Our total backlog at December 31, 2011 and 2010 was $16,160 and $14,616 million, respectively. We anticipate that approximately $12,018 million of the 2011 backlog will be filled in 2012. We believe that backlog is not necessarily a reliable indicator of our future sales because a substantial portion of the orders constituting this backlog may be canceled at the customer’s option.
We are subject to active competition in substantially all product and service areas. Competition is expected to continue in all geographic regions. Competitive conditions vary widely among the thousands of products and services provided by us, and vary by country. Our businesses compete on a variety of factors, such as price, quality, reliability, delivery, customer service, performance, applied technology, product innovation and product recognition. Brand identity, service to customers and quality are important competitive factors for our products and services, and there is considerable price competition. Other competitive factors include breadth of product line, research and development efforts and technical and managerial capability. While our competitive position varies among our products and services, we believe we are a significant competitor in each of our major product and service classes. A number of our products and services are sold in competition with those of a large number of other companies, some of which have substantial financial resources and significant technological capabilities. In addition, some of our products compete with the captive component divisions of original equipment manufacturers. See Item 1A “Risk Factors” for further discussion.
We are engaged in manufacturing, sales, service and research and development globally. U.S. exports and foreign manufactured products are significant to our operations. U.S. exports comprised 12, 11 and 12 percent of our total sales in 2011, 2010 and 2009, respectively. Foreign manufactured products and services, mainly in Europe and Asia, were 43, 42 and 40 percent of our total sales in 2011, 2010 and 2009, respectively.
Approximately 18 percent of total 2011 sales of Aerospace-related products and services were exports of U.S. manufactured products and systems and performance of services such as aircraft repair and overhaul. Exports were principally made to Europe, Asia, Canada, and Latin America. Foreign manufactured products and systems and performance of services comprised approximately 15 percent of total 2011 Aerospace sales. The principal manufacturing facilities outside the U.S. are in Europe, with less significant operations in Canada and Asia.
Approximately 3 percent of total 2011 sales of Automation and Control Solutions products and services were exports of U.S. manufactured products. Foreign manufactured products and performance of services accounted for 58 percent of total 2011 Automation and Control Solutions sales. The principal manufacturing facilities outside the U.S. are in Europe and Asia, with less significant operations in Canada and Australia.
Approximately 34 percent of total 2011 sales of Performance Materials and Technologies products and services were exports of U.S. manufactured products. Exports were principally made to Asia and Latin America. Foreign manufactured products and performance of services comprised 25 percent of total 2011 Performance Materials and Technologies sales. The principal manufacturing facilities outside the U.S. are in Europe, with less significant operations in Asia.
Approximately 3 percent of total 2011 sales of Transportation Systems products were exports of U.S. manufactured products. Foreign manufactured products accounted for 85 percent of total 2011 sales of Transportation Systems. The principal manufacturing facilities outside the U.S. are in Europe, with less significant operations in Asia and Latin America.
Financial information including net sales and long-lived assets related to geographic areas is included in Note 24 of Notes to Financial Statements in “Item 8. Financial Statements and Supplementary Data”. Information regarding the economic, political, regulatory and other risks associated with international operations is included in “Item 1A. Risk Factors.”
The principal raw materials used in our operations are generally readily available. Although we occasionally experience disruption in raw materials supply, we experienced no significant problems in the purchase of key raw materials and commodities in 2011. We are not dependent on any one supplier for a material
amount of our raw materials, except related to R240 (a key component in foam blowing agents), a raw material used in our Performance Materials and Technologies segment.
The costs of certain key raw materials, including cumene, fluorspar, perchloroethylene, R240, natural gas, sulfur and ethylene in our Performance Materials and Technologies business, nickel, steel and other metals in our Transportation Systems business, and nickel, titanium and other metals in our Aerospace business, are expected to remain volatile. We will continue to attempt to offset raw material cost increases with formula or long-term supply agreements, price increases and hedging activities where feasible. We do not presently anticipate that a shortage of raw materials will cause any material adverse impacts during 2012. See “Item 1A. Risk Factors” for further discussion.
Patents, Trademarks, Licenses and Distribution Rights
Our segments are not dependent upon any single patent or related group of patents, or any licenses or distribution rights. We own, or are licensed under, a large number of patents, patent applications and trademarks acquired over a period of many years, which relate to many of our products or improvements to those products and which are of importance to our business. From time to time, new patents and trademarks are obtained, and patent and trademark licenses and rights are acquired from others. We also have distribution rights of varying terms for a number of products and services produced by other companies. In our judgment, those rights are adequate for the conduct of our business. We believe that, in the aggregate, the rights under our patents, trademarks and licenses are generally important to our operations, but we do not consider any patent, trademark or related group of patents, or any licensing or distribution rights related to a specific process or product, to be of material importance in relation to our total business. See “Item 1A. Risk Factors” for further discussion.
We have registered trademarks for a number of our products and services, including Honeywell, Aclar, Ademco, Bendix, BW, Callidus, Enovate, Esser, Fire-Lite, Garrett, Genetron, Gent, Howard Leight, Jurid, Matrikon, Maxon, MK, North, Notifier, Novar, RMG, Silent Knight, Spectra, System Sensor, Trend, Tridium and UOP.
Research and Development
Our research activities are directed toward the discovery and development of new products, technologies and processes, and the development of new uses for existing products and software applications. The Company’s principal research and development activities are in the U.S., India, Europe and China.
Research and development (R&D) expense totaled $1,799, $1,450 and $1,321 million in 2011, 2010 and 2009, respectively. The increase in R&D expense of 24 percent in 2011 compared to 2010 was mainly due to increased expenditures on the development of new technologies to support existing and new aircraft platforms in our Aerospace segment, the development of turbocharging systems for new diesel and gas applications in our Transportation Systems segment and new product development in our Automation and Control Solutions segment. The increase in R&D expense of 10 percent in 2010 compared to 2009 was mainly due to additional product design and development costs in Automation and Control Solutions and increased expenditures on the development of products for new aircraft platforms. R&D as a percentage of sales was 4.9, 4.5 and 4.4 percent in2011, 2010 and 2009, respectively. Customer-sponsored (principally the U.S. Government) R&D activities amounted to an additional $867, $874 and $852 million in2011, 2010 and 2009, respectively.
Environment
We are subject to various federal, state, local and foreign government requirements regulating the discharge of materials into the environment or otherwise relating to the protection of the environment. It is our policy to comply with these requirements, and we believe that, as a general matter, our policies, practices and procedures are properly designed to prevent unreasonable risk of environmental damage, and of resulting financial liability, in connection with our business. Some risk of environmental damage is, however, inherent in some of our operations and products, as it is with other companies engaged in similar businesses.
We are and have been engaged in the handling, manufacture, use and disposal of many substances classified as hazardous by one or more regulatory agencies. We believe that, as a general matter, our policies, practices and procedures are properly designed to prevent unreasonable risk of environmental damage and personal injury, and that our handling, manufacture, use and disposal of these substances are in accord with environmental and safety laws and regulations. It is possible, however, that future knowledge or other developments, such as improved capability to detect substances in the environment or increasingly strict
11
environmental laws and standards and enforcement policies, could bring into question our current or past handling, manufacture, use or disposal of these substances.
Among other environmental requirements, we are subject to the federal superfund and similar state and foreign laws and regulations, under which we have been designated as a potentially responsible party that may be liable for cleanup costs associated with current and former operating sites and various hazardous waste sites, some of which are on the U.S. Environmental Protection Agency’s Superfund priority list. Although, under some court interpretations of these laws, there is a possibility that a responsible party might have to bear more than its proportional share of the cleanup costs if it is unable to obtain appropriate contribution from other responsible parties, we have not had to bear significantly more than our proportional share in multi-party situations taken as a whole.
We do not believe that existing or pending climate change legislation, regulation, or international treaties or accords are reasonably likely to have a material effect in the foreseeable future on the Company’s business or markets that it serves, nor on its results of operations, capital expenditures or financial position. We will continue to monitor emerging developments in this area.
Further information, including the current status of significant environmental matters and the financial impact incurred for remediation of such environmental matters, if any, is included in “Item 7. Management’s Discussion and Analysis of Financial Condition and Results of Operations,” in Note 21 of Notes to Financial Statements in “Item 8. Financial Statements and Supplementary Data,” and in “Item 1A. Risk Factors.”
Employees
We have approximately 132,000 employees at December 31, 2011, of which approximately 53,000 were located in the United States.
12
Cautionary Statement about Forward-Looking Statements
We have described many of the trends and other factors that drive our business and future results in “Item 7. Management’s Discussion and Analysis of Financial Condition and Results of Operations”, including the overview of the Company and each of our segments and the discussion of their respective economic and other factors and areas of focus for 2012. These sections and other parts of this report (including this Item 1A) contain “forward-looking statements” within the meaning of Section 21E of the Securities Exchange Act of 1934.
Forward-looking statements are those that address activities, events or developments that management intends, expects, projects, believes or anticipates will or may occur in the future. They are based on management’s assumptions and assessments in light of past experience and trends, current economic and industry conditions, expected future developments and other relevant factors. They are not guarantees of future performance, and actual results, developments and business decisions may differ significantly from those envisaged by our forward-looking statements. We do not undertake to update or revise any of our forward-looking statements. Our forward-looking statements are also subject to risks and uncertainties that can affect our performance in both the near-and long-term. These forward-looking statements should be considered in light of the information included in this Form 10-K, including, in particular, the factors discussed below.
Risk Factors
Our business, operating results, cash flows and financial condition are subject to the risks and uncertainties set forth below, any one of which could cause our actual results to vary materially from recent results or from our anticipated future results.
Industry and economic conditions may adversely affect the market and operating conditions of our customers, which in turn can affect demand for our products and services and our results of operations.
The operating results of our segments are impacted by general global industry and economic conditions that can cause changes in spending and capital investment patterns, demand for our products and services and the level of our manufacturing and shipping costs. The operating results of our Aerospace segment, which generated 31 percent of our consolidated revenues in 2011, are directly tied to cyclical industry and economic conditions, including global demand for air travel as reflected in new aircraft production, the deferral or cancellation of orders for new aircraft, delays in launch schedules for new aircraft platforms, the retirement of aircraft, global flying hours, and business and general aviation aircraft utilization rates, as well as changes in customer buying patterns with respect to aftermarket parts, supplier consolidation, factory transitions, capacity constraints, and the level and mix of U.S. Government appropriations for defense and space programs (as further discussed in other risk factors below). The challenging operating environment faced by the commercial airline industry may be influenced by a wide variety of factors including global flying hours, aircraft fuel prices, labor issues, airline consolidation, airline insolvencies, terrorism and safety concerns as well as changes in regulations. Future terrorist actions or pandemic health issues could dramatically reduce both the demand for air travel and our Aerospace aftermarket sales and margins. The operating results of our Automation and Control Solutions (ACS) segment, which generated 43 percent of our consolidated revenues in 2011, are impacted by the level of global residential and commercial construction (including retrofits and upgrades), capital spending and operating expenditures on building and process automation, industrial plant capacity utilization and expansion, inventory levels in distribution channels, and global economic growth rates. Performance Materials and Technologies’ operating results, which generated 15 percent of our consolidated revenues in 2011, are impacted by global economic growth rates, capacity utilization for chemical, industrial, refining, petrochemical and semiconductor plants, our customers’ availability of capital for refinery construction and expansion, and raw material demand and supply volatility. Transportation Systems’ operating results, which generated 11 percent of our consolidated revenues in 2011, are impacted by global production and demand for automobiles and trucks equipped with turbochargers, and regulatory changes regarding automobile and truck emissions and fuel economy, delays in launch schedules for new automotive platforms, and consumer demand and spending for automotive aftermarket products. Demand of global automotive and truck manufacturers will continue to be influenced by a wide variety of factors, including ability of consumers to obtain financing, ability to reduce operating costs and overall consumer and business confidence. Each of the segments is impacted by volatility in raw material prices (as further described below) and non-material inflation.
Raw material price fluctuations, the ability of key suppliers to meet quality and delivery requirements, or catastrophic events can increase the cost of our products and services, impact our ability to meet commitments to customers, and cause us to incur significant liabilities.
13
The cost of raw materials is a key element in the cost of our products, particularly in our Performance Materials and Technologies (cumene, fluorspar, perchloroethylene, R240, natural gas, sulfur and ethylene), Transportation Systems (nickel, steel and other metals) and Aerospace (nickel, titanium and other metals) segments. Our inability to offset material price inflation through increased prices to customers, formula or long-term fixed price contracts with suppliers, productivity actions or through commodity hedges could adversely affect our results of operations.
Our manufacturing operations are also highly dependent upon the delivery of materials (including raw materials) by outside suppliers and their assembly of major components, and subsystems used in our products in a timely manner and in full compliance with purchase order terms and conditions, quality standards, and applicable laws and regulations. In addition, many major components, product equipment items and raw materials are procured or subcontracted on a single-source basis with a number of domestic and foreign companies; in some circumstances these suppliers are the sole source of the component or equipment. Although we maintain a qualification and performance surveillance process to control risk associated with such reliance on third parties and we believe that sources of supply for raw materials and components are generally adequate, it is difficult to predict what effects shortages or price increases may have in the future. Our ability to manage inventory and meet delivery requirements may be constrained by our suppliers’ inability to scale production and adjust delivery of long-lead time products during times of volatile demand. Our suppliers may fail to perform according to specifications as and when required and we may be unable to identify alternate suppliers or to otherwise mitigate the consequences of their non-performance. The supply chains for our businesses could also be disrupted by suppliers’ decisions to exit certain businesses, bankruptcy and by external events such as natural disasters, extreme weather events, pandemic health issues, terrorist actions, labor disputes, governmental actions and legislative or regulatory changes (e.g., product certification or stewardship requirements, sourcing restrictions, product authenticity, climate change or greenhouse gas emission standards, etc.). Our inability to fill our supply needs would jeopardize our ability to fulfill obligations under commercial and government contracts, which could, in turn, result in reduced sales and profits, contract penalties or terminations, and damage to customer relationships. Transitions to new suppliers may result in significant costs and delays, including those related to the required recertification of parts obtained from new suppliers with our customers and/or regulatory agencies. In addition, because our businesses cannot always immediately adapt their cost structure to changing market conditions, our manufacturing capacity for certain products may at times exceed or fall short of our production requirements, which could adversely impact our operating costs, profitability and customer and supplier relationships.
Our facilities, distribution systems and information technology systems are subject to catastrophic loss due to, among other things, fire, flood, terrorism or other natural or man-made disasters. If any of these facilities or systems were to experience a catastrophic loss, it could disrupt our operations, result in personal injury or property damage, damage relationships with our customers and result in large expenses to repair or replace the facilities or systems, as well as result in other liabilities and adverse impacts. The same risk can also arise from the failure of critical systems supplied by Honeywell to large industrial, refining and petrochemical customers.
Our future growth is largely dependent upon our ability to develop new technologies that achieve market acceptance with acceptable margins.
Our businesses operate in global markets that are characterized by rapidly changing technologies and evolving industry standards. Accordingly, our future growth rate depends upon a number of factors, including our ability to (i) identify emerging technological trends in our target end-markets, (ii) develop and maintain competitive products, (iii) enhance our products by adding innovative features that differentiate our products from those of our competitors and prevent commoditization of our products, (iv) develop, manufacture and bring products to market quickly and cost-effectively, and (v) develop and retain individuals with the requisite expertise.
Our ability to develop new products based on technological innovation can affect our competitive position and requires the investment of significant resources. These development efforts divert resources from other potential investments in our businesses, and they may not lead to the development of new technologies or products on a timely basis or that meet the needs of our customers as fully as competitive offerings. In addition, the markets for our products may not develop or grow as we currently anticipate. The failure of our technologies or products to gain market acceptance due to more attractive offerings by our competitors could significantly reduce our revenues and adversely affect our competitive standing and prospects.
Protecting our intellectual property is critical to our innovation efforts.
We own or are licensed under a large number of U.S. and non-U.S. patents and patent applications, trademarks and copyrights. Our intellectual property rights may expire or be challenged, invalidated or infringed
14
upon by third parties or we may be unable to maintain, renew or enter into new licenses of third party proprietary intellectual property on commercially reasonable terms. In some non-U.S. countries, laws affecting intellectual property are uncertain in their application, which can affect the scope or enforceability of our patents and other intellectual property rights. Any of these events or factors could diminish or cause us to lose the competitive advantages associated with our intellectual property, subject us to judgments, penalties and significant litigation costs, and/or temporarily or permanently disrupt our sales and marketing of the affected products or services.
Cybersecurity incidents could disrupt business operations, result in the loss of critical and confidential information, and adversely impact our reputation and results of operations.
Global cybersecurity threats can range from uncoordinated individual attempts to gain unauthorized access to our information technology (IT) systems to sophisticated and targeted measures known as advanced persistent threats. While we employ comprehensive measures to prevent, detect, address and mitigate these threats (including access controls, data encryption, vulnerability assessments, continuous monitoring of our IT networks and systems and maintenance of backup and protective systems), cybersecurity incidents, depending on their nature and scope, could potentially result in the misappropriation, destruction, corruption or unavailability of critical data and confidential or proprietary information (our own or that of third parties) and the disruption of business operations. The potential consequences of a material cybersecurity incident include reputational damage, litigation with third parties, diminution in the value of our investment in research, development and engineering, and increased cybersecurity protection and remediation costs, which in turn could adversely affect our competitiveness and results of operations.
An increasing percentage of our sales and operations is in non-U.S. jurisdictions and is subject to the economic, political, regulatory and other risks of international operations.
Our international operations, including U.S. exports, comprise a growing proportion of our operating results. Our strategy calls for increasing sales to and operations in overseas markets, including developing markets such as China, India, the Middle East and other high growth regions.
In 2011, approximately 55 percent of our total sales (including products manufactured in the U.S. and sold outside the U.S. as well as products manufactured in international locations) were outside of the U.S. including approximately 30 percent in Europe and approximately 12 percent in Asia. Risks related to international operations include exchange control regulations, wage and price controls, employment regulations, foreign investment laws, import, export and other trade restrictions (such as embargoes), changes in regulations regarding transactions with state-owned enterprises, nationalization of private enterprises, government instability, and our ability to hire and maintain qualified staff and maintain the safety of our employees in these regions. We are also subject to U.S. laws prohibiting companies from doing business in certain countries, or restricting the type of business that may be conducted in these countries. The cost of compliance with increasingly complex and often conflicting regulations worldwide can also impair our flexibility in modifying product, marketing, pricing or other strategies for growing our businesses, as well as our ability to improve productivity and maintain acceptable operating margins.
Uncertain global economic conditions arising from circumstances such as sovereign debt issues and credit rating downgrades in certain European countries or speculation regarding changes to the composition or viability of the Euro zone could result in reduced customer confidence resulting in decreased demand for our products and services, disruption in payment patterns and higher default rates, a tightening of credit markets (see risk factor below regarding volatility of credit markets for further discussion), increased risk regarding supplier performance, increased counterparty risk with respect to the financial institutions with which we do business, and exchange rate fluctuations. While we employ comprehensive controls regarding global cash management to guard against cash or investment loss and to ensure our ability to fund our operations and commitments, a material disruption to the financial institutions with whom we transact business could expose Honeywell to financial loss.
Sales and purchases in currencies other than the US dollar expose us to fluctuations in foreign currencies relative to the US dollar and may adversely affect our results of operations. Currency fluctuations may affect product demand and prices we pay for materials, as a result, our operating margins may be negatively impacted. Fluctuations in exchange rates may give rise to translation gains or losses when financial statements of our non-U.S. businesses are translated into U.S. dollars. While we monitor our exchange rate exposures and seek to reduce the risk of volatility through hedging activities, such activities bear a financial cost and may not always be available to us or successful in significantly mitigating such volatility.
Volatility of credit markets or macro-economic factors could adversely affect our business.
15
Changes in U.S. and global financial and equity markets, including market disruptions, limited liquidity, and interest rate volatility, may increase the cost of financing as well as the risks of refinancing maturing debt. In addition, our borrowing costs can be affected by short and long-term ratings assigned by independent rating agencies. A decrease in these ratings could increase our cost of borrowing.
Delays in our customers’ ability to obtain financing, or the unavailability of financing to our customers, could adversely affect our results of operations and cash flow. The inability of our suppliers to obtain financing could result in the need to transition to alternate suppliers, which could result in significant incremental cost and delay, as discussed above. Lastly, disruptions in the U.S. and global financial markets could impact the financial institutions with which we do business.
We may be required to recognize impairment charges for our long-lived assets or available for sale investments.
At December 31, 2011, the net carrying value of long-lived assets (property, plant and equipment, goodwill and other intangible assets) and available for sale securities totaled approximately $19.1 billion and $0.4 billion, respectively. In accordance with generally accepted accounting principles, we periodically assess these assets to determine if they are impaired. Significant negative industry or economic trends, disruptions to our business, unexpected significant changes or planned changes in use of the assets, divestitures and market capitalization declines may result in impairments to goodwill and other long-lived assets. An other than temporary decline in the market value of our available for sale securities may also result in an impairment charge. Future impairment charges could significantly affect our results of operations in the periods recognized. Impairment charges would also reduce our consolidated shareowners’ equity and increase our debt-to-total-capitalization ratio, which could negatively impact our credit rating and access to the public debt and equity markets.
A change in the level of U.S. Government defense and space funding or the mix of programs to which such funding is allocated could adversely impact Aerospace’s defense and space sales and results of operations.
Sales of our defense and space-related products and services are largely dependent upon government budgets, particularly the U.S. defense budget. Sales as a prime contractor and subcontractor to the U.S. Department of Defense comprised approximately 29 and 9 percent of Aerospace and total sales, respectively, for the year ended December 31, 2011.We cannot predict the extent to which total funding and/or funding for individual programs will be included, increased or reduced as part of the 2012 and subsequent budgets ultimately approved by Congress, or be included in the scope of separate supplemental appropriations. We also cannot predict the impact of potential changes in priorities due to military transformation and planning and/or the nature of war-related activity on existing, follow-on or replacement programs. A shift in defense or space spending to programs in which we do not participate and/or reductions in funding for or termination of existing programs could adversely impact our results of operations.
As a supplier of military and other equipment to the U.S. Government, we are subject to unusual risks, such as the right of the U.S. Government to terminate contracts for convenience and to conduct audits and investigations of our operations and performance.
In addition to normal business risks, companies like Honeywell that supply military and other equipment to the U.S. Government are subject to unusual risks, including dependence on Congressional appropriations and administrative allotment of funds, changes in governmental procurement legislation and regulations and other policies that reflect military and political developments, significant changes in contract requirements, complexity of designs and the rapidity with which they become obsolete, necessity for frequent design improvements, intense competition for U.S. Government business necessitating increases in time and investment for design and development, difficulty of forecasting costs and schedules when bidding on developmental and highly sophisticated technical work, and other factors characteristic of the industry, such as contract award protests and delays in the timing of contract approvals. Changes are customary over the life of U.S. Government contracts, particularly development contracts, and generally result in adjustments to contract prices and schedules.
Our contracts with the U.S. Government are also subject to various government audits. Like many other government contractors, we have received audit reports that recommend downward price adjustments to certain contracts or changes to certain accounting systems or controls to comply with various government regulations. When appropriate and prudent, we have made adjustments and paid voluntary refunds in the past and may do so in the future.
U.S. Government contracts are subject to termination by the government, either for the convenience of the government or for our failure to perform consistent with the terms of the applicable contract. In the case of a termination for convenience, we are typically entitled to reimbursement for our allowable costs incurred, plus
16
termination costs and a reasonable profit. If a contract is terminated by the government for our failure to perform we could be liable for reprocurement costs incurred by the government in acquiring undelivered goods or services from another source and for other damages suffered by the government as permitted under the contract.
We are also subject to government investigations of business practices and compliance with government procurement regulations. If, as a result of any such investigation or other government investigations (including violations of certain environmental or export laws), Honeywell or one of its businesses were found to have violated applicable law, it could be suspended from bidding on or receiving awards of new government contracts, suspended from contract performance pending the completion of legal proceedings and/or have its export privileges suspended. The U.S. Government also reserves the right to debar a contractor from receiving new government contracts for fraudulent, criminal or other egregious misconduct. Debarment generally does not exceed three years.
Our reputation and ability to do business may be impacted by the improper conduct of employees, agents or business partners.
We cannot ensure that our extensive compliance controls, policies and procedures will, in all instances, protect us from reckless or criminal acts committed by our employees, agents or business partners that would violate the laws of the jurisdictions in which the Company operates, including laws governing payments to government officials, competition and data privacy. Any improper actions could subject us to civil or criminal investigations, monetary and non-monetary penalties and could adversely impact our ability to conduct business, results of operations and reputation.
Changes in legislation or government regulations or policies can have a significant impact on our results of operations.
The sales and margins of each of our segments are directly impacted by government regulations. Safety and performance regulations (including mandates of the Federal Aviation Administration and other similar international regulatory bodies requiring the installation of equipment on aircraft), product certification requirements and government procurement practices can impact Aerospace sales, research and development expenditures, operating costs and profitability. The demand for and cost of providing Automation and Control Solutions products, services and solutions can be impacted by fire, security, safety, health care, environmental and energy efficiency standards and regulations. Performance Materials and Technologies’ results of operations can be affected by environmental (e.g. government regulation of fluorocarbons), safety and energy efficiency standards and regulations, while emissions and energy efficiency standards and regulations can impact the demand for turbochargers in our Transportation Systems segment. Legislation or regulations regarding areas such as labor and employment, employee benefit plans, tax, health, safety and environmental matters, import, export and trade, intellectual property, product certification, and product liability may impact the results of each of our operating segments and our consolidated results.
Completed acquisitions may not perform as anticipated or be integrated as planned, and divestitures may not occur as planned.
We regularly review our portfolio of businesses and pursue growth through acquisitions and seek to divest non-core businesses. We may not be able to complete transactions on favorable terms, on a timely basis or at all. In addition, our results of operations and cash flows may be adversely impacted by (i) the failure of acquired businesses to meet or exceed expected returns, (ii) the discovery of unanticipated issues or liabilities, (iii) the failure to integrate acquired businesses into Honeywell on schedule and/or to achieve synergies in the planned amount or within the expected timeframe, (iv) the inability to dispose of non-core assets and businesses on satisfactory terms and conditions and within the expected timeframe, and (v) the degree of protection provided by indemnities from sellers of acquired companies and the obligations under indemnities provided to purchasers of our divested businesses.
We cannot predict with certainty the outcome of litigation matters, government proceedings and other contingencies and uncertainties.
We are subject to a number of lawsuits, investigations and disputes (some of which involve substantial amounts claimed) arising out of the conduct of our business, including matters relating to commercial transactions, government contracts, product liability (including asbestos), prior acquisitions and divestitures, employment, employee benefits plans, intellectual property, import and export matters and environmental, health and safety matters. Resolution of these matters can be prolonged and costly, and the ultimate results or judgments are uncertain due to the inherent uncertainty in litigation and other proceedings. Moreover, our potential liabilities are subject to change over time due to new developments, changes in settlement strategy or the impact of evidentiary requirements, and we may become subject to or be required to pay damage awards or
17
settlements that could have a material adverse effect on our results of operations, cash flows and financial condition. While we maintain insurance for certain risks, the amount of our insurance coverage may not be adequate to cover the total amount of all insured claims and liabilities. It also is not possible to obtain insurance to protect against all our operational risks and liabilities. The incurrence of significant liabilities for which there is no or insufficient insurance coverage could adversely affect our results of operations, cash flows, liquidity and financial condition.
Our operations and the prior operations of predecessor companies expose us to the risk of material environmental liabilities.
Mainly because of past operations and operations of predecessor companies, we are subject to potentially material liabilities related to the remediation of environmental hazards and to claims of personal injuries or property damages that may be caused by hazardous substance releases and exposures. We have incurred remedial response and voluntary clean-up costs for site contamination and are a party to lawsuits and claims associated with environmental and safety matters, including past production of products containing hazardous substances. Additional lawsuits, claims and costs involving environmental matters are likely to continue to arise in the future. We are subject to various federal, state, local and foreign government requirements regulating the discharge of materials into the environment or otherwise relating to the protection of the environment. These laws and regulations can impose substantial fines and criminal sanctions for violations, and require installation of costly equipment or operational changes to limit emissions and/or decrease the likelihood of accidental hazardous substance releases. We incur, and expect to continue to incur capital and operating costs to comply with these laws and regulations. In addition, changes in laws, regulations and enforcement of policies, the discovery of previously unknown contamination or new technology or information related to individual sites, the establishment of stricter state or federal toxicity standards with respect to certain contaminants, or the imposition of new clean-up requirements or remedial techniques could require us to incur costs in the future that would have a negative effect on our financial condition or results of operations.
Our expenses include significant costs related to employee and retiree health benefits.
With approximately 132,000 employees, including approximately 53,000 in the U.S., our expenses relating to employee health and retiree health benefits are significant. In recent years, we have experienced significant increases in certain of these costs, largely as a result of economic factors beyond our control, in particular, ongoing increases in health care costs well in excess of the rate of inflation. Continued increasing health-care costs, legislative or regulatory changes, and volatility in discount rates, as well as changes in other assumptions used to calculate retiree health benefit expenses, may adversely affect our financial position and results of operations.
Risks related to our defined benefit pension plans may adversely impact our results of operations and cash flow.
Significant changes in actual investment return on pension assets, discount rates, and other factors could adversely affect our results of operations and pension contributions in future periods. U.S. generally accepted accounting principles require that we calculate income or expense for the plans using actuarial valuations. These valuations reflect assumptions about financial markets and interest rates, which may change based on economic conditions. Funding requirements for our U.S. pension plans may become more significant. However, the ultimate amounts to be contributed are dependent upon, among other things, interest rates, underlying asset returns and the impact of legislative or regulatory changes related to pension funding obligations. For a discussion regarding the significant assumptions used to estimate pension expense, including discount rate and the expected long-term rate of return on plan assets, and how our financial statements can be affected by pension plan accounting policies, see “Critical Accounting Policies” included in “Item 7. Management’s Discussion and Analysis of Financial Condition and Results of Operations.”
Additional tax expense or additional tax exposures could affect our future profitability.
We are subject to income taxes in both the United States and various non-U.S. jurisdictions, and our domestic and international tax liabilities are dependent upon the distribution of income among these different jurisdictions. In 2011, our tax expense represented 18.3 percent of our income before tax, and includes estimates of additional tax which may be incurred for tax exposures and reflects various estimates and assumptions, including assessments of future earnings of the Company that could impact the valuation of our deferred tax assets. Our future results of operations could be adversely affected by changes in the effective tax rate as a result of a change in the mix of earnings in countries with differing statutory tax rates, changes in the overall profitability of the Company, changes in tax legislation and rates, changes in generally accepted accounting principles, changes in the valuation of deferred tax assets and liabilities, changes in the amount of earnings permanently
18
reinvested offshore, the results of audits and examinations of previously filed tax returns and continuing assessments of our tax exposures.
| |
Item 1B. | Unresolved Staff Comments |
Not Applicable
We have approximately 1,300 locations consisting of plants, research laboratories, sales offices and other facilities. Our headquarters and administrative complex is located in Morris Township, New Jersey. Our plants are generally located to serve large marketing areas and to provide accessibility to raw materials and labor pools. Our properties are generally maintained in good operating condition. Utilization of these plants may vary with sales to customers and other business conditions; however, no major operating facility is significantly idle. We own or lease warehouses, railroad cars, barges, automobiles, trucks, airplanes and materials handling and data processing equipment. We also lease space for administrative and sales staffs. Our properties and equipment are in good operating condition and are adequate for our present needs. We do not anticipate difficulty in renewing existing leases as they expire or in finding alternative facilities.
Our principal plants, which are owned in fee unless otherwise indicated, are as follows:
| | | | |
| | Aerospace | | |
Anniston, AL (leased) | | Olathe, KS | | Toronto, Canada |
Glendale, AZ (leased) | | Minneapolis, MN(partially leased) | | Olomouc, Czech Republic (leased) |
Phoenix, AZ | | Plymouth, MN | | Raunheim, Germany |
Tempe, AZ | | Rocky Mount, NC | | Penang, Malaysia |
Tucson, AZ | | Albuquerque, NM | | Chihuahua, Mexico |
Torrance, CA | | Urbana, OH | | Singapore (leased) |
Clearwater, FL | | Greer, SC | | Yeovil, UK (leased) |
South Bend, IN | | | | |
| | | | |
| | Automation and Control Solutions | | |
San Diego, CA (leased) | | Pleasant Prairie, WI (leased) | | Schonaich, Germany (leased) |
Northford, CT | | Shenzhen, China (leased) | | Pune, India (leased) |
Freeport, IL | | Suzhou, China | | Chihuahua, Mexico |
St. Charles, IL (leased) | | Tianjin, China (leased) | | Juarez, Mexico (partially leased) |
Golden Valley, MN | | Brno, Czech Republic (leased) | | Tijuana, Mexico (leased) |
York, PA (leased) | | Mosbach, Germany | | Emmen, Netherlands |
| | Neuss, Germany | | Newhouse, Scotland |
| | | | |
| | Performance Materials and Technologies | | |
Mobile, AL | | Shreveport, LA | | Colonial Heights, VA |
Des Plaines, IL | | Frankford, PA | | Hopewell, VA |
Metropolis, IL | | Pottsville, PA | | Spokane, WA |
Baton Rouge, LA | | Orange, TX | | Seelze, Germany |
Geismar, LA | | Chesterfield, VA | | |
| | | | |
| | Transportation Systems | | |
Shanghai, China | | Atessa, Italy | | Mexicali, Mexico (partially leased) |
Glinde, Germany | | Kodama, Japan | | Bucharest, Romania |
| | Ansan, Korea (leased) | | Pune India |
19
We are subject to a number of lawsuits, investigations and claims (some of which involve substantial amounts) arising out of the conduct of our business. See a discussion of environmental, asbestos and other litigation matters in Note 21 of Notes to Financial Statements.
Environmental Matters Involving Potential Monetary Sanctions in Excess of $100,000
Although the outcome of the matter discussed below cannot be predicted with certainty, we do not believe that it will have a material adverse effect on our consolidated financial position, consolidated results of operations or operating cash flows.
The United States Environmental Protection Agency and the United States Department of Justice are investigating whether the Company’s manufacturing facility in Hopewell, Virginia is in compliance with the requirements of the Clean Air Act and the facility’s air operating permit. Based on these investigations, the federal authorities have issued notices of violation with respect to the facility’s benzene waste operations, leak detection and repair program, emissions of nitrogen oxides and emissions of particulate matter. The Company has entered into negotiations with federal authorities to resolve the alleged violations.
20
Executive Officers of the Registrant
The executive officers of Honeywell, listed as follows, are elected annually by the Board of Directors. There are no family relationships among them.
| | |
Name, Age, Date First Elected an Executive Officer | | Business Experience |
David M. Cote, 59 2002(a) | | Chairman of the Board and Chief Executive Officer since July 2002. |
| | |
Alexandre Ismail, 46 2009 | | President and Chief Executive Officer Transportation Systems since April 2009. President Turbo Technologies from November 2008 to April 2009. President Global Passengers Vehicles from August 2006 to November 2008. |
| | |
Roger Fradin, 58 2004 | | President and Chief Executive Officer Automation and Control Solutions since January 2004. |
| | |
Timothy O. Mahoney, 55 2009 | | President and Chief Executive Officer Aerospace since September 2009. Vice President Aerospace Engineering and Technology and Chief Technology Officer from March 2007 to August 2009. President of Air Transport and Regional from July 2005 to March 2007. |
| | |
Andreas C. Kramvis, 59 2008 | | President and Chief Executive Officer Performance Materials and Technologies since March 2008. President of Environmental and Combustion Controls from September 2002 to February 2008. |
| | |
David J. Anderson, 62 2003 | | Senior Vice President and Chief Financial Officer since June 2003. |
| | |
Krishna Mikkilineni, 52 2010 | | Senior Vice President Engineering and Operations since April 2010 and President Honeywell Technology Solutions since January 2009. Vice President Honeywell Technology Solutions from July 2002 to January 2009. |
| | |
Katherine L. Adams, 47 2009 | | Senior Vice President and General Counsel since April 2009. Vice President and General Counsel from September 2008 to April 2009. Vice President and General Counsel for Performance Materials and Technologies from February 2005 to September 2008. |
| | |
Mark R. James, 50 2007 | | Senior Vice President Human Resources and Communications since November 2007. Vice President of Human Resources and Communications for Aerospace from October 2004 to November 2007. |
21
Part II.
| |
Item 5. | Market for Registrant’s Common Equity, Related Stockholder Matters and Issuer Purchases of Equity Securities |
Market and dividend information for Honeywell’s common stock is included in Note 26 of Notes to Financial Statements in “Item 8. Financial Statements and Supplementary Data.”
The number of record holders of our common stock at December 31, 2011 was 58,965.
Honeywell purchased 1,450,000 shares of its common stock, par value $1 per share, in the quarter ending December 31, 2011. Honeywell purchased a total of 20,250,000 shares of its common stock in 2011. Under the Company’s previously reported $3 billion share repurchase program, $1.9 billion remained available as of December 31, 2011 for additional share repurchases. Honeywell presently expects to repurchase outstanding shares from time to time during 2012 to offset the dilutive impact of employee stock based compensation plans, including future option exercises, restricted unit vesting and matching contributions under our savings plans. The amount and timing of future repurchases may vary depending on market conditions and the level of operating, financing and other investing activities.
The following table summarizes Honeywell’s purchase of its common stock, par value $1 per share, for the three months ended December 31, 2011:
| | | | | | | | | | | | | |
Issuer Purchases of Equity Securities | |
| | (a) | | (b) | | (c) | | | (d) | |
Period | | Total Number of Shares Purchased | | Average Price Paid per Share | | Total Number of Shares Purchased as Part of Publicly Announced Plans or Programs | | Approximate Dollar Value of Shares that May Yet be Purchased Under Plans or Programs (Dollars in millions) | |
| | | | | | | | | |
|
November 2011 | | | 1,250,000 | | | $ 52.67 | | | 1,250,000 | | | $ 1,925 | |
December 2011 | | | 200,000 | | | $ 50.09 | | | 200,000 | | | $ 1,915 | |
22
Performance Graph
The following graph compares the five-year cumulative total return on our Common Stock to the total returns on the Standard & Poor’s 500 Stock Index and a composite of Standard & Poor’s Industrial Conglomerates and Aerospace and Defense indices, on a 60%/40% weighted basis, respectively (the “Composite Index”). The weighting of the components of the Composite Index are based on our segments’ relative contribution to total segment profit. The selection of the Industrial Conglomerates component of the Composite Index reflects the diverse and distinct range of non-aerospace businesses conducted by Honeywell. The annual changes for the five-year period shown in the graph are based on the assumption that $100 had been invested in Honeywell stock and each index on December 31, 2006 and that all dividends were reinvested.
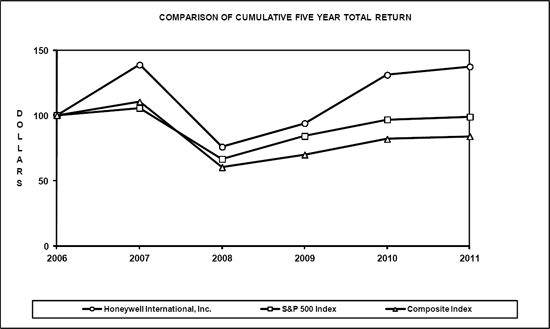
| | | | | | | | | | | | | | | | | | | |
| | Dec 2006 | | Dec 2007 | | Dec 2008 | | Dec 2009 | | Dec 2010 | | Dec 2011 | |
| | | | | | | | | | | | | |
Honeywell | | 100 | | | 138.64 | | | 75.77 | | | 93.82 | | | 130.89 | | | 137.22 | | |
S&P 500 Index® | | 100 | | | 105.49 | | | 66.46 | | | 84.05 | | | 96.71 | | | 98.76 | | |
Composite Index | | 100 | | | 110.34 | | | 60.12 | | | 69.70 | | | 81.74 | | | 83.81 | | |
23
HONEYWELL INTERNATIONAL INC.
The Consumer Products Group (CPG) automotive aftermarket business had historically been part of the Transportation Systems reportable segment. In accordance with generally accepted accounting principles, CPG is presented as discontinued operations in all periods presented. See Note 2 Acquisitions and Divestitures for further details. This selected financial data should be read in conjunction with Honeywell’s Consolidated Financial Statements and related Notes included elsewhere in this Annual Report as well as the section of this Annual Report titled Item 7. Management’s Discussion and Analysis of Financial Condition and Results of Operations.
| |
Item 6. | Selected Financial Data |
| | | | | | | | | | | | | | | | | | | | | | | | | | |
| | Years Ended December 31, | |
| | | |
| | 2011 | | 2010 | | 2009 | | 2008 | | 2007 | |
| | | | | | | | | | | |
| | (Dollars in millions, except per share amounts) | |
Results of Operations | | | | | | | | | | | | | | | | | | | | | | | | | | |
Net sales | | | $ | 36,529 | | | | $ | 32,350 | | | | $ | 29,951 | | | | $ | 35,520 | | | | $ | 33,462 | | |
Amounts attributable to Honeywell: | | | | | | | | | | | | | | | | | | | | | | | | | | |
Income from continuing operations less net income attributable to the noncontrolling interest | | | | 1,858 | | | | | 1,944 | | | | | 1,492 | | | | | 789 | | | | | 2,535 | | |
Income from discontinued operations(1) | | | | 209 | | | | | 78 | | | | | 56 | | | | | 17 | | | | | 59 | | |
| | | | | | | | | | | | | | | | | | | | | | | | | | |
Net income attributable to Honeywell(2) | | | | 2,067 | | | | | 2,022 | | | | | 1,548 | | | | | 806 | | | | | 2,594 | | |
Earnings Per Common Share | | | | | | | | | | | | | | | | | | | | | | | | | | |
Basic: | | | | | | | | | | | | | | | | | | | | | | | | | | |
Income from continuing operations | | | | 2.38 | | | | | 2.51 | | | | | 1.99 | | | | | 1.07 | | | | | 3.31 | | |
Income from discontinued operations | | | | 0.27 | | | | | 0.10 | | | | | 0.07 | | | | | 0.02 | | | | | 0.08 | | |
| | | | | | | | | | | | | | | | | | | | | | | | | | |
Net income attributable to Honeywell | | | | 2.65 | | | | | 2.61 | | | | | 2.06 | | | | | 1.09 | | | | | 3.39 | | |
Assuming dilution: | | | | | | | | | | | | | | | | | | | | | | | | | | |
Income from continuing operations | | | | 2.35 | | | | | 2.49 | | | | | 1.98 | | | | | 1.06 | | | | | 3.27 | | |
Income from discontinued operations | | | | 0.26 | | | | | 0.10 | | | | | 0.07 | | | | | 0.02 | | | | | 0.08 | | |
| | | | | | | | | | | | | | | | | | | | | | | | | | |
Net income attributable to Honeywell | | | | 2.61 | | | | | 2.59 | | | | | 2.05 | | | | | 1.08 | | | | | 3.35 | | |
Dividends per share | | | | 1.37 | | | | | 1.21 | | | | | 1.21 | | | | | 1.10 | | | | | 1.00 | | |
Financial Position at Year-End | | | | | | | | | | | | | | | | | | | | | | | | | | |
Property, plant and equipment—net | | | | 4,804 | | | | | 4,724 | | | | | 4,847 | | | | | 4,934 | | | | | 4,985 | | |
Total assets | | | | 39,808 | | | | | 37,834 | | | | | 35,993 | | | | | 35,570 | | | | | 33,805 | | |
Short-term debt | | | | 674 | | | | | 889 | | | | | 1,361 | | | | | 2,510 | | | | | 2,238 | | |
Long-term debt | | | | 6,881 | | | | | 5,755 | | | | | 6,246 | | | | | 5,865 | | | | | 5,419 | | |
Total debt | | | | 7,555 | | | | | 6,644 | | | | | 7,607 | | | | | 8,375 | | | | | 7,657 | | |
Shareowners’ equity | | | | 10,902 | | | | | 10,787 | | | | | 8,971 | | | | | 7,140 | | | | | 9,293 | | |
| | |
| |
| | |
(1) | For the year ended December 31, 2011, Income from discontinued operations includes a $178 million, net of tax gain, resulting from the sale of the CPG business which funded a portion of the 2011 repositioning actions. |
| |
(2) | For the year ended December 31, 2008, Net income attributable to Honeywell includes a $417 million, net of tax gain, resulting from the sale of our Consumables Solutions business as well as a charge of $465 million for environmental liabilities deemed probable and reasonably estimable during 2008. |
24
| |
Item 7. | Management’s Discussion and Analysis of Financial Condition and Results of Operations |
(Dollars in millions, except per share amounts)
The following Management’s Discussion and Analysis of Financial Condition and Results of Operations (“MD&A”) is intended to help the reader understand the results of operations and financial condition of Honeywell International Inc. (“Honeywell”) for the three years ended December 31, 2011. All references to Notes related to Notes to the Financial Statements in “Item 8-Financial Statements and Supplementary Data”.
The Consumer Products Group (CPG) automotive aftermarket business had historically been part of the Transportation Systems reportable segment. In accordance with generally accepted accounting principles, CPG results are excluded from continuing operations and are presented as discontinued operations in all periods presented. See Note 2 Acquisitions and Divestitures for further details.
CONSOLIDATED RESULTS OF OPERATIONS
Net Sales
| | | | | | | | | | | | | | | | |
| | 2011 | | 2010 | | 2009 | |
| | | | | | | |
Net sales | | | $ | 36,529 | | | | $ | 32,350 | | | | $ | 29,951 | | |
% change compared with prior period | | | | 13 | % | | | | 8 | % | | | | | | |
The change in net sales compared to the prior year period is attributable to the following:
| | | | | | | |
| | 2011 Versus 2010 | | 2010 Versus 2009 | |
| | | | | |
Volume | | 6 | % | | 5 | % | |
Price | | 2 | % | | 2 | % | |
Acquisitions/Divestitures | | 3 | % | | 1 | % | |
Foreign Exchange | | 2 | % | | 0 | % | |
| | | | | | | |
| | 13 | % | | 8 | % | |
| | | | | | | |
A discussion of net sales by segment can be found in the Review of Business Segments section of this MD&A.
Cost of Products and Services Sold
| | | | | | | | | | | | | | | | |
| | 2011 | | 2010 | | 2009 | |
| | | | | | | |
Cost of products and services sold | | | $ | 28,556 | | | | $ | 24,721 | | | | $ | 23,260 | | |
% change compared with prior period | | | | 16 | % | | | | 6 | % | | | | | | |
|
Gross Margin percentage | | | | 21.8 | % | | | | 23.6 | % | | | | 22.3 | % | |
Cost of products and services sold increased by $3,835 million or 16 percent in 2011 compared with 2010 principally due to an estimated increase in direct material costs, labor costs and indirect costs of approximately $2 billion, $520 million, and $280 million, respectively, driven substantially by a 13 percent increase in sales as a result of the factors (excluding price) discussed above and in the Review of Business Segments section of this MD&A, an increase in pension and other postretirement expense of approximately $880 million (primarily driven by the increase in the pension mark-to-market adjustment allocated to cost of goods sold of $1.1 billion) and an increase in repositioning and other charges of approximately $90 million.
Gross margin percentage decreased by 1.8 percentage points in 2011 compared with 2010 primarily due to higher pension and other postretirement expense (approximate 2.8 percentage point impact primarily driven by an unfavorable 3.3 percentage point impact resulting from the increase in the pension mark-to-market adjustment allocated to cost of goods sold) and repositioning and other charges (approximate 0.2 percentage point impact),
25
partially offset by higher sales volume driven by each of our business segments (approximate 1.2 percentage point impact).
