Exhibit 99.4
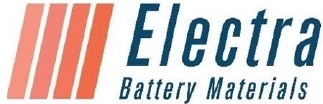
ELECTRA BATTERY MATERIALS CORPORATION
(Formerly First Cobalt Corp.)
ANNUAL INFORMATION FORM
For the fiscal year ended December 31, 2021
Dated April 8, 2022
401 Bay Street, 6th Floor
Toronto, Ontario, M5H 2Y4
TABLE OF CONTENTS
PRELIMINARY NOTES | 1 |
Date of Information | 1 |
Cautionary Notes to U.S. Investors Concerning Resource Estimates | 1 |
Currency | 1 |
Forward-Looking Information | 1 |
Future-Oriented Financial Information (FOFI) | 2 |
Certain Other Information | 3 |
CORPORATE STRUCTURE | 3 |
Name, Address and Incorporation | 3 |
Intercorporate Relationships | 3 |
GENERAL DEVELOPMENT OF THE BUSINESS | 4 |
Three Year History | 4 |
2019 Developments | 4 |
2020 Developments | 5 |
2021 Developments | 6 |
Subsequent Events | 8 |
Selected Financings | 9 |
THE BUSINESS | 10 |
Background | 10 |
Specialized Skills and Knowledge | 13 |
Competitive Conditions | 14 |
Components | 14 |
Business Cycles | 14 |
Environmental Protection | 14 |
Environmental and Social Governance | 14 |
Glencore Loan Agreement and Amended Glencore Loan Agreement | 15 |
Employees | 15 |
Reorganizations | 15 |
Foreign Operations | 15 |
REFINERY | 15 |
IRON CREEK PROJECT | 24 |
RISK FACTORS | 31 |
DIVIDENDS AND DISTRIBUTIONS | 43 |
CAPITAL STRUCTURE | 43 |
MARKET FOR SECURITIES | 43 |
Trading Price and Volume | 43 |
Prior Sales | 44 |
ESCROWED SECURITIES AND SECURITIES SUBJECT TO CONTRACTUAL RESTRICTIONS ON TRANSFER | 44 |
DIRECTORS AND OFFICERS | 44 |
Name, Province or State, Country of Residence and Offices Held | 44 |
Shareholdings of Directors and Officers | 46 |
Cease Trade Orders, Bankruptcies, Penalties or Sanctions | 46 |
Conflicts of Interest | 46 |
Management | 47 |
PROMOTERS | 49 |
AUDIT COMMITTEE | 49 |
Composition of the Audit Committee | 49 |
Relevant Education and Experience | 49 |
Audit Committee Oversight | 50 |
Reliance on Certain Exemptions | 50 |
Pre-approval Policies and Procedures | 50 |
External Auditor Service Fees (by Category) | 50 |
LEGAL PROCEEDINGS AND REGULATORY ACTIONS | 50 |
INTEREST OF MANAGEMENT AND OTHERS IN MATERIAL TRANSACTIONS | 50 |
AUDITORS, TRANSFER AGENT AND REGISTRAR | 51 |
Auditors | 51 |
Transfer Agents, Registrars or Other Agents | 51 |
MATERIAL CONTRACTS | 51 |
INTEREST OF EXPERTS | 51 |
ADDITIONAL INFORMATION | 51 |
PRELIMINARY NOTES
Date of Information
All information in this Annual Information Form (“AIF”) is as of April 8, 2022, unless otherwise indicated.
Cautionary Notes to U.S. Investors Concerning Resource Estimates
This AIF was prepared in accordance with Canadian standards for reporting of mineral resource estimates, which differ in some respects from United States standards. In particular, and without limiting the generality of the foregoing, the terms “inferred mineral resources,” “indicated mineral resources,” and “mineral resources” used or referenced in this AIF are Canadian mineral disclosure terms as defined in accordance with NI 43-101 under the guidelines set out in the Canadian Institute of Mining, Metallurgy and Petroleum Standards for Mineral Resources and Mineral Reserves, Definitions and Guidelines, May 2014 (the “CIM Standards”). Until recently, the CIM Standards differed significantly from standards in the United States. The U.S. Securities and Exchange Commission (the “SEC”) has adopted amendments to its disclosure rules to modernize the mineral property disclosure requirements for issuers whose securities are registered with the SEC under the U.S. Securities Exchange Act of 1934, as amended (the “Exchange Act”). These amendments became effective February 25, 2019 (the “SEC Modernization Rules”) with compliance required for the first fiscal year beginning on or after January 1, 2021. The SEC Modernization Rules replace the property disclosure requirements for mining registrants that were included in SEC Industry Guide 7, which will be rescinded from and after the required compliance date of the SEC Modernization Rules. As a result of the adoption of the SEC Modernization Rules, the SEC now recognizes estimates of “measured mineral resources”, “indicated mineral resources” and “inferred mineral resources”. In addition, the SEC has amended its definitions of “proven mineral reserves” and “probable mineral reserves” to be “substantially similar” to the corresponding definitions under the CIM Standards that are required under NI 43-101. Investors are cautioned that while the above terms are “substantially similar” to the corresponding CIM Definition Standards, there are differences in the definitions under the SEC Modernization Rules and the CIM Definition Standards. Accordingly, there is no assurance any mineral reserves or mineral resources that the Company may report as “proven mineral reserves”, “probable mineral reserves”, “measured mineral resources”, “indicated mineral resources” and “inferred mineral resources” under NI 43-101 would be the same had the Company prepared the mineral reserve or mineral resource estimates under the standards adopted under the SEC Modernization Rules. Readers are cautioned that “inferred mineral resources” have a great amount of uncertainty as to their existence, and great uncertainty as to their economic feasibility. It cannot be assumed that all or any part of an inferred mineral resource will ever be upgraded to a higher category. Under Canadian rules, estimates of inferred mineral resources may not form the basis of feasibility or other economic studies, except in limited circumstances. The term “resource” does not equate to the term “reserves”. Readers should not assume that all or any part of measured or indicated mineral resources will ever be converted into mineral reserves. Readers are also cautioned not to assume that all or any part of an inferred mineral resource exists or is economically mineable.
Currency
Except where otherwise indicated, all references to currency in this AIF are to thousands of Canadian Dollars (“$”).
Forward-Looking Information
Except for statements of historical fact, this AIF contains certain “forward-looking information” within the meaning of applicable Canadian securities legislation and “forward-looking statements” within the meaning of applicable United States securities legislation, together “forward-looking information”. Forward-looking statements include, but are not limited to, statements regarding anticipated burn rate and operations; planned exploration and development programs and expenditures; the Glencore Loan Agreement (as defined below); commercial agreements with respect to feedstock supply with Glencore (as defined below) and other parties; the Stratton Offtake Agreement (as defined below); the Glencore Offtake Agreement (as defined below); timelines and milestones with respect to the Refinery and the Battery Materials Park (as defined below); anticipated expenditures and programs at the Refinery, Iron Creek Project and Cobalt Camp (each as defined below); impact of COVID-19 on the Company; the estimation of mineral resources; magnitude or quality of mineral deposits; anticipated advancement of mineral properties and programs; future exploration prospects; proposed exploration plans and expected results of exploration; the Company’s ability to obtain licenses, permits and regulatory approvals required to implement expected future exploration plans; changes in commodity prices and exchange rates; future growth potential of Electra; future development plans; and currency and interest rate fluctuations. Any statements that express or involve discussions with respect to predictions, expectations, beliefs, plans, projections, objectives, assumptions or future events or performance (often, but not always, identified by words or phrases such as “expects”, “is expected”, “anticipates”, “believes”, “plans”, “projects”, “estimates”, “assumes”, “intends”, “strategy”, “goals”, “objectives”, “potential”, “possible” or variations thereof or stating that certain actions, events, conditions or results “may”, “could”, “would”, “should”, “might” or “will” be taken, occur or be achieved, or the negative of any of these terms and similar expressions) are not statements of fact and may be forward-looking statements. In particular, forward-looking information in this AIF includes, but is not limited to, statements with respect to future events and is subject to certain risks, uncertainties and assumptions. Although we believe that the expectations reflected in the forward-looking information are reasonable, there can be no assurance that such expectations will prove to be correct. We cannot guarantee future results, performance or achievements. Consequently, there is no representation that the actual results achieved will be the same, in whole or in part, as those set out in the forward-looking information.
Forward-looking statements are necessarily based upon a number of factors and assumptions that, if untrue, could cause actual results, performance or achievements to be materially different from future results, performance or achievements expressed or implied by such statements. Forward-looking statements are based upon a number of estimates and assumptions that, while considered reasonable by the Company at this time, are inherently subject to significant business, economic and competitive uncertainties and contingencies that may cause the Company’s actual financial results, performance, or achievements to be materially different from those expressed or implied herein. Some of the risks and other factors that could cause results to differ materially from those expressed in the forward-looking statements include, but are not limited to: the Refinery and general expectations with respect to the development of the Refinery; general economic conditions in Canada, the United States and globally; industry conditions, including the state of the electric vehicle (“EV”) market; governmental regulation of the mining industry, including environmental regulation; geological, technical and drilling problems; unanticipated operating events; competition for and/or inability to retain drilling rigs and other services; the availability of capital on acceptable terms; the need to obtain required approvals from regulatory authorities; stock market volatility; volatility in market prices for commodities; liabilities inherent in the mining industry; changes in tax laws and incentive programs relating to the mining industry; the future price of cobalt; anticipated costs and the Company’s ability to fund its programs; the Company’s ability to carry on exploration and development activities; the timing and results of drilling programs; the discovery of additional mineral resources on the Company’s mineral properties; the timely receipt of required approvals and permits, including those approvals and permits required for successful project permitting, construction and operation of projects; the costs of operating and exploration expenditures; the Company’s ability to operate in a safe, efficient and effective manner; the potential impact of natural disasters; the Company’s ability to obtain financing as and when required and on reasonable terms; the impacts and ongoing developments of the COVID-19 global pandemic and the Russo-Ukrainian war and the other factors described herein under “Risk Factors”, as well as in our public filings available at www.sedar.com. Readers are cautioned that this list of risk factors should not be construed as exhaustive.
The forward-looking information contained in this AIF is expressly qualified by this cautionary statement. We undertake no duty to update any of the forward-looking information to conform such information to actual results or to changes in our expectations, except as otherwise required by applicable securities legislation. Readers are cautioned not to place undue reliance on forward-looking information.
Future-Oriented Financial Information (FOFI)
This AIF also contains future-oriented financial information and outlook information (collectively, “FOFI”) about the Refinery and results of the Refinery Study. This information is subject to the same assumptions, risk factors, limitations and qualifications as set forth below in the below paragraphs. FOFI contained in this AIF is made as of the date of this AIF and is being provided for the purpose of providing further information with respect to the Refinery and results of the Refinery Study. The Company disclaims any intention or obligation to update or revise any FOFI contained in this AIF, whether as a result of new information, future events or otherwise, unless required pursuant to applicable law. Readers are cautioned that FOFI contained in this AIF should not be used for purposes other than for which it is disclosed herein.
Certain Other Information
Certain information in this AIF is obtained from third party sources, including public sources, and there can be no assurance as to the accuracy or completeness of such information. Although believed to be reliable, management of the Company has not independently verified any of the data from third party sources unless otherwise stated.
CORPORATE STRUCTURE
Name, Address and Incorporation
Electra Battery Materials Corporation (“Electra” or the “Company”) was incorporated under the provisions of the Business Corporations Act (British Columbia) (the “BCBCA”) on July 13, 2011 under the name Patrone Gold Corp. and became a reporting issuer in British Columbia and Alberta upon completion of an arrangement with Unity Energy Corp. on October 2, 2012. On October 3, 2013, the Company changed its name from Patrone Gold Corp. to Aurgent Gold Corp. On March 11, 2014, the Company changed its name from Aurgent Gold Corp. to Aurgent Resource Corp., and on September 22, 2016, the Company changed its name from Aurgent Resource Corp. to First Cobalt Corp. On October 26, 2017, shareholders of the Company approved a continuation under the Canada Business Corporations Act (the “CBCA”). The Company’s continuation under the CBCA was implemented as of September 4, 2018. On December 2, 2021, the Company changed its name from First Cobalt Corp. to Electra Battery Materials Corporation.
Electra is in the business of battery materials refining and the acquisition and exploration of resource properties. The Company is focused on building a diversified portfolio of assets that are highly leveraged to the cobalt market with assets located primarily in North America with the intent of providing a North American supply of battery materials.
Electra is planning to build a fully integrated, localized and environmentally sustainable battery materials park. Leveraging the Company’s own mining assets and business partners, the Battery Materials Park (as defined below) will host cobalt and nickel sulfate production plants, a large-scale lithium-ion battery recycling facility, and battery precursor materials production, which will serve both North American and global customers.
Electra has two significant North American assets:
| (1) | The only permitted cobalt refinery in North America capable of producing battery materials, (the “Refinery”); and |
| (2) | The Iron Creek Project in Idaho, the Company’s flagship mineral project (the “Iron Creek Project”). |
Electra is listed on the TSX Venture Exchange (“TSXV”) as a Tier 2 mining issuer, and trades under the symbol “ELBM” and on the OTCQX under the symbol “ELBMF”. The Company is a reporting issuer in all of the provinces and territories of Canada and files its continuous disclosure documents with the Canadian Securities Authorities in such jurisdictions. Such documents are available on SEDAR at www.sedar.com. Electra’s filings through SEDAR are not incorporated by reference in this AIF.
The Company’s registered office is located at Suite 2400, Bay Adelaide Centre, 333 Bay Street, Toronto, Ontario, M5H 2T6. The Company’s corporate head office is located at 401 Bay Street, 6th Floor, Toronto, Ontario, M5H 2Y4.
Intercorporate Relationships
Electra has four direct subsidiaries, being, Cobalt Industries of Canada Inc., Cobalt Projects International Corp. (“Cobalt Projects”), both of which are incorporated under the laws of the Province of Ontario, Canada, U.S. Cobalt Inc. (“US Cobalt”), which is incorporated under the laws of the Province of British Columbia, Canada, and Cobalt One Limited (“Cobalt One”), an Australian corporation. Electra is the registered and beneficial owner of all of the outstanding share capital in all four direct subsidiaries.
The following shows the Company’s intercorporate relationships. Electra owns, directly or indirectly, 100% of each subsidiary unless otherwise indicated.
Electra Battery Materials Corporation (Ontario)
(I) Cobalt Industries of Canada Inc. (Ontario)
(II) Cobalt Projects International Corp. (Ontario)
(III) U.S. Cobalt Inc. (British Columbia)
(i) Scientific Metals (Delaware) Corp. (Delaware)
(ii) 1086370 B.C. Ltd. (British Columbia)
(a) Idaho Cobalt Company (Idaho)
(iii) Orion Resources NV (Nevada)
(IV) Cobalt One Limited (Australia)
| (i) | Cobalt Camp Refinery Ltd. (British Columbia) |
| (ii) | Cobalt Camp Ontario Holdings Corp. (Ontario) |
| (iii) | Acacia Minerals Pty Ltd (Australia) |
| (iv) | Ophiolite Consultants Pty Ltd (Australia) |
Effective March 1, 2021, Electra transferred ownership of CobalTech Mining Inc. (“CobalTech”) to Kuya Silver Corporation (“Kuya”). Electra originally retained certain rights associated with a class of outstanding preferred shares of CobalTech but such rights were extinguished in September 2021 when the preferred shares were redeemed. Prior to the transfer, CobalTech was a wholly-owned subsidiary of Electra. This transfer of ownership was in connection with completion of the sale to Kuya of a portion of its exploration assets in the Cobalt Camp in Ontario (the “Cobalt Camp”). See “General Development of the Business – 2021 Developments” below.
GENERAL DEVELOPMENT OF THE BUSINESS
Three Year History
2019 Developments
On January 16, 2019, the Company announced the departure of Jeff Swinoga from the Company’s Board of Directors.
On February 21, 2019, the Company announced the appointment of three-term former Idaho Governor C.L. “Butch” Otter to its Board of Directors. Gov. Otter has had a long and prominent political career including both federal and state positions, as well as a more than 30-year career as a business leader.
On April 3, 2019, the Company announced that it had successfully produced a battery grade cobalt sulfate using the Refinery flowsheet. This was a significant milestone which brings the Company closer to recommissioning the only permitted primary cobalt refinery in North America. SGS Canada performed the testing using cobalt hydroxide as the feedstock. The test work concluded that processing cobalt hydroxide feed would not require the reactivation of the Refinery’s autoclaves, providing an opportunity for higher production potential than projected in the independent study prepared by Primero Group in 2018.
On May 1, 2019, the Company acquired, by way of a private share purchase agreement, a total of 9,640,500 common shares of eCobalt Solutions Inc. for investment purposes. In consideration for the private share purchase, the Company issued 21,265,809 common shares in the capital of the Company (“Common Shares”).
On May 10, 2019, the Australian Securities Exchange (the “ASX”) approved the Company’s request to voluntarily de-list. The Company delisted due to low ASX trading volumes compared to the TSXV, to reduce compliance costs, and because it has no material Australian cobalt projects or business operations.
On May 21, 2019, the Company announced it had signed a memorandum of understanding with Glencore AG (“Glencore”) to supply feedstock and financing to recommission the Refinery.
On May 28, 2019, the Company announced the results of an Ausenco Engineering Canada Inc. (“Ausenco”) scoping study, which concluded that by eliminating the Refinery’s autoclave circuit and addressing production constraints, annual production could reach over 5,000 tonnes of cobalt per annum, more than double previous estimates. The total capital costs associated with this production level is estimated as US$37.5M, representing only US$7.5M of incremental capital costs over previous estimates in order to double production.
On July 15, 2019, the Company announced an agreed term sheet with Glencore which outlined the framework to collaboratively recommission and expand the Refinery. The term sheet outlined Glencore’s support, subject to conditions, to provide funding for metallurgical testing, engineering and permitting work associated with the Refinery and to work towards forming a collaborative long-term relationship to supply refined cobalt to the North American market.
On August 26, 2019, the Company finalized a loan agreement with Glencore (the “Glencore Loan Agreement”) for a US$5M loan to support the next phase of Refinery advancement work, which entails metallurgical testing, engineering, cost estimating, field work and permitting activities to recommission the Refinery, including a definitive feasibility study for a 55 tpd Refinery expansion. The agreement also provides a framework for a fully funded, phased approach to recommissioning and expanding the Refinery. This could involve an interim step where the Refinery is recommissioned at 12 tpd in 2020 then expanded to 55 tpd in 2021 utilizing the current site infrastructure and buildings.
On October 1, 2019, the Company named John Pollesel as non-executive Chairman of the Board of Directors and Susan Uthayakumar as a new Director. John Pollesel has over 30 years of experience in mining and was previously COO and Director of Base Metals Operations for Vale’s North Atlantic Operations, where he was responsible for the largest underground mining and metallurgical operations in Canada. Prior to this, he was Vice President and General Manager for Vale’s Ontario Operations. More recently, he was Senior Vice President, Mining at Finning Canada. Mr. Pollesel also served as CFO for Compania Minera Antamina in Peru, responsible for executive management in one of the largest copper/zinc mining and milling operations in the world. Susan Uthayakumar is President of Schneider Electric Canada, a French-headquartered Fortune Global 500 company and a global leader in digital transformation of energy management and automation. As the Company transitions to a cobalt refiner and active operations, the global management experience of the updated Board will provide valuable contributions to the Company.
2020 Developments
On January 15, 2020, the Company announced a new mineral resource estimate for the Iron Creek Project in Idaho, USA. The new mineral resource estimate was based on infill drilling and limited step-out drilling which included the conversion of 49% of resources from the inferred mineral resource category to the indicated mineral resource category while also increasing the overall tonnage. The indicated mineral resource is now 2.2M tonnes grading 0.32% cobalt equivalent (0.26% cobalt and 0.61% copper) containing 12.3M pounds of cobalt and 29.1M pounds of copper. The inferred mineral resource is now 2.7M tonnes grading 0.28% cobalt equivalent (0.22% cobalt and 0.68% copper) for an additional 12.7M pounds of cobalt and 39.9M pounds of copper. See “Iron Creek Project” below.
On March 30, 2020, the Company announced it had produced battery grade cobalt sulfate using the Refinery flowsheet again, using cobalt alloy as the feedstock.
On April 15, 2020, the Company announced that it increased the size of its Idaho cobalt land position by 50%. The expanded property contains the Iron Creek cobalt-copper deposit, the Ruby target and several other surface exposures of cobalt-copper mineralization. A total of 43 new claims were staked to the west of the Iron Creek Project, expanding the total area from 1,700 acres to over 2,600 acres.
On May 4, 2020, the Company announced positive results from an independent engineering study on the Refinery. The study, titled “First Cobalt Refinery Project – AACE Class 3 Feasibility Study” (the “Refinery Study”), was prepared by Ausenco under the definitions of an Association for the Advancement of Cost Engineering (AACE) Class 3 Feasibility Study is dated July 9, 2020 and was filed on SEDAR under the Company’s profile at www.sedar.com. The Refinery Study contemplates expanding the existing facility and adapting it to be North America’s first producer of cobalt sulfate, an essential component in the manufacturing of batteries for EVs.
On August 17, 2020, the Company announced the appointment of Mark Trevisiol as Vice-President, Project Development. Mr. Trevisiol is a professional engineer with 30 years of experience in mineral processing, mining, capital project and executive management.
On September 24, 2020, the Company announced initial results from ongoing optimization programs with respect to the Refinery.
On October 19, 2020, the Company announced the resumption of exploration activities at the Iron Creek Project. The Company commenced geophysical surveys to trace extensions of mineralization and will follow up on geophysical anomalies detected by its previous work on the Iron Creek Project.
