CONSTRUCTION SERVICES
(“Owner”)
(“Contractor”)
ARTICLE I DEFINITIONS | 3 | |||
1.1Architect | 3 | |||
1.2Change, Change Order, Change Proposal and Construction Change Directive | 3 | |||
1.3Claim | 3 | |||
1.4Contract | 3 | |||
1.5Contract Documents | 3 | |||
1.6Contract Time | 4 | |||
1.7Cost of the Work | 4 | |||
1.8Drawings | 4 | |||
1.9Final Completion | 4 | |||
1.10Guaranteed Date of Substantial Completion | 4 | |||
1.11Guaranteed Maximum Price | 4 | |||
1.12Major Permits | 4 | |||
1.13Modification | 5 | |||
1.14Owner’s Lenders | 5 | |||
1.15Principal Interior Designer | 5 | |||
1.16Specifications | 5 | |||
1.17Subcontractor | 5 | |||
1.18Substantial Completion | 5 | |||
1.19Substitution | 5 | |||
1.20Vendor | 6 | |||
1.21Work | 6 | |||
ARTICLE II INTENT, INTERPRETATION AND CORRELATION | 6 | |||
2.1Intent of the Contract Documents | 6 | |||
2.2Order of Precedence | 7 | |||
2.3Contractor’s Compliance with Contract Documents | 7 | |||
ARTICLE III GUARANTEED MAXIMUM PRICE | 8 | |||
3.1Guaranteed Maximum Price | 8 | |||
3.2Cost of the Work | 13 | |||
3.3Non-Allowable Cost of the Work | 17 | |||
3.4Contractor’s Responsibility for Taxes | 20 | |||
3.5Discounts, Rebates and Refunds | 20 | |||
3.6No Duplication | 20 | |||
ARTICLE IV CONTRACT TIME AND INTERIM MILESTONE DATES | 21 | |||
4.1Definitions | 21 | |||
4.2Time is of the Essence | 21 | |||
4.3Completion Guarantees | 22 | |||
4.4Liquidated Damages | 22 | |||
ARTICLE V PAYMENTS TO CONTRACTOR | 23 | |||
5.1Schedule of Values | 23 | |||
5.2Applications for Progress Payments | 24 | |||
5.3Time of Payments | 27 | |||
5.4Owner’s Right To Withhold | 27 | |||
5.5Joint Payee Checks | 30 | |||
5.6Retention | 31 |
5.7Substantial Completion Payment | 31 | |||
5.8Final Payment | 31 | |||
5.9Disputed Payments | 33 | |||
5.10Ownership of Materials | 33 | |||
5.11Deposits and Payments | 34 | |||
5.12Waiver | 34 | |||
5.13Materials Off-Site | 34 | |||
ARTICLE VI OWNER’S RESPONSIBILITIES | 35 | |||
6.1Information and Services | 35 | |||
6.2Limitations | 36 | |||
6.3Project Representative | 36 | |||
6.4Approval of Major Purchases | 36 | |||
6.5Site Access | 36 | |||
6.6Payments | 37 | |||
6.7Proof of Funding | 37 | |||
6.8Good Faith | 37 | |||
6.9Timely Delivery of Drawings | 37 | |||
ARTICLE VII CONTRACTOR’S RESPONSIBILITIES | 37 | |||
7.1Contractor’s Specific Representations | 37 | |||
7.2General Description | 40 | |||
7.3Preconstruction Services | 43 | |||
7.4Systems and Procedures | 45 | |||
7.5Schedule Meetings and Records | 46 | |||
7.6Contractor’s Operations | 46 | |||
7.7Site Discipline | 47 | |||
7.8Site Security | 48 | |||
7.9Coordination with Others | 49 | |||
7.10Product and Design Substitutions | 50 | |||
7.11Tests and Inspections | 51 | |||
7.12Access to Stored Material | 52 | |||
7.13Shop Drawings, Product Data and Samples | 52 | |||
7.14Project Record Documents and As-Built Requirements | 53 | |||
7.15Site Clean Up | 54 | |||
7.16Construction Facilities and Temporary Controls | 56 | |||
7.17Cutting and Patching of Work | 56 | |||
7.18Performance and Payment Bond Requirements | 57 | |||
7.19Liens | 57 | |||
7.20Royalties and Patents | 58 | |||
7.21Training | 58 | |||
7.22Construction Photographs | 58 | |||
7.23Statement of Unpaid Claims | 58 | |||
ARTICLE VIII ARCHITECT | 59 | |||
8.1Architect’s Administration of the Contract | 59 | |||
ARTICLE IX SUBCONTRACTORS AND VENDORS | 60 | |||
9.1Subcontractors and Vendors | 60 | |||
9.2Consent To Use Proposed Subcontractors and Vendors | 60 | |||
9.3Form of Subcontracts and Purchase Orders | 60 | |||
9.4Subcontractors and Vendors Designated By Owner | 61 | |||
9.5Payments to Subcontractors from the Contractor | 61 | |||
9.6Subcontractor and Vendor Replacements | 61 | |||
9.7Communications with Subcontractors and Vendors | 61 | |||
9.8Assignment | 62 |
ARTICLE X WARRANTY OBLIGATIONS | 62 | |||
10.1Contractor’s Warranty | 62 | |||
10.2Contractor’s Warranty Period | 63 | |||
10.3Compliance with Contract Documents | 63 | |||
10.4Warranty Costs | 63 | |||
10.5Timeliness of Corrective Services | 64 | |||
10.6Warranty Survival | 64 | |||
10.7Owner’s Right to Correct | 65 | |||
10.8Owner’s Right to Supplement Work of Contractor | 65 | |||
10.9Acceptance of Non-Conforming Work | 65 | |||
10.10Warranty Exclusions | 65 | |||
10.11Written Guaranty | 65 | |||
ARTICLE XI SCHEDULING, DELAYS AND ACCELERATION | 66 | |||
11.1Owner’s Right to Modify | 66 | |||
11.2Project Schedule | 66 | |||
11.3Schedule Updates | 66 | |||
11.4Force Majeure Delay | 67 | |||
11.5Owner Delay | 67 | |||
11.6Extensions of Time and Guaranteed Maximum Price Increases for Delay | 67 | |||
11.7Limitations | 69 | |||
11.8Recovery Plans | 70 | |||
11.9Accelerations for Owner’s Convenience | 71 | |||
11.10Schedule Coordination | 71 | |||
11.12Partial Occupancy or Use | 72 | |||
11.13Other | 73 | |||
ARTICLE XII SUBSTANTIAL AND FINAL COMPLETION | 73 | |||
12.1Substantial Completion Procedures and Requirements | 73 | |||
12.2Final Completion Procedures and Requirements | 75 | |||
ARTICLE XIII CONCEALED CONDITIONS AND UNCOVERING OF WORK | 79 | |||
13.1Concealed Conditions | 79 | |||
13.2Covering of Work | 79 | |||
ARTICLE XIV INDEMNIFICATION | 80 | |||
14.1Indemnitee | 80 | |||
14.2Defense Costs | 81 | |||
14.3Hazardous Materials | 81 | |||
14.4Other Limitations | 81 | |||
14.5Survival of Indemnification Provisions | 82 | |||
14.6Risk | 82 | |||
ARTICLE XV INSURANCE | 83 | |||
15.1Owner Controlled Insurance Program | 83 | |||
15.2Evidence of Coverage | 84 | |||
15.3Deductibles | 84 | |||
15.4Cooperation by the Parties | 84 | |||
15.5Duration | 84 | |||
ARTICLE XVI SAFETY AND COMPLIANCE | 85 | |||
16.1Contractor’s Site Safety Responsibilities | 85 | |||
16.2Compliance | 87 |
ARTICLE XVII TERMINATION OR SUSPENSION OF THE CONTRACT | 87 | |||
17.1Material Default by Contractor | 87 | |||
17.2Termination for Convenience | 91 | |||
17.3Suspensions by Owner | 92 | |||
17.4Claims for Consequential Damages | 93 | |||
17.5Other Rights and Remedies | 94 | |||
17.6Contractor’s Remedies | 94 | |||
ARTICLE XVIII CHANGE IN THE WORK | 95 | |||
18.1Change | 95 | |||
18.2Change Order | 95 | |||
18.3Change Proposal Request | 96 | |||
18.4Construction Change Directive | 97 | |||
18.5Determination of Increases in Guaranteed Maximum Price | 98 | |||
18.6Simultaneous Submittal Requirements | 98 | |||
18.7Continued Performance | 98 | |||
18.8Effect of Change Orders | 99 | |||
18.9Verbal Instructions and Minor Changes in the Work | 99 | |||
18.10Waiver and Release of Contractor’s Rights | 100 | |||
ARTICLE XIX RECORD KEEPING AND AUDIT RIGHTS | 100 | |||
19.1Required Accounting Records | 100 | |||
19.2Purpose and Extent of Record Access | 101 | |||
19.3Record Keeping Formats | 101 | |||
19.4Certifications | 101 | |||
19.5Flow Down Provisions | 101 | |||
19.6Remedies | 102 | |||
19.7Record Retention | 102 | |||
ARTICLE XX CLAIMS | 102 | |||
20.1Definition | 102 | |||
20.2Notice | 102 | |||
20.3Pending Resolution | 103 | |||
20.4Final Settlement of Claims | 103 | |||
20.5Unresolved Claims | 103 | |||
ARTICLE XXI OWNER’S LENDERS | 103 | |||
21.1Owner’s Lenders | 103 | |||
21.2Assignment and Default | 104 | |||
21.3Owner’s Lenders Election | 104 | |||
21.4Payment and Work Continuation | 105 | |||
21.5Payments | 105 | |||
21.6Audit Rights | 105 | |||
21.7Access | 105 | |||
21.8[Intentionally Omitted] | 105 | |||
21.9General Cooperation | 105 | |||
ARTICLE XXII DISPUTE RESOLUTION AND GOVERNING LAW | 106 | |||
22.1Judicial Determination | 106 | |||
22.2Waiver of Jury Trial | 106 | |||
22.3Governing Law | 106 | |||
22.4Non-Waiver | 106 | |||
22.5Severability | 106 | |||
ARTICLE XXIII PROPRIETARY INFORMATION AND USE OF OWNER’S NAME | 107 | |||
23.1Proprietary Information | 107 | |||
23.2Advertising and Use of Owner’s Name | 107 | |||
23.3Use of Drawings | 107 |
ARTICLE XXIV MISCELLANEOUS PROVISIONS | 108 | |||
24.1Assignment | 108 | |||
24.2Subordination | 108 | |||
24.3No Third-Party Beneficiaries | 108 | |||
24.4Enforceability | 109 | |||
24.5Headings | 109 | |||
24.6Counterparts | 109 | |||
24.7Legal Fees | 109 | |||
24.8Waiver | 109 | |||
24.9Intent of the Parties | 109 | |||
24.10Survival | 110 | |||
24.11Independent Contractor | 110 | |||
24.12Privileged Business | 110 | |||
24.13Pinnacle Entertainment’s Compliance Committee | 111 | |||
24.14M/W/DBE and Missouri Businesses | 111 | |||
24.15Joint and Several Liability | 111 | |||
24.16 Entire Agreement | 111 | |||
ARTICLE XXV NOTICES | 112 | |||
25.1Notice Procedures | 112 | |||
25.2Notices to Owner | 112 | |||
25.3Notices to Contractor | 112 | |||
25.4Change of Address | 113 | |||
A. | Owner owns or leases the real property described onExhibit Aattached hereto and incorporated herein by the reference (“Site”). | |
B. | Owner desires to construct on the Site a first class luxury resort and casino, including casino and gaming areas, restaurants, retail, and exterior features, and all on-Site and off-Site improvements and infrastructure related thereto, all in full accordance with the Contract Documents, including the Drawings and Specifications, and including the Work (as defined below) (the “Project”). Contractor’s Work is only a portion of the Project. The Project also includes services and materials to be provided by Owner and other separate contractors and consultants. | |
C. | Contractor and Owner acknowledge that the Drawings and Specifications are not complete, and Contractor and Owner agree to work together to complete the Drawings and Specifications as provided in this Agreement, including consistent with the Guaranteed Maximum Price Premises and Assumptions and Project Schedule. | |
D. | Owner desires to engage Contractor to construct, and supervise the construction of, that portion of the Project comprising the Work as more fully described in this Agreement and Contractor desires to accept such engagement, upon the terms and conditions contained in this Agreement. |
2
DEFINITIONS
3
4
5
INTENT, INTERPRETATION AND CORRELATION
6
7
GUARANTEED MAXIMUM PRICE
8
9
10
(a) | if the portion of the Work is not an Allowance Item, Contractor shall perform such Work and such increase in costs shall be solely Contractor’s responsibility and Contractor shall not be entitled to, and will not seek, any increase in the Guaranteed Maximum Price (though Contractor shall be entitled to allocate a portion of the Construction Contingency to cover such cost increase if Contractor elects to the extent permitted in accordance withSection 3.1.6hereof; provided however, if no funds remain in the Construction Contingency, Contractor shall still be responsible for the increased cost of the Work); or | ||
(b) | if the portion of the Work is an Allowance Item, Contractor shall not be responsible for such excess cost of that Allowance Item over the Allowance Amount (subject toSection 3.1.8.3hereof), even if the Drawings and Specifications are in substantial conformance with the Guaranteed Maximum Price Premises and Assumptions, and in such case as to such increased costs Owner will make an election under clauses (a), (b), (c) or (d) ofSection 3.1.8.1above. |
11
(a) | if the portion of the Work is not an Allowance Item, the difference between those amounts shall be allocated to and included within the Construction Contingency; or | ||
(b) | if the portion of the Work is an Allowance Item, then such savings and difference shall reduce the Guaranteed Maximum Price. |
12
13
14
15
16
17
18
19
20
CONTRACT TIME AND INTERIM MILESTONE DATES
21
22
PAYMENTS TO CONTRACTOR
23
(a) | Work performed during such preceding calendar month. | ||
(b) | Amounts due for Contractor’s initial scope of Work satisfactorily completed during the preceding month as measured by the Contractor’s direct and actual costs incurred in accordance with the Cost of the Work described inSection 3.2of this Agreement, a list of all bills for supplies, materials, equipment, and fixtures incorporated in the Work (in detail reasonably sufficient to allow Owner to determine where each item is incorporated) and labor performed (in detail reasonably sufficient to allow Owner to determine where and on what portion of the Work the labor was performed, including, but not limited to, weekly labor payrolls with names, dates, hours and rates) in connection with the Work, together with copies of the actual bills to be paid. |
24
(c) | For each category and portion of the Work as shown on the Schedule of Values: (1) the amount requested on all previous Applications for Progress Payment, (2) the amount requested on the current Application for Progress Payment, and (3) the amount allocated to the Work yet to be completed. | ||
(d) | The percentage completion of each portion of the Work as of the end of the period covered by the Application for Progress Payment, shown as the percentage obtained by dividing (a) the expense which has actually been incurred by Contractor on account of that portion of the Work for which Contractor has made or intends to make actual payment prior to the next Application for Progress Payment, by (b) the amount allocated to that portion of the Work in the Schedule of Values. | ||
(e) | Amounts due which are attributable to the Contractor’s Fee earned as a result of the completion of Contractor’s scope of Work during such period covered by and included in the Application for Progress and approved by Owner. Under no circumstances shall Contractor include in any Application for Progress Payment, nor shall Owner be required to pay, an Application for Progress Payment for funds to pay an amount in excess of the then applicable pro rata portion of the Contractor’s Fee, using the ratio that the portion of the Work then completed bears to the total Work (as determined by the total Costs of the Work disbursed to date compared to the total approved Costs of the Work amount on the Schedule of Values). | ||
(f) | For all amounts due as the result of Change Orders and Construction Change Directives, the Contractor shall make submittals for each Change Order and Construction Change Directive. | ||
(g) | Reflect Retainage in the amount provided for pursuant toSection 5.6of this Agreement. | ||
(h) | Such additional information and documentation regarding the progress of the Work as Owner or Owner’s Lenders may reasonably require. |
25
26
27
28
29
30
31
32
33
34
OWNER’S RESPONSIBILITIES
35
36
CONTRACTOR’S RESPONSIBILITIES
37
38
39
40
41
42
43
44
45
46
47
48
49
50
51
52
53
(a) | removal of all wastes and rubbish; | ||
(b) | cleaning of all walls and other surfaces including tile, wood and glass surfaces; |
54
(c) | replacement of all broken glass (including removing labels, washing and polishing both sides); | ||
(d) | cleaning and polishing of all plumbing fixtures and equipment; | ||
(e) | restoring existing facilities such as roads, other paved surfaces, fencing and curbing at the Site to either their pre-existing condition unless more is required by the Contract Documents; | ||
(f) | requiring affected Subcontractors to promptly remove from the Site all temporary offices, tools, equipment, machinery and surplus materials not required for the continued performance of the Work and otherwise leaving the designated areas “vacuum clean;” | ||
(g) | machine-sweep and clean all drive-way surfaces; | ||
(h) | grind, smooth, and sweep clean any concrete surfaces, as necessary or desirable; | ||
(i) | remove temporary protections; | ||
(j) | remove marks, spots, dust, stains, fingerprints and other soil or dirt from all floors, tile, walls, finishes, marble, finished materials, fixtures, equipment and other Work, and wash or wipe clean and leave same in undamaged, new condition; | ||
(k) | clean tubs, toilets and other fixtures, cabinet work and equipment, removing stains, paint, dirt and dust, and leave same in undamaged new condition; | ||
(l) | clean all metal finished in accordance with recommendations of the manufacturer and accepted industry standards; and | ||
(m) | clean resilient floors thoroughly with a well rinsed mop containing only enough moisture to clean off any surface dirt or dust and buff dry by machine to bring the surfaces to sheen. |
55
56
57
58
ARCHITECT
59
SUBCONTRACTORS AND VENDORS
60
61
WARRANTY OBLIGATIONS
62
63
64
65
SCHEDULING, DELAYS AND ACCELERATION
66
67
68
69
70
71
72
SUBSTANTIAL AND FINAL COMPLETION
73
74
75
76
77
78
CONCEALED CONDITIONS AND UNCOVERING OF WORK
79
INDEMNIFICATION
80
81
82
INSURANCE
83
84
SAFETY AND COMPLIANCE
85
86
TERMINATION OR SUSPENSION OF THE CONTRACT
87
88
89
(a) | the (i) Cost of the Work actually and properly completed by Contractor in accordance with the Contract Documents up to the date of such termination (and not cancelable or refundable), plus (ii) the pro rata portion of Contractor’s Fee thereon (subject to satisfaction of the conditions applicable to progress and Final Payment contained in the Contract Documents as the case may be), but the foregoing amounts shall not exceed the portion of the Guaranteed Maximum Price (including Contractor’s Fee) fairly allocable to the Work so completed, exceeds |
90
(b) | the total of (i) all payments theretofore made to Contractor under the Contract Documents, and (ii) all damages and other costs and expenses incurred by Owner directly or indirectly, arising out of or as a result of, Contractor’s breach or default, including, without limitation, the cost of any additional consultants’ services, or managerial and administrative services required thereby, any additional costs incurred in retaining another contractor or other Subcontractors, any additional financing, interest or fees and other costs that Owner must pay by reason of a delay in completion of the Work, Owner’s termination of Contractor and the finishing of the Work by another method after such termination, attorneys’ fees and expenses, and any other damages, costs, and expenses Owner may incur in completing the Work as a result of Contractor’s breach or default including if Owner elects to complete the Project after such termination, the amount by which the actual cost of completing the Project (including components of the Project that are not part of the Work) is greater than what such actual cost (including the actual cost of components of the Project that are not part of the Work) would have been if Contractor had fulfilled its obligations under the Contract Documents, and if Owner elects to not complete the Project after such termination Contractor hereby acknowledges that Owner has the right to so elect without Owner waiving Contractor’s liability for damages arising out of the breach by Contractor that led to its termination, all damages suffered by Owner arising out of Contractor’s breach of this Agreement. |
91
92
1. | damages incurred by the Owner for rental expenses, for losses of use, income, profit, financing, business and reputation, and for loss of management or employee productivity or of the services of such persons; and |
2. | damages incurred by the Contractor for principal office expenses including the compensation of personnel stationed there, for losses of financing, business and reputation, and for loss of profit except for Contractor’s Fee due and payable for Work previously performed |
93
94
CHANGE IN THE WORK
(a) | a Change in the Work including a full description of such Change; | ||
(b) | the amount of the adjustment, if any, in the Guaranteed Maximum Price; and/or | ||
(c) | the extent of the adjustment, if any, in the Contract Time. |
95
96
(a) | mutual acceptance of a lump sum properly itemized and supported by sufficient substantiating data to permit evaluation; |
(b) | unit prices stated in the Contract Documents or subsequently agreed upon; or |
(c) | cost to be determined in a manner agreed upon by the parties and a mutually acceptable fixed or percentage fee, which cost shall be based upon a proposal by the appropriate party. Any proposals from Subcontractors shall not include any amounts for overhead and profit in excess of an aggregate of ten percent (10%) of the cost of such Subcontractor’s Work, unless approved by Owner. |
97
98
99
RECORD KEEPING AND AUDIT RIGHTS
100
101
CLAIMS
102
OWNER’S LENDERS
103
104
105
DISPUTE RESOLUTION AND GOVERNING LAW
106
PROPRIETARY INFORMATION AND USE OF OWNER’S NAME
107
MISCELLANEOUS PROVISIONS
108
109
110
111
NOTICES
President, Pinnacle Design & Construction
Pinnacle Entertainment, Inc.
3800 Howard Hughes Parkway
Suite 1800
Las Vegas, NV 89169
W.G. Yates & Sons Construction Company
115 Main Street
Biloxi, MS 39530
Phone: (228) 386-4387
Fax (228) 374-0380
112
OWNER: | CONTRACTOR: | |
CASINO ONE CORPORATION | W. G & YATES SONS | |
CONSTRUCTION COMPANY | ||
BY: /s/ Daniel R. Lee | BY: /s/ William G. Yates | |
ITS: Chairman/CEO | ITS: President & C.E.O. | |
PARIC CORPORATION | ||
BY: /s/ P. Joseph McKee | ||
ITS: President & CEO |
113
DESCRIPTION OF REAL PROPERTY
PROJECT SCHEDULE
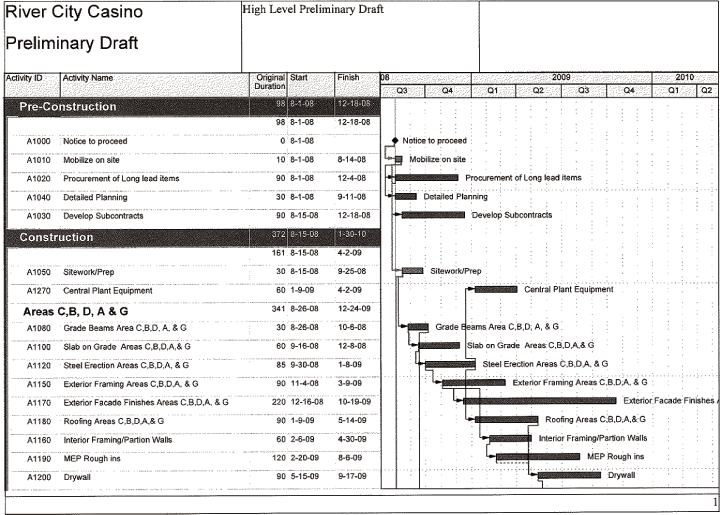
River City Casino Preliminary Draft |
High Level Preliminary Draft |
Activity ID ;: . Activity Name |
A1000 ! Notice to proceed A1010 Mobilize on site |
A1020 Procurement of Long lead items |
A1040 Detailed Planning A1030 Develop Subcontracts |
0 8-1-08 10 8-1-08 |
90 8-1-08 30 8-1-08 90 8-15-08 |
8-14-08 |
“12-4-08 |
9-11-08 |
12-18-OS |
Notice to proceed Mobilize:on site |
Procurement of Long lead items Detailed Planning |
Develop Subcontracts |
A1050 Sitework/Prep A1270 Central Plant EquipmentAreas _____ C,B, D, A & G A1080 Grade Beams Area C,B,D, A, & G A1100 Slab on Grade Areas C,B,D,A,& G A1120 Steel Erection Areas C,B,D,A, & G A1150 Exterior Framing Areas C,B,D,A, & G A1170 Exterior Facade Finishes Areas C,B,D,A, & G A1180 Roofing Areas C,B,D,A,& G A1160 Interior Framing/Parti on Walls A1190 WIEP Rough ins A1200 Drywall |
161 8-15-08 |
30 8-15-08 |
60 1-9-09 |
341 8-26-08 |
30 8-26-08 |
60 9-16-08 |
85 9-36-08 |
90 11-4-08 |
220 12-16-08 |
90 1-9-09 |
60 2-6-09 |
120 2-20-09 |
SO 5-15-09 |
4-2-09 |
9-25-08 |
4-2-09 |
12-24-09 10-6-08 12-8-08 |
1-8-09 |
3-9-09 |
10-19-09 |
5-14-09 4-30-09 8-6-09 9-17-09 |
Sitework/Prep |
Central Plant Equipment ..::.’• |
Grade E |
earns Area C,B,D, A, &G^: : :: : :• ‘. |
Slab on Grade Areas:C,B:,D,A,&G‘:’:’•’,’,’.’• |
Steel Erection Areas C,B,D,A, & G::• _____ .. Exterior Framing Areas C,B,D,A, & G ; |
Exterior; Facade Finishes / Roofing Areas C;B,D,A,&:G : : : : |
Interior Frarning/Partion Walls :: MEP Rough ins : : Drywall : : : |

Aditfity;tD.:::w Activity-Name^^y:...••^.-;-•:;:•::.;.v:::-::-;:\; ^••:•:Wi ±MiE~M^MM ^’ ;^’s:-:^ - -••-•-..•:•’:. Original :Start:::^: ::.v; Finishsa;‘•••’:•:•• ‘i-’-W-i—:M ;;::^’:7.^l<::;::^ iburatibh$;^:i$£$.•&Z&t2: —Wjjjjjij£ii[jjj^ — A1280 Ceilings 100 6-12-09 10-29-09 A1290\:^ ^ “^^T Millwork 1 00: 7-10-09 Tf-26-09 — A1300 Flooring 80 8-21-09 12-10-09 |
A1310 Trim Out 90 ; 8-2 1-09 ‘” 1 2-24-09 ~” — : A1490 FFE install 25 11-20-09 12-24-09 : , _____ , . : ^»*f:FE install. _____ .. : ; ^^“Clean/Punch : . :• ‘::::’• H*turn over to Owr^^mGrade Beams Areas U, V, &W••••’!.;.• —; A1330 Clean/Punch 15 12-4-09 12-24-09 |
— ; A1500 Turn over to Owner 1 12-24-09 12-24-09 |
— Areas U, V, & W3031°-7~08 : 12-1 1-09 — : A1090 Grade Beams Areas U,V, &W . 2510-7-08 i 11-10-08 — A1110 Slab on Grade Areas U, V, & W : 4510-28-08 12-29-08 ^*-^^^S Slab o;n Grade Areas U, V, ‘&W :: : *^M Steel Erection Areas:U, V, &W: : : : \: ^^»^^^»^ Exterior Framing Areas U,V,&W : |
— A1 1 30 Steel Erection Areas U , V, & W 3012-9-08 1-14-09 |
— A1210 Exterior Framing Areas U.V.&W 90 1-5-09 5-8-09 |
^*-f|PPp^^^ Ronfing Arpas U V, A W : |
A1230 Roofing Areas U, V, & W 75 1-15-09 4-29-09 |
A 1 220 Exterior Facade Finishes Areas U . V. & W 2002-16-09 11-20-09 |
— A1340 Interior F ram ing/Pa rtion Walis 60 4-20-09 7-10-09:: Interior Framing/Psrtion\NMK: —; ‘ : :• ; ; ; MEP Rough ins ;: A1350 MEP Rough ins 90 5-4-09 9-4-09 |
— A1360 Drywall 1006-1-09 10-16-09 |
: : ‘. : ;:rpilim,• : ; A1370 Ceilings 100 6-29-09 11-13-09 |
: : | ;:^^^^-M^; ; ; A1380 Millwork 90 7-27-09 11-27-09 |
— A1390 Flooring 90 8-10-09 12-11-09; ^: ^ ‘ : : ! — A1400 Trim Out 90 8-10-09 : 12-1 1-09 :’:;::::,;:: ; _____ ^W;iean/Puncn.’:’.’•’.: : : : : : *^ FFE Install ; : : : ; return. over to owner A1510 Clean/Punch 20 11-16-09 12-11-09 |
— A1530 FFE Install 2011-16-09 12-11-09 |
— A1520 Turn over to owner 1 12-11-09 12-11-09 |
— New Gaming Space 367 8-22-08 1-30-10 |
— 2 |
— |
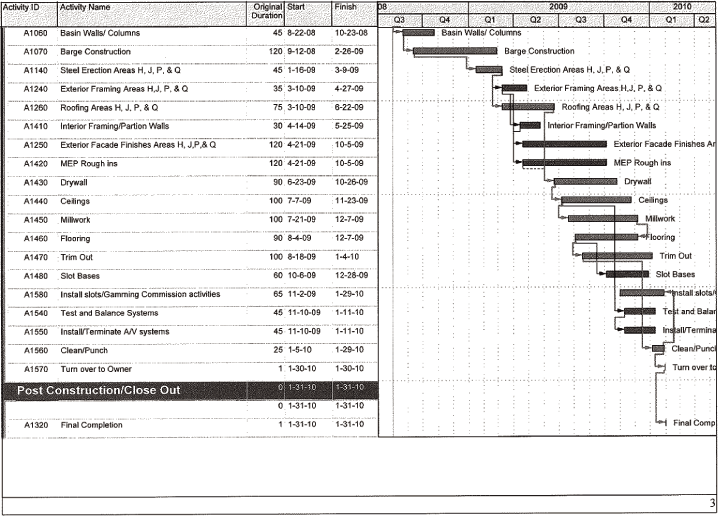
Activity ID .;:;;;::’; ‘Activity -Nairns^^:-y^:;:^>^:Starts-• -;:;;-::- ^SB:::;P.*M%:y::S-^’^^•••M.ff/K:^-:/prtginal _____ finishj^?>. — ‘/.••’ ;:••-.’•• .’-.•: :• ;’ v:;:.-:.:-"-!K’/^’-:- ^•imrn^f-::®:.y^x|;^^^^^^^j^i^j^^^^^^^^j^^^^j^jj^^•:.:•••:••• ::• -:•:[f;v‘:-.:f :•£’.: ‘•^•’••-.•’•,;•••:’•’ ••.: |
•;.’.^:K:^ A-’:;v;: .’••• .•.Duration —— —— — |
A1060 Basin Walls/ Columns 45 8-22-08 10-23-08.Basin Walls/ Columns••........................................................................................................................................... j™~: ::::::: : :::;-;:: |
—— —— — |
A1070 Barge Construction 120 9-12-08 2-26-09 Kargc(;on<;tnjrTinn — A1140 Steel Erection Areas H, J, P, & Q 45 1-16-09 3-9-09\ . ‘.: Steel Erection Areas H, J,P, &Q‘.’.’... —— — |
A1240 Exterior Framing Areas H,J, P, & O 35 3-10-09 4-27-09••*ym^m. Exterior Framing Areas. H,J, P, & Q . —— —— — |
A1260 Roofing Areas H, J, P, & Q 75 3-10-09 6-22-09 Roofing Areas H, .1, P, ^ O — A1410 Interior Framing/Partion Walls 30 4-14-09 : 5-25-09 :• ‘ ‘: ‘-fc^fc interior Framing/Parlion Wails ‘ ‘ j . : ::::.. —— —— — |
A1250 Exterior Facade Finishes Areas H, J,P,& Q. 120 4-21-09: 10-5-09• Exterior Facade Finishes Ar —— — |
A1420 MEP Rough ins 120 4-21-09 ; 10-5-09 ;.:.::;:.: I :::,::; —— —— — |
A1430 Drywall 90 6-23-09 10-26-09 Drywslt —r ...,:=. , _____ , ^5 ,..,,,.. , . |
— A1440 Ceilings 100 7-7-09 11-23-09 i . , . . r,pi?ings — i :::...:::: f . 1 . . : : : . |
— : A1450 Millwork 7-21-09 12-7-09iMillwork• 100 — A1460 Flooring 90 8-4-09 12-7-09 SSKW-ssHnorinq — A1470 Trim Out 100 8-18-09 1-4-10 ::;.::::::: Trim Out : |
—J i ‘• — A1480 SlotSases 60 10-6-09 12-28-09 |
— A1 580 Install slots/Gamming Commission activities 65 11-2-09 1-29-10 ^^^^^^^^tnstairslots/1 —: A1540 Test and Balance Systems 11-10-09 1-11-10;:: ; :: : : : :• tekiand: |
: 45 Balar —— — |
A1550 Install/Terminate A/V systems 45 11-10-09 1-11-10 i :;:!:•:::::: ; Inslall/Tarmins —— — |
A1560 Clean/Punch 25 A 1570 1-5-10 .1-29-10 1-30-10 j ; :::::: ::::::;: ^-rf^Clean/PuncI Turn over to Owner 1 1-30-10• z3 ^"urn °ver^c —— — |
: ‘: ‘:• ‘ ‘ ‘ ‘: 1-31-10 1-31-10 1-31-10 i.• ‘ .: j . ‘ ; i .: ‘:::::’:::: |
0 A1320 Final Completion 1 1-31-10 “*H Final Comp —— —— — |
CONTRACTOR’S PERSONNEL
* | Rates to be provide to Owner by separate document |
CONTRACTOR OWNED EQUIPMENT
Monthly | ||||
Rental Rate | ||||
based on 50 | ||||
hrs /Week for | ||||
Yates/Paric | ||||
Owned | ||||
Equipment | Equipment | |||
Forklifts | ||||
Wharehouse Forklift 8000# | $ | 1,179.52 | ||
Forklift 11,000 lbs TH580B | $ | 5,623.15 | ||
Forklift 6,000 lbs TH330B | $ | 4,023.21 | ||
Lull 10,000# 1044-C-54 | $ | 5,897.60 | ||
Lull 6,000# 644E-42 | $ | 4,747.27 | ||
Skytrak 6042 6000# | $ | 4,513.71 | ||
Skytrak 10042 10000# | $ | 5,319.52 | ||
Backhoe/Loaders | ||||
Backhoe 4wd 416E cat | $ | 2,840.28 | ||
Backhoe 2wd 416D cat | $ | 2,671.89 | ||
Backhoe 2wd Case 580M | $ | 3,003.07 | ||
Backhoe 4wd Case 580M | $ | 3,132.17 | ||
Backhoe 2wd John Deere 310G | $ | 2,784.15 | ||
Backhoe 4wd John Deere 310G | $ | 3,003.07 | ||
Tower Cranes SK415/405 | $ | 17,713.07 | ||
Personnel Hoists Alimak 650Dual | $ | 10,994.32 | ||
Trucks | ||||
Pickup Trucks 1/2 ton | $ | 735.00 | ||
Pickup Trucks 3/4 ton | $ | 825.00 | ||
Pickup truck 1/2 ton 4x4 | $ | 768.49 | ||
Water Tanker 3,000 gal | $ | 2,496.15 | ||
Hwy Truck Tractors 6x4 50,000# | $ | 3,906.01 | ||
On Highway rer dump 6x4 8-10CY | $ | 3,865.57 | ||
Excavators (Large) | ||||
Cat 312 | $ | 6,352.08 | ||
Cat 320 | $ | 8,492.45 | ||
Cat 330 | $ | 13,952.71 | ||
Cat 345 | $ | 22,111.44 | ||
JD120C | $ | 6,599.49 | ||
JD200LC | $ | 8,573.00 | ||
JD330C | $ | 12,807.72 | ||
JD450LC | $ | 18,532.65 | ||
Komatsu PC120 | $ | 5,935.51 | ||
Komatsu PC200 | $ | 7,681.18 | ||
Excavators (Mini) | ||||
Bobcat 335 | $ | 2,186.40 | ||
