UNITED STATES
SECURITIES AND EXCHANGE COMMISSION
Washington, D.C. 20549
FORM 10-K
| | | | |
(Mark One) | | | | |
x | | ANNUAL REPORT PURSUANT TO SECTION 13 OR 15(d) OF THE SECURITIES EXCHANGE ACT OF 1934 | | |
For the fiscal year ended December 31, 2005
OR
| | | | |
¨ | | TRANSITION REPORT PURSUANT TO SECTION 13 OR 15(d) OF THE SECURITIES EXCHANGE ACT OF 1934 | | |
For the transition period from to .
Commission File Number 1-7845
LEGGETT & PLATT, INCORPORATED
(Exact name of Registrant as specified in its charter)
| | |
Missouri | | 44-0324630 |
(State or other jurisdiction of incorporation or organization) | | (I.R.S. employer identification No.) |
| |
No. 1 Leggett Road Carthage, Missouri | | 64836 |
(Address of principal executive offices) | | (Zip code) |
Registrant’s telephone number, including area code: (417) 358-8131
SECURITIES REGISTERED PURSUANT TO SECTION 12(b) OF THE ACT:
| | |
Title of Each Class
| | Name of Each Exchange on Which Registered
|
Common Stock, $.01 par value | | New York Stock Exchange |
Preferred Stock Purchase Rights | | New York Stock Exchange |
Indicate by check mark if the Registrant is a well-known seasoned issuer, as defined in Rule 405 of the Securities Act. Yes x No ¨
Indicate by check mark if the Registrant is not required to file reports pursuant to Section 13 or Section 15(d) of the Act. Yes ¨ No x
Indicate by check mark whether the Registrant (1) has filed all reports required to be filed by Section 13 or 15(d) of the Securities Exchange Act of 1934 during the preceding 12 months (or for such shorter period that the registrant was required to file such reports), and (2) has been subject to such filing requirements for the past 90 days. Yes x No ¨
Indicate by check mark if disclosure of delinquent filers pursuant to Item 405 of Regulation S-K (Sec. 229.405 of this chapter) is not contained herein, and will not be contained, to the best of Registrant’s knowledge, in definitive proxy or information statements incorporated by reference in Part III of this Form 10-K or any amendment to this Form 10-K. x
Indicate by check mark whether the Registrant is a large accelerated filer, an accelerated filer, or a non-accelerated filer. See definition of “accelerated filer and large accelerated filer” in Rule 12b-2 of the Exchange Act.
Large accelerated filer x Accelerated filer ¨ Non-accelerated filer ¨
Indicate by check mark whether the Registrant is a shell company (as defined in Rule 12b-2 of the Act). Yes ¨ No x
The aggregate market value of the voting stock held by non-affiliates of the Registrant (based on the closing price of its common stock on the New York Stock Exchange) on June 30, 2005 was approximately $4,594,250,347.
There were 182,386,905 shares of the Registrant’s common stock outstanding as of February 15, 2006.
DOCUMENTS INCORPORATED BY REFERENCE
Items 10, 11, 12, 13 and 14 of Part III are incorporated by reference from the Company’s definitive Proxy Statement for the Annual Meeting of Shareholders to be held on May 10, 2006.
TABLE OF CONTENTS
LEGGETT & PLATT, INCORPORATED—FORM 10-K
FOR THE YEAR ENDED DECEMBER 31, 2005
Forward Looking Statements and Related Matters
This report and our other public disclosures, whether written or oral, may contain “forward-looking” statements including, but not limited to, estimates of the amounts and timing of charges resulting from our Restructuring Plan, as described beginning on page 28, and related reductions in revenues and the number of facilities to be closed pursuant to this plan; projections of revenue, income, earnings, capital expenditures, dividends, capital structure, cash flows or other financial items; possible plans, goals, objectives, prospects, strategies or trends concerning future operations; statements concerning future economic performance; and statements of the underlying assumptions relating to the forward-looking statements. These statements are identified either by the context in which they appear or by use of words such as “anticipate,” “believe,” “estimate,” “expect,” “intends,” “may,” “plans,” “should” or the like. All such forward-looking statements, whether written or oral, and whether made by us or on our behalf, are expressly qualified by the cautionary statements described in this provision.
Any forward-looking statement reflects only the beliefs of the Company or its management at the time the statement is made. Because all forward-looking statements deal with the future, they are subject to risks, uncertainties and developments which might cause actual events or results to differ materially from those envisioned or reflected in any forward-looking statement. Moreover, we do not have, and do not undertake, any duty to update or revise any forward-looking statement to reflect events or circumstances after the date on which the statement was made. For all of these reasons, forward-looking statements should not be relied upon as a prediction of actual future events, objectives, strategies, trends or results.
It is not possible to anticipate and list all risks, uncertainties and developments which may affect our future operations or performance of the Company, or which otherwise may cause actual events or results to differ from forward-looking statements. However, some of these risks and uncertainties include the following:
| • | | our ability to implement our Restructuring Plan, reduce overhead costs and maintain market share relating to the operations that are sold, consolidated or closed |
| • | | our ability to improve operations and realize cost savings (including our ability to improve the profitability of the Fixture & Display group) |
| • | | a significant decline in the long-term outlook for any given reporting unit (particularly our Fixture & Display group) that could result in goodwill impairment |
| • | | factors that could impact raw material costs, including the availability and pricing of steel rod and scrap, and other raw materials (including chemicals, fibers and resins), the reduction in the spread between the pricing of steel rod and steel scrap, energy costs (including natural gas, electricity and fuel) and the availability of labor |
| • | | our ability to pass along raw material cost increases to our customers through increased selling prices and our ability to maintain profit margins if our customers change the quantity and mix of our components in their finished goods because of increased raw materials costs |
| • | | price and product competition from foreign (particularly Asian) and domestic competitors |
| • | | future growth of acquired companies |
| • | | our ability to increase debt and maintain our current public debt and commercial paper credit ratings |
| • | | our ability to bring start up operations on line as budgeted in terms of expense and timing |
| • | | litigation risks, including litigation regarding product liability and warranty, intellectual property and workers compensation expense |
| • | | risks and uncertainties that could affect industries or markets in which we participate, such as growth rates and opportunities in those industries, changes in demand for certain products or trends in business capital spending |
1
| • | | changes in competitive, economic, legal and market conditions and related factors, such as the rate of economic growth in the United States and abroad, inflation, currency fluctuation, political risk, U.S. or foreign laws or regulations, interest rates, housing turnover, employment levels, consumer sentiment, taxation and the like |
Furthermore, we have made and expect to continue to make acquisitions. Acquisitions present significant challenges and risks, and depending upon market conditions, pricing and other factors, there can be no assurance that we can successfully negotiate and consummate acquisitions or successfully integrate acquired businesses into the Company.
The section in this report entitled “Management’s Discussion and Analysis of Financial Condition and Results of Operation” contains a disclosure on page 44 of the security ratings of the Company’s public debt. This discussion is not a recommendation to buy, sell or hold securities. Also, the security ratings are subject to revisions and withdrawal at any time by the rating organizations. Each rating should be evaluated independently of any other rating.
2
PART I
Item 1.Business.
Leggett & Platt, Incorporated and its subsidiaries are collectively referred to in this Form 10-K as “we,” “us,” “our,” “the Company” or “Leggett.” We were founded as a partnership in Carthage, Missouri in 1883 and became incorporated in 1901. The Company, a pioneer in the development of steel coil bedsprings, is a diversified manufacturer that conceives, designs and produces a wide range of engineered components and products that can be found in many homes, offices, retail stores and automobiles. Our business is organized into 29 business units, those units organized into 11 groups, and those groups into five segments, as indicated below.
Overview of the Residential Furnishings Segment
| | | | |
Segment
| | Groups
| | Business Units
|
Residential Furnishings | | Bedding | | U.S. Spring |
| | | | International Spring |
| | | | Adjustable Beds |
| | | | Wood Products |
| | Home Furniture & Consumer Products | | Furniture Hardware |
| | | | Seating Components |
| | | | Sofa Sleeper Components |
| | | | Ornamental Beds & Bedding Support Products |
| | Fabric, Foam & Fiber | | Fabric Converting |
| | | | Fibers |
| | | | Carpet Underlay |
| | | | Prime Foam Products |
| | | | Coated Fabrics |
| | | | Geo Components |
Our largest segment is Residential Furnishings. Our beginnings stem from an 1885 patent of the steel coil bedspring. Today, we supply a variety of components used by bedding and upholstered furniture manufacturers in the assembly of their finished products. We strive for competitive advantages based on a low cost structure, product innovation, a global presence, strong customer relationships and our internal production of key raw materials, including steel rod, wire, tubing, dimension lumber and plastics. Our wide range of products provides our customers with a single source for many of the components they need. For example, a bedding manufacturer can come to us for most components of a mattress and foundation, except the outer upholstery fabric. This is also true for manufacturers of upholstered recliner chairs, sofas and loveseats. We have long production runs and numerous production and assembly locations. Because of these advantages, we believe that we can generally produce components at a lower cost than our customers can produce the same parts for their own use. Sourcing components from Leggett allows our customers to focus on designing, merchandising and marketing their products. Listed below are examples of products manufactured or distributed by our Residential Furnishings groups:
Bedding
| • | | Innersprings (which are the sets of steel coils, bound together, that form the core of a mattress) |
| • | | Wood frames, steel coils and wire forms for mattress foundations |
| • | | Adjustable electric beds |
| • | | Cut-to-size dimension lumber |
3
Home Furniture & Consumer Products
| • | | Steel mechanisms and hardware (that enables furniture to recline, tilt, swivel, rock, elevate, etc.) for reclining chairs, sleeper sofas and other types of motion furniture |
| • | | Springs and seat suspensions for chairs, sofas and loveseats |
| • | | Steel tubular seat frames |
| • | | Bed frames, ornamental beds, comforters, decorative pillows, and other “top-of-bed” accessories |
Fabric, Foam & Fiber
| • | | Foam and fiber cushioning materials |
| • | | Specialty foam products (e.g. pillows and mattress toppers) |
| • | | Structural fabrics for mattresses, residential furniture and industrial uses |
| • | | Carpet underlay materials (bonded scrap foam, felt, rubber and prime foam) |
| • | | Coated fabrics (e.g. rug underlay, placemats and shelf liners) |
| • | | Geo components (a group of products that includes synthetic fabrics used in ground stabilization, geotextiles, drainage protection, erosion and weed control, geogrids, silt fencing, landscaping, chemicals, seed and fertilizer) |
Most of our Residential Furnishings customers are manufacturers of finished bedding products (mattresses and foundations) or upholstered furniture for residential use. We also sell a number of products including ornamental beds, bed frames, adjustable beds, carpet underlay, specialty foam products and top-of-bed accessories directly to retailers and distributors. Our geo components products are sold primarily to dealers, contractors, landscapers, road construction companies, golf courses and government agencies.
Key Strategies
Our ability to develop new, proprietary products provides an ongoing opportunity to increase business with customers, including those who continue to make some of their own components. Many of our capabilities, including product innovation, are being used as we move into new regions of the world. Internationally, we locate our operations close to our customers’ facilities in order to more efficiently supply them. Finally, we continue to look for acquisitions that expand our customer base, add new product lines or capabilities, or help establish a presence in new geographic regions.
In September 2005, the Company announced a significant broad-based restructuring project (Restructuring Plan) to reduce excess capacity and improve performance in a number of our businesses. As a part of the Restructuring Plan, we identified 36 underutilized or underperforming facilities to be closed, consolidated or sold (the Closure and Consolidation Initiative). To date, we have identified 16 facilities in the Residential Furnishings segment that will be closed, consolidated or sold. For further information on our Restructuring Plan, see Item 7, Management’s Discussion and Analysis of Financial Condition and Results of Operation beginning on page 28.
Overview of the Commercial Fixturing & Components Segment
| | | | |
Segment
| | Groups
| | Business Units
|
Commercial Fixturing & Components | | Fixture & Display | | Store Fixtures Point-of-Purchase Displays Commercial Vehicle Products* Storage Products |
| | Office Furniture Components | | U.S. Office Components International Office Components Plastics |
4
| * | The Company’s Commercial Vehicle Products unit, which primarily sells wire and steel racks, shelves and cabinets for the interior of service vans and utility vehicles, is reported in this Form 10-K in the Commercial Fixturing & Components segment. Effective October 31, 2005, the Company created the Commercial Vehicle Products group and unit in the Specialized Products segment following the acquisition of America’s Body Company. ABC’s main product categories include van interiors (the racks, shelving, cabinets, etc. installed in service vans) and truck bodies for cargo vans, flatbed trucks, service trucks and dump trucks. Effective January 1, 2006, the prior Commercial Vehicle Products unit was moved from the Commercial Fixturing & Components segment to the new Commercial Vehicle Products group in the Specialized Products segment. |
Our second largest segment is Commercial Fixturing & Components. This segment is divided into two groups, Fixture & Display and Office Furniture Components.
In the Fixture & Display group, we believe that we are the industry’s only “one-stop” supplier, with broad capabilities that include design, production, installation and project management. Products manufactured by our Fixture & Display group include:
| • | | Custom-designed, full store fixture packages, including shelving, counters, point-of-purchase displays, showcases, garment racks and decorative woodwork for retailers |
| • | | Standardized shelving used by large retailers, grocery stores and discount chains |
| • | | Commercial storage racks and carts (material handling systems) used primarily in the food service and healthcare industries |
| • | | Wire and steel racks, shelves and cabinets for the interior of service vans and utility vehicles |
Our Office Furniture Components group manufactures:
| • | | Bases, columns, back rests, casters and frames for office chairs, and control devices that allow office chairs to be adjusted to height, tilt and swivel |
| • | | Injection molded plastic components for manufacturers of lawn care products, power tools, office furniture and other consumer and commercial products |
Customers of the Commercial Fixturing & Components segment include:
| • | | Retail chains and specialty shops |
| • | | Brand name marketers and manufacturers |
| • | | Food service companies, healthcare providers and restaurants |
| • | | Office, institutional, and commercial furniture manufacturers |
Key Strategies
Our Fixture & Display group strategy is to be the industry’s most financially stable, and most customer oriented one-stop supplier of fixture and display products. Our focus is to increase volume within current markets and also look for opportunities to expand into new, related markets.
In October 2003, we announced the Fixture & Display group tactical plan to increase our attention and scrutiny of under-performing profit centers in the Fixture & Display group. This tactical plan was aimed at accomplishing improved operating efficiency, better adherence to standard costs, tighter inventory control, cost reduction, and more competent staffing. Over the past two years we made some progress. However, in 2005, we
5
were hampered in our efforts to improve operating margins by the impact of new program start-up costs and integration inefficiencies associated with the RHC Spacemaster acquisition. As part of the previously referenced Restructuring Plan and Closure and Consolidation Initiative, we have identified 10 facilities in Commercial Fixturing & Components, primarily in the Fixture & Display group, that will be consolidated, sold, or closed. For further information on our Restructuring Plan, see Item 7, Management’s Discussion and Analysis of Financial Condition and Results of Operation beginning on page 28.
In our businesses serving office furniture manufacturers, we plan to develop new products, providing opportunities to supply more components to customers. We also expect to continue making strategic acquisitions that add new products or expand operations into new regions of the world.
Principal growth strategies for our plastics operations include expanding our position in key markets, cross-selling to customers of other Leggett divisions, and supplying more of the Company’s internal requirements.
Overview of the Aluminum Products Segment
| | | | |
Segment
| | Groups
| | Business Units
|
Aluminum Products | | Aluminum | | Die Casting Tool & Die |
Our Aluminum Products segment is the leading independent producer of non-automotive aluminum die castings in North America. We also produce zinc and magnesium die castings. We work with customers from the design concept stage to market introduction and then through the product lifecycle to refine the product and reduce cost. We sell aluminum, zinc and magnesium die cast components to a diverse group of customers that manufacture industrial and consumer products. Our customers include:
| • | | Small engine and diesel engine builders |
| • | | Motorcycle, truck, off-road and recreational vehicle (including all-terrain vehicles and snowmobiles) and automobile makers |
| • | | Manufacturers of outdoor lighting fixtures, cable line amplifiers, wireless communications systems and other cable and telecommunication products |
| • | | Gas barbeque grill manufacturers |
| • | | Consumer appliance and power tool manufacturers |
| • | | Computer, electronic and electric motor producers |
We also manufacture and refurbish dies (also known as molds or tools) for all types and sizes of die casting machines. These are sold to customers that buy our die castings and to other die cast manufacturers. We also provide extensive machining, coating, finishing, sub-assembly and other value-added services related to our die cast components.
As planned, in December 2005 we completed construction of our new die casting facility in Auburn, Alabama. This facility is scheduled to supply aluminum components for Briggs & Stratton under a seven-year agreement. We expect the facility to be fully operational by the end of 2006.
Key Strategies
Market share growth is a major focus. We plan to continue to pursue large users of castings, target customers who currently make some of their own aluminum components, and look for opportunities to expand into new markets where die cast components are used. We plan to continue striving to develop technology that
6
allows opportunities for growth in new markets. Finally, we are committed to establishing a global presence, enabling us to supply customers as they take more production overseas. Acquisitions may play a part in accomplishing these plans.
Overview of the Industrial Materials Segment
| | | | |
Segment
| | Groups
| | Business Units
|
Industrial Materials | | Wire | | Wire Drawing |
| | | | Wire Products |
| | | | Steel Rod |
| | Tubing | | Steel Tubing |
The Industrial Materials segment produces steel rod, drawn wire and welded steel tubing, as well as specialty wire products. Drawn wire and welded steel tubing are important raw materials that are widely used to manufacture our products. About 50% of the drawn wire and about 25% of the welded steel tubing that we produce is used to manufacture other products made by the Company. For example, wire is used to make:
| • | | Bedding and furniture components |
| • | | Commercial fixtures and point-of-purchase displays |
| • | | Automotive seating components |
Welded steel tubing is used in many of the same products including:
| • | | Motion furniture mechanisms |
| • | | Store fixtures, displays, shelving and storage products |
| • | | ATV, RV and snowmobile accessories |
In addition to supplying a portion of our own raw material needs, we sell drawn wire and welded steel tubing to a diverse group of industrial customers, including:
| • | | Bedding and furniture makers |
| • | | Automotive seating manufacturers |
| • | | Lawn and garden equipment manufacturers |
| • | | Recreational equipment (e.g. ATV and RV) producers |
| • | | Mechanical spring makers |
We also produce specialty wire products such as:
| • | | Wire ties used by cotton gins to tie bales of cotton |
| • | | Wire tying heads used by waste recyclers and solid waste removal businesses to bale materials |
| • | | Shaped wire used by automotive companies and medical supply businesses |
Currently, our wire mills use over 800,000 tons of steel rod each year. Our steel rod mill provides a consistent supply of quality steel rod for the Industrial Materials segment. As of year end, we completed an expansion of the mill that is expected to increase future output by approximately 20%, raising annual rod output from 450,000 tons to approximately 540,000 tons. We expect to use nearly all of this steel rod in Leggett wire mills. This expansion does not signify a change in our rod strategy. We expect to continue to be a substantial
7
purchaser of rod on the open market, enabling us to maintain leverage with suppliers. We strive to maintain the efficiency of the mill by producing only a few sizes and types of rod, and operating the mill’s electric furnace (which has a capacity of about one million tons) during off-peak times to reduce energy costs. Also, the mill is located in a region that generates a significant amount of steel scrap. We expect that over the long term this scrap market will provide a consistent supply to the mill. Finally, the rod mill is also located near our wire mills.
Key Strategies
The core strategy of our wire and tubing businesses is to efficiently supply other Leggett businesses’ raw material requirements. We expect growth, to a large extent, to occur as our internal requirements expand, both domestically and abroad. We also expect to expand our capabilities to add value through the forming, shaping, and welding of our wire and tubing. This may occur through start-up operations or acquisitions.
As part of the previously referenced Restructuring Plan and Closure and Consolidation Initiative, we have identified five facilities in the Industrial Materials segment that will be consolidated, sold, or closed. For further information on our Restructuring Plan, see Item 7, Management’s Discussion and Analysis of Financial Condition and Results of Operation beginning on page 28.
Overview of the Specialized Products Segment
| | | | |
Segment
| | Groups
| | Business Units
|
Specialized Products | | Automotive | | Automotive |
| | Machinery | | Machinery |
| | Commercial Vehicle Products* | | Commercial Vehicle Products* |
| * | Effective October 31, 2005, the Company created the Commercial Vehicle Products group in the Specialized Products segment following the acquisition of America’s Body Company. ABC’s main product categories include van interiors (the racks, shelving, cabinets, etc. installed in service vans) and truck bodies for cargo vans, flatbed trucks, service trucks and dump trucks. The Company’s existing Commercial Vehicle Products unit, which primarily sells wire and steel racks, shelves and cabinets for the interior of service vans and utility vehicles, is reported in this Form 10-K in the Commercial Fixturing & Components segment but was moved to the new Commercial Vehicle Products group in the Specialized Products segment effective January 1, 2006. |
Our Specialized Products segment designs, produces and sells components for the automotive industry, specialized machinery and equipment, and van interiors and truck bodies for light-to-medium duty commercial trucks.
In the Automotive group, we manufacture:
| • | | Lumbar systems for automotive seating (including manual, 2-way power, 4-way power, massage systems and memory options) |
| • | | Seat suspension systems |
| • | | Automotive control cables, such as shift cables, cruise-control cables, seat belt cables, accelerator cables, seat control cables and latch release cables |
| • | | Stamped seat frames and formed metal parts |
Primary customers for these products are automobile seating manufacturers.
8
In the Machinery group, we primarily manufacture:
| • | | Highly automated quilting machines for fabrics used to cover mattresses and other home furnishings |
| • | | Machines used to shape wire into various types of springs |
| • | | Industrial sewing machines |
| • | | Material handling systems |
| • | | Wide format digital printing equipment |
| • | | Other equipment for factory automation |
The primary customers for these products are bedding manufacturers. We also design and produce some of these specialized products for our own use.
In the Commercial Vehicle Products group we primarily manufacture:
| • | | Van interiors (the racks, shelving, cabinets, etc. installed in service vans) |
| • | | Truck bodies (for cargo vans, flatbed trucks, service trucks, and dump trucks) |
The primary customers for these products are manufacturers and end-users of light-to-medium duty commercial trucks.
Key Strategies
In our Automotive group, we plan to continue the focus on research and development, looking for ways to improve the function and reduce the cost of our products. The introduction of new capabilities and products creates the potential for us to expand into new markets. Growing our global presence (to serve developing markets and to expand our sourcing options) will remain a key objective, as will assisting our customers with vendor consolidation (to reduce the complexity and cost of their supply chain).
Our Machinery group designs and manufactures equipment that is used to produce the proprietary innersprings we develop for our bedding customers. In most cases, this equipment is not available in the marketplace. Providing proprietary machinery is a critical function of our Machinery group, and a key factor contributing to the success of our bedding operations. In addition, we expect to continue to develop technology to improve efficiency in our own plants as well as those of our customers.
In our new Commercial Vehicle Products group, geographic expansion and new product development are key growth strategies. Certain markets for truck bodies in the United States are supplied by smaller regional manufacturers. We aim to expand into those markets which have high concentrations of end-users. Through a continued focus on product innovation, we expect to provide improved product functionality and quality to customers.
As part of the previously referenced Restructuring Plan and Closure and Consolidation Initiative we have identified five facilities in the Specialized Products segment that will be consolidated, sold or closed. For further information on our Restructuring Plan, see Item 7, Management’s Discussion and Analysis of Financial Condition and Results of Operation beginning on page 28.
Acquisitions and Divestitures
Our typical acquisition is a small, private, profitable, entrepreneurial company. Our acquisition targets are generally complementary to our existing businesses. Over the past ten years, the average acquisition target has had annual revenues between $15 and $20 million, which we believe makes the risk from any single acquisition
9
low. In our history, we have completed only five acquisitions of businesses with annual sales greater than $100 million. We do not follow a fixed timetable for buying companies. Rather, we aim to be opportunistic by taking advantage of circumstances as they arise. As a result, the pace and size of acquisitions in any given year could be significantly more or less than the average over the longer term.
In total, we acquired 12 businesses during 2005 representing approximately $320 million in annualized sales. The acquired businesses are expected to add approximate annualized sales within our segments as follows:
| | |
Residential Furnishings | | $170 million |
Specialized Products | | $150 million |
The largest of these acquisitions, America’s Body Company was acquired in late October and is expected to generate annual revenue of approximately $150 million. ABC’s main product categories include van interiors (the racks, shelving, cabinets, etc. installed in service vans) and truck bodies for cargo vans, flatbed trucks, service trucks, and dump trucks. This acquisition provided the basis to create our newly formed Commercial Vehicle Products group in the Specialized Products segment. As of January 1, 2006 our van interior operations were combined with ABC, consolidating the Commercial Vehicle Products group within the Specialized Products segment. With combined expected sales of approximately $250 million, we believe we are now the second largest supplier, in terms of revenue, in a $1.5 billion U.S. market. While the industry is fragmented, containing many small, regional manufacturers, we believe that only a few competitors provide as wide a range of products and service locations.
In another key expansion, we acquired two geo components operations in 2005 that are expected to collectively add approximately $80 million in revenue annually to the Residential Furnishings segment. These acquisitions expanded our presence in converting and distributing geo components. Geo components include geotextiles, or synthetic fabrics used in a variety of applications such as ground stabilization, drainage protection, erosion control and weed control. Products are sold primarily into the construction, landscaping and agriculture industries. The fragmented U.S. market for geotextiles is estimated at $900 million annually and contains many small regional suppliers.
We also divested a total of four businesses in 2005 with aggregate annualized sales of $22 million. In our Residential Furnishings segment we sold a wiping cloth business with annual sales of approximately $15 million. We also sold a small automotive cable producer in our Specialized Products segment. Finally, we sold assets relating to the production of stud wall fixture partitions and slotted wall displays, which were a part of the Commercial Fixturing & Components segment.
For further information on acquisitions and divestitures, see Note B and Note N of the Notes to Consolidated Financial Statements.
Segment Financial Information
For information on sales to external customers, sales by product line, earnings before interest and taxes, and total assets of each of our business segments, refer to Note L of the Notes to Consolidated Financial Statements.
Foreign Operations
The percentages of our trade sales from products manufactured outside the United States for the previous three years are shown in the table below.
| | | |
Year
| | Percent
| |
2005 | | 21 | % |
2004 | | 21 | % |
2003 | | 21 | % |
10
The majority of our international operations, measured by trade sales, are in Canada, Europe and Mexico.
The Canadian operations manufacture products including innersprings for mattresses, fabricated wire for the bedding, furniture and automotive industries, cut-to-size bed frame lumber and down comforters, mattress pads and pillows. We manufacture shelving for retailers, wire and steel storage systems and racks for the interior of service vans and utility vehicles, and point-of-purchase displays for retailers, as well as chair frames and bases, table bases and office chair controls, and plastic injection moldings. We also make lumbar supports for automotive seats.
Our operations in Europe produce, among other things, innersprings for mattresses, structural fabric for industrial and residential uses, various wire products, and lumbar and seat suspension systems for automotive seating. We also sell machinery and equipment designed to manufacture innersprings for mattresses and other bedding related components. Finally, we have one operation in Europe that designs and distributes point-of-purchase displays for retailers.
The Mexican operations manufacture products including innersprings and wire grid tops for mattresses, fabricated wire for the bedding industry, and structural fabric for industrial and residential uses. We produce aluminum die castings and provide machining, sub-assembly and other value added services related to aluminum die castings. We also produce commercial shelving, material handling equipment, and automotive control cable systems.
We continue to increase our presence in Asia, particularly in China where we now have 11 production facilities. Prior to 2003, we owned only three production facilities in China. Two of these plants produce mattress innersprings for sale into the Chinese market. The third plant produces machinery and replacement parts for machines used in the bedding industry.
In 2003, we increased to eight total Chinese operations. We began operations in our fourth plant, a facility to manufacture recliner mechanisms and various bases for upholstered furniture. This plant primarily sells products to furniture manufacturers in China (who produce upholstered furniture for export) and to some Leggett operations on an inter-company basis. The other four Chinese operations added in 2003 include a facility that produces small electric motors primarily used in lumbar systems for automotive seating; a facility that manufactures cables for these lumbar systems; an operation that produces innersprings for mattresses and sofa cushions; and a facility that manufactures innersprings and bedding machinery.
In 2005, we continued growing our presence in China with two acquisitions. One operation, in our Residential Furnishings segment, manufactures chair components. In our Fixture & Display group, we added a manufacturer of retail store fixtures and gondola shelving. In addition to these acquisitions, we bought assets and placed them into an existing location to create a manufacturer of stamped seat frames and formed-metal automotive products in our Automotive group.
Finally, our Ornamental Bed unit imports finished beds from Asia for sale in the United States. Many other business units of the Company have long-standing, well-established relationships with suppliers in Asia for components and finished products.
Our strategy regarding international expansion is to locate our operations where we believe demand for components is growing. In instances where our customers move the production of their finished products overseas, we need to be located nearby to supply them efficiently. In addition, these operations should allow us to supply growing demand in the local markets.
Our international operations face the risks associated with any operation in a foreign state. These risks include:
| • | | The nationalization of private enterprises |
| • | | Political instability in certain countries |
11
| • | | Differences in foreign laws that make it difficult to protect intellectual property and enforce contract rights |
| • | | Increased costs due to tariffs, customs and shipping rates |
| • | | Potential problems obtaining raw materials, and disruptions related to the availability of electricity and transportation during times of crisis or war |
| • | | Foreign currency fluctuation |
Such risks could result in increases in costs, reduction in profits, the inability to do business and other adverse effects on the Company’s business.
Geographic Areas of Operation
We have manufacturing, warehousing and distribution facilities in many foreign countries as listed in the chart below.
| | | | | | | | | | |
Segment
| | North America
| | Europe
| | South America
| | Asia / Pacific
| | Africa
|
Residential Furnishings | | Canada Mexico United States | | Croatia Denmark France Russia Spain United Kingdom | | Brazil | | Australia China Singapore | | South Africa |
| | | | | |
Commercial Fixturing & Components | | Canada Mexico United States | | United Kingdom | | | | China | | |
| | | | | |
Aluminum Products | | Mexico United States | | | | | | | | |
| | | | | |
Industrial Materials | | United States | | United Kingdom | | | | China | | |
| | | | | |
Specialized Products | | Canada Mexico United States | | Austria Belgium Croatia Germany Hungary Italy Sweden Switzerland United Kingdom | | | | China South Korea | | |
For further information concerning our long-lived assets and sales outside the United States, refer to Note L of the Notes to Consolidated Financial Statements.
12
Sales by Product Line
The following table shows the approximate percentages of our sales to external customers by product line for the last three years:
| | | | | | | | | |
| | 2005
| | | 2004
| | | 2003
| |
Product Line | | | | | | | | | |
Bedding Components | | 17.3 | % | | 17.6 | % | | 17.8 | % |
Residential Furniture Components | | 16.9 | | | 15.8 | | | 15.9 | |
Finished & Consumer Products | | 12.6 | | | 12.7 | | | 13.8 | |
Other Residential Furnishing Products | | 2.2 | | | 2.4 | | | 2.2 | |
Store Displays, Fixtures & Storage Products | | 15.3 | | | 16.2 | | | 17.0 | |
Office Furnishings & Plastic Components | | 6.1 | | | 4.9 | | | 4.9 | |
Aluminum Products | | 9.7 | | | 10.0 | | | 10.3 | |
Wire, Wire Products & Steel Tubing | | 10.1 | | | 10.4 | | | 8.4 | |
Automotive Products, Specialized Machinery & Commercial Vehicle Products | | 9.8 | | | 10.0 | | | 9.7 | |
Distribution of Products
In each of our segments, our products are sold and distributed primarily through the Company’s sales personnel. However, many of our businesses have relationships and agreements with sales representatives and distributors. We do not believe any of these agreements or relationships would, if terminated, have a material adverse effect on the consolidated financial condition or results of operations of the Company.
Raw Materials
We use a variety of raw materials in manufacturing our products. Some of the most important raw materials include:
| • | | Woven and non-woven fabrics |
| • | | Foam chemicals and foam scrap |
The raw materials for many of our businesses are supplied by our own facilities. For example, steel rod is used to produce steel wire, which we use to make innersprings and foundations for mattresses, springs and seat suspensions for chairs and sofas, displays, shelving and racks for retailers, and automotive seating components. Our own wire drawing mills supply nearly all of our U.S. requirements for steel wire. The steel rod produced at our rod mill currently supplies roughly half of our rod requirements. After the expansion of the rod mill and full ramp up (discussed further on page 7), we expect to produce approximately two-thirds of our steel rod requirements. We also produce welded steel tubing, dimension lumber and plastic components both for our own consumption and for sale to customers outside the Company.
13
We believe that worldwide supply sources are available for all the raw materials used by the Company. However, we have experienced higher raw material costs (most notably steel and oil-based materials such as chemicals, fibers and resins) during the past two years.
