
2003 Annual Report
Our Model for Success
Five Year Financial Highlights
| | | | | | | | | | | | | | | | | | | | |
For the years ended December 31
| | 2003
| | 2002
| | 2001
| | 2000
| | 1999
|
Income Statement Information($000) | | | | | | | | | | | | | | | | | | | | |
Revenues | | $ | 1,517,090 | | | $ | 1,403,275 | | | $ | 1,402,509 | | | $ | 1,530,978 | | | $ | 1,415,392 | |
EBIT | | | 55,386 | | | | 67,923 | | | | 38,759 | | | | 66,142 | | | | 59,220 | |
Adjusted EBIT (Notes) | | | 61,031 | | | | 70,411 | | | | 50,621 | | | | 66,142 | | | | 59,220 | |
Adjusted EBITDA (Notes) | | | 77,533 | | | | 85,603 | | | | 65,284 | | | | 80,387 | | | | 72,751 | |
Adjusted EBITDA to sales % | | | 5.1 | % | | | 6.1 | % | | | 4.7 | % | | | 5.3 | % | | | 5.1 | % |
Basic earnings per common share ($) | | $ | 0.41 | | | $ | 0.71 | | | $ | 0.17 | | | $ | 0.53 | | | $ | 0.74 | |
| | | | | | | | | | | | | | | | | | | | |
Balance Sheet Information($000) | | | | | | | | | | | | | | | | | | | | |
Metals | | | | | | | | | | | | | | | | | | | | |
Accounts receivable | | $ | 247,513 | | | $ | 197,653 | | | $ | 192,244 | | | $ | 246,093 | | | $ | 210,687 | |
Inventories | | | 303,048 | | | | 329,415 | | | | 265,417 | | | | 290,991 | | | | 254,527 | |
Prepaid expenses and other assets | | | 2,005 | | | | 2,770 | | | | 2,053 | | | | 1,587 | | | | 1,821 | |
Accounts payable and accrued liabilities | | | (207,886 | ) | | | (178,623 | ) | | | (157,300 | ) | | | (183,659 | ) | | | (168,546 | ) |
| | | | | | | | | | | | | | | | | | | | |
Net working capital – Metals | | | 344,680 | | | | 351,215 | | | | 302,414 | | | | 355,012 | | | | 298,489 | |
Fixed assets | | | 165,112 | | | | 88,898 | | | | 85,825 | | | | 75,297 | | | | 73,402 | |
Goodwill | | | 4,216 | | | | 2,709 | | | | 15,123 | | | | 7,843 | | | | 5,066 | |
| | | | | | | | | | | | | | | | | | | | |
Net assets employed in metals operations | | | 514,008 | | | | 442,822 | | | | 403,362 | | | | 438,152 | | | | 376,957 | |
Other operating assets | | | 23,257 | | | | 24,750 | | | | 26,434 | | | | 25,230 | | | | 25,304 | |
Non-core and discontinued assets and liabilities | | | 2,647 | | | | 4,046 | | | | 4,874 | | | | 6,610 | | | | 41,910 | |
Net income tax assets and liabilities | | | (1,468 | ) | | | 768 | | | | 13,326 | | | | 16,013 | | | | 3,970 | |
Deferred financing charges | | | 3,547 | | | | 4,962 | | | | 6,177 | | | | 7,613 | | | | 8,249 | |
Pension and benefit liabilities | | | (11,542 | ) | | | (9,590 | ) | | | (9,242 | ) | | | (9,143 | ) | | | (9,411 | ) |
Other corporate assets and liabilities | | | (8,120 | ) | | | (6,643 | ) | | | (1,259 | ) | | | (6,584 | ) | | | (2,232 | ) |
| | | | | | | | | | | | | | | | | | | | |
Total net assets employed | | $ | 522,329 | | | $ | 461,115 | | | $ | 443,672 | | | $ | 477,891 | | | $ | 444,747 | |
| | | | | | | | | | | | | | | | | | | | |
Capitalization($000) | | | | | | | | | | | | | | | | | | | | |
Bank indebtedness, net of cash | | $ | 59,085 | | | $ | (3,927 | ) | | $ | (17,151 | ) | | $ | 12,311 | | | $ | (19,968 | ) |
Long-term debt | | | 179,402 | | | | 212,602 | | | | 214,105 | | | | 217,525 | | | | 210,413 | |
| | | | | | | | | | | | | | | | | | | | |
Total interest bearing debt | | | 238,487 | | | | 208,675 | | | | 196,954 | | | | 229,836 | | | | 190,445 | |
Preferred shares | | | 30,000 | | | | 30,000 | | | | 30,000 | | | | 30,000 | | | | 30,000 | |
Market capitalization (Notes) | | | 378,175 | | | | 194,091 | | | | 136,733 | | | | 110,146 | | | | 182,360 | |
| | | | | | | | | | | | | | | | | | | | |
Total firm value | | $ | 646,662 | | | $ | 432,766 | | | $ | 363,687 | | | $ | 369,982 | | | $ | 402,805 | |
| | | | | | | | | | | | | | | | | | | | |
Other Information(Notes) | | | | | | | | | | | | | | | | | | | | |
Common shareholders’ equity ($000) | | $ | 253,842 | | | $ | 222,440 | | | $ | 216,718 | | | $ | 218,055 | | | $ | 224,302 | |
Free cash flow ($000) | | $ | 117,399 | | | $ | 13,753 | | | $ | 84,977 | | | $ | (18,253 | ) | | $ | 124,231 | |
Capital expenditures ($000) | | $ | 34,879 | | | $ | 12,768 | | | $ | 8,152 | | | $ | 13,020 | | | $ | 17,249 | |
Depreciation and amortization ($000) | | $ | 16,502 | | | $ | 15,192 | | | $ | 14,663 | | | $ | 14,245 | | | $ | 12,444 | |
Adjusted interest ($000) | | $ | 22,800 | | | $ | 20,324 | | | $ | 23,017 | | | $ | 23,849 | | | $ | 22,228 | |
Earnings multiple | | | 17.24 | | | | 6.80 | | | | 10.40 | | | | 5.50 | | | | 5.17 | |
Firm value as a multiple of Adjusted EBIT | | | 10.60 | | | | 6.15 | | | | 7.18 | | | | 5.59 | | | | 6.68 | |
Firm value as a multiple of Adjusted EBITDA | | | 8.34 | | | | 5.06 | | | | 5.57 | | | | 4.60 | | | | 5.54 | |
Interest bearing debt/Adjusted EBITDA | | | 3.08 | | | | 2.44 | | | | 3.02 | | | | 2.86 | | | | 2.62 | |
Adjusted EBITDA/interest | | | 3.40 | | | | 4.21 | | | | 2.84 | | | | 3.37 | | | | 3.27 | |
Market capitalization as a % of book value | | | 149 | % | | | 87 | % | | | 63 | % | | | 51 | % | | | 75 | % |
Interest bearing debt as a % of net metals working capital | | | 69 | % | | | 59 | % | | | 65 | % | | | 65 | % | | | 64 | % |
Return on capital employed (Adjusted EBIT/ net assets employed) | | | 11.7 | % | | | 15.3 | % | | | 11.4 | % | | | 13.8 | % | | | 12.8 | % |
| | | | | | | | | | | | | | | | | | | | |
Common Share Information | | | | | | | | | | | | | | | | | | | | |
Ending outstanding common shares | | | 43,023,342 | | | | 38,057,001 | | | | 37,981,501 | | | | 37,981,501 | | | | 47,489,547 | |
Average outstanding common shares | | | 40,021,479 | | | | 38,024,034 | | | | 37,981,501 | | | | 41,068,870 | | | | 49,573,917 | |
Common share dividends paid ($000) | | $ | 11,605 | | | $ | 6,466 | | | $ | 7,596 | | | $ | 5,854 | | | $ | — | |
Common share dividends ($) | | $ | 0.29 | | | $ | 0.17 | | | $ | 0.20 | | | $ | 0.15 | | | $ | — | |
Book value per share ($) | | $ | 5.90 | | | $ | 5.84 | | | $ | 5.71 | | | $ | 5.74 | | | $ | 4.72 | |
Price range of stock ($) | | | | | | | | | | | | | | | | | | | | |
Market price of common shares at December 31 | | $ | 8.79 | | | $ | 5.10 | | | $ | 3.60 | | | $ | 2.90 | | | $ | 3.84 | |
High | | $ | 8.90 | | | $ | 5.49 | | | $ | 3.90 | | | $ | 4.95 | | | $ | 4.40 | |
Low | | $ | 4.65 | | | $ | 3.46 | | | $ | 2.70 | | | $ | 2.75 | | | $ | 2.50 | |
| | | | | | | | | | | | | | | | | | | | |
Notes:
(1) In this annual report the Company uses certain financial measures that do not comply with Canadian generally accepted accounting principles (GAAP) or have standardized meanings and thus may not be comparable to similar measures presented by other issuers, for example Adjusted EBITDA and Other Information in the above table. Management believes that Adjusted EBITDA may be useful in assessing our operating performance and as an indicator of our ability to service or incur indebtedness, make capital expenditures and finance working capital requirements. The items excluded in determining Adjusted EBITDA are significant in assessing our operating results and liquidity. Therefore, Adjusted EBITDA should not be considered in isolation or as an alternative to cash from operating activities or other combined income or cash flow data prepared in accordance with Canadian GAAP. Adjusted EBITDA and a number of the ratios provided under Other Information are used by debt and equity analysts to compare our performance against other public companies.
This terminology is defined on page 46, under Definitions. See financial statements for GAAP earnings.
(2) Statements contained in this document that relate to Russel Metals’ beliefs or expectations as to certain future events are not statements of historical fact and are forward-looking statements. Russel Metals cautions readers that there are important factors, risks and uncertainties, including but not limited to economic, competitive and governmental factors affecting Russel Metals’ operations, markets, products, services and prices that could cause the Company’s actual results, performance or achievements to be materially different from those forecasted or anticipated by Russel Metals in such forward-looking statements. All dollar references in this report are in Canadian dollars unless otherwise stated.
Profile
Russel Metals is one of the largest metals distribution and processing companies in North America based on revenues, profits and tons sold. The Company conducts its distribution business primarily in three metals segments: service centers; energy sector pipe, tube, valves and fittings; and import/export. Russel Metals is one of the few metals distribution companies in the world to operate a significant international trading operation in conjunction with service centers.
Service Centers Purchases metal in large volumes from producers principally in North America, adds value by providing a wide range of value added services, and then distributes the product to a broad base of approximately 18,000 end users through a network of 58 Canadian and 4 U.S. locations.
Energy SectorThe business units distribute pipe, tube, valves and fittings, chiefly to the energy sector in Western Canada and the Western United States from 5 Canadian and 2 U.S. locations.
Import/ExportPrimarily imports foreign steel products into Canada and the United States for customers that include both steel mills and metals distribution companies.
2003 Highlights
| | |
 | | 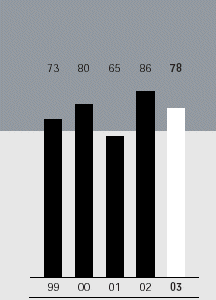 |
Revenues | | Adjusted EBITDA |
$ billions | | $ millions |
| | |
| | 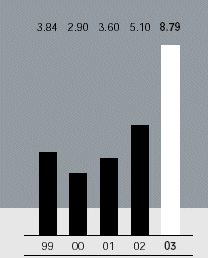 |
Adjusted EBITDA as a Percentage | | Market Price of |
of Net Assets Employed | | Common Shares |
% | | $ |
RUSSEL METALS 2003 ANNUAL REPORT 1
2003 Accomplishments
| | | | |
MANAGEMENT PRIORITIES | | | | ACCOMPLISHMENTS |
| | | | |
Be a sector leader | | > | | Generated 7th straight year of double digit return despite volatile steel pricing. |
in return on capital | | | | |
employed throughout | | | | |
the steel cycle | | | | |
| | | | |
Grow the Company’s | | > | | Acquired Acier Leroux, the largest steel distributor in Quebec. |
foundation through | | | | |
prudent acquisitions | | | | |
| | | | |
Optimize the Company’s | | > | | Restructured and integrated the Acier Leroux operations and balance sheet. |
application of capital | | | | |
| | > | | Generated $152.3 million in cash from operating activities. |
| | | | |
Provide leadership | | > | | Continued proactive management of health and safety issues resulted in a |
for employees through | | | | 9% reduction in lost time accidents in 2003. |
progressive health | | | | |
and safety practices | | > | | The accident severity measured by the number of days lost improved by 14% |
| | | | over the previous year. |
| | | | |
Provide shareholders | | > | | Dividends of $0.29 per share paid in 2003 – increased quarterly dividend 14% |
with superior common | | | | to $0.08 per share. |
share yields | | | | |
| | > | | Common share market value appreciated 72% in 2003. |
2 RUSSEL METALS 2003 ANNUAL REPORT
REPORT TO SHAREHOLDERS
ACQUISITION
1 In 2003, we purchased Acier Leroux. Our rationale
for acquiring Acier Leroux was primarily for its
profitable operations in Quebec and the Maritimes.
Edward M. Siegel, Jr.
President and
Chief Executive Officer
Defining the Model
2 RATIONALIZATION
Our strategy is to combine new acquisitions
with the existing Russel Metals operations
and then rationalize any duplication.
The rationalization of the Acier Leroux and 3
Russel Metals balance sheet went very
smoothly and represents a permanent
reduction in working capital and fixed
asset requirements.
CONSOLIDATION
Dear Shareholders
2003 was an extraordinary year in Canada,
and particularly for Russel Metals.
RUSSEL METALS 2003 ANNUAL REPORT 5
REPORT TO SHAREHOLDERS
This year, Canadians have witnessed many natural calamities that have affected their economy such as forest fires in British Columbia, Mad Cow once and revisited in Alberta, West Nile in the Prairies, the famous power outage and SARS in Ontario, and the hurricane in the Atlantic provinces to name a few. These events occurred in tandem with other issues such as the appreciation of the Canadian dollar and various disputes with the U.S. government including but not limited to softwood lumber, wheat and the galvanized steel reseller issue. Despite the effect of all of these on the economic environment, our Company finished the year in great shape and with its stock price trading at a ten-year high.
Our success in 2003 was due in part to the speedy integration of our acquisition of Acier Leroux, headquartered in Boucherville, Quebec, which positioned Russel Metals as the leading player in Quebec and increased our presence in the Maritimes and Ontario. Subsequent to this acquisition, we spent the second half of the year rationalizing and divesting assets, reducing the bank debt incurred for the acquisition and converting Acier Leroux’s computer system to the Russel Metals’ service center management information systems.
Not only were our activities focused on the Acier Leroux restructuring, we also completed the construction of a 156,000 square foot facility near Hamilton, Ontario, which is the new home of our B&T Steel flat rolled operations. We have expanded this operation by adding a new light gauge cut-to-length line, which increases our capacity and size range of flat rolled product.
Our fundamental business philosophy has not changed. We manage the business based on our working capital needs. We generate cash in a down cycle (less inventory and accounts receivable) and use more cash when the business improves (more inventory and accounts receivable). You may recall in last year’s annual report we stated that “we operate in a cyclical industry and our business model is predicated on principles intended to minimize significant earnings volatility.” These two guiding principles have become even more critical as the cyclicality of the steel business has become more profound, with shorter cycle times (peaks and troughs) than at any time in history.
Our management structure is flat. We have clearly defined operational goals for our business units and have provided our managers with the flexibility to react in the fastest manner possible. We consider this a necessity in this rapidly changing business environment.
In addition to shorter cycle times, a second important recent development in the steel industry is the changing correlation between supply and demand, and product pricing. In a traditional economic model, the price of a commodity will move in tandem with the demand for that same commodity, i.e., greater demand, higher prices; less demand, lower prices.
In the steel industry, this is no longer the case. During the last two years relatively flat demand has been accompanied by extraordinary price volatility. This has been caused in part by governmental intervention resulting in high tariffs on imported steel, the growth in Chinese consumption that has absorbed a significant amount of the raw materials at high prices that had
Acier Leroux
Our primary acquisition focus has been to strengthen our Canadian service center franchise. As a result of our acquisitions of A. J. Forsyth and Acier Leroux, Russel Metals now has a major presence in all the provinces of Canada.
The Model in Action
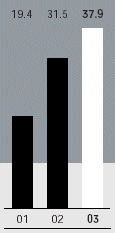
Service Center EBIT
$ millions
previously flowed to North America, and the weak U.S. dollar, which has made North America even less attractive for offshore materials.
Our emphasis on asset management has reduced the impact of price fluctuations and has consequently provided the Company with a relatively stable earnings stream. This has enabled us to provide stronger earnings compared to our competitors in an economic downturn, albeit with slightly lower earnings in periods of economic expansion. This reduces the volatility caused by the cycle and has enabled the Company to consistently generate earnings in the top decile of the industry. As an example, we have reported net earnings 27 out of the last 28 quarters and net earnings for seven consecutive years.
Steel is perceived to be a static industry. Russel Metals has, however, capitalized on two levers for growth. The first is participation in the steel distribution sector, which is a segment of the steel industry that continues to increase its market share of the overall consumption of steel. The second is growth through acquisition.
Within the past decade, metal service centers have continued to increase their share of overall steel mill shipments as the demand from their customers for finished parts, kits ready for assembly and inventory supplied on a just-in-time basis continues to expand. Buyers of metal products are looking to partner with suppliers who can improve their return on assets employed by reducing their working capital needs. With this in mind, Russel Metals has focused on acquiring equipment and developing processes that remove steps from our customers’ manufacturing and supply side operations. On the other hand, we have not made it a practice to involve ourselves in certain processes previously performed by the steel mills, such as cold reduction, temper rolling and pickling. These capital-intensive processes restrict the balance sheet flexibility required by Russel Metals to expand and contract with the steel cycle.
As mentioned earlier, the second driver of growth for Russel Metals has been selected acquisitions. Our primary acquisition focus has been to strengthen our Canadian service center franchise. As a result of our acquisitions of A. J. Forsyth and Acier Leroux, Russel Metals now has a major presence in all the provinces of Canada. Management is of the opinion that maintaining and growing this strong position is a major strategic goal.
Our aim is to be the market leader in every province in Canada. In markets where we are not the market leader, we will embark on a strategy to strengthen our market position. Our two most recent acquisitions, A. J. Forsyth in British Columbia and Acier Leroux in Quebec, were the most profitable operations in their provinces. Our business model is to seek out acquisition targets that are major players and profitable in their regions. Once the target has been acquired, our practice has been to combine the new acquisition with the existing Russel Metals operations, and then rationalize any geographic or product duplication that exists between the operations. In implementing this practice we reduce the working capital and reinforce the best of breed operational practices, facilities, equipment, operational teams and trade names, available in both the acquired company and Russel Metals.
In 2003, we purchased Acier Leroux. Our rationale for acquiring Acier Leroux was primarily for its profitable operations in Quebec and the Maritimes. The Acier Leroux USA and Ontario operations were unprofitable and the results were continuing to decline. At June 30, 2003, prior to this acquisition, Russel Metals had cash of $17.8 million. The cost of the Acier Leroux acquisition was $197.6 million funded by $20.0 million in new equity and borrowings of $177.6 million. Prior to the acquisition some stakeholders had expressed concern that an acquisition of this magnitude would adversely affect our balance sheet leverage. As of December 31, 2003, these concerns have been addressed as our net bank borrowing position was down almost $100 million from the transaction date. The rationalization of the combined balance sheets, coupled with lower import/export working capital levels, has enabled the Company to dramatically reduce this leverage. In addition, the Acier Leroux acquisition has been accretive to the net earnings of Russel Metals from the first month of the acquisition.
As stated earlier, our strategy is to combine new acquisitions with the existing Russel Metals operations and then rationalize any duplication. Immediately after the acquisition, the combined Russel Leroux regional teams evaluated the existing Russel Metals operations along with the new Acier Leroux operations and developed restructuring plans in order to provide Russel Metals with the strongest organization once the rationalization has been completed. This strategy was extraordinarily successful with the A. J. Forsyth acquisition completed in 2001.
In Quebec, the restructuring team has determined that all of the Acier Leroux facilities should remain open. In addition, we have changed the utilization of one of the two Acier Leroux, Boucherville facilities by transferring and expanding the Russel Metals non-ferrous business. We have also distributed the balance of our ferrous inventory to existing Acier Leroux facilities in Quebec to enable the sale of our 212,000 square foot facility in Lachine, Quebec. This building will be sold in 2004. The rationalization of staff levels in the region has been completed and the Quebec region is expected to generate results comparable to any region in Canada.
RUSSEL METALS 2003 ANNUAL REPORT 7
REPORT TO SHAREHOLDERS
In the Maritimes, we have realigned our distribution network with the addition of Acier Leroux’s Sackville, N.B. facility, which has allowed the Russel Metals Halifax operation to focus more on its immediate territory. We closed the Acier Leroux Dartmouth location and it will be sold in 2004.
In Ontario, we have begun the rationalization of the Russel Metals and Acier Leroux operations. Russel Metals’ Vantage Laser and Burlington plate operations, which were previously in leased facilities, are being combined in the vacant 124,000 square foot Acier Leroux Guelph facility. The refurbished Guelph facility will house all of our plate processing operations and plate inventory.
We will reduce the investment cost of the Acier Leroux acquisition with the sale of these aforementioned facilities in Dartmouth and Lachine.
Each regional team determined that converting the Acier Leroux operations to the Russel Metals management information systems would be of significant benefit to the regional operations. The conversion to the Russel Metals management information systems for most operations in each of Quebec, the Maritimes and Ontario was completed in 2003. I would like to take this opportunity to congratulate all of the Acier Leroux staff involved in the computer conversion for the professional manner in which they have handled the conversion and their positive outlook during what, for them, has been a traumatic transition.
Up until now, I have concentrated on our acquisition strategy as it relates to our Canadian steel service center franchise primarily because of its significance to our Company.
Acquisitions in the U.S. service center market or our energy and import/export segments will be considered if they provide us with a major presence in their geographic region or have a significant product niche. In the past, acquisitions such as the Sunbelt Trading Group and Triumph Tubulars have fallen into this category. Management is of the opinion that it is not possible to develop a franchise in the U.S. service center group similar to our Canadian service centers. Although the consolidation of the U.S. service center segment has slowed somewhat, no single service center has been able to develop a meaningful presence in terms of market share in the United States.
