UNITED STATES
SECURITIES AND EXCHANGE COMMISSION
WASHINGTON, D.C. 20549
FORM 10-K
x | ANNUAL REPORT PURSUANT TO SECTION 13 OR 15(d) OF THE SECURITIES EXCHANGE ACT OF 1934 |
For the fiscal year ended March 29, 2009
OR
¨ | TRANSITION REPORT PURSUANT TO SECTION 13 OR 15(d) OF THE SECURITIES EXCHANGE ACT OF 1934 |
For the transition period from to
Commission File No. 0-14225
EXAR CORPORATION
(Exact Name of Registrant as specified in its charter)
| | |
Delaware | | 94-1741481 |
(State or other jurisdiction of incorporation or organization) | | (I.R.S. Employer Identification Number) |
48720 Kato Road, Fremont, CA 94538
(Address of principal executive offices, Zip Code)
Registrant’s telephone number, including area code: (510) 668-7000
SECURITIES REGISTERED PURSUANT TO SECTION 12(b) OF THE ACT:
| | |
Title of each class | | Name of exchange on which registered |
Common Stock, $0.0001 Par Value | | The NASDAQ Global Market |
SECURITIES REGISTERED PURSUANT TO SECTION 12(g) OF THE ACT: NONE
Indicate by check mark if the Registrant is a well-known seasoned issuer, as defined in Rule 405 the Securities Act. Yes ¨ No x
Indicate by check mark if the Registrant is not required to file reports pursuant to Section 13 or 15(d) of the Act. Yes ¨ No x
Indicate by check mark whether the Registrant (1) has filed all reports required to be filed by Section 13 or 15(d) of the Securities Exchange Act of 1934 during the preceding 12 months (or for such shorter period that the Registrant was required to file such reports), and (2) has been subject to such filing requirements for the past 90 days. Yes x No ¨
Indicate by check mark whether the registrant has submitted electronically and posted on it corporate Website, if any, every Interactive Data File required to be submitted and posted pursuant to Rule 405 of Regulations S-T (§229.405 of this chapter) during the preceding 12 months (or for such shorter period that the registrant was required to submit post such files). Yes ¨ No ¨
Indicate by check mark if disclosure of delinquent filers pursuant to Item 405 of Regulation S-K is not contained herein, and will not be contained, to the best of Registrant’s knowledge, in definitive proxy or information statements incorporated by reference inPart III of this Form 10-K or any amendment to this Form 10-K. x
Indicate by check mark whether the Registrant is a large accelerated filer, an accelerated filer, a non-accelerated filer or a smaller reporting company. See the definitions of “large accelerated filer,” “accelerated filer” and “smaller reporting company” in Rule 12b-2 of the Exchange Act.
| | |
Large accelerated filer ¨ Accelerated filer x |
Non-accelerated filer ¨ (Do not check if a smaller reporting company) | | Smaller reporting company ¨ |
Indicate by check mark whether the Registrant is a shell company (as defined in Rule 12b-2 of the Act). Yes ¨ No x
The aggregate market value of the voting stock held by non-affiliates of the Registrant as of September 28, 2008 was $323,068,024 based upon the closing price reported on the NASDAQ Global Market as of the last business day of the Registrant’s most recently completed second fiscal quarter.
The number of shares outstanding of the Registrant’s Common Stock was 43,463,260 as of May 22, 2009, net of 19,924,369 treasury shares.
DOCUMENTS INCORPORATED BY REFERENCE
Portions of the Company’s 2009 Definitive Proxy Statement to be filed not later than 120 days after the close of the 2009 fiscal year are incorporated by reference intoPart III, Items 10, 11, 12, 13 and14 of this Report.
EXAR CORPORATION AND SUBSIDIARIES
INDEX TO
ANNUAL REPORT ON FORM 10-K
FOR FISCAL YEAR ENDED MARCH 29, 2009
2
PART I
FORWARD-LOOKING STATEMENTS
This Annual Report on Form 10-K (this “Annual Report”) contains forward-looking statements within the meaning of Section 27A of the Securities Act of 1933, as amended, and Section 21E of the Securities Exchange Act of 1934, as amended. Forward-looking statements are generally written in the future tense and/or may generally be identified by words such as “will,” “may,” “should,” “could,” “expect,” “suggest,” “believe,” “anticipate,” “intend,” “plan,” or other similar words. Forward-looking statements contained in this Annual Report include, among others, statements made in Part II, Item 7- Management’s Discussion and Analysis of Financial Condition and Results of Operations—Executive Summary” and elsewhere regarding (1) our revenue growth, (2) our future gross profits, (3) our future research and development efforts and related expenses, (4) our future selling, general and administrative expenses, (5) our cash and cash equivalents, short-term marketable securities and cash flows from operations being sufficient to satisfy working capital requirements and capital equipment needs for at least the next 12 months, (6) our ability to continue to finance operations with cash flows from operations, existing cash and investment balances, and some combination of long-term debt and/or lease financing and sales of equity securities, (7) the possibility of future acquisitions and investments, (8) our ability to accurately estimate our assumptions used in valuing stock-based compensation, (9) our ability to estimate and reconcile distributors’ reported inventories to their activities, (10) our ability to estimate future cash flows associated with long-lived assets and (11) anticipated results in connection with the merger with hi/fn, inc. (“Hifn”). Actual results may differ materially from those projected in the forward-looking statements as a result of various factors. Factors that could cause actual results to differ materially from those included herein include, but are not limited to the information contained under the captions Part I, Item 1—“Business,” Part I, Item 1A—“Risk Factors” and Part II, Item 7—“Management’s Discussion and Analysis of Financial Condition and Results of Operations.” We disclaim any obligation to update information in any forward-looking statement.
OVERVIEW
Exar Corporation and its subsidiaries (“Exar” or “we”) is a fabless semiconductor company that designs, sub-contracts manufacturing and sells highly differentiated silicon, software and subsystem solutions for industrial, datacom and storage applications. Our comprehensive knowledge of end-user markets along with our underlying analog, mixed signal and digital technology has enabled innovative solutions that meet the needs of the evolving connected world. Our product portfolio includes power management and interface components, datacom products, storage optimization solutions, network security and applied service processors. Applying both analog and digital technologies, our products are deployed in a wide array of applications such as portable electronic devices, set top boxes, digital video recorders, telecommunication systems, servers, enterprise storage systems and industrial automation equipment. We have the unique ability to provide customers with a breadth of component products and subsystem solutions based on advanced mixed signal silicon integration.
Exar was incorporated in California in 1971 and reincorporated in Delaware in 1991. Our common stock trades on The NASDAQ Global Market (“NASDAQ”) under the symbol “EXAR”. See the information inPart II, Item 8—“Financial Statements and Supplementary Data” for information on our financial position as of March 29, 2009 and March 30, 2008, and our results of operations and cash flows for fiscal years ended March 29, 2009, March 30, 2008 and March 31, 2007.
On April 3, 2009, Exar completed the acquisition of Hifn, a fabless semiconductor company that was founded in 1996, spun off from Stac, Inc. in 1999 and traded on the NASDAQ under the symbol “HIFN” since 1999. The acquisition of Hifn expands and complements our product offering in the enterprise storage, networking and telecom markets where we have had a significant base of business for more than 10 years. The Hifn technology adds world class compression and data deduplication products used in storage applications to optimize data and speed up data backup and retrieval. Hifn has also been a leading provider in security
3
acceleration technology by providing encryption and compression products to the leading networking and telecom system manufacturers. The Hifn products complement the existing Exar connectivity solutions and provide us with a more significant product offering to our customers.
On August 25, 2007, we acquired Sipex Corporation (“Sipex”), a fabless semiconductor company that designed, manufactured and marketed high performance, analog Integrated Circuits (“ICs”) used by Original Equipment Manufacturers (“OEMs”) in the computing, consumer electronics, communications and networking infrastructure markets. As a result of the acquisition, we have combined product offerings and increased technical expertise, distribution channels, customer base and geographic reach.
We believe our core competencies include:
Commitment to Connectivity—We remain steadfast in our commitment to connectivity—a strategic direction that drives our product strategies and serves as a foundation for customer engagements. Our connectivity solutions span a range of applications that serve industrial networking, storage and telecom applications. These solutions facilitate and optimize the virtual handshake between systems and across networks.
Leading Analog and Mixed-Signal Design Expertise—We have over 35 years of proven technical competency in developing analog and mixed-signal ICs. As a result, we have developed a deep understanding of the subtleties of analog and mixed-signal design and a comprehensive library of analog core blocks. For example, our high-speed, low-jitter Phase-Locked-Loop (“PLL”) capability plays a key role in our mixed-signal line interface units, transceivers, timing recovery, jitter attenuators and mapper products. As a result, we can provide our customers with solutions that typically exceed standard specifications and allow them flexibility in designing other system elements.
Comprehensive Solutions to Enhance System Integration—The combination of our design expertise, diverse technology and system-level expertise allows us to provide comprehensive solutions that encompass hardware, software and applications support. For example, we have developed many digital blocks and engines that are used in data aggregation, transmission, acceleration and compute offload. We believe that by using our solutions, OEMs can develop higher performance systems, better leverage their development resources and reduce their time-to-market.
Compelling Performance Solutions—We use our systems expertise and our analog, digital and mixed-signal design techniques to architect high-performance products based on standard Complementary Metal Oxide Semiconductor (“CMOS”) process technologies. The diversity of our technology allows us to integrate in order to develop further unique and differentiated solutions for our customers.
Conscious Preservation Initiative—Environmental concerns are having a direct impact on all electronic components and products. We are committed to reducing the impact that the end use and manufacturing of our products may have on the environment. We have taken the initiative to offer a portfolio of products that is truly “green” by transitioning our manufacturing processes such that we are able to offer parts which go beyond simply meeting Restriction of Hazardous Substances Directive (“RoHS”) requirements and are halogen-free.
MARKETS AND PRODUCTS
Datacom
The industry surrounding the network infrastructure and its underlying technologies continues to go through a significant transformation. The amount of data transferred by and stored within the network infrastructure is increasing rapidly. There are significantly more wired and wireless endpoints connected to the network in the form of mobile phones, personal computers, digital set-top boxes and many other devices each year. Telecommunications service providers are also looking towards Internet Protocol (“IP”) packet-based solutions within their infrastructure to simplify management and offer new, differentiated services to generate revenue. The mix of a large installed base of traditional Time Division Multiplexed (“TDM”) and packet-based infrastructure creates significant challenges for service providers.
4
Devices connected to the network infrastructure are capable of communicating at increasingly higher data rates, and with the emergence of large media-oriented data types such as high definition video and high resolution digital images, the size of the data sets being transferred is also growing rapidly. This trend puts a burden not only on the communications infrastructure but the resources used to store the data at the various network endpoints. The ability to manage the amount of data to be stored and the bandwidth necessary to transfer and secure that information for both storage and transmission are becoming critical.
To meet the needs of next generation network infrastructure solutions, suppliers have to address a number of key issues:
| • | | Increasing bandwidth through high-density, feature-rich and cost-effective products; |
| • | | Supporting both the installed base of TDM equipment and emerging packet-based solutions; |
| • | | Reducing cost of ownership through power efficiency and technologies reducing network bandwidth and storage capacity requirements; and |
| • | | Securing information for both storage and transmission across the network. |
To help address these needs, we acquired Hifn to complement our proven analog and digital design capabilities and understanding of the telecommunications market with Hifn’s leading-edge solutions addressing encryption, data reductions and packet processing. Hifn brings a comprehensive range of software, silicon and board-level solutions targeting both data reduction and encryption—offering continuous protection of data while in-transit or at rest.
T/E Carrier & SONET/SDH
The worldwide communications infrastructure market continues to transform into packet based infrastructure to support cost and service demands imposed by the deployment of new converged services. A significant portion of existing networks continues to be powered by TraverseEdge (“T/E”) and Synchronous Optical Network/Synchronous Digital Hierarchy (“SONET/SDH”) based infrastructure and to utilize technologies such as Ethernet over Plesiochronous Digital Hierarchy (“EoPDH”) and Ethernet Over SONET (“EoS”) to support packet-based traffic. Optical Transport Networks (“OTN”) are emerging as a medium to allow transfer of both packet-based and TDM traffic over the optical infrastructure. Our communications products primarily address equipment markets in two main segments: Metro-Access and Transport. The Metro-Access segment of the communications network covers both wired and wireless access equipment that aggregates data traffic from homes, wireless base-stations and businesses towards the Transport network. The Transport network primarily consists of fiber-optic based equipment that transports data at rates of 2.5 to 10 Gigabits per second or higher within a Metro or a larger area. In North America, the high-speed data traffic standard is SONET and in most of the rest of the world, it is SDH. Over optical fiber, the SONET/SDH standard ensures network reliability, data integrity and the interoperability of equipment deployed across the network from different manufacturers.
5
Our products for T/E carrier and SONET/SDH applications include high-speed analog, digital and mixed-signal physical interface and access control ICs. The physical interface IC consisting of a transmitter and receiver is called a transceiver. Transceivers interface with the physical transmission media. Most of these high-speed, mixed-signal ICs convert digital inputs in a parallel format into a single high-speed serial bit stream. Access control circuits are digital circuits that format or frame the data, perform error checking and, in some applications, aggregate signals by mapping multiple lower-speed data streams into one single higher-speed stream. The figure below illustrates where our products are utilized within networking equipment.
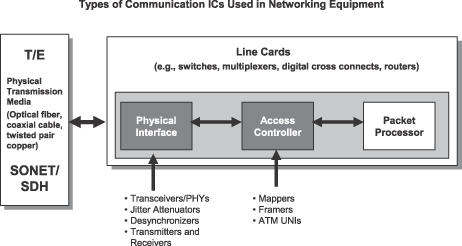
Exar products are used in networking equipment such as SONET/SDH Add/Drop Multiplexers (“ADMs”), Private Branch Exchange (“PBX”), central office switches, digital cross connects, multi-service provisioning platforms, routers and Digital Subscriber Loop Access Multiplexes (“DSLAMs”).
We offer a broad range of products in the T1/E1 segment including short-haul and long-haul Line Interface Units (“LIUs”) and LIU/framer combinations that incorporate reconfigurable, relayless redundancy (Exar R3 Technology™) with integrated termination resistors and jitter attenuation. Used individually or in chip sets, our T1/E1 devices offer customers key advantages including design flexibility, enhanced system reliability and standards compliance, which are critical components of high-density, low-power system boards and line-cards. In addition, our T1/E1/J1 Framer/LIU combination products simplify the design process by saving board space and by reducing complexity as a result of lowering component count. Our T1/E1 portfolio includes products with up to 21 channels for LIUs, up to 8 channels for LIU/framer combinations, and up to 28 channels for LIU/framer/SONET VT mapper combinations.
We have developed a diverse portfolio of single- and multi-channel T3/E3 physical interface solutions with integrated LIU logic and jitter attenuation that achieve high performance levels while reducing board space and overall power in multi-port applications. Extending our LIU and mapper jitter attenuation capabilities, we incorporate slip buffers as well as synchronization techniques to solve complex timing issues associated with mapping between SONET/SDH (synchronous) and T1/E1 (plesio-synchronous) environments. In addition, we have integrated our LIU and framer functions into a DS3/E3 LIU/framer combination device that offers customers additional design flexibility.
Our data aggregation mapper solutions leverage our expertise in T/E carrier and SONET/SDH, enabling us to provide unique solutions for the SONET/SDH marketplace. In addition to integrating the SONET Physical Layer (“PHY”) capability into our data aggregation mappers, we also offer a family of Optical Carrier (“OC”)-3/12/48 transceivers. Our access control products include framers, Asynchronous Transfer Mode Signaling User-to-Network Interfaces (“ATM UNIs”) and data aggregation mappers. Complementing our OC-3 to OC-48
6
SONET/SDH devices is a highly integrated Tethys™ family OC-3/Synchronous Transport Module (“STM”)-1 to OC-192/STM-64 multi-rate SONET/SDH framers/pointer processors. The high channel density of the Tethys devices enables significant flexibility in line card design coupled with cost, area and power savings.
Storage
Storage is becoming an increasingly important part of the network infrastructure. With greatly increasing storage requirements driven by large media-oriented file types and the pervasiveness of connected devices, the acquisition costs and overall costs to maintain these systems are increasing rapidly. Efficient utilization of storage resources is critical. Further, increasing societal, political and legal focus on corporate governance is driving not only the need for companies to retain more data for longer periods, but also their need to store information in a secure way.
Both enterprise and consumer storage solutions are increasingly offering features like encryption, compression and data deduplication. Historically, capabilities such as data deduplication were limited to archival storage in the enterprise. This technology is migrating into primary storage solutions in both enterprises and Small and Medium Businesses (“SMBs”).
The ability to compress data and look for redundancy across storage resources allows for significantly increased utilization within storage systems. Compression algorithms allow a file’s size to be reduced without loss of information prior to storing it. Data deduplication further increases efficiency by identifying redundancy at the file or even sub-file level, allowing data to be stored once with all other instances being referenced back to the original. With tools like email allowing for rapid propagation of large files throughout an enterprise, data reduction technologies like compression and deduplication enable a significant decrease in storage capacity requirements. An additional benefit of these technologies is the reduced bandwidth burden on the communications infrastructure while performing remote back-ups and replication of data at remote sites.
Innovative solutions are required to accelerate complex algorithms necessary for encryption and data reduction without affecting overall performance. Our acquisition of Hifn added software, silicon and board level solutions to our product portfolio that address these needs in both storage and communications applications.
The acquired Hifn Applied Services Processors (“ASPs”) perform the compute-intensive tasks of compression, encryption and authentication, providing our customers with high-performance, interoperable implementations of a wide variety of industry-standard networking and storage protocols. These processors allow OEMs to add both security and data reduction capabilities to systems. These products are available as chips and also integrated on the Data Security (“DS”) and Data Reduction (“DR”) families of adapter cards.
Storage connectivity is becoming a requirement across a range of consumer, enterprise, and embedded applications. The large capacities and low cost of Serial Advanced Technology Attachment (“SATA”) hard disk drives make them almost ubiquitous for all but the most demanding applications. SATA provides for both internal and external connection of disk drives. Our line of SATA storage components addresses the need to provide storage connectivity, expansion and high availability to a range of applications.
Interface
As a market leader, Exar offers the broadest line of industry-proven Universal Asynchronous Receiver/Transmitter (“UART”) solutions as well as synergistic serial transceiver devices into pervasive applications in industrial, telecommunications and consumer markets. Typical applications served by our serial communications products include Point-of-Sales (“POS”), process control and factory automation as well as servers, embedded systems, routers, network management equipment, remote access servers, wireless base-stations and repeaters. Additionally, our single and multi-channel UARTs are used in portable consumer applications such as multi-media, Global Positioning System (“GPS”), Personal Digital Assistant (“PDA”) and smart phone devices.
7
Our UART product portfolio ranges from cost-effective industry-standard devices to high-performance multi-channel UARTs with a broad range of First In, First Out (“FIFO”) depths and industry leading performance and features while supporting popular Central Processing Unit (“CPU”) bus interfaces such as 8-bit Industry Standard Architecture (“ISA”), 8-bit VLIO, 2-wire Inter-Integrate Circuit (“I2C”), 4-wire Serial Peripheral Interface (“SPI”) and Peripheral Component Interconnect (“PCI”). In addition, we were first to market with a wireless UART solution that includes a high-performance UART, controller and Radio Frequency (“RF”) functionality along with our proprietary firmware that enables the application to send and receive data wirelessly over a secure proprietary protocol.
Our serial transceiver solutions consist of Recommended Standard (“RS”)-232, RS-485 and multiprotocol devices that ensure reliable connectivity between computing devices. Our single protocol RS-232 and RS-485 transceivers comply with international standards in delivering multi-channel digital signals between two systems. Our proprietary multiprotocol transceivers enable network equipment to communicate with a large population of peripherals that use a diverse set of serial protocol standards without the added burden of multiple add-on boards and cables.
Our interface product strategy is to continue to enhance the product portfolio with higher speed, lower power and higher functionality devices that meet or exceed the growing demands of the serial communications market. Our interface product growth will be enabled by increased integration and value through the introduction of additional bridge products for popular and growing bus interfaces such as Universal Serial Bus (“USB”), Peripheral Component Interconnect Express (“PCIe”) and Ethernet, among others.
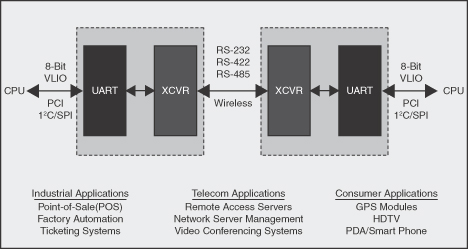
Power Management
The power management market has changed considerably over time. The practice of leaving power considerations to the final stages of the system design has given rise to increased difficulties in space, available energy and heat dissipation. Power management has now moved from the final design stage to one of the primary considerations when defining a system. As a result, power solutions today are challenged to solve a variety of these problems.
The latest generation of consumer, communication and industrial products brings with it the promise of lower-power, feature-rich systems. However, in order to create these new products, system architects are being inundated with several new and complex challenges. As embedded intelligence and features increase, the requirements for multiple voltages and currents, temperature stability and the associated power sequencing become daunting tasks for the system designer. These power challenges are being shared with IC manufacturer.
8
At Exar, we have established a differentiated, proprietary portfolio of power products with one clear goal in mind: to make power design easy. In doing so, we seek to remove the costs and labor burden on our customers of becoming analog “power experts” and enable them to focus on resolving their higher level system related challenges.
Our new generation of digital power management products utilizes proprietary technology that adds digital control and monitoring to our high performance analog circuitry designed to allow the system architect to create products that reduce wasted energy by orders of magnitude. We have developed proprietary technology that enables efficient digital and analog IC partitioning giving us the ability to tailor each new product to match the application requirements in a fraction of the area required by other technology.
Our portfolio of power products is focused on a range of solutions that offer power management, voltage conversion and Light-Emitting Diode (“LED”) lighting. In each product area, we have delivered products that offer differentiating capabilities based on innovative circuit design and integration. We have built upon our strong heritage of analog and mixed signal capability with the addition of proprietary technology enabling the creation of world class products that will continue to evolve as our customers’ requirements become ever more complex.
Strategy
We strive to be a leading provider of highly differentiated silicon, software and subsystem solutions for industrial, datacom and storage applications. To achieve our long-term business objectives, we employ the following strategies:
Leverage Analog and Mixed-Signal Design Expertise to Provide Integrated System-Level Solutions—Utilizing our analog and mixed-signal design expertise, we integrate mixed-signal physical interface devices for a broad range of silicon solutions. This capability continues to be the backbone of our integration strategy and enables us to offer optimized solutions in datacom, interface and power management. Our customers depend on analog and mixed signal integration for power reduction, size optimization and signal integrity.
Expand Product Portfolio—We have developed a strong presence in the broad industrial, datacom and storage markets where we have industry leading customers and proven technological capabilities. Our design expertise has enabled us to offer a diverse portfolio of both industry standard and proprietary products serving a range of connectivity and power management needs. Our extensive product portfolio provides the framework for customers to work with many of our products on a single board design. Our ability to serve the various needs of a customer’s design enables us to meet our customers’ procurement and support needs by reducing their number of vendors and providing a single point of contact for applications support and supply chain management for multiple components.
Grow Market Share with System Solutions—We create systems solutions by coupling system expertise, software and advanced silicon integration to provide an optimized solution that is designed to be technically compelling and cost effective, resulting in distinctive products like Tethys™, 10G Sonet Multiplexer (“Mux”)/DeMux, Flowthough® Security Processors, Bitwackr®, data deduplication solutions, XRP7704 and digital power management. These solutions and others provide platform engagements that involve software and hardware integration at the system level resulting in a cohesive bond with customers.
Strengthen and Expand Strategic OEM Relationships—To promote the early adoption of our solutions, we actively seek collaborative relationships with strategic OEMs during product development. We believe that OEMs recognize the value of our early involvement, because designing their system products in parallel with our development can accelerate time-to-market for their end products. Collaborative relationships also help us to obtain early design wins and to increase the likelihood of market acceptance of our new products.
9
Use Standard CMOS and Bipolar CMOS-DMOS (“BCD”) Process Technologies to Provide Compelling Price/Performance Solutions—We design our products to be manufactured using standard CMOS and BCD processes. We believe that these processes are proven, stable and predictable and benefit from the extensive semiconductor-manufacturing infrastructure devoted to CMOS and BCD processes. In certain specialized cases, we may use other process technologies to take advantage of their performance characteristics.
Employ Fabless Semiconductor Model—We have long-standing relationships with third-party wafer foundries, assembly and test subcontractors to manufacture our ICs. Our fabless approach allows us to avoid substantial capital spending, obtain competitive pricing, minimize the negative effects of industry cycles, reduce time-to-market, reduce technology and product risks, and facilitate the migration of our products to new CMOS and BCD process technologies. By employing the fabless model, we can focus on our core competencies in sales and marketing as well as in product design, development and support.
Broaden Sales Coverage with Channel Partners—We have strong relationships with our distributors and sales representatives throughout the world representing a significant portion of our total revenue. Through our partners, we have access to large market segments which we cannot directly support. Through these relationships, we extend our expertise and product exposure by enabling our partners to discover new demands for our solutions as well as aid us in defining our next generation solutions.
Expand our Business Through Acquisitions—The markets in which we compete require a wide variety of technologies, products and capabilities. The combination of technological complexity and rapid change within our markets makes it difficult for a single company to develop all the technological solutions that it desires to offer within its family of products. Through acquisitions, we aim to deliver a broader range of products to customers in target markets. We employ the following strategies to address the need for new or enhanced products: we develop new technologies and products internally; we acquire field proven third-party intellectual property cores to accelerate time to market; and we acquire all or parts of other companies.
Sales and Customers
We market our products globally through both direct and indirect channels. In the Americas, we are represented by 17 independent sales representatives and two independent, non-exclusive primary distributors, as well as our own direct sales organization. We currently have domestic presences in or near Atlanta, Boston, Chicago, Dallas, Philadelphia, Raleigh and Fremont, California.
Internationally, we are represented in Europe and the Asia Pacific region by our wholly-owned foreign subsidiaries and international support offices in Canada, China, France, Germany, Italy, Japan, Singapore, South Korea, Taiwan and the United Kingdom. In addition to these offices, approximately 37 independent sales representatives and other independent, non-exclusive distributors represent us in Europe, Japan and the Asia-Pacific region. Our international sales represented 75%, 69% and 56% of net sales for fiscal years ended March 29, 2009, March 30, 2008 and March 31, 2007, respectively. Sales to China accounted for 24%, 20% and 14% of net sales in fiscal years 2009, 2008 and 2007, respectively, while sales to Singapore accounted for 13% of net sales in fiscal year 2009 and sales to Italy accounted for 12% of net sales in fiscal year 2007. No other country accounted for sales in excess of 10% of net sales during fiscal years 2009, 2008 or 2007. We expect international sales to continue to be a significant portion of our net sales in the future. All of our sales to foreign entities are denominated in U.S. dollars. For a detailed description of our sales by geographic regions, seePart II, Item 7—“Management’s Discussion and Analysis of Financial Condition and Results of Operations, Net Sales by Geography” andPart II, Item 8—“Notes to Consolidated Financial Statement, Note 18—Segment and Geographic Information.” For a discussion of the risk factors associated with our foreign operations, seePart I, Item 1A—“Risk Factors—‘Our engagement with foreign customers could cause fluctuations in our operating results, which could materially and adversely impact our business, financial condition and results of operations’.”
10
We sell our products to distributors and OEMs throughout the world. Alcatel-Lucent accounted for 11% and 16% of our net sales in fiscal years 2008 and 2007, respectively. No other OEM customer accounted for 10% or more of our net sales in fiscal years 2009, 2008 and 2007. Future Electronics Inc. (“Future”), a related party, was our largest distributor and accounted for 35%, 24% and 20% of net sales in fiscal years 2009, 2008 and 2007, respectively. Our second largest distributor, Nu Horizons Electronics Corp. (“Nu Horizons”), accounted for 11% and 18% of net sales in fiscal years 2008 and 2007, respectively. No other distributor accounted for 10% or more of net sales for any of those three fiscal years.
We work directly with many key customers including, among others, Adtran Inc., Alcatel-Lucent, Apple Inc., Motorola, Inc., Cisco Systems Inc., Digi International Inc., Ericsson Inc., Fujitsu Limited, Huawei Technologies Co., Ltd., International Business Machines Corporation, LG Electronics Inc., Mitsubishi Electronics America Inc., NEC Corporation, Nokia Siemens Networks, Panasonic Corporation, Samsung Electronics, Tellabs, Inc. and ZTE Corporation. We expanded our relationship with Cisco Systems Inc. and Huawei Technologies Co., Ltd. through our acquisition of Hifn.
Manufacturing
We outsource all of our fabrication and assembly, as well as the majority of our testing operations. This fabless manufacturing model allows us to focus on sales and marketing as well as product design, development and support.
Our products are manufactured using standard CMOS, bipolar, BiCMOS (bipolar CMOS) and BCD process technologies. We use wafer foundries located in the United States and Asia to manufacture our semiconductor wafers.
Most of our semiconductor wafers are shipped directly from our foundries to our subcontractors in Asia for wafer test and assembly, where they are cut into individual die and packaged. Independent contractors in Malaysia, China, Indonesia and Taiwan perform most of our assembly work. Final test and quality assurance are performed either at our subcontractors’ facilities in Asia or at our Fremont, California facility. All our manufacturing partners have been certified to ISO 9001:2000 and are or soon will be automotive spec, TL16949 compliant.
For all acquired Hifn products, currently in production, we will continue to use the turnkey manufacturing model, with our suppliers delivering fully assembled and tested products based on our proprietary designs.
Research and Development
We believe that ongoing innovation and introduction of new products in our targeted and adjacent markets is essential to sustaining growth. Our ability to compete depends on our ability to offer technologically innovative products on a timely basis. As performance demands and the complexity of ICs have increased, the design and development process has become a multi-disciplinary effort requiring diverse competencies. Our research and development is focused on developing high-performance analog, digital and mixed-signal solutions addressing the high-bandwidth requirements of communications and storage systems OEMs and the high-current, high-voltage requirements of interface and power management OEMs. We make investments in advanced design tools, design automation and high-performance intellectual property libraries while taking advantage of readily available specialty intellectual property through licensing or purchases. We also augment our skill sets and intellectual property through university collaboration, incorporating talent through acquisition and by accessing needed skills with off-campus design centers. We continue to pursue the development of design methodologies that are optimized for reducing design-cycle time and increasing the likelihood of first-time success. While we continually upgrade our internal technology to develop innovative products, as a fabless company, we also work with foundries that provide our wafers. As a result of the Hifn acquisition we now have a substantive research and development presence in the People’s Republic of China (“PRC”). We spent $31.8 million, $30.7 million
11
and $25.8 million on research and development in fiscal years 2009, 2008 and 2007, respectively. For the explanation of our increased expenses in research and development, please seePart II, Item 7—“Management’s Discussion and Analysis of Financial Condition and Results of Operations.”
Competition
The semiconductor industry is intensely competitive and is characterized by rapid technological change and a history of price reductions as design improvements and production efficiencies are achieved in successive generations of products. Although the market for analog and mixed-signal ICs is generally characterized by longer product life cycles and less dramatic price reductions than the market for digital ICs, we face substantial competition in each market in which we participate.
We believe that the principal competitive factors in the portions of the semiconductor industry in which we operate are:
| • | | product performance, quality and reliability; |
| • | | customer support and services; |
| • | | rapid technological change; |
| • | | new product innovation; and |
| • | | compliance with and support of industry standards. |
We compete with many other companies and many of our current and potential competitors may have certain advantages over us, for example:
| • | | longer presence in key markets; |
| • | | greater name recognition; |
| • | | stronger financial position and liquidity; |
| • | | more secure supply chain; |
| • | | access to larger customer bases; and |
| • | | significantly greater sales and marketing, and other resources. |
Because IC markets are highly fragmented, we generally encounter different competitors in our various target markets. Competitors with respect to our communications products include Applied Micro Circuits Corporation, Integrated Device Technology, Inc., Maxim Integrated Products, Inc., Mindspeed Technologies, Inc., PMC-Sierra, Inc., TranSwitch Corporation and Vitesse Semiconductor Corporation. Competitors in storage include Silicon Image, Inc. and Marvell Technology Group Ltd. Competitors in serial interface include NXP B.V., Texas Instruments Incorporated, Analog Devices, Inc., Intersil Corporation, Linear Technology Corporation and Maxim Integrated Products, Inc. Our primary competitors in power include Advanced Analogic Technologies Incorporated, Analog Devices, Inc., Intersil Corporation, Linear Technology Corporation, Maxim Integrated Products, Inc., Micrel Incorporated, National Semiconductor Corporation, On Semiconductor Corporation, Pioneer Corporation, Semtech Corporation, Sharp Electronics Corporation, Sony Corporation and Texas Instruments Incorporated.
12
We believe that important competitive factors in the markets in which we offer the Hifn products include price-performance characteristics, rapid technological change, the continued emergence and compliance with and support of new industry standards, length of development cycles, design wins with major network and storage equipment vendors, support for new network and storage standards, features and functionality, adaptability of products to specific applications, reliability, technical service and support and protection of products by effective utilization of intellectual property laws. Our failure to develop products that compete successfully with those of other suppliers in these markets would harm our business, financial condition and results of operations. In addition, we must compete for the services of qualified distributors and sales representatives. To the extent that our competitors offer such distributors or sales representatives more favorable terms on a higher volume of business, such distributors or sales representatives may decline to carry, or discontinue carrying, our products. Our business, financial condition and results of operations could be harmed by any failure to maintain and expand our distribution network. SeeItem 1A. “Risk Factors—‘If we are unable to compete effectively with existing or new competitors, we will experience fewer customer orders, reduced revenues, reduced gross margins and lost market share’.”
Backlog
Our sales are made pursuant to either purchase orders for current delivery of standard items or agreements covering purchases over a period of time, which are frequently subject to revisions and, to a lesser extent, cancellations with little or no penalties. Lead times for the release of purchase orders depend on the scheduling practices of the individual customer, and our rate of bookings varies from month-to-month. Certain distributors’ agreements allow for stock rotations, scrap allowances and volume discounts. Further, we defer recognition of revenue on shipments to certain distributors until the product is resold. For all of these reasons, we believe backlog as of any particular date should not be used as a predictor of future sales.
Intellectual Property Rights
We believe that our intellectual property is critical to our current and future success. However, we do not believe that it is materially dependent upon any one patent. To protect our intellectual property, we rely on a combination of patents, mask work registrations, trademarks, copyrights, trade secrets, and employee and third-party nondisclosure agreements. We have 175 patents issued and 38 patent applications pending in the United States. We have 42 patents issued and 122 patent applications pending in various foreign countries. Our existing patents will expire between 2009 and 2026, or sooner if we choose not to pay renewal fees. We may also enter into license agreements or other agreements to gain access to externally developed products or technologies.
However, we may fail to adequately protect our intellectual property. Others may gain access to our trade secrets or disclose such trade secrets to third parties without our knowledge. Some or all of our pending and future patent applications may not result in issued patents that provide us with a competitive advantage. Even if issued, such patents, as well as our existing patents, may be challenged and later determined to be invalid or unenforceable. Others may develop similar or superior products without access to or without infringing upon our intellectual property, including intellectual property that is protected by trade secret and patent rights. In addition, the laws of certain territories in which our products are or may be developed, manufactured or sold, including Asia, Europe and Latin America, may not protect our products and intellectual property rights to the same extent as the laws of the United States of America.
We cannot be sure that our products or technologies do not infringe patents that may be granted in the future pursuant to pending patent applications or that our products do not infringe any patents or proprietary rights of third parties. Occasionally, we are informed by third parties of alleged patent infringement. In the event that any relevant claims of third-party patents are found to be valid and enforceable, we may be required to:
| • | | stop selling, incorporating or using our products that use the infringed intellectual property; |
| • | | obtain a license to make, sell or use the relevant technology from the owner of the infringed intellectual property, although, such license may not be available on commercially reasonable terms, if at all; or |
13
| • | | redesign our products so as not to use the infringed intellectual property, which may not be technically or commercially feasible or meet customer requirements. |
If we are required to take any of the actions described above or defend against any claims from third parties, our business, financial condition and results of operations could be harmed. SeePart I, Item 1A—“Risk Factors—‘We may be unable to protect our intellectual property rights, which could harm our competitive position’ and ‘We could be required to pay substantial damages or could be subject to various equitable remedies if it were proven that we infringed the intellectual property rights of others’.”
Employees
As of March 29, 2009, we employed 368 full-time employees, with 141 in research and development, 85 in operations, 88 in marketing and sales and 54 in administration. Of the 368 employees, 84 are located in our international offices. With the acquisition of Hifn, we added 158 employees, of which 73 are in China. SeePart I, Item 1A—“Risk Factors—‘We depend in part on the continued service of our key engineering and management personnel and our ability to identify, hire, incentivize and retain qualified personnel. If we lose key employees or fail to identify, hire, incentivize and retain these individuals, our business, financial condition and results of operations could be materially and adversely impacted’.” None of our employees are represented by a collective bargaining agreement, and we have never experienced a work stoppage due to labor issues.
Executive Officers of the Registrant
Our executive officers and their ages as of May 29, 2009, are as follows:
| | | | |
Name | | Age | | Position |
Pedro (Pete) P. Rodriguez | | 47 | | Chief Executive Officer, President and Director |
J. Scott Kamsler | | 61 | | Senior Vice President and Chief Financial Officer |
George Apostol | | 44 | | Chief Technology Officer |
Paul Pickering | | 49 | | Senior Vice President of Marketing |
Hung P. Le | | 48 | | Vice President of Engineering |
Bentley Long | | 47 | | Vice President of Worldwide Sales |
Thomas R. Melendrez | | 55 | | General Counsel, Secretary and Executive Vice President of Business Development |
Stephen W. Michael | | 62 | | Senior Vice President of Operations and Reliability & Quality Assurance |
Pedro (Pete) P. Rodriguez was appointed Chief Executive Officer and President of Exar in April 2008. He has served as a director of Exar since October 2005. Mr. Rodriguez has over 25 years of engineering, sales, marketing and executive management experience in the semiconductor industry. Mr. Rodriguez served, most recently, from June 2007 to April 2008, as Chief Marketing Officer of Virage Logic Corporation, a semiconductor intellectual property supplier for Systems on a Chip (“SoC”). Prior to his appointment at Virage Logic, Mr. Rodriguez served as President, Chief Executive Officer and Director of Xpedion Design Systems, Inc., a private, venture-funded developer of design solutions for Radio Frequency Integrated Circuits (“RFIC”) from May 2000 to August 2006. Mr. Rodriguez held this role for six years until shortly after Xpedion was acquired by Agilent Technologies, Inc. in 2006. Prior to Xpedion, he held various senior management positions in sales and marketing at Escalade Corporation, a provider of software for chip design, and LSI Corporation (formerly LSI Logic Corporation) as well as design engineering, product management and process engineering positions at Aerojet Electronics, Teledyne Microwave and Siliconix Incorporated. Mr. Rodriguez holds an MBA from Pepperdine University, an MSEE from California Polytechnic University and a BS in Chemical Engineering from California Institute of Technology.
J. Scott Kamsler joined us in February 2007 as our Senior Vice President and Chief Financial Officer. Prior to joining us, he was Vice President and Chief Financial Officer at Centillium Communications, Inc., a supplier of communications semiconductors, from July 2004 to February 2007. He also served as Vice President of Operations at Wyse Technology Inc., a supplier of server-centric thin client computers, from 2003 to 2004 and as
14
Chief Financial Officer at Tasman Networks, Inc., a supplier of access and aggregation routers, from 2000 to 2002. Prior to Tasman Networks, he served as Chief Financial Officer of four public companies: Symmetricom, Inc., DSP Technology Inc., Solitec, Inc. and E-H International, Inc. Earlier in his career, he held various finance positions at Intel Corporation and was an auditor with Peat Marwick Mitchell. Mr. Kamsler is a CPA and received his BA from Willamette University and his MBA from the University of Washington.
George Apostol joined us as Chief Technology Officer in May 2008. Mr. Apostol has over 20 years of experience in the systems electronics and semiconductor industries. From May 2005 to May 2008, Mr. Apostol served as Chief Technology Officer and Vice President of Engineering at PLX Technology, Inc., an integrated circuits company. He was Vice President of Engineering at Audience, Inc., a supplier of audio software and semiconductor systems, from May 2004 to May 2005 and Vice President of Engineering at BRECIS Communications Corporation, the inventor of the popular Multi-service Processor (MSP), from February 2000 to April 2004. Prior to that, he held various senior engineering and management positions at TiVo, Inc., LSI Corporation (formerly LSI Logic Corporation), Silicon Graphics, Inc. and Xerox Corporation. With a strong background designing systems on silicon, he holds several patents in the areas of system bus interface, clocking and buffer management design, and has written and deployed multiple Application-Specification Integrated Circuit (“ASIC”) design productivity tools. Mr. Apostol performed his academic research at the Dana Farber Cancer Institute and Massachusetts Institute of Technology Sloan School of Management and holds a BSEE from Massachusetts Institute of Technology.
Paul Pickeringwas appointed Senior Vice President of Marketing in June 2008. Mr. Pickering has over 26 years of semiconductor marketing and sales experience. Prior to his current position, Mr. Pickering was the Vice President of Field Operations for Innovative Silicon from March 2007 to June 2008, a venture-capital funded company that developed a pioneering memory—Z-RAM®—technology for stand-alone DRAM and embedded memory applications. Prior to Innovative Silicon, Mr. Pickering was executive vice-president of sales and marketing for Xpedion Design Systems from May 2003 to March 2007, a leading RF simulation company that was acquired by Agilent Technologies. Prior to Agilent Technologies, Mr. Pickering worked in senior management sales and marketing roles at Fairchild, Toshiba, LSI Logic, and PMC-Sierra.
Hung P. Le was appointed Vice President of Engineering in July 2007. Prior to his current position, Mr. Le was Division Vice President of Technology from October 2004 to July 2007. He joined Exar in March 1995 and served as Director of Technology when Exar acquired Startech Semiconductor, Inc. Prior to joining Startech in 1994, he was Manager of Technology at Sierra Semiconductor, Inc. Mr. Le has over 25 years of experience in semiconductor physics and design and holds eleven patents. He received his MS and BS in Electrical Engineering and Computer Science from Massachusetts Institute of Technology.
Bentley Long was appointed Vice President of Worldwide Sales in January 2008. Mr Long joined us as Vice President of North America Sales and Global Distribution in January 1997 and has over 20 years of semiconductor sales and marketing experience including the last 11 years at Exar. He has previously worked at VLSI Technology, Inc. as an Area Sales Manager and Worldwide Strategic Account Manager, and also held various technical positions at Texas Instruments Incorporated. He holds a Bachelor of Engineering Degree in Electrical Engineering and Mathematics from Vanderbilt University and an MBA from the University of Tennessee.
Thomas R. Melendrez joined us in April 1986 as our Corporate Attorney. He was promoted to Director, Legal Affairs in July 1991, and again to Corporate Vice President, Legal Affairs in March 1993. In March 1996, he was promoted to Corporate Vice President, General Counsel and in June 2001, he was appointed Secretary. In April 2003, he was promoted to General Counsel, Secretary and Vice President of Business Development and in July 2005, he was promoted to Senior Vice President of Business Development. In April 2007, he was promoted to his current position as General Counsel, Secretary and Executive Vice President of Business Development. Mr. Melendrez has over 25 years of legal experience in the semiconductor and related industries and he received a BA from the University of Notre Dame, a JD from University of San Francisco and an MBA from Pepperdine University.
