Exhibit 99.2
Management’s Discussion & Analysis
Index
This Management’s Discussion and Analysis (“MD&A”) is dated March 13, 2013 and should be read in conjunction with our consolidated financial statements and the accompanying notes for the year ended December 31, 2012. Except where otherwise noted, the financial information presented in this MD&A is prepared in accordance with International Financial Reporting Standards (IFRS) as issued by the International Accounting Standards Board. We use the United States dollar as our reporting currency and, except where otherwise noted, all currency amounts are stated in United States dollars.
At March 13, 2013 we had 94,743,044 common shares issued and outstanding and stock options and tandem share appreciation rights exercisable for 3,618,823 additional common shares.
Additional information relating to Methanex, including our Annual Information Form, is available on our website at www.methanex.com, the Canadian Securities Administrators’ SEDAR website at www.sedar.com and on the United States Securities and Exchange Commission’s EDGAR website at www.sec.gov.
OVERVIEW OF THE BUSINESS
Methanol is a clear liquid commodity chemical that is predominantly produced from natural gas and also, particularly in China, from coal. Approximately two-thirds of all methanol demand is used to produce traditional chemical derivatives, including formaldehyde, acetic acid and a variety of other chemicals that form the basis of a large number of chemical derivatives for which demand is influenced by levels of global economic activity. The remaining one-third of methanol demand comes from energy-related applications. There has been strong demand growth for direct methanol blending into gasoline, as a feedstock in the production of dimethyl ether (DME), which can be blended with liquefied petroleum gas for use in household cooking and heating, and in the production of biodiesel. Methanol is also used to produce methyl tertiary-butyl ether (MTBE), a gasoline component, and olefins. This latter use is emerging as a significant methanol demand driver.
We are the world’s largest supplier of methanol to the major international markets in Asia Pacific, North America, Europe and Latin America. Our total annual production capacity, including Methanex equity interests in jointly owned plants, is currently 9.5 million tonnes and is located in New Zealand, Trinidad, Egypt, Canada and Chile (refer to theProduction Summary section on page 9 for more information). We are currently relocating one of our Chile facilities to Geismar, Louisiana and we expect the relocated facility will be operational by the end of 2014. We have marketing rights for 100% of the production from the jointly owned plants in Trinidad and Egypt and this provides us with an additional 1.2 million tonnes per year of methanol offtake supply when the plants are operating at full capacity. In addition to the methanol produced at our sites, we purchase methanol produced by others under methanol offtake contracts and on the spot market. This gives us flexibility in managing our supply chain while continuing to meet customer needs and support our marketing efforts.
2012 Industry Overview & Outlook
Methanol is a global commodity and our earnings are significantly affected by fluctuations in the price of methanol, which is directly impacted by changes in methanol supply and demand.
Demand for methanol is driven primarily by levels of industrial production, energy prices and the strength of the global economy. Demand for methanol grew by 5% in 2012, leading to global demand of approximately 51 million tonnes, excluding demand from integrated methanol-to-olefins facilities. The increase in demand was driven by both traditional derivatives and energy-related applications in Asia, particularly in China.
Industry supply additions outside of China in 2012 consisted primarily of the restart of our second Motunui facility in New Zealand, which added 0.7 million tonnes to the site’s annual operating capacity, and the restart of a 0.7 million tonne facility in Beaumont, Texas. New production from supply additions inside China was consumed in that country and China continued to be a significant net importer of methanol.
| | | | |
| | Management’s Discussion & Analysis | | Methanex Corporation | Annual Report 2012 5 |
Management’s Discussion & Analysis
Overall, industry conditions were balanced in 2012 and this led to a relatively stable methanol pricing environment. Our average realized price for 2012 was $382 per tonne compared with $374 per tonne in 2011.
The outlook for methanol demand growth continues to be strong. The wide disparity between the price of crude oil and that of natural gas and coal has resulted in an increased use of methanol in energy-related applications, such as direct methanol blending into gasoline and DME and biodiesel production. Growth of direct methanol blending into gasoline in China has been particularly strong and we believe that future growth in this application is supported by numerous provincial and national fuel-blending standards, such as M15 or M85 (15% methanol and 85% methanol, respectively).
China is also leading the commercialization of methanol’s use as a feedstock to manufacture olefins. The use of methanol to produce olefins, at current energy prices, is proving to be cost competitive relative to the traditional production of olefins from naphtha. There are now five methanol-to-olefins (MTO) plants operating in China, with the capacity to consume approximately seven million tonnes of methanol annually. Three of these projects were not expected to impact the merchant methanol market as they are integrated projects – coal to methanol to olefins. However, over the past two years, these plants have purchased methanol to supplement their own methanol production. The two non-integrated plants (representing over 2 million tonnes of methanol demand annually) are dependent on merchant methanol supply. Several other integrated and non-integrated projects are currently under construction in China and the demand for methanol as a feedstock for producing olefins is anticipated to continue to grow.
While methanol demand in energy-related applications is strongest in China, there are an increasing number of countries around the world that have projects in place or are considering adopting these applications on a wider scale. Direct methanol blending into gasoline is being used in small quantities in the United Kingdom, Netherlands and Iceland, and other countries, including Australia and Israel, are conducting fuel-blending trials. DME is being produced and DME projects are under development in various countries including Japan, Taiwan, Turkey, the United States, Trinidad, India and Indonesia.
We believe demand potential into energy-related applications and olefins production will continue to grow.
We increased our operating capacity in 2012 and anticipate further increases over the next few years. We recently announced our commitment to add a further 0.7 million tonnes of operating capacity to our New Zealand site through the restart of the Waitara Valley facility and a debottlenecking project at the Motunui site. We are relocating one of our idle Chile facilities to Geismar, Louisiana and the plant is expected to commence operations by the end of 2014. We are also considering the relocation of a second facility to the Geismar site and expect to make a decision on this project by mid-2013.
Beyond our own capacity additions, there is a modest level of new capacity expected to come on stream over the next few years outside of China. There is a 0.8 million tonne plant expected to restart in Channelview, Texas in 2013 and a 0.7 million tonne plant expected to start up in Azerbaijan in 2013. We expect that production from new capacity in China will be consumed in that country and that higher-cost production capacity in China will need to operate in order to satisfy demand growth.
Entering 2013, methanol demand has continued to be healthy, supported by a higher energy price environment. With few industry capacity additions expected over the next few years relative to expected demand growth, we believe we are well positioned with several of our own initiatives to increase operating capacity. As production from these initiatives comes on line, we believe our leadership position in the industry will be strengthened and we will have significant upside potential to cash flows and earnings.
The methanol price will ultimately depend on the strength of the global economy, industry operating rates, global energy prices, new supply additions and the strength of global demand. We believe that our financial position and financial flexibility, outstanding global supply network and competitive cost position will provide a sound basis for Methanex to continue to be the leader in the methanol industry.
OUR STRATEGY
Our primary objective is to create value by maintaining and enhancing our leadership in the global production, marketing and delivery of methanol to customers. Our simple, clearly defined strategy – global leadership, low cost and operational excellence – has helped us achieve this objective.
| | | | |
6 Methanex Corporation | Annual Report 2012 | | Management’s Discussion & Analysis | | |
Management’s Discussion & Analysis
Global Leadership
Global leadership is a key element of our strategy. We are focused on maintaining and enhancing our position as the major supplier to the global methanol industry, enhancing our ability to cost-effectively deliver methanol supply to customers and supporting both traditional and energy-related global methanol demand growth.
We are the leading supplier of methanol to the major international markets in Asia Pacific, North America, Europe and Latin America. Our 2012 sales volumes of 7.5 million tonnes represented approximately 15% of global methanol demand. Our leadership position has enabled us to play an important role in the industry, which includes publishing Methanex reference prices that are generally used in each major market as the basis of pricing for most customer contracts.
The geographically diverse locations of our production sites allow us to deliver methanol cost-effectively to customers in all major global markets, while investments in global distribution and supply infrastructure, which include a dedicated fleet of ocean-going vessels and terminal capacity within all major international markets, enable us to enhance value to customers by providing reliable and secure supply.
A key component of our global leadership strategy is to strengthen our asset position and we have increased our operating capacity over the last two years. In 2011, we restarted our 0.5 million tonne per year Medicine Hat, Alberta facility and the 1.3 million tonne per year methanol plant in Egypt commenced operations. In 2012, we restarted a second facility in New Zealand and this increased our operating capacity in that country by 0.7 million tonnes. We have several other initiatives in progress in New Zealand that are expected to increase our operating capacity further and allow us to reach the site’s full production capacity of 2.4 million tonnes. Our New Zealand facilities are ideally situated to supply the growing Asia Pacific market.
During 2012, we operated our Chile methanol facilities significantly below site capacity. We expect to idle our Chile operations in March 2013 due to insufficient natural gas feedstock to operate the plant through the southern hemisphere winter (refer to theProduction Summary – Chilesection on page 10 for further information). We are in the process of relocating one of our four Chile facilities to Geismar, Louisiana. The Geismar facility will have an annual production capacity of approximately 1.0 million tonnes and is expected to be operational by the end of 2014. We are also considering other projects to increase the utilization of our Chile assets, including the potential to relocate an additional facility to the Geismar site.
Another key component of our global leadership strategy is our ability to supplement methanol production with methanol purchased from third parties to give us flexibility in our supply chain and continue to meet customer commitments. We purchase through a combination of methanol offtake contracts and spot purchases. We manage the cost of purchased methanol by taking advantage of our global supply chain infrastructure, which allows us to purchase methanol in the most cost-effective region while still maintaining overall security of supply.
The Asia Pacific region continues to lead global methanol demand growth and we have invested in and developed our presence in this important region. We have storage capacity in China, Korea and Japan that allows us to cost-effectively manage supply to customers and we have offices in Hong Kong, Shanghai, Beijing, Seoul and Tokyo to enhance customer service and industry positioning in the region. This enables us to participate in and improve our knowledge of the rapidly evolving and high growth methanol markets in China and other Asian countries. Our expanding presence in Asia has also helped us identify several opportunities to support the development of applications for methanol in the energy sector.
Low Cost
A low cost structure is an important competitive advantage in a commodity industry and is a key element of our strategy. Our approach to major business decisions is guided by a drive to improve our cost structure, expand margins and create value for shareholders. The most significant components of total costs are natural gas for feedstock and distribution costs associated with delivering methanol to customers.
Our ownership interest in production facilities in Trinidad and Egypt represents 2.8 million tonnes per year of competitive-cost production capacity. These facilities are well located to supply global methanol markets and are underpinned by natural gas purchase agreements where the gas price varies with methanol prices. This pricing relationship enables these facilities to be competitive throughout the methanol price cycle.
In January 2013, we entered into a 10-year agreement to purchase all of the natural gas required for the methanol plant we are relocating to Geismar, Louisiana. The agreement is structured so that the natural gas price is linked to the methanol price, which will enable the
| | | | |
| | Management’s Discussion & Analysis | | Methanex Corporation | Annual Report 2012 7 |
Management’s Discussion & Analysis
project to be profitable across a broad range of methanol prices. We also have a 0.5 million tonne facility located in Medicine Hat, Alberta and we believe that the long-term natural gas dynamics in North America will support the long-term operation of this facility.
The cost to distribute methanol from production locations to customers is also a significant component of total operating costs. These include costs for ocean shipping, in-market storage facilities and in-market distribution. We are focused on identifying initiatives to reduce these costs, including optimizing the use of our shipping fleet and taking advantage of prevailing conditions in the shipping market by varying the type and length of term of ocean vessel contracts. We are continuously investigating opportunities to further improve the efficiency and cost-effectiveness of distributing methanol from our production facilities to customers. We also look for opportunities to leverage our global asset position by entering into product exchanges with other methanol producers to reduce distribution costs.
Operational Excellence
We maintain a focus on operational excellence in all aspects of our business. This includes excellence in the manufacturing and supply chain processes, marketing and sales, human resources, corporate governance practices and financial management.
To differentiate ourselves from competitors, we strive to be the best operator in all aspects of our business and to be the preferred supplier to customers. We believe that reliability of supply is critical to the success of our customers’ businesses and our goal is to deliver methanol reliably and cost-effectively. We have a commitment to Responsible Care (a risk-minimization approach developed by the Chemistry Industry Association of Canada) and we use it as the umbrella under which we manage issues related to health, safety, the environment, community involvement, social responsibility, sustainability, security and emergency preparedness at each of our facilities and locations. We believe a commitment to Responsible Care helps us reduce the likelihood of unplanned events and achieve an excellent overall environmental and safety record.
Product stewardship is a vital component of a Responsible Care culture and guides our actions through the complete life cycle of our product. We aim for the highest safety standards to minimize risk to employees, customers and suppliers as well as to the environment and the communities in which we do business. We promote the proper use and safe handling of methanol at all times through a variety of internal and external health, safety and environmental initiatives, and we work with industry colleagues to improve safety standards. We readily share technical and safety expertise with key stakeholders, including customers, end-users, suppliers, logistics providers and industry associations in the methanol and methanol applications marketplace through active participation in local and international industry associations, seminars and conferences, and online education initiatives.
As a natural extension of the Responsible Care ethic, we have a Social Responsibility policy that aligns corporate governance, employee engagement and development, community involvement and social investment strategies with our core values and corporate strategy.
Our strategy of operational excellence also includes the financial management of the Company. We operate in a highly competitive commodity industry. Accordingly, we believe it is important to maintain financial flexibility and we have adopted a prudent approach to financial management. During 2012, we issued a total of $600 million of unsecured notes and a portion of the proceeds was used to repay $200 million of unsecured notes. Also during 2012, we extended the maturity on our undrawn revolving credit facility to 2016 and increased the amount to $400 million. At December 31, 2012, we had a strong balance sheet with a cash balance of $746 million, including $36 million relating to the non-controlling interest in Egypt. We believe we are well positioned to meet our financial commitments and continue investing to grow the Company.
