costs. To date, the overall slowdown in the economy that began in 2008 and has continued into 2009 has not significantly affected our operations, as many of our products are not used for elective procedures, and are not capital equipment.
For the year ended December 31, 2008, we reported net sales of $227.1 million, up $19.4 million or 9% over 2007 net sales. Net sales growth in 2008 was primarily driven by increased sales of our custom kit and procedure tray products (up 11%), stand-alone products (up 9%), including swabbable valves, stopcocks, OEM parts, tubing, and hemostasis valves and catheters (up 20%), particularly our Prelude® sheath product line, Mini Access Kit™ catheter product line, Micrus catheter product line and diagnostic cardiology catheters.
Our gross margins as a percentage of sales were 41.1% for the year ended December 31, 2008, compared to 38.4% for year ended December 31, 2007. This significant improvement resulted primarily from lower average fixed overhead unit costs resulting from increased production (unit costs decreased as fixed costs were shared over an increased number of units), lower unit costs for products manufactured in Mexico, price increases and production automation. These improvements also helped offset raw material and production labor cost increases that occurred during 2008.
Net income increased for the year ended December 31, 2008 to $20.7 million, compared to $15.6 million for the prior year. When compared to the prior year, net income for the year ended December 31, 2008 was positively affected by increased sales volumes and higher gross margins, and partially offset by a higher effective income tax rate.
RESULTS OF OPERATIONS
The following table sets forth certain operational data as a percentage of sales for the periods indicated:
| | 2008 | | 2007 | | 2006 | |
Sales | | 100.0 | % | 100.0 | % | 100.0 | % |
Gross profit | | 41.1 | | 38.4 | | 38.3 | |
Selling, general and administrative expenses | | 23.4 | | 23.2 | | 23.9 | |
Research and development expenses | | 4.0 | | 4.2 | | 4.5 | |
Income from operations | | 13.6 | | 11.1 | | 10.0 | |
Income before income tax expense | | 14.0 | | 11.3 | | 10.1 | |
Net income | | 9.1 | | 7.5 | | 6.5 | |
Our net sales increased by $19.4 million, or 9.3%, in 2008, compared to an increase of $17.1 million, or 9.0%, in 2007, and an increase of $24.1 million, or 14.5%, in 2006. We report sales in four product categories. Listed below are the sales relating to these product categories for the years ended December 31, 2008, 2007, 2006 and 2005:
| | December 31, | |
| | % Change | | 2008 | | % Change | | 2007 | | % Change | | 2006 | | 2005 | |
Stand-alone devices | | 9% | | $ | 68,005 | | 12% | | $ | 62,417 | | 19% | | $ | 55,824 | | $ | 46,900 | |
Custom kits & procedure trays | | 11% | | 66,584 | | 7% | | 60,013 | | 15% | | 56,009 | | 48,740 | |
Inflation devices | | 3% | | 61,656 | | 5% | | 59,595 | | 9% | | 56,978 | | 52,319 | |
Catheters | | 20% | | 30,898 | | 18% | | 25,743 | | 17% | | 21,863 | | 18,626 | |
Total | | 9% | | $ | 227,143 | | 9% | | $ | 207,768 | | 14% | | $ | 190,674 | | $ | 166,585 | |
Our sales increased during 2008, notwithstanding the fact that the markets for many of our products are experiencing slight pricing declines as our customers try to reduce their costs. Substantially all of the increase in our
18
Table of Contents
revenues was attributable to increased unit sales, except for a slight increase in revenues attributable to an increase in the exchange rate between the Euro and the U.S. Dollar which increased sales by 0.6% in 2008 compared to 2007, 0.9% in 2007 compared to 2006, and 0.1% in 2006 compared to 2005. Historically, an important part of our revenue growth came from increases in the number of procedures performed for patients in a given year. Starting in April 2007, the growth rate of coronary stents and other related procedures in the U.S. dropped significantly, reducing the traditional growth rate of our U.S. direct sales. New products are another source of revenue growth. In 2008, 2007 and 2006, our sales of new products represented 2%, 6% and 9% of sales, respectively. Included in those sales are revenues from recent acquisitions of 1%, 3% and 3% for 2008, 2007 and 2006, respectively. The third main source of revenue increases came from market share gains in our existing product lines.
International sales in 2008 were approximately $72.5 million, or 32% of total sales; international sales in 2007 were approximately $64.9 million, or 31% of total sales; international sales in 2006 were approximately $53.7 million, or 28% of total sales. These increases primarily resulted from greater acceptance of our products in international markets, ongoing growth in our European direct sales, and increased sales related to improvement in the exchange rate between the Euro and the U.S. Dollar, as discussed above. Our total direct sales in France, Germany, the U.K., Belgium, The Netherlands, Denmark, Sweden, Austria and Ireland were $27.1 million, $23.8 million, and $20.0 million in 2008, 2007 and 2006, respectively.
Our gross profit as a percentage of sales was 41.1%, 38.4%, and 38.3%, in 2008, 2007 and 2006, respectively. The increase in gross margins in 2008 resulted primarily from lower average fixed overhead unit costs resulting from increased production (unit costs decreased as fixed costs were shared over an increased number of units), lower unit costs for products manufactured in Mexico, customer price increases and production automation. These improvements also helped offset raw material and production labor cost increases that occurred during 2008. The increase in gross margins in 2007 was principally the result of production efficiencies resulting in lower headcount, product mix improvement, the transfer of the manufacturing process of four products to Mexico, and certain automation projects. The decline in gross margins in 2006 resulted primarily from investments made during the second half of 2005 for new facilities and related costs (i.e. utilities, maintenance, cleaning and taxes) and equipment. Gross margins in 2006 were also affected by the increased cost of direct labor, increased health insurance costs, our adoption of SFAS No. 123(R), Share-Based Payment, (“SFAS No. 123(R)”), effective January 1, 2006, and increased procedure tray sales in 2006, which have lower gross margins than our overall gross margins.
Our selling, general, and administrative expenses increased $5.0 million, or 10%, in 2008 over 2007; $2.6 million, or 6%, in 2007 over 2006; $6.9 million, or 18%, in 2006 over 2005. Selling, general and administrative expenses as a percentage of sales increased slightly in 2008 when compared to the prior year. This increase was primarily the result of higher commissions commensurate with higher sales, management and sales bonuses for meeting quarterly and annually objectives, increased travel-related expenses and increased national account administration fees. Selling, general and administrative expenses for 2008 were also affected by approximately $415,000 of damages (net of insurance reimbursement of $179,000) sustained by our Angleton, Texas facility during Hurricane Ike in September 2008. The significant (70 basis points) decrease in selling, general and administrative expenses in 2007 as a percentage of sales, was primarily the result of operating leverage from reducing head count, while increasing sales. The increase in selling, general, and administrative costs in 2006 as a percentage of sales, was primarily the result of a full year of costs associated with the hiring of 17 additional sales representatives in the second half of 2005, approximately $945,000 attributable to the adoption of SFAS No. 123(R) and an impairment charge of approximately $929,000, primarily relating to intellectual property assets acquired from Sub-Q in March 2005.
Research and development expenses increased 5% to $9.2 million in 2008, compared to $8.7 million in 2007. Our R&D expense for 2007 increased 1% to $8.7 million, compared to $8.6 million in 2006; R&D expenses for 2006 increased 23% to $8.6 million, compared to $7.0 million in 2005. The increase in R&D expenses in 2008, 2007 and 2006 was related primarily to R&D head count additions and indirect costs to support an increase in the number of new products we launched. Our R&D expenses as a percentage of sales were 4.0% for 2008, 4.2% for 2007 and 4.5% for 2006. We have a full pipeline of new products and management believes that we have an effective level of capabilities and expertise to continue the flow of new internally-developed products into the future.
Our effective income tax rates for 2008, 2007, and 2006 were 35%, 33%, and 36%, respectively. The increase in the effective income tax rate for 2008 over 2007 was primarily the result of investment losses sustained in our deferred compensation plan that are not deductible for tax purposes. The decrease in the effective income tax rate for 2007 over 2006 was primarily the result of the unrecognized tax benefits, related to Financial Accounting Standards Board Interpretation (“FIN”) No. 48, Accounting for Uncertainty in Income Taxes, which expired on our 2002 federal, state, and foreign tax returns and a non-taxed gain related to corporate-owned variable life insurance contracts for our deferred compensation plan. The increase in the effective tax rate for 2006 over 2005 was primarily the result of our reimbursement of costs incurred by our Irish subsidiary for the development of two new products which are taxed at a lower income tax rate than our U.S. operations.
19
Table of Contents
Our other income for 2008, 2007, and 2006 was approximately $861,000, $429,000, and $174,000, respectively. The increase in other income for 2008 over 2007 and 2007 over 2006 was primarily the result of an increase in interest income attributable to higher average cash balances and higher interest rates. The decrease in other income for 2006 over 2005 was primarily the result of a decrease in cash balances and a corresponding decrease in interest income of approximately $241,000.
Our net income for 2008, 2007, and 2006 was approximately $20.7 million, $15.6 million and $12.3 million, respectively. Net income for 2008 was positively affected by increased sales volumes and higher gross margins, and partially offset by higher effective income tax rates. Net income for 2007 was positively affected by increased sales volumes, higher gross margins, lower operating expenses as a percentage of sales and a lower effective income tax rate. Net income for 2006 was negatively affected by lower gross margins, higher research and development spending, increased selling, general and administrative expenses, and positively affected by increased sales volumes.
Under SFAS No. 142, Goodwill and Other Intangible Assets (“SFAS No. 142”), which we adopted effective January 1, 2002, we no longer amortize goodwill from business acquisitions, but review annually the impairment of goodwill, or more frequently if impairment indicators arise. We completed our initial testing of goodwill as of January 1, 2002 and determined that there was no impairment. We have elected to perform our annual testing of goodwill impairment as of July 1 of the applicable fiscal year. As of July 1, 2008, we performed our annual testing of goodwill for impairment and determined that there was no impairment. Also, as of December 31, 2008, we concluded there were no events or circumstances indicating that impairment had occurred. During the fourth quarter of 2006, we determined that it was unlikely we would pursue the product associated with the intellectual property acquired from Sub-Q due to our decision to pursue other priorities and opportunities that we believe are more favorable to us. Therefore, we recorded an impairment charge of approximately $929,000 in selling, general and administrative expense for 2006, which included approximately $500,000 related to goodwill. We had no impairments in goodwill for the years ended December 31, 2008 and 2007. The remaining unamortized amount of goodwill at December 31, 2008 was approximately $13.0 million.
LIQUIDITY AND CAPITAL RESOURCES
Capital Commitments and Contractual Obligations
The following table summarizes our capital commitments and contractual obligations as of December 31, 2008, including operating lease payments and office lease payments, as well as the future periods in which such payments are currently anticipated to become due:
| | Payment due by period (in thousands) | |
Contractual Obligations | | Total | | Less than 1 Year | | 1-3 Years | | 4-5 Years | | After 5 Years | |
Operating leases | | 19,381 | | 2,122 | | 3,791 | | 3,362 | | 10,106 | |
Royalty obligations | | 258 | | 50 | | 100 | | 50 | | 58 | |
Total contractual cash | | 19,639 | | 2,172 | | 3,891 | | 3,412 | | 10,164 | |
We have approximately $2.8 million of unrecognized tax positions that have been recognized as liabilities in accordance with FIN 48 that have not been included in the contractual obligations table due to uncertainty as to when such amounts may be settled.
Additional information regarding our capital commitments and contractual obligations, including royalty payments, is contained in notes 7, 8, and 12 of the notes to our consolidated financial statements, set forth in Item 8.
Cash Flows
Our cash flow from operations was $28.0 million in 2008, a decrease, of $4.0 million over 2007. This decrease in cash flow from operations in 2008, when compared to 2007, came mostly from an increase in inventories compared to a decrease in 2007 (an approximate change of $9.1 million), which was partially offset by an increase in net income in 2008 over 2007. Our working capital for 2008, 2007, and 2006 was $84.3 million, $60.2 million, and $55.0 million, respectively. The increase in working capital for 2008 over 2007 was primarily the result of an increase in cash generated from our net income and cash generated from the issuance of shares of Common Stock related to employee stock option exercises. The increase in working capital for 2007 over 2006 was primarily the result of an increase in cash net of the reduction in inventories of $4.5 million as we focused on improving our inventory turns. The increase in working capital for 2006 over 2005 was primarily the result of an increase in cash flow from operations of $8.0 million and a reduction in the amount of capital expenditures made, when compared to 2005.
20
Table of Contents
On December 7, 2006, we entered into an unsecured loan agreement with Bank of America, N.A. (“Bank of America”), whereby Bank of America agreed to provide us a line of credit in the amount of $30,000,000. Prior to December 7, 2006, we maintained a long-term revolving credit facility (the “Facility”) with Zions First National Bank (“Zions”). The Facility had a credit limit of $500,000 for years 2005 and 2006. The Facility expired on June 30, 2006. On December 8, 2006, we entered into an unsecured loan agreement with Zions, whereby Zions agreed to provide us a line of credit in the amount of $1,000,000. We had $0 outstanding under our lines of credit as of December 31, 2008, 2007 and 2006.
Historically, we have incurred significant expenses in connection with product development and introduction of new products. Substantial capital has also been required to finance the increase in our receivables and inventories associated with our increased sales. During 2008, we spent approximately $7.8 million on various production equipment related to automation, capacity increases, and product launches, and approximately $2.1 million to complete our new customer service and distribution facility for our European operations in The Netherlands. During 2007, we spent approximately $9.4 million on various production equipment related to automation and new product launches, approximately $3.0 million for construction costs on a new customer service and distribution facility for our European operations in The Netherlands and $2.0 million for improvements made to a production clean room in South Jordan, Utah. During 2006, we spent approximately $9.6 million for various production equipment, approximately $2.1 million on building and leasehold improvements, and approximately $1.7 million on the purchase of real estate in The Netherlands to build a distribution facility. Our principal source of funding for these and other expenses has been cash generated from operations, sales of equity, and bank lines of credit. We currently believe that our present sources of liquidity and capital are adequate for current operations and for the foreseeable future.
CRITICAL ACCOUNTING POLICIES AND ESTIMATES
The SEC has requested that all registrants address their most critical accounting policies. The SEC has indicated that a “critical accounting policy” is one which is both important to the representation of the registrant’s financial condition and results and requires management’s most difficult, subjective or complex judgments, often as a result of the need to make estimates about the effect of matters that are inherently uncertain. We base our estimates on past experience and on various other assumptions our management believes to be reasonable under the circumstances, the results of which form the basis for making judgments about carrying values of assets and liabilities that are not readily apparent from other sources. Actual results will differ, and may differ materially from these estimates under different assumptions or conditions. Additionally, changes in accounting estimates could occur in the future from period to period. Our management has discussed the development and selection of our most critical financial estimates with the audit committee of our Board of Directors. The following paragraphs identify our most critical accounting policies:
Inventory Obsolescence Reserve. Our management reviews on a regular basis inventory quantities on hand for unmarketable and/or slow-moving products that may expire prior to being sold. This review of inventory quantities for unmarketable and/or slow moving products is based on estimates of forecasted product demand prior to expiration lives. If market conditions become less favorable than those projected by our management, additional inventory write-downs may be required. We believe that the amount included in our obsolescence reserve has been a historically accurate estimate of the unmarketable and/or slow moving products that may expire prior to being sold. Our obsolescence reserve was approximately $2.3 million as of December 31, 2008.
Allowance for Doubtful Accounts. A majority of our receivables are with hospitals which, over our history, have demonstrated favorable collection rates. Therefore, we have experienced relatively minimal bad debts from hospital customers. In limited circumstances, we have written off minimal bad debts as the result of the termination of foreign distributors. The most significant write-offs over our history have come from U.S. packers who bundle our products in surgical trays.
