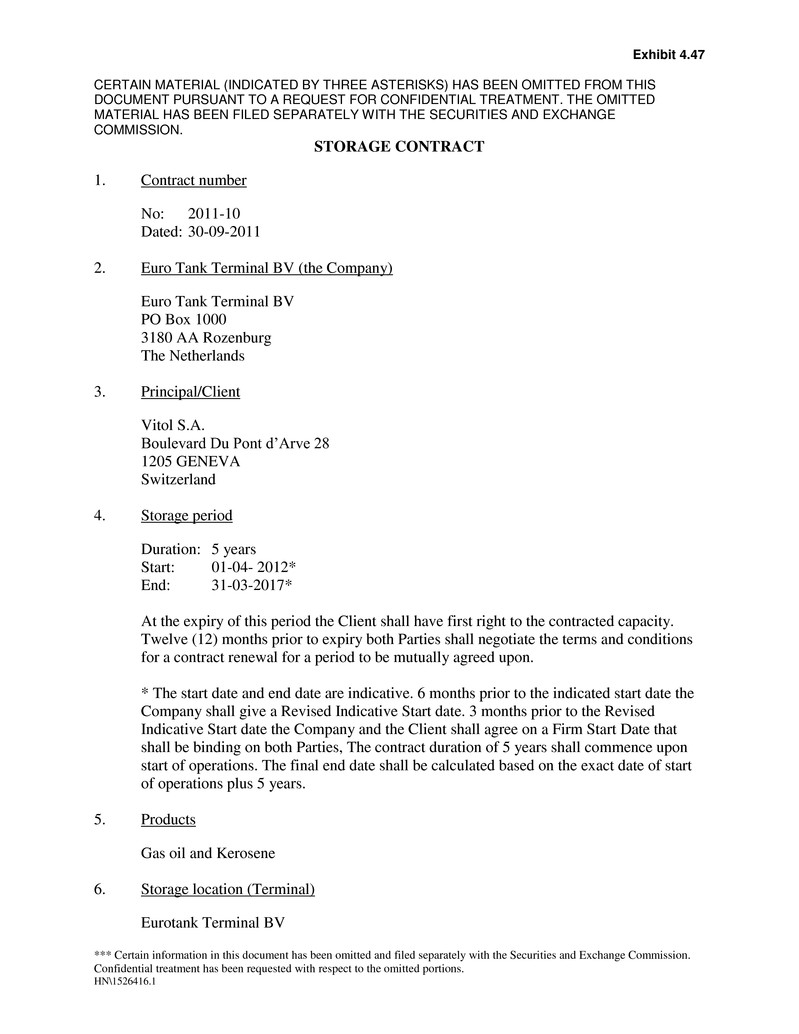
Exhibit 4.47 CERTAIN MATERIAL (INDICATED BY THREE ASTERISKS) HAS BEEN OMITTED FROM THIS DOCUMENT PURSUANT TO A REQUEST FOR CONFIDENTIAL TREATMENT. THE OMITTED MATERIAL HAS BEEN FILED SEPARATELY WITH THE SECURITIES AND EXCHANGE COMMISSION. *** Certain information in this document has been omitted and filed separately with the Securities and Exchange Commission. Confidential treatment has been requested with respect to the omitted portions. HN\1526416.1 STORAGE CONTRACT 1. Contract number No: 2011-10 Dated: 30-09-2011 2. Euro Tank Terminal BV (the Company) Euro Tank Terminal BV PO Box 1000 3180 AA Rozenburg The Netherlands 3. Principal/Client Vitol S.A. Boulevard Du Pont d’Arve 28 1205 GENEVA Switzerland 4. Storage period Duration: 5 years Start: 01-04- 2012* End: 31-03-2017* At the expiry of this period the Client shall have first right to the contracted capacity. Twelve (12) months prior to expiry both Parties shall negotiate the terms and conditions for a contract renewal for a period to be mutually agreed upon. * The start date and end date are indicative. 6 months prior to the indicated start date the Company shall give a Revised Indicative Start date. 3 months prior to the Revised Indicative Start date the Company and the Client shall agree on a Firm Start Date that shall be binding on both Parties, The contract duration of 5 years shall commence upon start of operations. The final end date shall be calculated based on the exact date of start of operations plus 5 years. 5. Products Gas oil and Kerosene 6. Storage location (Terminal) Eurotank Terminal BV

*** Certain information in this document has been omitted and filed separately with the Securities and Exchange Commission. Confidential treatment has been requested with respect to the omitted portions. Moezelweg 151 3198 LS Europoort – Rotterdam Netherlands Port and Draft restrictions : Ref. Appendix 1 Opening hours of the terminal : Ref. Appendix 1 Nominations and Operational procedures : : Ref. Appendix 2 7. Contractual Capacity Contractual capacity : approx 108,000m3 Products will be stored on a dedicated basis. Tank Contractual Capacity (m3) Nett capacity (m3) Roof Type Product Min flash TK 402 App. 54,000 TBD Domed + Floating Gas oil n.a. TK 403 App. 54,000 TBD Domed + Floating Gas oil n.a. The tanks are Class 1, meaning suitable for handling of product with