Selected Financial Data
(Millions of Dollars Except Per Share Amounts) | | 2002 | | | 2001 | | 2000 | | | 1999 | | 1998 |
|
|
Statement of Income Data: | | | | | | | | | | | | |
|
Sales and other operating revenue (including consumer excise taxes) | | $14,299 | | | $14,063 | | $14,514 | | | $10,045 | | $8,482 |
|
Income (loss) from continuing operations* | | $(47 | ) | | $398 | | $411 | | | $97 | | $280 |
|
Income from discontinued operations | | $— | | | $— | | $11 | ** | | $— | | $— |
|
Net income (loss) | | $(47 | ) | | $398 | | $422 | | | $97 | | $280 |
|
Per Share Data: | | | | | | | | | | | | |
|
Income (loss) from continuing operations: | | | | | | | | | | | | |
|
Basic | | $(.62 | ) | | $4.92 | | $4.72 | | | $1.07 | | $3.09 |
|
Diluted | | $(.62 | ) | | $4.85 | | $4.70 | | | $1.07 | | $2.95 |
|
Net income (loss): | | | | | | | | | | | | |
|
Basic | | $(.62 | ) | | $4.92 | | $4.85 | | | $1.07 | | $3.09 |
|
Diluted | | $(.62 | ) | | $4.85 | | $4.82 | | | $1.07 | | $2.95 |
|
Cash dividends on preference stock*** | | $— | | | $— | | $— | | | $— | | $1.6516 |
|
Cash dividends on common stock | | $1.00 | | | $1.00 | | $1.00 | | | $1.00 | | $1.00 |
|
Balance Sheet Data: | | | | | | | | | | | | |
|
Cash and cash equivalents | | $390 | | | $42 | | $239 | | | $87 | | $38 |
|
Total assets† | | $6,441 | | | $6,019 | | $5,537 | | | $5,289 | | $4,922 |
|
Short-term borrowings and current portion of long-term debt | | $2 | | | $302 | | $2 | | | $151 | | $189 |
|
Long-term debt | | $1,453 | | | $1,142 | | $933 | | | $878 | | $823 |
|
Shareholders’ equity | | $1,394 | | | $1,642 | | $1,702 | | | $1,506 | | $1,514 |
Shareholders’ equity per share | | $18.24 | | | $21.74 | | $20.06 | | | $16.76 | | $16.75 |
|
* | | Includes after-tax provisions for write-down of assets and other matters totalling $22, $1, $147, $1 and $31 million in 2002, 2001, 2000, 1999 and 1998, respectively, after-tax gains on settlement of insurance litigation totalling $5, $47 and $38 million in 2000, 1999 and 1998, respectively, gains on income tax settlements totalling $21 and $117 million in 2001 and 2000, respectively, and a $13 million tax benefit resulting from a change in tax election in 1998. (See Notes 2, 3 and 4 to the consolidated financial statements.) |
** | | Consists of a favorable adjustment to the 1996 gain on divestment of discontinued international oil and gas production operations. |
*** | | On May 28, 1998, the Company redeemed all of its outstanding shares of preference stock. The cash dividends per share of preference stock for 1998 represent the dividends paid through the redemption date. |
† | | Prior-year amounts have been reclassified to conform to the 2002 presentation. |
8
Management’s Discussion and Analysis of Financial Condition and Results of Operations
Management’s Discussion and Analysis is the Company’s analysis of its financial performance and of significant trends that may affect future performance. It should be read in conjunction with Sunoco’s consolidated financial statements and related notes. Those statements in Management’s Discussion and Analysis that are not historical in nature should be deemed forward-looking statements that are inherently uncertain. See “Forward-Looking Statements” on page 33 for a discussion of the factors that could cause actual results to differ materially from those projected.
Outlook
Sunoco’s profitability is primarily determined by refined product and chemical margins and the reliability and efficiency of its operations. The volatility of crude oil, refined product and chemical prices and the overall supply/demand balance for these commodities have had, and should continue to have, a dramatic impact on margins and financial results of the Company.
Throughout 2000 and the first half of 2001, refined product margins in Sunoco’s principal refining centers in the Northeast and Midwest were extremely strong, benefiting from exceptionally low industry refined product inventory levels and very strong product demand. However, product margins declined significantly in the second half of 2001 and remained low throughout the first nine months of 2002 due to high industry inventory levels, rising crude oil prices, a higher level of gasoline imports from Europe and warmer winter weather in early 2002. Chemical margins for most products were weak during 2001 and most of 2002 as a result of an oversupplied marketplace. In the latter part of 2002, refining margins began to improve as industry refined product inventory levels declined and chemical margins began to strengthen in response to chemical price increases due to phenol supply disruptions in the United States and an improvement in product demand.
In 2003, the Company believes refined product margins, including those for retail gasoline, will be higher than 2002. However, the absolute level of these margins is difficult to predict as they are influenced by a number of extremely volatile factors in the global marketplace including: crude oil price levels and availability; crude oil transportation costs; refined product inventory levels; refined product demand; refinery utilization rates; the level of refined product imports into the United States; and geopolitical events such as those in Venezuela and Iraq. The Company believes chemical margins and volumes will continue to improve in 2003 assuming a strengthening U.S. economy and ongoing industry rationalization moderates the supply/demand balance.
The Company expects 2003 operating results to be impacted by higher pension expense, which is expected to increase by approximately $30 million after tax. This increase is primarily attributable to the decline in pension plan assets due to the poor performance of equity markets over the past three years.
The Company’s future operating results and capital spending plans will also be impacted by environmental matters (see “Environmental Matters” below).
Given the very competitive marketplace and the highly volatile and uncertain margin environment in which the Company operates, Sunoco is committed to improving its results by:
• | | Delivering excellence in health and safety and environmental compliance; |
• | | Increasing reliability and realizing other efficiencies at each of the Company’s manufacturing facilities; |
• | | Continuing to expand and improve retail marketing through ongoing programs; |
• | | Prudently managing expenses and capital spending; and |
• | | Continuing to diversify, upgrade and grow its asset portfolio through strategic acquisitions and investments. |
9
Results of Operations
Earnings Profile of Sunoco Businesses (after tax)
(Millions of Dollars) | | 2002 | | | 2001* | | | 2000 | |
|
|
Refining and Supply** | | $ | (31 | ) | | $ | 290 | | | $ | 317 | |
|
Retail Marketing | | | 20 | | | | 87 | | | | 77 | |
|
Chemicals | | | 28 | | | | 6 | | | | 16 | |
|
Logistics | | | 33 | | | | 42 | | | | 46 | |
|
Coke | | | 42 | | | | 61 | | | | 61 | |
|
Corporate and Other: | | | | | | | | | | | | |
|
Corporate expenses | | | (26 | ) | | | (24 | ) | | | (23 | ) |
|
Net financing expenses and other | | | (91 | ) | | | (82 | ) | | | (56 | ) |
|
Income tax settlements | | | — | | | | 21 | | | | 117 | |
|
Insurance litigation settlements | | | — | | | | — | | | | 5 | |
|
Write-down of assets and other matters | | | (22 | ) | | | (1 | ) | | | (147 | ) |
|
Value Added and Eastern Lubricants** | | | — | | | | (2 | ) | | | (2 | ) |
|
Discontinued operations | | | — | | | | — | | | | 11 | |
|
Consolidated net income (loss) | | $ | (47 | ) | | $ | 398 | | | $ | 422 | |
|
* | | Consistent with the 2002 presentation, an $11 million after-tax expense accrual for environmental remediation activities has been reclassified from Write-down of Assets and Other Matters to Retail Marketing. |
** | | In connection with the Company’s decision to dispose of its Puerto Rico refinery, lubricants blending and packaging facilities and lubricants branded marketing assets (collectively, “Value Added and Eastern Lubricants”), commencing with the fourth quarter of 2000, those operations are reported as a separate item. Value Added and Eastern Lubricants losses of $29 million for the nine months ended September 30, 2000 are included in Refining and Supply. |
Analysis of Earnings Profile of Sunoco Businesses
In 2002, Sunoco, Inc. and its subsidiaries had a net loss of $47 million, or $.62 per share of common stock on a diluted basis, compared to net income of $398 million, or $4.85 per share in 2001 and net income of $422 million, or $4.82 per share in 2000.
The $445 million decrease in net income in 2002 was primarily due to significantly lower margins in Sunoco’s Refining and Supply ($451 million) and Retail Marketing ($70 million) businesses. Also contributing to the decline in earnings were a $9 million reduction in Logistics income largely due to the sale in February 2002 of a 25 percent interest in Sunoco Logistics Partners L.P., the Company’s master limited partnership; a $19 million reduction in Coke earnings, which were negatively impacted by the bankruptcy filing of a former long-term contract customer; the absence of gains on income tax settlements ($21 million); higher insurance and pension costs ($24 million); and higher provisions for write-down of assets and other matters ($21 million). Partially offsetting these negative factors were higher sales volumes of wholesale refined products ($47 million), retail gasoline ($14 million) and chemicals ($14 million) and lower refinery fuel costs ($92 million).
In 2001, the $24 million decrease in net income was primarily due to lower margins in Sunoco’s Northeast refining system ($114 million); lower gains on income tax settlements ($96 million); higher refinery fuel and volume-related costs ($68 million); and higher expenses in Retail Marketing ($52 million), primarily as a result of an increase in volumes. Also contributing to the decline were lower Chemicals income ($10 million); the absence of income from discontinued operations ($11 million); and higher net financing expenses ($26 million), primarily as a result of financing costs attributable to the Aristech acquisition. Partially offsetting these negative factors were lower provisions for write-down of assets and other matters ($146 million), improved margins in Sunoco’s MidContinent refining centers ($117 million) and Retail Marketing operations ($19 million), higher wholesale refined product sales volumes ($9 million), higher Retail Marketing gasoline sales volumes ($22 million) and non-gasoline income ($21 million) and the absence of the $29 million operating loss in Sunoco’s Value Added and Eastern Lubricants operations incurred in the first nine months of 2000.
10
Refining and Supply
The Refining and Supply business manufactures petroleum products at its Marcus Hook, Philadelphia, Toledo and Tulsa refineries and commodity petrochemicals at its Marcus Hook, Philadelphia and Toledo refineries and sells these products to other Sunoco businesses and to wholesale and industrial customers. This business also manufactures lubricant products at its Tulsa refinery which are sold into process oil, wholesale base oil and wax markets (“Western Lubricants”) and prior to the fourth quarter of 2000 included Value Added and Eastern Lubricants operations.
| | 2002 | | | 2001 | | 2000 | |
|
|
Income (loss) (millions of dollars) | | $(31 | ) | | $290 | | $317 | * |
|
Wholesale margin** (per barrel): | | | | | | | | |
|
Total Refining and Supply | | $3.59 | | | $6.04 | | $6.01 | |
|
Northeast Refining System | | $3.18 | | | $5.20 | | $6.08 | |
|
Toledo Refinery | | $4.45 | | | $8.13 | | $6.17 | |
|
Tulsa Refinery | | $4.61 | | | $7.49 | | $4.87 | |
|
Wholesale sales (thousands of barrels daily): | | | | | | | | |
|
To unaffiliated customers: | | | | | | | | |
|
Gasoline | | 152.5 | | | 137.5 | | 145.0 | |
|
Middle distillates | | 209.9 | | | 205.7 | | 219.5 | |
|
Residual fuel | | 62.6 | | | 59.8 | | 55.6 | |
|
Petrochemicals | | 13.2 | | | 13.5 | | 13.4 | |
|
Lubricants | | 13.4 | | | 9.3 | | 8.5 | |
|
Other | | 53.8 | | | 52.8 | | 52.0 | |
|
|
| | 505.4 | | | 478.6 | | 494.0 | |
|
To affiliates (primarily gasoline) | | 316.2 | | | 287.6 | | 263.7 | |
|
| | 821.6 | | | 766.2 | | 757.7 | |
|
|
Crude unit capacity (thousands of barrels daily) at December 31 | | 730.0 | | | 730.0 | | 730.0 | |
|
Crude unit capacity utilized | | 95% | | | 94% | | 92% | |
|
Conversion capacity*** (thousands of barrels daily) at December 31 | | 306.7 | | | 306.7 | | 306.7 | |
Conversion capacity utilized | | 95% | | | 90% | | 88% | |
|
* | | Includes losses of $29 million for the nine months ended September 30, 2000 attributable to Value Added and Eastern Lubricants operations. All other statistics in the table exclude amounts attributable to such operations for comparison purposes. |
** | | Wholesale sales price less cost of crude oil, other feedstocks, product purchases and related terminalling and transportation. |
*** | | Represents capacity to upgrade lower-value, heavier petroleum products into higher-value, lighter products. |
Refining and Supply segment results decreased $321 million in 2002 due to significantly lower realized margins ($451 million) compared to last year’s strong levels, partially offset by lower operating expenses due to a decline in refinery fuel costs ($67 million), higher production and sales volumes ($47 million) and a benefit attributable to LIFO inventory profits ($5 million). The margin decline resulted largely from rising crude oil prices throughout the year and high industry inventory levels. Warmer winter weather in early 2002, reduced jet fuel demand and much lower natural gas prices also impacted margins for distillates and other related fuel oil products. Margins at the Toledo and Tulsa refineries during 2001 were exceptionally high, in part, due to the industry supply disruptions in the Midwest during the second and third quarters of that year.
Refining and Supply segment income decreased $27 million in 2001 largely due to lower realized margins ($119 million) for wholesale fuels in the Northeast and petrochemicals produced across the refinery system and higher refinery fuel and volume-related operating costs ($68 million). Partially offsetting these negative factors were an increase in margins for wholesale fuels in the MidContinent and base oils produced at the Tulsa refinery ($122 million), higher refined product sales volumes ($9 million) and the absence of the $29 mil - -
11
lion operating loss in Sunoco’s Value Added and Eastern Lubricants operations incurred in the first nine months of 2000. Refined product margins and sales volumes were favorably impacted by a 7.7 million barrel, or 3 percent, increase in production to record levels.
During 2002, Sunoco recorded a $2 million after-tax charge to write off certain processing units at its Toledo refinery that were shut down as part of its decision to eliminate less efficient production capacity and established a $3 million after-tax accrual relating to a lawsuit concerning the Puerto Rico refinery, which was divested in December 2001 (see “Corporate and Other” below). During 2000, Sunoco announced its intention to sell its Value Added and Eastern Lubricants operations due to the inability to achieve an adequate return on capital employed in this business and recorded a $123 million after-tax charge to write down the assets held for sale to their estimated values. In connection therewith, Sunoco sold its lubricants marketing assets in March 2001, closed its lubricants blend plants in Marcus Hook, PA, Tulsa, OK and Richmond, CA in July 2001 and sold the Puerto Rico refinery in December 2001, which concluded the lubricants restructuring plan. As part of the restructuring, in 2001, Sunoco recorded a $10 million after-tax accrual for required exit costs, an $11 million after-tax accrual for employee terminations and an $11 million after-tax gain on the sale of the Puerto Rico refinery. During 2000, Sunoco also reversed into income the remaining $4 million after-tax loss accrual established in 1996 related to an MTBE purchase commitment. All of the above amounts are reported as part of the Write-Down of Assets and Other Matters shown separately under Corporate and Other in the Earnings Profile of Sunoco Businesses (see Note 3 to the consolidated financial statements).
For many years, sulfur gas generated during the refining process at Sunoco’s Marcus Hook refinery has been sent to a third party, General Chemical, for processing into sulfur. This arrangement with General Chemical generally functioned smoothly until 2002 when General Chemical experienced a series of operating failures. As a result of these incidents, Sunoco entered into a consent decree with the Delaware Department of Natural Resources and Environmental Control in the second quarter of 2002. The consent decree, among other things, provided for penalties of up to $10 thousand per day if Sunoco incinerates sulfur gas as a result of General Chemical’s failure to accept the gas. Sunoco believes it is in full compliance with the consent decree. As part of a long-term solution, in September 2002, Sunoco announced that it will build and operate its own sulfur plant at Marcus Hook. It is anticipated that construction of this facility, which is estimated to cost $40-$50 million, will be completed by early 2005. In October 2002, the parent company of General Chemical, GenTek, filed for Chapter 11 bankruptcy reorganization. Initially, General Chemical indicated it planned to continue to operate its sulfur plant while the parent company negotiates a plan of reorganization. However, on February 28, 2003, General Chemical announced its intent to close the sulfur processing portion of its facility on or about September 30, 2003. Sunoco is in negotiations with General Chemical and the State of Delaware to attempt to keep the facility operating until Sunoco’s sulfur recovery plant is operational. Sunoco is also investigating alternative technologies to allow for processing of its sulfur gas on an interim basis should General Chemical’s facility be shut down. Although Sunoco believes that it would not violate its permit or the consent decree to operate its Marcus Hook refinery without General Chemical’s sulfur recovery operation, this matter could have a significant impact on the Company’s results of operations.
12
Retail Marketing
The Retail Marketing business sells gasoline and middle distillates at retail and operates convenience stores in 23 states primarily on the East Coast and in the Midwest region of the United States.
| | 2002 | | 2001 | | | 2000 |
|
|
Income (millions of dollars) | | $20 | | $87 | * | | $77 |
|
Retail margin** (per barrel): | | | | | | | |
|
Gasoline | | $3.14 | | $4.27 | | | $3.87 |
|
Middle distillates | | $4.14 | | $4.72 | | | $4.97 |
|
Sales (thousands of barrels daily): | | | | | | | |
|
Gasoline | | 262.3 | | 244.1 | | | 225.3 |
|
Middle distillates | | 36.4 | | 35.0 | | | 31.7 |
|
| | 298.7 | | 279.1 | | | 257.0 |
|
Retail gasoline outlets | | 4,328 | | 4,151 | | | 3,635 |
|
* | | Consistent with the 2002 presentation, an $11 million after-tax expense accrual for environmental remediation activities has been reclassified from Write-down of Assets and Other Matters to Retail Marketing in the Earnings Profile of Sunoco Businesses. |
** | | Retail sales price less wholesale price and related terminalling and transportation costs. The retail sales price is the weighted average price received through the various branded marketing distribution channels. |
Retail marketing segment income decreased $67 million in 2002 primarily due to a lower average retail gasoline margin ($65 million), which was down 2.7 cents per gallon, or 26 percent, versus 2001. Higher expenses ($21 million), largely associated with volume growth, also reduced results. Partially offsetting these negative factors were higher retail gasoline sales volumes ($14 million), which increased 7 percent versus 2001 largely due to volumes associated with Coastal retail outlets acquired from El Paso Corporation during the 2001-2002 period, and higher non-gasoline income ($5 million). Sunoco acquired 397 and 473 Coastal retail gasoline outlets during 2002 and 2001, respectively, from El Paso Corporation. These outlets, which include approximately 110 convenience-store locations, are located primarily in the Northeastern and Southeastern United States. Average gasoline throughput per company-owned or leased outlet and convenience store sales per site were also up, increasing 5 and 8 percent, respectively.
Retail Marketing segment income increased $10 million in 2001 due to a higher average retail gasoline margin ($19 million), which was up 1.0 cents per gallon versus 2000, higher retail gasoline sales volumes ($22 million), which increased 8 percent versus 2000 largely due to the addition of the Coastal retail outlets, and higher non-gasoline income ($21 million), including increased earnings from retail heating oil operations. Partially offsetting these positive factors were higher marketing and administrative expenses ($52 million) largely attributable to an increase in company-operated locations primarily resulting from the acquisition of the Coastal outlets. The increase in expenses also included higher environmental remediation costs ($16 million) due largely to higher cost estimates for operating remediation systems at various retail sites and product terminals primarily due to use of MTBE in gasoline.
In January 2003, Sunoco signed an agreement to purchase 193 direct retail gasoline sites from a subsidiary of Marathon Ashland Petroleum LLC for $140 million plus inventory. The sites, which are located primarily in Florida and South Carolina, are all company-operated locations with convenience stores. Of the 193 outlets, 54 are subject to long-term lease agreements. This transaction is subject to regulatory approval.
13
Chemicals
The Chemicals business manufactures commodity and intermediate petrochemicals at the chemical plants acquired from Mitsubishi Corporation in 2001 located in Neal, WV; Haverhill, OH; Neville Island, PA; and Pasadena and LaPorte, TX that manufacture phenol and related products, polypropylene and plasticizers, at its Philadelphia cumene and phenol facilities, at its Mont Belvieu, TX joint venture MTBE facility (“BEF”) and at its Marcus Hook Epsilon Products Company, LLC joint venture polypropylene facility (“Epsilon”).
| | 2002 | | 2001 | | 2000 |
|
|
Income (millions of dollars) | | $28 | | $6 | | $16 |
|
Margin* (cents per pound): | | | | | | |
|
All products | | 6.4¢ | | 6.5¢ | | 4.3¢ |
|
Phenol and related products** | | 8.0¢ | | 8.4¢ | | 4.5¢ |
|
Polypropylene*** | | 9.5¢ | | 8.9¢ | | —¢ |
|
Sales (millions of pounds): | | | | | | |
|
Phenol and related products (including bisphenol-A) | | 2,831 | | 2,605 | | 1,771 |
|
Polypropylene*** | | 1,346 | | 1,384 | | — |
|
Plasticizers | | 615 | | 532 | | — |
|
Propylene | | 774 | | 715 | | 761 |
|
Other | | 178 | | 175 | | 297 |
|
| | 5,744 | | 5,411 | | 2,829 |
|
* | | Wholesale sales price less the cost of feedstocks and product purchases. The margin for all chemical products has also been reduced by related terminalling and transportation costs. |
** | | Consists of margin for phenol and byproducts divided by phenol sales volumes. Excludes margins and sales volumes attributable to a long-term, cost-based contract with Honeywell International, Inc. |
*** | | Excludes Epsilon Products Company, LLC polypropylene joint venture. |
Chemicals segment income increased $22 million in 2002 primarily as a result of higher sales volumes ($14 million), which increased 6 percent versus 2001. Also contributing to the increase were lower operating expenses ($6 million) due to a decline in both fuel costs and controllable expenses and higher equity income from Sunoco’s joint venture chemical operations ($7 million). Partially offsetting these positive factors were lower margins ($3 million), primarily for phenol and related products.
Chemicals segment income decreased $10 million in 2001 primarily due to a $15 million loss from the operations acquired from Mitsubishi Corporation effective January 1, 2001. Contributing to the decline were reduced product demand which adversely impacted production volumes and lower equity income from Sunoco’s joint venture chemical operations. Pretax equity income (loss) from the BEF and Epsilon joint ventures amounted to $5 and $(11) million, respectively, in 2001 compared to $12 and $(1) million, respectively, in 2000. Partially offsetting these negative factors was an increase in margins for phenol and related products at the Company’s Philadelphia cumene and phenol facilities ($7 million) and lower operating expenses ($6 million).
During 2002, Sunoco shut down a 200 million pounds-per-year polypropylene line at its LaPorte, TX plant. Subsequent to the shutdown, the Chemicals business continues to operate five polypropylene lines with capacity in excess of 2.0 billion pounds per year. In 2002, Sunoco also shut down its 170 million pounds-per-year aniline and diphenylamine production facility in Haverhill, OH. In connection with the shutdowns, the Company recorded a $14 million after-tax provision in 2002, primarily related to the write-off of the affected assets. This amount is reported as part of the Write-Down of Assets and Other Matters shown separately in Corporate and Other in the Earnings Profile of Sunoco Businesses (see Note 3 to the consolidated financial statements). The shutdowns are not expected to have a material impact on Chemicals’ future results of operations.
14
Effective January 1, 2001, Sunoco completed the acquisition of Aristech, a wholly owned subsidiary of Mitsubishi Corporation (“Mitsubishi”), for $506 million in cash and the assumption of $163 million in debt. The purchase price included $107 million for working capital. Contingent payments with a net present value as of the acquisition date of up to $167 million (the “earn out”) may also be made if realized margins for polypropylene and phenol exceed certain agreed upon thresholds through 2006. Since the $167 million represents a present value as of January 1, 2001, the actual amounts that could ultimately be paid under the earn out provisions increase over time by 11 percent per year. However, these contingent payments are limited to $90 million per year. Any earn out payments would be treated as adjustments to the purchase price. Sunoco also entered into a margin hedge agreement with Mitsubishi whereby Mitsubishi provided polypropylene margin protection for 2001 of up to $6.5 million per quarter. In connection with the margin hedge agreement, Sunoco received $19.5 million from Mitsubishi in 2001 related to Aristech’s operations for the first nine months and an additional $6.5 million in the first quarter of 2002 related to the 2001 fourth quarter’s operations. These payments were reflected as reductions in the purchase price when received. In addition, Mitsubishi is responsible during a 25-year indemnification period for up to $100 million of potential environmental liabilities for the business arising out of or related to the period prior to closing.
Effective June 15, 2000, Sunoco entered into the Epsilon joint venture which combined its polymer-grade propylene operations at the Marcus Hook refinery with the adjacent polypropylene business owned by Epsilon Products Company. In October 2001, Sunoco entered into an agreement with Epsilon under which Sunoco provides general administration, sales and support functions at cost to the joint venture. Under this agreement, the joint venture’s production is marketed under the Sunoco® name in combination with production from Sunoco’s own polypropylene plants. This operating structure has resulted in lower operating and administrative costs and the realization of synergies in production and marketing functions.
Sunoco supplies substantially all of the refinery-grade propylene and other feedstocks used by Epsilon in its production of polypropylene under a long-term supply contract with prices based on market conditions at time of delivery. Sunoco’s sales to Epsilon totaled $111 and $93 million during 2002 and 2001, respectively. Accounts receivable related to these sales amounted to $12 million at December 31, 2002. This supply arrangement is beneficial since it enables Chemicals to make these sales to an adjacent customer rather than seeking a lower-value alternative outlet for this production in the propylene market on the Gulf Coast of the United States. The joint venture currently has a $120 million term loan and $35 million outstanding under a $40 million revolving credit facility. Both of these borrowings are guaranteed by Sunoco; however, at this time, management does not believe that it is likely that the Company will have to perform under these guarantees. Although it is not currently anticipated, Sunoco and its partner could be required to fund any future cash deficiency in excess of the amount available under the revolving credit facility. At December 31, 2002, Sunoco’s investment in Epsilon consisted of a $31 million equity interest and a $19 million subordinated note receivable which bears interest at 12 percent.