We maintain allowances for doubtful accounts for estimated losses resulting from the inability of our customers to make required payments. The allowance is based upon historical experience and a review of individual customer balances. If the financial condition of our customers were to deteriorate, resulting in an impairment of their ability to make payments, additional allowances may be required. Our bad debt reserve was approximately $505,000 at December 31, 2008 which is consistent with historical collection experience.
Stock-Based Compensation. We account for stock-based compensation in accordance with SFAS No. 123(R). Under the fair value recognition provisions of this statement, we measure share-based compensation cost at the grant date based on the value of the award and recognize the cost as an expense over the term of the vesting period. Judgment is required in estimating the amount of share-based awards that are expected to be forfeited. If actual results differ
21
Table of Contents
significantly from these estimates, stock-based compensation expense and our results of operations could be materially impacted.
Income Taxes. We adopted the provisions of FIN 48 effective January 1, 2007. Under FIN 48, tax positions shall initially be recognized in the financial statements when it is more likely than not the position will be sustained upon examination by the tax authorities. Such tax positions shall initially and subsequently be measured as the largest amount of tax benefit that has a greater than 50% likelihood of being realized upon ultimate settlement with the tax authorities assuming full knowledge of the position and all relevant facts. Although we believe our provisions for FIN 48 unrecognized tax positions are reasonable, we can make no assurance that the final tax outcome of these matters will not be different from that which we have reflected in our income tax provisions and accruals. The tax law is subject to varied interpretations, and we have taken positions related to certain matters where the law is subject to interpretation. Such differences could have a material impact on our income tax provisions and operating results in the period(s) in which we make such determination.
Item 7A. | Quantitative and Qualitative Disclosure About Market Risk. |
Our principal market risk relates to changes in the value of the Euro and Great Britain Pound (“GBP”) relative to the value of the U.S. Dollar. Our consolidated financial statements are denominated in, and our principal currency is, the U.S. Dollar. A portion of our revenues ($25.6 million, representing approximately 11% of aggregate revenues), for the year ended December 31, 2008 was attributable to sales that were denominated in Euros and GBPs, all other international sales were denominated in U.S. Dollars. Certain expenses are also denominated in Euros and GBPs, which partially offsets risks associated with fluctuations of exchanges rates between the Euro and GBP on the one hand, and the U.S. Dollar on the other hand. Because of our Euro and GBP-denominated revenues and expenses, in a year in which our Euro and GBP-denominated revenues exceed our Euro and GBP-based expenses, the value of such Euro and GBP-denominated net income increases if the value of the Euro and GBP increase relative to the value of the U.S. Dollar, and decreases if the value of the Euro and GBP decrease relative to the value of the U. S. Dollar. During the year ended December 31, 2008, the exchange rate between the Euro and GBP against the U.S. Dollar resulted in an increase of our gross revenues of approximately $1.3 million and 0.10% in gross profit.
On November 28, 2008, we forecasted a net exposure for December 31, 2008 representing the difference between Euro and GBP denominated receivables and Euro and GBP denominated payables of approximately 147,000 Euros and 264,000 GBPs, respectively. In order to partially offset such risks, on November 28, 2007, we entered into a 30-day forward contract for Euros and GBPs. We generally enter into similar economic transactions at various times during the year to partially offset exchange rate risks we bear throughout the year. During the years ended December 31, 2008 and 2007, we experienced a net gain of approximately $52,000 and $29,000, respectively, from financing transactions executed during 2008 and 2007 in an effort to limit our exposure to fluctuations in the exchange rates of the Euro and GBP relative to the U.S. Dollar. We do not purchase or hold derivative financial instruments for speculative or trading purposes.
Another market risk relates to variable rate debt. As of December 31, 2008, we had no variable rate debt. As long as we do not have variable rate debt, our interest expense would not be affected by changes in interest rates.
22
Table of Contents
Item 8. | Financial Statements and Supplementary Data. |
REPORT OF INDEPENDENT REGISTERED PUBLIC ACCOUNTING FIRM
To the Board of Directors and Stockholders of Merit Medical Systems, Inc.:
We have audited the accompanying consolidated balance sheets of Merit Medical Systems, Inc., and subsidiaries (the “Company”) as of December 31, 2008 and 2007, and the related consolidated statements of income, stockholders’ equity, and cash flows for each of the three years in the period ended December 31, 2008. Our audits also included the financial statement schedule listed in the Index at Item 15. These financial statements and financial statement schedule are the responsibility of the Company’s management. Our responsibility is to express an opinion on the financial statements and financial statement schedule based on our audits.
We conducted our audits in accordance with the standards of the Public Company Accounting Oversight Board (United States). Those standards require that we plan and perform the audit to obtain reasonable assurance about whether the financial statements are free of material misstatement. An audit includes examining, on a test basis, evidence supporting the amounts and disclosures in the financial statements. An audit also includes assessing the accounting principles used and significant estimates made by management, as well as evaluating the overall financial statement presentation. We believe that our audits provide a reasonable basis for our opinion.
In our opinion, such consolidated financial statements present fairly, in all material respects, the financial position of the Company as of December 31, 2008 and 2007, and the results of its operations and its cash flows for each of the three years in the period ended December 31, 2008, in conformity with accounting principles generally accepted in the United States of America. Also, in our opinion, such financial statement schedule, when considered in relation to the basic consolidated financial statements taken as a whole, presents fairly, in all material respects, the information set forth therein.
As discussed in Note 1 to the consolidated financial statements, in 2006, the Company changed its method of accounting for stock-based compensation to conform to Statement of Financial Accounting Standards (“SFAS”) No. 123 (revised 2004), Share-Based Payment, in 2007, the Company changed its method of accounting for uncertain tax positions to conform to Financial Accounting Standards Board Interpretation (“FIN”) No. 48, Accounting for Uncertainty in Income Taxes, and in 2008, the Company adopted SFAS No. 157, Fair Value Measurements.
We have also audited, in accordance with the standards of the Public Company Accounting Oversight Board (United States), the Company’s internal control over financial reporting as of December 31, 2008, based on the criteria established in Internal Control — Integrated Framework issued by the Committee of Sponsoring Organizations of the Treadway Commission and our report dated March 2, 2009, expressed an unqualified opinion on the effectiveness of the Company’s internal control over financial reporting.
/s/ DELOITTE & TOUCHE LLP
Salt Lake City, Utah
March 2, 2009
23
Table of Contents
MERIT MEDICAL SYSTEMS, INC. AND SUBSIDIARIES
CONSOLIDATED BALANCE SHEETS
DECEMBER 31, 2008 AND 2007
(In thousands)
| | 2008 | | 2007 | |
ASSETS | | | | | |
| | | | | |
CURRENT ASSETS: | | | | | |
Cash and cash equivalents | | $ | 34,030 | | $ | 17,574 | |
Trade receivables — net of allowance for uncollectible accounts — 2008 – $505 and 2007 – $497 | | 27,749 | | 26,619 | |
Employee receivables | | 126 | | 144 | |
Other receivables | | 818 | | 1,140 | |
Inventories — net | | 38,358 | | 34,106 | |
Prepaid expenses and other assets | | 985 | | 1,297 | |
Deferred income tax assets | | 2,782 | | 811 | |
Income tax refund receivable | | 607 | | 297 | |
| | | | | |
Total current assets | | 105,455 | | 81,988 | |
| | | | | |
PROPERTY AND EQUIPMENT: | | | | | |
Land and land improvements | | 7,992 | | 7,977 | |
Buildings | | 49,793 | | 43,147 | |
Manufacturing equipment | | 68,184 | | 61,448 | |
Furniture and fixtures | | 16,689 | | 17,110 | |
Leasehold improvements | | 9,868 | | 9,870 | |
Construction-in-progress | | 7,599 | | 10,680 | |
| | | | | |
Total property and equipment | | 160,125 | | 150,232 | |
| | | | | |
Less accumulated depreciation | | (56,186 | ) | (50,536 | ) |
| | | | | |
Property and equipment — net | | 103,939 | | 99,696 | |
| | | | | |
OTHER ASSETS: | | | | | |
Intangibles — net of accumulated amortization — 2008 — $3,122 and 2007 – $2,171 | | 6,913 | | 6,163 | |
Goodwill | | 13,048 | | 9,527 | |
Other assets | | 2,325 | | 2,964 | |
Deferred income tax assets | | 23 | | 4 | |
Deposits | | 73 | | 78 | |
| | | | | |
Total other assets | | 22,382 | | 18,736 | |
| | | | | |
TOTAL | | $ | 231,776 | | $ | 200,420 | |
See notes to consolidated financial statements. | | | | (Continued) |
24
Table of Contents
MERIT MEDICAL SYSTEMS, INC. AND SUBSIDIARIES
CONSOLIDATED BALANCE SHEETS
DECEMBER 31, 2008 AND 2007
(In thousands)
| | 2008 | | 2007 | |
LIABILITIES AND STOCKHOLDERS’ EQUITY | | | | | |
| | | | | |
CURRENT LIABILITIES: | | | | | |
Trade payables | | $ | 10,622 | | $ | 10,275 | |
Accrued expenses | | 9,973 | | 9,492 | |
Advances from employees | | 211 | | 267 | |
Liabilities related to unrecognized tax positions | | | | 1,023 | |
Income taxes payable | | 366 | | 737 | |
| | | | | |
Total current liabilities | | 21,172 | | 21,794 | |
| | | | | |
DEFERRED INCOME TAX LIABILITIES | | 8,771 | | 6,082 | |
| | | | | |
LIABILITIES RELATED TO UNRECOGNIZED TAX POSITIONS | | 2,818 | | 2,588 | |
| | | | | |
DEFERRED COMPENSATION PAYABLE | | 2,348 | | 3,063 | |
| | | | | |
DEFERRED CREDITS | | 1,994 | | 2,105 | |
| | | | | |
OTHER LONG-TERM OBLIGATIONS | | 368 | | 420 | |
| | | | | |
Total liabilities | | 37,471 | | 36,052 | |
| | | | | |
COMMITMENTS AND CONTINGENCIES (Notes 2, 7, 8, 12 and 16) | | | | | |
| | | | | |
STOCKHOLDERS’ EQUITY: | | | | | |
Preferred stock — 5,000 shares authorized as of December 31, 2008 and 2007; no shares issued | | | | | |
Common stock, no par value; shares authorized — 2008 - 100,000 and 2007 - 50,000; issued shares as of December 31, 2008 - 28,093 and December 31, 2007 - 27,413 | | 61,689 | | 52,477 | |
Retained earnings | | 132,674 | | 111,947 | |
Accumulated other comprehensive loss | | (58 | ) | (56 | ) |
| | | | | |
Total stockholders’ equity | | 194,305 | | 164,368 | |
| | | | | |
TOTAL | | $ | 231,776 | | $ | 200,420 | |
See notes to consolidated financial statements. | (Concluded) |
25
Table of Contents
MERIT MEDICAL SYSTEMS, INC. AND SUBSIDIARIES
CONSOLIDATED STATEMENTS OF INCOME
YEARS ENDED DECEMBER 31, 2008, 2007, AND 2006
(In thousands except per share amounts)
| | 2008 | | 2007 | | 2006 | |
| | | | | | | |
NET SALES | | $ | 227,143 | | $ | 207,768 | | $ | 190,674 | |
| | | | | | | |
COST OF SALES | | 133,872 | | 127,977 | | 117,596 | |
| | | | | | | |
GROSS PROFIT | | 93,271 | | 79,791 | | 73,078 | |
| | | | | | | |
OPERATING EXPENSES: | | | | | | | |
Selling, general, and administrative | | 53,127 | | 48,133 | | 45,486 | |
Research and development | | 9,160 | | 8,688 | | 8,582 | |
| | | | | | | |
Total operating expenses | | 62,287 | | 56,821 | | 54,068 | |
| | | | | | | |
INCOME FROM OPERATIONS | | 30,984 | | 22,970 | | 19,010 | |
| | | | | | | |
OTHER INCOME (EXPENSE): | | | | | | | |
Interest income | | 781 | | 393 | | 250 | |
Interest expense | | (17 | ) | (3 | ) | (12 | ) |
Other income (expense) | | 97 | | 39 | | (64 | ) |
| | | | | | | |
Other income — net | | 861 | | 429 | | 174 | |
| | | | | | | |
INCOME BEFORE INCOME TAXES | | 31,845 | | 23,399 | | 19,184 | |
| | | | | | | |
INCOME TAX EXPENSE | | 11,118 | | 7,811 | | 6,883 | |
| | | | | | | |
NET INCOME | | $ | 20,727 | | $ | 15,588 | | $ | 12,301 | |
| | | | | | | |
EARNINGS PER COMMON SHARE: | | | | | | | |
Basic | | $ | 0.75 | | $ | 0.57 | | $ | 0.45 | |
| | | | | | | |
Diluted | | $ | 0.73 | | $ | 0.55 | | $ | 0.44 | |
| | | | | | | |
AVERAGE COMMON SHARES: | | | | | | | |
Basic | | 27,769 | | 27,425 | | 27,333 | |
| | | | | | | |
Diluted | | 28,550 | | 28,204 | | 28,245 | |
See notes to consolidated financial statements.
26
Table of Contents
MERIT MEDICAL SYSTEMS, INC. AND SUBSIDIARIES
CONSOLIDATED STATEMENTS OF STOCKHOLDERS’ EQUITY
YEARS ENDED DECEMBER 31, 2008, 2007, AND 2006
(In thousands)
| | | | | | | | | | Accumulated | |
| | | | | | | | | | Other | |
| | | | Common Stock | | Retained | | Comprehensive | |
| | Total | | Shares | | Amount | | Earnings | | Loss | |
| | | | | | | | | | | |
BALANCE — January 1, 2006 | | $ | 132,484 | | 27,163 | | $ | 48,198 | | $ | 84,668 | | $ | (382 | ) |
| | | | | | | | | | | |
Comprehensive income: | | | | | | | | | | | |
Net income | | 12,301 | | | | | | 12,301 | | | |
Foreign currency translation adjustment | | 231 | | | | | | | | 231 | |
| | | | | | | | | | | |
Total comprehensive income | | 12,532 | | | | | | | | | |
| | | | | | | | | | | |
Tax benefit attributable to appreciation of common stock options exercised | | 1,155 | | | | 1,155 | | | | | |
Stock-based compensation expense | | 1,502 | | | | 1,502 | | | | | |
Issuance of common stock under Employee Stock Purchase Plans | | 369 | | 29 | | 369 | | | | | |
Options exercised | | 3,170 | | 455 | | 3,170 | | | | | |
| | | | | | | | | | | |
BALANCE — December 31, 2006 | | 151,212 | | 27,647 | | 54,394 | | 96,969 | | (151 | ) |
| | | | | | | | | | | |
Comprehensive income: | | | | | | | | | | | |
Net income | | 15,588 | | | | | | 15,588 | | | |
Foreign currency translation adjustment | | 95 | | | | | | | | 95 | |
| | | | | | | | | | | |
Total comprehensive income | | 15,683 | | | | | | | | | |
| | | | | | | | | | | |
Cumulative effect of a change in accounting principle - adoption of FIN 48 | | (610 | ) | | | | | (610 | ) | | |
Tax benefit attributable to appreciation of common stock options exercised | | 500 | | | | 500 | | | | | |
Stock-based compensation expense | | 1,130 | | | | 1,130 | | | | | |
Issuance of common stock under Employee Stock Purchase Plans | | 323 | | 27 | | 323 | | | | | |
Stock repurchases | | (5,407 | ) | (464 | ) | (5,407 | ) | | | | |
Options exercised | | 1,537 | | 203 | | 1,537 | | | | | |
| | | | | | | | | | | |
BALANCE — December 31, 2007 | | 164,368 | | 27,413 | | 52,477 | | 111,947 | | (56 | ) |
| | | | | | | | | | | |
Comprehensive income: | | | | | | | | | | | |
Net income | | 20,727 | | | | | | 20,727 | | | |
Foreign currency translation adjustment | | (2 | ) | | | | | | | (2 | ) |
| | | | | | | | | | | |
Total comprehensive income | | 20,725 | | | | | | | | | |
| | | | | | | | | | | |
Tax benefit attributable to appreciation of common stock options exercised | | 2,044 | | | | 2,044 | | | | | |
Stock-based compensation expense | | 962 | | | | 962 | | | | | |
Issuance of common stock under Employee Stock Purchase Plans | | 305 | | 19 | | 305 | | | | | |
Warrants exercised | | 496 | | 49 | | 496 | | | | | |
Options exercised | | 5,405 | | 612 | | 5,405 | | | | | |
| | | | | | | | | | | |
BALANCE — December 31, 2008 | | $ | 194,305 | | 28,093 | | $ | 61,689 | | $ | 132,674 | | $ | (58 | ) |
See notes to consolidated financial statements.