We purchase about 1.3 million tons of steel annually, accounting for approximately 17% of our cost of goods sold. In 2004, inflation caused the Company to pay over $200 million more for steel than it did in 2003. Most steel vendors rescinded previous contracts, and moved to 30-day pricing. The Company announced or implemented steel-related price increases in most segments. In 2005, market prices for most types of steel were slightly lower at the end of the year than at the beginning of the year. Although the Company anticipates the costs for steel to stabilize, the future pricing of steel is uncertain and could increase in 2006. The degree to which we are able to mitigate or recover higher costs, should they occur, could be a significant factor influencing 2006 earnings.
The price increases in the steel market during 2004 led to an above average spread between scrap costs and rod prices. This spread continued throughout 2005, enhancing the earnings of our rod mill. We expect that the spread between the price of steel rod and steel scrap will narrow in 2006. If this occurs, it will negatively impact our results of operations.
We experienced significant inflation in chemicals, fibers and resins (generally driven by changes in oil prices) throughout 2005, but especially in the last half of the year. By year end 2005, the majority of these cost increases had been passed through to our customers. In addition to steel and oil-based materials, we also use significant amounts of aluminum. However, we are generally less exposed to cost changes in this commodity because of the pricing arrangements we have with our customers.
Heading into the fourth quarter of 2005, the availability of TDI, a chemical used to make polyurethane foam, was a concern. Overall industry capacity had been reduced early in the summer by the closure of two TDI plants and then hurricane damage to major chemical, refinery and natural gas facilities disrupted the production of TDI. These shortages abated by year end and we experienced no significant volume reductions.
In 2005, higher raw material costs led some of our customers to modify their product designs, changing the quantity and mix of our components in their finished goods. In some cases, our higher cost components were replaced with lower cost components, causing us to shift production accordingly. This has impacted our Residential Furnishings product mix and decreased profit margins. We expect that this will continue to be an issue in 2006 and could negatively impact our results of operations.
Customers
We serve thousands of customers worldwide, sustaining many long-term business relationships. No customer accounted for more than 5% of the Company’s consolidated revenues in 2005. Our top 10 customers accounted for less than 17% of our consolidated revenues in 2005. The Commercial Fixturing & Components segment has one customer whose sales exceeded 10% of total segment sales. This customer accounted for approximately 12% of the segment’s 2005 sales. Aluminum Products has one such customer, which accounted for approximately 13% of the segment’s 2005 sales, as well as two customers who account for just under 10% each. The Specialized Products segment has three customers with sales exceeding 10% of total segment sales. These customers accounted for approximately 17%, 13% and 11%, respectively, of the segment’s 2005 sales. The loss of any one of these customers may have a material adverse effect upon the relevant segment.
Patents and Trademarks
Leggett holds approximately 1,250 patents and has approximately 675 in process for its various product lines. We have registered over 950 trademarks, with more than 150 in process. No single patent or group of patents, or trademark or group of trademarks, is material to our business as a whole. Most of our patents and
14
trademarks relate to products sold in the Specialized Products and Residential Furnishings segments. Examples of our most significant trademarks include:
| • | | SEMI-FLEX®, LOK-Fast® andDYNA-Lock® (boxspring components and foundations) |
| • | | Mira-Coil®, Lura-Flex® andSuperlastic® (mattress innersprings) |
| • | | Nova-Bond® andRollout® (insulator pads for mattresses) |
| • | | ADJUSTAMAGIC® (adjustable electric beds) |
| • | | Wall Hugger® (recliner chair mechanisms) |
| • | | SUPER SAGLESS® (motion and sofa sleeper mechanisms) |
| • | | No-Sag® (wire forms used in seating) |
| • | | Tack & Jump® andPattern Link® (quilting machines) |
| • | | Hanes® (fiber materials) |
| • | | Schukra®, Pullmaflex® andFlex-O-Lators® (automotive seating products) |
| • | | Amco® andRHC® (fixtures and displays) |
| • | | Spuhl® (mattress innerspring manufacturing machines) |
| • | | Gribetz™ andPorter® (quilting and sewing machines) |
| • | | ABC America’s Body Co.®, QUIETFLEX®and Masterack® (equipment and accessories for vans and trucks) |
Research and Development
We maintain research, engineering and testing centers in Carthage, Missouri, and also do research and development work at many of our other facilities. We are unable to precisely calculate the cost of research and development because the personnel involved in product and machinery development also spend portions of their time in other areas. However, we estimate the cost of research and development was approximately $25 million in 2005, $25 million in 2004, and $24 million in 2003.
Employees
The Company has approximately 33,000 active employees, of which approximately 24,600 are engaged in production. Of the total active employees, roughly 10,700 are international employees. Approximately 5,400 of our employees were represented by labor unions. We did not experience any material work stoppage related to the negotiation of contracts with labor unions during 2005. Management is not aware of any circumstances likely to result in a material work stoppage related to the negotiation of contracts with labor unions during 2006.
The largest group of employees, approximately 13,700, works in the Residential Furnishings segment. Approximately 7,000 employees work in Commercial Fixturing & Components, while approximately 5,700 employees work in Specialized Products. Roughly 4,100 work in the Aluminum Products segment and approximately 1,600 are employed by our Industrial Materials segment.
Competition
Many companies offer products that compete with those manufactured and sold by Leggett. The number of competing companies varies by product line, but the markets for our products are highly competitive in all aspects. The primary competitive factors in our business include price, product quality, innovation, and customer service.
15
We believe we gain a competitive advantage over many competitors by having lower cost operations, significant internal production of key raw materials, superior manufacturing expertise and product innovation, higher quality products, extensive customer service capabilities, long-lived relationships with customers, and greater financial strength.
In certain of our markets, a portion of U.S. manufacturing is moving overseas. We face increasing price competition from foreign competitors, especially those in Asia, who are able to supply component parts to our customers’ Chinese and Asian manufacturing facilities. We have, and continue to develop, significant Asian supply sources. We also have, and continue to develop, a manufacturing presence in Asia.
When prices for key raw materials (such as steel, aluminum and chemicals) are relatively level throughout the world, we can generally produce our components at a lower cost in the U.S. (because many of our products have low labor content). However, in instances where our customers move production of their finished products overseas, our operations must be located nearby to supply them efficiently. At the end of 2005, we operated 11 facilities in China.
We believe Asian manufacturers currently benefit from lower commodity costs (certain commodities may sometimes be subsidized by Asian governments), lenient attitudes toward safety and environmental matters, and currency rates that are pegged to the U.S. dollar rather than free floating. However, when exporting to the U.S., Asian manufacturers must overcome higher transportation costs and increased working capital needs, and may have difficulty matching U.S. manufacturers’ level of service, flexibility and logistics.
We believe we are the largest independent manufacturer in North America, in terms of revenue, of the following:
| • | | Components for residential furniture and bedding |
| • | | Retail store fixtures and point-of-purchase displays |
| • | | Components for office furniture |
| • | | Non-automotive aluminum die castings |
| • | | Automotive seat support and lumbar systems |
| • | | Bedding industry machinery for wire forming, sewing and quilting |
Seasonality
We do not experience significant seasonality; however, quarter-to-quarter sales have generally varied in proportion to the total year by about 2.5%. The timing of acquisitions and economic factors in any year can distort the underlying seasonality in certain of our businesses. Nevertheless, for the Company as a whole, the second and third quarters typically have proportionately greater sales, while the first and fourth quarters are generally lower.
Residential Furnishings typically has the strongest sales in the second and third quarters due to increased consumer demand for bedding and furniture during the late summer and fall months. Commercial Fixturing and Components generally has heavy third quarter sales of its store fixture products, with the first and fourth quarters normally lower. This aligns with the industry’s normal construction cycle, and the opening of new stores and completion of remodeling projects in advance of the holiday season. Aluminum Products sales are proportionately greater in the first two calendar quarters due to typically stronger spring and early summer demand for lawn and garden equipment and barbeque grills. Industrial Materials and Specialized Products have
16
relatively little quarter-to-quarter variation in sales, although the automotive business is somewhat heavier in the second and fourth quarters of the year and somewhat lower in the third quarter, due to model changeovers and plant shutdowns in the automobile industry during the summer.
Backlog
Our relationships with our customers and our manufacturing and inventory practices do not provide for a significant backlog of orders. Production and inventory levels are geared primarily to the level of incoming orders and projections of future demand based on customer relationships.
Working Capital Items
For information regarding working capital items, see the discussion of “Cash from Operations” in Item 7, Management’s Discussion and Analysis of Financial Condition and Results of Operation, on page 42.
Environmental Regulation
The Company’s various operations are subject to federal, state, and local laws and regulations related to the protection of the environment. Environmental regulations include those relating to air and water emissions, underground storage tanks, waste handling, and the like. We have established policies in an effort to ensure that our operations are conducted in keeping with good corporate citizenship and with a positive commitment to the protection of the natural and workplace environments. While we cannot forecast policies that may be adopted by various regulatory agencies, management expects that compliance with these various laws and regulations will not have a material adverse effect on our competitive position, capital expenditures, consolidated financial condition or results of operations.
Internet Access to Other Information
Our annual reports on Form 10-K, quarterly reports on Form 10-Q, current reports on Form 8-K and all amendments to those reports are made available, without cost, on our website at http://www.leggett.com as soon as reasonably practicable after electronically filed with, or furnished to, the Securities and Exchange Commission. In addition to these reports, the Company’s Financial Code of Ethics, Code of Business Conduct and Ethics and Corporate Governance Guidelines, as well as charters for its Audit, Compensation, and Nominating and Corporate Governance Committees can be found on our website. Each of these documents is available in print, without cost, to any shareholder who requests it. Information contained on our website does not constitute part of this Annual Report on Form 10-K.
Item 1A.Risk Factors
Investing in our securities involves risk. Set forth below and elsewhere in this report are risks and uncertainties that could cause actual results to differ materially from the results contemplated by the forward-looking and other statements contained in this report. We may amend or supplement these risk factors from time to time by other reports we file with the SEC in the future.
Costs of raw materials could adversely affect our operating results.
Raw material cost increases (and our ability to respond to cost increases through selling price increases) can significantly impact our earnings. Steel is our largest raw material. During 2004 the price of certain types of steel nearly doubled. In 2005, market prices for most types of steel were slightly lower at the end of the year than at the beginning of the year. Although we anticipate the costs for steel to stabilize, the future pricing of steel is uncertain and could increase in 2006 even beyond current levels.
17
The price increases in the steel market during 2004 led to an above average spread between scrap costs and rod prices. This spread continued throughout 2005, enhancing the earnings of our rod mill. We expect that the spread between the price of steel rod and steel scrap will narrow in 2006. If this occurs, it will negatively impact our results of operations.
Our operations can also be impacted by other raw materials, including those affected by changes in oil prices, such as chemicals, fibers and resins, as well as aluminum and lumber. Throughout 2005, but particularly in the last half of the year, we experienced higher costs associated with the oil based raw materials. We may not be able to pass along future cost increases through selling price increases.
In 2005, higher raw material costs led some of our customers to modify their product designs, changing the quantity and mix of our components in their finished goods. In some cases, our higher cost components were replaced with lower cost components. This has impacted our Residential Furnishings product mix and decreased profit margins. We expect this to continue to be an issue in 2006 and could negatively impact our results of operations.
We may not be able to improve operating performance in our Fixture & Display group.
Our Fixture & Display group has experienced deterioration in profitability in recent years. We were hampered in our efforts to improve operating margins in 2005 by new program start-up costs and integration inefficiencies associated with the RHC Spacemaster acquisition. In September 2005, we announced a Restructuring Plan where eight facilities in the Fixture & Display group have been or will be consolidated, sold, or closed. We have estimated that our Fixture & Display group productive capacity will be reduced by approximately $100 million pursuant to the Restructuring Plan. If margins do not improve in the Fixture & Display group, we may incur further charges as we pursue additional restructuring activities in this group. For further information on our Restructuring Plan, see Item 7, Management’s Discussion and Analysis of Financial Condition and Results of Operation beginning on page 28.
Asian competition could adversely affect our operating results.
We operate in markets that are highly competitive. Depending on the particular product, we experience competition based on a number of factors, including quality, performance, price and availability. We face increasing pressure from foreign competitors as some of our customers source a portion of their components and finished product from Asia. If we are unable to purchase key raw materials, such as steel, aluminum and chemicals, at prices competitive with those of foreign suppliers, our ability to maintain market share and profit margins could likewise be harmed.
Also, if our customers move production of their finished products overseas, we believe that our operations must be located nearby to supply them efficiently, which is particularly true in China. At the end of 2005, we operated 11 facilities in China. If demand in China (and other foreign countries) increases at a more rapid rate than we are able to establish operations in these countries, our market share and results of operations could be negatively impacted.
We may fail to meet our acquisition growth goals.
One of our growth strategies is to increase our sales and earnings and expand our markets through acquisitions. In 2005 the Company acquired 12 businesses, including the third largest acquisition in our history in terms of revenue. We expect these acquisitions to add approximately $320 million in annual revenue.
18
Furthermore, we expect to continue to make acquisitions in the future when appropriate opportunities arise. However, we may not be able to identify and successfully negotiate suitable acquisitions that are sufficient to meet our goals. Further, our acquired companies may encounter unforeseen operating difficulties and may require significant financial and managerial resources, which would otherwise be available for the ongoing development or expansion of our existing operations. Our operating results may be adversely affected if we do not achieve our acquisition growth goals.
Higher energy costs could adversely affect our operating results.
Higher prices for natural gas, electricity and fuel increase our production and delivery costs. Many of our large manufacturing operations are heavy users of natural gas and electricity. In addition, certain of our sales are made with terms such that we incur the fuel cost associated with delivering the product to our customer’s facility. Energy costs increased throughout 2005 but especially in the last half of the year, in part due to supply disruptions caused by hurricanes. Our inability to respond to these cost increases (by raising selling prices) could negatively affect our operating results.
We have exposure to economic factors that may affect market demand for our products.
As a supplier of products to a variety of industries, we are adversely affected by general economic downturns. Our operating performance is heavily influenced by market demand for our components and products. This market demand is impacted by many broad economic factors, including consumer confidence, employment levels, housing turnover, energy costs and interest rates. These factors influence consumer spending on durable goods, and therefore drive demand for our components and products. Some of these factors also influence the level of business spending on facilities and equipment, which impacts approximately one quarter of our sales. Significant changes in these economic factors may negatively impact the demand for our products and our results of operations.
Our assets are subject to potential goodwill impairment.
A significant portion of our assets consists of goodwill and other intangible assets, the carrying value of which may be reduced if we determine that those assets are impaired. As of December 31, 2005, goodwill and other intangible assets represented approximately $1.2 billion, or 30% of our total assets. We test goodwill and other assets for impairment annually and whenever events or circumstances indicate an impairment may exist. We could be required to recognize reductions in our net income caused by the impairment of goodwill and other intangibles, which, if significant, could materially and adversely affect our results of operations.
As disclosed above, our Fixture & Display group has experienced deterioration in profitability compared to historical levels. We expect that the Restructuring Plan will lead to improved earnings in the Fixture & Display group. About $300 million of goodwill is associated with the Fixture & Display group. If our earnings in this group do not improve, a goodwill impairment charge against earnings may be required.
We are exposed to foreign currency risk.
We expect that international sales will continue to represent a significant percentage of our total sales, which exposes us to currency exchange rate fluctuations. In 2005, 21% of our sales were generated by international operations. The revenues and expenses of our foreign operations are generally denominated in local currencies; however, certain of our operations experience currency-related gains and losses where sales or purchases are denominated in currencies other than their local currency. We currently engage in limited currency hedging transactions. Further, our competitive position may be affected by the relative strength of the currencies in countries where our products are sold. We cannot predict whether foreign currency exchange risks inherent in doing business in foreign countries will have a material adverse effect on our future operations and financial results.
19
Item 1B.Unresolved Staff Comments.
None.
Item 2.Properties.
Our most important physical properties are our production plants. At December 31, 2005, we had approximately 255 production plants worldwide. About one-half of the production plants are in the Residential Furnishings segment. Facilities manufacturing, assembling or distributing products in Residential Furnishings are located in 27 U.S. states as well as Asia, Australia, Brazil, Canada, Europe, Mexico and South Africa. Commercial Fixturing & Components manufacturing plants and distribution facilities are located in 14 U.S. states, Canada, China, Mexico and the United Kingdom. The Aluminum Products segment has facilities in ten U.S. states and Mexico. The Industrial Materials facilities are located in 12 U.S. states and the United Kingdom. Specialized Products are produced and distributed in facilities in 13 U.S. states and other significant operations in Canada, China, Europe, Mexico and South Korea.
A majority of our major production facilities are owned by the Company. We also conduct certain operations in leased premises. Terms of the leases, including purchase options, renewals and maintenance costs, vary by lease. For additional information regarding lease obligations, reference is made to Note H of the Notes to Consolidated Financial Statements.
Properties of the Company include facilities that, in the opinion of management, are suitable and adequate for the manufacture, assembly and distribution of its products. These properties are located to allow quick and efficient deliveries and necessary service to our diverse customer base.
Item 3.Legal Proceedings.
The information contained in Note M to the Company’s Consolidated Financial Statements included in Item 15 to this Report and found on page 81 is incorporated herein by reference.
Item 4.Submission of Matters to a Vote of Security Holders.
Not applicable.
20
Supplemental Item.Executive Officers of the Registrant.
The following information is included in accordance with the provisions of Part III, Item 10 of Form 10-K.
The table below sets forth the names, ages and positions of all executive officers of the Company as of February 15, 2006. Executive officers are normally elected annually by the Board of Directors.
| | | | |
Name
| | Age
| | Position
|
Felix E. Wright | | 70 | | Chairman of the Board and Chief Executive Officer |
David S. Haffner | | 53 | | President and Chief Operating Officer |
Karl G. Glassman | | 47 | | Executive Vice President and President—Residential Furnishings Segment |
Jack D. Crusa | | 51 | | Senior Vice President and President—Specialized Products Segment |
Joseph D. Downes, Jr. | | 61 | | Senior Vice President and President—Industrial Materials Segment |
Matthew C. Flanigan | | 44 | | Senior Vice President—Chief Financial Officer |
Robert G. Griffin | | 53 | | Senior Vice President and President—Fixture & Display Group |
Daniel R. Hebert | | 62 | | Senior Vice President and President—Aluminum Products Segment |
Ernest C. Jett | | 60 | | Senior Vice President, General Counsel and Secretary |
William S. Weil | | 47 | | Vice President and Corporate Controller (Chief Accounting Officer) |
Subject to the employment agreements and severance benefit agreements listed as Exhibits to this report, the executive officers serve at the pleasure of the Board of Directors.
Felix E. Wright serves as Chairman of the Company’s Board of Directors and as Chief Executive Officer. Mr. Wright served as Vice Chairman of the Board from 1999 to 2002 and as Chief Operating Officer from 1979 to 1999. He has served in various other capacities since 1959.
David S. Haffner was elected President of the Company in 2002 and has served as the Company’s Chief Operating Officer since 1999. He previously served the Company as Executive Vice President from 1995 to 2002 and has served the Company in other capacities since 1983. Mr. Haffner is also head of the Commercial Fixturing & Components segment.
Karl G. Glassman was elected Executive Vice President of the Company in 2002, and has served as President of the Residential Furnishings Segment since 1999. Mr. Glassman previously served the Company as Senior Vice President from 1999 to 2002 and President of Bedding Components from 1996 through 1998. He has served in various other capacities since joining the Company in 1982.
Jack D. Crusa has served the Company as Senior Vice President since 1999 and President of Specialized Products since 2003. He previously served as President of the Industrial Materials Segment from 1999 through 2004, as President of the Automotive Group from 1996 through 1999, and in various other capacities since 1986.
Joseph D. Downes, Jr. was appointed Senior Vice President of the Company in January 2005 and President of the Industrial Materials Segment in 2004. He previously served the Company as President of the Wire Group from 1999 to 2004, and in various other capacities since 1976.
Matthew C. Flanigan has served the Company as Senior Vice President since August 2005 and as Chief Financial Officer since April 2003. Mr. Flanigan previously served the Company as Vice President since 2003, as Vice President and President of the Office Furniture Components Group since 1999 and as Staff Vice President of Operations from 1997 to 1999.
Robert G. Griffin has been employed by the Company since 1992. Mr. Griffin was named Vice President and Director of Mergers, Acquisitions and Strategic Planning in 1995, President of the Fixture and Display Group in 1998 and Senior Vice President in 1999.
21
Daniel R. Hebert became Senior Vice President of the Company and President of the Aluminum Products Segment in 2002. Mr. Hebert previously served as Executive Vice President of the Aluminum Products Segment from 2000 to 2002 and Vice President of Operations from 1996 to 2000.
Ernest C. Jett became Senior Vice President, General Counsel and Secretary in January 2005. He was appointed General Counsel in 1997, and Vice President and Secretary in 1995. He previously served the Company as Assistant General Counsel from 1979 to 1995 and as Managing Director of the Legal Department from 1991 to 1997.
William S. Weil was appointed the Chief Accounting Officer by the Board of Directors in February 2004. He became Vice President in 2000 and has served the Company as Corporate Controller since 1991. He previously served the Company in various other accounting capacities since 1983.
PART II
Item 5.Market for Registrant’s Common Equity, Related Stockholder Matters and Issuer Purchases of Equity Securities.
The Company’s common stock is listed on the New York Stock Exchange (symbol LEG). The table below highlights quarterly and annual stock market information for the last two years.
| | | | | | | | | | | |
| | Price Range
| | Volume of Shares Traded
| | Dividend Declared
|
| | High
| | Low
| | |
2005 | | | | | | | | | | | |
Fourth Quarter | | $ | 24.44 | | $ | 18.19 | | 56,700,000 | | $ | .16 |
Third Quarter | | | 28.60 | | | 19.54 | | 57,000,000 | | | .16 |
Second Quarter | | | 29.35 | | | 25.53 | | 39,100,000 | | | .16 |
First Quarter | | | 29.61 | | | 27.03 | | 32,400,000 | | | .15 |
| |
|
| |
|
| |
| |
|
|
For the Year | | $ | 29.61 | | $ | 18.19 | | 185,200,000 | | $ | .63 |
| |
|
| |
|
| |
| |
|
|
2004 | | | | �� | | | | | | | |
Fourth Quarter | | $ | 30.68 | | $ | 26.05 | | 35,100,000 | | $ | .15 |
Third Quarter | | | 28.81 | | | 25.56 | | 35,200,000 | | | .15 |
Second Quarter | | | 27.24 | | | 21.80 | | 43,800,000 | | | .14 |
First Quarter | | | 25.74 | | | 21.19 | | 33,400,000 | | | .14 |
| |
|
| |
|
| |
| |
|
|
For the Year | | $ | 30.68 | | $ | 21.19 | | 147,500,000 | | $ | .58 |
| |
|
| |
|
| |
| |
|
|
Price and volume data reflect composite transactions; price range reflects intra-day prices; data source is Bloomberg.
Shareholders
The Company estimates it has approximately 55,000 shareholders, which includes approximately 15,000 shareholders of record (i.e. stock certificates are issued in the name of the owner) as of February 22, 2006 and approximately 40,000 beneficial shareholders (i.e. stock is held for the owner by their stockbroker in the name of the brokerage firm). At year end, institutional investors (e.g. mutual funds, pension funds) as a group held an estimated 64% of the Company’s shares; the ten largest positions held an estimated 32%.
See the discussion of the Company’s target for dividend payout under “Uses of Cash” in Item 7, Management’s Discussion and Analysis of Financial Condition and Results of Operation on page 41.
22
Issuer Repurchases of Equity Securities
The table below is a listing of our repurchases of the Company’s common stock during the last quarter of 2005.
| | | | | | | | | |
Period
| | Total Number of Shares Purchased (1)
| | Average Price Paid per Share
| | Total Number of Shares Purchased as Part of a Publicly Announced Plan or Program (2)
| | Maximum Number of Shares that may yet be purchased under the Plans or Programs (2)
|
October 1, 2005 – October 31, 2005 | | 2,166,253 | | $ | 19.61 | | 2,161,832 | | 2,189,110 |
November 1, 2005 – November 30, 2005 | | 2,041,817 | | $ | 20.90 | | 2,036,460 | | 5,152,650 |
December 1, 2005 – December 31, 2005 | | 193,039 | | $ | 23.95 | | 187,805 | | 4,964,845 |
| |
| |
|
| |
| | |
Total | | 4,401,109 | | $ | 20.40 | | 4,386,097 | | |
| |
| |
|
| |
| | |
(1) | The shares purchased include 15,012 shares surrendered or withheld to cover the exercise price and/or tax withholding obligations in stock option exercises and other benefit plan transactions, as permitted under the Company’s Flexible Stock Plan. These shares were not repurchased as part of a publicly announced plan or program. |
(2) | On August 4, 2004, the Board authorized management to repurchase up to 10 million shares each calendar year beginning January 1, 2005. This authorization was first reported in the quarterly report on Form 10-Q for the period ended June 30, 2004. On November 2, 2005, the Board increased the calendar year 2005 authorization by five million shares, bringing the total 2005 authorization to 15 million shares. This modification was first reported in the Company’s press release dated November 2, 2005. This 15 million share authorization expired on December 31, 2005. For 2006 and years thereafter, the annual authorization will remain at 10 million shares, unless and until repealed or changed by the Board of Directors. |
Item 6.Selected Financial Data.
| | | | | | | | | | | | | | | |
(Unaudited) | | 2005
| | 2004
| | 2003
| | 2002
| | 2001
|
(Dollar amounts in millions, except per share data) | | | | | | | | | | |
Summary of Operations | | | | | | | | | | | | | | | |
Net sales | | $ | 5,299.3 | | $ | 5,085.5 | | $ | 4,388.2 | | $ | 4,271.8 | | $ | 4,113.8 |
Net earnings | | | 251.3 | | | 285.4 | | | 205.9 | | | 233.1 | | | 187.6 |
Earnings per share | | | | | | | | | | | | | | | |
Basic | | | 1.30 | | | 1.46 | | | 1.05 | | | 1.17 | | | .94 |
Diluted | | | 1.30 | | | 1.45 | | | 1.05 | | | 1.17 | | | .94 |
Cash dividends declared per share | | | .63 | | | .58 | | | .54 | | | .50 | | | .48 |
| |
|
| |
|
| |
|
| |
|
| |
|
|
Summary of Financial Position | | | | | | | | | | | | | | | |
Total assets | | $ | 4,052.6 | | $ | 4,197.2 | | $ | 3,889.7 | | $ | 3,501.1 | | $ | 3,412.9 |
Long-term debt | | | 921.6 | | | 779.4 | | | 1,012.2 | | | 808.6 | | | 977.6 |
| |
|
| |
|
| |
|
| |
|
| |
|
|
| Net earnings and earnings per share for 2001 and 2002 do not include stock option expense. As discussed in Note A of the Notes to Consolidated Financial Statements, the Company began recognizing stock option expense under SFAS No. 123 in 2003 for options granted after January 1, 2003. In addition, net earnings and earnings per share in 2001 include the amortization of goodwill. Beginning in 2002, under the provisions of SFAS No. 142, goodwill is no longer amortized into expense. Excluding goodwill amortization, but including stock option expense for options granted after January 1, 2001, net earnings for 2001 would have been $201.3; basic earnings per share would have been $1.01; and diluted earnings per share would have been $1.00. Including stock option expense under SFAS No. 123 for options granted after January 1, 2002, net earnings in 2002 would have been $226.9; basic earnings per share would have been $1.14; and diluted earnings per share would have been $1.14. |
23
Item 7.Management’s Discussion and Analysis of Financial Condition and Results of Operation.
2005 HIGHLIGHTS
For the full year 2005, we posted record sales but earnings declined mainly due to charges associated with our restructuring activities. Sales increased primarily from acquisitions and inflation.
In September, we launched a significant broad-based initiative (the Restructuring Plan) to reduce excess capacity and improve performance in a number of our businesses. We made significant progress on the restructuring in the fourth quarter and expect to have most of this activity completed by mid-2006. Future years’ earnings should benefit from the cost savings and improved asset utilization this restructuring activity is expected to bring.
Acquisition activity increased in 2005 as we completed 12 transactions, including the third largest in our history. These acquisitions should benefit Leggett by enhancing our position in current markets, increasing our product offerings and expanding our geographic presence.
Our use of cash in 2005 was consistent with our stated priorities:
| • | | We funded capital expenditures at levels slightly higher than 2004. |
| • | | Spending on acquisitions increased due to the size and number of opportunities we brought to completion. |
| • | | We raised our dividend for the 34th consecutive year. |
| • | | Cash used for share repurchases increased significantly; we bought back more shares than in any previous year. |
Cash from operations, our primary source of funds, was significantly higher in 2005 than in 2004. We also issued debt during the year and increased our percentage of net debt to net capital toward our long-term, targeted range.
These topics are discussed in more detail in the sections that follow.
EXECUTIVE OVERVIEW
What We Do
Leggett & Platt is a FORTUNE 500 diversified manufacturer that conceives, designs, and produces a broad range of engineered components and products that can be found in many homes, retail stores, offices, and automobiles. We make components that are often hidden within, but integral to, our customers’ products.
We are North America’s leading independent manufacturer of: components for residential furniture and bedding, adjustable beds, carpet underlay, retail store fixtures and point-of-purchase displays, components for office furniture, non-automotive aluminum die castings, drawn steel wire, automotive seat support and lumbar systems, and machinery used by the bedding industry for wire forming, sewing, and quilting.
24
Our Segments
Our 122-year-old company is composed of 29 business units under five reportable segments, with approximately 33,000 employee-partners, and more than 300 facilities located in over 20 countries around the world. Our five segments are Residential Furnishings, Commercial Fixturing & Components, Aluminum Products, Industrial Materials, and Specialized Products.
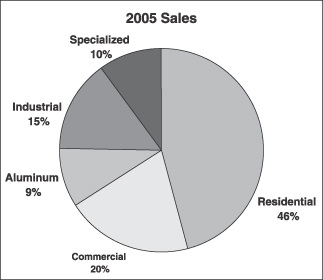
Residential Furnishings: This segment supplies a variety of components mainly used by bedding and upholstered furniture manufacturers in the assembly of their finished products. We also sell adjustable beds, bed frames, ornamental beds, carpet cushion, geo components, and other finished products.
Commercial Fixturing & Components: Operations in this segment produce: a) store fixtures, point-of-purchase displays, and storage products used by retailers; b) chair controls, bases, and other components for office furniture manufacturers; and c) injection molded plastic components used in a variety of end products.
Aluminum Products: This segment provides die cast aluminum components for customers that manufacture many products including motorcycles, diesel and small engines, outdoor lighting fixtures, gas barbeque grills, appliances, power tools, and consumer electronics, among others.
Industrial Materials: These operations primarily supply steel rod, drawn steel wire, and welded steel tubing to other Leggett operations and to external customers. Our wire and tubing is used to make bedding, furniture, automotive seats, retail store fixtures and displays, mechanical springs, and many other end products.
Specialized Products: From this segment we supply lumbar systems and wire components used by automotive seating manufacturers. We design, produce, and sell van interiors (the racks, shelving, cabinets, etc. installed in service vans) and truck bodies (for cargo vans, flatbed trucks, service trucks, and dump trucks) used in light-to-medium duty commercial trucks. We also design and produce machinery, both for our own use and for others, including bedding manufacturers.
Customers
We serve a broad suite of customers, with no single one representing 5% of our sales. Many are companies whose names are widely recognized; they include most manufacturers of furniture, bedding, and automobiles, many major retailers, and a variety of other manufacturers.
25
We primarily sell our products through our own sales employees, although we also use independent sales representatives and distributors in some of our businesses.
Competition
Most of our markets are highly competitive with the number of competitors varying by product line (they tend to be smaller, private companies).
We believe we gain competitive advantage in our global markets through low cost operations, significant internal production of key raw materials, superior manufacturing expertise and product innovation, higher quality products, extensive customer service capabilities, long-lived relationships with customers, and greater financial strength. Many of our competitors, both domestic and foreign, compete primarily on the basis of price. Our success has stemmed from the ability to remain price competitive, while delivering product quality, innovation, and customer service.
We face increasing pressure from foreign competitors as some of our customers source a portion of their components or finished products from Asia. When prices for key materials (such as steel, aluminum, and chemicals) are relatively level throughout the world, we can generally produce our components at a lower cost in the U.S. (because many of our products have low labor content). However, in instances where our customers move production of their finished products overseas, our operations must be located nearby to supply them efficiently. At the end of 2005, Leggett operated 11 facilities in China.
Asian manufacturers are currently thought to benefit from lower commodity costs (we believe certain commodities are sometimes subsidized by Asian governments), lenient attitudes toward safety and environmental matters, and currency rates that are pegged to the U.S. dollar rather than free floating. When exporting to the U.S., Asian manufacturers must overcome higher transportation costs, increased working capital needs, and difficulty matching U.S. manufacturers’ level of service, flexibility, and logistics.