Logistics
The Logistics business operates refined product and crude oil pipelines and terminals and conducts crude oil acquisition and marketing activities primarily in the Northeast, Midwest and South Central regions of the United States. In addition, the Logistics business has an ownership interest in several refined product and crude oil pipeline joint ventures.
15
Since February 8, 2002, the date of its initial public offering, logistics operations have been conducted primarily through Sunoco Logistics Partners L.P., the Company’s 75.3 percent owned master limited partnership (see “Capital Resources and Liquidity—Other Cash Flow Information” below).
| | 2002 | | 2001 | | 2000 |
|
|
Income (millions of dollars) | | $33 | | $42 | | $46 |
|
Pipeline throughput (thousands of barrels daily): | | | | | | |
|
Unaffiliated customers | | 627 | | 615 | | 748 |
|
Affiliated customers | | 1,137 | | 1,076 | | 1,052 |
|
| | 1,764 | | 1,691 | | 1,800 |
|
Logistics segment income decreased $9 million in 2002 primarily due to Sunoco’s reduced ownership interest in the partnership during the current period, partially offset by higher income from terminal facility operations. In 2001, Logistics segment income decreased $4 million primarily due to lower volumes associated with crude oil pipeline operations, lower storage revenue at the Company’s Nederland marine crude oil terminal, higher depreciation expense and higher ad valorem taxes. Partially offsetting these negative factors were higher revenues on the Eastern refined product pipeline system.
During 2002, Sunoco recorded a $3 million after-tax charge to reflect Sunoco Logistics Partners L.P.’s write-off of a pipeline located in Pennsylvania and New York and a related refined products terminal that were idled because they became uneconomic to operate. This amount is reported as part of the Write-Down of Assets and Other Matters shown separately in Corporate and Other in the Earnings Profile of Sunoco Businesses (see Note 3 to the consolidated financial statements).
In November 2002, the Logistics business completed the acquisition from an affiliate of Union Oil Company of California (“Unocal”) of interests in three Midwestern and Western U.S. products pipeline companies, consisting of a 31.5 percent interest in Wolverine Pipeline Company, a 9.2 percent interest in West Shore Pipeline Company and a 14.0 percent interest in Yellowstone Pipeline Company, for $54 million in cash. In November 2002, the Logistics business also completed the acquisition of an additional interest in West Texas Gulf pipeline for $6 million in cash, which increased its ownership interest in this pipeline from 17.3 percent to 43.8 percent.
Coke
The Coke business makes high-quality, blast furnace coke at Sunoco’s Indiana Harbor facility in East Chicago, IN and Jewell facility in Vansant, VA and produces metallurgical coal from mines in Virginia primarily for use at the Jewell cokemaking facility.
| | 2002 | | 2001 | | 2000 |
|
|
Income (millions of dollars) | | $42 | | $61 | | $61 |
Coke sales (thousands of tons) | | 2,158 | | 2,002 | | 2,011 |
|
Coke segment income decreased $19 million in 2002 due largely to lower income from Jewell Coke operations resulting from the Chapter 11 bankruptcy filing in early March 2002 by National Steel Corporation (“National”), Jewell’s former long-term contract customer. The 2002 results reflect lower sales prices and include a $4 million after-tax write-off of an account receivable from National. As part of the bankruptcy proceedings, National rejected its contract with Jewell. As a result, Jewell’s 2002 coke sales were made into lower-value short-term markets. Partially offsetting these factors were higher sales volumes and related tax benefits due to the liquidation of coke inventory at Jewell. In October 2002, the Coke business entered into a three-year sales contract with operating subsidiaries of the International Steel Group (“ISG”) under which the Coke business will provide to ISG approximately 700,000 tons of production from the Jewell cokemaking
16
facility annually during the 2003-2005 period. This sales contract provides for the semiannual adjustment of prices pursuant to a formula. ISG has also contracted to purchase approximately 150,000 tons of coke from Indiana Harbor during 2003. Coke segment income was essentially unchanged in 2001 as an increase in tax benefits recognized was offset by lower coke margins at Jewell.
The Coke business has third-party investors in its Jewell and Indiana Harbor cokemaking operations which are currently entitled to 98 percent of the cash flows and tax benefits from the respective cokemaking operations during a preferential return period which continues until they recover their investments and achieve a cumulative return thereon that averages approximately 10 percent after tax. Income in the Coke business is recognized as coke production and sales generate cash flows and tax benefits which are allocated to Sunoco and the third-party investors. The Coke business’ after-tax income attributable to the tax benefits, which primarily consist of nonconventional fuel credits, was $50, $48 and $47 million after tax in 2002, 2001 and 2000, respectively. In addition, expense is recognized to reflect the investors’ preferential returns. Such expense, which is included in Net Financing Expenses and Other under Corporate and Other in the Earnings Profile of Sunoco Businesses, totalled $27, $21 and $14 million after tax in 2002, 2001 and 2000, respectively.
Under the current tax law, beginning in 2003, a portion of the coke production at Jewell is no longer entitled to tax credits, which will result in a decline in annual Coke income of $6 million after tax. The remainder of the coke production at Jewell and all of the production at Indiana Harbor are eligible to generate credits through 2007.
In September 2000, the third-party investor in the Jewell operation made an additional $214 million cash investment which extended the preferential return period for this operation to 2007 and increased the investor’s interest in Jewell’s cash flows and tax benefits from 5 percent to 98 percent. The preferential return period from a prior investment in Jewell had ended in September 2000 at which time the investor’s interest had decreased from 95 percent to 5 percent. Due to anticipated lower income from the Jewell operation resulting from National’s Chapter 11 bankruptcy filing, the preferential return period for the Jewell operation is now estimated to extend to 2011. The preferential return period for the first investor in the Indiana Harbor operation ended in July 2002, at which time the first investor’s interest in the cash flows and tax benefits from Indiana Harbor decreased from 95 percent to 5 percent. As a result of an additional $215 million investment in July 2002, third-party investors’ interests increased from 5 percent to 98 percent. The new investor’s preferential return period for the Indiana Harbor operation is expected to end in 2007. The estimated lengths of these preferential return periods are based upon the Company’s current expectations of future operations, including sales volumes and prices, raw material and operating costs and capital expenditure levels. Better-than-expected results will shorten the investors’ preferential return periods, while lower-than-expected results will lengthen the periods.
After these preferential return periods, the investor in the Jewell operation will be entitled to a minority interest in the cash flows and tax benefits from Jewell amounting to 18 percent, while the investors in the Indiana Harbor operation will be entitled to a minority interest in the cash flows and tax benefits from Indiana Harbor initially amounting to 34 percent and declining to 10 percent by 2038.
17
Substantially all coke sales are currently made under long-term contracts with ISG and Ispat Inland Inc. (“Ispat”). ISG is a privately held company, and Ispat has a credit rating below investment-grade. Neither ISG nor Ispat have given any indication that they will not perform under their contracts. However, in the event of nonperformance, the Coke business’ results of operations and cash flows may be adversely affected and the period during which the third-party investors are entitled to preferential returns could be extended.
As a result of the expiration at the end of 2002 of tax credits attributable to a portion of the coke production at Jewell, a decrease in other tax benefits attributable to cokemaking operations and the anticipated prices associated with Jewell’s new coke sales contract, the Company estimates that the Coke business will earn approximately $40 million in 2003.
Corporate and Other
Net Financing Expenses and Other—Net financing expenses and other increased $9 million in 2002 primarily due to the $6 million increase in after-tax expense attributable to the preferential return of third-party investors in Sunoco’s cokemaking operations (see “Coke” above). Higher interest expense ($2 million) and lower interest income ($1 million) also contributed to the increase in net financing expenses in 2002. Partially offsetting these negative factors was higher capitalized interest ($2 million). In 2001, net financing expenses and other increased $26 million largely due to financing costs attributable to the Aristech acquisition and lower capitalized interest.
Income Tax Settlements—During 2001 and 2000, Sunoco settled certain federal income tax issues which increased net income by $21 and $117 million, respectively. (See Note 2 to the consolidated financial statements.)
Insurance Litigation Settlements—In 2000, Sunoco recognized $5 million of after-tax gains in connection with settlements of several insurance claims related to certain environmental matters of Sunoco, including its predecessor companies and subsidiaries, arising from ownership and operation of its businesses.
Write-Down of Assets and Other Matters—During 2002, Sunoco recorded a $14 million after-tax provision to write off a 200 million pounds-per-year polypropylene line at Chemicals’ LaPorte, TX plant and a 170 million pounds-per-year aniline and diphenylamine production facility at Chemicals’ Haverhill, OH plant and to recognize related shutdown costs, recorded a $2 million after-tax provision in connection with the shutdown of certain processing units at Refining and Supply’s Toledo refinery, recorded a $3 million after-tax provision to write-off an idled Logistics business refined products pipeline and terminal and established a $3 million after-tax accrual relating to a lawsuit concerning the Puerto Rico refinery.
During 2001, Sunoco recorded a $23 million after-tax charge for employee terminations and other required exit costs primarily related to the disposal of its Value Added and Eastern Lubricants operations, recorded an $11 million after-tax gain on the sale of the Company’s Puerto Rico refinery and reversed an $11 million after-tax accrual for warranty claims and other contingent liabilities established in connection with the disposal of the Company’s real estate business.
During 2000, Sunoco recorded a $123 million after-tax charge to write down the lubricants assets held for sale in its Value Added and Eastern Lubricants operations to their estimated values, established after-tax accruals totalling $19 million for employee terminations throughout the organization, reversed into income the remaining $4 million after-tax loss accrual related to a Refining and Supply MTBE purchase commitment and recorded an $11 million after-tax provision to write down the Chemicals Brandenburg, KY ethylene oxide plant and recognize related shutdown costs.
For a further discussion of the provisions for write-down of assets and other matters recorded during the 2000-2002 period, see Note 3 to the consolidated financial statements.
18
Discontinued Operations
During 2000, Sunoco recorded an $11 million after-tax favorable adjustment to the gain on divestment of Sunoco’s international oil and gas production business which was sold in 1996. (See Note 5 to the consolidated financial statements.)
Analysis of Consolidated Statements of Operations
Revenues—Total revenues were $14.38 billion in 2002, $14.14 billion in 2001 and $14.75 billion in 2000. The 2 percent increase in 2002 was primarily due to higher refined product sales volumes, higher consumer excise taxes, higher crude oil sales in connection with the crude oil gathering and marketing activities of the Company’s Logistics operations and higher merchandise sales at the Company’s convenience store outlets. Partially offsetting these increases were lower refined product sales prices. In 2001, the 4 percent decrease was primarily due to lower refined product prices and sales volumes and the absence of the income tax settlement gain in 2000. The decline in sales volumes in 2001 was largely attributable to lower sales from the Company’s Value Added and Eastern Lubricant operations, which were sold during 2001. Partially offsetting these decreases were higher chemical sales volumes as a result of the Aristech acquisition and higher consumer excise taxes.
Costs and Expenses—Total pretax costs and expenses were $14.46 billion in 2002, $13.56 billion in 2001 and $14.16 billion in 2000. The 7 percent increase in 2002 was primarily due to higher crude oil and refined product acquisition costs, higher consumer excise taxes, higher crude oil costs in connection with the crude oil gathering and marketing activities of the Company’s Logistics operations and the cost of higher merchandise sales at the Company’s convenience store outlets. Partially offsetting these increases were lower operating costs due to a decline in refinery fuel costs. In 2001, the 4 percent decrease was primarily due to lower crude oil and refined product acquisition costs and a decrease in the provision for write-down of assets and other matters, partially offset by costs and expenses attributable to Aristech’s operations, higher refinery fuel costs and higher consumer excise taxes.
Financial Condition
Capital Resources and Liquidity
Cash and Working Capital—At December 31, 2002, Sunoco had cash and cash equivalents of $390 million compared to $42 million at December 31, 2001 and $239 million at December 31, 2000 and had working capital of $122 million compared to a working capital deficit of $268 million at December 31, 2001 and working capital of $37 million at December 31, 2000. The $348 million increase in cash and cash equivalents in 2002 was due to $547 million of net cash provided by operating activities (“cash generation”) and $233 million of net cash provided by financing activities, partially offset by $432 million of net cash used in investing activities. The $197 million decrease in cash and cash equivalents in 2001 was due to an $833 million net use of cash in investing activities and a $143 million net use of cash in financing activities, partially offset by $779 million of net cash provided by operating activities. Sunoco’s working capital position is considerably stronger than indicated because of the relatively low historical costs assigned under the LIFO method of accounting for most of the inventories reflected in the consolidated balance sheets. The current replacement cost of all such inventories exceeded their carrying value at December 31, 2002 by $962 million. Inventories valued at LIFO, which consist of crude oil, and petroleum and chemical products, are readily marketable at their current replacement values. Management believes that the current levels of cash and working capital are adequate to support Sunoco’s ongoing operations.
19
Cash Flows from Operating Activities—In 2002, Sunoco’s cash generation was $547 million compared to $779 million in 2001 and $778 million in 2000. The $232 million decrease in cash generation in 2002 was primarily due to a decrease in net income and lower deferred income tax expense, partially offset by a decrease in working capital uses pertaining to operating activities. The cash generated from working capital changes in 2002 was largely the result of the liquidation of approximately 6 million barrels of crude oil and petroleum products. Increases in crude oil prices also contributed to the cash generation as the payment terms on Sunoco’s crude oil purchases are generally longer than the terms on product sales. The $1 million increase in cash generation in 2001 was largely due to higher deferred income tax expense and the liquidation of working capital in connection with the disposal of the lubricants assets. Partially offsetting these positive factors were a decrease in net income, the absence in 2001 of cash proceeds received in 2000 in connection with the settlement of several federal income tax issues and a decrease in proceeds received from insurance litigation settlements.
Other Cash Flow Information—Divestment activities have also been a source of cash. During the 2000-2002 period, proceeds from divestments totalled $105 million.
In 2002, Sunoco transferred an additional interest in its Indiana Harbor cokemaking operation to a third-party investor for $215 million in cash and, in 2000, transferred an additional interest in its Jewell cokemaking operations to a third-party investor for $214 million in cash. Sunoco did not recognize any gain or loss at the dates of these transactions. (See Note 14 to the consolidated financial statements.)
On February 8, 2002, the Company contributed a substantial portion of its Logistics business to Sunoco Logistics Partners L.P. (the “Partnership”) in exchange for a 73.2 percent limited partner interest, a 2 percent general partnership interest, incentive distribution rights and a $245 million special distribution, representing the net proceeds from the Partnership’s sale of $250 million ten-year 7.25 percent senior notes. The Partnership concurrently issued 5.75 million limited partnership units, representing a 24.8 percent interest in the Partnership, in an initial public offering at a price of $20.25 per unit. Proceeds from the offering, which totalled approximately $96 million net of underwriting discounts and offering expenses, were used by the Partnership to establish working capital that was not contributed to the Partnership by Sunoco. Sunoco liquidated this retained working capital subsequent to the Partnership’s formation. The proceeds from the liquidation and from the special distribution were used by Sunoco for general corporate purposes, including the repayment of outstanding commercial paper.
The Partnership, which is included in Sunoco’s consolidated financial statements, distributes to its general and limited partners all available cash (generally cash on hand at the end of each quarter less the amount of cash the general partner determines in its reasonable discretion is necessary or appropriate to: provide for the proper conduct of the Partnership’s business; comply with applicable law, any of the Partnership’s debt instruments or other agreements; pay fees and expenses, including payments to the general partner; or provide funds for distribution to unitholders and to the general partner for any one or more of the next four quarters). The minimum quarterly distribution is 2 percent of all available cash to the general partner and $.45 per limited partnership unit, or a total of $42 million per year. Sunoco’s 17.01 million limited partnership units consist of 5.63 million common units and 11.38 million subordinated units. Distributions on Sunoco’s subordinated units are payable only after the minimum quarterly distribution for the common units held by the public and Sunoco, including any arrearages, have been made. The subordinated units convert to common units when certain financial tests related to earning
20
and paying the minimum quarterly distribution for the preceding three consecutive one-year periods have been met. The Partnership earned and made its minimum quarterly distributions for 2002 and in 2003 increased the quarterly distribution to $.4875 per limited partnership unit.
The Partnership intends to implement growth opportunities in the future, both within its current system and with third-party acquisitions. The Partnership expects to finance these capital outlays with a combination of long-term borrowings and the issuance of additional limited partnership units to the public to maintain a balanced capital structure. Any issuance of limited partnership units to the public would dilute Sunoco’s ownership interest in the Partnership.
Concurrent with the offering, Sunoco entered into various agreements with the Partnership which require Sunoco to pay for minimum storage and throughput usage of certain Partnership assets. These commitments represent approximately 90 to 95 percent of Sunoco’s usage of the various assets during 2002 and generated approximately $125 million of revenue for the Partnership for the period February 8, 2002 through December 31, 2002. If, other than as a result of force majeure, Sunoco fails to meet its minimum obligations under these agreements, it would be required to pay the amount of any shortfall to the Partnership. Any such payments would be available as a credit in the following year after Sunoco’s minimum obligation for the year had been met. Sunoco’s obligations under these agreements may be reduced or suspended under certain circumstances. These agreements also establish fees for administrative services provided by Sunoco to the Partnership and indemnifications by Sunoco for certain environmental, toxic tort and other liabilities.
Financial Capacity—Management currently believes that future cash generation will be sufficient to satisfy Sunoco’s ongoing capital requirements, to fund its pension obligations (see “Pension Plan Funded Status” below) and to pay the current level of cash dividends on Sunoco’s common stock. However, from time to time, the Company’s short-term cash requirements may exceed its cash generation due to various factors including reductions in margins for products sold and the level of capital spending and working capital required. During those periods, the Company may supplement its cash generation with proceeds from financing activities.
In July 2002, the Company entered into a new revolving credit facility (the “Facility”) totaling $770 million and terminated its $500 million credit facility which would have matured in September 2002. The new facility structure consists of a $385 million commitment through July 2005 and a $385 million commitment that matures in July 2003. The Facility provides the Company with access to short-term financing and is intended to support the issuance of commercial paper and letters of credit. The Company also can borrow directly from the participating banks under the Facility. The Facility is subject to commitment fees, which are not material. Under the terms of the Facility, Sunoco is required to maintain tangible net worth (as defined in the Facility) in an amount greater than or equal to targeted tangible net worth (targeted tangible net worth being determined by adding $1.0 billion and 50 percent of adjusted net income (as defined in the Facility) for each quarter ended after March 31, 2002). At December 31, 2002, the Company’s tangible net worth was $1.4 billion and its targeted tangible net worth was $1.0 billion. The Facility also requires that Sunoco’s ratio of consolidated net indebtedness, including borrowings of Sunoco Logistics Partners L.P., to consolidated capitalization (as those terms are defined in the Facility) not exceed .60 to 1. At December 31, 2002, this ratio was .45 to 1. There were no borrowings under the Facility at December 31, 2002.
21
Concurrent with Sunoco Logistics Partners L.P.’s initial public offering, the Partnership entered into a three-year $150 million revolving credit facility. This credit facility, which is available to fund its working capital requirements, to finance acquisitions, and for general partnership purposes, includes a $20 million distribution sublimit that is available for distributions to third-party unitholders and Sunoco. At December 31, 2002, $65 million was outstanding under this credit facility. The credit facility contains covenants requiring the Partnership to maintain a ratio of up to 4 to 1 of its consolidated total debt to its consolidated EBITDA (each as defined in the credit facility) and an interest coverage ratio (as defined in the credit facility) of at least 3.5 to 1. At December 31, 2002, the Partnership’s ratio of its consolidated debt to its consolidated EBITDA was 3.0 to 1 and the interest coverage ratio was 5.0 to 1. On February 14, 2003, the revolving credit facility was amended to increase the total amount available thereunder to $200 million.
A wholly owned subsidiary of the Company, Sunoco Receivables Corporation, Inc., is a party to an accounts receivable securitization facility that terminates in 2006 under which the subsidiary may sell on a revolving basis up to a $200 million undivided interest in a designated pool of certain Sunoco accounts receivable. No receivables have been sold under this facility.
Debt—The following table sets forth Sunoco’s outstanding borrowings:
| | December 31
|
(Millions of Dollars) | | 2002 | | 2001 |
|
|
Short-term borrowings—commercial paper | | $ | — | | $ | 299 |
|
Current portion of long-term debt | | | 2 | | | 3 |
|
Long-term debt | | | 1,453 | | | 1,142 |
|
Total borrowings | | $ | 1,455 | | $ | 1,444 |
|
Sunoco’s ratio of debt (net of cash and cash equivalents) to total capital was 43.3 percent at December 31, 2002 compared to 46.1 percent at December 31, 2001. Management believes there is sufficient borrowing capacity available to pursue strategic investment opportunities as they arise. In addition, the Company has the option of issuing additional common or preference stock as a means of increasing its equity base.
The Company has an effective shelf registration statement which provides the Company with financing flexibility to offer senior and subordinated debt, common and preferred stock, warrants and trust preferred securities. At December 31, 2002, $1,300 million remains available under this shelf registration statement. The amount, type and timing of any financings will depend upon, among other things, the Company’s funding requirements, market conditions and compliance with covenants contained in the Company’s debt obligations and revolving credit facility.
Contractual Obligations—The following table sets forth the aggregate amount of long-term debt maturities, future annual rentals applicable to noncancellable operating leases and the fixed and determinable obligations to secure wastewater treatment services at the Toledo refinery and coal handling services at the Indiana Harbor cokemaking facility:
| | Payment Due Dates
| | |
(Millions of Dollars) | | 2003 | | 2004-2006 | | Thereafter | | Total |
|
|
Long-term debt | | $ | 2 | | $ | 323 | | $ | 1,130 | | $ | 1,455 |
|
Operating leases | | | 97 | | | 154 | | | 274 | | | 525 |
|
Unconditional purchase obligations | | | 9 | | | 24 | | | 71 | | | 104 |
|
|
| | $ | 108 | | $ | 501 | | $ | 1,475 | | $ | 2,084 |
|
22
Capital Expenditures and Acquisitions
The following table sets forth Sunoco’s planned and actual capital expenditures for additions to properties, plants and equipment. The actual capital expenditures are consistent with the presentation of the 2003 plan amounts in the table as well as with amounts presented in Sunoco’s consolidated financial statements. The Company’s significant acquisitions are included as footnotes to the table so that total capital outlays for each business unit can be determined.
(Millions of Dollars) | | 2003 Plan | | | 2002 | | | 2001 | | | 2000 | |
|
|
Refining and Supply | | $ | 281 | | | $ | 179 | | | $ | 122 | | | $ | 257 | * |
|
Retail Marketing | | | 154 | ** | | | 124 | | | | 173 | | | | 139 | |
|
Chemicals | | | 51 | | | | 36 | | | | 30 | *** | | | 21 | |
|
Logistics | | | 27 | | | | 41 | † | | | 61 | | | | 43 | |
|
Coke | | | 6 | | | | 5 | | | | 4 | | | | 5 | |
|
Consolidated capital expenditures | | $ | 519 | | | $ | 385 | | | $ | 390 | | | $ | 465 | |
|
* | | Includes $16 million attributable to the Value Added and Eastern Lubricants operations. |
** | | Excludes $140 million purchase of 193 retail gasoline outlets from Marathon Ashland Petroleum LLC located primarily in Florida and South Carolina which is subject to regulatory approval. |
*** | | Excludes $649 million acquisition of Aristech Chemical Corporation and related working capital. |
† | | Excludes $54 million purchase from an affiliate of Union Oil Company of California (“Unocal”) of interests in three Midwestern and Western U.S. products pipeline companies and a $6 million purchase which increased the Partnership’s ownership interest in the West Texas Gulf pipeline from 17.3 percent to 43.8 percent. |
The 2003 capital expenditure plan includes $360 million for base infrastructure, maintenance and regulatory spending, $89 million for turnarounds at the Company’s refineries and $70 million for income improvement projects. In addition to normal maintenance and infrastructure spending, base spending for 2003 includes approximately $70 million for additional investment to upgrade Sunoco’s existing retail network and enhance its APlus® convenience store presence. It also includes $22 million in outlays to comply with Clean Air Act requirements which phase in limitations on the sulfur content of gasoline beginning in 2004 and the sulfur content of on-road diesel fuel beginning in 2006. The Company expects to spend a total of $300-$400 million during the 2003-2006 period to comply with the new gasoline and diesel requirements. The 2003 regulatory spending also includes $10 million related to the construction of a sulfur plant at the Marcus Hook refinery. It is anticipated that construction of this facility, which is estimated to cost approximately $40-$50 million, will be completed by early 2005. The income improvement projects include expenditures to improve refinery technology and efficiency, and grow Sunoco’s retail network through acquisitions and new retail units, including outlays related to its retail gasoline initiative with Wal-Mart. At December 31, 2002, the Company had completed construction of 29 retail facilities at Wal-Mart locations.
In addition to the purchase of interests in three Midwestern and Western U.S. products pipeline companies from Unocal and the increased interest in the West Texas Gulf pipeline, the 2002 capital outlays included $248 million for base infrastructure, maintenance and regulatory spending, $82 million for refinery turnarounds and $55 million for various income improvement projects.
In addition to the Aristech acquisition, the 2001 capital outlays included $233 million for base infrastructure and legally required spending, $54 million for turnarounds at the Company’s refineries and $103 million for income improvement projects. The income improvement projects included expenditures to improve refinery efficiency, grow Sunoco’s retail marketing network and expand certain logistics assets. The income improvement outlays in retail marketing included the $59 million purchase from El Paso Corporation of 473 Coastal retail gasoline outlets located in the eastern United States.