27
Table of Contents
MERIT MEDICAL SYSTEMS, INC. AND SUBSIDIARIES
CONSOLIDATED STATEMENTS OF CASH FLOWS
YEARS ENDED DECEMBER 31, 2008, 2007, AND 2006
(In thousands)
| | 2008 | | 2007 | | 2006 | |
| | | | | | | |
CASH FLOWS FROM OPERATING ACTIVITIES: | | | | | | | |
Net income | | $ | 20,727 | | $ | 15,588 | | $ | 12,301 | |
| | | | | | | |
Adjustments to reconcile net income to net cash provided by operating activities: | | | | | | | |
Depreciation and amortization | | 10,240 | | 9,444 | | 8,275 | |
Losses on sales and/or abandonment of property and equipment | | 526 | | 317 | | 242 | |
Impairment of assets | | | | | | 929 | |
Write-off of certain patents and license agreement | | 164 | | 245 | | 40 | |
Amortization of deferred credits | | (111 | ) | (135 | ) | (175 | ) |
Purchase of trading investments | | (349 | ) | (267 | ) | (499 | ) |
Proceeds from sale of trading investments | | | | 218 | | | |
Unrealized (gains) losses on trading investments | | 987 | | (259 | ) | 206 | |
Deferred income taxes | | (183 | ) | 984 | | 376 | |
Tax benefit attributable to appreciation of common stock options exercised | | (2,044 | ) | (500 | ) | (1,155 | ) |
Stock-based compensation | | 962 | | 1,130 | | 1,502 | |
Changes in operating assets and liabilities net of effects from acquisitions: | | | | | | | |
Trade receivables | | (1,464 | ) | (496 | ) | 57 | |
Employee receivables | | 10 | | 52 | | (76 | ) |
Other receivables | | 304 | | (930 | ) | (52 | ) |
Inventories | | (4,036 | ) | 5,056 | | (6,045 | ) |
Prepaid expenses and other assets | | 301 | | (258 | ) | 6 | |
Income tax refund receivable | | (93 | ) | (194 | ) | | |
Other long-term assets | | | | | | 102 | |
Deposits | | 5 | | 12 | | 9 | |
Trade payables | | 758 | | (671 | ) | 305 | |
Accrued expenses | | 554 | | 872 | | (178 | ) |
Advances from employees | | (57 | ) | 11 | | (81 | ) |
Current liabilities related to unrecognized tax positions | | (1,023 | ) | 1,023 | | | |
Income taxes payable | | 1,692 | | 1,595 | | 2,724 | |
Non-current liabilities related to unrecognized tax positions | | 864 | | (1,010 | ) | | |
Deferred compensation payable | | (715 | ) | 194 | | 506 | |
Other long-term obligations | | (52 | ) | (16 | ) | | |
| | | | | | | |
Total adjustments | | 7,240 | | 16,417 | | 7,018 | |
| | | | | | | |
Net cash provided by operating activities | | 27,967 | | 32,005 | | 19,319 | |
| | | | | | | |
CASH FLOWS FROM INVESTING ACTIVITIES: | | | | | | | |
Capital expenditures for: | | | | | | | |
Property and equipment | | (14,476 | ) | (16,288 | ) | (14,715 | ) |
Patents and trademarks | | (432 | ) | (450 | ) | (283 | ) |
Proceeds from the sale of property and equipment | | 45 | | 11 | | 27 | |
Cash paid in acquisitions | | (5,112 | ) | (4,726 | ) | (3,923 | ) |
| | | | | | | |
Net cash used in investing activities | | (19,975 | ) | (21,453 | ) | (18,894 | ) |
| | | | | | | | | | |
See notes to consolidated financial statements. | | | | | | (Continued) |
28
Table of Contents
MERIT MEDICAL SYSTEMS, INC. AND SUBSIDIARIES
CONSOLIDATED STATEMENTS OF CASH FLOWS
YEARS ENDED DECEMBER 31, 2008, 2007, AND 2006
(In thousands)
| | 2008 | | 2007 | | 2006 | |
| | | | | | | |
CASH FLOWS FROM FINANCING ACTIVITIES: | | | | | | | |
Proceeds from issuance of common stock | | $ | 6,206 | | $ | 1,860 | | $ | 3,539 | |
Excess tax benefits from stock-based compensation | | 2,044 | | 500 | | 1,155 | |
Principal payments on notes payable to financial institutions and capital leases | | | | | | (2 | ) |
Common stock repurchased and retired | | | | (5,407 | ) | | |
| | | | | | | |
Net cash provided by (used in) financing activities | | 8,250 | | (3,047 | ) | 4,692 | |
| | | | | | | |
EFFECT OF EXCHANGE RATES ON CASH | | 214 | | 231 | | 76 | |
| | | | | | | |
NET INCREASE IN CASH AND CASH EQUIVALENTS | | 16,456 | | 7,736 | | 5,193 | |
| | | | | | | |
CASH AND CASH EQUIVALENTS: | | | | | | | |
Beginning of year | | 17,574 | | 9,838 | | 4,645 | |
| | | | | | | |
End of year | | $ | 34,030 | | $ | 17,574 | | $ | 9,838 | |
| | | | | | | |
SUPPLEMENTAL DISCLOSURES OF CASH FLOW INFORMATION — Cash paid during the year for: | | | | | | | |
Interest | | $ | 17 | | $ | 5 | | $ | 11 | |
| | | | | | | |
Income taxes | | $ | 9,853 | | $ | 5,354 | | $ | 3,736 | |
| | | | | | | |
SUPPLEMENTAL DISCLOSURES OF NON-CASH INVESTING AND FINANCING ACTIVITIES | | | | | | | |
Fixed asset purchases in accounts payable | | $ | 847 | | $ | 1,173 | | $ | 1,414 | |
| | | | | | | |
Adoption of FIN 48 | | | | $ | 610 | | | |
See notes to consolidated financial statements. | | | | | | (Continued) |
29
Table of Contents
MERIT MEDICAL SYSTEMS, INC. AND SUBSIDIARIES
CONSOLIDATED STATEMENTS OF CASH FLOWS
YEARS ENDED DECEMBER 31, 2008, 2007, AND 2006
SUPPLEMENTAL DISCLOSURES OF NON-CASH INVESTING AND FINANCING ACTIVITIES:
· During 2008, Merit Medical Systems, Inc. (“Merit” or “we” or “us”) entered into an asset purchase and supply agreement with Tran PA-C to purchase catheter extraction products for $1.5 million. We also accrued $11,000 in acquisition costs. The purchase price was preliminarily allocated to inventories for $71,228, property and equipment for $15,436, customer lists for $80,000, developed technology for $85,000, a covenant not to compete for $30,000 and goodwill for $1,229,336. See summary below (in thousands):
Fair value of assets acquired (including goodwill of $1,229) | | $ | 1,511 | |
Cash paid | | (1,500 | ) |
Accrued expenses | | (11 | ) |
| | | |
Liabilities assumed | | None | |
· During 2008, we entered into an asset purchase and supply agreement with Micrus Endovascular Corporation (“Micrus”) to purchase three catheter platforms for $3.0 million. We also paid $12,300 in acquisition costs. The purchase price was allocated to inventories for $143,939, customer lists for $270,000, developed technology for $330,000, and goodwill for $2,268,361. See summary below (in thousands):
Fair value of assets acquired (including goodwill of $2,268) | | $ | 3,012 | |
Cash paid | | (3,012 | ) |
| | | |
Liabilities assumed | | None | |
· During 2007, we negotiated a distribution agreement with Milamy Partners LLC, a limited liability company (“Milamy”), wherein we purchased the exclusive, worldwide right to distribute KanguruWeb® Abdominal Retraction System in vascular lab markets for $350,000. During 2008, we entered into an agreement with Milamy whereby Milamy agreed to terminate its exclusive license rights with McKnight Investments, LLC (“McKnight”) and substitute Merit as the exclusive licensee of the KanguruWeb® technology in exchange for our payment of $100,000. The purchase price was allocated to a distribution agreement for $450,000. See summary below (in thousands):
Fair value of assets acquired | | $ | 450 | |
Cash paid in 2007 | | (350 | ) |
Cash paid in 2008 | | (100 | ) |
| | | |
Liabilities assumed | | None | |
· During 2008, we paid $500,000 to GMA Company, Ltd (“GMA”) for reaching a milestone identified in a distribution agreement we executed with GMA in 2007. Pursuant to the distribution agreement, GMA granted to us the exclusive distribution rights to sell a micro-catheter. In 2007, we paid $1.0 million to GMA and incurred $4,000 for acquisition costs. An additional $500,000 is payable to GMA upon reaching a certain milestone identified in the distribution agreement. The purchase price was allocated to the distribution agreement for $1,504,000. See summary below (in thousands):
Fair value of assets acquired | | $ | 1,504 | |
Cash paid in 2007 | | (1,004 | ) |
Cash paid in 2008 | | (500 | ) |
| | | |
Liabilities assumed | | None | |
See notes to consolidated financial statements. | (Continued) |
30
Table of Contents
MERIT MEDICAL SYSTEMS, INC. AND SUBSIDIARIES
CONSOLIDATED STATEMENTS OF CASH FLOWS
YEARS ENDED DECEMBER 31, 2008, 2007, AND 2006
· During 2007, we entered into a patent assignment and royalty agreement with Lightek Corporation (“Lightek”), to manufacture and sell a radio-opaque band. We made an initial payment of $228,000 to Lightek and accrued an additional $200,000, which is payable upon reaching certain milestones identified in the patent assignment and royalty agreement. An additional $200,000 payment has not been accrued for as it is contingent upon reaching certain sales levels in the future. We paid $8,400 and accrued $1,600 for acquisition costs. The purchase price was allocated to developed technology for $78,000, customer lists for $240,000, and goodwill for $120,000. See summary below (in thousands):
Fair value of assets acquired (including goodwill of $120) | | $ | 438 | |
Cash paid in 2007 | | (236 | ) |
Accrued purchase price | | (202 | ) |
| | | |
Liabilities assumed | | None | |
· During 2007, we acquired customer relationships of Medrad Sweden, AB (“Medrad”), in a purchase transaction for $124,036. The purchase price was allocated to customer lists for $124,036. See summary below (in thousands):
Fair value of assets acquired | | $ | 124 | |
Cash paid | | (124 | ) |
| | | |
Liabilities assumed | | None | |
· During 2007, we entered into an asset purchase agreement with Datascope Corporation (“Datascope”) to purchase its ProGuide™ catheter in a purchase transaction for $3,290,731, including future minimum royalty payments of $279,181. The purchase price was allocated based on estimated fair values to property and equipment for $25,971, inventories for $778,659, a customer list for $300,000, developed technology for $150,000, a covenant not to compete for $20,000, a trademark for $150,000, and goodwill for $1,866,101. See summary below (in thousands):
Fair value of assets acquired (including goodwill of $1,866) | | $ | 3,291 | |
Cash paid | | (3,012 | ) |
Accrued minimum royalty | | (279 | ) |
| | | |
Liabilities assumed | | None | |
See notes to consolidated financial statements. | (Continued) |
31
Table of Contents
MERIT MEDICAL SYSTEMS, INC. AND SUBSIDIARIES
CONSOLIDATED STATEMENTS OF CASH FLOWS
YEARS ENDED DECEMBER 31, 2008, 2007, AND 2006
· During 2006, we acquired certain assets of Millimed A/S in a purchase transaction for $1,510,664. The purchase price was allocated between property and equipment for $135,590, inventories for $419,162, developed technology for $49,000, and goodwill for $906,912. See summary below (in thousands):
Fair value of assets acquired (including goodwill of $907) | | $ | 1,511 | |
Cash paid | | (1,511 | ) |
| | | |
Liabilities assumed | | None | |
· During 2006, we acquired certain assets and customer relationships of Hypoguard USA, Inc. (“Hypoguard) in a purchase transaction for $1,290,077. The purchase price was allocated between property and equipment for $203,944, inventories for $119,324, developed technology for $350,000 and goodwill for $616,809. See summary below (in thousands):
Fair value of assets acquired (including goodwill of $617) | | $ | 1,290 | |
Cash paid | | (1,290 | ) |
| | | |
Liabilities assumed | | None | |
· During 2006, we acquired certain know how and formulas for producing medical products from a medical device company in a purchase transaction for approximately $1.0 million. During 2006, we made three installment payments totaling $742,501. During 2007, we made a final payment of $254,904. The purchase price was allocated to developed technology for $997,405. See summary below (in thousands):
Fair value of assets acquired | | $ | 997 | |
Cash paid in 2007 | | (255 | ) |
Cash paid in 2006 | | (742 | ) |
| | | |
Liabilities assumed | | None | |
· During 2006, we acquired customer relationships of Q-Tech in a purchase transaction for $380,054. The purchase price was allocated to customer lists for $380,054. See summary below (in thousands):
Fair value of assets acquired | | $ | 380 | |
Cash paid | | (380 | ) |
| | | |
Liabilities assumed | | None | |
See notes to consolidated financial statements. | (Concluded) |
32
Table of Contents
MERIT MEDICAL SYSTEMS, INC. AND SUBSIDIARIES
NOTES TO CONSOLIDATED FINANCIAL STATEMENTS
YEARS ENDED DECEMBER 31, 2008, 2007, AND 2006
1. ORGANIZATION AND SUMMARY OF SIGNIFICANT ACCOUNTING POLICIES
Organization. Merit develops, manufactures and markets disposable medical products primarily used in diagnostic and interventional cardiology and radiology procedures. We consider our operations as one segment, sales of disposable medical devices, as products follow the same production, marketing, sales distribution channels and technology strategies. We manufacture our products in plants located in the United States, the Netherlands and in Ireland. We export sales to dealers and have direct sales forces in the United States and Western Europe (see Note 11). Our consolidated financial statements have been prepared in accordance with accounting principles generally accepted in the United States of America. The following is a summary of the more significant of such policies.
Use of Estimates in Preparing Financial Statements. The preparation of financial statements in conformity with accounting principles generally accepted in the United States of America requires management to make estimates and assumptions that affect the reported amounts of assets and liabilities and disclosure of contingent assets and liabilities at the date of the financial statements and the reported amounts of revenues and expenses during the reporting period. Actual results could differ from those estimates.
Principles of Consolidation. The consolidated financial statements include our wholly-owned subsidiaries. Intercompany balances and transactions have been eliminated.
Cash and Cash Equivalents. For purposes of the statements of cash flows, we consider interest bearing deposits with an original maturity date of three months or less to be cash equivalents.