Bobcat 430 | $ | 1,933.24 | ||
Komatsu PC35 | $ | 1,783.64 | ||
Komatsu PC50 | $ | 2,686.97 | ||
Bulldozers | ||||
Cat D4 | $ | 4,872.27 | ||
Cat D5 | $ | 5,444.81 | ||
Cat D6R | $ | 7,993.21 |
1
Monthly | ||||
Rental Rate | ||||
based on 50 | ||||
hrs /Week for | ||||
Yates/Paric | ||||
Owned | ||||
Equipment | Equipment | |||
Skidsteer | ||||
Cat 247B | $ | 2,699.95 | ||
Cat 257B | $ | 2,924.48 | ||
Cat 277B | $ | 3,525.10 | ||
Wheel Loader | ||||
Cat 914G | $ | 2,907.64 | ||
Cat 924G | $ | 3,856.28 | ||
Cat 928GZ | $ | 4,518.63 | ||
Cat 930G | $ | 4,872.27 | ||
Cat 950H | $ | 7,521.70 | ||
Cat 966H | $ | 9,929.77 | ||
Manlifts | ||||
Genie-S40 | $ | 3,693.87 | ||
Genie-S45 | $ | 4,315.27 | ||
Genie-S60 | $ | 5,466.01 | ||
Genie-S80 | $ | 8,072.43 | ||
JLG400S | $ | 3,636.33 | ||
JLG600S | $ | 5,575.33 | ||
JLG800S | $ | 7,859.54 | ||
Genie Z-30 | $ | 2,295.72 | ||
Genie Z-45 | $ | 2,583.41 | ||
Scissor lifts | ||||
21' to 30' | $ | 978.13 | ||
31' & up | $ | 1,478.70 | ||
to 20' | $ | 678.94 | ||
Air Compressors | ||||
185CFM diesel | $ | 772.94 | ||
Light Towers | ||||
portable diesel 20' | $ | 916.19 | ||
portable diesel 30' | $ | 1,398.72 | ||
Broce Broom | ||||
RC-350 | $ | 1,744.54 | ||
Georgia Buggies | ||||
10cu ft walk behind | $ | 685.92 | ||
14cu ft walk behind | $ | 786.30 | ||
16cu ft ride on | $ | 1,042.82 | ||
33 cu ft ride on | $ | 2,275.24 | ||
Smooth Drum Roller | ||||
433 Cat | $ | 4,062.77 | ||
563 Cat | $ | 6,170.01 | ||
433 Cat Sheepsfoot | $ | 3,972.86 | ||
563 Cat Sheepsfoot | $ | 5,619.32 | ||
Mule/ATV | $ | 439.77 | ||
Welding Machine |
2
Monthly | ||||
Rental Rate | ||||
based on 50 | ||||
hrs /Week for | ||||
Yates/Paric | ||||
Owned | ||||
Equipment | Equipment | |||
300 amp skid mounted | $ | 322.84 | ||
500 amp trailer mounted | $ | 493.06 | ||
Storage Containers/Trailers | ||||
8x32 conex type | $ | 201.13 | ||
40' float trailer | $ | 1,190.50 | ||
16' utility trailers | $ | 282.68 | ||
gooseneck 20t | $ | 701.25 | ||
12x60 office trailer | $ | 450.00 | ||
Pumps | ||||
3" trash pumps | $ | 791.88 | ||
4" trash pumps | $ | 1,005.91 | ||
6" trash pumps | $ | 1,455.35 | ||
Marine | ||||
Work barges 20x10 | $ | 717.71 | ||
Work barges 40x10 | $ | 1,132.63 | ||
140' Barge | $ | 16,557.77 | ||
160' Barge | $ | 18,963.22 | ||
200' Barge | $ | 30,384.89 | ||
16' runabouts | $ | 633.60 | ||
14' tenders | $ | 2,467.13 |
3
LIST OF DRAWINGS
ARCHITECTS• PLANNERS
TEL 702.940.0000• FAX 702.940.0001
BULLETIN F: 15-JUN-08 | ||
RIVER CITY CASINO, St. Louis, Missouri• Project No. 141005 | ADDENDUM 1: 16-JUN-08 |
1 | F | |||||||||||||||
SHEET | ISSUED FOR | ISSUED FOR | ||||||||||||||
NUMBER | SHEET TITLES | CONSTRUCTION | PLAN CHECK | |||||||||||||
REVISION | SHEET # | SHEET TITLES | 16-Jun-08 | 15-Jun-08 | ||||||||||||
ARCHITECTURAL SHEETS | 279 | 279 | ||||||||||||||
CIVIL SHEETS | 69 | 69 | ||||||||||||||
STRUCTURAL SHEETS | 134 | 134 | ||||||||||||||
MECHANICAL SHEETS | 32 | 32 | ||||||||||||||
PLUMBING SHEETS | 33 | 33 | ||||||||||||||
ELECTRICAL SHEETS | 88 | 88 | ||||||||||||||
LIGHTING SHEETS | 42 | 42 | ||||||||||||||
LOW VOLTAGE SHEETS | 69 | 69 | ||||||||||||||
FOOD SERVICE SHEETS | 102 | 102 | ||||||||||||||
INTERIOR DESIGN SHEETS | 196 | 196 | ||||||||||||||
LANDSCAPE SHEETS | 111 | 111 | ||||||||||||||
NAVAL ARCHITECT SHEETS | 30 | 30 | ||||||||||||||
TOTAL ALL SHEETS | 1185 | 1185 | ||||||||||||||
SUMMARY | 1 of 54 | 6/19/2008 10:14 AM |
ARCHITECTS• PLANNERS
TEL 702.940.0000• FAX 702.940.0001
BULLETIN F: 15-JUN-08 | ||
RIVER CITY CASINO, St. Louis, Missouri• Project No. 141005 | ADDENDUM 1: 16-JUN-08 |
1 | F | ||||||||
SHEET | ISSUED FOR | ISSUED FOR | |||||||
NUMBER | SHEET TITLES | CONSTRUCTION | PLAN CHECK | ||||||
ARCHITECTURAL | 16-Jun-08 | 15-Jun-08 | |||||||
REVISION | SHEET # | SHEET TITLES | |||||||
A0.0.0 | COVER SHEET | X | X | ||||||
A0.1.1 | SHEET INDEX 1ST SHEET | X | X | ||||||
A0.1.2 | SHEET INDEX 2ND SHEET | X | X | ||||||
A0.2.1 | PROJECT DATA, GEN NOTES, SYMBOL LEGEND & ABBREV | X | X | ||||||
A0.3.1 | ADA INFORMATION | X | X | ||||||
A0.3.2 | ADA INFORMATION | X | X | ||||||
A0.3.3 | ADA INFORMATION | X | X | ||||||
A0.3.4 | ADA INFORMATION | X | X | ||||||
A0.3.5 | ADA INFORMATION | X | X | ||||||
A0.3.6 | ADA INFORMATION | X | X | ||||||
A1.1.1 | SITE PLAN | X | X | ||||||
A1.1.11A | LIFE SAFETY PLAN CASINO LEVEL | X | X | ||||||
A1.1.11B | LIFE SAFETY PLAN CASINO LEVEL | X | X | ||||||
A1.1.12 | LIFE SAFETY PLAN SECOND LEVEL | X | X | ||||||
A1.2.0 | MASTER PLAN — BASIN LEVEL | X | X | ||||||
A1.2.1 | MASTER PLAN — CASINO LEVEL | X | X | ||||||
A1.2.2 | MASTER PLAN — SECOND LEVEL | X | X | ||||||
A1.3.1 | MASTER PLAN — ROOF LEVEL | X | X | ||||||
A2.1.1A | CASINO LEVEL PLAN — AREA A | X | X | ||||||
A2.1.1B | CASINO LEVEL PLAN — AREA B | X | X | ||||||
A2.1.1C | CASINO LEVEL PLAN — AREA C | X | X | ||||||
A2.1.1D | CASINO LEVEL PLAN — AREA D | X | X | ||||||
A2.1.1G | CASINO LEVEL PLAN — AREA G | X | X | ||||||
A2.1.1H | CASINO LEVEL PLAN — AREA H | X | X |
ARCHITECTURAL | 2 of 54 | 6/19/2008 10:14 AM |
ARCHITECTS• PLANNERS
TEL 702.940.0000• FAX 702.940.0001
BULLETIN F: 15-JUN-08 | ||
RIVER CITY CASINO, St. Louis, Missouri• Project No. 141005 | ADDENDUM 1: 16-JUN-08 |
1 | F | ||||||||
SHEET | ISSUED FOR | ISSUED FOR | |||||||
NUMBER | SHEET TITLES | CONSTRUCTION | PLAN CHECK | ||||||
ARCHITECTURAL | 16-Jun-08 | 15-Jun-08 | |||||||
REVISION | SHEET # | SHEET TITLES | |||||||
A2.1.1J | CASINO LEVEL PLAN — AREA J | X | X | ||||||
A2.1.1P | CASINO LEVEL PLAN — AREA P | X | X | ||||||
A2.1.1Q | CASINO LEVEL PLAN — AREA Q | X | X | ||||||
A2.1.1U | CASINO LEVEL PLAN — AREA U | X | X | ||||||
A2.1.1V | CASINO LEVEL PLAN — AREA V | X | X | ||||||
A2.1.1W | CASINO LEVEL PLAN — AREA W | X | X | ||||||
A2.1.2A | SECOND LEVEL PLAN — AREA A | X | X | ||||||
A2.1.2B | SECOND LEVEL PLAN — AREA B | X | X | ||||||
A2.1.2C | SECOND LEVEL PLAN — AREA C | X | X | ||||||
A2.1.2D | SECOND LEVEL PLAN — AREA D | X | X | ||||||
A2.5.1 | ROOF PLAN — AREA R1 | X | X | ||||||
A2.5.2 | ROOF PLAN — AREA R2 | X | X | ||||||
A2.5.3 | ROOF PLAN — AREA R3 | X | X | ||||||
A2.5.4 | ROOF PLAN — AREA R4 | X | X | ||||||
A2.6.1.1 | CASINO LEVEL — SLAB PLAN — AREA S1 | X | X | ||||||
A2.6.1.2 | CASINO LEVEL — SLAB PLAN — AREA S2 | X | X | ||||||
A2.6.1.3 | CASINO LEVEL — SLAB PLAN — AREA S3 | X | X | ||||||
A2.6.1.4 | CASINO LEVEL — SLAB PLAN — AREA S4 | X | X | ||||||
A2.6.2.1 | SECOND LEVEL — SLAB PLAN — AREA S1 | X | X | ||||||
A2.6.2.2 | SECOND LEVEL — SLAB PLAN — AREA S2 | X | X | ||||||
A2.6.3.1 | MAIN ROOF LEVEL SLAB PLAN AREA S1 | X | X | ||||||
A2.6.3.2 | MAIN ROOF LEVEL SLAB PLAN AREA S2 | X | X | ||||||
A2.6.3.3 | MAIN ROOF LEVEL SLAB PLAN AREA S3 | X | X | ||||||
A2.6.3.4 | MAIN ROOF LEVEL SLAB PLAN AREA S4 | X | X | ||||||
A2.6.4.1 | HIGH ROOF LEVEL SLAB PLANS | X | X | ||||||
A2.6.5.1 | CASINO LEVEL — SLAB PLAN — AREA S4 | X | X | ||||||
A2.6.5.2 | CASINO LEVEL — SLAB PLAN — AREA S1 | X | X |
ARCHITECTURAL | 3 of 54 | 6/19/2008 10:14 AM |
ARCHITECTS• PLANNERS
TEL 702.940.0000• FAX 702.940.0001
BULLETIN F: 15-JUN-08 | ||
RIVER CITY CASINO, St. Louis, Missouri• Project No. 141005 | ADDENDUM 1: 16-JUN-08 |
1 | F | ||||||||
SHEET | ISSUED FOR | ISSUED FOR | |||||||
NUMBER | SHEET TITLES | CONSTRUCTION | PLAN CHECK | ||||||
ARCHITECTURAL | 16-Jun-08 | 15-Jun-08 | |||||||
REVISION | SHEET # | SHEET TITLES | |||||||
A3.1.1 | OVERALL EXTERIOR ELEVATIONS | X | X | ||||||
A3.2.1 | EXTERIOR ELEVATION — NORTH | X | X | ||||||
A3.2.2 | EXTERIOR ELEVATION — EAST | X | X | ||||||
A3.2.3 | EXTERIOR ELEVATION — SOUTH | X | X | ||||||
A3.2.4 | EXTERIOR ELEVATION — WEST | X | X | ||||||
A3.2.5 | EXTERIOR ELEVATIONS | X | X | ||||||
A3.2.6 | EXTERIOR ELEVATIONS | X | X | ||||||
A3.3.1.1 | FACADE ELEVATION — F.D. KITCHEN | X | X | ||||||
A3.3.1.2 | FACADE ELEVATIONS — F.D. KITCHEN | X | X | ||||||
A3.3.1.3 | FACADE ELEVATIONS — F.D. KITCHEN | X | X | ||||||
A3.3.1.11 | FACADE PLANS — F.D. KITCHEN | X | X | ||||||
A3.3.1.12 | FACADE PLANS — F.D. KITCHEN | X | X | ||||||
A3.3.1.21 | WALL SECTIONS | X | X | ||||||
A3.3.1.22 | WALL SECTIONS | X | X | ||||||
A3.3.2.1 | FACADE ELEVATIONS — FINE DINING | X | X | ||||||
A3.3.2.2 | FACADE ELEVATION — FINE DINING | X | X | ||||||
A3.3.2.3 | FACADE ELEVATIONS — FINE DINING | X | X | ||||||
A3.3.2.4 | FACADE ELEVATIONS — FINE DINING | X | X | ||||||
A3.3.2.5 | FACADE ELEVATIONS — FINE DINING | X | X | ||||||
A3.3.2.11 | FACADE PLAN — FINE DINING | X | X | ||||||
A3.3.2.12 | FACADE PLAN — FINE DINING | X | X | ||||||
A3.3.2.13 | FACADE PLAN — FINE DINING | X | X | ||||||
A3.3.2.14 | FACADE PLAN — FINE DINING | X | X | ||||||
A3.3.2.21 | WALL SECTIONS | X | X | ||||||
A3.3.2.22 | WALL SECTIONS | X | X | ||||||
A3.3.2.23 | WALL SECTIONS | X | X |
ARCHITECTURAL | 4 of 54 | 6/19/2008 10:14 AM |
ARCHITECTS• PLANNERS
TEL 702.940.0000• FAX 702.940.0001
BULLETIN F: 15-JUN-08 | ||
RIVER CITY CASINO, St. Louis, Missouri• Project No. 141005 | ADDENDUM 1: 16-JUN-08 |
1 | F | ||||||||
SHEET | ISSUED FOR | ISSUED FOR | |||||||
NUMBER | SHEET TITLES | CONSTRUCTION | PLAN CHECK | ||||||
ARCHITECTURAL | 16-Jun-08 | 15-Jun-08 | |||||||
REVISION | SHEET # | SHEET TITLES | |||||||
A3.3.2.24 | WALL SECTIONS | X | X | ||||||
A3.3.2.25 | WALL SECTIONS | X | X | ||||||
A3.3.3.1 | FACADE ELEVATION — NORTH ENTRANCE EAST SIDE | X | X | ||||||
A3.3.3.11 | FACADE PLANS — NORTH ENTRANCE EAST SIDE | X | X | ||||||
A3.3.3.21 | WALL SECTIONS | X | X | ||||||
A3.3.4.1 | FACADE ELEVATIONS — NORTH ENTRANCE | X | X | ||||||
A3.3.4.2 | FACADE ELEVATIONS — NORTH ENTRANCE | X | X | ||||||
A3.3.4.11 | FACADE PLANS — NORTH ENTRANCE | X | X | ||||||
A3.3.4.21 | WALL SECTIONS | X | X | ||||||
A3.3.4.22 | WALL SECTIONS | X | X | ||||||
A3.3.5.1 | FACADE ELEVATION — NORTH ENTRANCE WEST SIDE | X | X | ||||||
A3.3.5.11 | FACADE PLANS — NORTH ENTRANCE WEST SIDE | X | X | ||||||
A3.3.5.21 | WALL SECTIONS | X | X | ||||||
A3.3.7.1 | FACADE ELEVATIONS — BUFFET | X | X | ||||||
A3.3.7.2 | FACADE ELEVATIONS — BUFFET | X | X | ||||||
A3.3.7.3 | FACADE ELEVATION — BUFFET | X | X | ||||||
A3.3.7.4 | FACADE ELEVATION — BUFFET | X | X | ||||||
A3.3.7.5 | FACADE ELEVATION — BUFFET | X | X | ||||||
A3.3.7.11 | FACADE PLANS — BUFFET | X | X | ||||||
A3.3.7.12 | FACADE PLANS — BUFFET | X | X | ||||||
A3.3.7.13 | FACADE PLANS — BUFFET | X | X | ||||||
A3.3.7.14 | FACADE PLANS — BUFFET | X | X | ||||||
A3.3.7.21 | WALL SECTIONS | X | X | ||||||
A3.3.7.22 | WALL SECTIONS | X | X | ||||||
A3.3.8.1 | FACADE ELEVATION — BUFFET KITCHEN | X | X |
ARCHITECTURAL | 5 of 54 | 6/19/2008 10:14 AM |
ARCHITECTS• PLANNERS
TEL 702.940.0000• FAX 702.940.0001
BULLETIN F: 15-JUN-08 | ||
RIVER CITY CASINO, St. Louis, Missouri• Project No. 141005 | ADDENDUM 1: 16-JUN-08 |
1 | F | ||||||||
SHEET | ISSUED FOR | ISSUED FOR | |||||||
NUMBER | SHEET TITLES | CONSTRUCTION | PLAN CHECK | ||||||
ARCHITECTURAL | 16-Jun-08 | 15-Jun-08 | |||||||
REVISION | SHEET # | SHEET TITLES | |||||||
A3.3.8.2 | FACADE ELEVATION — BUFFET | X | X | ||||||
A3.3.8.3 | FACADE ELEVATION — EDR | X | X | ||||||
A3.3.8.11 | FACADE PLANS — BUFFET KITCHEN | X | X | ||||||
A3.3.8.12 | FACADE PLANS — BUFFET KITCHEN | X | X | ||||||
A3.3.8.13 | FACADE PLANS — EDR | X | X | ||||||
A3.3.8.21 | WALL SECTIONS | X | X | ||||||
A3.3.10 | FACADE ELEVATION — WINDOW TYPES — NORTH | X | X | ||||||
A3.3.11 | FACADE ELEVATION — WINDOW TYPES — NORTH | X | X | ||||||
A3.3.20 | FACADE ELEVATION — DETAILS — NORTH | X | X | ||||||
A3.3.21 | FACADE ELEVATION — DETAILS — NORTH | X | X | ||||||
A3.3.22 | FACADE ELEVATION — DETAILS — NORTH | X | X | ||||||
A3.4.1.1 | FACADE ELEVATION — PROMENADE | X | X | ||||||
A3.4.1.2 | FACADE ELEVATION — PROMENADE | X | X | ||||||
A3.4.1.11 | FACADE PLANS — PROMENADE | X | X | ||||||
A3.4.1.12 | FACADE PLANS — PROMENADE | X | X | ||||||
A3.4.1.13 | FACADE PLANS — PROMENADE | X | X | ||||||
A3.4.1.21 | WALL SECTIONS | X | X | ||||||
A3.4.1.22 | WALL SECTIONS | X | X | ||||||
A3.4.2.1 | FACADE ELEVATION — CASINO | X | X | ||||||
A3.4.2.2 | FACADE ELEVATION — CASINO | X | X | ||||||
A3.4.2. 3 | FACADE ELEVATION — CASINO | X | X | ||||||
A3.4.2.11 | FACADE PLANS — CASINO | X | X | ||||||
A3.4.2.12 | FACADE PLANS — CASINO | X | X | ||||||
A3.4.2.13 | FACADE PLANS — CASINO | X | X | ||||||
A3.4.2.14 | FACADE PLANS — CASINO | X | X | ||||||
A3.4.2.15 | FACADE PLANS — CASINO | X | X | ||||||
A3.4.2.16 | FACADE PLANS — CASINO | X | X |
ARCHITECTURAL | 6 of 54 | 6/19/2008 10:14 AM |
ARCHITECTS• PLANNERS
TEL 702.940.0000• FAX 702.940.0001
BULLETIN F: 15-JUN-08 | ||
RIVER CITY CASINO, St. Louis, Missouri• Project No. 141005 | ADDENDUM 1: 16-JUN-08 |
1 | F | ||||||||
SHEET | ISSUED FOR | ISSUED FOR | |||||||
NUMBER | SHEET TITLES | CONSTRUCTION | PLAN CHECK | ||||||
ARCHITECTURAL | 16-Jun-08 | 15-Jun-08 | |||||||
REVISION | SHEET # | SHEET TITLES | |||||||
A3.4.2.17 | FACADE PLANS — CASINO | X | X | ||||||
A3.4.2.21 | WALL SECTIONS | X | X | ||||||
A3.4.3.1 | FACADE ELEVATION — LOBBY | X | X | ||||||
A3.4.3.2 | FACADE ELEVATION — LOBBY | X | X | ||||||
A3.4.3.11 | FACADE PLANS — LOBBY | X | X | ||||||
A3.4.3.12 | FACADE PLANS — LOBBY | X | X | ||||||
A3.4.3.21 | WALL SECTIONS | X | X | ||||||
A3.4.3.22 | WALL SECTIONS | X | X | ||||||
A3.4.3.23 | WALL SECTIONS | X | X | ||||||
A3.4.4.1 | FACADE ELEVATION — PORTE COCHERE | X | X | ||||||
A3.4.4.2 | FACADE ELEVATION — PORTE COCHERE | X | X | ||||||
A3.4.4.3 | FACADE ELEVATION — PORTE COCHERE | X | X | ||||||
A3.4.4.4 | FACADE ELEVATION — PORTE COCHERE | X | X | ||||||
A3.4.4.5 | FACADE ELEVATIONS — PORTE COCHERE | X | X | ||||||
A3.4.4.6 | FACADE PARTIAL SECTIONS — PORTE COCHERE | X | X | ||||||
A3.4.4.11 | FACADE PLANS — PORTE COCHERE | X | X | ||||||
A3.4.4.12 | FACADE PLANS — PORTE COCHERE | X | X | ||||||
A3.4.4.13 | FACADE PLANS — PORTE COCHERE | X | X | ||||||
A3.4.4.14 | FACADE PLANS — PORTE COCHERE | X | X | ||||||
A3.4.4.15 | FACADE PLANS — PORTE COCHERE | X | X | ||||||
A3.4.4.16 | FACADE PLANS — PORTE COCHERE | X | X | ||||||
A3.4.10 | FACADE ELEVATION — WINDOW TYPES — EAST | X | X | ||||||
A3.4.11 | FACADE ELEVATION — WINDOW TYPES — EAST | X | X | ||||||
A3.4.20 | FACADE ELEVATION — DETAILS — EAST | X | X | ||||||
A3.4.21 | FACADE ELEVATION — DETAILS — EAST | X | X | ||||||
A3.5.1.1 | FACADE ELEVATION — EMPLOYEE ENTRANCE | X | X |
ARCHITECTURAL | 7 of 54 | 6/19/2008 10:14 AM |
ARCHITECTS• PLANNERS
TEL 702.940.0000• FAX 702.940.0001
BULLETIN F: 15-JUN-08 | ||
RIVER CITY CASINO, St. Louis, Missouri• Project No. 141005 | ADDENDUM 1: 16-JUN-08 |
1 | F | ||||||||
SHEET | ISSUED FOR | ISSUED FOR | |||||||
NUMBER | SHEET TITLES | CONSTRUCTION | PLAN CHECK | ||||||
ARCHITECTURAL | 16-Jun-08 | 15-Jun-08 | |||||||
REVISION | SHEET # | SHEET TITLES | |||||||
A3.5.1.11 | FACADE PLANS — EMPLOYEE ENTRANCE | X | X | ||||||
A3.5.1.21 | WALL SECTIONS | X | X | ||||||
A3.5.1.22 | WALL SECTIONS | X | X | ||||||
A3.5.2.1 | FACADE ELEVATION — EMPLOYEE ENTRANCE | X | X | ||||||
A3.5.2.2 | FACADE ELEVATIONS — SOUTH ENTRANCE | X | X | ||||||
A3.5.2.11 | FACADE PLANS — EMPLOYEE ENTRANCE | X | X | ||||||
A3.5.2.21 | WALL SECTIONS | X | X | ||||||
A3.5.2.22 | WALL SECTIONS | X | X | ||||||
A3.5.3.1 | FACADE ELEVATION — SOUTH ENTRANCE | X | X | ||||||
A3.5.3.2 | FACADE ELEVATION — SOUTH ENTRANCE | X | X | ||||||
A3.5.3.11 | FACADE PLANS — SOUTH ENTRANCE | X | X | ||||||
A3.5.3.12 | FACADE PLANS — SOUTH ENTRANCE | X | X | ||||||
A3.5.3.21 | WALL SECTIONS | X | X | ||||||
A3.5.3.22 | WALL SECTIONS | X | X | ||||||
A3.5.10 | FACADE ELEVATION — WINDOW TYPES — SOUTH | X | X | ||||||
A3.5.20 | FACADE ELEVATION — DETAILS — SOUTH | X | X | ||||||
A3.5.21 | FACADE ELEVATION — DETAILS — SOUTH | X | X | ||||||
A3.6.1.1 | FACADE ELEVATION — CP/DOCK | X | X | ||||||
A3.6.1.2 | FACADE ELEVATION — CP/DOCK | X | X | ||||||
A3.6.1.3 | FACADE ELEVATION — CP/DOCK | X | X | ||||||
A3.6.1.4 | FACADE ELEVATION — CP/DOCK | X | X | ||||||
A3.6.1.21 | WALL SECTIONS | X | X | ||||||
A3.6.1.22 | WALL SECTIONS | X | X | ||||||
A3.6.1.23 | WALL SECTIONS | X | X | ||||||
A3.6.2.1 | FACADE ELEVATION — WEST SIDE | X | X |
ARCHITECTURAL | 8 of 54 | 6/19/2008 10:14 AM |
ARCHITECTS• PLANNERS
TEL 702.940.0000• FAX 702.940.0001
BULLETIN F: 15-JUN-08 | ||
RIVER CITY CASINO, St. Louis, Missouri• Project No. 141005 | ADDENDUM 1: 16-JUN-08 |
1 | F | ||||||||
SHEET | ISSUED FOR | ISSUED FOR | |||||||
NUMBER | SHEET TITLES | CONSTRUCTION | PLAN CHECK | ||||||
ARCHITECTURAL | 16-Jun-08 | 15-Jun-08 | |||||||
REVISION | SHEET # | SHEET TITLES | |||||||
A3.6.2.2 | FACADE ELEVATION — WEST SIDE | X | X | ||||||
A3.6.2.21 | WALL SECTIONS | X | X | ||||||
A3.6.3.1 | FACADE ELEVATION — WEST SIDE | X | X | ||||||
A3.6.3.21 | WALL SECTIONS | X | X | ||||||
A3.6.4.1 | FACADE ELEVATION — WEST SIDE | X | X | ||||||
A3.6.4.2 | FACADE ELEVATION — WEST SIDE | X | X | ||||||
A3.6.4.21 | WALL SECTIONS | X | X | ||||||
A3.6.20 | FACADE ELEVATION — DETAILS — WEST | X | X | ||||||
A4.1.1 | BUILDING SECTIONS — A & B | X | X | ||||||
A4.1.2 | BUILDING SECTIONS — C & D | X | X | ||||||
A4.1.3 | BUILDING SECTIONS — E & F | X | X | ||||||
A4.1.4 | BUILDING SECTIONS — G & K | X | X | ||||||
A4.1.5 | BUILDING SECTIONS — M | X | X | ||||||
A4.1.6 | BUILDING SECTIONS — L, N, P & Q | X | X | ||||||
A4.1.7 | BUILDING SECTIONS — R, S & T | X | X | ||||||
A4.2.1 | PARTIAL BUILDING SECTIONS | X | X | ||||||
A5.0.1 | MASTER RCP — CASINO LEVEL | X | X | ||||||
A5.0.2 | MASTER RCP — SECOND LEVEL | X | X | ||||||
A5.1.1A | CASINO LEVEL RCP — AREA A | X | X | ||||||
A5.1.1B | CASINO LEVEL RCP — AREA B | X | X | ||||||
A5.1.1C | CASINO LEVEL RCP — AREA C | X | X | ||||||
A5.1.1D | CASINO LEVEL RCP — AREA D | X | X | ||||||
A5.1.1G | CASINO LEVEL RCP — AREA G | X | X |
ARCHITECTURAL | 9 of 54 | 6/19/2008 10:14 AM |
ARCHITECTS• PLANNERS
TEL 702.940.0000• FAX 702.940.0001
BULLETIN F: 15-JUN-08 | ||
RIVER CITY CASINO, St. Louis, Missouri• Project No. 141005 | ADDENDUM 1: 16-JUN-08 |
1 | F | ||||||||
SHEET | ISSUED FOR | ISSUED FOR | |||||||
NUMBER | SHEET TITLES | CONSTRUCTION | PLAN CHECK | ||||||
ARCHITECTURAL | 16-Jun-08 | 15-Jun-08 | |||||||
REVISION | SHEET # | SHEET TITLES | |||||||
A5.1.1H | CASINO LEVEL RCP — AREA H | X | X | ||||||
A5.1.1J | CASINO LEVEL RCP — AREA J | X | X | ||||||
A5.1.1P | CASINO LEVEL RCP — AREA P | X | X | ||||||
A5.1.1Q | CASINO LEVEL RCP — AREA Q | X | X | ||||||
A5.1.1U | CASINO LEVEL RCP — AREA U | X | X | ||||||
A5.1.1V | CASINO LEVEL RCP — AREA V | X | X | ||||||
A5.1.1W | CASINO LEVEL RCP — AREA W | X | X | ||||||
A5.1.2A | SECOND LEVEL RCP — AREA A | X | X | ||||||
A5.1.2B | SECOND LEVEL RCP — AREA B | X | X | ||||||
A5.1.2C | SECOND LEVEL RCP — AREA C | X | X | ||||||
A6.2.1 | ELEVATOR PLANS & SECTIONS | X | X | ||||||
A6.3.1 | ELEVATOR DETAILS | X | X | ||||||
A6.4.1 | STAIR PLANS & SECTIONS | X | X | ||||||
A6.4.2 | STAIR PLANS & SECTIONS | X | X | ||||||
A6.4.3 | STAIR PLANS & SECTIONS | X | X | ||||||
A6.4.4 | STAIR PLANS & SECTIONS | X | X | ||||||
A6.4.5 | STAIR PLANS & SECTIONS | X | X | ||||||
A6.7.1 | STAIR DETAILS | X | X | ||||||
A6.7.2 | STAIR DETAILS | X | X | ||||||
A7.1.0 | TOILET ACCESSORY & FIXTURE MOUNTING HEIGHTS | X | X | ||||||
A7.1.1A | TOILET PLAN, RCP & ELEV — LOUNGE | X | X | ||||||
A7.1.1B | TOILET PLAN, RCP & ELEV — LOUNGE | X | X | ||||||
A7.1.1C | TOILET PLAN, RCP & ELEV — LOUNGE | X | X |
ARCHITECTURAL | 10 of 54 | 6/19/2008 10:14 AM |
ARCHITECTS• PLANNERS
TEL 702.940.0000• FAX 702.940.0001
BULLETIN F: 15-JUN-08 | ||
RIVER CITY CASINO, St. Louis, Missouri• Project No. 141005 | ADDENDUM 1: 16-JUN-08 |
1 | F | ||||||||
SHEET | ISSUED FOR | ISSUED FOR | |||||||
NUMBER | SHEET TITLES | CONSTRUCTION | PLAN CHECK | ||||||
ARCHITECTURAL | 16-Jun-08 | 15-Jun-08 | |||||||
REVISION | SHEET # | SHEET TITLES | |||||||
A7.1.2A | TOILET PLAN, RCP & ELEV — CASINO | X | X | ||||||
A7.1.2B | TOILET PLAN, RCP & ELEV — CASINO | X | X | ||||||
A7.1.2C | TOILET PLAN, RCP & ELEV — CASINO | X | X | ||||||
A7.1.3A | TOILET PLAN, RCP & ELEV — PROMENADE | X | X | ||||||
A7.1.3B | TOILET PLAN, RCP & ELEV — PROMENADE | X | X | ||||||
A7.1.3C | TOILET PLAN, RCP & ELEV — PROMENADE | X | X | ||||||
A7.1.4A | TOILET PLAN, RCP & ELEV — LOBBY | X | X | ||||||
A7.1.4B | TOILET PLAN, RCP & ELEV — LOBBY | X | X | ||||||
A7.1.5A | TOILET PLAN, RCP & ELEV — BUFFET | X | X | ||||||
A7.1.5B | TOILET PLAN, RCP & ELEV — BUFFET | X | X | ||||||
A7.1.6A | TOILET PLAN, RCP & ELEV — STAFF | X | X | ||||||
A7.1.6B | TOILET PLAN, RCP & ELEV — STAFF | X | X | ||||||
A7.1.7A | TOILET PLAN, RCP & ELEV — UNIFORM | X | X | ||||||
A7.1.7B | TOILET PLAN, RCP & ELEV — UNIFORM | X | X | ||||||
A7.1.8A | TOILET PLAN, RCP & ELEV — F.D. KITCHEN & HL | X | X | ||||||
A7.1.9A | TOILET PLAN, RCP & ELEV — UNISEX | X | X | ||||||
A7.1.10A | TOILET PLAN, RCP & ELEV — UNISEX | X | X | ||||||
A7.1.11A | TOILET PLAN, RCP & ELEV — VIP & OFFICES | X | X | ||||||
A7.1.11B | TOILET PLAN, RCP & ELEV — OFFICES | X | X | ||||||
A8.1.1 | EXTERIOR WALL DETAILS | X | X | ||||||
A8.3.1 | SITE & LOADING DOCK DETAILS | X | X | ||||||
A8.5.1 | ROOF DETAILS | X | X | ||||||
A8.5.2 | ROOF DETAILS | X | X | ||||||
A9.1.1 | DOOR TYPES, LEGEND & NOTES | X | X | ||||||
A9.1.11 | DOOR SCHEDULE | X | X | ||||||
A9.1.12 | DOOR SCHEDULE | X | X |
ARCHITECTURAL | 11 of 54 | 6/19/2008 10:14 AM |
ARCHITECTS• PLANNERS
TEL 702.940.0000• FAX 702.940.0001
BULLETIN F: 15-JUN-08 | ||
RIVER CITY CASINO, St. Louis, Missouri• Project No. 141005 | ADDENDUM 1: 16-JUN-08 |
1 | F | ||||||||
SHEET | ISSUED FOR | ISSUED FOR | |||||||
NUMBER | SHEET TITLES | CONSTRUCTION | PLAN CHECK | ||||||
ARCHITECTURAL | 16-Jun-08 | 15-Jun-08 | |||||||
REVISION | SHEET # | SHEET TITLES | |||||||
A9.1.21 | DOOR DETAILS | X | X | ||||||
A9.1.31 | DOOR THRESHOLD DETAILS | X | X | ||||||
A9.2.1 | WINDOW AND LOUVER TYPES, LEGEND & NOTES | X | X | ||||||
A9.2.11 | WINDOW DETAILS | X | X | ||||||
A9.4.1 | FINISH SCHEDULE — BACK-OF-HOUSE | X | X | ||||||
A9.4.2 | FINISH SCHEDULE | X | X | ||||||
A9.5.1 | PARTITION TYPE DETAILS | X | X | ||||||
A9.5.2 | PARTITION TYPE DETAILS | X | X | ||||||
A9.6.1 | PARTITION FRAMING DETAILS | X | X | ||||||
A9.6.2 | PARTITION FRAMING DETAILS | X | X | ||||||
A9.7.1 | MISCELLANEOUS DETAILS | X | X | ||||||
A9.7.2 | MISCELLANEOUS DETAILS | X | X | ||||||
A9.7.3 | COLUMN/BEAM DETAILS | X | X | ||||||
A9.8.1 | CEILING DETAILS | X | X | ||||||
A9.8.2 | CEILING DETAILS | X | X | ||||||
A10.1.1 | MILLWORK ELEVATIONS | X | X | ||||||
A10.1.2 | MILLWORK ELEVATIONS | X | X | ||||||
A10.1.3 | MILLWORK ELEVATIONS | X | X | ||||||
A10.1.4 | MILLWORK ELEVATIONS | X | X | ||||||
A10.1.5 | MILLWORK ELEVATIONS | X | X | ||||||
A10.1.6 | MILLWORK ELEVATIONS | X | X | ||||||
A10.1.7 | MILLWORK ELEVATIONS | X | X | ||||||
A10.1.8 | MILLWORK ELEVATIONS | X | X |
ARCHITECTURAL | 12 of 54 | 6/19/2008 10:14 AM |
ARCHITECTS• PLANNERS
TEL 702.940.0000• FAX 702.940.0001
BULLETIN F: 15-JUN-08 | ||
RIVER CITY CASINO, St. Louis, Missouri• Project No. 141005 | ADDENDUM 1: 16-JUN-08 |
1 | F | ||||||||||||
SHEET | ISSUED FOR | ISSUED FOR | |||||||||||
NUMBER | SHEET TITLES | CONSTRUCTION | PLAN CHECK | ||||||||||
ARCHITECTURAL | 16-Jun-08 | 15-Jun-08 | |||||||||||
REVISION | SHEET # | SHEET TITLES | |||||||||||
A10.2.1 | MILLWORK DETAILS | X | X | ||||||||||
A10.2.2 | MILLWORK DETAILS | X | X | ||||||||||
A10.2.3 | MILLWORK DETAILS | X | X | ||||||||||
A10.2.4 | MILLWORK DETAILS | X | X | ||||||||||
TOTAL ARCHITECTURAL SHEETS | 279 | 279 | |||||||||||
ARCHITECTURAL | 13 of 54 | 6/19/2008 10:14 AM |
ARCHITECTS• PLANNERS
TEL 702.940.0000• FAX 702.940.0001
BULLETIN F: 15-JUN-08 | ||
RIVER CITY CASINO, St. Louis, Missouri• Project No. 141005 | ADDENDUM 1: 16-JUN-08 |
1 | F | ||||||||
SHEET | ISSUED FOR | ISSUED FOR | |||||||
NUMBER | SHEET TITLES | CONSTRUCTION | PLAN CHECK | ||||||
CIVIL | 16-Jun-08 | 15-Jun-08 | |||||||
REVISION | SHEET # | SHEET TITLES | |||||||
C0.1 | COVER SHEET | X | X | ||||||
C0.2 | GENERAL NOTES | X | X | ||||||
C1.1 | TYPICAL SECTIONS | X | X | ||||||
C1.2 | TYPICAL SECTIONS | X | X | ||||||
C1.3 | TYPICAL SECTIONS & DETAILS | X | X | ||||||
C2.1 | OVERALL SITE PLAN & SHEET INDEX | X | X | ||||||
C2.2 | EXISTING PROPERTY INFORMATION | X | X | ||||||
C2.3 | EXISTING PROPERTY INFORMATION | X | X | ||||||
C2.4 | EXISTING PROPERTY INFORMATION | X | X | ||||||
C3.1 | SITE PLAN | X | X | ||||||
C3.2 | SITE PLAN | X | X | ||||||
C3.3 | SITE PLAN | X | X | ||||||
C3.4 | SITE PLAN | X | X | ||||||
C3.5 | SITE PLAN | X | X | ||||||
C3.6 | SITE PLAN | X | X | ||||||
C3.7 | SITE PLAN | X | X | ||||||
C3.8 | SITE PLAN | X | X | ||||||
C3.9 | SITE PLAN | X | X | ||||||
C3.10 | SITE PLAN | X | X | ||||||
C3.11 | SITE PLAN | X | X | ||||||
C3.12 | SITE PLAN | X | X | ||||||
C3.13 | SITE PLAN | X | X | ||||||
C3.14 | SITE PLAN | X | X |
CIVIL | 14 of 54 | 6/19/2008 10:14 AM |
ARCHITECTS• PLANNERS
TEL 702.940.0000• FAX 702.940.0001
BULLETIN F: 15-JUN-08 | ||
RIVER CITY CASINO, St. Louis, Missouri• Project No. 141005 | ADDENDUM 1: 16-JUN-08 |
1 | F | ||||||||
SHEET | ISSUED FOR | ISSUED FOR | |||||||
NUMBER | SHEET TITLES | CONSTRUCTION | PLAN CHECK | ||||||
CIVIL | 16-Jun-08 | 15-Jun-08 | |||||||
REVISION | SHEET # | SHEET TITLES | |||||||
C4.1 | GRADING PLAN | X | X | ||||||
C4.2 | GRADING PLAN | X | X | ||||||
C4.3 | GRADING PLAN | X | X | ||||||
C4.4 | GRADING PLAN | X | X | ||||||
C4.5 | GRADING PLAN | X | X | ||||||
C4.6 | GRADING PLAN | X | X | ||||||
C4.7 | GRADING PLAN | X | X | ||||||
C4.8 | GRADING PLAN | X | X | ||||||
C4.9 | GRADING PLAN | X | X | ||||||
C4.10 | GRADING PLAN | X | X | ||||||
C4.11 | GRADING PLAN | X | X | ||||||
C4.12 | GRADING PLAN | X | X | ||||||
C4.13 | GRADING PLAN | X | X | ||||||
C4.14 | GRADING PLAN | X | X | ||||||
C5.1 | ACCESS ROAD PROFILE | X | X | ||||||
C5.2 | ACCESS ROAD PROFILE | X | X | ||||||
C5.3 | SERVICE ROAD PROFILE | X | X | ||||||
C5.4 | SERVICE ROAD PROFILE | X | X | ||||||
C5.5 | SOUTH PARKING LOT ROAD & HOFFMEISTER CONNECTION PROFILES | X | X | ||||||
C5.6 | NORTH PARKING LOT ROADS PROFILES | X | X | ||||||
C5.7 | BIKE TRAIL PROFILE | X | X | ||||||
C5.8 | BIKE TRAIL PROFILE | X | X | ||||||
C6.1 | WALL A PROFILE | X | X | ||||||
C6.2 | WALL A & B PROFILES & DETAILS | X | X | ||||||
C6.3 | WALL C, D & E PROFILES & DETAILS | X | X |
CIVIL | 15 of 54 | 6/19/2008 10:14 AM |
ARCHITECTS• PLANNERS
TEL 702.940.0000• FAX 702.940.0001
BULLETIN F: 15-JUN-08 | ||
RIVER CITY CASINO, St. Louis, Missouri• Project No. 141005 | ADDENDUM 1: 16-JUN-08 |
1 | F | ||||||||||||
SHEET | ISSUED FOR | ISSUED FOR | |||||||||||
NUMBER | SHEET TITLES | CONSTRUCTION | PLAN CHECK | ||||||||||
CIVIL | 16-Jun-08 | 15-Jun-08 | |||||||||||
REVISION | SHEET # | SHEET TITLES | |||||||||||
C6.4 | WALL F & G PROFILES | X | X | ||||||||||
C7.1 | SANITARY SEWER PROFILES | X | X | ||||||||||
C7.2 | SANITARY LIFT STATION DETAILS | X | X | ||||||||||
C7.3 | SANITARY SEWER DETAILS | X | X | ||||||||||
C7.4 | SANITARY SEWER DETAILS | X | X | ||||||||||
C8.1 | STORM SEWER PROFILES — SYSTEM 1 | X | X | ||||||||||
C8.2 | STORM SEWER PROFILES — SYSTEM 1 | X | X | ||||||||||
C8.3 | STORM SEWER PROFILES — SYSTEM 1 | X | X | ||||||||||
C8.4 | STORM SEWER PROFILES — SYSTEM 2 | X | X | ||||||||||
C8.5 | STORM SEWER PROFILES — SYSTEM 2 | X | X | ||||||||||
C8.6 | STORM SEWER PROFILES — SYSTEM 2 | X | X | ||||||||||
C8.7 | STORM SEWER PROFILES — SYSTEM 2 | X | X | ||||||||||
C8.8 | STORM SEWER PROFILES — SYSTEM 2 | X | X | ||||||||||
C8.9 | STORM SEWER PROFILES — SYSTEM 2 | X | X | ||||||||||
C8.10 | STORM SEWER PROFILES — SYSTEM 2 & 3 | X | X | ||||||||||
C8.11 | STORM SEWER DETAILS | X | X | ||||||||||
C8.12 | STORM SEWER DETAILS | X | X | ||||||||||
C9.1 | UTILITY DETAILS | X | X | ||||||||||
C9.2 | UTILITY DETAILS | X | X | ||||||||||
C10.1 | STRIPIING AND SIGNING PLAN | X | X | ||||||||||
C10.2 | STRIPIING AND SIGNING PLAN | X | X | ||||||||||
TOTAL CIVIL SHEETS | 69 | 69 | |||||||||||
CIVIL | 16 of 54 | 6/19/2008 10:14 AM |
ARCHITECTS• PLANNERS
TEL 702.940.0000• FAX 702.940.0001
RIVER CITY CASINO, St. Louis, Missouri• Project No. 141005 | ADDENDUM 1: 16-JUN-08 |
1 | F | ||||||||
SHEET | ISSUED FOR | ISSUED FOR | |||||||
NUMBER | SHEET TITLES | CONSTRUCTION | PLAN CHECK | ||||||
STRUCTURAL | 16-Jun-08 | 15-Jun-08 | |||||||
REVISION | SHEET # | SHEET TITLES | |||||||
