
Kaman Corporation (NASDAQ-GS: KAMN)
Kaman Corporation (NASDAQ-GS: KAMN)
Investor Presentation
May 18, 2010

2
Distribution
56%
Aerospace
44%
2009 Sales
Distribution
14%
Aerospace
86%
2009 Segment
Operating Income*
2009 Sales $1,146 Million
4,373 Employees
Aerospace
Industrial
Distribution
NASDAQ GS: KAMN
KAMAN CORPORATION
* Operating profit after depreciation and before interest and corporate charges.
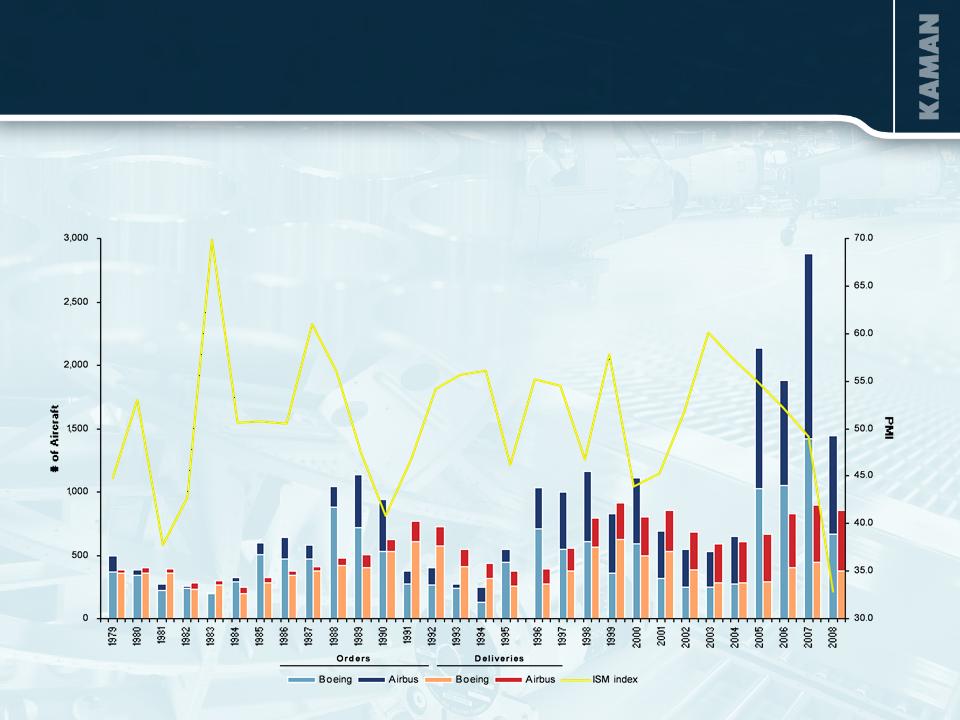
3
Source: Boeing and Airbus historical data and ISM
Aerospace Orders and Deliveries vs. ISM Index Over Time
WHY TWO BUSINESSES?

4
Source: Bloomberg, Barra, CapitalIQ, Kaman internal assessments, and projections and Goldman Sachs
Note: Aerospace index includes TransDigm, Woodward Governor, Heico, Moog, Curtiss-Wright, AAR Corp, Hexcel, BE Aerospace, Triumph, Esterline, LMI Aerospace, and Spirit.
Note: WACC assumes marginal tax rate of 35%. Assumes barra predicted beta post 2005 and Bloomberg beta pre 2005. Assumes Rf as 30 year treasury rate.
AEROSPACE - Strategic Perspective
(12.0)%
(8.0)%
(4.0)%
0.0%
4.0%
8.0%
12.0%
16.0%
20.0%
24.0%
28.0%
Jun-99
Dec-00
Jun-02
Dec-03
Jun-05
Dec-06
Jun-08
Average WACC
Average ROIC
Kaman Aerospace ROIC
Illustrative ROIC versus WACC Analysis Over Time | Last 10 Years

5
Source: Bloomberg, Barra, CapitalIQ, Kaman internal assessments and projections, and Goldman Sachs
Note: Distribution index includes Fastenal, MSC Industrial, WW Grainger, Genuine Parts, Applied Industrial Technologies, DXP, WESCO, Anixter, Watsco, and Interline.
Note: WACC assumes marginal tax rate of 35%. Assumes barra predicted beta post 2005 and Bloomberg beta pre 2005. Assumes Rf as 30 year treasury rate.
INDUSTRIAL DISTRIBUTION - Strategic Perspective
0.0%
5.0%
10.0%
15.0%
20.0%
25.0%
Jun-99
Dec-00
Jun-02
Dec-03
Jun-05
Dec-06
Jun-08
Average WACC
Average ROIC
Kaman Industrial Distribution ROIC
Illustrative ROIC versus WACC Analysis Over Time | Last 10 Years