Receivables. The allowance for uncollectible accounts receivable is based on our historical bad debt experience and on management’s evaluation of its ability to collect individual outstanding balances.
Reclassifications. Subsequent to the issuance of our Annual Report on Form 10-K for the year ended December 31, 2007, we determined that changes to our Deferred Compensation Plan balances should more properly be reflected as net cash provided by operating activities. Accordingly, we have reclassified such changes from investing activities and financing activities to operating activities. Management has concluded that the error was not material to our financial statements, and accordingly the prior period presentation has been revised for 2007 by decreasing net cash provided by operating activities by approximately $114,000 and increasing 2006 net cash provided by operating activities by approximately $213,000.
Inventories. We value our inventories at the lower of cost, determined on a first-in, first-out method, or market value. Market value for raw materials is based on replacement costs. Inventory costs include material, labor and manufacturing overhead. We review inventories on hand at least quarterly and record provisions for estimated excess, slow moving and obsolete inventory, as well as inventory with a carrying value in excess of net realizable value. The regular and systematic inventory valuation reviews include a current assessment of future product demand, historical experience and product expiration.
Goodwill and Intangible Assets. Goodwill is tested for impairment on an annual basis as of July 1, or whenever impairment indicators arise. We utilize several reporting units in evaluating goodwill for impairment. We assess the estimated fair value of reporting units based on discounted future cash flows. If the carrying amount of a reporting unit exceeds the fair value of the reporting unit, an impairment charge is recognized in an amount equal to the excess of the carrying amount of the reporting unit goodwill over the implied fair value of that goodwill.
33
Table of Contents
We evaluate the recoverability of intangible assets periodically and take into account events or circumstances that warrant revised estimates of useful lives or that indicate that impairment exists. All of our intangible assets are subject to amortization. During 2006, we recorded an impairment charge of approximately $929,000, relating to intellectual assets of $872,000 and production equipment of $57,000, which related to assets acquired from Sub-Q, Inc. (“Sub-Q”). Intangible assets are amortized over a straight line basis except that customer lists are generally amortized on an accelerated basis over the following useful lives:
Customer lists and developed technology | | 5–15 years |
Distribution agreements | | 3–11 years |
License agreements and trademarks | | 5–15 years |
Covenant not to compete | | 3-10 years |
Patents | | 17 years |
Royalty income | | 5 years |
Long-Lived Assets. We periodically review the carrying amount of our long-lived assets for impairment. An asset is considered impaired when estimated future cash flows are less than the carrying amount of the asset. In the event the carrying amount of such asset is not considered recoverable, the asset is adjusted to its fair value. Fair value is generally determined based on discounted future cash flow. There were no impairments of long-lived assets during the years ended December 31, 2008, 2007 and 2006, except as described in the preceding paragraph.
Property and Equipment. Property and equipment is stated at the historical cost of construction or purchase. Construction costs include payroll-related costs capitalized during construction. Maintenance and repairs of property and equipment are charged to operations as incurred. Leasehold improvements are amortized over the lesser of the base term of the lease or estimated life of the leasehold improvements. Construction-in-process consists of various production equipment being constructed internally and externally. Assets in construction-in-process will commence depreciating once the asset has been placed in service. Depreciation and amortization are computed using the straight-line method over estimated useful lives as follows:
Buildings | | 40 years | |
Automobiles | | 4-7 years | |
Manufacturing equipment | | 5–20 years | |
Furniture and fixtures | | 3–10 years | |
Land improvements | | 10–20 years | |
Leasehold improvements | | 4–25 years | |
Deferred Compensation. We have a deferred compensation plan that permits certain management employees to defer a portion of their salary until the future. We established a Rabbi trust to finance obligations under the plan with corporate-owned variable life insurance contracts. The cash surrender value totaled approximately $2.3 million and $3.0 million, as of December 31, 2008 and 2007, respectively, which is included in “Other assets” in our consolidated balance sheets. We have recorded a “Deferred Compensation Payable” of approximately $2.3 million and $3.1 million at December 31, 2008 and 2007, respectively, to reflect the liability to our employees under this plan.
Deferred Credits. Deferred credits consist of grant money received from the Irish government. Grant money is received for a percentage of expenditures on eligible property and equipment, specific research and development projects, and costs of hiring and training employees. Amounts related to the acquisition of property and equipment are amortized as a reduction of depreciation expense over the lives of the corresponding property and equipment.
Revenue Recognition. We sell our single-use disposable medical products through a direct sales force in the U.S., and through OEM relationships, custom packers and a combination of direct sales force and independent distributors in international markets. Revenues from these customers are recognized when all of the following have occurred: (i) persuasive evidence of an arrangement exists, (ii) delivery has occurred or services have been rendered, (iii) the price is fixed or determinable, and (iv) the ability to collect is reasonably assured. These criteria are generally satisfied at the time of shipment when risk of loss and title passes to the customer. We have certain written agreements with group purchasing organizations to sell our products to participating hospitals. These agreements have destination shipping terms which require us to defer the recognition of a sale until the product has arrived at the participating hospitals. We reserve for sales returns for defective products (i.e. warranty liability) as a reduction in revenue, based on our historical experience. We also offer sales rebates and discounts to purchasing groups. These reserves are recorded as a reduction in revenue and are not considered material to our consolidated statements of income for the years ended December 31, 2008, 2007, and 2006. In addition, we invoice our customers for taxes assessed by governmental authorities such as sales tax and value added taxes. We present these taxes on a net basis.
34
Table of Contents
Shipping and Handling. We bill our customers for shipping and handling charges, which are included in total revenues for the applicable period, and the corresponding shipping and handling expense is reported in cost of goods sold.
Cost of Sales. We include product costs (i.e. material, direct labor and overhead costs), shipping and handling expense, product royalty expense, developed technology expense, production related depreciation expense and product license agreement expense in cost of goods sold.
Research and Development. Research and development costs are expensed as incurred.
Income Taxes. We account for income taxes in accordance Statement of Financial Accounting Standards (“SFAS”) SFAS No. 109, Accounting for Income Taxes. This statement utilizes an asset and liability approach for financial accounting and reporting for income taxes. Deferred income taxes are provided for temporary differences in the basis of assets and liabilities as reported for financial statement and income tax purposes.
In July 2006, the Financial Accounting Standards Board (“FASB”) issued FIN 48, which clarifies the accounting for uncertainty in income taxes recognized in the financial statements in accordance with SFAS No. 109, Accounting for Income Taxes. Under FIN 48, tax positions shall initially be recognized in the financial statements when it is more likely than not the position will be sustained upon examination by the tax authorities. Such tax positions shall initially and subsequently be measured as the largest amount of tax benefit that has a greater than 50% likelihood of being realized upon ultimate settlement with the tax authority assuming full knowledge of the position and all relevant facts.
Earnings per Common Share. Net income per common share is computed by both the basic method, which uses the weighted average number of our common shares outstanding, and the diluted method, which includes the dilutive common shares from stock options and warrants, as calculated using the treasury stock method.
Fair Value Measurements. The fair value of a financial instrument is the amount that could be received upon the sale of an asset or paid to transfer a liability in an orderly transaction between market participants at the measurement date. Financial assets are marked to bid prices and financial liabilities are marked to offer prices. Fair value measurements do not include transaction costs. We adopted SFAS No. 157, Fair Value Measurements, on January 1, 2008. This statement defines fair value, establishes a framework to measure fair value, and expands disclosures about fair value measurements. SFAS No. 157 establishes a fair value hierarchy used to prioritize the quality and reliability of the information used to determine fair values. Categorization within the fair value hierarchy is based on the lowest level of input that is significant to the fair value measurement. The fair value hierarchy is defined into the following three categories:
Level 1: Quoted market prices in active markets for identical assets or liabilities.
Level 2: Observable market based inputs or unobservable inputs that are corroborated by market data.
Level 3: Unobservable inputs that are not corroborated by market data.
In February 2008, the FASB issued Staff Position (“FSP”) No. FAS 157-2, Effective Date of FASB Statement No. 157, which delays the effective date of SFAS No. 157 for non-financial assets and liabilities to fiscal years beginning after November 15, 2008. We are currently reviewing the requirements of FSP No. FAS 157-2, and at this point in time, have not determined what impact, if any, FSP No. FAS 157-2 will have on our results of operations and financial condition.
In October 2008, the FASB issued FSP No. FAS 157-3, Determining the Fair Value of a Financial Asset When the Market for That Asset is Not Active. This statement clarifies that determining fair value in an inactive or dislocated market depends on facts and circumstances and requires significant management judgment. This statement specifies that it is acceptable to use inputs based on management estimates or assumptions, or for management to make adjustments to observable inputs to determine fair value when markets are not active and relevant observable inputs are not available. We currently have no financial assets categorized as level 3.
We adopted SFAS No. 159, The Fair Value Option for Financial Assets and Financial Liabilities, effective January 1, 2008, and elected not to establish a fair value for our financial instruments and certain other items under this statement. Therefore, our adoption of this statement did not impact our financial statements during the year ended December 31, 2008.
35
Table of Contents
Stock-Based Compensation. Effective January 1, 2006, the fair value compensation cost relating to share-based payment transactions is recognized in financial statements in accordance with SFAS 123(R), Share-Based Payment (“SFAS No. 123(R)”). Under the provisions of SFAS No. 123(R), share-based compensation cost is measured at the grant date, based on the fair value of the award, and is recognized over the employee’s requisite service period, which is generally the vesting period. The fair value of our stock options is estimated using a Black-Scholes option valuation model. We adopted the fair value recognition provisions of SFAS No. 123(R) using the modified prospective transition method. Under this transition method, stock-based compensation cost is recognized beginning January 1, 2006, for all options granted after the date of adoption, as well as the unvested portion of previously granted options based on the estimated fair value. We elected to adopt the alternative transition method provided in the FASB Staff Position for calculating the tax effects of stock-based compensation pursuant to SFAS No. 123(R). The alternative transition method includes a simplified method to establish the beginning balance of the additional paid-in capital pool (“APIC”) related to the tax effects of employee stock-based compensation, and to determine the subsequent APIC pool and Consolidated Statements of Cash Flows of the tax effects of employee stock-based compensation awards that are outstanding upon adoption of SFAS No. 123(R). Stock-based compensation expense for the years ended December 31, 2008, 2007 and 2006 was $1.0 million, $1.1 million and $1.5 million, respectively.
Staff Accounting Bulletin (‘SAB”) No. 110, Share-Based Payment, was effective for us on January 1, 2008. SAB No. 110 amended SAB No. 107, and allows for the continued use, under certain circumstances, of the “simplified method” in developing an estimate of the expected term on stock options accounted for under SFAS No. 123(R). We believe we have sufficient employee exercise behavior to estimate an expected term for our stock option grants and have elected not to use the simplified method under provisions of SAB No. 110.
Concentration of Credit Risk. Financial instruments that potentially subject us to concentrations of credit risk consist primarily of cash and cash equivalents and accounts receivable. We provide credit, in the normal course of business, primarily to hospitals and independent third-party packers and distributors. We perform ongoing credit evaluations of our customers and maintain allowances for potential credit losses. Sales to our single largest customer approximated 7%, 7%, and 6% of total sales for the years ended December 31, 2008, 2007, and 2006, respectively.
Foreign Currency. The financial statements of our foreign subsidiaries are measured using local currencies as the functional currency, with the exception of Ireland which uses the U.S. Dollar as its functional currency. Assets and liabilities are translated into U.S. Dollars at year-end rates of exchange and results of operations are translated at average rates for the year. Gains and losses resulting from these translations are included in accumulated other comprehensive loss as a separate component of stockholders’ equity. Foreign currency transactions denominated in a currency other than the entity’s functional currency are included in determining net income for the period. Such foreign currency transaction gains and losses have not been significant.
Foreign Currency Forward Contracts. On November 28, 2008, we forecasted a net exposure for December 31, 2008 (representing the difference between Euro and Great Britain Pound (GBP) denominated receivables and Euro denominated payables) of approximately 147,000 Euros and 264,000 GBPs. In order to partially offset such risks at November 28, 2008, we entered into a 30-day forward contract for the Euro and GBP with a notional amount of approximately 147,000 Euros and notional amount of 264,000 GBPs. We enter into similar transactions at various times during the year to partially offset exchange rate risks we bear throughout the year. These contracts are marked to market at each month-end. During the year ended December 31, 2008 and 2007, we recorded a net (loss)/gain of approximately ($1,000) and $16,000, respectively, which is included in other income/(expense), on these forward contracts. We do not purchase or hold derivative financial instruments for speculative or trading purposes. The fair value of our open positions at December 31, 2008 and 2007, was not material.
Accumulated Other Comprehensive Loss. Accumulated other comprehensive loss consists entirely of foreign currency translation adjustments.
Recently Issued Financial Accounting Standards. In December 2007, the FASB issued SFAS No. 141(R), Business Combinations. SFAS 141(R) requires all business combinations completed after the effective date to be accounted for by applying the acquisition method (previously referred to as the purchase method). Companies applying this method will have to identify the acquirer, determine the acquisition date and purchase price and recognize at their acquisition-date fair values of the identifiable assets acquired, liabilities assumed, and any noncontrolling interests in the acquiree. In the case of a bargain purchase, the acquirer is required to reevaluate the measurements of the recognized assets and liabilities at the acquisition date and recognize a gain on that date if an excess remains. SFAS No. 141(R) becomes effective for fiscal periods beginning after December 15, 2008. This accounting standard will be applied to pending acquisitions as discussed in note 16. The adoption of this statement will require us to expense any costs related to an acquisitions made on or after January 1, 2009.
36
Table of Contents
2. ACQUISITIONS
On December 11, 2008 we entered into an asset purchase agreement with Tran PA-C to purchase catheter extraction products for $1.5 million. We also accrued $11,000 in acquisition costs. Additional payments totaling $1.5 million have not been accrued as they are contingent upon reaching future certain sales levels. In addition, we agreed to a running royalty payment of 6% of net sales for the catheter extractor for the next 10 years. The purchase price was preliminarily allocated to inventories for $71,228, property and equipment for $15,436, customer lists for $80,000, developed technology for $85,000, a covenant not to compete for $30,000, and goodwill for $1.2 million. We intend to amortize customer lists on an accelerated basis over 14 years, and developed technology over ten years. This product can used to extract chronic dialysis catheters, similar to our ProGuide™ dialysis catheter purchased from Datascope in 2007.
On January 29, 2008, we entered into an asset purchase and supply agreement with Micrus to purchase three catheter platforms for $3.0 million. We also paid $12,300 in acquisition costs. The purchase price was allocated to inventories for $143,939, customer lists for $270,000, developed technology for $330,000, and goodwill for approximately $2.3 million. We intend to amortize customer lists on an accelerated basis over fourteen years, and developed technology over fifteen years.
During 2007, we entered into a distribution agreement with Milamy, wherein we purchased the exclusive, worldwide right to distribute the KanguruWeb® Abdominal Retraction System in vascular lab markets for $350,000. During 2008, we entered into an agreement with Milamy whereby Milamy agreed to terminate their exclusive license rights with McKnight and substitute us as the exclusive licensee of the KanguruWeb® technology in exchange for our payment of $100,000. The purchase price was allocated to a distribution agreement for $450,000 and will be amortized over five years.
On August 7, 2007, we entered into a distribution agreement with GMA for the exclusive distribution rights to sell a micro-catheter. We paid to GMA an initial payment of $500,000 in September 2007, another payment of $500,000 in November 2007, and $500,000 in September 2008. We paid $4,000 in acquisition costs. An additional $500,000 is payable to GMA upon reaching a certain milestone identified in the Distribution Agreement. We have allocated the purchase price of $1.5 million as a distribution agreement and anticipate that it will be amortized over an estimated life of eleven years.