| | | | |
8 Methanex Corporation | Annual Report 2012 | | Management’s Discussion & Analysis | | |
Management’s Discussion & Analysis
FINANCIAL HIGHLIGHTS
| | | | | | | | |
| | |
($ MILLIONS, EXCEPT AS NOTED) | | 2012 | | | 2011 | |
Production (thousands of tonnes) (attributable to Methanex shareholders) | | | 4,071 | | | | 3,847 | |
Sales volumes (thousands of tonnes): | | | | | | | | |
Methanex-produced methanol (attributable to Methanex shareholders) | | | 4,039 | | | | 3,853 | |
Purchased methanol | | | 2,565 | | | | 2,815 | |
Commission sales1 | | | 855 | | | | 846 | |
Total sales volumes | | | 7,459 | | | | 7,514 | |
Methanex average non-discounted posted price ($ per tonne)2 | | | 443 | | | | 440 | |
Average realized price ($ per tonne)3 | | | 382 | | | | 374 | |
Revenue | | | 2,673 | | | | 2,608 | |
Adjusted EBITDA4 | | | 429 | | | | 427 | |
Adjusted cash flows from operating activities4 | | | 403 | | | | 392 | |
Cash flows from operating activities | | | 458 | | | | 480 | |
Adjusted net income4 | | | 180 | | | | 182 | |
Net income (loss) (attributable to Methanex shareholders) | | | (68 | ) | | | 201 | |
Adjusted net income per common share ($ per share)4 5 | | | 1.90 | | | | 1.93 | |
Basic net income (loss) per common share ($ per share) | | | (0.73 | ) | | | 2.16 | |
Diluted net income (loss) per common share ($ per share) | | | (0.73 | ) | | | 2.06 | |
Common share information (millions of shares): | | | | | | | | |
Weighted average number of common shares | | | 94 | | | | 93 | |
Diluted weighted average number of common shares | | | 94 | | | | 94 | |
Number of common shares outstanding, end of period | | | 94 | | | | 93 | |
1 | Commission sales represent volumes marketed on a commission basis related to the 36.9% of the Atlas methanol facility and 40% of the Egypt methanol facility that we do not own. | |
2 | Methanex average non-discounted posted price represents the average of our non-discounted posted prices in North America, Europe and Asia Pacific weighted by sales volume. Current and historical pricing information is available at www.methanex.com. | |
3 | Average realized price is calculated as revenue, excluding commissions earned and the Egypt non-controlling interest share of revenue, divided by the total sales volumes of Methanex-produced (attributable to Methanex shareholders) and purchased methanol. | |
4 | These items are non-GAAP measures that do not have any standardized meaning prescribed by GAAP and therefore are unlikely to be comparable to similar measures presented by other companies. Refer to the Supplemental Non-GAAP Measures section on page 34 for a description of each non-GAAP measure and reconciliations to the most comparable GAAP measures. | |
5 | For the year ended December 31, 2012, stock options have been excluded from the calculation of diluted net loss per common share (attributable to Methanex shareholders) as their effect would be anti-dilutive. However, for the calculation of adjusted net income per common share (attributable to Methanex shareholders) stock options have been included in the denominator and the diluted weighted average number of common shares for the year ended December 31, 2012 is 95 million. | |
PRODUCTION SUMMARY
The following table details the annual production capacity and actual production of our facilities in 2012 and 2011:
| | | | | | | | | | | | |
| | | |
(THOUSANDS OF TONNES) | | ANNUAL PRODUCTION CAPACITY1 | | | 2012 | | | 2011 | |
New Zealand2 | | | 2,430 | | | | 1,108 | | | | 830 | |
Atlas (Trinidad) (63.1% interest) | | | 1,125 | | | | 826 | | | | 891 | |
Titan (Trinidad) | | | 875 | | | | 786 | | | | 711 | |
Egypt (60% interest)3 | | | 760 | | | | 557 | | | | 532 | |
Medicine Hat (Canada)3 | | | 470 | | | | 481 | | | | 329 | |
Chile I, III and IV | | | 2,800 | | | | 313 | | | | 554 | |
Geismar, Louisiana (USA)4 | | | 1,000 | | | | – | | | | – | |
| | | 9,460 | | | | 4,071 | | | | 3,847 | |
1 | The annual production capacity of our production facilities may be higher than original nameplate capacity as, over time, these figures have been adjusted to reflect ongoing operating efficiencies at these facilities. Actual production for a facility in any given year may be higher or lower than annual production capacity due to a number of factors, including natural gas composition or the age of the facility’s catalyst. | |
2 | The annual production capacity of New Zealand represents the two facilities at Motunui and the currently idle facility at Waitara Valley. The current operating capacity of the Motunui facilities is 1.5 million tonnes due to distillation capacity constraints. We recently announced our commitment to restart the Waitara Valley facility and complete a debottlenecking project at the Motunui site, which we expect will allow our New Zealand operations to operate at their full production capacity of 2.4 million tonnes, depending on natural gas composition. | |
3 | The Egypt methanol facility commenced commercial production in March 2011 and the Medicine Hat facility was restarted in April 2011. | |
4 | We are relocating the Chile II facility to Geismar, Louisiana. The plant is expected to be operational by the end of 2014. | |
| | | | |
| | Management’s Discussion & Analysis | | Methanex Corporation | Annual Report 2012 9 |
Management’s Discussion & Analysis
New Zealand
In New Zealand, we produced 1.1 million tonnes of methanol in 2012 compared with 0.8 million tonnes in 2011. We have three plants in New Zealand with up to 2.4 million tonnes of annual production capacity. After operating one Motunui facility in 2011, we restarted the second facility in mid-2012 which increased our current operating capacity to 1.5 million tonnes. We recently committed to debottleneck the Motunui facility and restart the Waitara Valley facility and we expect this will allow us to produce at the site’s full production capacity, depending on natural gas composition. Our New Zealand facilities are ideally situated to supply the growing Asia Pacific market.
We have entered into several natural gas purchase agreements with various suppliers to underpin the future operation of our Motunui and Waitara Valley facilities. Each natural gas purchase agreement has base and variable components, where the gas price varies with methanol prices. We are also pursuing natural gas exploration and development opportunities in that country. We have an agreement with Kea Petroleum, an oil and gas exploration and development company, to explore areas of the Taranaki basin, which is close to our plants.
Trinidad
Our equity ownership of methanol facilities in Trinidad represents 2.0 million tonnes of competitive-cost annual capacity. The Titan and Atlas facilities in Trinidad are well located to supply global methanol markets and are underpinned by take-or-pay natural gas purchase agreements that expire in 2014 and 2024, respectively, where the gas price varies with methanol prices. These facilities produced a total of 1.6 million tonnes in each of 2012 and 2011.
The Atlas facility experienced an equipment failure in 2011. During 2012, the plant undertook two outages to repair the equipment failure and overcome a technical issue.
During 2011 and 2012, we experienced some natural gas curtailments to our Trinidad facilities due to a mismatch between upstream commitments to supply The National Gas Company of Trinidad and Tobago Limited (NGC) and downstream demand from NGC’s customers, which becomes apparent when an upstream supplier has a technical issue or planned maintenance that reduces gas delivery. We are engaged with key stakeholders to find a solution to this issue, but in the meantime expect to continue to experience some gas curtailments to the Trinidad site. Refer to theRisk Factors and Risk Management – Trinidad section on page 24 for more information.
Egypt
We have a 60% equity interest in the 1.26 million tonne per year methanol plant in Egypt and have marketing rights for 100% of the production. This facility is well located to supply the European market and is underpinned by a 25-year take-or-pay natural gas purchase agreement where the gas price varies with methanol prices. Production from the Egypt facility in 2012 was lower than capacity due to planned and unplanned maintenance outages and natural gas supply restrictions. Refer to theRisk Factors and Risk Management – Egyptsection on page 25 for more information.
Medicine Hat, Canada
We restarted the Medicine Hat, Alberta facility in 2011 and it operated well in 2012, producing 0.5 million tonnes. We are currently debottlenecking the Medicine Hat facility which we expect will add a further 0.1 million tonnes of annual production capacity by the end of the third quarter of 2013.
Chile
During 2012, we operated our Chile methanol facilities significantly below annual production capacity due to insufficient natural gas feedstock.
In 2007, our natural gas suppliers from Argentina curtailed all gas supply to our plants in Chile. Under the existing circumstances, we do not expect to receive any further natural gas supply from Argentina. As a result of the Argentinean natural gas supply issues, all of the methanol production at our Chile facilities since June 2007 has been produced with natural gas from Chile.
Over the past few years, investments have been made by us and others to accelerate the exploration and development of natural gas in southern Chile. However, the potential for a significant increase in gas production is more challenging than we had originally
| | | | |
10 Methanex Corporation | Annual Report 2012 | | Management’s Discussion & Analysis | | |
Management’s Discussion & Analysis
anticipated. As a result of the short-term outlook for gas supply in Chile, we expect to idle our Chile operations in March 2013 due to insufficient natural gas feedstock to keep the plant operating through the southern hemisphere winter. We are continuing to work with Empresa Nacional del Petroleo (ENAP) and others to secure sufficient natural gas to sustain our operations, and while the restart of a Chile plant is possible later in 2013, the restart is dependent on securing a sustainable natural gas position to operate over the medium term.
The future of our Chile operations is primarily dependent on the level of exploration and development in southern Chile and our ability to secure a sustainable natural gas supply to our facilities on economic terms. Refer to theRisk Factors and Risk Management – Chilesection on page 25 for more information.
HOW WE ANALYZE OUR BUSINESS
Our operations consist of a single operating segment – the production and sale of methanol. We review our financial results by analyzing changes in the components of Adjusted EBITDA (refer to theSupplemental Non-GAAP Measures section on page 34 for a description of Adjusted EBITDA and a reconciliation to the most comparable GAAP measure), mark-to-market impact of share-based compensation, Louisiana project relocation expenses and charges, asset impairment charges, depreciation and amortization, finance costs, finance income and other expenses, and income taxes.
In addition to the methanol that we produce at our facilities (“Methanex-produced methanol”), we also purchase and re-sell methanol produced by others (“purchased methanol”) and we sell methanol on a commission basis. We analyze the results of all methanol sales together, excluding commission sales volumes. The key drivers of change in Adjusted EBITDA are average realized price, cash costs and sales volume, which are defined and calculated as follows:
| | |
PRICE | | The change in Adjusted EBITDA as a result of changes in average realized price is calculated as the difference from period to period in the selling price of methanol multiplied by the current period total methanol sales volume excluding commission sales volume plus the difference from period to period in commission revenue. |
CASH COSTS | | The change in Adjusted EBITDA as a result of changes in cash costs is calculated as the difference from period to period in cash costs per tonne multiplied by the current period total methanol sales volume excluding commission sales volume in the current period. The cash costs per tonne is the weighted average of the cash cost per tonne of Methanex-produced methanol and the cash cost per tonne of purchased methanol. The cash cost per tonne of Methanex-produced methanol includes absorbed fixed cash costs per tonne and variable cash costs per tonne. The cash cost per tonne of purchased methanol consists principally of the cost of methanol itself. In addition, the change in Adjusted EBITDA as a result of changes in cash costs includes the changes from period to period in unabsorbed fixed production costs, consolidated selling, general and administrative expenses and fixed storage and handling costs. |
VOLUME | | The change in Adjusted EBITDA as a result of changes in sales volume is calculated as the difference from period to period in total methanol sales volume, excluding commission sales volumes, multiplied by the margin per tonne for the prior period. The margin per tonne for the prior period is the weighted average margin per tonne of Methanex-produced methanol and margin per tonne of purchased methanol. The margin per tonne for Methanex-produced methanol is calculated as the selling price per tonne of methanol less absorbed fixed cash costs per tonne and variable cash costs per tonne. The margin per tonne for purchased methanol is calculated as the selling price per tonne of methanol less the cost of purchased methanol per tonne. |
We own 63.1% of the Atlas methanol facility and market the remaining 36.9% of its production through a commission offtake agreement. We account for this investment using proportionate consolidation, which results in 63.1% of its results being included in revenues and expenses with the remaining 36.9% portion included as commission income.
We own 60% of the 1.26 million tonne per year Egypt methanol facility and market the remaining 40% of its production through a commission offtake agreement. We account for this investment using consolidation accounting, which results in 100% of the revenues and expenses being included in our financial statements with the other investors’ interest in the methanol facility being presented as “non-controlling interests”. For the purposes of analyzing our business, Adjusted EBITDA and Adjusted cash flows from operating activities exclude the amounts associated with the other investors’ 40% non-controlling interest, which are included in commission income on a consistent basis with how we present the Atlas facility.
| | | | |
| | Management’s Discussion & Analysis | | Methanex Corporation | Annual Report 2012 11 |
Management’s Discussion & Analysis
FINANCIAL RESULTS
For the year ended December 31, 2012, we reported Adjusted EBITDA of $429 million and Adjusted net income of $180 million ($1.90 per share on a diluted basis), compared with Adjusted EBITDA of $427 million and Adjusted net income of $182 million ($1.93 per share on a diluted basis) for the year ended December 31, 2011.
In addition, we recorded a non-cash before-tax asset impairment charge of $297 million ($193 million after-tax) related to the carrying value of our Chile assets and a before-tax $65 million charge to earnings related to Louisiana project relocation expenses and charges ($41 million after-tax). Including these items, we reported a net loss attributable to Methanex shareholders for the year ended December 31, 2012 of $68 million ($0.73 loss per share on a diluted basis), compared with net income attributable to Methanex shareholders for the year ended December 31, 2011 of $201 million ($2.06 income per share on a diluted basis).
We calculate Adjusted EBITDA and Adjusted net income by excluding amounts associated with the 40% non-controlling interest in Egypt that we do not own, the mark-to-market impact of share-based compensation as a result of changes in our share price and items that are considered by management to be non-operational, including asset impairment charges and Louisiana project relocation expenses and charges. Refer to theSupplemental Non-GAAP Measures section on page 34 for further discussion on how we calculate these measures.
A reconciliation from net income (loss) attributable to Methanex shareholders to Adjusted net income and the calculation of Adjusted diluted net income per common share is as follows:
| | | | | | | | |
| | |
($ MILLIONS EXCEPT NUMBER OF SHARES AND PER SHARE AMOUNTS) | | 2012 | | | 2011 | |
Net income (loss) attributable to Methanex shareholders | | $ | (68 | ) | | $ | 201 | |
Mark-to-market impact of share-based compensation, net of tax | | | 14 | | | | (19 | ) |
Louisiana project relocation expenses and charges, net of tax | | | | | | | | |
Cash expense | | | 23 | | | | – | |
Non-cash charge | | | 18 | | | | – | |
Asset impairment charge, net of tax | | | 193 | | | | – | |
Adjusted net income1 | | $ | 180 | | | $ | 182 | |
Diluted weighted average shares outstanding (millions) | | | 94 | | | | 94 | |
Adjusted diluted net income per common share1 2 | | $ | 1.90 | | | $ | 1.93 | |
1 | These items are non-GAAP measures that do not have any standardized meaning prescribed by GAAP and therefore are unlikely to be comparable to similar measures presented by other companies. Refer to the Supplemental Non-GAAP Measures section on page 34 for a description of the non-GAAP measures and a reconciliation to the most comparable GAAP measures. | |
2 | For the year ended December 31, 2012, stock options have been excluded from the calculation of diluted net loss per common share (attributable to Methanex shareholders) as their effect would be anti-dilutive. However, for the calculation of adjusted diluted net income per common share (attributable to Methanex shareholders) stock options have been included in the denominator and the diluted weighted average number of common shares for the year ended December 31, 2012 is 95 million. | |
We review our financial results by analyzing changes in the components of Adjusted EBITDA, mark-to-market impact of share-based compensation, Louisiana project relocation expenses and charges, asset impairment charges, depreciation and amortization, finance costs, finance income and other expenses, and income taxes.
| | | | |
12 Methanex Corporation | Annual Report 2012 | | Management’s Discussion & Analysis | | |
Management’s Discussion & Analysis
A summary of our consolidated statements of income for 2012 and 2011 is as follows:
| | | | | | | | |
| | |
($ MILLIONS) | | 2012 | | | 2011 | |
Consolidated statements of income: | | | | | | | | |
Revenue | | $ | 2,673 | | | $ | 2,608 | |
Cost of sales and operating expenses, excluding mark-to-market impact of share-based compensation | | | (2,171 | ) | | | (2,128 | ) |
| | | 502 | | | | 480 | |
Comprised of: | | | | | | | | |
Adjusted EBITDA (attributable to Methanex shareholders)1 | | | 429 | | | | 427 | |
Amounts attributable to non-controlling interests | | | 73 | | | | 53 | |
| | | 502 | | | | 480 | |
Mark-to-market impact of share-based compensation | | | (16 | ) | | | 21 | |
Louisiana project relocation expenses and charges | | | (65 | ) | | | – | |
Asset impairment charge | | | (297 | ) | | | – | |
Depreciation and amortization | | | (172 | ) | | | (157 | ) |
Operating income (loss)1 | | | (48 | ) | | | 344 | |
Finance costs | | | (71 | ) | | | (62 | ) |
Finance income and other expenses | | | 1 | | | | 2 | |
Income tax recovery (expense) | | | 84 | | | | (56 | ) |
Net income (loss) | | $ | (34 | ) | | $ | 228 | |
Net income (loss) attributable to Methanex shareholders | | $ | (68 | ) | | $ | 201 | |
1 | These items are non-GAAP measures that do not have any standardized meaning prescribed by GAAP and therefore are unlikely to be comparable to similar measures presented by other companies. Refer to the Supplemental Non-GAAP Measures section on page 34 for a description of the non-GAAP measures and a reconciliation to the most comparable GAAP measures. | |
Revenue
There are many factors that impact our global and regional revenue levels. The methanol business is a global commodity industry affected by supply and demand fundamentals. Due to the diversity of the end products in which methanol is used, demand for methanol largely depends upon levels of industrial production, energy prices and changes in general economic conditions, which can vary across the major international methanol markets. Methanol prices have been relatively stable over the past two years and our revenue for 2012 was $2.7 billion compared with 2011 revenue of $2.6 billion.
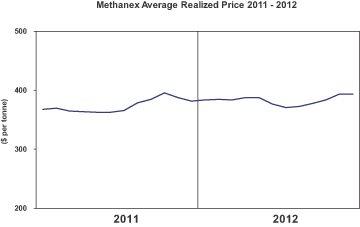
| | | | |
| | Management’s Discussion & Analysis | | Methanex Corporation | Annual Report 2012 13 |
Management’s Discussion & Analysis
Global methanol demand grew approximately 5% in 2012, to approximately 51 million tonnes, excluding methanol demand from integrated methanol-to-olefins facilities. Increases in demand were driven by both traditional derivatives and energy-related applications in Asia, particularly in China.