Major Factors That Impact Our Business
Many factors impact our business every year, but those that generally have the greatest impact are: market demand for our products, raw material cost trends, energy costs, and changes in foreign currency exchange rates. In recent years, weak performance by our Fixture & Display operations has also impacted our results.
Market Demand
Market demand is impacted by many broad economic factors, including consumer confidence, employment levels, housing turnover, energy costs, and interest rates. These factors influence consumer spending on durable goods, and therefore affect demand for our components and products. Some of these factors also influence the level of business spending on facilities and equipment, which impacts approximately one-quarter of our sales. Market demand can also be affected by inflation in raw materials (discussed below) when cost increases cause customers to change the design of their products (and the type of components they use) to offset higher costs.
Raw Materials
In many of our businesses we have a cost advantage from buying large quantities of raw materials. This purchasing leverage is a benefit that many of our competitors do not enjoy. Still, our costs can vary significantly as market prices for raw materials (many of which are commodities) increase and decrease.
Purchasing arrangements vary considerably across the company. Because we typically have short-term commitments from vendors, our raw material costs generally fluctuate with the market. In certain of our businesses, we have longer-term contracts with pricing terms that provide stability under reasonable market conditions. However, when commodities experience extreme inflation, vendors may not honor those contracts.
26
This situation occurred in 2004 when steel costs nearly doubled, and again in 2005 when the cost of chemicals, fibers, and resins increased significantly. Vendors were unable to honor the pricing terms in purchase contracts due to extreme market conditions.
Our ability to recover higher costs (through selling price increases) is a critical factor when we experience inflation. We have few long-term, fixed-pricing contracts with customers. When we experience significant increases in raw material costs, we implement price increases to recover the higher costs. Although we are generally able to pass through most cost increases, we encounter greater difficulty in businesses where we have a smaller market share and in products that are of a commodity nature. Inability to recover cost increases (or a delay in the recovery time) can impact our earnings.
Steel is our largest raw material. During 2004, the price of certain types of steel nearly doubled, but we were able to recover most of these higher costs through selling price increases. In 2005, market prices for most types of steel were slightly lower at the end of the year than at the beginning of the year.
Unprecedented price increases in the steel market during 2004 led to an above average spread between scrap costs and rod prices. This spread continued throughout 2005, enhancing the earnings of our steel rod mill. While we expect the average spread to be lower in 2006, scrap costs have been volatile and the spread is difficult to predict.
In 2005, we experienced significant inflation in chemicals, fibers, and resins (generally driven by changes in oil prices). By year end, the majority of these cost increases had been passed through to our customers.
In addition to steel and oil-based materials, we also use significant amounts of aluminum. However, we are generally less exposed to cost changes in this commodity because of the pricing arrangements we have with our customers.
Energy Costs
Higher prices for natural gas, electricity, and fuel increase our production and delivery costs. Many of our large manufacturing operations are heavy users of natural gas and electricity. In addition, certain of our sales are made with terms such that we incur the fuel cost associated with delivering the product to our customer’s facility. Our ability to respond to these cost increases (by raising selling prices) affects our operating results.
Higher energy costs can also reduce consumer demand for our products. As consumers pay more for fuel and utilities, they have less disposable income available to purchase products that contain our components.
Energy costs increased throughout 2005 but especially in the last half of the year, in part due to supply disruptions caused by the hurricanes. We continuously monitor natural gas trends and have locked in prices on a portion of our natural gas requirements for the next three years. The details of those arrangements are discussed in Note P to the financial statements (on page 85).
Foreign Currency
As we expand internationally, our exposure to foreign currencies grows. Our greatest exposures are currently to the Canadian dollar and the Euro. We occasionally use various types of contracts, options, and other arrangements to mitigate some of this exposure. The details of these arrangements are also discussed in Note P to the financial statements (on page 85). However, since these arrangements are used on a limited basis, our earnings are generally impacted by variability in the currency exchanges rates of countries where we operate.
In recent years, we’ve been particularly impacted by the weakening of the U.S. dollar versus the Canadian dollar. In certain operations, we incur costs in Canadian dollars and sell products in U.S. dollars. The decline of the U.S. dollar in recent years has reduced earnings of these operations.
27
Fixture & Display Performance
Two years ago, we initiated an effort to improve the performance of the Commercial segment and specifically the Fixture & Display operations. We made progress in 2004, as Commercial segment margins improved to 5.1% (from 2.8% in 2003). We expected further improvement in 2005 but it did not occur. Excluding restructuring, asset impairment, and inventory obsolescence charges, Commercial segment margins in 2005 were essentially unchanged from those of 2004. In 2005, benefits from our prior cost savings initiatives were offset by higher start-up costs associated with new fixture programs and operating inefficiencies related to the ongoing integration of RHC Spacemaster (a company we acquired in July 2003). We’re committed to improving the segment margins and expect to accomplish gains through our current restructuring efforts. However, earnings must improve appreciably from current levels or further restructuring may be initiated.
Restructuring and Asset Impairments
In 2005, we incurred restructuring-related and asset impairment charges totaling $55 million, compared to $9 million in 2004, and ($1) million in 2003. Through June 30, 2005, the level of restructuring activity was not unusual. However in the third quarter, we launched a significant broad-based restructuring project (Restructuring Plan) to reduce excess capacity and improve performance in a number of our businesses. We had maintained spare capacity for several years—expecting market demand to increase—but that incremental demand has not materialized. We made significant progress on the Restructuring Plan activities by year end.
As part of the Restructuring Plan, we identified 36 underutilized or underperforming facilities to be closed, consolidated, or sold (the Closure and Consolidation Initiative). We also took a more critical look at other underperforming operations; as a result, we modified or accelerated restructuring activities that were previously underway, and identified other operations with impaired assets.
Total expenses associated with the Restructuring Plan should approximate $78 million, of which about half will be non-cash charges. This estimate includes the cost of plant closures (building cleanup and repair), equipment relocation, employee severance pay, asset impairment, inventory obsolescence, and similar expenses. We incurred $55 million of these costs in 2005 and expect to incur the remaining $23 million in 2006, primarily in the first half of the year. These estimates do not include future benefits from the sales of buildings, real estate, or equipment, so our final net costs will be lower. More detail regarding the breakdown of these charges is shown below.
| | | | | | | | | |
| | Amount
| | Cash
| | Non-Cash
|
| | (Dollar amounts in millions) |
Restructuring charges | | $ | 11.9 | | | | | | |
Asset impairment charges | | | 16.0 | | | | | | |
Inventory obsolescence and other costs | | | 12.4 | | | | | | |
| |
|
| | | | | | |
2005 Closure & Consolidation Initiative | | | 40.3 | | $ | 13.6 | | $ | 26.7 |
Costs related to other activity | | | 14.6 | | | 9.8 | | | 4.8 |
| |
|
| |
|
| |
|
|
2005 costs for Restructuring Plan | | | 54.9 | | | 23.4 | | | 31.5 |
2006 expected costs for Restructuring Plan | | | 23.0 | | | 19.0 | | | 4.0 |
| |
|
| |
|
| |
|
|
Total anticipated Restructuring Plan costs | | $ | 77.9 | | $ | 42.4 | | $ | 35.5 |
| |
|
| |
|
| |
|
|
Of the 36 facilities under the Closure and Consolidation Initiative, about half are in Residential Furnishings, one-quarter are in Commercial Fixturing & Components, and the remainder are in Industrial Materials and Specialized Products. These operations had total revenue of roughly $400 million. Most of this volume should shift to surviving facilities, but a $90 million sales reduction is expected as we divest small, non-core operations and walk away from unprofitable business. The majority of this volume reduction should occur in the Residential and Commercial segments. We have determined which of our remaining locations will absorb displaced volume, and are addressing issues related to relocating equipment, inventory, and customer service.
28
We estimate an ongoing annual pre-tax earnings benefit from the Restructuring Plan of approximately $30-$35 million. At least half of this improvement should be realized in 2006 with the full benefit expected in subsequent years. This benefit results from the elimination of fixed costs associated with closed facilities, a reduction in the number of employees, and improved overhead absorption from increased volume at our remaining facilities. The Restructuring Plan should yield improved margins and returns in all segments. About one-half of the expected benefit should occur in Residential Furnishings, 15-20% of the benefit should impact Commercial Fixturing & Components, and approximately 10-15% of the benefit should occur in each of our other three segments.
Acquisitions
We completed 12 acquisitions in 2005 that should add about $320 million to annual sales. The two largest, America’s Body Company and Ikex/Jarex, establish sizeable new business platforms with opportunities for future growth.
America’s Body Company (ABC), was acquired in late October and generates annual revenue of approximately $150 million (this is the third largest acquisition in our history). ABC is a designer, manufacturer, and supplier of equipment for light-to-medium duty commercial trucks. Major product categories include van interiors (racks, shelving, and cabinets installed in service vans) and truck bodies (for cargo vans, flatbed trucks, service trucks, and dump trucks). This business joined our existing van interiors operations to form the Commercial Vehicle Products group (in our Specialized Products segment). With combined group sales of approximately $250 million, we are now the second largest supplier in a $1.5 billion U.S. market. While the industry is highly fragmented and contains many small, regional manufacturers, only a few competitors provide as wide a range of products and service locations.
Through the acquisition of Ikex/Jarex, we significantly expanded our presence in the conversion and distribution of geo components. This transaction was completed in early October and should add roughly $65 million in revenue, bringing our total annual sales in this business unit to approximately $80 million (this business unit is in our Residential Furnishings segment). Geo components include geotextiles, or synthetic fabrics (typically polypropylene, polyethylene, or polyester) used in a variety of applications such as ground stabilization, drainage protection, erosion control and weed control. These products are sold primarily into the construction, landscaping, and agricultural industries. The highly-fragmented U.S. market for geotextiles is believed to approximate $900 million annually, consisting mostly of small, regional suppliers. This acquisition should enhance our competitive position in the geo component market through national presence, high volume purchasing and manufacturing, and established distribution and marketing infrastructure.
We provide additional details about acquisitions in Note B to the financial statements on page 63.
RESULTS OF OPERATIONS—2005 vs. 2004
We achieved record sales in 2005, exceeding the prior year by 4%. Earnings for the year decreased primarily due to restructuring, asset impairment, and inventory obsolescence charges (related to the Restructuring Plan). Inflation was a challenge during the year, primarily in oil-based raw materials, but by year end we had recovered most of these higher costs through selling price increases. Further details about these items and our consolidated and segment results are discussed below.
29
CONSOLIDATED RESULTS
The following table shows the changes in sales and earnings from 2004 to 2005 and identifies the major factors contributing to the changes:
| | | | | | | |
| | Amount
| | | %
| |
| | (Dollar amounts in millions, except per share data) | | | | |
Net sales: | | | | | | | |
Year ended December 31, 2004 | | $ | 5,086 | | | | |
Acquisition sales growth (net of divestitures) | | | 107 | | | 2.1 | % |
Internal sales growth | | | 106 | | | 2.1 | % |
| |
|
|
| |
|
|
Year ended December 31, 2005 | | $ | 5,299 | | | 4.2 | % |
| |
|
|
| |
|
|
Net earnings: | | | | | | | |
Year ended December 31, 2004 | | $ | 285 | | | | |
| | |
Restructuring-related charges | | | (37 | ) | | | |
Higher workers’ compensation expense | | | (14 | ) | | | |
Lower tax rate | | | 10 | | | | |
Increased sales and other | | | 7 | | | | |
| |
|
|
| | | |
Year ended December 31, 2005 | | $ | 251 | | | | |
| |
|
|
| | | |
Earnings Per Share December 31, 2004 | | $ | 1.45 | | | | |
| |
|
|
| | | |
Earnings Per Share December 31, 2005 | | $ | 1.30 | | | | |
| |
|
|
| | | |
Internal growth and acquisitions each contributed about half the net sales increase. Internal sales growth (i.e. excluding acquisitions and divestitures) was mainly due to inflation—we implemented price increases to recover higher raw material costs. These increases related primarily to higher costs for steel early in the year (versus lower levels in early 2004) and for chemicals, fibers, and resins throughout 2005. By late 2005, steel costs had declined (versus peak levels in the last half of 2004) and we experienced modest deflation in a few businesses.
Unit volumes were mixed across our various markets. For the full year, we posted solid growth in our businesses supplying upholstered furniture components, but these gains were offset by declines in our bedding and automotive businesses. Volume was essentially flat in many of our other markets. These trends are discussed in the segment results below.
Inflation was a significant challenge again in 2005. The largest impact resulted from higher oil prices which affect the cost of raw materials such as chemicals, fibers, and resins. Many of these costs rose throughout the year, but the increases accelerated following last year’s hurricanes. In response, we raised prices to our customers, and by year end had recovered most of the higher costs.
Net earnings and earnings per share decreased versus 2004 primarily due to:
| • | | Restructuring-related charges: As shown in the table above, restructuring-related charges represent the majority of the decrease in 2005 earnings. These charges include the cost of plant closures, equipment relocation, employee severance pay, asset impairment, inventory obsolescence, and other similar costs associated with the Restructuring Plan discussed on page 28. |
| • | | Higher workers’ compensation expense: In 2005, we significantly increased our reserves for workers’ compensation to reflect higher cost of medical care and longer duration of claims (more treatment options are available and can continue over longer periods of time). |
| • | | Earnings were also affected by higher energy and transportation costs, and a weaker U.S. dollar (which caused margin declines in our Canadian operations that sell in U.S. dollars but incur costs in Canadian dollars). |
30
| • | | These declines were partially offset by benefits from sales growth and a tax benefit from a planned foreign entity restructuring and cash repatriation transaction. This transaction generated a net tax benefit of approximately $10 million. |
SEGMENT RESULTS
In the following section we discuss 2005 sales and earnings before interest and taxes (EBIT) for each of our segments. A reconciliation of segment EBIT to consolidated EBIT is provided in Note L to the financial statements on page 78.
All of our segments use the first-in, first-out (FIFO) method for valuing inventory. In 2004, segment margins generally benefited under the FIFO method from the effect of rising commodity costs. In 2005, declining steel costs caused margins (mainly in Residential and Industrial) to decrease under this same method. In our consolidated financials, we use the last-in, first-out (LIFO) method for determining cost of about half of our inventories. An adjustment is made at the corporate level (i.e. outside the segments) to convert the appropriate operations to the LIFO inventory method.
RESIDENTIAL FURNISHINGS
| | | | | | | | | | | |
| | Sales
| | | EBIT
| | | EBIT Margins
| |
| | (Dollar amounts in millions) | | | | |
Year ended December 31, 2005 | | $ | 2,622 | | | $ | 170 | | | 6.5 | % |
| | | |
Year ended December 31, 2004 | | | 2,482 | | | | 265 | | | 10.7 | % |
| |
|
|
| |
|
|
| | | |
Increase (decrease) | | $ | 140 | | | $ | (95 | ) | | | |
| |
|
|
| |
|
|
| | | |
% increase (decrease) | | | 6 | % | | | (36 | )% | | | |
Internal sales growth | | | 3 | % | | | | | | | |
Acquisition sales growth | | | 3 | % | | | | | | | |
Sales in Residential Furnishings increased in 2005 from a combination of internal growth and acquisitions. Inflation contributed the bulk of the internal sales growth. During the first half of 2005, sales increased over last year due to price increases (for the pass through of higher steel costs) implemented in the latter part of 2004. In the last half of 2005, declining steel costs (which were also passed through to our customers) resulted in slight deflation in certain businesses. When combined, these price-related factors led to higher full year sales.
Unit volume declines and changes in product mix partially offset sales growth from inflation in 2005. Unit volumes were down slightly, with decreases in bedding more than offsetting gains in upholstered furniture components. In addition, inflation in the raw materials used to produce finished bedding and upholstered furniture has, in certain cases, led our customers to change their product design, which has reduced the quantity and changed the mix of components they buy from us.
Market demand for bedding was weak for much of the year, but began to improve in early September and continued on a positive track through year end. For the past few years, bedding industry unit volume, including all types of mattresses, has been flat to slightly down. Overall consumer spending has been solid, but consumers have not been purchasing or replacing mattresses at historic rates. Bedding purchases are deferrable and are influenced by consumer confidence and the amount of cash consumers have available to spend on discretionary items. Higher gasoline and energy costs (as seen throughout 2005) reduce this discretionary spending. In addition, advertising expenditures by bedding manufacturers have also been lower in recent years. As the cost of materials (such as steel components and foam) increased significantly, these manufacturers cut expenditures in other areas (including advertising). Lower advertising levels negatively impact consumer demand for bedding.
31
For the full year 2005, we posted solid growth in our businesses supplying upholstered furniture components. We sell to most manufacturers of motion upholstered furniture. These customers include major public furniture producers as well as privately owned manufacturers. We also benefit from increased world-wide demand. Our international presence and depth of product line allow us to efficiently supply upholstered furniture manufacturers in many parts of the world. In addition, we’ve benefited from an industry trend to incorporate high quality motion features into more lines of furniture. Our consistent growth in this business since 2002 reflects all these factors.
EBIT and EBIT margins decreased versus 2004 due to several factors:
| • | | Restructuring-related and asset impairment charges ($26 million) |
| • | | Selling price decreases related to lower steel costs—We reduced selling prices (to reflect lower steel costs) more quickly than we were able to consume our higher cost inventories. |
| • | | Higher energy and transportation costs |
| • | | Increased workers’ compensation expense ($11 million) |
| • | | Changes in product mix (increased sales of lower margin components) |
| • | | Currency impacts (approximately $6 million)—In certain operations, we incur costs in Canadian dollars and sell products in U.S. dollars. The weaker U.S. dollar caused margin declines in these operations. |
| • | | Unit volume declines in bedding, which resulted in lower utilization rates and reduced overhead absorption |
| • | | Inflation in certain raw materials |
COMMERCIAL FIXTURING & COMPONENTS
| | | | | | | | | | | |
| | Sales
| | | EBIT
| | | EBIT Margins
| |
| | (Dollar amounts in millions) | | | | |
Year ended December 31, 2005 | | $ | 1,147 | | | $ | 39 | | | 3.4 | % |
| | | |
Year ended December 31, 2004 | | | 1,078 | | | | 55 | | | 5.1 | % |
| |
|
|
| |
|
|
| | | |
Increase (decrease) | | $ | 69 | | | $ | (16 | ) | | | |
| |
|
|
| |
|
|
| | | |
% increase (decrease) | | | 6 | % | | | (29 | )% | | | |
Internal sales growth | | | 5 | % | | | | | | | |
Acquisition sales growth | | | 1 | % | | | | | | | |
Internal growth accounted for the bulk of the sales increase in 2005. Inflation (primarily related to higher steel costs) and higher unit volumes each contributed about half of the internal sales growth.
Our Fixture & Display businesses experienced modest increases in unit volume during the year. Although volume declines have stopped, we have not yet seen notable, sustained improvements in demand. Many retailers remained reluctant to increase spending for remodeling programs and new store construction.
We also posted slight unit volume gains in office furniture components, which continued a trend of stable to improving market conditions that began mid-year 2003.
EBIT and EBIT margins decreased versus 2004 primarily due to:
| • | | Restructuring-related and asset impairment charges ($14 million) |
| • | | Currency impacts (approximately $6 million) |
| • | | Higher workers’ compensation expense ($5 million) |
These items were partially offset by benefits related to slightly higher unit volume and gains from assets sales (approximately $3 million).
32
ALUMINUM PRODUCTS
| | | | | | | | | | | |
| | Sales
| | | EBIT
| | | EBIT Margins
| |
| | (Dollar amounts in millions) | |
Year ended December 31, 2005 | | $ | 531 | | | $ | 31 | | | 5.8 | % |
| | | |
Year ended December 31, 2004 | | | 522 | | | | 46 | | | 8.7 | % |
| |
|
|
| |
|
|
| | | |
Increase (decrease) | | $ | 9 | | | $ | (15 | ) | | | |
| |
|
|
| |
|
|
| | | |
% increase (decrease) | | | 2 | % | | | (33 | )% | | | |
Internal sales growth | | | 2 | % | | | | | | | |
Acquisition sales growth | | | — | | | | | | | | |
Higher sales in 2005 were entirely due to internal growth. Unit volumes were up slightly, but inflation contributed most of the increase (as we passed through higher raw material costs). The rate of internal growth in this segment slowed as the year progressed and we reached the one year anniversary of the start-up of major new programs from 2004.
EBIT and EBIT margins decreased versus 2004 due to:
| • | | Restructuring-related and asset impairment charges ($3 million) |
| • | | Inefficiencies at some plants—primarily losses at a facility that is now closed and costs associated with the start-up of new programs |
| • | | A work stoppage at one facility |
INDUSTRIAL MATERIALS
| | | | | | | | | | | |
| | Sales
| | | EBIT
| | | EBIT Margins
| |
| | (Dollar amounts in millions) | |
Year ended December 31, 2005 | | $ | 844 | | | $ | 104 | | | 12.3 | % |
| | | |
Year ended December 31, 2004 | | | 818 | | | | 122 | | | 14.9 | % |
| |
|
|
| |
|
|
| | | |
Increase (decrease) | | $ | 26 | | | $ | (18 | ) | | | |
| |
|
|
| |
|
|
| | | |
% increase (decrease) | | | 3 | % | | | (15 | )% | | | |
Internal sales growth | | | 3 | % | | | | | | | |
Acquisition sales growth | | | — | | | | | | | | |
Internal growth contributed the entire sales increase in 2005, with inflation more than offsetting lower unit volumes. During the first half of 2005, sales increased over last year due to price increases (for the pass through of higher steel costs) implemented in the latter part of 2004. In the last half of 2005, declining steel costs (which were also passed through to our customers) resulted in deflation. When combined, these price-related factors led to higher full year sales.
Unit volumes declined for the year primarily due to weaker bedding demand (which impacts our wire operations) and lower production levels in the automotive industry (which impacts our tubing businesses). As bedding demand improved late in the year, unit volumes in this segment increased slightly.
EBIT and EBIT margins decreased versus 2004 due to several factors including:
| • | | Restructuring-related and asset impairment charges ($4 million) |
| • | | Higher energy and transportation costs |
| • | | Increased workers’ compensation expense ($3 million) |
| • | | Unit volume declines, which resulted in lower utilization rates and reduced overhead absorption |
33
SPECIALIZED PRODUCTS
| | | | | | | | | | | |
| | Sales
| | | EBIT
| | | EBIT Margins
| |
| | (Dollar amounts in millions) | |
Year ended December 31, 2005 | | $ | 579 | | | $ | 34 | | | 5.8 | % |
| | | |
Year ended December 31, 2004 | | | 564 | | | | 51 | | | 9.0 | % |
| |
|
|
| |
|
|
| | | |
Increase (decrease) | | $ | 15 | | | $ | (17 | ) | | | |
| |
|
|
| |
|
|
| | | |
% increase (decrease) | | | 3 | % | | | (34 | )% | | | |
Internal sales growth | | | (3 | )% | | | | | | | |
Acquisition sales growth | | | 6 | % | | | | | | | |
In 2005, a decline in internal sales was more than offset by acquisition growth. Volume decreased in our automotive and machinery businesses. Lower production levels in the automotive industry during 2005 led to reduced volume in our businesses that supply that industry. In addition, bedding manufacturers (the primary customers of our machinery business) reduced their capital spending in 2005 due to lower market demand for bedding throughout most of the year. This restricted spending impacted our machinery volume during the year.
EBIT and EBIT margins decreased versus 2004 primarily due to:
| • | | Restructuring-related and asset impairment charges ($8 million) |
| • | | Unit volume declines, which resulted in lower utilization rates and reduced overhead absorption |
| • | | Currency impacts (approximately $3 million) |
| • | | Higher workers’ compensation expense ($2 million) |
RESULTS OF OPERATIONS—2004 vs. 2003
Sales in 2004 exceeded our prior record (posted in 2003) by 16% and earnings increased substantially. Margins also improved for the full year. We were challenged during the year by rapidly escalating steel costs, but we were successful in recovering most of the higher costs through selling price increases. Our steel rod mill operated at full capacity for the year and brought significant earnings benefits. Improved performance of our Fixture & Display operations also contributed to our earnings growth. Further details about these items and our consolidated and segment results are discussed below.
34
CONSOLIDATED RESULTS
The following table shows the changes in sales and earnings from 2003 to 2004 and identifies the major factors contributing to the changes:
| | | | | | | |
| | Amount
| | | %
| |
| | (Dollar amounts in millions, except per share data) | | | | |
Net sales: | | | | | | | |
Year ended December 31, 2003 | | $ | 4,388 | | | | |
Acquisition sales growth | | | 189 | | | 4.3 | % |
Internal sales growth | | | 509 | | | 11.6 | % |
| |
|
|
| |
|
|
Year ended December 31, 2004 | | $ | 5,086 | | | 15.9 | % |
| |
|
|
| |
|
|
| | |
Net earnings: | | | | | | | |
Year ended December 31, 2003 | | $ | 206 | | | | |
Increased sales, operating improvements, and other | | | 71 | | | | |
Gains from asset sales | | | 9 | | | | |
Lower inventory obsolescence | | | 6 | | | | |
Lower tax rate | | | 9 | | | | |
Weaker U.S. dollar | | | (11 | ) | | | |
Higher restructuring costs | | | (5 | ) | | | |
| |
|
|
| | | |
Year ended December 31, 2004 | | $ | 285 | | | | |
| |
|
|
| | | |
Earnings Per Share December 31, 2003 | | $ | 1.05 | | | | |
| |
|
|
| | | |
Earnings Per Share December 31, 2004 | | $ | 1.45 | | | | |
| |
|
|
| | | |
Sales in 2004 increased 16% over 2003 levels. Internal sales growth (i.e. excluding acquisitions and divestitures) resulted from the combined effect of inflation, higher unit volumes, and currency rate changes.
| • | | Approximately two-thirds of the internal sales growth came from inflation—we raised prices to pass along higher raw material costs. |
| • | | Unit volumes improved in many businesses, but were strongest in upholstered furniture components, carpet underlay, aluminum components, and machinery. For the year, world-wide bedding units were roughly flat. Volume declined slightly in our Fixture & Display operations. |
| • | | Foreign currency rate changes also added to internal sales growth, but to a much lesser extent than inflation and unit volume gains. |
Rising steel costs were our largest challenge in 2004. We purchase roughly 1.3 million tons of steel each year, accounting for about 17% of our cost of goods sold. During 2004, prices increased significantly, and for the year we paid over $200 million more for steel than in 2003. Due to the magnitude of these increases, we were compelled to pass along our higher costs.
We experienced inflation in other raw materials during 2004. Chemical, fiber, and resin costs increased as oil prices rose. Aluminum costs also increased, but our earnings exposure to this commodity is currently limited by the pricing arrangements we have with our customers.
Net earnings and earnings per share also increased versus 2003 with several factors contributing to the improvement:
| • | | Sales increase: Internal sales growth was the primary factor behind 2004’s earnings improvement. Higher unit volumes led to improved overhead absorption in many of our businesses. In addition, prior years’ plant consolidations and cost cutting helped lower our fixed costs and allowed us to utilize capacity more efficiently as volume increased. Selling and administrative expenses increased at a slower rate than sales, also benefiting 2004 earnings. |
35
| • | | Gains from our steel rod mill: Earnings benefited in 2004 from full production at our steel rod mill. Operating efficiency improved significantly year-over-year since we were ramping up production in 2003. In addition, we benefited from an above-average market spread between scrap costs and rod selling prices. |
| • | | Improvements in our Fixture & Display operations: Steps taken under the 2003 Fixture & Display tactical plan contributed to the earnings growth we saw in 2004. |
| • | | Earnings also benefited from gains related to the sale of buildings, lower inventory obsolescence, and a lower income tax rate. The income tax rate fell from 34.7% in 2003 to 32.5% in 2004, due to our mix of domestic and foreign income and certain one-time factors. |
| • | | These benefits were partially offset by impacts from a weaker U.S. dollar and slightly higher costs associated with plant closings and consolidations. The U.S. dollar weakened in 2004, causing margin declines in our Canadian operations (that sell in U.S. dollars but incur their costs in Canadian dollars). |
RESIDENTIAL FURNISHINGS
| | | | | | | | | | | |
| | Sales
| | | EBIT
| | | EBIT Margins
| |
| | (Dollar amounts in millions) | |
Year ended December 31, 2004 | | $ | 2,482 | | | $ | 265 | | | 10.7 | % |
| | | |
Year ended December 31, 2003 | | | 2,186 | | | | 209 | | | 9.5 | % |
| |
|
|
| |
|
|
| | | |
Increase (decrease) | | $ | 295 | | | $ | 57 | | | | |
| |
|
|
| |
|
|
| | | |
% increase (decrease) | | | 14 | % | | | 27 | % | | | |
Internal sales growth | | | 11 | % | | | | | | | |
Acquisition sales growth | | | 3 | % | | | | | | | |
Sales in Residential Furnishings increased in 2004, with more than half the internal growth coming from inflation. Unit volumes gains were strongest in upholstered furniture components and carpet underlay, but these improvements were mitigated slightly by approximately flat world-wide bedding demand.
In 2004, we posted double-digit, world-wide unit sales growth in mechanisms for upholstered furniture. We benefited from market share gains (as our customers gain share), an industry trend to incorporate motion components into more lines of upholstered furniture, and a well-established international presence.
World-wide demand for bedding components was strong in early 2004, but moderated in the second and third quarters, and declined in the fourth quarter (primarily from weakness in the U.S. market). We believe that reduced advertising expenditures by bedding manufacturers during the fourth quarter led to less promotion by retailers and, in turn, lower demand for bedding. In early 2005, most bedding manufacturers implemented price increases to recover the higher costs they were absorbing late in 2004.
Earnings before interest and taxes (EBIT) also increased versus 2003 and EBIT margins improved. Gains came from:
| • | | Sales growth, which resulted in higher utilization rates and improved overhead absorption in certain businesses |
| • | | Prior cost reduction and plant consolidation efforts |
| • | | Selling price increases, primarily to recover escalating steel costs |
| • | | Gains related to the sale of buildings no longer used in operations ($7 million) |
These improvements were partially offset by higher raw material costs, the impact of a weaker U.S. dollar—primarily versus the Canadian dollar (approximately $9 million), and modest charges associated with plant closings and consolidations ($4 million).
36
COMMERCIAL FIXTURING & COMPONENTS
| | | | | | | | | | | |
| | Sales
| | | EBIT
| | | EBIT Margins
| |
| | (Dollar amounts in millions) | |
Year ended December 31, 2004 | | $ | 1,078 | | | $ | 55 | | | 5.1 | % |
| | | |
Year ended December 31, 2003 | | | 965 | | | | 27 | | | 2.8 | % |
| |
|
|
| |
|
|
| | | |
Increase (decrease) | | $ | 113 | | | $ | 28 | | | | |
| |
|
|
| |
|
|
| | | |
% increase (decrease) | | | 12 | % | | | 106 | % | | | |
Internal sales growth | | | 2 | % | | | | | | | |
Acquisition sales growth | | | 10 | % | | | | | | | |
For the full year 2004, acquisitions accounted for the bulk of the sales increase. Internal sales growth came from inflation, but was partially offset by a 2% decline in unit volumes. Slight unit declines in our Fixture & Display operations were partially offset by mid-single-digit unit growth in our office furniture components businesses. Weak demand for store fixtures reflected the continued reluctance on the part of many retailers to increase spending for construction of new stores and renovation of existing stores. The gains in office furniture components volume continued a trend of stable to improving market conditions.
EBIT increased and EBIT margins improved versus 2003 primarily due to:
| • | | Benefits from the 2003 Fixture & Display tactical plan, including cost savings and improved operational efficiency |
| • | | Non-recurrence of 2003’s inventory write-downs |
| • | | Higher sales in our office furniture components businesses |
| • | | Gains related to the sale of buildings no longer used in operations ($3 million) |
These items were partially offset by higher raw material costs, currency rate impacts (approximately $4 million), and modest restructuring charges ($3 million).
ALUMINUM PRODUCTS
| | | | | | | | | | | |
| | Sales
| | | EBIT
| | | EBIT Margins
| |
| | (Dollar amounts in millions) | |
Year ended December 31, 2004 | | $ | 522 | | | $ | 46 | | | 8.7 | % |
| | | |
Year ended December 31, 2003 | | | 467 | | | | 36 | | | 7.6 | % |
| |
|
|
| |
|
|
| | | |
Increase (decrease) | | $ | 55 | | | $ | 10 | | | | |
| |
|
|
| |
|
|
| | | |
% increase (decrease) | | | 12 | % | | | 28 | % | | | |
Internal sales growth | | | 12 | % | | | | | | | |
Acquisition sales growth | | | — | | | | | | | | |
Higher unit volumes contributed about three-quarters of the 2004 internal sales improvement. This growth reflected new programs for producers of motorcycles, small engines, large appliances, and others.
EBIT and EBIT margins also increased versus 2003. Earnings gains from higher sales were partially offset by inflation in aluminum costs.