Despite management’s beliefs noted above, we purchased Williams Steel in 2002 in an attempt to improve our Bahcall operations, which had been providing less than adequate returns. Unfortunately, the acquisition of Williams Steel and subsequent rationalization of the Russel Metals Bahcall location in Waukesha with Williams Steel did not generate positive returns. Neither Williams nor Bahcall were individually significant players in their market nor were they strong financial performers. The combination of the two resulted in a large regional player, but the execution of the rationalization has been disappointing. Williams Bahcall had an operating loss in 2003. The annual goodwill impairment evaluation has resulted in a write off of the Williams Bahcall goodwill of $2.4 million in the fourth quarter of 2003.
The construction of our B&T Steel flat rolled facility at Stoney Creek near Hamilton, Ontario during 2003 has been completed. This represents our first significant capital expenditure project in the past seven years. The 156,000 square foot facility will house two flat rolled cut-to-length lines, one
B&T Steel
The flat rolled facility at Stoney Creek near Hamilton, Ontario
will house a heavy gauge cut-to-length line previously located
at the B&T Steel facility and a new lighter gauge line.
The Model in Action
being the heavy gauge line previously located at the B&T Steel facility in Hamilton and a new lighter gauge line.
The balance sheet optimization generated during 2003 was very strong and the cash generated from operating activities was $152.3 million, which far exceeded expectations. This reflects the strong operating earnings experienced in 2003 and that the working capital levels were reduced in reaction to the flat demand experienced in the period particularly in the import/export operations. The inventory rationalization of the combined companies as part of the Acier Leroux restructuring further contributed to working capital reductions and our overall inventories as of December 31, 2003 were lower than the same period in 2002. The rationalization of the Acier Leroux and Russel Metals balance sheet went very smoothly and represents a permanent reduction in working capital and fixed asset requirements. This reduction in net assets employed since the acquisition enabled the Company to generate a return on capital employed of 11.7%, our seventh consecutive year of double digit returns.
In our 2002 Annual Report we included a section on corporate governance. At that time, there was a raft of corporate scandals calling into question the fundamental principles by which companies were governed. As a result, we clarified the Company’s corporate governance position in that report. 2003 has seen a continuance of governance failures on a global basis. We endeavour to be as open a company as possible. Effective January 1, 2003, the Company adopted the fair value method of accounting for stock-based compensation. In addition during 2003, senior management exercised a significant number of stock options earned since 1997. These individuals chose to reinvest most of the after tax gains in the Company’s common stock, which allows them to continue to invest in the ongoing growth and success of the Company.
On February 12, 2004, the Company issued 5,750,000 common shares at $9.00 per share. On February 20, 2004, the Company issued US$175 million of new 10-year Senior Notes with an interest rate of 6.375%. This financing enabled the Company to repurchase the US$95.5 million of 10% Senior Notes, $30 million of 8% Subordinated Debentures and $30 million of preferred shares, which on a before tax basis cost 11.9%. The Company will redeem the remaining US$20.1 million of 10% Senior Notes on June 1, 2004. The new debt issue will reduce the interest expense and preferred share dividend payments on an ongoing basis by approximately $6.7 million annually. The Company has swapped US$100 million of the notes to Canadian funds at a fixed interest rate of 7.12% to eliminate the exchange exposure.
The Company looks forward to 2004 positively, although we are going through a difficult period with the onslaught of surcharges that have been added to our costs by our suppliers, ostensibly to cover their higher cost for such items as energy and metallics. Much of what has driven these additional costs has been the strength of the metals market in China. The anticipation is that once that market becomes saturated, pricing will drop to normal levels.
With the acquisition of Acier Leroux, we have strengthened an area of the Company that has hereto not provided satisfactory results, and our anticipation is that there will be a general improvement in our overall performance based on the Acier Leroux acquisition.
We are seeing stronger results from our energy sector companies and we anticipate that the results for 2004 should finally reflect the high oil and gas prices we have seen during the past two years.
The import/export sector is an area of concern due to the continuing strength in China and the weakening of the U.S. dollar, which causes materials that have normally flowed to North America to be diverted to satisfy the market in China; however, we anticipate improvement in this sector once the Chinese bubble has run its course.
We are optimistic that 2004 will be an improvement on 2003 and that the Company is well situated to remain one of the most stable and consistently profitable financial performers in the metals distribution industry.
I would like to take this opportunity to welcome the Acier Leroux employee group and thank them for the enthusiasm they have shown since the acquisition, in what has been a very hectic period for all of us. The addition of Acier Leroux enables Russel Metals to strengthen its leading position in the Canadian service center industry. The combination of our world class import/export and energy operations and our strong Canadian service centers has created a company that continues to produce results at the forefront of the industry.
In closing, I would like to thank both Duncan Thomas, formerly General Manager of our British Columbia region, and Tom Oelkuch, formerly General Manager of our B&T Steel operation, who retired in 2003 and have been influential in our growth these past couple of years. I would also like to thank all our employees for another strong performance; without you, this success would not be possible.
(Signed) Edward M. Siegel, Jr.
Edward M. Siegel, Jr.
President and Chief Executive Officer
RUSSEL METALS 2003 ANNUAL REPORT 9
A Model of Balance
Service Centers
Purchase metal in large volumes from producers principally in North America, add value by providing a wide range of reliable services, and then distribute the product to a broad base of approximately 18,000 end users in a wide variety of industries through a network of 58 Canadian and 4 U.S. locations.
Energy
The business units distribute pipe, tube, valves and fittings, chiefly to the energy sector in Western Canada and the Western United States from 5 Canadian and 2 U.S. locations.
Import/Export
Imports foreign steel products into Canada and the United States for customers that include both steel mills and metals distribution companies and, to a lesser extent, exports North American steel products to international end users.
10 RUSSEL METALS 2003 ANNUAL REPORT
Service Centers
> 23% revenue increase to $922.8 million
> 20% increase in operating profits to $37.9 million
> Cash flow from operations of $99.1 million
> Industry leading inventory turns of 4.0
> Acquired Acier Leroux to strengthen Eastern Canada operations
Russel Metals believes it operates the largest service center operation in Canada based on revenues. Russel Metals processes and distributes products to a broad base of approximately 18,000 customers through a network of 58 locations across Canada. In addition, the Company has four U.S. locations.
Our service centers sell plate, flat rolled carbon and other general line carbon steel products, as well as some stainless steel, aluminum and other non-ferrous specialty metal products in a wide range of sizes, shapes and specifications. General line steel products, consisting of plate, structurals, bars, sheet, pipe, tubing and hollow structural steel tubing, are used by end users in a wide variety of industries.
Our service center operations also provide customized processing services to satisfy specifications established by end users. By providing these services, as well as by offering inventory management and just-in-time delivery, we enable end users to reduce their overall production costs and decrease capital required for raw materials and metals processing equipment.
Our service center operations provide products and services to end users in a wide variety of industries, including machinery and equipment manufacturing, construction, shipbuilding and natural resources, such as mining and petroleum.
On July 3, 2003, the Company purchased Acier Leroux inc., a company specializing in the processing and distribution of various steel products from service center locations mainly in Ontario, Quebec and the Maritimes.
Canadian OperationsWithin Canada, our steel service centers operate under the names Russel Metals, Métaux Russel, Drummond McCall, A. J. Forsyth, Acier Leroux, Acier Dollard, Acier Loubier, Ennisteel, Leroux Steel, Russel Leroux, Poutrelles Delta and Vantage Laser. Heavy gauge flat rolled operations are conducted by B&T Steel and McCabe, both located in Stoney Creek near Hamilton, Ontario.
U.S. OperationsOur U.S. service center operations are conducted under the names Russel Metals Williams Bahcall and Baldwin International. The Williams Bahcall operation focuses primarily on the distribution of general line carbon products through three facilities in Wisconsin. Baldwin International distributes specialty alloy products through its facility in Ohio.
| | |
| | |
| | Revenues |
| | $ millions |
| | |
| | |
| | EBITDA |
| | $ millions |
RUSSEL METALS 2003 ANNUAL REPORT 11
Energy
> 3% revenue increase to $297.5 million
> 1% increase in operating profits to $13.8 million
> Cash flow from operations of $13.2 million generated
> Stable 4.6% segment operating profit to revenues
Our energy sector consists of four businesses, each of which sells a distinct line of products. This segment distributes pipe, tube, valves and fittings primarily to the energy sector, from 5 Canadian and 2 U.S. locations.
Products are sourced from either the pipe processing arms of North American steel mills or from independent manufacturers of pipe and its accessories.
Each business in this segment sells a distinct line of products. These businesses include:
Fedmet TubularsA distributor of oil country tubular goods (which includes casing and tubing) and line pipe and related products. Fedmet Tubulars’ sales office is located in Calgary, Alberta.
Triumph Tubular & SupplyA distributor of oil country tubular goods. Triumph’s sales office is located in Calgary, Alberta.
Comco Pipe and Supply CompanyA distributor of pipe, valve and fitting products, specializing in the supply and distribution of pipe and fluid handling products to the energy, construction, manufacturing, pulp and paper and mining industries. These products are distributed through facilities in Calgary and Edmonton, Alberta; Stonewall, Manitoba; and Guelph and Sarnia, Ontario.
Pioneer PipeA distributor and processor of steel pipe products to the construction, oil and gas and ski industries in the Western United States. Pioneer Pipe has facilities in Aurora, Colorado and Lindon, Utah. These operations include Spartan Steel, headquartered in Evergreen, Colorado.
Import/Export
> 19% revenue decrease to $283.6 million
> Operating profits of $13.4 million, a decrease of 52%
> Cash flow from operations of $72.9 million
Russel Metals’ import/export operations import foreign steel products into Canada and the United States and, to a lesser extent, export North American steel products to international end users. These operations also provide the Company’s other business segments with valuable insight regarding international pricing trends and their potential impact in North America.
Revenues from these operations may vary substantially from year to year, depending primarily on general economic conditions and trade actions both in North America and in the export markets served by these operations. The import/export operations take title of the steel they acquire.
This segment specializes in the import into North America of carbon steel, plate, beams, channel, flat rolled products, rail and pipe products. Sales commitments for a significant portion of these products are obtained prior to their purchase or while the product is in production and transit. Products for which sales commitments have not been obtained are held in public warehouses for resale to North American service centers and other customers.
Our import/export segment is conducted through Wirth Steel located in Canada and the Sunbelt Group located in the United States.
12 RUSSEL METALS 2003 ANNUAL REPORT
Management’s Discussion and Analysis
For the Year Ended December 31, 2003
The following management’s discussion and analysis of financial condition and results of operations of Russel Metals Inc. and its subsidiaries (Russel Metals or the Company) provides information to assist the reader and should be read in conjunction with the audited Consolidated Financial Statements for the year ended December 31, 2003, including the notes thereto. Statements contained in this document that relate to Russel Metals’ beliefs or expectations as to certain future events are not statements of historical fact and are forward-looking statements. Russel Metals cautions readers that there are important factors, risks and uncertainties, including but not limited to economic, competitive and governmental factors affecting Russel Metals’ operations, markets, products, services and prices that could cause the Company’s actual results, performance or achievements to be materially different from those forecasted or anticipated by Russel Metals in such forward-looking statements. All dollar references in this report are in Canadian dollars unless otherwise stated.
The Management’s Discussion and Analysis includes a number of measures that are not prescribed by generally accepted accounting principles and as such may not be comparable to similar measures presented by other companies. The Company’s definition of gross margins, segment operating profits, Adjusted EBITDA, coverage ratio, and inventory turns are provided in the sections where used.
Overview
Russel Metals is one of the largest metal distribution companies in North America based on revenues and tons sold. The Company conducts business primarily in three metals distribution business segments: service centers; energy sector related pipe, tube, valves and fittings; and steel import/export.
2003 was an active year for Russel Metals highlighted by the acquisition of Acier Leroux in July. The Company reported $0.51 per common share earnings from continuing operations before other costs. The demand for steel by end users remained at similar levels to that experienced in 2002 in the service center sector on a same store basis.
The import/export operations experienced lower volumes driven by trade actions, increased domestic production capacity, the lower U.S. dollar, which made North American steel markets less attractive, and the demand for steel in the Far East, which diverted large portions of international steel movements to China.
The energy sector activity for the first six months of 2003 was strong but still not at levels expected given the high price of oil and gas. However, activity has increased in the oil country tubular goods (OCTG) area during the last six months of 2003.
In 2003, management concentration on working capital allowed the Company to report earnings in the first half of the year when many of our competitors had losses. The operations of Acier Leroux have been profitable since the acquisition in the third quarter, and the rationalization of working capital and fixed assets has generated profits and significant cash flow.
2002 was a year of contradictions in the steel sector, and was as unique as 2001, but for different reasons. Several factors contributed to the record $0.75 per common share earnings from operations before other costs of Russel Metals. The North American trade actions, coupled with the financial weakness of North American steel mills, which caused reduction in capacity, led to an unprecedented 40% price increase in flat rolled products, including plate. The supply side driven price increases were at odds with the demand side fundamentals, which remained static in 2002. The rapid price increases resulted in inventory holding gains and higher gross margin dollars per ton. In the case of Russel Metals, these higher per ton margins, despite the relatively flat demand, enabled the service center segment to generate stronger earnings than the previous year. In addition, the import/export operations experienced higher volumes and increasingly strong margins under the umbrella of the aforementioned higher steel prices.
Political uncertainty and merger and acquisition activity negatively influenced energy sector exploration and development and caused weak drilling activity in 2002, despite very strong oil and gas prices. This decline in activity led to lower revenues, gross margins and operating profits in our energy sector distribution businesses.
Strong balance sheet management resulted in lower borrowings and lower interest expense. Inventories did climb in the import/export operations during the later months of the year due to strong activity in our import/export operations. These elevated inventory levels were reduced during 2003.
Results of Operations
The following table provides a summary of revenues, segment operating profits (revenue minus cost of sales and operating expenses excluding corporate expenses and interest expense) and gross margins (revenue minus cost of sales) as a percentage of revenues for Russel Metals’ operating segments. The table shows the segments as they are reported to management and they are consistent with the segmented reporting in Note 13 to the Company’s 2003 Consolidated Financial Statements.
RUSSEL METALS 2003 ANNUAL REPORT 13
MANAGEMENT’S DISCUSSION AND ANALYSIS
| | | | | | | | | | | | | | | | | | | | |
| | | | | | | | | | | | | | 2003 | | 2002 |
| | | | | | | | | | | | | | Change | | Change |
(in thousands of dollars, | | | | | | | | | | | | | | as a % | | as a % |
except percentages)
| | 2003
| | 2002
| | 2001
| | of 2002
| | of 2001
|
Segment Revenues | | | | | | | | | | | | | | | | | | | | |
Service center distribution | | $ | 922,778 | | | $ | 750,878 | | | $ | 706,173 | | | | 22.9 | % | | | 6.3 | % |
Energy sector distribution | | | 297,532 | | | | 289,623 | | | | 360,515 | | | | 2.7 | % | | | (19.7 | %) |
Steel import/export | | | 283,579 | | | | 348,055 | | | | 321,454 | | | | (18.5 | %) | | | 8.3 | % |
Other | | | 13,201 | | | | 14,719 | | | | 14,367 | | | | (10.3 | %) | | | 2.5 | % |
| | | | | | | | | | | | | | | | | | | | |
| | $ | 1,517,090 | | | $ | 1,403,275 | | | $ | 1,402,509 | | | | 8.1 | % | | | 0.1 | % |
| | | | | | | | | | | | | | | | | | | | |
Segment Operating Profits | | | | | | | | | | | | | | | | | | | | |
Service center distribution | | $ | 37,903 | | | $ | 31,516 | | | $ | 19,352 | | | | 20.3 | % | | | 62.9 | % |
Energy sector distribution | | | 13,764 | | | | 13,612 | | | | 18,406 | | | | 1.1 | % | | | (26.0 | %) |
Steel import/export | | | 13,380 | | | | 28,090 | | | | 14,175 | | | | (52.4 | %) | | | 98.2 | % |
Other | | | 4,002 | | | | 5,732 | | | | 6,177 | | | | (30.2 | %) | | | (7.2 | %) |
Corporate expenses | | | (8,018 | ) | | | (8,539 | ) | | | (7,489 | ) | | | 6.1 | % | | | (14.0 | %) |
| | | | | | | | | | | | | | | | | | | | |
Operating profits from continuing operations | | $ | 61,031 | | | $ | 70,411 | | | $ | 50,621 | | | | (13.3 | %) | | | 39.1 | % |
| | | | | | | | | | | | | | | | | | | | |
Segment Gross Margins as a % of Revenues | | | | | | | | | | | | | | | | | | | | |
Service center distribution | | | 26.4 | % | | | 26.8 | % | | | 24.9 | % | | | | | | | | |
Energy sector distribution | | | 11.6 | % | | | 13.1 | % | | | 13.9 | % | | | | | | | | |
Steel import/export | | | 10.8 | % | | | 14.3 | % | | | 9.4 | % | | | | | | | | |
Total | | | 20.9 | % | | | 21.3 | % | | | 19.0 | % | | | | | | | | |
| | | | | | | | | | | | | | | | | | | | |
Segment Operating Profits as a % of Revenues | | | | | | | | | | | | | | | | | | | | |
Service center distribution | | | 4.1 | % | | | 4.2 | % | | | 2.7 | % | | | | | | | | |
Energy sector distribution | | | 4.6 | % | | | 4.7 | % | | | 5.1 | % | | | | | | | | |
Steel import/export | | | 4.7 | % | | | 8.1 | % | | | 4.4 | % | | | | | | | | |
| | | | | | | | | | | | | | | | | | | | |
Total | | | 4.0 | % | | | 5.0 | % | | | 3.6 | % | | | | | | | | |
| | | | | | | | | | | | | | | | | | | | |
Service Center Distribution
a) Description of operationsThe Company provides processing and distribution services to a broad base of more than 18,000 end users through a network of 58 Canadian locations. In addition, the Company has 4 U.S. locations. The Company’s network of service centers carries a broad line of products in a wide range of sizes, shapes and specifications, including carbon hot rolled and cold finished steel, pipe and tubular products, stainless steel and aluminum. Russel Metals purchases these products primarily from steel producers in North America and processes and packages them in accordance with end user specifications. The Company services all major geographic regions of Canada and the Midwest region in the United States. Within Canada, the service centers operate under the names Russel Metals, Métaux Russel, Drummond McCall, A. J. Forsyth, Acier Leroux, Acier Dollard, Acier Loubier, Ennisteel, Leroux Steel, Russel Leroux, Poutrelles Delta and Vantage Laser. Heavy gauge flat rolled operations are conducted by B&T Steel and McCabe Steel, both located near Hamilton, Ontario. Russel Metals’ U.S. service center operations are conducted under the names Russel Metals Williams Bahcall and Baldwin International. The Williams Bahcall operations focus primarily on the distribution of general line carbon products through three facilities in Wisconsin. Baldwin International distributes specialty alloy products through its facility in Ohio.
On July 3, 2003, the Company completed its acquisition of Acier Leroux inc. The merger plans have proceeded at a faster pace than predicted at the acquisition date and, consequently, management is in the final stages of merging the two operations. Acier Leroux was a publicly traded company with sales of approximately $471 million for the year prior to the acquisition date. Sales from Acier Leroux’s Canadian operations for such period were approximately $401 million. The balance of the revenue was from U.S. operations, which the Company has discontinued.
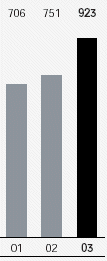
Service Center Revenues
$ millions
14 RUSSEL METALS 2003 ANNUAL REPORT
The results of operations of Acier Leroux for the period from acquisition to December 31, 2003 have been consolidated in the Russel Metals service center operations. The U.S. operations, which have been substantially closed, are reported as discontinued operations and thus are not included in the service center segment. The fourth quarter charge for discontinued operations was $0.2 million.
Acier Leroux specializes in the processing and distribution of steel products including reinforcing steel, steel bars, angles, channels, beams, tubing, pipes, plates and hot rolled sheets from service center locations mainly in Ontario, Quebec, New Brunswick and Nova Scotia.
In September 2002, the Company purchased the operating assets of a service center located in Milwaukee, Wisconsin formerly known as Williams Steel. This operation has been combined with the Russel Metals Bahcall operations. Williams Steel had sales of approximately $49 million for the year prior to the acquisition date.
b) Factors affecting results
The following is a general discussion on the significant factors affecting service center results. More specific information on how these factors impacted 2003, 2002 and 2001 is found in the sections that follow.
Steel pricing fluctuates significantly throughout the cycle. Steel prices are influenced by overall demand, trade sanctions and by product availability. Product availability is affected by supply side management practiced by steel producers in North America and international supply and demand which impacts steel imports. Trade sanctions are initiated either by steel mills or Governmental Agencies in North America, and less directly worldwide. Selling prices increased during the second quarter of 2002, as a result of trade tariffs in the United States increasing the price of imported steel. However, due to low demand and sufficient available mill capacity, selling prices have leveled out during the remainder of 2002 and 2003. The mills have implemented surcharges and price increases in 2004, which will result in increased selling prices and gross margins.
Demand is significantly affected by economic cycles with revenues and operating profit fluctuating with the level of general business activity in the markets served. The Company is most impacted by the non-automotive segments of the economy. General business activity and thus customer demand have been at low levels during the period 2001 to 2003. The U.S. operations of Williams Bahcall have been most significantly impacted by the general business conditions in the Wisconsin area. The Company does not foresee a pick up in demand in the near term.
Canadian steel service centers, which represent a large portion of the service center distribution segment operations, are particularly affected by regional general economic conditions. The Company has operations in all regions of Canada and has a market share of approximately 24%. This large market share and our diverse customer base of 18,000 customers means the Company’s results should mirror the performance of the regional economies. Alberta has been the region most significantly impacted due to the oil and gas rig activity, which reduced revenues 14% in 2002 compared to 2001. The rig activity has increased in 2003 resulting in higher tons in the Alberta region and a revenue increase of 6.7% over 2002.