Industry supply additions outside of China in 2012 consisted primarily of the restart of our second Motunui facility in New Zealand, which added 0.7 million tonnes to the site’s operating capacity on an annualized basis, and the restart of a 0.7 million tonne facility in Beaumont, Texas. New production from supply additions inside China was consumed in that country and China continued to be a significant net importer of methanol.
Overall, industry conditions were balanced in 2012 and this led to a relatively stable methanol pricing environment. Our average realized price for 2012 was $382 per tonne compared with $374 per tonne in 2011.
The methanol industry is highly competitive and prices are affected by supply and demand fundamentals. We publish regional non-discounted reference prices for each major methanol market and these posted prices are reviewed and revised monthly or quarterly based on industry fundamentals and market conditions. Most of our customer contracts use published Methanex reference prices as a basis for pricing, and we offer discounts to customers based on various factors. Our average non-discounted published reference price for 2012 was $443 per tonne compared with $440 per tonne in 2011.
Distribution of Revenue
The geographic distribution of revenue by customer location for 2012 was similar to 2011. Details are as follows:
| | | | | | | | | | | | | | | | |
| | |
($ MILLIONS, EXCEPT WHERE NOTED) | | 2012 | | | 2011 | |
Canada | | $ | 180 | | | | 7 | % | | $ | 176 | | | | 7 | % |
United States | | | 563 | | | | 21 | % | | | 632 | | | | 24 | % |
Europe | | | 772 | | | | 29 | % | | | 679 | | | | 26 | % |
China | | | 409 | | | | 15 | % | | | 431 | | | | 17 | % |
Korea | | | 286 | | | | 11 | % | | | 267 | | | | 10 | % |
Other Asia | | | 188 | | | | 7 | % | | | 155 | | | | 6 | % |
Latin America | | | 275 | | | | 10 | % | | | 268 | | | | 10 | % |
| | $ | 2,673 | | | | 100 | % | | $ | 2,608 | | | | 100 | % |
Adjusted EBITDA (Attributable to Methanex Shareholders)
2012 Adjusted EBITDA was $429 million compared with $427 million in 2011. The key drivers of changes in our Adjusted EBITDA are average realized price, sales volume and cash costs as described below (refer to theHow We Analyze Our Business section on page 11 for more information).
| | | | |
| |
($ MILLIONS) | | 2012 VS. 2011 | |
Average realized price | | $ | 57 | |
Sales volume | | | (5 | ) |
Total cash costs | | | (50 | ) |
Increase in Adjusted EBITDA | | $ | 2 | |
Average Realized Price
Our average realized price for the year ended December 31, 2012 was $382 per tonne compared with $374 per tonne for 2011, and this increased Adjusted EBITDA by $57 million (refer to theRevenue section on page 13 for more information).
Sales Volumes
Methanol sales volumes, excluding commission sales volumes, for the year ended December 31, 2012 were 64,000 tonnes lower than in 2011, and this decreased Adjusted EBITDA by $5 million. Including commission sales volumes from the Atlas and Egypt facilities, our total methanol sales volumes were 7.5 million tonnes in both 2012 and 2011.
| | | | |
14 Methanex Corporation | Annual Report 2012 | | Management’s Discussion & Analysis | | |
Management’s Discussion & Analysis
Total Cash Costs
The primary drivers of changes in our total cash costs are changes in the cost of methanol we produce at our facilities (Methanex-produced methanol) and changes in the cost of methanol we purchase from others (purchased methanol). All of our production facilities except Medicine Hat are underpinned by natural gas purchase agreements with pricing terms that include base and variable price components. We supplement our production with methanol produced by others through methanol offtake contracts and purchases on the spot market to meet customer needs and support our marketing efforts within the major global markets.
We have adopted the first-in, first-out method of accounting for inventories and it generally takes between 30 and 60 days to sell the methanol we produce or purchase. Accordingly, the changes in Adjusted EBITDA as a result of changes in Methanex-produced and purchased methanol costs primarily depend on changes in methanol pricing and the timing of inventory flows.
The changes in our total cash costs for 2012 compared with 2011 were due to the following:
| | | | |
| |
($ MILLIONS) | | 2012 VS. 2011 | |
Methanex-produced methanol costs | | $ | (34 | ) |
Purchased methanol costs | | | (22 | ) |
Proportion of Methanex-produced methanol sales | | | 36 | |
Other, net | | | (30 | ) |
Increase in total cash costs | | $ | (50 | ) |
Methanex-Produced Methanol Costs
Natural gas is the primary feedstock at our methanol facilities and is the most significant component of Methanex-produced methanol costs. We purchase natural gas for the New Zealand, Trinidad, Egypt and Chile methanol facilities under natural gas purchase agreements where the unique terms of each contract include a base price and a variable price component linked to the price of methanol to reduce our commodity price risk exposure. The variable price component of each gas contract is adjusted by a formula related to methanol prices above a certain level. We believe these pricing relationships enable each facility to be competitive throughout the methanol price cycle. Methanex-produced methanol costs were higher in 2012 compared with 2011 by $34 million, primarily due to the impact of higher realized methanol prices on our natural gas costs and a change in the mix of production sold from inventory. For additional information regarding our natural gas supply agreements refer to theSummary of Contractual Obligations and Commercial Commitments section on page 21.
Purchased Methanol Costs
A key element of our corporate strategy is global leadership, and as such we have built a leading market position in each of the major global markets where methanol is sold. We supplement our production with purchased methanol through methanol offtake contracts and on the spot market to meet customer needs and support our marketing efforts within the major global markets. In structuring purchase agreements, we look for opportunities that provide synergies with our existing supply chain that allow us to purchase methanol in the lowest-cost region. The cost of purchased methanol consists principally of the cost of the methanol itself, which is directly related to the price of methanol at the time of purchase. As a result of higher methanol prices in 2012, and the timing of purchases, the cost of purchased methanol per tonne increased and this decreased Adjusted EBITDA by $22 million compared with 2011.
Proportion of Methanex-Produced Methanol Sales
The cost of purchased methanol is directly linked to the selling price for methanol at the time of purchase and the cost of purchased methanol is generally higher than the cost of Methanex-produced methanol. Accordingly, an increase in the proportion of Methanex-produced methanol sales results in a decrease in our overall cost structure for a given period. The proportion of Methanex-produced methanol sales for the year ended 2012 was higher compared with 2011 and this increased Adjusted EBITDA by $36 million. We increased our sales volumes of methanol produced at the New Zealand, Egypt and Medicine Hat facilities and this more than offset the decrease in sales volumes from the Chile facility.
| | | | |
| | Management’s Discussion & Analysis | | Methanex Corporation | Annual Report 2012 15 |
Management’s Discussion & Analysis
Other, Net
Our investment in global distribution and supply infrastructure includes a dedicated fleet of ocean-going vessels. We utilize these vessels to enhance value to customers by providing reliable and secure supply and to optimize supply chain costs overall. For the year ended December 31, 2012 compared with 2011, ocean freight and other logistics costs were higher by $10 million, primarily as a result of a one-time charge to earnings to terminate a time charter vessel lease contract. In addition to changes in fuel prices, logistics costs can vary from period to period depending on the levels of production from each of our production facilities and the resulting impact on our supply chain.
We experienced an equipment failure at our Atlas facility in July 2011. Our operations are covered by business interruption insurance and we finalized our claim related to this event in 2012. We recorded a $17 million recovery in 2011 related to this event with the remaining $11 million recorded in 2012.
In October 2012, we completed a restructuring of our Chile operations which reduced the size of our workforce and resulted in a $5 million charge to earnings in 2012. The remaining change in other cash costs is primarily due to the timing of recognizing fixed manufacturing costs in earnings. We allocate fixed manufacturing costs to inventory based on the normal operating capacity of our manufacturing facilities. During 2012, primarily due to our Chile and Egypt facilities operating below capacity for certain periods, a portion of fixed manufacturing costs were charged directly to earnings rather than to inventory and this decreased Adjusted EBITDA in 2012.
Mark-to-Market Impact of Share-Based Compensation
We grant share-based awards as an element of compensation. Share-based awards granted include stock options, share appreciation rights, tandem share appreciation rights, deferred share units, restricted share units and performance share units. For all the share-based awards, share-based compensation is recognized over the related vesting period for the proportion of the service that has been rendered at each reporting date. Share-based compensation includes an amount related to the grant-date value and a mark-to-market impact as a result of subsequent changes in the Company’s share price. The grant-date value amount is included in Adjusted EBITDA and Adjusted net income. The mark-to-market impact of share-based compensation as a result of changes in our share price is excluded from Adjusted EBITDA and Adjusted net income and analyzed separately.
| | | | | | | | |
| | |
($ MILLIONS, EXCEPT AS NOTED) | | 2012 | | | 2011 | |
Methanex Corporation share price1 | | $ | 31.87 | | | $ | 22.82 | |
Grant-date fair value expense included in Adjusted EBITDA | | | 20 | | | | 16 | |
Mark-to-market impact due to change in share price | | | 16 | | | | (21 | ) |
Total share-based compensation expense (recovery) | | $ | 36 | | | $ | (5 | ) |
1 | US dollar share price of Methanex Corporation as quoted on NASDAQ Global Market on the last trading day of the respective period. | |
For stock options, the cost is measured based on an estimate of the fair value at the date of grant using the Black-Scholes option pricing model, and this grant-date fair value is recognized as compensation expense over the related vesting period with no subsequent re-measurement in fair value. Accordingly, share-based compensation expense associated with stock options will not vary significantly from period to period.
Share appreciation rights (SARs) and tandem share appreciation rights (TSARs) are units that grant the holder the right to receive a cash payment upon exercise for the difference between the market price of the Company’s common shares and the exercise price, which is determined at the date of grant. The fair values of SARs and TSARs are re-measured each quarter using the Black-Scholes option pricing model, which considers the market value of the Company’s common shares on the last trading day of each quarter.
Deferred, restricted and performance share units are grants of notional common shares that are redeemable for cash based on the market value of the Company’s common shares and are non-dilutive to shareholders. Performance share units have an additional feature where the ultimate number of units that vest will be determined by the Company’s total shareholder return in relation to a predetermined target over the period to vesting. The number of units that will ultimately vest will be in the range of 50% to 120% of the original grant. For deferred, restricted and performance share units, the value is initially measured at the grant date and subsequently re-measured based on the market value of the Company’s common shares on the last trading day of each quarter.
| | | | |
16 Methanex Corporation | Annual Report 2012 | | Management’s Discussion & Analysis | | |
Management’s Discussion & Analysis
Louisiana Project Relocation Expenses and Charges
In July 2012, we reached a final investment decision to proceed with the project to relocate an idle Chile facility to Geismar, Louisiana. The project will add approximately one million tonnes of operating capacity and is expected to be operational by the end of 2014. Under IFRS, certain costs associated with relocating an asset are not eligible for capitalization and are required to be charged directly to earnings. During 2012, we charged $39 million ($23 million after-tax) of Louisiana project relocation expenses directly to earnings. In addition, a non-cash charge of $26 million ($18 million after-tax) was recorded to earnings in 2012 related to the carrying value of the Chile facility that is being relocated to Louisiana.
Asset Impairment Charge
As a result of the continuing challenges related to securing a sustainable natural gas supply in Chile, we recorded a non-cash before-tax asset impairment charge of $297 million ($193 million after-tax) to write down the carrying value of our Chile assets at December 31, 2012 to $245 million. The remaining $245 million carrying value excludes the first Chile facility that is being relocated to Geismar, Louisiana but includes the second facility that management is also considering for relocation to Geismar. Refer to theCritical Accounting Estimates – Recoverability of Asset Carrying Values section on page 33 for more information.
Depreciation and Amortization
Depreciation and amortization was $172 million for the year ended December 31, 2012 compared with $157 million for the same period in 2011. The increase in depreciation and amortization in 2012 compared with 2011 is primarily a result of depreciation associated with the Egypt (100% basis) and Medicine Hat methanol facilities, which commenced operations in the first and second quarters of 2011, respectively, and depreciation associated with the second Motunui facility in New Zealand, which commenced operations in the third quarter of 2012.
Finance Costs
| | | | | | | | |
| | |
($ MILLIONS) | | 2012 | | | 2011 | |
Finance costs before capitalized interest | | $ | 73 | | | $ | 70 | |
Less capitalized interest | | | (2 | ) | | | (8 | ) |
Finance costs | | $ | 71 | | | $ | 62 | |
Finance costs before capitalized interest primarily relate to interest expense on the unsecured notes and limited recourse debt facilities. Capitalized interest in 2012 relates to interest costs capitalized for the Louisiana project while capitalized interest in 2011 relates to the Egypt project.
Finance Income and Other Expenses
Finance income and other expenses were $1 million and $2 million, respectively, for the years ended December 31, 2012 and 2011.
Income Taxes
A summary of our income taxes for 2012 compared with 2011 is as follows:
| | | | | | | | | | | | |
| |
| | YEAR ENDED DEC 31, 2012 | |
($ MILLIONS, EXCEPT WHERE NOTED) | | AMOUNTS EXCLUDING LOUISIANA PROJECT RELOCATION EXPENSESAND CHARGES AND ASSET IMPAIRMENT CHARGE | | | LOUISIANA PROJECT RELOCATION EXPENSES AND CHARGES AND ASSET IMPAIRMENT CHARGE | | | TOTAL | |
Income (loss) before income tax expense | | $ | 244 | | | $ | (362 | ) | | $ | (118 | ) |
Income tax recovery (expense) | | | (44 | ) | | | 128 | | | | 84 | |
Net income (loss) | | $ | 200 | | | $ | (234 | ) | | $ | (34 | ) |
Effective tax rate | | | 18 | % | | | 35 | % | | | 71 | % |
| | | | |
| | Management’s Discussion & Analysis | | Methanex Corporation | Annual Report 2012 17 |
Management’s Discussion & Analysis
| | | | | | | | | | | | |
| |
| | YEAR ENDED DEC 31, 2011 | |
($ MILLIONS, EXCEPT WHERE NOTED) | | AMOUNTS EXCLUDING LOUISIANA PROJECT RELOCATION EXPENSESAND CHARGES AND ASSET IMPAIRMENT CHARGE | | | LOUISIANA PROJECT RELOCATION EXPENSES AND CHARGES AND ASSET IMPAIRMENT CHARGE | | | TOTAL | |
Income before income tax expense | | $ | 284 | | | $ | – | | | $ | 284 | |
Income tax expense | | | (56 | ) | | | – | | | | (56 | ) |
Net income | | $ | 228 | | | $ | – | | | $ | 228 | |
Effective tax rate | | | 20 | % | | | – | | | | 20 | % |
For the year ended December 31, 2012, the effective tax rate excluding income taxes related to Louisiana project relocation expenses and charges and the asset impairment charge was 18% compared with 20% for the year ended December 31, 2011.
We earn the majority of our pre-tax earnings in New Zealand, Trinidad, Egypt, Canada and Chile. In Trinidad and Chile, the statutory tax rate is 35%, and in Egypt, the statutory tax rate is 25%. Our Atlas facility in Trinidad has partial relief from corporation income tax until 2014. We have significant loss carryforwards in Canada and New Zealand that have not been recognized for accounting purposes. During 2012, we earned a higher proportion of our consolidated income from methanol produced in jurisdictions with low effective tax rates and this contributed to a lower effective tax rate compared with 2011.
In Chile, the tax rate consists of a first-tier tax that is payable when income is earned and a second-tier tax that is due when earnings are distributed from Chile. The second category tax is initially recorded as future income tax expense and is subsequently reclassified to current income tax expense when earnings are distributed. Accordingly, the ratio of Chile’s current income tax expense to total income tax expense is dependent on the level of cash distributed from Chile.
For additional information regarding income taxes, refer to note 17 of our 2012 consolidated financial statements.