a flashpoint <21°c and an RVP < 14.7 psi. 8. Means of delivery Receipt ex seagoing vessel, barge or pump-over Redelivery into seagoing vessel, barge, railtankcar or pump over 9. Rates (expressed in Euro) a. Tank rental (from 2012) *** Expressed in cubic meter (M3) per contractual capacity per month or part thereof. Tank rental rate includes: Delivery from seagoing vessel or barge (in min. parcel size 1,000 Mt) Redelivery into seagoing vessel or barge (min. parcel size 1,000 Mt) Storage during the period Standard documentation on ship’s departure at terminal (B/L, AAD, T1, Timesheet, Master receipt document) *** free throughputs per *** (calculated as 1 import and export of the net tank capacity) b. Additional Throughput Surcharge (per M3) *** throughputs: *** *** throughputs: ***
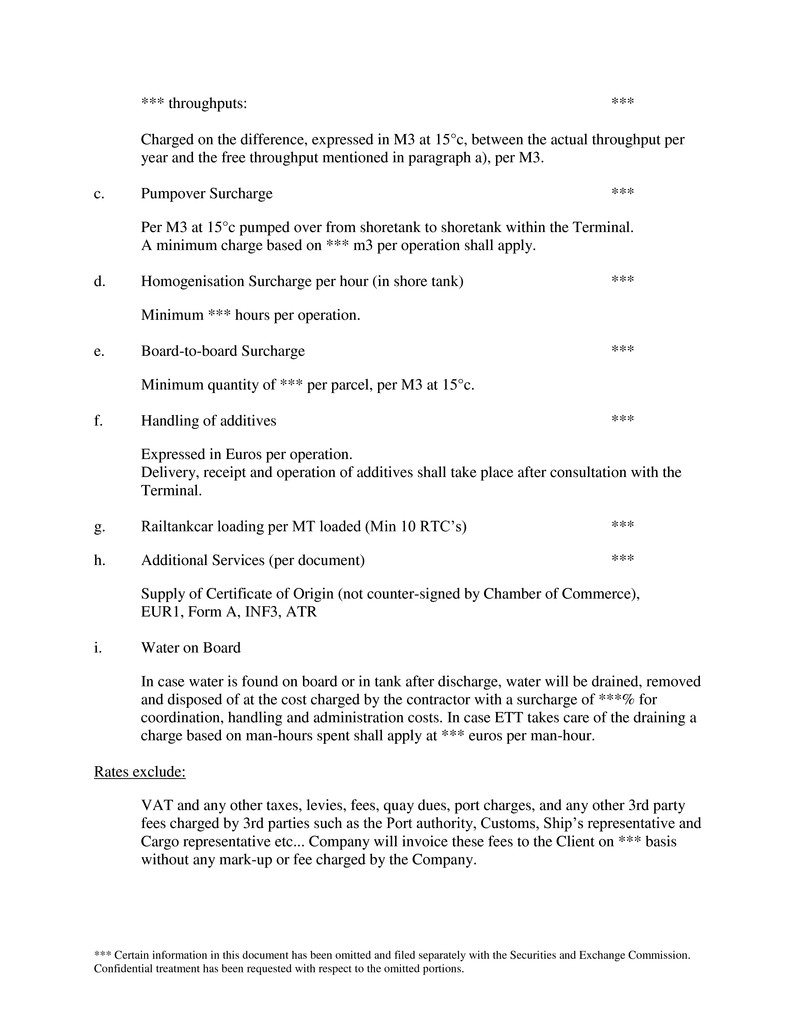
*** Certain information in this document has been omitted and filed separately with the Securities and Exchange Commission. Confidential treatment has been requested with respect to the omitted portions. *** throughputs: *** Charged on the difference, expressed in M3 at 15°c, between the actual throughput per year and the free throughput mentioned in paragraph a), per M3. c. Pumpover Surcharge *** Per M3 at 15°c pumped over from shoretank to shoretank within the Terminal. A minimum charge based on *** m3 per operation shall apply. d. Homogenisation Surcharge per hour (in shore tank) *** Minimum *** hours per operation. e. Board-to-board Surcharge *** Minimum quantity of *** per parcel, per M3 at 15°c. f. Handling of additives *** Expressed in Euros per operation. Delivery, receipt and operation of additives shall take place after consultation with the Terminal. g. Railtankcar loading per MT loaded (Min 10 RTC’s) *** h. Additional Services (per document) *** Supply of Certificate of Origin (not counter-signed by Chamber of Commerce), EUR1, Form A, INF3, ATR i. Water on Board In case water is found on board or in tank after discharge, water will be drained, removed and disposed of at the cost charged by the contractor with a surcharge of ***% for coordination, handling and administration costs. In case ETT takes care of the draining a charge based on man-hours spent shall apply at *** euros per man-hour. Rates exclude: VAT and any other taxes, levies, fees, quay dues, port charges, and any other 3rd party fees charged by 3rd parties such as the Port authority, Customs, Ship’s representative and Cargo representative etc... Company will invoice these fees to the Client on *** basis without any mark-up or fee charged by the Company.