The revenue growth recorded in 2002 was primarily due to the acquisition of A. J. Forsyth, and in 2003 was primarily due to the Acier Leroux acquisition.
c) Service center segment results – 2003 compared to 2002Revenues for 2003 increased 22.9% due to the acquisition of Acier Leroux. Revenues from operations excluding Acier Leroux were approximately the same as in 2002. The operations, excluding Acier Leroux, had tons and selling prices in 2003 that approximated the same levels as in 2002. Alberta and British Columbia had higher tons due to more activity related to the oil and gas industries and a slight pickup in the pulp and paper industry in British Columbia. Ontario flat rolled operations had lower tons, whereas the tons in other regions in 2003 were comparable to 2002. Our manufacturing customers in Ontario have experienced lower demands. Williams Bahcall volumes were higher due to the Williams acquisition, but the operation continued to be unprofitable due to generally weak customer demand in the Wisconsin region. Gross margins decreased from 26.8% in 2002 to 26.4% in 2003. The decline relates to inventory holding losses versus holding gains in 2002 in the Russel Metals operations. The Company has the centralized information systems necessary to manage change in the volatile steel sectors. Our focus is on inventory management and gross margin generation. Rising steel prices create inventory holding gains and declining prices result in inventory holding losses. The Company does not incur the expense to quantify these inventory holding gains/losses due to the complexity of our over fifty service center operations which buy and sell over 14,000 different SKUs. The Company proactively reacts to changes in market forces and this additional information would not be available on a timely basis.
| | |
| | |
| | Service Center Operating Profits |
| | $ millions |
| | |
| | |
| | Service Center EBIT To Sales |
| | % |
RUSSEL METALS 2003 ANNUAL REPORT 15
MANAGEMENT’S DISCUSSION AND ANALYSIS
Service center operating profits in 2003 increased $6.4 million or 20.3% compared to 2002. This increase is primarily a result of the acquisition of Acier Leroux partially offset by lower operating profits in certain of the remaining operations. The lower operating profits in the Russel Metals regions in 2003 excluding Acier Leroux resulted from the gross margin decline. Operating expenses for the operations excluding Acier Leroux were reduced $1.5 million in 2003.
Operating profits as a percentage of revenues in 2003 were 4.1% compared to 4.2% in 2002. In the first half of 2003, prior to the acquisition, the service center operating profits as a percentage of revenues were 3.5%. In the second half of 2003 after the acquisition, service center operating profits as a percentage of revenues improved to 4.5% due to the acquisition and improved conditions across Canada. In the second half of 2003, revenues were up 39.0% compared to the first half of 2003 as a result of the acquisition.
d) Service center segment results – 2002 compared to 2001Revenues for 2002 increased 6.3% due to higher selling prices and acquisitions compared to 2001. Revenue increases were most significant in the British Columbia region due to the acquisition of A. J. Forsyth in October 2001. Volume declines occurred in Alberta, due to lower oil and gas activity, and at our U.S. operation, Williams Bahcall, due to general lower customer demand in the Wisconsin region and customer facility closures.
The average selling price per ton was approximately 5% higher in 2002 compared to 2001. The average selling price started to increase during the second quarter of 2002, reflecting price increases implemented by the North American steel mills. The average selling price plateaued in the last half of 2002.
Gross margins improved from 24.9% for 2001 to 26.8% for 2002, mainly a result of rising selling prices during 2002, which resulted in inventory holding gains.
Service center operating profits for 2002 increased by 62.9% compared to 2001. This increase is a result of selling price increases and corresponding higher gross margins, and the acquisition of A. J. Forsyth. Operating expenses for 2002 were $13.6 million, or 8.7% higher than 2001. Approximately $10.2 million of the increase in operating costs relates to the British Columbia region due to the acquisition of A. J. Forsyth.
Operating profits as a percentage of revenues for 2002 were 4.2%, a significant improvement over 2001 at 2.7% in one of the weakest years on record for the industry.
Energy Sector Distribution
a) Description of operationsThese operations distribute pipe, tube, valves and fittings, primarily to the energy sector in Western Canada and the Western United States, from 5 Canadian and 2 U.S. locations. Russel Metals purchases these products either from the pipe processing arms of North American steel mills or from independent manufacturers of pipe and pipe accessories. The energy sector operates under the names Comco Pipe and Supply Company, Fedmet Tubulars, Triumph Tubular & Supply, Pioneer Pipe and Spartan Steel.
b) Factors affecting results
The following is a general discussion on the factors affecting our energy sector operations. More specific information on how these factors impacted 2003, 2002 and 2001 is found in the sections that follow.
Demand is significantly affected by oil and gas pricing, which impacts oil rig count and subsequent drilling activities particularly in Western Canada. Oil and gas pricing has been stable for the period from 2001 to 2003; however, demand was lower during 2002 due to financial consolidations and restructuring in the customer base we service. The drilling activity returned to expected levels during the second half of 2003 and is anticipated to continue in 2004.
Canadian operations can be affected by the U.S. dollar since some products are sourced outside Canada and are priced in U.S. dollars. The effect of the appreciation of the Canadian dollar on the 2003 results was negligible since this appreciation was offset by rising metal prices. The dollar was relatively constant for 2002 and 2001 and, therefore, was not a factor.
Pricing is influenced by overall demand, trade sanctions and by product availability. Trade sanctions are initiated either by steel mills or Governmental Agencies in North America. Trade sanctions have not been a factor for pipe products in the last three years.
| | |
| | |
| | Energy Sector Revenues |
| | $ millions |
| | |
| | |
| | Energy Sector Operating Profits |
| | $ millions |
16 RUSSEL METALS 2003 ANNUAL REPORT
c) Energy sector distribution results - 2003 compared to 2002Energy sector revenues increased 2.7% for 2003 compared to 2002. Stable oil and gas pricing and more rig activity in 2003 compared to 2002 have resulted in some volume increases for the oil country tubular goods operations in Western Canada. Comco Pipe, which distributes pipe, valves and fittings to other fluid handling industries as well as the energy sector and is heavily involved in project business, had decreased revenue of 24.5% in 2003 compared to 2002. Comco had significant revenues from large projects during 2002 that did not continue into 2003. Comco’s revenues for 2003 are comparable to 2001.
Energy sector operating profits increased by 1.1% in 2003, compared to 2002. The increase relates to higher volumes in the OCTG operations in Western Canada. The increase in volumes in the OCTG operations offset the lower volumes and profitability in our Comco operations due to lower project business.
d) Energy sector distribution results - 2002 compared to 2001Energy sector revenues decreased 19.7% for 2002 compared to 2001. Lower rig activity for 2002 compared to 2001 resulted in volume declines for the oil country tubular goods operations in Western Canada and the United States. Although oil pricing is comparable to 2001 levels, the consolidation of some large players and the restructuring to income trusts have impacted investment in capital and contributed to lower drilling levels in 2002.
Comco Pipe had increased revenue of 28.9% in 2002 compared to 2001. Comco Pipe’s revenue is more project oriented and as such is not as dependent on drilling levels.
Energy sector operating profits declined $4.8 million, or 26.0%, in 2002 compared to 2001. The decline is related to the drop in volume in the oil country tubular goods operations, partially offset by increased operating profits at Comco Pipe due to higher volumes from large projects.
Steel Import/Export
a) Description of operationsRussel Metals’ steel import/export business primarily imports foreign steel products into Canada and the United States. It also exports steel from Canada and the United States. The international presence provides the Company’s other business segments with valuable insight regarding international pricing trends and their potential impact on steel markets in North America.
The main steel products sourced by the import/export operations are structural beam, plate, coils, pipe and tubing. The operations in this sector are Wirth Steel and Sunbelt Group.
b) Factors affecting results
This section discusses the general factors affecting our import/export operations. More specific information on how these factors impacted 2003, 2002 and 2001 is found in the sections that follow.
Steel pricing is influenced by overall demand, trade sanctions and by product availability both domestically and worldwide. Trade sanctions are initiated either by steel mills or Governmental Agencies in North America. Mill capacity by product line in North America and international supply and demand impacts steel imports and significantly affects product availability. Higher steel prices resulting from U.S. trade actions significantly increased revenues and gross margin in 2002. Lack of product availability to import and increasing product supply from North American producers were the most significant factors reducing revenues and operating margins for 2003.
The Canadian import/export operations are affected by movement in the U.S. dollar since purchases are mainly in U.S. dollars. The effect of the appreciation of the Canadian dollar on 2003 results was negligible since the appreciation was offset by rising metal prices as Canadian suppliers increased their prices under the umbrella created by U.S. steel producers. The U.S. dollar versus the Canadian dollar was relatively constant in 2002 compared to 2001.
| | |
| | |
| | Energy Sector EBIT to Sales |
| | % |
| | |
| | |
| | Steel Import/Export Revenues |
| | $ millions |
RUSSEL METALS 2003 ANNUAL REPORT 17
MANAGEMENT’S DISCUSSION AND ANALYSIS
c) Steel import/export results - 2003 compared to 2002Steel import/export revenues decreased 18.5% in 2003 compared to 2002. Selling prices in 2003 have decreased compared to the high selling prices experienced in 2002. Lack of product availability due to high demand in the Far East, uncertainty due to Canadian trade actions, increased production by North American producers and the weaker U.S. dollar contributed to the reduced revenue and gross margin in 2003 compared to 2002. Gross margin as a percentage of revenue was 10.8% for 2003 and is a more normal level than the 14.3% reported in 2002. The high margins experienced in 2002 were directly related to U.S. trade actions, which artificially induced mill price increases on flat rolled steel. In addition, in 2002, lack of product from North American suppliers, who had temporarily banked their steel-making, resulted in higher selling prices and margins for inventory on hand.
Steel import/export operating profits decreased by 52.4% in 2003 compared to 2002. Lower demand and the return to more normal margins both contributed to this decrease. The reduced revenues and gross margins resulted in operating profit as a percentage of revenue decreasing from 8.1% for 2002 to 4.7% for 2003.
d) Steel import/export results - 2002 compared to 2001Steel import/export revenues increased 8.3% in 2002 compared to 2001. A decline in revenue was experienced during the first quarter of 2002 compared to the first quarter of 2001, when uncertainty existed related to the resolution of the U.S. and Canadian trade rulings. The U.S. made its ruling in March 2002, while the Canadian Safeguard initiative was under review during 2002. This resulted in increased steel pricing. Revenues during the remainder of 2002 were significantly higher than 2001 due to a slight improvement in customer demand and higher selling prices.
Steel price increases initiated by North American steel mills contributed to higher selling prices resulting in a stronger gross margin of 14.3% for 2002 compared to 9.4% for 2001. The gross margin as a percentage of revenue of 14.3% for 2002 is higher than normal and declined in 2003.
Steel import/export operating profits increased 98.2% to $28.1 million for 2002 compared to 2001. The increase was mainly related to a higher gross margin. This higher gross margin resulted in operating profits as a percentage of revenues of 8.1% for 2002 compared to 4.4% for 2001.
Other - 2003 compared to 2002 and 2001
Other revenue and income represents the results of the Company’s coal handling terminal in Thunder Bay. Revenue in 2003 was lower than 2002 and 2001 due to decreased coal volumes. The lower volumes resulted in lower earnings from operations.
Consolidated Results - 2003 compared to 2002
The following table discloses earnings from continuing operations net of income taxes, other costs net of income taxes, unusual items net of income taxes, and discontinued operations net of income taxes. Earnings per common share are disclosed to assist the reader in determining results from ongoing operations.
| | |
| | |
| | Steel Import/Export Operating Profits |
| | $ millions |
| �� | |
| | |
| | Steel Import/Export EBIT To Sales |
| | % |
18 RUSSEL METALS 2003 ANNUAL REPORT
| | | | | | | | | | | | |
(in thousands of dollars except per share data)
| | 2003
| | 2002
| | 2001
|
Operating profits from continuing operations | | $ | 61,031 | | | $ | 70,411 | | | $ | 50,621 | |
Interest expense | | | (22,800 | ) | | | (20,324 | ) | | | (23,017 | ) |
Income tax expense on above | | | (14,536 | ) | | | (19,340 | ) | | | (11,503 | ) |
Income tax rate adjustment | | | (900 | ) | | | — | | | | 378 | |
| | | | | | | | | | | | |
Earnings from continuing operations before other costs | | | 22,795 | | | | 30,747 | | | | 16,479 | |
| | | | | | | | | | | | |
Other costs | | | | | | | | | | | | |
Restructuring costs | | | (3,583 | ) | | | (2,749 | ) | | | (2,400 | ) |
Goodwill impairment | | | (2,410 | ) | | | — | | | | — | |
Foreign exchange gain (loss) | | | 348 | | | | 261 | | | | (1,383 | ) |
Debt repurchase costs | | | — | | | | — | | | | (391 | ) |
Income taxes recoverable on other costs | | | 2,137 | | | | 977 | | | | 1,627 | |
| | | | | | | | | | | | |
| | | (3,508 | ) | | | (1,511 | ) | | | (2,547 | ) |
| | | | | | | | | | | | |
Earnings before unusual items | | | 19,287 | | | | 29,236 | | | | 13,932 | |
| | | | | | | | | | | | |
Unusual items | | | | | | | | | | | | |
Loss on sale of business | | | — | | | | — | | | | (6,000 | ) |
Acquisition costs | | | — | | | | — | | | | (1,688 | ) |
Income taxes recoverable on unusual items | | | — | | | | — | | | | 2,364 | |
| | | | | | | | | | | | |
| | | — | | | | — | | | | (5,324 | ) |
| | | | | | | | | | | | |
Earnings from continuing operations | | | 19,287 | | | | 29,236 | | | | 8,608 | |
Net loss from discontinued operations | | | (788 | ) | | | — | | | | — | |
| | | | | | | | | | | | |
Net earnings | | $ | 18,499 | | | $ | 29,236 | | | $ | 8,608 | |
| | | | | | | | | | | | |
Basic earnings per common share from continuing operations before other costs | | $ | 0.51 | | | $ | 0.75 | | | $ | 0.37 | |
| | | | | | | | | | | | |
Basic earnings per common share from continuing operations | | $ | 0.43 | | | $ | 0.71 | | | $ | 0.17 | |
| | | | | | | | | | | | |
Basic earnings per common share after discontinued operations | | $ | 0.41 | | | $ | 0.71 | | | $ | 0.17 | |
| | | | | | | | | | | | |
Earnings from continuing operations before other costs were $22.8 million in 2003, compared to $30.7 million for 2002. A significant operating profit decline in the steel import/export segment was offset by an increase in service center operating profit due to the acquisition of Acier Leroux. Consolidated revenues for the entire Company increased by 8.1%, to $1,517.1 million, in 2003 compared to 2002. The revenue increase relates to the acquisition of Acier Leroux.
Consolidated interest expense in 2003 increased $2.5 million to $22.8 million compared to 2002. This is due to higher short-term debt outstanding related to the acquisition of Acier Leroux partially offset by lower exchange rates on U.S. denominated long-term debt in 2003 compared to 2002.
The rationalization of the duplicate Acier Leroux and Russel Metals operations in Eastern Canada has impacted Russel Metals locations. Russel Metals locations are incurring restructuring costs related to plant closures, employee severances and inventory moves. Generally accepted accounting principles in Canada and the U.S. require that these charges be included in the income statement in the period that they occur. Rationalization costs related to the Leroux facilities are charged to goodwill as a part of the purchase equation. During 2003, the Company recorded a charge of $3.6 million related to restructuring at Russel Metals locations. In September 2003, the employees at the Russel Metals’ Lachine, Quebec location were told that the location would be closed at the end of 2003. Employee severances and pension and benefits charges related to those employees were accrued at September 30, 2003. Employee related charges for Ontario and Atlantic region restructuring were also recorded during the six months from July to December 2003. Adjustments reducing the pension and benefit numbers accrued at September 30, 2003 were offset by costs incurred in the Ontario and Atlantic regions in the fourth quarter of 2003. The Company anticipates restructuring charges or income to be reported in subsequent quarters related to the restructuring of Atlantic, Quebec and Ontario regions of Russel Metals not completed at December 31, 2003.
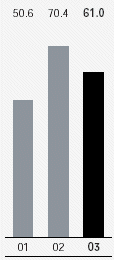
Earnings from Operations
$ millions
RUSSEL METALS 2003 ANNUAL REPORT 19
MANAGEMENT’S DISCUSSION AND ANALYSIS
In September 2002, the Company acquired the Williams Steel operation in Milwaukee, Wisconsin. Economic conditions in the Wisconsin region have resulted in significant deterioration in the Williams Bahcall customer base. As this operation continued to report losses in 2003 and does not project a significant improvement over the forecast period, the Company determined that goodwill of $2.4 million related to this acquisition was impaired. The goodwill related to Williams Bahcall was reduced to zero in the fourth quarter of 2003.
Income taxes for 2003 were $13.3 million compared to $18.4 million in 2002 due to lower earnings. The income tax expense for 2003 includes $0.9 million recorded in the fourth quarter of 2003 relating to an Ontario tax rate adjustment enacted, which reversed tax rate declines previously enacted for the years subsequent to 2003. The $0.9 million additional expense represents the difference in rates applied to future tax liabilities.
Net earnings from continuing operations for 2003 were $19.3 million compared to $29.2 million for 2002.
Net loss from discontinued operations was $0.8 million for the year. The loss relates to the U.S. operations of Acier Leroux. Russel Metals announced it would discontinue the U.S. operations of Acier Leroux at the time the Company made its offer. In October 2003, an assignment of the Company’s interest in the Acier Leroux U.S. joint venture to an unrelated party was completed. All U.S. branches except Plattsburgh, New York have been closed.
Basic earnings per common share from continuing operations before other costs for 2003 were $0.51 compared to $0.75 in 2002 and after other costs were $0.43 for 2003 compared to $0.71 in 2002.
The weighted average number of common shares outstanding for 2003 was 40,021,479 compared to 38,024,034 for 2002. The increase relates to the common shares issued on the acquisition of Acier Leroux and stock options exercised in 2003. The significant increase in the Company’s stock price during 2003 resulted in employees exercising stock options representing an aggregate of 1,419,567 common shares. The number of common shares outstanding at December 31, 2003 was 43,023,342.
Consolidated Results – 2002 compared to 2001
Earnings from operations were $70.4 million, an increase of 39.1% compared to 2001 at $50.6 million. This increase in operating profits for 2002 relates to higher volumes and margins in service center and import/export operations offset by lower volumes in the energy operations. Consolidated revenues for 2002 approximate revenues for 2001.
During the second quarter of 2001, the Company reported a number of items that are not representative of the Company’s ongoing business and thus were disclosed separately. The loss on sale of business related to the sale of the inventory and fixed assets of Total Distributors and the acquisition costs related to the cost of due diligence and legal expense of an unsuccessful acquisition attempt. These items are referred to as unusual items.
The acquisition of Williams Steel was completed in September 2002. Similar to the acquisition of A. J. Forsyth in 2001, the Williams Steel operation was a strategic acquisition. Williams Steel had one large operation in Milwaukee, which serviced most of Wisconsin and other nearby states. The restructuring with Bahcall resulted in the closure of the Bahcall location near Milwaukee in the first quarter of 2003. The closing of this location as well as employee terminations related to eliminating duplicate functions has been estimated to cost $3.1 million, pre-tax.
The 2001 reserve, which provided for the restructuring of A. J. Forsyth with the Russel Metals operation in British Columbia, was reduced in the fourth quarter of 2002 by $392,000, pre-tax. The facility closure costs were less than originally anticipated.
During 2002, the Company recorded a foreign exchange gain of $0.3 million related to U.S. denominated debt that was not designated as a hedge of the Company’s net investment in foreign subsidiaries. The movement in the Canadian dollar against the U.S. dollar caused the gain for 2002 versus the loss for 2001.
Consolidated interest expense decreased $2.7 million to $20.3 million for 2002 compared to 2001. This decrease is due to lower borrowing levels to fund working capital and lower U.S. denominated debt in 2002 due to the purchases of US$9.4 million of the U.S. Note in September and October 2001. The majority of the interest expense relates to the fixed term 10% Senior Notes and, therefore, no benefit was experienced from lower prime borrowing rates available through the bank credit facility.
Income taxes for 2002 were $18.4 million compared to $7.1 million for 2001. This dollar increase relates to higher operating earnings before tax for 2002 compared to 2001 and the unusual items recorded in 2001.
Basic earnings per share for 2002 were $0.71 compared to $0.17 for 2001. Earnings per share before other costs and unusual items were $0.75 for 2002 compared to $0.37 in 2001.
The weighted average number of common shares outstanding for 2002 was 38,024,034 compared to 37,981,501 for 2001. The increase relates to stock options exercised.
Interest Expense
The following table shows the components of interest expense.
| | | | | | | | | | | | |
(in thousands of dollars)
| | 2003
| | 2002
| | 2001
|
Interest on long-term debt | | $ | 18,839 | | | $ | 20,550 | | | $ | 21,396 | |
Other interest (income) | | | 3,961 | | | | (226 | ) | | | 1,621 | |
| | | | | | | | | | | | |
Total interest | | $ | 22,800 | | | $ | 20,324 | | | $ | 23,017 | |
| | | | | | | | | | | | |
20 RUSSEL METALS 2003 ANNUAL REPORT
The long-term debt interest expense relates to the 10% Senior Notes and the 8% Debentures. The decrease in the long-term debt interest relates to lower interest costs due to the lower foreign exchange on the U.S. denominated debt interest. The increase in other interest relates to bank indebtedness related to the acquisition of Acier Leroux.
EBITDA and Adjusted EBITDA
The following table shows the reconciliation of GAAP earnings from continuing operations to EBITDA and Adjusted EBITDA:
| | | | | | | | | | | | |
(in thousands of dollars)
| | 2003
| | 2002
| | 2001
|
Earnings from continuing operations | | $ | 19,287 | | | $ | 29,236 | | | $ | 8,608 | |
Income taxes | | | 13,299 | | | | 18,363 | | | | 7,134 | |
Interest expense - net | | | 22,800 | | | | 20,324 | | | | 23,017 | |
| | | | | | | | | | | | |
Earning before interest and income taxes (EBIT) | | | 55,386 | | | | 67,923 | | | | 38,759 | |
Depreciation and amortization | | | 16,502 | | | | 15,192 | | | | 14,663 | |
| | | | | | | | | | | | |
Earning before interest, income taxes, depreciation and amortization (EBITDA) | | | 71,888 | | | | 83,115 | | | | 53,422 | |
Restructuring costs | | | 3,583 | | | | 2,749 | | | | 2,400 | |
Goodwill impairment | | | 2,410 | | | | — | | | | — | |
Foreign exchange (gain) loss | | | (348 | ) | | | (261 | ) | | | 1,383 | |
Debt repurchase costs | | | — | | | | — | | | | 391 | |
Loss on sale of business | | | — | | | | — | | | | 6,000 | |
Acquisition costs | | | — | | | | — | | | | 1,688 | |
| | | | | | | | | | | | |
Adjusted EBITDA | | $ | 77,533 | | | $ | 85,603 | | | $ | 65,284 | |
| | | | | | | | | | | | |
Management believes that EBITDA and Adjusted EBITDA may be useful in assessing our operating performance and as an indicator of our ability to service or incur indebtedness, make capital expenditures and finance working capital requirements. The items excluded in determining EBITDA and Adjusted EBITDA are significant in assessing our operating results and liquidity. Therefore, EBITDA and Adjusted EBITDA should not be considered in isolation or as an alternative to cash from operating activities or other combined income or cash flow data prepared in accordance with Canadian GAAP.
| | |
| | |
| | Interest Expense |
| | $ millions |
| | |
| | |
| | Adjusted EBITDA to Interest |
| | times |
Adjusted EBITDA to Interest Expense Ratio
Russel Metals’ Adjusted EBITDA to interest expense ratio for 2003 strengthened in the second half of 2003. The Company’s ability to meet interest payments for the next two years remains strong.
| | | | | | | | | | | | |
(in thousands of dollars, except ratios)
| | 2003
| | 2002
| | 2001
|
Adjusted EBITDA | | $ | 77,533 | | | $ | 85,603 | | | $ | 65,284 | |
Interest expense | | | 22,800 | | | | 20,324 | | | | 23,017 | |
Adjusted EBITDA to interest expense | | | 3.4x | | | | 4.2x | | | | 2.8x | |
The Adjusted EBITDA and the Adjusted EBITDA to interest expense ratios are provided to assist readers in determining the ability of Russel Metals to generate cash from operations to cover its financial charges, income taxes and items not considered to be in the ordinary course of business.