LIQUIDITY AND CAPITAL RESOURCES
A summary of our consolidated statements of cash flows is as follows:
| | | | | | | | |
| | |
($ MILLIONS) | | 2012 | | | 2011 | |
Cash flows from operating activities: | | | | | | | | |
Cash flows from operating activities before changes in non-cash working capital1 | | $ | 436 | | | $ | 444 | |
Changes in non-cash working capital | | | 22 | | | | 36 | |
| | | 458 | | | | 480 | |
Cash flows from financing activities: | | | | | | | | |
Dividend payments | | | (68 | ) | | | (62 | ) |
Interest paid, including interest rate swap settlements | | | (65 | ) | | | (60 | ) |
Net proceeds on issue of long-term debt | | | 590 | | | | 3 | |
Repayment of long-term debt and limited recourse debt | | | (251 | ) | | | (50 | ) |
Other | | | (41 | ) | | | (11 | ) |
| | | 165 | | | | (180 | ) |
Cash flows from investing activities: | | | | | | | | |
Property, plant and equipment | | | (134 | ) | | | (126 | ) |
Louisiana project expenditures | | | (74 | ) | | | (1 | ) |
Oil and gas properties | | | (33 | ) | | | (30 | ) |
GeoPark repayments | | | 10 | | | | 7 | |
Changes in non-cash working capital relating to investing activities | | | 3 | | | | 7 | |
| | | (228 | ) | | | (143 | ) |
Increase in cash and cash equivalents | | | 395 | | | | 157 | |
Cash and cash equivalents, end of year | | $ | 746 | | | $ | 351 | |
1 | These items are non-GAAP measures that do not have any standardized meaning prescribed by GAAP and therefore are unlikely to be comparable to similar measures presented by other companies. Refer to the Supplemental Non-GAAP Measures section on page 34 for a description of the non-GAAP measures and a reconciliation to the most comparable GAAP measures. | |
| | | | |
18 Methanex Corporation | Annual Report 2012 | | Management’s Discussion & Analysis | | |
Management’s Discussion & Analysis
Cash Flow Highlights
Cash Flows from Operating Activities
Cash flows from operating activities for the year ended December 31, 2012 were $458 million compared with $480 million for 2011. The decrease in cash flows from operating activities is primarily due to lower net income (loss), after excluding depreciation and amortization, Louisiana project relocation non-cash charges, asset impairment charges and finance costs, and changes in non-cash working capital. The following table provides a summary of these items for 2012 and 2011:
| | | | | | | | |
| | |
($ MILLIONS) | | 2012 | | | 2011 | |
Net income (loss) | | $ | (34 | ) | | $ | 228 | |
Add (deduct) non-cash items: | | | | | | | | |
Depreciation and amortization | | | 172 | | | | 157 | |
Louisiana project relocation non-cash charges, net of tax | | | 18 | | | | – | |
Asset impairment charge, net of tax | | | 193 | | | | – | |
Finance costs | | | 71 | | | | 62 | |
Other | | | 16 | | | | (3 | ) |
Cash flows from operating activities before changes in non-cash working capital1 | | | 436 | | | | 444 | |
Changes in non-cash working capital: | | | | | | | | |
Trade and other receivables | | | (45 | ) | | | (59 | ) |
Inventories | | | 27 | | | | (44 | ) |
Prepaid expenses | | | (4 | ) | | | 2 | |
Accounts payable and accrued liabilities, including long-term payables | | | 44 | | | | 137 | |
| | | 22 | | | | 36 | |
Cash flows from operating activities | | $ | 458 | | | $ | 480 | |
Adjusted cash flows from operating activities (attributable to Methanex shareholders)1 | | $ | 403 | | | $ | 392 | |
1 | These items are non-GAAP measures that do not have any standardized meaning prescribed by GAAP and therefore are unlikely to be comparable to similar measures presented by other companies. Refer to the Supplemental Non-GAAP Measures section on page 34 for a description of the non-GAAP measures and a reconciliation to the most comparable GAAP measures. | |
For a discussion of the changes in net income (loss), depreciation and amortization, Louisiana project relocation expenses and charges, asset impairment charges and finance costs, refer to the analysis of our financial results on page 12.
Changes in non-cash working capital increased cash flows from operating activities by $22 million for the year ended December 31, 2012 compared with $36 million for the year ended December 31, 2011. Trade and other receivables increased in 2012 and this decreased cash flows from operating activities by $45 million, primarily due to the impact on customer receivables of a higher average realized methanol price. Inventories decreased primarily due to a lower volume of purchased methanol in ending inventory and this increased cash flows from operating activities by $27 million. Accounts payable and accrued liabilities, including long-term payables increased cash flows from operating activities by $44 million, primarily due to the impact of higher methanol prices on natural gas supply payables.
Adjusted cash flows from operating activities were $403 million for 2012 compared with $392 million for 2011 (refer to theSupplemental Non-GAAP Measures section on page 34 for a reconciliation of cash flows from operating activities to adjusted cash flows from operating activities).
Cash Flows from Financing Activities
During 2012, we increased our regular quarterly dividend by 9% to $0.185 per share, beginning with the dividend payable on June 30, 2012. Total dividend payments in 2012 were $68 million compared with $62 million in 2011.
Also during 2012, we issued two separate tranches of unsecured notes bearing interest rates of 5.25% (effective yield of 5.3%) and 3.25% (effective yield of 3.4%), respectively. The $250 million and $350 million of unsecured notes are due on March 1, 2022 and December 15, 2019, respectively.
During 2012, we repaid $200 million of unsecured notes bearing an interest rate of 8.75% and $51 million of other limited recourse debt. The other limited recourse debt consisted of $34 million of Egypt limited recourse debt facilities, $15 million of Atlas limited recourse debt facilities and $2 million of other limited recourse debt compared with total repayments in 2011 of $50 million. We have entered into interest rate swap contracts to swap the LIBOR-based interest payments on the Egypt limited recourse debt facilities for an average aggregated fixed rate of 4.8% plus a spread on approximately 75% of the Egypt limited recourse debt facilities for the period to March 31,
| | | | |
| | Management’s Discussion & Analysis | | Methanex Corporation | Annual Report 2012 19 |
Management’s Discussion & Analysis
2015 (refer to theFinancial Instruments section on page 23 for more information). The cash settlements associated with these interest rate swap contracts during 2012 and 2011 were included in interest paid of $65 million.
Cash Flows from Investing Activities
During 2012, we reached a final investment decision to proceed with the project to relocate an idle Chile facility to Geismar, Louisiana with an estimated project cost of approximately $550 million. During 2012, we incurred $113 million of expenditures in relation to the project, of which $74 million was capitalized to property, plant and equipment with the remaining amount charged to earnings.
Also during 2012, we incurred a total of $68 million to increase our production capability in New Zealand. We restarted a second Motunui facility in mid-2012 and recently announced our commitment to further increase capacity with the debottleneck of the Motunui site and the restart of the Waitara Valley facility. We also incurred $66 million of costs associated with turnarounds, catalyst and maintenance activities at our other facilities.
We incurred a total of $33 million in 2012 related to our share of oil and gas expenditures in southern Chile. In addition to other exploration blocks in which we are participating, we have an agreement with ENAP to invest in natural gas exploration and development in the Dorado Riquelme exploration block in southern Chile. Under the arrangement, we fund a 50% participation in the block and receive 100% of the natural gas produced in the block.
We also have agreements with GeoPark Chile Limited (GeoPark) under which we have provided $57 million in financing to support and accelerate GeoPark’s natural gas exploration and development activities in southern Chile. During 2012, GeoPark repaid approximately $10 million, bringing cumulative repayments for this financing to $50 million as at December 31, 2012. We have no further obligations to provide funding to GeoPark.
Liquidity and Capitalization
Our objectives in managing liquidity and capital are to provide financial capacity and flexibility to meet our strategic objectives, to provide an adequate return to shareholders commensurate with the level of risk and to return excess cash through a combination of dividends and share repurchases.
The following table provides information on our liquidity and capitalization position as at December 31, 2012 and December 31, 2011:
| | | | | | | | |
| | |
($ MILLIONS, EXCEPT WHERE NOTED) | | 2012 | | | 2011 | |
Liquidity: | | | | | | | | |
Cash and cash equivalents | | $ | 746 | | | $ | 351 | |
Undrawn credit facilities | | | 400 | | | | 200 | |
Total liquidity | | | 1,146 | | | | 551 | |
Capitalization: | | | | | | | | |
Unsecured notes | | | 739 | | | | 349 | |
Limited recourse debt facilities, including current portion | | | 506 | | | | 554 | |
Total debt | | | 1,245 | | | | 903 | |
Non-controlling interest | | | 188 | | | | 197 | |
Shareholders’ equity | | | 1,290 | | | | 1,405 | |
Total capitalization | | $ | 2,723 | | | $ | 2,505 | |
Total debt to capitalization1 | | | 46 | % | | | 36 | % |
Net debt to capitalization2 | | | 25 | % | | | 26 | % |
1 | Defined as total debt (including 100% of Egypt limited recourse debt facilities) divided by total capitalization. | |
2 | Defined as total debt (including 100% of Egypt limited recourse debt facilities) less cash and cash equivalents divided by total capitalization less cash and cash equivalents. | |
We manage our liquidity and capital structure and make adjustments to it in light of changes to economic conditions, the underlying risks inherent in our operations and the capital requirements to maintain and grow our business. The strategies we employ include the issue or repayment of general corporate debt, the issue of project debt, the issue of equity, the payment of dividends and the repurchase of shares.
We are not subject to any statutory capital requirements and have no commitments to sell or otherwise issue common shares except pursuant to outstanding employee stock options.
| | | | |
20 Methanex Corporation | Annual Report 2012 | | Management’s Discussion & Analysis | | |
Management’s Discussion & Analysis
We operate in a highly competitive commodity industry and believe that it is appropriate to maintain a conservative balance sheet and retain financial flexibility. At December 31, 2012, we had a strong balance sheet with a cash balance of $746 million, including $36 million relating to the non-controlling interest in Egypt, and a $400 million undrawn credit facility. We invest our cash only in highly rated instruments that have maturities of three months or less to ensure preservation of capital and appropriate liquidity.
At December 31, 2012, our long-term debt obligations included $750 million in unsecured notes ($150 million that matures in 2015, $350 million that matures in 2019 and $250 million that matures in 2022), $450 million related to the Egypt limited recourse debt facilities (100% basis), $50 million related to the Atlas limited recourse debt facilities and $17 million of other limited recourse debt.
We have covenant and default provisions on our long-term debt obligations and we also have certain covenants that could restrict access to the credit facility. The Egypt limited recourse debt facilities contain a covenant to complete by March 31, 2013 certain land title registrations and related mortgages that require action by Egyptian government entities and which we do not expect to complete by March 31, 2013. The Company is seeking a waiver from the lenders. We do not believe the finalization of these items is material to the security provided to the lenders.
At December 31, 2012, management believes the Company was in compliance with all of the covenants and default provisions related to its long-term debt obligations.
Our planned capital maintenance expenditure program directed towards maintenance, turnarounds and catalyst changes for existing operations is currently estimated to total approximately $160 million to the end of 2013, including major refurbishments at some of our plants. In July 2012, we reached a final investment decision to proceed with the project to relocate an idle Chile facility to Geismar, Louisiana with estimated project costs of approximately $550 million. The plant is expected to be operational by the end of 2014 and during 2012 we spent $113 million on the project. We are in the process of debottlenecking the Medicine Hat, Canada and Motunui, New Zealand facilities and restarting the Waitara Valley facility. These projects will result in additional capital expenditures of approximately $100 million by the end of 2013. We believe that we have the financial capacity to fund these growth initiatives with cash on hand, cash generated from operations and the undrawn bank facility.
We believe we are well positioned to meet our financial commitments, invest to grow the Company and continue to deliver on our commitment to return excess cash to shareholders.
Summary of Contractual Obligations and Commercial Commitments
A summary of the estimated amount and estimated timing of cash flows related to our contractual obligations and commercial commitments as at December 31, 2012 is as follows:
| | | | | | | | | | | | | | | | | | | | | | |
($ MILLIONS) | | 2013 | | | 2014-2015 | | | 2016-2017 | | | AFTER 2017 | | | | | TOTAL | |
Long-term debt repayments | | $ | 53 | | | $ | 262 | | | $ | 101 | | | $ | 852 | | | | | $ | 1,268 | |
Long-term debt interest obligations | | | 60 | | | | 99 | | | | 66 | | | | 102 | | | | | | 327 | |
Repayments of other long-term liabilities | | | 30 | | | | 110 | | | | 19 | | | | 88 | | | | | | 247 | |
Natural gas and other | | | 263 | | | | 366 | | | | 266 | | | | 1,020 | | | | | | 1,915 | |
Operating lease commitments | | | 124 | | | | 170 | | | | 134 | | | | 281 | | | | | | 709 | |
| | $ | 530 | | | $ | 1,007 | | | $ | 586 | | | $ | 2,343 | | | | | $ | 4,466 | |
Long-Term Debt Repayments and Interest Obligations
We have $150 million of unsecured notes that mature in 2015, $350 million of unsecured notes that mature in 2019 and $250 million of unsecured notes that mature in 2022. The remaining debt repayments represent the total expected principal repayments relating to the Egypt project debt, our proportionate share of expected principal repayments related to the Atlas limited recourse debt facilities and other limited recourse debt. Interest obligations related to variable interest rate long-term debt were estimated using current interest rates in effect at December 31, 2012. For additional information, refer to note 9 of our 2012 consolidated financial statements.
Repayments of Other Long-Term Liabilities
Repayments of other long-term liabilities represent contractual payment dates or, if the timing is not known, we have estimated the timing of repayment based on management’s expectations.
| | | | |
| | Management’s Discussion & Analysis | | Methanex Corporation | Annual Report 2012 21 |
Management’s Discussion & Analysis
Natural Gas and Other
We have commitments under take-or-pay contracts to purchase natural gas and to pay for transportation capacity related to this natural gas. We also have take-or-pay contracts to purchase oxygen and other feedstock requirements in Trinidad. Take-or-pay means that we are obliged to pay for the supplies regardless of whether we take delivery. Such commitments are common in the methanol industry. These contracts generally provide a quantity that is subject to take-or-pay terms that is lower than the maximum quantity that we are entitled to purchase. The amounts disclosed in the table represent only the minimum take-or-pay quantity.
The natural gas supply contracts for our facilities in New Zealand, Trinidad and Egypt are take-or-pay contracts denominated in United States dollars and include base and variable price components to reduce our commodity price risk exposure. The variable price component of each natural gas contract is adjusted by a formula related to methanol prices above a certain level. We believe this pricing relationship enables these facilities to be competitive at all points in the methanol price cycle and provides gas suppliers with attractive returns. The amounts disclosed in the table for these contracts represent only the base price component.
We have a program in place to purchase natural gas on the Alberta gas market to support the Medicine Hat facility and we believe that the long-term natural gas dynamics in North America will support the long-term operation of this facility. In the above table, we have included natural gas commitments at the contractual volumes and prices.
We also have arrangements with ENAP and GeoPark to accelerate natural gas exploration and development in southern Chile. Under the arrangements, we contribute capital to fund the exploration and development and have contracts to purchase any natural gas discovered. As we cannot determine the amount of natural gas that will be purchased under these agreements in the future, no amounts have been included in the above table.
The above table does not include costs for planned capital maintenance or expansion expenditures or any obligations with original maturities of less than one year.
We have supply contracts that expire between 2017 and 2025 with Argentinean suppliers for natural gas sourced from Argentina for a significant portion of the capacity of our facilities in Chile. We have excluded these potential purchase obligations from the table above. Since June 2007, our natural gas suppliers from Argentina have curtailed all gas supply to our plants in Chile. Under the current circumstances, we do not expect to receive any further natural gas supply from Argentina.
We also have contracts with ENAP to supply natural gas to produce approximately 0.8 million tonnes of methanol at our facilities in Chile. Over the last few years, deliveries from ENAP have been declining and ENAP has delivered significantly less than the full amount of natural gas that it was obligated to deliver under these contracts. We have excluded the potential purchase obligations from the table above.