On July 17, 2007, we entered into a patent assignment and royalty agreement with Lightek to manufacture and sell a radio-opaque marker band. We made an initial payment of $228,000 to Lightek and accrued an additional $200,000 payable upon reaching certain milestones identified in the patent assignment and royalty agreement. Achievement of the milestones is reasonably assured of occurring at this time. An additional $200,000 payment has not been accrued for as it is contingent upon reaching certain sales levels in the future. In addition, we agreed to a running royalty payment of 3% of net sales beginning with the issuance of the patent and continuing through the expiration of the patent. We paid $8,400 in 2007 and accrued $1,600 for acquisition costs. The purchase price was allocated to developed technology for $78,000, customer lists for $240,000, and goodwill for $120,000. Customer lists will be amortized on an accelerated basis over 14 years and developed technology over 15 years.
On February 26, 2007, we entered into an asset purchase agreement with Datascope to purchase certain assets for the manufacture and sale of the ProGuide™ catheter for approximately $3.3 million, including future minimum royalty payments of $279,181. In connection with this agreement, we acquired assets, inventories, a customer list, patents, and a trademark. The purchase price was allocated to property and equipment for $25,971, inventories for $778,659, a customer list for $300,000, developed technology for $150,000, a trademark for $150,000, a covenant not to compete for $20,000, and goodwill for approximately $1.9 million. In addition, we agreed to a running royalty payment of 5% of net sales through 2014, with a minimum annual payment of $50,000. Based on management’s evaluation of the purchase agreement, we recorded the additional minimum earn-out payment as an assumed liability and an addition to the cost of the acquisition. The minimum running royalty payment of $350,000 to be paid through 2014 was discounted using our incremental borrowing rate of 6% to arrive at an assumed liability of $279,181. Customer lists will be amortized on an accelerated basis over 14 years and developed technology and trademark over 15 years, and a covenant not to compete over 3 years.
On February 14, 2007, we terminated our exclusive sales distributor agreement with Medrad and purchased the customer list and information we believe will enable us to conduct direct sales in Sweden. The purchase price of $124,036 was allocated to property and equipment and customer lists. Customer lists will be amortized on an accelerated basis over 14 years.
On November 2, 2006, we entered into an agreement with our sales distributor, Q-Tech, to purchase customer lists for $380,054. The purchase price was allocated to customer lists for $380,054. We commenced direct sales efforts
37
Table of Contents
in Denmark beginning in 2007 with one sales representative. We expect over time that we will be able to expand our market share in Denmark. Customer lists will be amortized on an accelerated basis over 5 years.
On August 1, 2006, we entered in an exclusive agreement with a medical device company to purchase the product know-how and formulas for certain medical products for approximately $1.0 million. During 2006, we made three installment payments totaling $742,501. During 2007, we made a final payment of $254,904. The purchase price was allocated to developed technology for $997,405 and will be amortized over 15 years.
On April 7, 2006, we entered into an asset purchase agreement with Hypoguard to purchase certain assets for the manufacture and sale of auto-retractable safety scalpels, for a purchase price including legal fees of approximately $1.3 million. The purchase price was allocated between property and equipment for $203,944, inventories for $119,324, customer lists for $300,000, developed technology for $50,000, and goodwill for $616,809. Customer lists will be amortized on an accelerated basis over 5 years and developed technology will be amortized over 5 years.
On March 31, 2006, we entered into an asset purchase agreement with Millimed A/S to purchase certain assets for the manufacture and sale of a hemostasis valve, for a purchase price, including legal fees of approximately $1.5 million. The purchase price was allocated between property and equipment for $135,590, inventories for $419,162, developed technology for $49,000 and goodwill for $906,912. Developed technology will be amortized over 5 years.
Pro forma consolidated financial results for the acquisitions discussed above have not been included in our consolidated financial results because their effect would not be material.
3. INVENTORIES
Inventories at December 31, 2008 and 2007, consisted of the following (in thousands):
| | 2008 | | 2007 | |
| | | | | |
Finished goods | | $ | 17,818 | | $ | 17,090 | |
Work-in-process | | 4,790 | | 3,335 | |
Raw materials | | 15,750 | | 13,681 | |
| | | | | |
Total | | $ | 38,358 | | $ | 34,106 | |
38
Table of Contents
4. INTANGIBLE ASSETS
Intangible assets at December 31, 2008 and 2007, consisted of the following (in thousands):
| | 2008 | |
| | Gross | | | | Net | |
| | Carrying | | Accumulated | | Carrying | |
| | Amount | | Amortization | | Amount | |
| | | | | | | |
Patents | | $ | 2,704 | | $ | (1,019 | ) | $ | 1,685 | |
Distribution agreement | | 1,901 | | (178 | ) | 1,723 | |
License agreements | | 403 | | (242 | ) | 161 | |
Trademark | | 515 | | (314 | ) | 201 | |
Developed technology | | 1,730 | | (119 | ) | 1,611 | |
Covenant not to compete | | 50 | | (18 | ) | 32 | |
Customer lists | | 2,465 | | (1,073 | ) | 1,392 | |
Royalty agreements | | 267 | | (159 | ) | 108 | |
| | | | | | | |
Total | | $ | 10,035 | | $ | (3,122 | ) | $ | 6,913 | |
| | 2007 | |
| | Gross | | | | Net | |
| | Carrying | | Accumulated | | Carrying | |
| | Amount | | Amortization | | Amount | |
| | | | | | | |
Patents | | $ | 2,517 | | $ | (909 | ) | $ | 1,608 | |
Distribution agreement | | 1,354 | | (81 | ) | 1,273 | |
License agreements | | 283 | | (174 | ) | 109 | |
Trademark | | 515 | | (280 | ) | 235 | |
Developed technology | | 1,374 | | (51 | ) | 1,323 | |
Covenant not to compete | | 20 | | (6 | ) | 14 | |
Customer lists | | 2,004 | | (565 | ) | 1,439 | |
Royalty agreements | | 267 | | (105 | ) | 162 | |
| | | | | | | |
Total | | $ | 8,334 | | $ | (2,171 | ) | $ | 6,163 | |
Aggregate amortization expense for the years ended December 31, 2008, 2007, and 2006, was approximately $965,000, $807,000, and $475,000, respectively.
Estimated amortization expense for the intangible assets for the next five years consisted of the following (in thousands):
Year Ending | | | |
December 31 | | | |
| | | |
2009 | | $ | 932 | |
2010 | | 854 | |
2011 | | 552 | |
2012 | | 399 | |
2013 | | 380 | |
| | | | |
39
Table of Contents
5. INCOME TAXES
For the years ended December 31, 2008, 2007, and 2006, income before income taxes is broken out between U.S. and foreign-sourced operations and consisted of the following (in thousands):
| | 2008 | | 2007 | | 2006 | |
| | | | | | | |
Domestic | | $ | 28,184 | | $ | 22,033 | | $ | 16,756 | |
Foreign | | 3,661 | | 1,366 | | 2,428 | |
| | | | | | | |
Total | | $ | 31,845 | | $ | 23,399 | | $ | 19,184 | |
The components of the provision for income taxes for the years ended December 31, 2008, 2007, and 2006 consisted of the following (in thousands):
| | 2008 | | 2007 | | 2006 | |
| | | | | | | |
Current expense: | | | | | | | |
Federal | | $ | 9,693 | | $ | 5,660 | | $ | 5,130 | |
State | | 1,008 | | 800 | | 947 | |
Foreign | | 600 | | 367 | | 430 | |
| | | | | | | |
| | 11,301 | | 6,827 | | 6,507 | |
| | | | | | | |
Deferred (benefit) expense: | | | | | | | |
Federal | | (133 | ) | 752 | | 102 | |
State | | (44 | ) | 254 | | 88 | |
Foreign | | (6 | ) | (22 | ) | 186 | |
| | | | | | | |
| | (183 | ) | 984 | | 376 | |
| | | | | | | |
Total | | $ | 11,118 | | $ | 7,811 | | $ | 6,883 | |
The difference between the income tax expense reported and amounts computed by applying the statutory Federal rate of 35.0% to pretax income for the years ended December 31, 2008, 2007, and 2006 consisted of the following (in thousands):
| | 2008 | | 2007 | | 2006 | |
| | | | | | | |
Computed federal income tax expense at statutory rate of 35% | | $ | 11,146 | | $ | 8,189 | | $ | 6,714 | |
State income taxes | | 627 | | 685 | | 673 | |
Tax credits | | (271 | ) | (195 | ) | (135 | ) |
Extraterritorial income exclusion tax benefit and production activity deduction | | (114 | ) | (118 | ) | (314 | ) |
Income of subsidiaries recorded at foreign tax rates | | (822 | ) | (224 | ) | (227 | ) |
Tax-exempt interest income | | (45 | ) | (82 | ) | (100 | ) |
Uncertain tax positions | | 66 | | 13 | | | |
Deferred compensation insurance investments | | 398 | | (210 | ) | | |
Other — including the effect of graduated rates | | 133 | | (247 | ) | 272 | |
| | | | | | | |
Total income tax expense | | $ | 11,118 | | $ | 7,811 | | $ | 6,883 | |
40
Table of Contents
Deferred income tax assets and liabilities at December 31, 2008 and 2007, consisted of the following temporary differences and carry-forward items (in thousands):
| | Current | | Long-Term | |
| | 2008 | | 2007 | | 2008 | | 2007 | |
| | | | | | | | | |
Deferred income tax assets: | | | | | | | | | |
Allowance for uncollectible accounts receivable | | $ | 205 | | $ | 200 | | $ | — | | $ | — | |
Accrued compensation expense | | 699 | | 677 | | 966 | | 1,361 | |
Inventory capitalization for tax purposes | | 531 | | 315 | | | | | |
Inventory obsolescence reserve | | 510 | | 607 | | | | | |
Net operating loss carry-forwards | | | | | | 77 | | | |
Deferred revenue | | | | | | 173 | | 135 | |
Intangible assets | | | | | | 487 | | 319 | |
Stock based compensation | | | | | | 251 | | 922 | |
Uncertain tax positions | | 318 | | 1,156 | | 1,083 | | 273 | |
Other | | 705 | | 559 | | 6 | | 34 | |
| | | | | | | | | |
Total deferred income tax assets | | 2,968 | | 3,514 | | 3,043 | | 3,044 | |
| | | | | | | | | |
Deferred income tax liabilities: | | | | | | | | | |
Prepaid expenses | | (186 | ) | (2,615 | ) | | | | |
Property and equipment | | | | | | (11,161 | ) | (8,812 | ) |
Other | | | | (88 | ) | (630 | ) | (310 | ) |
| | | | | | | | | |
Net | | $ | 2,782 | | $ | 811 | | $ | (8,748 | ) | $ | (6,078 | ) |
| | | | | | | | | |
Reported as: | | | | | | | | | |
Deferred income tax assets | | $ | 2,782 | | $ | 811 | | $ | 23 | | $ | 4 | |
Deferred income tax liabilities | | | | | | (8,771 | ) | (6,082 | ) |
| | | | | | | | | |
Net | | $ | 2,782 | | $ | 811 | | $ | (8,748 | ) | $ | (6,078 | ) |
The long-term deferred income tax asset balances are not netted as they represent deferred amounts applicable to different taxing jurisdictions. Deferred income tax balances reflect the effects of temporary differences between the carrying amounts of assets and liabilities and their tax bases and are stated at enacted tax rates expected to be in effect when taxes are actually paid or recovered.
We have not provided U.S. deferred income taxes or foreign withholding taxes on the undistributed earnings of our non-U.S. subsidiaries since these earnings are intended to be reinvested indefinitely in operations outside the United States, in accordance with Accounting Principles Board (“APB”) Opinion No. 23. It is not practical to estimate the amount of additional taxes that might be payable on such undistributed earnings.
As of December 31, 2008, we had non-U.S. net operating loss carry-forwards of approximately $273,000, which have no expiration date.
We are subject to income taxes in the United States and numerous foreign jurisdictions. Significant judgment is required in determining our worldwide provision for income taxes and recording the related assets and liabilities. In the ordinary course of our business, there are many transactions and calculations where the ultimate tax determination is uncertain. We are regularly under audit by tax authorities. Our federal and state income tax returns for 2005 through 2008 are open tax years. We are in several foreign tax jurisdictions which have open tax years from 2003 through 2008.
We adopted the provisions of FIN 48 on January 1, 2007. As a result of this adoption, we recognized a cumulative-effect adjustment of approximately $610,000, increasing our liability for unrecognized tax benefits and reducing the January 1, 2007 balance of retained earnings.
41
Table of Contents
The total liability for unrecognized tax benefits at December 31, 2008 and 2007, including temporary tax differences, was approximately $2.8 million and $3.6 million, respectively, of which approximately $2.3 million and $2.2 million, respectively, would favorably impact our effective tax rate if recognized. As of December 31, 2008 and 2007, we accrued approximately $242,000 and $402,000, respectively, in interest and penalties related to unrecognized tax benefits. We account for interest expense and penalties for unrecognized tax benefits as part of our income tax provision. We do not anticipate that unrecognized tax benefits will significantly increase or decrease within 12 months of the reporting date.
During the year ended December 31, 2008, we reduced our liability for unrecognized tax benefits by approximately $793,000. This reduction in our unrecognized tax benefits was due primarily to the settlement of our Internal Revenue Service (“IRS”) audit. Included in this amount is a reduction of approximately $160,000 for the year ended December 31, 2008 related to interest expense. In addition, we recorded an unrecognized tax benefit related to the lapse of applicable statute of limitations of approximately $627,000, of which approximately $543,000 favorably impacted our effective tax rate. We also added approximately $816,000 to our liability for unrecognized tax benefits, of which we believe approximately $449,000 would favorably impact our effective tax rate, if recognized.
During the year ended December 31, 2007, the Company added approximately $816,000 to our liability for unrecognized tax benefits, of which approximately $321,000 would favorably impact our effective tax rate if recognized. Included in this amount is approximately $48,000 for the year ended December 31, 2007, related to interest expense. In addition, we recorded an unrecognized tax benefit related to the lapse of applicable statute of limitations of approximately $645,000, of which approximately $308,000 favorably impacted our effective tax rate.
Although we believe our estimates are reasonable, we can make no assurance that the final tax outcome of these matters will not be different from that which we have reflected in our historical income tax provisions and accruals. Such difference could have a material impact on our income tax provision and operating results in the period in which we make such determination.
A reconciliation of the beginning and ending amount of liabilities associated with uncertain tax positions consisted of the following:
FIN 48 Tabular Rollforward | | 2008 | | 2007 | |
| | | | | |
Unrecognized tax benefits, opening balance | | 3,611 | | 3,212 | |
Gross increases in tax positions taken in a prior year | | 257 | | 131 | |
Gross decreases in tax positions taken in a prior year | | (278 | ) | (4 | ) |
Gross increases in tax positions taken in the current year | | 547 | | 554 | |
Settlements with taxing authorities | | (842 | ) | — | |
Lapse of applicable statute of limitations | | (627 | ) | (542 | ) |
Unrecognized tax benefits, ending balance | | 2,668 | | 3,351 | |
The FIN48 tabular rollforward ending balance does not include interest expense (net of tax effect) and penalties related to unrecognized tax benefits. During the year ended December 31, 2008, we settled two open audits with the IRS related to certain temporary deductions. As a result of these settlements, we paid an additional $2.2 million on our 2007 federal and state extension payments. The reversal of these temporary differences and the payment of the additional taxes did not have a material impact on our financial statements for the year ended December 31, 2008, as the income tax liabilities had already been accrued in our financial statements. Of the amounts paid, $1.0 million was classified as a current liability related to unrecognized tax positions on the December 31, 2007 consolidated balance sheet.
