UNITED STATES
SECURITIES AND EXCHANGE COMMISSION
Washington, D.C. 20549
FORM 10-K
/X/ ANNUAL REPORT PURSUANT TO SECTION 13 OR 15(d) OF THE SECURITIES EXCHANGE ACT OF 1934 FOR THE FISCAL YEAR ENDED October 29, 2005 |
OR |
/ / TRANSITION REPORT PURSUANT TO SECTION 13 OR 15(d) OF THE SECURITIES EXCHANGE ACT OF 1934 FOR THE TRANSITION PERIOD From _________ to ________. |
Commission File number 1-9299 |
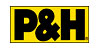
JOY GLOBAL INC.
(Exact Name of Registrant as Specified in Its Charter)
Delaware (State of Incorporation) | | 39-1566457 (I.R.S. Employer Identification No.) |
| | |
100 East Wisconsin Ave, Suite 2780, Milwaukee, Wisconsin (Address of principal executive offices) | | 53202 (Zip Code) |
| | |
Registrant’s Telephone Number, Including Area Code: (414) 319-8500 |
Securities registered pursuant to Section 12(b) of the Act:
8.75% Senior Subordinated Notes due 2012
(Title of Class)
Securities registered pursuant to Section 12(g) of the Act:
Common Stock, $1 Par Value
Preferred Stock Purchase Rights
(Title of Class)
Indicate by check mark whether the registrant (1) has filed all reports required to be filed by Section 13 or 15(d) of the Securities Exchange Act of 1934 during the preceding 12 months, and (2) has been subject to such filing requirements for the past 90 days. Yes [ X ] No [ ]
Indicate by check mark if disclosure of delinquent filers pursuant to Item 405 of Regulation S-K is not contained herein, and will not be contained, to the best of registrant’s knowledge, in definitive proxy or information statements incorporated by reference in Part III of this Form 10-K or any amendment to this Form 10-K. [ X ]
Indicate by check mark whether the registrant is an accelerated filer (as defined in Exchange Act Rule 12b-2) Yes [ X ] No [ ]
Indicate by check mark whether the registrant has filed all documents and reports required to be filed by Section 12, 13 or 15(d) of the Securities Exchange Act of 1934 subsequent to the distribution of securities under a plan confirmed by a court. Yes [ X ] No [ ]
The aggregate market value of Registrant’s Common Stock held by non-affiliates, as of April 29, 2005 the last business day of our most recently completed second fiscal quarter, based on a closing price of $22.58 per share, was approximately $2,723 million.
The number of shares outstanding of Registrant’s Common Stock, as of December 12, 2005, was 121,522,332.
Documents incorporated by reference: the information required by Part III, Items 10, 11, 12 and 13, is incorporated herein by reference to the Proxy Statement for the Company’s 2006 annual meeting of stockholders.
Joy Global Inc.
INDEX TO
ANNUAL REPORT ON FORM 10-K
For The Year Ended October 29, 2005
PART I
This document contains forward-looking statements. When used in this document, terms such as “anticipate,” “believe,” “estimate,” “expect,” “indicate,” “may be,” “objective,” “plan,” “predict,” “will be,” and the like are intended to identify forward-looking statements. Forward-looking statements involve risks and uncertainties and are not guarantees of future performance. Actual results may differ for a variety of reasons, many of which are beyond our control. Forward-looking statements are based upon our expectations at the time they are made. Although we believe that our expectations are reasonable, we can give no assurance that our expectations will prove to be correct. Important factors that could cause actual results to differ materially from such expectations (“Cautionary Statements”) are described generally below and disclosed elsewhere in this document. All subsequent written or oral forward-looking statements attributable to us or persons acting on our behalf are expressly qualified in their entirety by the Cautionary Statements. We undertake no obligation to publicly update or revise any forward-looking statements, whether as a result of new information, future events or otherwise.
Factors that could cause actual results to differ materially from those contemplated include:
Factors affecting our customers’ purchases of new equipment, rebuilds, parts and services such as: production capacity, stockpiles and production and consumption rates of coal, copper, iron ore, gold, oil sands and other ores and minerals; the cash flows and capital expenditures of our customers; the cost and availability of financing to our customers and their ability to obtain regulatory approval for investments in mining projects; consolidations among customers; changes in environmental regulations; work stoppages at customers or providers of transportation; and the timing, severity and duration of customer buying cycles.
Factors affecting our ability to capture available sales opportunities, including: our customers’ perceptions of the quality and value of our products and services as compared to our competitors’ products and services; our ability to commit to delivery schedules targeted by our customers; whether we have successful reference installations to display to customers; customers’ perceptions of our financial health and stability as compared to our competitors; our ability to assist customers with competitive financing programs; the availability of steel, castings, forgings, bearings and other materials; and the availability of manufacturing capacity at our factories.
Factors affecting general business levels, such as: political and economic turmoil in major markets such as the United States, Australia, Botswana, Brazil, Canada, Chile, China, Colombia, Europe, India, Indonesia, Mexico, Peru, Poland, Russia, South Africa, Venezuela and Zambia; environmental and trade regulations; commodity prices; and the stability and ease of exchange of currencies.
Factors affecting our ability to successfully manage sales we obtain, such as: the accuracy of our cost and time estimates for major projects and long-term maintenance and repair contracts; the adequacy of our systems to manage major projects and our success in completing projects on time and within budget; our success in recruiting and retaining managers and key employees; wage stability and cooperative labor relations; plant capacity and utilization; and whether acquisitions are assimilated and divestitures completed without notable surprises or unexpected difficulties.
Factors affecting our general business or financial position, such as: unforeseen patent, tax, product (including asbestos-related and silicosis liability), environmental, employee health and benefits, or contractual liabilities; changes in pension and post-retirement benefit costs; nonrecurring restructuring and other special charges; changes in accounting or tax rules or regulations; reassessments of asset valuations for such assets as receivables, inventories, fixed assets, intangible assets and deferred tax assets; and leverage and debt service.
Item 1. Business
General
Joy Global Inc. is the world’s leading manufacturer and servicer of high productivity mining equipment for the extraction of coal and other minerals and ores. Our equipment is used in major mining centers throughout the world to mine coal, copper, iron ore, oil sands and other minerals. We operate in two business segments: underground mining machinery (Joy Mining Machinery or “Joy”) and surface mining equipment (P&H Mining Equipment or “P&H”). Joy is a major manufacturer of underground mining equipment for the extraction of coal and other bedded minerals and offers comprehensive service locations near major mining regions worldwide. P&H is a major producer of surface mining equipment for the extraction of ores and minerals and provides extensive operational support for many types of equipment used in surface mining. Sales of original equipment for the mining industry, as a class of products, accounted for 27%, 31% and 37% of our consolidated sales for Fiscal 2003, Fiscal 2004 and Fiscal 2005, respectively. Aftermarket sales, which includes revenues from maintenance and repair services, mining equipment and electric motor rebuilds, equipment erection services and sales of replacement parts, account for the remainder of our consolidated sales for each of those years. Because these aftermarket sales generally include a combination of various products and services, it would be impracticable to determine whether any other class of products or services could be considered to exceed 10% of our consolidated revenues in any of the past three fiscal years.
We are the direct successor to a business begun over 120 years ago and were known as Harnischfeger Industries, Inc. (the “Predecessor Company”) prior to our emergence from protection under Chapter 11 of the U.S. Bankruptcy Code on July 12, 2001.
Underground Mining Machinery
Joy is the world’s largest producer of high productivity underground mining machinery for the extraction of coal and other bedded materials. It has significant facilities in Australia, South Africa, the United Kingdom, and the United States as well as sales offices and service facilities in China, India, Poland, and Russia. Joy products include: continuous miners; longwall shearers; roof supports; armored face conveyors; shuttle cars; flexible conveyor trains; continuous haulage systems; complete longwall mining systems (consisting of roof supports, an armored face conveyor and a longwall shearer); and roof bolters. Joy also maintains an extensive network of service and replacement parts distribution centers to rebuild and service equipment and to sell replacement parts in support of its installed base. This network includes seven service centers in the United States and ten outside of the United States, all of which are strategically located in major underground mining regions.
Products and Services:
Continuous miners – Electric, self-propelled continuous miners cut coal using carbide-tipped bits on a horizontal rotating drum. Once cut, the coal is gathered onto an internal conveyor and loaded into a haulage vehicle or continuous haulage system for transportation to the main mine belt.
Longwall shearers – A longwall shearer moves back and forth on a conveyor parallel to the coal face. Using carbide-tipped bits on cutting drums at each end, the shearer cuts a meter or more of coal on each pass and simultaneously loads the coal onto an armored face conveyor for transport to the main mine belt.
Roof supports – Roof supports support the mine roof during longwall mining. The supports advance with the longwall shearer, resulting in controlled roof falls behind the supports. A longwall face may range up to 400 meters in length.
Armored face conveyors – Armored face conveyors are used in longwall mining to transport coal cut by the shearer to the main mine belt.
Shuttle cars – Shuttle cars, a type of haulage vehicle, are electric, rubber-tired vehicles used to transport coal from continuous miners to the main mine belt where self-contained chain conveyors in the shuttle cars unload the coal onto the belt. Some models of Joy shuttle cars can carry up to 20 metric tons of coal.
Flexible conveyor trains (FCT)– FCT’s are electric-powered, self-propelled conveyor systems that provide continuous haulage of coal from a continuous miner to the main mine belt. The FCT’s coal conveyor belt operates independently from the track chain propulsion system, allowing the FCT to move and convey coal simultaneously. Available in lengths of up to 570 feet, the FCT is able to negotiate multiple 90-degree turns in an underground mine infrastructure.
Continuous chain haulage systems– A continuous chain haulage system transports coal from the continuous miner to the main mine belt on a continuous basis versus the batch process used by shuttle cars and battery haulers. It is made up of a series of connected bridge structures that use chain conveyors to transport coal from one bridge structure to the next bridge structure and ultimately to the main mine belt.
Roof bolters – Roof bolters are roof drills used to bore holes in the mine roof and to insert long metal bolts into the holes to reinforce the mine roof.
Joy’s aftermarket infrastructure quickly and efficiently provides customers with high-quality parts, exchange components, repairs, rebuilds, whole machine exchanges and services. Joy’s cost-per-ton programs allow its customers to pay fixed prices for each ton of material mined in order to match equipment costs with revenues, to reduce capital requirements, and to ensure quality aftermarket parts and services for the life of the contract. Joy sells its products and services directly to its customers through a global network of sales and marketing personnel.
The Joy business has demonstrated cyclicality over the years. This cyclicality is driven primarily by product life cycles, new product introductions, competitive pressures and other economic factors affecting the mining industry, such as commodity prices (particularly coal prices) and industry consolidation. Joy’s business is particularly sensitive to conditions in the coal mining industry, which accounts for over 90% of Joy’s sales.
Surface Mining Equipment
P&H is the world’s largest producer of electric mining shovels and a leading producer of rotary blasthole drills and walking draglines for open-pit mining operations. P&H has facilities in Australia, Brazil, Canada, Chile, China, South Africa, the United States, and Venezuela, as well as sales offices in India, Mexico, Peru, Russia, and the United Kingdom. P&H products are used in mining copper, coal, iron ore, oil sands, silver, gold, diamonds, phosphate, and other minerals and ores. P&H also provides a wide range of parts and services to mines through its P&H MinePro Services distribution group. In some markets, electric motor rebuilds and other selected products and services are provided to the industrial segment. P&H also sells used electric mining shovels in some markets. In November 2005, after the end of our latest fiscal year, P&H sold The Horsburgh & Scott Co., a subsidiary that makes industrial gears and mechanical gear drives for a range of industrial markets.
Products and Services:
Electric mining shovels – Mining shovels are primarily used to load copper ore, coal, iron ore, other mineral-bearing materials and overburden into trucks or other conveyances. There are two basic types of mining loaders — electric shovels and hydraulic excavators. Electric mining shovels feature larger buckets, allowing them to load greater volumes of material, while hydraulic shovels are smaller and more maneuverable. The electric mining shovel offers the lowest cost per ton of mineral mined. Its use is determined by the size of the mining operation and the availability of electricity. P&H manufactures only electric mining shovels. Dippers can range in size from 12 to 82 cubic yards.
Walking draglines – Draglines are primarily used to remove overburden to uncover a coal or mineral deposit and then to replace the overburden during reclamation activities. P&H’s draglines weigh from 500 to 7,500 tons, with bucket sizes ranging from 30 to 160 cubic yards.
Blasthole drills – Most surface mines require breakage or blasting of rock, overburden, or ore using explosives. A pattern of holes is created by a blasthole drill to contain the explosives. Drills are usually described in terms of the diameter of the hole they bore. Blasthole drills manufactured by P&H bore holes ranging in size from 8 5/8 to 22 inches in diameter.
P&H MinePro Services provides life cycle management support, including equipment erections, relocations, inspections, service, repairs, rebuilds, upgrades, used equipment, new and used parts, enhancement kits and training. The term “life cycle management” refers to our strategy to maximize the productivity of our equipment over the equipment’s entire operating life cycle through the optimization of the equipment, its operating and maintenance procedures and its upgrade and refurbishment. Each life cycle management program we offer is specifically designed for a particular customer and that customer’s application of our equipment. Under each life cycle management program, we provide the customer with specific aftermarket products and services to support the equipment during its operating life cycle. Under some of the programs, the customer pays us an amount based upon hours of operation or units of production achieved by the equipment. The amount to be paid per unit is determined by the economic model we develop on a case-by-case basis, and is set at a rate designed to include both the estimated costs we expect to incur and our anticipated profit. Through life cycle management contracts, MinePro reduces customer operating risk and guarantees availability levels.
P&H MinePro Services personnel and MinePro distribution centers are strategically located close to customers in major mining centers around the world, supporting P&H and other brands. P&H sells its products and services directly to its customers through a global network of sales and marketing personnel. The P&H MinePro Services distribution organization also represents other leading providers of equipment and services to the mining and associated industries, which we refer to as Alliance Partners. Some of the P&H Alliance Partner relationships include the following companies:
| |
---|
• AmeriCable Incorporated • Berkley Forge and Tool Inc. • Bridon American Corporation • Carbone of America • General Electric Industrial Systems • Hensley Industries Inc. • Hitachi Mining Division • Immersive Technologies Pty Ltd. • LeTourneau Inc. | • Lincoln Industrial • MacWhyte • Phillippi-Hagenbach Inc. • Prodinsa Wire Rope • Petro-Canada • Reedrill • Rimex Supply Ltd • Terex Materials Processing & Mining • Wire Rope Industries Ltd.
|
P&H’s businesses are subject to cyclical movements in the markets. Sales of original equipment are driven to a large extent by commodity prices. Copper mining, coal mining and iron ore mining accounted for approximately 40%, 26% and 17%, respectively, of total P&H sales in recent years. Rising commodity prices typically lead to the expansion of existing mines, opening of new mines or re-opening of less efficient mines. Although the aftermarket segment is much less cyclical, severe reductions in commodity prices can result in the removal of machines from mining production, and thus dampen demand for parts and services. Conversely, significant increases in commodity prices can result in higher use of equipment and generate requirements for more parts and services.
Both of our business segments are subject to moderate seasonality, with the first quarter of the fiscal year generally experiencing lower sales due to a decrease in production hours caused by the Thanksgiving and Christmas holidays.
Financial Information
Financial information about our business segments and geographic areas of operation is contained in Item 8 –Financial Statements and Supplementary Data and Item 15 –Exhibits and Financial Statement Schedules.
Employees
As of October 29, 2005, we employed approximately 7,900 people with approximately 3,800 employed in the United States. Local unions represent approximately 47% of our U.S. employees under collective bargaining agreements. Approximately 43% of our U.S. employees are covered by collective bargaining agreements which expire in Fiscal 2006. We believe that we maintain generally good relationships with our employees.
Customers
Joy and P&H sell their products primarily to large global and regional mining companies. No customer or affiliated group of customers accounted for 10% or more of our consolidated sales for Fiscal 2005.
Competitive Conditions
Joy and P&H conduct their domestic and foreign operations under highly competitive market conditions, requiring that their products and services be competitive in price, quality, service and delivery. The customers for these products are generally large mining companies with substantial purchasing power.
Joy’s continuous miners, longwall shearers, continuous haulage systems, roof supports and armored face conveyors compete with similar products made by a number of worldwide manufacturers of such equipment. Joy’s rebuild services compete with a large number of local repair shops. Joy competes with various regional suppliers in the sale of replacement parts for Joy equipment.
P&H’s shovels and draglines compete with similar products and with hydraulic excavators, large rubber-tired front-end loaders and bucket wheel excavators made by several international manufacturers. P&H’s large rotary blasthole drills compete with several worldwide drill manufacturers. Manufacturer location is not a significant advantage or disadvantage in this industry. P&H MinePro Services competes with a large number of primarily regional suppliers in the sale of parts.
Both Joy and P&H compete on the basis of providing superior productivity, reliability and service and lower overall cost of production to their customers. Both Joy and P&H compete with local and regional service providers in the provision of maintenance, rebuild and other services to mining equipment users.
Backlog
Backlog represents unfilled customer orders for our products and services. The customer orders that are included in the backlog represent commitments to purchase specific products or services from us by customers who have satisfied our credit review procedures. The following table provides backlog by business segment as of the fiscal year end. These backlog amounts exclude customer arrangements under long-term equipment life cycle management programs. Such programs extend for up to fourteen years and totaled approximately $528.8 million as of October 29, 2005. Sales already recognized by fiscal year-end under the percentage-of-completion method of accounting are also excluded from the amounts shown.
In thousands
| 2005
| 2004
| 2003
|
---|
Underground Mining Machinery | | | $ | 661,326 | | $ | 434,317 | | $ | 146,748 | |
Surface Mining Equipment | | | | 393,520 | | | 256,734 | | | 85,222 | |
|
| |
| |
| |
Total Backlog | | | $ | 1,054,846 | | $ | 691,051 | | $ | 231,970 | |
|
| |
| |
| |
The change in backlog for Underground Mining Machinery from October 30, 2004 to October 29, 2005 reflects more orders than shipments for continuous miners, shuttle cars and shearers. The increase in backlog for Surface Mining Equipment over the same period primarily reflects more orders than sales for new machines and parts partially offset by more sales than orders in service. Of the $1,055 million of backlog, approximately $77.1 million is expected to be recognized as revenue beyond the Fiscal 2006 year.
The change in backlog for Underground Mining Machinery from November 1, 2003 to October 30, 2004 substantially reflects more orders than shipments for continuous miners, shuttle cars, roof supports, armored face conveyors and aftermarket complete machine rebuilds. The increase in backlog for Surface Mining Equipment over the same period primarily reflects more orders than sales for new machines, parts and service.
Raw Materials
Joy purchases electric motors, gears, hydraulic parts, electronic components, forgings, steel, clutches and other components and raw materials from outside suppliers. Although Joy purchases certain components and raw material from a single source, alternative suppliers are generally available for all such items. During the second half of Fiscal 2005, we experienced some difficulty obtaining certain types of bearings that we had been purchasing from a sole supplier and at times we were not able to obtain these bearings from alternative sources, which delayed some of our product shipments. To mitigate the potential impact of this supply constraint, in Fiscal 2006 we expect to develop alternative sources for some of the new bearings we would otherwise procure from our sole supplier. Although we believe that it would be possible to obtain bearings from other sources in the event that supplies of bearings are reduced further, we expect that it would be difficult to do so and there would likely be some delay in securing these alternative sources. We expect that we could replace all other exclusive suppliers within a reasonable timeframe, although it is possible that we would experience delays in obtaining the relevant components and raw materials from these alternative sources as well. Due to the importance of bearings to our original equipment and aftermarket sales, substantially all the sales of our underground mining equipment business, which accounted for 59% of our consolidated sales in Fiscal 2005, depend on components and raw materials that we purchase from a single source.
P&H purchases raw and semi-processed steel, castings, forgings, copper and other materials from a number of suppliers. In addition, component parts such as engines, bearings, controls, hydraulic components and a wide variety of mechanical and electrical items are purchased from a group of pre-qualified suppliers.
During Fiscal 2004 and much of Fiscal 2005, worldwide steel prices rose in response to higher demand caused by a recovering end-market and higher consumption in emerging market countries, such as China. This has resulted in steel surcharges being added both directly and indirectly from suppliers of castings, forgings and other products. The availability of steel has also been problematic on occasion during Fiscal 2004 and Fiscal 2005. See “Management’s Discussion and Analysis of Financial Condition and Results of Operations” for a discussion of the impact of rapidly rising steel and component costs on Fiscal 2004 and Fiscal 2005 results and on our Fiscal 2006 outlook.
In Fiscal 2002 and Fiscal 2003, we combined our purchases of certain significant categories of raw materials and components at Joy and P&H and established strategic partnerships with selected suppliers. After a comprehensive evaluation, approximately 80 suppliers were awarded Strategic Alliance relationships. These relationships were established to leverage the combined purchases of Joy and P&H, raise standards for supplier performance, and enhance our ability to pursue additional process improvement and cost reduction opportunities.
Patents and Licenses
We own numerous patents and trademarks and have patent licenses from others relating to our products and manufacturing methods. Also, we have granted patent and trademark licenses to other manufacturers and receive royalties under most of these licenses. While we do not consider any particular patent or license or group of patents or licenses to be material to either of our business segments, we believe that in the aggregate our patents and licenses are significant in distinguishing many of our product lines from those of our competitors. The remaining duration of our patents and licenses range from less than one year to 20 years and averages approximately nine years.
Research and Development
We are strongly committed to pursuing technological development through the engineering of new products and systems, the improvement and enhancement of licensed technology, and synergistic acquisitions of technology. Research and development expenses were $8.5 million, $6.3 million and $3.8 million for Fiscal 2005, Fiscal 2004, and Fiscal 2003, respectively, not including application engineering.
Environmental, Health and Safety Matters
Our domestic activities are regulated by federal, state and local statutes, regulations and ordinances relating to both environmental protection and worker health and safety. These laws govern current operations, require remediation of environmental impacts associated with past or current operations, and under certain circumstances provide for civil and criminal penalties and fines as well as injunctive and remedial relief. Our foreign operations are subject to similar requirements as established by their respective countries.
We believe that we have substantially satisfied these diverse requirements. Because these requirements are complex and, in many areas, rapidly evolving, there can be no guarantee against the possibility of sizeable additional costs for compliance in the future. However, we do not expect that our compliance with environmental laws and regulations will have a material effect on our capital expenditures, earnings or competitive position, and do not expect to make any material capital expenditures for environmental control facilities in Fiscal 2006 or Fiscal 2007.
Our operations or facilities have been and may become the subject of formal or informal enforcement actions or proceedings for alleged noncompliance with either environmental or worker health and safety laws or regulations. Such matters have typically been resolved through direct negotiations with the regulatory agency and have typically resulted in corrective actions or abatement programs. However, in some cases, fines or other penalties have been paid.
International Operations
In Fiscal 2005, 2004 and 2003, approximately 55%, 54% and 53% of our sales were derived from sales outside the United States. Risks faced by our international operations include:
| • | | increased risk of litigation and other disputes with customers, such as the recently resolved disputes with Sokolovskaya Investment Company and the government of Egypt; |
| • | | regional or country-specific economic downturns, such as the 1997 Asian economic crisis; |
| • | | fluctuations in currency exchange rates, including the British pound sterling, South African rand and Australian dollar; |
| • | | unexpected changes in regulatory requirements, such as the possibility of new Black Economic Empowerment requirements in South Africa; |
| • | | higher tax rates and potentially adverse tax consequences, including restrictions on repatriating earnings, adverse tax withholding requirements and "double taxation"; |
| • | | costs and difficulties in integrating, staffing and managing international operations, especially in rapidly growing economies such as China; |
| • | | natural disasters and the greater difficulty in recovering from them, especially in countries prone to earthquakes, such as Indonesia, India, China and Chile; |
| • | | difficulties protecting our intellectual property; |
| • | | longer payment cycles and difficulty in collecting accounts receivable; |
| • | | complications in complying with a variety of foreign laws and regulations; |
| • | | customs matters and changes in trade policy or tariff regulations; |
| • | | transportation delays and interruptions; and |
| • | | uncertainties arising from local business practices, cultural considerations and international political and trade tensions. |
Available Information
Our internet address is:www.joyglobal.com. We make our annual report on Form 10-K, quarterly reports on Form 10-Q, current reports on Form 8-K, and amendments to those reports filed or furnished pursuant to Section 13(a) or 15(d) of the Exchange Act available free of charge through our website as soon as reasonably practicable after we electronically file such material with, or furnish it to, the SEC.
Item 2. Properties
As of October 29, 2005 the following principal properties of our operations were owned, except as indicated. Our worldwide corporate headquarters are currently housed in 10,000 square feet of leased space in Milwaukee, Wisconsin. All of these properties are generally suitable for the operations currently conducted at them.
Underground Mining Machinery Locations
Location
| Floor Space (Sq. Ft.)
| Land Area (Acres)
| Principal Operations
|
---|
Franklin, Pennsylvania Warrendale, Pennsylvania
Reno, Pennsylvania
Brookpark, Ohio
Solon, Ohio
* Bluefield, Virginia * Duffield, Virginia * Homer City, Pennsylvania * Mt. Vernon, Illinois * Wellington, Utah Lebanon, Kentucky
* McCourt Road, Australia Parkhurst, Australia Wollongong, Australia (1)
* Steeledale, South Africa * Wadeville, South Africa
Secunda, South Africa (2)
Pinxton, England
Wigan, England (3)
* Worcester, England
Baotou, China (1)
* Mikolow, Poland (4) | 739,000
71,250
121,400
85,000
101,200
102,160 100,350 89,920 107,130 76,250 88,250
101,450 48,570 27,000
250,381 212,245
2,002
76,000
60,000
178,000
20,550
42,266 | 58
13
22
4
11
15 11 10 12 60 13
33 15 4
13 29
1
10
3
14
3
3 | Component and parts production.
Administration and warehouse.
Chain manufacturing.
Gear manufacturing.
Machining manufacturing.
Component repair and complete machine rebuilds.
Original equipment, component repairs and complete machine rebuilds.
Component repair and complete machine rebuilds
Original equipment, component repairs and complete machine rebuilds.
Sales Office
Component repair and complete machine rebuilds.
Engineering and administration.
Original equipment and component repairs.
Component repair.
Component repair and complete machine rebuilds.
|
Surface Mining Equipment Locations
Location
| Floor Space (Sq. Ft.)
| Land Area (Acres)
| Principal Operations
|
---|
Milwaukee, Wisconsin
* Milwaukee, Wisconsin
Cleveland, Ohio (6)
* Gillette,Wyoming Evansville, Wyoming * Mesa, Arizona * Elko, Nevada Kilgore, Texas
Calgary, Canada (3)
* Bassendean, Australia * Mackay, Australia
* Hemmant, Australia * Rockdale, Australia
Johannesburg, South Africa (5)
* Belo Horizonte, Brazil
* Santiago, Chile * Antofagasta, Chile | 684,000
180,000
270,000
60,000 25,000 40,000 30,000 12,400
14,500
72,500 35,500
23,724 23,724
44,000
37,700
6,800 21,000 | 46
13
8
6 6 5 5 4
1
5 2
2 10
1
1
1 1 | Electric mining shovels, walking draglines and blasthole drills.
Electrical products.
Gearing manufacturing.
Rebuild service center.
Climate control system manufacturing.
Components and parts for mining machinery.
Motor rebuild service center.
Rebuild service center.
Components and parts for mining shovels.
Rebuild service center. |
(1) Under a month to month lease.
(2) Under a lease expiring in 2007.
(3) Under a lease expiring in 2010.
(4) Under a lease expiring in 2018.
(5) Under a lease expiring in 2006.
(6) This facility is owned by The Horsburgh & Scott Co., which was sold subsequent to year-end. See Footnote 16 — Discontinued Operations and Held for Sale Assets and Liabilities.
* Property includes a warehouse.
Joy also operates warehouses in Meadowlands, Pennsylvania, Green River, Wyoming; Pineville, West Virginia; Brookwood, Alabama; Carlsbad, New Mexico; Price, Utah; Norton, Virginia; Lovely and Henderson, Kentucky; Emerald, Moss Vale, Thornton and Lithgow, Australia; Hendrina and Secunda, South Africa; Siberia, Russia; and Chirimiri, India. All warehouses are owned except for the warehouses in Price, Utah; Lovely and Henderson, Kentucky; Moss Vale and Thornton, Australia; and Secunda, South Africa, which are leased.
