UNITED STATES
SECURITIES AND EXCHANGE COMMISSION
Washington, D.C. 20549
FORM 10-K
x | ANNUAL REPORT PURSUANT TO SECTION 13 OR 15(d) OF THE SECURITIES EXCHANGE ACT OF 1934 |
For the fiscal year ended June 30, 2008
or
¨ | TRANSITION REPORT PURSUANT TO SECTION 13 OR 15(d) OF THE SECURITIES EXCHANGE ACT OF 1934 |
For the transition period from to .
Commission file number: 0-27122
ADEPT TECHNOLOGY, INC.
(Exact name of registrant as specified in its charter)
| | |
Delaware | | 94-2900635 |
(State or other jurisdiction of incorporation or organization) | | (I.R.S. Employer Identification Number) |
| |
3011 Triad Drive, Livermore, California | | 94551 |
(Address of principal executive office) | | (Zip Code) |
Registrant’s telephone number, including area code: (925) 245-3400
Securities registered pursuant to Section 12(b) of the Act:
| | |
Title of each class | | Name of each exchange on which registered |
Common Stock, $0.001 par value | | NASDAQ Global Market |
Securities registered pursuant to Section 12(g) of the Act:
None
(Title of Class)
Indicate by check mark if the registrant is a well-known seasoned issuer, as defined in Rule 405 of the Securities Act. ¨ Yes x No
Indicate by check mark if the registrant is not required to file reports pursuant to Section 13 or Section 15(d) of the Act. ¨ Yes x No
Indicate by check mark whether the registrant: (1) has filed all reports required to be filed by Section 13 or 15(d) of the Securities Exchange Act of 1934 during the preceding 12 months (or for such shorter period that the registrant was required to file such reports), and (2) has been subject to such filing requirements for the past 90 days. x Yes ¨ No
Indicate by check mark if disclosure of delinquent filers pursuant to Item 405 of Regulation S-K is not contained herein, and will not be contained, to the best of registrant’s knowledge, in definitive proxy or information statements incorporated by reference in Part III of this Form 10-K or any amendment to this Form 10-K. ¨
Indicate by check mark whether the registrant is a large accelerated filer, an accelerated filer, a non-accelerated filer, or a smaller reporting company. See the definitions of “large accelerated filer”, “accelerated filer” and “smaller reporting company” in Rule 12b-2 of the Exchange Act.
| | | | | | |
Large accelerated filer ¨ | | Accelerated filer ¨ | | Non-accelerated filer ¨ | | Smaller reporting company x |
| | | | (Do not check if a smaller reporting company) | | |
Indicate by check mark whether the registrant is a shell company (as defined in Rule 12b-2 of the Exchange Act). ¨ Yes x No
The aggregate market value of the voting and non-voting common equity held by non-affiliates of the registrant computed by reference to the price at which the common equity was last sold as of the last business day of the registrant’s most recently completed second fiscal quarter (December 31, 2007) was $25,661,591. Shares of common stock held by each officer and director and by each person who beneficially owns 10% or more of common equity of the registrant may be deemed to be affiliates of the registrant.
As of September 8, 2008, approximately8,001,604 shares of the registrant’s common stock, $0.001 par value, were outstanding.
DOCUMENTS INCORPORATED BY REFERENCE
Portions of the registrant’s definitive proxy statement for the 2008 Annual Meeting of Stockholders are incorporated by reference into Part III hereof.
ADEPT TECHNOLOGY, INC.
ANNUAL REPORT ON FORM 10-K
TABLE OF CONTENTS
i
PART I
CAUTIONARY NOTE REGARDING FORWARD-LOOKING STATEMENTS
This Annual Report on Form 10-K and the documents incorporated by reference into this Annual Report contain forward-looking statements. Forward-looking statements are contained principally in the sections entitled “Business,” “Risk Factors,” “Management’s Discussion and Analysis of Financial Condition and Results of Operations” and “Controls and Procedures.” In some cases, you can identify forward-looking statements by terms such as “may,” “intend,” “might,” “will,” “should,” “could,” “would,” “expect,” “believe,” “estimate,” “predict,” “potential,” or the negative of these terms, and similar expressions intended to identify forward-looking statements. These statements reflect our current views with respect to future events. These statements involve known and unknown risks, uncertainties and other factors which may cause our actual results, performance or achievements to be materially different from any future results, performances or achievements expressed or implied by the forward-looking statements. Given these uncertainties, you should not place undue reliance on these statements. We discuss many of these risks and uncertainties in this Annual Report on Form 10-K in greater detail under the heading “Risk Factors.” Also, these statements represent our estimates and assumptions only as of the date of this Annual Report on Form 10-K, and we undertake no obligation to publicly update or revise these forward-looking statements.
In this report, unless the context indicates otherwise, the terms “Adept,” “we,” “us,” and “our” refer to Adept Technology, Inc., a Delaware corporation, and its subsidiaries.
This report contains trademarks and trade names of Adept and other companies. Adept has 140 trademarks of which 15 are registered trademarks, some of which include the Adept Technology logo. Our trademarks include (among others): AIM®, FireBlox®, HexSight®, Adept Cobra™, Adept Python™, Adept SmartServo™, AdeptOne™, AdeptSix™, AdeptViper™ , AdeptSight™, AdeptQuattro™, Adept Anyfeeder™, Adept ACE™, Cerebellum™ and ApproFlex™.
We are a global, leading provider of intelligent robotics systems and services that provide high performance and economic value throughout the production life cycle or automated procedure, enabling our customers to achieve precision, speed, quality and productivity in their assembly, handling, packaging, testing and other automated processes.
Adept helped pioneer the robotics industry, and with 25 years of operating expertise, we continue to lead in the development of innovative robotics solutions to meet the changing needs of automation. Our robotics solutions are targeted at automated applications and processes that require precision, flexibility and high productivity. Through sales to systems integrators, distributors, original equipment manufacturer (“OEM”) partners and end-user companies, we provide specialized, cost-effective robotics systems,software and services to emerging automation markets, including packaging, solar and medical; as well as to the disk drive/electronics market and traditional industrial markets, including machine tool automation and automotive electronics.
Our product range includes application software, integrated real-time vision and multi-axis motion controls, machine vision systems and software, industrial robots, and advanced vision-based flexible parts feeders. Our core offering combines our motion controls systems with application software, which we generally sell together with our own vision-guidance technology and/or our or third parties’ robot mechanisms. Our vision guidance technology is tightly integrated with our motion controls technology, and this is a key differentiator for Adept.
The Need for Automation
The benefits of automation include improved control, efficiency and productivity, higher and more consistent quality, and improved record keeping. For decades, industries such as automotive and electronics have utilized
1
robotic systems in their manufacturing operations in order to stay competitive, reduce costs and provide a safer environment for workers. Such industries are heavily dependent on automation to manufacture, assemble and package their products. In many other industries, the use of automation is only just beginning, spurred by changes in the regulatory and competitive environment, and always with a focus on achieving greater productivity at a lower cost.
Packaging—The use of packaging around commercial products has increased, as factors such as expediency, variety and safety have become more important to consumers. Additionally, in many cases the packaging around a product has become as important as the product itself, in terms of delivering benefits such as convenience, branding or market differentiation. Increased use of packaging is fueling the need for automation to address the challenges that arise in the packaging industry. These challenges include the need for flexibility, the need to maintain a clean or sterile environment, the ability to process high volumes and the ability to track products that are perishable or that may pose future unknown risks. For example, prescription medications must be packaged in a contamination-free environment, precisely measured or counted, accurately labeled and thoroughly documented. Automation provides a higher degree of precision and control over such processes to ensure that prescriptions are accurate, safe and traceable.
Cost considerations are also an important catalyst for automation, particularly in applications such as food, where products are often packaged locally for reasons including freshness, regional branding or specific regulatory requirements. Automation is often a more cost efficient alternative to maintaining a sufficient number of local employees because more productivity can be achieved more quickly, in less space and with less risk of contamination.
Packaging automation systems are increasingly being employed with applications such as food, consumer goods, cosmetics and pharmaceuticals. According to ARC Advisory Group, the overall market for parallel robots used in such applications is growing at an annual rate of 30%, of which a large share is being driven by packaging applications.
Solar—Rising oil prices and global concerns about fossil fuel pollution and global warming are spurring the commercial development of solar panels to provide clean, renewable energy. However, the infrastructure of equipment and expertise to manufacture solar energy production devices has not yet caught up with the demand. Today, government subsidies and technological expertise are fueling accelerated development of solar manufacturing in certain regions, such as Germany and Silicon Valley, California. Over the next several years, solar energy production is expected to increase in almost every area of the world. Automation brings benefits at many stages of the delicate and exacting process of solar cell and panel manufacturing. For example, automation allows manufacturers to produce higher volumes in less space, ensures that product specifications can be precisely replicated to ensure consistent product quality, and reduces breakage to enable higher yields.
According to investment research firm Credit Suisse, spending in the solar equipment market is expected to grow to $3.1 billion by 2010. Significant opportunity exists for automation suppliers such as Adept as solar product manufacturers set up their production facilities and develop capacity. Based on similarities in processes and products, the solar industry is expected to develop along similar lines as the heavily automated semiconductor industry over the longer term. Consequently, automation will likely continue to be an important tool for manufacturers as solar production technology evolves and changes such as smaller wafer dimensions, larger die size and a larger number of pins create additional challenges in terms of consistency, quality and yield.
Medical—Automation in the medical market is used in a range of medical, pharmaceutical and healthcare related applications, from the manufacture of medical devices, to automation of repetitive operations in diagnostic and pharmaceutical labs, to emerging techniques for computer assisted robot-based surgical procedures. The medical market is highly regulated and characterized by a high need for precision and safety. Automation provides many advantages, including minimizing opportunities for contamination, ensuring consistency and precision of processes and documentation of all process steps for subsequent tracking or review.
2
Disk Drive/Electronics—The combination of high volumes and continual price erosion in the disk drive/electronics market has long demanded the use of automation to ensure the highest yields at the lowest cost. Automation solutions are used to help manufacture and assemble a host of electronic products such as computer disk drives, cell phones and printer cartridges and components.
Automotive and Industrial—Automation enables important benefits in the automotive and industrial markets, including higher yields, better and more consistent quality and lower cost. In automotive applications, automation can provide the speed and precision required for small, high volume components such as sensors and electronic components. In industrial manufacturing applications, the automation of machine tools and other industrial equipment provides a more productive and safer alternative to human labor. Additionally, automation plays an important role in containing costs in high labor cost regions such as Europe, where governmental policies have encouraged automotive and industrial manufacturing to remain local.
Adept’s Automation Solutions
Adept’s business is focused towards delivering intelligent, flexible automation products, components and services for assembly, packaging, material handling inspection and lab automation applications under two operating segments: Robotics and Services and Support.
Our Robotics segment provides intelligent motion controls systems, vision inspection and guidance systems, production automation software and robot mechanisms to customers. With motion controls at the core, any of the other product components we offer can be combined to offer our customers a tailored solution to address specific application requirements.
Our Services and Support segment provides support services to customers including, spare parts for and/or remanufacture of robot mechanisms, information regarding the use of Adept’s automation equipment, ongoing support for installed systems, consulting services for applications, and training courses ranging from system operation and maintenance to advanced programming, geared towards manufacturing engineers who design and implement automation lines.
We market and sell our products worldwide through more than 200 systems integrators, distributors and OEMs as well as our direct sales force. Systems integrators and OEMs may add their own application-specific hardware and software to our products, resulting in solutions that are sold to Global 1000 companies across a range of industries. We have more than 30,000 motion control systems and more than 6,000 vision guidance systems installed worldwide, controlling an installed base of 25,000 Adept robots as well as other brands of robot mechanisms.
Founded in 1983, Adept is the largest U.S.-based manufacturer of industrial robots. We were incorporated in California in 1983 and reincorporated in Delaware in 2005. Our principal executive offices are located at 3011 Triad Drive, Livermore, California 94551. Our telephone number at that address is (925) 245-3400. Our website address is www.adept.com. Our annual reports on Form 10-K, our quarterly reports on Form 10-Q, our current reports on Form 8-K and any amendments to those reports filed or furnished pursuant to Section 13(a) or 15(d) of the Securities and Exchange Act of 1934, as amended, (the “Securities Exchange Act”) can be accessed, free of charge, at our website as soon as reasonably practicable after they are electronically filed with or furnished to the Securities and Exchange Commission (the “SEC”).
Robotics Segment
Adept is a pioneer and market innovator in developing intelligent robotics and advanced control systems. Our systems are designed for easy integration, deployment and use. We offer a unique robotic control system that combines tightly integrated vision, motion control and geometric object recognition. This tight integration helps to reduce development costs, risk associated with precision applications and the total cost of implementation, and is a key differentiator for Adept. We believe our vision-guided robotics systems remain the most robust and proven solutions in the market today.
3
Our robots include the widely employed 4-axis Cobra family of robots, which are SCARA (Selective Compliance Assembly Robot Arm) robot mechanisms designed for assembly and material handling tasks; Adept Viper 6-axis articulated robots for high-speed precision assembly; Adept Quattro robots for high-speed packaging, assembly and loading/unloading applications; and Modular Adept Python single axis robot mechanisms that are highly configurable by the user. To address the needs of our customers, we continue to expand our robot product lines and to develop advanced software and sensing technologies that enable robots to perform a wider range of functions.
We utilize our portfolio of high-performance motion controllers, application development software, vision-guidance technology and high-reliability robot mechanisms to deliver automation solutions that meet our customers’ increasingly complex manufacturing and automation requirements. We offer our customers comprehensive and tailored automation systems that reduce the time and cost to design, engineer and launch products into high-volume production or to perform repetitive tasks requiring a high degree of precision. The benefits of Adept automation products include increased manufacturing flexibility for future product generations, less customized engineering and reduced dependence on production engineers.
Advanced Controls and Software
Adept’s proprietary robotic control system, consisting of controls and software, is characterized by unique features, including tightly integrated vision, motion control and geometric object recognition; a compact design; scalability; and flexibility. These features combine to offer a powerful controls platform that enables our customers to reduce the cost and optimize the performance of their automation environment. Tight integration of vision and motion controls enables exceptional performance of robot mechanisms, for example, enabling increased dexterity, faster cycle times and better precision. Adept’s controls are the most compact in the automation industry, reducing the footprint of space needed and thus reducing costs for our customers. A scalable design allows Adept’s control platform to handle applications ranging from simple to very complex. Additionally, Adept’s control system is designed to work with both Adept robots and third party robot mechanisms. Adept also enables manufacturers to coordinate multiple Adept robots with one controls system, using Adept’s proprietary digital servo network distributed controls architecture based on the industry standard high-speed IEEE-1394 FireWire network.
Controls
The Adept SmartController CX is an ultra-compact high-performance robot and vision controller based on Adept’s proprietary SmartServo distributed architecture. The Adept SmartServo distributed servo control network seamlessly integrates motion control for up to 24 axes, vision guidance and inspection, and real-time networking and communications functions. Benefits of Adept SmartController include reduced costs, the smallest form factor in the industry, and simplified installation, wiring, and support while maintaining compliance with domestic and international safety specifications.
Adept MotionBlox technology offers convenient and economical scalability to add one or more axis to any Adept robot or Adept controller system. These self-contained multiple and single channel power amplifiers, with an on-board microprocessor, are mounted directly on (or in) the robot mechanism. Adept MotionBloxServo kits are plug compatible with Adept’s SmartServo distributed servo network. Additionally, Adept motion controls can be used with third party robot mechanisms, feeders, servo-controlled conveyors, or other servo and process-control axes
Adept controllers are unique in that they are able to operate both with Adept’s own robots and with third party European and Japanese robotic systems and to enable higher performance from all these robots. With more than 35 kinematic models, or configurations of controls and robot mechanisms, we are able to control and integrate multiple vendor products and systems.
4
Vision
Integrated vision is a key differentiator for Adept robotic solutions. Our AdeptVision family offers highly integrated machine vision products that are used for robot guidance and inspection applications. Utilizing proprietary geometric object recognition, the integration of our controller and vision systems software enables high speed vision applications such as vision servoing and on-the-fly vision refinement. For inspection applications such as gauging and dimensioning, the AdeptVision product is sold as an integrated inspection vision system comprised of a SmartController CX with an embedded vision board and software.
AdeptSight integrates PC-based vision with Adept’s robotic and motion control product and is designed to work seamlessly with Adept’s overall product line of robots, making the development and use of vision location, guidance and inspection applications simpler, faster, and more powerful. Based on Adept’s unique object locating technology, AdeptSight is a complete package that includes the application toolset, the vision software, vision and vision-to-robot calibration wizards, the camera and lens and the accessories to provide a complete out-of-the-box solution.
Software
Adept Automation Control Environment (ACE) is a real-time application software environment designed to make it easier to program, integrate and deploy one or more robots. Targeted at packing, handling and assembly applications in the packaging, solar and medical markets, ACE integrates the functionality of sophisticated robot applications such as robot motion, robot location, vision, conveyer tracking, and communications in a comprehensive, easy to use graphical application software interface. ACE is built on the Microsoft®. net platform, making it easy to install on any PC and compatible with the Microsoft Windows® application environment.
Adept developed the first modern programming language for robots, and our V+ real-time programming language allows software developers to create automation software systems and is the key enabling technology for our intelligent automation approach. This comprehensive programming environment provides a high-level language coupled with a multitasking operating system and built-in capability for integrating robots, machine vision, sensors, workcell control and general communications. These capabilities enable the development of sophisticated application software that can adaptively control mechanical systems based upon real-time sensory input while simultaneously maintaining communication with other factory equipment.
Adept ePLC Connect is a PLC interface enabling the entire Adept product line robots to be programmed using Rockwell PLC-based robot programming language. The Adept ePLC Connect provides a network for robots using Ethernet/IP connectivity. By eliminating the need to learn a new programming language, the ePLC Connect simplifies the installation and support of the robots, and maximizes the existing automation investment.
Adept Robot Mechanisms
We provide a broad range of robot mechanisms to address different markets and application needs. Each of these robot mechanisms offers unique features and capabilities, but all share a common software and hardware control platform (as described above in “Advanced Controls and Software”), which provides a more integrated, high performance and cost effective environment for our customers. Our broad product line allows systems integrators and end users to develop automation solutions for many industries and applications.
Adept’s most widely deployed robots are the Cobra family, which are 4-axis SCARA (Selective Compliance Assembly Robot Arm) robot mechanisms, designed for assembly and material handling tasks such as cell phone assembly, disk drive and printer head assembly and cosmetic kitting. SCARA robots utilize a combination of rotary and linear joints for high speed, high precision material handling, assembly and packaging. Our Cobra series robots are considered light-duty SCARA mechanisms that can be table or ceiling mounted and offer an efficient range of motions in limited space. Our Cobra robots can also be connected to Adept’s SmartController for integrated motion and vision or multi-mechanism configurations. Our Cobra robots include the Adept Cobra s600, Adept Cobra s800, Adept Cobra s350 and Adept Cobra Clean Room/ESD s350. We also offer an
5
embedded controller version of the Cobra line with the iCobra family, consisting of the Adept Cobra i600 and Adept Cobra i800. In May 2008, we introduced an inverted (ceiling mounted) SCARA robot, the Cobra s800 Inverted IP65.
Adept Python Linear Modules are single axis devices, similar in function to our Cobra robots, but sold as modular units that can be configured by the user to form application specific custom robot mechanisms ranging from two to four axes. Target markets for Adept Python products include disk drive/electronics and automotive electronics. Each Adept Python Module is powered by Adept MotionBlox, an integrated single axis motion controller and power amplifier, which reduces the amount of software programming and cabling required in a workcell or robotic system that performs a specific automation function. Additionally, Adept offers Clean Room Class 1 ESD versions of the Adept Python robot for precision assembly and handling applications in the solar, disk drive/electronics and medical markets.
The AdeptViper robot family are 6-axis articulated robots that combine speed and precision with a higher degree of flexibility and dexterity than traditional SCARA mechanisms. AdeptViper robots are targeted at precision assembly applications that require complex or fine manipulation of materials or products, for example, specialty assembly of components following curvatures or edges such as specialized electronic components, or surgical assist procedures. The AdeptViper s650 and AdeptViper s850 are designed for either table mounting or ceiling mounting and have a 5 kilogram maximum payload capacity. The AdeptViper s1300, Adept Viper s1700 and Adept Viper s2000 six-axis robots are extended-reach and higher-payload versions of the s650 and s850 robots models. These larger robots are well suited to handling heavier payloads such as solar panels.
Our newest robot, Adept Quattro, is a unique, proprietary four-parallel arm robot specifically designed for high-speed packaging and material handling. Introduced in February 2007, Adept Quattro has achieved the fastest growth of any Adept robot product. Adept Quattro currently offers the highest performance and most compact footprint in the automation industry. It is further differentiated by simplicity of integration and programming, which minimizes the use of engineering resources. Adept Quattro is targeted at applications such as loading/unloading, inspection, categorization and solar panel assembly in the solar industry and kitting, carton and case packing applications in the food, consumer goods, cosmetics and pharmaceutical industries.
Service and Support Segment
Adept Service and Support is dedicated to assuring the productivity of every Adept product installed at a customer location. We offer on-going training, service and applications support to our customers, and maintain a program of spare parts, field upgrades, and factory repair and remanufacturing capabilities. In some industries, support is a critical component of our overall solutions offering, and we work closely with our customers to configure the automation system that will best address their specific requirements.
We provide “evergreen” product paths that support our customers with service and upgrades for all products, including those no longer in production, to ensure that an investment in flexible automation from Adept will continue to be productive for the duration of a project or production requirement.
Our service and support organization includes a staff located at our headquarters and field personnel who are based in the United States, Europe and Asia to support customers worldwide.
Our product training personnel develop and deliver training courses on subjects ranging from basic system maintenance to advanced programming, which are offered through Adept offices and customer sites throughout the world.
Our field service organization maintains and repairs our products on location at the end user’s facilities. Personnel based at our service centers provide advice to customers on spare parts, product upgrades and preventative maintenance. We also operate toll-free telephone support lines to provide advice on issues such as product usage, software programming structure, layout problems and system installation.
6
In addition, our California manufacturing facility provides factory repair and remanufacture services which ensure that Adept products will continue to be productive over the extended timeframes common for automated production lines.
Customers
We sell our products to system integrators, distributors, Global 1000 companies and OEMs. Adept’s robotics solutions are targeted at companies that require greater precision, flexibility and productivity in their assembly, handling, packaging and testing processes. Through direct sales to companies, OEMs and via our systems integrators, Adept provides a suite of cost-effective robotics systems and services to the packaging, solar, medical, disk drive/electronics, automotive electronics and industrial markets. No one customer accounted for more than 10% of our revenues for any of the past three fiscal years.
Financial information regarding revenue derived from domestic and international customers based upon geographic area is included in Note 11 of our Notes to Consolidated Financial Statements included in this Annual Report on Form 10-K.
Sales and Distribution
We market our products through system integrators, sales representatives and distributors, our direct sales force and OEMs.
System Integrators. We ship a substantial portion of our products through system integrators, and we view our relationships with these organizations as important to our success. We have established relationships with over 200 system integrators worldwide that provide expertise and process knowledge for a wide range of specific applications. In the United States and Europe, these relationships are generally nonexclusive and not limited to specific geographical territories. In certain other international markets, Adept’s integrator relationships may include limited exclusive arrangements for a limited geographical territory in which the integrator markets and supports Adept functions directly. Generally a system integrator can purchase both standard and non-standard Adept solutions and components as opposed to OEM arrangements where generally one standard component or solution is purchased in higher volumes.
Sales Representatives and Distributors. We utilize a network of sales representatives and distributors to provide cost effective sales coverage in smaller markets where it is prohibitively expensive for us to allocate direct sales resources. We use a combination of exclusive (Adept product only) and non-exclusive sales representatives and distributors who sell our robot and vision guidance products in their standard forms. Adept also provides service and support for customers who have purchased Adept products through one of our sales representatives or distributors. As of June 30, 2008, we had 20 sales representatives and distributors in smaller, less strategic regions around the world.
Direct Sales Force. We employ a sales force of sales personnel and application engineers that is currently organized around our primary target markets and that sells to both end users and our indirect channel partners. With respect to end users, the sales force directs its efforts to communicate the capabilities of our products and support services and obtain up-to-date information regarding market requirements. Our sales force possesses expertise in automation solutions and advises end users on alternative production line designs, special application techniques, equipment sources and system integrator selection. Our sales force also works closely with system integrators and OEMs to integrate our product line into their systems, provides sales leads to certain system integrators and obtains intelligent automation system quotes from system integrators for end users. As of June 30, 2008, our North American sales channel included a direct sales force of 11 employees and seven sales agencies. We have three North American sales and customer support offices located in Livermore, California, Cincinnati, Ohio, and Charlotte, North Carolina. As of June 30, 2008, our international sales organization included 15 direct sales employees and 14 agents covering Europe, Asia and South America.
7
Some of our larger manufacturing end user customers, to whom we sell directly, have in-house engineering departments that are comparable to a captive systems integrator. These end user customers establish a corporate integrator relationship with us offering benefits similar to those provided to our integrator distribution channel; however, we may in some cases form strategic alliances for certain potentially high volume market opportunities with greater benefits to the customer than exist in system integrator arrangements, although the benefits may come with contractual restrictions.
OEMs.Our OEM customers typically purchase one standard product configuration, which the OEM integrates with additional hardware and software and sells under the OEM’s label to other resellers and end users. Unlike our system integrator channel, OEMs are responsible for all marketing, sales and customer support and for maintaining the associated spare parts to service the end users of the integrated product.
Research and Development
We focus our research and development efforts on the development of an integrated product line, which furthers our factory automation approach and which reduces costs, enhances performance, and improves ease of use for our customers. Research and development activities are focused on design of our motion and vision control hardware and the robotic mechanisms that utilize them along with advanced software for vision, motion control and applications.
As part of our corporate restructuring at the end of June 2007, we consolidated our primary research and development activities in Quebec, Canada into our Northern California facility. In the third quarter of 2008, we acquired Cerebellum Automation SAS and added a research and development facility in France.
We have devoted, and intend to devote in the future, a significant portion of our resources to research and development programs. As of June 30, 2008, we had 37 employees engaged in research, development and engineering. Our research, development and engineering expenses were approximately $5.4 million in fiscal 2008 and $7.2 million for fiscal 2007 and represented 8.8% and 14.8% of revenues in fiscal 2008 and fiscal 2007, respectively. With the acquisition of Cerebellum, we expect these expenses to increase in fiscal 2009.
Manufacturing
The majority of our robot mechanisms are sourced externally, and Adept’s manufacturing operations, which are located in Livermore, California and Dortmund, Germany, are focused on product assembly, integration and test. We strategically outsource sub-components of our systems, including electronics assemblies and mechanical mechanisms. Our manufacturing engineering organization develops test processes and detailed instructions for all manufacturing and test operations. These instructions are established in writing, implemented through training of the manufacturing workforce, and monitored to assure compliance. In addition, our manufacturing organization works closely with our suppliers to develop instructions, test methods and to remedy technical or quality problems if they arise.
Certain components and sub-assemblies incorporated into our products are obtained from a single source or a limited group of suppliers. We routinely monitor single source supply parts, and we endeavor to ensure that adequate inventory is available to maintain manufacturing schedules should the supply of any part be interrupted. Although we seek to reduce our dependence on sole or limited source suppliers, we have not qualified a second source for some of these products and the partial or complete loss of certain of these sources could have a negative impact on our results of operations and could damage customer relationships.
Backlog
Our product backlog at June 30, 2008 was approximately $10.9 million as compared to approximately $6.3 million at June 30, 2007. Customers who have placed orders with delivery dates beyond twelve months from the end of the fiscal quarter are not included in backlog, and thus we expect substantially all backlog at June 30, 2008 to ship during fiscal 2009. Because orders constituting our current backlog are subject to changes in
8
delivery schedules and in certain instances may be subject to cancellation without significant penalty to the customer, our backlog at any date may not be indicative of demand for our products or actual revenues for any period in the future. The increase in backlog for fiscal 2008 as compared to fiscal 2007 reflects the growing demand of our Quattro robot in the packaging and solar industries.
Employees
At June 30, 2008, we had 158 employees worldwide. Of the total, 37 were engaged in research and development, 31 in sales and marketing, 33 in service and support, 28 in operations, and 29 in finance and administration.
Competition
The market for intelligent automation products is highly competitive. We compete with a number of robot companies, motion control companies, and machine vision companies. Many of these companies are larger or have more resources than Adept. Many of our competitors in the robot market are integrated manufacturers of products that produce robotics equipment internally for their own use and may also compete with our products for sales to other customers. The basis for competition typically centers on price and performance. We believe that we favorably compete on the basis of higher performance, additional capabilities, greater combination of speed, precision and flexibility, and better support of our product line.
Our principal competitors in the SCARA robot and linear modules markets (including our Adept Cobra and Adept Python robots) include subsidiaries of Japanese companies, including Epson Corporation, Yamaha Corporation, Denso Corporation and IAI America, Inc. We also compete with a small group of European companies, principally Stäubli Corporation. Adept robots are differentiated by integrating more sophisticated controls and vision technology along with embedded controls.
In the 6-axis robot market where we sell our AdeptViper robots,we compete with the above companies, as well as manufacturers of 6-axis robots including ABB Robotics division, FANUC Robotics, Inc., and Motoman, Inc. In the 6-Axis robot market, Adept offers strong performance and more sophisticated controls and software.
In the machine vision market, our primary competition is from Cognex Corporation. Cognex Corporation has a broader, more extensive product line than Adept, but is focused on machine vision only.
In the parallel robot market, the primary competition for our Adept Quattro robot comes from ABB Robotics division and FANUC Robotics. The Adept Quattro robot offers higher performance and a more compact control solution than its competing products.
Intellectual Property
Because Adept’s success and competitiveness depends to an extent on the technical expertise, creativity, and knowledge of our personnel, we utilize patent, trademark, copyright, and trade secret protection to safeguard our competitive position. At June 30, 2008, we had 10 patents issued and current on various innovations in the field of robotics, motion control, and machine vision technology. In addition, we make use of non-disclosure agreements with customers, suppliers, employees, and consultants. Adept attempts to protect its intellectual property by restricting access to its proprietary information through a combination of technical and internal security measures. There can be no assurance, however, that any of the above measures will be adequate to protect the proprietary technology of Adept. Further, effective patent, trademark, copyright, and trade secret protection may be unavailable in certain foreign countries.
Seasonality
Historically, orders have been lower in the first half of our fiscal year and higher in the second half of our fiscal year, with a decline between the last quarter of our fiscal year and the first fiscal quarter of the next year. This
9
historical seasonality is due, in part, to the concentration of sales into the European market. Revenues in each quarter will vary based on European market seasonality and on the particular timing of major programs to key customers. We expect that this seasonality may be less dramatic in the foreseeable future as our Quattro packaging business increases and partially offsets the seasonal pattern.
