CE FRANKLIN
2010 ANNUAL REPORT
OURCUSTOMER SERVICE
MAKES USGREATER THAN
THESUM OF OUR PARTS
ANNUAL MEETING OF SHAREHOLDERS
CE Franklin’s 2011 Annual Meeting of Shareholders will be held at the Calgary Petroleum Club in the Cardium Room, 319-5th Ave SW, Calgary, Alberta on Wednesday, April 27th, 2011 at 2:30 pm Mountain time. Shareholders and other interested parties are invited to attend.
FORWARD-LOOKING STATEMENTS
The information in this annual report may contain “forward-looking statements” within the meaning of applicable securities legislation. All statements, other than statements of historical facts, that address activities, events, outcomes and other matters that CE Franklin plans, expects, intends, assumes, believes, budgets, predicts, forecasts, projects, estimates or anticipates (and other similar expressions) will, should or may occur in the future are forward-looking statements. These forward-looking statements are based on management’s belief, based on currently available information, as to the outcome and timing of future events. When considering forward-looking statements, you should keep in mind the risk factors and other cautionary statements in the Management’s Discussion and Analysis (“MD&A”), including those found under the caption “Risk Factors”.
CE Franklin is a leading supplier of products and services to the energy industry.
For over half a century, CE Franklin customers have relied on our commitment to quality and customer service.
We are where our customers need us.
With 45 branches situated in towns and cities throughout Western Canada, CE Franklin is geographically positioned to serve all of Canada’s key oil and gas producing fields and processing facilities. Our goal is to leverage our leading oilfield market position to provide similar products and services to the oil sands, midstream and other industrial end-use markets.
Shares of CE Franklin trade on the TSX (CFT) and NASDAQ (CFK) stock exchanges.
As of December 31, 2010, there were 17.5 million common shares outstanding.
On August 26, 2010, Schlumberger Limited (“Schlumberger”), a leading global oilfield service company, completed the acquisition of Smith International Inc. (“Smith”), a major oilfield service company based in the United States that owned approximately 56 percent of CE Franklin’s shares. We continue to leverage the relationship with Wilson Supply, a wholly owned, US subsidiary of Smith, now owned by Schlumberger, in order to offer North American solutions to our customers.
WE OFFER WHAT OUR CUSTOMERS NEED.
CE Franklin specializes in distributing more than 25,000 types of pipe, valves, flanges, fittings, production equipment, tubular products and other general industrial supplies, sourced from over 2,000 suppliers to Canadian industrial clients, mostly in the oil and gas sector. In addition to oil and gas producers, we serve the oil sands, midstream, refining, petrochemical and non-oilfield related industries.
Our industry leading distribution network ensures our more than 3,000 customers receive the right materials where and when they need them, and for the best value. Our Edmonton Distribution Centre is the heart of our distribution system, and maximizes our ability to provide our customers with enhanced product choice, delivery effectiveness and competitive pricing.
| | | | | |
(millions of Canadian dollars, except per share amounts) | 2010 | 2009 | 2008 | 2007 | 2006 |
Sales | 489.6 | 437.0 | 547.4 | 466.3 | 555.2 |
Gross profit | 75.0 | 76.6 | 107.7 | 84.6 | 103.5 |
EBITDA(1) | 12.5 | 12.4 | 35.8 | 25.7 | 40.1 |
EBITDA(1) as a % of sales | 2.5% | 2.8% | 6.5% | 5.5% | 7.2% |
Net income | 5.9 | 6.3 | 21.7 | 13.6 | 22.9 |
Net income per share | | | | | |
Basic | 0.34 | 0.36 | 1.19 | 0.74 | 1.27 |
Diluted | 0.33 | 0.35 | 1.17 | 0.72 | 1.22 |
Balance sheet highlights(3) | | | | | |
Net working capital (2) | 125.7 | 136.6 | 142.8 | 134.7 | 120.2 |
Bank operating loan and long term debt | 6.4 | 26.8 | 35.5 | 45.7 | 35.4 |
Shareholders’ equity | 150.5 | 142.6 | 139.3 | 118.2 | 102.5 |
Weighted average shares outstanding (basic) (MM) | 17.5 | 17.8 | 18.3 | 18.3 | 18.1 |
(1) See Management’s Discussion and Analysis on page 27 for a detailed description of EBITDA, a non-GAAP measure. (2) Net working capital is comprised of accounts receivable, inventory, and other assets, less accounts payable and accrued liabilities. (3) As at December 31. |
Message to our Shareholders
Despite a challenging business environment, CE Franklin demonstrated resilience and discipline through 2010. We are proud not only to have delivered solid operating results, but to have done so while maintaining our commitment to customer service and furthering our long term strategy.
We worked diligently on our strategies of product and market diversification as well as operational efficiency. This helped offset the product margin erosion the service and supply industry experienced due to the extremely competitive environment in 2010. Oil and gas industry activity levels in 2010 recovered somewhat from decade low levels in 2009, but are still 20 percent lower than the five year average.
2010 Highlights
Focusing on customer service
s
We continue to leverage our superior customer service and operational excellence to improve customer order fill rates, product availability, price competitiveness and quality – four key factors that differentiate market leaders.
s
Our revenue per industry well completion has increased by 48 percent in the last five years. By separating ourselves from our competition through superior customer service, we are gaining market share, positively impacting both our sales and overall profitability.
s
Over a 5 year period, our revenues have outperformed market activity. In 2010, our revenues increased by 12 percent over 2009 levels, driven by our customer service that is the cornerstone of all our performance achievements, making it even more critical going forward.