Cost of products and services sold increased by $1,461 million or 6 percent in 2010 compared with 2009, principally due to an estimated increase in direct material costs and indirect costs of approximately $1,250 million and $300 million, respectively, driven substantially by an 8 percent increase in sales as a result of the factors discussed above and in the Review of Business Segments section of this MD&A and approximately $130 million increase in repositioning and other charges (see Note 3 of Notes to Financial Statements), partially offset by a $300 million decrease in pension expense.
Gross margin percentage increased by 1.3 percentage points in 2010 compared with 2009, primarily due to lower pension expense (approximate 1 percentage point impact) and higher sales volume driven by our Automation and Control Solutions segment, Performance Materials and Technologies segment and Transportation Systems segment (approximate 0.7 percentage point impact), partially offset by higher repositioning and other charges (approximate 0.5 percentage point impact).
Selling, General and Administrative Expenses
| | | | | | | | | | | | | | | | |
| | 2011 | | 2010 | | 2009 | |
| | | | | | | |
Selling, general and administrative expense | | | $ | 5,399 | | | | $ | 4,618 | | | | $ | 4,323 | | |
|
Percent of sales | | | | 14.8 | % | | | | 14.3 | % | | | | 14.4 | % | |
Selling, general and administrative expenses (SG&A) increased as a percentage of sales by 0.5 percent in 2011 compared to 2010 driven by an estimated $430 million increase in labor costs resulting from acquisitions, investment for growth, and merit increases, an estimated increase of $240 million in pension and other postretirement expense (driven primarily by the allocated portion of the pension mark-to-market charge increase of approximately $270 million) and an estimated increase of $60 million in repositioning actions, partially offset by the impact of higher sales volume as a result of the factors discussed in the Review of Business Segments section of this MD&A.
Selling, general and administrative expenses (SG&A) decreased as a percentage of sales by 0.1 percent in 2010 compared to 2009 driven by the impact of higher sales volume, discussed above, and lower pension expense, partially offset by an estimated $500 million increase in labor costs (reflecting the absence of prior period labor cost actions).
| | | | | | | | | | | | | | | | |
Other (Income) Expense | | | | | | | | | | | | | | | | |
| | 2011 | | | 2010 | | 2009 | |
| | | | | | | | |
Equity (income)/loss of affiliated companies | | | $ | (51 | ) | | | $ | (28 | ) | | | $ | (26 | ) | |
Gain on sale of non-strategic businesses and assets | | | | (61 | ) | | | | — | | | | | (87 | ) | |
Interest income | | | | (58 | ) | | | | (39 | ) | | | | (33 | ) | |
Foreign exchange | | | | 50 | | | | | 12 | | | | | 45 | | |
Other, net | | | | 36 | | | | | (42 | ) | | | | 47 | | |
| | | | | | | | | | | | | | | | |
| | | $ | (84 | ) | | | $ | (97 | ) | | | $ | (54 | ) | |
| | | | | | | | | | | | | | | | |
Other income decreased by $13 million in 2011 compared to 2010 due primarily to a $29 million loss resulting from early redemption of debt in the first quarter of 2011, included within “Other, net”, and the absence of a $62 million pre-tax gain related to the consolidation of a joint venture within our Performance Materials and Technologies segment in the third quarter of 2010, included within “Other, net”, (see Note 4 of Notes to Financial Statements for further details), partially offset by a $61 million increase in gain on sale of non-strategic businesses and assets due primarily to a $50 million pre-tax gain related to the divestiture of the automotive on-board sensors products business within our Automation and Control Solutions segment and the reduction of approximately $12 million of acquisition related costs compared to 2010 included within “Other, net”.
Other income increased by $43 million in 2010 compared to 2009 primarily due to the consolidation of a joint venture resulting in a $62 million pre-tax gain within our Performance Materials and Technologies segment in the third quarter of 2010, included in “Other, net” (see Note 4 of Notes to Financial Statements for further details),
26
the absence of an other-than-temporary impairment chargeof$62 million in the second quarter of 2009, included within “Other, net”, partially offset by the absence of a $50 million deconsolidation gain related to a subsidiary within our Automation and Control Solutions segment in 2009, included within “Gain on sale of non-strategic businesses and assets”, and $22 million of acquisition related costs in 2010, included within “Other, net”.
| | | | | | | | | | | | | | | | |
Interest and Other Financial Charges | | | | | | | | | | | | | | | | |
| | 2011 | | 2010 | | 2009 | |
| | | | | | | |
Interest and other financial charges | | | $ | 376 | | | | $ | 386 | | | | $ | 458 | | |
% change compared with prior period | | | | (3 | )% | | | | (16 | )% | | | | | | |
Interest and other financial charges decreased by 3% percent in 2011 compared with 2010 primarily due to lower borrowing costs, partially offset by higher debt balances.
Interest and other financial charges decreased by 16% percent in 2010 compared with 2009 due to lower debt balances and lower borrowing costs.
Tax Expense
| | | | | | | | | | | | | | | | |
| | 2011 | | 2010 | | 2009 | |
| | | | | | | |
Tax expense | | | $ | 417 | | | | $ | 765 | | | | $ | 436 | | |
Effective tax rate | | | | 18.3 | % | | | | 28.1 | % | | | | 22.2 | % | |
The effective tax rate decreased by 9.8 percentage points in 2011 compared with 2010 primarily due to a change in the mix of earnings between U.S. and foreign related to higher U.S. pension expense (primarily driven by an approixmate 7.6 percentage point impact which resulted from the increase in pension mark-to-market expense), an increased benefit from manufacturing incentives, an increased benefit from the favorable settlement of tax audits and an increased benefit from a lower foreign effective tax rate. The foreign effective tax rate was 21.1 percent, a decrease of approximately 4.9 percentage points which primarily consisted of (i) a 5.1 percent impact from decreased valuation allowances on net operating losses primarily due to an increase in German earnings available to be offset by net operating loss carry forwards, (ii) a 2.4 percent impact from tax benefits related to foreign exchange and investment losses, iii) a 1.2 percent impact from an increased benefit in tax credits and lower statutory tax rates, and (iv) a 4.1 percent impact related to an increase in tax reserves. The effective tax rate was lower than the U.S. statutory rate of 35 percent primarily due to earnings taxed at lower foreign rates.
The effective tax rate increased by 5.9 percentage points in 2010 compared with 2009 primarily due to a change in the mix of earnings related to lower U.S. pension expense, the impact of an enacted change in the tax treatment of the Medicare Part D program, the absence of manufacturing incentives, a decreased impact from the settlement of audits and an increase in the foreign effective tax rate. The foreign effective tax rate increased by approximately 7 percentage points which primarily consisted of i) a 6 percentage point impact from the absence of tax benefits related to foreign exchange and investment losses and ii) a (0.1) percentage points impact from increased valuation allowances on net operating losses. The effective tax rate was lower than the U.S. statutory rate of 35 percent primarily due to earnings taxed at lower foreign rates.
In 2012, the effective tax rate could change based upon the Company’s operating results, mix of earnings and the outcome of tax positions taken regarding previously filed tax returns currently under audit by various Federal, State and foreign tax authorities, several of which may be finalized in the foreseeable future. The Company believes that it has adequate reserves for these matters, the outcome of which could materially impact the results of operations and operating cash flows in the period they are resolved.
27
| | | | | | | | | | | | | |
Net Income Attributable to Honeywell | | | | | | | | | | | | | |
| | 2011 | | 2010 | | 2009 | |
| | | | | | | |
Amounts attributable to Honeywell | | | | | | | | | | | | | |
Income from continuing operations | | $ | 1,858 | | | $ | 1,944 | | | $ | 1,492 | | |
Income from discontinued operations | | | 209 | | | | 78 | | | | 56 | | |
| | | | | | | | | | | | | |
Net income attributable to Honeywell | | $ | 2,067 | | | $ | 2,022 | | | $ | 1,548 | | |
| | | | | | | | | | | | | |
| | | | | | | | | | | | | |
Earnings per share of common stock – assuming dilution | | | | | | | | | | | | | |
Income from continuing operations | | $ | 2.35 | | | $ | 2.49 | | | $ | 1.98 | | |
Income from discontinued operations | | | 0.26 | | | | 0.10 | | | | 0.07 | | |
| | | | | | | | | | | | | |
Net income attributable to Honeywell | | $ | 2.61 | | | $ | 2.59 | | | $ | 2.05 | | |
| | | | | | | | | | | | | |
Earnings per share of common stock – assuming dilution increased by $0.02 per share in 2011 compared with 2010 primarily due to an increase in segment profit in each of our business segments, lower tax expense, the gain on disposal of discontinued operations, and lower other postretirement expense, partially offset by higher pension expense (primarily due to an increase in the pension mark-to-market adjustment) and higher repositioning and other charges.
Earnings per share of common stock – assuming dilution increased by $0.54 per share in 2010 compared with 2009 primarily due to increased segment profit in our Automation and Control Solutions, Performance Materials and Technologies and Transportation Systems segments and lower pension expense, partially offset by higher tax expense and higher repositioning and other charges.
For further discussion of segment results, see “Review of Business Segments”.
BUSINESS OVERVIEW
This Business Overview provides a summary of Honeywell and its four reportable operating segments (Aerospace, Automation and Control Solutions, Performance Materials and Technologies and Transportation Systems), including their respective areas of focus for 2012 and the relevant economic and other factors impacting their results, and a discussion of each segment’s results for the three years ended December 31, 2011. Each of these segments is comprised of various product and service classes that serve multiple end markets. See Note 23 to the financial statements for further information on our reportable segments and our definition of segment profit.
Economic and Other Factors
In addition to the factors listed below with respect to each of our operating segments, our consolidated operating results are principally driven by:
| | |
| • | Impact of change in global economic growth rates (U.S., Europe and emerging regions) and industry conditions on demand in our key end markets; |
| | |
| • | Overall sales mix, in particular the mix of Aerospace original equipment and aftermarket sales and the mix of Automation and Control Solutions (ACS) products, distribution and services sales; |
| | |
| • | The extent to which cost savings from productivity actions are able to offset or exceed the impact of material and non-material inflation; |
| | |
| • | The impact of the pension discount rate and asset returns on pension expense, including mark-to-market adjustments, and funding requirements; and |
| | |
| • | The impact of fluctuations in foreign currency exchange rates (Euro and other global currencies), relative to the U.S. dollar. |
| | |
Areas of Focus for 2012 |
| | |
| The areas of focus for 2012, which are generally applicable to each of our operating segments, include: |
| | |
| • | Driving profitable growth and margin expansion by building innovative products that address customer needs; |
28
| | |
| • | Achieving sales growth, technological excellence and manufacturing capability and capacity through global expansion, especially focused on emerging regions in China, India, the Middle East and other high growth regions; |
| | |
| • | Proactively managing raw material costs through formula and long term supply agreements, price increases and hedging activities, where feasible; |
| | |
| • | Driving cash flow conversion through effective working capital management and capital investment in our businesses, thereby enhancing liquidity, repayment of debt, strategic acquisitions, and the ability to return value to shareholders; |
| | |
| • | Maintaining a flexible cost structure to ensure our ability to proactively respond to trends in short-cycle end markets such as the Transportation Systems Turbo business, ACS Energy, Safety & Security businesses, Aerospace commercial after-market and Performance Materials and Technologies Advanced Materials business; |
| | |
| • | Aligning and prioritizing investments in long-term growth considering short-term demand volatility; |
| | |
| • | Driving productivity savings through execution of repositioning actions; |
| | |
| • | Controlling discretionary spending levels with focus on non-customer related costs; |
| | |
| • | Utilizing our enablers Honeywell Operating System (HOS), Functional Transformation and Velocity Product Development (VPD) to drive margin expansion by standardizing the way we work, reducing cycle time, optimizing effectiveness of R&D, increasing quality and reducing the costs of product manufacturing, reducing costs and enhancing the quality of our administrative functions and improving business operations through investments in systems and process improvements; |
| | |
| • | Monitoring both suppliers and customers for signs of liquidity constraints, limiting exposure to any resulting inability to meet delivery commitments or pay amounts due, and identifying alternate sources of supply as necessary; and |
| | |
| • | Controlling Corporate costs, including costs incurred for asbestos and environmental matters, pension and other post-retirement expenses and tax expense. |
29
Review of Business Segments
| | | | | | | | | | | | |
| | 2011 | | 2010 | | 2009 |
| | | | | | | |
Net Sales | | | | | | | | | | | | |
Aerospace | | | | | | | | | | | | |
Product | | $ | 6,494 | | | $ | 5,868 | | | $ | 5,930 | |
Service | | | 4,981 | | | | 4,815 | | | | 4,833 | |
| | | | | | | | | | | | |
Total | | | 11,475 | | | | 10,683 | | | | 10,763 | |
Automation and Control Solutions | | | | | | | | | | | | |
Product | | | 13,328 | | | | 11,733 | | | | 10,699 | |
Service | | | 2,207 | | | | 2,016 | | | | 1,912 | |
| | | | | | | | | | | | |
Total | | | 15,535 | | | | 13,749 | | | | 12,611 | |
Performance Materials and Technologies | | | | | | | | | | | | |
Product | | | 5,064 | | | | 4,449 | | | | 3,895 | |
Service | | | 595 | | | | 277 | | | | 249 | |
| | | | | | | | | | | | |
Total | | | 5,659 | | | | 4,726 | | | | 4,144 | |
Transportation Systems | | | | | | | | | | | | |
Product | | | 3,859 | | | | 3,192 | | | | 2,432 | |
Service | | | — | | | | — | | | | — | |
| | | | | | | | | | | | |
Total | | | 3,859 | | | | 3,192 | | | | 2,432 | |
Corporate | | | | | | | | | | | | |
Product | | | — | | | | — | | | | — | |
Service | | | 1 | | | | — | | | | 1 | |
| | | | | | | | | | | | |
Total | | | 1 | | | | — | | | | 1 | |
| | | | | | | | | | | | |
| | $ | 36,529 | | | $ | 32,350 | | | $ | 29,951 | |
| | | | | | | | | | | | |
| | | | | | | | | | | | |
Segment Profit | | | | | | | | | | | | |
Aerospace | | $ | 2,023 | | | $ | 1,835 | | | $ | 1,893 | |
Automation and Control Solutions | | | 2,083 | | | | 1,770 | | | | 1,588 | |
Performance Materials and Technologies | | | 1,042 | | | | 749 | | | | 605 | |
Transportation Systems | | | 485 | | | | 353 | | | | 61 | |
Corporate | | | (276 | ) | | | (222 | ) | | | (156 | ) |
| | | | | | | | | | | | |
| | $ | 5,357 | | | $ | 4,485 | | | $ | 3,991 | |
| | | | | | | | | | | | |
30
A reconciliation of segment profit to consolidated income from continuing operations before taxes are as follows:
| | | | | | | | | | | | |
| | Years Ended December 31, |
| | |
| | 2011 | | 2010 | | 2009 |
| | | | | | |
| | | | | | | | | | | | |
Segment Profit | | $ | 5,357 | | | $ | 4,485 | | | $ | 3,991 | |
Other income/ (expense)(1) | | | 33 | | | | 69 | | | | 28 | |
Interest and other financial charges | | | (376 | ) | | | (386 | ) | | | (458 | ) |
Stock compensation expense(2) | | | (168 | ) | | | (163 | ) | | | (117 | ) |
Pension expense-ongoing(2) | | | (105 | ) | | | (185 | ) | | | (287 | ) |
Pension mark-to-market adjustment(2) | | | (1,802 | ) | | | (471 | ) | | | (741 | ) |
Other postretirement income/(expense)(2) | | | 86 | | | | (29 | ) | | | 15 | |
Repositioning and other charges(2) | | | (743 | ) | | | (598 | ) | | | (467 | ) |
| | | | | | | | | | | | |
Income from continuing operations before taxes | | $ | 2,282 | | | $ | 2,722 | | | $ | 1,964 | |
| | | | | | | | | | | | |
| | |
(1) | Equity income/(loss) of affiliated companies is included in Segment Profit. |
| | |
(2) | Amounts included in cost of products and services sold and selling, general and administrative expenses. |
31
| | | | | | | | | | | | | | | | | | | |
| | | | | | | | | | | % Change | |
| | | | | | | | | | | | |
| | 2011 | | 2010 | | 2009 | | 2011 Versus 2010 | | 2010 Versus 2009 | |
| | | | | | | | | | | |
|
Aerospace Sales | | | | | | | | | | | | | | | | | | | |
Commercial: | | | | | | | | | | | | | | | | | | | |
Air transport and regional | | | | | | | | | | | | | | | | | | | |
Original equipment | | $ | 1,439 | | | $ | 1,362 | | | $ | 1,396 | | | 6 | % | | (2 | )% | |
Aftermarket | | | 2,828 | | | | 2,437 | | | | 2,419 | | | 16 | % | | 1 | % | |
Business and general aviation | | | | | | | | | | | | | | | | | | | |
Original equipment | | | 723 | | | | 513 | | | | 709 | | | 41 | % | | (28 | )% | |
Aftermarket | | | 1,207 | | | | 976 | | | | 902 | | | 24 | % | | 8 | % | |
Defense and Space Sales | | | 5,278 | | | | 5,395 | | | | 5,337 | | | (2 | )% | | 1 | % | |
| | | | | | | | | | | | | | | | | | | |
Total Aerospace Sales | | | 11,475 | | | | 10,683 | | | | 10,763 | | | | | | | | |
| | | | | | | | | | | | | | | | | | | |
Automation and Control Solutions Sales | | | | | | | | | | | | | | | | | | | |
Energy Safety & Security | | | 7,977 | | | | 6,789 | | | | 5,932 | | | 17 | % | | 14 | % | |
Process Solutions | | | 3,010 | | | | 2,678 | | | | 2,507 | | | 12 | % | | 7 | % | |
Building Solutions & Distribution | | | 4,548 | | | | 4,282 | | | | 4,172 | | | 6 | % | | 3 | % | |
| | | | | | | | | | | | | | | | | | | |
Total Automation and Control Solutions Sales | | | 15,535 | | | | 13,749 | | | | 12,611 | | | | | | | | |
| | | | | | | | | | | | | | | | | | | |
Performance Materials and Technologies Sales | | | | | | | | | | | | | | | | | | | |
UOP | | | 1,931 | | | | 1,556 | | | | 1,574 | | | 24 | % | | (1 | )% | |
Advanced Materials | | | 3,728 | | | | 3,170 | | | | 2,570 | | | 18 | % | | 23 | % | |
| | | | | | | | | | | | | | | | | | | |
Total Performance Materials and Technologies Sales | | | 5,659 | | | | 4,726 | | | | 4,144 | | | | | | | | |
| | | | | | | | | | | | | | | | | | | |
Transportation Systems Sales | | | | | | | | | | | | | | | | | | | |
Turbo Technologies | | | 3,859 | | | | 3,192 | | | | 2,432 | | | 21 | % | | 31 | % | |
| | | | | | | | | | | | | | | | | | | |
Total Transportation Systems Sales | | | 3,859 | | | | 3,192 | | | | 2,432 | | | | | | | | |
| | | | | | | | | | | | | | | | | | | |
Corporate | | | 1 | | | | — | | | | 1 | | | | | | | | |
| | | | | | | | | | | | | | | | | | | |
Net Sales | | $ | 36,529 | | | | 32,350 | | | | 29,951 | | | | | | | | |
| | | | | | | | | | | | | | | | | | | |
Aerospace
Overview
Aerospace is a leading global supplier of aircraft engines, avionics, and related products and services for aircraft manufacturers, airlines, aircraft operators, military services, and defense and space contractors. Our Aerospace products and services include auxiliary power units, propulsion engines, environmental control systems, electric power systems, engine controls, flight safety, communications, navigation, radar and surveillance systems, aircraft lighting, management and technical services, logistics services, advanced systems and instruments, aircraft wheels and brakes and repair and overhaul services. Aerospace sells its products to original equipment (OE) manufacturers in the air transport, regional, business and general aviation aircraft segments, and provides spare parts and repair and maintenance services for the aftermarket (principally to aircraft operators). The United States Government is a major customer for our defense and space products.
Economic and Other Factors
Aerospace operating results are principally driven by:
32
| | |
| • | New aircraft production rates and delivery schedules set by commercial air transport, regional jet, business and general aviation OE manufacturers, as well as airline profitability, platform mix and retirement of aircraft from service; |
| | |
| • | Global demand for commercial air travel as reflected in global flying hours and utilization rates for corporate and general aviation aircraft, as well as the demand for spare parts and maintenance and repair services for aircraft currently in use; |
| | |
| • | Level and mix of U.S. Government appropriations for defense and space programs and military activity; |
| | |
| • | Changes in customer platform development schedules, requirements and demands for new technologies; and |
| | |
| • | Availability and price volatility of raw materials such as titanium and other metals. |
| | | | | | | | | | | | | | | | | | | |
Aerospace | | | | | | | | | | | | | | | | | | | |
| | 2011 | | 2010 | | Change | | 2009 | | Change | |
| | | | | | | | | | | |
Net sales | | $ | 11,475 | | | $ | 10,683 | | | 7 | % | | $ | 10,763 | | | (1 | )% | |
| | | | | | | | | | | | | | | | | | | |
Cost of products and services sold | | | 8,665 | | | | 8,099 | | | | | | | 8,099 | | | | | |
Selling, general and administrative expenses | | | 591 | | | | 553 | | | | | | | 570 | | | | | |
Other | | | 196 | | | | 196 | | | | | | | 201 | | | | | |
| | | | | | | | | | | | | | | | | | | |
Segment profit | | $ | 2,023 | | | $ | 1,835 | | | 10 | % | | $ | 1,893 | | | (3 | )% | |
| | | | | | | | | | | | | | | | | | | |
| | | | | | | | | | | | | | |
| | 2011 vs. 2010 | | 2010 vs. 2009 | |
| | | | | |
|
Factors Contributing to Year-Over-Year Change | | | Sales | | Segment Profit | | Sales | | Segment Profit | |
| | | | | | | | | |
Organic growth/ Operational segment profit | | 7 | % | | 9 | % | | 0 | % | | 0 | % | |
Acquisitions and divestitures, net | | 0 | % | | 0 | % | | 0 | % | | 0 | % | |
Other | | 0 | % | | 1 | % | | (1 | )% | | (3 | )% | |
| | | | | | | | | | | | | |
Total % Change | | 7 | % | | 10 | % | | (1 | )% | | (3 | )% | |
| | | | | | | | | | | | | |
Aerospace sales by major customer end-markets were as follows:
| | | | | | | | | | | | | | | | | |
| | | % of Aerospace Sales | | % Change in Sales | |
| | | | | |
Customer End-Markets | | 2011 | | 2010 | | 2009 | | 2011 Versus 2010 | | 2010 Versus 2009 | |
| | | | | | | | | | | |
Commercial: | | | | | | | | | | | | | | | | |
Air transport and regional | | | | | | | | | | | | | | | | |
Original equipment | | 13 | % | | 13 | % | | 13 | % | | 6 | % | | (2 | )% | |
Aftermarket | | 25 | % | | 23 | % | | 22 | % | | 16 | % | | 1 | % | |
Business and general aviation | | | | | | | | | | | | | | | | |
Original equipment | | 6 | % | | 5 | % | | 7 | % | | 41 | % | | (27 | )% | |
Aftermarket | | 11 | % | | 9 | % | | 8 | % | | 24 | % | | 8 | % | |
Defense and Space | | 45 | % | | 50 | % | | 50 | % | | (2 | )% | | 1 | % | |
| | | | | | | | | | | | | | | | |
Total | | 100 | % | | 100 | % | | 100 | % | | 7 | % | | (1 | )% | |
| | | | | | | | | | | | | | | | |
2011 compared with 2010
Aerospace sales increased by 7 percent in 2011 compared with 2010 primarily due to an increase in organic growth of 7 percent primarily due to increased commercial sales volume.
33
| | |
| Details regarding the changes in sales by customer end-markets are as follows: |
| | |
| • | Air transport and regional original equipment (OE) sales increased by 6 percent in 2011 primarily driven by higher sales to our OE customers, consistent with higher production rates, platform mix and a higher win rate on selectables (components selected by purchasers of new aircraft). |
| | |
| • | Air transport and regional aftermarket sales increased by 16 percent for 2011 primarily due to (i) increased maintenance activity and spare parts sales driven by an approximately 6 percent increase in global flying hours, (ii) increased sales of avionics upgrades, and (iii) changes in customer buying patterns relating to spare parts and maintenance activity. |
| | |
| • | Business and general aviation OE sales increased by 41 percent in 2011 due to a rebound from near trough levels in 2010 and strong demand in the business jet end market, favorable platform mix, growth from acquisitions and lower OEM Payments (as defined below) during 2011. |
| | |
| • | Business and general aviation aftermarket sales increased by 24 percent in 2011 primarily due to increased sales of spare parts and revenue associated with maintenance service agreements. |
| | |
| • | Defense and space sales decreased by 2 percent in 2011 primarily due to anticipated program ramp downs, partially offset by higher domestic and international aftermarket sales, increased unmanned aerial vehicle (UAV) shipments and the EMS acquisition (refer to Note 2). |
Aerospace segment profit increased by 10 percent in 2011 compared with 2010 primarily due to an increase in operational segment profit of 9 percent and an increase of 1 percent due to lower OEM Payments made during 2011. The increase in operational segment profit is comprised of the positive impact from higher commercial aftermarket demand, price and productivity, net of inflation, partially offset by research, development and engineering investments. Cost of goods sold totaled $8.7 billion in 2011, an increase of approximately $566 million from 2010 which is primarily a result of the factors discussed above.
2010 compared with 2009
Aerospace sales decreased by 1 percent in 2010 compared with 2009 primarily due to a 1 percent reduction of revenue related to amounts recognized for payments to business and general aviation original equipment manufacturers to partially offset their pre-production costs associated with new aircraft platforms (OEM Payments).
Details regarding the decrease in sales by customer end-markets are as follows:
| | |
| • | Air transport and regional original equipment (OE) sales decreased by 2 percent in 2010 primarily due to lower sales to our air transport OE customers. |
| | |
| • | Air transport and regional aftermarket sales increased by 1 percent in 2010 primarily due to increased sales of spare parts driven by the impact of increased flying hours of approximately 6 percent in 2010. |
| | |
| • | Business and general aviation OE sales decreased by 27 percent in 2010 due to decreases in new business jet deliveries reflecting rescheduling and cancellations of deliveries by OE customers in the first six months and the impact of the OEM Payments discussed above. |
| | |
| • | Business and general aviation aftermarket sales increased by 8 percent in 2010 primarily due to increased sales of spare parts due to higher engine utilization, partially offset by lower revenue associated with licensing and maintenance service agreements. |
| | |
| • | Defense and space sales increased by 1 percent in 2010 primarily due to higher sales of logistics services partially offset by program wind-downs and completions and lower sales related to commercial helicopters. |
Aerospace segment profit decreased by 3 percent in 2010 compared to 2009 primarily due to a negative 3 percent impact from the OEM payments, discussed above. Operational segment profit was flat in 2010 with the approximate positive 4 percent impact from price and productivity, net of inflation (including the absence of prior period labor cost actions offset by the benefits from prior repositioning actions) offset by an approximate negative 4 percent impact from lower sales volume. Cost of goods sold totaled $8.1 billion in 2010, unchanged from 2009.
34
2012 Areas of Focus
Aerospace’s primary areas of focus for 2012 include:
| | |
| • | Driving customer satisfaction through operational excellence (product quality, cycle time reduction, and supplier management); |
| | |
| • | Aligning research and development and customer support costs with customer requirements and demand for new platforms; |
| | |
| • | Expanding sales and operations in international locations; |
| | |
| • | Global pursuit of new defense and space programs; |
| | |
| • | Focusing on cost structure initiatives to maintain profitability in face of potential defense and space budget reductions and program specific appropriations; |
| | |
| • | Continuing to design equipment that enhances the safety, performance and durability of aerospace and defense equipment, while reducing weight and operating costs; and |
| | |
| • | Continued deployment and optimization of our common enterprise resource planning (ERP) system. |
Automation and Control Solutions (ACS)
Overview
ACS provides innovative products and solutions that make homes, buildings, industrial sites and infrastructure more efficient, safe and comfortable. Our ACS products and services include controls for heating, cooling, indoor air quality, ventilation, humidification, lighting and home automation; advanced software applications for home/building control and optimization; sensors, switches, control systems and instruments for measuring pressure, air flow, temperature and electrical current; security, fire and gas detection; personal protection equipment; access control; video surveillance; remote patient monitoring systems; products for automatic identification and data collection, installation, maintenance and upgrades of systems that keep buildings safe, comfortable and productive; and automation and control solutions for industrial plants, including advanced software and automation systems that integrate, control and monitor complex processes in many types of industrial settings as well as equipment that controls, measures and analyzes natural gas production and transportation.
In 2011, we changed our presentation of ACS’s segment sales to better represent the key markets served (Energy, Safety & Security; Process Solutions; Building Solutions & Distribution). Prior period disclosure below has been conformed to this presentation format.
Economic and Other Factors
ACS’s operating results are principally driven by:
| | |
| • | Global commercial construction (including retrofits and upgrades); |
| | |
| • | Demand for residential security and environmental control retrofits and upgrades; |
| | |
| • | Demand for energy efficient products and solutions; |
| | |
| • | Industrial production; |
| | |
| • | Government and public sector spending; |
| | |
| • | Economic conditions and growth rates in developed (U.S. and Europe) and emerging markets; |
| | |
| • | The strength of global capital and operating spending on process (including petrochemical and refining) and building automation; |
| | |
| • | Inventory levels in distribution channels; and |
| | |
| • | Changes to energy, fire, security, health care, safety and environmental concerns and regulations. |
35
| | | | | | | | | | | | | | | | | | | |
Automation and Control Solutions | | | | | | | | | | | | | | | | | | | |
| | 2011 | | 2010 | | Change | | 2009 | | Change | |
| | | | | | | | | | | |
Net sales | | $ | 15,535 | | | $ | 13,749 | | | 13 | % | | $ | 12,611 | | | 9 | % | |
| | | | | | | | | | | | | | | | | | | |
Cost of products and services sold | | | 10,448 | | | | 9,312 | | | | | | | 8,561 | | | | | |
Selling, general and administrative expenses | | | 2,819 | | | | 2,480 | | | | | | | 2,256 | | | | | |
Other | | | 185 | | | | 187 | | | | | | | 206 | | | | | |
| | | | | | | | | | | | | | | | | | | |
Segment profit | | $ | 2,083 | | | $ | 1,770 | | | 18 | % | | $ | 1,588 | | | 11 | % | |
| | | | | | | | | | | | | | | | | | | |
| | | | | | | | | | | | | |
| | 2011 vs. 2010 | | 2010 vs. 2009 | |
| | | | | |
|
Factors Contributing to Year-Over-Year Change | | Sales | | Segment Profit | | Sales | | Segment Profit | |
| | | | | | | | | |
Organic growth/ Operational segment profit | | 5 | % | | 9 | % | | 6 | % | | 9 | % | |
Foreign exchange | | 2 | % | | 3 | % | | 0 | % | | 0 | % | |
Acquisitions and divestitures, net | | 6 | % | | 6 | % | | 3 | % | | 2 | % | |
| | | | | | | | | | | | | |
Total % Change | | 13 | % | | 18 | % | | 9 | % | | 11 | % | |
| | | | | | | | | | | | | |
2011 compared with 2010
Automation and Control Solutions (“ACS”) sales increased by 13 percent in 2011 compared with 2010, primarily due to a 6 percent growth from acquisitions, net of divestitures, 5 percent increase in organic revenue driven by increased sales volume and higher prices and 2 percent favorable impact of foreign exchange through the first nine months partially offset by the negative impact of foreign exchange in the fourth quarter. We expect sales growth to continue to moderate in the first quarter of 2012 due to European economic conditions and the anticipated negative impact of foreign exchange.
| | |
| • | Sales in our Energy, Safety & Security businesses increased by 17 percent (6 percent organically) in 2011 principally due to (i) the positive impact of acquisitions (most significantly Sperian and EMS), net of divestitures (ii) higher sales volume due to general industrial recovery and new product introductions and (iii) the favorable impact of foreign exchange. |
| | |
| • | Sales in our Process Solutions increased 12 percent (6 percent organically) in 2011 principally due to (i) increased volume reflecting conversion to sales from backlog (ii) the favorable impact of foreign exchange and (iii) the impact of acquisitions. Orders increased in 2011 compared to 2010 primarily driven by continued favorable macro trends in oil and gas infrastructure projects, growth in emerging regions and the positive impact of foreign exchange. |
| | |
| • | Sales in our Building Solutions & Distribution increased by 6 percent (4 percent organically) in 2011 driven principally due to (i) volume growth in our Building Solutions business reflecting conversion to sales from order backlog and increased sales volume in our Distribution business (ii) the favorable impact of foreign exchange and (iii) the impact of acquisitions, net of divestitures. |
ACS segment profit increased by 18 percent in 2011 compared with 2010 due to a 9 percent increase in operational segment profit, 6 percent increase from acquisitions, net of divestitures and 3 percent positive impact of foreign exchange. The increase in operational segment profit is comprised of an approximate 5 percent positive impact from price and productivity, net of inflation and investment for growth and a 4 percent positive impact from higher sales volumes. Cost of goods sold totaled $10.4 billion in 2011, an increase of approximately $1.1 billion which is primarily due to acquisitions, net of divestitures, higher sales volume, foreign exchange and inflation partially offset by positive impact from productivity.
2010 compared with 2009
ACS sales increased by 9 percent in 2010 compared with 2009, primarily due to a 6 percent increase in organic revenue driven by increased sales volume and 3 percent growth from acquisitions.
36
| | |
| • | Sales in our Energy, Safety & Security businesses increased by 14 percent in 2010 primarily reflecting higher sales volumes in our businesses tied to industrial production (environmental and combustion controls, sensing and control, gas detection, personal protective equipment and scanning and mobility products), new product introductions and acquisitions, primarily Sperian. |
| | |
| • | Sales in Process Solutions increased 7 percent in 2010 primarily due to the positive impact of increased volume, acquisitions (primarily the RMG Group), higher prices and industrial field solutions driven by order growth and conversion to sales from order backlog. |
| | |
| • | Sales in Building Solutions & Distribution increased by 3 percent in 2010 driven primarily by energy efficiency projects and conversion to sales from order backlog. |
ACS segment profit increased by 11 percent in 2010 compared with 2009 due to a 9 percent increase in operational segment profit and 2 percent increase from acquisitions. The increase in operational segment profit is comprised of an approximate 18 percent positive impact from higher sales volume, partially offset by an approximate 9 percent negative impact from inflation, net of price and productivity (including the absence of prior period labor cost actions, partially offset by the benefits of prior repositioning). Cost of goods sold totaled $9.3 billion in 2010, an increase of approximately $750 million which is primarily as a result of the factors discussed above.
2012 Areas of Focus
ACS’s primary areas of focus for 2012 include:
| | |
| • | Products and solutions for energy efficiency and asset management; |
| | |
| • | Extending technology leadership: lowest total installed cost and integrated product solutions; |
| | |
| • | Defending and extending our installed base through customer productivity and globalization; |
| | |
| • | Sustaining strong brand recognition through our brand and channel management; |
| | |
| • | Continued centralization and standardization of global software development capabilities; |
| | |
| • | Continuing to identify, execute and integrate acquisitions in or adjacent to the markets which we serve; |
| | |
| • | Continuing to establish and grow emerging markets presence and capability; |
| | |
| • | Continuing to invest in new product development and introductions; |
| | |
| • | Continued deployment and optimization of our common ERP system; and |
| | |
| • | Increased focus on commercial and R&D effectiveness. |
Performance Materials and Technologies (PMT)
Overview
During the fourth quarter of 2011, the Specialty Materials segment was renamed to Performance Materials and Technologies (‘PMT’). PMT better reflects the businesses’ expanded set of technology and product offerings that reach far beyond the traditional scope associated with specialty materials.
Performance Materials and Technologies develops and manufactures high-purity, high-quality and high-performance chemicals and materials for applications in the refining, petrochemical, automotive, healthcare, agricultural, packaging, refrigeration, appliance, housing, semiconductor, wax and adhesives segments. Performance Materials and Technologies also provides process technology, products and services for the petroleum refining, gas processing, petrochemical, renewable energy and other industries. Performance Materials and Technologies’ product portfolio includes fluorocarbons, hydrofluoroolefins, caprolactam, resins, ammonium sulfate for fertilizer, phenol, specialty films, waxes, additives, advanced fibers, customized research chemicals and intermediates, electronic materials and chemicals, catalysts, and adsorbents.
37
| | |
| Economic and Other Factors |
| | |
| Performance Materials and Technologies operating results are principally driven by: |
| | |
| • | Level and timing of capital spending and capacity and utilization rates in refining and petrochemical end markets; |
| | |
| • | Pricing volatility and industry supply conditions for raw materials such as cumene, fluorspar, perchloroethylene, R240, natural gas, sulfur and ethylene; |
| | |
| • | Impact of environmental and energy efficiency regulations; |
| | |
| • | Extent of change in order rates from global semiconductor customers; |
| | |
| • | Global demand for non-ozone depleting Hydro fluorocarbons (HFCs); |
| | |
| • | Condition of the U.S. residential housing and non residential industries and automotive demand; |
| | |
| • | Global demand for caprolactam and ammonium sulfate; and |
| | |
| • | Demand for new products including renewable energy and biofuels. |
| | | | | | | | | | | | | | | | |
Performance Materials and Technologies | | | | | | | | | | | | | | | | |
| | | | | | | | | | | | | | | | |
| | 2011 | | 2010 | | Change | | 2009 | | Change | |
| | | | | | | | | | | |
Net sales | | $ | 5,659 | | $ | 4,726 | | 20 | % | | $ | 4,144 | | 14 | % | |
|
Cost of products and services sold | | | 4,151 | | | 3,554 | | | | | | 3,127 | | | | |
Selling, general and administrative expenses | | | 420 | | | 345 | | | | | | 345 | | | | |
Other | | | 46 | | | 78 | | | | | | 67 | | | | |
| | | | | | | | | | | | | | | | |
Segment profit | | $ | 1,042 | | $ | 749 | | 39 | % | | $ | 605 | | 24 | % | |
| | | | | | | | | | | | | | | | |
| | | | | | | | | | | | | | | | | | | | | |
| | 2011 vs. 2010 | | 2010 vs. 2009 | |
| | | | | |
|
Factors Contributing to Year-Over-Year Change | | Sales | | Segment Profit | | Sales | | Segment Profit | |
| | | | | | | | | |
Organic growth/ Operational segment profit | | | | 16 | % | | | | 38 | % | | | | 14 | % | | | | 25 | % | |
Foreign exchange | | | | 1 | % | | | | 1 | % | | | | 0 | % | | | | (1 | )% | |
Acquisitions and divestitures, net | | | | 3 | % | | | | 0 | % | | | | 0 | % | | | | 0 | % | |
| | | | | | | | | | | | | | | | | | | | | |
Total % Change | | | | 20 | % | | | | 39 | % | | | | 14 | % | | | | 24 | % | |
| | | | | | | | | | | | | | | | | | | | | |
| | |
| | 2011 compared with 2010 |
| |
PMT sales increased by 20 percent in 2011 compared with 2010 due to a 16 percent increase in organic growth, 3 percent growth from acquisitions, and a 1 percent favorable impact of foreign exchange. |
|
| • | Advanced Materials sales increased by 18 percent (12 percent organically) in 2011 compared to 2010 primarily driven by (i) a 33 percent (18 percent organically) increase in Resins and Chemicals sales primarily due to higher prices driven by strong Asia demand, agricultural demand, formula pricing arrangements and increased sales resulting from the acquisition of a phenol plant, partially offset by decreased volumes primarily due to disruptions in phenol supply and weather related events, (ii) a 10 percent increase in our Fluorine Products business due to higher pricing reflecting robust global demand and tight industry supply conditions primarily in the first half of the year, which moderated in the second half of the year due to seasonally weaker demand and increased available capacity in the marketplace, (iii) a 12 percent increase in Specialty Products sales primarily due to higher sales volume in our armor, additives, and healthcare packaging products, and commercial excellence initiatives. We expect Advanced Materials sales growth to continue to moderate during the first half of 2012 due to slowing global demand and lower prices resulting from increased availability of refrigerants supply. |
38
| | |
• | UOP sales increased by 24 percent in 2011 compared to 2010 primarily driven by increased service, and licensing revenues and higher unit sales of refining and specialty catalysts, primarily reflecting continued strength in the refining and petrochemical industries. |
| | |
PMT segment profit increased by 39 percent in 2011 compared with 2010 due to a 38 percent increase in operational segment profit and a 1 percent favorable impact of foreign exchange. The increase in operational segment profit is primarily due to the favorable price to raw materials spread in Resins and Chemicals and Fluorine Products and higher service, product and licensing revenues in UOP, partially offset by continued investment in growth and plant optimization initiatives. Cost of goods sold totaled $4.2 billion in 2011, an increase of approximately $597 million which is primarily due to volume, material inflation, the phenol plant acquisition and continued investment in growth initiatives. |
|
| 2010 compared with 2009 |
| |
| PMT sales increased by 14 percent in 2010 compared with 2009 predominantly due to organic growth. |
| |
• | Advanced Materials sales increased by 23 percent in 2010 compared to 2009 primarily driven by (i) a 29 percent increase in Resins and Chemicals sales primarily due to higher prices driven by strong Asia demand, formula pricing arrangements and agricultural demand, (ii) a 21 percent increase in Specialty Products sales most significantly due to higher sales volume to our semiconductor, specialty additives, advanced fiber industrial applications and specialty chemicals customers, (iii) a 19 percent increase in our Fluorine Products business due to higher sales volume from increased demand for our refrigerants, insulating materials and industrial processing aids. |
| | |
• | UOP sales decreased by 1 percent in 2010 compared to 2009 primarily driven by lower new unit catalyst sales and timing of projects activity in the refining and petrochemical industries, partially offset by increased gas processing equipment sales. |
| | |
PMT segment profit increased by 24 percent in 2010 compared with 2009 due to a 25 percent increase in operational segment profit. The increase in operational segment profit is primarily due to a 24 percent positive impact from higher sales volumes. The positive impact from price and productivity was offset by the negative impact from inflation (including the absence of prior period labor cost actions). Cost of goods sold totaled $3.6 billion in 2010, an increase of approximately $400 million which is primarily as a result of the factors discussed above. |
| | |
| 2012 Areas of Focus |
| | |
| Performance Materials and Technologies primary areas of focus for 2012 include: |
| | |
| • | Continuing to develop new processes, products and technologies that address energy efficiency, the environment and security, as well as position the portfolio for higher value; |
| | |
| • | Commercializing new products and technologies in the petrochemical, gas processing and refining industries and renewable energy sector; |
| | |
| • | Investing to increase plant capacity and reliability and improving productivity and quality through operational excellence; |
| | |
| • | Driving sales and marketing excellence and expanding local presence in fast growing emerging markets; and |
| | |
| • | Managing exposure to raw material price and supply fluctuations through evaluation of alternative sources of supply and contractual arrangements. |
39
| | |
Transportation Systems |
| | |
| Overview |
| | |
Transportation Systems provides automotive products that improve the performance and efficiency of cars, trucks, and other vehicles through state-of-the-art technologies, world class brands and global solutions to customers’ needs. Transportation Systems’ products include turbochargers and thermal systems; and friction materials (Bendix(R) and Jurid(R)) and brake hard parts. Transportation Systems sells its products to original equipment (“OE”) automotive and truck manufacturers (e.g., BMW, Caterpillar, Daimler, Renault, Ford, and Volkswagen), wholesalers and distributors and through the retail aftermarket. |
| | |
| Economic and Other Factors |
| | |
| Transportation Systems operating results are principally driven by: |
| | |
| • | Financial strength and stability of automotive OE manufacturers; |
| | |
| • | Global demand, particularly in Western Europe, for automobile and truck production; |
| | |
| • | Turbo penetration rates for new engine platforms; |
| | |
| • | Global consumer preferences, particularly in Western Europe, for boosted diesel passenger cars; |
| | |
| • | Degree of volatility in raw material prices, including nickel and steel; |
| | |
| • | New automobile production rates and the impact of inventory levels of automotive OE manufacturers on demand for our products; |
| | |
| • | Regulations mandating lower emissions and improved fuel economy; |
| | |
| • | Consumers’ ability to obtain financing for new vehicle purchases; and |
| | |
| • | Impact of factors such as consumer confidence on automotive aftermarket demand. |
| | | | | | | | | | | | | | | | |
Transportation systems | | | | | | | | | | | |
| | | | | | | | | | | |
| | 2011 | | 2010 | | Change | | 2009 | | Change | |
| | | | | | | | | | | |
Net sales | | $ | 3,859 | | $ | 3,192 | | 21 | % | | $ | 2,432 | | 31 | % | |
|
Cost of products and services sold | | | 3,174 | | | 2,641 | | | | | | 2,190 | | | | |
Selling, general and administrative expenses | | | 161 | | | 149 | | | | | | 141 | | | | |
Other | | | 39 | | | 49 | | | | | | 40 | | | | |
| | | | | | | | | | | | | | | | |
|
Segment profit | | $ | 485 | | $ | 353 | | 37 | % | | $ | 61 | | 479 | % | |
| | | | | | | | | | | | | | | | |
| | | | | | | | | | | | | |
| | 2011 vs. 2010 | | 2010 vs. 2009 | |
| | | | | |
Factors Contributing to Year-Over-Year Change | | Sales | | Segment Profit | | Sales | | Segment Profit | |
| | | | | | | | | |
| | | | | | | | | | | | | |
Organic growth/ Operational segment profit | | 16 | % | | 32 | % | | 33 | % | | 490 | % | |
Foreign exchange | | 5 | % | | 5 | % | | (2 | )% | | (11 | )% | |
| | | | | | | | | | | | | |
Total % Change | | 21 | % | | 37 | % | | 31 | % | | 479 | % | |
| | | | | | | | | | | | | |
2011 compared with 2010
Transportation Systems sales increased by 21 percent in 2011 compared with the 2010 primarily due to a 16 percent increase in organic revenue driven by increased sales volume and a favorable impact of foreign exchange of 5 percent.
40
The sales increase in 2011 as compared with 2010 was primarily driven by (i) increased turbocharger sales to both light vehicle and commercial vehicle engine manufacturers primarily due to new platform launches and strong diesel penetration rates in Western Europe and (ii) the favorable impact of foreign exchange. We expect turbocharger year over year sales growth rate to moderate in the first quarter of 2012 primarily due to reduced European light vehicle production and the anticipated negative impact of foreign exchange.
Transportation Systems segment profit increased by 37 percent in 2011 compared with 2010 due to a 32 percent increase in operational segment profit and a 5 percent favorable impact of foreign exchange. The increase in operational segment profit is comprised of an approximate 25 percent positive impact from productivity, net of inflation and price, and 7 percent positive impact from higher sales volumes. Cost of goods sold totaled $3.2 billion in 2011, an increase of $533 million which is primarily a result of higher sales volume, foreign exchange and inflation, partially offset by positive impact from productivity.
2010 compared with 2009
Transportation Systems sales increased by 31 percent in 2010 compared with the 2009, primarily due to a 33 percent increase in organic revenue driven by increased sales volume, partially offset by an unfavorable impact of foreign exchange of 2 percent.
The sales increase in 2010 as compared with 2009 was primarily due to increased turbocharger sales to both light vehicle and commercial vehicle engine manufacturers partially offset by the negative impacts of foreign exchange.