15
Stephen W. Michael joined us in September 1992 as our Vice President of New Market Development. In July 1995, he was appointed Vice President of Operations, and in May 2001, he was appointed to Vice President of Operations and Reliability & Quality Assurance. In July 2007, he was appointed to Senior Vice President of Operations and Reliability & Quality Assurance. Prior to joining us, he was Vice President and General Manager of Analog and Custom Products with Catalyst Semiconductor. Prior to Catalyst Semiconductor, he served in various senior positions at GE Semiconductor, Intersil Corporation, Fairchild Camera and Instrument Corporation and National Semiconductor Corporation. Mr. Michael has over 30 years of semiconductor industry experience and holds a BS in Electrical Engineering from the University of California at Davis.
Available Information
We file electronically with the SEC our Annual Reports on Form 10-K, Quarterly Reports on Form 10-Q, current Reports on Form 8-K, and amendments to those Reports pursuant to Section 13 or 15(d) of the Securities Exchange Act of 1934. Those reports and statements: (1) may be read and copied at the SEC’s public reference room at 100 F Street, N.E., Washington, DC 20549, (2) are available at the SEC’s Internet site (http://www.sec.gov), which contains reports, proxy and information statements and other information regarding issuers that file electronically with the SEC; and (3) are available free of charge through our website (www.exar.com) as soon as reasonably practicable after electronic filing with, or furnishing to, the SEC. Information regarding the operation of the SEC’s public reference room may be obtained by calling the SEC at 1-800-SEC-0330. Copies of such documents may be requested by contacting our Investor Relations Department at (510) 668-7201 or by sending an e-mail through the Investor Relations page on our website. Information on our website is not incorporated by reference into this Report.
Global capital and credit market conditions, and resulting declines in consumer confidence and spending, could have a material adverse effect on our business, operating results, and financial condition.
Volatility and disruption in the global capital and credit markets in 2008 and 2009 have led to a tightening of business credit and liquidity, a contraction of consumer credit, business failures, higher unemployment, and declines in consumer confidence and spending in the United States and internationally. If global economic and financial market conditions deteriorate or remain weak for an extended period of time, many related factors could have a material adverse effect on our business, operating results, and financial condition, including the following:
| • | | slower spending may result in reduced demand for our products, reduced orders for our products, order cancellations, lower revenues, increased inventories, and lower gross margins; |
| • | | we may be unable to find suitable investments that are safe, liquid, and provide a reasonable return resulting in lower interest income or longer investment horizons, and disruptions to capital markets or the banking system may also impair the value of investments or bank deposits we currently consider safe or liquid; |
| • | | the failure of financial institution counterparties to honor their obligations to us under credit instruments could jeopardize our ability to rely on and benefit from those instruments, and our ability to replace those instruments on the same or similar terms may be limited under poor market conditions; |
| • | | continued volatility in the markets and prices for commodities and raw materials we use in our products and in our supply chain could have a material adverse effect on our costs, gross margins, and profitability; |
| • | | if distributors of our products experience declining revenues, or experience difficulty obtaining financing in the capital and credit markets to purchase our products, it could result in reduced orders for our products, order cancellations, inability to timely meet payment obligations to us, extended payment terms, higher accounts receivable, reduced cash flows, greater expense associated with collection efforts, and increased bad debt expense; |
| • | | if distributors of our products experience severe financial difficulty, some may become insolvent and cease business operations, which could reduce the availability of our products to customers; |
16
| • | | if contract manufacturers or foundries of our products or other participants in our supply chain experience difficulty obtaining financing in the capital and credit markets to purchase raw materials or to finance general working capital needs, it may result in delays or non-delivery of shipments of our products; |
| • | | potential shutdowns by our third-party foundry, assembly and test subcontractors due to slow business conditions could result in longer lead-times, higher buffer inventory levels and degraded on-time delivery performance; and |
| • | | the current macroeconomic environment also limits our visibility into future purchases by our customers and renewals of existing agreements, which may necessitate changes to our business model. |
Our financial results may fluctuate significantly because of a number of factors, many of which are beyond our control.
Our financial results may fluctuate significantly. Some of the factors that affect our financial results, many of which are difficult or impossible to control or predict, include:
| • | | the cyclical nature of the semiconductor industry; |
| • | | our difficulty in predicting revenues and ordering the correct mix of products from suppliers due to limited visibility provided by customers and channel partners; |
| • | | fluctuations of our revenue and gross profits due to the mix of product sales as our margins vary by product; |
| • | | the effect of the timing of sales by our resellers on our reported results as a result of our sell-through revenue recognition policies; and |
| • | | the reduction, rescheduling, cancellation or timing of orders by our customers, distributors and channel partners due to, among others, the following factors: |
| • | | management of customer, subcontractor and/or channel inventory; |
| • | | delays in shipments from our subcontractors causing supply shortages; |
| • | | inability of our subcontractors to provide quality products in a timely manner; |
| • | | dependency on a single product with a single customer and/or distributors; |
| • | | volatility of demand for equipment sold by our large customers, which in turn, introduces demand volatility for our products; |
| • | | disruption in customer demand as customers change or modify their complex subcontract manufacturing supply chain; |
| • | | disruption in customer demand due to technical or quality issues with our devices or components in their system; |
| • | | the inability of our customers to obtain components from their other suppliers; |
| • | | disruption in sales or distribution channels; |
| • | | our ability to maintain and expand distributor relationships; |
| • | | changes in sales and implementation cycles for our products; |
| • | | the ability of our suppliers and customers to remain solvent, obtain financing or fund capital expenditures as a result of global recession; |
| • | | risks associated with entering new markets; |
| • | | the announcement or introduction of products by our existing competitors or potential new competitors; |
17
| • | | loss of market share by our customers; |
| • | | competitive pressures on selling prices or product availability; |
| • | | pressures on selling prices overseas due to foreign currency exchange fluctuations; |
| • | | erosion of average selling prices coupled with the inability to sell newer products with higher average selling prices, resulting in lower overall revenue and margins; |
| • | | delays in product design releases; |
| • | | market and/or customer acceptance of our products; |
| • | | consolidation among our competitors, our customers and/or our customers’ customers; |
| • | | changes in our customers’ end user concentration or requirements; |
| • | | loss of one or more major customers; |
| • | | significant changes in ordering pattern by major customers; |
| • | | our or our channel partners’ ability to maintain and manage appropriate inventory levels; |
| • | | the availability and cost of materials and services, including foundry, assembly and test capacity, needed by us from our foundries and other manufacturing suppliers; |
| • | | disruptions in our or our customers’ supply chain due to natural disasters, fire, outbreak of communicable diseases, labor disputes, civil unrest or other reasons; |
| • | | delays in successful transfer of manufacturing processes to our subcontractors; |
| • | | fluctuations in the manufacturing output, yields, and capacity of our suppliers; |
| • | | fluctuation in suppliers’ capacity due to reorganization, relocation or shift in business focus or other reasons; |
| • | | problems, costs, or delays that we may face in shifting our products to smaller geometry process technologies and in achieving higher levels of design and device integration; |
| • | | our ability to successfully introduce and transfer into production new products and/or integrate new technologies; |
| • | | increased manufacturing costs; |
| • | | higher mask tooling costs associated with advanced technologies; |
| • | | the amount and timing of our investment in research and development; |
| • | | costs and business disruptions associated with stockholder or regulatory issues; |
| • | | the timing and amount of employer payroll tax to be paid on our employees’ gains on stock options exercised; |
| • | | inability to generate profits to utilize net operating losses; |
| • | | increased costs and time associated with compliance with new accounting rules or new regulatory requirements; |
| • | | changes in accounting or other regulatory rules, such as the requirement to record assets and liabilities at fair value; |
| • | | fluctuations in interest rates and/or market values of our marketable securities; |
| • | | litigation costs associated with the defense of suits brought or complaints made against us; and |
| • | | changes in or continuation of certain tax provisions. |
18
Our expense levels are based, in part, on expectations of future revenues and are, to a large extent, fixed in the short-term. Our revenues are difficult to predict and at times we have failed to achieve revenue expectations. We may be unable to adjust spending in a timely manner to compensate for any unexpected revenue shortfall. If revenue levels are below expectations for any reason, operating results are likely to be materially adversely affected.
Our stock price is volatile.
The market price of our common stock has fluctuated significantly to date. In the future, the market price of our common stock could be subject to significant fluctuations due to:
| • | | loss of or changes to key executives; |
| • | | our anticipated or actual operating results; |
| • | | announcements or introductions of new products by us or our competitors; |
| • | | technological innovations by us or our competitors; |
| • | | product delays or setbacks by us, our customers or our competitors; |
| • | | potential supply disruptions; |
| • | | sales channel interruptions; |
| • | | concentration of sales among a small number of customers; |
| • | | conditions in our customers’ markets and the semiconductor markets; |
| • | | the commencement and/or results of litigation; |
| • | | changes in estimates of our performance by securities analysts; |
| • | | decreases in the value of our investments or long-lived assets, thereby requiring an asset impairment charge against earnings; |
| • | | repurchasing shares of our common stock; |
| • | | announcements of merger or acquisition transactions; and/or |
| • | | general global economic and capital market conditions. |
In the past, securities and class action litigation has been brought against companies following periods of volatility in the market prices of their securities. We may be the target of one or more of these class action suits, which could result in significant costs and divert management’s attention, thereby harming our business, results of operations and financial condition.
In addition, at times the stock market has experienced and is currently experiencing extreme price, volume and value fluctuations that affect the market prices of many high technology companies, including semiconductor companies, and that are unrelated or disproportionate to the operating performance of those companies. Any such fluctuations may harm the market price of our common stock.
The general state of the U.S. and global economies, as well as our market, may materially and adversely impact our business, financial condition and results of operations.
Periodic declines or fluctuations in the U.S. dollar, corporate profits, interest rates, and capital markets, inflation, lower spending, the impact of conflicts throughout the world, terrorist acts, natural disasters, volatile energy costs, the outbreak of communicable diseases and other geopolitical factors have had, and may continue to have, a negative impact on the U.S. and global economies. Our revenue and profitability have generally followed market fluctuations in our industry, which fluctuations have affected the demand for our own and our
19
customers’ products, thus affecting our revenues and profitability. Our customers continue to experience consolidation in their industries which may result in project delays or cancellations. We are unable to predict the strength or duration of current market conditions or effects of consolidation. Uncertainties in anticipated spending levels or further consolidation may adversely affect our business, financial condition and results of operations.
We derive a substantial portion of our revenues from distributors, especially from our two primary distributors, Future Electronics Inc. (“Future”), a related party, and Nu Horizons Electronics Corp. (“Nu Horizons”). Our revenues would likely decline significantly if our primary distributors elected not to promote or sell our products or if they elected to cancel, reduce or defer purchases of our products.
Our distributors rely heavily on the availability of short-term capital at reasonable rates to fund their ongoing operations. If this capital is not available, or is only available on onerous term, certain distributors may not be able to pay for inventory received or we may experience a reduction in orders from these distributors, which would likely cause our revenue to decline and materially and adversely impact our business, financial condition and results of operations.
Future and Nu Horizons have historically accounted for a significant portion of our revenues, and they are our two primary distributors worldwide. We anticipate that sales of our products to these distributors will continue to account for a significant portion of our revenues. The loss of either Future or Nu Horizons as a distributor, or a significant reduction in orders from either of them would materially and adversely affect our operating results, business and financial condition.
Sales to Future and Nu Horizons are made under agreements that provide protection against price reduction for their inventory of our products. As such, we could be exposed to significant liability if the inventory value of the products held by Future and Nu Horizons declined dramatically. Our distributor agreements with Future and Nu Horizons do not contain minimum purchase commitments. As a result, Future and Nu Horizons could cease purchasing our products with short notice or cease distributing these products. In addition, they may defer or cancel orders without penalty, which would likely cause our revenues to decline and materially and adversely impact our business, financial condition and results of operations.
Any error in our sell-through revenue recognition judgment or estimates could lead to inaccurate reporting of our net sales, gross profit, deferred income and allowances on sales to distributors and net income.
Sell-through revenue recognition is highly dependent on receiving pertinent and accurate data from our distributors in a timely fashion. Distributors provide us periodic data regarding the product, price, quantity, and end customer when products are resold as well as the quantities of our products they still have in stock. We must use estimates and apply judgments to reconcile distributors’ reported inventories to their activities. Any error in our judgment could lead to inaccurate reporting of our net sales, gross profit, deferred income and allowances on sales to distributors and net income.
The complexity of our products may lead to errors, defects and bugs, which could subject us to significant costs or damages and adversely affect market acceptance of our products.
Although we, our customers and our suppliers rigorously test our products, they may contain undetected errors, weaknesses, defects or bugs when first introduced or as new versions are released. If any of our products contain production defects, reliability, quality or compatibility problems that are significant to our customers, our reputation may be damaged and customers may be reluctant to continue to buy our products, which could adversely affect our ability to retain and attract new customers. In addition, these defects or bugs could interrupt or delay sales of affected products, which could adversely affect our results of operations.
If defects or bugs are discovered after commencement of commercial production, we may be required to make significant expenditures of capital and other resources to resolve the problems. This could result in
20
significant additional development costs and the diversion of technical and other resources from our other development efforts. We could also incur significant costs to repair or replace defective products or may agree to be liable for certain damages incurred. These costs or damages could have a material adverse effect on our financial condition and results of operations.
If we fail to develop, introduce or enhance products that meet evolving market needs or which are necessitated by technological advances, or we are unable to grow revenues, then our business, financial condition and results of operations could be materially and adversely impacted.
The markets for our products are characterized by a number of factors, some of which are listed below:
| • | | evolving and competing industry standards; |
| • | | changing customer requirements; |
| • | | increasing price pressure; |
| • | | increasing product development costs; |
| • | | long design-to-production cycles; |
| • | | fluctuations in capital equipment spending levels and/or deployment; |
| • | | rapid adjustments in customer demand and inventory; |
| • | | increasing functional integration; |
| • | | moderate to slow growth; |
| • | | frequent product introductions and enhancements; |
| • | | changing competitive landscape (consolidation, financial viability); |
| • | | finite market windows for product introductions; and |
| • | | short end market product life cycles. |
Our growth depends in part on our successful development and acceptance of new products for our core markets. We must: (i) anticipate customer and market requirements and changes in technology and industry standards; (ii) properly define and develop new products on a timely basis; (iii) gain access to and use technologies in a cost-effective manner; (iv) have suppliers produce quality products; (v) continue to expand our technical and design expertise; (vi) introduce and cost-effectively manufacture new products on a timely basis; (vii) differentiate our products from our competitors’ offerings; and (viii) gain customer acceptance of our products. In addition, we must continue to have our products designed into our customers’ future products and maintain close working relationships with key customers to define and develop new products that meet their evolving needs. Moreover, we must respond in a rapid and cost-effective manner to shifts in market demands, the trend towards increasing functional integration and other changes. Migration from older products to newer products may result in volatility of earnings.
Products for our customers’ applications are based on continually evolving industry standards and new technologies. Our ability to compete will depend in part on our ability to identify and ensure compliance with these industry standards. The emergence of new standards could render our products incompatible. We could be required to invest significant time, effort and expenses to develop and qualify new products to ensure compliance with industry standards.
The process of developing and supporting new products is complex, expensive and uncertain, and if we fail to accurately predict and understand our customers’ changing needs and emerging technological trends, our
21
business may be harmed. In addition, we may make significant investments to modify new products according to input from our customers who may choose a competitor’s or an internal solution, or cancel their projects. We may not be able to identify new product opportunities successfully, develop and bring to market new products, achieve design wins, ensure when and which design wins actually get released to production, or respond effectively to technological changes or product announcements by our competitors. In addition, we may not be successful in developing or using new technologies or may incorrectly anticipate market demand and develop products that achieve little or no market acceptance. Our pursuit of technological advances may require substantial time and expense and may ultimately prove unsuccessful. Failure in any of these areas may materially and adversely harm our business, financial condition and results of operations.
If we are unable to convert a significant portion of our design wins into revenue, our business, financial condition and results of operations could be materially and adversely impacted.
We have secured a significant number of design wins for new and existing products. Such design wins are necessary for revenue growth. However, many of our design wins may never generate revenues if their end-customer projects are unsuccessful in the market place or the end-customer terminates the project, which may occur for a variety of reasons. Mergers and consolidations among our customers may lead to termination of certain projects before the associated design win generates revenue. If design wins do generate revenue, the time lag between the design win and meaningful revenue is typically between six months to greater than eighteen months. If we fail to convert a significant portion of our design wins into substantial revenue, our business, financial condition and results of operations could be materially and adversely impacted. Under current deteriorating global economic conditions, our design wins could be delayed even longer than the typical lag period and our eventual revenue could be less than anticipated from products that were introduced within the last eighteen to thirty-six months.
We may be exposed to additional credit risk
From time to time one of our customers has contributed more than 10% of our annual net sales. The acquisition of Hifn might result in additional customers, individually, contributing 10% or more of our annual net sales. Substantially all of Hifn’s customers are OEMs, or the manufacturing subcontractors of OEMs, which might result in an increase in concentrated credit risk with respect to our trade receivables. At September 30, 2008 (Hifn’s fiscal year end), three customers accounted for 66% of Hifn’s total accounts receivable.
We have made and in the future may make acquisitions and significant strategic equity investments, which may involve a number of risks. If we are unable to address these risks successfully, such acquisitions and investments could have a materially adverse effect on our business, financial condition and results of operations.
We have undertaken a number of strategic acquisitions and investments in the past and may do so from time to time in the future. The risks involved with these acquisitions and investments include:
| • | | the possibility that we may not receive a favorable return on our investment or incur losses from our investment or the original investment may become impaired; |
| • | | failure to satisfy or set effective strategic objectives; |
| • | | our assumption of known or unknown liabilities or other unanticipated events or circumstances; and |
| • | | the diversion of management’s attention from day-to-day operations of the business and the potential disruptions to the ongoing business. |
Additional risks involved with acquisitions include:
| • | | difficulties in integrating and managing various operations such as sales, engineering, marketing, and operations; |
22
| • | | difficulties in incorporating acquired technologies and intellectual property rights into new products; |
| • | | difficulties or delays in the transfer of manufacturing flows and supply chains of products of acquired businesses; |
| • | | failure to retain and integrate key personnel; |
| • | | failure to retain and maintain relationship with existing customers, distributors, channel partners and other parties; |
| • | | failure to manage and operate multiple geographic locations both effectively and efficiently; |
| • | | failure to coordinate research and development activities to enhance and develop new products and services in a timely manner that optimize the assets and resources of the combined company; |
| • | | difficulties in creating uniform standards, controls (including internal control over financial reporting), procedures, policies and information systems; |
| • | | unexpected capital equipment outlays and continuing expenses related to technical and operational integration; |
| • | | difficulties in entering markets or retaining current markets in which we have limited or no direct prior experience and where competitors in such markets may have stronger market positions; |
| • | | insufficient revenues to offset increased expenses associated with acquisitions; |
| • | | under-performance problems with an acquired company; |
| • | | issuance of common stock that would dilute our current stockholders’ percentage ownership; |
| • | | reduction in liquidity and interest income on lower cash balance; |
| • | | recording of goodwill and intangible assets that will be subject to periodic impairment testing and potential impairment charges against our future earnings; |
| • | | incurring amortization expenses related to certain intangible assets; |
| • | | the opportunity cost associated with committing capital in such investments; |
| • | | incurring large and immediate write-offs; and |
| • | | being subject to litigation. |
Risks involved with strategic equity investments include:
| • | | the possibility of litigation resulting from these types of investments; |
| • | | the possibility that we may not receive a financial return on our investments or incur losses from these investments; |
| • | | a changed or poorly executed strategic plan; and |
| • | | the opportunity cost associated with committing capital in such investments. |
We may not address these risks successfully without substantial expense, delay or other operational or financial problems, or at all. Any delays or other such operations or financial problems could adversely impact our business, financial condition and results of operations.
Because a significant portion of our total assets were, and may again be with future potential acquisitions, represented by goodwill and other intangible assets which are subject to mandatory annual impairment evaluations, we could be required to write off some or all of our goodwill and other intangible assets, which may adversely impact our financial condition and results of operations.
A significant portion of the purchase price for any business combination may be allocated to identifiable tangible and intangible assets and assumed liabilities based on estimated fair values at the date of consummation.
23
The excess purchase price, if any, over the fair value of these assets less liabilities would be allocated as required by generally accepted account principles utilized by Exar and would typically be allocated to goodwill. In accordance with the FAS 142, Goodwill and Other Intangible Assets, goodwill is not amortized but is reviewed for impairment annually or more frequently if impairment indicators arise. We typically conduct our annual analysis of our goodwill in the fourth quarter of our fiscal year. Intangible assets that are subject to amortization are reviewed for impairment in accordance with FAS 144, Accounting for the Impairment or Disposal of Long-Lived Assets.
The assessment of goodwill and other intangible assets impairment is a subjective process. Estimations and assumptions regarding future performance, results of our operations and comparability of our market capitalization and its net book value will be used. Changes in estimates and assumptions could have an adverse impact on our financial conditions and results of operations.
Occasionally, we enter into agreements that expose us to potential damages that exceed the value of the agreement.
We have given certain customers increased indemnification for product deficiencies that is in excess of our standard limited warranty indemnification and could possibly result in greater costs, in excess of the original contract value. In an attempt to limit this liability, we have purchased an errors and omissions insurance policy to partially offset these potential additional costs; however, our insurance coverage could be insufficient to prevent us from suffering material losses if the indemnification amounts are large enough.
If we are unable to accurately forecast demand for our products, we may be unable to efficiently manage our inventory.
Due to the absence of substantial non-cancelable backlog, we typically plan our production and inventory levels based on customer forecasts, internal evaluation of customer demand and current backlog, which can fluctuate substantially. As a consequence of inaccuracies inherent in forecasting, inventory imbalances periodically occur that result in surplus amounts of some of our products and shortages of others. Such shortages can adversely impact customer relations and surpluses can result in larger-than-desired inventory levels, which can adversely impact our financial position. Due to deteriorating global economic conditions and increased difficulty in forecasting demand for our products, we are currently experiencing and will likely continue to experience an increase in inventory levels.
Our business may be adversely impacted if we fail to effectively utilize and incorporate acquired technology.
We have acquired and may in the future acquire intellectual property in order to accelerate our time to market for new products. Acquisitions of intellectual property may involve risks such as successful technical integration into new products, market acceptance of new products and achievement of planned return on investment. Successful technical integration in particular requires a variety of factors which we may not currently have, such as available technical staff with sufficient time to devote to integration, the requisite skill sets to understand the acquired technology and the necessary support tools to effectively utilize the technology. The timely and efficient integration of acquired technology may be adversely impacted by inherent design deficiencies or application requirements. The potential failure of or delay in product introduction utilizing acquired intellectual property could lead to an impairment of capitalized intellectual property acquisition costs.
If we are unable to compete effectively with existing or new competitors, we will experience fewer customer orders, reduced revenues, reduced gross margins and lost market share.
We compete in markets that are intensely competitive, and which are subject to both rapid technological change and continued price erosion. Our competitors include many large domestic and foreign companies that have substantially greater financial, technical and management resources, name recognition and leverage than we have. As a result, they may be able to adapt more quickly to new or emerging technologies and changes in customer requirements or to devote greater resources to promote the sale of their products.
24
We have experienced increased competition at the design stage, where customers evaluate alternative solutions based on a number of factors, including price, performance, product features, technologies, and availability of long-term product supply and/or roadmap guarantee. Additionally, we experience, in some cases, severe pressure on pricing from some of our competitors or on-going cost reduction expectations from customers. Such circumstances may make some of our products unattractive due to price or performance measures and result in losing our design opportunities or causing a decrease in our revenue and margins. Also, competition from new companies in emerging economy countries with significantly lower costs could affect our selling price and gross margins. In addition, if competitors in Asia reduce prices on commodity products, it would adversely affect our ability to compete effectively in that region. Specifically, we have licensed rights to Hangzhou Silan Microelectronics Co. Ltd. and Hangzhou Silan Integrated Circuit Co. Ltd. (collectively “Silan”) in China to market our commodity interface products that could reduce our sales in the future should they become a meaningful competitor. Loss of competitive position could result in price reductions, fewer customer orders, reduced revenues, reduced gross margins and loss of market share, any of which would affect our operating results and financial condition. To the extent that our competitors offer distributors or sales representatives more favorable terms, these distributors and sales representatives may decline to carry, or discontinue carrying, our products. Our business, financial condition and results of operations could be harmed by any failure to maintain and expand our distribution network. Furthermore, many of our existing and potential customers internally develop solutions which attempt to perform all or a portion of the functions performed by our products. To remain competitive, we continue to evaluate our manufacturing operations for opportunities for additional cost savings and technological improvements. If we are unable to successfully implement new process technologies and to achieve volume production of new products at acceptable yields, our operating results and financial condition may be affected. Our future competitive performance depends on a number of factors, including our ability to:
| • | | increase device performance and improve manufacturing yields; |
| • | | accurately identify emerging technological trends and demand for product features and performance characteristics; |
| • | | develop and maintain competitive and reliable products; |
| • | | enhance our products by adding innovative features that differentiate our products from those of our competitors; |
| • | | bring products to market on a timely basis at competitive prices; |
| • | | respond effectively to new technological changes or new product announcements by others; |
| • | | adapt products and processes to technological changes; |
| • | | adopt or set emerging industry standards; |
| • | | meet changing customer requirements; and |
| • | | provide adequate technical service and support. |
Our design, development and introduction schedules for new products or enhancements to our existing and future products may not be met. In addition, these products or enhancements may not achieve market acceptance, or we may not be able to sell these products at prices that are favorable.
If our distributors or sales representatives stop selling or fail to successfully promote our products, our business, financial condition and results of operations could be adversely impacted.
We sell many of our products through sales representatives and distributors, many of which sell directly to OEMs, contract manufacturers and end customers. Our non-exclusive distributors and sales representatives may carry our competitors’ products, which could adversely impact or limit sales of our products. Additionally, they could reduce or discontinue sales of our products or may not devote the resources necessary to sell our products in the volumes and within the time frames that we expect. Our agreements with distributors contain limited
25
provisions for return of our products, including stock rotations whereby distributors may return a percentage of their purchases from us based upon a percentage of their most recent three months of shipments. In addition, in certain circumstances upon termination of the distributor relationship, distributors may return some portion of their prior purchases. The loss of business from any of our significant distributors or the delay of significant orders from any of them, even if only temporary, could materially and adversely harm our business, financial conditions and results of operations.
Moreover, we depend on the continued viability and financial resources of these distributors and sales representatives, some of which are small organizations with limited working capital. In turn, these distributors and sales representatives are subject to general economic and semiconductor industry conditions. We believe that our success will continue to depend on these distributors and sales representatives. If some or all of our distributors and sales representatives experience financial difficulties, or otherwise become unable or unwilling to promote and sell our products, our business, financial condition and results of operations could be adversely impacted.
Affiliates of Future, Alonim Investments Inc. and two of its affiliates (collectively “Alonim”), own approximately 18% of our common stock, and as such, Alonim is our largest stockholder. This ownership position will allow Future to significantly influence matters requiring stockholders’ approval. Future’s ownership may continue to increase as a percentage of our outstanding shares if we continue to repurchase our common stock. In addition, an executive officer of Future is on our board of directors, which could lead to actual or perceived influence from Future.
An affiliate of Future, our largest distributor, owns a significant percentage of our outstanding shares and Pierre Guilbault, the chief financial officer of Future, is a member of our board of directors. Due to its affiliate’s ownership of a significant percentage of our common stock, Future may be able to exert strong influence over actions requiring the approval of our stockholders, including the election of directors, many types of change of control transactions and amendments to our charter documents, although Future is bound by a Lock-Up and Standstill Agreement until August 25, 2009, prohibiting Future from either soliciting proxies or seeking to advise anyone with respect to voting our stock. The significant ownership percentage of Future could have the effect of delaying or preventing a change of control or otherwise discouraging a potential acquirer from obtaining control of us. Conversely, by virtue of Future’s percentage ownership of our stock, Future could facilitate a takeover transaction that our board of directors did not approve.
This relationship could also result in actual or perceived attempts to influence management to take actions beneficial to Future which may or may not be beneficial to us or in our best interests. Future could attempt to obtain terms and conditions more favorable than those we would typically provide our distributors because of its relationship with us. Any such actual or perceived preferential treatment could materially and adversely affect our business, financial condition and results of operations.
We depend on third-party subcontractors to manufacture our products. We utilize wafer foundries for processing our wafers and assembly and test subcontractors for manufacturing and testing our packaged products. Any disruption in or loss of subcontractors’ capacity to manufacture our products subjects us to a number of risks, including the potential for an inadequate supply of products and higher materials costs. These risks may lead to delayed product delivery or increased costs, which could materially and adversely impact our business, financial condition and results of operations.
We do not own or operate a semiconductor fabrication facility or a foundry. We utilize various foundries for different processes. Our products are based on Complementary Metal Oxide Semiconductor (“CMOS”) processes, bipolar processes and bipolar-CMOS (“BiCMOS”) processes. Chartered Semiconductor Manufacturing Ltd. (“Chartered”), located in Singapore, manufactures the majority of the CMOS wafers from which our communications and UART products are produced. Episil Technologies, Inc.(“Episil”), located in Taiwan, and Silan, located in China, manufacture the majority of CMOS and bipolar wafers from which our power and serial products are produced. High Voltage BiCMOS power products are supplied by Polar
26
Semiconductor (MN, USA) and Jazz Semiconductor (CA, USA). All of these foundries produce semiconductors for many other companies (many of which have greater requirements than us), and therefore, we may not have access on a timely basis to sufficient capacity or certain process technologies. In addition, we rely on our foundries’ continued financial health and ability to continue to invest in smaller geometry manufacturing processes and additional wafer processing capacity.
Many of our new products are designed to take advantage of smaller geometry manufacturing processes. Due to the complexity and increased cost of migrating to smaller geometries as well as process changes, we could experience interruptions in production or significantly reduced yields causing product introduction or delivery delays. If such delays occur, our products may have delayed market acceptance or customers may select our competitors’ products during the design process.
New process technologies or new products can be subject to especially wide variations in manufacturing yields and efficiency. There can be no assurance that our foundries or the foundries of our suppliers will not experience unfavorable yield variances or other manufacturing problems that result in delayed product introduction or delivery delays. This risk is particularly significant in the near term as we have recently transferred certain of our manufacturing processes to Silan.
We do not have long-term wafer supply agreements with Chartered that would guarantee wafer quantities, prices, and delivery or lead times, but we do provide minimum purchase commitments to Silan and Episil in accordance with our supply agreements. Subject to any such minimum purchase commitments, these foundries manufacture our products on a purchase order basis. We provide our foundries with rolling forecasts of our production requirements. However, the ability of our foundries to provide wafers is limited by the foundries’ available capacity. There can be no assurance that our third-party foundries will allocate sufficient capacity to satisfy our requirements.
Furthermore, any sudden reduction or elimination of any primary source or sources of fully processed wafers could result in a material delay in the shipment of our products. Any delays or shortages will materially and adversely impact our business, financial condition and operating results.
In addition, we may not continue to do business with our foundries on terms as favorable as our current terms. Significant risks associated with our reliance on third-party foundries include:
| • | | the lack of assured process technology and wafer supply; |
| • | | limited control over quality assurance, manufacturing yields and production costs; |
| • | | financial and operating stability of the foundries; |
| • | | limited control over delivery schedules; |
| • | | limited manufacturing capacity of the foundries; and |
| • | | potential misappropriation of our intellectual property. |
Our reliance on our wafer foundries and assembly and test subcontractors involves the following risks:
| • | | a manufacturing disruption or sudden reduction or elimination of any existing source or sources of semiconductor manufacturing materials or processes, which might include the potential closure, change of ownership, change in business conditions or relationships, change of management or consolidation by one of our foundries; |
| • | | disruption of manufacturing or assembly or test services due to relocation or limited capacity of the foundries or subcontractors; |
| • | | inability to obtain or develop technologies needed to manufacture our products; |
| • | | extended time required to identify, qualify and transfer to alternative manufacturing sources for existing or new products or the possible inability to obtain an adequate alternative; |
27
| • | | failure of our foundries or subcontractors to obtain raw materials and equipment; |
| • | | increasing cost of raw materials and energy resulting in higher wafer or package costs; |
| • | | long-term financial and operating stability of the foundries, or their suppliers or subcontractors and their ability to invest in new capabilities and expand capacity to meet increasing demand, to remain solvent, or to obtain financing in tight credit markets; |
| • | | we expect our suppliers will continue to take measures such as reductions in force, pay reductions, forced time off or shut down their production for extended periods of time to reduce and/or control operating expenses in response to weakened and weakening customer demand; |
| • | | subcontractors’ inability to transition to smaller package types or new package compositions; |
| • | | a sudden, sharp increase in demand for semiconductor devices, which could strain the foundries’ or subcontractors’ manufacturing resources and cause delays in manufacturing and shipment of our products; |
| • | | manufacturing quality control or process control issues, including reduced control over manufacturing yields, production schedules and product quality; |
| • | | disruption of transportation to and from Asia where most of our foundries and subcontractors are located; |
| • | | embargoes or other regulatory limitations affecting the availability of raw materials, equipment or changes in tax laws, tariffs, services and freight rates; and |
| • | | compliance with local or international regulatory requirements. |
Other additional risks associated with subcontractors include:
| • | | subcontractors imposing higher minimum order quantities for substrates; |
| • | | potential increase in assembly and test costs; |
| • | | our board level product volume may not be attractive to preferred manufacturing partners, which could result in higher pricing or having to qualify an alternative vendor; |
| • | | difficulties in selecting, qualifying and integrating new subcontractors; |
| • | | entry into “take-or-pay” agreements; and |
| • | | limited warranties from our subcontractors for products assembled and tested for us. |
To secure foundry capacity, we may be required to enter into financial and other arrangements with foundries, which could result in the dilution of our earnings or otherwise harm our operating results.
Allocation of a foundry’s manufacturing capacity may be influenced by a foundry customer’s size, the existence of a long-term agreement with the foundry or other commitments. To address foundry capacity constraints, we and other semiconductor companies that rely on third-party foundries have utilized various arrangements, including equity investments in or loans to foundries in exchange for guaranteed production capacity, joint ventures to own and operate foundries or “take or pay” contracts that commit a company to purchase specified quantities of wafers over extended periods. These arrangements may not be available to us on acceptable terms, if at all. Any of these arrangements could require us to commit substantial capital and, accordingly, could require us to reduce our cash holdings, incur additional debt or secure equity financing. This could result in the dilution of our earnings or the ownership of our stockholders or otherwise harm our operating results. Furthermore, we may not be able to obtain sufficient foundry capacity in the future pursuant to such arrangements.
28
We depend in part on the continued service of our key engineering and management personnel and our ability to identify, hire, incentivize and retain qualified personnel. If we lose key employees or fail to identify, hire, incentivize and retain these individuals, our business, financial condition and results of operations could be materially and adversely impacted.
Our future success depends, in part, on the continued service of our key design engineering, technical, sales, marketing and executive personnel and our ability to identify, hire, motivate and retain other qualified personnel.
Under certain circumstances, including a company acquisition or business downturn, current and prospective employees may experience uncertainty about their future roles with us. Volatility or lack of positive performance in our stock price and the ability to offer equity compensation to as many key employees or in amounts consistent with past practices, as a result of regulations regarding the expensing of equity awards, may also adversely affect our ability to retain key employees, all of whom have been granted equity awards. In addition, competitors may recruit employees, as is common in the high tech sector. If we are unable to retain personnel that are critical to our future operations, we could face disruptions in operations, loss of existing customers, loss of key information, expertise or know-how, and unanticipated additional recruitment and training costs.
Competition for skilled employees having specialized technical capabilities and industry-specific expertise is intense and continues to be a considerable risk inherent in the markets in which we compete. At times competition for such employees has been particularly notable in California and the PRC. Further, the PRC historically has been deficient in Western style management and financial reporting concepts and practices, as well as in modern banking, computer and other control systems, making the successful identification and employment of qualified personnel particularly important, and hiring and retaining a sufficient number of such qualified employees may be difficult. As a result of these factors, we may experience difficulty in establishing management, legal and financial controls, collecting financial data, books of account and records and instituting business practices that meet Western standards, which could negatively affect our business and results of operations.
Our employees are employed at-will, which means that they can terminate their employment at any time. The failure to recruit and retain, as necessary, key design engineers, technical, sales, marketing and executive personnel could harm our business, financial condition and results of operations.
Our results of operations could vary as a result of the methods, estimations and judgments we use in applying our accounting policies.
The methods, estimates and judgments we use in applying our accounting policies have a significant impact on our results of operations. Such methods, estimates and judgments are, by their nature, subject to substantial risks, uncertainties, assumptions and changes in rulemaking by the regulatory bodies; and factors may arise over time that lead us to change our methods, estimates, and judgments. Changes in those methods, estimates and judgments could significantly impact our results of operations. Our revenue reporting is highly dependent on receiving pertinent and accurate data from our distributors in a timely fashion. Distributors provide us periodic data regarding the product, price, quantity and end customer when products are resold as well as the quantities of our products they still have in stock. We must use estimates and apply judgment to reconcile distributors’ reported inventories to their activities. Any error in our judgment could lead to inaccurate reporting of our revenues, deferred income and allowances on sales to distributors and net income.
The final determination of our income tax liability may be materially different from our income tax provision, which could have an adverse effect on our results of operations.
Our future effective tax rates may be adversely affected by a number of factors including:
| • | | the jurisdictions in which profits are determined to be earned and taxed; |
| • | | the resolution of issues arising from tax audits with various tax authorities; |
29
| • | | changes in the valuation of our deferred tax assets and liabilities; |
| • | | adjustments to estimated taxes upon finalization of various tax returns; |
| • | | increases in expenses not deductible for tax purposes, including write-offs of acquired in-process research and development and impairment of goodwill in connection with acquisitions; |
| • | | changes in available tax credits; |
| • | | changes in share-based compensation expense; |
| • | | changes in tax laws or the interpretation of such tax laws and changes in generally accepted accounting principles; and/or |
| • | | the repatriation of non-U.S. earnings for which we have not previously provided for U.S. taxes. |
Any significant increase in our future effective tax rates could adversely impact net income for future periods. In addition, the U.S. Internal Revenue Service (“IRS”) and other tax authorities regularly examine our income tax returns. Our results of operations could be adversely impacted if these assessments or any other assessments resulting from the examination of our income tax returns by the IRS or other taxing authorities are not resolved in our favor.
We have acquired significant Net Operating Loss (“NOL”) carryforwards as a result of our acquisitions. The utilization of acquired NOL carryforwards is subject to the IRS’s complex limitation rules that carry significant burdens of proof. Our eventual ability to utilize our estimated NOL carryforwards is subject to IRS scrutiny and our future results may not benefit as a result of potential unfavorable IRS rulings.
Our engagement with foreign customers could cause fluctuations in our operating results, which could materially and adversely impact our business, financial condition and results of operations.
International sales have accounted for, and will likely continue to account for a significant portion of our revenues, which subjects us to the following risks, among others:
| • | | changes in regulatory requirements; |
| • | | tariffs and other barriers; |
| • | | timing and availability of export or import licenses; |
| • | | disruption of services due to political, civil, labor, and economic instability; |
| • | | disruption of services due to natural disasters outside the United States; |
| • | | disruptions to customer operations outside the United States due to the outbreak of communicable diseases; |
| • | | difficulties in accounts receivable collections; |
| • | | difficulties in staffing and managing foreign subsidiary and branch operations; |
| • | | difficulties in managing sales channel partners; |
| • | | difficulties in obtaining governmental approvals for communications and other products; |
| • | | limited intellectual property protection; |
| • | | foreign currency exchange fluctuations; |
| • | | the burden of complying with foreign laws and treaties; and |
| • | | potentially adverse tax consequences. |
30
In addition, because sales of our products have been denominated primarily in U.S. dollars, increases in the value of the U.S. dollar as compared with local currencies could make our products more expensive to customers in the local currency of a particular country resulting in pricing pressures on our products. Increased international activity in the future may result in foreign currency denominated sales. Furthermore, because some of our customers’ purchase orders and agreements are governed by foreign laws, we may be limited in our ability, or it may be too costly for us, to enforce our rights under these agreements and to collect damages, if awarded.
Because some of our integrated circuits products have lengthy sales cycles, we may experience substantial delays between incurring expenses related to product development and the revenue derived from these products.
A portion of our revenue is derived from selling integrated circuits to communications equipment vendors. Due to their product development cycle, we have typically experienced at least an eighteen-month time lapse between our initial contact with a customer and realizing volume shipments. We first work with customers to achieve a design win, which may take nine months or longer. Our customers then complete their design, test and evaluation process and begin to ramp-up production, a period which typically lasts an additional nine months. The customers of communications equipment manufacturers may also require a period of time for testing and evaluation, which may cause further delays. As a result, a significant period of time may elapse between our research and development efforts and our realization of revenue, if any, from volume purchasing of our communications products by our customers. Due to the length of the communications equipment vendors’ product development cycle, the risks of project cancellation by our customers, price erosion or volume reduction are present for an extended period of time.
Our backlog may not result in revenue.
Due to the possibility of customer changes in delivery schedules and quantities actually purchased, cancellation of orders, distributor returns or price reductions, our backlog at any particular date is not necessarily indicative of actual sales for any succeeding period. The current economic downturn increases the risk of purchase order cancellations or delays, product returns and price reductions. We may not be able to meet our expected revenue levels or results of operations if there is a reduction in our order backlog for any particular period and we are unable to replace those sales during the same period.
Fixed operating expenses and our practice of ordering materials in anticipation of projected customer demand could make it difficult for us to respond effectively to sudden swings in demand and result in higher than expected costs and excess inventory. Such sudden swings in demand could therefore have a material adverse impact on our business, financial condition and results of operations.
Our operating expenses are relatively fixed in the short to medium term, and therefore, we have limited ability to reduce expenses quickly and sufficiently in response to any revenue shortfall. In addition, we typically plan our production and inventory levels based on forecasts of customer demand, which is highly unpredictable and can fluctuate substantially. From time to time, in response to anticipated long lead times to obtain inventory and materials from our outside suppliers and foundries, we may order materials in advance of anticipated customer demand. This advance ordering may result in excess inventory levels or unanticipated inventory write-downs if expected orders fail to materialize. This incremental cost could have a materially adverse impact on our business, financial condition and results of operations.
We may be unable to protect our intellectual property rights, which could harm our competitive position.
Our ability to compete is affected by our ability to protect our intellectual property rights. We rely on a combination of patents, trademarks, copyrights, mask work registrations, trade secrets, confidentiality procedures and non-disclosure and licensing arrangements to protect our intellectual property rights. Despite these efforts, we may be unable to protect our proprietary information. Such intellectual property rights may not be recognized or if recognized, it may not be commercially feasible to enforce. Moreover, we cannot be certain that our competitors will not independently develop technology that is substantially similar or superior to our technology.
31
More specifically, our pending patent applications or any future applications may not be approved, and any issued patents may not provide us with competitive advantages or may be challenged by third parties. If challenged, our patents may be found to be invalid or unenforceable, and the patents of others may have an adverse effect on our ability to do business. Furthermore, others may independently develop similar products or processes, duplicate our products or processes or design around any patents that may be issued to us.
We could be required to pay substantial damages or could be subject to various equitable remedies if it were proven that we infringed the intellectual property rights of others.