37
INDUSTRIAL MATERIALS
| | | | | | | | | | | |
| | Sales
| | | EBIT
| | | EBIT Margins
| |
| | (Dollar amounts in millions) | |
Year ended December 31, 2004 | | $ | 818 | | | $ | 122 | | | 14.9 | % |
| | | |
Year ended December 31, 2003 | | | 579 | | | | 38 | | | 6.5 | % |
| |
|
|
| |
|
|
| | | |
Increase (decrease) | | $ | 239 | | | $ | 84 | | | | |
| |
|
|
| |
|
|
| | | |
% increase (decrease) | | | 41 | % | | | 222 | % | | | |
Internal sales growth | | | 41 | % | | | | | | | |
Acquisition sales growth | | | — | | | | | | | | |
The 2004 sales increase was almost entirely due to inflation, which resulted from the pass-through of higher steel costs. Unit volumes were up modestly in the first three quarters but declined in the fourth quarter due to weaker bedding demand. For the full year, unit volume was essentially flat.
EBIT and EBIT margins increased significantly versus 2003 levels. Earnings benefited from higher sales, full utilization of our steel rod mill, and an above average market spread between scrap costs and selling prices for rod (this spread benefited our rod mill).
SPECIALIZED PRODUCTS
| | | | | | | | | | | |
| | Sales
| | | EBIT
| | | EBIT Margins
| |
| | (Dollar amounts in millions) | |
Year ended December 31, 2004 | | $ | 564 | | | $ | 51 | | | 9.0 | % |
| | | |
Year ended December 31, 2003 | | | 486 | | | | 52 | | | 10.8 | % |
| |
|
|
| |
|
|
| | | |
Increase (decrease) | | $ | 77 | | | $ | (2 | ) | | | |
| |
|
|
| |
|
|
| | | |
% increase (decrease) | | | 16 | % | | | (3 | )% | | | |
Internal sales growth | | | 9 | % | | | | | | | |
Acquisition sales growth | | | 7 | % | | | | | | | |
Higher unit volumes and changes in currency rates each contributed about half of 2004’s internal sales growth. Our machinery operations posted double-digit gains for the full year, as bedding manufacturers increased spending on new equipment. In addition, we saw modest growth in our automotive businesses, reflecting benefits of new programs and increased product placement.
EBIT and EBIT margins decreased versus 2003. The earnings decline resulted from:
| • | | Currency impacts (approximately $2 million)—In certain automotive operations, we incur costs in Canadian dollars and sell products in U.S. dollars. The weaker U.S. dollar caused margin declines in these operations. |
| • | | Higher raw material costs—Due to the longer-term supply contracts we have with many automotive customers, we experienced lags in recovering higher steel costs. |
| • | | Other factors, including higher depreciation ($2 million), costs associated with plant closings and consolidations ($1 million), and new product development costs. |
These declines were partially offset by gains from higher sales.
38
LIQUIDITY AND CAPITALIZATION
In this section, we provide details about our
| • | | Debt position and total capitalization |
Our priorities for use of cash, in order of importance, are:
| • | | Finance internal growth and acquisitions |
| • | | Pay dividends and extend our record of annual increases |
Our operations provide much of the cash required to fund these priorities. In 2005, we also increased net debt and used excess cash to fund a portion of these items, including higher levels of acquisitions and share repurchases. Our long-term goal is to have net debt as a percent of net capital in the 30%-40% range while maintaining our longstanding “single A” debt rating. At the end of 2005, we were approaching the lower end of that range.
Uses of Cash
Finance Growth
We use cash to fund growth, both internally through capital expenditures and externally through acquisitions.
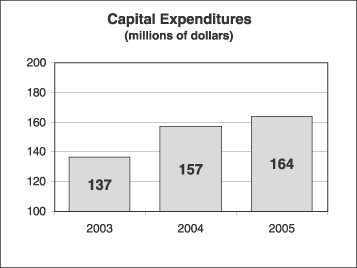
Capital expenditures are investments we make to modernize, maintain, and expand manufacturing capacity. We expect 2006 capital spending to be at about the same level as 2005.
39
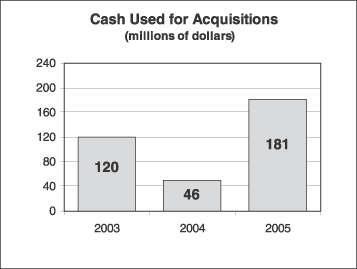
Acquisitions add to our business by expanding our markets, product lines, or manufacturing capabilities. Our level of spending increased in 2005 as we were able to complete several acquisitions (including the third largest in our history). In addition to the initial cash outlays for acquisitions (shown in the accompanying chart), we also assumed debt of $5 million, $2 million, and $35 million in our 2003, 2004 and 2005 transactions.
Our 2005 acquisitions (12 companies in three of our business segments) should contribute about $320 million in annual revenues.
| • | | Residential Furnishings: We added sales of about $170 million from 10 acquisitions. The largest acquisition in the segment in 2005 was Ikex/Jarex, the geo components business discussed on page 29. The other acquisitions in the segment: |
| • | | established, early in the year, a small foothold in geo components |
| • | | broadened our product offerings to include all major types of carpet underlay |
| • | | expanded our base of operations producing furniture mechanisms in China |
| • | | added to our businesses that produce and sell bedding components, upholstered furniture components, and top-of-the-bed products |
| • | | Commercial Fixturing & Components: We acquired one company which had been a key supplier to our Fixture & Display operations for many years. This company produces retail store fixtures and gondola shelving. Importantly, it gives us an operating presence in China from which to serve the growing domestic Chinese market. The acquisition expands our manufacturing capacity by $20 million but does not increase our reported sales since nearly all the product is sold to other Leggett operations for distribution in the U.S. |
| • | | Specialized Products: We added sales of about $150 million through the acquisition of America’s Body Company, a manufacturer of van interiors and truck bodies discussed on page 29. |
We provide additional details about acquisitions in Note B to the financial statements on page 63.
40
Pay Dividends
* | Actual Dividend Payout = annual dividend rate ÷ average EPS for prior three years |
In 2005, we increased our annual dividend for the 34th consecutive year. Over the last three years, dividends have grown at an 8% compound annual rate. Our long-term target for dividend payout is approximately one-third of the prior three years’ average earnings. We’ve been well above those levels in recent years, but as earnings grow, we expect to move back toward that target.
Repurchase Stock
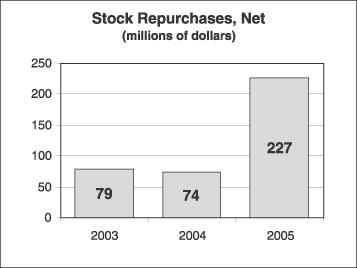
In 2005, we purchased 10.3 million of our shares, considerably more than in any previous year. This was an opportunistic move that was driven by two main factors: 1) additional cash was available as we increased net debt, and 2) a lower stock price in the last few months of the year presented an attractive buying opportunity. Almost six million shares were purchased during a nine week period in the third and fourth quarters, at an average price of about $20.25 per share. Share repurchases should be lower in 2006 (versus 2005), in part because we do not expect as large an increase in our net debt levels.
As we first mentioned in September 2004, we planned to increase our net debt levels toward the lower end of our targeted range and use the cash to fund growth, pay dividends, and repurchase shares. Going forward, the cash available to repurchase shares will fluctuate each year with earnings, capital spending, and the pace of acquisitions. At a minimum we typically repurchase shares to replace those issued for employee stock plans (approximately two million shares each year). Although no specific repurchase schedule has been established, we have been authorized by the Board of Directors to repurchase up to 10 million shares in 2006.
41
Cash from Operations
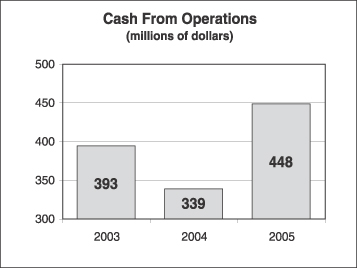
Cash from operations is our primary source of funds. Changes in earnings and working capital levels are the two broad factors that generally have the greatest impact on our cash from operations. Cash from operations in 2005 was 32% higher than in 2004 despite lower earnings. Working capital decreased in 2005 due to two main factors:
| • | | Accrued expenses and other current liabilities increased primarily from higher workers’ compensation accruals and restructuring liabilities. |
| • | | This impact was partially offset by higher inventories. Inventories increased primarily due to inflation in certain raw material costs, increased purchases in anticipation of rising costs, and new programs in certain businesses. |
Working capital management remains a priority and we expect to further improve these levels in 2006.
In 2004, cash from operations benefited from stronger earnings, but was reduced overall by an increase in working capital. The higher working capital levels were primarily the result of inflation. In 2003, cash from operations was relatively strong despite weak earnings, in part due to our ability to reduce working capital.
Working capital levels vary by segment, with the requirements of Aluminum Products and Commercial Fixturing & Components generally higher than company averages. Accounts receivable balances in these segments are typically higher due to the longer credit terms required to service certain customers of the Aluminum Die Casting and Fixture & Display businesses. These same businesses also require higher inventory investments due to the custom nature of their products, longer manufacturing lead times (in certain cases), and the needs of many customers to receive large volumes of product within short periods of time.
42
Capitalization
This table presents key debt and capitalization statistics at the end of the three most recent years.
| | | | | | | | | | | | |
| | 2005
| | | 2004
| | | 2003
| |
| | (Dollar amounts in millions) | |
Long-term debt outstanding: | | | | | | | | | | | | |
Scheduled maturities | | $ | 922 | | | $ | 779 | | | $ | 1,012 | |
Average interest rates | | | 5.0 | % | | | 4.1 | % | | | 4.1 | % |
Average maturities in years | | | 7.8 | | | | 5.6 | | | | 6.0 | |
Revolving credit/commercial paper | | | — | | | | — | | | | — | |
| |
|
|
| |
|
|
| |
|
|
|
Total long-term debt | | | 922 | | | | 779 | | | | 1,012 | |
Deferred income taxes and other liabilities | | | 144 | | | | 145 | | | | 138 | |
Shareholders’ equity | | | 2,249 | | | | 2,313 | | | | 2,114 | |
| |
|
|
| |
|
|
| |
|
|
|
Total capitalization* | | $ | 3,315 | | | $ | 3,237 | | | $ | 3,264 | |
| |
|
|
| |
|
|
| |
|
|
|
Unused committed credit: | | | | | | | | | | | | |
Long-term | | $ | 400 | | | $ | 342 | | | $ | 213 | |
Short-term | | | — | | | | — | | | | 127 | |
| |
|
|
| |
|
|
| |
|
|
|
Total unused committed credit | | $ | 400 | | | $ | 342 | | | $ | 340 | |
| |
|
|
| |
|
|
| |
|
|
|
Current maturities of long-term debt | | $ | 99 | | | $ | 401 | | | $ | 119 | |
| |
|
|
| |
|
|
| |
|
|
|
Cash and cash equivalents | | $ | 65 | | | $ | 491 | | | $ | 444 | |
| |
|
|
| |
|
|
| |
|
|
|
Ratio of earnings to fixed charges ** | | | 6.7x | | | | 8.0x | | | | 6.2x | |
| |
|
|
| |
|
|
| |
|
|
|
| * | Our calculation of “total capitalization,” may be different from similarly titled measures of other companies. |
| ** | Fixed charges include interest expense, capitalized interest, and implied interest included in operating leases. |
The next table shows the percent of long-term debt to total capitalization at December 31, 2005 and 2004. We show this calculation in two ways:
| • | | Long-term debt to total capitalization as reported in the previous table. |
| • | | Long-term debt to total capitalization each reduced by total cash and increased by current maturities of long-term debt. |
We believe that adjusting this measure for cash and current maturities allows more meaningful comparison to recent historical periods, during which cash has ranged from $65 million to $491 million. We use these adjusted measures to monitor our financial leverage.
| | | | | | | | |
| | 2005
| | | 2004
| |
| | (Dollar amounts in millions) | |
Long-term debt | | $ | 922 | | | $ | 779 | |
Current debt maturities | | | 99 | | | | 401 | |
Cash and cash equivalents | | | (65 | ) | | | (491 | ) |
| |
|
|
| |
|
|
|
Net debt | | $ | 956 | | | $ | 689 | |
| |
|
|
| |
|
|
|
Total capitalization | | $ | 3,315 | | | $ | 3,237 | |
Current debt maturities | | | 99 | | | | 401 | |
Cash and cash equivalents | | | (65 | ) | | | (491 | ) |
| |
|
|
| |
|
|
|
Net capitalization | | $ | 3,349 | | | $ | 3,147 | |
| |
|
|
| |
|
|
|
Long-term debt to total capitalization | | | 27.8 | % | | | 24.1 | % |
| |
|
|
| |
|
|
|
Net debt to net capitalization | | | 28.5 | % | | | 21.9 | % |
| |
|
|
| |
|
|
|
43
Total debt (which includes long-term debt and current debt maturities) decreased $161 million in 2005. During the year we repaid $433 million of debt that came due, and added $272 million, including $200 million of 10-year notes at a 5.0% coupon rate.
Since 2003, we’ve issued $730 million of fixed rate debt with an average remaining life at the end of 2005 of 9.5 years, and a weighted average coupon rate of 4.7%. To further facilitate the issuance of debt and other securities, $300 million remains available under a shelf registration.
In addition to issuing long-term notes, we can also raise cash by issuing up to $400 million in commercial paper through a program that is backed by a $400 million, five year revolving credit commitment. We expect any commercial paper issued under this agreement to be classified as long-term debt since we intend to maintain or increase the balance until it is replaced with long-term notes. At year-end, no commercial paper was outstanding.
With both the shelf registration and the commercial paper program in place, we believe we have sufficient funds available to support our ongoing operations and take advantage of growth opportunities.
Most of our debt has fixed repayment dates. At the end of 2005, this debt consisted primarily of term notes. Our term notes and public debt currently carries a Moody’s rating of A2 and a Standard & Poor’s rating of A+. Our commercial paper program carries a Moody’s rating of P-1 and a Standard & Poor’s rating of A-1. We have maintained a single A rating on our debt for over a decade.
CONTRACTUAL OBLIGATIONS
The following table summarizes our future contractual obligations and commitments:
| | | | | | | | | | | | | | | |
| | Total
| | Payments Due by Period
|
Contractual Obligations
| | | Less Than 1 Year
| | 1-3 Years
| | 3-5 Years
| | After 5 Years
|
| | (Dollar amounts in millions) |
Long-term debt* | | $ | 999 | | $ | 85 | | $ | 114 | | $ | 43 | | $ | 757 |
Capitalized leases | | | 21 | | | 14 | | | 4 | | | 2 | | | 1 |
Operating leases | | | 161 | | | 50 | | | 61 | | | 34 | | | 16 |
Purchase obligations** | | | 463 | | | 463 | | | — | | | — | | | — |
Interest payments*** | | | 376 | | | 48 | | | 84 | | | 73 | | | 171 |
Deferred income taxes | | | 59 | | | — | | | — | | | — | | | 59 |
Other obligations (including pension) | | | 85 | | | 5 | | | 9 | | | 8 | | | 63 |
| |
|
| |
|
| |
|
| |
|
| |
|
|
Total contractual cash obligations | | $ | 2,164 | | $ | 665 | | $ | 272 | | $ | 160 | | $ | 1,067 |
| |
|
| |
|
| |
|
| |
|
| |
|
|
*—The long-term debt payment schedule presented above could be accelerated if we were not able to make the principal and interest payments when due.
**—Purchase obligations primarily include open short-term (30-120 days) purchase orders that arise in the normal course of operating our facilities.
***—Interest payments are calculated on debt outstanding at December 31, 2005 at rates in effect at the end of the year.
CRITICAL ACCOUNTING POLICIES AND ESTIMATES
We prepare our consolidated financial statements in accordance with accounting principles generally accepted in the United States of America. To do so requires us to make estimates and judgments that affect the reported amounts of assets, liabilities, revenues and expenses, and the related disclosures. We periodically evaluate these estimates and judgments using historical experience and various assumptions that we believe to be reasonable under the circumstances. Different amounts could have been reported if we had used different
44
assumptions. Actual amounts may differ from the estimates and judgments reflected in our financial statements and future changes to these estimates could have a material effect on our financial condition and results of operations.
We consider accounting estimates to be critical if the estimates require us to make assumptions about matters that are highly uncertain, and if different estimates (that management could have reasonably used in the current period) or changes in the estimates (that are reasonably likely to occur) could materially impact the financial statements. The judgments and estimates we make which we believe could have a significant effect on our financial statements are discussed below. Critical judgments and estimates impacting our ongoing results relate to:
| • | | Asset and goodwill impairment |
| • | | Workers’ compensation, general liability and employee benefit programs |
| • | | Contingencies, including litigation |
More information regarding our significant accounting policies can be found in Note A to the financial statements on page 60.
Asset and Goodwill Impairment
Long-lived assets (primarily fixed assets and amortizable intangible assets) are tested annually and whenever there are indications that the book value of an asset may exceed the expected future cash flows from the use of the asset. In performing these tests, we must make judgments and estimates about the future cash flows expected to result from the use and eventual disposition of the assets and their fair market values. If actual future cash flows are less than our estimates, or our estimates change, we could incur future (unanticipated) impairment charges.
Goodwill represents the excess of the purchase price over the fair value of identifiable net assets acquired in business combinations. We assess goodwill of each of our reporting units for impairment on an annual basis and whenever events and circumstances warrant. Our reporting units for goodwill purposes are one level below our operating segments and are the same as the “Groups” disclosed in Item 1. Business of this report.
We estimate the fair market values of our reporting units using a discounted cash flow model. Key assumptions and estimates used in the cash flow model include discount rate, internal sales growth, margins, capital expenditure requirements, and working capital requirements. Recent performance of the reporting unit is an important factor (but not the only factor) in our assessment. Fair market values calculated for each reporting unit may go up or down each year based on a re-evaluation of the key assumptions. To date, none of our assessments has determined a goodwill impairment for any of our reporting units.
The excess, as a percent, of fair value over net carrying value for each of our reporting units as of June 30, 2005 (our annual testing date) ranged from approximately 50% to 300%, with an overall average of 136%. The total carrying value of goodwill as of December 31, 2005, was $1.1 billion.
One of our reporting units, the Fixture & Display group, has experienced deterioration in profitability in recent years compared to historical levels. If profitability does not continue to improve, there may be a future goodwill impairment in this reporting unit. About $300 million of goodwill is associated with these operations.
45
Inventory
We value our inventory at the lower of cost or fair market value by maintaining reserves for slow-moving and obsolete items. These reserves are based on turnover ratios (calculated by item) that reflect historical customer demand. Inventory with no activity (i.e. that has not been used or sold) in the previous 12 months are generally reserved at 100%, while active items with quantities exceeding 12 months usage are reserved at net realizable value. Obsolete and slow moving inventory reserves totaled $49 million as of December 31, 2005, or approximately 6% of total inventory valued on a FIFO basis.
Workers’ Compensation, General Liability and Employee Benefit Programs
We are self-insured for certain losses related to workers’ compensation, automobile, product and general liability, property, and medical insurance. Our self-insurance deductibles range from $1 million to $5 million per occurrence. Workers’ compensation losses in excess of self-insured levels are fully insured by third parties. Losses in excess of self-insured levels for automobile, product, and general liability are insured up to an aggregate annual maximum of $75 million, subject to certain limitations and exclusions. When estimating our self-insurance liabilities we consider a number of factors, including historical claim experience, demographic factors, and valuations provided by independent, third-party actuaries. Our self-insurance liabilities include estimates for both reported claims and for claims incurred but not yet reported. These estimates are subject to change from period to period if claim patterns differ from historical trends. Changes can have a material affect on our results of operations.
The average variation in the estimated yearly ultimate losses for worker’s compensation and general liability claims over the past five years has been approximately $5 million or 20%. A 20% change in our estimated self-insurance liabilities at December 31, 2005, would have affected pre-tax earnings for the year by approximately $13 million.
Credit Losses
Our customers are diverse. Many are small-to-medium sized companies, and some are highly leveraged. Bankruptcy can occur with some of these customers relatively quickly and with little warning, particularly in a changing economic environment. We regularly evaluate the collectibility of our accounts receivable based on a combination of factors. Significant customer accounts are evaluated individually. When we become aware of a specific customer’s inability to meet its financial obligations to us (such as in the case of a bankruptcy filing or deterioration in the customer’s operating results or financial position) we record a bad debt reserve to reflect the amount we reasonably believe is uncollectible. For smaller customers, we record bad debt reserves based on a variety of factors, including the length of time the receivables are past due, the financial health of the customer, industry and macroeconomic considerations, and historical experience.
The total amount of credit losses over the last three years is $20 million. At December 31, 2005, our reserves totaled $21 million against total consolidated accounts and other receivables of $868 million. In our year end evaluation, we identified $32 million in receivables considered to be less than fully collectible. Of the total reserved amount, $14 million relates to these accounts.
Pension Accounting
Accounting for our pension and postretirement benefit plans requires us to estimate the cost of benefits to be provided well into the future and the current value of our benefit obligations. The two most critical assumptions affecting these estimates are the discount rate and the expected return on assets. Other assumptions include rates of future compensation increases, participant withdrawal and mortality rates, and participant retirement ages. These estimates and assumptions impact the amount of net pension expense or income we recognize each year and the measurement of our reported benefit obligations under the plans. We use a September 30 measurement date for the majority of our plans.
46
To reflect market interest rates, in 2005 we reduced the discount rate for our major pension plans to 5.5% from the 6.0% which had been used in 2004 and 2003. We continued to assume long-term returns of 8.0% on the assets of these plans, the same as our assumptions for 2004 and 2003 and consistent with our experience over the past 10 years. Plan assets are invested in a diversified portfolio of equity, debt, and government securities. While we have historically targeted a weighted average portfolio of 70% equities and 30% bonds, the portfolio mix at year end (as well as the target going forward) was 75% equities and 25% bonds.
Sensitivity to changes in the critical assumptions for our major plans is as follows:
| • | | Discount rate—a 25 basis point decrease in the discount rate would increase pension expense in 2006 by approximately $.7 million and decrease the plans’ funded status by approximately $5.3 million. |
| • | | Expected return on assets—a 50 basis point reduction in the expected return on assets would increase pension expense in 2006 by $.9 million but have no effect on the plans’ funded status. |
The total of the unrecognized net actuarial losses of our major plans was $43 million for the year ended December 31, 2005, compared to $25 million for the year ended December 31, 2004. These losses are primarily the result of decreases in the discount rate since the implementation (in 1987) of the pension accounting rules established by Statement of Financial Accounting Standards No. 87. In 2006 net pension expense will reflect the amortization of approximately $23 million of these losses over an average of approximately 10 years. Approximately $10 million of the current year increase (in the unrecognized net actuarial losses) is due to a change in the life expectancies used in the calculation of the plans’ projected benefit obligations. The remainder of the increase is primarily due to the current year change in the discount rate from 6.0% to 5.5%. We do not expect any near-term significant funding requirements for our major plans. For 2006, we are projecting a $2 million contribution requirement, primarily for our foreign plans.
Income Taxes
In the ordinary course of business, many transactions occur for which the ultimate tax outcome is uncertain. In addition, respective tax authorities periodically audit our income tax returns. These audits examine our significant tax filing positions, including the timing and amounts of deductions and the allocation of income among tax jurisdictions. We adjust our income tax provision in the period in which we determine that the actual outcomes will likely be different from our estimates. As of December 31, 2005, six open years were either undergoing or subject to audit by the United States Internal Revenue Service and Canada Revenue Agency. Audits in both countries for 2000 and 2001 have been settled in all material respects with no significant adjustments.
At December 31, 2005 and 2004 we had $38.0 million and $18.5 million of net deferred tax assets on our balance sheet related to operating loss and tax credit carry-forwards. The ultimate realization of these net deferred tax assets is dependent on the amount and source of future taxable income. Valuation reserves are established against future potential tax benefits in order to reflect the amounts that we believe are more likely than not to be realized. In addition, certain assumptions have been made regarding the non-repatriation of earnings from certain subsidiaries. Those assumptions may change in the future, thereby affecting future period results for the tax impact of such earnings. Finally, income taxes are recorded at the rates in effect in the various tax jurisdictions in which we operate. Tax law and rate changes are reflected in the income tax provision in the period in which such changes are enacted.
Contingencies
Our disclosure and accrual of loss contingencies is based on an assessment of whether the likelihood of loss is remote, reasonably possible, or probable and whether the amount of potential loss can be estimated. Loss contingency assessments involve judgments that are subjective and can involve matters in litigation, the results of which are generally very unpredictable. Although we believe our assessment of the likelihood of loss contingencies is accurate, the resolution of any contingency is inherently uncertain and our assessment may ultimately prove to be materially incorrect.
47
In 2005, we recorded a deposit receivable of $4.8 million related to an on-going international dispute over countervailing duties (CVD) and anti-dumping duties (ADD) imposed by the United States on softwood lumber imported from Canada. This deposit receivable is our estimate of refunds due to the Company as a result of this dispute. See Note M to the financial statements on page 81 for further information regarding these actions.
NEW ACCOUNTING STANDARDS
In December 2004, the Financial Accounting Standards Board issued revised Statement of Financial Accounting Standards No. 123, “Share-Based Payment” (SFAS No. 123R). SFAS 123R clarifies and expands Statement 123’s guidance in several areas, including recognizing share-based compensation cost, measuring fair value, classifying an award as equity or as a liability, and attributing compensation cost to reporting periods. SFAS 123R is effective for Leggett & Platt beginning January 1, 2006, and applies to all awards granted, modified, repurchased or cancelled on or after that date. We adopted, as of January 1, 2003, the provisions of Statement 123 as originally issued and, having evaluated SFAS No. 123R, concluded it will not have a material impact on our financial condition or results of operations.
In December 2004, the Financial Accounting Standards Board issued FASB Staff Positions FAS 109-1, “Application of FASB Statement No. 109, Accounting for Income Taxes, to the Tax Deduction on Qualified Production Activities Provided by the American Jobs Creation Act of 2004” and FAS 109-2, “Accounting and Disclosure Guidance for the Foreign Earnings Repatriation Provision within the American Jobs Creation Act of 2004.” Although we will benefit from qualified production activities deductions provided under the Act, FASB Staff Position 109-1 has not had, nor is it expected to have, a material impact on our financial reporting or disclosures. Regarding FAS 109-2, we did not remit any amounts under the repatriation provision of the American Jobs Creation Act and, therefore, the provisions of this FASB staff position had no impact on our financial reporting or disclosures.
In March 2005, the FASB issued Interpretation No. 47, “Accounting for Conditional Asset Retirement Obligations—an Interpretation of FASB Statement No. 143” (FIN-47), which clarifies the termconditional asset retirement obligation as used in FASB No. 143 and requires recognition of a liability for the fair value of a conditional asset retirement obligation when incurred, if the fair value of the liability can be reasonably estimated. FIN-47 was effective for our fiscal year ended December 31, 2005 and did not have a material impact on our financial condition or results of operations.
In May 2005, the FASB issued SFAS No. 154, “Accounting Changes and Error Corrections,” which replaces APB Opinion No. 20, “Accounting Changes,” and SFAS No. 3, “Reporting Accounting Changes in Interim Financial Statements.” SFAS No. 154 applies to all voluntary changes in accounting principle and requires retrospective application (a term defined by the statement) to prior periods’ financial statements, unless it is impracticable to determine the effect of a change. It also applies to changes required by an accounting pronouncement that does not include specific transition provisions. SFAS No. 154 is effective for accounting changes and corrections of errors made in fiscal years beginning after December 15, 2005. We will adopt SFAS No. 154 as of January 1, 2006, and do not expect its adoption will have a material impact on our financial condition or results of operations.
Item 7A.Quantitative and Qualitative Disclosures About Market Risk.
(Unaudited)
(Dollar amounts in millions)
INTEREST RATES
The table below provides information about the Company’s debt obligations sensitive to changes in interest rates. The Company has no other significant financial instruments sensitive to changes in interest rates. During 2000, $350 of 7.65% fixed rate debt maturing in February 2005 and, in 1999, $14 of 6.90% fixed rate debt
48
maturing in June 2004 were issued and converted to variable rate debt by use of interest rate swap agreements. These swap agreements, which contained the same payment dates as the original issues, were used primarily by the Company to manage the fixed/variable interest rate mix of its debt portfolio. In March 2003, the Company sold its rights under the $350 interest rate swap agreement for $39.9.
Substantially all of the debt shown in the table below is denominated in United States dollars. The fair value of fixed rate debt was less than its carrying value by $23.5 at December 31, 2005, and greater than its carrying value by $6.6 at December 31, 2004. The fair value of fixed rate debt was calculated using the U.S. Treasury Bond rate as of December 31, 2005 and December 31, 2004 for similar remaining maturities, plus an estimated “spread” over such Treasury securities representing the Company’s interest costs under its medium-term note program. The fair value of variable rate debt is not significantly different from its recorded amount.
| | | | | | | | | | | | | | | | | | | | | | | | | | | | | | | | |
Long-term debt as of December 31,
| | Scheduled Maturity Date
| | | 2005
| | | 2004
| |
| 2006
| | | 2007
| | | 2008
| | | 2009
| | | 2010
| | | Thereafter
| | | |
Principal fixed rate debt | | $ | 75.0 | | | $ | 25.0 | | | $ | 71.5 | | | $ | 15.0 | | | $ | 0.0 | | | $ | 735.2 | | | $ | 921.7 | | | $ | 1,096.7 | |
Average interest rate | | | 7.12 | % | | | 7.40 | % | | | 6.31 | % | | | 7.26 | % | | | 0.00 | % | | | 4.74 | % | | | 5.17 | % | | | 4.22 | % |
Principal variable rate debt | | | 3.3 | | | | 9.1 | | | | 9.0 | | | | 9.0 | | | | 19.2 | | | | 22.5 | | | | 72.1 | | | | 35.5 | |
Average interest rate | | | 2.77 | % | | | 2.96 | % | | | 2.74 | % | | | 2.74 | % | | | 3.01 | % | | | 3.56 | % | | | 3.10 | % | | | 1.80 | % |
Miscellaneous debt | | | | | | | | | | | | | | | | | | | | | | | | | | | 26.4 | | | | 48.5 | |
| | | | | | | | | | | | | | | | | | | | | | | | | |
|
|
| |
|
|
|
Total debt | | | | | | | | | | | | | | | | | | | | | | | | | | | 1,020.2 | | | | 1,180.7 | |
Less: current maturities | | | | | | | | | | | | | | | | | | | | | | | | | | | (98.6 | ) | | | (401.3 | ) |
| | | | | | | | | | | | | | | | | | | | | | | | | |
|
|
| |
|
|
|
Total long-term debt | | | | | | | | | | | | | | | | | | | | | | | | | | $ | 921.6 | | | $ | 779.4 | |
| | | | | | | | | | | | | | | | | | | | | | | | | |
|
|
| |
|
|
|
EXCHANGE RATES
The Company does not hedge all net foreign currency exposures related to transactions denominated in other than its associated functional currencies. The Company may occasionally hedge firm specific commitments or other anticipated foreign currency cash flows. The decision by management to hedge any such transactions is made on a case-by-case basis. The amount of forward contracts outstanding at December 31, 2005 was approximately $15.9 (Pay USD/Receive MXN). The highest amount during 2005 was approximately $168.2 ($95.0 Pay EUR/Receive USD; $52.5 Pay USD/Receive EUR; $19.3 Pay USD/Receive MXN; $1.4 Pay GBP/Receive USD). In 2005, these contracts were primarily used to hedge known Euro-denominated purchases and receivables, about 70% of expected Mexican peso needs, and known British pound receivables.
The Company views its investment in foreign subsidiaries as a long-term commitment, and, except for the cross-currency swap agreement disclosed below, does not hedge translation exposures. The investment in a foreign subsidiary may take the form of either permanent capital or notes. The Company’s net investment in foreign subsidiaries subject to translation exposure at December 31 is as follows:
| | | | | | |
Functional Currency
| | 2005
| | 2004
|
Canadian Dollar | | $ | 311.2 | | $ | 280.9 |
European Currencies | | | 270.0 | | | 344.5 |
Mexican Peso | | | 80.0 | | | 56.7 |
Chinese Renminbi | | | 79.1 | | | 38.2 |
Other | | | 40.5 | | | 37.3 |
| |
|
| |
|
|
Total | | $ | 780.8 | | $ | 757.6 |
| |
|
| |
|
|
CROSS-CURRENCY SWAP AGREEMENT
In December 2003, the Company entered into a 38.3 million Swiss Francs (CHF) five year cross-currency rate swap agreement with Wachovia Bank, N.A. This agreement is designated as a net investment hedge. The
49
purpose of this swap is to hedge CHF denominated assets, thereby reducing exposure to volatility in the exchange rate. In addition, the terms of this agreement include that the Company will receive interest on $30 USD at a fixed rate of 6.35% and pay interest on 38.3 million CHF at a fixed rate of 4.71%. During 2005, the Company paid interest of $1.4 on the CHF portion and received interest of $1.9 on the USD portion of the agreement. At December 31, 2005, the market value loss on the cross-currency swap was approximately $.2.