S0.01 | COVER SHEET | X | X | ||||||
S0.02 | GENERAL NOTES | X | X | ||||||
S0.03 | GENERAL NOTES | X | X | ||||||
S0.04 | GENERAL NOTES | X | X | ||||||
S0.1.0A | SNOW LOADS PLAN — AREA A | X | X | ||||||
S0.1.0B | SNOW LOADS PLAN — AREA B | X | X | ||||||
S0.1.0C | SNOW LOADS PLAN — AREA C | X | X | ||||||
S0.1.0D | SNOW LOADS PLAN — AREA D | X | X | ||||||
S0.1.0G | SNOW LOADS PLAN — AREA G | X | X | ||||||
S0.1.0H | SNOW LOADS PLAN — AREA H | X | X | ||||||
S0.1.0J | SNOW LOADS PLAN — AREA J | X | X | ||||||
S0.1.0P | SNOW LOADS PLAN — AREA P | X | X | ||||||
S0.1.0Q | SNOW LOADS PLAN — AREA Q | X | X | ||||||
S0.1.0U | SNOW LOADS PLAN — AREA U | X | X | ||||||
S0.1.0V | SNOW LOADS PLAN — AREA V | X | X | ||||||
S0.1.0W | SNOW LOADS PLAN — AREA W | X | X | ||||||
S0.1.1A | WIND UPLIFT PLAN — AREA A | X | X | ||||||
S0.1.1B | WIND UPLIFT PLAN — AREA B | X | X | ||||||
S0.1.1C | WIND UPLIFT PLAN — AREA C | X | X | ||||||
S0.1.1D | WIND UPLIFT PLAN — AREA D | X | X | ||||||
S0.1.1G | WIND UPLIFT PLAN — AREA G | X | X | ||||||
S0.1.1H | WIND UPLIFT PLAN — AREA H | X | X | ||||||
S0.1.1J | WIND UPLIFT PLAN — AREA J | X | X | ||||||
S0.1.1P | WIND UPLIFT PLAN — AREA P | X | X | ||||||
S0.1.1Q | WIND UPLIFT PLAN — AREA Q | X | X | ||||||
S0.1.1U | WIND UPLIFT PLAN — AREA U | X | X |
STRUCTURAL | 17 of 54 | 6/19/2008 10:14 AM |
TEL 702.940.0000• FAX 702.940.0001
RIVER CITY CASINO, St. Louis, Missouri• Project No. 141005 | ADDENDUM 1: 16-JUN-08 |
1 | F | |||||||||||
SHEET | ISSUED FOR | ISSUED FOR | ||||||||||
NUMBER | SHEET TITLES | CONSTRUCTION | PLAN CHECK | |||||||||
STRUCTURAL | 16-Jun-08 | 15-Jun-08 | ||||||||||
REVISION | SHEET# | SHEET TITLES | ||||||||||
S0.1.1V | WIND UPLIFT PLAN — AREA V | X | X | |||||||||
S0.1.1W | WIND UPLIFT PLAN — AREA W | X | X | |||||||||
S0.1.1 | BASIN CONSTRUCTION JOINT PLAN | X | X | |||||||||
S2.00 | PILE CAPACITY PLAN | X | X | |||||||||
S2.1.0A | FOUNDATION PLAN — AREA A | X | X | |||||||||
S2.1.0B | FOUNDATION PLAN — AREA B | X | X | |||||||||
S2.1.0C | FOUNDATION PLAN — AREA C | X | X | |||||||||
S2.1.0D | FOUNDATION PLAN — AREA D | X | X | |||||||||
S2.1.0G | FOUNDATION PLAN — AREA G | X | X | |||||||||
S2.1.0H | FOUNDATION PLAN — AREA H | X | X | |||||||||
S2.1.0J | FOUNDATION PLAN — AREA J | X | X | |||||||||
S2.1.0P | FOUNDATION PLAN — AREA P | X | X | |||||||||
S2.1.0Q | FOUNDATION PLAN — AREA Q | X | X | |||||||||
S2.1.0U | FOUNDATION PLAN — AREA U | X | X | |||||||||
S2.1.0V | FOUNDATION PLAN — AREA V | X | X | |||||||||
S2.1.0W | FOUNDATION PLAN — AREA W | X | X | |||||||||
S2.1.1A | CASINO LEVEL FRAMING PLAN — AREA A | X | X | |||||||||
S2.1.1B | CASINO LEVEL FRAMING PLAN — AREA B | X | X | |||||||||
S2.1.1C | CASINO LEVEL FRAMING PLAN — AREA C | X | X | |||||||||
S2.1.1D | CASINO LEVEL FRAMING PLAN — AREA D | X | X | |||||||||
S2.1.1G | CASINO LEVEL FRAMING PLAN — AREA G | X | X | |||||||||
S2.1.1H | CASINO LEVEL FRAMING PLAN — AREA H | X | X | |||||||||
S2.1.1J | CASINO LEVEL FRAMING PLAN — AREA J | X | X | |||||||||
S2.1.1P | CASINO LEVEL FRAMING PLAN — AREA P | X | X |
STRUCTURAL | 18 of 54 | 6/19/2008 10:14 AM |
TEL 702.940.0000• FAX 702.940.0001
RIVER CITY CASINO, St. Louis, Missouri• Project No. 141005 | ADDENDUM 1: 16-JUN-08 |
1 | F | |||||||||||
SHEET | ISSUED FOR | ISSUED FOR | ||||||||||
NUMBER | SHEET TITLES | CONSTRUCTION | PLAN CHECK | |||||||||
STRUCTURAL | 16-Jun-08 | 15-Jun-08 | ||||||||||
REVISION | SHEET # | SHEET TITLES | ||||||||||
S2.1.1Q | CASINO LEVEL FRAMING PLAN — AREA Q | X | X | |||||||||
S2.1.1U | CASINO LEVEL FRAMING PLAN — AREA U | X | X | |||||||||
S2.1.1V | CASINO LEVEL FRAMING PLAN — AREA V | X | X | |||||||||
S2.1.1W | CASINO LEVEL FRAMING PLAN — AREA W | X | X | |||||||||
S2.1.2A | SECOND LEVEL FRAMING PLAN — AREA A | X | X | |||||||||
S2.1.2B | SECOND LEVEL FRAMING PLAN — AREA B | X | X | |||||||||
S2.1.2C | SECOND LEVEL FRAMING PLAN — AREA C | X | X | |||||||||
S2.1.2D | SECOND LEVEL FRAMING PLAN — AREA D | X | X | |||||||||
S2.1.2G | SECOND LEVEL FRAMING PLAN — AREA G | X | X | |||||||||
S2.1.2H | SECOND LEVEL FRAMING PLAN — AREA H | X | X | |||||||||
S2.1.2J | SECOND LEVEL FRAMING PLAN — AREA J | X | X | |||||||||
S2.1.2P | SECOND LEVEL FRAMING PLAN — AREA P | X | X | |||||||||
S2.1.2Q | SECOND LEVEL FRAMING PLAN — AREA Q | X | X | |||||||||
S2.1.2U | SECOND LEVEL FRAMING PLAN — AREA U | X | X | |||||||||
S2.1.2V | SECOND LEVEL FRAMING PLAN — AREA V | X | X | |||||||||
S2.1.2W | SECOND LEVEL FRAMING PLAN — AREA W | X | X | |||||||||
S2.1.3A | ROOF LEVEL FRAMING PLAN — AREA A | X | X | |||||||||
S2.1.3B | ROOF LEVEL FRAMING PLAN — AREA B | X | X | |||||||||
S2.1.3C | ROOF LEVEL FRAMING PLAN — AREA C | X | X | |||||||||
S2.1.3D | ROOF LEVEL FRAMING PLAN — AREA D | X | X | |||||||||
S2.1.3G | ROOF LEVEL FRAMING PLAN — AREA G | X | X | |||||||||
S2.1.3H | ROOF LEVEL FRAMING PLAN — AREA H | X | X | |||||||||
S2.1.3J | ROOF LEVEL FRAMING PLAN — AREA J | X | X | |||||||||
S2.1.3P | ROOF LEVEL FRAMING PLAN — AREA P | X | X | |||||||||
S2.1.3Q | ROOF LEVEL FRAMING PLAN — AREA Q | X | X | |||||||||
S2.1.3U | ROOF LEVEL FRAMING PLAN — AREA U | X | X |
STRUCTURAL | 19 of 54 | 6/19/2008 10:14 AM |
TEL 702.940.0000• FAX 702.940.0001
RIVER CITY CASINO, St. Louis, Missouri• Project No. 141005 | ADDENDUM 1: 16-JUN-08 |
1 | F | |||||||||||
SHEET | ISSUED FOR | ISSUED FOR | ||||||||||
NUMBER | SHEET TITLES | CONSTRUCTION | PLAN CHECK | |||||||||
STRUCTURAL | 16-Jun-08 | 15-Jun-08 | ||||||||||
REVISION | SHEET # | SHEET TITLES | ||||||||||
S2.1.3V | ROOF LEVEL AND CURB FRAMING PLANS — AREA V | X | X | |||||||||
S2.1.3W | ROOF LEVEL FRAMING PLAN — AREA W | X | X | |||||||||
S2.1.4V | TOWER ROOF FRAMING PLAN — AREA V | X | X | |||||||||
S2.1.4W | TOWER ROOF FRAMING PLAN — AREA W | X | X | |||||||||
S3.11 | BEAM ELEVATIONS | X | X | |||||||||
S3.12 | BEAM ELEVATIONS | X | X | |||||||||
S3.13 | BEAM ELEVATIONS | X | X | |||||||||
S3.14 | BEAM ELEVATIONS | X | X | |||||||||
S3.15 | BEAM ELEVATIONS | X | X | |||||||||
S3.16 | BEAM ELEVATIONS | X | X | |||||||||
S3.17 | BEAM ELEVATIONS | X | X | |||||||||
S3.18 | BEAM ELEVATIONS | X | X | |||||||||
S3.19 | BEAM ELEVATIONS | X | X | |||||||||
S3.20 | BEAM ELEVATIONS | X | X | |||||||||
S3.21 | BEAM ELEVATIONS | X | X | |||||||||
S3.22 | BEAM ELEVATIONS | X | X | |||||||||
S3.31 | BRACE ELEVATIONS | X | X | |||||||||
S3.32 | BRACE ELEVATIONS | X | X | |||||||||
S3.33 | BRACE ELEVATIONS | X | X | |||||||||
S3.34 | BRACE ELEVATIONS | X | X | |||||||||
S3.35 | BRACE ELEVATIONS | X | X | |||||||||
S3.36 | BRACE ELEVATIONS | X | X | |||||||||
S3.37 | BRACE ELEVATIONS | X | X | |||||||||
S3.41 | SIGN ELEVATIONS | X | X |
STRUCTURAL | 20 of 54 | 6/19/2008 10:14 AM |
TEL 702.940.0000• FAX 702.940.0001
RIVER CITY CASINO, St. Louis, Missouri• Project No. 141005 | ADDENDUM 1: 16-JUN-08 |
1 | F | |||||||||||
SHEET | ISSUED FOR | ISSUED FOR | ||||||||||
NUMBER | SHEET TITLES | CONSTRUCTION | PLAN CHECK | |||||||||
STRUCTURAL | 16-Jun-08 | 15-Jun-08 | ||||||||||
REVISION | SHEET # | SHEET TITLES | ||||||||||
S3.51 | WALL ELEVATIONS | X | X | |||||||||
S4.21 | BEAM SECTIONS | X | X | |||||||||
S4.22 | BEAM SECTIONS | X | X | |||||||||
S4.23 | BEAM SECTIONS | X | X | |||||||||
S5.01 | FOUNDATION SECTIONS | X | X | |||||||||
S5.02 | FOUNDATION SECTIONS | X | X | |||||||||
S5.03 | FOUNDATION SECTIONS | X | X | |||||||||
S5.04 | FOUNDATION SECTIONS | X | X | |||||||||
S5.05 | FOUNDATION SECTIONS | X | X | |||||||||
S5.06 | FOUNDATION SECTIONS | X | X | |||||||||
S5.07 | FOUNDATION SECTIONS | X | X | |||||||||
S5.08 | FOUNDATION SECTIONS | X | X | |||||||||
S5.09 | FOUNDATION SECTIONS | X | X | |||||||||
S5.10 | FOUNDATION SECTIONS | X | X | |||||||||
S5.11 | CONCRETE SECTIONS | X | X | |||||||||
S5.12 | CONCRETE SECTIONS | X | X | |||||||||
S5.13 | CONCRETE SECTIONS | X | X | |||||||||
S5.31 | MASONRY WALL SECTIONS | X | X | |||||||||
S5.32 | MASONRY WALL SECTIONS | X | X | |||||||||
S5.41 | MISCELLANEOUS SECTIONS | X | X | |||||||||
S5.51 | STEEL SECTIONS | X | X |
STRUCTURAL | 21 of 54 | 6/19/2008 10:14 AM |
TEL 702.940.0000• FAX 702.940.0001
RIVER CITY CASINO, St. Louis, Missouri• Project No. 141005 | ADDENDUM 1: 16-JUN-08 |
1 | F | |||||||||||
SHEET | ISSUED FOR | ISSUED FOR | ||||||||||
NUMBER | SHEET TITLES | CONSTRUCTION | PLAN CHECK | |||||||||
STRUCTURAL | 16-Jun-08 | 15-Jun-08 | ||||||||||
REVISION | SHEET # | SHEET TITLES | ||||||||||
S5.52 | STEEL SECTIONS | X | X | |||||||||
S5.53 | STEEL SECTIONS | X | X | |||||||||
S5.54 | STEEL SECTIONS | X | X | |||||||||
S5.55 | STEEL SECTIONS | X | X | |||||||||
S5.56 | STEEL SECTIONS | X | X | |||||||||
S5.57 | STEEL SECTIONS | X | X | |||||||||
S5.58 | STEEL SECTIONS | X | X | |||||||||
S5.59 | STEEL SECTIONS | X | X | |||||||||
S5.510 | STEEL SECTIONS | X | X | |||||||||
S5.511 | STEEL SECTIONS | X | X | |||||||||
S5.512 | STEEL SECTIONS | X | X | |||||||||
S7.11 | PILE CAP PLANS | X | X | |||||||||
S7.12 | PILE CAP PLANS | X | X | |||||||||
TOTAL STRUCTURAL SHEETS | 134 | 134 | ||||||||||
STRUCTURAL | 22 of 54 | 6/19/2008 10:14 AM |
TEL 702.940.0000• FAX 702.940.0001
BULLETIN F: 15-JUN-08 | ||
RIVER CITY CASINO, St. Louis, Missouri• Project No. 141005 | ADDENDUM 1: 16-JUN-08 |
1 | F | |||||||||||
SHEET | ISSUED FOR | ISSUED FOR | ||||||||||
NUMBER | SHEET TITLES | CONSTRUCTION | PLAN CHECK | |||||||||
MECHANICAL | 16-Jun-08 | 15-Jun-08 | ||||||||||
REVISION | SHEET # | SHEET TITLES | ||||||||||
M1.0.1 | MECHANICAL NOTE AND SCHEDULES | X | X | |||||||||
M1.0.2 | MECHANICAL OUTSIDE AIR CALCULATIONS | X | X | |||||||||
M2.1.1A | CASINO LEVEL MECHANICAL PLAN AREA A | X | X | |||||||||
M2.1.1B | CASINO LEVEL MECHANICAL PLAN AREA B | X | X | |||||||||
M2.1.1C | CASINO LEVEL MECHANICAL PLAN AREA C | X | X | |||||||||
M2.1.1D | CASINO LEVEL MECHANICAL PLAN AREA D | X | X | |||||||||
M2.1.1G | CASINO LEVEL MECHANICAL PLAN AREA G | X | X | |||||||||
M2.1.1H | CASINO LEVEL MECHANICAL PLAN AREA H | X | X | |||||||||
M2.1.1J | CASINO LEVEL MECHANICAL PLAN AREA J | X | X | |||||||||
M2.1.1P | CASINO LEVEL MECHANICAL PLAN AREA P | X | X | |||||||||
M2.1.1Q | CASINO LEVEL MECHANICAL PLAN AREA Q | X | X | |||||||||
M2.1.1U | CASINO LEVEL MECHANICAL PLAN AREA U | X | X | |||||||||
M2.1.1V | CASINO LEVEL MECHANICAL PLAN AREA V | X | X | |||||||||
M2.1.1W | CASINO LEVEL MECHANICAL PLAN AREA W | X | X | |||||||||
M2.1.2A | SECOND LEVEL MECHANICAL PLAN AREA A | X | X | |||||||||
M2.1.2B | SECOND LEVEL MECHANICAL PLAN AREA B | X | X | |||||||||
M2.1.2C | SECOND LEVEL MECHANICAL PLAN AREA C | X | X | |||||||||
M2.1.2D | SECOND LEVEL MECHANICAL PLAN AREA D | X | X | |||||||||
M2.1.2H | SECOND LEVEL MECHANICAL PLAN AREA H | X | X | |||||||||
M2.1.2P | SECOND LEVEL MECHANICAL PLAN AREA P | X | X | |||||||||
M2.1.3 | MECHANICAL PLAN ROOF | X | X | |||||||||
M8.1.1 | MECHANICAL ENLARGED PACKAGED CHILLED WATER PLANT | X | X | |||||||||
M8.1.2 | MECHANICAL ENLARGED HEATING PLANT | X | X |
MECHANICAL | 23 of 54 | 6/19/2008 10:14 AM |
TEL 702.940.0000• FAX 702.940.0001
BULLETIN F: 15-JUN-08 | ||
RIVER CITY CASINO, St. Louis, Missouri• Project No. 141005 | ADDENDUM 1: 16-JUN-08 |
1 | F | |||||||||||
SHEET | ISSUED FOR | ISSUED FOR | ||||||||||
NUMBER | SHEET TITLES | CONSTRUCTION | PLAN CHECK | |||||||||
MECHANICAL | 16-Jun-08 | 15-Jun-08 | ||||||||||
REVISION | SHEET # | SHEET TITLES | ||||||||||
M9.1.1 | MECHANICAL PIPING SCHEMATICS | X | X | |||||||||
M9.1.2 | MECHANICAL PIPING SCHEMATICS | X | X | |||||||||
M9.1.3 | MECHANICAL PIPING SCHEMATICS | X | X | |||||||||
M10.1.1 | MECHANICAL DETAILS | X | X | |||||||||
M10.1.2 | MECHANICAL DETAILS | X | X | |||||||||
M10.1.3 | MECHANICAL DETAILS | X | X | |||||||||
M11.1.1 | MECHANICAL SCHEDULES | X | X | |||||||||
M11.1.2 | MECHANICAL SCHEDULES | X | X | |||||||||
M11.1.3 | MECHANICAL SCHEDULES | X | X | |||||||||
TOTAL MECHANICAL SHEETS | 32 | 32 | ||||||||||
MECHANICAL | 24 of 54 | 6/19/2008 10:14 AM |
TEL 702.940.0000• FAX 702.940.0001
BULLETIN F: 15-JUN-08 | ||
RIVER CITY CASINO, St. Louis, Missouri• Project No. 141005 | ADDENDUM 1: 16-JUN-08 |
1 | F | |||||||||||
SHEET | ISSUED FOR | ISSUED FOR | ||||||||||
NUMBER | SHEET TITLES | CONSTRUCTION | PLAN CHECK | |||||||||
PLUMBING | 16-Jun-08 | 15-Jun-08 | ||||||||||
REVISION | SHEET # | SHEET TITLES | ||||||||||
P2.1.1A | CASINO LEVEL PLUMBING PLAN AREA A | X | X | |||||||||
P2.1.1B | CASINO LEVEL PLUMBING PLAN AREA B | X | X | |||||||||
P2.1.1C | CASINO LEVEL PLUMBING PLAN AREA C | X | X | |||||||||
P2.1.1D | CASINO LEVEL PLUMBING PLAN AREA D | X | X | |||||||||
P2.1.1G | CASINO LEVEL PLUMBING PLAN AREA G | X | X | |||||||||
P2.1.1H | CASINO LEVEL PLUMBING PLAN AREA H | X | X | |||||||||
P2.1.1J | CASINO LEVEL PLUMBING PLAN AREA J | X | X | |||||||||
P2.1.1P | CASINO LEVEL PLUMBING PLAN AREA P | X | X | |||||||||
P2.1.1Q | CASINO LEVEL PLUMBING PLAN AREA Q | X | X | |||||||||
P2.1.1U | CASINO LEVEL PLUMBING PLAN AREA U | X | X | |||||||||
P2.1.1V | CASINO LEVEL PLUMBING PLAN AREA V | X | X | |||||||||
P2.1.1W | CASINO LEVEL PLUMBING PLAN AREA W | X | X | |||||||||
P2.1.2A | SECOND LEVEL PLUMBING PLAN AREA A | X | X | |||||||||
P2.1.2B | SECOND LEVEL PLUMBING PLAN AREA B | X | X | |||||||||
P2.1.2C | SECOND LEVEL PLUMBING PLAN AREA C | X | X | |||||||||
P2.1.3 | ROOF LEVEL PLAN | X | X | |||||||||
P3.1.1 | �� | CASINO LEVEL FIRE PROTECTION PLAN | X | X | ||||||||
P3.1.2 | SECOND LEVEL FIRE PROTECTION PLAN | X | X | |||||||||
P5.1.1 | PLUMBING RISER DIAGRAMS | X | X | |||||||||
P10.1.1 | PLUMBING DETAILS SCHEDULES AND LEGENDS | X | X | |||||||||
P10.1.2 | PLUMBING DETAILS SCHEDULES AND LEGENDS | X | X |
PLUMBING | 25 of 54 | 6/19/2008 10:14 AM |
TEL 702.940.0000• FAX 702.940.0001
BULLETIN F: 15-JUN-08 | ||
RIVER CITY CASINO, St. Louis, Missouri• Project No. 141005 | ADDENDUM 1: 16-JUN-08 |
1 | F | |||||||||||
SHEET | ISSUED FOR | ISSUED FOR | ||||||||||
NUMBER | SHEET TITLES | CONSTRUCTION | PLAN CHECK | |||||||||
PLUMBING | 16-Jun-08 | 15-Jun-08 | ||||||||||
REVISION | SHEET # | SHEET TITLES | ||||||||||
PFS-1.0 | CASINO LEVEL WAREHOUSE PLUMBING PLAN | X | X | |||||||||
PFS-2.0 | CASINO LEVEL MAIN KITCHEN PLUMBING PLAN | X | X | |||||||||
PFS-3.0 | CASINO LEVEL BUFFET PLUMBING PLAN | X | X | |||||||||
PFS-4.0 | CASINO LEVEL EMPLOYEE DINING ROOM PLUMBING PLAN | X | X | |||||||||
PFS-5.0 | CASINO LEVEL FINE DINING PLUMBING PLAN | X | X | |||||||||
PFS-6.0 | CASINO LEVEL 24 HOUR RESTAURANT PLUMBING PLAN | X | X | |||||||||
PFS-7.0 | CASINO LEVEL ENTERTAINMENT BAR PLUMBING PLAN | X | X | |||||||||
PFS-8.0 | CASINO LEVEL CASINO BARS PLUMBING PLAN | X | X | |||||||||
PFS-9.0 | CASINO LEVEL BEER HALL PLUMBING PLAN | X | X | |||||||||
PFS-10.0 | CASINO LEVEL BEER GARDEN KITCHEN PLUMBING PLAN | X | X | |||||||||
PFS-11.0 | CASINO LEVEL HIGH LIMIT SERVICE BAR PLUMBING PLAN | X | X | |||||||||
PFS-12.0 | CASINO LEVEL SOUTHEAST SERVICE BAR PLUMBING PLAN | X | X | |||||||||
TOTAL PLUMBING SHEETS | 33 | 33 | ||||||||||
PLUMBING | 26 of 54 | 6/19/2008 10:14 AM |
TEL 702.940.0000• FAX 702.940.0001
BULLETIN F: 15-JUN-08 | ||
RIVER CITY CASINO, St. Louis, Missouri• Project No. 141005 | ADDENDUM 1: 16-JUN-08 |
1 | F | |||||||||||
SHEET | ISSUED FOR | ISSUED FOR | ||||||||||
NUMBER | SHEET TITLES | CONSTRUCTION | PLAN CHECK | |||||||||
ELECTRICAL | 16-Jun-08 | 15-Jun-08 | ||||||||||
REVISION | SHEET # | SHEET TITLES | ||||||||||
E1.0.1 | ELECTRICAL NOTES, SYMBOLS AND SCHEDULES | X | X | |||||||||
E1.3.2 | ELECTRICAL SITE PLAN | X | X | |||||||||
E1.4.1 | ELECTRICAL SITE LIGHTING PLAN | X | X | |||||||||
E1.4.2 | ELECTRICAL SITE LIGHTING PLAN | X | X | |||||||||
E2.1.1A | CASINO LEVEL ELECTRICAL PLAN AREA A | X | X | |||||||||
E2.1.1B | CASINO LEVEL ELECTRICAL PLAN AREA B | X | X | |||||||||
E2.1.1C | CASINO LEVEL ELECTRICAL PLAN AREA C | X | X | |||||||||
E2.1.1D | CASINO LEVEL ELECTRICAL PLAN AREA D | X | X | |||||||||
E2.1.1G | CASINO LEVEL ELECTRICAL PLAN AREA G | X | X | |||||||||
E2.1.1H | CASINO LEVEL ELECTRICAL PLAN AREA H | X | X | |||||||||
E2.1.1J | CASINO LEVEL ELECTRICAL PLAN AREA J | X | X | |||||||||
E2.1.1P | CASINO LEVEL ELECTRICAL PLAN AREA P | X | X | |||||||||
E2.1.1Q | CASINO LEVEL ELECTRICAL PLAN AREA Q | X | X | |||||||||
E2.1.1U | CASINO LEVEL ELECTRICAL PLAN AREA U | X | X | |||||||||
E2.1.1V | CASINO LEVEL ELECTRICAL PLAN AREA V | X | X | |||||||||
E2.1.1W | CASINO LEVEL ELECTRICAL PLAN AREA W | X | X | |||||||||
E2.1.2A | SECOND LEVEL ELECTRICAL PLAN AREA A | X | X | |||||||||
E2.1.2B | SECOND LEVEL ELECTRICAL PLAN AREA B | X | X | |||||||||
E2.1.2C | SECOND LEVEL ELECTRICAL PLAN AREA C | X | X | |||||||||
E2.4.1 | ELECTRICAL PLAN ROOF LEVEL | X | X | |||||||||
E2.5.1 | ELECTRICAL GROUNDING PLAN | X | X | |||||||||
E5.1.1A | CASINO LEVEL LIGHTING PLAN AREA A | X | X | |||||||||
E5.1.1B | CASINO LEVEL LIGHTING PLAN AREA B | X | X | |||||||||
E5.1.1C | CASINO LEVEL LIGHTING PLAN AREA C | X | X | |||||||||
E5.1.1D | CASINO LEVEL LIGHTING PLAN AREA D | X | X |
ELECTRICAL | 27 of 54 | 6/19/2008 10:14 AM |
TEL 702.940.0000• FAX 702.940.0001
BULLETIN F: 15-JUN-08 | ||
RIVER CITY CASINO, St. Louis, Missouri• Project No. 141005 | ADDENDUM 1: 16-JUN-08 |
1 | F | |||||||||||
SHEET | ISSUED FOR | ISSUED FOR | ||||||||||
NUMBER | SHEET TITLES | CONSTRUCTION | PLAN CHECK | |||||||||
ELECTRICAL | 16-Jun-08 | 15-Jun-08 | ||||||||||
REVISION | SHEET # | SHEET TITLES | ||||||||||
E5.1.1G | CASINO LEVEL LIGHTING PLAN AREA G | X | X | |||||||||
E5.1.1H | CASINO LEVEL LIGHTING PLAN AREA H | X | X | |||||||||
E5.1.1J | CASINO LEVEL LIGHTING PLAN AREA J | X | X | |||||||||
E5.1.1P | CASINO LEVEL LIGHTING PLAN AREA P | X | X | |||||||||
E5.1.1Q | CASINO LEVEL LIGHTING PLAN AREA Q | X | X | |||||||||
E5.1.1U | CASINO LEVEL LIGHTING PLAN AREA U | X | X | |||||||||
E5.1.1V | CASINO LEVEL LIGHTING PLAN AREA V | X | X | |||||||||
E5.1.1W | CASINO LEVEL LIGHTING PLAN AREA W | X | X | |||||||||
E5.1.2A | SECOND LEVEL LIGHTING PLAN AREA A | X | X | |||||||||
E5.1.2B | SECOND LEVEL LIGHTING PLAN AREA B | X | X | |||||||||
E5.1.2C | SECOND LEVEL LIGHTING PLAN AREA C | X | X | |||||||||
E5.1.2D | SECOND LEVEL LIGHTING PLAN AREA D | X | X | |||||||||
E5.1.2J | SECOND LEVEL LIGHTING PLAN AREA J | X | X | |||||||||
E5.1.2Q | SECOND LEVEL LIGHTING PLAN AREA Q | X | X | |||||||||
E5.1.2U | SECOND LEVEL LIGHTING PLAN AREA U | X | X | |||||||||
E5.1.2V | SECOND LEVEL LIGHTING PLAN AREA V | X | X | |||||||||
E5.1.2W | SECOND LEVEL LIGHTING PLAN AREA W | X | X | |||||||||
E8.1.1 | ONE-LINE DIAGRAMS NORMAL POWER MSA/MSB | X | X | |||||||||
E8.1.2 | ONE-LINE DIAGRAMS EMERGENCY POWER EMSA/EMSB | X | X | |||||||||
E9.1.1 | ELECTRICAL RISER DIAGRAM NORMAL POWER MSA/MSB | X | X | |||||||||
E9.1.2 | ELECTRICAL RISER DIAGRAMS EMERGENCY POWER EMSA/EMSB | X | X | |||||||||
E9.1.3 | FIRE ALARM DIAGRAMS AND FIRE ALARM MATRIX | X | X | |||||||||
E10.1.1 | ELECTRICAL PANEL SCHEDULES MSA | X | X |
ELECTRICAL | 28 of 54 | 6/19/2008 10:14 AM |
TEL 702.940.0000• FAX 702.940.0001
BULLETIN F: 15-JUN-08 | ||
RIVER CITY CASINO, St. Louis, Missouri• Project No. 141005 | ADDENDUM 1: 16-JUN-08 |
1 | F | |||||||||||
SHEET | ISSUED FOR | ISSUED FOR | ||||||||||
NUMBER | SHEET TITLES | CONSTRUCTION | PLAN CHECK | |||||||||
ELECTRICAL | 16-Jun-08 | 15-Jun-08 | ||||||||||
REVISION | SHEET # | SHEET TITLES | ||||||||||
E10.1.2 | ELECTRICAL PANEL SCHEDULES MSA | X | X | |||||||||
E10.1.3 | ELECTRICAL PANEL SCHEDULES MSB | X | X | |||||||||
E10.1.4 | ELECTRICAL PANEL SCHEDULES MSB | X | X | |||||||||
E10.1.5 | ELECTRICAL PANEL SCHEDULES EMSA | X | X | |||||||||
E10.1.6 | ELECTRICAL PANEL SCHEDULES EMSA | X | X | |||||||||
E10.1.7 | ELECTRICAL PANEL SCHEDULES EMSB | X | X | |||||||||
E10.1.8 | ELECTRICAL PANEL SCHEDULES EMSB | X | X | |||||||||
E10.1.9 | ELECTRICAL PANEL SCHEDULES EMSB | X | x | |||||||||
E10.1.10 | ELECTRICAL PANEL SCHEDULES EMSB | X | X | |||||||||
E10.1.11 | ELECTRICAL PANEL SCHEDULES EMSB | X | X | |||||||||
E10.1.12 | ELECTRICAL PANEL SCHEDULES EMSB | X | X | |||||||||
E10.1.13 | ELECTRICAL PANEL SCHEDULES EMSB | X | X | |||||||||
E10.2.1 | ELECTRICAL RELAY SCHEDULES | X | X | |||||||||
E10.2.2 | ELECTRICAL RELAY SCHEDULES | X | X | |||||||||
E10.3.1 | ELECTRICAL DIMMER SCHEDULES | X | X | |||||||||
E10.3.2 | ELECTRICAL DIMMER SCHEDULES | X | X | |||||||||
E10.3.3 | ELECTRICAL DIMMER SCHEDULES | X | X | |||||||||
E10.3.4 | ELECTRICAL DIMMER SCHEDULES | X | X | |||||||||
E11.1.1 | ELECTRICAL CALCULATIONS | X | X | |||||||||
EFS-1.0 | CASINO LEVEL WAREHOUSE ELECTRICAL PLAN AND SCHEDULE | X | X | |||||||||
EFS-2.0 | CASINO LEVEL MAIN KITCHEN ELECTRICAL PLAN | X | X | |||||||||
EFS-2.01 | CASINO LEVEL MAIN KITCHEN ELECTRICAL FOOD SERVICE EQUIP. | X | X | |||||||||
EFS-3.0 | CASINO LEVEL BUFFET ELECTRICAL PLANS AND SCHEDULE | X | X |
ELECTRICAL | 29 of 54 | 6/19/2008 10:14 AM |
TEL 702.940.0000• FAX 702.940.0001
BULLETIN F: 15-JUN-08 | ||
RIVER CITY CASINO, St. Louis, Missouri• Project No. 141005 | ADDENDUM 1: 16-JUN-08 |
1 | F | |||||||||||
SHEET | ISSUED FOR | ISSUED FOR | ||||||||||
NUMBER | SHEET TITLES | CONSTRUCTION | PLAN CHECK | |||||||||
ELECTRICAL | 16-Jun-08 | 15-Jun-08 | ||||||||||
REVISION | SHEET # | SHEET TITLES | ||||||||||
EFS-3.01 | CASINO LEVEL BUFFET ELECTRICAL FOOD SERVICE EQUIP. SCHEDULE | X | X | |||||||||
EFS-4.0 | CASINO LEVEL EMPLOYEE DINING ROOM ELECTRICAL PLAN AND SCHEDULE | X | X | |||||||||
EFS-5.0 | CASINO LEVEL FINE DINING ELECTRICAL PLAN | X | X | |||||||||
EFS-5.01 | CASINO LEVEL FINE DINING ELECTRICAL FOOD SERVICE EQUIP. SCHEDULE | X | X | |||||||||
EFS-5.02 | CASINO LEVEL FINE DINING ELECTRICAL FOOD SERVICE EQUIP. SCHEDULE | X | X | |||||||||
EFS-6.0 | CASINO LEVEL 24 HOUR RESTAURANT ELECTRICAL PLAN | X | X | |||||||||
EFS-6.01 | CASINO LEVEL 24 HOUR RESTAURANT ELECTRICAL FOOD- SERVICE | X | X | |||||||||
EFS-7.0 | CASINO LEVEL ENTERTAINMENT BAR ELECTRICAL PLAN | X | X | |||||||||
EFS-7.01 | CASINO LEVEL ENTERTAINMENT LOUNGE ELECTRICAL FOOD- SERVICE | X | X | |||||||||
EFS-8.0 | CASINO LEVEL CASINO BAR ELECTRICAL PLAN | X | X | |||||||||
EFS-8.01 | CASINO LEVEL CASINO BAR ELECTRICAL FOOD- SERVICE EQUIPMENT | X | X | |||||||||
EFS-9.0 | CASINO LEVEL BEER HALL ELECTRICAL PLAN AND SCHEDULE | X | X | |||||||||
EFS-10.0 | CASINO LEVEL BEER GARDEN KITCHEN ELECTRICAL PLAN AND SCHEDULE | X | X | |||||||||
EFS-11.0 | CASINO LEVEL SERVICE BAR ELECTRICAL PLAN AND SCHEDULE | X | X | |||||||||
EFS-12.0 | CASINO LEVEL SERVICE BAR ELECTRICAL PLAN AND SCHEDULE | X | X | |||||||||
EFS-13.0 | SECOND LEVEL VIP BAR ELECTRICAL PLAN AND SCHEDULE | X | X | |||||||||
EFS-14.0 | CASINO LEVEL SOUTHWEST COFFEE BAR ELECTRICAL PLAN AND | X | X | |||||||||
TOTAL ELECTRICAL SHEETS | 88 | 88 | ||||||||||
ELECTRICAL | 30 of 54 | 6/19/2008 10:14 AM |
TEL 702.940.0000• FAX 702.940.0001
BULLETIN F: 15-JUN-08 | ||
RIVER CITY CASINO, St. Louis, Missouri• Project No. 141005 | ADDENDUM 1: 16-JUN-08 |
1 | F | ||||||||
SHEET | ISSUED FOR | ISSUED FOR | |||||||
NUMBER | SHEET TITLES | CONSTRUCTION | PLAN CHECK | ||||||
LIGHTING | 16-Jun-08 | 15-Jun-08 | |||||||
REVISION | SHEET # | SHEET TITLES | |||||||
SL1.1.1 | SITE LIGHTING PLAN | X | X | ||||||
SL1.2.1 | MASTER PLAN CASINO LEVEL LIGHTING | X | X | ||||||
SL1.2.2 | MASTER PLAN SECOND LEVEL LIGHTING | X | X | ||||||
SL1.3.1 | MASTER PLAN ROOF LEVEL LIGHTING | X | X | ||||||
SL2.1.1G | CASINO LEVEL LIGHTING PLAN AREA G | X | X | ||||||
SL2.1.1H | CASINO LEVEL PLAN LIGHTING AREA H | X | X | ||||||
SL2.1.1J | CASINO LEVEL PLAN LIGHTING AREA J | X | X | ||||||
SL2.1.1P | CASINO LEVEL PLAN LIGHTING AREA P | X | X | ||||||
SL2.1.1Q | CASINO LEVEL PLAN LIGHTING AREA Q | X | X | ||||||
SL2.1.1U | CASINO LEVEL PLAN LIGHTING AREA U | X | X | ||||||
SL2.1.1V | CASINO LEVEL PLAN LIGHTING AREA V | X | X | ||||||
SL2.1.2D | SECOND LEVEL PLAN LIGHTING AREA D | X | X | ||||||
SL3.1.1 | OVERALL LIGHTING EXT. ELEVATIONS | X | X | ||||||
SL3.2.1 | EXTERIOR ELEVATION NORTH — LIGHTING | X | X | ||||||
SL3.2.2 | EXTERIOR ELEVATION EAST — LIGHTING | X | X | ||||||
SL3.2.3 | EXTERIOR ELEVATION SOUTH — LIGHTING | X | X | ||||||
SL3.2.4 | EXTERIOR ELEVATION WEST — LIGHTING | X | X | ||||||
SL3.2.5 | EXTERIOR ELEVATION — LIGHTING | X | X | ||||||
SL5.0.1 | MASTER LIGHTING RCP CASINO LEVEL | X | X | ||||||
SL5.0.2 | MASTER LIGHTING RCP SECOND LEVEL | X | X | ||||||
SL5.1.1C | CASINO LEVEL LIGHTING RCP AREA C | X | X |
LIGHTING | 31 of 54 | 6/19/2008 10:14 AM |
TEL 702.940.0000• FAX 702.940.0001
BULLETIN F: 15-JUN-08 | ||
RIVER CITY CASINO, St. Louis, Missouri• Project No. 141005 | ADDENDUM 1: 16-JUN-08 |
1 | F | ||||||||
SHEET | ISSUED FOR | ISSUED FOR | |||||||
NUMBER | SHEET TITLES | CONSTRUCTION | PLAN CHECK | ||||||
LIGHTING | 16-Jun-08 | 15-Jun-08 | |||||||
REVISION | SHEET# | SHEET TITLES | |||||||
SL5.1.1DA | CASINO LEVEL LIGHTING RCP AREA D | X | X | ||||||
SL5.1.1DB | CASINO LEVEL LIGHTING WALL AREA D | X | X | ||||||
SL5.1.1GA | CASINO LEVEL LIGHTING RCP AREA G | X | X | ||||||
SL5.1.1GB | CASINO LEVEL LIGHTING WALL AREA G | X | X | ||||||
SL5.1.1HA | CASINO LEVEL LIGHTING RCP AREA H | X | X | ||||||
SL5.1.1HB | CASINO LEVEL LIGHTING WALL AREA H | X | X | ||||||
SL5.1.1JA | CASINO LEVEL LIGHTING RCP AREA J | X | X | ||||||
SL5.1.1JB | CASINO LEVEL LIGHTING WALL AREA J | X | X | ||||||
SL5.1.1PA | CASINO LEVEL LIGHTING RCP AREA P | X | X | ||||||
SL5.1.1PB | CASINO LEVEL LIGHTING WALL AREA P | X | X | ||||||
SL5.1.1QA | CASINO LEVEL LIGHTING RCP AREA Q | X | X | ||||||
SL5.1.1QB | CASINO LEVEL LIGHTING WALL AREA Q | X | X | ||||||
SL5.1.1UA | CASINO LEVEL LIGHTING RCP AREA U | X | X | ||||||
SL5.1.1UB | CASINO LEVEL LIGHTING WALL AREA U | X | X | ||||||
SL5.1.1VA | CASINO LEVEL LIGHTING RCP AREA V | X | X | ||||||
SL5.1.1VB | CASINO LEVEL LIGHTING WALL AREA V | X | X | ||||||
SL5.1.1WA | CASINO LEVEL LIGHTING RCP AREA W | X | X | ||||||
SL5.1.1WB | CASINO LEVEL LIGHTING WALL AREA W | X | X | ||||||
SL5.1.2C | SECOND LEVEL LIGHTING RCP AREA C | X | X | ||||||
SL5.1.2DA | SECOND LEVEL LIGHTING RCP AREA D | X | X | ||||||
SL5.1.2DB | SECOND LEVEL LIGHTING WALL AREA D | X | X | ||||||
TOTAL LIGHTING SHEETS | 42 | 42 |
LIGHTING | 32 of 54 | 6/19/2008 10:14 AM |
TEL 702.940.0000• FAX 702.940.0001
BULLETIN F: 15-JUN-08 | ||
RIVER CITY CASINO, St. Louis, Missouri• Project No. 141005 | ADDENDUM 1: 16-JUN-08 |
1 | F | ||||||||
SHEET | ISSUED FOR | ISSUED FOR | |||||||
NUMBER | SHEET TITLES | CONSTRUCTION | PLAN CHECK | ||||||
LOW VOLTAGE | 16-Jun-08 | 15-Jun-08 | |||||||
REVISION | SHEET # | SHEET TITLES | |||||||
VD.00.000 | NOTES AND SYMBOLS | X | X | ||||||
VD.00.001 | SECTION 27 00 00 GENERAL CONDITIONS | X | X | ||||||
VD.00.002 | SECTION 27 00 00 GENERAL CONDITIONS | X | X | ||||||
VD.00.003 | SECTION 27 10 00 COMMUNICATIONS CABLING | X | X | ||||||
VD.00.004 | SECTION 27 10 00 COMMUNICATIONS CABLING | X | X | ||||||
VD.00.005 | SECTION 27 10 00 COMMUNICATIONS CABLING | X | X | ||||||
VD.00.100 | DEVICE LEGEND | X | X | ||||||
VD.00.101 | LVL 1 WIRE TRAY LAYOUT | X | X | ||||||
VD.00.102A | SYSTEM RISER DIAGRAMS | X | X | ||||||
VD.00.102B | SYSTEM RISER SCHEDULES | X | X | ||||||
VD.00.103 | TELECOM GROUNDING SYSTEM | X | X | ||||||
VD.01.001 | IDF-1A & IDF-1B OUTLET LOCATIONS | X | X | ||||||
VD.01.002 | IDF-1C OUTLET LOCATIONS | X | X | ||||||
VD.01.003 | IDF-1D, IDF-1E, & IDF-1F OUTLET LOCATIONS | X | X | ||||||
VD.01.004 | IDF-1G & IDF-1H LVL 1 OUTLET LOCATIONS | X | X | ||||||
VD.01.005 | IDF-1H LVL1 FLOOR OUTLET LOCATIONS | X | X | ||||||
VD.01.006 | MDF-2 LVL1 OUTLET LOCATIONS | X | X | ||||||
VD.01.101 | IDF-1A BUILD OUT | X | X | ||||||
VD.01.102 | IDF-1B BUILD OUT | X | X | ||||||
VD.01.103 | IDF-1C BUILD OUT | X | X | ||||||
VD.01.104 | IDF-1D BUILD OUT | X | X | ||||||
VD.01.105 | IDF-1E BUILD OUT | X | X | ||||||
VD.01.106 | IDF-1F BUILD OUT | X | X | ||||||
VD.01.107 | IDF-1G BUILD OUT | X | X | ||||||
VD 01.108 | IDF-1H BUILD OUT | X | X | ||||||
VD.02.007 | IDF-2A & MDF-2 LVL 2 OUTLET LOCATIONS | X | X | ||||||
VD.02.109A | MDF-2 BUILD OUT | X | X |
LOW VOLTAGE | 33 of 54 | 6/19/2008 10:14 AM |
TEL 702.940.0000• FAX 702.940.0001
BULLETIN F: 15-JUN-08 | ||
RIVER CITY CASINO, St. Louis, Missouri• Project No. 141005 | ADDENDUM 1: 16-JUN-08 |
1 | F | ||||||||
SHEET | ISSUED FOR | ISSUED FOR | |||||||
NUMBER | SHEET TITLES | CONSTRUCTION | PLAN CHECK | ||||||
LOW VOLTAGE | 16-Jun-08 | 15-Jun-08 | |||||||