As a general matter, the semiconductor industry is characterized by substantial litigation regarding patents and other intellectual property rights. If a third party were to prove that our technology infringed its intellectual property rights, we could be required to pay substantial damages for past infringement and could be required to pay license fees or royalties on future sales of our products. If we were required to pay such license fees whenever we sold our products, such fees could exceed our revenue. In addition, if it was proven that we willfully infringed a third party’s proprietary rights, we could be held liable for three times the amount of the damages that we would otherwise have to pay. Such intellectual property litigation could also require us to:
| • | | stop selling, incorporating or using our products that use the infringed intellectual property; |
| • | | obtain a license to make, sell or use the relevant technology from the owner of the infringed intellectual property, which license may not be available on commercially reasonable terms, if at all; and/or |
| • | | redesign our products so as not to use the infringed intellectual property, which may not be technically or commercially feasible. |
The defense of infringement claims and lawsuits, regardless of their outcome, would likely be expensive and could require a significant portion of management’s time. In addition, rather than litigating an infringement matter, we may determine that it is in our best interests to settle the matter. Terms of a settlement may include the payment of damages and our agreement to license technology in exchange for a license fee and ongoing royalties. These fees could be substantial. If we were required to pay damages or otherwise became subject to such equitable remedies, our business, financial condition and results of operations would suffer. Similarly, if we were required to pay license fees to third parties based on a successful infringement claim brought against us, such fees could exceed our revenue.
Earthquakes and other natural disasters may damage our facilities or those of our suppliers and customers.
Our corporate headquarters in Fremont, California is located near major earthquake faults that have experienced seismic activity. In addition, some of our customers and suppliers are in locations which may be subject to similar natural disasters. In the event of a major earthquake or other natural disaster near our headquarters, our operations could be disrupted. Similarly, a major earthquake or other natural disaster affecting one or more of our major customers or suppliers could adversely impact the operations of those affected, which could disrupt the supply of our products and harm our business.
ITEM 1B. | UNRESOLVED STAFF COMMENTS |
None.
Our executive offices and our marketing and sales, research and development, manufacturing, test and engineering operations are located in Fremont, California in two adjacent buildings that we own, which consist of approximately 151,000 square feet. Additionally, we own approximately 4.5 acres of partially developed property adjacent to our headquarters, which is presently being held for future office expansion.
32
We also lease smaller facilities in Belgium, Canada, China, Germany, Japan, Korea, Malaysia, Taiwan and the United States, which are occupied by administrative offices, sales offices, design centers and field application engineers.
Based upon our estimates of future hiring, we believe that our current facilities will be adequate to meet our requirements at least through the next fiscal year.
We also lease one additional building in California, totaling approximately 95,700 square feet, which is subleased to a tenant. The sublease began on April 15, 2008 and expires March 31, 2011. For further discussion of this facility and its effect on our financial condition and results of operations, seePart II, Item 7—“Management’s Discussion and Analysis of Financial Condition and Results of Operations”and in Part II, Item 8—”Financial Statements and Supplementary Data”and“Notes to Consolidated Financial Statements, Note 14—Lease Financing Obligation.”
Information required by this item is set forth inPart II, Item 8—”Financial Statements and Supplementary Data”and“Notes to Consolidated Financial Statements, Note 16—Legal Proceedings” of this Annual Report on Form 10-K and is incorporated by reference herein.
ITEM 4. | SUBMISSION OF MATTERS TO A VOTE OF SECURITY HOLDERS |
No matters were submitted to a vote of security holders during the fourth fiscal quarter of 2009.
33
PART II
ITEM 5. | MARKET FOR REGISTRANT’S COMMON EQUITY, RELATED STOCKHOLDER MATTERS AND ISSUER PURCHASES OF EQUITY SECURITIES |
Market Information
Our common stock is traded on The NASDAQ Global Market under the symbol “EXAR.” The following table set forth the range of high and low sales prices of our common stock for the periods indicated, as reported by The NASDAQ Global Market.
| | | | | | |
| | Common Stock Prices |
| | High | | Low |
FISCAL 2009 | | | | | | |
Fourth quarter ended March 29, 2009 | | $ | 7.25 | | $ | 4.94 |
Third quarter ended December 28, 2008 | | $ | 7.75 | | $ | 4.93 |
Second quarter ended September 28, 2008 | | $ | 8.91 | | $ | 6.51 |
First quarter ended June 29, 2008 | | $ | 9.20 | | $ | 7.33 |
| | |
FISCAL 2008 | | | | | | |
Fourth quarter ended March 30, 2008 | | $ | 8.50 | | $ | 6.50 |
Third quarter ended December 30, 2007 | | $ | 13.51 | | $ | 7.60 |
Second quarter ended September 30, 2007 | | $ | 15.24 | | $ | 12.57 |
First quarter ended June 30, 2007 | | $ | 14.26 | | $ | 13.06 |
The closing sales price for our common stock on May 22, 2009, was $6.16 per share. As of May 22, 2009, the approximate number of record holders of our common stock was 216 (not including beneficial owners of stock held in street name).
Dividend Policy
We have never declared or paid any cash dividends on our capital stock and we do not currently intend to pay any cash dividends on our common stock. We expect to retain future earnings, if any, to fund the development and growth of our business. Any future determination to pay dividends on our common stock will be, subject to applicable law, at the discretion of our board of directors and will depend upon, among other factors, our results of operations, financial condition, capital requirements and contractual restrictions.
Unregistered Sales of Equity Securities and Use of Proceeds
(a) None.
(b) None.
(c) Issuer Purchases of Equity Securities
From time to time, we acquire outstanding common stock in the open market to partially offset dilution from our stock programs, to increase our return on our invested capital and to bring our cash to a more appropriate level for our company. At March 29, 2009, approximately $11.8 million remained available under our previously announced repurchase program. We may continue to utilize the stock repurchase program, which would reduce our cash, cash equivalents and/or short-term investments available to fund future operations and to meet other liquidity requirements.
34
The following table sets forth our stock repurchase activities for the fourth fiscal quarter of 2009 were as follows:
| | | | | | | | | | |
Fiscal Period | | Total Number of Shares Purchased | | Average Price Paid per Share | | Total Number of Shares Purchased as Part of Publicly Announced Plans or Programs(1) | | Maximum Dollar Value of Shares that May Yet Be Purchased Under the Plans or Programs (in thousands)(1) |
Balance as of December 28, 2008 | | 12,423,011 | | $ | 10.32 | | 12,413,011 | | $ | 11,823 |
| | | | | | | | | | |
12/29/2008—1/25/2009 | | 1,358 | | | 6.01 | | 1,358 | | $ | 11,815 |
1/26/2009—2/22/2009 | | — | | | — | | — | | $ | 11,815 |
2/23/2009—3/29/2009 | | — | | | — | | — | | $ | 11,815 |
| | | | | | | | | | |
Total shares purchased | | 1,358 | | $ | 6.01 | | 1,358 | | | |
| | | | | | | | | | |
Balance as of March 29, 2009 | | 12,424,369 | | $ | 10.32 | | 12,414,369 | | | |
| | | | | | | | | | |
(1) | On August 28, 2007, we established a share repurchase plan (“2007 SRP”) and authorized the repurchase of up to $100 million of our common stock. As of March 29, 2009, $11.8 million remained available to repurchase the Company’s common stock under the Company’s August 27, 2007 share repurchase plan. |
35
Stock Price Performance
The following table and graph showed a five-year comparison of cumulative total stockholder returns for Exar, The NASDAQ Composite Index, and The NASDAQ Electronic Components Index (SIC code 3670-3679). The table and graph assumed the investment of $100 in stock or index on March 31, 2004 and that all dividends, if any, were reinvested. We have never paid cash dividends on our common stock. The performance shown is not necessarily indicative of future performance.

| | | | | | | | | | | | |
| | Cumulative Total Return as of |
| | March 31, 2004 | | March 31, 2005 | | March 31, 2006 | | March 31, 2007 | | March 30, 2008 | | March 29, 2009 |
Exar Corporation Stock | | 100.00 | | 72.83 | | 77.61 | | 71.96 | | 44.73 | | 33.53 |
NASDAQ Composite Index | | 100.00 | | 101.44 | | 120.49 | | 127.08 | | 118.90 | | 78.48 |
NASDAQ Electronic Components Index | | 100.00 | | 83.84 | | 93.40 | | 86.25 | | 84.44 | | 56.29 |
36
ITEM 6. | SELECTED FINANCIAL DATA |
On August 25, 2007, we acquired Sipex which was accounted for as a purchase of a business. Accordingly, the results of operations of Sipex have been included in our consolidated financial statements since August 26, 2007. SeePart II, Item 8—“Financial Statements and Supplementary Data”and“Notes to Consolidated Financial Statements, Note 3—Business Combinations.”
The following selected financial data should be read in conjunction with the consolidated financial statements and notes thereto and“Management’s Discussion and Analysis of Financial Condition and Results of Operations” included inPart II, Item 7 of this Report.
| | | | | | | | | | | | | | | | | | | | |
| | As of and For the Years Ended | |
| | March 29, 2009(5) | | | March 30, 2008(4) | | | March 31, 2007(3) | | | March 31, 2006(2) | | | March 31, 2005(1) | |
Consolidated Statements of Operations Data: | | | | | | | | | | | | | | | | | | | | |
Net Sales | | $ | 115,118 | | | $ | 89,743 | | | $ | 68,502 | | | $ | 67,024 | | | $ | 57,369 | |
Gross Profit | | | 50,245 | | | | 40,112 | | | | 46,534 | | | | 45,475 | | | | 39,156 | |
Income (loss) from operations | | | (80,222 | ) | | | (202,438 | ) | | | (4,229 | ) | | | (507 | ) | | | (2,321 | ) |
Net income (loss) | | | (73,036 | ) | | | (195,879 | ) | | | 8,024 | | | | 7,786 | | | | 5,319 | |
| | | | | |
Net Income (loss) per share: | | | | | | | | | | | | | | | | | | | | |
Basic | | $ | (1.70 | ) | | $ | (4.55 | ) | | $ | 0.22 | | | $ | 0.20 | | | $ | 0.13 | |
Diluted | | $ | (1.70 | ) | | $ | (4.55 | ) | | $ | 0.22 | | | $ | 0.20 | | | $ | 0.13 | |
| | | | | |
Shares used in computation of net income (loss) per share: | | | | | | | | | | | | | | | | | | | | |
Basic | | | 42,887 | | | | 43,090 | | | | 36,255 | | | | 38,152 | | | | 41,532 | |
Diluted | | | 42,887 | | | | 43,090 | | | | 36,480 | | | | 38,510 | | | | 42,423 | |
| | | | | |
Consolidated Balance Sheets Data: | | | | | | | | | | | | | | | | | | | | |
Cash, cash equivalents and short-term investments | | $ | 256,343 | | | $ | 268,860 | | | $ | 356,079 | | | $ | 329,528 | | | $ | 446,285 | |
Working capital | | | 257,179 | | | | 266,060 | | | | 357,068 | | | | 335,896 | | | | 447,292 | |
Total assets | | | 336,389 | | | | 424,220 | | | | 421,174 | | | | 401,397 | | | | 503,203 | |
Long-term obligations | | | 16,869 | | | | 18,091 | | | | 191 | | | | 222 | | | | 265 | |
Retained earnings (accumulated deficit) | | | (170,516 | ) | | | (97,480 | ) | | | 98,164 | | | | 90,140 | | | | 82,354 | |
Stockholders’ equity | | $ | 292,094 | | | $ | 371,077 | | | $ | 406,756 | | | $ | 387,405 | | | $ | 490,047 | |
(1) | Fiscal 2005 included a gain on legal settlement of $1.2 million in connection with a commercial dispute. |
(2) | Fiscal 2006 included an impairment charge of $1.2 million related to our investment in non-marketable securities. |
(3) | Fiscal 2007 included $4.4 million of stock-based compensation expense, an impairment charges of $1.0 million related to our non-marketable securities and separation costs of $1.6 million related to the resignations of two former executives. |
(4) | Fiscal 2008 included $5.0 million of stock-based compensation expense, $5.4 million of amortization of intangible assets acquired in connection with the Sipex acquisition, $8.8 million of IPR&D purchased in connection with the Sipex acquisition, $165.2 million impairment charge on goodwill and other intangible assets, separation expenses of $0.5 million related to our former chief executive officer and $0.6 million impairment loss related to our non-marketable securities. |
(5) | Fiscal 2009 included $59.7 million impairment charge on goodwill and other intangible assets, $4.9 million of stock-based compensation expense, $2.7 million of amortization of intangible assets acquired in connection with the Sipex acquisition, $1.2 million charge for accelerated depreciation on abandoned equipment and $1.8 million impairment loss related to our investment in marketable and non-marketable securities. |
37
ITEM 7 | MANAGEMENT’S DISCUSSION AND ANALYSIS OF FINANCIAL CONDITION AND RESULTS OF OPERATIONS |
The following Management’s Discussion and Analysis of Financial Condition and Results of Operations, as well as information contained in “Risk Factors” above and elsewhere in this Annual Report on Form 10-K contains “forward-looking statements” within the meaning of Section 27A of the Securities Act of 1933, as amended, and Section 21E of the Securities Exchange Act of 1934, as amended, that involve risks and uncertainties. Please see “Forward Looking Statements” in Part I above. Actual results may differ materially from those projected in the forward-looking statements as a result of various factors, including, among others, those identified above under Part I, Item 1A—“Risk Factors.”
COMPANY OVERVIEW
Exar Corporation and its subsidiaries (“Exar” or “we”) is a fabless semiconductor company that designs, sub-contracts manufacturing and sells highly differentiated silicon, software and subsystem solutions for industrial, datacom and storage applications. Our comprehensive knowledge of end-user markets along with our underlying analog, mixed signal and digital technology has enabled innovative solutions that meet the needs of the evolving connected world. Our product portfolio includes power management and interface components, datacom products, storage optimization solutions, network security and applied service processors. Applying both analog and digital technologies, our products are deployed in a wide array of applications such as portable electronic devices, set top boxes, digital video recorders, telecommunication systems, servers, enterprise storage systems and industrial automation equipment. We have the unique ability to provide customers with a breadth of component products and subsystem solutions based on advanced mixed signal silicon integration.
We market our products worldwide with sales offices and personnel located throughout the Americas, Europe and Asia. Our products are sold in the United States through a number of manufacturers’ representatives and distributors. Internationally, our products are sold through various global and regional distributors with locations in thirty-three countries around the globe. In addition to our sales offices, we also employ a worldwide team of field application engineers to work directly with our customers.
Our international sales are generally denominated in U.S. dollars. Our international related operations expenses expose us to fluctuations in currency exchange rates because our foreign operating expenses are denominated in foreign currency while our sales are denominated in U.S. dollars. Although foreign sales within certain countries or foreign sales comprised of certain products may subject us to tariffs, our gross profit margin on international sales, adjusted for differences in product mix, is not significantly different from that realized on our sales to domestic customers. Our operating results are subject to quarterly and annual fluctuations as a result of several factors that could materially and adversely affect our future profitability as described in“Part II, Item 1A. Risk Factors—Our Financial Results May Fluctuate Significantly Because Of A Number Of Factors, Many Of Which Are Beyond Our Control.”
On April 3, 2009, we completed the acquisition of Hifn, a leading provider of network- and storage-security and data reduction products that simplify the way major network and storage original equipment manufacturers, as well as small-and-medium enterprises, efficiently and securely share, retain, access and protect critical data. We believe the acquisition has enabled us to expand both our market presence and revenue without compromising our financial condition.
In December 2007, we changed our fiscal year end from a fiscal year ending March 31 to a 52-53 week fiscal year ending on the Sunday closest to March 31. As part of this change, each fiscal quarter will also end on the Sunday closest to the end of the corresponding calendar quarter. As a result of the change in our fiscal year end, our fiscal year ended March 29, 2009 contains 364 days and our fiscal years ended March 30, 2008 and March 31, 2007 each contained 365 days. Fiscal years ended March 29, 2009, March 30, 2008 and March 31, 2007 are also referred to herein as “2009,” “2008” and “2007” unless otherwise indicated.
38
In August 2007, we completed the acquisition of Sipex Corporation (“Sipex”), a company that designed, manufactured and marketed high performance, analog Integrated Circuits (“ICs”) used by OEMs in the computing, consumer electronics, datacom and networking infrastructure markets. As a result of the acquisition, we have combined product offerings, increased technical expertise, distribution channels, customer base and geographic reach as well as reduced expenses due to significant cost synergies.
EXECUTIVE SUMMARY
During fiscal year 2009, we continued to execute on our strategy of growing the company through new product introductions and through acquisitions.
We acquired Sipex in August 2007, and fiscal year 2009 represents our first full year of combined operations. We have completed the integration of the organization and information systems, and the rationalization of our sales channels, development projects, business processes, compensation plans and internal controls. We also achieved annualized cost savings in the first quarter of fiscal 2009, which exceeded the targeted savings for that quarter when we announced the proposed acquisition of Sipex in May 2007.
We commenced a tender offer for the shares of Hifn in the fourth quarter of fiscal 2009 and subsequently closed the transaction on April 3, 2009. We expect to benefit by combining the encryption and data deduplication technologies of Hifn together with our network and storage technology into new products.
Our net sales for fiscal year 2009 were $115.1 million, an increase of $25.4 million or 28% as compared to net sales for fiscal year 2008. The increase was primarily due to growth in net sales of $31.8 million associated with Sipex products acquired in August 2007. The transition of the recognition of revenue through our two primary distributors from the sell-in to the sell-through basis reduced net sales in fiscal year 2008 by an estimated $6.9 million. As this fiscal year progressed, our net sales were severely impacted by the economic recession and resulting decline in end customer demand. Our net sales in the second fiscal quarter grew 2% over the first fiscal quarter, then declined 20% and 9% on a sequential basis in the third and fourth fiscal quarters.
For fiscal year 2009, sales of our datacom products represented 24% of our net sales, as compared to 31% in fiscal year 2008 and 42% in fiscal year 2007. For fiscal year 2009, sales of our interface products represented 55% of our net sales, as compared to 56% in fiscal year 2008 and 58% in fiscal year 2007. For fiscal years 2009 and 2008, sales of our power management products, a new line of products that we acquired from Sipex, represented 21% and 13% of our net sales, respectively.
The gross margin percentage in fiscal year 2009 was 44% as compared to 45% for fiscal year 2008 and 68% for fiscal year 2007. The reduction in gross margin in fiscal year 2008 compared to fiscal year 2007 resulted primarily from lower gross margins on acquired Sipex products and to the amortization of intangible assets associated with the Sipex acquisition. In addition, in fiscal year 2008, the gross margin was also reduced by the amortization of the fair value adjustment for inventories acquired in connection with the Sipex acquisition.
Our operating expenses for fiscal year 2009 were $130.5 million, or $112.1 million lower than fiscal year 2008, and included a non-cash charge of $59.7 million for the impairment of goodwill and other intangible assets as compared to a similar charge of $165.2 million in fiscal year 2008.
For fiscal year 2009, our loss from operations was $80.2 million. Interest income and other, net was $9.7 million and interest expense was $1.3 million. We also recorded an impairment charge of $1.8 million associated with our marketable and non-marketable securities during the period. The net loss for fiscal year 2009 was $73.0 million, or $1.70 loss per share.
CRITICAL ACCOUNTING POLICIES AND ESTIMATES
The preparation of our financial statements and accompanying disclosures in conformity with GAAP, the accounting principles generally accepted in the United States, requires estimates and assumptions that affect the
39
reported amounts of assets, liabilities, revenues and expenses, and related disclosures of contingent assets and liabilities in the consolidated financial statements and the accompanying notes. The U.S. Securities and Exchange Commission (“SEC”) has defined a company’s critical accounting policies as policies that are most important to the portrayal of a company’s financial condition and results of operations, and which require a company to make its most difficult and subjective judgments, often as a result of the need to make estimates of matters that are inherently uncertain. Based on this definition, we have identified our most critical accounting policies and estimates to be as follows: (1) revenue recognition; (2) inventories; (3) income taxes; (4) stock-based compensation; (5) goodwill and long-lived assets; each of which is addressed below. We also have other key accounting policies that involve the use of estimates, judgments and assumptions that are significant to understanding our results. For additional information, see Part II, Item 8—“Financial Statements and Supplementary Data” and “Notes to Consolidated Financial Statements, Note 2—Accounting Policies.”Although we believe that our estimates, assumptions and judgments are reasonable, they are based upon information presently available. Actual results may differ significantly from these estimates if the assumptions, judgments and conditions upon which they are based turn out to be inaccurate.
Revenue Recognition
We recognize revenue in accordance with SEC Staff Accounting Bulletin 104,“Revenue Recognition” (“SAB 104”). SAB 104 requires that four basic criteria must be met before revenue can be recognized: (1) persuasive evidence of an arrangement exists; (2) delivery has occurred or services rendered; (3) the price is fixed or determinable; and (4) collectability is reasonably assured.
We derive revenue principally from the sale of our products to distributors and to OEMs or their contract manufacturers. Our delivery terms are primarily FOB shipping point, at which time title and all risks of ownership are transferred to the customer. For fiscal years ended March 29, 2009, March 30, 2008 and March 31, 2007, approximately 44%, 35% and 38%, respectively, of our net sales were derived from product sales to our two primary distributors, Future Electronics Inc. (“Future”) and Nu Horizons Electronics Corp. (“Nu Horizons”); and approximately 56%, 65% and 62%, respectively, of our net sales were derived from sales to other distributors, OEM customers and other non-distributors.
Non-distributors
For non-distributors, revenue is recognized when title to the product is transferred to the customer, which occurs upon shipment or delivery, depending upon the terms of the customer order, provided that persuasive evidence of a sales arrangement exists, the price is fixed or determinable, collection of the resulting receivables is reasonably assured, there are no customer acceptance requirements and there are no remaining significant obligations. Provisions for returns and allowances for non-distributor customers are provided at the time product sales are recognized. An allowance for sales returns and allowances for non-distributor customers are recorded based on historical experience or specific identification of an event necessitating an allowance.
Distributors
Our two primary distributors’ agreements permit the return of 3% to 5% of their purchases during the preceding quarter for purposes of stock rotation. For one of these distributors, a scrap allowance of 2% of the preceding quarter’s purchases is permitted. We also provide discounts to certain distributors based on volume of product they sell for a specific product with a specific volume range for a given customer over a period not to exceed one year.
We recognize revenue from each of our distributors using either of the following basis. Once adopted, the basis for revenue recognition for a distributor is maintained unless there is a change in circumstances indicating the basis for revenue recognition for that distributor is no longer appropriate.
| • | | Sell-in Basis—Revenue is recognized upon shipment if we conclude we meet the same criteria as for non-distributors discussed above and we can reasonably estimate the credits for returns, pricing |
40
| allowances and/or other concessions. We record an estimated allowance, at the time of shipment, based upon historical patterns of returns, pricing allowances and other concessions (i.e., “sell-in” basis). |
| • | | Sell-through Basis—Revenue and the related costs of sales are deferred until the resale to the end customer if we grant more than limited rights of return, pricing allowances and/or other concessions or if we cannot reasonably estimate the level of returns and credits issuable (i.e., “sell-through” basis). Under the sell-through basis, accounts receivable are recognized and inventory is relieved upon shipment to the distributor as title to the inventory is transferred upon shipment, at which point we have a legally enforceable right to collection under normal terms. The associated sales and cost of sales are deferred and are included in deferred income and allowance on sales to distributors in the consolidated balance sheet. When the related product is sold by our distributors to their end customers, at which time the ultimate price we receive is known, we recognize previously deferred income as sales and cost of sales. |
Sell-through revenue recognition is highly dependent on receiving pertinent and accurate data from our distributors in a timely fashion. Distributors provide us periodic data regarding the product, price, quantity, and end customer when products are resold as well as the quantities of our products they still have in stock. We must use estimates and apply judgments to reconcile distributors’ reported inventories to their activities. Any error in our judgment could lead to inaccurate reporting of our net sales, gross profit, deferred income and allowances on sales to distributors and net income.
Our historical patterns of returns, pricing allowances and other concessions with distributors had been fairly consistent, which enabled us to reasonably estimate such allowances at the time of shipment. Therefore, we historically recognized revenue on sales to all distributors on the sell-in basis and recorded an estimated allowance, at the time of shipment, based on authorized and historical patterns of returns and other concessions. Concurrent with the acquisition of Sipex, we reassessed our expected ability to continue to reasonably estimate such allowances for each of our distributors as well as for Sipex’s distributors. Prior to the acquisition, Sipex recognized revenue on sales to all distributors on the sell-through basis. Consistent with Sipex’s past practice, we concluded that we were not able to reasonably estimate such allowances at the time of shipment of products to Sipex’s distributors. Therefore, we determined that consistent with Sipex’s past practice, we will continue to recognize sales to Sipex’s distributors on the sell-through basis. In addition, as a result of the acquisition, our relationships, marketing and sales practices with our two primary distributors had changed. Further, as disclosed in“Part II, Item 8—Financial Statements and Supplementary Data”and“Notes to Consolidated Financial Statements, Note 5— Related Party Transaction,” Future is a related party of Exar. As a result of these changes, we have concluded that we can no longer reasonably estimate returns, pricing allowances and other concessions at the time of shipment of products to these distributors. Accordingly, concurrent with our consummation of the Sipex acquisition on August 25, 2007, we determined it was appropriate that revenue on all sales to our two primary distributors, Future and Nu Horizons, be recognized on the sell-through basis.
Inventories
Our policy is to establish a provision for excess inventories, based on the nature of the specific product that is greater than six or twelve months of forecasted demand unless there are other factors indicating that the inventories will be sold at a profit after such periods. Among other factors, management considers known backlog of orders, projected sales and marketing forecasts, shipment activity, inventory-on-hand at our primary distributors, past and current market conditions, anticipated demand for our products, changing lead times in the manufacturing process and other business conditions when determining if a provision for excess inventory is required. Our net inventories at March 29, 2009 were $15.7 million, compared with $14.2 million at March 30, 2008. The increase was primarily due to the rapid decline in demand caused by the recession, versus the cycle time required for us to reduce orders from our wafer subcontractors. Should the assumptions used by management in estimating the provision for excess inventory differ from actual future demand or should market conditions become less favorable than those projected by management, additional inventory write-downs may be required, which would have a negative impact on our gross margins. SeePart I, Item 1A. “Risk Factors—’Our Financial Results May Fluctuate Significantly Because Of A Number Of Factors, Many Of Which Are Beyond Our Control’.”
41
Income Taxes
We account for income taxes under the provisions of Statement of Financial Accounting Standards No. 109,“Accounting for Income Taxes” (“FAS 109”). Under this method, we determine our deferred tax assets and liabilities based upon the difference between the financial statement and tax bases of our assets and liabilities. We make certain estimates and judgments in determining income tax expense for financial statement purposes. These estimates and judgments occur in the calculation of certain deferred tax assets and liabilities, which arise from timing differences in the recognition of revenue and expense for tax and financial statement purposes. Such deferred income tax assets and liabilities are recognized for the future tax consequences attributable to differences between the financial statement carrying amounts of existing assets and liabilities and their respective tax base, operating losses and tax credit carryforwards. Changes in tax rates affect the deferred income tax assets and liabilities and are recognized in the period in which the tax rates or benefits are enacted. SeePart II, Item 8—“Financial Statements and Supplementary Data”and“Notes to Consolidated Financial Statements, Note 17—Income Taxes” for more details about our deferred tax assets and liabilities.
We must determine the probability that we will be able to utilize our deferred tax assets. A valuation allowance is provided when it is more likely than not that some portion or all of a deferred tax asset will not be realized. As of March 29, 2009 and March 30, 2008, we maintained a full valuation allowance and our net deferred tax assets recorded on our consolidated balance sheets is zero.
Uncertain Income Tax Provisions
Effective April 1, 2007, we adopted Financial Accounting Standards Interpretation No. 48,“Accounting for Uncertainty in Income Taxes—an interpretation of FASB Statement No. 109” (“FIN 48”). FIN 48 prescribes a recognition threshold and measurement attribute for the financial statement recognition and measurement of uncertain tax positions taken or expected to be taken in our income tax return, and also provides guidance on derecognition, classification, interest and penalties, accounting in interim periods, disclosure and transition.
The unrecognized tax benefits increased by $0.5 million during the fiscal year ended March 29, 2009 to $9.9 million. If recognized, $8.2 million of these unrecognized tax benefits (net of federal benefit) would be recorded as a reduction of future income tax provision before consideration of changes in valuation allowance.
Stock-Based Compensation
We compute the fair value of stock options utilizing the Black-Scholes model. Calculating stock-based compensation expense requires the input of highly subjective assumptions. The assumptions used in calculating the fair value of stock-based compensation represent our estimates, which involve inherent uncertainties and the application of management judgment. As a result, if factors change and we use different assumptions, our stock-based compensation expense could be materially different in the future. In addition, we are required to estimate the expected forfeiture rate and only recognize expense for those shares expected to vest. If our actual forfeiture rate is materially different from our estimate, the stock-based compensation expense could be significantly different from what we have recorded in the current period. Additionally, a change in the estimated forfeiture rate will have a significant effect on reported stock-based compensation expense, as the effect of adjusting the rate for all unamortized expense after April 1, 2006 is recognized in the period the forfeiture estimate is changed. SeePart II, Item 8—“Financial Statements and Supplementary Data”and“Notes to the Consolidated Financial Statements, Note 12—Stock-Based Compensation” for more details about our assumptions used in calculating the stock-based compensation expenses and activities of our stock-based compensation.
In fiscal year 2007, our stockholders ratified the Exar Corporation 2006 Equity Incentive Plan (the “2006 Plan”). Within the terms of the 2006 Plan, we now grant stock options and Restricted Stock Units (“RSUs”). At March 29, 2009, unrecognized stock-based compensation was $6.0 million and $2.0 million for stock-options and RSUs, respectively, with remaining weighted average recognition periods of 3.03 years and 1.14 years, respectively.
42
Option Exchange Program
On October 23, 2008, we commenced a tender offer (the “Offer”) and filed a Schedule TO with the SEC pursuant to which holders of options with exercise prices equal to or greater than $11.00 per share and an expiration date after March 31, 2009 could tender their options in exchange for RSU awards. The exchange ratio of shares subject to such eligible options to shares subject to new awards issued was 4-to-1, 5-to-1 or 6-to-1, depending on the exercise price of the option being exchanged. New awards received in exchange for eligible options are subject to a two-year vesting schedule with 50% vesting at each anniversary of the grant date.
Pursuant to the Offer, 242 eligible participants tendered, and we accepted for exchange, options to purchase an aggregate of 1,650,231 shares of our common stock, representing approximately 94% of the 1,755,691 shares subject to options that were eligible to be exchanged in the Offer as of the commencement of the Offer on October 23, 2008. On November 24, 2008, upon the terms and subject to the conditions set forth in the Offer to Exchange Certain Outstanding Options for Restricted Stock Units, filed as an exhibit to the Schedule TO, we issued RSUs covering an aggregate of 344,020 shares of our common stock in exchange for the options surrendered pursuant to the Offer.
The new awards were granted with a price of $6.51, the closing price of our common stock on November 24, 2008 as reported on the NASDAQ Global Select Market. The fair value of the options exchanged was measured as the total of the unrecognized compensation cost of the original options tendered and the incremental compensation cost of the RSUs awarded on November 24, 2008, the date of exchange. The incremental compensation cost of $1.2 million was measured as the excess of the fair value of the RSUs over the fair value of the options immediately before cancellation based on the share price and other pertinent factors at that date. The amount will be amortized over the two years service period. During fiscal year 2009, we recorded approximately $208,000 of such incremental stock-based compensation expense.
Goodwill and Long-Lived Assets
Goodwill represents the excess of the purchase price over the fair value of the net tangible and identifiable intangible assets acquired in a business combination. We follow the provisions of Statement of Financial Accounting Standards No. 142,“Goodwill and Other Intangible Assets”(“FAS 142”), under which we evaluate goodwill for impairment on an annual basis or whenever events and changes in circumstances suggest that the carrying amount may not be recoverable. We conduct our annual impairment analysis in the fourth quarter of each fiscal year. Impairment of goodwill is tested at the reporting unit level by comparing the reporting unit’s carrying amount, including goodwill, to the fair value of the reporting unit. The fair values of the reporting units are estimated using a combination of the income approach that uses discounted cash flows and the market approach that utilizes comparable companies’ data. If the carrying amount of the reporting unit exceeds its fair value, goodwill is considered impaired and a second step is performed to measure the amount of impairment loss, if any. Because we have one reporting unit under FAS 142, we utilize an entity-wide approach to assess goodwill for impairment. SeePart II, Item 8—“Financial Statements and Supplementary Data”and“Notes to the Consolidated Financial Statements, Note 3—Business Combinations”and“Note 8—Goodwill and Intangible Assets”for more details about our assumptions used in calculating the stock-based compensation expenses and activities of our stock-based compensation.
Our long-lived assets include land, buildings, equipment, furniture and fixtures and other intangible assets. Long-lived assets are evaluated for impairment whenever events or changes in circumstances indicate that the carrying amount of an asset may not be recoverable. We evaluate the recoverability of our long-lived assets in accordance with Statement of Financial Accounting Standards No. 144,“Accounting for the Impairment or Disposal of Long-Lived Assets” (“FAS 144”). We compare the carrying value of long-lived assets to our projection of future undiscounted cash flows attributable to such assets and, in the event that the carrying value exceeds the future undiscounted cash flows, we record an impairment charge equal to the excess of the carrying value over the asset’s fair value.
43
Fiscal Year 2009
The rapid and severe deterioration of worldwide economic conditions has affected our industry and led customers to scale down their levels of production. As a result of third quarter fiscal year 2009 impairment indicators, we considered the potential impairment of goodwill and other long-lived assets including intangible assets. Indicators that required us to perform an interim impairment review consisted of further weakening in new orders from our customers throughout the third quarter and into the fourth quarter of fiscal year 2009, as well as the uncertainty of the magnitude and duration of the current recession as evidenced by industry analysts expectations that demand for semiconductors will remain weak until economic conditions improve. In addition, we experienced a significant decline in our stock price that reduced our market capitalization below our net asset carrying value for an extended period of time. As a result of the goodwill and long-lived asset impairment assessments, we recorded a charge totaling $59.7 million in the third quarter of fiscal year 2009. This charge is comprised of $46.2 million related to goodwill and $13.5 million related to intangible assets, which is included in the “Goodwill and other intangible asset impairment” line item in the consolidated statements of operations.
Given the impairment indicators discussed above, we performed an interim goodwill impairment analysis during the third quarter of fiscal year 2009 using a combination of the income approach and the market approach, in accordance with the provisions of FAS 142. The analysis performed compared the implied fair value of goodwill to the carrying amount of goodwill on our balance sheet. Our estimate of the implied fair value of the goodwill was based on the quoted market price of our common stock and the discounted value of estimated future cash flows over a seven-year period with residual value. The analysis resulted in an impairment charge of approximately $46.2 million, which is included in the “Goodwill and other intangible asset impairment” line item in the consolidated statements of operations, that reduced our carrying value of goodwill to zero.
Solely for the purposes of establishing inputs for the fair value calculations described above related to goodwill impairment testing, we made the following assumptions. We assumed that the current economic recession would continue through fiscal year 2010, followed by a recovery period in fiscal years 2011 through 2013 and long-term industry growth past fiscal year 2013. In addition, we applied gross margin assumptions consistent with our historical trends and used a 3% growth factor to calculate the terminal value of the company, which was consistent with the rate used in the prior year’s annual impairment test. We used a 14% discount rate to calculate the present value of cash flows and the terminal value, which is slightly higher than the 12.5% discount rate we used in the prior year’s annual impairment test, primarily due to increases to the required market risk and small stock premiums.
The change in the carrying amount of goodwill for fiscal years 2009 and 2008 are as follows (in thousands):
| | | | |
| | Amount | |
Balance as of March 31, 2007 | | $ | 5,190 | |
Goodwill acquired in connection with the Sipex acquisition | | | 171,127 | |
Goodwill adjustment | | | (187 | ) |
Impairment charge | | | (128,504 | ) |
| | | | |
Balance as of March 30, 2008 | | | 47,626 | |
Goodwill adjustment | | | (1,449 | ) |
Impairment charge | | | (46,177 | ) |
| | | | |
Balance as of March 29, 2009 | | $ | — | |
| | | | |
Given the impairment indicators discussed above, we also performed a test of purchased intangible assets for recoverability. The assessment of recoverability was based upon the assumptions and underlying cash flow projections prepared for the concurrent interim goodwill impairment test. Our estimate of the implied fair value of the intangible assets was based on the discounted value of estimated future cash flows over a five-year period using a discount rate of 14%.
44
The analysis determined that the carrying amount of the intangible assets exceeded the implied fair value under the test for impairment per FAS 144 and the difference was allocated to the intangible assets of the impacted asset group on a pro-rata basis using the relative carrying amounts of the assets. We recorded an impairment charge of approximately $13.5 million, which is included in the “Goodwill and other intangible asset impairment” line item in the consolidated statements of operations, of which $9.8 million related to existing technology, $1.4 million to patents/core technology, $1.3 million to distributor relationships, $0.9 million to customer relationships and $0.1 million to tradenames/trademarks.
Our purchased intangible assets at March 29, 2009 and March 30, 2008 were as follows (in thousands):
| | | | | | | | | | | | | | | | | | | | |
| | March 29, 2009 | | March 30, 2008 |
| | New Carrying Amount(2) | | Accumulated Amortization | | | Net Carrying Amount | | Carrying Amount(1) | | Accumulated Amortization | | | Net Carrying Amount |
Existing technology | | $ | 16,870 | | $ | (10,798 | ) | | $ | 6,072 | | $ | 26,646 | | $ | (6,517 | ) | | $ | 20,129 |
Patents/Core technology | | | 1,692 | | | (1,189 | ) | | | 503 | | | 3,159 | | | (781 | ) | | | 2,378 |
Customer backlog | | | 340 | | | (340 | ) | | | — | | | 340 | | | (340 | ) | | | — |
Distributor relationships | | | 1,264 | | | (817 | ) | | | 447 | | | 2,539 | | | (537 | ) | | | 2,002 |
Customer relationships | | | 770 | | | (460 | ) | | | 310 | | | 1,647 | | | (301 | ) | | | 1,346 |
Tradenames/Trademarks | | | 177 | | | (150 | ) | | | 27 | | | 263 | | | (99 | ) | | | 164 |
| | | | | | | | | | | | | | | | | | | | |
| | $ | 21,113 | | $ | (13,754 | ) | | $ | 7,359 | | $ | 34,594 | | $ | (8,575 | ) | | $ | 26,019 |
| | | | | | | | | | | | | | | | | | | | |
(1) | The carrying amount is net of intangible asset impairment charges of approximately $36.7 million taken during the fourth quarter of fiscal 2008. |
(2) | The new carrying amount is net of intangible asset impairment charges of approximately $36.7 million and $13.5 million taken during the fourth quarter of fiscal 2008 and the third quarter of fiscal 2009, respectively. |
Given the current volatile worldwide economic environment and the resulting uncertainties regarding its impact on our business, our estimates and assumptions regarding the duration of the ongoing economic downturn, or the period or strength of any future recovery, made for purposes of our goodwill impairment testing and intangible asset impairment testing during the third quarter of fiscal year 2009 may prove to be inaccurate. If our assumptions regarding projected revenue or gross margin rates are not achieved, we may be required to record additional intangible asset impairment charges in future periods, if any such change or other factor constitutes a triggering event. It is not possible at this time to determine if any such future impairment charge would result or, if it does, whether such charge would be material. As of March 29, 2009 there were no indicators that required us to perform an intangible assets impairment review and therefore we did not record an impairment charge during the fourth quarter of fiscal 2009.
Fiscal Year 2008
In the fourth quarter of fiscal year 2008, we conducted our annual impairment review and determined that, based on the then current market conditions in the semiconductor industry and our stock price over the prior six months, the carrying amount of our goodwill exceeded its implied fair value under the test for impairment as per FAS 142 and recorded a goodwill impairment charge of approximately $128.5 million, which is included in the “Goodwill and other intangible asset impairment” line item in the consolidated statements of operations. Our estimate of the implied fair value of the goodwill was based on the quoted market price of our common stock and the discounted value of estimated future cash flows over a seven-year period with residual value and discount rates between 12.5% and 18.8%.
In the fourth quarter of fiscal year 2008, based on the then current market conditions in the semiconductor industry and our stock price over the prior six months, certain intangible assets acquired in our acquisition of Sipex were tested for recoverability. As a result of an unfavorable product architecture decision by a market leading end customer, our reassessment of potential product cost reductions and delay in introducing new
45
proprietary products to markets, we reduced our projections of our future cash flows and determined that the carrying amount of the purchased Sipex intangible assets exceeded the implied fair value under the test for impairment as per FAS 144 and recorded an impairment charge of approximately $36.7 million, which is included in the “Goodwill and other intangible asset impairment” line item in the consolidated statements of operations. Our estimate of the implied fair value of the intangible assets was based on the discounted value of estimated future cash flows over a six-year period with residual value and a discount rate of 12.5%.
RESULTS OF OPERATIONS
We acquired Sipex in August 2007 and consequently, our results of operations are combined in fiscal years 2009 and 2008 for twelve and seven months, respectively. We were precluded from recognizing net sales for products shipped to Sipex’s distributors prior to the acquisition, and began to recognize revenue at those distributors once products shipped to the distributors after the acquisition were sold to end customers. Also as described above in Critical Accounting Policies and Estimates, we began to recognize revenue on shipments to our two primary distributors, Future and Nu Horizons, on the sell-through basis beginning August 26, 2007. Consequently, our net sales were lower until products shipped to those distributors after August 25, 2007 were sold to end customers.
Net Sales by Product Line
The following table shows net sales by product line in dollars and as a percentage of net sales for the periods indicated (in thousands):
| | | | | | | | | | | | | | | | | | | | | | | | |
| | March 29, 2009 | | | March 30, 2008 | | | March 31, 2007 | | | 2009 vs. 2008 Change | | | 2008 vs. 2007 Change | |
Net sales: | | | | | | | | | | | | | | | | | | | | | | | | |
Datacom | | $ | 27,833 | | 24 | % | | $ | 27,946 | | 31 | % | | $ | 28,462 | | 42 | % | | — | | | (2 | )% |
Interface | | | 63,036 | | 55 | % | | | 49,904 | | 56 | % | | | 40,040 | | 58 | % | | 26 | % | | 25 | % |
Power management | | | 24,249 | | 21 | % | | | 11,893 | | 13 | % | | | — | | — | | | 104 | % | | 100 | % |
| | | | | | | | | | | | | | | | | | | | | | | | |
Total | | $ | 115,118 | | 100 | % | | $ | 89,743 | | 100 | % | | $ | 68,502 | | 100 | % | | | | | | |
| | | | | | | | | | | | | | | | | | | | | | | | |
* | Revenue from Sipex products was included starting from August 26, 2007. |
Fiscal Year 2009 versus Fiscal Year 2008
Datacom
Net sales of datacom products, including network access and transmission products and storage products as well as optical products acquired from Sipex, for fiscal year 2009 decreased $0.1 million as compared to fiscal year 2008.
Net sales of network access and transmission products decreased $1.3 million primarily due to reduced customer demand and price erosion on certain SONET products, partially offset by a full years recognition of sales to our primary distributors on the sell-through basis of revenue recognition. Net sales of optical products increased $1.2 million primarily due to the five additional months of combined results in fiscal year 2009.