Following through on our diversification strategy
s
Our diversification strategy continues to benefit from our ability to successfully leverage and enhance our existing capabilities, product base and scale.
s
Growing our major projects revenue, which supports oil sands and conventional business growth, has been critical to our past and future success. We are growing our project competence and market place credibility. Oil sands revenue represents approximately 13 percent, or $61.3 million of our total revenue.
s
Our valve actuation and other product diversification strategies helped us grow our business with existing customers and further penetrate the midstream sector.
Increasing efficiency
s
One of our key strategies is to respond to changing market pressures. We worked throughout 2010 to further transform our business processes and efficiencies to facilitate operational flexibility and growth.
s
Deliberately shifting our supply chain model to centralize more services through our Edmonton Distribution Centre has helped facilitate our major projects growth, as well as growth in our oilfield business. This “Load Shifting” ensures consistent customer service despite seasonal and project demand fluctuations placed on our business. We are better positioned to meet customer demand and allow our branch level staff to focus their efforts on new customer capture and further enhance our customer service capability.
s
Our revenue grew by $52.6 million year over year and our Selling, General & Administrative (“SG&A”) expense dropped by $1.6 million, a significant productivity improvement.
Achieving solid operating results
s
We generated $10.7 million in cash flow from operating activities before net changes in non-cash operating working capital balances. Working capital performance improved, resulting in a $10.9 million reduction of net working capital balances, despite increased sales in 2010. We reduced our borrowing balances by $20.4 million to end the year at $6.4 million and extended the maturity of our borrowing facility until 2013.
s
We achieved a net income per share (basic) of $0.34 in 2010, our eighth consecutive year of profitable operations.
We are growing despite difficult market fundamentals
Extended economic uncertainty continued to impact overall market activity – particularly on the natural gas side - through 2010, resulting in a difficult year for both oil and gas producers and the companies that service that sector, such as CE Franklin. The natural gas market remained extremely fragile due to oversupply, low demand, and the strong Canadian dollar. With that said, we are pleased to report optimism increased throughout the industry as the year progressed, and activity levels started to accelerate in the latter half of 2010.
Oil and gas capital expenditures in Western Canada are rebounding from decade low levels in 2009. Well completions in 2010 – still down 49 percent from the industry peak in 2006 – were up 50 percent on a year over year basis. Likewise, the average operating rig count increased 54 percent to 332, up from an average of 215 in 2009. We are encouraged to see an increasing number of stalled and postponed projects in the process of being restarted, evidence that the industry has now weathered the worst of the economic storm.
CE Franklin’s operating results are improving as well. Our revenue for 2010 was $489.6 million, an increase of $52.6 million compared to the prior year. Revenues strengthened as the year progressed, with the fourth quarter outperforming the first quarter. This improvement on a quarter over quarter basis is a very positive leading indicator, given that historically, first quarter (winter drilling season) revenues are the highest. The increased activity and the Company’s improving results are a reflection of industry economics strengthening and the Company continuing to gain traction on its strategies.
Despite confidence slowly returning to the oil and gas industry, industry well completion levels, which drive demand for CE Franklin products, remain far below five and ten year averages. Well completions in 2010 were comparable to those in 2002. However, our revenues are approximately double what we achieved in 2002, demonstrating that our growth strategies are taking hold and we are gaining significant traction in the marketplace.
Countering strong revenue growth through 2010 is the fact that we experienced significant sales margin erosion on a year over year basis. Industry activity and economic weakness resulted in our customers focusing more and more on decreasing their supply chain costs. This pressure, in combination with inconsistent pricing (due in part to significant fluctuations in steel prices and competitive pricing activity) resulted in our average sales margins declining from 17.5 percent in 2009 to 15.3 percent in 2010. We expect some market correction as companies that are cutting margins to non-sustainable levels drop out of the business or shift their practices.
We are committed to long-term sustainability for shareholders rather than short term market share gain. Therefore, we were not willing to cut our prices to the point of sacrificing our customer service, execution capability and shareholder value. Fortunately, our product and sales diversification strategies allowed us to partially offset the sales margin decreases to our bottom line.
We do not expect sales margins to return to normal levels immediately. Rather, we expect moderate improvements in pricing as industry fundamentals improve, combined with our focus on improving customer service and operating efficiencies, will drive our profitability up. We will continue to leverage our supply chain to ensure disciplined growth has flow through to the bottom line.
Our geographic diversification continued to prove advantageous in 2010. We are flexible and responsive to shifts in the industry’s geographic focus, and are well positioned to take advantage of regionalized activity increases across the Western Canadian Sedimentary Basin. Noteworthy growth in industry activity through 2010 occurred in the Horn River, Bakken and Heavy Oil regions, a substantial shift in the geographic focus of industry activity from just a few years ago. Both mining and steam assisted gravity drainage (SAGD) construction projects increased in the oil sands region. Conventional natural gas regions should follow suit as natural gas fundamentals improve.
Our diversification and efficiency strategies generate results
Though we anticipate growth in the oil and gas industry going forward, we are not relying solely on a rebound in market activity to grow our business. We remain focused on actively pursuing our three growth strategies: growing our customer base, diversifying our product lines, and end use markets, while driving more efficiency into our distribution infrastructure through our load shifting strategies.