23
In 2000, capital expenditures included: $298 million for base infrastructure and legally required spending; $81 million for the turnaround of numerous units throughout the Company’s refinery network; and $86 million for income improvement projects. The income improvement projects included outlays to upgrade or acquire additional Sunoco® retail marketing locations.
Pension Plan Funded Status
During 2002, the market value of the investments in Sunoco’s defined benefit pension plans declined by $232 million, or 21 percent, due to plan benefit payments of $141 million and a net investment loss of $91 million resulting from the poor performance of the equity markets in 2002. As a result, during 2002, the Company contributed $52 million to the plans to improve their funded status. Despite this contribution, the accumulated benefit obligation of these plans continued to exceed the market value of plan assets at December 31, 2002. Accordingly, the Company was required to record an after-tax charge totalling $176 million to the accumulated other comprehensive loss component of shareholders’ equity in its consolidated balance sheet at December 31, 2002. Management currently intends to make additional contributions of approximately $50 million to the plans during 2003 and expects pension expense to increase by approximately $30 million after tax in 2003 primarily due to the decline in pension plan assets resulting from the poor performance of the equity markets. Management believes any additional contributions to the pension plans can be funded without any significant impact on liquidity. Continued poor performance in the equity markets could result in additional significant charges to the accumulated other comprehensive loss component of shareholders’ equity and additional significant increases in future pension expense and funding requirements.
Environmental Matters
Sunoco is subject to numerous federal, state and local laws and regulations which regulate the discharge of materials into the environment or that otherwise relate to the protection of the environment. As with the industry generally, compliance with existing and anticipated laws and regulations increases the overall cost of operating Sunoco’s business, including capital costs to construct, maintain and upgrade equipment and facilities. These laws and regulations have required, and are expected to continue to require, Sunoco to make significant expenditures of both a capital and expense nature. The following table summarizes Sunoco’s expenditures for environmental projects and compliance activities:
(Millions of Dollars) | | 2002 | | 2001 | | 2000 |
|
|
Pollution abatement capital* | | $ | 47 | | $ | 45 | | $ | 52 |
|
Remediation | | | 49 | | | 38 | | | 39 |
|
Operations, maintenance and administration | | | 147 | | | 158 | | | 156 |
|
| | $ | 243 | | $ | 241 | | $ | 247 |
|
* | Capital expenditures for pollution abatement are expected to approximate $90 and $165 million in 2003 and 2004, respectively. |
These laws and regulations also result in liabilities and loss contingencies at Sunoco’s facilities and at third-party or formerly owned sites. Sunoco accrues environmental remediation costs for work at identified sites where an assessment has indicated that cleanup costs are probable and reasonably estimable. Such accruals are undiscounted and are based on currently available information, estimated timing of remedial actions and related inflation assumptions, existing technology and presently enacted laws and regulations. If a range of probable environmental cleanup costs exists for an identified site, FASB Interpretation No. 14, “Reasonable Estimation of the Amount of a Loss” requires that the minimum of the range be accrued unless some other point or points in the range are more likely in which case the most likely amount in the range is accrued. Engineering studies, historical experience and other factors are used to identify and evaluate remediation alternatives and their related costs in determining the estimated accruals for environmental remediation activities. Losses attributable to unasserted claims are also reflected in the accruals to the
24
extent they are probable of occurrence and reasonably estimable. The accrued liability for environmental remediation is classified in the consolidated balance sheets as follows:
| | December 31
|
(Millions of Dollars) | | 2002 | | 2001 |
|
|
Accrued liabilities | | $ | 43 | | $ | 39 |
|
Other deferred credits and liabilities | | | 116 | | | 106 |
|
| | $ | 159 | | $ | 145 |
|
The following table sets forth the accrued liability for environmental remediation activities by category:
(Millions of Dollars) | | Refineries | | | Marketing Sites | | | Chemicals Facilities | | | Pipelines and Terminals | | | Hazardous Waste Sites | | | Other | | Total | |
|
|
At December 31, 1999 | | $ | 74 | | | $ | 53 | | | $ | — | | | $ | 19 | | | $ | 11 | | | $ | 3 | | $ | 160 | |
|
Accruals | | | 1 | | | | 3 | | | | — | | | | 13 | | | | — | | | | — | | | 17 | |
|
Payments | | | (6 | ) | | | (17 | ) | | | — | | | | (13 | ) | | | (3 | ) | | | — | | | (39 | ) |
|
Other* | | | — | | | | 3 | | | | — | | | | — | | | | — | | | | — | | | 3 | |
|
|
At December 31, 2000 | | $ | 69 | | | $ | 42 | | | $ | — | | | $ | 19 | | | $ | 8 | | | $ | 3 | | $ | 141 | |
|
Accruals | | | (2 | ) | | | 21 | | | | — | | | | 10 | | | | 2 | | | | — | | | 31 | |
|
Payments | | | (6 | ) | | | (19 | ) | | | — | | | | (11 | ) | | | (2 | ) | | | — | | | (38 | ) |
|
Acquisitions | | | — | | | | — | | | | 10 | | | | — | | | | — | | | | — | | | 10 | |
|
Other* | | | — | | | | 1 | | | | — | | | | — | | | | — | | | | — | | | 1 | |
|
|
At December 31, 2001 | | $ | 61 | | | $ | 45 | | | $ | 10 | | | $ | 18 | | | $ | 8 | | | $ | 3 | | $ | 145 | |
|
Accruals | | | (2 | ) | | | 36 | | | | 1 | | | | 7 | | | | — | | | | — | | | 42 | |
|
Payments | | | (7 | ) | | | (24 | ) | | | (3 | ) | | | (12 | ) | | | (3 | ) | | | — | | | (49 | ) |
|
Other* | | | — | | | | 15 | | | | — | | | | 6 | | | | — | | | | — | | | 21 | |
|
At December 31, 2002 | | $ | 52 | | | $ | 72 | | | $ | 8 | | | $ | 19 | | | $ | 5 | | | $ | 3 | | $ | 159 | |
|
* | Consists of increases in the accrued liability for which recovery from third parties is probable. |
Total future costs for the environmental remediation activities identified above will depend upon, among other things, the identification of any additional sites, the determination of the extent of the contamination at each site, the timing and nature of required remedial actions, the technology available and needed to meet the various existing legal requirements, the nature and terms of cost sharing arrangements with other potentially responsible parties, the nature and extent of future environmental laws, inflation rates and the determination of Sunoco’s liability at the sites, if any, in light of the number, participation level and financial viability of the other parties. Management believes it is reasonably possible (i.e., less than probable but greater than remote) that additional environmental remediation losses will be incurred. At December 31, 2002, the aggregate of the estimated maximum additional reasonably possible losses, which relate to numerous individual sites, totaled $90 million. However, the Company believes it is very unlikely that it will realize the maximum loss at every site. Furthermore, the recognition of additional losses, if and when they might occur, would likely extend over many years and, therefore, would not have a material impact on the Company’s financial position.
Under various environmental laws, including the Resource Conservation and Recovery Act (“RCRA”), Sunoco has initiated corrective remedial action at its facilities, formerly owned facilities and third-party sites. At the Company’s major manufacturing facilities, Sunoco has consistently assumed continued industrial use and a containment/remediation strategy focused on eliminating unacceptable risks to human health or the environment. The remediation accruals for these sites reflect that strategy. Accruals include amounts to prevent off-site migration and to contain the impact on the facility property, as well as to address known, discrete areas requiring remediation within the plants. Activities include closure of RCRA solid waste management units, recovery of hydrocarbons, handling of impacted soil, mitigation of surface water impacts and prevention of off-site migration.
Most of Sunoco’s current terminals are being addressed with the above containment/remediation strategy. At some smaller or less impacted facilities and previously divested terminals, the focus is on remediating discrete interior areas to attain regulatory closure.
25
Future costs for environmental remediation activities at the Company’s marketing sites will also be influenced by the extent of MTBE contamination of groundwater aquifers, the cleanup of which will be driven by thresholds based on drinking water protection. Though not all groundwater is used for drinking, several states have initiated or proposed more stringent MTBE cleanup requirements. Cost increases result directly from extended operations and maintenance on sites that previously could otherwise have been completed, installation of additional remedial or monitoring wells and purchase of more expensive equipment because of the presence of MTBE. While actual cleanup costs for specific sites are variable and depend on many of the factors discussed above, expansion of similar MTBE remediation thresholds to additional states or adoption of even more stringent requirements for MTBE remediation would result in further cost increases.
The accrued liability for hazardous waste sites in the table above is attributable to potential obligations to remove or mitigate the environmental effects of the disposal or release of certain pollutants at third party sites pursuant to the Comprehensive Environmental Response Compensation and Liability Act (“CERCLA”). Under CERCLA, Sunoco is potentially subject to joint and several liability for the costs of remediation at sites at which it has been identified as a “potentially responsible party” (“PRP”). As of December 31, 2002, Sunoco had been named as a PRP at 44 sites identified or potentially identifiable as “Superfund” sites under federal and state law. The Company is usually one of a number of companies identified as a PRP at a site. Sunoco has reviewed the nature and extent of its involvement at each site and other relevant circumstances and, based upon the other parties involved or Sunoco’s negligible participation therein, believes that its potential liability associated with such sites will not be significant.
Management believes that none of the current remediation locations is individually material to Sunoco as its largest accrual for any one Superfund site, operable unit or remediation area is less than $7 million at December 31, 2002. As a result, Sunoco’s exposure to adverse developments with respect to any individual site is not expected to be material, and these current sites are in various stages of ongoing remediation. However, if changes in environmental regulations occur, such changes could impact multiple Sunoco facilities and formerly owned and third-party sites at the same time. As a result, from time to time, significant charges against income for environmental remediation may occur.
The Company maintains insurance programs that cover certain of its existing or potential environmental liabilities, which programs vary by year, type and extent of coverage. For underground storage tank remediations, the Company can also seek reimbursement through various state funds of certain remediation costs above a deductible amount. For certain acquired properties, the Company has entered into arrangements with the sellers or others that allocate environmental liabilities and provide indemnities to the Company for remediating contamination that occurred prior to the acquisition dates. Some of these environmental indemnifications are subject to caps and limits. No accruals have been recorded for any potential contingent liabilities that will be funded by the prior owners as management does not believe, based on current information, that it is likely that any of the former owners will not perform under any of these agreements. Other than the preceding arrangements, the Company has not entered into any arrangements with third parties to mitigate its exposure to loss from environmental contamination. Claims for recovery of environmental liabilities that are probable of realization totalled $27 million at December 31, 2002 and are included primarily in deferred charges and other assets in the consolidated balance sheets.
In December 1999, the U.S. Environmental Protection Agency (“EPA”) adopted a rule under the Clean Air Act which phases in limitations on the sulfur content of gasoline beginning in 2004 and, in January 2001, adopted another rule which will require limitations on the allowable sulfur content of on-road diesel fuel beginning in 2006. The rules include banking and trading credit systems, which could provide refiners flexibility until 2006 for
26
the low-sulfur gasoline and until 2010 for the on-road low-sulfur diesel. These rules are expected to have a significant impact on Sunoco and its operations primarily with respect to the capital and operating expenditures at its four refineries. Most of the capital spending is likely to occur in the 2003-2006 period, while the higher operating costs will be incurred when the low-sulfur fuels are produced. The Company estimates that the total capital outlays to comply with the new gasoline and diesel requirements will be in the range of $300-$400 million, of which $22 million is expected to be spent in 2003. The ultimate impact of the rules may be affected by such factors as technology selection, the effectiveness of the banking and trading credit systems, timing uncertainties created by permitting requirements and construction schedules and any effect on prices created by changes in the level of gasoline and diesel fuel production.
Pursuant to the Clean Air Act, in April 2002 the EPA issued a final rule to reduce hazardous air pollutants (including organics, reduced sulfur compounds, inorganics and particulate metals) from certain sources at petroleum refineries, including catalytic cracking and reforming units and sulfur recovery units (“MACT II”). The rule requires all petroleum refineries that are major sources of hazardous air pollutants to meet emission standards reflecting the application of the maximum achievable control technology at the affected sources by 2005. Analysis of this rule to determine its impact is ongoing. Although the ultimate impact of the rule cannot be determined at this time, it could have a significant impact on Sunoco and its operations, primarily with respect to capital expenditures at its four refineries.
Since the late 1990s, the EPA has undertaken significant enforcement initiatives under authority of the Clean Air Act. These enforcement initiatives have been targeted at industries that have large manufacturing facilities and that are significant sources of emissions, such as the refining, paper and pulp, and electric power generating industries. The basic premise of the enforcement initiative is the EPA’s assertion that many of these industrial establishments have modified or expanded their operations over time without complying with New Source Review regulations that require permits and new emission controls in connection with any significant facility modifications or expansions that can result in emission increases above certain thresholds, and have violated various other provisions of the Clean Air Act, including New Source Review and Prevention of Significant Deterioration (“NSR/PSD”) Programs, Benzene Waste Organic National Emissions Standards for Hazardous Air Pollutants (“NESHAP”), Leak Detection and Repair (“LDAR”) and flaring requirements. As part of this enforcement initiative, the EPA has entered into consent agreements with several refiners that require them to pay civil fines and penalties and make significant capital expenditures to install emissions control equipment at selected facilities. For some of these refineries, the cost of the required emissions control equipment is significant, depending on the size, age and configuration of the refinery. Sunoco received information requests in 2000, 2001 and 2002 in connection with the enforcement initiative pertaining to its four current refineries, the Puerto Rico refinery divested by Sunoco in 2001 and its phenol facility in Philadelphia, PA. Sunoco has completed its responses to the EPA, which is focusing solely on the refineries at this time.
Sunoco has received Notices of Violation and Findings of Violation from the EPA relating to its Marcus Hook, Philadelphia and Toledo refineries. The Notices and Findings of Violation allege failure to comply with certain requirements relating to benzene wastewater emissions at the Company’s Marcus Hook, Toledo and Philadelphia refineries and failure to comply with certain requirements relating to leak detection and repair at the Toledo refinery. In addition, the EPA has alleged that: at the Company’s Philadelphia refinery, certain modifications were made to one of the fluid catalytic cracking units in 1992 and 1998 without obtaining requisite permits; at the Company’s Marcus Hook refinery, certain modifications were made to the fluid catalytic cracking unit in 1990 and 1996 without obtaining requisite permits; and at the Company’s Toledo refinery, certain physical and operational changes were made to the fluid catalytic cracking unit in 1985 with - -
27
out obtaining requisite permits. The EPA has also alleged that at the Company’s Toledo refinery, certain physical and operational changes were made to the sulfur plant in 1995, 1998 and 1999 without obtaining requisite permits; certain physical and operational changes were made to a flare system without obtaining requisite permits; and that the flare system was not being operated in compliance with the Clean Air Act. Sunoco has met with representatives of the EPA on these Notices and Findings of Violation and is currently evaluating its position. Although Sunoco does not believe that it has violated any Clean Air Act requirements, as part of this initiative, Sunoco could be required to make significant capital expenditures, operate these refineries at reduced levels and pay significant penalties. There are no liabilities accrued at December 31, 2002 in connection with this initiative.
During the 2001-2002 session, the U.S. Congress was considering energy policy legislation. Congress failed to approve the legislation during the session. The Senate and House both approved bills, which included provisions concerning ethanol and MTBE; however, a conference committee was unable to resolve differences between the two pieces of legislation. Provisions concerning MTBE, ethanol, and fuels standards were among the disputed issues. It is expected that these issues will be on the Congressional agendas in 2003. Sunoco uses MTBE and ethanol as an oxygenate in different geographic areas of its refining and marketing system. While federal action to ban or phase down MTBE or to require increased usage of ethanol is uncertain, some states are scheduled to begin enforcing MTBE bans within the next year. Sunoco is currently evaluating its options to produce MTBE-free gasoline when the additive is banned in states where it markets, including Connecticut (October 2003) and New York (January 2004). While Sunoco does not market in California, that state’s ban on MTBE (January 2004) could have an impact on market conditions. Numerous other states are expected to consider legislation to ban MTBE during their 2003 legislative sessions. If MTBE is banned throughout the United States or on a state-by-state basis, the effect on Sunoco and the industry in general could be significant. It will depend on the specific regulations, the impact on gasoline supplies, the cost and availability of alternative oxygenates if the minimum oxygenate requirements remain in effect, and the ability of Sunoco and the industry in general to recover their costs in the marketplace.
Sunoco is a one-third partner in Belvieu Environmental Fuels (“BEF”), a joint venture that owns and operates an MTBE production facility in Mont Belvieu, TX. The Company had a $51 million investment in this operation at December 31, 2002 and had after-tax equity income of $6, $3 and $8 million attributable to the joint venture in 2002, 2001 and 2000, respectively. The joint venture is currently evaluating alternative uses for this facility in the event MTBE is banned, including the conversion from the production of MTBE to the production of alkylate or some other gasoline blending component. If the Company determines that it is uneconomic to convert the facility, the write-down of its investment in this operation may be necessary.
During 2001, the EPA issued its final rule addressing emissions of toxic air pollutants from mobile sources (the Mobile Source Air Toxics (“MSAT”) Rule). The rule is currently being challenged by certain environmental organizations and a number of states, and by a member of the petroleum industry. It requires refiners to produce gasoline which maintains their average 1998-2000 gasoline toxic emission performance level. If the rule survives the challenges and if MTBE is banned, it could result in significant additional expenditures or significant reductions in reformulated gasoline production levels for Sunoco as well as the industry.
Management believes that the environmental matters discussed above are potentially significant with respect to results of operations or cash flows for any one year. However, management does not believe that such matters will have a material impact on Sunoco’s consolidated financial position or, over an extended period of time, on Sunoco’s cash flows or liquidity.
28
Derivative Instruments
Sunoco uses futures and forward contracts from time to time to achieve ratable pricing of its crude oil purchases and to convert certain refined product sales to fixed or floating prices. In addition, price collars, swaps and option contracts may be used to lock in a portion of the Company’s electricity and natural gas costs. Sunoco also uses swaps, price collars and other contracts from time to time to hedge against significant increases in crude oil prices and to lock in what Sunoco considers to be acceptable margins for various refined products. Sunoco does not hold or issue derivative instruments for trading purposes.
Sunoco is at risk for possible changes in the market value of all of its derivative contracts; however, such risk would be mitigated by price changes in the underlying hedged items. At December 31, 2002, Sunoco had accumulated net derivative gains, before income taxes, of $2 million on its open derivative contracts. The potential loss on these derivatives from a hypothetical 10 percent adverse change in the year-end market prices of the underlying commodities that were being hedged by derivative contracts at December 31, 2002 was estimated to be $4 million. This hypothetical loss was estimated by multiplying the difference between the hypothetical and the actual year-end market prices of the underlying commodities by the contract volume amounts. The Company also had accumulated net derivative gains, before income taxes, of $1 million at December 31, 2002 on closed options and futures contracts, which relate to hedged transactions occurring in 2003.
Sunoco also is exposed to credit risk in the event of nonperformance by derivative counterparties. Management believes this risk is negligible as its counterparties are either regulated by exchanges or are major international financial institutions or corporations with investment-grade credit ratings. (See Note 17 to the consolidated financial statements.)
Cash Dividends and Share Repurchases
The Company has paid cash dividends on a regular quarterly basis since 1904. During the 2000-2002 period, the quarterly cash dividend paid on common stock amounted to $.25 per share ($1.00 per year). The Company expects to continue to pay the quarterly common stock cash dividend at its current level.
The Company did not repurchase any of its common stock in 2002. During the 2000-2001 period, the Company repurchased 15.9 million shares of its common stock for $537 million. At December 31, 2002, the Company had a remaining authorization from its Board of Directors to purchase up to $327 million of Company common stock in the open market or through privately negotiated transactions from time to time depending on prevailing market conditions and available cash.
Critical Accounting Policies
A summary of the Company’s significant accounting policies is included in Note 1 to the consolidated financial statements. Management believes that the application of these policies on a consistent basis enables the Company to provide the users of the financial statements with useful and reliable information about the Company’s operating results and financial condition. The preparation of Sunoco’s consolidated financial statements requires management to make estimates and assumptions that affect the reported amounts of assets, liabilities, revenues and expenses, and the disclosures of contingent assets and liabilities. Significant items that are subject to such estimates and assumptions consist of retirement benefit liabilities, long-lived assets and environmental remediation activities. Although management bases its estimates on historical experience and various other assumptions that are believed to be reasonable under the circumstances, actual results may differ to some extent from the estimates on which the Company’s consolidated financial statements are prepared at any given point in time. Despite these inherent limitations, management believes the Company’s Management’s Discussion and Analysis and consolidated financial statements provide a meaningful and fair perspective of the Company. Management has reviewed the estimates affecting its critical accounting policies with the Audit Committee of Sunoco’s Board of Directors.
29
Retirement Benefit Liabilities
Sunoco has noncontributory defined benefit pension plans which provide retirement benefits for approximately one-half of its employees. Sunoco also has postretirement benefit plans which provide health care and life insurance benefits for substantially all of its retirees. The postretirement benefit plans are unfunded and the costs are shared by Sunoco and its retirees. The levels of required retiree contributions to these plans are adjusted periodically, and the plans contain other cost-sharing features, such as deductibles and coinsurance.
The principal assumptions that impact the determination of both expense and benefit obligations for Sunoco’s pension plans are the discount rate, the long-term rate of return on plan assets and the rate of compensation increase. The discount rate and the health care cost trend are the principal assumptions that impact the determination of expense and benefit obligations for Sunoco’s postretirement health care and life insurance plans.
The discount rates used to determine the present value of future pension payments, medical costs and life insurance benefits are based on the yields on high-quality, fixed income investments (such as Moody’s Aa-rated long-term corporate bonds). The present values of Sunoco’s future pension and other postretirement obligations were determined using discount rates of 6.75 percent at December 31, 2002 and 7.25 percent at December 31, 2001. Sunoco’s expense under these plans is determined using the discount rate as of the beginning of the year, which was 7.25 percent for 2002, 7.50 percent for 2001, 7.75 percent for 2000, and is 6.75 percent for 2003.
The long-term rate of return on plan assets and the rate of compensation increase were assumed to be 9 percent and 4 percent, respectively, for each of the last three years. A rate of return of 8.75 percent on plan assets and a rate of compensation increase of 4 percent will be used to determine Sunoco’s pension expense for 2003. In determining pension expense, the Company applies the expected rate of return to the market-related value of plan assets at the beginning of the year, which is determined using a quarterly average of plan assets from the preceding year. The expected return on plan assets is designed to be a long- term assumption. It generally will differ from the actual return which is subject to considerable year-to-year variability. As permitted by existing accounting rules, the Company does not recognize the difference between the expected and actual return on assets currently in pension expense. Rather, the difference is deferred along with other actuarial gains or losses resulting from differences between actuarial assumptions used in accounting for the plans (primarily the discount rate) and actual experience. If such unrecognized gains and losses on a cumulative basis exceed 10 percent of the projected benefit obligation, the excess is amortized into income as a component of pension or postretirement benefits expense over the remaining service period of plan participants still employed with the Company, which currently is approximately 12 years. At December 31, 2002, the unrecognized net loss for defined benefit and postretirement benefit plans was $450 and $52 million, respectively. The actual returns on plan assets have been below the expected amounts in each of the last three years. For 2002, the pension plan assets generated a loss of 8.2 percent, compared to a loss of 2.9 percent in 2001 and .6 percent in 2000. Over the last five years, Sunoco’s pension plan assets have generated a compounded annual investment return of 3.5 percent. Although those returns are below the long-term assumption, this measurement period included a three-year period of declining performance of the equity markets. For the fifteen-year period ended December 31, 2002, the compounded annual investment return on Sunoco’s pension plan assets was 9.2 percent. The rate of compensation increase assumption has been indicative of actual results during the 2000-2002 period.
The initial health care cost trend assumptions used to compute the accumulated postretirement benefit obligation were increases of 12.2 percent, 8.3 percent and 8.4 percent at December 31, 2002, 2001 and 2000, respectively. These trend rates were assumed to decline
30
gradually to 5.5 percent in 2008 and to remain at that level thereafter. In 1993, Sunoco implemented a dollar cap on its future contributions for its principal postretirement health care benefits plan, which significantly reduces the impact of future cost increases on the estimated postretirement benefit expense and benefit obligation.
Set forth below are the estimated increases in pension and postretirement benefits expense and benefit obligations that would occur in 2003 from a one percentage point change in the indicated assumptions:
| | Expense
| | |
(Millions of Dollars) | | Service and Interest Cost | | Amortization of Unrecognized Losses | | Total | | Benefit Obligation* |
|
|
Pension benefits: | | | | | | | | |
|
Decrease in the discount rate | | $1 | | $12 | | $13 | | $150 |
|
Decrease in the long-term rate of return on plan assets | | $11 | | $— | | $11 | | $— |
|
Increase in rate of compensation | | $4 | | $3 | | $7 | | $36 |
|
Postretirement benefits: | | | | | | | | |
|
Decrease in the discount rate | | $— | | $1 | | $1 | | $34 |
Increase in the annual health care cost trend rates | | $1 | | $— | | $1 | | $12 |
|
* | Represents the projected benefit obligations for defined benefit plans and the accumulated postretirement benefit obligations for postretirement benefit plans. |
Long-Lived Assets
The cost of plants and equipment is generally depreciated on a straight-line basis over the estimated useful lives of the assets. Useful lives are based on historical experience and are adjusted when changes in planned use, technological advances or other factors show that a different life would be more appropriate. Changes in useful lives that do not result in the impairment of an asset are recognized prospectively. There have been no significant changes in the useful lives of the Company’s plants and equipment during the 2000-2002 period.
Long-lived assets, other than those held for sale, are reviewed for impairment whenever events or circumstances indicate that the carrying amount of the assets may not be recoverable. Such events and circumstances include, among other factors: operating losses; unused capacity; market value declines; technological developments resulting in obsolescence; changes in demand for the Company’s products or in end-use goods manufactured by others utilizing the Company’s products as raw materials; changes in the Company’s business plans or those of its major customers or suppliers; changes in competition and competitive practices; uncertainties associated with the United States and world economies; changes in the expected level of environmental capital, operating or remediation expenditures; and changes in governmental regulations or actions. Additional factors impacting the economic viability of long-lived assets are described under “Forward-Looking Statements” below.