COMMODITY PRICES
Other than for planned purchases of natural gas, the Company does not generally use derivative commodity instruments to hedge its exposures to changes in commodity prices. At December 31, 2005, approximately $13.0 of natural gas forward contracts were outstanding at an average price of $7.47 per mmbtu, of which the contracts hedging January and February 2006 usage totaled approximately $3.1. At December 31, 2005, the total unrealized gain recorded in other comprehensive income on natural gas contracts was approximately $3.5, net of tax.
Subsequent to year-end, the Company entered into an additional $22.0 of natural gas forward contracts at an average price of $9.19 per mmbtu. At February 28, 2006, the Company had contracts in place hedging approximately 75% of its anticipated natural gas consumption for March 2006, approximately 65% of its anticipated monthly consumption for the 6-month period beginning April 2006, approximately 50% of its anticipated monthly consumption for the 3-month period beginning October 2006, approximately 20% of its anticipated monthly consumption for 2007, and approximately 5-15% of its anticipated monthly consumption for 2008. Contracts in place at February 28, 2006 totaled $31.9 at an average price of $8.40 per mmbtu.
Item 8.Financial Statements and Supplementary Data.
The Consolidated Financial Statements and supplementary data included in this Report are listed in Item 15 and begin immediately after Item 15, and are incorporated herein by reference.
Item 9.Changes In and Disagreements With Accountants on Accounting and Financial Disclosure.
Not applicable.
Item 9A.Controls and Procedures.
Effectiveness of the Company’s Disclosure Controls and Procedures.
An evaluation as of December 31, 2005 was carried out by the Company’s management, with the participation of the Company’s Chief Executive Officer and Chief Financial Officer, of the effectiveness of the Company’s disclosure controls and procedures (as defined in Rule 13a-15(e) under the Securities Exchange Act of 1934, as amended (the “Exchange Act”)). Based upon this evaluation, the Chief Executive Officer and Chief Financial Officer have concluded the Company’s disclosure controls and procedures were effective, as of December 31, 2005, to provide reasonable assurance that information that is required to be disclosed by the Company in the reports that it files or submits under the Exchange Act is recorded, processed, summarized, and reported, within the time periods specified by the Securities and Exchange Commission’s rules and forms. Disclosure controls and procedures, include without limitation, controls and procedures designed to ensure that information required to be disclosed by the Company in the reports that it files or submits under the Exchange Act is accumulated and communicated to the Company’s management, including its Chief Executive Officer and Chief Financial Officer, or persons performing similar functions, as appropriate to allow timely decisions regarding required disclosure.
Management’s Report on Internal Control over Financial Reporting and Auditors Attestation Report.
Management’s Report on Internal Control over Financial Reporting can be found on page 53, and the Attestation Report regarding management’s assessment and the effectiveness of the Company’s Internal Control over Financial Reporting of PricewaterhouseCoopers LLP can be found on pages 53 through 55 of this Form 10-K. Each is incorporated by reference into this Item 9A.
50
Changes in the Company’s Internal Control Over Financial Reporting.
In the second quarter of 2005, the Company began the rollout of a redesigned procurement process incorporating PeopleSoft/Oracle purchasing and payables software and trade import facilitation software from NextLinx. Spanning the purchasing, receiving and accounts payable processes, this initiative will centralize purchasing information for operations in the United States and Canada. The primary objectives of this initiative are to enable strategic sourcing with our suppliers and reduce total procurement costs. We believe the effectiveness of the Company’s internal control over financial reporting will be maintained or enhanced by the redesigned system. We believe implementation risk will be controlled through a staged rollout and on-going process of monitoring and evaluation. Approximately seven percent of the Company’s operations in the United States and Canada were converted as of December 31, 2005. Based upon our experience converting the initial branches, the Company anticipates that 30% to 40% of United States and Canadian branches will be converted in 2006. The rollout is expected to be completed by the end of 2007.
There were no other changes in the Company’s internal control over financial reporting that occurred during the quarter ending December 31, 2005 that have materially affected, or are reasonably likely to materially affect, the Company’s internal control over financial reporting.
Item 9B.Other Information.
On February 23, 2006, the Compensation Committee amended the 2004 Key Officers Incentive Plan to make the plan compliant with Section 409A of the Internal Revenue Code. The amendment specifies that a participant’s award under the plan will be paid no later than March 15 of the year the award becomes payable. The 2004 Key Officers Incentive Plan, amended and restated effective January 1, 2006, is attached hereto as Exhibit 10.13 and incorporated herein by reference. Reference is made to the Award Formula under the plan, which is a part of Exhibit 10.9. Because this Annual Report on Form 10-K is being filed within four business days from February 23, 2006, the amendment to the 2004 Key Officers Incentive Plan is being disclosed hereunder rather than under Item 1.01 of Form 8-K.
PART III
Item 10.Directors and Executive Officers of the Registrant.
The section entitled “Proposal No. 1—Election of Directors” and subsections entitled “Board Structure and Committee Composition” and “Section 16(a) Beneficial Ownership Reporting Compliance” in the Company’s definitive Proxy Statement for the Company’s Annual Meeting of Shareholders to be held on May 10, 2006, are incorporated by reference.
Please see the “Supplemental Item” in Part I hereof, for a listing of and a description of the positions and offices held by the executive officers of the Company.
The Company has adopted a code of ethics that applies to its chief executive officer, chief financial officer, principal accounting officer and corporate controller called the Leggett & Platt, Incorporated Financial Code of Ethics. The Company has also adopted a Code of Business Conduct and Ethics for directors, officers and employees and Corporate Governance Guidelines. The Financial Code of Ethics, the Code of Business Conduct and Ethics and the Corporate Governance Guidelines are available on the Company’s Internet website at http://www.leggett.com, Investor Relations, Corporate Governance. Each of these documents is available in print to any shareholder, without charge, upon request. The Company intends to satisfy the disclosure requirement under Item 5.05 of Form 8-K by posting any amendment or waiver to its Financial Code of Ethics, within four business days, on its website at the above address for at least a 12 month period. The Company’s website does not constitute part of this Annual Report on Form 10-K.
51
Item 11. Executive Compensation.
The subsection entitled “Director Compensation,” and the section entitled “Executive Compensation and Related Matters” (excluding the subsection “Compensation Committee Report on Executive Compensation”) in the Company’s definitive Proxy Statement for the Company’s Annual Meeting of Shareholders to be held on May 10, 2006, are incorporated by reference.
Item 12.Security Ownership of Certain Beneficial Owners and Management and Related Stockholder Matters.
The sections entitled “Common Stock Ownership of Certain Beneficial Owners and Management” and “Equity Compensation Plan Information” in the Company’s definitive Proxy Statement for the Company’s Annual Meeting of Shareholders to be held on May 10, 2006, are incorporated by reference.
Item 13.Certain Relationships and Related Transactions.
The section entitled “Related Party Transactions” in the Company’s definitive Proxy Statement for the Company’s Annual Meeting of Shareholders to be held on May 10, 2006 is incorporated by reference.
Item 14.Principal Accounting Fees and Services.
The section entitled “Independent Auditor Fees and Services” in the Company’s definitive Proxy Statement for the Company’s Annual Meeting of Shareholders to be held on May 10, 2006 is incorporated by reference.
PART IV
Item 15.Exhibits and Financial Statement Schedules.
(a) Financial Statements and Financial Statement Schedules.
The Reports, Financial Statements and Financial Statement Schedules listed below are included in this Form 10-K:
| • | | Management’s Report on Internal Control Over Financial Reporting |
| • | | Report of Independent Registered Public Accounting Firm |
| • | | Consolidated Statements of Earnings for each of the years in the three-year period ended December 31, 2005 |
| • | | Consolidated Balance Sheets at December 31, 2005 and 2004 |
| • | | Consolidated Statements of Cash Flows for each of the years in the three-year period ended December 31, 2005 |
| • | | Consolidated Statements of Changes in Shareholders’ Equity for each of the years in the three-year period ended December 31, 2005 |
| • | | Notes to Consolidated Financial Statements |
| • | | Quarterly Summary of Earnings (Unaudited) |
| • | | Schedule II—Valuation and Qualifying Accounts and Reserves |
All other information schedules have been omitted as the required information is inapplicable, not required, or the information is included in the financial statements or notes thereto.
52
(b) Exhibits—See Exhibit Index.
No other long-term debt instruments are filed since the total amount of securities authorized under any such instrument does not exceed ten percent of the total assets of the Company and its subsidiaries on a consolidated basis. The Company agrees to furnish a copy of such instruments to the SEC upon request.
MANAGEMENT’S REPORT ON INTERNAL CONTROL OVER FINANCIAL REPORTING
Management of Leggett & Platt, Incorporated is responsible for establishing and maintaining adequate internal control over financial reporting as defined in Exchange Act Rule 13a-15(f). Leggett & Platt’s internal control over financial reporting is a process designed to provide reasonable assurance regarding the reliability of financial reporting and the preparation of financial statements for external purposes in accordance with accounting principles generally accepted in the United States of America. The Company’s internal control over financial reporting includes those written policies and procedures that:
| • | | Pertain to the maintenance of records that, in reasonable detail, accurately and fairly reflect the transactions and dispositions of the assets of Leggett & Platt; |
| • | | Provide reasonable assurance that transactions are recorded as necessary to permit preparation of financial statements in accordance with accounting principles generally accepted in the United States of America, and that receipts and expenditures of Leggett & Platt are being made only in accordance with authorizations of management and directors of Leggett & Platt; and |
| • | | Provide reasonable assurance regarding prevention or timely detection of unauthorized acquisition, use or disposition of assets that could have a material effect on the consolidated financial statements. |
Because of its inherent limitations, internal control over financial reporting may not prevent or detect misstatements. Also, projections of any evaluation of effectiveness to future periods are subject to the risk that controls may become inadequate because of changes in conditions, or that the degree of compliance with the policies or procedures may deteriorate.
Under the supervision and with the participation of management (including ourselves), we conducted an evaluation of the effectiveness of Leggett & Platt’s internal controls over financial reporting, as of December 31, 2005, based on the criteria inInternal Control—Integrated Frameworkissued by the Committee of Sponsoring Organizations of the Treadway Commission. Based on the evaluation under this framework, we concluded that Leggett & Platt’s internal control over financial reporting was effective as of December 31, 2005.
Management’s assessment of the effectiveness of the Company’s internal control over financial reporting as of December 31, 2005 has been audited by PricewaterhouseCoopers LLP, an independent registered public accounting firm, as stated in their report which appears herein.
| | |
/S/ FELIX E. WRIGHT
| | /S/ MATTHEW C. FLANIGAN
|
Felix E. Wright | | Matthew C. Flanigan |
Chairman and Chief Executive Officer | | Senior Vice President and |
| | Chief Financial Officer |
| |
February 24, 2006 | | February 24, 2006 |
Report of Independent Registered Public Accounting Firm
To the Board of Directors and Shareholders of
Leggett & Platt, Incorporated:
We have completed integrated audits of Leggett & Platt, Incorporated’s 2005 and 2004 consolidated financial statements and of its internal control over financial reporting as of December 31, 2005, and an audit of its 2003 consolidated financial statements in accordance with the standards of the Public Company Accounting Oversight Board (United States). Our opinions, based on our audits, are presented below.
53
Consolidated financial statements and financial statement schedule
In our opinion, the consolidated financial statements listed in the index appearing under Item 15(a) present fairly, in all material respects, the financial position of Leggett & Platt, Incorporated and its subsidiaries at December 31, 2005 and 2004, and the results of their operations and their cash flows for each of the three years in the period ended December 31, 2005 in conformity with accounting principles generally accepted in the United States of America. In addition, in our opinion, the financial statement schedule listed in the index appearing under Item 15(a) presents fairly, in all material respects, the information set forth therein when read in conjunction with the related consolidated financial statements. These financial statements and financial statement schedule are the responsibility of the Company’s management. Our responsibility is to express an opinion on these financial statements and financial statement schedule based on our audits. We conducted our audits of these statements in accordance with the standards of the Public Company Accounting Oversight Board (United States). Those standards require that we plan and perform the audit to obtain reasonable assurance about whether the financial statements are free of material misstatement. An audit of financial statements includes examining, on a test basis, evidence supporting the amounts and disclosures in the financial statements, assessing the accounting principles used and significant estimates made by management, and evaluating the overall financial statement presentation. We believe that our audits provide a reasonable basis for our opinion.
Internal control over financial reporting
Also, in our opinion, management’s assessment, included in the accompanying Management’s Report on Internal Control Over Financial Reporting, that the Company maintained effective internal control over financial reporting as of December 31, 2005 based on criteria established inInternal Control—Integrated Framework issued by the Committee of Sponsoring Organizations of the Treadway Commission (COSO), is fairly stated, in all material respects, based on those criteria. Furthermore, in our opinion, the Company maintained, in all material respects, effective internal control over financial reporting as of December 31, 2005 based on criteria established inInternal Control—Integrated Framework issued by the COSO. The Company’s management is responsible for maintaining effective internal control over financial reporting and for its assessment of the effectiveness of internal control over financial reporting. Our responsibility is to express opinions on management’s assessment and on the effectiveness of the Company’s internal control over financial reporting based on our audit. We conducted our audit of internal control over financial reporting in accordance with the standards of the Public Company Accounting Oversight Board (United States). Those standards require that we plan and perform the audit to obtain reasonable assurance about whether effective internal control over financial reporting was maintained in all material respects. An audit of internal control over financial reporting includes obtaining an understanding of internal control over financial reporting, evaluating management’s assessment, testing and evaluating the design and operating effectiveness of internal control, and performing such other procedures as we consider necessary in the circumstances. We believe that our audit provides a reasonable basis for our opinions.
A company’s internal control over financial reporting is a process designed to provide reasonable assurance regarding the reliability of financial reporting and the preparation of financial statements for external purposes in accordance with generally accepted accounting principles. A company’s internal control over financial reporting includes those policies and procedures that (i) pertain to the maintenance of records that, in reasonable detail, accurately and fairly reflect the transactions and dispositions of the assets of the company; (ii) provide reasonable assurance that transactions are recorded as necessary to permit preparation of financial statements in accordance with generally accepted accounting principles, and that receipts and expenditures of the company are being made only in accordance with authorizations of management and directors of the company; and (iii) provide reasonable assurance regarding prevention or timely detection of unauthorized acquisition, use, or disposition of the company’s assets that could have a material effect on the financial statements.
54
Because of its inherent limitations, internal control over financial reporting may not prevent or detect misstatements. Also, projections of any evaluation of effectiveness to future periods are subject to the risk that controls may become inadequate because of changes in conditions, or that the degree of compliance with the policies or procedures may deteriorate.
|
/s/ PricewaterhouseCoopers LLP |
St. Louis, MO |
February 24, 2006 |
55
LEGGETT & PLATT, INCORPORATED
Consolidated Statements of Earnings
| | | | | | | | | | | |
| | Year ended December 31
| |
| | 2005
| | 2004
| | | 2003
| |
| | (Amounts in millions, except per share data) | |
Net sales | | $ | 5,299.3 | | $ | 5,085.5 | | | $ | 4,388.2 | |
Cost of goods sold | | | 4,386.5 | | | 4,169.7 | | | | 3,616.5 | |
| |
|
| |
|
|
| |
|
|
|
Gross profit | | | 912.8 | | | 915.8 | | | | 771.7 | |
Selling and administrative expenses | | | 468.8 | | | 460.2 | | | | 409.9 | |
Amortization of intangibles | | | 10.3 | | | 10.5 | | | | 8.4 | |
Other expense (income), net | | | 37.5 | | | (16.6 | ) | | | (1.9 | ) |
| |
|
| |
|
|
| |
|
|
|
Earnings before interest and income taxes | | | 396.2 | | | 461.7 | | | | 355.3 | |
Interest expense | | | 46.7 | | | 45.9 | | | | 46.9 | |
Interest income | | | 6.7 | | | 6.8 | | | | 6.7 | |
| |
|
| |
|
|
| |
|
|
|
Earnings before income taxes | | | 356.2 | | | 422.6 | | | | 315.1 | |
Income taxes | | | 104.9 | | | 137.2 | | | | 109.2 | |
| |
|
| |
|
|
| |
|
|
|
Net earnings | | $ | 251.3 | | $ | 285.4 | | | $ | 205.9 | |
| |
|
| |
|
|
| |
|
|
|
Earnings per share | | | | | | | | | | | |
Basic | | $ | 1.30 | | $ | 1.46 | | | $ | 1.05 | |
| |
|
| |
|
|
| |
|
|
|
Diluted | | $ | 1.30 | | $ | 1.45 | | | $ | 1.05 | |
| |
|
| |
|
|
| |
|
|
|
The accompanying notes are an integral part of these financial statements.
56
LEGGETT & PLATT, INCORPORATED
Consolidated Balance Sheets
| | | | | | | | |
| | December 31
| |
| | 2005
| | | 2004
| |
| | (Amounts in millions, except per share data) | |
ASSETS | | | | | | | | |
Current Assets | | | | | | | | |
Cash and cash equivalents | | $ | 64.9 | | | $ | 491.3 | |
Accounts and other receivables | | | 847.6 | | | | 790.7 | |
Inventories | | | | | | | | |
Finished goods | | | 391.2 | | | | 365.0 | |
Work in process | | | 97.7 | | | | 96.7 | |
Raw materials and supplies | | | 341.9 | | | | 331.6 | |
LIFO reserve | | | (63.7 | ) | | | (87.6 | ) |
| |
|
|
| |
|
|
|
Total inventories | | | 767.1 | | | | 705.7 | |
Other current assets | | | 83.7 | | | | 77.1 | |
| |
|
|
| |
|
|
|
Total current assets | | | 1,763.3 | | | | 2,064.8 | |
Property, Plant and Equipment—at cost | | | | | | | | |
Machinery and equipment | | | 1,493.9 | | | | 1,415.2 | |
Buildings and other | | | 716.0 | | | | 681.1 | |
Land | | | 70.8 | | | | 65.0 | |
| |
|
|
| |
|
|
|
Total property, plant and equipment | | | 2,280.7 | | | | 2,161.3 | |
Less accumulated depreciation | | | 1,309.6 | | | | 1,200.6 | |
| |
|
|
| |
|
|
|
Net property, plant and equipment | | | 971.1 | | | | 960.7 | |
Other Assets | | | | | | | | |
Goodwill | | | 1,102.5 | | | | 1,028.9 | |
Other intangibles, less accumulated amortization of $31.3 in 2005 and $32.5 in 2004 | | | 133.5 | | | | 68.4 | |
Sundry | | | 82.2 | | | | 74.4 | |
| |
|
|
| |
|
|
|
Total other assets | | | 1,318.2 | | | | 1,171.7 | |
| |
|
|
| |
|
|
|
TOTAL ASSETS | | $ | 4,052.6 | | | $ | 4,197.2 | |
| |
|
|
| |
|
|
|
LIABILITIES AND SHAREHOLDERS’ EQUITY | | | | | | | | |
Current Liabilities | | | | | | | | |
Current maturities of long-term debt | | $ | 98.6 | | | $ | 401.3 | |
Accounts payable | | | 254.2 | | | | 224.4 | |
Accrued expenses | | | 279.3 | | | | 239.5 | |
Other current liabilities | | | 105.9 | | | | 94.4 | |
| |
|
|
| |
|
|
|
Total current liabilities | | | 738.0 | | | | 959.6 | |
| | |
Long-Term Debt | | | 921.6 | | | | 779.4 | |
| | |
Other Liabilities | | | 84.6 | | | | 79.7 | |
| | |
Deferred Income Taxes | | | 59.4 | | | | 65.4 | |
| | |
Shareholders’ Equity | | | | | | | | |
Capital stock | | | | | | | | |
Preferred stock—authorized, 100.0 shares; none issued Common stock—authorized, 600.0 shares of $.01 par value; issued 198.8 shares in 2005 and 2004 | | | 2.0 | | | | 2.0 | |
Additional contributed capital | | | 464.4 | | | | 452.5 | |
Retained earnings | | | 2,093.1 | | | | 1,961.5 | |
Accumulated other comprehensive income | | | | | | | | |
Foreign currency translation adjustments | | | 71.3 | | | | 89.6 | |
Fair market value of natural gas hedges | | | 3.5 | | | | — | |
Minimum pension liability adjustments | | | (8.5 | ) | | | (7.3 | ) |
Less treasury stock—at cost (16.2 and 7.9 shares in 2005 and 2004, respectively) | | | (376.8 | ) | | | (185.2 | ) |
| |
|
|
| |
|
|
|
Total shareholders’ equity | | | 2,249.0 | | | | 2,313.1 | |
| |
|
|
| |
|
|
|
TOTAL LIABILITIES AND SHAREHOLDERS’ EQUITY | | $ | 4,052.6 | | | $ | 4,197.2 | |
| |
|
|
| |
|
|
|
The accompanying notes are an integral part of these financial statements.
57
LEGGETT & PLATT, INCORPORATED
Consolidated Statements of Cash Flows
| | | | | | | | | | | | |
| | Year ended December 31
| |
| | 2005
| | | 2004
| | | 2003
| |
| | (Amounts in millions) | |
Operating Activities | | | | | | | | | | | | |
Net earnings | | $ | 251.3 | | | $ | 285.4 | | | $ | 205.9 | |
Adjustments to reconcile net earnings to net cash provided by operating activities | | | | | | | | | | | | |
Depreciation | | | 160.8 | | | | 164.3 | | | | 158.6 | |
Amortization | | | 10.3 | | | | 10.5 | | | | 8.4 | |
Losses on writedown of inventories | | | 24.9 | | | | 11.6 | | | | 16.8 | |
Asset impairment | | | 24.3 | | | | 2.4 | | | | 1.3 | |
(Gain) loss from sales of assets | | | (6.3 | ) | | | (16.3 | ) | | | 1.9 | |
Deferred income tax (benefit) expense | | | (35.6 | ) | | | 3.4 | | | | 15.9 | |
Other | | | 9.5 | | | | (13.8 | ) | | | (19.4 | ) |
Other changes, excluding effects from purchases of companies | | | | | | | | | | | | |
(Increase) in accounts receivable | | | (18.0 | ) | | | (96.5 | ) | | | (64.3 | ) |
(Increase) decrease in inventories | | | (50.4 | ) | | | (68.7 | ) | | | 29.0 | |
Decrease (increase) in other current assets | | | 9.9 | | | | (11.0 | ) | | | 1.0 | |
Increase in accounts payable | | | — | | | | 17.4 | | | | .2 | |
Increase in accrued expenses and other current liabilities | | | 67.6 | | | | 50.2 | | | | 37.9 | |
| |
|
|
| |
|
|
| |
|
|
|
Net Cash Provided by Operating Activities | | | 448.3 | | | | 338.9 | | | | 393.2 | |
Investing Activities | | | | | | | | | | | | |
Additions to property, plant and equipment | | | (164.2 | ) | | | (157.1 | ) | | | (136.6 | ) |
Purchases of companies, net of cash acquired | | | (181.0 | ) | | | (46.4 | ) | | | (120.4 | ) |
Proceeds from liquidation of interest rate swap agreement | | | — | | | | — | | | | 39.9 | |
Proceeds from sales of assets | | | 14.9 | | | | 42.0 | | | | 6.7 | |
Other | | | (8.2 | ) | | | (8.9 | ) | | | 4.3 | |
| |
|
|
| |
|
|
| |
|
|
|
Net Cash Used for Investing Activities | | | (338.5 | ) | | | (170.4 | ) | | | (206.1 | ) |
Financing Activities | | | | | | | | | | | | |
Additions to debt | | | 246.0 | | | | 189.5 | | | | 355.2 | |
Payments on debt | | | (433.0 | ) | | | (130.5 | ) | | | (143.8 | ) |
Dividends paid | | | (118.4 | ) | | | (109.9 | ) | | | (102.7 | ) |
Issuances of common stock | | | 9.5 | | | | 26.1 | | | | 3.8 | |
Purchases of common stock | | | (236.4 | ) | | | (99.9 | ) | | | (82.8 | ) |
| |
|
|
| |
|
|
| |
|
|
|
Net Cash (Used for) Provided by Financing Activities | | | (532.3 | ) | | | (124.7 | ) | | | 29.7 | |
| |
|
|
| |
|
|
| |
|
|
|
Effect of Exchange Rate Changes on Cash | | | (3.9 | ) | | | 3.6 | | | | 2.1 | |
| |
|
|
| |
|
|
| |
|
|
|
| | | |
(Decrease) Increase in Cash and Cash Equivalents | | | (426.4 | ) | | | 47.4 | | | | 218.9 | |
Cash and Cash Equivalents—Beginning of Year | | | 491.3 | | | | 443.9 | | | | 225.0 | |
| |
|
|
| |
|
|
| |
|
|
|
Cash and Cash Equivalents—End of Year | | $ | 64.9 | | | $ | 491.3 | | | $ | 443.9 | |
| |
|
|
| |
|
|
| |
|
|
|
Supplemental Information | | | | | | | | | | | | |
Interest paid | | $ | 56.5 | | | $ | 66.9 | | | $ | 53.8 | |
Income taxes paid | | | 138.9 | | | | 137.1 | | | | 93.7 | |
Property, plant and equipment acquired through capital leases | | | 5.0 | | | | 3.2 | | | | 3.3 | |
Liabilities assumed of acquired companies | | | 99.7 | | | | 16.9 | | | | 21.2 | |
Common stock issued for employee stock plans | | | 38.4 | | | | 36.4 | | | | 33.1 | |
| |
|
|
| |
|
|
| |
|
|
|
The accompanying notes are an integral part of these financial statements.
58
LEGGETT & PLATT, INCORPORATED
Consolidated Statements of Changes in Shareholders’ Equity
| | | | | | | | | | | | |
| | Year ended December 31
| |
| | 2005
| | | 2004
| | | 2003
| |
| | (Amounts in millions, except per share data) | |
Common Stock | | | | | | | | | | | | |
Balance, beginning and end of period | | $ | 2.0 | | | $ | 2.0 | | | $ | 2.0 | |
| |
|
|
| |
|
|
| |
|
|
|
Additional Contributed Capital | | | | | | | | | | | | |
Balance, beginning of period | | $ | 452.5 | | | $ | 433.7 | | | $ | 422.9 | |
Stock options and benefit plans transactions | | | 18.8 | | | | 20.4 | | | | 14.2 | |
Treasury stock issued | | | (9.0 | ) | | | (10.6 | ) | | | (4.1 | ) |
Tax benefit related to stock options | | | 2.1 | | | | 9.0 | | | | .7 | |
| |
|
|
| |
|
|
| |
|
|
|
Balance, end of period | | $ | 464.4 | | | $ | 452.5 | | | $ | 433.7 | |
| |
|
|
| |
|
|
| |
|
|
|
Retained Earnings | | | | | | | | | | | | |
Balance, beginning of period | | $ | 1,961.5 | | | $ | 1,788.3 | | | $ | 1,687.3 | |
Net earnings | | | 251.3 | | | | 285.4 | | | | 205.9 | |
Cash dividends declared (per share: 2005—$.63; 2004—$.58; 2003—$.54) | | | (119.7 | ) | | | (112.2 | ) | | | (104.9 | ) |
| |
|
|
| |
|
|
| |
|
|
|
Balance, end of period | | $ | 2,093.1 | | | $ | 1,961.5 | | | $ | 1,788.3 | |
| |
|
|
| |
|
|
| |
|
|
|
Treasury Stock | | | | | | | | | | | | |
Balance, beginning of period | | $ | (185.2 | ) | | $ | (144.4 | ) | | $ | (96.3 | ) |
Treasury stock purchased | | | (238.9 | ) | | | (103.6 | ) | | | (83.3 | ) |
Treasury stock issued | | | 47.3 | | | | 62.8 | | | | 35.2 | |
| |
|
|
| |
|
|
| |
|
|
|
Balance, end of period | | $ | (376.8 | ) | | $ | (185.2 | ) | | $ | (144.4 | ) |
| |
|
|
| |
|
|
| |
|
|
|
Accumulated Other Comprehensive Income (Loss) | | | | | | | | | | | | |
Balance, beginning of period | | $ | 82.3 | | | $ | 34.4 | | | $ | (39.0 | ) |
Foreign currency translation adjustments | | | (18.3 | ) | | | 55.2 | | | | 73.4 | |
Change in fair market value of natural gas hedges | | | 3.5 | | | | — | | | | — | |
Minimum pension liability adjustments | | | (1.2 | ) | | | (7.3 | ) | | | — | |
| |
|
|
| |
|
|
| |
|
|
|
Balance, end of period | | $ | 66.3 | | | $ | 82.3 | | | $ | 34.4 | |
| |
|
|
| |
|
|
| |
|
|
|
Total Shareholders’ Equity | | $ | 2,249.0 | | | $ | 2,313.1 | | | $ | 2,114.0 | |
| |
|
|
| |
|
|
| |
|
|
|
Comprehensive Income | | | | | | | | | | | | |
Net earnings | | $ | 251.3 | | | $ | 285.4 | | | $ | 205.9 | |
Foreign currency translation adjustments, net of income tax expense (benefit): 2005—$2.2; 2004—$(.9); 2003—$1.6 | | | (18.3 | ) | | | 55.2 | | | | 73.4 | |
Change in fair market value of natural gas hedges, net of income tax expense: 2005—$2.2 | | | 3.5 | | | | — | | | | — | |
Minimum pension liability adjustments, net of income tax (benefit): 2005—$(.9); 2004—$(4.0) | | | (1.2 | ) | | | (7.3 | ) | | | — | |
| |
|
|
| |
|
|
| |
|
|
|
Total Comprehensive Income | | $ | 235.3 | | | $ | 333.3 | | | $ | 279.3 | |
| |
|
|
| |
|
|
| |
|
|
|
The accompanying notes are an integral part of these financial statements.
59
Leggett & Platt, Incorporated
Notes to Consolidated Financial Statements
(Dollar amounts in millions, except per share data)
December 31, 2005, 2004 and 2003
A—Summary of Significant Accounting Policies
PRINCIPLES OF CONSOLIDATION: The consolidated financial statements include the accounts of Leggett & Platt, Incorporated and its majority-owned subsidiaries (the Company). To facilitate timely financial reporting, many of the Company’s subsidiaries outside of the United States are consolidated as of a fiscal year which ended November 30. All intercompany transactions and accounts have been eliminated in consolidation.
ESTIMATES: The preparation of financial statements in conformity with generally accepted accounting principles requires management to make estimates and assumptions that affect the reported amounts of assets, liabilities, revenues and expenses and the disclosure of contingencies. Actual results could differ from those estimates.
CASH EQUIVALENTS: Cash equivalents include cash in excess of daily requirements which is invested in various financial instruments with original maturities of three months or less.
ACCOUNTS RECEIVABLE AND ALLOWANCE FOR DOUBTFUL ACCOUNTS: Trade accounts receivable are recorded at the invoiced amount and generally do not bear interest. The allowance for doubtful accounts is an estimate of the amount of probable credit losses determined from individual account reviews by management. Account balances are charged off against the allowance when it is probable the receivable will not be recovered.
INVENTORIES: All inventories are stated at the lower of cost or market. Cost includes materials, labor and production overhead. The cost for approximately $425, or 51%, of the Company’s inventories is determined by the last-in, first-out (LIFO) method. Finished goods of $221, work-in-process of $50 and raw materials of $154 are valued under the LIFO method. Approximately 40% of these inventories are composed of materials and products the cost of which is closely linked to steel costs. Another 40% are part of a pool closely linked to the cost of raw wire and wire products. The remainder consists primarily of wood and plastics related products and materials. The first-in, first-out (FIFO) method is principally used for the remainder of our inventories. The FIFO cost of inventories at December 31, 2005 and 2004 approximated their expected replacement cost. Obsolete and slow moving inventory reserves valued on a FIFO basis totaled $48.5 and $40.2, as of December 31, 2005 and 2004, respectively.
PROPERTY, PLANT AND EQUIPMENT: Property, plant and equipment is stated at cost, less accumulated depreciation. Assets are depreciated by the straight-line method over their estimated useful lives and in the case of leasehold improvements over their respective lease terms, if shorter. Depreciable lives primarily range from 3 to 18 years for machinery and equipment with a weighted average life of 9 years; 10 to 40 years for buildings with a weighted average of 27 years; and 3 to 15 years for other items with a weighted average of 7 years. Accelerated methods are used for tax purposes.
INTANGIBLE ASSETS: Goodwill and other intangible assets with indefinite lives are not amortized, but, instead, are reviewed for impairment annually and whenever events or circumstances indicate there may be an impairment. Other intangible assets are amortized by the straight-line method over their estimated lives ranging from 2 to 50 years with a weighted average of 12 years.
The Company has selected June in which to do its annual evaluation of goodwill impairment. As of June 30, 2005 and 2004, it was determined that the carrying value of goodwill did not exceed its fair value and, accordingly, no impairment loss existed. There were no indicators of impairment subsequent to this annual review that required further assessment.