P&H also operates warehouses in Cleveland, Ohio; Hibbing and Virginia, Minnesota; Charleston, West Virginia; Negaunee, Michigan; Hinton, Sparwood, Labrador City, Fort McMurray, Sept. Iles and Baie-Comeau, Canada; Mt. Thorley, Australia; Iquique and Calama, Chile; Johannesburg, South Africa; and Puerto Ordaz, Venezuela. The warehouses in Hibbing, Fort McMurray, Johannesburg, Mt. Thorley, and Calama are owned; the others are leased. In addition, P&H leases sales offices throughout the United States and in principal surface mining locations in other countries.
Item 3. Legal Proceedings
We and our subsidiaries are involved in various unresolved legal matters that arise in the normal course of operations, the most prevalent of which relate to product liability (including over 1,000 asbestos and silica-related cases), employment and commercial matters. Although the outcome of these matters cannot be predicted with certainty and favorable or unfavorable resolutions may affect the results of operations on a quarter-to-quarter basis, we believe that the outcome of such legal and other matters will not have a materially adverse effect on our consolidated financial position, results of operations or liquidity.
In litigation commenced in 2001 in the United States District Court for the District of Massachusetts, John G. Kling, purportedly on his own behalf and in a representative capacity for the Harnischfeger Industries Employees’ Savings Plan (the “Plan”), filed suit against us and certain of our present and former employees, officers and directors. This action was based on, among other things, allegations that certain of the defendants failed to properly discharge their fiduciary obligations under ERISA with respect to the “Harnischfeger Common Stock Fund” in the Harnischfeger Industries Employees’ Savings Plan. In September 2005, the parties entered into a Memorandum of Understanding setting forth the terms of a negotiated resolution of this lawsuit. We expect that a Stipulation of Settlement will be filed with the court early in 2006. The settlement is subject to review by an independent fiduciary appointed by the Plan and subject to approval by the court, which must provide prior notice to members of the provisional settlement class and hold a fairness hearing to consider any objections. Upon approval of the settlement, our insurers will be responsible for all payments required under its terms.
On November 9, 2005, Joy Mining Machinery Limited (“Joy MM”), a subsidiary located in the United Kingdom, entered into a settlement agreement with the government of Egypt, pursuant to which the parties agreed to terminate arbitration proceedings between them in the Cairo Arbitration Centre and related litigation. The proceedings related to an agreement entered into in 1998 between Joy MM and the General Organization for Industrial and Mining Projects, an agency of the government of Egypt, relating to underground mining equipment for the Abu Tartur project in Egypt.
On September 19, 2005, the arbitration panel in the ICC International Court of Arbitration proceedings between Sokolovskaya Investment Company (“SIC”) and Joy MM rendered a final decision and awarded damages and partial reimbursement of costs and legal fees to SIC. The dispute arose out of contracts for the supply of underground mining equipment and related services entered into between Joy MM and SIC, a Russian mining company, in 1995 and 1996. Under the rules applicable to ICC arbitration, we are prohibited from publicly disclosing the amount of the arbitration award. As a result of the award, in the fourth quarter of Fiscal 2005, we booked a charge against earnings of less than $0.03 per share.
On August 19, 2005, the United States Bankruptcy Court for the District of Delaware issued a final decree closing our Chapter 11 reorganization proceedings.
From time to time we and our subsidiaries become involved in proceedings relating to environmental matters. We believe that the resolution of such environmental matters will not have a materially adverse effect on our consolidated financial position, results of operations or liquidity.
Item 4. Submission of Matters to a Vote of Security Holders
No matters were submitted to a vote of security holders during the fourth quarter of Fiscal 2005.
Executive Officers of the Registrant
The following table shows certain information for each of our executive officers, including position with the corporation and business experience. Our executive officers are elected each year at the organizational meeting of our Board of Directors, which follows the annual meeting of shareholders, and at other meetings as appropriate.
Name
| Age
| Current Office and Principal Occupation
| Years as Officer
|
---|
John Nils Hanson Donald C. Roof
James A. Chokey
John J. Fons
Dennis R. Winkleman
Mark E. Readinger
Michael W. Sutherlin | 63 53
62
48
55
52
59 | President and Chief Operating Officer since 2000. He has been an officer of the registrant since 1995 and director since 1996. Executive Vice President, Chief Financial Officer and Treasurer since 2001. President and Chief Executive Officer of Heafner Tire Group, Inc. from 1999 to 2001 and Senior Vice President and Chief Financial Officer from 1997 to 1999.
Executive Vice President since 1997 and General Counsel from 1997 to 2005.
Executive Vice President and General Counsel since 2005. He was an independent consultant specializing in corporate governance and compliance from 2002 to 2005. Vice President, Secretary and General Counsel of Metso Minerals Industries, Inc. from 1995 to 2002 and Secretary and General Counsel from 1990 to 1995.
Executive Vice President Human Resources since 2000. Mr. Winkleman held similar positions with Midwest Generation LLC in 2000 and Beloit Corporation from 1997 to 2000.
Executive Vice President of Joy Global Inc. and President and Chief Operating Officer of P&H Mining Equipment, since 2002. President and Chief Executive Officer of Armillaire Technologies from 2001 to 2002. President and Chief Operating Officer of Beloit Corporation from 1998 to 2001. President and Chief Operating Officer of Joy Mining Machinery from 1996 to 1998.
Executive Vice President of Joy Global Inc. and President and Chief Operating Officer of Joy Mining Machinery, since 2003. President and Chief Operating Officer of Varco International, Inc. from 1999 to 2002 and Vice President of European Businesses and Senior Executive for Europe, Africa and Asia from 1995 to 1999. | 10
5
9
1
5
3
3 |
PART II
Item 5. Market for Registrant’s Common Equity, Related Stockholder Matters and Issuer Purchasesof
Equity Securities
Our common stock is traded on the Nasdaq National Market under the symbol “JOYG.” As of October 29, 2005, there were approximately 15,000 shareholders of record. The following table sets forth the high and low sales prices and dividend payments for our common stock for the periods indicated. All per share data shown below has been adjusted to reflect our 3-for-2 stock splits completed on January 21, 2005 and December 12, 2005.
| Price per Share
| Dividends
|
---|
| High
| Low
| Per Share
|
---|
2005 | | | | | | | | | | | |
First Quarter | | | $ | 19 | .57$ | | 14 | .56$ | | 0 | .050 |
Second Quarter | | | $ | 25 | .89$ | | 18 | .41$ | | 0 | .075 |
Third Quarter | | | $ | 27 | .31$ | | 22 | .15$ | | 0 | .075 |
Fourth Quarter | | | $ | 34 | .16$ | | 26 | .51$ | | 0 | .075 |
2004 | | | | | |
First Quarter | | | $ | 12 | .54$ | | 8 | .32$ | | 0 | .022 |
Second Quarter | | | $ | 13 | .56$ | | 11 | .00$ | | 0 | .033 |
Third Quarter | | | $ | 13 | .76$ | | 10 | .43$ | | 0 | .033 |
Fourth Quarter | | | $ | 16 | .12$ | | 11 | .97$ | | 0 | .033 |
2003 | | | | | |
First Quarter | | | $ | 5 | .85$ | | 4 | .09$ | | — | |
Second Quarter | | | $ | 5 | .67$ | | 4 | .41$ | | — | |
Third Quarter | | | $ | 7 | .29$ | | 5 | .38$ | | — | |
Fourth Quarter | | | $ | 8 | .58$ | | 6 | .31$ | | — | |
We made no repurchase of equity securities in the fourth quarter of Fiscal 2005.
Item 6. Selected Financial Data
The following table sets forth certain selected historical financial data on a consolidated basis. The selected consolidated financial data was derived from our Consolidated Financial Statements. As a result of the application of fresh start accounting, our financial statements are not comparable to those of the Predecessor Company. Accordingly, data for Fiscal 2001 is presented separately for the Predecessor Company’s fiscal period from November 1, 2000 to June 23, 2001 (“2001 Eight Months”) and our period from June 24, 2001 to October 31, 2001 (“2001 Four Months”). During the first quarter of Fiscal 2002, we amended our by-laws to adopt a 52- or 53-week fiscal year and changed our fiscal year-end date from October 31 to the Saturday nearest October 31. Beginning with the first quarter of Fiscal 2002, each of our fiscal quarters consists of 13 weeks, except for any fiscal years consisting of 53 weeks that will add one week to the first quarter. This change did not have a material effect on our revenue or results of operations for Fiscal 2002. The selected consolidated financial data should be read in conjunction with our Consolidated Financial Statements appearing in Item 8 –Financial Statements and Supplementary Data and Item 15 –Exhibits and Financial Statement Schedules. All per share data shown below has been adjusted to reflect our 3-for-2 stock splits completed on January 21, 2005 and December 12, 2005.
RESULTS OF OPERATIONS
In thousands except per share amounts
| Year Ended October 29, 2005
| Year Ended October 30, 2004
| Year Ended November 1, 2003
| Year Ended November 2, 2002
| 2001 Four Months
| Predecessor Company - -----------------
2001 Eight Months
|
---|
Net sales | | | $ | 1,927,474 | | $ | 1,399,357 | | $ | 1,185,701 | | $ | 1,126,349 | | $ | 397,180 | | $ | 719,069 | |
Operating income (loss) | | | | 266,690 | | | 107,846 | | | 48,033 | | | (14,054 | ) | | (52,101 | ) | | 44,269 | |
Income (loss) from continuing operations | | | $ | 146,921 | | $ | 55,456 | | $ | 18,769 | | $ | (27,432 | ) | $ | (76,741 | ) | $ | 50,138 | |
Income (loss) from discontinued operations | | | | 1,128 | | | (134 | ) | | (253 | ) | | (585 | ) | | 243 | | | (2,676 | ) |
Gain on disposal of discontinued operations | | | | — | | | — | | | — | | | — | | | — | | | 256,353 | |
Extraordinary gain on debt discharge | | | | — | | | — | | | — | | | — | | | — | | | 1,124,083 | |
|
| |
| |
| |
| |
| |
| |
Net income (loss) | | | $ | 148,049 | | $ | 55,322 | | $ | 18,516 | | $ | (28,017 | ) | $ | (76,498 | ) | $ | 1,427,898 | |
Basic Earnings (Loss) Per Share | | |
Income (loss) from continuing operations | | | $ | 1.21 | | $ | 0.47 | | $ | 0.17 | | $ | (0.24 | ) | $ | (0.68 | ) | $ | 1.07 | |
Income (loss) from and net gain on disposal of | | |
discontinued operations | | | | 0.01 | | | — | | | (0.01 | ) | | (0.01) | | | — | | | 5.42 | |
Extraordinary gain on debt discharge | | | | — | | | — | | | — | | | — | | | — | | | 24.01 | |
|
| |
| |
| |
| |
| |
| |
Net income (loss) per common share | | | $ | 1.22 | | $ | 0.47 | | $ | 0.16 | | $ | (0.25 | ) | $ | (0.68 | ) | $ | 30.50 | |
Diluted Earnings (Loss) Per Share | | |
Income (loss) from continuing operations | | | $ | 1.19 | | $ | 0.46 | | $ | 0.16 | | $ | (0.24 | ) | $ | (0.68 | ) | $ | 1.07 | |
Income from and net gain on disposal of | | |
discontinued operations | | | | 0.01 | | | — | | | — | | | (0.01) | | | — | | | 5.42 | |
Extraordinary gain on debt discharge | | | | — | | | — | | | — | | | — | | | — | | | 24.01 | |
|
| |
| |
| |
| |
| |
| |
Net income (loss) per common share | | | $ | 1.20 | | $ | 0.46 | | $ | 0.16 | | $ | (0.25 | ) | $ | (0.68 | ) | $ | 30.50 | |
Dividends Per Common Share | | | $ | 0.275 | | $ | 0.122 | | $ | — | | $ | — | | $ | — | | $ | — | |
Working capital | | | $ | 517,170 | | $ | 560,200 | | $ | 450,861 | | $ | 382,702 | | $ | 443,313 | | $ | 242,278 | |
Total Assets | | | | 1,648,528 | | | 1,440,359 | | | 1,286,729 | | | 1,257,339 | | | 1,371,714 | | | 1,314,451 | |
Total Long-Term Obligations | | | | 2,667 | | | 203,682 | | | 204,302 | | | 216,252 | | | 289,936 | | | 1,417,982 | |
Item 7. Management's Discussion and Analysis of Financial Condition and Results of Operations
The following discussion should be read in conjunction with the Consolidated Financial Statements and related notes. References made to years are for fiscal year periods. Dollar amounts are in thousands, except share and per-share data and as indicated. All per share data shown below has been adjusted to reflect our 3-for-2 stock splits completed on January 21, 2005 and December 12, 2005.
The purpose of this discussion and analysis is to enhance the understanding and evaluation of the results of operations, financial position, cash flows, indebtedness, and other key financial information of Joy Global Inc. and its subsidiaries for Fiscal 2005, Fiscal 2004, and Fiscal 2003. For a more complete understanding of this discussion, please read the Notes to Consolidated Financial Statements included in this report.
Overview
We are the direct successor to businesses that have been manufacturing mining equipment for over 120 years. We operate in two business segments: Underground Mining Machinery, comprised of our Joy Mining Machinery business (“Joy”), and Surface Mining Equipment, comprised of our P&H Mining Equipment business (“P&H”). Joy is the world’s largest producer of high productivity electric-powered underground mining equipment used primarily for the extraction of coal. P&H is the world’s largest producer of high productivity electric mining shovels and a leading producer of walking draglines and large rotary blasthole drills, used primarily for surface mining copper, coal, iron ore, oil sands and other minerals.
Over 87% of our sales are to the coal and copper mining industries. In addition to selling new equipment, we provide parts, components, repairs, rebuilds, diagnostic analysis, fabrication, training and other aftermarket services for our installed base of machines. In the case of Surface Mining Equipment, we also provide aftermarket services for equipment manufactured by other companies, including manufacturers with which we have ongoing relationships and which we refer to as “Alliance Partners.” We emphasize our aftermarket products and services as an integral part of lowering our customers’ cost per unit of production and are focused on continuing to grow this part of our business.
Demand for new equipment is cyclical in nature, being driven by commodity prices and other factors. Our new equipment sales over the last five years have ranged from a high of $716.8 million in Fiscal 2005 to a low of $316.4 million in Fiscal 2001. In contrast, our aftermarket business has shown consistent growth over the past five years despite commodity production restrictions and price volatility, and helps moderate the effects of changes in new equipment demand on our financial performance. Our aftermarket sales over the last five years have grown from $799.8 million in Fiscal 2001 to $1,210.7 million in Fiscal 2005.
Approximately 83% of our sales in Fiscal 2005 were recorded at the time of shipment of the product or delivery of the service. The remaining 17% of sales was recorded using percentage of completion accounting, a practice we follow in recognizing revenue on the sale of long lead-time equipment such as electric mining shovels, walking draglines and roof supports. Under percentage of completion accounting, revenue is recognized on firm orders from customers as the product is manufactured based on the ratio of actual costs incurred to estimated total costs to be incurred. We generally receive progress payments on long lead-time equipment.
The major components of our cost of sales are manufacturing overhead, labor and raw materials such as steel. We have taken significant steps to reduce manufacturing overhead. In recent years, we have been adversely affected by increases in the cost of raw materials, especially steel. The mix of original equipment and aftermarket sales affects our operating profit. Our aftermarket products generally carry higher margins than our original equipment and increases in our aftermarket sales have a favorable impact on our profitability. Although steel prices increased, our gross profit margin in Fiscal 2005 increased to 29.2% from 27.0% in Fiscal 2004.
In Fiscal 2005, approximately 45% of our sales were made to customers from the United States. With the exception of South Africa and Australia, our domestic and international sales are largely denominated in U.S. dollars or pounds sterling. From time to time, we hedge specifically identified committed cash flows using foreign currency sale or purchase contracts.
Results of Operations
2005 Compared with 2004
Sales
The following table sets forth Fiscal 2005 and Fiscal 2004 net sales as derived from our Consolidated Statement of Income:
In thousands
| Fiscal 2005
| Fiscal 2004
| $ Change
| % Change
|
---|
Net Sales | | | | | | | | | | | | | | |
Underground Mining Machinery | | | $ | 1,132,334 | | $ | 820,121 | | $ | 312,213 | | | 38 | .1% |
Surface Mining Equipment | | | | 795,140 | | | 579,236 | | | 215,904 | | | 37 | .3% |
|
| |
| |
| | |
Total | | | $ | 1,927,474 | | $ | 1,399,357 | | $ | 528,117 | | | 37 | .7% |
|
| |
| |
| | |
Total net sales for Fiscal 2005 increased by $528.1 million, or 37.7%, over Fiscal 2004 net sales. Net sales in the United States increased by $230.4 million, or 36.0%, and international net sales rose by $297.7 million, or 39.2%. Reflecting the cyclical upturn in commodities, original equipment revenues increased by approximately 65% to $716.8 million in Fiscal 2005, accounting for 37.2% of total revenues for the year. Aftermarket sales, which include sales of parts and services, increased approximately 26% to $1,210.7 million for Fiscal 2005.
The increase in net sales for Underground Mining Machinery in Fiscal 2005 compared to Fiscal 2004 was the result of a $188.5 million increase in shipments of original equipment combined with a $123.7 million increase in aftermarket products and service. The primary increases in original equipment sales were $77.3 million, $67.1 million and $43.3 million in the emerging markets served out of the United Kingdom, the United States and Australia, respectively. The increase in original equipment sales reflects the continuing strong activity levels for new equipment for both replacement of existing equipment and for new mining capacity. Increases in aftermarket net sales were reported in substantially all of our markets. Higher aftermarket sales in the United States accounted for approximately 60% of the overall increase in aftermarket sales. Approximately 40% of the increase in aftermarket sales was due to the increase in repair parts sales, another 40% due to complete machine rebuilds and the remaining increase was due to component repairs. The strong level of aftermarket sales in Fiscal 2005 reflected the continued high level of coal mining activity on a global basis.
The increase in net sales for Surface Mining Equipment in Fiscal 2005 compared to Fiscal 2004 was the result of a $90.7 million increase in original equipment combined with a $125.2 million increase in aftermarket parts and service. Increases in original equipment sales were reported in Canada, Mexico, the international markets we serve out of the United Kingdom (primarily Russia), Australia, Venezuela and Chile. Approximately 40% of the original equipment sales increase was due to shipments of electric mining shovels to Canada and approximately 20% was due to primarily to shipments of electric mining shovels to the international markets we serve out of the United Kingdom (primarily Russia) with the remainder attributable to the other markets. Increases in aftermarket sales were reported for the United States, Australia, Canada, Chile, Brazil, Russia, Mexico and Southern Africa. Approximately 73% of the aftermarket sales increase was due to the higher repair parts sales, with the remaining increase due to higher aftermarket service sales. The strong level of both original equipment and aftermarket sales in Fiscal 2005 reflects the continued high level of activity in the mining of copper, coal, iron ore, oil sands and gold.
Operating Income
The following table sets forth Fiscal 2005 and Fiscal 2004 operating income as derived from our Consolidated Statement of Income:
| Fiscal 2005
| Fiscal 2004
|
---|
In thousands
| Operating Income (loss)
| % of Net Sales
| Operating Income (loss)
| % of Net Sales
|
---|
Operating income (loss): | | | | | | | | | | | | | | |
Underground Mining Machinery | | | $ | 187,288 | | | 16 | .5% | $ | 91,376 | | | 11 | .1% |
Surface Mining Equipment | | | | 114,375 | | | 14 | .4% | | 53,354 | | | 9 | .2% |
Corporate Expense | | | | (34,973) | | | | | | (36,884) | | | | |
|
| | |
| | |
| | | | |
Total | | | $ | 266,690 | | | 13 | .8% | $ | 107,846 | | | 7 | .7% |
|
| | |
| | |
Operating income as a percentage of net sales for Underground Mining Machinery increased from 11.1% in Fiscal 2004 to 16.5% in Fiscal 2005. The higher volume of sales favorably impacted operating income in Fiscal 2005. Increased production activity allowed for higher levels of manufacturing overhead absorption that exceeded the increase in the variable overhead spending in the United States, United Kingdom and Australia. Product development and selling expenses were essentially flat year over year, and were down significantly as a percent of revenues. These favorable impacts were partially offset by $10.5 million in administrative expenses.
Operating income as a percentage of net sales for Surface Mining Equipment increased from 9.2% in Fiscal 2004 to 14.4% in Fiscal 2005. This improvement in profitability was due primarily to an $8.7 million improvement in the relationship between manufacturing overhead spending and manufacturing overhead absorption, partially offset by a $15.0 million increase in product development, selling and administrative expenses.
Product Development, Selling and Administrative Expense
Product development, selling and administrative expense for Fiscal 2005 was $297.9 million as compared to $273.0 million for Fiscal 2004. The increase in product development, selling and administrative expense was due primarily to a $4.2 million increase in compensation expense associated with performance-based incentive programs, approximately $4.4 million for an arbitration award and approximately $2.6 million for the implementation of the SAP enterprise software system, as well as the impact of general cost inflation. Product development, selling and administrative expense as a percentage of sales for Fiscal 2005 decreased to 15.5% as compared to 19.5% in Fiscal 2004.
Interest Expense
Interest expense for Fiscal 2005 decreased to $15.2 million as compared to $24.3 million for Fiscal 2004. This decrease was principally due to our repurchase of substantially all of our 8.75% Senior Subordinated Notes in June 2005. There were no direct borrowings under our revolving credit agreement at the end of Fiscal 2005. Cash interest paid in Fiscal 2005 and Fiscal 2004 was $16.5 million and $22.0 million, respectively.
Provision for Income Taxes
Our effective consolidated income tax rates from continuing operations for Fiscal 2005 and Fiscal 2004 were approximately 35.4% and 41.5%, respectively. For Fiscal 2005, the consolidated income tax rate approximated the statutory rate of 35%. Consolidated income tax expense from continuing operations increased to $80.5 million in Fiscal 2005 as compared to $39.3 million in Fiscal 2004. The increase in income tax expense is primarily attributable to the substantial increase in our pre-tax income. Additionally, the consolidated income tax expense and effective income tax rate for Fiscal 2004 were negatively impacted by a $13.4 million increase in our deferred tax valuation reserves relating to Australian corporate income taxes that was not repeated in Fiscal 2005.
2004 Compared with 2003
Sales
The following table sets forth Fiscal 2004 and Fiscal 2003 net sales as derived from our Consolidated Statement of Income:
In thousands
| Fiscal 2004
| Fiscal 2003
| $ Change
| % Change
|
---|
Net Sales | | | | | | | | | | | | | | |
Underground Mining Machinery | | | $ | 820,121 | | $ | 685,999 | | $ | 134,122 | | | 19 | .6% |
Surface Mining Equipment | | | | 579,236 | | | 499,702 | | | 79,534 | | | 15 | .9% |
|
| |
| |
| | |
Total | | | $ | 1,399,357 | | $ | 1,185,701 | | $ | 213,656 | | | 18 | .0% |
|
| |
| |
| | |
Total net sales for Fiscal 2004 increased by $213.7 million, or 18%, over Fiscal 2003 net sales. Net sales in the United States increased by $87.3 million, or 15.8%, and net sales in the rest of the world rose by $126.3 million, or 19.9%. Reflecting the cyclical upturn in commodities, original equipment revenues increased by approximately 35% to $437.6 million in Fiscal 2004, accounting for 31.3% of total revenues for the year. Aftermarket sales, which include sales of parts, components, rebuilds and services, increased approximately 11% to $961.8 million for Fiscal 2004.
The increase in Underground Mining Machinery net sales in Fiscal 2004 was the result of an $80.6 million increase in original equipment product shipments and $53.5 million increase in aftermarket sales. New machine sales recorded through the United Kingdom increased by $55.0 primarily due to a large roof support order and an increase in armored face conveyor shipments to both the United Kingdom and China. South Africa increased $18.1 million, recovering from depressed levels of prior year new machine sales with increased shipments of continuous miners in Fiscal 2004. New machine sales increased by $14.3 million in Australia primarily due to an increase in shipments of roof supports, longwall shearers and armored face conveyors, which were partially offset by a decline in sales of continuous miners. United States new machine sales were down slightly due to decreases in shipments of roof supports and armored face conveyors partially offset by increased shipments of continuous miners and shuttle cars. Aftermarket sales showed significant improvement in the United States, growing by $42.6 million, while revenues from South Africa grew by $11.5 million, benefiting from the weakness of the U.S. dollar and the favorable impact of translating South African Rand sales into U.S. dollars. Those increases in aftermarket sales were partially offset by a decrease in complete machine rebuilds of $7.7 million in Australia primarily due to unusually high levels of sales in Fiscal 2003. Throughout the markets we serve both our new machine and aftermarket sales have benefited from the prices our customers receive for their coal. Activity levels in the emerging markets, including China, continued the high level of activity we began to see in Fiscal 2003.
The increase in Surface Mining Equipment net sales in Fiscal 2004 was a result of a $37.6 increase in new and used equipment shipments, as well as a $41.9 million aftermarket parts and service sales. The increase in new equipment was due to higher sales of electric mining shovels in both Russia and the United States (accounting for $11.7 million and $28.6 million, respectively) and higher U.S. sales of loading equipment manufactured by our Alliance Partners (accounting for $6.2 million). The increase in U.S. new equipment sales was driven by stronger demand in the coal and iron ore markets. The Russian shovel sale, which was the first new electric mining shovel sold in Russia, was attributable to increased activity in the coal market. An increase in sales of used electric mining shovels was attributable to shipments to both Russia and Zambia. In the aftermarket, sales increased primarily in South America and the Southwestern United States (accounting for $26.7 million and $12.8 million, respectively). Service sales were strong in Brazil, Chile, South Africa and the United States, partially offset by lower service sales in Canada.
Operating Income
The following table sets forth Fiscal 2004 and Fiscal 2003 operating income as derived from our Consolidated Statement of Income:
| Fiscal 2004
| Fiscal 2003
|
---|
In thousands
| Operating Income (loss)
| % of Net Sales
| Operating Income (loss)
| % of Net Sales
|
---|
Operating income (loss): | | | | | | | | | | | | | | |
Underground Mining Machinery | | | $ | 91,376 | | | 11 | .1% | $ | 43,573 | | | 6 | .4% |
Surface Mining Equipment | | | | 53,354 | | | 9 | .2% | | 27,923 | | | 5 | .6% |
Corporate Expense | | | | (36,884 | ) | | | | | (23,463) | | | | |
|
| | |
| | |
| | | | |
Total | | | $ | 107,846 | | | 7 | .7% | $ | 48,033 | | | 4 | .1% |
|
| | |
| | |
Operating income for Underground Mining Machinery increased by approximately $47.8 million in Fiscal 2004 as compared to Fiscal 2003. During Fiscal 2004, charges for the depreciation and amortization of the fresh start accounting items decreased by approximately $3.0 million. Excluding the impact of the charges for fresh start, the increase in operating income for Fiscal 2004 was $44.8 million. The higher volume of sales favorably impacted operating income in Fiscal 2004. Increased sales activity allowed for higher levels of manufacturing overhead absorption that exceeded the increase in the variable overhead spending. These favorable impacts were partially offset by an increase of approximately $9 million in our administrative expenses. Expenses in the United States and United Kingdom in Fiscal 2004 were positively affected by the restructuring activity that took place in Fiscal 2003.
Operating income for Surface Mining Equipment increased by approximately $25.4 million in Fiscal 2004 as compared to Fiscal 2003. During Fiscal 2004, charges for the depreciation and amortization of the fresh start accounting items decreased by approximately $3.4 million. Excluding the impact of the charges for fresh start, the increase in operating income for Fiscal 2004 was $22.0 million. The increase in operating income for Surface Mining Equipment was the result of an increase in net sales in Fiscal 2004 and a significant increase in manufacturing absorption associated with the higher volume of production of new machines and parts in this segment's manufacturing facilities. These favorable impacts on margins were partially offset by approximately $12.9 million in product development, selling and administrative expenses.
The increase in the corporate expense was primarily attributable to compensation expense associated with performance-based incentive programs which is due in part to the increase in our stock price.
Product Development, Selling and Administrative Expense
Product development, selling and administrative expense for Fiscal 2004 was $273.0 million, after fresh start charges of $2.8 million, as compared to $237.0 million, after fresh start charges of $9.0 million, for Fiscal 2003. The increase in product development, selling and administrative expense was due primarily to a $16.3 million increase in compensation expense associated with performance-based incentive programs, a $6.5 million increase in pension expense and a $9.7 million increase for the impact associated with the translation of non-U.S. expenses into U.S. dollars due to exchange rate fluctuations, as well as the impact of general cost inflation. These increases were partially offset by cost reductions associated with the Fiscal 2003 restructuring programs. Product development, selling and administrative expense as a percentage of sales for Fiscal 2004 decreased to 19.5% as compared to 20.0% in Fiscal 2003.