On November 10, 2020, the Company announced that it had re-focused commercial arrangements with Glencore towards a long-term feed purchase contract rather than a tolling arrangement. The Company also announced that it had extended the maturity date on the Glencore Loan Agreement by a year from August 23, 2021 to August 23, 2022.
On November 23, 2020, the Company announced that it had filed amended and restated audited consolidated financial statements for the year-ended December 31, 2019 and amended and restated condensed interim consolidated financial statements for the interim periods ended March 31, 2020 and June 30, 2020, along with amended and restated management discussion and analysis for these periods.
On November 26, 2020, the Company filed a final short form base shelf prospectus (the “Base Prospectus”) with the securities regulators in all provinces and territories of Canada. The Base Prospectus allows the Company to make offerings of Common Shares, subscription receipts, warrants, units or any combination thereof for up to an aggregate total of $20,000 during the 25-month period that the Base Prospectus remains effective. The specific terms of any offering of securities, including the use of proceeds from any offering, will be set forth in a shelf prospectus supplement.
On December 16, 2020, the Company entered into contribution agreements with the Government of Canada and the Government of Ontario to receive $10,000 in public funding pursuant to the Federal Economic Development Initiative for Northern Ontario and the Northern Ontario Heritage Fund Corporation, respectively. The funding is anticipated to be used for recommissioning and expansion of the Refinery. The funding from the Government of Canada is a $5,000 zero-interest loan. This loan will be repaid starting one year after production is commenced at the Refinery and must be repaid within 5 years from the first payment date. The funding from the Government of Ontario is a $5,000 non-repayable grant.
On December 18, 2020, the Company filed a Notice of Change of Auditors on SEDAR in connection with a change of the Company’s auditors from MNP LLP, Chartered Professional Accountants (“MNP”) to KPMG LLP, Chartered Professional Accountants (“KPMG”) effective December 10, 2020.
2021 Developments
On January 12, 2021, the Company announced long-term cobalt hydroxide feed arrangements with Glencore and IXM SA (“IXM”), a fully owned subsidiary of China Molybdenum Co., Ltd (“CMOC”), which will provide a total of 4,500 tonnes of contained cobalt per year to the Refinery commencing in late 2022. The contained cobalt will be provided from Glencore’s KCC mine and CMOC’s Tenke Fungurume mine and represents 90% of the projected capacity of the Refinery.
On January 26, 2021, the Company announced that it has commenced certain pre-construction activities for the Refinery, including detailed engineering and the tendering process for long lead equipment items. The vendor for the cobalt crystallizer, a critical piece of equipment in the expanded Refinery, has been selected and the equipment engineering work has started.
On February 9, 2021, the Company announced the appointment of Regan Watts as Vice-President, Corporate Affairs and Dr. George Puvvada as its Refinery Technical Manager.
On February 22, 2021, the Company filed a supplement to its Base Prospectus to establish an at-the-market equity program that allowed the Company to issue up to $10,000 of Common shares from treasury to the public from time to time, at the Company’s discretion. Distributions of Common shares through the at-the-market equity program were made pursuant to the terms of an equity distribution agreement between the Company and Cantor Fitzgerald Canada Corporation (“Cantor”). On August 23, 2021, in the context of arranging for the US$45,000 combined secured convertible debt and brokered equity financing, as further described under the heading “Selected Financings” below, the Company provided notice to Cantor of the Company’s intention to terminate the at-the-market equity program. The Company raised a total of $686 under the at-the-market equity program. Effective as of September 2, 2021, all sales under the at-the-market equity program were suspended.
On March 1, 2021, the Company announced that it completed its transaction with Kuya to sell a portion of its silver and cobalt exploration assets in the Cobalt Camp and form a joint venture to advance the remaining mineral assets. Kuya acquired a 100% interest in the properties located in the Kerr silver district as consideration for which the Company received $1,000 in cash and 1,437,470 common shares of Kuya. Kuya also acquired an option to earn a 70% interest in the remainder of the Cobalt Camp assets in exchange for staged payments totaling a further $2,000 ($1,000 of which has been paid) and expenditures aggregating to $4,000 in advance of September 1, 2024. Kuya is to make a milestone payment of $2,500 upon completion of a maiden mineral resource estimate of at least 10,000,000 silver equivalent ounces on either of the Kerr area properties or the remaining Cobalt Camp assets. The quantum of the payment increases to $5,000 should the resource exceed 25,000,000 silver equivalent ounces. The Company will have a right of first offer to refine base metal concentrates produced at the Refinery as well as a back-in right for any discovery of a primary cobalt deposit on the remaining Cobalt Camp assets.
On March 29, 2021, the Company announced that it had signed a flexible, long-term, offtake agreement (the “Stratton Offtake Agreement”) with Stratton Metal Resources Limited (“Stratton Metals”) for the sale of future cobalt sulfate production from the Refinery. The Company will have the option to sell up to 100% of its annual cobalt sulfate production to Stratton Metals, subject to a minimum annual quantity. The Stratton Offtake Agreement has a five year term, with quantities to be determined by Electra in advance of each calendar year, and subject to a minimum annual quantity. Pricing will be based on prevailing market prices at the time of the shipment.
Effective April 7, 2021, the Company executed a loan amendment agreement with Glencore to repay the full amount of the existing loan, approximately US$5,506 inclusive of capitalized interest, by issuing common shares of the Company. The amendment and settlement were made via a “shares for debt” provision under TSXV rules. Therefore, the Glencore loan payable and associated derivative liability were settled and derecognized for accounting purposes in the second quarter of 2021, with a resulting loss booked by the Company at that time. The shares were issued at a 15% discount to market, consistent with the original loan agreement terms which gave Glencore the right to convert the balance owing to shares of Electra at a discount of 15% at maturity. A total of 23,849,737 shares were issued to Glencore at a deemed price of $0.29 per share.
On April 7, 2021, the Company announced the appointment of Michael Insulan as Vice President, Commercial. Mr. Insulan has nearly 20 years of experience across oil and gas, bulk commodities, base and minor metals. He has worked for Royal Dutch Shell, CRU, and Eurasian Resources Group. He holds a PhD in Economics, focused on the extractive industries.
On April 28, 2021, the Company announced it had been awarded funding from the US Department of Energy’s Critical Materials Institute (CMI) to research innovative mineral processing techniques for the Iron Creek project. The funding from CMI will consist of US$600 over a two-year period, with an in-kind match from the Company, as part of a total US$1.2 million program.
On May 11, 2021 the Company announced it had acquired additional mining claims known as the West Fork Property to the west of the Iron Creek Project. This transaction effectively doubled the Company’s Idaho land position. Geophysical surveys will be conducted at the West Fork property to test for cobalt and copper mineralization extensions.
On May 25, 2021, the Company announced another transaction, acquiring the Redcastle property to the east of the Iron Creek Project to further expand its land position in Idaho.
On September 1, 2021, Kuya exercised its option to earn up to a 70% interest in the Remaining Assets. To exercise the option, Kuya issued 671,141 common shares at a 20-day VWAP of $1.49 per common share. Over a 3-year earn-in period, Kuya will be required to make $1,000 in additional payments to the Company and invest $4,000 in exploration activities on the properties to earn a 70% interest. Additional milestone payments would be made to the Company in the event a significant silver mineral resource estimate is completed.
On October 5, 2021, the Company announced that it awarded a contract to Metso Outotec for the design and manufacturing for the design and manufacturing of solvent extraction cells as well as technical support for the layout of a new solvent extraction plant and its process control.
On November 30, 2021, the Company announced that it had filed an amendment to the Base Prospectus to increase the total offering price of the securities of the Company that may be offered from time to time under the Prospectus from $20,000 to $70,000 (or the equivalent thereof in U.S. dollars or other currencies).
On December 30, 2021, the Company announced it signed a five-year cobalt tolling contract and amended the previous concluded five-year cobalt hydroxide feed purchase agreement with Glencore.
Subsequent Events
On January 13, 2022, the Company filed a prospectus supplement announced that it has established an at-the-market equity program that allows the Company to issue up to $20,000 of Common Shares from the treasury to the public from time to time, at the Company’s discretion (the “ATM Program”). Distributions of the Common Shares through the ATM Program, if any, will be made pursuant to the terms of an equity distribution agreement (the “ATM Distribution Agreement”) between the Company and CIBC Capital Markets (“CIBC”). The volume and timing of distributions under the ATM Program, if any, will be determined at the Company’s sole discretion. The Company is not obligated to make any sales of Common Shares under the ATM Program. The ATM Program will be effective until the earlier of the issuance and sale of all of the Common Shares issuable pursuant to the ATM Program and December 26, 2022, unless terminated prior to such date by the Company or the Agent. The ATM Program is being facilitated pursuant to a prospectus supplement dated January 13, 2022 to the Company’s base shelf prospectus dated November 26, 2020 as amended pursuant to amendment no. 1 dated November 30, 2021 filed with the securities commissions in each of the provinces of Canada, which are available online under the Company’s profile on SEDAR at www.sedar.com.
On January 19, 2022, the Company announced that it signed a battery recycling and cobalt sulfate supply agreement with Japanese conglomerate Marubeni Corporation.
On February 10, 2022, the Company announced that it received its Industrial Sewage Works Environmental Compliance Approval from the Ontario Ministry of the Environment, Conservation and Parks, and that it has filed its final closure plan for the Refinery.
On February 23, 2022, the Company announced that it was partnering with the Government of Ontario, Glencore plc and Talon Metals Corp., to launch a battery materials park study. The partners will collaborate on engineering, permitting, socio-economic and cost studies associated with the construction of a nickel sulfate plant as well as a battery precursor cathode materials (PCAM) plant adjacent to the Refinery.
On March 1, 2022, the Company announced a financial commitment of $250 from the Government of Ontario in support of the study.
On March 4, 2022, the Company’s closure plan for its Refinery received final approval.
On April 5, 2022, the Company announced its intention to submit a formal application to list its Common Shares on the Nasdaq Stock Market LLC.
On April 5, 2022, the Company announced that it would be undertaking a consolidation of its share capital on the basis of eighteen (18) existing Common Shares for one (1) new Common Shares. The Company anticipates that the consolidation will take effect on or about April 11, 2022.
On April 6, 2022, the Company announced that it had entered into an offtake agreement (the “Glencore Offtake Agreement”) for nickel and cobalt produced from a battery recycling plant that it expects to commission in 2023 at its Battery Materials Park (as defined below). Under the agreement, Glencore will purchase nickel and cobalt products until the end of 2024 on market-based terms.
Selected Financings
The Company has completed the following financings over the last three completed financial years.
On March 29, 2019, the Company completed a non-brokered private placement of 8,913,251 units at a price of $0.18 per unit for gross proceeds of $1,604. Each unit consists of one Common Share and one Common Share purchase warrant. Each warrant entitles the holder thereof to purchase one additional Common Share at a price of $0.27 for a period of two years. The warrants are subject to an acceleration clause such that, if the closing price of the Common Share is equal to or greater than $0.37 per Common Share for a period of ten consecutive trading days, the Company shall have the option, but not the obligation, to effect an accelerated expiration date that shall be 20 calendar days from the issuance of a notice of acceleration.
On February 5, 2020, the Company completed a non-brokered private placement by issuing 15,097,430 units at a price of $0.14 per unit for gross proceeds of $2,114. Each unit consists of one Common Share and one Common Share purchase warrant. Each warrant entitles the holder thereof to purchase one additional Common Share at a price of $0.21 for a period of two years. The warrants are subject to an acceleration clause such that, if the closing price of the Common Shares is equal to or greater than $0.37 per share for a period of 10 consecutive trading days, the Company shall have the option, but not the obligation, to effect an accelerate expiration date that shall be 20 calendar days from the issuance of a notice of acceleration.
On August 28, 2020, the Company announced the closing of a non-brokered private placement of 8,225,000 units at a price of $0.14 per unit and 8,528,643 flow-through units at a price of $0.16 per flow-through unit for aggregate gross proceeds of $2,510. Each unit consists of one Common Share and one warrant. Each flow-through unit consists of one Common Share qualifying as a ‘flow-through share’ and one half of one warrant. The warrants issued in connection with the units and flow-through units entitle the holder to purchase a Common Share at a price of $0.21 per Common Share for a period of 24 months from the date of issuance.
On January 22, 2021, the Company completed a bought deal prospectus offering, pursuant to a prospectus supplement to the Base Prospectus, of 31,533,000 units at a price of $0.31 per unit for gross proceeds of $9,775. Each unit consists of one Common Share and one-half of one Common Share purchase warrant. Each whole warrant is exercisable into one Common Share at an exercise price of $0.50 per Common Share for a period of 24 months from the closing of the offering. The underwriters received a cash commission equal to 6% of the gross proceeds of the offering and 1,891,980 compensation warrants, each compensation warrant being exercisable to acquire one Common Share at $0.31 per Common Share, for a period of 24 months from the closing of the offering.
On August 23, 2021, the Company entered into subscription agreements with certain institutional investors in the United States for US$37,500 principal amount of 6.95% senior secured convertible notes due December 1, 2026 (“Notes”), led by Cantor Fitzgerald Co. as placement agent (the “Note Offering”), and announced a brokered overnight-marketed public offering of Common Shares of approximately $9,500 to be priced in the context of the market (the “Equity Offering”) for aggregate proceeds to the Company of approximately US$45,000. On September 2, 2021 an aggregate of 38,150,000 common shares were issued at a price of $0.25 per share pursuant to the Equity Offering. The investors in the Note Offering also had an option to increase the principal amount of notes subscribed for by up to an additional aggregate amount of US$7,500. This option was exercised in full by the noteholders and the additional Notes were subsequently issued on October 22, 2021. The initial conversion rate of the Notes is 4,058.24 Common Shares per US$1 (equivalent to an initial conversion price of approximately US$0.25 per Common Share), subject to certain adjustments set forth in the indenture governing the Notes.
THE BUSINESS
Background
The Company was incorporated on July 13, 2011 under the BCBCA. On September 4, 2018, the Company was continued under the CBCA. On December 6, 2021, the Company changed its name from “First Cobalt Corp.” to “Electra Battery Materials Corporation”. The Company is in the business of producing battery materials for the electric vehicle supply chain. The Company is focused on building an ethical supply of cobalt, nickel and battery precursor material.
The Company owns two main assets – the Refinery located in Ontario, Canada and the Iron Creek cobalt-copper project located in Idaho, United States. It also controls a number of properties in Ontario known as the Cobalt Camp.
The Company has been progressing plans to recommission and expand the Refinery with a view to becoming the only refiner of battery grade cobalt sulfate in North America. It’s primary focus for 2022 is advancing the expansion and recommissioning of the Company’s Refinery (Phase 1 of the Company’s four-phased approach to build the Battery Materials Park (as defined below)) and continuing to expand its cobalt-copper resource at Iron Creek.
The Refinery and the Battery Materials Park
The Company is working towards restarting its wholly owned cobalt Refinery in Ontario, Canada, as the first phase in a four-phase strategy to create North America’s only fully integrated, localized and environmentally sustainable battery materials park (the “Battery Materials Park”), which will provide battery grade nickel and cobalt, recycled battery materials and precursor material to the North American and global electric vehicle battery market. The Company is pursuing a four-phased approach to build the Battery Materials Park, as follows:
| • | Phase 1 entails an expansion and recommissioning of the Company’s Refinery. The Company anticipates the refinery will produce at an initial rate of 5,000 tonnes per annum of battery cobalt contained in cobalt sulfate from cobalt hydroxide intermediate product supplied from Glencore and CMOC mining operations in the Democratic Republic of Congo. The Company has purchased larger equipment such that a step up in production to 6,500 tonnes per annum in the future is possible. |
| • | Phase 2 entails the recycling of black mass from spent lithium-ion batteries supplied by various black mass producers (battery shredders) in the United States and elsewhere. |
| • | Phase 3 entails the construction of a nickel sulfate plant, thereby providing all of the necessary components (other than manganese) to attract a precursor manufacturer to establish a facility adjacent to these refining operations. |
| • | Phase 4 entails the construction of a precursor cathode active materials facility (“PCAM”), potentially in conjunction with an industry partner, to produce a nickel-cobalt-manganese PCAM product for the electric vehicle supply chain. |
On May 4, 2020, the Company announced positive results from an engineering study performed for the Refinery by Ausenco Engineering Canada (the “Refinery Study”). The Refinery Study outlined the Refinery’s ability to reach annual production of 25,000 tonnes of battery grade cobalt sulfate from third party feed, representing 5% of the total global refined cobalt market and 100% of North American cobalt supply with strong operating cash flows and a globally competitive cost structure.
The Refinery Study was prepared to summarize the results of an engineering study prepared at a feasibility level related to the Refinery. The Company confirms that the report does not constitute a feasibility study within the definition employed by the Canadian Institute of Mining, Metallurgy and Petroleum (“CIM”), as it relates to a standalone industrial project and does not concern a mineral project of Electra. As a result, disclosure standards prescribed by NI 43-101 are not applicable to the scientific and technical disclosure in the report. Any references to scoping study, prefeasibility study or feasibility study by Electra, in relation to the Refinery, are not the same as terms defined by the CIM Definition Standards and used in NI 43-101. The Refinery Study is also not based on any existing mineral reserves or mineral resources of the Company and the Company does not contemplate that any of the Company’s current mineral projects will provide a source of feedstock for the Refinery.
Subsequent to the Refinery Study, additional metallurgical testing, engineering work, flow-sheet optimization and market analysis has been completed, certain equipment has been ordered and the Company has entered the full development phase of the refinery expansion project. As the project has progressed and changed from the Refinery Study, the original economic outputs should no longer be relied upon.
Additionally, in response to strong customer demand, the Company has invested in increased capacity for its cobalt crystallizer, which will result in installed capacity of 6,500 tonnes of annual contained cobalt production, a 30% increased from the engineering study design of 5,000 tonnes. Future permit amendments will be sought to permit this increased output level. The Company has also been reviewing opportunities to utilize black mass from recycled lithium-ion batteries as supplemental refinery feedstock, with a scoping study in progress.
The Company has achieved several additional key milestones on its development path for the Refinery, including:
| • | January 2021 | – Feedstock arrangements announced with Glencore and IXM |
| • | January 2021 | – Commencement of detailed engineering and pre-construction activities |
| • | February 2021 | – ATM Program launched for issuance of up to $10,000 of common shares |
| • | March 2021 | – Sale of Cobalt Camp properties to Kuya Silver for $4,000 in cash and shares |
| • | March 2021 | – Warrant exercises of $7.1 million from Dec 2020 through March 2021 |
| • | March 2021 | – Flexible, long-term offtake arrangement for up to 100% of production |
| • | September 2021 | – Convertible note and equity offering for US$45,000 to fund construction |
| • | October 2021 | – Solvent extraction design and manufacturing contract awarded to Metso-Outotec |
| • | October 2021 | – Additional convertible notes of US$7,500 issued |
| • | November 2021 | – Increased cobalt crystallizer capacity and formalized new project capital budget |
| • | December 2021 | – Five-year tolling contract and amended feed purchase agreement with Glencore |
| • | January 2022 | – Establishment of the $20,000 ATM Program with CIBC |
| • | February 2022 | – Receipt of Industrial Sewage Works approval |
| • | March 2022 | – Receipt of final approval for closure plan for the Refinery |
The construction remains on schedule to commission the expanded refinery in Q4 2022 and initially ramp-up to 5,000 tonnes of contained cobalt production per year. Ground excavation has commenced for the solvent extraction facility, and major equipment contracts have been awarded. The project has now advanced beyond the study phase, with detailed engineering now significantly more advanced and numerous equipment orders finalized. Therefore, the Company has completed a new capital budget that is more defined and representative of the project. The updated capital budget is US$67,000, including a contingency amount of US$3,900.
The Company received approval for its Air and Noise permit and its Permit to Take Water, and as noted above, the Company has received final approvals for its Industrial Sewage Works permit amendment and its revised Refinery closure plan. An update to the Permit to Take Water is in progress to ensure the volumes match the Industrial Sewage Works Permit, which will need to be completed in advance of operation.
The current estimated timeline to bring the Refinery into production is outlined below:
| • | Q2 2022 – Receive updated permit to take water |
| • | Q2 2022 to Q4 2022 – On site construction activities |
| • | Q4 2022 – Refinery Commissioning |
The Company continues to make progress towards achieving its objective of providing the world’s most sustainable battery materials for the electric vehicle market. The Company continues to work with engineering firms, its commercial partners, process experts and financial advisers to finalize and execute on the plans for its phase one recommissioning and expansion of the Refinery.
See “Refinery” for more information with respect to the Refinery Study.

The Iron Creek Project
Following the completion of the acquisition of US Cobalt, the Company owns 100% of the Iron Creek Project which is located about 42 kilometres southwest of Salmon, Idaho, within the historic Blackbird cobalt-copper district of the Idaho cobalt belt. The project consists of seven patented Federal lode claims that straddle Iron Creek, and a surrounding group of 83 unpatented Federal lode claims. As noted above, the Company announced a new mineral resource estimate for the Iron Creek Project in Idaho, USA in January 2020. The new mineral resource estimate was based on infill drilling and limited step-out drilling which included the conversion of 49% of resources from the inferred mineral resource category to the indicated mineral resource category while also increasing the overall tonnage. The indicated mineral resource is now 2.2M tonnes grading 0.32% cobalt equivalent (0.26% cobalt and 0.61% copper) containing 12.3M pounds of cobalt and 29.1M pounds of copper. The inferred mineral resource is now 2.7M tonnes grading 0.28% cobalt equivalent (0.22% cobalt and 0.68% copper) for an additional 12.7M pounds of cobalt and 39.9M pounds of copper. In April 2020, the Company announced additional staking added 43 new claims to the Company’s Idaho land package. The Company further increased its property position around Iron Creek in May 2021, with the acquisition of the West Fork Property and the announcement of the Redcastle property earn-in agreement. In June 2021, the Company announced the commencement of its 2021 Idaho exploration program encompassing 4,500 metres of drilling, geophysical surveys and bedrock geological mapping at a budgeted cost of $2.5 million. Together, the patented and unpatented claims cover an area of approximately 5,900 acres. See “Iron Creek Project” for more information with respect to the Iron Creek Project.