A long-lived asset is considered to be impaired when the undiscounted net cash flows expected to be generated by the asset are less than its carrying amount. Such estimated future cash flows are highly subjective and are based on numerous assumptions about future operations and market conditions. The impairment recognized is the amount by which the carrying amount exceeds the fair market value of the impaired asset. It is also difficult to precisely estimate fair market value because quoted market prices for the Company’s long-lived assets may not be readily available. Therefore, fair market value is generally based on the present values of estimated future cash flows using discount rates commensurate with the risks associated with the assets being reviewed for impairment.
Sunoco had asset impairments totalling $18 and $129 million after tax during 2002 and 2000, respectively. There were no asset impairments during 2001. The impairments in 2002 related to the shutdown of a polypropylene line at the Company’s LaPorte, TX plant, an aniline and diphenylamine production facility in Haverhill, OH, certain processing
31
units at the Toledo refinery and a refined products pipeline and terminal owned by Sunoco Logistics Partners L.P. The chemical facilities and the Toledo refinery processing units were shut down to eliminate less efficient production capacity, while the pipeline and terminal were idled because they became uneconomic to operate. The impairment in 2000 resulted primarily from the Company’s decision to exit the Value Added and Eastern Lubricants business due to its inability to achieve an adequate return on capital employed in this business. For a further discussion of these asset impairments, see Note 3 to the consolidated financial statements.
Environmental Remediation Activities
Sunoco is subject to numerous federal, state and local laws and regulations which regulate the discharge of materials into the environment or that otherwise relate to the protection of the environment. These laws and regulations require environmental assessment and/or remediation efforts at many of Sunoco’s facilities and at formerly owned or third-party sites.
Sunoco’s accrual for environmental remediation activities amounted to $159 million at December 31, 2002. This accrual is for work at identified sites where an assessment has indicated that cleanup costs are probable and reasonably estimable. The accrual is undiscounted and is based on currently available information, estimated timing of remedial actions and related inflation assumptions, existing technology and presently enacted laws and regulations. It is often extremely difficult to develop reasonable estimates of future site remediation costs due to changing regulations, changing technologies and their associated costs, and changes in the economic environment. In the above instances, if a range of probable environmental cleanup costs exists for an identified site, FASB Interpretation No. 14, “Reasonable Estimation of the Amount of a Loss” requires that the minimum of the range be accrued unless some other point or points in the range are more likely, in which case the most likely amount in the range is accrued. Engineering studies, historical experience and other factors are used to identify and evaluate remediation alternatives and their related costs in determining the estimated accruals for environmental remediation activities. Losses attributable to unasserted claims are also reflected in the accruals to the extent they are probable of occurrence and reasonably estimable.
Management believes that none of the current remediation locations is individually material to Sunoco as its largest accrual for any one Superfund site, operable unit or remediation area is less than $7 million at December 31, 2002. As a result, Sunoco’s exposure to adverse developments with respect to any individual site is not expected to be material. However, if changes in environmental regulations occur, such changes could impact several of Sunoco’s facilities and formerly owned and third-party sites at the same time. As a result, from time to time, significant charges against income for environmental remediation may occur.
Under various environmental laws, including the Resource Conservation and Recovery Act (“RCRA”), Sunoco has initiated corrective remedial action at its facilities, formerly owned facilities and third-party sites. At the Company’s major manufacturing facilities, Sunoco has consistently assumed continued industrial use and a containment/remediation strategy focused on eliminating unacceptable risks to human health and the environment. The remediation accruals for these sites reflect that strategy. Accruals include amounts to prevent off-site migration and to contain the impact on the facility property, as well as to address known, discrete areas requiring remediation within the plants. Activities include closure of RCRA solid waste management units, recovery of hydrocarbons, handling of impacted soil, mitigation of surface water impacts and prevention of off-site migration.
Most of Sunoco’s current terminals are being addressed with the above containment/remediation strategy. At some smaller or less impacted facilities and previously divested terminals, the focus is on remediating discrete interior areas to attain regulatory closure.
32
Future costs for environmental remediation activities at the Company’s marketing sites will also be influenced by the extent of MTBE contamination of groundwater aquifers, the cleanup of which will be driven by thresholds based on drinking water protection. Though not all groundwater is used for drinking, several states have initiated or proposed more stringent MTBE cleanup requirements. Cost increases result directly from extended operations and maintenance on sites that previously could otherwise have been completed, installation of additional remedial or monitoring wells and purchase of more expensive equipment because of the presence of MTBE. While actual cleanup costs for specific sites are variable and depend on many of the factors discussed above, expansion of similar MTBE remediation thresholds to additional states or adoption of even more stringent requirements for MTBE remediation would result in further cost increases.
In summary, total future costs for environmental remediation activities will depend upon, among other things, the identification of any additional sites, the determination of the extent of the contamination at each site, the timing and nature of required remedial actions, the technology available and needed to meet the various existing legal requirements, the nature and terms of cost sharing arrangements with other potentially responsible parties and the nature and extent of future environmental laws, inflation rates and the determination of Sunoco’s liability at the sites, if any, in light of the number, participation level and financial viability of other parties.
New Accounting Pronouncements
For a discussion of recently issued accounting pronouncements requiring adoption subsequent to December 31, 2002, see Note 1 to the consolidated financial statements.
Forward-Looking Statements
Statements and financial discussion and analysis contained in this Annual Report to Shareholders that are not historical facts are forward-looking statements made pursuant to the safe harbor provisions of the Private Securities Litigation Reform Act of 1995. Such statements generally will be accompanied by words such as “anticipate,” “believe,” “could,” “estimate,” “expect,” “forecast,” “intend,” “may,” “possible,” “potential,” “predict,” “project,” or other similar words that convey the uncertainty of future events or outcomes. Although Sunoco believes these forward-looking statements are reasonable, they are based upon a number of assumptions concerning future conditions, any or all of which may ultimately prove to be inaccurate. Forward-looking statements involve a number of risks and uncertainties. Important factors that could cause actual results to differ materially from the forward-looking statements include, without limitation:
• | | Changes in refining, marketing and chemical margins; |
• | | Variation in petroleum-based commodity prices and availability of crude oil supply or transportation; |
• | | Volatility in the marketplace which may affect supply and demand for Sunoco’s products; |
• | | Changes in competition and competitive practices, including the impact of foreign imports; |
• | | Changes in the reliability and efficiency of the Company’s operating facilities or those of third parties; |
• | | Changes in the level of operating expenses and hazards common to operating facilities (including equipment malfunction, explosions, fires, oil spills, and the effects of severe weather conditions); |
• | | Changes in the expected level of environmental capital, operating or remediation expenditures; |
• | | Delays related to work on facilities and the issuance of applicable permits; |
• | | Changes in product specifications; |
33
• | | Availability and pricing of oxygenates such as MTBE and ethanol; |
• | | Phase-outs or restrictions on the use of MTBE; |
• | | Political and economic conditions in the markets in which the Company operates, including the impact of potential terrorist acts and international hostilities; |
• | | Changes in the availability and cost of debt and equity financing; |
• | | Changes in insurance markets impacting costs and the level and types of coverage available; |
• | | Changes in financial markets impacting pension expense and funding requirements; |
• | | Risks related to labor relations; |
• | | Nonperformance by major customers or suppliers; |
• | | General economic, financial and business conditions which could affect Sunoco’s financial condition and results of operations; |
• | | Changes in applicable statutes and government regulations or their interpretations; |
• | | Claims of the Company’s noncompliance with statutory and regulatory requirements; and |
• | | Changes in the status of litigation to which the Company is a party. |
The factors identified above are believed to be important factors (but not necessarily all of the important factors) that could cause actual results to differ materially from those expressed in any forward-looking statement made by Sunoco. Unpredictable or unknown factors not discussed herein could also have material adverse effects on forward-looking statements. All forward-looking statements included in this Annual Report to Shareholders are expressly qualified in their entirety by the foregoing cautionary statements. The Company undertakes no obligation to update publicly any forward-looking statement (or its associated cautionary language) whether as a result of new information or future events.
34
Consolidated Statements of Operations | Sunoco, Inc. and Subsidiaries |
(Millions of Dollars and Shares Except Per Share Amounts) | | | | | | | | |
|
|
For the Years Ended December 31 | | 2002 | | | 2001 | | 2000 | |
|
Revenues | | | | | | | | | | | |
|
Sales and other operating revenue (including consumer excise taxes) | | $ | 14,299 | | | $ | 14,063 | | $ | 14,514 | |
|
Interest income | | | 7 | | | | 9 | | | 14 | |
|
Other income (Note 2) | | | 78 | | | | 71 | | | 224 | |
|
|
| | | 14,384 | | | | 14,143 | | | 14,752 | |
Costs and Expenses | | | | | | | | | | | |
|
Cost of products sold and operating expenses | | | 11,430 | | | | 10,699 | | | 11,349 | |
|
Consumer excise taxes | | | 1,834 | | | | 1,741 | | | 1,636 | |
|
Selling, general and administrative expenses | | | 622 | | | | 583 | | | 502 | |
|
Depreciation, depletion and amortization | | | 329 | | | | 321 | | | 298 | |
|
Payroll, property and other taxes | | | 100 | | | | 103 | | | 79 | |
|
Provision for write-down of assets and other matters (Note 3) | | | 34 | | | | 6 | | | 214 | |
|
Interest cost and debt expense | | | 111 | | | | 103 | | | 82 | |
|
Interest capitalized | | | (3 | ) | | | — | | | (4 | ) |
|
|
| | | 14,457 | | | | 13,556 | | | 14,156 | |
|
Income (loss) from continuing operations before income tax expense (benefit) | | | (73 | ) | | | 587 | | | 596 | |
|
Income tax expense (benefit) (Note 4) | | | (26 | ) | | | 189 | | | 185 | |
|
|
Income (loss) from continuing operations | | | (47 | ) | | | 398 | | | 411 | |
|
Income from discontinued operations (Note 5) | | | — | | | | — | | | 11 | |
|
Net Income (Loss) | | $ | (47 | ) | | $ | 398 | | $ | 422 | |
|
Earnings Per Share of Common Stock: | | | | | | | | | | | |
|
Basic: | | | | | | | | | | | |
|
Income (loss) from continuing operations | | | $(.62 | ) | | | $4.92 | | | $4.72 | |
|
Income from discontinued operations | | | — | | | | — | | | .13 | |
|
Net income (loss) | | | $(.62 | ) | | | $4.92 | | | $4.85 | |
|
|
Diluted: | | | | | | | | | | | |
|
Income (loss) from continuing operations | | | $(.62 | ) | | | $4.85 | | | $4.70 | |
|
Income from discontinued operations | | | — | | | | — | | | .12 | |
|
Net income (loss) | | | $(.62 | ) | | | $4.85 | | | $4.82 | |
|
|
Weighted Average Number of Shares Outstanding (Note 6): | | | | | | | | | | | |
|
Basic | | | 76.2 | | | | 80.9 | | | 87.0 | |
Diluted | | | 76.2 | | | | 82.0 | | | 87.5 | |
|
Cash Dividends Paid Per Share of Common Stock | | | $1.00 | | | | $1.00 | | | $1.00 | |
|
(See Accompanying Notes)
35
Consolidated Balance Sheets | Sunoco, Inc. and Subsidiaries |
(Millions of Dollars) | | | | | | |
|
|
At December 31 | | 2002 | | | 2001 | |
|
Assets | | | | | | | | |
Current Assets | | | | | | | | |
|
Cash and cash equivalents | | $ | 390 | | | $ | 42 | |
|
Accounts and notes receivable, net | | | 923 | | | | 700 | |
|
Inventories (Note 7) | | | 491 | | | | 652 | |
|
Deferred income taxes (Note 4) | | | 94 | | | | 116 | |
|
|
Total Current Assets | | | 1,898 | | | | 1,510 | |
|
|
Investments and long-term receivables (Note 8) | | | 220 | | | | 165 | |
|
Properties, plants and equipment, net (Note 9) | | | 4,099 | | | | 4,099 | |
|
Prepaid retirement costs (Note 10) | | | 5 | | | | 87 | |
|
Deferred charges and other assets | | | 219 | | | | 158 | |
|
Total Assets | | $ | 6,441 | | | $ | 6,019 | |
|
Liabilities and Shareholders’ Equity | | | | | | | | |
Current Liabilities | | | | | | | | |
|
Accounts payable | | $ | 1,316 | | | $ | 986 | |
|
Accrued liabilities | | | 339 | | | | 351 | |
|
Short-term borrowings (Note 11) | | | — | | | | 299 | |
|
Current portion of long-term debt (Note 12) | | | 2 | | | | 3 | |
|
Taxes payable | | | 119 | | | | 139 | |
|
Total Current Liabilities | | | 1,776 | | | | 1,778 | |
|
|
Long-term debt (Note 12) | | | 1,453 | | | | 1,142 | |
|
Retirement benefit liabilities (Note 10) | | | 653 | | | | 488 | |
|
Deferred income taxes (Note 4) | | | 490 | | | | 551 | |
|
Other deferred credits and liabilities (Note 13) | | | 196 | | | | 195 | |
|
Commitments and contingent liabilities (Note 13) | | | | | | | | |
|
Minority interests (Note 14) | | | 479 | | | | 223 | |
Shareholders’ Equity(Notes 15 and 16) | | | | | | | | |
|
Common stock, par value $1 per share Authorized—200,000,000 shares; Issued, 2002—134,760,400 shares; Issued, 2001—133,795,605 shares | | | 135 | | | | 134 | |
|
Capital in excess of par value | | | 1,489 | | | | 1,446 | |
|
Earnings employed in the business | | | 2,143 | | | | 2,266 | |
|
Accumulated other comprehensive loss | | | (195 | ) | | | (28 | ) |
|
Common stock held in treasury, at cost 2002—58,321,433 shares; 2001—58,266,818 shares | | | (2,178 | ) | | | (2,176 | ) |
|
|
Total Shareholders’ Equity | | | 1,394 | | | | 1,642 | |
|
Total Liabilities and Shareholders’ Equity | | $ | 6,441 | | | $ | 6,019 | |
|
(See Accompanying Notes)
36
Consolidated Statements of Cash Flows | Sunoco, Inc. and Subsidiaries |
(Millions of Dollars) | | | | | | | | | |
|
|
For the Years Ended December 31 | | 2002 | | | 2001 | | | 2000 | |
|
Increases (Decreases) in Cash and Cash Equivalents | | | | | | | | | | | | |
Cash Flows from Operating Activities: | | | | | | | | | | | | |
|
Net income (loss) | | $ | (47 | ) | | $ | 398 | | | $ | 422 | |
|
Adjustments to reconcile net income (loss) to net cash provided by operating activities: | | | | | | | | | | | | |
|
Income from discontinued operations | | | — | | | | — | | | | (11 | ) |
|
Provision for write-down of assets and other matters | | | 34 | | | | 6 | | | | 214 | |
|
Noncash reduction in minority interest in cokemaking operations (Note 14) | | | (35 | ) | | | (37 | ) | | | (46 | ) |
|
Depreciation, depletion and amortization | | | 329 | | | | 321 | | | | 298 | |
|
Deferred income tax expense | | | 19 | | | | 203 | | | | 66 | |
|
Payments in excess of expense for retirement plans | | | (42 | ) | | | (12 | ) | | | (39 | ) |
|
Changes in working capital pertaining to operating activities, net of effect of acquisitions: | | | | | | | | | | | | |
|
Accounts and notes receivable | | | (230 | ) | | | 357 | | | | (57 | ) |
|
Inventories | | | 161 | | | | (59 | ) | | | (63 | ) |
|
Accounts payable and accrued liabilities | | | 319 | | | | (276 | ) | | | (82 | ) |
|
Taxes payable | | | 10 | | | | (110 | ) | | | 75 | |
|
Other | | | 29 | | | | (12 | ) | | | 1 | |
|
|
Net cash provided by operating activities | | | 547 | | | | 779 | | | | 778 | |
|
Cash Flows from Investing Activities: | | | | | | | | | | | | |
|
Capital expenditures | | | (385 | ) | | | (390 | ) | | | (465 | ) |
|
Acquisitions, net of debt assumed of $163 in 2001 (Note 18) | | | (54 | ) | | | (486 | ) | | | — | |
|
Proceeds from divestments | | | 22 | | | | 47 | | | | 36 | |
|
Other | | | (15 | ) | | | (4 | ) | | | (7 | ) |
|
|
Net cash used in investing activities | | | (432 | ) | | | (833 | ) | | | (436 | ) |
|
Cash Flows from Financing Activities: | | | | | | | | | | | | |
|
Net proceeds from (repayments of) short-term borrowings | | | (299 | ) | | | 299 | | | | (150 | ) |
|
Proceeds from issuance of long-term debt | | | 311 | | | | 200 | | | | — | |
|
Repayments of long-term debt | | | (3 | ) | | | (152 | ) | | | — | |
|
Net proceeds from issuance of Sunoco Logistics Partners L.P. limited partnership units (Note 14) | | | 96 | | | | — | | | | — | |
|
Proceeds from transferred interests in cokemaking operations | | | 215 | | | | — | | | | 214 | |
|
Cash distributions to investors in cokemaking operations | | | (24 | ) | | | (56 | ) | | | (27 | ) |
|
Cash dividend payments | | | (76 | ) | | | (82 | ) | | | (87 | ) |
|
Purchases of common stock for treasury | | | — | | | | (393 | ) | | | (144 | ) |
|
Proceeds from issuance of common stock under management incentive and employee option plans | | | 23 | | | | 41 | | | | 6 | |
|
Other | | | (10 | ) | | | — | | | | (2 | ) |
|
|
Net cash provided by (used in) financing activities | | | 233 | | | | (143 | ) | | | (190 | ) |
|
|
Net increase (decrease) in cash and cash equivalents | | | 348 | | | | (197 | ) | | | 152 | |
|
Cash and cash equivalents at beginning of year | | | 42 | | | | 239 | | | | 87 | |
|
Cash and cash equivalents at end of year | | $ | 390 | | | $ | 42 | | | $ | 239 | |
|
(See Accompanying Notes)
37
Consolidated Statements of Comprehensive Income and Shareholders’ Equity
(Dollars in Millions, Shares in Thousands) | | | Sunoco, Inc. and Subsidiaries |
|
|
| | | | | Shareholders’ Equity
|
|
| | | | | Common Stock
| | Capital in Excess of Par Value | | Earnings Employed in the Business | | | Accumulated Other Comprehensive Loss | | | Common Stock Held in Treasury
|
| | Comprehensive Income (Loss) | | | Number of Shares | | Par Value | | | | | Shares | | Cost |
|
At December 31, 1999 | | | | | | 132,172 | | $ | 132 | | $ | 1,397 | | $ | 1,615 | | | $ | — | | | 42,303 | | $ | 1,638 |
|
Net income | | $ | 422 | | | — | | | — | | | — | | | 422 | | | | — | | | — | | | — |
|
Cash dividend payments | | | — | | | — | | | — | | | — | | | (87 | ) | | | — | | | — | | | — |
|
Purchases for treasury | | | — | | | — | | | — | | | — | | | — | | | | — | | | 5,203 | | | 144 |
|
Issued under management incentive and employee option plans | | | — | | | 203 | | | — | | | 6 | | | — | | | | — | | | — | | | — |
|
Other | | | — | | | — | | | — | | | — | | | — | | | | — | | | 38 | | | 1 |
|
|
Total | | $ | 422 | | | | | | | | | | | | | | | | | | | | | | |
| |
|
|
| | | | | | | | | | | | | | | | | | | | | |
|
At December 31, 2000 | | | | | | 132,375 | | $ | 132 | | $ | 1,403 | | $ | 1,950 | | | $ | — | | | 47,544 | | $ | 1,783 |
|
Net income | | $ | 398 | | | — | | | — | | | — | | | 398 | | | | — | | | — | | | — |
|
Other comprehensive loss: | | | | | | | | | | | | | | | | | | | | | | | | | |
|
Minimum pension liability adjustment (net of related tax benefit of $12) | | | (21 | ) | | — | | | — | | | — | | | — | | | | (21 | ) | | — | | | — |
|
Net hedging losses (net of related tax benefit of $6) | | | (11 | ) | | — | | | — | | | — | | | — | | | | (11 | ) | | — | | | — |
|
Reclassifications of net hedging losses to earnings (net of related tax expense of $2) | | | 4 | | | — | | | — | | | — | | | — | | | | 4 | | | — | | | — |
|
Cash dividend payments | | | — | | | — | | | — | | | — | | | (82 | ) | | | — | | | — | | | — |
|
Purchases for treasury | | | — | | | — | | | — | | | — | | | — | | | | — | | | 10,717 | | | 393 |
|
Issued under management incentive and employee option plans | | | — | | | 1,421 | | | 1 | | | 40 | | | — | | | | — | | | — | | | — |
|
Other | | | — | | | — | | | 1 | | | 3 | | | — | | | | — | | | 6 | | | — |
|
|
Total | | $ | 370 | | | | | | | | | | | | | | | | | | | | | | |
| |
|
|
| | | | | | | | | | | | | | | | | | | | | |
|
At December 31, 2001 | | | | | | 133,796 | | $ | 134 | | $ | 1,446 | | $ | 2,266 | | | $ | (28 | ) | | 58,267 | | $ | 2,176 |
|
Net loss | | $ | (47 | ) | | — | | | — | | | — | | | (47 | ) | | | — | | | — | | | — |
|
Other comprehensive loss: | | | | | | | | | | | | | | | | | | | | | | | | | |
|
Minimum pension liability adjustment (net of related tax benefit of $94) | | | (176 | ) | | — | | | — | | | — | | | — | | | | (176 | ) | | — | | | — |
|
Net hedging gains (net of related tax expense of $2) | | | 5 | | | — | | | — | | | — | | | — | | | | 5 | | | — | | | — |
|
Reclassifications of net hedging losses to earnings (net of related tax expense of $2) | | | 4 | | | — | | | — | | | — | | | — | | | | 4 | | | — | | | — |
|
Cash dividend payments | | | — | | | — | | | — | | | — | | | (76 | ) | | | — | | | — | | | — |
|
Issued under management incentive and employee option plans | | | — | | | 964 | | | 1 | | | 27 | | | — | | | | — | | | — | | | — |
|
Net increase in equity related to unissued shares under management incentive plans | | | — | | | — | | | — | | | 15 | | | — | | | | — | | | — | | | — |
|
Other | | | — | | | — | | | — | | | 1 | | | — | | | | — | | | 54 | | | 2 |
|
|
Total | | $ | (214 | ) | | | | | | | | | | | | | | | | | | | | | |
| |
|
|
| | | | | | | | | | | | | | | | | | | | | |
At December 31, 2002 | | | | | | 134,760 | | $ | 135 | | $ | 1,489 | | $ | 2,143 | | | $ | (195 | ) | | 58,321 | | $ | 2,178 |
|
(See Accompanying Notes)
38
Notes to Consolidated Financial Statements | Sunoco, Inc. and Subsidiaries |
1. Summary of Significant Accounting Policies
Principles of Consolidation
The consolidated financial statements of Sunoco, Inc. and subsidiaries (collectively, “Sunoco” or the “Company”) contain the accounts of all operations that are controlled (generally more than 50 percent owned). Corporate joint ventures and other investees over which the Company has the ability to exercise significant influence but that are not controlled (generally 20 to 50 percent owned) are accounted for by the equity method.
Use of Estimates
The preparation of financial statements in conformity with accounting principles generally accepted in the United States requires management to make estimates and assumptions that affect the amounts reported in the financial statements and accompanying notes. Actual amounts could differ from these estimates.
Revenue Recognition
The Company sells various refined products (including gasoline, middle distillates, residual fuel, petrochemicals and lubricants), coke and coal and also sells crude oil in connection with the crude oil gathering and marketing activities of its logistics operations. In addition, the Company sells a broad mix of merchandise such as groceries, fast foods and beverages at its convenience stores and provides a variety of car care services at its retail gasoline outlets. Revenues related to the sale of products are recognized when title passes, while service revenues are recognized when services are provided. Title passage generally occurs when products are shipped or delivered in accordance with the terms of the respective sales agreements. In addition, revenues are not recognized until sales prices are fixed or determinable and collectability is reasonably assured.
Crude oil exchange transactions, which are entered into primarily to acquire crude oil of a desired quality or at a desired location, are netted in cost of products sold and operating expenses in the consolidated statements of operations.
Consumer excise taxes on sales of refined products and merchandise are included in both revenues and costs and expenses, with no effect on net income.
Cash Equivalents
Sunoco considers all highly liquid investments with a remaining maturity of three months or less at the time of purchase to be cash equivalents. These cash equivalents consist principally of time deposits and money market investments.
Inventories
Inventories are valued at the lower of cost or market. The cost of crude oil and petroleum and chemical product inventories is determined using the last-in, first-out method (“LIFO”). The cost of materials, supplies and other inventories is determined using principally the average cost method.
Depreciation and Retirements
Plants and equipment are generally depreciated on a straight-line basis over their estimated useful lives. Gains and losses on the disposals of fixed assets are generally reflected in net income.
Impairment of Long-Lived Assets
Long-lived assets other than those held for sale are reviewed for impairment whenever events or changes in circumstances indicate that the carrying amount of the assets may not be recoverable. An asset is considered to be impaired when the undiscounted estimated net cash flows expected to be generated by the asset are less than its carrying amount. The impairment recognized is the amount by which the carrying amount exceeds the fair market value of the impaired asset. Long-lived assets held for sale are recorded at the lower of their carrying amount or fair market value less cost to sell the assets. Effective January 1, 2002, Sunoco adopted Statement of Financial Accounting Standards No. 144, “Accounting for the Impairment or Disposal of Long-Lived Assets” (“SFAS No. 144”) which, among other things, changed the criteria that would have to be met to classify an asset as held-for-sale. SFAS No. 144 had no impact on Sunoco’s consolidated financial statements during 2002.
