Stillwater mining company
Technical report for the
Mining operations at
Stillwater mining company
Stillwater mine, 45°23'n, 109°53'w
East boulder mine, 45°30'n, 109°05'w
(behre dolbear project 11-030)
March 2011
Prepared by:
Mr. David m. Abbott, jr., cpg
Dr. Richard l. Bullock, p.e.
Ms. Betty gibbs
Mr. Richard s. Kunter
BEHRE DOLBEAR & COMPANY, LTD.
999 Eighteenth Street, Suite 1500
Denver, Colorado 80202
(303) 620-0020
A Member of the Behre Dolbear Group Inc.
© 2011, Behre Dolbear Group Inc. All Rights Reserved.
www.dolbear.com
Technical Report for the Mining Operations at Stillwater Mining Company
March 2011
TABLE OF CONTENTS | |
| | | | |
3.0 | SUMMARY | 1 |
| 3.1 | INTRODUCTION | 1 |
| 3.2 | EXPLORATION | 1 |
| 3.3 | GEOLOGY AND MINERALIZATION | 2 |
| 3.4 | DRILLING, SAMPLING METHOD, AND ANALYSES | 3 |
| 3.5 | RESOURCES AND RESERVES | 3 |
| 3.6 | DEVELOPMENT AND OPERATIONS | 5 |
| | 3.6.1 | Mining Operation | 5 |
| | 3.6.2 | Processing and Smelter | 5 |
| 3.7 | ENVIRONMENTAL COMPLIANCE AND RECLAMATION | 6 |
| 3.8 | CONCLUSIONS AND RECOMMENDATIONS | 7 |
4.0 | | INTRODUCTION | 8 |
| 4.1 | PERSONNEL INVOLVED AND QUALIFICATIONS | 8 |
| 4.2 | SITE EXAMINATIONS | 9 |
| 4.3 | UNITS AND DEFINITIONS | 9 |
5.0 | RELIANCE ON OTHER EXPERTS | 10 |
6.0 | PROPERTY DESCRIPTIONS AND LOCATIONS | 11 |
7.0 | ACCESSIBILITY, CLIMATE, LOCAL RESOURCES, INFRASTRUCTURE | |
| AND PHYSIOGRAPHY | 13 |
8.0 | HISTORY | 15 |
9.0 | GEOLOGICAL SETTING | 16 |
| 9.1 | THE J-M REEF | 16 |
| | 9.2 STRUCTURAL GEOLOGY | 17 |
| | 9.2.1 | Cross Faults | 19 |
| | 9.2.2 | Intrusions | 19 |
10.0 | DEPOSIT TYPES | 20 |
11.0 | MINERALIZATION | 21 |
| 11.1 | LARGE-SCALE REGULARITY OF THE J-M REEF | 21 |
12.0 | EXPLORATION | 23 |
13.0 | DRILLING | 24 |
14.0 | SAMPLING METHOD AND APPROACH | 26 |
| 14.1 | COMMENTS ON SMC'S QUALITY ASSURANCE/QUALITY CONTROL (QA/QC) PROCEDURES | 26 |
15.0 | SAMPLE PREPARATION, ANALYSES, AND SECURITY | 29 |
16.0 | DATA VERIFICATION | 30 |
| 16.1 | DRILLING | 30 |
| 16.2 | SAMPLING AND ANALYSIS | 30 |
17.0 | ADJACENT PROPERTIES | 31 |
18.0 | MINERAL PROCESSING AND METALLURGICAL TESTING | 32 |
| 18.1 | STILLWATER CONCENTRATOR | 32 |
| | 18.1.1 | Stillwater Primary Crushing | 32 |
| | 18.1.2 | Stillwater Grinding Circuit | 32 |
| | 18.1.3 | Stillwater Flotation Circuit | 32 |
| | 18.1.4 | Stillwater Tailings | |
Technical Report for the Mining Operations at Stillwater Mining Company
March 2011
TABLE OF CONTENTS |
(CONTINUED) |
|
| 18.2 | EAST BOULDER CONCENTRATOR | 34 |
| | 18.2.1 | East Boulder Grinding Circuit | 35 |
| | 18.2.2 | East Boulder Flotation Circuit | 35 |
| | 18.2.3 | East Boulder Tailings | 35 |
| 18.3 | COLUMBUS METALLURGICAL OPERATION | 37 |
| | 18.3.1 | SMC's Smelter | 37 |
| | 18.3.2 | SMC's Base Metal Refinery | 37 |
| | 18.3.3 | SMC's Catalyst Recycle Facility | 38 |
19.0 | MINERAL RESOURCE AND MINERAL RESERVE ESTIMATES | 39 |
| 19.1 | DRILL SECTION INTERPRETATIONS AND WIREFRAME CONSTRUCTION | 39 |
| 19.2 | BLOCK MODELING | 39 |
| 19.3 | GRADE ESTIMATION - EAST BOULDER MINE | 40 |
| 19.4 | GRADE ESTIMATION - STILLWATER MINE | 41 |
| 19.5 | RESOURCE/RESERVE DEFINITIONS | 42 |
| 19.6 | SMC'S MINERAL RESOURCE ESTIMATES | 43 |
| 19.7 | SMC'S PROVEN AND PROBABLE MINERAL RESERVE ESTIMATES | 44 |
| 19.8 | MINE LIFE | 48 |
20.0 | OTHER RELEVANT DATA AND INFORMATION | 49 |
21.0 | INTERPRETATION AND CONCLUSIONS | 50 |
22.0 | RECOMMENDATIONS | 51 |
23.0 | REFERENCES | 52 |
24.0 | DATE AND SIGNATURE PAGE | 53 |
| | Richard L. Bullock | 58 |
25.0 | ADDITIONAL REQUIREMENTS FOR TECHNICAL REPORTS ON DEVELOPMENT PROPERTIES AND PRODUCTION PROPERTIES | 62 |
| 25.1 | MINING | 62 |
| | 25.1.1 | Stillwater and East Boulder Mining Methods | 62 |
| | 25.1.2 | Stillwater Mine Operation | 67 |
| | 25.1.3 | The Major Stillwater Mine Off-shaft Deep Mine Development | 68 |
| | 25.1.4 | Normal Stillwater Mine Operations | 72 |
| | 25.1.5 | Stillwater Mine Production | 73 |
| | 25.1.6 | Stillwater Mine Services | 75 |
| | 25.1.7 | East Boulder Operation | 75 |
| | 25.1.8 | East Boulder Mine Production | 77 |
| | 25.1.9 | East Boulder Mine Services | 78 |
| | 25.1.10 | SMC's Mining Safety and Health | 78 |
| 25.2 | MARKETS | 79 |
| 25.3 | CONTRACTS | 80 |
| 25.4 | TAXES | 81 |
| 25.5 | CAPITAL AND OPERATING COSTS | 81 |
| | 25.5.1 | Operating and Capital Cost of the Stillwater Mine | 81 |
| | 25.5.2 | Operating and Capital Cost of the East Boulder Mine | |
Technical Report for the Mining Operations at Stillwater Mining Company
March 2011
| |
| (CONTINUED) |
| |
| | | |
| 25.6 | ENVIRONMENTAL COMPLIANCE AND RECLAMATION | 83 |
| | 25.6.1 | Introduction | 83 |
| | 25.6.2 | Summary and Conclusions | 83 |
| | 25.6.3 | Stillwater Air Permit | 84 |
| | 25.6.4 | Stillwater Montana Department of Environmental Quality Permit | 84 |
| | 25.6.5 | Revisions to Water Treatment Facilities at East Boulder | 84 |
| | 25.6.6 | Groundwater Study at East Boulder | 85 |
| | 25.6.7 | Environmental Impact Statement | 85 |
| | 25.6.8 | Reclamation Bonding Changes | 85 |
| | 25.6.9 | Storm Water Permit at Metallurgical Complex | 86 |
| | 25.6.10 | Future Waste Disposal Issues | 86 |
| | 25.6.11 | Other Matters | 86 |
| 25.7 | CATALYTIC CONVERTER RECYCLE BUSINES | |
Technical Report for the Mining Operations at Stillwater Mining Company
March 2011
| LIST OF TABLES | |
| | |
Table 3.1 | SMC's Estimated Proven and Probable Mineral Reserves | 4 |
Table 3.2 | SMC's Estimated Mineralized Material (United States reporting) or Inferred Mineral Resources (Canadian reporting) in the J-M Reef | 5 |
Table 6.1 | Summary of SMC's Mining Claims | 12 |
Table 7.1 | Billings, Montana Climate | 14 |
Table 12.1 | Surface and Adit Exploration Drill Holes | 23 |
Table 18.1 | Stillwater Concentrator Summary Statistics for 2010 | 33 |
Table 18.2 | East Boulder Concentrator Statistics for 2010 | 36 |
Table 19.1 | SMC's Estimated Mineralized Material (United States Reporting) or Inferred Mineral Resources (Canadian Reporting) in the J-M Reef | 44 |
Table 25.1 | Minimum Mining Widths by Area of the Mine and Mining Method1 | 72 |
Table 25.2 | Stillwater Mine Production | 74 |
Table 25.3 | East Boulder Minimum Mining Widths by Type of Mining Methods | 77 |
Table 25.4 | East Boulder Mine Production | 77 |
Table 25.5 | SMC's Accident Incident Rate | 78 |
Table 25.6 | Stillwater Mine Operating Cost | 81 |
Table 25.7 | Previous Stillwater Mine Capital Costs | 81 |
Table 25.8 | East Boulder Mine Operating Cost | 82 |
Table 25.9 | Previous East Boulder Mine Capital Costs | |
Technical Report for the Mining Operations at Stillwater Mining Company
March 2011
| LIST OF FIGURES | |
| | |
Figure 6.1 | The location of SMC's properties and mining claims | 11 |
Figure 7.1 | Looking south up the Stillwater River Valley toward the Stillwater Mine and the Beartooth Mountains beyond | 13 |
Figure 9.1 | Cross section through the Stillwater Mine showing the effects of the thrust faulting | 18 |
Figure 10.1 | The original layering in the Stillwater Complex | 20 |
Figure 13.1 | Drill fans used to delineate the J-M Reef | 24 |
Figure 14.1 | Illustration of statistical homogeneity and the effect of the size of mineralization | 27 |
Figure 18.1 | A simplified circuit diagram of the Stillwater concentrator | 34 |
Figure 18.2 | East Boulder concentrator's simplified flow sheet 2010 | 36 |
Figure 19.1 | Stillwater Mine wire frame model of the mineralized J-M Reef | 40 |
Figure 25.1 | Overhand captive cut and fill stoping | 63 |
Figure 25.2 | Overhand captive conventional cut and fill stoping | 64 |
Figure 25.3 | Overhand R&F mining method with sand backfill as applied at Stillwater Mine | 65 |
Figure 25.4 | Undercut R&F mining method using paste backfill as applied at Stillwater Mine | 66 |
Figure 25.5 | Sublevel long hole open stoping with subsequent backfilling | 67 |
Figure 25.6 | 2500 Level pump station | 69 |
Figure 25.7 | New locomotive repair shop | 69 |
Figure 25.8 | New locomotive battery charging station | 69 |
Figure 25.9 | Shaft breakthrough on 3500 Level | 70 |
Figure 25.10 | New Granby type dump station | 70 |
Figure 25.11 | Kiruna truck shop with truck being assembled; notice the three-wire trolley | 71 |
Figure 25.12 | Two of six new Nordic chutes | 71 |
Figure 25.13 | New Biodiesel storage area | 71 |
Figure 25.14 | One of two recently commissioned Kiruna trucks | 71 |
Figure 25.15 | Stillwater Mine mining method mix change over time | 73 |
Figure 25.16 | The planned changes in mining methods for the East Boulder Mine | 76 |
Figure 25.17 | Platinum supply and demand | 80 |
Figure 25.18 | Palladium supply and demand | |
Technical Report for the Mining Operations at Stillwater Mining Company
March 2011
3.0 SUMMARY
3.1 INTRODUCTION
This Technical Report was prepared for Stillwater Mining Company (SMC) on its Montana properties. The report will be used to satisfy the listing requirements of the Toronto Stock Exchange and is compliant with Canadian National Instrument 43-101.
SMC’s mining claims are located in Stillwater, Sweet Grass, and Park counties Montana and within the Custer and Gallatin National Forests. The Stillwater Mine and the Smelter and Refinery are located in Stillwater County, and the East Boulder Mine is located in Sweet Grass County. The Stillwater Mine has been producing since 1986, and the East Boulder Mine has been producing since 2002. SMC holds or leases 1,006 patented and unpatented lode, placer, or mill site claims encompassing over 16,000 acres.
The boundaries of the mining claims have all been surveyed, and these locations have been integrated into SMC’s electronic databases so that the relationships between claim boundaries and mine workings can be readily identified. Some of the claims are subject to royalties. In addition to its mining claims, SMC owns a number of fee parcels that have been purchased over the years.
SMC has operating permits for its mines from the U.S. Forest Service and the Montana Department of Environmental Quality. It also has a “Good Neighbor” agreement covering its operations and provides bus service for employees to minimize traffic on secondary roads.
The Stillwater Mine is accessible by paved roads. The East Boulder Mine is accessible by paved and wellmaintained gravel roads. The mines are located south of Interstate 90 west of Billings, Montana. The southern Montana region is in rugged country and is well served by the electrical grid system.
3.2 EXPLORATION
Since 1883, the Stillwater Complex and adjacent areas have been known to contain copper, nickel, and chromium deposits. The Stillwater layered igneous complex was first geologically mapped and described in the 1930s by Princeton University geologists operating out of their base camp in Red Lodge.
In 1998, a drill hole, located in the Stillwater River Canyon at the Stillwater Mine, intersected the major thrust splay underlying the Stillwater Mine at 800 feet above sea level, more than 4,000 feet below surface. Additional deep drilling penetrated two regional thrust splays of the Beartooth master thrust system.
Between 1969 and 1995, SMC and predecessor firms drilled 944 holes from the surface and from the Frog Pond and West Fork adits over 28 miles along the strike of the J-M Reef, establishing the known strike length of the well-mineralized length of the J-M Reef at 26 miles. The results from these drill holes were used to define the estimated mineralization in the sectors, which are bounded by geologic features that are often major fault offsets.
Surface exploration drilling is no longer being undertaken. Ongoing exploration at both the Stillwater and East Boulder Mines consists of driving the primary development footwall laterals and then drilling advance probe holes from these laterals to ensure that the J-M Reef is being appropriately followed.
Project 11-030 | 1 | BEHRE DOLBEAR |
Technical Report for the Mining Operations at Stillwater Mining Company
March 2011
3.3 GEOLOGY AND MINERALIZATION
The J-M Reef, which SMC exploits, is a small part of the large, layered igneous intrusive known as the Stillwater Complex. The exposed Stillwater Complex is considered to be a small part of a much larger intrusive body, the bulk of which (estimated to be about 4,400 square kilometers (km2)) underlies the thick sedimentary cover to the northeast.
The Stillwater Complex intruded into the surrounding metasedimentary rocks about 2.7 billion years ago. The Stillwater Complex rocks are primarily composed of large, euhedral (clearly formed) to subhedral (somewhat rounded) cumulus-phase crystals that formed during the cooling of the Stillwater magma(s). The Stillwater Complex is subdivided into three major series; from bottom to top, these are the Basal Series, the Ultramafic Series, and the Banded Series.
The J-M Reef specifically refers to the stratiform deposition of platinum-group elements and sulfide minerals in a distinctive stratigraphic zone within the Stillwater Complex. The J-M Reef formed as a more or less flat-lying, tabular layer as a part of the crystallization of the Stillwater Complex, and its laterally persistent character reflects this origin.
The reef package, which hosts the J-M Reef, is predominately an olivine-rich cumulate. The footwall is gabbro, and the hanging wall is a plagioclase-rich cumulate. The J-M Reef generally strikes westnorthwest throughout its 26 miles of strike length. At the Stillwater Mine, the J-M Reef dips north at angles varying between overturned and vertical in the eastern part of the mine (east of about the 4000E mine coordinate), about 62° in the central portion of the mine (from about 4000E to about 9000W), and around 45° to 50° in the Upper West area of the mine. At the East Boulder Mine, the dip averages about 52°.
In some places, the J-M Reef is interrupted by mafic intrusive dikes. The J-M Reef and related stratigraphy are clearly identifiable on either side of the dikes; however, the dikes may be sufficiently wide to result in J-M Reef offsets and/or to split the J-M Reef. It should be stressed that these dikes do not have more than a minor impact on mining.
Another feature of the J-M Reef within the Stillwater Mine is the occurrence of thickened areas of mineralized reef, known as “ballrooms.” Ballrooms contain significant ore-grade tons and ounces within the J-M Reef. Ballrooms have not yet been encountered in the East Boulder Mine, although there are zones of greater reef thickness at East Boulder.
When the J-M Reef is considered as a whole reef package, or in large, geologically bounded segments, mineralization is predictably and relatively evenly distributed throughout the unit. Although precise relationships vary in fine detail, the method of drilling delineation from the footwall laterals, used by SMC, provides sufficiently precise locations to guide mining. On the scale (tens to hundreds of feet) important in mine planning, the J-M Reef can be consistently located and delineated to allow mine planning. This regularity of mineralization is unlike that of most precious- and base-metal deposits and emphasizes the fact that the J-M Reef should be compared with mineral deposits formed in sedimentary environments rather than with precious metal veins.
Specifically, the J-M Reef probably was formed as a chemical precipitate during crystallization of a magma in a chamber that is tens of miles in diameter. Therefore, reserve estimation procedures for the J-M Reef for the probable mineral reserve should be, and are, more similar to those used for nonmagmatic or sedimentary iron or coal deposits than to those typically used for precious metal deposits.
Project 11-030 | 2 | BEHRE DOLBEAR |
Technical Report for the Mining Operations at Stillwater Mining Company
March 2011
The author has investigated the exploration procedure used to delineate the mineral resources and agrees that widely spaced drilling can accurately predict the character of platinum-palladium mineralization within large areas of the J-M Reef. Prior to the end of 2004, when conversion to the use of Vulcan™ mine planning software was fully implemented, Behre Dolbear (who audits the reserve calculations) and SMC consistently analyzed the J-M Reef using the vertical plane rather than the plane of the dipping J-M Reef. Since SMC commenced using Vulcan™ mine planning software, the J-M Reef is modeled on actual drill intercepts of the Reef, and the use of vertical or dipping planes is no longer an issue.
3.4 DRILLING, SAMPLING METHOD, AND ANALYSES
The primary sources of geological data at the Stillwater and East Boulder Mines are mine development, surface diamond drill holes, and underground diamond drill holes.
Two types of underground core drilling are routinely conducted at the Stillwater and East Boulder Mines. The first type consists of probe holes drilled ahead of advancing footwall laterals with the twin objectives of maintaining the footwall laterals within the desired distance of the J-M Reef and testing for rock quality, water, and any other characteristics that might affect mining. The second type of drilling consists of fans normally drilled at 50-foot intervals along the footwall laterals to delineate the mineralization in the J-M Reef.
Drill core (BQ size, 1.433 inches in diameter) is transported from the rigs to core logging rooms at the surface of both the Stillwater and East Boulder Mines. These logging rooms each have storage racks and several well-lit logging stations. Only mineralized zones and adjacent hanging and footwall zones are sampled, and the logging geologist selects zones visually. The log data are entered into a computerized database using bar code sheets containing codes for all the common parameters.
SMC maintains an assay laboratory in Columbus, Montana. The geologic and mill samples are transported from the mines to the lab in the cargo areas of the buses transporting employees from the mines to Columbus. Sample tampering is not an issue.
Routine analyses are done by X-ray methods, which are verified for accuracy by fire assays. Sample runs routinely contain standard and duplicate samples as part of the laboratory’s internal Quality Assurance/Quality Control (QA/QC) program.
3.5 RESOURCES AND RESERVES
The estimated mineral resources and mineral reserves contained in this report are current as of December 31, 2010 and consist of SMC’s regular year-end mineral reserve estimates. The reserve estimates are made in conformance with the U.S. Securities and Exchange Commission’s (SEC) Industry Guide 7,1 which Behre Dolbear audited. The geological data used in this report primarily were collected and compiled by SMC personnel. The Behre Dolbear author has carefully reviewed and examined this information, over the years, when conducting annual mineral resource and reserve audits for SMC and on related assignments.
The combined estimated Stillwater and East Boulder Mine reserves are shown in Table 3.1.
1 Part 7 of Canadian National Instrument 43-101 permits use of the SEC’s Industry Guide 7 for reporting estimates of proven and probable mineral reserves by foreign issuers, such as SMC.
Project 11-030 | 3 | BEHRE DOLBEAR |
Technical Report for the Mining Operations at Stillwater Mining Company
March 2011
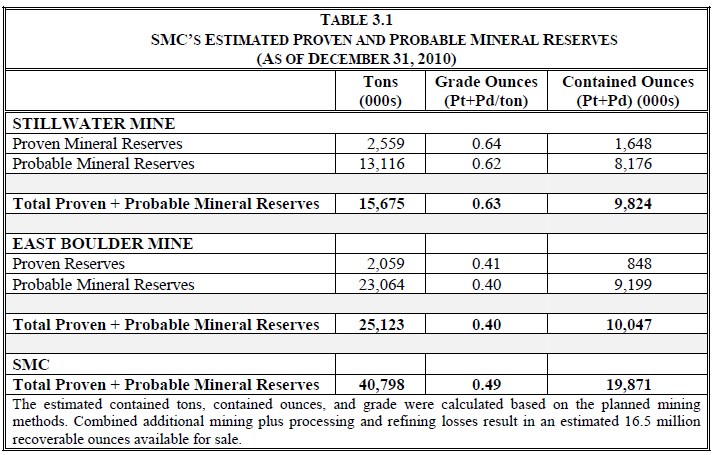
TABLE 3.1
SMC'S ESTIMATED PROVEN AND PROBABLE MINERAL RESERVES
(AS OF DECEMBER 31, 2010)
Tons Grade Ounces Contained Ounces
(000s) (Pt+Pd/ton) (Pt+Pd) (000s)
STILLWATER MINE
Proven Mineral Reserves 2,559 0.64 1,648
Probable Mineral Reserves 13,116 0.62 8,176
Total Proven + Probable Mineral Reserves 15,675 0.63 9,824
EAST BOULDER MINE
Proven Reserves 2,059 0.41 848
Probable Mineral Reserves 23,064 0.40 9,199
Total Proven + Probable Mineral Reserves 25,123 0.40 10,047
SMC
Total Proven + Probable Mineral Reserves 40,798 0.49 19,871
The estimated contained tons, contained ounces, and grade were calculated based on the planned mining
methods. Combined additional mining plus processing and refining losses result in an estimated 16.5 million
recoverable ounces available for sale. The SEC’s Industry Guide 7 does not provide for the disclosure of mineral resource categories, so SMC has been reporting estimates of “mineralized material” in areas of the J-M Reef that have not been drilled at the densities required for the estimation of probable reserves. As such drilling does occur as the mines expand, the delineated mineralization is converted directly into probable and then proven reserves, which include provision for mining and processing losses, rather than reporting the intermediate, in-situ estimates of indicated or measured mineral resources typical in Canadian reports. SMC’s “mineralized material” estimates correspond to the “inferred mineral resource” category in the Canadian definitions for mineral resources and mineral reserves.
During 2010, SMC undertook a 10-year strategic planning program to examine mining opportunities at the Stillwater and East Boulder Mines and in areas between the mines, west of the East Boulder Mine and east of the Stillwater Mine. This program resulted in the re-definition of some sector boundaries (both in the east-west dimensions and in the depth of projection), the re-assessment of the estimation parameters for the “mineralized material” (United States reporting) or Inferred Mineral Resource category (Canadian reporting). Adjustments were also made to the estimated quantities near both mines due to the conversion of some of this material to Probable Mineral Reserves during 2010.
SMC’s estimated mineralized inventory (United States reporting) or Inferred Mineral Resources (Canadian reporting) as of December 31, 2010 is presented in Table 3.2.
Project 11-030 | 4 | BEHRE DOLBEAR |
Technical Report for the Mining Operations at Stillwater Mining Company
March 2011
TABLE 3.2
SMC'S ESTIMATED MINERALIZED MATERIAL (UNITED STATES REPORTING) OR INFERRED MINERAL RESOURCES (CANADIAN REPORTING) IN THE J-M REEF
(AS OF DECEMBER 31, 2010)
Tons (millions) Grade Ounces (Pt+Pd/ton)
Stillwater Mine 55.5 0.53
East Boulder Mine 53.1 0.43
Total Estimated Mineralized Material/Inferred Mineral Resources 108.6 0.48
3.6 DEVELOPMENT AND OPERATIONS
SMC's mining operations consist of two underground mines that have been developed on the 26-mile strike length of the palladium-platinum mineralized J-M Reef. The Stillwater Mine is located near the Stillwater River and was started in 1986. The East Boulder Mine is located father west along the J-M Reef near the East Boulder River. Development of the East Boulder Mine began in 1998, and commercial production began in 2002. The two mines are the only major palladium-platinum primary metal producing mines in North or South America.