Interface
Net sales of interface products, including UARTs, video, imaging and other products as well as transceiver products acquired from Sipex, for fiscal year 2009 increased $13.1 million as compared to fiscal year 2008.
Net sales of UART products for fiscal year 2009 decreased $5.1 million as compared to fiscal year 2008 primarily due to decreased customer demand and price erosion on certain products partially offset by a full year’s
46
recognition of sales to our primary distributors on the sell-through basis of revenue recognition. Net sales of transceiver products for fiscal year 2009 were $18.2 million higher as compared to fiscal year 2008 primarily due to the five additional months of combined results with Sipex in fiscal year 2009.
Power Management
Net sales of power management products, including DC-DC regulators and LED drivers acquired from Sipex, for fiscal year of 2009 increased $12.4 million as compared to fiscal year 2008 primarily due to the five additional months of combined results with Sipex in fiscal year 2009.
Fiscal Year 2008 versus Fiscal Year 2007
Datacom
Net sales of datacom products for fiscal year 2008 included $1.6 million of additional sales from optical products. We estimate the change of revenue recognition to the sell-through basis at our two primary distributors reduced net sales of network access and transmission products by approximately $1.7 million for fiscal year 2008.
Net of these effects, net sales of network access and transmission products for fiscal year 2008 decreased $0.4 million as compared to fiscal year 2007, primarily due to price erosion on certain T/E carrier products and reduced sales from last time buys partially offset by increased volumes of T/E carrier and SONET product sales.
Interface
Net sales of interface products for fiscal year 2008 included $14.6 million of additional sales relating to sales of transceiver products. We estimate the change of revenue recognition to the sell-through basis at our primary distributors reduced the UART product sales by $5.3 million for fiscal year 2008.
Net of these effects, net sales of interface products for fiscal year 2008 were $0.6 million higher as compared to fiscal year 2007, primarily due to increased volume of UART sales partially offset by a shift in mix to lower priced UARTs, price erosion on certain UART products and reduced sales from last time buy orders.
Power Management
Power management products increased net sales for fiscal year 2008 by $11.9 million as we recognized our first revenue from power management products.
Net Sales by Channel
Net sales by channel for prior years have been reclassified to be consistent with the presentation of fiscal year 2009. The net sales to our two primary distributors are shown in sell-through distributors, as per their current classification, despite sales to them in fiscal 2007 and five months of fiscal 2008 being recorded on the sell-in basis of revenue recognition.
The following table shows net sales by channel in dollars and as a percentage of net sales for the periods indicated (in thousands):
| | | | | | | | | | | | | | | | | | | | | | | | |
| | March 29, 2009 | | | March 30, 2008 | | | March 31, 2007 | | | 2009 vs. 2008 Change | | | 2008 vs. 2007 Change | |
Net sales: | | | | | | | | | | | | | | | | | | | | | | | | |
Sell-through distributors | | $ | 68,762 | | 60 | % | | $ | 41,438 | | 46 | % | | $ | 25,956 | | 38 | % | | 66 | % | | 60 | % |
Direct and others | | | 46,356 | | 40 | % | | | 48,305 | | 54 | % | | | 42,546 | | 62 | % | | (4 | )% | | 14 | % |
| | | | | | | | | | | | | | | | | | | | | | | | |
Total | | $ | 115,118 | | 100 | % | | $ | 89,743 | | 100 | % | | $ | 68,502 | | 100 | % | | | | | | |
| | | | | | | | | | | | | | | | | | | | | | | | |
* | Revenue from Sipex products was included starting from August 26, 2007. |
47
Fiscal Year 2009 versus Fiscal Year 2008
Net sales to our distributors, for which we recognize revenue on the sell-through basis, for fiscal year 2009 increased by $27.3 million primarily due to increased sales of the products acquired from Sipex of $25.7 million and a full year’s recognition of sales to our primary distributors on the sell-through basis of revenue recognition partially offset by reduced customer demand.
Net sales to direct customers and other distributors for fiscal year 2009 decreased $1.9 million primarily due to reduced customer demand and price erosion on a SONET product and certain UART products partially offset by increased sales of products acquired from Sipex of $6.1 million.
Fiscal Year 2008 versus Fiscal Year 2007
Net sales to our distributors, for which we recognize revenue on the sell-through basis, for fiscal year 2008, included $19.4 million in sales of the products acquired from Sipex. Furthermore, as a result of transitioning revenue recognition used for sales to our two primary distributors from the sell-in to the sell-through basis as of August 26, 2007, net sales for fiscal year 2008 were lower by $6.9 million.
Net sales to direct customers and other distributors for fiscal year 2008 included $8.7 million in sales of the products acquired in the Sipex acquisition.
Net Sales by Geography
The following table shows net sales by geography in dollars and as a percentage of net sales for the periods indicated (in thousands):
| | | | | | | | | | | | | | | | | | | | | | | | |
| | March 29, 2009 | | | March 30, 2008 | | | March 31, 2007 | | | 2009 vs. 2008 Change | | | 2008 vs. 2007 Change | |
Net sales: | | | | | | | | | | | | | | | | | | | | | | | | |
Americas | | $ | 28,996 | | 25 | % | | $ | 27,626 | | 31 | % | | $ | 30,163 | | 44 | % | | 5 | % | | (8 | )% |
Asia | | | 61,029 | | 53 | % | | | 39,953 | | 44 | % | | | 20,322 | | 30 | % | | 53 | % | | 97 | % |
Europe | | | 25,093 | | 22 | % | | | 22,164 | | 25 | % | | | 18,017 | | 26 | % | | 13 | % | | 23 | % |
| | | | | | | | | | | | | | | | | | | | | | | | |
Total | | $ | 115,118 | | 100 | % | | $ | 89,743 | | 100 | % | | $ | 68,502 | | 100 | % | | | | | | |
| | | | | | | | | | | | | | | | | | | | | | | | |
* | Revenue from Sipex products was included starting from August 26, 2007. |
Fiscal Year 2009 versus Fiscal Year 2008
Net sales in the Americas for fiscal year 2009 included $16.5 million in sales of products acquired in the Sipex acquisition and a full year’s recognition of sales to our primary distributors on the sell-through basis of revenue recognition.
Net sales in Asia and Europe for fiscal year 2009 included $34.6 million and $8.7 million, respectively, of sales of products acquired in the Sipex acquisition.
Fiscal Year 2008 versus Fiscal Year 2007
Net sales in the Americas for fiscal year 2008 included $5.6 million in sales of products acquired in the Sipex acquisition. We estimate the change of revenue recognition to the sell-through basis at our two primary distributors decreased our net sales in the Americas by $6.9 million for fiscal year 2008.
Net sales in Asia and Europe for fiscal year 2008 included $17.2 million and $5.3 million, respectively, of sales of products acquired in the Sipex acquisition.
48
Gross Profit
The following table shows gross profit and cost of sales in dollars and as a percentage of net sales for the periods indicated (in thousands):
| | | | | | | | | | | | | | | | | | | | | | | | |
| | March 29, 2009 | | | March 30, 2008 | | | March 31, 2007 | | | 2009 vs. 2008 Change | | | 2008 vs. 2007 Change | |
Net sales | | $ | 115,118 | | | | | $ | 89,743 | | | | | $ | 68,502 | | | | | | | | | |
Cost of sales: | | | | | | | | | | | | | | | | | | | | | | | | |
Cost of sales | | | 61,744 | | 54 | % | | | 41,948 | | 47 | % | | | 21,008 | | 31 | % | | 47 | % | | 100 | % |
Fair value adjustment of acquired inventories | | | — | | — | | | | 2,231 | | 2 | % | | | — | | — | | | (100 | )% | | 100 | % |
Amortization of acquired intangible assets | | | 3,129 | | 3 | % | | | 5,452 | | 6 | % | | | 960 | | 1 | % | | (43 | )% | | 468 | % |
| | | | | | | | | | | | | | | | | | | | | | | | |
Gross profit | | $ | 50,245 | | 44 | % | | $ | 40,112 | | 45 | % | | $ | 46,534 | | 68 | % | | 25 | % | | (14 | )% |
| | | | | | | | | | | | | | | | | | | | | | | | |
* | Incremental revenue and gross profit from Sipex products was included starting from August 26, 2007. |
Gross profit represents net sales less cost of sales. Cost of sales includes:
| • | | the cost of purchasing finished silicon wafers manufactured by independent foundries; |
| • | | the costs associated with assembly, packaging, test, quality assurance and product yields; |
| • | | the cost of personnel and equipment associated with manufacturing support and manufacturing engineering; |
| • | | the cost of stock-based compensation associated with manufacturing engineering and support personnel; |
| • | | fair value adjustment of inventory acquired from Sipex; |
| • | | the amortization of purchased intangible assets; and |
| • | | the provision for excess and obsolete inventory. |
Fiscal Year 2009 versus Fiscal Year 2008
Gross profit for fiscal year 2009 increased $10.1 million, but as a percentage of net sales decreased 1%, as compared to fiscal year 2008. The decrease in gross profit as a percentage of sales was primarily due to an increase of $31.8 million in sales of lower gross margin products acquired from Sipex, higher charges of $1.2 million for excess and obsolete inventory, a decrease of $5.1 million in sales of network and UART products that typically have higher gross margins, partially offset by lower amortization of acquired intangible assets and the sale last year of acquired inventory which had been written-up to fair value.
We recorded impairment charges against purchased intangible assets in the third fiscal quarter of 2009 and in the fourth fiscal quarter of 2008.
Stock-based compensation expense recorded in cost of sales were $0.6 million and $0.4 million for fiscal year 2009 and 2008, respectively.
Fiscal Year 2008 versus Fiscal Year 2007
The decrease in gross profit for fiscal year 2008 was primarily due to lower gross margins of Sipex’s products, an incremental amortization expense of $4.5 million associated with the purchased intangible assets as a result of the Sipex acquisition, the amortization of the fair value adjustment to acquired inventories of $2.2 million and charges associated with excess and obsolete inventories.
49
In fiscal year 2008, we fully amortized the fair value adjustment of acquired Sipex inventories. In addition, we recorded an impairment charge against purchased intangible assets in the fourth fiscal quarter of 2008.
Stock-based compensation expense recorded in cost of sales was $0.4 million for fiscal year 2008 as compared to $0.1 million for fiscal year of 2007. The increase in stock-based compensation expense when compared to the prior year is primarily attributable to assumed unvested stock options in connection with the Sipex acquisition.
Other Costs and Expenses
The following table shows other costs and expenses in dollars and as a percentage of net sales for the periods indicated (in thousands):
| | | | | | | | | | | | | | | | | | | | | | | | |
| | March 29, 2009 | | | March 30, 2008 | | | March 31, 2007 | | | 2009 vs. 2008 Change | | | 2008 vs. 2007 Change | |
Net sales | | $ | 115,118 | | | | | $ | 89,743 | | | | | $ | 68,502 | | | | | | | | | |
Research and development | | | 31,829 | | 28 | % | | | 30,660 | | 34 | % | | | 25,838 | | 38 | % | | 4 | % | | 19 | % |
Selling, general and administrative | | | 38,962 | | 34 | % | | | 37,899 | | 42 | % | | | 24,925 | | 36 | % | | 3 | % | | 52 | % |
Goodwill and other intangible asset impairment | | | 59,676 | | 52 | % | | | 165,191 | | 184 | % | | | — | | — | | | (64 | )% | | 100 | % |
Acquired in-process research and development | | | — | | — | | | | 8,800 | | 10 | % | | | — | | — | | | (100 | )% | | 100 | % |
* | Incremental revenue and gross profit from Sipex products was included starting from August 26, 2007. |
Research and Development (“R&D”)
Our research and development costs consist primarily of:
| • | | the salaries, stock-based compensation, and related expenses of employees engaged in product research, design and development activities; |
| • | | costs related to engineering design tools, mask tooling costs, test hardware, engineering supplies and services, and use of in-house test equipment; |
| • | | amortization of purchased intellectual property; and |
Fiscal Year 2009 versus Fiscal Year 2008
The $1.2 million, or 4% increase in R&D expenses for fiscal year 2009 as compared to a year ago was primarily due to increased labor, equipment depreciation and patent expenses associated with operating the entire fiscal year with the resources acquired from Sipex partially offset by lower EDA software license costs.
Fiscal Year 2008 versus Fiscal Year 2007
The $4.8 million, or 19% increase in R&D expenses for fiscal year 2008 as compared to fiscal year 2007 was primarily a result of incremental expense of $4.3 million due to the growth of our company as a result of the Sipex acquisition and $0.4 million in severance costs of our employees, partially offset by lower labor related costs.
50
Selling, General and Administrative (“SG&A”)
Selling, general and administrative expenses consist primarily of:
| • | | salaries, stock-based compensation and related expenses; |
| • | | professional and legal fees; |
| • | | amortization of purchased intangible assets; and |
Fiscal Year 2009 versus Fiscal Year 2008
The $1.1 million, or 3% increase in SG&A expenses for fiscal year 2009, as compared to fiscal year 2008, was primarily due to increased labor, travel, insurance and subsidiary support expenses associated with operating the entire fiscal year with the resources acquired from Sipex partially offset by lower stock-based compensation expense, employee bonuses, audit and legal fees and acquisition related costs.
Fiscal Year 2008 versus Fiscal Year 2007
The $13.0 million, or 52% increase in SG&A expenses for fiscal year 2008, as compared to fiscal year 2007, was primarily a result of incremental expense of $8.4 million due to the growth of our company as a result of the Sipex acquisition, $1.1 million in severance costs of our employees, the amortization of acquired Sipex intangible assets of $0.9 million, other acquisition related costs of $0.6 million and increased legal costs of $0.5 million partially offset by lower labor-related expenses.
Stock-based compensation expense recorded in SG&A expenses was $3.4 million for fiscal year 2008 as compared to $3.1 million in the prior year. The increase in stock-based compensation expense when compared to fiscal year 2007 is primarily attributable to assumed unvested stock options in connection with the Sipex acquisition.
Separation costs for certain executive officers were $0.5 million and $1.6 million in fiscal years 2008 and 2007, respectively.
Acquired In-Process Research and Development
We recorded a charge of $8.8 million in acquired In-Process Research and Development (“IPR&D”), associated with our acquisition of Sipex in the three months ended September 30, 2007. We allocated the purchase price related to IPR&D through established valuation techniques. IPR&D was expensed upon acquisition because technological feasibility had not been established and no future alternative uses existed. The fair value of technology under development is determined using the income approach, which discounts expected future cash flows to present value, taking into account the stage of completion, estimated costs to complete, utilization of patents and core technology, the risks related to successful completion, and the markets served. The cash flows derived from the IPR&D were discounted at discount rates ranging from 25% to 40%. The percentage of completion for these projects ranged from 20% to 87% at the acquisition date.
The IPR&D projects underway at Sipex at the acquisition date were in the interface and power management product families. Within interface products, specific projects relate to new products in its multiprotocol and RS485 families. Within power management, development activities relate to the commercialization of its digital power technology, LED drivers, DC-DC regulators and controllers. Of these projects, four have been released to production, four require further development and testing to release them to production and five have been cancelled. IPR&D projects for power management required $0.2 million to complete and some product shipments began in early fiscal year 2009. IPR&D projects for interface required $0.6 million to complete with expected revenue generation beginning in fiscal year 2010. All power management and interface projects are scheduled to be completed by the middle of fiscal year 2010.
51
Other Income and Expenses
The following table shows other income and expenses in dollars and as a percentage of net sales for the periods indicated (in thousands):
| | | | | | | | | | | | | | | | | | | | | | | | | | | |
| | March 29, 2009 | | | March 30, 2008 | | | March 31, 2007 | | | 2009 vs. 2008 Change | | | 2008 vs. 2007 Change | |
Net sales | | $ | 115,118 | | | | | | $ | 89,743 | | | | | | $ | 68,502 | | | | | | | | | | |
Interest income and other, net | | | 9,693 | | | 8 | % | | | 16,037 | | | 18 | % | | | 16,526 | | | 24 | % | | (40 | )% | | (3 | )% |
Interest expense | | | (1,253 | ) | | (1 | )% | | | (771 | ) | | (1 | )% | | | — | | | — | | | 63 | % | | 100 | % |
Impairment charges on investments, net | | | | | | | | | | | | | | | | | | | | | | | | | | | |
Impairment charges on non-marketable securities | | | (1,203 | ) | | (1 | )% | | | (591 | ) | | (1 | )% | | | (957 | ) | | (1) | % | | 104 | % | | (38 | )% |
Loss on investments in short-term marketable securities | | | (586 | ) | | (1 | )% | | | — | | | — | | | | — | | | — | | | 100 | % | | — | |
Interest Income and Other, Net
Interest income and other, net primarily consists of:
| • | | foreign exchange gains or losses; and |
| • | | gains or losses on the sale or disposal of equipment. |
Fiscal Year 2009 versus Fiscal Year 2008
The $6.3 million or 40% decrease in interest income and other, net during fiscal year 2009 as compared to fiscal year 2008 was primarily attributable to a decrease in interest income as a result of lower invested cash balances, as we repurchased 1.6 million of our shares of common stock for $13.4 million and lower yields and increased investment management fees as we transitioned the internally managed portion of our portfolio to our professional investment managers, partially offset by increased sublease income.
Our Hillview facility located in Milpitas, California (the “Hillview Facility”), originally leased from Mission West Properties, L.P., was sublet to a tenant in April 2008. The sublease expires on March 31, 2011 with average annual rent of approximately $1.4 million.
Fiscal Year 2008 versus Fiscal Year 2007
The $0.5 million or 3% decrease in interest income and other, net during fiscal year 2008 as compared to fiscal year 2007 was primarily attributable to a decrease in interest income as a result of lower invested cash balances partially offset by higher market interest rates. Cash and short-term investments balances decreased $87.2 million during fiscal year 2008 as compared to fiscal year 2007 primarily as result of stock repurchases of 9.3 million shares totaling $93.0 million.
We expect that our interest income will continue to fluctuate due to changes in interest rates.
Interest expense
In fiscal year 2008, in connection with the acquisition of Sipex, we assumed a lease financing obligation related to Hillview Facility. We have accounted for this sale and leaseback transaction as a financing transaction which is included in the “Long-term lease financing obligation” line item on the consolidated balance sheet. The effective interest rate is 8.2%.
52
We have acquired engineering design tools (“design tools”) under capital leases. We acquired $5.2 million of design tools in December 2007 under a four-year license and $3.7 million of design tools in November 2008 under a three-year license, which were accounted for as capital leases and recorded in the “Property, plant and equipment, net” line item on the consolidated balance sheets. The related design tool obligations were included in the “Long-term lease financing obligations” line on our consolidated balance sheets. The effective interest rates for the design tools are 7.25% for the four-year tools and 4.0% for the three-year tools.
Interest expense for the Hillview Facility lease financing and the design tools lease obligations for fiscal year 2009 totaled approximately $1.3 million. Interest expense for the Hillview Facility lease financing and the design tools lease obligations for fiscal year 2008 totaled approximately $0.7 million.
Impairment Charges on Investments
We follow the guidance provided by FASB Staff Position No. 115-1,“The Meaning of Other-Than-Temporary Impairment and Its Application to Certain Investments” (“FSP 115-1”), to assess whether our investments with unrealized loss positions are other-than-temporarily impaired. We regularly review our investments in unrealized loss positions for other-than-temporary impairments. This evaluation includes, but is not limited to, significant quantitative and qualitative assessments and estimates regarding credit ratings, collateralized support, the length of time and significance of a security’s loss position and intent and ability to hold a security to maturity or forecasted recovery. Realized gains and losses and declines in value of our investments, both marketable and non-marketable, judged to be other-than-temporary are reported in the “Impairment charges on investments, net of realized gain” line item in the consolidated statements of operations. In September 2008, Lehman Brothers Holdings Inc. (“Lehman”) filed a petition under Chapter 11 of the U.S. Bankruptcy Code with the U.S. Bankruptcy Court for the Southern District of New York. As a result of Lehman’s bankruptcy filing, we recorded an other-than-temporary impairment charge of $0.6 million in fiscal year 2009.
Our long-term investments consist of the investments in TechFarm Ventures L.P. (Q), L.P. (“TechFarm Fund”) and Skypoint Telecom Fund II (US), L.P. (“Skypoint Fund”). Both TechFarm Fund and Skypoint Fund are venture capital funds which invest primarily in private companies in the telecommunications and/or networking industry. We account for these non-marketable equity securities under the cost method. In accordance with EITF 03-1,The Meaning of Other-Than-Temporary Impairment and its Application to Certain Investments, we periodically review and determine whether the investments are other-than-temporarily impaired, in which case the investments are written down to their impaired value.
TechFarm Fund
In fiscal year 2009, we analyzed the fair value of the underlying investment in TechFarm Fund and concluded that the remaining carrying value in TechFarm Fund was other-than-temporarily impaired and recorded an impairment charge of $0.5 million. As such, we reduced the carrying value of our investment in TechFarm Fund to zero.
In fiscal year 2008, we did not record any impairment charges after our assessment of the valuation of the fund performance.
In fiscal year 2007, we determined that the TechFarm Fund management fees continued to deplete the fund capital without any appreciation in the valuation of portfolio companies and concluded that a portion of the carrying value of our investment in the fund was other-than-temporarily impaired. As a result, we recorded a $0.1 million impairment charge in September 2006.
Skypoint Fund
In fiscal year 2009, we analyzed the fair value of the underlying investments of Skypoint Fund and concluded a portion of the carrying value was other-than-temporarily impaired and recorded an impairment charge of $0.7 million.
53
In fiscal year 2008, we performed a review of our investments and determined that two of the portfolio companies in the Skypoint Fund had limited cash on hand and financing opportunities were minimal. We concluded that a portion of the carrying value had been other-than-temporarily impaired and recorded a $0.6 million impairment charge during the year.
In fiscal year 2007, we became aware that two Skypoint Fund portfolio companies would be liquidated. We believed a portion of the carrying value of our investment in the fund was permanently impaired. As a result, we recorded a $0.8 million impairment charge against our earnings in September 2006.
Provision for Income Taxes
Fiscal Year 2009
Our effective tax rate for fiscal year 2009 was 0.7%. The provision for fiscal year 2009 differs from the amount computed by applying the statutory federal rate of 35%. This difference is principally due to changes in valuation allowance and net operating loss benefited during fiscal year 2009.
Fiscal Year 2008
Our effective tax rate for fiscal year 2008 was (4.3%). The provision for fiscal year 2008 differs from the amount computed by applying the statutory federal rate of 35%. This difference is principally due to nondeductible goodwill impairment charges, the write-down of purchased intangible assets which is not deducted for tax purposes, and the impact of valuation allowance against our deferred tax assets.
Fiscal Year 2007
Our effective tax rate for fiscal year 2007 was 29.2%. The provision for fiscal year 2007 differs from the amount computed by applying the statutory federal rate of 35%. This difference is principally due to benefits claimed for tax-exempt interest and research and development tax credits generated during the fiscal year, partially offset by state income taxes and stock-based compensation not currently deductible.
LIQUIDITY AND CAPITAL RESOURCES
| | | | | | | | | | | | |
| | Fiscal Years Ended | |
| | March 29, 2009 | | | March 30, 2008 | | | March 31, 2007 | |
| | (dollars in thousands) | |
Cash and cash equivalents | | $ | 89,002 | | | $ | 122,016 | | | $ | 119,809 | |
Short-term marketable securities | | | 167,341 | | | | 146,844 | | | | 236,270 | |
| | | | | | | | | | | | |
Total cash, cash equivalents, and short-term marketable securities | | | 256,343 | | | | 268,860 | | | | 356,079 | |
| | | | | | | | | | | | |
Percentage of total assets | | | 76 | % | | | 63 | % | | | 85 | % |
| | | |
Net cash provided by operating activities | | | 3,268 | | | | 13,820 | | | | 22,645 | |
Net cash provided by (used in) investing activities | �� | | (25,038 | ) | | | 82,849 | | | | (96,740 | ) |
Net cash provided by (used in) financing activities | | | (11,244 | ) | | | (94,336 | ) | | | 6,553 | |
Effect of exchange rate change on cash | | | — | | | | (126 | ) | | | (259 | ) |
| | | | | | | | | | | | |
Net increase (decrease) in cash and cash equivalents | | | (33,014 | ) | | | 2,207 | | | | (67,801 | ) |
| | | | | | | | | | | | |
Fiscal Year 2009
Operating Activities—Our net loss was $73.0 million. After adjustments for non-cash items and changes in working capital, we generated $3.3 million of cash from operating activities.
54
Significant non-cash charges included:
| • | | Goodwill and other intangible assets impairment charge of $59.7 million; |
| • | | Depreciation and amortization expenses of $14.4 million; |
| • | | Provision for sales returns and allowances of $7.8 million; |
| • | | Stock-based compensation expense of $4.9 million; and |
| • | | Losses on investments of $1.8 million. |
Working capital changes included:
| • | | a $3.4 million decrease in accounts receivable primarily due to decreased net sales; |
| • | | a $3.4 million decrease in accounts payable primarily due to reduced purchases of inventory; and |
| • | | a $1.7 million decrease in deferred income and allowances on sales to distributors as our distributors have reduced their inventory in response to reduced end customer demand. |
Investment Activities—In fiscal year 2009, net cash used in investing activities includes net purchases of short-term marketable securities of $22.6 million and $2.3 million in purchases of property, plant and equipment and intellectual property.
Financing Activities—In fiscal year 2009, net cash used in financing activities reflects the repurchase of 1.6 million shares of our common stock in fiscal year 2009 for $13.4 million and the $1.3 million repayment of lease financing partially offset by $3.5 million of proceeds associated with our employee stock plans.
As of March 29, 2009, we are obligated to contribute our remaining committed capital of approximately $0.5 million as required by the Skypoint Fund’s General Partner and in accordance with the partnership agreement between the Skypoint Fund and us. To meet our capital commitment to the Skypoint Fund, we may need to use our existing cash, cash equivalents and marketable securities.
From time to time, we acquire outstanding shares of our common stock in the open market to partially offset dilution from our equity awards, to increase our return on our invested capital and to bring our cash to a more appropriate level for our company. We may continue to utilize our share repurchase plan, which would reduce our cash, cash equivalents and/or short-term investments available to fund future operations and to meet other liquidity requirements.
During fiscal year 2009 we repurchased approximately 1.6 million shares of our common stock for $13.4 million. As of March 29, 2009 we had $11.8 million available to repurchase common stock under the share repurchase plan (“2007 SRP”).
To date, inflation has not had a significant impact on our operating results.
We anticipate that we will continue to finance our operations with cash flows from operations, existing cash and investment balances, and some combination of long-term debt and/or lease financing and additional sales of equity securities. The combination and sources of capital will be determined by management based on our needs and prevailing market conditions.
55
The following table summarizes our investments in marketable securities (in thousands):
| | | | | | | | | | | | | |
| | March 29, 2009 |
| | Amortized Cost | | Gross Unrealized Gains | | Gross Unrealized Losses | | | Fair Value |
Money market funds | | $ | 26,332 | | $ | — | | $ | — | | | $ | 26,332 |
Corporate bonds and commercial paper | | | 28,755 | | | 160 | | | (141 | ) | | | 28,774 |
U.S. government and agency securities | | | 163,750 | | | 1,379 | | | (38 | ) | | | 165,091 |
Asset-backed and mortgage-backed securities | | | 35,070 | | | 317 | | | (364 | ) | | | 35,023 |
| | | | | | | | | | | | | |
Total at March 29, 2009 | | $ | 253,907 | | $ | 1,856 | | $ | (543 | ) | | $ | 255,220 |
| | | | | | | | | | | | | |
| |
| | March 30, 2008 |
| | Amortized Cost | | Gross Unrealized Gains | | Gross Unrealized Losses | | | Fair Value |
Money market funds | | $ | 28,274 | | $ | — | | $ | — | | | $ | 28,274 |
Corporate bonds and commercial paper | | | 158,790 | | | 354 | | | (233 | ) | | | 158,911 |
U.S. government and agency securities | | | 50,146 | | | 1,413 | | | — | | | | 51,559 |
Asset-backed and mortgage-backed securities | | | 28,543 | | | 462 | | | (97 | ) | | | 28,908 |
| | | | | | | | | | | | | |
Total at March 30, 2008 | | $ | 265,753 | | $ | 2,229 | | $ | (330 | ) | | $ | 267,652 |
| | | | | | | | | | | | | |
As of March 29, 2009, our fixed income investment securities included asset-backed and mortgage-backed securities that accounted for 3.4% and 10.4%, respectively, of our total investments in marketable securities of $255.2 million. The asset-backed securities are comprised primarily of premium tranches of auto loans and credit card receivables, while our mortgage-backed securities are primarily from Federal agencies. We do not own auction rate securities nor do we own securities that are classified as sub-prime. As of the date of this Report, we believe we have sufficient liquidity and do not intend to sell these securities nor realize any significant losses in the short term. As of March 29, 2009, the net unrealized loss of our asset-backed and mortgage-backed securities totaled $47,000 or less than 0.02% of our total investments.
We believe that our cash and cash equivalents, short-term marketable securities and cash flows from operations will be sufficient to satisfy working capital requirements and capital equipment needs for at least the next 12 months. However, should the demand for our products decrease in the future, the availability of cash flows from operations may be limited, thus having a material adverse effect on our financial condition. From time to time, we evaluate potential acquisitions, strategic arrangements and equity investments complementary to our design expertise and market strategy, which may include investments in wafer fabrication foundries. To the extent that we pursue or position ourselves to pursue these transactions, we could consume a significant portion of our capital resources or choose to seek additional equity or debt financing. There can be no assurance that additional financing could be obtained on terms acceptable to us. The sale of additional equity or convertible debt could result in dilution to our stockholders.
Fiscal Year 2008
Operating Activities—Our net loss was $195.9 million. After adjustments for non-cash items and changes in working capital, we generated $13.8 million of cash from operating activities.
Significant non-cash charges included:
| • | | Goodwill and other intangible assets impairment charge of $165.2 million; |
| • | | Depreciation and amortization expenses of $12.6 million; |
| • | | Acquired IPR&D expense of $8.8 million; and |
56
| • | | Stock-based compensation expense of $5.0 million. |
Working capital changes included:
| • | | a $6.8 million increase in accounts receivable primarily due to increased net sales; |
| • | | a $3.8 million decrease in other accrued expenses as a result of payments of liabilities acquired in connection with the Sipex acquisition; and |
| • | | a $10.0 million increase in deferred income and allowances on sales to distributors due to our change in revenue recognition on sales to our two primary distributors. |
Investment Activities—In fiscal year 2008, net cash provided by investing activities reflected net sales of short-term marketable securities of $91.2 million partially offset by $4.9 million in purchases of property, plant and equipment and intellectual property and $2.9 million in net assets acquired in the acquisition of Sipex. The purchases of property, plant and equipment and intellectual property includes $3.2 million associated with the purchase of FyreStorm Inc.’s intellectual property.
Financing Activities—In fiscal year 2008, net cash used in financing activities reflected the repurchase of 9.3 million shares of our common stock in fiscal year 2008 for $93.0 million and the $5.3 million repayment of bank borrowings partially offset by $4.3 million of proceeds associated with our employee stock plans.
Fiscal Year 2007
Operating Activities—Net income, adjusted for non-cash related items provided cash of $22.6 million during fiscal year 2007.
Investment Activities—In fiscal year 2007, net cash used in investing activities reflected net purchases of $93.0 million of short-tem marketable securities and $3.0 million of purchases of property, plant and equipment and intellectual property.
Financing Activities—In fiscal year 2007, net cash provided by financing activities was primarily attributable to $15.8 million of proceeds associated with our employee stock plans, partially offset by the repurchase of approximately 0.7 million shares for $9.9 million under the stock repurchase plan authorized in March 2001.
OFF-BALANCE SHEET ARRANGEMENTS
As of March 29, 2009, we had no off-balance sheet arrangements as defined in Item 303(a)(4) of the SEC’s Regulation S-K.
CONTRACTUAL OBLIGATIONS AND COMMITMENTS
Our contractual obligations and commitments at March 29, 2009 are as follows (in thousands):
| | | | | | | | | | |
| | Payments due by period |
| | Total | | Less than 1 year | | 1-3 years | | 3-5 years | | More than 5 years |
Purchase commitment(1) | | 4,073 | | 4,073 | | — | | — | | — |
Long-term lease financing obligation(2) | | 9,299 | | 4,085 | | 5,214 | | — | | — |
Lease obligations(3) | | 1,282 | | 846 | | 436 | | — | | — |
Long-term investment commitments | | — | | — | | — | | — | | — |
(Skypoint Fund)(4) | | 510 | | 510 | | — | | — | | — |
Remediation commitment(5) | | 250 | | 200 | | 10 | | 40 | | — |
| | | | | | | | | | |
Total | | 15,414 | | 9,714 | | 5,660 | | 40 | | — |
| | | | | | | | | | |
57
Note: | The table above excludes the liability for uncertain tax positions of approximately $1.1 million at March 29, 2009 since we cannot predict with reasonable reliability the timing of cash settlements with the respective taxing authorities. |
(1) | We place purchase orders with wafer foundries and other vendors as part of our normal course of business. We expect to receive and pay for wafers, capital equipment and various service contract over the next 12 to 18 months from our existing cash balances. |
(2) | Lease payments (excluding $12.2 million estimated final obligation settlement with the lessor by returning the Hillview facility at the end of lease term due on our Hillview facility in Milpitas, California under a 5-year Standard Form Lease agreement that we signed with Mission West Properties L.P. on March 9, 2006, as amended on August 25, 2007). It also includes a $6.5 million licensing agreement related to engineering design software. |
(3) | Includes lease payments related to worldwide offices and buildings. |
(4) | The commitment related to the Skypoint Fund does not have a set payment schedule and thus will become payable upon the request from the Fund’s General Partner. |
(5) | The commitment relates to the environmental remediation activities of Micro Power Systems, Inc. |
RECENT ACCOUNTING PRONOUNCEMENTS
Please refer toPart II, Item 8—“Financial Statements and Supplementary Data”and“Notes to Consolidated Financial Statements, Note 2—Accounting Policies.”
SUBSEQUENT EVENT
Please refer toPart II, Item 8—“Financial Statements and Supplementary Data”and“Notes to Consolidated Financial Statements, Note 20—Subsequent Event.”
ITEM 7A. | QUANTITATIVE AND QUALITATIVE DISCLOSURES ABOUT MARKET RISK |
Foreign Currency Fluctuations. We are exposed to foreign currency fluctuations primarily through our foreign operations. This exposure is the result of foreign operating expenses being denominated in foreign currency. Operational currency requirements are typically forecasted for a one-month period. If there is a need to hedge this risk, we may enter into transactions to purchase currency in the open market or enter into forward currency exchange contracts.
If our foreign operations forecasts are overstated or understated during periods of currency volatility, we could experience unanticipated currency gains or losses. For fiscal year ended March 29, 2009, we did not have significant foreign currency denominated net assets or net liabilities positions, and had no foreign currency contracts outstanding.
Interest Rate Sensitivity. We maintain investment portfolio holdings of various issuers, types, and maturity dates with various professional money managers, banks and investment banking institutions. The market value of these investments on any given day during the investment term may vary as a result of market interest rate fluctuations. Our investment portfolio consisted of cash, money market funds and fixed income securities of $254.6 million as of March 29, 2009 and $267.7 million as of March 30, 2008. These securities, like all fixed income instruments, are subject to interest rate risk and will vary in value as market interest rates fluctuate. If market interest rates were to increase or decline immediately and uniformly by less than 10% from levels as of March 29, 2009, the increase or decline in the fair value of the portfolio would not be material. At March 29, 2009, the difference between the fair market value and the underlying cost of the investment portfolio was a gross unrealized gain of $1.3 million.
Our short-term investments are classified as “available-for-sale” securities and the cost of securities sold is based on the specific identification method. At March 29, 2009, short-term investments consisted of asset-backed securities, corporate bonds and government agency securities of $167.3 million.
58
ITEM 8. | FINANCIAL STATEMENTS AND SUPPLEMENTARY DATA |
INDEX TO CONSOLIDATED FINANCIAL STATEMENTS
59
Report of Independent Registered Public Accounting Firm
To the Board of Directors and Stockholders of Exar Corporation:
In our opinion, the accompanying consolidated balance sheets and the related consolidated statements of operations, stockholders’ equity and comprehensive income (loss), and cash flows present fairly, in all material respects, the financial position of Exar Corporation and its subsidiaries at March 29, 2009 and March 30, 2008, and the results of their operations and their cash flows for each of the three years in the period ended March 29, 2009 in conformity with accounting principles generally accepted in the United States of America. Also in our opinion, the Company maintained, in all material respects, effective internal control over financial reporting as of March 29, 2009, based on criteria established inInternal Control—Integrated Framework issued by the Committee of Sponsoring Organizations of the Treadway Commission (COSO). The Company’s management is responsible for these financial statements, for maintaining effective internal control over financial reporting and for its assessment of the effectiveness of internal control over financial reporting, included in Management’s Report on Internal Control over Financial Reporting. Our responsibility is to express opinions on these financial statements and on the Company’s internal control over financial reporting based on our integrated audits. We conducted our audits in accordance with the standards of the Public Company Accounting Oversight Board (United States). Those standards require that we plan and perform the audits to obtain reasonable assurance about whether the financial statements are free of material misstatement and whether effective internal control over financial reporting was maintained in all material respects. Our audits of the financial statements included examining, on a test basis, evidence supporting the amounts and disclosures in the financial statements, assessing the accounting principles used and significant estimates made by management, and evaluating the overall financial statement presentation. Our audit of internal control over financial reporting included obtaining an understanding of internal control over financial reporting, assessing the risk that a material weakness exists, and testing and evaluating the design and operating effectiveness of internal control based on the assessed risk. Our audits also included performing such other procedures as we considered necessary in the circumstances. We believe that our audits provide a reasonable basis for our opinions.
As discussed in Note 2 to the consolidated financial statements, the Company changed the manner in which it accounts for uncertain tax positions in fiscal year 2008.
A company’s internal control over financial reporting is a process designed to provide reasonable assurance regarding the reliability of financial reporting and the preparation of financial statements for external purposes in accordance with generally accepted accounting principles. A company’s internal control over financial reporting includes those policies and procedures that (i) pertain to the maintenance of records that, in reasonable detail, accurately and fairly reflect the transactions and dispositions of the assets of the company; (ii) provide reasonable assurance that transactions are recorded as necessary to permit preparation of financial statements in accordance with generally accepted accounting principles, and that receipts and expenditures of the company are being made only in accordance with authorizations of management and directors of the company; and (iii) provide reasonable assurance regarding prevention or timely detection of unauthorized acquisition, use, or disposition of the company’s assets that could have a material effect on the financial statements.
Because of its inherent limitations, internal control over financial reporting may not prevent or detect misstatements. Also, projections of any evaluation of effectiveness to future periods are subject to the risk that controls may become inadequate because of changes in conditions, or that the degree of compliance with the policies or procedures may deteriorate.
/s/ PricewaterhouseCoopers LLP
San Jose, CA
June 12, 2009
60
EXAR CORPORATION AND SUBSIDIARIES
CONSOLIDATED BALANCE SHEETS
(In thousands, except share amounts)
| | | | | | | | |
| | March 29, 2009 | | | March 30, 2008 | |
ASSETS | | | | | | | | |
Current assets: | | | | | | | | |
Cash and cash equivalents | | $ | 89,002 | | | $ | 122,016 | |
Short-term marketable securities | | | 167,341 | | | | 146,844 | |
Accounts receivable (net of allowances of $572 and $714) | | | 7,452 | | | | 9,943 | |
Accounts receivable, related party (net of allowances of $736 and $1,421) | | | 1,796 | | | | 3,712 | |
Inventories | | | 15,678 | | | | 14,201 | |
Other current assets | | | 3,274 | | | | 3,889 | |
Deferred income taxes, net | | | 62 | | | | 507 | |
| | | | | | | | |
Total current assets | | | 284,605 | | | | 301,112 | |
Property, plant and equipment, net | | | 42,549 | | | | 46,130 | |
Goodwill | | | — | | | | 47,626 | |
Intangible assets, net | | | 7,359 | | | | 26,019 | |
Other non-current assets | | | 1,876 | | | | 3,333 | |
| | | | | | | | |
Total assets | | $ | 336,389 | | | $ | 424,220 | |
| | | | | | | | |
| | |
LIABILITIES AND STOCKHOLDERS’ EQUITY | | | | | | | | |
Current liabilities: | | | | | | | | |
Accounts payable | | $ | 5,391 | | | $ | 8,801 | |
Accrued compensation and related benefits | | | 4,773 | | | | 5,744 | |
Deferred income and allowances on sales to distributors | | | 3,208 | | | | 3,253 | |
Deferred income and allowances on sales to distributors, related party | | | 7,040 | | | | 9,118 | |
Other accrued expenses | | | 7,014 | | | | 8,136 | |
| | | | | | | | |
Total current liabilities | | | 27,426 | | | | 35,052 | |
Long-term lease financing obligations | | | 15,633 | | | | 16,379 | |
Other non-current obligations | | | 1,236 | | | | 1,712 | |
| | | | | | | | |
Total liabilities | | | 44,295 | | | | 53,143 | |
| | | | | | | | |
Commitments and contingencies (Notes 14, 15 and 16) | | | | | | | | |
| | |
Total stockholders’ equity: | | | | | | | | |
Preferred stock, $.0001 par value; 2,250,000 shares authorized; no shares outstanding | | | — | | | | — | |
Common stock, $.0001 par value; 100,000,000 shares authorized; 43,036,271 and 43,928,762 shares issued and outstanding at March 29, 2009 and March 30, 2008, respectively (net of treasury shares) | | | 4 | | | | 4 | |
Additional paid-in capital | | | 710,787 | | | | 702,218 | |
Accumulated other comprehensive income | | | 802 | | | | 1,873 | |
Treasury stock at cost, 19,924,369 and 18,288,021 shares at March 29, 2009 and March 30, 2008, respectively | | | (248,983 | ) | | | (235,538 | ) |
Accumulated deficit | | | (170,516 | ) | | | (97,480 | ) |
| | | | | | | | |
Total stockholders’ equity | | | 292,094 | | | | 371,077 | |
| | | | | | | | |
Total liabilities and stockholders’ equity | | $ | 336,389 | | | $ | 424,220 | |
| | | | | | | | |
See accompanying notes to consolidated financial statements.