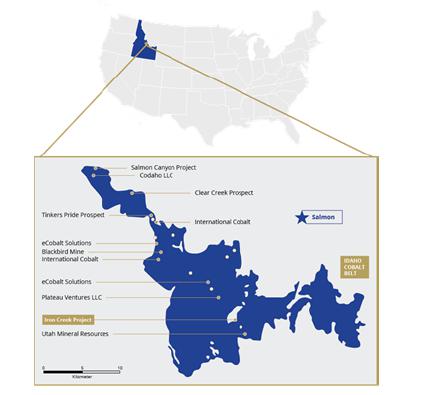
The Cobalt Camp
As further discussed under “General Development of the Business – 2021 Developments” above, on March 1, 2021, the Company announced that it completed its transaction with Kuya to sell a portion of its silver and cobalt mineral exploration assets its Cobalt Camp and form a joint venture to advance the remaining mineral assets comprising the Cobalt Camp. The Cobalt Camp is approximately a five-hour drive from Toronto, Ontario. The Cobalt Camp is not material property for the purpose of this AIF.

Specialized Skills and Knowledge
Successful exploration, development and operation of the Company’s cobalt projects will require access to personnel in a wide variety of disciplines, including engineers, geologists, geophysicists, drillers, managers, project managers, accounting, financial and administrative staff, and others. Since the project locations are also in jurisdictions familiar with and friendly to advanced manufacturing and resource extraction, management believes that the Company’s access to the skills and experience needed for success is sufficient.
Competitive Conditions
The Company’s activities are directed towards the potential recommissioning and expansion of the Refinery and the exploration, evaluation and development of mineral deposits. There is no certainty that the expenditures to be made by the Company will result in the recommissioning and expansion of the Refinery or discoveries of commercial quantities of mineral deposits. There is aggressive competition within the mining industry for the discovery and acquisition of properties considered to have commercial potential. The Company will compete with other interests, many of which have greater financial resources than it will have, for the opportunity to participate in promising projects. Significant capital investment is required to achieve commercial production from successful exploration efforts, and the Company may not be able to successfully raise funds required for any such capital investment. See “Risk Factors – Competition” below.
Components
The Company’s Refinery expansion depends on the sourcing, pricing and availability of mine production for refining. Most of the cobalt consumed today is mined in the DRC and then shipped to China for refining. There are no primary cobalt refining facilities operating in North America, which gives the Refinery a strategic advantage in the EV supply chain. The ability of the Refinery to Company produce battery grade cobalt sulfate using different types of feedstock will assist in diversifying sourcing of mine production for the Refinery. As noted above, while the Company and Glencore initially anticipated using the results of the Refinery Study to negotiate the terms of a tolling agreement and financing arrangement, the Company announced that it has since re-focused commercial arrangements with Glencore towards a long-term feed purchase contract rather than a tolling arrangement.
Business Cycles
Mining is a cyclical industry and commodity prices fluctuate according to global economic trends and conditions. See “Risk Factors – Risk Related to the Cyclical Nature of the Mining Business” below.
Environmental Protection
The Company’s Refinery expansion and exploration activities are subject to various levels of federal, provincial, state and local laws and regulations relating to the protection of the environment, including requirements for closure and reclamation of mining properties.
The Refinery has active permits and is subject to a reclamation bond and closure plan. The total provision for reclamation and closure cost obligations at December 31, 2021 was $1,204. The Company submitted a new closure plan, which covers activities still to take place at site, with a total closure cost of $3,450. A surety bond for this same $3,450 amount has been deposited with the Province of Ontario.
The Iron Creek Project is located within Salmon National Forecast, under the administration of the United States Forest Service (“USFS”). The Company manages all activities on site to ensure all work is performed in compliance with existing environmental regulations. It is understood that water and particulates from any drilling or other work should be prevented from entering any body of water without first being treated so there is no sediment or other contaminants entering the water.
Environmental and Social Governance
The Company’s mission is to be one of the most sustainable producers of battery materials.
Cobalt is a key element in fueling the lithium-ion batteries used in electric vehicles and for electric battery storage, both of which are essential technologies in the reduction of global carbon emissions.
The Company strives to be a leader amongst its peer group in the area of Environmental and Social Governance (“ESG”). Cobalt is essential to the global transition to electric mobility and Electra is committed to sustainable production and employing industry leading ESG practices at its Refinery.
The Company will provide a clean and ethical supply of cobalt for the EV market from large, commercial mining operations that provide ethically sourced cobalt and the highest quality cobalt hydroxide globally. As a member of the Cobalt Institute, the Company will follow the Cobalt Industry Responsible Assessment Framework (CIRAF), an industry-wide risk management tool that helps cobalt supply chain players identify production and sourcing related risks. Electra also committed to the Responsible Minerals Initiative, which will include a third-party audit of the systems in place to responsibly source minerals in line with current global standards.
The Refinery is projected to have a lower quartile carbon intensity cobalt by virtue of hydro powered mining operations supplying its hydro powered refining operation. In October 2020, results were released from an independent Life Cycle Assessment (“LCA”) which affirmed the low carbon footprint of the Refinery. The report concluded that the environmental impacts associated with refining cobalt at the Refinery will be materially lower than the published impacts of a leading Chinese refiner.
The Company takes a proactive, risk-based approach to environmental management and human rights with robust measures intended to minimize the environmental impact of operations and prevent the use of child labor at any level in the supply chain. Electra believes that these and other ESG practices will help it establish a premium brand of cobalt sulfate for the electric vehicle market.
Glencore Loan Agreement and Amended Glencore Loan Agreement
On August 26, 2019, the Company finalized the Glencore Loan Agreement to fund the next phase of activities required to advance the Refinery, which included metallurgical testing, engineering, cost estimating, field work and permitting activities to recommission the Refinery, including an engineering study for a 55 tpd Refinery expansion. While the maturity date on the Glencore Loan Agreement was extended by a year from August 23, 2021 to August 23, 2022, the Company then entered an amending agreement, pursuant to which Electra had the right to repay the loan by issuing Common Shares. In particular, the Company and Glencore agreed that, subject to the terms of the amended Glencore Loan Agreement, the Company would repay the loan, which represented an outstanding debt of US$5,506 by issuing 23,849,737 Common Shares at a deemed price of $0.29 (being a 15% discount to the market price on the TSXV on March 24, 2021). The Common Shares were issued on April 7, 2021 and the loan has now been fully repaid. The U.S. dollar denominated debt was converted from United States dollars into Canadian dollars using an exchange rate of US$1.00 = $1.2562.
Employees
As of December 31, 2021, the Company had 19 staff members made up of full-time employees and contractors.
Reorganizations
There have been no corporate reorganizations of the Company.
Foreign Operations
The Company’s Iron Creek Project is located in Idaho, U.S. Mineral exploration and mining activities in the United States may be affected in varying degrees by government regulations to the mining industry. Any changes in regulations or shifts in political conditions may adversely affect the Company’s business. Operations may be affected in varying degrees by government restrictions on permitting, production, price controls, income taxes, expropriation of property, environmental legislation and mine safety. The Refinery is likely to also rely substantially on mine production from foreign jurisdictions. As such, the Company may indirectly be exposed to various levels of political, economic and other risks and uncertainties associated with operations in a foreign jurisdiction.
REFINERY
The Refinery
The Refinery is 100% owned by Cobalt Camp Refinery Limited (“CCRL”), a subsidiary of Electra. The Refinery is currently under development with permit amendments mostly complete. The refinery business plan involves modifying the existing flowsheet to treat cobalt hydroxide feed material to produce cobalt sulphate used in the manufacture of batteries for electric vehicles. The flowsheet changes from the feasibility study were supported by bench and pilot scale metallurgical test work. It is proposed to refurbish and expand the refinery to produce 6,500 tpa (6.5 thousand tpa) of cobalt contained in cobalt sulfate.
Refinery Description and Location
The Refinery is located at approximately 47.40640° north and 79.62225° west in Lorrain Township near the town of North Cobalt, Ontario. The Refinery is located approximately 1.5 km east of the town of North Cobalt, along Highway 567, locally referred to as “Silver Centre Road”.
The facility was permitted in 1996 with a nominal throughput of 12 tpd and operated intermittently until 2015, producing a cobalt carbonate product along with nickel carbonate and silver precipitate. The facility is located on approximately 250 acres, with two settling ponds and an autoclave pond. The current footprint also includes a large warehouse building that once housed a conventional mill.
Infrastructure and Physiography
The Refinery is located near the town of North Cobalt and the city of Temiskaming Shores. Temiskaming Shores is an amalgamation of the towns of New Liskeard, Dymond, Haileybury and North Cobalt. Geographically, the Refinery is closest to the town of North Cobalt approximately 140 km north of the city of North Bay. The Refinery is accessed from the town of North Cobalt via an all-weather road from Silver Centre Road (Highway 567).
The region experiences a typical continental-style climate, with cold winters and warm summers. Daily average temperature ranges from -15°C in January to 18.3°C in July. The coldest months are December to March, during which the temperature is often below -20°C and can fall below -30°C. During summer, temperatures can exceed 30°C. Snow accumulation begins in November and generally remains until the spring thaw in mid-March to April, with the average monthly snowfall peaking at 40 cm in January and a yearly average of 181 cm.
Basic services are available locally in Temiskaming Shores, and further services are available in Sudbury. Sudbury is located 200 km by road southwest of the Refinery, and is considered a world-class mining centre and major hub for retail, economic, health, and education sectors in Northern Ontario. Most of the resources for the restart of the Refinery will likely be provided from the local townships, Sudbury, and North Bay areas.
Power for the refinery is provided from the grid by Hydro One through 115 kV and 230 kV transmission lines. The feeder to the Refinery is 44 kV. Fresh water is sourced from the nearby Lake Timiskaming. Many roads, trails, and powerlines span the area. Ontario Northland Railway services the town of North Cobalt, linking North Bay with the rest of north-eastern Ontario. Ontario Northland’s rail line passes approximately 2 km west-northwest of the refinery road. An existing road provides access to the site.
The Refinery is located within a well-established site. Local topography is dominated by Lake Temiskaming and the Montreal River, both of which are within the Ottawa River watershed. Topography within the property boundaries of the refinery is generally flat. General physiography is typical of the Precambrian Shield in north-eastern Ontario, with rocky, rolling bedrock hills with locally steep ledges and cliffs, separated by valleys filled with clay, glacial material, swamps and streams. Given the presence of the Clay Belt, some farms are present nearby. In this boreal region, coniferous and mixed-wood forests dominate. The main conifer species are black and white spruce, jack pine, balsam fir, tamarack and eastern white cedar. The predominant deciduous (hardwood) species are poplar and white birch. Swampy low-lying areas contain abundant tag alders.
History
In the 1980s, the location was the site of the Hellens-Eplett underground mine, which featured a traditional silver and cobalt mill that was quite common in the historic Cobalt Mining Camp. The property and mill were purchased by Cobatec Ltd. in the 1990s and construction of the refinery took place in 1994 and 1995. The integrated mining, milling and refining operation processed ore from the mine in the mill to produce concentrate, and then produce a refined cobalt and silver product from the concentrate in the Refinery. Initial start-up was in 1996. The Refinery was built with a nominal 12 tpd feed rate and made a cobalt-carbonate product from four feedstocks over different periods. Cobatec eventually shut down the Refinery on January 2, 1999. The Refinery was operational for approximately one of the three years between start-up and shutdown.
The Refinery was subsequently owned and operated by several owners until Electra entered into a 50-50 joint venture with Australian-listed Cobalt One Limited to acquire the Refinery in 2017.
The previous owners included:
| • | 1999-2003: Canmine Resources Corporation |
| • | 2003-2012: Yukon Refinery AG |
| • | 2012-2015: United Commodities |
| • | 2015-2017: Yukon Refinery AG |
Metallurgical Testing
Phase I – Initial Testing
Metallurgical testing was completed at SGS Canada Inc. (“SGS”) between Q4 2018 and Q2 2020. The test work program was managed by Electra with input from Ausenco. For purposes of the Refinery Study, the initial phase of test work was conducted under 17070-01 and 17070-03 programs.
The programs evaluated two different cobalt hydroxide feed materials. The composition of each feed material is summarized in the table below.
Cobalt Hydroxide Feed Sample Analysis
Program | | | Co % | | | Cu % | | | Fe % | | | Mn % | | | Mg % | | | Si % | | | Zn g/t | | | Ni g/t | | | Al g/t | | | Cr g/t | |
| 17070-01 | | | | 23.2 | | | | 1.61 | | | | 2.39 | | | | 3.27 | | | | 3.45 | | | | 1.05 | | | | 1920 | | | | 3870 | | | | 6390 | | | | 52 | |
| 17070-03 | | | | 29.2 | | | | 0.46 | | | | 0.12 | | | | 4.85 | | | | 5.67 | | | | 0.77 | | | | 403 | | | | 9410 | | | | 1200 | | | | <100 | |
The 17070-01 sample had a lower cobalt content (23.2% dry weight (“w/w”)) than the 17070-03 sample (29.2% w/w), as well as higher levels of copper, iron, silica, zinc and aluminium all of which are impurities. The source of the 17070-01 was from an operation in the DRC. The source of the 17070-03 sample was Glencore’s Mutanda operation in the DRC and a mass of 570 kg (gross) was supplied.
The purpose of the 17070-01 campaign was to demonstrate that battery-grade cobalt sulphate could be produced from a cobalt hydroxide feedstock using most of the current flowsheet at the refinery. The definition of a battery-grade cobalt sulphate product was based on specifications received by Electra from potential end users.
The program achieved a high purity cobalt sulphate product with a cobalt grade of 20.8 %w/w, with impurity levels that we within range of lithium-ion battery market specifications.
The purpose of the 17070-03 program was to provide data for the Refinery Study, such as process conditions and operating targets for the various unit operations. The tests conducted included re-leaching and neutralisation, impurity solvent extraction (“ISX”), CoSX, solid/liquid separation testing, environmental and tailings testing.
Following the SX testwork performed at SGS and METSIM™ modelling by Ausenco, results were provided to Solvay to evaluate the SX processes on a continuous basis. The modelling results were incorporated into the basis of design.
Environmental testwork was also conducted to determine operating parameters for the effluent treatment circuit. Synthetic solutions were prepared based on compositions predicted in the METSIM™ model and were supplied to Story Environmental Inc. (“SEI”) for effluent treatment testing and Aquatox Testing and Consulting Inc. for toxicity testing.
Key results from the testwork program and Solvay modelling are listed in the table below:
Key Results from the 17070-03 Testwork Program & Solvay Modelling
Description | | Unit | | Value | |
Re-leach and neutralisation recovery | | % | | | 93.5 | |
Neutralisation pH | | - | | | 5.0 | |
Average sulphuric acid addition | | kg/t (dry basis) | | | 633 | |
Limestone addition | | kg/t (dry basis) | | | 161 | |
ISX configuration | | extract / scrub / strip | | | 3 / 2 / 2 | |
ISX extractant concentration | | % | | | 20 | |
ISX cobalt recovery (to extraction raffinate) | | % | | | 99.6 | |
CoSX configuration | | extract / scrub / strip | | | 3 / 6 / 2 | |
CoSX extractant concentration | | % | | | 40 | |
CoSX cobalt recovery (to strip solution) | | % | | | 99.6 | |
Effluent treatment final pH | | - | | | 11.0 | |
Based on the results of the Solvay modelling, it was determined that ion exchange and manganese precipitation would not be required.
The testwork demonstrated that high-purity, battery-grade cobalt sulphate can be produced from the cobalt hydroxide samples that were provided. The overall cobalt recovery of the process was 93% based on the testwork results conducted. The final cobalt sulfate produced in this test work graded 21.4% cobalt, exceeding the minimum cobalt specification for battery grade cobalt sulfate.
Phase II – Testing and Piloting
Subsequent to the Refinery Study, the Company continued to advance metallurgical testwork with SGS, including pilot plant testing using new sample material from Kamoto Copper Company SARL (“KCC”; majority owned by Glencore’s Katanga Mining) in the DRC, which better represents the material that would be expected to be processed through the refinery when in operation. This testwork yielded recoveries significantly higher than those from the Refinery Study analysis.
The pilot study consisted of the following unit operations such as a) Leaching; b) Solvent Extraction; and c) Effluent Treatment.
The solvent extraction pilot study resulted in removing the impurities from the leach liquor and generating a concentrated cobalt sulfate product solution that is used to produce battery grade cobalt sulfate crystals. The waste streams of the solvent extraction pilot were treated using lime in a separate continuous pilot run, and the effluent generated from this study was found to meet the discharge limits prescribed by the Ontario Ministry of Environment, Conservation and Parks. The gypsum residue generated as a solid waste will be stored in the on-site tailings storage facility.
Recovery Methods
The refinery takes in cobalt hydroxide feed containing anywhere from 30 to 50% of contained cobalt. The refinery uses sulfuric acid to leach the cobalt hydroxide material into solution. Following the leaching process the liquor is neutralized before being sent to solvent extraction circuits where further impurities are removed. The final liquid from solvent extraction contains a high percentage of cobalt and that product is put through a crystallization process where battery grade cobalt sulphate is produced as the plants final product which then goes to market.
The process design is consistent with other operations, including:
| • | Vale, Long Harbour: impurity SX followed by CoSX |
| • | WMC, Bulong Refinery: CoSX with Cyanex 272 followed by sulphide precipitation and impurity SX with D2EHPA |
| • | Finland, Terrafame: crystallisation of high purity cobalt sulphate heptahydrate |
Process Description
Cobalt hydroxide is received on site at 66% w/w moisture in 1-tonne bulk bags and stored in the warehouse. The bags are lifted by forklift and broken in a bag breaker before being fed into a storage bin by conveyors. The material is fed into a re-pulper where it is mixed with recycled water into a slurry and stored in a feed tank.
The slurry is pumped to a leach tank and leached with sulphuric acid to solubilise cobalt and other metals. The leach slurry then gravity flows to pre neutralisation tanks where process steps such as a) water dilution and b) removal of impurities take place. The pre-neutralised slurry would then advance to thickeners and the thickener underflow is filtered using plate and frame filter presses. The leach thickener overflow and the leach filtrate would advance to secondary neutralisation stage.
The overflow of the neutralisation thickener is filtered to remove suspended solids. This filtrate is the feed stock for solvent extraction plant for further purification.
The solvent extraction step consists of two phases, the impurity solvent extraction (ISX) and cobalt solvent extraction (CoSX). The feed solution initially processed through ISX which consists of extraction, scrubbing, and stripping stages to separate various impurities. The cobalt-rich ISX raffinate reports to CoSX, while the impurities report to effluent treatment.
The ISX raffinate reports to CoSX and is processed through extraction, scrubbing and stripping stages to separate impurities from the cobalt. The CoSX raffinate is treated in the effluent treatment plant, while the cobalt-rich strip solution is sent to crystallisation.
The strip solution from CoSX reports to the forced circulation mechanical vapour recompression cobalt sulphate crystalliser. Cobalt sulphate is crystallised and subsequently dewatered in a thickener, centrifuge and fluid bed dryer. The dry product is then bagged and stored in the warehouse prior to shipment.
Some of the reagents used in the process include:
| • | flocculant, including a mixing and dosing system for the residue and effluent thickeners |
| • | sulphuric acid, including a storage tank, dilution and dosing system |
| • | lime (CaO), including a storage silo, slaker and ring main |
| • | sodium hydroxide, including a heated storage tank, dilution and dosing system |
Services supplied to the process include:
| • | fire water and fire suppression systems |
| • | plant and instrument air |
Process Design Criteria
The design criteria are based on data supplied by Electra, bench and pilot test work, vendor data and modelling, industry standards and HATCH’s in-house database.
Site Infrastructure
The major project facilities include the existing refinery building with expanded facilities, a new SX building and three existing ponds.
Power to the Refinery is provided via an existing 44 kV feeder from the Hydro One grid. It is then stepped down via a 2.5 MVA 44kV/600V transformer for distribution throughout the facilities.
Fresh water is supplied to the refinery from Lake Timiskaming by an overland pipeline and pumping system. The pumphouse contains two freshwater pumps in a duty/standby configuration. Water is pumped 2.5 km through a buried pipeline, in an existing easement, to the Refinery site, where it is stored in the filtered water tank. The water is predominantly used for cooling and does not touch the process liquids. The warm water is returned to Lake Timiskaming through a similar buried pipeline along the same easement.
Market Studies and Commercial Contracts
Electra has retained numerous firms to provide market studies and battery metals industry outlooks and expertise. Subsequent to the Refinery Study and in the normal course of business, Electra has now entered into the following contracts:
| • | a 5-year contract for the purchase of cobalt hydroxide feedstock from Glencore’s KCC mine |
| • | a 5-year cobalt tolling agreement with Glencore for material from the KCC mine, |
| • | a 5-year contract IXM SA for the purchase of cobalt hydroxide feedstock from the Tenke Fungurume mine |
| • | a flexible, long-term cobalt sulfate offtake agreement with Stratton Metals for the sale of finished product from the refinery. |
All of these arrangements are linked to future benchmark cobalt prices, with the exception of the cobalt tolling agreement which stipulates a tolling fee to Electra.