Our strategies to increase market share in both the conventional and oil sands markets are paying off. Sales to oil sands and other major project customers continue to draw an increasingly wide base of customers and are resulting in sales growth of both existing and new products.
In the past five years, we have invested significantly in improved product, distribution and project management infrastructure. Throughout this last year, we leveraged these investments to strengthen our market position, win customers, and improve both supply chain and process efficiency.
Our Edmonton Distribution Centre acts as the centralized hub of our business. Our focus on centralization is taking pressure off branch-level staff, allowing them to commit more effort to new customer capture and further enhancements to customer service. We refer to this as “Load Shifting” our work.
Additionally, the Distribution Centre has allowed us to expand into new, value-added service offerings, such as our fluid control and instrumentation (FC&I) product strategy launched in 2009. We are pleased that our FC&I product sales achieved year over year growth and is already realizing profitable return on investment. The most significant component of our FC&I strategy is our valve actuation service. Having the capacity to assemble complete valve and actuator packages at our Distribution Centre means that we can provide customers with faster order turn-around times, thereby improving our credibility, increasing our sales to existing customers, and drawing in new customers. We will continue to look for this kind of value-added opportunity and aggressively leverage such successes in our sales and marketing strategies.
Efficiency, both in terms of processes and supply, is a key priority that is generating bottom line results. Automating processes to increase our order fill speed, shipping directly from our Distribution Centre to our customers to eliminate double handling, and improving internal communications and logistical capability have all allowed us to lower the overall transaction cost per revenue dollar.
We’ve established business processes, improved project execution and increased supply volumes to enable the management of multiple major projects at the same time. Additionally, our increasing efficiency and proactive investment means we are now able to sell further up the project planning cycle, allowing for the forward booking of project business.
Increasing efficiency resulted in direct savings in our SG&A costs. While revenue increased by $52.6 million in 2010, SG&A decreased by $1.6 million. Some of these savings are attributable to the absence of costs incurred to integrate the oilfield supply business acquired in June of 2009. However, a good portion of the savings resulted from load shifting and centralizing work processes.
The current highly competitive nature of our business makes operational efficiency and lower costs per transaction vital. We will continue to focus on driving efficiency into our business.
We remain committed to achieving solid shareholder returns
Our strong financial position allowed us to continue our share buy-back program under the Normal Course Issuer Bid. In 2010, 61,769 shares were purchased through the buy-back. We have continued this program into 2011, as we believe purchasing our own stock represents good value.
During 2010, we extended the maturity of our $60 million bank facility to 2013 and reduced borrowing levels. This financial strength positions us to support revenue growth, execute large projects for our customers and be opportunistic in the pursuit of our strategies.
We are pleased to welcome our new major shareholder
On August 26th, 2010, Schlumberger acquired Smith, which on that date owned 56 percent of our shares. This transaction means that Schlumberger is now our majority shareholder.
We are pleased that Schlumberger shows a high level of support for and confidence in our company. Our operations and strategy remain consistent subsequent to the transaction and we are further strengthened by Schlumberger’s backing as we move forward.
Schlumberger is the most successful oilfield services company in the world. We look forward to leveraging their industry knowledge, reach and best practices to improve our efficiencies and economics, bolstering shareholder value. We continue to work on improving our interaction with Wilson Supply, our sister company operating in the United States, which was acquired from Smith by Schlumberger.
I would personally like to thank Doug Rock and John Yearwood, former CEF board members and CEO’s of Smith, for their support of CE Franklin. They represented a very supportive shareholder. I would also like to thank Don McKenzie, past President and CEO of Smith subsidiary, MI Swaco, for his years of guidance and service on the CE Franklin board.
I welcome the addition of Kjell-Eric Oestdahl, Vice President Operations, Schlumberger Limited, to the CE Franklin Board of Directors in October, 2010. I would also like to welcome Bradley Thompson and Keith Turnbull who joined our Board in April 2010. The addition of these Directors makes our Board of Directors stronger than ever. We also appreciate the ongoing guidance and support of John Kennedy, President of Schlumberger’s distribution unit, who has been a key member of our Board since 1999 and the continuing guidance of Michael Hogan and Robert McClinton.
Thanks to our strong team, the future looks bright
Differentiated from our competition by customer service, supply efficiency and product choice, we remain committed to market leadership in our sector. We will continue to focus on building customer relationships, refining supply chain efficiencies, and strengthening corporate sustainability for the future.
Our strategies have proven beneficial in all cycles of the industry. Not only have they enabled us to remain profitable through the recent industry downturn, we are confident they will provide very strong incremental profit flow-through during periods of industry growth. We look forward to leveraging the work done on our strategies as the industry recovers.
Our ongoing commitment to efficiency, proven track record of profitability and experienced leadership give us the capacity to out-perform market activity. We are proud to possess one other very significant competitive advantage: a strong balance sheet. Our balance sheet gives our customers and suppliers confidence that we can facilitate, invest in and execute both our own priorities, as well as theirs, now and into the future.
I would like to thank our team of 483 staff for their hard work and dedication, especially as we have moved through the downturn of the last couple years. We have worked hard to recruit and retain the best staff in the industry. Our continued success would not be possible without their hard work, commitment to customer service and willingness to take on challenges. I am proud to be part of this dynamic team.
Additionally, I would like to acknowledge our operating and supply partners, and key financial stakeholders for their continued support.