61
EXAR CORPORATION AND SUBSIDIARIES
CONSOLIDATED STATEMENTS OF OPERATIONS
(In thousands, except per share amounts)
| | | | | | | | | | | | |
| | Fiscal Years Ended | |
| | March 29, 2009 | | | March 30, 2008 | | | March 31, 2007 | |
Sales: | | | | | | | | | | | | |
Net sales | | $ | 74,620 | | | $ | 67,925 | | | $ | 54,580 | |
Net sales, related party | | | 40,498 | | | | 21,818 | | | | 13,922 | |
| | | | | | | | | | | | |
Total net sales | | | 115,118 | | | | 89,743 | | | | 68,502 | |
| | | | | | | | | | | | |
Cost of sales: | | | | | | | | | | | | |
Cost of sales | | | 41,811 | | | | 33,773 | | | | 17,041 | |
Cost of sales, related party | | | 19,933 | | | | 10,406 | | | | 3,967 | |
Amortization of purchased intangible assets | | | 3,129 | | | | 5,452 | | | | 960 | |
| | | | | | | | | | | | |
Total cost of sales | | | 64,873 | | | | 49,631 | | | | 21,968 | |
| | | | | | | | | | | | |
Gross profit | | | 50,245 | | | | 40,112 | | | | 46,534 | |
| | | | | | | | | | | | |
Operating expenses: | | | | | | | | | | | | |
Research and development | | | 31,829 | | | | 30,660 | | | | 25,838 | |
Selling, general and administrative | | | 38,962 | | | | 37,899 | | | | 24,925 | |
Goodwill and other intangible asset impairment | | | 59,676 | | | | 165,191 | | | | — | |
Acquired in-process research and development | | | — | | | | 8,800 | | | | — | |
| | | | | | | | | | | | |
Total operating expenses | | | 130,467 | | | | 242,550 | | | | 50,763 | |
Loss from operations | | | (80,222 | ) | | | (202,438 | ) | | | (4,229 | ) |
Other income and expense: | | | | | | | | | | | | |
Interest income and other, net | | | 9,693 | | | | 16,037 | | | | 16,526 | |
Interest expense | | | (1,253 | ) | | | (771 | ) | | | — | |
Impairment charges on investments | | | (1,789 | ) | | | (591 | ) | | | (957 | ) |
| | | | | | | | | | | | |
Total other income and expense | | | 6,651 | | | | 14,675 | | | | 15,569 | |
Income (loss) before income taxes | | | (73,571 | ) | | | (187,763 | ) | | | 11,340 | |
Provision for (benefit from) income taxes | | | (535 | ) | | | 8,116 | | | | 3,316 | |
| | | | | | | | | | | | |
Net income (loss) | | $ | (73,036 | ) | | $ | (195,879 | ) | | $ | 8,024 | |
| | | | | | | | | | | | |
Earnings (loss) per share: | | | | | | | | | | | | |
Basic earnings (loss) per share | | $ | (1.70 | ) | | $ | (4.55 | ) | | $ | 0.22 | |
| | | | | | | | | | | | |
Diluted earnings (loss) per share | | $ | (1.70 | ) | | $ | (4.55 | ) | | $ | 0.22 | |
| | | | | | | | | | | | |
Shares used in the computation of earnings (loss) per share: | | | | | | | | | | | | |
Basic | | | 42,887 | | | | 43,090 | | | | 36,255 | |
| | | | | | | | | | | | |
Diluted | | | 42,887 | | | | 43,090 | | | | 36,480 | |
| | | | | | | | | | | | |
See accompanying notes to consolidated financial statements.
62
EXAR CORPORATION AND SUBSIDIARIES
CONSOLIDATED STATEMENTS OF STOCKHOLDERS’ EQUITY AND COMPREHENSIVE INCOME (LOSS)
(In thousands, except share amounts)
| | | | | | | | | | | | | | | | | | | | | | | | | | | | | |
| | Common Stock | | Treasury Stock | | | Additional Paid-in- Capital | | | Retained Earnings (Accumulated Deficit) | | | Accum- ulated Other Compre- hensive Income (Loss) | | | Total Stockholders’ Equity | |
| | Shares | | | Amount | | Shares | | | Amount | | | | | |
Balance, March 31, 2006 | | 43,898,555 | | | $ | 4 | | (8,267,110 | ) | | $ | (132,702 | ) | | $ | 430,380 | | | $ | 90,140 | | | $ | (417 | ) | | $ | 387,405 | |
Comprehensive income: | | | | | | | | | | | | | | | | | | | | | | | | | | | | | |
Net income | | | | | | | | | | | | | | | | | | | | 8,024 | | | | | | | | 8,024 | |
Other comprehensive income: | | | | | | | | | | | | | | | | | | | | | | | | | | | | | |
Foreign currency translation adjustments, net of tax expense of $102 | | | | | | | | | | | | | | | | | | | | | | | | (155 | ) | | | (155 | ) |
Unrealized gains on marketable securities net of tax benefit of $426 | | | | | | | | | | | | | | | | | | | | | | | | 648 | | | | 648 | |
| | | | | | | | | | | | | | | | | | | | | | | | | | | | | |
Total comprehensive income | | | | | | | | | | | | | | | | | | | | | | | | | | | $ | 8,517 | |
| | | | | | | | | | | | | | | | | | | | | | | | | | | | | |
Issuance of common stock through employee stock plans | | 1,254,817 | | | | | | | | | | | | | | 15,844 | | | | | | | | | | | | 15,844 | |
Tax benefit from stock plans | | | | | | | | | | | | | | | | 510 | | | | | | | | | | | | 510 | |
Issuance of common stock for services | | 16,700 | | | | | | | | | | | | | | | | | | | | | | | | | | | |
Stock-based compensation | | | | | | | | | | | | | | | | 4,350 | | | | | | | | | | | | 4,350 | |
Acquisition of treasury stock | | | | | | | | (748,147 | ) | | | (9,870 | ) | | | | | | | | | | | | | | | (9,870 | ) |
| | | | | | | | | | | | | | | | | | | | | | | | | | | | | |
Balance, March 31, 2007 | | 45,170,072 | | | $ | 4 | | (9,015,257 | ) | | $ | (142,572 | ) | | $ | 451,084 | | | $ | 98,164 | | | $ | 76 | | | $ | 406,756 | |
| | | | | | | | | | | | | | | | | | | | | | | | | | | | | |
Comprehensive loss: | | | | | | | | | | | | | | | | | | | | | | | | | | | | | |
Net loss | | | | | | | | | | | | | | | | | | | | (195,879 | ) | | | | | | | (195,879 | ) |
Cumulative effect adjustment to retained earnings related to the adoption of FIN 48 | | | | | | | | | | | | | | | | | | | | 235 | | | | | | | | 235 | |
Other comprehensive income: | | | | | | | | | | | | | | | | | | | | | | | | | | | | | |
Foreign currency translation adjustments, net of tax benefit of $50 | | | | | | | | | | | | | | | | | | | | | | | | (77 | ) | | | (77 | ) |
Unrealized gains on marketable securities | | | | | | | | | | | | | | | | | | | | | | | | 1,874 | | | | 1,874 | |
| | | | | | | | | | | | | | | | | | | | | | | | | | | | | |
Total comprehensive loss | | | | | | | | | | | | | | | | | | | | | | | | | | | $ | (193,847 | ) |
| | | | | | | | | | | | | | | | | | | | | | | | | | | | | |
Issuance of common stock in connection with the Sipex acquisition | | 16,459,076 | | | | | | | | | | | | | | 229,999 | | | | | | | | | | | | 229,999 | |
Fair value of vested options assumed in connection with the Sipex acquisition | | | | | | | | | | | | | | | | 10,401 | | | | | | | | | | | | 10,401 | |
Fair value of warrants assumed in connection with the Sipex acquisition | | | | | | | | | | | | | | | | 1,489 | | | | | | | | | | | | 1,489 | |
Issuance of common stock through employee stock plans | | 518,193 | | | | | | | | | | | | | | 4,288 | | | | | | | | | | | | 4,288 | |
Tax deficit from stock plans | | | | | | | | | | | | | | | | (55 | ) | | | | | | | | | | | (55 | ) |
Issuance of common stock for vested restricted stock units | | 69,442 | | | | | | | | | | | | | | | | | | | | | | | | | | | |
Stock-based compensation | | | | | | | | | | | | | | | | 5,012 | | | | | | | | | | | | 5,012 | |
Acquisition of treasury stock | | | | | | | | (9,272,764 | ) | | | (92,966 | ) | | | | | | | | | | | | | | | (92,966 | ) |
| | | | | | | | | | | | | | | | | | | | | | | | | | | | | |
Balance, March 30, 2008 | | 62,216,783 | | | $ | 4 | | (18,288,021 | ) | | $ | (235,538 | ) | | $ | 702,218 | | | $ | (97,480 | ) | | $ | 1,873 | | | $ | 371,077 | |
| | | | | | | | | | | | | | | | | | | | | | | | | | | | | |
Comprehensive loss: | | | | | | | | | | | | | | | | | | | | | | | | | | | | | |
Net loss | | | | | | | | | | | | | | | | | | | | (73,036 | ) | | | | | | | (73,036 | ) |
Other comprehensive income: | | | | | | | | | | | | | | | | | | | | | | | | | | | | | |
Change in unrealized gains, including tax of $485 | | | | | | | | | | | | | | | | | | | | | | | | (1,071 | ) | | | (1,071 | ) |
| | | | | | | | | | | | | | | | | | | | | | | | | | | | | |
Total comprehensive loss | | | | | | | | | | | | | | | | | | | | | | | | | | | $ | (74,107 | ) |
| | | | | | | | | | | | | | | | | | | | | | | | | | | | | |
Issuance of common stock through employee stock plans | | 635,959 | | | | | | | | | | | | | | 3,518 | | | | | | | | | | | | 3,518 | |
Reclassification of deferred compensation liability | | | | | | | | | | | | | | | | 210 | | | | | | | | | | | | 210 | |
Issuance of common stock for vested restricted stock units | | 117,437 | | | | | | | | | | | | | | | | | | | | | | | | | | | |
Withholding of common shares for tax obligations on vested restricted stock units | | (9,539 | ) | | | | | | | | | | | | | (60 | ) | | | | | | | | | | | (60 | ) |
Stock-based compensation | | | | | | | | | | | | | | | | 4,901 | | | | | | | | | | | | 4,901 | |
Acquisition of treasury stock | | | | | | | | (1,636,348 | ) | | | (13,445 | ) | | | | | | | | | | | | | | | (13,445 | ) |
| | | | | | | | | | | | | | | | | | | | | | | | | | | | | |
Balance, March 29, 2009 | | 62,960,640 | | | $ | 4 | | (19,924,369 | ) | | $ | (248,983 | ) | | $ | 710,787 | | | $ | (170,516 | ) | | $ | 802 | | | $ | 292,094 | |
| | | | | | | | | | | | | | | | | | | | | | | | | | | | | |
See accompanying notes to consolidated financial statements.
63
EXAR CORPORATION AND SUBSIDIARIES
CONSOLIDATED STATEMENTS OF CASH FLOWS
(In thousands)
| | | | | | | | | | | | |
| | Fiscal Years Ended | |
| | March 29, 2009 | | | March 30, 2008 | | | March 31, 2007 | |
Cash flows from operating activities: | | | | | | | | | | | | |
Net income (loss) | | $ | (73,036 | ) | | $ | (195,879 | ) | | $ | 8,024 | |
Reconciliation of net income (loss) to net cash provided by operating activities: | | | | | | | | | | | | |
Goodwill and other intangible asset impairment | | | 59,676 | | | | 165,191 | | | | — | |
Depreciation and amortization | | | 14,446 | | | | 12,615 | | | | 5,257 | |
Deferred income taxes | | | (485 | ) | | | 7,895 | | | | 529 | |
Acquired in-process research and development | | | — | | | | 8,800 | | | | — | |
Stock-based compensation expense | | | 4,934 | | | | 4,979 | | | | 4,350 | |
Provision for sales returns and allowances | | | 7,824 | | | | 3,273 | | | | 3,964 | |
Fair value adjustment of acquired inventories included in cost of sales | | | — | | | | 2,231 | | | | — | |
Other than temporary loss on investment in non-marketable securities | | | 1,202 | | | | 591 | | | | 957 | |
Other than temporary loss on investments in marketable securities | | | 587 | | | | — | | | | — | |
Tax benefits (deficit) from stock plans | | | — | | | | (55 | ) | | | 510 | |
Gross tax windfall from stock-based compensation | | | — | | | | — | | | | (579 | ) |
Changes in operating assets and liabilities, net of effect of the Sipex acquisition: | | | | | | | | | | | | |
Accounts receivable | | | (3,417 | ) | | | (6,842 | ) | | | (902 | ) |
Inventories | | | (1,510 | ) | | | 626 | | | | 752 | |
Prepaid expenses and other assets | | | 819 | | | | 1,145 | | | | (303 | ) |
Accounts payable | | | (3,410 | ) | | | 223 | | | | (505 | ) |
Other accrued expenses | | | (1,720 | ) | | | (3,798 | ) | | | 575 | |
Income taxes payable | | | 94 | | | | 543 | | | | 497 | |
Deferred income and allowance on sales to distributors | | | (1,704 | ) | | | 9,956 | | | | — | |
Accrued compensation and related benefits | | | (1,032 | ) | | | 2,326 | | | | (481 | ) |
| | | | | | | | | | | | |
Net cash provided by operating activities | | | 3,268 | | | | 13,820 | | | | 22,645 | |
| | | | | | | | | | | | |
Cash flows from investing activities: | | | | | | | | | | | | |
Purchases of property, plant and equipment and intellectual property | | | (2,255 | ) | | | (4,923 | ) | | | (2,952 | ) |
Purchases of short-term marketable securities | | | (264,087 | ) | | | (322,279 | ) | | | (362,585 | ) |
Proceeds from maturities of short-term marketable securities | | | 199,064 | | | | 374,460 | | | | 257,493 | |
Proceeds from sales of short-term marketable securities | | | 42,467 | | | | 39,064 | | | | 12,103 | |
Contributions to long-term investments, net | | | (227 | ) | | | (557 | ) | | | (799 | ) |
Acquisition of Sipex, net of cash acquired and transaction costs | | | — | | | | (2,916 | ) | | | — | |
| | | | | | | | | | | | |
Net cash provided by (used in) investing activities | | | (25,038 | ) | | | 82,849 | | | | (96,740 | ) |
| | | | | | | | | | | | |
Cash flows from financing activities: | | | | | | | | | | | | |
Repurchase of common stock | | | (13,445 | ) | | | (92,965 | ) | | | (9,870 | ) |
Proceeds from issuance of common stock | | | 3,518 | | | | 4,288 | | | | 15,844 | |
Repayment of bank borrowings | | | — | | | | (5,291 | ) | | | — | |
Repayment of lease financing obligations | | | (1,317 | ) | | | (368 | ) | | | — | |
Gross tax windfall from stock-based compensation | | | — | | | | — | | | | 579 | |
| | | | | | | | | | | | |
Net cash provided (used in) by financing activities | | | (11,244 | ) | | | (94,336 | ) | | | 6,553 | |
Effect of exchange rate changes on cash | | | — | | | | (126 | ) | | | (259 | ) |
| | | | | | | | | | | | |
Net increase (decrease) in cash and cash equivalents | | | (33,014 | ) | | | 2,207 | | | | (67,801 | ) |
Cash and cash equivalents at the beginning of year | | | 122,016 | | | | 119,809 | | | | 187,610 | |
| | | | | | | | | | | | |
Cash and cash equivalents at the end of year | | $ | 89,002 | | | $ | 122,016 | | | $ | 119,809 | |
| | | | | | | | | | | | |
Supplemental disclosure of non-cash investing and financing activities: | | | | | | | | | | | | |
Issuance of common stock in consideration for acquired assets and liabilities of Sipex | | $ | — | | | $ | 229,999 | | | $ | — | |
Assumption of vested options and warrants of Sipex | | | — | | | | 11,890 | | | | — | |
Cash paid for income taxes | | | 164 | | | | 2,088 | | | | 2,018 | |
Cash paid for interest | | | 1,200 | | | | 738 | | | | — | |
Property, plant and equipment acquired under capital lease | | | 2,571 | | | | 5,154 | | | | — | |
See accompanying notes to consolidated financial statements.
64
EXAR CORPORATION AND SUBSIDIARIES
NOTES TO CONSOLIDATED FINANCIAL STATEMENTS
FISCAL YEARS ENDED MARCH 29, 2009, MARCH 30, 2008 AND MARCH 31, 2007
NOTE 1. DESCRIPTION OF BUSINESS
Exar Corporation was incorporated in California in 1971 and reincorporated in Delaware in 1991. Exar Corporation and its subsidiaries (“Exar” or “we”) is a fabless semiconductor company that designs, sub-contracts manufacturing and sells highly differentiated silicon, software and subsystem solutions for industrial, datacom and storage applications. Our comprehensive knowledge of end-user markets along with our underlying analog, mixed signal and digital technology has enabled innovative solutions that meet the needs of the evolving connected world. Our product portfolio includes power management and interface components, datacom products, storage optimization solutions, network security and applied service processors. Applying both analog and digital technologies, our products are deployed in a wide array of applications such as portable electronic devices, set top boxes, digital video recorders, telecommunication systems, servers, enterprise storage systems and industrial automation equipment. We have the unique ability to provide customers with a breadth of component products and subsystem solutions based on advanced mixed signal silicon integration.
On August 25, 2007, we acquired Sipex Corporation (“Sipex”). Sipex was a company that designed, manufactured and marketed high performance, analog Integrated Circuits (“IC”) used by Original Equipment Manufacturers (“OEM”), in the computing, consumer electronics, datacom and networking infrastructure markets. The results of operations of Sipex and estimated fair value of assets acquired and liabilities assumed were included in our consolidated financial statements beginning August 26, 2007.
NOTE 2. ACCOUNTING POLICIES
Basis of Presentation—In December 2007, we changed our fiscal year end from a fiscal year ending March 31 to a 52-53 week fiscal year ending on the Sunday closest to March 31. As part of this change, each fiscal quarter will also end on the Sunday closest to the end of the corresponding calendar quarter. As a result of the change in our fiscal year end, our fiscal year ended March 29, 2009 contains 364 days and our fiscal years ended March 30, 2008 and March 31, 2007 each contain 365 days. Fiscal years ended March 29, 2009, March 30, 2008 and March 31, 2007 are also referred to as “2009,” “2008” and “2007” unless otherwise indicated.
In conjunction with the Sipex acquisition, we reassessed our ability to estimate returns and allowances and consequently, on August 26, 2007, changed the revenue recognition used for sales to our two primary distributors, Future Electronics Inc. (“Future”) and Nu Horizons Electronics Corp. (“Nu Horizons”), from the sell-in basis to the sell-through basis (See “Note 2 – Accounting Policies, Revenue Recognition”).
In December 2007, in connection with integrating and realigning our combined operations with Sipex, we reassessed the economic facts and circumstances of each of our foreign subsidiaries and changed the functional currencies for our foreign subsidiaries to the U.S. dollar. Accumulated other comprehensive loss reported in the consolidated balance sheet before December 1, 2007 related to the cumulative foreign currency translation adjustments of our subsidiaries prior to changing our functional currency was immaterial.
The accounts of foreign subsidiaries have been remeasured into U.S. dollars in accordance with the Financial Accounting Standards Board (“FASB”) Statement of Financial Accounting Standards No. 52, “Foreign Currency Translation” (“FAS 52”). Accordingly, foreign currency is remeasured to U.S. dollars for financial purposes by using the U.S. dollar as the functional currency and exchange gains and losses are reported in income and expenses. These currency gains or losses are reported in interest and other income, net in the consolidated statements of operations. Monetary balance sheet accounts are remeasured using the current exchange rate in effect at the balance sheet date. For non-monetary items, the accounts are remeasured at the historical exchange rate. Revenues and expenses are remeasured at the average exchange rates for the period.
65
EXAR CORPORATION AND SUBSIDIARIES
NOTES TO CONSOLIDATED FINANCIAL STATEMENTS—(CONTINUED)
FISCAL YEARS ENDED MARCH 29, 2009, MARCH 30, 2008 AND MARCH 31, 2007
Principles of Consolidation—The consolidated financial statements include the accounts of Exar Corporation and its wholly-owned subsidiaries. All intercompany accounts and transactions have been eliminated.
Use of Management Estimates—The preparation of consolidated financial statements in conformity with generally accepted accounting principles in the United States requires management to make estimates, judgments and assumptions that affect the reported amounts of assets, liabilities, revenues and expenses and related disclosure of contingent assets and liabilities. On an on-going basis, we evaluate our estimates, including (1) revenue recognition; (2) valuation of inventories; (3) income taxes; (4) stock-based compensation; (5) goodwill; and (6) long-lived assets. Actual results could differ from these estimates and material effects on operating results and financial position may result.
Business Combinations—The estimated fair value of acquired assets and assumed liabilities and the results of operations of acquired businesses are included in our consolidated financial statements from the effective date of the purchase. The total purchase price is allocated to the estimated fair value of assets acquired and liabilities assumed based on management estimates as per Statement of Financial Accounting Standards No. 141,“Business Combinations” (“FAS 141”). The purchase price includes direct transaction costs consisting of investment banking, legal and accounting fees.
Cash and Cash Equivalents—We consider all highly liquid debt securities and investments with a maturity from the date of purchase of 90 days or less to be classified as cash and cash equivalents. Cash and cash equivalents also consist of cash on deposit with banks and money market funds.
Inventories—Inventories are recorded at the lower of cost or market, determined on a first-in, first-out basis. Cost is computed using the standard cost, which approximates average actual cost. Inventory is written down when conditions indicate that the selling price could be less than cost due to physical deterioration, obsolescence, changes in price levels, or other causes. The write-down of excess inventories is generally based on inventory levels in excess of either six or twelve months of demand, as judged by management, for each specific product.
Our inventories consisted of the following (in thousands) as of the dates indicated:
| | | | | | |
| | March 29, 2009 | | March 30, 2008 |
Work-in-process | | $ | 9,175 | | $ | 8,775 |
Finished goods | | | 6,503 | | | 5,426 |
| | | | | | |
Inventories | | $ | 15,678 | | $ | 14,201 |
| | | | | | |
Property, Plant and Equipment—Property, plant and equipment, including capital leases and leasehold improvements, are stated at cost less accumulated depreciation and amortization. Depreciation for machinery and equipment is computed using the straight-line method over the estimated useful lives of the assets, which ranges from three to ten years. Buildings are depreciated using the straight-line method over an estimated useful life of 30 years. Assets held under capital leases and leasehold improvements are amortized over the shorter of the terms of the leases or their estimated useful lives. Land is not depreciated.
66
EXAR CORPORATION AND SUBSIDIARIES
NOTES TO CONSOLIDATED FINANCIAL STATEMENTS—(CONTINUED)
FISCAL YEARS ENDED MARCH 29, 2009, MARCH 30, 2008 AND MARCH 31, 2007
Our property, plant and equipment consisted of the following (in thousands) as of the dates indicated:
| | | | | | | | |
| | March 29, 2009 | | | March 30, 2008 | |
Land | | $ | 11,960 | | | $ | 11,960 | |
Buildings | | | 22,641 | | | | 22,584 | |
Machinery and equipment | | | 69,675 | | | | 65,215 | |
| | | | | | | | |
Property, plant and equipment, total | | | 104,276 | | | | 99,759 | |
Accumulated depreciation and amortization | | | (61,727 | ) | | | (53,629 | ) |
| | | | | | | | |
Property, plant and equipment, net | | $ | 42,549 | | | $ | 46,130 | |
| | �� | | | | | | |
Depreciation and amortization expense for fiscal years ended March 29, 2009, March 30, 2008 and March 31, 2007 was $8.4 million, $5.9 million and $4.6 million, respectively. Included in the March 29, 2009 depreciation and amortization expense was a charge for accelerated depreciation of $1.2 million associated with the abandonment of an energy generation equipment at our Fremont Facility.
Non-Marketable Equity Securities—Non-marketable equity investments are accounted for at historical cost and are presented on our consolidated balance sheets as other non-current assets.
Other-Than-Temporary Impairment
All of our marketable and non-marketable investments are subject to a periodic impairment review. Investments are considered to be impaired when a decline in fair value is judged to be other-than-temporary, for the following investments:
Marketable investmentwhen the resulting fair value is significantly below cost basis and/or the significant decline has lasted for an extended period of time. The evaluation that we use to determine whether a marketable equity security is other than temporarily impaired is based on the specific facts and circumstances present at the time of assessment, which include significant quantitative and qualitative assessments and estimates regarding credit ratings, collateralized support, the length of time and significance of a security’s loss position and intent and ability to hold a security to maturity or forecasted recovery. Realized gains and losses and declines in value of our investments judged to be other-than-temporary are reported in the “Impairment charges on investments” line item in the consolidated statements of operations.
Non-marketable equity investmentwhen events or circumstances are identified that would likely have a significant adverse effect on the fair value of the investment and the fair value is significantly below cost basis and/or the significant decline has lasted for an extended period of time. The indicators that we use to identify those events and circumstances include:
| • | | the investment manager’s evaluation; |
| • | | the investee’s revenue and earnings trends relative to predefined milestones and overall business prospects; |
| • | | the technological feasibility of the investee’s products and technologies; |
| • | | the general market conditions in the investee’s industry; and |
| • | | the investee’s liquidity, debt ratios and the rate at which the investee is using cash. |
67
EXAR CORPORATION AND SUBSIDIARIES
NOTES TO CONSOLIDATED FINANCIAL STATEMENTS—(CONTINUED)
FISCAL YEARS ENDED MARCH 29, 2009, MARCH 30, 2008 AND MARCH 31, 2007
Investments identified as having an indicator of impairment are subject to further analysis to determine if the investment is other than temporarily impaired, in which case the investment is written down to its impaired value. When an investee is not considered viable from a financial or technological point of view, the entire investment is written down. Impairment of non-marketable equity investment is recorded in the “Other-than-temporary loss on long-term investments” line item in the consolidated statements of operations.
Goodwill—Goodwill represents the excess of the purchase price over the fair value of the net tangible and identifiable intangible assets acquired in a business combination. We follow the provisions of Statement of Financial Accounting Standards No. 142,“Goodwill and Other Intangible Assets” (“FAS 142”), under which goodwill is no longer subject to amortization. We evaluate goodwill for impairment on an annual basis or whenever events and changes in circumstances suggest that the carrying amount may not be recoverable. Impairment of goodwill is tested at the reporting unit level by comparing the reporting unit’s carrying amount, including goodwill, to the fair value of the reporting unit. The fair values of the reporting units are estimated using a combination of the income, or discounted cash flows, approach and the market approach, which utilize comparable companies’ data. If the carrying amount of the reporting unit exceeds its fair value, goodwill is considered impaired and a second step is performed to measure the amount of impairment loss, if any. Because we have one reporting unit under FAS 142, we utilized the entity-wide approach to assess goodwill for impairment. The rapid and severe deterioration of worldwide economic conditions has affected our industry and led customers to scale down their levels of production. As a result of third quarter fiscal 2009 impairment indicators, we considered the potential impairment of goodwill. Indicators that required us to perform an interim impairment review consisted of further weakening in new orders from our customers throughout the third quarter and into the fourth quarter of fiscal 2009, as well as the uncertainty of the magnitude and duration of the current recession as evidenced by industry analysts expectations that demand for semiconductors will remain weak until economic conditions improve. In addition, we experienced a significant decline in our stock price that reduced our market capitalization below our net asset carrying value for an extended period of time. We performed an interim goodwill impairment analysis during the third fiscal quarter of 2009 pursuant to the requirements under FAS 142 and recorded a $46.2 million impairment loss that was included in the “Goodwill and other intangible asset impairment” line item in the consolidated statements of operations. During our annual goodwill impairment analysis in the fourth quarter fiscal 2008, we recorded a $128.5 million impairment loss that was included in the “Goodwill and other intangible asset impairment” line item in the consolidated statements of operations. (See “Note 8—Goodwill and Intangible Assets”).
Long-Lived Assets—Our long-lived assets include land, buildings, equipment, furniture and fixtures and other intangible assets. Long-lived assets are evaluated for impairment whenever events or changes in circumstances indicate that the carrying amount of an asset may not be recoverable. We evaluate the recoverability of our long-lived assets in accordance with Statement of Financial Accounting Standards No. 144, “Accounting for the Impairment or Disposal of Long-Lived Assets” (“FAS 144”). We compare the carrying value of long-lived assets to our projection of future undiscounted cash flows attributable to such assets and, in the event that the carrying value exceeds the future undiscounted cash flows, we record an impairment charge against income equal to the excess of the carrying value over the asset’s fair value. The rapid and severe deterioration of worldwide economic conditions has affected our industry and led customers to scale down their levels of production. As a result of third quarter fiscal 2009 impairment indicators, we considered the potential impairment of other long-lived assets including intangible assets. Indicators that required us to perform an interim impairment review consisted of further weakening in new orders from our customers throughout the third quarter and into the fourth quarter of fiscal 2009, as well as the uncertainty of the magnitude and duration of the current recession as evidenced by industry analysts expectations that demand for semiconductors will remain weak until economic conditions improve. In addition, we experienced a significant decline in our stock price that reduced
68
EXAR CORPORATION AND SUBSIDIARIES
NOTES TO CONSOLIDATED FINANCIAL STATEMENTS—(CONTINUED)
FISCAL YEARS ENDED MARCH 29, 2009, MARCH 30, 2008 AND MARCH 31, 2007
our market capitalization below our net asset carrying value for an extended period of time. The analysis determined that the carrying amount of the intangible assets exceeded the implied fair value under the test for impairment per FAS 144 and the difference was allocated to the intangible assets of the impacted asset group on a pro-rata basis using the relative carrying amounts of the assets. We recorded an impairment charge of approximately $13.5 million, of which $9.8 million related to existing technology, $1.4 million to patents/core technology, $1.3 million to distributor relationships, $0.9 million to customer relationships and $0.1 million to tradenames/trademarks. During the fourth quarter of fiscal 2008, we recorded a $36.7 million impairment loss on our intangibles assets that was included in the “Goodwill and other intangible asset impairment” line item in the consolidated statements of operations. (See “Note 8—Goodwill and Intangible Assets”). Substantially all of our property, plant and equipment and other long-lived assets are located in the United States.
Income Taxes—Income taxes are reported under Statement of Financial Accounting Standards No. 109, “Accounting for Income Taxes” (“FAS 109”) and accordingly, deferred taxes are recognized using the asset and liability method, whereby deferred tax assets and liabilities are recognized for the future tax consequence attributable to differences between the financial statement carrying amounts of existing assets and liabilities and their respective tax base, and operating loss and tax credit carryforwards. Valuation allowances are provided if it is more likely than not that some or all of the deferred tax assets will not be realized.
Revenue Recognition—We recognize revenue in accordance with the Securities and Exchange Commission (“SEC”) Staff Accounting Bulletin 104,“Revenue Recognition” (“SAB 104”). SAB 104 requires that four basic criteria must be met before revenue can be recognized: (1) persuasive evidence of an arrangement exists; (2) delivery has occurred or services rendered; (3) the price is fixed or determinable; and (4) collectability is reasonably assured.
We derive revenue principally from the sale of our products to distributors and to OEMs or their contract manufacturers. Our delivery terms are primarily FOB shipping point, at which time title and all risks of ownership are transferred to the customer. For fiscal years ended March 29, 2009, March 30, 2008 and March 31, 2007, approximately 44%, 35% and 38%, respectively, of our net sales were derived from product sales to our two primary distributors, Future and Nu Horizons; and approximately 56%, 65% and 62%, respectively, of our net sales were derived from sales to other distributors, OEM customers and other non-distributors.
Non-distributors
For non-distributors, revenue is recognized when title to the product is transferred to the customer, which occurs upon shipment or delivery, depending upon the terms of the customer order, provided that persuasive evidence of a sales arrangement exists, the price is fixed or determinable, collection of the resulting receivables is reasonably assured, there are no customer acceptance requirements and there are no remaining significant obligations. Provisions for returns and allowances for non-distributor customers are provided at the time product sales are recognized. An allowance for sales returns and allowances for non-distributor customers are recorded based on historical experience or specific identification of an event necessitating an allowance.
Distributors
Our two primary distributors’ agreements permit the return of 3% to 5% of their purchases during the preceding quarter for purposes of stock rotation. For one of these distributors, a scrap allowance of 2% of the preceding quarter’s purchases is permitted. We also provide discounts to certain distributors based on volume of product they sell for a specific product with a specific volume range for a given customer over a period not to exceed one year.
69
EXAR CORPORATION AND SUBSIDIARIES
NOTES TO CONSOLIDATED FINANCIAL STATEMENTS—(CONTINUED)
FISCAL YEARS ENDED MARCH 29, 2009, MARCH 30, 2008 AND MARCH 31, 2007
We recognize revenue from each of our distributors using either of the following basis. Once adopted, the basis for revenue recognition for a distributor is maintained unless there is a change in circumstances indicating the basis for revenue recognition for that distributor is no longer appropriate.
| • | | Sell-in Basis—Revenue is recognized upon shipment if we conclude we meet the same criteria as for non-distributors and we can reasonably estimate the credits for returns, pricing allowances and/or other concessions. We record an estimated allowance, at the time of shipment, based upon historical patterns of returns, pricing allowances and other concessions (i.e., “sell-in” basis). |
| • | | Sell-through Basis—Revenue and the related costs of sales are deferred until the resale to the end customer if we grant more than limited rights of return, pricing allowances and/or other concessions or if we cannot reasonably estimate the level of returns and credits issuable (i.e., “sell-through” basis). Under the sell-through basis, accounts receivable are recognized and inventory is relieved upon shipment to the distributor as title to the inventory is transferred upon shipment, at which point we have a legally enforceable right to collection under normal terms. The associated sales and cost of sales are deferred and are included in deferred income and allowance on sales to distributors in the consolidated balance sheet. When the related product is sold by our distributors to their end customers, at which time the ultimate price we receive is known, we recognize previously deferred income as sales and cost of sales. |
Sell-through revenue recognition is highly dependent on receiving pertinent and accurate data from our distributors in a timely fashion. Distributors provide us periodic data regarding the product, price, quantity, and end customer when products are resold as well as the quantities of our products they still have in stock. We must use estimates and apply judgments to reconcile distributors’ reported inventories to their activities. Any error in our judgment could lead to inaccurate reporting of our net sales, gross profit, deferred income and allowances on sales to distributors and net income.
Our historical patterns of returns, pricing allowances and other concessions with distributors had been fairly consistent, which enabled us to reasonably estimate such allowances at the time of shipment. Therefore, we historically recognized revenue on sales to all distributors on the sell-in basis and recorded an estimated allowance, at the time of shipment, based on authorized and historical patterns of returns and other concessions. Concurrent with the acquisition of Sipex, we reassessed our expected ability to continue to reasonably estimate such allowances for each of our distributors as well as for Sipex’s distributors. Prior to the acquisition, Sipex recognized revenue on sales to all distributors on the sell-through basis. Consistent with Sipex’s past practice, we concluded that we were not able to reasonably estimate such allowances at the time of shipment of products to Sipex’s distributors. Therefore, we determined that consistent with Sipex’s past practice, we will continue to recognize sales to Sipex’s distributors on the sell-through basis. In addition, as a result of the acquisition, our relationships, marketing and sales practices with our two primary distributors had changed. Further, as disclosed inPart II, Item 8—“Financial Statements and Supplementary Data”and“Notes to Consolidated Financial Statements, Note 5—Related Party Transaction,” Future is a related party of Exar. As a result of these changes, we have concluded that we can no longer reasonably estimate returns, pricing allowances and other concessions at the time of shipment of products to these distributors. Accordingly, concurrent with our consummation of the Sipex acquisition on August 25, 2007, we determined it was appropriate that revenue on all sales to our two primary distributors, Future and Nu Horizons, be recognized on the sell-through basis.
Research and Development Expenses—Research and development expenses consist primarily of the salaries and related expenses of those employees engaged in research, design and development activities; expenses related to design tools, license expenses related to intellectual property; contract R&D mask tooling costs; supplies and services; and facilities expenses. All research and development expenses that have no alternative future use are expensed as incurred.
70
EXAR CORPORATION AND SUBSIDIARIES
NOTES TO CONSOLIDATED FINANCIAL STATEMENTS—(CONTINUED)
FISCAL YEARS ENDED MARCH 29, 2009, MARCH 30, 2008 AND MARCH 31, 2007
Comprehensive Income (Loss)—Comprehensive income (loss) includes charges or credits to equity as a result of foreign currency translation adjustments, net of taxes, and unrealized gains or losses on marketable securities, net of taxes. Comprehensive income (loss) for fiscal years ended March 29, 2009, March 30, 2008 and March 31, 2007 has been disclosed within the consolidated statements of stockholders’ equity and comprehensive income (loss).
Foreign Currency—The accounts of foreign subsidiaries are remeasured into U.S. dollars in accordance with the Statement of Financial Accounting Standards No. 52, “Foreign Currency Translation” (“FAS 52”). Accordingly, foreign currency is remeasured to U.S. dollars for financial reporting purposes by using the U.S. dollar as the functional currency and exchange gains and losses are reported in income and expenses. These currency gains or losses are reported in interest income and other, net in the consolidated statements of operations. Monetary balance sheet accounts are remeasured using the current exchange rate in effect at the balance sheet date. For non-monetary items, the accounts are remeasured at the historical exchange rate. Revenues and expenses are remeasured at the average exchange rates for the period. Foreign currency transaction losses were approximately $199,000, $65,000 and $20,000 for fiscal years ended March 29, 2009, March 30, 2008 and March 31, 2007, respectively.
Concentration of Credit Risk and Significant Customers—Financial instruments potentially subjecting us to concentrations of credit risk consist primarily of accounts receivable, cash, cash equivalents, short-term marketable securities and long-term investments. The majority of our sales are derived from distributors and manufacturers in the communications, industrial and computer industries. We perform ongoing credit evaluations of our customers and generally do not require collateral for sales on credit. We maintain allowances for potential credit losses, and such losses have been within management’s expectations. Charges to bad debt expense were insignificant for fiscal years 2009, 2008 and 2007, respectively. Our policy is to place our cash, cash equivalents and short-term marketable securities with high credit quality financial institutions and limit the amounts invested with any one financial institution or in any type of financial instrument. We do not hold or issue financial instruments for trading purposes.
We sell our products to distributors and OEMs throughout the world. Alcatel-Lucent accounted for 11% and 16% of our net sales in fiscal years 2008 and 2007, respectively. No other OEM customer accounted for 10% or more of our net sales in fiscal years 2009, 2008 and 2007. Future, a related party, was and continues to be our largest distributor. Future, on a worldwide basis, represented 35%, 24% and 20% of net sales in fiscal years 2009, 2008 and 2007, respectively. Our second largest distributor, Nu Horizons, accounted for 11% and 18%, of net sales in fiscal years of 2008 and 2007, respectively. No other distributor customer accounted for 10% or more of our net sales for any of the three fiscal years.
Concentration of Other Risks—The majority of our products are currently fabricated at Chartered Semiconductor Manufacturing Ltd. (“Chartered”) in Singapore, Episil Technologies Inc. (“Episil”) in Taiwan, and Hangzhou Silan Microelectronics Co. Ltd. and Hangzhou Silan Integrated Circuit Co. Ltd. (collectively “Silan”) in the People’s Republic of China (“PRC”), and are assembled and tested by other third-party sub-contractors located in Asia. A significant disruption in the operations of one or more of these sub-contractors would impact the production of our products for a substantial period of time which could have a material adverse effect on our business, financial condition and results of operations.
Fair Value of Financial Instruments—We estimate the fair value of our financial instruments by using available market information and valuation methodologies considered to be appropriate. However, considerable judgment is required in interpreting market data to develop the estimates of fair value. The use of different market assumptions and/or estimation methodologies could have a material effect on estimated fair value
71
EXAR CORPORATION AND SUBSIDIARIES
NOTES TO CONSOLIDATED FINANCIAL STATEMENTS—(CONTINUED)
FISCAL YEARS ENDED MARCH 29, 2009, MARCH 30, 2008 AND MARCH 31, 2007
amounts. The estimated fair value of our carrying values of cash and cash equivalents, short-term investments, accounts receivable, accounts payable and accrued liabilities at March 29, 2009, March 30, 2008 and March 31, 2007 was not materially different from the carrying values presented in the consolidated balance sheets due to the relatively short periods to maturity of the instruments.
Stock-Based Compensation—On April 1, 2006, we adopted Statement of Financial Accounting Standards No. 123 (revised 2004),“Share-Based Payment” (“FAS 123R”) by using the modified prospective transition method. In accordance with this transition method, we began recognizing compensation expense for all share-based awards granted after April 1, 2006 plus unvested awards granted prior to April 1, 2006. Under this method of implementation, no restatement of prior periods has been made. The estimated fair value of the equity-based awards, less expected forfeitures, is amortized over the awards’ vesting period on a straight-line basis. Determining the fair value of stock-based awards at the grant date requires considerable judgment, including estimating expected volatility, expected term and risk-free rate. If factors change and we employ different assumptions, stock-based compensation expense may differ significantly from what we have recorded in the prior years. In addition, we follow the “with-and-without” intra-period allocation approach as described in EITF Topic D-32 for purposes of the utilization of tax attributes.
Recent Accounting Pronouncements
In April 2009, the FASB issued FSP FAS 115-2 and FAS 124-2,“Recognition and Presentation of Other-Than-Temporary Impairment” (“FSP 115-2/124-2”). FSP 115-2/124-2 amends the requirements for the recognition and measurement of other-than-temporary impairments for debt securities by modifying the pre-existing “intent and ability” indicator. Under FSP 115-2/124-2, an other-than-temporary impairment is triggered when there is an intent to sell the security, it is more likely than not that the security will be required to be sold before recovery, or the security is not expected to recover the entire amortized cost basis of the security. Additionally, FSP 115-2/124-2 changes the presentation of an other-than-temporary impairment in the income statement for those impairments involving credit losses. The credit loss component will be recognized in earnings and the remainder of the impairment will be recorded in other comprehensive income. FSP FSP 115-2/124-2 is effective for periods ending after June 15, 2009. Early adoption is permitted, however, we elected to adopt FSP 115-2/124-2 during our first quarter of fiscal year 2010. The adoption of FSP 115-2/124-2 is not expected to have a significant impact on our consolidated financial statements.
In April 2009, the FASB issued FSP FAS 107-1 and APB 28-1,“Interim Disclosure about Fair Value of Financial Instruments”(“FSP 107-1/APB 28-1”). FSP 107-1/APB 28-1 requires interim disclosures regarding the fair values of financial instruments that are within the scope of FAS 107,“Disclosures about the Fair Value of Financial Instruments.” (“FAS 107”). Additionally, FSP 107-1/APB 28-1 requires disclosure of the methods and significant assumptions used to estimate the fair value of financial instruments on an interim basis as well as changes of the methods and significant assumptions from prior periods. The FSP will now require these disclosures on a quarterly basis, providing qualitative and quantitative information about fair value estimates for all those financial instruments not measured on the balance sheet at fair value. FSP 107-1/APB 28-1 is effective for periods ending after June 15, 2009. Early adoption is permitted, however, we elected to adopt FSP 107-1/APB 28-1 during our first quarter of fiscal year 2010. The adoption of FSP 107-1/APB 28-1 is not expected to have a significant impact on our consolidated financial statements.
In April 2009, the FASB issued FSP FAS 157-4,“Determining Fair Value When Volume and Level of Activity for the Asset or Liability Have Significantly Decreased and Identifying Transactions That Are Not Orderly” (“FSP 157-4”). FSP 157-4 provides guidance on how to determine the fair value of assets and liabilities when the volume and level of activity for the asset/liability has significantly decreased. FSP 157-4 also provides
72
EXAR CORPORATION AND SUBSIDIARIES
NOTES TO CONSOLIDATED FINANCIAL STATEMENTS—(CONTINUED)
FISCAL YEARS ENDED MARCH 29, 2009, MARCH 30, 2008 AND MARCH 31, 2007
guidance on identifying circumstances that indicate a transaction is not orderly. In addition, FSP 157-4 requires disclosure in interim and annual periods of the inputs and valuation techniques used to measure fair value and a discussion of changes in valuation techniques. FSP 157-4 is effective for periods ending after June 15, 2009. Early adoption is permitted, however, we elected to adopt FSP 157-4 during our first quarter of fiscal year 2010. The adoption of FSP 157-4 is not expected to have a significant impact on our consolidated financial statements.