Both mines employ the same types of mining methods. The three principle mining methods are conventional overhand cut and fill (Conv. C&F), as captive stopes; ramp and fill (R&F), as both overhand and underhand cut and fill; and sublevel extraction (SLE) by longhole open stoping with subsequent backfill. Since considerable tonnage is produced from the development of the sublevels in the reef, this is carried separately as sublevel development (SLD) tonnage.
Over the past five years, the main production areas in the Stillwater Mine have been the Upper West area and the Off-shaft area. The current production goal is 2,000 tons per day.
The East Boulder Mine, which began commercial production at the beginning of 2002, is accessed by two approximately 18,700-foot-long bored tunnels. In 2003, R&F stoping was introduced to the East Boulder Mine to provide more flexibility and more efficient extraction in areas of the J-M Reef lacking the uniform width best exploited by sublevel stoping. From 2005 through 2007, there was an increase in Conv. C&F stoping in an effort to increase the overall production grade, but the resulting decrease in productivity led to a reduction in the use of this method in 2008 to 2010 and an increase in the use of the sublevel extraction method and R&F stoping.
3.6.2 Processing and Smelter
SMC's Stillwater Mill produces a nickel-copper concentrate containing platinum group metals (PGM). The present available mill capacity is 2,750 tons per day or more. An underground jaw crusher reduces the Off-shaft concentrator feed to minus 4 inches, and the crushed ore is hoisted to the surface and conveyed to a 3,000-ton ore silo. The mill averages about 92% PGM recovery.
The flotation tailings from the scavenger circuit are pumped to the paste plant and sand fill plant, where up to 50% is used in the mine backfill process. The remaining mill tails and sand plant cyclone overflow report to a tailings depository.
Project 11-030 | 5 | BEHRE DOLBEAR |
Technical Report for the Mining Operations at Stillwater Mining Company
March 2011
The East Boulder Concentrator was constructed to allow expansion to 3,000 tons per day from the originally planned 2,000 tons per day operation. A surface jaw crusher reduces ore to minus 6 inches, and the ore is conveyed to a stockpile. A flash flotation cell, installed to process cyclone underflow ahead of the ball mill, recovers readily floatable sulfides, reducing the possibility of over grinding liberated material. The flash flotation cell recovers up to 50% of the total recovered PGMs that report directly to a cleaner circuit and then to concentrate containers following thickening and pressure filtration. Overall PGM recovery is about 89%.
Tails from the flash flotation circuit report to the ball mill and then to a Knelson gravity concentrator that recovers 2.9% of total platinum and 2.3% of the total recovered gold. The flotation tailings from the scavenger circuit, which contained about 0.0406 opt combined PGMs in 2007, are pumped to an underground sand plant, where 50% is used in the mine as backfill. The remaining concentrator tails and sand plant cyclone overflow report to a tailings pond.
SMC's metallurgical complex, consisting of a smelter and base metal refinery (BMR), is located in Columbus, Montana. The smelter handles wet concentrate from both the Stillwater and East Boulder Mills, as well as recycled automotive catalysts and other PGM-bearing materials, averaging 21 ounces of platinum plus palladium per ton.
The BMR leaches the base metals present in the matte in hydrometallurgical circuits without affecting dissolution of the PGMs. The refinery has a capacity of up to 1,000 pounds per hour of smelter matte.
In 2010, the smelter and refinery processed 5,927 tons of recycled catalysts containing approximately 399,000 combined troy ounces of platinum, palladium, and rhodium.
3.7 ENVIRONMENTAL COMPLIANCE AND RECLAMATION
Behre Dolbear has considered a number of environmental factors that could potentially affect SMC, with current investigations focused primarily on changes since 2008. The following review is based on a visit to the SMC office for SMC staff interviews and assessment of conditions in mid-2010, as updated by a desktop review and interview with the Stillwater Environmental Manager in January 2011 to assess conditions through end of 2010. Inquiry was made into issues associated with air emissions, water discharges, water treatment, ground water, tailings disposal, waste rock disposal, smelter slag, smelter scrubber sludge, reclamation, reclamation bonding, and community relations. The inquiries covered the Stillwater Mine site, the East Boulder Mine site, and the metallurgical complex at Columbus, Montana.
The waste rock, tailings, and ore have been shown by testing to not be acid generating. In general, the environmental problems at the SMC operations are minor in nature compared to other large metal mining operations, and the operations are viewed by the regulatory agencies and non-governmental organizations (NGOs) as being properly managed from an environmental perspective.
Preparation of an Environmental Impact Statement (EIS) has finally been completed after several years of discussions, negotiations, and operational improvements. A Draft EIS was issued for review in November 2010. Public comments were accepted through 24 February 2011. The EIS focuses on closure and post-closure Water Management Plans at both the Stillwater and East Boulder Mines and on prospective use and operational flexibility of the Boe Ranch Land Application Disposal (LAD) site for process water disposal in the vicinity of the East Boulder Mine. This EIS is a joint effort by the U.S. Forest Service and the Montana Department of Environmental Quality.
Project 11-030 | 6 | BEHRE DOLBEAR |
Technical Report for the Mining Operations at Stillwater Mining Company
March 2011
The Stillwater Mine's bond is currently US$19.5 million, and the East Boulder Mine's bond is US$13.5 million. Negotiations on bond adjustments continue with the agencies, and revised bonding amounts to address current plans are expected to total in the US$45 million to US$55 million range for both operations. SMC staff are confident that new controlling interests (following the recent Norilsk equity sale) will provide management support for such environmental expenditures.
3.8 CONCLUSIONS AND RECOMMENDATIONS
SMC's Stillwater and East Boulder Mines have been successfully mining platinum and palladium from the J-M Reef in the Stillwater layered igneous complex of south-central Montana since 1986 and 2002, respectively. Over the years, the mines have expanded the estimated proven and probable reserves into new areas of the J-M Reef while extracting previously identified reserves. This process is expected to continue for some time, although not forever. Ultimate mine life depends on a number of factors, including metal prices, mining costs, changing mining technology, and regulatory issues, among other things that cannot be predicted at this time. SMC's geologic, mining, metallurgical, environmental, and other practices and procedures are excellent and appropriate for the type of deposit being mined. Differences from practices and procedures used at other mining properties reflect differences in the types of deposits being exploited.
Project 11-030 | 7 | BEHRE DOLBEAR |
Technical Report for the Mining Operations at Stillwater Mining Company
March 2011
4.0 INTRODUCTION
This Technical Report was prepared for Stillwater Mining Company (SMC) on its Montana properties. The report will be used to satisfy the listing requirements of the Toronto Stock Exchange and is compliant with Canadian National Instrument 43-101.
The estimated mineral resources and mineral reserves contained in this report are current as of December 31, 2010 and consist of SMC's regular year-end mineral reserve estimates made in conformance with the U.S. Securities and Exchange Commission's (SEC) Industry Guide 7. Behre Dolbear audited these year-end mineral reserve estimates.
The technical report has been co-authored by Mr. David M. Abbott, Jr., CPG; Dr. Richard L. Bullock, PE; Ms. Betty Gibbs; and Mr. Richard S. Kunter. Mr. Bernard J. Guarnera performed a quality control review of the report.
4.1 personnel involved and qualifications
The following Qualified Persons worked on this assignment.
Mr. David M. Abbott, Jr., Senior Associate, Principal, and geologist, served as the project manager and examined the geologic aspects of the assignment. Mr. Abbott has been involved with audits of SMC's reserve estimates since 1997. He is an AIPG Certified Professional Geologist, holds the European Geologist title, and is a Fellow and a Chartered Professional (Geology) with the Australasian Institute of Mining and Metallurgy and, thus, is a Qualified Person in Canada and a Competent Person in Australia.
Dr. Richard L. Bullock, Senior Associate, Principal, and mining engineer, examined the mine planning and execution aspects of the assignment. Dr. Bullock is professor emeritus of mining engineering at the University of Missouri-Rolla and an underground mining specialist. He worked on SMC's 1997, 2004, and 2006 year-end audits. Dr. Bullock is a licensed Professional Engineer in Missouri, New York, Tennessee, and Nevada and holds a Qualified Professional status from the Mining and Metallurgical Society of America and, thus, is a Qualified Person in Canada.
Ms. Betty L. Gibbs, Senior Associate and mining engineer, examined the ore reserves and mine planning aspects of the assignment. Ms. Gibbs holds Engineer of Mines and Master of Science degrees in Mining Engineering from the Colorado School of Mines. She holds a Qualified Professional status from the Mining and Metallurgical Society of America and, thus, is a Qualified Person in Canada. She worked on SMC's 2006 year-end audit.
Mr. Richard S. Kunter, Senior Associate, Principal, and processing engineer, reviewed the current status of SMC's concentrators and smelter/BMR. He conducted a thorough examination of these facilities in connection with Behre Dolbear's 2003, 2005, and 2006 reserve audits. He is a Fellow of the Australasian Institute of Mining and Metallurgy and, thus, is a Qualified Person in Canada.
Mr. Neil J. Eurick, President of Behre Dolbear Environmental Services Inc. and an environmental compliance specialist, reviewed SMC's compliance with its operating permits and relations with applicable regulatory agencies and non-governmental organizations (NGOs) during the site visit in August 2010.
Project 11-030 | 8 | BEHRE DOLBEAR |
Technical Report for the Mining Operations at Stillwater Mining Company
March 2011
Dr. Scott Mernitz, an environmental compliance specialist, reviewed SMC's compliance with its operating permits and relations with applicable regulatory agencies and non-governmental organizations (NGOs) as of year-end 2010. Dr. Mernitz has worked on previous SMC audits.
Mr. William F. Jennings, Senior Associate, Principal, and a mineral economist and geologist, verified the economic tests of this assignment. He is Behre Dolbear's foremost financial modeler. He is a Certified Mineral Appraiser and a Qualified Person in Canada.
Mr. Bernard J. Guarnera, president and CEO of Behre Dolbear Group Inc. and geologist, served as the project advisor and provided quality control for the written reports. He has served in a similar capacity for Behre Dolbear's previous assignments for SMC, over the years. Prior to joining Behre Dolbear, he was in charge of Boise Cascade's mineral development division. Mr. Guarnera is a Certified Mineral Appraiser with the American Institute of Mineral Appraisers, a Registered Professional Engineer (Texas) and Geologist (Idaho and Oregon), and a Fellow and Chartered Professional (Geology) with the Australasian Institute of Mining and Metallurgy and, thus, a Qualified Person in Canada and a Competent Person in Australia.
4.2 SITE EXAMINATIONS
All Behre Dolbear personnel employed in preparing this report, except Dr. Mernitz, conducted a site visit to SMC on August 11 to 13, 2010 and again on January 31 to February 3, 2011.2 All have visited SMC's operations at one time or another in the past; several of them have visited these operations many times over the years. Mr. Abbott, the project manager, initially visited the Stillwater Mine in 1997 and has made a number of subsequent visits to the Stillwater and East Boulder Mines; the smelter base-metal refinery (BMR) and analytical lab in Columbus, Montana; and SMC's headquarters in Columbus or Billings. Dr. Bullock, the project's mining engineer, visited the Stillwater Mine in 1997 and most recently visited the Stillwater Mine, the East Boulder Mine, and SMC's Billings headquarters in 2006, 2007, 2008, and January 2010. Ms. Gibbs visited the Stillwater Mine in 2007 and both the Stillwater and East Boulder Mines in 2008, 2009, and 2010. Mr. Kunter visited both mines and the smelter/BMR in 2006, 2007, and January 2010. Mr. Guarnera has visited SMC's operations many times since 1992.
4.3 UNITS AND DEFINITIONS
The units commonly used in the United States, short tons of 2,000 pounds (tons), troy ounces per short ton (opt), miles, feet, etc. are the major units used in this report. Where metric units are used, such are noted. The currency used is United States (US) dollars.
Project 11-030 | 9 | BEHRE DOLBEAR |
Technical Report for the Mining Operations at Stillwater Mining Company
March 2011
5.0 RELIANCE ON OTHER EXPERTS
The geological data used in this report primarily was collected and compiled by SMC personnel over the years. The Qualified Persons writing this Technical Report have carefully reviewed and examined this information over the years in conducting annual mineral resource and reserve audits for SMC and on related assignments. Where appropriate, references to published information and private reports prepared by others are given in the text, and the authors, dates, titles, and source of these documents are listed in the References chapter.
SMC retained an independent consulting firm in early 2010 to perform a Technical and Operational Review of [SMC's] mining and processing facilities. This review was done in the context of the recently completed 10-Year mine plan. This report commented negatively on the way in which SMC calculates its Probable Reserves, on some of the methodology used in the sampling Quality Assurance/Quality Control (QA/QC) program, and other aspects of SMC's 10-Year mining plan. These comments will be addressed in detail in appropriate portions of this report. In summary, both SMC and the Qualified Person are of the opinion that the independent technical reviewer's adverse comments reflect a lack of understanding of the layered-intrusive-complex character of the platinum and palladium mineralization in the J-M Reef.
Project 11-030 | 10 | BEHRE DOLBEAR |
Technical Report for the Mining Operations at Stillwater Mining Company
March 2011
6.0 PROPERTY DESCRIPTIONS AND LOCATIONS
SMC's mining claims are located in Stillwater, Sweet Grass, and Park counties and within the Custer and Gallatin National Forests. The Stillwater Mine and the smelter and refinery are located in Stillwater County, and the East Boulder Mine is located in Sweet Grass County. Figure 6.1 is a map showing the location of SMC's properties and mining claims with south-central Montana.
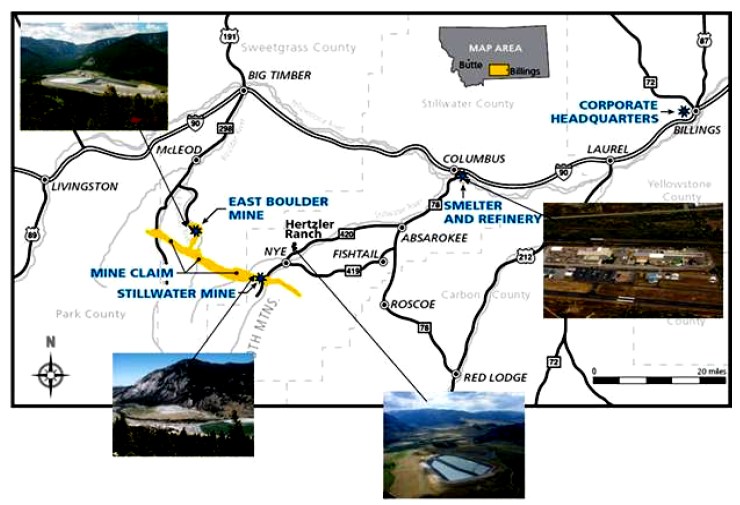
Figure 6.1. The location of SMC's properties and mining claims
The Stillwater Mine has been producing since 1986, and the East Boulder Mine has been producing since 2002.
SMC holds or leases 1,006 patented and unpatented lode, placer, or mill site claims encompassing over 16,000 acres covering:
● | 100% of the known apex of the J-M Reef (approximately 141 of the claims)3 |
● | areas to the north that will allow construction of ventilation and other shafts to the surface from lower levels in the northward-dipping J-M Reef |
3 The apex of the J-M Reef controlled by SMC extends from west of the Boulder River on the west to about West Fishtail Creek on the east. SMC and its predecessor companies have been unable to trace the J-M Reef east of West Fishtail Creek.
Project 11-030 | 11 | BEHRE DOLBEAR |
Technical Report for the Mining Operations at Stillwater Mining Company
March 2011
● | some land to the south of the apex |
● | the East Boulder Mine's access adits and plant site |
Table 6.1 presents a summary of SMC's mining claims as of the end of December 2010.
TABLE 6.1
SUMMARY OF SMC'S MINING CLAIMS
Stillwater County Sweet Grass County Park County
Patented Claims
44 117 0
9 0 0
53 117 0
Unpatented Claims
152 519 34
4 0 0
1 126 0
157 645 34
210 762 34
The boundaries of the mining claims have all been surveyed, and these locations have been integrated into SMC's electronic databases so that the relationships between claim boundaries and mine workings can be readily identified.
In addition to its mining claims, SMC owns a number of fee parcels that have been purchased over the years. Some of these parcels are currently used for operations, while others may be so used in the future. In addition to title to the lands, ownership of these parcels provides SMC with water rights.
Of the 1,006 SMC-controlled claims, 869 are subject to royalties, including 711 subject to a 5% net smelter return (NSR) royalty payable to Franco-Nevada Corporation, 143 are subject to a maximum 0.35% NSR royalty payable to the Mouat family, and 102 are subject to both royalties. Only some of these claims have been mined or are being mined during any one year. During 2010, Stillwater incurred royalties of $13.7 million, which compares with $10.6 million incurred in 2009 and $14.6 million incurred in 2008. The differences reflect metal sales prices.
SMC has operating permits for its mines from the U.S. Forest Service and the Montana Department of Environmental Quality. It also has a "Good Neighbor" agreement covering its operations, which has proven very useful in maintaining good relationships with individuals and organizations affected by SMC's operations. These permits and agreement are discussed more fully in the Environmental Section of Chapter 25.
Project 11-030 | 12 | BEHRE DOLBEAR |
Technical Report for the Mining Operations at Stillwater Mining Company
March 2011
7.0 ACCESSIBILITY, CLIMATE, LOCAL RESOURCES, INFRASTRUCTURE AND PHYSIOGRAPHY
As shown in Figure 6.1, Interstate 90 (I-90) is the main highway through the area of SMC's properties. Montana Rail Link's main line approximately follows I-90 and the Yellowstone River, including access to Columbus, the site of SMC's smelter and refinery. Excellent secondary roads connect I-90 to the mine sites. The roads to the Stillwater Mine are entirely paved, while the roads to the East Boulder Mine are paved from I-90 to south of McLeod, followed by a well-maintained gravel road along the East Boulder River to the mine site.
Billings is the main population center in the region and is home to many of SMC's employees. Many SMC employees also live in a number of smaller towns: Laurel, Columbus, Absarokee, Big Timber, Livingston, and Red Lodge, among others. As part of its "Good Neighbor" agreements, SMC provides bus service from most of these towns to the mines in order to limit mine-related traffic on the secondary roads.
The southern Montana region is well served by the state's electrical grid system. The electric transmission lines to the Stillwater Mine can deliver 22 megawatts, although current peak use is 18 megawatts. The East Boulder Mine can receive 14 megawatts, to the site, and current peak use is 11 megawatts.
The Stillwater and East Boulder Mines are located on the northern part of the Beartooth Mountains and are surrounded by extremely rugged country, some of which is above timberline (Figure 7.1). Snow, low temperatures, and high winds can present periodic problems to mine access during the winter. The climatic conditions in the towns along the Yellowstone River are more moderate, although subject to similar winter weather conditions.
Figure 7.1. Looking south up the Stillwater River Valley toward the Stillwater Mine and the Beartooth Mountains beyond
Project 11-030 | 13 | BEHRE DOLBEAR |
Technical Report for the Mining Operations at Stillwater Mining Company
March 2011
Table 7.1 shows the average temperatures and precipitation for Billings.
TABLE 7.1 BILLINGS, MONTANA CLIMATE
Average Temperature Low (F) Average Temperature High (F) Precipitation (inches)
January 13 37 0.62
February 18 44 0.49
March 25 53 0.87
April 34 63 1.55
May 43 72 2.39
June 51 81 1.98
July 56 88 1.19
August 55 88 0.92
September 45 77 1.42
October 35 65 1.32
November 24 48 0.64
December 16 39 0.57
Annual 35 63 13.96
Project 11-030 | 14 | BEHRE DOLBEAR |
Technical Report for the Mining Operations at Stillwater Mining Company
March 2011
8.0 HISTORY
Since 1883, the Stillwater Complex and adjacent areas have been known to contain copper, nickel, and chromium deposits. The Stillwater layered igneous complex was first geologically mapped and described in the 1930s by Princeton University geologists operating out of their base camp in Red Lodge. Chromite was mined during World War II and processed at a plant at the site of the current Stillwater Mine surface facilities. Sulfides containing the platinum-group metals (PGM) were discovered in the early 1930s, but significant exploration for PGMs did not start until the 1960s by two separate groups, the Anaconda Minerals Company and the Johns-Manville Corporation. In 1973, Johns-Manville geologists identified what is now known as the J-M Reef (Page and others, 1985). Surface exploration, on the eastern part of the J-M Reed in the vicinity of the Stillwater Mine, was initiated by Anaconda Minerals Company in 1977 and led to the driving of the Minneapolis Adit between 1979 and 1981; portal at 5,140 feet in elevation. In 1983, the Stillwater Mining Company, a partnership of Chevron Resources Company, the Manville Corporation, and Anaconda Minerals Company, was formed to pursue exploration westward and eastward along the J-M Reef from both the surface and underground at the Minneapolis Adit (Turner and others, 1985).
In 1998, a drill hole located in the Stillwater River Canyon at the Stillwater Mine intersected the major thrust splay underlying the Stillwater Mine. An additional deep drill hole farther to the west allowed further delineation of the J-M Reef at depth and of the bounding thrust fault. These deep drill holes allow projection of thrust fault positions that currently define the lower limits of estimated probable reserves in areas near the deep drilling.
Commercial underground mining at the Stillwater Mine began in 1986. In 1992, SMC was incorporated and on October 1, 1993, Chevron Resources Company and Manville Corporation transferred substantially all of their assets, liabilities, and operations at the Stillwater property to SMC with each partner retaining 50% of the stock (Anaconda had previously left the partnership). In September 1994, SMC redeemed Chevron Resources Company's 50% interest, and in December 1994, SMC completed its initial public offering. Manville Corporation sold a portion of its stock during the public offering and its interest was reduced to 27%. In August 1995, Manville Corporation sold its remaining interest to a group of institutional investors (SMC, 2010).
The East Boulder Mine was placed in commercial production in January 2002.
Project 11-030 | 15 | BEHRE DOLBEAR |
Technical Report for the Mining Operations at Stillwater Mining Company
March 2011
The J-M Reef, which SMC exploits, is a small part of a large, layered igneous intrusive known as the Stillwater Complex. The Stillwater Complex is located in the northern Beartooth Mountains of south- central Montana and adjacent northwestern Wyoming. The exposed Stillwater Complex is considered to be a small part of a much larger intrusive body, the bulk of which (estimated to be about 4,400 km2) underlies the thick sedimentary cover to the northeast.
The Stillwater Complex intruded into the surrounding metasedimentary rocks about 2.7 billion years ago. The Stillwater Complex rocks are primarily composed of large, euhedral (clearly formed) to subhedral (somewhat rounded) cumulus-phase crystals that formed during the cooling of the Stillwater magma(s). The Stillwater Complex is subdivided into three major series: from bottom to top, these are the Basal Series, the Ultramafic Series, and the Banded Series. Each series is further subdivided into distinctive stratigraphic units (see Figure 10.1).
The Basal Series is composed of norites and bronzitites that are discontinuous and appear chilled near contacts with the intruded metasediments. The Ultramafic Series is subdivided into two main subunits, an olivine-bearing peridotite or hartzburgite zone and an overlying bronzitite zone. The upper part of the Ultramafic Series is a 1,200-foot to 1,300-foot-thick bronzitite unit, with a well-defined contact with the plagioclase-bearing Norite I zone that forms the base of the overlying Banded Series that can be mapped over much of the Stillwater Complex.
The Banded Series is comprised of plagioclase-rich cumulate rocks. SMC subdivides the more than 14,000-foot-thick Banded Series into six megacycle units (identified by the Roman numbers I through VI). The megacycle units are further subdivided into zones according to their major lithology. The J-M Reef occurs near the base of the Banded Series and is associated with the first thin troctolite-anorthosite zone (TAZ I) occurring above the contact with the underlying bronzitite at the top of the Ultramafic Series; it occurs above the Norite I and Gabbro I zones defined by SMC.
Although there are alternative hypotheses for the formation of the Stillwater Complex and the J-M Reef, all hypotheses agree on the general regularity of the layering sequences and the persistent presence of the J-M Reef in the immediate vicinity of the reappearance of olivine cumulates above the basal norite megasequence of the Banded Series of the Stillwater Complex.