Demand
Cobalt is used in a range of applications, but the largest single market is lithium-ion (Li-ion) batteries. The three primary segments for Li-ion batteries are consumer electronic devices, electric vehicles and both stationary and grid energy storage. All three segments have a strong growth profile over the coming years and as such, the market for Li-ion batteries is expected to grow sharply. EVs are forecast to be the largest market for Li-ion batteries.
Growth in cobalt demand through 2040 will be almost entirely dominated by the battery sector, fuelled predominantly by increased EV penetration uptake. Demand growth is forecast to outpace the ability of suppliers to keep up by the mid-2020s. It should be expected that cobalt producers will not only be able to sell their products, but that strong prices should be able to be commanded due to the predicted shortfall.
Supply
Cobalt is mainly produced as a by-product from copper and nickel operations. Over 70% of mined cobalt originates from the copper operations of the African Copper Belt, in the DRC. Much of that production is exported to China, which is responsible for the majority of global refined supply.
Cobalt refining typically takes place away from mine sites. Vale, Glencore and Sherritt are among some of the mining companies that refine cobalt from their own mining operations, but they produce metallic cobalt products. None of them refines cobalt sulfate, which is a key input for the battery market.
Besides Electra, to the Company’s knowledge, there are no plans for new cobalt sulfate refineries outside of China. However, with the current focus by governments and industry on the battery sector, supply chains are expected to develop outside of China. Putting aside permitting considerations, refineries can often be built and commissioned in 18-36 months.
Environmental Permits and Social or Community Impact
Electra has regularly kept local municipalities and Indigenous communities apprised of their activities. Local municipalities with an interest in the Refinery include the Township of Coleman, the Town of Cobalt and the City of Temiskaming Shores. Electra has engaged the following Indigenous communities to keep them informed and obtain their input on recommencing operations at the refinery, and the permits relating to the refinery:
| • | Matachewan First Nation (MFN) |
| • | Temagami First Nation (TemFN) |
| • | Timiskaming First Nation (TFN) |
| • | Métis Nation of Ontario (MNO) |
| • | Beaverhouse First Nation (BFN) |
Electra is committed to continuing their engagement and consultation activities with stakeholders and Indigenous communities. All engagement and consultation activities related to the Refinery will continue to be entered into the Record of Consultation.
The Refinery requires 3 key environmental permits to operate and an approved closure plan prior to certain construction aspects. The Company received final approved and acceptance of its closure plan by the Ministry of Northern Development, Mines, Natural Resources and Forestry in March 2022.
The Company received new or amended environmental permits as follows:
| • | Permit to Take Water (PTTW) in May 2021 |
| • | Air and Noise Environmental Compliance Approval in October 2021 |
| • | Industrial Sewage Works Environmental Compliance Approval in February 2021 |
The Company is in the process of amending its PTTW to match the water volumes in the recently approved Industrial Sewage Works permit.
Capital and Operating Costs
Capital Costs
The capital cost estimate for the expansion of refinery is USD $67 million, as outlined below:
US$ million | | Refinery Project Capital Budget | |
Feed Prep, Leaching and Solvent Extraction | | | 30.6 | |
Crystallization and Sulfate Handling | | | 9.4 | |
Tailings, Site Services and Reagent Storage | | | 7.6 | |
Other Infrastructure | | | 2.7 | |
Project Management and Indirects | | | 6.8 | |
Spares, First Fills, and Owners Costs | | | 6.0 | |
Contingency | | | 3.9 | |
Total | | | 67.0 | |
Operating Costs
The refinery operating costs include the following:
| • | labour for operating, maintenance and supervision |
| • | fuels, reagents, consumables and maintenance materials |
| • | fuels, lubricants, tires and maintenance materials for operating and maintaining equipment |
| • | operating costs for the on-site laboratory |
Reagents are expected to be the largest component of the Refinery’s operating costs. Key reagents include sodium hydroxide, sulfuric acid, quicklime, and cyanex.
Refinery Updates
See “General Development of the Business – Three Year History” and “- Subsequent Events” above for additional Refinery updates.
IRON CREEK PROJECT
The bulk of the information in this section is derived from the technical report titled “Technical Report with Updated Mineral Resources, Iron Creek Cobalt Project, Lemhi County, Idaho, USA” dated November 27, 2019 with an effective date of November 27, 2019 (the “Iron Creek Technical Report”). The Iron Creek Technical Report was prepared by Steven J. Ristorcelli, C.P.G., P.G, and Joseph Schlitt, MMSA QP, each of whom is a Qualified Person and “independent” as such term is defined in NI 43-101. Mr. Ristorcelli was employed as Principal Geologist by Mine Development Associates, Inc. (“MDA”). Mr. Schlitt wass employed as President of Hydrometal Inc.
Project Description, Location and Access
The Iron Creek Project is located about 18 miles southwest of Salmon, Idaho, within the historic Blackbird cobalt-copper district of the Idaho cobalt belt. Access to the property is via the paved, all-weather U.S. Highway 93, and County Road 45 located 23 miles south of Salmon, Idaho.
The property consists of seven patented Federal lode claims that straddle Iron Creek, and a surrounding group of 296 unpatented Federal lode claims. Together the patented and unpatented claims cover an area of 5,900 acres. The center of the property is located at approximately 44° 57′ 42″ North, and 114° 06′ 57″ West.
Iron Creek property map

Electra currently controls 296 unpatented federal lode claims as part of the Iron Creek property. Idaho Cobalt Company (“Idaho Cobalt”), of Boise, Idaho a wholly owned subsidiary of Electra is the legal owner of 241 claims including the BR, BRS, and JA claims. The 103 JA claims are subject to a 1% NSR of which ½ of 1% is purchasable for $750,000 CDN. Scientific Metals (Delaware) Corp., owned subsidiary of Electra, controls an additional 25 NBR claims.
Electra is earning into a Joint Venture with Borah Resources Inc and Phoenix Copper Limited on 30 SCOB claims. Subject to the Earn-in agreement Electra can earn 75% interest in the claims by spending a minimum of 3,000,000 USD over 5 years on Exploration, Development, and related work.
The seven patented claims were acquired from the Chester Mining Company (OTC: CHMN) (“Chester”) in 2018. The patented claims are described as: Iron #118, Iron #135, Iron #136, Iron #143, Iron #144 Iron #182, and Iron #189, of the Idaho Mineral Survey No. 3613, located in portions of Section 20 and Section 21, Township 19 North, Range 20 East, B.M., Parcel #RP9900000109A, Blackbird Mining District, Lemhi County, Idaho. Idaho Cobalt holds 100% of the patented claims.
The unpatented claims are on Federal public lands administered by the United States Forest Service (“USFS”). Ownership of the unpatented mining claims is in the name of the holder (locator), subject to the paramount title of the United States of America, under the administration of the USFS. Under the Mining Law of 1872, which governs the location of unpatented mining claims on federal lands, the locator has the right to explore, develop, and mine minerals on unpatented mining claims without payments of production royalties to the U.S. government, subject to the surface management regulation of the USFS. Currently, annual claim-maintenance fees are the only Federal payments related to unpatented mining claims, and these fees have been paid in full to September 1, 2020. The unpatented claims have no expiration date as long as the annual claim-maintenance fees are paid by August 31 of each year. For the patented claims, which are real property, annual property taxes are paid to Lemhi County, Idaho. The total annual land-holding costs are estimated to be US$50,000.
Scientific Metals Corp. (“STM”), later known as US Cobalt, and now Electra, entered into a mining lease agreement with Chester dated August 23, 2016, with an option to purchase a 100% interest in the seven patented claims. Under the terms of the lease agreement, STM was required to pay Chester the sum of US$45,000 upon signing of the lease agreement and Chester retained a 4.0% NSR royalty. The terms of the agreement also required STM to make advance royalty payments on the NSR of US$3,000 per month for the first two years of the lease agreement, increasing to US$4,000 per month for the subsequent two years, and US$5,000 per month for subsequent years. At any time during the term of the lease, STM held the right to purchase a 100% interest in the seven claims and reduce the NSR held by Chester from 4.0% to 1.0%, all for consideration of a cash payment US$1,500,000. The NSR may subsequently be purchased for a cash payment of US$500,000 for every 1.0% of the NSR elected to be acquired by STM (now Electra).
On September 4, 2018 Electra announced an agreement had been reached to eliminate the advance royalty payments, purchase the patented claims, and eliminate the 4.0% NSR royalty for US$1.07M, which has been paid in full. As of the date of this report, Electra owns a 100% interest in the seven patented claims and the 83 unpatented claims.
A separate exploration program is planned for the Ruby zone within the unpatented claims. This will require a plan of operations (POO) to be approved by the USFS. Electra has submitted a POO to the USFS which has been ruled complete and will be implemented following posting of the appropriate reclamation bond which is anticipated to be $66,000 USD.
History
The first mining claims were staked in the Iron Creek area in 1967 on copper-stained material in what later became known as the “No Name” zone. In 1970, these claims were leased to Sachem Prospects Corporation (“Sachem”) of Salt Lake City, Utah. Sachem drilled 11 diamond-core holes and drove three underground exploratory drifts known as the Adit-1 (East Adit), Adit-2 (West Adit) and an unnamed adit. Hanna Mining optioned the property in 1972 through its wholly owned subsidiaries, Coastal Mining Co. and Idaho Mining Co., and acquired it outright in 1973.
From 1979 through 1996 the property was explored by Noranda Exploration, Inc., Inspiration Mines, Inc., Centurion Gold, and Cominco American Resources Inc. Various campaigns of drilling, geophysical surveys, and surface and underground geochemical sampling were conducted. Between all these programs, a total of 57 holes were drilled on the property prior to 1996.
Between 1996 and 2016 the patented and unpatented claims were acquired by Chester. STM acquired the Iron Creek property from Chester in 2016 and changed its name to US Cobalt in 2017. US Cobalt conducted surface exploration drilling in 2017, and underground drilling from the 6500 Level Adit (Adit-2) during the winter of 2017 and into 2018. The 2017 drilling results drew the interest of Electra. In March 2018, Electra entered into a definitive agreement with US Cobalt to acquire all of the issued and outstanding shares of US Cobalt and the Iron Creek Project. Completion of the acquisition was announced by Electra on September 4, 2018. Electra continued the surface- and underground-drilling campaign to expand the deposit along strike.
Several historical estimates of “reserves” have been made for mineralized zones in the No Name zone. These historical estimates are considered relevant for historical interest with respect to the exploration history at Iron Creek, and they are superseded by the current mineral resource estimates. There has been no historical commercial production of cobalt or copper from the Iron Creek Project.
Geological Setting, Mineralization and Deposit Types
The Iron Creek Project is situated in the Blackbird copper-cobalt ± gold mining district, the Idaho Cobalt Belt (“ICB”), in the eastern part of the Salmon River Mountains, central Idaho. The project area is underlain mainly by mid-Proterozoic metasedimentary siltite and quartzite of the Apple Creek Formation, which is part of the Belt Supergroup. Bedding and foliation generally strike northwest and dip 60° to 80° northeast. Ash-flow tuff of the Eocene Challis Volcanic Group unconformably caps the Apple Creek units that host the cobalt and copper mineralization within the property.
Five zones of stratabound cobalt and copper mineralization have been identified on surface within the property. That mineralization occurs within sequences of dominantly argillite and siltite enveloped by quartzite-rich units of the Apple Creek Formation. Specifically, mineralization is associated with thin quartzite layers cross bedded within the argillite-siltite units. The main zone in which the resources reported in the Iron Creek Technical Report occur is at Iron Creek. The other zones on the property are the Sulfate, Footwall, Magnetite and Ruby zones, which are now exploration targets.
The principal mineral assemblage consists of pyrite, chalcopyrite, pyrrhotite, and magnetite with much lesser quantities of native copper and arsenopyrite locally. Scanning-electron and microprobe tests indicate the cobalt occurs largely or entirely within pyrite and there is a distinct lack of cobaltite. Drill results demonstrate that the cobalt and copper mineralization are in part separated from each other spatially, and in part overlapping.
The cobalt and copper mineralization at the Iron Creek Project belong to a class of deposits variably described as “Blackbird Co-Cu” or “Blackbird Sediment-hosted Cu-Co” in and adjacent to the Blackbird mining district of Idaho. The Blackbird mining district contains several cobalt-copper ± gold deposits and prospects in proximity that are hosted in similar meta-sedimentary rocks.
Exploration
Electra (formerly STM, and US Cobalt) commenced exploration of the Iron Creek Project in 2016 with the compilation of historical geological, drilling, geophysical and geochemical data. In 2017 and 2018, Electra rehabilitated about 1,260 feet of underground workings in Adit-1 (East adit) and Adit-2 (West adit), which provide subsurface access to portions of the No Name zone within the Iron Creek mineralized zone. The objectives for US Cobalt in 2017 were as follows:
| • | Diamond-core drill approximately 35,000ft from surface along a 1,500ft strike length of the No Name Zone, twinning historical holes in an effort to confirm and increase confidence in historical estimates of cobalt mineralization; and |
| • | Re-habilitate the underground workings of the Adit-1 (East Adit) and Adit-2 (West adit; 6500-level Adit) for underground diamond drilling and channel sampling. |
During 2017, Electra drilled 40 diamond-core holes from the surface, for a total of 34,704ft of core drilling. The aforementioned surface drill program was completed in December of 2017. In addition to twinning previous holes, the drilling further delineated portions of the No Name Zone and left the mineralized zone open to further expansion along strike. The 2017 drilling also identified a second mineralized zone stratigraphically lower than the No Name Zone called the Waite Zone, which may have been previously referred to as the Footwall No Name Zone. This drilling also encountered diabase dikes that cross-cut the Apple Creek host rocks.
A total of 18,507ft were drilled in 29 core holes collared at surface and from underground locations in Adit-2 and Adit-1. The results have been incorporated in the current estimated mineral resources. Of the 29 holes, 25 were drilled in Adit-2 and four were drilled in Adit-1. All but two of the holes in Adit-2 were collared in a drill bay at the western face of the adit and were intended to extend the No Name and Waite Zones to the west, as well as explore possible copper targets to the north-northwest. The other two holes were drilled in a secondary bay approximately 300ft inside the portal and targeted the Waite Zone to the south. The four holes drilled in Adit-1 were designed to be collared in the No Name Zone and further explore the Waite Zone.
The entire length of Adit-1 was channel sampled and geologically mapped in detail by Electra geologists. A total of 133 channel samples (each five feet in length) were collected from both ribs along the crosscut and drift in Adit-1. The samples were collected using air-powered chisels, with average sample weights of about 7.3lb. The underground channel samples were transported by a Electra geologist from Adit-1 to the laboratory of American Assay Laboratories (“AAL”) in Sparks, Nevada.
Road-cut sampling was started but not completed along the roads cross-cutting the No Name and Waite zones on the west side of the North Fork of Iron Creek.
During 2018, Electra initiated mineralogical and petrograhic studies of mineralized material from the No Name zone. A total of 20 samples of drill core from 13 of the 2017 and 2018 drill holes were sent to SGS Minerals (“SGS”) in Lakefield, Ontario for detailed mineralogical descriptions. The purpose of the study was to identify and quantify metallic mineral species over a range of cobalt grades as identified by geochemical analyses. Specific attention was made in this study to identify cobalt- bearing minerals. Core logging and underground mapping found a diversity of pyrite textures and a range of grain sizes that had not been systematically analyzed for cobalt content.
The SGS samples were derived from drill core and underground grab samples of pyrite-rich material. SGS prepared polished mounts of each sample for analysis using QEMSCAN, a standard method to derive high-resolution mineralogic images. Individual minerals are identified on each image manually by a mineralogist.
The principal metallic mineral in all 20 samples was pyrite. In six samples, chalcopyrite was identified to a maximum of over 14% in one sample. Pyrrhotite was identified in one sample. Magnetite and/or hematite are present in all samples; one sample contains over 75% iron oxide. The cobalt-bearing minerals cobaltite, glaucodot, and gersdorffite were identified in four samples, but generally are in minor concentrations (maximum of 0.33%). Arsenopyrite was not found in any of the 20 samples.
During 2020 Electra completed a 18.5 line kilometre pold-dipole IP survey on the project. The survey targeted extensions of the mineralization to the east and west of the known resource. Multiple high chargeability low resistivity anomalies were identified in this survey that could provide targets for future drill campaigns.
During 2021 Electra completed a surface exploration work focused on mapping and sampling the area surrounding the Iron Creek deposit. Sampling included 204 rock samples and 39 sediment samples. These samples define the Ruby target in the Jackass Creek drainage as a high priority target for follow up exploration activities.
Multiple collaborative research programs were initiated in 2021 including a system footprint study with the Colorado School of Mines under the supervision of Katharina Pffaf, a metallurgical study on innovative mineral processing techniques under the supervision of Corby Anderson, and a mineralogy study at the University of Idaho. Electra provided samples of Iron Creek ore from underground samples and drill core to researchers as in-kind support for these studies.
No drilling was completed in 2020.
In 2021 five HQ core holes and one HQ wedge hole were drilled from the surface for a total of 2433 m. All holes were drilled by Major Drilling of Salt Lake City, Utah with a track mounted LF-90 drill rig. Holes IC21-01, IC21-02, and IC21-03 targeted the western extension of the ore body. Holes IC21-04 IC21-05, and IC21-05A targeted the eastern extension of the mineralization.
Drilling
The project database has had 169 holes drilled from 1969 through to January 2019. That total includes five sets of underground channel samples entered into the database as “drill holes”. Of the 169 drill holes, 115 (including the five sets of underground channel samples) were drilled and/or sampled by Electra and were used in the estimate in some fashion. Five holes were lost and drilled again. Records for the historical drill holes are incomplete, but all are believed to have been drilled with diamond-core methods. The total footage drilled within the property is at least 130,535ft. Five of the holes were vertical (four historical and one drilled in 2017) and the balance were inclined with dips of +40° to -85°. None of the drill holes completed before Electra were used.
Electra began drilling in July of 2017 and by the end of the program in 2019, a total of 94,870ft was drilled in 110 holes. All the holes were drilled from the surface or from underground using diamond-core and wireline methods to recover HQ- and NQ-diameter core.
The 2017 drilling was focused on the No Name zone to confirm, in fill and potentially expand the mineralized zones known from the historical drilling. The drilling did substantially confirm what was indicated in the pre-Electra drilling. The drilling contractor was Timberline Drilling (“Timberline”) of Hayden Lake, Idaho. Two modular Atlas Copco U8 underground type core drills were used. Both drills were operated on two 12-hour shifts each day.
In 2018, Electra commenced underground core drilling in Adit-2 with Timberline as the drilling contractor. A single Sandvik DE-130 underground drill was used to drill 26 NQ-diameter diamond-core holes in Adit-2. A total of four core holes were drilled in Adit-1. Timberline also drilled 14 HQ-diameter diamond-core holes from the surface before being evacuated from the project area due to a wildfire. Another 18 surface core holes were drilled later in 2018. The 2018 surface drilling was carried out by Timberline with two Atlas Copco CS-14 track-mounted rigs, one modular Atlas Copco U8 underground rig and one UDR track-mounted rig.
Electra did use AK Drilling of Butte, Montana who completed two drill holes (ICS18-20 and ICS18-23). They used an LF90 drill rig coring HQ-size core.
Core drilling from the surface was also conducted in 2019. Four holes were drilled for a total of 3,790ft.
The results of the 2017, 2018 and 2019 drilling have generally confirmed the cobalt and copper mineralization encountered by historical drilling in the No Name and Footwall (Waite) zones and also confirmed the known orientation and general thickness of mineralization. Most importantly, the drilling has enabled Electra to recognize that the cobalt and copper mineralized zones are distinct from each other but overlap spatially in some areas.
No drilling was completed in 2020.
In 2021 five HQ core holes and one HQ wedge hole were drilled from the surface for a total of 2433 m. All holes were drilled by Major Drilling of Salt Lake City, Utah with a track mounted LF-90 drill rig. Holes IC21-01, IC21-02, and IC21-03 targeted the western extension of the ore body. Holes IC21-04 IC21-05, and IC21-05A targeted the eastern extension of the mineralization.
Sampling, Analysis and Data Verification
In 2021 Electra drill core was transported by Electra geologists from the drill sites to Electra’s core-processing facility in Salmon, Idaho. Core recovery, and rock quality designation (“RQD”) were measured by Electra geologists and recorded in spreadsheets on notebook computers. Digital photographs were taken of all whole core. Electra geologists logged core and marked sample intervals which ranged from 0.2 to 3.2 m. Core was marked with crayon and sample numbers were assigned to each interval using barcoded sample books. Sample tags were inserted into the core boxes prior to cutting. Electra geologists entered a control in approximately 1 in every 20 samples in the sample books and recorded the associated standard, blank, or duplicate in spreadsheet form. Standards were randomly selected from one of five certified reference materials purchased from OREAS laboratories and certified for Cu and Co. Blanks were inserted as coarse material from a location of unmineralized chalice volcanics on the property. Duplicates were quarter sawn core intervals that were submitted after the original sample half.
Core samples were sawn into two equal halves with an Almonite core saw by technicians employed by Electra. One half of each interval of core was placed in polyethylene sample bags with barcoded sample tags and zip tied shut. Sample bags were placed in rice bags with control samples for shipment. Samples were transported to ALS laboratories prep facility in Twin Falls, Idaho by Electra staff members. ALS is an independent commercial lab and all ALS geochemical hub laboratories are accredited to ISO/IEC17025:2017 and ISO9001:2015 International Standards.