Transportation Systems segment profit increased by $292 million in 2010 compared with 2009 predominantly due to the positive impact from increased sales volume. Cost of goods sold totaled $2.6 billion in 2010, an increase of approximately $450 million which is also primarily a result of increased sales volume.
| | |
| 2012 Areas of Focus |
| |
| Transportation Systems primary areas of focus in 2012 include: |
| |
| • | Sustaining superior turbocharger technology through successful platform launches; |
| | |
| • | Maintaining the high quality of current products while executing new product introductions; |
| | |
| • | Increasing global penetration and share of diesel and gasoline turbocharger OEM demand; |
| | |
| • | Addressing capacity challenges and improving cost structure through increasing plant productivity and expansion of global manufacturing footprint; |
| | |
| • | Aligning cost structure with current economic outlook, and successful execution of repositioning actions; and |
| | |
| • | Aligning development efforts and costs with new turbo platform launch schedules. |
Repositioning and Other Charges
See Note 3 to the financial statements for a discussion of repositioning and other charges incurred in 2011, 2010, and 2009. Our repositioning actions are expected to generate incremental pretax savings of approximately $150 million in 2012 compared with 2011 principally from planned workforce reductions. Cash expenditures for severance and other exit costs necessary to execute our repositioning actions were $159, $147, and $193 million in 2011, 2010, and 2009, respectively. Such expenditures for severance and other exit costs have been funded principally through operating cash flows. Cash expenditures for severance and other costs necessary to execute the remaining actions are expected to be approximately $150 million in 2012 and will be funded through operating cash flows.
The following tables provide details of the pretax impact of total net repositioning and other charges by segment.
41
| | | | | | | | | | | | | | | |
| | Years Ended December 31, |
| | |
| | 2011 | | 2010 | | 2009 |
| | | | | | |
Aerospace | | | | | | | | | |
Net repositioning charge | | $ | | 29 | | | $ | | 32 | | | $ | | 31 | |
| | | | | | | | | | | | | | | |
| | | | | | | | | | | | | | | |
| | Years Ended December 31, |
| | |
| | 2011 | | 2010 | | 2009 |
| | | | | | |
Automation and Control Solutions | | | | | | | | | |
Net repositioning charge | | $ | | 191 | | | $ | | 79 | | | $ | | 70 | |
| | | | | | | | | | | | | | | |
| | | | | | | | | | | | | | | |
| | Years Ended December 31, |
| | |
| | 2011 | | 2010 | | 2009 |
| | | | | | |
Performance Materials and Technologies | | | | | | | | | |
Net repositioning charge | | $ | | 41 | | | $ | | 18 | | | $ | | 9 | |
| | | | | | | | | | | | | | | |
| | | | | | | | | | | | | | | |
| | Years Ended December 31, |
| | |
| | 2011 | | 2010 | | 2009 |
| | | | | | |
Transportation Systems | | | | | | | | | |
Net repositioning charge | | $ | | 82 | | | $ | | 20 | | | $ | | 50 | |
Asbestos related litigation charges, net of insurance | | | | 146 | | | | | 158 | | | | | 112 | |
| | | | | | | | | | | | | | | |
|
| | $ | | 228 | | | $ | | 178 | | | $ | | 162 | |
| | | | | | | | | | | | | | | |
| | | | | | | | | | | | | | | |
| | Years Ended December 31, |
| | |
| | 2011 | | 2010 | | 2009 |
| | | | | | |
Corporate | | | | | | | | | |
Net repositioning charge | | $ | | 11 | | | $ | | — | | | $ | | — | |
Asbestos related litigation charges, net of insurance | | | | 3 | | | | | 17 | | | | | 43 | |
Probable and reasonably estimable environmental liabilities | | | | 240 | | | | | 212 | | | | | 145 | |
Other | | | | — | | | | | 62 | | | | | 7 | |
| | | | | | | | | | | | | | | |
|
| | $ | | 254 | | | $ | | 291 | | | $ | | 195 | |
| | | | | | | | | | | | | | | |
LIQUIDITY AND CAPITAL RESOURCES
The Company continues to manage its businesses to maximize operating cash flows as the primary source of liquidity. In addition to our available cash and operating cash flows, additional sources of liquidity include committed credit lines, short-term debt from the commercial paper market, long-term borrowings, and access to the public debt and equity markets, as well as the ability to sell trade accounts receivables. We continue to balance our cash and financing uses through investment in our existing core businesses, acquisition activity, share repurchases and dividends.
Cash Flow Summary
Our cash flows from operating, investing and financing activities, as reflected in the Consolidated Statement of Cash Flows for the years ended 2011, 2010 and 2009, are summarized as follows:
42
| | | | | | | | | | | | | | | |
| | 2011 | | 2010 | | 2009 |
| | | | | | |
Cash provided by (used for): | | | | | | | | | |
Operating activities | | $ | | 2,833 | | | $ | | 4,203 | | | $ | | 3,946 | |
Investing activities | | | | (611 | ) | | | | (2,269 | ) | | | | (1,133 | ) |
Financing activities | | | | (1,114 | ) | | | | (2,047 | ) | | | | (2,152 | ) |
Effect of exchange rate changes on cash | | | | (60 | ) | | | | (38 | ) | | | | 75 | |
| | | | | | | | | | | | | | | |
|
Net increase/(decrease) in cash and cash equivalents | | $ | | 1,048 | | | $ | | (151 | ) | | $ | | 736 | |
| | | | | | | | | | | | | | | |
2011 compared with 2010
Cash provided by operating activities decreased by $1,370 million during 2011 compared with 2010 primarily due to i) increased voluntary cash contributions of $1,050 million to our U.S. pension plans, ii) an unfavorable impact from decreased deferred taxes (excluding the impact of cash taxes) of approximately $710 million, and iii) higher cash tax payments of approximately $500 million, partially offset by an $863 million increase of net income before the non-cash pension mark-to-market adjustment.
Cash used for investing activities decreased by $1,658 million during 2011 compared with 2010 primarily due to an increase in proceeds from sale of businesses of $1,149 million (most significantly the divestiture of the Consumer Products Group business and the automotive on-board sensor products business within our Automation and Control Solutions segment), a decrease in cash paid for acquisitions of $330 million, and a net $315 million decrease in investments of short-term marketable securities.
Cash used for financing activities decreased by $933 million during 2011 compared to 2010 primarily due to an increase in the net proceeds from debt of $1,734 million and a decrease of $293 million in the payment of debt assumed with acquisitions, partially offset by an increase of $1,085 million of repurchases of common stock.
2010 compared with 2009
Cash provided by operating activities increased by $257 million during 2010 compared with 2009 primarily due to i) increased accrued expenses of $690 million (due to increased customer advances and incentive compensation accruals), ii) a $550 million impact from increased deferred taxes (excluding the impact of cash taxes), iii) increased net income of $474 million, iv) lower cash tax payments of approximately $300 million and v) a $219 million decrease in payments for repositioning and other charges, partially offset by a i) $1,059 unfavorable impact from working capital driven by higher receivables and increased purchases of raw materials and component inventory to support higher demand, partially offset by a corresponding increase to accounts payable, ii) increased pension and other postretirement payments of $598 million and iii) the absence of $155 million sale of long-term receivables in 2009.
Cash used for investing activities increased by $1,136 million during 2010 compared with 2009 primarily due to an increase in cash paid for acquisitions of $835 million (most significantly Sperian Protection), and a net $341 million increase in investments in short-term marketable securities
Cash used for financing activities decreased by $105 million during 2010 compared with 2009 primarily due to a decrease in the net repayment of debt (including commercial paper) of $287 million and an increase in the proceeds from the issuance of common stock, primarily related to stock option exercises of $158 million, partially offset by the repayment of $326 million of debt assumed in the acquisition of Sperian Protection.
Liquidity
Each of our businesses is focused on implementing strategies to increase operating cash flows through revenue growth, margin expansion and improved working capital turnover. Considering the current economic environment in which each of the businesses operate and their business plans and strategies, including the focus on growth, cost reduction and productivity initiatives, the Company believes that cash balances and operating cash flows are the principal source of liquidity. In addition to the available cash and operating cash flows, additional sources of liquidity include committed credit lines, short term debt from the commercial paper markets, long-term borrowings, and access to the public debt and equity markets, as well as the ability to sell trade accounts receivables. At December 31, 2011, a substantial portion of the Company’s cash and cash equivalents were held by foreign subsidiaries. If the amounts held outside of the U.S. were to be repatriated, under current
43
law, they would be subject to U.S. federal income taxes, less applicable foreign tax credits. However, our intent is to permanently reinvest these funds outside of the U.S. It is not practicable to estimate the amount of tax that might be payable if some or all of such earnings were to be repatriated, and the amount of foreign tax credits that would be available to reduce or eliminate the resulting U.S. income tax liability.
A source of liquidity is our ability to issue short-term debt in the commercial paper market. Commercial paper notes are sold at a discount and have a maturity of not more than 365 days from date of issuance. Borrowings under the commercial paper program are available for general corporate purposes as well as for financing potential acquisitions. There was $599 million of commercial paper outstanding at December 31, 2011.
Our ability to access the commercial paper market, and the related cost of these borrowings, is affected by the strength of our credit rating and market conditions. Our credit ratings are periodically reviewed by the major independent debt-rating agencies. As of December 31, 2011, Standard and Poor’s (S&P), Fitch, and Moody’s have ratings on our long-term debt of A, A and A2 respectively, and short-term debt of A-1, F1 and P1 respectively. S&P, Fitch and Moody’s have Honeywell’s rating outlook as “stable”. To date, the company has not experienced any limitations in our ability to access these sources of liquidity.
We also have a current shelf registration statement filed with the Securities and Exchange Commission under which we may issue additional debt securities, common stock and preferred stock that may be offered in one or more offerings on terms to be determined at the time of the offering. Net proceeds of any offering would be used for general corporate purposes, including repayment of existing indebtedness, capital expenditures and acquisitions.
As a source of liquidity, we sell interests in designated pools of trade accounts receivables to third parties. As of December 31, 2011 and 2010, none of the receivables in the designated pools had been sold to third parties. When we sell receivables, they are over-collateralized and we retain a subordinated interest in the pool of receivables representing that over-collateralization as well as an undivided interest in the balance of the receivables pools. The terms of the trade accounts receivable program permit the repurchase of receivables from the third parties at our discretion, providing us with an additional source of revolving credit. As a result, program receivables remain on the Company’s balance sheet with a corresponding amount recorded as either Short-term borrowings or Long-term debt.
In February 2011, the Company issued $800 million 4.25% Senior Notes due 2021 and $600 million 5.375% Senior Notes due 2041 (collectively, the “Notes”). The Notes are senior unsecured and unsubordinated obligations of Honeywell and rank equally with all of Honeywell’s existing and future senior unsecured debt and senior to all of Honeywell’s subordinated debt. The offering resulted in gross proceeds of $1,400 million, offset by $19 million in discount and closing costs related to the offering.
In the first quarter of 2011, the Company repurchased the entire outstanding principal amount of its $400 million 5.625% Notes due 2012 via a cash tender offer and a subsequent optional redemption. The costs relating to the early redemption of the Notes, including the “make-whole premium”, was $29 million.
In March 2011, the Company entered into a $2,800 million Five Year Credit Agreement (“Credit Agreement”) with a syndicate of banks. Commitments under the Credit Agreement can be increased pursuant to the terms of the Credit Agreement to an aggregate amount not to exceed $3,500 million. The Credit Agreement is maintained for general corporate purposes, including support for the issuance of commercial paper, and replaces the previous $2,800 million five year credit agreement dated May 14, 2007 (“Prior Agreement”). At December 31, 2011, there were no borrowings or letters of credit issued under the credit facility. The credit facility does not restrict Honeywell’s ability to pay dividends, nor does it contain financial covenants.
In the fourth quarter of 2011, the Company repaid $500 million of its 6.125% notes at maturity. The repayment was funded with cash provided by operating activities.
We monitor the third-party depository institutions that hold our cash and cash equivalents on a daily basis. Our emphasis is primarily on safety of principal and secondarily on maximizing yield on those funds. We diversify our cash and cash equivalents among counterparties to minimize exposure to any one of these entities.
Global economic conditions or a tightening of credit markets could adversely affect our customers’ or suppliers’ ability to obtain financing, particularly in our long-cycle businesses and airline and automotive end markets. Customer or supplier bankruptcies, delays in their ability to obtain financing, or the unavailability of financing could adversely affect our cash flow or results of operations. To date we have not experienced material impacts from customer or supplier bankruptcy or liquidity issues. We continue to monitor and take measures to limit our exposure.
44
In February 2011, the Board of Directors authorized the repurchase of up to a total of $3 billion of Honeywell common stock. During 2011, the Company repurchased $1,085 million of outstanding shares to offset the dilutive impact of employee stock based compensation plans, including future option exercises, restricted unit vesting and matching contributions under our savings plans (see Part II, Item 5 for share repurchases in the fourth quarter of 2011).
In July 2011, the Company sold its Consumer Products Group business (CPG) to Rank Group Limited. The sale was completed for approximately $955 million in cash proceeds, resulting in a pre-tax gain of approximately $301 million and approximately $178 million net of tax. The gain was recorded in net income from discontinued operations after taxes in the Company’s Consolidated Statement of Operations for the year ended December 31, 2011. The net income attributable to the non-controlling interest for the discontinued operations is insignificant. The sale of CPG, which had been part of the Transportation Systems segment, is consistent with the Company’s strategic focus on its portfolio of differentiated global technologies. See Acquisitions and Divestitures in Note 2 to the financial statements for further discussion.
In August 2011, the Company completed the acquisition of EMS, a leading provider of connectivity solutions for mobile networking, rugged mobile computers and satellite communications. The aggregate value, net of cash acquired, was approximately $513 million. See Acquisitions and Divestitures in Note 2 to the financial statements for further discussion.
In December 2011, the Company acquired King’s Safetywear Limited (KSW), a leading international provider of branded safety footwear. The aggregate value, net of cash acquired, was approximately $331 million (including the assumption of debt of $33 million). See Acquisitions and Divestitures in Note 2 to the financial statements for further discussion.
During 2011, the Company made voluntary cash contributions to its U.S. pension plans of $1,650 million to improve the funded status of our plans.
In addition to our normal operating cash requirements, our principal future cash requirements will be to fund capital expenditures, debt repayments, dividends, employee benefit obligations, environmental remediation costs, asbestos claims, severance and exit costs related to repositioning actions, share repurchases and any strategic acquisitions.
Specifically, we expect our primary cash requirements in 2012 to be as follows:
| | |
| • | Capital expenditures—we expect to spend approximately $1.1 billion for capital expenditures in 2012 primarily for growth, production and capacity expansion, cost reduction, maintenance, and replacement. |
| | |
| • | Share repurchases— Under the Company’s previously reported $3 billion share repurchase program, $1.9 billion remained available as of December 31, 2011 for additional share repurchases. Honeywell presently expects to repurchase outstanding shares from time to time during 2012 to offset the dilutive impact of employee stock based compensation plans, including future option exercises, restricted unit vesting and matching contributions under our savings plans. The amount and timing of future repurchases may vary depending on market conditions and the level of operating, financing and other investing activities. |
| | |
| • | Dividends—we expect to pay approximately $1.2 billion in dividends on our common stock in 2012, reflecting the 12 percent increase in the dividend rate effective with the fourth quarter 2011 dividend. |
| | |
| • | Asbestos claims—we expect our cash spending for asbestos claims and our cash receipts for related insurance recoveries to be approximately $240 and $75 million, respectively, in 2012. See Asbestos Matters in Note 21 to the financial statements for further discussion of possible funding obligations in 2012 related to the Narco Trust. |
| | |
| • | Pension contributions—In 2012, we plan to make cash contributions of $800 million to $1 billion ($250 million was made in January 2012) to our plans to improve the funded status of the plans. These contributions principally consist of voluntary contributions to our U.S. plans. The timing and amount of contributions may be impacted by a number of factors, including the funded status of the plans. |
| | |
| • | Repositioning actions—we expect that cash spending for severance and other exit costs necessary to execute the previously announced repositioning actions will approximate $150 million in 2012. |
45
| | |
| • | Environmental remediation costs—we expect to spend approximately $300 million in 2012 for remedial response and voluntary clean-up costs. See Environmental Matters in Note 21 to the financial statements for additional information. |
We continuously assess the relative strength of each business in our portfolio as to strategic fit, market position, profit and cash flow contribution in order to upgrade our combined portfolio and identify business units that will most benefit from increased investment. We identify acquisition candidates that will further our strategic plan and strengthen our existing core businesses. We also identify businesses that do not fit into our long-term strategic plan based on their market position, relative profitability or growth potential. These businesses are considered for potential divestiture, restructuring or other repositioning actions subject to regulatory constraints. In 2011 we realized $1,156 million in cash proceeds from sales of non-strategic businesses.
Based on past performance and current expectations, we believe that our operating cash flows will be sufficient to meet our future operating cash needs. Our available cash, committed credit lines, access to the public debt and equity markets as well as our ability to sell trade accounts receivables, provide additional sources of short-term and long-term liquidity to fund current operations, debt maturities, and future investment opportunities.
Contractual Obligations and Probable Liability Payments
Following is a summary of our significant contractual obligations and probable liability payments at December 31, 2011:
| | | | | | | | | | | | | | | | | | | | | | | | | |
| | | | Payments by Period | | |
| | | | | | |
| | Total(6) | | 2012 | | 2013- 2014 | | 2015- 2016 | | Thereafter |
| | | | | | | | | | |
Long-term debt, including capitalized | | | | | | | | | | | | | | | |
leases(1) | | $ | | 6,896 | | | $ | | 15 | | | $ | | 1,241 | | | $ | | 456 | | | $ | | 5,184 | |
Interest payments on long-term debt, including capitalized leases | | | | 2,836 | | | | | 258 | | | | | 420 | | | | | 357 | | | | | 1,801 | |
Minimum operating lease payments | | | | 1,213 | | | | | 311 | | | | | 432 | | | | | 227 | | | | | 243 | |
Purchase obligations(2) | | | | 1,566 | | | | | 1,086 | | | | | 294 | | | | | 122 | | | | | 64 | |
Estimated environmental liability | | | | | | | | | | | | | | | | | | | | | | | | | |
payments(3) | | | | 723 | | | | | 300 | | | | | 285 | | | | | 110 | | | | | 28 | |
Asbestos related liability payments(4) | | | | 1,736 | | | | | 237 | | | | | 805 | | | | | 460 | | | | | 234 | |
Asbestos insurance recoveries(5) | | | | 780 | | | | | 71 | | | | | 205 | | | | | 122 | | | | | 382 | |
| | | | | | | | | | | | | | | | | | | | | | | | | |
| | | | | | | | | | | | | | | | | | | | | | | | | |
| | $ | | 15,750 | | | $ | | 2,278 | | | $ | | 3,682 | | | $ | | 1,854 | | | $ | | 7,936 | |
| | | | | | | | | | | | | | | | | | | | | | | | | |
| |
(1) | Assumes all long-term debt is outstanding until scheduled maturity. |
| |
(2) | Purchase obligations are entered into with various vendors in the normal course of business and are consistent with our expected requirements. |
| |
(3) | The payment amounts in the table only reflect the environmental liabilities which are probable and reasonably estimable as of December 31, 2011. See Environmental Matters in Note 21 to the financial statements for additional information. |
| |
(4) | These amounts are estimates of asbestos related cash payments for NARCO and Bendix based on our asbestos related liabilities which are probable and reasonably estimable as of December 31, 2011. Except for amounts due upon the effective date of the NARCO Plan of Reorganization ($76 million), we have assumed funding for the NARCO Trust will occur in 2013 and beyond. Projecting the timing of NARCO payments is dependent on, among other things, the effective date of the Trust which could cause the timing of payments to be earlier or later than that projected. Projecting future events is subject to many uncertainties that could cause asbestos liabilities to be higher or lower than those projected and recorded. See Asbestos Matters in Note 21 to the financial statements for additional information. |
| |
(5) | These amounts represent our insurance recoveries that are deemed probable for asbestos related liabilities as of December 31, 2011. The timing of insurance recoveries are impacted by the terms of insurance settlement agreements, as well as the documentation, review and collection process required to collect on |
46
| |
| insurance claims. Where probable insurance recoveries are not subject to definitive settlement agreements with specified payment dates, but instead are covered by insurance policies, we have assumed collection will occur beyond 2016. Projecting the timing of insurance recoveries is subject to many uncertainties that could cause the amounts collected to be higher or lower than those projected and recorded or could cause the timing of collections to be earlier or later than that projected. We reevaluate our projections concerning insurance recoveries in light of any changes or developments that would impact recoveries or the timing thereof. See Asbestos Matters in Note 21 to the financial statements for additional information. |
| |
(6) | The table excludes $815 million of uncertain tax positions. See Note 6 to the financial statements. |
The table also excludes our pension and other postretirement benefits (OPEB) obligations. In 2012, we plan to make cash contributions of $800 million to $1 billion ($250 million was made in January 2012) to our plans to improve the funded status of the plans. These contributions principally consist of voluntary contributions to our U.S. plans. The timing and amount of contributions may be impacted by a number of factors, including the funded status of the plans. Beyond 2012, the actual amounts required to be contributed are dependent upon, among other things, interest rates, underlying asset returns and the impact of legislative or regulatory actions related to pension funding obligations. Payments due under our OPEB plans are not required to be funded in advance, but are paid as medical costs are incurred by covered retiree populations, and are principally dependent upon the future cost of retiree medical benefits under our plans. We expect our OPEB payments to approximate $167 million in 2012 net of the benefit of approximately $13 million from the Medicare prescription subsidy. See Note 22 to the financial statements for further discussion of our pension and OPEB plans.
Off-Balance Sheet Arrangements
Following is a summary of our off-balance sheet arrangements:
Guarantees—We have issued or are a party to the following direct and indirect guarantees at December 31, 2011:
| | | | | |
| | Maximum Potential Future Payments |
| | |
Operating lease residual values | | $ | | 43 | |
Other third parties’ financing | | | | 5 | |
Unconsolidated affiliates’ financing | | | | 12 | |
Customer financing | | | | 13 | |
| | | | | |
| | | | | |
| | $ | | 73 | |
| | | | | |
We do not expect that these guarantees will have a material adverse effect on our consolidated results of operations, financial position or liquidity.
In connection with the disposition of certain businesses and facilities we have indemnified the purchasers for the expected cost of remediation of environmental contamination, if any, existing on the date of disposition. Such expected costs are accrued when environmental assessments are made or remedial efforts are probable and the costs can be reasonably estimated.
Environmental Matters
We are subject to various federal, state, local and foreign government requirements relating to the protection of the environment. We believe that, as a general matter, our policies, practices and procedures are properly designed to prevent unreasonable risk of environmental damage and personal injury and that our handling, manufacture, use and disposal of hazardous substances are in accordance with environmental and safety laws and regulations. However, mainly because of past operations and operations of predecessor companies, we, like other companies engaged in similar businesses, have incurred remedial response and voluntary cleanup costs for site contamination and are a party to lawsuits and claims associated with environmental and safety matters, including past production of products containing hazardous substances. Additional lawsuits, claims and costs involving environmental matters are likely to continue to arise in the future.
47
With respect to environmental matters involving site contamination, we continually conduct studies, individually or jointly, with other potentially responsible parties, to determine the feasibility of various remedial techniques to address environmental matters. It is our policy (see Note 1 to the financial statements) to record appropriate liabilities for environmental matters when remedial efforts or damage claim payments are probable and the costs can be reasonably estimated. Such liabilities are based on our best estimate of the undiscounted future costs required to complete the remedial work. The recorded liabilities are adjusted periodically as remediation efforts progress or as additional technical or legal information becomes available. Given the uncertainties regarding the status of laws, regulations, enforcement policies, the impact of other potentially responsible parties, technology and information related to individual sites, we do not believe it is possible to develop an estimate of the range of reasonably possible environmental loss in excess of our recorded liabilities. We expect to fund expenditures for these matters from operating cash flow. The timing of cash expenditures depends on a number of factors, including the timing of litigation and settlements of remediation liability, personal injury and property damage claims, regulatory approval of cleanup projects, execution timeframe of projects, remedial techniques to be utilized and agreements with other parties.
Remedial response and voluntary cleanup costs charged against pretax earnings were $240, $225 and $151 million in 2011, 2010 and 2009, respectively. At December 31, 2011 and 2010, the recorded liabilities for environmental matters was $723 and $753 million, respectively. In addition, in 2011 and 2010 we incurred operating costs for ongoing businesses of approximately $102 and $86 million, respectively, relating to compliance with environmental regulations.
Remedial response and voluntary cleanup payments were $270, $266 and $318 million in 2011, 2010 and 2009, respectively, and are currently estimated to be approximately $300 million in 2012. We expect to fund such expenditures from operating cash flow.
Although we do not currently possess sufficient information to reasonably estimate the amounts of liabilities to be recorded upon future completion of studies, litigation or settlements, and neither the timing nor the amount of the ultimate costs associated with environmental matters can be determined, they could be material to our consolidated results of operations or operating cash flows in the periods recognized or paid. However, considering our past experience and existing reserves, we do not expect that environmental matters will have a material adverse effect on our consolidated financial position.
See Note 21 to the financial statements for a discussion of our commitments and contingencies, including those related to environmental matters and toxic tort litigation.
Financial Instruments
As a result of our global operating and financing activities, we are exposed to market risks from changes in interest and foreign currency exchange rates and commodity prices, which may adversely affect our operating results and financial position. We minimize our risks from interest and foreign currency exchange rate and commodity price fluctuations through our normal operating and financing activities and, when deemed appropriate, through the use of derivative financial instruments. We do not use derivative financial instruments for trading or other speculative purposes and do not use leveraged derivative financial instruments. A summary of our accounting policies for derivative financial instruments is included in Note 1 to the financial statements. We also hold investments in marketable equity securities, which exposes us to market volatility, as discussed in Note 16 to the financial statements.
We conduct our business on a multinational basis in a wide variety of foreign currencies. Our exposure to market risk from changes in foreign currency exchange rates arises from international financing activities between subsidiaries, foreign currency denominated monetary assets and liabilities and anticipated transactions arising from international trade. Our objective is to preserve the economic value of non-functional currency cash flows. We attempt to hedge transaction exposures with natural offsets to the fullest extent possible and, once these opportunities have been exhausted, through foreign currency forward and option agreements with third parties. Our principal currency exposures relate to the U.S. dollar, Euro, British pound, Canadian dollar, Hong Kong dollar, Mexican peso, Swiss franc, Czech koruna, Chinese renminbi, Indian rupee, Singapore dollar, Swedish krona, Korean won and Thai baht.
Our exposure to market risk from changes in interest rates relates primarily to our net debt and pension obligations. As described in Notes 14 and 16 to the financial statements, we issue both fixed and variable rate debt and use interest rate swaps to manage our exposure to interest rate movements and reduce overall borrowing costs.
48
Financial instruments, including derivatives, expose us to counterparty credit risk for nonperformance and to market risk related to changes in interest or currency exchange rates. We manage our exposure to counterparty credit risk through specific minimum credit standards, diversification of counterparties, and procedures to monitor concentrations of credit risk. Our counterparties are substantial investment and commercial banks with significant experience using such derivative instruments. We monitor the impact of market risk on the fair value and expected future cash flows of our derivative and other financial instruments considering reasonably possible changes in interest and currency exchange rates and restrict the use of derivative financial instruments to hedging activities.
The following table illustrates the potential change in fair value for interest rate sensitive instruments based on a hypothetical immediate one-percentage-point increase in interest rates across all maturities, the potential change in fair value for foreign exchange rate sensitive instruments based on a 10 percent weakening of the U.S. dollar versus local currency exchange rates across all maturities, and the potential change in fair value of contracts hedging commodity purchases based on a 20 percent decrease in the price of the underlying commodity across all maturities at December 31, 2011 and 2010.
| | | | | | | | | | | | | | | | | |
| | Face or Notional Amount | | Carrying Value(1) | | Fair Value(1) | | Estimated Increase (Decrease) in Fair Value | | |
| | | | | | | | | | | | | |
December 31, 2011 | | | | | | | | | | | | | | | | | |
Interest Rate Sensitive Instruments | | | | | | | | | | | | | | | | | |
Long-term debt (including current maturities) | | $ | 6,896 | | | $ | (6,896 | ) | | $ | (7,896 | ) | | $ | (578 | ) | |
Interest rate swap agreements | | | 1,400 | | | | 134 | | | | 134 | | | | (74 | ) | |
Foreign Exchange Rate Sensitive Instruments | | | | | | | | | | | | | | | | | |
Foreign currency exchange contracts(2) | | | 7,108 | | | | (26 | ) | | | (26 | ) | | | 274 | | |
Commodity Price Sensitive Instruments | | | | | | | | | | | | | | | | | |
Forward commodity contracts(3) | | | 59 | | | | (9 | ) | | | (9 | ) | | | (10 | ) | |
| | | | | | | | | | | | | | | | | |
December 31, 2010 | | | | | | | | | | | | | | | | | |
Interest Rate Sensitive Instruments | | | | | | | | | | | | | | | | | |
Long-term debt (including current maturities) | | $ | 6,278 | | | $ | (6,278 | ) | | $ | (6,835 | ) | | $ | (399 | ) | |
Interest rate swap agreements | | | 600 | | | | 22 | | | | 22 | | | | (18 | ) | |
Foreign Exchange Rate Sensitive Instruments | | | | | | | | | | | | | | | | | |
Foreign currency exchange contracts(2) | | | 5,733 | | | | 2 | | | | 2 | | | | 102 | | |
Commodity Price Sensitive Instruments | | | | | | | | | | | | | | | | | |
Forward commodity contracts(3) | | | 23 | | | | — | | | | — | | | | (4 | ) | |
| |
(1) | Asset or (liability). |
| |
(2) | Changes in the fair value of foreign currency exchange contracts are offset by changes in the fair value or cash flows of underlying hedged foreign currency transactions. |
| |
(3) | Changes in the fair value of forward commodity contracts are offset by changes in the cash flows of underlying hedged commodity transactions. |
The above discussion of our procedures to monitor market risk and the estimated changes in fair value resulting from our sensitivity analyses are forward-looking statements of market risk assuming certain adverse market conditions occur. Actual results in the future may differ materially from these estimated results due to actual developments in the global financial markets. The methods used by us to assess and mitigate risk discussed above should not be considered projections of future events.
49
CRITICAL ACCOUNTING POLICIES
The preparation of our consolidated financial statements in accordance with generally accepted accounting principles is based on the selection and application of accounting policies that require us to make significant estimates and assumptions about the effects of matters that are inherently uncertain. We consider the accounting policies discussed below to be critical to the understanding of our financial statements. Actual results could differ from our estimates and assumptions, and any such differences could be material to our consolidated financial statements.
We have discussed the selection, application and disclosure of these critical accounting policies with the Audit Committee of our Board of Directors and our Independent Registered Public Accountants. New accounting standards effective in 2011 which had a material impact on our consolidated financial statements are described in the Recent Accounting Pronouncements section in Note 1 to the financial statements.
Contingent Liabilities—We are subject to a number of lawsuits, investigations and claims (some of which involve substantial dollar amounts) that arise out of the conduct of our global business operations or those of previously owned entities, including matters relating to commercial transactions, government contracts, product liability (including asbestos), prior acquisitions and divestitures, employee benefit plans, intellectual property, and environmental, health and safety matters. We recognize a liability for any contingency that is probable of occurrence and reasonably estimable. We continually assess the likelihood of any adverse judgments or outcomes to our contingencies, as well as potential amounts or ranges of probable losses, and recognize a liability, if any, for these contingencies based on a careful analysis of each matter with the assistance of outside legal counsel and, if applicable, other experts. Such analysis includes making judgments concerning matters such as the costs associated with environmental matters, the outcome of negotiations, the number and cost of pending and future asbestos claims, and the impact of evidentiary requirements. Because most contingencies are resolved over long periods of time, liabilities may change in the future due to new developments (including new discovery of facts, changes in legislation and outcomes of similar cases through the judicial system), changes in assumptions or changes in our settlement strategy. For a discussion of our contingencies related to environmental, asbestos and other matters, including management’s judgment applied in the recognition and measurement of specific liabilities, see Notes 1 and 21 to the financial statements.
Asbestos Related Contingencies and Insurance Recoveries—We are a defendant in personal injury actions related to products containing asbestos (refractory and friction products). We recognize a liability for any asbestos related contingency that is probable of occurrence and reasonably estimable. Regarding North American Refractories Company (NARCO) asbestos related claims, we accrued for pending claims based on terms and conditions in agreements with NARCO, its former parent company, and certain asbestos claimants, and an estimate of the unsettled claims pending as of the time NARCO filed for bankruptcy protection. We also accrued for the estimated value of future NARCO asbestos related claims expected to be asserted against the NARCO trust through 2018 as described in Note 21 to the financial statements. In light of the inherent uncertainties in making long term projections and in connection with the initial operation of a 524(g) trust, as well as the stay of all NARCO asbestos claims since January 2002, we do not believe that we have a reasonable basis for estimating NARCO asbestos claims beyond 2018. Regarding Bendix asbestos related claims, we accrued for the estimated value of pending claims using average resolution values for the previous five years. We also accrued for the estimated value of future anticipated claims related to Bendix for the next five years based on historic claims filing experience and dismissal rates, disease classifications, and average resolution values in the tort system for the previous five years. In light of the uncertainties inherent in making long-term projections, as well as certain factors unique to friction product asbestos claims, we do not believe that we have a reasonable basis for estimating asbestos claims beyond the next five years. We will continue to update the resolution values used to estimate the cost of pending and future Bendix claims during the fourth quarter each year. For additional information see Note 21 to the financial statements. We continually assess the likelihood of any adverse judgments or outcomes to our contingencies, as well as potential ranges of probable losses and recognize a liability, if any, for these contingencies based on an analysis of each individual issue with the assistance of outside legal counsel and, if applicable, other experts.
In connection with the recognition of liabilities for asbestos related matters, we record asbestos related insurance recoveries that are deemed probable. In assessing the probability of insurance recovery, we make judgments concerning insurance coverage that we believe are reasonable and consistent with our historical experience with our insurers, our knowledge of any pertinent solvency issues surrounding insurers, various judicial determinations relevant to our insurance programs and our consideration of the impacts of any settlements with our insurers. Our insurance is with both the domestic insurance market and the London excess market. While the substantial majority of our insurance carriers are solvent, some of our individual carriers are insolvent, which has been considered in our analysis of probable recoveries. Projecting future events is subject to
50
various uncertainties that could cause the insurance recovery on asbestos related liabilities to be higher or lower than that projected and recorded. Given the inherent uncertainty in making future projections, we reevaluate our projections concerning our probable insurance recoveries in light of any changes to the projected liability, our recovery experience or other relevant factors that may impact future insurance recoveries. See Note 21 to the financial statements for a discussion of management’s judgments applied in the recognition and measurement of insurance recoveries for asbestos related liabilities.
Defined Benefit Pension Plans—We sponsor both funded and unfunded U.S. and non-U.S. defined benefit pension plans covering the majority of our employees and retirees.
We recognize changes in the fair value of plan assets and net actuarial gains or losses in excess of 10 percent of the greater of the market-related value of plan assets or the plans’ projected benefit obligation (the corridor) annually in the fourth quarter each year (MTM Adjustment). Netactuarial gains and losses occur when the actual experience differs from any of the various assumptions used to value our pension plans or when assumptions change as they may each year. The primary factors contributing to actuarial gains and losses are changes in the discount rate used to value pension obligations as of the measurement date each year and the differences between expected and actual returns on plan assets.This accounting method also results in the potential for volatile and difficult to forecast MTM adjustments. MTM adjustments were $1,802, $471 and $741 million in 2011, 2010 and 2009, respectively. The remaining components of pension expense, primarily service and interest costs and assumed return on plan assets, are recorded on a quarterly basis (On-going Pension Expense).
For financial reporting purposes, net periodic pension expense is calculated based upon a number of actuarial assumptions, including a discount rate for plan obligations and an expected long-term rate of return on plan assets. We determine the expected long-term rate of return on plan assets utilizing historical plan asset returns over varying long-term periods combined with our expectations on future market conditions and asset mix considerations (see Note 22 to the financial statements for details on the actual various asset classes and targeted asset allocation percentages for our pension plans). The discount rate reflects the market rate on December 31 (measurement date) for high-quality fixed-income investments with maturities corresponding to our benefit obligations and is subject to change each year. Further information on all our major actuarial assumptions is included in Note 22 to the financial statements.
The key assumptions used in developing our 2011, 2010 and 2009 net periodic pension expense for our U.S. plans included the following:
| | | | | | | | | | | | | |
| | 2011 | | 2010 | | 2009 | |
| | | | | | | | | | |
Discount rate | | | 5.25 | % | | | 5.75 | % | | | 6.95 | % | |
Assets: | | | | | | | | | | | | | |
Expected rate of return | | | 8 | % | | | 9 | % | | | 9 | % | |
Actual rate of return | | | 0 | % | | | 19 | % | | | 20 | % | |
Actual 10 year average annual compounded rate of return | | | 6 | % | | | 6 | % | | | 4 | % | |
The discount rate can be volatile from year to year because it is determined based upon prevailing interest rates as of the measurement date. We will use a 4.89 percent discount rate in 2012, reflecting the decrease in the market interest rate environment since December 31, 2010. We plan to continue to use an expected rate of return on plan assets of 8 percent for 2012 as this is a long-term rate based on historical plan asset returns over varying long-term periods combined with our expectations on future market conditions and the asset mix of the plan’s investments.
In addition to the potential for MTM adjustments, changes in our expected rate of return on plan assets and discount rate resulting from economic events also affects future on-going pension expense. The following table highlights the sensitivity of our U.S. pension obligations and on-going expense to changes in these assumptions, assuming all other assumptions remain constant. These estimates exclude any potential MTM adjustment:
51
| | | | | | | |
Change in Assumption | | Impact on 2012 On-Going Pension Expense | | Impact on PBO | |
| | | | | |
0.25 percentage point decrease in discount rate | | Decrease $10 million | | | Increase $410 million | | |
0.25 percentage point increase in discount rate | | Increase $8 million | | | Decrease $400 million | | |
0.25 percentage point decrease in expected rate of return on assets | | Increase $32 million | | | — | | |
0.25 percentage point increase in expected rate of return on assets | | Decrease $32 million | | | — | | |
On-going pension expense for all of our pension plans is expected to be approximately $60 million in 2012, a decrease of $45 million from 2011, due primarily to the impact of planned cash contributions in 2012. Also, if required, an MTM adjustment will be recorded in the fourth quarter of 2012 in accordance with our pension accounting method as previously described. It is difficult to reliably forecast or predict whether there will be a MTM adjustment in 2012, and if one is required what the magnitude of such adjustment will be. MTM adjustments are primarily driven by events and circumstances beyond the control of the Company such as changes in interest rates and the performance of the financial markets.
In 2011, 2010 and 2009, we were not required to make contributions to satisfy minimum statutory funding requirements in our U.S. pension plans. However, we made voluntary contributions of $1,650, $1,000 and $740 million to our U.S. pension plans in2011, 2010 and 2009, respectively, primarily to improve the funded status of our plans which has been adversely impacted by relatively low discount rates and asset losses in 2011 and 2008 resulting from the poor performance of the equity markets. In 2012, we plan to make cash contributions of $800 million to $1 billion($250 million was made in January 2012)to our plans to improve the funded status of the plans. These contributions principally consist of voluntary contributions to our U.S. plans.The timing and amount of contributions may be impacted by a number of factors, including the funded status of the plans.
Long-Lived Assets (including Tangible and Definite-Lived Intangible Assets)—To conduct our global business operations and execute our business strategy, we acquire tangible and intangible assets, including property, plant and equipment and definite-lived intangible assets. At December 31, 2011, the net carrying amount of these long-lived assets totaled approximately $6.5 billion. The determination of useful lives (for depreciation/amortization purposes) and whether or not these assets are impaired involves the use of accounting estimates and assumptions, changes in which could materially impact our financial condition or operating performance if actual results differ from such estimates and assumptions. We periodically evaluate the recoverability of the carrying amount of our long-lived assets whenever events or changes in circumstances indicate that the carrying amount of a long-lived asset group may not be fully recoverable. The principal factors we consider in deciding when to perform an impairment review are as follows:
| | |
| • | significant under-performance (i.e., declines in sales, earnings or cash flows) of a business or product line in relation to expectations; |
| | |
| • | annual operating plans or five-year strategic plans that indicate an unfavorable trend in operating performance of a business or product line; |
| | |
| • | significant negative industry or economic trends; and |
| | |
| • | significant changes or planned changes in our use of the assets. |
Once it is determined that an impairment review is necessary, recoverability of assets is measured by comparing the carrying amount of the asset grouping to the estimated future undiscounted cash flows. If the carrying amount exceeds the estimated future undiscounted cash flows, the asset grouping is considered to be impaired. The impairment is then measured as the difference between the carrying amount of the asset grouping and its fair value. We endeavor to utilize the best information available to measure fair value, which is usually either market prices (if available), level 1 or level 2 in the fair value hierarchy or an estimate of the future discounted cash flow, level 3 of the fair value hierarchy. The key estimates in our discounted cash flow analysis include expected industry growth rates, our assumptions as to volume, selling prices and costs, and the discount rate selected. As described in more detail in Note 16 to the financial statements, we have recorded impairment charges related to long-lived assets of $127 million and $30 million in 2011 and 2010, respectively, principally related to manufacturing plant and equipment in facilities scheduled to close or be downsized.
52
Goodwill Impairment Testing—Goodwill represents the excess of acquisition costs over the fair value of the net tangible assets and identifiable intangible assets acquired in a business combination. Goodwill is not amortized, but is subject to impairment testing. Our Goodwill balance, $11.9 billion as of December 31, 2011, is subject to impairment testing annually as of March 31, or whenever events or changes in circumstances indicate that the carrying amount may not be fully recoverable. This testing compares carrying values to fair values and, when appropriate, the carrying value is reduced to fair value. The fair value of our reporting units is estimated utilizing a discounted cash flow approach utilizing cash flow forecasts in our five year strategic and annual operating plans adjusted for terminal value assumptions. This impairment test involves the use of accounting estimates and assumptions, changes in which could materially impact our financial condition or operating performance if actual results differ from such estimates and assumptions. To address this uncertainty we perform sensitivity analysis on key estimates and assumptions.
We completed our annual impairment test as of March 31, 2011 and determined that there was no impairment as of that date. However, significant negative industry or economic trends, disruptions to our business, unexpected significant changes or planned changes in use of the assets, divestitures and market capitalization declines may have a negative effect on the fair value of our reporting units.
Income Taxes—Deferred tax assets and liabilities are determined based on the difference between the financial statements and tax basis of assets and liabilities using enacted tax rates in effect for the year in which the differences are expected to reverse. Our provision for income taxes is based on domestic and international statutory income tax rates in the jurisdictions in which we operate. Significant judgment is required in determining income tax provisions as well as deferred tax asset and liability balances, including the estimation of valuation allowances and the evaluation of tax positions.
As of December 31, 2011, we recognized a net deferred tax asset of $2,421 million, less a valuation allowance of $591 million. Net deferred tax assets are primarily comprised of net deductible temporary differences, net operating loss carryforwards and tax credit carryforwards that are available to reduce taxable income in future periods. The determination of the amount of valuation allowance to be provided on recorded deferred tax assets involves estimates regarding (1) the timing and amount of the reversal of taxable temporary differences, (2) expected future taxable income, and (3) the impact of tax planning strategies. A valuation allowance is established to offset any deferred tax assets if, based upon the available evidence it is more likely than not that some or all of the deferred tax asset will not be realized. In assessing the need for a valuation allowance, we consider all available positive and negative evidence, including past operating results, projections of future taxable income and the feasibility of ongoing tax planning strategies. The projections of future taxable income include a number of estimates and assumptions regarding our volume, pricing and costs. Additionally, valuation allowances related to deferred tax assets can be impacted by changes to tax laws.
Our net deferred tax asset of $2,421 million consists of $1,516 million related to U.S. operations and $905 million related to non-U.S. operations. The U.S. net deferred tax asset of $1,516 million consists of net deductible temporary differences, tax credit carryforwards, federal and state tax net operating losses which we believe will more likely than not be realized through the generation of future taxable income in the U.S. and tax planning strategies. We maintain a valuation allowance of $5 million against such asset related to state net operating losses. The non-U.S. net deferred tax asset of $905 million consists principally of net operating and capital loss carryforwards, mainly in France, Netherlands, Luxembourg and Germany. We maintain a valuation allowance of $588 million against these deferred tax assets reflecting our historical experience and lower expectations of taxable income over the applicable carryforward periods. As more fully described in Note 6 to the financial statements, our valuation allowance decreased by $45 million in 2011 and increased by $58 million and $133 million in 2010 and 2009, respectively. In the event we determine that we will not be able to realize our net deferred tax assets in the future, we will reduce such amounts through a charge to income in the period such determination is made. Conversely, if we determine that we will be able to realize net deferred tax assets in excess of the carrying amounts, we will decrease the recorded valuation allowance through a credit to income in the period that such determination is made.
Significant judgment is required in determining income tax provisions and in evaluating tax positions. We establish additional reserves for income taxes when, despite the belief that tax positions are fully supportable, there remain certain positions that do not meet the minimum recognition threshold. The approach for evaluating certain and uncertain tax positions is defined by the authoritative guidance and this guidance determines when a tax position is more likely than not to be sustained upon examination by the applicable taxing authority. In the normal course of business, the Company and its subsidiaries are examined by various Federal, State and foreign tax authorities. We regularly assess the potential outcomes of these examinations and any future examinations for the current or prior years in determining the adequacy of our provision for income taxes. We continually
53
assess the likelihood and amount of potential adjustments and adjust the income tax provision, the current tax liability and deferred taxes in the period in which the facts that give rise to a revision become known.
Sales Recognition on Long-Term Contracts—In 2011, we recognized approximately 16 percent of our total net sales using the percentage-of-completion method for long-term contracts in our Automation and Control Solutions, Aerospace and Performance Materials and Technologies segments. These long-term contracts are measured on the cost-to-cost basis for engineering-type contracts and the units-of-delivery basis for production-type contracts. Accounting for these contracts involves management judgment in estimating total contract revenue and cost. Contract revenues are largely determined by negotiated contract prices and quantities, modified by our assumptions regarding contract options, change orders, incentive and award provisions associated with technical performance and price adjustment clauses (such as inflation or index-based clauses). Contract costs are incurred over a period of time, which can be several years, and the estimation of these costs requires management judgment. Cost estimates are largely based on negotiated or estimated purchase contract terms, historical performance trends and other economic projections. Significant factors that influence these estimates include inflationary trends, technical and schedule risk, internal and subcontractor performance trends, business volume assumptions, asset utilization, and anticipated labor agreements. Revenue and cost estimates are regularly monitored and revised based on changes in circumstances. Anticipated losses on long-term contracts are recognized when such losses become evident. We maintain financial controls over the customer qualification, contract pricing and estimation processes to reduce the risk of contract losses.
54
OTHER MATTERS
Litigation
See Note 21 to the financial statements for a discussion of environmental, asbestos and other litigation matters.
Recent Accounting Pronouncements
See Note 1 to the financial statements for a discussion of recent accounting pronouncements.
Item 7A. Quantitative and Qualitative Disclosures About Market Risk
Information relating to market risk is included in Item 7. Management Discussion and Analysis of Financial Condition and Results of Operations under the caption “Financial Instruments”.
55
ITEM 8. Financial Statements and Supplementary Data
Honeywell International Inc.