Interest Expense
Interest expense for Fiscal 2004 decreased to $24.3 million as compared to $27.0 million for Fiscal 2003. This decrease was principally due to our repayment of two industrial revenue bonds in late Fiscal 2003. There were no direct borrowings under our revolving credit agreement in Fiscal 2004. Cash interest paid in Fiscal 2004 and Fiscal 2003 was $22.0 million and $23.1 million, respectively.
Provision for Income Taxes
Our effective consolidated income tax rates for Fiscal 2004 and Fiscal 2003 were approximately 41.5% and 33.5%, respectively. Consolidated income tax expense increased to $39.3 million in Fiscal 2004 as compared to $9.4 million in Fiscal 2003. The increase in income tax expense is primarily attributable to the substantial increase in our pre-tax income and a $13.4 million increase in our deferred tax valuation reserves relating to Australian corporate income taxes. These factors were partially offset by the fact that a higher proportion of our taxable income earned in Fiscal 2004 was earned in jurisdictions where we are able to utilize net operating loss carryforwards.
We increased our deferred tax valuation reserves for Australia because such reserves are required under FAS No.109, “Accounting for Income Taxes,” to the extent that we conclude that it is more likely than not that the associated deferred tax assets will not be realized. FAS No.109 states that this determination should be based on a weighing of all available positive and negative evidence. At the end of Fiscal 2003, we had projected that our Australian operations, which were restructured during the course of Fiscal 2003, would be profitable during Fiscal 2004 and begin to utilize the loss carryforwards that existed at the end of Fiscal 2003. As a result, the positive evidence regarding the realizability of the Australian deferred tax assets was considered to outweigh the negative evidence, and no incremental reserve was required under FAS No. 109. However, our Australian operations ultimately recorded a net loss for Fiscal 2004. As a result, at the end of Fiscal 2004, we concluded that the additional allowance of $13.4 million was merited because the negative evidence, namely the cumulative losses of our Australian subsidiary (including the loss in Fiscal 2004), outweighed the positive evidence regarding realizability of the deferred tax asset.
Because this incremental Australian valuation reserve increased our provision for income taxes without a corresponding increase in our pre-tax income, it had the effect of substantially increasing our effective tax rate for Fiscal 2004. Excluding the impact of this incremental reserve, our consolidated income tax expense would have been $25.8 million and our consolidated effective income tax rate would have been 27.3%. This rate differs from the 33.6% reported for Fiscal 2003 primarily attributable to the reversal of a $6.3 million deferred tax liability related to the projected tax to be due on a distribution of previously untaxed foreign earnings that was recorded in an earlier year but was not needed as the jurisdiction receiving the distribution was able to utilize foreign tax credits to fully offset the tax impacts of the distribution. This reversal was recorded as a discreet item in the third quarter of Fiscal 2004 and was disclosed in the Form 10-Q filed for that period. Excluding the reversal of this reserve and the valuation reserves discussed above, the effective rate for Fiscal 2004 would have been 33.9%.
Reorganization Items
Reorganization items include income, expenses and losses that were realized or incurred by the Predecessor Company as a result of it's decision to reorganize under Chapter 11 of the Bankruptcy Code.
Net reorganization items for Fiscal 2005, Fiscal 2004 and Fiscal 2003 consisted of the following:
In thousands - (income) expense
| Fiscal 2005
| Fiscal 2004
| Fiscal 2003
|
---|
Professional fees reimbursement | | | $ | (1,500 | ) | $ | — | | $ | — | |
Legal reserve reversal | | | | (1,422 | ) | | — | | | — | |
Beloit U.K. claim settlement | | | | (1,092 | ) | | (1,774 | ) | | (3,333 | ) |
Professional fees directly related to the reorganization | | | | 826 | | | 1,165 | | | 1,495 | |
Distribution from the Beloit Liquidating Trust | | | | — | | | (2,856 | ) | | — | |
Beloit Liquidating Trust settlement | | | | — | | | (2,336 | ) | | — | |
Other - net | | | | 378 | | | (1,041 | ) | | (573 | ) |
|
| |
| |
| |
Net reorganization income | | | $ | (2,810 | ) | $ | (6,842 | ) | $ | (2,411 | ) |
|
| |
| |
| |
Restructuring and Other Special Charges
Costs associated with restructuring activities other than those activities covered by SFAS No. 144, “Accounting for the Impairment or Disposal of Long-Lived Assets,” or that involve an entity newly acquired in a business combination, are accounted for in accordance with SFAS No. 146, “Accounting for Costs Associated with Exit or Disposal Activities.” Costs associated with such activities are recorded as restructuring costs in the consolidated statement of income when the liability is incurred.
During Fiscal 2003, we began implementing a manufacturing capacity rationalization at our P&H Mining Equipment Milwaukee location that reduced factory space by 350,000 square feet and resulted in a facility that is more efficient. The rationalization was completed in Fiscal 2004 at a cost of $2.0 million and resulted in approximately $5.5 million in cost savings primarily in cost of sales in Fiscal 2004.
During Fiscal 2003, Joy Mining Machinery began implementing a manufacturing capacity rationalization plan for North America. Total costs for the Joy North American manufacturing capacity rationalization were $3.7 million. Included in this amount is $1.5 million for one-time termination benefits for 132 employees, $0.8 million for abandoned assets, and $1.4 million for other associated costs. Also during Fiscal 2003, Joy Mining Machinery began implementing a manufacturing capacity rationalization plan for the United Kingdom and Australia. The total costs for the United Kingdom manufacturing capacity rationalization were $1.6 million for one-time termination benefits for 26 employees. The total costs for the Australian manufacturing capacity rationalization were $0.2 million for one-time termination benefits for 27 employees. We realized approximately $5.8 million in cost savings in Fiscal 2004 as a result of the Fiscal 2003 rationalization plan at Joy. These savings consisted of $4.7 million reflected in our cost of sales and $1.1 million reflected in our product development, selling and administrative expenses. These savings are sustainable in future years, but will vary based upon sales.
During Fiscal 2005, Joy Mining Machinery began implementing a capacity rationalization plan for North America. Total costs incurred in Fiscal 2005 were $0.8 million and consisted of one-time termination benefits for 173 employees. All benefits are expected to be paid by February 2006.
Below is a summary of the activity related to restructuring costs recorded pursuant to SFAS No. 144 and SFAS No.146.
In thousands
| One-time Termination Benefits
| Abandoned Assets
| Other Associated Costs
| Total Charges
|
---|
Fiscal 2003 | | | | | | | | | | | | | | |
P&H Mining Equipment | | | $ | — | | $ | 1,154 | | $ | 612 | | $ | 1,766 | |
Joy Mining Machinery | | | | 3,384 | | | 715 | | | 1,050 | | | 5,149 | |
|
| |
| |
| |
| |
| | | | |
| | | $ | 3,384 | | $ | 1,869 | | $ | 1,662 | | $ | 6,915 | |
|
| |
| |
| |
| |
Fiscal 2004 | | |
P&H Mining Equipment | | | $ | — | | $ | — | | $ | 253 | | $ | 253 | |
Joy Mining Machinery | | | | 200 | | | — | | | 172 | | | 372 | |
|
| |
| |
| |
| |
| | | | |
| | | $ | 200 | | $ | — | | $ | 425 | | $ | 625 | |
|
| |
| |
| |
| |
Fiscal 2005 | | |
P&H Mining Equipment | | | $ | — | | $ | — | | $ | — | | $ | — | |
Joy Mining Machinery | | | | 849 | | | — | | | — | | | 849 | |
|
| |
| |
| |
| |
| | | | |
| | | $ | 849 | | $ | — | | $ | — | | $ | 849 | |
|
| |
| |
| |
| |
Cumulative Total | | |
P&H Mining Equipment | | | $ | — | | $ | 1,154 | | $ | 865 | | $ | 2,019 | |
Joy Mining Machinery | | | | 4,433 | | | 715 | | | 1,222 | | | 6,370 | |
|
| |
| |
| |
| |
| | | | |
| | | $ | 4,433 | | $ | 1,869 | | $ | 2,087 | | $ | 8,389 | |
|
| |
| |
| |
| |
Critical Accounting Policies
Our discussion and analysis of financial condition and results of operations is based upon our Consolidated Financial Statements, which have been prepared in accordance with accounting principles generally accepted in the United States. The preparation of these Consolidated Financial Statements requires us to make estimates and judgments that affect the reported amounts of assets, liabilities, revenues and expenses, and related disclosure of contingent assets and liabilities. We continually evaluate our estimates and judgments, including those related to bad debts, excess inventory, warranty, intangible assets, income taxes, performance-based incentive programs and contingencies. We base our estimates on historical experience and assumptions that we believe to be reasonable under the circumstances. Actual results may differ from these estimates.
We believe the accounting policies described below are the ones that most frequently require us to make estimates and judgments, and therefore are critical to the understanding of our results of operations:
Revenue Recognition
We generally recognize revenue at the time of shipment and passage of title for sales of products and at the time of performance for sales of services. We recognize revenue on long-term contracts, such as the manufacture of mining shovels, drills, draglines and roof support systems, using either the percentage-of-completion or inventory sales methods. When using the percentage-of-completion method, sales and gross profit are recognized as work is performed based on the relationship between actual costs incurred and total estimated costs at completion. Sales and gross profit are adjusted prospectively for revisions in estimated total contract costs and contract values. Estimated losses are recognized in full when identified.
We have life cycle management contracts with customers to supply parts and service for terms of 1 to 13 years. These contracts are set up based on the projected costs and revenues of servicing the respective machines over the specified contract terms. Accounting for these contracts requires us to make various estimates, including estimates of the relevant machine’s long-term maintenance requirements. Under these contracts, customers are generally billed monthly and the respective deferred revenues are recorded when billed. Revenue is recognized in the period in which parts are supplied or services provided. These contracts are reviewed periodically and revenue recognition is adjusted appropriately for future estimated costs. If a loss is expected at any time, the full amount of the loss is recognized immediately.
Revenue recognition involves judgments, assessments of expected returns, the likelihood of nonpayment, and estimates of expected costs and profits on long-term contracts. We analyze various factors, including a review of specific transactions, historical experience, credit-worthiness of customers and current market and economic conditions, in determining when to recognize revenue. Changes in judgments on these factors could impact the timing and amount of revenue recognized with a resulting impact on the timing and amount of associated income.
Inventories
Inventories are carried at the lower of cost or net realizable value using the first-in, first-out ("FIFO") method for all inventories. We evaluate the need to record adjustments for inventory on a regular basis. Our policy is to evaluate all inventory including raw material, work-in-process, finished goods, and spare parts. Inventory in excess of our estimated usage requirements is written down to its estimated net realizable value. Inherent in the estimates of net realizable value are estimates related to our future manufacturing schedules, customer demand, possible alternative uses and ultimate realization of potentially excess inventory.
Intangible Assets
Intangible assets include drawings, patents, trademarks, technology and other specifically identifiable assets. Indefinite-lived intangible assets are not being amortized. Finite-lived intangible assets are amortized to reflect the pattern of economic benefits consumed which is principally the straight-line method. Intangible assets are evaluated for impairment annually, or more frequently if events or changes occur that suggest impairment in carrying value.
Accrued Warranties
We record accruals for potential warranty claims based on prior claim experience. Warranty costs are accrued at the time revenue is recognized. These warranty costs are based upon management’s assessment of past claims and current experience. However, actual claims could be higher or lower than amounts estimated, as the amount and value of warranty claims are subject to variation as a result of many factors that cannot be predicted with certainty.
Pension and Postretirement Benefits and Costs
We have pension and postretirement benefits and expenses which are developed from actuarial valuations. These valuations are based on assumptions including, among other things, discount rates, expected returns on plan assets, retirement ages, years of service, future salary increases, and future health care cost trend rates. Future changes affecting the assumptions will change the related pension benefit or expense.
Income Taxes
Deferred taxes are accounted for under the asset and liability method whereby deferred tax assets and liabilities are recognized for the future tax consequences attributable to differences between the financial statement carrying amounts of existing assets and liabilities and their respective tax bases. Deferred tax assets and liabilities are measured using statutory tax rates. Deferred income tax provisions are based on changes in the deferred tax assets and liabilities from period to period, adjusted for certain reclassifications under fresh start accounting. Additionally, we analyze our ability to recognize currently the net deferred tax assets created in each jurisdiction in which we operate to determine if valuation allowances are necessary because realizability of the tax assets is deemed to not be more likely than not.
As required under the application of fresh start accounting, the release of pre-emergence tax valuation reserves was not recorded in the income statement but instead was treated first as a reduction of excess reorganization value until exhausted, then intangibles until exhausted, and thereafter reported as additional paid in capital. Consequently, a net tax charge will be incurred in future years when these tax assets are utilized. We will continue to monitor the appropriateness of the existing valuation allowances and determine annually the amount of valuation allowances that are required to be maintained.
Similar to the treatment of pre-emergence deferred tax valuation reserves, amounts reserved pre-emergence relating to future income tax contingencies also require special treatment under fresh start accounting. Reversals of tax contingency reserves that are no longer required due to the resolution of the underlying tax issue and were recorded at the emergence date will first reduce any excess reorganization value until exhausted, then other intangibles until exhausted, and thereafter are reported as an adjustment to income tax expense. Consistent with prior years, we have reviewed the amounts so reserved and adjusted the balances to the amounts deemed appropriate with the corresponding adjustment treated as a reduction to other intangibles.
We estimate the effective tax rate expected to be applicable for the full fiscal year during the course of the year on an interim basis. The estimated effective tax rate contemplates the expected jurisdiction where income is earned (e.g. United States compared to non-United States) as well as tax planning strategies. If the actual results are different from these estimates, adjustments to the effective tax rate may be required in the period such determination is made. Additionally, discreet items are treated separately from the effective rate analysis and are recorded separately as an income tax provision or benefit at the time they are recognized. To the extent recognized, these items will impact the effective tax rate in aggregate but will not adjust the amount used for future periods within the same fiscal year.
Liquidity and Capital Resources
Working capital and cash flow are two financial measurements which provide an indication of our ability to meet our financial obligations. We currently use cash generated by operations to fund continuing operations.
The following table summarizes the major elements of our working capital at the end of Fiscal 2005 and Fiscal 2004:
In millions
| October 29, 2005
| October 30, 2004
|
---|
Cash and cash equivalents | | | $ | 143 | .9 | $ | 231 | .7 |
Accounts receivable | | | | 351 | .5 | | 260 | .0 |
Inventories | | | | 548 | .2 | | 443 | .8 |
Other current assets | | | | 73 | .1 | | 56 | .6 |
Short-term debt | | | | (1 | .0) | | (3 | .1) |
Accounts payable | | | | (160 | .6) | | (139 | .2) |
Employee compensation and benefits | | | | (91 | .1) | | (82 | .5) |
Advance payments and progress billings | | | | (187 | .7) | | (87 | .5) |
Accrued warranties | | | | (34 | .2) | | (31 | .3) |
Other current liabilities | | | | (124 | .9) | | (88 | .3) |
|
| |
| |
Working Capital | | | $ | 517 | .2 | $ | 560 | .2 |
|
| |
| |
Our businesses are working capital intensive and require funding for purchases of production and replacement parts inventories. In addition, cash is required for capital expenditures for the repair, replacement and upgrading of existing facilities. We have debt service requirements, including commitment and letter of credit fees under our revolving credit facility. We believe that cash generated from operations, together with borrowings available under our credit facility, provides us with adequate liquidity to meet our operating and debt service requirements and planned capital expenditures.
Cash provided by operations for Fiscal 2005 was $201.3 million as compared to $62.3 million provided by operations for Fiscal 2004. The primary change in our cash from operations was attributable to the increase in net income and the decrease in contributions to our pension plans partially offset by the increase in non-cash working capital. Approximately $50.6 million was used by additions to working capital in Fiscal 2005 while approximately $30.9 million was provided by reductions in working capital in Fiscal 2004. The most significant working capital changes affecting the use of cash from Fiscal 2004 to Fiscal 2005 related to inventories and accounts receivable. Inventories were increased to accommodate the increase in manufacturing while the timing of year-end sales resulted in a significant increase in outstanding accounts receivable. The most significant working capital changes providing an increase of cash from Fiscal 2004 to Fiscal 2005 related to advance payments, due primarily to the timing of cash received from customers.
During Fiscal 2005, we contributed $60.2 million to our worldwide pension plans compared to $95.4 million during Fiscal 2004. As a result of the additional contributions in Fiscal 2005, we do not expect that additional contributions for U.S. plans will be required in Fiscal 2006. However, we currently believe we will make voluntary contributions for our employee pension plans in the range of $10 million to $15 million in Fiscal 2006. Beyond Fiscal 2006, the investment performance of the plans’ assets and the actual results of the other actuarial assumptions will determine the funding requirements of the pension plans.
Cash used by investment activities for Fiscal 2005 was $35.7 million as compared to $11.1 million used by investment activities for Fiscal 2004. Approximately $38.8 million and $21.1 million were used for capital expenditures in Fiscal 2005 and Fiscal 2004, respectively. For Fiscal 2006, we anticipate capital expenditures between $40 million and $45 million, primarily for the upgrade of existing facilities, completion of SAP implementation, and other projects.
Cash used by financing activities for Fiscal 2005 was $250.8 million as compared to $27.6 million provided by financing activities for Fiscal 2004. This decrease in Fiscal 2005 primarily resulted from the repurchase of approximately $200 million of our 8.75% Senior Subordinated Notes at a cost of $224.5 and the payment of approximately $33.6 million for dividends partially offset by the exercise of stock options generating $12.0 million.
Credit Facilities
On October 28, 2005, we entered into a $400 million unsecured revolving credit facility expiring on November 15, 2010. It replaced the $275 million facility expiring on October 15, 2008. We recorded a pre-tax charge of $3.3 million related to deferred financing costs associated with the $275 million facility. Outstanding borrowings bear interest equal to either LIBOR plus the applicable margin (.5% to 1.25%) or the Base Rate (defined as the higher of the Prime Rate or the Federal Funds Effective Rate plus 0.50%) at our option. We pay a commitment fee ranging from 0.125% to 0.25% on the unused portion of the revolving credit facility. The Credit Agreement requires the maintenance of certain financial covenants including leverage, interest coverage, minimum net worth and capital expenditures covenants. On October 29, 2005, we were in compliance with all financial covenants in the credit agreement.
In 2002, we issued $200 million principal amount 8.75% Senior Subordinated Notes due March 15, 2012. During Fiscal 2005, we have purchased substantially all $200 million principal amount Senior Subordinated Notes through a tender offer and in several open market purchases. These transactions, which resulted in a $29.1 million loss on repurchase, consisted of approximately $224.5 million of cash payments and the write-down of unamortized finance costs of $4.6 million.
At October 29, 2005, there were no outstanding direct borrowings under the Credit Agreement. Outstanding letters of credit issued under the Credit Agreement, which count toward the $400 million credit limit, totaled $101.6 million. At October 29, 2005, there was $298.4 million available for borrowings under the Credit Agreement.
Off-Balance Sheet Arrangements
We lease various assets under operating leases. The aggregate payments under operating leases as of October 29, 2005 are disclosed in the table of Disclosures about Contractual Obligations and Commercial Commitments below. No significant changes to lease commitments have occurred since October 30, 2004. We have no other off-balance sheet arrangements.
Disclosures about Contractual Obligations and Commercial Commitments
The following table sets forth our contractual obligations and commercial commitments as of October 29, 2005:
In thousands
| Total
| Less than 1 year
| 1 - 3 years
| 3 - 5 years
| More than 5 years
|
---|
Long-Term Debt | | | $ | 220 | | $ | 54 | | $ | 118 | | $ | 48 | | $ | — | |
Capital Lease Obligations | | | | 2,447 | | | 910 | | | 599 | | | 938 | | | — | |
Purchase Obligations | | | | 20,818 | | | 7,339 | | | 12,119 | | | 1,360 | | | — | |
Operating Leases | | | | 32,320 | | | 10,695 | | | 13,367 | | | 4,919 | | | 3,339 | |
|
| |
| |
| |
| |
| |
Total | | | $ | 55,805 | | $ | 18,998 | | $ | 26,203 | | $ | 7,265 | | $ | 3,339 | |
|
| |
| |
| |
| |
| |
Market Conditions and Outlook
Market conditions in most of the commodity markets served by our customers remain robust. Coal markets in the United States continue to strengthen in both pricing and demand. Higher spot coal prices are expected over time to be reflected in higher prices in supply contracts. Demand for coal is being positively affected by continued high natural gas prices and increases in exports of metallurgical coal from the United States. Coal producers in the United States are increasing their production levels and capital spending plans. The increase in production levels is primarily occurring in existing mine operations, which we believe is leading to the increasing demand for replacement equipment as operators drive for more production from the same reserves.
The international coal markets continue to be strong with rising prices for both thermal and metallurgical coal. Capacity levels in port facilities have resulted in shipping constraints in both South Africa and Australia. China continues to take steps in the long-term to convert its underground coal industry to high productivity mining methods. Efforts by the Chinese government to encourage investments in power plants, railroads, and coal should be a positive contributor to this conversion. We continue to believe we will experience solid, long-term, double-digit growth in China, both for our underground mining machinery and our aftermarket parts and service activities.
Markets served by P&H in surface mining are strong across the board. Copper, iron ore and gold selling prices remain at high levels. Higher oil prices are driving both current production and new projects in the Canadian oil sands sector. As a result, total shovel orders in Fiscal 2005 exceeded current shovel capacity. We anticipate more of the same in Fiscal 2006, driven by coal and copper demand in the near-term and new projects in the oil sands longer term. As with Joy on the underground side of our business, we are booking orders well into Fiscal 2007.
Several factors temper our outlook. We believe that the current increases in purchases for mining equipment and services will be affected by our customers’ efforts to constrain their production and capital spending. As we increase our production to meet the increased demand for mining equipment, our challenge is to manage our working capital and the other aspects of our business so that we meet the needs of our customers while maximizing returns to shareholders. We will need to continue to control pension and health care costs. Our ability to grow revenues is constrained by the capacity of our plants, our ability to supplement that capacity with outside sources, and our success in securing critical supplies such as castings, forgings, bearings and other purchased components. The positive effects we are seeing on our business as a result of higher customer production and capital spending levels could be offset by customer restraints on production and capital spending, capacity limitations at our facilities, and continuing tight supplies.
New Accounting Pronouncements
Our new accounting pronouncements are set forth under Item 8 of this annual report and are incorporated herein by reference.
Item 7a. Quantitative and Qualitative Disclosures about Market Risk
Volatility in interest rates and foreign exchange rates can impact our earnings, equity and cash flow. From time to time we undertake transactions to hedge this impact. Under governing accounting guidelines, a hedge instrument is considered effective if it offsets partially or completely the impact on earnings, equity and cash flow due to fluctuations in interest and foreign exchange rates. In accordance with our policy, we do not execute derivatives that are speculative or that increase our risk from interest rate or foreign exchange rate fluctuations.
Interest Rate Risk
We are exposed to market risk from changes in interest rates on long-term debt obligations. We manage this risk through the use of a combination of fixed and variable rate debt (See Note 4 – Borrowings and Credit Facilities). At October 29, 2005 we were not party to any interest rate derivative contracts.
Foreign Currency Risk
Most of our foreign subsidiaries use local currencies as their functional currency. For consolidation purposes, assets and liabilities are translated at month-end exchange rates. Items of income and expense are translated at average exchange rates. Translation gains and losses are not included in determining net income (loss) but are accumulated as a separate component of shareholders’ equity. Gains (losses) arising from foreign currency transactions are included in determining net income (loss). During Fiscal 2005, we incurred a gain of $3.9 million arising from foreign currency transactions. Foreign exchange derivatives at October 29, 2005 were in the form of forward exchange contracts executed over the counter. There is a concentration of these contracts held with LaSalle Bank, N.A. as agent for ABN Amro Bank, N.V. which maintains an investment grade rating.
We have adopted a Foreign Exchange Risk Management Policy. It is a risk-averse policy under which significant exposures that impact earnings and cash flow are fully hedged. Exposures that impact only equity or do not have a cash flow impact are generally not hedged with derivatives. There are two categories of foreign exchange exposures that are hedged: assets and liabilities denominated in a foreign currency, which include net investment in a foreign subsidiary, and future committed receipts or payments denominated in a foreign currency. These exposures normally arise from imports and exports of goods and from intercompany trade and lending activity.