Finally, I would like to thank our customers for choosing to make CE Franklin their supplier of choice.
Given our hard working team, our proactive diversification strategies, and evidence of improving industry trends, I look forward to the challenges and opportunities of 2011.
Sincerely,
Michael S. West,
President and Chief Executive Officer
February 2, 2011.
Operations Review
PROJECT MANAGEMENT EXECUTION AND DISTRIBUTION EFFICIENCY
+
TOP QUALITY PRODUCTS AND SUPERIOR SERVICE
+
THE VERY BEST EMPLOYEES
+
BEST PRACTICES IN SAFETY AND ENVIRONMENT
+
STRONG TIES TO OUR COMMUNITIES
=
Our Continued Success
At CE Franklin, we recognize that our long-term business success is directly tied to how well we support and balance the needs of all of our stakeholders. In order to be sustainable, we must efficiently meet the product and service requirements of our customers. We must provide safe and rewarding employment to our staff and be a strong connectivity partner for our suppliers. Most importantly, we must support the communities we operate in, all while providing solid investment returns for our shareholders.
We have been in business for over half a century and are proud to be one of the largest distributors serving the Canadian energy industry. Many of our customer and supplier relationships span decades. We strive to lead our industry in solutions-oriented customer service, understanding that our actions today are an important part of what will draw our customers back tomorrow.
Our size, experience and ability to diversify and execute have positioned us to outperform market activity. Our industry-leading capability to leverage our assets and supply chain increases our efficiency and overall rate of return. This translates into value for our stakeholders, making CE Franklin an attractive partner, employer, community member and investment.
We remain focused on maintaining a healthy balance sheet, as our ability to meet the needs of our stakeholders is enabled by our strong financial position. At the end of 2010, CE Franklin had a debt to debt plus equity ratio of 4 percent.
Finally, we remain committed to good corporate governance, financial transparency and shareholder dialogue. We meet or exceed all of the reporting requirements for publicly traded companies and welcome conversation with all stakeholders about our results and positioning.
Project Management Execution and Distribution Efficiency
CE Franklin is a market leader in the delivery of products and services to the Canadian energy industry. We continually strive to develop our project management execution and distribution efficiency. Our industry reputation for expertise in expediting, warehousing, project management, and document control for any type of major project continues to grow.
Our Edmonton Distribution Centre is the largest distribution facility in the Canadian oilfield supply industry. Centralizing processes through our Distribution Centre have reduced transactions and related costs, improved order fulfillment efficiency due to scale and specialized resources, and increased asset efficiency resulting from central inventory utilization.
Additionally, it has provided us the necessary capability for specialization, enabling us to expand our service offering into major projects and other value-added opportunities. Our ability to execute major projects has positively impacted oil sands revenue as well as larger scale projects in our conventional business. Our oil sands revenue now represents 13 percent of our overall revenues. Our major project capability will help facilitate growth in 2011. Our valve actuation centre, where our highly skilled staff builds complete valve and actuator packages, is an increasing revenue stream made possible by being situated adjacent to the centralized inventory and logistics capability at our Distribution Centre.
By refining and automating operations, communications and logistics, we have been able to leverage our Distribution Centre to significantly improve our overall efficiency. We are able to ship directly to customers. Our front-line branch staff are able to commit more time to new customer capture and customer service and our inventory management is becoming increasingly streamlined and organized. In 2010, our Distribution Centre processed over $99.3 million of customer sales orders. Our load shifting strategies will increase the amount of revenue put through our Distribution Centre in 2011, focusing our front line branch staff on customer service.
+
Top Quality Products and Superior Service
We are more than a supplier of products: we are proud to be a productivity partner for many of our customers. Our customers rely on CE Franklin to consistently provide high quality products and services at competitive prices. Just as importantly, they depend on our superior customer service and our technical expertise on a broad spectrum of requirements from bottom hole pump repair to pumping well equipment design/performance evaluation, and from valve automation solutions to product standardization. Our branch network reach means we can help our customers consistently execute their capital and operations programs across all of their operating locations.
Sourcing quality, well-priced products from suppliers in a consistent, timely and cost-efficient way is a key component of our success. How do we do it? We start with quality: all of our suppliers and all 25,000 of our regularly stocked products have to meet our rigorous standards of excellence. Then, we focus on minimizing pricing and maximizing efficiency. With over 50 years of experience in this business and our specialized operational processes which allow us to leverage our supply chain, we are accelerating our asset velocity and ensuring the right products are delivered when and where our customers need them.
Looking forward, we plan to continue to build our end use customer base and diversify into additional product lines and service offerings. Additional diversification will not only enhance our resiliency towards the variable and cyclical nature of the oil and gas industry, it will allow us to continue to best respond to the changing needs of our customers.
+
The Very Best Employees
CE Franklin values the effort, input and expertise of our employees. We recognize that our employees are critical to the design and execution of our strategies, and that our business could not exist without their hard work and dedication. We appreciate the pride each one of our staff takes in delivering top quality customer service, optimal operational efficiency, and shareholder value.
We continue to offer more tools and training to ensure our employees’ success. We have mapped out career development opportunities and succession plans, recognizing that improving our employees’ knowledge and skill levels is good for both the employee and the company as a whole.
CE Franklin employees prove daily that our Mission Statement and Operating Values are the foundation of our business and people strategy.