Risks Related to Our Business
Our operating results fluctuate from quarter to quarter due to factors that are difficult to forecast, are often out of our control and can be extremely volatile.
Our past revenues and other operating results may not be accurate indicators of our future performance, and you should not rely on such results to predict our future performance. Our operating results have been subject to significant fluctuations in the past, and could be subject to fluctuations in the future. The factors that may contribute to these fluctuations include:
| • | | fluctuations in aggregate capital spending, cyclicality and other economic conditions domestically and internationally in one or more industries in which we sell our products; |
| • | | changes or reductions in demand in the disk drive/electronics, automotive, packaging, medical, solar and other markets we serve; |
| • | | a change in market acceptance of our products or a shift in demand for our products; |
| • | | changes in our strategy and organizational changes made to execute changes in our strategy; |
| • | | new product introductions by us or by our competitors; |
| • | | changes in product mix and pricing by us, our suppliers or our competitors; |
| • | | pricing and related availability of components and raw materials for our products; |
| • | | our failure to manufacture a sufficient volume of products in a timely and cost-effective manner; |
| • | | our failure to anticipate the changing product requirements of our customers; |
| • | | changes in the mix of sales by distribution channels; |
| • | | our ability to effectively manage our working capital; |
| • | | impact of new accounting pronouncements; |
| • | | exchange rate fluctuations; |
| • | | shifts in geographic concentration of our sales or operations between domestic and international; |
| • | | seasonal fluctuations in demand and our associated revenue, for which demand is generally lower in the first half of the fiscal year; |
| • | | costs incurred in connection with compliance with SEC and NASDAQ requirements; |
| • | | costs incurred in connection with regulatory compliance for the industries we serve; |
| • | | our ability to expand our product offerings through acquired technologies and products; and |
| • | | extraordinary events such as litigation, product liability claims or mergers and acquisitions activity, and unforeseen costs in international or industry expansion. |
Revenue levels also impact our gross margins. Our gross margins can vary greatly for a number of reasons, and our operating results tend to fluctuate as a result of the variance in gross margins. The mix of products we sell can vary from period to period, particularly with respect to the volume of lower margin hardware products (such as mechanical subsystems purchased from third party vendors) and higher margin controller products or robotics
10
mechanisms. While we intend to more aggressively pursue opportunities to sell our higher margin products, we cannot give any assurances regarding the growth of our sales of these products in the future. Other factors that impact gross margins include costs listed above and:
| • | | currency exchange rate fluctuations for our international sales; |
| • | | the average selling prices of products we sell including changes in the average discounts offered; |
| • | | the costs to manufacture, service and support our products and enhancements; |
| • | | the costs to customize our systems; |
| • | | the volume of products produced and associated production volume variances, if any, generated; |
| • | | our efforts to enter new markets, in particular the growth of our sales in Asia; and |
| • | | certain inventory-related costs including obsolescence of products and component demand changes resulting in excess inventory. |
We generally recognize product revenues upon shipment or, for certain international sales, upon receipt by customers. As a result, our net revenues and results of operations for a fiscal period will be affected by the timing of orders received and orders shipped during the period. A significant percentage of our product shipments occur in the last month of each fiscal quarter. Historically, this has been due, in part, to our inability to forecast the level of demand for our products or the product mix for a particular fiscal quarter. To address this problem we periodically stock inventory levels of completed robots, machine controllers and certain strategic components. A delay in shipments near the end of a fiscal period, for example, due to product development delays or delays in obtaining materials, may cause sales to fall below expectations and harm our operating results for the period.
Similarly, our indirect costs, production capacity and operating expenses are largely fixed in the short run. Continued investments in research and development, capital equipment and ongoing customer service and support capabilities, in addition to the expense of being a public reporting company and executing a growth strategy, result in significant fixed costs that we cannot reduce rapidly or at all. As a result, if our sales for a particular fiscal period are below expected levels, our cost of revenue increases and our operating results for the period could be materially adversely affected. Further, if shipments of our products fail to meet forecasted levels, the increased inventory levels and increased operating expenses in anticipation of sales that do not materialize could adversely affect our business and substantially impact our liquidity. In the event that in some fiscal quarter our net revenues or operating results fall below the expectations of public market analysts and investors, the price of our common stock may fall. We may not be able to increase or sustain our profitability on a quarterly or annual basis in the future.
We are subject to lawsuits relating to our Livermore facilities which could be expensive and disruptive.
We are currently engaged in litigation with the landlord of our Livermore, California facilities. Our landlord has initiated multiple lawsuits seeking to remove Adept from its Livermore facility in an unlawful detainer action and declaratory relief in favor of its interpretation of a lease termination agreement, and alleging damages exceeding an alleged $1 million termination fee it claims is due from Adept and additionally making claims for tortious interference with a lease with a new lessee and potentially lost lease payments for its entire new 13-year lease of the Livermore facilities with a new tenant, plus attorneys fees and costs. Such litigation have been, and are expected to continue to be, costly and time consuming and could divert management’s attention from our day-to-day operations. In addition, in connection with this litigation, we may choose to or be forced to move our operations from our Livermore facilities in a very short timeframe, which could be disruptive to our operations. If our defense is not successful in one or all of the litigation matters, we may be liable to pay our landlord damages. We cannot assure you that such litigation will be ultimately resolved in our favor or that an adverse outcome will not have a material adverse effect on our business, results of operations and financial condition. Even if this lawsuit is ultimately resolved in favor of Adept, Adept still expects that it would incur substantial legal fees and expenses in defending the lawsuits.
11
Our international operations and sales and foreign suppliers subject us to foreign currency exchange risks, divergent regulatory requirements and other financial and operating risks outside of our control that may harm our operating results.
We have significant and expanding operations outside the United States and a substantial majority of our revenue is derived from non-U.S. sales. International sales represented 68% and 60% of revenues for fiscal 2008 and fiscal 2007, respectively. We expect that revenue from our international operations will continue to account for a significant portion of our total revenue. We also purchase some critical components and mechanical subsystems from, and increasingly rely upon, foreign suppliers. As a result, our operating results are subject to the risks inherent in international sales and purchases, which include the following:
| • | | unexpected changes in regulatory requirements; |
| • | | political, military and economic changes and disruptions, including terrorist activity; |
| • | | transportation costs and delays; |
| • | | foreign currency fluctuations; |
| • | | export/import controls; |
| • | | tariff regulations and other trade barriers; |
| • | | difficulties in staffing and managing foreign sales, service and manufacturing operations; |
| • | | stringent local jurisdictional requirements regarding employees and union activity; |
| • | | greater difficulty in and longer time required for accounts receivable collection in foreign jurisdictions; and |
| • | | potentially adverse tax consequences. |
Ongoing global economic and political developments and the resulting changes in currency exchange rates, most notably between the U.S. dollar, the euro, and the Japanese yen, have had, and may in the future have, a significant effect on our business, operating results and financial condition. The decline in value of the U.S. dollar to the euro in fiscal 2005 through 2008 resulted in a currency exchange gain for us, and future fluctuations may result in significant gains or losses. If there is an increase in the rate at which a foreign currency exchanges into U.S. dollars and the dollar appreciates relative to the foreign currency, it will take more of the foreign currency to equal the same amount of U.S. dollars than before the rate increase. Additionally, we make yen-denominated purchases of certain components and mechanical subsystems from certain of our sole or single source Japanese suppliers and thus remain subject to the transaction exposures that arise from foreign exchange movements between the dates foreign currency export sales or purchase transactions are recorded and the dates cash is received or payments are made in foreign currencies. Our non-U.S. operations use its respective local currency as the functional currency. In Europe, we manufacture locally and thereby incur a greater part of our costs and expenses in the local currency. Our Asian headquarters in Singapore incurs a high percentage of local currency expenses. These operations result in exposure to currency exchange risk. Continued change in the values of the euro, yen or changes in the values of other foreign currencies could have a negative impact on our business, financial condition and results of operations.
Approximately two-thirds of our revenues come from international sales and collection times on those sales are longer because of longer delivery times, time required to clear customs, and generally slower payment patterns in some international markets. If our international sales increase, delays in receiving payment in connection with such sales may also have a greater impact on our revenue and liquidity.
In addition to our international sales, maintaining operations in different countries requires us to expend significant resources to keep our operations coordinated and subjects us to differing laws and regulatory regimes that may affect our offerings and revenue.
12
We have experienced operating losses and negative cash flow in the past, and our doing so in the future could impair our operations and revenue-generating activities and adversely affect our results of operations.
We currently depend on funds generated from operating activities to meet our operating requirements and execute on our growth plan. Our $5 million credit facility, under which no amounts had been borrowed, recently expired, and therefore we do not intend to renew or replace it at this time. Because of certain regulatory restrictions impeding our ability to move certain cash reserves from our foreign operations to our U.S. operations, we may have limited access to a portion of our existing cash balances.
In the past, we have experienced operating losses and negative cash flow. If our projected revenue falls below current estimates or if operating expenses exceed current expectations, we may not be able to take advantage of market opportunities, develop or enhance new products to an extent desirable to execute our strategic growth plan, pursue acquisitions that would complement our existing product offerings or enhance our technical capabilities to fully execute our business plan or otherwise adequately respond to competitive pressures or unanticipated requirements. Any of these actions would adversely impact our business and results of operations.
The long sales cycle, customer evaluation process, and implementation period of our products may increase the costs of obtaining orders and reduce the predictability of our earnings.
Our products are technologically complex. Prospective customers generally must commit significant resources to test and evaluate our products and to install and integrate them into larger systems. Orders expected in one quarter may shift to another quarter or be cancelled with little advance notice as a result of customers’ budgetary constraints, internal acceptance reviews, and other factors affecting the timing of customers’ purchase decisions. In addition, customers often require a significant number of product presentations and demonstrations, in some instances evaluating equipment on site, before reaching a sufficient level of confidence in the product’s performance and compatibility with the customer’s requirements to place an order. As a result, our sales process is often subject to delays associated with lengthy evaluation and approvals that typically accompany capital expenditure approval processes. The sales cycles of our products often last for many months or even years. In addition, the time required for our customers to incorporate our products into their systems can vary significantly with the needs of our customers and generally exceeds several months, which further complicates our planning processes and reduces the predictability of our operating results. Longer sales cycles require us to invest significant resources in attempting to secure sales, which may not be realized in the near term and therefore may delay or prevent the generation of revenue. In addition, should our financial condition deteriorate, prospective customers may be reluctant to purchase our products, which would have an adverse effect on our revenue.
Sales of our products depend on the capital spending patterns of our customers, which tend to be cyclical; we have experienced reduced demand in some of the industries in which we operate, which has and may continue to adversely affect our revenue and we may not be able to quickly ramp up if demand significantly increases.
Intelligent automation systems using our products can range in price from $25,000 to $500,000. Accordingly, our success is directly dependent upon the capital expenditure budgets of our customers. Our future operations may be subject to substantial fluctuations as a consequence of domestic and foreign economic conditions, industry patterns and other factors affecting capital spending. Domestic or international recessions or a downturn in one or more of our major markets, such as the solar, electronic/communications, packaging or European automotive or industrial industries, and any resulting cutbacks in capital spending would have a direct, negative impact on our business.
Downturns in the industries we serve often occur in connection with, or anticipation of, maturing product cycles for both companies and their customers as well as declines in general economic conditions. Industry downturns have been characterized by reduced demand for devices and equipment, production over-capacity and accelerated decline in average selling prices. During a period of declining demand, we must be able to quickly and
13
effectively reduce expenses while at the same time, continue to motivate and retain key employees. In the last few years, we have seen demand from traditional U.S. manufacturing markets decline. We implemented a worldwide restructuring program at the end of fiscal 2007 and early fiscal 2008 to realign our businesses to the changes in our industry and our customers’ decrease in capital spending. However, our ability to reduce expenses in response to any downturn in any of our industries is limited by our need for continued investment in engineering and research and development and extensive ongoing customer service and support requirements, in addition to administrative costs that we incur as a public company. The long lead-time for production and delivery of some of our products creates a risk that we may incur expenditures or purchase inventories for products that we cannot sell. We believe our future performance will continue to be affected by the cyclical nature of the industries in which we participate, and thus, any future downturn in these industries could therefore harm our revenue and gross margin if demand drops or average selling prices decline.
Upturns in industries such as disk drive or electronics have been characterized by abrupt increases in demand for devices and equipment as well as production under-capacity. During a period of increasing demand and rapid growth, we must be able to quickly increase our manufacturing capacity to meet customer demand and hire and assimilate a sufficient number of qualified personnel to service our customers. Our inability to ramp-up in times of increased demand could harm our reputation and cause some of our existing or potential customers to place orders with our competitors.
We have engaged in substantial restructuring activities in the past, and may need to implement further restructurings in the future, and our restructuring efforts may negatively impact our business.
The intelligent automation industry is subject to rapid change, including shifts between particular markets and geographies that actively purchase and implement automation systems. These changes can have a substantial impact on our business, as our sales into established markets may decrease more rapidly than our sales into new markets, resulting in insufficient revenue levels compared to our operational overhead and product investment. From time to time, we have responded to such changes by restructuring our operations. At the end of fiscal 2007, we restructured our operations to lower fixed operating costs and redistribute sales and engineering resources to our higher growth target markets. The restructuring included headcount reductions and the closure or consolidation of certain Adept sites in Canada and the U.S., consolidation of certain sales activities in the Company’s Singapore location, the realignment of our sales force to address target vertical markets and additional outsourcing for the manufacture of non-core functions and standard products. Despite our efforts to structure our company and our business to operate in a cost-effective manner while adequately facing competitive pressures and fulfilling customer needs, we cannot assure you that the reductions in sites, workforce and other cost-cutting measures will not harm our future business operations and prospects. We also cannot be certain that we will not be required to implement further restructuring activities, make additions or other changes to our management or reductions in workforce based on other cost reduction measures or changes in the markets and industry in which we compete. Our inability to structure our operations based on evolving market conditions could negatively impact our business. Restructuring activities can create unanticipated consequences and negative impacts on the business, and we cannot be sure that any future restructuring efforts will be successful.
We have significant dependence on outsourced manufacturing capabilities and single source suppliers. If we experience disruptions in the supply of one or more key components, we may be unable to meet product demand and we may lose customers and suffer decreased revenue.
We outsource a predominant portion of our manufacturing function. We obtain many key components and materials and most of our mechanical subsystems from sole or single source suppliers with whom we have no guaranteed supply arrangements. In addition, some of our sole or single sourced components and mechanical subsystems incorporated into our products have long procurement lead times. Our increased reliance on outsourced manufacturing and other capabilities, and particularly our reliance on sole or single source suppliers, involves certain significant risks including:
| • | | loss of control over the manufacturing process decreasing our flexibility in meeting customer delivery requirements and in reducing the cost of our products; |
14
| • | | potential absence of adequate supplier capacity; |
| • | | potential for significant price increases in the components and mechanical subsystems; |
| • | | potential inability to obtain an adequate supply of required components, materials or mechanical subsystems; and |
| • | | reduced control over manufacturing yields, costs, timely delivery, reliability and quality of components, materials and mechanical subsystems. |
We do not have contracts with certain of our sole or single source suppliers. If any one of our suppliers were unable or unwilling to manufacture the components, materials or mechanical subsystems we need in the volumes we require, we would have to identify and qualify acceptable replacements. The process of qualifying suppliers may be lengthy, and additional sources may not be available to us on a timely basis, on acceptable terms or at all. If sufficient quantities of these items were not available from our existing suppliers and a relationship with an alternative vendor could not be developed in a timely manner, shipments of our products could be interrupted and reengineering of these products could be required. We have limited control over the quality of certain manufactured products and their acceptance by our customers. In the past, we have experienced quality control or specification problems with certain key components provided by sole source suppliers, and have had to design around the particular flawed item. Any quality issues could result in customer dissatisfaction, lost sales, and increased warranty costs. In addition, some of the components that we use in our products are in short supply. In the past, we have also experienced delays in filling customer orders due to the failure of certain suppliers to meet our volume and schedule requirements. Some of our suppliers have also ceased manufacturing components that we require for our products, and we have been required to purchase sufficient supplies for the estimated life of such product line. Problems of this nature with our suppliers may occur in the future.
Disruption, significant price increases, or termination of our supply sources could require us to seek alternative sources of supply, could delay our product shipments and damage relationships with current and prospective customers, require us to absorb a significant price increase or risk pricing ourselves out of the market, or prevent us from taking other business opportunities, any of which could have a material adverse effect on our business. If we incorrectly forecast product mix for a particular period and we are unable to obtain sufficient supplies of any components or mechanical subsystems on a timely and cost effective basis due to long procurement lead times, our business, financial condition and results of operations could be substantially impaired. Moreover, if demand for a product for which we have purchased a substantial amount of components fails to meet our expectations, or due to component price increases causes us to be priced out of the market, we would be required to write off the excess inventory. A prolonged inability to obtain adequate timely deliveries of key components or obtain components at prices within our business model could have a material adverse effect on our business, financial condition and results of operations.
We are considering outsourcing our information technology functions, which will make us more dependent upon third parties.
In an effort to increase our information technology, or IT, capabilities and reduce potential disruptions, we are considering outsourcing almost all of our information technology functions. If we outsource our IT functions, as is the case with our outsourced manufacturing, we will be relying on third parties to ensure that our IT needs are sufficiently met. This reliance subjects us to risks arising from the loss of control over IT processes, changes in pricing that may affect our operating results, and potentially, termination of provision of these services by our supplier. A failure of our service providers to perform may have a significant adverse affect on our business.
Our business will decline if we cannot keep up with the rapid pace of technological change and new product development that characterize the intelligent automation industry.
The intelligent automation industry is characterized by rapid technological change and new product introductions and enhancements. Our ability to remain competitive greatly depends upon the technological quality of our products and processes compared to those of our competitors and our ability both to continue to develop new and
15
enhanced products and to introduce those products at competitive prices and on a timely and cost-effective basis. We may not be successful in selecting, developing, and manufacturing new products or in enhancing our existing products on a timely basis or at all. Our new or enhanced products may not achieve market acceptance. Our failure to successfully select, develop, and manufacture new products, or to timely enhance existing technologies and meet customers’ technical specifications for any new products or enhancements on a timely basis, or to successfully market new products, could harm our business. If we cannot successfully develop and manufacture new products or meet specifications, our products could lose market share, our revenue and profits could decline, or we could experience operating losses. New technology or product introductions by our competitors could also cause a decline in sales or loss of market acceptance for our existing products or force us to significantly reduce the prices of our existing products.
Growth of our business depends upon the development and successful commercial acceptance of our new products.
From time to time, we have experienced delays in the introduction of, and certain technical and manufacturing difficulties with, some of our products, and we may experience technical and manufacturing difficulties and delays in future introductions of new products and enhancements. Our failure to develop, manufacture, and sell new products in quantities sufficient to offset a decline in revenue from existing products or to successfully manage product and related inventory transitions could harm our business.
Our success in developing, introducing, selling, and supporting new and enhanced products depends upon a variety of factors, including timely and efficient completion of hardware and software design and development, implementation of manufacturing processes, and effective sales, marketing, and customer service. Because of the complexity of our products, significant delays may occur between a product’s initial introduction and commencement of volume production.
The development and commercialization of new products involve many difficulties, including:
| • | | the identification of new product opportunities; |
| • | | the retention and hiring of appropriate research and development personnel; |
| • | | the determination of the product’s technical specifications; |
| • | | the successful completion of the development process; |
| • | | the successful marketing of the product and the risk of having customers embrace new technological advances; and |
| • | | additional customer service and warranty costs associated with supporting new product introductions and/or effecting subsequent potential field upgrades. |
The development of new products may not be completed in a timely manner, and these products may not achieve acceptance in the market. The development of new products has required, and will require, that we expend significant financial and management resources. If we are unable to continue to successfully develop new products in response to customer requirements or technological changes, our business may be harmed. Additionally, a failure of our new products to be commercially successful may have a significant adverse impact on our operating results in the future.
In connection with our cost control efforts, we have limited resources to allocate to research and development and must allocate our resources among a wide variety of projects. Because of intense competition in our industry, the cost of failing to invest in strategic products is high. If we fail to adequately invest in research and development, we may be unable to compete effectively in the intelligent automation markets in which we operate.
16
We are making significant investments in emerging markets, including solar, packaging and medical, which subject Adept to the risks of increased regulation and potential product liability; however, we can make no assurances of success in these target markets or that risks related to these industries will not have an adverse affect on our business.
Our systems and controls are sold in a variety of industries. We have, and are continuing to, invest resources in certain emerging markets including solar, packaging and medical. There is no assurance that our products will receive market acceptance in these markets or that these markets will continue to grow at their current pace. In addition, as part of our increased focus on the medical market, we have increased our sales focus on certain applications that are highly regulated, including the manufacture of medical devices, the automation of repetitive operations in diagnostic and pharmaceutical labs, and computer assisted robot-based surgical procedures. We must obtain and monitor compliance for our products and systems with various regulatory requirements relevant to medical applications. This may increase certain costs necessary for the operation of our business. Additionally, our failure to obtain or maintain compliance with these requirements could have an adverse effect on our ability to sell our products or subject us to regulatory actions or fines.
As we further penetrate the medical market, our business exposure to product liability claims will increase. The medical device industry has historically been litigious, and we would face financial exposure to product liability claims if the use of our products were to cause injury or death. There is also the possibility that defects in the design or manufacture of our products might necessitate a product recall. Any weaknesses in training and services associated with our products may also be subject to product liability lawsuits. Medical applications subject us to greater risk of claims and product liability which are not a part of our historical operations or sales in other industries.
We face costs and risks associated with maintaining effective internal controls over financial reporting, and if we fail to achieve and maintain adequate internal controls over financial reporting, our business, results of operations and financial condition, and investors’ confidence in us, could be materially affected.
Under Sections 302 and 404 of the Sarbanes-Oxley Act of 2002, our management is required to make certain assessments and certifications regarding our disclosure controls and internal controls over financial reporting. We have dedicated, and expect to continue to dedicate, significant management, financial and other resources in connection with our compliance with Section 404 of the Sarbanes-Oxley Act. In our efforts to develop internal controls that comply with Section 404, we have undertaken certain actions including the preparation of an internal plan, which includes a timeline and schedule of activities for the evaluation, testing and remediation, as necessary, of internal controls. These actions have resulted in, and are likely to continue to result in increased and significant expense, and have required and are likely to continue to require significant efforts by management and other employees. During the course of our evaluation, we may identify areas requiring improvement and may be required to design enhanced processes and controls to address issues identified through this review. This could result in significant delays and costs to us and require us to divert substantial resources, including management time, from other activities. We have found material weaknesses in our internal controls in the past and we cannot be certain in the future that we will be able to report that our controls are without material weakness or to complete our evaluation of those controls in a timely fashion.
In the future, our independent auditors must evaluate and render an opinion on the effectiveness of our internal controls over financial reporting. We cannot be certain that our internal control measures will be timely or successful to ensure that we implement and maintain adequate controls over our financial processes and reporting in the future and our independent auditors may not be able to render an unqualified attestation concerning the effectiveness of our internal controls and disclosure controls.
If we fail to maintain an effective system of disclosure controls or internal control over financial reporting, we may not be able to rely on the integrity of our financial results, which could result in inaccurate or late reporting of our financial results and investigation by regulatory authorities. If we fail to achieve and maintain adequate
17
internal controls the financial position of our business could be harmed; current and potential future shareholders could lose confidence in us and/or our reported financial results, which may cause a negative effect on the trading price of our common stock; and we could be exposed to litigation or regulatory proceedings, which may be costly or divert management attention.
In addition, all internal control systems, no matter how well designed and operated, can only provide reasonable assurance that the objectives of the control system are met. Because there are inherent limitations in all control systems, no evaluation of control can provide absolute assurance that all control issues and instances of fraud, if any, within the Company have been or will be detected. Projections of any evaluation of controls effectiveness to future periods are subject to risks. Over time, controls may become inadequate because of changes in conditions or deterioration in the degree of compliance with policies or procedures. Any failure of our internal control systems to be effective could adversely affect our business.
Our future success depends on our continuing ability to attract, integrate, retain and motivate highly-qualified managerial and technical personnel.
Competition for qualified personnel in the intelligent automation industry is intense. Our inability to recruit, train, motivate and retain qualified management and technical personnel on a timely basis would adversely affect our ability to manage our operations and design, manufacture, market, and support our products, in addition to our ability to meet our requirements as a public company. We have reduced headcount in connection with our restructurings in prior fiscal years and made changes in other senior personnel which may create uncertainty for employees and cause difficulties retaining key employees.
We may incur credit risk-related losses because many of the resellers we sell to are small operations with limited financial resources.
Substantial portions of our sales are to system integrators that specialize in designing and building production lines for manufacturers. Many of these companies are small operations with limited financial resources, and we have from time to time experienced difficulty in collecting payments from certain of these companies. As a result, we perform ongoing credit evaluations of our customers. To the extent we are unable to mitigate this risk of collections from system integrators, our results of operations may be harmed. In addition, due to their limited financial resources, during extended market downturns the viability of some system integrators may be in question, which would also result in a reduction in our revenue or credit losses.
We do not generally have long-term contracts with our customers, and our order bookings and backlog cannot be relied upon as a future indicator of sales.
We generally do not have long-term contracts with our customers and existing contracts and purchase commitments may, under certain circumstances, be cancelled. As a result, our agreements with our customers do not provide meaningful assurance of future sales. Furthermore, our customers are not required to make minimum purchases and may cease purchasing our products at any time without penalty. Backlog should not be relied on as a measure of anticipated demand for our products or future revenue, because the orders constituting our backlog are subject to changes in delivery schedules and in certain instances are subject to cancellation without significant penalty to the customer. Because our customers are free to purchase products from our competitors, we are exposed to competitive price pressure on each order. Any reductions, cancellations or deferrals in customer orders could have a negative impact on our financial condition and results of operations.
We market and sell our products primarily through an indirect channel comprised of third party resellers, and are subject to certain risks associated with this method of product marketing and distribution.
We believe that our ability to sell products to system integrators and OEMs will continue to be important to our success. However, our relationships with system integrators and OEMs are generally not exclusive, and some of
18
our system integrators and OEMs may expend a significant amount of effort or give higher priority to selling products of our competitors. In the future, any of our system integrators or our OEMs may discontinue their relationships with us or form additional competing arrangements with our competitors. The loss of, or a significant reduction in revenue from system integrators or OEMs to which we sell a significant amount of our product could negatively impact our business, financial condition or results of operations.
We cannot control the procurement, either with respect to the timing or amount of orders placed, by our resellers. We also cannot control the sales or marketing efforts of the system integrators and OEMs who sell our products, which may result in lower revenue if they do not successfully market and sell our products or choose instead to promote competing products.
As we enter new geographic and applications markets, we must locate and establish relationships with system integrators and OEMs to assist us in building sales in those markets. It can take an extended period of time and significant resources to establish a profitable relationship with a system integrator or OEM because of product integration expenses, training in product and technologies and sales training. We may not be successful in obtaining effective new system integrators or OEMs or in maintaining sales relationships with them. In the event a number of our system integrators and/or OEMs experience financial problems, terminate their relationships with us or substantially reduce the amount of our products they sell, or in the event we fail to build or maintain an effective systems integrator or OEM channel in any existing or new markets, our business, financial condition and results of operations could be adversely affected.
If we cannot identify and make acquisitions of other technologies and products, our ability to expand our operations and increase our revenue may be impaired.
A meaningful portion of our historical growth has been attributable to acquisitions of other technologies and businesses. We are continually exploring mergers and acquisitions opportunities, and expect that acquisitions of complementary products and technologies in the future will likely again play an important role in our ability to expand our operations and increase our revenue. Our ability to make acquisitions is restricted by our cash constraints, the level and volatility of our common stock price and thin trading volume affecting liquidity considerations, making equity transactions more expensive. If we are unable to identify suitable targets for acquisition or complete acquisitions on acceptable terms, our ability to expand our product and/or service offerings and increase our revenue will be impaired.
Any acquisition we may make in the future could disrupt our business, increase our expenses and adversely affect our financial condition or operations.
In the future we may make acquisitions of, or investments in, other businesses that offer products, services, and technologies that management believes will further our strategic objectives. We cannot be certain that we would successfully integrate any businesses, technologies or personnel that we might acquire, and any acquisitions might divert our management’s attention away from our core business. Any future acquisitions or investments we might make would present risks commonly associated with these types of transactions, including:
| • | | difficulty in combining the product offerings, operations, or workforce of an acquired business; |
| • | | potential loss of key personnel of an acquired business; |
| • | | adverse effects on existing relationships with suppliers and customers; |
| • | | disruptions of our on-going businesses; |
| • | | difficulties in realizing our potential financial and strategic objectives through the successful integration of the acquired business; |
| • | | difficulty in maintaining uniform standards, controls, procedures and policies; |
19
| • | | potential negative impact on results of operations due to goodwill impairment write-offs, amortization of intangible assets other than goodwill, or assumption of anticipated liabilities; |
| • | | risks associated with entering markets in which we have limited previous experience; |
| • | | potential negative impact of unanticipated liabilities or litigation; and |
| • | | the diversion of management attention. |
The risks described above, either individually or in the aggregate, could significantly harm our business, financial condition and results of operations. We expect that future acquisitions, if any, could provide for consideration to be paid in cash, shares of our common stock, or a combination of cash and common stock. In addition, we may issue additional equity in connection with future acquisitions, which could result in dilution of our stockholders’ equity interest. Fluctuations in our stock price may make acquisitions more expensive or prevent us from being able to complete acquisitions on terms that are acceptable to us.
If we become subject to unfair hiring or termination claims, we could be prevented from hiring needed personnel, incur liability for damages and/or incur substantial costs in defending ourselves.
Companies in our industry whose employees accept positions with competitors frequently claim that these competitors have engaged in unfair hiring practices or that the employment of these persons would involve the disclosure or use of trade secrets. These claims could prevent us from hiring personnel or cause us to incur liability for damages. We could also incur substantial costs in defending ourselves or our employees against these claims, regardless of their merits. We may also experience actions against us for employment terminations which are perceived to be unjustified. Although to date we have not experienced any material claims, defending ourselves from these claims could divert the attention of our management away from our operations.
Our hardware and software products may contain defects that could increase our expenses and exposure to liabilities and or harm our reputation and future business prospects.
Our hardware and software products are complex and, despite extensive testing, our new or existing products or enhancements may contain defects, errors or performance problems when first introduced, when new versions or enhancements are released, or even after these products or enhancements have been used in the marketplace for a period of time. We may discover product defects only after a product has been installed and used by customers. We may discover defects, errors, or performance problems in future shipments of our products. These problems could result in expensive and time consuming design modifications or large warranty charges, expose us to liability for damages, damage customer relationships, and result in loss of market share, any of which could harm our reputation and future business prospects. We generate revenue from sales of several relatively recently released products, and expect sales of our new products to increase in the current fiscal year. As a result, the negative impact on our business resulting from defects in such products could be significant. In addition, increased development and warranty costs could reduce our operating profits and could result in losses.