42
Table of Contents
6. ACCRUED EXPENSES
Accrued expenses at December 31, 2008 and 2007, consisted of the following (in thousands):
| | 2008 | | 2007 | |
| | | | | |
Payroll taxes | | $ | 640 | | $ | 735 | |
Payroll | | 2,377 | | 2,196 | |
Bonuses | | 482 | | 701 | |
Commissions | | 699 | | 519 | |
Vacation | | 2,438 | | 2,304 | |
Other accrued expenses | | 3,337 | | 3,037 | |
| | | | | |
Total | | $ | 9,973 | | $ | 9,492 | |
7. REVOLVING CREDIT FACILITY AND LONG-TERM DEBT
On December 7, 2006, we entered into an unsecured loan agreement with Bank of America, N.A. (“Bank of America”), whereby the Bank of America agreed to provide us with a line of credit in the amount of $30.0 million expiring on December 7, 2010. The loan agreement requires us to pay interest at a rate equal to the lesser of (i) the maximum lawful rate of interest permitted under applicable usury laws, or (ii) the Bank of America’s prime rate, plus a negative margin, as defined in the loan agreement. Alternatively, we may elect optional interest rates based on the London Inter-Bank Offered Rate (LIBOR) during interest periods agreed to by the Bank of America and us. There were no outstanding borrowings on this loan as of December 31, 2008 and 2007.
On December 8, 2006, we entered into an unsecured loan agreement with Zions First National Bank (“Zions”), whereby they agreed to provide us a line of credit in the amount of $1.0 million. The Zions loan agreement requires we pay interest at a rate of prime minus 0.35% and will expire on December 1, 2009. There were no outstanding borrowings on this loan as of December 31, 2008 and 2007.
We believe we are in compliance with the covenants in our loan agreements, which require the maintenance of certain financial ratios and minimum working capital, and also include, among other things, limitations on additional indebtedness, the pledging or sale of assets and we are restricted from paying dividends to shareholders.
8. COMMITMENTS AND CONTINGENCIES
Leases. We have non-cancelable operating lease agreements for off-site office and production facilities and equipment. The leases for the off-site office and production facilities are for one to five years and some have renewal options for three years. In September 2007, the leases for our Murray, Utah off-site and production facilities expired and are currently on a month-to-month lease. Total rental expense on these operating leases and on our manufacturing and office building (see below) for the years ended December 31, 2008, 2007, and 2006, approximated $2.6 million, $2.6 million, and $3.2 million, respectively.
In June 1993, we entered into a 25-year lease agreement with a developer for a manufacturing and office building. Under the agreement, we were granted an option to purchase the building at fair market value at the end of the lease term.
43
Table of Contents
The future minimum lease payments for operating leases as of December 31, 2008, consisted of the following (in thousands):
Years Ending | | Operating | |
December 31 | | Leases | |
| | | |
2009 | | $ | 2,122 | |
2010 | | 1,986 | |
2011 | | 1,805 | |
2012 | | 1,697 | |
2013 | | 1,665 | |
Thereafter | | 10,106 | |
| | | |
Total minimum lease payments | | $ | 19,381 | |
Irish Government Development Agency Grants. As of December 31, 2008, we had entered into several grant agreements with the Irish Government Development Agency. We have recorded the grants related to research and development projects and costs of hiring and training employees as a reduction of operating expenses in 2008 and 2007, in the amounts of approximately $158,000 and $266,000, respectively. Grants related to the acquisition of property and equipment purchased in Ireland are amortized as a reduction to depreciation expense over lives corresponding to the depreciable lives of such property and equipment. The balance of deferred credits related to such grants as of December 31, 2008 and 2007, is approximately $1,994,000 and $2,105,000, respectively. During 2008, 2007, and 2006, approximately $111,000, $135,000, and $164,000, respectively, of the deferred credit was amortized as a reduction of operating expenses.
There is a commitment to repay the Irish government for grants received if we were to cease production in Ireland prior to the expiration of the grant liability period. The grant liability period is usually between 5-8 years from the last claim made on a grant. As of December 31, 2008, the total amount of grants that could be subject to refund was approximately $4.1 million. Management does not believe it will ever have to repay any of these grant monies as we have no intention of ceasing operation in Ireland.
Litigation. In the ordinary course of business, we are involved in litigation and claims which management believes will not have a materially adverse effect on our financial position or results of operations.
9. EARNINGS PER COMMON SHARE (EPS)
The computation of weighted average shares outstanding and the basic and diluted earnings per common share consisted of the following (in thousands except per share amounts):
| | Net | | | | Per Share | |
| | Income | | Shares | | Amount | |
| | | | | | | |
Year ended December 31, 2008: | | | | | | | |
Basic EPS | | $ | 20,727 | | 27,769 | | $ | 0.75 | |
Effect of dilutive stock options and warrants | | | | 781 | | | |
| | | | | | | |
Diluted EPS | | $ | 20,727 | | 28,550 | | $ | 0.73 | |
| | | | | | | |
Year ended December 31, 2007: | | | | | | | |
Basic EPS | | $ | 15,588 | | 27,425 | | $ | 0.57 | |
Effect of dilutive stock options and warrants | | | | 779 | | | |
| | | | | | | |
Diluted EPS | | $ | 15,588 | | 28,204 | | $ | 0.55 | |
| | | | | | | |
Year ended December 31, 2006: | | | | | | | |
Basic EPS | | $ | 12,301 | | 27,333 | | $ | 0.45 | |
Effect of dilutive stock options and warrants | | | | 912 | | | |
| | | | | | | |
Diluted EPS | | $ | 12,301 | | 28,245 | | $ | 0.44 | |
44
Table of Contents
For the years ended December 31, 2008, 2007, and 2006, approximately 984,000, 1,422,000, and 584,000, respectively, of stock options were not included in the computation of diluted earnings per share because they would have been antidilutive.
Repurchase of Our Common Stock. On February 24, 2007, our Board of Directors approved the repurchase of 344,084 shares of our common stock in a private transaction with a non-institutional private investor for $4.1 million, which occurred during the first quarter of 2007. On April 30, 2007, our Board of Directors approved the repurchase of up to 1,400,000 shares of our common stock. During the second and third quarters of 2007, we repurchased a total of 119,900 shares for a total of $1.3 million.
10. EMPLOYEE STOCK PURCHASE PLAN AND STOCK OPTIONS AND WARRANTS.
Our stock-based compensation primarily consists of the following plans:
Stock Incentive Plan. During 1999, we adopted the Merit Medical Systems, Inc. Stock Incentive Plan (formerly the 1999 Omnibus Stock Incentive Plan), which provides for the issuance of incentive stock options, non-statutory stock options and certain corresponding stock appreciation rights (the “Stock Incentive Plan”). Options may be granted to directors, officers, outside consultants and key employees and may be granted upon such terms and such conditions as the compensation committee of our Board of Directors in their sole discretion shall determine. Options typically vest 20% per year over either a 4.5 or 5 year life with contractual lives of 5, 7 and 10 years. The Plan also provides for options that vest 100% upon grant with contractual lives of 10 years. In no event, however, may the exercise price be less than the fair market value on the date of grant. Under a provision of our stock incentive plan, participants are allowed to surrender mature shares of our common stock for the payment of the option price and minimum statutory taxes associated with the exercise of options. The shares surrendered must be shares the participant has held for more than six months. The value of the mature shares surrendered is based on the closing price of our common stock on the date of exercise by the participant. As of December 31, 2008, a total of 206,000 shares remained available to be issued under the Stock Incentive Plan.
2006 Long-Term Incentive Plan. Our Board of Directors adopted and the shareholders approved the Merit Medical Systems, Inc. 2006 Long-Term Incentive Plan (the “2006 Incentive Plan”) in May 2006. The 2006 Incentive Plan provides for the granting of stock options, stock appreciation rights, restricted stock, stock units (including restricted stock units) and performance awards. Options may be granted to directors, officers, outside consultants and key employees and may be granted upon such terms and such conditions as the compensation committee of our Board of Directors shall determine. Options will typically vest on an annual basis over a 3 to 5 year life (or 1 year if performance based) with contractual lives of 7-10 years. As of December 31, 2008, a total of 478,000 shares remained available to be issued under the 2006 Long-Term Incentive Plan.
Employee Stock Purchase Plan. We have a qualified and a non-qualified Employee Stock Purchase Plan (“ESPP”), which will expire on June 30, 2016. As of December 31, 2008, the total number of shares that remained available to be issued under our qualified plan was approximately 274,000 shares and 86,000 shares for our non-qualified plan. ESPP participants purchase shares on a quarterly basis at a price equal to 95% of the market price of the common stock at the end of the applicable offering period.
Stock-Based Compensation Expense. The stock-based compensation expense before income tax expense for the years ended December 31, 2008, 2007 and 2006 consisted of the following (in thousands):
| | 2008 | | 2007 | | 2006 | |
| | | | | | | |
Cost of goods sold | | $ | 101 | | $ | 261 | | $ | 399 | |
Research and development | | 37 | | 81 | | 158 | |
Selling, general and administrative | | 824 | | 788 | | 945 | |
Stock-based compensation expense before taxes | | $ | 962 | | $ | 1,130 | | $ | 1,502 | |
We recognize stock-based compensation expense (net of a forfeiture rate) for those awards which are expected to vest on a straight-line basis over the requisite service period. We estimate the forfeiture rate based on our historical experience and expectations about future forfeitures. As of December 31, 2008, the total remaining unrecognized compensation cost related to non-vested stock options, net of forfeitures, was approximately $4.1 million and is expected to be recognized over a weighted average period of 3.88 years. The total 2008 and 2007 income tax benefit related to share-based compensation recorded in capital in excess of par value was approximately $2.0 million and $500,000, respectively, and was shown as a cash inflow from financing activities in our cash flow statement.
45
Table of Contents
In applying the Black-Scholes methodology to the option grants, the fair value of our stock-based awards granted were estimated using an expected annual dividend yield of 0% and the following assumptions:
| | 2008 | | 2007 | | 2006 | |
| | | | | | | |
Risk-free interest rate | | 3.24%-3.55% | | 3.64%-5.00% | | 4.98% | |
Expected option life | | 4.2-6.0 years | | 6.0 years | | 6.1 years | |
Expected price volatility | | 38.0%-41.7% | | 44.3%-47.8% | | 41.9% | |
The average risk-free interest rate is determined using the U.S. Treasury rate in effect as of the date of grant, based on the expected term of the stock option. We determine the expected term of the stock options using the historical exercise behavior of employees. The expected price volatility was determined using a weighted average of daily historical volatility of our stock price over the corresponding expected option life and implied volatility based on recent trends of the daily historical volatility. For options with a vesting period, compensation expense is recognized on a straight-line basis over the service period, which corresponds to the vesting period. Compensation expense is recognized immediately for options that are fully vested on the date of grant. During the years ended December 31, 2008, 2007, and 2006, 499,000, 425,500, and 105,000 stock-based compensation grants were made for a total fair value of approximately $2.5 million, $2.5 million, and $0.5 million, net of estimated forfeitures, respectively.
The table below presents information related to stock option activity for the years ended December 31, 2008, 2007, and 2006 (in thousands):
| | 2008 | | 2007 | | 2006 | |
| | | | | | | |
Total intrinsic value of stock options exercised | | $ | 6,150 | | $ | 1,471 | | $ | 3,195 | |
Cash received from stock option exercises | | 5,405 | | 1,537 | | 3,170 | |
Net income tax benefit from the exercises of stock options | | 2,044 | | 500 | | 1,155 | |
| | | | | | | | | | |
46
Table of Contents
Changes in stock options for the years ended December 31, 2008, 2007, and 2006 consisted of the following (in thousands):
| | | | Weighted | | Remaining | | | |
| | Number | | Average | | Contractual | | | |
| | of | | Exercise | | Term | | Intrinsic | |
| | Shares | | Price | | (in Years) | | Value | |
| | | | | | | | | |
2006: | | | | | | | | | |
Beginning balance | | 4,288 | | | | | | | |
Granted | | 105 | | $ | 11.52 | | | | | |
Exercised | | 455 | | 7.48 | | | | | |
Forfeited/expired | | 141 | | 11.90 | | | | | |
Outstanding at December 31 | | 3,797 | | 11.03 | | 6.5 | | $ | 20,615 | |
Exercisable | | 3,433 | | 11.11 | | 6.5 | | 18,605 | |
Ending vested and expected to vest | | 3,788 | | 11.03 | | 6.5 | | 20,568 | |
| | | | | | | | | |
Weighted average fair value of options granted during year | | | | $ | 5.58 | | | | | |
| | | | | | | | | |
2007: | | | | | | | | | |
Beginning balance | | 3,797 | | | | | | | |
Granted | | 426 | | $ | 12.14 | | | | | |
Exercised | | 203 | | 6.40 | | | | | |
Forfeited/expired | | 69 | | 14.27 | | | | | |
Outstanding at December 31 | | 3,951 | | 11.34 | | 5.7 | | $ | 13,754 | |
Exercisable | | 3,353 | | 11.28 | | 5.7 | | 12,405 | |
Ending vested and expected to vest | | 3,908 | | 11.33 | | 5.6 | | 13,669 | |
| | | | | | | | | |
Weighted average fair value of options granted during year | | | | $ | 6.34 | | | | | |
| | | | | | | | | |
2008: | | | | | | | | | |
Beginning balance | | 3,951 | | | | | | | |
Granted | | 499 | | $ | 14.41 | | | | | |
Exercised | | 612 | | 8.85 | | | | | |
Forfeited/expired | | 5 | | 18.84 | | | | | |
Outstanding at December 31 | | 3,833 | | 12.12 | | 5.0 | | $ | 23,579 | |
Exercisable | | 2,964 | | 11.74 | | 4.7 | | 19,665 | |
Ending vested and expected to vest | | 3,785 | | 12.11 | | 5.0 | | 23,367 | |
| | | | | | | | | |
Weighted average fair value of options granted during year | | | | $ | 5.32 | | | | | |
47
Table of Contents
On November 17, 2004, we acquired all of the assets and assumed certain liabilities of MedSource Packaging Concepts LLC (“MedSource”). In connection with this acquisition we issued 100,000 warrants to MedSource at a fair value of approximately $323,170. Changes in these warrants for the years ended December 31, 2008, 2007, and 2006, consisted of the following (in thousands):
| | | | Weighted | | Remaining | | | |
| | Number | | Average | | Contractual | | | |
| | of | | Exercise | | Term | | Intrinsic | |
| | Shares | | Price | | (in Years) | | Value | |
| | | | | | | | | |
2006: | | | | | | | | | |
Beginning balance | | 100 | | | | | | | |
Outstanding at December 31 | | 100 | | $ | 10.13 | | 2.9 | | $ | 571 | |
Exercisable | | 100 | | 10.13 | | 2.9 | | 571 | |
| | | | | | | | | |
2007: | | | | | | | | | |
Beginning balance | | 100 | | | | | | | |
Outstanding at December 31 | | 100 | | $ | 10.13 | | 1.9 | | $ | 377 | |
Exercisable | | 100 | | 10.13 | | 1.9 | | 377 | |
| | | | | | | | | |
2008: | | | | | | | | | |
Beginning balance | | 100 | | | | | | | |
Exercised | | 49 | | $ | 10.13 | | | | | |
Outstanding at December 31 | | 51 | | $ | 10.13 | | 0.9 | | $ | 369 | |
Exercisable | | 51 | | 10.13 | | 0.9 | | 369 | |
The following table summarizes information about stock options outstanding at December 31, 2008 (shares in thousands):
| | Options Outstanding | | Options Exercisable | |
| | | | Weighted | | | | | | | |
| | | | Average | | | | | | | |
| | | | Remaining | | Weighted | | | | Weighted | |
Range of | | | | Contractual | | Average | | | | Average | |
Exercise | | Number | | Life | | Exercise | | Number | | Exercise | |
Prices | | Outstanding | | (in years) | | Price | | Exercisable | | Price | |
| | | | | | | | | | | |
$2.07—$9.74 | | 1,157 | | 3.1 | | $ | 6.68 | | 1,157 | | $ | 6.68 | |
$10.47—$12.14 | | 1,049 | | 5.7 | | 11.77 | | 686 | | 11.61 | |
$13.22—$15.03 | | 1,187 | | 6.1 | | 14.49 | | 683 | | 14.56 | |
$15.12—$21.67 | | 440 | | 5.2 | | 20.90 | | 438 | | 20.91 | |
| | | | | | | | | | | |
$2.07—$21.67 | | 3,833 | | 5.0 | | $ | 12.12 | | 2,964 | | $ | 11.74 | |
11. SEGMENT REPORTING AND FOREIGN OPERATIONS
We report sales in four product categories. Sales relating to these product categories for the years ended December 31, 2008, 2007, and 2006 consisted of the following (in thousands):
| | Twelve Months Ended | |
| | December 31, | |
| | % Change | | 2008 | | % Change | | 2007 | | % Change | | 2006 | | 2005 | |
Stand-alone devices | | 9% | | $ | 68,005 | | 12% | | $ | 62,417 | | 19% | | $ | 55,824 | | $ | 46,900 | |
Custom kits & procedure trays | | 11% | | 66,584 | | 7% | | 60,013 | | 15% | | 56,009 | | 48,740 | |
Inflation devices | | 3% | | 61,656 | | 5% | | 59,595 | | 9% | | 56,978 | | 52,319 | |
Catheters | | 20% | | 30,898 | | 18% | | 25,743 | | 17% | | 21,863 | | 18,626 | |
Total | | 9% | | $ | 227,143 | | 9% | | $ | 207,768 | | 14% | | $ | 190,674 | | $ | 166,585 | |
During the years ended December 31, 2008, 2007, and 2006, we had foreign sales of approximately $72,500,000, $64,900,000, and $53,700,000 or approximately 32%, 31%, and 28%, respectively, of total sales, primarily
48
Table of Contents
in Japan, Germany, France and the United Kingdom. Foreign sales are attributed based on location of the customer receiving the product.