At the ALS laboratory Drill core samples are dried, weighed, crushed to 70% passing -2mm, split to 250g pulps crushed to 85% passing minus 75 microns. Samples were dissolved with a sodium peroxide fusion with gravimetric dilution in glassless labware and analyzed using super trace methods via ICP-MS and ICP-AES. Analyses for Ag, As, Ba, Be, Bi, Ca, Cd, Ce, Co, Cs, Cu, Dy, Er, Eu, Fe, Ga, Gd, Ge, Ho, In, K, La, Li, Lu, Mg, Mn, Mo, Nb, Nd, Ni, Pb, Pr, Rb, Re, Sb, Se, Sm, Sn, Sr, Ta, Tb, Te, Th, Ti, Tl, Tm, U, V, W, Y, Yb, and Zn. Samples over 2% Copper were analyzed with a HF-HNO3-HClO4 digest and analyzed with ICP-AES.
The QA/QC samples inserted in the sample stream demonstrate that sampling, sub-sampling and analyses yield results suitable for reliable resource estimation. However, some additional care must be used when handling samples and recording sample numbers. The suitability of one of the CRMs should be checked. Electra can use a blank material with lower concentrations of cobalt. Rhyolite of the Challis Volcanic Group exposed within the property should contain less than 10ppm Co.
Mineral Processing and Metallurgical Testing
Electra’s metallurgical testing has been limited to work on two bulk samples obtained from adjacent spots in Adit-1 and one bulk sample from a nearby single location in Adit-2. It is not clear how closely they represent the average life-of-mine cobalt and copper levels. However, both the cobalt and copper levels in the samples do fall within the expected grade ranges, so are representative in that sense.
All three samples responded very well when subjected to rougher flotation using standard conditions at the natural pH of 6 to 8. More than 96% of the sulfide sulfur reported to the bulk concentrate and cobalt recovery also averaged over 96%. Copper recovery into the bulk concentrate averaged over 97% for the two high-grade samples and 92.5% for the low-grade sample.
An initial round of cleaner flotation tests was performed on the sulfide rougher concentrates. Optimum performance was achieved by regrinding the rougher concentrate and floating at pH 12 to depress the pyrite. For the two high-grade copper samples, 75% to 85% of the copper was recovered into copper concentrates that would be suitable for conventional copper smelting. The low-grade copper sample appears to need some further flotation optimization in order to produce acceptable smelter feed.
The cobalt was recovered in the pyrite product that represents the cleaner flotation tailings. For all three bulk samples this product contained more than 90% of the cobalt at grades of 1.2% to 1.8% Co. Higher grades may be difficult to obtain, as the cobalt is bound up within the pyrite crystal structure.
Following completion of the flotation tests, mineralogical studies were performed on four cleaner flotation products. These confirmed that pyrite and chalcopyrite are the principal sulfide minerals and that the pyrite is also the major carrier for both cobalt and arsenic. The main contaminants in the low-grade concentrate are liberated pyrite grains and non-sulfide gangue. Most of the copper losses in the cleaner tails are liberated grains of chalcopyrite. Most of the pyrite lost in the cleaner tails is also liberated. These findings suggest that optimization of the flotation parameters should improve both metal recovery and concentrate quality.
No testwork has yet been done on recovery of the cobalt from the pyrite concentrates. However, two approaches appear to be technically viable. One is to roast the concentrate, then leach the cobalt from the resulting cinder and concentrate the cobalt using solvent extraction. Final recovery of the cobalt would be as a salt or electrowon metal. In this case the roaster off-gas would be treated to recover the contained sulfur as commercial-grade sulfuric acid. The other approach is to use an autoclave to oxidize the pyrite and solubilize the cobalt, then use solvent extraction as with roasting. With this approach a sludge containing the iron and arsenic would be produced requiring an environmentally sound treatment.
Mineral Resource Estimate
Following the initial inferred mineral resource published October 15, 2018, Electra completed an infill drilling campaign to improve the confidence of mineralization continuity as well as to test the extensions of mineralization.
The geochemical database contains 21,456 assay records, all of which were deemed usable in modeling metal domains and density, but only those from core holes drilled by Electra were used to estimate cobalt and copper resources at the Iron Creek Project. Historical drilling was excluded due to lack of original source data and sometimes conflicting collar locations and no down-hole survey data. Inverse distance was used to estimate the block-diluted indicated and inferred mineral resources shown below.
All mineral resources tabulated below are based on the presumption that the most likely method of exploitation will be from underground. Technical and economic factors likely to influence the “reasonable prospects for eventual economic extraction” were evaluated using the best judgement of the author of the Iron Creek Technical Report responsible for the mineral resources. Potential for underground mining was assessed by running stope optimizations in 2018. Having passed that test and after updating the mineral resource estimate, a grade shell with grades above 0.10%CoEq were made. Isolated and discontinuous zones were eliminated, and then that solid was used to constrain the reported resources. The reporting cutoff 0.18%CoEq is fractionally lower than what was determined by using mining costs ($100/ton), processing costs ($22/ton), anticipated metallurgical recoveries (81% for copper and 88% for cobalt), and appropriate G&A ($10/ton) costs for similar size operations in the western United States. The cutoff grades are based on US$30/lb Co and US$3/lb Cu as they were in 2018.
The Iron Creek reported mineral resources are the fully block-diluted estimates. The blocks are 10ft long along strike, 5ft across, and 10ft high. The resources are reported at a cutoff of 0.18%CoEq for potentially underground minable material. Cobalt equivalent was based on the simple formula of:
%CoEq = %Co + (%Cu / 10)
No metallurgical recoveries were applied to either metal because it is expected that the metallurgical recoveries will be similar for both metals.
Indicated | |
Cutoff | | | | Tons | | | | Grade | | | | Grade | | | | Pounds | | | | Grade | | | | Pounds | |
%CoEq | | | | | | | | %CoEq | | | | %Co | | | | Cobalt | | | | %Cu | | | | Copper | |
0.18 | | | | 2,374,000 | | | | 0.32 | | | | 0.26 | | | | 12,250,000 | | | | 0.61 | | | | 29,058,000 | |
Inferred | |
Cutoff | | | | Tons | | | | Grade | | | | Grade | | | | Pounds | | | | Grade | | | | Pounds | |
%CoEq | | | | | | | | %CoEq | | | | %Co | | | | Cobalt | | | | %Cu | | | | Copper | |
0.18 | | | | 2,950,000 | | | | 0.28 | | | | 0.22 | | | | 12,685,000 | | | | 0.68 | | | | 39,943,000 | |
1. | Mineral resources, which are not Mineral Reserves, do not have demonstrated economic viability. The inferred mineral resource in this estimate has a lower level of confidence than that applied to an indicated mineral resource and must not be converted to a mineral reserve. It is reasonably expected that the majority of the inferred mineral resource could be upgraded to an indicated mineral resource with continued exploration. The mineral resources herein were estimated using the CIM, CIM Standards on Mineral Resources and Reserves, Definitions and Guidelines prepared by the CIM Standing Committee on Reserve Definitions and adopted by CIM Council. |
2. | CoEq calculated as %Co + %Cu÷10. |
3. | The cutoff grade utilized in the above table was derived from US$30/lb Co and US$3/lb Cu, consistent with the 2018 resource estimate. |
4. | Three types of statistical estimates were completed: nearest neighbour, inverse distance, and kriging. Each method was run several times in order to determine sensitivity to estimation parameters as well as optimize the estimation parameters. Results using the inverse distance estimate are reported in Table 1. |
5. | Block size employed of 10ft along strike, 5ft across, and 10ft high reflect assumed underground mining extraction dimensions. |
6. | Mineral resources are reported in the Iron Creek Technical Report in imperial tons. |
7. | The effective date of the mineral resource estimate is October 23, 2019. |
8. | The effective date of the of the geochemical database on which the mineral resource estimate is based is February 18, 2019. |
Exploration and Development
As described above under “General Development of the Business – Three Year History”, on January 15, 2020, the Company announced a new mineral resource estimate for Iron Creek Project. The new mineral resource estimate was based on infill drilling and limited step-out drilling which included the conversion of 49% of resources from the inferred mineral resource category to the indicated mineral resource category while also increasing the overall tonnage. The indicated mineral resource is now 2.2M tonnes grading 0.32% cobalt equivalent (0.26% cobalt and 0.61% copper) containing 12.3M pounds of cobalt and 29.1M pounds of copper. The inferred mineral resource is now 2.7M tonnes grading 0.28% cobalt equivalent (0.22% cobalt and 0.68% copper) for an additional 12.7M pounds of cobalt and 39.9M pounds of copper. The Company also announced that it increased the size of its Idaho cobalt land position by 50%. The expanded property contains the Iron Creek cobalt-copper deposit, the Ruby target and several other surface exposures of cobalt-copper mineralization. A total of 43 new claims were staked to the west of the Iron Creek Project, expanding the total area from 1,700 acres to over 2,600 acres.
In February 2021, the Company announced that a geophysical survey of its Iron Creek cobalt-copper deposit identified several new drill targets on the property.
On May 11, 2021 the Company announced it had acquired additional mining claims known as the West Fork Property to the west of the Iron Creek Project. This transaction effectively doubled the Company’s Idaho land position. Geophysical surveys will be conducted at the West Fork property to test for cobalt and copper mineralization extensions. On May 25, 2021, the Company announced that it had entered into an earn-in agreement with Phoenix Copper Limited to acquire the Redcastle property to the east of the Iron Creek Project to further expand its land position in Idaho to over 1,820 hectares.
In June 2021, the Company commenced a $2.5 million exploration program at Iron Creek, which will include a total of 4,500 metres of drilling focusing on testing the western and eastern extensions to the Iron Creek deposit identified in IP-Resistivity surveys and potentially other targets on the property. Drilling will also test geophysical anomalies similar to the signature of the Iron Creek deposit to identify new zones of mineralization. The Company’s overall objective of this drilling program is to meaningfully increase the resource size at the Iron Creek Project.
On March 14, 2022 the Company announced that drill results to the west of the Iron Creek Project had successfully extended mineralization by 130 metres along strike and by 110 metres at depth.
RISK FACTORS
There are a number of risks that may have a material and adverse impact on the future operating and financial performance of the Company and could cause the Company’s operating and financial performance to differ materially from the estimates described in forward-looking statements relating to the Company. These include widespread risks associated with any form of business and specific risks associated with the Company’s business and its involvement in the cobalt exploration and development industry.
This section describes risk factors identified as being potentially significant to the Company and its material properties, the Refinery and the Iron Creek Project. Additional risk factors may be included in technical reports or other documents previously disclosed by the Company. In addition, other risks and uncertainties not discussed to date or not known to management could have material and adverse effects on the valuation of our securities, existing business activities, financial condition, results of operations, plans and prospects.
Financing Risks
The Company’s Refinery construction, purchase of feedstock inventories, and exploration activities may require additional external financing. There can be no assurance that additional capital or other types of financing will be available when needed or that, if available, the terms of such financing will be acceptable to the Company. Furthermore, if the Company raises additional capital by offering equity securities or securities convertible into equity securities, any additional financing may involve substantial dilution to existing shareholders. Failure to obtain sufficient financing could result in the delay or indefinite postponement of exploration, development, construction or production of any or all of the Company’s mineral properties as well as the advancement of the Refinery. The cost and terms of such financing may significantly reduce the expected benefits from new developments or render such developments uneconomic.
Substantial Capital Requirements and Liquidity
The Company anticipates that it will incur substantial expenditures for the continued exploration and development of its projects in the future. The Company currently has no revenue and may have limited ability to undertake or complete future drilling or exploration programs, process and engineering studies and the design and recommissioning of the Refinery. There can be no assurance that debt or equity financing, or cash generated by operations will be available or sufficient to meet these requirements or for other corporate purposes or, if debt or equity financing is available, that it will be on terms acceptable to the Company. Moreover, future activities may require the Company to alter its capitalization significantly. The inability of the Company to access sufficient capital for its operations could have a material adverse effect on the Company’s financial condition, results of operations or prospects. Sales of substantial amounts of securities may have a highly dilutive effect on the ownership or share structure of the Company. Sales of a large number of Common Shares in the public markets, or the potential for such sales, could decrease the trading price of the Common Shares and could impair the Company’s ability to raise capital through future sales of Common Shares.
The Company has not yet commenced commercial production at any of its properties and as such, it has not generated positive cash flows to date and has no reasonable prospects of doing so unless the Refinery is successfully recommissioned or successful commercial production can be achieved at the Iron Creek Project. The Company expects to continue to incur negative investing and operating cash flows until such time as it recommissions the Refinery or enters into commercial production at one of its mineral properties. This will require the Company to deploy its working capital to fund such negative cash flow. The Company will also require a working capital arrangement in order to fund inventory purchases once in operation, which may require the Company and to seek additional sources of financing.
There is no assurance that any such financing sources will be available or sufficient to meet the Company’s requirements. There is no assurance that the Company will be able to continue to raise equity capital or that the Company will not continue to incur losses.
Volatility of the Market Price of the Company’s Common Shares
The Company’s Common Shares are listed on the TSXV under the symbol “ELBM” and on the OTCQX under the symbol “ELBMF”. Securities of junior companies have experienced substantial volatility in the past, often based on factors unrelated to the financial performance or prospects of the companies involved. These factors include macroeconomic developments in North America and globally and market perceptions of the attractiveness of particular industries. The Company’s Common Share price is also likely to be significantly affected by delays experienced in progressing with development plans, a decrease in investor appetite for junior stocks, or in adverse changes in the Company’s financial condition or results of operations as reflected in the Company’s quarterly and annual financial statements. Other factors unrelated to performance that could have an effect on the price of the Company’s Common Shares include the following:
| (a) | The trading volume and general market interest in the Company’s Common Shares could affect a shareholder’s ability to trade significant numbers of Common Shares; and |
| (b) | The size of the public float in the Company’s Common Shares may limit the ability of some institutions to invest in the Company’s securities. |
As a result of any of these or other factors, the market price of the Company’s Common Shares at any given point in time might not accurately reflect the Company’s long-term value. Securities class action litigation has been brought against companies following years of volatility in the market price of their securities. The Company could in the future be the target of similar litigation. Securities litigation could result in substantial costs and damages and divert management’s attention and resources.
Technical Capabilities of the Refinery
The Company’s strategic priority is the advancement of the Refinery, with significant metallurgical test work and engineering work completed. There is no assurance that the Refinery with have the capabilities to produce specific end products. Furthermore, no assurance can be given that operating the Refinery will be economically viable. The Company will manage these risks through contracting technical experts on metallurgy and engineering to perform the required analysis and studies on the capability of the Refinery and its projected economics.
Global Pandemic
The current outbreak and resurgence of novel COVID-19, and the emergence of multiple COVID-19 variants, continues to significantly impact global economies and global economic conditions which may adversely impact the Company’s operations, and the operations of its suppliers, contractors and service providers, the ability to obtain financing and maintain necessary liquidity, the demand for and ability to transport the Company’s products, commodity prices and its ability to advance its projects and other growth initiatives. Any future emergence and spread of similar pathogens could have similar adverse impacts.
The COVID-19 outbreak and its declaration as a global pandemic are causing companies and governments around the world to impose sweeping restrictions on the movement of people and goods, including social distancing measures and restrictions on group gatherings, isolation and quarantine requirements, closure of business and government offices, travel advisories and travel restrictions. While these effects are expected to be temporary, the duration of these measures, and the related business, social and government disruptions and financial impacts, cannot be reasonably fully estimated at this time. The Company cannot estimate whether or to what extent these measures, and the resulting impacts, will continue to impact the Company’s business, financial condition and results of operations. Furthermore, government bodies may introduce new, or modify existing, laws, regulations, orders or other measures that could impact the Company’s ability to operate or affect the actions of its suppliers, contractors and service providers.
To date, the Company has been able to continue operations largely unaffected since the outbreak of the COVID-19 pandemic. However, the Company cannot provide any assurances that its planned operations, production and capital expenditure for the foreseeable future will not be delayed, postponed or cancelled as a result of the COVID-19 pandemic or otherwise. Should the responses of companies and governments be insufficient to contain the spread and impact of COVID-19, this may lead to further economic downturn that may adversely impact the Company’s business, financial condition and results of operations. The outbreak and resurgence of the COVID-19 pandemic could also continue to affect financial markets, including the price of gold and the trading price of the Company’s shares, may adversely affect the Company’s ability to raise capital, and could cause continued interest rate volatility and movements that could make obtaining financing or refinancing debt obligations more challenging or more expensive or unavailable on commercially reasonable terms or at all. In addition, if any number of employees, contractors or consultants of the Company or any key supplier become infected with COVID-19 or similar pathogens and/or the Company is unable to source necessary replacements, consumables or supplies or transport its products, due to government restrictions or otherwise, it could have a material negative impact on the Company’s operations and prospects, including the complete shutdown of one or more of its operations. An outbreak of COVID-19 at the Company’s operations could also cause reputational harm and negatively impact the Company’s social license to operate. The COVID-19 pandemic has also increased cybersecurity and information technology risks due to the rise in fraudulent activity and increased number of employees working remotely.
Furthermore, the Company may also experience regional risks which include, but are not limited to, delays in the supply chain of critical equipment components, reagents, consumables and parts, and the impact on the delivery of critical capital projects, and such circumstances could have a material adverse effect on the Company’s business, financial condition and results of operations.
As a result of measures it has taken, there is no assurance as to whether the Company will be affected by the current COVID-19 pandemic or potential future health crises. The Company will continue to work actively to monitor the situation and implement further measures as required to mitigate and/or deal with any repercussions that may occur as a result of the COVID-19 outbreak.
Exploration and Development
Exploring and developing natural resource projects bears a high potential for all manner of risks. Additionally, few exploration projects successfully achieve development due to factors that cannot be predicted or foreseen. Moreover, even one such factor may result in the economic viability of a project being detrimentally impacted, such that it is neither feasible nor practical to proceed. Natural resource exploration involves many risks, which even a combination of experience, knowledge and careful evaluation may not be able to overcome. Operations in which the Company has a direct or indirect interest will be subject to all the hazards and risks normally incidental to exploration, development and production of natural resources, any of which could result in work stoppages, damage to property, and possible environmental damage. If any of the Company’s exploration programs are successful, there is a degree of uncertainty attributable to the calculation of resources and corresponding grades and in the analysis of the economic viability of future mine development and mineral extraction. Until actually extracted and processed, the quantity of cobalt reserves and grade must be considered as estimates only. In addition, the quantity of reserves and resources may vary depending on commodity prices and various technical and economic assumptions. Any material change in quantity of reserves, grade or recovery ratio, may affect the economic viability of the Company’s properties. In addition, there can be no assurance that results obtained in small-scale laboratory tests or pilot plants will be duplicated in larger scale tests under on-site conditions or during production. The Company closely monitors its activities and those factors which could impact them, and employs experienced consulting, engineering, and legal advisors to assist in its risk management reviews where it is deemed necessary.
Mineral Resource Uncertainties
Mineral resources that are not mineral reserves do not have demonstrated economic viability. Due to the uncertainty which may attach to mineral resources, there can be no assurances that mineral resources will be upgraded to mineral reserves as a result of continued exploration or during the course of operations.
There can be no assurances that any of the mineral resources stated in this AIF or published technical reports of the Company will be realized. Until a deposit is actually extracted and processed, the quantity of mineral resources or reserves, grades, recoveries and costs must be considered as estimates only. In addition, the quantity of mineral resources or reserves may vary depending on, among other things, product prices. Any material change in the quantity of mineral resources or reserves, grades, dilution occurring during mining operations, recoveries, costs or other factors may affect the economic viability of stated mineral resources or reserves. In addition, there is no assurance that mineral recoveries in limited, small scale laboratory tests or pilot plants will be duplicated by larger scale tests or during production. Fluctuations in cobalt prices, results of future drilling, metallurgical testing, actual mining and operating results, and other events subsequent to the date of stated mineral resources and reserves estimates may require revision of such estimates. Any material reductions in estimates of mineral resources or reserves could have a material adverse effect on the Company.
Permitting
The Company’s operations, Refinery and exploration activities are subject to receiving and maintaining licenses, permits and approvals, including regulatory relief or amendments, (collectively, “permits”) from appropriate governmental authorities. Before any development on any of its properties the Company must receive numerous permits, and continued operations at the Company’s mines is also dependent on maintaining, complying with and renewing required permits or obtaining additional permits.
The Company may be unable to obtain on a timely basis or maintain in the future all necessary permits required to explore and develop its properties, commence construction or operation of mining facilities and properties or maintain continued operations. Delays may occur in connection with obtaining necessary renewals of permits for the Company’s existing operations and activities, additional permits for existing or future operations or activities, or additional permits associated with new legislation. It is possible that previously issued permits may become suspended or revoked for a variety of reasons, including through government or court action.
Future Share Issuances May Affect the Market Price of the Common Shares
In order to finance future operations, the Company may raise funds through the issuance of additional Common Shares or the issuance of debt instruments or other securities convertible into Common Shares. The Company cannot predict the size of future issuances of Common Shares or the issuance of debt instruments or other securities convertible into Common Shares or the dilutive effect, if any, that future issuances and sales of the Company’s securities will have on the market price of the Common Shares.