The existence of any defects, errors, or failures in our products could also lead to product liability claims or lawsuits against us, our channel partners, or against our customers. Although we maintain product liability insurance, the coverage limits of these policies may not be adequate to cover future claims. Particularly as sales of our products increase, we may be unable to maintain product liability insurance in the future at satisfactory rates or in adequate amounts. A product liability claim, regardless of its merit or eventual outcome, could result in significant legal defense costs. A product liability claim or any product recalls could divert management’s attention and resources, could also harm our reputation and result in a decline in revenues and other negative impacts on our business and financial condition.
20
If our hardware products do not comply with standards set forth by the European Union, we will not be able to sell them in Europe.
The hardware products we sell in the European Union are required to comply with European Union Low Voltage, Electro-Magnetic Compatibility and Machinery Safety directives. The European Union mandates that our products carry the CE mark denoting that these products are manufactured in strict accordance to design guidelines in support of these directives. These guidelines are subject to change and to varying interpretation. New guidelines impacting machinery design go into effect each year. We continue to use TUV Rheinland to help certify that our controller-based products, including some of our robots, meet applicable European Union directives and guidelines. Adept hardware products have been declared as exempt by TUV Rheinland from the EU Directive WEEE/RoHS (Waste Electrical and Electronics Equipment/Reduction of Hazardous Substances). Although our existing certified products meet the requirements of the applicable European Union directives, we cannot provide any assurance that future products can be designed, within market window constraints, to meet the future requirements. If any of our robot products or any other major hardware products do not meet the requirements of the European Union directives, we would be unable to legally sell these products in Europe. Thus, our business, financial condition and results of operations could be harmed. Such directives and guidelines could change in the future, forcing us to redesign or withdraw from the market one or more of our existing products that may have been originally approved for sale.
Our failure to protect our intellectual property and proprietary technology may significantly impair our competitive advantage.
Our success and ability to compete depend in large part upon protecting our proprietary technology and trade secrets. We rely on a combination of patent, trademark and trade secret protection, and nondisclosure agreements to protect our proprietary rights, but have not always sought patent or similar protection on our technology where it may have been available. The steps we have taken may not be sufficient to prevent the misappropriation of our intellectual property, particularly in foreign countries where the laws may not protect our proprietary rights as fully as in the United States. The patent and trademark law and trade secret protection may not be adequate to deter third party infringement or misappropriation of our patents, trademarks, and similar proprietary rights. In addition, patents issued to Adept may be challenged, invalidated, or circumvented. Our rights granted under those patents may not provide competitive advantages to us, and the claims under our patent applications may not be allowed. We may be subject to or may initiate interference proceedings in the United States Patent and Trademark Office, which can demand significant financial and management resources. The process of seeking patent protection can be time consuming and expensive, and patents may not be issued from currently pending or future applications. Moreover, our existing patents or any new patents that may be issued may not be sufficient in scope or strength to provide meaningful protection or any commercial advantage to us.
We may in the future initiate claims or litigation against third parties for infringement of our proprietary rights in order to determine the scope and validity of our proprietary rights or the proprietary rights of our competitors. These claims could result in costly litigation and the diversion of our technical and management personnel.
We may face costly intellectual property infringement claims.
We have received in the past, and may receive in the future, communications from third parties asserting that we are infringing certain patents and other intellectual property rights of others or seeking indemnification against such alleged infringement. The asserted claims and/or initiated litigation could include claims against us or our manufacturers, suppliers, or customers, alleging infringement of their proprietary rights with respect to our existing or future products or components of those products. There are numerous patents in the automation components industry. It is not always practicable to determine in advance whether a product or any of its components infringes the intellectual property rights of others. As a result, from time to time, we may be forced to respond to intellectual property infringement claims to protect our rights or defend a customer’s rights. These claims, regardless of merit, could consume valuable management time, result in costly litigation, or cause product shipment delays, all of which could seriously harm our business, operating results and financial
21
condition. In settling these claims, we may be required to enter into royalty or licensing agreements with the third parties claiming infringement. These royalty or licensing agreements, if available, may not have terms favorable to us. Being forced to enter into a license agreement with unfavorable terms could seriously harm our business, operating results and financial condition. Any potential intellectual property litigation could force us to do one or more of the following:
| • | | pay damages, license fees or royalties to the party claiming infringement; |
| • | | stop selling products or providing services that use the challenged intellectual property; |
| • | | obtain a license from the owner of the infringed intellectual property to sell or use the relevant technology, which license may not be available on reasonable terms, or at all; or |
| • | | redesign the challenged technology, which could be time-consuming and costly. |
If we were forced to take any of these actions, our business, financial condition and results of operations may suffer.
Forecasting our estimated annual effective tax rate is complex and subject to uncertainty, and material differences between forecasted and actual tax rates could have a material impact on our results of operations.
Forecasts of our income tax position and resultant effective tax rate are complex and subject to uncertainty because our income tax position for each year combines the effects of a mix of profits and losses earned by us and our subsidiaries in tax jurisdictions with a broad range of income tax rates as well as benefits from available deferred tax assets and costs resulting from tax audits. To forecast our global tax rate, pre-tax profits and losses by jurisdiction are estimated and tax expense by jurisdiction is calculated. If the mix of profits and losses, our ability to use tax credits, or effective tax rates by jurisdiction is different than those estimates, our actual tax rate could be materially different than forecasted, which could have a material impact on our results of operations.
Risks Related to Our Industry
The market for intelligent automation products is intensely competitive, which may make it difficult to manage and grow our business or to maintain or enhance our profitability.
We compete with a number of robot, motion control, machine vision, and simulation software companies. Many of our competitors have substantially greater financial, technical, and marketing resources than we do. In addition, we may in the future face competition from new entrants in one or more of our markets.
Many of our competitors in the robot market are integrated manufacturers of products that produce robotics equipment internally for their own use and may also compete with our products for sales to other customers. Some of these large manufacturing companies have greater flexibility in pricing because they generate substantial unit volumes of robots for internal demand and may have access through their parent companies to large amounts of capital. Any of our competitors may seek to expand their presence in other markets in which we compete.
We believe that other principal competitive factors affecting the market for our products are:
| • | | product functionality and reliability; |
| • | | delivery, including timeliness, predictability, and reliability of delivery commitment dates; and |
| • | | product features such as flexibility, programmability, and ease of use. |
22
Our current or potential competitors may develop products comparable or superior in terms of price and performance features to those developed by us or adapt more quickly than we can to new or emerging technologies and changes in customer requirements. We may be required to make substantial additional investments in connection with our research, development, engineering, marketing, and customer service efforts in order to meet any competitive threat, so that we will be able to compete successfully in the future. We expect that in the event the intelligent automation market expands, competition in the industry will intensify as additional competitors enter our markets and current competitors expand their product lines. Increased competitive pressure could result in a loss of sales or market share or cause us to lower prices for our products, any of which could harm our business.
If we are unable to effectively support the distinct needs of the multiple industries of our customers, the demand for our products may decrease and our revenue may decline.
We market products for the packaging, solar, medical, disk drive/electronics, automotive electronics and industrial industries. Because we operate in multiple industries, we must work constantly to understand the needs, standards, and technical requirements of numerous different industries and must devote significant resources to developing different products for these industries. Our results of operations are also subject to the cyclicality and downturns in these markets. Product development is costly and time consuming. Many of our products are used by our customers to develop, manufacture, and test their own products. As a result, we must anticipate trends in our customers’ industries and develop products before our customers’ products are commercialized. If we do not accurately predict our customers’ needs and future activities, we may invest substantial resources in developing products that do not achieve broad market acceptance. Our decision to continue to offer products to a given market or to penetrate new markets is based in part on our judgment of the size, growth rate, and other factors that contribute to the attractiveness of a particular market. If our product offerings in any particular market are not competitive or our analyses of a market are incorrect, our business and results of operations could be harmed.
We may not receive significant revenue from our current research and development efforts for several years, if at all.
Internally developing intelligent automation products is expensive, and these investments often require a long time to generate returns. Our strategy involves significant investments in research and development and related product opportunities. We believe that we must continue to dedicate a significant amount of resources to our research and development efforts to maintain our competitive position. However, we cannot predict that we will receive significant revenue from these investments, if at all.
If we do not comply with environmental regulations, we may incur significant costs causing our overall business to suffer.
We are subject to a variety of environmental regulations relating to the use, storage, handling, and disposal of certain hazardous substances used in the manufacturing and assembly of our products. We believe that we are currently in compliance with all material environmental regulations in connection with our manufacturing operations, and that we have obtained all necessary environmental permits to conduct our business. However, our failure to comply with present or future regulations could subject us to such consequences as: the imposition of substantial fines, suspension of production, and alteration of manufacturing processes or cessation of operations.
Compliance with environmental regulations could require us to acquire expensive remediation equipment or to incur substantial expenses. Our failure to control the use, disposal, removal, storage, or to adequately restrict the discharge of or assist in the cleanup of hazardous or toxic substances, could subject us to significant liabilities, including joint and several liability under certain statutes. The imposition of liabilities of this kind would harm our financial condition.
23
Risks Related to our Stock
The sale of a substantial amount of our common stock, including shares issued upon exercise of outstanding options and warrants in the public market, and the concentration of our equity ownership by a small number of stockholders, could adversely affect the liquidity of Adept securities and the prevailing market price of our common stock and could permit a small number of stockholders to effectively control all decisions of stockholders of our company.
We had an aggregate of 8,001,604 shares of common stock outstanding on September 8, 2008 shortly before the filing of this Annual Report on Form 10-K. In 2003, we completed a private placement of an aggregate of approximately 2.2 million shares of common stock to several accredited investors, referred to as the 2003 financing. Investors in the 2003 financing also received warrants to purchase an aggregate of approximately 1.1 million shares of common stock at an exercise price of $6.25 per share, with certain proportionate anti-dilution protections. These warrants expire in November 2008 and could be exercised at any time, so are expected to be exercised soon after the date of this Annual Report on Form 10-K. In 2006, we also issued 731,251 shares to Crosslink entities in a private placement, referred to as the 2006 financing. In 2007, in connection with our settlement of a dispute with Crosslink, referred to as the 2007 settlement, we issued 225,000 additional shares of common stock to Crosslink entities. We have registered for resale by the investors the shares of common stock issued, and to be issuable upon exercise of the warrants in the 2003 financing, the 2006 financing and the 2007 settlement. The selling security holders from these offerings may offer up to an aggregate of approximately 4.3 million shares of our common stock under these existing registration statements, including more than 1.1 million shares of which are not currently outstanding but are likely to be in the future. The investors in our private placements beneficially own a substantial portion of our total outstanding equity securities, and these investors along with a few other stockholders unrelated to these stockholders together hold the substantial majority of our outstanding common stock, which may affect the trading market for our stock and control the results of any questions of corporate governance.
Additionally, at June 30, 2008, options to purchase approximately 987,733 shares of our common stock were outstanding under our equity compensation plans, and an additional 592,230 shares of common stock were reserved for future grant and issuance under such plans. We also issue restricted shares under our employee stock purchase plan. Shares of common stock issued under these plans generally will be freely tradable in the public market, subject to the Rule 144 limitations applicable to our affiliates. The exercise of options and conversion of the warrants will significantly increase the number of common shares outstanding, diluting the ownership interests of our existing stockholders. Further, the sale of a substantial amount of our common stock, including shares issued upon exercise of these outstanding options or issuable upon exercise of our warrants, or future options in the public market could adversely affect the prevailing market price of our common stock. In connection with our Cerebellum acquisition, we may issue shares of our common stock as consideration to the sellers in that transaction. Our use of equity to raise additional financing or as consideration in connection with a future acquisition or other transaction could result in the further dilution of our stockholders’ equity interest.
The ability of our Board of Directors to issue additional preferred stock could delay or impede a change of control of our company and may adversely affect the price an acquirer is willing to pay for our common stock.
The Board of Directors has the authority to issue, without further action by our stockholders, up to 1,000,000 shares of preferred stock in one or more series and to fix the price, rights, preferences, privileges and restrictions thereof, including dividend rights, dividend rates, conversion rights, voting rights, terms of redemption, redemption prices, liquidation preferences, and the number of shares constituting a series or the designation of such series. The issuance of preferred stock, while providing desirable flexibility in connection with possible acquisitions, financings, and other corporate purposes, could have the effect of delaying, deferring, or preventing a change in control of Adept without further action by the stockholders and may adversely affect the market price of, and the voting and other rights of, the holders of common stock. Additionally, the conversion of preferred stock into common stock may have a dilutive effect on the holders of common stock.
24
Our stock price has fluctuated and may continue to fluctuate widely.
The market price of our common stock has fluctuated substantially in the past, and will continue to be subject to significant fluctuations in the future in response to a variety of factors, including:
| • | | fluctuations in operating results and restatements of historical financial statements; |
| • | | our liquidity needs and constraints; |
| • | | effectiveness of cost control measures; |
| • | | changes in our business focus and operational organization; |
| • | | our restructuring activities and changes in management and other personnel; |
| • | | the trading of our common stock on NASDAQ or another exchange; |
| • | | the business environment, including the operating results and stock prices of companies in the industries we serve; |
| • | | general conditions in the intelligent automation industry; |
| • | | announcements concerning our business or that of our competitors or customers; |
| • | | the introduction of new products or changes in product pricing policies by us or our competitors; |
| • | | litigation or claims regarding our restatement, internal controls, proprietary rights or other matters; |
| • | | developments in the financial markets; and |
| • | | perceived dilution from stock issuances. |
Furthermore, stock prices for many companies, and high technology companies in particular, fluctuate widely for reasons that may be unrelated to their operating results. Those fluctuations and general economic, political and market conditions, such as recessions, terrorist or other military actions, or international currency fluctuations, as well as public perception of equity values of publicly-traded companies may adversely affect the market price of our common stock.
We may be subject to claims, securities class action and other litigation if our stock price remains volatile or operating results suffer, which could result in substantial costs, distract management, and damage our reputation.
In the past, securities class action and other litigation has often been brought against companies following periods of volatility in the market price of their securities or where operating results suffer. Companies like ours, which are involved in rapidly changing markets, are particularly subject to this risk. We have incurred net operating losses in recent fiscal years and our stock price remains volatile. To date, there has been no litigation commenced with respect to such matters; however, we may be the target of litigation of this kind in the future. Any securities or other litigation could result in substantial costs, divert management’s attention and resources from our operations, and negatively affect our public image and reputation.
Recent legislation, liability insurance costs and other increased costs of being public are likely to impact our future consolidated financial position and results of operations.
Significant federal regulation, including the Sarbanes-Oxley Act of 2002 and rules and regulations promulgated as a result of the Sarbanes-Oxley Act, and accounting pronouncements or regulatory rulings will have an impact on our future financial position and results of operations. These regulatory requirements have, and in the future, are expected to increase general and administrative costs. In addition, costs of insurance have, in some instances, increased after these regulatory changes. These and other potential changes could materially increase the expenses we report under generally accepted accounting principles and adversely affect our financial position and operating results.
25
ITEM 1B. | UNRESOLVED STAFF COMMENTS |
Not applicable.
Our headquarters are located in a leased building of approximately 75,000 square feet in Livermore, California. Effective with our restructuring efforts in the fourth quarter of fiscal 2007, we consolidated our operations in Livermore and eliminated 20% of our building requirements so we now operate within 60,000 square feet. The lease agreement provides that the lease expires in May 2011 and obligates us to lease payments with 4.0% annual increases, plus insurance, property taxes and common area maintenance. We are currently in a dispute with our landlord for these facilities, including the landlord’s purported termination of the lease and our right to occupy the Livermore facilities. See Item 3, “Legal Proceedings”. With the acquisition of Cerebellum we added a leased location in Annecy, France. We also lease facilities for sales and operations in Dortmund, Germany. Other Adept facilities include Cincinnati, Ohio, Charlotte, North Carolina, Pomona, California, Vancouver, Canada, Massy, France, and Singapore. All of our facilities are used by both of our two reportable business segments.
On April 14, 2008, Tri-Valley Technology Campus LLC, the landlord of Adept’s Livermore, California offices (referred to as Landlord) sent Adept a lease termination notice, purporting to terminate the Livermore lease 90 days following the date of such notice. The notice indicated that a termination fee of $1 million was due from Adept to terminate Adept’s obligations under the lease on July 14, 2008, other than certain express obligations intended to survive termination. The Landlord subsequently delivered a new lease termination notice to Adept, indicating that the Livermore lease would terminate on August 26, 2008, and demanding payment of a $1 million termination fee no later than June 27, 2008. The notices were delivered based on the Landlord’s interpretation of a Lease Termination Agreement dated December 16, 2007 between Adept and the Landlord.
On May 30, 2008, the Landlord commenced litigation with the matterTri-Valley Campus I LLC vs. Adept Technology, Inc.in California Superior Court in Contra Costa County seeking declaratory relief in favor of its interpretation of the Lease Termination Agreement, including seeking a declaration that the terms of the Lease Termination Agreement required Adept to pay $1 million to the Landlord and to vacate the premises no later than August 26, 2008, and sought attorneys’ fees and costs. The Landlord dismissed this action on July 31, 2008 and instituted an action in California Superior Court in Alameda County, bringing claims for declaratory relief, breach of contract, breach of the implied covenant of good faith and fair dealing, intentional interference with contract, and intentional interference with prospective economic advantage. The Landlord seeks a declaration that the terms of the Lease Termination Agreement required Adept to pay $1 million to the landlord and to vacate the premises no later than August 26, 2008, and pay damages, punitive damages, attorneys’ fees, and costs. Among other things, the Landlord alleges that the Landlord is required to deliver possession of the Livermore facilities to its new tenant no later than September 1, 2008, and is seeking damages and punitive damages, including but not limited to the value of the 13-year lease with its new tenant.
On July 29, 2008, the Landlord filed an unlawful detainer action withTri-Valley Technology Campus, LLC v. Adept Technology, Inc .in California Superior Court in Alameda County seeking to recover immediate possession of the Livermore facilities, claiming the failure to pay the termination payment also constituted a breach of the lease agreement for such facilities. In addition to seeking to repossess the premises, the Landlord also seeks payment of $1 million as a termination fee, the forfeiture of the lease, and attorneys’ fees and costs. On August 28, 2008, the Court denied a motion to compel arbitration of the dispute. On August 29, 2008, the Court issued an order setting trial starting September 16, 2008, and Adept appealed the Court’s denial of the motion to compel arbitration and has sought a stay of the trial proceedings.
Adept disputes the Landlord’s interpretation of the Lease Termination Agreement, including its alleged obligations and the effect of Adept’s choosing not to pay $1 million in combination with relinquishing the leased
26
property. Adept currently occupies its Livermore facility and is vigorously defending these litigation matters with its Landlord and exploring its leasing alternatives, but the outcome of these matters cannot be determined at this time.
From time to time, the Company is party to various legal proceedings or claims, either asserted or unasserted, which arise in the ordinary course of its business. The Company has reviewed pending legal matters and believes that the resolution of these matters will not have a material adverse effect on its business, financial condition or results of operations.
Adept has in the past received communications from third parties asserting that it has infringed certain patents and other intellectual property rights of others, or seeking indemnification against alleged infringement. While it is not feasible to predict or determine the likelihood or outcome of any actual or potential actions from such assertions against the Company, the Company believes the ultimate resolution of these matters will not have a material adverse effect on its financial position, results of operations or cash flows.
ITEM 4. | SUBMISSION OF MATTERS TO A VOTE OF SECURITY HOLDERS |
No matters were submitted to a vote of security holders during the fourth quarter of 2008.
EXECUTIVE OFFICERS OF THE REGISTRANT
| | | | |
Name | | Age | | Position |
John Dulchinos | | 46 | | Chief Executive Officer, President and Assistant Secretary |
Lisa M. Cummins | | 38 | | Vice President of Finance and Chief Financial Officer, Secretary |
Gordon Deans | | 48 | | Vice President, Business Development |
Joachim Melis | | 43 | | Vice President, Worldwide Sales |
David Pap Rocki | | 54 | | Vice President, Worldwide Operations |
John Dulchinos was appointed Chief Executive Officer and President effective September 3, 2008 and was previously President and Chief Operating Officer since June 2007. Mr. Dulchinos joined Adept in October 1987 as a Regional Sales Engineer, and has held various positions at Adept including Director of OEM business, Vice President of North American Sales, Vice President of Worldwide Sales and Vice President, Robotics. Mr. Dulchinos holds both Bachelors and Masters degrees in Mechanical Engineering with a concentration in Robotics from Renssalaer Polytechnic Institute in Troy, New York.
Lisa M. Cummins joined Adept in May 2007 as Corporate Controller and was appointed Vice President and Chief Financial Officer in July 2007. Since September 2005 and prior to joining Adept, Ms. Cummins served as Assistant Corporate Controller with Pacer International, Inc., a publicly-traded logistics and intermodal freight transportation provider. From 2001 to 2005, Ms. Cummins held several positions, most recently as Manager of Financial Planning and Analysis, with APL Logistics, an independent unit of Neptune Orient Lines Limited, a global transportation and logistics company. Ms. Cummins is a Certified Public Accountant and has an MBA from St. Mary’s College in Moraga, CA, and a Bachelors degree from the University of California in Santa Barbara, CA.
Gordon Deans joined Adept in June 2004 as Vice President Business Development. From March 2002 until joining Adept, Mr. Deans held the position of President of Telere Technologies, Inc., a consulting firm providing product marketing and business development services to high-tech organizations. Mr. Deans holds a Master of Electrical Engineering degree from Carleton University in Ottawa, Ontario and a Bachelor of Science degree in Electrical Engineering from Queens University in Kingston, Ontario.
27
Joachim Melis was appointed Vice President, Worldwide Sales in June 2007. He joined Adept in October 1990 as an Applications Engineer in our German office and served as Applications Supervisor and then Manager of European Customer Service from 1992 to 1998. In 1998, Mr. Melis became Managing Director of the RDA Services Division. In July 2000, Mr. Melis became the Managing Director for Sales and Service in Germany, and in September 2002, added Sales and Service in France. In August 2004 Mr. Melis was appointed Vice President, Europe in which position he served until June 2007. Mr. Melis holds a Degree in Electronics from the University of Dortmund, Germany.
Dave Pap Rocki was appointed Vice President, Worldwide Operations in September 2008 after serving as Chief Technical officer since July 2006. He joined Adept in February 2000 as Director of Robotic Systems and has also held the position of Director of Hardware. Previously, Mr. Pap Rocki worked in the semiconductor industry from 1988 to 2000 at Novellus and SVG, managing systems and electrical engineering groups responsible for developing control platforms for front-end wafer production equipment. Prior to this, Mr. Pap Rocki was a founding member of Adept in 1983, leaving as the manager of systems in 1988. He has also worked at Unimation, a pioneer in the field of industrial robotics. At Unimation, SVG and Adept, Mr. Pap Rocki has been involved in the development of a number of successful robots including the PUMA, AdeptOne, i/sCobra and silicon wafer handling mechanisms. Mr. Pap Rocki holds a bachelor of science in electrical engineering from DeVry Technology in Phoenix, Arizona.
28
PART II
ITEM 5. | MARKET FOR REGISTRANT’S COMMON EQUITY, RELATED STOCKHOLDER MATTERS AND ISSUER PURCHASES OF EQUITY SECURITIES |
Market for Registrant’s Common Stock and Related Stockholder Matters
Our common stock is traded on the NASDAQ Global Market under the symbol ADEP.
The following table reflects the range of high and low sales prices for Adept common stock for each full quarterly period within the two most recent fiscal years as reported for trading on the NASDAQ Global Market.
| | | | | | | | | | | | | | | | | | | | | | | | |
| | Three Months Ended |
| | Jun. 30, 2008 | | Mar. 31, 2008 | | Dec. 31, 2007 | | Sep. 30, 2007 | | Jun. 30, 2007 | | Mar. 31, 2007 | | Dec. 31, 2006 | | Sep. 30, 2006 |
High | | $ | 12.24 | | $ | 9.98 | | $ | 8.34 | | $ | 6.74 | | $ | 9.89 | | $ | 12.41 | | $ | 11.99 | | $ | 16.95 |
Low | | $ | 7.90 | | $ | 5.95 | | $ | 5.35 | | $ | 5.61 | | $ | 5.71 | | $ | 6.40 | | $ | 7.40 | | $ | 8.90 |
At September 8, 2008, there were approximately 259 stockholders of record of our common stock.
To date, we have neither declared nor paid cash dividends on shares of our common stock. We do not anticipate paying cash dividends on our common stock in the foreseeable future and we may be restricted from doing so under or a future credit facility. In September 2008, we announced the adoption by our Board of Directors of a stock repurchase program to acquire up to $2.5 million of our common stock.
Recent Sales of Unregistered Securities
None.
Purchases of Equity Securities by the Issuer and Affiliated Purchasers
None.
29
PERFORMANCE GRAPH
The following graph compares the five-year cumulative total stockholder return of Adept Technology, Inc. as compared to the Major Market Index, and an Industry Index/Peer Group index including ten other companies. The graph assumes an investment of $100.00 in our common stock and each index (including reinvestment of dividends) on June 30, 2003 and shown through June 30, 2008.
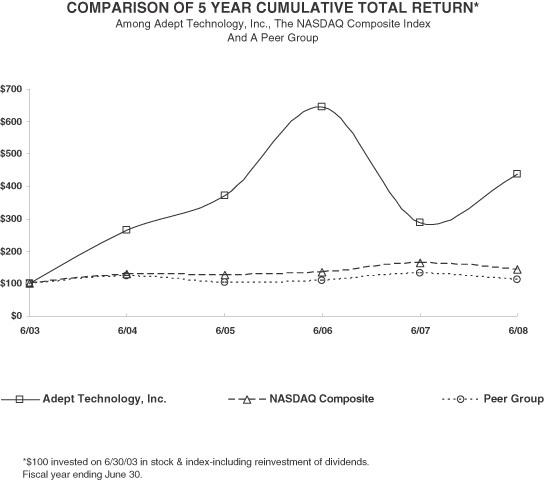
| | | | | | | | | | | | |
| | 6/03 | | 6/04 | | 6/05 | | 6/06 | | 6/07 | | 6/08 |
Adept Technology, Inc. | | 100.00 | | 263.64 | | 370.45 | | 645.45 | | 287.73 | | 438.18 |
NASDAQ Composite | | 100.00 | | 129.09 | | 127.97 | | 136.00 | | 164.15 | | 142.67 |
Peer Group | | 100.00 | | 123.78 | | 104.99 | | 108.32 | | 133.86 | | 111.73 |
| • | | This peer group is comprised of the following companies: Asyst Technologies Inc., Brooks Automation Inc., Cognex Corporation, Cyberoptics Corporation, Esterline Technologies Corporation, Gerber Scientific, Integralvision Inc., KLA Tencor Corporation, Nordson Corporation, and Perceptron Inc. The total return for each member of this peer group has been weighted according to each member’s stock market capitalization. |
ITEM 6. | SELECTED FINANCIAL DATA |
Not applicable to Adept as a smaller reporting company.
30
ITEM 7. | MANAGEMENT’S DISCUSSION AND ANALYSIS OF FINANCIAL CONDITION AND RESULTS OF OPERATIONS |
We provide intelligent robotics systems, the core of which are our motion controls systems, integrated vision-guidance technology and application software, that are sold in combination with our own proprietary or our third parties’ robot mechanisms. Our vision guidance technology is tightly integrated with our motion controls technology, and this is a key differentiator for Adept. In addition, we provide a full complement of robotics services and support for our customers. Through sales to system integrators, original equipment manufacturer (“OEM”) partners and end-user companies, we sell our robotics systems and services into a few broad industries where we believe we can provide the best solutions for particular applications. Our growth strategy focuses on four global vertical markets: packaging, solar, medical and disk drive/electronics, as well as on traditional industrial markets in Europe, including automotive electronics and machine tool automation. We believe these markets represent significant opportunity over the next several years for growth and product differentiation.
Overview
Over the past several years we have experienced a significant shift in the composition and focus of our business as demand in the U.S. automotive and industrial markets declined sharply due to deterioration in those industries, and demand in the global disk drive market decreased due to consolidation and ongoing deferment of capital investment. To counter these trends and the related decline in our revenues, we adopted a strategy focusing on a few vertical markets where the use of automation is growing or is expected to grow. The markets we have selected are: packaging, solar, medical and disk drive/electronics. Currently, we are focusing the majority of our investments on opportunities in the global packaging market and on the emerging solar market, as we believe these industries offer significant opportunity in both the near and long term. In addition, we have continued to focus on the automotive and industrial markets in Germany, which have remained robust. Over the longer term, we believe that demand in the disk drive/electronics market will also grow.
Because much of the demand for our products in recent periods has come from Europe, over the past several quarters we have also intensified our efforts to strengthen our operational and sales capabilities in this region. We believe Europe will continue to be an important market for our products both in traditional sectors such as automotive electronics and in our target vertical markets.
To further diversify our revenue base and expand sales of our products for packaging and solar applications into additional geographies, during fiscal 2008 we added distribution capabilities in Brazil and Argentina through agreements with new channel partners, and in February 2008, we added a distribution partner in Korea. In early fiscal 2009, we signed our first distribution partner in India. In the fourth quarter of fiscal 2008, we also launched new marketing programs to expand sales of our Quattro robot, currently sold primarily in Germany and France, into additional countries in Europe as well as into Asia.
To better address the needs of the packaging and emerging solar markets, in fiscal 2007 we introduced an important new robot to our portfolio, Quattro, which offers industry leading speed and performance for high speed automation applications. Sales of Quattro have helped drive Adept’s revenue growth in fiscal 2008, and we believe the product will continue to be an important revenue driver. The Quattro robot is a unique kinematic licensed exclusively to Adept and covered under patent protection in Adept’s key geographic markets.
Additionally, in May 2008, we introduced a new inverted SCARA robot, the Adept Cobra s800, to address applications in the packaging market such as mechanical assembly, material handling and packaging of packaged goods.
As a result of our recent strategies, we experienced 25% sales growth in fiscal 2008 as compared to fiscal 2007, and the composition of our sales has shifted to include a higher proportion of revenues from our target vertical markets of packaging, solar and medical, as well as a higher proportion of revenues from Europe than from the United States and Asia.
31
To augment our technical and sales capabilities in the medical and packaging markets, in the third quarter of fiscal 2008 we acquired Cerebellum Automation SAS, a leader in specialized OEM robotics and motion control solutions for medical and packaging applications. Our results for the third quarter and year ended June 30, 2008 include the operations of Cerebellum.