6
AEROSPACE SEGMENT
2009 Sales $501 million

7
Commercial
Military
Business/Regional
28%
69%
3%
Note: Based on 2009 sales
AEROSPACE - Business Mix

8
Manufacture of cockpit
Blade erosion coating
Manufacture and assembly
of tail rotor pylon
of tail rotor pylon
Sub assembly and
joining of fuselage
joining of fuselage
Blade manufacture, repair
and overhaul
and overhaul
Driveline couplings
Bushings
Flight control bearings
Bearing products
AEROSPACE - Programs/Capabilities

9
Fixed trailing edge
Fuel tank access doors
Top covers
Bearing products
Nose landing gear
Rudder
Main landing gear
Flaps
Horizontal stabilizer
Doors
Engine/thrust reverser
Flight controls
AEROSPACE - Programs/Capabilities

10
HARPOON
FMU-139
TOMAHAWK
STANDARD
MISSILE
MISSILE
SLAM-ER
AMRAAM
KPP Fuzes are on a Majority of Major Weapons
Systems
Systems
STANDARD
MISSILE
MISSILE
JPF
SLAM-ER
TOMAHAWK
AMRAAM
MAVERICK
AGM-65M
AEROSPACE - Programs/Capabilities
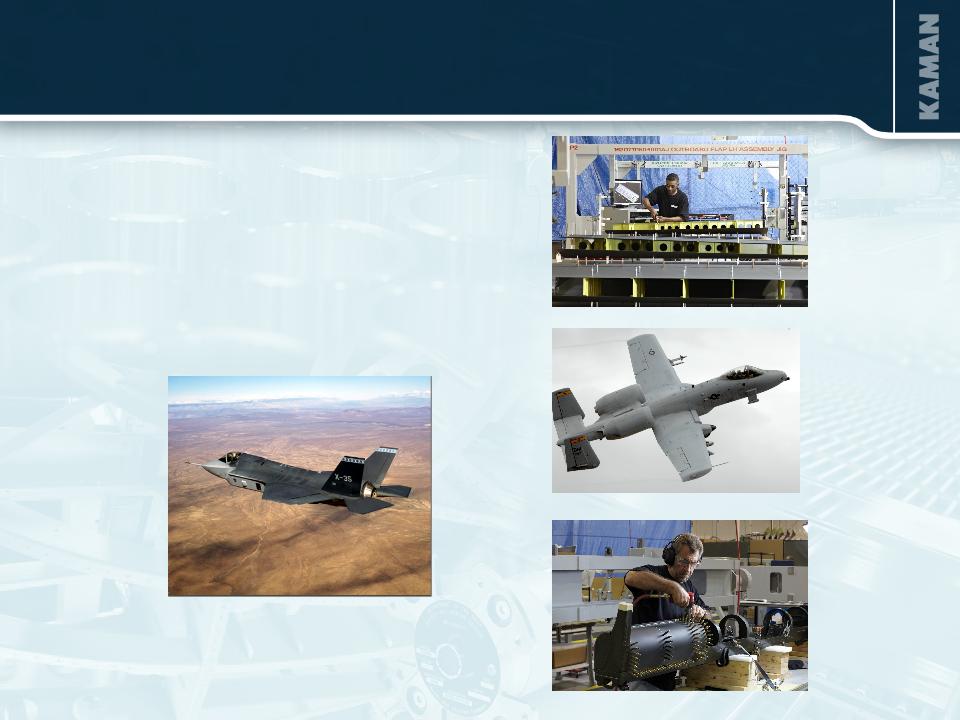
11
AEROSPACE - Programs/Capabilities
§ Tooling design and manufacture

12
JSF
C-17
A-10
E-2D
Typhoon
UH-60
A400
CH-47
AEROSPACE - Principal Military Platforms
Boeing NewGen Tanker
MH-92

13
AEROSPACE - Commercial Significant Platforms
Airbus A320
Boeing 777
Airbus A330
Bell Helicopter
Boeing 787
Boeing 737
Airbus A350