Goodwill and Indefinite-Lived Intangible Assets
Effective January 1, 2002, Statement of Financial Accounting Standards No. 142, “Goodwill and Other Intangible Assets” (“SFAS No. 142”), was adopted. SFAS No. 142 requires the testing of goodwill, which represents the excess of the purchase price over the fair value of net assets acquired, and indefinite-lived intangible assets for impairment rather than amortizing them. Sunoco ceased amortizing goodwill effective January 1, 2002 and de - -
39
termined during 2002 that its goodwill is not impaired. Prior to January 1, 2002, goodwill was amortized on a straight-line basis over its estimated useful life. Sunoco’s amortization of goodwill and indefinite-lived intangible assets amounted to $5 and $4 million after tax during 2001 and 2000, respectively.
Environmental Remediation
Sunoco accrues environmental remediation costs for work at identified sites where an assessment has indicated that cleanup costs are probable and reasonably estimable. Such accruals are undiscounted and are based on currently available information, estimated timing of remedial actions and related inflation assumptions, existing technology and presently enacted laws and regulations. If a range of probable environmental cleanup costs exists for an identified site, the minimum of the range is accrued unless some other point or points in the range are more likely in which case the most likely amount in the range is accrued.
Maintenance Shutdowns
Maintenance and repair costs in excess of $500 thousand incurred in connection with major maintenance shutdowns are capitalized when incurred and amortized over the period benefited by the maintenance activities.
Derivative Instruments
Sunoco uses swaps, options, futures, forwards and other derivative instruments from time to time to hedge its exposure to crude oil, petroleum product, electricity and natural gas price volatility. Effective January 1, 2001, such contracts are accounted for using derivative accounting as prescribed by Statement of Financial Accounting Standards No. 133, “Accounting for Derivative Instruments and Hedging Activities,” as amended by Statement of Financial Accounting Standards No. 138, “Accounting for Certain Derivative Instruments and Certain Hedging Activities” (collectively, “new derivative accounting”). The new derivative accounting requires the recognition of all derivative contracts in the consolidated balance sheet at their fair value. Changes in fair value of derivative contracts that are not hedges are recognized in net income as they occur. If the derivative contracts are designated as hedges, depending on their nature, the effective portions of changes in their fair values are either offset in net income against the changes in the fair values of the items being hedged or reflected initially as a separate component of shareholders’ equity and subsequently recognized in net income when the hedged items are recognized in net income. The ineffective portions of changes in the fair values of derivative contractsdesignated as hedges are immediately recognized in net income. The impact of the new derivative accounting on Sunoco’s consolidated net income during 2001 was not material. Sunoco does not hold or issue derivative instruments for trading purposes.
Prior to January 1, 2001, derivative contracts which effectively met the Company’s risk reduction and correlation criteria were accounted for using derivative accounting as prescribed by Statement of Financial Accounting Standards No. 80, “Accounting for Futures Contracts” (“prior derivative accounting”). Effectiveness was measured based upon the correlation between the gains and losses on the derivative contracts and the corresponding offsetting changes in the market value of the items being hedged. Under the prior derivative accounting, gains or losses on derivative contracts (including positions which had been closed) were deferred and recognized in cost of products sold and operating expenses in the same periods as the items being hedged.
Minority Interests in Cokemaking Operations
Cash investments by third parties are recorded as an increase in minority interests in the consolidated balance sheets. There is no recognition of any gain at the dates of these transactions as the third-party investors are entitled to a preferential return on their investments.
Nonconventional fuel credit and other net tax benefits generated by the Company’s cokemaking operations and allocated to third-party investors are recorded as a reduction in minority interests. The investors’ preferential return is recorded as an increase in minority interests. The net of these two amounts represents a noncash reduction in minority interests in cokemaking operations, which is recognized in other income in the consolidated statements of operations.
Cash payments, representing the distributions of the investors’ share of cash generated by the cokemaking operations, are also recorded as a reduction in minority interests.
Stock-Based Compensation
During the fourth quarter of 2002, Sunoco adopted the fair value method of accounting for employee stock compensation plans as prescribed by Statement of Financial Accounting Standards No. 123, “Accounting for Stock-Based Compensation” (“SFAS No. 123”) and amended by Statement of Financial Accounting Standards No. 148, “Accounting for Stock-Based Compensation—Transition and Disclosure” (“SFAS No. 148”). The Company recognized $6 million of expense ($4 million after tax) in 2002 for all unvested stock options attributable to the vesting
40
that occurred in 2002 retroactive to January 1, 2002 using the “modified prospective method” transition rules of SFAS No. 148. Prior to January 1, 2002, the Company followed the intrinsic value method of accounting for employee stock compensation plans prescribed by Accounting Principles Board Opinion No. 25, “Accounting for Stock Issued to Employees” (“APB No. 25”). Under APB No. 25, the Company did not recognize compensation expense for stock options because the exercise price of the options equaled the market price of the underlying stock on the date of grant (Note 16).
New Accounting Principles
In August 2001, Statement of Financial Accounting Standards No. 143, “Accounting for Asset Retirement Obligations” (“SFAS No. 143”), was issued. Sunoco is adopting SFAS No. 143 effective January 1, 2003 when adoption is mandatory. This statement significantly changes the method of accruing for costs that an entity is legally obligated to incur associated with the retirement of fixed assets. Under SFAS No. 143, the fair value of a liability for an asset retirement obligation will be recognized in the period in which it is incurred if a reasonable estimate of fair value can be made. The associated asset retirement costs will be capitalized as part of the carrying amount of the fixed asset and depreciated over its estimated useful life. Under existing accounting principles, a liability for an asset retirement obligation is recognized using a cost-accumulation measurement approach. Adoption of SFAS No. 143 is not expected to have a significant impact on the Company’s consolidated financial statements.
In July 2002, Statement of Financial Accounting Standards No. 146, “Accounting for Costs Associated with Exit or Disposal Activities” (“SFAS No. 146”), was issued. SFAS No. 146 supersedes Emerging Issues Task Force (“EITF”) Issue No. 94-3, “Liability Recognition for Certain Employee Termination Benefits and Other Costs to Exit an Activity (including Certain Costs Incurred in a Restructuring).” SFAS No. 146 requires that a liability for a cost associated with an exit or disposal activity be recognized when the liability is incurred. Under SFAS No. 146, an entity’s commitment to a plan, by itself, does not create an obligation that meets the definition of a liability. SFAS No. 146 also establishes fair value as the objective for initial measurement of the liability. Severance pay would be recognized over time rather than at the plan commitment date if the benefit arrangement requires employees to render future service beyond a“minimum retention period.” The provisions of SFAS No. 146 are effective for exit or disposal activities that are initiated after December 31, 2002. The Company has traditionally recognized certain costs associated with restructuring plans as of the date of commitment to the plan. Adoption of SFAS No. 146 could result in the deferral of recognition of such costs for restructuring plans initiated in periods subsequent to December 31, 2002 from the date the Company commits to the plan to the date that it incurs a liability for the costs. As SFAS No. 146 only applies to prospective items, Sunoco is unable to determine the impact, if any, that adoption of SFAS No. 146 would have on the Company’s future financial position or results of operations.
In November 2002, FASB Interpretation No. 45, “Guarantor’s Accounting and Disclosure Requirements for Guarantees, Including Indirect Guarantees of Indebtedness of Others” (“FASB Interpretation No. 45”), was issued. The accounting recognition provisions of FASB Interpretation No. 45 are effective January 1, 2003 on a prospective basis. They require that a guarantor recognize, at the inception of a guarantee, a liability for the fair value of the obligation undertaken in issuing the guarantee. Under prior accounting principles, a guarantee would not have been recognized as a liability until a loss was probable and reasonably estimable. As FASB Interpretation No. 45 only applies to prospective transactions, Sunoco is unable to determine the impact, if any, that adoption of the accounting recognition provisions of FASB Interpretation No. 45 would have on the Company’s future financial position or results of operations.
In January 2003, FASB Interpretation No. 46, “Consolidation of Variable Interest Entities” (“FASB Interpretation No. 46”), was issued. It clarifies the application of Accounting Research Bulletin No. 51, “Consolidated Financial Statements”, to certain entities in which the equity investors do not have a controlling financial interest or do not have sufficient equity at risk. FASB Interpretation No. 46 is effective on January 31, 2003 for entities acquired after such date. The effective date for entities acquired on or before January 31, 2003 is July 1, 2003. Sunoco has not completed its evaluation of FASB Interpretation No. 46 and, therefore, is unable to estimate its impact on the Company’s consolidated financial statements at this time (Note 8).
Reclassifications
Certain amounts in the prior years’ financial statements have been reclassified to conform to the current year presentation.
41
2. Other Income
(Millions of Dollars) | | 2002 | | | 2001 | | | 2000 | |
|
|
Gain on income tax settlements | | $ | — | | | $ | — | | | $ | 120 | |
|
Equity income (loss): | | | | | | | | | | | | |
|
Belvieu Environmental Fuels | | | | | | | | | | | | |
|
(MTBE joint venture) | | | | | | | | | | | | |
|
(Notes 8 and 13) | | | 9 | | | | 5 | | | | 12 | |
|
Epsilon Products Company, LLC (polypropylene joint venture) (Notes 8, 13 and 18) | | | (3 | ) | | | (11 | ) | | | (1 | ) |
|
Pipeline joint ventures (Notes 8 and 18) | | | 14 | | | | 11 | | | | 10 | |
|
Other | | | 3 | | | | 3 | | | | 1 | |
|
Noncash reduction in minority interests in cokemaking operations (Note 14) | | | 35 | | | | 37 | | | | 46 | |
|
Gain on settlement of insurance litigation | | | — | | | | — | | | | 7 | |
|
Other | | | 20 | | | | 26 | | | | 29 | |
|
| | $ | 78 | | | $ | 71 | | | $ | 224 | |
|
During 2001 and 2000, Sunoco settled certain federal income tax issues that had been in dispute, which increased net income by $21 and $117 million, respectively. In connection with the 2000 settlement, Sunoco received cash proceeds of $132 million in the fourth quarter of 2000. Sunoco did not receive any cash proceeds in connection with the 2001 settlement. The following table sets forth summary information relating to the 2000 income tax settlement:
(Millions of Dollars) | | Pretax Gain | | After-Tax Gain | | Cash Proceeds |
|
|
Interest income: | | | | | | | | | |
|
Recognized currently | | $ | 30 | | $ | 19 | | $ | 30 |
|
Previously recognized* | | | — | | | — | | | 17 |
|
Reversal of tax reserve and related interest** | | | 90 | | | 68 | | | — |
|
Refund of income taxes*** | | | — | | | 30 | | | 85 |
|
|
| | $ | 120 | | $ | 117 | | $ | 132 |
|
* | | Gain recognized in 1998 upon agreement by the Internal Revenue Service to allow a disputed bad debt tax deduction. No cash was received at the time of this settlement due to the pending dispute which was settled in 2000. |
** | | A previously established reserve was reversed upon approval of the settlement by the Joint Committee on Taxation in 2000. |
*** | | The $85 million of cash proceeds includes a $55 million refund of prepaid taxes. |
In 2000, Sunoco settled several insurance claims related to certain environmental matters of Sunoco, including its predecessor companies and subsidiaries, arising from ownership and operation of its businesses. The Company received net cash proceeds totalling $37 million in 2000 related to these settlements and similar agreements recognized in 1998 and 1999. The 2000 settlements increased net income by $5 million.
3. Write-Down of Assets and Other Matters
The following table sets forth summary information regarding the provisions for write-down of assets and other matters:
(Millions of Dollars) | | Pretax Provisions | | | After-Tax Provisions | |
|
2002 | | | | | | | | |
|
Chemical facilities: | | | | | | | | |
|
Asset write-off | | $ | 20 | | | $ | 13 | |
|
Exit costs | | | 1 | | | | 1 | |
|
Toledo refinery processing units | | | 4 | | | | 2 | |
|
Pipeline and related terminal | | | 5 | | | | 3 | |
|
Litigation reserve | | | 4 | | | | 3 | |
|
|
| | $ | 34 | | | $ | 22 | |
|
2001 | | | | | | | | |
|
Value Added and Eastern Lubricants: | | | | | | | | |
|
Exit costs | | $ | 15 | | | $ | 10 | |
|
Employee terminations | | | 16 | | | | 11 | |
|
Puerto Rico refinery sale | | | (12 | ) | | | (11 | ) |
|
Other employee terminations | | | 4 | | | | 2 | |
|
Real estate accrual adjustment | | | (17 | ) | | | (11 | ) |
|
|
| | $ | 6 | | | $ | 1 | |
|
2000 | | | | | | | | |
|
Value Added and Eastern Lubricants | | $ | 177 | | | $ | 123 | |
|
Employee terminations and related costs | | | 29 | | | | 19 | |
|
Brandenburg ethylene oxide plant | | | 18 | | | | 11 | |
|
MTBE purchase commitment | | | (7 | ) | | | (4 | ) |
|
Other | | | (3 | ) | | | (2 | ) |
|
|
| | $ | 214 | | | $ | 147 | |
|
During 2002, Sunoco shut down a polypropylene line at its LaPorte, TX plant, an aniline and diphenylamine production facility in Haverhill, OH, certain processing units at its Toledo refinery and a pipeline located in Pennsylvania and New York and a related refined products terminal. The chemical facilities and the Toledo refinery processing units were shut down to eliminate less efficient production capacity, while the pipeline and terminal were idled because they became uneconomic to operate. In connection with these shutdowns, Sunoco recorded provisions to write off the affected units and established accruals for related exit costs. During 2002, the Company also established an accrual relating to a lawsuit concerning the Puerto Rico refinery, which was divested in December 2001.
During 2000, Sunoco announced its intention to sell its Puerto Rico refinery, lubricants blending and packaging facilities in Marcus Hook, PA, Tulsa, OK and Richmond, CA and lubricants branded marketing assets (which include the Kendall® motor oil brand and the customer lists for both the Sunoco® and the Kendall® lubricants brands) (collectively, “Value Added and Eastern Lubricants”). The Company elected to exit the Value Added and Eastern Lubricants business due to its inability to achieve an adequate return on capital employed in this business. During 2000, Sunoco recorded a $177 million non-cash charge ($123 million after tax) to write down
42
the assets held for sale to their estimated values. In connection with this decision, Sunoco sold its lubricants branded marketing assets in March 2001, closed its lubricants blending and packaging facilities in July 2001 and sold the Puerto Rico refinery in December 2001 to conclude the lubricants restructuring plan. As part of the restructuring, in 2001, Sunoco recorded a $15 million accrual ($10 million after tax) for required exit costs including amounts for contract settlements, lease abandonments and environmental and other cleanup activities, a $16 million accrual ($11 million after tax) for employee terminations and a $12 million gain ($11 million after tax) on the sale of the Puerto Rico refinery.
Value Added and Eastern Lubricants incurred after-tax operating losses of $2 and $31 million in 2001 and 2000, respectively. The disposal of the lubricants assets generated cash of approximately $125 million in 2001, which included $27 million attributable to the sale of the branded marketing operations and the Puerto Rico refinery with the balance generated from the liquidation of working capital in the normal course of business.
Sunoco also established other employee termination accruals totalling $4 and $29 million ($2 and $19 million after tax) in 2001 and 2000, respectively. The 2000 accrual included pension settlement losses totalling $11 million ($7 million after tax). The termination accruals recorded in 2001 were for approximately 350 employee terminations, primarily in the lubricants business, while the termination accruals recorded in 2000 were for approximately 115 employee terminations, primarily at corporate and in refining and supply operations. Payments charged against these accruals are expected to continue through 2003.
The following table summarizes the changes in the accrual for exit costs and terminations:
(Millions of Dollars) | | 2002 | | | 2001 | | | 2000 | |
|
|
Balance at beginning of year | | $ | 24 | | | $ | 26 | | | $ | 6 | |
|
Additional accruals | | | 1 | | | | 35 | | | | 26 | * |
|
Payments charged against the accruals | | | (15 | ) | | | (37 | ) | | | (6 | ) |
|
Balance at end of year | | $ | 10 | | | $ | 24 | | | $ | 26 | |
|
* | Excludes pension settlement losses totalling $11 million. |
The Company reversed an accrual for warranty claims and other contingent liabilities associated with its former real estate business during 2001. The accrual was established during 1991 as part of the costs expected to be incurred in connection with the disposal of this business. The accrual reversal resulted from the favorable settlement of certain litigation claims and upon expiration of various statute-of-limitation periods during 2001.
During 2000, the Company recorded a write-down of its Brandenburg, KY ethylene oxide plant and recognized related shutdown costs. The Company also reversed into income the remaining loss accrual related to an MTBE fixed-price purchase commitment. This accrual was established in 1996 and 1998 for the estimated future losses expected to be realized on the fixed-price purchase commitment through May 2000. After that date, Sunoco is paying spot-market-related prices for the last four years of the agreement. As a result, the remaining accrual was reversed into income at that time when the fixed-price portion of the contract ended.
4. Income Taxes
The components of income tax expense (benefit) from continuing operations are as follows:
(Millions of Dollars) | | 2002 | | | 2001 | | | 2000 |
|
|
Income taxes currently payable: | | | | | | | | | | | |
|
U.S. federal | | $ | (47 | ) | | $ | (19 | ) | | $ | 104 |
|
State and other | | | 2 | | | | 5 | | | | 15 |
|
|
| | | (45 | ) | | | (14 | ) | | | 119 |
|
|
Deferred taxes: | | | | | | | | | | | |
|
U.S. federal | | | 18 | | | | 195 | | | | 56 |
|
State and other | | | 1 | | | | 8 | | | | 10 |
|
|
| | | 19 | | | | 203 | | | | 66 |
|
| | $ | (26 | ) | | $ | 189 | | | $ | 185 |
|
The reconciliation of income tax expense (benefit) at the U.S. statutory rate to the income tax expense (benefit) pertaining to continuing operations is as follows:
(Millions of Dollars) | | 2002 | | | 2001 | | | 2000 | |
|
|
Income tax expense (benefit) at U.S. statutory rate of 35 percent | | $ | (26 | ) | | $ | 205 | | | $ | 209 | |
|
Increase (reduction) in income taxes resulting from: | | | | | | | | | | | | |
|
Income tax settlements (Note 2) | | | — | | | | (21 | ) | | | (39 | ) |
|
State income taxes net of Federal income tax effects | | | 2 | | | | 9 | | | | 11 | |
|
Puerto Rico operations | | | — | | | | — | | | | 8 | * |
|
Dividend exclusion for affiliated companies | | | (3 | ) | | | (3 | ) | | | (3 | ) |
|
Nonconventional fuel credit | | | — | | | | (2 | ) | | | (3 | ) |
|
Other | | | 1 | | | | 1 | | | | 2 | |
|
| | $ | (26 | ) | | $ | 189 | | | $ | 185 | |
|
* | During 2000, the Company recorded an $8 million charge to establish deferred income taxes attributable to the unremitted earnings of its operations in Puerto Rico which had been deemed indefinitely reinvested prior to Sunoco’s decision to sell these operations (Note 3). |
43
The tax effects of temporary differences which comprise the net deferred income tax liability are as follows:
| | December 31
| |
(Millions of Dollars) | | 2002 | | | 2001 | |
|
|
Deferred tax assets: | | | | | | | | |
|
Retirement benefit liabilities | | $ | 219 | | | $ | 140 | |
|
Environmental remediation liabilities | | | 46 | | | | 51 | |
|
Other liabilities not yet deductible | | | 261 | | | | 199 | |
|
Alternative minimum tax credit carryforward* | | | 71 | | | | — | |
|
Other | | | 89 | | | | 107 | |
|
Valuation allowance** | | | (32 | ) | | | (32 | ) |
|
|
| | | 654 | | | | 465 | |
|
|
Deferred tax liabilities: | | | | | | | | |
|
Properties, plants and equipment | | | (1,001 | ) | | | (865 | ) |
|
Other | | | (49 | ) | | | (35 | ) |
|
|
| | | (1,050 | ) | | | (900 | ) |
|
Net deferred income tax liability | | $ | (396 | ) | | $ | (435 | ) |
|
* | | Alternative minimum tax credit carryforwards may be carried forward indefinitely. |
** | | The valuation allowance reduces the benefit of certain state net operating loss carryforwards to the amount that will more likely than not be realized. |
The net deferred income tax liability is classified in the consolidated balance sheets as follows:
| | December 31
| |
(Millions of Dollars) | | 2002 | | | 2001 | |
|
|
Current asset | | $ | 94 | | | $ | 116 | |
|
Noncurrent liability | | | (490 | ) | | | (551 | ) |
|
| | $ | (396 | ) | | $ | (435 | ) |
|
Cash payments for (refunds of) income taxes were $(49), $100 and $36 million in 2002, 2001 and 2000, respectively. The $36 million payment in 2000 is net of an $85 million cash refund received in the fourth quarter of 2000 in connection with the settlement of certain federal income tax issues (Note 2).
5. Discontinued Operations
During 2000, Sunoco recorded an $11 million after-tax favorable adjustment (including a $7 million tax benefit) to the gain recognized in 1996 in connection with the divestment of the Company’s international oil and gas production business. The adjustment resulted from the favorable resolution of certain United Kingdom income tax issues. At the time of the sale, this business was treated as a discontinued operation; therefore, this adjustment has been classified similarly in the consolidated statement of operations for the year ended December 31, 2000.
6. Earnings Per Share Data
The following table sets forth the reconciliation of the weighted average number of common shares used to compute basic earnings per share (“EPS”) to those used to compute diluted EPS for 2002, 2001 and 2000:
(In Millions) | | 2002* | | 2001 | | 2000 |
|
|
Weighted average number of common shares outstanding—basic | | 76.2 | | 80.9 | | 87.0 |
|
Add effect of dilutive stock incentive awards | | — | | 1.1 | | .5 |
|
Weighted average number of shares—diluted | | 76.2 | | 82.0 | | 87.5 |
|
* | Since the assumed issuance of common stock under stock incentive awards would not have been dilutive, the weighted average number of shares used to compute diluted EPS is equal to the weighted average number of shares used in the basic EPS computation. |
7. Inventories
| | December 31
|
(Millions of Dollars) | | 2002 | | 2001 |
|
|
Crude oil | | $ | 153 | | $ | 245 |
|
Petroleum and chemical products | | | 227 | | | 290 |
|
Materials, supplies and other | | | 111 | | | 117 |
|
| | $ | 491 | | $ | 652 |
|
The current replacement cost of all inventories valued at LIFO exceeded their carrying value by $962 and $516 million at December 31, 2002 and 2001, respectively. During 2002, Sunoco reduced certain inventory quantities which were valued at lower LIFO costs prevailing in prior years. The effect of this reduction was to increase 2002 results of operations by $5 million after tax.
8. Investments and Long-Term Receivables
| | December 31
|
(Millions of Dollars) | | 2002 | | 2001 |
|
|
Investments in and advances to affiliated companies: | | | | | | |
|
Belvieu Environmental Fuels (MTBE joint venture) (Notes 2 and 13) | | $ | 51 | | $ | 54 |
|
Epsilon Products Company, LLC (polypropylene joint venture) (Notes 2, 13 and 18) | | | 50 | | | 52 |
|
Pipeline joint ventures (Notes 2 and 18) | | | 81 | | | 21 |
|
Other | | | 16 | | | 12 |
|
|
| | | 198 | | | 139 |
|
Accounts and notes receivable | | | 22 | | | 26 |
|
| | $ | 220 | | $ | 165 |
|
Dividends received from affiliated companies amounted to $27, $18 and $21 million in 2002, 2001 and 2000, respectively. Earnings employed in the business at December 31, 2002 include $46 million of undistributed earnings of affiliated companies.
44
Summarized financial information for all entities accounted for using the equity method is set forth below. Amounts attributable to acquired interests (Note 18) have been included in the table since the acquisition dates.
| | 100 Percent
| | | | Sunoco Proportionate Share
|
(Millions of Dollars) | | 2002 | | 2001 | | 2000 | | | | 2002 | | 2001 | | 2000 |
|
|
Balance Sheet Information, at December 31: | | | | | | | | | | | | | | |
|
Current assets | | $297 | | $203 | | $204 | | | | $94 | | $67 | | $75 |
|
Other assets | | $762 | | $498 | | $519 | | | | $211 | | $161 | | $168 |
|
Current liabilities | | $166 | | $90 | | $275 | | | | $49 | | $28 | | $119 |
|
Other liabilities | | $596 | | $344 | | $163 | | | | $159 | | $108 | | $24 |
|
Income Statement Information, for the years ended December 31: | | | | | | | | | | | | | | |
|
Revenues | | $992 | | $927 | | $955 | | | | $358 | | $339 | | $348 |
|
Income before income tax expense | | $166 | | $104 | | $126 | | | | $31 | | $15 | | $28 |
|
Net income | | $115 | | $65 | | $93 | | | | $23 | | $8 | | $22 |
|
Although the Company has not completed its evaluation of FASB Interpretation No. 46, it is reasonably possible that Sunoco will be required to consolidate its investment in the Epsilon Products Company, LLC joint venture, effective July 1, 2003 (Note 1). The Epsilon joint venture, which had revenues totaling $189 million for the year ended December 31, 2002 and assets totaling $203 million at December 31, 2002, produces polypropylene at a facility adjacent to the Company’s Marcus Hook, PA refinery. Sunoco’s maximum exposure to loss as a result of its involvement with Epsilon amounted to $222 million at December 31, 2002, consisting of its $50 million investment in Epsilon, $12 million of trade accounts receivable and the guarantee of the joint venture’s $120 million term loan and $40 million revolving credit facility.