The J-M Reef specifically refers to the stratiform deposition of platinum-group elements and sulfide minerals in a distinctive stratigraphic zone within the Stillwater Complex. The J-M Reef formed as a more or less flat-lying, tabular layer as a part of the crystallization of the Stillwater Complex, and its laterally persistent character reflects this origin.4 It occurs within the Banded Series of the Stillwater Complex in the unit known as Troctolite-Anorthosite Zone I (TAZ I). The reef package, which hosts the J-M Reef, is predominately an olivine-rich cumulate. The footwall is gabbro, and the hanging wall is a plagioclase-rich cumulate. The J-M Reef generally strikes west-northwest throughout its 26 miles of well- mineralized strike length. At the Stillwater Mine, the J-M Reef dips north at angles varying between overturned and vertical in the eastern part of the mine (east of about the 4000E mine coordinate), about 62° in the central portion of the mine (from about 4000E to about 9000W), and around 45° to 50° in the Upper West area of the mine. At the East Boulder Mine, the dip averages about 52°. During core logging, which usually commences on the footwall side of the J-M Reef, the reappearance of olivine cumulate or sulfides above a thick sequence of gabbro usually marks the lower boundary of the reef package.
Project 11-030 | 16 | BEHRE DOLBEAR |
Technical Report for the Mining Operations at Stillwater Mining Company
March 2011
In some places, the J-M Reef is interrupted by mafic intrusive dikes. The J-M Reef and the related stratigraphy are clearly identifiable on either side of the dikes; however, the dikes may be sufficiently wide to result in J-M Reef offsets and/or to split the J-M Reef. It should be stressed that these dikes do not have more than a minor impact on mining.
Another feature of the J-M Reef within the Stillwater Mine is the occurrence of thickened areas of mineralized reef, known as "ballrooms." Ballrooms contain significant ore-grade tons and ounces within the J-M Reef. SMC has conducted studies of the ballrooms in an effort to more fully understand their spacing and size. To date these studies have not resulted in discernable trends, and the specific size and distribution of ballrooms cannot be predicted. The cause of ballroom formation is unknown.
Ballrooms have not yet been encountered in the East Boulder Mine, although there are zones of greater reef thickness that are not accompanied by corresponding increases in grade. Ore grade mineralization, delineated at the East Boulder Mine to date, is more consistently distributed than at the Stillwater Mine. As the Stillwater Mine has extended west into the Dow Sector, the character of the mineralization appears to change. Among the characteristics marking this change in mineralization character is a change in the in-situ platinum :palladium (Pt:Pd) ratio to 1:3.9, compared with an in-situ Pt:Pd ratio of 1:3.5 for the entire Stillwater Mine.
Because drilling, even at 50-foot spacing, does not specifically delineate ballrooms (ore grade drill intercepts that are wider than 20 plus feet horizontal, reef thickness may indicate their presence), the distribution of ballrooms outside the developed area of the Stillwater Mine is uncertain. The existence of such wider intercepts from the surface drilling and in some of the initial underground drilling has previously been interpreted as supporting the distribution of ballrooms throughout the Stillwater Complex.
The Stillwater Complex is similar in many ways to the much larger Bushveld Complex of South Africa, which contains the world's largest PGM resource.5 The Merensky Reef in the Bushveld Complex is the closest analog to the J-M Reef. However, there are some important differences between the J-M Reef and the Merensky Reef. The UG2 Reef, in the Bushveld Complex, is also a major PGM producer, but it is in a chromite-rich horizon and has other characteristics, including greater PGM variability, that does not make it a good analog for the J-M Reef.
During the Laramide Orogeny in the Late Cretaceous and early Tertiary geologic periods, the presently exposed portion of the Stillwater Complex was faulted away from the rest of the original, relatively flat- lying, lopolithic igneous body and into its current position. Thrust faulting related to this orogenic event forms the lower boundary of the currently exploitable portion of the Stillwater Complex. Figure 9.1 shows a cross section through the Stillwater Mine showing the effects of the thrust faulting and the placement of the currently exploitable and steeply dipping portion of the J-M Reef.
5 The other major source of the world's PGM production, the Norilsk intrusive in western Siberia, geologically differs from the J-M and Merensky Reefs in both mode of occurrence and origin.
Project 11-030 | 17 | BEHRE DOLBEAR |
Technical Report for the Mining Operations at Stillwater Mining Company
March 2011
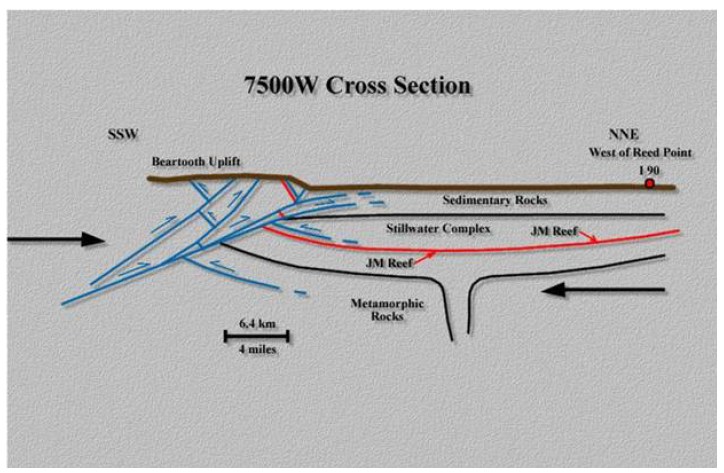
Figure 9.1. Cross section through the Stillwater Mine showing the effects of the thrust faulting
The lower structural boundary of the exposed Stillwater Complex is a sled-runner thrust fault6 separating the upthrust portion of the Stillwater Complex lying within the Beartooth Mountains frontal blocks from deeper and more shallowly dipping portions of the undeformed Stillwater Complex forming part of the Precambrian basement underlying the Crazy Mountains Basin to the northeast. One regional thrust fault system associated with uplift of the Beartooth structural block during the Laramide Orogeny in Latest Cretaceous to Paleocene time does cut the J-M Reef and forms the regional lower limit of mining on the J-M Reef.
One splay of the Beartooth thrust system was intersected in 1998 by a drill hole located in the Stillwater River Canyon at the Stillwater Mine. Another deep drill hole located further to the west also tested the depth to the bounding thrust fault. These projected fault positions currently define the lower limits of estimated probable reserves in areas near the deep drilling.
6 A sled-runner thrust fault is another name for decollement-type thrust fault that has come into recent usage. The name comes from the similarity of the fault's shape to the runners of a sled.
Project 11-030 | 18 | BEHRE DOLBEAR |
Technical Report for the Mining Operations at Stillwater Mining Company
March 2011
9.2.1 Cross Faults
Several major more or less northerly striking cross faults with 200-foot to 1,500-foot offsets cut the J-M Reef and are known from surface and underground mapping and drilling. All of the major fault systems encountered during production mining at the Stillwater Mine since 1986 have been handled routinely, and none have presented major interruptions to continued mining of the J-M Reef. Other than offset, these faults have minimal effect on mineral remobilization and, in effect, cause limited, local adverse mining conditions.
9.2.2 Intrusions
The potential for post-Stillwater Complex intrusions cutting off the J-M Reef at depth has been assessed. First and foremost, it is unlikely that later intrusions could cut off significant portions of the J-M Reef because the magma chemistry required to consume or assimilate significant quantities of existing Stillwater Complex rocks would have to be more refractory (i.e., having a higher melting temperature) than rocks of the complex itself. Magmas with a higher melting temperature than the ultramafic to mafic Stillwater Complex are relatively rare, and there are no indications that such magmas are present in the region around the Stillwater Complex. Regional gravity and magnetic anomalies give no indication of buried, large-scale younger intrusions.
Numerous diabase and more felsic dikes cut and offset the J-M Reef in both the Stillwater and East Boulder Mines, the West Fork and Frog Pond adits, and throughout the Stillwater Complex on surface. These dikes make use of pre-existing faults and fractures that provide pathways and allow dilational offset of Stillwater Complex rock layers and mineralized zones. Many of these dikes are known from surface mapping, and most are intersected in underground drilling and drifting and are routinely handled as part of the mining process. These dikes dilate the J-M Reef but do not destroy mineralization. They do have limited (within 30 feet) contact alteration zones that cause adverse ground-support conditions within and adjacent to the dike contacts in some areas of the mines. However, these conditions do not present significant obstacles to mining and have been and are routinely addressed as mining proceeds.
Project 11-030 | 19 | BEHRE DOLBEAR |
Technical Report for the Mining Operations at Stillwater Mining Company
March 2011
The Stillwater Complex is a layered ultramafic to mafic igneous complex formed by the gradual cooling of an enormous subterranean intrusion. In such intrusions, the gradual cooling leads to the formation of layers of crystals with similar geochemical properties. Some of these layers are essentially mono- mineralic (anorthosites composed of high-calcium plagioclase), while others have additional minerals such as troctolites, which contain both high-calcium plagioclase and olivine. The layering is very distinct and resembles the layering of sedimentary rocks even though the rocks of the complex are igneous. These layers form over extremely large areas. The fact of this layering is critically important to understanding the deposition of the palladium- and platinum-bearing minerals in the J-M Reef. Figure 10.1 illustrates both the original, essentially horizontal layering of the Stillwater Complex.
Figure 10.1. The original layering in the Stillwater Complex
Another aspect of the layers within layered igneous complexes is that the crystals in the layers are large, often 1 to 2 centimeters on a side. While platinum- and palladium-bearing minerals and associated copper and nickel sulfides that comprise the mineralization in the J-M Reef are not as large, they nevertheless frequently form in large clots, a fact that complicates the sampling processes discussed elsewhere in this report.
Project 11-030 | 20 | BEHRE DOLBEAR |
Technical Report for the Mining Operations at Stillwater Mining Company
March 2011
The J-M Reef is recognized by the presence of chalcopyrite, pyrrhotite, pentlandite, and, rarely, pyrite within the reef package. Other base-metal sulfides have been identified, but their presence is subordinate. The platinum group minerals can rarely be recognized with a hand lens. SMC (2001) reported that platinum occurs primarily (67%) as sulfide, 25% as the metal alloy, isoferroplatinum, and 8% as the telluride, moncheite. Palladium occurs primarily (80%) as a solid-solution in pentlandite, 15% as sulfides, and 5% in the telluride, moncheite. The platinum:palladium ratio averages 1:3.5 in-situ at the Stillwater Mine, except for the Dow (Upper West) area of the mine, where the platinum:palladium ratio increases to 1:3.9 in-situ, and averages 1:3.6 to 3.7 in-situ at the East Boulder Mine. The currently delineated proven reserves at the East Boulder Mine have a lower PGM grade and higher copper plus nickel content than the Stillwater Mine. At the west end of the Stillwater Mine in the Dow sector, an area of higher copper plus nickel content has been identified that is similar to the East Boulder Mine mineralization.
11.1 LARGE-SCALE REGULARITY OF THE J-M REEF
When the J-M Reef is considered as a whole reef package, or in large, geologically bounded segments, mineralization is predictably and relatively evenly distributed throughout the unit. Although precise relationships vary in fine detail, the method of drilling delineation from the footwall laterals used by SMC provides sufficiently precise locations to guide mining. On the scale (tens to hundreds of feet) important in mine planning, the J-M Reef can be consistently located and delineated to allow mine planning. This regularity of mineralization is unlike that of most precious- and base-metal deposits and emphasizes the fact that the J-M Reef should be compared with mineral deposits formed in sedimentary environments rather than with precious metal veins. Specifically, the J-M Reef probably was formed as a chemical precipitate during crystallization of a magma in a chamber that is tens of miles in diameter. Therefore, reserve estimation procedures for the J-M Reef for the probable mineral reserve should be, and are, more similar to those used for non-magmatic or sedimentary iron or coal deposits than those typically used for precious metal deposits.
The J-M Reef is an integral rock-forming component of the Stillwater Complex. In this respect, it has geological analogy to mineral deposits, such as coal, sedimentary iron formation, bedded salt, and potash deposits and certain syngenetic copper deposits; all characterized by uniformity and predictability over large areas and generally delineated in exploration and mine development by widely spaced drilling.
In this respect, the J-M Reef is quite unlike most gold, silver, copper, lead, and zinc deposits, where the metal is introduced, often many aeons after the rock is completely solidified and has been tectonized. Such metal deposits are generally restricted in occurrence to structural openings and replacements along such features, which are generally much more random in occurrence, and consequently require more closely spaced drilling for reliable overall reasonable definition.
Platinum-palladium mineralization is predictably and statistically overall relatively evenly distributed through the J-M Reef throughout the complex unless the Reef is removed by later faulting, shearing, or dyke and sill intrusion. This overall general distribution is consistent with a complex-wide event.
Project 11-030 | 21 | BEHRE DOLBEAR |
Technical Report for the Mining Operations at Stillwater Mining Company
March 2011
Succinctly, the author observed and opines that widely spaced drilling can accurately predict the character of platinum-palladium mineralization within large areas of the J-M Reef. As applied to probable reserve estimation within the J-M Reef, geologically homogeneous bodies (Turner and Weiss, 1963) are areas that exceed 1,000 feet of strike length up to several thousand feet and up to 1,000 or more feet vertically. Prior to the end of 2004, when conversion to the use of Vulcan™ mine planning software was fully implemented, SMC consistently analyzed the J-M Reef using the vertical plane rather than the plane of the dipping J-M Reef. The vertical and dipping planes can be converted using trigonometry. The results obtained from the use of vertical planes have been consistently substantiated at SMC's Stillwater and East Boulder Mines in probable reserve estimation. Since SMC commenced using Vulcan™ mine planning software, the J-M Reef is modeled on actual drill intercepts of the Reef, and the use of vertical or dipping planes is no longer an issue.
Project 11-030 | 22 | BEHRE DOLBEAR |
Technical Report for the Mining Operations at Stillwater Mining Company
March 2011
Between 1969 and 1995, SMC and predecessor firms drilled 944 holes from the surface and from the Frog Pond and West Fork adits over 28 miles along the strike of the J-M Reef, establishing the currently known strike length of the well-delineated J-M Reef at 26 miles. The results from these drill holes were used to define the estimated mineralization in the sectors, which are bounded by geologic characteristics that are often major fault offsets. Table 12.1 lists the sectors arranged from west to east along the J-M Reef and the number of drill holes in each.
TABLE 12.1
SURFACE AND ADIT EXPLORATION DRILL HOLES
Sector
(Listed from West to East, Number of Holes
2000 Sector Boundaries)
Tecate 13
Boulder West 28
Boulder East 52
Frog Pond West 104
Frog Pond Adit (in Frog Pond West) 94
Frog Pond East 59
Brass Monkey West 46
Brass Monkey East 83
West Fork West 41
West Fork East 99
West Fork Adit (in West Fork East) 95
Dow 38
Stillwater West 88
Stillwater East 74
Blitz 30
Total Drill Holes 944
The data from the drilling in the Tecate Sector, which is west of the Boulder River on the far west end of exploratory drilling, resulted in the decision not to estimate mineralization in this Sector.
In addition, exploratory drilling was conducted at the Stillwater Mine to determine the location of the thrust fault that effectively cuts the mineralization off at depth. Below this fault, the J-M Reef is displaced a significant distance to the south. The projection of this fault places a lower boundary on estimated mineralization, particularly on the eastern side of the Stillwater Mine, and its location is included in the longitudinal sections of the mine.
Ongoing exploration, at both the Stillwater and East Boulder Mines, consists of driving the primary development footwall laterals and then drilling advance probe holes from these laterals to ensure that the J-M Reef is being appropriately followed. From these footwall laterals, the drill fans used to delineate the Proven Reserves are drilled at 50-foot intervals. These are drill holes are discussed in greater detail in Section 13.0 of this report.
Project 11-030 | 23 | BEHRE DOLBEAR |
Technical Report for the Mining Operations at Stillwater Mining Company
March 2011
The primary sources of geological data at the Stillwater and East Boulder Mines are mine development, surface diamond drill holes, and underground diamond drill holes. Exploration holes drilled from the surface provided the original data that established the deposit characteristics (Section 12.0). These holes have been as widely spaced as 1,000 feet. Statistical studies have determined that a reasonable estimate of grades can be obtained from the widely spaced exploration drilling for the purpose of defining probable reserves. Surface drilling is no longer routinely performed.
Two types of underground core drilling are routinely conducted at the Stillwater and East Boulder Mines. The first type consists of probe holes drilled ahead of advancing footwall laterals with the twin objectives of maintaining the footwall laterals within the desired distance of the J-M Reef and testing for rock quality, ground water, and any other characteristics that might affect mining. The second type of drilling consists of fans normally drilled at 50-foot intervals along the footwall laterals to delineate the mineralization in the J-M Reef. Each fan consists of 5 or 6 holes drilled at angles designed to intersect the J-M Reef at 50-foot vertical intervals. Figure 13.1 shows drill fans drilled from the 4100E Level and the 3800E Level into the J-M Reef and adjacent geologic units.
Figure 13.1. Drill fans used to delineate the J-M Reef
Project 11-030 | 24 | BEHRE DOLBEAR |
Technical Report for the Mining Operations at Stillwater Mining Company
March 2011
Probable ore reserves at both mines are estimated from surface and underground drill intersections of the J-M Reef. Projections of drilling information are extended up to 1,000 feet vertically and laterally from sampling points in the J-M Reef (mostly drill intersections) except where a major geologic boundary, such as the underlying thrust faults below the Stillwater Mine, limit the projection distance. The projection distances used are justified by the general, large-scale uniformity of mineralization within the J-M Reef and geostatistical work justifies an extension of projection up to 1,600 feet from known data.
Typically, 3 to 5 drill rigs are active at any one time. In 2010, the diamond drilling program at Stillwater Mine generated some 288,000 feet of diamond drill core. As of December 31, 2010, the diamond drill hole database for the Stillwater Mine contained 31,768 drill holes for a total of 6.74 million feet and 167,647 sampled intervals.
In 2010, the diamond drilling program at the East Boulder Mine generated about 81,474 feet of diamond drill core. At the end of 2010, the definition diamond drill hole database contained 4,969 drill holes with a total of 1.32 million feet and 33,238 assay intervals.
Drill hole collars are surveyed after drilling, but the down hole deviation is generally not surveyed because the length of these holes is short enough that deviation is not a major concern. Each drill hole is visually checked in Vulcan™ against surveyed 3-D models of the footwall lateral drifts to ensure that the collar coordinates, azimuth, and dip of each are correct. Assay data are imported into the database from electronic files prepared at SMC's assay lab in Columbus. Lithologic data are imported from electronic files created by the DatCol® program that is used by the development geologists in the core room.
Project 11-030 | 25 | BEHRE DOLBEAR |
Technical Report for the Mining Operations at Stillwater Mining Company
March 2011
14.0 SAMPLING METHOD AND APPROACH
Drill core (BQ size, 1.433 inches in diameter) is brought from the rigs to core logging rooms at the surface of both the Stillwater and East Boulder Mines. These logging rooms each have storage racks and several well-lit logging stations. Only mineralized zones and adjacent hanging and footwall zones are sampled, and the logging geologist selects zones visually.7
The drill core is logged by a trained geologist, who recognizes the mineralized zones. The geologist identifies the J-M Reef intercepts as well as intervals directly above and below the Reef and pulls the intercepts from the cores to sample for platinum (Pt) and palladium (Pd). Mineralized sections of the core are sampled in 0.5- to 3.0-foot segments and usually include a foot below and above the mineralized section. The core segments are sent whole to the lab for analysis. All other core is discarded due to the volume of the core obtained each year.8 Core from select holes is split and saved for reference at the East Boulder Mine but not at the Stillwater Mine (see Section 14.1).
At the Stillwater Mine, the log data are entered into a computerized database using bar code sheets containing codes for all the common parameters (distance from and to, rock type, mineralization, alteration, geotechnical data, etc.). An Ore QMS (master) database was created to store and manage the diamond drill core information. Diamond drill hole header information, along with lithologic, geotechnical, structural, assay, and mineralization data, are imported into the master database from electronic files created by the DatCol® program. The diamond drill hole data, stored in Ore QMS, is exported to Vulcan™ on demand after surveyed collars are entered. The Ore QMS system is not yet used at the East Boulder Mine.
At the East Boulder Mine, digital photographs are taken of most of the sampled core and then kept in the files and on separate disks. This practice is not followed at the Stillwater Mine. Core recovery is usually above 90%.
In addition to the commonly used parameters, the geologist has the discretion to enter any other pertinent information. This method of logging avoids transcription errors, and each screen within the logging database is programmed to ensure that all required data are entered. This helps ensure that the logging database is complete and "clean" from the time data are initially entered. The logging data are available on the company's computer network for reserve estimation and mine planning as soon as they are entered.
14.1 COMMENTS ON SMC'S QUALITY ASSURANCE/QUALITY CONTROL (QA/QC) PROCEDURES
In a 2010 report, an independent review report conducted for SMC commented on SMC's QA/QC procedures and discussed what it believed were SMC's departures from industry standard practices.
Twin Samples: The independent report noted that drill core should be split in half so that one-half can be retained for reference while the other half of the core is sent for analysis. Common practice is to select some of the retained half core, split it in half again to a quarter-core sample, and have this quarter-core sample submitted as a duplicate sample to check the validity of the sample collection, preparation, and analytical steps. The independent report noted that SMC does not split its core but submits the entire core for analysis.
7 Blank samples are periodically collected from well into the footwall of selected cores.
8 SMC has determined that is cheaper to re-drill a hole than save core. Re-drilling of holes is very seldom needed.
Project 11-030 | 26 | BEHRE DOLBEAR |
Technical Report for the Mining Operations at Stillwater Mining Company
March 2011
This common practice is inapplicable for the J-M Reef due to the very coarse-grained nature of the rock and contained mineralization in the J-M Reef and similar samples from layered igneous intrusions. Because of the size of crystals in the core and the clotty nature of the platinum-palladium mineralization, analyses of split core do not result in closely identical results. The common practice inherently assumes that mineralization is statistically homogeneous (Turner and Weiss, 1963) within the core; therefore, one should expect a high degree of correlation between samples. Correlation between samples that are statistically homogeneous should have R2 values of 0.90 or better if the sample collection, preparation, and analytical procedures provide accurate results. Figure 14.1 illustrates what Turner and Weiss' Figure 2-1 (1963) mean by statistically homogeneous.
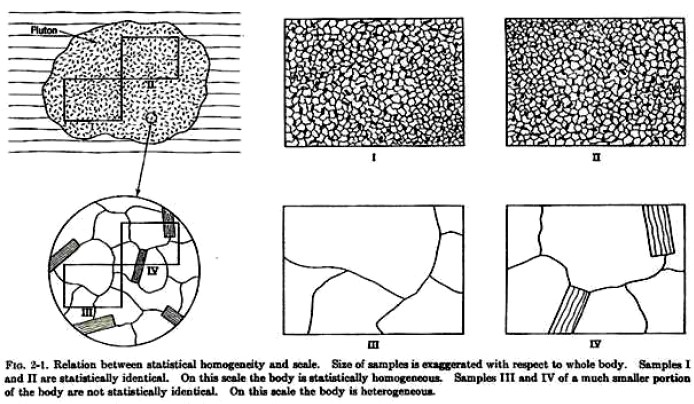
Figure 14.1. Illustration of statistical homogeneity and the effect of the size of mineralization
The character of mineralization in the cumulate crystallization of layered igneous complex, like the Stillwater Complex, is similar to Figure 14.1. For purposes of this discussion, assume that diagrams III and IV are the separate halves (or quarters) of split core. If we were testing for the quantity of the mineral shown by the wavy internal lines, which are present in diagram IV but not diagram III, there obviously is going to be no correlation between analyses of the two samples.
The author examined another platinum-palladium-bearing igneous intrusive complex with similar very coarse-grained, clotty mineralization where the common practice of splitting core and submitting duplicate quarter-core samples was followed. Comparison of the duplicate analysis showed very poor correlation between the analyses, as would be expected. The R2 correlation for the duplicate samples from this property was 0.53 for platinum plus palladium and 0.0027 for gold, and this, therefore, is not an appropriate practice for SMC to follow.
Project 11-030 | 27 | BEHRE DOLBEAR |
Technical Report for the Mining Operations at Stillwater Mining Company
March 2011
Duplicate Samples: The independent report commented that common industry practice is to take duplicate samples after the first crushing and splitting step in the preparation process. The author believes that this practice is inapplicable for very coarse-grained, statistically inhomogeneous samples for the same reason that duplicates of the split core do not correlate and this, therefore, is not an appropriate practice for SMC to follow.
SMC resubmits sample pulps for re-assay to verify the accuracy of the analytical procedure. At the Stillwater Mine, 497 pulp duplicates have been submitted over the years, and the R2 correlation coefficient between the original and the duplicate assay is 0.95. For the East Boulder Mine, 738 pulp duplicate samples have been submitted, and the R2 correlation coefficient between the original and the duplicate assay is 0.94. The high R2 correlation coefficient values indicate excellent agreement between the original and duplicate samples. When discrepancies occur, which occasionally happens, the reason for the discrepancy is investigated.