Economic and Financial Market Instability
Global financial markets have been volatile and unstable at times since the global financial crisis, which began in 2007. Bank failures, the risk of sovereign defaults, other economic conditions and intervention measures have caused significant uncertainties in the markets. The resulting disruptions in credit and capital markets have negatively impacted the availability and terms of credit and capital. High levels of volatility and market turmoil could also adversely impact commodity prices, exchange rates and interest rates. In the short term, these factors, combined with the Company’s financial position, may impact the Company’s ability to obtain equity or debt financing in the future and, if obtained, the terms that are available to the Company. In the longer term, these factors, combined with the Company’s financial position could have important consequences, including the following:
| (a) | Increasing the Company’s vulnerability to general adverse economic and industry conditions; |
| (b) | Limiting the Company’s ability to obtain additional financing to fund future working capital, capital expenditures, operating and exploration costs and other general corporate requirements; |
| (c) | Limiting the Company’s flexibility in planning for, or reacting to, changes in the Company’s business and the industry; and |
| (d) | Placing the Company at a disadvantage when compared to competitors that have less debt relative to their market capitalization. |
No Revenue and Negative Cash Flow
The Company has negative cash flow from operating activities and does not currently generate any revenue. Lack of cash flow from the Company’s operating activities could impede its ability to raise capital through debt or equity financing to the extent required to fund its business operations. In addition, working capital deficiencies could negatively impact the Company’s ability to satisfy its obligations promptly as they become due. If the Company does not generate sufficient cash flow from operating activities, it will remain dependent upon external financing sources. There can be no assurance that such sources of financing will be available on acceptable terms or at all.
Ability to meet Debt Service Obligations
The Company now has debt service obligations arising from its convertible notes, which include ongoing coupon payments and payment of principal at maturity. In the event the refinery construction is not completed as planned or sufficient cash flow from refinery operations is note generated, there is a risk that the Company may not have sufficient available capital to meet its debt obligations. In this event, the assets pledged may be transferred to the lenders. There can be no assurance that refinery cash flows will be sufficient to meet future debt service obligations.
Reliance on Key Personnel
The senior officers of the Company are critical to its success. In the event of the departure of a senior officer, the Company believes that it will be successful in attracting and retaining qualified successors, but there can be no assurance of such success. Recruiting qualified personnel as the Company grows is critical to its success. The number of persons skilled in the acquisition, exploration and development of mining properties is limited, and competition for such persons is intense. As the Company’s business activity grows, it will require additional key financial, administrative, engineering, geological and other personnel. If the Company is not successful in attracting and training qualified personnel, the efficiency of its operations could be affected, which could have an adverse impact on future cash flows, earnings, results of operations and the financial condition of the Company. The Company is particularly at risk at this state of its development as it relies on a small management team, the loss of any member of which could cause severe adverse consequences.
Property Commitments
The Company’s mining properties may be subject to various land payments, royalties and/or work commitments. Failure by the Company to meet its payment obligations or otherwise fulfill its commitments under these agreements could result in the loss of related property interests.
Operational Risks
The Company will be subject to a number of operational risks and may not be adequately insured for certain risks, including: environmental contamination, liabilities arising from historic operations, accidents or spills, industrial and transportation accidents, which may involve hazardous materials, labor disputes, catastrophic accidents, fires, blockades or other acts of social activism, changes in the regulatory environment, impact of non-compliance with laws and regulations, natural phenomena such as inclement weather conditions, floods, earthquakes, ground movements, cave-ins, and encountering unusual or unexpected geological conditions and technological failure of exploration methods.
There is no assurance that the foregoing risks and hazards will not result in damage to, or destruction of, the property of the Company, personal injury or death, environmental damage or, regarding the exploration or development activities of the Company, increased costs, monetary losses and potential legal liability and adverse governmental action. These factors could all have an adverse impact on the Company’s future cash flows, earnings, results of operations and financial condition.
Additionally, the Company may be subject to liability or sustain loss for certain risks and hazards against which the Company cannot insure or which the Company may elect not to insure because of the cost. This lack of insurance coverage could have an adverse impact on the Company’s future cash flows, earnings, results of operations and financial condition.
Construction Risks
As a result of the substantial expenditures involved in development projects, developments are prone to material cost overruns versus budget. The capital expenditures and time required to develop new mines are considerable and changes in cost or construction schedules can significantly increase both the time and capital required to build the project.
Construction costs and timelines can be impacted by a wide variety of factors, many of which are beyond the control of the Company. These include, but are not limited to, weather conditions, ground conditions, performance of the mining fleet and availability of appropriate rock and other material required for construction, availability and performance of contractors and suppliers, delivery and installation of equipment, design changes, accuracy of estimates and availability of accommodations for the workforce.
Project development schedules are also dependent on obtaining the governmental approvals necessary for the operation of a project. The timeline to obtain these government approvals is often beyond the control of the Company. A delay in start-up or commercial production would increase capital costs and delay receipt of revenues.
Environmental Risks
All phases of mineral exploration and development businesses, including with respect to the Refinery, present environmental risks and hazards and are subject to environmental regulations. Environmental legislation provides for, among other things, restrictions and prohibitions on spills, releases or emissions of various substances used and or produced in association with natural resource exploration and production operations. The legislation also requires that facility sites be operated, maintained, abandoned and reclaimed to the satisfaction of applicable regulatory authorities. Compliance with such legislation can require significant expenditures, and a breach may result in the imposition of fines and penalties, some of which may be material.
Environmental legislation is evolving in a manner expected to result in stricter standards and enforcement, larger fines and liability and potentially increased capital expenditures and operating costs. The discharge of pollutants into the air, soil or water may give rise to liabilities to foreign governments and third parties and may require the Company to incur costs to remedy such discharge. Based on risk assessments conducted by the Company, climate change is not an immediate material risk faced by the Company. However, no assurance can be given that the application of environmental laws to the business and operations of the Company will not result in a curtailment of production or a material increase in the costs of production, development or exploration activities or otherwise adversely affect the Company’s financial condition, results of operations or prospects.
Commodity Price Fluctuations
The prices of commodities vary on a daily basis. Price volatility could have dramatic effects on the results of operations and the ability of the Company to execute its business plan. The price of cobalt materials may also be reduced by the discovery of new cobalt deposits, which could not only increase the overall supply of cobalt (causing downward pressure on its price), but could draw new firms into the cobalt industry which would compete with the Company. As the Company’s refinery business plan involves both buying cobalt products and selling cobalt products, its ultimate economics will be significantly impacted by market commodity prices.
Cost Estimates
The Company prepares estimates of operating costs and/or capital costs for each operation and project. The Company’s actual costs are dependent on a number of factors, including royalties, the price of cobalt and by-product metals and the cost of inputs used in exploration activities.
The Company’s actual costs may vary from estimates for a variety of reasons, including labour and other input costs, commodity prices, general inflationary pressures and currency exchange rates. Failure to achieve cost estimates or material increases in costs could have an adverse impact on the Company’s future cash flows, profitability, results of operations and financial condition.
Industry Competition and International Trade Restrictions
The international resource industries are highly competitive. The value of any future reserves discovered and developed by the Company may be limited by competition from other world resource mining companies, or from excess inventories. Existing international trade agreements and policies and any similar future agreements, governmental policies or trade restrictions are beyond the control of the Company and may affect the supply of and demand for minerals, including cobalt, around the world.
Governmental Regulation and Policy
Mining operations and exploration activities are subject to extensive laws and regulations. Such regulations relate to production, development, exploration, exports, imports, taxes and royalties, labor standards, occupational health, waste disposal, protection and remediation of the environment, mine decommissioning and reclamation, mine safety, toxic and radioactive substances, transportation safety and emergency response, and other matters. Compliance with such laws and regulations increases the costs of exploring, drilling, developing, constructing, operating and closing mines and refining and other facilities. It is possible that, in the future, the costs, delays and other effects associated with such laws and regulations may impact decisions of the Company with respect to the exploration and development of properties such as the Iron Creek Project, the Refinery or the Cobalt Camp, or any other properties in which the Company has an interest. The Company will be required to expend significant financial and managerial resources to comply with such laws and regulations. Since legal requirements change frequently, are subject to interpretation and may be enforced in varying degrees in practice, the Company is unable to predict the ultimate cost of compliance with these requirements or their effect on operations. Furthermore, future changes in governments, regulations and policies and practices, such as those affecting exploration and development of the Company’s properties could materially and adversely affect the results of operations and financial condition of the Company in a particular year or in its long-term business prospects.
The development of mines and related facilities is contingent upon governmental approvals, licenses and permits which are complex and time consuming to obtain and which, depending upon the location of the project, involve multiple governmental agencies. The receipt, duration and renewal of such approvals, licenses and permits are subject to many variables outside the control of the Company, including potential legal challenges from various stakeholders such as environmental groups or non-government organizations. Any significant delays in obtaining or renewing such approvals, licenses or permits could have a material adverse effect on the Company, including delays and cost increases in the advancement of the Iron Creek Project, the Refinery and the Cobalt Camp.
Risk Related to the Cyclical Nature of the Mining Business
The mining business and the marketability of the products that are produced are affected by worldwide economic cycles. At the present time, the significant demand for cobalt and other commodities in many countries is driving increased prices, but it is difficult to assess how long such demand may continue. Fluctuations in supply and demand in various regions throughout the world are common.
As the Company’s mining and exploration business is in the exploration stage and as the Company does not carry on production activities, its ability to fund ongoing exploration is affected by the availability of financing which is, in turn, affected by the strength of the economy and other general economic factors.
Title Claims and First Nations Rights
The Company has investigated its rights to explore and exploit its projects and, to the best of its knowledge, its rights in relation to lands covering the projects are in good standing. Nevertheless, no assurance can be given that such rights will not be revoked, or significantly altered, to the Company’s detriment. There can also be no assurance that the Company’s rights will not be challenged or impugned by third parties.
Although the Company is not aware of any existing title uncertainties with respect to lands covering material portions of its projects, there is no assurance that such uncertainties will not result in future losses or additional expenditures, which could have an adverse impact on the Company’s future cash flows, earnings, results of operations and financial condition.
Certain of the Company’s properties may be subject to the rights or the asserted rights of various community stakeholders, including First Nations and other indigenous peoples. The presence of community stakeholders may impact the Company’s ability to develop or operate its mining properties and its projects or to conduct exploration activities. Accordingly, the Company is subject to the risk that one or more groups may oppose the continued operation, further development or new development or exploration of the Company’s current or future mining properties and projects.
Such opposition may be directed through legal or administrative proceedings, or through protests or other campaigns against the Company’s activities.
Governments in many jurisdictions must consult with, or require the Company to consult with, indigenous peoples with respect to grants of mineral rights and the issuance or amendment of project authorizations. Consultation and other rights of indigenous peoples may require accommodation including undertakings regarding employment, royalty payments and other matters. This may affect the Company’s ability to acquire within a reasonable time frame effective mineral titles, permits or licenses in any jurisdictions in which title or other rights are claimed by First Nations and other indigenous peoples, and may affect the timetable and costs of development and operation of mineral properties in these jurisdictions. The risk of unforeseen title claims by indigenous peoples also could affect existing operations as well as development projects. These legal requirements may also affect the Company’s ability to expand or transfer existing operations or to develop new projects.
Community Relations and License to Operate
The Company’s relationship with the host communities where it operates is critical to ensure the future success of its existing operations and the construction and development of its projects. There is an increasing level of public concern relating to the perceived effect of mining activities on the environment and on communities impacted by such activities. Certain non-governmental organizations (“NGOs”), some of which oppose globalization and resource development, are often vocal critics of the mining industry and its practices, including the use of cyanide and other hazardous substances in processing activities. Adverse publicity generated by such NGOs or others related to extractive industries generally, or the Company’s exploration or development activities specifically, could have an adverse effect on the Company’s reputation. Reputation loss may result in decreased investor confidence, increased challenges in developing and maintaining community relations and an impediment to the Company’s overall ability to advance its projects, which could have a material adverse impact on the Company’s results of operations, financial condition and prospects. While the Company is committed to operating in a socially responsible manner, there is no guarantee that the Company’s efforts in this respect will mitigate this potential risk.
Acquisition and Integration Risks
As part of its business strategy, the Company has sought and will continue to seek new operating, development and exploration opportunities in the mining industry. In pursuit of such opportunities, the Company may fail to select appropriate acquisition candidates or negotiate acceptable arrangements, including arrangements to finance acquisitions or integrate the acquired businesses and their personnel into the Company. The Company cannot assure that it can complete any acquisition or business arrangement that it pursues, or is pursuing, on favourable terms, if at all, or that any acquisition or business arrangement completed will ultimately benefit its business. Such acquisitions may be significant in size, may change the scale of the Company’s business and may expose the Company to new geographic, political, operating, financial or geological risks. Further, any acquisition the Company makes will require a significant amount of time and attention of Electra’s management, as well as resources that otherwise could be spent on the operation and development of the Company’s existing business.
Any future acquisitions would be accompanied by risks, such as a significant decline in the relevant metal price after the Company commits to complete an acquisition on certain terms; the quality of the mineral deposit acquired proving to be lower than expected; the difficulty of assimilating the operations and personnel of any acquired companies; the potential disruption of the Company’s ongoing business; the inability of management to realize anticipated synergies and maximize the Company’s financial and strategic position; the failure to maintain uniform standards, controls, procedures and policies; the impairment of relationships with employees, customers and contractors as a result of any integration of new management personnel; and the potential for unknown or unanticipated liabilities associated with acquired assets and businesses, including tax, environmental or other liabilities. In addition, the Company may need additional capital to finance an acquisition. Debt financing related to any acquisition may expose the Company to the risks related to increased leverage, while equity financing may cause existing shareholders to suffer dilution. There can be no assurance that any business or assets acquired in the future will prove to be profitable, that the Company will be able to integrate the acquired businesses or assets successfully or that it will identify all potential liabilities during the course of due diligence. Any of these factors could have a material adverse effect on the Company’s business, prospects, results of operations and financial condition.
Legal and Litigation
All industries, including the mining industry, are subject to legal claims, with and without merit. Defense and settlement costs of legal claims can be substantial, even with respect to claims that have no merit. Due to the inherent uncertainty of the litigation process, the resolution of any particular legal proceeding to which the Company may become subject could have a material adverse effect on the Company’s business, prospects, financial condition, and operating results. There are no current claims or litigation outstanding against the Company.
Insurance
The Company is also subject to a number of operational risks and may not be adequately insured for certain risks, including: accidents or spills, industrial and transportation accidents, which may involve hazardous materials, labor disputes, catastrophic accidents, fires, blockades or other acts of social activism, changes in the regulatory environment, impact of non-compliance with laws and regulations, natural phenomena such as inclement weather conditions, floods, earthquakes, tornados, thunderstorms, ground movements, cave-ins, and encountering unusual or unexpected geological conditions and technological failure of exploration methods.
There is no assurance that the foregoing risks and hazards will not result in damage to, or destruction of, the properties of the Company, personal injury or death, environmental damage or, regarding the exploration or development activities of the Company, increased costs, monetary losses and potential legal liability and adverse governmental action, all of which could have an adverse impact on the Company’s future cash flows, earnings, results of operations and financial condition. The payment of any such liabilities would reduce the funds available to the Company. If the Company is unable to fully fund the cost of remedying an environmental problem, it might be required to suspend operations or enter into costly interim compliance measures pending completion of a permanent remedy.
No assurance can be given that insurance to cover the risks to which the Company’s activities are subject will be available at all or at commercially reasonable premiums. The Company is not currently covered by any form of environmental liability insurance, since insurance against environmental risks (including liability for pollution) or other hazards resulting from exploration and development activities is unavailable or prohibitively expensive. This lack of environmental liability insurance coverage could have an adverse impact on the Company’s future cash flows, earnings, results of operations and financial condition.
Conflicts of Interest
The Company’s directors and officers are or may become directors or officers of other mineral resource companies or reporting issuers or may acquire or have significant shareholdings in other mineral resource companies and, to the extent that such other companies may participate in ventures in which the Company may, or may also wish to participate, the directors and officers of the Company may have a conflict of interest with respect to such opportunities or in negotiating and concluding terms respecting the extent of such participation.
The Company and its directors and officers will attempt to minimize such conflicts. If such a conflict of interest arises at a meeting of the directors of the Company, a director who has such a conflict will abstain from voting for or against the approval of such participation or such terms. In appropriate cases, the Company will establish a special committee of independent directors to review a matter in which several directors, or officers, may have a conflict. In determining whether or not the Company will participate in a particular program and the interest to be acquired by it, the directors will primarily consider the potential benefits to the Company, the degree of risk to which the Company may be exposed and its financial position at that time. Other than as indicated, the Company has no other procedures or mechanisms to deal with conflicts of interest.
Decommissioning and Reclamation
Environmental regulators are increasingly requiring financial assurances to ensure that the cost of decommissioning and reclaiming sites is borne by the parties involved, and not by government. It is not possible to predict what level of decommissioning and reclamation (and financial assurances relating thereto) may be required in the future by regulators. The Company’s ability to advance its projects could be adversely affected by any inability on its part to obtain or maintain the required financial assurances.
Dividends
The Company has never paid cash dividends on our Common Shares, and does not expect to pay any cash dividends in the future in favor of utilizing cash to support the development of our business. Any future determination relating to the Company’s dividend policy will be made at the discretion of the Company’s Board of Directors and will depend on a number of factors, including future operating results, capital requirements, financial condition and the terms of any credit facility or other financing arrangements the Company may obtain or enter into, future prospects and other factors the Company’s Board of Directors may deem relevant at the time such payment is considered. As a result, shareholders will have to rely on capital appreciation, if any, to earn a return on their investment in the Common Shares for the foreseeable future.
Time and Cost Estimates
Actual time and costs may vary significantly from estimates for a variety of reasons, both within and beyond the control of the Company. Failure to achieve time estimates and significant increases in costs may adversely affect the Company’s ability to continue exploration, develop the Iron Creek Project, the Refinery and the Cobalt Camp, and ultimately generate sufficient cash flows. There is no assurance that the Company’s estimates of time and costs will be achievable.
Consumables Availability and Costs
The Company’s planned exploration, development and operating activities, including the profitability thereof, will continue to be affected by the availability and costs of consumables used in connection with the Company’s activities. Of significance, this may include concrete, steel, copper, piping, diesel fuel and electricity. Other inputs such as labour, consultant fees and equipment components are also subject to availability and cost volatility. If inputs are unavailable at reasonable costs, this may delay or indefinitely postpone planned activities. Furthermore, many of the consumables and specialized equipment used in exploration, development and operating activities are subject to significant volatility. There is no assurance that consumables will be available at all or at reasonable costs.
Russo-Ukrainian War
The continued escalation of the Russo-Ukrainian War has resulted in significant volatility in commodity prices and global markets and an increased risk of cybersecurity and information technology attacks. The ongoing war has caused foreign governments, including Canada and the United States, to impose economic sanctions on Russia. While the Company does not operate in Russia and its operational activities are not currently impacted by sanctions, continued volatility could impact the Company’s ability to obtain necessary financing and market liquidity. Expansion of the war outside of the Ukraine may adversely impact global markets and commodity prices as well as the ability of the Company to secure the necessary employees and resources to sustain planned operations.
Global Financial Conditions
Global financial conditions have been subject to continued volatility. Government debt, the risk of sovereign defaults, political instability and wider economic concerns in many countries have been causing significant uncertainties in the markets. Disruptions in the credit and capital markets can have a negative impact on the availability and terms of credit and capital. Uncertainties in these markets could have a material adverse effect on the Company’s liquidity, ability to raise capital and cost of capital. High levels of volatility and market turmoil could also adversely impact commodity prices, exchange rates and interest rates and have a detrimental effect on the Company’s business.
Infrastructure
Mining, processing, development and exploration activities depend on adequate infrastructure. Reliable roads, bridges, power sources and water supply are important determinants which affect capital and operating costs. Unusual or infrequent weather phenomena, sabotage, or community, government or other interference in the maintenance or provision of such infrastructure could adversely affect the Company’s operations, financial condition and results of operations.
Competition
The Company faces strong competition from other mining companies in connection with the identification and acquisition of properties producing, or capable of producing, precious and base metals. Many of these companies have greater financial resources, operational experience and technical capabilities than the Company. As a result of this competition, the Company may be unable to identify, maintain or acquire attractive mining properties on acceptable terms or at all. In addition, the Company faces competition sourcing mine production for the Refinery. The Company’s plan for the Refinery, in part, includes African mine production from China to North America. Most cobalt is currently mined in the DRC and shipped to China for refining. The Company faces significant competition in diverting mine production, particularly ethically sourced mine production, to the Refinery and as a result, may be unable to identify, maintain or acquire mine production for the Refinery on acceptable terms or at all. Consequently, the Company’s prospects, revenues, operations and financial condition could be materially adversely affected.
Shareholder Activism
In recent years, publicly-traded companies have been increasingly subject to demands from activist shareholders advocating for changes to corporate governance practices, such as executive compensation practices, social issues, or for certain corporate actions or reorganizations. There can be no assurances that activist shareholders will not publicly advocate for the Company to make certain corporate governance changes or engage in certain corporate actions. Responding to challenges from activist shareholders, such as proxy contests, media campaigns or other activities, could be costly and time consuming and could have an adverse effect on the Company reputation and divert the attention and resources of the Company management and the Company’s board of directors, which could have an adverse effect on the Company’s business and results of operations. Even if the Company does undertake such corporate governance changes or corporate actions, activist shareholders may continue to promote or attempt to effect further changes, and may attempt to acquire control of the Company to implement such changes.
If shareholder activists seeking to increase short-term shareholder value are elected to the Company’s board of directors, this could adversely affect its business and future operations. Additionally, shareholder activism could create uncertainty about the Company’s future strategic direction, resulting in loss of future business opportunities, which could adversely effect the Company’s business, future operations, profitability and ability to attract and retain qualified personnel.
Public Company Obligations
The Company’s business is subject to evolving corporate governance and public disclosure regulations that have increased both the Company’s compliance costs and the risk of non-compliance, which could have a material adverse impact on the Company’s share price.
The Company is subject to changing rules and regulations promulgated by a number of governmental and self-regulated organizations, including the Canadian Securities Administrators, the TSXV, and the International Accounting Standards Board. These rules and regulations continue to evolve in scope and complexity creating many new requirements. The Company’s efforts to comply with rules and obligations could result in increased general and administration expenses and a diversion of management time and attention from revenue-generating activities.