9. Properties, Plants and Equipment
(Millions of Dollars) December 31 | | Gross Investments, at Cost | | Accumulated Depreciation, Depletion And Amortization | | Net Investment |
|
2002 | | | | | | | | | |
|
Refining and supply | | $ | 3,637 | | $ | 2,019 | | $ | 1,618 |
|
Retail marketing* | | | 1,400 | | | 639 | | | 761 |
|
Chemicals | | | 1,072 | | | 171 | | | 901 |
|
Logistics | | | 1,012 | | | 427 | | | 585 |
|
Coke | | | 401 | | | 167 | | | 234 |
|
|
| | $ | 7,522 | | $ | 3,423 | | $ | 4,099 |
|
2001 | | | | | | | | | |
|
Refining and supply | | $ | 3,488 | | $ | 1,871 | | $ | 1,617 |
|
Retail marketing* | | | 1,472 | | | 656 | | | 816 |
|
Chemicals | | | 1,042 | | | 108 | | | 934 |
|
Logistics | | | 819 | | | 328 | | | 491 |
|
Coke | | | 400 | | | 159 | | | 241 |
|
|
| | $ | 7,221 | | $ | 3,122 | | $ | 4,099 |
|
* | Includes assets leased to third parties with a gross investment totalling $563 and $577 million at December 31, 2002 and 2001, respectively. Related accumulated depreciation totalled $302 and $293 million at December 31, 2002 and 2001, respectively. |
In connection with the initial public offering of Sunoco Logistics Partners L.P. (the “Partnership”), the Company contributed a substantial portion of its Logistics business as well as certain assets from its Refining and Supply and Retail Marketing businesses to the Partnership (Note 14). The contributions from Refining and Supply and Retail Marketing, which were effective January 1, 2002, consisted of properties, plants and equipment with a gross investment of $27 and $131 million, respectively, and related accumulated depreciation of $9 and $64 million, respectively.
Annual future minimum rentals due Sunoco, as lessor, on noncancelable operating leases at December 31, 2002 are as follows (in millions of dollars):
|
|
Year ending December 31: | | | |
|
2003 | | $ | 37 |
|
2004 | | | 23 |
|
2005 | | | 10 |
|
2006 | | | 3 |
|
2007 | | | 1 |
|
Thereafter | | | — |
|
|
| | $ | 74 |
|
10. Retirement Benefit Plans
Defined Benefit Pension Plans and Postretirement Health Care and Life Insurance Plans
Sunoco has noncontributory defined benefit pension plans (“defined benefit plans”) which provide retirement benefits for approximately one-half of its employees. Sunoco also has plans which provide health care and life insurance benefits for substantially all of its retirees (“postretirement benefit plans”). The postretirement benefit plans are unfunded and the costs are shared by Sunoco and its retirees.
45
Pension and postretirement health care and life insurance expense consisted of the following components:
| | Defined Benefit Plans
| | | Postretirement Benefit Plans
| |
(Millions of Dollars) | | 2002 | | | 2001 | | | 2000 | | | 2002 | | | 2001 | | | 2000 | |
|
|
Service cost (cost of benefits earned during the year) | | $ | 33 | | | $ | 32 | | | $ | 28 | | | $ | 7 | | | $ | 6 | | | $ | 5 | |
|
Interest cost on benefit obligations | | | 89 | | | | 92 | | | | 94 | | | | 28 | | | | 26 | | | | 24 | |
|
Expected return on plan assets | | | (100 | ) | | | (120 | ) | | | (118 | ) | | | — | | | | — | | | | — | |
|
Amortization of: | | | | | | | | | | | | | | | | | | | | | | | | |
|
Prior service cost (benefit) | | | 2 | | | | 2 | | | | 3 | | | | (10 | ) | | | (9 | ) | | | (9 | ) |
|
Unrecognized (gains) losses | | | 2 | | | | (2 | ) | | | (4 | ) | | | 2 | | | | — | | | | — | |
|
Net settlement/curtailment losses (Note 3) | | | — | | | | 1 | | | | 11 | | | | — | | | | 2 | | | | — | |
|
| | $ | 26 | | | $ | 5 | | | $ | 14 | | | $ | 27 | | | $ | 25 | | | $ | 20 | |
|
Pension and postretirement health care and life insurance expense is determined using actuarial assumptions as of the beginning of the year. The discount rates were 7.25 percent for 2002, 7.50 percent for 2001 and 7.75 percent for 2000. The long-term rate of return on plan assets and the rate of compensation increase were assumed to be 9 percent and 4 percent, respectively, for each of the last three years.
The following tables set forth the components of the changes in benefit obligations and fair value of plan assets during 2002 and 2001 as well as the funded status and amounts both recognized and not recognized in the consolidated balance sheets at December 31, 2002 and 2001:
| | Defined Benefit Plans
| | | Postretirement Benefit Plans
| |
| | 2002
| | | 2001
| | |
(Millions of Dollars) | | Funded Plans | | | Unfunded Plans | | | Funded Plans | | | Unfunded Plans | | | 2002 | | | 2001 | |
|
|
Benefit obligations at beginning of year* | | $ | 1,143 | | | $ | 122 | | | $ | 1,107 | | | $ | 118 | | | $ | 374 | | | $ | 348 | |
|
Service cost | | | 32 | | | | 1 | | | | 31 | | | | 1 | | | | 7 | | | | 6 | |
|
Interest cost | | | 81 | | | | 8 | | | | 83 | | | | 9 | | | | 28 | | | | 26 | |
|
Actuarial losses | | | 118 | | | | 2 | | | | 48 | | | | 7 | | | | 19 | | | | 6 | |
|
Acquisitions and divestments | | | — | | | | — | | | | 11 | | | | — | | | | — | | | | 15 | |
|
Benefits paid | | | (141 | ) | | | (13 | ) | | | (138 | ) | | | (13 | ) | | | (34 | ) | | | (34 | ) |
|
Premiums paid by participants | | | — | | | | — | | | | — | | | | — | | | | 4 | | | | 5 | |
|
Other | | | 2 | | | | (2 | ) | | | 1 | | | | — | | | | — | | | | 2 | |
|
Benefit obligations at end of year* | | $ | 1,235 | | | $ | 118 | | | $ | 1,143 | | | $ | 122 | | | $ | 398 | | | $ | 374 | |
|
|
Fair value of plan assets at beginning of year** | | $ | 1,110 | | | | | | | $ | 1,287 | | | | | | | | | | | | | |
|
Actual loss on plan assets | | | (91 | ) | | | | | | | (42 | ) | | | | | | | | | | | | |
|
Employer contributions | | | 52 | | | | | | | | 1 | | | | | | | | | | | | | |
|
Acquisitions and divestments | | | — | | | | | | | | 1 | | | | | | | | | | | | | |
|
Benefits paid from plan assets | | | (141 | ) | | | | | | | (137 | ) | | | | | | | | | | | | |
| | |
| | | | | | |
Fair value of plan assets at end of year** | | $ | 930 | | | | | | | $ | 1,110 | | | | | | | | | | | | | |
|
|
Unfunded accumulated obligation | | $ | (176 | ) | | $ | (110 | ) | | $ | 82 | | | $ | (114 | ) | | | | | | | | |
|
Provision for future salary increases | | | (129 | ) | | | (8 | ) | | | (115 | ) | | | (8 | ) | | | | | | | | |
| | | | |
|
Benefit obligations in excess of plan assets at end of year | | | (305 | ) | | | (118 | ) | | | (33 | ) | | | (122 | ) | | $ | (398 | ) | | $ | (374 | ) |
|
Unrecognized prior service cost (benefit) | | | 20 | | | | (4 | ) | | | 20 | | | | (2 | ) | | | (20 | ) | | | (30 | ) |
|
Unrecognized net loss | | | 407 | | | | 43 | | | | 98 | | | | 43 | | | | 52 | | | | 35 | |
|
Net amount recognized in balance sheet at end of year | | $ | 122 | | | $ | (79 | ) | | $ | 85 | | | $ | (81 | ) | | $ | (366 | ) | | $ | (369 | ) |
|
* | | Represents the projected benefit obligations for defined benefit plans and the accumulated postretirement benefit obligations (“APBO”) for postretirement benefit plans. |
** | | Less than 1 percent of plan assets was invested in Company stock. |
46
The net amount recognized in the consolidated balance sheets at December 31, 2002 and 2001 is classified as follows:
| | Defined Benefit Plans
| | | Postretirement Benefit Plans
| |
(Millions of Dollars) | | 2002 | | | 2001 | | | 2002 | | | 2001 | |
|
|
Prepaid retirement costs | | $ | 5 | | | $ | 87 | | | $ | — | | | $ | — | |
|
Retirement benefit liabilities | | | (287 | ) | | | (119 | ) | | | (366 | ) | | | (369 | ) |
|
Deferred charges and other assets* | | | 22 | | | | 3 | | | | — | | | | — | |
|
Accumulated other comprehensive loss (before related tax benefit)** | | | 303 | | | | 33 | | | | — | | | | — | |
|
| | $ | 43 | | | $ | 4 | | | $ | (366 | ) | | $ | (369 | ) |
|
* | | Represents an intangible asset for which an equivalent additional minimum liability is included in retirement benefit liabilities. |
** | | Represents a separate component of shareholders’ equity for which an equivalent additional minimum liability is included in retirement benefit liabilities. |
The following weighted-average assumptions were used at December 31, 2002 and 2001 to determine benefit obligations for the plans:
| | Defined Benefit Plans
| | Postretirement Benefit Plans
|
| | 2002 | | 2001 | | 2002 | | 2001 |
|
Discount rate | | 6.75% | | 7.25% | | 6.75%
| | 7.25%
|
Rate of compensation increase | | 4.00% | | 4.00% | | | | |
| | | | |
The health care cost trend assumption used at December 31, 2002 to compute the APBO for the postretirement benefit plans was an increase of 12.2 percent (8.3 percent at December 31, 2001), which is assumed to decline gradually to 5.5 percent in 2008 and to remain at that level thereafter.
A one-percentage point change each year in assumed health care cost trend rates would have the following effects at December 31, 2002:
(Millions of Dollars) | | 1-Percentage Point Increase | | 1-Percentage Point Decrease | |
|
|
Effect on total of service and interest cost components of postretirement benefits expense | | $ | 1 | | $ | (1 | ) |
|
Effect on APBO | | $ | 12 | | $ | (10 | ) |
|
Defined Contribution Pension Plans
Sunoco has defined contribution pension plans which provide retirement benefits for most of its employees. Sunoco’s contributions, which are principally based on a percentage of employees’ annual base compensation and are charged against income as incurred, amounted to $19, $19 and $17 million in 2002, 2001 and 2000, respectively.
Sunoco’s principal defined contribution plan is SunCAP. Sunoco matches 100 percent of employee contributions to this plan up to 5 percent of an employee’s base compensation. SunCAP is a combined profit sharing and employee stock ownership plan which contains a provision designed to permit SunCAP, only upon approval by the Company’s Board of Directors (“Board”), to borrow in order to purchase shares of Company common stock. As of December 31, 2002, no such borrowings had been approved.
11. Short-Term Borrowings and Credit Facilities
In July 2002, the Company entered into a new revolving credit facility (the “Facility”) totaling $770 million and terminated its $500 million credit facility which would have matured in September 2002. The new facility structure consists of a $385 million commitment through July 2005 and a $385 million commitment that matures in July 2003. The Facility provides the Company with access to short-term financing and is intended to support the issuance of commercial paper and letters of credit. The Company also can borrow directly from the participating banks under the Facility. The Facility is subject to commitment fees, which are not material. Under the terms of the Facility, Sunoco is required to maintain tangible net worth (as defined in the Facility) in an amount greater than or equal to targeted tangible net worth (targeted tangible net worth being determined by adding $1.0 billion and 50 percent of adjusted net income (as defined in the Facility) for each quarter ended after March 31, 2002). At December 31, 2002, the Company’s tangible net worth was $1.4 billion and its targeted tangible net worth was $1.0 billion. The Facility also requires that Sunoco’s ratio of consolidated net indebtedness, including borrowings of Sunoco Logistics Partners L.P., to consolidated capitalization (as those terms are defined in the Facility) not exceed .60 to 1. At December 31, 2002, this ratio was .45 to 1. At December 31, 2001, $299 million of commercial paper was outstanding (with a weighted-average interest rate of 2.92 percent). There were no short-term borrowings at December 31, 2002.
47
In February 2002, Sunoco Logistics Partners L.P. entered into a three-year $150 million revolving credit facility, which is available to fund the Partnership’s working capital requirements, to finance acquisitions, and for general partnership purposes. It includes a $20 million distribution sublimit that is available for distributions to third-party unitholders and Sunoco. At December 31, 2002, $65 million was outstanding under this credit facility (Note 12). The credit facility contains covenants requiring the Partnership to maintain a ratio of up to 4 to 1 of its consolidated total debt to its consolidated EBITDA (each as defined in the credit facility) and an interest coverage ratio (as defined in the credit facility) of at least 3.5 to 1. At December 31, 2002, the Partnership’s ratio of its consolidated debt to its consolidated EBITDA was 3.0 to 1 and the interest coverage ratio was 5.0 to 1. On February 14, 2003, the revolving credit facility was amended to increase the total amount available thereunder to $200 million.
12. Long-Term Debt
| | December 31
|
(Millions of Dollars) | | 2002 | | 2001 |
|
|
9 3/8% debentures due 2016 | | $ | 200 | | $ | 200 |
|
9% debentures due 2024 | | | 100 | | | 100 |
|
7¾% notes due 2009 | | | 200 | | | 200 |
|
7.60% environmental industrial revenue bonds due 2024 | | | 100 | | | 100 |
|
7¼% notes due 2012 (Note 14) | | | 250 | | | — |
|
7 1/8% notes due 2004 | | | 100 | | | 100 |
|
6 7/8% notes due 2006 | | | 150 | | | 150 |
|
6¾% notes due 2011 | | | 200 | | | 200 |
|
6¾% convertible debentures due 2012 (Note 15) | | | 10 | | | 10 |
|
Revolving credit loans, floating interest rate (2.12% at January 1, 2003) due 2005 (Note 11) | | | 65 | | | — |
|
Other | | | 87 | | | 91 |
|
|
| | | 1,462 | | | 1,151 |
|
Less: unamortized discount | | | 7 | | | 6 |
|
current portion | | | 2 | | | 3 |
|
| | $ | 1,453 | | | $1,142 |
|
The aggregate amount of long-term debt maturing and sinking fund requirements in the years 2003 through 2007 is as follows (in millions of dollars):
|
|
2003 | | $ | 2 | | 2006 | | $ | 153 |
|
2004 | | $ | 103 | | 2007 | | $ | 7 |
|
2005 | | $ | 67 | | | | | |
|
Cash payments for interest related to short-term borrowings and long-term debt (net of amounts capitalized) were $100, $98 and $79 million in 2002, 2001 and 2000, respectively.
The following table summarizes Sunoco’s long-term debt by issuer:
| | December 31
|
(Millions of Dollars) | | 2002 | | 2001 |
|
|
Sunoco, Inc. | | $ | 807 | | $ | 807 |
|
Sunoco Logistics Partners L.P. | | | 317 | | | — |
|
Other | | | 329 | | | 335 |
|
| | $ | 1,453 | | $ | 1,142 |
|
13. Commitments and Contingent Liabilities
Sunoco, as lessee, has noncancelable operating leases for marine transportation vessels, service stations, office space and other property and equipment. Total rental expense for such leases for the years 2002, 2001 and 2000 amounted to $136, $145 and $118 million, respectively. Approximately 6 percent of total rental expense was recovered through related sublease rental income during 2002.
The aggregate amount of future minimum annual rentals applicable to noncancelable operating leases are as follows (in millions of dollars):
|
|
Year ending December 31: | | | |
|
2003 | | $ | 97 |
|
2004 | | | 74 |
|
2005 | | | 45 |
|
2006 | | | 35 |
|
2007 | | | 32 |
|
Thereafter | | | 242 |
|
|
| | $ | 525 |
|
48
Sunoco is contingently liable under an arrangement which guarantees a $120 million term loan due in 2006 of the Epsilon Products Company, LLC polypropylene joint venture in which the Company is a partner (Notes 2, 8 and 18). Under this arrangement, Sunoco also guarantees borrowings under the joint venture’s $40 million revolving credit facility maturing in 2006, which amounted to $35 million at December 31, 2002. Sunoco is also contingently liable under various other arrangements which guarantee debt of other third parties aggregating approximately $13 million at December 31, 2002. At this time, management does not believe that it is likely that the Company will have to perform under any of these guarantees.
Over the years, Sunoco has sold thousands of retail gasoline outlets as well as refineries, coal mines, oil and gas properties and various other assets. In connection with these sales, the Company has indemnified the purchasers for potential environmental and other contingent liabilities related to the period prior to the transaction dates. In most cases, the effect of these arrangements was to afford protection for the purchasers with respect to obligations for which the Company was already primarily liable. While some of these indemnities have spending thresholds which must be exceeded before they become operative, or limits on Sunoco’s maximum exposure, they generally are not limited. The Company accrues for any obligations under these agreements when a loss is probable and reasonably estimable. The Company cannot reasonably estimate the maximum potential amount of future payments under these agreements.
Sunoco is a party under agreements which provide for future payments to secure wastewater treatment services at its Toledo refinery and coal handling services at its Indiana Harbor cokemaking facility. The fixed anddeterminable amounts of the obligations under these agreements are as follows (in millions of dollars):
|
|
Year ending December 31: | | | | |
|
2003 | | $ | 9 | |
|
2004 | | | 8 | |
|
2005 | | | 8 | |
|
2006 | | | 8 | |
|
2007 | | | 8 | |
|
2008 through 2018 | | | 63 | |
|
|
Total | | | 104 | |
|
Less: Amount representing interest | | | (37 | ) |
|
|
Total at present value | | $ | 67 | |
|
Payments under these agreements, including variable components, totalled $18 million in each of the years 2002, 2001 and 2000.
Sunoco is subject to numerous federal, state and local laws and regulations which regulate the discharge of materials into the environment or that otherwise relate to the protection of the environment. As with the industry generally, compliance with existing and anticipated laws and regulations increases the overall cost of operating Sunoco’s businesses, including capital costs to construct, maintain and upgrade equipment and facilities. These laws and regulations result in liabilities and loss contingencies for remediation at Sunoco’s facilities and at third-party or formerly owned sites. The accrued liability for environmental remediation is classified in the consolidated balance sheets as follows:
| | December 31
|
(Millions of Dollars) | | 2002 | | 2001 |
|
|
Accrued liabilities | | $ | 43 | | $ | 39 |
|
Other deferred credits and liabilities | | | 116 | | | 106 |
|
| | $ | 159 | | $ | 145 |
|
The following table sets forth the accrued liability for environmental remediation activities by category:
(Millions of Dollars) | | Refineries | | | Marketing Sites | | | Chemicals Facilities | | | Pipelines and Terminals | | | Hazardous Waste Sites | | | Other | | Total | |
|
At December 31, 1999 | | $ | 74 | | | $ | 53 | | | $ | — | | | $ | 19 | | | $ | 11 | | | $ | 3 | | $ | 160 | |
|
Accruals | | | 1 | | | | 3 | | | | — | | | | 13 | | | | — | | | | — | | | 17 | |
|
Payments | | | (6 | ) | | | (17 | ) | | | — | | | | (13 | ) | | | (3 | ) | | | — | | | (39 | ) |
|
Other* | | | — | | | | 3 | | | | — | | | | — | | | | — | | | | — | | | 3 | |
|
At December 31, 2000 | | $ | 69 | | | $ | 42 | | | $ | — | | | $ | 19 | | | $ | 8 | | | $ | 3 | | $ | 141 | |
|
Accruals | | | (2 | ) | | | 21 | | | | — | | | | 10 | | | | 2 | | | | — | | | 31 | |
|
Payments | | | (6 | ) | | | (19 | ) | | | — | | | | (11 | ) | | | (2 | ) | | | — | | | (38 | ) |
|
Acquisitions | | | — | | | | — | | | | 10 | | | | — | | | | — | | | | — | | | 10 | |
|
Other* | | | — | | | | 1 | | | | — | | | | — | | | | — | | | | — | | | 1 | |
|
At December 31, 2001 | | $ | 61 | | | $ | 45 | | | $ | 10 | | | $ | 18 | | | $ | 8 | | | $ | 3 | | $ | 145 | |
|
Accruals | | | (2 | ) | | | 36 | | | | 1 | | | | 7 | | | | — | | | | — | | | 42 | |
|
Payments | | | (7 | ) | | | (24 | ) | | | (3 | ) | | | (12 | ) | | | (3 | ) | | | — | | | (49 | ) |
|
Other* | | | — | | | | 15 | | | | — | | | | 6 | | | | — | | | | — | | | 21 | |
|
At December 31, 2002 | | $ | 52 | | | $ | 72 | | | $ | 8 | | | $ | 19 | | | $ | 5 | | | $ | 3 | | $ | 159 | |
|
*Consists | | of increases in the accrued liability for which recovery from third parties is probable. |
49
Sunoco’s accruals for environmental remediation activities reflect its estimates of the most likely costs that will be incurred over an extended period to remediate identified conditions for which the costs are both probable and reasonably estimable. Engineering studies, historical experience and other factors are used to identify and evaluate remediation alternatives and their related costs in determining the estimated accruals for environmental remediation activities. Losses attributable to unasserted claims are also reflected in the accruals to the extent they are probable of occurrence and reasonably estimable.
Total future costs for the environmental remediation activities identified above will depend upon, among other things, the identification of any additional sites, the determination of the extent of the contamination at each site, the timing and nature of required remedial actions, the technology available and needed to meet the various existing legal requirements, the nature and terms of cost sharing arrangements with other potentially responsible parties, the nature and extent of future environmental laws, inflation rates and the determination of Sunoco’s liability at the sites, if any, in light of the number, participation level and financial viability of the other parties. Management believes it is reasonably possible (i.e., less than probable but greater than remote) that additional environmental remediation losses will be incurred. At December 31, 2002, the aggregate of the estimated maximum additional reasonably possible losses, which relate to numerous individual sites, totaled $90 million. However, the Company believes it is very unlikely that it will realize the maximum loss at every site. Furthermore, the recognition of additional losses, if and when they might occur, would likely extend over many years and, therefore, would not have a material impact on the Company’s financial position.
Under various environmental laws, including the Resource Conservation and Recovery Act (“RCRA”), Sunoco has initiated corrective remedial action at its facilities, formerly owned facilities and third-party sites. At the Company’s major manufacturing facilities, Sunoco has consistently assumed continued industrial use and a containment/remediation strategy focused on eliminating unacceptable risks to human health or the environment. The remediation accruals for these sites reflect that strategy. Accruals include amounts to prevent off-site migration and to contain the impact on the facility property, as well as to address known, discrete areas requiring remediation within the plants. Activities include closure of RCRA solid waste management units, recovery of hydrocarbons, handling of impacted soil, mitigation of surface water impacts and prevention of off-site migration.
Most of Sunoco’s current terminals are being addressed with the above containment/remediation strategy. At some smaller or less impacted facilities and previously divested terminals, the focus is on remediating discrete interior areas to attain regulatory closure.
Future costs for environmental remediation activities at the Company’s marketing sites will also be influenced by the extent of MTBE contamination of groundwater aquifers, the cleanup of which will be driven by thresholds based on drinking water protection. Though not all groundwater is used for drinking, several states have initiated or proposed more stringent MTBE cleanup requirements. Cost increases result directly from extended operations and maintenance on sites that previously could otherwise have been completed, installation of additional remedial or monitoring wells and purchase of more expensive equipment because of the presence of MTBE. While actual cleanup costs for specific sites are variable and depend on many of the factors discussed above, expansion of similar MTBE remediation thresholds to additional states or adoption of even more stringent requirements for MTBE remediation would result in further cost increases.
The accrued liability for hazardous waste sites in the table above is attributable to potential obligations to remove or mitigate the environmental effects of the disposal or release of certain pollutants at third-party sites pursuant to the Comprehensive Environmental Response Compensation and Liability Act (“CERCLA”). Under CERCLA, Sunoco is potentially subject to joint and several liability for the costs of remediation at sites at which it has been identified as a “potentially responsible party” (“PRP”). As of December 31, 2002, Sunoco had been named as a PRP at 44 sites identified or potentially identifiable as “Superfund” sites under federal and state law. The Company is usually one of a number of companies identified as a PRP at a site. Sunoco has reviewed the nature and extent of its involvement at each site and other relevant circumstances and, based upon the other parties involved or Sunoco’s negligible participation therein, believes that its potential liability associated with such sites will not be significant.
Management believes that none of the current remediation locations is individually material to Sunoco as its largest accrual for any one Superfund site, operable unit or remediation area is less than $7 million at December 31, 2002. As a result, Sunoco’s exposure to adverse developments with respect to any individual site is not expected to be material, and these current sites are in various stages of ongoing remediation. However, if changes in environmental regulations occur, such changes could impact multiple Sunoco facilities and for - -
50
merly owned and third-party sites at the same time. As a result, from time to time, significant charges against income for environmental remediation may occur.
The Company maintains insurance programs that cover certain of its existing or potential environmental liabilities, which programs vary by year, type and extent of coverage. For underground storage tank remediations, the Company can also seek reimbursement through various state funds of certain remediation costs above a deductible amount. For certain acquired properties, the Company has entered into arrangements with the sellers or others that allocate environmental liabilities and provide indemnities to the Company for remediating contamination that occurred prior to the acquisition dates. Some of these environmental indemnifications are subject to caps and limits. No accruals have been recorded for any potential contingent liabilities that will be funded by the prior owners as management does not believe, based on current information, that it is likely that any of the former owners will not perform under any of these agreements. Other than the preceding arrangements, the Company has not entered into any arrangements with third parties to mitigate its exposure to loss from environmental contamination. Claims for recovery of environmental liabilities that are probable of realization totalled $27 million at December 31, 2002 and are included primarily in deferred charges and other assets in the consolidated balance sheets.