*** Certain information in this document has been omitted and filed separately with the Securities and Exchange Commission. Confidential treatment has been requested with respect to the omitted portions. 10. Terms of Operation Oil movement planning including quality and quantity must be clearly identified and detailed by the Client in writing and intimated to the Company well in advance for execution. The Company will not be responsible for any effect of oil movement planning whatsoever. In implementing the oil movement planning, the Company shall follow the instructions of the Client, but the Client should always observe and consider the Quality and Quantity requirements of tank heels bottoms i.e. ROB. 11. Product Acceptance procedure Upon nomination of a vessel/barge for a discharge operation the Client shall provide actual specifications of the cargo on board, containing at least the following: • Density • Colour* • Sulphur • Conductivity • Pour Point • Viscosity The product shall meet all of the following criteria: Specification Max/Min Method Viscosity Max 20 CST @ 40 °C Pour Point Max 0°c (will be reviewed on case by case basis as per ambient temperature) If the Terminal requests all or any of the abovementioned specifications and is not properly informed by the Client the Terminal shall have the right to refuse discharge. If product does not meet the abovementioned specification Company shall have the right to refuse discharge. * If colour is > 2.5 Client shall provide material with which lines can be flushed. Terminal shall also be informed of SDS and REACH Number for each delivery prior to discharge. 12. Tank cleaning Tanks are prepared for their respective products prior to commencement of the Contract. On completion of the Contract the tank shall be re-delivered in a state suitable for CPP storage. If required, cleaning shall have taken place prior to contract expiry. Costs involved in cleaning the tanks to their original condition in preparation for the next service and the disposal of wastes if any are to the Client’s account. A copy invoice of the cleaning company will be attached to our invoice with a surcharge of ***% for coordination and administration costs.

