Exhibit 6.13
| AGREEMENT 746-R-2768R
REPORT
PHASE 1 &2
REVISED FINAL REPORT
Laboratory Evaluation of
______________ as a Bituminous or
Lignite Coal Combustion Catalyst |
PULVERIZED COAL COMBUSTION FACILITY
| To TransAlta Utilities Corporation March 1, 1990 |
Battell [Logo]
REVISED
FINAL REPORT
for
PHASE 1 AND 2
on
LABORATORY EVALUATION OF ___________________________________
AS A BITUMINOUS OR LIGNITE COAL COMBUSTION CATALYST
to
____________________________
March 1, 1990
by
James J. Reuther
BATTELLE
Columbus Division
505 King Avenue
Columbus, Ohio 43201
Battelle does not engage in research for advertising, sales promotion, or endorsement of our clients' interests including raising investment capital or recommending investment decisions, or other publicity purposes, or for any use in litigation.
Battelle endeavors at all times to produce work of the highest quality, consistent with our contract commitments. However, because of the research and/or experimental nature of this work the client undertakes the sole responsibility for the consequences of any use, misuse, or inability to use, any information, apparatus, process or result obtained from Battelle, and Battelle, its employees, officers, or Trustees have no legal liability for the accuracy, adequacy, or efficacy thereof.
TABLE OF CONTENTS
ACKNOWLEDGEMENTS | iv |
| |
RESEARCH SUMMARY | v |
| |
1.0. INTRODUCTION | 1 |
| |
2.0. PROJECT OBJECTIVE | 1 |
| |
3.0. PROJECT APPROACH | 2 |
| |
4.0. EXPERIMENTAL PROCEDURES | |
4.1. Preliminary Preparation | |
4.1.1. Combustion Hardware | |
4.1.1.1. Combustor and "Pseudo-Combustor" | |
4.1.1.1.1. Firing-Rate Scaling | |
4.1.1.2. Fuel-Handling System | |
4.1.1.3. Coal Burner/Carbonex Injector | |
4.1.2. Combustion Diagnostics | |
4.1.3. Test Coals and_____ | |
4.1.3.1. Coal Rank | |
4.1.3.2. Coal Particle Size Distribution | |
4.1.3.3. Combustion Catalyst: ____ | |
4.1.4. Combustion Test Procedures | |
4.1.4.1. General Combustor Operation | |
4.1.4.2. Parametric Combustor Operation | |
4.1.4.3. Additive Injection | |
4.1.4.3.1. Injection Location | |
4.1.4.3.2. Injected Amount | |
4.1.5. TGA Procedures | |
4.1.6. Quality Assurance/Quality Control | |
4.1.6.1. Experimental Issues | |
4.1.6.2. Analytical Issues | |
4.1.6.2.1. Method 5 Analysis | |
4.1.6.2.2. ASTM Analyses | |
4.1.6.2.3. Routine Analyses | |
4.1.6.3. Data Interpretation Issues | |
4.1.6.3.1. Uncertainty | |
4.1.6.3.2. Combustion Efficiency | |
4.1.6.3.3. Biases | |
5.0. DIRECT COMBUSTION RESULTS AND DISCUSSION | |
5.1. Combustion Test Results | |
5.1.1. Baseline Performance | |
5.1.2. Effect of_____ on Baseline Performance | |
5.1.3. Effect of Reduced Excess Air, Without/With ____ | . |
5.1.4. Effect of Secondary Air Swirl, Without/With ____ | |
5.1.5. Effect of Coal Particle Size, Without/With ____ | |
5.2. Rationale of Test Data | |
| |
6.0. INDIRECT (TGA) COMBUSTION RESULTS | |
| |
7.0. SIGNIFICANCE OF RESULTS | |
7.1. Excess Air Requirements | |
7.2. Coal-Grinding Requirements | |
7.3. Electrostatic Precipitator Performance | |
7.4. Slagging, Fouling, and Corrosion | |
7.5. Coal-Specificity and Applicability | |
| |
8.0. RESEARCH SUMMARY | |
9.0. REFERENCES | |
LIST OF TABLES
Table 1. Test Coal Characteristics | |
Table 2. Results of Combustion Tests on Pulverized Bituminous Coal | |
Flames Injected with____________ as a Function of Swirl, ExcessAir, and Particle Size | |
LIST OF FIGURES
Figure 1. Battelle Laboratory-Scale Combustion Facility | |
Figure 2. Cross Section of Swirl-Stabilized Pulverized Coal Burner. | |
Figure 3. dTGA Burning Profiles of Black and Brown Coal, Without/With | |
RESEARCH SUMMARY
Standarized experiments and analyses were performed by Battelle under laboratory-simulated utility-boiler conditions to determine, with certainty, the effect of a coal combustion catalyst called _________ on the combustion performance of high-volatibituminous and lignite coal. These tests employed either a pilot-scale furnace to obtain direct data on combustion performance, without or with _____, and/or a thermogravimetric analyzer to obtain indirect data on the same. The influence of flame-injected or pretreated __________ (5 ppm) evaluated at two levels of excess combustion air (10 or 26%) as a function secondary combustion air swirl (tuned or detuned) and coal particle size (6 or 80% minus 200 mesh). The characteristics of neat pulverized coal flames injected with an equal volume of _____ free xylene carrier established basel combustion performance.