REVISION | SHEET # | SHEET TITLES | |||||||
VD.02.109B | SPOT POLLING ROOM | X | X | ||||||
VD.02.110 | IDF-2A BUILD OUT | X | X | ||||||
AV.00.000 | SECTION 27 41 00 AUDIO-VIDEO SYSTEMS | X | X | ||||||
AV.00.001 | SECTION 27 41 00 AUDIO-VIDEO SYSTEMS | X | X | ||||||
AV.00.101 | AUDIO BACKBONE LINE DIAGRAM | X | X | ||||||
AV.01.001 | IDF-1A & IDF-1B A/V DEVICES | X | X | ||||||
AV.01.002 | IDF-1C A/V DEVICES | X | X | ||||||
AV.01.003 | CASINO FLOOR SOUTH AV DEVICES | X | X | ||||||
AV.01.004 | CASINO FLOOR NORTH AV DEVICES | X | X | ||||||
AV.01.005 | IDF-1H NON-CASINO LVL 1 AV DEVICES | X | X | ||||||
AV.01.006 | MDF-2 LVL1 AV DEVICES | X | X | ||||||
AV.01.008 | LVL 1 SPEAKER ZONES | X | X | ||||||
AV.01.101 | IDF-1D AV LINE DIAGRAM | X | X | ||||||
AV.01.102 | IDF-1F AV LINE DIAGRAM | X | X | ||||||
AV.01.103 | IDF-1H AV LINE DIAGRAM | X | X | ||||||
AV.02.007 | IDF-2A & MDF-2 LVL 2 AV DEVICES | X | X | ||||||
AV.02.009 | LVL 2 SPEAKER ZONES | X | X | ||||||
AV.02.101 | AV HEAD END BUILD OUT | X | X | ||||||
AV.02.102 | AV HE AUDIO LINE DIAGRAM | X | X | ||||||
AV.02.103 | AV HE CONTROL LINE DIAGRAM | X | X | ||||||
AV.02.104 | IDF-2A AV LINE DIAGRAM | X | X | ||||||
AV.02.105 | LVL 2 CONF ROOMS LINE DIAGRAM | X | X | ||||||
SC.00.000 | SECTION 28 00 00 SECURITY SYSTEMS | X | X | ||||||
SC.00.001 | SECTION 28 00 00 SECURITY SYSTEMS | X | X | ||||||
SC.00.002 | SECTION 28 00 00 SECURITY SYSTEMS | X | X | ||||||
SC.01.001A | IDF-1A & IDF-1B AREA CAMERAS | X | X | ||||||
SC.01.001B | IDF-1A & IDF-1B AREA SECURITY DEVICES | X | X |
LOW VOLTAGE | 34 of 54 | 6/19/2008 10:14 AM |
TEL 702.940.0000• FAX 702.940.0001
BULLETIN F: 15-JUN-08 | ||
RIVER CITY CASINO, St. Louis, Missouri• Project No. 141005 | ADDENDUM 1: 16-JUN-08 |
1 | F | ||||||||
SHEET | ISSUED FOR | ISSUED FOR | |||||||
NUMBER | SHEET TITLES | CONSTRUCTION | PLAN CHECK | ||||||
LOW VOLTAGE | 16-Jun-08 | 15-Jun-08 | |||||||
REVISION | SHEET # | SHEET TITLES | |||||||
SC.01.002A | IDF-1C AREA CAMERAS | X | X | ||||||
SC.01.002B | IDF-1C AREA SECURITY DEVICES | X | X | ||||||
SC.01.003A | IDF-1F-SOUTH CAMERA LOCATIONS | X | X | ||||||
SC.01.003B | IDF-1F-SOUTH SECURITY DEVICES | X | X | ||||||
SC.01.004A | IDF-1G IDF-1H LVL 1 CAMERA LOCATIONS | X | X | ||||||
SC.01.004B | IDF-1G & IDF-1H LVL 1 SECURITY DEVICES | X | X | ||||||
SC.01.005A | IDF-1H NON-CASINO LVL 1 CAMERA LOCATIONS | X | X | ||||||
SC.01.005B | IDF-1H NON-CASINO LVL 1 SECURITY DEVICES | X | X | ||||||
SC.01.006A | MDF-2 LVL 1 CAMERA LOCATIONS | X | X | ||||||
SC.01.006B | MDF-2 LVL 1 SECURITY DEVICES | X | X | ||||||
SC.01.102 | CASINO ENTRANCE TURNSTILES | X | X | ||||||
SC.01.103 | ACCESS CONTROLLED DOOR DETAIL | X | X | ||||||
SC.02.007A | LVL 2 SECURITY DEVICE LOCATIONS | X | X | ||||||
SC.02.007B | LVL 2 SECURITY DEVICE LOCATIONS | X | X | ||||||
SC.02.101 | SURVEILLANCE ROOM LAYOUT | X | X | ||||||
TOTAL LOW VOLTAGE SHEETS | 69 | 69 |
LOW VOLTAGE | 35 of 54 | 6/19/2008 10:14 AM |
TEL 702.940.0000• FAX 702.940.0001
BULLETIN F: 15-JUN-08 | ||
RIVER CITY CASINO, St. Louis, Missouri• Project No. 141005 | ADDENDUM 1: 16-JUN-08 |
1 | F | ||||||||
SHEET | ISSUED FOR | ISSUED FOR | |||||||
NUMBER | SHEET TITLES | CONSTRUCTION | PLAN CHECK | ||||||
FOOD SERVICE | 16-Jun-08 | 15-Jun-08 | |||||||
REVISION | SHEET # | SHEET TITLES | |||||||
FS-1.0M | CASINO LEVEL MASTER PLAN | X | X | ||||||
FS-1.0 | CASINO LEVEL WAREHOUSE EQUIPMENT PLAN | X | X | ||||||
FS-1.1 | CASINO LEVEL WAREHOUSE ELECTRICAL PLAN | X | X | ||||||
FS-1.2 | CASINO LEVEL WAREHOUSE PLUMBING PLAN | X | X | ||||||
FS-1.3 | CASINO LEVEL WAREHOUSE MECHANICAL PLAN | X | X | ||||||
FS-1.4 | CASINO LEVEL WAREHOUSE BLDG. WORKS PLAN | X | X | ||||||
FS-1.5 | CASINO LEVEL WAREHOUSE BEER CONDUIT PLAN | X | X | ||||||
FS-1.6 | CASINO LEVEL WAREHOUSE SODA CONDUIT PLAN | X | X | ||||||
FS-1.7 | CASINO LEVEL WAREHOUSE LIQUOR CONDUIT PLAN | X | X | ||||||
FS-2.0 | CASINO LEVEL MAIN KITCHEN EQUIPMENT PLAN | X | X | ||||||
FS-2.S | CASINO LEVEL MAIN KITCHEN EQUIPMENT SCHEDULE | X | X | ||||||
FS-2.1 | CASINO LEVEL MAIN KITCHEN ELECTRICAL PLAN | X | X | ||||||
FS-2.2 | CASINO LEVEL MAIN KITCHEN ELECTRICAL SCHEDULE | X | X | ||||||
FS-2.3 | CASINO LEVEL MAIN KITCHEN PLUMBING PLAN | X | X | ||||||
FS-2.4 | CASINO LEVEL MAIN KITCHEN FLOOR SINK PLAN | X | X | ||||||
FS-2.5 | CASINO LEVEL MAIN KITCHEN PLUMBING SCHEDULE | X | X | ||||||
FS-2.6 | CASINO LEVEL MAIN KITCHEN MECHANICAL PLAN | X | X | ||||||
FS-2.7 | CASINO LEVEL MAIN KITCHEN BUILDING WORKS PLAN | X | X | ||||||
FS-2.8 | CASINO LEVEL MAIN KITCHEN ELEVATIONS | X | X | ||||||
FS-2.9 | CASINO LEVEL MAIN KITCHEN ELEVATIONS | X | X | ||||||
FS-2.10 | CASINO LEVEL MAIN KITCHEN HOOD DETAILS | X | X | ||||||
FS-3.0 | CASINO LEVEL BUFFET EQUIPMENT PLAN | X | X | ||||||
FS-3.0S | CASINO LEVEL BUFFET EQUIPMENT SCHEDULE | X | X | ||||||
FS-3.1 | CASINO LEVEL BUFFET ELECTRICAL PLAN | X | X | ||||||
FS-3.2 | CASINO LEVEL BUFFET ELECTRICAL SCHEDULE | X | X | ||||||
FS-3.3 | CASINO LEVEL BUFFET PLUMBING PLAN | X | X | ||||||
FS-3.4 | CASINO LEVEL BUFFET FLOOR SINK PLAN | X | X |
FOOD SERVICE | 36 of 54 | 6/19/2008 10:14 AM |
TEL 702.940.0000• FAX 702.940.0001
BULLETIN F: 15-JUN-08 | ||
RIVER CITY CASINO, St. Louis, Missouri• Project No. 141005 | ADDENDUM 1: 16-JUN-08 |
1 | F | ||||||||
SHEET | ISSUED FOR | ISSUED FOR | |||||||
NUMBER | SHEET TITLES | CONSTRUCTION | PLAN CHECK | ||||||
FOOD SERVICE | 16-Jun-08 | 15-Jun-08 | |||||||
REVISION | SHEET # | SHEET TITLES | |||||||
FS-3.5 | CASINO LEVEL BUFFET PLUMBING SCHEDULE | X | X | ||||||
FS-3.6 | CASINO LEVEL BUFFET MECHANICAL PLAN | X | X | ||||||
FS-3.7 | CASINO LEVEL BUFFET BUILDING WORKS PLAN | X | X | ||||||
FS-3.8 | CASINO LEVEL BUFFET ELEVATIONS | X | X | ||||||
FS-3.9 | CASINO LEVEL BUFFET ELEVATIONS | X | X | ||||||
FS-3.10 | CASINO LEVEL BUFFET ELEVATIONS | X | X | ||||||
FS-3.11 | CASINO LEVEL BUFFET HOOD DETAILS | X | X | ||||||
FS-3.12 | CASINO LEVEL BUFFET HOOD DETAILS | X | X | ||||||
FS-4.0 | CASINO LEVEL EMPLOYEE DINING ROOM EQUIPMENT PLAN | X | X | ||||||
FS-4.1 | CASINO LEVEL EMPLOYEE DINING ROOM ELECTRICAL PLAN | X | X | ||||||
FS-4.2 | CASINO LEVEL EMPLOYEE DINING ROOM PLUMBING PLAN | X | X | ||||||
FS-4.3 | CASINO LEVEL EMPLOYEE DINING ROOM BLDG. WORKS PLAN | X | X | ||||||
FS-4.4 | CASINO LEVEL EMPLOYEE DINING ROOM ELEVATIONS | X | X | ||||||
FS-4.5 | CASINO LEVEL EMPLOYEE DINING ROOM HOOD DETAILS | X | X | ||||||
FS-5.0 | CASINO LEVEL FINE DINING — EQUIPMENT PLAN | X | X | ||||||
FS-5.S | CASINO LEVEL FINE DINING EQUIPMENT SCHEDULE | X | X | ||||||
FS-5.1 | CASINO LEVEL FINE DINING ELECTRICAL PLAN | X | X | ||||||
FS-5.2 | CASINO LEVEL FINE DINING ELECTRICAL SCHEDULE | X | X | ||||||
FS-5.3 | CASINO LEVEL FINE DINING PLUMBING PLAN | X | X | ||||||
FS-5.4 | CASINO LEVEL FINE DINING FLOOR SINK PLAN | X | X | ||||||
FS-5.5 | CASINO LEVEL FINE DINING PLUMBING SCHEDULE | X | X | ||||||
FS-5.6 | CASINO LEVEL FINE DINING MECHANICAL PLAN | X | X | ||||||
FS-5.7 | CASINO LEVEL FINE DINING BUILDING WORKS PLAN | X | X | ||||||
FS-5.8 | CASINO LEVEL FINE DINING ELEVATIONS | X | X | ||||||
FS-5.9 | CASINO LEVEL FINE DINING ELEVATIONS | X | X | ||||||
FS-5.10 | CASINO LEVEL FINE DINING KITCHEN HOOD DETAILS | X | X |
FOOD SERVICE | 37 of 54 | 6/19/2008 10:14 AM |
TEL 702.940.0000• FAX 702.940.0001
BULLETIN F: 15-JUN-08 | ||
RIVER CITY CASINO, St. Louis, Missouri• Project No. 141005 | ADDENDUM 1: 16-JUN-08 |
1 | F | ||||||||
SHEET | ISSUED FOR | ISSUED FOR | |||||||
NUMBER | SHEET TITLES | CONSTRUCTION | PLAN CHECK | ||||||
FOOD SERVICE | 16-Jun-08 | 15-Jun-08 | |||||||
REVISION | SHEET # | SHEET TITLES | |||||||
FS-6.0 | CASINO LEVEL 24 HOUR RESTAURANT EQUIPMENT PLAN | X | X | ||||||
FS-6.1 | CASINO LEVEL 24 HOUR RESTAURANT ELECTRICAL PLAN | X | X | ||||||
FS-6.2 | CASINO LEVEL 24 HOUR RESTAURANT PLUMBING PLAN | X | X | ||||||
FS-6.3 | CASINO LEVEL 24 HOUR RESTAURANT MECHANICAL PLAN | X | X | ||||||
FS-6.4 | CASINO LEVEL 24 HOUR RESTAURANT BLDG WORKS PLAN | X | X | ||||||
FS-6.5 | CASINO LEVEL 24 HOUR RESTAURANT ELEVATIONS 1 | X | X | ||||||
FS-6.6 | CASINO LEVEL 24 HOUR RESTAURANT ELEVATIONS 2 | X | X | ||||||
FS-6.7 | CASINO LEVEL 24 HOUR RESTAURANT HOOD DETAILS | X | X | ||||||
FS-7.0 | CASINO LEVEL ENTERTAINMENT BAR — EQUIP. PLAN | X | X | ||||||
FS-7.S | CASINO LEVEL ENTERTAINMENT BAR SCHEDULE | X | X | ||||||
FS-7.1 | CASINO LEVEL ENTERTAINMENT BAR — ELECT. PLAN | X | X | ||||||
FS-7.2 | CASINO LEVEL ENTERTAINMENT BAR — PLUMB. PLAN | X | X | ||||||
FS-7.3 | CASINO LEVEL ENTERTAINMENT BAR — FLOOR SINK PLAN | X | X | ||||||
FS-7.4 | CASINO LEVEL ENTERTAINMENT BAR — UTILITY SCHEDULE | X | X | ||||||
FS-7.5 | CASINO LEVEL ENTERTAINMENT BAR — MECH. PLAN | X | X | ||||||
FS-7.6 | CASINO LEVEL ENTERTAINMENT BAR — BUILDING WORKS PLAN | ||||||||
FS-7.7 | CASINO LEVEL ENTERTAINMENT BAR ELEVATIONS | X | X | ||||||
FS-8.0 | CASINO LEVEL CASINO BARS EQUIPMENT PLAN | X | X | ||||||
FS-8.S | CASINO LEVEL CASINO BARS SCHEDULE | X | X | ||||||
FS-8.1 | CASINO LEVEL CASINO BARS ELECTRICAL PLAN | X | X | ||||||
FS-8.2 | CASINO LEVEL CASINO BARS PLUMBING PLAN | X | X | ||||||
FS-8.3 | CASINO LEVEL CASINO BARS FLOOR SINK PLAN | X | X | ||||||
FS-8.4 | CASINO LEVEL CASINO BARS UTILITY SCHEDULE | X | X | ||||||
FS-8.5 | CASINO LEVEL CASINO BARS MECHANICAL PLAN | X | X | ||||||
FS-8.6 | CASINO LEVEL CASINO BARS BUILDING WORKS PLAN | X | X | ||||||
FS-8.7 | CASINO LEVEL CASINO BARS ELEVATIONS | X | X |
FOOD SERVICE | 38 of 54 | 6/19/2008 10:14 AM |
TEL 702.940.0000• FAX 702.940.0001
BULLETIN F: 15-JUN-08 | ||
RIVER CITY CASINO, St. Louis, Missouri• Project No. 141005 | ADDENDUM 1: 16-JUN-08 |
1 | F | ||||||||
SHEET | ISSUED FOR | ISSUED FOR | |||||||
NUMBER | SHEET TITLES | CONSTRUCTION | PLAN CHECK | ||||||
FOOD SERVICE | 16-Jun-08 | 15-Jun-08 | |||||||
REVISION | SHEET # | SHEET TITLES | |||||||
FS-9.0 | �� | CASINO LEVEL BEER HALL EQUIPMENT PLAN | X | X | |||||
FS-9.1 | CASINO LEVEL BEER HALL ELECTRICAL PLAN | X | X | ||||||
FS-9.2 | CASINO LEVEL BEER HALL PLUMBING PLAN | X | X | ||||||
FS-9.3 | CASINO LEVEL BEER HALL CONDUIT & FL. SINK PLAN | X | X | ||||||
FS-9.4 | CASINO LEVEL BEER HALL MECHANICAL & BLDG WORKS PLAN | X | X | ||||||
FS-9.5 | CASINO LEVEL BEER HALL ELEVATIONS | X | X | ||||||
FS-10.0 | CASINO LEVEL BEER GARDEN KITCHEN EQUIPMENT PLAN | X | X | ||||||
FS-10.1 | CASINO LEVEL BEER GARDEN KITCHEN ELECTRICAL PLAN | X | X | ||||||
FS-10.2 | CASINO LEVEL BEER GARDEN KITCHEN PLUMBING PLAN | X | X | ||||||
FS-10.3 | CASINO LEVEL BEER GARDEN KITCHEN MECHANICAL PLAN | X | X | ||||||
FS-10.4 | CASINO LEVEL BEER GARDEN KITCHEN BLDG. WORKS PLAN | X | X | ||||||
FS-10.5 | CASINO LEVEL BEER GARDEN KITCHEN ELEVATIONS | X | X | ||||||
FS-10.6 | CASINO LEVEL BEER GARDEN KITCHEN HOOD DETAILS | X | X | ||||||
FS-11.0 | CASINO LEVEL HIGH LIMIT/ BEVARAGE COUNTER EQUIPMENT PLAN | X | X | ||||||
FS-11.1 | CASINO LEVEL HIGH LIMIT/ BEVERAGE COUNTER ELECTRICAL PLAN | X | X | ||||||
FS-11.2 | CASINO LEVEL HIGH LIMIT/ BEVERAGE COUNTER PLUMBING PLAN | X | X | ||||||
FS-11.3 | CASINO LEVEL HIGH LIMIT/ BEVERAGE COUNTER BLDG WORKS PLAN | X | X | ||||||
FS-11.4 | CASINO LEVEL HIGH LIMIT/ BEVERAGE COUNTER ELEVATIONS | X | X | ||||||
FS-12.0 | CASINO LEVEL SOUTHEAST SERVICE BAR EQUIPMENT PLAN | X | X | ||||||
FS-12.1 | CASINO LEVEL SOUTHEAST SERVICE BAR ELECTRICAL PLAN | X | X | ||||||
FS-12.2 | CASINO LEVEL SOUTHEAST SERVICE BAR PLUMBING PLAN | X | X | ||||||
FS-12.3 | CASINO LEVEL SOUTHEAST SERVICE BAR BLDG WORKS PLAN | X | X | ||||||
FS-12.4 | CASINO LEVEL SOUTHEAST SERVICE BAR ELEVATIONS | X | X | ||||||
TOTAL FOOD SERVICE SHEETS | 102 | 102 |
FOOD SERVICE | 39 of 54 | 6/19/2008 10:14 AM |
TEL 702.940.0000• FAX 702.940.0001
BULLETIN F: 15-JUN-08 | ||
RIVER CITY CASINO, St. Louis, Missouri• Project No. 141005 | ADDENDUM 1: 16-JUN-08 |
1 | F | ||||||||
SHEET | ISSUED FOR | ISSUED FOR | |||||||
NUMBER | SHEET TITLES | CONSTRUCTION | PLAN CHECK | ||||||
INTERIOR DESIGN | 16-Jun-08 | 15-Jun-08 | |||||||
REVISION | SHEET # | SHEET TITLES | |||||||
10.1.0 | COVER SHEET | X | X | ||||||
10.1.1 | GENERAL NOTES, SYMBOL LEGENDS & ABBREVIATIONS | X | X | ||||||
10.1.2 | SHEET INDEX | X | X | ||||||
10.2.1 | FINISH & MATERIALS LIST — GRAND COURT | X | X | ||||||
10.2.2 | FINISH & MATERIALS LIST — 24 DINER | X | X | ||||||
10.2.3 | FINISH & MATERIALS LIST — BIERHAUS | X | X | ||||||
10.2.4 | FINISH & MATERIALS LIST — VIP | X | X | ||||||
10.2.5 | FINISH & MATERIALS LIST — CASINO | X | X | ||||||
10.2.5A | FINISH & MATERIALS LIST — CASINO | X | X | ||||||
10.2.5B | FINISH & MATERIALS LIST — CASINO | X | X | ||||||
10.2.6 | FINISH&MATERIALS LIST — BUFFET | X | X | ||||||
10.2.7 | FINISH & MATERIALS LIST — PROMENADE | X | X | ||||||
10.2.8 | FINISH & MATERIALS LIST — PUBLIC RESTROOMS | X | X | ||||||
10.2.9 | FINISH & MATERIALS LIST — COFFE SHOP | X | X | ||||||
11.1.1 | OVERALL MASTER LOCATION PLAN — CASINO LEVEL | X | X | ||||||
11.1.2 | OVERALL MASTER LOCATION PLAN — SECOND LEVEL | X | X | ||||||
1.1.100 | REFERENCE PLAN — GRAND COURT | X | X | ||||||
1.1.200 | REFLECTED CEILING PLAN — GRAND COURT | X | X | ||||||
1.2.201 | REFLECTED CEILING PLAN — GRAND COURT | X | X | ||||||
1.1.300 | POWER PLAN — GRAND COURT | X | X | ||||||
1.1.400 | FLOOR FINISH PLAN — GRAND COURT | X | X | ||||||
1.1.500 | FF & A PLAN — GRAND COURT | X | X | ||||||
1.1.600 | INTERIOR ELEVATIONS — GRAND COURT | X | X | ||||||
1.1.601 | INTERIOR ELEVATIONS — GRAND COURT | X | X | ||||||
1.1.602 | INTERIOR ELEVATIONS — GRAND COURT | X | X | ||||||
1.1.603 | INTERIOR ELEVATIONS — GRAND COURT | X | X |
FOOD SERVICE | 40 of 54 | 6/19/2008 10:14 AM |
TEL 702.940.0000• FAX 702.940.0001
BULLETIN F: 15-JUN-08 | ||
RIVER CITY CASINO, St. Louis, Missouri• Project No. 141005 | ADDENDUM 1: 16-JUN-08 |
1 | F | ||||||||
SHEET | ISSUED FOR | ISSUED FOR | |||||||
NUMBER | SHEET TITLES | CONSTRUCTION | PLAN CHECK | ||||||
INTERIOR DESIGN | 16-Jun-08 | 15-Jun-08 | |||||||
REVISION | SHEET # | SHEET TITLES | |||||||
1.1.604 | INTERIOR ELEVATIONS — GRAND COURT | X | X | ||||||
1.1.605 | INTERIOR ELEVATIONS — GRAND COURT | X | X | ||||||
1.1.606 | INTERIOR ELEVATIONS — GRAND COURT | X | X | ||||||
1.1.607 | INTERIOR ELEVATIONS — GRAND COURT | X | X | ||||||
1.1.608 | INTERIOR ELEVATIONS — GRAND COURT | X | X | ||||||
1.1.800 | INTERIOR ARCHITECTURE DETAILS — GRAND COURT | X | X | ||||||
1.1.801 | INTERIOR ARCHITECTURE DETAILS — GRAND COURT | X | X | ||||||
1.1.802 | INTERIOR ARCHITECTURE DETAILS — GRAND COURT | X | X | ||||||
1.1.803 | INTERIOR ARCHITECTURE DETAILS — GRAND COURT | X | X | ||||||
1.1.804 | INTERIOR ARCHITECTURE DETAILS — GRAND COURT | X | X | ||||||
1.1.805 | INTERIOR ARCHITECTURE DETAILS — GRAND COURT | X | X | ||||||
1.1.806 | INTERIOR ARCHITECTURE DETAILS — GRAND COURT | X | X | ||||||
1.1.900 | MILLWORK DETAILS — GRAND COURT | X | X | ||||||
1.1.901 | MILLWORK DETAILS — GRAND COURT | X | X | ||||||
1.1.902 | MILLWORK DETAILS — GRAND COURT | X | X | ||||||
1.2.100 | REFERENCE PLAN — 24 DINER | X | X | ||||||
1.2.200 | REFLECTED CEILING PLAN — 24 DINER | X | X | ||||||
1.2.300 | POWER PLAN — 24 DINER | X | X | ||||||
1.2.400 | FLOOR FINISH PLAN — 24 DINER | X | X | ||||||
1.2.500 | FF&A PLAN — 24 DINER | X | X | ||||||
1.2.600 | INTERIOR ELEVATIONS — 24 DINER | X | X | ||||||
1.2.800 | INTERIOR ARCHITECTURE DETAILS — 24 DINER | X | X | ||||||
1.2.801 | INTERIOR ARCHITECTURE DETAILS — 24 DINER | X | X | ||||||
1.2.802 | INTERIOR ARCHITECTURE DETAILS — 24 DINER | X | X | ||||||
1.2.803 | INTERIOR ARCHITECTURE DETAILS — 24 DINER | X | X | ||||||
1.2.900 | MILLWORK DETAILS — 24 DINER | X | X | ||||||
1.3.100 | REFERENCE PLAN — BIERHAUS | X | X |
INTERIOR DESIGN | 41 of 54 | 6/19/2008 10:14 AM |
TEL 702.940.0000• FAX 702.940.0001
BULLETIN F: 15-JUN-08 | ||
RIVER CITY CASINO, St. Louis, Missouri• Project No. 141005 | ADDENDUM 1: 16-JUN-08 |
1 | F | ||||||||
SHEET | ISSUED FOR | ISSUED FOR | |||||||
NUMBER | SHEET TITLES | CONSTRUCTION | PLAN CHECK | ||||||
INTERIOR DESIGN | 16-Jun-08 | 15-Jun-08 | |||||||
REVISION | SHEET # | SHEET TITLES | |||||||
1.3.200 | REFLECTED CEILING PLAN — BIERHAUS | X | X | ||||||
1.3.300 | POWER PLAN — BIERHAUS | X | X | ||||||
1.3.400 | FLOOR FINISH PLAN — BIERHAUS | X | X | ||||||
1.3.500 | FF&A PLAN — BIERHAUS | X | X | ||||||
1.3.600 | INTERIOR ELEVATIONS — BIERHAUS | X | X | ||||||
1.3.601 | INTERIOR ELEVATIONS — BIERHAUS | X | X | ||||||
1.3.800 | INTERIOR ARCHITECTURE DETAILS — BIERHAUS | X | X | ||||||
1.3.801 | INTERIOR ARCHITECTURE DETAILS — BIERHAUS | X | X | ||||||
1.3.900 | MILLWORK DETAILS — BIERHAUS | X | X | ||||||
1.4.100 | REFERENCE PLAN — VIP | X | X | ||||||
1.4.100A | REFERENCE PLAN — VIP | X | X | ||||||
1.4.200 | REFLECTED CEILING PLAN — VIP | X | X | ||||||
1.4.300 | POWER PLAN — VIP | X | X | ||||||
1.4.400 | FLOOR FINISH PLAN — VIP | X | X | ||||||
1.4.500 | FF&A PLAN — VIP | X | X | ||||||
1.4.600 | INTERIOR ELEVATIONS — VIP | X | X | ||||||
1.4.601 | INTERIOR ELEVATIONS — VIP | X | X | ||||||
1.4.800 | INTERIOR ARCHITECTURE DETAILS — VIP | X | X | ||||||
1.4.801 | INTERIOR ARCHITECTURE DETAILS — VIP | X | X | ||||||
1.4.900 | MILLWORK DETAILS — VIP | X | X | ||||||
1.5.1 | CASINO ZONING PLAN | X | X | ||||||
1.5.2 | CASINO ZONING REFLECTED CEILING PLAN | X | X | ||||||
1.5.100 | REFERENCE PLAN — CASINO A | X | X | ||||||
1.5.101 | REFERENCE PLAN — CASINO B | X | X | ||||||
1.5.102 | REFERENCE PLAN — CASINO C | X | X | ||||||
1.5.103 | REFERENCE PLAN — CASINO D | X | X | ||||||
1.5.104 | REFERENCE PLAN — CASINO E | X | X |
INTERIOR DESIGN | 42 of 54 | 6/19/2008 10:14 AM |
ARCHITECTS • PLANNERS
TEL 702.940.0000• FAX 702.940.0001
BULLETIN F: 15-JUN-08 | ||
RIVER CITY CASINO, St. Louis, Missouri• Project No. 141005 | ADDENDUM 1: 16-JUN-08 |
1 | F | ||||||||
SHEET | ISSUED FOR | ISSUED FOR | |||||||
NUMBER | SHEET TITLES | CONSTRUCTION | PLAN CHECK | ||||||
INTERIOR DESIGN | 16-Jun-08 | 15-Jun-08 | |||||||
REVISION | SHEET # | SHEET TITLES | |||||||
1.5.200 | REFLECTED CEILING PLAN — CASINO A | X | X | ||||||
1.5.201 | REFLECTED CEILING PLAN — CASINO B | X | X | ||||||
1.5.202 | REFLECTED CEILING PLAN — CASINO C | X | X | ||||||
1.5.203 | REFLECTED CEILING PLAN — CASINO D | X | X | ||||||
1.5.204 | REFLECTED CEILING PLAN — CASINO E | X | X | ||||||
1.5.400 | FLOOR FINISH PLAN — CASINO A | X | X | ||||||
1.5.401 | FLOOR FINISH PLAN — CASINO B | X | X | ||||||
1.5.402 | FLOOR FINISH PLAN — CASINO C | X | X | ||||||
1.5.403 | FLOOR FINISH PLAN — CASINO D | X | X | ||||||
1.5.404 | FLOOR FINISH PLAN — CASINO E | X | X | ||||||
1.5.500 | FF&A PLAN — CASINO A | X | X | ||||||
1.5.501 | FF&A PLAN — CASINO B | X | X | ||||||
1.5.502 | FF&A PLAN — CASINO C | X | X | ||||||
1.5.503 | FF&A PLAN — CASINO D | X | X | ||||||
1.5.504 | FF&A PLAN — CASINO E | X | X | ||||||
1.5.600 | INTERIOR ELEVATIONS — CASINO | X | X | ||||||
1.5.601 | INTERIOR ELEVATIONS — CASINO | X | X | ||||||
1.5.602 | INTERIOR ELEVATIONS — CASINO | X | X | ||||||
1.5.603 | INTERIOR ELEVATIONS — CASINO | X | X | ||||||
1.5.603-A | INTERIOR ELEVATIONS — CASINO | X | X | ||||||
1.5.604 | INTERIOR ELEVATIONS — CASINO | X | X | ||||||
1.5.605 | INTERIOR ELEVATIONS — CASINO | X | X | ||||||
1.5.606 | INTERIOR ELEVATIONS — CASINO | X | X | ||||||
1.5.607 | INTERIOR ELEVATIONS — CASINO | X | X | ||||||
1.5.608 | INTERIOR ELEVATIONS — CASINO | X | X | ||||||
1.5.609 | INTERIOR ELEVATIONS — CASINO | X | X | ||||||
1.5.610 | INTERIOR ELEVATIONS — CASINO | X | X |
INTERIOR DESIGN | 43 of 54 | 6/19/2008 10:14 AM |
ARCHITECTS • PLANNERS
TEL 702.940.0000• FAX 702.940.0001
BULLETIN F: 15-JUN-08 | ||
RIVER CITY CASINO, St. Louis, Missouri• Project No. 141005 | ADDENDUM 1: 16-JUN-08 |
1 | F | ||||||||
SHEET | ISSUED FOR | ISSUED FOR | |||||||
NUMBER | SHEET TITLES | CONSTRUCTION | PLAN CHECK | ||||||
INTERIOR DESIGN | 16-Jun-08 | 15-Jun-08 | |||||||
REVISION | SHEET # | SHEET TITLES | |||||||
1.5.611 | INTERIOR ELEVATIONS — CASINO | X | X | ||||||
1.5.612 | INTERIOR ELEVATIONS — CASINO | X | X | ||||||
1.5.613 | INTERIOR ELEVATIONS — CASINO | X | X | ||||||
1.5.614 | ELEVATIONS — CASINO | X | X | ||||||
1.5.700 | ENLARGED HIGH LIMIT RESTROOMS — CASINO | X | X | ||||||
1.5.800 | INTERIOR ARCHITECTURE DETAILS — CASINO | X | X | ||||||
1.5.801 | INTERIOR ARCHITECTURE DETAILS — CASINO | X | X | ||||||
1.5.802 | INTERIOR ARCHITECTURE DETAILS — CASINO | X | X | ||||||
1.5.803 | INTERIOR ARCHITECTURE DETAILS — CASINO | X | X | ||||||
1.5.804 | INTERIOR ARCHITECTURE DETAILS — CASINO | X | X | ||||||
1.5.805 | INTERIOR ARCHITECTURE DETAILS — CASINO | X | X | ||||||
1.5.806 | INTERIOR ARCHITECTURE DETAILS — CASINO | X | X | ||||||
1.5.807 | INTERIOR ARCHITECTURE DETAILS — CASINO | X | X | ||||||
1.5.808 | INTERIOR ARCHITECTURE DETAILS — CASINO | X | X | ||||||
1.5.809 | INTERIOR ARCHITECTURE DETAILS — CASINO | X | X | ||||||
1.5.810 | INTERIOR ARCHITECTURE DETAILS — CASINO | X | X | ||||||
1.5.811 | INTERIOR ARCHITECTURE DETAILS — CASINO | X | X | ||||||
1.5.812 | INTERIOR ARCHITECTURE DETAILS — CASINO | X | X | ||||||
1.5.813 | INTERIOR ARCHITECTURE DETAILS — CASINO | X | X | ||||||
1.5.900 | MILLWORK DETAILS — CASINO | X | X | ||||||
1.5.901 | MILLWORK DETAILS — CASINO | X | X | ||||||
1.5.902 | MILLWORK DETAILS — CASINO | X | X | ||||||
1.5.903 | MILLWORK DETAILS — CASINO | X | X | ||||||
1.5.904 | MILLWORK DETAILS — CASINO | X | X | ||||||
1.5.906 | MILLWORK DETAILS — CASINO | X | X | ||||||
1.6.100 | REFERENCE PLAN — BUFFET | X | X |
INTERIOR DESIGN | 44 of 54 | 6/19/2008 10:14 AM |
ARCHITECTS • PLANNERS
TEL 702.940.0000• FAX 702.940.0001
BULLETIN F: 15-JUN-08 | ||
RIVER CITY CASINO, St. Louis, Missouri• Project No. 141005 | ADDENDUM 1: 16-JUN-08 |
1 | F | ||||||||
SHEET | ISSUED FOR | ISSUED FOR | |||||||
NUMBER | SHEET TITLES | CONSTRUCTION | PLAN CHECK | ||||||
INTERIOR DESIGN | 16-Jun-08 | 15-Jun-08 | |||||||
REVISION | SHEET # | SHEET TITLES | |||||||
1.6.200 | REFLECTED CEILING PLAN — BUFFET | X | X | ||||||
1.6.300 | POWER PLAN — BUFFET | X | X | ||||||
1.6.400 | FLOOR FINISH PLAN — BUFFET | X | X | ||||||
1.6.500 | FF&A PLAN — BUFFET | X | X | ||||||
1.6.600 | INTERIOR ELEVATIONS — BUFFET | X | X | ||||||
1.6.601 | INTERIOR ELEVATIONS — BUFFET | X | X | ||||||
1.6.602 | INTERIOR ELEVATIONS — BUFFET | X | X | ||||||
1.6.603 | INTERIOR ELEVATIONS — BUFFET | X | X | ||||||
1.6.800 | INTERIOR ARCHITECTURE DETAILS — BUFFET | X | X | ||||||
1.6.900 | MILLWORK DETAILS — BUFFET | X | X | ||||||
1.6.901 | MILLWORK DETAILS — BUFFET | X | X | ||||||
1.6.902 | MILLWORK DETAILS — BUFFET | X | X | ||||||
1.6.903 | MILLWORK DETAILS — BUFFET | X | X | ||||||
1.7.100 | REFERENCE PLAN — PROMENADE | X | X | ||||||
1.7.200 | REFLECTED CEILING PLAN — PROMENADE | X | X | ||||||
1.7.300 | POWER PLAN — PROM FLOOR FINISH PLAN — PROMENADE | X | X | ||||||
1.7.400 | FF&A PLAN — PROMENADE | X | X | ||||||
1.7.600 | INTERIOR ELEVATIONS — PROMENADE | X | X | ||||||
1.7.601 | INTERIOR ELEVATIONS — PROMENADE | X | X | ||||||
1.8.100 | REFERENCE PLAN — PUBLIC RESTROOMS | X | X | ||||||
1.8.100A | PLUMBING FIXTURE REF. PLAN — PUBLIC RESTROOMS | X | X | ||||||
1.8.101 | REFERENCE PLAN — PUBLIC RESTROOMS | X | X | ||||||
1.8.101A | PLUMBING REF. PLAN — PUBLIC RESTROOMS | X | X | ||||||
1.8.200 | REFLECTED CEILING PLAN — PUBLIC RESTROOMS | X | X | ||||||
1.8.201 | REFLECTED CEILING PLAN — PUBLIC RESTROOMS | X | X | ||||||
1.8.300 | POWER PLAN — PUBLIC RESTROOMS | X | X | ||||||
1.8.301 | POWER PLAN — PUBLIC RESTROOMS | X | X |
INTERIOR DESIGN | 45 of 54 | 6/19/2008 10:14 AM |
ARCHITECTS • PLANNERS
TEL 702.940.0000• FAX 702.940.0001
BULLETIN F: 15-JUN-08 | ||
RIVER CITY CASINO, St. Louis, Missouri• Project No. 141005 | ADDENDUM 1: 16-JUN-08 |
1 | F | ||||||||
SHEET | ISSUED FOR | ISSUED FOR | |||||||
NUMBER | SHEET TITLES | CONSTRUCTION | PLAN CHECK | ||||||
INTERIOR DESIGN | 16-Jun-08 | 15-Jun-08 | |||||||
REVISION | SHEET # | SHEET TITLES | |||||||
1.8.400 | FLOOR FINISH PLAN — PUBLIC RESTROOMS | X | X | ||||||
1.8.401 | FLOOR FINISH PLAN — PUBLIC RESTROOMS | X | X | ||||||
1.8.500 | FF&A PLAN — PUBLIC RESTROOMS | X | X | ||||||
1.8.501 | FF&A PLAN — PUBLIC RESTROOMS | X | X | ||||||
1.8.600 | INTERIOR ELEVATIONS — PUBLIC RESTROOMS | X | X | ||||||
1.8.601 | INTERIOR ELEVATIONS — PUBLIC RESTROOMS | X | X | ||||||
1.8.602 | INTERIOR ELEVATIONS — PUBLIC RESTROOMS | X | X | ||||||
1.8.603 | INTERIOR ELEVATIONS — PUBLIC RESTROOMS | X | X | ||||||
1.8.604 | INTERIOR ELEVATIONS — PUBLIC RESTROOMS | X | X | ||||||
1.8.605 | INTERIOR ELEVATIONS — PUBLIC RESTROOMS | X | X | ||||||
1.8.606 | INTERIOR ELEVATIONS — PUBLIC RESTROOMS | X | X | ||||||
1.8.607 | INTERIOR ELEVATIONS — PUBLIC RESTROOMS | X | X | ||||||
1.8.608 | INTERIOR ELEVATIONS — PUBLIC RESTROOMS | X | X | ||||||
1.8.609 | INTERIOR ELEVATIONS — PUBLIC RESTROOMS | X | X | ||||||
1.8.800 | INTERIOR ARCHITECTURE DETAILS | X | X | ||||||
1.8.900 | MILLWORK DETAILS | X | X | ||||||
1.8.901 | MILLWORK DETAILS | X | X | ||||||
1.8.902 | MILLWORK DETAILS | X | X | ||||||
1.9.100 | REFERENCE PLAN & RCP — COFFEE SHOP | X | X | ||||||
1.9.200 | POWER, FLOOR FIN & FF& A PLAN — COFFEE SHOP | X | X | ||||||
1.9.600 | INTERIOR ELEVATIONS — COFFEE SHOP | X | X | ||||||
1.9.800 | INTERIOR ARCHITECTURE DETAILS — COFFEE HOUSE | X | X | ||||||
1.9.801 | INTERIOR ARCHITECTURE DETAILS — COFFEE HOUSE | X | X | ||||||
1.9.900 | MILLWORK DETAILS — COFFEE SHOP | X | X | ||||||
1.9.901 | MILLWORK DETAILS — COFFEE SHOP | X | X | ||||||
1.9.902 | MILLWORK DETAILS — COFFEE SHOP | X | X | ||||||
1.12.1 | PLUMBING SCHEDULE | X | X |
INTERIOR DESIGN | 46 of 54 | 6/19/2008 10:14 AM |
ARCHITECTS • PLANNERS
TEL 702.940.0000• FAX 702.940.0001
BULLETIN F: 15-JUN-08 | ||
RIVER CITY CASINO, St. Louis, Missouri• Project No. 141005 | ADDENDUM 1: 16-JUN-08 |
1 | F | ||||||||
SHEET | ISSUED FOR | ISSUED FOR | |||||||
NUMBER | SHEET TITLES | CONSTRUCTION | PLAN CHECK | ||||||
INTERIOR DESIGN | 16-Jun-08 | 15-Jun-08 | |||||||
REVISION | SHEET # | SHEET TITLES | |||||||
1.12.2 | PLUMBING & SPECIAL EQUIPMENT SCHEDULE | X | X | ||||||
1.12.3 | PLUMBING & SPECIAL EQUIPMENT SCHEDULE | X | X | ||||||
1.12.4 | PLUMBING & SPECIAL EQUIPMENT SCHEDULE | X | X | ||||||
1.12.5 | PLUMBING & SPECIAL EQUIPMENT SCHEDULE | X | X | ||||||
1.12.6 | PLUMBING & SPECIAL EQUIPMENT SCHEDULE | X | X | ||||||
1.12.7 | PLUMBING & SPECIAL EQUIPMENT SCHEDULE | X | X | ||||||
1.12.8 | PLUMBING & SPECIAL EQUIPMENT SCHEDULE | X | X | ||||||
1.12.9 | PLUMBING & SPECIAL EQUIPMENT SCHEDULE | X | X | ||||||
1.12.10 | PLUMBING & SPECIAL EQUIPMENT SCHEDULE | X | X | ||||||
TOTAL INTERIOR DESIGN SHEETS | 196 | 196 | |||||||
INTERIOR DESIGN | 47 of 54 | 6/19/2008 10:14 AM |
ARCHITECTS • PLANNERS
TEL 702.940.0000• FAX 702.940.0001
BULLETIN F: 15-JUN-08 | ||
RIVER CITY CASINO, St. Louis, Missouri• Project No. 141005 | ADDENDUM 1: 16-JUN-08 |
1 | F | ||||||||
SHEET | ISSUED FOR | ISSUED FOR | |||||||
NUMBER | SHEET TITLES | CONSTRUCTION | PLAN CHECK | ||||||
LANDSCAPE | 16-Jun-08 | 15-Jun-08 | |||||||
REVISION | SHEET # | SHEET TITLES | |||||||
L-0.01 | COVER SHEET | X | X | ||||||
L-0.02 | SHEET INDEX | X | X | ||||||
L-0.03 | SITE ORIENTATION/ SHEET LAYOUT | X | X | ||||||
L-0.04 | GENERAL CONSTRUCTION NOTES & LEGENDS | X | X | ||||||
L-1.00 | FINISH SCHEDULE | X | X | ||||||
L-2.01 | GRADING & DRAINAGE CONCEPT PLAN | X | X | ||||||
L-2.02 | GRADING & DRAINAGE CONCEPT PLAN | X | X | ||||||
L-2.03 | GRADING & DRAINAGE CONCEPT PLAN | X | X | ||||||
L-2.04 | GRADING & DRAINAGE CONCEPT PLAN | X | X | ||||||
L-2.05 | GRADING & DRAINAGE CONCEPT PLAN | X | X | ||||||
L-2.06 | GRADING & DRAINAGE CONCEPT PLAN | X | X | ||||||
L-2.07 | GRADING & DRAINAGE CONCEPT PLAN | X | X | ||||||
L-2.08 | GRADING & DRAINAGE CONCEPT PLAN | X | X | ||||||
L-2.09 | GRADING & DRAINAGE CONCEPT PLAN — INTERIOR GRAND COURT | X | X | ||||||
L-3.01 | CONSTRUCTION PLAN CALLOUT | X | X | ||||||
L-3.02 | CONSTRUCTION PLAN CALLOUT | X | X | ||||||
L-3.03 | CONSTRUCTION PLAN CALLOUT | X | X | ||||||
L-3.04 | CONSTRUCTION PLAN CALLOUT | X | X | ||||||
L-3.05 | CONSTRUCTION PLAN CALLOUT | X | X | ||||||
L-3.06 | CONSTRUCTION PLAN CALLOUT | X | X | ||||||
L-3.07 | CONSTRUCTION PLAN CALLOUT | X | X | ||||||
L-3.08 | CONSTRUCTION PLAN CALLOUT | X | X | ||||||
L-3.09 | CONSTRUCTION PLAN CALLOUT — INTERIOR | X | X | ||||||