*** Certain information in this document has been omitted and filed separately with the Securities and Exchange Commission. Confidential treatment has been requested with respect to the omitted portions. 13. Dyeing Adding of dye can only be performed on board and not in tank or line of the terminal. 14. Contractual loss Contractual loss during Operations and Storage will be actual loss as determined after unloading & loading operations on basis of the shore tanks gauging. Product losses will be to the account of the Client. 15. Rates/conditions are exclusively for the client The client is not authorised to cede or subcontract the Contractual Capacity as well as any right granted by this Contract without the Terminal prior written approval. Sub-leasing of Clients tank to a 3rd Party In case the Client wishes to sub-lease one or more of the contracted tanks it may request the Company to do so on its behalf. In this case the Company shall at its discretion approach potentially interested parties and negotiate a sub-lease contract acceptable to the Client for the tank and period agreed with the Client provided that: (i) the Client remains fully responsible for the performance of the sublease contract and especially the payment of the rates outlined in Article 9 (ii) the sublease termination date is always earlier than the termination date of the present Contract (iii) the sublease does not comprise any option to renew or extend or increase the duration or the capacity or any conditions referred to in the Sub lease Agreement. The Client is not allowed to enter into any direct negotiations or discussions concerning its contracted tanks with a 3rd Party and the Company is under no obligation to accept any 3rd parties as a sub-lessee. In case the company is not able to find a sub-lessee on its own accord the Client may propose a suitable alternative, approval of which shall not be unreasonably withheld. The proceeds of any sub-lease arrangement shall be *** between Company and Client. 16. Index / escalation clause The rates in Article 9 will be (de)escalated by the CPI as published by the Netherlands CBS annually. Initial rates in 2012 are as stated in Article 9a and b.

*** Certain information in this document has been omitted and filed separately with the Securities and Exchange Commission. Confidential treatment has been requested with respect to the omitted portions. 17. Long term Maintenance The Company shall have the right to perform long term or emergency maintenance during the contract period. The normal storage rate of Article 9a shall be payable during such maintenance for a period of maximum 30 days for the entire contract period. 18. Invoicing and payment Tank Rental fee will be invoiced monthly; invoices will be issued at the beginning of each calendar month, in advance. All other charges (Pumpovers, Homogenization, Additivation, Additional throughput, etc.„) for any other services rendered will be invoiced upon expiry of the month in which the respective service was rendered. Excess throughput as per Article 9b shall be invoiced on a monthly basis once the free throughput allowed under this contract has been achieved. Invoices are payable in the currency as invoiced and within 15 days after the date of invoice and before final lifting of product. 19. Insurance a) Title and risks of the oil products will remain with Client at all times. b) Client will be responsible for insuring the oil stored under this Contract at their cost and expense. c) Both Parties will be responsible for procuring third party liability insurance to cover their respective legal liabilities arising from their responsibilities under this Contract. d) Company shall at no time be liable for any damage to or loss of product stored. 20. General terms and conditions The General Conditions for Tankstorage in the Netherlands (VOTOB) and the VOTOB jetty conditions shall be applicable to this Contract. 21. Modification of the General Conditions The provisions set forth in the Contract may be modified by a decision of the Terminal in accordance with technical or legal requirements. In this case the Terminal shall endeavour to give at least three months notice, except in the event of urgency in particular regarding regulations and safety measures. By exception to the abovementioned General Conditions, the Parties agree that in case any storage capacity of the Client becomes unavailable due to maintenance or repairs undertaken by ETT the tank rental rate mentioned in Article 9a will be *** for the period that the capacity is unavailable.