We have marketing rights for 100% of the production from our jointly owned Atlas and Egypt plants which results in purchase commitments of an additional 1.2 million tonnes per year of methanol offtake supply when these plants operate at capacity. At December 31, 2012, we also have methanol purchase commitments with other suppliers under contracts for approximately 0.5 million tonnes for 2013 and 2.6 million tonnes thereafter. The pricing under these purchase commitments is referenced to pricing at the time of purchase or sale, and accordingly, no amounts have been included in the above table.
We are in the process of relocating one of the idled Chile methanol plants to Geismar, Louisiana. It is anticipated that this plant will have a production capacity of 1.0 million tonnes and commence operations by the end of 2014. Subsequent to December 31, 2012, we entered into a ten-year natural gas agreement for the supply of all of the plant’s natural gas requirements. Contractual deliveries and obligations under the contract commence on the first date of commercial operations. Also subsequent to December 31, 2012, we entered into a natural gas purchase agreement to support the restart of the 0.5 million tonne per year Waitara Valley facility in New Zealand. No amounts have been included in the above table related to these contracts.
Operating Lease Commitments
The majority of these commitments relate to time charter vessel agreements with terms of up to 15 years. Time charter vessels typically meet most of our ocean-shipping requirements.
| | | | |
22 Methanex Corporation | Annual Report 2012 | | Management’s Discussion & Analysis | | |
Management’s Discussion & Analysis
Off-Balance Sheet Arrangements
At December 31, 2012, we did not have any off-balance sheet arrangements, as defined by applicable securities regulators in Canada and the United States, that have, or are reasonably likely to have, a current or future material effect on our results of operations or financial condition.
Financial Instruments
A financial instrument is any contract that gives rise to a financial asset of one party and a financial liability or equity instrument of another party. Financial instruments are either measured at amortized cost or fair value. Held-to-maturity investments, loans and receivables and other financial liabilities are measured at amortized cost. Held-for-trading financial assets and liabilities and available-for-sale financial assets are measured on the balance sheet at fair value. From time to time we enter into derivative financial instruments to limit our exposure to commodity price, foreign exchange and variable interest rate volatility and to contribute towards achieving cost structure and revenue targets. Until settled, the fair value of derivative financial instruments will fluctuate based on changes in commodity prices, foreign exchange rates and variable interest rates. Derivative financial instruments are classified as held-for-trading and are recorded on the Consolidated Statements of Financial Position at fair value unless exempted. Changes in fair value of held-for-trading derivative financial instruments are recorded in earnings unless the instruments are designated as cash flow hedges.
The following table shows the carrying value of each of our categories of financial assets and liabilities and the related balance sheet item as at December 31, 2012 and December 31, 2011:
| | | | | | | | |
| | |
($ MILLIONS) | | 2012 | | | 2011 | |
Financial assets: | | | | | | | | |
Loans and receivables: | | | | | | | | |
Cash and cash equivalents | | $ | 746 | | | $ | 351 | |
Trade and other receivables, excluding tax receivable and current portion of GeoPark financing | | | 371 | | | | 333 | |
Project financing reserve accounts included in other assets | | | 45 | | | | 40 | |
GeoPark financing, including current portion | | | 8 | | | | 18 | |
Total financial assets1 | | $ | 1,170 | | | $ | 742 | |
Financial liabilities: | | | | | | | | |
Other financial liabilities: | | | | | | | | |
Trade, other payables and accrued liabilities, excluding tax payable | | $ | 339 | | | $ | 306 | |
Deferred gas payments included in other long-term liabilities | | | 83 | | | | 51 | |
Long-term debt, including current portion | | | 1,245 | | | | 903 | |
Financial liabilities held-for-trading: | | | | | | | | |
Derivative instruments designated as cash flow hedges2 | | | 33 | | | | 42 | |
Total financial liabilities | | $ | 1,700 | | | $ | 1,302 | |
1 | The carrying amount of the financial assets represents the maximum exposure to credit risk at the respective reporting periods. | |
2 | The euro hedges and the Egypt interest rate swaps designated as cash flow hedges are measured at fair value based on industry accepted valuation models and inputs obtained from active markets. | |
At December 31, 2012, all of the financial instruments were recorded on the Consolidated Statements of Financial Position at amortized cost with the exception of held-for-trading derivative financial instruments, which are recorded at fair value.
The Egypt limited recourse debt facilities bear interest at LIBOR plus a spread. We have entered into interest rate swap contracts to swap the LIBOR-based interest payments for an average aggregated fixed rate of 4.8% plus a spread on approximately 75% of the Egypt limited recourse debt facilities for the period to March 31, 2015. These interest rate swaps had outstanding notional amounts of $342 million as at December 31, 2012. The notional amount decreases over the expected repayment of the Egypt limited recourse debt facilities. At December 31, 2012, these interest rate swap contracts had a negative fair value of $33 million (December 31, 2011 – negative $42 million) recorded in other long-term liabilities. The fair value of these interest rate swap contracts will fluctuate until maturity.
The Company also designates as cash flow hedges forward exchange contracts to sell euros at a fixed US dollar exchange rate. At December 31, 2012, the Company had outstanding forward exchange contracts designated as cash flow hedges to sell a notional amount of 5.8 million euros in exchange for US dollars and these euro contracts had a negative fair value of $0.2 million (2011 – positive fair value of $0.3 million) recorded in trade, other payables and accrued liabilities.
| | | | |
| | Management’s Discussion & Analysis | | Methanex Corporation | Annual Report 2012 23 |
Management’s Discussion & Analysis
Changes in the fair value of derivative financial instruments designated as cash flow hedges have been recorded in other comprehensive income.
RISK FACTORS AND RISK MANAGEMENT
We are subject to risks that require prudent risk management. We believe the following risks, in addition to those described in theCritical Accounting Estimates section on page 32, to be among the most important for understanding the issues that face our business and our approach to risk management.
Security of Natural Gas Supply and Price
Natural gas is the principal feedstock for producing methanol and it accounts for a significant portion of our operating costs. Accordingly, our results from operations depend in large part on the availability and security of supply and the price of natural gas. If, for any reason, we are unable to obtain sufficient natural gas for any of our plants on commercially acceptable terms or we experience interruptions in the supply of contracted natural gas, we could be forced to curtail production or close such plants, which could have an adverse effect on our results of operations and financial condition.
New Zealand
We have three plants in New Zealand with a total production capacity of up to 2.4 million tonnes per year. Two plants are located at Motunui and the third is located at nearby Waitara Valley. In 2012, we restarted a second Motunui facility and we recently committed to debottleneck the Motunui site and restart the Waitara Valley facility. Upon completion of the current projects in New Zealand, we expect to be able to operate the site at its annual production capacity of 2.4 million tonnes, depending on natural gas composition. We have entered into several agreements with various suppliers to underpin our New Zealand operations with terms that range in length up to ten years. All agreements in New Zealand are take-or-pay agreements and include base and variable price components where the variable price component is adjusted by a formula related to methanol prices above a certain level. We believe this pricing relationship enables these facilities to be competitive at all points in the methanol price cycle and provides gas suppliers with attractive returns. Certain of these contracts require the supplier to deliver a minimum amount of natural gas with additional volumes dependent on the success of exploring and developing the related natural gas field.
We continue to pursue opportunities to contract additional natural gas supply to our plants in New Zealand and are also pursuing natural gas exploration and development opportunities in that country. We have an agreement with Kea Petroleum, an oil and gas exploration and development company, to explore areas of the Taranaki basin, which is close to our plants.
The future operation of our New Zealand facilities depends on methanol industry supply and demand, the ability of our contracted suppliers to meet their commitments, and the success of ongoing exploration and development activities. We cannot provide assurance that our contracted suppliers will be able to meet their commitments or that the ongoing exploration and development activities in New Zealand will be successful to enable our operations to operate at capacity.
Trinidad
Natural gas for our two methanol production facilities in Trinidad, with our share of total production capacity being 2.0 million tonnes per year, is supplied under long-term contracts with NGC. The contracts for Titan and Atlas expire in 2014 and 2024, respectively, and have base and variable price components where the variable portion changes with methanol prices. Although Titan and Atlas are located close to other natural gas reserves in Trinidad, which we believe could be a source of supply after the expiration of these natural gas supply contracts, we cannot provide assurance that we would be able to secure access to such natural gas under long-term contracts on commercially acceptable terms and that this will not have an adverse impact on our results of operations and financial condition.
Since 2011, large industrial consumers in Trinidad, including our Titan and Atlas facilities, have experienced periodic curtailments of natural gas supply due to a mismatch between upstream commitments to supply NGC and downstream demand from NGC’s customers, which becomes apparent when an upstream supplier has a technical issue or planned maintenance that reduces gas delivery. We are engaged with key stakeholders to find a solution to this issue, but in the meantime expect to continue to experience some gas curtailments to our Trinidad facilities. We cannot provide assurance that we will not experience longer or greater than
| | | | |
24 Methanex Corporation | Annual Report 2012 | | Management’s Discussion & Analysis | | |
Management’s Discussion & Analysis
anticipated curtailments due to upstream outages or other issues in Trinidad and that these curtailments will not be material and that this would not have an adverse impact on our results of operations and financial condition.
Egypt
Natural gas for the 1.26 million tonne per year production facility in Egypt, which commenced commercial production in March 2011, is supplied under a 25-year contract with the government-owned Egyptian Natural Gas Holding Company (EGAS). The contractual gas price includes base and variable price components where the variable portion changes with methanol prices. Natural gas is supplied to this facility from the same gas delivery grid infrastructure that supplies other industrial users in Egypt, as well as the general Egyptian population.
The Egypt facility experienced periodic natural gas supply constraints commencing in mid-2012 and since that time has operated below full capacity. Egypt’s government is currently in a transition, which has resulted in ongoing civil unrest, political uncertainty and an adverse impact on the country’s economy. We believe that the political uncertainty is causing delays in decision-making within the Egyptian government including with respect to upstream natural gas development and this, as well as the economic situation in the country, is contributing to constraints in the development of new supplies of natural gas coming to market. In addition, domestically produced natural gas is increasingly being used instead of more expensive imported energy for the purpose of generating domestic electricity. These factors have led to periodic natural gas supply restrictions to the EMethanex facility. This situation may persist in the future and become more acute during the summer months when electricity demand is at its peak.
Canada
We restarted our 0.5 million tonne per year facility in Medicine Hat, Alberta in April 2011. We have a program in place to purchase natural gas on the Alberta gas market and we believe that the long-term natural gas dynamics in North America will support the long-term operation of this facility.
The future operation of our Medicine Hat facility depends on methanol industry supply and demand and our ability to secure sufficient natural gas on commercially acceptable terms. There can be no assurance that we will be able to continue to secure sufficient natural gas for our Medicine Hat facility on commercially acceptable terms and that this will not have an adverse impact on our results of operations and financial condition.
Chile
Since 2007, we have operated our methanol facilities in Chile significantly below site capacity primarily due to curtailments of natural gas supply from Argentina. In June 2007, our natural gas suppliers from Argentina curtailed all gas supply to our plants in Chile. Under the existing circumstances, we do not expect to receive any further natural gas supply from Argentina. As a result of the Argentinean natural gas supply issues, all of the methanol production at our Chile facilities since June 2007 has been produced with natural gas from Chile.
Over the past few years, investments have been made by us and others to accelerate the exploration and development of natural gas in southern Chile. However, the potential for a significant increase in gas production is more challenging than we had originally anticipated. As a result of the short-term outlook for gas supply in Chile, we expect to idle our Chile operations in March 2013 due to insufficient natural gas feedstock to keep our plant operating through the southern hemisphere winter. We are continuing to work with ENAP and others to secure sufficient natural gas to sustain our operations, and while the restart of a Chile plant is possible later in 2013, the restart is dependent on securing a sustainable natural gas position to operate over the medium term.
The future of our Chile operations is primarily dependent on the level of exploration and development in southern Chile and our ability to secure a sustainable natural gas supply to our facilities on economic terms. We cannot provide assurance that we will be able to restart our Chile operations later in 2013 and that this will not have an adverse impact on our results of operations or financial condition.
United States
We are in the process of relocating one of our idled Chile methanol plants to Geismar, Louisiana. It is anticipated that this plant will have a production capacity of 1.0 million tonnes and commence operations by the end of 2014. We have recently entered into a ten-year natural gas agreement for the supply of all of the plant’s natural gas requirements. Contractual deliveries and obligations commence on the first
| | | | |
| | Management’s Discussion & Analysis | | Methanex Corporation | Annual Report 2012 25 |
Management’s Discussion & Analysis
date of commercial operations. Once the contract is in effect, the supplier is obligated to supply, and we are obliged to take and pay for, a specified annual quantity of natural gas. The price to be paid for the gas is based on a US dollar base price plus a variable price component that is determined with reference to methanol prices. We cannot provide assurance that the facility will commence commercial operations on the planned date or that our natural gas supplier will supply the contracted gas and that this will not have an adverse impact on our results of operations or financial condition.
Methanol Price Cyclicality and Methanol Supply and Demand
The methanol business is a highly competitive commodity industry and prices are affected by supply and demand fundamentals. Methanol prices have historically been, and are expected to continue to be, characterized by cyclicality. New methanol plants are expected to be built and this will increase overall production capacity. Additional methanol supply can also become available in the future by restarting idle methanol plants, carrying out major expansions of existing plants or debottlenecking existing plants to increase their production capacity. Historically, higher-cost plants have been shut down or idled when methanol prices are low, but there can be no assurance that this practice will occur in the future. Demand for methanol largely depends upon levels of global industrial production, changes in general economic conditions and the level of energy prices.
We are not able to predict future methanol supply and demand balances, market conditions, global economic activity, methanol prices or energy prices, all of which are affected by numerous factors beyond our control. Since methanol is the only product we produce and market, a decline in the price of methanol would have an adverse effect on our results of operations and financial condition.
Global Economic Conditions
Volatile global economic conditions over the past few years have added significant risks and uncertainties to our business, including risks and uncertainties related to the global supply and demand for methanol, its impact on methanol prices, changes in capital markets and corresponding effects on our investments, our ability to access existing or future credit and increased risk of defaults by customers, suppliers and insurers. While the demand for methanol grew in 2012 and methanol prices were relatively stable, there can be no assurance that future global economic conditions will not have an adverse impact on the methanol industry and that this will not have an adverse impact on our results of operations and financial condition.
Methanol Demand
Demand for Methanol – General
Methanol is a global commodity and customers base their purchasing decisions principally on the delivered price of methanol and reliability of supply. Some of our competitors are not dependent on revenues from a single product and some have greater financial resources than we do. Our competitors also include state-owned enterprises. These competitors may be better able than we are to withstand price competition and volatile market conditions.
Changes in environmental, health and safety laws, regulations or requirements could impact methanol demand. The US Environmental Protection Agency (EPA) is currently evaluating the human health effects of methanol as part of a standard review of chemicals under its Integrated Risk Information System (IRIS). Methanol is currently unclassified under IRIS. A draft assessment for methanol was released by the EPA in 2010 classifying methanol as “Likely to Be Carcinogenic to Humans.” As of 2010, the EPA’s draft methanol assessment was placed “on hold.” In 2011, the EPA announced that it was dividing the draft assessment for methanol into carcinogenic and non-carcinogenic assessments. The timeline for the carcinogenic assessment remains unknown while the non-carcinogenic assessment is expected in 2013. We are unable to determine whether the current draft classification will be maintained in the final assessment or if this will lead other government agencies to reclassify methanol. Any reclassification could reduce future methanol demand, which could have an adverse effect on our results of operations and financial condition.
Demand for Methanol in the Production of Formaldehyde
In 2012, methanol demand for the production of formaldehyde represented approximately 32% of global demand. The largest use for formaldehyde is as a component of urea-formaldehyde and phenol-formaldehyde resins, which are used in adhesives for plywood, particleboard, oriented strand board, medium-density fibreboard and other reconstituted or engineered wood products. There is also demand for formaldehyde as a raw material for engineering plastics and in the manufacture of a variety of other products, including elastomers, paints, building products, foams, polyurethane and automotive products.
| | | | |
26 Methanex Corporation | Annual Report 2012 | | Management’s Discussion & Analysis | | |
Management’s Discussion & Analysis
The current EPA IRIS carcinogenicity classification for formaldehyde is “Likely to Be Carcinogenic to Humans;” however, the EPA is reviewing this classification for formaldehyde as part of a standard review of chemicals. In 2010, the EPA released its draft formaldehyde assessment, proposing formaldehyde as “Known to be Carcinogenic to Humans.” The release of the final assessment of formaldehyde is expected in 2013.