14
AEROSPACE - Kaman Helicopters
Kaman SH-2G Naval Helicopters
§ Support and Upgrades
§ Currently in service with Egypt,
New Zealand, Poland
New Zealand, Poland
§ Remarketing eleven SH-2G(I)s,
formerly Royal Australian Navy aircraft
formerly Royal Australian Navy aircraft

15
Kaman K-MAX®
§ K-MAX Commercial Helicopter
Support
Support
§ Teamed with Lockheed Martin to
develop an unmanned military version
of the K-MAX
develop an unmanned military version
of the K-MAX
§ Successfully demonstrated unmanned
K-MAX to the U.S. Marine Corps in
January 2010
K-MAX to the U.S. Marine Corps in
January 2010
AEROSPACE - Kaman Helicopters

16
AEROSPACE - Market Environment/Opportunities
§ Existing funded programs
- C-17
- JPF
- BLACKHAWK
§ Production ramp up
- A-10 re-wing
- Bell Helicopters
- B787
- JSF
- A380
§ Continuation of outsourcing trend - primes and super tier 1’s
§ Unmanned K-MAX program
§ Sale of SH-2G(I) helicopters
§ Acquisitions providing complementary capabilities and platforms

17
INDUSTRIAL DISTRIBUTION SEGMENT
2009 Sales $645 million

18
INDUSTRIAL DISTRIBUTION SEGMENT
§ Third largest industrial distribution firm serving $15 billion of a $23 billion power
transmission / motion control market.
transmission / motion control market.
§ 207 branches and 5 distribution centers
§ Major product categories:
- Bearings
- Mechanical and electrical power transmission
- Fluid Power
- Motion control
- Automation
- Material handling
§ Statistics
- $371,000 sales per employee (2009)
- 2,000 employees (approximately one third outside sales)
- 3.5 million SKUs
- 50,000+ customers
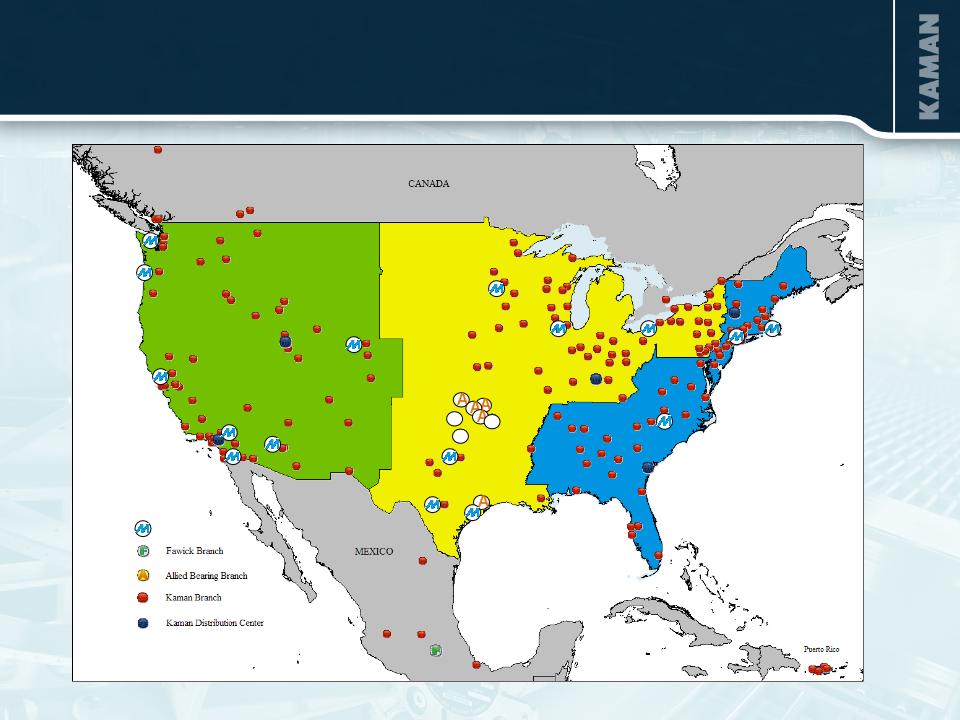
19
INDUSTRIAL DISTRIBUTION SEGMENT
A
A
A
Minarik