*** Certain information in this document has been omitted and filed separately with the Securities and Exchange Commission. Confidential treatment has been requested with respect to the omitted portions. 22. Equity Clause In the event of unexpected, heavy changes in exploitation costs, or important disruption of the general economy, or any duty or tax not already included, the parties to this Contract will meet to discuss the necessity of modifying part or all of the conditions of this Contract. 23. Law and jurisdiction: Dutch law and English language will govern the present Contract. For every dispute not settled amicably the only qualified jurisdiction will be Rotterdam Courts. 24. Notices All notices which may be given under any provisions of this Contract shall be in writing in English and deemed to have been duly given when (a) served by (i) facsimile or other written electronic means and communication confirmed by registered airmail, (ii) personally or (iii) mailed by certified or registered first class mail, return receipt requested, postage prepaid and (b) properly addressed to the Parties at their addresses first above written or to such other address as each of the Parties may designate in writing to the other Parties in the manner provided in this Clause 13, together with copies as follows: In case of notice to ETT: Euro Tank Terminal BV PO Box 1000 3180 AA Rozenburg The Netherlands In case of notice to Vitol Distillate Matrix Vitol Distillates E-mail: Vitol S.A. Boulevard Du Pont D’ Arve 28 1205 GENEVA

*** Certain information in this document has been omitted and filed separately with the Securities and Exchange Commission. Confidential treatment has been requested with respect to the omitted portions. Eurotank Terminal B.V. /s/ Jack de Moel Date: September 30, 2011 Vitol S.A. /s/ Roland Favre Director Date: May 15, 2014 Appendix 1 Jetties available for gas oil loading and discharge operations Jetty No. Draught (m) Max Beam (m) Min/Max LOA (m) Operational Date Sea going vessels berths Caland East – (A) 20.95 not restricted 145 - 280 Operational Max freeboard 2.29 m x 20.54 m Caland Centre – (B) 20.95 not restricted 180 - 360 Operational Max freeboard 2.29 m x 20.54 m Caland West – (D) 17.85 not restricted 125 - 280 Operational Max freeboard 2.29 m x 20.54 m Jetty 1 (M) 16.00 not restricted 80 - 260 T.B.A Max freeboard 2.29 m x 20.54 m Barges berths Caland East inside – (A) 