Accounting Policies and Estimates
a) Change in accounting policiesDuring 2003, the Canadian Institute of Chartered Accountants issued two Emerging Issues Committee Abstracts that impacted Russel Metals in 2003. EIC-134 Accounting for Severance and Termination Benefits and EIC-135 Accounting for Costs Associated with Exit and Disposal Activities (Including Costs Incurred in a Restructuring) apply to events occurring after March 31, 2003. Russel Metals has applied these abstracts to the restructuring steps taken subsequent to the Acier Leroux acquisition.
Effective with the Acier Leroux acquisition, the Company adopted the new Canadian accounting standard for the disposal of long-lived assets and discontinued operations. This standard has been applied to the U.S. operations of Acier Leroux.
During the fourth quarter of 2003, the Company adopted the fair value-based accounting method for stock-based compensation effective January 1, 2003 and expensed stock options issued in 2003. The amount expensed was $217,000 for 2003, which represents less than $0.01 per share.
RUSSEL METALS 2003 ANNUAL REPORT 21
MANAGEMENT’S DISCUSSION AND ANALYSIS
b) OtherThe preparation of the Company’s financial statements requires management to make estimates and judgements that affect the reported amounts. On an ongoing basis, the Company evaluates its estimates, including those related to bad debts, inventories, fixed asset useful lives, income taxes, restructuring costs, pensions and other post-retirement benefits, environmental, contingencies and litigation. The Company bases its estimates on historical experience and on various other assumptions that are believed to be reasonable under the circumstances, the results of which form the basis for making judgements about the carrying values of assets and liabilities that are not readily apparent from other sources. Actual results may differ from these estimates under different assumptions or conditions.
The Company’s most significant assets consist of accounts receivable and inventory. The Company maintains allowances for doubtful accounts for estimated losses resulting from the inability of its customers to make required payments. If the financial condition of the Company’s customers were to deteriorate, resulting in an impairment of their ability to make payments, additional allowances may be required. The Company reviews its inventory for obsolescence and to ensure that the cost of inventory is not in excess of the estimated market value. Inventory reserves or write-downs are recorded if required.
Capital Expenditures
Capital expenditures in 2003 were $34.9 million compared to $12.8 million in 2002. During 2003, the Company expended $22.5 million on the relocation of B&T Steel related to the purchase of land, construction of a new building, a new cut-to-length line and cranes. The B&T Steel operation relocated to this facility in December 2003.
Russel Metals’ normal capital expenditures are mainly related to maintenance capital, the purchase of additional processing equipment across a broad base of the operations and upgrades to its existing facilities and computer systems.
Depreciation expense was $15.3 million in 2003 and $14.0 million in 2002. The increase in depreciation relates to the depreciation on the assets of Acier Leroux for six months. Depreciation expense will increase in 2004 due to higher fixed assets for the full year.
Liquidity
Russel Metals stresses working capital management to ensure working capital is minimized and leverage reduced over the economic cycle. As anticipated in 2002, during 2003 the Company reduced the inventory bulge that existed at December 31, 2002. Inventory in the import/export operations was $80.0 million lower at December 2003 compared to December 2002. Factors including dumping tariffs from trade actions and high demand for product in China have resulted in lower inventory levels in the import/export operations. Service center inventories were higher by $57.1 million related to the Acier Leroux branches acquired in the year. It is anticipated that an improvement in the economy would cause the working capital employed by Russel Metals to increase to support the incremental revenues.
On July 3, 2003, the Company acquired 99.52% of the outstanding Class A shares, 97.53% of the outstanding Class B shares, 86.61% of the outstanding 8% unsecured convertible debentures and 87.2% of the outstanding 7.25% unsecured convertible debentures of Acier Leroux inc. in relation to its offers. The Company issued 3,546,874 common shares of Russel Metals and paid cash pursuant to the offers. In August 2003, the Company acquired the remaining Class A and B shares and redeemed the remaining debentures.
The total consideration for the Acier Leroux acquisition including shares issued, cash paid and debt assumed was $197.6 million. This amount includes transaction costs. The total cash paid and debt assumed as a result of the acquisition was $177.6 million. The Company used bank borrowings under its credit facility to finance the cash portion. At December 31, 2003, the Company had reduced its bank indebtedness, net of cash, to $59.1 million. The Company had a net cash position, cash less bank indebtedness, of $3.9 million at December 31, 2002. The bank indebtedness, net of cash, is lower than initially projected due to significant reductions in inventory levels at the import/export operations and reduced inventory levels in the Acier Leroux operations.
During 2003, cash generated from operating activities was $41.0 million and from changes in non-cash working capital was $111.3 million. For 2002, cash generated from operating activities was $55.7 million and from changes in non-cash working capital was $(29.1) million.
The balances disclosed in the consolidated cash flow statements are adjusted to remove the non-cash component related to foreign exchange rate changes impacting inventory, accounts receivable, accounts payable and income tax balances of the U.S. operations. Assets purchased as part of the Acier Leroux acquisition are also shown separately based on balances at the date of the transaction.
Reductions in inventory levels generated cash of $91.4 million in 2003. Inventory turns for 2003 remained stable with seasonal buildup in the energy sector distribution inventories during the fourth quarter of 2003 and a significant reduction in the import/export inventories during the last half of 2003.
Inventory turns
| | | | | | | | | | | | | | | | | | | | |
| | Quarters Ended,
|
| | Dec 31, | | Sep 30, | | Jun 30, | | Mar 31, | | Dec 31, |
| | 2003
| | 2003
| | 2003
| | 2003
| | 2002
|
Service center distribution | | | 4.0 | | | | 4.3 | | | | 4.5 | | | | 4.4 | | | | 4.2 | |
Energy sector distribution | | | 3.1 | | | | 4.1 | | | | 3.9 | | | | 4.2 | | | | 3.4 | |
Steel import/export | | | 7.1 | | | | 5.1 | | | | 4.0 | | | | 4.2 | | | | 2.7 | |
Total | | | 4.1 | | | | 4.3 | | | | 4.2 | | | | 4.3 | | | | 3.5 | |
| | | | | | | | | | | | | | | | | | | | |
Inventory turns are calculated using the cost of sales for the quarter annualized divided by the ending inventory position.
22 RUSSEL METALS 2003 ANNUAL REPORT
Service center inventory turns declined slightly due to the inventory levels at the Acier Leroux operations. The Acier Leroux operations historically had inventory turns closer to the industry average. Russel Metals management is actively reducing the inventory levels. Russel Metals’ service center inventory turns can be compared with the service center industry turns estimated to be 3.9 for 2003 as derived from the monthly Metals Activity Report published for the United States by the Metals Service Center Institute. It is management’s goal to achieve service center inventory turns at significantly higher levels than the industry norm.
The other major component of working capital is accounts payable and accrued liabilities, which utilized cash of $12.7 million for 2003. Accounts payable in the import/export operations decreased caused by lower inventory purchases.
During 2003, the Company utilized cash of $34.9 million on capital expenditures and $13.9 million on common and preferred share dividends. During 2002, the Company utilized cash of $12.8 million on capital expenditures and $8.7 million on common and preferred share dividends. The 2003 capital expenditure included a special project for $22.5 million. Future years’ capital expenditures are expected to return to previous levels.
For several years, the Company’s cash flows were positively impacted by its ability to utilize income tax losses. In 2003, the Company was required to make payments related to 2002 as well as installments for 2003. The Company made income tax payments of $7.8 million in 2003.
| | |
| | |
| | Long Term Debt |
| | $ millions |
Debt and Credit Facilities
The Company manages its cash position based on bank borrowings net of cash. The bank credit facilities table provides the split between loans and cash on deposit.
Bank credit facilities
| | | | | | | | | | | | |
| | Russel | | U.S. | | |
| | Metals | | Subsidiary | | |
($ millions)
| | Facility
| | Facility
| | Total
|
Bank loans | | $ | 79.0 | | | $ | — | | | $ | 79.0 | |
On deposit | | | 5.9 | | | | 14.0 | | | | 19.9 | |
| | | | | | | | | | | | |
Net borrowings (cash) | | | 73.1 | | | | (14.0 | ) | | | 59.1 | |
Letters of credit | | | 25.7 | | | | 12.1 | | | | 37.8 | |
| | | | | | | | | | | | |
| | $ | 98.8 | | | $ | (1.9 | ) | | $ | 96.9 | |
| | | | | | | | | | | | |
Facility availability | | $ | 253.8 | | | $ | 45.2 | | | $ | 299.0 | |
| | | | | | | | | | | | |
The Company has two long-term debt instruments outstanding. The $30 million 8% Subordinated Debentures mature in 2006. The 10% Senior Notes mature in 2009. The balance outstanding on the Senior Notes at December 31, 2003 was US$115.6 million, unchanged from December 31, 2002. The Canadian dollar equivalent of the Senior Notes fluctuates with the exchange rate. At December 31, 2003, the long-term debt balance was $179.4 million. See subsequent events for information on debt restructuring.
Russel Metals has a bank credit facility with a syndicate of Canadian and U.S. banks. The $253.8 million credit facility expires on June 19, 2005. The Company may extend this facility with the consent of the banks. Russel Metals is entitled to borrow under this facility, on a revolving basis, up to an amount equal to the sum of specified percentages of eligible accounts receivable and inventories, to a maximum of $253.8 million. At December 31, 2003, Russel Metals was entitled to borrow $253.8 million, including letters of credit under this facility. At December 31, 2003, Russel Metals had $79.0 million of borrowings and had $25.7 million in letters of credit under this facility. At December 31, 2002, Russel Metals had borrowings of $5.8 million and $8.0 million in letters of credit under this facility.
In addition, certain U.S. subsidiaries of Russel Metals have their own one-year bank credit facility. The maximum borrowing under this facility is US$35.0 million. At December 31, 2003, these subsidiaries had no borrowings and letters of credit of US$9.4 million. At December 31, 2002, these subsidiaries had borrowings of US$11.8 million and letters of credit of US$5.6 million.
Subsequent to the year-end, the Company issued approximately $51.8 million of common equity and US$175 million 6.375% Senior Notes due in 2014. The net proceeds will be used to purchase or redeem all of the US$115.6 million 10% Senior Notes, the $30 million 8% debentures, and the Company’s outstanding preferred shares of $30 million. The remaining proceeds will be used to pay down the bank facility and pay fees associated with the refinancing. As a result of the debt redemptions, the Company has no principal payments until 2014 and has reduced annual interest and eliminated preferred share dividend payments by $6.7 million to approximately $18 million annually based on December 31, 2003 borrowing levels.
The metals distribution business experiences significant swings in cash flow to fund working capital. Russel Metals has one of the most working capital intensive balance sheets in the industry. Total inventory and accounts receivable represent 70% of the total assets employed by the Company. The existing bank credit facilities are used to fund the growth in working capital caused by demand or steel price increases which require higher inventory and accounts receivable levels to support the higher activity levels. Based on the
RUSSEL METALS 2003 ANNUAL REPORT 23
MANAGEMENT’S DISCUSSION AND ANALYSIS
Company’s recent experience, a $100 million increase in revenues would require approximately $30 million of net working capital to support the higher activity levels. When the demand weakens, or the price of steel declines, cash is generated from the reduction of inventory and lower accounts receivable levels. This cash is used to reduce the borrowings under the bank credit facilities.
The other major funding requirement of the Company is the purchase of fixed assets, which is projected to be between $15 million and $20 million, annually.
Cash generated from operating activities before working capital changes has averaged $45.0 million over the last three years. The cash generated from operating activities combined with the available bank facilities of $202.1 million at December 31, 2003 is projected to be sufficient to fund interest obligations and fixed asset purchases with the balance available to fund working capital expansion. These available funds provide the Company with the ability to fund the working capital necessary to support up to a $500 million increase in revenues, which management feels is sufficient for any foreseeable pick-up in the economy.
The Company has made several acquisitions over the last three years and believes it can continue to grow by acquisition. Russel Metals believes it has the ability to fund these acquisitions through the utilization of the existing bank facilities and the issuance of new equity, if required. Due to the high level and quality of accounts receivable and inventory the Company could also select to finance working capital growth and acquisitions through an asset-backed facility.
Contractual Obligations
As at December 31, 2003, the Company was contractually obligated to payments under its long-term agreements and operating lease obligations that come due during the following periods. Subsequent to year-end, the long-term debt was refinanced with the maturity being 2014.
| | | | | | | | | | | | | | | | |
| | Long-Term Debt | | Interest | | Lease | | |
(in thousands of dollars)
| | Maturities
| | Obligations
| | Obligations
| | Total
|
2004 | | $ | — | | | $ | 17,340 | | | $ | 8,862 | | | $ | 26,202 | |
2005 | | | — | | | | 17,340 | | | | 8,054 | | | | 25,394 | |
2006 | | | 30,000 | | | | 16,140 | | | | 5,991 | | | | 52,131 | |
2007 | | | — | | | | 14,940 | | | | 4,347 | | | | 19,287 | |
2008 | | | — | | | | 14,940 | | | | 3,425 | | | | 18,365 | |
2009 and beyond | | | 149,402 | | | | 7,470 | | | | 6,705 | | | | 163,577 | |
| | | | | | | | | | | | | | | | |
Total | | $ | 179,402 | | | $ | 88,170 | | | $ | 37,384 | | | $ | 304,956 | |
| | | | | | | | | | | | | | | | |
Off-Balance Sheet Arrangements
The Company does not have any material off-balance sheet arrangements other than the letters of credit referred to in the bank credit facilities table.
Dividends and Share Capital
The ability to pay dividends on common shares is impacted by restrictions associated with the 10% Senior Notes due June 2009. Dividends on common shares and the repurchase of common and preferred shares are considered to be restricted payments under the Note Indenture. The Company increased its quarterly common share dividend twice during 2003. In the first quarter of 2003 the dividend was increased $0.01 to $0.07 per share and in the fourth quarter of 2003 it was again increased $0.01 to $0.08 per share. During 2003, the Company paid in aggregate common share dividends of $0.29 per share resulting in a payment of $11.6 million for the year. At December 31, 2003, the Company had $13.2 million available for restricted payments such as the common share dividend.
The ability to make restricted payments is adjusted quarterly by 50% of the quarterly net income or loss. Net income is adjusted for certain exclusions that include: extraordinary items, gains or losses on asset dispositions and unrealized foreign exchange gains and losses. In addition to adjustments due to net income, the ability to make restricted payments is enhanced by the proceeds on the issuance of share capital.
As at February 4, 2004, the Company had 43,023,342 common shares and 1,200,000 class II preferred shares outstanding. See subsequent events.
| | |
| | 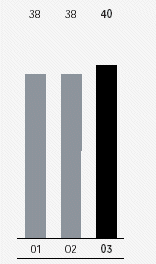 |
| | |
| | Weighted Average Shares Outstanding $ millions |
Vision and Strategy
The metals distribution business is a segment of a mature, cyclical industry. The use of distributors by both manufacturers and end users of steel continues to grow. This is evidenced by the growth in the percentage of total steel shipments from steel producers to distributors. As the distribution segment’s share of steel industry shipments continues to grow, steel distributors such as Russel Metals can grow their business over the course of a cycle.
24 RUSSEL METALS 2003 ANNUAL REPORT
Russel Metals strives to deal with the cyclical nature of the business by operating with the lowest possible net assets throughout the course of a cycle. In addition, its aim is to be more profitable through the various successive peaks and troughs as the steel cycles progress. In order to achieve this, management emphasizes profitability rather than revenue growth. This intensive asset management reduces borrowings and therefore interest expense in declining periods in the economic cycle and creates higher more stable returns on net assets over the course of the cycle. Our conservative management approach creates relatively stronger trough earnings but could cause peak earnings to be somewhat muted. Management strongly believes that it is more prudent to be profitable throughout a cycle, without the spikes in earnings caused by less emphasis on asset management, and have average earnings over the full range of the cycle in the top decile of the industry.
Growth from selective acquisitions is also a core management philosophy. The Company focuses on investment opportunities in businesses that have strong market niches or provide mass to existing Russel Metals operations. On July 3, 2003, the Company successfully completed the Acier Leroux acquisition. The Company believed it required stronger market positions in Quebec, Ontario and the Maritime Provinces and believes the Acier Leroux acquisition provides this result.
In the energy and import/export segments all of the companies in the Russel Metals group have significant operations in the market niche that they service. Consistent with our acquisition philosophy, any new acquisitions in these areas could likely be either major stand-alone operations or complements to existing operations.
In the future, we believe that the length of the steel-based economic cycle will continue to shorten and a management structure and philosophy that allows the fastest reaction to the changes will be the most successful. The Company will continue to invest in business systems to enable faster reaction times to changing business conditions. In addition, management believes the high level of service and flexibility provided by service centers will enable this distribution channel to capture an increasing percentage of total steel revenues to end users, allowing for increased growth within the sector.
Outlook
The Company looks forward to 2004 in a positive fashion although we are going through a difficult period with the onslaught of surcharges that have been added to our costs by our suppliers, ostensibly to cover their higher cost for such items as energy and metallics. Much of what has driven these additional costs has been the strength of the metals market in China. The anticipation is that once that market becomes saturated, pricing will drop to more normal levels.
With the acquisition of Acier Leroux, we have strengthened an area of the Company that has hereto not provided satisfactory results, and our anticipation is that there will be a general improvement in our overall results based on the Acier Leroux acquisition.
We are seeing stronger results from our energy sector companies and we anticipate that the results for 2004 should finally reflect the high oil and gas prices we have seen in the past two years.
The import/export sector is an area of concern due to the continuing strength in China and the weakening of the U.S. dollar, which causes materials that have normally flowed to North America to be diverted to satisfy the market in China.
We are optimistic that 2004 will be an improvement upon 2003 and that the Company is well situated to remain one of the most stable and consistently profitable financial performers in the metals distribution industry.
Subsequent Events
Subsequent to year-end, the Company issued 5,750,000 common shares at an issue price of $9.00 per share for net proceeds of $49.2 million. In addition, the Company made an offer to purchase and a consent solicitation to its holders of the 10% Senior Notes due June 1, 2009 whereby in addition to a consent fee of US$20.00 per US$1,000 Note, the Company would repurchase the bonds for a price of US$1,052.50 per US$1,000 Note. The Company sold on a private placement basis US$175 million of Senior Notes and is using these proceeds to repurchase or redeem its US$115.6 million 10% Senior Notes, $30 million 8% Debentures and its $30 million Class II preferred shares. Deferred financing costs of $2.6 million will be charged to income as a result of this refinancing. In addition, the consent fee and redemption premium will result in a one-time charge estimated to be $10.5 million.
RUSSEL METALS 2003 ANNUAL REPORT 25
Management’s Report to the Shareholders
The accompanying consolidated financial statements, management’s discussion and analysis and all information in the Annual Report have been prepared by management and approved by the Audit Committee and the Board of Directors of the Company. The consolidated financial statements were prepared in accordance with Canadian generally accepted accounting principles and, where appropriate, reflect management’s best estimates and judgements. Management is responsible for the accuracy, integrity and objectivity of the consolidated financial statements and management’s discussion and analysis within reasonable limits of materiality and for the consistency of financial data included in the text of the Annual Report with that contained in the consolidated financial system.
To assist management in the discharge of these responsibilities, the Company maintains a system of internal controls designed to provide reasonable assurance that its assets are safeguarded; that only valid and authorized transactions are executed; and that accurate, timely and comprehensive financial information is prepared.
The Company’s Audit Committee is appointed annually by the Board of Directors and is comprised of Directors, all of whom are neither employees nor officers of the Company. The Audit Committee meets with management as well as with external auditors to satisfy itself that management is properly discharging its financial reporting responsibilities and to review the consolidated financial statements, the independent auditors’ report and the management’s discussion and analysis. The Audit Committee reports its findings to the Board of Directors for consideration in approving the consolidated financial statements and management discussion and analysis for presentation to the shareholders. The external auditors have direct access to the Audit Committee of the Board of Directors.
The consolidated financial statements have been independently audited by Deloitte & Touche LLP. Their report outlines the nature of their audits and expresses their opinion on the consolidated financial statements of the Company.
| | |
(Signed) E. M. Siegel, Jr. | | (Signed) Brian R. Hedges |
| | |
E. M. Siegel, Jr. | | Brian R. Hedges |
President and Chief Executive Officer | | Executive Vice President and Chief Financial Officer |
26 RUSSEL METALS 2003 ANNUAL REPORT
Auditors’ Report
To the Shareholders of Russel Metals Inc.
We have audited the consolidated balance sheets of Russel Metals Inc. as at December 31, 2003 and 2002 and the consolidated statements of earnings and retained earnings and of cash flows for each of the years in the three-year period ended December 31, 2003. These financial statements are the responsibility of the Company’s management. Our responsibility is to express an opinion on these financial statements based on our audits.
We conducted our audits in accordance with Canadian generally accepted auditing standards. Those standards require that we plan and perform an audit to obtain reasonable assurance whether the financial statements are free of material misstatement. An audit includes examining, on a test basis, evidence supporting the amounts and disclosures in the financial statements. An audit also includes assessing the accounting principles used and significant estimates made by management, as well as evaluating the overall financial statement presentation.