We operate primarily in one segment in which we develop, manufacture and market disposable medical products, principally for use in the diagnosis and treatment of cardiovascular disease. Major operations outside the United States include a manufacturing facility in Ireland, a distribution facility in The Netherlands, and sales subsidiaries in Europe. The following is a summary of how we managed and reported our worldwide operations for fiscal years 2008, 2007, and 2006 (in thousands):
| | | | Transfers | | | | | |
| | Sales to | | Between | | | | | |
| | Unaffiliated | | Geographic | | Net | | Identifiable | |
| | Customers | | Areas | | Sales | | Assets | |
| | | | | | | | | |
Year ended December 31, 2008: | | | | | | | | | |
United States, Canada and international distributors | | $ | 184,708 | | $ | | $ | 184,708 | | $ | 188,579 | |
Europe direct and European distributors | | 42,435 | | 20,889 | | 63,324 | | 43,197 | |
Eliminations | | | | (20,889 | ) | (20,889 | ) | | |
| | | | | | | | | |
Consolidated | | $ | 227,143 | | $ | — | | $ | 227,143 | | $ | 231,776 | |
| | | | | | | | | |
Year ended December 31, 2007: | | | | | | | | | |
United States, Canada and international distributors | | $ | 169,704 | | $ | 2,491 | | $ | 172,195 | | $ | 159,491 | |
Europe direct and European distributors | | 38,064 | | 16,487 | | 54,551 | | 40,929 | |
Eliminations | | | | (18,978 | ) | (18,978 | ) | | |
| | | | | | | | | |
Consolidated | | $ | 207,768 | | $ | — | | $ | 207,768 | | $ | 200,420 | |
| | | | | | | | | |
Year ended December 31, 2006: | | | | | | | | | |
United States, Canada and international distributors | | $ | 158,488 | | $ | 2,423 | | $ | 160,911 | | $ | 147,134 | |
Europe direct and European distributors | | 32,186 | | 16,421 | | 48,607 | | 35,534 | |
Eliminations | | | | (18,844 | ) | (18,844 | ) | | |
| | | | | | | | | |
Consolidated | | $ | 190,674 | | $ | — | | $ | 190,674 | | $ | 182,668 | |
Transfers between geographic areas are accounted for at amounts which are generally above cost and consistent with the rules and regulations of governing tax authorities. Such transfers are eliminated in the consolidated financial statements. Net income by geographic areas reflects foreign earnings reported by the foreign entities. Identifiable assets are those assets that can be directly associated with a particular foreign entity and thus do not include assets used for general corporate purposes.
Our long-lived assets by geographic area consisted of the following (in thousands):
| | 2008 | | 2007 | |
| | | | | |
United States | | $ | 78,920 | | $ | 76,880 | |
Ireland | | 16,584 | | 16,826 | |
Other foreign countries | | 8,435 | | 5,990 | |
| | | | | |
Total | | $ | 103,939 | | $ | 99,696 | |
49
Table of Contents
12. ROYALTY AGREEMENTS
Pursuant to a 1992 settlement agreement, we entered into a license agreement with another medical product manufacturer (the “Licensor”), whereby the Licensor granted to us a nonexclusive right and license to manufacture and sell products which are subject to the patents issued to the Licensor. The license agreement terminated in August 2008 upon the expiration of the last related patent. For the rights and license granted under the agreement, we paid the Licensor a nonrefundable prepaid royalty in the amount of $600,000. In addition to the prepaid royalty, we agreed to pay the Licensor a continuing royalty of 5.75% of sales (which will not exceed $450,000 for any calendar year) made in the United States, of products covered by the license agreement. Royalties of $450,000 were paid or accrued in each of the years ended December 31, 2008, 2007, and 2006.
During 2006, in connection with the purchase of the Futura® safety scalpel device from Hypoguard, we acquired a license agreement with a medical product manufacturer (the “Licensor”), whereby the Licensor granted to us an exclusive worldwide license to manufacture and sell products which are subject to the patents issued to the Licensor. For the rights and license granted under the agreement, we agreed to pay the Licensor a royalty of 4% of net sales, with annual minimum royalty payments of $144,000 for calendar years 2007 through 2014, and $108,000 for 2015. During the years ended December 31, 2008, 2007, and 2006, we paid or accrued a royalty of $108,000, $144,000, and $108,000 respectively, under this license agreement. During January 2008, we negotiated to purchase from the Licensor the patents related to this product for $432,000. The patent will amortize over the remaining life of the patents, which is approximately five and one-half years. In connection with the purchase of the patents, the licensor forgave the three months ended December 31, 2008 royalties due of $36,000.
During 2007, in connection with the purchase of the ProGuide™ chronic dialysis catheter from Datacope, we entered into a running royalty agreement as partial consideration of the assignment of acquired intellectual property to us. Under this agreement, we agreed to pay Datascope a royalty of 5% of net sales, with annual minimum royalty payments of $50,000 for calendar years 2008 through 2013. During the years ended December 31, 2008 and 2007, we paid or accrued a royalty of $50,000 and $42,000, respectively, under this agreement.
13. EMPLOYEE BENEFIT PLANS
We have a contributory 401(k) savings and profit sharing plan (the “Plan”) covering all U.S. full-time employees who are at least 18 years of age. The Plan has a-90 day minimum service requirement. We may contribute, at our discretion, matching contributions based on the employees’ compensation. Contributions made by us to the Plan for the years ended December 31, 2008, 2007, and 2006, totaled approximately $0, $510,000, and $845,000, respectively. We have defined contribution plans covering some of our foreign employees. We contribute 3-36% for certain foreign non-management employees, 10-36% for certain foreign management employees, and 48% for a foreign executive employee. Contributions made to these plans for the years ended December 31, 2008, 2007, and 2006, totaled approximately $541,000, $635,000, and $389,000, respectively.
50
Table of Contents
14. QUARTERLY RESULTS OF OPERATIONS (UNAUDITED)
Quarterly data for the years ended December 31, 2008, 2007, and 2006, consisted of the following (in thousands except per share amounts):
| | Quarter Ended | |
| | March 31 | | June 30 | | September 30 | | December 31 | |
| | | | | | | | | |
2008 | | | | | | | | | |
| | | | | | | | | |
Net sales | | $ | 53,553 | | $ | 57,441 | | $ | 58,153 | | $ | 57,996 | |
Gross profit | | 21,592 | | 24,502 | | 23,684 | | 23,493 | |
Income from operations | | 6,604 | | 9,009 | | 7,169 | | 8,202 | |
Income tax expense | | 2,432 | | 3,337 | | 2,198 | | 3,151 | |
Net income | | 4,317 | | 5,818 | | 5,200 | | 5,392 | |
Basic earnings per common share | | 0.16 | | 0.21 | | 0.19 | | 0.19 | |
Diluted earnings per common share | | 0.15 | | 0.21 | | 0.18 | | 0.19 | |
| | | | | | | | | |
2007 | | | | | | | | | |
| | | | | | | | | |
Net sales | | $ | 51,030 | | $ | 51,811 | | $ | 50,584 | | $ | 54,343 | |
Gross profit | | 18,858 | | 19,536 | | 19,783 | | 21,614 | |
Income from operations | | 4,479 | | 5,471 | | 6,086 | | 6,934 | |
Income tax expense | | 1,598 | | 1,937 | | 1,891 | | 2,385 | |
Net income | | 2,969 | | 3,596 | | 4,295 | | 4,728 | |
Basic earnings per common share | | 0.11 | | 0.13 | | 0.16 | | 0.17 | |
Diluted earnings per common share | | 0.10 | | 0.13 | | 0.15 | | 0.17 | |
| | | | | | | | | |
2006 | | | | | | | | | |
| | | | | | | | | |
Net sales | | $ | 45,040 | | $ | 48,121 | | $ | 46,697 | | $ | 50,816 | |
Gross profit | | 17,050 | | 18,996 | | 18,068 | | 18,964 | |
Income from operations* | | 3,705 | | 5,476 | | 5,136 | | 4,693 | |
Income tax expense | | 1,351 | | 1,951 | | 1,900 | | 1,681 | |
Net income | | 2,401 | | 3,522 | | 3,325 | | 3,053 | |
Basic earnings per common share | | 0.09 | | 0.13 | | 0.12 | | 0.11 | |
Diluted earnings per common share | | 0.09 | | 0.13 | | 0.12 | | 0.11 | |
*Income from operations was adjusted in the first quarter of 2006, from what was reported, as the result of the reclassification of losses on disposal of assets from other income (expense) to selling, general and administrative expense.
During the quarter ended December 31, 2006, we determined it was not likely that we would pursue the product associated with the intellectual property and assets acquired from Sub-Q due to other priorities and opportunities. Therefore, we recorded an impairment charge of approximately $929,000 during the fourth quarter, primarily relating to intellectual property assets acquired from Sub-Q in March 2005.
15. FAIR VALUE MEASUREMENTS.
Our financial assets and liabilities carried at fair value measured on a recurring basis as of December 31, 2008 consisted of the following (in thousands):
| | | Fair Value Measurements Using | |
Description | | Total Fair Value at December 31, 2008 | | Quoted prices in active markets (Level 1) | | Significant other observable inputs (Level 2) | | Significant Unobservable inputs (Level 3) | |
| | | | | | | | | |
Commercial paper (1) | | $ | 19,995 | | | | $ | 19,995 | | | |
Deferred compensation investments (2) | | 2,325 | | 274 | | 2,051 | | | |
| | | | | | | | | | | |
(1) The fair value of the commercial paper is based on a fixed-income approach over a straight-line basis. In the event a transaction is observed on the same security in the market place, the price is adjusted to reflect the quoted market price.
(2) The deferred compensation investments are held in a Rabbi trust under an insurance-based deferred compensation plan. The investments of the Rabbi trust are valued based upon unit values multiplied by the
51
Table of Contents
number of units held. The unit value is based upon the investment’s net asset value adjusted for some administrative fees.
During the year ended December 31, 2008, we had no significant measurements of assets or liabilities at fair value (as defined in SFAS No. 157) on a nonrecurring basis subsequent to their initial recognition. As indicated in Note 1, of the notes to our consolidated financial statements, the aspects of SFAS No. 157 for which the effective date for us was deferred under FSP No. 157-2 until January 1, 2009 relate to nonfinancial assets and liabilities that are measured at fair value, but are recognized or disclosed at fair value on a nonrecurring basis. This deferral applies to such items as nonfinancial assets and liabilities initially measured at fair value in a business combination (but not measured at fair value in subsequent periods) or nonfinancial long-lived asset groups measured at fair value for an impairment assessment. During the year ended December 31, 2008, such measurements of fair value impacted by the deferral under FSP No. 157-2 related primarily to the nonfinancial assets and liabilities with respect to all previous business combinations we have made.
16. SUBSEQUENT EVENTS
On February 18, 2009, we entered into an asset purchase agreement to acquire substantially all the assets of Alveolus, Inc. (“Alveolus”), located in Charlotte, North Carolina, for approximately $19.0 million. We expect to close the Alveolus acquisition shortly after March 6, 2009. Alveolus produces non-vascular interventional stents used for esophageal, tracheobronchial, and biliary stenting procedures. Also, on February 19, 2009, we entered into an asset purchase and supply agreement with Biosearch Medical Products, Inc., a wholly-owned subsidiary of Hydromer, Inc. (“Biosearch”), to acquire two products that are being sold on an OEM basis to major medical device companies in the gastroenterology market. The anticipated purchase price for the Biosearch assets is approximately $1.6 million. We made an initial payment of approximately $1.1 million on February 23, 2009.
52
Table of Contents
SUPPLEMENTARY FINANCIAL DATA
The supplementary financial information required by Item 302 of Regulation S-K is contained in Note 14 to the consolidated financial statements of the Company set forth above.
Item 9. Changes in and Disagreements with Accountants on Accounting and Financial Disclosure.
None
Item 9A. Controls and Procedures.
MERIT MEDICAL SYSTEMS, INC. AND SUBSIDIARIES
MANAGEMENT’S REPORT ON INTERNAL CONTROL OVER FINANCIAL REPORTING
Our management is responsible for establishing and maintaining adequate internal control over financial reporting as defined in Rules 13a-15(f) and 15d-15(f) under the Securities Exchange Act of 1934, as amended. Our internal control over financial reporting is a process designed to provide reasonable assurance regarding the reliability of financial reporting and the preparation of financial statements for external purposes in accordance with accounting principles generally accepted in the United States of America. Internal control over financial reporting includes those written policies and procedures that:
· Pertain to the maintenance of records that, in reasonable detail, accurately and fairly reflect the transactions and dispositions of the assets of Merit Medical Systems, Inc.;
· Provide reasonable assurance that transactions are recorded as necessary to permit preparation of financial statements in accordance with accounting principles generally accepted in the United States of America;
· Provide reasonable assurance that our receipts and expenditures are being made only in accordance with authorization of our management and directors; and
· Provide reasonable assurance regarding prevention or timely detection of the unauthorized acquisition, use or disposition of assets that could have a material effect on the consolidated financial statements.
Internal control over financial reporting includes the controls themselves, monitoring and internal auditing practices and actions taken to correct deficiencies as identified. Because of its inherent limitations, internal control over financial reporting may not prevent or detect misstatements. Also, projections of any evaluation of effectiveness to future periods are subject to the risk that controls may become inadequate because of changes in conditions, or that the degree of compliance with the policies or procedures may deteriorate.