To lower our expense base and more efficiently utilize our sales resources, at the end of fiscal 2007 we implemented a restructuring program, under which we reduced facility and headcount costs, consolidated development activities to fewer locations and realigned our U.S. sales resources around our target vertical markets. As a result, we reduced our quarterly expense rate by a significant amount, which we believe will help us to maintain profitability in the future and provide cash flows to invest into our target vertical markets.
This discussion summarizes the significant factors affecting our consolidated operating results, financial condition, liquidity and cash flow during the two-year period ended June 30, 2008, each year therein referred to as fiscal 2008 and 2007, reflecting requirements applicable to Adept as a smaller reporting company. Unless otherwise indicated, references to any year in this Management’s Discussion and Analysis of Financial Condition and Results of Operations refer to our fiscal year ended June 30. This discussion should be read with the consolidated financial statements and financial statement footnotes included in this Annual Report on Form 10-K.
Critical Accounting Policies
Management’s discussion and analysis of Adept’s financial condition and results of operations are based upon Adept’s consolidated financial statements which have been prepared in conformity with U.S. generally accepted accounting principles. The preparation of these financial statements requires management to make estimates, judgments and assumptions that affect reported amounts of assets and liabilities and disclosure of contingent assets and liabilities at the date of the financial statements and the reported amounts of revenues and expenses during the reporting period. On an on-going basis, we evaluate our estimates, including those related to warranty obligations, bad debt, inventories, cancellation costs associated with long-term commitments, investments, intangible assets, income taxes, restructuring expenses, service contracts, stock-based compensation, contingencies and litigation. We base our estimates on historical experience and on various other assumptions that we believe to be reasonable under the circumstances, the results of which form the basis for making estimates and judgments about the carrying value of assets and liabilities that are not readily apparent from other sources. Estimates, by their nature, are based on judgment and available information. Therefore, actual results could differ from those estimates and could have a material impact on our consolidated financial statements, and it is possible that such changes could occur in the near term.
Reclassifications
Certain reclassifications have been made to prior-period balances to present the financial statements on a consistent basis with current year presentation. Such reclassifications have not changed previously reported net income (loss) or stockholders’ equity.
Critical Accounting Policies
We have identified the accounting principles which we believe are most critical to our consolidated financial statements while considering accounting policies that involve the most complex or subjective decisions or assessments. These critical accounting policies described below include:
| • | | allowance for doubtful accounts; |
32
| • | | capitalization of software development costs; |
| • | | deferred tax valuation allowance; |
| • | | foreign currency accounting; |
| • | | long-lived assets and goodwill; |
| • | | valuation of stock-based awards; and |
| • | | commitments and contingencies |
Revenue Recognition.
We generate revenues primarily from sales of production automation equipment and parts, and to a lesser extent from support and service activities associated with this equipment. Non-software product revenue consists primarily of sales of robots, refurbished robots and spare parts. We recognize non-software product revenue in accordance with Staff Accounting Bulletin 104 (“SAB 104”),Revenue Recognition, when persuasive evidence of a non-cancelable arrangement exists, delivery has occurred and/or services have been rendered, the price is fixed or determinable, collectibility is reasonably assured, legal title and economic risk is transferred to the customer, and when an economic exchange has taken place. We use the signed purchase contract or purchase order as evidence of an arrangement. Product revenues are normally recognized at the point of shipment from Adept facilities since title and risk of loss passes to the customers at that time. Customers have no right of return other than for product defects covered by our warranty. Adept maintains a warranty liability based on its historical warranty experience and managements’ best estimate of Adept’s warranty liability at each balance sheet date. There are no acceptance criteria on our standard non-software products. We do not deem the fee to be fixed or determinable where a significant portion of the price is due after our normal payment terms, which are 30 to 90 days from the invoice date. In recording revenue, management exercises judgment about the collectibility of receivables based on a number of factors, including the customer’s past payment history and its current creditworthiness. If we conclude that collection is not reasonably assured, then the revenue is deferred until the uncertainty is removed, generally upon receipt of payment. Our experience is that we have been able to reliably determine whether collection is reasonably assured.
Adept’s robots and controllers have features that are enabled or enhanced through the use of software enabling tools and other software elements, which are embedded within our robot and controller products. Our software enabling tools or other software elements do not operate independently of the robots or controllers, and they are not sold separately and cannot be used without the robots or controllers. We also sell optional software used to enhance capability of our products. Adept believes that the software component of our products is incidental to our products and services taken as a whole.
We recognize software revenue in accordance with the American Institute of Certified Public Accountants’ Statement of Position 97-2 (“SOP 97-2”),Software Revenue Recognition, as amended by SOP 98-9,Modification of SOP 97-2, And Software Revenue Recognition With Respect To Certain Transactions. Under SOP 97-2, revenue attributable to an element in a customer arrangement is recognized when (i) persuasive evidence of an arrangement exists, (ii) delivery has occurred, (iii) the fee is fixed or determinable, (iv) collectibility is probable and (v) the arrangement does not require services that are essential to the functionality of the software. License revenue is recognized on shipment of the product provided that no significant vendor or post-contract support obligations remain and that collection of the resulting receivable is deemed probable by management. Insignificant vendor and post-contract support obligations are accrued upon shipment of the licensed product. For software that is installed and integrated by the customer, revenue is recognized upon shipment assuming functionality has already been proven in prior sales and there are no customizations that would cause a substantial acceptance risk.
33
Service and Support revenue consists primarily of sales of spare parts and refurbished robots. Service revenue also includes training, consulting and customer support, the latter of which includes all field service activities; i.e., maintenance, repairs, system modifications or upgrades. Revenues from training and consulting are recognized at the time the service is performed and the customer has accepted the work. These revenues are not essential to the product functionality and, therefore, do not bear on the revenue recognition policy for Adept’s component products.
Deferred revenues represent payments received from customers in advance of the delivery of products and/or services, or before the satisfaction of all revenue recognition requirements enumerated above, as well as cases in which we have invoiced the customer but cannot yet recognize the revenue for the same reasons discussed above.
Revenue for robot refurbishment relates to Adept-owned or customer-owned remanufactured robots and components. Adept receives parts returned from customers under warranty contracts, or Adept purchases surplus used parts available from customers or suppliers. These parts traditionally have lower cost, and internal analysis indicates that on average, we pay a percentage of the new part cost to acquire these components. The standard cost for acquired parts is therefore set at such percentage of cost in compliance with GAAP as reflected in the SAB 100,Restructuring Charges, Impairments, and Related Issues, pronouncement requiring valuation of inventory at “lower of cost or market”. By contrast, the cost basis starting point for customer-owned remanufactured or repaired robots is zero since Adept does not own the robots. For all refurbishment and remanufacturing, we track all related costs and activities (materials and labor) required to bring the robots up to standard using work orders. This revenue stream is included within the Services and Support segment.
Allowance for Doubtful Accounts. We maintain allowances for doubtful accounts for estimated losses resulting from the inability of our customers to make required payments. We assess the customer’s ability to pay based on a number of factors, including our past transaction history with the customer and creditworthiness of the customer. Management specifically analyzes accounts receivable and historical bad debts, customer concentrations, customer creditworthiness, current economic trends and changes in our customer payment terms when evaluating the adequacy of the allowances for doubtful accounts. Adept performs ongoing credit evaluations of its customers and does not generally request collateral from our customers. However, Adept may require customers to make payments in advance of shipment or provide a letter of credit under certain circumstances. If the financial condition of our customers were to deteriorate in the future, resulting in an impairment of their ability to make payments, additional allowances may be required.
Our policy is to record specific allowances against known doubtful accounts. An additional allowance is also calculated based on the greater of 0.5% of consolidated accounts receivable or 20% of consolidated accounts receivable more than 120 days past due. Specific allowances are netted out of the respective receivable balances for purposes of calculating this additional allowance. On an ongoing basis, we evaluate the creditworthiness of our customers and, should the default rate change or the financial positions of our customers change, we may increase this additional allowance percentage.
Inventories. Inventories are stated at the lower of standard cost or market value. We perform a detailed assessment of inventory at each balance sheet date, which includes, among other factors, a review of component demand requirements, product lifecycle and product development plans, and quality issues. As a result of this assessment, we write down inventory for estimated obsolescence or unmarketable inventory equal to the difference between the cost of the inventory and the estimated liquidation value based upon assumptions about future demand and market conditions. If actual demand and market conditions are less favorable than those projected by management, additional inventory write-downs may be required.
Manufacturing inventory includes raw materials, work-in-process, and finished goods. The inventory valuation provisions are based on an excess and obsolete systems report, which captures all obsolete parts and products and all other inventory, which have quantities on hand in excess of one year’s projected demand. Individual line item
34
exceptions are identified for either inclusion or exclusion from the inventory valuation provision. The materials control group and cost accounting function monitor the line item exceptions and make periodic adjustments as necessary.
Warranties. Our warranty policy is included in our Terms of Sale, generally as a two year parts and one year labor limited warranty on most hardware and component products, and states that there are no rights of return, and that a refund may be made at Adept’s discretion, and only if there is an identified fault in the product and the customer has complied with Adept’s approved maintenance schedules and procedures, and the product has not been subject to abuse. We provide for the estimated cost of product warranties at the time revenue is recognized. Factors that affect our warranty liability include the number of installed units, historical and anticipated rates of warranty claims, and costs per claim for repair or replacement. While we engage in extensive product quality programs and processes, including actively monitoring and evaluating the quality of our components suppliers, our warranty obligation is affected by product failure rates, material usage and service labor and delivery costs incurred in correcting a product failure. Should actual product failure rates, material usage, service labor or delivery costs differ from our estimates, revisions to the estimated warranty liability would be required.
Capitalization of Software Development Costs. We capitalize certain software development costs in accordance with Statement of Financial Accounting Standards (“SFAS”) No. 86,Accounting for the Costs of Computer Software to Be Sold, Leased, or Otherwise Marketed. We begin capitalizing software development costs upon the establishment of technological feasibility, which is established upon the completion of a working model or a detailed program design. Costs incurred prior to technological feasibility are charged to expense as incurred. Capitalization ceases when the product is considered available for general release to customers. Capitalized software development costs are amortized to costs of revenues over the estimated economic lives of the software products based on product life expectancy. Generally, estimated economic lives of the software products do not exceed three years.
Deferred Tax Valuation Allowance. We record a valuation allowance to reduce deferred tax assets to the amount that is more likely than not to be realized. While we have considered future taxable income and ongoing prudent and feasible tax planning strategies in assessing the need for the valuation allowance, in the event we were to determine that we would be able to realize deferred tax assets in the future in excess of our net recorded amount, an adjustment to the deferred tax asset would increase income in the period such determination was made. Likewise, should we have a net deferred tax asset and determine that we would not be able to realize all or part of our net deferred tax asset in the future, an adjustment to the deferred tax assets would be charged to income in the period that such determination was made.
Foreign Currency Accounting.Adept applies SFAS 52, Foreign Currency Translation, with respect to our international operations, which include manufacturing, sales and service entities. Each of our non-U.S. operations uses its respective local currency as the functional currency. Our foreign subsidiaries’ balance sheet accounts are translated at current period ending exchange rates and statements of operations are translated at the average rate for the period. Translation gains and losses are recorded as a separate component of accumulated other comprehensive income (loss) in stockholders’ equity.
Gains and losses realized from transactions, including intercompany balances not considered to be a permanent investment, denominated in currencies other than an entity’s functional currency are included in other income (expense), net in the accompanying consolidated statements of operations.
We do not currently apply a hedging strategy against our currency positions as defined under Statement of Financial Accounting Standards No. 133 (“SFAS 133”),Accounting for Derivative Instruments and Hedging Activities.
Long-Lived Assets and Goodwill. The carrying value of goodwill and other intangible assets are reviewed for possible impairment in accordance with SFAS No. 142,Goodwill and Other Intangible Assets. Our impairment review is based on a discounted cash flow approach that requires significant management judgment with respect
35
to future sales and production volumes, revenue and expense growth rates, changes in working capital use, foreign exchange rates and selection of an appropriate discount rate. Impairment occurs when the carrying value of a reporting unit exceeds the fair value of that reporting unit. An impairment charge is recorded for the difference between the carrying value and the net present value of estimated future cash flows, which represents the estimated fair value of the reporting unit. The intangibles and goodwill were acquired and valued in the third quarter of fiscal 2008. We test our intangible assets annually unless there are indications during an interim period that such assets may have become impaired. We use our judgment in assessing whether intangible assets may have become impaired between annual valuations. Indicators such as unexpected adverse economic factors, unanticipated technological change or competitive activities may signal that an intangible asset has become impaired.
On January 2, 2008, Adept acquired all outstanding common shares of Cerebellum Automation SAS. Of the $804,000 of acquired intangible assets, all was assigned to Cerebellum’s ApproFlex system software system, which has an approximate useful life of 3 years. The $81,000 of goodwill was assigned to the Adept’s Robotics segment. During the year, currency translation will affect the amounts recorded on the consolidated financial statements. In addition, the purchase price allocation for goodwill has been increased and includes the impact of recording a deferred tax liability of $289,000 related to the non-tax deductible amortization of the acquired intangibles. At the end of fiscal 2008 the remaining amount of intangible assets and goodwill related to Cerebellum was $725,000 and $377,000 respectively.
In fiscal 2007, Adept concluded that the carrying value of goodwill related to its acquisitions of Hexavision and META was not supportable because the estimate of future cash flows related to these intangible assets was not sufficient to recover the carrying value of such intangibles. Accordingly, Adept wrote down the entire value of goodwill related to these acquisitions and took a charge of $3.2 million under SFAS 142 for intangible asset impairment.
Valuation of Stock-Based Awards. We account for stock-based compensation in accordance with the fair value recognition provisions of SFAS No. 123R. Under SFAS No. 123R, stock-based compensation cost is measured at the grant date based on the value of the award and is recognized as expense over the vesting period of the individual equity instrument. Determining the fair value of stock-based awards at the grant date requires judgment, including estimating the expected term of stock options, the expected volatility of our stock, and expected dividends. The computation of the expected volatility assumption used in the Black-Scholes calculation for option grants is based on historical volatility as options on our stock are not traded. When establishing the expected life assumption, we review annual historical employee exercise behavior of option grants with similar vesting periods. In addition, judgment is also required in estimating the amount of stock-based awards that are expected to be forfeited. If actual forfeitures differ significantly from these estimates, stock-based compensation expense and our results of operations could be materially affected.
Commitments and Contingencies.In accordance with SFAS No. 5, we evaluate potential commitments and contingencies based on their anticipated outcome. If we determine, after consideration of all known facts and consultation with legal counsel, that a loss related to the potential matter is neither probable or cannot be reasonably estimated as of the date of issuance of our fiscal period-end reports, we do not accrue for the potential liability. If a loss is reasonably possible related to the matter, we will disclose the relevant facts of the matter along with an estimated loss amount or range if such amount or range can be reasonably estimated.
Acquisitions
From time to time, we may make acquisitions of products, technologies or other businesses. On January 2, 2008, the Company acquired all outstanding common shares of Cerebellum Automation SAS. The results of Cerebellum’s operations have been included in the consolidated financial statements since that date. Cerebellum, based in France, is a provider of Custom Robotics and Motion Control products and components.
36
The initial purchase price paid at closing, excluding all items tied to contingent employee-retention compensation, amounted to $732,971. This included an initial cash payment of $350,000, accrued liabilities of $297,500 due within one year and paid direct costs of $85,471. Additional contingent deferred cash consideration of $32,500 in cash and $167,500 payable in shares of Adept common stock payable upon the first anniversary of the acquisition provided that certain employees remain employed by Cerebellum, will be amortized monthly during the first year following the acquisition. Additional contingent consideration of $65,000 in cash and $385,000 payable in shares of Adept common stock, which may be paid on the second anniversary provided that certain employees remain employed by Cerebellum, will be amortized monthly during the second year following the acquisition (months 13 to 24 post-acquisition). Additionally, there are contingent amounts payable up to a maximum aggregate amount of €312,000 in Adept common stock based on Cerebellum’s meeting certain revenue milestones in each of the first and second years after the date of the acquisition. The amounts achieved will be added to Goodwill upon realization of the associated revenue milestones. In no event will Adept issue common stock in an amount greater than 20% of its outstanding stock at the time of the acquisition, and any amount which would exceed this maximum will instead be paid in cash.
In fiscal 2003, we acquired a 67% ownership interest in Meta Control Technologies, Inc. (“Meta”), a provider of automation solutions, with the remaining 33% ownership interest in Meta being held in escrow for the benefit of one stockholder. The acquisition agreement provided that Adept would acquire all of these remaining shares in return for the provision of discounts and royalty payments to the stockholder and its affiliates of up to $1.7 million through August 2008 but would, in any event and regardless of whether discounts were incurred or royalties paid, acquire 100% of the stock of Meta no later than August 2008 for no additional consideration. No discounts and royalties were paid to the stockholder, and Adept acquired the remaining equity of Meta in August 2008. Management decided to discontinue selling META products in fiscal 2008, other than a last time buy opportunity for the remaining customer for those products. As a result of this decision to discontinue sales of all META products, management has determined the entire amount of goodwill related to the acquisition of META is fully impaired.
Results of Operations
Revenues
The following table sets forth our annual revenues and year-to-year change in revenues by business segment for the fiscal years ended June 30, 2008 and 2007:
| | | | | | | | | | | |
| | Fiscal 2008 | | | % Change 2007 to 2008 | | | Fiscal 2007 | |
| ($’s in thousands) | |
Revenue by Segment | | | | | | | | | | | |
Robotics | | | | | | | | | | | |
Revenues | | $ | 46,691 | | | 52 | % | | $ | 30,743 | |
Percentage of total revenues | | | 77 | % | | | | | | 63 | % |
Services and Support | | | | | | | | | | | |
Revenues | | $ | 14,092 | | | (21 | )% | | $ | 17,945 | |
Percentage of total revenues | | | 23 | % | | | | | | 37 | % |
| | | | | | | | | | | |
Total revenues | | $ | 60,783 | | | 25 | % | | $ | 48,688 | |
| | | | | | | | | | | |
Revenues.
Revenues were $60.8 million in fiscal 2008, up $12.1 million, or 25%, from $48.7 million in fiscal 2007. The increase in revenues resulted from an increase in sales in our Robotics segment, offset by a decrease in sales in our Service and Support segment.
37
Robotics segment revenues were $46.7 million in fiscal 2008, up 52% from $30.7 million in fiscal 2007. Higher robotics revenues in fiscal 2008 were primarily the result of increased sales in Europe of our Viper and Cobra products for applications in the automotive electronics and packaging markets, as well as sales of our new Quattro robot in the packaging and emerging solar markets. Demand from the disk drive / electronics market continued to be weak in fiscal 2008. Sales to the medical market, comprised primarily of medical device manufacturing, were modestly higher in fiscal 2008 compared with the previous year.
Services and Support segment revenues were $14.1 million in fiscal 2008, down 21% from $18.0 million in fiscal 2007. The decrease was primarily due to lower sales of remanufactured robotics to disk drive/electronics manufacturers in the U.S. and Asia. We expect Service and Support revenues will continue to comprise a similar percentage of sales as they have in fiscal 2008.
The following table sets forth our annual revenues and year-to-year change in revenues by geographic region for the fiscal years ended June 30, 2008 and 2007:
| | | | | | | | | | | |
| | Fiscal 2008 | | | % Change 2007 to 2008 | | | Fiscal 2007 | |
| | ($’s in thousands) | |
Revenue by Geography | | | | | | | | | | | |
United States | | | | | | | | | | | |
Revenues | | $ | 19,199 | | | (2 | )% | | $ | 19,507 | |
Percentage of total revenues | | | 32 | % | | | | | | 40 | % |
| | | | | | | | | | | |
Europe | | | | | | | | | | | |
Revenues | | | 33,527 | | | 43 | % | | | 23,410 | |
Percentage of total revenues | | | 55 | % | | | | | | 48 | % |
Asia | | | | | | | | | | | |
Revenues | | | 4,141 | | | 5 | % | | | 3,951 | |
Percentage of total revenues | | | 7 | % | | | | | | 8 | % |
Other Countries | | | | | | | | | | | |
Revenues | | | 3,916 | | | 115 | % | | | 1,820 | |
Percentage of total revenues | | | 6 | % | | | | | | 4 | % |
| | | | | | | | | | | |
Total International revenues | | $ | 41,584 | | | 43 | % | | $ | 29,181 | |
Percentage of total revenues | | | 68 | % | | | | | | 60 | % |
| | | | | | | | | | | |
Total revenues | | $ | 60,783 | | | 25 | % | | $ | 48,688 | |
| | | | | | | | | | | |
Our domestic revenues were $19.2 million in fiscal 2008, down 2% from $19.5 million in fiscal 2007. This decrease was primarily due to reduced sales of both new robotic systems and refurbished robots to the disk drive/electronics industry, offset by new sales of our Quattro robots and increased sales of our Viper and Cobra robots for applications in our target packaging and solar markets. U.S. sales to the medical market were modestly higher in fiscal 2008 compared with the previous year, although still a small portion of our overall revenues.
Our international revenues were $41.6 million in fiscal 2008, up 43% from $29.2 million in fiscal 2007. Higher international revenues primarily resulted from increased sales in Europe, as well as increased sales in Canada and new sales in South America (shown collectively in the table above under “Other Countries”). European sales were $33.5 million in fiscal 2008, up 43% from $23.4 million in fiscal 2007, driven by continued strong demand from the automotive electronics and machine tool automation markets and increasing demand from the emerging solar market in Germany, as well as increased demand in France for our products for packaging applications. Sales to Other Countries rose 115% to $3.9 million in fiscal 2008, compared with $1.8 million in fiscal 2007. This increase was driven primarily by increased sales in Canada for packaging applications. Sales also increased in South America as a result of new channel distribution agreements during fiscal 2008. Asian sales increased 5%
38
in fiscal 2008 to $4.1 million, compared with $4.0 million in fiscal 2007 due to sales of Quattro by our new Korean distributor into the packaging industry.
Gross Margin.
The following table sets forth our gross margin and year-to-year change in gross margin by business segment for the fiscal years ended June 30, 2008 and 2007:
| | | | | | | | | | | |
| | Fiscal 2008 | | | % Change 2007 to 2008 | | | Fiscal 2007 | |
| | ($’s in thousands) | |
Revenues | | $ | 60,783 | | | | | | $ | 48,688 | |
Gross margin | | $ | 30,092 | | | 43 | % | | $ | 21,077 | |
Gross margin % | | | 49.5 | % | | | | | | 43.3 | % |
Gross margin as a percentage of revenues was 49.5% in fiscal 2008, compared to 43.3% in fiscal 2007. The increase in gross margin in fiscal 2008 was the result of several factors, including: favorable product mix, primarily as a result of higher sales volumes of higher margin products in Europe, where we have focused more of our sales efforts in the last several quarters; lower product costs as a result of our ongoing efforts to reduce manufacturing overhead, reduce component costs and improve inventory management; and the recognition of software license revenue in the first half of 2008 which is not expected to continue at the same magnitude in the future and accounted for an incremental two percentage points of gross margin for the full fiscal year.
We may experience significant fluctuations in our gross margin percentage from period to period due to changes in volume, changes in availability of components, changes in product configuration, increased price-based competition, changes in sales mix of products and/or changes in operating costs
Operating Expenses
Research, Development and Engineering
| | | | | | | | | | | |
| | Fiscal 2008 | | | % Change 2007 to 2008 | | | Fiscal 2007 | |
| | ($’s in thousands) | |
Expenses | | $ | 5,354 | | | (26 | )% | | $ | 7,220 | |
Percentage of revenue | | | 9 | % | | | | | | 15 | % |
Research, development and engineering (“R&D”) expenses in fiscal 2008 were $5.4 million, or 9% of revenues, a decrease of 26% from $7.2 million, or 15% of revenues, in fiscal 2007. Included in R&D expenses in fiscal 2008 was approximately $173,000 of incremental expenses from Cerebellum, which Adept acquired during the third quarter of 2008. The decrease in R&D expense in fiscal 2008 was due primarily to restructuring actions taken by Adept at the end of fiscal 2007, including the consolidation of development activities into fewer locations, as well as lower expenses associated with the productization of the Quattro robot, for which the majority of development was completed at the end of fiscal 2007.
Adept’s capitalization of software costs was $370,000 in fiscal 2008 and $737,000 in fiscal 2007.
39
Selling, General and Administrative Expenses.
| | | | | | | | | | | |
| | Fiscal 2008 | | | % Change 2007 to 2008 | | | Fiscal 2007 | |
| | ($’s in thousands) | |
Expenses | | $ | 21,441 | | | 7 | % | | $ | 20,132 | |
Percentage of revenue | | | 35 | % | | | | | | 41 | % |
Selling, general and administrative (“SG&A”) expenses consist primarily of employee compensation, professional fees arising from legal, auditing and other consulting services, as well as tradeshow participation and other marketing costs.
Selling, general and administrative expenses increased 7% to $21.4 million, or 35% of revenues in fiscal 2008, compared with $20.1 million, or 41% of revenues in fiscal 2007. The increase in SG&A expenses in 2008 compared with the prior year was primarily due to higher consulting and legal fees in the fourth quarter of fiscal 2008 related to various corporate activities including Sarbanes-Oxley compliance, merger and acquisition related activities and our lease dispute, and also the accrual of certain corporate employee bonuses earned in fiscal 2008, and higher marketing expenses related to programs to promote Adept’s solutions for the solar market in additional geographic regions. Additionally, included in SG&A expenses in fiscal 2008 were approximately $422,000 of ongoing expenses to operate the newly acquired Cerebellum, and approximately $280,000 of costs related to Sarbanes-Oxley compliance, discussed below. Offsetting higher SG&A expenses in the fourth quarter of fiscal 2008 were lower expenses in the first nine months of fiscal 2008 that resulted from reductions in headcount and facility space utilized as a result of our restructuring actions initiated at the end of fiscal 2007.
During fiscal 2008, we undertook and have now completed the actions necessary to become compliant with Sarbanes-Oxley Section 404 with respect to our internal controls. We recognized the majority of the related expense for these actions in our SG&A expenses during fiscal 2008. We do expect continued expenses for our Sarbanes-Oxley compliance efforts in fiscal 2009.
Amortization.Amortization of intangible assets was $216,000 in fiscal 2008, compared with $33,000 in 2007. Higher levels of amortization in fiscal 2008 resulted from the amortization of additional intangible assets acquired with the purchase of Cerebellum in the third quarter of fiscal 2008.
Impairment of Goodwill and Intangibles.As required under SFAS 142, Adept evaluates the carrying value of goodwill and indefinite-lived intangible assets on our balance sheet at least annually and we record a charge for impairment whenever events or changes in circumstances indicate that the carrying amount of long-lived assets may not be recoverable.
On January 2, 2008, Adept acquired all outstanding common shares of Cerebellum. Of the $804,000 of acquired intangible assets, all was assigned to Cerebellum’s ApproFlex software system, which has an approximate useful life of 3 years. At the end of fiscal 2008 the remaining amount of intangible assets and goodwill related to Cerebellum was $725,000 and $377,000, respectively.
In fiscal 2007, we concluded that the carrying value of goodwill related to the acquisitions of Hexavision and META was not supportable because the estimate of future cash flows related to these intangible assets was not sufficient to recover the carrying value of such intangibles. Accordingly, we wrote down the entire value of goodwill related to the acquisitions and recorded a charge of $3.2 million for asset impairment.
Stock Compensation Expense. Under the provisions of SFAS 123R, we recorded stock-based compensation expense of $769,000 in fiscal 2008 and $1.3 million in fiscal 2007 for our stock option plans and ESPP. We did not record an income-tax benefit for the stock compensation expense in any of these years because of the extent of our net operating loss carry forwards. See Note 2 of the Notes to the Consolidated Financial Statements for more information about our recognition of stock compensation expense.
40
Crosslink Settlement Costs. During fiscal 2007, we recorded a $1.9 million non-cash expense paid in common shares associated with the settlement of our dispute with Crosslink. This was a one-time expense and did not impact subsequent fiscal periods.
Restructuring Charges. We recorded $254,000 in restructuring charges in 2008 primarily related to lease terminations. We recorded $1.0 million in restructuring charges in fiscal 2007, primarily related to facility closure, lease termination and employee severance as part of our business restructuring at the end of June 2007.
Operating Income (Loss). Operating income was $2.8 million in fiscal 2008 compared with an operating loss of $12.4 million in fiscal 2007. Operating income in fiscal 2008 was the result of higher revenues and gross margin and lower operating expenses than in the previous year. Our operating loss in fiscal 2007 was the result of lower revenues and gross margin, combined with higher operating expenses, as well as a one-time settlement expense related to Crosslink, restructuring charges related to the restructuring implemented at the end of fiscal 2007 and impairment of goodwill.
Interest Income (Expense), Net. Interest income, net of interest expense, was $306,000 in fiscal 2008, compared with interest income of $445,000 in fiscal 2007. The decrease in interest income, net in fiscal 2008 compared with the prior year was primarily due to lower interest rates on investment cash and securities in the fiscal 2008 period.
Foreign Currency Transaction Gain (Loss). Foreign currency transaction gains were $755,000 in fiscal 2008 and $208,000 in fiscal 2007. The 2008 foreign currency gains recorded resulted primarily from the settlement of previously considered permanent USD-denominated inter-company balances. In 2007, all the intercompany balances were considered permanent. In 2008, a portion of the debt was considered non-permanent and was primarily settled, so the transactional gains and losses flowed through to other earnings.
Provision (Benefit) for Income Taxes. The provision for income taxes for fiscal 2008 was $252,000 as compared with a benefit of ($202,000) in fiscal 2007. The fiscal 2008 provision represents federal and state alternative minimum tax requirements as well as foreign tax expense primarily related to our German and France operations. The fiscal 2007 benefit is net of various state and foreign minimum tax expenses and arose primarily from the reversal of liabilities which Adept believes are no longer probable, and as such have been adjusted. Adept adjusts its tax liabilities and assets based on consideration of a variety of factors, including interpretations of statutes and regulations as well as estimates and judgments for financial statement purposes. Adept has previously had net operating losses available to offset most of its domestic and foreign tax obligations except when yearly net operating loss limitations exist for domestic and foreign jurisdictions that result in some tax expense.
Backlog. Our product backlog related to continuing operations at June 30, 2008 was approximately $10.9 million, compared with $6.3 million at June 30, 2007. Backlog is calculated based on orders that are expected to ship during the twelve months following each fiscal year end. Customers who have placed orders with delivery dates beyond twelve months from the end of the fiscal period are not included in backlog, and thus we expect a substantial amount of the backlog at June 30, 2008 to ship during fiscal 2009. Because orders constituting our current backlog are subject to changes in delivery schedules and in certain instances may be subject to cancellation without significant penalty to the customer, our backlog at any date may not be indicative of demand for our products or actual net revenues for any period in the future.