In our opinion, these consolidated financial statements present fairly, in all material respects, the financial position of the Company as at December 31, 2003 and 2002 and the results of its operations and its cash flows for each of the years in the three-year period ended December 31, 2003 in accordance with Canadian generally accepted accounting principles.
(Signed) Deloitte & Touche LLP
Chartered Accountants
Toronto, Ontario
January 30, 2004
Comments by Auditors on Canada - U.S. Reporting Differences
In the United States of America, reporting standards for auditors require the addition of an explanatory paragraph (following the opinion paragraph) when there is a change in accounting principles that have a material effect on the comparability of the Company’s financial statements, such as the changes described in Note 2 to the financial statements. Our report to the Shareholders, dated January 30, 2004, is expressed in accordance with Canadian reporting standards, which does not require a reference to such a change in accounting principles in the auditors’ report when the change is properly accounted for and adequately disclosed in the financial statements.
(Signed) Deloitte & Touche LLP
Chartered Accountants
Toronto, Ontario
January 30, 2004
RUSSEL METALS 2003 ANNUAL REPORT 27
Consolidated Balance Sheets
| | | | | | | | |
At December 31 ($000)
| | 2003
| | 2002
|
Assets | | | | | | | | |
Current | | | | | | | | |
Cash | | $ | 19,008 | | | $ | 25,068 | |
Accounts receivable | | | 248,904 | | | | 201,675 | |
Inventories | | | 303,048 | | | | 329,415 | |
Prepaid expenses and other assets | | | 5,028 | | | | 6,077 | |
Income taxes recoverable | | | 5,912 | | | | 1,306 | |
Discontinued operations (Note 3d) | | | 1,107 | | | | — | |
| | | | | | | | |
| | | 583,007 | | | | 563,541 | |
Property, Plant and Equipment (Note 5) | | | 184,929 | | | | 110,512 | |
Assets Held for Sale (Note 3d) | | | 1,622 | | | | — | |
Deferred Financing Charges (Note 17) | | | 3,547 | | | | 4,962 | |
Goodwill (Note 3) | | | 4,216 | | | | 2,709 | |
Future Income Tax Assets (Note 10) | | | 10,458 | | | | 10,698 | |
Other Assets (Note 6) | | | 2,840 | | | | 3,172 | |
| | | | | | | | |
| | $ | 790,619 | | | $ | 695,594 | |
| | | | | | | | |
Liabilities and Shareholders’ Equity | | | | | | | | |
Current | | | | | | | | |
Bank indebtedness (Note 7) | | $ | 78,093 | | | $ | 21,141 | |
Accounts payable and accrued liabilities | | | 217,173 | | | | 188,585 | |
Income taxes payable | | | 11,729 | | | | 2,487 | |
Discontinued operations (Note 3d) | | | 2,729 | | | | — | |
| | | | | | | | |
| | | 309,724 | | | | 212,213 | |
Long-Term Debt (Notes 8 and 17) | | | 179,402 | | | | 212,602 | |
Pensions and Benefits (Note 14) | | | 11,542 | | | | 9,590 | |
Future Income Tax Liabilities (Note 10) | | | 6,109 | | | | 8,749 | |
| | | | | | | | |
| | | 506,777 | | | | 443,154 | |
| | | | | | | | |
Contingencies and Commitments (Note 15) Shareholders’ Equity | | | | | | | | |
Preferred shares (Notes 11 and 17) | | | 30,000 | | | | 30,000 | |
Shareholders’ equity (Note 11) | | | 253,842 | | | | 222,440 | |
| | | | | | | | |
| | | 283,842 | | | | 252,440 | |
| | | | | | | | |
| | $ | 790,619 | | | $ | 695,594 | |
| | | | | | | | |
On Behalf of the Board,
| | |
(Signed) C. R. Fiora | | (Signed) A. C. Thorsteinson |
Director | | Director |
28 RUSSEL METALS 2003 ANNUAL REPORT
Consolidated Statements of Earnings and Retained Earnings
| | | | | | | | | | | | |
For the years ended December 31 ($000 except per share data)
| | 2003
| | 2002
| | 2001
|
Revenues | | $ | 1,517,090 | | | $ | 1,403,275 | | | $ | 1,402,509 | |
Cost of sales and operating expenses | | | 1,456,059 | | | | 1,332,864 | | | | 1,351,888 | |
| | | | | | | | | | | | |
Earnings before the following | | | 61,031 | | | | 70,411 | | | | 50,621 | |
Restructuring costs (Note 3b) | | | 3,583 | | | | 2,749 | | | | 2,400 | |
Foreign exchange (gain) loss (Note 12) | | | (348 | ) | | | (261 | ) | | | 1,383 | |
Goodwill impairment (Note 3c) | | | 2,410 | | | | — | | | | — | |
Debt repurchase costs | | | — | | | | — | | | | 391 | |
Interest expense – net (Note 9) | | | 22,800 | | | | 20,324 | | | | 23,017 | |
Loss on sale of business (Note 4) | | | — | | | | — | | | | 6,000 | |
Acquisition costs (Note 3) | | | — | | | | — | | | | 1,688 | |
| | | | | | | | | | | | |
Earnings before income taxes | | | 32,586 | | | | 47,599 | | | | 15,742 | |
Provision for income taxes (Note 10) | | | (13,299 | ) | | | (18,363 | ) | | | (7,134 | ) |
| | | | | | | | | | | | |
Earnings from continuing operations | | | 19,287 | | | | 29,236 | | | | 8,608 | |
Loss from discontinued operations (Note 3d) | | | (788 | ) | | | — | | | | — | |
| | | | | | | | | | | | |
Net earnings for the year | | | 18,499 | | | | 29,236 | | | | 8,608 | |
Retained Earnings – | | | | | | | | | | | | |
Dividends on preferred shares | | | (2,250 | ) | | | (2,250 | ) | | | (2,250 | ) |
| | | | | | | | | | | | |
Earnings available to common shareholders | | | 16,249 | | | | 26,986 | | | | 6,358 | |
Dividends on common shares | | | (11,605 | ) | | | (6,466 | ) | | | (7,596 | ) |
Retained earnings, beginning of the year | | | 105,858 | | | | 100,461 | | | | 101,699 | |
Goodwill impairment (Note 2) | | | — | | | | (15,123 | ) | | | — | |
| | | | | | | | | | | | |
Retained earnings, end of the year (Note 11) | | $ | 110,502 | | | $ | 105,858 | | | $ | 100,461 | |
| | | | | | | | | | | | |
Basic earnings per common share – continuing operations | | $ | 0.43 | | | $ | 0.71 | | | $ | 0.17 | |
| | | | | | | | | | | | |
Basic earnings per common share | | $ | 0.41 | | | $ | 0.71 | | | $ | 0.17 | |
| | | | | | | | | | | | |
Diluted earnings per common share – continuing operations | | $ | 0.41 | | | $ | 0.68 | | | $ | 0.17 | |
| | | | | | | | | | | | |
Diluted earnings per common share | | $ | 0.39 | | | $ | 0.68 | | | $ | 0.17 | |
| | | | | | | | | | | | |
RUSSEL METALS 2003 ANNUAL REPORT 29
Consolidated Cash Flow Statements
| | | | | | | | | | | | |
For the years ended December 31 ($000)
| | 2003
| | 2002
| | 2001
|
Operating activities | | | | | | | | | | | | |
Earnings from continuing operations | | $ | 19,287 | | | $ | 29,236 | | | $ | 8,608 | |
Depreciation and amortization | | | 16,502 | | | | 15,192 | | | | 14,663 | |
Future income taxes | | | (464 | ) | | | 8,708 | | | | 3,503 | |
Loss (gain) on sale of fixed assets | | | (89 | ) | | | 26 | | | | (113 | ) |
Restructuring costs | | | 3,162 | | | | 2,749 | | | | 2,400 | |
Stock-based compensation | | | 217 | | | | — | | | | — | |
Goodwill impairment | | | 2,410 | | | | — | | | | — | |
Foreign exchange (gain) loss | | | — | | | | (261 | ) | | | 1,093 | |
Debt repurchase costs | | | — | | | | — | | | | 391 | |
Loss on sale of business | | | — | | | | — | | | | 6,000 | |
Acquisition costs | | | — | | | | — | | | | 1,688 | |
| | | | | | | | | | | | |
Cash from operating activities before working capital | | | 41,025 | | | | 55,650 | | | | 38,233 | |
| | | | | | | | | | | | |
Changes in non-cash working capital items | | | | | | | | | | | | |
Accounts receivable | | | 18,193 | | | | (210 | ) | | | 69,182 | |
Inventories | | | 91,439 | | | | (55,841 | ) | | | 36,772 | |
Accounts payable and accrued liabilities | | | (12,669 | ) | | | 23,926 | | | | (46,328 | ) |
Current income taxes | | | 11,719 | | | | 3,919 | | | | (4,397 | ) |
Other | | | 2,571 | | | | (923 | ) | | | (323 | ) |
| | | | | | | | | | | | |
Change in non-cash working capital | | | 111,253 | | | | (29,129 | ) | | | 54,906 | |
| | | | | | | | | | | | |
Cash from operating activities | | | 152,278 | | | | 26,521 | | | | 93,139 | |
| | | | | | | | | | | | |
Financing activities | | | | | | | | | | | | |
Increase (decrease) in bank borrowing | | | 56,952 | | | | 21,141 | | | | (38,441 | ) |
Repayment of debt assumed | | | (99,262 | ) | | | — | | | | — | |
Dividends on common shares | | | (11,605 | ) | | | (6,466 | ) | | | (7,596 | ) |
Dividends on preferred shares | | | (2,250 | ) | | | (2,250 | ) | | | (2,250 | ) |
Repurchase of long-term debt | | | — | | | | — | | | | (14,808 | ) |
Issue of common shares (Note 11) | | | 5,663 | | | | 253 | | | | — | |
Deferred financing costs | | | (77 | ) | | | (14 | ) | | | (29 | ) |
| | | | | | | | | | | | |
Cash from (used in) financing activities | | | (50,579 | ) | | | 12,664 | | | | (63,124 | ) |
| | | | | | | | | | | | |
Investing activities | | | | | | | | | | | | |
Purchase of fixed assets | | | (34,879 | ) | | | (12,768 | ) | | | (8,152 | ) |
Proceeds on sale of fixed assets | | | 1,804 | | | | 2,328 | | | | 255 | |
Purchase of businesses (Note 3) | | | (70,359 | ) | | | (21,406 | ) | | | (25,288 | ) |
Proceeds on sale of businesses (Note 4) | | | — | | | | — | | | | 10,397 | |
Other | | | (4,628 | ) | | | 578 | | | | 1,001 | |
| | | | | | | | | | | | |
Cash used in investing activities | | | (108,062 | ) | | | (31,268 | ) | | | (21,787 | ) |
| | | | | | | | | | | | |
Discontinued operations | | | | | | | | | | | | |
Operating activities | | | (788 | ) | | | — | | | | — | |
Investing activities | | | 1,091 | | | | — | | | | — | |
| | | | | | | | | | | | |
Cash from discontinued operations | | | 303 | | | | — | | | | — | |
| | | | | | | | | | | | |
Increase (decrease) in cash | | | (6,060 | ) | | | 7,917 | | | | 8,228 | |
Cash, beginning of the year | | | 25,068 | | | | 17,151 | | | | 8,923 | |
| | | | | | | | | | | | |
Cash, end of the year | | $ | 19,008 | | | $ | 25,068 | | | $ | 17,151 | |
| | | | | | | | | | | | |
30 RUSSEL METALS 2003 ANNUAL REPORT
Notes to the Consolidated Financial Statements
1. Summary of Significant Accounting Policies
a) Principles of consolidationThe consolidated financial statements include the accounts of Russel Metals Inc. and its subsidiary companies herein referred to as the Company. The reporting currency is Canadian dollars unless otherwise noted. All material inter-company balances, transactions and profits have been eliminated.
These consolidated financial statements have been prepared in accordance with Canadian generally accepted accounting principles. Material differences from accounting principles generally accepted in the U.S. are disclosed in Note 16.
b) InventoriesInventories are recorded at the lower of cost and net realizable value. Cost is determined on either an average cost basis or an actual cost basis depending on the business unit.
c) Property, plant, equipment and depreciationProperty, plant, equipment and leasehold improvements are recorded at cost. Depreciation is provided on a straight-line basis at rates that charge the original cost of such assets to operations over their estimated useful lives. The rates used are 20 to 40 years for buildings, 10 years for machinery and equipment, 2 to 5 years for computer equipment and over the lease term for leasehold improvements. Depreciation expense was $15,312,000 in 2003 (2002: $13,973,000; 2001: $12,993,000).
d) Deferred financing charges and amortizationCosts incurred that relate to financing are deferred and amortized over the period of the related financing. Deferred financing charges are recorded at cost less accumulated amortization. Amortization of deferred financing charges was $1,190,000 in 2003 (2002: $1,219,000; 2001: $1,243,000).
e) Goodwill and amortizationGoodwill represents the excess purchase price paid on acquisitions over the value assigned to identifiable net assets acquired. Goodwill on acquisitions subsequent to July 1, 2001 is not amortized but is subject to an annual permanent impairment test (see Note 3). Goodwill on acquisitions prior to July 1, 2001 was amortized on a straight-line basis over a period not exceeding 40 years or written down when there has been a permanent impairment in value. Effective January 1, 2002 all goodwill ceased to be amortized and is subject to an annual permanent impairment test. Amortization recorded in 2001 was $427,000.
f) PensionsThe cost of pension benefits earned by employees covered under defined benefit plans is determined using the projected benefit method prorated on service and is charged to expense as services are rendered. Aggregate gains and losses are amortized on a straight-line basis over the estimated average remaining service lives of the employee groups, using the corridor approach. The cost of post-retirement benefits other than pensions is recognized on an accrual basis over the working lives of employees.
g) Income taxesThe Company uses the liability method of income tax allocation. Under this method, future tax assets and liabilities are determined based on differences between the financial accounting and tax bases of assets and liabilities and are measured using the substantively enacted tax rates and laws that will be in effect when the differences are expected to reverse.
h) Foreign currency translationThe accounts of foreign subsidiaries are translated into Canadian dollars at the noon spot rates in effect at the balance sheet date. For 2003, the U.S. dollar published exchange rate was 1.2924 (2002: 1.5796). Revenues and expenses are translated at the average rate of exchange for the year. For 2003, the U.S. dollar published average exchange rate was 1.4010 (2002: 1.5703; 2001: 1.5489). The resulting gains or losses are accumulated as a separate component of shareholders’ equity.
Effective January 1, 2001, the Company adopted the Canadian accounting standards on foreign currency translation and accordingly, exchange gains or losses on long-term debt denominated in foreign currencies not designated as a hedge are expensed as incurred (see Note 12). Exchange gains or losses on the translation of long-term debt denominated in a foreign currency designated as a hedge of the Company’s net investment in foreign subsidiaries are included in the separate component of shareholders’ equity.
i) Earnings per shareBasic earnings per common share are calculated using the weighted daily average number of common shares outstanding. The weighted average number of common shares for 2003 was 40,021,479 (2002: 38,024,034; 2001: 37,981,501).
j) Stock-based compensationEffective January 1, 2003, the Company adopted the fair value method of accounting for stock-based payments. Prior to 2003, the Company had chosen to account for the employee stock-based compensation plans using the intrinsic value-based method. Pro forma net income and earnings per share have been provided as if the fair value-based accounting method had been used since January 1, 2001 (see Note 11).
k) Revenue recognitionRevenue is recognized when the goods are shipped to the customer when collection is reasonably assured. Revenue on certain sales in the energy segment, where the Company acts as an agent, is presented on a net basis.
l) Derivative financial instrumentsThe Company uses foreign exchange contracts to manage foreign exchange risk on certain committed cash outflows. Realized and unrealized foreign exchange gains and losses not designated as a hedge are included in income. Derivatives are not entered into for speculative purposes and the use of derivative contracts is governed by documented risk management policies.
m) CashCash includes short-term investments with a maturity of less than 30 days.
n) Use of estimatesThe preparation of consolidated financial statements in conformity with Canadian generally accepted accounting principles requires management to make estimates and assumptions that affect the reported assets and liabilities and disclosure of contingent assets and liabilities at the date of the financial statements and the reported amounts of revenue and expenses during the reporting periods. In particular, inventories, accounts receivable, other contingencies and assigned values on net assets acquired represent management’s best estimates. Actual results could differ from these estimates.
RUSSEL METALS 2003 ANNUAL REPORT 31
NOTES TO THE CONSOLIDATED FINANCIAL STATEMENTS
2. Change in Accounting Policies
a)In the fourth quarter of 2003, the Company prospectively adopted, effective January 1, 2003, the fair value method of accounting for employee stock-based payments issued after that date. The impact of the adoption of this standard for the year ended December 31, 2003 resulted in additional compensation expense of $217,000. If this standard had been adopted prior to the release of the quarterly statements, the effect on the first, second and third quarters would have been an increase in compensation expense of $48,000, $53,000 and $55,000 respectively. The Company has not restated its quarterly results. For options issued prior to January 1, 2003, the Company had chosen to account for the employee stock-based compensation plans using the intrinsic value-based method as allowed by the Canadian standard adopted on January 1, 2001. As required by the transitional provisions of the standard, pro forma net income and earnings per share information have been provided as if the fair value-based accounting method had been used since January 1, 2001 for options issued prior to January 1, 2003 (see Note 11).
b)Effective May 1, 2003, the Company adopted the new accounting standard for Long-Lived Assets and Discontinued Operations. This standard, along with emerging issues abstracts EIC-134 Accounting for Severance and Termination Benefits and EIC-135 Accounting for Costs Associated with Exit and Disposal Activities (Including Costs Incurred in a Restructuring) have been applied to the restructuring as a result of the Acier Leroux Inc. acquisition (see Note 3).
c)In 2003, the Company also adopted the new standard on financial statement presentation and new accounting guideline on disclosure of guarantees. The implementation of these standards did not have a material effect on the Company’s results of operations, financial position or cash flows.
d)Effective January 1, 2002, the Company adopted the provisions of the Canadian accounting standard for goodwill and other intangibles. Under this standard, goodwill is no longer amortized but is subject to an impairment test at least annually. As required by the standard, the Company has performed a transitional goodwill impairment evaluation based on discounted cash flows in each reporting unit as at January 1, 2002. The transitional impairment loss of $15,123,000 as a result of this evaluation has been charged to retained earnings at January 1, 2002.
The following table presents the impact on comparative net earnings and earnings per share had the new standard been in effect January 1, 2001.
| | | | | | | | | | | | |
($000 except per share data)
| | 2003
| | 2002
| | 2001
|
Net earnings as reported | | $ | 18,499 | | | $ | 29,236 | | | $ | 8,608 | |
Goodwill amortization | | | — | | | | — | | | | 427 | |
| | | | | | | | | | | | |
Net income adjusted | | $ | 18,499 | | | $ | 29,236 | | | | 9,035 | |
| | | | | | | | | | | | |
Basic earnings per share – as reported | | $ | 0.41 | | | $ | 0.71 | | | $ | 0.17 | |
Basic earnings per share – adjusted | | $ | 0.41 | | | $ | 0.71 | | | $ | 0.18 | |
| | | | | | | | | | | | |
e)Effective July 1, 2001, the Company adopted the accounting standard for business combinations. The Company has applied this new standard in its acquisitions subsequent to July 1, 2001 (see Note 3) and as required by the standard’s transitional provisions, the goodwill generated from these acquisitions was not amortized.
f)Effective January 1, 2001, the Company adopted the Canadian accounting standards for earnings per share and foreign currency translation. Under the earnings per share standard, the treasury stock method is used for determining the dilutive effect of stock options issued. Under the accounting standard for foreign currency translation, foreign exchange gains and losses on long-term debt are no longer deferred and amortized. The implementation of these standards does not have a material effect on the Company’s results of operations, financial position or cash flows.
3. Business Acquisitions
a)On July 3, 2003, the Company successfully completed its offers to purchase Acier Leroux inc. Acier Leroux is a service center operation with Canadian locations in Ontario, Quebec and the Atlantic provinces. Acier Leroux Class A multiple voting shares validly tendered under the offer represented 99.52% of the issued and outstanding Class A shares. Acier Leroux Class B subordinate voting shares validly tendered under the offer represented 97.53% of the issued and outstanding Class B shares. Acier Leroux debentures validly tendered under the offer represented 86.61% of the outstanding 8% convertible unsecured subordinated debentures and 87.2% of the outstanding 7.25% convertible unsecured subordinated debentures. The Company issued 3,546,874 shares and paid $48,947,000 in cash in consideration for the shares and $16,684,000 in cash in consideration for debentures tendered under the offer. In addition, the Company entered into an arrangement with the former Chairman and Chief Executive Officer of Acier Leroux requiring payments over a three-year period in the amount of $1,350,000, which has been accrued as a transaction cost.
On August 19, 2003, the Company, under the provisions of theCompanies Act (Quebec), acquired the remaining shares of Acier Leroux for $1,190,000 in cash. On August 27, 2003, Acier Leroux redeemed the debentures not acquired in the offer.
32 RUSSEL METALS 2003 ANNUAL REPORT
Effective September 9, 2002, the Company purchased substantially all of the assets of the Milwaukee, Wisconsin service center operation formerly known as Williams Steel for $17.0 million in cash. This acquisition was intended to strengthen the existing Bahcall operations in Wisconsin and led to the restructuring of these operations. Costs associated with the restructuring of the Williams Steel location of $0.2 million were included in goodwill. Effective March 1, 2002, the Company purchased the operations and the fixed assets of Arrow Steel Processors, a coil processor of customer owned material located in Texas, for $4.4 million cash.
Effective October 15, 2001, the Company purchased 100% of the shares of A. J. Forsyth and Company Limited, a Canadian service center operation located in British Columbia, for cash consideration of $22.0 million and assumed bank debt of $13.9 million. The acquisition was made to strengthen the B.C. region and led to the restructuring of the B.C. service center operations. Costs of $1.2 million associated with the restructuring of the A. J. Forsyth locations were included in goodwill on acquisition, which totaled $7.6 million.
Effective August 16, 2001, the Company purchased 100% of the shares of Spartan Steel Products, Inc., a U.S. distributor of energy sector pipe, for cash consideration of $3.0 million and assumed bank debt of $3.3 million. Effective October 9, 2001, the Company purchased 100% of the shares of 1377804 Ontario Inc., a Canadian service center operation located in Ontario, for cash consideration of $255,000.
Effective September 1, 2000, the Company purchased Triumph Tubular & Supply Ltd., a Calgary, Alberta distributor of oil country tubular goods. Additional amounts under an earnout based on results may be paid over five years and will be incremental to goodwill. The additional amount related to 2003 is $nil (2002: $nil; 2001: $102,000).