L-4.01 | CONSTRUCTION PLAN LAYOUT | X | X | ||||||
L-4.02 | CONSTRUCTION PLAN LAYOUT | X | X | ||||||
L-4.03 | CONSTRUCTION PLAN LAYOUT | X | X | ||||||
L-4.04 | CONSTRUCTION PLAN LAYOUT | X | X |
LANDSCAPE | 48 of 54 | 6/19/2008 10:14 AM |
ARCHITECTS • PLANNERS
TEL 702.940.0000• FAX 702.940.0001
BULLETIN F: 15-JUN-08 | ||
RIVER CITY CASINO, St. Louis, Missouri• Project No. 141005 | ADDENDUM 1: 16-JUN-08 |
1 | F | ||||||||
SHEET | ISSUED FOR | ISSUED FOR | |||||||
NUMBER | SHEET TITLES | CONSTRUCTION | PLAN CHECK | ||||||
LANDSCAPE | 16-Jun-08 | 15-Jun-08 | |||||||
REVISION | SHEET # | SHEET TITLES | |||||||
L-4.05 | CONSTRUCTION PLAN LAYOUT | X | X | ||||||
L-4.06 | CONSTRUCTION PLAN LAYOUT | X | X | ||||||
L-4.07 | CONSTRUCTION PLAN LAYOUT | X | X | ||||||
L-4.08 | CONSTRUCTION PLAN LAYOUT | X | X | ||||||
L-4.09 | CONSTRUCTION PLAN LAYOUT — INTERIOR | X | X | ||||||
L-5.01 | CONSTRUCTION PLAN PAVING & TILE | X | X | ||||||
L-5.02 | CONSTRUCTION PLAN PAVING&TILE | X | X | ||||||
L-5.03 | CONSTRUCTION PLAN PAVING & TILE | X | X | ||||||
L-5.04 | CONSTRUCTION PLAN PAVING & TILE | X | X | ||||||
L-5.05 | CONSTRUCTION PLAN PAVING&TILE | X | X | ||||||
L-5.06 | CONSTRUCTION PLAN PAVING & TILE | X | X | ||||||
L-5.07 | CONSTRUCTION PLAN PAVING & TILE | X | X | ||||||
L-5.08 | CONSTRUCTION PLAN PAVING & TILE | X | X | ||||||
L-6.01 | CONSTRUCTION DETAILS | X | X | ||||||
L-6.02 | CONSTRUCTION DETAILS | X | X | ||||||
L-6.03 | CONSTRUCTION DETAILS | X | X | ||||||
L-6.04 | CONSTRUCTION DETAILS | X | X | ||||||
L-6.05 | CONSTRUCTION DETAILS | X | X | ||||||
L-7.00 | IRRIGATION LEGEND AND NOTES | X | X | ||||||
L-7.01 | IRRIGATION PLAN TREES | X | X | ||||||
L-7.02 | IRRIGATION PLAN TREES | X | X | ||||||
L-7.03 | IRRIGATION PLAN TREES | X | X | ||||||
L-7.04 | IRRIGATION PLAN TREES | X | X | ||||||
L-7.05 | IRRIGATION PLAN TREES | X | X | ||||||
L-7.06 | IRRIGATION PLAN TREES | X | X | ||||||
L-7.07 | IRRIGATION PLAN TREES | X | X | ||||||
L-7.08 | IRRIGATION PLAN TREES | X | X |
LANDSCAPE | 49 of 54 | 6/19/2008 10:14 AM |
ARCHITECTS • PLANNERS
TEL 702.940.0000• FAX 702.940.0001
BULLETIN F: 15-JUN-08 | ||
RIVER CITY CASINO, St. Louis, Missouri• Project No. 141005 | ADDENDUM 1: 16-JUN-08 |
1 | F | ||||||||
SHEET | ISSUED FOR | ISSUED FOR | |||||||
NUMBER | SHEET TITLES | CONSTRUCTION | PLAN CHECK | ||||||
LANDSCAPE | 16-Jun-08 | 15-Jun-08 | |||||||
REVISION | SHEET # | SHEET TITLES | |||||||
L-7.09 | IRRIGATION PLAN TREES | X | X | ||||||
L-7.10 | IRRIGATION PLAN TREES | X | X | ||||||
L-7.11 | IRRIGATION PLAN TREES | X | X | ||||||
L-7.12 | IRRIGATION PLAN TREES | X | X | ||||||
L-7.13 | IRRIGATION PLAN TREES | X | X | ||||||
L-7.14 | IRRIGATION PLAN TREES | X | X | ||||||
L-7.15 | IRRIGATION PLAN TREES — INTERIOR | X | X | ||||||
L-7.16 | IRRIGATION PLAN SHRUBS | X | X | ||||||
L-7.17 | IRRIGATION PLAN SHRUBS | X | X | ||||||
L-7.18 | IRRIGATION PLAN SHRUBS | X | X | ||||||
L-7.19 | IRRIGATION PLAN SHRUBS | X | X | ||||||
L-7.20 | IRRIGATION PLAN SHRUBS | X | X | ||||||
L-7.21 | IRRIGATION PLAN SHRUBS | X | X | ||||||
L-7.22 | IRRIGATION PLAN SHRUBS | X | X | ||||||
L-7.23 | IRRIGATION PLAN SHRUBS | X | X | ||||||
L-7.24 | IRRIGATION PLAN SHRUBS | X | X | ||||||
L-7.25 | IRRIGATION PLAN SHRUBS | X | X | ||||||
L-7.26 | IRRIGATION PLAN SHRUBS | X | X | ||||||
L-7.27 | IRRIGATION PLAN SHRUBS | X | X | ||||||
L-7.28 | IRRIGATION PLAN SHRUBS | X | X | ||||||
L-7.29 | IRRIGATION PLAN SHRUBS | X | X | ||||||
L-7.30 | IRRIGATION PLAN SHRUBS | X | X | ||||||
L-8.01 | IRRIGATION DETAILS | X | X | ||||||
L-8.02 | IRRIGATION DETAILS | X | X | ||||||
L-8.03 | IRRIGATION DETAIL | X | X | ||||||
L-9.01 | PLANTING PLAN (TREES & G.C.) | X | X | ||||||
L-9.02 | PLANTING PLAN (TREES & G.C.) | X | X |
LANDSCAPE | 50 of 54 | 6/19/2008 10:14 AM |
ARCHITECTS • PLANNERS
TEL 702.940.0000• FAX 702.940.0001
BULLETIN F: 15-JUN-08 | ||
RIVER CITY CASINO, St. Louis, Missouri• Project No. 141005 | ADDENDUM 1: 16-JUN-08 |
1 | F | ||||||||
SHEET | ISSUED FOR | ISSUED FOR | |||||||
NUMBER | SHEET TITLES | CONSTRUCTION | PLAN CHECK | ||||||
LANDSCAPE | 16-Jun-08 | 15-Jun-08 | |||||||
REVISION | SHEET # | SHEET TITLES | |||||||
L-9.03 | PLANTING PLAN (TREES & G.C.) | X | X | ||||||
L-9.04 | PLANTING PLAN (TREES & G.C.) | X | X | ||||||
L-9.05 | PLANTING PLAN (TREES & G.C.) | X | X | ||||||
L-9.06 | PLANTING PLAN (TREES & G.C.) | X | X | ||||||
L-9.07 | PLANTING PLAN (TREES & G.C.) | X | X | ||||||
L-9.08 | PLANTING PLAN (TREES & G.C.) | X | X | ||||||
L-9.09 | PLANTING PLAN (TREES & G.C.) | X | X | ||||||
L-9.10 | PLANTING PLAN (TREES & G.C.) | X | X | ||||||
L-9.11 | PLANTING PLAN (TREES & G.C.) | X | X | ||||||
L-9.12 | PLANTING PLAN (TREES & G.C.) | X | X | ||||||
L-9.13 | PLANTING PLAN (TREES&G.C.) | X | X | ||||||
L-9.14 | PLANTING PLAN (TREES & G.C.) | X | X | ||||||
L-9.15 | PLANTING PLAN (TREES & G.C.) — INTERIOR GRAND COURT | X | X | ||||||
L-10.01 | PLANTING PLAN (SHRUBS&VINES) | X | X | ||||||
L-10.02 | PLANTING PLAN (SHRUBS&VINES) | X | X | ||||||
L-10.03 | PLANTING PLAN (SHRUBS&VINES) | X | X | ||||||
L-10.04 | PLANTING PLAN (SHRUBS&VINES) | X | X | ||||||
L-10.05 | PLANTING PLAN (SHRUBS&VINES) | X | X | ||||||
L-10.06 | PLANTING PLAN (SHRUBS&VINES) | X | X | ||||||
L-10.07 | PLANTING PLAN (SHRUBS&VINES) | X | |||||||
L-10.08 | PLANTING PLAN (SHRUBS&VINES) | X | X | ||||||
L-10.09 | PLANTING PLAN (SHRUBS&VINES) | X | X | ||||||
L-10.10 | PLANTING PLAN (SHRUBS&VINES) | X | X | ||||||
L-10.11 | PLANTING PLAN (SHRUBS&VINES) | X | X | ||||||
L-10.12 | PLANTING PLAN (SHRUBS&VINES) | X | X | ||||||
L-10.13 | PLANTING PLAN (SHRUBS&VINES) | X | X | ||||||
L-10.14 | PLANTING PLAN (SHRUBS&VINES) | X | X |
LANDSCAPE | 51 of 54 | 6/19/2008 10:14 AM |
ARCHITECTS • PLANNERS
TEL 702.940.0000• FAX 702.940.0001
BULLETIN F: 15-JUN-08 | ||
RIVER CITY CASINO, St. Louis, Missouri• Project No. 141005 | ADDENDUM 1: 16-JUN-08 |
1 | F | ||||||||
SHEET | ISSUED FOR | ISSUED FOR | |||||||
NUMBER | SHEET TITLES | CONSTRUCTION | PLAN CHECK | ||||||
LANDSCAPE | 16-Jun-08 | 15-Jun-08 | |||||||
REVISION | SHEET # | SHEET TITLES | |||||||
L-10.15 | PLANTING PLAN (SHRUBS&VINES) — INTERIOR GRAND COURT | X | X | ||||||
L-11.01 | PLANTING DETAILS | X | X | ||||||
L-11.02 | PLANTING DETAILS | X | X | ||||||
TOTAL LANDSCAPE SHEETS | 111 | 111 | |||||||
LANDSCAPE | 52 of 54 | 6/19/2008 10:14 AM |
ARCHITECTS • PLANNERS
TEL 702.940.0000 • FAX 702.940.0001
BULLETIN F: 15-JUN-08 | ||
RIVER CITY CASINO, St. Louis, Missouri• Project No. 141005 | ADDENDUM 1: 16-JUN-08 |
1 | F | ||||||||
SHEET | ISSUED FOR | ISSUED FOR | |||||||
NUMBER | SHEET TITLES | CONSTRUCTION | PLAN CHECK | ||||||
NAVAL ARCHITECT | 16-Jun-08 | 15-Jun-08 | |||||||
REVISION | SHEET # | SHEET TITLES | |||||||
NA-W40 | DRAWING INDEX | X | X | ||||||
NA-A11 | HOLD ARRANGEMENT | X | X | ||||||
NA-A12 | MAIN DECK ARRANGEMENT | X | X | ||||||
NA-A15 | TYPICAL SECTIONS | X | X | ||||||
NA-A16 | PILASTER DETAILS | X | X | ||||||
NA-A24 | MAIN DECK STRUCTURAL SLAB | X | X | ||||||
NA-A25 | BARGE BOTTOM KEEL SLAB ARRANGEMENT | X | X | ||||||
NA-A35 | TANK CAPACITY PLAN | X | X | ||||||
NA-A36.0 | WIREMOLD FLOORING ARRANGEMENT & DETAILS | X | X | ||||||
NA-A36.1 | WIREMOLD FLOORING INSTALLATION & DETAILS | X | X | ||||||
NA-A36.2 | WIREMOLD FLOORING INSTALLATION&DETAILS | X | X | ||||||
NA-A37.0 | PRECAST PANEL SCHEDULE | X | X | ||||||
NA-A37.1 | PRECAST BULKHEAD DETAILS | X | X | ||||||
NA-A37.2 | PRECAST BULKHEAD DETAILS | X | X | ||||||
NA-A37.3 | PRECAST BULKHEAD DETAILS | X | X | ||||||
NA-A37.4 | PRECAST BULKHEAD DETAILS | X | X | ||||||
NA-A38 | TANK ACCESS PLAN | X | X | ||||||
NA-F30.0 | RAMP ARRANGEMENT & DETAILS | X | X | ||||||
NA-F30.1 | RAMP ARRANGEMENT & DETAILS | X | X | ||||||
NA-F30.2 | RAMP ARRANGEMENT & DETAILS | X | X | ||||||
NA-F31 | RUBRAIL & ACCESS PLAN | X | X | ||||||
NA-P10.0 | BILGE AND BALLAST DIAGRAM | X | X | ||||||
NA-P10.1 | BILGE AND BALLAST DIAGRAM | X | X | ||||||
NA-P38 | TANK VENTS DIAGRAM | X | X | ||||||
NA-P44.0 | SEWAGE PIPING DIAGRAM | X | X | ||||||
NA-P44.1 | SEWAGE PIPING DIAGRAM | X | X | ||||||
NA-P44.2 | SEWAGE PIPING DIAGRAM | X | X |
NAVAL | 53 of 54 | 6/19/2008 10:14 AM |
ARCHITECTS • PLANNERS
TEL 702.940.0000 • FAX 702.940.0001
BULLETIN F: 15-JUN-08 | ||
RIVER CITY CASINO, St. Louis, Missouri• Project No. 141005 | ADDENDUM 1: 16-JUN-08 |
1 | F | ||||||||
SHEET | ISSUED FOR | ISSUED FOR | |||||||
NUMBER | SHEET TITLES | CONSTRUCTION | PLAN CHECK | ||||||
NAVAL ARCHITECT | 16-Jun-08 | 15-Jun-08 | |||||||
REVISION | SHEET # | SHEET TITLES | |||||||
NA-P44.3 | SEWAGE PIPING DIAGRAM | X | X | ||||||
NA-P44.4 | SEWAGE PIPING DIAGRAM | X | X | ||||||
NA-E25 | HOLD LIGHTING PLAN | X | X | ||||||
TOTAL NAVAL ARCHITECT SHEETS | 30 | 30 |
NAVAL | 54 of 54 | 6/19/2008 10:14 AM |

DWG. NO. | DRAWING TITLE | DRAWING DATE | ||
SPECIFICATIONS | ||||
CS | COVER SHEET | 06-15-2008 | ||
00 01 10 | TABLE OF CONTENTS | 06-15-2008 | ||
DIVISION 00 | ||||
00 63 13 | REQUESTS FOR INFORMATION/INTERPRETATION | 06-15-2008 | ||
00 63 25 | SUBSTITUTION REQUEST (AFTER THE BIDDING PHASE) | 06-15-2008 | ||
DIVISION 01 | ||||
01 11 00 | SUMMARY OF WORK | 06-15-2008 | ||
01 22 00 | UNIT PRICES | 06-15-2008 | ||
01 23 00 | ALTERNATES | 06-15-2008 | ||
01 26 13 | CONTRACTOR’S REQUEST FOR INFORMATION/ INTERPRETATION | 06-15-2008 | ||
01 33 00 | SUBMITTALS | 06-15-2008 | ||
01 42 00 | REFERENCE STANDARDS | 06-15-2008 | ||
01 45 00 | QUALITY CONTROL | 06-15-2008 | ||
01 50 00 | CONSTRUCTION FACILITIES AND TEMPORARY CONTROLS | 06-15-2008 | ||
01 60 00 | MATERIAL AND EQUIPMENT | 06-15-2008 | ||
01 73 00 | EXECUTION REQUIREMENTS | 06-15-2008 | ||
01 73 29 | CUTTING AND PATCHING | 06-15-2008 | ||
01 77 00 | CONTRACT CLOSEOUT | 06-15-2008 | ||
DIVISION 2 | ||||
02810 | LANDSCAPE IRRIGATION SYSTEM | 06-15-2008 | ||
02905 | LANDSCAPE PLANTING | 06-15-2008 | ||
DIVISION 3 | ||||
03 05 05 | FLY ASH | 06-15-2008 | ||
03 10 00 | CONCRETE FORMWORK | 06-15-2008 | ||
03 20 00 | CONCRETE REINFORCEMENT | 06-15-2008 | ||
03 30 00 | CAST-IN-PLACE CONCRETE | 06-15-2008 | ||
03 35 33 | SPECIAL CONCRETE FINISHES | 06-15-2008 | ||
03 49 00 | GLASS-FIBER REINFORCED CONCRETE (GFRC) | 06-15-2008 | ||
DIVISION 4 | ||||
04 01 20.52 | UNIT MASONRY CLEANING | 06-15-2008 | ||
04 05 15 | MORTAR AND MASONRY GROUT | 06-15-2008 | ||
04 05 23 | MASONRY ACCESSORIES | 06-15-2008 | ||
04 21 13 | BRICK UNIT MASONRY | 06-15-2008 | ||
04 21 13.13 | THIN BRICK VENEER | 06-15-2008 | ||
04 22 00 | CONCRETE MASONRY UNITS | 06-15-2008 | ||
04 43 13 | STONE MASONRY VENEER | 06-15-2008 | ||
04 73 16 | SIMULATED STONE VENEER | 06-15-2008 | ||
DIVISION 5 | ||||
05 10 00 | STRUCTURAL STEEL FRAMING | 06-15-2008 | ||
05 21 19 | OPEN-WEB STEEL JOISTS | 06-15-2008 | ||
05 31 00 | STEEL DECK | 06-15-2008 | ||
05 36 00 | STEEL COMPOSITE DECK | 06-15-2008 | ||
05 41 00 | STRUCTURAL METAL STUD FRAMING | 06-15-2008 |
DWG. NO. | DRAWING TITLE | DRAWING DATE | ||
05 50 00 | METAL FABRICATIONS | 06-15-2008 | ||
05 51 00 | METAL STAIRS | 06-15-2008 | ||
05 52 00 | METAL RAILINGS | 06-15-2008 | ||
05 70 00 | DECORATIVE METAL | 06-15-2008 | ||
05 73 00 | ORNAMENTAL RAILINGS | 06-15-2008 | ||
DIVISION 06 | ||||
06 10 53 | MISCELLANEOUS CARPENTRY | 06-15-2008 | ||
06 20 00 | FINISH CARPENTRY | 06-15-2008 | ||
06 40 00 | ARCHITECTURAL WOODWORK | 06-15-2008 | ||
06 60 00 | COATED POLYSTYRENE FABRICATIONS | 06-15-2008 | ||
06 82 00 | GLASS-FIBER REINFORCED PLASTIC FABRICATIONS | 06-15-2008 | ||
DIVISION 07 | ||||
07 13 13 | BITUMINOUS SHEET MEMBRANE WATERPROOFING | 06-15-2008 | ||
07 18 13 | PEDESTRIAN TRAFFIC COATING | 06-15-2008 | ||
07 19 00 | WATER REPELLENTS | 06-15-2008 | ||
07 21 00 | BUILDING INSULATION | 06-15-2008 | ||
07 24 19 | WATER MANAGED EXTERIOR INSULATION AND FINISH SYSTEM | 06-15-2008 | ||
07 26 00 | WEATHER RESISTIVE BARRIERS | 06-15-2008 | ||
07 31 26 | SLATE SHINGLES | 06-15-2008 | ||
07 32 16 | CONCRETE ROOFING TILES | 06-15-2008 | ||
07 43 13 | METAL ROOF AND WALL PANELS | 06-15-2008 | ||
07 54 23 | THERMOPLASTIC-POLYOLEFIN ROOFING | 06-15-2008 | ||
07 60 00 | FLASHING AND SHEET METAL | 06-15-2008 | ||
07 72 00 | ROOF ACCESSORIES | 06-15-2008 | ||
07 81 00 | SPRAY-APPLIED FIRE RESISTIVE MATERIALS | 06-15-2008 | ||
07 84 00 | FIRESTOPPING | 06-15-2008 | ||
07 88 00 | FIRE BARRIER DUCT WRAP | 06-15-2008 | ||
07 92 00 | JOINT SEALERS | 06-15-2008 | ||
07 92 19 | ACOUSTICAL SEALANTS | 06-15-2008 | ||
07 92 23 | FACADE SEALANTS | 06-15-2008 | ||
07 95 13 | EXPANSION JOINT COVER ASSEMBLIES | 06-15-2008 | ||
DIVISION 08 | ||||
08 11 13 | STEEL DOORS AND FRAMES | 06-15-2008 | ||
08 14 00 | WOOD DOORS | 06-15-2008 | ||
08 31 13 | ACCESS DOORS AND FRAMES | 06-15-2008 | ||
08 33 00 | COILING DOORS AND GRILLES | 06-15-2008 | ||
08 41 13 | ALUMINUM ENTRANCES AND STOREFRONTS | 06-15-2008 | ||
08 41 26 | INTERIOR ALUMINUM ENTRANCES AND STOREFRONTS | 06-15-2008 | ||
08 42 26 | ALL GLASS ENTRANCES | 06-15-2008 | ||
08 42 29.33 | LOW-ENERGY SWING ENTRANCE AUTOMATIC DOOR OPERATORS | 06-15-2008 | ||
08 42 33 | REVOLVING ENTRANCE DOORS | 06-15-2008 | ||
08 51 13.13 | ALUMINUM WINDOWS | 06-15-2008 | ||
08 63 00 | METAL-FRAMED SKYLIGHTS | 06-15-2008 | ||
08 71 00 | DOOR HARDWARE | 06-15-2008 | ||
08 80 00 | GLAZING | 06-15-2008 | ||
08 83 00 | MIRROR GLASS | 06-15-2008 | ||
08 91 00 | LOUVERS | 06-15-2008 | ||
DIVISION 09 | ||||
09 21 19 | SHAFT WALL ASSEMBLIES | 06-15-2008 | ||
09 22 16 | NON-STRUCTURAL METAL FRAMING | 06-15-2008 | ||
09 24 00 | PORTLAND CEMENT PLASTER (STUCCO) | 06-15-2008 | ||
09 26 13 | VENETIAN PLASTER | 06-15-2008 | ||
09 27 13 | GLASS FIBER REINFORCED GYPSUM (GFRG) | 06-15-2008 | ||
09 29 00 | GYPSUM BOARD | 06-15-2008 |
DWG. NO. | DRAWING TITLE | DRAWING DATE | ||
09 29 13 | EXTERIOR GYPSUM SHEATHING | 06-15-2008 | ||
09 30 00 | TILE | 06-15-2008 | ||
09 30 16 | QUARRY TILE | 06-15-2008 | ||
09 30 33 | NATURAL STONE TILE | 06-15-2008 | ||
09 51 00 | ACOUSTICAL AND SPECIALTY CEILINGS | 06-15-2008 | ||
09 54 26 | LINEAR WOOD CEILING SYSTEM | 06-15-2008 | ||
09 64 00 | WOOD FLOORING | 06-15-2008 | ||
09 65 16.13 | LINOLEUM SHEET FLOORING | 06-15-2008 | ||
09 65 19 | RESILIENT TILE FLOORING | 06-15-2008 | ||
09 68 00 | CARPET | 06-15-2008 | ||
09 69 00 | ACCESS FLOORING | 06-15-2008 | ||
09 72 00 | WALL COVERINGS | 06-15-2008 | ||
09 75 00 | INTERIOR STONE FACINGS | 06-15-2008 | ||
09 77 33 | FRP WALL PANELS | 06-15-2008 | ||
09 81 00 | ACOUSTICAL INSULATION | 06-15-2008 | ||
09 84 00 | ACOUSTICAL WALL PANELS | 06-15-2008 | ||
09 91 00 | PAINTING | 06-15-2008 | ||
09 94 13 | TEXTURED ACRYLIC COATING | 06-15-2008 | ||
DIVISION 10 | ||||
10 14 00 | SIGNAGE | 06-15-2008 | ||
10 21 13.16 | PLASTIC LAMINATE TOILET COMPARTMENTS | 06-15-2008 | ||
10 21 13.40 | STONE TOILET COMPARTMENTS | 06-15-2008 | ||
10 22 26 | OPERABLE PARTITIONS | 06-15-2008 | ||
10 26 00 | CORNER GUARDS | 06-15-2008 | ||
10 28 13 | TOILET ACCESSORIES | 06-15-2008 | ||
10 44 00 | FIRE PROTECTION SPECIALTIES | 06-15-2008 | ||
10 51 00 | LOCKERS | 06-15-2008 | ||
10 73 13 | FABRIC AWNINGS | 06-15-2008 | ||
DIVISION 11 | ||||
11 12 00 | PARKING CONTROL EQUIPMENT | 06-15-2008 | ||
11 13 00 | LOADING DOCK EQUIPMENT | 06-15-2008 | ||
11 23 43 | UNIFORM CONVEYOR SYSTEM | 06-15-2008 | ||
11 52 00 | AUDIO FISUAL MOUNTING SYSTEMS | 06-15-2008 | ||
11 82 26 | WASTE HANDLING EQUIPMENT | 06-15-2008 | ||
DIVISION 12 | ||||
12 26 40 | STONE COUNTERTOPS | 06-15-2008 | ||
DIVISION 14 | ||||
14 21 00 | ELECTRIC TRACTION ELEVATORS | 06-15-2008 | ||
14 42 00 | WHEELCHAIR LIFT | 06-15-2008 | ||
DIVISION 21 | ||||
21 00 00 | FIRE PROTECTION SYSTEMS | 06-15-2008 | ||
21 12 00 | FIRE SUPPRESSION STAND PIPES | 06-15-2008 | ||
21 13 00 | FIRE SUPPRESSION SPRINKLER SYSTEMS | 06-15-2008 | ||
21 40 00 | FIRE SUPPRESSION HF C227 EA SYSTEMS | 06-15-2008 | ||
DIVISION 22 | ||||
22 01 00 | GENERAL INSTRUCTIONS, MECHANICAL | 06-15-2008 | ||
22 02 00 | PLUMBING, MISCELLANEOUS | 06-15-2008 | ||
22 03 00 | TESTING AND ADJUSTING | 06-15-2008 | ||
22 05 00 | PLUMBING PIPING BASIC REQUIREMENTS | 06-15-2008 | ||
22 06 00 | PLUMBING DRAINS & SPECIALTIES | 06-15-2008 | ||
22 07 00 | PLUMBING PIPE INSULATION | 06-15-2008 | ||
22 11 00 | DOMESTIC WATER PIPING SYSTEM | 06-15-2008 | ||
22 11 13 | FACILITY WATER DISTRIBUTION PIPING | 06-15-2008 | ||
22 13 00 | SANITARY PIPING SYSTEM | 06-15-2008 |
DWG. NO. | DRAWING TITLE | DRAWING DATE | ||
22 13 13 | FACILITY SANITARY SEWERS | 06-15-2008 | ||
22 13 43 | FACILITY PACKAGED SEWAGE PUMPING STATIONS | 06-15-2008 | ||
22 14 00 | STORM PIPING SYSTEM | 06-15-2008 | ||
22 15 00 | GAS PIPING SYSTEM | 06-15-2008 | ||
22 17 00 | FUEL OIL | 06-15-2008 | ||
22 30 00 | PLUMBING EQUIPMENT | 06-15-2008 | ||
22 40 00 | PLUMBING FIXTURES | 06-15-2008 | ||
DIVISION 23 | ||||
23 05 01 | GENERAL INSTRUCTIONS, MECHANICAL | 06-15-2008 | ||
23 05 02 | MECHANICAL, MISCELLANEOUS | 06-15-2008 | ||
23 05 13 | MOTORS | 06-15-2008 | ||
23 05 14 | VARIABLE SPEED MOTOR DRIVES (PWM) | 06-15-2008 | ||
23 05 48 | SEISMIC AND VIBRATION CONTROL | 06-15-2008 | ||
23 05 93 | TESTING AND ADJUSTING | 06-15-2008 | ||
23 07 13 | DUCT INSULATION | 06-15-2008 | ||
23 07 16 | MECHANICAL EQUIPMENT INSULATION | 06-15-2008 | ||
23 07 19 | MECHANICAL PIPE INSULATION | 06-15-2008 | ||
23 09 23 | AIR CONDITIONING CONTROLS (DDC) | 06-15-2008 | ||
23 21 13 | HVAC PIPING BASIC REQUIREMENTS | 06-15-2008 | ||
23 21 14 | HVAC WATER PIPING SYSTEM | 06-15-2008 | ||
23 21 23 | PUMPS, VERTICAL INLINE SPLIT COUPLED | 06-15-2008 | ||
23 21 24 | PUMPS, PIPE MOUNTED | 06-15-2008 | ||
23 23 20 | REFRIGERANT DETECTION MONITORING SYSTEM | 06-15-2008 | ||
23 25 13 | WATER TREATMENT | 06-15-2008 | ||
23 31 00 | AIR CONDITIONING SHEET METAL WORK | 06-15-2008 | ||
23 33 19 | SOUND ATTENUATORS | 06-15-2008 | ||
23 34 16 | FANS | 06-15-2008 | ||
23 36 16 | VAV TERMINAL BOX | 06-15-2008 | ||
23 36 17 | VAV SIDE PICKET FAN TERMINAL BOX | 06-15-2008 | ||
23 37 13 | AIR DEVICES | 06-15-2008 | ||
23 37 23 | ROOF AIR INTAKES & RELIEFS | 06-15-2008 | ||
23 52 16 | GAS FIRED (FORCE DRAFT)-CONDENSING BOILER | 06-15-2008 | ||
23 55 23 | GAS FIRED INFRA-RED UNIT HEATERS | 06-15-2008 | ||
23 57 19 | HEAT EXCHANGER- PLATE AND FRAME TYPE | 06-15-2008 | ||
23 64 16 | CENTRIFUGAL WATER CHILLERS | 06-15-2008 | ||
23 65 13 | COOLING TOWER-FACTORY FABRICATED | 06-15-2008 | ||
23 72 13 | ENERGY RECOVERY WRAP-AROUND HEAT PIPES | 06-15-2008 | ||
23 74 33 | ROOF TOP HEAT RECOVERY AIR HANDLING UNITS | 06-15-2008 | ||
23 74 34 | HEAT RECOVERY WHEEL | 06-15-2008 | ||
23 75 13 | PACKAGED OUTDOOR ROOF TOP CENTRAL | 06-15-2008 | ||
STATION AIR HANDLING UNIT | 06-15-2008 | |||
23 81 23 | PACKAGED COMPUTER ROOM UNITS | 06-15-2008 | ||
23 82 16 | HYDRONIC DUCT COILS | 06-15-2008 | ||
23 82 19 | HORIZONTAL FAN COIL (UNITS LESS THAN 2200 CFM) | 06-15-2008 | ||
23 82 39 | HYDRONIC CABINET UNIT HEATERS | 06-15-2008 | ||
23 90 00 | PACKAGED CENTRAL ENERGY PLAN (PCEP) | 06-15-2008 | ||
DIVISION 26 | ||||
26 05 00 | COMMON WORK RESULTS FOR ELECTRICAL | 06-15-2008 | ||
26 05 05 | FIRESTOPPING FOR ELECTRICAL PENETRATIONS | 06-15-2008 | ||
26 05 19 | ELECTRICAL WIRING | 06-15-2008 | ||
26 05 26 | GROUNDING | 06-15-2008 | ||
26 05 27 | WATER FEATURES ELECTRICAL SYSTEMS | 06-15-2008 | ||
26 05 33 | RACEWAY SYSTEMS | 06-15-2008 | ||
26 05 34 | SURFACE METAL RACEWAY | 06-15-2008 |
DWG. NO. | DRAWING TITLE | DRAWING DATE | ||
26 05 36 | CABLE TRAY SYSTEM | 06-15-2008 | ||
26 05 43 | UNDERGROUND DUCT SYSTEM | 06-15-2008 | ||
26 05 43 | AMERENUE UNDERGROUND DUCTS AND STRUCTURES | 06-15-2008 | ||
26 08 10 | SPECIAL TESTING | 06-15-2008 | ||
26 09 15 | ELECTRICAL CONTROL SYSTEMS | 06-15-2008 | ||
26 09 23 | CONTACT DEVICES | 06-15-2008 | ||
26 09 33 | ARCHITECTURAL DIMMING CONTROL SYSTEMES | 06-15-2008 | ||
26 09 43 | RELAY LIGHTING CONTROL SYSTEM | 06-15-2008 | ||
26 24 05 | ELECTRIC SERVICE ENTRANCES | 06-15-2008 | ||
26 27 00 | ELECTRICAL DISTRIBUTION EQUIPMENT | 06-15-2008 | ||
26 27 26 | WIRING DEVICES | 06-15-2008 | ||
26 32 00 | PACKAGED ENGINE-GENERATOR SYSTEMS | 06-15-2008 | ||
26 33 53 | UNINTERRUPTIBLE POWER SYSTEMS (UPS) | 06-15-2008 | ||
26 35 33 | AUTOMATIC POWER FACTOR CONTROLLERS | 06-15-2008 | ||
26 41 13 | LIGHTNING PROTECTION SYSTEM | 06-15-2008 | ||
26 43 13 | SURGE PROTECTIVE DEVICES | 06-15-2008 | ||
26 50 00 | LIGHTING | 06-15-2008 | ||
26 55 00 | SPECIALTY LIGHTING | 06-15-2008 | ||
DIVISION 27 | ||||
27 00 00 | GENERAL CONDITIONS COMMUNICATIONS SYSTEM | 06-15-2008 | ||
27 05 28 | TELECOMMUNICATIONS PATHWAYS SYSTEM | 06-15-2008 | ||
27 10 00 | COMMUNICATIONS CABLING SYSTEM | 06-15-2008 | ||
27 41 00 | AUDIO VISUAL SYSTEMS | 06-15-2008 | ||
DIVISION 28 | ||||
28 00 00 | SECURITY SYSTEMS | 06-15-2008 | ||
28 31 00 | FIRE ALARM SYSTEM | 06-15-2008 | ||
DIVISION 31 | ||||
31 10 00 | SITE CLEARING | 06-15-2008 | ||
31 20 00 | EARTH MOVING | 06-15-2008 | ||
31 23 19 | DEWATERING | 06-15-2008 | ||
31 50 00 | EXCAVATION SUPPORT AND PROTECTION | 06-15-2008 | ||
31 63 16 | AUGERED CAST-IN-PLACE PILES | 06-15-2008 | ||
DIVISION 32 | ||||
32 12 16 | ASPHALT PAVING | 06-15-2008 | ||
32 13 13 | CONCRETE PAVING | 06-15-2008 | ||
32 41 00 | SEGMENTAL RETAINING WALLS | 06-15-2008 | ||
32 42 00 | STONE STRONG RETAINING WALLS | 06-15-2008 | ||
32 92 00 | TURF AND GRASSES | 06-15-2008 | ||
DIVISION 33 | ||||
33 41 00 | STORM UTILITY DRAINAGE PIPING | 06-15-2008 | ||
DIVISION 35 | ||||
35 00 00 | MARINE CONSTRUCTION | 06-15-2008 |
GMP, GMP CLARIFICATIONS AND ADJUSTMENTS
Estimate Summary | Bid date: 8/7/2008 | |||||||
Standard Construction Project | ||||||||
Management Computer Controls, Inc. | 0.3 | |||||||
5350 Poplar Avenue, Suite 600 | sqft | |||||||
Memphis | ||||||||
TN |
% | Labor | Material | Equipment | Subcontract | Temp Material | Equip Rental | Other | Totals | ||||||||||||||||||||||||||||
Direct costs | ||||||||||||||||||||||||||||||||||||
Base labor | $ | 4,590,442 | $ | 2,572,983 | $ | 673,880 | $ | 126,552,425 | $ | 0 | $ | 0 | $ | 0 | $ | 134,389,730 | ||||||||||||||||||||
Labor burden | 30.00 | % | $ | 1,377,133 | $ | 1,377,133 | ||||||||||||||||||||||||||||||
Labor fringes | $ | 0 | $ | 0 | ||||||||||||||||||||||||||||||||
Labor manhours | 73,508 | |||||||||||||||||||||||||||||||||||
Material sales tax | 6.08 | % | $ | 156,309 | $ | 156,309 | ||||||||||||||||||||||||||||||
Equipment Surcharge | 6.08 | % | $ | 40,938 | $ | 40,938 | ||||||||||||||||||||||||||||||
Temporary material markup | 6.08 | % | $ | 0 | $ | 0 | ||||||||||||||||||||||||||||||
Equipment rental markup | 6.08 | % | $ | 0 | $ | 0 | ||||||||||||||||||||||||||||||
Other markup | 0.00 | % | $ | 0 | $ | 0 | ||||||||||||||||||||||||||||||
Gross cost | $ | 5,967,575 | $ | 2,729,292 | $ | 714,818 | $ | 126,552,425 | $ | 0 | $ | 0 | $ | 0 | $ | 135,964,110 | ||||||||||||||||||||
Building Permits/Plan Review Fees | 0.00 | % | by owner | $ | 0 | |||||||||||||||||||||||||||||||
Builder’s risk insurance | 0.00 | % | by owner | $ | 0 | |||||||||||||||||||||||||||||||
Overall | ||||||||||||||||||||||||||||||||||||
Overhead | 0.00 | % | 0.00 | % | 0.00 | % | 0.00 | % | 0.00 | % | 0.00 | % | 0.00 | % | 0.00 | % | ||||||||||||||||||||
$ | 0 | $ | 0 | $ | 0 | $ | 0 | $ | 0 | $ | 0 | $ | 0 | $ | 0 | $ | 0 | |||||||||||||||||||
Profit | 4.00 | % | 0.00 | % | 0.00 | % | 0.00 | % | 0.00 | % | 0.00 | % | 0.00 | % | 0.00 | % | ||||||||||||||||||||
$ | 5,518,237 | $ | 0 | $ | 0 | $ | 0 | $ | 0 | $ | 0 | $ | 0 | $ | 0 | $ | 5,518,237 | |||||||||||||||||||
Subcontract bond | 0.00 | % | $ | 0 | ||||||||||||||||||||||||||||||||
Performance bond | 1.25 | % | $ | 1,784,125 | ||||||||||||||||||||||||||||||||
GL | 0.93 | % | $ | 1,264,466 | ||||||||||||||||||||||||||||||||
Contractor Controlled Contingency | $ | 4,300,000 | ||||||||||||||||||||||||||||||||||
Total | $ | 148,830,937 | ||||||||||||||||||||||||||||||||||
Cut/Add | $ | 0 | ||||||||||||||||||||||||||||||||||
Project total | $ | 148,830,937 | ||||||||||||||||||||||||||||||||||
Page 1
Recap — Without Taxes and Insurance | Group 1: Divisions | |
Group 2: Major ItemCode Groups | ||
Estimator : SGD | ||
Project Size : 0 |
Description | Quantity UM | Tot. Unit Cost | Total Cost | $/???? | ||||||||||||
ALLOWANCE | ||||||||||||||||
ALLOWANCE | 1,970,000.00 | |||||||||||||||
*Total ALLOWANCE | 1,970,000.00 | |||||||||||||||
General requirements | ||||||||||||||||
GENERAL REQUIREMENTS | 7,133,226.00 | |||||||||||||||
MISCELLANEOUS OVERHEAD | 290,000.00 | |||||||||||||||
*Total General requirements | 7,423,226.00 | |||||||||||||||
Sitework | ||||||||||||||||
EXCAVATION, GRADING & BACKFILL | ||||||||||||||||
PILING & CAISSONS | ||||||||||||||||
SITE DRAINAGE & UTILITIES | ||||||||||||||||
ROADS & WALKS | 485,731.00 | |||||||||||||||
SITE IMPROVEMENTS | 56,435.00 | |||||||||||||||
LAWNS & PLANTING | 3,301,875.00 | |||||||||||||||
*Total Sitework | 3,844,041.00 | |||||||||||||||
Concrete | ||||||||||||||||
CONCRETE FINISHING | ||||||||||||||||
FORMWORK | 12,182,250.00 | |||||||||||||||
REINFORCING STEEL | ||||||||||||||||
CAST IN PLACE CONCRETE | ||||||||||||||||
GROUT | ||||||||||||||||
*Total Concrete | 12,182,250.00 | |||||||||||||||
Masonry | ||||||||||||||||
MASONRY | 1,511,090.00 | |||||||||||||||
STONE | ||||||||||||||||
*Total Masonry | 1,511,090.00 | |||||||||||||||
Metals | ||||||||||||||||
STRUCTURAL METALS | 7,550,365.00 | |||||||||||||||
MISCELLANEOUS & ORNAMENTAL METALS | 184,078.00 | |||||||||||||||
*Total Metals | 7,734,443.00 | |||||||||||||||
Wood and plastics | ||||||||||||||||
ROUGH CARPENTRY | 633,700.00 | |||||||||||||||
FINISH CARPENTRY | 15,650,000.00 | |||||||||||||||
LAMINATED WOOD | ||||||||||||||||
*Total Wood and plastics | 16,283,700.00 | |||||||||||||||
Thermal and moisture | ||||||||||||||||
FIREPROOFING | 750,000.00 | |||||||||||||||
PREFORMED ROOFING & SIDING | 33,750.00 | |||||||||||||||
ROOFING, SHEETMETAL & ACCESSORIES | 2,525,000.00 | |||||||||||||||
CAULKING, SEALANTS & FASTENERS | 425,000.00 | |||||||||||||||
*Total Thermal and moisture | 3,733,750.00 |
Page 1 | 8/6/2008 12:55 PM |
Recap — Without Taxes and Insurance | Group 1: Divisions | |
Group 2: Major ItemCode Groups | ||
Estimator : SGD | ||
Project Size : 0 |
Description | Quantity UM | Tot. Unit Cost | Total Cost | $/???? | ||||||||||||
Doors and windows | ||||||||||||||||
METAL DOORS & FRAMES | 844,100.00 | |||||||||||||||
SPECIAL DOORS | 53,500.00 | |||||||||||||||
METAL WINDOWS | ||||||||||||||||
GLASS & GLAZING | 2,743,457.00 | |||||||||||||||
*Total Doors and windows | 3,641,057.00 | |||||||||||||||
Finishes | ||||||||||||||||
DRYWALL | 20,000,000.00 | |||||||||||||||
TILE & TERRAZZO | 1,900,000.00 | |||||||||||||||
ACOUSTICAL TREATMENT | ||||||||||||||||
FLOORING | ||||||||||||||||
SPECIAL FINISHES | 254,200.00 | |||||||||||||||
PAINTING & WALL COVERING | 1,228,013.00 | |||||||||||||||
*Total Finishes | 23,382,213.00 | |||||||||||||||
Specialties | ||||||||||||||||
SPECIALTIES | 480,476.00 | |||||||||||||||
*Total Specialties | 480,476.00 | |||||||||||||||
Equipment | ||||||||||||||||
EQUIPMENT | 7,289,115.00 | |||||||||||||||
*Total Equipment | 7,289,115.00 | |||||||||||||||
Conveying systems | ||||||||||||||||
CONVEYING SYSTEMS | 490,069.00 | |||||||||||||||
*Total Conveying systems | 490,069.00 | |||||||||||||||
Mechanical | ||||||||||||||||
PLUMBING SYSTEMS & EQUIPMENT | 5,640,000.00 | |||||||||||||||
FIRE PROTECTION SYSTEMS & EQUIPMENT | 1,542,300.00 | |||||||||||||||
HVAC SYSTEMS & EQUIPMENT | 15,210,000.00 | |||||||||||||||
*Total Mechanical | 22,392,300.00 | |||||||||||||||
Electrical | ||||||||||||||||
ELECTRICAL SYSTEMS & EQUIPMENT | 22,032,000.00 | |||||||||||||||
*Total Electrical | 22,032,000.00 | |||||||||||||||
BUILDING AUTOMATION SYSTEM | ||||||||||||||||
BUILDING AUTOMATION SYSTEM | ||||||||||||||||
*Total BUILDING AUTOMATION SYSTEM | ||||||||||||||||
Total Estimate | 134,389,730.00 |
Page 2 | 6/06/2008 12:55 PM |
ST. LOUIS, MO
W.G. Yates & Sons Construction Company | 2 | River City Casino | ||||
Gulf Coast Division — Confidential | St. Louis, MO |
W.G. Yates & Sons Construction Company | 3 | River City Casino | ||||
Gulf Coast Division — Confidential | St. Louis, MO |
W.G. Yates & Sons Construction Company | 4 | River City Casino | ||||
Gulf Coast Division — Confidential | St. Louis, MO |
Copper roof at dome is included with manufacturer’s standard warranty, if available.