Long-Lived Assets
Our long-lived assets consist primarily of fixed assets of $3.4 million and $3.6 million (net of depreciation) at June 30, 2008 and 2007, respectively. Financial information regarding the geographic breakdown of our long-lived assets is included in Note 11 of our Notes to Consolidated Financial Statements included in this Annual Report on Form 10-K.
41
Litigation
Adept is currently involved in litigation with its landlord of its Livermore, California facilities, referred to as Landlord (See Item 3 Legal Proceedings). The Landlord has delivered lease termination notices to Adept, most recently indicating that the Livermore lease would terminate on August 26, 2008, and demanding payment of a $1 million termination fee no later than June 27, 2008 based on the Landlord’s interpretation of a Lease Termination Agreement dated December 16, 2007 between Adept and the Landlord.
During the fourth quarter of fiscal 2008, the Landlord filed an unlawful detainer action seeking to recover immediate possession of the Livermore facilities, claiming the failure to pay the termination payment constituted a breach of the lease agreement for such facilities (in addition to a breach of the Lease Termination Agreement) and seeking payment of $1 million as a termination fee, the forfeiture of the lease, and attorneys’ fees and costs. This action is currently scheduled to go to trial on September 16, 2008.
On July 31, 2008, the Landlord initiated additional litigation seeking a declaration that the terms of the Lease Termination Agreement required Adept to pay $1 million to the Landlord and to vacate the premises no later than August 26, 2008, and pay damages, punitive damages, attorneys’ fees, and costs. Among other things, the Landlord alleges that the Landlord was required to deliver possession of the Livermore facilities to its new tenant, no later than September 1, 2008, and is seeking damages and punitive damages, including but not limited to the value of the 13-year lease with the new tenant.
Adept disputes the Landlord’s interpretation of the Lease Termination Agreement, including its alleged obligations and the effect of Adept’s choosing not to pay $1 million in combination with relinquishing the leased property, and is vigorously defending these litigation matters with its Landlord. The outcome of these litigation matters cannot be determined at this time and significant legal costs are expected to be incurred in the future to defend these actions even if no damages are ultimately paid by Adept.
From time to time, the Company is party to various legal proceedings or claims, either asserted or unasserted, which arise in the ordinary course of its business. The Company has reviewed pending legal matters and believes that the resolution of these matters will not have a material adverse effect on its business, financial condition or results of operations.
Adept has in the past received communications from third parties asserting that it has infringed certain patents and other intellectual property rights of others, or seeking indemnification against alleged infringement. While it is not feasible to predict or determine the likelihood or outcome of any actual or potential actions from such assertions against the Company, we believe the ultimate resolution of these matters will not have a material adverse effect on our financial position, results of operations or cash flows.
Liquidity and Capital Resources
We had an aggregate cash and short term investments balance of $15.2 million and $10.9 million for fiscal years end June 30, 2008 and 2007, respectively. We also had a credit facility of up to $5.0 million, with no outstanding balance at year-end or borrowings during both fiscal years. We depend on funds generated from operations and collections of accounts receivable to meet our operating requirements. We believe our sources of funds will be sufficient to finance our operations through at least fiscal 2009 and have therefore not renewed our credit facility allowing it to expire per its terms in August 2008.
Cash and cash equivalents and short-term investments increased $4.3 million and decreased $3.2 million during 2008 and 2007, respectively. In fiscal year 2008, net cash provided by operating activities of $6.7 million was attributable to our net income of $3.6 million augmented by $2.6 million of non-cash charges including depreciation, amortization, and stock-based compensation. In fiscal year 2007, net cash used by operating activities of $932,000 was attributable to our net loss of $11.5 million augmented by $9.5 million of non-cash charges including depreciation, amortization, goodwill impairment, stock compensation, settlement costs, as well as a decrease of inventory and accounts receivable, and partially offset by a $1.8 million decrease in accounts payable.
42
In fiscal year 2008, cash provided by investing activities of $604,000 primarily reflects the redemption of short-term investments of $2.0 million, offset by the purchase of intangibles as part of our acquisition of Cerebellum, as well as capital expenditures for computer hardware and software, including capitalized software development costs. In fiscal year 2007, cash used in investing activities of $1.7 million reflects capital expenditures primarily for computer hardware and software, including capitalized software development costs, tooling, marketing show booths and sales demo equipment, especially the Quattro Robot.
Cash provided by financing activities of $189,000 and $491,000 in fiscal years 2008 and 2007, respectively, represent proceeds from our employee stock purchase plan and the exercise of stock options of $337,000 and $615,000 in fiscal years 2008 and 2007, respectively, offset by payments of $148,000 and $124,000 on capital leases in fiscal 2008 and 2007, respectively.
In fiscal 2009, the Adept Board of Directors has approved a stock repurchase program for up to $2.5 million of Adept stock. The timing and amount of shares repurchased will depend on a variety of factors including the stock price, corporate and contractual and regulatory requirements, alternative investment opportunities and other market and economic conditions. Adept expects to fund its purchases from its working capital. The Company has no obligation to purchase a specific amount of common stock under its program.
The Adept Board of Directors has also adopted a new Employee Stock Purchase Program, which, subject to approval of Adept stockholders, will provide for the sale of additional shares of common stock to employees and result in additional cash and stock-based compensation expense for Adept. Additionally, it approved a new executive and senior management payment plan which contemplates possible cash and/or restricted stock payments to Adept employees based upon the Company’s revenue and operating income for fiscal 2009.
Tabular disclosure of contractual obligations is not applicable to Adept as a smaller reporting company.
New Accounting Pronouncements
In December 2007, FASB issued SFAS No. 141 (revised 2007),Business Combinations. Under SFAS No. 141(R), an entity is required to recognize the assets acquired, liabilities assumed, contractual contingencies, and contingent consideration at their fair value on the acquisition date. It further requires that acquisition-related costs be recognized separately from the acquisition and expensed as incurred, restructuring costs generally be expensed in periods subsequent to the acquisition date, and changes in accounting for deferred tax asset valuation allowances and acquired income tax uncertainties after the measurement period impact income tax expense. In addition, acquired in-process research and development (IPR&D) is capitalized as an intangible asset and amortized over its estimated useful life. The adoption of SFAS No. 141(R) will change our accounting treatment for business combinations entered into after the first quarter of fiscal year 2009.
In February 2007, the FASB issued SFAS No. 159, “The Fair Value Option for Financial Assets and Financial Liabilities” (“SFAS No. 159”). SFAS No. 159 allows companies to choose to measure certain financial instruments and certain other items at fair value. The statement requires that unrealized gains and losses are reported in earnings for items measured using the fair value option and establishes presentation and disclosure requirements. SFAS No. 159 is effective July 1, 2008 for the Company. The Company does not believe the adoption of SFAS No. 159 will have a material effect on our consolidated financial statements.
In December 2007, the FASB issued SFAS No. 160, “Noncontrolling Interests in Consolidated Financial Statements”, an amendment of Accounting Research Bulletin No. 51. SFAS No. 160 will change the accounting and reporting for minority interests, which will be recharacterized as noncontrolling interests and classified as a component of equity. SFAS No. 160 is effective for fiscal years beginning after December 15, 2008. Early adoption is not permitted. We are currently evaluating the impact that SFAS No. 160 will have on our consolidated financial statements.
43
ITEM 7A. | QUANTITATIVE AND QUALITATIVE DISCLOSURES ABOUT MARKET RISK |
Not applicable to Adept as a smaller reporting company.
ITEM 8. | FINANCIAL STATEMENTS AND SUPPLEMENTARY DATA |
Consolidated Financial Statements and a Financial Statement Schedule as of June 30, 2008 and 2007 and for each of the two years in the period ended June 30, 2008 are included in Items 15(a)(1) and (2) included in this Annual Report on Form 10-K.
No Supplementary Financial Data is required in this Annual Report on Form 10-K as such data is not required of Adept as a smaller reporting company.
ITEM 9. | CHANGES IN AND DISAGREEMENTS WITH ACCOUNTANTS ON ACCOUNTING AND FINANCIAL DISCLOSURE |
None.
ITEM 9A. | CONTROLS AND PROCEDURES |
Evaluation of Disclosure Controls and Procedures
As of the end of the fiscal year ended June 30, 2008, Adept carried out an evaluation, under the supervision and with the participation of members of our management, including our former Chief Executive Officer and our Chief Financial Officer (“CFO”), of the effectiveness of the design and operation of Adept’s disclosure controls and procedures pursuant to Rule 13a-15(b) of the Securities Exchange Act of 1934. Our new Chief Executive Officer (“new CEO”), who assumed that position in the first quarter of fiscal 2009, and our CFO have concluded, based on their evaluation as of June 30, 2008, that Adept’s disclosure controls and procedures were effective at the end of the fiscal year to ensure that information required to be disclosed by us in the reports that we file or submit under the Securities Exchange Act is recorded, processed, summarized and reported within the time periods specified in the SEC’s rules and forms and is accumulated and communicated to our management, including the CEO and CFO, as appropriate to allow timely decisions regarding required disclosure. It should be noted that our new CEO’s certification as to our disclosure controls and procedures as of the end of fiscal 2008 is necessarily based in part on an evaluation of facts that existed before he served in the capacity of Chief Executive Officer of Adept.
Management’s Annual Report on Internal Control over Financial Reporting
The Company’s management is responsible for establishing and maintaining adequate internal control over financial reporting (as defined in Rule 13a-15(f) under the Securities Exchange Act). The Company’s management assessed the our internal control over financial reporting based on the Internal Control—Integrated Framework issued by the Committee of Sponsoring Organizations of the Treadway Commission (“COSO”) . Based on the results of this evaluation, the Company’s management concluded that our internal control over financial reporting was effective, as of June 30, 2008 based on these criteria.
A control system, no matter how well conceived and operated, can provide only reasonable, not absolute, assurance that the objectives of the control system are met under all potential conditions, regardless of how remote, and may not prevent or detect all error and all fraud. Because of the inherent limitations in all control systems, no evaluation of controls can provide absolute assurance that all control issues and instances of fraud, if any, within Adept have been prevented or detected. Our internal control over financial reporting is designed to provide reasonable assurance regarding the reliability of financial reporting and the preparation of financial statements for external purposes in accordance with generally accepted accounting principles.
44
Auditor’s Report on Internal Control over Financial Reporting
This annual report does not include an attestation report of the company’s registered public accounting firm regarding internal control over financial reporting. Management’s report was not subject to attestation by the Company’s registered public accounting firm pursuant to temporary rules of the Securities and Exchange Commission that permit the company to provide only management’s report in this annual report.
Changes in Internal Controls over Financial Reporting
There have not been any changes in the Company’s internal control over financial reporting (as such term is defined in Rules 13a-15(f) and 15d-15(f) under the Securities Exchange Act) during the quarter ended June 30, 2008 that have materially affected, or are reasonably likely to materially affect, Adept’s internal control over financial reporting. Prior to the fourth quarter, Adept completed procedures to achieve Sarbanes-Oxley 404 compliance, which were tested during and since the fourth quarter.
ITEM 9B. | OTHER INFORMATION |
Change of Management
On September 3, 2008, John Dulchinos, previously our President and Chief Operating Officer, was appointed as Chief Executive Officer of the Company, succeeding Robert H. Bucher, who now serves as the Executive Chairman of the Board of Directors of Adept. Mr. Dulchinos was also appointed to serve as a member of our Board of Directors.
45
PART III
ITEM 10. | DIRECTORS, EXECUTIVE OFFICERS AND CORPORATE GOVERNANCE |
See the information included under the heading “Executive Officers” elsewhere in this Annual Report on Form 10-K. Certain information required by this item is incorporated by reference from our Proxy Statement related to the 2008 Annual Meeting of Stockholders to be filed by us with the Securities and Exchange Commission within 120 days of the end of our fiscal year pursuant to General Instruction G(3) of Form 10-K, referred to as the Proxy Statement.
ITEM 11. | EXECUTIVE COMPENSATION |
The information required by this item is incorporated by reference from our Proxy Statement.
ITEM 12. | SECURITY OWNERSHIP OF CERTAIN BENEFICIAL OWNERS AND MANAGEMENT AND RELATED STOCKHOLDER MATTERS |
The information required by this item is incorporated by reference from our Proxy Statement.
ITEM 13. | CERTAIN RELATIONSHIPS AND RELATED TRANSACTIONS, AND DIRECTOR INDEPENDENCE |
The information required by this item is incorporated by reference from our Proxy Statement.
ITEM 14. | PRINCIPAL ACCOUNTING FEES AND SERVICES |
The information required by this item is incorporated by reference from our Proxy Statement.
46
PART IV
ITEM 15. | EXHIBITS AND FINANCIAL STATEMENT SCHEDULES. |
(a)(1) Financial Statements
The financial statements (including the Notes thereto set forth in Item 8 of Part II of this Form 10-K) are filed as part of this Annual Report on Form 10-K.
(a)(2) Financial Statement Schedules
The following financial statement schedule is included herein:
Schedule II—Valuation and Qualifying Accounts. Additional schedules are not required under the related schedule instructions or are inapplicable, and therefore have been omitted.
(a)(3) Exhibits
EXHIBIT INDEX
| | |
2.1 | | Agreement and Plan of Merger dated November 4, 2005 between Adept Technology, Inc., a Delaware corporation (“Adept-Delaware”) and Adept Technology, Inc., a California corporation (“Adept-California”) (incorporated by reference to Exhibit 2.1 to the Current Report on Form 8-K filed with the Securities and Exchange Commission on November 8, 2005). |
| |
2.2 | | Share Purchase Agreement effective January 1, 2008, by and among the Company, Adept Technology France and the shareholders of Cerebellum Automation (incorporated by reference to Exhibit 2.1 to the Registrant’s Quarterly Report on Form 10-Q for the 2008 second fiscal quarter ended December 29, 2007, filed with the Securities and Exchange Commission on February 11, 2008). |
| |
2.3 | | Amendment dated January 18, 2008 to the Share Purchase Agreement effective January 1, 2008, by and among the Company, Adept Technology France and the shareholders of Cerebellum Automation (incorporated by reference to Exhibit 2.2 to the Registrant’s Quarterly Report on Form 10-Q for the 2008 second fiscal quarter ended December 29, 2007, filed with the Securities and Exchange Commission on February 11, 2008). |
| |
3.1 | | Certificate of Incorporation of Adept-Delaware (incorporated by reference to Exhibit 3.1 to the Registrant’s Current Report on Form 8-K12G3 filed with the Securities and Exchange Commission on November 10, 2005). |
| |
3.2 | | Certificate of Amendment of Certificate of Incorporation of Adept-Delaware (incorporated by reference to Exhibit 3.2 to the Registrant’s Current Report on Form 8-K12G3 filed with the Securities and Exchange Commission on November 10, 2005). |
| |
3.3 | | Bylaws of Adept-Delaware (incorporated by reference to Exhibit 3.3 to the Registrant’s Current Report on Form 8-K12G3 filed with the Securities and Exchange Commission on November 10, 2005). |
| |
4.1 | | Specimen of Common Stock Certificate of Adept-Delaware (incorporated by reference to Exhibit 4.1 to the Registrant’s Current Report on Form 8-K12G3 filed with the Securities and Exchange Commission on November 10, 2005). |
| |
4.2 | | Registration Rights Agreement, dated as of June 9, 2006 by and among the Registrant and the investors party thereto (incorporated by reference to Exhibit 10.2 to the Registrant’s Current Report on Form 8-K/A filed with the Securities and Exchange Commission on June 23, 2006). |
47
| | |
4.3 | | Registration Rights Agreement, dated as of May 13, 2007 by and among the Registrant and the investors party thereto (incorporated by reference to Exhibit 10.1 to the Registrant’s Current Report on Form 8-K/A filed with the Securities and Exchange Commission on May 16, 2007). |
| |
4.4 | | Form of Registration Rights Agreement, dated as of November 18, 2003 by and among the Registrant and the investors party thereto (incorporated by reference to Exhibit 4.5 to the Registrant’s Registration Statement on Form S-2 (No. 333-112360) filed on January 30, 2004). |
| |
10.1* | | 1993 Stock Plan as amended, and form of Option Agreement thereto (incorporated by reference to Exhibit 4.1 to the Registrant’s Registration Statement on Form S-8 filed with the Securities and Exchange Commission on November 20, 2000, No. 333-50296). |
| |
10.2* | | 1998 Employee Stock Purchase Plan as amended, and form of Agreements thereto (incorporated by reference to Exhibit 10.1 to the Registrant’s Form 10-Q for the fiscal 2003 first quarter ended September 28, 2002, filed with the Securities and Exchange Commission on November 12, 2002). |
| |
10.3* | | 1995 Director Option Plan as amended, and form of Option Agreement thereto (incorporated by reference to Exhibit 10.4 to the Registrant’s Form 10-K for the 1997 fiscal year ended June 30, 1997, filed with the Securities and Exchange Commission on September 26, 1997. |
| |
10.4 | | Form of Indemnification Agreement between Adept-California and its officers and directors (incorporated by reference to Exhibit 10.5 to the Registrant’s Registration Statement on Form S-1 (No. 33-98816.)) |
| |
10.5 | | Form of Indemnification Agreement between the Registrant and its officers and directors (incorporated by reference to Exhibit 10.1 to the Registrant’s Current Report on Form 8-K12G3 filed with the Securities and Exchange Commission on November 10, 2005). |
| |
10.6* | | 2003 Stock Option Plan, as amended (incorporated by reference to Exhibit 10.2 to the Registrant’s Quarterly Report on Form 10-Q for the fiscal 2006 third quarter ended April 1, 2006, filed with the Securities and Exchange Commission on May 16, 2006). |
| |
10.7* | | Form of Option Agreements under the 2003 Stock Option Plan (incorporated by reference to Exhibits 10.2 and 10.3 to the Registrant’s Registration Statement on Form S-8 (Registration No. 333-112148) filed with the Securities and Exchange Commission on January 19, 2005). |
| |
10.8** | | Original Equipment Manufacturing Agreement between Registrant and Yaskawa Electric Corp. dated August 29, 2000 (incorporated by reference to Exhibit 10.34 to the Registrant’s Amendment to its Annual Report on Form 10-K for the 2000 fiscal year ended June 30, 2000). |
| |
10.9 | | Industrial R&D Lease Agreement dated October 31, 2000 between Registrant and Tri-Valley Campus I, LLC for premises located at Livermore, California (incorporated by reference to Exhibit 10.1 to the Registrant’s Quarterly Report on Form 10-Q for the 2001 first fiscal quarter ended September 30, 2000, filed with the Securities and Exchange Commission on November 13, 2000). |
| |
10.10* | | 2001 Stock Option Plan, as amended (incorporated by reference to Exhibit 10.1 to the Registrant’s Quarterly Report on Form 10-Q for the fiscal 2006 third quarter ended March 31, 2006, filed with the Securities and Exchange Commission on May 16, 2006). |
| |
10.11* | | Form of Option Agreement under 2001 Stock Option Plan (incorporated by reference to Exhibit 10.4 to the Registrant’s Current Report on Form 8-K filed with the Securities and Exchange Commission on March 15, 2005). |
| |
10.12 | | Accounts Receivable Purchase Agreement dated as of March 21, 2003 between the Registrant and Silicon Valley Bank (incorporated by reference to Exhibit 10.1 to the Registrant’s Quarterly Report on Form 10-Q for the fiscal 2003 third quarter ended March 29, 2003, filed with the Securities and Exchange Commission on May 13, 2003). |
48
| | |
10.13 | | Intellectual Property Security Agreement dated as of March 21, 2003 between the Registrant and Silicon Valley Bank (incorporated by reference to Exhibit 10.2 to the Registrant’s Quarterly Report on Form 10-Q for the fiscal 2003 third quarter ended March 29, 2003, filed with the Securities and Exchange Commission on May 13, 2003). |
| |
10.14 | | Convertible Subordinated Note issued by Registrant to Tri-Valley Campus, LLC dated August 6, 2003 (incorporated by reference to Exhibit 4.1 to the Registrant’s Current Report on Form 8-K filed with the Securities and Exchange Commission on August 6, 2003). |
| |
10.15 | | Amendment to Lease Amendment dated as of August 6, 2003 between the Registrant and Tri-Valley Campus LLC (incorporated by reference to Exhibit 10.26 to the Registrant’s Annual Report on Form 10-K filed for the fiscal year ended June 30, 2003). |
| |
10.16** | | Original Equipment Manufacturer Agreement between the Registrant and Hirata Corporation dated January 31, 1995 (incorporated by reference to Exhibit 10.31 to the Registrant’s Amendment to its Annual Report on Form 10-K for the 2000 fiscal year ended June 30, 2000). |
| |
10.17 | | Form of Warrant, dated November 18, 2003 to purchase common stock of the Registrant issued to investors (incorporated by reference to Exhibit 4.6 to the Registrant’s Registration Statement on Form S-2 (No. 333-112360) filed with the Securities and Exchange Commission on January 30, 2004). |
| |
10.18 | | Purchase Agreement, dated as of November 14, 2003 by and among the Registrant and the investors named therein (incorporated by reference to Exhibit 10.28 and 10.29 to the Registrant’s Registration Statement on Form S-2 (No. 333-112360) filed with the Securities and Exchange Commission on January 30, 2004). |
| |
10.19* | | Robert H. Bucher Offer Letter dated November 3, 2003 (incorporated by reference to Exhibit 10.27 to the Registrant’s Amendment to its Annual Report on Form 10-K/A filed with the Securities and Exchange Commission on November 12, 2003). |
| |
10.20 | | Amendment to Loan Documents, dated as of April 22, 2004 by and between the Registrant and Silicon Valley Bank (incorporated by reference to Exhibit 10.3 to the Registrant’s Quarterly Report on Form 10-Q for the 2004 fiscal third quarter ended March 27, 2004, filed with the Securities and Exchange Commission on May 11, 2004). |
| |
10.21 | | Loan and Security Agreement, dated April 22, 2004, by and between the Registrant and Silicon Valley Bank (incorporated by reference to Exhibit 10.4 to the Registrant’s Quarterly Report on Form 10-Q for the 2004 fiscal third quarter ended March 27, 2004, filed with the Securities and Exchange Commission on May 11, 2004). |
| |
10.22* | | Termination Letter Agreement from Adept Technology, Inc. to Michael Overby dated October 19, 2004 (incorporated by reference to Exhibit 10.1 to the Registrant’s Current Report on Form 8-K filed with the Securities and Exchange Commission on October 25, 2004). |
| |
10.23* | | Amended and Restated 2004 Director Option Plan (incorporated by reference to Appendix A to Adept Technology, Inc. Proxy Statement on Schedule 14A for the 2006 Annual Meeting of Stockholders filed with the Securities and Exchange Commission on October 20, 2006). |
| |
10.24* | | Form of Director Option Agreement for Initial Grant under the 2004 Director Option Plan (incorporated by reference to Exhibit 10.1 to the Registrant’s Current Report on Form 8-K filed with the Securities and Exchange Commission on May 2, 2006). |
| |
10.25* | | Form of Director Option Agreement for Annual Grant under the 2004 Director Option Plan (incorporated by reference to Exhibit 10.10 to the Registrant’s Quarterly Report on Form 10-Q for the period ended March 31, 2006, filed with the Securities and Exchange Commission on May 16, 2006). |
49
| | |
10.26 | | Amendment to Loan Documents, dated as of June 15, 2005 by and between the Registrant and Silicon Valley Bank (incorporated by reference to Exhibit 10.1 to the Registrant’s Current Report on Form 8-K filed with the Securities and Exchange Commission on June 15, 2005). |
| |
10.27* | | Second Half Fiscal Year 2005 Executive Bonus Plan (incorporated by reference to Exhibit 10.3 to the Registrant’s Current Report on Form 8-K filed with the Securities and Exchange Commission on March 15, 2005). |
| |
10.28* | | Option Agreement for Performance-Based Non-Qualified Stock Options to Robert H. Bucher dated as of August 18, 2006 as amended (incorporated by reference to Item 10.1 of Registrant’s Current Report on Form 8-K filed with the Securities and Exchange Commission on April 27, 2006). |
| |
10.29* | | Adept Technology, Inc. Fiscal 2006 Executive Bonus Plan (incorporated by reference to Exhibit 10.1 to the Registrant’s Current Report on Form 8-K filed with the Securities and Exchange Commission on August 24, 2005). |
| |
10.30* | | 2005 Equity Incentive Plan (incorporated by reference to Exhibit 10.3 the Registrant’s Quarterly Report on Form 10-Q for the 2006 fiscal third quarter ended March 31, 2006, filed with the Securities and Exchange Commission on May 16, 2006). |
| |
10.31* | | Form of Restricted Stock and Option Agreements to 2005 Equity Incentive Plan (incorporated by reference to Exhibits 10.4, 10.5 and 10.6 to the Registrant’s Quarterly Report on Form 10-Q for the 2006 fiscal third quarter ended March 31, 2006, filed with the Securities and Exchange Commission on May 16, 2006). |
| |
10.32** | | Letter of Understanding dated as of December 9, 2005 between Adept Technology, Inc. and Parker Hannifin Corporation (incorporated by reference to Exhibit 10.1 of the Registrant’s Quarterly Report on Form 10-Q for the 2006 fiscal second quarter ended December 31, 2005, filed with the Securities and Exchange Commission on February 14, 2006). |
| |
10.33* | | Performance Option Grant to Robert H. Bucher dated as of May 5, 2006 (Incorporated by reference to Exhibit 10.1 of Registrant’s Current Report on Form 8-K filed with the Securities and Exchange Commission on May 9, 2006). |
| |
10.34* | | Offer Letter Agreement between Adept Technology, Inc. and Steven L. Moore dated June 12, 2006 (incorporated by reference to Exhibit 10.1 to Registrant’s Current Report on Form 8-K filed with the Securities and Exchange Commission on June 13, 2006). |
| |
10.35 | | Common Stock Purchase Agreement, dated as of June 9, 2006 by and among the Registrant and the purchasers named therein affiliated with Crosslink Capital Partners (incorporated by reference to Exhibit 10.1 to the Registrant’s Current Report on Form 8-K/A filed with the Securities and Exchange Commission on June 23, 2006). |
| |
10.36 | | Amendment to Loan Documents, dated as of August 15, 2006, by and between the Registrant and Silicon Valley Bank (incorporated by reference to Exhibit 10.1 to the Registrant’s Current Report on Form 8-K, filed with the Securities and Exchange Commission on August 21, 2006). |
| |
10.37 | | Amendment to Loan Documents, dated as of August 14, 2007, by and between the Registrant and Silicon Valley Bank on August 23, 2007 (incorporated by reference to Exhibit 10.1 to Registrant’s Current Report on 8-K filed with the Securities and Exchange Commission on August 24, 2007). |
| |
10.38* | | Summary of Non-employee Director Compensation. |
| |
10.39* | | Summary of Executive Officer Compensation (incorporated by reference to Exhibit 10.1 to the Registrant’s Current Report on Form 8-K filed with the Securities and Exchange Commission on September 3, 2008). |
| |
10.40* | | Fiscal 2007 Executive Bonus Plan (incorporated by reference to Exhibit 10.1 to the Registrant’s Current Report on Form 8-K filed with the Securities and Exchange Commission on November 20, 2006). |
50
| | |
10.41* | | Fiscal 2007 Performance Stock Guidelines (incorporated by reference to Exhibit 10.2 to the Registrant’s Current Report on Form 8-K filed with the Securities and Exchange Commission on November 20, 2006). |
| |
10.42* | | Option Agreement for Robert H. Bucher, dated May 5, 2006 as amended (incorporated by reference to Exhibit 10.1 to the Registrant’s Current Report on Form 8-K filed with the Securities and Exchange Commission on October 16, 2006). |
| |
10.43** | | License Agreement between Registrant and Fundacion Fatronik dated December 21, 2006. (incorporated by reference to Exhibit 10.1 to the Registrant’s Quarterly Report on Form 10-Q for the quarter ended March 29, 2008 filed with the Securities and Exchange Commission on May 13, 2008). |
| |
10.44* | | Offer Letter Agreement between Adept Technology and Lisa M. Cummins (incorporated by reference to Exhibit 10.1 to the Registrant’s Current Report on Form 8-K filed with the Securities and Exchange Commission on July 19, 2007). |
| |
10.45 | | Settlement Agreement by and among Adept Technology, Inc. and the purchasers named therein affiliated with Crosslink Capital Partners, dated as of May 13, 2007 (incorporated by reference to Exhibit 10.1 to Registrant’s Current Report on 8K/A filed with the Securities and Exchange Commission on May 16, 2007). |
| |
10.46* | | Severance Agreement dated as of August 27, 2007 between Adept Technology, Inc. and Matthew J. Murphy (incorporated by reference to Exhibit 10.1 to Registrant’s Current Report on 8-K filed with the Securities and Exchange Commission on September 13, 2007). |
| |
10.47* | | Fiscal 2008 Executive and Senior Management Payment Plan (incorporated by reference to Exhibit 10.1 to Registrant’s Current Report on 8-K filed with the Securities and Exchange Commission on October 10, 2007). |
| |
10.48* | | Amendment of Fiscal 2008 Executive and Senior Management Payment Plan (incorporated by reference to Exhibit 10.1 to Registrant’s Quarterly Report on Form 10-Q for the 2008 fiscal second quarter ended December 29, 2007, filed with the Securities and Exchange Commission on February 11, 2008). |
| |
10.49* | | Fiscal 2009 Executive and Senior Management Payment Plan. |
| |
10.50* | | Letter agreement re Employment terms between John Dulchinos and Adept Technology dated September 2, 2008. |
| |
10.51* | | Letter agreement re Employment terms between Robert Bucher and Adept Technology dated September 2, 2008. |
| |
10.52* | | 2008 Employee Stock Purchase Plan. |
| |
10.53* | | Form of Option Agreement for Consultants (incorporated by reference to Exhibit 10.4 to Registrant’s Quarterly Report on Form 10-Q for the 2008 fiscal first quarter ended September 29, 2007, filed with the Securities and Exchange Commission on November 13, 2007). |
| |
10.54 | | Lease Termination Agreement dated as of December 16, 2007 by and between Tri-Valley Technology Campus LLC and Adept Technology, Inc. (incorporated by reference to Exhibit 10.1 to Registrant’s Quarterly Report on Form 10-Q for the quarter ended March 29, 2008 filed with the Securities and Exchange Commission on May 13, 2008). |
| |
14.1 | | Code of Business Conduct, as amended (incorporated by reference to Exhibit 14.1 to the Registrant’s Current Report on Form 8-K filed with the Securities and Exchange Commission on November 20, 2006). |
| |
21.1 | | Subsidiaries of the Registrant. |
| |
23.1 | | Consent of Independent Registered Public Accounting Firm. |
51
| | |
24.1 | | Power of Attorney (See Signature Page to this Form 10-K). |
| |
31.1 | | Certification by the Chief Executive Officer Pursuant to Rule 13a-14(a)/15d-14(a) under the Securities Exchange Act of 1934 as adopted pursuant to Section 302 of the Sarbanes-Oxley Act of 2002. |
| |
31.2 | | Certification by the Chief Financial Officer Pursuant to Rule 13a-14(a)/15d-14(a) under the Securities Exchange Act of 1934 as adopted pursuant to Section 302 of the Sarbanes-Oxley Act of 2002. |
| |
32.1 | | Certification by the Chief Executive Officer and the Chief Financial Officer Pursuant to 18 U.S.C. Section 1350, as adopted pursuant to Section 906 of the Sarbanes-Oxley Act of 2002. |
* | Management contract or compensatory plan or arrangement. |
** | Confidential treatment has been requested as to certain portions of this exhibit. An unredacted version of this exhibit has been filed separately with the SEC. |
(b) Exhibits.