The fair value of our forward exchange contracts at October 29, 2005 is analyzed in the following table of dollar equivalent terms:
In thousands of US Dollars
| Maturing in 2006
|
---|
| Buy
| Sell
|
---|
U.S. Dollar | | | $ | 314 | | $ | (988 | ) |
Australian Dollar | | | | (15 | ) | | (1 | ) |
British Pound Sterling | | | | (690 | ) | | (1 | ) |
South African Rand | | | | (63 | ) | | 2 | |
Euro | | | | (193 | ) | | 33 | |
Exchange Rate Sensitivity Table As of October 29, 2005
| |
---|
| Expected Maturity or Transaction Date (000,s)
| | |
---|
$US Functional Currency: Forward Exchange Agreements
| Fiscal 2006
| Fiscal 2007
| Fiscal 2008
| Fiscal 2009
| Fiscal 2010
| There- after
| Total
| Fair Value
|
---|
Receive AUD Pay ZAR Contract Amount | ($ 120.3) | $ 0.0 | $ 0.0 | $ 0.0 | $ 0.0 | $ 0.0 | ($ 120.3) | $ 3.2 |
| | | | | | | | | | |
Average Rate | 0.7368 | 0.0000 | 0.0000 | 0.0000 | 0.0000 | 0.0000 | 0.7368 |
Receive USD Pay ZAR Contract Amount | ($ 4,651.9) | $ 0.0 | $ 0.0 | $ 0.0 | $ 0.0 | $ 0.0 | ($ 4,651.9) | $ 270.3 |
Average Rate | 6.5451 | 0.0000 | 0.0000 | 0.0000 | 0.0000 | 0.0000 | 6.5451 |
Receive GBP Pay ZAR Contract Amount | ($ 1,933.3) | $ 0.0 | $ 0.0 | $ 0.0 | $ 0.0 | $ 0.0 | ($ 1,933.3) | $ 40.8 |
Average Rate | 1.7620 | 0.0000 | 0.0000 | 0.0000 | 0.0000 | 0.0000 | 1.7620 |
Pay USD Receive GBP Contract Amount | $ 97,811.1 | $ 0.0 | ($ 0.0 | $ 0.0 | $ 0.0 | $ 0.0 | $ 97,811.1 | ($ 990.7) |
Average Rate | 1.7875 | 0.0000 | 0.0000 | 0.0000 | 0.0000 | 0.0000 | 1.7875 |
Receive GBP Pay USD Contract Amount | ($ 58,820.5) | $ 0.0 | $ 0.0 | $ 0.0 | $ 0.0 | $ 0.0 | ($ 58,820.5) | ($ 731.9) |
Average Rate | 1.7997 | 0.0000 | 0.0000 | 0.0000 | 0.0000 | 0.0000 | 1.7997 |
Pay USD Receive AUD Contract Amount | $ 7,000.0 | $ 0.0 | $ 0.0 | $ 0.0 | $ 0.0 | $ 0.0 | $ 7,000.0 | $ 46.0 |
Average Rate | 0.7412 | 0.0000 | 0.0000 | 0.0000 | 0.0000 | 0.0000 | 0.7412 |
Receive AUD Pay USD Contract Amount | ($ 3,270.4) | $ 0.0 | $ 0.0 | $ 0.0 | $ 0.0 | $ 0.0 | ($ 3,270.4) | ($ 19.1) |
Average Rate | 0.7526 | 0.0000 | 0.0000 | 0.0000 | 0.0000 | 0.0000 | 0.7526 |
Receive EUR Pay USD Contract Amount | ($ 1,530.1) | $ 0.0 | $ 0.0 | $ 0.0 | $ 0.0 | $ 0.0 | ($ 1,530.1) | ($ 159.3) |
Average Rate | 1.3306 | 0.0000 | 0.0000 | 0.0000 | 0.0000 | 0.0000 | 1.3306 |
Receive Zar Pay BWP Contract Amount | ($ 832.8) | $ 0.0 | $ 0.0 | $ 0.0 | $ 0.0 | $ 0.0 | ($ 832.8) | ($ 18.5) |
Average Rate | 6.5711 | 0.0000 | 0.0000 | 0.0000 | 0.0000 | 0.0000 | 6.5711 |
Receive ZAR Pay USD Contract Amount | ($ 2,666.8) | $ 0.0 | $ 0.0 | $ 0.0 | $ 0.0 | $ 0.0 | ($ 2,666.8) | ($ 31.0) |
Average Rate | 6.8318 | 0.0000 | 0.0000 | 0.0000 | 0.0000 | 0.0000 | 6.8318 |
Receive ZAR Pay GBP Contract Amount | ($ 1,308.1) | $ 0.0 | $ 0.0 | $ 0.0 | $ 0.0 | $ 0.0 | ($ 1,308.1) | ($ 11.0) |
Average Rate | 12.1627 | 0.0000 | 0.0000 | 0.0000 | 0.0000 | 0.0000 | 12.1627 |
|
|
|
|
|
|
|
|
|
Contract Amount | $ 29,676.9 | $ 0.0 | $ 0.0 | $ 0.0 | $ 0.0 | $ 0.0 | $ 29,676.9 | ($ 1,601.2) |
|
|
|
|
|
|
|
|
|
Exchange Rate Sensitivity Table As of October 30, 2004
| |
---|
| Expected Maturity or Transaction Date (000,s)
| | |
---|
$US Functional Currency: Forward Exchange Agreements
| Fiscal 2005
| Fiscal 2006
| Fiscal 2007
| Fiscal 2008
| Fiscal 2009
| There- after
| Total
| Fair Value
|
---|
Receive AUD Pay ZAR Contract Amount | ($ 300.9) | $ 0.0 | $ 0.0 | $ 0.0 | $ 0.0 | $ 0.0 | ($ 300.9) | ($ 14.6) |
| | | | | | | | | | |
Average Rate | 0.7900 | 0.0000 | 0.0000 | 0.0000 | 0.0000 | 0.0000 | 0.7900 |
Receive USD Pay ZAR Contract Amount | ($ 7,542.8) | $ 0.0 | $ 0.0 | $ 0.0 | $ 0.0 | $ 0.0 | ($ 7,542.8) | ($ 957.5) |
Average Rate | 7.0290 | 0.0000 | 0.0000 | 0.0000 | 0.0000 | 0.0000 | 7.0290 |
Receive GBP Pay ZAR Contract Amount | ($ 571.1) | $ 0.0 | $ 0.0 | $ 0.0 | $ 0.0 | $ 0.0 | ($ 571.10) | ($ 38.3) |
Average Rate | 1.9784 | 0.0000 | 0.0000 | 0.0000 | 0.0000 | 0.0000 | 1.9784 |
Pay USD Receive GBP Contract Amount | $ 106,473.2 | $ 4,109.2 | $ 0.0 | $ 0.0 | $ 0.0 | $ 0.0 | $ 110,582.3 | $ 2,125.9 |
Average Rate | 1.7787 | 1.7701 | 0.0000 | 0.0000 | 0.0000 | 0.0000 | 1.7784 |
Receive GBP Pay USD Contract Amount | ($ 10,038.2) | ($ 2,999.5) | $ 0.0 | $ 0.0 | $ 0.0 | $ 0.0 | ($ 13,037.6) | $ 141.6 |
Average Rate | 1.8251 | 1.7313 | 0.0000 | 0.0000 | 0.0000 | 0.0000 | 1.8035 |
Pay USD Receive AUD Contract Amount | $ 4,723.1 | $ 0.0 | $ 0.0 | $ 0.0 | $ 0.0 | $ 0.0 | $ 4,723.1 | $ 44.8 |
Average Rate | 0.7212 | 0.0000 | 0.0000 | 0.0000 | 0.0000 | 0.0000 | 0.7212 |
Receive AUD Pay USD Contract Amount | ($ 11,435.7) | $ 0.0 | $ 0.0 | $ 0.0 | $ 0.0 | $ 0.0 | ($ 11,435.7) | $ 28.7 |
Average Rate | 0.7233 | 0.0000 | 0.0000 | 0.0000 | 0.0000 | 0.0000 | 0.7233 |
Receive EUR Pay USD Contract Amount | ($ 157.9) | $ 0.0 | $ 0.0 | $ 0.0 | $ 0.0 | $ 0.0 | ($ 157.9) | $ 15.2 |
Average Rate | 1.1622 | 0.0000 | 0.0000 | 0.0000 | 0.0000 | 0.0000 | 1.1622 |
Pay EUR Receive GBP Contract Amount | $ 2,061.3 | $ 0.0 | $ 0.0 | $ 0.0 | $ 0.0 | $ 0.0 | $ 2,061.3 | ($ 3.2) |
Average Rate | 1.2753 | 0.0000 | 0.0000 | 0.0000 | 0.0000 | 0.0000 | 1.2753 |
Receive ZAR Pay BWP Contract Amount | ($ 1,073.8) | $ 0.0 | $ 0.0 | $ 0.0 | $ 0.0 | $ 0.0 | ($ 1,073.8) | ($ 151.1) |
Average Rate | 5.3316 | 0.0000 | 0.0000 | 0.0000 | 0.0000 | 0.0000 | 5.3316 |
|
|
|
|
|
|
|
|
|
Contract Amount | $ 82,137.3 | $ 1,109.7 | $ 0.0 | $ 0.0 | $ 0.0 | $ 0.0 | $ 83,247.0 | $ 1,191.5 |
|
|
|
|
|
|
|
|
|
Item 8. Financial Statements and Supplementary Data
Unaudited Quarterly Financial Data
Our Consolidated Financial Statements are included with Item 15. of this Form 10-K beginning on page F-1.
The following table sets forth certain unaudited quarterly financial data for our fiscal years ended October 29, 2005, and October 30, 2004. All per share data shown below has been adjusted to reflect our 3-for-2 stock splits completed on January 21, 2005 and December 12, 2005.
| 2005 Fiscal Quarter Ended
|
---|
(In thousands except per share amounts)
| January 31
| April 30
| July 30
| October 29
|
---|
| | | | | | | | | | (1) | | | | |
Net sales | | | $ | 373,868 | | $ | 472,506 | | $ | 512,874 | | $ | 568,226 | |
Gross profit | | | | 111,201 | | | 137,051 | | | 145,185 | | | 168,541 | |
Operating income | | | | 42,185 | | | 64,301 | | | 72,260 | | | 87,944 | |
Income from continuing operations | | | | 22,122 | | | 38,430 | | | 30,451 | | | 55,918 | |
Income from discontinued operations, net of tax | | | | 62 | | | 393 | | | 331 | | | 342 | |
Net income | | | | 22,184 | | | 38,823 | | | 30,782 | | | 56,260 | |
Basic Earnings Per Share: | | |
Continuing operations | | | $ | 0.18 | | $ | 0.32 | | $ | 0.25 | | $ | 0.46 | |
Discontinued operations | | | $ | — | | $ | — | | $ | — | | $ | — | |
Net income | | | $ | 0.18 | | $ | 0.32 | | $ | 0.25 | | $ | 0.46 | |
Diluted Earnings Per Share: | | |
Continuing operations | | | $ | 0.18 | | $ | 0.31 | | $ | 0.25 | | $ | 0.45 | |
Discontinued operations | | | $ | — | | $ | — | | $ | — | | $ | — | |
Net income | | | $ | 0.18 | | $ | 0.31 | | $ | 0.25 | | $ | 0.45 | |
Dividends Per Share | | | $ | 0.05 | | $ | 0.075 | | $ | 0.075 | | $ | 0.075 | |
|
| |
| |
| |
| |
| 2004 Fiscal Quarter Ended
|
---|
(In thousands except per share amounts)
| January 31
| May 1
| July 31
| October 30
|
---|
| (2) |
---|
Net sales | | | $ | 276,625 | | $ | 331,736 | | $ | 374,153 | | $ | 416,843 | |
Gross profit | | | | 69,038 | | | 90,277 | | | 98,886 | | | 119,822 | |
Operating income | | | | 8,021 | | | 22,702 | | | 30,070 | | | 47,053 | |
Income from continuing operations | | | | 1,126 | | | 18,964 | | | 16,340 | | | 19,026 | |
Income (loss) from discontinued operations, net of tax | | | | (188 | ) | | (124 | ) | | (85 | ) | | 263 | |
Net income | | | | 938 | | | 18,840 | | | 16,255 | | | 19,289 | |
Earnings Per Share: | | |
Continuing operations | | | $ | 0.01 | | $ | 0.16 | | $ | 0.14 | | $ | 0.16 | |
Discontinued operations | | | $ | — | | $ | — | | $ | — | | $ | — | |
Net income | | | $ | 0.01 | | $ | 0.16 | | $ | 0.14 | | $ | 0.16 | |
Diluted Earnings Per Share: | | |
Continuing operations | | | $ | 0.01 | | $ | 0.16 | | $ | 0.13 | | $ | 0.16 | |
Discontinued operations | | | $ | — | | $ | — | | $ | — | | $ | — | |
Net income | | | $ | 0.01 | | $ | 0.16 | | $ | 0.13 | | $ | 0.16 | |
Dividends Per Share | | | $ | 0.022 | | $ | 0.033 | | $ | 0.033 | | $ | 0.033 | |
|
| |
| |
| |
| |
(1) - For the third quarter of Fiscal 2005 our net income was adversely affected by a $24.2 million loss on debt repurchase resulting from our successful tender offer for substantially all of our outstanding 8.75% Senior Subordinated Notes.
(2) — For the fourth quarter of Fiscal 2004 our net income was adversely affected by an unusually high provision for income taxes attributable to a $13.4 million increase (including a $9.9 million adjustment) in our Australian deferred tax valuation reserves. The increase in the valuation reserves was due to concerns about the realizability of the underlying deferred tax assets. This item had the effect of decreasing fourth quarter net income by $13.4 million, or 11 cents per share on a fully-diluted basis. For a further discussion of this increase to our deferred tax valuation reserves, please see Item 7, under the heading “Management’s Discussion and Analysis of Financial Condition and Results of Operations—Results of Operations—2004 Compared with 2003—Provision for Income Taxes.”
Item 9. Changes in and Disagreements with Accountants on Accounting and Financial Disclosure
None
Item 9a. Controls and Procedures
(a) Evaluation of Disclosure Controls and Procedures
Our management, with the participation of our Chief Executive Officer and Chief Financial Officer, has evaluated the effectiveness of our disclosure controls and procedures (as such term is defined in Rules 13a-15(e) and 15d-15(e) under the Securities Exchange Act of 1934, as amended (the "Exchange Act")) as of October 29, 2005. Based on such evaluation, our Chief Executive Officer and Chief Financial Officer have concluded that, as of such date, our disclosure controls and procedures are effective (1) in recording, processing, summarizing and reporting, on a timely basis, information required to be disclosed by us in the reports that we file or submit under the Exchange Act and (2) to ensure that information required to be disclosed in the reports we file or submit under the Exchange Act is accumulated and communicated to our management, including our Chief Executive Officer and Chief Financial Officer, to allow timely decisions regarding required disclosure.
(b) Management’s Report on Internal Control over Financial Reporting
Our management’s annual report on internal control over financial reporting is set forth under Item 8 of this annual report and is incorporated herein by reference.
(c) Changes in Internal Control over Financial Reporting
There was no change in our internal control over financial reporting that occurred during the most recently completed fiscal quarter that has materially affected, or is reasonably likely to materially affect, our internal control over financial reporting.
Item 9b. Other Information
None
PART III
Item 10. Directors and Executive Officers of the Registrant
We incorporate by reference herein the section entitled “ELECTION OF DIRECTORS,” “BOARD OF DIRECTORS; AUDIT COMMITTEE FINANCIAL EXPERT” and “OTHER INFORMATION — Section 16(a) Beneficial Ownership Reporting Compliance” in our Proxy Statement to be mailed to stockholders in connection with our 2006 annual meeting.
Information regarding executive officers is included in Part I of this Form 10-K as permitted by General Instruction G(3) and incorporated herein by reference.
Our Code of Ethics for CEO and Senior Financial Officers is available on our website. We intend to satisfy the disclosure requirement under Item 5.05 of Form 8-K regarding any amendment to, or waiver from, a provision of this code of ethics by posting such information on our website.
Item 11. Executive Compensation
We incorporate by reference herein the section entitled “EXECUTIVE COMPENSATION” in our Proxy Statement to be mailed to stockholders in connection with our 2006 annual meeting.
Item 12. Security Ownership of Certain Beneficial Owners and Management and Related Stockholder Matters
We incorporate by reference herein the section entitled “SECURITY OWNERSHIP OF CERTAIN BENEFICIAL OWNERS AND MANAGEMENT AND RELATED STOCKHOLDER MATTERS” and “EXECUTIVE COMPENSATION – Equity Compensation Plan Information” in our Proxy Statement to be mailed to stockholders in connection with our 2006 annual meeting.
Item 13. Certain Relationships and Related Transactions
We incorporate by reference herein the section “EXECUTIVE COMPENSATION — Certain Business Relationships” in our Proxy Statement to be mailed to stockholders in connection with our 2006 annual meeting.
Item 14. Principal Accountant Fees and Services
We incorporate by reference herein the section entitled “AUDITORS, AUDIT FEES AND AUDITOR INDEPENDENCE” in our Proxy Statement to be mailed to stockholders in connection with our 2006 annual meeting.
PART IV
Item 15. Exhibits and Financial Statement Schedules
(a) The following documents are filed as part of this report:
(1) | Financial Statements: |
The response to this portion of Item 15 is submitted in a separate section of this report. See the audited Consolidated Financial Statements and Financial Statement Schedule of Joy Global Inc. attached hereto and listed on the index to this report.
(2) | Financial Statement Schedules: |
The response to this portion of Item 15 is submitted in a separate section of this report. See the audited Consolidated Financial Statements and Financial Statement Schedule of Joy Global Inc. attached hereto and listed on the index to this report.
Exhibits
| Number
| Exhibit
|
| 2.1 | Third Amended Joint Plan of Reorganization, as modified, of the Debtors Under Chapter 11 of the Bankruptcy Code (incorporated by reference to Exhibit 2.1 to current report of Joy Global Inc. on Form 8-K dated July 12, 2001, File No. 01-9299). |
| 3.1 | Amended and Restated Certificate of Incorporation of Joy Global Inc. (incorporated by reference to Exhibit 3.1 to current report of Joy Global Inc. on Form 8-K dated July 12, 2001, File No. 01-9299). |
| 3.2 | Amended and Restated Bylaws of Joy Global Inc. as amended on August 23, 2005 (incorporated by reference to Exhibit 99 to current report of Joy Global Inc. on Form 8-K dated August 29, 2005, File No. 01-9299). |
| 3.3 | Certificate of Designations of Joy Global Inc. dated July 15, 2002 (incorporated by reference to Exhibit 3(a) to report of Joy Global Inc. on Form 10-Q for the quarter ended August 3, 2002, File No. 01-9299). |
| 4.1 | Specimen common stock certificate of Joy Global Inc. (incorporated by reference to Exhibit 4.4 to current report of Joy Global Inc. on Form 8-K dated July 12, 2001, File No. 01-9299). |
| 4.2 | Indenture dated as of March 18, 2002, among Joy Global Inc., the Subsidiary Guarantors and Wells Fargo Bank Minnesota, N.A. relating to 8.75% Senior Subordinated Notes due 2012 (incorporated by reference to Exhibit 4.1 to current report of Joy Global Inc. on Form 8-K dated March 13, 2002, File No. 01-9299). |
| 4.3 | Form of 8.75% Senior Subordinated Notes due 2012 (incorporated by reference to Exhibit 4.4 to current report of Joy Global Inc. on Form 8-K dated March 13, 2002, File No. 01-9299). |
| 4.4 | Rights Agreement, dated as of July 16, 2002, between Joy Global Inc. and American Stock Transfer and Trust Company, as rights agent, including the Form of Certificate of Designations, the Form of Rights Certificate and the Summary of Rights to Purchase Preferred Shares attached thereto as Exhibits A, B and C (incorporated by reference to Exhibit 4.1 to Joy Global Inc.’s Form 8-A filed on July 17, 2002, File No. 01-9299). |
| 4.5 | Supplemental Indenture dated as of June 16, 2005 and entered into by and among Joy Global Inc. and its direct and indirect subsidiaries identified therein as guarantors and Wells Fargo Bank, N.A., as trustee (incorporated by reference to Exhibit 10(b) to report of Joy Global Inc. on Form 10-Q for the quarter ended July 30, 2005, File No. 01-9299). |
| 10.1 | Amended and Restated Credit Agreement, dated as of June 25, 2002, among Joy Global inc. as Borrower, the lenders listed therein, Deutsche Bank Trust Company Americas, as Agents, Heller Financial, Inc. and Fleet Capital Corporation, as Co-Syndication Agents, CIT Group/Business Credit, as Documentation Agent and Deutsche Bank Securities Inc., as Lead Arranger and Sole Book Running Manager (incorporated by reference to Exhibit 10(a) to report of Joy Global Inc. on Form 10-Q for the quarter ended August 3, 2002, File No. 01-9299). |
| 10.2 | First Amendment to Amended and Restated Credit Agreement dated as of October 31, 2002 and entered into by and among Joy Global Inc., as Borrower, the lenders named therein, as Lenders, Deutsche Bank Trust Company Americas, as Agents, Heller Financial, Inc. and Fleet Capital Corporation, as Co-Syndication Agents, and CIT Group/Business Credit, as Documentation Agent (incorporated by reference to Exhibit 10(b) to report of Joy Global Inc. on Form 10-K for the year ended November 2, 2002, File No. 01-9299). |
| 10.3 | Joy Global Inc. 2001 Stock Incentive Plan, as amended October 16, 2001 (incorporated by reference to Exhibit 10(c) to report of Joy Global Inc. on Form 10-K for the year ended October 31, 2001, File No. 01-9299). * |
| 10.4 | Harnischfeger Industries, Inc. Supplemental Retirement Plan, as amended and restated as of June 3, 1999 (incorporated by reference to Exhibit 10(d) to report of Harnischfeger Industries, Inc. on Form 10-K for the year ended October 31, 1999, File No. 01-9299). * |
| 10.5 | Form of Change in Control Agreement made and entered into as of September 30, 1999, between Harnischfeger Industries, Inc. and James A. Chokey and John Nils Hanson and made and entered into as of May 22, 2000, and June 11, 2001, with Dennis R. Winkleman and Donald C. Roof, respectively (incorporated by reference to Exhibit 10(e) to report of Joy Global Inc. on Form 10-K for the year ended October 31, 2001, File No. 01-9299). * |
| 10.6 | Change in Control Agreement made and entered into as of November 17, 2000 by and between Harnischfeger Industries, Inc. and Michael S. Olsen (incorporated by reference to Exhibit 10(f) to report of Joy Global Inc. on Form 10-K for the year ended October 31, 2001, File No. 01-9299). * |
| 10.7 | Form of Stock Option Agreement dated July 16, 2001 (incorporated by reference to Exhibit 10(g) to report of Joy Global Inc. on Form 10-K for the year ended October 31, 2001, File No. 01-9299). * |
| 10.8 | Form of Performance Unit Agreement entered into as of August 27, 2001, between Joy Global Inc. and James A. Chokey, John Nils Hanson, Michael S. Olsen, Donald C. Roof and Dennis R. Winkleman (incorporated by reference to Exhibit 10(h) to report of Joy Global Inc. on Form 10-K for the year ended October 31, 2001, File No. 01-9299). * |
| 10.9 | Form of Stock Option Agreement dated November 1, 2001 (incorporated by reference to Exhibit 10(i) to report of Joy Global Inc. on Form 10-K for the year ended October 31, 2001, File No. 01-9299). * |
| 10.10 | Joy Global Inc. Annual Bonus Compensation Plan (incorporated by reference to Exhibit 10(j) to report of Joy Global Inc. on Form 10-K for the year ended October 31, 2001, File No. 01-9299).* |
| 10.11 | Form of Stock Option Agreement dated February 1, 2002 (incorporated by reference to Exhibit (a) to report of Joy Global Inc. on Form 10-Q for the quarter ended February 2, 2002, File No. 01-9299). * |
| 10.12 | Form of Director Stock Option Agreement dated February 27, 2002 (incorporated by reference to Exhibit 10(d) to report of Joy Global Inc. on Form 10-Q for the quarter ended August 3, 2002, File No. 01-9299). |
| 10.13 | Form of Stock Option Agreement dated May 1, 2002 (incorporated by reference to Exhibit 10(b) to report of Joy Global Inc. on Form 10-Q for the quarter ended August 3, 2002, File No. 01-9299). * |
| 10.14 | Form of Director Stock Option Agreement dated July 16, 2001 (incorporated by reference to Exhibit 10(c) to report of Joy Global Inc. on Form 10-Q for the quarter ended August 3, 2002, File No. 01-9299). |
| 10.15 | Form of Change of Control Employment Agreement entered into as of May 20, 2003 between Joy Global Inc. and each of James A. Chokey, John Nils Hanson, Michael S. Olsen, Mark E. Readinger, Donald C. Roof, Thomas J. Stanczyk, Michael W. Sutherlin and Dennis R. Winkleman, and entered into as of August 1, 2005 between Joy Global Inc. and John J. Fons (incorporated by reference to Exhibit 10(t) to report of Joy Global Inc. on Form 10-K for the year ended November 1, 2003, File No. 01-9299). * |
| 10.16 | Second Amended and Restated Credit Agreement and Consent dated as of January 23, 2004 and entered into by and among Joy Global Inc. as Borrower, the lenders named therein, as Lenders, Deutsche Bank Trust Company America, as Agent, Heller Financial, Inc. and Fleet Capital Corporation, as Co-Syndication Agents, and CIT Group/Business Credit, as Documentation Agent (incorporated by reference to Exhibit 10 to current report of Joy Global Inc. on Form 8-K dated February 10, 2004, File No. 01-9299). |
| 10.17 | Amendment No. 1 to Joy Global Inc. 2001 Stock Incentive Plan (incorporated by reference to Exhibit 10(b) to report of Joy Global Inc. on Form 10-Q for the quarter ended May 3, 2003, File No. 01-9299). * |
| 10.18 | Joy Global Inc. 2003 Stock Incentive Plan (incorporated by reference to Exhibit 10(a) to report of Joy Global Inc. on Form 10-Q for the quarter ended May 3, 2003, File No. 01-9299). * |
| 10.19 | Form of Change of Control Employment Agreement dated as of May 20, 2003. (incorporated by reference to Exhibit 10(t) to report of Joy Global Inc. on Form 10-K for the year ended November 1, 2003, File No. 01-9299)* |
| 10.20 | Second Amendment to Amended and Restated Credit Agreement dated as of August 26, 2003 and entered into by and among Joy Global Inc., as Borrower, the lenders named therein, as Lenders, Deutsche Bank Trust Company Americas, as Agents, Heller Financial, Inc. and Fleet Capital Corporation, as Co-Syndication Agents, and CIT Group/Business Credit, as Documentation Agent (incorporated by reference to Exhibit 10(u) to report of Joy Global Inc. on Form 10-K for the year ended November 1, 2003, File No. 01-9299). |
| 10.21 | Form of Amendment to Performance Unit Agreement (incorporated by reference to Exhibit 10(v) to report of Joy Global Inc. on Form 10-K for the year ended November 1, 2003, File No. 01-9299).* |
| 10.22 | First Amendment to Second Amended and Restated Credit Agreement and Consent dated as of April 19, 2004 and entered into by and among Joy Global Inc., as Borrower, the lenders named therein, as Lenders, Deutsche Bank Trust Company America, as Agent, Heller Financial, Inc. and Fleet Capital Corporation, as Co-Syndication Agents, and CIT Group/Business Credit, as Documentation Agent (incorporated by reference to Exhibit 10(a) to report of Joy Global Inc. on Form 10-Q for the quarter ended May 1, 2004, File No. 01-9299). |
| 10.23 | Second Amendment to Second Amended and Restated Credit Agreement and Consent dated as of June 1, 2005 and entered into by and among Joy Global Inc. as Borrower, the lenders named therein, as Lenders, Deutsche Bank Trust Company America, as Agent, Heller Financial, Inc. and Fleet Capital Corporation, as Co-Syndication Agents, and CIT Group/Business Credit, as Documentation Agent (incorporated by reference to Exhibit 10(a) to report of Joy Global Inc. on Form 10-Q for the quarter ended July 30, 2005, File No. 01-9299). |
| 10.24 | Form of Stock Option Agreement entered into as of November 15, 2004 (incorporated by reference to Exhibit 10(c) to report of Joy Global Inc. on Form 10-Q for the quarter ended July 30, 2005, File No. 01-9299). |
| 10.25 | Form of Restricted Stock Unit Award Agreement entered into as of November 15, 2004 between Joy Global Inc. and each of James A. Chokey, John Nils Hanson, Michael S. Olsen, Mark E. Readinger, Donald C. Roof, Thomas J. Stanczyk, Michael W. Sutherlin and Dennis R. Winkleman and entered into as of August 1, 2005 between Joy Global Inc. and John J. Fons (incorporated by reference to Exhibit 10(d) to report of Joy Global Inc. on Form 10-Q for the quarter ended July 30, 2005, File No. 01-9299). |
| 10.26 | Form of Performance Share Agreement entered into as of November 15, 2004 between Joy Global Inc. and each of James A. Chokey, John Nils Hanson, Michael S. Olsen, Mark E. Readinger, Donald C. Roof, Thomas J. Stanczyk, Michael W. Sutherlin and Dennis R. Winkleman and entered into as of August 1, 2005 between Joy Global Inc. and John J. Fons (incorporated by reference to Exhibit 10(e) to report of Joy Global Inc. on Form 10-Q for the quarter ended July 30, 2005, File No. 01-9299). |
| 10.27 | Form of Restricted Stock Unit Award Agreement entered into as of February 22, 2005 between Joy Global Inc. and each of the registrant's non-employee directors. * |
| 10.28 | Credit Agreement dated as of October 28, 2005 entered into by and among Joy Global Inc., certain of its domestic subsidiaries, Bank of America, N.A., LaSalle Bank National Association, Deutsche Bank AG New York Branch, Harris N.A., JPMorgan Chase Bank, N.A., and the other lenders named therein. |
| 21 | Subsidiaries of the Registrant. |
| 23 | Consent of Ernst & Young LLP. |
| 24 | Powers of Attorney. |
| 31.1 | Chief Executive Officer Rule 13a-14(a)/15d-14(a) Certifications. |
| 31.2 | Chief Financial Officer Rule 13a-14(a)/15d-14(a) Certifications. |
| 32 | Section 1350 Certifications. |
| * | Represents a management contract or compensatory plan or arrangement required to be filed as an exhibit pursuant to Item 15(c) of Form 10-K. |
Joy Global Inc.
Form 10-K Item 8 and Items 15(a)(1) and 15(a)(2)
Index to Consolidated Financial Statements
And Financial Statement Schedule
The following Consolidated Financial Statements of Joy Global Inc. and the related Reports of Independent Registered Public Accounting Firm are included in Item 8 –Financial Statements and Supplementary Data and Item 15 –Exhibits and Financial Statement Schedules:
Item 15(a) (1):
| Page in This Form 10-K
|
---|
Reports of Independent Registered Public Accounting Firm
Management's Report on Internal Control Over Financial Reporting
Consolidated Statement of Income for the fiscal years ended October 29, 2005, October 30, 2004 and November 1, 2003
Consolidated Balance Sheet at October 29, 2005 and October 30, 2004
Consolidated Statement of Cash Flows for the fiscal years ended October 29, 2005, October 30, 2004 and November 1, 2003
Consolidated Statement of Shareholders’ Equity for the fiscal years ended October 29, 2005, October 30, 2004 and November 1, 2003
Notes to Consolidated Financial Statements |
|
| |
The following Consolidated Financial Statement schedule of Joy Global Inc. is included in Item 15(a)(2):
All other schedules are omitted because they are either not applicable or the required information is shown in the financial statements or notes thereto.
Report of Independent Registered Public Accounting Firm
The Board of Directors and Shareholders
Joy Global Inc.
We have audited the accompanying consolidated balance sheets of Joy Global Inc. as of October 29, 2005 and October 30, 2004, and the related consolidated statements of income, shareholders’ equity, and cash flows for each of the three years in the period ended October 29, 2005. Our audits also included the financial statement schedule listed in the Index at Item 15(a)(2). These financial statements and schedule are the responsibility of the Company’s management. Our responsibility is to express an opinion on these financial statements and schedule based on our audits.