Waste Samples: The independent report noted that SMC's practice for submitting waste core blanks consisted of collecting either footwall or hanging wall core intervals taken away from the J-M Reef. The independent report noted that some of these blank samples contained detectable values of platinum plus palladium, which in the independent report's opinion, hindered the usefulness of these samples to unambiguously identify contamination in the sample collection, preparation, and analysis procedures. The author agrees that many of these "blank" samples do contain detectable values of platinum plus palladium. This results from the fact that low platinum plus palladium values do occur some distance into the hanging and footwalls. Only a small percentage of the samples report platinum plus palladium values exceeding 0.1 ounces per ton, 4.7% for the East Boulder Mine and 3.8% for the Stillwater Mine. In most cases, these samples were taken too close to the J-M Reef. While this is not viewed as a significant issue, SMC re-revised its blank core sampling protocol in order to submit blank samples from further into the footwall that do not contain detectable platinum plus palladium.
The independent report's final comment on SMC's QA/QC program was that the mine geology departments do not submit standard samples to verify the accuracy of the analysis. However, SMC's analytical lab in Columbus, Montana regularly assays its standards. Therefore, there is really no need for the mine geology departments to submit standard samples or to submit samples to outside labs. One problem with sending samples to outside labs is that there are not many labs that can accurately analyze for platinum group elements. In fact, SMC material is the base source for most of the PGM standard reference materials used in North America.
Project 11-030 | 28 | BEHRE DOLBEAR |
Technical Report for the Mining Operations at Stillwater Mining Company
March 2011
15.0 SAMPLE PREPARATION, ANALYSES, AND SECURITY
SMC's assay laboratory, located at the metallurgical complex in Columbus, Montana, receives four different sample streams, which, because each stream has differing PGM concentrations, are prepared in separate lab flow streams to avoid cross-sample contamination. The four samples streams are:
1) | Geologic samples, primarily the core samples collected by the geologists logging the core and other samples collected from stope faces |
2) | Mill samples collected during the concentration processes |
3) | Metallurgical complex process samples |
4) | Recycled catalytic converters |
The geologic samples and mill samples are transported from the mines to the SMC lab in the cargo areas of the buses transporting employees from the mines to Columbus, Montana. Due to the number of samples involved and the producing character of the mines, sample tampering is not an issue. After drying, the samples are given lab numbers, and the sample and lab numbers are entered into the computer. The geologic samples are crushed in jaw crushers in two stages, the second of which is the first blending step in addition to size reduction.
Routine analyses are done by X-ray methods, which are verified for accuracy by fire assays. Sample runs routinely contain standard and duplicate samples as part of the laboratory's internal QA/QC program.
Because no one sample out of the thousands submitted each year by the geology departments at both mines is particularly significant in the overall estimation of mineral reserves or for planning the locations of specific stopes, sample security does not present the problem that can be present in an exploration setting. The author believes that no significant security problem exists for SMC's sampling procedures.
Project 11-030 | 29 | BEHRE DOLBEAR |
Technical Report for the Mining Operations at Stillwater Mining Company
March 2011
16.1 DRILLING
Each drill hole location has been visually checked in VulcanTM against surveyed 3-D models of the footwall lateral drifts to ensure that the collar coordinates, azimuth, and dip of each are correct.
16.2 SAMPLING AND ANALYSIS
The QA/QC sampling provides documented assurance that the drill core assays are reliable values. This program covers more steps in the sample collection and analysis than the QA/QC program conducted by SMC's Columbus, Montana laboratory and is independent from the laboratory's QA/QC program, which includes round-robin sample analysis with other labs.
The QA/QC program employed by the geology departments at the Stillwater and East Boulder Mines consists of two parts. The first consists of the regular collection and submission of waste core samples, and the second consists of the regular resubmission of the pulp samples, as discussed in Section 14.1.
Project 11-030 | 30 | BEHRE DOLBEAR |
Technical Report for the Mining Operations at Stillwater Mining Company
March 2011
There is no relevant adjacent property information. SMC controls the J-M Reef along its known strike length, and the J-M Reef is the only PGM-bearing layer that can be economically exploited, given current and expected economic conditions.
Project 11-030 | 31 | BEHRE DOLBEAR |
Technical Report for the Mining Operations at Stillwater Mining Company
March 2011
18.0 MINERAL PROCESSING AND METALLURGICAL TESTING 18.1 STILLWATER CONCENTRATOR
18.1.1 Stillwater Primary Crushing
Since 1986, SMC's Stillwater Mill operation has been producing a nickel-copper concentrate containing PGMs. Several expansions have increased the capacity from an initial 500 tons per concentrator operating day in 1987 to a present available capacity of 2,750 tons per day or more. The ore types being fed to the concentrator consist of Off-shaft material, with a lower hardness (Bond Work Index 18), and Upper West material, with a higher hardness (Bond Work Index 21). Both the Off-shaft and Upper West areas contain 10% to 20% talc. Reef waste and slag/brick from the smelter are included in the total concentrator feed.
An underground jaw crusher reduces the Off-shaft concentrator feed to minus 4 inches, and the crushed ore is hoisted to the surface and conveyed to a 3,000-ton ore silo. Ore from the silo is conveyed by an apron feeder to the concentrator feed bin.
A surface jaw crusher reduces Upper West concentrator feed to minus 6 inches; a cone crusher further reduces it to minus inches; and a conveyor transfers it to the concentrator feed bin.
18.1.2 Stillwater Grinding Circuit
The current grinding circuit consists of an 800-horse power (HP), fixed-speed, semi-autogenous grinding (SAG) mill and a 2,500-HP ball mill in closed circuit with a cluster of 15-inch cyclones. The SAG screen oversize (minus 3/s-inch) reports to a cone crusher that reduces it to minus 3/s-inch and discharges it to the ball mill discharge sump. A tertiary grinding 1,250-HP Verti-mill is installed in closed circuit with a cluster of 15-inch cyclones to grind rougher flotation tails prior to middling and scavenger flotation. Two small regrind mills are installed in the flotation circuit to grind middling concentrate and cleaner concentrate in open circuits with one 10-inch cyclone; the mill discharges are now floated directly rather than recycled back to the cleaner circuit. The philosophy at this concentrator has been to float liberated minerals as soon as possible and minimize recycling streams, which also contain talc that interferes with the flotation response and subsequent recovery.
18.1.3 Stillwater Flotation Circuit
The mill processes up to 2,750 tons per day of feed and averages about 92% PGM recovery. Plant recoveries have been steadily improving since 2002, primarily as a result of adopting innovative circuit modifications on a continuous basis and an advanced degree of automation.
The circuit operates in a multiple grind/float mode that minimizes over grinding of soft minerals prior to flotation. One of these soft minerals is pentlandite, a nickel sulfide containing the majority of the palladium, and the other is talc, a gangue mineral. The objective of the multiple grind/float circuit is to float the pentlandite mineral grains containing the palladium as quickly as possible after they have been liberated and before they are over ground or become coated with fine slime particles.
Increased slimes in the circuit interfere with flotation in at least two ways. First, the sulfides that become coated with slimes require longer flotation times and usually require increased reagent dosages to enable the flotation, because the slimes adsorb the flotation reagents. Second, the talc in the ore is naturally floatable and slimes readily, thus requiring the addition of suppressants to the flotation circuit to keep it from floating along with the sulfides. The talc suppressant reagent, currently being used in the Stillwater concentrator, is carboxymethyl cellulose (CMC).
Project 11-030 | 32 | BEHRE DOLBEAR |
Technical Report for the Mining Operations at Stillwater Mining Company
March 2011
A flash flotation cell installed to process cyclone underflow from the SAG-ball mill circuit recovers readily floatable sulfides, reducing the possibility of over grinding liberated material. The flash flotation cell recovers up to 50% of the total recovered PGMs, which directly report to a cleaner circuit and then to the product stock tank following thickening.
SAG and ball mill discharge is fed to the 15-inch cyclones. The process cyclone overflow product, at P80 145 microns, reports to the rougher conditioner for subsequent flotation. Rougher and middling concentrate undergo cleaning and join the final concentrate stream. Scavenger concentrate and middling cleaner tails undergo regrinding in closed circuit with cleaner and column cell flotation, prior to discharge into the final concentrate stream. Two new regrind mills have been ordered to decrease the particle size in the regrind circuit to improve recovery. These mills are expected to be operational by the 4th quarter of 2011.
18.1.4 Stillwater Tailings
The flotation tailings from the scavenger circuit are pumped to the paste plant and sand fill plant, where up to 50% is used in the mine backfill process. The remaining mill tails and sand plant cyclone overflow report to a tailings depository. The majority of the approximately 0.047 ounces of PGM per ton content in the tails is palladium contained in fine pentlandite grains, together with some unfloated tellurides and native alloy PGMs. The addition of soda ash to the circuit has softened the process water, reducing calcium scale and improving recoveries during grinding and flotation, with a reduction in recycle streams containing talc. Concentration ratios have increased along with the concentrate grade, although recoveries are a bit lower from treating lower-grade feed.
Table 18.1 presents a summary of statistics for the Stillwater Concentrator for 2010.
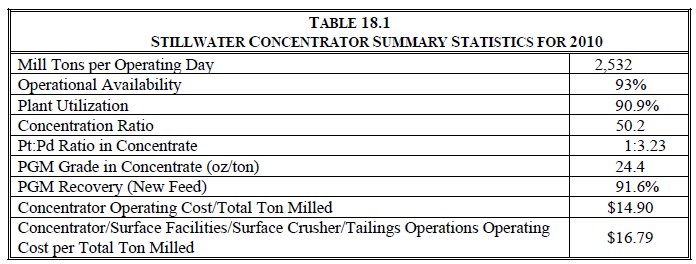
TABLE 18.1
STILLWATER CONCENTRATOR SUMMARY STATISTICS FOR 2010
Mill Tons per Operating Day 2,532
Operational Availability 93%
Plant Utilization 90.9%
Concentration Ratio 50.2
Pt:Pd Ratio in Concentrate 1:3.23
PGM Grade in Concentrate (oz/ton) 24.4
PGM Recovery (New Feed) 91.6%
Concentrator Operating Cost/Total Ton Milled $14.90
Concentrator/Surface Facilities/Surface Crusher/Tailings Operations Operating Cost per Total Ton Milled $16.79
Figure 18.1 is a diagrammatic flow chart for the Stillwater concentrator.
Project 11-030 | 33 | BEHRE DOLBEAR |
Technical Report for the Mining Operations at Stillwater Mining Company
March 2011
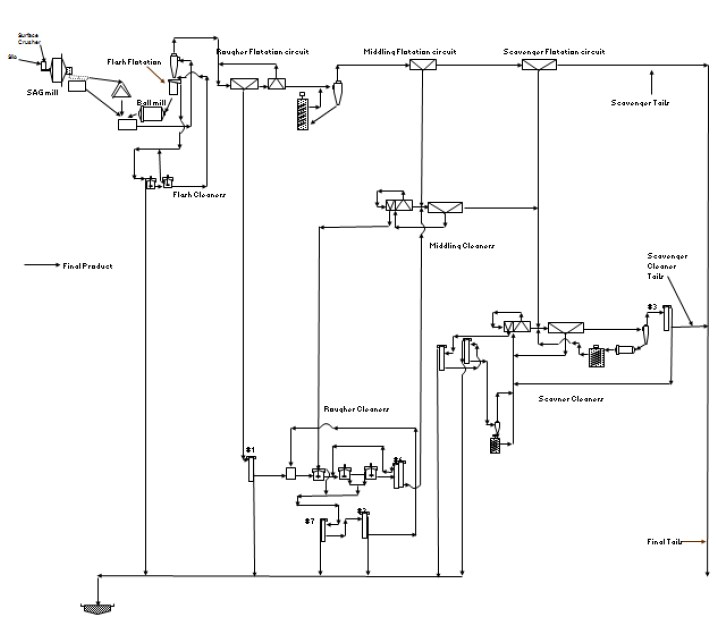
Figure 18.1. A simplified circuit diagram of the Stillwater concentrator
18.2 EAST BOULDER CONCENTRATOR
The East Boulder concentrator began operations in mid-June 2001. The concentrator was constructed to allow expansion to 4,000 tons per day from the originally planned 2,000 tons per day operation. The mill is capable of processing in excess of 2,000 tons per day of feed, but concentrator throughput has been significantly limited by mining rates. The concentrator operated on a 24 hours per day, 7 days per week schedule, but it shuts down 3 days per week, depending upon ore supply and maintenance requirements. In 2010, it averaged 1,932 tons per day throughput calculated on a 208 operating day basis. PGM recoveries in 2010 to mid-year were similar to previous year recoveries, averaging 89.5%.
The ore feed to the concentrator is generally uniform in grade, with a lower hardness (Bond Work Index 18), lower talc content (5% to 10%), lower platinum plus palladium grade, and higher base metal content (copper and nickel) than composite feed to the Stillwater concentrator. The processing circuit at East Boulder was modeled directly after the Stillwater concentrator experience, although there are a few differences.
Project 11-030 | 34 | BEHRE DOLBEAR |
Technical Report for the Mining Operations at Stillwater Mining Company
March 2011
A surface jaw crusher reduces ore to minus 6 inches, and the ore is conveyed to a stockpile. An apron feeder recovers ore from the stockpile and conveys it to a SAG mill.
18.2.1 East Boulder Grinding Circuit
The grinding circuit consists of a 2,000-HP SAG variable speed mill and a 2,000-HP ball mill in closed circuit with a cluster of 15-inch cyclones. The SAG trommel oversize is recycled back to the SAG mill, and undersize is fed either directly to the flotation circuit or to the ball mills for further grinding. Downstream, a tertiary grinding 125-HP Verti-mill is installed in closed circuit with a cluster of 10-inch cyclones to regrind rougher cleaner tails, middling cleaner tails, and scavenger concentrate.
A test of copper sulfate additions to the East Boulder concentrator resulted in an increase in PGM recovery. Copper sulfate is a traditional activator for sulfide minerals that are slow to float and acts by coating mineral surfaces with a layer of copper ions, which readily attach to collectors, thereby promoting flotation. The addition of copper sulfate was initiated on a regular basis during 2006. The Stillwater concentrator has a copper sulfate system installed but has discontinued its use as it was no longer effective relative to its cost. The recycle water at Stillwater has a greater content of dissolved elements compared to East Boulder, as it has been in production for a much longer time; so the surface chemistry issues are somewhat different.
18.2.2 East Boulder Flotation Circuit
A flash flotation cell installed to process cyclone underflow ahead of the ball mill recovers readily floatable sulfides, reducing the possibility of over grinding liberated material. The flash flotation cell recovers up to 50% of the total recovered PGMs, which report directly to a cleaner circuit and then to concentrate containers following thickening and pressure filtration.
Tails from the flash flotation circuit report to the ball mill and then to a Knelson gravity concentrator that recovers 2.9% of total platinum and 2.3% of the total recovered gold. The gravity concentrate is shipped separately from the flotation concentrates to the smelter for refining. In-house flotation tests on the gravity concentrate revealed less than optimum platinum and gold recoveries, justifying the inclusion of the Knelson concentrator as a means to improving overall precious metal recoveries. The presence of a ferro-platinum mineral has been confirmed.
SAG and ball mill discharge is fed to the 15-inch cyclones. The process cyclone overflow product, at P80 of 97 to 100 microns, reports to the rougher conditioner for subsequent flotation. Rougher and middling concentrate undergoes cleaning and joins the final concentrate stream. Scavenger concentrate joins the rougher and middling cleaner circuit tails and undergoes regrinding in closed circuit with cleaner and column cell flotation prior to discharge into the final concentrate stream.
As in the Stillwater concentrator, the use of carboxymethyl cellulose to suppress talc is effective.
18.2.3 East Boulder Tailings
The flotation tailings from the scavenger circuit, which contained about 0.041 opt combined PGMs in 2010, are pumped to an underground sand plant, where 50% is used in the mine as backfill. The remaining concentrator tails and sand plant cyclone overflow report to a tailings pond.
Project 11-030 | 35 | BEHRE DOLBEAR |
Technical Report for the Mining Operations at Stillwater Mining Company
March 2011
A new tailings impoundment, Phase II, was constructed and lined during the summer of 2006 as the old impoundment was nearing its maximum storage capacity.
Table 18.2 presents the summary operating statistics for the East Boulder Mill in 2010.
TABLE 18.2
EAST BOULDER CONCENTRATOR STATISTICS FOR 2010
Mill Tons per Operating Day 2,003
Operational Availability 99.85%
Plant Utilization 54.8%
Concentration Ratio 41.1
Pt:Pd Ratio in Concentrate 1:3.3
PGM Grade in Concentrate (oz/ton) 16.0
Overall PGM Recovery 89.22%
Concentrator Operating Cost per Total Ton Milled $12.64
Concentrator/Surface Facilities/Sand Plant/Tails Operating Cost per Total Ton Milled $16.44
Figure 18.2 is a schematic diagram of the East Boulder Concentrator flotation circuit configuration.
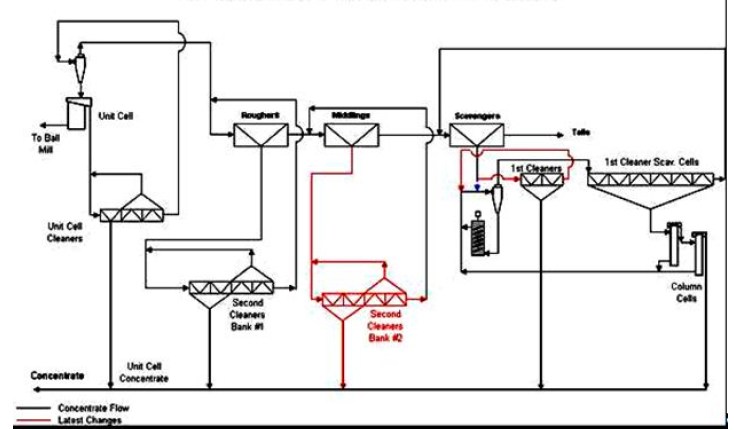
East Boulder Simplified Float Circuit Configuration (as of January 2005)
Figure 18.2. East Boulder concentrator's simplified flow sheet 2010
Project 11-030 | 36 | BEHRE DOLBEAR |
Technical Report for the Mining Operations at Stillwater Mining Company
March 2011
18.3 COLUMBUS METALLURGICAL OPERATION
SMC's metallurgical complex, consisting of a smelter and BMR, is located in Columbus. SMC's analytical laboratory is also located in the metallurgical complex.
18.3.1 SMC's Smelter
Wet concentrate from both the Stillwater and East Boulder Mills, averaging 10% moisture, is trucked in 10-ton tote bins to the smelter in Columbus, Montana. Following tube sampling for moisture and initial assays, the material is introduced into a fluidized-bed, natural-gas dryer that reduces moisture to less than 1%. It is then conveyed to a feed storage bin and sampled in duplicate.
Recycled automotive catalysts and other PGM-bearing materials, averaging 60 ounces of platinum plus palladium per ton, constitute a separate source of smelter feed. These materials are weighed, crushed, sampled, and stored in bulk bags prior to being fed to the electric furnace (EF).
The combined stock of concentrates and spent catalysts, together with 0.05 to 0.1 ton of limestone per ton of feed, is continuously introduced at 5,000 to 9,500 pounds per hour into a new 150-ton electric arc furnace. The old furnace, capable of handling up to 110 tons per day of feed, is currently being re-bricked for use as a standby furnace or potentially to be used for cleaning the slag from the new furnace. The matte layer, containing 200 to 250 ounces of platinum plus palladium per ton collected in the furnace bottom, is tapped and granulated in high-pressure water. The supernatant slag layer, containing 0.15 to 0.30 ounces of platinum plus palladium per ton, is tapped, air cooled, and shipped to the Stillwater Mill for reprocessing.
Exhaust gases and particulates from the EF enter a bag house. The dust is recycled back to the furnace, and the gases, primarily sulfur dioxide, are scrubbed with caustic solution prior to atmospheric discharge at levels well under the facility's air quality permit. The resulting CaSO4^2H2O (gypsum) precipitate is collected and disposed of as an agricultural soil amendment product.
The granulated matte from the EF is fed with pebbled lime into an oxygen-lanced top-blown rotary converter (TBRC). Slag is recycled to the EF following granulation and drying. The granulated and dried minus 10 mesh TBRC matte is feed for the BMR and averages 350 to 700 ounces of platinum plus palladium per ton, 28% to 30% copper, 40% to 42% nickel, 0.3% to 0.7% cobalt, 20% to 22% sulfur, and <2% iron, together with some gold, silver, rhodium, selenium, and tellurium.
18.3.2 SMC's Base Metal Refinery
The BMR leaches the base metals present in the matte in hydrometallurgical circuits without affecting dissolution of the PGMs. The refinery has a capacity of up to 1,000 pounds per hour of smelter matte.
TBRC matte is ground in a tower mill to 85% passing 74 microns and fed as slurry to an agitated, five- tank, nickel atmospheric leach (NAL) circuit that dissolves iron, nickel, and cobalt in an environment that is acidic, the temperature is just under boiling, and the circuit is at atmospheric pressure. The leach circuit discharge enters a thickener, and the overflow solution is treated for iron removal by oxygen injection and ammonia addition. The iron sludge is recycled to the smelter, and the nickel-rich solution feeds a crystallizer circuit that evaporates the solution and promotes nickel sulfate crystal formation.
Project 11-030 | 37 | BEHRE DOLBEAR |
Technical Report for the Mining Operations at Stillwater Mining Company
March 2011
The thickener underflow solids from the leach circuit enter a horizontal, stainless steel, 3-compartment acid autoclave that leaches copper, selenium, and tellurium at 50-psig oxygen overpressure, a 275°F temperature, and a 3-hour residence time. The autoclave discharge is pumped to a thickener, and the overflow solution reports to a selenium and tellurium removal circuit. Injected sulfurous acid is used to precipitate selenium, tellurium, and some copper. The remaining copper-rich solution is pumped to a multiple-pass electrowinning circuit, where copper is plated onto stainless steel cathodes.
The thickener underflow solids from the copper dissolve autoclave circuit are routed to two vertical polishing leach autoclaves, operated at up to 150-psig oxygen overpressure and up to 270°F temperature, that remove remnants of iron, nickel, and copper from the solids. The autoclave discharge slurry is pumped to a filter press, and the filter cake residue containing up to 50% platinum plus palladium is dried and shipped for further refining to one of two refiners.
● | Johnson Matthey Company in New Jersey |
● | Heraeus Company in California |
In 2010, production from the refinery included 853,00 troy ounces of platinum plus palladium (including 370,000 troy ounces of recycled material), 413 tons of copper, 700 tons of nickel, 5 tons of cobalt, 6,700 troy ounces of silver, 9,300 troy ounces of gold, and 31,500 troy ounces of rhodium.
18.3.3 SMC's Catalyst Recycle Facility
In 2010, the smelter and refinery processed 5,927 tons of recycled catalysts containing 399,000 troy ounces of platinum, palladium, and rhodium. This amount compares with the 2009 totals of 3,600 tons of recycled material containing 251,000 troy ounces of platinum, palladium, and rhodium.
A new sampling and assay facility to handle catalyst lots is currently being commissioned.
Project 11-030 | 38 | BEHRE DOLBEAR |
Technical Report for the Mining Operations at Stillwater Mining Company
March 2011
19.0 MINERAL RESOURCE AND MINERAL RESERVE ESTIMATES
SMC estimates year-end proven reserves using the VulcanTM mining software package for both the Stillwater Mine and East Boulder Mine. A mid-year reserve update is also prepared, although without some of the rigor of the year-end estimates. The reserve estimation procedures and parameters for the Stillwater Mine and the East Boulder Mine have been used for at least five years with only minor modification to the variogram model and the grade estimation procedures. The changes have resulted in only insignificant differences in the global estimations.
During the latter half of 2010, geostatistical studies were performed for both the East Boulder Mine and the Stillwater Mine. The geostatistics were last reviewed in 2005. Approximately 2,000 holes have been drilled since that time, and the Proven and Probable reserve extents have been expanded.
19.1 DRILL SECTION INTERPRETATIONS AND WIREFRAME CONSTRUCTION
The geological resource is created from zones picked by the geologists during examination of the drill cores. In addition to the mineralized zones, the geologists have delineated several major faults and intrusive dikes that intersect and offset or replace the mineralized reef in places.
The drilling database contains special rock codes for dike and fault intercepts, used to construct models for each. Faults were modeled as planes, using both drilling data and geologic mapping where the faults can be identified in the footwall lateral drifts. Dikes were similarly modeled as 3-D solids. Both dikes and faults were projected to be beyond the limit of drilled reef where necessary.
The zones as identified in the drill holes are viewed on each 50-foot section line for the extent of the mine polygon, which is drawn to outline the "zone pick" or mineralized J-M Reef from one drill hole fan and then continued to the next drill hole fan. The polygons are constructed not in true section, but rather so that each node is attached to the drill hole trace, even if it is a few feet off section on either side. The polygons are extended to just beyond the last drill hole at the top and bottom of the section. The polygons are terminated or offset when they intersect a fault or dike that has been modeled, as described above.