6.00 22 max 145 Operational Caland West inside – (C) 5.00 22 max 145 Operational Quay wall East – (E) 8.52 22 max 145 Operational Quay Wall East – (F) 4.62 22 max 135 Operational

*** Certain information in this document has been omitted and filed separately with the Securities and Exchange Commission. Confidential treatment has been requested with respect to the omitted portions. Quay Wall West G 4.62 22 max 135 T.B.A. Quay Wall West H 4.82 22 max 135 T.B.A. Berth P 4.62 22 max 135 T.B.A. Berth – 2 Q 7.00 22 Max 135 T.B.A. 1. Above stated draughts are general figures. Contact the local harbour authorities for the latest draught restrictions. Minimum vessel capabilities Vessels calling at the Terminal with a DWT tonnage of more than 25,000 shall be able to maintain a minimum pumping or receiving rate of 1000 m3 per hour or 7 bar at the ships manifold. Vessels calling at the Terminal with a DWT tonnage between 10,000 and 25,000 shall be able to maintain a minimum pumping or receiving rate of 800 m3 per hour Vessels calling at the Terminal with a DWT tonnage between 5,000 and 10,000 shall be able to maintain a minimum pumping or receiving rate of 600 m3 per hour. Vessels calling at the Terminal with a DWT tonnage lower than 5,000 shall be able to maintain a minimum pumping or receiving rate of 400 m3 per hour. In the event that the abovementioned performance criteria are not met by a vessel, the Terminal shall have the right to unberth such vessel if it is causing delays to other vessels’ operations. Surveying Before loading and unloading of vessels the Principal must appoint an independent surveying company. When failing to do so the Terminal may nominate one, on behalf of the Principal and all costs will be for account of and invoiced to the Principal. Working hours and overtime: For operations the Terminal is working on a 365/7/24 basis For emergency please contact key-personnel at below stated phone numbers. Emergency contact details Key-personnel: General Manager : Jack de Moel E-mail : jdm@ett.vtti.com Tel : 0181-240024

*** Certain information in this document has been omitted and filed separately with the Securities and Exchange Commission. Confidential treatment has been requested with respect to the omitted portions. Terminal Manager : C. Saaltink E-mail : cls@ett.vtti.com Tel : 0181-240024 Commercial Manager : J.L.D. Koomen E-mail : jpk@vtti.com Tel : 0623897646
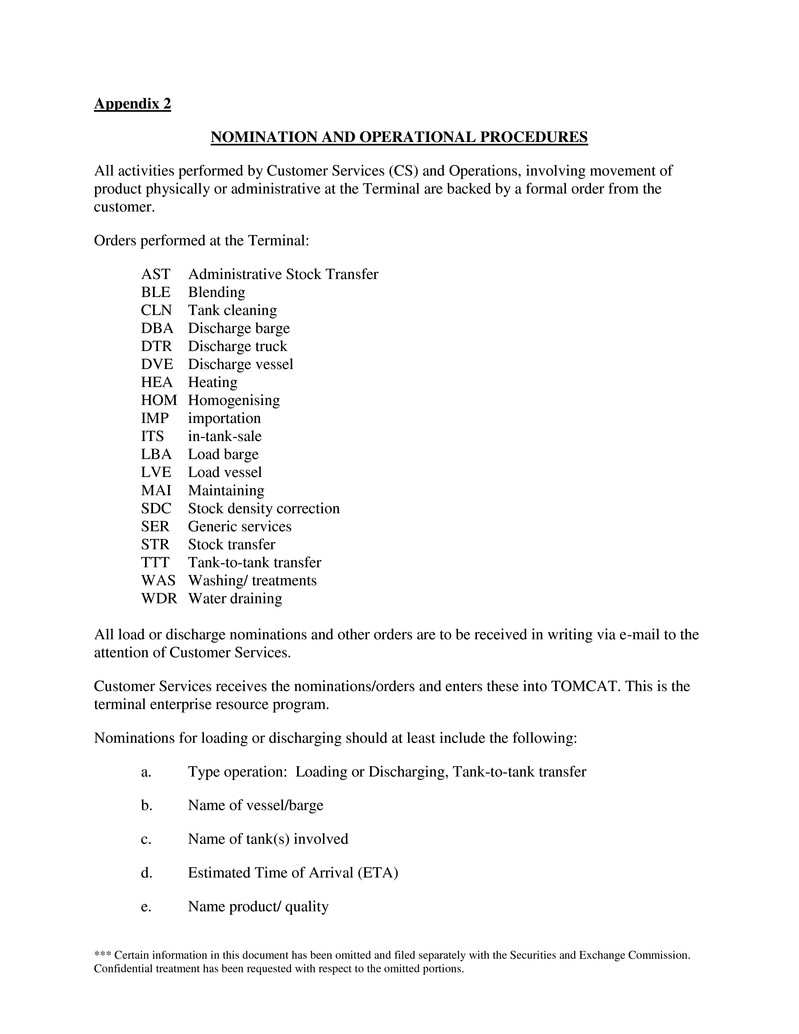