We conducted our audits in accordance with the standards of the Public Company Accounting Oversight Board (United States). Those standards require that we plan and perform the audit to obtain reasonable assurance about whether the financial statements are free of material misstatement. An audit includes examining, on a test basis, evidence supporting the amounts and disclosures in the financial statements. An audit also includes assessing the accounting principles used and significant estimates made by management, as well as evaluating the overall financial statement presentation. We believe that our audits provide a reasonable basis for our opinion.
In our opinion, the financial statements referred to above present fairly, in all material respects, the consolidated financial position of Joy Global Inc. at October 29, 2005 and October 30, 2004, and the consolidated results of its operations and its cash flows for each of the three years in the period ended October 29, 2005, in conformity with U.S. generally accepted accounting principles. Also, in our opinion, the related financial statement schedule, when considered in relation to the basic financial statements taken as a whole, present fairly in all material respects the information set forth therein.
We also have audited, in accordance with the standards of the Public Company Accounting Oversight Board (United States), the effectiveness of Joy Global Inc.‘s internal control over financial reporting as of October 29, 2005, based on criteria established in Internal Control – Integrated Framework issued by the Committee of Sponsoring Organizations of the Treadway Commission and our report dated December 15, 2005 expressed an unqualified opinion thereon.
/s/ Ernst & Young LLP
Milwaukee, Wisconsin
December 15, 2005
Report of Independent Registered Public Accounting Firm
The Board of Directors and Shareholders
Joy Global Inc.
We have audited management’s assessment, included in the accompanying Management’s Report on Internal Control Over Financial Reporting, that Joy Global Inc. maintained effective internal control over financial reporting as of October 29, 2005, based on criteria established in Internal Control—Integrated Framework issued by the Committee of Sponsoring Organizations of the Treadway Commission (the COSO criteria). Joy Global Inc.‘s management is responsible for maintaining effective internal control over financial reporting and for its assessment of the effectiveness of internal control over financial reporting. Our responsibility is to express an opinion on management’s assessment and an opinion on the effectiveness of the company’s internal control over financial reporting based on our audit.
We conducted our audit in accordance with the standards of the Public Company Accounting Oversight Board (United States). Those standards require that we plan and perform the audit to obtain reasonable assurance about whether effective internal control over financial reporting was maintained in all material respects. Our audit included obtaining an understanding of internal control over financial reporting, evaluating management’s assessment, testing and evaluating the design and operating effectiveness of internal control, and performing such other procedures as we considered necessary in the circumstances. We believe that our audit provides a reasonable basis for our opinion.
A company’s internal control over financial reporting is a process designed to provide reasonable assurance regarding the reliability of financial reporting and the preparation of financial statements for external purposes in accordance with generally accepted accounting principles. A company’s internal control over financial reporting includes those policies and procedures that (1) pertain to the maintenance of records that, in reasonable detail, accurately and fairly reflect the transactions and dispositions of the assets of the company; (2) provide reasonable assurance that transactions are recorded as necessary to permit preparation of financial statements in accordance with generally accepted accounting principles, and that receipts and expenditures of the company are being made only in accordance with authorizations of management and directors of the company; and (3) provide reasonable assurance regarding prevention or timely detection of unauthorized acquisition, use, or disposition of the company’s assets that could have a material effect on the financial statements.
Because of its inherent limitations, internal control over financial reporting may not prevent or detect misstatements. Also, projections of any evaluation of effectiveness to future periods are subject to the risk that controls may become inadequate because of changes in conditions, or that the degree of compliance with the policies or procedures may deteriorate.
In our opinion, management’s assessment that Joy Global Inc. maintained effective internal control over financial reporting as of October 29, 2005, is fairly stated, in all material respects, based on the COSO criteria. Also, in our opinion, Joy Global Inc. maintained, in all material respects, effective internal control over financial reporting as of October 29, 2005, based onthe COSO criteria.
We also have audited, in accordance with the standards of the Public Company Accounting Oversight Board (United States), the 2005 consolidated financial statements of Joy Global Inc. and our report dated December 15, 2005 expressed an unqualified opinion thereon.
/s/ Ernst & Young LLP
Milwaukee, Wisconsin
December 15, 2005
Management’s Report on Internal Control Over Financial Reporting
Our management is responsible for establishing and maintaining adequate internal control over financial reporting (as defined in Rule 13a-15(f) under the Exchange Act), to provide reasonable assurance regarding the reliability of our financial reporting and the preparation of financial statements for external purposes in accordance with generally accepted accounting principles.
Due to its inherent limitations, internal control over financial reporting may not prevent or detect misstatements. Also, projections of any evaluation of effectiveness to future periods are subject to the risk that controls may become inadequate due to changes in conditions, or that the degree of compliance with the policies or procedures may deteriorate.
Under the supervision and with the participation of our management, including our Chief Executive Officer and Chief Financial Officer, we conducted an evaluation of the effectiveness of our internal control over financial reporting using the criteria set forth by the Committee of Sponsoring Organizations of the Treadway Commission in Internal Control—Integrated Framework. Based on its evaluation, our management concluded that our internal control over financial reporting was effective as of October 29, 2005.
Ernst & Young LLP, an independent registered public accounting firm, has audited the Consolidated Financial Statements included in this Annual Report on Form 10-K and, as part of its audit, has issued its reports, included herein, (1) on our management’s assessment of the effectiveness of our internal control over financial reporting and (2) on the effectiveness of our internal control over financial reporting.
Joy Global Inc.
Consolidated Statement of Income
(In thousands, except for per share data)
| Fiscal Years Ended
|
---|
| October 29, 2005
| October 30, 2004
| November 1, 2003
|
---|
Net sales | | | $ | 1,927,474 | | $ | 1,399,357 | | $ | 1,185,701 | |
Cost of sales | | | | 1,365,496 | | | 1,021,334 | | | 896,712 | |
Product development, selling | | |
and administrative expenses | | | | 297,904 | | | 272,967 | | | 237,004 | |
Other income | | | | (3,465 | ) | | (3,415 | ) | | (2,963 | ) |
Restructuring charges | | | | 849 | | | 625 | | | 6,915 | |
|
| |
| |
| |
Operating income | | | | 266,690 | | | 107,846 | | | 48,033 | |
Interest income | | | | 5,575 | | | 4,333 | | | 5,065 | |
Interest expense | | | | (15,191 | ) | | (24,284 | ) | | (27,031 | ) |
Loss on early retirement of debt | | | | (32,431 | ) | | — | | | (261 | ) |
|
| |
| |
| |
Income from continuing operations | | |
before reorganization items | | | | 224,643 | | | 87,895 | | | 25,806 | |
Reorganization items | | | | 2,810 | | | 6,842 | | | 2,411 | |
|
| |
| |
| |
Income from continuing operations | | |
before income taxes | | | | 227,453 | | | 94,737 | | | 28,217 | |
Provision for income taxes | | | | (80,532 | ) | | (39,281 | ) | | (9,448 | ) |
|
| |
| |
| |
Income from continuing operations | | | | 146,921 | | | 55,456 | | | 18,769 | |
Income (loss) from discontinued operations, net of applicable income taxes | | | | 1,128 | | | (134 | ) | | (253 | ) |
|
| |
| |
| |
| | |
Net income | | | $ | 148,049 | | $ | 55,322 | | $ | 18,516 | |
|
| |
| |
| |
Basic earnings (loss) per share* (Note 9): | | |
Continuing operations | | | $ | 1.21 | | $ | 0.47 | | $ | 0.17 | |
Discontinued operations | | | $ | 0.01 | | $ | — | | $ | (0.01 | ) |
|
| |
| |
| |
Net income | | | $ | 1.22 | | $ | 0.47 | | $ | 0.16 | |
|
| |
| |
| |
Diluted earnings per share* (Note 9): | | |
Continuing operations | | | $ | 1.19 | | $ | 0.46 | | $ | 0.16 | |
Discontinued operations | | | $ | 0.01 | | $ | — | | $ | — | |
|
| |
| |
| |
Net income | | | $ | 1.20 | | $ | 0.46 | | $ | 0.16 | |
|
| |
| |
| |
Dividends per common share* | | | $ | 0.275 | | $ | 0.122 | | $ | .122 | |
|
| |
| |
| |
Weighted average common shares* | | |
Basic | | | | 121,121 | | | 117,277 | | | 113,045 | |
|
| |
| |
| |
Diluted | | | | 123,443 | | | 120,654 | | | 113,799 | |
|
| |
| |
| |
*Adjusted for three-for-two stock splits effective both January 21, 2005 and December 12, 2005
See accompanying notes to consolidated financial statements
Joy Global Inc.
Consolidated Balance Sheet
(In thousands)
| October 29, 2005
| October 30, 2004
|
---|
ASSETS | | | | | | | | |
Current Assets: | | |
Cash and cash equivalents | | | $ | 143,917 | | $ | 231,706 | |
Accounts receivable, net | | | | 351,501 | | | 259,897 | |
Inventories | | | | 548,195 | | | 443,810 | |
Other current assets | | | | 73,070 | | | 56,639 | |
|
| |
| |
Total Current Assets | | | | 1,116,683 | | | 992,052 | |
|
| |
| |
Property, Plant and Equipment: | | |
Land and improvements | | | | 14,959 | | | 14,388 | |
Buildings | | | | 81,700 | | | 73,649 | |
Machinery and equipment | | | | 251,884 | | | 250,927 | |
|
| |
| |
| | | | 348,543 | | | 338,964 | |
Accumulated depreciation | | | | (149,363 | ) | | (128,208 | ) |
|
| |
| |
| | |
Total Property, Plant and Equipment | | | | 199,180 | | | 210,756 | |
|
| |
| |
Other Assets: | | |
Intangible assets, net | | | | 6,515 | | | 37,431 | |
Deferred income taxes | | | | 225,138 | | | 129,424 | |
Prepaid benefit cost | | | | 87,308 | | | 49,119 | |
Other non-current assets | | | | 13,704 | | | 21,577 | |
|
| |
| |
| | |
Total Other Assets | | | | 332,665 | | | 237,551 | |
|
| |
| |
Total Assets | | | $ | 1,648,528 | | $ | 1,440,359 | |
|
| |
| |
See accompanying notes to consolidated financial statements
Joy Global Inc.
Consolidated Balance Sheet
(In thousands)
| October 29, 2005
| October 30, 2004
|
---|
LIABILITIES AND SHAREHOLDERS' EQUITY | | | | | | | | |
Current Liabilities: | | |
Short-term notes payable, including current | | |
portion of long-term obligations | | | $ | 964 | | $ | 3,110 | |
Trade accounts payable | | | | 160,627 | | | 139,178 | |
Employee compensation and benefits | | | | 91,172 | | | 82,472 | |
Advance payments and progress billings | | | | 187,710 | | | 87,507 | |
Accrued warranties | | | | 34,183 | | | 31,259 | |
Other accrued liabilities | | | | 124,857 | | | 88,326 | |
|
| |
| |
Total Current Liabilities | | | | 599,513 | | | 431,852 | |
|
| |
| |
Long-term Obligations | | | | 1,703 | | | 202,869 | |
Other Non-current Liabilities: | | |
Liability for postretirement benefits | | | | 43,504 | | | 44,345 | |
Accrued pension costs | | | | 301,161 | | | 268,933 | |
Other | | | | 35,021 | | | 40,312 | |
|
| |
| |
Total Other Non-current Liabilities | | | | 379,686 | | | 353,590 | |
Commitments and Contingencies (Note 18) | | | | — | | | — | |
Shareholders' Equity: | | |
Common stock, $1 par value | | |
(authorized 150,000,000 shares; 121,769,427* and | | |
53,239,858 deemed shares issued at October 29, | | |
2005 and October 30, 2004, respectively.) | | | | 121,769 | | | 53,240 | |
Capital in excess of par value | | | | 704,932 | | | 640,883 | |
Retained earnings (deficit) | | | | 69,766 | | | (45,042 | ) |
Accumulated other comprehensive loss | | | | (228,841 | ) | | (197,033 | ) |
|
| |
| |
Total Shareholders' Equity | | | | 667,626 | | | 452,048 | |
|
| |
| |
Total Liabilities and Shareholders' Equity | | | $ | 1,648,528 | | $ | 1,440,359 | |
|
| |
| |
*Adjusted for three-for-two stock splits effective both January 21, 2005 and December 12, 2005
See accompanying notes to consolidated financial statements
Joy Global Inc.
Consolidated Statement of Cash Flows
(In thousands)
| Fiscal Years Ended
|
---|
| October 29, 2005
| October 30, 2004
| November 1, 2003
|
---|
Operating Activities: | | | | | | | | | | | |
Net income | | | $ | 148,049 | | $ | 55,322 | | $ | 18,516 | |
Add (deduct) - items not affecting cash: | | |
Loss on early retirement of debt | | | | 32,431 | | | — | | | 261 | |
Depreciation and amortization | | | | 41,885 | | | 46,177 | | | 52,542 | |
Amortization of financing fees | | | | 1,424 | | | 3,190 | | | 3,546 | |
Increase (decrease) in deferred income taxes, net | | |
of change in valuation allowance | | | | 65,509 | | | (2,390 | ) | | (11,642 | ) |
Change in long-term accrued pension costs | | | | 9,419 | | | 15,031 | | | (1,121 | ) |
Other, net | | | | 1,579 | | | 2,151 | | | 3,645 | |
Contributions to U.S. qualified pension plans | | | | (48,400 | ) | | (88,104 | ) | | (47,612 | ) |
Changes in Working Capital Items: | | |
(Increase) in accounts receivable, net | | | | (101,835 | ) | | (57,719 | ) | | (10,510 | ) |
(Increase) decrease in inventories | | | | (123,436 | ) | | (48,146 | ) | | 65,293 | |
(Increase) decrease in other current assets | | | | (5,434 | ) | | 4,750 | | | 7,377 | |
Increase in trade accounts payable | | | | 25,828 | | | 45,442 | | | 7,601 | |
Increase in employee compensation and benefits | | | | 15,015 | | | 30,037 | | | 30,753 | |
Increase in advance payments and progress billings | | | | 111,357 | | | 49,290 | | | 5,695 | |
Increase (decrease) in other accrued liabilities | | | | 27,906 | | | 7,230 | | | (18,699 | ) |
|
| |
| |
| |
Net cash provided by operating activities | | | | 201,297 | | | 62,261 | | | 105,645 | |
|
| |
| |
| |
Investment Activities: | | |
Property, plant and equipment acquired | | | | (38,753 | ) | | (21,135 | ) | | (28,620 | ) |
Proceeds from sale of property, plant and equipment | | | | 1,694 | | | 2,330 | | | 2,996 | |
Purchase of equity interest in subsidiary | | | | — | | | — | | | (12,316 | ) |
Other, net | | | | 1,356 | | | 7,668 | | | 7,393 | |
|
| |
| |
| |
Net cash used by investment activities | | | | (35,703 | ) | | (11,137 | ) | | (30,547 | ) |
|
| |
| |
| |
Financing Activities: | | |
Exercise of stock options | | | | 11,984 | | | 44,716 | | | 1,917 | |
Dividends paid | | | | (33,580 | ) | | (14,026 | ) | | — | |
Increase (decrease) in short-term notes payable | | | | (2,297 | ) | | (1,080 | ) | | 1,512 | |
Payments on long-term obligations | | | | (817 | ) | | (1,010 | ) | | (13,174 | ) |
Financing fees | | | | (1,615 | ) | | (1,000 | ) | | (250 | ) |
Redemption of 8.75% Senior Subordinated Notes | | | | (224,521 | ) | | — | | | — | |
|
| |
| |
| |
Net cash provided (used) by financing activities | | | | (250,846 | ) | | 27,600 | | | (9,995 | ) |
|
| |
| |
| |
Effect of Exchange Rate Changes on Cash and | | |
Cash Equivalents | | | | (2,537 | ) | | 4,477 | | | 12,496 | |
|
| |
| |
| |
(Decrease) Increase in Cash and Cash Equivalents | | | | (87,789 | ) | | 83,201 | | | 77,599 | |
Cash and Cash Equivalents at Beginning of Year | | | | 231,706 | | | 148,505 | | | 70,906 | |
|
| |
| |
| |
Cash and Cash Equivalents at End of Year | | | $ | 143,917 | | $ | 231,706 | | $ | 148,505 | |
|
| |
| |
| |
Supplemental cash flow information | | |
Interest paid | | | $ | 16,538 | | $ | 22,022 | | $ | 23,075 | |
Income taxes paid | | | | 14,389 | | | 13,745 | | | 19,067 | |
See accompanying notes to consolidated financial statements
Joy Global Inc.
Consolidated Statement of Shareholders’ Equity
(In thousands)
| Common Stock
| Capital in Excess of | Retained Earnings | Accumulated Other Comprehensive | |
---|
| Shares
| Amount
| Par Value
| (Deficit)
| Income (Loss)
| Total
|
---|
Balance at November 2, 2002 | | | | 50,228 | | $ | 50,228 | | $ | 585,370 | | $ | (104,515 | ) | $ | (180,467 | ) | $ | 350,616 | |
Comprehensive income (loss): | | |
Net income | | | | — | | | — | | | — | | | 18,516 | | | — | | | 18,516 | |
Change in additional minimum pension liability | | | | — | | | — | | | — | | | — | | | (33,652 | ) | | (33,652 | ) |
Derivative instrument fair market value adjustment | | | | — | | | — | | | — | | | — | | | 585 | | | 585 | |
Currency translation adjustment | | | | — | | | — | | | — | | | — | | | 31,974 | | | 31,974 | |
| | | | | |
| |
Total comprehensive income | | | | | | | | | | | | | | | | | | | 17,423 | |
Exercise of stock options | | | | 145 | | | 145 | | | 1,910 | | | — | | | — | | | * 2,055 | |
Tax benefit from exercise of stock options | | | | | | | | | | 179 | | | — | | | — | | | 179 | |
|
| |
| |
| |
| |
| |
| |
Balance at November 1, 2003 | | | | 50,373 | | $ | 50,373 | | $ | 587,459 | | $ | (85,999 | ) | $ | (181,560 | ) | $ | 370,273 | |
Comprehensive income (loss): | | |
Net income | | | | — | | | — | | | — | | | 55,322 | | | — | | | 55,322 | |
Change in additional minimum pension liability | | | | — | | | — | | | — | | | — | | | (22,158 | ) | | (22,158 | ) |
Derivative instrument fair market value adjustment | | | | — | | | — | | | — | | | — | | | 3,088 | | | 3,088 | |
Currency translation adjustment | | | | — | | | — | | | — | | | — | | | 3,597 | | | 3,597 | |
| | | | | |
| |
Total comprehensive income | | | | | | | | | | | | | | | | | | | 39,849 | |
Dividends | | | | — | | | — | | | — | | | (14,365 | ) | | — | | | (14,365 | ) |
Exercise of stock options | | | | 2,867 | | | 2,867 | | | 41,711 | | | — | | | — | | | * 44,578 | |
Tax benefit from exercise of stock options | | | | — | | | — | | | 11,713 | | | — | | | — | | | 11,713 | |
|
| |
| |
| |
| |
| |
| |
Balance at October 30, 2004 | | | | 53,240 | | $ | 53,240 | | $ | 640,883 | | $ | (45,042 | ) | $ | (197,033 | ) | $ | 452,048 | |
Comprehensive income (loss): | | |
Net income | | | | — | | | — | | | — | | | 148,049 | | | — | | | 148,049 | |
Change in additional minimum pension liability, net of taxes | | | | — | | | — | | | — | | | — | | | (21,173 | ) | | (21,173 | ) |
Derivative instrument fair market value adjustment, net of taxes | | | | — | | | — | | | — | | | — | | | (4,391 | ) | | (4,391 | ) |
Currency translation adjustment | | | | — | | | — | | | — | | | — | | | (6,244 | ) | | (6,244 | ) |
| | | | | |
| |
Total comprehensive income | | | | | | | | | | | | | | | | | | | 116,241 | |
3 for 2 stock split effective January 21, 2005 | | | | 26,728 | | | 26,728 | | | (26,728 | ) | | — | |
Restricted stock expense and other | | | | (1 | ) | | (1 | ) | | 1,435 | | | — | | | — | | | 1,434 | |
Deferred tax adjustment | | | | — | | | — | | | 100,088 | | | — | | | — | | | 100,088 | |
Dividends | | | | — | | | — | | | — | | | (33,241 | ) | | — | | | (33,241 | ) |
Issuance of performance units | | | | 135 | | | 135 | | | 10,290 | | | — | | | — | | | 10,425 | |
Exercise of stock options | | | | 1,077 | | | 1,077 | | | 10,907 | | | — | | | — | | | 11,984 | |
Tax benefit from exercise of stock options | | | | — | | | — | | | 8,647 | | | — | | | — | | | 8,647 | |
3 for 2 stock split effective December 12, 2005 | | | | 40,590 | | | 40,590 | | | (40,590 | ) | | — | | | — | | | — | |
|
| |
| |
| |
| |
| |
| |
Balance at October 29, 2005 | | | | 121,769 | | $ | 121,769 | | $ | 704,932 | | $ | 69,766 | | $ | (228,841 | ) | $ | 667,626 | |
|
| |
| |
| |
| |
| |
| |
| | | | | | |
* Difference between the consoldiated Statement of Shareholders' Equity and Consoldiated Statement of Cash Flows represents $138 of cash received in Fiscal 2004 relating to stock options exercised in Fiscal 2003.
See accompanying notes to the consolidated financial statements
Joy Global Inc.