The final product of this work is a series of near continuous polygons spaced about 50 feet apart that outline the "zone pick" or mineralized reef throughout the drilled portion of the J-M Reef. In areas where the reef terminated or there was a lack of drilling, an "end plate" was built by making a copy of the last drill supported polygon and moving it 25 feet along strike. This "half the drill spacing rule" was always used except where a modeled fault or dike could be used to truncate the shape and is a standard method of terminating a shape.
19.2 BLOCK MODELING
All blocks in the models for Stillwater Mine and East Boulder Mine are 10 feet by 10 feet in the J-M Reef plane. Since the block model is rotated to conform to the average strike and dip of the J-M Reef, the Y direction is at, or very near, the true thickness of the mineralized zone. The Y-Length of each block is variable to represent the true thickness of the main mineralized zone wireframe shape in that area.
The block model is filled with mineralized and waste blocks. Some blocks outside the mineralized zone are necessary for volume and tonnage calculations of dilution and development waste. In the waste zone outside the "zone pick" wireframe, the blocks are 10 feet by 10 feet in X and Z and are limited to a maximum of 100 feet in Y. The waste blocks still conform to the mineralized shape within 0.5 foot.
Project 11-030 | 39 | BEHRE DOLBEAR |
Technical Report for the Mining Operations at Stillwater Mining Company
March 2011
A tonnage check is used to confirm that the block model correctly represents the wireframe models of mineralized zones. A fixed value of 11.6 cubic feet per ton is used to calculate the tonnage within the modeled wireframes and the blocks in the final model.
At the Stillwater Mine, six individual block models were constructed to cover the extent of drilled resource. Each block model covers the same basic extents as the five "zone pick" wire frame models that were used to create them. There is a small overlap of about 100 feet in each of the adjoining models to allow for those cases where previous or planned mining activities may cross over the block model boundaries.
The individual block models are nearly identical, but each may differ by the location and orientation of the block model frame. The internal construction, number of variables, contents, etc. is identical for each model. The limits of each of the block models were set to totally encompass the mineralized reef model and the associated waste envelope. The orientation of each model was chosen to best conform to the average strike and dip of the mineralized zone within that area. Thus, the blocks in each model align very closely and report the true thickness of the JM Reef.
Figure 19.1 shows the mineralized reef wire frame with the block model limit outline for each of the six block models. Also shown are the 500-foot envelopes that enclose each of the zone pick wire frames.
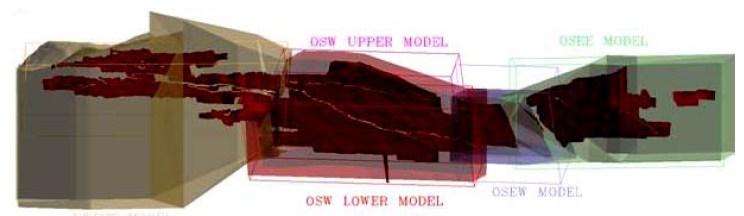
Figure 19.1. Stillwater Mine wire frame model of the mineralized J-M Reef 19.3 GRADE ESTIMATION - EAST BOULDER MINE
Variography: The 2010 reserve block model was calculated using parameters redefined in the geostatistical study performed in 2010. Composited samples, within the mineralized zone, were analyzed using the Vulcan™ geostatistical package. The J-M Reef is divided into the East reserve block and the West reserve block. The blocks were analyzed separately and as a whole. Even though there is a grade variation between the two blocks, the mine was evaluated as a whole because fewer samples were available from the East block. The West block resembles the average grade of the entire mine.
The variogram model nugget was determined to be 10%, which improves the block model as a local estimator. The variograms indicate two structures, a departure from the previous single structure. The search radius for the first structure was decreased from 50 feet to 30 feet, and the intermediate structure radius was determined to be 150 feet.
Project 11-030 | 40 | BEHRE DOLBEAR |
Technical Report for the Mining Operations at Stillwater Mining Company
March 2011
The statistical evaluation also resulted in changing the maximum number of samples used to influence a block during ordinary kriging from 5 to 15. Using a larger number of samples decreases the influence of both very low and very high grade samples on the final block grade.
The recalculated East Boulder 12-31-10 proven reserves using the revised variography and estimation parameters, as compared to the 2009 reserves, show no difference in ore tons or thickness and only 2% difference in ore grade and ounces. Several checks were made to test for bias in the estimates, and no global bias was demonstrated. The changes in estimation parameters do not significantly impact or bias the grade thickness values of the estimated blocks.
It was determined that there was no advantage or bias when estimating platinum and palladium independently; therefore, estimating platinum plus palladium as a combined grade is appropriate.
An isotropic model is clearly defined. Omni-directional and directional correlograms were calculated for platinum plus palladium and for platinum and palladium independently. It was discovered that the population is clearly isotropic, and models were the same for platinum plus palladium, platinum, and palladium.
Grade Capping: Analysis of the composite data set showed that there are a few very high-grade samples in the model area. In order to reduce the effect of this high-grade "tail" in the grade estimation runs, a capping grade was applied in the Vulcan™ kriging routines. After review of the data distributions, the cap was applied at the 99th percentile 1.71 ounces of platinum plus palladium per ton.
Kriging Plan: Composited grade values from drilled regions of the mine were analyzed in detail. New studies performed in 2010 included the review of basic statistics and variography for platinum and palladium grades separately and for the combined grades. In all areas of the mine, the results for the individual assays and the combined values were the same. Thus, the combined platinum plus palladium grades were estimated directly in the model.
19.4 GRADE ESTIMATION - STILLWATER MINE
Grade Capping: Analysis of the composite data sets showed a few very high-grade samples in each of the six block model areas. In order to reduce the effect of this high-grade "tail" in the grade estimation runs, a capping grade was applied in the Vulcan™ kriging routines. After review of the data distributions, the cap was applied at the 99th percentile of each of the six datasets representing the six modeled divisions of the mine.
Kriging Plan: Composited grade values from each of the six main regions of the mine were analyzed in detail. Studies included the review of basic statistics and variography for platinum and palladium grades separately and for the combined grades. In all areas of the mine, the results for the individual assays and the combined values were similar. Thus, in all six block models, the combined platinum plus palladium grades were estimated directly in the models.
High Yield Limit: Reconciliation work using interim block models showed that even with the application of a high-grade "cap" to the samples used, some remaining higher-grade samples were having a large-scale effect on the estimated block grades. In order to reduce this effect, a high yield limit was applied in the Vulcan™ kriging plan. The high yield limit has the effect of giving a very limited range of influence to samples above the grade threshold. All block estimations below this limited range do not include the high-grade sample, i.e., it is not cut, the sample is removed from the kriging matrix for that block.
Project 11-030 | 41 | BEHRE DOLBEAR |
Technical Report for the Mining Operations at Stillwater Mining Company
March 2011
2010 Evaluation of Conversion of Probable Reserves to Proven Reserves: During 2010, a study was made of the factors that influence the conversion of Probable to Proven reserves. The goal of the study was to identify what factors are affecting probable to proven conversion.
Below is a summary of the recommendations.
● | The boundaries between the reserve blocks should be revised to reflect information obtained from new drilling. |
● | The level of uncertainty of Probable reserve estimation varies between reserve blocks and needs to be quantified to minimize risk associated with mine plans. |
● | Ballrooms (areas of very high grade) happen occasionally and are not predictable. |
● | Mineability factors applied to reserve blocks reflect the differences between tonnages above cutoff and what can be mined selectively. Some clusters of blocks are too small to be of economic interest but could have a significant influence on the mineability factor. These block clusters should be further evaluated. |
● | Cutoff grade can potentially be lowered. |
19.5 RESOURCE/RESERVE DEFINITIONS
Because SMC is registered with the U.S. Securities and Exchange Commission (SEC), it has been following the SEC's definitions for Proven and Probable reserves in reporting its estimated reserves. These definitions are:
● | Probable Reserves: Reserves for which quantity and grade and/or quality are computed from information similar to that used for Proven reserves, but the sites for inspection, sampling, and measurement are farther apart or are otherwise less adequately spaced. The degree of assurance, although lower than that for Proven (measured) reserves, is high enough to assume continuity between points of observation. |
● | Proven Reserves: Reserves for which (a) quantity is computed from dimensions revealed in outcrops, trenches, workings, or drill holes; grade and/or quality are computed from the results of detailed sampling; and (b) the sites for inspection, sampling, and measurement are spaced so closely and the geologic character is so well defined that size, shape, depth, and mineral content of reserves are well established. |
These definitions are compatible with the definitions used by the Canadian Institute of Mining, Metallurgy, and Petroleum (CIM), whose definitions are used for Canadian National Instrument 43-101 reports.1 The relevant CIM definitions for this report are:
A "Mineral Resource" is a concentration or occurrence of diamonds, natural solid inorganic material, or natural solid fossilized organic material including base and precious metals, coal, and industrial minerals in or on the Earth's crust in such form and quantity and of such a grade or quality that it has reasonable prospects for economic extraction. The location, quantity, grade, geological characteristics and continuity of a Mineral Resource are known, estimated or interpreted from specific geological evidence and knowledge.
Project 11-030 | 42 | BEHRE DOLBEAR |
Technical Report for the Mining Operations at Stillwater Mining Company
March 2011
An 'Inferred Mineral Resource' is that part of a Mineral Resource for which quantity and grade or quality can be estimated on the basis of geological evidence and limited sampling and reasonably assumed, but not verified, geological and grade continuity. The estimate is based on limited information and sampling gathered through appropriate techniques from locations such as outcrops, trenches, pits, workings and drill holes.
A 'Probable Mineral Reserve' is the economically mineable part of an Indicated, and in some circumstances a Measured Mineral Resource demonstrated by at least a Preliminary Feasibility Study. This Study must include adequate information on mining, processing, metallurgical, economic, and other relevant factors that demonstrate, at the time of reporting, that economic extraction can be justified.
A 'Proven Mineral Reserve' is the economically mineable part of a Measured Mineral Resource demonstrated by at least a Preliminary Feasibility Study. This Study must include adequate information on mining, processing, metallurgical, economic, and other relevant factors that demonstrate, at the time of reporting, that economic extraction is justified.
The SEC does not define mineral resources, and material that is classified as a Mineral Resource by the CIM is designated "non-reserve mineralized material" or similar terms.
19.6 SMC'S MINERAL RESOURCE ESTIMATES
During 2010, SMC undertook a strategic planning program of the Stillwater Complex to examine mining opportunities at the Stillwater and East Boulder Mines and in areas west of the East Boulder Mine, between the mines, and east of the Stillwater Mine. This program resulted in the redefinition of some sector boundaries (both in the east-west dimensions and in the depth of projection) and the reassessment of the estimation parameters for the "mineralized material" (United States reporting) or Inferred Mineral Resource category (Canadian reporting). Adjustments to the estimated quantities near both of the mines were also made due to the conversion of some of this material to Probable Mineral Reserves during 2010. The bases for the estimation of Inferred Mineral Resources include:
● | surface drilling along the strike-length of the J-M Reef |
● | the interpreted deposition of the J-M Reef as part of the cooling of the Stillwater igneous complex that is supported by the overall continuity of the J-M Reef at both mines |
● | the underground delineation drilling for Proven and Probable Reserves at both the Stillwater and East Boulder Mines as they have expanded both laterally and vertically over the years |
● | deep drilling undertaken at the Stillwater Mine to locate the underlying Horseman Thrust Fault that offsets the Stillwater igneous complex and thereby limits the depths to which mining could extend |
● | the successful conversion of material previously classified as "mineralized material" or Inferred Mineral Resource to Probable and Proven reserves as both mines have expanded over the years |
SMC's estimated mineralized inventory (United States reporting) or Inferred Mineral Resources (Canadian reporting) as of December 31, 2010 is presented in Table 19.1
Project 11-030 | 43 | BEHRE DOLBEAR |
Technical Report for the Mining Operations at Stillwater Mining Company
March 2011
TABLE 19.1
SMC'S ESTIMATED MINERALIZED MATERIAL (UNITED STATES REPORTING) OR INFERRED MINERAL RESOURCES (CANADIAN REPORTING) IN THE J-M REEF
(AS OF DECEMBER 31, 2010)
Tons (millions) Grade Ounces (Pt+Pd/ton)
Stillwater Mine 55.5 0.53
East Boulder Mine 53.1 0.43
Total Estimated Mineralized Material/Inferred Mineral Resources 108.6 0.48
There are no estimated Mineral Resources in the Indicated or Measured categories. Canadian National Instrument 43-101 assumes that exploration precedes mine development and that mineral deposits are fairly thoroughly delineated prior to mine development. This assumption does not hold for producing mines exploiting steeply dipping deposits like the J-M Reef. It is simply not economically feasible to do exploratory and delineation drilling at the depths at which these deposits are exploited. As the mine's horizontal and vertical workings extend into areas classified as Inferred resources, the underground core drilling, sampling, and analytical results not only provide the geologic assurance required for delineating Proven and Probable reserves, but also permit detailed mine planning and stope design to proceed. Probable and Proven reserves are thus estimated as soon as the relevant data from underground drilling becomes available. Estimation of Indicated and Measured resources would be meaningless and possibly confusing for producing mining operations such as the Stillwater and East Boulder Mines.
19.7 SMC'S PROVEN AND PROBABLE MINERAL RESERVE ESTIMATES
SMC's Proven reserve estimates are based on the 50-foot fan drilling. The Probable reserve estimates are based on 1,000-foot projections from a drill hole or other J-M Reef sample (unless there is a known geologic boundary, such as fault or mafic dike that dictates a lesser projection distance). Although a geostatistical basis for using 1,600-foot projections and similarly long projections are used in the Bushveld Complex of South Africa, the most comparable deposit to the J-M Reef, SMC elected to use 1,000-foot projections following discussions with the SEC in 2002.
The independent review conducted for SMC in 2010 commented that, in its opinion, SMC used an unconventional method of estimating Probable reserves by estimating mineralization outside of a drilling grid (extrapolation) rather than within a more widely spaced drilling grid than would be used for Proven reserves (interpolation). This comment ignores the fact that estimates of mineral resources and reserves routinely include extrapolated areas of mineralization as well as interpolated areas. It also failed to recognize that SMC's approach is similar to that used for the Bushveld Complex.
The independent review noted that the percentage of estimated Probable reserves to Proven reserves, which has been kept on an annual basis since 1997 at the Stillwater Mine, has been declining over the past 10 years even though the average conversion between 1997 and 2010 is 88%. The percentage conversion from Probable to Proven reserves is expected to vary from year to year, depending on the areas within the J-M Reef in which the footwall laterals are being driven each year. The author evaluated the year-by-year changes in conversion percentage using a runs test, a non-parametric statistical technique to test whether changes in sequentially collected data, such as the conversion percentages, were random or not. The runs test determined that the year-to-year changes were random in direction, that is, either greater or less than the conversion percentage in the previous year.
Project 11-030 | 44 | BEHRE DOLBEAR |
Technical Report for the Mining Operations at Stillwater Mining Company
March 2011
Nevertheless, SMC followed up on the issue during 2010. An independent statistical review of the issue identified a number of complexly interacting factors affecting the estimation of Probable reserves at the Stillwater Mine. Some changes were made prior to the 2010 year-end estimates, including adjustments to the block boundaries within the Stillwater Mine used for estimation. Other modifications will be studied during the first half of 2011.
The conversion rate for Probable reserves to Proven reserves at the East Boulder Mine are made using the same procedure that is used at the Stillwater Mine, and the conversion rate at the East Boulder Mine was 95%.
SMC's estimated Proven and Probable reserves, as of December 31, 2010, total approximately 40.8 million tons and 19.9 million ounces of platinum and palladium, at an average combined grade of 0.49 troy ounces of platinum and palladium per ton. Of the 19.9 million total reserve ounces, an estimated 16.7 million ounces are recoverable, as presented in Table 19.2. These estimates are based on operating plan projections that use the 12-quarter trailing average prices of $1,464.02 for platinum and of $380.59 for palladium, or $624.05 on a combined troy ounce of platinum plus palladium at SMC's production ratio for platinum and palladium.
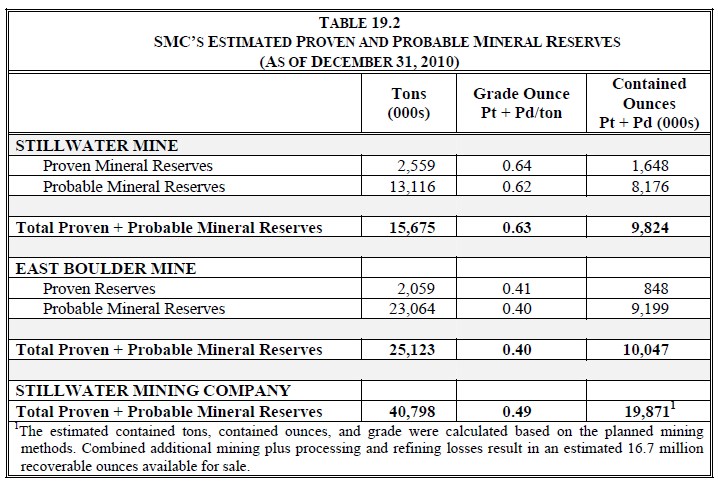
TABLE 19.2 SMC'S ESTIMATED PROVEN AND PROBABI (As OF DECEMBER 31, 2010 ,E MINERAL RESERVES
Tons (000s) Grade Ounce Pt + Pd/ton Contained Ounces Pt + Pd (000s)
STILLWATER MINE
Proven Mineral Reserves 2,559 0.64 1,648
Probable Mineral Reserves 13,116 0.62 8,176
Total Proven + Probable Mineral Reserves 15,675 0.63 9,824
EAST BOULDER MINE
Proven Reserves 2,059 0.41 848
Probable Mineral Reserves 23,064 0.40 9,199
Total Proven + Probable Mineral Reserves 25,123 0.40 10,047
STILLWATER MINING COMPANY
Total Proven + Probable Mineral Reserves 40,798 0.49 19,8711
1The estimated contained tons, contained ounces, and grade were calculated based on the planned mining methods. Combined additional mining plus processing and refining losses result in an estimated 16.7 million recoverable ounces available for sale.
The following notes apply to the mineral reserve estimates.
1) | In 2010, the overall recovered ratio of platinum to palladium was 1:3.45 at the Stillwater Mine, was 1:3.45 at the East Boulder Mine, and was 1:3.45 for the combined mines. |
Project 11-030 | 45 | BEHRE DOLBEAR |
Technical Report for the Mining Operations at Stillwater Mining Company
March 2011
2) | 'Mineralized J-M Reef is a platinum-palladium-bearing geologic horizon whose presence is indicated by surface trenching, surface drilling, and underground exploration. This material has been found to contain a sufficient amount of PGM to warrant further evaluation. While this material is not currently and may never be converted to reserves, the potential for such conversion reasonably exists, particularly in those areas adjacent to the Stillwater and East Boulder Mines. Over the years, much of this material has been converted to Probable and Proven reserves, as the mines have expanded. The geologic character and continuity of this material has been established, but further detailed technical and economic factors must be evaluated prior to conversion to reserves. |
3) | SMC has divided its strike-length holdings along the platinum and palladium-bearing J-M Reef into a series of sectors. These sectors have been divided into roughly equal portions and assigned to the Stillwater and to East Boulder Mines. |
The estimates presented in the mineral inventory tables reflect a combination of factors related to:
● | reclassification based on new underground drilling that upgraded mineralized J-M Reef to Probable reserves and Probable reserves to Proven reserves |
● | deletion of mine production |
● | changes in the mix of mining methods to be employed in the future |
● | additions and subtractions due to changes in estimation parameters for Probable reserves and the mineralized J-M Reef |
Mineral reserve estimates are inherently forward-looking statements subject to error. Although experience in mining at the Stillwater and East Boulder Mines has provided improved understanding of the mineralization and improved modeling ability, estimation errors cannot be eliminated. The major expected sources of error in the estimates, in order of importance, include metal prices, estimated mining and production costs, increased manpower requirements, regulatory changes, unknown geologic conditions, estimation methodologies, and inherent sample variability. These factors are continually being reviewed to determine whether any adjustments are needed. The timing and effect of such changes cannot be predicted.
● | Metal Prices: The prices for platinum and palladium fluctuate. The spot prices of both platinum and palladium generally rose during 2010. The 2010 average prices, $1,609 per ounce of platinum and $526 per ounce of palladium, were higher than the average 2009 prices of $1,204 for platinum and $263 for palladium.9 The December 2010 average price for platinum was $1,673 and for palladium was $716. The palladium market primarily depends on the gasoline engine market, while platinum can be used in both gasoline and diesel engines. During 2010, Johnson Matthey reported that the palladium supply and demand were about equal following several years in which supply exceeded demand. Likewise, platinum demand was much closer to the supply than was the case in 2009.10 As mining progresses to greater distances from the shaft or surface openings, the cost of mining will necessarily go up, and the sensitivity of economic recovery to price fluctuations will increase. The differential between platinum and palladium prices can result in shifts in demand toward the lower-priced metal for use as autocatalysts, which are a major market for SMC's production. Many factors affect both price and demand projections that cannot be accurately predicted, at this time. Should significantly lower prices of platinum and palladium occur in the future, a change in mine plans could result in material reserve estimate revisions. |
9 Behre Dolbear used Kitco.com's London PM price fixes for these reported prices
Project 11-030 | 46 | BEHRE DOLBEAR |
Technical Report for the Mining Operations at Stillwater Mining Company
March 2011
● | Mining and Production Costs: Mining and production costs have increased dramatically at all mines, world-wide, since 2006. SMC experienced this dramatic increase in costs from 2005 through 2008. These increases were, in part, due to the mining inflation cost occurring globally but also due to large expenditures for mine infrastructure and equipment capital costs. SMC's future plans incorporate increased site productivity, changes in planned production rates, and long-term capital expense reduction. While Behre Dolbear believes that these plans are reasonably based and achievable based on past production data, there remains risk that these objectives will not be achieved in either the estimated amounts or at the estimated times. The estimated revenue per combined ounce of platinum plus palladium over the reserve life varies depending on which parts of the mines are being exploited and the amount of production from each mine. SMC's long-range plans project positive cash flows for both mines on an undiscounted basis over the life of the currently delineated Proven and Probable reserves. |
● | Manpower Requirements: SMC's long-range mine plans depend on the Company's ability to attract, develop, and maintain the increased staff required to achieve the planned development and mining rates. When the mining industry was in a downturn, this was not as significant a problem as it had been in the past. However, as the mining industry continues its recovery, it may become a more significant problem in the future. While SMC is recruiting and training new employees, the success of this effort cannot be assured, at this time. |
● | Regulatory Changes: Although SMC is currently in compliance with all regulatory requirements, there is no assurance that the regulatory environment will not change in the future in a manner that would adversely impact SMC's ability to exploit the J-M Reef. |
● | Unknown Geologic Conditions: Although the geologic character of the mineralized J-M Reef has been established by systematic surface drilling along 26 miles of strike length and underground development at two mines separated by 8 miles and although produced metal in general has conformed to estimated reserves, there still may be geologic surprises. Significant amounts of metal are periodically found in the Stillwater Mine within features known as 'ballrooms,' whose precise spacing and size have not proven predictable. Ballrooms have not been identified at the East Boulder Mine. Other unexpected geologic conditions have been and can be expected to be encountered as mining proceeds. This is particularly true for faulting and its effects on units that are close to the J-M Reef in some areas, which can result in additional dilution of grade during mining. |
● | Estimation Methodologies: Although comparison of estimated tonnages and grades and actual production support the conclusion that the estimation methodologies used produce acceptable results, these methodologies employ assumptions about the geology of the J-M Reef and assumptions inherent in the calculation algorithms. The parameters used in these calculations are periodically reviewed, and such a review at the East Boulder Mine in 2010 resulted in an improved 2010 estimate. |
Project 11-030 | 47 | BEHRE DOLBEAR |
Technical Report for the Mining Operations at Stillwater Mining Company
March 2011
● | Inherent Sample Variability: There is an inherent variability in the grade distribution within the deposit that cannot be reduced by economically reasonable sampling methods. This variability is random and tends to cancel out over larger volumes. Because of this variability, no more than three significant figures can be considered relevant in the estimated amounts, even though the computer programs used to estimate the mineral reserves and other mineralized material report far more significant figures. |
19.8 MINE LIFE
SMC prepares a detailed ore reserve economic test at the end of each calendar year to determine that all of the estimated Proven and Probable reserves can be profitably extracted over the life of the mines. This economic test is, in turn, based on detailed infrastructure creation, extraction, and capital investment sequencing plans developed for each mine. At the end of 2010, the estimated life of the Stillwater Mine continued until 2031, and the estimated life of the East Boulder Mine continued until 2074.