20
INDUSTRIAL DISTRIBUTION SEGMENT - Key Suppliers
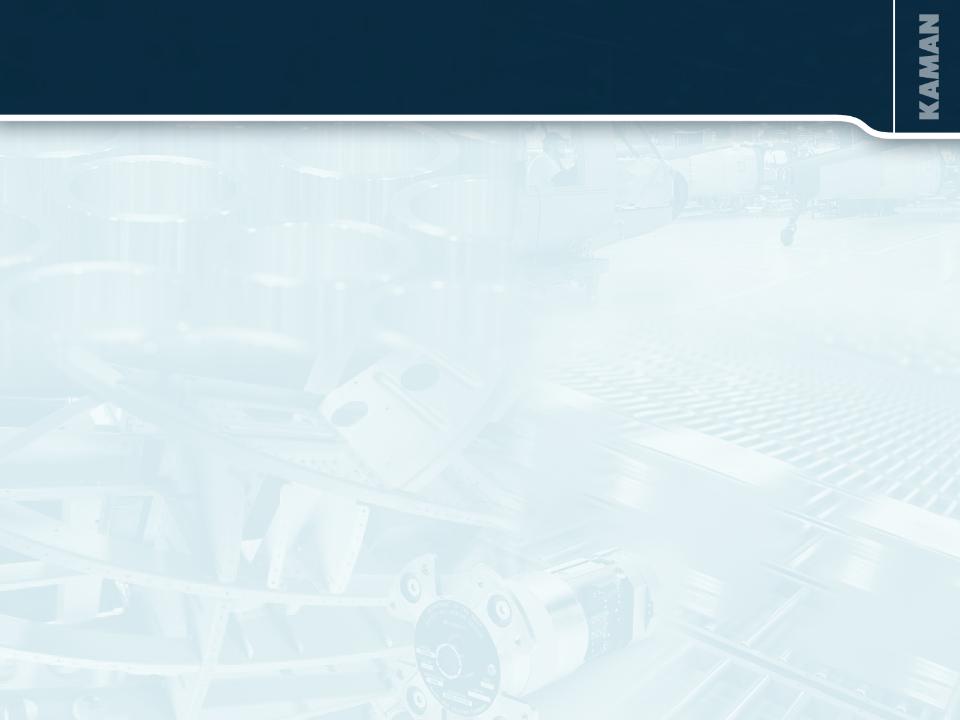
21
INDUSTRIAL DISTRIBUTION - Market Environment
§ Market recovery - positive ISM index points to improving market
environment
environment
§ Sales per sales day were up 7%, 10%, and 14% sequentially in January,
February and March, respectively, as compared to the fourth quarter of
2009
February and March, respectively, as compared to the fourth quarter of
2009
§ February was the first month of positive year over year sales growth
since October 2008
since October 2008
§ April sales were encouraging
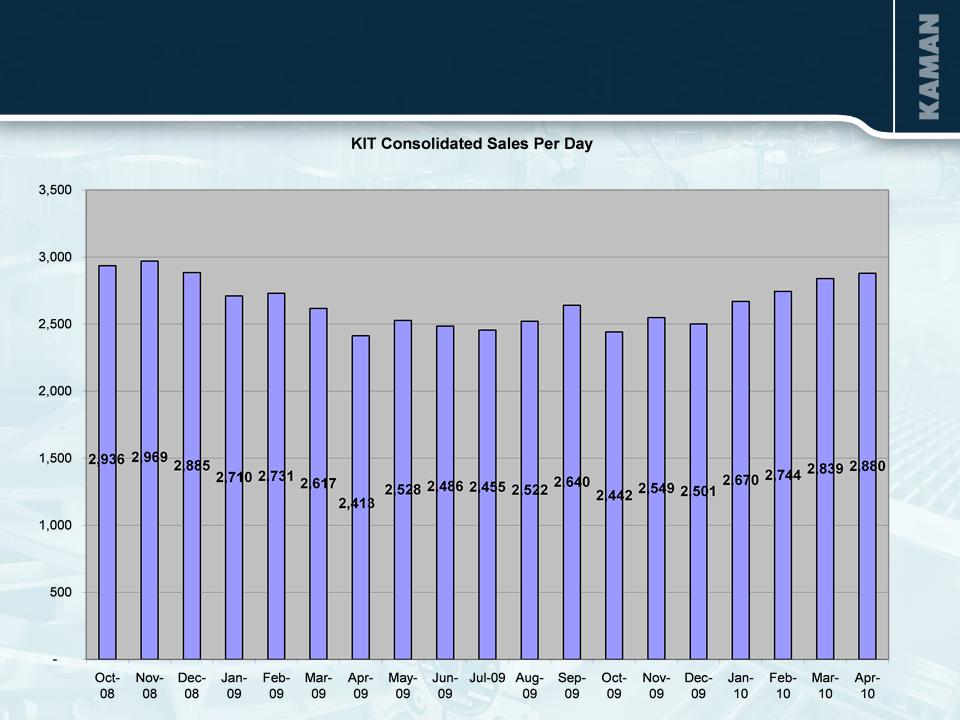
22
SALES PER DAY - $(000)