Consolidated Statement of Operations
| | | | | | | | | | | | | |
| | Years Ended December 31, | |
| | | |
|
| | 2011 | | 2010 | | 2009 | |
| | | | | | | |
| | | | | | | | | | | | | |
| | (Dollars in millions, except per share amounts) | |
| | | | | | | | | | | | | |
Product sales | | $ | 28,745 | | | $ | 25,242 | | | $ | 22,957 | | |
Service sales | | | 7,784 | | | | 7,108 | | | | 6,994 | | |
| | | | | | | | | | | | | |
Net sales | | | 36,529 | | | | 32,350 | | | | 29,951 | | |
| | | | | | | | | | | | | |
|
Costs, expenses and other | | | | | | | | | | | | | |
Cost of products sold | | | 23,220 | | | | 19,903 | | | | 18,565 | | |
Cost of services sold | | | 5,336 | | | | 4,818 | | | | 4,695 | | |
| | | | | | | | | | | | | |
| | | 28,556 | | | | 24,721 | | | | 23,260 | | |
Selling, general and administrative expenses | | | 5,399 | | | | 4,618 | | | | 4,323 | | |
Other (income) expense | | | (84 | ) | | | (97 | ) | | | (54) | | |
Interest and other financial charges | | | 376 | | | | 386 | | | | 458 | | |
| | | | | | | | | | | | | |
| | | 34,247 | | | | 29,628 | | | | 27,987 | | |
| | | | | | | | | | | | | |
Income from continuing operations before taxes | | | 2,282 | | | | 2,722 | | | | 1,964 | | |
Tax expense | | | 417 | | | | 765 | | | | 436 | | |
| | | | | | | | | | | | | |
Income from continuing operations after taxes | | | 1,865 | | | | 1,957 | | | | 1,528 | | |
Income from discontinued operations after taxes | | | 209 | | | | 78 | | | | 56 | | |
| | | | | | | | | | | | | |
Net income | | | 2,074 | | | | 2,035 | | | | 1,584 | | |
| | | | | | | | | | | | | |
Less: Net income attributable to the noncontrolling interest | | | 7 | | | | 13 | | | | 36 | | |
| | | | | | | | | | | | | |
Net income attributable to Honeywell | | $ | 2,067 | | | $ | 2,022 | | | $ | 1,548 | | |
| | | | | | | | | | | | | |
| | | | | | | | | | | | | |
Amounts attributable to Honeywell: | | | | | | | | | | | | | |
Income from continuing operations less net income attributable to the noncontrolling interest | | | 1,858 | | | | 1,944 | | | | 1,492 | | |
Income from discontinued operations | | | 209 | | | | 78 | | | | 56 | | |
| | | | | | | | | | | | | |
Net income attributable to Honeywell | | $ | 2,067 | | | $ | 2,022 | | | $ | 1,548 | | |
| | | | | | | | | | | | | |
| | | | | | | | | | | | | |
Earnings per share of common stock - basic: | | | | | | | | | | | | | |
Income from continuing operations | | | 2.38 | | | | 2.51 | | | | 1.99 | | |
Income from discontinuing operations | | | 0.27 | | | | 0.10 | | | | 0.07 | | |
| | | | | | | | | | | | | |
Net income | | $ | 2.65 | | | $ | 2.61 | | | $ | 2.06 | | |
| | | | | | | | | | | | | |
| | | | | | | | | | | | | |
Earnings per share of common stock - assuming dilution: | | | | | | | | | | | | | |
Income from continuing operations | | | 2.35 | | | | 2.49 | | | | 1.98 | | |
Income from discontinuing operations | | | 0.26 | | | | 0.10 | | | | 0.07 | | |
| | | | | | | | | | | | | |
Net income | | $ | 2.61 | | | $ | 2.59 | | | $ | 2.05 | | |
| | | | | | | | | | | | | |
| | | | | | | | | | | | | |
Cash dividends per share of common stock | | $ | 1.37 | | | $ | 1.21 | | | $ | 1.21 | | |
| | | | | | | | | | | | | |
The Notes to Financial Statements are an integral part of this statement.
56
Honeywell International Inc.
Consolidated Balance Sheet
| | | | | | | | | |
| | December 31, | | |
| | 2011 | | | 2010 | | |
| | | | | | | |
|
| | | (Dollars in millions) |
ASSETS | | | |
Current assets: | | | | | | | | | |
Cash and cash equivalents | | $ | 3,698 | | | $ | 2,650 | | |
Accounts, notes and other receivables | | | 7,228 | | | | 6,841 | | |
Inventories | | | 4,264 | | | | 3,822 | | |
Deferred income taxes | | | 460 | | | | 877 | | |
Investments and other current assets | | | 484 | | | | 455 | | |
Assets held for sale | | | — | | | | 841 | | |
| | | | | | | | | |
Total current assets | | | 16,134 | | | | 15,486 | | |
| | | | | | | | | |
Investments and long-term receivables | | | 494 | | | | 616 | | |
Property, plant and equipment - net | | | 4,804 | | | | 4,724 | | |
Goodwill | | | 11,858 | | | | 11,275 | | |
Other intangible assets - net | | | 2,477 | | | | 2,537 | | |
Insurance recoveries for asbestos related liabilities | | | 709 | | | | 825 | | |
Deferred income taxes | | | 2,132 | | | | 1,221 | | |
Other assets | | | 1,200 | | | | 1,150 | | |
| | | | | | | | | |
Total assets | | $ | 39,808 | | | $ | 37,834 | | |
| | | | | | | | | |
| | | | | | | | | |
LIABILITIES | | | | | | | | | |
Current liabilities: | | | | | | | | | |
Accounts payable | | $ | 4,738 | | | $ | 4,199 | | |
Short-term borrowings | | | 60 | | | | 67 | | |
Commercial paper | | | 599 | | | | 299 | | |
Current maturities of long-term debt | | | 15 | | | | 523 | | |
Accrued liabilities | | | 6,863 | | | | 6,446 | | |
Liabilities related to assets held for sale | | | — | | | | 190 | | |
| | | | | | | | | |
Total current liabilities | | | 12,275 | | | | 11,724 | | |
| | | | | | | | | |
Long-term debt | | | 6,881 | | | | 5,755 | | |
Deferred income taxes | | | 676 | | | | 636 | | |
Postretirement benefit obligations other than pensions | | | 1,417 | | | | 1,477 | | |
Asbestos related liabilities | | | 1,499 | | | | 1,557 | | |
Other liabilities | | | 6,158 | | | | 5,898 | | |
| | | | | | | | | |
SHAREOWNERS’ EQUITY | | | | | | | | | |
Capital - common stock issued | | | 958 | | | | 958 | | |
- additional paid-in capital | | | 4,157 | | | | 3,977 | | |
Common stock held in treasury, at cost | | | (8,948 | ) | | | (8,299 | ) | |
Accumulated other comprehensive income (loss) | | | (1,444 | ) | | | (1,067 | ) | |
Retained earnings | | | 16,083 | | | | 15,097 | | |
| | | | | | | | | |
Total Honeywell shareowners’ equity | | | 10,806 | | | | 10,666 | | |
Noncontrolling interest | | | 96 | | | | 121 | | |
| | | | | | | | | |
Total shareowners’ equity | | | 10,902 | | | | 10,787 | | |
| | | | | | | | | |
Total liabilities and shareowners’ equity | | $ | 39,808 | | | $ | 37,834 | | |
| | | | | | | | | |
The Notes to Financial Statements are an integral part of this statement.
57
Honeywell International Inc.
Consolidated Statement of Cash Flows
| | | | | | | | | | | | | |
| | Years Ended December 31, | |
| | | |
| | 2011 | | 2010 | | 2009 | |
| | | | | | | |
| | (Dollars in millions) | |
Cash flows from operating activities: | | | | | | | | | | | | | |
Net income attributable to Honeywell | | $ | 2,067 | | | $ | 2,022 | | | $ | 1,548 | | |
Adjustments to reconcile net income attributable to Honeywell to net cash provided by operating activities: | | | | | | | | | | | | | |
Depreciation and amortization | | | 957 | | | | 987 | | | | 957 | | |
Gain on sale of non-strategic businesses and assets | | | (362 | ) | | | — | | | | (87 | ) | |
Repositioning and other charges | | | 743 | | | | 600 | | | | 478 | | |
Net payments for repositioning and other charges | | | (468 | ) | | | (439 | ) | | | (658 | ) | |
Pension and other postretirement expense | | | 1,823 | | | | 689 | | | | 1,022 | | |
Pension and other postretirement benefit payments | | | (1,788 | ) | | | (787 | ) | | | (189 | ) | |
Stock compensation expense | | | 168 | | | | 164 | | | | 118 | | |
Deferred income taxes | | | (331 | ) | | | 878 | | | | 47 | | |
Excess tax benefits from share based payment arrangements | | | (42 | ) | | | (13 | ) | | | (1 | ) | |
Other | | | 194 | | | | (24 | ) | | | 261 | | |
Changes in assets and liabilities, net of the effects of acquisitions and divestitures: | | | | | | | | | | | | | |
Accounts, notes and other receivables | | | (316 | ) | | | (688 | ) | | | 360 | | |
Inventories | | | (310 | ) | | | (300 | ) | | | 475 | | |
Other current assets | | | 25 | | | | (26 | ) | | | (43 | ) | |
Accounts payable | | | 527 | | | | 592 | | | | (169 | ) | |
Accrued liabilities | | | (54 | ) | | | 548 | | | | (173 | ) | |
| | | | | | | | | | | | | |
Net cash provided by operating activities | | | 2,833 | | | | 4,203 | | | | 3,946 | | |
| | | | | | | | | | | | | |
Cash flows from investing activities: | | | | | | | | | | | | | |
Expenditures for property, plant and equipment | | | (798 | ) | | | (651 | ) | | | (609 | ) | |
Proceeds from disposals of property, plant and equipment | | | 6 | | | | 14 | | | | 31 | | |
Increase in investments | | | (380 | ) | | | (453 | ) | | | (24 | ) | |
Decrease in investments | | | 354 | | | | 112 | | | | 1 | | |
Cash paid for acquisitions, net of cash acquired | | | (973 | ) | | | (1,303 | ) | | | (468 | ) | |
Proceeds from sales of businesses,net of fees paid | | | 1,156 | | | | 7 | | | | 1 | | |
Other | | | 24 | | | | 5 | | | | (65 | ) | |
| | | | | | | | | | | | | |
Net cash used for investing activities | | | (611 | ) | | | (2,269 | ) | | | (1,133 | ) | |
| | | | | | | | | | | | | |
| | | | | | | | | | | | | |
Cash flows from financing activities: | | | | | | | | | | | | | |
Net increase/(decrease) in commercial paper | | | 300 | | | | 1 | | | | (1,133 | ) | |
Net (decrease)/increase in short-term borrowings | | | (2 | ) | | | 20 | | | | (521 | ) | |
Payment of debt assumed with acquisitions | | | (33 | ) | | | (326 | ) | | | — | | |
Proceeds from issuance of common stock | | | 304 | | | | 195 | | | | 37 | | |
Proceeds from issuance of long-term debt | | | 1,390 | | | | — | | | | 1,488 | | |
Payments of long-term debt | | | (939 | ) | | | (1,006 | ) | | | (1,106 | ) | |
Excess tax benefits from share based payment arrangements | | | 42 | | | | 13 | | | | 1 | | |
Repurchases of common stock | | | (1,085 | ) | | | — | | | | — | | |
Cash dividends paid | | | (1,091 | ) | | | (944 | ) | | | (918 | ) | |
| | | | | | | | | | | | | |
Net cash used for financing activities | | | (1,114 | ) | | | (2,047 | ) | | | (2,152 | ) | |
| | | | | | | | | | | | | |
| | | | | | | | | | | | | |
Effect of foreign exchange rate changes on cash and cash equivalents | | | (60 | ) | | | (38 | ) | | | 75 | | |
| | | | | | | | | | | | | |
Net increase/(decrease) in cash and cash equivalents | | | 1,048 | | | | (151 | ) | | | 736 | | |
Cash and cash equivalents at beginning of period | | | 2,650 | | | | 2,801 | | | | 2,065 | | |
| | | | | | | | | | | | | |
Cash and cash equivalents at end of period | | $ | 3,698 | | | $ | 2,650 | | | $ | 2,801 | | |
| | | | | | | | | | | | | |
The Notes to Financial Statements are an integral part of this statement.
58
Honeywell International Inc.
Consolidated Statement of Shareowners’ Equity
| | | | | | | | | | | | | | | | | | | |
| | Years Ended December 31, | |
| | 2011 | | 2010 | | 2009 | |
| | | | | | | |
| | Shares | | $ | | Shares | | $ | | Shares | | $ | |
| | | | | | | |
| | (in millions) | |
Common stock, par value | | 957.6 | | | 958 | | | 957.6 | | | 958 | | | 957.6 | | | 958 | | |
| | | | | | | | | | | | | | | | | | | |
Additional paid-in capital | | | | | | | | | | | | | | | | | | | |
Beginning balance | | | | | 3,977 | | | | | | 3,823 | | | | | | 3,994 | | |
Issued for employee savings and option plans | | | | | 14 | | | | | | (35 | ) | | | | | (99 | ) | |
Contributed to pension plans | | | | | — | | | | | | 32 | | | | | | (190 | ) | |
Stock-based compensation expense | | | | | 168 | | | | | | 157 | | | | | | 118 | | |
Other owner changes | | | | | (2 | ) | | | | | — | | | | | | — | | |
| | | | | | | | | | | | | | | | | | | |
Ending balance | | | | | 4,157 | | | | | | 3,977 | | | | | | 3,823 | | |
| | | | | | | | | | | | | | | | | | | |
Treasury stock | | | | | | | | | | | | | | | | | | | |
Beginning balance | | (174.6 | ) | | (8,299 | ) | | (193.4 | ) | | (8,995 | ) | | (223.0 | ) | | (10,206 | ) | |
Reacquired stock or repurchases of common stock | | (20.3 | ) | | (1,085 | ) | | — | | | — | | | — | | | — | | |
Issued for employee savings and option plans | | 12.0 | | | 436 | | | 8.9 | | | 328 | | | 6.6 | | | 281 | | |
Contributed to pension plans | | — | | | — | | | 9.9 | | | 368 | | | 23.0 | | | 930 | | |
| | | | | | | | | | | | | | | | | | | |
Ending balance | | (182.9 | ) | | (8,948 | ) | | (174.6 | ) | | (8,299 | ) | | (193.4 | ) | | (8,995 | ) | |
| | | | | | | | | | | | | | | | | | | |
Retained earnings | | | | | | | | | | | | | | | | | | | |
Beginning balance | | | | | 15,097 | | | | | | 14,023 | | | | | | 13,391 | | |
Net income attributable to Honeywell | | | | | 2,067 | | | | | | 2,022 | | | | | | 1,548 | | |
Dividends paid on common stock | | | | | (1,081 | ) | | | | | (948 | ) | | | | | (916 | ) | |
| | | | | | | | | | | | | | | | | | | |
Ending balance | | | | | 16,083 | | | | | | 15,097 | | | | | | 14,023 | | |
| | | | | | | | | | | | | | | | | | | |
Accumulated other comprehensive income (loss) | | | | | | | | | | | | | | | | | | | |
Beginning balance | | | | | (1,067 | ) | | | | | (948 | ) | | | | | (1,078 | ) | |
Foreign exchange translation adjustment | | | | | (146 | ) | | | | | (249 | ) | | | | | 259 | | |
Pensions and other post retirement benefit adjustments | | | | | (209 | ) | | | | | 44 | | | | | | (271 | ) | |
Changes in fair value of available for sale investments | | | | | 12 | | | | | | 90 | | | | | | 112 | | |
Changes in fair value of effective cash flow hedges | | | | | (34 | ) | | | | | (4 | ) | | | | | 30 | | |
| | | | | | | | | | | | | | | | | | | |
Ending balance | | | | | (1,444 | ) | | | | | (1,067 | ) | | | | | (948 | ) | |
| | | | | | | | | | | | | | | | | | | |
Non controlling interest | | | | | | | | | | | | | | | | | | | |
Beginning balance | | | | | 121 | | | | | | 110 | | | | | | 82 | | |
Acquisitions | | | | | — | | | | | | 2 | | | | | | 5 | | |
Interest sold (bought) | | | | | (5 | ) | | | | | 4 | | | | | | — | | |
Net income attributable to non controlling interest | | | | | 7 | | | | | | 13 | | | | | | 36 | | |
Foreign exchange translation adjustment | | | | | (4 | ) | | | | | 2 | | | | | | (1 | ) | |
Dividends paid | | | | | (23 | ) | | | | | (10 | ) | | | | | (9 | ) | |
Other owner changes | | | | | — | | | | | | — | | | | | | (3 | ) | |
| | | | | | | | | | | | | | | | | | | |
Ending balance | | | | | 96 | | | | | | 121 | | | | | | 110 | | |
| | | | | | | | | | | | | | | | | | | |
Total shareowners equity | | 774.7 | | | 10,902 | | | 783.0 | | | 10,787 | | | 764.2 | | | 8,971 | | |
| | | | | | | | | | | | | | | | | | | |
Comprehensive income | | | | | | | | | | | | | | | | | | | |
Net income | | | | | 2,074 | | | | | | 2,035 | | | | | | 1,584 | | |
Foreign exchange translation adjustment | | | | | (146 | ) | | | | | (249 | ) | | | | | 259 | | |
Pensions and other post retirement benefit adjustments | | | | | (209 | ) | | | | | 44 | | | | | | (271 | ) | |
Changes in fair value of available for sale investments | | | | | 12 | | | | | | 90 | | | | | | 112 | | |
Changes in fair value of effective cash flow hedges | | | | | (34 | ) | | | | | (4 | ) | | | | | 30 | | |
| | | | | | | | | | | | | | | | | | | |
Total comprehensive income | | | | | 1,697 | | | | | | 1,916 | | | | | | 1,714 | | |
Comprehensive income attributable to non controlling interest | | | | | (3 | ) | | | | | (15 | ) | | | | | (36 | ) | |
| | | | | | | | | | | | | | | | | | | |
Comprehensive income (loss) attributable to Honeywell | | | | | 1,694 | | | | | | 1,901 | | | | | | 1,678 | | |
| | | | | | | | | | | | | | | | | | | |
The Notes to Financial Statements are integral part of this statement.
59
Note 1. Summary of Significant Accounting Policies
Accounting Principles—The financial statements and accompanying notes are prepared in accordance with accounting principles generally accepted in the United States of America. The following is a description of Honeywell’s significant accounting policies..
Principles of Consolidation—The consolidated financial statements include the accounts of Honeywell International Inc. and all of its subsidiaries and entities in which a controlling interest is maintained. Our consolidation policy requires equity investments that we exercise significant influence over but do not control the investee and are not the primary beneficiary of the investee’s activities to be accounted for using the equity method. Investments through which we are not able to exercise significant influence over the investee and which we do not have readily determinable fair values are accounted for under the cost method. All intercompany transactions and balances are eliminated in consolidation.
The Consumer Products Group (CPG) automotive aftermarket business had historically been part of the Transportation Systems reportable segment. In accordance with generally accepted accounting principles, CPG is presented as discontinued operations in all periods presented. See Note 2 Acquisitions and Divestitures for further details.
Cash and Cash Equivalents—Cash and cash equivalents include cash on hand and on deposit and highly liquid, temporary cash investments with an original maturity of three months or less.
Inventories—Inventories are valued at the lower of cost or market using the first-in, first-out or the average cost method and the last-in, first-out (LIFO) method for certain qualifying domestic inventories.
Investments—Investments in affiliates over which we have a significant influence, but not a controlling interest, are accounted for using the equity method of accounting. Other investments are carried at market value, if readily determinable, or at cost. All equity investments are periodically reviewed to determine if declines in fair value below cost basis are other-than-temporary. Significant and sustained decreases in quoted market prices or a series of historic and projected operating losses by investees are strong indicators of other-than-temporary declines. If the decline in fair value is determined to be other-than-temporary, an impairment loss is recorded and the investment is written down to a new carrying value.
Property, Plant and Equipment—Property, plant and equipment are recorded at cost, including any asset retirement obligations, less accumulated depreciation. For financial reporting, the straight-line method of depreciation is used over the estimated useful lives of 10 to 50 years for buildings and improvements and 2 to 16 years for machinery and equipment. Recognition of the fair value of obligations associated with the retirement of tangible long-lived assets is required when there is a legal obligation to incur such costs. Upon initial recognition of a liability, the cost is capitalized as part of the related long-lived asset and depreciated over the corresponding asset’s useful life. See Note 11 and Note 17 for additional details.
Goodwill and Indefinite-Lived Intangible Assets—Goodwill represents the excess of acquisition costs over the fair value of tangible net assets and identifiable intangible assets of businesses acquired. Goodwill and certain other intangible assets deemed to have indefinite lives are not amortized. Intangible assets determined to have definite lives are amortized over their useful lives. Goodwill and indefinite lived intangible assets are subject to impairment testing annually as of March 31, or whenever events or changes in circumstances indicate that the carrying amount may not be fully recoverable. This testing compares carrying values to fair values and, when appropriate, the carrying value of these assets is reduced to fair value. We completed our annual goodwill impairment test as of March 31, 2011 and determined that there was no impairment as of that date. See Note 12 for additional details on goodwill balances.
Other Intangible Assets with Determinable Lives—Other intangible assets with determinable lives consist of customer lists, technology, patents and trademarks and other intangibles and are amortized over their estimated useful lives, ranging from 2 to 24 years.
Long-Lived Assets—We periodically evaluate the recoverability of the carrying amount of long-lived assets (including property, plant and equipment and intangible assets with determinable lives) whenever events or changes in circumstances indicate that the carrying amount of an asset may not be fully recoverable. We evaluate events or changes in circumstances based on a number of factors including operating results, business plans and forecasts, general and industry trends and, economic projections and anticipated cash flows. An impairment is assessed when the undiscounted expected future cash flows derived from an asset are less than its carrying amount. Impairment losses are measured as the amount by which the carrying value of an asset exceeds its fair value and are recognized in earnings. We also continually evaluate the estimated useful lives of all long-lived assets and periodically revise such estimates based on current events.
60
Sales Recognition—Product and service sales are recognized when persuasive evidence of an arrangement exists, product delivery has occurred or services have been rendered, pricing is fixed or determinable, and collection is reasonably assured. Service sales, principally representing repair, maintenance and engineering activities in our Aerospace and Automation and Control Solutions segments, are recognized over the contractual period or as services are rendered. Sales under long-term contracts in the Aerospace and Automation and Control Solutions segments are recorded on a percentage-of-completion method measured on the cost-to-cost basis for engineering-type contracts and the units-of-delivery basis for production-type contracts. Provisions for anticipated losses on long-term contracts are recorded in full when such losses become evident. Revenues from contracts with multiple element arrangements are recognized as each element is earned based on the relative fair value of each element provided the delivered elements have value to customers on a standalone basis. Amounts allocated to each element are based on its objectively determined fair value, such as the sales price for the product or service when it is sold separately or competitor prices for similar products or services.
Allowance for Doubtful Accounts—We maintain allowances for doubtful accounts for estimated losses as a result of customer’s inability to make required payments. We estimate anticipated losses from doubtful accounts based on days past due, as measured from the contractual due date, historical collection history and incorporate changes in economic conditions that may not be reflected in historical trends for example, customers in bankruptcy, liquidation or reorganization. Receivables are written-off against the allowance for doubtful accounts when they are determined uncollectible. Such determination includes analysis and consideration of the particular conditions of the account, including time intervals since last collection, success of outside collection agencies activity, solvency of customer and any bankruptcy proceedings.
Environmental Expenditures—Environmental expenditures that relate to current operations are expensed or capitalized as appropriate. Expenditures that relate to an existing condition caused by past operations, and that do not provide future benefits, are expensed as incurred. Liabilities are recorded when environmental remedial efforts or damage claim payments are probable and the costs can be reasonably estimated. Such liabilities are based on our best estimate of the undiscounted future costs required to complete the remedial work. The recorded liabilities are adjusted periodically as remediation efforts progress or as additional technical, regulatory or legal information becomes available. Given the uncertainties regarding the status of laws, regulations, enforcement policies, the impact of other potentially responsible parties, technology and information related to individual sites, we do not believe it is possible to develop an estimate of the range of reasonably possible environmental loss in excess of our recorded liabilities.
Asbestos Related Contingencies and Insurance Recoveries—Honeywell is a defendant in personal injury actions related to products containing asbestos (refractory and friction products). We recognize a liability for any asbestos related contingency that is probable of occurrence and reasonably estimable. Regarding North American Refractories Company (NARCO) asbestos related claims, we accrued for pending claims based on terms and conditions in agreements with NARCO, its former parent company, and certain asbestos claimants, and an estimate of the unsettled claims pending as of the time NARCO filed for bankruptcy protection. We also accrued for the estimated value of future NARCO asbestos related claims expected to be asserted against the NARCO Trust through 2018 as described in Note 21. In light of the inherent uncertainties in making long term projections and in connection with the initial operation of a 524(g) trust, as well as the stay of all NARCO asbestos claims since January 2002, we do not believe that we have a reasonable basis for estimating NARCO asbestos claims beyond 2018. Regarding Bendix asbestos related claims, we accrued for the estimated value of pending claims using average resolution values for the previous five years. We also accrued for the estimated value of future anticipated claims related to Bendix for the next five years based on historic claims filing experience and dismissal rates, disease classifications, and average resolution values in the tort system for the previous five years. In light of the uncertainties inherent in making long-term projections, as well as certain factors unique to friction product asbestos claims, we do not believe that we have a reasonable basis for estimating asbestos claims beyond the next five years. We will continue to update the resolution values used to estimate the cost of pending and future Bendix claims during the fourth quarter each year. For additional information see Note 21. We continually assess the likelihood of any adverse judgments or outcomes to our contingencies, as well as potential ranges of probable losses and recognize a liability, if any, for these contingencies based on an analysis of each individual issue with the assistance of outside legal counsel and, if applicable, other experts.
In connection with the recognition of liabilities for asbestos related matters, we record asbestos related insurance recoveries that are deemed probable. In assessing the probability of insurance recovery, we make judgments concerning insurance coverage that we believe are reasonable and consistent with our historical experience with our insurers, our knowledge of any pertinent solvency issues surrounding insurers, various judicial determinations relevant to our insurance programs and our consideration of the impacts of any settlements with our insurers.
61
Aerospace Sales Incentives—We provide sales incentives to commercial aircraft manufacturers and airlines in connection with their selection of our aircraft equipment, predominately wheel and braking system hardware and auxiliary power units, for installation on commercial aircraft. These incentives principally consist of free or deeply discounted products, but also include credits for future purchases of product and upfront cash payments. These costs are recognized in the period incurred as cost of products sold or as a reduction to sales, as appropriate. For aircraft manufacturers, incentives are recorded when the products are delivered; for airlines, incentives are recorded when the associated aircraft are delivered by the aircraft manufacturer to the airline.
Research and Development—Research and development costs for company-sponsored research and development projects are expensed as incurred. Such costs are principally included in Cost of Products Sold and were $1,799, $1,450 and $1,321 million in 2011, 2010 and 2009, respectively.
Stock-Based Compensation Plans—The principal awards issued under our stock-based compensation plans, which are described in Note 20, include non-qualified stock options and restricted stock units (RSUs). The cost for such awards is measured at the grant date based on the fair value of the award. The value of the portion of the award that is ultimately expected to vest is recognized as expense over the requisite service periods (generally the vesting period of the equity award) and is included in selling, general and administrative expense in our Consolidated Statement of Operations. Forfeitures are required to be estimated at the time of grant in order to estimate the portion of the award that will ultimately vest. The estimate is based on our historical rates of forfeiture.
Pension Benefits—We sponsor both funded and unfunded U.S. and non-U.S. defined benefit pension plans covering the majority of our employees and retirees. We recognize changes in the fair value of plan assets and net actuarial gains or losses in excess of 10 percent of the greater of the market-related value of plan assets or the plans’ projected benefit obligation (the corridor) annually in the fourth quarter each year (MTM Adjustment). The remaining components of pension expense, primarily service and interest costs and assumed return on plan assets, are recorded on a quarterly basis (On-going Pension Expense).
Foreign Currency Translation—Assets and liabilities of subsidiaries operating outside the United States with a functional currency other than U.S. dollars are translated into U.S. dollars using year-end exchange rates. Sales, costs and expenses are translated at the average exchange rates in effect during the year. Foreign currency translation gains and losses are included as a component of Accumulated Other Comprehensive Income (Loss). For subsidiaries operating in highly inflationary environments, inventories and property, plant and equipment, including related expenses, are remeasured at the exchange rate in effect on the date the assets were acquired, while monetary assets and liabilities are remeasured at year-end exchange rates. Remeasurement adjustments for these subsidiaries are included in earnings.
Derivative Financial Instruments—As a result of our global operating and financing activities, we are exposed to market risks from changes in interest and foreign currency exchange rates and commodity prices, which may adversely affect our operating results and financial position. We minimize our risks from interest and foreign currency exchange rate and commodity price fluctuations through our normal operating and financing activities and, when deemed appropriate through the use of derivative financial instruments. Derivative financial instruments are used to manage risk and are not used for trading or other speculative purposes and we do not use leveraged derivative financial instruments. Derivative financial instruments used for hedging purposes must be designated and effective as a hedge of the identified risk exposure at the inception of the contract. Accordingly, changes in fair value of the derivative contract must be highly correlated with changes in fair value of the underlying hedged item at inception of the hedge and over the life of the hedge contract.
All derivatives are recorded on the balance sheet as assets or liabilities and measured at fair value. For derivatives designated as hedges of the fair value of assets or liabilities, the changes in fair values of both the derivatives and the hedged items are recorded in current earnings. For derivatives designated as cash flow hedges, the effective portion of the changes in fair value of the derivatives are recorded in Accumulated Other Comprehensive Income (Loss) and subsequently recognized in earnings when the hedged items impact earnings. Cash flows of such derivative financial instruments are classified consistent with the underlying hedged item.
Transfers of Financial Instruments—Sales, transfers and securitization of financial instruments are accounted for under authoritative guidance for the transfers and servicing of financial assets and extinguishments of liabilities.
We sell interests in designated pools of trade accounts receivables to third parties. The terms of the trade accounts receivable program permit the repurchase of receivables from the third parties at our discretion. As a
62
result, these program receivables are not accounted for as a sale and remain on the Consolidated Balance Sheet with a corresponding amount recorded as either Short-term borrowings or Long-term debt.
At times we also transfer trade and other receivables that qualify as a sale and are thus are removed from the Consolidated Balance Sheet at the time they are sold. The value assigned to any subordinated interests and undivided interests retained in receivables sold is based on the relative fair values of the interests retained and sold. The carrying value of the retained interests approximates fair value due to the short-term nature of the collection period for the receivables.
Income Taxes—Deferred tax liabilities or assets reflect temporary differences between amounts of assets and liabilities for financial and tax reporting. Such amounts are adjusted, as appropriate, to reflect changes in tax rates expected to be in effect when the temporary differences reverse. A valuation allowance is established to offset any deferred tax assets if, based upon the available evidence, it is more likely than not that some or all of the deferred tax assets will not be realized. The determination of the amount of a valuation allowance to be provided on recorded deferred tax assets involves estimates regarding (1) the timing and amount of the reversal of taxable temporary differences, (2) expected future taxable income, and (3) the impact of tax planning strategies. In assessing the need for a valuation allowance, we consider all available positive and negative evidence, including past operating results, projections of future taxable income and the feasibility of ongoing tax planning strategies. The projections of future taxable income include a number of estimates and assumptions regarding our volume, pricing and costs. Additionally, valuation allowances related to deferred tax assets can be impacted by changes to tax laws.
Significant judgment is required in determining income tax provisions and in evaluating tax positions. We establish additional reserves for income taxes when, despite the belief that tax positions are fully supportable, there remain certain positions that do not meet the minimum recognition threshold. The approach for evaluating certain and uncertain tax positions is defined by the authoritative guidance and this guidance determines when a tax position is more likely than not to be sustained upon examination by the applicable taxing authority. In the normal course of business, the tax filings of the Company and its subsidiaries are examined by various Federal, State and foreign tax authorities. We regularly assess the potential outcomes of these examinations and any future examinations for the current or prior years in determining the adequacy of our provision for income taxes. We continually assess the likelihood and amount of potential adjustments and adjust the income tax provision, the current tax liability and deferred taxes in the period in which the facts that give rise to a revision become known.
Earnings Per Share—Basic earnings per share is based on the weighted average number of common shares outstanding. Diluted earnings per share is based on the weighted average number of common shares outstanding and all dilutive potential common shares outstanding.
Use of Estimates—The preparation of consolidated financial statements in conformity with generally accepted accounting principles requires management to make estimates and assumptions that affect the reported amounts in the financial statements and related disclosures in the accompanying notes. Actual results could differ from those estimates. Estimates and assumptions are periodically reviewed and the effects of revisions are reflected in the consolidated financial statements in the period they are determined to be necessary.
Reclassifications—Certain prior year amounts have been reclassified to conform to the current year presentation.
Recent Accounting Pronouncements—Changes to accounting principles generally accepted in the United States of America (U.S. GAAP) are established by the Financial Accounting Standards Board (FASB) in the form of accounting standards updates (ASU’s) to the FASB’s Accounting Standards Codification.
The Company considers the applicability and impact of all ASU’s. ASU’s not listed below were assessed and determined to be either not applicable or are expected to have minimal impact on our consolidated financial position and results of operations.
In May 2011, the FASB issued amendments to disclosure requirements for common fair value measurement. These amendments, effective for the interim and annual periods beginning on or after December 15, 2011 (early adoption is prohibited), result in common definition of fair value and common requirements for measurement of and disclosure requirements between U.S. GAAP and IFRS. Consequently, the amendments change some fair value measurement principles and disclosure requirements. The implementation of this amended accounting guidance is not expected to have a material impact on our consolidated financial position and results of operations.
63
In June 2011, the FASB issued amendments to disclosure requirements for presentation of comprehensive income. This guidance, effective retrospectively for the interim and annual periods beginning on or after December 15, 2011 (early adoption is permitted), requires presentation of total comprehensive income, the components of net income, and the components of other comprehensive income either in a single continuous statement of comprehensive income or in two separate but consecutive statements. In December 2011, the FASB issued an amendment to defer the presentation on the face of the financial statements the effects of reclassifications out of accumulated other comprehensive income on the components of net income and other comprehensive income for annual and interim financial statements. The implementation of the two aforementioned amendments is not expected to have a material impact on our consolidated financial position and results of operations.
In September 2011, the FASB issued amendments to the goodwill impairment guidance which provides an option for companies to use a qualitative approach to test goodwill for impairment if certain conditions are met. The amendments are effective for annual and interim goodwill impairment tests performed for fiscal years beginning after December 15, 2011 (early adoption is permitted). The implementation of amended accounting guidance is not expected to have a material impact on our consolidated financial position and results of operations.
Note 2. Acquisitions and Divestitures
Acquisitions –We acquired businesses for an aggregate cost of $973, $1,303, and $468 million in 2011 2010 and 2009, respectively. For all of our acquisitions the acquired businesses were recorded at their estimated fair values at the dates of acquisition. Significant acquisitions made in these years are discussed below.
In December 2011, the Company acquired King’s Safetywear Limited (KSW), a leading international provider of branded safety footwear. The aggregate value, net of cash acquired, was approximately $331 million (including the assumption of debt of $33 million) and was allocated to tangible and identifiable intangible assets acquired and liabilities assumed based on their estimated fair values at the acquisition date. On a preliminary basis, the Company has assigned approximately $178 million to identifiable intangible assets, predominantly trademarks, technology, and customer relationships. The definite lived intangible assets are being amortized over their estimated lives, using straight-line and accelerated amortization methods. The value assigned to trademarks of approximately $91 million is classified as indefinite lived intangibles. The excess of the purchase price over the estimated fair values of net assets acquired (approximately $163 million), was recorded as goodwill. This goodwill arises primarily from the avoidance of the time and costs which would be required (and the associated risks that would be encountered) to enhance our product offerings to key target markets and serve as entry into new and profitable segments, and the expected cost synergies that will be realized through the consolidation of the acquired business into our Automation and Control Solutions segment. Their cost synergies are expected to be realized principally in the areas of selling, general and administrative expenses, material sourcing and manufacturing. This goodwill is non–deductible for tax purposes.
The results from the acquisition date through December 31, 2011 are included in the Automation and Control Solutions segment and were not material to the consolidated financial statements. As of December 31, 2011, the purchase accounting for KSW is subject to final adjustment primarily for the valuation of inventory, property, plant and equipment, useful lives of intangible assets, amounts allocated to intangible assets and goodwill, tax balances, and for certain pre-acquisition contingencies.
In August 2011, the Company acquired 100 percent of the issued and outstanding shares of EMS Technologies, Inc. (EMS), a leading provider of connectivity solutions for mobile networking, rugged mobile computers and satellite communications. EMS had reported 2010 revenues of approximately $355 million.
The aggregate value, net of cash acquired, was approximately $513 million and was allocated to tangible and identifiable intangible assets acquired and liabilities assumed based on their estimated fair values at the acquisition date. On a preliminary basis, the Company has assigned approximately $119 million to identifiable intangible assets, of which approximately $89 million and approximately $30 million were recorded within the Aerospace and Automation and Control segments, respectively. The intangible assets are predominantly customer relationships, existing technology and trademarks. These intangible assets are being amortized over their estimated lives, using straight-line and accelerated amortization methods. The excess of the purchase price over the estimated fair values of net assets acquired (approximating $326 million), was recorded as goodwill. This goodwill arises primarily from the avoidance of the time and costs which would be required (and the
64
associated risks that would be encountered) to enhance our product offerings to key target markets and serve as entry into new and profitable segments, and the expected cost synergies that will be realized through the consolidation of the acquired business into our Aerospace and Automation and Control Solutions segments. These cost synergies are expected to be realized principally in the areas of selling, general and administrative expenses, material sourcing and manufacturing. This goodwill is non-deductible for tax purposes.
The results from the acquisition date through December 31, 2011 are included in the Aerospace and Automation and Control Solutions segments and were not material to the consolidated financial statements. As of December 31, 2011, the purchase accounting for EMS is subject to final adjustment primarily for the valuation of inventory and property, plant and equipment, useful lives of intangible assets, amounts allocated to intangible assets and goodwill, and for certain pre-acquisition contingencies.
In October 2010, we completed the acquisition of the issued and outstanding shares of Sperian Protection (Sperian), a French company that operates globally in the personal protection equipment design and manufacturing industry. Sperian had reported 2009 revenues of approximately $900 million.
The aggregate value, net of cash acquired, was approximately $1,475 million (including the assumption of approximately $326 million of outstanding debt) and was allocated to tangible and identifiable intangible assets acquired and liabilities assumed based on their estimated fair values at the acquisition date.
The following amounts represent the final determination of the fair value of the identifiable assets acquired and liabilities assumed.
| | | | | |
Accounts and other receivables | | $ | 117 | | |
Inventories | | | 166 | | |
Other current assets | | | 8 | | |
Property, plant and equipment | | | 108 | | |
Intangible assets | | | 539 | | |
Other assets and deferred charges | | | 4 | | |
Accounts payable | | | (63 | ) | |
Accrued liabilities | | | (114 | ) | |
Deferred income taxes | | | (156 | ) | |
Long-term debt | | | (326 | ) | |
Other long-term liabilities | | | (64 | ) | |
| | | | | |
Net assets acquired | | | 219 | | |
Goodwill | | | 930 | | |
| | | | | |
Purchase price | | $ | 1,149 | | |
| | | | | |
We have assigned $539 million to intangible assets, predominantly customer relationships, trade names, and technology. These intangible assets are being amortized over their estimated lives which range from 3 to 20 years using straight line and accelerated amortization methods.Included in this amount, a value of approximately $246 million has been assigned to trade names intangibles determined to have indefinite lives. The excess of the purchase price over the estimated fair values of net assets acquired is approximately $930 million and was recorded as goodwill. This goodwill arises primarily from the avoidance of the time and costs which would be required (and the associated risks that would be encountered) to develop a business with a product offering and customer base comparable to Sperian and the expected cost synergies that will be realized through the consolidation of the acquired business into our Automations and Controls Solutions segment. These cost synergies are expected to be realized principally in the areas of selling, general and administrative expenses, material sourcing and manufacturing. This goodwill is non-deductible for tax purposes. The results from the acquisition date through December 31, 2010 are included in the Automation and Control Solutions segment and were not material to the consolidated financial statements.
In August 2009, the Company completed the acquisition of the RMG Group (RMG Regel + Messtechnik GmbH), a natural gas measuring and control products, services and integrated solutions company, for a purchase price of approximately $416 million, net of cash acquired. The purchase price for the acquisition was allocated to the tangible and identifiable intangible assets acquired and liabilities assumed based on their estimated fair values at the acquisition date. The Company has assigned $174 million to identifiable intangible assets, predominantly customer relationships, existing technology and trademarks. These intangible assets are being
65
amortized over their estimated lives which range from 1 to 15 years using straight-line and accelerated amortization methods. The excess of the purchase price over the estimated fair values of net assets acquired (approximating $225 million), was recorded as goodwill. This goodwill is non-deductible for tax purposes. The results from the acquisition date through December 31, 2009 are included in the Automation and Control Solutions segment and were not material to the consolidated financial statements.
In connection with all acquisitions in 2011, 2010 and 2009, the amounts recorded for transaction costs and the costs of integrating the acquired businesses into Honeywell were not material.
The pro forma results for 2011, 2010 and 2009, assuming these acquisitions had been made at the beginning of the comparable prior year, would not be materially different from consolidated reported results.
Divestitures–In July 2011, the Company sold its Consumer Products Group business (CPG) to Rank Group Limited. The sale was completed for approximately $955 million in cash proceeds, resulting in a pre-tax gain of approximately $301 million and approximately $178 million net of tax. The gain was recorded in net income from discontinued operations after taxes in the Company’s Consolidated Statement of Operations for the year ended December 31, 2011. The net income attributable to the non-controlling interest for the discontinued operations is insignificant. The sale of CPG, which had been part of the Transportation Systems segment, is consistent with the Company’s strategic focus on its portfolio of differentiated global technologies.
The key components of income from discontinued operations related to CPG were as follows:
| | | | | | | | | | | | | |
| | Year Ended December 31, | |
| | | |
| | 2011 | | 2010 | | 2009 | |
| | | | | | | |
Net sales | | $ | 530 | | | $ | 1,020 | | | $ | 957 | | |
Costs, expenses and other | | | 421 | | | | 798 | | | | 752 | | |
Selling, general and administrative expense | | | 63 | | | | 99 | | | | 120 | | |
Other (income) expense | | | (2 | ) | | | 2 | | | | — | | |
| | | | | | | | | | | | | |
(Loss) income before taxes | | | 48 | | | | 121 | | | | 85 | | |
| | | | | | | | | | | | | |
Gain on disposal of discontinued operations | | | 301 | | | | — | | | | — | | |
| | | | | | | | | | | | | |
Net income from discontinued operations before taxes | | | 349 | | | | 121 | | | | 85 | | |
| | | | | | | | | | | | | |
Tax expense | | | 140 | | | | 43 | | | | 29 | | |
| | | | | | | | | | | | | |
Net income from discontinued operations after taxes | | $ | 209 | | | $ | 78 | | | $ | 56 | | |
| | | | | | | | | | | | | |
The components of assets and liabilities classified as discontinued operations and included in other current assets and other current liabilities related to the CPG business consisted of the following:
| | | | |
| | December 31, 2010 | |
| | | |
Accounts, notes and other receivables | | $ | 227 | |
Inventories | | | 136 | |
Property, plant and equipment - net | | | 116 | |
Goodwill and other intangibles - net | | | 359 | |
Other | | | 3 | |
| | | | |
Total assets | | $ | 841 | |
| | | | |
Accounts payable | | $ | 145 | |
Accrued and other liabilities | | | 45 | |
| | | | |
Total liabilities | | $ | 190 | |
| | | | |
Note 3. Repositioning and Other Charges
66
A summary of repositioning and other charges follows:
| | | | | | | | | | |
| | Years Ended December 31, | |
| | | |
| | 2011 | | 2010 | | 2009 | |
| | | | | | | |
Severance | | $ | 246 | | | $ | 144 | | | $ | 197 | | |
Asset impairments | | | 86 | | | | 21 | | | | 6 | | |
Exit costs | | | 48 | | | | 14 | | | | 10 | | |
Reserve adjustments | | | (26 | ) | | | (30 | ) | | | (53 | ) | |
| | | | | | | | | | | | | |
Total net repositioning charge | | | 354 | | | | 149 | | | | 160 | | |
| | | | | | | | | | | | | |
|
Asbestos related litigation charges, net of insurance | | | 149 | | | | 175 | | | | 155 | | |
Probable and reasonably estimable environmental liabilities | | | 240 | | | | 212 | | | | 145 | | |
Other | | | — | | | | 62 | | | | 7 | | |
| | | | | | | | | | | | | |
Total net repositioning and other charges | | $ | 743 | | | $ | 598 | | | $ | 467 | | |
| | | | | | | | | | | | | |
The following table summarizes the pretax distribution of total net repositioning and other charges by income statement classification:
| | | | | | | | | | |
| | Years Ended December 31, | |
| | | |
| | 2011 | | 2010 | | 2009 | |
| | | | | | | |
Cost of products and services sold | | $ | 646 | | $ | 558 | | $ | 404 | |
Selling, general and administrative expenses | | | 97 | | | 40 | | | 63 | |
| | | | | | | | | | |
| | $ | 743 | | $ | 598 | | $ | 467 | |
| | | | | | | | | | |
The following table summarizes the pretax impact of total net repositioning and other charges by segment:
| | | | | | | | | | |
| | Years Ended December 31, | |
| | | |
| | 2011 | | 2010 | | 2009 | |
| | | | | | | |
Aerospace | | $ | 29 | | $ | 32 | | $ | 31 | |
Automation and Control Solutions | | | 191 | | | 79 | | | 70 | |
Performance Materials and Technologies | | | 41 | | | 18 | | | 9 | |
Transportation Systems | | | 228 | | | 178 | | | 162 | |
Corporate | | | 254 | | | 291 | | | 195 | |
| | | | | | | | | | |
| | $ | 743 | | $ | 598 | | $ | 467 | |
| | | | | | | | | | |
In 2011, we recognized repositioning charges totaling $380 million including severance costs of $246 million related to workforce reductions of 3,188 manufacturing and administrative positions across all of our segments. The workforce reductions were primarily related to the planned shutdown of a manufacturing facility in our Transportation Systems segment, cost savings actions taken in connection with our ongoing functional transformation and productivity initiatives, factory transitions in connection with acquisition-related synergies in our Automation and Control Solutions and Aerospace segments, the exit from and/or rationalization of certain product lines and markets in our Performance Materials and Technologies and Automation and Control Solutions segments, the consolidation of repair facilities in our Aerospace segment, and factory consolidations and/or rationalizations and organizational realignments of businesses in our Automation and Control Solutions segment. The repositioning charges included asset impairments of $86 million principally related to the write-off of certain intangible assets in our Automation and Control Solutions segment due to a change in branding strategy and manufacturing plant and equipment associated with the planned shutdown of a manufacturing facility and the exit of a product line and a factory transition as discussed above. The repositioning charges also included exit costs of $48 million principally for costs to terminate contracts related to the exit of a market and product line and a factory transition as discussed above. Exit costs also included closure obligations associated with the planned shutdown of a manufacturing facility and exit of a product line also as discussed above. Also, $26 million of previously established accruals, primarily for severance at our Aerospace and Automation and Control Solutions segments, were returned to income in 2011 due principally to fewer employee separations than originally planned associated with prior severance programs.
67
In 2010, we recognized repositioning charges totaling $179 million including severance costs of $144 million related to workforce reductions of 2,781 manufacturing and administrative positions primarily in our Automation and Control Solutions, Aerospace and Transportation Systems segments. The workforce reductions were primarily related to the planned shutdown of certain manufacturing facilities in our Automation and Control Solutions and Transportation Systems segments, cost savings actions taken in connection with our ongoing functional transformation and productivity initiatives, factory transitions in our Aerospace, Automation and Control Solutions and Performance Materials and Technologies segments to more cost-effective locations, achieving acquisition-related synergies in our Automation and Control Solutions segment, and the exit and/or rationalization of certain product lines in our Performance Materials and Technologies segment. The repositioning charge also included asset impairments of $21 million principally related to manufacturing plant and equipment associated with the exit and/or rationalization of certain product lines and in facilities scheduled to close. Also, $30 million of previously established accruals, primarily for severance at our Automation and Control Solutions, Transportation Systems and Aerospace segments, were returned to income in 2010 due to fewer employee separations than originally planned associated with prior severance programs.
In 2009, we recognized repositioning charges totaling $213 million primarily for severance costs related to workforce reductions of 4,145 manufacturing and administrative positions mainly in our Automation and Control Solutions, Transportation Systems and Aerospace segments. The workforce reductions were primarily related to the adverse market conditions experienced by many of our businesses, cost savings actions taken in connection with our ongoing functional transformation initiative, the planned downsizing or shutdown of certain manufacturing facilities, and organizational realignments of portions of our Aerospace and Transportation Systems segments. Also, $53 million of previously established accruals, primarily for severance at our Automation and Control Solutions, Aerospace, and Transportation Systems segments, were returned to income in 2009 due to fewer employee separations than originally planned associated with prior severance programs and changes in the scope of previously announced repositioning actions.
The following table summarizes the status of our total repositioning reserves:
| | | | | | | | | | | | | | | | |
| | Severance Costs | | Asset Impairments | | Exit Costs | | Total | |
| | | | | | | | | | | | |
Balance at December 31, 2008 | | $ | 358 | | | $ | — | | | $ | 36 | | | $ | 394 | |
| | | | | | | | | | | | | | | | |
2009 charges | | | 197 | | | | 6 | | | | 10 | | | | 213 | |
2009 usage - cash | | | (186 | ) | | | — | | | | (7 | ) | | | (193 | ) |
2009 usage - noncash | | | — | | | | (6 | ) | | | — | | | | (6 | ) |
Adjustments | | | (51 | ) | | | — | | | | (2 | ) | | | (53 | ) |
Divestitures(1) | | | (24 | ) | | | — | | | | — | | | | (24 | ) |
| | | | | | | | | | | | | | | | |
Balance at December 31, 2009 | | | 294 | | | | — | | | | 37 | | | | 331 | |
| | | | | | | | | | | | | | | | |
2010 charges | | | 144 | | | | 21 | | | | 14 | | | | 179 | |
2010 usage - cash | | | (130 | ) | | | — | | | | (17 | ) | | | (147 | ) |
2010 usage - noncash | | | — | | | | (21 | ) | | | — | | | | (21 | ) |
Adjustments | | | (30 | ) | | | — | | | | — | | | | (30 | ) |
Foreign currency translation | | | (8 | ) | | | — | | | | — | | | | (8 | ) |
| | | | | | | | | | | | | | | | |
Balance at December 31, 2010 | | | 270 | | | | — | | | | 34 | | | | 304 | |
| | | | | | | | | | | | | | | | |
2011 charges | | | 246 | | | | 86 | | | | 48 | | | | 380 | |
2011 usage - cash | | | (136 | ) | | | — | | | | (23 | ) | | | (159 | ) |
2011 usage - noncash | | | — | | | | (86 | ) | | | — | | | | (86 | ) |
Adjustments | | | (26 | ) | | | — | | | | — | | | | (26 | ) |
Foreign currency translation | | | (1 | ) | | | — | | | | — | | | | (1 | ) |
| | | | | | | | | | | | | | | | |
Balance at December 31, 2011 | | $ | 353 | | | $ | — | | | $ | 59 | | | $ | 412 | |
| | | | | | | | | | | | | | | | |
(1) Relates to businesses divested during 2009 included in Gain on Sale of Non-Strategic Businesses and Assets see Note 4, Other (Income) Expense.
Certain repositioning projects in our Aerospace, Automation and Control Solutions and Transportation Systems segments included exit or disposal activities, the costs related to which will be recognized in future periods when the actual liability is incurred. The nature of these exit or disposal costs includes asset set-up and moving, product recertification and requalification, and employee retention, training and travel. The following tables
68
summarize by segment, expected, incurred and remaining exit and disposal costs related to 2011 and 2010 repositioning actions which we were not able to recognize at the time the actions were initiated.
| | | | | | | | | | | | | | | | |
2011 Repositioning Actions | | Aerospace | | Automation and Control Solutions | | Transportation Systems | | Total |
| | | | | | | | | | | | |
Expected exit and disposal costs | | $ | 15 | | | $ | 15 | | | $ | 7 | | | $ | 37 | |
Costs incurred year ended December 31, 2011 | | | (1 | ) | | | — | | | | — | | | | (1 | ) |
| | | | | | | | | | | | | | | | |
Remaining exit and disposal costs at December 31, 2011 | | $ | 14 | | | $ | 15 | | | $ | 7 | | | $ | 36 | |
| | | | | | | | | | | | | | | | |
| | | | | | | | | | | | | | | | |
2010 Repositioning Actions | | Aerospace | | Automation and Control Solutions | | Transportation Systems | | Total |
| | | | | | | | | | | | |
Expected exit and disposal costs | | $ | 11 | | | $ | 10 | | | $ | 2 | | | $ | 23 | |
Costs incurred year ended December 31, 2011 | | | (2 | ) | | | (3 | ) | | | (1 | ) | | | (6 | ) |
Costs incurred year ended December 31, 2010 | | | — | | | | — | | | | — | | | | — | |
| | | | | | | | | | | | | | | | |
Remaining exit and disposal costs at December 31, 2011 | | $ | 9 | | | $ | 7 | | | $ | 1 | | | $ | 17 | |
| | | | | | | | | | | | | | | | |
In 2011, we recognized a charge of $240 million for environmental liabilities deemed probable and reasonably estimable during the year. We recognized asbestos related litigation charges, net of insurance, of $149 million. Environmental and Asbestos matters are discussed in detail in Note 21, Commitments and Contingencies.
In 2010, we recognized a charge of $212 million for environmental liabilities deemed probable and reasonably estimable during the year. We recognized asbestos related litigation charges, net of insurance, of $175 million. We also recognized other charges of $62 million in connection with the evaluation of potential resolution of certain legal matters.
In 2009, we recognized a charge of $145 million for environmental liabilities deemed probable and reasonably estimable during the year. We recognized asbestos related litigation charges, net of insurance, of $155 million.
Note 4. Other (income) expense
| | | | | | | | | | | | |
| | Years Ended December 31, |
| | |
| | 2011 | | 2010 | | 2009 |
| | | | | | |
| | | | | | | | | | | | |
Equity (income)/loss of affiliated companies | | $ | (51 | ) | | $ | (28 | ) | | $ | (26 | ) |
Gain on sale of non-strategic businesses and assets | | | (61 | ) | | | — | | | | (87 | ) |
Interest income | | | (58 | ) | | | (39 | ) | | | (33 | ) |
Foreign exchange | | | 50 | | | | 12 | | | | 45 | |
Other, net | | | 36 | | | | (42 | ) | | | 47 | |
| | | | | | | | | | | | |
| | $ | (84 | ) | | $ | (97 | ) | | $ | (54 | ) |
| | | | | | | | | | | | |
Gain on sale of non-strategic businesses and assets for 2011 includes a $50 million pre-tax gain, $31 million net of tax, related to the divestiture of the automotive on-board sensor products business within our Automation and Control Solutions segment.
Other, net in 2011 includes a loss of $29 million resulting from early redemption of debt in the first quarter of 2011. See Note 14 Long-term Debt and Credit Agreements for further details.
69
Other, net for 2010 includes a $62 million pre-tax gain, $39 million net of tax, related to the consolidation of a joint venture within our Performance Materials and Technologies segment. The Company obtained control and the ability to direct those activities most significant to the joint venture’s economic performance in the third quarter, resulting in consolidation. Accordingly, we have i) recognized the assets and liabilities at fair value, ii) included the results of operations in the consolidated financial statements from the date of consolidation and iii) recognized the above noted gain representing the difference between the carrying amount and fair value of our previously held equity method investment. The Company has assigned $24 million to intangibles, predominantly the joint venture’s customer contracts. These intangible assets are being amortized over their estimated lives using the straight line method. The excess of the book value over the estimated fair values of the net assets consolidated approximating $132 million, was recorded as goodwill. This goodwill is non-deductible for tax purposes. The results from the consolidation date through December 31, 2010 are included in the Performance Materials and Technologies segment and were not material to the consolidated financial statements.
Gain on sale of non-strategic businesses and assets for 2009 includes a $50 million pre-tax gain, $42 million net of tax, related to the deconsolidation of a subsidiary within our Automation and Control Solutions segment. The subsidiary achieved contractual milestones at December 31, 2009 and as a result, we are no longer the primary beneficiary, resulting in deconsolidation. We continue to hold a non-controlling interest which was recorded at its estimated fair value of $67 million upon deconsolidation. The fair value was estimated using a combination of a market and income approaches utilizing observable market data for comparable businesses and discounted cash flow modeling. Our non-controlling interest, classified within Investments and long-term receivables on our Balance Sheet will be accounted for under the equity method on a prospective basis.
Other, net for 2009 includes an other than-temporary impairment charge of $62 million. See Note 16 Financial Instruments and Fair Value Measures for further details.
Note 5. Interest and Other Financial Charges
| | | | | | | | | | | | |
| | Years Ended December 31, |
| | |
| | 2011 | | 2010 | | 2009 |
| | | | | | |
Total interest and other financial charges | | $ | 389 | | | $ | 402 | | | $ | 473 | |
Less—capitalized interest | | | (13 | ) | | | (16 | ) | | | (15 | ) |
| | | | | | | | | | | | |
| | $ | 376 | | | $ | 386 | | | $ | 458 | |
| | | | | | | | | | | | |
The weighted average interest rate on short-term borrowings and commercial paper outstanding at December 31, 2011 and 2010 was 0.84 percent and 1.64 percent, respectively.
Note 6. Income Taxes
Income from continuing operations before taxes
| | | | | | | | | | | | |
| | Years Ended December 31, |
| | |
| | 2011 | | 2010 | | 2009 |
| | | | | | |
United States | | $ | 318 | | | $ | 1,157 | | | $ | 1,068 | |
Foreign | | | 1,964 | | | | 1,565 | | | | 896 | |
| | | | | | | | | | | | |
| | $ | 2,282 | | | $ | 2,722 | | | $ | 1,964 | |
| | | | | | | | | | | | |
70
| | | | | | | | | | | | |
Tax expense (benefit) | | | | | | | | | | | | |
| | Years Ended December 31, |
| | |
| | 2011 | | 2010 | | 2009 |
| | | | | | |
| | | | | | | | | | | | |
United States | | $ | 3 | | | $ | 358 | | | $ | 272 | |
Foreign | | | 414 | | | | 407 | | | | 164 | |
| | | | | | | | | | | | |
| | $ | 417 | | | $ | 765 | | | $ | 436 | |
| | | | | | | | | | | | |
| | | | | | | | | | | | |
| | | Years Ended December 31, |
| | |
| | 2011 | | 2010 | | 2009 |
| | | | | | |
| | | | | | | | | | | | |
Tax Expense consists of Current: | | | | | | | | | | | | |
United States | | $ | 171 | | | $ | (501 | ) | | $ | (47 | ) |
State | | | 13 | | | | 3 | | | | 19 | |
Foreign | | | 564 | | | | 385 | | | | 417 | |
| | | | | | | | | | | | |
| | $ | 748 | | | $ | (113 | ) | | $ | 389 | |
| | | | | | | | | | | | |
| | | | | | | | | | | | |
Deferred: | | | | | | | | | | | | |
United States | | $ | (185 | ) | | $ | 784 | | | $ | 283 | |
State | | | 4 | | | | 72 | | | | 17 | |
Foreign | | | (150 | ) | | | 22 | | | | (253 | ) |
| | | | | | | | | | | | |
| | | (331 | ) | | | 878 | | | | 47 | |
| | | | | | | | | | | | |
| | $ | 417 | | | $ | 765 | | | $ | 436 | |
| | | | | | | | | | | | |
| | | | | | | | | | | | |
| | Years Ended December 31, |
| | |
| | 2011 | | 2010 | | 2009 |
| | | | | | |
The U.S. statutory federal income tax rate is reconciled to our effective income tax rate as follows: | | | | | | | | | | | | |
Statutory U.S. federal income tax rate | | | 35.0 | % | | | 35.0 | % | | | 35.0 | % |
Taxes on foreign earnings below U.S. tax rate(1) | | | (10.4 | ) | | | (7.3 | ) | | | (8.3 | ) |
State income taxes(1) | | | 0.7 | | | | 1.5 | | | | 1.5 | |
Manufacturing incentives | | | (1.7 | ) | | | — | | | | (1.6 | ) |
ESOP dividend tax benefit | | | (1.1 | ) | | | (0.8 | ) | | | (1.1 | ) |
Tax credits | | | (2.3 | ) | | | (1.2 | ) | | | (1.9 | ) |
Audit settlements | | | (2.0 | ) | | | 0.1 | | | | (0.7 | ) |
All other items—net | | | 0.1 | | | | 0.8 | | | | (0.7 | ) |
| | | | | | | | | | | | |
| | | 18.3 | % | | | 28.1 | % | | | 22.2 | % |
| | | | | | | | | | | | |
(1) Net of changes in valuation allowance and tax reserves
The effective tax rate decreased by 9.8 percentage points in 2011 compared with 2010 primarily due to a change in the mix of earnings related to higher U.S. pension expense (primarily driven by an approximate 7.6 percentage point impact which resulted from the increase in pension mark-to-market expense), an increased benefit from manufacturing incentives, an increased benefit from the favorable settlement of tax audits and an increased benefit from a lower foreign effective tax rate. The foreign effective tax rate was 21.1 percent, a decrease of approximately 4.9 percentage points which primarily consisted of (i) a 5.1 percent impact from decreased valuation allowances on net operating losses primarily due to an increase in German earnings available to be offset by net operating loss carry forwards; (ii) a 2.4 percent impact from tax benefits related to foreign exchange and investment losses; iii) a 1.2 percent impact from an increased benefit in tax credits and lower statutory tax rates and (iv) a 4.1 percent impact related to an increase in tax reserves. The effective tax rate was lower than the U.S. statutory rate of 35 percent primarily due to earnings taxed at lower foreign rates.
71
The effective tax rate increased by 5.9 percentage points in 2010 compared to 2009 primarily due to a change in the mix of earnings related to lower U.S. pension expense, the impact of an enacted change in the tax treatment of the Medicare Part D program, the absence of manufacturing incentives, a decreased impact from the settlement of audits and an increase in the foreign effective tax rate. The foreign effective tax rate increased by approximately 7 percentage points which primarily consisted of i) a 6 percentage point impact from the absence of tax benefits related to foreign exchange and investment losses and ii) a (0.1) percentage point impact from increased valuation allowances on net operating losses.
Deferred tax assets (liabilities)
Deferred income taxes represent the future tax effects of transactions which are reported in different periods for tax and financial reporting purposes. The tax effects of temporary differences and tax carryforwards which give rise to future income tax benefits and payables are as follows:
| | | | | | | | |
| | December 31, |
| | | |
| | 2011 | | 2010 |
| | | | | | |
|
Property, plant and equipment basis differences | | $ | (1,097 | ) | | $ | (1,107 | ) |
Postretirement benefits other than pensions and post employment benefits | | | 571 | | | | 674 | |
Investment and other asset basis differences | | | (970 | ) | | | (993 | ) |
Other accrued items | | | 2,852 | | | | 2,348 | |
Net operating and capital losses | | | 810 | | | | 873 | |
Tax credits | | | 379 | | | | 249 | |
Undistributed earnings of subsidiaries | | | (57 | ) | | | (40 | ) |
All other items—net | | | (67 | ) | | | 15 | |
| | | | | | | | |
| | | 2,421 | | | | 2,019 | |
Valuation allowance | | | (591 | ) | | | (636 | ) |
| | | | | | | | |
| | $ | 1,830 | | | $ | 1,383 | |
| | | | | | | | |
There were $3 million of U.S. federal tax net operating losses available for carryforward at December 31, 2011 which have expiration dates through 2029. The Company has state tax net operating loss carryforwards of $3.5 billion at December 31, 2011 with varying expiration dates through 2032. We also have foreign net operating and capital losses of $2.7 billion which are available to reduce future income tax payments in several countries, subject to varying expiration rules.
We have U.S. federal tax credit carryforwards of $35 million at December 31, 2011, including alternative minimum tax credits which are not subject to expiration. We also have state tax credit carryforwards of $61 million at December 31, 2011, including carryforwards of $38 million with various expiration dates through 2026 and tax credits of $23 million which are not subject to expiration.
The valuation allowance against deferred tax assets decreased by $45 million in 2011 and increased by $58 million and $133 million in 2010 and 2009, respectively. The 2011 decrease in the valuation allowance was primarily due to decreased foreign net operating losses related to the Netherlands and Germany, partially offset by the increase in the valuation allowance of France, Luxembourg and Canada. The 2010 increase in the valuation allowance was primarily due to increased foreign net operating losses related to France, Luxembourg, and the Netherlands offset by the reversal of a valuation allowance related to Germany. The 2010 increase in valuation allowance also includes adjustments related to purchase accounting for various acquisitions. The 2009 increase in the valuation allowance was primarily due to increased foreign net operating losses related to Germany, Luxembourg, and the Netherlands.
Federal income taxes have not been provided on undistributed earnings of the majority of our international subsidiaries as it is our intention to reinvest these earnings into the respective subsidiaries. At December 31, 2011 Honeywell has not provided for U.S. federal income and foreign withholding taxes on approximately $8.1 billion of such earnings of our non-U.S. operations. It is not practicable to estimate the amount of tax that might be payable if some or all of such earnings were to be repatriated, and the amount of foreign tax credits that would be available to reduce or eliminate the resulting U.S. income tax liability.
We had $815 million, $757 million and $720 million of unrecognized tax benefits as of December 31, 2011, 2010, and 2009 respectively. If recognized, $815 million would be recorded as a component of income tax
72
expense as of December 31, 2011. For the years ended December 31, 2011 and 2010, the Company increased its unrecognized tax benefits by $58 million and $37 million, respectively, due to additional reserves for various international and U.S. tax audit matters, partially offset by adjustments related to our ongoing assessments of the likelihood and amount of potential outcomes of current and future examinations, the expiration of various statute of limitations, and settlements with tax authorities. The following table summarizes the activity related to our unrecognized tax benefits:
| | | | | | | | | | | | |
| | 2011 | | 2010 | | 2009 |
| | | | | | | | | |
Change in unrecognized tax benefits: | | | | | | | | | | | | |
Balance at beginning of year | | $ | 757 | | | $ | 720 | | | $ | 671 | |
Gross increases related to current period tax positions | | | 46 | | | | 37 | | | | 86 | |
Gross increases related to prior periods tax positions | | | 327 | | | | 84 | | | | 86 | |
Gross decreases related to prior periods tax positions | | | (56 | ) | | | (41 | ) | | | (77 | ) |
Decrease related to settlements with tax authorities | | | (237 | ) | | | (23 | ) | | | (44 | ) |
Expiration of the statute of limitations for the assessment of taxes | | | (12 | ) | | | (8 | ) | | | (8 | ) |
Foreign currency translation | | | (10 | ) | | | (12 | ) | | | 6 | |
| | | | | | | | | | | | |
Balance at end of year | | $ | 815 | | | $ | 757 | | | $ | 720 | |
| | | | | | | | | | | | |
Generally, our uncertain tax positions are related to tax years that remain subject to examination by the relevant tax authorities. The following table summarizes these open tax years by major jurisdiction as of December 31, 2011:
| | | | |
| | Open Tax Year |
| | |
Jurisdiction | | Examination in progress | | Examination not yet initiated |
| | | | |
United States(1) | | 2001–2009 | | 2005–2011 |
United Kingdom | | N/A | | 2010-2011 |
Canada(1) | | 2006-2010 | | 2011 |
Germany(1) | | 2004-2009 | | 2010-2011 |
France | | 2009-2010 | | 2000–2008, 2011 |
Netherlands | | 2007-2009 | | 2010-2011 |
Australia | | N/A | | 2009-2011 |
China | | 2009-2010 | | 2006-2008, 2011 |
India | | 2000–2009 | | 2010-2011 |
| |
(1) | includes federal as well as state, provincial or similar local jurisdictions, as applicable. |
Based on the outcome of these examinations, or as a result of the expiration of statute of limitations for specific jurisdictions, it is reasonably possible that the related unrecognized tax benefits for tax positions taken regarding previously filed tax returns will materially change from those recorded as liabilities for uncertain tax positions in our financial statements. In addition, the outcome of these examinations may impact the valuation of certain deferred tax assets (such as net operating losses) in future periods. Based on the number of tax years currently under audit by the relevant U.S federal, state and foreign tax authorities, the Company anticipates that several of these audits may be finalized in the foreseeable future. However, based on the status of these examinations, the protocol of finalizing audits by the relevant taxing authorities, and the possibility that the Company might challenge certain audit findings (which could include formal legal proceedings), at this time it is not possible to estimate the impact of any amount of such changes, if any, to previously recorded uncertain tax positions.
Unrecognized tax benefits for examinations in progress were $482 million, $274 million and $261 million, as of December 31, 2011, 2010, and 2009, respectively. These increases are primarily due to an increase in tax examinations. Estimated interest and penalties related to the underpayment of income taxes are classified as a component of Tax Expense in the Consolidated Statement of Operations and totaled $63 million, $33 million and $13 million for the years ended December 31, 2011, 2010, and 2009, respectively. Accrued interest and penalties were $247 million, $183 million and $150 million, as of December 31, 2011, 2010, and 2009, respectively.
73
Note 7. Earnings Per Share
The details of the earnings per share calculations for the years ended December 31, 2011, 2010 and 2009 are as follows:
| | | | | | | | | | | | |
| | Years Ended December 31, |
| | |
| | 2011 | | 2010 | | 2009 |
| | | | | | | | | |
Basic | | | | | | | | | | | | |
Income from continuing operations less net income attributable to the non controlling interest | | $ | 1,858 | | | $ | 1,944 | | | $ | 1,492 | |
Income from discontinued operations | | | 209 | | | | 78 | | | | 56 | |
| | | | | | | | | | | | |
Net income attributable to Honeywell | | $ | 2,067 | | | $ | 2,022 | | | $ | 1,548 | |
| | | | | | | | | | | | |
| | | | | | | | | | | | |
Weighted average shares outstanding | | | 780.8 | | | | 773.5 | | | | 752.6 | |
| | | | | | | | | | | | |
Earnings per share of common stock: | | | | | | | | | | | | |
Income from continuing operations | | $ | 2.38 | | | $ | 2.51 | | | $ | 1.99 | |
Income from discontinued operations | | | 0.27 | | | | 0.10 | | | | 0.07 | |
| | | | | | | | | | | | |
Net Income attributable to Honeywell | | $ | 2.65 | | | $ | 2.61 | | | $ | 2.06 | |
| | | | | | | | | | | | |
| | | | | | | | | | | | |
| | Years Ended December 31, |
| | |
| | 2011 | | 2010 | | 2009 |
| | | | | | |
Assuming Dilution | | | | | | | | | | | | |
Income from continuing operations less net income attributable to the noncontrolling interest | | $ | 1,858 | | | $ | 1,944 | | | $ | 1,492 | |
Income from discontinued operations | | | 209 | | | | 78 | | | | 56 | |
| | | | | | | | | | | | |
Net income attributable to Honeywell | | $ | 2,067 | | | $ | 2,022 | | | $ | 1,548 | |
| | | | | | | | | | | | |
| | | | | | | | | | | | |
Average Shares | | | | | | | | | | | | |
Weighted average shares outstanding | | | 780.8 | | | | 773.5 | | | | 752.6 | |
Dilutive securities issuable - stock plans | | | 10.8 | | | | 7.4 | | | | 3.1 | |
| | | | | | | | | | | | |
Total weighted average diluted shares outstanding | | | 791.6 | | | | 780.9 | | | | 755.7 | |
| | | | | | | | | | | | |
| | | | | | | | | | | | |
Earnings per share of common stock - assuming dilution: | | | | | | | | | | | | |
Income from continuing operations | | $ | 2.35 | | | $ | 2.49 | | | $ | 1.98 | |
Income from discontinuing operations | | | 0.26 | | | | 0.10 | | | | 0.07 | |
| | | | | | | | | | | | |
Net income attributable to Honeywell | | $ | 2.61 | | | $ | 2.59 | | | $ | 2.05 | |
| | | | | | | | | | | | |
The diluted earnings per share calculations exclude the effect of stock options when the options’ assumed proceeds exceed the average market price of the common shares during the period. In 2011, 2010, and 2009 the weighted number of stock options excluded from the computations were 9.5, 14.8, and 34.0 million, respectively. These stock options were outstanding at the end of each of the respective periods.
Note 8. Accounts, Notes and Other Receivables
| | | | | | | | |
| | December 31, |
| | |
| | 2011 | | 2010 |
| | | | | | |
Trade | | $ | 6,926 | | | $ | 6,471 | |
Other | | | 555 | | | | 642 | |
| | | | | | | | |
| | | 7,481 | | | | 7,113 | |
Less - Allowance for doubtful accounts | | | (253 | ) | | | (272 | ) |
| | | | | | | | |
| | $ | 7,228 | | | $ | 6,841 | |
| | | | | | | | |
74
Trade Receivables includes $1,404, and $1,307 million of unbilled balances under long-term contracts as of December 31, 2011 and December 31, 2010, respectively. These amounts are billed in accordance with the terms of customer contracts to which they relate.
Note 9. Inventories
| | | | | | | | | |
| | December 31, | |
| | | |
| | 2011 | | 2010 | |
| | | | | |
Raw materials | | $ | 1,222 | | | $ | 1,139 | | |
Work in process | | | 958 | | | | 792 | | |
Finished products | | | 2,253 | | | | 2,045 | | |
| | | | | | | | | |
| | | 4,433 | | | | 3,976 | | |
Reduction to LIFO cost basis | | | (169 | ) | | | (154 | ) | |
| | | | | | | | | |
| | $ | 4,264 | | | $ | 3,822 | | |
| | | | | | | | | |
Inventories valued at LIFO amounted to $302 and $198 million at December 31, 2011 and 2010, respectively. Had such LIFO inventories been valued at current costs, their carrying values would have been approximately $169 and $154 million higher at December 31, 2011 and 2010, respectively.
Note 10. Investments and Long-Term Receivables
| | | | | | | | | |
| | December 31, | | |
| | | |
| | 2011 | | 2010 | |
| | | | | |
| | | | | | | | | |
Investments | | $ | 362 | | | $ | 413 | | |
Long-term trade and other receivables | | | 81 | | | | 83 | | |
Long-term financing receivables | | | 51 | | | | 120 | | |
| | | | | | | | | |
| | $ | 494 | | | $ | 616 | | |
| | | | | | | | | |
Long-Term Trade and Other Receivables include $29 and $19 million of unbilled balances under long-term contracts as of December 31, 2011 and 2010, respectively. These amounts are billed in accordance with the terms of the customer contracts to which they relate.
The following table summarizes long term trade, financing and other receivables by segment, including current portions and allowances for credit losses.
| | | | | |
| | December 31, 2011 | |
| | | |
Aerospace | | $ | 13 | | |
Automation and Control Solutions | | | 90 | | |
Performance Materials and Technologies | | | 7 | | |
Transportation Systems | | | 7 | | |
Corporate | | | 19 | | |
| | | | | |
| | $ | 136 | | |
| | | | | |
Allowance for credit losses for the above detailed long-term trade, financing and other receivables totaled $5 million and $7 million as of December 31, 2011 and 2010, respectively. The receivables are evaluated for impairment on an individual basis, including consideration of credit quality. The above detailed financing receivables are predominately with commercial and governmental counterparties of investment grade credit quality.
75
Note 11. Property, Plant and Equipment
| | | | | | | | | |
| | December 31, | |
| | | |
| | 2011 | | 2010 | |
| | | | | |
Land and improvements | | $ | 376 | | | $ | 375 | | |
Machinery and equipment | | | 9,937 | | | | 9,878 | | |
Buildings and improvements | | | 2,897 | | | | 2,750 | | |
Construction in progress | | | 513 | | | | 398 | | |
| | | | | | | | | |
| | | 13,723 | | | | 13,401 | | |
Less—Accumulated depreciation | | | (8,919 | ) | | | (8,677 | ) | |
| | | | | | | | | |
| | $ | 4,804 | | | $ | 4,724 | | |
| | | | | | | | | |
Depreciation expense was $699, $707 and $686 million in 2011, 2010 and 2009, respectively.
Note 12. Goodwill and Other Intangible Assets - Net
The change in the carrying amount of goodwill for the years ended December 31, 2011 and 2010 by segment is as follows:
| | | | | | | | | | | | | | | | | | | | | |
| | December 31, 2010 | | Acquisitions | | Divestitures | | Currency Translation Adjustment | | December 31, 2011 | |
| | | | | | | | | | | |
Aerospace | | $ | 1,883 | | | $ | 212 | | | $ | — | | | $ | — | | | $ | 2,095 | | |
Automation and Control Solutions | | | 7,907 | | | | 365 | | | | (12 | ) | | | — | | | | 8,260 | | |
Performance Materials and Technologies | | | 1,291 | | | | 15 | | | | — | | | | — | | | | 1,306 | | |
Transportation Systems | | | 194 | | | | — | | | | — | | | | 3 | | | | 197 | | |
| | | | | | | | | | | | | | | | | | | | | |
| | $ | 11,275 | | | $ | 592 | | | $ | (12 | ) | | $ | 3 | | | $ | 11,858 | | |
| | | | | | | | | | | | | | | | | | | | | |
| | | | | | | | | | | | | | | | | | | | | | | | | |
| | December 31, 2011 | | December 31, 2010 | |
| | | | | |
| | Gross Carrying Amount | | Accumulated Amortization | | Net Carrying Amount | | Gross Carrying Amount | | Accumulated Amortization | | Net Carrying Amount | |
| | | | | | | | | | | | | |
Determinable life intangibles: | | | | | | | | | | | | | | | | | | | | | | | |
Patents and technology | | $ | 1,151 | | | $ | (761 | ) | | $ | 390 | | | $ | 1,101 | | | $ | (676 | ) | | $ | 425 | | |
Customer relationships | | | 1,718 | | | | (493 | ) | | | 1,225 | | | | 1,688 | | | | (399 | ) | | | 1,289 | | |
Trademarks | | | 155 | | | | (84 | ) | | | 71 | | | | 186 | | | | (84 | ) | | | 102 | | |
Other | | | 211 | | | | (145 | ) | | | 66 | | | | 512 | | | | (404 | ) | | | 108 | | |
| | | | | | | | | | | | | | | | | | | | | | | | | |
| | | 3,235 | | | | (1,483 | ) | | | 1,752 | | | | 3,487 | | | | (1,563 | ) | | | 1,924 | | |
| | | | | | | | | | | | | | | | | | | | | | | | | |
| | | | | | | | | | | | | | | | | | | | | | | | | |
Indefinite life intangibles: | | | | | | | | | | | | | | | | | | | | | | | | | |
Trademarks | | | 725 | | | | — | | | | 725 | | | | 613 | | | | — | | | | 613 | | |
| | | | | | | | | | | | | | | | | | | | | | | | | |
| | $ | 3,960 | | | $ | (1,483 | ) | | $ | 2,477 | | | $ | 4,100 | | | $ | (1,563 | ) | | $ | 2,537 | | |
| | | | | | | | | | | | | | | | | | | | | | | | | |
Intangible assets amortization expense was $249, $263, and $250 million in 2011, 2010, 2009, respectively. Estimated intangible asset amortization expense for each of the next five years approximates $250 million in 2012, $226 million in 2013, $200 million in 2014, $166 million in 2015, and $141 in 2016.
Note 13. Accrued Liabilities
76
| | | | | | | | | |
| | | December 31, | |
| | | | |
| | | 2011 | | | 2010 | |
| | | | | | | |
| Compensation, benefit and other employee related | | $ | 1,555 | | | $ | 1,363 | |
| Customer advances and deferred income | | | 1,914 | | | | 1,703 | |
| Asbestos related liabilities | | | 237 | | | | 162 | |
| Repositioning | | | 414 | | | | 306 | |
| Product warranties and performance guarantees | | | 367 | | | | 380 | |
| Environmental costs | | | 303 | | | | 328 | |
| Income taxes | | | 318 | | | | 466 | |
| Accrued interest | | | 108 | | | | 116 | |
| Other taxes (payroll, sales, VAT etc.) | | | 233 | | | | 249 | |
| Insurance | | | 180 | | | | 179 | |
| Other (primarily operating expenses) | | | 1,234 | | | | 1,194 | |
| | | | | | | |
| | | $ | 6,863 | | | $ | 6,446 | |
| | | | | | | |
Note 14. Long -term Debt and Credit Agreements
| | | | | | | | |
| | December 31, | |
| | | |
| | 2011 | | | 2010 | |
| | | | | | |
6.125% notes due 2011 | | $ | — | | | $ | 500 | |
5.625% notes due 2012 | | | — | | | | 400 | |
4.25% notes due 2013 | | | 600 | | | | 600 | |
3.875% notes due 2014 | | | 600 | | | | 600 | |
5.40% notes due 2016 | | | 400 | | | | 400 | |
5.30% notes due 2017 | | | 400 | | | | 400 | |
5.30% notes due 2018 | | | 900 | | | | 900 | |
5.00% notes due 2019 | | | 900 | | | | 900 | |
4.25% notes due 2021 | | | 800 | | | | — | |
5.375% notes due 2041 | | | 600 | | | | — | |
Industrial development bond obligations, floating rate maturing at various dates through 2037 | | | 37 | | | | 46 | |
6.625% debentures due 2028 | | | 216 | | | | 216 | |
9.065% debentures due 2033 | | | 51 | | | | 51 | |
5.70% notes due 2036 | | | 550 | | | | 550 | |
5.70% notes due 2037 | | | 600 | | | | 600 | |
Other (including capitalized leases), 0.6%-9.5% maturing at various dates through 2023 | | | 242 | | | | 115 | |
| | | | | | | | |
| | | 6,896 | | | | 6,278 | |
Less: current portion | | | (15 | ) | | | (523 | ) |
| | | | | | | | |
| | $ | 6,881 | | | $ | 5,755 | |
| | | | | | |
77
The schedule of principal payments on long term debt is as follows:
| | | | |
| | December 31, 2011 | |
| | | |
2012 | | $ | 15 | |
2013 | | | 628 | |
2014 | | | 613 | |
2015 | | | 1 | |
2016 | | | 455 | |
Thereafter | | | 5,184 | |
| | | | |
| | | 6,896 | |
Less-current portion | | | (15 | ) |
| | | | |
| | $ | 6,881 | |
| | | | |
In February 2011, the Company issued $800 million 4.25 percent Senior Notes due 2021 and $600 million 5.375 percent Senior Notes due 2041 (collectively, the “Notes”). The Notes are senior unsecured and unsubordinated obligations of Honeywell and rank equally with all of Honeywell’s existing and future senior unsecured debt and senior to all of Honeywell’s subordinated debt. The offering resulted in gross proceeds of $1,400 million, offset by $19 million in discount and closing costs related to the offering.
In the first quarter of 2011, the Company repurchased the entire outstanding principal amount of its $400 million 5.625 percent Notes due 2012 via a cash tender offer and a subsequent optional redemption. The cost relating to the early redemption of the Notes, including the “make-whole premium”, was $29 million.
In March 2011, the Company entered into a $2,800 million Five Year Credit Agreement (“Credit Agreement”) with a syndicate of banks. Commitments under the Credit Agreement can be increased pursuant to the terms of the Credit Agreement to an aggregate amount not to exceed $3,500 million. The Credit Agreement contains a $700 million sub-limit for the issuance of letters of credit. The Credit Agreement is maintained for general corporate purposes, including support for the issuance of commercial paper, and replaces the previous $2,800 million five year credit agreement dated May 14, 2007 (“Prior Agreement”). There have been no borrowings under the Credit Agreement or the Prior Agreement.
The Credit Agreement does not restrict our ability to pay dividends and contains no financial covenants. The failure to comply with customary conditions or the occurrence of customary events of default contained in the credit agreement would prevent any further borrowings and would generally require the repayment of any outstanding borrowings under the credit agreement. Such events of default include: (a) non-payment of credit agreement debt, interest or fees; (b) non-compliance with the terms of the credit agreement covenants; (c) cross-default to other debt in certain circumstances; (d) bankruptcy; and (e) defaults upon obligations under Employee Retirement Income Security Act. Additionally, each of the banks has the right to terminate its commitment to lend additional funds or issue letters of credit under the agreement if any person or group acquires beneficial ownership of 30 percent or more of our voting stock, or, during any 12-month period, individuals who were directors of Honeywell at the beginning of the period cease to constitute a majority of the Board of Directors.
Loans under the Credit Agreement are required to be repaid no later than March 31, 2016. We have agreed to pay a facility fee of 0.125 percent per annum on the aggregate commitment.
Interest on borrowings under the Credit Agreement would be determined, at Honeywell’s option, by (a) a competitive bidding procedure; (b) the highest of the floating base rate publicly announced by Citibank, N.A. 0.5 percent above the Federal funds rate or Libor plus 1 percent; or (c) the Eurocurrency rate plus Honeywell’s credit default swap spread, subject to a floor and a cap (applicable margin).
The facility fee, the applicable margin over the Eurocurrency rate and the letter of credit issuance fee, are subject to change, based upon a grid determined by our long term debt ratings. The Credit Agreement is not subject to termination based upon a decrease in our debt ratings or a material adverse change.
In the fourth quarter of 2011, the Company repaid $500 million of its 6.125% notes. The repayment was funded with cash provided by operating activities.
78
In the first quarter of 2010, the Company repaid $1,000 million of its 7.50% notes. The repayment was funded with cash provided by operating activities.
As a source of liquidity, we sell interests in designated pools of trade accounts receivables to third parties. As of December 31, 2011 and December 31, 2010, none of the receivables in the designated pools had been sold to third parties. When we sell receivables, they are over-collateralized and we retain a subordinated interest in the pool of receivables representing that over-collateralization as well as an undivided interest in the balance of the receivables pools. The terms of the trade accounts receivable program permit the repurchase of receivables from the third parties at our discretion, providing us with an additional source of revolving credit. As a result, program receivables remain on the Company’s balance sheet with a corresponding amount recorded as either Short-term borrowings or Long-term debt.
Note 15. Lease Commitments
Future minimum lease payments under operating leases having initial or remaining noncancellable lease terms in excess of one year are as follows:
| | | | |
| | At December 31, 2011 | |
| | | |
2012 | | $ | 311 | |
2013 | | | 248 | |
2014 | | | 184 | |
2015 | | | 135 | |
2016 | | | 92 | |
Thereafter | | | 243 | |
| | | | |
| | $ | 1,213 | |
| | | | |
We have entered into agreements to lease land, equipment and buildings. Principally all our operating leases have initial terms of up to 25 years, and some contain renewal options subject to customary conditions. At any time during the terms of some of our leases, we may at our option purchase the leased assets for amounts that approximate fair value. We do not expect that any of our commitments under the lease agreements will have a material adverse effect on our consolidated results of operations, financial position or liquidity.
Rent expense was $386, $369 and $366 million in 2011, 2010 and 2009, respectively.
Note 16. Financial Instruments and Fair Value Measures
Credit and Market Risk—Financial instruments, including derivatives, expose us to counterparty credit risk for nonperformance and to market risk related to changes in interest and currency exchange rates and commodity prices. We manage our exposure to counterparty credit risk through specific minimum credit standards, diversification of counterparties, and procedures to monitor concentrations of credit risk. Our counterparties in derivative transactions are substantial investment and commercial banks with significant experience using such derivative instruments. We monitor the impact of market risk on the fair value and cash flows of our derivative and other financial instruments considering reasonably possible changes in interest rates, currency exchange rates and commodity prices and restrict the use of derivative financial instruments to hedging activities.
We continually monitor the creditworthiness of our customers to which we grant credit terms in the normal course of business. The terms and conditions of our credit sales are designed to mitigate or eliminate concentrations of credit risk with any single customer. Our sales are not materially dependent on a single customer or a small group of customers.
Foreign Currency Risk Management—We conduct our business on a multinational basis in a wide variety of foreign currencies. Our exposure to market risk for changes in foreign currency exchange rates arises from international financing activities between subsidiaries, foreign currency denominated monetary assets and liabilities and transactions arising from international trade. Our objective is to preserve the economic value of non-functional currency denominated cash flows. We attempt to hedge transaction exposures with natural offsets to the fullest extent possible and, once these opportunities have been exhausted, through foreign currency exchange forward and option contracts with third parties.
79
We hedge monetary assets and liabilities denominated in non-functional currencies. Prior to conversion into U.S. dollars, these assets and liabilities are remeasured at spot exchange rates in effect on the balance sheet date. The effects of changes in spot rates are recognized in earnings and included in Other (Income) Expense. We partially hedge forecasted sales and purchases, which predominantly occur in the next twelve months and are denominated in non-functional currencies, with currency forward contracts. Changes in the forecasted non-functional currency cash flows due to movements in exchange rates are substantially offset by changes in the fair value of the currency forward contracts designated as hedges. Market value gains and losses on these contracts are recognized in earnings when the hedged transaction is recognized. Open foreign currency exchange forward contracts mature predominantly in the next twelve months. At December 31, 2011 and 2010, we had contracts with notional amounts of $7,108 million and $5,733 million, respectively, to exchange foreign currencies, principally the U.S. dollar, Euro, British pound, Canadian dollar, Hong Kong dollar, Mexican peso, Swiss franc, Czech koruna, Chinese renminbi, Indian rupee, Singapore dollar, Swedish krona, Korean won and Thai baht.
Commodity Price Risk Management—Our exposure to market risk for commodity prices can result in changes in our cost of production. We primarily mitigate our exposure to commodity price risk through the use of long-term, fixed-price contracts with our suppliers and formula price agreements with suppliers and customers. We also enter into forward commodity contracts with third parties designated as hedges of anticipated purchases of several commodities. Forward commodity contracts are marked-to-market, with the resulting gains and losses recognized in earnings when the hedged transaction is recognized. At December 31, 2011 and 2010, we had contracts with notional amounts of $59 million and $23 million, respectively, related to forward commodity agreements, principally base metals and natural gas.
Interest Rate Risk Management— We use a combination of financial instruments, including long-term, medium-term and short-term financing, variable-rate commercial paper, and interest rate swaps to manage the interest rate mix of our total debt portfolio and related overall cost of borrowing. At December 31, 2011 and 2010, interest rate swap agreements designated as fair value hedges effectively changed $1,400 and $600 million, respectively, of fixed rate debt at a rate of 4.09 and 3.88 percent, respectively, to LIBOR based floating rate debt. Our interest rate swaps mature through 2021.
Fair Value of Financial Instruments— The FASB’s accounting guidance defines fair value as the price that would be received to sell an asset or paid to transfer a liability in an orderly transaction between market participants at the measurement date (exit price). The FASB’s guidance classifies the inputs used to measure fair value into the following hierarchy:
| | | |
| Level 1 | Unadjusted quoted prices in active markets for identical assets or liabilities | |
| | | |
| Level 2 | Unadjusted quoted prices in active markets for similar assets or liabilities, or | |
| | Unadjusted quoted prices for identical or similar assets or liabilities in markets that are not active, or | |
| | Inputs other than quoted prices that are observable for the asset or liability | |
| | | |
| Level 3 | Unobservable inputs for the asset or liability | |
The Company endeavors to utilize the best available information in measuring fair value. Financial and nonfinancial assets and liabilities are classified in their entirety based on the lowest level of input that is significant to the fair value measurement. The Company has determined that our available for sale investments in marketable equity securities are level 1 and our remaining financial assets and liabilities are level 2 in the fair value hierarchy. The following table sets forth the Company’s financial assets and liabilities that were accounted for at fair value on a recurring basis as of December 31, 2011 and 2010:
80
| | | | | | | |
| | December 31, 2011 | | December 31, 2010 | |
| | | | | |
Assets: | | | | | | | |
Foreign currency exchange contracts | | $ | 26 | | $ | 16 | |
Available for sale investments | | | 359 | | | 322 | |
Interest rate swap agreements | | | 134 | | | 22 | |
Forward commodity contracts | | | 1 | | | 2 | |
| | | | | | | |
Liabilities: | | | | | | | |
Foreign currency exchange contracts | | $ | 52 | | $ | 14 | |
Forward commodity contracts | | | 10 | | | 2 | |
The foreign currency exchange contracts, interest rate swap agreements, and forward commodity contracts are valued using broker quotations, or market transactions in either the listed or over-the-counter markets. As such, these derivative instruments are classified within level 2. The Company also holds investments in commercial paper, certificates of deposits, and time deposits that are designated as available for sale and are valued using market transactions in over-the-counter markets. As such, these investments are classified within level 2.
The carrying value of cash and cash equivalents, trade accounts and notes receivables, payables, commercial paper and short-term borrowings contained in the Consolidated Balance Sheet approximates fair value. The following table sets forth the Company’s financial assets and liabilities that were not carried at fair value:
| | | | | | | | | | | | | | |
| | December 31, 2011 | | | December 31, 2010 | |
| | | | | | |
| | Carrying Value | | Fair Value | | | Carrying Value | | Fair Value | |
| | | | | | | | | | |
Assets | | | | | | | | | | | | | | |
Long-term receivables | | $ | 132 | | $ | 132 | | | $ | 203 | | $ | 199 | |
Liabilities | | | | | | | | | | | | | | |
Long-term debt and related current maturities | | $ | 6,896 | | $ | 7,896 | | | $ | 6,278 | | $ | 6,835 | |
In the years ended December 31, 2011 and 2010, the Company had assets with a net book value of $262 million and $32 million, respectively, specifically property, plant and equipment, software and intangible assets, which were accounted for at fair value on a nonrecurring basis. These assets were tested for impairment and based on the fair value of these assets the Company recognized losses of $127 million and $30 million, respectively, in the years ended December 31, 2011 and 2010, primarily in connection with our repositioning actions (see Note 3 Repositioning and Other Charges). The Company has determined that the fair value measurements of these nonfinancial assets are level 3 in the fair value hierarchy.
The Company holds investments in marketable equity securities that are designated as available for sale securities. Due to an other-than-temporary decline in fair value of these investments, the Company recognized an impairment charge of $62 million in the second quarter of 2009 that is included in Other (Income) Expense.
The derivatives utilized for risk management purposes as detailed above are included on the Consolidated Balance Sheet and impacted the Statement of Operations as follows:
81
Fair value of derivatives classified as assets consist of the following:
| | | | | | | | | | | |
Designated as a Hedge | | Balance Sheet Classification | | December 31, 2011 | | December 31, 2010 | |
| | | | | | | | | |
Foreign currency exchange contracts | | Accounts, notes, and other receivables | | $ | 18 | | | $ | 10 | | |
Interest rate swap agreements | | Other assets | | | 134 | | | | 22 | | |
Commodity contracts | | Accounts, notes, and other receivables | | | 1 | | | | 2 | | |
| | | | | | | | | | | |
Not Designated as a Hedge | | Balance Sheet Classification | | December 31, 2011 | | December 31, 2010 | |
| | | | | | | | | |
Foreign currency exchange contracts | | Accounts, notes, and other receivables | | $ | 8 | | | $ | 6 | | |
| | | | | | | | | | |
Fair value of derivatives classified as liabilities consist of the following: |
| | | | | | | | | | | |
Designated as a Hedge | | Balance Sheet Classification | | December 31, 2011 | | December 31, 2010 | |
| | | | | | | | | |
Foreign currency exchange contracts | | Accrued liabilities | | $ | 50 | | | $ | 9 | | |
Commodity contracts | | Accrued liabilities | | | 10 | | | | 2 | | |
| | | | | | | | | | | |
Not Designated as a Hedge | | Balance Sheet Classification | | December 31, 2011 | | December 31, 2010 | |
| | | | | | | | | |
Foreign currency exchange contracts | | Accrued liabilities | | $ | 2 | | | $ | 5 | | |
| | | | | | | |
Gains (losses) recognized in OCI (effective portions) consist of the following: |
| | | | | | | |
| | Year Ended December 31, |
| | |
Designated Cash Flow Hedge | | 2011 | | 2010 | |
| | | | | |
Foreign currency exchange contracts | | $ | (42 | ) | $ | 12 | |
Commodity contracts | | | (12 | ) | | (7 | ) |
| | | | | | | | | |
Gains (losses) reclassified from AOCI to income consist of the following: |
| | | | | | | | | |
| | | | Year Ended December 31, |
Designated Cash Flow Hedge | | Income Statement Location | | 2011 | | 2010 | |
| | | | | | | |
Foreign currency exchange contracts | | Product sales | | $ | 29 | | $ | (19 | ) |
| | Cost of products sold | | | (34 | ) | | 30 | |
| | Sales & general administrative | | | (8 | ) | | (3 | ) |
| | | | | | | | | |
Commodity contracts | | Cost of products sold | | $ | (2 | ) | $ | (8 | ) |
Ineffective portions of commodity derivative instruments designated in cash flow hedge relationships were insignificant in the years ended December 31, 2011 and 2010 and are located in cost of products sold.
82
Interest rate swap agreements are designated as hedge relationships with gains or (losses) on the derivative recognized in Interest and other financial charges offsetting the gains and losses on the underlying debt being hedged. Gains or (losses) on interest rate swap agreements recognized in earnings were $112 and $24 million in the years ended December 31, 2011 and 2010 respectively. These gains were fully offset by losses on the underlying debt being hedged.
We also economically hedge our exposure to changes in foreign exchange rates principally with forward contracts. These contracts are marked-to-market with the resulting gains and losses recognized in earnings offsetting the gains and losses on the non-functional currency denominated monetary assets and liabilities being hedged. We recognized $30 million of income and $18 million of expense, in Other (Income) Expense for the years ended December 31, 2011 and 2010, respectively.
Note 17. Other Liabilities
| | | | | | | | |
| | Year Ended December 31, |
| | |
| | 2011 | | 2010 |
| | | | |
Pension and other employee related | | $ | 4,308 | | | $ | 4,216 | |
Environmental | | | 420 | | | | 425 | |
Income taxes | | | 856 | | | | 562 | |
Insurance | | | 218 | | | | 177 | |
Asset retirement obligations(1) | | | 74 | | | | 80 | |
Deferred income | | | 77 | | | | 94 | |
Other | | | 205 | | | | 344 | |
| | | | | | | | |
| | $ | 6,158 | | | | 5,898 | |
| | | | | | | | |
| | | | | | | | |
(1) Asset retirement obligations primarily relate to costs associated with the future retirement of nuclear fuel conversion facilities in our Performance Materials and Technologies segment and the future retirement of facilities in our Automation and Control Solutions segment. |
A reconciliation of our liability for asset retirement obligations for the year ended December 31, 2011, is as follows:
| | | | | | | |
| | 2011 | | 2010 | |
| | | | |
Change in asset retirement obligations: | | | | | | | |
Balance at beginning of year | | $ | 80 | | $ | 79 | |
Liabilities settled | | | (6 | ) | | (3 | ) |
Adjustments | | | (2 | ) | | 2 | |
Accretion expense | | | 2 | | | 2 | |
| | | | | | |
Balance at end of year | | $ | 74 | | $ | 80 | |
| | | | | | | |
Note 18. Capital Stock
We are authorized to issue up to 2,000,000,000 shares of common stock, with a par value of $1. Common shareowners are entitled to receive such dividends as may be declared by the Board, are entitled to one vote per share, and are entitled, in the event of liquidation, to share ratably in all the assets of Honeywell which are available for distribution to the common shareowners. Common shareowners do not have preemptive or conversion rights. Shares of common stock issued and outstanding or held in the treasury are not liable to further calls or assessments. There are no restrictions on us relative to dividends or the repurchase or redemption of common stock.
The Board of Directors has authorized the repurchase of up to a total of $3.0 billion of Honeywell common stock, which amount includes $1.9 billion that remained available under the Company’s previously reported share repurchase program. We purchased a total of approximately 20.3 million shares of our common stock in 2011 for $1,085 million.
83
We are authorized to issue up to 40,000,000 shares of preferred stock, without par value, and can determine the number of shares of each series, and the rights, preferences and limitations of each series. At December 31, 2011, there was no preferred stock outstanding.
Note 19. Accumulated Other Comprehensive Income (Loss)
Total accumulated other comprehensive income (loss) is included in the Consolidated Statement of Shareowners’ Equity. Comprehensive Income (Loss) attributable to non-controlling interest consisted predominantly of net income. The changes in Accumulated Other Comprehensive Income (Loss) are as follows:
| | | | | | | | | | | | |
| | Pretax | | Tax | | After Tax |
| | | | | | |
Year Ended December 31, 2011 | | | | | | | | | | | | |
Foreign exchange translation adjustment | | $ | (146 | ) | | $ | — | | | $ | (146 | ) |
Pensions and other post retirement benefit adjustments | | | (317 | ) | | | 108 | | | | (209 | ) |
Changes in fair value of available for sale investments | | | 12 | | | | — | | | | 12 | |
Changes in fair value of effective cash flow hedges | | | (41 | ) | | | 7 | | | | (34 | ) |
| | | | | | | | | | | | |
| | $ | (492 | ) | | $ | 115 | | | $ | (377 | ) |
| | | | | | | | | | | | |
| | | | | | | | | | | | |
Year Ended December 31, 2010 | | | | | | | | | | | | |
Foreign exchange translation adjustment | | $ | (249 | ) | | $ | — | | | $ | (249 | ) |
Pensions and other post retirement benefit adjustments | | | 26 | | | | 18 | | | | 44 | |
Changes in fair value of available for sale investments | | | 90 | | | | — | | | | 90 | |
Changes in fair value of effective cash flow hedges | | | (6 | ) | | | 2 | | | | (4 | ) |
| | | | | | | | | | | | |
| | $ | (139 | ) | | $ | 20 | | | $ | (119 | ) |
| | | | | | | | | | | | |
| | | | | | | | | | | | |
Year Ended December 31, 2009 | | | | | | | | | | | | |
Foreign exchange translation adjustment | | $ | 259 | | | $ | — | | | $ | 259 | |
Pensions and other post retirement benefit adjustments | | | (407 | ) | | | 136 | | | | (271 | ) |
Changes in fair value of available for sale investments(1) | | | 112 | | | | — | | | | 112 | |
Changes in fair value of effective cash flow hedges | | | 38 | | | | (8 | ) | | | 30 | |
| | | | | | | | | | | | |
| | $ | 2 | | | $ | 128 | | | $ | 130 | |
| | | | | | | | | | | | |
| |
| (1) Includes reclassification adjustment for losses included in net income |
| | | | | | | | | |
Components of Accumulated Other Comprehensive Income (Loss) |
| | | | | | | |
| | December 31, |
| | |
| | 2011 | | | 2010 | | |
| | | | | | | |
Cumulative foreign exchange translation adjustment | | $ | 74 | | | $ | 220 | | |
Pensions and other post retirement benefit adjustments | | | (1,650 | ) | | | (1,441 | ) | |
Change in fair value of available for sale investments | | | 163 | | | | 151 | | |
Change in fair value of effective cash flow hedges | | | (31 | ) | | | 3 | | |
| | | | | | | | | |
| | $ | (1,444 | ) | | $ | (1,067 | ) | |
| | | | | | | | | |
Note 20. Stock-Based Compensation Plans
We have stock-based compensation plans available to grant non-qualified stock options, incentive stock options, stock appreciation rights, restricted units and restricted stock to key employees. The 2011 Stock Incentive Plan of Honeywell International Inc. and its Affiliates (the Plan) was approved by the shareowners at the Annual Meeting of Shareowners effective on April 26, 2011. Following approval of the Plan on April 26, 2011 we have not and will not grant any new awards to key employees under any previously existing stock-based compensation plans. There were 39,582,132 shares available for future grants under the terms of the Plan at December 31, 2011. Additionally, under the 2006 Stock Plan for Non-Employee Directors of Honeywell International Inc. (the Directors Plan) there were 229,000 shares of Honeywell common stock available for future grant as of December 31, 2011.
84
Stock Options—The exercise price, term and other conditions applicable to each option granted under our stock plans are generally determined by the Management Development and Compensation Committee of the Board. The exercise price of stock options is set on the grant date and may not be less than the fair market value per share of our stock on that date. The fair value is recognized as an expense over the employee’s requisite service period (generally the vesting period of the award). Options generally vest over a four-year period and expire after ten years.
The fair value of each option award is estimated on the date of grant using the Black-Scholes option-pricing model. Expected volatility is based on implied volatilities from traded options on Honeywell common stock. We used a Monte Carlo simulation model to derive an expected term. Such model uses historical data to estimate option exercise activity and post-vest termination behavior. The expected term represents an estimate of the time options are expected to remain outstanding. The risk-free rate for periods within the contractual life of the option is based on the U.S. treasury yield curve in effect at the time of grant.
Compensation cost on a pre-tax basis related to stock options recognized in operating results (included in selling, general and administrative expenses) in 2011, 2010 and 2009 was $59, $55 and $39 million, respectively. The associated future income tax benefit recognized in 2011, 2010 and 2009 was $19, $16 and $13 million, respectively.
The following table sets forth fair value per share information, including related weighted-average assumptions, used to determine compensation cost:
| | | | | | | | | | | | |
| | Years Ended December 31, | |
| | | |
| | 2011 | | | 2010 | | | 2009 | |
| | | | | | | | | |
Weighted average fair value per share of options granted during the year(1) | | $ | 12.56 | | | $ | 8.96 | | | $ | 6.73 | |
Assumptions: | | | | | | | | | | | | |
Expected annual dividend yield | | | 2.68 | % | | | 3.00 | % | | | 4.26 | % |
Expected volatility | | | 27.60 | % | | | 29.39 | % | | | 35.78 | % |
Risk-free rate of return | | | 2.47 | % | | | 2.64 | % | | | 2.53 | % |
Expected option term (years) | | | 5.8 | | | | 5.4 | | | | 5.8 | |
| |
(1) | Estimated on date of grant using Black-Scholes option-pricing model. |
The following table summarizes information about stock option activity for the three years ended December 31, 2011:
85
| | | | | | | | |
| | Number of Options | | | Weighted Average Exercise Price | |
| | | | | | |
Outstanding at December 31, 2008 | | | 40,933,522 | | | $ | 43.97 | |
Granted | | | 9,159,650 | | | | 28.40 | |
Exercised | | | (645,201 | ) | | | 31.66 | |
Lapsed or canceled | | | (8,537,598 | ) | | | 53.90 | |
| | | | | | | | |
Outstanding at December 31, 2009 | | | 40,910,373 | | | | 38.58 | |
Granted | | | 7,607,950 | | | | 40.29 | |
Exercised | | | (5,211,526 | ) | | | 34.77 | |
Lapsed or canceled | | | (2,515,266 | ) | | | 44.14 | |
| | | | | | | | |
Outstanding at December 31, 2010 | | | 40,791,531 | | | | 39.05 | |
Granted | | | 7,625,950 | | | | 57.08 | |
Exercised | | | (7,984,840 | ) | | | 36.39 | |
Lapsed or canceled | | | (1,516,271 | ) | | | 42.38 | |
| | | | | | | | |
Outstanding at December 31, 2011 | | | 38,916,370 | | | $ | 43.01 | |
| | | | | | | | |
Vested and expected to vest at December 31, 2011(1) | | | 35,845,642 | | | $ | 42.49 | |
| | | | | | | | |
Exercisable at December 31, 2011 | | | 21,672,281 | | | $ | 40.71 | |
| | | | | | | | |
| |
(1) | Represents the sum of vested options of 21.7 million and expected to vest options of 14.1 million. Expected to vest options are derived by applying the pre-vesting forfeiture rate assumption to total outstanding unvested options 17.2 million. |
The following table summarizes information about stock options outstanding and exercisable at December 31, 2011:
| | | | | | | | | | | | | | | | | | | | | | | | | | | | |
| | Options Outstanding | | Options Exercisable |
| | | | |
Range of Exercise prices | | Number Outstanding | | | Weighted Average Life (1) | | | Weighted Average Exercise Price | | | Aggregate Intrinsic Value | | | Number Exercisable | | | Weighted Average Exercise Price | | | Aggregate Intrinsic Value | |
| | | | | | | | | | | | | | | | | | | | | |
$21.75–$32.99 | | | 8,037,712 | | | | 5.90 | | | $ | 27.53 | | | $ | 216 | | | | 4,346,486 | | | $ | 26.79 | | | $ | 120 | |
$33.00–$39.99 | | | 5,219,120 | | | | 2.75 | | | | 36.22 | | | | 95 | | | | 5,219,120 | | | | 36.22 | | | | 95 | |
$40.00–$49.99 | | | 14,259,988 | | | | 6.31 | | | | 42.61 | | | | 167 | | | | 8,978,375 | | | | 43.96 | | | | 93 | |
$50.00–$74.95 | | | 11,399,550 | | | | 8.10 | | | | 57.52 | | | | — | | | | 3,128,300 | | | | 58.23 | | | | — | |
| | | | | | | | | | | | | | | | | | | | | | | | | | | | |
| | | 38,916,370 | | | | 6.27 | | | | 43.01 | | | $ | 478 | | | | 21,672,281 | | | | 40.71 | | | $ | 308 | |
| | | | | | | | | | | | | | | | | | | | | | | | | | | | |
(1) Average remaining contractual life in years.
There were 24,722,493 and 27,427,023 options exercisable at weighted average exercise prices of $39.43 and $38.85 at December 31, 2010 and 2009, respectively.
The total intrinsic value of options (which is the amount by which the stock price exceeded the exercise price of the options on the date of exercise) exercised during 2011, 2010 and 2009 was $164, $54 and $4 million, respectively. During 2011, 2010 and 2009, the amount of cash received from the exercise of stock options was $290, $181 and $20 million, respectively, with an associated tax benefit realized of $54, $18 and $1 million, respectively. In 2011, 2010 and 2009 we classified $42, $13 and $1 million, respectively, of this benefit as a financing cash inflow in the Consolidated Statement of Cash Flows, and the balance was classified as cash from operations.
At December 31, 2011 there was $119 million of total unrecognized compensation cost related to non-vested stock option awards which is expected to be recognized over a weighted-average period of 2.52 years. The total fair value of options vested during 2011, 2010 and 2009 was $52, $41 and $51 million, respectively.
86
Restricted Stock Units—Restricted stock unit (RSU) awards entitle the holder to receive one share of common stock for each unit when the units vest. RSUs are issued to certain key employees at fair market value at the date of grant as compensation. RSUs typically become fully vested over periods ranging from three to seven years and are payable in Honeywell common stock upon vesting.
The following table summarizes information about RSU activity for the three years ended December 31, 2011:
| | | | | | | | | |
| | Number of Restricted Stock Units | | Weighted Average Grant Date Fair Value Per Share | |
| | | | | |
Non-vested at December 31, 2008 | | 6,825,717 | | | $ | | 46.63 | | |
Granted | | 3,691,129 | | | | | 30.16 | | |
Vested | | (1,313,975 | ) | | | | 40.44 | | |
Forfeited | | (940,094 | ) | | | | 44.51 | | |
| | | | | | | | | |
Non-vested at December 31, 2009 | | 8,262,777 | | | | | 40.49 | | |
Granted | | 3,842,367 | | | | | 42.33 | | |
Vested | | (1,593,979 | ) | | | | 48.71 | | |
Forfeited | | (537,212 | ) | | | | 40.45 | | |
| | | | | | | | | |
Non-vested at December 31, 2010 | | 9,973,953 | | | | | 39.89 | | |
Granted | | 1,887,733 | | | | | 55.11 | | |
Vested | | (1,509,528 | ) | | | | 49.48 | | |
Forfeited | | (605,725 | ) | | | | 40.11 | | |
| | | | | | | | | |
Non-vested at December 31, 2011 | | 9,746,433 | | | $ | | 41.35 | | |
| | | | | | | | | |
As of December 31, 2011, there was approximately $179 million of total unrecognized compensation cost related to non-vested RSUs granted under our stock plans which is expected to be recognized over a weighted-average period of 1.8 years. Compensation expense related to RSUs was $109, $109 and $79 million in 2011, 2010, and 2009, respectively.
Non-Employee Directors’ Plan—Under the Directors’ Plan each new non-employee director receives a one-time grant of 3,000 restricted stock units that will vest on the fifth anniversary of continuous Board service.
In 2011, each non-employee director received an annual grant to purchase 5,000 shares of common stock at the fair market value on the date of grant. In 2012, the annual equity grant will change from a fixed number of shares to a target value of $75,000 and will consist of 50 percent options and 50 percent RSUs. Options will become exercisable over a four-year period and expire after ten years. RSUs will generally vest on the third anniversary of the date of grant.
Note 21. Commitments and Contingencies
Environmental Matters
We are subject to various federal, state, local and foreign government requirements relating to the protection of the environment. We believe that, as a general matter, our policies, practices and procedures are properly designed to prevent unreasonable risk of environmental damage and personal injury and that our handling, manufacture, use and disposal of hazardous substances are in accordance with environmental and safety laws and regulations. However, mainly because of past operations and operations of predecessor companies, we, like other companies engaged in similar businesses, have incurred remedial response and voluntary cleanup costs for site contamination and are a party to lawsuits and claims associated with environmental and safety matters, including past production of products containing hazardous substances. Additional lawsuits, claims and costs involving environmental matters are likely to continue to arise in the future.
With respect to environmental matters involving site contamination, we continually conduct studies, individually or jointly with other potentially responsible parties, to determine the feasibility of various remedial
87
techniques. It is our policy to record appropriate liabilities for environmental matters when remedial efforts or damage claim payments are probable and the costs can be reasonably estimated. Such liabilities are based on our best estimate of the undiscounted future costs required to complete the remedial work. The recorded liabilities are adjusted periodically as remediation efforts progress or as additional technical, regulatory or legal information becomes available. Given the uncertainties regarding the status of laws, regulations, enforcement policies, the impact of other potentially responsible parties, technology and information related to individual sites, we do not believe it is possible to develop an estimate of the range of reasonably possible environmental loss in excess of our recorded liabilities. We expect to fund expenditures for these matters from operating cash flow. The timing of cash expenditures depends on a number of factors, including the timing of remedial investigations and feasibility studies, the timing of litigation and settlements of remediation liability, personal injury and property damage claims, regulatory approval of cleanup projects, remedial techniques to be utilized and agreements with other parties.
The following table summarizes information concerning our recorded liabilities for environmental costs:
| | | | | | | | | | | | | | | |
| | Years Ended December 31, |
| | |
| | 2011 | | 2010 | | 2009 |
| | | | | | |
Beginning of year | | $ | | 753 | | | $ | | 779 | | | $ | | 946 | |
Accruals for environmental matters deemed probable and reasonably estimable | | | | 240 | | | | | 225 | | | | | 151 | |
Environmental liability payments | | | | (270 | ) | | | | (266 | ) | | | | (318 | ) |
Other | | | | — | | | | | 15 | | | | | — | |
| | | | | | | | | | | | | | | |
End of year | | $ | | 723 | | | $ | | 753 | | | $ | | 779 | |
| | | | | | | | | | | | | | | |
Environmental liabilities are included in the following balance sheet accounts:
| | | | | | | | | | | |
| | December 31, 2011 | | December 31, 2010 | |
| | | | | |
Accrued liabilities | | $ | | 303 | | | $ | | 328 | | |
Other liabilities | | | | 420 | | | | | 425 | | |
| | | | | | | | | | | |
| | $ | | 723 | | | $ | | 753 | | |
| | | | | | | | | | | |
Although we do not currently possess sufficient information to reasonably estimate the amounts of liabilities to be recorded upon future completion of studies, litigation or settlements, and neither the timing nor the amount of the ultimate costs associated with environmental matters can be determined, they could be material to our consolidated results of operations or operating cash flows in the periods recognized or paid. However, considering our past experience and existing reserves, we do not expect that these environmental matters will have a material adverse effect on our consolidated financial position.
New Jersey Chrome Sites—The excavation and offsite disposal of approximately one million tons of chromium residue present at a predecessor Honeywell site located in Jersey City, New Jersey, known as Study Area 7, was completed in January 2010. We are also implementing related groundwater remedial actions, and are seeking the appropriate permits from state and federal agencies for related river sediment work approved by the federal court. Provisions have been made in our financial statements for the estimated cost of these remedies.
The above-referenced site is the most significant of the 21 sites located in Hudson County, New Jersey that are the subject of an Administrative Consent Order (ACO) entered into with the New Jersey Department of Environmental Protection (NJDEP) in 1993 (the “Honeywell ACO Sites”). Remedial investigations and activities consistent with the ACO and other applicable settlement orders have been conducted and are underway at the other Honeywell ACO Sites. In addition, a settlement order was entered by the New Jersey State Superior Court in the third quarter of 2011 resolving litigation brought by the NJDEP against Honeywell and two other companies regarding the investigation and remediation of the remaining sites in the area that allegedly have chromium contamination (known as the Publicly Funded Sites). Under the settlement, Honeywell has accepted responsibility to remediate 24 of the 53 Publicly Funded Sites and will also bear 50 percent of the costs at another 10 Publicly Funded Sites. Honeywell is developing a schedule for the investigation and remediation of these Publicly Funded Sites. We have recorded reserves for the Honeywell ACO Sites and the applicable Publicly Funded Sites where
88
appropriate under the accounting policy described above.
Dundalk Marine Terminal, Baltimore, MD—Chrome residue from legacy chrome plant operations in Baltimore was deposited as fill at the Dundalk Marine Terminal (“DMT”), which is owned and operated by the Maryland Port Administration (“MPA”). Honeywell and the MPA have been sharing costs to investigate and mitigate related environmental issues, and have entered into a cost sharing agreement under which Honeywell will bear 77 percent of the costs of developing and implementing permanent remedies for the DMT facility. In January 2011, the MPA and Honeywell submitted to the Maryland Department of the Environment (“MDE”) a Corrective Measures Alternatives Analysis (“CMAA”) of certain potential remedies for DMT to assist MDE in selection of a final remedy, which has not yet occurred. Provision has been made in our financial statements for the CMAA consistent with the accounting policy described above. We have negotiated a Consent Decree with the MPA and MDE with respect to the investigation and remediation of the DMT facility. The Consent Decree is being challenged in federal court by BUILD, a Baltimore community group, together with a local church and two individuals (collectively “BUILD”). In October 2007, the Court dismissed with prejudice BUILD’s state law claims and dismissed without prejudice BUILD’s RCRA claims regarding neighborhoods near the DMT facility. In August 2008, the Court held a hearing on the Company’s motion to dismiss BUILD’s remaining claims on the grounds that MDE is diligently prosecuting the investigation and remediation of the DMT. We are awaiting the Court’s decision. We do not believe that this matter will have a material adverse impact on our consolidated financial position or operating cash flows. Given the scope and complexity of this project, it is possible that the cost of remediation, when determinable, could have a material adverse impact on our results of operations in the periods recognized.
Onondaga Lake, Syracuse, NY—We are implementing a combined dredging/capping remedy of Onondaga Lake pursuant to a consent decree approved by the United States District Court for the Northern District of New York in January 2007. We have accrued for our estimated cost of remediating Onondaga Lake based on currently available information and analysis performed by our engineering consultants. Honeywell is also conducting remedial investigations and activities at other sites in Syracuse. We have recorded reserves for these investigations and activities where appropriate under the accounting policy described above.
Honeywell has entered into a cooperative agreement with potential natural resource trustees to assess alleged natural resource damages relating to this site. It is not possible to predict the outcome or duration of this assessment, or the amounts of, or responsibility for, any damages.
Asbestos Matters
Like many other industrial companies, Honeywell is a defendant in personal injury actions related to asbestos. We did not mine or produce asbestos, nor did we make or sell insulation products or other construction materials that have been identified as the primary cause of asbestos related disease in the vast majority of claimants.
Honeywell’s predecessors owned North American Refractories Company (NARCO) from 1979 to 1986. NARCO produced refractory products (bricks and cement used in high temperature applications). We sold the NARCO business in 1986 and agreed to indemnify NARCO with respect to personal injury claims for products that had been discontinued prior to the sale (as defined in the sale agreement). NARCO retained all liability for all other claims. NARCO and/or Honeywell are defendants in asbestos personal injury cases asserting claims based upon alleged exposure to NARCO asbestos-containing products. Claimants consist largely of individuals who allege exposure to NARCO asbestos-containing refractory products in an occupational setting. These claims, and the filing of subsequent claims, have been stayed continuously since January 4, 2002, the date on which NARCO sought bankruptcy protection (see discussion below).
Honeywell’s Bendix friction materials (Bendix) business manufactured automotive brake parts that contained chrysotile asbestos in an encapsulated form. Claimants consist largely of individuals who allege exposure to asbestos from brakes from either performing or being in the vicinity of individuals who performed brake replacements.
The following tables summarize information concerning NARCO and Bendix asbestos related balances:
89
| | | | | | | | | | | | | | | | | | | | | | | | | | | | | | | | | | | | | | | | | | | | | | |
| | | | | | | |
Asbestos Related Liabilities |
| | Year Ended December 31, 2011 | | Year Ended December 31, 2010 | | Year Ended December 31, 2009 | |
| | | | | | | |
| | Bendix | | NARCO | | Total | | Bendix | | NARCO | | Total | | Bendix | | NARCO | | Total | |
| | | | | | | | | | | | | | | | | | | |
Beginning of year | | $ | | 594 | | | $ | | 1,125 | | | $ | | 1,719 | | | $ | | 566 | | | $ | | 1,128 | | | $ | | 1,694 | | | $ | | 578 | | | $ | | 1,131 | | | $ | | 1,709 | | |
Accrual for update to estimated liability | | | | 167 | | | | | 3 | | | | | 170 | | | | | 162 | | | | | 3 | | | | | 165 | | | | | 127 | | | | | 5 | | | | | 132 | | |
Change in estimated cost of future claims | | | | 16 | | | | | — | | | | | 16 | | | | | 16 | | | | | — | | | | | 16 | | | | | 11 | | | | | — | | | | | 11 | | |
Update of expected resolution values for pending claims | | | | 2 | | | | | — | | | | | 2 | | | | | 7 | | | | | — | | | | | 7 | | | | | (2 | ) | | | | — | | | | | (2 | ) | |
Asbestos related liability payments | | | | (166 | ) | | | | (5 | ) | | | | (171 | ) | | | | (157 | ) | | | | (6 | ) | | | | (163 | ) | | | | (148 | ) | | | | (8 | ) | | | | (156 | ) | |
| | | | | | | | | | | | | | | | | | | | | | | | | | | | | | | | | | | | | | | | | | | | | | |
End of year | | $ | | 613 | | | $ | | 1,123 | | | $ | | 1,736 | | | $ | | 594 | | | $ | | 1,125 | | | $ | | 1,719 | | | $ | | 566 | | | $ | | 1,128 | | | $ | | 1,694 | | |
| | | | | | | | | | | | | | | | | | | | | | | | | | | | | | | | | | | | | | | | | | | | | | |
| | | | | | | | | | | | | | | | | | | | | | | | | | | | | | | | | | | | | | | | | | | | | | |
Insurance Recoveries for Asbestos Related Liabilities |
| | | | | | | | | | | | | | | | | | | | | | | | | | | | |
| | Year Ended December 31, 2011 | | Year Ended December 31, 2010 | | Year Ended December 31, 2009 | |
| | | | | | | |
| | Bendix | | NARCO | | Total | | Bendix | | NARCO | | Total | | Bendix | | NARCO | | Total | |
| | | | | | | | | | | | | | | | | | | |
Beginning of year | | $ | | 157 | | | $ | | 718 | | | $ | | 875 | | | $ | | 172 | | | $ | | 831 | | | $ | | 1,003 | | | $ | | 156 | | | $ | | 877 | | | $ | | 1,033 | | |
Probable insurance recoveries related to estimated liability | | | | 29 | | | | | — | | | | | 29 | | | | | 26 | | | | | — | | | | | 26 | | | | | 24 | | | | | — | | | | | 24 | | |
Insurance receipts for asbestos related liabilities | | | | (34 | ) | | | | (100 | ) | | | | (134 | ) | | | | (41 | ) | | | | (100 | ) | | | | (141 | ) | | | | (8 | ) | | | | (8 | ) | | | | (16 | ) | |
Insurance receivables settlements and write offs | | | | 10 | | | | | — | | | | | 10 | | | | | — | | | | | (13 | ) | | | | (13 | ) | | | | — | | | | | (38 | ) | | | | (38 | ) | |
| | | | | | | | | | | | | | | | | | | | | | | | | | | | | | | | | | | | | | | | | | | | | | |
End of year | | $ | | 162 | | | $ | | 618 | | | $ | | 780 | | | $ | | 157 | | | $ | | 718 | | | $ | | 875 | | | $ | | 172 | | | $ | | 831 | | | $ | | 1,003 | | |
| | | | | | | | | | | | | | | | | | | | | | | | | | | | | | | | | | | | | | | | | | | | | | |
NARCO and Bendix asbestos related balances are included in the following balance sheet accounts:
| | | | | | | | |
| | December 31, |
| | |
| | 2011 | | 2010 |
| | | | |
Other current assets | | $ | 71 | | | $ | 50 | |
Insurance recoveries for asbestos related liabilities | | | 709 | | | | 825 | |
| | | | | | | | |
| | $ | 780 | | | $ | 875 | |
| | | | | | | | |
| | | | | | | | |
Accrued liabilities | | $ | 237 | | | $ | 162 | |
Asbestos related liabilities | | | 1,499 | | | | 1,557 | |
| | | | | | | | |
| | $ | 1,736 | | | $ | 1,719 | |
| | | | | | | | |
NARCO Products – On January 4, 2002, NARCO filed a petition for reorganization under Chapter 11 of the U.S. Bankruptcy Code. In connection with the filing of NARCO’s petition in 2002, the Bankruptcy Court issued an injunction staying the prosecution of NARCO-related asbestos claims against the Company, which stay has
90
continuously remained in place. In November 2007, the U.S. Bankruptcy Court for the Western District of Pennsylvania confirmed NARCO’s Third Amended Plan of Reorganization (NARCO Plan of Reorganization). All challenges to the NARCO Plan of Reorganization were fully resolved in the third quarter of 2010. The NARCO Plan of Reorganization cannot become effective, however, until unrelated issues pertaining to certain NARCO affiliates which are pending in Bankruptcy Court are resolved. It is not possible to predict the timing or outcome of the Bankruptcy Court proceedings in the affiliates’ case or whether discussions between the parties will resolve the matter. We expect that the stay enjoining litigation against NARCO and Honeywell will remain in effect until the effective date of the NARCO Plan of Reorganization.
In connection with NARCO’s bankruptcy filing, we agreed to certain obligations which will be triggered upon the effective date of the NARCO Plan of Reorganization. Honeywell will provide NARCO with $20 million in financing and simultaneously forgive such indebtedness. We will also pay $40 million to NARCO’s former parent company and $16 million to certain asbestos claimants whose claims were resolved during the pendency of the NARCO bankruptcy proceedings. These amounts have been classified as Accrued Liabilities in the Consolidated Balance Sheet as of December 31, 2011.
When the NARCO Plan of Reorganization becomes effective, in connection with its implementation, a federally authorized 524(g) trust (“NARCO Trust”) will be established for the evaluation and resolution of all existing and future NARCO asbestos claims. When the NARCO Trust is established, both Honeywell and NARCO will be entitled to a permanent channeling injunction barring all present and future individual actions in state or federal courts and requiring all asbestos related claims based on exposure to NARCO products to be made against the Trust. The NARCO Trust will review submitted claims and determine award amounts in accordance with established Trust Distribution Procedures approved by the Bankruptcy Court which set forth all criteria claimants must meet to qualify for compensation including, among other things, exposure and medical criteria that determine the award amount.
Once the NARCO Trust is established and operational, Honeywell will be obligated to fund NARCO asbestos claims submitted to the trust which qualify for payment under the Trust Distribution Procedures, subject to annual caps up to $150 million in any year, provided, however, that the first $100 million of claims processed through the NARCO Trust (the “Initial Claims Amount”) will not count against the first year annual cap and any unused portion of the Initial Claims Amount will roll over to subsequent years until fully utilized.
Once the NARCO Trust is established and operational, Honeywell will also be responsible for the following funding obligations which are not subject to the annual cap described above: a) previously approved payments due to claimants pursuant to settlement agreements reached during the pendency of the NARCO bankruptcy proceedings which provide that a portion of these settlements is to be paid by the NARCO Trust, which amounts are estimated at $130 million and are expected to be paid during the first year of trust operations and, b) payments due to claimants pursuant to settlement agreements reached during the pendency of the NARCO bankruptcy proceedings that provide for the right to submit claims to the NARCO Trust subject to qualification under the terms of the settlement agreements and Trust Distribution Procedures criteria, which amounts are estimated at $150 million and are expected to be paid during the first two years of trust operations.
Our consolidated financial statements reflect an estimated liability for the amounts discussed above, unsettled claims pending as of the time NARCO filed for bankruptcy protection and for the estimated value of future NARCO asbestos claims expected to be asserted against the NARCO Trust through 2018. In light of the uncertainties inherent in making long-term projections and in connection with the initial operation of a 524(g) trust, as well as the stay of all NARCO asbestos claims since January 2002, we do not believe that we have a reasonable basis for estimating NARCO asbestos claims beyond 2018. In the absence of actual trust experience on which to base the estimate, Honeywell projected the probable value, including trust claim handling costs, of asbestos related future liabilities based on Company specific and general asbestos claims filing rates, expected rates of disease and anticipated claim values. Specifically, the valuation methodology included an analysis of the population likely to have been exposed to asbestos containing products, epidemiological studies to estimate the number of people likely to develop asbestos related diseases, NARCO asbestos claims filing history, general asbestos claims filing rates in the tort system and in certain operating asbestos trusts, and the claims experience in those forums, the pending inventory of NARCO asbestos claims, disease criteria and payment values contained in the Trust Distribution Procedures and an estimated approval rate of claims submitted to the NARCO Trust. This methodology used to estimate the liability for future claims has been commonly accepted by numerous bankruptcy courts addressing 524(g) trusts and resulted in a range of estimated liability for future claims of $743 to $961 million. We believe that no amount within this range is a better estimate than any other amount and accordingly, we have recorded the minimum amount in the range.
Our insurance receivable corresponding to the liability for settlement of pending and future NARCO asbestos claims reflects coverage which reimburses Honeywell for portions of the costs incurred to settle NARCO
91
related claims and court judgments as well as defense costs and is provided by a large number of insurance policies written by dozens of insurance companies in both the domestic insurance market and the London excess market. At December 31, 2011, a significant portion of this coverage is with insurance companies with whom we have agreements to pay full policy limits. We conduct analyses to determine the amount of insurance that we estimate is probable of recovery in relation to payment of current and estimated future claims. While the substantial majority of our insurance carriers are solvent, some of our individual carriers are insolvent, which has been considered in our analysis of probable recoveries. We made judgments concerning insurance coverage that we believe are reasonable and consistent with our historical dealings with our insurers, our knowledge of any pertinent solvency issues surrounding insurers and various judicial determinations relevant to our insurance programs.
In 2006, Travelers Casualty and Insurance Company (“Travelers”) filed a declaratory judgment action in the Supreme Court of New York, County of New York against Honeywell and other insurance carriers that provide coverage for NARCO asbestos claims, seeking a declaration regarding coverage obligations for NARCO asbestos claims under high excess insurance coverage issued by Travelers and the other insurance carriers. The other insurance carriers asserted cross claims against Honeywell seeking declarations regarding their coverage obligations for NARCO asbestos claims under high excess insurance coverage issued by them. Since then, the Company has entered into settlement agreements resolving all NARCO-related asbestos coverage issues with certain of these insurance carriers, including Travelers. Approximately $57 million of remaining unsettled coverage is included in our NARCO-related insurance receivable at December 31, 2011. Honeywell believes it is entitled to the coverage at issue and expects to prevail in this matter. In 2007, Honeywell prevailed on a critical choice of law issue concerning the appropriate method of allocating NARCO-related asbestos liabilities to triggered policies. The plaintiffs appealed and the trial court’s ruling was upheld by the intermediate appellate court in 2009. Plaintiffs’ further appeal to the New York Court of Appeals, the highest court in New York, was denied in October 2009. A related New Jersey action brought by Honeywell has been dismissed, but all coverage claims against plaintiffs have been preserved in the New York action. Based upon (i) our understanding of relevant facts and applicable law, (ii) the terms of insurance policies at issue, (iii) our experience on matters of this nature, and (iv) the advice of counsel, we believe that the amount due from the remaining insurance carriers is probable of recovery. While Honeywell expects to prevail in this matter, an adverse outcome could have a material impact on our results of operations in the period recognized but would not be material to our consolidated financial position or operating cash flows.
Projecting future events is subject to many uncertainties that could cause the NARCO related asbestos liabilities or assets to be higher or lower than those projected and recorded. There is no assurance that the plan of reorganization will become final, that insurance recoveries will be timely or whether there will be any NARCO related asbestos claims beyond 2018. Given the inherent uncertainty in predicting future events, we review our estimates periodically, and update them based on our experience and other relevant factors. Similarly, we will reevaluate our projections concerning our probable insurance recoveries in light of any changes to the projected liability or other developments that may impact insurance recoveries.
Friction Products—The following tables present information regarding Bendix related asbestos claims activity:
92
| | | | | | | | | | | |
| | Year Ended December 31, | |
| | | |
Claims Activity | | 2011 | | 2010 | |
| | | | | |
Claims Unresolved at the beginning of year | | | | 22,480 | | | | | 19,940 | | |
Claims Filed(a) | | | | 3,592 | | | | | 4,302 | | |
Claims Resolved(b) | | | | (3,501 | ) | | | | (1,762 | ) | |
| | | | | | | | | | | |
Claims Unresolved at the end of year | | | | 22,571 | | | | | 22,480 | | |
| | | | | | | | | | | |
(a) The number of claims filed in 2010 includes approximately 1,541 non-malignant claims (with an accrued liability of approximately $575 thousand in the aggregate), a majority of which had previously been dismissed in Mississippi and re-filed in Arkansas.
(b) The number of claims resolved in 2011 includes approximately 351 claims previously classified as inactive (82% non-malignant and accrued liability of approximately $1.7 million) which were activated during 2011. The number of claims resolved in 2010 includes approximately 1,300 claims previously classified as inactive (95% non-malignant and accrued liability of approximately $2.0 million) which were activated during 2010.
| | | | | | | | | | | |
| | December 31, | |
| | | |
Disease Distribution of Unresolved Claims | | 2011 | | 2010 | |
| | | | | |
| | | | | | | | | | | |
Mesothelioma and Other Cancer Claims | | | | 4,943 | | | | | 4,856 | | |
Nonmalignant Claims | | | | 17,628 | | | | | 17,624 | | |
| | | | | | | | | | | |
Total Claims | | | | 22,571 | | | | | 22,480 | | |
| | | | | | | | | | | |
Honeywell has experienced average resolution values per claim excluding legal costs as follows:
| | | | | | | | | | | | | | | | | | | | | |
| | Year Ended December 31, | |
| | | |
| | 2011 | | 2010 | | 2009 | | 2008 | | 2007 | |
| | | | | | | | | | | |
| | (in whole dollars) | |
Malignant claims | | $ | 48,000 | | | $ | 54,000 | | | $ | 50,000 | | | $ | 65,000 | | | $ | 33,000 | | |
Nonmalignant claims | | $ | 1,000 | | | $ | 1,300 | | | $ | 200 | | | $ | 1,500 | | | $ | 500 | | |
It is not possible to predict whether resolution values for Bendix related asbestos claims will increase, decrease or stabilize in the future.
Our consolidated financial statements reflect an estimated liability for resolution of pending (claims actually filed as of the financial statement date) and future Bendix related asbestos claims. We have valued Bendix pending and future claims using average resolution values for the previous five years. We update the resolution values used to estimate the cost of Bendix pending and future claims during the fourth quarter each year.
The liability for future claims represents the estimated value of future asbestos related bodily injury claims expected to be asserted against Bendix over the next five years. Such estimated cost of future Bendix related asbestos claims is based on historic claims filing experience and dismissal rates, disease classifications, and resolution values in the tort system for the previous five years. In light of the uncertainties inherent in making long-term projections, as well as certain factors unique to friction product asbestos claims, we do not believe that we have a reasonable basis for estimating asbestos claims beyond the next five years. The methodology used to estimate the liability for future claims is similar to that used to estimate the future NARCO related asbestos claims liability.
Our insurance receivable corresponding to the liability for settlement of pending and future Bendix asbestos claims reflects coverage which is provided by a large number of insurance policies written by dozens of insurance companies in both the domestic insurance market and the London excess market. Based on our
93
ongoing analysis of the probable insurance recovery, insurance receivables are recorded in the financial statements simultaneous with the recording of the estimated liability for the underlying asbestos claims. This determination is based on our analysis of the underlying insurance policies, our historical experience with our insurers, our ongoing review of the solvency of our insurers, our interpretation of judicial determinations relevant to our insurance programs, and our consideration of the impacts of any settlements reached with our insurers. Insurance receivables are also recorded when structured insurance settlements provide for future fixed payment streams that are not contingent upon future claims or other events. Such amounts are recorded at the net present value of the fixed payment stream.
On a cumulative historical basis, Honeywell has recorded insurance receivables equal to approximately 40 percent of the value of the underlying asbestos claims recorded. However, because there are gaps in our coverage due to insurance company insolvencies, certain uninsured periods, and insurance settlements, this rate is expected to decline for any future Bendix related asbestos liabilities that may be recorded. Future recoverability rates may also be impacted by numerous other factors, such as future insurance settlements, insolvencies and judicial determinations relevant to our coverage program, which are difficult to predict. Assuming continued defense and indemnity spending at current levels, we estimate that the cumulative recoverability rate could decline over the next five years to approximately 33 percent.
Honeywell believes it has sufficient insurance coverage and reserves to cover all pending Bendix related asbestos claims and Bendix related asbestos claims estimated to be filed within the next five years. Although it is impossible to predict the outcome of either pending or future Bendix related asbestos claims, we do not believe that such claims would have a material adverse effect on our consolidated financial position in light of our insurance coverage and our prior experience in resolving such claims. If the rate and types of claims filed, the average resolution value of such claims and the period of time over which claim settlements are paid (collectively, the “Variable Claims Factors”) do not substantially change, Honeywell would not expect future Bendix related asbestos claims to have a material adverse effect on our results of operations or operating cash flows in any fiscal year. No assurances can be given, however, that the Variable Claims Factors will not change.
Other Matters
We are subject to a number of other lawsuits, investigations and disputes (some of which involve substantial amounts claimed) arising out of the conduct of our business, including matters relating to commercial transactions, government contracts, product liability, prior acquisitions and divestitures, employee benefit plans, intellectual property, and environmental, health and safety matters. We recognize a liability for any contingency that is probable of occurrence and reasonably estimable. We continually assess the likelihood of adverse judgments of outcomes in these matters, as well as potential ranges of possible losses (taking into consideration any insurance recoveries), based on a careful analysis of each matter with the assistance of outside legal counsel and, if applicable, other experts. Included in these other matters are the following:
Allen, et al. v. Honeywell Retirement Earnings Plan—Pursuant to a settlement approved by the U.S. District Court for the District of Arizona in February 2008, 18 of 21 claims alleged by plaintiffs in this class action lawsuit were dismissed with prejudice in exchange for approximately $35 million (paid from the Company’s pension plan) and the maximum aggregate liability for the remaining three claims (alleging that Honeywell impermissibly reduced the pension benefits of certain employees of a predecessor entity when the plan was amended in 1983 and failed to calculate benefits in accordance with the terms of the plan) was capped at $500 million. In October 2009, the Court granted summary judgment in favor of the Honeywell Retirement Earnings Plan with respect to the claim regarding the calculation of benefits. In May 2011, the parties engaged in mediation and reached an agreement in principle to settle the three remaining claims for $23.8 million (also to be paid from the Company’s pension plan). Settlement documents have been submitted to the court for classwide approval. A preliminary settlement order has been approved by the court and a fairness hearing on the settlement is scheduled for April 2012. Upon court approval of the settlement, all claims in this matter will be fully resolved.
Quick Lube—On March 31, 2008, S&E Quick Lube, a filter distributor, filed suit in U.S. District Court for the District of Connecticut alleging that twelve filter manufacturers, including Honeywell, engaged in a conspiracy to fix prices, rig bids and allocate U.S. customers for aftermarket automotive filters. This suit is a purported class action on behalf of direct purchasers of filters from the defendants. Parallel purported class actions, including on behalf of indirect purchasers of filters, have been filed by other plaintiffs in a variety of jurisdictions in the United States and Canada. The U.S cases have been consolidated into a single multi-district litigation in the Northern District of Illinois. In June 2011, plaintiff’s principal witness pled guilty to a felony count of having made false statements to federal investigators. In February 2012, Honeywell reached an agreement in principle to resolve the multi-district litigation class action as to all plaintiffs, subject to finalization of the agreement and approval by the court. As previously reported, the Antitrust Division of the Department of Justice notified Honeywell in January
94
2010 that it had officially closed its investigation into possible collusion in the replacement auto filters industry.
Honeywell v. United Auto Workers (“UAW”) et. al—In July 2011, Honeywell filed an action in federal court (District of New Jersey) against the UAW and all former employees who retired under a series of Master Collective Bargaining Agreements (“MCBAs”) between Honeywell and the UAW. The Company is seeking a declaratory judgment that certain express limitations on its obligation to contribute toward the healthcare coverage of such retirees (the “CAPS”) set forth in the MCBAs may be implemented, effective January 1, 2012. In September 2011, the UAW and certain retiree defendants filed a motion to dismiss the New Jersey action and filed suit in the Eastern District of Michigan alleging that the MCBAs do not provide for CAPS on the Company’s liability for healthcare coverage. The UAW and retiree plaintiffs subsequently filed a motion for class certification and a motion for partial summary judgment in the Michigan action, seeking a ruling that retirees who retired prior to the initial inclusion of the CAPS in the 2003 MCBA are not covered by the CAPS as a matter of law. In December 2011, the New Jersey action was dismissed on jurisdictional grounds. Honeywell has filed a motion for expedited review of the New Jersey court’s dismissal with the United States Court of Appeals for the Third Circuit and the parties are awaiting the court’s instructions with respect to how the Michigan action is to proceed. Honeywell is confident that the CAPS will be upheld and that its liability for healthcare coverage premiums with respect to the putative class will be limited as negotiated and expressly set forth in the applicable MCBAs. In the event of an adverse ruling, however, Honeywell’s other postretirement benefits for pre-2003 retirees would increase by approximately $150 million, reflecting the estimated value of these CAPS.
Given the uncertainty inherent in litigation and investigations (including the specific matters referenced above), we do not believe it is possible to develop estimates of reasonably possible loss in excess of current accruals for these matters. Considering our past experience and existing accruals, we do not expect the outcome of these matters, either individually or in the aggregate, to have a material adverse effect on our consolidated financial position. Because most contingencies are resolved over long periods of time, potential liabilities are subject to change due to new developments, changes in settlement strategy or the impact of evidentiary requirements, which could cause us to pay damage awards or settlements (or become subject to equitable remedies) that could have a material adverse effect on our results of operations or operating cash flows in the periods recognized or paid.
Warranties and Guarantees—We have issued or are a party to the following direct and indirect guarantees at December 31, 2011:
| | | | | | |
| | Maximum Potential Future Payments | |
| | | |
Operating lease residual values | | $ | | 43 | | |
Other third parties’ financing | | | | 5 | | |
Unconsolidated affiliates’ financing | | | | 12 | | |
Customer financing | | | | 13 | | |
| | | | | | |
| | $ | | 73 | | |
| | | | | | |
We do not expect that these guarantees will have a material adverse effect on our consolidated results of operations, financial position or liquidity.
In connection with the disposition of certain businesses and facilities we have indemnified the purchasers for the expected cost of remediation of environmental contamination, if any, existing on the date of disposition. Such expected costs are accrued when environmental assessments are made or remedial efforts are probable and the costs can be reasonably estimated.
In the normal course of business we issue product warranties and product performance guarantees. We accrue for the estimated cost of product warranties and performance guarantees based on contract terms and historical experience at the time of sale. Adjustments to initial obligations for warranties and guarantees are made as changes in the obligations become reasonably estimable. The following table summarizes information concerning our recorded obligations for product warranties and product performance guarantees:
95
| | | | | | | | | | | | | | | | |
| | Years Ended December 31, | |
| | | |
| | 2011 | | 2010 | | 2009 | |
| | | | | | | |
Beginning of year | | $ | | 415 | | | $ | | 407 | | | $ | | 417 | | |
Accruals for warranties/guarantees issued during the year | | | | 197 | | | | | 214 | | | | | 188 | | |
Adjustment of pre-existing warranties/guarantees | | | | (2 | ) | | | | (13 | ) | | | | (7 | ) | |
Settlement of warranty/guarantee claims | | | | (208 | ) | | | | (193 | ) | | | | (191 | ) | |
| | | | | | | | | | | | | | | | |
End of year | | $ | | 402 | | | $ | | 415 | | | $ | | 407 | | |
| | | | | | | | | | | | | | | | |
Product warranties and product performance guarantees are included in the following balance sheet accounts:
| | | | | | | | | | | |
| | 2011 | | 2010 | |
| | | | | |
Accrued liabilities | | $ | | 364 | | | $ | | 380 | | |
Other liabilities | | | | 38 | | | | | 35 | | |
| | | | | | | | | | | |
| | $ | | 402 | | | $ | | 415 | | |
| | | | | | | | | | | |
96
Note 22. Pension and Other Postretirement Benefits
We sponsor both funded and unfunded U.S. and non-U.S. defined benefit pension plans covering the majority of our employees and retirees. Pension benefits for substantially all U.S. employees are provided through non-contributory, qualified and non-qualified defined benefit pension plans. U.S. defined benefit pension plans comprise 77 percent of our projected benefit obligation. Non-U.S. employees, who are not U.S. citizens, are covered by various retirement benefit arrangements, some of which are considered to be defined benefit pension plans for accounting purposes. Non-U.S. defined benefit pension plans comprise 23 percent of our projected benefit obligation.
We also sponsor postretirement benefit plans that provide health care benefits and life insurance coverage to eligible retirees. Our retiree medical plans mainly cover U.S. employees who retire with pension eligibility for hospital, professional and other medical services. Most of the U.S. retiree medical plans require deductibles and copayments, and virtually all are integrated with Medicare. Retiree contributions are generally required based on coverage type, plan and Medicare eligibility. All non-union hourly and salaried employees joining Honeywell after January 1, 2000 are not eligible to participate in our retiree medical and life insurance plans. Only approximately 5 percent of Honeywell’s U.S. employees are eligible for a retiree medical subsidy from the Company; and this subsidy is limited to a fixed-dollar amount. In addition more than half of its current retirees either have no Company subsidy or have a fixed dollar subsidy amount. This significantly limits our exposure to the impact of future health care cost increases. The retiree medical and life insurance plans are not funded. Claims and expenses are paid from our operating cash flow.
In 2011, in connection with new collective bargaining agreements reached with several of its union groups, Honeywell amended its U.S. retiree medical plans eliminating the subsidy for those union employees resulting in curtailment gains totaling $167 million. The curtailment gains represent the recognition in net periodic postretirement benefit cost of prior service credits attributable to the future years of service of the union groups for which future accrual of benefits has been eliminated.
In 2010, Honeywell amended its U.S. retiree medical plan to no longer offer certain post-age-65 retirees Honeywell group coverage and facilitate their purchase of an individual plan in the Medicare marketplace. This plan amendment reduced the accumulated postretirement benefit obligation by $137 million which will be recognized as part of net periodic postretirement benefit cost over the average future service period to full eligibility of the remaining active union employees still eligible for a retiree medical subsidy. Also in 2010, in connection with a new collective bargaining agreement reached with one of its union groups, Honeywell amended its U.S. retiree medical plan eliminating the subsidy for those union employees who retire after February 1, 2013. This plan amendment reduced the accumulated postretirement benefit obligation by $39 million which will be recognized as part of net periodic postretirement benefit cost over the average future service period to full eligibility of the remaining active union employees still eligible for a retiree medical subsidy. This plan amendment also resulted in a curtailment gain of $37 million in 2010 which represented the recognition in net periodic postretirement benefit cost of prior service credits attributable to the future years of service of the union group for which future accrual of benefits was eliminated.
In 2009, Honeywell amended the U.S. retiree medical plan eliminating the subsidy for active non-union employees who retire after September 1, 2009. Employees already retired or who retired on or before September 1, 2009 were not affected by this change. This plan amendment reduced the accumulated postretirement benefit obligation by $180 million representing the elimination of benefits attributable to years of service already rendered by active non-union employees who are not eligible to retire and those eligible non-union employees who were assumed not to retire prior to September 1, 2009. This reduction in the accumulated postretirement benefit obligation will be recognized as part of net periodic postretirement benefit cost over the average future service period to full eligibility of the remaining active union employees still eligible for a retiree medical subsidy. This plan amendment also resulted in a curtailment gain of $98 million in 2009 which represented the recognition in net periodic post retirement benefit cost of prior service credits attributable to the future years of service of the employee group for which future accrual of benefits was eliminated.
97
The following tables summarize the balance sheet impact, including the benefit obligations, assets and funded status associated with our significant pension and other postretirement benefit plans at December 31, 2011 and 2010.
| | | | | | | | | | | | | | | | | |
| | Pension Benefits | | |
| | | |
| | U.S. Plans | | | Non-U.S. Plans | | |
| | | | | |
| | 2011 | | 2010 | | 2011 | | 2010 | |
| | | | | | | | | |
Change in benefit obligation: | | | | | | | | | | | | | | | | | |
Benefit obligation at beginning of year | | $ | 14,990 | | | $ | 13,620 | | | $ | 4,373 | | | $ | 4,266 | | |
Service cost | | | 232 | | | | 221 | | | | 59 | | | | 51 | | |
Interest cost | | | 761 | | | | 768 | | | | 239 | | | | 228 | | |
Plan amendments | | | 5 | | | | 117 | | | | — | | | | — | | |
Actuarial losses | | | 566 | | | | 1,211 | | | | 171 | | | | 150 | | |
Divestitures | | | (26 | ) | | | — | | | | — | | | | — | | |
Benefits paid | | | (952 | ) | | | (947 | ) | | | (189 | ) | | | (181 | ) | |
Settlements and curtailments | | | — | | | | — | | | | (25 | ) | | | — | | |
Other | | | 24 | | | | — | | | | 20 | | | | (141 | ) | |
| | | | | | | | | | | | | | | | | |
Benefit obligation at end of year | | | 15,600 | | | | 14,990 | | | | 4,648 | | | | 4,373 | | |
| | | | | | | | | | | | | | | | | |
Change in plan assets: | | | | | | | | | | | | | | | | | |
Fair value of plan assets at beginning of year | | | 12,181 | | | | 10,306 | | | | 3,939 | | | | 3,488 | | |
Actual return on plan assets | | | (41 | ) | | | 1,788 | | | | 87 | | | | 414 | | |
Company contributions | | | 1,681 | | | | 1,034 | | | | 124 | | | | 313 | | |
Divestitures | | | (33 | ) | | | — | | | | — | | | | — | | |
Benefits paid | | | (952 | ) | | | (947 | ) | | | (189 | ) | | | (181 | ) | |
Settlements and curtailments | | | — | | | | — | | | | (25 | ) | | | — | | |
Other | | | — | | | | — | | | | 22 | | | | (95 | ) | |
| | | | | | | | | | | | | | | | | |
Fair value of plan assets at end of year | | | 12,836 | | | | 12,181 | | | | 3,958 | | | | 3,939 | | |
| | | | | | | | | | | | | | | | | |
Funded status of plans | | $ | (2,764 | ) | | $ | (2,809 | ) | | $ | (690 | ) | | $ | (434 | ) | |
| | | | | | | | | | | | | | | | | |
Amounts recognized in Consolidated Balance | | | | | | | | | | | | | | | | | |
Sheet consist of: | | | | | | | | | | | | | | | | | |
Prepaid pension benefit cost(1) | | $ | — | | | $ | — | | | $ | 84 | | | $ | 135 | | |
Accrued pension liability(2) | | | (2,764 | ) | | | (2,809 | ) | | | (774 | ) | | | (569 | ) | |
| | | | | | | | | | | | | | | | | |
Net amount recognized | | $ | (2,764 | ) | | $ | (2,809 | ) | | $ | (690 | ) | | $ | (434 | ) | |
| | | | | | | | | | | | | | | | | |
| |
(1) | Included in Other Assets on Consolidated Balance Sheet |
(2) | Included in Other Liabilities - Non-Current on Consolidated Balance Sheet |
98
| | | | | | | | | |
| | Other Postretirement Benefits | |
| | | |
| | 2011 | | 2010 | |
| | | | | |
Change in benefit obligation: | | | | | | | | | |
Benefit obligation at beginning of year | | $ | 1,628 | | | $ | 1,748 | | |
Service cost | | | 1 | | | | 2 | | |
Interest cost | | | 69 | | | | 81 | | |
Plan amendments | | | (22 | ) | | | (176 | ) | |
Actuarial losses | | | 6 | | | | 160 | | |
Benefits paid | | | (138 | ) | | | (187 | ) | |
Settlements and curtailments | | | (10 | ) | | | — | | |
| | | | | | | | | |
Benefit obligation at end of year | | | 1,534 | | | | 1,628 | | |
| | | | | | | | | |
Change in plan assets: | | | | | | | | | |
Fair value of plan assets at beginning of year | | | — | | | | — | | |
Actual return on plan assets | | | — | | | | — | | |
Company contributions | | | — | | | | — | | |
Benefits paid | | | — | | | | — | | |
| | | | | | | | | |
Fair value of plan assets at end of year | | | — | | | | — | | |
| | | | | | | | | |
Funded status of plans | | $ | (1,534 | ) | | $ | (1,628 | ) | |
| | | | | | | | | |
| | | | | | | | | |
Amounts recognized in Consolidated Balance Sheet consist of: | | | | | | | | | |
| | | | | | | | | |
Accrued liabilities | | | (167 | ) | | | (197 | ) | |
Postretirement benefit obligations other than pensions(1) | | | (1,367 | ) | | | (1,431 | ) | |
| | | | | | | | | |
Net amount recognized | | $ | (1,534 | ) | | $ | (1,628 | ) | |
| | | | | | | | | |
| |
(1) | Excludes Non-U.S. plans of $50 and $46 million in 2011 and 2010, respectively. |
Amounts recognized in Accumulated Other Comprehensive (Income) Loss associated with our significant pension and other postretirement benefit plans at December 31, 2011 and 2010 are as follows.
| | | | | | | | | | | | | | | | | |
| | Pension Benefits | |
| | | |
| | U.S. Plans | | Non-U.S. Plans | |
| | | | | |
| | 2011 | | 2010 | | 2011 | | 2010 | |
| | | | | | | | | |
Transition obligation | | $ | — | | | $ | — | | | $ | 7 | | | $ | 9 | | |
Prior service cost (credit) | | | 148 | | | | 177 | | | | (17 | ) | | | (19 | ) | |
Net actuarial loss | | | 1,559 | | | | 1,499 | | | | 430 | | | | 321 | | |
| | | | | | | | | | | | | | | | | |
Net amount recognized | | $ | 1,707 | | | $ | 1,676 | | | $ | 420 | | | $ | 311 | | |
| | | | | | | | | | | | | | | | | |
| | | | | | | | | |
| | Other Postretirement Benefits | |
| | | |
| | 2011 | | 2010 | |
| | | | | |
Prior service (credit) | | $ | (67 | ) | | $ | (264 | ) | |
Net actuarial loss | | | 391 | | | | 425 | | |
| | | | | | | | | |
Net amount recognized | | $ | 324 | | | $ | 161 | | |
| | | | | | | | | |
The components of net periodic benefit cost and other amounts recognized in other comprehensive (income) loss for our significant plans for the years ended December 31, 2011, 2010, and 2009 include the following components:
99
| | | | | | | | | | | | | | | | | | | | | | | | | |
| | Pension Benefits | |
| | | |
| | U.S. Plans | | Non-U.S. Plans | |
| | | | | |
Net Periodic Benefit Cost | | 2011 | | 2010 | | 2009 | | 2011 | | 2010 | | 2009 | |
| | | | | | | | | | | | | |
Service cost | | $ | 232 | | | $ | 221 | | | $ | 183 | | | $ | 59 | | | $ | 51 | | | $ | 41 | | |
Interest cost | | | 761 | | | | 768 | | | | 785 | | | | 239 | | | | 228 | | | | 208 | | |
Expected return on plan assets | | | (1,014 | ) | | | (902 | ) | | | (767 | ) | | | (284 | ) | | | (248 | ) | | | (221 | ) | |
Amortization of transition obligation | | | — | | | | — | | | | — | | | | 2 | | | | 1 | | | | 1 | | |
Amortization of prior service cost (credit) | | | 33 | | | | 32 | | | | 26 | | | | (2 | ) | | | (1 | ) | | | (1 | ) | |
Recognition of actuarial losses | | | 1,568 | | | | 182 | | | | 447 | | | | 234 | | | | 289 | | | | 308 | | |
Settlements and curtailments | | | 24 | | | | — | | | | — | | | | 1 | | | | 4 | | | | — | | |
| | | | | | | | | | | | | | | | | | | | | | | | | |
Net periodic benefit cost | | $ | 1,604 | | | $ | 301 | | | $ | 674 | | | $ | 249 | | | $ | 324 | | | $ | 336 | | |
| | | | | | | | | | | | | | | | | | | | | | | | | |
| | | | | | | | | | | | | | | | | | | | | | | | | |
Other Changes in Plan Assets and Benefits Obligations Recognized in Other Comprehensive (Income) Loss | | | | | |
| U.S. Plans | | Non-U.S. Plans | |
| | | | |
| 2011 | | 2010 | | 2009 | | 2011 | | 2010 | | 2009 | |
| | | | | | | | | | | | | |
Actuarial (gains)/losses | | $ | 1,628 | | | $ | 325 | | | $ | 686 | | | $ | 368 | | | $ | (20 | ) | | $ | 449 | | |
Prior service cost (credit) | | | 5 | | | | 117 | | | | — | | | | — | | | | — | | | | 2 | | |
Transition obligation recognized during year | | | — | | | | — | | | | — | | | | (2 | ) | | | (1 | ) | | | (1 | ) | |
Prior service (cost) credit recognized during year | | | (33 | ) | | | (32 | ) | | | (26 | ) | | | 2 | | | | 1 | | | | 1 | | |
Actuarial losses recognized during year | | | (1,568 | ) | | | (182 | ) | | | (447 | ) | | | (234 | ) | | | (289 | ) | | | (308 | ) | |
Foreign exchange translation adjustments | | | — | | | | — | | | | — | | | | (11 | ) | | | (17 | ) | | | 42 | | |
| | | | | | | | | | | | | | | | | | | | | | | | | |
Total recognized in other comprehensive (income) loss | | $ | 32 | | | $ | 228 | | | $ | 213 | | | $ | 123 | | | $ | (326 | ) | | $ | 185 | | |
| | | | | | | | | | | | | | | | | | | | | | | | | |
Total recognized in net periodic benefit cost and other comprehensive (income) loss | | $ | 1,636 | | | $ | 529 | | | $ | 887 | | | $ | 372 | | | $ | (2 | ) | | $ | 521 | | |
| | | | | | | | | | | | | | | | | | | | | | | | | |
The estimated prior service cost for pension benefits that will be amortized from accumulated other comprehensive (income) loss into net periodic benefit cost in 2012 are expected to be $28 million and $(2) million for U.S. and Non-U.S. benefit plans, respectively.
100
| | | | | | | | | | | | | |
| | Other Postretirement Benefits Years Ended December 31, | |
| | | |
Net Periodic Benefit Cost | | 2011 | | 2010 | | 2009 | |
| | | | | | | |
Service cost | | $ | 1 | | | $ | 2 | | | $ | 6 | | |
Interest cost | | | 69 | | | | 81 | | | | 104 | | |
Amortization of prior service (credit) | | | (34 | ) | | | (44 | ) | | | (44 | ) | |
Recognition of actuarial losses | | | 38 | | | | 34 | | | | 13 | | |
Settlements and curtailments | | | (167 | ) | | | (47 | ) | | | (98 | ) | |
| | | | | | | | | | | | | |
Net periodic benefit (income) cost | | $ | (93 | ) | | $ | 26 | | | $ | (19 | ) | |
| | | | | | | | | | | | | |
| | | | | | | | | | | | | |
Other Changes in Plan Assets and Benefits Obligations Recognized in Other Comprehensive (Income) Loss | | Years Ended December 31, | |
| | |
| 2011 | | 2010 | | 2009 | |
| | | | | | | |
Actuarial losses | | $ | 6 | | | $ | 160 | | | $ | 46 | | |
Prior service (credit) | | | (21 | ) | | | (176 | ) | | | (180 | ) | |
Prior service credit recognized during year | | | 34 | | | | 44 | | | | 44 | | |
Actuarial losses recognized during year | | | (38 | ) | | | (34 | ) | | | (13 | ) | |
Settlements and curtailments | | | 167 | | | | 47 | | | | 98 | | |
| | | | | | | | | | | | | |
Total recognized in other comprehensive loss (income) | | $ | 148 | | | $ | 41 | | | $ | (5 | ) | |
| | | | | | | | | | | | | |
Total recognized in net periodic benefit cost and other comprehensive loss (income) | | $ | 55 | | | $ | 67 | | | $ | (24 | ) | |
| | | | | | | | | | | | | |
The estimated net loss and prior service (credit) for other postretirement benefits that will be amortized from accumulated other comprehensive (income) loss into net periodic benefit cost in 2012 are expected to be $40 and $(15) million, respectively.
Major actuarial assumptions used in determining the benefit obligations and net periodic benefit cost for our significant benefit plans are presented in the following table.
| | | | | | | | | | | | | | | | | | | |
| | Pension Benefits | |
| | | |
| | U.S. Plans | | Non-U.S. Plans | |
| | | | | |
| | 2011 | | 2010 | | 2009 | | 2011 | | 2010 | | 2009 | |
| | | | | | | | | | | | | |
Actuarial assumptions used to determine benefit obligations as of December 31: | | | | | | | | | | | | | | | | | | | |
Discount rate | | 4.89 | % | | 5.25 | % | | 5.75 | % | | 4.84 | % | | 5.40 | % | | 5.71 | % | |
Expected annual rate of compensation increase | | 4.50 | % | | 4.50 | % | | 4.50 | % | | 3.67 | % | | 3.79 | % | | 3.87 | % | |
Actuarial assumptions used to determine net periodic benefit cost for years ended December 31: | | | | | | | | | | | | | | | | | | | |
Discount rate | | 5.25 | % | | 5.75 | % | | 6.95 | % | | 5.40 | % | | 5.71 | % | | 6.21 | % | |
Expected rate of return on plan assets | | 8.00 | % | | 9.00 | % | | 9.00 | % | | 7.06 | % | | 7.51 | % | | 7.52 | % | |
Expected annual rate of compensation increase | | 4.50 | % | | 4.50 | % | | 4.50 | % | | 3.79 | % | | 3.87 | % | | 3.33 | % | |
101
| | | | | | | | | | |
| | Other Postretirement Benefits | |
| | | |
| | 2011 | | 2010 | | 2009 | |
| | | | | | | |
Actuarial assumptions used to determine benefit obligations as of December 31: | | | | | | | | | | |
Discount rate | | 4.00 | % | | 4.70 | % | | 5.25 | % | |
Actuarial assumptions used to determine net periodic benefit cost for years ended December 31: | | | | | | | | | | |
Discount rate | | 4.70 | % | | 5.25 | % | | 6.00 | % | |
The discount rate for our U.S. pension and other postretirement benefits plans reflects the current rate at which the associated liabilities could be settled at the measurement date of December 31. To determine discount rates for our U.S. pension and other postretirement benefit plans, we use a modeling process that involves matching the expected cash outflows of our benefit plans to a yield curve constructed from a portfolio of high quality, fixed-income debt instruments. We use the average yield of this hypothetical portfolio as a discount rate benchmark. The discount rate used to determine the other postretirement benefit obligation is lower principally due to a shorter expected duration of other postretirement plan obligations as compared to pension plan obligations.
Our expected rate of return on U.S. plan assets of 8 percent is a long-term rate based on historical plan asset returns over varying long-term periods combined with our expectations on future market conditions and the asset mix of the plan’s investments. We review the expected rate of return on an annual basis and revise it as appropriate.
For non-U.S. benefit plans, none of which was individually material, assumptions reflect economic assumptions applicable to each country.
Pension Benefits
Included in the aggregate data in the tables above are the amounts applicable to our pension plans with accumulated benefit obligations exceeding the fair value of plan assets. Amounts related to such plans were as follows:
| | | | | | | | | | | | | | | | | |
| | December 31, | |
| | | |
| | U.S. Plans | | Non-U.S. Plans | |
| | | | | |
| | 2011 | | 2010 | | 2011 | | 2010 | |
| | | | | | | | | |
Projected benefit obligation | | $ | 15,600 | | | $ | 14,990 | | | $ | 4,141 | | | $ | 1,990 | | |
Accumulated benefit obligation | | $ | 14,845 | | | $ | 14,260 | | | $ | 3,912 | | | $ | 1,883 | | |
Fair value of plan assets | | $ | 12,836 | | | $ | 12,181 | | | $ | 3,367 | | | $ | 1,474 | | |
Accumulated benefit obligation for our U.S. defined benefit pension plans were $14.8 and $14.3 billion and our Non-U.S. defined benefit plans were $4.4 and $4.1 billion at December 31, 2011 and 2010, respectively.
Our asset investment strategy for our U.S. pension plans focuses on maintaining a diversified portfolio using various asset classes in order to achieve our long-term investment objectives on a risk adjusted basis. Our actual invested positions in various securities change over time based on short and longer-term investment opportunities. To achieve our objectives, we have established long-term target allocations as follows: 60-70 percent equity securities, 10-20 percent fixed income securities and cash, 5-15 percent real estate investments, and 10-20 percent other types of investments. Equity securities include publicly-traded stock of companies located both inside and outside the United States. Fixed income securities include corporate bonds of companies from diversified industries, mortgage-backed securities, and U.S. Treasuries. Real estate investments include direct investments in commercial properties and investments in real estate funds. Other types of investments include investments in private equity and hedge funds that follow several different strategies. We review our assets on a regular basis to ensure that we are within the targeted asset allocation ranges and, if necessary, asset balances are adjusted back within target allocations.
Our non-U.S. pension assets are typically managed by decentralized fiduciary committees with the Honeywell Corporate Investments group providing standard funding and investment guidance. Local regulations, local funding rules, and local financial and tax considerations are part of the funding and investment allocation process in each country. While our non-U.S. investment policies are different for each country, the long-term investment objectives are generally the same as those for the U.S. pension assets.
102
The fair values of both our U.S. and non-U.S. pension plans assets at December 31, 2011 and 2010 by asset category are as follows:
| | | | | | | | | | | | | | | | | |
| | U.S. Plans | |
| | | |
| | December 31, 2011 | |
| | | |
| | Total | | Level 1 | | Level 2 | | Level 3 | |
| | | | | | | | | |
Common stock/preferred stock: | | | | | | | | | | | | | | | | | |
Honeywell common stock | | $ | 1,012 | | | $ | 1,012 | | | $ | — | | | $ | — | | |
U.S. large cap stocks | | | 2,697 | | | | 2,416 | | | | 281 | | | | — | | |
U.S. mid cap stocks | | | 1,087 | | | | 1,087 | | | | — | | | | — | | |
U.S. small cap stocks | | | 272 | | | | 272 | | | | — | | | | — | | |
International stocks | | | 2,010 | | | | 1,993 | | | | 17 | | | | — | | |
Real estate investment trusts | | | 32 | | | | 32 | | | | — | | | | — | | |
Fixed income investments: | | | | | | | | | | | | | | | | | |
Short term investments | | | 941 | | | | 941 | | | | — | | | | — | | |
Government securities | | | 291 | | | | — | | | | 291 | | | | — | | |
Corporate bonds | | | 1,984 | | | | — | | | | 1,984 | | | | — | | |
Mortgage/Asset-Backed securities | | | 435 | | | | — | | | | 435 | | | | — | | |
Insurance contracts | | | 6 | | | | — | | | | 6 | | | | — | | |
Investments in private funds: | | | | | | | | | | | | | | | | | |
Private funds | | | 1,039 | | | | — | | | | — | | | | 1,039 | | |
Hedge funds | | | 60 | | | | — | | | | — | | | | 60 | | |
Real estate funds | | | 256 | | | | — | | | | — | | | | 256 | | |
Direct investments: | | | | | | | | | | | | | | | | | |
Direct private investments | | | 161 | | | | — | | | | — | | | | 161 | | |
Real estate properties | | | 553 | | | | — | | | | — | | | | 553 | | |
| | | | | | | | | | | | | | | | | |
| | $ | 12,836 | | | $ | 7,753 | | | $ | 3,014 | | | $ | 2,069 | | |
| | | | | | | | | | | | | | | | | |
| | | | | | | | | | | | | |
| | U.S. Plans | |
| | | |
| | December 31, 2010 | |
| | | |
| | Total | | Level 1 | | Level 2 | | Level 3 | |
| | | | | | | | | |
Common stock/preferred stock: | | | | | | | | | | | | | | | | | |
Honeywell common stock | | $ | 986 | | | $ | 986 | | | $ | — | | | $ | — | | |
U.S. large cap stocks | | | 2,349 | | | | 2,349 | | | | — | | | | — | | |
U.S. mid cap stocks | | | 1,049 | | | | 1,049 | | | | — | | | | — | | |
U.S. small cap stocks | | | 301 | | | | 301 | | | | — | | | | — | | |
International stocks | | | 2,197 | | | | 2,176 | | | | 21 | | | | — | | |
Real estate investment trusts | | | 38 | | | | 38 | | | | — | | | | — | | |
Fixed income investments: | | | | | | | | | | | | | | | | | |
Short term investments | | | 1,242 | | | | 1,242 | | | | — | | | | — | | |
Government securities | | | 240 | | | | — | | | | 240 | | | | — | | |
Corporate bonds | | | 1,342 | | | | — | | | | 1,342 | | | | — | | |
Mortgage/Asset-Backed securities | | | 422 | | | | — | | | | 422 | | | | — | | |
Insurance contracts | | | 10 | | | | — | | | | 10 | | | | — | | |
Investments in private funds: | | | | | | | | | | | | | | | | | |
Private funds | | | 1,053 | | | | — | | | | — | | | | 1,053 | | |
Hedge funds | | | 77 | | | | — | | | | — | | | | 77 | | |
Real estate funds | | | 214 | | | | — | | | | — | | | | 214 | | |
Direct investments: | | | | | | | | | | | | | | | | | |
Direct private investments | | | 167 | | | | — | | | | — | | | | 167 | | |
Real estate properties | | | 494 | | | | — | | | | — | | | | 494 | | |
| | | | | | | | | | | | | | | | | |
| | $ | 12,181 | | | $ | 8,141 | | | $ | 2,035 | | | $ | 2,005 | | |
| | | | | | | | | | | | | | | | | |
103
| | | | | | | | | | | | | | | | | |
| | Non-U.S. Plans | |
| | | |
| | December 31, 2011 | |
| | | |
| | Total | | Level 1 | | Level 2 | | Level 3 | |
| | | | | | | | | |
Common stock/preferred stock: | | | | | | | | | | | | | | | | | |
U.S. companies | | $ | 371 | | | $ | 249 | | | $ | 122 | | | $ | — | | |
Non-U.S. companies | | | 1,343 | | | | 233 | | | | 1,110 | | | | — | | |
Fixed income investments: | | | | | | | | | | | | | | | | | |
Short-term investments | | | 78 | | | | 78 | | | | — | | | | — | | |
Government securities | | | 1,175 | | | | — | | | | 1,175 | | | | — | | |
Corporate bonds | | | 463 | | | | — | | | | 463 | | | | — | | |
Mortgage/Asset-backed securities | | | 5 | | | | — | | | | 5 | | | | — | | |
Insurance contracts | | | 197 | | | | — | | | | 197 | | | | — | | |
Investments in private funds: | | | | | | | | | | | | | | | | | |
Private funds | | | 112 | | | | — | | | | — | | | | 112 | | |
Hedge funds | | | 54 | | | | — | | | | — | | | | 54 | | |
Real estate funds | | | 160 | | | | — | | | | — | | | | 160 | | |
| | | | | | | | | | | | | | | | | |
| | $ | 3,958 | | | $ | 560 | | | $ | 3,072 | | | $ | 326 | | |
| | | | | | | | | | | | | | | | | |
| | | | | | | | | | | | | | | | | |
| | Non-U.S. Plans | |
| | | |
| | December 31, 2010 | |
| | | |
| | Total | | Level 1 | | Level 2 | | Level 3 | |
| | | | | | | | | |
Common stock/preferred stock: | | | | | | | | | | | | | | | | | |
U.S. companies | | $ | 338 | | | $ | 327 | | | $ | 11 | | | $ | — | | |
Non-U.S. companies | | | 1,556 | | | | 336 | | | | 1,220 | | | | — | | |
Fixed income investments: | | | | | | | | | | | | | | | | | |
Short-term investments | | | 176 | | | | 176 | | | | — | | | | — | | |
Government securities | | | 915 | | | | — | | | | 915 | | | | — | | |
Corporate bonds | | | 431 | | | | — | | | | 431 | | | | — | | |
Mortgage/Asset-backed securities | | | 14 | | | | — | | | | 14 | | | | — | | |
Insurance contracts | | | 196 | | | | — | | | | 196 | | | | — | | |
Investments in private funds: | | | | | | | | | | | | | | | | | |
Private funds | | | 89 | | | | — | | | | — | | | | 89 | | |
Hedge funds | | | 55 | | | | — | | | | — | | | | 55 | | |
Real estate funds | | | 169 | | | | — | | | | — | | | | 169 | | |
| | | | | | | | | | | | | | | | | |
| | $ | 3,939 | | | $ | 839 | | | $ | 2,787 | | | $ | 313 | | |
| | | | | | | | | | | | | | | | | |
The following tables summarize changes in the fair value of Level 3 assets for the years ended December 31, 2011 and 2010:
104
| | | | | | | | | | | | | | | | | | | | | |
| | U.S. Plans | |
| | | |
| | Private Funds | | Direct Private Investments | | Hedge Funds | | Real Estate Funds | | Real Estate Properties | |
| | | | | | | | | | | |
Balance at December 31, 2009 | | $ | 911 | | | $ | 149 | | | $ | 78 | | | $ | 132 | | | $ | 452 | | |
Actual return on plan assets: | | | | | | | | | | | | | | | | | | | | | |
Relating to assets still held at year-end | | | 42 | | | | (9 | ) | | | 11 | | | | 36 | | | | 45 | | |
Relating to assets sold during the year | | | 29 | | | | — | | | | 1 | | | | 1 | | | | 10 | | |
Purchases, sales and settlements | | | 71 | | | | 27 | | | | (13 | ) | | | 45 | | | | (13 | ) | |
| | | | | | | | | | | | | | | | | | | | | |
Balance at December 31, 2010 | | | 1,053 | | | | 167 | | | | 77 | | | | 214 | | | | 494 | | |
Actual return on plan assets: | | | | | | | | | | | | | | | | | | | | | |
Relating to assets still held at year-end | | | (9 | ) | | | 4 | | | | (7 | ) | | | 26 | | | | 41 | | |
Relating to assets sold during the year | | | — | | | | 8 | | | | 4 | | | | — | | | | — | | |
Purchases, sales and settlements | | | (5 | ) | | | (18 | ) | | | (14 | ) | | | 16 | | | | 18 | | |
| | | | | | | | | | | | | | | | | | | | | |
Balance at December 31, 2011 | | $ | 1,039 | | | $ | 161 | | | $ | 60 | | | $ | 256 | | | $ | 553 | | |
| | | | | | | | | | | | | | | | | | | | | |
| | | | | | | | | | | | | |
| | Non-U.S. Plans | |
| | | |
| | Private Funds | | Hedge Funds | | Real Estate Funds | |
| | | | | | | |
Balance at December 31, 2009 | | $ | 81 | | | $ | 51 | | | $ | 137 | | |
Actual return on plan assets: | | | | | | | | | | | | | |
Relating to assets still held at year-end | | | 2 | | | | 4 | | | | 2 | | |
Relating to assets sold during the year | | | 3 | | | | — | | | | 5 | | |
Purchases, sales and settlements | | | 3 | | | | — | | | | 25 | | |
| | | | | | | | | | | | | |
Balance at December 31, 2010 | | | 89 | | | | 55 | | | | 169 | | |
Actual return on plan assets: | | | | | | | | | | | | | |
Relating to assets still held at year-end | | | 2 | | | | (1 | ) | | | 7 | | |
Relating to assets sold during the year | | | 3 | | | | — | | | | 2 | | |
Purchases, sales and settlements | | | 18 | | | | — | | | | (18 | ) | |
| | | | | | | | | | | | | |
Balance at December 31, 2011 | | $ | 112 | | | $ | 54 | | | $ | 160 | | |
| | | | | | | | | | | | | |
Our U.S. pension assets at December 31, 2011 and 2010 include $976 and $834 million, respectively, in notional derivative exposure primarily related to outstanding equity futures contracts. The Company enters into futures contracts to gain exposure to certain markets.
Common stocks, preferred stocks, real estate investment trusts, and short-term investments are valued at the closing price reported in the active market in which the individual securities are traded. Corporate bonds, mortgages, asset-backed securities, and government securities are valued either by using pricing models, bids provided by brokers or dealers, quoted prices of securities with similar characteristics or discounted cash flows and as such include adjustments for certain risks that may not be observable such as credit and liquidity risks. Certain securities are held in commingled funds which are valued using net asset values provided by the
105
administrators of the funds. Investments in private equity, debt, real estate and hedge funds and direct private investments are valued at estimated fair value based on quarterly financial information received from the investment advisor and/or general partner. Investments in real estate properties are valued on a quarterly basis using the income approach. Valuation estimates are periodically supplemented by third party appraisals.
Our general funding policy for qualified pension plans is to contribute amounts at least sufficient to satisfy regulatory funding standards. In 2011, 2010 and 2009, we were not required to make contributions to our U.S. pension plans, however, we made voluntary contributions of $1,650, $1,000 and $740 million, respectively, primarily to improve the funded status of our plans. These contributions do not reflect benefits paid directly from Company assets. In 2012, we expect to make cash contributions of $800 million to $1 billion ($250 million was made in January 2012) to our global defined benefit pension plans principally to improve the funded status of our plans and also to satisfy regulatory funding standards in our non-U.S. plans.
Benefit payments, including amounts to be paid from Company assets, and reflecting expected future service, as appropriate, are expected to be paid as follows:
| | | | | | | |
| | U.S. Plans | | Non-U.S. Plans | |
| | | | | |
2012 | | $ | 1,025 | | $ | 185 | |
2013 | | | 1,025 | | | 189 | |
2014 | | | 1,051 | | | 193 | |
2015 | | | 1,101 | | | 197 | |
2016 | | | 1,084 | | | 203 | |
2017-2021 | | | 5,473 | | | 1,097 | |
Other Postretirement Benefits
The Medicare Prescription Drug, Improvement and Modernization Act of 2003 (the Act) provides subsidies for employers that sponsor postretirement health care plans that provide prescription drug coverage that is at least actuarially equivalent to that offered by Medicare Part D. The March 2010 enactment of the Patient Protection and Affordable Care Act, including modifications made in the Health Care and Education Reconciliation Act of 2010 resulted in a one-time, non-cash charge of $13 million related to income taxes in the first quarter of 2010. The charge results from a change in the tax treatment of the Medicare Part D program.
| | | | | | | |
| | December 31, | |
| | | |
| | 2011 | | 2010 | |
| | | | | |
Assumed health care cost trend rate: | | | | | | | |
Health care cost trend rate assumed for next year | | | 7.50 | % | | 8.00 | % |
Rate that the cost trend rate gradually declines to | | | 5.00 | % | | 5.00 | % |
Year that the rate reaches the rate it is assumed to remain at | | | 2017 | | | 2017 | |
The assumed health care cost trend rate has a significant effect on the amounts reported. A one-percentage-point change in the assumed health care cost trend rate would have the following effects:
| | | | | | | |
| | 1 percentage point | |
| | | |
| | Increase | | Decrease | |
| | | | | |
Effect on total of service and interest cost components | | $ | 5 | | $ | (3 | ) |
Effect on postretirement benefit obligation | | $ | 126 | | $ | (80 | ) |
Benefit payments reflecting expected future service, as appropriate, are expected to be paid as follows:
106
| | | | | | | | | | | |
| | Without Impact of Medicare Subsidy | | Net of Medicare Subsidy | |
| | | | | |
2012 | | | $ | 180 | | | | $ | 167 | | |
2013 | | | | 168 | | | | | 156 | | |
2014 | | | | 157 | | | | | 145 | | |
2015 | | | | 147 | | | | | 136 | | |
2016 | | | | 137 | | | | | 126 | | |
2017-2021 | | | | 551 | | | | | 499 | | |
Employee Savings Plans
We sponsor employee savings plans under which we match, in the form of our common stock, savings plan contributions for certain eligible employees. Shares issued under the stock match plans were 2.6, 2.4, and 4.8 million at a cost of $138, $105 and $158 million in 2011, 2010, and 2009, respectively.
Note 23. Segment Financial Data
We globally manage our business operations through four reportable operating segments serving customers worldwide with aerospace products and services, control, sensing and security technologies for buildings, homes and industry, automotive products and chemicals. Segment information is consistent with how management reviews the businesses, makes investing and resource allocation decisions and assesses operating performance. Our four reportable segments are as follows:
| | |
| • | Aerospace includes Air Transport and Regional, Business and General Aviation and Defense and Space and provides products and services which include auxiliary power units; propulsion engines; environmental control systems; electric power systems, engine controls; repair and overhaul services; flight safety, communications, navigation, radar and surveillance systems; aircraft lighting; management and technical services; logistic services; advanced systems and instruments; and aircraft wheels and brakes. |
| | |
| • | Automation and Control Solutions includes Energy, Safety & Security (controls for heating, cooling, indoor air quality, ventilation, humidification, lighting and home automation; advanced software applications for home/building control and optimization; sensors, switches, control systems and instruments for measuring pressure, air flow, temperature and electrical current; security, fire and gas detection; personal protection equipment; access control; video surveillance equipment; remote patient monitoring systems; and automatic identification and data collection); Process Solutions (provides a full range of automation and control solutions for industrial plants, offering advanced software and automation systems that integrate, control and monitor complex processes in many types of industrial settings as well as equipment that controls, measures and analyzes natural gas production and transportation); and Building Solutions & Distribution (installs, distributes, maintains and upgrades systems that keep buildings safe, comfortable and productive). |
| | |
| • | Performance Materials and Technologies includes Advanced Materials (fluorocarbons, hydrofluoroolefins, caprolactam, resins, ammonium sulfate for fertilizer, specialty films, waxes, additives, advanced fibers, customized research chemicals and intermediates, and electronic materials and chemicals) and UOP (catalysts and adsorbents). |
| | |
| • | Transportation Systems includes turbochargers, thermal systems, brake hard parts and other friction materials. |
The accounting policies of the segments are the same as those described in Note 1. Honeywell’s senior management evaluates segment performance based on segment profit. Segment profit is measured as business unit income (loss) before taxes excluding general corporate unallocated expense, other income (expense), interest and other financial charges, pension and other postretirement benefits (expense), stock compensation expense, repositioning and other charges and accounting changes.
107
| | | | | | | | | | | | |
| | Years Ended December 31, |
| | |
| | 2011 | | 2010 | | 2009 |
| | | | | | |
Net Sales | | | | | | | | | | | | |
| | | | | | | | | | | | |
Aerospace | | | | | | | | | | | | |
Product | | $ | 6,494 | | | $ | 5,868 | | | $ | 5,930 | |
Service | | | 4,981 | | | | 4,815 | | | | 4,833 | |
| | | | | | | | | | | | |
Total | | | 11,475 | | | | 10,683 | | | | 10,763 | |
Automation and Control Solutions | | | | | | | | | | | | |
Product | | | 13,328 | | | | 11,733 | | | | 10,699 | |
Service | | | 2,207 | | | | 2,016 | | | | 1,912 | |
| | | | | | | | | | | | |
Total | | | 15,535 | | | | 13,749 | | | | 12,611 | |
Performance Materials and Technologies | | | | | | | | | | | | |
Product | | | 5,064 | | | | 4,449 | | | | 3,895 | |
Service | | | 595 | | | | 277 | | | | 249 | |
| | | | | | | | | | | | |
Total | | | 5,659 | | | | 4,726 | | | | 4,144 | |
Transportation Systems | | | | | | | | | | | | |
Product | | | 3,859 | | | | 3,192 | | | | 2,432 | |
Service | | | — | | | | — | | | | — | |
| | | | | | | | | | | | |
Total | | | 3,859 | | | | 3,192 | | | | 2,432 | |
Corporate | | | | | | | | | | | | |
Product | | | — | | | | — | | | | — | |
Service | | | 1 | | | | — | | | | 1 | |
| | | | | | | | | | | | |
Total | | | 1 | | | | — | | | | 1 | |
| | | | | | | | | | | | |
| | $ | 36,529 | | | $ | 32,350 | | | $ | 29,951 | |
| | | | | | | | | | | | |
| | | | | | | | | | | | |
Depreciation and amortization | | | | | | | | | | | | |
Aerospace | | $ | 208 | | | $ | 224 | | | $ | 217 | |
Automation and Control Solutions | | | 364 | | | | 368 | | | | 352 | |
Performance Materials and Technologies | | | 216 | | | | 222 | | | | 209 | |
Transportation Systems | | | 96 | | | | 97 | | | | 98 | |
Corporate | | | 64 | | | | 59 | | | | 60 | |
| | | | | | | | | | | | |
| | $ | 948 | | | $ | 970 | | | $ | 936 | |
| | | | | | | | | | | | |
| | | | | | | | | | | | |
Segment Profit | | | | | | | | | | | | |
Aerospace | | $ | 2,023 | | | $ | 1,835 | | | $ | 1,893 | |
Automation and Control Solutions | | | 2,083 | | | | 1,770 | | | | 1,588 | |
Performance Materials and Technologies | | | 1,042 | | | | 749 | | | | 605 | |
Transportation Systems | | | 485 | | | | 353 | | | | 61 | |
Corporate | | | (276 | ) | | | (222 | ) | | | (156 | ) |
| | | | | | | | | | | | |
| | $ | 5,357 | | | $ | 4,485 | | | $ | 3,991 | |
| | | | | | | | | | | | |
| | | | | | | | | | | | |
Capital expenditures | | | | | | | | | | | | |
Aerospace | | $ | 174 | | | $ | 158 | | | $ | 184 | |
Automation and Control Solutions | | | 153 | | | | 131 | | | | 114 | |
Performance Materials and Technologies | | | 282 | | | | 188 | | | | 153 | |
Transportation Systems | | | 133 | | | | 78 | | | | 66 | |
Corporate | | | 48 | | | | 89 | | | | 88 | |
| | | | | | | | | | | | |
| | $ | 790 | | | $ | 644 | | | $ | 605 | |
| | | | | | | | | | | | |
| | | | | | | | | | | |
| | December 31, |
| | |
| | 2011 | | 2010 | | 2009 |
| | | | | | |
Total Assets | | | | | | | | | | | | |
| | | | | | | | | | | |
Aerospace | | $ | 9,109 | | | $ | 8,604 | | | $ | 8,386 | |
Automation and Control Solutions | | | 19,127 | | | | 18,183 | | | | 15,474 | |
Performance Materials and Technologies | | | 5,402 | | | | 4,938 | | | | 4,657 | |
Transportation Systems | | | 1,991 | | | | 1,806 | | | | 1,680 | |
Corporate | | | 4,179 | | | | 4,303 | | | | 5,796 | |
| | | | | | | | | | | | |
| | $ | 39,808 | | | $ | 37,834 | | | $ | 35,993 | |
| | | | | | | | | | | | |
108
A reconciliation of segment profit to consolidated income from continuing operations before taxes are as follows:
| | | | | | | | | | | | |
| | Years Ended December 31, | |
| | | |
| | 2011 | | | 2010 | | | 2009 | |
| | | | | | | | | |
| | | | | | | | | | | | |
Segment Profit | | $ | 5,357 | | | $ | 4,485 | | | $ | 3,991 | |
Other income/ (expense)(1) | | | 33 | | | | 69 | | | | 28 | |
Interest and other financial charges | | | (376 | ) | | | (386 | ) | | | (458 | ) |
Stock compensation expense(2) | | | (168 | ) | | | (163 | ) | | | (117 | ) |
Pension expense-ongoing(2) | | | (105 | ) | | | (185 | ) | | | (287 | ) |
Pension mark-to-market adjustment(2) | | | (1,802 | ) | | | (471 | ) | | | (741 | ) |
Other postretirement income/(expense)(2) | | | 86 | | | | (29 | ) | | | 15 | |
Repositioning and other charges(2) | | | (743 | ) | | | (598 | ) | | | (467 | ) |
| | | | | | | | | | | | |
Income from continuing operations before taxes | | $ | 2,282 | | | $ | 2,722 | | | $ | 1,964 | |
| | | | | | | | | | | | |
| |
| (1) Equity income/(loss) of affiliated companies is included in Segment Profit. |
| |
| (2) Amounts included in cost of products and services sold and selling, general and administrative expenses. |
Note 24. Geographic Areas - Financial Data
| | | | | | | | | | | | | | | | | | | | | | | | |
| | Net Sales(1) | | | Long-lived Assets(2) | |
| | Years Ended December 31, | | | Years Ended December 31, | |
| | | | | | |
| | 2011 | | | 2010 | | | 2009 | | | 2011 | | | 2010 | | | 2009 | |
| | | | | | | | | | | | | | | | | | |
United States | | $ | 21,005 | | | $ | 18,858 | | | $ | 18,000 | | | $ | 12,426 | | | $ | 12,267 | | | $ | 11,645 | |
Europe | | | 9,604 | | | | 8,367 | | | | 7,594 | | | | 3,991 | | | | 3,973 | | | | 3,798 | |
Other International | | | 5,920 | | | | 5,125 | | | | 4,357 | | | | 2,728 | | | | 2,296 | | | | 2,072 | |
| | | | | | | | | | | | | | | | | | | | | | | | |
| | $ | 36,529 | | | $ | 32,350 | | | $ | 29,951 | | | $ | 19,145 | | | $ | 18,536 | | | $ | 17,515 | |
| | | | | | | | | | | | | | | | | | | | | | | | |
(1) Sales between geographic areas approximate market and are not significant. Net sales are classified according to their country of origin. Included in United States net sales are export sales of $4,549, $3,629 and $3,548 million in 2011, 2010 and 2009, respectively.