60
Leggett & Platt, Incorporated
Notes to Consolidated Financial Statements—(Continued)
LONG-LIVED ASSETS AND ASSET IMPAIRMENT: The Company accounts for impairments of long-lived assets subject to amortization in accordance with Statement of Financial Accounting Standards (SFAS) No. 144, “Accounting for Impairment or Disposal of Long-Lived Assets.” As such, the Company evaluates long-lived assets for impairment annually and whenever events or circumstances indicate that the carrying amount may not be recoverable. When undiscounted future cash flows are not expected to be sufficient to recover the carrying amount, the asset or asset group is written down to its fair value.
STOCK-BASED COMPENSATION: Prior to 2003, the Company applied the intrinsic value based method of accounting prescribed by APB Opinion No. 25 and related interpretations in accounting for stock-based compensation plans. Accordingly, compensation cost for stock options granted prior to 2003 was measured as the excess, if any, of the quoted market price of the Company’s stock at the date of grant over the amount an employee must pay to acquire the stock.
Effective January 1, 2003, the Company adopted the preferable fair value recognition provisions of SFAS No. 123, “Accounting For Stock-Based Compensation.” The Company selected the prospective transition method permitted by SFAS No. 148, “Accounting For Stock-Based Compensation—Transition and Disclosures.” Accordingly, after January 1, 2003 the Company began expensing the fair value of stock options granted and began expensing the 15% and 20% purchase discounts allowed for under its employee stock plans. The following table illustrates the effect on net income and earnings per share as if the fair value method had been applied to all outstanding and unvested awards in each period:
| | | | | | | | | | | | |
| | 2005
| | | 2004
| | | 2003
| |
Net earnings—as reported | | $ | 251.3 | | | $ | 285.4 | | | $ | 205.9 | |
Add: Stock-based compensation cost, net of taxes, included in net earnings as reported | | | 9.6 | | | | 9.6 | | | | 7.5 | |
| | | |
Deduct: Stock-based compensation cost, net of taxes, if the fair value based method had been applied to all awards | | | (9.9 | ) | | | (11.0 | ) | | | (9.2 | ) |
| |
|
|
| |
|
|
| |
|
|
|
Pro forma net income | | $ | 251.0 | | | $ | 284.0 | | | $ | 204.2 | |
| |
|
|
| |
|
|
| |
|
|
|
Earnings per share | | | | | | | | | | | | |
Basic—as reported | | $ | 1.30 | | | $ | 1.46 | | | $ | 1.05 | |
Basic—pro forma | | | 1.30 | | | | 1.45 | | | | 1.04 | |
Diluted—as reported | | | 1.30 | | | | 1.45 | | | | 1.05 | |
Diluted—pro forma | | | 1.30 | | | | 1.44 | | | | 1.04 | |
SALES RECOGNITION: The Company recognizes sales when title and risk of loss pass to the customer. The terms of the Company’s sales are split approximately evenly between FOB shipping point and FOB destination. The timing of the Company’s recognition of FOB destination sales is determined based on shipping date and distance to the destination. The Company has no significant and unusual price protection, right of return or acceptance provisions with its customers nor is it the Company’s practice to replace goods damaged or lost in transit. Sales allowances and discounts can be reasonably estimated throughout the period and are deducted from sales in arriving at net sales. Certain aluminum segment customers have fixed pricing arrangements covering specified aggregate quantities of aluminum contained in their purchases over the terms of the agreements. The Company generally purchases in advance sufficient quantities of aluminum inventory to “hedge” this fixed pricing commitment.
SHIPPING AND HANDLING FEES AND COSTS: The Company reports Shipping and Handling Fees and Costs in accordance with Emerging Issues Task Force (“EITF”) issue No. 00-10, “Accounting for Shipping and Handling Fees and Costs.” As such, in the Consolidated Statement of Earnings all amounts billed to customers by the Company related to shipping and handling are included in “Net Sales” and the Company’s shipping and handling costs are included in “Cost of goods sold”.
61
Leggett & Platt, Incorporated
Notes to Consolidated Financial Statements—(Continued)
RESTRUCTURING COSTS: In accordance with SFAS No. 146, “Accounting for Costs Associated with Exit or Disposal Activities,” except for certain one-time termination benefits the Company recognizes a liability for costs associated with an exit or disposal activity when the liability is incurred. Certain termination benefits for which employees are required to render service are recognized ratably over the respective future service periods.
INCOME TAXES: The Company records, using enacted rates, deferred tax assets and liabilities for the future tax consequences of temporary differences between the financial reporting and tax bases of its assets and liabilities. A valuation allowance is provided to the extent realization of deferred tax assets is not considered likely.
Annual tax provisions include amounts considered sufficient to pay assessments that may result from examinations of prior year tax returns; however, the amount ultimately paid may differ from the amounts accrued. The Company accrues for tax contingencies when it is probable that a liability has been incurred and the amount of the contingency can be reasonably estimated. Provision is made for taxes on undistributed earnings of foreign subsidiaries and related companies to the extent that such earnings are not deemed to be permanently invested. The tax effect of most distributions would be offset by available foreign tax credits.
CONCENTRATION OF CREDIT RISKS, EXPOSURES AND FINANCIAL INSTRUMENTS: The Company manufactures, markets, and distributes engineered products for the various end markets described in Note L. Operations are principally located in the United States, although the Company also has operations in Canada, Europe, Latin America, Asia, Australia and South Africa.
The Company performs ongoing credit evaluations of its customers’ financial conditions and generally requires no collateral from its customers, some of which are highly leveraged. The Company maintains allowances for potential credit losses and such losses have generally been within management’s expectations.
The Company has no material guarantees or liabilities for product warranties which would require disclosure under Financial Accounting Standards Board Interpretation (FIN) No. 45, “Guarantor’s Accounting and Disclosure Requirements for Guarantees, Including Indirect Guarantees of Indebtedness of Others.”
From time to time, the Company will enter into contracts to hedge foreign currency denominated transactions, natural gas purchases, and interest rates related to the Company’s debt. To minimize the risk of counter party default, we only use highly-rated financial institutions that meet certain requirements. We do not anticipate that any of the financial institution counter parties that we deal with will default on their obligations.
The carrying value of cash and short-term financial instruments approximates fair value due to the short maturity of those instruments.
OTHER RISKS: The Company obtains insurance for workers’ compensation, automobile, product and general liability, property loss and medical claims. However, the Company has elected to retain a significant portion of expected losses through the use of deductibles. Our self-insurance liabilities include estimates for both reported claims and for claims incurred but not yet reported. Provisions for losses are recorded based upon the Company’s estimates of the aggregate liability for claims incurred utilizing the Company’s prior experience and information provided by its third-party administrators and insurance carriers.
FOREIGN CURRENCY TRANSLATION: The functional currency for most foreign operations is the local currency. The translation of foreign currencies into U.S. dollars is performed for balance sheet accounts using current exchange rates in effect at the balance sheet date and for income and expense accounts using monthly
62
Leggett & Platt, Incorporated
Notes to Consolidated Financial Statements—(Continued)
average exchange rates. The cumulative effects of translating the functional currencies into the U.S. dollar are included in comprehensive income. Foreign entities whose functional currency is the U.S. dollar are not significant.
RECLASSIFICATIONS: Certain reclassifications have been made to the prior years’ consolidated financial statements to conform to the 2005 presentation.
NEW ACCOUNTING STANDARDS: In December 2004, the Financial Accounting Standards Board issued revised Statement of Financial Accounting Standards No. 123, “Share-Based Payment” (SFAS No. 123R). SFAS 123R clarifies and expands Statement 123’s guidance in several areas, including recognizing share-based compensation cost, measuring fair value, classifying an award as equity or as a liability, and attributing compensation cost to reporting periods. SFAS 123R is effective for Leggett & Platt beginning January 1, 2006, and applies to all awards granted, modified, repurchased or cancelled on or after that date. We adopted, as of January 1, 2003, the provisions of Statement 123 as originally issued and, having evaluated SFAS No. 123R, concluded it will not have a material impact on our financial condition or results of operations.
In December 2004, the Financial Accounting Standards Board issued FASB Staff Positions FAS 109-1, “Application of FASB Statement No. 109, Accounting for Income Taxes, to the Tax Deduction on Qualified Production Activities Provided by the American Jobs Creation Act of 2004” and FAS 109-2, “Accounting and Disclosure Guidance for the Foreign Earnings Repatriation Provision within the American Jobs Creation Act of 2004.” Although we will benefit from qualified production activities deductions provided under the Act, FASB Staff Position 109-1 has not had, nor is it expected to have, a material impact on our financial reporting or disclosures. Regarding FAS 109-2, we did not remit any amounts under the repatriation provision of the American Jobs Creation Act and, therefore, the provisions of this FASB staff position had no impact on our financial reporting or disclosures.
In March 2005, the FASB issued Interpretation No. 47, “Accounting for Conditional Asset Retirement Obligations—an Interpretation of FASB Statement No. 143” (FIN-47), which clarifies the termconditional asset retirement obligation as used in FASB No. 143 and requires recognition of a liability for the fair value of a conditional asset retirement obligation when incurred, if the fair value of the liability can be reasonably estimated. FIN-47 was effective for our fiscal year ended December 31, 2005 and did not have a material impact on our financial condition or results of operations.
In May 2005, the FASB issued SFAS No. 154, “Accounting Changes and Error Corrections,” which replaces APB Opinion No. 20, “Accounting Changes,” and SFAS No. 3, “Reporting Accounting Changes in Interim Financial Statements.” SFAS No. 154 applies to all voluntary changes in accounting principle and requires retrospective application (a term defined by the statement) to prior periods’ financial statements, unless it is impracticable to determine the effect of a change. It also applies to changes required by an accounting pronouncement that does not include specific transition provisions. SFAS No. 154 is effective for accounting changes and corrections of errors made in fiscal years beginning after December 15, 2005. We will adopt SFAS No. 154 as of January 1, 2006, and do not expect its adoption will have a material impact on our financial condition or results of operations.
B—Acquisitions
During 2005, the Company acquired 12 businesses for $174.3 in cash (net of cash acquired) plus assumed debt of $35.4, of which $34.6 was repaid shortly after closing. Including debt assumed, the total cost of current year acquisitions was $209.7. In addition, $6.7 was paid as additional consideration for prior year acquisitions
63
Leggett & Platt, Incorporated
Notes to Consolidated Financial Statements—(Continued)
bringing the total cash paid in 2005 for acquisitions to $181.0. The excess of the purchase price over the fair value of the net identifiable assets acquired, and reclassifications for prior year acquisitions, increased goodwill by $85.4, of which $64.0 is expected to provide an income tax benefit.
The Company has not yet obtained all information required to complete the purchase price allocation related to certain recent acquisitions. The Company does not believe that the additional information will materially modify the preliminary purchase price allocations. In Residential Furnishings, the Company acquired ten businesses. The largest converts and/or distributes geotextiles, erosion control products and silt fencing for the geotextile, landscape, and agricultural markets. The second largest manufactures rubber and felt carpet underlay. In Specialized Products, the Company acquired a business that designs, manufactures and supplies equipment for light and medium duty commercial trucks. In Commercial Fixturing & Components, the Company acquired a business that manufactures metal fixtures and displays.
The unaudited pro forma consolidated net sales, as though the 2005 acquisitions had occurred on January 1 of each year presented, were $5,544.0 and $5,362.1 for the years ended December 31, 2005 and 2004, respectively. The unaudited pro forma consolidated net earnings and earnings per share are not materially different from the amounts reflected in the accompanying financial statements. These pro forma amounts are not necessarily indicative of either results of operations that would have occurred had the purchases been made on January 1 of each year or of future results of the combined companies.
During 2004, the Company acquired nine businesses for $38.9 in cash (net of cash acquired) plus assumed debt of $2.2, all of which was repaid shortly after closing. Including debt assumed, the total cost of 2004 acquisitions was $41.1. In addition, $7.5 was paid as additional consideration for prior year acquisitions bringing the total cash paid in 2004 for acquisitions to $46.4. The excess of the purchase price over the fair value of the net assets acquired and reclassifications for prior year acquisitions increased goodwill by $13.3, of which $13.2 is expected to provide an income tax benefit. In Residential Furnishings, the Company acquired three businesses. The largest designs and produces comforters, decorative pillows, and other “top-of-bed” accessories. In Commercial Fixturing & Components, the Company added three businesses. Two of these businesses produce injection-molded plastic components used primarily in office furniture. The Company added three businesses to the Specialized Products segment. The largest makes tubing and wire products used primarily in automotive seating.
During 2003, the Company acquired 15 businesses for $120.4 in cash (net of cash acquired) plus assumed debt of $5.3, of which $4.5 was repaid shortly after closing. Including debt assumed, the total cost of 2003 acquisitions was $125.7. The excess of the purchase price over the fair value of the net assets acquired and reclassifications for prior year acquisitions increased goodwill by $54.5, of which $43.7 is expected to provide an income tax benefit. In Residential Furnishings, the Company acquired nine businesses. The largest designs, manufactures and markets adjustable beds in the “leisure” product category. In Commercial Fixturing & Components, the Company acquired three businesses. The largest manufactures a broad range of standard and custom metal and wood store fixtures. In Specialized Products, the Company acquired three businesses.
The results of operations of the above acquired companies have been included in the consolidated financial statements since the dates of acquisition. The terms of certain of the Company’s acquisition agreements provide for additional consideration to be paid if the acquired company’s performance exceeds certain targeted levels. Such additional consideration may be paid in cash, and is recorded when earned as additional purchase price. At December 31, 2005, the maximum remaining amount of additional consideration is approximately $17 and will be payable, if earned, through 2008.
64
Leggett & Platt, Incorporated
Notes to Consolidated Financial Statements—(Continued)
C—Goodwill and Other Intangible Assets
The changes in the carrying amount of goodwill are as follows:
| | | | | | | | | | | | | | | | | | | | | | | |
| | Residential Furnishings
| | | Commercial Fixturing & Components
| | | Aluminum Products
| | Industrial Materials
| | | Specialized Products
| | | Total
| |
Balance as of January 1, 2004 | | $ | 336.1 | | | $ | 372.4 | | | $ | 83.3 | | $ | 29.9 | | | $ | 167.8 | | | $ | 989.5 | |
Additions | | | 2.4 | | | | 8.7 | | | | — | | | — | | | | 8.5 | | | | 19.6 | |
Adjustments to finalize purchase price allocation | | | (6.5 | ) | | | (.2 | ) | | | — | | | .3 | | | | .1 | | | | (6.3 | ) |
| |
|
|
| |
|
|
| |
|
| |
|
|
| |
|
|
| |
|
|
|
| | | (4.1 | ) | | | 8.5 | | | | — | | | .3 | | | | 8.6 | | | | 13.3 | |
Goodwill written off related to sale of facilities | | | — | | | | — | | | | — | | | — | | | | (.1 | ) | | | (.1 | ) |
Foreign currency translation adjustment/other | | | 6.9 | | | | 5.6 | | | | — | | | .4 | | | | 13.3 | | | | 26.2 | |
| |
|
|
| |
|
|
| |
|
| |
|
|
| |
|
|
| |
|
|
|
Balance as of December 31, 2004 | | | 338.9 | | | | 386.5 | | | | 83.3 | | | 30.6 | | | | 189.6 | | | | 1,028.9 | |
Additions | | | 37.2 | | | | 2.2 | | | | — | | | — | | | | 45.2 | | | | 84.6 | |
Adjustments to finalize purchase price allocation | | | — | | | | .4 | | | | — | | | — | | | | .4 | | | | .8 | |
| |
|
|
| |
|
|
| |
|
| |
|
|
| |
|
|
| |
|
|
|
| | | 37.2 | | | | 2.6 | | | | — | | | — | | | | 45.6 | | | | 85.4 | |
Goodwill written off related to sale of facilities | | | (1.1 | ) | | | — | | | | — | | | — | | | | (.8 | ) | | | (1.9 | ) |
Foreign currency translation adjustment/other | | | (1.7 | ) | | | .7 | | | | — | | | (.4 | ) | | | (8.5 | ) | | | (9.9 | ) |
| |
|
|
| |
|
|
| |
|
| |
|
|
| |
|
|
| |
|
|
|
Balance as of December 31, 2005 | | $ | 373.3 | | | $ | 389.8 | | | $ | 83.3 | | $ | 30.2 | | | $ | 225.9 | | | $ | 1,102.5 | |
| |
|
|
| |
|
|
| |
|
| |
|
|
| |
|
|
| |
|
|
|
Intangible assets acquired during the year and included in “Other intangibles” on the Consolidated Balance Sheets are as follows:
| | | | | | | | | | |
| | 2005
| | 2004
|
| | Gross Carrying Amount
| | Weighted Average Amortization Period in Years
| | Gross Carrying Amount
| | Weighted Average Amortization Period in Years
|
Non-compete agreements | | $ | 9.6 | | 7.6 | | $ | 7.3 | | 6.9 |
Customer related intangibles | | | 52.7 | | 12.1 | | | 7.9 | | 9.5 |
Patents and trademarks | | | 9.3 | | 11.3 | | | 12.6 | | 18.6 |
Deferred financing and other costs | | | 7.8 | | 7.0 | | | 3.3 | | 7.9 |
| |
|
| |
| |
|
| |
|
| | $ | 79.4 | | 10.9 | | $ | 31.1 | | 11.8 |
| |
|
| |
| |
|
| |
|
Out of $79.4 additions to intangibles, $68.5 is related to business acquisitions.
65
Leggett & Platt, Incorporated
Notes to Consolidated Financial Statements—(Continued)
The gross carrying amount and accumulated amortization by major amortized intangible asset class is as follows:
| | | | | | | | | | | | |
| | December 31
|
| | 2005
| | 2004
|
| | Gross Carrying Amount
| | Accumulated Amortization
| | Gross Carrying Amount
| | Accumulated Amortization
|
Non-compete agreements | | $ | 29.5 | | $ | 9.5 | | $ | 26.8 | | $ | 12.7 |
Customer related intangibles | | | 64.7 | | | 3.6 | | | 12.7 | | | 1.5 |
Patents and trademarks | | | 48.0 | | | 11.4 | | | 42.6 | | | 9.8 |
Deferred financing and other costs | | | 22.6 | | | 6.8 | | | 18.8 | | | 8.5 |
| |
|
| |
|
| |
|
| |
|
|
| | $ | 164.8 | | $ | 31.3 | | $ | 100.9 | | $ | 32.5 |
| |
|
| |
|
| |
|
| |
|
|
Aggregate amortization expense for other intangible assets was $10.3, $10.5 and $8.4 for the years ended December 31, 2005, 2004 and 2003, respectively.
Estimated amortization expense for each of the five years following 2005 is as follows:
| | | |
2006 | | $ | 16.0 |
2007 | | | 15.3 |
2008 | | | 13.7 |
2009 | | | 12.5 |
2010 | | | 11.1 |
D—Accounts and Other Receivables
Accounts and other receivables consisted of the following at December 31, 2005 and 2004:
| | | | | | | | |
| | 2005
| | | 2004
| |
Trade | | $ | 832.4 | | | $ | 779.2 | |
Other | | | 36.0 | | | | 29.5 | |
| |
|
|
| |
|
|
|
Total accounts and other receivables | | | 868.4 | | | | 808.7 | |
Allowance for doubtful accounts | | | (20.8 | ) | | | (18.0 | ) |
| |
|
|
| |
|
|
|
Total | | $ | 847.6 | | | $ | 790.7 | |
| |
|
|
| |
|
|
|
66
Leggett & Platt, Incorporated
Notes to Consolidated Financial Statements—(Continued)
E—Earnings Per Share
Basic and diluted earnings per share were calculated as follows:
| | | | | | | | | |
| | 2005
| | 2004
| | 2003
|
Basic | | | | | | | | | |
Weighted average shares outstanding, including shares issuable for little or no cash | | | 192,637,308 | | | 195,699,972 | | | 196,548,473 |
| |
|
| |
|
| |
|
|
Net earnings | | $ | 251.3 | | $ | 285.4 | | $ | 205.9 |
| |
|
| |
|
| |
|
|
Earnings per share | | $ | 1.30 | | $ | 1.46 | | $ | 1.05 |
| |
|
| |
|
| |
|
|
Diluted | | | | | | | | | |
Weighted average shares outstanding, including shares issuable for little or no cash | | | 192,637,308 | | | 195,699,972 | | | 196,548,473 |
Additional dilutive shares principally from the assumed exercise of outstanding stock options | | | 937,379 | | | 1,175,643 | | | 405,403 |
| |
|
| |
|
| |
|
|
| | | 193,574,687 | | | 196,875,615 | | | 196,953,876 |
| |
|
| |
|
| |
|
|
Net earnings | | $ | 251.3 | | $ | 285.4 | | $ | 205.9 |
| |
|
| |
|
| |
|
|
Earnings per share | | $ | 1.30 | | $ | 1.45 | | $ | 1.05 |
| |
|
| |
|
| |
|
|
In 2005, approximately 3.5 million of the total 12.4 million shares issuable under employee and non-employee stock options were excluded from the calculation of diluted earnings per share as their inclusion would have been anti-dilutive.
F—Supplemental Balance Sheet Information
Sundry assets, accrued expenses, and other current liabilities at December 31 consist of the following:
| | | | | | |
| | 2005
| | 2004
|
Sundry assets | | | | | | |
Prepaid pension costs | | $ | 35.1 | | $ | 35.0 |
Other | | | 47.1 | | | 39.4 |
| |
|
| |
|
|
| | $ | 82.2 | | $ | 74.4 |
| |
|
| |
|
|
Accrued expenses | | | | | | |
Wages and commissions payable | | $ | 69.1 | | $ | 68.7 |
Workers’ compensation, medical, auto and product liability | | | 68.4 | | | 42.1 |
Sales promotions | | | 42.9 | | | 37.5 |
Other | | | 98.9 | | | 91.2 |
| |
|
| |
|
|
| | $ | 279.3 | | $ | 239.5 |
| |
|
| |
|
|
Other current liabilities | | | | | | |
Outstanding checks in excess of book balances | | $ | 57.7 | | $ | 46.5 |
Dividends payable | | | 29.3 | | | 28.5 |
Other | | | 18.9 | | | 19.4 |
| |
|
| |
|
|
| | $ | 105.9 | | $ | 94.4 |
| |
|
| |
|
|
67
Leggett & Platt, Incorporated
Notes to Consolidated Financial Statements—(Continued)
G—Long-Term Debt
Long-term debt, weighted average interest rates and due dates at December 31 are as follows:
| | | | | | |
| | 2005
| | 2004
|
Term notes, net—average interest rates of 5.2% and 4.2% for 2005 and 2004, respectively, due dates through 2018 | | $ | 913.0 | | $ | 1,089.5 |
Industrial development bonds, principally variable interest rates of 4.0% and 2.5% for 2005 and 2004, respectively, due dates through 2030 | | | 40.2 | | | 40.7 |
Bank note, variable interest rate based on 90-day Euribor plus .25%, principal and interest due quarterly through 2010 | | | 37.1 | | | — |
Capitalized leases | | | 20.5 | | | 34.5 |
Other, partially secured | | | 9.4 | | | 16.0 |
| |
|
| |
|
|
| | | 1,020.2 | | | 1,180.7 |
Less current maturities | | | 98.6 | | | 401.3 |
| |
|
| |
|
|
| | $ | 921.6 | | $ | 779.4 |
| |
|
| |
|
|
On August 12, 2005, the Company issued $200 of 10-year notes with a coupon rate of 5.0%. The Company had treasury lock agreements in the amount of $80 attached to this issuance, a $2.3 gain on which is being amortized over the life of the notes. This was the Company’s fourth debt offering since early 2003. These four issuances comprise $730 of long-term debt, with a weighted average remaining life of 9.5 years and a weighted average coupon of 4.7%.
During the first quarter of 2003, the Company liquidated an interest rate swap agreement it had entered into in February 2000 on a $350 term note, and received $39.9 in cash proceeds. The market value adjustment at the date the swap was liquidated (equivalent to the proceeds from liquidation of the swap agreement) was amortized over the remaining life of the term note, which matured on February 15, 2005. The unamortized market value adjustment of the liquidated swap agreement was $2.5 at December 31, 2004.
On December 16, 2003, the Company entered into a cross-currency rate swap agreement with Wachovia Bank, N.A. See Note P for more discussion of this agreement.
At December 31, 2005, the Company had $400 of debt capital available through a commercial paper program supported by $400 in syndicated revolving credit agreements. Under the syndicated agreements, the Company may elect to pay interest based on 1) the bank’s base lending rate, 2) LIBOR, 3) an adjusted certificate of deposit rate, or 4) the money market rate, as specified in the revolving credit agreements. These agreements will terminate on July 31, 2010, at which time any outstanding balances will become due. There were no amounts outstanding under any revolving credit agreements at December 31, 2005 and 2004.
The revolving credit agreements and certain other long-term debt contain restrictive covenants which, among other restrictions, limit the amount of debt in relation to the Company’s total capitalization, the total amount of secured debt, and asset sales. The Company remained in compliance with all such covenants during the years ended December 31, 2005 and 2004.
68
Leggett & Platt, Incorporated
Notes to Consolidated Financial Statements—(Continued)
Maturities of long-term debt are as follows:
| | | |
Year ended December 31 | | | |
2006 | | $ | 98.6 |
2007 | | | 36.1 |
2008 | | | 82.5 |
2009 | | | 25.7 |
2010 | | | 19.3 |
Thereafter | | | 758.0 |
| |
|
|
| | $ | 1,020.2 |
| |
|
|
H—Lease Obligations
The Company leases certain operating facilities, most of its automotive and trucking equipment and various other assets. Lease terms, including purchase options, renewals and maintenance costs, vary by lease.
Total rental expense included in the results of operations was $62.0, $59.0 and $55.4 for the years ended December 31, 2005, 2004 and 2003, respectively.
Future minimum rental commitments for all long-term noncancelable operating leases are as follows:
| | | |
Year ended December 31 | | | |
2006 | | $ | 49.6 |
2007 | | | 35.3 |
2008 | | | 25.9 |
2009 | | | 19.3 |
2010 | | | 14.5 |
Later years | | | 16.0 |
| |
|
|
| | $ | 160.6 |
| |
|
|
The above lease obligations expire at various dates through 2014. Certain leases contain renewal and/or purchase options. Aggregate rental commitments above include renewal amounts where it is the intention of the Company to renew the lease.
69
Leggett & Platt, Incorporated
Notes to Consolidated Financial Statements—(Continued)
I—Capital Stock and Stock Based Compensation
STOCK ACTIVITY
Activity in the Company’s stock accounts for each of the three years ended December 31 is as follows:
| | | | | |
| | Common Stock
| | Treasury Stock
| |
Balance, January 1, 2003 | | 198,799,543 | | (4,300,923 | ) |
Shares issued | | — | | 1,614,003 | |
Treasury stock purchased | | — | | (4,009,929 | ) |
| |
| |
|
|
Balance, December 31, 2003 | | 198,799,543 | | (6,696,849 | ) |
Shares issued | | — | | 2,813,791 | |
Treasury stock purchased | | — | | (4,030,467 | ) |
| |
| |
|
|
Balance, December 31, 2004 | | 198,799,543 | | (7,913,525 | ) |
Shares issued | | — | | 1,960,433 | |
Treasury stock purchased | | — | | (10,269,917 | ) |
| |
| |
|
|
Balance, December 31, 2005 | | 198,799,543 | | (16,223,009 | ) |
| |
| |
|
|
The Company issues shares for employee and director stock plans and acquisitions. The Company purchases its common stock to replace shares issued under the employee stock plans and those issued in acquisitions, to satisfy contractual obligations, and for investment purposes. The Company also receives shares surrendered to pay the exercise price in stock option exercises.
At December 31, 2005, a combined total of 23,353,005 common shares were authorized for issuance under employee and non-employee stock plans. This amount represents 12,449,938 unexercised options, 2,145,733 outstanding stock units, and 8,757,334 shares available for grant under the Company’s Flexible Stock Plan. All stock units are considered equivalent to outstanding common shares for accounting and earnings per share purposes.
Stock-Based Compensation Plans
The Company’s total expense related to its stock-based compensation plans was $14.1, $12.0 and $11.9 for 2005, 2004 and 2003, respectively. Upon the adoption of SFAS No. 123 on January 1, 2003, we began expensing both the fair value of granted options and the purchase discounts provided for under our various stock-based programs as described below. As such, these amounts reflect the options granted and discounts provided after that date.
The Company has a stock plan (the Flexible Stock Plan) that provides for the grant of various types of equity awards to employees, non-employee directors, and consultants. We grant stock options annually on a discretionary basis to a broad group of employees. Options generally become exercisable over 42 months in one-third increments beginning 18 months after the date of grant, have a maximum term of ten years, and are issued with exercise prices at market. We currently limit our use of restricted stock to non-employee directors.
The Company offers a deferred compensation program under which senior management may elect to receive stock options and/or stock units in lieu of cash compensation. Prior to 2005, options granted under the program were below market. In 2005, the Company began to exclusively grant “at market” stock options under the program. Options granted after December 31, 2003, have a maximum term of ten years. Previously, the
70
Leggett & Platt, Incorporated
Notes to Consolidated Financial Statements—(Continued)
options had 15-year terms. Options granted under the program vest as the associated compensation is earned and are exercisable beginning 15 months after the date of grant. Stock units are issued under the program at a 20% discount to the market price of the Company’s common stock and vest as the associated compensation is earned.
The Company has two stock-based retirement plans: the tax-qualified Stock Bonus Plan (SBP) and the non-qualified Executive Stock Unit Program (ESUP). The Company makes contributions of 50% of the amount of employee contributions under both plans. In addition, the Company fully matches its contributions when certain profitability levels, as defined in the SBP and the ESUP, have been attained. Contributions to the ESUP acquire stock units at 85% of the market price while contributions to the SBP are used to purchase the Company’s common stock at market prices.
Finally, the Company offers a tax-qualified employee stock purchase plan, the Discount Stock Plan (DSP). Under the DSP, eligible employees may purchase shares of Company common stock at 85% of the closing market price on the last business day of each month. Shares purchased under the DSP were 654,283 in 2005, 636,842 in 2004, and 765,388 in 2003. Purchase prices ranged from $16 to $25 per share. Since inception of the DSP in 1982, a total of 19,284,048 shares have been purchased by employees. A maximum of 23,000,000 shares may be purchased under the plan.
STOCK OPTIONS
A summary of the Company’s employee stock option plans as of December 31, 2005, 2004 and 2003, and changes during the years then ended, is as follows:
| | | | | | |
| | Shares
| | | Weighted Average Exercise Price per Share
|
Outstanding at January 1, 2003 | | 10,051,727 | | | $ | 14.49 |
Granted | | 2,237,727 | | | | 14.39 |
Exercised | | (344,051 | ) | | | 11.84 |
Forfeited | | (609,805 | ) | | | 21.64 |
| |
|
| |
|
|
Outstanding at December 31, 2003 | | 11,335,598 | | | | 14.17 |
Granted | | 1,951,475 | | | | 22.80 |
Exercised | | (1,682,967 | ) | | | 16.87 |
Forfeited | | (240,835 | ) | | | 19.31 |
| |
|
| |
|
|
Outstanding at December 31, 2004 | | 11,363,271 | | | | 15.31 |
Granted | | 1,941,472 | | | | 25.87 |
Exercised | | (748,668 | ) | | | 17.17 |
Forfeited | | (273,265 | ) | | | 21.26 |
| |
|
| |
|
|
Outstanding at December 31, 2005 | | 12,282,810 | | | $ | 16.75 |
| |
|
| |
|
|
Options exercisable at | | | | | | |
December 31, 2005 | | 9,117,447 | | | $ | 14.35 |
December 31, 2004 | | 7,912,044 | | | | 12.47 |
December 31, 2003 | | 7,716,615 | | | | 12.89 |
71
Leggett & Platt, Incorporated
Notes to Consolidated Financial Statements—(Continued)
The following table summarizes information about employee stock options outstanding at December 31, 2005:
| | | | | | | | | | | | |
| | Options Outstanding
| | Options Exercisable
|
Range of Exercise Prices
| | Number Outstanding
| | Weighted-Average Remaining Contractual Life In Years
| | Weighted- Average Exercise Price
| | Number Exercisable
| | Weighted- Average Exercise Price
|
$ .01–$ .25 | | 1,014,568 | | 5.5 | | $ | .06 | | 1,014,568 | | $ | .06 |
3.09– 4.82 | | 2,240,963 | | 10.5 | | | 3.90 | | 2,240,963 | | | 3.90 |
10.00– 15.00 | | 35,222 | | 2.9 | | | 13.85 | | 35,222 | | | 13.85 |
15.31– 20.00 | | 3,728,107 | | 4.8 | | | 18.79 | | 3,331,993 | | | 18.90 |
20.03– 28.67 | | 5,263,950 | | 8.0 | | | 24.01 | | 2,494,701 | | | 23.48 |
| |
| |
| |
|
| |
| |
|
|
$ .01–$28.67 | | 12,282,810 | | 7.3 | | $ | 16.75 | | 9,117,447 | | $ | 14.35 |
| |
| |
| |
|
| |
| |
|
|
The following table summarizes the weighted-average fair value per share of each option granted during the years 2005, 2004 and 2003 as of the grant date. These values are calculated using the Black-Scholes option pricing model based on these weighted-average assumptions.
| | | | | | | | | | | | |
| | 2005
| | | 2004
| | | 2003
| |
Weighted-average fair value of options: | | | | | | | | | | | | |
Granted at market price | | $ | 5.35 | | | $ | 4.65 | | | $ | 3.35 | |
Granted below market price | | | N/A | | | $ | 16.85 | | | $ | 9.44 | |
Weighted-average exercise price of options: | | | | | | | | | | | | |
Granted at market price | | $ | 25.87 | | | $ | 22.99 | | | $ | 18.27 | |
Granted below market price | | | N/A | | | $ | 3.63 | | | $ | 4.09 | |
Principal assumptions: | | | | | | | | | | | | |
Risk-free interest rate | | | 4.0 | % | | | 3.2 | % | | | 2.9 | % |
Expected life in years | | | 6.3 | | | | 6.0 | | | | 6.4 | |
Expected volatility (over expected life) | | | 25.7 | % | | | 28.3 | % | | | 29.3 | % |
Expected dividend yield (over expected life) | | | 3.3 | % | | | 3.7 | % | | | 4.4 | % |
SHAREHOLDER PROTECTION RIGHTS PLAN
In 1989, the Company declared a dividend distribution of one preferred stock purchase right (a Right) for each share of common stock. The Rights are attached to and traded with the Company’s common stock. The Rights become exercisable only under certain circumstances involving actual or potential acquisitions of the Company’s common stock. The Rights currently remain in existence until February 2009, unless they are exercised, exchanged or redeemed at an earlier date. Depending upon the circumstances, if these Rights become exercisable, the holder may be entitled to purchase shares of Series A junior preferred stock of the Company, shares of the Company’s common stock or shares of common stock of the acquiring entity.