In 2009, the US National Cancer Institute (NCI) published a report on the health effects of occupational exposure to formaldehyde and a possible link to leukemia, multiple myeloma and Hodgkin’s disease. The NCI report concluded that there may be an increased risk of cancers of the blood and bone marrow related to a measure of peak formaldehyde exposure. The NCI report is the first part of an update of the 2004 NCI study that indicated possible links between formaldehyde exposure and nasopharyngeal cancer and leukemia. The NCI has not outlined its expected schedule with regards to the second portion of the study, which focuses on nasopharyngeal cancer and other cancers. The International Agency for Research on Cancer also concluded that there is sufficient evidence in humans of a causal association of formaldehyde with leukemia. In 2011, the US Department of Health and Human Services’ National Toxicology Program released its 12th Report on Carcinogens, modifying its listing of formaldehyde from “Reasonably Anticipated to be a Human Carcinogen” to “Known to be a Human Carcinogen.”
We are unable to determine at this time if the EPA or other governments or government agencies will reclassify formaldehyde or what limits could be imposed related to formaldehyde emissions in the United States or elsewhere. Any such actions could reduce future methanol demand for use in producing formaldehyde, which could have an adverse effect on our results of operations and financial condition.
Demand for Methanol in the Production of MTBE
In 2012, methanol demand for the production of MTBE represented approximately 12% of global methanol demand. Demand growth has been strong, particularly in China. MTBE is used primarily as a source of octane and as an oxygenate for gasoline to reduce the amount of harmful exhaust emissions from motor vehicles.
Several years ago, environmental concerns and legislative action related to gasoline leaking into water supplies from underground gasoline storage tanks in the United States resulted in the phase-out of MTBE as a gasoline additive in the United States. We believe that methanol has not been used in the United States to make MTBE for use in domestic fuel blending since 2007. However, approximately 0.7 million tonnes of methanol was used in the United States in 2012 to produce MTBE for export markets, where demand for MTBE has continued at strong levels. While we currently expect demand for methanol for MTBE production in the United States for 2013 to remain steady, it could decline materially if export demand was impacted by legislation or policy changes.
Additionally, the EPA in the United States is preparing an IRIS review of the human health effects of MTBE, including its potential carcinogenicity. The timeline for the final report is currently unknown.
The European Union issued a final risk assessment report on MTBE in 2002 that permitted the continued use of MTBE, although several risk-reduction measures relating to the storage and handling of fuels were recommended. Governmental efforts in recent years in some countries, primarily in the European Union and Latin America, to promote biofuels and alternative fuels through legislation or tax policy put competitive pressures on the use of MTBE in gasoline in these countries. However, due to strong MTBE demand in other countries, particularly in Asia, we have observed methanol demand growth for MTBE production.
Although MTBE demand has remained strong outside of the United States, we cannot provide assurance that further legislation banning or restricting the use of MTBE or promoting alternatives to MTBE will not be passed or that negative public perceptions will not develop outside of the United States, either of which could lead to a decrease in the global demand for methanol for use in MTBE. Declines in demand for methanol for use in MTBE could have an adverse effect on our results of operations and financial condition.
Foreign Operations
The majority of our operations and investments are located outside of North America, in New Zealand, Trinidad, Egypt, Chile, Europe and Asia. We are subject to risks inherent in foreign operations such as loss of revenue, property and equipment as a result of expropriation; import or export restrictions; anti-dumping measures; nationalization, war, insurrection, civil unrest, terrorism and other political risks; increases in duties, taxes and governmental royalties; renegotiation of contracts with governmental entities; as well as changes in laws
| | | | |
| | Management’s Discussion & Analysis | | Methanex Corporation | Annual Report 2012 27 |
Management’s Discussion & Analysis
or policies or other actions by governments that may adversely affect our operations. Many of the foregoing risks related to foreign operations may also exist for our domestic operations in North America.
Because we derive the majority of our revenues from production and sales by subsidiaries outside of Canada, the payment of dividends or the making of other cash payments or advances by these subsidiaries may be subject to restrictions or exchange controls on the transfer of funds in or out of the respective countries or result in the imposition of taxes on such payments or advances.
We have organized our foreign operations in part based on certain assumptions about various tax laws (including capital gains and withholding taxes), foreign currency exchange and capital repatriation laws and other relevant laws of a variety of foreign jurisdictions. While we believe that such assumptions are reasonable, we cannot provide assurance that foreign taxation or other authorities will reach the same conclusion. Further, if such foreign jurisdictions were to change or modify such laws, we could suffer adverse tax and financial consequences.
The dominant currency in which we conduct business is the United States dollar, which is also our reporting currency. The most significant components of our costs are natural gas feedstock and ocean-shipping costs and substantially all of these costs are incurred in United States dollars. Some of our underlying operating costs, purchases of methanol and capital expenditures, however, are incurred in currencies other than the United States dollar, principally the Canadian dollar, the Chilean peso, the Trinidad and Tobago dollar, the New Zealand dollar, the euro and the Egyptian pound. We are exposed to increases in the value of these currencies that could have the effect of increasing the United States dollar equivalent of cost of sales and operating expenses and capital expenditures. A portion of our revenue is earned in euros, Canadian dollars and British pounds. We are exposed to declines in the value of these currencies compared to the United States dollar, which could have the effect of decreasing the United States dollar equivalent of our revenue.
Trade in methanol is subject to duty in a number of jurisdictions. Methanol sold in China from any of our producing regions is currently subject to duties ranging from 0% to 5.5%. In 2010, the Chinese Ministry of Commerce investigated allegations made by domestic Chinese producers related to the dumping into China of imported methanol. In December 2010, the Ministry recommended that duties of approximately 9% be imposed on methanol imports from New Zealand, Malaysia and Indonesia for five years starting from December 24, 2010. However, citing special circumstances, the Customs Tariff Commission of the State Council, which is China’s chief administrative authority, suspended enforcement of the recommended dumping duties with the effect that methanol will continue to be allowed to be imported from these three countries without the imposition of additional duties. If the suspension is lifted, we do not expect there to be a significant impact on industry supply/demand fundamentals and we would realign our supply chain to minimize the payment of duties. However, we cannot provide assurance that the suspension will not be lifted or that the Chinese government will not impose duties or other measures in the future, which actions could have an adverse effect on our results of operations and financial condition.
Methanol is a globally traded commodity that is produced by many producers at facilities located in many countries around the world. Some producers and marketers may have direct or indirect contacts with countries that may, from time to time, be subject to international trade sanctions or other similar prohibitions (“Sanctioned Countries”). In addition to the methanol we produce, we purchase methanol from third parties under purchase contracts or on the spot market in order to meet our commitments to customers, and we also engage in product exchanges with other producers and marketers. We believe that we are in compliance with all applicable laws with respect to sales and purchases of methanol and product exchanges. However, as a result of the participation of Sanctioned Countries in our industry, we cannot provide assurance that we will not be exposed to reputational or other risks that could have an adverse impact on our results of operations and financial condition.
Liquidity Risk
During 2012, we entered into a $400 million revolving credit facility with a syndicate of banks, which remains undrawn at December 31, 2012. The facility expires in December 2016 and our ability to access the facility is subject to certain financial covenants, including an EBITDA to interest coverage ratio and a debt to capitalization ratio, as defined.
| | | | |
28 Methanex Corporation | Annual Report 2012 | | Management’s Discussion & Analysis | | |
Management’s Discussion & Analysis
At December 31, 2012, our long-term debt obligations include $750 million in unsecured notes ($150 million that matures in 2015, $350 million that matures in 2019 and $250 million that matures in 2022), $450 million related to the Egypt limited recourse debt facilities (100% basis), $50 million related to the Atlas limited recourse debt facilities (63.1% basis) and $17 million related to other limited recourse debt. The covenants governing the unsecured notes, which are specified in an indenture, apply to the Company and its subsidiaries, excluding the Atlas joint venture and Egypt entity (“limited recourse subsidiaries”), and include restrictions on liens, sale and lease-back transactions, a merger or consolidation with another corporation or sale of all or substantially all of the Company’s assets. The indenture also contains customary default provisions. The Atlas and Egypt limited recourse debt facilities are described as limited recourse as they are secured only by the assets of the Atlas joint venture and the Egypt entity, respectively. Accordingly, the lenders to the limited recourse debt facilities have no recourse to the Company or its other subsidiaries. The Atlas and Egypt limited recourse debt facilities have customary covenants and default provisions that apply only to these entities, including restrictions on the incurrence of additional indebtedness, a requirement to fulfill certain conditions before the payment of cash or other distributions and a restriction on these distributions if there is a default subsisting.
The Egypt limited recourse debt facilities contain a covenant to complete by March 31, 2013 certain land title registrations and related mortgages that require action by Egyptian government entities and which we do not expect to complete by March 31, 2013. We do not believe that the finalization of these items is material to the security provided to the lenders. The Company is seeking a waiver from the lenders. We cannot provide assurance that we will be able to obtain a waiver from the lenders.
For additional information regarding long-term debt, refer to note 9 of our 2012 consolidated financial statements.
We cannot provide assurance that we will be able to access new financing in the future or that the financial institutions providing the credit facility will have the ability to honour future draws. Additionally, failure to comply with any of the covenants or default provisions of the long-term debt facilities described above could result in a default under the applicable credit agreement that would allow the lenders to not fund future loan requests and to accelerate the due date of the principal and accrued interest on any outstanding loans. Any of these factors could have a material adverse effect on our results of operations, our ability to pursue and complete strategic initiatives or on our financial condition.
Customer Credit Risk
Our customers are large global or regional petrochemical manufacturers or distributors and a number are highly leveraged. We monitor our customers’ financial status closely; however, some customers may not have the financial ability to pay for methanol in the future and this could have an adverse effect on our results of operations and financial condition. Although credit losses have not been significant in the past, this risk still exists.
Operational Risks
Production Risks
Most of our earnings are derived from the sale of methanol produced at our plants. Our business is subject to the risks of operating methanol production facilities, such as equipment breakdowns, interruptions in the supply of natural gas and other feedstocks, power failures, longer-than-anticipated planned maintenance activities, loss of port facilities, natural disasters or any other event, including unanticipated events beyond our control, that could result in a prolonged shutdown of any of our plants or impede our ability to deliver methanol to our customers. A prolonged plant shutdown at any of our major facilities could have an adverse effect on our results of operations and financial condition.
Purchased Product Price Risk
In addition to the sale of methanol produced at our plants, we also purchase methanol produced by others on the spot market and through purchase contracts to meet our customer commitments and support our marketing efforts. We have adopted the first-in, first-out method of accounting for inventories and it generally takes between 30 and 60 days to sell the methanol we purchase. Consequently, we have the risk of holding losses on the resale of this product to the extent that methanol prices decrease from the date of purchase to the date of sale. Holding losses, if any, on the resale of purchased methanol could have an adverse effect on our results of operations and financial condition.
| | | | |
| | Management’s Discussion & Analysis | | Methanex Corporation | Annual Report 2012 29 |
Management’s Discussion & Analysis
Distribution Risks
Excess capacity within our fleet of ocean vessels resulting from a prolonged plant shutdown or other event could have an adverse effect on our results of operations and financial condition as our vessel fleet is subject to fixed time charter costs. In the event we have excess shipping capacity, we may be able to mitigate some of the excess costs by entering into sub-charters or third-party backhaul arrangements, although the success of this mitigation is dependent on conditions within the broader global shipping industry. If we suffer any disruptions in our distribution system and are unable to mitigate these costs this could have an adverse effect on our results of operations and financial condition.
Insurance Risks
Although we maintain operational and construction insurances, including business interruption insurance and delayed start-up insurance, we cannot provide assurance that we will not incur losses beyond the limits of, or outside the coverage of, such insurance or that insurers will be financially capable of honouring future claims. From time to time, various types of insurance for companies in the chemical and petrochemical industries have not been available on commercially acceptable terms or, in some cases, have been unavailable. We cannot provide assurance that in the future we will be able to maintain existing coverage or that premiums will not increase substantially.
Construction Projects and Louisiana Relocation Project
We believe that our estimates of project costs and anticipated completion dates for our expansion projects in New Zealand, Medicine Hat and Louisiana are reasonable. However, we cannot provide any assurance that the cost estimates will not be exceeded or that the facilities will begin commercial production within the anticipated schedules, if at all, or that the facilities will operate at their designed capacity or on a sustained basis. Any changes to the expected timing of completion or cost to complete these projects could have an adverse impact on results of operations and financial condition.
New Capital Projects
As part of our strategy to strengthen our position as the global leader in the production and marketing of methanol, we intend to continue pursuing new opportunities to enhance our strategic position in the methanol industry. Our ability to successfully identify, develop and complete new capital projects is subject to a number of risks, including finding and selecting favourable locations for new facilities or relocation of existing facilities where sufficient natural gas and other feedstock is available through long-term contracts with acceptable commercial terms, obtaining project or other financing on satisfactory terms, constructing and completing the projects within the contemplated budgets and schedules and other risks commonly associated with the design, construction and start-up of large complex industrial projects. We cannot provide assurance that we will be able to identify or develop new methanol projects.
Environmental Regulation
The countries in which we operate all have laws and regulations to which we are subject governing the environment and the management of natural resources as well as the handling, storage, transportation and disposal of hazardous or waste materials. We are also subject to laws and regulations governing emissions and the import, export, use, discharge, storage, disposal and transportation of toxic substances. The products we use and produce are subject to regulation under various health, safety and environmental laws. Non-compliance with these laws and regulations may give rise to compliance orders, fines, injunctions, civil liability and criminal sanctions.
Laws and regulations protecting the environment have become more stringent in recent years and may, in certain circumstances, impose absolute liability rendering a person liable for environmental damage without regard to negligence or fault on the part of such person. Such laws and regulations may also expose us to liability for the conduct of, or conditions caused by, others, or for our own acts even if we complied with applicable laws at the time such acts were performed. To date, environmental laws and regulations have not had a significant adverse effect on our capital expenditures, earnings or competitive position. However, operating petrochemical manufacturing plants and distributing methanol exposes us to risks in connection with compliance with such laws and we cannot provide assurance that we will not incur significant costs or liabilities in the future.
| | | | |
30 Methanex Corporation | Annual Report 2012 | | Management’s Discussion & Analysis | | |
Management’s Discussion & Analysis
Management of Emissions
We believe that minimizing emissions and waste from our business activities is good business practice. Carbon dioxide (“CO2”) is a by-product of the methanol production process. The amount of CO2 generated by the methanol production process depends on the production technology (and hence often the plant age), the feedstock and any export of by-product hydrogen. We continually strive to increase the energy efficiency of our plants, which not only reduces the use of energy but also reduces CO2 emissions. We have reduced CO2 emission intensity in our manufacturing operations by 30% between 1994 and 2012 through asset turnover, improved plant reliability and energy efficiency and emissions management. Plant efficiency, and thus CO2 emissions, is highly dependent on the design of the methanol plant. Therefore, the CO2 emission figure may vary from year to year depending on the asset mix that is operating. We also recognize that CO2 is generated from our marine operations, and in that regard we measure the consumption of fuel by our ocean vessels based on the volume of product transported. Between 2002 and 2012, we reduced our CO2 intensity (tonnes of CO2 from fuel burned per tonne of product moved) from marine operations by nearly 27%. We also actively support global industry efforts to voluntarily reduce both energy consumption and CO2 emissions.
We manufacture methanol in New Zealand, Trinidad, Egypt, Canada and Chile. All of these countries signed and ratified the Kyoto Protocol; however, Canada has since removed itself from that Agreement. We are not currently required to reduce greenhouse gases (GHG) in Trinidad, Egypt and Chile, but our production in New Zealand and Canada is subject to GHG reduction regulations.