In January 2009, the Financial Accounting Standards Board (“FASB”) issued FASB Staff Position Emerging Issues Task Force (“EITF”) 99-20-1, “Amendments to the Impairment Guidance of EITF Issue No. 99-20” (“FSP EITF 99-20-1”). FSP EITF 99-20-1 amends the impairment guidance in EITF Issue No. 99-20,“Recognition of Interest Income and Impairment on Purchased Beneficial Interests and Beneficial Interests That Continue to be Held by a Transferor in Securitized Financial Assets,” to achieve a more consistent determination of whether an other-than-temporary impairment has occurred. The FSP also reemphasized the objective of an other-than-temporary impairment assessment and the related disclosure requirements in FASB Statement No. 115,“Accounting for Certain Investments in Debt and Equity Securities”(“FAS 115”). FSP EITF 99-20-1 is effective for interim and annual reporting periods ending after December 15, 2008. As of March 30, 2009, the first day of our fiscal year 2010, we adopted FSP EITF 99-20-1and the adoption had no material impact on our financial position, results of operations and liquidity.
In June 2008, the FASB issued FASB Staff Position EITF 03-6-1,“Determining Whether Instruments Granted in Share-Based Payment Transactions Are Participating Securities” (“FSP EITF 03-6-1”). FSP EITF 03-6-1 addresses whether participating share-based payment awards, that contain non-forfeitable rights to dividends or dividend equivalents (paid or unpaid) prior to vesting, should be included in the computation of earnings per share under the two-class method. FSP EITF 03-6-1 will be effective for financial statements issued for fiscal years beginning after December 15, 2008. The Company is currently evaluating the potential impact, if any, of the adoption of FSP EITF 03-6-1 on its financial position, cash flows and results of operations.
In April 2008, the FASB issued Staff Position No. FAS 142-3,“Determination of the Useful Life of Intangible Assets”(“FSP FAS 142-3”). FSP 142-3 amends the factors that should be considered in developing renewal or extension assumptions used to determine the useful life of a recognized intangible asset under Statement of Financial Accounting Standards No. 142, “Goodwill and Other Intangible Assets” (“FAS 142”). FSP 142-3 is intended to improve the consistency between the useful life of a recognized intangible asset under FAS 142 and the period of expected cash flows used to measure the fair value of the asset under Statement of Financial Accounting Standards No. 141 (revised 2007), “Business Combinations” (“FAS 141R”), and other guidance under GAAP. FSP 142-3 is effective for fiscal years beginning after December 15, 2008. As of March 30, 2009, the first day of our fiscal year 2010, we adopted FSP 142-3 and the adoption had no material impact on our financial position, results of operations and liquidity.
In December 2007, FASB issued SFAS No. 141 (revised 2007),“Business Combinations”(“SFAS 141R”) and SFAS No. 160,“Noncontrolling Interests in Consolidated Financial Statements”(“SFAS 160”), an amendment of Accounting Research Bulletin No. 51. SFAS 141R will change how business acquisitions are accounted for and will impact financial statements both on the acquisition date and in subsequent periods. SFAS 160 will change the accounting and reporting for minority interests, which will be recharacterized as noncontrolling interests and classified as a component of equity. SFAS 141R and SFAS 160 are effective beginning in the first quarter of fiscal 2010. Early adoption is not permitted. The Company expects the adoption of SFAS No. 141(R) to have a material effect on the Company’s financial position and results of operations subsequent to adoption on March 30, 2009, the first day of our fiscal year 2010, as realization of any acquired tax attributes will benefit the tax provision as opposed to recording the benefit to Goodwill. The Company is currently evaluating the impact that SFAS 160 will have on its consolidated financial statements.”
73
EXAR CORPORATION AND SUBSIDIARIES
NOTES TO CONSOLIDATED FINANCIAL STATEMENTS—(CONTINUED)
FISCAL YEARS ENDED MARCH 29, 2009, MARCH 30, 2008 AND MARCH 31, 2007
NOTE 3. BUSINESS COMBINATIONS
We periodically evaluate strategic acquisitions that build upon our existing library of intellectual property, human capital and engineering talent, and seek to increase our leadership position in the areas in which we operate.
Acquisition of Sipex Corporation
On August 25, 2007, we acquired Sipex Corporation (“Sipex”), a company that designed, manufactured and marketed high performance analog ICs used by OEMs in the computing, consumer electronics, communications and networking infrastructure markets. As a result of the acquisition, we combined product offerings, increased technical expertise, distribution channels, customer base and geographic reach, and reduced expenses due to significant cost synergies.
The acquisition was accounted for as a purchase of a business in accordance with FAS 141. Accordingly, Sipex’s results of operations and estimated fair value of assets acquired and liabilities assumed were included in our consolidated financial statements beginning August 26, 2007.
The total purchase price of the Sipex acquisition is summarized as follows (in thousands):
| | | |
| | Amounts |
Fair value of Exar common stock issued | | $ | 229,999 |
Fair value of options and warrants assumed | | | 16,701 |
Direct transaction costs | | | 4,038 |
| | | |
Total purchase price | | $ | 250,738 |
| | | |
Purchase Price Allocation
The allocation of the purchase price to Sipex’s tangible and identifiable intangible assets acquired and liabilities assumed was based on their estimated fair values. The excess of the purchase price over the tangible and identifiable intangible assets acquired and liabilities assumed has been allocated to goodwill. Goodwill resulted primarily from our expectations of synergies from integration of Sipex’s product offerings with our product offerings. Goodwill is not deductible for tax purposes. We had up to twelve months from the closing date of the acquisition to adjust pre-acquisition contingencies, if any.
74
EXAR CORPORATION AND SUBSIDIARIES
NOTES TO CONSOLIDATED FINANCIAL STATEMENTS—(CONTINUED)
FISCAL YEARS ENDED MARCH 29, 2009, MARCH 30, 2008 AND MARCH 31, 2007
The purchase price was adjusted as follows (in thousands):
| | | | | | | | | | | |
| | As of March 30, 2008 | | | Adjustments | | | As of March 29, 2009 | |
Cash | | $ | 1,122 | | | | | | $ | 1,122 | |
Accounts receivable | | | 5,720 | | | | | | | 5,720 | |
Inventory | | | 12,245 | | | | | | | 12,245 | |
Other assets | | | 2,056 | | | | | | | 2,056 | |
Property, plant and equipment | | | 19,883 | | | | | | | 19,883 | |
Accounts payable | | | (6,439 | ) | | | | | | (6,439 | ) |
Other liabilities | | | (10,530 | ) | | 1,449 | | | | (9,081 | ) |
Long-term financing obligations and others | | | (18,470 | ) | | | | | | (18,470 | ) |
| | | | | | | | | | | |
Net tangible assets acquired | | | 5,587 | | | | | | | 7,036 | |
Identifiable intangible assets | | | 60,600 | | | | | | | 60,600 | |
In-process research and development | | | 8,800 | | | | | | | 8,800 | |
Fair value of unvested options assumed | | | 4,811 | | | | | | | 4,811 | |
Goodwill | | | 170,940 | | | (1,449 | ) | | | 169,491 | |
| | | | | | | | | | | |
Total purchase price | | $ | 250,738 | | | | | | $ | 250,738 | |
| | | | | | | | | | | |
During fiscal 2009, goodwill was reduced by $1.4 million, principally in connection with the reduction of $0.4 million in the allowance for sales returns and volume price discounts for Sipex’s products in the distribution channel, and $0.9 million related to employee related liabilities which were initially estimated in August 2007. We recorded a goodwill impairment loss of approximately $41.0 million and $128.5 million, associated with the Sipex acquisition during fiscal years ended March 29, 2009 and March 30, 2008, respectively.
Identifiable Intangible Assets
The following table sets forth the components of the identifiable intangible assets acquired in the Sipex acquisition, which are being amortized over their estimated useful lives on a straight-line basis (in thousands):
| | | | | |
| | Fair Value | | Useful Life (in years) |
Existing technology | | $ | 40,900 | | 6.0 |
Patents/Core technology | | | 7,900 | | 5.0 |
Customer backlog | | | 400 | | 0.5 |
Distributor relationships | | | 6,500 | | 6.0 |
Customer relationships | | | 4,300 | | 7.0 |
Tradenames/Trademarks | | | 600 | | 3.0 |
| | | | | |
Total acquired identifiable intangible assets | | $ | 60,600 | | |
| | | | | |
We recorded an impairment loss of approximately $11.7 million and $36.7 million related to the purchased Sipex intangible assets during fiscal year ended March 29, 2009 and March 30, 2008, respectively. (See“Note 8—Goodwill and Intangible Assets”).
75
EXAR CORPORATION AND SUBSIDIARIES
NOTES TO CONSOLIDATED FINANCIAL STATEMENTS—(CONTINUED)
FISCAL YEARS ENDED MARCH 29, 2009, MARCH 30, 2008 AND MARCH 31, 2007
Acquired In-Process Research and Development
We recorded a charge of $8.8 million in acquired In-Process Research and Development (“IPR&D”), associated with the acquisition of Sipex in fiscal quarter ended September 30, 2007. We allocated the purchase price related to IPR&D through established valuation techniques. IPR&D was expensed upon acquisition because technological feasibility had not been established and no future alternative uses existed. The fair value of technology under development was determined using the income approach, which discounted expected future cash flows to present value, taking into account the stage of completion, estimated costs to complete, utilization of patents and core technology, the risks related to successful completion, and the markets served. The cash flows derived from the IPR&D were discounted at discount rates ranging from 25% to 40%. The percentage of completion for these projects ranged from 20% to 87% at the acquisition date.
The IPR&D projects underway at Sipex at the acquisition date were in the interface and power management product families. Within interface products, specific projects relate to new products in its multiprotocol and RS485 families. Within power management, development activities relate to the commercialization of its digital power technology, LED drivers, DC-DC regulators and controllers. Of these projects, four have been released to production, four require further development and testing to release them to production and five have been cancelled. IPR&D projects for power management required $0.6 million to complete and some product shipments began in early fiscal 2009. IPR&D projects for interface required $0.2 million to complete with expected revenue generation beginning in fiscal year 2010. All power management and interface projects are scheduled to be completed by the middle of fiscal year 2010.
If the projects discussed above are not successfully developed and/or successfully marketed, our sales and profitability may be adversely affected in future periods.
Pro Forma Financial Information
The following unaudited pro forma financial information was based on the respective historical financial statements of Exar and Sipex. The unaudited pro forma financial information reflected the consolidated results of operations as if the acquisition of Sipex occurred at the beginning of each period and included the amortization of the resulting identifiable acquired intangible assets, effects of the estimated write-up of Sipex inventory to fair value on cost of goods sold, the exclusion of interest expense on Sipex’s senior convertible notes and stock-based compensation expenses. These unaudited pro forma financial information adjustments reflect their related tax effects. The pro forma data for fiscal year ended March 30, 2008 also included a non-recurring charge of $8.8 million for acquired IPR&D. The unaudited pro forma financial data is provided for illustrative purposes only and is not necessarily indicative of the consolidated results of operations for future periods or that actually would have been realized had Exar and Sipex been a consolidated entity during the periods presented.
The following summary includes the impact of certain adjustments mentioned in the previous paragraph (in thousands except per share information):
| | | | |
| | March 30, 2008 | |
Pro forma net sales | | $ | 117,825 | |
Pro forma net loss | | $ | (215,767 | ) |
Pro forma basic and diluted net loss per share | | $ | (4.34 | ) |
76
EXAR CORPORATION AND SUBSIDIARIES
NOTES TO CONSOLIDATED FINANCIAL STATEMENTS—(CONTINUED)
FISCAL YEARS ENDED MARCH 29, 2009, MARCH 30, 2008 AND MARCH 31, 2007
NOTE 4. CASH, CASH EQUIVALENTS AND SHORT-TERM MARKETABLE SECURITIES
Fair Value of Financial Instruments
Fair value is defined under SFAS 157,“Fair Value Measurements”(“SFAS 157”), as the exchange price that would be received for an asset or paid to transfer a liability in the principal or most advantageous market for the asset or liability in an orderly transaction between market participants on the measurement date. Valuation techniques used to measure fair value under SFAS 157 must maximize the use of observable inputs and minimize the use of unobservable inputs. The standard describes a fair value hierarchy based on three levels of inputs, of which the first two are considered observable and the last unobservable, that may be used to measure fair value which are the following:
Level 1—Quoted prices in active markets for identical assets or liabilities.
Level 2—Inputs other than Level 1 that are observable, either directly or indirectly, such as quoted prices for similar assets or liabilities; quoted prices in markets that are not active; or other inputs that are observable or can be corroborated by observable market data for substantially the full term of the assets or liabilities.
Level 3—Unobservable inputs that are supported by little or no market activity and that are significant to the fair value of the assets or liabilities.
Our investment assets, measured at fair value on a recurring basis, as of March 29, 2009 were as follows (in thousands):
| | | | | | | | | |
| | Total | | Level 1 | | Level 2 |
Assets | | | | | | | | | |
Money market funds and U.S. Treasury securities | | $ | 30,659 | | $ | 30,659 | | $ | — |
Asset-backed securities | | | 8,559 | | | — | | | 8,559 |
Mortgage-backed securities | | | 26,464 | | | — | | | 26,464 |
Other fixed income available-for-sale securities | | | 188,952 | | | — | | | 188,952 |
| | | | | | | | | |
Total financial instruments owned | | $ | 254,634 | | $ | 30,659 | | $ | 223,975 |
| | | | | | | | | |
Our cash, cash equivalents and short-term marketable securities at March 29, 2009 and March 30, 2008 were as follows (in thousands):
| | | | | | |
| | March 29, 2009 | | March 30, 2008 |
Cash and cash equivalents | | | | | | |
Cash in financial institutions | | $ | 1,709 | | $ | 1,208 |
| | | | | | |
Cash equivalents | | | | | | |
Money market funds | | | 26,332 | | | 28,274 |
Corporate bonds and commercial paper | | | — | | | 86,553 |
U.S. government and agency securities | | | 60,961 | | | 5,981 |
| | | | | | |
Total cash equivalents | | | 87,293 | | | 120,808 |
| | | | | | |
Total cash and cash equivalents | | | 89,002 | | | 122,016 |
| | | | | | |
Available-for-sale securities | | | | | | |
U.S. government and agency securities | | $ | 104,130 | | $ | 72,358 |
Corporate bonds and commercial paper | | | 28,188 | | | 45,578 |
Asset-backed securities | | | 8,559 | | | 10,943 |
Mortgage-backed securities | | | 26,464 | | | 17,965 |
| | | | | | |
Total short-term marketable securities | | $ | 167,341 | | $ | 146,844 |
| | | | | | |
77
EXAR CORPORATION AND SUBSIDIARIES
NOTES TO CONSOLIDATED FINANCIAL STATEMENTS—(CONTINUED)
FISCAL YEARS ENDED MARCH 29, 2009, MARCH 30, 2008 AND MARCH 31, 2007
Our marketable securities include municipal securities, commercial paper, asset-backed securities, corporate bonds and government securities. We classify investments as available-for-sale at the time of purchase and re-evaluate such designation as of each consolidated balance sheet date. We amortize premiums and accrete discounts to interest income over the life of the investment. Our available-for-sale securities are classified as cash equivalents if the maturity from the date of purchase is ninety days or less and as short-term marketable securities for those with maturities, from the date of purchase, in excess of ninety days which we intend to sell as necessary to meet our liquidity requirements.
All marketable securities are reported at fair value based on the estimated or quoted market prices as of each consolidated balance sheet date, with unrealized gains or losses recorded in accumulated other comprehensive income within stockholders’ equity except those unrealized losses that are deemed to be other than temporary which are reflected in the other income and expense section in the consolidated statement of operations.
Realized gains or losses on the sale of marketable securities are determined on the specific identification method and are reflected in “Interest income and other, net” line item on the consolidated statements of operation. Net realized gains on marketable securities for fiscal years ended March 29, 2009, March 30, 2008 and March 31, 2007, were $578,000, $174,000 and $52,000, respectively.
The following table summarizes our investments in marketable securities as of March 29, 2009 and March 30, 2008 (in thousands):
| | | | | | | | | | | | | |
| | March 29, 2009 |
| | Amortized Cost | | Gross Unrealized Gains | | Gross Unrealized Losses | | | Fair Value |
Money market funds | | $ | 26,332 | | $ | — | | $ | — | | | $ | 26,332 |
Corporate bonds and commercial paper | | | 28,169 | | | 160 | | | (141 | ) | | | 28,188 |
U.S. government and agency securities | | | 163,750 | | | 1,379 | | | (38 | ) | | | 165,091 |
Asset-backed and mortgage-backed securities | | | 35,070 | | | 317 | | | (364 | ) | | | 35,023 |
| | | | | | | | | | | | | |
Total at March 29, 2009 | | $ | 253,321 | | $ | 1,856 | | $ | (543 | ) | | $ | 254,634 |
| | | | | | | | | | | | | |
| |
| | March 30, 2008 |
| | Amortized Cost | | Gross Unrealized Gains | | Gross Unrealized Losses | | | Fair Value |
Money market funds | | $ | 28,274 | | $ | — | | $ | — | | | $ | 28,274 |
Corporate bonds and commercial paper | | | 158,790 | | | 354 | | | (233 | ) | | | 158,911 |
U.S. government and agency securities | | | 50,146 | | | 1,413 | | | — | | | | 51,559 |
Asset-backed and mortgage-backed securities | | | 28,543 | | | 462 | | | (97 | ) | | | 28,908 |
| | | | | | | | | | | | | |
Total at March 30, 2008 | | $ | 265,753 | | $ | 2,229 | | $ | (330 | ) | | $ | 267,652 |
| | | | | | | | | | | | | |
As of March 29, 2009, asset-backed and mortgage-backed securities, accounted for 3.4% and 10.4%, respectively, of our total investments in marketable securities of $255.0 million. The asset-back securities are comprised primarily of premium tranches of auto loans and credit card receivables, while our mortgage-backed securities are primarily from Federal agencies. We do not own auction rate securities nor do we own securities that are classified as sub-prime. As of March 29, 2009, the net unrealized loss of our asset-backed and mortgage-backed securities totaled $47,000 or less than 0.02% of our total investments.
78
EXAR CORPORATION AND SUBSIDIARIES
NOTES TO CONSOLIDATED FINANCIAL STATEMENTS—(CONTINUED)
FISCAL YEARS ENDED MARCH 29, 2009, MARCH 30, 2008 AND MARCH 31, 2007
We account for our investments in debt and equity instruments under the Statement of Financial Accounting Standards No. 115, “Accounting for Certain Investments in Debt and Equity Securities” (“FAS 115”). Management determines the appropriate classification of cash equivalents or short-term marketable securities at the time of purchase and reevaluates such classification as of each balance sheet date. The investments are adjusted for amortization of premiums and discounts to maturity and such amortization is included in the “Interest income and other, net” line item in the consolidated statement of operations. Cash equivalents and short-term marketable securities are reported at fair value with the related unrealized gains and losses included in the “Accumulated other comprehensive income” line item in the consolidated balance sheets. As of March 29, 2009, there was approximately $0.8 million of net unrealized gains including tax expense from our level 1 and level 2 investments.
We follow the guidance provided by FASB Staff Position No. 115-1, “The Meaning of Other-Than-Temporary Impairment and Its Application to Certain Investments” (“FSP 115-1”), to assess whether our investments with unrealized loss positions are other-than-temporarily impaired. We regularly review our investments in unrealized loss positions for other-than-temporary impairments. This evaluation includes, but is not limited to, significant quantitative and qualitative assessments and estimates regarding credit ratings, collateralized support, the length of time and significance of a security’s loss position and intent and ability to hold a security to maturity or forecasted recovery. Realized gains and losses and declines in value of our investments judged to be other-than-temporary are reported in the “Impairment charges on investments” line item in the consolidated statements of operations. In September 2008, Lehman Brothers Holdings Inc. (“Lehman”) filed a petition under Chapter 11 of the U.S. Bankruptcy Code with the U.S. Bankruptcy Court for the Southern District of New York. As a result of Lehman’s bankruptcy filing, we recorded an other-than-temporary impairment charge of $0.6 million during our fiscal year ended March 29, 2009.
The amortized cost and estimated fair value of cash equivalents and marketable securities classified as available-for-sale at March 29, 2009 and March 30, 2008 by expected maturity were as follows (in thousands):
| | | | | | | | | | | | |
| | March 29, 2009 | | March 30, 2008 |
| | Amortized Cost | | Fair Value | | Amortized Cost | | Fair Value |
Less than 1 year | | $ | 183,724 | | $ | 183,742 | | $ | 197,609 | | $ | 197,734 |
Due in 1 to 5 years | | | 69,597 | | | 70,892 | | | 68,144 | | | 69,918 |
| | | | | | | | | | | | |
Totals | | $ | 253,321 | | $ | 254,634 | | $ | 265,753 | | $ | 267,652 |
| | | | | | | | | | | | |
79
EXAR CORPORATION AND SUBSIDIARIES
NOTES TO CONSOLIDATED FINANCIAL STATEMENTS—(CONTINUED)
FISCAL YEARS ENDED MARCH 29, 2009, MARCH 30, 2008 AND MARCH 31, 2007
The following table summarizes the gross unrealized losses and fair values of our investments in an unrealized loss position as of March 29, 2009 and March 30, 2008, aggregated by investment category and length of time that individual securities have been in a continuous unrealized loss position (in thousands).
| | | | | | | | | | | | | | | | | | | | | |
| | March 29, 2009 | |
| | Less than 12 months | | | 12 months or greater | | | Total | |
| | Fair Value | | Gross Unrealized Losses | | | Fair Value | | Gross Unrealized Losses | | | Fair Value | | Gross Unrealized Losses | |
Corporate bonds and commercial paper | | | 10,144 | | | (106 | ) | | | 3,614 | | | (35 | ) | | | 13,758 | | | (141 | ) |
U.S. government and agency obligations | | | 62,128 | | | (38 | ) | | | — | | | — | | | | 62,128 | | | (38 | ) |
Asset-backed and mortgage-backed obligations | | | 8,913 | | | (50 | ) | | | 887 | | | (314 | ) | | | 9,800 | | | (364 | ) |
| | | | | | | | | | | | | | | | | | | | | |
Total at March 29, 2009 | | $ | 81,185 | | $ | (194 | ) | | $ | 4,501 | | $ | (349 | ) | | $ | 85,686 | | $ | (543 | ) |
| | | | | | | | | | | | | | | | | | | | | |
| |
| | March 30, 2008 | |
| | Less than 12 months | | | 12 months or greater | | | Total | |
| | Fair Value | | Gross Unrealized Losses | | | Fair Value | | Gross Unrealized Losses | | | Fair Value | | Gross Unrealized Losses | |
Corporate bonds and commercial paper | | $ | 10,431 | | $ | (169 | ) | | $ | 3,155 | | $ | (64 | ) | | $ | 13,586 | | $ | (233 | ) |
U.S. government and agency obligations | | | 750 | | | — | | | | — | | | — | | | | 750 | | | — | |
Asset-backed and mortgage-backed obligations | | | 1,915 | | | (34 | ) | | | 1,268 | | | (63 | ) | | | 3,183 | | | (97 | ) |
| | | | | | | | | | | | | | | | | | | | | |
Total at March 30, 2008 | | $ | 13,096 | | $ | (203 | ) | | $ | 4,423 | | $ | (127 | ) | | $ | 17,519 | | $ | (330 | ) |
| | | | | | | | | | | | | | | | | | | | | |
NOTE 5. RELATED PARTY TRANSACTION
Affiliates of Future, Alonim Investments Inc. and two of its affiliates (collectively “Alonim”), own approximately 7.7 million shares, or approximately 18% of our outstanding common stock as of March 29, 2009. As such, Alonim is our largest stockholder.
Our sales to Future are made under an agreement that provides protection against price reduction for its inventory of our products and other sales allowances. We recognize revenue on sales to Future under the distribution agreement when Future sells the products to its end customers. Future has historically accounted for a significant portion of our net sales. It is our largest distributor worldwide and accounted for 35%, 24% and 20% of our total net sales for fiscal years ended March 29, 2009, March 30, 2008 and March 31, 2007, respectively.
We reimbursed Future for approximately $52,000, $56,000 and $6,000 of expenses for marketing promotional materials for fiscal years ended March 29, 2009, March 30, 2008 and March 31, 2007, respectively.
NOTE 6. RESTRUCTURING
In connection with the Sipex acquisition in August 2007, our management approved and initiated plans to restructure the operations of the combined company to eliminate certain duplicative activities, reduce costs and better align product and operating expenses with current economic conditions. The Sipex restructuring costs were accounted for as liabilities assumed as part of the purchase business combination in accordance with the EITF Issue No. 95-3,“Recognition of Liabilities in Connection with a Purchase Business Combination” (“EITF 95-3”).
80
EXAR CORPORATION AND SUBSIDIARIES
NOTES TO CONSOLIDATED FINANCIAL STATEMENTS—(CONTINUED)
FISCAL YEARS ENDED MARCH 29, 2009, MARCH 30, 2008 AND MARCH 31, 2007
Our restructuring liabilities were included in the “Other accrued expenses” line item in our consolidated balance sheets, and the activities affecting the liabilities for fiscal year ended March 29, 2009 are summarized as follows (in thousands):
| | | | | | | | | | | | |
| | Facility costs | | | Severance costs | | | Total restructuring liabilities | |
Balance at March 30, 2008 | | $ | 491 | | | $ | 200 | | | $ | 691 | |
Payments | | | (116 | ) | | | (192 | ) | | | (308 | ) |
| | | | | | | | | | | | |
Balance at March 29, 2009 | | $ | 375 | | | $ | 8 | | | $ | 383 | |
| | | | | | | | | | | | |
The remaining facility related balance of approximately $375,000 is expected to be paid during the remaining term of the lease contract which extends through 2012. The severance related balance of approximately $8,000 is expected to be paid in April 2009.
NOTE 7. LONG-TERM INVESTMENTS
Our long-term investments consist of our investments in TechFarm Ventures L.P. (Q), L.P. (“TechFarm Fund”) and Skypoint Telecom Fund II (US), L.P. (“Skypoint Fund”). Both TechFarm Fund and Skypoint Fund are venture capital funds that invest primarily in private companies in the telecommunications and/or networking industry. We account for these non-marketable equity securities under the cost method. In accordance with EITF 03-1,“The Meaning of Other-Than-Temporary Impairment and its Application to Certain Investments,” we periodically review and determine whether the investments are other-than-temporarily impaired, in which case the investments are written down to their impaired value.
As of March 29, 2009 and March 30, 2008, our long-term investments balances which is included in “other non-current assets” line item on the consolidated balance sheet were as follows (in thousands):
| | | | |
| | March 29, 2009 | | March 30, 2008 |
TechFarm Fund | | — | | 466 |
Skypoint Fund | | 1,660 | | 2,170 |
| | | | |
Long-term investments | | 1,660 | | 2,636 |
| | | | |
TechFarm Fund
We have made a total of approximately $4.0 million in capital contributions to TechFarm Fund since we became a limited partner in May 2001. We have reached our total commitment to the fund and made no capital contribution to the fund during either fiscal year 2009 or fiscal year 2008. As a result, we have no capital contribution obligation to the TechFarm Fund at March 29, 2009.
The carrying amount of zero at March 29, 2009 reflected the net of the capital contribution and the accumulative impairment charges. We have never received any capital distribution from the fund.
Impairment
In fiscal year 2009, we analyzed the fair value of the underlying investment in TechFarm Fund and concluded that the remaining carrying value in TechFarm Fund was other-than-temporarily impaired and recorded an impairment charge of $0.5 million. As such, we reduced the carrying value of our investment in TechFarm Fund to zero.
81
EXAR CORPORATION AND SUBSIDIARIES
NOTES TO CONSOLIDATED FINANCIAL STATEMENTS—(CONTINUED)
FISCAL YEARS ENDED MARCH 29, 2009, MARCH 30, 2008 AND MARCH 31, 2007
In fiscal year 2008, we did not record any impairment charges after our assessment of the valuation of the fund performance.
In fiscal year 2007, we determined that the TechFarm Fund management fees continued to deplete the fund capital without any appreciation in the valuation of portfolio companies and concluded that a portion of the carrying value of our investment in the fund was other-than-temporarily impaired. As a result, we recorded a $0.1 million impairment charge in September 2006.
Skypoint Fund
We have made approximately $4.5 million in capital contributions to Skypoint Fund since we became a limited partner in July 2001. Our total capital commitment is $5.0 million. We contributed $0.2 million and $0.6 million to the fund during fiscal years of 2009 and 2008, respectively. As of March 29, 2009, we have a remaining obligation of approximately $0.5 million to the fund upon its request.
The approximate carrying amount of $1.7 million reflected the net of the capital contribution, accumulative impairment charges and capital distributions. We did not receive any distribution during fiscal years of 2009 and 2008.
Impairment
In fiscal year 2009, we analyzed the fair value of the underlying investments of Skypoint Fund and concluded a portion of the carrying value was other-than-temporarily impaired and recorded an impairment charge of $0.7 million.
In fiscal year 2008, we performed a review of our investments and determined that two of the portfolio companies in the Skypoint Fund had limited cash on hand and financing opportunities were minimal. We concluded that a portion of the carrying value had been other-than-temporarily impaired and recorded a $0.6 million impairment charge during the year.
In fiscal year 2007, we became aware that two Skypoint Fund portfolio companies would be liquidated. We believed a portion of the carrying value of our investment in the fund was permanently impaired. As a result, we recorded a $0.8 million impairment charge against our earnings in September 2006.
NOTE 8. GOODWILL AND INTANGIBLE ASSETS
The rapid and severe deterioration of worldwide economic conditions has affected our industry and led customers to scale down their levels of production. As a result of third quarter fiscal 2009 impairment indicators, we considered the potential impairment of goodwill and other long-lived assets including intangible assets. Indicators that required us to perform an interim impairment review consisted of further weakening in new orders from our customers throughout the third quarter and into the fourth quarter of fiscal 2009, as well as, the uncertainty of the magnitude and duration of the current recession as evidenced by industry analysts expectations that demand for semiconductors will remain weak until economic conditions improve. In addition, we experienced a significant decline in our stock price that reduced our market capitalization below our net asset carrying value for an extended period of time. As a result of the goodwill and long-lived asset impairment
82
EXAR CORPORATION AND SUBSIDIARIES
NOTES TO CONSOLIDATED FINANCIAL STATEMENTS—(CONTINUED)
FISCAL YEARS ENDED MARCH 29, 2009, MARCH 30, 2008 AND MARCH 31, 2007
assessments, we recorded a charge totaling $59.7 million in the third quarter of fiscal 2009. This charge is comprised of $46.2 million related to goodwill and $13.5 million related to intangible assets.
Described below is a summary of our goodwill and intangible assets and the related impairment assessments.
Goodwill
Goodwill represents the excess of the purchase price over the fair value of the net tangible and identifiable intangible assets acquired in a business combination. We follow the provisions of Statement of Financial Accounting Standards No. 142,“Goodwill and Other Intangible Assets” (“FAS 142”), under which we evaluate goodwill for impairment on an annual basis or whenever events and changes in circumstances suggest that the carrying amount may not be recoverable. We conduct our annual impairment analysis in the fourth quarter of each fiscal year. Impairment of goodwill is tested at the reporting unit level by comparing the reporting unit’s carrying amount, including goodwill, to the fair value of the reporting unit. The fair values of the reporting units are estimated using a combination of the income approach that uses discounted cash flows and the market approach that utilizes comparable companies’ data. If the carrying amount of the reporting unit exceeds its fair value, goodwill is considered impaired and a second step is performed to measure the amount of impairment loss. Because we have one reporting unit under FAS 142, we utilize an entity-wide approach to assess goodwill for impairment.
Given the impairment indicators discussed above, we performed an interim goodwill impairment analysis during the third quarter of fiscal 2009 using a combination of the income approach and the market approach, in accordance with the provisions of FAS 142. The analysis performed compared the implied fair value of goodwill to the carrying amount of goodwill on our balance sheet. Our estimate of the implied fair value of the goodwill was based on the quoted market price of our common stock and the discounted value of estimated future cash flows over a seven-year period with residual value. The analysis resulted in an impairment charge of approximately $46.2 million, which is included in the “Goodwill and other intangible asset impairment” line item in the consolidated statements of operations, that reduced our carrying value of goodwill to zero.
Solely for the purposes of establishing inputs for the fair value calculations described above related to goodwill impairment testing, we made the following assumptions. We assumed that the current economic recession would continue through fiscal year 2010, followed by a recovery period in fiscal years 2011 through 2013 and long-term industry growth past fiscal year 2013. In addition, we applied gross margin assumptions consistent with our historical trends and used a 3% growth factor to calculate the terminal value of the company, which was consistent with the rate used in the prior year’s annual impairment test. We used a 14% discount rate to calculate the present value of cash flows and the terminal value, which is slightly higher than the 12.5% discount rate we used in the prior year’s annual impairment test, primarily due to increases to the required market risk and small stock premiums.
In the fourth fiscal quarter of 2008, we conducted our annual impairment review and determined that, based on the current market conditions in the semiconductor industry and our stock price over the prior six months, the carrying amount of our goodwill exceeded its implied fair value under the test for impairment as per FAS 142 and recorded a goodwill impairment charge of approximately $128.5 million which is included in the “Goodwill and other intangible asset impairment” line item in the consolidated statements of operations (See “Note 2—Accounting Policies”). Our estimate of the implied fair value of the goodwill was based on the quoted market price of our common stock and the discounted value of estimated future cash flows over a seven-year period with residual value and discount rates between 12.5% and 18.8%.
83
EXAR CORPORATION AND SUBSIDIARIES
NOTES TO CONSOLIDATED FINANCIAL STATEMENTS—(CONTINUED)
FISCAL YEARS ENDED MARCH 29, 2009, MARCH 30, 2008 AND MARCH 31, 2007
The changes in the carrying amount of goodwill for fiscal years 2009 and 2008 are as follows (in thousands):
| | | | |
| | Amount | |
Balance as of March 31, 2007 | | $ | 5,190 | |
Goodwill acquired in connection with the Sipex acquisition | | | 171,127 | |
Goodwill adjustment (see Note 3) | | | (187 | ) |
Impairment charge | | | (128,504 | ) |
| | | | |
Balance as of March 30, 2008 | | | 47,626 | |
Goodwill adjustment (see Note 3) | | | (1,449 | ) |
Impairment charge | | | (46,177 | ) |
| | | | |
Balance as of March 29, 2009 | | $ | — | |
| | | | |
Intangible Assets
Our purchased intangible assets at March 29, 2009 and March 30, 2008 were as follows (in thousands):
| | | | | | | | | | | | | | | | | | | | |
| | March 29, 2009 | | March 30, 2008 |
| | New Carrying Amount(2) | | Accumulated Amortization | | | Net Carrying Amount | | Carrying Amount(1) | | Accumulated Amortization | | | Net Carrying Amount |
Existing technology | | $ | 16,870 | | $ | (10,798 | ) | | $ | 6,072 | | $ | 26,646 | | $ | (6,517 | ) | | $ | 20,129 |
Patents/Core technology | | | 1,692 | | | (1,189 | ) | | | 503 | | | 3,159 | | | (781 | ) | | | 2,378 |
Customer backlog | | | 340 | | | (340 | ) | | | — | | | 340 | | | (340 | ) | | | — |
Distributor relationships | | | 1,264 | | | (817 | ) | | | 447 | | | 2,539 | | | (537 | ) | | | 2,002 |
Customer relationships | | | 770 | | | (460 | ) | | | 310 | | | 1,647 | | | (301 | ) | | | 1,346 |
Tradenames/Trademarks | | | 177 | | | (150 | ) | | | 27 | | | 263 | | | (99 | ) | | | 164 |
| | | | | | | | | | | | | | | | | | | | |
| | $ | 21,113 | | $ | (13,754 | ) | | $ | 7,359 | | $ | 34,594 | | $ | (8,575 | ) | | $ | 26,019 |
| | | | | | | | | | | | | | | | | | | | |
(1) | The carrying amount is net of intangible asset impairment charges of approximately $36.7 million taken during the fourth quarter of fiscal 2008. |
(2) | The new carrying amount is net of intangible asset impairment charges of approximately $36.7 million and $13.5 million taken during the fourth quarter of fiscal 2008 and the third quarter of fiscal 2009, respectively. |
Our long-lived assets include land, buildings, equipment, furniture and fixtures and other intangible assets. Long-lived assets are evaluated for impairment whenever events or changes in circumstances indicate that the carrying amount of an asset may not be recoverable. We evaluate the recoverability of our long-lived assets in accordance with Statement of Financial Accounting Standards No. 144,“Accounting for the Impairment or Disposal of Long-Lived Assets” (“FAS 144”). We compare the carrying value of long-lived assets to our projection of future undiscounted cash flows attributable to such assets and, in the event that the carrying value exceeds the future undiscounted cash flows, we record an impairment charge equal to the excess of the carrying value over the asset’s fair value.
Given the impairment indicators discussed above, we performed a test of purchased intangible assets for recoverability. The assessment of recoverability was based upon the assumptions and underlying cash flow
84
EXAR CORPORATION AND SUBSIDIARIES
NOTES TO CONSOLIDATED FINANCIAL STATEMENTS—(CONTINUED)
FISCAL YEARS ENDED MARCH 29, 2009, MARCH 30, 2008 AND MARCH 31, 2007
projections prepared for the concurrent interim goodwill impairment test. Our estimate of the implied fair value of the intangible assets was based on the discounted value of estimated future cash flows over a five-year period using a discount rate of 14%.
The analysis determined that the carrying amount of the intangible assets exceeded the implied fair value under the test for impairment per FAS 144 and the difference was allocated to the intangible assets of the impacted asset group on a pro-rata basis using the relative carrying amounts of the assets. We recorded an impairment charge of approximately $13.5 million, which is included in the “Goodwill and other intangible asset impairment” line item in the consolidated statements of operations of which $9.8 million related to existing technology, $1.4 million to patents/core technology, $1.3 million to distributor relationships, $0.9 million to customer relationships and $0.1 million to tradenames/trademarks.
Given the current volatile worldwide economic environment and the resulting uncertainties regarding its impact on our business, our estimates and assumptions regarding the duration of the ongoing economic downturn, or the period or strength of any future recovery, made for purposes of our intangible asset impairment testing during the third quarter of fiscal 2009 may prove to be inaccurate. If our assumptions regarding projected revenue or gross margin rates are not achieved, we may be required to record additional intangible asset impairment charges in future periods, if any such change or other factor constitutes a triggering event. It is not possible at this time to determine if any such future impairment charge would result or, if it does, whether such charge would be material. As of March 29, 2009 there were no indicators that required us to perform an intangible assets impairment review and therefore we did not record an impairment charge during the fourth quarter of fiscal 2009.
During the fourth fiscal quarter of 2008, we concluded that our market capitalization was below our net book value for an extended period of time and as a result, the long-lived assets were tested for recoverability. The sales and margin projections for Sipex products have declined due to the impact of the weakening economy, delays in sales ramp up of new high margin proprietary products, and delays in achieving manufacturing cost reductions initially projected. As a result, we reduced our projections of our future cash flows and determined that the carrying amount of the purchased Sipex intangible assets exceeded the implied fair value under the test for impairment as per FAS 144 and recorded an impairment charge of approximately $36.7 million, which is included in the “Goodwill and other intangible asset impairment” line item in the consolidated statements of operations (See“Note 2—Accounting Policies”). Our estimate of the implied fair value of the intangible assets was based on the discounted value of estimated future cash flows over a six-year period with residual value and a discount rate of 12.5%.
The aggregate amortization expenses for our purchased intangible assets for fiscal years ended March 29, 2009, March 30, 2008 and March 31, 2007 were as follows (in thousands):
| | | | | | | | | | | |
| | Weighted Average Lives | | March 29, 2009 | | March 30, 2008 | | March 31, 2007 |
| | (in months) | | | | | | |
Existing technology | | 68 | | $ | 4,281 | | $ | 4,640 | | $ | 960 |
Patents/Core technology | | 60 | | | 408 | | | 781 | | | — |
Customer backlog | | 6 | | | — | | | 340 | | | — |
Distributor relationships | | 72 | | | 280 | | | 537 | | | — |
Customer relationships | | 84 | | | 159 | | | 301 | | | — |
Tradenames/Trademarks | | 36 | | | 52 | | | 99 | | | — |
| | | | | | | | | | | |
Total | | | | $ | 5,180 | | $ | 6,698 | | $ | 960 |
| | | | | | | | | | | |
85
EXAR CORPORATION AND SUBSIDIARIES
NOTES TO CONSOLIDATED FINANCIAL STATEMENTS—(CONTINUED)
FISCAL YEARS ENDED MARCH 29, 2009, MARCH 30, 2008 AND MARCH 31, 2007
The estimated future amortization expenses for our purchased intangible assets are summarized below (in thousands):
| | | |
Amortization Expense (by fiscal year) |
2010 | | | 2,938 |
2011 | | | 2,199 |
2012 | | | 984 |
2013 | | | 857 |
2014 | | | 358 |
2015 and thereafter | | | 23 |
| | | |
| | $ | 7,359 |
| | | |
NOTE 9. EARNINGS (LOSS) PER SHARE
Basic earnings (loss) per share excludes dilution and is computed by dividing net income (loss) by the weighted average number of common shares outstanding for the periods in accordance with FASB Statement of Financial Accounting Standards No. 128, “Earnings Per Share” (“FAS 128”). Diluted earnings per share (“EPS”) reflects the potential dilution that would occur if outstanding stock options or warrants to issue common stock were exercised for common stock, and the common stock underlying restricted stock units (“RSUs”) and restricted stock awards (“RSAs”) were issued by using the treasury stock method.
A summary of our earnings (loss) per share for the three fiscal years of 2009, 2008 and 2007 was as follows (in thousands, except per share amounts):
| | | | | | | | | | | |
| | March 29, 2009 | | | March 30, 2008 | | | March 31, 2007 |
Net income (loss) | | $ | (73,036 | ) | | $ | (195,879 | ) | | $ | 8,024 |
| | | | | | | | | | | |
Shares used in computation: | | | | | | | | | | | |
Weighted average shares of common stock outstanding used in computation of basic earnings (loss) per share | | | 42,887 | | | | 43,090 | | | | 36,255 |
Dilutive effect of stock options and restricted stock units | | | — | | | | — | | | | 225 |
| | | | | | | | | | | |
Shares used in computation of diluted earnings (loss) per share | | | 42,887 | | | | 43,090 | | | | 36,480 |
| | | | | | | | | | | |
Earnings (loss) per share—basic and diluted | | $ | (1.70 | ) | | $ | (4.55 | ) | | $ | 0.22 |
| | | | | | | | | | | |
For fiscal year ended March 29, 2009, as we incurred a net loss, the weighted average number of common shares outstanding equaled the weighted average number of common shares and common share equivalents assuming dilution. Options to purchase common shares and RSUs for common shares in the aggregate amount of approximately 214,000 shares for the period ended March 29, 2009 were excluded from our loss per share calculation under the treasury stock method. Had we had income for these periods, our diluted shares would have increased by the aforementioned amount.
For fiscal year ended March 29, 2009, options to purchase approximately 4.5 million shares of common stock, at exercise prices ranging from $5.44 to $86.10, were outstanding but were not included in the computation of diluted loss per share because they were anti-dilutive under the treasury stock method.
86
EXAR CORPORATION AND SUBSIDIARIES
NOTES TO CONSOLIDATED FINANCIAL STATEMENTS—(CONTINUED)
FISCAL YEARS ENDED MARCH 29, 2009, MARCH 30, 2008 AND MARCH 31, 2007
Approximately 280,000 warrants outstanding were also excluded from the computation of diluted loss per share because they were anti-dilutive under the treasury stock method for fiscal year ended March 29, 2009. Unvested restricted stock units of 56,000 with a grant date fair value of $7.12 were outstanding at March 29, 2009 and were not included in the computation of diluted net loss per share because they were anti-dilutive under the treasury stock method.