Notes to Consolidated Financial Statements
October 29, 2005
1. Description of Business
| Joy Global Inc. is the world’s leading manufacturer and servicer of high productivity mining equipment for the extraction of coal and other minerals and ores. Our equipment is used in major mining centers throughout the world to mine coal, copper, iron ore, oil sands and other minerals. We operate in two business segments: underground mining machinery (Joy Mining Machinery or “Joy”) and surface mining equipment (P&H Mining Equipment or “P&H”). Joy is a major manufacturer of underground mining equipment for the extraction of coal and other bedded minerals and offers comprehensive service locations near major mining regions worldwide. P&H is a major producer of surface mining equipment for the extraction of ores and minerals and provides extensive operational support for many types of equipment used in surface mining. |
2. Significant Accounting Policies
Our significant accounting policies are as follows:
| Basis of Presentation and Principles of Consolidation — The Consolidated Financial Statements are presented in accordance with accounting principles generally accepted in the United States. The Consolidated Financial Statements include the accounts of Joy Global Inc. and our subsidiaries, all of which are wholly owned. All significant intercompany balances and transactions have been eliminated. |
| Use of Estimates — The preparation of financial statements in conformity with accounting principles generally accepted in the United States requires us to make estimates and assumptions that affect the reported amounts of assets and liabilities at the date of the financial statements, and the reported amounts of revenues and expenses during the reporting period. Ultimate realization of assets and settlement of liabilities in the future could differ from those estimates. |
| Stock Splits –Except on the Consolidated Balance Sheet and Consolidated Statement of Shareholders’ Equity, all previously presented earnings per share, share amounts, and stock price data have been adjusted for three-for-two stock splits, effective both January 21, 2005 and December 12, 2005. |
| Cash Equivalents — All highly liquid investments with original maturities of three months or less when issued are considered cash equivalents. These primarily consist of money market funds and to a lesser extent, certificates of deposit and commercial paper. Cash equivalents were $81.5 million and $189.5 million at October 29, 2005 and October 30, 2004, respectively. |
| Inventories — Our inventories are carried at the lower of cost or net realizable value using the first-in, first-out (“FIFO”) method for all inventories. We evaluate the need to record adjustments for inventory on a regular basis. Our policy is to evaluate all inventory including raw material, work-in-process, finished goods, and spare parts. Inventory in excess of our estimated usage requirements is written down to its estimated net realizable value. Inherent in the estimates of net realizable value are estimates related to our future manufacturing schedules, customer demand, possible alternative uses and ultimate realization of potentially excess inventory. |
| Property, Plant and Equipment — Property, plant and equipment are stated at historical cost. Expenditures for major renewals and improvements are capitalized, while maintenance and repair costs that do not significantly improve the related asset or extend its useful life are charged to expense as incurred. For financial reporting purposes, plant and equipment are depreciated primarily by the straight-line method over the estimated useful lives of the assets which generally range from 5 to 20 years for improvements, from 33 to 50 years for buildings, from 3 to 15 years for machinery and equipment and 3 years for software. Depreciation expense was $37.8 million, $40.5 million and $41.5 million for Fiscal 2005, Fiscal 2004, and Fiscal 2003, respectively. Depreciation claimed for income tax purposes is computed by accelerated methods. |
| Impairment of Long-Lived Assets — Our policy is to assess the realizability of our held and used long-lived assets and to evaluate such assets for impairment whenever events or circumstances indicate that the carrying amount of such assets (or group of assets) may not be recoverable. Impairment is determined to exist if the estimated future undiscounted cash flows related to such assets is less than the carrying value. If an impairment is determined to exist, any related impairment loss is calculated based on the fair value of the asset compared to its carrying value. |
| Intangible Assets —Intangible assets include drawings, patents, trademarks, technology and other specifically identifiable assets. Indefinite-lived intangible assets are not being amortized. Finite-lived intangible assets are amortized to reflect the pattern of economic benefits consumed which is principally the straight-line method. Intangible assets are evaluated for impairment annually, or more frequently if events or changes occur that suggest impairment in carrying value. |
| Foreign Currency Translation — Exchange gains or losses incurred on transactions conducted by one of our operations in a currency other than the operation’s functional currency are normally reflected in cost of sales in our Consolidated Statement of Income. An exception is made where the transaction is a long-term intercompany loan that is not expected to be repaid in the foreseeable future, in which case the transaction gain or loss is included in shareholders’ equity as an element of accumulated other comprehensive income (loss). Assets and liabilities of international operations that have a functional currency that is not the U.S. dollar are translated into U.S. dollars at year-end exchange rates and revenue and expense items are translated using weighted average exchange rates. Any adjustments arising on translations are included in shareholders’ equity as an element of accumulated other comprehensive income (loss). Assets and liabilities of operations which have the U.S. dollar as their functional currency (but which maintain their accounting records in local currency) have their values remeasured into U.S. dollars at year-end exchange rates, except for non-monetary items for which historical rates are used. Exchange gains or losses arising on remeasurement of the values into U.S. dollars are recognized in cost of sales. Pre-tax foreign exchange gains (losses) included in operating income were $3.9 million, $(0.6) million and $(0.3) million for Fiscal 2005, Fiscal 2004, and Fiscal 2003, respectively. |
| Foreign Currency Hedging and Derivative Financial Instruments — We enter into derivative contracts, primarily foreign currency forward contracts, to protect against fluctuations in exchange rates. These contracts are for committed transactions, receivables and payables denominated in foreign currencies and net investment hedges and not for speculative purposes. All current contracts mature within 12 months. Statement of Financial Accounting Standards (“SFAS”) No. 133, “Accounting for Derivative Instruments and Hedging Activities”, as amended, requires companies to record derivatives on the balance sheet as assets or liabilities, measured at fair value. Any changes in fair value of these instruments are recorded in the income statement or in the balance sheet as other comprehensive income (loss). |
| During Fiscal 2005, 2004 and 2003, there were no derivative instruments that were deemed to be ineffective. The amounts included in Accumulated Other Comprehensive Loss will be reclassified into income when the forecasted transaction occurs, generally within the next twelve months. |
| Comprehensive Income (Loss) — SFAS No. 130, “Reporting Comprehensive Income”, requires the reporting of comprehensive income in addition to net income. Comprehensive income is a more inclusive financial reporting method that includes disclosure of financial information that historically has not been recognized in the calculation of net income. We have chosen to report Comprehensive Income (Loss) and Accumulated Other Comprehensive Income (Loss) which encompasses net income, foreign currency translation, minimum pension liability and unrealized gain (loss) on derivatives in the Consolidated Statement of Shareholders’ Equity. Accumulated other comprehensive loss consists of the following: |
| October 29, 2005
| October 30, 2004
| November 1, 2003
|
---|
Minimum pension liability | | | $ | (260 | .2) | $ | (239 | .0) | $ | (216 | .9) |
Unrealized gain (loss) on derivatives | | | | (0 | .9) | | 3 | .5 | | 0 | .4 |
Foreign currency translation | | | | 32 | .3 | | 38 | .5 | | 34 | .9 |
|
| |
| |
| |
Accumulated other comprehensive loss | | | $ | (228 | .8) | $ | (197 | .0) | $ | (181 | .6) |
|
| |
| |
| |
| Minimum pension liability and unrealized gain (loss) on derivatives are net of $14.9 and $0.6 million of income tax benefits, respectively, at October 29, 2005. |
| Revenue Recognition — We generally recognize revenue at the time of shipment and passage of title for sales of products and at the time of performance for sales of services. We recognize revenue on long-term contracts, such as the manufacture of mining shovels, drills, draglines and roof support systems, using either the percentage-of-completion or inventory sales method. We generally recognize revenue using the percentage-of-completion method for equipment that requires a minimum of six months to produce. When using the percentage-of-completion method, sales and gross profit are recognized as work is performed based on the relationship between actual costs incurred and total estimated costs at completion. Sales and gross profit are adjusted prospectively for revisions in estimated total contract costs and contract values. Estimated losses are recognized in full when identified. |
| We have life cycle management contracts with customers to supply parts and service for terms of 1 to 13 years. These contracts are set up based on the projected costs and revenues of servicing the respective machines over the specified contract terms. Accounting for these contracts requires us to make various estimates, including estimates of the relevant machine’s long-term maintenance requirements. Under these contracts, customers are generally billed monthly and the respective deferred revenues are recorded when billed. Revenue is recognized in the period in which parts are supplied or services provided. These contracts are reviewed periodically and revenue recognition is adjusted appropriately for future estimated costs. If a loss is expected at any time, the full amount of the loss is recognized immediately. |
| Revenue recognition involves judgments, assessments of expected returns, the likelihood of nonpayment, and estimates of expected costs and profits on long-term contracts. We analyze various factors, including a review of specific transactions, historical experience, credit-worthiness of customers and current market and economic conditions, in determining when to recognize revenue. Changes in judgments on these factors could impact the timing and amount of revenue recognized with a resulting impact on the timing and amount of associated income. |
| Sales Incentives –In accordance with the Financial Accounting Standards Board’s Emerging Issues Task Force Issue (“EITF”) No. 01-09, “Accounting for Consideration Given by a Vendor to a Customer or a Reseller of the Vendor’s Product,” we account for cash consideration (such as sales incentives and cash discounts) given to our customers or resellers as a reduction of revenue rather than an operating expense. |
| Shipping and Handling Fees and Costs –We account for shipping and handling fees and costs in accordance with EITF Issue No. 00-10, “Accounting for Shipping and Handling Fees and Costs.” Under EITF No. 00-10 amounts billed to a customer in a sale transaction related to shipping costs are reported as net sales and the related costs incurred for shipping are reported as cost of sales. |
| Income Taxes — Deferred income taxes are recognized for the tax consequences of temporary differences by applying enacted statutory tax rates applicable to future years to differences between the financial statement carrying amounts and the tax bases of existing assets and liabilities, and for tax loss carryforwards. Valuation allowances are provided for deferred tax assets where it is considered more likely than not that we will not realize the benefit of such assets. Certain tax benefits existed as of our emergence from protection under Chapter 11 of the U.S. Bankruptcy Code on July 12, 2001 (the “Effective Date”) but were offset by valuation allowances. The utilization of these pre-emergence benefits to reduce income taxes paid to federal, state, and foreign jurisdictions does not reduce our income tax expense. Realization of net operating loss, tax credits and other deferred tax benefits from pre-emergence attributes will first reduce other intangibles until exhausted, and thereafter will be credited to additional paid in capital. |
| Accounting For Stock Options – We account for stock-based employee compensation arrangements in accordance with Accounting Principles Board Opinion No. 25, “Accounting for Stock Issued to Employees” (“APB 25”) and related interpretations and complies with the disclosure provisions of Statement of Financial Accounting Standards No. 123, “Accounting for Stock-Based Compensation,” (“SFAS 123”), as amended by SFAS No. 148, “Accounting for Stock-Based Compensation—Transition and Disclosure.” |
| We are required under SFAS 123 to disclose pro forma information regarding the stock awards made to its employees based on specified valuation techniques that produce estimated compensation charges. The pro forma information is as follows (in thousands, except per share data): |
| Fiscal 2005
| Fiscal 2004
| Fiscal 2003
|
---|
Net income, as reported | | | $ 148,049 | | | $ 55,322 | | | $ 18,516 | | |
Add: Stock-based employee compensation | | |
expense included in reported net income, net | | |
of related taxes | | | 11,116 | | | 9,363 | | | 2,852 | | |
Deduct: Stock -based employee compensation | | |
expense determined under fair value based | | |
method for all awards, net of related taxes | | | (7,979) | | | (9,097) | | | (6,977) | | |
|
| |
| |
| |
| | | |
Pro forma net income | | | $ 151,186 | | | $ 55,588 | | | $ 14,391 | | |
|
| |
| |
| |
Earnings per share: | | |
Basic-as reported | | | $ 1.22 | | | $ 0.47 | | | $ 0.16 | | |
|
| |
| |
| |
Basic-pro forma | | | $ 1.25 | | | $ 0.47 | | | $ 0.13 | | |
|
| |
| |
| |
Diluted-as reported | | | $ 1.20 | | | $ 0.46 | | | $ 0.16 | | |
|
| |
| |
| |
Diluted-pro forma | | | $ 1.22 | | | $ 0.46 | | | $ 0.13 | | |
|
| |
| |
| |
| The fair value of the stock awards is the estimated present value at grant date using the Black Scholes valuation model with weighted average assumptions and the resulting estimated fair value for the years 2005, 2004 and 2003 as follows: |
| Fiscal 2005
| Fiscal 2004
| Fiscal 2003
|
---|
Risk free interest rate | | | | 3.5% | | | 4.2% | | | 4.5% | |
Expected volatility | | | | 47% | | | 51% | | | 37% | |
Expected life | | | 4.1 years | 5.0 years | 7.0 years |
Dividend yield | | | | 1.13% | | | 1.14% | | | — | |
Weighted average estimated fair value at grant date | | | $ | 6.71 | | $ | 5.23 | | $ | 2.08 | |
| Research and Development Expenses — Research and development costs are expensed as incurred. Such costs incurred in the development of new products or significant improvements to existing products amounted to $8.5 million, $6.3 million and $3.8 million for Fiscal 2005, 2004 and 2003, respectively. |
| Earnings Per Share — Basic earnings (loss) per share is computed by dividing net earnings by the weighted average number of common shares outstanding during the reporting period. Diluted earnings (loss) per common share is computed similar to basic earnings per share except that the weighted average number of shares outstanding is increased to include additional shares from the assumed exercise of stock options, performance units and restricted stock units if dilutive. See Note 9 –Earnings PerShare for further information. |
| New Accounting Pronouncements — On December 16, 2004, the Financial Accounting Standards Board (“FASB”) issued SFAS No. 123 (revised 2004), “Share-Based Payments” (“SFAS 123(R)”). SFAS 123(R) replaces FASB Statement No. 123, “Accounting forStock-Based Compensation,” and supersedes APB Opinion No. 25, “Accounting for Stock Issued to Employees.”SFAS 123(R) generally requires compensation cost related to share-based payment transactions, including stock options, performance units and restricted units, to be recognized in the financial statements. Compensation cost will be measured using an option pricing model and will be recognized over the requisite service period. We have adopted SFAS 123(R) effective October 30, 2005. SFAS 123(R) will apply to all awards granted after the implementation date and to previously granted awards unvested as of the implementation date. The effect of adoption of SFAS 123(R) is currently estimated to be an incremental expense of approximately $5.0 to $8.0 million ($.04 to $.07 per share) after-tax for Fiscal 2006. However, our actual share-based compensation expense in 2006 depends on a number of factors, including fair value of awards at the time of grant. |
| In December 2004, the FASB issued Statement No. 153 (“FAS 153”), “Exchanges of Nonmonetary Assets – an amendment of APB Opinion No. 29, Accounting for Nonmonetary Transactions” (“APB 29”). FAS 153 is based on the principle that nonmonetary asset exchanges should be recorded and measured at the fair value of the assets exchanged, with certain exceptions. This standard requires exchanges of productive assets to be accounted for at fair value, rather than at carryover basis, unless (i) neither the asset received nor the asset surrendered has a fair value that is determinable within reasonable limits or (ii) the transactions lack commercial substance (as defined). In addition, the FASB decided to retain the guidance in APB 29 for assessing whether the fair value of a nonmonetary asset is determinable within reasonable limits. The new standard is the result of the convergence project between the FASB and the International Accounting Standards Board (“IASB”). We will adopt this standard for nonmonetary asset exchanges beginning in Fiscal 2006. The adoption of FAS 153 is not expected to have a significant impact on our consolidated financial statements. |
| In November 2004, FASB issued Statement No. 151 (“FAS 151”), “Inventory Costs, an amendment of ARB No. 43, Chapter 4", to improve financial reporting and global comparability of inventory accounting. The amendment, which adopted language similar to that used in the IASB International Accounting Standard 2 (“IAS 2”), clarifies that inventory related expenses, such as abnormal amounts of idle facility expense, freight, handling costs, and wasted or spoiled materials should be recognized as current period charges. The statement also requires fixed production overhead allocations to inventory based on normal capacity of the production facilities. The guidance is effective for inventory costs incurred beginning in Fiscal 2006. The adoption of FAS 151 is not expected to have a significant impact on our consolidated financial statements. |
| Reclassifications – Certain prior year amounts have been reclassified to conform to the current year presentation. The reclassifications did not impact net income or earnings per share. |
3. Intangible Assets
| Goodwill and intangible assets with indefinite useful lives are not amortized but are tested for impairment at least annually. Intangible assets with finite useful lives are amortized over their respective estimated useful lives to their estimated residual values, and reviewed for impairment in accordance with SFAS No. 144, “Accounting for the Impairment or Disposal of Long-Lived Assets.” |
| | October 29, 2005
| October 30, 2004
|
---|
In thousands
| Estimated Useful Lives
| Gross Carrying Amount
| Accumulated Amortization
| Gross Carrying Amount
| Accumulated Amortization
|
---|
Finite lived intangible assets: | | | | | | | | | | | | | | | | | |
Engineering drawings | | | 10-15 years | | | $ | - | (1) | $ | — | | $ | 3,432 | (1) | $ | (698 | ) |
Repair and maintenance contracts | | | 2-5 years | | | | - | (1) | | — | | | 1,208 | (1) | | (645 | ) |
Patents | | | 11-14 years | | | | 4,343 | | | (3,154 | ) | | 7,131 | (1) | | (2,828 | ) |
Unpatented technology | | | 35 years | | | | 1,147 | | | (70 | ) | | 16,858 | (1) | | (970 | ) |
| |
| |
| |
| |
| |
Subtotal | | | | | | | 5,490 | | | (3,224 | ) | | 28,629 | | | (5,141 | ) |
Indefinite lived intangible assets: | | |
Trademarks | | | | | | | - | (1) | | — | | | 9,486 | | | — | |
Pension | | | | | | | 4,249 | | | — | | | 4,457 | | | — | |
| |
| |
| |
| |
| |
Subtotal | | | | | | | 4,249 | | | — | | | 13,943 | | | — | |
| |
| |
| |
| |
| |
Total intangible assets | | | | | | $ | 9,739 | | $ | (3,224 | ) | $ | 42,572 | | $ | (5,141 | ) |
| |
| |
| |
| |
| |
(1) | | During Fiscal 2005 and Fiscal 2004, we adjusted valuation allowances and other tax accruals (see Note 5 –Income Taxes). In accordance with the provisions of SOP 90-7 and FAS No. 109, adjustments to these allowances and other tax accruals that existed as of the emergence date will first reduce any excess reorganization value until exhausted, then other intangibles until exhausted, and thereafter will be included as additional paid in capital in the case of valuation allowance or a reduction of income tax expense in the case of other tax accruals. As of October 29, 2005, all intangibles created upon emerge from reorganization have been eliminated. |
| The following table summarizes the impact of the tax valuation allowance and tax accrual adjustments on our intangible assets. Intangible asset adjustments were allocated on a pro rata share based on their net carrying value. |
In thousands
| Carrying Amount
| Valuation Allowance and Other Tax Accruals
| Adjusted Carrying Amount
|
---|
Fiscal 2005 | | | | | | | | | | | |
Trademarks | | | $ | 9,486 | | $ | (9,486 | ) | $ | — | |
Unpatented technology | | | | 15,406 | | | (14,329 | ) | | 1,077 | |
Engineering drawings | | | | 2,378 | | | (2,378 | ) | | — | |
Patents | | | | 3,182 | | | (1,993 | ) | | 1,189 | |
Repair and maintenance contracts | | | | 303 | | | (303 | ) | | — | |
|
| |
| |
| |
| | | $ | 30,755 | | $ | (28,489 | ) | $ | 2,266 | |
|
| |
| |
| |
Fiscal 2004 | | |
Trademarks | | | $ | 19,777 | | $ | (10,291 | ) | $ | 9,486 | |
Unpatented technology | | | | 32,911 | | | (16,053 | ) | | 16,858 | |
Engineering drawings | | | | 6,235 | | | (2,803 | ) | | 3,432 | |
Patents | | | | 9,511 | | | (2,380 | ) | | 7,131 | |
Repair and maintenance contracts | | | | 2,042 | | | (834 | ) | | 1,208 | |
|
| |
| |
| |
| | | $ | 70,476 | | $ | (32,361 | ) | $ | 38,115 | |
|
| |
| |
| |
| Amortization expense was $2.2 million, $3.7 million and $9.1 million for Fiscal 2005, Fiscal 2004 and Fiscal 2003, respectively. Estimated future annual amortization expense is as follows: |
In thousands
|
|
---|
For the fiscal year ending: | | | | | |
2006 | | | $ | 869 | |
2007 | | | | 392 | |
2008 | | | | 35 | |
2009 | | | | 35 | |
2010 | | | | 35 | |
Our reportable segments have been defined as reporting units for purposes of testing intangible assets for impairment.
4. Borrowings and Credit Facilities
| On October 28, 2005, we entered into a $400.0 million unsecured revolving credit facility expiring on November 15, 2010. It replaced the $275.0 million facility scheduled to expire on October 15, 2008. We recorded a pre-tax charge of $3.3 million related to deferred financing costs associated with the $275.0 million facility. Outstanding borrowings bear interest equal to LIBOR plus the applicable margin (.5% to 1.25%) or the Base Rate (defined as the higher of the Prime Rate or the Federal Funds Effective Rate plus 0.50%) at our option. We pay a commitment fee ranging from 0.125% to 0.25% on the unused portion of the revolving credit facility. The Credit Agreement requires the maintenance of certain financial covenants including leverage, interest coverage and capital expenditures covenants. The agreement also requires a minimum net worth of approximately $396 million, increased by 25% of net income on a quarterly basis beginning with the fourth quarter of Fiscal 2005. On October 29, 2005, we were in compliance with all financial covenants in the credit agreement. |
| At October 29, 2005, there were no outstanding direct borrowings under the Credit Agreement. Outstanding letters of credit issued under the Credit Agreement, which count toward the $400 million credit limit, totaled $101.6 million. At October 29, 2005, there was $298.4 million available for borrowings under the Credit Agreement. |
| In 2002, we issued $200 million par value 8.75% Senior Subordinated Notes due March 15, 2012. During Fiscal 2005, we have purchased approximately all $200.0 million par value Senior Subordinated Notes through a tender offer and in several open market purchases. These transactions, which resulted in a $29.1 million loss on repurchase, consisted of approximately $224.5 million of cash payments and the required write-down of unamortized finance costs of $4.6 million. |
Direct borrowings and capital lease obligations consisted of the following:
In thousands
| October 29, 2005
| October 30, 2004
|
---|
Domestic: | | | | | | | | |
Credit Facility | | | $ | — | | $ | — | |
8.75% Senior Subordinated Notes | | | | 48 | | | 200,000 | |
Capital leases | | | | 182 | | | 230 | |
Foreign: | | |
Capital leases | | | | 2,265 | | | 3,185 | |
Other | | | | 172 | | | 267 | |
Short-term notes payable and bank overdrafts | | | | — | | | 2,297 | |
|
| |
| |
| | | | 2,667 | | | 205,979 | |
Less: Amounts due within one year | | | | (964 | ) | | (3,110 | ) |
|
| |
| |
Long-term Obligations | | | $ | 1,703 | | $ | 202,869 | |
|
| |
| |
| The aggregate maturities of debt consist of the following (in thousands): Fiscal 2006 — $964; Fiscal 2007 — $455; Fiscal 2008 — $262; Fiscal 2009 — $358, Fiscal 2010 — $628. |
5. Income Taxes
The consolidated provision (benefit) for income taxes included in the Consolidated Statement of Income consisted of the following:
In thousands
| Fiscal 2005
| Fiscal 2004
| Fiscal 2003
|
---|
Current provision | | | | | | | | | | | |
Federal | | | $ | 9,000 | | $ | 11,651 | | $ | 659 | |
State | | | | 2,318 | | | 716 | | | 387 | |
Foreign | | | | 20,705 | | | 15,028 | | | 20,949 | |
|
| |
| |
| |
Total current | | | | 32,023 | | | 27,395 | | | 21,995 | |
|
| |
| |
| |
Deferred provision (benefit) | | |
Federal | | | | 33,843 | | | 5,355 | | | (2,884 | ) |
State | | | | 7,946 | | | 1,576 | | | (413 | ) |
Foreign | | | | 6,720 | | | 4,955 | | | (9,250 | ) |
|
| |
| |
| |
Total deferred | | | | 48,509 | | | 11,886 | | | (12,547 | ) |
|
| |
| |
| |
Total consolidated income tax | | |
provision | | | $ | 80,532 | | $ | 39,281 | | $ | 9,448 | |
|
| |
| |
| |
| The components of income (loss) from continuing operations before income taxes for our domestic and foreign operations were as follows: |
In thousands
| Fiscal 2005
| Fiscal 2004
| Fiscal 2003
|
---|
Domestic income (loss) | | | $ | 115,079 | | $ | 53,182 | | $ | (6,629 | ) |
Foreign income | | | | 112,374 | | | 41,555 | | | 34,846 | |
|
| |
| |
| |
Pre-tax income from | | |
continuing operations | | | $ | 227,453 | | $ | 94,737 | | $ | 28,217 | |
|
| |
| |
| |
| The reconciliation between the income tax provision recognized in our Consolidated Statement of Income and the income tax provision computed by applying the statutory federal income tax rate to the income from continuing operations are as follows: |
In thousands
| Fiscal 2005
| Fiscal 2004
| Fiscal 2003
|
---|
Income tax computed at federal | | | | | | | | | | | |
statutory tax rate | | | $ | 79,609 | | $ | 33,158 | | $ | 9,876 | |
Sub-part F income and foreign | | |
dividends | | | | 1,430 | | | 3,703 | | | 1,414 | |
Tax on undistributed foreign earnings | | | | — | | | (5,509 | ) | | 5,509 | |
Differences in foreign and U.S. | | |
tax rates | | | | (7,568 | ) | | (6,098 | ) | | (4,807 | ) |
State income taxes, net of federal | | |
tax impact | | | | 712 | | | (1,490 | ) | | (280 | ) |
Resolution of prior years' tax issues | | | | (3,487 | ) | | (3,492 | ) | | (7,993 | ) |
Other items, net | | | | 1,823 | | | 681 | | | 737 | |
Valuation allowance | | | | 8,013 | | | 18,328 | | | 4,992 | |
|
| |
| |
| |
| | | $ | 80,532 | | $ | 39,281 | | $ | 9,448 | |
|
| |
| |
| |
The components of the net deferred tax asset are as follows:
In thousands
| Fiscal 2005
| Fiscal 2004
|
---|
Deferred tax assets: | | | | | | | | |
Reserves not currently deductible | | | $ | 18,189 | | $ | 29,415 | |
Employee benefit related items | | | | 127,557 | | | 130,141 | |
Tax credit carryforwards | | | | 18,763 | | | 21,437 | |
Tax loss carryforwards | | | | 387,870 | | | 430,924 | |
Inventories | | | | 16,036 | | | 20,340 | |
Other, net | | | | 19,858 | | | 19,635 | |
Valuation allowance | | | | (316,962 | ) | | (435,167 | ) |
|
| |
| |
Total deferred tax assets | | | | 271,311 | | | 216,725 | |
|
| |
| |
Deferred tax liabilities: | | |
Depreciation and amortization in excess | | |
of book expense | | | | 30,935 | | | 40,084 | |
Intangibles | | | | — | | | 11,927 | |
|
| |
| |
Total deferred tax liabilities | | | | 30,935 | | | 52,011 | |
|
| |
| |
Net deferred tax asset | | | $ | 240,376 | | $ | 164,714 | |
|
| |
| |
The net deferred tax assets are reflected in the accompanying balance sheets as follows:
In thousands
| Fiscal 2005
| Fiscal 2004
|
---|
Current deferred tax assets | | | $ | 27,882 | | $ | 35,290 | |
Long term deferred tax asset | | | | 225,138 | | | 129,424 | |
Current deferred tax liability | | | | — | | | — | |
Long term deferred tax liability | | | | (12,644 | ) | | — | |
|
| |
| |
Net deferred tax asset | | | $ | 240,376 | | $ | 164,714 | |
|
| |
| |
| At October 29, 2005, we had general business tax credits of $11.2 million expiring in 2008 through 2013 and alternative minimum tax credit carryforwards of $7.5 million, which do not expire. |
| We have tax loss carryforwards consisting of a gross U.S. Federal operating loss carryforward of $730.0 million expiring in 2020 through 2023 with a net tax benefit of $255.5 million; tax benefits related to U.S. state operating loss carryforwards of $98.6 million with various expiration dates; and tax benefits related to foreign carryforwards of $33.8 million with tax benefits of $33.1 million that have no expiration date. For financial statement purposes, future tax benefits related to the recognition of net operating losses are subject to review as to the future realizability of these amounts. As such, valuation reserves have been established against those loss carryforward amounts for which realizability was not considered more likely than not. |
| Because our Plan of Reorganization provided for substantial changes in our ownership, there are annual limitations on the portions of the federal and state net operating loss carryforwards that existed at the time of our emergence from bankruptcy which we may be able to utilize on our income tax returns. This annual limitation is an amount equal to the value of our stock immediately before the ownership change adjusted to reflect the increase in value of the Company resulting from the cancellation of creditor’s claims multiplied by a federally mandated long-term tax exempt rate. The annual federal limitation originally calculated was approximately $45.7 million and could be increased by certain transactions which result in recognition of “built-in” gains – unrecognized gains existing as of the date we emerged from bankruptcy. During Fiscal 2003, the Internal Revenue Service issued Notice 2003-65, which allows for additional modifications to the annual limitation as originally determined. Based upon the guidance from this ruling and applying it to our facts at the time of emergence from bankruptcy, the Company has recomputed the amount of U.S. net operating loss that it is entitled to utilize since Fiscal 2001. As a result of this recalculation, the total amount of the U.S. Federal net operating loss carryforwards not subject to the annual limitation was approximately $517.8 million at October 29, 2005. The U.S. state limitations vary by taxing jurisdiction. |
| Annually, we reassess our position on the creation and continuation of valuation allowances and adjust the allowance balances where we feel it appropriate based upon past, current, and projected profitability in the various geographical areas in which we conduct business and available tax strategies. Additionally, the U.S. carryforwards were reduced upon emergence from bankruptcy due to the rules and regulations in the Internal Revenue Code related to cancellation of indebtedness income that is excluded from taxable income. These adjustments are included in the net operating loss values detailed above. |
| At October 29, 2005, our net deferred tax asset, including loss and credit carryforwards and including valuation allowances, was $240.4 million. We have reviewed the realization of net operating losses, tax credits, and net other deferred tax assets in each statutory location in which we conduct our business and established valuation allowances against those net deferred tax assets whose realizability we have determined does not meet the more likely than not criteria of Financial Accounting Standards Board No. 109, “Accounting for Income Taxes.” The continued need for valuation allowances will be assessed at least annually to determine the propriety of recognizing additional deferred tax assets. Additionally, our emergence from bankruptcy in Fiscal 2001 did not create a new tax reporting entity. Accordingly, the adjustments required to adopt fresh start accounting are not applicable for our tax reporting. Therefore, the fresh start adjustments created new deferred tax items which have been recognized concurrently with the recognition of the respective fresh start accounting adjustments since Fiscal 2001 and into Fiscal 2005. |
| In addition, as it relates to the valuation allowances currently recorded that arose in pre-emergence years, our reorganization has resulted in a significantly modified capital structure by which SOP 90-7 requires us to apply fresh start accounting. Under fresh start accounting, reversals of valuation allowances recorded against deferred tax assets that existed as of the emergence date will first reduce any excess reorganization value until exhausted, then other intangibles until exhausted, and thereafter are reported as additional paid in capital. Consequently, we will recognize cash tax savings in the year of asset recognition without the corresponding benefit to income tax expense. The balance of the amount of valuation allowances for which this treatment is required was $157.4 million at October 29, 2005. |
| Similar to the treatment of pre-emergence deferred tax valuation allowances, amounts accrued for pre-emergence relating to future income tax contingencies also require special treatment under fresh start accounting. Reversals of tax contingency reserves that are no longer required due to the resolution of the underlying tax issue and were recorded at the emergence date will first reduce any excess reorganization value until exhausted, then other intangibles until exhausted, and thereafter are reported as an adjustment to income tax expense. Consistent with prior years, we have reviewed the amounts so accrued and adjusted the balances to the amounts deemed appropriate with the corresponding adjustment treated as a reduction to other intangibles. |
| As of October 29, 2005, all other intangibles recorded under fresh start accounting have been reduced to zero. All future reversals of pre-emergence valuation allowances will be reversed to paid in capital. Future reversals of accruals related to pre-emergence tax contingencies will be recognized as a component of income tax expense in the period reversed. |
| As of October 29, 2005, U.S. income taxes, net of foreign taxes paid or payable, have not been provided on the undistributed profits of foreign subsidiaries as all undistributed profits of foreign subsidiaries are deemed to be permanently reinvested outside of the U.S. It is not practical to determine the United States federal income tax liability, if any, which would be payable if such earnings were not permanently reinvested. Such unremitted earnings of subsidiaries which have been or are intended to be permanently reinvested were $366.5 million at October 29, 2005. |
| On October 22, 2004, the American Jobs Creation Act of 2004 was signed into law. Included in this Act was a provision that provided for a special one-time tax deduction of 85% of certain foreign earnings that are repatriated within a specified statutory time frame. At October 30, 2004 we had estimated the range of potential distributions to be between $0 and $44 million. We assessed the potential distributions that were available under this provision and elected to make no foreign repatriation under these rules for the year ended October 29, 2005. |
| Cash taxes paid for Fiscal 2003, Fiscal 2004, and Fiscal 2005 were $19.1 million, $13.7 million, and $14.4 million, respectively. |
6. Accounts Receivable
Consolidated accounts receivable consisted of the following:
In thousands
| October 29, 2005
| October 30, 2004
|
---|
Trade receivables | | | $ | 297,694 | | $ | 235,918 | |
Unbilled receivables (due within one year) | | | | 59,602 | | | 29,657 | |
Allowance for doubtful accounts | | | | (5,795 | ) | | (5,678 | ) |
|
| |
| |
| | | $ | 351,501 | | $ | 259,897 | |
|
| |
| |
We provide for doubtful accounts on a specific account identification basis.