Taxation
The Company is affected by the tax regimes of various local, regional and national authorities. Revenues, expenditures, income, investments, land use, intercompany transactions and all other business conditions can be taxed. Tax regulations, interpretations and enforcement policies may differ from the Company’s applied methods and may change over time due to circumstances beyond the Company’s control. The effect of such events could have material adverse effects on the Company’s anticipated tax consequences. There is no assurance regarding the nature or rate of taxation, assessments and penalties that may be imposed.
“Passive Foreign Investment Company” Under the U.S. Internal Revenue Code
U.S. investors should be aware that they could be subject to certain adverse U.S. federal income tax consequences in the event that the Company is classified as a “passive foreign investment company” (“PFIC”) for U.S. federal income tax purposes. The determination of whether the Company is a PFIC for a taxable year depends, in part, on the application of complex U.S. federal income tax rules, which are subject to differing interpretations, and the determination will depend on the composition of the Company’s income, expenses and assets from time to time and the nature of the activities performed by the Company’s officers and employees. The Company may be a PFIC in one or more prior tax years, in the current tax year and in subsequent tax years. Prospective investors should consult their own tax advisers regarding the likelihood and consequences of the Company being treated as a PFIC for U.S. federal income tax purposes, including the advisability of making certain elections that may mitigate certain possible adverse U.S. federal income tax consequences that may result in an inclusion in gross income without receipt of such income.
Foreign Exchange Rate Risk
The Company reports its consolidated financial statements in Canadian dollars; however, the Company has operations in the United States. As a consequence, the financial results of the Company’s operations as reported in Canadian dollars are subject to changes in the value of the Canadian dollar relative to the U.S. dollar. Exploration and development activities in the U.S. are held in the Company’s U.S. subsidiaries and are primarily incurred in U.S. dollars. and translated into Canadian dollars within the consolidated financial statements. Given the time period between initial recognition and settlement of payments, as such, the Company can be exposed to significant fluctuations in the exchange rate between the U.S. dollar and the Canadian dollar. In addition, a significant change in the exchange rate between the U.S. dollar and Canadian dollar can impact the Company’s available liquidity to perform exploration and development activities. The Company does not currently enter into any foreign exchange hedges to limit exposure to exchange rate fluctuations. The Board of Directors continually assesses the Company’s strategy toward its foreign exchange rate risk, depending on market conditions.
Enforcement of US Judgments
United States investors may not be able to obtain enforcement of civil liabilities against the Company.
The enforcement by investors of civil liabilities under the United States federal or state securities laws may be affected adversely by the fact that the Company is governed by the CBCA, that the majority of the Company’s officers and directors are residents of Canada, and that all, or a substantial portion of their assets and a portion of the Company’s assets, are located outside the United States. It may not be possible for investors to effect service of process within the United States on certain of its directors and officers or enforce judgments obtained in the United States courts against the Company or certain of the Company’s directors and officers based upon the civil liability provisions of United States federal securities laws or the securities laws of any state of the United States.
DIVIDENDS AND DISTRIBUTIONS
The Company has not, for any of the three most recently completed financial years or its current financial year, declared or paid any dividends on its Common Shares, and does not currently have a policy with respect to the payment of dividends. For the foreseeable future, we anticipate that we will not pay dividends but will retain future earnings and other cash resources for the operation and development of our business. The payment of dividends in the future will depend on our earnings, if any, our financial condition and such other factors as our directors consider appropriate.
CAPITAL STRUCTURE
Common Shares
The authorized share capital of the Company consists of an unlimited number of Common Shares. As of the date of this AIF, 564,443,309 Common Shares were issued and outstanding. In addition, as of the date of this AIF, there were 17,269,270 Common Shares issuable on the exercise of incentive stock options, 3,813,908 Common Shares issuable on the exercise of deferred share units, 1,268,458 Common Shares issuable on the exercise of restricted share units, 1,900,000 Common Shares issuable on the exercise of performance share units and 22,946,123 Common Shares issuable on the exercise of Common Share purchase warrants.
Holders of Common Shares are entitled to receive notice of any meeting of shareholders of the Company, to attend and to cast one vote per share at such meetings. Holders of Common Shares are also entitled to receive on a pro-rata basis such dividends, if any, as and when declared by the Board of Directors at its discretion from funds legally available therefor and upon the liquidation, dissolution or winding up of the Company are entitled to receive on a pro-rata basis, the net assets of the Company after payment of debts and other liabilities, in each case subject to the rights, privileges, restrictions and conditions attaching to any other series or class of shares ranking senior in priority. The Common Shares do not carry any pre-emptive, subscription, redemption or conversion rights.
MARKET FOR SECURITIES
Trading Price and Volume
The Common Shares are listed for trading on the TSXV under the trading symbol “ELBM”. From January 2021 to December 6, 2021, the Common Shares were listed for trading on the TSXV under the trading symbol “FCC”. The following table sets forth the high and low prices and total monthly volume of the Common Shares as traded on the TSXV for the periods indicated. All share prices are shown in Canadian dollars.
Period | | High | | | Low | | | Total Volume | |
January 2021 | | | 0.41 | | | | 0.26 | | | | 63,043,114 | |
February 2021 | | | 0.46 | | | | 0.275 | | | | 53,315,621 | |
March 2021 | | | 0.385 | | | | 0.29 | | | | 27,767,679 | |
April 2021 | | | 0.39 | | | | 0.335 | | | | 14,289,107 | |
May 2021 | | | 0.36 | | | | 0.32 | | | | 7,437,062 | |
June 2021 | | | 0.345 | | | | 0.29 | | | | 17,209,504 | |
July 2021 | | | 0.34 | | | | 0.26 | | | | 9,996,284 | |
August 2021 | | | 0.325 | | | | 0.275 | | | | 9,410,623 | |
September 2021 | | | 0.305 | | | | 0.26 | | | | 11,735,226 | |
October 2021 | | | 0.335 | | | | 0.255 | | | | 11,770,075 | |
November 2021 | | | 0.425 | | | | 0.29 | | | | 42,853,106 | |
December 2021 | | | 0.36 | | | | 0.295 | | | | 13,611,548 | |
Prior Sales
The Company issued the following securities which are outstanding but not listed or quoted on a marketplace during the most recently completed financial year:
Date | | Class of Security | | Amount Issued | | Issue Price | |
22-Jan-2021 | | Warrants | | | 15,766,500(1) | | $ | 0.50 | |
22-Jan-2021 | | Warrants | | | 1,891,980(2) | | $ | 0.31 | |
17-Feb-2021 | | RSUs | | | 148,456(3) | | $ | 0.405 | |
17-Feb-2021 | | DSUs | | | 30,864(4) | | $ | 0.405 | |
17-Feb-2021 | | Options | | | 100,000(3) | | $ | 0.405 | |
16-Apr-2021 | | RSUs | | | 115,000(5) | | $ | 0.345 | |
16-Apr-2021 | | DSUs | | | 218,116(3) | | $ | 0.345 | |
16-Apr-2021 | | PSUs | | | 1,575,000(3) | | $ | 0.345 | |
16-Apr-2021 | | Options | | | 575,000(5) | | $ | 0.345 | |
2-Sep-2021 | | Convertible Senior | | | 4,058.24 Common Shares per | | US$ | 37,500,000 | |
22-Oct-2021 | | Secured Notes | US$1,000 principal amount of Notes(6) | | US$ | 7,500,000 | |
8-Nov-2021 | | DSUs | | | 35,714(3) | | $ | 0.35 | |
8-Nov-2021 | | RSUs | | | 50,000(3) | | $ | 0.35 | |
8-Nov-2021 | | Options | | | 250,000(3) | | $ | 0.35 | |
| Notes: |
| (1) | Issued pursuant to a bought-deal financing. |
| (2) | Issued as agent compensation warrants relating to a bought-deal financing. |
| (3) | Issued to directors, officers, employees and contractors under the Company’s long-term incentive plan. |
| (4) | Issued to directors of the Company in lieu of earned fees. |
| (5) | Issued as initial grant to new officer or employee. |
| (6) | Issued pursuant to the Note Offering. |
ESCROWED SECURITIES AND SECURITIES SUBJECT TO CONTRACTUAL RESTRICTIONS ON TRANSFER
As of the date of this AIF, there are no securities held in escrow or subject to contractual restrictions on transfer.
DIRECTORS AND OFFICERS
Name, Province or State, Country of Residence and Offices Held
The following table sets forth the name of each of our directors and executive officers, their province or state and country of residence, their position(s) with the Company, their principal occupation during the preceding five years and the date they first became a director of the Company. Each director’s term will expire immediately prior to the following annual meeting of shareholders.
Name and Residence | Position(s)with the Company | Principal Occupation During Past Five Years | Director Since |
Trent Mell(3) Toronto, Ontario, Canada | President, Chief Executive Officer and Director | Current President& CEO of the Company; former President of PearTree Securities; and former President& CEO of Falco Resources | March 14, 2017 |
John Pollesel(1)(2)(3)(4) Edmonton, Alberta, Canada | Director | Current CEO of Boreal Agrominerals Inc., an agromineral fertilizer company; and former SVP of Mining of Finning Canada | May 17, 2017 |
Garett Macdonald(1)(2)(4) West Lorne, Ontario, Canada | Director | Current President& CEO of Maritime Resources Corp., a mineral exploration company; former Vice President of Business Development of JDS Energy& Mining; and former Project Director of New Gold Inc. | June 4, 2018 |
C.L. “Butch” Otter(1)(3) Star, Idaho, USA | Director | Retired Governor of Idaho | February 21, 2019 |
Susan Uthayakumar(1)(2) Toronto, Ontario, Canada | Director | Current Chief Energy and Sustainability Officer at Prologis Inc.; former President Sustainability Business Division of Schneider Electric, former Country President, Schneider Electric Canada, an energy technology company | October 1, 2019 |
Ryan Snyder Oakville, Ontario, Canada | Chief Financial Officer | Current CFO of the Company; former CFO of Primero Mining Corp and former Director of Finance and Treasurer of Primero Mining Corp | N/A |
Michael Insulan Luxembourg | Vice President, Commercial | Current VP Commercial of the Company; former Senior Market Analyst at Eurasian Resources Group; former Managing Consultant, Team Leader, Aluminium Raw Materials | N/A |
Mark Trevisiol Sudbury, Ontario, Canada | Vice President, Project Development | Current VP of Project Development of the Company; former Site Manager of Northern Sun Mining | N/A |
Regan P. Watts Toronto, Ontario, Canada | Vice President, Corporate Affairs | Current VP of Corporate Affairs of the Company; former member of the IBM Innovation, Corporate Citizenship and Government Affair team, former member of the Executive Committee of Lafarge Canada Inc. | N/A |
| Notes: |
| (1) | Independent Director |
| (2) | Member of the Audit Committee |
| (3) | Member of the Compensation, Governance and Nominating Committee |
| (4) | Member of the Technical and Sustainability Committee |
Shareholdings of Directors and Officers
As the date of this AIF, the Company’s directors and executive officers beneficially own, control or direct, directly or indirectly, 7,362,062 Common Shares.
Cease Trade Orders, Bankruptcies, Penalties or Sanctions
None of our directors or executive officers is, as at the date hereof, or was within 10 years before the date hereof, a director, chief executive officer or chief financial officer of any company (including the Company) that (a) was subject to a cease trade order, an order similar to a cease trade order or an order that denied the relevant issuer access to any exemption under securities legislation, that was in effect for a period or more than 30 consecutive days (a “Cease Trade Order”) that was issued while the director or executive officer was acting in the capacity as director, chief executive officer or chief financial officer of such issuer, or (b) was subject to a Cease Trade Order that was issued after the director or executive officer ceased to be a director, chief executive officer or chief financial officer and which resulted from an event that occurred while that person was acting in the capacity as director, chief executive officer or chief financial officer.
None of our directors or executive officers, nor, to our knowledge, any shareholder holding a sufficient number of our securities to affect materially the control of the Company (a) is, as at the date hereof, or has been within the 10 years before the date hereof, a director or executive officer of any company (including ours) that, while that person was acting in that capacity, or within a year of that person ceasing to act in that capacity, became bankrupt, made a proposal under any legislation relating to bankruptcy or insolvency or was subject to or instituted any proceedings, arrangement or compromise with creditors or had a receiver, receiver manager or trustee appointed to hold its assets, or (b) has, within the 10 years before the date hereof, become bankrupt, made a proposal under any legislation relating to bankruptcy or insolvency, or become subject to or instituted any proceedings, arrangement or compromise with creditors, or had a receiver, receiver manager or trustee appointed to hold the assets of such director, executive officer or shareholder.
None of our directors or executive officers, nor, to our knowledge, any shareholder holding a sufficient number of our securities to affect materially the control of the Company, has been subject to (a) any penalties or sanctions imposed by a court relating to securities legislation or by a securities regulatory authority or has entered into a settlement agreement with a securities regulatory authority, or (b) any other penalties or sanctions imposed by a court or regulatory body that would likely be considered important to a reasonable investor in making an investment decision.
Conflicts of Interest
Unless otherwise noted in this AIF, to the best of our knowledge, there are no known existing or potential material conflicts of interest between the Company or its subsidiaries and any of our directors or officers or a director or officer of our subsidiaries. However, certain of our directors and officers are, or may become, directors or officers of other companies, with businesses that may conflict with our business. Accordingly, conflicts of interest may arise which could influence these individuals in evaluating possible acquisitions or in generally acting on behalf of the Company. Pursuant to the CBCA, directors are required to act honestly and in good faith with a view to the best interests of the Company. As required under the CBCA and our Articles:
| • | A director or executive officer who holds any office or possesses any property, right or interest that could result, directly or indirectly, in the creation of a duty or interest that materially conflicts with that individual’s duty or interest as a director or executive officer of the Company, must promptly disclose the nature and extent of that conflict. |
| • | A director who holds a disclosable interest (as that term is used in the CBCA) in a contract or transaction into which the Company has entered or proposes to enter may generally not vote on any directors’ resolution to approve the contract or transaction. |
Generally, as a matter of practice, directors or executive officers who have disclosed a material interest in any transaction or agreement that our Board of Directors is considering will not take part in any Board of Directors discussion respecting that contract or transaction. If on occasion such directors do participate in the discussions, they will abstain from voting on any matters relating to matters in which they have disclosed a material interest. In appropriate cases, we will establish a special committee of independent directors to review a matter in which directors, or management, may have a conflict.
Management
Trent Mell, President, Chief Executive Officer & Director – Mr. Trent Mell is a mining executive with almost 20 years of operating and capital markets experience. Over his career, he has been involved in transactions around the world, including $2.9B in equity and debt financings, mergers and acquisitions, offtake agreements and joint ventures. Mr. Mell was President and CEO of Falco Resources, which acquired the Horne Mine Complex area and 13 other former producers in the Rouyn-Noranda mining district in Quebec, Canada. Falco completed a feasibility study demonstrating the viability of a 15-year mine life with the potential to generate $6.6B in gross revenue. Immediately prior to joining Electra, Mr. Mell built a mining team with PearTree Securities to advise mining companies and investors on Canadian exploration and development opportunities. In 2016, his team placed $300M in equity investments and became the largest provider of flow-through capital to the Canadian resource industry. Mr. Mell began his career as a mining and securities lawyer with one of Canada’s leading law firms. He subsequently joined Barrick Gold and was part of the team that completed a US$10.4B hostile takeover of Placer Dome, creating the world’s largest gold company. He has also worked with nickel-cobalt producer Sherritt International and Ni-Cu-PGM producer North American Palladium. As Executive Vice President of AuRico Gold, Mr Mell led the team that competed an all-cash US$750M sale of the Ocampo Gold Mine in Mexico at the peak of the gold market in 2012. Mr Mell holds a B.A., B.C.L. and LL.B. from McGill University (Montreal), LL.M from Osgoode Hall (Toronto), as well as an MBA from Northwestern University (Chicago) and the Schulich School of Business (Toronto).
Mark Trevisiol, Vice President, Project Development – Mr. Trevisiol is a professional engineer with 30 years of experience in mineral processing, mining, capital projects and executive management. Mr. Trevisiol spent over 20 years with Glencore predecessor companies Falconbridge Ltd. and Xstrata Nickel, where he was General Manager of Business Development and Strategy, General Manager of the Sudbury Smelter Business Unit, Manager of Smelter Operations and Superintendent of the Kidd Creek Zinc Plant. More recently, Mark held a number of executive leadership and board positions, including CEO positions at Crowflight Minerals and Silver Bear Resources. During his career, Mr. Trevisiol has had responsibility in mining and mineral processing for teams of up to 300 people, with responsibility for operations, safety & environment, custom feed, engineering, maintenance and technology. He has a demonstrated track record of increasing plant efficiency and margins, notably in treating third party feeds. With Falconbridge Ltd., Mr. Trevisiol championed a new recycling facility primarily designed to handle spent cobalt-based lithium batteries. He has worked across several commodities, including nickel, cobalt, zinc, copper, lithium, gold, and silver. Mr. Trevisiol holds an Engineering degree from the University of Waterloo.
Michael Insulan, Vice President, Commercial – Mr. Insulan has nearly 20 years of experience across oil and gas, bulk commodities, base and minor metals. He has worked for Royal Dutch Shell, CRU, and Eurasian Resources Group. Over the past four years, Mr. Insulan has been primarily focused on the cobalt market where he has built a reputation as an industry expert. Mr. Insulan previously served as Senior Market Analyst at Eurasian Resources Group (Amsterdam and Luxembourg) where he was responsible for cobalt market intelligence, supporting sales and strategy. Prior to that he served as Managing Consultant and Team Leader at Aluminium Raw Materials assisting on the market intelligence and price reporting end for aluminium raw materials (alumina, bauxite, anode and cathode materials). Mr. Insulan has also served as a consultant at CRU Consulting where he would sell and lead consulting assignments for various commodity producers and consumers globally.
Regan P. Watts, Vice President, Corporate Affairs – Mr. Watts is a seasoned and entrepreneurial executive with more than 20 years of public and private sector experience in corporate communications, strategy, innovation, and regulatory and corporate affairs. His experience spans various industries including infrastructure, transportation, industrial manufacturing, information technology and financial services. Mr. Watts has provided services to Electra since 2019 and has been instrumental in helping communicate Electra’s priorities and plans to the Government of Canada and the Government of Ontario. In his executive capacity, Mr. Watts will add U.S. corporate and regulatory affairs to his responsibilities. Electra has ambitious plans for its Iron Creek copper-cobalt project in Idaho, which align with President Biden’s US$2 trillion green energy plan. Prior to working with Electra, Mr. Watts was a member of IBM Canada’s senior leadership group, heading the Innovation, Citizenship and Government Affairs team. Prior to IBM, he served on the Executive Committee of Lafarge Canada, where he led corporate communications, public and regulatory affairs, and corporate social responsibility. Mr. Watts had an extensive career in public service, serving in leadership roles in the Government of Canada across four federal departments. From 2006 to 2012, he served at Finance Canada, Transport Canada, Health Canada, and Foreign Affairs and International Trade Canada. In 2012, Mr. Watts was awarded the Queen Elizabeth II Diamond Jubilee Medal for his public service to Canada. A published author, Mr. Watts holds an MBA from the Ivey Business School at Western University and is President of consultancy Fratton Park Inc.
Ryan Snyder, Chief Financial Officer – Mr. Snyder has more than a decade of experience in finance. Previously, he spent five years in operations finance with Inmet Mining Corporation, where he led the worldwide annual budgeting and quarterly forecasting processes, oversaw operational financial reporting and analysis, and conducted scenario analysis for strategic decision-making. He then joined Enirgi Group Corporation where he oversaw financial planning, asset modeling and corporate governance. Most recently he was with Primero Mining Corp., initially as Director of Finance and Treasurer and later as Chief Financial Officer, where he was part of the team that negotiated the friendly merger of Primero with First Majestic Silver in 2018. Prior to entering the mining industry, Mr. Snyder obtained his Chartered Professional Accountant designation with KPMG LLP.
Non-Executive Directors
John Pollesel, Chairman and Director – Mr. John Pollesel has over 30 years of experience in the mining industry and is currently Chief Executive Officer of Boreal Agrominerals Inc. Prior to this, he was Senior Vice President, Mining at Finning Canada. Mr. Pollesel previously served as Chief Operating Officer and Director of Base Metals Operations for Vale SA’s North Atlantic Operations, where he was responsible for the largest underground mining and metallurgical operations in Canada. Prior to this, he was Vice President and General Manager for Vale’s Ontario Operations. Mr. Pollesel also served as the Chief Financial Officer for Compania Minera Antamina in Peru, with executive management responsibilities for one of the largest copper-zinc mining and milling operations in the world. Mr. Pollesel holds an MBA from Laurentian University and is a FCPA and CMA.
Garett Macdonald, Director – Mr. Macdonald is a mining engineer with extensive experience in project development and mine operations with over 23 years of industry experience. He has managed large technical programs through the concept, feasibility, and into construction stages and has senior management and board-level experience with several public companies. Garett led JDS Energy and Mining’s Eastern Canadian business operations as Vice President of Project Development. He also held roles in mine operations and engineering with senior Canadian mining firms Teck Corporation, Placer Dome and Suncor Energy, as well as the Vice President of Operations role for Rainy River Resources prior to the $310M sale of Rainy River to New Gold Inc. in 2013. Mr. Macdonald is currently the President and CEO of Maritime Resources. He holds a Master of Business Administration from Western University’s Ivey Business School and a Bachelor of Engineering (Mining) from Laurentian University.