The company and each of our employees prioritize safety. Providing a healthy, safe, respectful and productive work environment allows our employees to commit their full efforts to their work tasks and makes CE Franklin an employer of choice in our industry.
Finding and retaining the very best staff is a key priority for our company. We recognize that we must invest in our employees’ professional and personal priorities. To this end, we work to ensure our compensation, benefits and rewards programs are both competitive and responsive to the changing needs of our staff. We offer a profit share program that rewards employee efforts and results, and aligns employee actions with shareholder interests.
We encourage and thank our employees for participating in and supporting the communities we operate in.
+
Best Practices in Safety and Environment
Keeping our employees, customers, partners, as well as our environment, safe is our highest priority. We consistently remind ourselves through the great care that we put into our work, that even greater care must be taken to avoid compromising the health of our employees, customers and the surrounding environment.
We are proud of our proactive safety and environmental policies. Our comprehensive “4 Life” program details the Quality, Health, Safety and Environment best practices within which all CE Franklin staff work. Important highlights of our program include:
s
Continuous improvement with hazard identification and management as a critical element of our safety program.
s
Our Edmonton Distribution Centre and our Calgary and Fort McMurray branches are ISO 9001-2000 certified (the highest global standard of quality management system), and we operate to the same standards in all 45 of our branches across Canada.
s
We have also adopted the IRP-16 comprehensive management system, a program of safety and environmental management practices developed by the petroleum industry.
s
CE Franklin is an accredited member of the Partners in Injury Reduction, a collaborative initiative with the Workers’ Compensation Board.
s
Our Alberta branches have all achieved the Certificate of Recognition through the Petroleum Industry Training Service, and our other Canadian branches are working towards this recognition.
s
In 2010, we improved our overall safety record and will always strive for 0 incidents.
+
Strong Ties to Our Communities
At CE Franklin, we take seriously our responsibility – both as individuals and as a company – to contribute to the growth and strength of our communities. In order to develop sustainable and growing financial results, we need to build a trusted name in our communities by being a forward-thinking industry leader and community builder.
We encourage all of our employees to volunteer in the communities in which we operate. We financially support numerous community projects. Additionally, we contribute to more than 100 charities, including the United Way, Canadian Diabetes Association, Alberta Lung Association, Canadian Cancer Society, MS Society of Canada, and Alberta Children’s Hospital Foundation.
CE Franklin 3 on 3 Challenge Cup
In 2010, we initiated a major fundraising event in partnership with the Calgary Health Trust. The CE Franklin 3 on 3 Challenge Cup is an amateur hockey tournament designed to engage a wide cross-section of corporate sponsors as well as their employees and families in support of critically ill and premature infants. In 2010, the CE Franklin 3 on 3 Challenge Cup raised in excess of $155,000, all of which went towards the purchase of state-of-the-art equipment for neonatal intensive care units (NICUs) at the Foothills Medical Centre, Rockyview General Hospital and Peter Lougheed Centre in Calgary. The second annual CE Franklin 3 on 3 Challenge Cup will take place on September 10, 2011.
Athlete Ambassadors
CE Franklin is proud to support world speed skating champions and Olympians, Christine Nesbitt and Denny Morrison; Canada’s leading heptathlete and Beijing Olympic contender, Jessica Zelinka; and Professional Chuckwagon Driver and 2007 WPCA Rookie of the Year, Codey McCurrach. These athletes personify dedication, perseverance, hard work and a determination to win. These are the same values our employees exude daily.
Board of Directors
ROBERT MCCLINTON
Mr. McClinton was elected to the Board in 2006, and appointed Chairman in 2008. Robert McClinton, a Chartered Accountant, has been an independent business consultant since April 2005. From September 2007 to October 2008, he served as Chief Financial Officer of CEP International Petroleum Ltd., a private company. Mr. McClinton was a major shareholder and President & CEO of BMP Energy Systems (“BMP”) from 1992 to 2005, when BMP was sold to a public company. During the 10 years prior to joining BMP, Mr. McClinton served as director and senior financial officer of Canadian Turbo Inc. He began his career in 1969 with Deloitte & Touche in Northern Ireland, where he obtained his Chartered Accountant designation before immigrating to Canada in 1974. Mr. McClinton is a member of the Alberta and Canadian Institute of Chartered Accountants and the Institute of Corporate Directors (“ICD”).
KJELL-ERIK OESTDAHL
Mr. Oestdahl was appointed to the Board on October 28, 2010. Mr. Oestdahl is Vice President, Operations of Schlumberger. He holds a Master of Science degree in Electrical Engineering. Mr. Oestdahl joined the Schlumberger group of companies in 1990 as a field engineer in China and has held increasingly senior positions in operations, business development and marketing for Schlumberger Oilfield Services in Europe and North America. Mr. Oestdahl also worked as Chief Procurement Officer of StatoilHydro in 2007-2008. In Canada, he is a member of the ICD.
MICHAEL J.C. HOGAN
Mr. Hogan was appointed to the Board in 2006. Michael Hogan is a business consultant and 30 year veteran of the electric power industry. He is President and CEO of Enact Power Ltd., providing business development support to companies pursuing electric power investment in Canada and internationally. From 1995 to 1998, Mr. Hogan was President and CEO of SaskPower Commercial Inc., the international development arm of SaskPower. He is a member of the Association of Professional Engineers, Geologists, and Geophysicists of Alberta (APEGGA) and the ICD. Mr. Hogan has also completed the Director Education Program and holds the ICD.D designation.