See Item 15(a)(3) above.
(c) Financial Statement Schedules.
See Item 15(a)(2) above.
52
SIGNATURES
Pursuant to the requirements of Section 13 or 15(d) of the Securities Exchange Act of 1934, the Registrant has duly caused this report to be signed on its behalf by the undersigned, thereunto duly authorized.
| | |
ADEPT TECHNOLOGY, INC. |
| |
By: | | /s/ LISA M. CUMMINS |
| | Lisa M. Cummins |
| | Vice President, Finance and Chief Financial Officer |
| |
By: | | /s/ JOHN DULCHINOS |
| | John Dulchinos |
| | President and Chief Executive Officer |
Date: September 10, 2008
53
POWER OF ATTORNEY
KNOW ALL PERSONS BY THESE PRESENTS, that each person whose signature appears below constitutes and appoints John Dulchinos and Lisa M. Cummins and each of them, his true and lawful attorneys-in-fact and agents, each with full power of substitution and resubstitution, to sign any and all amendments to this Annual Report on Form 10-K and to file the same, with all exhibits thereto and other documents in connection therewith, with the Securities and Exchange Commission, granting unto said attorneys-in-fact and agents, and each of them, full power and authority to do and perform each and every act and thing requisite and necessary to be done in connection therewith, as fully to all intents and purposes as he or she might or could do in person, hereby ratifying and confirming all that said attorneys-in-fact and agents, or their substitute or substitutes, or any of them, shall do or cause to be done by virtue hereof.
Pursuant to the requirements of the Securities Exchange Act of 1934, this Report has been signed below by the following persons on behalf of the Registrant and in the capacities and on the dates indicated:
| | | | |
Signature | | Title | | Date |
| | |
/s/ JOHN DULCHINOS (John Dulchinos) | | President and Chief Executive Officer (Principal Executive Officer) | | September 10, 2008 |
| | |
/s/ LISA M. CUMMINS (Lisa M. Cummins) | | Vice President, Finance and Chief Financial Officer (Principal Financial and Principal Accounting Officer) | | September 10, 2008 |
| | |
/s/ ROBERT H. BUCHER (Robert H. Bucher) | | Executive Chairman of the Board | | September 10, 2008 |
| | |
/s/ MICHAEL P. KELLY (Michael P. Kelly) | | Lead Independent Director | | September 10, 2008 |
| | |
/s/ A. RICHARD JUELIS (A. Richard Juelis) | | Director | | September 10, 2008 |
| | |
/s/ HERBERT J. MARTIN (Herbert Martin) | | Director | | September 10, 2008 |
| | |
/s/ ROBERT J. MAJTELES (Robert J. Majteles) | | Director | | September 10, 2008 |
54
FINANCIAL STATEMENTS AND SUPPLEMENTARY DATA
ADEPT TECHNOLOGY, INC.
INDEX TO CONSOLIDATED FINANCIAL STATEMENTS
55
REPORT OF INDEPENDENT REGISTERED PUBLIC ACCOUNTING FIRM
The Board of Directors and Stockholders
Adept Technology, Inc.
Livermore, CA
We have audited the accompanying consolidated balance sheets of Adept Technology, Inc. as of June 30, 2008 and June 30, 2007, and the related consolidated statements of operations and comprehensive income (loss), stockholders’ equity and cash flows for each of the years in the two year period ended June 30, 2008. Our audits also included the financial statement schedule for each of the years in the two year period ended June 30, 2008 listed in the Index at Item 15(a)(2). These consolidated financial statements and schedule are the responsibility of the Company’s management. Our responsibility is to express an opinion on these consolidated financial statements based on our audits.
We conducted our audits in accordance with the standards of the Public Company Accounting Oversight Board (United States). Those standards require that we plan and perform the audits to obtain reasonable assurance about whether the financial statements are free of material misstatement. We were not engaged to perform an audit of the Company’s internal control over financial reporting. Our audits included consideration of internal control over financial reporting as a basis for designing audit procedures that are appropriate in the circumstances, but not for the purpose of expressing an opinion on the effectiveness of the Company’s internal control over financial reporting. Accordingly, we express no such opinion. An audit also includes examining, on a test basis, evidence supporting the amounts and disclosures in the financial statements, assessing the accounting principles used and significant estimates made by management, and evaluating the overall financial statement presentation. We believe that our audits provide a reasonable basis for our opinion.
In our opinion, the consolidated financial statements referred to above present fairly, in all material respects, the financial position of Adept Technology, Inc. as of June 30, 2008 and 2007, and the results of its operations and its cash flows for each of the years in the two year period ended June 30, 2008 in conformity with accounting principles generally accepted in the United States of America. Also, in our opinion, the related financial statement schedule for the years ended June 30, 2008 and 2007, when considered in relation to the consolidated financial statements as a whole, presents fairly in all material respects the information set forth therein.
/s/ Armanino McKenna LLP
San Ramon, California
September 9, 2008
56
ADEPT TECHNOLOGY, INC.
CONSOLIDATED BALANCE SHEETS
| | | | | | | | |
| | June 30, 2008 | | | June 30, 2007 | |
| | (in thousands, except per share data) | |
ASSETS | | | | |
Current assets: | | | | | | | | |
Cash and cash equivalents | | $ | 15,185 | | | $ | 8,900 | |
Short-term investments | | | — | | | | 1,962 | |
Accounts receivable, less allowance for doubtful accounts of $485 in fiscal 2008 and $506 in fiscal 2007 | | | 11,757 | | | | 10,185 | |
Inventories | | | 10,234 | | | | 9,806 | |
Other current assets | | | 431 | | | | 598 | |
| | | | | | | | |
Total current assets | | | 37,607 | | | | 31,451 | |
Property and equipment at cost | | | 14,805 | | | | 14,903 | |
Accumulated depreciation and amortization | | | (11,451 | ) | | | (11,271 | ) |
| | | | | | | | |
Property and equipment, net | | | 3,354 | | | | 3,632 | |
Goodwill | | | 377 | | | | — | |
Other intangible assets, net | | | 800 | | | | — | |
Other assets | | | 152 | | | | 152 | |
| | | | | | | | |
Total assets | | $ | 42,290 | | | $ | 35,235 | |
| | | | | | | | |
LIABILITIES AND STOCKHOLDERS’ EQUITY | | | | | | | | |
Current liabilities: | | | | | | | | |
Accounts payable | | $ | 5,972 | | | $ | 5,175 | |
Accrued payroll and related expenses | | | 2,267 | | | | 1,708 | |
Accrued warranty | | | 1,259 | | | | 1,207 | |
Deferred revenue | | | 70 | | | | 33 | |
Accrued restructuring charges, current | | | 217 | | | | 449 | |
Accrued income tax | | | 392 | | | | 2 | |
Other accrued liabilities | | | 741 | | | | 436 | |
| | | | | | | | |
Total current liabilities | | | 10,918 | | | | 9,010 | |
Long-term liabilities: | | | | | | | | |
Accrued restructuring charges, long-term | | | 416 | | | | 637 | |
Other long-term liabilities | | | 461 | | | | 184 | |
| | | | | | | | |
Total liabilities | | | 11,795 | | | | 9,831 | |
| | | | | | | | |
Commitments and contingencies | | | — | | | | — | |
Stockholders’ equity: | | | | | | | | |
Preferred stock, $0.001 par value: 1,000 shares authorized, none issued and outstanding | | | — | | | | — | |
Common stock, $0.001 par value: 19,000 shares authorized, 7,985 and 7,914 shares issued and outstanding in fiscal 2008 and 2007, respectively | | | 163,490 | | | | 162,385 | |
Accumulated deficit | | | (134,021 | ) | | | (137,457 | ) |
Accumulated other comprehensive income | | | 1,026 | | | | 476 | |
| | | | | | | | |
Total stockholders’ equity | | | 30,495 | | | | 25,404 | |
| | | | | | | | |
Total liabilities and stockholders’ equity | | $ | 42,290 | | | $ | 35,235 | |
| | | | | | | | |
See accompanying notes.
57
ADEPT TECHNOLOGY, INC.
CONSOLIDATED STATEMENTS OF OPERATIONS
AND COMPREHENSIVE INCOME (LOSS)
| | | | | | | | |
| | Year Ended June 30, | |
| | 2008 | | | 2007 | |
| | (in thousands, except per share data) | |
| | |
Revenues | | $ | 60,783 | | | $ | 48,688 | |
Cost of revenues | | | 30,691 | | | | 27,611 | |
| | | | | | | | |
Gross margin | | | 30,092 | | | | 21,077 | |
Operating expenses: | | | | | | | | |
Research, development and engineering | | | 5,354 | | | | 7,220 | |
Selling, general and administrative | | | 21,441 | | | | 20,132 | |
Restructuring charges | | | 254 | | | | 1,023 | |
Amortization of other intangible assets | | | 216 | | | | 33 | |
Goodwill impairment | | | — | | | | 3,176 | |
Crosslink settlement costs | | | — | | | | 1,861 | |
| | | | | | | | |
Total operating expenses | | | 27,265 | | | | 33,445 | |
| | | | | | | | |
Operating income (loss) | | | 2,827 | | | | (12,368 | ) |
Currency exchange gain | | | 755 | | | | 208 | |
Interest income | | | 347 | | | | 481 | |
Interest expense | | | (41 | ) | | | (36 | ) |
| | | | | | | | |
Income (loss) before income taxes | | | 3,888 | | | | (11,715 | ) |
Provision for (benefit from) income taxes | | | 252 | | | | (202 | ) |
| | | | | | | | |
Net income (loss) | | $ | 3,636 | | | $ | (11,513 | ) |
| | | | | | | | |
Basic net income (loss) per share | | $ | 0.46 | | | $ | (1.50 | ) |
| | | | | | | | |
Diluted net income (loss) per share | | $ | 0.44 | | | $ | (1.50 | ) |
| | | | | | | | |
Basic number of shares used in computing per share amounts: | | | 7,957 | | | | 7,676 | |
| | | | | | | | |
Diluted number of shares used in computing per share amounts: | | | 8,246 | | | | 7,676 | |
| | | | | | | | |
Comprehensive income (loss) | | | | | | | | |
Net income (loss) | | $ | 3,636 | | | $ | (11,513 | ) |
Foreign currency translation adjustment | | | 550 | | | | 476 | |
| | | | | | | | |
Total comprehensive income (loss) | | $ | 4,186 | | | $ | (11,037 | ) |
| | | | | | | | |
See accompanying notes.
58
ADEPT TECHNOLOGY, INC.
CONSOLIDATED STATEMENTS OF STOCKHOLDERS’ EQUITY
| | | | | | | | | | | | | | | | |
| | Common Stock | | (Accumulated Deficit) | | | Accumulated Other Comprehensive Income | | Total Stockholders’ Equity | |
| Shares | | Amount | | | |
| | (in thousands) | |
| | | | | |
Balance at June 30, 2006 | | 7,583 | | $ | 158,633 | | $ | (125,944 | ) | | $ | — | | $ | 32,689 | |
| | | | | |
Common stock issued under employee stock incentive program and employee stock purchase plan | | 106 | | | 614 | | | — | | | | — | | | 614 | |
Common stock issued in Crosslink settlement | | 225 | | | 1,861 | | | — | | | | — | | | 1,861 | |
Stock-based compensation | | — | | | 1,277 | | | — | | | | — | | | 1,277 | |
Net loss | | — | | | — | | | (11,513 | ) | | | — | | | (11,513 | ) |
Foreign currency translation adjustment | | — | | | — | | | — | | | | 476 | | | 476 | |
| | | | | | | | | | | | | | | | |
Balance at June 30, 2007 | | 7,914 | | $ | 162,385 | | $ | (137,457 | ) | | $ | 476 | | $ | 25,404 | |
| | | | | |
Common stock issued under employee stock incentive program and employee stock purchase plan | | 71 | | | 336 | | | — | | | | — | | | 336 | |
Stock-based compensation | | — | | | 769 | | | — | | | | — | | | 769 | |
FIN 48 adjustment | | — | | | — | | | (200 | ) | | | — | | | (200 | ) |
Net income | | — | | | — | | | 3,636 | | | | — | | | 3,636 | |
Foreign currency translation adjustment | | — | | | — | | | — | | | | 550 | | | 550 | |
| | | | | | | | | | | | | | | | |
Balance at June 30, 2008 | | 7,985 | | $ | 163,490 | | $ | (134,021 | ) | | $ | 1,026 | | $ | 30,495 | |
| | | | | | | | | | | | | | | | |
See accompanying notes.
59
ADEPT TECHNOLOGY, INC.
CONSOLIDATED STATEMENTS OF CASH FLOWS
| | | | | | | | |
| | Year Ended June 30, | |
| | 2008 | | | 2007 | |
| | (in thousands) | |
Operating activities | | | | | | | | |
Net income (loss) | | $ | 3,636 | | | $ | (11,513 | ) |
Adjustments to reconcile net income (loss) to net cash provided by (used in) operating activities: | | | | | | | | |
Depreciation | | | 1,626 | | | | 1,335 | |
Loss on disposal of property and equipment | | | 38 | | | | 425 | |
Stock-based compensation | | | 769 | | | | 1,277 | |
Amortization of other intangible assets | | | 216 | | | | 33 | |
Goodwill impairment | | | — | | | | 3,176 | |
Crosslink settlement costs | | | — | | | | 1,861 | |
Reversal of previously accrued taxes | | | — | | | | (223 | ) |
Net changes in operating assets and liabilities: | | | | | | | | |
Accounts receivable, net | | | (19 | ) | | | 1,769 | |
Inventories | | | (244 | ) | | | 1,963 | |
Other current assets | | | 223 | | | | (154 | ) |
Other assets | | | 4 | | | | 18 | |
Accounts payable | | | 164 | | | | (1,810 | ) |
Other accrued liabilities and deferred revenue | | | 466 | | | | 105 | |
Accrued restructuring charges | | | (221 | ) | | | 931 | |
Other long-term liabilities | | | (119 | ) | | | (125 | ) |
| | | | | | | | |
Net cash provided by (used in) operating activities | | | 6,539 | | | | (932 | ) |
| | | | | | | | |
Investing activities | | | | | | | | |
Purchase of property and equipment | | | (610 | ) | | | (2,061 | ) |
Proceeds from sale of property and equipment | | | 173 | | | | 67 | |
Purchase of license fees | | | (150 | ) | | | — | |
Capitalized software | | | (370 | ) | | | (737 | ) |
Payment for purchase of Cerebellum, net of cash acquired | | | (401 | ) | | | — | |
Maturities of short-term investments | | | 1,962 | | | | 22,071 | |
Purchase of short-term investments | | | — | | | | (21,031 | ) |
| | | | | | | | |
Net cash provided by (used in) investing activities | | | 604 | | | | (1,691 | ) |
| | | | | | | | |
Financing activities | | | | | | | | |
Principal payments on capital leases | | | (148 | ) | | | (124 | ) |
Proceeds from employee stock incentive program and employee stock purchase plan, net of repurchases and cancellations | | | 337 | | | | 615 | |
| | | | | | | | |
Net cash provided by financing activities | | | 189 | | | | 491 | |
| | | | | | | | |
Effect of exchange rates on cash and cash equivalents | | | (1,047 | ) | | | (22 | ) |
| | | | | | | | |
Increase (decrease) in cash and cash equivalents | | | 6,285 | | | | (2,154 | ) |
Cash and cash equivalents, beginning of period | | | 8,900 | | | | 11,054 | |
| | | | | | | | |
Cash and cash equivalents, end of period | | $ | 15,185 | | | $ | 8,900 | |
| | | | | | | | |
Supplemental disclosure of non-cash investing and financing activities: | | | | | | | | |
Cash paid during the period for: | | | | | | | | |
Interest | | $ | 41 | | | $ | 23 | |
Income taxes paid (refunded) | | $ | 104 | | | $ | (11 | ) |
Supplemental disclosure of non-cash investing and financing activities: | | | | | | | | |
Transferred from inventory to property and equipment | | $ | 497 | | | $ | — | |
The Company purchased all of the capital stock of Cerebellum. In conjunction with the acquisition, liabilities were assumed as follows: | | | | | | | | |
Fair value of assets acquired | | | 1,544 | | | | — | |
Cash paid for the capital stock | | | (468 | ) | | | — | |
| | | | | | | | |
Liabilities assumed | | $ | 1,076 | | | $ | — | |
| | | | | | | | |
Non-cash item: | | | | | | | | |
Deferred tax liability related to the non-tax deductible amortization of acquired goodwill | | $ | 289 | | | $ | — | |
| | | | | | | | |
See accompanying notes.
60
ADEPT TECHNOLOGY, INC.
NOTES TO CONSOLIDATED FINANCIAL STATEMENTS
June 30, 2008 and 2007
1. | Company and Summary of Significant Accounting Policies |
Company
Adept Technology, Inc. (“Adept” or the “Company”) was incorporated under the laws of the state of California on June 14, 1983 and reincorporated in Delaware in November 2005. Through sales to system integrators, original equipment manufacturer (“OEM”) partners and end-user companies, we provide specialized, cost-effective robotics systems and services to emerging automation markets including packaging, solar and medical; as well as to the disk drive/electronics market and traditional industrial markets, including machine tool automation and automotive electronics.
Basis of Presentation
The accompanying consolidated financial statements as of June 30, 2008 and 2007 and for each of the two years in the period ended June 30, 2008 include the accounts of Adept and its wholly owned subsidiaries. All significant intercompany transactions and balances are eliminated upon consolidation. Adept includes consolidated financial statements for two fiscal years in its Annual Report on Form 10-K as a smaller reporting company.
Unless otherwise indicated, references to any year in these Notes to Consolidated Financial Statements refer to Adept’s fiscal year ended June 30.
Use of Estimates
The preparation of financial statements in conformity with U.S. generally accepted accounting principles requires management to make estimates and assumptions that affect reported amounts of assets and liabilities and disclosure of contingent assets and liabilities at the dates of the financial statements and the reported amounts of revenues and expenses during the reporting periods. Actual results could differ from those estimates.
Reclassifications
Certain reclassifications have been made to prior-period balances to present the financial statements on a consistent basis with current year presentation. Such reclassifications have not changed previously reported net income (loss) or stockholders’ equity.
Foreign Currency
The Company applies Statement of Financial Accounting Standards (“SFAS”) No. 52 (“SFAS 52”),Foreign Currency Translation, with respect to its international operations, which include manufacturing, sales and service entities. Each of Adept’s non-U.S. operations uses its respective local currency as the functional currency. The Company’s foreign subsidiaries’ balance sheet accounts are translated at current period ending exchange rates and statements of operations are translated at the average rate for the period.
Foreign currency transaction gains were $755,000 in fiscal 2008 and $208,000 in fiscal 2007. The 2008 foreign currency transaction gains recorded resulted primarily from the settlement of non-permanent in nature, USD-denominated inter-company balances. In 2008, a portion of the inter-company debt was considered non-permanent and to be settled, resulting in transactional gains. Translation gains and losses are recorded as a separate component of accumulated other comprehensive income (loss) in stockholders equity.
61
Cash, Cash Equivalents and Short-Term Investments
The Company considers all highly liquid investments purchased with an original maturity of three months or less to be cash equivalents. Short-term investments in marketable securities typically consist principally of debt instruments with maturities between three and twelve months. Investments are classified as held-to-maturity, trading, or available-for-sale at time of purchase.
At June 30, 2007, all of the Company’s investments in marketable securities were classified as available-for-sale and were carried at fair market value, which approximated cost. Fair market value is based on quoted market prices on the last day of the year. The cost of securities is based upon specific identification method.
| | | | | | |
| | June 30, |
| | 2008 | | 2007 |
| | (in thousands) |
Cash and cash equivalents: | | | | | | |
Cash | | $ | 8,770 | | $ | 4,219 |
Money market funds | | | 6,415 | | | 1,093 |
Fixed income securities | | | — | | | 3,588 |
| | | | | | |
Total cash and cash equivalents | | $ | 15,185 | | $ | 8,900 |
| | | | | | |
Short-term investments: | | | | | | |
Auction rate securities | | $ | — | | $ | 1,962 |
| | | | | | |
Total short-term investments | | $ | — | | $ | 1,962 |
| | | | | | |
Realized gains or losses, interest, and dividends are included in interest income. Realized and unrealized gains or losses from available-for-sale securities were not material in 2008 or 2007.
Fair Values of Financial Instruments
The carrying amounts for cash, accounts receivables and accounts payable approximate fair value due to the short-term nature of these instruments.
Comprehensive Income (Loss)
In years ended June 30, 2008 and 2007, comprehensive income (loss) included $550,000 and $476,000, respectively, of foreign currency translation adjustments stemming from Adept’s non-U.S. subsidiaries’ use of respective local currencies as their functional currency.
Inventories
Inventories are stated at the lower of standard cost or market value. The components of inventories are as follows:
| | | | | | |
| | June 30, |
| | 2008 | | 2007 |
| | (in thousands) |
Raw materials | | $ | 7,553 | | $ | 6,639 |
Work-in-process | | | 126 | | | 96 |
Finished goods | | | 2,555 | | | 3,071 |
| | | | | | |
| | $ | 10,234 | | $ | 9,806 |
| | | | | | |
62
Manufacturing inventory includes raw materials, work-in-process, and finished goods. The inventory valuation provisions are based on an excess and obsolete systems report, which captures all obsolete parts and products and all other inventory, which have quantities on hand in excess of one year’s projected demand. Individual line item exceptions are identified for either inclusion or exclusion from the inventory valuation provision. The materials control group and cost accounting function monitor the line item exceptions and make periodic adjustments as necessary.
During the years ended June 30, 2008 and 2007, the Company recognized revenues of approximately $78,000 and $500,000, respectively, from sales of inventory that had been previously considered excess or obsolete and written-off. Consequently, there was no cost of revenues recognized in connection with these product sales in fiscal 2008 and 2007. Total cumulative reductions for excess or obsolete inventory totaled approximately $1.3 million at June 30, 2008 and $1.5 million at June 30, 2007.
Warranties
The Company’s warranty policy is included in its terms of sale and states that there are no rights of return, and that a refund may be made at Adept’s discretion, and only if there is an identified fault in the product and the customer has complied with Adept’s approved maintenance schedules and procedures, and the product has not been subject to abuse. The Company provides for the estimated cost of product warranties at the time revenue is recognized. Factors that affect the Company’s warranty liability include the number of installed units, historical and anticipated rates of warranty claims, and costs per claim for repair or replacement. While the Company engages in extensive product quality programs and processes, including actively monitoring and evaluating the quality of its components suppliers, the Company’s warranty obligation is affected by product failure rates, material usage and service labor and delivery costs incurred in correcting a product failure. Should actual product failure rates, material usage, service labor or delivery costs differ from the Company’s estimates, revisions to the estimated warranty liability would be required.
Changes in the Company’s warranty liability are as follows:
| | | | | | | | |
| | June 30, | |
| | 2008 | | | 2007 | |
| | (in thousands) | |
Balance at beginning of period | | $ | 1,207 | | | $ | 1,638 | |
Warranties issued | | | 1,193 | | | | 690 | |
Change in estimated warranty provision, including expirations | | | — | | | | (155 | ) |
Warranty claims | | | (1,141 | ) | | | (966 | ) |
| | | | | | | | |
Balance at end of period | | $ | 1,259 | | | $ | 1,207 | |
| | | | | | | | |
Accounts Receivable and Allowance for Doubtful Accounts
Adept manufactures and sells its products to system integrators, end users and original equipment manufacturers, or OEMs, in diversified industries. Adept performs ongoing credit evaluations of its customers and generally does not require collateral. However, Adept may require customers to make payments in advance of shipment or to provide a letter of credit under certain circumstances.
Adept maintains allowances for doubtful accounts for estimated losses resulting from the inability of its customers to make required payments, and such losses have been within management’s expectations. Adept assesses the customer’s ability to pay based on a number of factors, including its past transaction history with the customer and creditworthiness of the customer. Management specifically analyzes accounts receivable and historical bad debts, customer concentrations, customer creditworthiness, current economic trends and changes in the Company’s customer payment terms when evaluating the adequacy of the allowances for doubtful accounts.
63
If the financial condition of the customers were to deteriorate in the future, resulting in an impairment of their ability to make payments, additional allowances may be required. Uncollectible accounts receivable are written off against the allowance for doubtful accounts when all efforts to collect them have been exhausted, and recoveries are recognized when they are received.
Adept’s policy is to record specific allowances against known doubtful accounts. An additional allowance is also calculated based on the greater of 0.5% of consolidated accounts receivable or 20% of consolidated accounts receivable more than 120 days past due. Specific allowances are netted out of the respective receivable balances for purposes of calculating this additional allowance. On an ongoing basis, Adept evaluates the creditworthiness of customers and, should the default rate change or the financial positions of Adept customers change, Adept may increase this additional allowance percentage. Amounts charged to bad debt expense were $49,000 and $69,000, in 2008 and 2007, respectively.
Property and Equipment
Property and equipment are recorded at cost.
The components of property and equipment are summarized as follows:
| | | | | | | | |
| | June 30, | |
| | 2008 | | | 2007 | |
| | (in thousands) | |
Cost: | | | | | | | | |
Machinery and equipment | | $ | 5,340 | | | $ | 4,622 | |
Computer equipment | | | 5,737 | | | | 6,583 | |
Office furniture and equipment | | | 2,166 | | | | 2,506 | |
Software development costs | | | 1,562 | | | | 1,192 | |
| | | | | | | | |
| | | 14,805 | | | | 14,903 | |
Accumulated depreciation and amortization | | | (11,451 | ) | | | (11,271 | ) |
| | | | | | | | |
Net property and equipment | | $ | 3,354 | | | $ | 3,632 | |
| | | | | | | | |
Depreciation is computed using the straight-line method over the estimated useful lives of the assets, which range from three to five years.
Capitalization of Software Development Cost
The Company capitalizes certain software development costs in accordance with SFAS 86,Accounting for the Costs of Computer Software to be Sold, Leased, or Otherwise Marketed. The Company begins capitalizing software development costs upon the establishment of technological feasibility, which is established upon the completion of a working model or a detailed program design. Costs incurred prior to technological feasibility are charged to expense as incurred. Capitalization ceases when the product is considered available for general release to customers. Capitalized software development costs are amortized to costs of revenues over the estimated economic lives of the software products based on product life expectancy. Generally, estimated economic lives of the software products do not exceed three years.
Long-Lived Assets
The Company periodically assesses the impairment of long-lived assets used in operations in accordance with the provisions of SFAS 144,Accounting for the Impairment or Disposal of Long-Lived Assets. An impairment review is performed whenever events or changes in circumstances indicate that the carrying value may not be recoverable. Factors the Company considers important, which could trigger an impairment review include, but are not limited to, significant under-performance relative to historical or projected future operating results,
64
significant changes in the manner of use of the acquired assets or the strategy for the Company’s overall business, and significant industry or economic trends. When the Company determines that the carrying value of the long-lived assets may not be recoverable based upon the existence of one or more of the above indicators, the Company measures any impairment based on a discounted future cash flow method using a discount rate commensurate with the risk inherent in its current business model. Impairment charges are recorded when determined.
In fiscal 2007, Adept concluded that the carrying value of goodwill related to the acquisitions of Hexavision and META was not supportable because the estimate of future cash flows related to these intangible assets was not sufficient to recover the carrying value of such intangibles. Accordingly, the Company wrote down the entire value of goodwill related to these acquisitions and took a charge of $3.2 million under SFAS 142 for intangible asset impairment.
Revenue Recognition
We generate revenues primarily from sales of production automation equipment and parts, and to a lesser extent from support and service activities associated with this equipment. Non-software product revenue consists primarily of sales of robots, refurbished robots and spare parts. We recognize non-software product revenue in accordance with Staff Accounting Bulletin 104 (“SAB 104”),Revenue Recognition, when persuasive evidence of a non-cancelable arrangement exists, delivery has occurred and/or services have been rendered, the price is fixed or determinable, collectibility is reasonably assured, legal title and economic risk is transferred to the customer, and when an economic exchange has taken place. We use the signed purchase contract or purchase order as evidence of an arrangement. Product revenues are normally recognized at the point of shipment from Adept facilities since title and risk of loss passes to the customers at that time. Customers have no right of return other than for product defects covered by our warranty. Adept maintains a warranty liability based on its historical warranty experience and managements’ best estimate of Adept’s warranty liability at each balance sheet date. There are no acceptance criteria on our standard non-software products. We do not deem the fee to be fixed or determinable where a significant portion of the price is due after our normal payment terms, which are 30 to 90 days from the invoice date. In recording revenue, management exercises judgment about the collectibility of receivables based on a number of factors, including the customer’s past payment history and its current creditworthiness. If we conclude that collection is not reasonably assured, then the revenue is deferred until the uncertainty is removed, generally upon receipt of payment. Our experience is that we have been able to reliably determine whether collection is reasonably assured.
Adept’s robots and controllers have features that are enabled or enhanced through the use of software enabling tools and other software elements, which are embedded within our robot and controller products. Our software enabling tools or other software elements do not operate independently of the robots or controllers, and they are not sold separately and cannot be used without the robots or controllers. We also sell optional software used to enhance capability of our products. Adept believes that the software component of our products is incidental to our products and services taken as a whole.
We recognize software revenue in accordance with the American Institute of Certified Public Accountants’ Statement of Position 97-2 (“SOP 97-2”),Software Revenue Recognition, as amended by SOP 98-9,Modification of SOP 97-2, And Software Revenue Recognition With Respect To Certain Transactions. Under SOP 97-2, revenue attributable to an element in a customer arrangement is recognized when (i) persuasive evidence of an arrangement exists, (ii) delivery has occurred, (iii) the fee is fixed or determinable, (iv) collectibility is probable and (v) the arrangement does not require services that are essential to the functionality of the software. License revenue is recognized on shipment of the product provided that no significant vendor or post-contract support obligations remain and that collection of the resulting receivable is deemed probable by management. Insignificant vendor and post-contract support obligations are accrued upon shipment of the licensed product. For software that is installed and integrated by the customer, revenue is recognized upon shipment assuming functionality has already been proven in prior sales and there are no customizations that would cause a substantial acceptance risk.