Since the late 1990s, the Environmental Protection Agency (“EPA”) has undertaken significant enforcement initiatives under authority of the Clean Air Act. These enforcement initiatives have been targeted at industries that have large manufacturing facilities and that are significant sources of emissions, such as the refining, paper and pulp, and electric power generating industries. The basic premise of the enforcement initiative is the EPA’s assertion that many of these industrial establishments have modified or expanded their operations over time without complying with New Source Review regulations that require permits and new emission controls in connection with any significant facility modifications or expansions that can result in emission increases above certain thresholds, and have violated various other provisions of the Clean Air Act, including New Source Review and Prevention of Significant Deterioration (“NSR/PSD”) Program, Benzene Waste Organic National Emissions Standards for Hazardous Air Pollutants (“NESHAP”), Leak Detection and Repair (“LDAR”) and flaring requirements. As part of this enforcement initiative, the EPA has entered into consent agreements with several refiners that require them to pay civil fines and penalties and make significant capital expenditures to install emissions control equipment at selected facilities. For some of these refineries, the cost of the required emissions control equipment is significant, depending on the size, age and configuration of the refinery. Sunoco received information requests in 2000, 2001 and 2002 in connection with the enforcement initiative pertaining to its four current refineries, the Puerto Rico refinery divested by Sunoco in 2001 and its phenol facility in Philadelphia, PA. Sunoco has completed its responses to the EPA, which is focusing solely on the refineries at this time.
Sunoco has received Notices of Violation and Findings of Violation from the EPA relating to its Marcus Hook, Philadelphia and Toledo refineries. The Notices and Findings of Violation allege failure to comply with certain requirements relating to benzene wastewater emissions at the Company’s Marcus Hook, Toledo and Philadelphia refineries and failure to comply with certain requirements relating to leak detection and repair at the Toledo refinery. In addition, the EPA has alleged that: at the Company’s Philadelphia refinery, certain modifications were made to one of the fluid catalytic cracking units in 1992 and 1998 without obtaining requisite permits; at the Company’s Marcus Hook refinery, certain modifications were made to the fluid catalytic cracking unit in 1990 and 1996 without obtaining requisite permits; and at the Company’s Toledo refinery, certain physical and operational changes were made to the fluid catalytic cracking unit in 1985 without obtaining requisite permits. The EPA has also alleged that at the Company’s Toledo refinery, certain physical and operational changes were made to the sulfur plant in 1995, 1998 and 1999 without obtaining requisite permits; certain physical and operational changes were made to a flare system without obtaining requisite permits; and that the flare system was not being operated in compliance with the Clean Air Act. Sunoco has met with representatives of the EPA on these Notices and Findings of Violation and is currently evaluating its position. Although Sunoco does not believe that it has violated any Clean Air Act requirements, as part of this initiative, Sunoco could be required to make significant capital expenditures, operate these refineries at reduced levels and pay significant penalties. There are no liabilities accrued at December 31, 2002 in connection with this initiative.
During the 2001-2002 session, the U.S. Congress was considering energy policy legislation. Congress failed to approve the legislation during the session. The Senate and House both approved bills, which included provisions concerning ethanol and MTBE; however, a conference committee was unable to resolve differences between the two pieces of legislation. Provisions concerning MTBE, ethanol, and fuels standards were among the disputed issues. It is expected that these issues will be on the Congressional agendas in 2003. Sunoco uses MTBE and ethanol as an oxygenate in different geographic areas
51
of its refining and marketing system. While federal action to ban or phase down MTBE or to require increased usage of ethanol is uncertain, some states are scheduled to begin enforcing MTBE bans within the next year. Sunoco is currently evaluating its options to produce MTBE-free gasoline when the additive is banned in states where it markets, including Connecticut (October 2003) and New York (January 2004). While Sunoco does not market in California, that state’s ban on MTBE (January 2004) could have an impact on market conditions. Numerous other states are expected to consider legislation to ban MTBE during their 2003 legislative sessions. If MTBE is banned throughout the United States or on a state-by-state basis, the effect on Sunoco and the industry in general could be significant. It will depend on the specific regulations, the impact on gasoline supplies, the cost and availability of alternative oxygenates if the minimum oxygenate requirements remain in effect, and the ability of Sunoco and the industry in general to recover their costs in the marketplace.
Sunoco is a one-third partner in Belvieu Environmental Fuels (“BEF”), a joint venture that owns and operates an MTBE production facility in Mont Belvieu, TX. The joint venture is currently evaluating alternative uses for this facility in the event MTBE is banned, including the conversion from the production of MTBE to the production of alkylate or some other gasoline blending component. If the Company determines that it is uneconomic to convert the facility, the write-down of its $51 million investment in this operation may be necessary. In order to obtain a secure supply of oxygenates for the manufacture of reformulated gasoline, Sunoco entered into an off-take agreement with BEF whereby Sunoco agreed to purchase all of the MTBE production from the plant. Sunoco’s total MTBE purchases under this agreement, which expires in 2004, were $234, $207 and $272 million during 2002, 2001 and 2000, respectively (Notes 2, 3 and 8).
Many other legal and administrative proceedings are pending or possible against Sunoco from its current and past operations, including proceedings related to commercial and tax disputes, product liability, antitrust, employment claims, leaks from pipelines and underground storage tanks, premises-liability claims, allegations of exposures of third parties to toxic substances (such as benzene or asbestos) at Sunoco assets or facilities and general environmental claims. The ultimate outcome of these proceedings and the matters discussed above cannot be ascertained at this time; however, it is reasonably possible that some of them could be resolved unfavorably to Sunoco. Management believes that these matters could have a significant impact on results of operations for any one year. However, management does not believe that any additional liabilities which may arise pertainingto such matters would be material in relation to the consolidated financial position of Sunoco at December 31, 2002.
14. Minority Interests
Cokemaking Operations
In July 2002, Sunoco transferred an additional interest in its Indiana Harbor cokemaking operation to a third-party investor for $215 million in cash and in September 2000, transferred an additional interest in its Jewell cokemaking operation to a third-party investor for $214 million in cash. Since 1995, Sunoco has received $724 million in exchange for interests in its Indiana Harbor and Jewell cokemaking operations in four separate transactions. Sunoco did not recognize any gain at the dates of these transactions as the third-party investors are entitled to a preferential return on their investments, currently equal to 98 percent of the cash flows and tax benefits from the respective cokemaking operations, during a preferential return period which continues until they recover their investments and achieve a cumulative return that averages approximately 10 percent after tax thereon. Income is recognized as coke production and sales generate cash flows and tax benefits which are allocated to Sunoco and the third-party investors, while expense is recognized to reflect the investors’ preferential returns.
The preferential return period for the Jewell operation, which had been projected to end in 2007, is now estimated to extend to 2011 due to anticipated lower income from the Jewell operation resulting from the Chapter 11 bankruptcy filing in March 2002 by National Steel Corporation, Jewell’s former long-term contract customer. The preferential return period for the first investor in the Indiana Harbor operation ended in July 2002, at which time the first investor’s interest in the cash flows and tax benefits from Indiana Harbor decreased from 95 percent to 5 percent. As a result of the additional investment in July 2002, third-party investors’ interests increased from 5 percent to 98 percent. The new investor’s preferential return period for the Indiana Harbor operation is expected to end in 2007. The estimated lengths of these preferential return periods are based upon the Company’s current expectations of future operations, including sales volumes and prices, raw material and operating costs and capital expenditure levels. Better-than-expected results will shorten the investors’ preferential return periods, while lower-than-expected results will lengthen the periods.
After these preferential return periods, the investor in the Jewell operation will be entitled to a minority interest in the cash flows and tax benefits from Jewell amounting to 18 percent, while the investors in the Indiana Harbor operation will be entitled to a minority interest in the cash flows and tax benefits from Indiana Harbor initially
52
amounting to 34 percent and declining to 10 percent by 2038.
The following table sets forth the minority interest balances and the changes in these balances attributable to the investors’ interests in cokemaking operations:
(Millions of Dollars) | | 2002 | | | 2001 | | | 2000 | |
|
|
Balance at beginning of year | | $ | 223 | | | $ | 316 | | | $ | 175 | |
|
Nonconventional fuel credit and other tax benefits* | | | (77 | ) | | | (69 | ) | | | (68 | ) |
|
Preferential return* | | | 42 | | | | 32 | | | | 22 | |
|
Additional cash investments by third-party investors | | | 215 | | | | — | | | | 214 | |
|
Cash distributions to third-party investors | | | (24 | ) | | | (56 | ) | | | (27 | ) |
|
Balance at end of year | | $ | 379 | | | $ | 223 | | | $ | 316 | |
|
* | The nonconventional fuel credit and other tax benefits and the preferential return, which comprise the noncash reduction in the minority interest in cokemaking operations, are included in other income in the consolidated statements of operations (Note 2). |
In each of the four transactions in which the Company transferred interests in its cokemaking operations to third-party investors, Sunoco has provided tax indemnifications to the third parties for certain tax benefits allocated to them during the preferential return periods. In certain of these cases, the Company also has the option to purchase the third-party investors’ interests. These indemnifications would require the Company to make payments in the event the Internal Revenue Service disallows the tax deductions and benefits allocated to the third parties or if there is a change in the tax laws that reduces the amount of nonconventional fuel tax credits which would be available to them. These tax indemnifications are in effect until the applicable tax returns are no longer subject to Internal Revenue Service review. Although the Company believes it is remote that it will be required to make any payments under these indemnifications, at December 31, 2002, the maximum potential payment under the tax indemnifications and the options to purchase the third-party investors’ interests, if exercised, would have been approximately $850 million. If this occurs, the minority interest balance would be reduced by approximately $340 million.
Logistics Operations
On February 8, 2002, the Company contributed a substantial portion of its Logistics business to Sunoco Logistics Partners L.P., its master limited partnership formed in 2001, in exchange for a 73.2 percent limited partnership interest, a 2 percent general partnership interest, incentive distribution rights and a $245 million special distribution, representing the net proceeds from the Partnership’s issuance of $250 million of ten-year 7 1/4 percent senior notes (Note 12). The Partnership concurrently issued 5.75 million limited partnership units,representing a 24.8 percent interest in the Partnership, in an initial public offering at a price of $20.25 per unit. Proceeds from the offering, which totalled approximately $96 million net of underwriting discounts and offering expenses, were used by the Partnership to establish working capital that was not contributed to the Partnership by Sunoco. Sunoco liquidated this retained working capital subsequent to the Partnership’s formation. The accounts of the Partnership continue to be included in Sunoco’s consolidated financial statements. No gain or loss was recognized on this transaction.
Concurrent with the offering, Sunoco entered into various agreements with the Partnership which require Sunoco to pay for minimum storage and throughput usage of certain Partnership assets. These agreements also establish fees for administrative services provided by Sunoco to the Partnership and indemnifications by Sunoco for certain environmental, toxic tort and other liabilities.
The following table sets forth the changes in the minority interest balance attributable to the third-party investors’ interests in Sunoco Logistics Partners L.P. during 2002 subsequent to the initial public offering (in millions of dollars):
(Millions of Dollars) | | | |
|
|
Net proceeds from the initial public offering on February 8, 2002 | | $ | 96 | |
|
Minority interest share of income * | | | 11 | |
|
Cash distributions to third-party investors | | | (7 | ) |
|
Balance at end of year | | $ | 100 | |
|
* | Included in selling, general and administrative expenses in the consolidated statement of operations. |
15. Shareholders’ Equity
Each share of Company common stock is entitled to one full vote. The $10 million of outstanding 6 3/4 percent debentures are convertible into shares of Sunoco common stock at any time prior to maturity at a conversion price of $40.81 per share and are redeemable at the option of the Company. At December 31, 2002, there were 242,981 shares of common stock reserved for this potential conversion (Note 12).
The Company did not repurchase any of its common stock in 2002. During the 2000-2001 period, the Company repurchased 15.9 million shares of its common stock for $537 million. At December 31, 2002, the Company had a remaining authorization from its Board to purchase up to $327 million of Company common stock in the open market or through privately negotiated transactions from time to time depending on prevailing market conditions and available cash.
53
The Company’s Articles of Incorporation authorize the issuance of up to 15,000,000 shares of preference stock without par value, subject to approval by the Board. The Board also has authority to fix the number, designation, rights, preferences and limitations of these shares, subject to applicable laws and the provisions of the Articles of Incorporation. At December 31, 2002, no such shares had been issued.
On February 1, 1996, the Company adopted a shareholder rights plan and designated 1,743,019 shares of its preference stock as Series B participating cumulative preference stock. Pursuant to the plan, the Company declared a dividend of one stock purchase right (“Right”) for each share of common stock outstanding on February 12, 1996. A Right will be granted for each share of common stock issued after such date and prior to the expiration date of the rights plan. The Rights are attached to the common stock until they become exercisable. Generally, the Rights become exercisable a specified period after a party acquires 15 percent or more of the aggregate outstanding common stock or announces a tender offer for 15 percent or more of the common stock. Each Right initially entitles a holder to purchase one one-hundredth of a share of the Series B participating cumulative preference stock for $100. After a party has acquired 15 percent or more of the common stock, each Right will entitle a holder to pay $100 for the number of shares of Company common stock (or in certain situations, common stock of the acquiring party) having a then current market value of $200. Alternatively, the Company has the option to exchange one share of Company common stock for each Right at any time after a party has acquired at least 15 percent but less than 50 percent of the common stock.The Company may redeem each Right for $.01 per Right at any time until a party has acquired 15 percent or more of the common stock. In general, none of the benefits of the Rights will be available to a holder of 15 percent or more of the common stock. The Rights will expire on February 12, 2006, unless earlier exchanged or redeemed.
The following table sets forth the components (net of related income taxes) of the accumulated other comprehensive loss balances in shareholders’ equity:
| | December 31
| |
(Millions of Dollars) | | 2002 | | | 2001 | |
|
|
Minimum pension liability adjustment | | $ | (197 | ) | | $ | (21 | ) |
|
Hedging activities | | | 2 | | | | (7 | ) |
|
| | $ | (195 | ) | | $ | (28 | ) |
|
16. Management Incentive Plans
Sunoco’s principal management incentive plans are the Executive Incentive Plan (“EIP”) and the Long-Term Performance Enhancement Plan II (“LTPEP II”). The EIP provides for the payment of annual cash incentive awards while the LTPEP II provides for the award of stock options, common stock units and related rights to directors, officers and other key employees of Sunoco. The options granted under LTPEP II have a ten-year term, are not exercisable until two years after the date of grant and permit optionees to purchase Company common stock at its fair market value on the date of grant. LTPEP II authorizes the use of four million shares of common stock for awards. No awards may be granted under LTPEP II after December 31, 2006, unless the Board extends this date to a date no later than December 31, 2011.
54
The following table summarizes information with respect to common stock option awards under Sunoco’s management incentive plans as well as the Employee Option Plan:
| | Management Incentive Plans
| | Employee Option Plan*
|
| | Shares Under Option | | | Weighted- Average Option Price Per Share | | Shares Under Option | | | Option Price Per Share |
|
|
Outstanding, December 31, 1999 | | 4,585,067 | | | $ | 29.83 | | 535,174 | | | $ | 28.00 |
|
Granted | | 702,210 | | | $ | 28.22 | | — | | | | |
|
Exercised | | (80,923 | ) | | $ | 28.47 | | (5,025 | ) | | $ | 28.00 |
|
Canceled | | (151,000 | ) | | $ | 29.91 | | (21,130 | ) | | $ | 28.00 |
|
|
Outstanding, December 31, 2000 | | 5,055,354 | | | $ | 29.63 | | 509,019 | | | $ | 28.00 |
|
Granted | | 754,960 | | | $ | 37.61 | | — | | | | |
|
Exercised | | (1,279,910 | ) | | $ | 29.38 | | (118,100 | ) | | $ | 28.00 |
|
Canceled | | (32,710 | ) | | $ | 32.12 | | (12,020 | ) | | $ | 28.00 |
|
|
Outstanding, December 31, 2001 | | 4,497,694 | | | $ | 31.02 | | 378,899 | | | $ | 28.00 |
|
Granted | | 733,360 | | | $ | 30.27 | | — | | | | |
|
Exercised | | (604,264 | ) | | $ | 27.34 | | (213,470 | ) | | $ | 28.00 |
|
Canceled | | (95,480 | ) | | $ | 35.60 | | (6,225 | ) | | $ | 28.00 |
|
Outstanding, December 31, 2002 | | 4,531,310 | | | $ | 31.29 | | 159,204 | | | $ | 28.00 |
|
|
Exercisable, December 31 | | | | | | | | | | | | |
|
|
2000 | | 3,358,264 | | | $ | 31.22 | | 509,019 | | | $ | 28.00 |
|
2001 | | 3,051,724 | | | $ | 30.02 | | 378,899 | | | $ | 28.00 |
2002 | | 3,111,490 | | | $ | 30.13 | | 159,204 | | | $ | 28.00 |
|
|
Available for Grant, December 31 | | | | | | | | | | | | |
|
|
2000 | | 468,652 | | | | | | — | | | | |
|
2001 | | 3,547,040 | | | | | | — | | | | |
2002 | | 2,526,780 | | | | | | — | | | | |
|
*Options | were granted to employees (other than executives) during 1993 and 1994. |
The following table provides additional information concerning all options outstanding at December 31, 2002:
| | Options Outstanding
| | Options Exercisable
|
Range of Exercise Prices | | Shares Under Option | | Weighted- Average Remaining Contractual Life (Years) | | Weighted- Average
Exercise Price | | Shares Under Option | | Weighted- Average
Exercise Price |
|
|
$23.25—$26.44 | | 951,385 | | 6 | | $ | 24.95 | | 951,385 | | $ | 24.95 |
|
$27.25—$28.88 | | 909,044 | | 6 | | $ | 27.78 | | 909,044 | | $ | 27.78 |
|
$30.15—$32.88 | | 1,644,885 | | 7 | | $ | 31.30 | | 913,185 | | $ | 32.19 |
|
$35.24—$39.88 | | 1,185,200 | | 7 | | $ | 38.62 | | 497,080 | | $ | 39.88 |
|
|
$23.25—$39.88 | | 4,690,514 | | 7 | | $ | 31.18 | | 3,270,694 | | $ | 30.03 |
|
55
Common stock unit awards entitle the holder to receive Company common stock upon completion of a restriction period or upon attainment of predetermined performance targets. The following table summarizes information with respect to common stock unit awards under Sunoco’s management incentive plans:
| | 2002 | | | 2001 | | | 2000 | |
|
|
Outstanding at beginning of year | | 519,290 | | | 436,292 | | | 364,213 | |
|
Granted* | | 151,650 | | | 114,500 | | | 174,585 | |
|
Performance factor adjustment** | | (53,372 | ) | | — | | | 22,240 | |
|
Matured | | (147,061 | ) | | (22,902 | ) | | (117,889 | ) |
|
Canceled | | (8,295 | ) | | (8,600 | ) | | (6,857 | ) |
|
Outstanding at end of year | | 462,212 | | | 519,290 | | | 436,292 | |
|
* | | The weighted average price for common stock awards on the date of grant was $30.14, $37.07 and $28.51 for awards granted in 2002, 2001 and 2000, respectively. |
** | | Consists of adjustments to performance-based awards to reflect actual performance. The adjustments are required since the original grants of these awards were at 100 percent of the targeted amounts. |
During the fourth quarter of 2002, Sunoco adopted the fair value method of accounting for employee stock compensation plans (Note 1). Stock-based compensation expense for 2002 determined utilizing this method amounted to $11 million ($7 million after tax), which consisted of $6 million related to stock option awards and $5 million related to common stock unit awards. Had the fair value method been followed during 2001 and 2000, the pro forma impact on Sunoco’s net income and net income per share of common stock on a diluted basis would have been as follows:
(Millions of Dollars, Except Per Share Amounts) | | 2001 | | | 2000 | |
|
|
Net income, as reported: | | $ | 398 | | | $ | 422 | |
|
Add back after-tax stock-based compensation expense included in reported net income | | | 4 | | | | 1 | |
|
Less after-tax stock-based compensation expense determined under SFAS No. 123 | | | (7 | ) | | | (4 | ) |
|
|
Net income, pro forma | | $ | 395 | | | $ | 419 | |
|
|
Net income per share: | | | | | | | | |
|
As reported | | $ | 4.85 | | | $ | 4.82 | |
|
Pro forma | | $ | 4.82 | | | $ | 4.79 | |
|
The 2002 historical amounts and the 2001 and 2000 pro forma amounts above have been computed in accordance with the fair value method and reflect the estimated fair values of $7.08, $10.38 and $6.95 per option granted during 2002, 2001 and 2000, respectively. These values are calculated using the Black-Scholes option pricing model based on the following weighted-average assumptions:
| | 2002 | | 2001 | | 2000 |
|
|
Expected life (years) | | 6 | | 6 | | 6 |
|
Risk-free interest rate | | 3.7% | | 4.8% | | 5.4% |
|
Dividend yield | | 3.3% | | 2.7% | | 3.6% |
Expected volatility | | 29.3% | | 29.3% | | 28.1% |
|
17. Financial Instruments
The estimated fair value of financial instruments has been determined based on the Company’s assessment of available market information and appropriate valuation methodologies. However, these estimates may not necessarily be indicative of the amounts that the Company could realize in a current market exchange.
Sunoco’s current assets (other than inventories and deferred income taxes) and current liabilities are financial instruments. The estimated fair value of these financial instruments approximates their carrying amounts. At December 31, 2002 and 2001, the estimated fair value of Sunoco’s long-term debt was $1,593 and $1,215 million, respectively, compared to carrying amounts of $1,453 and $1,142 million, respectively. Long-term debt that is publicly traded was valued based on quoted market prices while the fair value of other debt issues was estimated by management based upon current interest rates available to Sunoco at the respective balance sheet dates for similar issues.
The Company guarantees the debt of affiliated companies and others (Note 13). Due to the complexity of these guarantees and the absence of any market for these financial instruments, the Company does not believe it is practicable to estimate their fair value.
Sunoco uses a variety of derivative instruments for hedging purposes. Sunoco is at risk for possible changes in the market value for these derivative instruments. However, it is anticipated that such risk would be mitigated by price changes in the underlying hedged items. In addition, Sunoco is exposed to credit risk in the event of nonperformance by counterparties. Management believes this risk is negligible as its counterparties are either regulated by exchanges or are major international financial institutions or corporations with investment-grade credit ratings. Market and credit risks associated with all of Sunoco’s derivative contracts are reviewed regularly by management.
Sunoco uses futures and forward contracts from time to time to achieve ratable pricing of its crude oil purchases and to convert certain refined product sales to fixed or floating prices. In addition, price collars, swaps and option contracts may be used to lock in a portion of the Company’s electricity and natural gas costs. Sunoco also uses swaps, price collars and other contracts from time to time to hedge against significant increases in crude oil prices and to lock in what Sunoco considers to be acceptable margins for various refined products.
56
At December 31, 2002, the Company had recorded assets totalling $2 million for hedging gains, which represented their fair value as determined using various indices and dealer quotes. The amount of hedge ineffectiveness on derivative contracts during the 2000-2002 period was not material. Open contracts as of December 31, 2002 vary in duration but do not extend beyond 2003.
18. Acquisitions and Polypropylene Joint Venture
Acquisitions
Pipeline Joint Ventures—In November 2002, Sunoco’s Logistics business completed the acquisition from an affiliate of Union Oil Company of California (“Unocal”) of interests in three Midwestern and Western U.S. products pipeline companies, consisting of a 31.5 percent interest in Wolverine Pipeline Company, a 9.2 percent interest in West Shore Pipeline Company and a 14.0 percent interest in Yellowstone Pipeline Company, for $54 million in cash. In November 2002, Sunoco’s Logistics business also completed the acquisition of an additional interest in West Texas Gulf pipeline for $6 million in cash, which increased its ownership interest in this pipeline from 17.3 percent to 43.8 percent. The Company’s share of the results of operations of these joint ventures has been included in equity income in the consolidated statement of operations since the acquisition dates. The purchase prices have been reflected as investments and long-term receivables in the consolidated balance sheet. The Company’s pro forma share of the results of operations of the joint ventures in 2002 and 2001 was not material in relation to Sunoco’s consolidated results of operations.
Aristech Chemical Corporation—Effective January 1, 2001, Sunoco completed the acquisition of Aristech Chemical Corporation (“Aristech”), a wholly owned subsidiary of Mitsubishi Corporation (“Mitsubishi”), for $506 million in cash and the assumption of $163 million of debt. The purchase price included $107 million for working capital. Contingent payments with a net present value as of the acquisition date of up to $167 million (the “earn out”) may also be made if realized margins for polypropylene and phenol exceed certain agreed-upon thresholds through 2006. Since the $167 million represents a present value as of January 1, 2001, the actual amounts that could ultimately be paid under the earn out provisions increase over time by 11 percent per year. However, the contingent payments are limited to $90 million per year. Any earn out payments would be treated as adjustments to the purchase price. Sunoco also enteredinto a margin hedge agreement with Mitsubishi whereby Mitsubishi provided polypropylene margin protection for 2001 of up to $6.5 million per quarter. In connection with the margin hedge agreement, Sunoco received $19.5 million from Mitsubishi in 2001 related to Aristech’s operations for the first nine months and an additional $6.5 million in the first quarter of 2002 related to the 2001 fourth quarter’s operations. These payments were reflected as reductions in the purchase price when received. In addition, Mitsubishi is responsible during a 25-year indemnification period for up to $100 million of potential environmental liabilities for the business arising out of or related to the period prior to the acquisition date.
Included in the purchase are Aristech’s five chemical plants located at Neal, WV; Haverhill, OH; Neville Island, PA; and Pasadena and LaPorte, TX and a research center in Pittsburgh, PA. These facilities produce polypropylene, phenol and related derivatives (including biphenol-A) and plasticizers.
The acquisition has been accounted for as a purchase. The results of operations of Aristech have been included in the consolidated statements of operations from the date of acquisition. The purchase price has been allocated to the assets acquired and liabilities assumed based on their relative estimated fair market values at the acquisition date.