JOHN J. KENNEDY
Mr. Kennedy was appointed to the Board in 1999. John Kennedy is President of Wilson Supply, a distribution unit of Schlumberger. Previously, he was Senior Vice-President and CFO of Smith. He has worked in the energy industry for over 30 years in various executive and management positions. Mr. Kennedy is a member of several professional bodies in both the United Kingdom and United States, including the Energy Institute, the Association of Corporate Treasurers, the ICD, and is a member of the board of directors of the Petroleum Equipment Supplier Association.
KEITH S. TURNBULL
Mr. Turnbull was appointed to the Board on April 6, 2010. Mr. Turnbull is a chartered accountant and business consultant. He retired as a Partner from KPMG on December 31, 2009, after nearly 30 years of service. Mr. Turnbull has extensive experience in all aspects of public company accounting and finance matters, including serving as Office Managing Partner at KPMGLLP’s (“KPMG”) Calgary office, where he was responsible for the strategic direction and growth of the Calgary practice, as well its audit, tax and advisory business. Mr. Turnbull is a member of the Alberta and Canadian Institute of Chartered Accountants and the ICD.
BRADLEY J. THOMSON
Mr. Thomson was appointed to the Board on April 6, 2010. Mr. Thomson is a business consultant. He is a Chartered Accountant with over 25 years of diverse experience as a senior executive and corporate director in the energy services industry, including natural gas marketing, trading and transportation, oilfield services, and electricity generation, transmission and telecommunications. From 2004 to 2009 (and from 1994 to 1998), he was a member of the senior executive team of TransCanada Corporation. Mr. Thomson also held senior positions with Northridge Canada Inc. and KPMG LLP (“KPMG”). He is a member of the Alberta and Canadian Institute of Chartered Accountants and the ICD. Mr. Thomson has also completed the Director Education Program and holds the ICD.D designation.
MICHAEL S. WEST
Mr. West is President and Chief Executive Officer of CE Franklin. He was appointed President and Chief Executive Officer and to CE Franklin’s Board of Directors in January 2002. Mr. West has held executive positions in the oilfield supply and distribution business for 14 years. Prior to joining the oil and gas sector in 1996, he worked for 11 years in various capacities in the automotive aftermarkets industry. He is a member of the ICD.
Leadership Team
MICHAEL S. WEST
Mr. West is President and Chief Executive Officer of CE Franklin. He was appointed President and Chief Executive Officer and to CE Franklin’s Board of Directors in January 2002. Mr. West has held executive positions in the oilfield supply and distribution business for 14 years. Prior to joining the oil and gas sector in 1996, he worked for 11 years in various capacities in the automotive aftermarkets industry.
W. MARK SCHWEITZER
Mr. Schweitzer is Vice President and Chief Financial Officer of CE Franklin and was appointed in August 2007. Prior to joining CE Franklin, Mr. Schweitzer was the Executive Vice President and Chief Financial Officer of a large diversified business income fund and has extensive financial experience in oil and gas, mining and other industry sectors.
MERV DAY
Mr. Day is Senior Vice President, Business Development and joined CE Franklin in 2008. Prior to joining CE Franklin, Mr. Day was President of a major Canadian valve manufacturer. He has over 30 years experience in the manufacturing and distribution of valves, pipe, fittings and instrumentation in the Canadian and international energy industry.
JAMES E. BAUMGARTNER
Mr. Baumgartner is Vice President, Commercial Strategies and has been with the Company since 2001. Prior to joining CE Franklin, Mr. Baumgartner was the General Manager for a competitor in the oilfield and industrial project supply distribution business. He has over 29 years experience in distribution of pipe, valves and fittings to the energy industry in Canada as well as internationally.
RONALD L. KOPER
Mr. Koper is Vice President, Business Effectiveness and joined the Company in 2000. Over the last 26 years he has worked with a variety of large and mid-sized corporations in the human resources and organizational development profession. Mr. Koper graduated from the University of Calgary in 1984 with a Bachelor of Commerce degree.
TIMOTHY M. RITCHIE
Mr. Ritchie is Vice President, Sales. He began his career with Franklin Supply in the field over 17 years ago and has progressively taken on roles that are more senior for the Company. Mr. Ritchie graduated from the University of Lethbridge with a Bachelor of Arts in 1993 and in 2000 earned his MBA from the University of Calgary.
RODERICK H. TATHAM
Mr. Tatham is Vice President, Operations. He is responsible for overall operational performance. Prior to joining CE Franklin in 2002, he worked in various management capacities including Business Process & Design, Quality, Branch Management and Materials Management in the oilfield supply industry.
Management’s Discussion and Analysis
As at February 2, 2011
The following Management’s Discussion and Analysis (“MD&A”) is provided to assist readers in understanding CE Franklin Ltd.’s (“CE Franklin” or the “Company”) financial performance and position during the periods presented and significant trends that may impact future performance of CE Franklin and should be read in conjunction with the audited comparative consolidated financial statements of CE Franklin and the related notes thereto.
All amounts are expressed in Canadian dollars and in accordance with Canadian generally accepted accounting principles (“Canadian GAAP”), except where otherwise noted. For a discussion of the principal differences between CE Franklin’s financial results as calculated under US GAAP, see note 16 to the consolidated financial statements of CE Franklin.