23
SALES PER DAY GROWTH RATE

24
INDUSTRIAL DISTRIBUTION - Opportunities
§ Broaden our product offerings to gain additional business
from existing customers and new opportunities from a wider
slice of the market
from existing customers and new opportunities from a wider
slice of the market
- Product line additions from vendors such as:
• ASCO/Numatics
• Sheffer Corporation
• GEM® Steam Trap
• Bison Gear
- Launched ReliaMark brand of bearings,
roller chains, oil seals, and shaft collars
§ Recognize sales and cost synergies from the three
acquisitions completed in 2010
acquisitions completed in 2010
§ Expand our geographic footprint through acquisitions in major
industrial markets to enhance our position in the competition
for national and regional accounts
industrial markets to enhance our position in the competition
for national and regional accounts

25
§ Minarik is a national distributor of motion control and automation products
§ 2009 Sales - $84 million
Vision Systems Motors & Gear Motors Actuators
AC & DC Drives Servo Motors Safety
& Controls
ACQUISITIONS - Minarik

26
§ Minarik has 16 stocking distributor locations and 3 Minarik Applied Products
and Systems Centers (MAPS Centers) locations and approx. 215 employees
and Systems Centers (MAPS Centers) locations and approx. 215 employees
§ Expands KIT’s geographic coverage in key markets
§ Adds branch locations in 3 of the top 15 markets where KIT is not well
represented (San Jose, Cleveland, Chicago)
represented (San Jose, Cleveland, Chicago)
ACQUISITIONS - Minarik

27
§ Expands KIT’s product offering
§ Positions Kaman as an industry leader in US motion control and automation
markets
markets
§ Diversifies traditional MRO customer base through primary OEM presence
§ Organizational and cultural fit:
- Minarik will substantially strengthen KIT’s Automation Specialist group
- Minarik is realigning organization in a similar manner as KIT
ACQUISITIONS - Minarik

28
ACQUISITIONS
Business Overview
•Bearing & power transmission dist.
•Headquartered in Tulsa, OK
(October 31) 2007 2008 2009
Sales $28 MM $30 MM $22 MM
•8 branches located in Oklahoma, Arkansas
and Texas; 70+ employees
Strategic Rationale
•Geographic penetration
•Adds volume in our core product lines
•Provides access to chemical and petro-
chemical industries and oil and gas
industries
Transaction Summary
•Transaction closed April 5, 2010
•Purchase price $15MM
Strengths
•Product knowledge in our core bearing
and power transmission product lines
•Vendor authorizations with premier
brands
§ Allied Bearings Supply, Co., Inc.

29
§ Fawick De Mexico
Business Overview
•Mexico City based fluid power distributor
•Headquartered in same building complex
as Kaman’s Delamac business
$ Pesos MM 2008 2009
Sales $43 MM $50 MM
Exchange Rate: 13.4 Pesos / US $
Strategic Rationale
•Adds fluid power to Delamac’s product
offering
•Adds higher margin product lines to
improve overall profitability of Delamac
•Adds exclusive franchises for Mexico
•Ensures that a Delamac competitor does
not occupy the premises
Transaction Summary
•Closed transaction 2/26/10
•Purchase price $4.4MM
Strengths
•Knowledge in fluid power product
applications
•Sales force covers almost all of Mexico
ACQUISITIONS