Our management assessed the effectiveness of our internal control over financial reporting as of December 31, 2008. In making this assessment, our management used the criteria set forth by the Committee of Sponsoring Organizations of the Treadway Commission (COSO) in Internal Control-Integrated Framework. Based on those criteria and management’s assessment, we believe that, as of December 31, 2008, our internal control over financial reporting is effective.
Our independent registered public accountants have also issued an audit report on the Company’s internal control over financial reporting. This report appears below.
53
Table of Contents
REPORT OF INDEPENDENT REGISTERED PUBLIC ACCOUNTING FIRM
To the Board of Directors and Stockholders of Merit Medical Systems, Inc.
We have audited the internal control over financial reporting of Merit Medical Systems, Inc. and subsidiaries (the “Company”) as of December 31, 2008, based on criteria established in Internal Control — Integrated Framework issued by the Committee of Sponsoring Organizations of the Treadway Commission. The Company’s management is responsible for maintaining effective internal control over financial reporting and for its assessment of the effectiveness of internal control over financial reporting, included in the accompanying Management’s Report on Internal Control over Financial Reporting. Our responsibility is to express an opinion on the Company’s internal control over financial reporting based on our audit.
We conducted our audit in accordance with the standards of the Public Company Accounting Oversight Board (United States). Those standards require that we plan and perform the audit to obtain reasonable assurance about whether effective internal control over financial reporting was maintained in all material respects. Our audit included obtaining an understanding of internal control over financial reporting, assessing the risk that a material weakness exists, testing and evaluating the design and operating effectiveness of internal control based on the assessed risk, and performing such other procedures as we considered necessary in the circumstances. We believe that our audit provides a reasonable basis for our opinion.
A company’s internal control over financial reporting is a process designed by, or under the supervision of, the company’s principal executive and principal financial officers, or persons performing similar functions, and effected by the company’s board of directors, management, and other personnel to provide reasonable assurance regarding the reliability of financial reporting and the preparation of financial statements for external purposes in accordance with generally accepted accounting principles. A company’s internal control over financial reporting includes those policies and procedures that (1) pertain to the maintenance of records that, in reasonable detail, accurately and fairly reflect the transactions and dispositions of the assets of the company; (2) provide reasonable assurance that transactions are recorded as necessary to permit preparation of financial statements in accordance with generally accepted accounting principles, and that receipts and expenditures of the company are being made only in accordance with authorizations of management and directors of the company; and (3) provide reasonable assurance regarding prevention or timely detection of unauthorized acquisition, use, or disposition of the company’s assets that could have a material effect on the financial statements.
Because of the inherent limitations of internal control over financial reporting, including the possibility of collusion or improper management override of controls, material misstatements due to error or fraud may not be prevented or detected on a timely basis. Also, projections of any evaluation of the effectiveness of the internal control over financial reporting to future periods are subject to the risk that the controls may become inadequate because of changes in conditions, or that the degree of compliance with the policies or procedures may deteriorate.
In our opinion, the Company maintained, in all material respects, effective internal control over financial reporting as of December 31, 2008, based on the criteria established in Internal Control — Integrated Framework issued by the Committee of Sponsoring Organizations of the Treadway Commission.
We have also audited, in accordance with the standards of the Public Company Accounting Oversight Board (United States), the consolidated financial statements and financial statement schedule as of and for the year ended December 31, 2008, of the Company and our report dated March 2, 2009 expressed an unqualified opinion on those financial statements and financial statement schedule and included an explanatory paragraph regarding the adoption of Statement of Financial Accounting Standards (“SFAS”) No. 123 (revised 2004), Share-Based Payment, Financial Accounting Standards Board Interpretation (“FIN”) No. 48, Accounting for Uncertainty in Income Taxes, and SFAS No. 157, Fair Value Measurement.
/s/ DELOITTE & TOUCHE LLP | |
| |
Salt Lake City, Utah | |
March 2, 2009 | |
54
Table of Contents
Item 9B. Other Information.
None.
PART III
Items 10, 11, 12, 13 and 14.
These items are incorporated by reference to our definitive proxy statement relating to our Annual Meeting of Shareholders scheduled for May 20, 2009. We anticipate that our definitive proxy statement will be filed with the SEC not later than 120 days after December 31, 2008, pursuant to Regulation 14A of the Securities Exchange Act of 1934, as amended.
PART IV
Item 15. Exhibit and Financial Statement Schedules.
(a) Documents filed as part of this report:
(1) Financial Statements. The following consolidated financial statements and the notes thereto, and the Reports of Independent Registered Public Accounting Firm are incorporated by reference as provided in Item 8 and Item 9A of this report:
· Report of Independent Registered Public Accounting Firm — Internal Control
· Report of Independent Registered Public Accounting Firm — Financial Statements
· Consolidated Balance Sheets as of December 31, 2008 and 2007
· Consolidated Statements of Income for the Years Ended December 31, 2008, 2007 and 2006
· Consolidated Statements of Stockholders’ Equity for the Years Ended December 31, 2008, 2007 and 2006
· Consolidated Statements of Cash Flows for the Years Ended December 31, 2008, 2007 and 2006
· Notes to Consolidated Financial Statements
55
Table of Contents
(2) Financial Statement Schedule.
· Schedule II - Valuation and qualifying accounts
VALUATION AND QUALIFYING ACCOUNTS
YEARS ENDED DECEMBER 31, 2008, 2007 AND 2006
(In Thousands)
Description | | Balance at Beginning of Year | | Additions Charged to Costs Expenses (a) | | Deduction (b) | | Balance at End of Year | |
| | | | | | | | | |
ALLOWANCE FOR UNCOLLECTIBLE ACCOUNTS: | | | | | | | | | |
| | | | | | | | | |
2006 | | (767 | ) | (154 | ) | 361 | | (560 | ) |
2007 | | (560 | ) | (19 | ) | 82 | | (497 | ) |
2008 | | (497 | ) | (139 | ) | 131 | | (505 | ) |
(a) The Company records a bad debt provision based upon historical experience and a review of individual customer balances.
(b) When an individual customer balance becomes impaired and is deemed uncollectible a deduction is made against the allowance for uncollectible accounts.
Description | | Balance at Beginning of Year | | Additions Charged to Costs Expenses (c) | | Deductions(d) | | Balance at End of Year | |
| | | | | | | | | |
RESERVE FOR INVENTORY OBSOLESCENCE: | | | | | | | | | |
| | | | | | | | | |
2006 | | (1,708 | ) | (1,074 | ) | 677 | | (2,105 | ) |
2007 | | (2,105 | ) | (1,416 | ) | 1,186 | | (2,335 | ) |
2008 | | (2,335 | ) | (1,096 | ) | 1,170 | | (2,261 | ) |
(c) The Company writes down its inventory for estimated obsolescence for ummarketable and/or slow moving products that may expire prior to being sold.
(d) When a previously reserved for inventory item is either disposed of or sold the Company records a deduction to its reserve for obsolescence inventory.
All other schedules have been omitted because they are not required, not applicable, or the information is otherwise set forth in the financial statements or notes thereto.
(b) none
56
Table of Contents
(c) Exhibits:
The following exhibits required by Item 601 of Regulation S—K are filed herewith or have been filed previously with the SEC as indicated below:
| | Description | | Exhibit No. |
3.1 | | Articles of Incorporation of the Company, as amended and restated* | | [Form 10-Q filed August 14, 1996, Exhibit No. 1] |
| | | | |
3.2 | | Bylaws of the Company* | | [Form S—18 filed October 19, 1989, Exhibit No. 2] |
| | | | |
3.3 | | Amended and Restated Bylaws of Merit Medical Systems, Inc.* | | [Form 10-Q filed November 8, 2007, Exhibit No. 3.3] |
| | | | |
4 | | Specimen Certificate of the Company’s Common Stock, no par value* | | [Form S—18 filed October 19, 1989, Exhibit No. 10] |
| | | | |
4.3 | | Articles of Amendment of the Articles of Incorporation dated May 14, 1993* | | [Form S-3 filed February 14, 2005, Exhibit 4.3] |
| | | | |
4.4 | | Articles of Amendment to Articles of Incorporation dated June 6, 1996* | | [Form S-3 filed February 14, 2005, Exhibit 4.4] |
| | | | |
4.5 | | Articles of Amendment to Articles of Incorporation dated June 12, 1997* | | [Form S-3 filed February 14, 2005, Exhibit 4.5] |
| | | | |
4.7 | | Articles of Amendment to the Articles of Incorporation dated May 22, 2003* | | [Form S-3 filed February 14, 2005, Exhibit 4.7] |
| | | | |
4.8 | | Articles of Amendment to the Articles of Incorporation of Merit Medical Systems, Inc., dated May 23, 2008* | | [Form 8-K filed May 28, 2008, Exhibit 3.1] |
| | | | |
10.1 | | Merit Medical Systems, Inc. Long Term Incentive Plan (as amended and restated) dated March 25, 1996* | | [Form 10-Q filed August 14, 1996, Exhibit No. 2] |
| | | | |
10.2 | | Merit Medical Systems, Inc. 401(k) Profit Sharing Plan (as amended effective January 1, 1991* | | [Form S—1 filed February 14, 1992, Exhibit No. 8] |
| | | | |
10.3 | | License Agreement, dated April 8, 1992 between the Company and Utah Medical Products, Inc.* | | [Form S—1 filed February 14, 1992, Exhibit No. 5] |
| | | | |
10.4 | | Lease Agreement dated as of June 8, 1993 for office and manufacturing facility* | | [Form 10—K for year ended December 31, 1994, Exhibit No. 10.4] |
| | | | |
10.12 | | Amended and Restated Deferred Compensation plan* | | [Form 10-K for year ended December 31, 2003, Exhibit No. 10.12] |
| | | | |
10.13 | | Purchase agreement dated November 17, 2004 between the Company and MedSource Packaging Concepts LLC* | | [Form 10-K for year ended December 31, 2004, Exhibit No. 10.13] |
| | | | |
10.17 | | Unsecured Loan Agreement with Bank of America, N.A.* | | [Form 8-K filed December 7, 2006, Exhibit 10.1] |
| | | | |
10.18 | | Seventh Amendment to the First Restatement of the Merit Medical Systems, Inc. 401(k) Profit Sharing Plan* | | [Form 10-K for year ended December 31, 2006, Exhibit No. 10.18] |
| | | | |
10.19 | | Stock Purchase Agreement by and between Merit Medical Systems, Inc. and Sheen Man Co. LTD, dated April 1, 2007* | | [Form 10-Q filed May 9, 2007, Exhibit No. 10.19] |
| | | | |
10.20 | | Eighth Amendment to the First Restatement of the Merit Medical Systems, Inc. 401(k) Profit Sharing Plan* | | [Form 10-K for year ended December 31, 2007, Exhibit No. 10.20] |
57
Table of Contents
10.21 | | Ninth Amendment to the First Restatement of the Merit Medical Systems, Inc. 401(k) Profit Sharing Plan* | | [Form 10-K for year ended December 31, 2007, Exhibit No. 10.21] |
| | | | |
10.22 | | Tenth Amendment to the First Restatement of the Merit Medical Systems, Inc. 401(k) Profit Sharing Plan* | | [Form 10-K for year ended December 31, 2007, Exhibit No. 10.22] |
| | | | |
10.23 | | Merit Medical Systems, Inc. Amended and Restated Deferred Compensation Plan, Effective January 1, 2008* | | [Form 8-K filed December 18, 2008, Exhibit 10.1] |
| | | | |
10.24 | | Employment Agreement, made on December 31, 2008, by and between Merit Medical Systems, Inc. and Fred P. Lampropoulos* | | [Form 8-K filed January 7, 2009, Exhibit 10.1] |
| | | | |
10.25 | | Employment Agreement, made on December 31, 2008, by and between Merit Medical Systems, Inc. and Kent W. Stanger* | | [Form 8-K filed January 7, 2009, Exhibit 10.2] |
| | | | |
10.26 | | Employment Agreement, made on December 31, 2008, by and between Merit Medical Systems, Inc. and Martin R. Stephens* | | [Form 8-K filed January 7, 2009, Exhibit 10.3] |
| | | | |
10.27 | | Employment Agreement, made on December 31, 2008, by and between Merit Medical Systems, Inc. and Arlin D. Nelson* | | [Form 8-K filed January 7, 2009, Exhibit 10.4] |
| | | | |
10.28 | | Employment Agreement, made on December 31, 2008, by and between Merit Medical Systems, Inc. and Rashelle Perry* | | [Form 8-K filed January 7, 2009, Exhibit 10.5] |
| | | | |
10.29 | | Eleventh Amendment to the First Restatement of the Merit Medical Systems, Inc. 401(k) Profit Sharing Plan | | Filed herewith |
| | | | |
10.30 | | Twelfth Amendment to the First Restatement of the Merit Medical Systems, Inc. 401(k) Profit Sharing Plan | | Filed herewith |
| | | | |
21 | | Subsidiaries Of Merit Medical Systems, Inc | | Filed herewith |
| | | | |
23.1 | | Consent of Independent Registered Public Accounting Firm | | Filed herewith |
| | | | |
31.1 | | Certification of Chief Executive Officer | | Filed herewith |
| | | | |
31.2 | | Certification of Chief Financial Officer | | Filed herewith |
| | | | |
32.1 | | Certification of Chief Executive Officer | | Filed herewith |
| | | | |
32.2 | | Certification of Chief Financial Officer | | Filed herewith |
* These exhibits are incorporated herein by reference.
58
Table of Contents
SIGNATURES
Pursuant to the requirements of Section 13 or 15(d) of the Securities Exchange Act of 1934, the Registrant has duly caused this Annual Report on Form 10-K to be signed on its behalf by the undersigned, thereunto duly authorized, on March 4, 2009.
| MERIT MEDICAL SYSTEMS, INC. |
| |
| |
| By: | /s/ FRED P. LAMPROPOULOS |
| Fred P. Lampropoulos, President and Chief Executive Officer |
ADDITIONAL SIGNATURE AND POWER OF ATTORNEY
Pursuant to the requirements of the Securities Exchange Act of 1934, this report has been signed below by the following persons on behalf of the registrant and in the capacities indicated on March 4, 2009. In addition, each person whose signature to this report appears below hereby constitutes and appoints Fred P. Lampropoulos and Kent W. Stanger, and each of them, as his true and lawful attorney-in-fact and agent, with full power of substitution, to sign on his behalf individually and in the capacity stated below and to perform any acts necessary to be done in order to file all amendments and post-effective amendments to this report, and any and all instruments or documents filed as part of or in connection with this report or the amendments thereto and each of the undersigned does hereby ratify and confirm all that said attorney-in-fact and agent, or his substitutes, shall do or cause to be done by virtue hereof.
Signature | | Capacity in Which Signed |
| | |
| | |
/s/: FRED P. LAMPROPOULOS | | President, Chief Executive Officer and Director |
Fred P. Lampropoulos | | (Principal executive officer) |
| | |
| | |
/s/: KENT W. STANGER | | Chief Financial Officer, Secretary, Treasurer and |
Kent W. Stanger | | Director (Principal financial and accounting officer) |
| | |
| | |
/s/: RICHARD W. EDELMAN | | Director |
Richard W. Edelman | | |
| | |
| | |
/s/: REX C. BEAN | | Director |
Rex C. Bean | | |
| | |
| | |
/s/: JAMES J. ELLIS | | Director |
James J. Ellis | | |
| | |
| | |
/s/: MICHAEL E. STILLABOWER | | Director |
Michael E. Stillabower | | |
| | |
| | |
/s/: FRANKLIN J. MILLER | | Director |
Franklin J. Miller | | |
59