>
7. Inventories
Consolidated inventories consisted of the following:
In thousands
| October 29, 2005
| October 30, 2004
|
---|
Finished goods | | | $ | 292,786 | | $ | 244,244 | |
Work-in-process and purchased parts | | | | 192,344 | | | 164,660 | |
Raw materials | | | | 63,065 | | | 34,906 | |
|
| |
| |
| | | $ | 548,195 | | $ | 443,810 | |
|
| |
| |
8. Warranties
| We provide for the estimated costs that may be incurred under product warranties to remedy deficiencies of quality or performance of our products. These product warranties extend over either a specified period of time, units of production or machine hours depending upon the product subject to the warranty. We accrue a provision for estimated future warranty costs based upon the historical relationship of warranty costs to sales. We periodically review the adequacy of the accrual for product warranties and adjust the warranty percentage and accrued warranty reserve for actual experience as necessary. |
The following table reconciles the changes in the product warranty reserve:
In thousands
| Fiscal 2005
| Fiscal 2004
|
---|
Balance, beginning of year | | | $ | 31,259 | | $ | 30,443 | |
Accrual for warranty expensed during the year | | | | 22,071 | | | 20,654 | |
Settlements made during the year | | | | (17,716 | ) | | (19,881 | ) |
Change in liability for pre-existing warranties | | |
during the year, including expirations | | | | 83 | | | (1,826 | ) |
Effect of foreign currency translation | | | | (974 | ) | | 1,869 | |
Other | | | | (540 | ) | | - | |
|
| |
| |
Balance, end of year | | | $ | 34,183 | | $ | 31,259 | |
|
| |
| |
9. Earnings Per Share
| The following is a reconciliation of the numerators and denominators of basic and diluted earnings per share computations in accordance with SFAS No. 128: |
In thousands except per share amounts
| Fiscal 2005
| Fiscal 2004
| Fiscal 2003
|
---|
Numerator: | | | | | | | | | | | |
Income from continuing operations | | | $ | 146,921 | | $ | 55,456 | | $ | 18,769 | |
Income (loss) from discontinued operations | | | | 1,128 | | | (134 | ) | | (253 | ) |
|
| |
| |
| |
Net income | | | $ | 148,049 | | $ | 55,322 | | $ | 18,516 | |
|
| |
| |
| |
Denominator: | | |
Denominator for basic earnings per share - | | |
Weighted average shares | | | | 121,121 | | | 117,277 | | | 113,045 | |
Effect of dilutive securities: | | |
Stock options, restricted stock and | | |
performance units | | | | 2,322 | | | 3,377 | | | 754 | |
|
| |
| |
| |
Denominator for diluted earnings per share - | | |
Adjusted weighted average shares and | | |
assumed conversions | | | | 123,443 | | | 120,654 | | | 113,799 | |
|
| |
| |
| |
Basic earnings (loss) per share* | | |
Continuing operations | | | $ | 1.21 | | $ | 0.47 | | $ | 0.17 | |
Discontinued operations | | | | 0.01 | | | — | | | (0.01 | ) |
|
| |
| |
| |
Net income | | | $ | 1.22 | | $ | 0.47 | | $ | 0.16 | |
|
| |
| |
| |
Diluted earnings per share* | | |
Continuing operations | | | $ | 1.19 | | $ | 0.46 | | $ | 0.16 | |
Discontinued operations | | | | 0.01 | | | — | | | — | |
|
| |
| |
| |
Net income | | | $ | 1.20 | | $ | 0.46 | | $ | 0.16 | |
|
| |
| |
| |
| | |
*Adjusted for the three-for-two stock splits effective both January 21, 2005 and December 12, 2005.
10. Pensions and Other Employee Benefits
| The Company and its subsidiaries have a number of defined benefit, defined contribution and government mandated pension plans covering substantially all employees. Benefits from these plans are based on factors that include various combinations of years of service, fixed monetary amounts per year of service, employee compensation during the last years of employment and the recipient’s social security benefit. Our funding policy with respect to qualified plans is to contribute annually not less than the minimum required by applicable law and regulation nor more than the amount which can be deducted for income tax purposes. We also have an unfunded nonqualified supplemental pension plan that is based on credited years of service and compensation during the last years of employment. For our qualified and non-qualified pension plans and the post-retirement welfare plans we use the last Saturday closest to October 31 as our measurement date which coincides with our fiscal year end. |
| Certain plans outside the United States, which supplement or are coordinated with government plans, many of which require funding through mandatory government retirement or insurance company plans, have pension funds or balance sheet accruals which approximate the actuarially computed value of accumulated plan benefits as of October 29, 2005 and October 30, 2004. |
| We also have a defined contribution benefit plan (401(k) plan). Substantially every U.S. employee of the Company (except any employee who is covered by a collective bargaining agreement which does not provide for such employee’s participation in the plan) is eligible to participate in the plan. Under the terms of the plan, the Company generally matches 25% of participant salary reduction contributions up to the first 6% of the participant’s compensation, subject to limitations. We recognized costs for matching contributions of $1.7 million, $1.5 million, and $1.2 million, for Fiscal 2005, Fiscal 2004 and Fiscal 2003, respectively. |
| We recorded additional minimum pension liabilities of $35.9 million and $22.4 million in Fiscal 2005 and Fiscal 2004, respectively, to recognize the unfunded accumulated benefit obligations of certain plans. Corresponding amounts are required to be recognized as intangible assets to the extent of the unrecognized prior service cost and the unrecognized net transition obligation on an individual plan basis. Any excess of the minimum pension liability above the intangible asset is recorded as a separate component and reduction in shareholders’ equity. The balance of $260.2 million and $239.0 million in Fiscal 2005 and Fiscal 2004, respectively, were included in shareholders’ equity. |
| Total pension expense for all defined benefit plans was $22.6 million, $22.0 million and $14.2 million for Fiscal 2005, Fiscal 2004 and Fiscal 2003, respectively. Total pension expense for all defined contribution plans was $3.8 million, $3.8 million and $2.1 million for Fiscal 2005, Fiscal 2004 and Fiscal 2003, respectively. |
Net periodic pension costs for U.S. plans and plans of subsidiaries outside the United States included the following components:
| U.S. Pension Plans
| Non-U.S. Pension Plans
|
---|
In thousands
| Fiscal 2005
| Fiscal 2004
| Fiscal 2003
| Fiscal 2005
| Fiscal 2004
| Fiscal 2003
|
---|
Components of Net | | | | | | | | | | | | | | | | | | | | |
Periodic Benefit Cost (Income) | | |
Service cost | | | $ | 12,944 | | $ | 11,389 | | $ | 10,441 | | $ | 5,893 | | $ | 5,529 | | $ | 4,533 | |
Interest cost | | | | 43,079 | | | 42,990 | | | 42,825 | | | 27,729 | | | 27,140 | | | 23,496 | |
Expected return on assets | | | | (48,363 | ) | | (42,113 | ) | | (38,476 | ) | | (32,664 | ) | | (32,855 | ) | | (29,401 | ) |
Amortization of: | | |
Prior service cost | | | | 442 | | | 361 | | | 360 | | | 1 | | | 1 | | | 1 | |
Actuarial loss | | | | 10,412 | | | 6,676 | | | 421 | | | 3,132 | | | 2,840 | | | 33 | |
Total net periodic benefit cost (income) | | | $ | 18,514 | | $ | 19,303 | | $ | 15,571 | | $ | 4,091 | | $ | 2,655 | | $ | (1,338 | ) |
|
| |
| |
| |
| |
| |
| |
| Changes in the projected benefit obligations and pension plan assets relating to the Company’s defined benefit pension plans together with a summary of the amounts recognized in the Consolidated Balance Sheet are set forth in the following table: |
| U.S. Pension Plans
| Non-U.S. Pension Plans
|
---|
In thousands
| October 29, 2005
| October 30, 2004
| October 29, 2005
| October 30, 2004
|
---|
Change in Benefit Obligations | | | | | | | | | | | | | | |
Net benefit obligations at beginning of year | | | $ | 759,606 | | $ | 696,354 | | $ | 499,302 | | $ | 460,091 | |
Service cost | | | | 12,944 | | | 11,389 | | | 5,893 | | | 5,529 | |
Interest cost | | | | 43,079 | | | 42,990 | | | 27,729 | | | 27,140 | |
Plan participants' contributions | | | | — | | | — | | | 1,469 | | | 1,364 | |
Plan amendments | | | | 264 | | | 658 | | | — | | | — | |
Actuarial loss (gain) | | | | 45,171 | | | 46,375 | | | 56,563 | | | (10,969 | ) |
Currency fluctuations | | | | — | | | — | | | (18,107 | ) | | 37,946 | |
Gross benefits paid | | | | (37,690 | ) | | (38,160 | ) | | (21,343 | ) | | (21,799 | ) |
|
| |
| |
| |
| |
Net benefit obligations at end of year | | | $ | 823,374 | | $ | 759,606 | | $ | 551,506 | | $ | 499,302 | |
|
| |
| |
| |
| |
Change in Plan Assets | | |
Fair value of plan assets at beginning of year | | | $ | 541,241 | | $ | 430,834 | | $ | 428,683 | | $ | 381,128 | |
Actual return on plan assets | | | | 62,906 | | | 59,389 | | | 55,559 | | | 29,819 | |
Currency fluctuations | | | | — | | | — | | | (15,182 | ) | | 31,931 | |
Employer contributions | | | | 50,602 | | | 89,178 | | | 9,554 | | | 6,241 | |
Plan participants' contributions | | | | — | | | — | | | 1,469 | | | 1,363 | |
Gross benefits paid | | | | (37,690 | ) | | (38,160 | ) | | (21,343 | ) | | (21,799 | ) |
|
| |
| |
| |
| |
Fair value of plan assets at end of year | | | $ | 617,059 | | $ | 541,241 | | $ | 458,740 | | $ | 428,683 | |
|
| |
| |
| |
| |
Funded Status, Realized and Unrealized Amounts | | |
Funded status at end of year | | | $ | (206,315 | ) | $ | (218,365 | ) | $ | (92,765 | ) | $ | (70,619 | ) |
Unrecognized net actuarial loss | | | | 218,530 | | | 198,313 | | | 137,740 | | | 109,997 | |
Unrecognized prior service cost | | | | 4,051 | | | 4,229 | | | 16 | | | 16 | |
|
| |
| |
| |
| |
Net amount recognized at end of year | | | $ | 16,266 | | $ | (15,823 | ) | $ | 44,991 | | $ | 39,394 | |
|
| |
| |
| |
| |
Amounts Recognized in the Consolidated | | |
Balance Sheet Consist of: | | |
Prepaid benefit cost | | | $ | 35,713 | | $ | 2,870 | | $ | 51,595 | | $ | 46,249 | |
Deferred tax asset | | | | 7,273 | | | — | | | 7,636 | | | — | |
Accrued benefit liability | | | | (19,447 | ) | | (18,693 | ) | | (6,605 | ) | | (6,855 | ) |
Additional minimum liability | | | | (182,628 | ) | | (165,425 | ) | | (96,721 | ) | | (78,050 | ) |
Intangible asset | | | | 4,233 | | | 4,441 | �� | | 16 | | | 16 | |
Accumulated other comprehensive loss | | | | 171,122 | | | 160,984 | | | 89,070 | | | 78,034 | |
|
| |
| |
| |
| |
Net amount recognized at end of year | | | $ | 16,266 | | $ | (15,823 | ) | $ | 44,991 | | $ | 39,394 | |
|
| |
| |
| |
| |
Accumulated Benefit Obligation | | | $ | 783,421 | | $ | 722,489 | | $ | 508,188 | | $ | 466,181 | |
| The principal assumptions used in determining the funded status and net periodic benefit cost of our pension plans are set forth in the following tables. The assumptions for non-U.S. plans were developed on a basis consistent with that for U.S. plans, adjusted to reflect prevailing economic conditions and interest rate environments. |
| Significant assumptions used in determining net periodic benefit cost as of the fiscal year ended are as follows (in weighted averages): |
| U.S. Pension Plan
| Non-U.S. Pension Plans
|
---|
| 2005
| 2004
| 2003
| 2005
| 2004
| 2003
|
---|
Discount rate | | | | 5 | .75% | | 6 | .25% | | 7 | .00% | | 5 | .59% | | 5 | .92% | | 5 | .63% |
Expected return on plan assets | | | | 9 | .00% | | 9 | .00% | | 9 | .00% | | 7 | .55% | | 7 | .60% | | 7 | .55% |
Rate of compensation increase | | | | 3 | .75% | | 3 | .75% | | 4 | .00% | | 4 | .03% | | 4 | .12% | | 4 | .08% |
| Significant assumptions used in determining benefit obligations as of the fiscal year ended are as follows (in weighted averages): |
| U.S. Pension Plan
| Non-U.S. Pension Plans
|
---|
| 2005
| 2004
| 2005
| 2004
|
---|
Discount rate | | | | 5 | .80% | | 5 | .75% | | 5 | .07% | | 5 | .59% |
Rate of compensation increase | | | | 4 | .25% | | 3 | .75% | | 4 | .01% | | 4 | .03% |
| The defined benefit plans had the following target allocation and weighted-average asset allocations as of October 29, 2005 and October 30, 2004. |
| Percentage of Plan Assets
|
---|
| U.S. Pension Plan
| Non-U.S. Pension Plans
|
---|
Asset Category
| Target Allocation
| Fiscal 2005
| Fiscal 2004
| Target Allocation
| Fiscal 2005
| Fiscal 2004
|
---|
Equity Securities | | | | 58 | .0% | | 58 | .0% | | 69 | .9% | | 49 | .0% | | 52 | .5% | | 51 | .5% |
Debt Securities | | | | 32 | .0% | | 30 | .9% | | 30 | .1% | | 41 | .0% | | 38 | .6% | | 39 | .4% |
Other | | | | 10 | .0% | | 11 | .1% | | 0 | .0% | | 10 | .0% | | 8 | .9% | | 9 | .1% |
|
| |
| |
| |
| |
| |
| |
Total | | | | 100 | .0% | | 100 | .0% | | 100 | .0% | | 100 | .0% | | 100 | .0% | | 100 | .0% |
| The plans assets are invested to maximize funded ratios over the long-term while managing the risk that funded ratios fall meaningfully below 100%. This objective to maximize the plan’s funded ratio is based on a long-term investment horizon, so that interim fluctuations should be viewed with appropriate perspective. |
| The desired investment return objective is a long-term average annual real rate of return on assets that is approximately 6.5% greater than the assumed inflation rate. The target rate of return is based upon an analysis of historical returns supplemented with an economic and structural review for each asset class. There is no assurance that these objectives will be met. |
| The following pension benefit payments (which include expected future service) are expected to be paid in each of the following fiscal years. |
In thousands
| U.S. Pension Plans
| Non-U.S. Pension Plans
|
---|
2006 | | | $ | 39,744 | | $ | 19,920 | |
2007 | | | | 40,811 | | | 20,730 | |
2008 | | | | 42,200 | | | 22,715 | |
2009 | | | | 43,691 | | | 22,190 | |
2010 | | | | 45,181 | | | 22,809 | |
2011 - 2015 | | | | 252,933 | | | 130,229 | |
| The projected benefit obligations, accumulated benefits obligations and fair value of plan assets for underfunded and overfunded plans have been combined for disclosure purposes. The projected benefit obligations, accumulated benefit obligations, and fair value of assets for pension plans with a projected benefit obligation in excess of plan assets and pension plans with an accumulated benefit obligation in excess of plan assets are as follows: |
| Projected Benefit Obligation Exceeds the Fair Value of Plan's Assets
| Accumulated Benefit Obligation Exceeds the Fair Value of Plan's Assets
|
---|
In thousands
| 2005
| 2004
| 2005
| 2004
|
---|
Projected Benefit Obligation | | | $ | 1,364,924 | | $ | 1,220,280 | | $ | 1,333,178 | | $ | 1,220,280 | |
Accumulated Benefit Obligation | | | | 1,284,328 | | | 1,152,853 | | | 1,255,655 | | | 1,152,853 | |
Fair Value of Plan Assets | | | | 1,063,336 | | | 929,764 | | | 1,032,783 | | | 929,764 | |
| For the fiscal year ending October 28, 2006, we expect to voluntarily contribute between $10 million and $15 million to our employee pension plans. |
11. Postretirement Benefits Other Than Pensions
| In 1993, our Board of Directors approved a general approach that culminated in the elimination of all Company contributions towards postretirement health care benefits. Increases in costs paid by us were capped for certain plans beginning in 1994 extending through 1998 and Company contributions were eliminated as of January 11, 1999 for most employee groups, excluding Joy, certain early retirees and specific discontinued operation groups. For Joy, based upon existing plan terms, future eligible retirees will participate in a premium cost-sharing arrangement which is based upon age as of March 1, 1993 and position at the time of retirement. Active employees under age 45 as of March 1, 1993 and any new hires after April 1, 1993 will be required to pay 100% of the applicable premium. |
| The components of the net periodic benefit cost associated with our postretirement benefit plans (other than pensions), all of which relate to operations in the U.S., are as follows: |
In thousands
| Fiscal 2005
| Fiscal 2004
| Fiscal 2003
|
---|
Components of net periodic benefit cost: | | | | | | | | | | | |
Service cost | | | $ | 169 | | $ | 149 | | $ | 142 | |
Interest cost | | | | 2,867 | | | 3,143 | | | 3,747 | |
Amortization of actuarial (gain) loss | | | | 208 | | | 193 | | | 258 | |
|
| |
| |
| |
Total net periodic benefit cost | | |
of continuing operations | | | $ | 3,244 | | $ | 3,485 | | $ | 4,147 | |
|
| |
| |
| |
| The following table sets forth the benefit obligations, plan assets, funded status and amounts recognized in our Consolidated Balance Sheets: |
In thousands
| Fiscal 2005
| Fiscal 2004
|
---|
Change in Benefit Obligations | | | | | | | | |
Net benefit obligations at beginning of year | | | $ | 52,020 | | $ | 57,880 | |
Service cost | | | | 169 | | | 149 | |
Interest cost | | | | 2,867 | | | 3,144 | |
Actuarial (gain) loss | | | | 4,879 | | | (5,133 | ) |
Gross benefits paid | | | | (4,053 | ) | | (4,020 | ) |
|
| |
| |
Net benefit obligations at end of year | | | $ | 55,882 | | $ | 52,020 | |
|
| |
| |
Change in Plan Assets | | |
Fair value of plan assets at beginning of year | | | $ | — | | $ | — | |
Employer contributions | | | | 4,053 | | | 4,020 | |
Gross benefits paid | | | | (4,053 | ) | | (4,020 | ) |
|
| |
| |
Fair value of plan assets at end of year | | | $ | — | | $ | — | |
|
| |
| |
Funded Status, Recognized and Unrecognized Amounts | | |
Funded status at end of year | | | $ | (55,882 | ) | $ | (52,020 | ) |
Unrecognized net actuarial loss | | | | 8,328 | | | 3,655 | |
|
| |
| |
Net amount recognized at end of year | | | $ | (47,554 | ) | $ | (48,365 | ) |
|
| |
| |
Amounts recognized in the Consolidated | | |
Balance Sheet consist of: | | |
Accrued benefit liability | | |
- short term portion | | | $ | (4,050 | ) | $ | (4,020 | ) |
- long term portion | | | | (43,504 | ) | | (44,345 | ) |
|
| |
| |
Net amount recognized at end of year | | | $ | (47,554 | ) | $ | (48,365 | ) |
|
| |
| |
| The following postretirement benefit payments (which include expected future service) are expected to be paid in each of the following fiscal years. |
In thousands
| Prior to Medicare Part D
| After Medicare Part D
| Impact of Medicare Part D
|
---|
2006 | | | $ | 4,050 | | $ | 4,050 | | $ | — | |
2007 | | | | 5,087 | | | 4,936 | | | 151 | |
2008 | | | | 5,095 | | | 4,946 | | | 149 | |
2009 | | | | 5,010 | | | 4,864 | | | 146 | |
2010 | | | | 4,935 | | | 4,796 | | | 139 | |
2011 - 2015 | | | | 22,901 | | | 22,320 | | | 581 | |
| For postretirement benefit obligation measurement purposes, the weighted average discount rate is 5.60 % and 5.75% for Fiscal 2005 and Fiscal 2004, respectively, and the assumed annual rate of increase in the per capita cost of covered health care benefits is 10% for both Fiscal 2005 and 2004. The annual increase in the per capita cost of covered health care benefits rate is assumed to decrease 1% per year to an ultimate 5% by Fiscal 2010, and remain at that level thereafter. The health care cost trend rate assumption has an effect on the amounts reported. A one percentage point increase in the assumed health care cost trend rates each year would increase the accumulated postretirement benefit obligation as of October 29, 2005 by $3.8 million. The service cost and interest cost components of the net periodic postretirement benefit cost for the year would increase by $.2 million. A one percentage point decrease in the assumed health care cost trend rates each year would decrease the accumulated postretirement benefit obligation as of October 29, 2005 by $3.4 million. The service cost and interest cost components of the net periodic postretirement benefit cost for the year would decrease by $.2 million. Postretirement life insurance benefits have a minimal effect on the total benefit obligation. |
| On December 8, 2003, the Medicare Prescription Drug Improvement and Modernization Act of 2003 became law. This Act introduced a prescription drug benefit under Medicare (Medicare Part D) as well as a federal subsidy to sponsors of retiree health care benefits plans that provide a benefit that is at least actuarially equivalent to Medicare Part D. We currently sponsor retiree health care plans that provide prescription drug benefits to our U.S. retirees. |
| We have one retiree medical plan which will qualify for the federal subsidy. We elected to prospectively recognize the effects of the Act during the fourth quarter of Fiscal 2004, which reduced the accumulated benefit obligation by approximately $1.0 million and is recognized as an actuarial gain in the preceding table and reduced the net periodic benefit cost by approximately $.2 million for Fiscal 2005 as compared with the amount calculated without considering the effects of the subsidy. |
12. Shareholders’ Equity and Stock Options
| We have 150,000,000 shares of authorized common stock, par value $1.00 per share, 50,000,000 of which were distributed in connection with our July 12, 2001 emergence from bankruptcy. The last distribution of 1,233,423 shares (2,775,111 shares after January 1, 2005 and December 12, 2005 stock splits) were distributed starting on January 28, 2005 in accordance with the Plan of Reorganization. |
| We are authorized to issue 5,000,000 shares of preferred stock, of which 1,000,000 shares have been designated as Series A Junior Participating Preferred Stock of $1 par value. None of the preferred shares have been issued. On July 15, 2002, our Board of Directors declared a dividend of one preferred share purchase right for each outstanding share of common stock. Each right entitles the holder to purchase one one-hundredth of a share of our Series A Junior Participating Preferred Stock for $100. Under certain circumstances, if a person or group acquires 15% or more of our outstanding common stock, holders of the rights (other than the person or group triggering their exercise) will be able to purchase, in exchange for the $100 exercise price, shares of our common stock or of any company into which we are merged having a value of $200. The rights expire on August 5, 2012 unless extended by our Board of Directors. Because the rights may substantially dilute the stock ownership of a person or group attempting to take us over without the approval of our Board of Directors, our rights plan could make it more difficult for a third party to acquire us (or a significant percentage of our outstanding capital stock) without first negotiating with our Board of Directors regarding such acquisition. |
| Our stock incentive plan authorizes the grant of up to 18,126,000 stock options, performance units, restricted stock units and other stock-based awards to officers, employees and directors. As of October 29, 2005, stock option grants aggregating approximately 12.8 million shares of common stock had been made to approximately 260 individuals. Stock options vest over a three-year period with one-third vesting on the first, second and third anniversaries of the grant date. Options to purchase 33,750 shares have also been granted to each of our six outside directors. On February 25, 2003, February 24, 2004, and February 22, 2005 restricted stock unit grants of 12,560, 4,858 and 3,081, respectively, were made to each of our six outside directors. These restricted stock units vest one year after the grant date and provide that a number of shares of common stock equal to the number of vested units will be delivered one year after the director’s service on the board terminates. On January 21, 2004 and November 15, 2004, grants of 106,796 and 77,850 restricted stock units were made to certain executive officers and key employees. These restricted stock units vest over a five-year period with one-third vesting on the third, fourth and fifth anniversaries of the grant date and provide that a number of shares of common stock equal to the number of vested units will be delivered to the individual as the units vest. Individuals are credited with additional units to reflect cash dividends paid on the underlying common stock. In the event of a change in control, the units will be paid out in cash based on the market price of the common stock as of the date of the change in control. |
| The Performance Unit Award Programs under our stock incentive plan provide long-term incentive compensation opportunities to certain senior executives. Up to approximately 904,610 shares of common stock may be earned by the senior executives under the Performance Unit Award Programs if, at the end of a three year award cycle, cumulative net cash flow, as defined in the performance award agreements, exceeds certain threshold amounts. During the year ended October 29, 2005, 89,475 units were granted under the 2005 Performance Unit Award Program. Each performance unit represents the right to earn one share of common stock. Awards can range from 0% to 150% of the target award opportunities and may be paid out in stock, cash or a combination of stock and cash at the discretion of the Company. In the event of a change in control, the performance units are paid out in cash based on the greater of actual performance or target award. The final awards for the Fiscal 2003 Performance Unit Program amounted to 586,407 units and will be paid out entirely in stock beginning in January 2006. |
A summary of stock option activity under all plans is as follows:
| Number of Options
| Weighted- Average Exercise Price per Share
|
---|
Outstanding at November 2, 2002 | | | | 7,939,130 | | $ | 7 | .18 |
|
| |
|
Options granted | | | | 2,458,912 | | | 4 | .71 |
Options exercised | | | | (326,637 | ) | | 6 | .29 |
Options forfeited or cancelled | | | | (331,524 | ) | | 5 | .69 |
|
| |
|
Outstanding at November 1, 2003 | | | | 9,739,881 | | $ | 6 | .61 |
|
| |
|
Options granted | | | | 1,137,825 | | | 11 | .78 |
Options exercised | | | | (6,449,155 | ) | | 7 | .34 |
Options forfeited or cancelled | | | | (93,656 | ) | | 6 | .91 |
|
| |
|
Outstanding at October 30, 2004 | | | | 4,334,895 | | $ | 7 | .52 |
|
| |
|
Options granted | | | | 1,116,750 | | | 17 | .63 |
Options exercised | | | | (1,696,612 | ) | | 7 | .07 |
Options forfeited or cancelled | | | | (82,383 | ) | | 9 | .73 |
|
| |
|
Outstanding at October 29, 2005 | | | | 3,672,650 | | $ | 10 | .75 |
|
| |
|
The following table summarizes information about stock options outstanding at October 29, 2005:
| Outstanding
| Exercisable
|
---|
Exercise price range
| Shares
| Average life (a)
| Average exercise price
| Shares
| Average exercise price
|
---|
$3.57 to $7.77 | | | | 1,696,250 | | | 6 | .7 | $ | 5 | .74 | | 937,060 | | $ | 6 | .56 |
$7.78 to $14.98 | | | | 881,025 | | | 8 | .2 | | 11 | .81 | | 152,225 | | | 11 | .80 |
$14.99 to $28.08 | | | | 1,095,375 | | | 9 | .1 | | 17 | .65 | | — | | | — | |
|
| | |
| |
| |
| |
| |
Total | | | | 3,672,650 | | | 7 | .8 | $ | 10 | .75 | | 1,089,285 | | $ | 7 | .29 |
|
| | |
| |
| |
| |
| |
(a) - Average contractual life remaining in years
| At October 29, 2005 and October 30, 2004, approximately 1.1 million and 1.7 million outstanding options were vested and exercisable, respectively. The weighted average exercise prices for vested and exercisable outstanding options were $7.29 and $7.26 at October 29, 2005 and October 30, 2004, respectively. |
13. Operating Leases
| We lease certain plant, office and warehouse space as well as machinery, vehicles, data processing and other equipment. Certain of the leases have renewal options at reduced rates and provisions requiring us to pay maintenance, property taxes and insurance. Amortization of assets reported as capital leases is included in depreciation expense. Generally, all rental payments are fixed. Our assets and obligations under capital lease arrangements are not significant. |
| Total rental expense under operating leases, excluding maintenance, taxes and insurance, was $16.3 million, $16.9 million and $17.4 million for Fiscal 2005, Fiscal 2004, and Fiscal 2003, respectively. |
| At October 29, 2005, the future payments for all operating leases with remaining lease terms in excess of one year, and excluding maintenance, taxes and insurance were as follows: |
In thousands
|
|
---|
2006 | | | $ | 10,695 | |
2007 | | | | 7,811 | |
2008 | | | | 5,556 | |
2009 | | | | 3,526 | |
2010 | | | | 1,393 | |
Thereafter | | | | 3,339 | |
|
| |
Total | | | | 32,320 | |
|
| |
14. Reorganization Items
| Reorganization items include income, expenses and losses that were realized or incurred by the Predecessor Company as a result of its decision to reorganize under Chapter 11 of the Bankruptcy Code. |
Net reorganization items for Fiscal 2005, Fiscal 2004 and Fiscal 2003 consisted of the following:
In thousands - (income) expense
| Fiscal 2005
| Fiscal 2004
| Fiscal 2003
|
---|
Distribution from the Beloit Liquidating Trust | | | $ | — | | $ | (2,856 | ) | $ | — | |
Beloit Liquidating Trust settlement | | | | — | | | (2,336 | ) | | — | |
Beloit U.K. claim settlement | | | | (1,092 | ) | | (1,774 | ) | | (3,333 | ) |
Professional fees directly related to the reorganization | | | | 826 | | | 1,165 | | | 1,495 | |
Professional fees reimbursement | | | | (1,500 | ) | | — | | | — | |
Legal reserve reversal | | | | (1,422 | ) | | — | | | — | |
Other - net | | | | 378 | | | (1,041 | ) | | (573 | ) |
|
| |
| |
| |
Net reorganization items | | | $ | (2,810 | ) | $ | (6,842 | ) | $ | (2,411 | ) |
|
| |
| |
| |
15. Restructuring and Other Special Charges
| Costs associated with restructuring activities other than those activities covered by SFAS No. 144, “Accounting for the Impairment or Disposal of Long-Lived Assets,” or that involve an entity newly acquired in a business combination, are accounted for in accordance with SFAS No. 146, “Accounting for Costs Associated with Exit or Disposal Activities.” Costs associated with such activities are recorded as restructuring costs in the consolidated statement of income when the liability is incurred. |
| During Fiscal 2003, we began implementing a manufacturing capacity rationalization at our P&H Mining Equipment Milwaukee location that reduced factory space by 350,000 square feet and resulted in a facility that is more efficient. The rationalization was completed in Fiscal 2004 at a total cost of $2.0 million and resulted in approximately $5.5 million in cost savings principally in cost of sales in Fiscal 2004. |
| During Fiscal 2003, Joy Mining Machinery began implementing a manufacturing capacity rationalization plan for North America. Total costs for the Joy North American manufacturing capacity rationalization were $3.7 million in Fiscal 2003. Included in this amount is $1.5 million for one-time termination benefits for 132 employees, $0.8 million for abandoned assets, and $1.4 million for other associated costs. Also during Fiscal 2003, Joy Mining Machinery began implementing a manufacturing capacity rationalization plan for the United Kingdom and Australia. The total costs for the United Kingdom manufacturing capacity rationalization were $1.6 million for one-time termination benefits for 26 employees. The total costs for the Australian manufacturing capacity rationalization were $0.2 million for one-time termination benefits for 27 employees. We realized approximately $5.8 million in cost savings in Fiscal 2004 as a result of the Fiscal 2003 rationalization plan at Joy. These savings consisted of $4.7 million reflected in our cost of sales and $1.1 million reflected in our product development, selling and administrative expenses. These savings are expected to be sustainable in future years, but will vary based upon sales volume. |
| During Fiscal 2005, Joy Mining Machinery continued its capacity rationalization plan for North America. Total costs incurred in Fiscal 2005 were $0.8 million and consisted of one-time termination benefits for 173 employees. All benefits are expected to be paid by February 2006. |
Below is a summary of the activity related to restructuring costs recorded pursuant to SFAS No. 144 and SFAS No.146.