Project 11-030 | 48 | BEHRE DOLBEAR |
Technical Report for the Mining Operations at Stillwater Mining Company
March 2011
20.0 OTHER RELEVANT DATA AND INFORMATION
There is no other pertinent information.
Project 11-030 | 49 | BEHRE DOLBEAR |
Technical Report for the Mining Operations at Stillwater Mining Company
March 2011
21.0 INTERPRETATION AND CONCLUSIONS
SMC's Stillwater and East Boulder Mines have been successfully mining platinum and palladium from the J-M Reef in the Stillwater layered igneous complex of south-central Montana since 1986 and 2002, respectively. Over the years, the mines have expanded the estimated Proven and Probable reserves into new areas of the J-M Reef while extracting previously identified reserves. This process is expected to continue for some time, although not forever. Ultimate mine life depends on a number of factors, including metal prices, mining costs, changing mining technology, and regulatory issues, among other things that cannot be predicted, at this time. SMC's geologic, mining, metallurgical, environmental, and other practices and procedures are excellent and appropriate for the type of deposit being mined. Differences from practices and procedures used at other mining properties reflect differences in the types of deposits being exploited.
The means that SMC employs to obtain relevant data to estimate its mineral reserves and the estimation methodology used are proper and are, in the opinion of the Behre Dolbear Qualified Person conducted in an exemplary fashion.
Project 11-030 | 50 | BEHRE DOLBEAR |
Technical Report for the Mining Operations at Stillwater Mining Company
March 2011
22.0 RECOMMENDATIONS
Behre Dolbear is not making any recommendations at this time. SMC has already undertaken or commenced addressing the issues that would have been recommended.
Project 11-030 | 51 | BEHRE DOLBEAR |
Technical Report for the Mining Operations at Stillwater Mining Company
March 2011
23.0 REFERENCES
Canadian Institute of Mining, Metallurgy, and Petroleum (CIM), 2010, CIM Definition Standards for Mineral Resources and Mineral Reserves, 10 pages.
Johnson Matthey, 2010, Platinum 2010 Interim Review, 44 pages.
Page, N.J., Zientek, M.L., Lipin, B.R., Mann, E.L., Schmidt, E.A., Turner, A.R., Czamanske, G.K., and Raedeke, 1985, Exploration and Mining History of the Stillwater Complex and Adjacent Rocks Adit in Czamanske, G.K. and
Zientek, M.L., eds., The Stillwater Complex, Montana: Geology and Guide: Montana Bureau of Mining and Geology Special Publication 92, p. 77-92.
Stillwater Mining Company, 2010, 2009 Annual Report Form 10-K, p. 9.
Turner, F.J. and Weiss, L.E., 1963, Structural Analysis of Metamorphic Tectonites: McGraw-Hill Book Company, 545 pages.
Turner, A.R., Wolfgram, D., and Barnes, S.J., 1985, Geology of the Stillwater County Sector of the J-M Reef, including the Minneapolis Adit in Czamanske, G.K. and Zientek, M.L., eds., The Stillwater Complex,
Montana: Geology and Guide: Montana Bureau of Mining and Geology Special Publication 92, p. 210-230.
Project 11-030 | 52 | BEHRE DOLBEAR |
Technical Report for the Mining Operations at Stillwater Mining Company
March 2011
24.0 DATE AND SIGNATURE PAGE
The undersigned prepared this Technical Report, titled "Technical Report for the Mining Operations of Stillwater Mining Company" dated March 14, 2011.
The format and content of the report are intended to conform to Form 43-101F of Canadian National Instrument 43-101 (NI 43-101) of the Canadian Securities Administrators.
Signed and Sealed
David M. Abbott, Jr., CPG-4570
"Original Document signed and sealed by Richard L. Bullock"
Richard L. Bullock, PE
"Original Document signed and sealed by Richard S. Kunter"
Richard S. Kunter
"Original Document signed and sealed by Betty L. Gibbs"
Betty L. Gibbs
Project 11-030 | 53 | BEHRE DOLBEAR |
Technical Report for the Mining Operations at Stillwater Mining Company
March 2011
CERTIFICATE OF QUALIFICATIONS
I, David M. Abbott, Jr., of Denver, Colorado do hereby certify that:
(a) | I am a Senior Associate and Principal with Behre Dolbear & Company (USA), Inc. at the address 2266 Forest Street, Denver, Colorado, USA 80207. |
(b) | I am a graduate of Dartmouth College with an AB degree in Earth Science and of the Colorado School of Mines with an MS in Geology. |
(c) | I am an Honorary Member in good standing of the American Institute of Professional Geologists, which has designated me as Certified Professional Geologist (CPG) 4560. I am also licensed as a Professional Geologist by the State of Wyoming, PG-2660, and as a Professional Geoscientist by the State of Texas, PG-312. |
(d) | I have practiced my profession since 1975. My relevant experience for the purpose of the Technical Report is: |
● | Serving as a geologist for the U.S. Securities and Exchange Commission (SEC) from February 1975 until March 1996, where I reviewed the adequacy of disclosures made by junior mining and oil and gas companies filing to sell securities and investigated mining and oil and gas frauds. This work involved a wide variety of minerals and application of the SEC's reserve classification standards to a wide variety of deposit types. |
● | Conducting annual mineral reserve and resource audits of Stillwater Mining Company since the audit for December 31, 1997. I have also worked on other assignments for Stillwater Mining Company related to the definition, delineation, and classification of its mineral resources and reserves. |
● | Conducting an independent review of the exploration program at the Marathon PGM-Cu deposit near Marathon, Ontario in 2007. |
● | Writing papers and giving talks to professional organizations on the application of reserve and resource classification schemes, including their application to industrial minerals. |
(e) | I have read the definition of "Qualified Person" as set out in National Instrument 43-101 (NI 43-101) and certify that by reason of my education, affiliation with a professional association (as defined in NI 43-101), and past relevant work experience, I fulfill the requirements to be a "Qualified Person" for the purposes of NI 43-101. |
(f) | I am responsible for the overall preparation of and specifically for Sections 7.0 to 14.0, 18.0 to 22.0, 25.2 to 25.4, and 25.6 and 25.7 of this Technical Report titled "Technical Report for the Mining Operations at Stillwater Mining Company" dated March 2011. |
(g) | I have personally undertaken many visits to the properties that are the subject of this report, beginning in the fall of 1997. |
Project 11-030 | 54 | BEHRE DOLBEAR |
Technical Report for the Mining Operations at Stillwater Mining Company
March 2011
(e) | I am independent of Stillwater Mining Company, as set out in Section 1.4 of National Instrument 43-101. |
(f) | I have previously reported on annual mineral resource and mineral reserve audits of Stillwater Mining Company, beginning with the year ending December 31, 1997. |
(j) | I have read National Instrument 43-101, and the technical report has been prepared in compliance with National Instrument 43-101 and Form 43-101F1. |
(k) | As of the date of the certificate, to the best of my knowledge, information, and belief, the technical report contains all scientific and technical information that is required to be disclosed to make the technical report not misleading. |
(l) | I consent to the filing of this Technical Report with any stock exchange and other regulatory authority and any publication by them, including electronic publication in the public company files on their websites accessible by the public. |
Signed and dated this March 14, 2011 at Denver Colorado.
Signature
Project 11-030 | 55 | BEHRE DOLBEAR |
Technical Report for the Mining Operations at Stillwater Mining Company
March 2011
CERTIFICATE OF QUALIFICATIONS
Betty L. Gibbs
I, Betty L. Gibbs, of Boulder, Colorado do hereby certify that:
(a) | I am a Senior Associate with Behre Dolbear & Company (USA), Inc. at the address 91 Camino Bosque, Boulder, Colorado, USA 80302. |
(b) | I am a graduate of the Colorado School of Mines with an EM (Engineer of Mines) degree in Mining Engineering and a MS degree in Mining Engineering. |
(c) | I am a Member in good standing of the Mining and Metallurgical Society of America, which has designated me a Qualified Professional (Mining). I am also a Member in good standing of the Society for Mining, Metallurgy, and Exploration. |
(d) | I have practiced my profession since 1969. My relevant experience for the purpose of the Technical Report is: |
● | Contributed to the annual mineral reserve and resource audits of Stillwater Mining Company since the audit for December 31, 2005. |
● | Performed database due diligence and mineral resource estimations for a gold deposit in Kazakhstan. |
● | Provided due diligence and resource audit of a vein-type silver/copper deposit in South America. |
● | Contributed to the preparation of the NI 43-101 report for the Great Basin Gold in Nevada. Behre Dolbear did not verify the reserve portion of that report. |
● | Prepared and presented courses about using computer software for database development, geologic modeling, resource estimation, and mine planning. |
(e) | I have read the definition of "Qualified Person" as set out in National Instrument 43-101 (NI 43-101) and certify that by reason of my education, affiliation with a professional association (as defined in NI 43-101), and past relevant work experience, I fulfill the requirements to be a "Qualified Person" for the purposes of NI 43-101. |
(f) | I am responsible in part for preparation of Sections 13.0 to 16.0, and 19.0 of this Technical Report titled "Technical Report for the Mining Operations at Stillwater Mining Company" dated March 2011. |
(g) | I have personally undertaken many visits to the properties that are the subject of this report, beginning in the winter of 2007. |
(h) | I am independent of Stillwater Mining Company, as set out in Section 1.4 of National Instrument 43-101. |
(i) | I have previously contributed to the reports on the ore reserves related sections of the annual mineral resource and mineral reserve audits of Stillwater Mining Company, beginning with the year ending December 31, 2006. |
Project 11-030 | 56 | BEHRE DOLBEAR |
Technical Report for the Mining Operations at Stillwater Mining Company
March 2011
(j) | I have read National Instrument 43-101, and the technical report has been prepared in compliance with National Instrument 43-101 and Form 43-101F1. |
(k) | As of the date of the certificate, to the best of my knowledge, information, and belief, the technical report contains all scientific and technical information that is required to be disclosed to make the technical report not misleading. |
(l) | I consent to the filing of this Technical Report with any stock exchange and other regulatory authority and any publication by them, including electronic publication in the public company files on their websites accessible by the public. |
Signed and dated this March 14, 2011 at Boulder Colorado.
"Original Document signed and sealed by Betty L. Gibbs"
Signature
Project 11-030 | 57 | BEHRE DOLBEAR |
Technical Report for the Mining Operations at Stillwater Mining Company
March 2011
CERTIFICATE OF QUALIFICATIONS
I, Richard L. Bullock, of Longview, Washington do hereby certify that:
(a) | I am a Senior Associate with Behre Dolbear & Company (USA), and a Professor Emeritus, Distance Learning Professor, Missouri University of Science and Technology at the address 217 Sunset Drive, Longview, Washington, USA 98632. |
(b) | I am a graduate of the University of Missouri School of Mines with a BS degree in Mining Engineering (1951), an MS degree in Mining Engineering (1955), and a Doctorate of Engineer in Mining Engineering (1975). |
(c) | I was awarded an Honorary Engineer of Mines by the University of Missouri, Rolla, in 1986. I was elected to the honorary Missouri School of Mines and Metallurgy Academy, 1995, when only 20 others of over 6,000 living alumni had been so honored. |
(d) | I have been a licensed Professional Engineer since 1957, Missouri, (PE No. 8000); 1975, New York, (PE No. 55387); 1977, Tennessee (PE No. 12002); and 1994, Nevada, (10996). |
(e) | I have practiced my mining engineering profession since 1951. My relevant experience for the purpose of the Technical Report is: |
● | Performed some sort of engineering analysis, due diligence, or feasibility study on over 250 mineral properties during my career (List available upon request). |
● | Taught a graduate level course 13 times on mineral property feasibility and evaluation to over 125 students for the Missouri University of Science and Technology. Recently, this included an introduction to NI 43-101. |
● | Has over 40 years of experience in the mining industry in managing mineral property evaluations, mine developments, projects, ongoing operations, mining research, and multi-disciplined engineering design groups. |
● | Personally visited the Stillwater Mine in 2002 and assisted in conducting five independent mining reviews of the annual mineral reserve and resource audits of Stillwater Mining Company since 2005. |
● | Was the Behre Dolbear Project Manager of a group that prepared the NI 43-101 report for Great Basin Gold in Nevada, but Behre Dolbear did not verify the reserve portion of that report. |
● | Recently wrote the chapter on Mineral Property Feasibility and Evaluation Studies for the new Mining Engineering Handbook for the Society for Mining, Metallurgy and Exploration, Inc. This new book will be published in February 2011. |
(f) | I have read the definition of "Qualified Person" as set out in National Instrument 43-101 (NI 43-101) and certify that by reason of my education, affiliation with a professional association (as defined in NI 43-101), and past relevant work experience, I fulfill the requirements to be a "Qualified Person" for the purposes of NI 43-101. This has been verified by the Mining and Metallurgical Society of America, which designated me as a Qualified Professional" with expertise in Mining and Ore Reserves, Certificate No. 1105QP. |
Project 11-030 | 58 | BEHRE DOLBEAR |
Technical Report for the Mining Operations at Stillwater Mining Company
March 2011
(g) | I am responsible for preparation of the mining sections, 25.1 and 25.5 of this Technical Report titled "Technical Report for the Mining Operations at Stillwater Mining Company" dated March 2011. |
(h) | I have personally undertaken many visits to the properties that are the subject of this report, beginning in 1997. |
(i) | I am independent of Stillwater Mining Company, as set out in Section 1.4 of National Instrument 43-101. |
(j) | I have previously reported on the mining aspects related to the annual mineral resource and mineral reserve audits of Stillwater Mining Company, beginning with the year ending December 31, 2005. |
(k) | I have read National Instrument 43-101, and the technical report has been prepared in compliance with National Instrument 43-101 and Form 43-101F1. |
(l) | As of the date of the certificate, to the best of my knowledge, information, and belief, the technical report contains all scientific and technical information that is required to be disclosed to make the technical report not misleading. |
(m) | I consent to the filing of this Technical Report with any stock exchange and other regulatory authority and any publication by them, including electronic publication in the public company files on their websites accessible by the public. |
Signed and dated this March 14, 2011 in Longview, Washington.
"Original Document signed and sealed by Richard L. Bullock"
Signature
Project 11-030 | 59 | BEHRE DOLBEAR |
Technical Report for the Mining Operations at Stillwater Mining Company
March 2011
CERTIFICATE OF QUALIFICATIONS
Richard S. Kunter
I, Richard S. Kunter, of Golden, Colorado do hereby certify that:
(a) | I am a Senior Associate and Principal with Behre Dolbear & Company (USA), Inc. at the address 181 Mesa Verde Street, Golden, Colorado, USA 80401. |
(b) | I am a graduate of the University of Idaho with a BS (Met Engr) degree in Metallurgical Engineering and a MS (Met Engr) degree in Metallurgical Engineering. |
(c) | I am a Member in good standing of the Mining and Metallurgical Society of America, which has designated me a Qualified Professional (Metallurgy and Environmental). I am also a Fellow of the Australasian Institute of Mining and Metallurgy and a Chartered Professional, Registration number 100346. I am also a Member in good standing of the Society for Mining, Metallurgy, and Exploration and of the Minerals, Metals, and Materials Society, both constituent societies of the American Institute of Mining, Metallurgical, and Petroleum Engineers. |
(d) | I have practiced my profession since 1969. My relevant experience for the purpose of the Technical Report is: |
● | Serving as a research metallurgist and project metallurgist for Western Mining Corporation in Perth, Western Australia from February 1971 to June 1976, where I worked on nickel flotation and precious metal projects and in the hydrometallurgical refinery for nickel production at Kwinana and at the nickel smelter in Kalgoorlie. These operations have commonality with the concentration, smelting, and refining operations of Stillwater. |
● | Serving as Mill Superintendent for Newmont Australia at Telfer Gold Project from July 1976 to November 1978, where I was in charge of the commissioning and operation of a gold processing facility. |
● | Serving as Senior Corporate Metallurgist for Homestake Mining Company from February 1979 to February 1989 where I was involved in process development of many of Homestake's operating plants and exploration projects. |
● | Conducting the metallurgical portion of the annual mineral reserve and resource audits of Stillwater Mining Company since the audit for December 31, 2000. I have also worked on other assignments for Stillwater Mining Company related to the audit of the metallurgical operations of their concentrators, base metal smelter, and refinery. |
● | Conducting independent reviews of the PGM-Cu-Ni exploration projects of Birch Lake and Mesaba in the Taconite District of northern Minnesota. |
(e) | I have read the definition of "Qualified Person" as set out in National Instrument 43-101 (NI 43-101) and certify that by reason of my education, affiliation with a professional association (as defined in NI 43-101), and past relevant work experience, I fulfill the requirements to be a "Qualified Person" for the purposes of NI 43-101. |
Project 11-030 | 60 | BEHRE DOLBEAR |
Technical Report for the Mining Operations at Stillwater Mining Company
March 2011
(f) | I am responsible for preparation of Section 18.0 of this Technical Report titled "Technical Report for the Mining Operations at Stillwater Mining Company" dated March 2011. |
(g) | I have personally undertaken many visits to the properties that are the subject of this report, beginning in the spring of 2001. |
(h) | I am independent of Stillwater Mining Company, as set out in Section 1.4 of National Instrument 43-101. |
(i) | I have previously reported on the metallurgical related sections of the annual mineral resource and mineral reserve audits of Stillwater Mining Company, beginning with the year ending December 31, 2000. |
(j) | I have read National Instrument 43-101, and the technical report has been prepared in compliance with National Instrument 43-101 and Form 43-101F1. |
(k) | As of the date of the certificate, to the best of my knowledge, information, and belief, the technical report contains all scientific and technical information that is required to be disclosed to make the technical report not misleading. |
(l) | I consent to the filing of this Technical Report with any stock exchange and other regulatory authority and any publication by them, including electronic publication in the public company files on their websites accessible by the public. |
Signed and dated this March 14, 2011 at Golden Colorado.
"Original Document signed and sealed by Richard S Kunter"
Signature
Project 11-030 | 61 | BEHRE DOLBEAR |
Technical Report for the Mining Operations at Stillwater Mining Company
March 2011
25.0 ADDITIONAL REQUIREMENTS FOR TECHNICAL REPORTS ON DEVELOPMENT PROPERTIES AND
PRODUCTION PROPERTIES
This section contains discussions of the following topics:
● | the mining operations at the Stillwater and East Boulder Mines, including mine safety issues |
● | SMC's environmental compliance |
● | SMC's catalytic converter recycling business |
SMC's mining operations consist of two underground mines that have been developed on the 26-mile strike length of the platinum-palladium mineralized J-M Reef. The Stillwater Mine located near the Stillwater River was started in 1986. The East Boulder Mine is located farther west along the J-M Reef near the East Boulder River. Development of the East Boulder Mine began in 1998, and commercial production began in 2002. Combined, the two mines have produced approximately 9 million ounces of platinum and palladium through 2010. They are the only major platinum-palladium primary metal producing mines in the North or South America. A description of the two mining operations will follow and is based on information gathered on five previous annual site visits and an additional operations review in August 2010. All of the information contained herein was obtained from Stillwater management personnel and internal reports.
25.1.1 Stillwater and East Boulder Mining Methods
Both mines employ the same types of mining methods. The three principle mining methods are conventional overhand cut and fill (Conv. C&F), as captive stopes; ramp and fill (R&F) as both overhand and underhand cut and fill; and sublevel extraction (SLE) by longhole open stoping with subsequent backfill. Since considerable tonnage is produced from the development of the sublevels in the Reef, this is carried separately tonnage as sublevel development (SLD) tonnage.
Conventional Overhand Cut and Fill: Several variations of Conv. C&F, which have been practiced at Stillwater, two of which are shown on Figure 25.1 and Figure 25.2.
Project 11-030 | 62 | BEHRE DOLBEAR |
Technical Report for the Mining Operations at Stillwater Mining Company
March 2011
Figure 25.1. Overhand captive cut and fill stoping
Project 11-030 | 63 | BEHRE DOLBEAR |
Technical Report for the Mining Operations at Stillwater Mining Company
March 2011
Figure 25.2. Overhand captive conventional cut and fill stoping
The other variation of captive overhand cut and fill involves using a raise-bored access hole, rather than an Alimak raise climber, which remains captive to the stope. Uncemented sand fill (cycloned mill tailings) is used for the backfill material. All of the Stillwater Mine's Conv. C&F stopes use hand held jackleg drills for drilling and electric slushers for moving the ore from the headings to the ore pass. This equipment remains in the captive stope as it advances upward.
Ramp and Fill (R&F): R&F stopes are the predominant mining method at the Stillwater Mine. While the primary method is by overhand mining, some undercut and fill is used. The two different applications, as practiced at Stillwater, are shown on Figure 25.3 and Figure 25.4. The backfill for the overhand R&F is uncemented sand fill, while the backfill for the undercut and fill is a paste backfill. Where ground conditions permit, the overhand method is preferred and is more cost effective. Where less stable ground conditions dictate, undercut R&F is applied, and the more expensive paste backfill must be used. Most of the R&F stopes are drilled by breast holes using single-boom drill jumbos, and the rock is loaded by small 4-cubic-yard Load-Haul-Dump (LHD) units.
Project 11-030 | 64 | BEHRE DOLBEAR |
Technical Report for the Mining Operations at Stillwater Mining Company
March 2011
Figure 25.3. Overhand R&F mining method with sand backfill as applied at Stillwater Mine
Project 11-030 | 65 | BEHRE DOLBEAR |
Technical Report for the Mining Operations at Stillwater Mining Company
March 2011
Figure 25.4. Undercut R&F mining method using paste backfill as applied at Stillwater Mine
Sublevel Extraction and Sublevel Development: Where the reef structure and the hanging wall are much more competent, sublevel open stoping, using relatively short "long holes" (compared to other mining districts) can be applied. This extraction method is shown in Figure 25.5. The sublevels are driven on the reef structure at 25- to 50-foot intervals. Since considerable amount of tonnage is generated by driving sublevels in the Reef, this tonnage is accounted for as a separate mining method of SLD, as separate from SLE tonnage. The sublevel sills are driven with narrow single-boom jumbos. The long holes are drilled by long hole pneumatic drill rigs.
Project 11-030 | 66 | BEHRE DOLBEAR |
Technical Report for the Mining Operations at Stillwater Mining Company
March 2011
Figure 25.5. Sublevel long hole open stoping with subsequent backfilling
Once the sublevels are driven, a drop raise is drilled and blasted at the end of the stope over the full width of the Reef at that point. Blast holes are then drilled downward on a pattern between the sublevels and blasted toward the open cavity of a slot raise. The ore is mucked from the sublevel below, using remote controlled, diesel-powered LHD units, and the ore is then trammed to the nearest ore pass.
Presently at the Stillwater Mine, the R&F methods are used predominantly in the Off-shaft areas, and the sublevel stoping is used predominantly in the Upper West areas. The captive cut and fill stopes are used in all areas where there are isolated remnants of ore blocks that adapt to this smaller vein type mining system.
25.1.2 Stillwater Mine Operation
The Stillwater Mine was developed by a series of footwall lateral adits driven from the Stillwater River valley. It was the objective to keep these footwall developments approximately 100 feet from the J-M Reef, so that a fan of diamond drill holes could be drilled across the Reef at 50-foot intervals. The footwall laterals were driven on 200-foot vertical intervals initially, but this spacing was more recently increased to 300 feet. A total of seven adits have been driven from the Stillwater River valley; the main high-speed rail haulage adits are the 5000 Level and the 3500 Level. The overall length of the present mine is approximately six miles.
The other major access to the mine is the 18-foot-diameter concrete lined shaft, which extends from about the 5,000-foot elevation at the surface to the bottom at 3,030 feet of elevation. This shaft is used for hoisting ore, men, and materials. It was commissioned in 1997. It uses two 11-ton counter-balanced skips and a 50-person capacity service cage. It supports the production from the 4400 Level down to the 2000 Level. Over the past three years, a new ramp and all related mine infrastructure have been developed down to the 2000 Level, which will serve production from the 2900, the 2600, and the 2300 Levels. The ore will be hauled up the ramp to the 3500 Level by electric-trolley Kiruna trucks.
Project 11-030 | 67 | BEHRE DOLBEAR |
Technical Report for the Mining Operations at Stillwater Mining Company
March 2011
The Stillwater Mine has been subdivided into three large mining areas: the Off-shaft area (all areas east of the shaft and all areas west of the shaft to the 9000 West Fault Line); the Upper West area (all areas west of the West Fault Line above 5000 Level); and the Lower West area (all areas west of the West Fault Line below the 5000 Level).