C.L. “Butch” Otter, Director – Mr. Otter is an American businessman and politician. He held the longest serving consecutive terms as Governor of Idaho, a position he held from 2007 to 2019. Mr. Otter was also the longest serving Lieutenant Governor of Idaho with 14-year tenure from 1997 to 2001, before being elected to the U.S. Congress from 2001 to 2007. Butch spent 30 years working with J.R. Simplot Company, a privately-owned global food and agribusiness with interests in seed production, farming, fertilizer manufacturing, frozen-food processing, and food brands and distribution. He worked his way up from a Simplot Caldwell Potato Plant to the position of President of Simplot International, during which he traveled to nearly 80 countries to promote the company. Mr. Otter also served in the military from 1968 to 1973. He was part of the Idaho Army National Guard’s 116th Armored Cavalry.
Susan Uthayakumar, Director – Ms. Uthayakumar is a business executive with almost 25 years of experience in finance and executive management. She has been with Schneider Electric for the past 15 years, served as President of Schneider Electric Canada with overall responsibility for Canadian operations and was most recently the President of the Sustainability Business Division of Schneider Electric. Susan now serves as the Chief Energy and Sustainability Officer at Prologist Inc. She began her career as a CA with Deloitte, where she held positions of increasing responsibilities before joining McCain, where she executed global growth strategies and acquisitions across North America, Europe and Asia. Ms. Uthayakumar is a CA and CPA and has an Executive MBA from the Kellogg School of Management as well as a Bachelor of Arts and a Master of Accounting from the University of Waterloo.
PROMOTERS
During the fiscal years ended December 31, 2020 and 2021, no person or company has been a promoter of the Company or any subsidiary of the Company.
AUDIT COMMITTEE
Composition of the Audit Committee
The current members of the Audit Committee are Susan Uthayakumar (chair), John Pollesel and Garett Macdonald. All of the members of the Audit Committee are financially literate.
National Instrument 52-110 – Audit Committees (“NI 52-110”) provides that a member of an audit committee is “independent” if the member has no direct or indirect material relationship with the Company, which could, in the view of the Board of Directors, reasonably interfere with the exercise of the member’s independent judgment. All members of the Audit Committee are “independent” within the meaning of NI 52-110.
Relevant Education and Experience
The following sets out the Audit Committee members’ education and experience that is relevant to the performance of his responsibilities as an audit committee member.
Susan Uthayakumar (Committee Chair) – Ms. Uthayakumar has almost 25 years of experience in finance and executive management. For the past 15 years, she has been with Schneider Electric, a global leader in energy management and automation. Ms. Uthayakumar is a CA and CPA and holds an Executive MBA from the Kellogg School of Management as well as a Bachelor of Arts and a Master of Accounting from the University of Waterloo.
John Pollesel – Mr. Pollesel has over 30 years of experience in the mining industry and has held senior management roles with several publicly listed companies. Mr. Pollesel holds an HBA and MBA from the University of Waterloo and Laurentian University, respectively. He is a FCPA and FCMA.
Garett Macdonald – Mr. Macdonald has over 20 years of experience in the resource sector and currently holds the role of Chief Executive Officer with Maritime Resources. He has held numerous senior management roles and is a director of two other publicly listed junior mining companies. Mr. Macdonald holds an MBA from Western University’s Ivey Business School and a Bachelor of Engineering (Mining) from Laurentian University.
Audit Committee Oversight
At no time since the commencement of the Company’s most recent completed financial year was a recommendation of the Audit Committee to nominate or compensate an external auditor not adopted by the Board of Directors.
Reliance on Certain Exemptions
At no time since the commencement of the Company’s most recently completed financial year has the Company relied on the exemption in Section 2.4 of NI 52-110 (De Minimis Non-audit Services), or an exemption from NI 52-110, in whole or in part, granted under Part 8 of NI 52-110.
The Company is relying upon the exemption in Section 6.1 of NI 52-110.
Pre-approval Policies and Procedures
See Schedule “A” – Audit Committee Mandate for specific policies and procedures for the engagement of non-audit services.
External Auditor Service Fees (by Category)
The aggregate fees billed by the Company’s external auditors in each of the last two fiscal years for audit fees are as follows:
Fees in Canadian dollars | | December 31, 2021 | | | December 31, 2020(5)(6) | |
Audit fees(1) | | $ | 317,900 | | | $ | 126,838 | |
Audit-related fees(2) | | $ | Nil | | | $ | Nil | |
Tax fees(3) | | $ | Nil | | | $ | Nil | |
All other fees(4) | | $ | Nil | | | $ | 5,350 | |
Total | | $ | 317,900 | | | $ | 132,188 | |
Notes:
| (1) | The aggregate fees billed for audit services, including fees relating to the review of quarterly financial statements, statutory audits of the Company’s subsidiaries. |
| (2) | The aggregate fees billed for assurance and related services that are reasonably related to the performance of the audit or review of the Company’s financial statements and are not disclosed in the “Audit Fees” row. |
| (3) | The aggregate fees billed for tax compliance, tax advice and tax planning services. |
| (4) | Fees billed in relation to valuation services. |
| (5) | For the fiscal years ended December 31, 2020 and December 31, 2021, none of the Company’s audit-related fees, tax fees or all other fees described in the table above made use of the de minimis exception to pre-approval provisions contained in Section 2.4 of NI 52-110. |
| (6) | For the 2020 fees, a total of $90,950 related to KPMG LLP and $41,238 related to MNP LLP |
LEGAL PROCEEDINGS AND REGULATORY ACTIONS
Ausenco Engineering Canada Inc. has commenced a legal proceeding against the Company in relation to a dispute over final amounts owing for refinery engineering work. The amount of this claim is not material and the Company’s is progressing its legal defense on this matter.
Other than as noted above, there are no other legal proceedings or regulatory actions material to us to which we are a party, or to which we have been a party since our incorporation, or of which any property of the Company is or has been the subject matter of, since the beginning of the financial year ended December 31, 2021, and no such proceedings are known by us to be contemplated. There have been no penalties or sanctions imposed against us by a court relating to provincial or territorial securities legislation or by any securities regulatory authority, there have been no penalties or sanctions imposed by a court or regulatory body against us, and we have not entered into any settlement agreements before a court relating to provincial or territorial securities legislation or with any securities regulatory authority since our incorporation.
INTEREST OF MANAGEMENT AND OTHERS IN MATERIAL TRANSACTIONS
Other than disclosed elsewhere in this AIF, no director, senior officer or principal shareholder of the Company and no associate or affiliate of the foregoing have had a material interest, direct or indirect, in any transaction in which the Company has participated within the three-year period prior to the date of this AIF, or will have any material interest in any proposed transaction, which has materially affected or will materially affect the Company.
AUDITORS, TRANSFER AGENT AND REGISTRAR
Auditors
The Company’s auditors are KPMG, having an address at Suite 4600, 333 Bay Street, Toronto, Ontario, M5H 2S5. KPMG was first appointed as auditors of the Company on December 10, 2020.
Transfer Agents, Registrars or Other Agents
The transfer agent and registrar for the Common Shares in Canada is AST Trust Company (Canada), at its principal offices in Vancouver, British Columbia and Toronto, Ontario.
MATERIAL CONTRACTS
There have been no materials contracts entered into by the Company within the most recently completed financial year or before the most recently completed financial year that are still in effect, other than contracts made in the ordinary course of business.
INTEREST OF EXPERTS
Experts who have prepared reports for Electra in the financial year ending December 31, 2021 include the following:
KPMG LLP, who prepared the auditors’ report accompanying the audited financial statements of the Company for the most recent year end, have confirmed with respect to the Company that they are independent within the meaning of the relevant rules and related interpretations prescribed by the relevant professional bodies in Canada and any applicable legislation or regulations.
Steven J. Ristorcelli, C.P.G., P.G, and Joseph Schlitt, MMSA QP, have acted as “Qualified Persons” under NI 43-101 in connection with the Iron Creek Technical Report and have reviewed and approved the information related to the Iron Creek Project in this AIF.
All other scientific and technical information in this annual information form has been reviewed and approved by Dan Pace, Principal Geologist at Electra, who is a “Qualified Person” under NI 43-101.
None of the experts whom are named in this AIF as having prepared reports or having been responsible for reporting exploration results relating to our mineral properties and whose profession or business gives authority to such reports, or any director, officer, partner, or employee thereof, as applicable, received or has received a direct or indirect interest in our property or of any of our associates or affiliates. As at the date hereof, such persons, and the directors, officers, partners and employees, as applicable, of each of the experts beneficially own, directly or indirectly, in the aggregate, less than one percent of the securities of the Company and they did not receive any direct or indirect interest in any securities of the Company or of any associate or affiliate of the Company in connection with the preparation of such report.
None of such persons, or any director, officer or employee, as applicable, of any such companies or partnerships, is currently expected to be elected, appointed or employed as a director, officer or employee of the Company or of any associate or affiliate of the Company.
ADDITIONAL INFORMATION
Additional information relating to the Company may be found on SEDAR at www.sedar.com. Additional information including directors’ and officers’ remuneration and indebtedness, principal holders of our securities, securities authorized for issuance under equity compensation plans and a statement as to the interest of insiders in material transactions, was contained in the management proxy circular for the annual and special meeting of shareholders held on December 2, 2021. Additional financial information is provided in the audited financial statements and management discussion and analysis for the most recent year-end. The foregoing additional information is available on SEDAR at www.sedar.com under the Company’s profile.
SCHEDULE “A”
Audit Committee Charter
Electra battery materials corporation
audit Committee Charter
Adopted April 8, 2022
The purpose of the Audit Committee (the “Committee”) of the Board of Directors (the “Board”) of Electra Battery Materials Corporation (the “Company”) is to oversee the accounting and financial reporting processes of the Company and its subsidiaries and the audits of the financial statements of the Company, as well as related disclosure, internal controls, regulatory compliance and risk management functions.
The members of the Committee shall be appointed annually by the Board. The Chair shall be elected by the members of the Committee. The Committee shall consist of a minimum of three independent directors of the Company, and each member of the Committee shall be qualified to serve on the Committee pursuant to the requirements of the Nasdaq Stock Market (“Nasdaq”) and any additional requirements that the Board deems appropriate. In addition, at least one member of the Committee must be designated by the Board to be an “audit committee financial expert” as defined by the U.S. Securities and Exchange Commission (the “SEC”).
Independence is defined by, and subject to the exemptions and other provisions set out in, applicable laws, rules and regulations, as well as the rules of relevant stock exchanges (the “Applicable Laws”).
| III. | QUALIFICATIONS & EXPERIENCE |
Each member of the Committee must be financially literate, meaning that the director has the ability to read and understand a set of financial statements that present the breadth and level of complexity of accounting issues that can reasonably be expected to be raised by the Company’s financial statements.
At least one member of the Committee must be designated by the Board to be an “audit committee financial expert” as defined by the SEC and a “financial expert” within the meaning of Applicable Laws. The financial expert should have the following competencies:
| • | An understanding of financial statements and accounting principles used by the Company to prepare its financial statements; |
| • | The ability to assess the general application of such accounting principles in connection with the accounting for estimates, accruals and reserves; |
| • | Experience preparing, auditing, analyzing or evaluating financial statements that present a breadth and level of complexity comparable to the Company’s financial statements, or experience actively supervising one or more persons engaged in such activities; |
| • | An understanding of internal controls and procedures for financial reporting; and |
| • | An understanding of audit committee functions. |
In addition to the specific responsibilities enumerated below, the Committee shall be responsible for reviewing financial risks of the business and overseeing the implementation and evaluation of appropriate risk management practices. This will involve inquiring with management regarding how financial risks are managed and seeking opinions from management and the independent public accounting firm engaged for the purpose of preparing or issuing an auditor report for inclusion in the Company’s annual report or performing other audit, review or attest services for the Company (the “independent auditor”) regarding the adequacy of risk mitigation strategies.
| V. | COMMITTEE RESPONSIBILITIES |
In addition to such other duties as may be delegated by the Board, the Committee shall:
| • | Financial Statements: Review the Company’s interim and annual financial statements, MD&A and related press releases before the Company publicly discloses this information and recommend Board approval of such documents. The Committee shall also oversee procedures for the review of the Company’s public disclosure of financial information and shall periodically assess the adequacy of those procedures. |
| • | Variances: Obtain explanations from management for significant variances between comparative reporting periods and question management and the independent auditor regarding any significant financial reporting issues raised during the fiscal period and the method of resolution. |
| • | Internal Controls: Inquire as to the adequacy of the Company’s system of internal controls and review periodic reports from management regarding internal controls, which should include an assessment of risk with respect to financial reporting. |
| • | Auditor: Be directly responsible for the appointment, compensation, retention and oversight of the work of the Company’s independent auditor; ensure that the independent auditor reports directly to the Committee; and ensure that any disagreements between management and the independent auditor regarding financial reporting are resolved. |
| • | Auditor Performance and Independence Evaluation: Review the performance of the independent auditor, including the lead partner of the independent auditor. The Committee shall ensure its receipt from the independent auditor of a formal written statement delineating all relationships between the auditor and the Company, actively engage in a dialogue with the independent auditor with respect to any disclosed relationships or services that may impact the objectivity and independence of the auditor and take, or recommend that the full Board take, appropriate action to oversee the independence of the independent auditor. |
| • | Non-audit Services: Review and, in its sole discretion, approve in advance the independent auditor’s annual engagement letter and all audit and non-audit services to be provided to the Company and its subsidiaries by the independent auditor. In order to obtain pre-approval, management should detail the work to be performed by the independent auditor and obtain the assurance from the independent auditor that the proposed work will not impair their independence. |
| • | Whistleblower: Establish procedures for (i) the receipt, retention and treatment of complaints received by the Company regarding accounting, internal accounting controls or auditing matters, and (ii) the confidential, anonymous submission by employees of the Company of concerns regarding questionable accounting or auditing matters and other potential violations of the Company’s Code of Business Conduct and Ethics (the “Code”). |
| • | Hiring: Review and approve the Company’s policies regarding the hiring of current and past partners and employees of the Company’s present or former independent auditor. |
| • | Funding: Provide for appropriate funding, as determined by the Committee, in its capacity as a committee of the Board, for the payment of: |
| • | compensation to the independent auditor; |
| • | compensation to any advisors employed by the Committee; and |
| • | ordinary administrative expenses of the Committee that are necessary or appropriate in carrying out its duties. |
| • | Reporting: Report to the Board on a quarterly basis on the proceedings of Committee meetings. |
| • | Related Person Transactions: Oversee the Company’s related persons transactions policy and review proposed transactions or courses of dealings requiring approval or ratification under such policy. |
| • | Code of Conduct: Review the Company’s program to monitor compliance with the Code. The Committee shall also oversee the investigation of any alleged breach of the Code and the taking of appropriate corrective actions where a breach of the Code has occurred. |
| • | Miscellaneous: Perform such additional activities, and consider such other matters, within the scope of its responsibilities, as the Committee or the Board deems necessary or appropriate. |
| VI. | CHAIR RESPONSIBILITIES |
The Chair shall have the responsibilities and duties set out in the Position Description for the Chair of the Audit Committee.
| VII. | RESPONSIBILITIES AND DUTIES OF THE CHAIR |
The Chair shall have the responsibilities and duties set out in the Position Description for the Chair of the Compensation, Governance, and Nominating Committee.
The Committee has authority to:
| • | Appoint, compensate, and oversee the work of any registered public accounting firm retained by the Company. |
| • | Conduct or authorize investigations into or studies of matters within its scope of responsibility, including with respect to whistleblower submissions, and may retain, at the Company’s expense, independent legal, accounting or other advisors as it deems necessary to assist the Committee in carrying out its duties or to assist in the conduct of an investigation. |
| • | Meet with management, the independent auditor and other advisors, as necessary. |
| • | Obtain full access to the books, records, facilities and personnel of the Company and its subsidiaries. |
| • | Call a meeting of the Board to consider any matter of concern to the Committee. |
The Committee shall meet as often as it deems necessary, but not less frequently than quarterly. A quorum for the transaction of business at all meetings shall be a majority of members. Decisions shall be made by an affirmative vote of the majority of members in attendance and the Committee Chair shall not have a deciding or casting vote. An in-camera session of independent directors shall take place at least quarterly. The Committee should also meet separately on a periodic basis with (i) management, (ii) the director of the Company’s internal auditing department or other person responsible for the internal audit function, if applicable, and (iii) the Company’s independent auditor. The Committee may also request to meet separately with management, internal auditors, independent auditors or other advisors.
Meeting minutes shall be recorded and maintained, as directed by the Chair of the Committee.
| X. | DELEGATION OF AUTHORITY |
The Committee may form subcommittees for any purpose that the Committee deems appropriate and may delegate to such subcommittees such power and authority as the Committee deems appropriate; provided, however, that no subcommittee shall consist of fewer than two members, and provided further that the Committee shall not delegate to a subcommittee any power or authority required by any law, regulation or listing standard to be exercised by the Committee as a whole.
| XI. | LIMITATION ON COMMITTEE’S DUTIES |
The Committee shall discharge its responsibilities, and shall assess the information provided by the Company’s management and the external auditor, in accordance with its business judgment. Members of the Committee are not full-time employees of the Company and are not, and do not represent themselves to be, professional accountants or auditors. The authority and responsibilities set forth in this Charter do not reflect or create any duty or obligation of the Committee to (i) plan or conduct any audits; (ii) determine or certify that the Company’s financial statements are complete, accurate, fairly presented or in accordance with generally accepted accounting principles or applicable law; (iii) guarantee the external auditor’s reports; or (iv) provide any expert or special assurance as to the Company’s internal controls or management of risk. Members of the Committee are entitled to rely, absent knowledge to the contrary, on the integrity of the persons and organizations from whom they receive information, the accuracy and completeness of the information provided and representations made by management as to any audit or non-audit services provided by the external auditor.
Nothing in this Charter is intended or may be construed as imposing on any member of the Committee or the Board a standard of care or diligence that is in any way more onerous or extensive than the standard to which the directors are subject under applicable law. This Charter is not intended to change or interpret the constating documents of the Company or any federal, provincial, state or exchange law, regulation or rule to which the Company is subject, and this Charter should be interpreted in a manner consistent with the Applicable Laws. The Board may, from time to time, permit departures from the terms hereof, either prospectively or retrospectively, and no provision contained herein is intended to give rise to civil liability to shareholders, competitors, employees or other persons, or to any other liability whatsoever.
Any action that may or is to be taken by the Committee may, to the extent permitted by law or regulation, be taken directly by the Board.
| XII. | EVALUATION OF COMMITTEE |
The Committee shall, on an annual basis, review and evaluate its performance. In conducting this review, the Committee shall address such matters that the Committee considers relevant to its performance and evaluate whether this Charter appropriately addresses the matters that are or should be within its scope. The review and evaluation shall be conducted in such a manner as the Committee deems appropriate.
The Committee shall deliver to the Board a report, which may be oral, setting forth the results of its review and evaluation, including any recommended changes to this Charter and any recommended changes to the Company’s or the Board’s policies or procedures, as it deems necessary or appropriate.
Appendix A
electra battery materials corporation
POSITION DESCRIPTION FOR THE CHAIR OF THE AUDIT COMMITTEE
Adopted April 8, 2022
The board of directors (the “Board”) of Electra Battery Materials Corporation (the “Company”) shall select one of the members of the Board who meets the criteria for independence established by National Instrument 52-110 – Audit Committees, adopted by the Canadian securities administrators and by applicable United States securities laws and exchange requirements, to be appointed as Chair (the “Chair”) of the Audit Committee (the “Audit Committee”) of the Board.
| I. | DUTIES AND RESPONSIBILITIES OF THE CHAIR |
| (a) | Providing leadership to enable the Audit Committee to effectively carry out its duties and responsibilities as described in the Charter of the Audit Committee, and as may otherwise be appropriate. |
| (b) | Chairing meetings of the Audit Committee and encouraging a free and open discussion at the meetings. |
| (c) | Assisting the Audit Committee and the individual members of the Audit Committee in understanding and discharging their respective duties and responsibilities. |
| (d) | Ensuring the Audit Committee meets as necessary or appropriate to fulfill its mandate. |
| (e) | Ensuring there is an effective relationship between the senior executives (including internal auditors of the Company, if any), the external auditors of the Company and the members of the Audit Committee. |
| (f) | Acting as liaison between the Audit Committee and each of the Company’s management and external auditor. |
| (g) | Establishing and overseeing procedures to govern the work of the Audit Committee and the discharge of the duties of the Audit Committee, including procedures relating to: |
| (i) | the development of the agendas for meetings of the Audit Committee in consultation, as appropriate, with the Chair or lead director of the Board, the Chief Executive Officer and Chief Financial Officer of the Company and other senior executives of the Company; |
| (ii) | the receipt of appropriate information from senior executives of the Company to enable the Audit Committee to effectively exercise its duties; |
| (iii) | access to senior executives of the Company as the Audit Committee may require from time to time; |
| (iv) | the tabling of items requiring the approval of the Audit Committee or the review and recommendation of Audit Committee for approval by the Board; |
| (v) | the proper flow of information to the Audit Committee, including the adequacy and timing of information and materials that may be required by the Audit Committee; and |
| (vi) | the retention of appropriately qualified and independent external auditors, and other external advisors as appropriate and support of their independent functions. |
| (h) | Discussing as necessary with the Chair of the Compensation, Governance, and Nominating Committee the skills, experience and talents required for the members of the Audit Committee on an ongoing basis. |
| (i) | Overseeing the assessment of the performance of the Audit Committee. |
| (j) | Reporting to the Board, where appropriate, on matters reviewed and on any decisions or recommendations made by the Audit Committee. |
| (k) | Attending meetings of shareholders and responding to such questions from shareholders as may be put to the Chair. |
| (l) | Carrying such other duties as may be requested by the Board from time to time. |