In thousands
| One-time Termination Benefits
| | Abandoned Assets
| | Other Associated Costs
| | Total Charges
|
---|
Fiscal 2003 | | | | | | | | | | | | | | |
P&H Mining Equipment | | | $ | — | | $ | 1,154 | | $ | 612 | | $ | 1,766 | |
Joy Mining Machinery | | | | 3,384 | | | 715 | | | 1,050 | | | 5,149 | |
|
| |
| |
| |
| |
| | | | |
| | | $ | 3,384 | | $ | 1,869 | | $ | 1,662 | | $ | 6,915 | |
|
| |
| |
| |
| |
Fiscal 2004 | | |
P&H Mining Equipment | | | $ | — | | $ | — | | $ | 253 | | $ | 253 | |
Joy Mining Machinery | | | | 200 | | | — | | | 172 | | | 372 | |
|
| |
| |
| |
| |
| | | | |
| | | $ | 200 | | $ | — | | $ | 425 | | $ | 625 | |
|
| |
| |
| |
| |
Fiscal 2005 | | |
P&H Mining Equipment | | | $ | — | | $ | — | | $ | — | | $ | — | |
Joy Mining Machinery | | | | 849 | | | — | | | — | | | 849 | |
|
| |
| |
| |
| |
| | | | |
| | | $ | 849 | | $ | — | | $ | — | | $ | 849 | |
|
| |
| |
| |
| |
Cumulative Total | | |
P&H Mining Equipment | | | $ | — | | $ | 1,154 | | $ | 865 | | $ | 2,019 | |
Joy Mining Machinery | | | | 4,433 | | | 715 | | | 1,222 | | | 6,370 | |
|
| |
| |
| |
| |
| | | $ | 4,433 | | $ | 1,869 | | $ | 2,087 | | $ | 8,389 | |
|
| |
| |
| |
| |
16. Discontinued Operations and Held for Sale Assets and Liabilities
| During the fourth quarter of Fiscal 2005, Horsburgh & Scott (“H&S”), a wholly owned subsidiary of the Company, has met all of the criteria of SFAS No. 144, “Accounting for the Impairment of Disposal of Long-Lived Assets” to be classified as held for sale. H&S is a premier designer and manufacturer of industrial gears and gear drives and was classified as part of the Surface Mining Equipment segment. |
| In November 2005, we concluded the sale of the stock of H&S to members of the management team for cash and a note receivable of approximately $12.0 million. The gain on the sale between $1.5-$2.5 million will be deferred until realizability is reasonably assured. The major classes of assets included in the consolidated balance sheets as assets held for sale and held for sale liabilities are disclosed below. Approximately $3.4 million is recorded as accumulated other comprehensive income at October 29, 2005 relating to the minimum pension liability associated with H&S. |
In thousands
| October 29, 2005
| October 30, 2004
|
---|
Assets held for sale: | | | | | | | | |
Cash | | | $ | 58 | | $ | 311 | |
Accounts receivable | | | | 6,993 | | | 9,510 | |
Inventories | | | | 10,789 | | | 5,862 | |
Other current assets | | | | 62 | | | 218 | |
Deferred tax asset | | | | 1,804 | | | 1,263 | |
Property, plant and equipment, net | | | | 7,295 | | | 8,821 | |
|
| |
| |
Total assets held for sale | | | $ | 27,001 | | $ | 25,985 | |
|
| |
| |
Held for sale liabilities: | | |
Accounts payable | | | $ | 2,928 | | $ | 2,898 | |
Employee compensation and benefits | | | | 1,955 | | | 1,249 | |
Advance payments and progress billings | | | | 8,843 | | | 5,413 | |
Other accounts payable and accruals | | | | 3,107 | | | 3,022 | |
Accrued pension costs | | | | 4,150 | | | 3,285 | |
|
| |
| |
Total held for sale liabilities | | | $ | 20,983 | | $ | 15,867 | |
|
| |
| |
| H&S is classified as a discontinued operation in accordance with SFAS No. 144. The Consolidated Statements of Income for all prior periods have been reclassified to reflect the discontinuance of operations. The operating results of H&S for all periods is as follows (dollars in thousands): |
| Fiscal Years Ended
|
---|
| October 29, 2005
| October 30, 2004
| November 1, 2003
|
---|
Net sales | | | $ | 39,418 | | $ | 32,810 | | $ | 30,265 | |
Income (loss) before income taxes | | | | 2,073 | | | (165 | ) | | (351 | ) |
(Provision) benefit for income taxes | | | | (945 | ) | | 31 | | | 98 | |
|
| |
| |
| |
Discontinued operations, net of tax | | | $ | 1,128 | | $ | (134 | ) | $ | (253 | ) |
|
| |
| |
| |
| H&S will meet the definition of a variable interest entity (“VIE”) in accordance with FASB Interpretation No. 46, “ Consolidation of Variable Interest Entities – an Interpretation on ARB No. 51” (“FIN 46”). We will not be required to consolidate the VIE based on the requirements of the interpretation as we will not be the primary beneficiary of the residual interests in the VIE. |
17. Acquisitions
| Effective November 4, 2002, we acquired the 25% interest in our Australian surface mining equipment subsidiary owned by Kobelco Construction Machinery Co. Limited. The purchase price of approximately $12.3 million included $11.2 million of minority interest and $1.1 million in intangible assets. As a result, our ownership of the subsidiary increased to 100% and we removed minority interest from our Consolidated Financial Statements. |
18. Commitments, Contingencies and Off-Balance-Sheet Risks
| We and our subsidiaries are involved in various unresolved legal matters that arise in the normal course of operations, the most prevalent of which relate to product liability (including over 1,000 asbestos and silica-related cases), employment and commercial matters. Also, as a normal part of operations, our subsidiaries undertake contractual obligations, warranties and guarantees in connection with the sale of products or services. Although the outcome of these matters cannot be predicted with certainty and favorable or unfavorable resolutions may affect the results of operations on a quarter-to-quarter basis, we believe that the outcome of such legal and other matters will not have a materially adverse effect on our consolidated financial position, results of operations or liquidity. |
| On August 19, 2005, the United States Bankruptcy Court for the District of Delaware issued a final decree closing our Chapter 11 reorganization proceedings. |
| In litigation commenced in 2001 in the United States District Court for the District of Massachusetts, John G. Kling, purportedly on his own behalf and in a representative capacity for the Harnischfeger Industries Employees’ Savings Plan (the “Plan”), filed suit against us and certain of our present and former employees, officers and directors. This action was based on, among other things, allegations that certain of the defendants failed to properly discharge their fiduciary obligations under ERISA with respect to the “Harnischfeger Common Stock Fund” in the Harnischfeger Industries Employees’ Savings Plan. In September 2005, the parties entered into a Memorandum of Understanding setting forth the terms of a negotiated resolution of this lawsuit. We expect that a Stipulation of Settlement will be filed with the court early in 2006. The settlement is subject to review by an independent fiduciary appointed by the Plan and subject to approval by the court, which must provide prior notice to members of the provisional settlement class and hold a fairness hearing to consider any objections. Upon approval of the settlement, our insurers will be responsible for all payments required under its terms. |
| On November 9, 2005, Joy Mining Machinery Limited (“Joy MM”), a subsidiary located in the United Kingdom, entered into a settlement agreement with the government of Egypt, pursuant to which the parties agreed to terminate arbitration proceedings between them in the Cairo Arbitration Centre and related litigation. The proceedings related to an agreement entered into in 1998 between Joy MM and the General Organization for Industrial and Mining Projects, an agency of the government of Egypt, relating to underground mining equipment for the Abu Tartur project in Egypt. |
| On September 19, 2005, the arbitration panel in the ICC International Court of Arbitration proceedings between Sokolovskaya Investment Company (“SIC”) and Joy MM rendered a final decision and awarded damages and partial reimbursement of costs and legal fees to SIC. The dispute arose out of contracts for the supply of underground mining equipment and related services entered into between Joy MM and SIC, a Russian mining company, in 1995 and 1996. Under the rules applicable to ICC arbitration, we are prohibited from publicly disclosing the amount of the arbitration award. As a result of the award, in the fourth quarter of Fiscal 2005, we booked a charge against earnings of less than $0.03 per share. |
| In Fiscal 2004, Joy Global (SA)(Pty) Ltd. (“Joy SA”) declared and paid a dividend in the amount of 320 million South African Rand to Joy MM, its direct shareholder. Joy SA did not pay Secondary Tax on Companies (“STC”) on the dividend based upon legal advice to the effect that no such tax was payable due to the Double Tax Agreement between South Africa and the United Kingdom, and filed a 2004 tax return reflecting this position. On September 19, 2005, the South African Revenue Service (the “SARS”) issued an assessment for STC in the amount of 40 million South African Rand (approximately $6 million) and notified Joy SA that the SARS was disputing the position taken in the company’s tax return. Joy SA filed an objection to the assessment and an application for deferral of payment, and in November 2005 the SARS disallowed the objection but granted the deferral of payment pending final resolution of this matter. We intend to appeal the disallowance through the South African court system. As of October 29, 2005, the amount of the STC tax liability claimed by the SARS would have been approximately 46.1 million South African Rand (approximately $6.9 million at the exchange rate in effect at October 29, 2005), including interest at the prescribed rate, currently 10.5% per year, which will continue to accrue until payment. |
| At October 29, 2005, we were contingently liable to banks, financial institutions and others for approximately $141.6 million for outstanding letters of credit, bank guarantees and surety bonds securing performance of sales contracts and other guarantees in the ordinary course of business. Of the $141.6 million, approximately $6.1 million remains in place and is substantially attributable to remaining workers compensation obligations of Beloit Corporation. At October 29, 2005, there were $21.7 million of outstanding letters of credit or other guarantees issued by non-U.S. banks for non-U.S. subsidiaries under locally provided credit facilities. |
| From time to time we and our subsidiaries become involved in proceedings relating to environmental matters. We believe that the resolution of such environmental matters will not have a materially adverse effect on our consolidated financial position, results of operations or liquidity of the Company. |
| We have entered into various forward foreign exchange contracts with major international financial institutions for the purpose of hedging our risk of loss associated with changes in foreign exchange rates. These contracts involve off-balance-sheet market and credit risk. As of October 29, 2005, the nominal or face value of forward foreign exchange contracts, in absolute U.S. dollar equivalent terms, was $236.3 million. |
| Forward exchange contracts are entered into to protect the value of committed future foreign currency receipts and disbursements and net investment hedges and consequently any market related loss on the forward contract would be offset by changes in the value of the hedged item. As a result, we are not exposed to net market risk associated with these instruments. |
| We are exposed to credit-related losses in the event of non-performance by counterparties to our forward exchange contracts. We currently have a concentration of these contracts held with LaSalle Bank, N.A. as agent for ABN Amro Bank, N.V., which maintains an investment grade rating. We do not expect any counterparties, including LaSalle Bank, N.A. to fail to meet their obligations. A contract is generally subject to credit risk only when it has a positive fair value and the maximum exposure is the amount of the positive fair value. |
19. Disclosure About Fair Value of Financial Instruments
| The following methods and assumptions were used to estimate the fair value of each class of financial instruments for which it is practicable to estimate that value: |
| Cash and Cash Equivalents: The carrying value approximates fair value because of the short maturity of those instruments. |
| Credit Facility: The carrying value of the Credit Facility approximates fair value as the facility bears a floating rate of interest expressed in relation to LIBOR or the Base Rate (previously defined). Consequently, the cost of this instrument always approximates the market cost of borrowing for an equivalent maturity and risk class. |
| Senior Subordinated Notes: The fair market value of the Senior Subordinated Notes is estimated based on market quotations at year-end. |
| Other Borrowings: The carrying value of other borrowings approximates fair value because these instruments consist predominantly of capital leases. |
| Forward Exchange Contracts: The fair value of forward exchange contracts represents the estimated amounts receivable (payable) to terminate such contracts at the reporting date based on foreign exchange market prices at that date. |
The estimated fair values of financial instruments at October 29, 2005 and October 30, 2004 are as follows:
In thousands
| Carrying Value
| Fair Value
|
---|
Fiscal 2005 | | | | | | | | |
Cash and cash equivalents | | | $ | 143,917 | | $ | 143,917 | |
8.75 % Senior Subordinated Notes | | | | 48 | | | 48 | |
Other borrowings | | | | 2,619 | | | 2,619 | |
Forward exchange contracts | | | | — | | | (1,602 | ) |
Fiscal 2004 | | |
Cash and cash equivalents | | | $ | 231,706 | | $ | 231,706 | |
8.75 % Senior Subordinated Notes | | | | 200,000 | | | 225,815 | |
Other borrowings | | | | 5,979 | | | 5,979 | |
Forward exchange contracts | | | | — | | | 1,192 | |
| The fair values of forward exchange contracts at October 29, 2005 are analyzed in the following table of U.S. dollar equivalent terms: |
| Maturing in 2006
|
---|
In thousands
| Buy
| Sell
|
---|
U.S. Dollar | | | | 314 | | | (988 | ) |
Australian Dollar | | | | (15 | ) | | (1 | ) |
British Pound Sterling | | | | (690 | ) | | (1 | ) |
South African Rand | | | | (63 | ) | | 2 | |
Euro | | | | (193 | ) | | 33 | |
| We are exposed to fluctuations in foreign currency exchange rates and interest rates. To manage these risks, we use derivative instruments, in this case, forward exchange contracts. Derivative instruments used in hedging activities are viewed as risk management tools, involve little complexity, and are not used for trading or speculative purposes. |
| As part of ongoing control procedures, we monitor concentrations of credit risk associated with financial institutions. We also monitor the creditworthiness of our customers to which we grant credit terms in the normal course of business. Our customers are, almost exclusively, in the mining industry. Our concentration of credit risk associated with our trade receivables are considered minimal due to the broad customer base and the generally sound financial standing of our major customers. Bad debts have not been significant. We often require and receive letters of credit or bank guarantees as collateral for our credit sales, especially when the customer is located outside the United States and other developed markets. |
20. Subsequent Events
| On November 15, 2005 our Board of Directors declared a three-for-two split of our common shares, payable on December 12, 2005 to shareholders of record on November 28, 2005. In connection with the stock split, each holder of Joy Global common stock will receive one share of Joy Global common stock for each two shares of such stock owned. Cash will be distributed in lieu of fractional shares. New shares will be issued by our transfer agent, and will begin trading on the Nasdaq National Market on a split-adjusted basis on December 13, 2005. Except on the Consolidated Balance Sheet and Consolidated Statement of Shareholders’ Equity, all previously reported earnings per share, share amounts, and stock price data have been adjusted for this split. |
| On November 15, 2005, our Board of Directors declared a cash dividend of $0.1125 per outstanding share of common stock. The dividend will be paid on December 29, 2005 to all stockholders of record at the close of business on December 15, 2005. This represents a 50% increase from the previous split adjusted quarterly rate of $0.075 per share. |
| In November 2005, we commenced a share repurchase program. Under the program, management is authorized to repurchase up to $300.0 million in shares in the open market or through privately negotiated transactions. We have repurchased approximately $10.0 million of common stock, representing 327,450 shares, under the program through November 2005. |
21. Segment Information
Business Segment Information
| At October 29, 2005, we had two reportable segments, underground mining machinery (Joy) and surface mining equipment (P&H). Joy is a major manufacturer of underground mining equipment for the extraction of coal and other bedded minerals and offers comprehensive service locations near major mining regions worldwide. P&H is a major producer of surface mining equipment for the extraction of ores and minerals and provides extensive operational support for many types of equipment used in surface mining. The accounting policies of the segments are the same as those described in Note 2 —Significant Accounting Policies. Operating income (loss) of segments does not include interest income or expense and provision for income taxes. Identifiable assets are those used in our operations in each segment. Corporate assets consist primarily of deferred financing costs, cash and cash equivalents, and deferred income taxes and prepaid benefit cost. |
In thousands
| Net Sales
| Operating Income (Loss)
| Depreciation and Amortization
| Capital Expenditures
| Total Assets
|
---|
Fiscal 2005 | | | | | | | | | | | | | | | | | |
Underground Mining | | | $ | 1,132,334 | | $ | 187,288 | | $ | 24,755 | | $ | 23,906 | | $ | 764,593 | |
Surface Mining | | | | 795,140 | | | 114,375 | | | 15,189 | | | 14,533 | | | 505,330 | |
|
| |
| |
| |
| |
| |
Total operations | | | | 1,927,474 | | | 301,663 | | | 39,944 | | | 38,439 | | | 1,269,923 | |
Corporate | | | | — | | | (34,973 | ) | | 1,546 | | | 26 | | | 351,604 | |
|
| |
| |
| |
| |
| |
Total Continuing | | |
Operations | | | | 1,927,474 | | | 266,690 | | | 41,490 | | | 38,465 | | | 1,621,527 | |
Discontinued Operation | | | | 39,418 | | | 2,073 | | | 1,819 | | | 288 | | | 27,001 | |
|
| |
| |
| |
| |
| |
Total | | | $ | 1,966,892 | | $ | 268,763 | | $ | 43,309 | | $ | 38,753 | | $ | 1,648,528 | |
|
| |
| |
| |
| |
| |
Fiscal 2004 | | |
Underground Mining | | | $ | 820,121 | | $ | 91,376 | | $ | 28,012 | | $ | 11,914 | | $ | 641,053 | |
Surface Mining | | | | 579,236 | | | 53,354 | | | 16,052 | | | 8,835 | | | 406,094 | |
|
| |
| |
| |
| |
| |
Total operations | | | | 1,399,357 | | | 144,730 | | | 44,064 | | | 20,749 | | | 1,047,147 | |
Corporate | | | | — | | | (36,884 | ) | | 3,345 | | | — | | | 367,227 | |
|
| |
| |
| |
| |
| |
Total Continuing | | |
Operations | | | | 1,399,357 | | | 107,846 | | | 47,409 | | | 20,749 | | | 1,414,374 | |
Discontinued Operation | | | | 32,810 | | | (165 | ) | | 1,958 | | | 386 | | | 25,985 | |
|
| |
| |
| |
| |
| |
Total | | | $ | 1,432,167 | | $ | 107,681 | | $ | 49,367 | | $ | 21,135 | | $ | 1,440,359 | |
|
| |
| |
| |
| |
| |
Fiscal 2003 | | |
Underground Mining | | | $ | 685,999 | | $ | 43,573 | | $ | 31,635 | | $ | 19,376 | | $ | 679,919 | |
Surface Mining | | | | 499,702 | | | 27,923 | | | 18,817 | | | 8,245 | | | 444,287 | |
|
| |
| |
| |
| |
| |
Total operations | | | | 1,185,701 | | | 71,496 | | | 50,452 | | | 27,621 | | | 1,124,206 | |
Corporate | | | | — | | | (23,463 | ) | | 3,710 | | | — | | | 140,052 | |
|
| |
| |
| |
| |
| |
Total Continuing | | |
Operations | | | | 1,185,701 | | | 48,033 | | | 54,162 | | | 27,621 | | | 1,264,258 | |
Discontinued Operation | | | | 30,265 | | | (351 | ) | | 1,926 | | | 999 | | | 22,471 | |
|
| |
| |
| |
| |
| |
Total | | | $ | 1,215,966 | | $ | 47,682 | | $ | 56,088 | | $ | 28,620 | | $ | 1,286,729 | |
|
| |
| |
| |
| |
| |
Geographical Segment Information
In thousands
| Total Sales
| Interarea Sales
| Sales to Unaffiliated Customers
| Operating Income (Loss)
| Long- Lived Assets
|
---|
Fiscal 2005 | | | | | | | | | | | | | | | | | |
United States | | | $ | 1,149,126 | | $ | (279,334 | ) | $ | 869,792 | | $ | 194,852 | | $ | 170,768 | |
Europe | | | | 447,290 | | | (118,625 | ) | | 328,665 | | | 53,153 | | | 78,958 | |
Australia | | | | 316,496 | | | (11,126 | ) | | 305,370 | | | 30,886 | | | 27,449 | |
Other Foreign | | | | 438,935 | | | (15,288 | ) | | 423,647 | | | 68,546 | | | 23,017 | |
Interarea Eliminations | | | | (424,373 | ) | | 424,373 | | | — | | | (45,774 | ) |
|
| |
| |
| |
| |
| |
| | | $ | 1,927,474 | | $ | — | | $ | 1,927,474 | | $ | 301,663 | | $ | 300,192 | |
|
| |
| |
| |
| |
| |
Fiscal 2004 | | |
United States | | | $ | 830,832 | | $ | (191,415 | ) | $ | 639,417 | | $ | 88,241 | | $ | 142,871 | |
Europe | | | | 270,887 | | | (60,102 | ) | | 210,785 | | | 24,870 | | | 75,123 | |
Australia | | | | 223,244 | | | (7,434 | ) | | 215,810 | | | 12,574 | | | 25,455 | |
Other Foreign | | | | 337,580 | | | (4,235 | ) | | 333,345 | | | 50,493 | | | 23,593 | |
Interarea Eliminations | | | | (263,186 | ) | | 263,186 | | | — | | | (31,448 | ) | | — | |
|
| |
| |
| |
| |
| |
| | | $ | 1,399,357 | | $ | — | | $ | 1,399,357 | | $ | 144,730 | | $ | 267,042 | |
|
| |
| |
| |
| |
| |
Fiscal 2003 | | |
United States | | | $ | 731,002 | | $ | (178,916 | ) | $ | 552,086 | | $ | 32,666 | | $ | 166,683 | |
Europe | | | | 218,632 | | | (71,784 | ) | | 146,848 | | | 27,227 | | | 68,582 | |
Australia | | | | 213,773 | | | (11,643 | ) | | 202,130 | | | 8,902 | | | 23,849 | |
Other Foreign | | | | 286,139 | | | (1,502 | ) | | 284,637 | | | 35,534 | | | 27,115 | |
Interarea Eliminations | | | | (263,845 | ) | | 263,845 | | | — | | | (32,833 | ) | | — | |
|
| |
| |
| |
| |
| |
| | | $ | 1,185,701 | | $ | — | | $ | 1,185,701 | | $ | 71,496 | | $ | 286,229 | |
|
| |
| |
| |
| |
| |
Product Information
In thousands
| Fiscal 2005
| Fiscal 2004
| Fiscal 2003
|
---|
Original equipment | | | $ | 716,798 | | $ | 437,556 | | $ | 319,398 | |
Aftermarket | | | | 1,210,676 | | | 961,801 | | | 866,303 | |
|
| |
| |
| |
Total revenues | | | $ | 1,927,474 | | $ | 1,399,357 | | $ | 1,185,701 | |
|
| |
| |
| |
| Pursuant to the requirements of Section 13 or 15(d) of the Securities Exchange Act of 1934, the Registrant has duly caused this report to be signed on its behalf by the undersigned, thereunto duly authorized, in the City of Milwaukee, Wisconsin, on the 22nd day of December, 2004. |
JOY GLOBAL INC.
(Registrant)
/s/ John Nils Hanson
John Nils Hanson
Chairman, President
And Chief Executive Officer
| Pursuant to the requirements of the Securities Exchange Act of 1934, this report has been signed below by the following persons on behalf of the registrant and in the capacities indicated on December 22, 2005. |
| | |
---|
Signature | | Title |
/s/ John Nils Hanson John Nils Hanson | | Chairman, President and Chief Executive Officer |
/s/ Donald C. Roof Donald C. Roof | | Executive Vice President, Chief Financial Officer and Treasurer |
/s/ Michael S. Olsen Michael S. Olsen | | Vice President, Controller and Chief Accounting Officer |
(1) Stephen L. Gerard | | Director |
(1) Ken C. Johnsen | | Director |
(1) James R. Klauser | | Director |
(1) Richard B. Loynd | | Director |
(1) P. Eric Siegert | | Director |
(1) James H. Tate | | Director |
(1) | | John Nils Hanson, by signing his name hereto, does hereby sign and execute this report on behalf of each of the above-named Directors of Joy Global Inc. pursuant to powers of attorney executed by each of such Directors and filed with the Securities and Exchange Commission as an exhibit to this report.
|
December 22, 2005
| By:/s/ John Nils Hanson John Nils Hanson, Attorney-in-fact |
JOY GLOBAL INC.
SCHEDULE II
VALUATION AND QUALIFYING ACCOUNTS
(In thousands)
Classification
| Balance at Beginning of Period
| Additions Charged to Expense
| Deductions (1)
| Currency Translation Effects
| Discontinued Operations
| Balance at End of Year
|
---|
Allowance Deducted in Balance Sheet from Accounts | | | | | | | | | | | | | | | | | | | | |
Receivable: | | |
Fiscal 2005 | | | $ | 5,678 | | $ | 1,259 | | $ | (944 | ) | $ | 11 | | $ | (209) | | $ | 5,795 | |
|
| |
| |
| |
| |
| |
| |
Fiscal 2004 | | | $ | 7,645 | | $ | 463 | | $ | (2,539 | ) | $ | 109 | | $ | — | | $ | 5,678 | |
|
| |
| |
| |
| |
| |
| |
Fiscal 2003 | | | $ | 7,654 | | $ | 575 | | $ | (1,587 | ) | $ | 1,003 | | $ | — | | $ | 7,645 | |
|
| |
| |
| |
| |
| |
| |
(1) Represents write-off of bad debts, net of recoveries.
Classification
| Balance at Beginning of Year
| Additions Charged to Comprehensive Loss
| Allocated to Tax Expense
| Allocated to Intangibles
| Allocated to APIC
| Reclass to L-T Deferred Tax Assets
| Balance at End of Year
|
---|
Allowance Deducted in Balance Sheet from Deferred | | | | | | | | | | | | | | | | | | | | | | | |
Tax Assets: | | |
Fiscal 2005 | | | $ | 435,167 | | $ | — | | $ | 8,013 | | $ | (13,736 | ) | $ | (100,088 | ) | $ | (12,394 | ) | $ | 316,962 | |
|
| |
| |
| |
| |
| |
| |
| |
Fiscal 2004 | | | $ | 396,911 | | $ | 8,387 | | $ | 18,328 | | $ | (419 | ) | $ | — | | $ | 11,960 | | $ | 435,167 | |
|
| |
| |
| |
| |
| |
| |
| |
Fiscal 2003 | | | $ | 399,468 | | $ | 13,461 | | $ | 4,992 | | $ | (48,271 | ) | $ | — | | $ | 27,261 | | $ | 396,911 | |
|
| |
| |
| |
| |
| |
| |
| |