72
Leggett & Platt, Incorporated
Notes to Consolidated Financial Statements—(Continued)
J—Employee Benefit Plans
This footnote provides information at December 31 as to the Company’s sponsored domestic and foreign defined benefit pension plans as required by Statement of Financial Accounting Standards 132 (revised 2003), “Employers’ Disclosures about Pensions and Other Postretirement Benefits.” The Company uses a September 30 measurement date for the majority of its plans.
| | | | | | | | | | | | |
| | 2005
| | | 2004
| | | 2003
| |
Change in Benefit Obligation | | | | | | | | | | | | |
Benefit obligation, beginning of period | | $ | 192.2 | | | $ | 168.2 | | | $ | 155.5 | |
Service cost | | | 5.2 | | | | 5.2 | | | | 4.2 | |
Interest cost | | | 10.9 | | | | 10.2 | | | | 9.0 | |
Plan participants’ contributions | | | 6.2 | | | | 5.9 | | | | 5.6 | |
Actuarial losses | | | 25.9 | | | | 11.1 | | | | 1.1 | |
Benefits paid | | | (10.8 | ) | | | (10.9 | ) | | | (9.9 | ) |
Foreign currency exchange rate changes | | | (2.1 | ) | | | 2.5 | | | | 2.7 | |
| |
|
|
| |
|
|
| |
|
|
|
Benefit obligation, end of period | | | 227.5 | | | | 192.2 | | | | 168.2 | |
Change in Plan Assets | | | | | | | | | | | | |
Fair value of plan assets, beginning of period | | | 189.1 | | | | 174.5 | | | | 154.2 | |
Actual return on plan assets | | | 21.9 | | | | 16.0 | | | | 21.3 | |
Employer contributions | | | 1.8 | | | | 2.2 | | | | 1.5 | |
Plan participants’ contributions | | | 6.2 | | | | 5.9 | | | | 5.6 | |
Benefits paid | | | (10.8 | ) | | | (10.9 | ) | | | (9.9 | ) |
Foreign currency exchange rate changes | | | (1.1 | ) | | | 1.4 | | | | 1.8 | |
| |
|
|
| |
|
|
| |
|
|
|
Fair value of plan assets, end of period | | | 207.1 | | | | 189.1 | | | | 174.5 | |
Plan Assets (Under) Over Benefit Obligations | | | (20.4 | ) | | | (3.1 | ) | | | 6.3 | |
Unrecognized net actuarial losses | | | 50.5 | | | | 33.2 | | | | 24.8 | |
Unrecognized net transition asset | | | — | | | | — | | | | .1 | |
Unrecognized prior service cost | | | 2.0 | | | | 2.5 | | | | 2.6 | |
| |
|
|
| |
|
|
| |
|
|
|
Net prepaid pension cost | | $ | 32.1 | | | $ | 32.6 | | | $ | 33.8 | |
| |
|
|
| |
|
|
| |
|
|
|
The net prepaid pension cost amount recognized in the Consolidated Balance Sheets at December 31 is as follows: | | | | | | | | | | | | |
Prepaid pension costs | | $ | 35.1 | | | $ | 35.0 | | | $ | 40.4 | |
Accrued pension benefit liabilities | | | (18.8 | ) | | | (17.0 | ) | | | (6.6 | ) |
Intangible assets | | | 2.6 | | | | 3.3 | | | | — | |
Accumulated other comprehensive income | | | 13.2 | | | | 11.3 | | | | — | |
| |
|
|
| |
|
|
| |
|
|
|
Net amount recognized | | $ | 32.1 | | | $ | 32.6 | | | $ | 33.8 | |
| |
|
|
| |
|
|
| |
|
|
|
Components of Net Pension (Expense) Income | | | | | | | | | | | | |
Service cost | | $ | (5.2 | ) | | $ | (5.2 | ) | | $ | (4.2 | ) |
Interest cost | | | (10.9 | ) | | | (10.2 | ) | | | (9.0 | ) |
Expected return on plan assets | | | 14.8 | | | | 14.0 | | | | 12.4 | |
Amortization of net transition asset | | | — | | | | (.1 | ) | | | (.1 | ) |
Recognized net actuarial loss | | | (1.0 | ) | | | (1.9 | ) | | | (1.4 | ) |
| |
|
|
| |
|
|
| |
|
|
|
Net pension (expense) | | $ | (2.3 | ) | | $ | (3.4 | ) | | $ | (2.3 | ) |
| |
|
|
| |
|
|
| |
|
|
|
Weighted Average Assumptions:* | | | | | | | | | | | | |
Discount rate | | | 5.5 | % | | | 5.9 | % | | | 6.0 | % |
Expected return on plan assets | | | 7.9 | % | | | 7.9 | % | | | 7.9 | % |
Rate of compensation increase | | | 4.1 | % | | | 4.5 | % | | | 4.5 | % |
| * | Used in the calculation of both benefit obligations and net pension costs. |
73
Leggett & Platt, Incorporated
Notes to Consolidated Financial Statements—(Continued)
The Company uses the average of the Citigroup Pension Liability Index rate and Merrill Lynch AA-AAA 10 yr. Bond Index rate to determine the discount rate used for its major pension plans (rounded to the nearest 25 basis points). The Citigroup Index rate is a calculated rate using yearly spot rates matched against expected future benefit payments. The Merrill Lynch Index rate is based on the weighted average yield of a portfolio of high grade Corporate Bonds with an average duration approximating the plans’ projected benefit payments, adjusted for any callable bonds included in the portfolio. In 2005, we reduced the discount rate for our major pension plans to 5.5% from the 6.0% which had been used in 2004 and 2003. The discount rates used for the Company’s other, primarily foreign, plans are based on rates appropriate for the respective country and plan obligations.
The overall expected long-term rate of return is based on each plans’ historical experience and the Company’s expectations of future returns based upon each plans’ investment holdings.
The accumulated benefit obligation for all defined benefit pension plans was $207.0, $174.6 and $152.4 at December 31, 2005, 2004 and 2003, respectively.
Those plans that have benefit obligations in excess of plan assets at December 31 are recapped below.
| | | | | | | | | |
| | 2005
| | 2004
| | 2003
|
Aggregated plans with accumulated benefit obligations in excess of plan assets: | | | | | | | | | |
Projected benefit obligation | | $ | 74.0 | | $ | 66.9 | | $ | 47.8 |
Accumulated benefit obligation | | | 71.5 | | | 64.0 | | | 46.7 |
Fair value of plan assets | | | 52.3 | | | 47.5 | | | 35.2 |
Aggregated plans with projected benefit obligations in excess of plan assets: | | | | | | | | | |
Projected benefit obligation | | | 123.7 | | | 99.8 | | | 87.6 |
Accumulated benefit obligation | | | 108.6 | | | 87.3 | | | 75.6 |
Fair value of plan assets | | | 115.0 | | | 100.6 | | | 93.5 |
The increase in minimum pension liability included in other comprehensive income is $1.2, net of tax of $.9.
Included in the above plans is a subsidiary’s unfunded supplemental executive retirement plan. The subsidiary owns insurance policies with cash surrender values of $2.0, $1.8 and $2.0 at December 31, 2005, 2004 and 2003, respectively, for the participants in this non-qualified plan. These insurance policies are not included in the plan’s assets.
Plan assets are invested in diversified portfolios of equity, debt and government securities. The aggregate allocation of these investments is as follows:
| | | | | | | | | |
| | 2005
| | | 2004
| | | 2003
| |
Asset Category | | | | | | | | | |
Equity securities | | 69 | % | | 66 | % | | 58 | % |
Debt securities | | 22 | | | 26 | | | 27 | |
Other, including cash | | 9 | | | 8 | | | 15 | |
| |
|
| |
|
| |
|
|
Total | | 100 | % | | 100 | % | | 100 | % |
| |
|
| |
|
| |
|
|
The Company’s investment policy and strategies are established with a long-term view in mind. The Company strives for a sufficiently diversified asset mix to minimize the risk of a material loss to a portfolio’s value due to the devaluation of any single investment. In determining the appropriate asset mix, the Company’s financial strength and ability to fund potential shortfalls that might result from poor investment performance are considered. The Company’s weighted average target percentages of the asset portfolios are 75% equities and 25% bonds.
74
Leggett & Platt, Incorporated
Notes to Consolidated Financial Statements—(Continued)
The Company expects to contribute $2.1 to its defined benefit pension plans in 2006.
Estimated benefit payments, which reflect expected future service, to be paid over the next ten years are: 2006—$11.6; 2007—$12.4; 2008—$12.8; 2009—$13.9; 2010—$14.6; and 2011-2015—$88.7.
Total net pension expense, including multiemployer plans and other defined contribution plans, was $7.9, $8.8 and $7.0 in 2005, 2004 and 2003, respectively.
Contributions to union sponsored, defined benefit, multiemployer pension plans were less than $1.5 in 2005, 2004 and 2003. These plans are not administered by the Company and contributions are determined in accordance with provisions of negotiated labor contracts. While the Company has no present intention of withdrawing from any of these plans, nor has it been informed that there is an intention to terminate any such plan, the Company does not believe there would be a material withdrawal liability in such event.
K—Income Taxes
The components of earnings before income taxes are as follows:
| | | | | | | | | |
| | Year ended December 31
|
| | 2005
| | 2004
| | 2003
|
Domestic | | $ | 317.8 | | $ | 347.7 | | $ | 247.6 |
Foreign | | | 38.4 | | | 74.9 | | | 67.5 |
| |
|
| |
|
| |
|
|
| | $ | 356.2 | | $ | 422.6 | | $ | 315.1 |
| |
|
| |
|
| |
|
|
Income tax expense is comprised of the following components:
| | | | | | | | | | | | |
| | Year ended December 31
| |
| | 2005
| | | 2004
| | | 2003
| |
Current | | | | | | | | | | | | |
Federal | | $ | 113.1 | | | $ | 100.4 | | | $ | 66.3 | |
State and local | | | 9.1 | | | | 11.3 | | | | 4.1 | |
Foreign | | | 18.3 | | | | 22.1 | | | | 22.9 | |
| |
|
|
| |
|
|
| |
|
|
|
| | | 140.5 | | | | 133.8 | | | | 93.3 | |
Deferred | | | | | | | | | | | | |
Federal | | | (21.8 | ) | | | 11.3 | | | | 14.2 | |
State and local | | | (3.0 | ) | | | (6.5 | ) | | | 3.5 | |
Foreign | | | (10.8 | ) | | | (1.4 | ) | | | (1.8 | ) |
| |
|
|
| |
|
|
| |
|
|
|
| | | (35.6 | ) | | | 3.4 | | | | 15.9 | |
| |
|
|
| |
|
|
| |
|
|
|
| | $ | 104.9 | | | $ | 137.2 | | | $ | 109.2 | |
| |
|
|
| |
|
|
| |
|
|
|
75
Leggett & Platt, Incorporated
Notes to Consolidated Financial Statements—(Continued)
Deferred income taxes are provided for the temporary differences between the financial reporting basis and the tax basis of the Company’s assets and liabilities. The major temporary differences that give rise to deferred tax assets or liabilities are as follows:
| | | | | | | | | | | | | | | | |
| | December 31
| |
| | 2005
| | | 2004
| |
| | Assets
| | | Liabilities
| | | Assets
| | | Liabilities
| |
Property, plant and equipment | | $ | 8.3 | | | $ | (84.5 | ) | | $ | — | | | $ | (83.5 | ) |
Accrued expenses | | | 105.3 | | | | — | | | | 81.9 | | | | — | |
Net operating loss and tax credit carryforwards | | | 74.9 | | | | — | | | | 47.5 | | | | — | |
Pension cost | | | 7.2 | | | | (15.4 | ) | | | — | | | | (10.6 | ) |
Intangible assets | | | 8.0 | | | | (75.1 | ) | | | 9.2 | | | | (50.8 | ) |
Other | | | 13.7 | | | | (40.0 | ) | | | 10.1 | | | | (25.8 | ) |
| |
|
|
| |
|
|
| |
|
|
| |
|
|
|
Gross deferred tax assets (liabilities) | | | 217.4 | | | | (215.0 | ) | | | 148.7 | | | | (170.7 | ) |
Valuation allowance | | | (38.0 | ) | | | — | | | | (29.0 | ) | | | — | |
| |
|
|
| |
|
|
| |
|
|
| |
|
|
|
Total deferred taxes | | $ | 179.4 | | | $ | (215.0 | ) | | $ | 119.7 | | | $ | (170.7 | ) |
| |
|
|
| |
|
|
| |
|
|
| |
|
|
|
Net deferred tax liability | | | | | | $ | (35.6 | ) | | | | | | $ | (51.0 | ) |
| | | | | |
|
|
| | | | | |
|
|
|
The valuation allowance primarily relates to net operating loss and tax credit carryforwards for which utilization is uncertain. Cumulative tax losses in certain state and foreign jurisdictions during recent years, and limited carryforward periods in certain jurisdictions, were factors considered in determining the valuation allowance. Generally, no significant amount of carryforwards expire in any one year. However, $16.2 of the carryforwards will expire in 2016.
The Company recognized excess tax benefits of approximately $2.2, $4.4 and $.6 in 2005, 2004 and 2003, respectively, related to the exercise of employee stock options, which have been recorded as increases to additional contributed capital.
In 2005, the Company completed a foreign entity restructuring and cash repatriation transaction that resulted in the recognition of a deferred tax asset related to foreign losses and foreign taxes. Overall, the transaction generated a gross Foreign Tax Credit (FTC) benefit of $17.5 which was reduced by an $8 valuation allowance. The valuation allowance was recorded due to significant uncertainty regarding the Company’s ability to realize all of the FTC benefit. It is reasonably possible that changes in facts and circumstances will occur within the next year that will require an adjustment to the valuation allowance.
Deferred income taxes and withholding taxes have been provided on earnings of the Company’s foreign subsidiaries to the extent it is anticipated that the earnings will be remitted in the future as dividends. The tax effect of most distributions would be significantly offset by available foreign tax credits.
Deferred income taxes and withholding taxes have not been provided on undistributed earnings which management has deemed to be permanently reinvested. The cumulative undistributed earnings as of December 31, 2005 which the Company has deemed to be permanently reinvested are approximately $84.1. If such earnings were distributed, the resulting incremental taxes would be approximately $10.7 based on present income tax laws, which are subject to change.
76
Leggett & Platt, Incorporated
Notes to Consolidated Financial Statements—(Continued)
Deferred tax assets and liabilities included in the consolidated balance sheets are as follows:
| | | | | | | | |
| | December 31
| |
| | 2005
| | | 2004
| |
Other current assets | | $ | 23.8 | | | $ | 14.4 | |
Deferred income taxes | | | (59.4 | ) | | | (65.4 | ) |
| |
|
|
| |
|
|
|
| | $ | (35.6 | ) | | $ | (51.0 | ) |
| |
|
|
| |
|
|
|
Income tax expense, as a percentage of earnings before income taxes, differs from the statutory federal income tax rate as follows:
| | | | | | | | | |
| | Year ended December 31
| |
| | 2005
| | | 2004
| | | 2003
| |
Statutory federal income tax rate | | 35.0 | % | | 35.0 | % | | 35.0 | % |
Increases (decreases) in rate resulting from: | | | | | | | | | |
State taxes, net of federal benefit | | 1.2 | | | .9 | | | 1.6 | |
Taxes on foreign earnings | | (1.8 | ) | | (1.1 | ) | | (.7 | ) |
Recognition of foreign deferred tax assets | | (2.6 | ) | | (.9 | ) | | (1.3 | ) |
Permanent differences | | (1.2 | ) | | (.8 | ) | | (.5 | ) |
Other | | (1.1 | ) | | (.6 | ) | | .6 | |
| |
|
| |
|
| |
|
|
Effective tax rate | | 29.5 | % | | 32.5 | % | | 34.7 | % |
| |
|
| |
|
| |
|
|
L—Segment Information
Reportable segments are primarily based upon the Company’s management organizational structure. This structure is generally focused on broad end-user markets for the Company’s diversified products. Residential Furnishings derives its revenues from components for bedding, furniture and other furnishings, as well as related consumer products. Commercial Fixturing & Components derives its revenues from retail store fixtures, displays, storage and material handling systems, components for office and institutional furnishings, and plastic components. The Aluminum Products revenues are derived from die castings, custom tooling and secondary machining and coating. Industrial Materials derives its revenues from drawn steel wire, steel rod, specialty wire products and welded steel tubing sold to trade customers as well as other Leggett segments. Specialized Products derives its revenues from the automotive industry, specialized machinery and equipment, and van interiors and truck bodies.
The accounting principles used in the preparation of the segment information are the same as used for the consolidated financial statements, except that the segment assets and income reflect the FIFO basis of accounting for inventory. Certain inventories are accounted for using the LIFO basis in the consolidated financial statements. The Company evaluates performance based on earnings from operations before interest and income taxes (EBIT). Intersegment sales are made primarily at prices that approximate market-based selling prices. Centrally incurred costs are allocated to the segments based on estimates of services used by the segment. Certain general and administrative costs and miscellaneous corporate income and expense of the Company are allocated to the segments based on sales and EBIT. Asset information for the segments includes only inventory, trade receivables, net property, plant and equipment and unamortized purchased intangibles. These segment assets are reflected in the segment information at their estimated average for the year. Acquired companies’ long-lived assets as disclosed include property, plant and equipment, goodwill and other intangibles, and long-term assets. Centrally incurred costs, allocated general and administrative costs and miscellaneous corporate income and
77
Leggett & Platt, Incorporated
Notes to Consolidated Financial Statements—(Continued)
expense include depreciation and other costs and income related to assets that are not allocated or otherwise included in the segment assets.
Summarized financial information concerning the Company’s reportable segments is shown in the following tables:
| | | | | | | | | | | | | |
| | Year ended December 31
| |
| | External Sales
| | Inter- Segment Sales
| | Total Sales
| | EBIT
| |
2005 | | | | | | | | | | | | | |
Residential Furnishings | | $ | 2,598.8 | | $ | 22.7 | | $ | 2,621.5 | | $ | 170.4 | |
Commercial Fixturing & Components | | | 1,134.6 | | | 12.8 | | | 1,147.4 | | | 39.1 | |
Aluminum Products | | | 516.0 | | | 15.4 | | | 531.4 | | | 30.6 | |
Industrial Materials | | | 533.4 | | | 310.4 | | | 843.8 | | | 104.2 | |
Specialized Products | | | 516.5 | | | 62.5 | | | 579.0 | | | 33.5 | |
Intersegment eliminations | | | | | | | | | | | | (5.5 | ) |
Adjustment to LIFO method | | | | | | | | | | | | 23.9 | |
| |
|
| |
|
| |
|
| |
|
|
|
| | $ | 5,299.3 | | $ | 423.8 | | $ | 5,723.1 | | $ | 396.2 | |
| |
|
| |
|
| |
|
| |
|
|
|
2004 | | | | | | | | | | | | | |
Residential Furnishings | | $ | 2,467.5 | | $ | 14.1 | | $ | 2,481.6 | | $ | 265.0 | |
Commercial Fixturing & Components | | | 1,072.2 | | | 6.0 | | | 1,078.2 | | | 55.3 | |
Aluminum Products | | | 505.7 | | | 16.0 | | | 521.7 | | | 45.5 | |
Industrial Materials | | | 530.3 | | | 287.2 | | | 817.5 | | | 121.5 | |
Specialized Products | | | 509.8 | | | 54.0 | | | 563.8 | | | 50.5 | |
Intersegment eliminations | | | | | | | | | | | | .4 | |
Adjustment to LIFO method | | | | | | | | | | | | (76.5 | ) |
| |
|
| |
|
| |
|
| |
|
|
|
| | $ | 5,085.5 | | $ | 377.3 | | $ | 5,462.8 | | $ | 461.7 | |
| |
|
| |
|
| |
|
| |
|
|
|
2003 | | | | | | | | | | | | | |
Residential Furnishings | | $ | 2,180.1 | | $ | 6.3 | | $ | 2,186.4 | | $ | 208.5 | |
Commercial Fixturing & Components | | | 957.8 | | | 7.2 | | | 965.0 | | | 26.8 | |
Aluminum Products | | | 453.5 | | | 13.2 | | | 466.7 | | | 35.6 | |
Industrial Materials | | | 369.2 | | | 209.6 | | | 578.8 | | | 37.7 | |
Specialized Products | | | 427.6 | | | 58.8 | | | 486.4 | | | 52.3 | |
Intersegment eliminations | | | | | | | | | | | | (3.8 | ) |
Adjustment to LIFO method | | | | | | | | | | | | (1.8 | ) |
| |
|
| |
|
| |
|
| |
|
|
|
| | $ | 4,388.2 | | $ | 295.1 | | $ | 4,683.3 | | $ | 355.3 | |
| |
|
| |
|
| |
|
| |
|
|
|
78
Leggett & Platt, Incorporated
Notes to Consolidated Financial Statements—(Continued)
| | | | | | | | | | | | | |
| | Year ended December 31
|
| | Assets
| | | Additions to Property, Plant and Equipment
| | Acquired Companies’ Long-Lived Assets
| | Depreciation And Amortization
|
2005 | | | | | | | | | | | | | |
Residential Furnishings | | $ | 1,504.4 | | | $ | 60.1 | | $ | 81.0 | | $ | 74.2 |
Commercial Fixturing & Components | | | 969.9 | | | | 14.6 | | | 15.5 | | | 25.1 |
Aluminum Products | | | 387.2 | | | | 40.2 | | | — | | | 22.1 |
Industrial Materials | | | 338.2 | | | | 15.7 | | | — | | | 14.3 |
Specialized Products | | | 530.2 | | | | 23.2 | | | 94.6 | | | 24.9 |
Unallocated assets | | | 218.9 | | | | 10.4 | | | — | | | 10.5 |
Adjustment to year-end vs. average assets | | | 103.8 | | | | | | | | | | |
| |
|
|
| |
|
| |
|
| |
|
|
| | $ | 4,052.6 | | | $ | 164.2 | | $ | 191.1 | | $ | 171.1 |
| |
|
|
| |
|
| |
|
| |
|
|
2004 | | | | | | | | | | | | | |
Residential Furnishings | | $ | 1,395.7 | | | $ | 59.9 | | $ | 3.6 | | $ | 70.4 |
Commercial Fixturing & Components | | | 964.9 | | | | 17.7 | | | 15.2 | | | 32.1 |
Aluminum Products | | | 375.8 | | | | 22.3 | | | — | | | 23.4 |
Industrial Materials | | | 303.3 | | | | 14.9 | | | .3 | | | 14.5 |
Specialized Products | | | 480.0 | | | | 31.9 | | | 26.3 | | | 23.1 |
Unallocated assets | | | 626.8 | | | | 10.4 | | | — | | | 11.3 |
Adjustment to year-end vs. average assets | | | 50.7 | | | | | | | | | | |
| |
|
|
| |
|
| |
|
| |
|
|
| | $ | 4,197.2 | | | $ | 157.1 | | $ | 45.4 | | $ | 174.8 |
| |
|
|
| |
|
| |
|
| |
|
|
2003 | | | | | | | | | | | | | |
Residential Furnishings | | $ | 1,328.0 | | | $ | 50.7 | | $ | 45.7 | | $ | 70.2 |
Commercial Fixturing & Components | | | 950.2 | | | | 20.8 | | | 24.6 | | | 30.2 |
Aluminum Products | | | 376.3 | | | | 18.5 | | | — | | | 23.0 |
Industrial Materials | | | 263.2 | | | | 14.7 | | | — | | | 17.2 |
Specialized Products | | | 414.2 | | | | 23.0 | | | 14.4 | | | 16.8 |
Unallocated assets | | | 615.3 | | | | 8.9 | | | — | | | 9.6 |
Adjustment to year-end vs. average assets | | | (57.5 | ) | | | | | | | | | |
| |
|
|
| |
|
| |
|
| |
|
|
| | $ | 3,889.7 | | | $ | 136.6 | | $ | 84.7 | | $ | 167.0 |
| |
|
|
| |
|
| |
|
| |
|
|
79
Leggett & Platt, Incorporated
Notes to Consolidated Financial Statements—(Continued)
Revenues from external customers, by product line, are as follows:
| | | | | | | | | |
| | Year Ended December 31
|
| | 2005
| | 2004
| | 2003
|
Residential Furnishings | | | | | | | | | |
Bedding components | | $ | 915.3 | | $ | 895.2 | | $ | 778.7 |
Residential furniture components | | | 895.0 | | | 805.1 | | | 697.1 |
Finished & consumer products | | | 669.4 | | | 643.0 | | | 606.4 |
Other residential furnishings products | | | 119.1 | | | 124.2 | | | 97.9 |
| |
|
| |
|
| |
|
|
| | | 2,598.8 | | | 2,467.5 | | | 2,180.1 |
Commercial Fixturing & Components | | | | | | | | | |
Store displays, fixtures & storage products | | | 810.2 | | | 824.2 | | | 744.0 |
Office furnishings & plastic components | | | 324.4 | | | 248.0 | | | 213.8 |
| |
|
| |
|
| |
|
|
| | | 1,134.6 | | | 1,072.2 | | | 957.8 |
Aluminum Products | | | | | | | | | |
Die cast products | | | 481.5 | | | 474.6 | | | 422.4 |
Tool & die operations | | | 34.5 | | | 31.1 | | | 31.1 |
| |
|
| |
|
| |
|
|
| | | 516.0 | | | 505.7 | | | 453.5 |
Industrial Materials | | | | | | | | | |
Wire, wire products & steel tubing | | | 533.4 | | | 530.3 | | | 369.2 |
| | | |
Specialized Products | | | | | | | | | |
Automotive products, commercial vehicle products & specialized machinery | | | 516.5 | | | 509.8 | | | 427.6 |
| |
|
| |
|
| |
|
|
| | $ | 5,299.3 | | $ | 5,085.5 | | $ | 4,388.2 |
| |
|
| |
|
| |
|
|
The Company’s operations outside of the United States are principally in Canada, Europe and Mexico. The geographic information that follows regarding sales is based on the area of manufacture.
| | | | | | | | | |
| | Year Ended December 31
|
| | 2005
| | 2004
| | 2003
|
External sales | | | | | | | | | |
United States | | $ | 4,163.4 | | $ | 4,029.3 | | $ | 3,467.7 |
Canada | | | 458.7 | | | 412.5 | | | 424.0 |
Europe | | | 373.8 | | | 403.2 | | | 315.1 |
Mexico | | | 155.0 | | | 145.7 | | | 135.3 |
Other | | | 148.4 | | | 94.8 | | | 46.1 |
| |
|
| |
|
| |
|
|
| | $ | 5,299.3 | | $ | 5,085.5 | | $ | 4,388.2 |
| |
|
| |
|
| |
|
|
Long-lived assets | | | | | | | | | |
United States | | $ | 1,694.0 | | $ | 1,553.9 | | $ | 1,551.8 |
Canada | | | 231.3 | | | 227.9 | | | 207.8 |
Europe | | | 197.9 | | | 228.2 | | | 198.5 |
Mexico | | | 83.8 | | | 71.9 | | | 68.0 |
Other | | | 82.3 | | | 50.5 | | | 44.2 |
| |
|
| |
|
| |
|
|
| | $ | 2,289.3 | | $ | 2,132.4 | | $ | 2,070.3 |
| |
|
| |
|
| |
|
|
80
Leggett & Platt, Incorporated
Notes to Consolidated Financial Statements—(Continued)
M—Contingencies
The Company is involved in various legal proceedings including matters which involve claims against the Company under employment, intellectual property, environmental and other laws. When it appears probable in management’s judgment that the Company will incur monetary damages or other costs in connection with claims and proceedings, and the costs can be reasonably estimated, appropriate liabilities are recorded in the financial statements and charges are made against earnings. No claim or proceeding resulted in a material charge against earnings, nor are the total liabilities recorded material to the Company’s financial position. While the results of any ultimate resolution are uncertain, management believes the possibility of a material adverse effect on the Company’s consolidated financial position, results of operations and cash flows from claims and proceedings is remote.
Countervailing and Anti-Dumping Duties
On April 2, 2001, the Coalition for Fair Lumber Imports filed two petitions with the U.S. Department of Commerce (Commerce) and the International Trade Commission (ITC), claiming that production of softwood lumber in Canada was being subsidized by Canada and that imports from Canada were being “dumped” into the U.S. market (sold at less than fair value). As a result, beginning on May 22, 2002, Commerce began imposing countervailing duty (CVD) and anti-dumping (AD) duty deposit requirements on softwood lumber imported from Canada. Through December 2005, the Company has paid or accrued approximately $21.0 million in CVD and AD deposits related to this action. Deposits are expensed when paid or accrued.
The CVD and AD tariff rates are determined by Commerce on an annual basis, with the actual final rate established at the end of each rate period via an annual review process. The annual CVD periods run from April 1 through March 31 and the annual AD periods run from May 1 through April 30. Any difference between the deposit rates and the final assessment rates are to be settled at the time of finalization. Subsequent deposit rates are subject to adjustment by Commerce based on the findings of the most recent administrative review. The annual review process will be repeated in successive one-year periods. After five years, both the CVD and AD orders will be automatically reviewed in a “sunset” proceeding to determine whether the tariffs should be continued or revoked.
As noted above, the Company began making cash deposits relating to the CVD and AD actions beginning in May 2002. The Company’s initial combined deposit rate for the CVD and AD tariffs was 27.22% for the first and second administrative review periods. Based upon the results of the first and second administrative reviews, the Company’s combined duty rates have been finalized at 21.15% for the first administrative review period and 11.35% for the second administrative review period.
Legal challenges have been filed by Canadian and U.S. parties before various authorities including the Court of International Trade, the North American Free Trade Agreement dispute panels, and the WTO Dispute Settlement Body. The appeal and challenge processes are on-going and the parties, primarily the U.S. and Canadian governments, continue to discuss the possibility of a negotiated settlement. Until this dispute is ultimately resolved, the Company cannot be entirely certain what the ultimate costs to the Company will be, if any. AD and CVD rates could rise or fall and will not be final until the conclusion of the litigation. The Company expects that whatever the ultimate resolution is, the CVD and AD rates for the periods covered by the first and second administrative reviews will be no higher than the final rates that have been set by Commerce in those reviews. As such, in 2005 the Company recorded $4.8 million as a receivable and a partial reversal of the previously recorded expense which represents the difference between the deposit rates and final rates for the 2002 through 2004 periods covered by the first and second administrative reviews.
81
Leggett & Platt, Incorporated
Notes to Consolidated Financial Statements—(Continued)
Following is a summary of the CVD and AD charges/deposits and reversal/receivable recorded in the Company’s consolidated financial statements through December 2005:
| | | | | | | | | | | | | | | | | |
| | 2005
| | | 2004
| | 2003
| | 2002
| | Total
| |
Charges for CVD and anti-dumping duties | | $ | 5.1 | | | $ | 5.6 | | $ | 5.9 | | $ | 4.4 | | $ | 21.0 | |
Reversal associated with first and second administrative reviews | | | (4.8 | ) | | | — | | | — | | | — | | | (4.8 | ) |
| |
|
|
| |
|
| |
|
| |
|
| |
|
|
|
Net charges | | $ | 0.3 | | | $ | 5.6 | | $ | 5.9 | | $ | 4.4 | | $ | 16.2 | |
| |
|
|
| |
|
| |
|
| |
|
| |
|
|
|
N—Special Charges
In each of the three years ending December 31, 2005, the Company has implemented various cost reduction initiatives to improve its operating cost structures. These cost initiatives have, among other actions, included workforce reductions and the closure or consolidation of certain operations. Except for the 2005 Closure and Consolidation Initiative described below, none of these initiatives has individually resulted in a material charge to earnings for any of the periods presented.