New Zealand passed legislation to establish an Emissions Trading Scheme (“ETS”) that came into force in 2010. The ETS imposes a carbon price on producers of fossil fuels, including natural gas, which is passed on to Methanex, increasing the cost of gas that Methanex purchases in New Zealand. However, as a trade-exposed company, Methanex is entitled to a free allocation of emissions units to partially offset those increased costs. Recently, the New Zealand government concluded that the legislation will continue providing further moderation and free allocation of any residual cost exposure until at least 2015. Consequently, our ETS-related costs are not expected to be significant to the end of 2015. However, after this date, the moderating features are expected to be removed and our eligibility for free allocation of emissions units may also be progressively reduced. As a consequence, we may incur increasing costs after 2015. It is impossible to accurately quantify the impact on our business of ETS-related costs after 2015 and therefore we cannot provide assurance that the ETS will not have a significant impact on our results of operations and financial condition beyond 2015.
Medicine Hat is located in the Canadian province of Alberta, which has an established GHG reduction regulation that applies to our plant. The regulation requires that facilities reduce emissions intensities by up to 12% of their established emissions intensity baseline. “Emissions intensity” means the quantity of specified GHGs released per unit of production. In order to meet the reduction obligation, a facility can choose to make emissions reduction improvements or it can purchase either offset credits or “technology fund” credits for CDN$15 per tonne of CO2 equivalent. Financial obligations are set to begin in 2014 and based on the expected GHG baseline intensity, we do not believe that, when applied, the cost will be significant.
The federal government of Canada is in the process of developing a sector-by-sector approach to reduce GHG emissions in support of its commitment to reduce GHGs from 2005 levels by 17% by 2020. Final proposed regulations are expected by the end of 2013. As the sole methanol producer in Canada, Methanex is engaged in a consultative process to ensure achievable performance standards are set and that these incorporate equivalency agreements with existing regulations in Alberta to prevent the potential of paying double for GHG emissions under both provincial and federal regimes.
We are currently in the process of relocating one of our idle methanol plants in Chile to Geismar, Louisiana. The reassembled plant in Geismar is expected to be operational by the end of 2014. Today, there is no GHG legislation that impacts our business in the United States. We continue to monitor the development of potential GHG legislation in the US and Louisiana to ensure compliance with any potential future requirements once the plant becomes operational. At this time, it unknown what impact, if any, potential new GHG legislation or regulation could have on our operations in Geismar.
We cannot provide assurance over ongoing compliance with existing legislation or that future laws and regulations to which we are subject governing the environment and the management of natural resources as well as the handling, storage, transportation and disposal of hazardous or waste materials will not have an adverse effect on our results of operations and financial condition.
Legal Proceedings
The Board of Inland Revenue of Trinidad and Tobago has issued assessments against our 63.1% owned joint venture, Atlas Methanol Company Unlimited (“Atlas”), in respect of the 2005 and 2006 financial years. All subsequent tax years remain open to assessment. The
| | | | |
| | Management’s Discussion & Analysis | | Methanex Corporation | Annual Report 2012 31 |
Management’s Discussion & Analysis
assessments relate to the pricing arrangements of certain long-term fixed-price sales contracts that extend to 2014 and 2019 related to methanol produced by Atlas. The impact of the amounts in dispute for the 2005 and 2006 financial years is not significant. Atlas has partial relief from corporation income tax until 2014.
The Company has lodged objections to the assessments. Based on the merits of the cases and legal interpretation, management believes its position should be sustained.
CRITICAL ACCOUNTING ESTIMATES
We believe the following selected accounting policies and issues are critical to understanding the estimates, assumptions and uncertainties that affect the amounts reported and disclosed in our consolidated financial statements and related notes. See note 2 to our 2012 consolidated financial statements for our significant accounting policies.
Property, Plant and Equipment
Our business is capital intensive and has required, and will continue to require, significant investments in property, plant and equipment. At December 31, 2012, the net book value of our property, plant and equipment was $2,015 million.
Capitalization
Property, plant and equipment are initially recorded at cost. The cost of purchased equipment includes expenditures that are directly attributable to the purchase price, delivery and installation. The cost of self-constructed assets includes the cost of materials and direct labour, any other costs directly attributable to bringing the assets to the location and condition for their intended use, the costs of dismantling and removing the items and restoring the site on which they are located, and borrowing costs on self-constructed assets that meet certain criteria. Routine repairs and maintenance costs are expensed as incurred.
At December 31, 2012, we have accrued $22.6 million for site restoration costs relating to the decommissioning and reclamation of our methanol production sites and oil and gas properties. Inherent uncertainties exist in this estimate because the restoration activities will take place in the future and there may be changes in governmental and environmental regulations and changes in removal technology and costs. It is difficult to estimate the future costs of these activities as our estimate of fair value is based on current regulations and technology. Because of uncertainties related to estimating the cost and timing of future site restoration activities, future costs could differ materially from the amounts estimated.
Depreciation and Amortization
Depreciation and amortization is generally provided on a straight-line basis at rates calculated to amortize the cost of property, plant and equipment from the commencement of commercial operations over their estimated useful lives to estimated residual value.
The estimated useful lives of the Company’s buildings, plant installations and machinery, excluding costs related to turnarounds, range from 10 to 25 years depending on the specific asset component and the production facility to which it is related. The Company determines the estimated useful lives of individual asset components based on the shorter of its physical life or economic life. The physical life of these assets is generally longer than the economic life. The economic life is primarily determined by the nature of the natural gas feedstock available to our various production facilities. Factors that influence the nature of natural gas feedstock availability include the terms of individual natural gas supply contracts, access to natural gas supply through open markets, regional factors influencing the exploration and development of natural gas, and the expected price of securing natural gas supply. We review the factors related to each production facility on an annual basis to determine if changes are required to the estimated useful lives.
Oil and Gas Properties
Exploration and evaluation costs incurred for oil and natural gas exploration properties that do not have proven reserves are capitalized to other assets. Upon determination of proven reserves and internal approval for development, these costs are transferred to property, plant and equipment. Costs are also transferred to property, plant and equipment and become subject to depreciation when the associated properties have been deemed abandoned by management. Subsequent costs incurred for oil and natural gas properties with proven reserves are capitalized to property, plant and equipment. Oil and gas costs included in property, plant and equipment are depreciated using a unit-of-production method, taking into consideration estimated proven reserves and estimated future development costs.
| | | | |
32 Methanex Corporation | Annual Report 2012 | | Management’s Discussion & Analysis | | |
Management’s Discussion & Analysis
Proven and probable reserves for oil and natural gas properties are estimated based on independent reserve reports and represent the estimated quantities of natural gas that are considered commercially feasible. These reserve estimates are used to determine depreciation and to assess the carrying value of oil and natural gas properties.
Recoverability of Asset Carrying Values
Property, Plant and Equipment and Oil and Gas Properties
Long-lived assets are tested for recoverability whenever events or changes in circumstances indicate that the carrying amount may not be recoverable. Examples of such events or changes in circumstances related to our long-lived assets include, but are not restricted to: a significant adverse change in the extent or manner in which the asset is being used or in its physical condition; a significant change in the price or availability of natural gas feedstock required to manufacture methanol; a significant adverse change in legal factors or in the business climate that could affect the asset’s value, including an adverse action or assessment by a foreign government that impacts the use of the asset; or a current-period operating or cash flow loss combined with a history of operating or cash flow losses, or a projection or forecast that demonstrates continuing losses associated with the asset’s use.
We recently announced that we expect to idle our Chile operations in March 2013 due to an expected shortfall of natural gas feedstock to keep the plant operating through the southern hemisphere winter. We are continuing to work with our natural gas suppliers to secure sufficient natural gas to sustain our operations, and while the restart of a Chile plant is possible later in 2013, the restart is dependent on securing a sustainable natural gas position to operate over the medium term.
As a consequence of the uncertain outlook for the future supply of natural gas feedstock, the carrying value of our Chile assets was tested for recoverability at December 31, 2012.
Recoverability of long-lived assets is measured by comparing the carrying value of an asset or cash-generating unit to the estimated recoverable amount, which is the higher of its estimated fair value less costs to sell or its value in use. Value in use was determined by measuring the pre-tax cash flows expected to be generated from the cash-generating unit over its estimated useful life discounted by a pre-tax discount rate. The pre-tax discount rate used of 13% was derived from the Company’s estimated cost of capital. An impairment writedown was recorded for the difference that the carrying value exceeded the recoverable amount. An impairment writedown recognized in prior periods for an asset or cash-generating unit is reversed if there has been a subsequent recovery in the value of the asset or cash-generating unit due to changes in events and circumstances. For the purposes of recognition and measurement of an impairment writedown, we group our long-lived assets with other assets and liabilities to form a “cash-generating unit” at the lowest level for which identifiable cash flows are largely independent of the cash flows of other assets and liabilities. To the extent that our methanol facilities in a particular location are interdependent as a result of common infrastructure and/or feedstock from shared sources that can be shared within a facility location, we group our assets based on site locations for the purpose of determining impairment.
There are two key variables that impact our estimate of future cash flows: (1) the methanol price and (2) the price and availability of natural gas feedstock. Short-term methanol price estimates are based on current supply and demand fundamentals and current methanol prices. Long-term methanol price estimates are based on our view of long-term supply and demand, and consideration is given to many factors, including, but not limited to, estimates of global industrial production rates, energy prices, changes in general economic conditions, future global methanol production capacity, industry operating rates and the global industry cost structure. Our estimate of the price and availability of natural gas takes into consideration the current contracted terms, as well as factors that we believe are relevant to supply under these contracts and supplemental natural gas sources. Other assumptions included in our estimate of future cash flows include the estimated cost incurred to maintain the facilities, estimates of transportation costs and other variable costs incurred in producing methanol in each period. Changes in these assumptions will impact our estimates of future cash flows and could impact our estimates of the useful lives of property, plant and equipment. Consequently, it is possible that our future operating results could be adversely affected by further asset impairment charges or by changes in depreciation and amortization rates related to property, plant and equipment.
| | | | |
| | Management’s Discussion & Analysis | | Methanex Corporation | Annual Report 2012 33 |
Management’s Discussion & Analysis
Based on the test performed at December 31, 2012 related to our Chile assets, we recorded a non-cash before-tax asset impairment charge of $297 million ($193 million after-tax) to write down the carrying value of the Chile assets at December 31, 2012 to $245 million. The remaining carrying value of $245 million excludes the first Chile facility that is being relocated to Geismar, Louisiana but includes the second facility that management is also considering for relocation to Geismar. Refer to note 6 of the consolidated financial statements for the year ended December 31, 2012.
We believe the estimated recoverable amount of all long-lived assets except our Chile cash-generating unit substantially exceeded their carrying value as at December 31, 2012.
Income Taxes
Deferred income tax assets and liabilities are determined using enacted or substantially enacted tax rates for the effects of net operating losses and temporary differences between the book and tax bases of assets and liabilities. We recognize deferred tax assets to the extent it is probable that taxable profit will be available against which the asset can be utilized. In making this determination, certain judgments are made relating to the level of expected future taxable income and to available tax-planning strategies and their impact on the use of existing loss carryforwards and other income tax deductions. We also consider historical profitability and volatility to assess whether we believe it is probable that the existing loss carryforwards and other income tax deductions will be used to offset future taxable income otherwise calculated. Our management routinely reviews these judgments. At December 31, 2012, we had recognized future tax assets of $147 million and unrecognized future income tax assets of approximately $144 million. The determination of income taxes requires the use of judgment and estimates. If certain judgments or estimates prove to be inaccurate, or if certain tax rates or laws change, our results of operations and financial position could be materially impacted.
Financial Instruments
We enter into derivative financial instruments from time to time to manage certain exposures to commodity price volatility, foreign exchange volatility and variable interest rate volatility, which contributes towards managing our cost structure. Derivative financial instruments are classified as held-for-trading and are recorded on the balance sheet at fair value unless exempted. Changes in the fair value of held-for-trading derivative financial instruments are recorded in earnings unless the instruments are designated as cash flow hedges, in which case the effective portion of any changes in fair value are recorded in other comprehensive income. Assessment of contracts as derivative instruments, the valuation of financial instruments and derivatives, and hedge effectiveness assessments require a high degree of judgment and are considered critical accounting estimates due to the complex nature of these products and the potential impact on our financial statements.
At December 31, 2012, the fair value of our derivative financial instruments used to limit our exposure to variable interest rate volatility that have been designated as cash flow hedges approximated their carrying value of negative $33 million. Until settled, the fair value of the derivative financial instruments will fluctuate based on changes in variable interest rates.
ANTICIPATED CHANGES TO INTERNATIONAL FINANCIAL REPORTING STANDARDS
Consolidation and Joint Arrangement Accounting
In May 2011, the IASB issued new accounting standards related to consolidation and joint arrangement accounting. The IASB has revised the definition of “control,” which is a criterion for consolidation accounting. In addition, changes to IFRS in the accounting for joint arrangements were issued that, under certain circumstances, removed the option for proportionate consolidation accounting so that the equity method of accounting for such interests would need to be applied. We currently account for our 63.1% interest in Atlas Methanol Company using proportionate consolidation accounting and upon adoption of these new standards effective January 1, 2013 we will account for this entity using equity accounting. The impact of applying equity accounting does not result in any change to net earnings or shareholders’ equity but will result in changes to the presentation of our Consolidated Statements of Income and Consolidated Statements of Financial Position.
SUPPLEMENTAL NON-GAAP MEASURES
In addition to providing measures prepared in accordance with International Financial Reporting Standards (IFRS), we present certain supplemental measures that are not defined terms under IFRS (non-GAAP measures). These are adjusted EBITDA, adjusted net
| | | | |
34 Methanex Corporation | Annual Report 2012 | | Management’s Discussion & Analysis | | |
Management’s Discussion & Analysis
income, adjusted diluted net income per share, adjusted cash flows from operating activities, cash flow from operating activities before changes in non-cash working capital and operating income. These measures do not have any standardized meaning prescribed by IFRS and therefore are unlikely to be comparable to similar measures presented by other companies. We believe these measures are useful in assessing the operating performance and liquidity of the Company’s ongoing business. We also believe Adjusted EBITDA is frequently used by securities analysts and investors when comparing our results with those of other companies.
These measures should be considered in addition to, and not as a substitute for, net income, cash flows and other measures of financial performance and liquidity reported in accordance with IFRS.
Adjusted EBITDA (Attributable to Methanex Shareholders)
Adjusted EBITDA differs from the most comparable GAAP measure, net income (loss) attributable to Methanex shareholders, because it excludes finance costs, finance income and other expenses, income tax expense (recovery), depreciation and amortization, mark-to-market impact of share-based compensation, Louisiana project relocation expenses and charges and asset impairment charges.
Adjusted EBITDA and Adjusted net income exclude the mark-to-market impact of share-based compensation related to the impact of changes in our share price on share appreciation rights, tandem share appreciation rights, deferred share units, restricted share units and performance share units. The mark-to-market impact related to performance share units that is excluded from Adjusted EBITDA and Adjusted net income is calculated as the difference between the grant-date value determined using a Methanex total shareholder return factor of 100% and the fair value recorded at each period-end. As share-based awards will be settled in future periods, the ultimate value of the units is unknown at the date of grant and therefore the grant-date value recognized in Adjusted EBITDA and Adjusted net income may differ from the total settlement cost.