For fiscal year ended March 30, 2008, as we incurred a net loss, the weighted average number of common shares outstanding equaled the weighted average number of common and common share equivalents assuming dilution. Options to purchase common shares and RSUs for common shares in the aggregate amount of approximately 405,000 shares for the period ended March 30, 2008 were excluded from our loss per share calculation under the treasury method. If we had income for the period, our diluted shares would have increased by the aforementioned amount.
For fiscal year ended March 30, 2008, options to purchase approximately 5.2 million shares of common stock, at exercise prices ranging from $8.78 to $86.10, were outstanding but were not included in the computation of diluted loss per share because they were anti-dilutive under the treasury stock method. Approximately 280,000 warrants outstanding were also excluded from the computation of diluted loss per share because they were anti-dilutive under the treasury stock method for fiscal year ended March 30, 2008. Unvested restricted stock units of 37,901 with a grant date fair value of $11.39 were outstanding at March 30, 2008 and were not included in the computation of diluted net loss per share because they were anti-dilutive under the treasury stock method.
For fiscal year ended March 31, 2007, options to purchase approximately 5.0 million shares of common stock, at exercise prices ranging from $12.09 to $54.75, were outstanding but were not included in the computation of diluted earnings per share because they were anti-dilutive under the treasury stock method. Unvested restricted stock units of 1,603 with a grant date fair value of $13.40 were outstanding at March 31, 2007 and were not included in the computation of diluted net income per share because they were anti-dilutive under the treasury stock method.
Our application of the treasury stock method includes assumed cash proceeds from option exercised, the average unamortized stock-based compensation expense for the period, and the estimated deferred tax benefit or detriment associated with stock-based compensation expense.
NOTE 10. COMMON STOCK REPURCHASES
From time to time, we acquire outstanding common stock in the open market to partially offset dilution from our equity award programs, to increase our return on our invested capital and to bring our cash to a more appropriate level for our company. We may continue to utilize the share repurchase plan, which would reduce our cash, cash equivalents and/or short-term investments available to fund future operations and to meet other liquidity requirements.
On August 31, 2007, we established a new share repurchase plan (“2007 SRP”) and authorized the repurchase of up to $100 million of our common stock. The 2007 SRP was in addition to a share repurchase plan announced in March 6, 2001 (“2001 SRP”), which covered the repurchase of up to $40 million of our common stock.
During fiscal year ended March 29, 2009, we repurchased a total of 1.6 million shares of our common stock at an aggregate cost of $13.4 million under the 2007 SRP.
87
EXAR CORPORATION AND SUBSIDIARIES
NOTES TO CONSOLIDATED FINANCIAL STATEMENTS—(CONTINUED)
FISCAL YEARS ENDED MARCH 29, 2009, MARCH 30, 2008 AND MARCH 31, 2007
During fiscal year ended March 30, 2008, we repurchased a total of 9.3 million shares of our common stock at an aggregate cost of $93.0 million under the 2007 SRP and 2001 SRP.
We have fully utilized the 2001 SRP. As of March 29, 2009, the remaining authorized amount for share repurchases under the 2007 SRP was $11.9 million. The 2007 SRP does not have a termination date.
NOTE 11. EMPLOYEE BENEFIT PLANS
Exar Savings Plans
The Exar Savings Plan, as amended and restated, covers our eligible U.S. employees. The Exar Savings Plan provides for voluntary salary reduction contributions in accordance with Section 401(k) of the Internal Revenue Code as well as matching contributions from the company based on the achievement of specified operating results. Our matching contributions to the plan were $0.4 million, $0.3 million and $0.3 million for fiscal years ended March 29, 2009, March 30, 2008 and March 31, 2007, respectively.
Executive and Key Employee Incentive Compensation Programs
Our incentive compensation programs provide for incentive awards for substantially all employees based on the achievement of personal objectives and operating performance results. During fiscal years ended March 29, 2009 and March 30, 2008, we paid approximately $468,000 and $699,000 in incentive compensation, respectively. Unpaid incentive compensation at March 29, 2009 and March 30, 2008 was approximately $300,000 and $600,000, respectively. For fiscal year ended March 31, 2007, no incentive compensation was earned. Our incentive compensation programs may be amended or discontinued at the discretion of our board of directors.
NOTE 12. STOCK-BASED COMPENSATION
Employee Stock Participation Plan (“ESPP”)
Our ESPP permits employees to purchase common stock through payroll deductions at a purchase price that is equal to 95% of our common stock price on the last trading day of each three-calendar-month offering period. Our ESPP is non-compensatory under FAS 123R.
At March 29, 2009 and March 30, 2008, approximately 1,607,697 and 1,663,000 shares of common stock, respectively, were authorized and reserved for future issuance under our ESPP.
For fiscal years ended March 29, 2009, March 30, 2008 and March 31, 2007, we issued 55,617, 33,705 and 36,832 shares at weighted average prices of $7.08, $10.07 and $12.53, respectively, to the participating employees.
Equity Incentive Plans
We currently have four equity incentive plans including the Exar Corporation 2006 Equity Incentive Plan (the “2006 Plan”) and three other equity plans assumed upon our acquisition of Sipex: the Sipex Corporation 2000 Non-Qualified Stock Option Plan, the Sipex Corporation Amended and Restated 2002 Non-Statutory Stock Option Plan and the Sipex Corporation 2006 Equity Incentive Plan (collectively, the “Sipex Plans”).
88
EXAR CORPORATION AND SUBSIDIARIES
NOTES TO CONSOLIDATED FINANCIAL STATEMENTS—(CONTINUED)
FISCAL YEARS ENDED MARCH 29, 2009, MARCH 30, 2008 AND MARCH 31, 2007
The 2006 Plan authorizes the issuance of stock options, stock appreciation rights, restricted stock, stock bonuses and other forms of awards granted or denominated in common stock or units of common stock, as well as cash bonus awards. RSUs granted under the 2006 Plan are counted against authorized shares available for future issuance on a basis of two shares for every RSU issued. The 2006 Plan allows for performance-based vesting and partial vesting based upon level of performance. Grants under the Sipex Plans are only available to former Sipex employees or employees of the combined company hired after the acquisition. At March 29, 2009, there were approximately 4.6 million shares available for future grant under all our equity incentive plans.
As of March 29, 2009 and March 30, 2008, there were options to purchase approximately 3.4 million and 5.1 million shares of our common stock outstanding under all stock option plans, respectively.
The following table summarizes information about our stock options outstanding at March 29, 2009 (in thousands, except number of years and per-share data):
| | | | | | | | | | | | | | |
| | | | OPTIONS OUTSTANDING | | OPTIONS EXERCISABLE |
Range of Exercise Prices | | Number Outstanding As of 03/29/2009 | | Weighted Average Remaining Contractual Terms in Years | | Weighted Average Exercise Price | | Number Exercisable As of 03/29/2009 | | Weighted Average Exercise Price |
$3.60 | | $7.34 | | 789,733 | | 5.96 | | $ | 6.55 | | 168,057 | | $ | 5.61 |
7.42 | | 8.48 | | 955,877 | | 6.00 | | | 8.13 | | 45,516 | | | 7.80 |
8.57 | | 9.53 | | 698,685 | | 6.10 | | | 8.64 | | 40,015 | | | 9.28 |
9.80 | | 13.93 | | 686,740 | | 4.30 | | | 12.76 | | 449,079 | | | 12.56 |
14.32 | | 86.10 | | 275,056 | | 2.28 | | | 16.51 | | 275,056 | | | 16.51 |
| | | | | | | | | | | | | | |
$3.60 | | $86.10 | | 3,406,091 | | 5.37 | | $ | 9.48 | | 977,723 | | $ | 12.12 |
| | | | | | | | | | | | | | |
Valuation Assumptions
The assumptions used in calculating the fair value of stock-based compensation represent our estimates, but these estimates involve inherent uncertainties and the application of management judgments which include the expected term of the share-based awards, stock price volatility and forfeiture rates. As a result, if factors change and we use different assumptions, our stock-based compensation expense could be materially different in the future.
Valuation Method—we compute the fair value of stock options utilizing the Black-Scholes option pricing model.
Expected Term—we estimate the expected life of options granted based on historical exercise and post-vest cancellation patterns, which we believe are representative of future behavior.
Volatility—our expected volatility is based on historical data of the market closing price for our common stock as reported by The NASDAQ Global Market under the symbol “EXAR” and the expected term of our stock options.
Risk-Free Interest Rate—the risk-free interest rate assumption is based on the observed interest rate of the U.S. Treasury appropriate for the expected term of the option to be valued.
89
EXAR CORPORATION AND SUBSIDIARIES
NOTES TO CONSOLIDATED FINANCIAL STATEMENTS—(CONTINUED)
FISCAL YEARS ENDED MARCH 29, 2009, MARCH 30, 2008 AND MARCH 31, 2007
Dividend Yield—we do not currently pay dividends and have no plans to do so in the future. Therefore, we have assumed a dividend yield of zero.
We have used the following weighted average assumptions to calculate the fair values of options granted during the years presented:
| | | | | | | | | | | | |
| | Stock Option Plans | |
| | March 29, 2009 | | | March 30, 2008 | | | March 31, 2007 | |
Expected term of options (years) | | | 4.6 - 4.8 | | | | 4.5 - 5.0 | | | | 5.1 - 5.3 | |
Risk-free interest rate | | | 1.7 - 3.2 | % | | | 2.6 - 4.8 | % | | | 4.6 - 4.9 | % |
Expected volatility | | | 30 - 38 | % | | | 30 - 36 | % | | | 38 - 51 | % |
Expected dividend yield | | | — | | | | — | | | | — | |
Weighted average estimated fair value | | $ | 2.56 | | | $ | 4.12 | | | $ | 5.66 | |
We amended our ESPP on April 1, 2006 to permit employees to purchase common stock at a purchase price that is equal to 95% of the fair market value of the common stock on the last trading day of each three-month offering period. The amendment to the employees’ discount and the elimination of the look-back period resulted in the ESPP being considered non-compensatory under SFAS 123R.
Stock Option Activities
A summary of stock option transactions during the periods indicated for all stock option plans is as follows:
| | | | | | | | | | | |
| | Outstanding | | | Weighted Average Exercise Price per Share | | Weighted Average Remaining Contractual Life (in Years) | | Aggregate Intrinsic Value |
Balance at March 31, 2006 | | 7,508,898 | | | $ | 17.34 | | 2.25 | | $ | 5,471,874 |
Options granted | | 607,300 | | | | 13.02 | | | | | |
Options exercised | | (1,217,985 | ) | | | 12.26 | | | | | |
Options cancelled | | (1,409,124 | ) | | | 23.33 | | | | | |
Options forfeited | | (194,972 | ) | | | 13.18 | | | | | |
| | | | | | | | | | | |
Balance at March 31, 2007 | | 5,294,117 | | | $ | 16.57 | | 3.09 | | $ | 1,367,158 |
Options assumed from Sipex | | 2,215,421 | | | | 6.84 | | | | | |
Options granted | | 848,539 | | | | 11.80 | | | | | |
Options exercised | | (484,490 | ) | | | 8.11 | | | | | |
Options cancelled | | (1,896,679 | ) | | | 19.82 | | | | | |
Options forfeited | | (890,611 | ) | | | 11.34 | | | | | |
| | | | | | | | | | | |
Balance at March 30, 2008 | | 5,086,297 | | | $ | 13.23 | | 3.85 | | $ | 2,383,110 |
Options granted | | 2,152,475 | | | | 7.92 | | | | | |
Options exercised | | (579,142 | ) | | | 5.38 | | | | | |
Options cancelled | | (2,526,228 | ) | | | 16.18 | | | | | |
Options forfeited | | (727,311 | ) | | | 11.07 | | | | | |
| | | | | | | | | | | |
Balance at March 29, 2009 | | 3,406,091 | | | $ | 9.48 | | 5.37 | | $ | 128,514 |
| | | | | | | | | | | |
Vested and expected to vest, March 29, 2009 | | 2,956,690 | | | $ | 9.63 | | 5.26 | | $ | 123,719 |
| | | | | | | | | | | |
Vested and exercisable, March 29, 2009 | | 977,723 | | | $ | 12.12 | | 3.50 | | $ | 100,548 |
| | | | | | | | | | | |
90
EXAR CORPORATION AND SUBSIDIARIES
NOTES TO CONSOLIDATED FINANCIAL STATEMENTS—(CONTINUED)
FISCAL YEARS ENDED MARCH 29, 2009, MARCH 30, 2008 AND MARCH 31, 2007
The aggregate intrinsic values in the table above represented the total pre-tax intrinsic value which was based on the fair value of our common stock of $6.17, $8.19 and $13.24 as of March 29, 2009, March 30, 2008 and March 31, 2007, respectively. These were the values which would have been received by option holders if all option holders exercised their options as of that date.
The total number of in-the-money options vested and exercisable was 0.2 million, 0.7 million and 0.8 million for fiscal years ended March 29, 2009, March 30, 2008 and March 31, 2007.
Total intrinsic value of options exercised was approximately $1.3 million, $1.4 million and $1.7 million for fiscal years ended March 29, 2009, March 30, 2008 and March 31, 2007, respectively.
Total cash received related to option exercises was $3.1 million, $3.9 million and $14.9 million for fiscal years ended March 29, 2009, March 30, 2008 and March 31, 2007, respectively. Upon option exercise, we issue shares of common stock.
We recorded a tax benefit of $1.3 million, $1.4 million and $0.5 million related to the option exercises for fiscal years ended March 29, 2009, March 30, 2008 and March 31, 2007, respectively.
Total unrecognized stock-based compensation cost was $6.0 million at March 29, 2009, which was expected to be recognized over a weighted average period of 3.03 years. Total unrecognized stock-based compensation cost was $5.0 million at March 30, 2008, which was expected to be recognized over a weighted average period of 2.64 years.
RSUs and RSAs
In the second fiscal quarter of 2007, we began issuing RSUs to employees and non-employee directors. RSUs currently granted by us generally vest on the first or third anniversary date from the grant date, although the RSUs issued in exchange for options tendered in our option exchange program in the third quarter of fiscal year 2009 vest in two equal annual installments. RSUs granted under the 2006 Plan are counted against authorized shares available for future issuance on the basis of two shares for every RSU issued. Prior to vesting, RSUs do not have dividend equivalent rights, do not have voting rights and the shares underlying the RSUs are not considered issued and outstanding. Shares are issued on the date the RSUs vest.
91
EXAR CORPORATION AND SUBSIDIARIES
NOTES TO CONSOLIDATED FINANCIAL STATEMENTS—(CONTINUED)
FISCAL YEARS ENDED MARCH 29, 2009, MARCH 30, 2008 AND MARCH 31, 2007
A summary of RSUs and RSAs is as follows:
| | | | | | | | | | | |
| | Shares | | | Weighted Average Grant-Date Fair Market Value | | Weighted Average Remaining Contractual Term (years) | | Aggregate Intrinsic Value |
Non-vested at March 31, 2006 | | — | | | $ | — | | | | | |
Granted | | 214,437 | | | | 13.18 | | | | | |
Issued and released | | (6,000 | ) | | | 13.74 | | | | | |
Cancelled | | (3,519 | ) | | | 12.69 | | | | | |
| | | | | | | | | | | |
Non-vested at March 31, 2007 | | 204,918 | | | $ | 13.18 | | 2.05 | | $ | 2,713,114 |
| | | | | | | | | | | |
Granted | | 253,650 | | | | 11.92 | | | | | |
Issued and released | | (69,442 | ) | | | 11.08 | | | | | |
Cancelled | | (84,193 | ) | | | 13.25 | | | | | |
| | | | | | | | | | | |
Non-vested at March 30, 2008 | | 304,933 | | | $ | 12.20 | | 1.41 | | $ | 2,497,401 |
| | | | | | | | | | | |
Granted | | 598,409 | | | | 7.18 | | | | | |
Issued and released | | (117,437 | ) | | | 6.90 | | | | | |
Cancelled | | (55,668 | ) | | | 9.16 | | | | | |
| | | | | | | | | | | |
Non-vested at March 29, 2009 | | 730,237 | | | $ | 8.36 | | 1.14 | | $ | 4,505,562 |
| | | | | | | | | | | |
Vested and expected to vest at March 29, 2009 | | 619,220 | | | $ | 8.14 | | 1.11 | | $ | 3,820,586 |
| | | | | | | | | | | |
The aggregate intrinsic value of RSUs represents the closing price per share of our common stock at the end of the periods presented, multiplied by the number of unvested RSUs and RSAs or the number of vested and expected to vest RSUs, as applicable, at the end of each period.
For RSUs, stock-based compensation expense was calculated based on our stock price on the date of grant, multiplied by the number of RSUs granted. The grant date fair value of RSUs, less estimated forfeitures, was recognized on a straight-line basis, over the vesting period.
At March 29, 2009, there were 730,237 RSUs outstanding. The unrecognized stock-based compensation cost was $2.0 million at March 29, 2009 and was expected to be recognized as compensation expense over a weighted average period of 1.14 years.
At March 30, 2008, there were 304,933 RSUs outstanding. The unrecognized stock-based compensation cost was $2.5 million at March 30, 2008 and was expected to be recognized as compensation expense over a weighted average period of 1.41 years.
At March 31, 2007, there were approximately 204,918 RSUs outstanding. The unrecognized stock-based compensation cost was $2.7 million at March 31, 2007 and was expected to be recognized as compensation expense over a weighted average period of 2.05 years.
During fiscal year of 2008, we granted performance-based RSUs covering approximately 22,000 shares to certain executives, issuable on March 31, 2008. Based on our assessment of meeting the performance targets established for each individual and the probability that these targets will be achieved, we recorded approximately $135,000 of compensation expense related to these grants for the year ended March 30, 2008. No such grants were made in either fiscal year 2007 or 2009.
92
EXAR CORPORATION AND SUBSIDIARIES
NOTES TO CONSOLIDATED FINANCIAL STATEMENTS—(CONTINUED)
FISCAL YEARS ENDED MARCH 29, 2009, MARCH 30, 2008 AND MARCH 31, 2007
Stock-Based Compensation Expenses
The following table summarizes stock-based compensation expense related to stock options, RSAs and RSUs under FAS 123R for fiscal years ended March 29, 2009, March 30, 2008 and March 31, 2007 (in thousands):
| | | | | | | | | |
| | March 29, 2009 | | March 30, 2008 | | March 31, 2007 |
Cost of sales | | $ | 595 | | $ | 406 | | $ | 92 |
Research and development | | | 1,614 | | | 1,207 | | | 1,181 |
Selling, general and administrative | | | 2,725 | | | 3,366 | | | 3,077 |
| | | | | | | | | |
Stock-based compensation expense | | $ | 4,934 | | $ | 4,979 | | $ | 4,350 |
| | | | | | | | | |
At March 29, 2009, there was no unamortized stock-based compensation cost capitalized in inventory. At March 30, 2008, there was approximately $33,000 of total unamortized stock-based compensation cost capitalized in inventory. At March 31, 2007, there was no unamortized compensation cost capitalized in inventory.
During fiscal year 2008, we modified options to purchase approximately 298,000 shares held by our former chief executive officer and one other officer upon their departures in December 2007 and February 2008, respectively. The modification provided an extended exercise period of six months following termination as compared to three months as defined by the plan. As a result of the modifications, we recorded additional stock-based compensation expenses of approximately $18,000 during fiscal year ended March 30, 2008.
During fiscal year of 2007, we recorded stock-based compensation expense of $0.4 million in connection with modifications of approximately 0.8 million stock options related to the separations of our former chief executive officer and chief financial officer.
Option Exchange Program
On October 23, 2008, we commenced a tender offer (the “Offer”) and filed a Schedule TO with the SEC pursuant to which holders of options with exercise prices equal to or greater than $11.00 per share and an expiration date after March 31, 2009 could tender their options in exchange for RSUs awards. The exchange ratio of shares subject to such eligible options to shares subject to new awards issued was 4-to-1, 5-to-1 or 6-to-1, depending on the exercise price of the option being exchanged. New awards received in exchange for eligible options are subject to a two-year vesting schedule with 50% vesting at each anniversary of the grant date.
Pursuant to the Offer, 242 eligible participants tendered, and we accepted for exchange, options to purchase an aggregate of 1,650,231 shares of our common stock, representing approximately 94% of the 1,755,691 shares subject to options that were eligible to be exchanged in the Offer as of the commencement of the Offer on October 23, 2008. On November 24, 2008, upon the terms and subject to the conditions set forth in the Offer to Exchange Certain Outstanding Options for Restricted Stock Units, filed as an exhibit to the Schedule TO, we issued RSU awards covering an aggregate of 344,020 shares of our common stock in exchange for the options surrendered pursuant to the Offer.
The new awards were granted with a price of $6.51 per share, the closing price of our common stock on November 24, 2008 as reported on the NASDAQ Global Select Market. The fair value of the options exchanged was measured as the total of the unrecognized compensation cost of the original options tendered and the incremental compensation cost of the RSUs awarded on November 24, 2008, the date of exchange. The
93
EXAR CORPORATION AND SUBSIDIARIES
NOTES TO CONSOLIDATED FINANCIAL STATEMENTS—(CONTINUED)
FISCAL YEARS ENDED MARCH 29, 2009, MARCH 30, 2008 AND MARCH 31, 2007
incremental compensation cost of $1.2 million, was measured as the excess of the fair value of the RSUs over the fair value of the options immediately before cancellation based on the share price and other pertinent factors at that date. The amount will be amortized over the two years service period. During fiscal year 2009, we recorded approximately $208,000 of such incremental stock-based compensation expense.
Income Tax
We record our stock-based compensation expense in multiple jurisdictions. In jurisdictions where an income tax deduction is allowed and an income tax benefit is realizable, we have recognized an income tax benefit. In jurisdictions where an income tax deduction is not allowed or where an income tax benefit is not realizable, an income tax benefit has not been recognized.
NOTE 13. WARRANTS
In connection with the Sipex acquisition, we assumed warrants, which enable the holders, to purchase a total of approximately 280,000 shares of our common stock. The warrants are exercisable at any time for shares of our common stock at an initial exercise price of $9.63 per share, subject to adjustment upon certain events. The warrants expire on May 18, 2011. As of March 29, 2009, there were warrants to purchase approximately 280,000 shares of our common stock outstanding.
NOTE 14. LEASE FINANCING OBLIGATION
In connection with the Sipex acquisition, we assumed a lease financing obligation related to the Hillview Facility. The lease term expires in March 2011 with average lease payments of approximately $1.4 million per year.
The fair value of the Hillview Facility was estimated at $13.4 million at the time of the acquisition and was included in the “Property, plant and equipment, net” line item on the consolidated balance sheet. In accordance with purchase accounting, we have accounted for this sale and leaseback transaction as a financing transaction which was included in the “Long-term lease financing obligations” line item on our consolidated balance sheet. The effective interest rate is 8.2%. Depreciation for the Hillview Facility was recorded over the straight-line method for the remaining useful life and was $0.4 million and $0.2 million in fiscal years 2009 and 2008, respectively. There was no depreciation expense in fiscal year 2007. At the end of the lease term, the estimated final lease obligation is approximately $12.2 million, which we will settle by returning the Hillview Facility to the lessor.
For fiscal years 2009 and 2008, interest expense totaled approximately $1.1 million and $0.6 million, respectively, for the Hillview Facility lease financing obligation.
We sublet the Hillview Facility in April 2008. The sublease expires in March 2011 and we expect annual sublease income of approximately $1.4 million for the duration of the sublease term. The sublease income of $1.4 million for fiscal year 2009 was recorded in the “Interest income and other, net” line item in our condensed consolidated statements of operations.
We have also acquired engineering design tools (“design tools”) under capital leases. We acquired $5.2 million of design tools in December 2007 under a four-year license and $3.7 million of design tools in November 2008 under a three-year license, which were accounted for as capital leases and recorded in the “Property, plant and equipment, net” line item on the condensed consolidated balance sheets. The related design tool obligations were included in the “Long-term lease financing obligations” line item in our condensed consolidated balance sheets. The effective interest rates for the design tools are 7.25% for the four-year tools and 4.0% for the three-
94
EXAR CORPORATION AND SUBSIDIARIES
NOTES TO CONSOLIDATED FINANCIAL STATEMENTS—(CONTINUED)
FISCAL YEARS ENDED MARCH 29, 2009, MARCH 30, 2008 AND MARCH 31, 2007
year tools based upon prevailing interest rates at the time of the respective acquisitions. Amortization on the design tools is recorded using the straight-line method over the remaining useful life and was $1.6 million and $0.3 million, respectively, for fiscal years 2009 and 2008. There was no amortization expense in fiscal year 2007.
Future minimum lease payments for the lease financing obligations as of March 29, 2009 were as follows (in thousands):
| | | | | | | | | | | | | | | |
Fiscal Years | | Hillview Facility | | | Design Tools | | | Total | | | Expected Sublease Income |
2010 | | | 1,415 | | | | 2,670 | | | | 4,085 | | | | 1,412 |
2011 | | | 13,624 | | | | 2,670 | | | | 16,294 | | | | 1,412 |
2012 | | | — | | | | 1,087 | | | | 1,087 | | | | — |
| | | | | | | | | | | | | | | |
Total minimum lease payments | | | 15,039 | | | | 6,427 | | | | 21,466 | | | | 2,824 |
Less: amount representing interest | | | (2,073 | ) | | | (682 | ) | | | (2,755 | ) | | | — |
Less: amount representing maintenance | | | — | | | | (618 | ) | | | (618 | ) | | | — |
| | | | | | | | | | | | | | | |
Present value of minimum lease payments | | | 12,966 | | | | 5,127 | | | | 18,093 | | | | 2,824 |
Less: current portion of lease financing obligation | | | (362 | ) | | | (2,098 | ) | | | (2,460 | ) | | | — |
| | | | | | | | | | | | | | | |
Long-term lease financing obligation | | $ | 12,604 | | | $ | 3,029 | | | $ | 15,633 | | | $ | 2,824 |
| | | | | | | | | | | | | | | |
NOTE 15. COMMITMENTS AND CONTINGENCIES
In 1986, Micro Power Systems Inc. (“MPSI”), a subsidiary that we acquired in June 1994, identified low-level groundwater contamination at its principal manufacturing site. Although the area and extent of the contamination appear to have been defined, the source of the contamination has not been identified. MPSI previously reached an agreement with a prior tenant to share in the cost of ongoing site investigations and the operation of remedial systems to remove subsurface chemicals. The frequency and number of wells monitored at the site was reduced with prior regulatory approval for a plume stability analysis as an initial step towards site closure. No significant rebound concentrations have been observed. The groundwater treatment system remains shut down during its two-year plume stability evaluation. In July 2008, we evaluated the effectiveness of the plume stability and decided to initiate a treatment program and pursue a no further action order for the site. As such, we accrued an additional $58,000, increasing our liability to $250,000. This accrual includes approximately $200,000 for various remediation options under consideration and $50,000 for future annual monitoring.
Sipex, which we acquired in August 2007, had entered into a definitive Master Agreement with Hangzhou Silan Microelectronics Co. Ltd. and Hangzhou Silan Integrated Circuit Co. Ltd. (collectively “Silan”) in China. Silan is a China-based semiconductor foundry. This transaction was related to the closing of Sipex wafer fabrication operations located in Milpitas, California. Under this agreement, Sipex and Silan would work together to enable Silan to manufacture semiconductor wafers using Sipex process technology. The Master Agreement includes a Process Technology Transfer and License Agreement which contemplates the transfer of eight of our processes and related product manufacturing to Silan. Subject to our option to suspend in whole or in part, there is a purchase commitment under the Wafer Supply Agreement obligating us to purchase from Silan an average of at least one thousand equivalent wafers per week, calculated on a quarterly basis, for five years beginning February 2006. There were open purchase orders for approximately $0.3 million outstanding as of March 29, 2009.
Generally, we warrant all of our products against defects in materials and workmanship for a period ranging from ninety days to two years from the delivery date. Reserve requirements are recorded in the period of sale and
95
EXAR CORPORATION AND SUBSIDIARIES
NOTES TO CONSOLIDATED FINANCIAL STATEMENTS—(CONTINUED)
FISCAL YEARS ENDED MARCH 29, 2009, MARCH 30, 2008 AND MARCH 31, 2007
are based on an assessment of the products sold with warranty and historical warranty costs incurred. Our liability is generally limited to replacing, repairing or issuing credit, at our option, for the product if it has been paid for. The warranty does not cover damage which results from accident, misuse, abuse, improper line voltage, fire, flood, lightning or other damage resulting from modifications, repairs or alterations performed other than by us, or resulting from failure to comply with our written operating and maintenance instructions. Warranty expense has historically been immaterial for our products. The warranty liability related to our products was immaterial at the end of fiscal 2009.
Additionally, our sales agreements indemnify our customers for expenses or liability resulting from alleged or claimed infringement by our products of any U.S. letter patents of third parties. However, we are not liable for any collateral, incidental or consequential damages arising out of patent infringement. The terms of these indemnification agreements are perpetual, commencing after execution of the sales agreement or the date indicated on our order acknowledgement. The maximum amount of potential future indemnification is unlimited. However, to date, we have not paid any claims or been required to defend any lawsuits with respect to any such indemnity claim.
NOTE 16. LEGAL PROCEEDINGS
From time to time, we are involved in various claims, legal actions and complaints arising in the normal course of business. Although the ultimate outcome of the matters discussed below and other matters is not presently determinable, management currently believes that the resolution of all such pending matters will not have a material adverse effect on our financial position, results of operations or liquidity.
Ericsson Wireless Communications, Inc. and Vicor Corporation
On November 16, 2004, Ericsson Wireless Communications, Inc. (now known as Ericsson Inc.) (“Ericsson”) initiated a lawsuit against us in San Diego County Superior Court. In its Third Amended Complaint, Ericsson asserted causes of action against us for negligence, strict product liability, and unfair competition, seeking monetary damages and unspecified injunctive relief. Based on discovery responses, Ericsson claimed that its damages exceeded $1 billion. The case is based on Ericsson’s purchase of allegedly defective products from Vicor Corporation, our former customer to whom we sold untested, semi-custom wafers. We disputed the allegations in Ericsson’s Third Amended Complaint, believed that we had meritorious defenses, and defended the lawsuit vigorously. On December 1, 2006, we entered into a Settlement Agreement with Ericsson to resolve the claims it asserted. Based on further events in the case, our total liability to Ericsson under the Settlement Agreement was $500,000, which was paid by our insurance carriers. Following payment, Ericsson dismissed its claims against us with prejudice.
On April 5, 2005, Vicor Corporation (“Vicor”) filed a cross-complaint against us in San Diego County Superior Court that asserted various contract, tort, and indemnity based claims. Vicor alleged, among other things, that we sold it integrated circuits that were defective and failed to meet agreed-upon specifications, and that we intentionally concealed material facts regarding the specifications of the integrated circuits that Vicor alleges it bought from us. Vicor alleged that it is entitled to indemnification from us for the damages that Vicor paid to Ericsson because of Ericsson’s direct claims against Vicor. On May 9, 2005, we filed a demurrer to all but one of Vicor’s causes of action against us, which the San Diego Superior Court sustained without leave to amend on June 17, 2005, except for Vicor’s claims for indemnity. We answered those causes of action on July 5, 2005. We disputed the allegations in Vicor’s cross-complaint, believed that we had meritorious defenses, and defended the lawsuit vigorously.
96
EXAR CORPORATION AND SUBSIDIARIES
NOTES TO CONSOLIDATED FINANCIAL STATEMENTS—(CONTINUED)
FISCAL YEARS ENDED MARCH 29, 2009, MARCH 30, 2008 AND MARCH 31, 2007
After entering the Settlement Agreement with Ericsson, we filed a motion on December 20, 2006 for an order finding the Settlement Agreement was in good faith. On January 22, 2007, the Court entered an order finding that we entered into the Settlement Agreement in good faith. The result of the finding of good faith was that Vicor’s indemnity claims were subject to dismissal. Vicor filed a petition for writ of mandate with the California Court of Appeal challenging the good faith finding, which the Court of Appeal summarily denied on February 28, 2007. The San Diego Superior Court dismissed Vicor’s indemnity claims and entered judgment in our favor on July 10, 2007. After entering judgment, the San Diego Superior Court awarded us costs against Vicor in the amount of $84,405 and monetary sanctions against Vicor in the amount of $44,266.91. Vicor filed a notice of appeal on September 6, 2007. Oral argument on the appeal was held on January 12, 2009, but no decision has been issued yet.
On March 4, 2005, we filed a complaint in Santa Clara County Superior Court against Vicor. In the complaint, we sought a declaration regarding the respective rights and obligations, including warranty and indemnity rights and obligations, under the written contracts between us and Vicor for the sale of untested, semi-custom wafers. In addition, we sought a declaration that we were not responsible for any damages that Vicor must pay to Ericsson or any other customer of Vicor arising from claims that Vicor sold allegedly defective products. On March 17, 2005, Vicor filed a cross-complaint against us and Rohm Device USA, LLC and Rohm Co., Ltd, the owners and operators of the foundry which supplied the untested, semi-custom wafers that we sold to Vicor. In the cross-complaint, Vicor asserted allegations similar to those in its cross-complaint in the Ericsson San Diego County action discussed above, and also alleged that it is entitled to indemnification from us for any damages that Vicor must pay to Ericsson or other Vicor customers that may make claims against Vicor. In the cross-complaint, Vicor asserted various contract, tort, and indemnity based causes of action against us. On May 23, 2005, we filed a demurrer to each cause of action in Vicor’s cross-complaint, and on July 15, 2005, the Santa Clara County Superior Court sustained our demurrer to each of the causes of action. The Court granted Vicor leave to amend the cross-complaint to assert a reciprocal cause of action for declaratory relief only. On August 1, 2005, Vicor filed its amended cross-complaint asserting a reciprocal declaratory relief claim against us and a declaration that we were obligated to indemnify it for any damages resulting from claims brought against Vicor by its customers. Vicor’s amended cross-complaint does not seek damages. We answered Vicor’s amended cross-complaint on September 2, 2005. The Santa Clara action was transferred to San Diego for coordination with the Ericsson San Diego County action on August 18, 2006. No trial date has been set.
DiPietro v. Sipex
In April 2003, plaintiff Frank DiPietro (former chief financial officer of Sipex) brought an action for breach of contract against Sipex in the Middlesex Superior Court in the state of Massachusetts. Mr. DiPietro was seeking approximately $800,000 in severance benefits. Sipex counterclaimed for approximately $150,000, which it was owed under a promissory note signed by Mr. DiPietro. In August 2004, Sipex filed two motions for summary judgment (one for Mr. DiPietro’s claims against it and one for its counterclaim against Mr. DiPietro). In June 2005, the Middlesex Superior Court granted both Sipex’s motions for summary judgment. Soon thereafter, Mr. DiPietro filed a notice of appeal. Sipex then filed motions for costs and pre-judgment interest. Sipex was successful in its motion for prejudgment interest and it was successful in requiring Mr. DiPietro to pay over $900 in deposition costs.
On June 21, 2006, Mr. DiPietro served Sipex with his appeal brief. On July 20, 2006, Sipex served its opposition and Mr. DiPietro’s reply brief was served on August 3, 2006. On December 12, 2006, the Massachusetts Appeals Court heard arguments in DiPietro v. Sipex and asked for a letter clarifying a legal issue that Sipex provided on December 28, 2006. On January 12, 2007, Mr. DiPietro sent a letter responding to Sipex’s letter.
97
EXAR CORPORATION AND SUBSIDIARIES
NOTES TO CONSOLIDATED FINANCIAL STATEMENTS—(CONTINUED)
FISCAL YEARS ENDED MARCH 29, 2009, MARCH 30, 2008 AND MARCH 31, 2007
On May 14, 2007, the Appeals Court issued its decision reversing the Middlesex Superior Court’s grant of summary judgment and remanding the case for further proceedings. Sipex immediately filed a motion for enlargement of time to file a petition for rehearing and an application for further appellate review. Sipex’s petition for rehearing was filed on June 13, 2007, in the Massachusetts Appeals Court and its application for further appellate review was filed on June 28, 2007, in the Massachusetts Supreme Judicial Court. Thereafter, on July 9, 2007, DiPietro filed his opposition to Sipex’s application for further appellate review and on July 18, 2007, filed his response to Sipex’s petition for rehearing. In early September 2007, the Massachusetts Appeals Court amended its decision to clarify issues addressed in Sipex’s petition for rehearing.
On October 31, 2007, Sipex’s application for further appellate review was denied. The case was remanded to Middlesex Superior Court and will proceed.
On June 16, 2008, we attended a pretrial conference. At the Court clerk’s suggestion, Sipex served its motion for leave to file renewed motions for summary judgment on August 11, 2008, and Mr. DiPietro served his opposition on August 21, 2008. The parties attended a status conference on October 14, 2008, and at that time, the Court heard arguments on Sipex’s motion for leave to file renewed motions for summary judgment. The Court denied Sipex’s motion on October 16, 2008. A pre-trial conference was held on February 3, 2009. At that time, opposing counsel requested a continuance due to a family emergency, and the trial was rescheduled for April 27, 2009. In early April, DiPietro made a settlement offer to Sipex, and the trial was continued again until July 27, 2009, to allow the parties time to engage in settlement discussions.
Cypress v. Sipex, Exar and Ralph Schmitt
On October 12, 2007, Cypress Semiconductor Corporation (“Cypress”) filed an action against Sipex, Exar, Ralph Schmitt and Does 1 through 50 in the Superior Court of the State of California, County of Santa Clara, Cypress Semiconductor Corp. v. Sipex Corp., et al., Case No. 1-07-CV096311, alleging claims for: (1) misappropriation of trade secrets; (2) violation of the Computer Fraud and Abuse Act, 18 U.S.C. §1030; (3) unfair competition under Cal. Bus. & Prof. Code §§17200 et seq.; (4) tortious interference with contract; (5) interference with actual and prospective economic advantage; (6) breach of fiduciary duty and breach of the duty of loyalty; (7) inducement of breach of fiduciary duty; (8) breach of written contract; (9) breach of the covenant of good faith and fair dealing; (10) conversion; and (11) unjust enrichment. The second, sixth, eighth and ninth causes of action are alleged against Mr. Schmitt only. Mr. Schmitt was Chief Executive Officer and President and a member of the board of directors of Exar from August 25, 2007 to December 6, 2007. Prior to Exar’s acquisition of Sipex, he was Chief Executive Officer and a member of the board of directors of Sipex. Exar filed an answer to the complaint on November 13, 2007. The case was removed to federal court on November 14, 2007, Cypress Semiconductor Corp. v. Sipex Corp., et al., United States District Court, Northern District of California, Case No. C 07-05778 JF. The parties exchanged Initial Disclosures pursuant to Federal Rules of Civil Procedure, Rule 26(a)(1) on March 7, 2008. A Case Management Conference was held on March 14, 2008 before the Honorable Jeremy Fogel. At the Case Management Conference, Judge Fogel ordered that discovery be stayed for 60 days to allow the parties the opportunity to discuss settlement. A Settlement Conference took place before Magistrate Judge Seeborg on May 13, 2008 which resulted in a settlement of the case. The terms of the settlement are confidential and the settlement amount was not material to our financial condition, results of operations or liquidity. On May 28, 2008, Judge Fogel issued a conditional Order of Dismissal of the case with prejudice.
98
EXAR CORPORATION AND SUBSIDIARIES
NOTES TO CONSOLIDATED FINANCIAL STATEMENTS—(CONTINUED)
FISCAL YEARS ENDED MARCH 29, 2009, MARCH 30, 2008 AND MARCH 31, 2007
NOTE 17. INCOME TAXES
The components of the provision for (benefit from) income taxes are as follows (in thousands) as of the dates indicated:
| | | | | | | | | | | | |
| | March 29, 2009 | | | March 30, 2008 | | | March 31, 2007 | |
Current: | | | | | | | | | | | | |
Federal | | $ | (8 | ) | | $ | (458 | ) | | $ | 2,963 | |
State | | | (234 | ) | | | 488 | | | | 432 | |
Foreign | | | 192 | | | | 191 | | | | 32 | |
| | | | | | | | | | | | |
Total current | | | (50 | ) | | | 221 | | | | 3,427 | |
| | | | | | | | | | | | |
Deferred: | | | | | | | | | | | | |
Federal | | | (450 | ) | | | 6,195 | | | | (72 | ) |
State | | | (35 | ) | | | 1,700 | | | | (39 | ) |
| | | | | | | | | | | | |
Total deferred | | | (485 | ) | | | 7,895 | | | | (111 | ) |
| | | | | | | | | | | | |
Total provision for (benefit from) income taxes | | $ | (535 | ) | | $ | 8,116 | | | $ | 3,316 | |
| | | | | | | | | | | | |
Consolidated pre-tax income included foreign income of $212,000, $218,000 and $184,000 for the fiscal years ended March 29, 2009, March 30, 2008 and March 31, 2007, respectively. Undistributed earnings of approximately $4.4 million of our foreign subsidiaries are considered to be indefinitely reinvested and accordingly, no provisions for federal and state income taxes have been provided thereon. Upon distribution of those earnings in the form of a dividend or otherwise, we would be subject to both U.S. income taxes (subject to an adjustment for foreign tax credits) and withholding taxes payable to the various foreign countries.
Significant components of our net deferred tax assets are as follows (in thousands) as of the dates indicated:
| | | | | | | | | | | | |
| | March 29, 2009 | | | March 30, 2008 | | | March 31, 2007 | |
Deferred tax assets: | | | | | | | | | | | | |
Reserves and expenses not currently deductible | | $ | 7,701 | | | $ | 10,261 | | | $ | 3,765 | |
Net operating loss carryforwards | | | 84,528 | | | | 84,340 | | | | 141 | |
Tax credits | | | 15,960 | | | | 14,753 | | | | 12,244 | |
Losses on investments | | | 16,995 | | | | 15,319 | | | | 16,552 | |
Capitalized R&D expenses | | | 4,048 | | | | 2,480 | | | | 2,790 | |
Deferred margin | | | 3,846 | | | | 4,743 | | | | — | |
Depreciation | | | 197 | | | | — | | | | — | |
| | | | | | | | | | | | |
Total deferred tax assets | | | 133,275 | | | | 131,896 | | | | 35,492 | |
Deferred tax liabilities: | | | | | | | | | | | | |
Depreciation | | | — | | | | (1,555 | ) | | | (956 | ) |
Non-goodwill intangibles | | | (1,547 | ) | | | (7,142 | ) | | | — | |
| | | | | | | | | | | | |
Total deferred tax liabilities | | | (1,547 | ) | | | (8,697 | ) | | | (956 | ) |
Valuation allowance | | | (131,728 | ) | | | (123,199 | ) | | | (23,125 | ) |
| | | | | | | | | | | | |
Net deferred tax assets | | $ | — | | | $ | — | | | $ | 11,411 | |
| | | | | | | | | | | | |
The net valuation allowance increased by approximately $8.5 million during fiscal year 2009.