For many years, the Stillwater Mine has been divided into blocks based on mineralization character, although the block boundaries have been redefined as appropriate, including adjustments during 2005 and 2007. The blocks are distributed through the major mining areas as follows:
● | in the Upper West area, which is above the 5000 Level in the Dow Sector, Block 1, and Block 2 |
● | in the Off-shaft west area in Blocks 3 and 6 |
● | in the Off-shaft east area in Blocks 7, 8, and 10 |
● | in the Lower West area, which is below the 5000 Level and west of 10,000W grid, are the Dow Sector and Blocks 1 and 2 |
25.1.3 The Major Stillwater Mine Off-shaft Deep Mine Development
Over the past five years, the main production areas in the Stillwater Mine have been from the Upper West area and the Off-shaft Dow area. The production has been split approximately equally between the two areas. However, the main planning for the future Stillwater production, which began in 2005 and 2006, is for the area below the 3200 Level (the Below 3200 Project). During 2006 and 2007, various trade-off studies were conducted to determine the optimal method of moving ore from the lower portions of the mine, both short term and long term. The options considered were:
● | declines with conveyors |
● | declines with Kiruna electric 35-ton trucks |
● | extend existing shaft to 1900 Level, with access to footwall laterals below 3200 Level |
● | a rail dump on 2000 Level feeding a new crusher station on 1900 Level |
The optimal selection was the Kiruna electric 35-ton trucks. A tremendous amount of development capital and non-development capital went into the project.
At present, the haulage ramp has been driven down to the 2800 Level. To set up this lower area for future mine production, considerable effort has been devoted to building the mine infrastructure on the lower levels.
Project 11-030 | 68 | BEHRE DOLBEAR |
Technical Report for the Mining Operations at Stillwater Mining Company
March 2011
A working ramp has been driven down to the 2000 Level. A new pump station was installed on the 2500 Level, consisting of 3 sets of pumps capable of pumping 750 gallons per minute (Figure 25.6). These pumps will discharge to the 3100 Level, where a similar set up will discharge to the 4400 Level pump station that discharges to the surface clarifier on 5100 Level. The surface clarifier furnishes needed underground water make up for drilling, spray bars, backfill, etc.
A new rail locomotive and rail car shop constructed on the 3500 main rail haulage Level. The large excavation, with one motor pit, has been completed, with
concrete floor and shotcrete reinforcement on the back and ribs (Figure 25.7 and Figure 25.8).
Figure 25.7. New locomotive repair shop Figure 25.8.New locomotive battery charging station
Project 11-030 | 69 | BEHRE DOLBEAR |
Technical Report for the Mining Operations at Stillwater Mining Company
March 2011
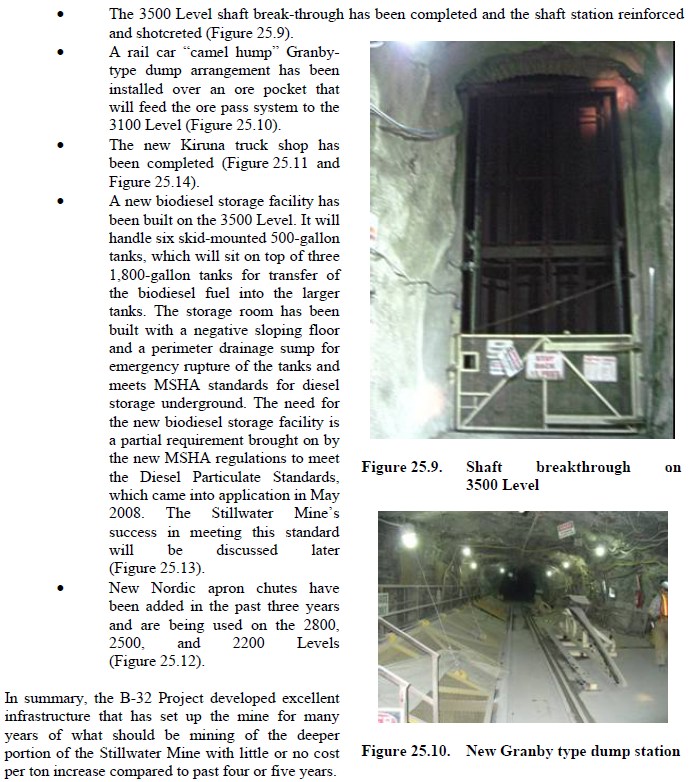
The 3500 Level shaft break-through and shotcreted (Figure 25.9).
A rail car "camel hump" Granby- type dump arrangement has been installed over an ore pocket that will feed the ore pass system to the 3100 Level (Figure 25.10).
The new Kiruna truck shop has been completed (Figure 25.11 and Figure 25.14).
A new biodiesel storage facility has been built on the 3500 Level. It will handle six skid-mounted 500-gallon tanks, which will sit on top of three 1,800-gallon tanks for transfer of the biodiesel fuel into the larger tanks. The storage room has been built with a negative sloping floor and a perimeter drainage sump for emergency rupture of the tanks and meets MSHA standards for diesel storage underground. The need for the new biodiesel storage facility is a partial requirement brought on by the new MSHA regulations to meet the Diesel Particulate Standards, which came into application in May 2008. The Stillwater Mine's success in meeting this standard will be discussed later (Figure 25.13).
New Nordic apron chutes have been added in the past three years and are being used on the 2800, 2500, and 2200 Levels (Figure 25.12).
been completed and the shaft station reinforced
Figure 25.9. Shaft breakthrough on 3500 Level
Figure 25.10. New Granby type dump station
In summary, the B-32 Project developed excellent infrastructure that has set up the mine for many years of what should be mining of the deeper portion of the Stillwater Mine with little or no cost per ton increase compared to past four or five years.
Project 11-030 | 70 | BEHRE DOLBEAR |
Technical Report for the Mining Operations at Stillwater Mining Company
March 2011
Figure 25.11. Kiruna truck shop with truck being assembled; notice the three-wire trolley
Figure 25.12. Two of six new Nordic chutes
Figure 25.13. New Biodiesel storage area
Figure 25.14. One of two recently commissioned Kiruna trucks
Project 11-030 | 71 | BEHRE DOLBEAR |
Technical Report for the Mining Operations at Stillwater Mining Company
March 2011
25.1.4 Normal Stillwater Mine Operations
Within the Stillwater Mine, the J-M Reef varies in dip from 40° to 90° to the north,11 with an average dip of 60°. Reef thickness varies from inches to tens of feet. The mining methods applied are based on the true width of the ore zone as is shown in Table 25.1. The planned total dilution in these minimum mining widths varies from 17% to 40%. These minimum widths have not changed over the past four years. Large mineralized extensions into the footwall of the reef package, referred to as ballrooms, are an occasional feature and a significant contributor to ore production. The J-M Reef is somewhat sinuous in both the strike and dip planes. Geotechnical conditions vary from good to poor, and all headings require ground support to varying degrees.
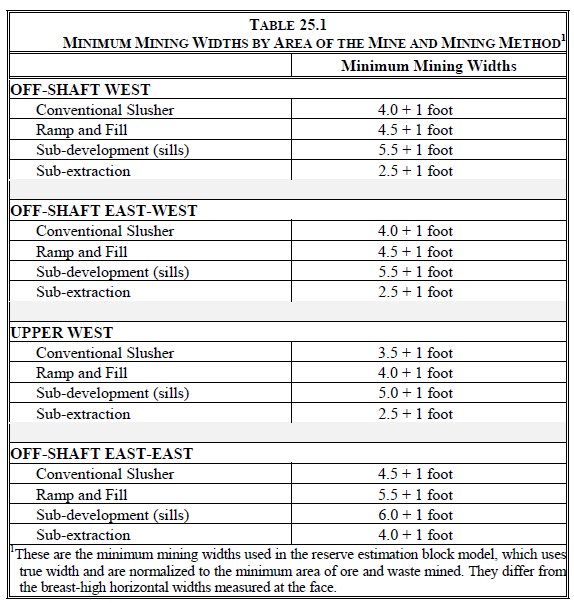
TABLE 25.1
MINIMUM MINING WIDTHS BY AREA OF THE MINE AND MINING METHOD1
Minimum Mining Widths
OFF-SHAFT WEST
Conventional Slusher 4.0 + 1 foot
Ramp and Fill 4.5 + 1 foot
Sub-development (sills) 5.5 + 1 foot
Sub-extraction 2.5 + 1 foot
OFF-SHAFT EAST-WEST
Conventional Slusher 4.0 + 1 foot
Ramp and Fill 4.5 + 1 foot
Sub-development (sills) 5.5 + 1 foot
Sub-extraction 2.5 + 1 foot
UPPER WEST
Conventional Slusher 3.5 + 1 foot
Ramp and Fill 4.0 + 1 foot
Sub-development (sills) 5.0 + 1 foot
Sub-extraction 2.5 + 1 foot
OFF-SHAFT EAST-EAST
Conventional Slusher 4.5 + 1 foot
Ramp and Fill 5.5 + 1 foot
Sub-development (sills) 6.0 + 1 foot
Sub-extraction 4.0 + 1 foot
1These are the minimum mining widths used in the reserve estimation block model, which uses true width and are normalized to the minimum area of ore and waste mined. They differ from the breast-high horizontal widths measured at the face.
Dilution of ore beyond that which is planned is a persistent challenge in every precious metal vein type of mine; Stillwater is no exception. In the earlier years, there was considerably more dilution from over break in the R&F stopes than there is today. Also, the SLE method tends to yield more dilution because sometimes the reef structure undulates or thins and swells vertically whereas the drill holes are straight. Thus, there are more ore losses and more dilution from this method than in R&F or Conv. C&F. There is a trend over the past few years to mine more of the ore bodies by R&F and less by SLD and SLE. This trend can be seen in Figure 25.15.
11 The steepest dips occur on the east side of the Stillwater River, and in some places, the J-M Reef is overturned.
Project 11-030 | 72 | BEHRE DOLBEAR |
Technical Report for the Mining Operations at Stillwater Mining Company
March 2011
Figure 25.15. Stillwater Mine mining method mix change over time
"Conv. C&F" is conventional cut and fill, which includes the Alimak cut and fill; "SLD" is sublevel development; and "SLE" is sublevel extraction.
25.1.5 Stillwater Mine Production
The original objective of the Stillwater Mine production was to reach and maintain approximately 2,500 tons per day. This was reached in 2001, but with the development of East Boulder Mine and all of the pressure put on the work force by the recruiting of Stillwater employees by the other mining camps of the Northwest during the worldwide mining boom, it was just too much to try to maintain that level of production. Thus, for the years 2002 through 2006, the production level was maintained at approximately 2,200 tons per day. In 2007, the tonnage dropped further to 1,900 tons per day, partly due to labor unrest and a subsequent strike period. The management of SMC delivered its 10-year plan in November 2008 at a time of severe economic conditions due to a precipitous fall in platinum and palladium prices in the latter half of the year. In order to adjust to the severe economic changes, some major reorganizational changes for the mining operation were made. Some of the changes are listed below.
Project 11-030 | 73 | BEHRE DOLBEAR |
Technical Report for the Mining Operations at Stillwater Mining Company
March 2011
● | The operation went from two 10-hour to two 11^-hour shifts, with four rotating shifts, changing four days on and four days off, resulting in a continuous 7-day-per-week operation. |
● | A significant decrease in the manpower from 927 (including contractors) to 873. This was accomplished by drastically decreasing the mine operations support workers by 20%, temporarily (2009) decreasing the mine development from three crews to one crew, and decreasing mine service staff. |
● | At the Stillwater Mine, approximately 13% of the mobile diesel fleet was parked and was moth-balled or sold. |
● | Elimination of most of the mine's contractors, which allowed Stillwater Mine to absorb 44 of the East Boulder miners who were laid off. |
The 2010 year-end Stillwater Mine operation manpower stood at 850. However, the 10-year mine plan varies from a high of 921 to a low of 852, with an average of 861. The primary reason for the increase in manpower is the increase in development crews, the added effort going into ore haulage, and adjustments in the number and size of support crews.
In November 2009, SMC settled on a production rate at the Stillwater Mine of approximately 2,000 tons per day for the 10-year plan. The production history and projections are shown in Table 25.2.
TABLE 25.2 STILLWATER MINE PRODUCTION (000s)
Year Actual
Tons PGM (ounces) PGM (opt)
2006 739.4 409.4 0.55
2007 714.7 359.3 0.50
2008 760.9 347.7 0.46
2009 777.2 393.8 0.51
2010 780.4 351.7 0.45
Note: All grades are stated as of net of processing recoveries.
For planning and budgeting purposes, the mine development is divided into two categories, primary development, which consists of footwall lateral drives and ramps, and secondary development, which consists of cross cuts and raises. The previous mine plan had a policy of maintaining a minimum of 18 months of identified stope ore ahead of production. This required that primary development be accelerated in the years 2004 through 2006 to correct a development deficit. Likewise, secondary development was accelerated in the years 2007 through 2008. At that time, the primary development schedule appeared adequate to support the mine plan production goals, assuming that the tons of reserves developed per foot of footwall lateral drive remains near the current factor of 75. Due to the 2008-2009 development curtailment, stope development fell slightly behind. To correct this, the mine recently added back one development crew, which should be adequate to sustain the current level of production. The budgeted amount of secondary development was not verified by Behre Dolbear; however, the methodology used was reviewed and found to be acceptable.
Project 11-030 | 74 | BEHRE DOLBEAR |
Technical Report for the Mining Operations at Stillwater Mining Company
March 2011
25.1.6 Stillwater Mine Services
The Stillwater Mine generates 1,300,000 cubic feet per minute of fresh ventilation, with intake air coming from various ventilation shafts and adits. This amount of air is more than adequate for a mine of this size with the amount of personnel and production equipment in use within the mine. This level of ventilation should be adequate for the 10-year plan; although, if the mine begins the development into the lower Reef structure on the east side of the Stillwater River, then some other ventilation development may have to take place.
The pumping capacity of the mine from the lower Off-shaft area is approximately 1,500 gallons per minute from the deepest main pump station on the 2500 Level. This pumping capacity is more than double the expected amount of water mine inflow, which is currently 550 gallons per minute. Gravity drainage from the Upper West area is an additional 100 gallons per minute. The power furnished to the mine is 22 megawatts, with the current usage at 18 megawatts. The mine is also equipped with a leaky feeder system for the mobile radios that are used on all mobile equipment throughout the mine. The mine is also equipped with a Gaitronic Paging phone system, with stations located strategically throughout the mine.
25.1.7 East Boulder Operation
The East Boulder Mine, which began commercial production at the beginning of 2002, is accessed by two, approximately 18,700-foot long, bored tunnels. The deposit is reached by ramps and footwall laterals on 260-foot to 300-foot vertically spaced levels. Ore reserves are delineated by diamond drilling from these headings, which are also used for stope access and development. The current mine is approximately two miles long and 1,000 feet in vertical extent.
The main adit haulage level is the 6500 Level. A ramp has been driven to the 7900 Level. Except for the adit rail haulage, the mine is operated as a trackless operation. The stopes are accessed from footwall laterals located approximately 150 to 200 feet from the reef. The 6500 Level footwall lateral extends for a nominal 14,000 feet, and the 6700 Level footwall lateral extends for a nominal 12,000 feet. The levels are connected by spiral ramps, and the Reef is accessed by cross cuts.
The principal stoping method is R&F stoping (combined with the SLD production). However, SLE stopes contribute a significant tonnage, and a minor amount of ore comes from Conv. C&F stopes. Figure 25.1, Figure 25.2, Figure 25.3, and Figure 25.5 are all applicable to the East Boulder Mine. The mine has a cycloned tailings sand plant but no paste backfill plant, so Figure 25.4 showing undercut and fill does not apply.
Prior to 2003, almost all production was by the sublevel long hole stoping method. Initially, sublevels were based on a 43-vertical foot sublevel interval. This was modified to a 35-vertical foot sublevel interval in an effort to reduce dilution. The current sublevel sill drifts are narrower than in previous mining in an effort to reduce dilution. The nominal sill width is now 8.0 feet, with a minimum stoping width of 7.5 feet. The change to pneumatic long hole drills from hydraulic-electric drills allowed a reduction in the size of the sill drifts and also the in size of the drilled holes, which reduced over break.
In 2003, R&F stoping was introduced to the East Boulder Mine to provide more flexibility and more efficient extraction in areas of the J-M Reef lacking the uniform width best exploited with sublevel stoping. From 2005 through 2007, there was an increase in Conv. C&F stoping in an effort to increase the overall production grade, but the decrease in productivity led to a decrease in these methods in 2008 to 2010 and an increase in SLE method. This can be seen in Figure 25.16.
Project 11-030 | 75 | BEHRE DOLBEAR |
Technical Report for the Mining Operations at Stillwater Mining Company
March 2011
Figure 25.16. The planned changes in mining methods for the East Boulder Mine
"Conv. C&F" is conventional cut and fill, which includes the Alimak cut and fill; "SLD" is sublevel development; and "SLE" is sublevel extraction.
As at the Stillwater Mine, the selection of mining methods is constrained by geotechnical conditions that require that the ribs and the "shanty shaped" back of all openings that workers access must have ground support installed. This limits the minimum stoping width to a nominal 6 feet. Table 25.3 presents the minimum true mining widths for the mining methods used in the different areas of the East Boulder Mine. The widths vary in different areas of the mine due to differences in the average dip of the J-M Reef from area to area and to the mining method applied. In the East Boulder Mine, the J-M Reef dips 50° to 55° to the north; however, the dip may flatten to as little as 35° in the far west area of the 6500 Level footwall lateral.
Project 11-030 | 76 | BEHRE DOLBEAR |
Technical Report for the Mining Operations at Stillwater Mining Company
March 2011
TABLE 25.3
EAST BOULDER MINIMUM MINING WIDTHS BY TYPE OF MINING METHODS
Mining Method True Width (Minimum + Constant Add) Remarks Dilution -50 Dip
Ramp and Fill 8 + 3 feet
Sublevel Development 8 + 3 feet
Sublevel Extraction 5 + 2.75 feet 75% Recovery
Cut and Fill Slusher 5.5 + 2 feet
Drifting On Reef 10 + 4.5 feet
These are the minimum mining widths used in the reserve estimation block model, which use true width and
are normalized to the minimum area of ore and waste mined. They differ from the breast-high horizontal
widths measured at the face.
25.1.8 East Boulder Mine Production
The 2008 East Boulder Mine plan production was 439,662 tons for the year, or 1,202 tons per day. Following the rationalization that took place from the 2-week shutdown in the fourth quarter of 2008, the mine's 2009 actual production was reduced to 406,038 tons. Table 25.4 presents the actual production for the East Boulder Mine for the years 2006 through 2010. Planned production levels are reduced to approximately 352,300 tons per year for the next 9 years. The budgeted ore grades are within the Proven and Probable ore reserve grades and the mine's production record. The East Boulder Mine staff has prepared a comprehensive mine plan that was reviewed by the author and found to meet industry standards.
TABLE 25.4 EAST BOULDER MINE PRODUCTION (000s)
Year Actual
Tons PGM (ounces) PGM (opt)
2006 540.9 191.2 0.35
2007 529.0 178.2 0.34
2008 438.8 149.5 0.34
2009 407.4 136.1 0.33
2010 400.4 133.4 0.33
Note: All grades are net of processing recovery
The current production comes from 7,200 feet of strike length that has been developed vertically for several levels, but for 2009/2010, the active strike length being mined was reduced to mining from only five relatively close areas. Starting in 2004, the East Boulder Mine resumed extending the portal level footwall lateral to the west, followed by definitional diamond drilling. During 2008, the tunnel boring machine was again used to extend the footwall lateral, but this was discontinued when the economic downturn became obvious. However, it was reactivated in October 2010 to extend the footwall laterals and will continue into 2011.
Project 11-030 | 77 | BEHRE DOLBEAR |
Technical Report for the Mining Operations at Stillwater Mining Company
March 2011
25.1.9 East Boulder Mine Services
The East Boulder Mine generates 500,000 cubic feet per minute of fresh ventilation with intake air coming from various ventilation shafts and adits. This amount of air is more than adequate for a mine of this size with the amount of personnel and production equipment in use within the mine. This level of ventilation should be adequate for the 10-year plan; although if the mine begins the development into the lower reef structure, then some other ventilation developments may have to take place.
The pumping capacity of the mine is only approximately 400 gallons per minute from the deepest main pump station on the 6500 Level. This mine is primarily an "upside down" mine in that most of the mining is above the main haulage adits, which drain the mine by gravity of most of its mine water. Therefore, this pumping capacity is more than double the expected amount of water mine inflow. At present, the total maximum water flow is only 200 gallons per minute.
The power furnished to the mine is 14 megawatts, with the current usage at only 11 megawatts. The mine is also equipped with a leaky feeder system for the mobile radios that are used on all mobile equipment throughout the mine.
25.1.10 SMC's Mining Safety and Health
Safety Performance: Mine safety is continuing to improve at both the Stillwater Mine and the East Boulder Mine, and the combined Incident Accident Rate (Table 25.5) has continued to drop. In the year 2000, the Incident Rate was at 14.28 as compared to an industry incident rate of 9.19. However, since that time, it has dropped every year, except 2009. The reportable incident rate has been under the national U.S. Industry underground metal mine average since 2004; again except in 2009. The problems in 2009 were probably related to the reorganization, new job reassignments, and a temporary loss of focus on real safety issues rather than the multitude of minor Mining Safety and Health Administration (MSHA) citations.
TABLE 25.5 SMC's ACCIDENT INCIDENT RATE Year 2000 2001 2002 2003 2004 2005 2006 2007 2008 2009 2010 SMC Mines 14.28 8.67 8.63 8.92 5.73 4.33 3.89 3.87 3.56 4.89 4.20 U.S. Industry Underground Metal Mines 9.19 7.13 6.38 6.11 5.76 5.52 4.61 5.43 4.91 4.05 4.46
MSHA Citations: Despite continuing improvement in safety records, the problems of MSHA Citations have become more frequent, both for SMC and for the U.S. mining industry as a whole. For the last three to four years, since several serious coal mine disasters brought criticism to the mining industry and more specifically to the MSHA inspectors, MSHA has greatly accelerated the issuing of MSHA Citations.
At SMC, MSHA inspections have been following the industry pattern. SMC mines went from 163 non- S&S Citations and 26 S&S Citations in 2006 to 316 non-S&S Citations and 66 S&S Citations in 2008; and for 2010, SMC had 337 non-S&S Citations and 81 S&S Citations. While SMC's management disagrees with many of the citations and notes that the MSHA inspector's interpretations and method of inspections are inconsistent, SMC's management acknowledges that they must apply manpower to this problem in order to continue to operate. SMC is working hard to continually educate its mine workers at every level of supervision; and also with union management to meet the challenge of these inspections while conducting a real safety program and operating safe mines.
Project 11-030 | 78 | BEHRE DOLBEAR |
Technical Report for the Mining Operations at Stillwater Mining Company
March 2011
Diesel Particulate Matter (DPM) Compliance: The Stillwater Industrial Health group has led the way in the United States in research and development to bring their diesel operations into MSHA DPM compliance. They have been in virtual compliance with the 160 micrograms of total carbon standard since 2008. This is not to say that there may not be an occasional problem in the future, with an equipment failure or human error that may result in a violation. So far, SMC has received no DPM citations. SMC's in-house sampling and testing far exceeds anything that MSHA is doing.
PGMs comprise six closely related metals: platinum, palladium, rhodium, ruthenium, iridium, and osmium, which commonly occur together in nature in varying proportions and are among the scarcest of the metallic elements. Nearly all of the world's supply of these metals is extracted from deposits in four countries, Russia, Canada, the United States, and the Republic of South Africa, which is the only country producing all six PGMs in substantial quantities. PGMs have become critical to industry because of their physical and chemical properties, the most important of which is their catalytic character. Since the mid- 1970s and continuing today, automobile manufacturers have used catalytic converters containing platinum, palladium, and rhodium to reduce automobile emissions. Similarly, the chemical and petroleum refining industries have relied on PGM catalysts to produce a wide variety of chemical and petroleum products. Electronic and jewelry uses are additional major uses of PGMs. Figure 25.17 and Figure 25.18 present data from Johnson Matthey's 2010 Interim Review on the platinum and palladium supply and demand from 2000 through their estimated total for 2010.
SMC's major market has been automobile catalysts, and for the past several years, it has had sales contracts with one or more automobile manufacturers. The Company's remaining automobile contract with Ford Motor Company expired at year-end 2010; however, it has signed some new PGM supply agreements, as discussed below.
SMC believes that the increased platinum and palladium prices that have occurred since the middle of 2009 are sustainable in the future and that the fundamentals could lead to a higher equilibrium price of palladium relative to platinum due to the surging increase in worldwide automobile production and increased regulatory requirements for catalytic converters.