These acquisitions have been accounted for using the purchase method and their results of operations have been consolidated since their respective acquisition dates.
Net assets acquired, at assigned values at acquisition dates:
| | | | | | | | | | | | |
($000)
| | 2003
| | 2002
| | 2001
|
Accounts receivable | | $ | 74,483 | | | $ | 4,110 | | | $ | 12,323 | |
Inventories | | | 82,880 | | | | 8,567 | | | | 15,945 | |
Fixed assets | | | 60,769 | | | | 6,273 | | | | 16,693 | |
Other assets | | | 2,122 | | | | 54 | | | | 510 | |
Goodwill | | | 4,216 | | | | 2,680 | | | | 8,321 | |
| | | | | | | | | | | | |
Total assets – continuing operations | | | 224,470 | | | | 21,684 | | | | 53,792 | |
Accounts payable and accrued liabilities | | | (44,778 | ) | | | (346 | ) | | | (8,203 | ) |
Accrued pension and benefit liability | | | (1,380 | ) | | | — | | | | — | |
Future income taxes | | | 11,278 | | | | 68 | | | | (3,181 | ) |
| | | | | | | | | | | | |
Net identifiable assets – continuing operations | | | 189,590 | | | | 21,406 | | | | 42,408 | |
Discontinued operations | | | 8,010 | | | | — | | | | — | |
Debt assumed, net of cash | | | (123,956 | ) | | | — | | | | (17,120 | ) |
| | | | | | | | | | | | |
Net assets acquired | | $ | 73,644 | | | $ | 21,406 | | | $ | 25,288 | |
| | | | | | | | | | | | |
Consideration: | | | | | | | | | | | | |
Cash | | $ | 50,137 | | | $ | 21,406 | | | $ | 25,288 | |
Russel Metals common shares | | | 19,969 | | | | — | | | | — | |
Transaction costs, net of taxes | | | 3,538 | | | | — | | | | — | |
| | | | | | | | | | | | |
| | $ | 73,644 | | | $ | 21,406 | | | $ | 25,288 | |
| | | | | | | | | | | | |
The preliminary net assets acquired in the Leroux transaction include certain contingencies and estimates such as the expected proceeds on disposition of certain Leroux assets. The purchase price allocation is expected to be final in the second quarter of 2004.
The goodwill for 2003 and 2002 has been allocated to the service center segment and for 2001 $7.6 million was allocated to the service center segment with the balance in energy. The tax-deductible portion of goodwill is $nil (2002: $2.7 million; 2001: $0.8 million). Cash included in debt assumed was $2.7 million (2001: $nil).
In May 2001, the Company announced that it had been unsuccessful in finalizing an agreement for the acquisition of a U.S. service center operation. The due diligence process and legal expenses resulted in a write off of costs of $1.7 million.
b) RestructuringIn 2003, a restructuring charge of $3.6 million was recorded relating to the severance, employee benefits and termination costs of the closure of the Russel Metals’ operations as a result of the acquisition of Acier Leroux. These costs primarily relate to the closure of the Russel Metals’ Lachine, Quebec location. These costs also relate to employee related charges in the Atlantic and Ontario regions. Operations ceased at Lachine on December 31, 2003, at which time the building was being readied for sale.
The continuity of the restructuring provision is as follows:
RUSSEL METALS 2003 ANNUAL REPORT 33
NOTES TO THE CONSOLIDATED FINANCIAL STATEMENTS
| | | | | | | | | | | | | | | | |
($000)
| | 2003
|
| | Special | | Contractual | | | | |
| | Termination | | Termination | | | | |
| | Costs
| | Costs
| | Other
| | Total
|
Restructuring charged in the year | | $ | 327 | | | $ | 2,507 | | | $ | 749 | | | $ | 3,583 | |
Cash payments | | | (99 | ) | | | (105 | ) | | | (217 | ) | | | (421 | ) |
| | | | | | | | | | | | | | | | |
Balance at end of year | | $ | 228 | | | $ | 2,402 | | | $ | 532 | | | $ | 3,162 | |
| | | | | | | | | | | | | | | | |
In 2002, costs of restructuring the Bahcall locations, including the closure of the Waukesha location and employee terminations, of $3.1 million were charged to income.
In 2001, the costs of restructuring the Russel Metals B.C. locations of $2.4 million were charged to income. During 2002, $0.4 million of this provision, not required for restructuring, was included in income.
| | | | | | | | |
($000)
| | 2002
| | 2001
|
Restructuring – Russel Metals B.C. operations | | $ | (392 | ) | | $ | 2,400 | |
Restructuring – Bahcall operations | | | 3,141 | | | | — | |
| | | | | | | | |
Restructuring costs | | $ | 2,749 | | | $ | 2,400 | |
| | | | | | | | |
As at December 31, 2003, the remaining balance in these reserves was $0.7 million (2002: $3.9 million).
c) Goodwill impairmentThe Company completed its annual goodwill impairment test during the fourth quarter of 2003. This evaluation concluded that the fair value associated with the service center segment’s Williams Bahcall operation could not support the carrying value of the goodwill and accordingly, the Company recorded a goodwill impairment charge of $2.4 million.
d) Discontinued operationsAs part of the acquisition of Acier Leroux, the Company adopted a formal plan to dispose of their U.S. operations. At December 31, 2003, all of these operations have been divested except a service center in Plattsburgh, New York. This service center and certain other Acier Leroux assets are expected to be sold in the next year and consequently have been included in discontinued operations. The revenue generated by the service center since acquisition was $3.3 million.
4. Divestitures
Divestitures include the sale of the inventory and fixed assets of Total Distributors, the Company’s Tulsa-based energy sector operation for cash of $9.6 million on June 15, 2001. This sale resulted in a loss on sale of business of $6.0 million.
5. Property, Plant and Equipment
| | | | | | | | | | | | | | | | |
($000)
| | 2003
| | 2002
|
| | Cost
| | Net
| | Cost
| | Net
|
Land and buildings | | $ | 139,850 | | | $ | 106,460 | | | $ | 73,983 | | | $ | 43,008 | |
Machinery and equipment | | | 179,548 | | | | 68,140 | | | | 163,044 | | | | 56,686 | |
Leasehold improvements | | | 25,454 | | | | 10,329 | | | | 25,777 | | | | 10,818 | |
| | | | | | | | | | | | | | | | |
| | $ | 344,852 | | | $ | 184,929 | | | $ | 262,804 | | | $ | 110,512 | |
| | | | | | | | | | | | | | | | |
6. Other Assets
Other assets included a demand loan to an officer at interest rates prescribed by tax authorities for the purchase of Company shares in the amount of $nil (2002: $710,820). This loan was repaid in its entirety in February 2003.
7. Revolving Credit Facilities
The Company has a credit facility with a syndicate of banks, which provides a line of credit to a maximum of $253.8 million, including letters of credit. The Company has extended the facility to June 19, 2005. Borrowings under this facility are restricted by certain financial covenants with which the Company was in compliance at December 31, 2003. The obligations of the Company under this agreement are secured by a pledge of trade accounts receivable and inventories of a significant portion of the Company’s operations. At December 31, 2003, the Company had borrowings of $79.0 million (2002: $5.8 million) and letters of credit of $25.8 million (2002: $8.0 million) under this facility.
34 RUSSEL METALS 2003 ANNUAL REPORT
In addition, certain U.S. subsidiaries of the Company have their own credit facility. The maximum borrowing under this facility is US$35.0 million. At December 31, 2003, these subsidiaries had no borrowings (2002: US$11.8 million) and letters of credit of US$9.4 million (2002: US$5.6 million) under this facility.
8. Long-Term Debt
| | | | | | | | |
($000)
| | 2003
| | 2002
|
10% Senior Notes US$115.6 million due June 1, 2009 | | $ | 149,402 | | | $ | 182,602 | |
8% Subordinated Debentures due June 15, 2006 | | | 30,000 | | | | 30,000 | |
| | | | | | | | |
| | $ | 179,402 | | | $ | 212,602 | |
| | | | | | | | |
a) 10% Senior NotesDuring 2003 and 2002, US$69.4 million of these are notes of Russel Metals Inc., legal entity, and have been designated as a hedge of the Company’s net investment in foreign subsidiaries. The remaining US$46.2 million are notes of RMI USA LLC, a U.S. subsidiary of Russel Metals Inc.
The notes are redeemable, as units, in whole or in part, at the joint option of the Company and the U.S. subsidiary, on or after June 1, 2004 at 105% of the principal amount declining rateably to 100% of the principal amount on or after June 1, 2007. In addition, the notes are also redeemable, in whole, at the option of the Company at any time at 100% of the principal amount in the event of certain changes affecting Canadian withholding taxes. The notes contain certain restrictions on the payment of common share dividends.
During the year ended December 31, 2001, the Company repurchased US$9.4 million of the 10% Senior Notes for US$9.4 million in cash.
b) 8% Subordinated DebenturesThe 8% Subordinated Debentures, which are unsecured and mature in June 2006, are redeemable at face value subject to certain conditions being met.
9. Interest Expense
| | | | | | | | | | | | |
($000)
| | 2003
| | 2002
| | 2001
|
Interest on long-term debt | | $ | 18,839 | | | $ | 20,550 | | | $ | 21,396 | |
Other interest expense (income) | | | 3,961 | | | | (226 | ) | | | 1,621 | |
| | | | | | | | | | | | |
| | $ | 22,800 | | | $ | 20,324 | | | $ | 23,017 | |
| | | | | | | | | | | | |
Total interest paid by the Company in 2003 was $21,746,000 (2002: $20,298,000; 2001: $23,272,000).
10. Income Taxes
a)The non-current future income tax balances consist of:
| | | | | | | | |
($000)
| | 2003
| | 2002
|
Future income tax assets | | | | | | | | |
Tax benefits of loss carryforwards | | $ | 8,820 | | | $ | 8,988 | |
Plant and equipment | | | 198 | | | | 1,677 | |
Pensions and benefits | | | 974 | | | | 988 | |
Other timing | | | 3,294 | | | | 3,362 | |
| | | | | | | | |
Gross future income tax assets | | | 13,286 | | | | 15,015 | |
Valuation allowance | | | (2,828 | ) | | | (4,317 | ) |
| | | | | | | | |
Total future income tax assets | | | 10,458 | | | | 10,698 | |
| | | | | | | | |
Future income tax liabilities | | | | | | | | |
Plant and equipment | | | (6,650 | ) | | | (5,930 | ) |
Pension and benefits | | | 2,608 | | | | 2,174 | |
Other timing | | | 1,117 | | | | (8,028 | ) |
Unrealized foreign exchange charged to equity | | | (3,184 | ) | | | 3,035 | |
| | | | | | | | |
Total future income tax liabilities | | | (6,109 | ) | | | (8,749 | ) |
| | | | | | | | |
Net future income taxes | | $ | 4,349 | | | $ | 1,949 | |
| | | | | | | | |
RUSSEL METALS 2003 ANNUAL REPORT 35
NOTES TO THE CONSOLIDATED FINANCIAL STATEMENTS
b)The Company’s effective income tax rate is derived as follows:
| | | | | | | | | | | | |
| | 2003
| | 2002
| | 2001
|
Average combined statutory rate | | | 37.0 | % | | | 39.0 | % | | | 41.9 | % |
Statutory tax rate changes | | | 2.8 | % | | | — | | | | (2.4 | %) |
Large Corporation Tax | | | 0.6 | % | | | 0.5 | % | | | 2.8 | % |
Rate difference of U.S. companies | | | — | | | | (1.1 | %) | | | 4.1 | % |
Other | | | 0.4 | % | | | 0.2 | % | | | (1.1 | %) |
| | | | | | | | | | | | |
Average effective tax rate | | | 40.8 | % | | | 38.6 | % | | | 45.3 | % |
| | | | | | | | | | | | |
c)The details of the income tax provision are as follows:
| | | | | | | | | | | | |
($000)
| | 2003
| | 2002
| | 2001
|
Current provision | | $ | 13,763 | | | $ | 9,655 | | | $ | 3,631 | |
Future provision | | | (1,364 | ) | | | 8,708 | | | | 3,881 | |
Statutory rate adjustments | | | 900 | | | | — | | | | (378 | ) |
| | | | | | | | | | | | |
| | $ | 13,299 | | | $ | 18,363 | | | $ | 7,134 | |
| | | | | | | | | | | | |
d)Income taxes paid in 2003 were $7,777,000 (2002: $5,942,000; 2001: $2,058,000).
e)The Company has Canadian net operating losses carried forward for tax purposes for which a valuation allowance has been recorded. They expire as follows:
| | | | | | | | |
($000)
| | Year of Expiry
| | Amount
|
| | | 2005 | | | $ | 195 | |
| | | 2006 | | | | 651 | |
| | | 2007 | | | | 838 | |
| | | 2008 | | | | 585 | |
| | | 2009 | | | | 4 | |
| | | 2010 | | | | 1,013 | |
| | | | | | | | |
In addition, the Company has recorded a valuation allowance for timing differences of approximately $4.8 million (2002: $7.7 million).
11. Shareholders’ Equity
a)The components of shareholders’ equity are as follows:
| | | | | | | | |
($000)
| | 2003
| | 2002
|
Common shares | | $ | 147,981 | | | $ | 122,324 | |
Retained earnings | | | 110,502 | | | | 105,858 | |
Contributed surplus | | | 192 | | | | — | |
Cumulative translation adjustment | | | (4,833 | ) | | | (5,742 | ) |
| | | | | | | | |
| | $ | 253,842 | | | $ | 222,440 | |
| | | | | | | | |
b)At December 31, 2003, the authorized share capital of the Company consists of:
| (i) | | an unlimited number of common shares without nominal or par value; |
| (ii) | | an unlimited number of Class I preferred shares without nominal or par value, issuable in series; and |
| (iii) | | an unlimited number of Class II preferred shares without nominal or par value, issuable in series. |
The Company has 1,200,000 cumulative, redeemable Class II preferred shares, Series C with annual cash dividends of $1.875 per share payable in quarterly installments authorized, issued and outstanding as of December 31, 2003 and 2002. This series of Class II preferred shares is non-voting and is redeemable at a price of $25 per share without condition.
The Directors have the authority to issue the Class I and Class II preferred shares in series and fix the designation, rights, privileges and conditions to be attached to each series, except the Class I shares shall be entitled to preference over the Class II shares with respect to the payment of dividends and the distribution of assets in the event of liquidation, dissolution or winding-up of the Company.
36 RUSSEL METALS 2003 ANNUAL REPORT
c)The number of common shares issued and outstanding at December 31 was as follows:
| | | | | | | | |
| | Number | | Amount |
| | of Shares
| | ($000)
|
Balance, December 31, 2001 | | | 37,981,501 | | | $ | 122,071 | |
Stock options exercised | | | 75,500 | | | | 253 | |
| | | | | | | | |
Balance December 31, 2002 | | | 38,057,001 | | | | 122,324 | |
Shares issued – Acier Leroux acquisition | | | 3,546,874 | | | | 19,969 | |
Stock options exercised | | | 1,419,567 | | | | 5,688 | |
Shares cancelled | | | (100 | ) | | | — | |
| | | | | | | | |
Balance, December 31, 2003 | | | 43,023,342 | | | $ | 147,981 | |
| | | | | | | | |
d)The Company has a shareholder approved share option plan, the purpose of which is to provide the Directors and employees of the Company and its subsidiaries with the opportunity to participate in the growth and development of the Company. The number of common shares that may be issued under the share option plan is 4,500,000. The options are exercisable on a cumulative basis to the extent of either 331/3% or 20% per year of total options granted, except that under certain specified conditions the options become exercisable immediately. The consideration paid by employees for purchase of common shares is added to share capital.
The following is a continuity schedule of options outstanding:
| | | | | | | | | | | | | | | | |
| | Number | | Weighted Average |
| | of Options | | Exercise Price |
| | 2003
| | 2002
| | 2003
| | 2002
|
Balance, beginning of the year | | | 2,682,100 | | | | 2,293,600 | | | $ | 3.94 | | | $ | 3.97 | |
Granted | | | 795,000 | | | | 604,000 | | | | 5.22 | | | | 3.87 | |
Exercised | | | (1,419,567 | ) | | | (75,500 | ) | | | 3.99 | | | | 3.35 | |
Expired | | | (26,400 | ) | | | (140,000 | ) | | | 4.30 | | | | 4.54 | |
| | | | | | | | | | | | | | | | |
Balance, end of the year | | | 2,031,133 | | | | 2,682,100 | | | $ | 4.40 | | | $ | 3.94 | |
| | | | | | | | | | | | | | | | |
Exercisable | | | 795,922 | | | | 1,651,600 | | | $ | 4.46 | | | $ | 4.21 | |
| | | | | | | | | | | | | | | | |
The outstanding options at December 31, 2003 have exercise prices ranging from $5.50 – $6.00 (87,000 options); $3.50 – $5.49 (484,600 options) and $3.00 – $3.49 (1,459,533 options). In 2002, the exercise price of the options ranged from $3.00 to $6.375. The options expire in the years 2005 to 2012 and have a weighted average remaining contractual life of 7.1 years (2002: 7.7 years).
On January 1, 2003, the Company adopted the fair value-based method of accounting for stock-based compensation. Prior to January 1, 2003, the Company accounted for stock options using the intrinsic value-based method.
As required by the standard, disclosure of pro forma net earnings and earnings per share, as calculated under the fair value-based method as if this method had been adopted since January 1, 2001, is as follows:
| | | | | | | | | | | | |
($000 except per share data)
| | 2003
| | 2002
| | 2001
|
Net earnings – as reported | | $ | 18,499 | | | $ | 29,236 | | | $ | 8,608 | |
Additional compensation expense | | | (496 | ) | | | (764 | ) | | | (901 | ) |
| | | | | | | | | | | | |
Net earnings | | $ | 18,003 | | | $ | 28,472 | | | $ | 7,707 | |
| | | | | | | | | | | | |
Basic earnings per common share | | $ | 0.39 | | | $ | 0.69 | | | $ | 0.14 | |
Diluted earnings per common share | | $ | 0.38 | | | $ | 0.66 | | | $ | 0.14 | |
| | | | | | | | | | | | |
The Black Scholes option-pricing model assumptions used to compute compensation expense under the fair value-based method are as follows:
| | | | | | | | | | | | |
| | 2003
| | 2002
| | 2001
|
Dividend yield | | | 5.0 | % | | | 5.0 | % | | | 5.0 | % |
Expected volatility | | | 34.6 | % | | | 39.6 | % | | | 41.8 | % |
Expected life | | 7 yrs | | 7 yrs | | 10 yrs |
Risk free rate of return | | | 5.0 | % | | | 5.0 | % | | | 5.0 | % |
Weighted average fair value of options granted | | $ | 1.30 | | | $ | 1.09 | | | $ | 0.91 | |
| | | | | | | | | | | | |
RUSSEL METALS 2003 ANNUAL REPORT 37
NOTES TO THE CONSOLIDATED FINANCIAL STATEMENTS
e)Diluted share amounts were computed as follows:
| | | | | | | | | | | | |
| | 2003
| | 2002
| | 2001
|
Weighted average shares outstanding | | | 40,021,479 | | | | 38,024,034 | | | | 37,981,501 | |
Shares assumed issued – options | | | 1,981,324 | | | | 1,948,942 | | | | 461,667 | |
| | | | | | | | | | | | |
Diluted weighted average shares outstanding | | | 42,002,803 | | | | 39,972,976 | | | | 38,443,168 | |
| | | | | | | | | | | | |
12. Financial Instruments
a) Fair valueThe fair value of long-term debt as at December 31, 2003 and 2002 is estimated based on the last quoted trade price, where they exist, or on the current rates available to the Company for similar debt of the same remaining maturities.
| | | | | | | | |
($000)
| | 2003
| | 2002
|
Long-term debt | | | | | | | | |
Carrying amount | | $ | 179,402 | | | $ | 212,602 | |
Fair value | | | 187,912 | | | | 219,032 | |
| | | | | | | | |
As at December 31, 2003 and 2002, the estimated fair value of financial assets, liabilities and off-balance sheet instruments approximates their carrying values.
b) Credit riskThe Company, in the normal course of business, is exposed to credit risk from its customers. This risk is mitigated by the fact that its customer base is geographically diverse and in different industries. The Company is also exposed to credit risk from the potential default by any of its counterparties on its foreign exchange forward contracts. The Company mitigates this risk by entering into forward contracts with Canadian chartered banks only.
c) Interest rate riskThe Company is not exposed to significant interest rate risk. The Company’s long-term debt is at fixed rates. The Company’s bank debt that is used to finance working capital, which is short-term in nature, is at floating interest rates.
d) Foreign exchange riskThe Company uses foreign exchange contracts to manage foreign exchange risk on certain future committed cash outflows. As at December 31, 2003, the Company had outstanding forward foreign exchange contracts in the amounts of US$15.3 million (2002: US$3.0 million) and €1.825 million (2002: €nil). The foreign exchange gain included in 2003 net earnings from continuing operations was $881,000 (2002 loss: $560,000; 2001 loss: $190,000).
The Company has designated US$69.4 million of the Senior Notes and other U.S. borrowings as a hedge of its net investment in foreign subsidiaries. The exchange gains and losses on U.S. borrowing not designated as a hedge of its net investment are charged to income as incurred. This resulted in a foreign exchange gain of $348,000 (2002 gain: $261,000; 2001 loss: $1.4 million).
13. Segmented Information
The Company conducts business primarily in three metals business segments.
(i) | | Service center distribution |
| | The Company’s network of service centers carries a full line of metal products in a wide range of sizes, shapes and specifications, including carbon hot rolled and cold finished steel, pipe and tubular products, stainless steel and aluminum. The Company services all major geographic regions of Canada and certain regions in the Midwestern United States. |
|
(ii) | | Energy sector distribution |
|
| | The Company’s energy sector distribution operations carry a more specialized and limited product line than the service centers. These operations distribute pipe, tube, valves and fittings, primarily to the energy sector in Western Canada and the Western United States. |
|
(iii) | | Steel import/export |
|
| | The Company’s steel import/export business primarily imports foreign steel products into Canada and the United States for sale to third party steel service centers and other customers. |
The Company has segmented its operations on the basis of management reporting and the geographic segments in which it operates.