30
SUMMARY

31
2010 OUTLOOK UPDATE
Aerospace segment
§ We expect full year sales to be approximately flat in comparison to 2009
§ We expect the full year operating margin to be between 15.5% and 16.5%
Industrial Distribution segment
§ We expect full year organic sales growth to be up 6% to 8% for the full year as
compared to 2009
compared to 2009
§ Including completed acquisitions we expect full year sales to be in a range of
$765 million to $785 million
$765 million to $785 million
§ We expect operating margins for the full year of approximately 2.8% to 3.2%
Other
§ We expect corporate expenses, on average, to be in a range of $9.0 million to
$10.0 million per quarter
$10.0 million per quarter
§ We expect full year interest expense to be approximately $10.7 million
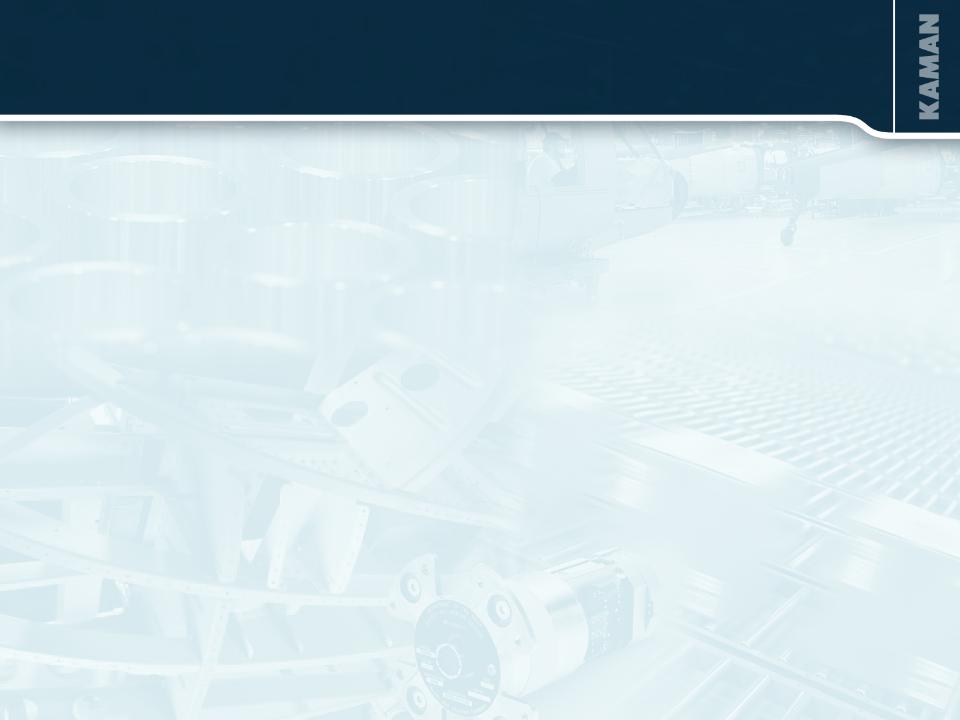
32
KAMAN CORPORATION - Summary
§ High margin aerospace business led by specialty bearing product lines
§ Industrial distribution business gaining market share in a fragmented
market via national account growth, geographic and product line
expansion
market via national account growth, geographic and product line
expansion
§ Long-term organic growth opportunities in both segments
§ Potential to further accelerate growth and increase scale through
additional acquisitions
additional acquisitions
§ Initiatives to optimize profit, increase cash flow generation, strengthen
competitive position
competitive position
§ Strong balance sheet to fund growth and strategic initiatives

33
APPENDIX
44%
2009 Sales $1,146 million

34
1 Corporate expense percentage is to Total Sales
(In thousands) SEGMENTS | Net Sales | Operating Income/(Loss) | Operating Margin | |||
Q1 2010 | Q1 2009 | Q1 2010 | Q1 2009 | Q1 2010 | Q1 2009 | |
Industrial Distribution | $179,259 | $176,906 | $4,812 | $2,779 | 2.7% | 1.6% |
Aerospace | 97,513 | 117,129 | 9,633 | 15,297 | 9.9% | 13.1% |
Net gain/(loss) on sale of assets | 576 | 93 | ||||
Corporate expense | (10,528) | (8,766) | 1 (3.8%) | 1(3.0%) | ||
Sales/Op. inc. from continuing ops | $276,772 | $294,035 | $4,493 | $9,403 | 1.6% | 3.2% |
INCOME STATEMENT HIGHLIGHTS
For the quarters ended April 2, 2010 and April 3, 2009
For the quarters ended April 2, 2010 and April 3, 2009

35
1 Corporate expense percentage is to Total Sales
(In thousands) SEGMENTS | Net Sales | Operating Income/(Loss) | Operating Margin | |||
2009 | 2008 | 2009 | 2008 | 2009 | 2008 | |
Industrial Distribution | $645,535 | $776,970 | $12,612 | $35,397 | 2.0% | 4.6% |
Aerospace | 500,696 | 476,625 | 74,996 | 61,608 | 15.0% | 12.9% |
Net gain/(loss) on sale of assets | (4) | 221 | ||||
Corporate expense | (33,662) | (31,960) | 1 (2.9%) | 1(2.5%) | ||
Sales/Op. inc. from continuing ops | $1,146,231 | $1,253,595 | $53,942 | $65,266 | 4.7% | 5.2% |
INCOME STATEMENT HIGHLIGHTS
For the years ended December 31
For the years ended December 31