The following is a summary of the effects of this transaction on Sunoco’s consolidated financial position:
(Millions of Dollars): | | | |
|
|
Allocation of purchase price: | | | | |
|
Accounts and notes receivable, net | | $ | 156 | |
|
Inventories | | | 130 | |
|
Investments and long-term receivables | | | 8 | |
|
Properties, plants and equipment, net | | | 674 | |
|
Accounts payable | | | (110 | ) |
|
Accrued liabilities | | | (57 | ) |
|
Current portion of long-term debt | | | (1 | ) |
|
Taxes payable | | | (10 | ) |
|
Long-term debt | | | (162 | ) |
|
Retirement benefit liabilities | | | (25 | ) |
|
Deferred income taxes | | | (103 | ) |
|
Other deferred credits and liabilities | | | (20 | ) |
|
Cash paid, net of cash received under margin hedge agreement and cash acquired | | $ | 480 | |
|
57
The unaudited pro forma sales and other operating revenue of Sunoco for the year ended December 31, 2000, as if the acquisition of these assets had occurred on January 1, 2000, was $15,385 million. The unaudited pro forma income from continuing operations for the year ended December 31, 2000 was $340 million ($3.89 per share on a diluted basis). The pro forma information does not purport to be indicative of the results that actually would have been obtained if the combined operations had been conducted during the period presented and is not intended to be a projection of future results. Accordingly, the pro forma results do not reflect any restructuring costs, changes in operating levels, or potential cost savings and other synergies.
Polypropylene Joint Venture
Effective June 15, 2000, Sunoco entered into a joint venture (named Epsilon Products Company, LLC) which combined the Company’s polymer-grade propylene operation at its Marcus Hook, PA refinery with its partner’s adjacent polypropylene business (Notes 2, 8 and 13). Sunoco did not recognize any gain or loss on this transaction. The following is a summary of the effects of the transaction on Sunoco’s consolidated financial position:
(Millions of Dollars) | | | |
|
|
Increase (decrease) in: | | | | |
|
Properties, plants and equipment, net | | $ | (49 | ) |
|
Investments and long-term receivables | | | 64 | |
|
|
Cash advances to the joint venture | | $ | 15 | |
|
19. | | Business Segment Information |
Sunoco is principally a petroleum refiner and marketer and chemicals manufacturer with interests in logistics and cokemaking. Sunoco’s operations are organized into five business segments.
The Refining and Supply segment manufactures petroleum products at Sunoco’s Marcus Hook, Philadelphia, Toledo and Tulsa refineries and commodity petrochemicals at Sunoco’s Marcus Hook, Philadelphia and Toledo refineries and sells these products to other Sunoco businesses and to wholesale and industrial customers. This segment also manufactures lubricant products at Sunoco’s Tulsa refinery which are sold into process oil, wholesale base oil and wax markets (“Western Lubricants”) and, prior to the completion of the restructuring of lubricants operations in December 2001, included Value Added and Eastern Lubricants (Note 3).
The Retail Marketing segment sells gasoline and middle distillates at retail and operates convenience stores in 23 states primarily on the East Coast and in the Midwest region of the United States.
The Chemicals segment manufactures commodity and intermediate petrochemicals primarily at the chemical plants acquired from Mitsubishi Corporation effective January 1, 2001 located in Neal, WV; Haverhill, OH; Neville Island, PA; and Pasedena and LaPorte, TX that manufacture phenol and related products, polypropylene and plasticizers and at its Philadelphia cumene and phenol facilities, at its Mont Belvieu, TX joint venture MTBE facility and at its Marcus Hook joint venture polypropylene facility since June 2000. This segment also distributes and markets these products.
The Logistics segment operates refined product and crude oil pipelines and terminals and conducts crude oil acquisition and marketing activities primarily in the Northeast, Midwest and South Central regions of the United States. In addition, the Logistics segment has an ownership interest in several refined product and crude oil pipeline joint ventures. Since February 8, 2002, the date of the initial public offering, logistics operations have been conducted primarily through Sunoco Logistics Partners L.P., the Company’s 75.3 percent owned master limited partnership (Note 14).
The Coke segment makes high-quality, blast-furnace coke at Sunoco’s Indiana Harbor facility in East Chicago, IN and Jewell facility in Vansant, VA, and produces metallurgical coal from mines in Virginia primarily for use at the Jewell cokemaking facility. Substantially all of the coke sales are made under long-term contracts with two steel companies.
Income tax amounts give effect to the tax credits earned by each segment. Overhead expenses that can be identified with a segment have been included as deductions in determining pretax and after-tax segment income. The remainder are included in Corporate and Other. Also included in Corporate and Other are net financing expenses and other, which consist principally of interest cost, debt and other financing expenses less interest income and interest capitalized, and significant unusual and infrequently occurring items not allocated to a segment for purposes of reporting to the chief operating decision maker. Corporate and Other also includes the preferential return of third-party investors in the Company’s cokemaking operations (Note 14). Intersegment revenues are accounted for based on the prices negotiated by the segments which approximate market. Identifiable assets are those assets that are utilized within a specific segment.
58
Segment Information
(Millions of Dollars) | | Refining and Supply | | | Retail Marketing | | | Chemicals | | | Logistics | | | Coke | | | Corporate and Other | | | Consolidated | |
|
2002 | | | | | | | | | | | | | | | | | | | | | | | | | | | | |
|
Sales and other operating revenue (including consumer excise taxes): | | | | | | | | | | | | | | | | | | | | | | | | | | | | |
Unaffiliated customers | | $ | 5,827 | | | $ | 6,172 | | | $ | 1,362 | | | $ | 690 | | | $ | 248 | | | $ | — | | | $ | 14,299 | |
|
Intersegment | | $ | 3,828 | | | $ | — | | | $ | — | | | $ | 1,158 | | | $ | — | | | $ | — | | | $ | — | |
|
|
Pretax segment income (loss) | | $ | (46 | ) | | $ | 31 | | | $ | 43 | | | $ | 47 | | | $ | 65 | | | $ | (213 | ) | | $ | (73 | ) |
|
Income tax (expense) benefit | | | 15 | | | | (11 | ) | | | (15 | ) | | | (14 | ) | | | (23 | ) | | | 74 | | | | 26 | |
|
After-tax segment income (loss) | | $ | (31 | ) | | $ | 20 | | | $ | 28 | | | $ | 33 | | | $ | 42 | | | $ | (139 | )* | | $ | (47 | ) |
|
Equity income | | $ | 3 | | | $ | — | | | $ | 6 | | | $ | 14 | | | $ | — | | | $ | — | | | $ | 23 | |
|
Depreciation, depletion and amortization | | $ | 153 | | | $ | 95 | | | $ | 44 | | | $ | 25 | | | $ | 12 | | | $ | — | | | $ | 329 | |
|
Capital expenditures | | $ | 179 | | | $ | 124 | | | $ | 36 | | | $ | 41 | ** | | $ | 5 | | | $ | — | | | $ | 385 | |
|
Investments in and advances to affiliated companies | | $ | 16 | | | $ | — | | | $ | 101 | | | $ | 81 | | | $ | — | | | $ | — | | | $ | 198 | |
|
Identifiable assets | | $ | 2,252 | | | $ | 1,135 | | | $ | 1,325 | | | $ | 1,021 | | | $ | 278 | | | $ | 452 | *** | | $ | 6,441 | † |
|
* | | Consists of $26 million of after-tax corporate expenses, $91 million of after-tax net financing expenses and other and a $22 million after-tax provision for write-down of assets and other matters (Note 3). |
** | | Excludes $54 million purchase from Unocal of interests in three Midwestern and Western U.S. products pipeline companies and a $6 million purchase which increased the Company’s ownership interest in the West Texas Gulf pipeline. |
*** | | Consists of Sunoco’s $94 million consolidated deferred income tax asset, $5 million of prepaid retirement costs and $353 million attributable to corporate activities. |
† | | After elimination of intersegment receivables. |
(Millions of Dollars) | | Refining and Supply* | | | Retail Marketing | | | Chemicals | | | Logistics | | | Coke | | | Corporate and Other | | | Consolidated | |
|
2001 | | | | | | | | | | | | | | | | | | | | | | | | | | | | |
|
Sales and other operating revenue (including consumer excise taxes): | | | | | | | | | | | | | | | | | | | | | | | | | | | | |
Unaffiliated customers | | $ | 5,999 | | | $ | 6,019 | | | $ | 1,264 | | | $ | 545 | | | $ | 236 | | | $ | — | | | $ | 14,063 | |
|
Intersegment | | $ | 3,711 | | | $ | — | | | $ | — | | | $ | 1,068 | | | $ | — | | | $ | — | | | $ | — | |
|
|
Pretax segment income (loss) | | $ | 459 | | | $ | 137 | | | $ | 9 | | | $ | 61 | | | $ | 91 | | | $ | (170 | ) | | $ | 587 | |
|
Income tax (expense) benefit | | | (171 | ) | | | (50 | ) | | | (3 | ) | | | (19 | ) | | | (30 | ) | | | 84 | | | | (189 | ) |
|
|
After-tax segment income (loss) | | $ | 288 | | | $ | 87 | | | $ | 6 | | | $ | 42 | | | $ | 61 | | | $ | (86 | )** | | $ | 398 | |
|
|
Equity income (loss) | | $ | 3 | | | $ | — | | | $ | (6 | ) | | $ | 11 | | | $ | — | | | $ | — | | | $ | 8 | |
|
|
Depreciation, depletion and amortization | | $ | 150 | | | $ | 100 | | | $ | 41 | | | $ | 18 | | | $ | 12 | | | $ | — | | | $ | 321 | |
|
|
Capital expenditures | | $ | 122 | | | $ | 173 | | | $ | 30 | *** | | $ | 61 | | | $ | 4 | | | $ | — | | | $ | 390 | |
|
|
Investments in and advances to affiliated companies | | $ | 12 | | | $ | — | | | $ | 106 | | | $ | 21 | | | $ | — | | | $ | — | | | $ | 139 | |
|
|
Identifiable assets | | $ | 2,346 | | | $ | 1,131 | | | $ | 1,325 | | | $ | 699 | | | $ | 293 | | | $ | 241 | † | | $ | 6,019 | †† |
|
* | | Includes Value Added and Eastern Lubricants operations (Note 3). |
** | | Consists of $24 million of after-tax corporate expenses, $82 million of after-tax net financing expenses and other, a $21 million after-tax gain on income tax settlement (Note 2) and a $1 million after-tax provision for write-down of assets and other matters (Note 3). |
*** | | Excludes the $649 million acquisition of Aristech Chemical Corporation and related working capital. |
† | | Consists of Sunoco’s $116 million consolidated deferred income tax asset, $87 million of prepaid retirement costs and $38 million attributable to corporate activities. |
†† | | After elimination of intersegment receivables. |
59
Segment Information
(Millions of Dollars) | | Refining and Supply* | | | Retail Marketing | | | Chemicals | | | Logistics | | | Coke | | | Corporate and Other | | | Consolidated | |
|
2000 | | | | | | | | | | | | | | | | | | | | | | | | | | | | |
|
Sales and other operating revenue (including consumer excise taxes): | | | | | | | | | | | | | | | | | | | | | | | | | | | | |
Unaffiliated customers | | $ | 7,207 | | | $ | 5,849 | | | $ | 729 | | | $ | 507 | | | $ | 222 | | | $ | — | | | $ | 14,514 | |
|
Intersegment | | $ | 3,968 | | | $ | — | | | $ | — | | | $ | 1,305 | | | $ | — | | | $ | — | | | $ | — | |
|
|
Pretax segment income (loss) | | $ | 498 | | | $ | 122 | | | $ | 26 | | | $ | 68 | | | $ | 91 | | | $ | (209 | ) | | $ | 596 | |
|
Income tax (expense) benefit | | | (183 | ) | | | (45 | ) | | | (10 | ) | | | (22 | ) | | | (30 | ) | | | 105 | | | | (185 | ) |
|
|
After-tax segment income (loss) | | $ | 315 | | | $ | 77 | | | $ | 16 | | | $ | 46 | | | $ | 61 | | | $ | (104 | )** | | $ | 411 | |
|
|
Equity income | | $ | 1 | | | $ | — | | | $ | 11 | | | $ | 10 | | | $ | — | | | $ | — | | | $ | 22 | |
|
|
Depreciation, depletion and amortization | | $ | 159 | | | $ | 98 | | | $ | 13 | | | $ | 16 | | | $ | 12 | | | $ | — | | | $ | 298 | |
|
|
Capital expenditures | | $ | 257 | | | $ | 139 | | | $ | 21 | | | $ | 43 | | | $ | 5 | | | $ | — | | | $ | 465 | |
|
|
Investments in and advances to affiliated companies | | $ | 9 | | | $ | — | | | $ | 119 | | | $ | 19 | | | $ | — | | | $ | — | | | $ | 147 | |
|
|
Identifiable assets | | $ | 2,481 | | | $ | 1,142 | | | $ | 496 | | | $ | 736 | | | $ | 317 | | | $ | 456 | *** | | $ | 5,537 | † |
|
* | | Includes Value Added and Eastern Lubricants operations (Note 3). |
** | | Consists of $23 million of after-tax corporate expenses, $56 million of after-tax net financing expenses and other, a $117 million after-tax gain on income tax settlement (Note 2), a $5 million after-tax gain on settlement of insurance litigation (Note 2) and a $147 million after-tax provision for write-down of assets and other matters (Note 3). |
*** | | Consists of Sunoco’s $94 million consolidated deferred income tax asset, $111 million of prepaid retirement costs and $251 million attributable to corporate activities. |
† | | After elimination of intersegment receivables. |
The following table sets forth Sunoco’s sales to unaffiliated customers and other operating revenue by product or service:
(Millions of Dollars) | | 2002 | | 2001 | | 2000 |
|
|
Gasoline: | | | | | | | | | |
|
Wholesale | | $ | 1,787 | | $ | 1,690 | | $ | 1,986 |
|
Retail | | | 3,545 | | | 3,542 | | | 3,597 |
|
Middle distillates | | | 2,736 | | | 2,861 | | | 3,510 |
|
Residual fuel | | | 549 | | | 525 | | | 639 |
|
Petrochemicals | | | 1,599 | | | 1,508 | | | 876 |
|
Lubricants | | | 263 | | | 476 | | | 607 |
|
Other refined products | | | 510 | | | 450 | | | 552 |
|
Other products and services | | | 596 | | | 543 | | | 437 |
|
Resales of purchased crude oil | | | 632 | | | 491 | | | 452 |
|
Coke and coal | | | 248 | | | 236 | | | 222 |
|
Consumer excise taxes | | | 1,834 | | | 1,741 | | | 1,636 |
|
| | $ | 14,299 | | $ | 14,063 | | $ | 14,514 |
|
In January 2003, Sunoco signed an agreement to purchase 193 direct retail gasoline sites from a subsidiary of Marathon Ashland Petroleum LLC for $140 million plus inventory. The sites, which are located primarily in Florida and South Carolina, are all company-operated locations with convenience stores. Of the 193 outlets, 54 are subject to long-term lease agreements. This transaction is subject to regulatory approval.
60
Report of Management
To the Shareholders of Sunoco, Inc.
The accompanying consolidated financial statements of Sunoco, Inc. and its subsidiaries (“Sunoco”) and the related information are the responsibility of management. The financial statements, which include amounts based on informed estimates and judgments, were prepared using accounting principles generally accepted in the United States and deemed appropriate in the circumstances. Management believes that these financial statements present fairly, in all material respects, Sunoco’s financial position, results of operations and cash flows. Other financial information presented in this Annual Report is consistent with that in the financial statements.
To fulfill its responsibility for the financial statements, Sunoco maintains a system of internal control which in management’s opinion provides reasonable assurance of achieving the objectives of internal control. These objectives include safeguarding of assets from loss through unauthorized use or disposition and maintaining reliable records permitting the preparation of financial statements and accountability for assets. The system of internal control is subject to ongoing evaluation of its continuing effectiveness.
Sunoco’s independent auditors, Ernst & Young LLP, have expressed an opinion on the fairness of management’s financial statements in their report presented on this page.
The Audit Committee of the Board of Directors, which met thirteen times during 2002, is comprised only of directors who meet the independence requirements of the New York Stock Exchange. It assists the Board of Directors in discharging its duties relating to accounting and reporting practices and internal control, and it assesses the performance and approves the appointment of the independent auditors, and recommends the ratification of their appointment to the shareholders. Both the independent auditors and Sunoco’s internal auditors have unrestricted access to the Committee to discuss audit findings and other financial matters.
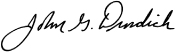
John G. Drosdick
Chairman, Chief Executive Officer & President

Thomas W. Hofmann
Senior Vice President & Chief Financial Officer
Report of Independent Auditors
To the Shareholders and Board of Directors,
Sunoco, Inc.
We have audited the accompanying consolidated balance sheets of Sunoco, Inc. and subsidiaries as of December 31, 2002 and 2001, and the related consolidated statements of operations, comprehensive income and shareholders’ equity and cash flows for each of the three years in the period ended December 31, 2002. These financial statements are the responsibility of the Company’s management. Our responsibility is to express an opinion on these financial statements based on our audits.
We conducted our audits in accordance with auditing standards generally accepted in the United States. Those standards require that we plan and perform the audit to obtain reasonable assurance about whether the financial statements are free of material misstatement. An audit includes examining, on a test basis, evidence supporting the amounts and disclosures in the financial statements. An audit also includes assessing the accounting principles used and significant estimates made by management, as well as evaluating the overall financial statement presentation. We believe that our audits provide a reasonable basis for our opinion.
In our opinion, the financial statements referred to above present fairly, in all material respects, the consolidated financial position of Sunoco, Inc. and subsidiaries at December 31, 2002 and 2001 and the consolidated results of their operations and their cash flows for each of the three years in the period ended December 31, 2002, in conformity with accounting principles generally accepted in the United States.
As discussed in Note 1 to the consolidated financial statements, the Company changed its methods of accounting for goodwill and other indefinite-lived intangible assets and employee stock compensation plans in 2002 and its method of accounting for derivative instruments in 2001.
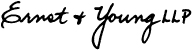
Philadelphia, Pennsylvania
February 14, 2003
61
Supplemental Financial and Operating Information(Unaudited)
Refining and Supply and Retail Marketing
Segments Data
Refinery Utilization* | | 2002 | | 2001 | | 2000 |
|
Refinery crude unit capacity at December 31 | | 730.0 | | 730.0 | | 730.0 |
Input to crude units | | 689.9 | | 687.7 | | 673.3 |
Refinery crude unit capacity utilized | | 95% | | 94% | | 92% |
|
*Thousands | | of barrels daily except percentages. |
Refined Product Sales* | | 2002 | | 2001 | | 2000 |
|
Gasoline: | | | | | | |
|
Wholesale | | 152.5 | | 137.5 | | 145.0 |
|
Retail | | 262.3 | | 244.1 | | 225.3 |
Middle distillates | | 246.3 | | 240.7 | | 251.2 |
Residual fuel | | 62.6 | | 59.8 | | 55.6 |
Petrochemicals** | | 13.2 | | 13.5 | | 13.4 |
Lubricants | | 13.4 | | 9.3 | | 8.5 |
|
Other | | 53.8 | | 52.8 | | 52.0 |
|
| | 804.1 | | 757.7 | | 751.0 |
|
* | | Thousands of barrels daily to third parties. Excludes amounts attributable to Value Added and Eastern Lubricants operations. |
** | | Consists of sales of petrochemicals produced at Sunoco’s Marcus Hook, Philadelphia and Toledo refineries excluding cumene, which is included in the Chemicals segment. |
Inventories* | | 2002 | | 2001 | | 2000 |
|
Crude oil | | 17.0 | | 20.2 | | 18.8 |
Refined products** | | 17.4 | | 19.8 | | 18.7 |
|
* | | Millions of barrels at December 31. |
** | | Includes petrochemical inventories produced at Sunoco’s Marcus Hook, Philadelphia and Toledo refineries excluding cumene, which is included in the Chemicals segment. |
Retail Gasoline Outlets | | 2002 | | 2001 | | 2000 |
|
Direct outlets: | | | | | | |
|
Company owned or leased | | 1,384 | | 1,433 | | 1,287 |
|
Dealer owned | | 682 | | 686 | | 550 |
|
Total direct outlets | | 2,066 | | 2,119 | | 1,837 |
|
Distributor outlets | | 2,262 | | 2,032 | | 1,798 |
|
| | 4,328 | | 4,151 | | 3,635 |
|
Throughput per Direct Outlet* | | 2002 | | 2001 | | 2000 |
|
Company owned or leased | | 113.8 | | 108.2 | | 109.8 |
|
Dealer owned | | 85.3 | | 81.1 | | 85.6 |
|
Average-total direct outlets | | 104.6 | | 99.3 | | 102.6 |
|
* | Thousands of gallons of gasoline monthly. |
Chemicals Segment Data
Chemical Sales* | | 2002 | | 2001 | | 2000 |
|
Phenol and related products | | 2,831 | | 2,605 | | 1,771 |
Polypropylene** | | 1,346 | | 1,384 | | — |
Plasticizers | | 615 | | 532 | | — |
Propylene | | 774 | | 715 | | 761 |
|
Other | | 178 | | 175 | | 297 |
|
| | 5,744 | | 5,411 | | 2,829 |
|
** | | Excludes Epsilon Products Company, LLC polypropylene joint venture. |
Other Data | | 2002 | | 2001 | | 2000 |
|
Chemical inventories* | | 499 | | 453 | | 155 |
|
|
*Millions of pounds. | | | | | | |
Logistics Segment Data
Pipeline Shipments* | | 2002 | | 2001 | | 2000 |
|
Crude oil | | 51.2 | | 52.2 | | 54.0 |
Refined products | | 38.4 | | 31.3 | | 30.2 |
|
* | Billions of barrel miles. Includes 100 percent of the pipeline shipments of Sunoco Logistics Partners L.P., Sunoco’s 75.3 percent-owned master limited partnership and Sunoco’s proportionate share of shipments in joint venture pipelines in which it has an ownership interest. |
Other Data | | 2002 | | 2001 | | 2000 |
|
Crude oil inventory* | | 1.9 | | 2.4 | | 1.9 |
|
|
*Millions of barrels at December 31. | | | | | | |
Coke Segment Data*
| | 2002 | | 2001 | | 2000 |
|
Coke production | | 2,001 | | 2,006 | | 2,010 |
Coke sales | | 2,158 | | 2,002 | | 2,011 |
|
62
Quarterly Financial and Stock Market Information(Unaudited)
(Millions of Dollars Except Per Share Amounts and Common Stock Prices)
| | 2002
| | | 2001
| |
| | First Quarter | | | Second Quarter | | | Third Quarter | | | Fourth Quarter | | | First Quarter | | | Second Quarter | | | Third Quarter | | | Fourth Quarter | |
|
Sales and other operating revenue (including consumer excise taxes) | | $2,918 | | | $3,527 | | | $3,789 | | | $4,065 | | | $ | 3,627 | | | $ | 3,916 | | | $ | 3,588 | | | $ | 2,932 | |
|
Gross profit* | | $16 | | | $193 | | | $170 | | | $279 | | | | $336 | | | | $475 | | | | $295 | | | | $151 | |
|
Net income (loss)** | | $(107 | ) | | $9 | *** | | $(10 | ) | | $61 | † | | | $106 | †† | | | $196 | ††† | | | $92 | # | | | $4 | ## |
|
Net income (loss) per share of common stock**: | | | | | | | | | | | | | | | | | | | | | | | | | | | | |
|
Basic | | $(1.41 | ) | | $.12 | | | $(.13 | ) | | $.80 | | | | $1.26 | | | | $2.38 | | | | $1.15 | | | | $.05 | |
|
Diluted | | $(1.41 | )### | | $.12 | | | $(.13 | )### | | $.79 | | | | $1.24 | | | | $2.35 | | | | $1.14 | | | | $.05 | |
|
Cash dividends per share of common stock | | $.25 | | | $.25 | | | $.25 | | | $.25 | | | | $.25 | | | | $.25 | | | | $.25 | | | | $.25 | |
|
Common stock price@—high | | $42.25 | | | $40.81 | | | $37.58 | | | $33.57 | | | $ | 37.00 | | | $ | 42.73 | | | $ | 38.80 | | | $ | 39.20 | |
—low | | $36.25 | | | $34.11 | | | $29.65 | | | $27.02 | | | $ | 29.13 | | | $ | 31.30 | | | $ | 32.00 | | | $ | 34.34 | |
—end of period | | $40.01 | | | $35.63 | | | $30.16 | | | $33.18 | | | $ | 32.43 | | | $ | 36.63 | | | $ | 35.60 | | | $ | 37.34 | |
|
* | | Gross profit equals sales and other operating revenue less cost of products sold and operating expenses; depreciation, depletion and amortization; and consumer excise, payroll and other applicable taxes. |
** | | Reflects decreases in results of operations of $1 million and earnings per share of common stock (both basic and diluted) of $.01 for each of the quarters ended March 31, June 30 and September 30, 2002, respectively, compared to amounts previously reported on Securities and Exchange Commission Form 10-Q. These decreases are due to expense recognition for all unvested stock options commencing in the fourth quarter of 2002, retroactive to January 1, 2002, utilizing the fair value method of accounting for employee compensation plans. Prior to January 1, 2002, the Company followed the intrinsic value method of accounting for employee benefit plans under which there was no expense recognized for stock options. |
*** | | Includes a $17 million after-tax provision for write-down of assets and other matters. |
† | | Includes a $5 million after-tax provision for write-down of assets and other matters. |
†† | | Includes a $7 million after-tax provision for write-down of assets and other matters. |
††† | | Includes a $6 million after-tax provision for write-down of assets and other matters. |
# | | Includes a $21 million after-tax gain on income tax settlement and a $2 million after-tax provision for write-down of assets and other matters. |
## | | Includes a $14 million after-tax benefit for write-down of assets and other matters. |
### | | Since the assumed issuance of common stock related to stock incentive awards would have resulted in a reduction in the loss per share, the diluted per share amounts are equal to the basic per share amounts. |
@ | | The Company’s common stock is principally traded on the New York Stock Exchange, Inc. under the symbol “SUN.” The Company had approximately 26,500 holders of record of common stock as of January 31, 2003. |
63