38 RUSSEL METALS 2003 ANNUAL REPORT
a) Results by business segment:
| | | | | | | | | | | | |
($000)
| | 2003
| | 2002
| | 2001
|
Segment Revenues | | | | | | | | | | | | |
Service center distribution | | $ | 922,778 | | | $ | 750,878 | | | $ | 706,173 | |
Energy sector distribution | | | 297,532 | | | | 289,623 | | | | 360,515 | |
Steel import/export | | | 283,579 | | | | 348,055 | | | | 321,454 | |
| | | | | | | | | | | | |
| | | 1,503,889 | | | | 1,388,556 | | | | 1,388,142 | |
Other | | | 13,201 | | | | 14,719 | | | | 14,367 | |
| | | | | | | | | | | | |
| | $ | 1,517,090 | | | $ | 1,403,275 | | | $ | 1,402,509 | |
| | | | | | | | | | | | |
Segment Operating Profits | | | | | | | | | | | | |
Service center distribution | | $ | 37,903 | | | $ | 31,516 | | | $ | 19,352 | |
Energy sector distribution | | | 13,764 | | | | 13,612 | | | | 18,406 | |
Steel import/export | | | 13,380 | | | | 28,090 | | | | 14,175 | |
| | | | | | | | | | | | |
| | | 65,047 | | | | 73,218 | | | | 51,933 | |
Other income | | | 4,002 | | | | 5,732 | | | | 6,177 | |
Corporate expenses | | | (8,018 | ) | | | (8,539 | ) | | | (7,489 | ) |
| | | | | | | | | | | | |
| | $ | 61,031 | | | $ | 70,411 | | | $ | 50,621 | |
| | | | | | | | | | | | |
Capital Expenditures | | | | | | | | | | | | |
Service center distribution | | $ | 33,466 | | | $ | 11,416 | | | $ | 6,639 | |
Energy sector distribution | | | 1,032 | | | | 1,009 | | | | 1,347 | |
Steel import/export | | | 77 | | | | 202 | | | | 32 | |
Other | | | 304 | | | | 141 | | | | 134 | |
| | | | | | | | | | | | |
| | $ | 34,879 | | | $ | 12,768 | | | $ | 8,152 | |
| | | | | | | | | | | | |
Depreciation Expense | | | | | | | | | | | | |
Service center distribution | | $ | 12,747 | | | $ | 11,549 | | | $ | 10,846 | |
Energy sector distribution | | | 1,126 | | | | 1,010 | | | | 1,110 | |
Steel import/export | | | 529 | | | | 502 | | | | 148 | |
Other | | | 910 | | | | 912 | | | | 889 | |
| | | | | | | | | | | | |
| | $ | 15,312 | | | $ | 13,973 | | | $ | 12,993 | |
| | | | | | | | | | | | |
Identifiable Assets | | | | | | | | | | | | |
Service center distribution | | $ | 501,433 | | | $ | 312,999 | | | $ | 298,098 | |
Energy sector distribution | | | 144,809 | | | | 145,670 | | | | 149,623 | |
Steel import/export | | | 71,436 | | | | 162,776 | | | | 112,941 | |
| | | | | | | | | | | | |
Identifiable assets by segment | | | 717,678 | | | | 621,445 | | | | 560,662 | |
Assets not included in segments | | | | | | | | | | | | |
Cash | | | 19,008 | | | | 25,068 | | | | 17,151 | |
Income tax assets | | | 16,370 | | | | 12,004 | | | | 17,950 | |
Deferred financing charges | | | 3,547 | | | | 4,962 | | | | 6,177 | |
Other assets | | | 2,840 | | | | 3,172 | | | | 3,197 | |
Corporate and other operating assets | | | 31,176 | | | | 28,943 | | | | 31,732 | |
| | | | | | | | | | | | |
Total assets | | $ | 790,619 | | | $ | 695,594 | | | $ | 636,869 | |
| | | | | | | | | | | | |
RUSSEL METALS 2003 ANNUAL REPORT 39
NOTES TO THE CONSOLIDATED FINANCIAL STATEMENTS
b) Results by geographic segment:
| | | | | | | | | | | | |
($000)
| | 2003
| | 2002
| | 2001
|
Segment Revenues | | | | | | | | | | | | |
Canada | | $ | 1,137,906 | | | $ | 991,821 | | | $ | 941,105 | |
United States | | | 365,983 | | | | 396,735 | | | | 447,037 | |
| | | | | | | | | | | | |
| | $ | 1,503,889 | | | $ | 1,388,556 | | | $ | 1,388,142 | |
| | | | | | | | | | | | |
Segment Operating Profits | | | | | | | | | | | | |
Canada | | $ | 55,784 | | | $ | 54,899 | | | $ | 46,940 | |
United States | | | 9,263 | | | | 18,319 | | | | 4,993 | |
| | | | | | | | | | | | |
| | $ | 65,047 | | | $ | 73,218 | | | $ | 51,933 | |
| | | | | | | | | | | | |
Identifiable Assets | | | | | | | | | | | | |
Canada | | $ | 580,955 | | | $ | 439,910 | | | $ | 425,564 | |
United States | | | 136,723 | | | | 181,535 | | | | 135,098 | |
| | | | | | | | | | | | |
| | $ | 717,678 | | | $ | 621,445 | | | $ | 560,662 | |
| | | | | | | | | | | | |
14. Pensions and Benefits
The Company maintains defined benefit pension plans, post-retirement benefit plans and defined contribution pension plans in Canada and 401(k) defined contribution pension plans in the United States.
The components for the Company’s pension and benefit expense include the following:
| | | | | | | | | | | | |
($000)
| | 2003
| | 2002
| | 2001
|
Defined benefit pension plans | | | | | | | | | | | | |
Benefits earned during the year | | $ | 1,538 | | | $ | 1,399 | | | $ | 1,237 | |
Interest cost on benefit obligation | | | 3,825 | | | | 3,639 | | | | 3,469 | |
Expected return on plan assets | | | (3,353 | ) | | | (3,333 | ) | | | (3,396 | ) |
Curtailment loss | | | 225 | | | | — | | | | — | |
Settlement loss | | | 648 | | | | — | | | | — | |
Other | | | 170 | | | | 208 | | | | (110 | ) |
| | | | | | | | | | | | |
| | | 3,053 | | | | 1,913 | | | | 1,200 | |
Post-retirement benefits | | | 112 | | | | 390 | | | | 380 | |
Defined contribution plans | | | | | | | | | | | | |
Paid during the year | | | 794 | | | | 834 | | | | 522 | |
| | | | | | | | | | | | |
| | | 3,959 | | | | 3,137 | | | | 2,102 | |
Related to discontinued operations | | | (462 | ) | | | (475 | ) | | | (498 | ) |
| | | | | | | | | | | | |
Pension and benefit expense | | $ | 3,497 | | | $ | 2,662 | | | $ | 1,604 | |
| | | | | | | | | | | | |
The actuarial determinations were based on the following assumptions in each year:
| | | | | | | | | | | | |
| | 2003
| | 2002
| | 2001
|
Assumed discount rate – year-end | | | 6.5 | % | | | 6.5 | % | | | 6.5 | % |
Expected long-term rate of return on plan assets | | | 7.0 | % | | | 7.0 | % | | | 7.0 | % |
Rate of increase in future compensation | | | 4.0 | % | | | 4.0 | % | | | 4.0 | % |
Rate of increase in future government benefits | | | 3.5 | % | | | 3.5 | % | | | 3.5 | % |
| | | | | | | | | | | | |
The health care cost trend rates used were 5% for dental and 9% (2002: 9%; 2001: 8%) graded out for medical, which is reduced 1% per year until 5% and 5% thereafter. A 1% change in trend rates would result in an increase in the accrued benefit obligation for post- retirement benefits of $639,000 or a decrease of $571,000 and an increase in net periodic cost of $68,000 or a decrease of $57,000.
40 RUSSEL METALS 2003 ANNUAL REPORT
The following information pertains to the Company’s defined benefit pension and other benefit plans, excluding those which are in the process of being wound up.
| | | | | | | | | | | | | | | | |
| | Pension Plans | | Other Benefit Plans |
($000)
| | 2003
| | 2002
| | 2003
| | 2002
|
Reconciliation of accrued benefit obligation | | | | | | | | | | | | | | | | |
Balance, beginning of the year | | $ | 54,808 | | | $ | 55,541 | | | $ | 5,828 | | | $ | 5,605 | |
Acquisition | | | 5,603 | | | | — | | | | — | | | | — | |
Current service cost | | | 1,538 | | | | 1,399 | | | | 48 | | | | 44 | |
Participant contribution | | | 337 | | | | 351 | | | | — | | | | — | |
Interest cost | | | 3,825 | | | | 3,639 | | | | 372 | | | | 357 | |
Benefits paid | | | (2,682 | ) | | | (2,587 | ) | | | (300 | ) | | | (273 | ) |
Plan amendments | | | 141 | | | | 92 | | | | — | | | | — | |
Corporate restructuring giving rise to: | | | | | | | | | | | | | | | | |
Settlement | | | (3,447 | ) | | | — | | | | — | | | | — | |
Curtailment | | | 225 | | | | — | | | | (305 | ) | | | — | |
Actuarial (gain) loss | | | 364 | | | | (3,627 | ) | | | — | | | | 95 | |
| | | | | | | | | | | | | | | | |
Balance, end of the year | | $ | 60,712 | | | $ | 54,808 | | | $ | 5,643 | | | $ | 5,828 | |
| | | | | | | | | | | | | | | | |
Reconciliation of fair value of plan assets | | | | | | | | | | | | | | | | |
Balance, beginning of the year | | $ | 45,825 | | | $ | 47,852 | | | $ | — | | | $ | — | |
Acquisition | | | 4,223 | | | | — | | | | — | | | | — | |
Actual return of plan assets | | | 6,310 | | | | (1,576 | ) | | | — | | | | — | |
Employer contributions | | | 2,322 | | | | 1,785 | | | | 300 | | | | 273 | |
Employee contributions | | | 337 | | | | 351 | | | | — | | | | — | |
Corporate restructuring giving rise to: | | | | | | | | | | | | | | | | |
Settlement | | | (3,447 | ) | | | — | | | | — | | | | | |
Benefits paid | | | (2,682 | ) | | | (2,587 | ) | | | (300 | ) | | | (273 | ) |
| | | | | | | | | | | | | | | | |
Balance, end of the year | | $ | 52,888 | | | $ | 45,825 | | | $ | — | | | $ | — | |
| | | | | | | | | | | | | | | | |
Unamortized amounts | | | | | | | | | | | | | | | | |
Funded status – (deficit) | | $ | (7,824 | ) | | $ | (8,983 | ) | | $ | (5,643 | ) | | $ | (5,828 | ) |
Unrecognized prior service cost | | | 264 | | | | 163 | | | | — | | | | — | |
Unamortized net actuarial loss (gain) | | | 2,134 | | | | 5,534 | | | | (473 | ) | | | (476 | ) |
| | | | | | | | | | | | | | | | |
Accrued benefit liability | | $ | (5,426 | ) | | $ | (3,286 | ) | | $ | (6,116 | ) | | $ | (6,304 | ) |
| | | | | | | | | | | | | | | | |
As at December 31, 2003 and 2002, five of the Company’s pension plans, included in the previous table, had a projected benefit obligation of $42,694,000 (2002: $42,814,000), a fair value of plan assets of $39,092,000 (2002: $37,186,000) and an unfunded obligation of $3,602,000 (2002: $5,628,000). The closure of Lachine (see Note 3) resulted in a partial settlement and curtailment of one of the Company’s plans. The plan acquired with the Leroux acquisition, which is discussed below, is excluded from these figures.
In 2003, the Company acquired two pension plans as part of the Leroux acquisition. These plans had assets of $4,223,000 and an accrued benefit obligation of $5,603,000 as of the acquisition date. The deficit in the plan of $1,380,000 was included in the net assets acquired in the Leroux acquisition. The year-end discount rate used for this plan was 6.25%. Also at December 31, 2003, the Company has certain unfunded executive arrangements with an accrued benefit obligation of $4,693,000 (2002: $4,524,000).
The Company expects to contribute approximately $2.3 million to its defined benefit plans and $0.4 million to its other benefit plans in 2004.
RUSSEL METALS 2003 ANNUAL REPORT 41
NOTES TO THE CONSOLIDATED FINANCIAL STATEMENTS
The other benefit plans primarily represent obligations to retired employees of sold or closed businesses. Less than 1% of all active employees are entitled to retirement benefits.
| | | | | | | | |
($000)
| | 2003
| | 2002
|
Defined contribution plans | | | | | | | | |
Fair value of plan assets | | | | | | | | |
Canadian plans | | $ | 5,588 | | | $ | 5,142 | |
401(k) U.S. plans | | | 18,181 | | | | 17,273 | |
| | | | | | | | |
| | $ | 23,769 | | | $ | 22,415 | |
| | | | | | | | |
| | | | | | | | |
($000)
| | 2003
| | 2002
|
Plans in the process of being wound up | | | | | | | | |
Fair value of plan assets | | $ | 2,616 | | | $ | 2,455 | |
Projected benefit obligation | | | — | | | | — | |
| | | | | | | | |
Surplus | | $ | 2,616 | | | $ | 2,455 | |
| | | | | | | | |
The plans in the process of being wound up relate to previously discontinued operations. The resolution of the surplus may result in sharing arrangements with employees of those operations.
As at December 31, 2003, approximately 44% of all pension plan assets were invested in equities, 30% in fixed income securities, and 26% in cash and cash equivalents. The expected return on plan assets is based on historical returns on the Company’s Master Trust. Management endeavours to have an asset mix of approximately 55% in equities, 40% in fixed income securities and 5% in cash and cash equivalents. The volatility of the markets has caused management to invest a greater percentage of the pension plan assets in cash and cash equivalents. The plan assets are not invested in either derivatives or real estate assets.
15. Contingencies, Guarantees and Commitments
a)The Company and certain of its subsidiaries have been named defendants in a number of legal actions. Although the outcome of these claims cannot be determined, management intends to defend all claims and has recorded provisions based on its best estimate of the potential losses. In the opinion of management the resolution of these matters is not expected to have a materially adverse effect on the Company’s financial position, cash flows or operations.
b)The Company and its subsidiary companies have operating lease commitments, with varying terms, requiring approximate annual payments as follows: 2004: $8,862,000; 2005: $8,054,000; 2006: $5,991,000; 2007: $4,347,000; 2008: $3,425,000; 2009 and beyond: $6,705,000. Rental expenses on operating leases were as follows: 2003: $10,104,000; 2002: $9,753,000 and 2001: $10,645,000.
c)The Company is incurring site cleanup and restoration costs related to properties held for resale. Remedial actions are currently underway at several sites. The estimated costs of these cleanups have been provided for based on management’s best estimates. Additional costs may be incurred at these or other sites, as site cleanup and restoration progress, but the amounts cannot be quantified at this time.
42 RUSSEL METALS 2003 ANNUAL REPORT
16. United States Generally Accepted Accounting Principles
The following table represents the material differences between Canadian and U.S. generally accepted accounting principles (GAAP):
| | | | | | | | | | | | |
($000 except per share amounts)
| | 2003
| | 2002
| | 2001
|
Net earnings for the year under Canadian GAAP | | $ | 18,499 | | | $ | 29,236 | | | $ | 8,608 | |
Amortization of transitional obligation – pensions | | | (561 | ) | | | (561 | ) | | | (561 | ) |
Goodwill impairment – transitional loss | | | — | | | | (15,123 | ) | | | — | |
Income taxes | | | — | | | | — | | | | (360 | ) |
| | | | | | | | | | | | |
Net earnings – U.S. GAAP | | | 17,938 | | | | 13,552 | | | | 7,687 | |
Other comprehensive income items: | | | | | | | | | | | | |
Change in currency translation adjustment | | | 7,074 | | | | 425 | | | | (2,803 | ) |
Tax effect of change in currency translation adjustment | | | (6,165 | ) | | | (353 | ) | | | 2,704 | |
Unrealized gain in available for sale securities | | | 262 | | | | — | | | | — | |
Minimum pension liability | | | 1,395 | | | | 1,762 | | | | (5,178 | ) |
| | | | | | | | | | | | |
Comprehensive earnings – U.S. GAAP | | $ | 20,504 | | | $ | 15,386 | | | $ | 2,410 | |
| | | | | | | | | | | | |
Opening retained earnings and comprehensive earnings – U.S. GAAP | | $ | 102,250 | | | $ | 95,580 | | | $ | 103,016 | |
Dividends on common shares | | | (11,605 | ) | | | (6,466 | ) | | | (7,596 | ) |
Dividends on preferred shares | | | (2,250 | ) | | | (2,250 | ) | | | (2,250 | ) |
Comprehensive earnings – U.S. GAAP | | | 20,504 | | | | 15,386 | | | | 2,410 | |
| | | | | | | | | | | | |
Closing retained earnings and comprehensive earnings – U.S. GAAP | | $ | 108,899 | | | $ | 102,250 | | | $ | 95,580 | |
| | | | | | | | | | | | |
Basic earnings per common share – U.S. GAAP – continuing operations | | $ | 0.41 | | | $ | 0.30 | | | $ | 0.14 | |
| | | | | | | | | | | | |
Fully diluted earnings per common share – U.S. GAAP – continuing operations | | $ | 0.39 | | | $ | 0.29 | | | $ | 0.14 | |
| | | | | | | | | | | | |
Basic earnings per common share – U.S. GAAP | | $ | 0.39 | | | $ | 0.30 | | | $ | 0.14 | |
| | | | | | | | | | | | |
Fully diluted earnings per common share – U.S. GAAP | | $ | 0.37 | | | $ | 0.29 | | | $ | 0.14 | |
| | | | | | | | | | | | |
a)Statement of Financial Accounting Standards (“SFAS”) No. 87, Employer’s Accounting for Pensions, requires that the transitional obligation be amortized over the expected average service lives of the employee group rather than charged to retained earnings immediately as allowed under the Canadian standards. In addition, the U.S. standard requires the recognition of an additional minimum pension liability. Three of the Company’s plans and one executive arrangement have a minimum liability, which has been charged to other comprehensive income under U.S. GAAP.
b)In June 2001, the Financial Accounting Standards Board (“FASB”) issued SFAS 141, Business Combinations and SFAS 142, Goodwill and Other Intangible Assets. The effect of adopting these standards is not materially different from the adoption of the Canadian standards (see Note 2) except that the transitional impairment loss is charged to earnings as a cumulative effect of a change in accounting principle under U.S. GAAP. Certain additional disclosures on business combinations are required by the U.S. standard.
These disclosures have been included with the Canadian disclosures (see Note 3) except the pro forma disclosure noted below.
RUSSEL METALS 2003 ANNUAL REPORT 43
NOTES TO THE CONSOLIDATED FINANCIAL STATEMENTS
The following table includes the compilation of the results of the Company in accordance with Canadian GAAP on a pro forma basis as if Acier Leroux had been acquired January 1, 2002.
| | | | | | | | |
($000 except per share amounts)
| | 2003
| | 2002
|
Revenue | | $ | 1,683,334 | | | $ | 1,765,181 | |
Net income – continuing operations | | | 14,588 | | | | 26,825 | |
Net income | | | 10,184 | | | | 19,168 | |
Basic earnings per common share – continuing operations | | $ | 0.30 | | | $ | 0.59 | |
Basic earnings per common share | | $ | 0.19 | | | $ | 0.41 | |
| | | | | | | | |
c)Canadian standards require an adjustment to income when changes in income tax rates have been substantively enacted. A proposed change in income tax rates resulted in a charge to income of $360,000 for the year ended December 31, 2000. As at December 31, 2000, this tax rate change had not been enacted as required by the U.S. standards. In 2001, this proposed change was enacted.
d)Other cumulative comprehensive income also includes changes in the cumulative translation account of $7.1 million and the taxes of $6.2 million thereon. This account represents a reduction in the Company’s shareholders’ equity and represents unrealized translation adjustments, which arise on the translation to Canadian dollars of U.S. denominated assets and liabilities. The Company has designated certain U.S. denominated debt as a hedge of its net investment in these U.S. subsidiaries (see Note 12). The change in the cumulative exchange account relating to debt designated as a hedge of the Company’s net investment in its foreign subsidiaries is a gain of $25.1 million in 2003 (2002 gain: $1.1 million; 2001 loss: $8.0 million).
e)The Company has certain available for sale securities that are recorded at the lower of cost or market for Canadian accounting standards and marked to market through other comprehensive income in the amount of $262,000, net of tax of $141,000 as required by U.S. standards.
f)During 2003, the Company adopted SFAS 143, Accounting for Asset Retirement Obligations, SFAS 144, Accounting for the Impairment or Disposal of Long-Lived Assets, SFAS 148, Accounting for Stock-based Compensation, Transition and Disclosure and EITF 02-16 Accounting by a Customer for Certain Consideration Received from a Vendor. The implementation of these standards did not differ materially from the corresponding Canadian standards except that the Company adopted the Canadian Asset Retirement Obligation standard January 1, 2004. The Company has asset retirement obligations relating to its land lease for its Thunder Bay Terminal operations. The landlord has the option to retain the facilities or to require the Company to remove them. The probability weighted cost of removal is not material.
g)During 2002, FASB issued SFAS 145, Rescission of FASB Statements No. 4, 44 and 64 and FASB Interpretation No. 45, Guarantor’s Accounting and Disclosure Requirements for Guarantees, Including Indirect Guarantees of Indebtedness of Others, which did not have a material impact on the Company’s consolidated results of operations, financial position or cash flows. Also, during 2002, FASB issued SFAS 146, Accounting for Costs Associated with Exit or Disposal Activities. The Company implemented this standard for transactions entered into subsequent to December 31, 2002.
h)On January 1, 2001, the Company adopted SFAS 133, Accounting for Derivative Instruments and Hedging Activities and the corresponding amendments under SFAS 138. SFAS 133, as amended by SFAS 138, did not have a material impact on the Company’s consolidated results of operations, financial position or cash flows.
i)U.S. accounting standards do not permit certain subtotals in the cash flow statement such as cash from operating activities. Accounts receivable includes an allowance for doubtful accounts of $4.5 million (2002: $4.4 million).
j)The following table indicates the significant items in the consolidated balance sheets that would have been affected had the consolidated financial statements been prepared in accordance with U.S. GAAP.
| | | | | | | | |
($000)
| | 2003
| | 2002
|
Cash | | $ | 13,372 | | | $ | 14,942 | |
Other assets | | | 3,244 | | | | 2,461 | |
Bank indebtedness | | | 89,575 | | | | 23,406 | |
Accounts payable | | | 201,484 | | | | 176,194 | |
Income taxes payable | | | 11,871 | | | | 9,590 | |
Pension and benefits | | | 5,936 | | | | 1,179 | |
Shareholders’ equity | | | 291,051 | | | | 262,926 | |
| | | | | | | | |
44 RUSSEL METALS 2003 ANNUAL REPORT
In addition to the effect of the GAAP differences noted above, this table reflects reclassification of outstanding cheques from accounts payable and deduction of the shareholder loan (Note 6) from equity. Cumulative other comprehensive income balances included in the shareholders’ equity above are $(7.2 million) (2002: $(9.8 million)).
k)In January 2003, FASB issued FIN 46, Consolidation of Variable Interest Entities. The Company expects to adopt this standard in fiscal 2004 and it is not expected to have a material effect on the Company’s results of operations, financial position or cash flows.