Overview
CE Franklin is a leading distributor of pipe, valves, flanges, fittings, production equipment, tubular products and other general industrial supplies, primarily to the oil and gas industry in Canada through its 45 branches situated in towns and cities that serve oil and gas fields of the western Canadian sedimentary basin. In addition, the Company distributes similar products to the oil sands, midstream, refining, petrochemical industries and non-oilfield related industries such as forestry and mining.
The Company’s branch operations service over 3,000 customers by providing the right materials where and when they are needed, and for the best value. Our branches, supported by our centralized Distribution Centre in Edmonton, Alberta, stock over 25,000 stock keeping units sourced from over 2,000 suppliers. This infrastructure enables us to provide our customers with the products they need on a same day or over-night basis. Our centralized inventory and procurement capabilities allow us to leverage our scale to enable industry leading hub and spoke purchasing, logistics and project execution capabilities. The branches are also supported by services provided by the Company’s corporate office in Calgary, Alberta including sales, marketing, product expertise, logistics, invoicing, credit and collection and other business services.
The Company’s common shares trade on the TSX (“CFT”) and NASDAQ (“CFK”) stock exchanges. Schlumberger Limited (“Schlumberger”), a major oilfield service company based in Paris, France, owns approximately 56% of the Company’s shares.
Business Strategy
The Canadian oilfield equipment supply industry is highly competitive and fragmented. There are approximately 230 oilfield supply stores in Canada which generate annual estimated sales of $2 billion to $3 billion. CE Franklin competes with three other large oilfield product distributors and with numerous local and regional distributors as well as specialty equipment distributors and manufacturers. The oilfield equipment market is part of the larger industrial equipment supply market, which is also serviced by numerous competitors. The oil sands and niche industrial product markets are more specialized and solutions oriented and require more in-depth product knowledge and supplier relationships to service specific customer requirements.
Oilfield equipment distributors compete based on price and level of service. Service includes the ability to consistently provide required products to a customer’s operating site when needed, project management services, product expertise and support, billing and expenditure management services, and related equipment services.
Demand for oilfield products and services is driven by the level of oil and gas industry capital expenditures in the Western Canadian sedimentary basin as well as by production related maintenance, repair and operating (“MRO”) requirements. MRO demand tends to be relatively stable over time and predictable in terms of product and service requirements and typically comprise 40% to 50% of the Company’s annual sales. Capital project demand fluctuates over time with oil and gas commodity prices, which directly impacts the economic returns realized by oil and gas companies.
The mix of products sold and customers served will affect profitability. Local walk in relationship business will typically generate higher profit margins compared to project bids, which are typically larger orders where the Company can take advantage of volume discounts and longer lead times. Larger oil and gas customers tend to have a broader geographic operating reach requiring multi-site service capability, conduct larger capital projects, and require more sophisticated billing and project management services than do smaller customers. The Company has entered into a number of formal alliances with larger customers where the scale and repeat nature of business enables efficiencies which are shared with the customer through lower profit margins.
Barriers to entry in the oilfield supply business are low with start up operations typically focused on servicing local relationship based MRO customers. To compete effectively on capital project business and to service larger customers requires multi-location branch operations, increased financial, procurement, product expertise and breadth of product lines, information systems and process capability.
The Company’s 45 branch operations provide substantial geographic coverage across the oil and gas producing regions in western Canada. Each branch competes for local business supported by centralized support services provided by the Company’s Distribution Centre and corporate office in Calgary. The Company’s large branch network, coupled with its centralized capabilities enables it to develop strong supply chain relationships with suppliers and provide it with a competitive advantage over local independent oilfield and specialty equipment distributors for larger customers who are seeking multi-location, one stop shopping and more comprehensive service. The Company’s relationship with Wilson Supply, a leading oilfield equipment distributor operating in the United States, and a wholly owned subsidiary of Schlumberger, enables it to provide North American solutions to its customer base and provides increased purchasing scale with equipment suppliers.
THE COMPANY IS PURSUING THE FOLLOWING STRATEGIES TO GROW ITS BUSINESS PROFITABLY:
s
Expand the reach and market share serviced by the Company’s distribution network. The Company is focusing its sales efforts and product offering on servicing complex, multi-location needs of large and emerging customers in the energy sector. Organic growth may be complemented by selected acquisitions.
s
Expand production equipment service capability to capture more of the product life cycle requirements for the equipment the Company sells such as down hole pump repair, oilfield engine maintenance, well optimization and on site project management. This will differentiate the Company’s service offering from its competitors and deepen relationships with its customers.
s
Expand oil sands and industrial project and MRO business by leveraging our existing supply chain infrastructure, product and major project expertise.
s
Increase the resourcing of customer project sales quotation and order fulfillment services provided by our Distribution Centre to augment local branch capacity to address seasonal and project driven fluctuations in customer demand. By doing so, we aim to increase our capacity flexibility and improve operating efficiency while providing consistent customer service.