In the Company’s fourth quarter 2005 press release issued January 26, 2006, we disclosed that the total expected cost of certain recent restructuring activities would be approximately $76. This cost is now estimated to total $77.9. The details regarding all of our restructuring activities are provided below.
Restructuring and other special charges for each of the three years ended December 31 were comprised of:
| | | | | | | | | | | |
| | December 31
| |
| | 2005
| | | 2004
| | 2003
| |
Severance and other restructuring costs | | $ | 20.0 | | | $ | 6.9 | | $ | .6 | |
Asset impairment charges | | | 24.3 | | | | 2.4 | | | 1.3 | |
Inventory obsolescence and other | | | 14.1 | | | | — | | | — | |
(Gains) on sales | | | (3.5 | ) | | | — | | | (2.5 | ) |
| |
|
|
| |
|
| |
|
|
|
Total restructuring and other special charges | | $ | 54.9 | | | $ | 9.3 | | $ | (.6 | ) |
| |
|
|
| |
|
| |
|
|
|
2005 Closure and Consolidation Initiative
In September 2005, the Company launched a significant broad-based restructuring initiative to reduce excess capacity and improve performance in a number of its businesses. As a result, management identified 36 operations to be closed, consolidated or sold and which currently constitute the “2005 Closure and Consolidation Initiative.” The Company’s current estimate of the charges it expects to incur in connection with this initiative is $58.2, of which $40.3 was expensed in 2005 and $17.9 is expected to be incurred in 2006. These amounts do not incorporate any offsets from potential gains on the sale of equipment, buildings or real estate. The extent of any potential offsetting gains will not be known until such time as the Company has made a final determination of which assets will be sold, and has prepared or obtained estimates of the related fair market values.
82
Leggett & Platt, Incorporated
Notes to Consolidated Financial Statements—(Continued)
The following table contains, by each major type of cost associated with the 2005 Closure and Consolidation Initiative, the total amount of costs expected to be incurred and the cumulative amount incurred to date:
| | | | | | |
| | Total Amount Expected to be Incurred
| | Total Amount Incurred in 2005
|
Type of charge: | | | | | | |
Employee termination costs | | $ | 12.7 | | $ | 8.4 |
Contract termination costs | | | 1.9 | | | .8 |
Other exit costs, primarily plant closure and asset relocation | | | 12.6 | | | 2.7 |
| |
|
| |
|
|
Total restructuring costs (1) | | | 27.2 | | | 11.9 |
Asset impairment charges (2) | | | 18.3 | | | 16.0 |
Inventory obsolescence and other (3) | | | 12.7 | | | 12.4 |
| |
|
| |
|
|
Total costs | | $ | 58.2 | | $ | 40.3 |
| |
|
| |
|
|
(1) | Restructuring costs associated with the 2005 Closure and Consolidation Initiative are reported on the Statement of Earnings in “Other expense (income), net.” |
(2) | Asset impairment charges relate primarily to the write down of property, plant and equipment at the impacted facilities. These facilities include six in the Fixture & Display group; four in Bedding; four in Fabric, Foam & Fiber; four in Wire; two in Automotive and one in Home Furniture & Consumer Products. Current fair market values were estimated based primarily on prices for similar assets. Asset impairment charges for the 2005 Closure and Consolidation Initiative are reported in “Other expense (income), net.” |
(3) | Inventory obsolescence and other charges for the 2005 Closure and Consolidation Initiative are reported in “Cost of Goods Sold.” |
These amounts are good faith estimates, and the amounts of actual charges may vary due to a variety of factors. Other than the inventory obsolescence and asset impairment charges, the costs associated with the 2005 Closure and Consolidation Initiative primarily represent cash charges. The Company currently anticipates that the remaining $17.9 will be incurred by the end of 2006, at which time the 2005 Closure and Consolidation Initiative activities are expected to be essentially complete.
The following table contains information, by segment, regarding the total amount of costs expected to be incurred in connection with the 2005 Closure and Consolidation Initiative and the amount incurred in the current year:
| | | | | | | | | | | | | | | |
| | Total Estimated Cost at Completion
| | Amounts Incurred in 2005
|
| | | Restructuring Charges
| | Asset Impairment Charges
| | Inventory Obsolescence and Other Charges
| | Total Amount Incurred Year-to-Date
|
Residential Furnishings | | $ | 23.3 | | $ | 2.4 | | $ | 11.5 | | $ | 2.0 | | $ | 15.9 |
Commercial Fixturing & Components | | | 18.4 | | | 8.4 | | | 1.5 | | | 4.7 | | | 14.6 |
Aluminum Products | | | — | | | — | | | — | | | — | | | — |
Industrial Materials | | | 4.1 | | | .5 | | | 2.3 | | | .4 | | | 3.2 |
Specialized Products | | | 12.4 | | | .6 | | | .7 | | | 5.3 | | | 6.6 |
| |
|
| |
|
| |
|
| |
|
| |
|
|
Total | | $ | 58.2 | | $ | 11.9 | | $ | 16.0 | | $ | 12.4 | | $ | 40.3 |
| |
|
| |
|
| |
|
| |
|
| |
|
|
83
Leggett & Platt, Incorporated
Notes to Consolidated Financial Statements—(Continued)
At December 31, 2005, the accrued liability associated with the 2005 Closure and Consolidation Initiative consisted of the following:
| | | | | | | | | | | | | | | | |
| | Balance at September 19, 2005
| | Subsequent Accruals
| | Non-Cash Settlements and Other Adjustments
| | Payments
| | | Balance at December 31, 2005
|
Termination benefits | | $ | — | | $ | 8.4 | | $ | — | | $ | (1.7 | ) | | $ | 6.7 |
Contract termination costs | | | — | | | .8 | | | — | | | ( .1 | ) | | | .7 |
Other restructuring costs | | | — | | | 2.7 | | | — | | | (1.3 | ) | | | 1.4 |
| |
|
| |
|
| |
|
| |
|
|
| |
|
|
| | $ | — | | $ | 11.9 | | $ | — | | $ | (3.1 | ) | | $ | 8.8 |
| |
|
| |
|
| |
|
| |
|
|
| |
|
|
All remaining payments relating to the 2005 Closure and Consolidation Initiative are expected to be paid in 2006.
Other Initiatives
Apart from the 2005 Closure and Consolidation Initiative, the Company has implemented various cost reduction initiatives over the last three years to improve its operating cost structures. None of these actions has individually resulted in a material charge to earnings. In 2006, the Company expects to incur an additional $5.1, primarily composed of $4.5 in employee termination costs, to complete these initiatives. Costs associated with these activities have had the following impact on the Company’s financial statements:
| | | | | | | | | | | |
| | Year ended December 31
| |
| | 2005
| | | 2004
| | 2003
| |
Charged to other (income) expense, net: | | | | | | | | | | | |
Severance and other restructuring costs | | $ | 8.1 | | | $ | 3.9 | | $ | .6 | |
Write-downs of property, plant & equipment | | | 8.3 | | | | .2 | | | 1.3 | |
(Gains) on sales | | | (3.5 | ) | | | — | | | (2.5 | ) |
| |
|
|
| |
|
| |
|
|
|
| | $ | 12.9 | | | $ | 4.1 | | $ | (.6 | ) |
| |
|
|
| |
|
| |
|
|
|
Charged to cost of goods sold: | | | | | | | | | | | |
Severance and other restructuring costs | | $ | 1.7 | | | $ | 3.0 | | $ | — | |
Write-down of property, plant & equipment | | | — | | | | 2.2 | | | — | |
| |
|
|
| |
|
| |
|
|
|
| | $ | 1.7 | | | $ | 5.2 | | $ | — | |
| |
|
|
| |
|
| |
|
|
|
Total of Other Initiatives | | $ | 14.6 | | | $ | 9.3 | | $ | (.6 | ) |
| |
|
|
| |
|
| |
|
|
|
Restructuring liabilities at year-end | | $ | 2.1 | | | $ | 1.4 | | $ | .6 | |
| |
|
|
| |
|
| |
|
|
|
Adjustments of previously established liabilities relating to these activities have been negligible.
Net sales for the 12-month period prior to divestiture for businesses sold were $22 in 2005, $0 in 2004, and $23 in 2003. The earnings impact from these divested businesses is not material; as such, the Company has chosen not to report them as discontinued operations.
84
Leggett & Platt, Incorporated
Notes to Consolidated Financial Statements—(Continued)
O—Other (Income) Expense
The components of other (income) expense were as follows:
| | | | | | | | | | | | |
| | Year ended December 31
| |
| | 2005
| | | 2004
| | | 2003
| |
(Gain) loss on asset sale | | $ | (6.3 | ) | | $ | (16.3 | ) | | $ | 1.9 | |
Restructuring charges | | | 20.0 | | | | 3.9 | | | | (1.9 | ) |
Asset impairments | | | 24.3 | | | | .2 | | | | 1.3 | |
Currency (gain) | | | (1.2 | ) | | | (2.1 | ) | | | (.1 | ) |
Other | | | .7 | | | | (2.3 | ) | | | (3.1 | ) |
| |
|
|
| |
|
|
| |
|
|
|
| | $ | 37.5 | | | $ | (16.6 | ) | | $ | (1.9 | ) |
| |
|
|
| |
|
|
| |
|
|
|
P—Derivative Financial Instruments
The Company’s risk management strategies include the use of derivative instruments to manage the fixed/variable interest rate mix of its debt portfolio, to hedge its exposure to fluctuating natural gas prices, and to hedge against its exposure to variability in interest and foreign exchange rates. It is the Company’s policy not to speculate in derivative instruments.
The Company has managed a portion of the fixed/variable interest rate risk of its debt portfolio through the use of interest rate swap agreements. During 2000, $350 of 7.65% fixed rate debt which matured on February 15, 2005 was issued and converted to variable rate debt by use of an interest rate swap agreement. In March 2003, the Company sold its rights under the interest rate swap agreement for $39.9 in cash proceeds. The unamortized market value of the swap agreement was $2.5 at December 31, 2004.
Other than for planned purchases of natural gas, the Company does not generally use derivative commodity instruments to hedge its exposures to changes in commodity prices. At December 31, 2005, approximately $13.0 of natural gas forward contracts were outstanding at an average price of $7.47 per mmbtu, of which the contracts hedging January and February 2006 usage totaled approximately $3.1. At December 31, 2005, the total unrealized gain recorded in other comprehensive income on natural gas contracts was approximately $3.5, net of tax.
Subsequent to year-end, the Company entered into an additional $22.0 of natural gas forward contracts at an average price of $9.19 per mmbtu. At February 28, 2006, the Company had contracts in place hedging approximately 75% of its anticipated natural gas consumption for March 2006, approximately 65% of its anticipated monthly consumption for the 6-month period beginning April 2006, approximately 50% of its anticipated monthly consumption for the 3-month period beginning October 2006, approximately 20% of its anticipated monthly consumption for 2007, and approximately 5-15% of its anticipated monthly consumption for 2008. Contracts in place at February 28, 2006 totaled $31.9 at an average price of $8.40 per mmbtu.
The Company may use forward contracts, options and currency swaps in the normal course of business to mitigate foreign currency exposures. Where appropriate, the Company may designate forward currency contracts as hedges against the Company’s exposure to variability in exchange rates on certain cash flows denominated in foreign currencies. In December 2003, the Company hedged a portion of anticipated Mexican peso expenses for certain subsidiaries through 2004. During 2004, hedges were used to reduce exposure from anticipated U.S. dollar (USD) raw material purchases at certain United Kingdom subsidiaries, and again to hedge a portion of its Mexican peso (MXN) needs for 2005. The amount of foreign currency forward contracts outstanding at
85
Leggett & Platt, Incorporated
Notes to Consolidated Financial Statements—(Continued)
December 31, 2005 was approximately $15.9 (pay USD/receive MXN). At December 31, 2005, the unrealized gain recorded in other comprehensive income on these contracts was approximately $.8, net of tax.
The changes in fair value of the unexpired natural gas and foreign currency contracts are recorded in other comprehensive income and reclassified to cost of goods sold in the period in which earnings are impacted by the hedged items.
In December 2003, the Company entered into a 38.3 Swiss Francs (CHF) five-year cross-currency swap agreement with Wachovia Bank, N.A. This agreement is designated as a net investment hedge of the Company’s Swiss subsidiaries. In addition, the terms of this agreement include that the Company will receive interest on $30 USD at a fixed rate of 6.35% and pay interest on 38.3 CHF at a fixed rate of 4.71%. At December 31, 2005, the unrealized loss on this agreement was approximately $.1, net of tax, and is included in the foreign currency translation component of accumulated other comprehensive income.
All derivative financial instruments accorded hedge accounting treatment are considered highly effective. There were no transactions that ceased to qualify for hedge accounting treatment in the years ended December 31, 2005 and 2004.
86
Quarterly Summary of Earnings
Leggett & Platt, Incorporated
(Unaudited)
(Dollar amounts in millions, except per share data)
| | | | | | | | | | | | | | | |
Year ended December 31
| | First
| | Second
| | Third
| | Fourth
| | Total
|
2005 | | | | | | | | | | | | | | | |
Net sales | | $ | 1,301.3 | | $ | 1,309.8 | | $ | 1,348.6 | | $ | 1,339.6 | | $ | 5,299.3 |
Gross profit | | | 232.4 | | | 246.2 | | | 215.1 | | | 219.1 | | | 912.8 |
Earnings before income taxes | | | 107.7 | | | 118.2 | | | 77.6 | | | 52.7 | | | 356.2 |
Net earnings | | | 72.8 | | | 79.2 | | | 54.0 | | | 45.3 | | | 251.3 |
Earnings per share | | | | | | | | | | | | | | | |
Basic | | $ | .37 | | $ | .41 | | $ | .28 | | $ | .24 | | $ | 1.30 |
| |
|
| |
|
| |
|
| |
|
| |
|
|
Diluted | | $ | .37 | | $ | .41 | | $ | .28 | | $ | .24 | | $ | 1.30 |
| |
|
| |
|
| |
|
| |
|
| |
|
|
2004 | | | | | | | | | | | | | | | |
Net sales | | $ | 1,187.2 | | $ | 1,278.1 | | $ | 1,338.0 | | $ | 1,282.2 | | $ | 5,085.5 |
Gross profit | | | 215.1 | | | 243.4 | | | 242.5 | | | 214.8 | | | 915.8 |
Earnings before income taxes | | | 93.0 | | | 116.4 | | | 121.1 | | | 92.1 | | | 422.6 |
Net earnings | | | 62.8 | | | 76.8 | | | 80.2 | | | 65.6 | | | 285.4 |
Earnings per share | | | | | | | | | | | | | | | |
Basic | | $ | .32 | | $ | .39 | | $ | .41 | | $ | .34 | | $ | 1.46 |
| |
|
| |
|
| |
|
| |
|
| |
|
|
Diluted | | $ | .32 | | $ | .39 | | $ | .41 | | $ | .33 | | $ | 1.45 |
| |
|
| |
|
| |
|
| |
|
| |
|
|
In the third quarter of 2005, the Company launched a broad-based restructuring initiative resulting in unusually high restructuring and other special charges in both the third and fourth quarters of 2005. Restructuring and other special charges totaled $14.2 and $37.3 for the 2005 third and fourth quarters, respectively. See Note N to the Consolidated Financial Statements for further discussion of these charges.
87
LEGGETT & PLATT, INCORPORATED
SCHEDULE II—VALUATION AND QUALIFYING ACCOUNTS AND RESERVES
(Amounts in millions)
| | | | | | | | | | | | | |
Column A
| | Column B
| | Column C
| | Column D
| | | Column E
|
Description
| | Balance at Beginning of Period
| | Additions Charged to Cost and Expenses
| | Deductions
| | | Balance at End of Period
|
Year ended December 31, 2005 | | | | | | | | | | | | | |
Allowance for doubtful receivables | | $ | 18.0 | | $ | 6.8 | | $ | 4.0 | (A) | | $ | 20.8 |
| |
|
| |
|
| |
|
|
| |
|
|
Excess and obsolete inventory reserve, LIFO basis | | $ | 25.1 | | $ | 24.9 | | $ | 15.8 | | | $ | 34.2 |
| |
|
| |
|
| |
|
|
| |
|
|
Tax valuation allowance | | $ | 29.0 | | $ | 12.8 | | $ | 3.8 | (B) | | $ | 38.0 |
| |
|
| |
|
| |
|
|
| |
|
|
Year ended December 31, 2004 | | | | | | | | | | | | | |
Allowance for doubtful receivables | | $ | 17.9 | | $ | 9.0 | | $ | 8.9 | (A) | | $ | 18.0 |
| |
|
| |
|
| |
|
|
| |
|
|
Excess and obsolete inventory reserve, LIFO basis | | $ | 29.7 | | $ | 11.6 | | $ | 16.2 | | | $ | 25.1 |
| |
|
| |
|
| |
|
|
| |
|
|
Tax valuation allowance | | $ | 24.4 | | $ | 4.8 | | $ | .2 | (B) | | $ | 29.0 |
| |
|
| |
|
| |
|
|
| |
|
|
Year ended December 31, 2003 | | | | | | | | | | | | | |
Allowance for doubtful receivables | | $ | 19.4 | | $ | 3.9 | | $ | 5.4 | (A) | | $ | 17.9 |
| |
|
| |
|
| |
|
|
| |
|
|
Excess and obsolete inventory reserve, LIFO basis | | $ | 17.1 | | $ | 16.8 | | $ | 4.2 | | | $ | 29.7 |
| |
|
| |
|
| |
|
|
| |
|
|
Tax valuation allowance | | $ | 23.1 | | $ | 1.4 | | $ | .1 | (B) | | $ | 24.4 |
| |
|
| |
|
| |
|
|
| |
|
|
(A) | Uncollectible accounts charged off, net of recoveries |
(B) | Federal tax effect of State net operating loss carryforwards and credits |
88
SIGNATURES
Pursuant to the requirements of Section 13 or 15(d) of the Securities Exchange Act of 1934, the Registrant has duly caused this report to be signed on its behalf by the undersigned, thereunto duly authorized.
| | |
LEGGETT & PLATT, INCORPORATED |
| |
By: | | /s/ FELIX E. WRIGHT
|
| | Felix E. Wright Chairman of the Board and Chief Executive Officer |
Dated: March 1, 2006
Pursuant to the requirements of the Securities Exchange Act of 1934, this report has been signed by the following persons on behalf of the Registrant and in the capacities and on the dates indicated.
| | | | |
Signature
| | Title
| | Date
|
| | |
(a) Principal Executive Officer: | | | | |
| | |
/s/ FELIX E. WRIGHT
Felix E. Wright | | Chairman of the Board and Chief Executive Officer | | March 1, 2006 |
| | |
(b) Principal Financial Officer: | | | | |
| | |
/s/ MATTHEW C. FLANIGAN
Matthew C. Flanigan | | Senior Vice President and Chief Financial Officer | | March 1, 2006 |
| | |
(c) Principal Accounting Officer: | | | | |
| | |
/s/ WILLIAM S. WEIL
William S. Weil | | Vice President and Corporate Controller | | March 1, 2006 |
| | |
(d) Directors: | | | | |
| | |
RAYMOND F. BENTELE*
Raymond F. Bentele | | Director | | |
| | |
RALPH W. CLARK*
Ralph W. Clark | | Director | | |
| | |
Harry M. Cornell, Jr. | | Director | | |
| | |
ROBERT TED ENLOE, III*
Robert Ted Enloe, III | | Director | | |
| | |
RICHARD T. FISHER*
Richard T. Fisher | | Director | | |
89
| | | | |
Signature
| | Title
| | Date
|
| | |
KARL G. GLASSMAN*
Karl G. Glassman | | Director | | |
| | |
DAVID S. HAFFNER*
David S. Haffner | | Director | | |
| | |
JOSEPH W. MCCLANATHAN*
Joseph W. McClanathan | | Director | | |
| | |
JUDY C. ODOM*
Judy C. Odom | | Director | | |
| | |
MAURICE E. PURNELL, JR.*
Maurice E. Purnell, Jr. | | Director | | |
| | |
PHOEBE A. WOOD*
Phoebe A. Wood | | Director | | |
| | |
FELIX E. WRIGHT*
Felix E. Wright | | Chairman | | |
| | | | | | | | |
| | | | |
*By: | | /s/ ERNEST C. JETT | | | | | | March 1, 2006 |
| | Ernest C. Jett | | | | | | |
| | Attorney-in-Fact Under Power-of-Attorney dated February 23, 2006 | | | | | | |
90
EXHIBIT INDEX
| | |
Exhibit No.
| | Document Description
|
| |
3.1 | | Restated Articles of Incorporation of the Company as of May 13, 1987; Amendment dated May 12, 1993; and Amendment dated May 20, 1999, filed March 11, 2004 as Exhibit 3.1 to the Company’s Annual Report on Form 10-K for the year ended December 31, 2003, are incorporated by reference. (SEC File No. 1-7845) |
| |
3.2 | | Bylaws of the Company as amended through February 24, 2005, filed February 28, 2005 as Exhibit 3.2 to the Company’s Annual Report on Form 10-K for the year ended December 31, 2004, is incorporated by reference. (SEC File No. 1-7845) |
| |
4.1 | | Article III of the Company’s Restated Articles of Incorporation, as amended, filed as Exhibit 3.1 hereto, is incorporated by reference. |
| |
4.2 | | Form of 1999 Rights Agreement effective February 15, 1999 between the Company and UMB Bank, N.A., as successor Rights Agent to ChaseMellon Shareholder Services, LLC, which includes the form of Certificate of Designation, setting forth the terms of the Series A Junior Participating Preferred Stock, no par value, as Exhibit A; the form of Right Certificate as Exhibit B; and the Summary of Preferred Stock Purchase Rights as Exhibit C, filed December 1, 1998 as Exhibit 4 to the Company’s Current Report on Form 8-K, is incorporated by reference. (SEC File No. 1-7845) |
| |
4.3 | | Indenture, dated as of November 24, 1999 between the Company and JPMorgan Chase Bank (formerly known as the Chase Manhattan Bank), as Trustee, and Form of Note included therein under Sections 202 and 203 filed November 5, 1999 as Exhibit 4.1 to Registration Statement No. 333-90443 on Form S-3, is incorporated herein by reference. (SEC File No. 1-7845) |
| |
4.4 | | Senior Indenture dated May 6, 2005 between the Company and JPMorgan Chase Bank, N.A., as Trustee, filed May 10, 2005 as Exhibit 4.1 to the Company’s Current Report on Form 8-K, is incorporated by reference. (SEC File No. 1-7845) |
| |
4.5 | | Form of Fixed Rate Note filed May 10, 2005 as Exhibit 4.2 to the Company’s Current Report on Form 8-K, is incorporated by reference. (SEC File No. 1-7845) |
| |
4.6 | | Form of Floating Rate Note filed May 10, 2005 as Exhibit 4.3 to the Company’s Current Report on Form 8-K, is incorporated by reference. (SEC File No. 1-7845) |
| |
4.7 | | Form of $200,000,000 4.7% Notes due 2013 issued pursuant to the Indenture dated November 24, 1999, and filed March 20, 2003 as Exhibit 4.1 to the Company’s Form 8-K, is incorporated herein by reference. (SEC File No. 1-7845) |
| |
4.8 | | Form of $150,000,000 4.4% Notes due 2018 issued pursuant to the Indenture dated November 24, 1999, and filed June 20, 2003 as Exhibit 4.1 to the Company’s Form 8-K, is incorporated herein by reference. (SEC File No. 1-7845) |
| |
4.9 | | Form of $180,000,000 4.65% Notes due 2014 issued pursuant to the Indenture dated November 24, 1999, and filed November 9, 2004 as Exhibit 4.1 to the Company’s Form 8-K, is incorporated herein by reference. (SEC File No. 1-7845) |
| |
4.10 | | Form of $200,000,000 5.00% Notes due 2015 issued pursuant to the Senior Indenture dated May 6, 2005, and filed August 11, 2005 as Exhibit 4.1 to the Company’s Current Report on Form 8-K, is incorporated by reference. (SEC File No. 1-7845) |
| |
10.1(1) | | Restated and Amended Employment Agreement between the Company and Felix E. Wright dated March 1, 1999, filed March 31, 1999 as Exhibit 10.2(1) to the Company’s Form 10-K for the year ended December 31, 1998; Amendment No. 1 to the Restated and Amended Employment Agreement of Felix E. Wright, dated October 1, 2002, filed November 13, 2002 as Exhibit 10 to the Company’s Form 10-Q for the quarter ended September 30, 2002; Letter Agreement between |
91
| | |
Exhibit No.
| | Document Description
|
| |
| | the Company and Felix E. Wright, dated August 6, 2003, filed August 6, 2003 as Exhibit 10.1 to the Company’s Form 10-Q for the quarter ended June 30, 2003; and Amendment No. 2 to the Restated and Amended Employment Agreement of Felix E. Wright, dated August 4, 2004, filed August 5, 2004 as Exhibit 10.1 to the Company’s Form 10-Q for the quarter ended June 30, 2004; all of which are incorporated by reference. (SEC File No. 1-7845) |
| |
10.2(1) | | Employment Agreement between the Company and David S. Haffner, dated July 30, 2001, filed October 31, 2001 as Exhibit 10 to the Company’s Form 10-Q for the quarter ended September 30, 2001, is incorporated by reference. (SEC File No. 1-7845) |
| |
10.3(1) | | Employment Agreement between the Company and Karl G. Glassman, dated November 1, 2005, filed November 3, 2005 as Exhibit 10.1 to the Company’s Form 10-Q for the quarter ended September 30, 2005, is incorporated by reference. (SEC File No. 1-7845) |
| |
10.4(1) | | Restated and Amended Employment Agreement between the Company and Harry M. Cornell, Jr. dated as of August 14, 1996, and Amendment No. 1 to Employment Agreement dated January 1, 1999, and Letter Agreement dated April 24, 2000 extending term of Employment Agreement and Letter Agreement dated March 1, 2001 extending term of Employment Agreement, all of which was filed as of March 28, 2002 as Exhibit 10.1(1) to the Company’s Form 10-K for the year ended December 31, 2001, and Letter Agreement dated November 15, 2002, filed March 18, 2003 as Exhibit 10.2(1) to the Company’s Form 10-K for the year ended December 31, 2002, all of which are incorporated by reference. (SEC File No. 1-7845) |
| |
10.5(1) | | Severance Benefit Agreement between the Company and Felix E. Wright dated May 9, 1984, filed March 29, 2001 as Exhibit 10.5(1) to the Company’s Form 10-K for the year ended December 31, 2000, is incorporated by reference. (SEC File No. 1-7845) |
| |
10.6(1) | | Severance Benefit Agreement between the Company and David S. Haffner, dated July 30, 2001, filed October 31, 2001 as Exhibit 10 to the Company’s Form 10-Q for the quarter ended September 30, 2001, is incorporated by reference. (SEC File No. 1-7845) |
| |
10.7(1) | | Severance Benefit Agreement between the Company and Karl G. Glassman, dated November 1, 2005, filed November 3, 2005 as Exhibit 10.2 to the Company’s Form 10-Q for the quarter ended September 30, 2005, is incorporated by reference. (SEC File No. 1-7845) |
| |
10.8(1) | | Form of Indemnification Agreement approved by the shareholders of the Company and entered into between the Company and its directors and certain executive officers, filed March 28, 2002, as Exhibit 10.11(1) to the Company’s Form 10-K for the year ended December 31, 2001 is incorporated by reference. (SEC File No. 1-7845) |
| |
10.9(1)* | | Summary Sheet of Executive Cash Compensation and Award Formula under the 2004 Key Officers Incentive Plan. |
| |
10.10(1) | | Summary Sheet for Director Compensation filed August 4, 2005 as Exhibit 10.2 to the Company’s Form 10-Q for the quarter ended June 30, 2005, is incorporated by reference. (SEC File No. 1-7845) |
| |
10.11(1) | | The Company’s Flexible Stock Plan, amended and restated, effective as of May 4, 2005, filed March 23, 2005 as Appendix B to the Company’s Definitive Proxy Statement for the Annual Meeting of Shareholders; Form of Non-Qualified Stock Option Award pursuant to the Company’s Flexible Stock Plan, filed November 3, 2004 as Exhibit 10.1 to the Company’s Form 10-Q for the quarter ended September 30, 2004; Form of Restricted Stock Agreement pursuant to the Company’s Flexible Stock Plan, filed November 3, 2004 as Exhibit 10.2 to the Company’s Form 10-Q for the quarter ended September 30, 2004; all of which are incorporated by reference. (SEC File No. 1-7845) |
| |
10.12(1) | | Description of the Company’s Key Management Incentive Compensation Plan as amended as of January 1, 2004, filed March 11, 2004 as Exhibit 10.9(1) to the Company’s Form 10-K for the year ended December 31, 2003, is incorporated by reference. (SEC File No. 1-7845) |
92
| | |
Exhibit No.
| | Document Description
|
| |
10.13(1)* | | The Company’s 2004 Key Officers Incentive Plan, amended and restated effective January 1, 2006. |
| |
10.14(1) | | The Company’s Director Stock Option Plan, as amended and restated November 13, 2002, filed March 18, 2003 as Exhibit 10.13(1) to the Company’s Form 10-K for the year ended December 31, 2002, is incorporated by reference. (SEC File No. 1-7845) |
| |
10.15(1) | | The Company’s Deferred Compensation Program, Amended and Restated, Effective as of December 1, 2005, filed December 2, 2005 as Exhibit 10.1 to the Company’s Current Report on Form 8-K, is incorporated by reference. (SEC File No. 1-7845) |
| |
10.16(1) | | The Company’s Executive Deferred Stock Program, filed March 31, 1999 as Exhibit 10.16 to the Company’s Form 10-K for the year ended December 31, 1998, is incorporated by reference. (SEC File No. 1-7845) |
| |
10.17(1) | | The Company’s Pre-2005 Executive Stock Unit Program, as amended and restated, effective as of December 31, 2004, filed December 10, 2004 as Exhibit 10.2 to the Company’s Form 8-K, is incorporated by reference. (SEC File No. 1-7845) |
| |
10.18(1) | | The Company’s 2005 Executive Stock Unit Program, as amended, effective as of December 30, 2005, filed December 2, 2005 as Exhibit 10.2 to the Company’s Current Report on Form 8-K, is incorporated by reference. (SEC File No. 1-7845) |
| |
10.19(1) | | Description of long-term disability arrangements between the Company and certain executives filed March 11, 2004 as Exhibit 10.11(1) to the Company’s Form 10-K for the year ended December 31, 2003, is incorporated herein by reference. (SEC File No. 1-7845) |
| |
10.20(1) | | Description of Excess Retirement Benefit Arrangements with Certain Executive Officers filed August 4, 2005 as Exhibit 10.1 to the Company’s Form 10-Q for the quarter ended June 30, 2005, is incorporated by reference. (SEC File No. 1-7845) |
| |
10.21 | | Credit Agreement, dated August 5, 2005 among the Company, Wachovia Bank, N.A., as syndication agent, JPMorgan Chase Bank, N.A., as administrative agent, and the participating banking institutions named therein, filed August 9, 2005 as Exhibit 10.1 to the Company’s Current Report on Form 8-K, is incorporated by reference. (SEC File No. 1-7845) |
| |
12* | | Computation of Ratio of Earnings to Fixed Charges. |
| |
21* | | Schedule of Subsidiaries of the Company. |
| |
23* | | Consent of Independent Registered Public Accounting Firm. |
| |
24* | | Power of Attorney executed by members of the Company’s Board of Directors regarding this Form 10-K. |
| |
31.1* | | Certification of Felix E. Wright, pursuant to Rule 13a-14(a), as adopted pursuant to Section 302 of the Sarbanes-Oxley Act of 2002, dated March 1, 2006. |
| |
31.2* | | Certification of Matthew C. Flanigan, pursuant to Rule 13a-14(a), as adopted pursuant to Section 302 of the Sarbanes-Oxley Act of 2002, dated March 1, 2006. |
| |
32.1* | | Certification of Felix E. Wright, pursuant to 18 U.S.C. Section 1350, as adopted pursuant to Section 906 of the Sarbanes-Oxley Act of 2002, dated March 1, 2006. |
| |
32.2* | | Certification of Matthew C. Flanigan, pursuant to 18 U.S.C. Section 1350, as adopted pursuant to Section 906 of the Sarbanes-Oxley Act of 2002, dated March 1, 2006. |
(1) | Denotes management contract or compensatory plan or arrangement. |
| * Denotes filed or furnished herewith |
93