65
Service and Support revenue consists primarily of sales of spare parts and refurbished robots. Service revenue also includes training, consulting and customer support, the latter of which includes all field service activities; i.e., maintenance, repairs, system modifications or upgrades. Revenues from training and consulting are recognized at the time the service is performed and the customer has accepted the work. These revenues are not essential to the product functionality and, therefore, do not bear on revenue recognition policy for Adept’s component products.
Deferred revenues represent payments received from customers in advance of the delivery of products and/or services, or before the satisfaction of all revenue recognition requirements enumerated above, as well as cases in which we have invoiced the customer but cannot yet recognize the revenue for the same reasons discussed above.
Revenue for robot refurbishment relates to Adept-owned or customer-owned remanufactured robots and components. Adept receives parts returned from customers under warranty contracts, or Adept purchases surplus used parts available from customers or suppliers. These parts traditionally have lower cost, and internal analysis indicates that on average, we pay a percentage of the new part cost to acquire these components. The standard cost for acquired parts is therefore set at such percentage of cost in compliance with GAAP as reflected in the SAB 100,Restructuring Charges, Impairments, and Related Issues, pronouncement requiring valuation of inventory at “lower of cost or market”. By contrast, the cost basis starting point for customer-owned remanufactured or repaired robots is zero since Adept does not own the robots. For all refurbishment and remanufacturing, we track all related costs and activities (materials and labor) required to bring the robots up to standard using work orders. This revenue stream is included within the Services and Support segment.
Shipping and Handling
Adept manages incoming and outgoing product shipments through a third party shipping manager. Outgoing product is primarily shipped by customer-selected carriers and freight costs are billed directly to the customer. Incoming material is usually shipped via Adept-selected carriers with freight cost incurred by Adept and recorded as cost of goods sold, and title transfers at time of shipment.
Concentration of Credit Risk
Financial instruments that potentially subject the Company to concentrations of credit risk consist primarily of cash and cash equivalents and trade receivables. The Company places its cash and cash equivalents with high credit-quality financial institutions. The Company invests its excess cash in money market mutual funds, commercial paper, readily marketable debt instruments and obligations of U.S., state and municipal government entities. Adept has established guidelines relative to credit ratings, diversification and maturities that seek to maintain safety and liquidity. The Company is exposed to credit risk in the event of default by the financial institutions holding the cash and cash equivalents to the extent of the amount recorded on the balance sheets in excess of insured limits.
Adept manufactures and sells its products to system integrators, end users and OEMs in diversified industries. Adept performs ongoing credit evaluations of its customers and does not require collateral. However, Adept may require customers to make payments in advance of shipment or to provide a letter of credit. No customer accounted for more than 10% of revenues or trade receivables for any of the past two fiscal years.
Research, Development and Engineering Costs
Research, development and engineering costs, other than purchased computer software and capital equipment, are charged to expense when incurred. The Company has in the past offset research, development and engineering expenses against third party funding as the Company retains the rights to any technology that is developed. The Company did not receive any third party funding in fiscal 2008 or 2007. The Company is not presently a party to any such research and development arrangements.
66
Advertising Costs
Advertising costs are expensed in the period incurred. Advertising costs were $241,000 in 2008 and $208,000 in 2007. The Company does not incur any direct response advertising costs.
Income Taxes
The liability method is used to account for income taxes. Deferred tax assets and liabilities are determined based on differences between the financial reporting and tax bases of assets and liabilities and are measured using the enacted tax rates and laws that will be in effect when the differences are expected to reverse. The Company records a valuation allowance to reduce deferred tax assets to the amount that is expected to be realized on a more-likely-than-not basis. Deferred tax expense results from the change in the net deferred tax asset or liability between periods.
Net Income (Loss) Per Share
Statement of Financial Accounting Standard 128 (“SFAS128”),Earnings Per Share, requires the presentation of basic and diluted earnings per share (“EPS”). Basic EPS excludes dilution and is computed by dividing net income (loss) available to common stockholders by the weighted-average number of common shares outstanding for the period. Diluted EPS reflects the potential dilution that could occur if securities or other contracts to issue common stock were exercised or converted into common stock or resulted in the issuance of common stock that then participates in the earnings of the Company. Unless their effect is antidilutive, dilutive common equivalent shares consist of stock options calculated using the treasury stock method and shares issued from the conversion of outstanding warrants.
The basis for the diluted EPS calculation is as follows:
| | | | | | | |
| | 2008 | | 2007 | |
| | (in thousands) | |
Numerator: | | | | | | | |
Net income (loss), as reported | | $ | 3,636 | | $ | (11,513 | ) |
| | |
Denominator: | | | | | | | |
Basic shares | | | 7,957 | | | 7,676 | |
Plus: Dilutive options | | | 80 | | | — | |
Plus: Dilutive warrants | | | 209 | | | — | |
| | | | | | | |
| | | 8,246 | | | 7,676 | |
| | | | | | | |
Diluted income (loss) per share | | $ | 0.44 | | $ | (1.50 | ) |
| | | | | | | |
If the company had reported net income for the year ended June 30, 2007, the calculation of diluted earnings per share would have included additional common equivalent shares of approximately 585,453 related to outstanding employee stock options and warrants not included above.
The computation of diluted net income per share for fiscal 2008 and 2007 does not include certain securities, on a weighted average basis, because the effect of their inclusion would be anti-dilutive. Items excluded are options to purchase common stock in the amount of 737,795 shares for fiscal 2008 and 509,074 shares for fiscal year 2007.
Commitments and Contingencies.In accordance with SFAS No. 5, we evaluate potential commitments and contingencies based on their anticipated outcome. If we determine, after consideration of all known facts and consultation with legal counsel, that a loss related to the potential matter is neither probable or cannot be reasonably estimated as of the date of issuance of our fiscal period-end reports, we do not accrue for the potential liability. If a loss is reasonably possible related to the matter, we will disclose the relevant facts of the matter along with an estimated loss amount or range if such amount or range can be reasonably estimated.
67
New Accounting Pronouncements
In December 2007, FASB issued SFAS No. 141 (revised 2007),Business Combinations. Under SFAS No. 141(R), an entity is required to recognize the assets acquired, liabilities assumed, contractual contingencies, and contingent consideration at their fair value on the acquisition date. It further requires that acquisition-related costs be recognized separately from the acquisition and expensed as incurred, restructuring costs generally be expensed in periods subsequent to the acquisition date, and changes in accounting for deferred tax asset valuation allowances and acquired income tax uncertainties after the measurement period impact income tax expense. In addition, acquired in-process research and development (IPR&D) is capitalized as an intangible asset and amortized over its estimated useful life. The adoption of SFAS No. 141(R) will change our accounting treatment for business combinations on a prospective basis beginning in the first quarter of fiscal year 2009.
In February 2007, the FASB issued SFAS No. 159, “The Fair Value Option for Financial Assets and Financial Liabilities” (“SFAS No. 159”). SFAS No. 159 allows companies to choose to measure certain financial instruments and certain other items at fair value. The statement requires that unrealized gains and losses are reported in earnings for items measured using the fair value option and establishes presentation and disclosure requirements. SFAS No. 159 is effective July 1, 2008 for the Company. The Company does not believe the adoption of SFAS No. 159 will have a material effect on our consolidated financial statements.
In December 2007, the FASB issued SFAS No. 160, “Noncontrolling Interests in Consolidated Financial Statements”, an amendment of Accounting Research Bulletin No. 51. SFAS No. 160 will change the accounting and reporting for minority interests, which will be recharacterized as noncontrolling interests and classified as a component of equity. SFAS No. 160 is effective for fiscal years beginning after December 15, 2008. Early adoption is not permitted. We are currently evaluating the impact that SFAS No. 160 will have on our consolidated financial statements.
2. | Stock-Based Compensation |
The Company has adopted equity incentive plans that provide for the grant to employees of stock-based awards, including stock options and restricted shares, of Adept common stock. In addition, these plans permit the grant of nonstatutory stock-based awards to paid consultants and outside directors. To date, Adept has generally granted options under its existing stock plans, with some limited use in 2006 of restricted stock grants to non-executive employees. No restricted stock grants were issued in 2007 but are contemplated to be granted pursuant to awards to be made pursuant to the Adept Technology, Inc. Fiscal 2008 Executive and Senior Management Executive Payment Plan. Option awards are granted with an exercise price equal to the market price of the Company’s stock on the date of grant. Those option awards generally vest evenly over the next four years of continuous service and have ten-year contractual terms. The Company also has an employee stock purchase plan (“ESPP”) expiring in fiscal 2009 that allows employees to purchase a limited number of shares of its common stock at a discount of 15% of the market value at certain plan-defined dates that are established at six-month intervals.
Adept has one employee stock purchase plan and four equity compensation plans currently in effect under which options, restricted stock or other rights can be granted, including the 2001 Stock Option Plan, 2003 Stock Option Plan, 2004 Director Option Plan and 2005 Equity Incentive Plan, as described in Note 8 to the Notes to Consolidated Financial Statements. As of June 30, 2008, there are 450,741 shares available for issuance under the 1998 Employee Stock Purchase Plan. The plan, which expires September 2008, provides for an annual automatic increase in the number of shares available for issuance by the lesser of 120,000 shares, 3% of the shares outstanding, or a lesser amount as may be determined by the Board of Directors. Under the 2001 Stock Option Plan, there are 261,656 shares subject to outstanding options with 90,921 available for grant. Under the 2003 Stock Option Plan, there are 355,000 shares subject to outstanding options with 27,640 available for grant. The 2004 Director Option Plan has 57,166 shares subject to outstanding options with 73,210 available for grant. The 2005 Equity Incentive Plan has 184,500 shares subject to outstanding options with 400,459 available for
68
grant. Options are also outstanding pursuant to two equity compensation plans which have expired. They include the 1993 Stock Option Plan and the 1995 Director Stock Option Plan, which have, respectively, 122,811 and 6,600 shares subject to outstanding options. Under all of these plans, for employee grants, except for certain performance grants to Adept’s former Chief Executive Officer and restricted stock which may be granted under an Executive and Senior Management Executive Payment Plan, vesting is generally monthly in equal installments over a four or five year period. In fiscal 2006, certain restricted stock grants were made to non-executive employees with six month vesting provisions. Under the director option plan, initial director grants vest one-fourth on the first anniversary of the grant, then monthly in equal installments thereafter for three years. Annual director grants vest monthly in equal installments over a four year period.
The Company adopted SFAS 123R,Share–Based Payment, effective July 1, 2005. SFAS 123R requires the recognition of the fair value of stock compensation as an expense in the calculation of net income (loss). Adept recognizes the stock compensation expense ratably over the vesting period of the individual equity instruments. All stock compensation recorded since adoption has been accounted for as an equity instrument. Prior to July 1, 2005 Adept followed the Accounting Principles Board (“APB”) Opinion 25,Accounting for Stock Issued to Employees, and related interpretations for the Company’s stock compensation.
The Company has elected the modified prospective transition method for adopting SFAS 123R. Under this method, the provisions of SFAS 123R apply to all stock-based awards granted or other awards granted that are subsequently reclassified into equity. The unrecognized expense of awards not yet vested as of July 1, 2005, the date of SFAS 123R adoption by the Company, is now being recognized as expense in the calculation of net income using the same valuation method (the Black-Scholes model) and assumptions disclosed prior to Adept’s adoption of SFAS 123R. Determining the fair-value of stock-awards at the grant date requires judgment in estimating the expected term of stock options, the expected volatility of Adept common stock, expected forfeitures and expected dividends. The computation of the expected volatility assumption in the Black-Scholes calculation is based on historical volatility as options on the Company’s stock are not traded. When establishing the expected life assumption, the Company reviews annual historical employer exercise behavior of option grants with similar vesting periods. In addition, judgment is also required in estimating the amount of stock-based awards that are expected to be forfeited. As of July 1, 2005, Adept had an unrecorded deferred stock-based compensation balance related to stock options and ESPP of $1.1 million after estimated forfeitures. The unamortized compensation cost (previously being recognized under FAS 123 on a pro-forma basis) for options and ESPP rights granted but not vested as of July 1, 2005 will be recognized ratably over the remaining vesting period of such options and ESPP purchases.
Under the provisions of SFAS 123R, the Company recorded $769,000 and $1,277,000 of stock-based compensation expense on its consolidated statements of operations for the years ended June 30, 2008 and 2007, respectively, for its stock option plans and ESPP. The Company did not record an income tax benefit for the stock compensation expense because of the extent of the Company’s net operating loss carry forwards. Adept utilized the Black-Scholes valuation model for estimating the fair value of the compensation after the adoption of SFAS 123R. The weighted average grant-date fair values of the options granted under the stock option plans and shares subject to purchase under the ESPP for the year ended June 30, 2008 were $2.93 and $2.26, respectively, and for the year ended June 30, 2007 were $4.62 and $3.28, respectively, using the following weighted average assumptions:
| | | | | | | | | | | | |
| | Year Ended June 30, 2008 | | | Year Ended June 30, 2007 | |
| | Stock Option Plans | | | Stock Purchase Plan | | | Stock Option Plan | | | Stock Purchase Plan | |
Risk free interest rate | | 4.05 | % | | 3.45 | % | | 3.88 | % | | 4.95 | % |
Expected life (in years) | | 3.38 | | | 0.50 | | | 2.87 | | | 0.50 | |
Expected volatility | | 0.71 | | | 0.61 | | | 0.53 | | | 0.71 | |
Dividend yield | | 0.00 | % | | 0.00 | % | | 0.00 | % | | 0.00 | % |
69
The dividend yield of zero is based on the fact that the Company has never paid cash dividends and has no present intention to pay cash dividends. Expected volatility is based on the historical volatility of Adept’s common stock over the period commensurate with the expected life of the options or ESPP shares. The risk-free interest rate is based on observed and expected time to post-vesting exercise and forfeitures of options or ESPP shares by Adept’s employees. The expected life in years is based on the historic time to post-vesting exercise and forfeitures of the options or ESPP shares.
A summary of stock option activity under the option plans as of June 30, 2008 and changes during the year then ended is presented below:
| | | | | | | | | | | |
Options | | Shares (in thousands) | | | Weighted- Average Exercise Price | | Weighted- Average Remaining Contractual Term (years) | | Aggregate Intrinsic Value (in thousands) |
Outstanding at June 30, 2007 | | 1,084 | | | $ | 12.24 | | | | | |
Granted | | 147 | | | | 5.80 | | | | | |
Exercised | | (38 | ) | | | 4.41 | | | | | |
Forfeited or Expired | | (205 | ) | | | 16.40 | | | | | |
| | | | | | | | | | | |
Outstanding at June 30, 2008 | | 988 | | | $ | 10.73 | | 6.88 | | $ | 2,308 |
| | | | | | | | | | | |
Vested/Expected to Vest at June 30, 2008 | | 829 | | | $ | 11.28 | | 6.60 | | $ | 1,964 |
| | | | | | | | | | | |
Exercisable at June 30, 2008 | | 632 | | | $ | 12.39 | | 6.01 | | $ | 1,505 |
| | | | | | | | | | | |
During the year ended June 30, 2008, Adept granted options for 147,000 shares of common stock with an estimated total grant date fair market value of $852,910. The intrinsic value of options exercised during the year ended June 30, 2008 was $73,249. Cash received from stock option exercises and ESPP purchases was$336,633 for the year ended June 30, 2008. As of June 30, 2008, there was $427,363 of total unrecognized compensation cost related to non-vested stock options granted and outstanding; that cost is expected to be recognized through fiscal year 2012, with a weighted average remaining period of 1.24 years.
At the end of June 2007, the Company executed its restructuring plan which involved closure of facilities in Quebec, Canada, Southbury, Connecticut and a portion of Adept’s Livermore, California facility. Any remaining work at these facilities is being either outsourced or absorbed within Adept’s Livermore facility.
Also, a reduction in force was made of approximately 34 employees, located primarily in Canada and the United States.
As part of its restructuring actions, the Company consolidated its office space at the Livermore facility, vacating approximately 20% of the building. The costs of excess space will be offset against the accrued restructuring charge through the end of the Livermore facility lease term of May 2011. Lease termination costs of $246,000 related to the Quebec and Connecticut facilities were expensed and paid in the first quarter of 2008.
70
The following table summarizes the activity in Adept’s accrued restructuring charges during the years ended June 30, 2008 and 2007.
Fiscal 2008
| | | | | | | | | | | | | | |
(in thousands) | | Balance June 30, 2007 | | Additional Charges/ (Reversals) Fiscal 2008 | | | Cash Payment Fiscal 2008 | | | Balance June 30, 2008 |
Employee severance costs | | $ | 236 | | $ | (19 | ) | | $ | (217 | ) | | $ | — |
Lease commitments | | | 850 | | | 246 | | | | (463 | ) | | | 633 |
Other costs | | | — | | | 27 | | | | (27 | ) | | | — |
| | | | | | | | | | | | | | |
Total | | $ | 1,086 | | $ | 254 | | | $ | (707 | ) | | $ | 633 |
| | | | | | | | | | | | | | |
Fiscal 2007
| | | | | | | | | | | | | |
(in thousands) | | Balance June 30, 2006 | | Additional Charges/ (Reversals) Fiscal 2007 | | Cash Payment Fiscal 2007 | | | Balance June 30, 2007 |
Employee severance costs | | $ | — | | $ | 249 | | $ | (13 | ) | | $ | 236 |
Lease commitments | | | — | | | 878 | | | (28 | ) | | | 850 |
Other costs | | | — | | | 51 | | | (51 | ) | | | — |
| | | | | | | | | | | | | |
Total | | $ | — | | $ | 1,178 | | $ | (92 | ) | | $ | 1,086 |
| | | | | | | | | | | | | |
4. | Goodwill and Other Intangible Assets |
Under SFAS 142,Goodwill and Other Intangible Assets,goodwill (and other intangible assets deemed to have indefinite lives) are not amortized but are subject to annual impairment tests. Other intangible assets with finite lives are amortized over those useful lives. Statement 142 requires goodwill and other intangible assets to be evaluated for impairment at least annually and Adept has chosen April 1 as the annual date to conduct this evaluation. Any impairment charges are determined using a fair value approach, incorporating the discounted cash flow method.
The results of Adept’s fiscal 2008 annual impairment evaluation did not indicate impairment of the Company’s goodwill.
In fiscal 2007, Adept concluded that the carrying value of goodwill related to the acquisitions of Hexavision and META was not supportable because the estimate of future cash flows related to these intangible assets was not sufficient to recover the carrying value of such intangibles. Accordingly, the Company wrote down the entire value of goodwill related to these acquisitions and took a charge of $3.2 million under SFAS 142 for intangible asset impairment.
In accordance with SFAS 142, the following is a summary of the gross carrying amount, the accumulated amortization and the aggregate amortization expense related to the intangible assets subject to amortization.
| | | | | | | | | | | | | | | | | | | | |
(in thousands) | | June 30, 2008 | | June 30, 2007 |
Amortizable intangible assets | | Gross Carrying Amount | | Accumulated Amortization | | | Net Carrying Amount | | Gross Carrying Amount | | Accumulated Amortization | | | Net Carrying Amount |
| | | | | | | (in thousands) | | | | | |
Developed technology | | $ | 1,020 | | $ | (220 | ) | | $ | 800 | | $ | 2,389 | | $ | (2,389 | ) | | $ | — |
Non compete agreements | | | — | | | — | | | | — | | | 380 | | | (380 | ) | | | — |
| | | | | | | | | | | | | | | | | | | | |
Total | | $ | 1,020 | | $ | (220 | ) | | $ | 800 | | $ | 2,769 | | $ | (2,769 | ) | | $ | — |
| | | | | | | | | | | | | | | | | | | | |
71
The aggregate amortization expense totaled $216,000 for 2008 and $33,000 for 2007.
Estimated amortization expense in future fiscal years ending June 30 is as follows:
| | | |
(in thousands) | | |
2009 | | $ | 365 |
2010 | | | 290 |
2011 | | | 145 |
| | | |
TOTAL | | $ | 800 |
| | | |
On January 2, 2008, the Company acquired the outstanding common shares of Cerebellum Automation SAS. The results of Cerebellum’s operations have been included in Adept’s consolidated financial statements since that date. Cerebellum, based in France, is a provider of custom robotics and motion control products and components.
The initial purchase price paid at closing, excluding all items tied to retention compensation, amounted to $732,971. This includes an initial cash payment of $350,000, accrued liabilities of $297,500 due within one year and paid direct costs of $85,471. The payment of additional contingent deferred cash consideration of $32,500 in cash and $167,500 payable in shares of common stock of the Company on the first anniversary, provided that certain employees remain employed by Cerebellum, will be amortized monthly during the first year following the acquisition. Additional contingent consideration of $65,000 in cash and $385,000 payable in shares of common stock of the Company, which may be paid on the second anniversary provided that certain employees remain employed by Cerebellum, will be amortized monthly during the second year following the acquisition (months 13 to 24). Additionally, there are contingent amounts payable up to a maximum aggregate amount of €312,000 in common stock of the Company based on Cerebellum’s meeting of certain revenue milestones in each of the first and second years after the date of the acquisition. The amounts achieved will be added to Goodwill upon realization of the associated revenue milestones.
The following table summarizes the estimated fair values of the assets acquired and liabilities assumed at the date of acquisition.
At January 2, 2008
(in thousands)
| | | |
Current assets | | $ | 659 |
Intangible assets | | | 804 |
Goodwill | | | 81 |
| | | |
Total assets acquired | | | 1,544 |
| | | |
Current liabilities | | | 555 |
Long-term debt | | | 252 |
Other long-term liabilities | | | 4 |
| | | |
Total liabilities assumed | | | 811 |
| | | |
Net assets acquired | | $ | 733 |
| | | |
Of the $804,000 of acquired intangible assets, all was assigned to Cerebellum’s ApproFlex software system, which has an approximate useful life of 3 years. The $81,000 of goodwill was assigned to the Company’s Robotics segment. The purchase price allocation for goodwill has been increased and includes the impact of recording a deferred tax liability of $289,000 related to the non-tax deductible amortization of the acquired intangibles. We do not expect the $81,000 of goodwill and $804,000 of the intangible amortization to be deductible for French tax purposes.
72
Effective August 14, 2007, Adept entered into an Amendment to Loan Documents with Silicon Valley Bank (“SVB”) which effectively extended the maturity date of the agreement to August 14, 2008. All of the provisions of the August 15, 2006 amendment are still applicable as noted below.
Effective August 15, 2006, Adept entered into an Amendment to Loan Documents (the “August 2006 Amendment”) with Silicon Valley Bank (“SVB”), which effectively extended and increased Adept’s line of credit with SVB. The August 2006 Amendment provides that Adept may borrow amounts under the credit facility not to exceed the lesser of (i) $5.0 million or (ii) the sum of 80% of Adept’s eligible accounts receivable plus any overadvance loans that may be granted by SVB from time to time in its sole and absolute discretion, plus foreign accounts, plus non-formula loans that SVB may make up to $3.0 million. Such lesser amount as determined in (i) or (ii) above, shall be reduced by the amount of all outstanding letters of credit and the FX Reserve, which is 10% of the total FX Forward Contracts (as discussed below) outstanding for purposes of determining the “Credit Limit” under the loan facility. The aggregate of over advance loans may not exceed the lesser of $1.0 million or 30% of Adept’s eligible accounts receivable. For purposes of application under the loan facility, foreign accounts must meet the same eligibility requirements as domestic receivables, and are permitted up to a maximum of 25% of the total eligible accounts receivable.
As amended, the loan facility authorizes SVB to issue letters of credit for Adept’s account subject to certain limits. The aggregate amount of all letters of credit outstanding will not exceed (i) the lesser of $3.5 million minus the FX Reserve or (ii) the lesser of the Credit Limit or the Borrowing Base minus the FX Reserve and all outstanding loans.
Adept may also enter into foreign exchange forward contracts with SVB (“FX Forward Contracts”), provided that Adept has loans available in an amount of at least 10% of the amount of the FX Forward Contract, and the total FX Forward Contracts outstanding at any one time may not exceed 10 times the amount of the lesser of $3.5 million minus the amount of all outstanding letters of credit or the lesser of the Credit Limit or the Borrowing Base minus the amount of all outstanding letters of credit and all outstanding loans.
The amendments dated June 15, 2005, June 12, 2006, August 15, 2006 and August 14, 2007, are to the Loan and Security Agreement between Adept and SVB, dated April 22, 2004, which amended and restated a predecessor Accounts Receivable Purchase Agreement (the “Purchase Agreement”). In connection with the Loan and Security Agreement, Adept granted to SVB a security interest in substantially all of its assets. In addition, certain agreements, instruments and other related documents initially entered into between Adept and SVB in connection with the Purchase Agreement remain in effect, including the security interest in substantially all of Adept’s assets granted to SVB by Adept.
The Loan and Security Agreement currently provides that interest rates vary depending on Adept’s Adjusted Quick Ratio. The Adjusted Quick Ratio is the ratio of Adept’s cash and cash equivalents held at SVB plus 80% of Adept’s eligible accounts to Adept’s current liabilities, less the current portion of Adept’s deferred revenues. If the Adjusted Quick Ratio as of the end of a month is 1.5 to 1.0 or greater, then the interest rate will be equal to the prime rate announced from time to time by SVB (“Prime Rate”), plus 0.5%. If the Adjusted Quick Ratio as of the end of a month is less than 1.5 to 1.0, then the interest rate will be the Prime Rate plus 1.5%. Adept must make quarterly payments for any unused available loan amounts at a rate of 0.20% per annum.
The Loan and Security Agreement includes certain financial and other covenants with which Adept must comply. The loan agreement has minimum tangible net worth financial covenant applicable to Adept, such that Adept must maintain tangible net worth of at least $19.0 million plus 40% of the consideration received upon issuance of any equity securities or subordinated debt, plus 25% of Adept’s net income in each fiscal quarter. Once an increase in the minimum tangible net worth of Adept takes effect, it remains in effect thereafter, and does not decrease. Other covenants with which Adept must comply, include, but are not limited to, the payment of Adept’s tax obligations as and when due and the maintenance of Adept’s primary operating deposit accounts
73
with SVB. Adept cannot make any transfers to any of its subsidiaries of money or other assets with an aggregate value in excess of $300,000 in any fiscal quarter and is subject to customary default provisions. In the event of default under the Loan and Security Agreement, SVB may, among other things, cease making loans to Adept; accelerate and declare all or any part of Adept’s obligations to be immediately due and payable, and enforce its security against the collateral. Adept was in compliance with the covenants of the Loan and Security Agreement as of June 30, 2007.
On November 18, 2003, Adept completed a private placement (the “2003 financing”) of an aggregate of approximately 2.2 million shares of common stock to several accredited investors for net proceeds after estimated costs and expenses of approximately $9.4 million. The investors also received warrants to purchase an aggregate of approximately 1.11 million shares of common stock at an exercise price of $6.25 per share, with certain proportionate anti-dilution protections. The warrants expire on November 18, 2008. Under the terms of these warrants, Adept may call the warrants, thereby forcing a cash exercise, in certain circumstances after the common stock has closed at or above $12.50 per share, subject to any further adjustment for stock splits or similar events, for 20 consecutive trading days during which a registration statement covering the warrant shares is effective to permit sales under the registration statement for at least 15 trading days. The call right is subject to a 30-day advance notice by Adept, which notice period must be extended for a number of days equal to the number of days for which the registration statement covering the warrant shares is not effective to permit sales under the registration statement.
7. | Commitments and Contingencies |
Commitments
Future minimum lease payments under non-cancelable operating leases with original terms in excess of one year as of June 30, 2008 are as follows:
| | | |
(in thousands) | | |
| |
Fiscal Year | | | |
2009 | | $ | 1,946 |
2010 | | | 1,643 |
2011 | | | 1,486 |
2012 | | | 155 |
2013 | | | 144 |
Thereafter | | | 169 |
| | | |
Total minimum lease payments | | $ | 5,543 |
| | | |
Rent expense, net of sublease income, was $1.4 million in 2008 and $1.6 million in 2007.
Rent payments for the Livermore facilities increase at a rate of 4.0% annually for cost of living increases on June 1 of each year. The related rent expense is recognized on a straight-line basis.
In connection with the restructuring of the Livermore facility lease, the lease amendment carries liquidated damages equivalent to one year of rent obligations on the original lease that are triggered in the event of default on the lease payments.
In the event of Adept’s bankruptcy or a failure to make payments to the landlord of the Livermore, California facilities owed under the lease within three days after a written notice from the landlord, a default would occur and the liquidated damages would be triggered on the lease.
At June 30, 2008, Adept had capital lease obligations totaling $207,602, which are included in other accrued liabilities and other long-term liabilities. These related to three leases with bargain purchase options, with terms ranging from three to five years, and with interest rates between 5% and 9%.
74
At June 30, 2008, Adept had $16.3 million of inventory purchase obligations. Purchase obligations are in the form of purchase orders, generally for custom components and sub-assemblies. These purchase orders typically cannot be cancelled without penalty. Penalties may range up to 30% of the canceled order, but cancellations are not common and the usual practice is to reschedule delivery dates if adjustment is needed.
Legal Proceedings
The Company has from time to time received communications from third parties asserting that the Company is infringing certain patents and other intellectual property rights of others, or seeking indemnification against alleged infringement. While it is not feasible to predict or determine the likelihood or outcome of any actions brought against it, the Company believes the ultimate resolution of these matters will not have a material adverse effect on its financial position, results of operations or cash flows.
On April 14, 2008, Tri-Valley Technology Campus LLC, the landlord of Adept’s Livermore, California offices (referred to as Landlord) sent Adept a lease termination notice, purporting to terminate the Livermore lease 90 days following the date of such notice. The notice indicated that a termination fee of $1 million was due from Adept to terminate Adept’s obligations under the lease on July 14, 2008, other than certain express obligations intended to survive termination. The Landlord subsequently delivered a new lease termination notice to Adept, indicating that the Livermore lease would terminate on August 26, 2008, and demanding payment of a $1 million termination fee no later than June 27, 2008. The notices were delivered based on the Landlord’s interpretation of a Lease Termination Agreement dated December 16, 2007 between Adept and the Landlord.