36
(In Millions) | As of 04/02/10 | As of 12/31/09 | As of 12/31/08 |
Cash and Cash Equivalents | $18.3 | $18.0 | $8.2 |
Notes Payable and Long-term Debt | $88.6 | $63.6 | $94.2 |
Shareholders’ Equity | $333.0 | $312.9 | $274.3 |
Debt as % of Total Capitalization | 21.0% | 16.9% | 25.6% |
Capital Expenditures | $3.6 | $13.6 | $16.0 |
Depreciation & Amortization | $4.5 | $16.1 | $12.8 |
BALANCE SHEET AND CAPITAL FACTORS

37
Sales
EPS
Stock Price (one year)
Return on Invested Capital
PERFORMANCE METRICS

38
Pension Plans
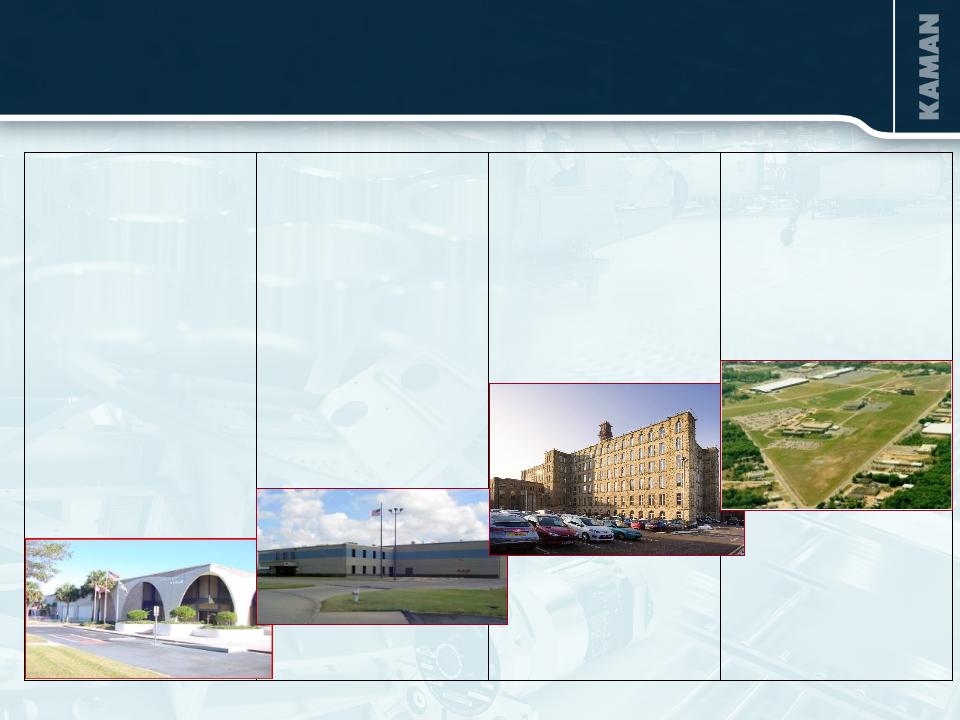
39
Bloomfield, CT
700,000 sq ft
•Mechanical
•Composites
•Large Assembly
Wichita, KS
168,000 sq ft
•Composites
•Structural
Bondments
•Composite
Assemblies
Jacksonville, FL
220,000 sq ft
•Fabrication-
ØMachining
ØSheet Metal Form
ØExtrusion
•Assembly
ØMajor Subs
ØFinal Structure
•Product Integration
Darwen, UK
208,000 sq ft
•Composites
•Metal Fabrication
•Tooling
•Assembly
AEROSPACE - Primary Facilities
•Helicopter assembly
and test facilities
•Bearing manufacturing

40
Manchester, UK
63,000 sq ft
•Aerospace
manufacturing
facility
manufacturing
facility
Orlando, FL
90,000 sq ft
•Bomb safe and
arming device
manufacturing
facility
arming device
manufacturing
facility
80 acre test range
Middletown, CT
202,000 sq ft
•Manufacturing facility
•Missile safe and
arming devices
arming devices
•Bomb safe and
arming devices
arming devices
•Ruggedized
memory
products
memory
products
•Measuring
products
products
Dachsbach, Germany
30,000 sq ft
•Manufacturing facility
•Spherical
bearings
bearings
•Ball bearings
•Rod ends
•Bushings
•Specialty
components
components
AEROSPACE - Primary Facilities