Roof hatches are included.
Ceiling access doors and frames are included separate from door allowance.
Coiling doors and grilles are included separate from door allowance.
Aluminum entrances and storefront are included with standard hardware.
Revolving doors are included as Stanley tourinex revolvers 16’ x 7’ with 12 high canopies.
W.G. Yates & Sons Construction Company | 5 | River City Casino | ||||
Gulf Coast Division — Confidential | St. Louis, MO |
• | 3500 lbs/200 feet per minute | ||
• | 20’ rise | ||
• | Two stops | ||
• | Two front openings only | ||
• | 8’-6“x7’ -10” deep hoistway | ||
• | 6’-8” wide x 5’-5” deep clear car inside dimensions | ||
• | 17’-1” clear overhead | ||
• | 5’-6” clear pit depth | ||
• | Cab enclosure is Series 5 front return, header and satin bronze cab door, Otis round handrail, Otis hands free phone, Otis DC-22 ceiling with suspended aluminum frame and lay in panels, fluorescent lighting, 7’ high cab doors and 7’-41/2” clear under ceiling height. | ||
• | 12 month warranty |
W.G. Yates & Sons Construction Company | 6 | River City Casino | ||||
Gulf Coast Division — Confidential | St. Louis, MO |
W.G. Yates & Sons Construction Company | 7 | River City Casino | ||||
Gulf Coast Division — Confidential | St. Louis, MO |
We exclude fire protection under the casino floor in the barge area.
We exclude all standpipe systems, unless required by code.
We exclude pre-action systems.
W.G. Yates & Sons Construction Company | 8 | River City Casino | ||||
Gulf Coast Division — Confidential | St. Louis, MO |
W.G. Yates & Sons Construction Company | 9 | River City Casino | ||||
Gulf Coast Division — Confidential | St. Louis, MO |
Type MC cable and modular wiring shall be used where allowed by code.
W.G. Yates & Sons Construction Company | 10 | River City Casino | ||||
Gulf Coast Division — Confidential | St. Louis, MO |
RIVER CITY CASINO — YATES / PARIC | ||
GMP ADJUSTMENT INFORMATION | August 7, 2008 |
GMP — RECAP | ||||
Construction Cost (With Bond) | $ | 144,530,937 | ||
Contingency | $ | 4,300,000 | ||
TOTAL | $ | 148,830,937 | ||
Potential Adds to GMP: | ||||
1 Month Acceleration to Schedule | $ | 3,672,133 | ||
Porte Cochere Revisions | TBD | |||
VIP Balcony | TBD |
Carried as | ||||||||||||||||
Carried in GMP as | Carried in GMP as | ADD to the | ||||||||||||||
GMP Comments, Qualifications & Allowances: | Fixed Price | Allowance Value | GMP | Comments | ||||||||||||
Changing load bearing masonry in Area “A” to steel framing with [ILLEGIBLE] non-loadbearing infill | $ | (80,000 | ) | $ | — | $ | — | In GMP | ||||||||
Changing VIP stair to front of house type finish | $ | 30,000 | $ | — | $ | — | In GMP | |||||||||
Design information on approximately 450 sqft of decorative metal panels @ building facade. | $ | 33,750 | $ | — | $ | — | In GMP |
GMP ALLW-COST LIST (CONTRACT) | Confidential | Page 1 |
Carried as | ||||||||||||||
Carried in GMP as | Carried in GMP as | ADD to the | ||||||||||||
GMP Comments, Qualifications & Allowances: | Fixed Price | Allowance Value | GMP | Comments | ||||||||||
Discuss exterior windows needing to be storefront in lieu of punch windows due to radius and manufacturers comments about not being able to provide the product. | Need | Need | Need | In GMP | ||||||||||
Discuss exterior cladding and design assist input from cladding subcontractor to maintain budget. | $ | 20,000,000 | $ | — | $ | — | Includes Exterior Cladding & Interior Drywall. Breakout Value being established. | |||||||
Design information needed for VIP area and 2nd floor balcony. | $ | — | $ | — | $ | 261,000 | Carried as Add to GMP (R.O.M. Value) | |||||||
Design information needed for Porte Cochere revisions. | $ | — | $ | — | Need | Carried as Add to GMP (R.O.M. Value) Need to discuss with Design Team to Finalize ROM. | ||||||||
Coffee shop currently included as designed. Discuss how to set up allowance to track drawing revisions as final design develops. | $ | 221,700 | $ | — | $ | — | Carried in GMP as Build Out Value. ROM Value established for Coffee Shop Conversion. Per 8-5-08 discussion this item will be Retail Only. | |||||||
Fine Dining currently included as designed. Discuss how to set up allowance to track drawing revisions as final design develops. | Need Break-Out Value Established | $ | — | $ | — | Currently in GMP as Fixed Price but in several subcontractor values. | ||||||||
Food service equipment currently included per schedule in 100% CD drawings. Need final food service equipment cut sheets and data. | $ | 6,961,785 | $ | — | $ | — | Food Service Value only. Doesnot Include MEPS Costs | |||||||
Design information of glass canopies. | $ | 187,500 | $ | — | $ | — | In GMP | |||||||
Precon Costs from Allowance to Lump Sum included in GMP | $ | 50,000 | $ | — | $ | — | In GMP | |||||||
Casework — Original Proposal stipulated unspecified stone to be class B. Requested evaluation to go to similar specified stone. Carried in GMP as per CD Documents | $ | — | $ | — | $ | — | In GMP |
GMP ALLW-COST LIST (CONTRACT) | Confidential | Page 2 | ||
Carried as | ||||||||||||||
Carried in GMP as | Carried in GMP as | ADD to the | ||||||||||||
GMP Comments, Qualifications & Allowances: | Fixed Price | Allowance Value | GMP | Comments | ||||||||||
Exterior skin travel cost for 2 trips to Las Vegas 5 people. | $ | — | $ | — | $ | — | To be bought in Drywall / Cladding Subcontract | |||||||
SWPPP Maintenance Allowance. Note regarding North Lot was mistake. This value is a Lump Sum | $ | — | $ | — | $ | — | In Fred Weber Inc Contract | |||||||
OFCI Lighting systems. Added quantities as per RFI 112. The add is for the fixture support & installation. | $ | — | $ | — | $ | — | In GMP as per REVISION # 2 dated 7-09-2008 | |||||||
Drywall revisions for Hard Count security items | $ | — | $ | — | $ | — | To be bought in Drywall / Cladding Subcontract | |||||||
Add painting of Mech / Elec items in Casino Area | $ | — | $ | — | $ | — | In GMP | |||||||
Revisions to plumbing fixture package for hard wired ILO battery flush valves | $ | — | $ | — | $ | — | Included in GMP as Hard Wired | |||||||
Heat tracing budget increase for FS Drains | $ | 12,000 | $ | — | $ | — | In GMP | |||||||
Verification that all wire mold accessories were included | $ | — | $ | — | $ | — | In GMP | |||||||
LOW VOLTAGE MATRIX ADJUSTMENTS per CD Addendum # 1 dated 07/09/08: | $ | — | $ | — | $ | — | In GMP | |||||||
Verify expansion joint costs for decorative finish in F.O.H. | $ | — | $ | — | $ | — | In GMP | |||||||
Gas Piping Outside Ruby’s Seating Area | $ | — | $ | — | $ | — | In GMP | |||||||
Basin Water Test | $ | 250,000 | $ | — | $ | — | In GMP | |||||||
Delete basin wall admixtures and sheet waterproofing on exterior side of basin wall end add liquid applied product to interior side of basin wall | $ | — | $ | — | $ | — | In GMP | |||||||
Eliminate FT Lumber requirement for millwork as per CCI | $ | — | $ | — | $ | — | In GMP | |||||||
Provide gas piping encasement | $ | — | $ | — | $ | — | In GMP | |||||||
Add 3 air curtains at Loading Dock | $ | — | $ | — | $ | — | In GMP | |||||||
Provide pre action / FM systems and add HFC227EA system to 4 rooms | $ | — | $ | — | $ | — | In GMP | |||||||
Add FP System to 16,000 sf Attic Space | $ | — | $ | — | $ | — | In GMP | |||||||
Add for centering of heads in Fire Protection Scope (Stipulated as Allowance) | $ | — | $ | — | $ | — | In GMP | |||||||
Cover Plate Finish on FP Devices | $ | — | $ | — | $ | — | In GMP | |||||||
Coffee Shop Food Service Equipment | $ | — | $ | — | $ | — | In GMP Food Service Equipment per CD Schedule | |||||||
Add 6 Infrared heaters at Porte Cochere | $ | — | $ | — | $ | — | In GMP | |||||||
Water Softener change from Culligan to Unity | $ | 80,000 | $ | — | $ | — | In GMP | |||||||
Sleeves for Irrigation System to facilitate Sitework | $ | — | $ | — | $ | — | In FWI Contract | |||||||
Uniform Retrieval Equipment | $ | 292,555 | $ | — | $ | — | In GMP |
GMP ALLW-COST LIST (CONTRACT) | Confidential | Page 3 | ||
Carried as | ||||||||||||||
Carried in GMP as | Carried in GMP as | ADD to the | ||||||||||||
GMP Comments, Qualifications & Allowances: | Fixed Price | Allowance Value | GMP | Comments | ||||||||||
ALLOWANCES: | ||||||||||||||
Design information needed on added millwork scope from Scope Review & Clarification Items dated July 15, 2008. (Millwork locations are: Stands at 24 Hr Restaurant, Bierhaus, Valet, Buffet, VIP Hostess, Casino Host Cash Machine Millwork at 7 group/5machine ATM’s, 1 Group/4 Machine ATM’s, Card Swipe & Security Podiums 2 each Casino Entrance Locations) | $ | — | $ | 250,000 | $ | — | In GMP | |||||||
Discuss $1,800/leaf Allowance for doors, frames, hardware and installation. | $ | — | $ | 844,100 | $ | — | In GMP | |||||||
Discuss $100,000 Allowance for glass door pulls. Allowance is for Fabrication & Installation of Pulls Only | $ | — | $ | 100,000 | $ | — | In GMP | |||||||
Design information needed on MGC Camera & Security Offices/Surveillance. | $ | — | $ | 32,500 | $ | — | In GMP | |||||||
Design information needed on fireplaces. Allowance is for Two (2) Interior fireplaces only | $ | — | $ | 80,000 | $ | — | In GMP | |||||||
Design information needed on secondary framing to support owner furnished theatrical equipment Allowance is for Fabrication & Installation of Supports Only | $ | — | $ | 100,000 | $ | — | In GMP | |||||||
Bilge & Tank Level Indicator to be in GMP. Allowance value for this has been added | $ | — | $ | 100,000 | $ | — | In GMP | |||||||
Retail Build Out at $300 / SF. Allowance is for Interior Finishes Costs only beyond “White Box” | $ | — | $ | 221,700 | $ | — | In GMP | |||||||
Chiller Plant Scope Gap Allowance | $ | — | $ | 150,000 | $ | — | In GMP | |||||||
Add Buffet Decorative pie case Allowance. Value carried in Food Service Equipment Line Item | $ | — | $ | 20,000 | $ | — | In GMP | |||||||
Include Setting of Gaming Equipment (Stipulated as Allowance) | $ | — | $ | — | $ | — | In GMP. Need Final Value Established | |||||||
Boiler Scope Gap Cost | $ | — | $ | 30,000 | $ | — | In GMP | |||||||
Waterfeatures Allowance is for Exterior Features and includes General, MEPS & Low Voltage Costs. | $ | — | $ | 500,000 | $ | — | In GMP | |||||||
Casino Floor Mock — Up as per RFI issued during RFP process. | $ | — | $ | 375,000 | $ | — | In GMP | |||||||
Misc. Reinforcing Steel for Owner Driven Changes Only | $ | — | $ | 20,000 | $ | — | In GMP | |||||||
Exterior Wall Mock— Up as per RFI issued during the RFP Process | $ | — | $ | 275,000 | $ | — | In GMP | |||||||
Misc. Steel Fabrication for Owner Driven Changes Only | $ | — | $ | 150,000 | $ | — | In GMP | |||||||
Misc. Steel Installation for Owner Driven Changes Only | $ | — | $ | 75,000 | $ | — | In GMP | |||||||
Metal Stair Re-Work | $ | — | $ | 15,000 | $ | — | In GMP | |||||||
Misc. Firestopping for Owner Driven Changes | $ | — | $ | 20,000 | $ | — | In GMP | |||||||
Misc. Joint Sealers for Scope Coverage | $ | — | $ | 5,000 | $ | — | In GMP | |||||||
Spray Fireproofing Modifications for Owner Driven Changes Only | $ | — | $ | 35,000 | $ | — | In GMP | |||||||
Signage -(As per RFP, Allowance is for Support/Electric/Data at Interior wayfinding. Directional, Venue, & Slot Signage) | $ | — | $ | 500,000 | $ | — | In GMP | |||||||
Design information on approximately 450 sqft of decorative metal panels @ building facade. | $ | — | $ | 33,750 | $ | — | In GMP | |||||||
Design information to finalize custom color selection of skylight frame. | $ | — | $ | 87,000 | $ | — | In GMP | |||||||
Design information on glass cab enclosure for VIP elevator. | $ | — | $ | 75,000 | $ | — | In GMP (Total Elevator Budget is $363,096) |
GMP ALLW-COST LIST (CONTRACT) | Confidential | Page 4 | ||
OMITTED
CONDITIONAL LIEN WAIVER
Date:
(Conditional) (To Be an Attachment With Each Payment Application)
The undersigned, being first duly sworn on my oath, certify and state that I hold the position of |
for (“Contractor”) and |
(Title)(Name of Contractor) |
that I am the authorized representative for the Contractor named in the contract by and between the Contractor and Pinnacle Entertainment, Inc. (“Owner”), dated the _____ day of , 200___, (the “Contract”) for the project located at . |
(Description of Project) |
Signature: | ||
Company/Title: | ||
STATE OF | ) | |||||
) | ss | |||||
COUNTY OF | ) |
Notary Public |
My Commission Expires: | ||
2
Date:
Project Name:
(Conditional) (To Be An Attachment With Each Payment Application)
SUBCONTRACTOR | ||||
By: | ||||
Name: | ||||
Title: | ||||
Address: | ||||
Date: | ||||
STATE OF | ) | |||||
) | ss | |||||
COUNTY OF | ) |
Notary Public in for said County and State | ||
My Commission Expires: | ||
UNCONDITIONAL LIEN WAIVER
(Unconditional) (To Be An Attachment With Each Payment Application)
The undersigned, being first duly sworn on my oath, certify and state that I hold the position of |
for (“Contractor”) and |
(Title)(Name of Contractor) |
that I am the authorized representative for the Contractor named in the contract by and between the Contractor and Pinnacle Entertainment, Inc. (“Owner”), dated the _____ day of , 200___, (the “Contract”) for the project located at . |
(Description of Project) |
Signature: | ||
Name (print): | ||
Company/Title: | ||
STATE OF | ) | |||||
) | ss | |||||
COUNTY OF | ) |
Notary Public | ||
My Commission Expires: | ||
2
Project:
(Unconditional) (To Be An Attachment With Each Payment Application)
The undersigned, being first duly sworn on my oath, certify and state that I hold the position of |
for (“Contractor”) and |
(Title)(Name of Subcontractor/Supplier) |
that I am the authorized representative for the subcontractor/supplier named in the subcontract/purchase order by and between the undersigned and the General Contractor, dated the _____ day of , 200___, for the project located at . |
(Description of Project) |
Signature: | ||
Company/Title: | ||
STATE OF | ) | |||||
) | ss | |||||
COUNTY OF | ) |
Notary Public | ||
My Commission Expires: | ||
CONTRACTOR’S CERTIFICATE TO
BE INCLUDED WITH PAY APPLICATION
Amount Owed as of the end of the period Covered by the above-referenced Application | Contractor: | |||||||
For Payment: | By: | |||||||
$ | Its: | |||||||
Disputed Claims Amount included within Amount Owed, if any: | ||||||||
$ |
TECHNICAL STUDIES AND REPORTS
PERMITS, APPROVALS AND ENTITLEMENTS
OMITTED
UNCONDITIONAL FINAL WAIVER
Payment Application No. | FINAL | |
Date: | ||
Project: | ||
(Unconditional)
The undersigned, being first duly sworn on my oath, certify and state that I hold the position of |
for (“Contractor”) and |
(Title)(Name of Contractor) |
that I am the authorized representative for the Contractor named in the contract by and between the Contractor and Pinnacle Entertainment, Inc. (“Owner”), dated the day of , 200__, (the “Contract”) for the project located at . |
(Description of Project) |
Signature: | ||||||
Company/Title: | ||||||
STATE OF | ) | |
) ss | ||
COUNTY OF | ) |
Notary Public | ||
My Commission Expires: | ||
2
Payment Approval | FINAL | |
Date: | ||
Project: | ||
(Unconditional)
The undersigned, being first duly sworn on my oath, certify and state that I hold the position of |
for |
(Title)(Name of Subcontractor/Supplier) |
and that I am the authorized representative for the subcontractor/supplier named in the subcontract/purchase order by and between the undersigned and the General Contractor, dated the day of , 200__, for the project located at . |
(Description of Project) |
Signature: | ||||||
Company/Title: | ||||||
STATE OF | ) | |
) ss | ||
COUNTY OF | ) |
Notary Public | ||
My Commission Expires: | ||
SAFETY AND HEALTH GUIDELINES

Casino & Hotel
SITE SPECIFIC SAFETY PLAN
Job Number 53838
August 7, 2008
1. | Purpose |
The Purposes of this Policy are as follows: |
a. | To establish and maintain a safe, healthy working environment for all employees; | ||
b. | To insure the reputation of Yates/Paric and its employees as good, responsible citizens worthy of the licenses and franchises entrusted to them; | ||
c. | To reduce absenteeism, tardiness and indifferent job performance; and | ||
d. | To reduce the incidence of accidental injury to persons or property. |
2. | Benefits, Insurance, Cooperation | ||
Those employees with drug abuse problems make up only a small fraction of the work force, and we regret any inconvenience that may be caused by the problems of the few. It is believed, however, that the benefits to be derived from the reduction in the number of accidents, and the greater safety of all employees, will more than make up for any inconvenience of loss the rest of us must experience. Yates/Paric earnestly solicits the understanding and cooperation of all employees in implementing the Policy as set forth herein. | |||
3. | Definitions |
a. | The term “business premises”, as used herein includes all property of any customer, contractor or subcontractor with whom Yates/Paric is doing business or at any other location at any time while acting in the course of and scope of employment. | ||
b. | “Employees” shall be defined as employees of Yates/Paric and its invitees, and subcontractors and their employees. |
c. | “Reasonable suspicion” is a belief based on objective and articulable facts sufficient to lead a prudent and reasonable person to suspect that an employee is using or has used drugs or alcohol and/or is under any degree of influence of one or both. |
d. | The words, “illegal drugs”, “drugs”, and/or “substances” include at all times the following. |
(1) | drugs that are not legally obtainable; | ||
(2) | drugs that are legally obtainable, but have been obtained illegally; | ||
(3) | drugs that are legally obtained, but are knowingly used for other than prescribed purpose or in other than prescribed manner; | ||
(4) | so-called “designer drugs” or drug substances that are not approved for medical or other use by the Food and Drug Administration and not available in the United States retail markets; and also includes, for purposes of this Policy, any substance that alters behavior. |
4. | Policy | ||
This is to notify all employees, including employees of other contractors, subcontractors and invitees that the use, possession, concealment, transportation, promotion, being on the job under the influence of or sale of the following items or substances are strictly prohibited from all of the above-mentioned business premises: |
• | Illegal drugs, controlled substances, (including trace amounts), look-a-likes, and designer drugs; | ||
• | Drug paraphernalia; | ||
• | All Prescription drugs, except under the following conditions: |
5. | Searches and Inspections | ||
Yates/Paric reserves the right, at all times, while an employee is on the business premises and properties described above or at any location at any time while acting in the course of the scope of employment to have a Supervisor and/or authorized Search and Inspection Specialist conduct searches and inspections of employees or other persons and their lockers, business-provided living quarters, baggage, desk, tool boxes, clothing and vehicles. A search may also be conducted on an employee’s personal property brought on the job for the purpose of determining if such employees or other persons are in possession, use, transportation or concealment of any of the prohibited items and substances subject to this Policy. |
• | Pre-employment testing (testing prior to or within five (5) days of employment); | ||
• | At any time, upon request by management, as part of an overall work unit, department or business-wide testing of employees; | ||
• | When required and/or requested by a customer to comply with their testing policy; | ||
• | When required to comply with any federal, state, and/or local law, statute, ordinance, etc. | ||
• | Pre-placement testing; | ||
• | To comply with contractual agreements with other contractors and/or project owners; | ||
• | Part of an overall Search and Inspection or an employee’s work area or location of employment; | ||
• | When an employee’s supervisor has reasonable suspicion that an employee is using or under any degree of influence of drugs; | ||
• | When an employee or person is found in possession of suspected illicit or unauthorized drugs, or when any of these items are found in any area controlled or used exclusively by designated employees; | ||
• | Following any work-related accident, regardless of whether personal injury is sustained, and also following any incident, which may result in Yates/Paric being charged with any liability or responsibility. |
a) | Shirt with a 4” sleeve | ||
b) | Proper Work Boots | ||
c) | Hard Hat | ||
d) | Safety Glasses (tinted outdoors; clear indoors) | ||
e) | Long pants | ||
f) | High Visibility Vest (Class I or Higher) | ||
• | All items MUST meet OSHA / ANSI standards (hard hats, eyewear, etc.) Anyone wearing clothing with offensive logos, wording, etc. will be asked to leave the job site. |
1. | Valve protection caps must be in place and secured. |
2. | When cylinders are hoisted, they will be secured on a cradle, slingboard, or pallet. They must never be hoisted or transported by means of magnets or choker slings. |
3. | Cylinders should be moved by tilting and rolling them on their bottom edges. They must never be intentionally dropped, struck, or permitted to strike each other violently. |
4. | When cylinders are transported by powered vehicles, they will be secured in a vertical position. |
5. | Valve protection caps will not be used for lifting cylinders from one vertical position to another. Bars will not be used under valves or valve protection caps to pry cylinders loose when frozen. Warm, not boiling, water must be used to thaw cylinders loose. |
6. | Regulators will be removed and valve protection caps put in place before cylinders are moved. |
7. | A suitable cylinder truck, chain, or other steadying device will be used to keep cylinders from being knocked over while in use. |
8. | When work is finished, when cylinders are empty, or when cylinders are moved at any time, the cylinder valve is to be closed and the valve protection cap put in place. |
9. | Compressed gas cylinders must be secured in an upright position at all times. |
10. | Oxygen cylinders in storage will be separated from fuel-gas cylinders or combustible materials (especially oil or grease), a minimum distance of 20 feet (6.1m) or by a noncombustible barrier at least 5 feet (1.5m) high having a fire resistance rating of at least one-half hour. |
11. | Inside of buildings, cylinders must be stored in a well-protected, well-ventilated, dry location, at least 20 feet (6.1m) from highly combustible materials such as oil or excelsior. Cylinders should be store in specific assigned places away from elevators, stairs, or gangways. Assigned storage places will be located where cylinders will not be knocked over or damaged by passing or falling objects, or subject to tampering. |
12. | The handling, storage, and utilization of all compressed gases in cylinders, portable tanks, rail tank cars, or motor vehicle cargo tanks shall be in accordance with Compressed Gas Association Pamphlet P-1-1965. |
13. | A 10-lb ABC fire extinguisher will be located within 25 feet of storage and use areas. | ||
14. | “No Smoking” or “Open Flame” signs will be located in the area. |
15. | Cylinders must not be stored within 40 feet of an occupied dwelling-i.e.—Office trailer. |
1. | Cylinders must be kept far enough away from the actual welding or cutting operation so that sparks, hot slag, or flame will not reach them. When this is impractical, fire-resistant shields must be provided. |
2. | Cylinders will be placed where they cannot become part of an electrical circuit. Electrodes must never be struck against a cylinder to strike an arc. |
3. | Fuel gas cylinders are to be placed with valve end up whenever they are in use. They will not be placed in a location where they would be subject to open flame, hot metal, or other sources of artificial heat. | ||
4. | Cylinders containing oxygen or acetylene or other fuel gas will not be taken into confined spaces. |
1. | Cylinders, whether full or empty, will not be used as rollers or supports. |
2. | No person other than the gas supplier will attempt to mix gases in a cylinder. No one except the owner of the cylinder or person authorized by the owner shall refill a cylinder. No one is to use a cylinder’s contents for purposes other than those intended by the supplier. All cylinders used must meet the Department of Transportation requirements published in 49 CFR Part 178, Subpart C, Specification for Cylinders. |
3. | No damaged or defective cylinder will be used. NOTE: Damaged cylinders are to be removed from service and tagged out of service. |
1. | General |
2. | Material storage |
January — Orange | ||||
February — Blue | ||||
March — Red | ||||
April — Yellow May — Orange June — Blue July — Red August — Yellow September — Orange October — Blue November — Red December — Yellow |
a. | All cranes, hoists, motor vehicles, elevators, conveyors, and heavy equipment must be operated and maintained to conform to established standards. | ||
b. | Equipment rental companies are required to supply the Safety Department with a current “inspections Certificate” for each individual crane to work on the project. A certified inspector, testing laboratory, manufacturer, or metallurgist will sign off this certificate or facsimile. A copy of the last annual crane inspection must accompany the rental agreement. Terms and conditions for rental equipment places the responsibility of lessor to furnish copy of certifications of annual inspections of various pieces of lifting equipment and cranes as required by OSHA. The Project Superintendent must ensure this documentation is in hand and in order prior to placing the equipment in service. | ||
c. | All cranes, hoists, motor vehicles, elevators, and heavy equipment must be inspected prior to use on each shift. All deficiencies must be repaired before the equipment is used. | ||
d. | Operators of such equipment must keep inspection records required by this procedure. | ||
e. | Rated load capacity charts, recommended operating speeds, special hazard warnings, and other essential information will be visible to the operator while they are at their control station. | ||
f. | Prior to initial use, all new, extensively repaired, and altered cranes should be tested by or under the direction of an appointed or authorized person, confirming the load rating of the crane. | ||
g. | Operators must take signals from only one person; in an emergency, however, a STOP signal can be given by anyone. | ||
h. | Only standard hand signals will be acknowledged. A copy of the hand signals must be provided on equipment visible to employees. | ||
i. | Routine maintenance, fueling, and repairs must not be performed while the equipment is in use or the power on. | ||
j. | When handling or recharging batteries or using jumper cables, wear a face shield. |
k. | The starting procedure is as follows: |
1. | Prior to start-up, make a walk-around inspection to check the condition of the machine and see that everyone is in the clear. | ||
2. | Check the engine oil and coolant prior to the initial start-up each shift. | ||
3. | Before working machine, allow sufficient time for a warm-up period after engine is started. | ||
4. | Prior to attempting to work the machine, the operator should thoroughly familiarize himself with all controls. | ||
5. | All controls should be tested by the operator at the start of a new shift. If controls do not operated properly, they will be adjusted or repaired before working the machine. Check wheel brakes before moving machine. |
2. | Operators of Material Handling Equipment |
a. | Cranes will be operated only by the following personnel: | ||
b. | Designated operator — The operator assigned by the employer as being qualified to perform specific duties. | ||
c. | Learners under the direct supervision of a designated operator. | ||
d. | Maintenance and test personnel, when it is necessary in the performance of their duties. |
1. | No one, other than personnel specified, will enter an operator station or crane cab, with the exception of persons such as helpers and supervisors whose duties require them to do so, and then only in the performance of their duties and with the knowledge of the operator or other appointed person. | ||
2. | It will be the responsibility of the Project Superintendent to assign a competent person to indoctrinate operators in the operating procedures and OSHA regulations concerning hoist and crane operation, prior to starting work. |
e. | Each operator for mobile cranes rated 50 tons or larger must be qualified in accordance with accepted Operator Qualification procedure. This qualification must be met at the beginning of each project and at least annually thereafter. If there is any question about physical or mental fitness of any operator, he may be referred to Project Superintendent for arrangement for doctor examination. |
f. | The operator will be responsible for those operations under his direct control. Whenever there is any doubt as to safety, the operator will stop and refuse to handle the load until safety, such as proper rigging, has been assured. | ||
g. | While actually engaged in operating the crane, the operator will not engage in any practice that will divert his attention. | ||
h. | The operator will familiarize himself with the equipment and its proper care. If adjustments or repairs are necessary, or any defects are known, he will report he same promptly to his supervisor and will also notify the next operator of the defects upon changing shift. | ||
i. | The operator will avoid swinging loads over employees. The operator will sound the horn when swinging a suspended load. | ||
j. | The operator will not leave his position at the controls while the load is suspended. Before leaving his crane unattended, the operator will: |
1) | Land any attached load, bucket, lifting magnet, or other device. | ||
2) | Disengage clutch. | ||
3) | Set travel, swing, boom brakes, and other locking devices. | ||
4) | Put controls in the “off” position. | ||
5) | Stop the engine. | ||
6) | Secure crane against accidental travel. |
k. | Safety latches are required on all hooks on lifting and pulling devices. |
p. Mobile Equipment Operation and Operator Training | |||
Cranes, Derricks, Hoists, Conveyors, and Aerial Lifts |
A. | General Requirements |
1. | All cranes, hoists, motor vehicles, elevators, conveyors, and heavy equipment must be operated and maintained to conform to established standards. |
2. | Equipment rental companies are required to supply the Safety Department with a current “inspections Certificate” for each individual crane to work on the project. A certified inspector, testing laboratory, manufacturer, or metallurgist will sign off this certificate or facsimile. A copy of the new annual crane inspection must accompany the rental agreement. Terms and conditions for rental equipment places the responsibility of lessor to furnish copy of certifications of annual inspections of various pieces of lifting equipment and cranes as required by OSHA. The site management team must ensure this documentation is in hand and in order prior to placing the equipment in service. | ||
3. | All cranes, hoists, motor vehicles, elevators, and heavy equipment must be inspected prior to use on each shift. All deficiencies must be repaired before the equipment is used. | ||
4. | Operators of such equipment must keep inspection records required by this procedure. | ||
5. | Rated load capacity charts, recommended operating speeds, special hazard warnings, and other essential information will be visible to the operator while they are at their control station. | ||
6. | Prior to initial use, all new, extensively repaired, and altered cranes should be tested by or under the direction of an appointed or authorized person, confirming the load rating of the crane. | ||
7. | Operators must take signals from only one person; in an emergency, however, a STOP signal can be given by anyone. | ||
8. | Only standard hand signals will be acknowledged. A copy of the hand signals must be provided on equipment visible to employees. | ||
9. | Routine maintenance, fueling, and repairs must not be performed while the equipment is in use or the power on. | ||
10. | When handling or recharging batteries or using jumper cables, wear a face shield. |
11. | The starting procedure is as follows: |
a) | Prior to start-up, make a walk-around inspection to check the condition of the machine and see that everyone is in the clear. | ||
b) | Check the engine oil and coolant prior to the initial start-up each shift. | ||
c) | Before working any machine, allow sufficient time for a warm-up period after engine is started. | ||
d) | Prior to attempting to work the machine, the operator should thoroughly familiarize himself with all controls. | ||
e) | All controls should be tested by the operator at the start of a new shift. If controls do not operated properly, they will be adjusted or repaired before working the machine. Check wheel brakes before moving machine. |
1. | Cranes will be operated only by the following personnel: |
a) | Designated operator — The operator assigned by the employer as being qualified to perform specific duties. | ||
b) | Learners under the direct supervision of a designated operator. | ||
c) | Maintenance and test personnel, when it is necessary in the performance of their duties. |
2. | No one, other than personnel specified, will enter an operator station or crane cab, with the exception of persons such as helpers and supervisors whose duties require them to do so, and then only in the performance of their duties and with the knowledge of the operator or other appointed person. | ||
3. | It will be the responsibility of the Crane and Equipment Safety Manager or his designee to indoctrinate operators in the operating procedures and OSHA regulations concerning hoist and crane operation, prior to starting work. | ||
4. | Each operator for all equipment must be qualified in accordance with accepted Operator Qualification procedure. This qualification must be met at the beginning of each project and as determined thereafter. If there is any question about physical or mental fitness of any operator, he may be referred to the Crane and Equipment Safety Manager or his designee for referral to Human Resources for evaluation. | ||
5. | The operator will be responsible for those operations under his direct control. Whenever there is any doubt as to safety, the operator will stop and refuse to handle the load untilsafety, such as proper rigging, has been assured. | ||
6. | While actually engaged in operating the crane, the operator willnot engage in any practice that will divert his attention. |
7. | The operator will familiarize himself with the equipment and its proper care. If adjustments or repairs are necessary, or any defects are known, he will report the same promptly to his supervisor and will also notify the next operator of the defects upon changing shift. If these adjustments, repairs or defects are such that they may jeopardize the safe operation of the equipment, the equipmentmust be removed from service immediately and tagged out of service. | ||
8. | The operator will avoid swinging loads over employees. The operator will sound the horn when swinging a suspended load. | ||
9. | The operator will not leave his position at the controls while the load is suspended. Before leaving his crane unattended, the operator will: |
a) | Land any attached load, bucket, lifting magnet, or other device. | ||
b) | Disengage clutch. | ||
c) | Set travel, swing, boom brakes, and other locking devices. | ||
d) | Put controls in the “off” position. | ||
e) | Stop the engine. | ||
f) | Secure crane against accidental travel. |
10. | Safety latches are required on all hooks on lifting and pulling devices. |
a. | No one but the operator will be allowed in or on the machine while it is operating. (This meansNO RIDERS). | ||
b. | NO RIDERsigns will be posted in cab of crane. | ||
c. | Boom angle indicators must be in working order at all times. Load movement devices or load indicating devices will be installed where required. | ||
d. | All wire ropes will be in good repair. | ||
e. | All belts, gears, shafts, pulleys, sprockets, drums, flywheels, or chains will be properly guarded. | ||
f. | Accessible areas within the swing radius of all cranes must be barricaded. | ||
g. | The swing radius will be free of outside material such as water cans, tool boxes, and miscellaneous storage. | ||
h. | All exhaust systems will be in good repair and guarded. |
i. | All windows will be of safety glass and free of distortion such as cracks. | ||
j. | Guardrails and hand holds will be appropriately built and secured and antiskid surfaces placed on walkways and platforms. | ||
k. | There will be an accessible 10-lb ABC fire extinguisher at all operator stations or cabs. | ||
l. | The load block, headache ball, and safety hook will be kept in good repair. | ||
m. | No employee will ride on a cable, ball, chain, sling, or any other hoisting attachment or on the material being moved by means of a winch line, crane, or truck. | ||
n. | Backup alarms will be installed and operational on truck cranes and pickers. | ||
o. | With motor cranes, all four outriggers should be firmly set for every lift. In case of a rolling lift, the ground area must be firm and level and outriggers pads set to just clear ground. | ||
p. | Booms and boom members will be kept in good repair, free of cracks, dents, and broken parts. | ||
q. | Boom and crane rigging should be inspected at the start of every shift. At least once a week, lines should be checked thoroughly and lubricated. Aerosol can-type lubricant seems to be the most generally acceptable. It must be a lubricant that will penetrate the cables. | ||
r. | A monthly Crane Inspection Report must be completed and submitted to the Project Office. In addition, this report must be completed as soon as the piece of equipment arrives on the job site. | ||
s. | Never repair a damaged boom or any section thereof. The only safe procedure is to contact the manufacturer giving crane identification information and following their instructions. | ||
t. | Jibs will be used only when necessary for inward reach and will be equipped with positive jib stops when available. | ||
u. | Cranes will not be operated when any part of the machine can come within 10 feet of a high voltage conductor. For this purpose, anything over 220 volts will be considered high voltage. When operating in proximity to a high voltage line, riggers will not pull the load line at an angle to make a hook up. If it is necessary to operate a crane close to high voltage lines, make arrangements through management to have the line de-energized if possible. |
v. | For lines rated over 50 kV, the minimum clearance between the lines and any part of the crane or load must be 10 feet plus 0.4 inch for each 10 kV over 50 kV. | ||
w. | During transit, with no load and the boom lowered, the minimum equipment clearance must be 4 feet for 50 kV or less, 10 feet for 50 kV to 345 kV, and 16 feet for voltages up to 750 kV. | ||
x. | A designated employee must observe clearance of the equipment and give timely warning for all operations where the operator’s vision is obstructed. | ||
y. | Any overhead line must be considered energized unless the responsible utility company or client representative verifies that it is not energized. | ||
z. | Buffers will be installed at each end of the tracks for stops on rail-mounted cranes. |
• | Specific areas recommended by the manufacturer. | ||
• | Proper readable load chart in Cab. | ||
• | Angle Indicator functions. | ||
• | If two-block device is not functioning; discussion with Crane and Equipment Safety Manager is required. | ||
• | Rated 10ABC Fire Extinguisher. | ||
• | Cab maintenance and cleanliness. | ||
• | Main and side crane windows not blocked with paper. | ||
• | Out riggers fully extend and support crane weight. | ||
• | Tires inflated properly. | ||
• | Lattice boom crane — chord — connections inspected. | ||
• | Note: Chord damage of any level shall have crane rejected. | ||
• | Deformed, cracked, or corroded members in the crane structure and entire boom. | ||
• | Loose bolts or rivets. | ||
• | Cracked or worn sheaves and drums. | ||
• | Worn, cracked or distorted parts such as pins, bearings, shafts, gears, rollers and locking devices. | ||
• | Excessive wear on brake and clutch system parts, linings, pawls and ratchets. | ||
• | Load, boom angle, and other indicators over their full range, for any significant inaccuracies Note: If load indicator is not functioning or absent discussion with Crane and Equipment Safety Manager is required. |
• | Excessive wear of chain drive sprockets and excessive chain stretch. | ||
• | Crane hooks for cracks (visual). | ||
• | Travel steering, braking and locking devices for malfunction. | ||
• | Excessively worn or damaged tires. |
a. | Evidence of leakage at the surface of the flexible hose or its junction with the metal and couplings. | ||
b. | Blistering or deformation of the outer covering of the hydraulic or pneumatic hose. | ||
c. | Leakage at threaded or clamped joint that cannot be eliminated by normal tightening or recommended procedures. | ||
d. | Evidence of excessive abrasion or scrubbing on the outer surface of a hose, rigid tube or fitting. Means shall be taken to eliminate the interference of elements in contact or otherwise protect the components. |
a. | Loose bolts or fasteners | ||
b. | Leaks at joints between sections | ||
c. | Shaft seal leaks | ||
d. | Unusual noises or vibration | ||
e. | Loss of operating speed | ||
f. | Excessive heating of the fluid | ||
g. | Loss of pressure |
a. | Cracks in valve housing | ||
b. | Improper return of spool to neutral position | ||
c. | Leaks at spools or joints | ||
d. | Sticking spools | ||
e. | Failure of relief valves to attain correct pressure setting | ||
f. | Relief valve pressures as specified by the manufacturer |
a. | Drifting caused by fluid leaking across the piston | ||
b. | Rod seals leakage | ||
c. | Leaks at welded joints | ||
d. | Scored, nicked or dented cylinder rods | ||
e. | Dented case (barrel) |
f. | Loose or deformed rod eyes or connecting joints | ||