On May 30, 2008, the Landlord commenced litigation with the matterTri-Valley Campus I LLC vs. Adept Technology, Inc.in California Superior Court in Contra Costa County seeking declaratory relief in favor of its interpretation of the Lease Termination Agreement, including seeking a declaration that the terms of the Lease Termination Agreement required Adept to pay $1 million to the Landlord and to vacate the premises no later than August 26, 2008, and sought attorneys’ fees and costs. The Landlord dismissed this action on July 31, 2008 and instituted an action in California Superior Court in Alameda County, bringing claims for declaratory relief, breach of contract, breach of the implied covenant of good faith and fair dealing, intentional interference with contract, and intentional interference with prospective economic advantage. The Landlord seeks a declaration that the terms of the Lease Termination Agreement required Adept to pay $1 million to the landlord and to vacate the premises no later than August 26, 2008, and pay damages, punitive damages, attorneys’ fees, and costs. Among other things, the Landlord alleges that the Landlord is required to deliver possession of the Livermore facilities to its new tenant no later than September 1, 2008, and is seeking damages and punitive damages, including but not limited to the value of the 13-year lease with its new tenant.
On July 29, 2008, the Landlord filed an unlawful detainer action withTri-Valley Technology Campus, LLC v. Adept Technology, Inc .in California Superior Court in Alameda County seeking to recover immediate possession of the Livermore facilities, claiming the failure to pay the termination payment also constituted a breach of the lease agreement for such facilities. In addition to seeking to repossess the premises, the Landlord also seeks payment of $1 million as a termination fee, the forfeiture of the lease, and attorneys’ fees and costs. On August 28, 2008, the Court denied a motion to compel arbitration of the dispute. On August 29, 2008, the Court issued an order setting trial starting September 16, 2008, and Adept appealed the Court’s denial of the motion to compel arbitration and has sought a stay of the trial proceedings.
Adept disputes the Landlord’s interpretation of the Lease Termination Agreement, including its alleged obligations and the effect of Adept’s choosing not to pay $1 million in combination with relinquishing the leased property. Adept currently occupies its Livermore facility and is vigorously defending these litigation matters with its Landlord and exploring its leasing alternatives, but the outcome of these matters cannot be determined at this time.
75
From time to time, the Company is party to various legal proceedings or claims, either asserted or unasserted, which arise in the ordinary course of its business. The Company has reviewed pending legal matters and believes that the resolution of these matters will not have a material adverse effect on its business, financial condition or results of operations.
In October 2006, Adept was informed by Crosslink Capital Partners that Crosslink believed Adept made misrepresentations regarding Adept’s consolidated financial statements relating to periods after June 2005 in the common stock purchase agreement, dated as of June 9, 2006 (the “Purchase Agreement”) between Crosslink Capital Partners and Adept, and requested compensation for these alleged misrepresentations.
On May 13, 2007, Adept and the entities affiliated with Crosslink Capital Partners (collectively, “Crosslink Entities”), which were party to the purchase agreement dated June 9, 2006, entered into a settlement agreement. Pursuant to the settlement agreement, Adept agreed to issue an aggregate of 225,000 shares of its common stock to the Crosslink Entities with registration rights in lieu of cash consideration for the settlement. The Crosslink Entities agreed to waive and release any claims against Adept, its officers, directors and other related parties arising from their purchase of Adept common stock pursuant to the Purchase Agreement, including without limitation, any claims for indemnification for breaches of representations or warranties thereunder as well as under any federal or state securities laws. Adept agreed to waive and release the Crosslink Entities from claims by Adept relating to the same matters. Additionally, the Crosslink Entities agreed to terminate the survival of Adept’s representations and warranties, and the indemnification obligations related thereto, in the Purchase Agreement effective on the date of the settlement agreement.
The Company is also subject to various other lawsuits and claims relating to issues such as contract disputes, product liability, and employee and other matters. Although the results of claims and litigation cannot be predicted with certainty, it is the opinion of management that the ultimate disposition of these matters, to the extent not previously provided for, will not have a material adverse effect, individually or in the aggregate, on the Company’s consolidated financial statements taken as a whole.
Preferred Stock
The Board of Directors has the authority to issue, without further action by the stockholders, up to 1.0 million shares of preferred stock in one or more series and to fix the price, rights, preferences, privileges and restrictions thereof, including dividend rights, dividend rates, conversion rights, voting rights, terms of redemption, redemption prices, liquidation preferences and the number of shares constituting a series or the designation of such series, without any further vote or action by the Company’s stockholders. The issuance of preferred stock, while providing desirable flexibility in connection with possible financings, acquisitions and other corporate purposes, could have the effect of delaying, deferring or preventing a change in control of the Company without further action by the stockholders and may adversely affect the market price of, and the voting and other rights of, the holders of common stock. No shares of preferred stock are outstanding.
Common Stock
On November 18, 2003, the Company completed a private placement of an aggregate of approximately 2.2 million shares of common stock to several accredited investors for a total purchase price of $10.0 million, referred to as the 2003 financing. Net proceeds from the 2003 financing after estimated costs and expenses were approximately $9.4 million. The investors also received warrants to purchase an aggregate of approximately 1.11 million shares of common stock at an exercise price of $6.25 per share, with certain proportionate anti-dilution protections. The warrants expire on November 18, 2008.
76
On June 22, 2006, Adept completed the issuance and sale to affiliates of Crosslink Capital Partners (“Crosslink”), pursuant to a common stock purchase agreement dated June 9, 2006 (the “Purchase Agreement”) of 731,251 shares of its common stock for aggregate consideration of $10 million, representing a purchase price of $13.6752 per share, in a transaction not registered under the Securities Act of 1933, as amended (the transactions contemplated by the Purchase Agreement are referred to as the “Financing”).
The Purchase Agreement includes certain representations and warranties, covenants and agreements of Adept in connection with its private placement of stock, including retaining its existence, NASDAQ listing and reporting status. In connection with the Financing, the Company granted to Crosslink the right to designate an individual to serve as a director of Adept so long as Crosslink holds more than 5% of Adept’s outstanding stock, certain inspection rights of Company information, indemnification for breaches of representations and warranties and agreements in the Purchase Agreement and customary indemnification under the registration rights agreement for any violations of the securities laws or any material misstatements or omissions, and paid $35,000 for certain legal expenses of Crosslink incurred in connection with the Financing. As required under the registration rights agreement entered into at the time of the sales of the shares, Adept has registered the shares it sold for resale to the public. Adept must keep this registration statement effective for two years or until all of the shares issued in the Financing are sold in a public offering (under the registration statement or otherwise) or can be sold without restriction under Rule 144(k). Adept, however, does have the ability to suspend the registration statement for one or more periods of up to 20 consecutive days subject to a maximum of 45 days in any 12 months where Adept determines in good faith, on advice of counsel, that such disclosure required by the registration statement would not be in the best interest of Adept.
In May 2007, pursuant to a settlement agreement, Adept issued 225,000 shares of common stock to affiliates of Crosslink that were parties to the Purchase Agreement in settlement of potential claims by Crosslink in lieu of a cash settlement payment. In connection with the issuance, Adept and the Crosslink entities entered into a registration rights agreement substantially similar to the agreement entered into in connection with the 2006 Financing.
The Company has reserved shares of common stock for future issuance at June 30, 2008 as follows:
| | |
(in thousands) | | |
Stock options outstanding | | 988 |
Stock options available for grant | | 592 |
Conversion of warrants issued in 2003 financing | | 1,111 |
Employee stock purchase plan shares available for purchase | | 451 |
| | |
| | 3,142 |
| | |
Stock Option Plans
The Company’s 1993 Stock Plan (the “1993 Plan”) was adopted by the Board of Directors in April 1993 and approved by the stockholders of the Company in June 1993. This Plan expired in April 2003, so no shares remain available for grant thereunder. At June 30, 2008, there were a total of 122,811 outstanding options under the 1993 Plan.
The Company’s 1995 Director Option Plan (the “Director Plan”) was adopted by the Board of Directors and approved by the stockholders of the Company in October 1995. The Director Plan expired in 2005, so no shares remain available for grant thereunder. The option grants under the Director Plan were automatic and nondiscretionary, with an exercise price of the options equal to the fair market value of the Company’s common stock on the date of grant. As of June 30, 2008, there were a total of 6,600 outstanding options under the 1995 Plan.
77
On August 9, 2001, the Board of Directors adopted the 2001 Stock Option Plan (the “2001 Plan”) with 520,000 shares of common stock to be reserved for issuance under the 2001 Plan. As amended, options under the 2001 Plan may be granted to employees either from time to time at the discretion of the Compensation Committee of the Board of Directors or automatically upon the occurrence of specified events, including, without limitation, reduction of at will employees’ salaries and the achievement of performance goals. The exercise price of the options is at the fair market value of the Company’s common stock on the date of the grant. Options generally vest over a time period specified by the Compensation Committee. However, at the Compensation Committee’s discretion, options granted for reduction of at will employees’ salaries vest in equal monthly increments over the salary reduction period. All stock options granted under the 2001 Plan have an expiration date of 10 years from the date of the grant. As of June 30, 2008, there were a total of 261,656 outstanding options under the 2001 Plan.
The Company’s 2003 Stock Plan (the “2003 Plan”) was adopted and approved by the stockholders of the Company in January 2004 and an amendment to the 2003 Plan was approved by the stockholders in November 2004. The 2003 Plan provides for grants of up to 400,000 shares upon exercise of incentive stock options to employees (including officers and employee directors) and non statutory stock options to employees (including officers and employee directors) and consultants of the Company. In general, options granted under the 2003 Plan vest and become exercisable starting one year after the date of grant, with 25% of the shares subject to the option vesting and becoming exercisable at that time and an additional 1/48th of the shares subject to the option vesting and becoming exercisable each month thereafter. The terms of the options granted under the 2003 Plan generally may not exceed ten years. The Board of Directors determines the exercise price of the options, which must be at least equal to the fair market value of the common stock on the date of grant. As of June 30, 2008, there were a total of 355,000 outstanding options under the 2003 Plan.
The Company’s 2004 Director Stock Option Plan (the “2004 Plan”) was approved by the stockholders of the Company in November 2004. In March 2005, the Board of Directors approved increases to the automatic, nondiscretionary initial and annual option grants available to non-employee directors under the 2004 Plan. The size of initial option grants to new directors was increased from 3,000 shares to 10,000 shares, and annual director option grants from 1,000 to 2,000 shares, which was subsequently increased to 3,000 shares by an amendment approved by the Board in January 2006. The 2004 Plan provides for the annual director option grant to be made on the date of the first meeting of the Board following Adept’s annual meeting of stockholders. In November 2006, the stockholders approved the increase in authorized shares under the 2004 Plan by an additional 72,000 shares. As of June 30, 2008, there were a total of 57,166 outstanding options under the 2004 Plan.
On June 16, 2005, the Board of Directors adopted the 2005 Equity Incentive Plan (“2005 Plan”) which was approved by the stockholders in November 2005. The 2005 Plan authorizes the issuance of up to 600,000 shares of common stock to employees and non-employee directors. The 2005 Plan provides for the granting of stock options, stock appreciation rights, restricted stock, restricted stock units and performance award units (including incentives that may be paid in cash). Included in the 600,000 shares of common stock to employees and non-employee are 200,000 shares that were approved in November 2007 by the stockholders. As of June 30, 2008, there were 184,500 outstanding options under the 2005 Plan.
78
The following table summarizes option activities under the Company’s stock option plans:
| | | | | | | | | | | | | |
| | Options |
| | Available for Grant | | | No. of Options Outstanding | | | Aggregate Price | | | Weighted Average Exercise Price Per Share |
| | (in thousands, except per share data) |
Balance at June 30, 2006 | | 541 | | | 921 | | | $ | 12,316 | | | $ | 13.33 |
| | | | | | | | | | | | | |
Additional shares authorized | | 72 | | | — | | | | — | | | | — |
Granted | | (355 | ) | | 355 | | | $ | 3,199 | | | | 9.01 |
Canceled | | 128 | | | (128 | ) | | | (1,921 | ) | | | 14.96 |
Exercised | | — | | | (64 | ) | | | (328 | ) | | | 5.13 |
Expired | | (18 | ) | | — | | | | — | | | | — |
| | | | | | | | | | | | | |
Balance at June 30, 2007 | | 368 | | | 1,084 | | | $ | 13,266 | | | $ | 12.24 |
| | | | | | | | | | | | | |
Additional shares authorized | | 200 | | | | | | | | | | | |
Granted | | (147 | ) | | 147 | | | $ | 853 | | | $ | 5.80 |
Canceled | | 205 | | | (205 | ) | | | (3,354 | ) | | | 16.40 |
Exercised | | — | | | (38 | ) | | | (170 | ) | | | 4.41 |
Expired | | (34 | ) | | — | | | | — | | | | — |
| | | | | | | | | | | | | |
Balance at June 30, 2008 | | 592 | | | 988 | | | $ | 10,595 | | | $ | 10.73 |
| | | | | | | | | | | | | |
The following table summarizes information concerning outstanding and exercisable options at June 30, 2008:
| | | | | | | | | | | | |
| | Options Outstanding | | Options Exercisable |
Range of Exercise Prices | | Options Outstanding | | Weighted Average Remaining Contractual Life | | Weighted Average Exercise Price | | Options Exercisable | | Weighted Average Exercise Price |
| | (in thousands) | | (years) | | (per share) | | (in thousands) | | (per share) |
$ 1.50 - $ 5.50 | | 88.9 | | 5.70 | | $ | 3.84 | | 81.7 | | $ | 3.70 |
5.74 - 5.74 | | 127.0 | | 9.26 | | | 5.74 | | 21.2 | | | 5.74 |
6.05 - 6.05 | | 120.0 | | 5.35 | | | 6.05 | | 120.0 | | | 6.05 |
6.15 - 7.14 | | 102.0 | | 7.29 | | | 6.66 | | 66.4 | | | 6.58 |
8.00 - 8.00 | | 159.0 | | 7.15 | | | 8.00 | | 110.3 | | | 8.00 |
8.07 - 8.07 | | 183.0 | | 8.38 | | | 8.06 | | 72.4 | | | 8.06 |
8.25 - 13.94 | | 112.4 | | 7.35 | | | 12.30 | | 64.9 | | | 12.22 |
13.95 - 120.00 | | 94.6 | | 2.45 | | | 40.04 | | 94.6 | | | 40.04 |
245.63 - 245.63 | | 0.3 | | 2.26 | | | 245.63 | | 0.3 | | | 245.63 |
248.75 - 248.75 | | 0.5 | | 2.17 | | | 248.75 | | 0.5 | | | 248.75 |
| | | | | | | | | | | | |
$ 1.50 - 248.75 | | 987.7 | | 6.88 | | $ | 10.73 | | 632.3 | | $ | 12.39 |
79
Employee Stock Purchase Plan
The 1998 Employee Stock Purchase Plan (the “1998 ESPP”) has overlapping 12-month offering periods that begin every six months, starting on the first trading day on or after September 1 and March 1 of each year. Each 12-month offering period is divided into two six-month purchase periods. For every six-month purchase period, the plan allows eligible employees, through payroll deductions of a maximum of 15% of individual salary, to purchase up to a maximum of 600 shares of the Company’s common stock at 85% of fair market value on either the first day of the offering period or the last day of the purchase period, whichever is lower.
9. | Employee Savings and Investment Plan |
The Company maintains a 401(k) savings and investment plan in which all employees are eligible to participate. The Company did not match any contributions for fiscal years ended June 30, 2008 and 2007.
The provision for (benefit from) income taxes consists of the following:
| | | | | | | | |
| | Year Ended June 30, | |
(in thousands) | | 2008 | | | 2007 | |
Current: | | | | | | | | |
Federal | | $ | 57 | | | $ | (223 | ) |
State | | | 15 | | | | 13 | |
Foreign | | | 227 | | | | 8 | |
| | | | | | | | |
Total current | | | 299 | | | | (202 | ) |
| | | | | | | | |
Deferred: | | | | | | | | |
Federal | | | — | | | | — | |
State | | | — | | | | — | |
Foreign | | | (47 | ) | | | — | |
| | | | | | | | |
Total deferred | | | (47 | ) | | | — | |
| | | | | | | | |
Provision for (benefit from) income taxes | | $ | 252 | | | $ | (202 | ) |
| | | | | | | | |
The difference between the provision for (benefit from) income taxes and the amount computed by applying the federal statutory income tax rate to income (loss) income before provision for (benefit from) income taxes is explained below:
| | | | | | | | |
| | Year Ended June 30, | |
(in thousands) | | 2008 | | | 2007 | |
Tax at federal statutory rate | | $ | 1,322 | | | $ | (3,983 | ) |
State taxes, net of federal benefit | | | 9 | | | | 9 | |
Net operating losses not benefited (benefited) | | | (1,814 | ) | | | 3,431 | |
Foreign taxes | | | 267 | | | | 8 | |
Tax credits | | | (57 | ) | | | (119 | ) |
Non-deductible meals and entertainment | | | 25 | | | | 25 | |
Goodwill impairment | | | — | | | | 266 | |
Federal alternative minimum taxes | | | 59 | | | | — | |
Change in valuation allowance | | | 243 | | | | 165 | |
Non-deductible stock compensation | | | 130 | | | | 221 | |
Reversal of previously accrued income taxes | | | (40 | ) | | | (223 | ) |
Other | | | 108 | | | | (2 | ) |
| | | | | | | | |
Provision for (benefit from) income taxes | | $ | 252 | | | $ | (202 | ) |
| | | | | | | | |
80
Deferred income taxes reflect the net tax effects of temporary differences between the carrying amounts of assets and liabilities for financial reporting purposes and the amounts used for income tax purposes. Significant components of the Company’s deferred tax assets and liabilities are as follows:
| | | | | | | | |
(in thousands) | | June 30, | |
| 2008 | | | 2007 | |
Deferred tax assets: | | | | | | | | |
Net operating loss carry forwards | | $ | 31,450 | | | $ | 33,331 | |
Tax credit carry forwards | | | 1,022 | | | | 6,759 | |
Inventory valuation | | | 591 | | | | 707 | |
Depreciation /amortization | | | 2,176 | | | | 2,281 | |
Other accruals not currently deductible for tax purposes | | | 2,157 | | | | 2,054 | |
Capitalized research and development expenses | | | 688 | | | | 992 | |
Other | | | 256 | | | | 269 | |
| | | | | | | | |
Total deferred tax assets | | | 38,340 | | | | 46,393 | |
Valuation allowance | | | (38,340 | ) | | | (46,393 | ) |
| | | | | | | | |
Net deferred tax assets | | | — | | | | — | |
| | | | | | | | |
Deferred tax liabilities: | | | | | | | | |
Purchased intangibles | | | (242 | ) | | | — | |
| | | | | | | | |
Net deferred tax liabilities | | | (242 | ) | | | — | |
| | | | | | | | |
Total net deferred tax assets | | $ | (242 | ) | | $ | — | |
| | | | | | | | |
For financial reporting purposes, the Company’s deferred tax assets have been fully offset by a valuation allowance due to uncertainties about the Company’s ability to generate future taxable income. The change in the valuation allowance was a net increase (decrease) of approximately $(8.1) million and $7.4 million for the periods ended June 30, 2008 and June 30, 2007, respectively.
The accumulated tax benefits associated with employee stock options provide a deferred benefit of approximately $1.0 million which has been fully offset by the valuation allowance. The deferred tax benefit associated with the employee stock options will be credited to additional paid-in capital when realized.
The reversal of previously accrued income taxes reflects management’s reassessment of the appropriate level of tax liabilities for the Company based on the Company’s current level of operating activities and recent filing of its federal, state and international tax returns.
At June 30, 2008, the Company has net operating loss carry forwards for federal income tax purposes of approximately $80.0 million, which will expire in the years 2022 through 2027 if unused. The Company had net operating loss carryforwards for California income tax purposes of approximately $25.6 million which will expire in 2014 through 2017. The Company has net operating loss carry forwards for other state income tax purposes of approximately $16.4 million, which will expire in the years 2021 through 2027 if unused.
The Company also has tax credit carry forwards of approximately $3.8 million for federal income tax purposes and $4.8 million for state income tax purposes. The federal tax credit and a portion of the state tax credit will expire in the years 2008 through 2027 if unused. Utilization of the net operating loss and tax credit carry forwards may be subject to a substantial annual limitation due to the change in ownership limitations provided in the Internal Revenue Code. The annual limitation may result in the expiration of the net operating losses and credits before utilization.
The Company has foreign net operating loss carryforwards of approximately $8.5 million which have no expiration date.
81
Effective July 1, 2007, we adopted Financial Accounting Standards Interpretation No. 48,Accounting for Uncertainty in Income Taxes-An Interpretation of FASB Statement No. 109(“FIN 48”). As a result of adoption of FIN 48, we recognized a charge of $200,000 to the Company’s accumulated deficit as of July 1, 2007. This charge was classified as a long-term liability because payment of the liability is not anticipated within one year of the balance sheet date. Also as a result of the adoption of FIN 48, we recorded a $2.75 million reduction to deferred tax assets for unrecognized tax benefits, all of which is currently offset by a full valuation allowance that had no effect on the beginning balance of accumulated deficit or the net balance sheet. As of June 30, 2008, the total unrecognized tax benefit of $2.95 million increased to $7.32 million of which $7.20 million is offset by a full valuation allowance. In addition, we do not expect any material changes to the estimated amount of the liability associated with our uncertain tax positions within the next twelve months.
We file income tax returns in the U.S. federal jurisdiction, California and various state and foreign tax jurisdictions in which we have a subsidiary or branch operation. The tax years 1995 to 2008 remain open to examination by the U.S. and state tax authorities, and the tax years 2005 to 2008 remain open to examination by the foreign tax authorities.
Our policy is that we recognize interest and penalties accrued on any unrecognized tax benefits as a component of income tax expense. As of the date of adoption of FIN 48, we had no accrued interest or penalties associated with unrecognized tax benefits.
The following table summarizes the activity related to our unrecognized tax benefits:
| | | | |
| | Total | |
| | (In thousands) | |
Balance at July 1, 2007 | | $ | 2,950 | |
Increases related to current year tax positions | | $ | — | |
Increases related to prior year tax positions | | $ | 4,410 | |
Decreases related to prior year tax positions | | $ | (40 | ) |
| | | | |
Balance at June 30, 2008 | | $ | 7,320 | |
SFAS 131,Disclosures about Segments of an Enterprise and Related Information, requires disclosures of certain information regarding operating segments, products and services, geographic areas of operation and major customers. Statement 131 reporting is based upon the “management approach”. This requires management to organize the Company’s operating segments for which separate financial information is: (i) available and (ii) evaluated regularly by the chief operating decision maker in deciding how to allocate resources and in assessing performance. Adept’s chief operating decision maker is its President and Chief Operating Officer.
Adept’s business is focused towards delivering intelligent flexible production automation products, components and services for assembly, packaging, material handling and lab automation applications under two operating segments: Robotics and Services and Support.
| • | | The Robotics segment provides intelligent motion control systems, production automation software, including vision-guidance and application software, and robot mechanisms to customers. |
| • | | The Services and Support segment provides support services to customers including: spare parts for, and/or remanufacture of, robot mechanisms; information regarding the use of the Company’s automation equipment; ongoing support of installed systems; consulting services for applications; and training courses ranging from system operation and maintenance to advanced programming, geared towards manufacturing engineers who design and implement automation lines. |
82
The Company evaluates performance and allocates resources based on segment revenue and segment operating income (loss). Segment operating income (loss) is comprised of income before unallocated research, development and engineering expenses, unallocated selling, general and administrative expenses, interest income, and interest and other expenses.
Management does not fully allocate research, development and engineering expenses and selling, general and administrative expenses when making capital spending and expense funding decisions or assessing segment performance. There is no inter-segment revenue recognized. Transfers of materials or labor between segments are recorded at cost.
Segment information for total assets and capital expenditures is not presented as such information is not used in measuring segment performance or allocating resources between segments.
| | | | | | | | |
| | Fiscal Years Ended | |
(in thousands) | | June 30, 2008 | | | June 30, 2007 | |
Revenue: | | | | | | | | |
Robotics | | $ | 46,691 | | | $ | 30,743 | |
Services and Support | | | 14,092 | | | | 17,945 | |
| | | | | | | | |
Total revenue | | $ | 60,783 | | | $ | 48,688 | |
| | | | | | | | |
Operating income (loss): | | | | | | | | |
Robotics | | $ | 12,104 | | | $ | 1,436 | |
Services and support | | | 2,556 | | | | 3,555 | |
| | | | | | | | |
Segment profit | | | 14,660 | | | | 4,991 | |
Unallocated research, development and engineering and selling, general and administrative expenses | | | (11,363 | ) | | | (11,266 | ) |
Restructuring (charges) reversals, net | | | (254 | ) | | | (1,023 | ) |
Goodwill impairment expense | | | — | | | | (3,176 | ) |
Crosslink settlement costs | | | — | | | | (1,861 | ) |
Amortization of other intangible assets | | | (216 | ) | | | (33 | ) |
Other income | | | — | | | | — | |
Interest income (expense), net | | | 306 | | | | 445 | |
Currency exchange gain | | | 755 | | | | 208 | |
| | | | | | | | |
Income (loss) before income taxes | | $ | 3,888 | | | $ | (11,715 | ) |
| | | | | | | | |
83
Management also assesses the Company’s performance, operations and assets by geographic areas, and, therefore, revenue and long-lived assets related to continuing operations are summarized in the following table:
| | | | | | | | | | | | |
| | Fiscal Year Ended June 30, | |
(in thousands) | | 2008 | | % of total | | | 2007 | | % of total | |
Revenue: | | | | | | | | | | | | |
United States | | $ | 19,199 | | 31.6 | % | | $ | 19,507 | | 40.1 | % |
| | | | | | | | | | | | |
Europe | | | | | | | | | | | | |
Germany | | | 17,780 | | 29.3 | % | | | 10,314 | | 21.2 | % |
France | | | 6,246 | | 10.3 | % | | | 5,288 | | 10.9 | % |
Switzerland | | | 2,372 | | 3.9 | % | | | 2,383 | | 4.9 | % |
Other European countries | | | 7,129 | | 11.7 | % | | | 5,425 | | 11.1 | % |
Asia | | | | | | | | | | | | |
Singapore | | | 2,436 | | 4.0 | % | | | 2,826 | | 5.8 | % |
Malaysia | | | 1,705 | | 2.8 | % | | | 1,125 | | 2.3 | % |
Other countries | | | 3,916 | | 6.4 | % | | | 1,820 | | 3.7 | % |
| | | | | | | | | | | | |
Total International | | | 41,584 | | 68.4 | % | | | 29,181 | | 59.9 | % |
| | | | | | | | | | | | |
Total | | $ | 60,783 | | 100.0 | % | | $ | 48,688 | | 100.0 | % |
| | | | | | | | | | | | |
Long-Lived Assets
| | | | | | |
(in thousands) | | June 30, 2008 | | June 30, 2007 |
Long-lived tangible assets: | | | | | | |
United States | | $ | 2,821 | | $ | 3,130 |
All other countries | | | 685 | | | 654 |
| | | | | | |
Total long-lived assets | | $ | 3,506 | | $ | 3,784 |
| | | | | | |
Adept’s revenues are reported by geographic region based on the ship to location of the customer order. Revenues by country are broken out when they exceed 5% of total revenue or deemed useful.
Employee Stock Purchase Plan
The Board of Directors did not authorize any additional shares to be issued pursuant to the 1998 Employee Stock Purchase Plan (other than the remaining shares authorized for issuance under such plan). Effective September 1, 2008, the Board of Directors adopted the 2008 Employee Stock Purchase Plan (the “2008 ESPP”) which has overlapping 24-month offering periods that begin every six months, starting on the first trading day on or after September 1 and March 1 of each year. Each 24-month offering period is divided into two six-month purchase periods. For every six-month purchase period, the plan allows eligible employees, through payroll deductions of a maximum of 15% of individual salary, to purchase up to a maximum of 1,200 shares of the Company’s common stock at 85% of fair market value on either the first day of the offering period or the last day of the purchase period, whichever is lower. The 2008 ESPP is subject to the approval of Adept’s stockholders.
In August 2008, the loan agreement with SVB expired by its terms and was not renewed by Adept.
84
Stock Repurchase Program
On September 2, 2008, the Board of Directors approved a stock repurchase program for up to $2.5 million of Adept stock effective immediately. Stock repurchases under this program may be made through a variety of methods, which may include open market purchases, privately negotiated transactions, block trades, accelerated share repurchase transactions or otherwise, or by any combination of such methods. The timing and actual number of shares repurchased will depend on a variety of factors including the stock price, corporate and contractual and regulatory requirements, alternative investment opportunities and other market and economic conditions. Adept expects to fund its purchases from its working capital. The Company has no obligation to purchase a specific amount of common stock, and the stock repurchase program may be suspended or discontinued at any time.
Adoption of Fiscal 2008 Executive and Senior Management Payment Plan
On September 2, 2008, the Adept Board of Directors approved the adoption by the Company of the Executive and Senior Management Payment Plan for fiscal year 2009 (the “Bonus Plan”). The Bonus Plan establishes the terms and targets of performance bonuses payable in cash and/or restricted stock grants for Adept’s executive officers and certain other key employees of the Company for the 2009 fiscal year, as recommended by Adept’s Compensation Committee of the Board of Directors. Under the Bonus Plan, executive performance bonuses are based on various target revenue (weighted at 60%) and operating income (weighted at 40%) in target formulae, and executive sales commissions are based upon applicable sales revenue. The Bonus Plan is not subject to the approval of Adept stockholders. Non-sales commission awards ultimately granted under the Plan would consist of a portion payable in cash (generally targeted to be 30% of the bonus payment) and a portion payable in shares of restricted stock (generally targeted to be 70% of the bonus payment) to be granted after completion of fiscal 2009 under the Adept 2005 Equity Incentive Plan (the “2005 Plan”), to vest in equal quarterly installments over a two year period. The Compensation Committee shall determine the amount of the non-sales commission bonus payments to be made after review of the fiscal year’s audited results, the individual’s performance as presented by management, and projected financials for the next fiscal year. Adept’s Board and the Compensation Committee reserves the right to adjust or eliminate a bonus at any time or to grant bonuses to executives on a discretionary basis.
Change of Management
On September 3, 2008, John Dulchinos, previously our President and Chief Operating Officer, was appointed as Chief Executive Officer of the Company, succeeding Robert H. Bucher, who now serves as the Executive Chairman of the Board of Directors of Adept. Mr. Dulchinos was also appointed to serve as a member of the Adept Board of Directors.
85
SCHEDULE II
ADEPT TECHNOLOGY, INC.
VALUATION AND QUALIFYING ACCOUNTS
(in thousands)
| | | | | | | | | | | | | |
Description | | Balance at Beginning of Period | | Additions Charged to Costs and Expenses | | Deductions (1) | | | Balance at End of Period |
Year ended June 30, 2007: | | | | | | | | | | | | | |
Allowance for doubtful accounts | | $ | 467 | | $ | 69 | | $ | (30 | ) | | $ | 506 |
Year ended June 30, 2008: | | | | | | | | | | | | | |
Allowance for doubtful accounts | | $ | 506 | | $ | 49 | | $ | (70 | ) | | $ | 485 |
(1) | Includes write-offs, net of recoveries. |
86