41
FORWARD-LOOKING STATEMENTS
This presentation contains forward-looking information relating to the company's business and prospects, including the Aerospace and
Industrial Distribution businesses, operating cash flow, and other matters that involve a number of uncertainties that may cause actual results
to differ materially from expectations. Those uncertainties include, but are not limited to: 1) the successful conclusion of competitions for
government programs and thereafter contract negotiations with government authorities, both foreign and domestic; 2) political conditions in
countries where the company does or intends to do business; 3) standard government contract provisions permitting renegotiation of terms
and termination for the convenience of the government; 4) domestic and foreign economic and competitive conditions in markets served by
the company, particularly the defense, commercial aviation and industrial production markets; 5) risks associated with successful
implementation and ramp up of significant new programs; 6) management's success in increasing the volume of profitable work at the
Aerospace Wichita facility; 7) successful negotiation of the Sikorsky Canadian MH-92 program price; 8) successful resale of the SH-2G(I)
aircraft, equipment and spare parts; 9) receipt and successful execution of production orders for the JPF U.S. government contract,
including the exercise of all contract options and receipt of orders from allied militaries, as all have been assumed in connection with goodwill
impairment evaluations; 10) satisfactory resolution of the company’s litigation relating to the FMU-143 program; 11) continued support of the
existing K-MAX helicopter fleet, including sale of existing K-MAX spare parts inventory; 12) cost estimates associated with environmental
remediation activities at the Bloomfield, Moosup and New Hartford, CT facilities and our U.K. facilities; 13) profitable integration of acquired
businesses into the company's operations; 14) changes in supplier sales or vendor incentive policies; 15) the effects of price increases or
decreases; 16) the effects of pension regulations, pension plan assumptions and future contributions; 17) future levels of indebtedness and
capital expenditures; 18) continued availability of raw materials and other commodities in adequate supplies and the effect of increased costs
for such items; 19) the effects of currency exchange rates and foreign competition on future operations; 20) changes in laws and regulations,
taxes, interest rates, inflation rates and general business conditions; 21) future repurchases and/or issuances of common stock; and 22) other
risks and uncertainties set forth in the company's annual, quarterly and current reports, and proxy statements. Any forward-looking
information provided in this presentation should be considered with these factors in mind. The company assumes no obligation to update any
forward-looking statements contained in this presentation.
Industrial Distribution businesses, operating cash flow, and other matters that involve a number of uncertainties that may cause actual results
to differ materially from expectations. Those uncertainties include, but are not limited to: 1) the successful conclusion of competitions for
government programs and thereafter contract negotiations with government authorities, both foreign and domestic; 2) political conditions in
countries where the company does or intends to do business; 3) standard government contract provisions permitting renegotiation of terms
and termination for the convenience of the government; 4) domestic and foreign economic and competitive conditions in markets served by
the company, particularly the defense, commercial aviation and industrial production markets; 5) risks associated with successful
implementation and ramp up of significant new programs; 6) management's success in increasing the volume of profitable work at the
Aerospace Wichita facility; 7) successful negotiation of the Sikorsky Canadian MH-92 program price; 8) successful resale of the SH-2G(I)
aircraft, equipment and spare parts; 9) receipt and successful execution of production orders for the JPF U.S. government contract,
including the exercise of all contract options and receipt of orders from allied militaries, as all have been assumed in connection with goodwill
impairment evaluations; 10) satisfactory resolution of the company’s litigation relating to the FMU-143 program; 11) continued support of the
existing K-MAX helicopter fleet, including sale of existing K-MAX spare parts inventory; 12) cost estimates associated with environmental
remediation activities at the Bloomfield, Moosup and New Hartford, CT facilities and our U.K. facilities; 13) profitable integration of acquired
businesses into the company's operations; 14) changes in supplier sales or vendor incentive policies; 15) the effects of price increases or
decreases; 16) the effects of pension regulations, pension plan assumptions and future contributions; 17) future levels of indebtedness and
capital expenditures; 18) continued availability of raw materials and other commodities in adequate supplies and the effect of increased costs
for such items; 19) the effects of currency exchange rates and foreign competition on future operations; 20) changes in laws and regulations,
taxes, interest rates, inflation rates and general business conditions; 21) future repurchases and/or issuances of common stock; and 22) other
risks and uncertainties set forth in the company's annual, quarterly and current reports, and proxy statements. Any forward-looking
information provided in this presentation should be considered with these factors in mind. The company assumes no obligation to update any
forward-looking statements contained in this presentation.
###
Contact: Eric Remington, V.P.
Investor Relations
(860) 243-6334
Eric.Remington@kaman.com