g. | Hydraulic filters for evidence of rubber particles on the filter element that may indicate hose, “O” ring or other rubber component deterioration. Metal chips or pieces on the filter may denote failure in pumps, motors or cylinders.Further checking will be necessaryto determine the origin of the problem before corrective action can be taken. |
1. | In warm weather, remove and store doors to prevent blind spots or slide back in the locked position. | ||
2. | Wear seat belts at all times while traveling the crane. | ||
3. | In addition to filing the Monthly Crane Safety Report, “a daily check of the following items will be made before starting the shift: |
a. | All deficiencies on the machine or unsafe conditions are to be reported to your supervisor promptly. | ||
b. | No modifications or additions that affect the capacity and operation of the equipment will be made without the manufacturer’s written approval. | ||
c. | Check wire rope condition and dead end for wedges and clamps. Keep wire rope lubricated. |
d. | Check hook and block. Make sure hook has an operational safety latch. | ||
e. | Check boom pivot pins and pin retainers. | ||
f. | Check mountings for hydraulic boom cylinders. | ||
g. | Check outriggers, pivot pins and retainers, and cylinder mountings. | ||
h. | Check for buildup of dirt and rocks under outrigger cylinders. Check outrigger frames for cracks. | ||
i. | Check all steering linkage. | ||
j. | Check winch mounting. | ||
k. | Check for any leaks of the hydraulic, engine oil, and coolant systems. | ||
l. | Test brakes prior to moving machine. | ||
m. | Make sure hydraulic pump is disengaged before moving machine if applicable. | ||
n. | Check horn, turn signals, and lights for proper operation. | ||
o. | Inspect tires for condition and proper inflation. | ||
p. | Check back-up alarm for proper functioning. |
D. | Outriggers |
1. | The crane must be level withall outriggers down on firm ground or footing prior to lifting loads or swinging the boom over the side, except as noted under the “Traveling” heading. Without the outriggers down and even with no load, it is possible to tip the crane over by simply swinging the boom over the side. | ||
2. | The transporting of materials on the outriggers is prohibited. | ||
3. | Use appropriate pads under outriggers when soil conditions warrant or there is not a firm, stable foundation for the outrigger to be placed on, especially when making heavy picks or when working near maximum radius. | ||
4. | When setting up near trenches or excavations, stay a safe distance back from the hole a minimum of 2 feet or an evaluation must be conducted by a competent person to determine if the footing is stable to support the machine. |
E. | Hoisting |
1. | Know the weight of the load and the location to which it is being moved. | ||
2. | No crane is to be loaded beyond its rated capacity. | ||
3. | The operator will test the machine each time a load approaching the rated load is handled, by raising it a few inches and holding the load. | ||
4. | Extreme care should be exercised when a load approaching the rated load capacity is handled. Whenever possible, this load should be tested keeping it close to the ground and booming out to the maximum radius required prior to making the actual lift into place. Be sure actual operating conditions do not exceed test conditions. | ||
5. | Use extreme caution when extending the boom with loads suspended. As working radius increases, load capacity decreases and can cause the machine to tip over. Most hydraulic cranes differ from a friction machine in that a load cannot be lowered fast enough to overcome a tipping action once the machine becomes over-balanced. | ||
6. | When the boom is extended, care should be exercised to avoid “two blocking” sheave block with boom. | ||
7. | During hoisting, swing, or lowering operations, there will be no sudden acceleration or deceleration of the moving load. |
F. | Traveling |
1. | When traveling, the boom will be fully retracted and positioned over the front of the machine in the direction of travel. | ||
2. | Use a signalman when traveling mobile cranes. The operator’s visibility is very poor towards the rear of some machines. | ||
3. | The warning signal will be sounded each time before traveling, and intermittently during travel, particularly when approaching employees. | ||
4. | Traveling with a load is not encouraged. However, if there is no alternative means to accomplish the task, follow the manufactures guidelines when traveling with a load. | ||
5. | Load must be positioned over the front of the machine in the direction of travel. |
6. | ALL TRAVELED LOADS MUST BE TIED OFF TO THE MACHINE BY A TAG LINE AND NOT HELD OR BALANCED BY EMPLOYEES WALKING ALONG SIDE OF LOAD. | ||
7. | Some loads will require the positioning of outriggers close to the ground. | ||
8. | Route to be traveled will be level, compacted, and free of potholes. | ||
9. | No one will be permitted to ride on any crane or picker except the operator or driver. |
1. | Suspended work platform will not be permitted if there is another reasonable method consistent with construction practices to accomplish the task. | ||
2. | Each suspended work platform brought onto the project must be inspected and approved for use by the Crane and Equipment Safety Manager or his designee. | ||
3. | The Crane and Equipment Manager or his designee must specifically approve each individual use of suspended work platform. | ||
4. | Suspended work platforms will be constructed in accordance with C.F.R. 1926.550(G)(4)(i) | ||
5. | E. A critical lift plan must be completed by the Crane and Equipment Safety Manager or his designee. |
1. | The erection and operation of personnel hoists must conform to established standards. | ||
2. | Hoists must be guarded at ground elevation by suitable barricades and signs, and, on all elevations, the entrance to the platform should be barricaded. | ||
3. | Personnel hoists will be enclosed on all sides and the top, except sides used for entrances and exits, which will have car gates or doors. | ||
4. | The maximum allowable distance between the floor of the lifting car and the landing platform is six inches. | ||
5. | Prior to placing a hoist into service, functions and safety devices must be tested thoroughly under the supervision of the manufacturer’s representative or other similarly qualified person in the presence of the Project Superintendent or his designee. | ||
6. | At least every four months, the manufacturer’s representative as required by ANSI must make a full inspection and test to include a drop test. | ||
7. | Records of such inspections and tests must be kept on the job site with copies to the Safety Department. | ||
8. | Operators of personnel hoists will receive orientation and training in the safe and proper operation in accordance with the manufacturer’s instructions. |
1. | General Requirements: |
a) | The design and operation of all movable personnel hoists will be in accordance with the manufacturer’s recommended procedures for safe operation. | ||
b) | All personnel who operate aerial work platforms will be trained and qualified in the safe operating procedures, using the manufacturer’s operator book. | ||
c) | The operator will have,on his person or on the job site, the documentation issued by the Safety Department stating his competency in operating the specific model of equipment. Arrangements should be made for instructor personnel to be periodically trained and upgraded by the manufacturer’s representative or the vendor. |
d) | At least every three months, the manufacturers must make a full inspection and test representative. Records of such inspections and tests must be kept on the job site with copies forwarded to the Safety Department. | ||
e) | The movable personnel hoist is to be inspected for proper mechanical condition and is not to be used for lifting personnel unless in proper working order. | ||
f) | All outriggers must be extended and firmly set before personnel are elevated. | ||
g) | Never position steps, ladders, or similar items on platforms to provide additional reach. | ||
h) | Aerial work platform are not designed to be use as a lifting device for materials. It is designed to safely lift workmen, small incidental materials and their tools. | ||
i) | If any questionable situation arises as to the capabilities or use of a movable personnel hoist, the Safety Department or manufacturer’s representative is to be consulted prior to use. | ||
j) | All mechanical, hydraulic, and structural parts and systems of the lift will be inspected before each use. Any defects will be corrected before use. | ||
k) | The equipment operator must know the equipment’s capacity and operate within the safe operating limits. |
1. | Two 10-lb ABC fire extinguishers will be maintained on each J.L.G., one in the main basket, one on the machine base on the ground. | ||
2. | The counterweight swing radius is to be barricaded any time the equipment is in operation. The area directly underneath the J.L.G. must be barricaded if the work presents a hazard to workers at lower levels. | ||
3. | Lift will be operated only on level ground with wheels choked unless controls are located in basket of equipment. |
4. | Steering wheels should not be turned on concrete floors, unless lift is in motion. | ||
5. | Safety harnesses will be worn in basket with lanyards secured to anchor point provided in the lift. | ||
6. | Gate on basket will be kept closed and locked at all times when in use. | ||
7. | No material will be lifted with J.L.G. lift. | ||
8. | Fuel, motor oil, and hydraulic oil will be checked before each shift. | ||
9. | Lift will not be used for any purpose other than to provide a mobile scaffold for workers. | ||
10. | Machine platforms will be kept a minimum of 10 feet from electrical power lines. | ||
11. | Personnel cannot stand on handrails for purposes of work. They must remain inside the basket. | ||
12. | In the event that a person must exit the basket to perform work, the 100% tie off rule must be followed. The person must be tied off to an appropriate anchor point outside of the basket prior to unhooking from the anchor point inside the basket. |
• | Inspections are required when in use other than daily mandated inspection. | ||
• | Inspect all control mechanisms for maladjustment interfering with proper operation. | ||
• | Inspect all control mechanisms for excessive wear of components and contamination by lubricants or other foreign matter. | ||
• | Inspect all safety devices for malfunction. | ||
• | Inspect all hydraulic hoses, and particularly those which flex in normal operation of crane functions, should be visually inspected. | ||
• | Inspect crane hooks for deformations or cracks. Hooks with cracks, or having more than 15 percent in excess of normal throat opening, or more than 10-degree twist from the plane of the unbent hook must not be used. | ||
• | Inspect rope reaving for compliance with crane manufacturer’s specifications. | ||
• | Inspect electrical apparatus for malfunctioning, signs of excessive deterioration, dirt and moisture accumulation | ||
• | Inspect tires for recommended inflation pressure. |
• | It is the primary responsibility of the operator to see that the equipment is operated within the designed specifications. | ||
• | The operator will have the primary responsibility for inspecting and maintaining hoisting equipment. | ||
• | All hydraulic booms will be stowed at end of work shift. | ||
• | All lattice boom cranes will have the boom “dogged off” to an approved location at end of work shift. | ||
• | The operator must be in position at the controls before starting a crane and will never attempt to start a crane while standing on the ground outside the cab. | ||
• | The operator must make sure all other personnel are clear of the crane before starting and/or moving the crane. | ||
• | The operator must not leave the controls position while a load is suspended. | ||
• | The operator must never climb on or off a crane or equipment while it is in motion. | ||
• | The operator and the rigger will be responsible to ensure all systems used with the hoisting equipment are within design capacity. This includes blocks, slings, ropes, etc. | ||
• | The operator will apply power to load lines slowly. | ||
• | The operator will receive signals from only one signal person at a time. The operator will stop the hoist / lift if there is confusion or uncertainty regarding the movement of the load or crane. |
• | The lift supervisor will be responsible to ensure that proper barricades are placed around the swing radius of cranes or other lifting equipment. | ||
• | Personnel operating cranes will be competent to operate such equipment and must have current certification / qualification card issued by the Crane and Equipment Safety Manager. | ||
• | The operator will ensure that a fire extinguisher is on the equipment with a rating of 10ABC or larger and is readily accessible. | ||
• | When handling or recharging batteries or using jumper cables, wear a face shield. |
• | A signal person must guide and direct the movement of the rig. | ||
• | Close cooperation between the operator and signal person must be exercised. The operator will not make any move unless signals are clearly understood. | ||
• | Sudden starts and stops are to be avoided. | ||
• | Swing speed must be controlled so that the load does not swing out beyond the radius at which it can safely be handled. | ||
• | The operator will avoid hoisting and carrying loads over personnel. |
• | The bottom tip should always be positioned directly above the load being hoisted. A crane boom should never be used for dragging loads sideways. | ||
• | The load should never be allowed to strike the boom, outriggers or crane body, and the boom should never strike a structure. If a boom strikes any object, the crane must be remove crane from service for re-inspection. | ||
• | The weight of the hook, spreader bar, load block and other material to be lifted must be included when calculating the total weight of a load. | ||
• | All personnel will stand clear of all lines under strain. | ||
• | All personnel should stand clear of the bight of a line (i.e., where the line makes a loop or a turn over a sheave or block). | ||
• | All rigging hardware is to be used per the manufacturer’s instructions, applicable standards and good practice. Hardware should never be loaded beyond its safe working load. | ||
• | In the event of a possible failure where the crane could potentially contact an electrical energy source, the lift operator shall ensure the crane is grounded through the superstructure. | ||
• | Rated capacities, special warnings and instructions will be legibly posted on all equipment so they are visible by the operator. | ||
• | Tag lines will be used when lifting materials with any cranes or other lifting device. | ||
• | A rope sling will never be used on material contaminated with caustic or acids. | ||
• | The use of barricade rope as a hand line is prohibited. | ||
• | A bar should be used to guide cable or line onto a drum of a hoist. The employee’s hands or feet should never be used as a cable guide. | ||
• | Pads or mats will always be used under outriggers when setting up a crane on unstable ground or in areas where the strength of the slab/roadway is not known (The operator will be responsible for this action). | ||
• | Weather conditions and lightning potential must always be considered before handling a load. During heavy rain and especially during lightening,stop work and find shelter. | ||
• | Boatswain chair lifts with a crane are prohibited. |
• | Load lines will be capable of supporting, without failure, at least seven- (7) times maximum intended load. Anti-rotation rope will be capable of supporting ten — (10) times the maximum intended load. |
• | Load and boom hoist brakes, swing brakes, and locking devices will be engaged when man basket is in a stationary working position. |
• | The load line hoist drum will have controlled load lowering. Free-fall is prohibited. |
• | The crane will be uniformly level, within one percent (1%) level grade on firm footing; and outriggers with pads shall be used, if not crawler crane. |
• | Total weight of the loaded platform and rigging will not exceed 50% of the rated capacity for the radius and configuration of the crane. |
• | Cranes will be equipped with and have in good working order the following: |
• | Cranes having a live boom will not be used. |
• | A qualified engineer with a Professional Engineer (PE) stamp competent in structural design will endorse and will design the man basket and suspension system. |
• | Welded by approved welder and welding inspection report required with submission. |
• | Man basket will be properly hung so that it will not turn or overturn while personnel are in inside. |
• | The personnel platform will have a safety factor of five (5) of its intended capacity. |
• | A minimum of six (6) feet of headroom will be provided where required. |
• | Each platform must have a perimeter protection up from the floor forty-three (43) inches — (1100mm) minimum, which will be of solid construction of expanded metal with no greater than one-half inch (1/2) — 12.7mm openings. | ||
• | A grab rail will be provided inside the platform. |
• | If a gate is provided, it will swing inward and will be equipped with a device to prevent accidental opening. |
• | Overhead protection must be provided when workers may be exposed to falling objects. | ||
• | Signs will be permanently affixed to the man basket displaying: |
• | Regulatory requirements where more stringent will supersede and apply. |
• | Only workers performing the work task will occupy the man basket; 2x men maximum. |
• | Man basket will be used only to lift workers and their tools and material to do the job. All work materials well be secured and distributed evenly in the man basket. |
• | No additional load will be lifted with the crane while man baskets are in use. |
• | When a wire rope bridle is used to connect the man basket to the load line, the bridle legs will be connected to a single ring or shackle. Bridles used as a connection for the personnel platform must not be used for any other purpose. |
• | Hook throat openings will be closed and locked. “Mousing” (using wire rope to close the hook opening) is not permitted. |
• | All rigging will have a minimum safety factor of seven (7) of the intended load. |
• | All eyes in wire rope must be fabricated with thimbles. |
• | A trial liftwith the unoccupied man basket will be made by the crane operator for each new work location and a new permit issued for the beginning of each shift to ensure that all controls and safety devices are functioning properly. |
• | A new work location is any new lift where the radius has changed or additional weight is required or physical movement of the crane location. |
• | Prior to hoisting workers for the first time at each new set up location, the crane operator will make a full cycle test of the man basket by lifting the unoccupied man basket loaded to 125% of the posted rated capacity. |
• | Lifting and lowering of the man basket will be performed in a slow and controlled manner with no sudden moves. |
• | Workers will keep all parts of their body inside the man basket during raising, lowering, and positioning. |
• | Traveling the crane will be prohibited while the man basket is occupied. |
• | The crane operator will remain at the controls while the man basket is occupied. |
• | The use of the man baskets shall be prohibited upon indication of any dangerous weather conditions. |
• | Workers being hoisted shall remain in continuous sight of or continuous communication with the operator or signal person. |
• | Workers occupying the man basket must wear a safety harness with lanyard connected above the load block or fall ball. |
• | No lifts shall be made on another of the crane load lines while personnel are suspended in a man basket. |
• | A pre-lift meeting prior to hoisting at each new location, shall be held between the crane operator, persons to be lifted, Crane and Equipment Manager or his designee, to assure the safeguards mentioned in this procedure are followed and there is clear understanding of each person’s job scope and requirements. |
• | Controls will be clearly marked as to their function. |
• | The design and operation of all movable personnel hoists will be in accordance with the manufacturer’s recommended procedures for safe operation. |
• | All personnel who operate aerial work platforms will be trained and certified in the safe operating procedures, using the manufacturer’s operator book. |
• | The operator will have, a certificate issued by an authorized Yates/Paric trainer. Verification of training may be accomplished by contacting the Safety Training Manage. |
• | The movable personnel hoist is to be inspected for proper mechanical condition and is not to be used for lifting personnel unless in proper working order. |
• | All outriggers must be extended and firmly set before personnel are elevated. |
• | While traveling, the basket must always follow behind the boom and must always be in a down position. |
• | Never position steps, ladders, or similar items on platforms to provide additional reach. |
• | Never lift any materials with the hoist. It is designed to lift workmen and their tools safely. |
• | If any questionable situation arises as to the capabilities or use of a movable personnel hoist, the Safety Department or manufacturer’s representative is to be consulted prior to use. |
• | All mechanical, hydraulic, and structural parts and systems of the lift will be inspected before each use. Any defects will be corrected before use. | ||
• | Know equipment’s capacity and operate within it. |
• | Two 10-lb ABC fire extinguishers will be maintained on each J.L.G., one in the main basket, one on the machine base on the ground. |
• | The counterweight swing radius is to be barricaded any time the equipment is in operation. Area directly underneath overhead work should also be barricaded. |
• | Lift will be operated only from level ground with wheels choked unless controls are located in basket of equipment. |
• | Steering wheels will not be turned on concrete floors, unless lift is in motion. |
• | Safety harnesses will be worn in basket with lanyards secured to bar provided. |
• | Gate on basket will be kept closed and locked at all times when in use. | ||
• | No material will be lifted with J.L.G. lift. | ||
• | Fuel, motor oil, and hydraulic oil will be checked before each shift. |
• | Lift will not be used for any purpose other than to provide a mobile scaffold for workers. |
• | Machine platforms will be kept a minimum of 10 feet from electrical power lines. |
• | Personnel cannot stand on handrails for purposes of work. They must remain inside the basket. |
• | A 10-lb ABC fire extinguisher will be mounted and maintained on the inside of the work platform. |
• | When platform is raised for maintenance of rig; or before working under the platform, the platform will be positively blocked up to prevent the platform from falling. |
• | Lower platform fully at end of work operation, and never climb up to extended platform. |
• | The erection and operation of hoists must conform to established standards. |
• | The maximum allowable distance between the floor of the lifting car and the landing platform is six inches. |
• | A sign stating “No Riders Allowed” must be posted on the car frame. Employees are prohibited from riding material hoists except for authorized purposes of inspection and maintenance. |
• | Material hoists will not be operated near ladders, passageways, etc. |
• | The Dead Man Control Switch must be operable by the person operating the equipment and not wired in the “on or open” position. |
• | Equipment will not operate closer than 20 feet to and energized power lines rated at 50 KV or less unless the aerial device is insulated for the work, and personnel for such operations perform the work. |
• | Engine must be able to be started from the controls in the basket as well as from controls on the engine compartment. |
• | A copy of the operator’s manual must be available and read by each operator, before use. |
• | No employee will be permitted to use or operate lifts or platforms unless he/she has been instructed, trained and certified by a competent person in the use and operation of such equipment. |
• | Equipment will not be moved when the boom is elevated in a working position with employees in the basket or on an elevated platform. Manufacturer’s specifications and limitations will be observed. |
• | No employee will sit or climb on the guardrail of the basket, with the lanyard being attached to the boom or basket. |
• | Employees who tamper with controls and/or bypass safety devices, such as dead-man switches, etc. may be terminated. |
• | Lift truck operators should be physically qualified as follows: |
• | No physical or mental condition that would jeopardize the safe operation of the truck (dizzy spells, medication, bad back, etc.). |
• | Good vision — at least 20/40, corrected if necessary; depth perception at least 90 percent of normal. | ||
• | Normal hearing, preferably without need of a hearing aid. | ||
• | Normal reflexes and reaction time. | ||
• | Ability to understand and read instructions, signs, etc. in English/Spanish. |
• | Only trained and authorized operators will be permitted to operate an industrial power truck (forklift). Those authorized employees will demonstrate their ability to operate the forklift and an employee qualification will be issued. |
• | Upon successfully completing training requirements established by Crane and Equipment Safety Manager, a record will be established and the matrix of these record will be maintained by the Safety Training Manager. |
• | The certification will be issued for the forklift on which the operator is trained and should be renewed yearly by training operations rules, the manufacturer’s operation’s manual, and by passing a manipulative test. | ||
• | The person must successfully pass an operational skills test on the forklift. | ||
• | The person qualified must read and understand the manufacturer’s operator’s manual. |
Rough Terrain Fork Lifts
• | P.I.T.’s will be equipped with a 5-lb ABC rated dry chemical type fire extinguisher, within reach of the operator. | ||
• | P.I.T.’s will be equipped at all times with approved overhead protection, in addition to roll over protection. | ||
• | Where possible, P.I.T.’s will be kept off of public roads. | ||
• | P.I.T.’s will not be operated on public roads during hours of darkness. | ||
• | P.I.T.’s must never exceed 10mph on project. |
• | P.I.T.’s will be equipped with back-up alarms and/or a single amber flashing or revolving warning light. |
• | P.I.T.’s will be equipped with a 10-inch convex rear view mirror on the blind side of the machine. |
• | Forklifts will not be used as an elevator for employees unless equipped with a personnel lift platform designed and approved by the forklift manufacturer and used according to the OSHA standard. | ||
• | Seat belts will be worn by operator. |
• | No person will be allowed to stand or pass under the elevated portion of any truck, whether loaded or empty. |
• | No personnel will be permitted to ride on industrial power trucks or the load. |
• | The operator will not allow arms or legs to be placed between the uprights of the mast or outside the running lines of the truck at any time while in operations. |
• | When an industrial power truck is unattended, load-engaging means will be fully lowered, controls will be neutralized, power will be shut off and brakes will be set. Wheels will be blocked if the truck is parked on an incline. |
• | A safe distance will be maintained from the edge of ramps or platforms while on any elevated dock, or platform. Trucks will not be used for opening or closing freight doors. |
• | Brakes will be set and wheel blocks will be in place to prevent movement of trucks, trailers while loading and unloading. Fixed jacks are necessary to support a semi-trailer during loading or unloading when the trailer is not coupled to a tractor. | ||
• | The flooring of trucks and trailers will be checked for breaks and weakness before they are driven on or across by the forklift. |
• | There will be sufficient headroom under overhead installations, lights, pipes, sprinkler system, etc. | ||
• | An overhead guard will be used to protect against falling objects. | ||
• | Fire aisles, access to stairways and fire equipment will be kept clear. |
protection from the impact of small packages, boxes, bagged material, etc., representative of the job application; but not to withstand the impact of a falling capacity load.
• | Safeguard the pedestrians at all times. Do not drive a truck up to anyone standing in front of a bench or other fixed object. |
• | Do not allow anyone to stand or pass under the elevated portion of any truck, whether loaded or empty. |
• | Unauthorized personnel will not be permitted to ride on powered industrial trucks. A safe place to ride will be provided where riding of trucks is authorized. |
• | Do not put arms or legs between the uprights of the mast or outside the running lines of the truck. |
• | When leaving a powered industrial truck unattended, load engaging means will be fully lowered, controls will be neutralized, power shut off, brakes set, key or connector plug removed. Block wheels if truck is parked on an incline. |
• | Maintain a safe distance from the edge of ramps or platforms and do not, while on any elevated dock or platform, push freight cars. Do not use trucks for opening or closing freight doors. |
• | Be sure of sufficient headroom under overhead installations, lights, pipes, sprinkler systems, etc. |
• | Use a load backrest extension whenever necessary to minimize the possibility of the load or part of it from falling rearward. |
• | Report all accidents involving personnel, building structures and equipment to the site superintendent immediately. |
• | Personnel will not use lift trucks for elevated work platforms. |
• | Fully licensed and approved under regulatory requirements. | ||
• | Operator shall have appropriate license for vehicle type. | ||
• | Vehicle and personal insurance. | ||
• | Vehicles unlicensed for public roads are not allowed within the site. | ||
• | Vehicles used for the transporting of material will have a“back-up alarm” wired into the vehicle reverse gear. Back-up alarm will be fully audible for(20) feet. |
• | When operated offsite all vehicles will be maintained and driven according to traffic laws and regulations. | ||
• | Inside the site speed limit is maximum (15/mph). | ||
• | Vehicle backing-up with areas blind to the operator will require a signal-man. | ||
• | Vehicles will never block a road way at any time. | ||
• | Vehicle keys should remain inside vehicle at all times. | ||
• | Vehicle operator will not leave vehicle running and unattended. |
• | Vehicle may be required to be parked in designated parking spaces. | ||
• | During any emergencies or alarms all vehicle will pull to the side of the road — turn-off engine and personnel will walk to designated assembly point. |
1. | Steel erection activities include hoisting, laying out, placing, connecting, welding, burning, guying, bracing, bolting, plumbing and rigging structural steel, steel joists and metal buildings; installing metal decking, curtain walls, window walls, siding systems, miscellaneous metals, ornamental iron and similar materials; and moving point-to-point while performing these activities. |
2. | The following activities are covered by this plan when they occur during and are a part of steel erection activities: rigging, hoisting, laying out, placing, connecting, guying, bracing, dismantling, burning, welding, bolting, grinding, sealing, caulking, and all related activities for construction, alteration and/or repair of materials and assemblies such as structural steel; ferrous metals and alloys; non-ferrous metals and alloys; glass; plastics and synthetic composite materials; structural metal framing and related bracing and assemblies; anchoring devices; structural cabling; cable stays; permanent and temporary bents and towers; false work for temporary supports of permanent steel members; stone and other non-precast concrete architectural materials mounted on steel frames; safety systems for steel erection; steel and metal joists; metal decking and raceway systems and accessories; metal roofing and accessories; metal siding; bridge flooring; cold formed steel framing; elevator beams; grillage; shelf racks; multi-purpose supports; crane rails and accessories; miscellaneous, architectural and ornamental metals and metal work; ladders; railings; handrails; fences and gates; gratings; trench covers; floor plates; castings; sheet metal fabrications; metal panels and panel wall systems; louvers; column covers; enclosures and pockets; stairs; perforated metals; ornamental iron work, expansion control including bridge expansion joint assemblies; slide bearings; hydraulic structures; fascias; soffit panels; penthouse enclosures; skylights; joint fillers; gaskets; sealants and seals; doors; windows; hardware; detention/security equipment and doors, windows and hardware; conveying systems; building specialties; building equipment; machinery and plant equipment, furnishings and special construction. |
walking/working surface. Pre-engineered holes in cellular decking (for wires, cables, etc.) are not included in this definition.
rigging suppliers that facilitates the attachment of up to five independent loads to the hoist rigging of a crane.
• | Securely connect members of support systems, | ||
• | Safely install support systems, | ||
• | Never overload members of support systems, and | ||
• | Install other structural members to carry loads imposed on the support system when temporary removal of individual members is necessary. |
• | Keep materials or equipment that might fall or roll into an excavation at least 2 feet from the edge of excavations, or have retaining devices, or both. |
• | Provide scaling to remove loose rock or soil or install protective barricades and other equivalent protection to protect employees against falling rock, soil, or materials. |
• | Prohibit employees from working on faces of sloped or benched excavations at levels above other employees unless employees at lower levels are adequately protected from the hazard of falling, rolling, or sliding material or equipment. |
• | Prohibit employees under loads that are handled by lifting or digging equipment. To avoid being struck by any spillage or falling materials, require employees to stand away from vehicles being loaded or unloaded. |
1. | All open trenches and excavations will be barricaded to protect pedestrians and vehicles. |
2. | When possible, the barricades will be set up prior to excavation so there will not be a lag time between opening the excavation and erecting the barricade. |
3. | Excavations requiring wooden barricades constructed with 2” by 4” top rail at 39” to 45” in height and 2” by 4” mid-rail including 2” by 4” uprights no further apart than eight feet are: |
a) | Any excavation to be open more than 36 hours. |
b) | Any excavation that cuts an accepted established walkway, sidewalk, or aisle way. |
4. | Excavations requiring sawhorse-type barricades with flashing lights are: |
5. | All other excavations may be barricaded with pennant flagging or yellow and black barrier tape. |
1. | Broken or damaged ladders must not be used. Repair or destroy them immediately. Ladders to be repaired must be tagged “Unsafe, Do Not Use.” | ||
2. | Ladders will not be spliced together. | ||
3. | Ladders should not be placed against movable objects. | ||
4. | The areas around the top and base of ladders must be free of tripping hazards such as loose materials, trash, and electric cords. | ||
5. | To prevent ladders that project into passageways from being struck by personnel, moving equipment, or materials being handled, barricades or guards must protect them. | ||
6. | You must face the ladder at all times when ascending or descending. Three points of contact must be maintained at all times. | ||
7. | When ascending or descending a ladder, an employee will have hands free, grip the sides or rungs with both hands, and face the ladder. | ||
8. | Under no circumstances will an employee ascend or descend a ladder while carrying tools or material in their hand. A hand line is recommended when hoisting or lowering tools and materials. | ||
9. | Be sure that shoes are free of mud, grease, or other substances that could cause a slip or fall. | ||
10. | The use of metal ladders is prohibited. | ||
11. | Boxes, crates, chairs, or equipment should never be used as a substitute for ladders. | ||
12. | Only one employee will work from a ladder at one time. | ||
13. | A competent person will inspect ladders frequently and immediately repair or replace ladders when found defective. | ||
14. | Straight or extension ladders used for access to a floor or platform must extend a least 3 feet above the landing and must be secured. | ||
15. | The feet of all ladders will be equipped with “safety shoes” | ||
16. | Ladder feet will always be placed on a level, substantial base. |
17. | One employee must always hold the base of the ladder stationary whenever the climber is ascending or descending an unsecured ladder. Ladders shall be tied off at the top prior to starting work. |
18. | A ladder or any part of a ladder must not be used as a scaffold platform. |
19. | Extension ladders will be placed one foot out at the horizontal base for four feet of vertical rise. |
20. | Extension ladders will not be separated in order to create “two” ladders. |
21. | If three points of contact cannot be accomplished and the working height is 6 foot or greater, then a full body harness, lanyard and the off point must be used. |
1. | The following procedures will be followed: | ||
a. | Notify all affected employees that a lockout and tagout system is going to be utilized and the reason for it. The authorized employee shall know the type and magnitude of energy that the machine or equipment utilizes and shall understand the hazards associated with it. | ||
b. | If the machine or equipment is operating, shut it down by the normal stopping procedure. | ||
c. | Operate the switch or other isolating device so that the equipment is isolated from its energy source or sources. Restrain any stored energy, such as springs, elevated parts of machines, rotating members and air, gas, steam or pressurized water by blocking, bleeding, repositioning or other effective means. |
d. | Lockout and tagout the energy isolating devices with assigned individual locks, tags, or other additional safety measures. Lockout locks shall be keyed individually to insure each lock’s integrity. | ||
e. | After ensuring that no personnel are exposed, and as a check on having disconnected the energy sources, operate the normal operating controls to make certain the equipment will not operate. CAUTION — Return operating controls to “Neutral” or “Off” position after the test. An individual familiar with the start up of the equipment must do this test. Also, a qualified electrician must use test equipment to ensure that electrical parts and circuit elements have been de-energized. | ||
f. | The equipment is now locked and tagged out. |
Gating at security access/egress points will be of the same materials of construction as the perimeter fencing. Gates will be capable of being secured and locked.
OCIP MANUAL
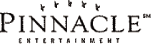
INSURANCE MANUAL
I.Introduction | 1 | |||
II.Administration Directory | 2 | |||
III.Insurance Policy Reference | 4 | |||
IV.Program Definitions | 5 | |||
V.TheInsuranceProgram | 7 | |||
A. 11.1 —Owner Controlled Insurance Program | 7 | |||
B. 11.1.2 —Applicability of the OCIP | 7 | |||
C. 11.2 —Contractor Insurance Cost Identification | 8 | |||
D. 11.2.1 —Change Order Pricing | 9 | |||
E. 11.2.2 —Audit and Recovery of Contractor and/or Subcontractor “Insurance Cost” | 9 | |||
F. 11.3 —RIVER CITY CASINO & HOTEL PROJECT OCIP—OCIP Provided Coverages | 11 | |||
G. 11.3.1 —Certificates and Policies | 12 | |||
H. 11.3.2 —Termination/Modification of the OCIP Warranty Work | 12 | |||
I. 11.4 —Contractor-Provided Coverage | 13 | |||
J. 11.4.1 —Deductibles on Contractor Policies | 14 | |||
K. 11.4.2 —Certificates of Insurance | 14 | |||
L. 11.4.3 —Other Insurance | 15 | |||
M. 11.4.4 —Contractor Responsibilities | 15 | |||
N. 11.4.5 —Contractor’s Responsibility for its Subcontractors | 16 | |||
O. 11.4.6 —Assignment of Return Premiums | 16 | |||
P. 11.4.7 —Waiver of Subrogation | 16 | |||
Q. 11.4.8 —No Release | 16 | |||
R. 11.4.9 —Approval of Forms and Companies | 16 | |||
S. 11.4.10 —Coverage to be Provided by Contractor During Warranty Period | 17 | |||
T. 11.4.11 —Claims Responsibilities | 17 | |||
U. 11.4.12 —Project Safety Administration | 17 | |||
VI.Insurance Administration | ||||
A.Exhibit11b — Enrollment Process Table | 20 | |||
VII.AccidentReporting and Claims Procedures | 21 | |||
VII.Sample Forms |
River City Casino & Hotel | August 11, 2008 | |||
OCIP Manual |
• | Describes the OCIP and details the insurance-related responsibilities of the various parties involved. | ||
• | Provides a basic description of the OCIP structure and operation, with an overview of coverage provided by the OCIP and guidelines for carrying out specific administrative and audit procedures. | ||
• | Provides answers to questions that are likely to arise during the course of the project. Because it is impossible to anticipate every question or situation that may arise, the directory lists those involved in the administration of the OCIP and their areas of expertise. Please feel free to call with any questions. | ||
• | Will be updated as changes dictate during the course of this project. | ||
• | Does not and is not intended to provide coverage interpretations. The terms and conditions of the policies alone govern how coverage is applied. |
River City Casino & Hotel | 1 | August 11, 2008 | ||
OCIP Manual |
224 N. Hwy 67 Suite 193
Florissant, MO 63031
Office Phone: 314-395-6615
Fax: 314-395-1880
Cell Phone: 817-681-5710
E-mail: gina.neal@willis.com
Willis—National Wrap-Up Team
One Galleria Tower
13355 Noel Road, Suite 400
Dallas, TX 75240
Phone: 972-715-6229
Cell Phone: 214-878-0481
E-mail: james.tingley@willis.com
Willis of Nevada, Inc.