17. Subsequent Events
Subsequent to year-end, the Company entered into an agreement to issue 5,000,000 common shares at an issue price of $9.00 per share for net proceeds of $42.7 million. The Company has also granted the investment dealer an option to purchase an additional 750,000 common shares. In addition, the Company made an offer to purchase and a consent solicitation to its holders of the 10% Senior Notes due June 1, 2009, whereby in addition to a consent fee of US$20.00 per US$1,000 Note, the Company would repurchase the bonds for a price of US$1,052.50 per US$1,000 Note. The Company has also announced that it intends to sell on a private placement basis up to US$175 million of Senior Notes and will use these proceeds to repurchase its US$115.6 million 10% Senior Notes, $30 million 8% Debentures and its $30 million Class II preferred shares. Deferred financing costs of $2.6 million will be charged to income as a result of this refinancing. In addition, the consent fee and redemption premium will result in a one-time charge estimated to be $10.5 million.
RUSSEL METALS 2003 ANNUAL REPORT 45
Summarized Quarterly Financial Information
2003
| | | | | | | | | | | | | | | | | | | | |
| | Three Months Ended
| | Year Ended |
(Unaudited)
| | Mar. 31
| | June 30
| | Sept. 30
| | Dec. 31
| | Dec. 31
|
Revenues ($000) | | $ | 367,021 | | | $ | 339,756 | | | $ | 392,490 | | | $ | 417,823 | | | $ | 1,517,090 | |
Earnings from operations ($000) | | | 10,609 | | | | 10,601 | | | | 17,245 | | | | 22,576 | | | | 61,031 | |
Earnings before taxes ($000) | | | 5,853 | | | | 5,730 | | | | 7,185 | | | | 13,818 | | | | 32,586 | |
Net earnings – continuing operations ($000) | | | 3,587 | | | | 3,575 | | | | 4,314 | | | | 7,811 | | | | 19,287 | |
Basic earnings per common share – continuing operations | | $ | 0.08 | | | $ | 0.08 | | | $ | 0.09 | | | $ | 0.17 | | | $ | 0.43 | |
Basic earnings per common share | | $ | 0.08 | | | $ | 0.08 | | | $ | 0.07 | | | $ | 0.17 | | | $ | 0.41 | |
Market price of common shares | | | | | | | | | | | | | | | | | | | | |
High | | $ | 5.65 | | | $ | 6.00 | | | $ | 6.39 | | | $ | 8.90 | | | $ | 8.90 | |
Low | | $ | 4.85 | | | $ | 4.65 | | | $ | 5.20 | | | $ | 6.18 | | | $ | 4.65 | |
Number of common shares traded | | | 1,841,038 | | | | 3,918,050 | | | | 6,237,389 | | | | 5,016,721 | | | | 17,013,198 | |
| | | | | | | | | | | | | | | | | | | | |
2002
| | | | | | | | | | | | | | | | | | | | |
| | Three Months Ended
| | Year Ended |
(Unaudited)
| | Mar. 31
| | June 30
| | Sept. 30
| | Dec. 31
| | Dec. 31
|
Revenues ($000) | | $ | 325,863 | | | $ | 351,523 | | | $ | 374,079 | | | $ | 351,810 | | | $ | 1,403,275 | |
Earnings from operations ($000) | | | 11,024 | | | | 19,020 | | | | 21,848 | | | | 18,519 | | | | 70,411 | |
Earnings before taxes ($000) | | | 5,884 | | | | 14,829 | | | | 16,108 | | | | 10,778 | | | | 47,599 | |
Net earnings ($000) | | | 3,514 | | | | 9,102 | | | | 9,980 | | | | 6,640 | | | | 29,236 | |
Basic earnings per common share – continuing operations | | $ | 0.08 | | | $ | 0.22 | | | $ | 0.25 | | | $ | 0.16 | | | $ | 0.71 | |
Basic earnings per common share | | $ | 0.08 | | | $ | 0.22 | | | $ | 0.25 | | | $ | 0.16 | | | $ | 0.71 | |
Market price of common shares | | | | | | | | | | | | | | | | | | | | |
High | | $ | 4.28 | | | $ | 5.49 | | | $ | 5.25 | | | $ | 5.20 | | | $ | 5.49 | |
Low | | $ | 3.46 | | | $ | 4.29 | | | $ | 4.10 | | | $ | 4.22 | | | $ | 3.46 | |
Number of common shares traded | | | 4,294,572 | | | | 2,354,671 | | | | 3,208,781 | | | | 2,149,368 | | | | 12,007,392 | |
| | | | | | | | | | | | | | | | | | | | |
Definitions
Adjusted interest– Interest for 1999 includes pre-tax interest on the 9% convertible debentures recorded as dividends.
Adjusted EBIT– Earnings from continuing operations before deduction of interest, income taxes, restructuring costs, goodwill impairment, foreign exchange gain (loss), debt repurchase costs, loss on sales of business and acquisition costs.
Adjusted EBITDA– Earnings from continuing operations before interest, income taxes, depreciation, amortization, restructuring costs, goodwill impairment, foreign exchange gain (loss), debt repurchase costs, loss on sales of business and acquisition costs.
(See table page 21).
Free cash flow– Cash from operating activities less capital expenditures.
Market capitalization– Outstanding common shares times market price of a common share at December 31.
Return on capital employed– Adjusted EBIT over net assets employed.
46 RUSSEL METALS 2003 ANNUAL REPORT
Corporate Governance
The members of the Board of Directors are:
| | | | |
James F. Dinning | | Robbert Hartog | | Edward M. Siegel, Jr. |
Executive Vice President | | President | | President and Chief Executive Officer |
TransAlta Corporation | | Robhar Investments Ltd. | | Russel Metals Inc. |
| | | | |
Carl R. Fiora | | Lise Lachapelle | | Arni C. Thorsteinson |
Corporate Director, | | Corporate Director | | President |
steel industry executive | | | | Shelter Canadian Properties Limited |
| | | | |
Anthony F. Griffiths | | John W. Robinson | | |
Corporate Director, | | Corporate Director, | | |
Chairman of the Board | | steel industry executive | | |
Russel Metals Inc. | | | | |
Russel Metals’ Board of Directors places high value on the responsible fulfilment of its duties to the Company and its shareholders. The Company’s corporate governance practices are aligned with the best practices as recommended in the Toronto Stock Exchange’s corporate governance guidelines. The Board continues to monitor and to adapt the Company’s corporate governance practices, as appropriate, to reflect developments in best practices for Canadian public companies including the best practice guidelines released by Canadian securities regulatory authorities in January 2004.
Mandate of the BoardThe Board’s mandate is to supervise the management of the business and affairs of the Company. Through the Board’s stewardship of the Company, the goal is to enhance long-term value for the shareholders. The Board discharges its responsibility by delegating to management responsibility for day-to-day operations of the business, by monitoring the Company’s performance and by considering and approving the Company’s strategic direction. The Board has implemented a number of practices to promote effective governance, including a written job description for the CEO, an annual written questionnaire to all directors and at least two annual Board meetings where management is not present for portions of the meeting.
Composition of the BoardThe Directors bring to the Company a balance of industry and operational expertise as well as backgrounds in other areas which the Board believes are of benefit. The Board has concluded that all of the Directors of the Company, other than Mr. Siegel, are unrelated within the meaning of the Toronto Stock Exchange Guidelines.
Committees of the BoardThe Board delegates certain of its functions to four committees of the Board to facilitate more detailed consideration of certain issues. Each of the committees is comprised entirely of unrelated directors.
Audit CommitteeThe Audit Committee meets quarterly to review the Company’s financial statements, management’s discussion and analysis and press releases. The Audit Committee monitors the integrity of internal control and management information through discussions with management and regular meetings with the external auditors. In addition, the Committee reviews other public disclosure documents, including the annual information forms, registrations and prospectuses. The members are: J. F. Dinning, C. R. Fiora, R. Hartog (chair) and A. C. Thorsteinson.
Corporate Governance CommitteeThe Corporate Governance Committee develops comprehensive written mandates for each of the Board committees, monitors and evaluates the corporate governance system, recommends candidates for election to the Board and serves as a forum for concerns of directors which may not be appropriate for discussion in full Board meetings. The members are: J. F. Dinning, C. R. Fiora and A. F. Griffiths (chair).
Management Resources and Compensation CommitteeThe Management Resources and Compensation Committee reviews compensation policies for the Company’s executive officers and is responsible for succession planning for the most senior members of management. The members are: A. F. Griffiths, R. Hartog, L. Lachapelle (chair) and J. W. Robinson.
Environmental Management and Health & Safety CommitteeThe Company has established an Environmental Management and Health & Safety Committee for the purpose of reviewing compliance policies and procedures in accordance with legislative and regulatory requirements with regard to Environmental and Health and Safety issues. The members are: L. Lachapelle, J. W. Robinson (chair) and A. C. Thorsteinson.
Additional information about the Company’s governance practices may be found in the Management Proxy Circular.
RUSSEL METALS 2003 ANNUAL REPORT 47
Russel Metals Inc. Directory
Head Office
1900 Minnesota Court, Ste. 210, Mississauga, Ontario, Canada, L5N 3C9
Tel: (905) 819-7777 Fax: (905) 819-7409
E-mail: info@russelmetals.com Internet: www.russelmetals.com
Officers
| | | | |
Anthony F. Griffiths | | Edward M. Siegel, Jr. | | Brian R. Hedges |
Chairman of the Board | | President and | | Executive Vice President |
Toronto | | Chief Executive Officer | | and Chief Financial Officer |
| | Mississauga | | Mississauga |
| | | | |
Marion E. Britton | | | | |
Vice President, Controller | | Elaine G. Hillis | | William M. O’Reilly |
and Assistant Secretary | | Assistant Secretary | | Secretary |
Mississauga | | Mississauga | | Davies Ward Phillips & Vineberg, LLP |
| | | | Toronto |
Shareholder Information
Stock Symbol:The Toronto Stock Exchange – RUS
Transfer Agent and Registrar
CIBC Mellon Trust Company
P.O. Box 7010, Adelaide Street Postal Stn., Toronto, Ontario, Canada, M5G 2W9
Answer line: Toronto (416) 643-5500
Toll Free: 1-800-387-0825
E-mail: inquiries@cibcmellon.ca Internet: www.cibcmellon.ca
Operations
Energy
CANADA
Comco Pipe and Supply Company
Edmonton, Alberta
5910 – 17th Street, T6P 1S5
Tel: (780) 440-2000
Calgary, Alberta
9307 – 48th Street South East,
T2C 2R1
Tel: (403) 203-0766
Stonewall, Manitoba
116 – 4th Street East, R0C 2Z0
Tel: (204) 467-8797
Guelph, Ontario
Kerr Industrial Park, N1H 6H9
Tel: (519) 763-1114
Sarnia, Ontario
1018 Gladwish Drive North,
N7T 7H3
Tel: (519) 332-6666
Fedmet Tubulars
Calgary, Alberta
700 – 9th Avenue South West,
Ste. 2200, T2P 3V4
Tel: (403) 237-0955
Triumph Tubular & Supply
Calgary, Alberta
441 – 5th Avenue South West,
Ste. 875, T2P 2V1
Tel: (403) 262-3777
UNITED STATES
Pioneer Pipe
Denver, Colorado
1660 Lincoln Street,
Ste. 2300, 80264
Tel: (303) 289-3201
Lindon, Utah (Provo)
1610 West 200 South, 84042
Tel: (801) 224-8739
Houston, Texas
2203 Timberloch Place,
Ste. 125-1,
The Woodlands, 77380
Tel: (281) 292-2875
Spartan Steel Products
Evergreen, Colorado
2942 Evergreen Pkwy,
Ste. 207, 80439
Tel: (303) 670-9048
Import/Export
CANADA
Wirth Steel
Montreal, Quebec
1 Westmount Square,
Ste. 200, H3Z 2P9
Tel: (514) 939-5555
Burnaby, British Columbia
4603 Kingsway,
Ste. 308, V5H 4M4
Tel: (604) 436-1741
UNITED STATES
Sunbelt Group
Houston, Texas
1990 Post Oak Blvd.,
Ste. 950, 77056-3817
Tel: (713) 840-0550
Overland Park, Kansas
7300 W. 110th Street,
Ste. 660, 66210
Tel: (913) 491-6660
Continental Wood Trading
Houston, Texas
1990 Post Oak Blvd.,
Ste. 1550, 77056-3817
Tel: (713) 629-1701
Arrow Steel Processors
Houston, Texas
8710 Clinton Drive, 77029
Tel: (713) 673-0666
Other
CANADA
Thunder Bay Terminals Ltd.
Thunder Bay, Ontario
Station F, McKellar Island,
P7C 5J7
Tel: (807) 625-7800
48 RUSSEL METALS 2003 ANNUAL REPORT
Service Centers
Operating under the name
Russel Metals, unless
otherwise noted.
CANADA
BRITISH COLUMBIA
Operating under the name
A. J. Forsyth throughout B.C.
Delta (Vancouver) – Regional Office
830 Carlisle Road, V3M 5P4
Tel: (604) 525-0544
Campbell River
2710 Vigar Road, V9W 6A3
Tel: (250) 287-8841
Fort St. John
Mile 49-1/2 Alaska Highway,
V1J 4M6
Tel: (250) 785-5641
Kelowna
668 Willow Park Road, V1X 5C4
Tel: (250) 765-3123
Kitimat
815 Enterprise Avenue, V8C 2P1
Tel: (250) 632-4702
Nanaimo
1950 East Wellington Road,
V9S 5V2
Tel: (250) 753-1555
Prince George
1154 Pacific Street, V2N 5S3
Tel: (250) 563-1274
990 Industrial Way, V2N 5S1
(Specializing in flat rolled)
Tel: (250) 563-1274
ALBERTA
Calgary
5724 – 40th Street South East,
T2C 2A1
Tel: (403) 279-6600
Edmonton
7016 – 99th Street, T6E 4T2
Tel: (780) 439-2051
Russel Drilling & Industrial Supply
3751 – 69th Avenue, T6B 3G4
Tel: (780) 440-0779
Grande Prairie
11035 – 89th Avenue, T8V 5B9
Tel: (780) 539-3193
Red Deer
6724 Golden West Avenue, T4P 1A8
Tel: (403) 346-2096
SASKATCHEWAN
Regina
445 – 1st Avenue East, S4N 4Z3
Tel: (306) 721-6411
Russel Drilling & Industrial Supply
475 – 1st Avenue East, S4N 4Z3
Tel: (306) 721-9355
Saskatoon
922 – 51st Street East,
S7K 5C7
Tel: (306) 931-3338
MANITOBA
Winnipeg
Drummond McCall
1359 St. James Street, R3H 0K9
Tel: (204) 772-0321
Russel Metals
1510 Clarence Avenue, R3T 1T6
Tel: (204) 475-8584
ONTARIO
Mississauga (Toronto) –
Regional Office
1900 Minnesota Court,
Ste. 210, L5N 3C9
(Ontario General Line Sales)
Tel: (905) 819-7777
Burlington
3455 North Service Road, L7N 3G2
Tel: (905) 819-7777
Milspec Industries
5036 South Service Road, L7L 5Y7
(Specializing in strapping)
Tel: (905) 333-0646
Cambridge
Russel Leroux
15 Cherry Blossom Road,
N3H 4R7
Tel: (519) 650-1666
Guelph
Vantage Laser Cutting
24 Nicholas Beaver Road,
N1H 6H9
Tel: (519) 653-1588
Hamilton
175 Shaw Street, L8N 3S2
(Specializing in non-ferrous sales)
Tel: (905) 522-5930
(Specializing in chain)
Tel: (905) 522-1130
Kingston
191 Dalton Avenue, K7K 6C2
Tel: (613) 546-1281
London
685 Hale Street, N5W 1J1
Tel: (519) 451-1140
Milton
York Steel
8725 Holgate Crescent, L9T 2X7
(Specializing in structurals)
Tel: (905) 875-1447
Ottawa
Russel Leroux
2420 Stevenage Drive, K1G 3W3
Tel: (613) 738-2961
Port Robinson
Ennisteel
200 South Street North, L0S 1K0
Tel: (905) 384-9794
Stoney Creek (Hamilton)
B&T Steel
1052 South Service Road,
L8E 6G3
(Specializing in flat rolled)
Tel: (905) 643-3008
McCabe Steel
687 Arvin Avenue, L8E 5R2
Tel: (905) 643-8284
Thunder Bay
Drummond McCall
620 Norah Crescent, P7C 5V8
Tel: (807) 622-8898
Windsor
3702 Walker Road, N8W 3S8
Tel: (519) 250-3788
QUEBEC
Boucherville – Regional Office
Acier Leroux
1331, rue Graham-Bell, J4B 6A1
Tel: (450) 641-4360
Amos
Acier Leroux
1675, route de l’aéroport, J9T 3A8
Tel: (819) 732-8381
Baie-Comeau
Acier Leroux
55 William Dobel, G4Z 1T8
Tel: (418) 296-8626
Chicoutimi
Acier Leroux
2149, rue de la Fonderie, G7H 5B1
Tel: (418) 545-8881
Longueuil
Armabec
2300, rue Garneau, J4G 1E8
(Specializing in rebar)
Tel: (450) 442-9527
Montreal
Dollard Steel
6600, boul. Décarie, H3X 2K4
Tel: (514) 343-3804
Quebec
Acier Loubier
5225, rue John Molson, G1X 3X4
Tel: (418) 656-0668
Rimouski
Acier Leroux
221, rue des Négociants, G5M 1B7
Tel: (418) 724-4937
Saguenay
Métaux Russel
2420, rue Bauman, G7S 4S4
Tel: (418) 548-3103
Sainte-Marie
Delta Joist
1270 2E Rue, Parc Industriel,
G6E 1G8
Tel: (418) 387-6611
St-Augustin-de-Desmaures
Acier Leroux
167, rue Rotterdam, G3A 2K2
Tel: (418) 878-5737
Sept-Iles
Acier Leroux
533, boul. Laure Est, G4R 4K2
Tel: (418) 962-6374
Terrebonne
Acier Leroux
1025, boul. des Entreprises,
J6Y 1V2
(Specializing in structurals)
Tel: (450) 622-2060
Thetford Mines
Megantic Metal
1400, boul. Smith Nord,
G6G 5R9
Tel: (418) 338-3188
NEW BRUNSWICK
Edmundston
25 Rue Richards, E3V 4H4
Tel: (506) 739-9561
Sackville
141 Crescent Street, E4L 3V2
Tel: (506) 364-1234
Saint John
37 McIlveen Drive,
McAllister Industrial Park,
E2L 4B3
Tel: (506) 635-0005
NOVA SCOTIA
Halifax – Regional Office
28 Lakeside Park Drive,
B3T 1A3
Tel: (902) 876-7861
NEWFOUNDLAND
Mount Pearl
Donovans Industrial Estates
A1N 5B7
Tel: (709) 364-3300
UNITED STATES
Russel Metals Williams Bahcall
Appleton, Wisconsin
975 North Meade Street,
54912
Tel: (920) 734-9271
Green Bay, Wisconsin
895 Hinkle Street, 54303
Tel: (920) 497-1020
Milwaukee, Wisconsin
999 West Armour Avenue,
53221
Tel: (414) 481-7100
Federal Pipe & Steel
Plattsburg, New York
4 Martina Circle, 12901
Tel: (518) 563-5885
Baldwin International
Solon, Ohio
30403 Bruce Industrial Pkwy.,
44139
Tel: (440) 248-9500

Our Values
Management looks to maintain superior returns throughout the current and future economic cycles. Both short and long-term success in any business depends on the development and retention of strong relationships. At Russel Metals, these relationships include our customers, suppliers, employees, community, and, of course, our shareholders.
Our CustomersCritical to our relationship with our customers is providing competitively priced, quality product with on-time delivery. Our geographically diverse network of locations throughout Canada and various areas in the United States enables us to store our product close to our customer locations and respond to their needs on a timely basis. We at Russel Metals strive to meet our customers’ quality expectations by promoting high quality standards throughout the organization. The vast majority of our locations are ISO 9000 certified and our Regional Quality Leaders strive to enhance Best Practices in their region.
Our SuppliersWithout the support of our suppliers, the Company would not be successful. We endeavour to pay fair market value for the goods we buy for either resale or for further processing. We look upon our suppliers as partners, and we reward those suppliers who we feel support us with the majority of our purchases.
Our EmployeesRussel Metals has approximately 2,500 employees with offices and operations throughout North America. The Company continues to elevate awareness of health and safety throughout the organization from the shop floor to the Board of Directors. In 2003, as a result of proactive initiatives in this area, the number of accidents decreased by 9% and the accident severity, as measured by the number of days lost, improved 14% over the previous year.
The Company encourages the implementation of results oriented bonus plans at all levels of the organization. This helps to ensure that the interests of the employees and the shareholders are aligned. In addition, our Value Sharing Plan provides financial incentives to every employee to participate in the ownership of our Company.
Our CommunityOur management does not administer social responsibility, including charitable donations, at the corporate level. Rather, branch management, in our diverse locations throughout North America, are encouraged to sponsor community-based local initiatives both in donations of cash and in employee time.
Our EnvironmentThe business practices involved in the metals distribution business of the Company present minimal environmental exposure. The Company has implemented rigorous environmental standards and an ongoing audit process. The Environmental Manager proactively reports to both management and our Board of Directors on any changes in legislation and the effect, if any, on our continuing operations.
The ongoing environmental cleanup costs expended by the Company relate to non-metals operations previously sold or discontinued, not the metals operations. The Company has actively honoured its legacy environmental costs for non-metals operations and over the last 10 years has spent in excess of $18 million on environmental cleanups.
Our ShareholdersThe above, coupled with our emphasis on bottom line performance and effective asset management throughout the organization, enables us to be a sector leader in dividend yield and share appreciation.
www.russelmetals.com