The following were significant findings of the evaluation:
| · | The ability of _______ to enhance the combustibility of already efficiently burning bituminous or lignite coals was unambiguous proof-of-concept for ____________ a combustion catalyst. |
| · | The use of ______ in pulverized bituminous or lignite coal flames offers a means by which to maintain high levels of combustion efficiency (99+%) at reduced levels (10-%) of excombustion air. |
| · | The use of ______ allows strategic technology supplements low-excess-air-firing, such as swirl and coal particle size modification, to be used effectively to control NOxemission without a penalty to combustion efficiency. |
| · | ____ usage offers an effective means by which to achieve net reduction in NOx emissions to compliance levels, while maintaining efficient pulverized coal combustion. |
| · | ____ usage will probably enhance the performance of electrostatic precitipation for particulate control. |
In summary, this study confirms that ____________________ is viable catalyst for the improved combustion of bituminous and lignite coal
FINAL REPORT
On
EVALUATION OF CLEANBOOST GOLD
AS A DIESEL ENGINE COMBUSTION ADDITIVE
To
COMBUSTION TECHNOLOGIES USA LLC
February 23, 2015
By
Dr. James J. Reuther
505 King Avenue
Columbus, Ohio 43201
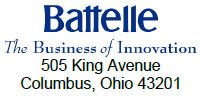
RESEARCH SUMMARY
Standardized combustion tests were performed by Battelle in a production diesel engine to determine with certainty the effect of various levels of the additive called CleanBoost Gold, which is manufactured by Combustion Technologies USA LLC. This fuel additive contained organoiron compounds diluted in an aromatic hydrocarbon solvent carrier. The influence of two levels of CleanBoost Gold (150 and 250 ppm by volume) was evaluated in a 4-stroke, 6-cylinder, 4300 cubic-inch diesel engine, rated at 1400 brake-horsepower and 1200 revolutions per minute at full load. The diesel engine was operated at about 85 percent of full load to artificially create a particulate emissions problem and simulate how a working engine might perform in the field.
The measurable and reproducible results provided the following information:
| • | The addition to conventional diesel fuel of 150 to 250 ppm of CleanBoost Gold: |
| o | Reduced CO emissions 7-10 percent, |
| o | Reduced HC emissions 3-9 percent, |
| o | Reduced particulate carbon 13-26 percent, |
| o | Reduced particulate emissions 29-43 percent, |
| o | Increased combustion efficiency 0.2-0.4 percent, and |
| o | Had no adverse effect on NOx emissions. |
| • | Use of CleanBoost Gold is superior to other diesel particulate control technologies in that it does not result in increased NOx emissions or diminished fuel economy. |
| • | CleanBoost Gold is competitive with other chemical additives for diesel particulate reduction because less of the active metal (iron) is required to accomplish the reduction. |
In summary, CleanBoost Gold appears to be a viable fuel additive for stationary and mobile diesel engines for both environmental and economic reasons. By reducing particulate emissions ahead of in-line particulate traps or filters, CleanBoost Gold will also improve the operating efficiency and regeneration performance of these devices.