7251 W. Lake Mead, Suite 300
Las Vegas, NV 89128
Phone: 702-458-1877
Fax: 702-562-4340
E-mail: chuck.halsey@willis.com
WilIis—National Wrap-Up Team
13355 Noel Rd., Suite 400
Dallas, Texas 75240
Phone: 972-715-6316
Fax: 972-386-5561
E-mail: edwards_bl@willis.com
River City Casino & Hotel OCIP Manual | 2 | August 11, 2008 |
CLAIMS OFFICES/TEAMS
P.O. BOX 20048
Kansas City, MO 64195
Toll free: 800-777-9005
FAX: 913-345-1582
Phone: 913-345-4349
E-Mail:kimberly.ellis@zurichna.com
Phone: 913-345-4336
E-Mail: alan.barzee@zurichna.com
Phone: 913-345-4391
E-Mail: tammy.richardson@zurichna.com
Phone: 913-345-4370
E-Mail: joanna.ko@zurichna.com
Phone: 913-345-4327
E-Mail: william.cherry@zurichna.com
Phone: 913-345-4331
E-Mail: fred.taylor@zurichna.com
River City Casino & Hotel | 3 | August 11, 2008 | ||
OCIP Manual |
Policy Number: Varies by Subcontractor
Policy Number: GLO5379534-00
Policy Number: AEC5379534-00
Limits: $25,000,000 excess of primary
Policy Number: G21979296001
Limits: $25,000,000 excess $25,000,000 excess primary
Policy Number: UK73761
Limits: $50,000,000 excess $50,000,000 excess primary
NAMED INSURED: Union Pacific Railroad
Policy Number: RRP 3878359-00
Limits: $2,000,000 per occurrence/$6,000,000 aggregate
Policy Number: IM 9002897-00
River City Casino & Hotel | 4 | August 11, 2008 | ||
OCIP Manual |
Owner Controlled Insurance Program (OCIP) | The Program under which Workers’ Compensation, Employer’s Liability, Commercial General Liability, Excess Liability, Railroad Protective Liability, Builder’s Risk are procured or provided on a project “wrap-up” basis for Contractor/Subcontractor(s) of any tier, who have been properly enrolled, while performing operations ata designated Project Site. | |
Insured | River City Casino & Hotel Contractor(s) and Subcontractors of any tier who are enrolled in the OCIP and who have been named in a policy, certificate of insurance, or advice of insurance. | |
Insurer | Insurance Companies, identified in the Administrative Directory providing coverage for theRiver City Casino & Hotel OCIP. | |
OCIP Administrator | The firm responsible for the brokering and administration of the Owner Controlled Insurance Program. | |
OCIP Safety Consultants | These representatives are employees of the Insurer and Willis who will provide safety consulting services to theRiver City Casino & Hotel Project OCIP,its Contractors and Subcontractors of all tiers enrolled in the OCIP. | |
Project Site | River City Casino & Hotel Lemay Missouri Project,located@ 599 E. Arlee Avenue, St. Louis, MO 63125,consisting of approximately “80 acres within the boundary of the River Des Peres on the North, The Mississippi River on the East, The Union Pacific Railroad on the West and private property on the South.” | |
River City Road Lemay Missouri Project is described as“An approximate two mile length of 4-lane road including a new bridge over existing railroad tracks. The site includes new and renovated road sections extending from the project’s northwest property line to Interstate 55. The roadway limits generally follow the south side of River Des Peres.” | ||
On-Site Activities | Those activities atthe Project sites or emanating there from such as adjacent sidewalks, streets and contiguous areas. The OCIP does not provide insurance coverage for permanent yards or other locations of any Contractor/Subcontractor, except as specifically requested by Contractor and endorsed by owner, and as outlined by the Builders’ Risk policy. | |
Eligible Contractors (Included in the Program) | Eligible Contractors include all subcontractors providing direct labor on theProject Sites (see definition of ineligible subcontractors below). Temporary labor services and leasing companies are to be treated as a subcontractor. |
River City Casino & Hotel | 5 | August 11, 2008 | ||
OCIP Manual |
Ineligible Contractors (Not included in the Program) | The OCIP does not cover consultants, suppliers (that do not perform or subcontract installation), vendors, materials dealers, guard services, janitorial services, truckers (including trucking to the project where delivery is the only scope work performed), and other temporary project services. | |
Certificate of Insurance | Written evidence of the existence of coverage terms of a particular insurance policy. | |
Bid Deduct | Contractor/subcontractor original scope of work and subsequent change orders will be bidwith insurance costs included. Each Contractor shall complete the Insurance Cost Identification Form 2. Requirements are further defined in Section 11.2. | |
Composite Rating | Composite rate is the combination of all basic rates, increased factors, credits and surcharges into a combined rate. For the purpose of this program, any credit for self insurance or deductibles must be identified but will not be allowed. | |
Corporate Allocation | A rate assigned for a branch, office or subsidiary by the corporate office for designated costs. For the purpose of the program, this rate is not allowed, actual cost must be identified. | |
Loss Fund | The fund set up by each contractor to pay for any claims within the deductible or self insured level of the contractor/subcontractor’s primary insurance program. This fund amount is a cost normally passed back to the Owner in the final bid. For purposes of this program, this amount is not allowed; the credit amount given on the rate must be identified. | |
Sponsor/Owner | Casino One Corporation. |
River City Casino & Hotel | 6 | August 11, 2008 | ||
OCIP Manual |
(a) | Any Contractor or Subcontractor who applies for enrollment in the OCIP ten (10) days or more after they commence working on the Project, will be required to provide a “No Known Loss Letter” to the Carrier along with the enrollment documentation. If the loss occurs prior to enrollment, the loss may not be covered under the OCIP. The Owner retains the sole discretion to determine whether to enroll any Contractor or Subcontractor in the OCIP. |
River City Casino & Hotel | 7 | August 11, 2008 | ||
OCIP Manual |
a) | First dollar Workers’ Compensation coverage is provided underThe Project OCIP for all Contractors/Subcontractors enrolled in the program. Contractor Insurance Programs that include high deductibles; self-retention levels; self-insured portions (Workers’ Compensation or General Liability) must use the following for their calculations: |
i) | Although Deductible or Self-Retention Credits or Self-Insured amounts are to be identified, they will not be allowed. Policies usingComposite rates must show at a minimum the deductible/self-retention/self-insured amount and the rating breakdown. If the credit percentage is not available, minimum and maximum rates for the program must be identified.Corporate allocations will not be allowed; the same format for calculation as shown for Composite Rates must be shown on the Form-2 and furnished with the bid documents. | ||
ii) | Any credits (other than credits for deductibles or self-retention or self-insured plans), or surcharges shown on the dec and/or rating sheets should be used to calculate contractor’s actual insurance cost. | ||
iii) | A copy of the Workers’ Compensation, General Liability, and Excess Liability policy declarations page and rating schedules to be submitted to the OCIP administrator to confirm information included on the Form 2. |
(1) | Workers’ Compensation and Employer’s Liability Insurance: |
(a) | $1,000,000 Bodily Injury with Accident — Each Accident; | ||
(b) | $1,000,000 Bodily Injury by Disease — Policy Limit | ||
(c) | $1,000,000 Bodily Injury by Disease — Each Employee |
(2) | Commercial or General Liability Insurance: |
(a) | $1,000,000 Bodily Injury/Property Damage each occurrence | ||
(b) | $2,000,000 Products/Completed Operations Aggregate | ||
(c) | $2,000,000 General Aggregate | ||
(d) | $1,000,000 Each Occurrence | ||
(e) | $50,000 Fire Damage | ||
(f) | $5,000 Medical |
River City Casino & Hotel | 8 | August 11, 2008 | ||
OCIP Manual |
1. | Contractual Liability to cover liability assumed under the agreement; | ||
2. | Product and Completed Operations Liability insurance | ||
3. | Broad Form Property Damage Liability Insurance | ||
4. | Explosion, collapse and underground hazards (deletion of the X,C,U exclusions) if such exposure exists; | ||
5. | Independent Contractors; | ||
6. | Such policy shall include all of the coverages which may be included in coverages A, B and C contained in the Commercial General Liability Policy, without deletion. Such policy must be issued upon an “occurrence” basis, as distinguished from a “claims made” basis. | ||
7. | Products and Completed Operations to be maintained for two (2) year after final payment. |
(3) | Excess Insurance: | ||
$25,000,000-General Contractor Requirement *$ 5,000,000 |
* | Limits required of Subcontractors unless otherwise noted in Bid Documents. |
River City Casino & Hotel | 9 | August 11, 2008 | ||
OCIP Manual |
• | A final audit will be conducted at the end of each contract, of the actual on-site payroll, receipts, and insurance costs. The insurance costs will be based on the rates, credits and surcharges shown on the approved Enrollment Form 2. These rates will be applied to the entire actual project payroll and/or receipts. The final adjustment will be calculated based on the actual payroll or receipts less those estimated during the bidding and less OCIP change order process. | ||
• | The OCIP Administrator will provide the Contractor with a close-out form and notify the Sponsor and/or awarding Contractor of the final calculation and the difference will be adjusted in the contract amount prior to release of retainage. |
River City Casino & Hotel | 10 | August 11, 2008 | ||
OCIP Manual |
(1) | Workers’ Compensation and Employer’s Liability Insurance: | ||
WORKERS’ COMPENSATION INSURANCE STATUTORY BENEFITS as provided by state statute; and EMPLOYER’S LIABILITY LIMITS: |
(a) | $1,000,000 Bodily Injury with Accident — Each Accident; | ||
(b) | $1,000,000 Bodily Injury by Disease — Policy Limit | ||
(c) | $1,000,000 Bodily Injury by Disease — Each Employee |
(2) | Commercial General Liability Insurance, placed by the OCIP Administrator (Willis), will be provided on an “occurrence” form under a master liability policy. Certificates of insurance will be provided to the Prime Contractor/Subcontractor and all tiers of Subcontractors reflecting the following Limits of Liability, Coverages, and Terms: |
(a) | Limit of Liability: |
1. | $2,000,000 Bodily Injury and Property Damage Liability Each Occurrence | ||
2. | $4,000,000 General Aggregate Reinstated Annually | ||
3. | $4,000,000 Products and Completed Operations | ||
4. | $5,000 Property Damage Deductible per occurrence to be the responsibility of the Contractor or Subcontractor who caused the loss. |
(b) | Coverage and Terms: |
1. | Occurrence Basis; | ||
2. | Contractual Liability specifically designating the indemnity provision of this agreement as an insured contract; | ||
3. | Completed Operations (Ten Year Term); | ||
4. | Independent Contractor/Subcontractor’s Liability; | ||
5. | Designated Premises Only. |
(3) | Railroad Protective Liability |
(a) | $ 2,000,000 each occurrence limit | ||
(b) | $ 6,000,000 aggregate limit Policy issued to Union Pacific Railroad |
(4) | Excess Liability Insurance |
(a) | $100,000,000 per occurrence | ||
(b) | $100,000,000 aggregate |
River City Casino & Hotel | 11 | August 11, 2008 | ||
OCIP Manual |
(5) | Builders Risk |
River City Casino & Hotel | 12 | August 11, 2008 | ||
OCIP Manual |
(a) | $1,000,000 Bodily Injury with Accident — Each Accident; | ||
(b) | $1,000,000 Bodily Injury by Disease — Policy Limit | ||
(c) | $1,000,000 Bodily Injury by Disease — Each Employee; and | ||
(d) | The policy will be endorsed to exclude“The Project”if you are a participant in the OCIP. |
River City Casino & Hotel | 13 | August 11, 2008 | ||
OCIP Manual |
* | Limits required of Subcontractors unless otherwise noted in Bid Documents. |
Excess of General Liability
Excess of Employer’s Liability
Completed Operations
River City Casino & Hotel | 14 | August 11, 2008 | ||
OCIP Manual |
C/o Gina Neal — Willis
224 N. Hwy 67 Suite 193
Florissant, MO 63031
(1) | Compliance with all rules and regulations of the applicable State Insurance Bureau/Board; failure to meet state requirements may result in fines being assessed, if this occurs, the Contractor shall deduct from monies due or to become due under the provisions of this subcontract for any applicable fines that are assessed against the Owner/contractor/subcontractor; | ||
(2) | Compliance with applicable Construction Safety Program; | ||
(3) | Provision of necessary contract, operations and insurance information; | ||
(4) | Cooperation with any insurance company or Insurance Administrator with respect to requests for claims, payroll or other information required under the program; |
River City Casino & Hotel | 15 | August 11, 2008 | ||
OCIP Manual |
(1) | Identify all applicable insurance costs associated with their contract work; and cooperate with the OCIP Administrator in the confirmation of the insurance cost as shown in paragraph 11.2. | ||
(2) | Irrevocably assign to and for the benefit of The Owner, all return premiums, premium refunds, premium discounts, dividends, retentions, credits, and any other monies in connection with the OCIP insurance. Contractor agrees to evidence such assignment by executing and delivering the Form-2. Contractor further agrees to require each subcontractor to execute the assignment on the Form-2, for the benefit of The Owner. |
River City Casino & Hotel | 16 | August 11, 2008 | ||
OCIP Manual |
a. | Company commitment to and philosophy on safety. | ||
b. | Company acknowledgement that they will support and participate in the light duty/return to work policy. | ||
c. | Company acknowledgement that they will commit to drug free workplace. | ||
d. | Company acknowledgement that they will comply with OSHA Standards 29 CFR 1926, 29 CFR 1910 and 46 CFR (if applicable). | ||
e. | Project Safety Representative’s name and lines of authority, his authority regarding safety matters. | ||
f. | The following attachments should follow the commitment letter: |
1. | Project Safety Representative’s and Alternate. | ||
2. | Safety Representative’s resumes must meet Qualifications listed below. |
River City Casino & Hotel | 17 | August 11, 2008 | ||
OCIP Manual |
a. | Specific Project Requirements | ||
b. | Safe Work Practices | ||
c. | Housekeeping | ||
d. | Work Zone Safety | ||
e. | Personal Protective Equipment, Respiratory Protection, Hearing Protection | ||
f. | Fire Protection | ||
g. | Compressed Gas Cylinders | ||
h. | Material Handling, Storage, Usage | ||
i. | Tool Safety | ||
j. | Welding and Cutting | ||
k. | Electrical Safety | ||
l. | Scaffolding | ||
m. | 100% Fall Protection over 6’ on all work activities | ||
n. | Cranes & Rigging — Personal hoists/manlifts | ||
o. | Mobile Equipment Operation and Operator Training |
River City Casino & Hotel | 18 | August 11, 2008 | ||
OCIP Manual |
p. | Excavation and Trenching | ||
q. | Concrete and Masonry Construction | ||
r. | Steel Erection | ||
s. | Underground Construction | ||
t. | Demolition | ||
u. | Explosives | ||
v. | Power Transmission | ||
w. | Confined Space Entry Program | ||
x. | Ladder, Stairway and Ramp Safety | ||
y. | Lockout Tagout Procedures | ||
z. | Hazardous Communication Compliance, Hazardous Material Handling | ||
aa. | Site Security | ||
bb. | Evacuation Plan | ||
cc. | Crisis Management Plan | ||
dd. | Miscellaneous — Include any applicable items not covered above needed to successfully complete your contract. |
River City Casino & Hotel | 19 | August 11, 2008 | ||
OCIP Manual |
Form 1 — | Notice of Subcontract Award: When an Eligible Contractor or Subcontractor of any tier awards a subcontract, the awarding Eligible Subcontractor shall complete Notice of Subcontract Award Form 1 and immediately forward to the OCIP Administrator. A copy of the Manual should be given to each Eligible Subcontractor. | |
Form 2 — | Insurance Cost Identification Worksheet: The awarding Eligible Subcontractor shall assure that their subcontractors complete and immediately forward to the OCIP administrator and attach a copy of WC, GL, and Excess declarations page and rating schedules from the policies. |
Form 2A — | Supplemental Insurance Information Form: This form is required if the contracts issues are a Time and Material contract or if under $30,000 (project cumulative total) or Contracts 30 days or less. | |
Form 3 — | Supplemental Insurance Information Form: If an Eligible Subcontractor has been awarded more than one contract on this Project, Insurance Cost Identification Worksheet (Form 2) must be completed by the subcontractor on the first contract. For each additional contract, Supplemental Insurance Information (Form 3) must be completed and forwarded to the OCIP Administrator. | |
Form 4 — | Notice of Anticipation Completion: When subcontractor is 85% complete, this form should be completed by the Eligible Subcontractor and sent to the OClP Administrator. | |
Form 5 — | Project Site Payroll Reporting Form: To be submitted by the 10th of each month to the OClP Administrator. If not received, pay may be held to the subcontractor. Each Eligible Subcontractor is also responsible for receipt of each lower-tier’s Form 5 also. |
River City Casino & Hotel | 20 | August 11, 2008 | ||
OCIP Manual |
A. | Workers’ Compensation Claims |
1. | Seek immediate medical attention for the injured person(s). | ||
2. | Immediately notify your supervisor and project manager of the situation. | ||
3. | The Supervisor must then notify the OCIP Claims Coordinator and Project Safety Manager or their designate. If you cannot reach, please leave a voice mail message. | ||
4. | Complete the Accident Investigation and the Applicable State Form (include appropriate Location Code) and forward to the OCIP Claims Coordinator and Project Safety Manager in a timely manner, but no later than the close of business day on the day of the accident. | ||
5. | The Contractor’s safety representative or designated person will transport the injured worker to: |
Joe McMillan — Center Administrator
1617 South 3rd Street
St. Louis, MO 63104
Hours: 8am – 5:00pm, M-F
Ph: (314)-421-2557
Fax: (314)-421-2046
6. | TheOCIP Claims Coordinator will report claim with appropriate location code to Zurich. | ||
7. | Employer must complete theFirst Notice of Injury Formand forward toOCIP Claims Coordinator. | ||
8. | Upon receipt of Acknowledgement of Claim fromZurich Insurance Company,OCIP Administrator will provide the Contractor/Subcontractor with a copy so you can record the Claim number for future reference. | ||
9. | All medical bills, hospital bills, etc should be forwarded toZurich Insurance Companyidentifying the injured employee and claim number. |
River City Casino & Hotel | 21 | August 11, 2008 | ||
OCIP Manual |
B. | General Liability Claims |
1. | Seek immediate medical attention for any injured person(s). | ||
2. | Immediately notify your supervisor and project manager of the situation. | ||
3. | The Supervisor must then notify the OCIP Administrator and Project Safety Manager or their designate. If you cannot reach, please leave a voice mail message. | ||
4. | Complete the Accident Investigation and forward to the OCIP Claims Coordinator and Project Safety Manager in a timely manner, but no later than the close of business day on the day of the accident. | ||
5. | TheOCIP Claims Coordinator will report claims with appropriate location code to Zurich. | ||
6. | Upon receipt of Acknowledgement of Claim fromZurich Insurance Company,OCIP Claims Coordinator will provide Contractor/Subcontractor with a copy so you can record the Claim number for future reference. | ||
7. | All investigation reports, pictures, medical bills, hospital bills, etc should be forwarded toZurich Insurance Companyidentifying the injured individual, claimant and claim number. |
C. | Duties in the Event of Occurrence, Claims or Suit |
a) | Follow the claims reporting procedures above. | ||
b) | You must see to it that the OCIP Claims Coordinator is notified promptly of an “occurrence” which may result in a claim. Notice should include: |
• | How, when and where the “occurrence” took place, and; | ||
• | The names and addresses of any injured persons and witnesses. |
c) | If a claim is made or “lawsuit” is brought against any insured, you provide written notice of the claim or “lawsuit” to: |
• | OCIP Claims Coordinator |
d) | You and any other involved insured must: |
• | Cooperate with the Insurer in their investigation, settlement or defense of the claims or “suit”; and | ||
• | Assist the Insurer, upon their request, in the enforcement of any right against any person or organization which may be liable to the insured because of injury or damage to which this insurance may also apply. |
e) | No Insureds will, except at their own cost, voluntarily make a payment, assume any obligation or incur any expense, other than for first aid, without Insurer’s consent. |
D. | Automobile Claims |
River City Casino & Hotel | 22 | August 11, 2008 | ||
OCIP Manual |
E. | Contractor’s Equipment Claims |
F. | Miscellaneous Claims Notes |
1) | Any incident that involved injury to persons or property is to be reported to the OCIP Claims Coordinator office immediately. | ||
2) | Any claims adjuster representing a Contractor/Subcontractor’s normal insurer who seeks to come ontoThe Project sitemust obtain written authorization from the OCIP Claims Coordinator prior to coming on the site. There will be no exceptions to this stipulation. |
River City Casino & Hotel | 23 | August 11, 2008 | ||
OCIP Manual |
Incident Investigation Report | (To be completed within 24 hours by Supervisor at time of incident) |
Employee Name | Male | Female | Date of Birth | Ht. | Wt. | |||||||||||||||||
Employee Address | ||||||||||
Street | City | State | Zip Code | Home Phone |
Employer Name | Address | |||||
Date of Incident | Time | AM/PM | Jobsite/Area | |||||||||
Employee Job Title | Length of Employment | |||||
Weather Condition | Shift | Supervisor | ||||||||
UNSAFE ACTS | UNSAFE CONDITIONS |
What actions caused or contributed to the incident? | What conditions of tools, equipment, or environment contributed to incident? | |||||||
Operating equipment without authority | Inadequate guard/barrier/safety device | |||||||
Failure to warn/signal | Inadequate/improper protective equipment | |||||||
Failure to secure/lock out/tag out | Inadequate warning system | |||||||
Reaching into/servicing equipment in operation | Defective or work tools/equipment materials | |||||||
Making safety devices inoperable | Congestion or restricted area | |||||||
Used defective equipment | Fire or explosion hazard | |||||||
Took unsafe/improper position | Hazardous storage method | |||||||
Horseplay, disruptive actions | Unsecured against movement | |||||||
Improper lifting or movement | Lighting/noise/visual obstruction | |||||||
Other: | Environmental/atmospheric conditions | |||||||
No unsafe action | Other: | |||||||
No unsafe condition | ||||||||
What actions caused or influenced above unsafe acts? | What caused or influenced above unsafe condition? | |||||||
Unaware of job hazards | Defective/worn from normal use | |||||||
Inattention to hazards | Defective/worn from abuse/misuse | |||||||
Unaware of safe method/procedure | Housekeeping/cleaning failure | |||||||
Tried to gain or safe time | Lack of preventative maintenance | |||||||
Influence of fatigue/illness | Inadequate maintenance | |||||||
Influence of emotions/stress | Exposure to environment | |||||||
Defective vision/bodily defects | Inadequate purchasing | |||||||
Under influence of alcohol or drugs | Safety inspection failure | |||||||
Failure to enforce procedures/rules | Other: | |||||||
Other: | Unknown |
Describe the nature and extent of injury/illness (body part affected, type of injury, etc.) | ||||
Was first aid administered? | Yes _____ | No _____ | If yes, what type and by whom | |||||
Was employee taken to hospital/clinic? | Yes | No | If yes, list name, address and phone number of |
hospital/physician/nurse attending | ||
List any eyewitnesses to the incident and others who might provide information about the incident | ||||
River City Casino & Hotel | Page 1 of 2 | July 31, 2008 | ||
OCIP Manual |
Incident/Illness Evaluation (continued)
Type of exertion/body motion during injury: | Pull | Lift | Bend | Reach | Twist | Other | ||||||||||||||||||||
Was this the employee’s regular job? | Yes | No | How much experience does this employee have on this job? | |||||||||||
Was the employee trained in this job or task? | Yes | No | When was last training on this task? | |||||||||
Was this the employee’s first job-related injury or illness? | Yes | No | If no, briefly describe previous injuries (date, nature, | |||||||
extent, etc.) | ||
Hours of overtime worked in last 24 hours | Did this possibly contribute to incident? If so, describe | |||||
Does a safety rule or policy apply to this task? | Yes | No | If yes, describe rule and how employee followed or violated | |||||||
Does a specific procedure for task exist? | Yes | No | If yes, describe procedure briefly and if it was followed | |||||||||
Is protective equipment required for this task? | Yes | No | If yes, describe equipment, if it was used, if it was | |||||||
adequate/functioned properly, and if the employee(s) were trained on it. | ||
Is there possibly any third party which contributed to the incident? (Other contractors, employee, etc.) | Yes | No | ||||||
If yes, describe. | ||
Did any unsafe physical/environmental conditions exist? | Yes | No | If yes, describe conditions (physical, | |||||||
mechanical, electrical, etc.) which contributed to the incident | ||||||||||
Is material handling equipment required for this task? | Yes | No | If yes, was it used and did it function properly? | |||||||
Reinstruction of employee(s) involved | Do/revise Job Safety Analysis | Repair/replace/modify equipment | ||||||||
Preventative instruction of others who do job | Revise/establish safety rule | Improve clean-up procedure | ||||||||
Training of employee(s) | Reassign employee to another job | Improve inspection procedure | ||||||||
Action to improve enforcement | Require/replace protective equipment | Eliminate/reduce congestion | ||||||||
Reprimand/discipline of employee(s) involved | Install safety guard device | Improve design/construction | ||||||||
Improve environmental conditions |
Completion | ||||||||||||||||
Estimated | Confirmed | |||||||||||||||
What was/will be done | By Whom | Completion Date | Date | Initials |
Incident discussed with employee to prevent reoccurrence? | Yes | No | Date | |||||||||||
Any disciplinary action taken? Yes No If yes, describe what type. |
YES | NO | Incident site reviewed by supervisor with employee (and safety coordinator if applicable.) | ||||||||
YES | NO | Incident review meeting conducted. Attended by | ||||||||
YES | NO | Employee or supervisor reviewed incident with work group. | ||||||||
YES | NO | Employee reviewed injury with safety committee | ||||||||
YES | NO | Project Safety informed of incident | ||||||||
Date of Report | Prepared by | Title | ||||||||
Signature | ||||||||||
Reviewed by | Superintendent | |||||||||
River City Casino & Hotel | Page 2 of 2 | July 31, 2008 | ||
OCIP Manual |
RIVER CITY OCIP | ||||
FORM 1 |
Notice of Subcontract Award
Request for Insurance
Willis. | ||||
Attn: Gina Neal | Phone: | 314-395-6615 | ||
224 N. Hwy 67 Suite 193 | Fax: | 314-395-1880 | ||
Florissant, MO 63031 | E-mail: | Gina.Neal@willis.com |
RE: | Project Name: | |||||
Name of Firm: | ||
Address: | City: | State: | Zip: | |||||||||||
Phone: ( ) | Fax: ( ) | Federal Employer��s ID#: | ||||||||
Office Contact: | E-Mail: | |||||
Safety Contact: | E-Mail: | |||||
Type of Work: | Job | |||||
*Start Date: | Estimated Completion Date: | Contract Value: | ||||||||
Estimated Payroll: $ | Est Manhours: | Est. # of Subcontractors: | ||||||||
Awarding Contractor: | ||||||
By: | ||||||
Title: | ||||||
Date: | ||||||
Prime Contractor (if different) | ||||||
River City Casino & Hotel | Page 1 of 1 | July 31, 2008 | ||
OCIP Manual |
FORM 2
INSURANCE COST IDENTIFICATION WORKSHEET
Contractor: | Indv | Ptshp | Corp | J/V | ||||||||||||||
Address: | FEIN: | |||||||||||||||||
Office Contact: | Phone: | Fax: | E-mail: | |||||||||||
Site Contact: | Phone: | Fax: | E-mail: | |||||||||||
Safety Contact: | Phone: | Fax: | E-mail: | |||||||||||
Insurance Contact: | Phone: | Fax: | E-mail: | |||||||||||
Payroll Contact: | Phone: | Fax: | E-mail: | |||||||||||
Address (if different): | ||||||||||||||
CONTRACT INFORMATION | Contract Value: $ |
Job Name/Description: | Contract/JOB #: | |||||
Awarding Contractor: | Prime Contractor: | |||||
Award Date: | Start Date: | Est. Completion Date: | Self Preformed %, $ | |||||||||||
Subcontracted %; | $ Est. # of Subcontractors | Est. Manhours | DBE/MBE/WBE: | |||||||||
Company Name: | Contact: | |||||||
City: | Phone: | ( ) | ||||||
Current WC Ins Co: | Policy Period: | |||||||||||||
Experience Modifier: | Rate Date: | Deductible: | Retention: | |||||||||||
Attach additional pages if required. Attach copy of declaration page and rate sheets for WC Policy
W.C. Rate/ | |||||||||||||||
W.C. Classification | W.C. Code | $100 Payroll | Estimated Payroll | Premium | |||||||||||
1. | |||||||||||||||
2. | |||||||||||||||
3. | |||||||||||||||
4. | |||||||||||||||
5. | |||||||||||||||
6. | |||||||||||||||
Subtotal | |||||||||||||||
*It is extremely important to accurately estimate all onsite payroll anticipated for this contract. Payroll should be raw wages without burden, fringes, or overtime premium: but should include sick, vacation, holiday pay and imputed income. All WC rules for Missouri are applicable. Composite Rates and Corporate Allocations, must reflect the breakout of insurance cost (actual rating calculations).See Section 11.2 of the OCIP Manual. | Increased Limit Factor: | $ | |||||||||||||
Experience Modifier | $ | ||||||||||||||
Discounts | $ | ||||||||||||||
Surcharges/Assessments | $ | ||||||||||||||
$ | |||||||||||||||
Although Deductible and Self-Retention Credits are to be identified, they should not be used in the calculation of insurance cost. | Deductible Credit^ OR | $ | |||||||||||||
Self Insured | $ | ||||||||||||||
Retention | |||||||||||||||
The OCIP provides first dollar coverage for all contractors. | Total WC Premium | A.$ |
River City Casino & Hotel OCIP Manual | Page 1 of 2 | July 31, 2008 |
INSURANCE COST IDENTIFICATION WORKSHEET
Contractor Name: | ||||||
Current GL Ins Co: | Policy Period: | |||||
If GL is based other than Payroll/Receipts describe: | Deductible: Retention: | |||||
Total WC Premium from previous page | A.$ | |||||||||
B. General Liability (Project Site Payroll/Receipts Only) | ||||||||||
Attach additional pages if required. Attach copy of declaration page and rate sheets for GL Policy | ||||||||||
G.L. Rate per basis | Estimated | |||||||||
G.L. Classification | G.L. Code | shown above | Payroll*/Receipts | Premium | ||||||
1. | $ | $ | ||||||||
2. | $ | $ | ||||||||
3. | $ | $ | ||||||||
4. | $ | $ | ||||||||
5. | Subcontracted Work | 91581 or | $ | $ |
Composite Rates and Corporate Allocations must reflect the breakout of insurance cost (actual rating calculations). Although Deductible and Self-Retention Credits are to be identified, they should not be used in the calculation of insurance cost.The OCIP has a $5,000 property damage deductible See Section 11.2 of the OCIP Manual. | Deductible Credit^ OR Self Insured Retention Credit^ | $ $ | ||||||
*It is extremely important to accurately estimate payrolls anticipated for this contract. Payroll should be raw wages without burden, fringes or overtime premium: but should include sick, vacation, holiday pay and imputed income. | Total General Liability Premium | B.$ | ||||||
C. | Umbrella Excess (Attach copy of declaration page and rate sheets for XS. | C.$ | ||||||
Rate: per $ | ||||||||
Name of Insurer: Term: | ||||||||
D. | Estimated Subcontractor Premiums (Attach Cost Identification Sheet for Each Subcontractor or calculate 2.5% of Subcontract value for each subcontractor’s estimated insurance cost). See Section 11.1.2.a of the OCIP Manual. | D.$ | ||||||
E. | TOTAL PREMIUMS (A + B + C + D) “Total Premiums” indicated in E represent the Total Insurance Cost the Contractor has identified | E.$ |
Signed | Title | Date | ||||||||
Send this Form to: | Gina Neal—Willis, 224 N. Hwy 67 Suite 193, Florissant, MO 63031 | |
Phone: 314-395-6615 Fax: 314-395-1880 E-mail: gina.neal@willis.com |
River City Casino & Hotel | Page 2 of 2 | July 31, 2008 | ||
OCIP Manual |
Supplemental Insurance Cost Identification Worksheet*
Contractors: | Indv | Ptshp | Corp | J/V | ||||||||||||||
Address: | FEIN: | |||||
Office Contact: | Phone: | Fax: | E-Mail: | |||||||||||
Site Contact: | Phone: | Fax: | E-Mail: | |||||||||||
Safety Contact: | Phone: | Fax: | E-Mail: | |||||||||||
CONTRACT INFORMATION | Contract Value: $ |
Job Name/Description: | Contract/JOB #: | |||||
Awarding Contractors: | Prime Contractors: | |||||
Award Date: | Start Date: | Est Completion Date: | Self Preformed | %, $ | ||||||||||||||
Subcontracted | %; $ | Est. # of Subcontractors | Est. Manhours | DBE/MBE/WBE: | ||||||||||||||
Contractor’s Insurance Broker/Agent:Company Name: | Contact: | |||||
City/State/Zip: | Phone: ( ) E-Mail: | |||||
Current WC Ins Co: | Policy Period: | Experience Modifier: | Deductible/Retention: | |||||||||||
Current GL Ins Co: | Policy Period: | Deductible: | Retention: | |||||||||||
�� |
WC Code | Manhours | WC/GL | ||||||||||||||||
Classification | GL Code | Incl OT | Rates | Estimated Payroll/Receipts | Premium | |||||||||||||
l. WC | ||||||||||||||||||
2. WC | ||||||||||||||||||
3. WC | ||||||||||||||||||
4. WC | ||||||||||||||||||
5. WC | ||||||||||||||||||
*Although Deductible and Self-Retention Credits are to be identified, they will not be allowed. Composite Rating will not be allowed without breakdown; Corporate Allocations will not be allowed, actual cost must be shown. If you need assistance, contact the OCIP Administrator. * It is extremely important to accurately estimate payrolls anticipated for this contract. Payroll should be raw wages without burden, fringes or overtime premium; but should include sick, vacation, holiday pay, and imputed income. Missouri Rules and Regulations for Payroll apply. See Section 11.2 of the OCIP Manual. | WC Sub Total | $ | ||||||||||||||||
Increased Limits Factor | $ | |||||||||||||||||
WC Experience Mod. | $ | |||||||||||||||||
$ | ||||||||||||||||||
$ | ||||||||||||||||||
$ | ||||||||||||||||||
Total WC Premium | A.$ | |||||||||||||||||
1. GL | ||||||||||||||||||
2. GL | ||||||||||||||||||
3. GL | ||||||||||||||||||
4. GL | ||||||||||||||||||
5. GL | ||||||||||||||||||
6. GL Subcontracted Work | 91585 | |||||||||||||||||
The OCIP provides first dollar WC coverage for all contractors. | TotalGL Premium | B.$ | ||||||||||||||||
C. Umbrella Excess | Rate: per $ | Total XS Prem | C.$ | |||||||||||||||
D. SUBCONTRACTORS PREMIUM (3% of Subcontractors’ contracts’ value) See section 11.1.2.a of the OCIP Manual. | Total Subs Premium or % | D.$ | ||||||||||||||||
TOTAL PREMIUM (A+B+C+D). | Total A,B,C,D | E.$ |
Signed | Title | Date | ||||||||
Send this Form to: | Gina Neal— Willis, 224 N. Hwy 67 Suites 193, Florissant, MO 63031 Phone: 314-395-6615 Fax: 314-395-1880 E-mail: gina.neal@willis.com |
River City Casino & Hotel | Page 1 of 1 | July 31, 2008 | ||
OCIP Manual |
River City OCIP FORM 3 |
SUPPLEMENTAL INSURANCE INFORMATION FORM
Contractor: | Contact: | E-mail: | ||||||||
Address: | City: | State: | Zip: | Phone: | Fax: | |||||||||||||||||||
oNew ContractName/Description: | Contract/JOB #: | Contract Value: $ | ||||||||
oExisting ContractName/Description: | Contract/JOB #: | Change Order Value: $ | ||||||||
Awarding Contractor: | Prime Contractor: | |||||
Award Date: | Start Date: | Est Completion Date: | Self Preformed | %, $ | ||||||||||||||
Subcontracted | %; $ | Est. # of Subcontractors | Est. Manhours | DBE/MBE/WBE: | ||||||||||||||
A.Workers Compensation | ||||||||||||||||||
Classification | Code | Rate | Estimated Payroll | Premium | ||||||||||||||
l. | $ | $ | ||||||||||||||||
2. | $ | $ | ||||||||||||||||
3. | $ | $ | ||||||||||||||||
4. | $ | $ | ||||||||||||||||
WC SUBTOTAL | $ | $ | ||||||||||||||||
It is extremely important to accurately estimate payrolls anticipated for this contract. Payroll should be raw wages without burden, fringes, or overtime premium: but should include sick, vacation, holiday pay and imputed income. Although Deductible and Self-Retention Credits are to be identified, they will not be allowed. Since these types of programs also require loss funding, the credits will be substituted for the loss pick. The OCIP provides first dollar coverage for all contractors. Composite rates must show all surcharges and credits. Corporate allocations will not be allowed, actual rating must be shown as required above | Increased Limits Factor | $ | ||||||||||||||||
WC Experience Mod. | $ | |||||||||||||||||
WC Discounts | $ | |||||||||||||||||
WC Discounts | $ | |||||||||||||||||
WC Surcharges | $ | |||||||||||||||||
Secondary Fund | $ | |||||||||||||||||
WC State Assessments | $ | |||||||||||||||||
Total WC Premium | A.$ | |||||||||||||||||
B.General Liability | Estimated | |||||||||||||||||
Classification | Code | Rate | Payroll/Receipts* | Premium | ||||||||||||||
1. | $ | $ | ||||||||||||||||
2. | $ | $ | ||||||||||||||||
3. | $ | $ | ||||||||||||||||
4. | $ | $ | ||||||||||||||||
5. Subcontracted Work | 91585 | $ | $ | |||||||||||||||
Total General Liability | B.$ | |||||||||||||||||
C. Umbrella/Excess Liability | $ | C.$ | ||||||||||||||||
D. Estimated Subcontractor Premiums (Attach Form 1/2 for Each Subcontractor (including leasing and/or temporary labor companies). | D.$ | |||||||||||||||||
E. Total insurance cost, included in bid or change order documents | TOTAL (A+B+C+D) | E.$ |
Signed | Title | Date | ||||||||
Send this Form to: | Gina Neal— Willis, 224 N. Hwy 67 Suite 193, Florissant, MO 63031 Phone: 314-395-6615 Fax: 314-395-1880 E-mail: gina.neal@willis.com |
River City Casino & Hotel | Page 1 of 1 | July 31, 2008 | ||
OCIP Manual |
River City OCIP | ||
FORM 4 |
NOTICE OF ANTICIPATED COMPLETION
Willis | ||||
Attn: Gina Neal | Phone: | 314-395-6615 | ||
224 N. Hwy 67 Suite 193 | Fax: | 314-395-1880 | ||
Florissant, MO 63031 | E-mail: | gina.neal@willis.com |
Please be advised, we, | are scheduled to complete our work for: | |||
(Name of Contractor Film) |
Awarding Contractor | Prime: | |||||
Job Name/Description: | Start Date: | Completion Date: | ||||||||
^Original Contract Value: $ | ^Final Contract Value: $ | |||||
^Self Performed Work: $ | ^Subcontracted Work: $ | |||||
*Change Orders: | ||
Original Actual Payroll: $ | Final Actual Payroll: $ | |||||
Subcontractors | Final Contract Value | |||
$ | ||||
$ | ||||
$ | ||||
$ | ||||
Subcontractors | Final Contract Value | |||
$ | ||||
$ | ||||
$ | ||||
$ | ||||
This is our only contract at the | Project. | |||||||
We are still working on the following jobs at the | Project. | |||||||
Awarding Contractors | Job Name/Description | Prime | ||
Your Company’s Name: | Date: | |||||
By: | Title | |||||
Name: | Phone: | Fax: | E-Mail: | |||||||||||
Address: | City: | State: | Zip | |||||||||||
River City Casino & Hotel | Page 1 of 1 | July 31, 2008 | ||
OCIP Manual |
River City OCIP - | ||
FORM 5 |
PROJECT SITE PAYROLL REPORTING FORM
Contractor: | ||
Address: | City: | State: | Zip: | |||||||||||
Phone: | Fax: | |||||
Awarding Contractor: | Construction Manager: | |||||
LOCATION CODE (For this Contract): | MONTH ENDING): | |||||
WORKER’S COMPENSATION | ||||||||||||
WC Classification Description | Manhours | WC Code | Actual Payroll | |||||||||
1. | ||||||||||||
2. | ||||||||||||
3. | ||||||||||||
4. | ||||||||||||
5. | ||||||||||||
Total |
GENERAL LIABILITY | ||||||||||||
GL Classification Description | Manhours | GLCode | Receipts/Other | |||||||||
1. | ||||||||||||
2. | ||||||||||||
3. | ||||||||||||
4. | ||||||||||||
5. | ||||||||||||
6. Subcontracted Work | 95185 | |||||||||||
Total | ||||||||||||
Monthly Receipts (Amount on Monthly Pay Application) | $ |
• | It is extremely important to accurately estimate payrolls anticipated for this contract. Payroll should be raw wageswithout burden, fringes, or overtime premium: but should include sick, vacation, holiday pay and imputed income. | |
• | Earnings for overtime should be included only at straight hourly rates. Do Not Include the Extra Wages Paid for Overtime Hours. Overtime means those hours in excess of 8 hours worked each day, 40 hours in any week or on Saturdays, Sundays, or holidays, but only when there is an increase in the hourly rate to work such hours. | |
• | Hours should be shown on overtime. | |
* | If GL is based on payroll – only show the classification description and codes, manhours and payroll are already shown under WC. |
Signature: | ||
Title: | Date | |||||
Send this Form to: | Gina Neal—Willis, 224 N. Hwy 67 Suite 193, Florissant, MO 63031 | |||
Phone: 314-395-6615 Fax: 314-395-1880 E-mail: gina.neal@willis.com |
River City Casino & Hotel | Page 1 of 1 | July 31, 2008 | ||
OCIP Manual |
Revision | ||||
Date | Page Number | Description of Change | ||
8/11/08 | 4 | Clarified the Builders’ Risk Deductible is to be borne by the Contractor/Subcontractor(s) who caused the loss | ||
5 | On-Site Activities — added wording “and as outlined by the Builders’ Risk policy”. | |||
11 | Item (2) CGL — Clarified Item a) 4. to read that the $5,000 PD deductible is the responsibility of the contractor who cause the loss. | |||
13 | Contractor-Provided Coverage-included wording as stated in the contract that the products-completed operations should be carried for two year after completion on the project. | |||
07/31/08 | 13-14 | Additional Insured Language — Consultants added for RCC as they apply to Yates/Paric | ||
Pinnacle Entertainment, Inc. name added with endorsed name Casino One | ||||
07/22/08 | 4 | Builders Risk Policy Number and Deductible | ||
21 | St Anthony’s Medical Clinic Updated to Concentra Medical Center (Soulard Clinic) | |||
03/12/08 | 4 | Deleted — Builders Risk Language, (TBD) | ||
5 | Addition of site description specific to the River City Road Project | |||
6, 7, 13, & 14 | Pinnacle Entertainment, Inc endorsement. Named changed toCasino One Corporation | |||
01/14/08 | 2 | Deleted — One of Willis’ OCIP Consultant information, Pam Robertson — “employee change in work duty” | ||
3 | Updated — New Fax number for Zurich claims | |||
From — 913-345-4327 to 913-345-1582 | ||||
Medical Only Adjuster — changed from Lyla Grady to Joanna KO | ||||
14 | Additional Insured Wording — | |||
Added Fred Weber, Inc. as additional insured | ||||
01/17/07 | Pinnacle Entertainment OCIP Policy and Procedures Manual | Original Printing of the Policy and Procedure Manual |
River City Casino & Hotel OCIP Manual | Page 1 of 1 | July 31, 2008 |
OMITTED
REQUIRED INSURANCE COVERAGES
Coverage shall include the following: