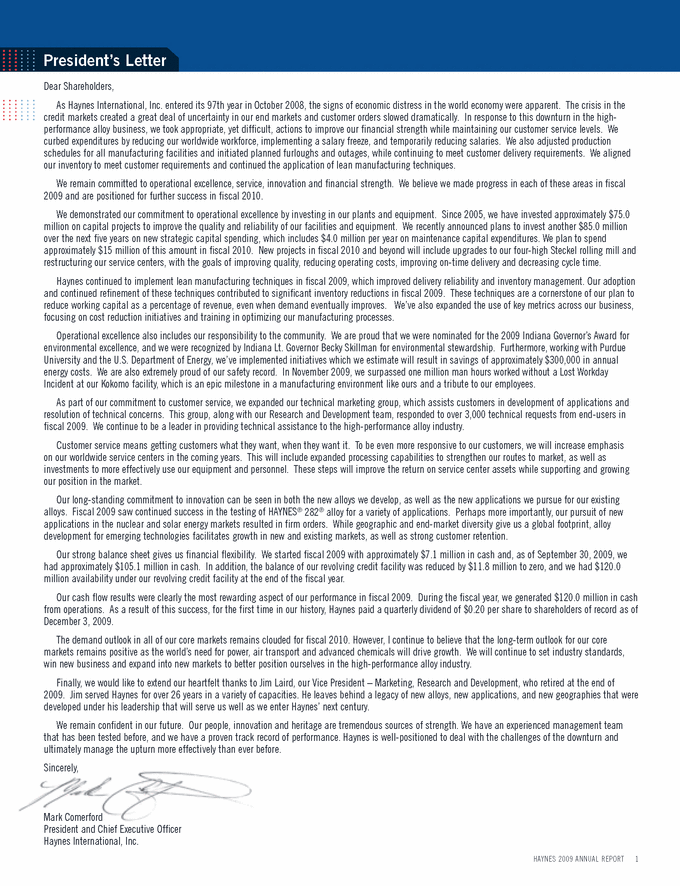
| Dear Shareholders, As Haynes International, Inc. entered its 97th year in October 2008, the signs of economic distress in the world economy were apparent. The crisis in the credit markets created a great deal of uncertainty in our end markets and customer orders slowed dramatically. In response to this downturn in the high-performance alloy business, we took appropriate, yet difficult, actions to improve our financial strength while maintaining our customer service levels. We curbed expenditures by reducing our worldwide workforce, implementing a salary freeze, and temporarily reducing salaries. We also adjusted production schedules for all manufacturing facilities and initiated planned furloughs and outages, while continuing to meet customer delivery requirements. We aligned our inventory to meet customer requirements and continued the application of lean manufacturing techniques. We remain committed to operational excellence, service, innovation and financial strength. We believe we made progress in each of these areas in fiscal 2009 and are positioned for further success in fiscal 2010. We demonstrated our commitment to operational excellence by investing in our plants and equipment. Since 2005, we have invested approximately $75.0 million on capital projects to improve the quality and reliability of our facilities and equipment. We recently announced plans to invest another $85.0 million over the next five years on new strategic capital spending, which includes $4.0 million per year on maintenance capital expenditures. We plan to spend approximately $15 million of this amount in fiscal 2010. New projects in fiscal 2010 and beyond will include upgrades to our four-high Steckel rolling mill and restructuring our service centers, with the goals of improving quality, reducing operating costs, improving on-time delivery and decreasing cycle time. Haynes continued to implement lean manufacturing techniques in fiscal 2009, which improved delivery reliability and inventory management. Our adoption and continued refinement of these techniques contributed to significant inventory reductions in fiscal 2009. These techniques are a cornerstone of our plan to reduce working capital as a percentage of revenue, even when demand eventually improves. We’ve also expanded the use of key metrics across our business, focusing on cost reduction initiatives and training in optimizing our manufacturing processes. Operational excellence also includes our responsibility to the community. We are proud that we were nominated for the 2009 Indiana Governor’s Award for environmental excellence, and we were recognized by Indiana Lt. Governor Becky Skillman for environmental stewardship. Furthermore, working with Purdue University and the U.S. Department of Energy, we’ve implemented initiatives which we estimate will result in savings of approximately $300,000 in annual energy costs. We are also extremely proud of our safety record. In November 2009, we surpassed one million man hours worked without a Lost Workday Incident at our Kokomo facility, which is an epic milestone in a manufacturing environment like ours and a tribute to our employees. As part of our commitment to customer service, we expanded our technical marketing group, which assists customers in development of applications and resolution of technical concerns. This group, along with our Research and Development team, responded to over 3,000 technical requests from end-users in fiscal 2009. We continue to be a leader in providing technical assistance to the high-performance alloy industry. Customer service means getting customers what they want, when they want it. To be even more responsive to our customers, we will increase emphasis on our worldwide service centers in the coming years. This will include expanded processing capabilities to strengthen our routes to market, as well as investments to more effectively use our equipment and personnel. These steps will improve the return on service center assets while supporting and growing our position in the market. Our long-standing commitment to innovation can be seen in both the new alloys we develop, as well as the new applications we pursue for our existing alloys. Fiscal 2009 saw continued success in the testing of HAYNES® 282® alloy for a variety of applications. Perhaps more importantly, our pursuit of new applications in the nuclear and solar energy markets resulted in firm orders. While geographic and end-market diversity give us a global footprint, alloy development for emerging technologies facilitates growth in new and existing markets, as well as strong customer retention. Our strong balance sheet gives us financial flexibility. We started fiscal 2009 with approximately $7.1 million in cash and, as of September 30, 2009, we had approximately $105.1 million in cash. In addition, the balance of our revolving credit facility was reduced by $11.8 million to zero, and we had $120.0 million availability under our revolving credit facility at the end of the fiscal year. Our cash flow results were clearly the most rewarding aspect of our performance in fiscal 2009. During the fiscal year, we generated $120.0 million in cash from operations. As a result of this success, for the first time in our history, Haynes paid a quarterly dividend of $0.20 per share to shareholders of record as of December 3, 2009. The demand outlook in all of our core markets remains clouded for fiscal 2010. However, I continue to believe that the long-term outlook for our core markets remains positive as the world’s need for power, air transport and advanced chemicals will drive growth. We will continue to set industry standards, win new business and expand into new markets to better position ourselves in the high-performance alloy industry. Finally, we would like to extend our heartfelt thanks to Jim Laird, our Vice President – Marketing, Research and Development, who retired at the end of 2009. Jim served Haynes for over 26 years in a variety of capacities. He leaves behind a legacy of new alloys, new applications, and new geographies that were developed under his leadership that will serve us well as we enter Haynes’ next century. We remain confident in our future. Our people, innovation and heritage are tremendous sources of strength. We have an experienced management team that has been tested before, and we have a proven track record of performance. Haynes is well-positioned to deal with the challenges of the downturn and ultimately manage the upturn more effectively than ever before. Sincerely, Mark Comerford President and Chief Executive Officer Haynes International, Inc. HAYNES 2009 ANNUAL REPORT 1 President’s Letter |