Project 11-030 | 79 | BEHRE DOLBEAR |
Technical Report for the Mining Operations at Stillwater Mining Company
March 2011
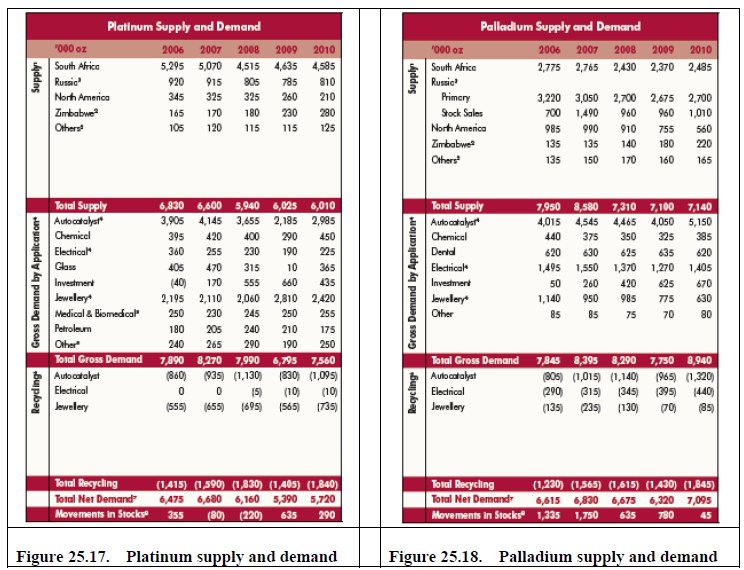
Until year-end 2010, SMC had a sales agreement with Ford Motor Company covering a portion of production from its mines that guaranteed floor and ceiling prices for metal delivered. Metal sales under the agreement, when not affected by the guaranteed floor or ceiling prices, were priced at a slight discount to market. Under this sales agreement, SMC committed 70% of its platinum production and 80% of its palladium production from mining through 2010.
In December 2010, SMC announced a new three-year agreement with General Motors to supply stipulated quantities of palladium each month at a price based on the trailing month's market price. The company has also signed two smaller agreements, one with BASF, a large producer of catalytic converters, to supply fixed month quantities of palladium and platinum, and one with Tiffany's to provide a stipulated annual quantity of platinum for jewelry. Pricing in all of these agreements is market-based. SMC also reported in February 2011 that it was in the midst of negotiating one or two more supply contracts. Any SMC production that is not committed to supply contacts will be sold in the spot market.
At sufficiently low PGM price levels, the absence of the pricing floors that were a part of the Ford Motor Company contract could have a material adverse effect on SMC. SMC restructured its operations in order to mitigate this exposure and has reduced its operating costs significantly, but the loss of the Ford Motor Company agreement will increase SMC's financial exposure to low PGM prices.
Figure 25.17. Platinum supply and demand Figure 25.18. Palladium supply and demand
Project 11-030 | 80 | BEHRE DOLBEAR |
Technical Report for the Mining Operations at Stillwater Mining Company
March 2011
25.4 TAXES
SMC's non-income taxes, royalty payments, and insurance costs are contractual or governmental obligations outside of the control of SMC's mining operations, and in the case of royalties and most taxes, are driven more by the level of sales realizations than by operating efficiency. SMC combines these costs for financial reporting purposes. In 2009, these costs totaled $26.6 million, compared to $34.3 million in 2008 and $33.4 million in 2007 (SMC's 2009 Form 10-K).
25.5 CAPITAL AND OPERATING COSTS
25.5.1 Operating and Capital Cost of the Stillwater Mine
As can be seen in Table 25.6, the Stillwater Mine production cost per ton increased by 13.7% from 2006 to 2008 but then increased by only 1.3% from 2008 through 2010. The Production Cost per ounce of PGM increased by 27.8% between 2006 and 2008 but then increased by only 2.5% between 2008 and 2010.
TABLE 25.6 STILLWATER MINE OPERATING COST
2006 2007 2008 2009 20] 10
$/ton $/oz $/ton $/ oz $/ton $/ oz $/ton $/ oz $/ton $/ oz
Total Cash Cost 143 280 147 292 170 373 174 344 171 380
Total Production Cost 205 400 213 423 233 511 238 469 236 524
Table 25.7 presents the capital costs for the Stillwater Mine for the past 8 years.
TABLE 25.7
PREVIOUS STILLWATER MINE CAPITAL COSTS ($ MILLIONS)
Capital Cost 2002 2003 2004 2005 2006 2007 2008 2009 2010
Capitalized Development 28.5 31.5 34.2 43.4 36.6 37.1 35.9 19.2 25.0
Other Capital 9.8 10.6 12.8 9.7 17.0 10.8 10.7 7.5 9.1
Total CAPEX 38.3 42.0 47.0 53.0 53.6 47.9 46.7 26.7 34.1
25.5.2 Operating and Capital Cost of the East Boulder Mine
As can be seen in Table 25.8, the East Boulder Mine's production cost per ton increased by 32.8% from 2006 to 2008 but then decreased 13.0% from 2008 through 2010. The production cost per ounce PGM increased by 35.3% between 2006 and 2008 but then decreased by 10.9% between 2008 and 2010. The production cost per ounce PGM ranged from a high of $678 down to a low of $501, with a weighted average of $528 per ounce PGM. This adequately reflects the economies of the new schedule of production rate as it is decreased from the previous forecast to reflect the drastic changes in the East Boulder Mine's work force.
12 Oz. is the returnable ounce of PGM and equals the palladium and platinum content and ratio in the mill concentrate for each mine times 0.992, which accounts for the losses from the smelter/BMR
13 Production Cost includes Depreciation, Depletion, Amortization, and Site General and Administrative cost.
Project 11-030 | 81 | BEHRE DOLBEAR |
Technical Report for the Mining Operations at Stillwater Mining Company
March 2011
TABLE 25.8 EAST BOULDER MINE OPERATING COST
2006 2007 2008 2009 20] 10
$/tons $/oz12 $/tons $/ oz $/tons $/oz $/tons $/ oz $/tons $/ oz
Total Cash Cost 113 326 136 403 154 451 136 407 147 442
Total Production Cost 174 501 206 611 231 678 191 571 201 604
The author reviewed the production estimates for the period and found them to be possible for the following reasons.
● | Most operations at the East Boulder Mine went from two 12-hour shifts to 11^-hour shifts, 24/7, with four rotating shifts, changing 4-days off. |
● | There were renegotiations with the union for such things as changing the off time "call- in" procedures and the elimination of several job classifications so that miners could perform any of the functional mining tasks needed without bringing other classified workers to the job location. |
● | The manpower at the East Boulder Mine decreased from 536 to 250. This was accomplished by drastically decreasing the operations worker support, temporarily decreasing the mine development for 2009 from three crews to one crew, and decreasing mine service staff. |
● | Approximately one-half of the mobile diesel fleet has been parked and will be mothballed or sold. |
● | Elimination of most of the mine contractors. |
● | Concentration of all of the mining in only five areas so as to make mining support much more efficient. |
The current East Boulder Mine Operation's manpower stands at about 274. However, manpower during the 10-year plan varies from a high of 281 to a low of 274, with an average of 275.6. The primary reason for the fluctuation is the use of more or less development crews and the adjustments in the size and number of maintenance crews.
Table 25.9 presents the capital costs for the East Boulder Mine for the past 8 years.
14 Production Cost includes Depreciation, Depletion, Amortization, and Site General and Administrative cost.
Project 11-030 | 82 | BEHRE DOLBEAR |
Technical Report for the Mining Operations at Stillwater Mining Company
March 2011
TABLE 25.9
PREVIOUS EAST BOULDER MINE CAPITAL COSTS ($ MILLIONS)
Capital Cost 2002 2003 2004 2005 2006 2007 2008 2009 2010
Capitalized Development 8.5 10.0 18.2 24.0 27.5 24.9 16.5 4.1 4.7
Other Capital 12.6 3.1 6.9 14.1 13.6 9.1 2.6 0.4 1.8
Total CAPEX 21.1 13.1 25.1 38.1 41.1 34.0 19.1 4.5 6.5
While the author believes that the 10-year productivities are possible, the "belt tightening" that took place at the end of 2008 must be maintained and cost controls must be extremely tight to reach the 10-year plan objectives. Some increases in spending have been noted for 2009 and these must be held in check.
25.6 ENVIRONMENTAL COMPLIANCE AND RECLAMATION
25.6.1 Introduction
Behre Dolbear considered a number of environmental factors that potentially could affect SMC, with its current investigations focused primarily on changes since 2008 as updated by a mid-2010 visit to SMC's offices and staff interviews, and a desk update through the end of 2010. Inquiry was made into issues associated with air emissions, water discharges, water treatment, ground water, tailings disposal, waste rock disposal, smelter slag, smelter scrubber sludge, reclamation, reclamation bonding, and community relations. The inquiries covered the Stillwater Mine site, the East Boulder Mine site, and the metallurgical complex at Columbus, Montana.
25.6.2 Summary and Conclusions
The waste rock, tailings, and ore generated at SMC's mining operations have been shown by testing to not be acid generating. This characteristic has positive implications both for current operations and for future closure and reclamation of the facilities. Also, the facilities do not use significant amounts of problematic chemicals. In particular, cyanide is not required by any of the processing operations. These have been positive factors for SMC, especially as regards for obtaining and renewing environmental permits.
The principal constituents of concern in mine water discharge from SMC mines are nitrites and nitrates, and to a lesser extent ammonia, all resulting from the use of blasting agents in the mining operations. These constituents are controlled by treating the mine drainage water in treatment facilities using an anaerobic bacteria system. All mine drainage water is treated, even though much of it is returned to the mines for use in the mining operations or used as make-up water in the mills. No water, not even storm water, is discharged at the metallurgical complex in Columbus, Montana.
After inquiry into and review of the various issues and discussion with SMC's environmental managers, review of NGO websites, and review of supporting legal documents, Behre Dolbear concludes that it has been, for the most part, "business as usual" regarding environmental issues at SMC operations during the period since 2008.
The only significant increase in environmental expense has been a recent increase in reclamation bonding. SMC appears to be meeting all of its environmental obligations, in spite of some reduction in
staffing that was necessitated by reduced PGM prices. As noted in the Executive Summary, bonding increases are under negotiation and may raise total amounts in the $10 million to $20 million range for the two sites. Funding support for environmental matters from SMC management and controlling interests, following the recent Norilsk equity sale, appears to be a non-issue.
Project 11-030 | 83 | BEHRE DOLBEAR |
Technical Report for the Mining Operations at Stillwater Mining Company
March 2011
SMC appears to be meeting all of its environmental obligations. Recent comments in early 2011 by the SMC Vice President of Environmental and Governmental Affairs suggest that one new staff position may be added at Nye and one at the Smelter/BMR to handle additional duties. Funding for active environmental management continues and is supported further by recent favorable economic conditions.
In general, the environmental problems at the SMC operations are minor in nature compared to other large metal mining operations, and the operations are viewed by the regulatory agencies and NGOs as being properly managed from an environmental perspective.
25.6.3 Stillwater Air Permit
The Title V air permit for the Stillwater Mine and mill was reissued in July 2007. A change from the previous permit requires corrective action if any visible emissions are observed. Although allowable opacity limits remained the same at 5% to 7%, this corrective action provision could require additional maintenance expenditures, although such expenses would probably be minor. In addition, an emission point was added for the soda ash handling equipment. An inspection by Montana Department of Environmental Quality in August 2008 found no deficiencies with respect to the air permit. (Note that a Title V permit is required only for sources classified as "major," and that neither East Boulder Mine nor the metallurgical plant at Columbus, Montana are so classified. The Stillwater Mine reaches the threshold due to the amount of diesel equipment running in the mine, which contributes to the loading on mine exhaust fan emissions.)
At this time, there is no indication that, if Title V permits were to be required for these operations, there would be any significant issues or delays in obtaining the permits. It is estimated that the East Boulder Mine operations could reach the permitting threshold in five to six years and the metallurgical complex in three to five years.
25.6.4 Stillwater Montana Department of Environmental Quality Permit
A new water discharge permit was issued effective November 1, 2008 by Montana Department of Environmental Quality. The previous permit had expired several years earlier but had been administratively extended by Montana Department of Environmental Quality pending their having the time and resources to process the renewal application, which had been submitted by SMC before expiration of the previous permit. The new permit adds a number of parameters that must be included in SMC's self-monitoring reports. Many of these parameters were included in the previous permits several years ago but were dropped from the permit when sampling and analysis consistently showed them to be below detection limits. It is expected that this will again be the case and that these parameters will again be dropped from the permit after a year or two. No problems are expected from these additional monitoring requirements, other than the higher analytical costs incurred.
25.6.5 Revisions to Water Treatment Facilities at East Boulder
In 2007, SMC's environmental personnel were concerned that nitrogen loading in the discharge at the East Boulder Mine was increasing, even though it was below the limits prescribed in the permit. This was believed to be due to the nitrogen in ammonia, as ammonia was not being treated. Accordingly, one of the biological treatment cells was modified to convert ammonia to nitrates and nitrites, the effluent from which goes to the remaining cells for de-nitrification. This procedure has been effective in lowering total nitrogen load in the discharge. A reverse osmosis unit is being constructed as a backup system at the site.
Project 11-030 | 84 | BEHRE DOLBEAR |
Technical Report for the Mining Operations at Stillwater Mining Company
March 2011
25.6.6 Groundwater Study at East Boulder
Nitrate levels in the ground water at the East Boulder Mine resulted in a Water Quality Act enforcement action by the State of Montana against SMC. Nitrates were reaching levels above the permit allowances in 2008, 2009, and 2010. Violation notices were sent to SMC. Subsequently, SMC and the State entered into an Administrative Order on Consent whereby SMC provided to the State of Montana a Mitigation Plan in late 2010. The State of Montana is satisfied with SMC's signing of the Administrative Order of Consent to the extent that $130,000 in Notice of Violation fines were waived. SMC's innovative measures taken to date as noted in the Mitigation Plan, including installation of de-nitrification wells to control groundwater quality in discharges to control the plume emanating from the pond and other sources, have been well received. Behre Dolbear believes that this issue is being resolved to the satisfaction of the state and community and will not be a significant issue going forward.
25.6.7 Environmental Impact Statement
As noted in previous Behre Dolbear reports, preparation of an Environmental Impact Statement (EIS) had been ongoing for several years. Finally in November 2010, the Draft EIS was issued for public comment. Comments were due 24 February 2011. This is a joint effort by the U.S. Forest Service and the Montana Department of Environmental Quality. A brief review of the Executive Summary of the EIS shows it to address three major issues:
● | closure and post-closure water management plans at the Stillwater Mine and Hertzler Ranch LAD |
● | closure and post-closure water management plans at East Boulder Mine |
● | prospective use of the Boe Ranch LAD at East Boulder, its operational flexibility, and related matters |
Nine alternatives are addressed, and Agency Preferred Alternatives are described.
The EIS was in planning stages for an extended period to address a number of closure issues at both mines as well as some miscellaneous issues that have arisen since earlier EISs were undertaken. In the current EIS, closure issues include design of caps to be placed over waste and tailings, post closure water quality, and water management for all adit, tailings, and storm water generated during operations, closure, and post-closure. The EIS also addresses potential land application of water from East Boulder operations at the Boe Ranch, if it should be needed in the future. From Behre Dolbear's brief review, it appears that the above issues are carefully and thoroughly addressed.
25.6.8 Reclamation Bonding Changes
The Stillwater Mine's bond is $19.5 million and the East Boulder Mine's bond is $13.5 million. Negotiations on bond adjustments continue with the agencies, and revised bonding amounts to address current plans could total in the $45 million to $55 million range for both operations. SMC's staff are confident that new controlling interests (following the recent Norilsk equity sale by Norilsk Nickel of its
SMC shares, representing about 51.3% of the company's equity) will support such environmental expenditures.
Project 11-030 | 85 | BEHRE DOLBEAR |
Technical Report for the Mining Operations at Stillwater Mining Company
March 2011
25.6.9 Storm Water Permit at Metallurgical Complex
The acquisition of an additional parcel of land for potential future expansion of the metallurgical complex gave rise to concerns that a major storm event could result in discharge of storm water (the metallurgical complex has been a no-discharge facility from inception). It is expected that the facility will retain the no- discharge status even with future expansion; however, should a major storm event or failure of an impoundment structure occur, the permit would assure that the facility would not be in the serious position of discharging without a permit. The storm water permit became effective during 2008, and the required Pollution Prevention Plan, incorporating Best Management Practices, was prepared. One improvement incorporated into the planning to handle storm water was the capture of precipitation falling on the plant roof for use as industrial water in the metallurgical complex.
25.6.10 Future Waste Disposal Issues
At the Stillwater Mine, the increasing the height of the mine waste rock storage areas will accommodate anticipated production of such rock until about 2018. Regulatory authorities were more favorable to raising the elevation of the storage areas than to expanding rock storage to new ground. The mine received permission to raise the storage area another 100 feet, which would provide about 10 more years of operation.
Mill tailings from the Stillwater Mine will be accommodated at the Hertzler site (Stage 2) until 2014 or 2015, and Stage 3, which has already been permitted, will probably begin construction in 2012 and serve until 2025 to 2030. At the Hertzler site, a groundwater plume was discovered whose source was determined to be a hole in the liner. Mitigation plans and enhancements to future expansions were approved by the Montana Department of Environmental Quality and the U.S. Forest Service, and the situation is determined to be to the satisfaction of all parties.
At the East Boulder Mine, the present tailing disposal area is believed to be sufficient for the known ore reserves. Because mine waste rock is used for construction of the tailings impoundment, no other provision for storage of such rock is deemed necessary, and, in fact, a borrow area has been permitted because it is anticipated that there will be a shortage of rock for dam construction from time-to-time.
At the metallurgical complex, smelter slag is not regarded as waste material but rather as a by-product containing valuable metals. Accordingly, slag is sent to one of the mills (both mills have been used) for recovery of these metals in the flotation process. Periodically, the recoverable metals in the slag are determined and documented so that SMC will be able to refute any possible future charge of "sham recycling." Although SMC had been planned to install equipment for granulating smelter slag to improve handling, a reduction in capital spending, due to lower prices for SMC's products, has caused this improvement to be delayed for an undetermined period of time. The sludge from the air scrubbing system is gypsum, which is sold for use as an agricultural soil amendment.
25.6.11 Other Matters
Restructuring of operations at East Boulder in 2008 resulted in some personnel reduction in the environmental group, although the duties and responsibilities of the group have not been reduced. Any periodic shortfalls in personnel have been made up by borrowing help from other SMC operations or by the use of consultants, and all responsibilities are reportedly being met. As noted above, two new hires are currently planned to handle increasing environmental responsibilities.
Project 11-030 | 86 | BEHRE DOLBEAR |
Technical Report for the Mining Operations at Stillwater Mining Company
March 2011
The Good Neighbor Agreement, which legally binds SMC and the local NGOs to find collaborative solutions to environmental and economic issues, celebrated its 10th anniversary in 2010. This agreement has contributed to the stability in the regulatory environment that has been beneficial to SMC's operations. The Good Neighbor Agreement appears to be active and effective.
United States Environmental Protection Agency (EPA) financial assurance bonding of mine sites under CERCLA is an issue that could have a potentially significant financial impact to SMC's operations. The so-called CERCLA bonding regime will be focused at any mine site that has, or is projected to have, long-term water treatment issues. As of late 2010, the schedule is for the proposed rule for mining to be issued in the fall of 2011, followed by other industries in the summer of 2012. At the present time, it is anticipated that this rule, if enacted, could impact SMC sometime in 2014. Although SMC is not expected to have "serious" long-term water treatment issues, the potential exists for additional cash bonding requirements in the future. The update in late 2010 continues to suggest that SMC is very proactive in anticipating problems in this aspect of the operations.
25.7 CATALYTIC CONVERTER RECYCLE BUSINESS
SMC recycles automotive catalytic converters at its metallurgical complex in Columbus, Montana. In 2009, a second electric furnace became fully operational and allowed a 50% increase in concentrate processing. The recycled catalytic converters are added to the concentrate from the mines in this furnace. The copper and nickel sulfides in the mine concentrates enhance the recovery of the PGMs in the catalytic converters. Thus, the recycling business depends on the concentrates shipped from the mines as a significant part of the economic viability of the business.
The amount of recycled catalytic converters received fluctuates with the prices of PGMs. Following the steep decline in prices in the second half of 2008, the amount of catalytic converters received for recycling also declined. As prices recovered during 2009, the amount of recycled catalytic converters received also increased. Overall, during 2009, SMC fed 251,000 recycled PGM ounces into the smelter, down 37% from the 398,000 ounces fed during 2008. However, by the fourth quarter of 2009, volumes had recovered to nearly their 2008 level. SMC estimates that at present only about 50% of catalytic converters are recycled and that the average age of these converters is about 12 years. SMC expects that with increased loadings of catalytic converters in newer vehicles and increasing PGM prices, the percentage of catalytic converters that are recycled will increase to 70%.
Due to the investment in the second electric furnace, other capital improvements related to the recycling business (a new processing and sampling plant and a new X-ray assay lab) and SMC's projected increases in recycling volumes, SMC formed a new subsidiary, Stillwater Metals Company, in February 2010 to oversee the recycling business. Stillwater Metals Company operates its recycling business on both purchase and toll bases.1 Among other things, the new X-ray assay lab, which will provide faster assay results, will allow Stillwater Metals Company to provide faster returns to recycled catalytic converter suppliers, increasing its competitive status in the recycled PGM market. The formation of Stillwater Metals Company will also allow SMC greater protection from downturns in PGM prices and resulting declines in the quantity of catalytic converters received for recycling.
15 In the purchase basis option, Stillwater Metals Company buys the recycled catalytic converters from the supplier at a price depending on spot PGM prices. If the prices increase between the time of purchase and the time the contained PGMs are recovered and sold, Stillwater Metals Company comes out ahead. If PGM prices decline, the reverse is true. In the toll basis option, the supplier pays Stillwater Metals Company a fee for processing and recovering the contained PGMs but retains ownership of the contained PGM ounces.
Project 11-030 | 87 | BEHRE DOLBEAR |
TO: Alberta Securities Commission
Saskatchewan Financial Services Commission
Registrar of Securities, Prince Edward Island
RE: Technical Report entitled “Technical Report for the Mining Operations of Stillwater Mining Company” dated March 14, 2011 of Stillwater Mining Company (“Stillwater”)
I, David M. Abbott, Jr., am an author of the technical report entitled “Technical Report for the Mining Operations of Stillwater Mining Company”, dated March 14, 2011, (the “Technical Report”) and hereby consent to the public filing by Stillwater of the Technical Report and to the filing of the Technical Report with the securities regulatory authorities referred to above.
[Remainder of page intentionally left blank.]
Dated this 23rd day of June, 2011.
___________________________
Signature of Qualified Person
David M. Abbott, Jr.
____________________________
Name of Qualified Person
TO: Alberta Securities Commission
Saskatchewan Financial Services Commission
Registrar of Securities, Prince Edward Island
RE: Technical Report entitled “Technical Report for the Mining Operations of Stillwater Mining Company” dated March 14, 2011 of Stillwater Mining Company (“Stillwater”)
I, Richard L. Bullock, am an author of the technical report entitled “Technical Report for the Mining Operations of Stillwater Mining Company”, dated March 14, 2011, (the “Technical Report”) and hereby consent to the public filing by Stillwater of the Technical Report and to the filing of the Technical Report with the securities regulatory authorities referred to above.
[Remainder of page intentionally left blank.]
Dated this 23rd day of June, 2011.
___________________________
Signature of Qualified Person
__Richard L. Bullock___________
Name of Qualified Person
TO: Alberta Securities Commission
Saskatchewan Financial Services Commission
Registrar of Securities, Prince Edward Island
RE: Technical Report entitled “Technical Report for the Mining Operations of Stillwater Mining Company” dated March 14, 2011 of Stillwater Mining Company (“Stillwater”)
I, Betty L. Gibbs, am an author of the technical report entitled “Technical Report for the Mining Operations of Stillwater Mining Company”, dated March 14, 2011, (the “Technical Report”) and hereby consent to the public filing by Stillwater of the Technical Report and to the filing of the Technical Report with the securities regulatory authorities referred to above.
[Remainder of page intentionally left blank.]
Dated this 23rd day of June, 2011.
___________________________
Signature of Qualified Person
Betty L. Gibbs
____________________________
Name of Qualified Person
TO: Alberta Securities Commission
Saskatchewan Financial Services Commission
Registrar of Securities, Prince Edward Island
RE: Technical Report entitled “Technical Report for the Mining Operations of Stillwater Mining Company” dated March 14, 2011 of Stillwater Mining Company (“Stillwater”)
I, Richard S. Kunter, am an author of the technical report entitled “Technical Report for the Mining Operations of Stillwater Mining Company”, dated March 14, 2011, (the “Technical Report”) and hereby consent to the public filing by Stillwater of the Technical Report and to the filing of the Technical Report with the securities regulatory authorities referred to above.
[Remainder of page intentionally left blank.]
Dated this 23rd day of June, 2011.
Signature of Qualified Person
____________________________
Name of Qualified Person