(2) Long-lived assets are comprised of property, plant and equipment, goodwill and other intangible assets.
Note 25. Supplemental Cash Flow Information
109
| | | | | | | | | | | | |
| | Years Ended December 31, | |
| | | |
| | 2011 | | | 2010 | | | 2009 | |
| | | | | | | | | |
Payments for repositioning and other charges: | | | | | | | | | | | | |
Severance and exit cost payments | | $ | (161 | ) | | $ | (151 | ) | | $ | (200 | ) |
Environmental payments | | | (270 | ) | | | (266 | ) | | | (318 | ) |
Insurance receipts for asbestos related liabilities | | | 134 | | | | 141 | | | | 16 | |
Asbestos related liability payments | | | (171 | ) | | | (163 | ) | | | (156 | ) |
| | | | | | | | | | | | |
| | $ | (468 | ) | | $ | (439 | ) | | $ | (658 | ) |
| | | | | | | | | | | | |
| | | | | | | | | | | | |
Interest paid, net of amounts capitalized | | $ | 378 | | | $ | 410 | | | $ | 469 | |
Income taxes paid, net of refunds | | | 578 | | | | 80 | | | | 361 | |
Non-cash investing and financing activities: | | | | | | | | | | | | |
Common stock contributed to savings plans | | | 138 | | | | 105 | | | | 153 | |
Common stock contributed to U.S. pension plans | | | — | | | | 400 | | | | 740 | |
Marketable securities contributed to non-U.S. pension plans | | | — | | | | 242 | | | | — | |
Note 26. Unaudited Quarterly Financial Information
110
| | | | | | | | | | | | | | | | | | | | |
| | 2011 | |
| | | |
| | Mar. 31 | | | June 30 | | | Sept. 30 | | | Dec. 31 | | | Year | |
| | | | | | | | | | | | | | | |
Net Sales | | $ | 8,672 | | | $ | 9,086 | | | $ | 9,298 | | | $ | 9,473 | | | $ | 36,529 | |
Gross Profit | | | 2,248 | | | | 2,422 | | | | 2,265 | | | | 1,038 | | | | 7,973 | |
Amounts attributable to Honeywell | | | | | | | | | | | | | | | | | | | | |
Income (loss) from continuing operations less net income attributable to the noncontrolling interest | | | 687 | | | | 796 | | | | 685 | | | | (310 | ) | | | 1,858 | |
Income from discontinued operations(1) | | | 18 | | | | 14 | | | | 177 | | | | — | | | | 209 | |
| | | | | | | | | | | | | | | | | | | | |
Net Income (loss) attributable to Honeywell | | | 705 | | | | 810 | | | | 862 | | | | (310 | ) | | | 2,067 | |
Earnings per share - basic | | | | | | | | | | | | | | | | | | | | |
Income (loss) from continuing operations | | | 0.87 | | | | 1.01 | | | | 0.88 | | | | (0.40 | ) | | | 2.38 | |
Income from discontinued operations | | | 0.03 | | | | 0.02 | | | | 0.23 | | | | — | | | | 0.27 | |
| | | | | | | | | | | | | | | | | | | | |
Net Income (loss) attributable to Honeywell | | | 0.90 | | | | 1.03 | | | | 1.11 | | | | (0.40 | ) | | | 2.65 | |
Earnings per share - assuming dilution | | | | | | | | | | | | | | | | | | | | |
Income (loss) from continuing operations | | | 0.86 | | | | 1.00 | | | | 0.87 | | | | (0.40 | ) | | | 2.35 | |
Income from discontinued operations | | | 0.02 | | | | 0.02 | | | | 0.23 | | | | — | | | | 0.26 | |
| | | | | | | | | | | | | | | | | | | | |
Net Income (loss) attributable to Honeywell | | | 0.88 | | | | 1.02 | | | | 1.10 | | | | (0.40 | ) | | | 2.61 | |
Dividends paid per share | | | 0.3325 | | | | 0.3325 | | | | 0.3325 | | | | 0.3725 | | | | 1.37 | |
Market Price per share | | | | | | | | | | | | | | | | | | | | |
High | | | 59.71 | | | | 62.00 | | | | 60.44 | | | | 54.98 | | | | 62.00 | |
Low | | | 53.48 | | | | 55.53 | | | | 41.94 | | | | 42.32 | | | | 41.94 | |
| | | | | | | | | | | | | | | | | | | | |
| | 2010 | |
| | | |
| | Mar. 31 | | | June 30 | | | Sept. 30 | | | Dec. 31 | | | Year | |
| | | | | | | | | | | | | | | |
Net Sales | | $ | 7,536 | | | $ | 7,926 | | | $ | 8,139 | | | $ | 8,749 | | | $ | 32,350 | |
Gross Profit | | | 1,869 | | | | 1,959 | | | | 1,969 | | | | 1,832 | | | | 7,629 | |
Amounts attributable to Honeywell | | | | | | | | | | | | | | | | | | | | |
Income from continuing operations less net income attributable to the noncontrolling interest | | | 471 | | | | 550 | | | | 579 | | | | 344 | | | | 1,944 | |
Income from discontinued operations | | | 18 | | | | 16 | | | | 19 | | | | 25 | | | | 78 | |
| | | | | | | | | | | | | | | | | | | | |
Net Income attributable to Honeywell | | | 489 | | | | 566 | | | | 598 | | | | 369 | | | | 2,022 | |
Earnings per share - basic | | | | | | | | | | | | | | | | | | | | |
Income from continuing operations | | | 0.61 | | | | 0.72 | | | | 0.75 | | | | 0.44 | | | | 2.51 | |
Income from discontinued operations | | | 0.02 | | | | 0.02 | | | | 0.02 | | | | 0.03 | | | | 0.10 | |
| | | | | | | | | | | | | | | | | | | | |
Net Income attributable to Honeywell | | | 0.63 | | | | 0.74 | | | | 0.77 | | | | 0.47 | | | | 2.61 | |
Earnings per share - assuming dilution | | | | | | | | | | | | | | | | | | | | |
Income from continuing operations | | | 0.61 | | | | 0.71 | | | | 0.74 | | | | 0.44 | | | | 2.49 | |
Income from discontinued operations | | | 0.02 | | | | 0.02 | | | | 0.02 | | | | 0.03 | | | | 0.10 | |
| | | | | | | | | | | | | | | | | | | | |
Net Income attributable to Honeywell | | | 0.63 | | | | 0.73 | | | | 0.76 | | | | 0.47 | | | | 2.59 | |
Dividends paid per share | | | 0.3025 | | | | 0.3025 | | | | 0.3025 | | | | 0.3025 | | | | 1.21 | |
Market Price per share | | | | | | | | | | | | | | | | | | | | |
High | | | 45.27 | | | | 48.52 | | | | 44.46 | | | | 53.72 | | | | 53.72 | |
Low | | | 36.87 | | | | 39.03 | | | | 38.53 | | | | 43.61 | | | | 36.87 | |
(1) For the year ended December 31, 2011, Income from discontinued operations includes a $178 million, net of tax gain, resulting from the sale of the CPG business which funded a portion of the 2011 repositioning actions.
111
Report of Independent Registered Public Accounting Firm
TO THE BOARD OF DIRECTORS AND SHAREHOLDERS OF
HONEYWELL INTERNATIONAL INC.;
In our opinion, the consolidated financial statements listed in the index appearing under Item 15(a)(1) present fairly, in all material respects, the financial position of Honeywell International Inc. and its subsidiaries at December 31, 2011 and 2010, and the results of their operations and their cash flows for each of the three years in the period ended December 31, 2011 in conformity with accounting principles generally accepted in the United States of America. In addition, in our opinion, the financial statement schedule listed in the index appearing under item 15(a)(2) presents fairly, in all material respects, the information set forth therein when read in conjunction with the related consolidated financial statements. Also in our opinion, the Company maintained, in all material respects, effective internal control over financial reporting as of December 31, 2011, based on criteria established in Internal Control - Integrated Framework issued by the Committee of Sponsoring Organizations of the Treadway Commission (COSO). The Company’s management is responsible for these financial statements and the financial statement schedule, for maintaining effective internal control over financial reporting and for its assessment of the effectiveness of internal control over financial reporting, included in Management’s Report on Internal Control over Financial Reporting under Item 9A. Our responsibility is to express opinions on these financial statements, on the financial statement schedule and on the Company’s internal control over financial reporting based on our integrated audits. We conducted our audits in accordance with the standards of the Public Company Accounting Oversight Board (United States). Those standards require that we plan and perform the audits to obtain reasonable assurance about whether the financial statements are free of material misstatement and whether effective internal control over financial reporting was maintained in all material respects. Our audits of the financial statements included examining, on a test basis, evidence supporting the amounts and disclosures in the financial statements, assessing the accounting principles used and significant estimates made by management, and evaluating the overall financial statement presentation. Our audit of internal control over financial reporting included obtaining an understanding of internal control over financial reporting, assessing the risk that a material weakness exists, and testing and evaluating the design and operating effectiveness of internal control based on the assessed risk. Our audits also included performing such other procedures as we considered necessary in the circumstances. We believe that our audits provide a reasonable basis for our opinions.
A company’s internal control over financial reporting is a process designed to provide reasonable assurance regarding the reliability of financial reporting and the preparation of financial statements for external purposes in accordance with generally accepted accounting principles. A company’s internal control over financial reporting includes those policies and procedures that (i) pertain to the maintenance of records that, in reasonable detail, accurately and fairly reflect the transactions and dispositions of the assets of the company; (ii) provide reasonable assurance that transactions are recorded as necessary to permit preparation of financial statements in accordance with generally accepted accounting principles, and that receipts and expenditures of the company are being made only in accordance with authorizations of management and directors of the company; and (iii) provide reasonable assurance regarding prevention or timely detection of unauthorized acquisition, use, or disposition of the company’s assets that could have a material effect on the financial statements.
Because of its inherent limitations, internal control over financial reporting may not prevent or detect misstatements. Also, projections of any evaluation of effectiveness to future periods are subject to the risk that controls may become inadequate because of changes in conditions, or that the degree of compliance with the policies or procedures may deteriorate.
/s/ PricewaterhouseCoopers LLP
Florham Park, New Jersey
February 17, 2012
112
| |
Item 9. | Changes in and Disagreements with Accountants on Accounting and Financial Disclosure |
Not Applicable
| |
Item 9A. | Controls and Procedures |
Honeywell management, including the Chief Executive Officer and Chief Financial Officer, conducted an evaluation of the effectiveness of our disclosure controls and procedures as of the end of the period covered by this Annual Report on Form 10-K. Based upon that evaluation, the Chief Executive Officer and the Chief Financial Officer concluded that such disclosure controls and procedures were effective as of the end of the period covered by this Annual Report on Form 10-K to ensure information required to be disclosed in the reports that Honeywell files or submits under the Exchange Act is recorded, processed, summarized, and reported within the time periods specified in the Securities and Exchange Commission rules and forms and that it is accumulated and communicated to our management, including our Chief Executive Officer, our Chief Financial Officer and our Controller, as appropriate, to allow timely decisions regarding required disclosure. There have been no changes that have materially affected, or are reasonably likely to materially affect, Honeywell’s internal control over financial reporting that have occurred during the quarter ended December 31, 2011.
Management’s Report on Internal Control Over Financial Reporting
Honeywell management is responsible for establishing and maintaining adequate internal control over financial reporting as defined in Rules 13a-15(f) and 15d-15(f) under the Securities Exchange Act of 1934. Honeywell’s internal control over financial reporting is a process designed to provide reasonable assurance regarding the reliability of financial reporting and the preparation of financial statements for external purposes in accordance with generally accepted accounting principles. Honeywell’s internal control over financial reporting includes those policies and procedures that:
| |
| (i) pertain to the maintenance of records that, in reasonable detail, accurately and fairly reflect the transactions and dispositions of Honeywell’s assets; |
| |
| (ii) provide reasonable assurance that transactions are recorded as necessary to permit preparation of financial statements in accordance with generally accepted accounting principles, and that receipts and expenditures of the company are being made only in accordance with authorizations of Honeywell’s management and directors; and |
| |
| (iii) provide reasonable assurance regarding prevention or timely detection of unauthorized acquisition, use or disposition of Honeywell’s assets that could have a material effect on the financial statements. |
Because of its inherent limitations, internal control over financial reporting may not prevent or detect misstatements. Also, projections of any evaluation of effectiveness to future periods are subject to the risk that controls may become inadequate because of changes in conditions, or that the degree of compliance with the policies or procedures may deteriorate.
Management assessed the effectiveness of Honeywell’s internal control over financial reporting as of December 31, 2011. In making this assessment, management used the criteria set forth by the Committee of Sponsoring Organizations of the Treadway Commission (COSO) inInternal Control – Integrated Framework.
Based on this assessment, management determined that Honeywell maintained effective internal control over financial reporting as of December 31, 2011.
The effectiveness of Honeywell’s internal control over financial reporting as of December 31, 2011 has been audited by PricewaterhouseCoopers LLP, an independent registered public accounting firm, as stated in their report which is included in “Item 8. Financial Statements and Supplementary Data.”
113
| |
Item 9B. | Other Information |
| |
Not Applicable |
| |
Item 10. | Directors and Executive Officers of the Registrant |
Information relating to the Directors of Honeywell, as well as information relating to compliance with Section 16(a) of the Securities Exchange Act of 1934, will be contained in our definitive Proxy Statement involving the election of the Directors, which will be filed with the SEC pursuant to Regulation 14A not later than 120 days after December 31, 2011, and such information is incorporated herein by reference. Certain other information relating to the Executive Officers of Honeywell appears in Part I of this Annual Report on Form 10-K under the heading “Executive Officers of the Registrant”.
The members of the Audit Committee of our Board of Directors are: George Paz (Chair), Kevin Burke, Scott Davis, Linnet Deily, and Judd Gregg. The Board has determined that Mr. Paz is the “audit committee financial expert” as defined by applicable SEC rules and that Mr. Paz, Mr. Davis, and Ms. Deily satisfy the “accounting or related financial management expertise” criteria established by the NYSE. All members of the Audit Committee are “independent” as that term is defined in applicable SEC Rules and NYSE listing standards.
Honeywell’s Code of Business Conduct is available, free of charge, on our website under the heading “Investor Relations” (see “Corporate Governance”), or by writing to Honeywell, 101 Columbia Road, Morris Township, New Jersey 07962, c/o Vice President and Corporate Secretary. Honeywell’s Code of Business Conduct applies to all Honeywell directors, officers (including the Chief Executive Officer, Chief Financial Officer and Controller) and employees. Amendments to or waivers of the Code of Business Conduct granted to any of Honeywell’s directors or executive officers will be published on our website within five business days of such amendment or waiver.
| |
Item 11. | Executive Compensation |
Information relating to executive compensation is contained in the Proxy Statement referred to above in “Item 10. Directors and Executive Officers of the Registrant,” and such information is incorporated herein by reference.
| |
Item 12. | Security Ownership of Certain Beneficial Owners and Management and Related Stockholder Matters |
Information relating to security ownership of certain beneficial owners and management and related stockholder matters is contained in the Proxy Statement referred to above in “Item 10. Directors and Executive Officers of the Registrant,” and such information is incorporated herein by reference.
EQUITY COMPENSATION PLANS
As of December 31, 2011 information about our equity compensation plans is as follows:
114
| | | | | | | | | | | | |
Plan category | | Number of Shares to be Issued Upon Exercise of Outstanding Options, Warrants and Rights | | | Weighted- Average Exercise Price of Outstanding Options, Warrants and Rights | | | Number of Securities Remaining Available for Future Issuance Under Equity Compensation Plans (Excluding Securities Reflected in Column (a)) | |
| | | | | | | | | |
| | (a) | | | (b) | | | (c) | |
Equity compensation plans approved by security holders | | | 49,895,073 | (1) | | $ | 43.01 | (2) | | | 42,195,484 | (3) |
Equity compensation plans not approved by security holders | | | 626,868 | (4) | | | N/A | (5) | | | N/A | (6) |
| | | | | | | | | | | | |
Total | | | 50,521,941 | | | | 43.01 | | | | 42,195,484 | |
| | | | | | | | | | | | |
| |
(1) | Equity compensation plans approved by shareowners that are included in column (a) of the table are the 2011 Stock Incentive Plan of Honeywell International Inc. and its Affiliates (the “2011 Stock Incentive Plan”), the 2006 Stock Incentive Plan of Honeywell International Inc. and its Affiliates (the “2006 Stock Incentive Plan”), the 2003 Stock Incentive Plan of Honeywell International Inc. and its Affiliates (the “2003 Stock Incentive Plan”) and the 1993 Stock Plan for Employees of Honeywell International Inc. and its Affiliates (the “1993 Stock Plan”) (38,562,720 shares of Common Stock to be issued for options with a weighted average term of 6.27 years; 31,150 shares to be issued for stock appreciation rights (“SARs”); 9,746,433 RSUs subject to continued employment; 130,891 performance shares subject to continued employment; and 1,092,879 deferred RSUs of earned and vested awards where delivery of shares has been deferred); and the 2006 Stock Plan for Non-Employee Directors of Honeywell International Inc. (the “2006 Non-Employee Director Plan”) and the 1994 Stock Plan for Non-Employee Directors of Honeywell International Inc. (the “1994 Non-Employee Director Plan”) (322,000 shares of Common Stock to be issued for options; and 9,000 RSUs subject to continued services). RSUs included in column (a) of the table represent the full number of RSUs awarded and outstanding whereas the number of shares of Common Stock to be issued upon vesting will be lower than what is reflected on the table due to the net share settlement process used by the Company (whereas the value of shares required to meet employee statutory minimum tax withholding requirements are not issued). |
| |
| 1,266,309 growth plan units were issued for the performance cycle commencing on January 1, 2010 and ending December 31, 2011 pursuant to the 2006 Stock Incentive Plan. The ultimate value of any growth plan award may be paid in cash or shares of Common Stock and, thus, growth plan units are not included in the table above. The ultimate value of growth plan units depends upon the achievement of pre-established performance goals during the two-year performance cycle. 50% of the payment related to these growth plan units will be paid in March 2012 and the remaining 50% will be paid in March 2013, subject to active employment on the payment dates. |
| |
| Because the number of future shares that may be distributed to employees participating in the Honeywell Global Stock Plan is unknown, no shares attributable to that plan are included in column (a) of the table above. |
| |
(2) | Column (b) relates to stock options and does not include any exercise price for RSUs, performance shares, or growth plan units granted to employees or non-employee directors under equity compensation plans approved by shareowners. RSUs do not have an exercise price because their value is dependent upon attainment of certain performance goals or continued employment or service and they are settled for shares of Common Stock on a one-for-one basis. Growth plan units are denominated in cash units and the ultimate value of the award is dependent upon attainment of certain performance goals. |
| |
(3) | The number of shares that may be issued under the 2011 Stock Incentive Plan as of December 31, 2011 is 39,582,132 which includes the following additional shares under the 2011 Stock Incentive Plan (or any Prior |
115
| |
| Plan as defined in the 2011 Stock Incentive Plan) that may again be available for issuance: shares that are settled for cash, expire, are canceled, are tendered in satisfaction of an option exercise price or tax withholding obligations, are reacquired with cash tendered in satisfaction of an option exercise price or with monies attributable to any tax deduction enjoyed by Honeywell to the exercise of an option, and are under any outstanding awards assumed under any equity compensation plan of an entity acquired by Honeywell. No securities are available for future issuance under the 2006 Stock Incentive Plan, the 2003 Stock Incentive Plan, the 1993 Stock Plan, or the 1994 Non-Employee Director Plan. |
| |
| The number of shares that may be issued under the Honeywell Global Stock Plan as of December 31, 2011 is 2,384,352. This plan is an umbrella plan for four plans maintained solely for eligible employees of participating non-U.S. countries. More than 50% of the shares distributed under the Honeywell Global Stock Plan have been distributed to participants in one sub-plan, the Global Employee Stock Purchase Plan. As of January 1, 2011, the Global Employee Stock Purchase Plan was suspended, although company matching shares awarded to participants in 2008 vested in November 2011. |
| |
| Another sub-plan of the Honeywell Global Stock Plan, the UK Sharebuilder Plan, allows an eligible UK employee to contribute a specified percentage of taxable earnings that is then invested in shares. The company matches those shares and dividends paid are used to purchase additional shares. The company increased the match share percentage from 50% to 62.50% effective March 1, 2011. Matched shares are subject to a three-year vesting schedule. Shares taken out of the plan before five years lose their tax-favored status. For the year ending December 31, 2011, 105,015 shares were credited to participants’ accounts under the UK Sharebuilder Plan. |
| |
| The remaining two sub-plans of the Honeywell Global Stock Plan, the Honeywell International Technologies Employees Share Ownership Plan (Ireland) and the Honeywell Measurex (Ireland) Limited Group Employee Profit Sharing Scheme, allow eligible Irish employees to contribute specified percentages of base pay, bonus or performance pay that are then invested in shares. Shares must be held in trust for at least two years and lose their tax-favored status if they are taken out of the plan before three years. For the year ending December 31, 2011, 23,881 shares were credited to participants’ accounts under these two plans. |
| |
| The remaining 229,000 shares included in column (c) are shares remaining for future grants under the 2006 Non-Employee Director Plan. |
| |
(4) | Equity compensation plans not approved by shareowners that are included in the table are the Supplemental Non-Qualified Savings Plan for Highly Compensated Employees of Honeywell International Inc. and its Subsidiaries, and the AlliedSignal Incentive Compensation Plan for Executive Employees of AlliedSignal Inc. and its Subsidiaries. |
| |
| The Supplemental Non-Qualified Savings Plan for Highly Compensated Employees of Honeywell International Inc. and its Subsidiaries is an unfunded, non-tax qualified plan that provides benefits equal to the employee deferrals and company matching allocations that would have been provided under Honeywell’s U.S. tax-qualified savings plan if the Internal Revenue Code limitations on compensation and contributions did not apply. The company matching contribution is credited to participants’ accounts in the form of notional shares of Common Stock. The notional shares are distributed in the form of actual shares of Common Stock when payments are made to participants under the plan. The number of shares to be issued under this plan based on the value of the notional shares as of December 31, 2011 is 592,957. |
| |
| The AlliedSignal Incentive Compensation Plan for Executive Employees of AlliedSignal Inc. and its Subsidiaries was a cash incentive compensation plan maintained by AlliedSignal Inc. This plan has expired. Employees were permitted to defer receipt of a cash bonus payable under the plan and invest the deferred bonus in notional shares of Common Stock. The notional shares are distributed in the form of actual shares of Common Stock when payments are made to participants under the plan. No further deferrals can be made under this plan. The number of shares of Common Stock that remain to be issued under this expired plan as of December 31, 2011 is 33,911. |
| |
| The Deferred Compensation Plan for Non-Employee Directors of Honeywell International Inc. provides for mandatory and elective deferral of certain payments to non-employee directors. Mandatory deferrals are invested in notional shares of Common Stock. Directors may also invest any elective deferrals in notional shares of Common Stock. Because the notional shares are distributed in the form of cash when payments are made to directors under the plan, they are not included in the table above. |
116
| |
(5) | Column (b) does not include any exercise price for notional shares allocated to employees under Honeywell’s equity compensation plans not approved by shareowners because all of these shares are notionally allocated as a matching contribution under the non-tax qualified savings plans or as a notional investment of deferred bonuses or fees under the cash incentive compensation and directors’ plans as described in note 4 and are only settled for shares of Common Stock on a one-for-one basis. |
| |
(6) | No securities are available for future issuance under the AlliedSignal Incentive Compensation Plan for Executive Employees of AlliedSignal Inc. and its Subsidiaries and the Deferred Compensation Plan for Non-Employee Directors of Honeywell International Inc. The cash incentive compensation plan has expired. All notional investments in shares of Common Stock are converted to cash when payments are made under the directors’ plan. The amount of securities available for future issuance under the Supplemental Non-Qualified Savings Plan for Highly Compensated Employees of Honeywell International Inc. and its Subsidiaries is not determinable because the number of securities that may be issued under this plan depends upon the amount deferred to the plan by participants in future years. |
| |
| The table does not contain information for employee benefit plans of Honeywell that are intended to meet the requirements of Section 401(a) of the Internal Revenue Code and a small number of foreign employee benefit plans that are similar to such Section 401(a) plans. |
| |
Item 13. | Certain Relationships and Related Transactions |
Information relating to certain relationships and related transactions is contained in the Proxy Statement referred to above in “Item 10. Directors and Executive Officers of the Registrant,” and such information is incorporated herein by reference.
| |
Item 14. | Principal Accounting Fees and Services |
Information relating to fees paid to and services performed by PricewaterhouseCoopers LLP in 2011 and 2010 and our Audit Committee’s pre-approval policies and procedures with respect to non-audit services are contained in the Proxy Statement referred to above in “Item 10. Directors and Executive Officers of the Registrant,” and such information is incorporated herein by reference.
117
| |
Item 15. | Exhibits and Financial Statement Schedules |
118
SIGNATURES
Pursuant to the requirements of the Securities Exchange Act of 1934, the registrant has duly caused this report to be signed on its behalf by the undersigned thereunto duly authorized.
| | | |
| HONEYWELL INTERNATIONAL INC. |
| | |
Date: February 17, 2012 | By: | /s/ Kathleen A. Winters | |
| | | |
| | Kathleen A. Winters |
| | Vice President and Controller |
| | (on behalf of the Registrant |
| | and as the Registrant’s |
| | Principal Accounting Officer) |
Pursuant to the requirements of the Securities Exchange Act of 1934, this annual report has been signed below by the following persons on behalf of the Registrant and in the capacities and on the date indicated:
| | | | |
| Name | | Name | |
| | | | |
| * | | * | |
| | | | |
| David M. Cote | | Linnet F. Deily | |
| Chairman of the Board, | | Director | |
| Chief Executive Officer | | | |
| and Director | | | |
| | | | |
| * | | * | |
| | | | |
| Gordon M. Bethune | | Clive R. Hollick | |
| Director | | Director | |
| | | | |
| * | | * | |
| | | | |
| Kevin Burke | | George Paz | |
| Director | | Director | |
| | | | |
| * | | * | |
| | | | |
| Jaime Chico Pardo | | Bradley T. Sheares, Ph.D. | |
| Director | | Director | |
| | | | |
| * | | * | |
| | | | |
| D. Scott Davis | | Judd Gregg | |
| Director | | Director | |
| | | | |
| /s/ David J. Anderson | | /s/ Kathleen A. Winters | |
| | | | |
| David J. Anderson | | Kathleen A. Winters | |
| Senior Vice President and | | Vice President and Controller | |
| Chief Financial Officer | | (Principal Accounting Officer) | |
| (Principal Financial Officer) | | | |
| | | | |
*By: | /s/ David J. Anderson | | | |
| | | | |
| (David J. Anderson | | | |
| Attorney-in-fact) | | | |
| February 17, 2012 | | | |
119
EXHIBIT INDEX
| | |
Exhibit No. | | Description |
| | |
| | |
3(i) | | Amended and Restated Certificate of Incorporation of Honeywell International Inc., as amended April 26, 2010 (incorporated by reference to Exhibit 3(i) to Honeywell’s Form 8-K filed April 27, 2010) |
| | |
3(ii) | | By-laws of Honeywell International Inc., as amended April 26, 2010 (incorporated by reference to Exhibit 3(ii) to Honeywell’s Form 8-K filed April 27, 2010) |
| | |
4 | | Honeywell International Inc. is a party to several long-term debt instruments under which, in each case, the total amount of securities authorized does not exceed 10% of the total assets of Honeywell and its subsidiaries on a consolidated basis. Pursuant to paragraph 4(iii)(A) of Item 601(b) of Regulation S-K, Honeywell agrees to furnish a copy of such instruments to the Securities and Exchange Commission upon request. |
| | |
10.1* | | 2003 Stock Incentive Plan of Honeywell International Inc. and its Affiliates (incorporated by reference to Honeywell’s Proxy Statement, dated March 17, 2003, filed pursuant to Rule 14a-6 of the Securities and Exchange Act of 1934), and amended by Exhibit 10.1 to Honeywell’s Form 8-K filed December 21, 2004, Exhibit 10.1 to Honeywell’s Form 10-K for the year ended December 31, 2006 and Exhibit 10.1 to Honeywell’s Form 10-K for the year ended December 31, 2008 |
| | |
10.2* | | Deferred Compensation Plan for Non-Employee Directors of Honeywell International Inc., as amended and restated (incorporated by reference to Exhibit 10.2 to Honeywell’s Form 10-Q for quarter ended June 30, 2003), and amended by Exhibit 10.1 to Honeywell’s Form 8-K filed December 21, 2004 and Exhibit 10.2 to Honeywell’s Form 10-K for the year ended December 31, 2005 |
| | |
10.3* | | Stock Plan for Non-Employee Directors of AlliedSignal Inc., as amended (incorporated by reference to Exhibit 10.3 to Honeywell’s Form 10-Q for the quarter ended June 30, 2003), and amended by Exhibit 10.2 to Honeywell’s Form 10-Q for the quarter ended June 30, 2007 and Exhibit 10.1 to Honeywell’s Form 10-Q for the quarter ended September 30, 2008 |
| | |
10.4* | | Honeywell International Inc. Incentive Compensation Plan for Executive Employees, as amended and restated (incorporated by reference to Honeywell’s Proxy Statement, dated March 10, 2011, filed pursuant to Rule 14a-6 of the Securities and Exchange Act of 1934) |
| | |
10.5* | | Supplemental Non-Qualified Savings Plan for Highly Compensated Employees of Honeywell International Inc. and its Subsidiaries, as amended and restated (incorporated by reference to Exhibit 10.6 to Honeywell’s Form 10-K for the year ended December 31, 2008), and amended by Exhibit 10.5 to Honeywell’s Form 10-K for the year ended December 31, 2010 |
| | |
10.6* | | Honeywell International Inc. Severance Plan for Senior Executives, as amended and restated (incorporated by reference to Exhibit 10.7 to Honeywell’s Form 10-K for the year ended December 31, 2008), and amended by Exhibit 10.7 to Honeywell’s Form 10-K for the year ended December 31, 2009 |
| | |
10.7* | | Salary and Incentive Award Deferral Plan for Selected Employees of Honeywell International Inc., and its Affiliates, as amended and restated (incorporated by reference to Exhibit 10.8 to Honeywell’s Form 10-K for the year ended December 31, 2008) |
| | |
10.8* | | 1993 Stock Plan for Employees of Honeywell International Inc. and its Affiliates, as amended (incorporated by reference to Exhibit A to Honeywell’s Proxy Statement, dated March 10, 1994, filed pursuant to Rule 14a-6 of the Securities and Exchange Act of 1934), and amended by Exhibit 10.1 to Honeywell’s Form 8-K filed December 21, 2004, Exhibit 10.9 to Honeywell’s Form 10-K for |
120
| | |
Exhibit No. | | Description |
| | |
| | the year ended December 31, 2006, Exhibit 10.3 to Honeywell’s Form 10-Q for the quarter ended June 30, 2007 and Exhibit 10.9 to Honeywell’s Form 10-K for the year ended December 31, 2008 |
| | |
10.9* | | Honeywell International Inc. Supplemental Pension Plan, as amended and restated (incorporated by reference to Exhibit 10.10 to Honeywell’s Form 10-K for the year ended December 31, 2008), and amended by Exhibit 10.10 to Honeywell’s Form 10-K for the year ended December 31, 2009 |
| | |
10.10* | | Honeywell International Inc. Supplemental Executive Retirement Plan for Executives in Career Band 6 and Above, as amended and restated (incorporated by reference to Exhibit 10.12 to Honeywell’s Form 10-K for the year ended December 31, 2008), and amended by Exhibit 10.12 to Honeywell’s Form 10-K for the year ended December 31, 2009 |
| | |
10.11* | | Honeywell Supplemental Defined Benefit Retirement Plan, as amended and restated (incorporated by reference to Exhibit 10.13 to Honeywell’s Form 10-K for the year ended December 31, 2008), and amended by Exhibit 10.13 to Honeywell’s Form 10-K for the year ended December 31, 2009 |
| | |
10.12* | | Letter between David J. Anderson and Honeywell International Inc. dated June 12, 2003 (incorporated by reference to Exhibit 10.26 to Honeywell’s Form 10-Q for the quarter ended June 30, 2003), and amended by Exhibit 10.14 to Honeywell’s Form 10-K for the year ended December 31, 2008 |
| | |
10.13* | | Honeywell International Inc. Severance Plan for Corporate Staff Employees (Involuntary Termination Following a Change in Control), as amended and restated (incorporated by reference to Exhibit 10.16 to Honeywell’s Form 10-K for the year ended December 31, 2008) |
| | |
10.14* | | Employment Agreement dated as of February 18, 2002 between Honeywell and David M. Cote (incorporated by reference to Exhibit 10.24 to Honeywell’s Form 8-K filed March 4, 2002), and amended by Exhibit 10.3 to Honeywell’s Form 10-Q for the quarter ended September 30, 2008 and Exhibit 10.17 to Honeywell’s Form 10-K for the year ended December 31, 2008 |
| | |
10.15* | | 2003 Stock Incentive Plan for Employees of Honeywell International Inc. and its Affiliates Award Agreement (incorporated by reference to Exhibit 10.1 to Honeywell’s Form 8-K filed February 7, 2005) |
| | |
10.16* | | 2003 Stock Incentive Plan for Employees of Honeywell International Inc. and its Affiliates Restricted Unit Agreement (incorporated by reference to Exhibit 10.21 to Honeywell’s Form 10-K for the year ended December 31, 2005) |
| | |
10.17* | | Stock Plan For Non-Employee Directors of Honeywell International Inc. Option Agreement (incorporated by reference to Exhibit 10.1 to Form 8-K filed April 29, 2005) |
| | |
10.18* | | Deferred Compensation Agreement dated August 4, 2006 between Honeywell and David M. Cote (incorporated by reference to Exhibit 10.22 to Honeywell’s Form 10-K for the year ended December 31, 2006) and amended by Exhibit 10.22 to Honeywell’s Form 10-K for the year ended December 31, 2009 |
| | |
10.19* | | Letter Agreement dated July 27, 2001 between Honeywell and Larry E. Kittelberger (incorporated by reference to Exhibit 10.23 to Honeywell’s Form 10-K for the year ended December 31, 2006), and amended by Exhibit 10.23 to Honeywell’s Form 10-K for the year ended December 31, 2008 |
| | |
10.20* | | Honeywell Supplemental Retirement Plan (incorporated by reference to Exhibit 10.24 to Honeywell’s Form 10-K for the year ended December 31, 2006) |
| | |
10.21* | | Pittway Corporation Supplemental Executive Retirement Plan (incorporated by reference to Exhibit 10.25 to Honeywell’s Form 10-K for the year ended December 31, 2006) and amended by Exhibit |
121
| | |
Exhibit No. | | Description |
| | |
| | 10.25 to Honeywell’s Form 10-K for the year ended December 31, 2008 and Exhibit 10.25 to Honeywell’s 10-K for the year ended December 31, 2009 |
| | |
10.22* | | 2006 Stock Incentive Plan of Honeywell International Inc. and Its Affiliates, as amended and restated (incorporated by reference to Exhibit 10.26 to Honeywell’s Form 10-K for the year ended December 31, 2008), and amended by Exhibit 10.1 to Honeywell’s 10-Q for the quarter ended March 31, 2011 |
| | |
10.23* | | 2006 Stock Incentive Plan of Honeywell International Inc. and Its Affiliates—Form of Option Award Agreement (incorporated by reference to Exhibit 10.2 to Honeywell’s Form 10-Q for the quarter ended March 31, 2009) |
| | |
10.24* | | 2006 Stock Incentive Plan of Honeywell International Inc. and Its Affiliates—Form of Restricted Unit Agreement (incorporated by reference to Exhibit 10.1 to Honeywell’s Form 10-Q for the quarter ended March 31, 2009) |
| | |
10.25* | | 2006 Stock Incentive Plan of Honeywell International Inc. and Its Affiliates—Form of Growth Plan Agreement (incorporated by reference to Exhibit 10.1 to Honeywell’s Form 10-Q for the quarter ended March 31, 2010) |
| | |
10.26* | | 2006 Stock Incentive Plan of Honeywell International Inc. and Its Affiliates— Form of Performance Share Agreement (incorporated by reference to Exhibit 10.30 to Honeywell’s Form 10-K for the year ended December 31, 2006) |
| | |
10.27* | | 2006 Stock Plan for Non-Employee Directors of Honeywell International Inc., as amended and restated (incorporated by reference to Exhibit 10.31 to Honeywell’s Form 10-K for the year ended December 31, 2008), and amended by the attached amendment (filed herewith) |
| | |
10.28* | | 2006 Stock Plan for Non-Employee Directors of Honeywell International Inc.—Form of Option Agreement (incorporated by reference to Exhibit 10.7 to Honeywell’s Form10-Q for the quarter ended June 30, 2006) |
| | |
10.29* | | 2006 Stock Plan for Non-Employee Directors of Honeywell International Inc.—Form of Restricted Stock Agreement (incorporated by reference to Exhibit 10.8 to Honeywell’s Form 10-Q for the quarter ended June 30, 2006) |
| | |
10.30* | | 2006 Stock Plan for Non-Employee Directors of Honeywell International Inc.—Form of Restricted Unit Agreement (incorporated by reference to Exhibit 10.34 to Honeywell’s Form 10-K for the year ended December 31, 2008) |
| | |
10.31* | | 2007 Honeywell Global Employee Stock Plan (incorporated by reference to Honeywell’s Proxy Statement, dated March 12, 2007, filed pursuant to Rule 14a-6 of the Securities and Exchange Act of 1934) |
| | |
10.32* | | Letter Agreement dated July 20, 2007 between Honeywell and Roger Fradin (incorporated by reference to Exhibit 10.1 to Honeywell’s Form 10-Q for the quarter ended September 30, 2007) and amended by Exhibit 10.36 to Honeywell’s Form 10-K for the year ended December 31, 2009 |
| | |
10.33* | | Consulting Agreement dated March 24, 2010 between Honeywell and Larry Kittelberger (incorporated by reference to Exhibit 10.2 to Honeywell’s Form 10-Q for the quarter ended March 31, 2010) |
| | |
10.34* | | Letter Agreement dated October 6, 2010 between Honeywell and Roger Fradin (incorporated by reference to Exhibit 10.34 to Honeywell’s Form 10-K for the year ended December 31, 2010)) |
122
| | |
Exhibit No. | | Description |
| | |
10.35* | | Employee Non-Competition Agreement dated October 26, 2010 for Andreas Kramvis (incorporated by reference to Exhibit 10.35 to Honeywell’s Form 10-K for the year ended December 31, 2010) |
| | |
10.36* | | 2006 Stock Incentive Plan of Honeywell International Inc. and its Affiliates — Form of Restricted Unit Agreement, Form 2 (incorporated by reference to Exhibit 10.2 to Honeywell’s Form 10-Q for the quarter ended June 30, 2010) |
| | |
10.37* | | 2006 Stock Incentive Plan of Honeywell International Inc. and Its Affiliates—Form of Option Award Agreement, Form 2 (incorporated by reference to Exhibit 10.37 to Honeywell’s Form 10-K for the year ended December 31, 2010) |
| | |
10.38* | | Letter Agreement dated September 3, 2009 between Honeywell and Timothy Mahoney (incorporated by reference to Exhibit 10.38 to Honeywell’s Form 10-K for the year ended December 31, 2010) |
| | |
10.39* | | Form of Honeywell International Inc. Noncompete Agreement for Senior Executives (incorporated by reference to Exhibit 10.39 to Honeywell’s Form 10-K for the year ended December 31, 2010)) |
| | |
10.40* | | 2011 Stock Incentive Plan of Honeywell International Inc. and its Affiliates (incorporated by reference to Honeywell’s Proxy Statement, dated March 10, 2011, filed pursuant to Rule 14a-6 of the Securities and Exchange Act of 1934) |
| | |
10.41* | | 2011 Stock Incentive Plan of Honeywell International Inc. and its Affiliates—Form of Restricted Unit Agreement (incorporated by reference to Exhibit 10.2 to Honeywell’s Form 10-Q for the quarter ended June 30, 2011) |
| | |
10.42* | | 2011 Stock Incentive Plan of Honeywell International Inc. and Its Affiliates—Form of Option Award Agreement (filed herewith) |
| | |
10.43* | | 2011 Stock Incentive Plan of Honeywell International Inc. and Its Affiliates—Form of Growth Plan Agreement (filed herewith) |
| | |
10.44* | | Letter Agreement dated August 4, 2011 between Honeywell International Inc. and David M. Cote (incorporated by reference to Exhibit 10.1 to Honeywell’s Form 10-Q for the quarter ended September 30, 2011) |
| | |
10.45 | | Five Year Credit Agreement dated as of March 31, 2011 by and among Honeywell International Inc., the banks, financial institutions and other institutional lenders parties thereto, Citibank, N.A., as administrative agent, Citibank International PLC, as swing line agent, JPMorgan Chase Bank, N.A., as syndication agent, Bank of America, N.A., Barclays Bank PLC, Deutsche Bank AG New York Branch, Goldman Sachs Bank USA, Morgan Stanley MUFG Loan Partners, LLC and The Royal Bank of Scotland PLC, as documentation agents, and Citigroup Global Markets Inc. and J.P. Morgan Securities LLC, as joint lead arrangers and co- book managers (incorporated by reference to Exhibit 10.1 to Honeywell’s 8-K filed April 4, 2011) |
| | |
10.46 | | Purchase and Sale Agreement between Catalysts, Adsorbents and Process Systems, Inc., and Honeywell Specialty Materials, LLC, dated September 30, 2005 (incorporated by reference to Exhibit 10.23 to Honeywell’s Form 10-Q for the quarter ended September 30, 2005) |
| | |
10.47 | | Stock Purchase Agreement by and between Honeywell International Inc. and M&F Worldwide Corp. (incorporated by reference to Exhibit 2.1 to Honeywell’s Form 8-K filed November 1, 2005) |
| | |
10.48 | | Stock Purchase Agreement dated April 3, 2008 by and among Honeywell International Inc., Safety Products Holdings, Inc., the selling shareholders party thereto, and Odyssey Investment Services, L.L.C. (incorporated by reference to Exhibit 10.1 to Honeywell’s Form 8-K filed April 7, 2008) |
123
| | |
Exhibit No. | | Description |
| | |
10.49 | | Stock and Asset Purchase Agreement dated June 9, 2008, by and between Honeywell International Inc. and BE Aerospace, Inc. (incorporated by reference to Exhibit 10.1 to Honeywell’s Form 8-K filed June 11, 2008) |
| | |
10.50 | | Tender Offer Agreement dated May 19, 2010 by and among Sperian Protection S.A., Honeywell International Inc. and Honeywell Holding France SAS (incorporated by reference to Exhibit 10.1 to Honeywell’s Form 10-Q for the quarter ended June 30, 2010) |
| | |
10.51 | | Stock and Asset Purchase Agreement dated January 27, 2011 by and among Honeywell International Inc., Rank Group Limited and Autoparts Holdings Limited, (incorporated by reference to Exhibit 10.1 to Honeywell’s Form 8-K filed January 31, 2011) |
| | |
12 | | Statement re: Computation of Ratio of Earnings to Fixed Charges (filed herewith) |
| | |
21 | | Subsidiaries of the Registrant (filed herewith) |
| | |
23 | | Consent of PricewaterhouseCoopers LLP (filed herewith) |
| | |
24 | | Powers of Attorney (filed herewith) |
| | |
31.1 | | Certification of Principal Executive Officer Pursuant to Section 302 of the Sarbanes-Oxley Act of 2002 (filed herewith) |
| | |
31.2 | | Certification of Principal Financial Officer Pursuant to Section 302 of the Sarbanes-Oxley Act of 2002 (filed herewith) |
| | |
32.1 | | Certification of Principal Executive Officer Pursuant to 18 U.S.C. Section 1350, as Adopted Pursuant to Section 906 of the Sarbanes-Oxley Act of 2002 (filed herewith) |
| | |
32.2 | | Certification of Principal Financial Officer Pursuant to 18 U.S.C. Section 1350, as Adopted Pursuant to Section 906 of the Sarbanes-Oxley Act of 2002 (filed herewith) |
| | |
101.INS | | XBRL Instance Document (furnished herewith) |
| | |
101.SCH | | XBRL Taxonomy Extension Schema (furnished herewith) |
| | |
101.CAL | | XBRL Taxonomy Extension Calculation Linkbase (furnished herewith) |
| | |
101.DEF | | XBRL Taxonomy Extension Definition Linkbase (furnished herewith) |
| | |
101.LAB | | XBRL Taxonomy Extension Label Linkbase (furnished herewith) |
| | |
101.PRE | | XBRL Taxonomy Extension Presentation Linkbase (furnished herewith) |
| |
| |
| |
The Exhibits identified above with an asterisk (*) are management contracts or compensatory plans or arrangements. |
124
Honeywell International Inc.
SCHEDULE II - VALUATION AND QUALIFYING ACCOUNTS
Three Years Ended December 31, 2011
(Dollars in millions)
| | | | |
Allowance for Doubtful Accounts: | | | | |
| | | | |
Balance December 31, 2008 | | $ | 182 | |
Provision charged to income | | | 176 | |
Deductions from reserves | | | (134 | ) |
Acquisitions | | | 6 | |
| | | | |
| | | | |
Balance December 31, 2009 | | | 230 | |
Provision charged to income | | | 145 | |
Deductions from reserves | | | (111 | ) |
Acquisitions | | | 8 | |
| | | | |
| | | | |
Balance December 31, 2010 | | | 272 | |
Provision charged to income | | | 79 | |
Deductions from reserves | | | (112 | ) |
Acquisitions | | | 14 | |
| | | | |
Balance December 31, 2011 | | $ | 253 | |
| | | | |
| | | | |
Deferred Tax Assets—Valuation Allowance | | | | |
| | | | |
Balance December 31, 2008 | | $ | 445 | |
Additions charged to income tax expense | | | 142 | |
Reductions credited to income tax expense | | | (30 | ) |
Reductions charged to deferred tax assets due to expiring NOLs | | | 3 | |
Reductions charged to deferred tax assets due to capital loss carryforwards | | | (9 | ) |
Additions charged to equity | | | 27 | |
| | | | |
| | | | |
Balance December 31, 2009 | | | 578 | |
Additions charged to income tax expense | | | 129 | |
Reductions credited to income tax expense | | | (90 | ) |
Reductions charged to deferred tax asset due to expired NOL | | | (7 | ) |
Reductions charged to deferred tax assets due to capital loss carryforwards | | | (1 | ) |
Additions charged to equity | | | (17 | ) |
Additions charged to goodwill | | | 44 | |
| | | | |
| | | | |
Balance December 31, 2010 | | | 636 | |
Additions charged to income tax expense | | | 109 | |
Reductions credited to income tax expense | | | (152 | ) |
Reductions charged to deferred tax asset due to expired NOL | | | (8 | ) |
Reductions charged to deferred tax assets due to capital loss carryforwards | | | (5 | ) |
Additions charged to equity | | | (13 | ) |
Additions charged to goodwill | | | 24 | |
| | | | |
Balance December 31, 2011 | | $ | 591 | |
| | | | |
125