*** Certain information in this document has been omitted and filed separately with the Securities and Exchange Commission. Confidential treatment has been requested with respect to the omitted portions. Appendix 2 NOMINATION AND OPERATIONAL PROCEDURES All activities performed by Customer Services (CS) and Operations, involving movement of product physically or administrative at the Terminal are backed by a formal order from the customer. Orders performed at the Terminal: AST Administrative Stock Transfer BLE Blending CLN Tank cleaning DBA Discharge barge DTR Discharge truck DVE Discharge vessel HEA Heating HOM Homogenising IMP importation ITS in-tank-sale LBA Load barge LVE Load vessel MAI Maintaining SDC Stock density correction SER Generic services STR Stock transfer TTT Tank-to-tank transfer WAS Washing/ treatments WDR Water draining All load or discharge nominations and other orders are to be received in writing via e-mail to the attention of Customer Services. Customer Services receives the nominations/orders and enters these into TOMCAT. This is the terminal enterprise resource program. Nominations for loading or discharging should at least include the following: a. Type operation: Loading or Discharging, Tank-to-tank transfer b. Name of vessel/barge c. Name of tank(s) involved d. Estimated Time of Arrival (ETA) e. Name product/ quality
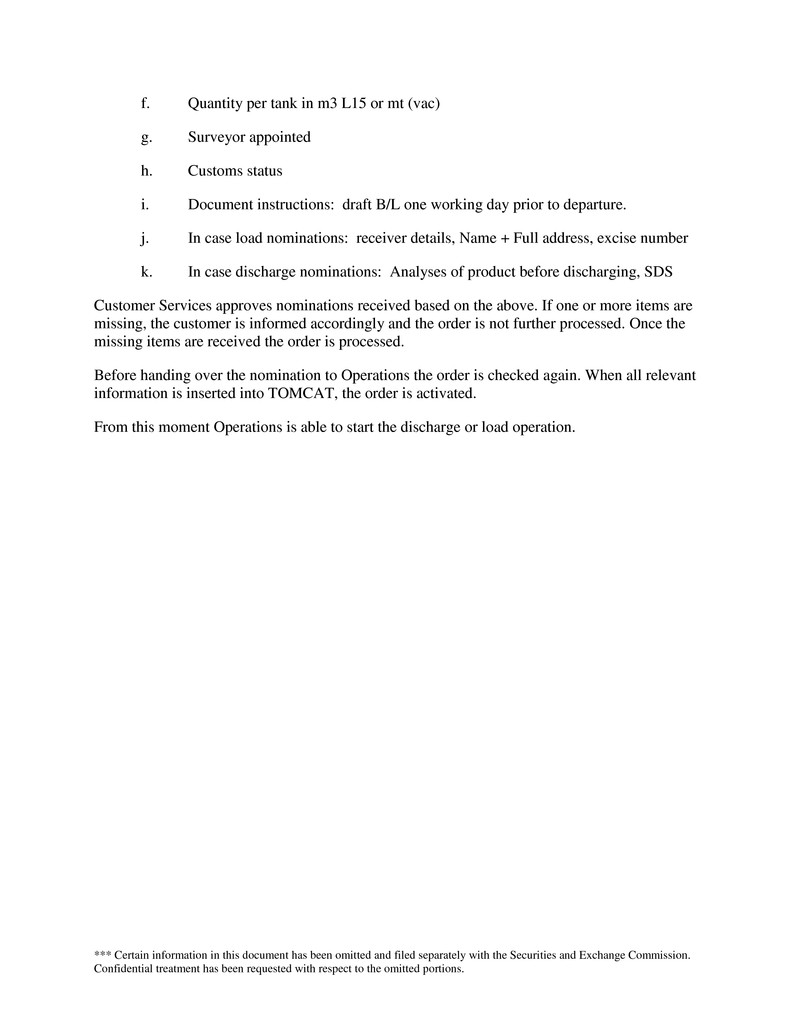
*** Certain information in this document has been omitted and filed separately with the Securities and Exchange Commission. Confidential treatment has been requested with respect to the omitted portions. f. Quantity per tank in m3 L15 or mt (vac) g. Surveyor appointed h. Customs status i. Document instructions: draft B/L one working day prior to departure. j. In case load nominations: receiver details, Name + Full address, excise number k. In case discharge nominations: Analyses of product before discharging, SDS Customer Services approves nominations received based on the above. If one or more items are missing, the customer is informed accordingly and the order is not further processed. Once the missing items are received the order is processed. Before handing over the nomination to Operations the order is checked again. When all relevant information is inserted into TOMCAT, the order is activated. From this moment Operations is able to start the discharge or load operation.