99
EXAR CORPORATION AND SUBSIDIARIES
NOTES TO CONSOLIDATED FINANCIAL STATEMENTS—(CONTINUED)
FISCAL YEARS ENDED MARCH 29, 2009, MARCH 30, 2008 AND MARCH 31, 2007
Reconciliations of the income tax provision at the statutory rate to our provision for (benefit from) income tax are as follows (in thousands) as of the dates indicated:
| | | | | | | | | | | | |
| | March 29, 2009 | | | March 30, 2008 | | | March 31, 2007 | |
Income tax provision (benefit from) at statutory rate | | $ | (25,750 | ) | | $ | (65,717 | ) | | $ | 3,969 | |
State income taxes, net of federal tax benefit | | | (1,970 | ) | | | (6,566 | ) | | | 638 | |
Deferred tax assets not benefited | | | 11,560 | | | | 29,203 | | | | 379 | |
Tax-exempt interest income | | | — | | | | (150 | ) | | | (473 | ) |
Tax credits | | | (8 | ) | | | (368 | ) | | | (1,465 | ) |
Stock-based compensation | | | 498 | | | | 374 | | | | 253 | |
Settlement of tax audit | | | — | | | | (1,934 | ) | | | — | |
In-process R&D | | | — | | | | 3,401 | | | | — | |
Goodwill impairment | | | 15,491 | | | | 49,656 | | | | — | |
Other, net | | | (356 | ) | | | 217 | | | | 15 | |
| | | | | | | | | | | | |
Provision for (benefit from) income taxes | | $ | (535 | ) | | $ | 8,116 | | | $ | 3,316 | |
| | | | | | | | | | | | |
As of March 29, 2009, our federal and state net operating loss carryforwards for income tax purposes were approximately $227.2 million and $95.4 million, respectively. If not utilized, $6.0 million of the federal net operating loss carryforwards will expire in calendar year 2009, while the state net operating losses will begin to expire in 2011. Additionally, we have capital loss carryforwards of approximately $39.6 million, which will begin to expire in calendar year 2010 if not utilized.
As of March 29, 2009, our federal and state tax credit carryforwards were $8.0 million and $10.7 million, respectively. The federal and state credits will begin to expire in 2012 and 2010, respectively. Utilization of these federal and state net operating loss and tax credit carryforwards may be subject to a substantial annual limitation due to the ownership change limitations provided by the Internal Revenue Code of 1986, as amended, and similar state provisions.
We have evaluated our deferred tax assets and concluded that a valuation allowance is required for that portion of the total deferred tax assets that are not considered more likely than not to be realized in future periods. To the extent that the deferred tax assets with a valuation allowance become realizable in future periods, we will have the ability, subject to carryforward limitations, to benefit from these amounts. Approximately $8.5 million of these deferred tax assets pertain to certain net operating loss and credit carryforwards resulting from the exercise of employee stock options. When recognized, the tax benefit of these carryforwards is accounted for as a credit to additional paid-in capital rather than a reduction of the income tax provision.
Uncertain Income Tax Benefits
Effective April 1, 2007, we adopted Financial Accounting Standards Board Interpretation No. 48,“Accounting for Uncertainty in Income Taxes—an interpretation of FASB Statement No. 109” (“FIN 48”). FIN 48 prescribes a recognition threshold and measurement attribute for the financial statement recognition and measurement of uncertain tax positions taken or expected to be taken in our income tax return, and also provides guidance on derecognition, classification, interest and penalties, accounting in interim periods, disclosure and transition. The total amount of unrecognized tax benefit on the adoption date was $7.6 million.
100
EXAR CORPORATION AND SUBSIDIARIES
NOTES TO CONSOLIDATED FINANCIAL STATEMENTS—(CONTINUED)
FISCAL YEARS ENDED MARCH 29, 2009, MARCH 30, 2008 AND MARCH 31, 2007
Our total amount of gross unrecognized tax benefits as of March 30, 2008 was $9.4 million. The unrecognized tax benefits increased by $0.5 million during the fiscal year ended March 29, 2009 to $9.9 million. If recognized, $8.2 million of these unrecognized tax benefits (net of federal benefit) would be recorded as a reduction of future income tax provision before consideration of changes in valuation allowance.
A reconciliation of the beginning and ending amount of the unrecognized tax benefits during the tax year ended March 29, 2009 is as follows (in thousands):
| | | | |
| | Amount | |
Unrecognized tax benefits as of April 1, 2007 | | $ | 7,584 | |
Gross increase related to prior year tax positions | | | 3,079 | |
Gross increase related to current year tax positions | | | 648 | |
Settlement | | | (1,901 | ) |
| | | | |
Unrecognized tax benefits as of March 30, 2008 | | | 9,410 | |
Gross increase related to prior year tax positions | | | — | |
Gross increase related to current year tax positions | | | 592 | |
Lapses in statutes of limitations | | | (70 | ) |
| | | | |
Unrecognized tax benefits as of March 29, 2009 | | $ | 9,932 | |
| | | | |
The reconciliation of the unrecognized gross tax benefit of $9.9 million is as follows: $1.1 million in income taxes payable, non-current, and $8.8 million as a reduction to deferred tax assets. We do not anticipate a significant increase or decrease to our unrecognized tax benefits within the next twelve months. The total amount of unrecognized tax benefit (net of federal benefit), if recognized would affect the effective rate is $8.2 million.
Estimated interest and penalties related to the underpayment of income taxes were classified as a component of the provision for income taxes in the condensed consolidated statement of operations. Accrued interest and penalties were $0.3 million and $0.2 million as of March 29, 2009 and March 30, 2008, respectively which is included in the “Other non-current obligations” line item on the consolidated balance sheet.
Our only major tax jurisdictions are the United States (federal) and various U.S. states. The fiscal years 1997 through 2008 remain open and subject to examinations by the appropriate governmental agencies in the United States with fiscal years 2000 through 2008 open to audits in certain of our U.S. state jurisdictions.
NOTE 18. SEGMENT AND GEOGRAPHIC INFORMATION
We operate in one reportable segment. We design, develop and market high-performance, analog and mixed-signal silicon solutions for a variety of markets including power management, interface and datacom. The nature of our products and production processes as well as the type of customers and distribution methods are consistent among all of our products.
Our net sales by product lines are summarized as follows (in thousands):
| | | | | | | | | |
| | March 29, 2009 | | March 30, 2008 * | | March 31, 2007 |
Datacom | | $ | 27,833 | | $ | 27,946 | | $ | 28,462 |
Interface | | | 63,036 | | | 49,904 | | | 40,040 |
Power management | | | 24,249 | | | 11,893 | | | — |
| | | | | | | | | |
Total net sales | | $ | 115,118 | | $ | 89,743 | | $ | 68,502 |
| | | | | | | | | |
* | Revenue from Sipex products was included starting from August 26, 2007. |
101
EXAR CORPORATION AND SUBSIDIARIES
NOTES TO CONSOLIDATED FINANCIAL STATEMENTS—(CONTINUED)
FISCAL YEARS ENDED MARCH 29, 2009, MARCH 30, 2008 AND MARCH 31, 2007
Our foreign operations are conducted primarily through our wholly-owned subsidiaries in Canada, China, France, Germany, Italy, Japan, South Korea, Taiwan, Malaysia and the United Kingdom. Our principal markets include North America, Europe and the Asia Pacific region. Net sales by geographic areas represent sales to unaffiliated customers.
Our net sales by geographic areas are summarized as follows (in thousands):
| | | | | | | | | |
| | March 29, 2009 | | March 30, 2008* | | March 31, 2007 |
United States | | $ | 28,517 | | $ | 27,471 | | $ | 30,061 |
China | | | 27,384 | | | 17,724 | | | 9,511 |
Singapore | | | 14,894 | | | 7,727 | | | 3,219 |
Japan | | | 7,170 | | | 6,865 | | | 4,859 |
Italy | | | 5,607 | | | 7,768 | | | 8,265 |
Europe (excludes Italy) | | | 19,486 | | | 14,395 | | | 9,752 |
Rest of world | | | 12,060 | | | 7,793 | | | 2,835 |
| | | | | | | | | |
Total net sales | | $ | 115,118 | | $ | 89,743 | | $ | 68,502 |
| | | | | | | | | |
* | Revenue from Sipex products was included starting from August 26, 2007. |
Substantially all of our long-lived assets at March 29, 2009 and March 30, 2008 were located in the United States.
NOTE 19. ALLOWANCES FOR SALES RETURNS AND DOUBTFUL ACCOUNTS
We had the following activities for the allowance for sales returns and allowances and bad debt reserves (in thousands):
| | | | | | | | | | | | | |
Classification | | Balance at Beginning of Year | | Additions | | | Write-offs and Recoveries(1) | | Balance at End of Year |
Allowance for sales return: | | | | | | | | | | | | | |
| | | | |
Year ended March 29, 2009 | | $ | 1,992 | | $ | 7,871 | | | $ | 8,650 | | $ | 1,213 |
Year ended March 30, 2008 | | $ | 1,078 | | $ | 3,190 | | | $ | 2,276 | | $ | 1,992 |
Year ended March 31, 2007 | | $ | 965 | | $ | 4,013 | | | $ | 3,900 | | $ | 1,078 |
| | | | |
Allowance for doubtful accounts: | | | | | | | | | | | | | |
| | | | |
Year ended March 29, 2009 | | $ | 143 | | $ | (47 | ) | | $ | 1 | | $ | 95 |
Year ended March 30, 2008 | | $ | 60 | | $ | 83 | | | $ | — | | $ | 143 |
Year ended March 31, 2007 | | $ | 109 | | $ | (49 | ) | | $ | — | | $ | 60 |
(1) | Write-offs and recoveries reflect credits issued to distributors for stock rotations and volume discounts and write-offs of uncollectible accounts receivable. |
NOTE 20. SUBSEQUENT EVENT
On June 5, 2009, we announced that the Company has entered into a definitive agreement to acquire Galazar Networks Inc. Galazar Networks Inc., based in Ottawa, Canada, is a fabless semiconductor and software supplier focused on carrier grade transport over telecom networks. Galazar’s product portfolio addresses transport of a wide range of datacom and telecom services including Ethernet, SAN, TDM and video over SONET/SDH, PDH and OTN networks.
102
EXAR CORPORATION AND SUBSIDIARIES
NOTES TO CONSOLIDATED FINANCIAL STATEMENTS—(CONTINUED)
FISCAL YEARS ENDED MARCH 29, 2009, MARCH 30, 2008 AND MARCH 31, 2007
On April 3, 2009, we completed the acquisition of all of the outstanding shares of common stock of hi/fn, inc. (“Hifn”). Hifn is a provider of network- and storage-security and data reduction products that simplify the way major network and storage original equipment manufacturers (“OEMs”), as well as small-and-medium enterprises (“SMEs”), efficiently and securely share, retain, access and protect critical data. As a result of the transaction, we issued approximately 378,000 shares of our common stock and paid approximately $56.8 million in cash.
NOTE 21. SUPPLEMENTARY QUARTERLY FINANCIAL DATA (UNAUDITED)
The following table contains selected unaudited quarterly financial data for the years ended March 29, 2009 and March 30, 2008. In the opinion of management, this unaudited information has been prepared on the same basis as the audited information and includes all adjustments, consisting only of normal and recurring adjustments necessary to state fairly the information set forth therein. Results for a given quarter are not necessarily indicative of results for any subsequent quarter (in thousands, except per share data).
| | | | | | | | | | | | | | | | | | | | | | | | | | | | | | | | |
| | Fiscal Year 2009 | | | Fiscal Year 2008 | |
| | March 29, 2009(1) | | | December 28, 2008(2) | | | September 28, 2008(3) | | | June 29, 2008(4) | | | March 30, 2008(5) | | | December 30, 2007(6) | | | September 30, 2007(7) | | | June 30, 2007 | |
Consolidated Statements of Operations Data: | | | | | | | | | | | | | | | | | | | | | | | | | | | | | | | | |
Net sales | | $ | 23,854 | | | $ | 26,305 | | | $ | 32,748 | | | $ | 32,211 | | | $ | 28,262 | | | $ | 25,207 | | | $ | 19,173 | | | $ | 17,101 | |
Gross profit | | | 10,066 | | | | 10,704 | | | | 15,005 | | | | 14,470 | | | | 10,705 | | | | 7,567 | | | | 10,484 | | | | 11,357 | |
Income (loss) from operations | | | (6,262 | ) | | | (66,163 | ) | | | (2,874 | ) | | | (4,923 | ) | | | (174,538 | ) | | | (13,394 | ) | | | (14,271 | ) | | | (232 | ) |
Net income (loss) | | | (4,565 | ) | | | (63,823 | ) | | | (2,187 | ) | | | (2,461 | ) | | | (172,398 | ) | | | (11,682 | ) | | | (16,410 | ) | | | 4,611 | |
Net income (loss) per share: | | | | | | | | | | | | | | | | | | | | | | | | | | | | | | | | |
Basic(8) | | $ | (0.11 | ) | | $ | (1.49 | ) | | $ | (0.05 | ) | | $ | (0.06 | ) | | $ | (3.77 | ) | | $ | (0.24 | ) | | $ | (0.39 | ) | | $ | 0.13 | |
Diluted(8) | | $ | (0.11 | ) | | $ | (1.49 | ) | | $ | (0.05 | ) | | $ | (0.06 | ) | | $ | (3.77 | ) | | $ | (0.24 | ) | | $ | (0.39 | ) | | $ | 0.13 | |
Shares used in the computation of net income (loss) per share: | | | | | | | | | | | | | | | | | | | | | | | | | | | | | | | | |
Basic | | | 42,950 | | | | 42,889 | | | | 42,735 | | | | 42,973 | | | | 45,712 | | | | 49,301 | | | | 41,796 | | | | 35,998 | |
Diluted | | | 42,950 | | | | 42,889 | | | | 42,735 | | | | 42,973 | | | | 45,712 | | | | 49,301 | | | | 41,796 | | | | 36,134 | |
(1) | Included $0.2 million amortization expenses related to purchased assets in connection with the Sipex acquisition; $0.8 million in acquisition related costs;$0.7 million benefit from a partial reversal of estimated fiscal year 2009 incentive compensation liabilities in light of the economic recession, $0.6 million of idle capacity charges and $0.3 million impairment charge against our long-term non-marketable securities (see Note 7). |
(2) | Included $59.7 million impairment charges in goodwill and other intangible assets (See Note 8); $0.7 million amortization expenses related to purchased assets in connection with the Sipex acquisition; and $1.2 million in acceleration of depreciation on abandoned equipment. |
(3) | Included $0.9 million amortization expenses related to purchased assets in connection with the Sipex acquisition; $0.6 million impairment charge against our marketable securities and $0.9 million impairment charge against our long-term non-marketable securities (see Note 7). |
103
EXAR CORPORATION AND SUBSIDIARIES
NOTES TO CONSOLIDATED FINANCIAL STATEMENTS—(CONTINUED)
FISCAL YEARS ENDED MARCH 29, 2009, MARCH 30, 2008 AND MARCH 31, 2007
(4) | Included $0.9 million amortization expenses related to purchased assets in connection with the Sipex acquisition. |
(5) | Included $165.2 million impairment charges in goodwill and other intangible assets (See Note 8); $1.5 million amortization expenses related to purchased assets in connection with the Sipex acquisition; $0.4 million related to the fair value adjustment to the acquired inventories in connection with the Sipex acquisition; $0.8 million in acquisition related costs; and $0.1 million impairment charge against our long-term non-marketable securities (see Note 7). |
(6) | Included $2.8 million amortization expenses related to purchased assets in connection with the Sipex acquisition; $1.5 million related to the fair value adjustment to the acquired inventories in connection with the Sipex acquisition; $0.5 million in acquisition related costs; and $0.5 million in separation cost to our former chief executive officer. |
(7) | Included $1.1 million amortization expenses related to purchased assets in connection with the Sipex acquisition; $0.3 million related to the fair value adjustment to the acquired inventories in connection with the Sipex acquisition; $1.0 million in acquisition related costs; $8.8 million in acquired in-process research and development charge in connection with the Sipex acquisition (see Note 3); and $0.4 million impairment charge against our long-term non-marketable securities (see Note 7). |
(8) | Basic and diluted earnings per share are computed independently for each of the quarters presented. Therefore, the sum of quarterly basic and diluted per share information may not equal annual basic and diluted earnings per share. |
104
ITEM 9. | CHANGES IN AND DISAGREEMENTS WITH ACCOUNTANTS ON ACCOUNTING AND FINANCIAL DISCLOSURE |
None.
ITEM 9A. | CONTROLS AND PROCEDURES |
Disclosure Controls and Procedures
Evaluation of Disclosure Controls and Procedures (“Disclosure Controls”). We evaluated the effectiveness of the design and operation of our Disclosure Controls, as defined by the rules and regulations of the SEC (the “Evaluation”), as of the end of the period covered by this Report. This Evaluation was performed under the supervision and with the participation of management, including our Chief Executive Officer (the “CEO”), as principal executive officer, and Chief Financial Officer (the “CFO”), as principal financial officer.
Attached as Exhibits 31.1 and 31.2 of this Report are the certifications of the CEO and the CFO, respectively, in compliance with Section 302 of the Sarbanes-Oxley Act of 2002 (the “Certifications”). This section of the Report provides information concerning the Evaluation referred to in the Certifications and should be read in conjunction with the Certifications.
Disclosure Controls are controls and procedures designed to ensure that information required to be disclosed in the reports filed or submitted under the Securities Exchange Act of 1934, as amended, is recorded, processed, summarized and reported within the time periods as specified in the SEC’s rules and forms. In addition, Disclosure Controls are designed to ensure the accumulation and communications of information required to be disclosed in reports filed or submitted under the Securities Exchange Act of 1934, as amended, to our management, including the CEO and CFO, to allow timely decisions regarding required disclosure.
Based on the Evaluation, our CEO and CFO have concluded that our Disclosure Controls are effective as of the end of fiscal year 2009.
Inherent Limitations on the Effectiveness of Disclosure Controls
Our management, including the CEO and CFO, does not expect that the Disclosure Controls will prevent all errors and all fraud. Disclosure Controls, no matter how well conceived, managed, utilized and monitored, can provide only reasonable assurance that the objectives of such controls are met. Therefore, because of the inherent limitation of Disclosure Controls, no evaluation of such controls can provide absolute assurance that all control issues and instances of fraud, if any, within us have been detected.
Management’s Annual Report on Internal Control over Financial Reporting
Management is responsible for establishing and maintaining adequate internal control over financial reporting. Management conducted an assessment of our internal control over financial reporting as of March 29, 2009 based on the framework established by the Committee of Sponsoring Organizations of the Treadway Commission in Internal Control—Integrated Framework. Based on this assessment, management concluded that, as of March 29, 2009, our internal control over financial reporting was effective.
Internal control over financial reporting cannot provide absolute assurance of achieving financial reporting objectives because of its inherent limitations. Internal control over financial reporting is a process that involves human diligence and compliance, and is subject to lapses in judgment and breakdowns resulting from human failures. Internal control over financial reporting also can be circumvented by collusion or improper management override. Because of such limitations, there is a risk that material misstatements may not be prevented or detected on a timely basis by internal control over financial reporting. However, these inherent limitations are known features of the financial reporting process. Therefore it is possible to design into the process safeguards to reduce, though not eliminate, this risk.
105
Our independent registered public accounting firm has audited the financial statements included in Item 8 of this report and has issued an attestation report on our internal control over financial reporting, which is included at page 58.
Changes in Internal Control over Financial Reporting
There was no change in our internal control over financial reporting that occurred during the fourth quarter of fiscal 2009 that has materially affected, or is reasonably likely to materially affect, our internal control over financial reporting.
ITEM 9B. | OTHER INFORMATION |
None.
106
PART III
ITEM 10. | DIRECTORS, EXECUTIVE OFFICERS AND CORPORATE GOVERNANCE |
Executive Officers
A listing of Executive Officers of Exar and certain other information required by Item 10 with respect to our executive officers is set forth under the caption “Executive Officers of the Registrant” inPart I, Item 1 of this Report and is incorporated herein by reference.
Directors
The information required by this item with respect to our directors is incorporated by reference from the information set forth under the caption “Election of Directors—Executive Officers and Directors” in our Definitive Proxy Statement in connection with our 2009 Annual Meeting of Stockholders (“2009 Definitive Proxy Statement”) which will be filed with the Securities and Exchange Commission no later than 120 days after March 29, 2009.
Audit Committee
The information required by this item with respect to our audit committee is set forth under the caption “Audit Committee” in our 2009 Definitive Proxy Statement and is incorporated by reference.
Section 16(a) Beneficial Ownership Reporting Compliance
The information required by this item is set forth under the caption “Section 16(a) Beneficial Ownership Reporting Compliance” in our 2009 Definitive Proxy Statement and is incorporated herein by reference.
Code of Ethics
We have adopted a Code of Ethics for Principal Executives, Executive Management and Senior Financial Officers, a Code of Business Conduct and Ethics and a Financial Integrity Compliance Policy. These documents can be found on our website:www.exar.com. We will post any amendments to the codes and policy, as well as any waivers that are required to be disclosed by the rules of either the SEC or the NASDAQ on our website, or by filing a Form 8-K. Hard copy can be obtained free of charge by submit a written request to:
Exar Corporation
48720 Kato Road
Fremont, California 94538
Attn: Investor Relations, M/S 210
ITEM 11. | EXECUTIVE COMPENSATION |
The information required by this item is set forth under the caption “Executive Compensation” in our 2009 Definitive Proxy Statement and is incorporated herein by reference.
107
ITEM 12. | SECURITY OWNERSHIP OF CERTAIN BENEFICIAL OWNERS AND MANAGEMENT AND RELATED STOCKHOLDER MATTERS |
The information required by this Item is hereby incorporated by reference from our 2009 Definitive Proxy Statement.
ITEM 13. | CERTAIN RELATIONSHIPS AND RELATED TRANSACTIONS, AND DIRECTOR INDEPENDENCE |
The information required by this Item is hereby incorporated by reference from our 2009 Definitive Proxy Statement.
ITEM 14. | PRINCIPAL ACCOUNTING FEES AND SERVICES |
The information required by this Item is hereby incorporated by reference from our 2009 Definitive Proxy Statement.
108
PART IV
ITEM 15. | EXHIBITS, FINANCIAL STATEMENT SCHEDULES |
(a) The following documents are filed as part of this Form 10-K:
(1) Schedules
SeePart II, Item 8—“Financial Statements and Supplementary Data”and“Notes to Consolidated Financial Statements, Note 19—Allowance for Sales Return and Doubtful Accounts.”
(2) Exhibits.
See the Exhibit Index, which follows the signature page to this Report.
109
SIGNATURES
Pursuant to the requirements of Section 13 or 15(d) of the Securities Exchange Act of 1934, the Registrant has duly caused this Report to be signed on its behalf by the undersigned, thereunto duly authorized.
| | |
EXAR CORPORATION |
| |
By: | | /S/ PEDRO (PETE) P. RODRIGUEZ |
| | Pedro (Pete) P. Rodriguez |
| | Chief Executive Officer and President |
| | (Principal Executive Officer) |
Date: June 12, 2009
KNOW ALL PERSONS BY THESE PRESENTS, that each person whose signature appears below constitutes and appoints Pedro (Pete) P. Rodriguez and J. Scott Kamsler, and each of them, as his true and lawful attorneys-in-fact and agents, with full power of substitution and re-substitution, for him and in his name, place, and stead, in any and all capacities, to sign any and all amendments to this Report, and to file the same, with all exhibits thereto, and other documents in connection therewith, with the Securities and Exchange Commission, granting unto said attorneys-in-fact and agents, and each of them, full power and authority to do and perform each and every act and thing requisite and necessary to be done in connection therewith, as fully to all intents and purposes as he might or could do in person, hereby ratifying and confirming that all said attorneys-in-fact and agents, or any of them or their or his substitute or substituted, may lawfully do or cause to be done by virtue hereof.
Pursuant to the requirements of the Securities Exchange Act of 1934, this Report has been signed below by the following persons on behalf of the Registrant and in the capacities and on the dates indicated.
| | | | |
Signature | | Title | | Date |
| | |
/s/ PEDRO (PETE) P. RODRIGUEZ (Pedro (Pete) P. Rodriguez) | | Chief Executive Officer, President and Director (Principal Executive Officer) | | June 12, 2009 |
| | |
/s/ J. SCOTT KAMSLER (J. Scott Kamsler) | | Senior Vice President and Chief Financial Officer (Principal Financial and Accounting Officer) | | June 12, 2009 |
| | |
/s/ DR. IZAK BENCUYA (Dr. Izak Bencuya) | | Director | | June 12, 2009 |
| | |
/s/ PIERRE G. GUILBAULT | | Director | | June 12, 2009 |
(Pierre G. Guilbault) | | | | |
| | |
/s/ BRIAN HILTON | | Director | | June 12, 2009 |
(Brian Hilton) | | | | |
| | |
/s/ RICHARD L. LEZA (Richard L. Leza) | | Chairman of the Board | | June 12, 2009 |
| | |
/s/ GARY MEYERS | | Director | | June 12, 2009 |
(Gary Meyers) | | | | |
| | |
/s/ J. OSCAR RODRIGUEZ (J. Oscar Rodriguez) | | Director | | June 12, 2009 |
| | |
/s/ ALBERT E. SISTO (Albert E. Sisto) | | Director | | June 12, 2009 |
110
EXHIBIT INDEX
| | | | | | | | | | | | |
Exhibit Number | | | | Incorporated by Reference | | Filed Herewith |
| Exhibit | | Form | | File No. | | Exhibit | | Filing Date | |
2.1++ | | Purchase Agreement between Exar Corporation and Infineon Technologies North America Corp., dated April 6, 2005. | | 10-K | | 0-14225 | | 2.1 | | 6/14/2005 | | |
| | | | | | |
2.2 | | Agreement and Plan of Merger by and among Exar Corporation, Sipex Corporation and Side Acquisition Corp., dated as of May 7, 2007. | | 8-K | | 0-14225 | | 2.1 | | 5/8/2007 | | |
| | | | | | |
2.3 | | Agreement and Plan of Merger, dated as of February 23, 2009, among Exar Corporation, Hybrid Acquisition Corp. and hi/fn, inc. | | 8-K | | 0-14225 | | 2.1 | | 2/27/2009 | | |
| | | | | | |
3.1 | | Amended and Restated Certificate of Incorporation of Exar Corporation, as amended. | | 10-K | | 0-14225 | | 3.1 | | 6/12/2007 | | |
| | | | | | |
3.2 | | Amended and Restated Bylaws of the Company. | | 8-K | | 0-14225 | | 3.1 | | 12/10/2007 | | |
| | | | | | |
4.1 | | Warrant Agent Agreement between Sipex Corporation and Wells Fargo Bank, National Association, dated May 16, 2006. | | S-3 | | 333-147154 | | 4.1 | | 11/5/2007 | | |
| | | | | | |
4.2 | | Amendment, dated August 28, 2007, to Warrant Agent Agreement between Sipex Corporation, Exar Corporation and Wells Fargo Bank, National Association, dated May 16, 2006. | | S-3 | | 333-147154 | | 4.2 | | 11/5/2007 | | |
| | | | | | |
4.3 | | Registration Rights Agreement, among Sipex Corporation and the buyers listed on the Schedule of Buyers therein, dated May 16, 2006. | | S-3 | | 333-147154 | | 4.3 | | 11/5/2007 | | |
| | | | | | |
10.1*+++ | | 1989 Employee Stock Participation Plan, as amended, and related Offering documents. | | 10-K | | 0-14225 | | 10.1 | | 6/12/2006 | | |
| | | | | | |
10.2*+++ | | 1996 Non-Employee Directors’ Stock Option Plan, as amended, and related forms of stock option grant and exercise. | | 10-K | | 0-14225 | | 10.6 | | 6/12/2006 | | |
| | | | | | |
10.3* | | 1997 Equity Incentive Plan, as amended, and related forms of stock option grant and exercise. | | 10-K | | 0-14225 | | 10.7 | | 6/14/2005 | | |
| | | | | | |
10.4* | | 2000 Equity Incentive Plan, as amended, and related forms of stock option grant and exercise. | | 10-K | | 0-14225 | | 10.9 | | 6/14/2005 | | |
| | | | | | |
10.5* | | Form of Letter Agreement Regarding Change of Control for each of the following: Thomas R. Melendrez and Stephen W. Michael. | | 10-K | | 0-14225 | | 10.11 | | 6/27/2001 | | |
111
| | | | | | | | | | | | |
Exhibit Number | | | | Incorporated by Reference | | Filed Herewith |
| Exhibit | | Form | | File No. | | Exhibit | | Filing Date | |
10.6* | | Form of Indemnity Agreement between the Company and each of the following: Guy W. Adams, J. Scott Kamsler, John S. McFarlane, John W. Herzing, Kevin S. Bauer, Levent Ozcolak, Mir Bahram Ghaderi, Pete Rodriguez, Richard L. Leza, Stephen W. Michael and Thomas R. Melendrez. | | 10-Q | | 0-14225 | | 10.12 | | 11/13/2002 | | |
| | | | | | |
10.7* | | Separation and General Release Agreement between Exar Corporation and Roubik Gregorian, dated February 22, 2007. | | 10-K | | 0-14225 | | 10.25 | | 6/12/2007 | | |
| | | | | | |
10.8* | | Separation and General Release Agreement between Exar Corporation and Ronald W. Guire, dated June 29, 2006. | | 8-K | | 0-14225 | | 10.1 | | 7/6/2006 | | |
| | | | | | |
10.9* | | Consulting Agreement between Exar Corporation and Richard L. Leza, dated February 22, 2007. | | 10-K | | 0-14225 | | 10.27 | | 6/12/2007 | | |
| | | | | | |
10.10* | | Amendment to Consulting Agreement between Exar Corporation and Richard L. Leza, dated May 22, 2007. | | 10-K | | 0-14225 | | 10.28 | | 6/12/2007 | | |
| | | | | | |
10.11 | | Amendment No. 3, entered October 29, 2007, to that certain Distributor Agreement, dated July 1, 1997, by and between Exar Corporation and Future Electronics Incorporated. | | 10-Q | | 0-14225 | | 10.1 | | 2/8/2008 | | |
| | | | | | |
10.12 | | Amendment No. 4, entered October 29, 2007, to that certain Domestic Distributor Agreement, dated December 1, 2001, by and between Exar Corporation and NuHorizons, Inc. | | 10-Q | | 0-14225 | | 10.2 | | 2/8/2008 | | |
| | | | | | |
10.13 | | Amendment No. 8, entered October 21, 2007, to the Worldwide Authorized Distributor Market Price Agreement, dated July 22, 1993, by and between Sipex and Future Electronics Inc. (the “Sipex Agreement”), which terminates the Sipex Agreement. | | 10-Q | | 0-14225 | | 10.3 | | 2/8/2008 | | |
| | | | | | |
10.14* | | Sipex Corporation 2006 Equity Incentive Plan. | | S-8 | | 333-145751 | | 4.1 | | 8/28/2007 | | |
| | | | | | |
10.15* | | Sipex Corporation Amended and Restated 2002 Nonstatutory Stock Option Plan. | | S-8 | | 333-145751 | | 4.2 | | 8/28/2007 | | |
| | | | | | |
10.16* | | Sipex Corporation 2000 Non-Qualified Stock Option Plan. | | S-8 | | 333-145751 | | 4.3 | | 8/28/2007 | | |
| | | | | | |
10.17* | | Sipex Corporation 1999 Stock Plan. | | S-8 | | 333-145751 | | 4.4 | | 8/28/2007 | | |
112
| | | | | | | | | | | | |
Exhibit Number | | | | Incorporated by Reference | | Filed Herewith |
| Exhibit | | Form | | File No. | | Exhibit | | Filing Date | |
10.18* | | Sipex Corporation 1997 Stock Option Plan. | | S-8 | | 333-145751 | | 4.5 | | 8/28/2007 | | |
| | | | | | |
10.19* | | Amendment, dated August 24, 2007, to Employment Agreement, dated May 7, 2007, between the Company and Ralph Schmitt. | | 8-K | | 0-14225 | | 10.1 | | 8/30/2007 | | |
| | | | | | |
10.20* | | Agreement, dated August 24, 2007, by and among the Company, Guy W. Adams, GWA Capital Partners LLC, GWA Master Fund LP and GWA Investments LLC. | | 8-K | | 0-14225 | | 10.2 | | 8/30/2007 | | |
| | | | | | |
10.21* | | Separation Agreement between the Company and John Herzing, dated July 30, 2007. | | 8-K | | 0-14225 | | 10.1 | | 8/1/2007 | | |
| | | | | | |
10.22* | | Separation Agreement between the Company and Bahram Ghaderi, dated July 12, 2007. | | 8-K | | 0-14225 | | 10.1 | | 7/17/2007 | | |
| | | | | | |
10.23+ | | Master Agreement between Sipex, Hangzhou Silan Microelectronics Co., Ltd. and Hangzhou Silan Integrated Circuit Co., Ltd., dated February 27, 2006. | | 8-K/A† | | 0-27892 | | 10.1 | | 7/26/2006 | | |
| | | | | | |
10.24 | | Worldwide Authorized Distributor Market Price Agreement, dated July 22, 1993, by and between Sipex and Future Electronics Inc. | | 10-K† | | 0-27892 | | 10.27 | | 3/31/2003 | | |
| | | | | | |
10.25 | | Amendment, dated October 1, 2002 to Worldwide Authorized Distributor Market Price Agreement, dated July 22, 1993, by and between Sipex and Future Electronics Inc. | | 10-Q† | | 0-27892 | | 10.1 | | 9/21/2006 | | |
| | | | | | |
10.26 | | Addendum “A”, dated February 7, 2003, to Worldwide Authorized Distributor Market Price Agreement, dated July 22, 1993, by and between Sipex and Future Electronics Inc. | | 10-K† | | 0-27892 | | 10.28 | | 3/31/2003 | | |
| | | | | | |
10.27 | | Addendum “B”, dated August 26, 2003, to Worldwide Authorized Distributor Market Price Agreement, dated July 22, 1993, by and between Sipex and Future Electronics Inc. | | 10-Q† | | 0-27892 | | 10.2 | | 9/21/2006 | | |
| | | | | | |
10.28 | | Amendment #3, dated September 15, 2003, to Worldwide Authorized Distributor Market Price Agreement, dated July 22, 1993, by and between Sipex and Future Electronics Inc. | | 10-Q† | | 0-27892 | | 10.3 | | 9/21/2006 | | |
113
| | | | | | | | | | | | |
Exhibit Number | | | | Incorporated by Reference | | Filed Herewith |
| Exhibit | | Form | | File No. | | Exhibit | | Filing Date | |
10.29 | | Amendment #4, dated April 25, 2006, to Worldwide Authorized Distributor Market Price Agreement, dated July 22, 1993, by and between Sipex and Future Electronics Inc. | | 10-Q† | | 0-27892 | | 10.4 | | 9/21/2006 | | |
| | | | | | |
10.30 | | Amendment #7, dated November 1, 2006, to Worldwide Authorized Distributor Market Price Agreement, dated July 22, 1993, by and between Sipex and Future Electronics Inc. | | 8-K† | | 0-27892 | | 10.1 | | 11/7/2006 | | |
| | | | | | |
10.31* | | Letter agreement as of August 24, 2005 with Mr. Edward Lam joining Sipex as the new Senior Vice President of Marketing and Business Development. | | 8-K† | | 0-27892 | | 10.1 | | 9/23/2005 | | |
| | | | | | |
10.32 | | Agreement for Purchase and Sale of Real Property, dated March 9, 2006, by and between Sipex and Mission West Properties, L.P. | | 8-K† | | 0-27892 | | 10.1 | | 3/13/2006 | | |
| | | | | | |
10.33 | | First Amendment, dated August 23, 2007, to Agreement for Purchase and Sale of Real Property, dated March 9, 2006, by and between Exar and Mission West Properties, L.P. | | 10-Q | | 0-14225 | | 10.23 | | 9/30/2007 | | |
| | | | | | |
10.34 | | Standard Form Lease, dated March 9, 2006, by and between Sipex and Mission West Properties, L.P. | | 8-K† | | 0-27892 | | 10.2 | | 3/13/2006 | | |
| | | | | | |
10.35 | | Securities Purchase Agreement, dated May 16, 2006, by and among Sipex and the Buyers listed on the Schedule of Buyers. | | 8-K† | | 0-27892 | | 10.1 | | 5/22/2006 | | |
| | | | | | |
10.36 | | Amendment No. 1, dated May 24, 2006 to Securities Purchase Agreement, dated May 16, 2006, by and among Sipex and the Buyers listed on the Schedule of Buyers. | | 8-K† | | 0-27892 | | 10.1 | | 5/30/2006 | | |
| | | | | | |
10.37 | | Securities Purchase Agreement, dated March 29, 2007, by and between Sipex and Rodfre Holdings LLC. | | 10-K† | | 0-27892 | | 10.36 | | 3/30/2007 | | |
| | | | | | |
10.38 | | Form of Sipex Voting Agreement | | 8-K | | 0-14225 | | 10.1 | | 5/8/2007 | | |
| | | | | | |
10.39 | | Form of Exar Voting Agreement | | 8-K | | 0-14225 | | 10.2 | | 5/8/2007 | | |
| | | | | | |
10.40 | | Lock-up and Standstill Agreement between Exar Corporation and Rodfre Holdings LLC, dated May 7, 2007. | | 8-K | | 0-14225 | | 10.3 | | 5/8/2007 | | |
| | | | | | |
10.41* | | Employment Agreement by and between Exar Corporation and Ralph Schmitt, dated May 7, 2007. | | 8-K | | 0-14225 | | 10.4 | | 5/8/2007 | | |
114
| | | | | | | | | | | | |
Exhibit Number | | | | Incorporated by Reference | | Filed Herewith |
| Exhibit | | Form | | File No. | | Exhibit | | Filing Date | |
10.42 | | Form of Affiliate Agreement. | | S-4 | | 333-143243 | | 10.4 | | 5/24/2007 | | |
| | | | | | |
10.43* | | Fiscal 2009 Senior Executive Incentive Compensation Program. | | 8-K | | 0-14225 | | 10.1 | | 3/10/2008 | | |
| | | | | | |
10.44* | | Agreement between Exar Corporation and John S. McFarlane, dated December 19, 2007. | | 8-K | | 0-14225 | | 10.1 | | 12/20/2007 | | |
| | | | | | |
10.45* | | Separation and General Release Agreement between Exar Corporation and Ralph Schmitt, dated December 29, 2007. | | 8-K | | 0-14225 | | 10.1 | | 1/10/2008 | | |
| | | | | | |
10.46 | | Amendment #6, dated September 27, 2006, to Worldwide Authorized Distributor Market Price Agreement, dated July 22, 1993, by and between Sipex and Future Electronics Inc. (as previously filed as Exhibit 10.1 to Sipex’s Current Report). | | 8-K† | | 0-27892 | | 10.1 | | 10/3/2006 | | |
| | | | | | |
10.47 | | Sublease Agreement, dated January 16, 2008, by and between Exar Corporation and Kovio, Inc., under that certain Standard Form Lease entered into with Mission West Properties, L.P., dated March 9, 2006. | | 8-K | | 0-14225 | | 10.1 | | 1/23/2008 | | |
| | | | | | |
10.48 | | Agreement for Public Sale of Assets of FyreStorm, Inc. by Horizon Technology Funding Company LLC and Sand Hill Venture Debt III, LLC to Exar Corporation, dated January 31, 2008. | | 8-K | | 0-14225 | | 10.1 | | 2/12/2008 | | |
| | | | | | |
10.49* | | Executive Officers’ Group II Change of Control Severance Benefit Plan. | | 10-Q | | 0-14225 | | 10.1 | | 2/6/2009 | | |
| | | | | | |
10.50* | | 2006 Equity Incentive Plan. | | DEF 14A | | 0-14225 | | | | 8/9/2006 | | |
| | | | | | |
10.51* | | Form of Notice of Grant and Terms and Conditions of Nonqualified Stock Option for the 2006 Equity Incentive Plan. | | 8-K | | 0-14225 | | 10.2 | | 9/13/2006 | | |
| | | | | | |
10.52* | | Form of Notice of Grant and Terms and Conditions of Incentive Stock Option for the 2006 Equity Incentive Plan. | | 8-K | | 0-14225 | | 10.3 | | 9/13/2006 | | |
| | | | | | |
10.53* | | Form of Director Nonqualified Stock Option Agreement for the 2006 Equity Incentive Plan | | 8-K | | 0-14225 | | 10.6 | | 9/13/2006 | | |
| | | | | | |
10.54* | | Form of Stock Unit Award Agreement for the 2006 Equity Incentive Plan. | | 10-Q | | 0-14225 | | 10.2 | | 2/6/2009 | | |
115
| | | | | | | | | | | | |
Exhibit Number | | | | Incorporated by Reference | | Filed Herewith |
| Exhibit | | Form | | File No. | | Exhibit | | Filing Date | |
10.55* | | Form of Director Restricted Stock Unit Award Agreement for the 2006 Equity Incentive Plan. | | 10-Q | | 0-14225 | | 10.3 | | 2/6/2009 | | |
| | | | | | |
10.56* | | Form of Performance Stock Unit Award Agreement for the 2006 Equity Incentive Plan. | | 10-Q | | 0-14225 | | 10.4 | | 2/6/2009 | | |
| | | | | | |
10.57* | | Amended and Restated Employment Agreement, dated December 31, 2008, by and between Exar Corporation and J. Scott Kamsler. | | 10-Q | | 0-14225 | | 10.5 | | 2/6/2009 | | |
| | | | | | |
10.58* | | Amended and Restated Employment Agreement, dated December 19, 2008, by and between Exar Corporation and Pedro (Pete) P. Rodriguez. | | 10-Q | | 0-14225 | | 10.6 | | 2/6/2009 | | |
| | | | | | |
10.59 | | Tender and Voting Agreement, dated as of February 23, 2009, among Exar Corporation and the Stockholders signatory thereto. | | 8-K | | 0-14225 | | 99.1 | | 2/27/2009 | | |
| | | | | | |
21.1 | | Subsidiaries of the Company. | | | | | | | | | | X |
| | | | | | |
23.1 | | Consent of Independent Registered Public Accounting Firm, PricewaterhouseCoopers LLP. | | | | | | | | | | X |
| | | | | | |
24.1 | | Power of Attorney. Reference is made to the signature page 93. | | | | | | | | | | X |
| | | | | | |
31.1 | | Principal Executive Officer Certification pursuant to Section 302 of the Sarbanes-Oxley Act of 2002. | | | | | | | | | | X |
| | | | | | |
31.2 | | Principal Financial Officer Certification pursuant to Section 302 of the Sarbanes-Oxley Act of 2002. | | | | | | | | | | X |
| | | | | | |
32.1 | | Certification of Chief Executive Officer Pursuant to 18 U.S.C. Section 1350, as Adopted Pursuant to Section 906 of the Sarbanes-Oxley Act of 2002. | | | | | | | | | | X |
| | | | | | |
32.2 | | Certification of Chief Financial Officer Pursuant to 18 U.S.C. Section 1350, as Adopted Pursuant to Section 906 of the Sarbanes-Oxley Act of 2002. | | | | | | | | | | X |
* | Indicates management contracts or compensatory plans or arrangements filed pursuant to Item 601(b)(10) of Regulation S-K. |
+ | Portions of this agreement have been omitted pursuant to a request for confidential treatment and the omitted portions have been filed separately with the Securities and Exchange Commission. |
++ | Portions of this agreement have been omitted pursuant to a request for confidential treatment and the omitted portions have been filed separately with the Securities and Exchange Commission. Schedules, exhibits and similar attachments have also been excluded, copies of which will be furnished supplemental to the Securities and Exchange Commission upon request. |
+++ | Related Forms of Stock Option Grant and Exercise filed as part of an exhibit to Exar’s Annual Report on Form 10-K for fiscal year ended March 31, 2005, and incorporated herein by reference. |
116