The following table shows a reconciliation from net income (loss) attributable to Methanex shareholders to Adjusted EBITDA:
| | | | | | | | |
| | |
($ MILLIONS) | | 2012 | | | 2011 | |
Net income (loss) attributable to Methanex shareholders | | $ | (68 | ) | | $ | 201 | |
Finance costs | | | 71 | | | | 62 | |
Finance income and other expenses | | | (1 | ) | | | (2 | ) |
Income tax expense (recovery) | | | (84 | ) | | | 56 | |
Depreciation and amortization | | | 172 | | | | 157 | |
Mark-to-market impact of share-based compensation | | | 16 | | | | (21 | ) |
Louisiana project relocation expenses and charges | | | 65 | | | | – | |
Asset impairment charge | | | 297 | | | | – | |
Non-controlling interests adjustments1 | | | (39 | ) | | | (26 | ) |
Adjusted EBITDA (attributable to Methanex shareholders) | | $ | 429 | | | $ | 427 | |
1 | This adjustment represents finance costs, finance income and other expenses, income tax expense, and depreciation and amortization associated with the 40% non-controlling interest in the methanol facility in Egypt. | |
| | | | |
| | Management’s Discussion & Analysis | | Methanex Corporation | Annual Report 2012 35 |
Management’s Discussion & Analysis
Adjusted Net Income and Adjusted Net Income per Common Share (Attributable to Methanex Shareholders)
Adjusted net income and Adjusted net income per common share are non-GAAP measures because they exclude the mark-to-market impact of share-based compensation and items that are considered by management to be non-operational, including asset impairment charges and Louisiana project relocation charges and expenses. The following table shows a reconciliation from net income (loss) attributable to Methanex shareholders to Adjusted net income and the calculation of Adjusted diluted net income per common share:
| | | | | | | | |
| | |
($ MILLIONS, EXCEPT NUMBER OF SHARES AND PER SHARE AMOUNTS) | | 2012 | | | 2011 | |
Net income (loss) attributable to Methanex shareholders | | $ | (68 | ) | | $ | 201 | |
Mark-to-market impact of share-based compensation | | | 16 | | | | (21 | ) |
Louisiana project relocation expenses and charges | | | | | | | | |
Cash expense | | | 39 | | | | – | |
Non-cash charge | | | 26 | | | | – | |
Asset impairment charge | | | 297 | | | | – | |
Income expense (recovery) related to above items | | | (130 | ) | | | 2 | |
Adjusted net income | | $ | 180 | | | $ | 182 | |
Diluted weighted average shares outstanding | | | 94 | | | | 94 | |
Adjusted net income per common share1 | | $ | 1.90 | | | $ | 1.93 | |
1 | For the year ended December 31, 2012, stock options have been excluded from the calculation of diluted net loss per common share (attributable to Methanex shareholders) as their effect would be anti-dilutive. However, for the calculation of adjusted diluted net income per common share, stock options have been included in the denominator and the diluted weighted average number of common shares for the year ended December 31, 2012 is 95 million. | |
Adjusted Cash Flows from Operating Activities (Attributable to Methanex Shareholders)
Adjusted cash flows from operating activities differs from the most comparable GAAP measure, cash flows from operating activities, because it does not include cash flows associated with the 40% non-controlling interest in the methanol facility in Egypt, changes in non-cash working capital and the cash portion of Louisiana project relocation expenses and charges.
The following table shows a reconciliation of cash flows from operating activities to adjusted cash flows from operating activities:
| | | | | | | | |
| | |
($ MILLIONS) | | 2012 | | | 2011 | |
Cash flows from operating activities | | $ | 458 | | | $ | 480 | |
Deduct non-controlling interests adjustment: | | | | | | | | |
Net income | | | (33 | ) | | | (26 | ) |
Non-cash items | | | (39 | ) | | | (26 | ) |
Changes in non-cash working capital | | | (22 | ) | | | (36 | ) |
Cash portion of Louisiana project relocation expenses and charges | | | 39 | | | | – | |
Adjusted cash flow from operating activities (attributable to Methanex shareholders) | | $ | 403 | | | $ | 392 | |
Operating Income and Cash Flows from Operating Activities before Changes in Non-Cash Working Capital
Operating income and cash flows from operating activities before changes in non-cash working capital are reconciled to GAAP measures in our Consolidated Statements of Income and Consolidated Statements of Cash Flows, respectively.
| | | | |
36 Methanex Corporation | Annual Report 2012 | | Management’s Discussion & Analysis | | |
Management’s Discussion & Analysis
QUARTERLY FINANCIAL DATA (UNAUDITED)
| | | | | | | | | | | | | | | | |
($ MILLIONS, EXCEPT PER SHARE AMOUNTS) | | THREE MONTHS ENDED | |
| DEC 31 | | | SEP 30 | | | JUN 30 | | | MAR 31 | |
2012 | | | | | | | | | | | | | | | | |
Revenue | | $ | 696 | | | $ | 655 | | | $ | 656 | | | $ | 666 | |
Adjusted EBITDA1 | | | 119 | | | | 104 | | | | 113 | | | | 93 | |
Adjusted net income1 | | | 61 | | | | 36 | | | | 44 | | | | 39 | |
Net income (loss)2 | | | (140 | ) | | | (3 | ) | | | 52 | | | | 22 | |
Adjusted net income per share1 | | | 0.64 | | | | 0.38 | | | | 0.47 | | | | 0.41 | |
Basic net income (loss) per common share2 | | | (1.49 | ) | | | (0.03 | ) | | | 0.56 | | | | 0.24 | |
Diluted net income (loss) per common share2 | | | (1.49 | ) | | | (0.03 | ) | | | 0.50 | | | | 0.23 | |
| | | | |
2011 | | | | | | | | | | | | | | | | |
Revenue | | $ | 696 | | | $ | 670 | | | $ | 623 | | | $ | 619 | |
Adjusted EBITDA1 | | | 133 | | | | 111 | | | | 102 | | | | 81 | |
Adjusted net income1 | | | 65 | | | | 40 | | | | 39 | | | | 37 | |
Net income2 | | | 64 | | | | 62 | | | | 41 | | | | 35 | |
Adjusted net income per share2 | | | 0.69 | | | | 0.43 | | | | 0.41 | | | | 0.39 | |
Basic net income per common share2 | | | 0.69 | | | | 0.67 | | | | 0.44 | | | | 0.37 | |
Diluted net income per common share2 | | | 0.68 | | | | 0.59 | | | | 0.43 | | | | 0.37 | |
1 | These items are non-GAAP measures that do not have any standardized meaning prescribed by GAAP and therefore are unlikely to be comparable to similar measures presented by other companies. Refer to the Supplemental Non-GAAP Measures section on page 34 for a description of each non-GAAP measure and reconciliations to the most comparable GAAP measures. | |
2 | Attributable to Methanex Corporation shareholders. | |
A discussion and analysis of our results for the fourth quarter of 2012 is set out in our fourth quarter of 2012 Management’s Discussion and Analysis filed with the Canadian Securities Administrators and the U.S. Securities and Exchange Commission and incorporated herein by reference.
SELECTED ANNUAL INFORMATION
| | | | | | | | | | | | |
| | | |
($ MILLIONS, EXCEPT PER SHARE AMOUNTS) | | 2012 | | | 2011 | | | 2010 | |
Revenue | | $ | 2,673 | | | $ | 2,608 | | | $ | 1,967 | |
Adjusted EBITDA1 | | | 429 | | | | 427 | | | | 291 | |
Adjusted net income1 | | | 180 | | | | 182 | | | | 91 | |
Net income (loss)2 | | | (68 | ) | | | 201 | | | | 96 | |
Adjusted net income per share1 | | | 1.90 | | | | 1.93 | | | | 0.98 | |
Basic net income (loss) per share2 | | | (0.73 | ) | | | 2.16 | | | | 1.04 | |
Diluted net income (loss) per share2 | | | (0.73 | ) | | | 2.06 | | | | 1.03 | |
Cash dividends declared per share | | | 0.725 | | | | 0.665 | | | | 0.620 | |
Total assets | | | 3,545 | | | | 3,394 | | | | 3,141 | |
Total long-term financial liabilities | | | 1,434 | | | | 886 | | | | 1,105 | |
1 | These items are non-GAAP measures that do not have any standardized meaning prescribed by GAAP and therefore are unlikely to be comparable to similar measures presented by other companies. Refer to the Supplemental Non-GAAP Measures section on page 34 for a description of each non-GAAP measure and reconciliations to the most comparable GAAP measures. | |
2 | Attributable to Methanex Corporation shareholders. | |
CONTROLS AND PROCEDURES
Disclosure Controls and Procedures
Disclosure controls and procedures are those controls and procedures that are designed to ensure that the information required to be disclosed in the filings under applicable securities regulations is recorded, processed, summarized and reported within the time periods specified. As at December 31, 2012, under the supervision and with the participation of our management, including our Chief Executive Officer and Chief Financial Officer, we conducted an evaluation of the effectiveness of the design and operation of the Company’s disclosure controls and procedures. Based on this evaluation, the Chief Executive Officer and Chief Financial Officer have concluded that our disclosure controls and procedures are effective.
| | | | |
| | Management’s Discussion & Analysis | | Methanex Corporation | Annual Report 2012 37 |
Management’s Discussion & Analysis
Management’s Annual Report on Internal Control over Financial Reporting
Management is responsible for establishing and maintaining adequate internal control over financial reporting. Internal control over financial reporting includes those policies and procedures that: (1) pertain to the maintenance of records that, in reasonable detail, accurately and fairly reflect the transactions and dispositions of our assets; (2) provide reasonable assurance that transactions are recorded as necessary to permit preparation of financial statements in accordance with generally accepted accounting principles, and that our receipts and expenditures are being made only in accordance with authorizations of our management and directors; and (3) provide reasonable assurance regarding prevention or timely detection of unauthorized acquisition, use or disposition of our assets that could have a material effect on the financial statements.
The design of any system of controls and procedures is based in part upon certain assumptions about the likelihood of future events. There can be no assurance that any design will succeed in achieving its stated goals under all potential future conditions, regardless of how remote.
Under the supervision and with the participation of our Chief Executive Officer and our Chief Financial Officer, management conducted an evaluation of the effectiveness of our internal control over financial reporting, as of December 31, 2012, based on the framework set forth in Internal Control – Integrated Framework issued by the Committee of Sponsoring Organizations of the Treadway Commission. Based on its evaluation under this framework, management concluded that our internal control over financial reporting was effective as of that date.
KPMG LLP, an independent registered public accounting firm that audited and reported on our consolidated financial statements, has issued an attestation report on the effectiveness of our internal control over financial reporting as of December 31, 2012. The attestation report is included in our consolidated financial statements on page 43.
Changes in Internal Control over Financial Reporting
There have been no changes during the year ended December 31, 2012 to internal control over financial reporting that have materially affected, or are reasonably likely to materially affect, internal control over financial reporting.
FORWARD-LOOKING STATEMENTS
This 2012 Management’s Discussion and Analysis (“MD&A”) contains forward-looking statements with respect to us and our industry. These statements relate to future events or our future performance. All statements other than statements of historical fact are forward-looking statements. Statements that include the words “believes,” “expects,” “may,” “will,” “should,” “potential,” “estimates,” “anticipates,” “aim”, “goal” or other comparable terminology and similar statements of a future or forward-looking nature identify forward-looking statements.
More particularly, and without limitation, any statements regarding the following are forward-looking statements:
n | | expected demand for methanol and its derivatives, |
n | | expected new methanol supply or restart of idled capacity and timing for start-up of the same, |
n | | expected shutdowns (either temporary or permanent) or restarts of existing methanol supply (including our own facilities), including, without limitation, the timing and length of planned maintenance outages, |
n | | expected methanol and energy prices, |
n | | expected levels of methanol purchases from traders or other third parties, |
n | | expected levels, timing and availability of economically priced natural gas supply to each of our plants, |
n | | capital committed by third parties towards future natural gas exploration and development in the vicinity of our plants, |
n | | our expected capital expenditures, including, without limitation, those to support natural gas exploration and development for our plants and the restart of our idled methanol facilities, |
n | | anticipated production rates of our plants, |
n | | expected operating costs, including natural gas feedstock costs and logistics costs, |
n | | expected tax rates or resolutions to tax disputes, |
n | | expected cash flows, earnings capability and share price, |
n | | ability to meet covenants or obtain waivers associated with our long-term debt obligations, including, without limitation, the Egypt limited recourse debt facilities that have conditions associated with finalization of certain land title registration and related mortgages that require actions by Egyptian governmental entities, |
| | | | |
38 Methanex Corporation | Annual Report 2012 | | Management’s Discussion & Analysis | | |
Management’s Discussion & Analysis
n | | availability of committed credit facilities and other financing, |
n | | our shareholder distribution strategy and anticipated distributions to shareholders, |
n | | commercial viability and timing of, or our ability to execute, future projects, plant restarts, capacity expansions, plant relocations, or other business initiatives or opportunities, including the planned relocation of one of our idle Chile methanol plants to Geismar, Louisiana (“Geismar”) and certain initiatives in New Zealand and Canada, |
n | | our financial strength and ability to meet future financial commitments, |
n | | expected global or regional economic activity (including industrial production levels), |
n | | expected outcomes of litigation or other disputes, claims and assessments, |
n | | expected actions of governments, government agencies, gas suppliers, courts, tribunals or other third parties, and |
n | | expected impact on our operations in Egypt or our financial condition as a consequence of civil unrest or actions taken or inaction by the Government of Egypt and its agencies. |
We believe that we have a reasonable basis for making such forward-looking statements. The forward-looking statements in this document are based on our experience, our perception of trends, current conditions and expected future developments as well as other factors. Certain material factors or assumptions were applied in drawing the conclusions or making the forecasts or projections that are included in these forward-looking statements, including, without limitation, future expectations and assumptions concerning the following:
n | | supply of, demand for, and price of, methanol, methanol derivatives, natural gas, coal, oil and oil derivatives, |
n | | the success of our natural gas exploration and development in Chile and New Zealand and our ability to procure economically priced natural gas in Chile, New Zealand, Trinidad, Canada and the United States, |
n | | production rates of our facilities, |
n | | receipt of remaining required permits in connection with the Geismar project, |
n | | receipt or issuance of third-party consents or approvals, including, without limitation, governmental registrations of land title and related mortgages in Egypt, governmental approvals related to natural gas exploration rights or rights to purchase natural gas, |
n | | receipt of governmental approvals related to natural gas exploration rights, |
n | | the establishment of new fuel standards, |
n | | operating costs including natural gas feedstock and logistics costs, capital costs, tax rates, cash flows, foreign exchange rates and interest rates, |
n | | the availability of committed credit facilities and other financing, |
n | | timing of completion and cost of the Geismar project and our initiatives to increase production in New Zealand and Canada, |
n | | global and regional economic activity (including industrial production levels), |
n | | absence of a material negative impact from major natural disasters, |
n | | absence of a material negative impact from changes in laws or regulations, |
n | | absence of a material negative impact from political instability in the countries in which we operate, |
n | | enforcement of contractual arrangements and ability to perform contractual obligations by customers, natural gas and other suppliers and other third parties, and |
n | | satisfaction of conditions precedent contained in the Geismar project natural gas supply agreement. |
| | | | |
| | Management’s Discussion & Analysis | | Methanex Corporation | Annual Report 2012 39 |
Management’s Discussion & Analysis
However, forward-looking statements, by their nature, involve risks and uncertainties that could cause actual results to differ materially from those contemplated by the forward-looking statements. The risks and uncertainties primarily include those attendant with producing and marketing methanol and successfully carrying out major capital expenditure projects in various jurisdictions, including, without limitation:
n | | conditions in the methanol and other industries including fluctuations in the supply, demand for and price of methanol and its derivatives, including demand for methanol for energy uses, |
n | | the price of natural gas, coal, oil and oil derivatives, |
n | | the success of natural gas exploration and development activities in southern Chile and New Zealand and our ability to obtain any additional gas in Chile and New Zealand on commercially acceptable terms, |
n | | the ability to successfully carry out corporate initiatives and strategies, |
n | | actions of competitors, suppliers and financial institutions, |
n | | conditions within the natural gas delivery systems that may prevent delivery of our natural gas supply requirements, |
n | | competing demand for natural gas, especially with respect to domestic needs for gas and electricity in Chile and Egypt, |
n | | actions of governments and governmental authorities, including, without limitation, the implementation of policies or other measures that could impact the supply of or demand for methanol or its derivatives, |
n | | changes in laws or regulations, |
n | | import or export restrictions, anti-dumping measures, increases in duties, taxes and government royalties, and other actions by governments that may adversely affect our operations or existing contractual arrangements, |
n | | worldwide economic conditions, |
n | | satisfaction of conditions precedent contained in the Geismar project natural gas supply agreement, and |
n | | other risks described in the 2012 Management’s Discussion and Analysis. |
Having in mind these and other factors, investors and other readers are cautioned not to place undue reliance on forward-looking statements. They are not a substitute for the exercise of one’s own due diligence and judgment. The outcomes anticipated in forward-looking statements may not occur and we do not undertake to update forward-looking statements except as required by applicable securities laws.
| | | | |
40 Methanex Corporation | Annual Report 2012 | | Management’s Discussion & Analysis | | |