STRATEGY ACCOMPLISHMENTS:
s
In the spring of 2008, the Company moved into a new 153,000 square foot Distribution Centre and nine acre pipe yard located in Edmonton, Alberta. The new Distribution Centre provided a 76% increase in functional warehousing capacity over our previous facility, increasing our capability to support and grow sales through our branch network. The larger facility also enabled us to increase the Company’s central project execution capability and processes, to service larger projects and ship direct to customers, avoiding double handling of material by branches. The Company opened a new branch operation in Red Earth, Alberta and expanded two existing branch facilities.
s
In June of 2009, the Company increased its market share, customer base, and branch network through the acquisition of a western Canadian oilfield supply competitor (the “Acquired Business”). The Acquired Business operated 23 supply stores of which 18 stores were proximate to existing Company branches and were integrated. The remaining 5 operations were focused in the east Alberta heavy oil corridor, and have extended the Company’s distribution network reach. Total oilfield supply sales have increased an estimated 15% as a result of the acquisition. The Company’s Fort St. John and Lloydminster branches moved to larger locations during the year, increasing capacity to service customer requirements in these important markets. Sales to oil sands customers increased for the fifth year in a row, reaching a record $64.5 million in 2009, comprising 15% of total Company sales. The Company added process automation products to its product line and opened a valve actuation centre at our Edmonton Distribution Centre, to broaden the spectrum of solutions the Company provides to existing oilfield, oil sands, and other industrial customers, and enhancing its ability to attract new customers. The Company recruited new product, operations and supply chain expertise into the organization to advance its strategies.
s
In 2010, we made advances in centrally resourcing project work by processing $99.3 million (2009 – $87.4 million) of sales orders through our Edmonton distribution centre, representing 20% of total Company sales. This enabled us to service the 12% year over year increase in sales while marginally decreasing our selling, general and administrative costs (“SG&A”) resulting in improved operating efficiency. SG&A costs improved to 13% of sales in 2010 compared to 15% in 2009.
Business Outlook
Oil and gas industry activity in 2011 is expected to increase modestly from 2010 levels. Natural gas prices remain depressed as North American production capacity and inventory levels currently dominate demand. Natural gas capital expenditure activity is focused on the emerging shale gas plays in north eastern British Columbia and liquids rich gas plays in north-western Alberta where the Company has strong market positions. Conventional and heavy oil economics are reasonable at current price levels leading to moderate capital expenditure activity in eastern Alberta and south east Saskatchewan. Oil sands project announcements continue to gain momentum at current oil price levels. Approximately 50% to 60% of the Company’s total sales are driven by our customer’s capital expenditure requirements. CE Franklin’s revenues are expected to increase modestly in 2011 due to increased oil and gas industry activity and the expansion of the Company’s product lines.
Sales margins are expected to remain under pressure as customers that produce natural gas, focus on reducing their costs to maintain acceptable project economics and due to continued aggressive oilfield supply industry competition. The Company will continue to manage its cost structure to protect profitability while maintaining service capacity and advancing strategic initiatives.
Over the medium to longer term, the Company’s strong financial and competitive positions will enable profitable growth of its distribution network through the expansion of its product lines, supplier relationships and capability to service additional oil and gas and other industrial end use markets.
Operating Results
The following table summarizes the consolidated results of operations of the Company for the last three years:
| | | | | | |
(in millions of Cdn. dollars except per share data) |
Years Ended December 31 | 2010 | 2009 | 2008 |
| $ | % | $ | % | $ | % |
Sales | 489.6 | 100.0% | 437.0 | 100.0% | 547.4 | 100.0% |
Cost of sales | (414.6) | (84.7)% | (360.4) | (82.5)% | (439.7) | (80.3)% |
Gross profit | 75.0 | 15.3% | 76.6 | 17.5% | 107.7 | 19.7% |
Selling, general and administrative expenses | (62.6) | (12.8)% | (64.2) | (14.7)% | (71.6) | (13.1)% |
Foreign exchange gain/(loss) | 0.1 | 0.0% | – | 0.0% | (0.2) | (0.0)% |
EBITDA(1) | 12.5 | 2.5% | 12.4 | 2.8% | 35.8 | 6.5% |
Amortization | (2.5) | (0.5)% | (2.5) | (0.6)% | (2.4) | (0.4)% |
Interest | (0.7) | (0.1)% | (0.9) | (0.2)% | (1.0) | (0.2)% |
Income before taxes | 9.3 | 1.9% | 8.9 | 2.0% | 32.4 | 6.0% |
Income tax expense | (3.4) | (0.7)% | (2.6) | (0.6)% | (10.7) | (2.0)% |
Net income | 5.9 | 1.2% | 6.3 | 1.4% | 21.7 | 4.0% |
Net income per share | | | | | | |
Basic (Cdn. $) | $0.34 | | $0.36 | | $1.19 | |
Diluted (Cdn. $) | $0.33 | | $0.35 | | $1.17 | |
Weighted average number of shares outstanding (000’s) | | | | | | |
Basic | 17,499 | | 17,750 | | 18,255 | |
Diluted | 18,000 | | 17,953 | | 18,561 | |
(1) EBITDA represents net income before interest, taxes, depreciation and amortization. EBITDA is a supplemental non-GAAP financial measure used by management, as well as industry analysts, to evaluate operations. Management believes that EBITDA, as presented, represents a useful means of assessing the performance of the Company’s ongoing operating activities, as it reflects the Company’s earnings trends without showing the impact of certain charges. The Company is also presenting EBITDA, incremental flow through to EBITDA and EBITDA as a percentage of sales because it is used by management as a supplemental measure of profitability. The use of EBITDA by the Company has certain material limitations because it excludes the recurring expenditures of interest, income tax, and amortization expenses. Interest expense is a necessary component of the Company’s expenses because the Company borrows money to finance its working capital and capital expenditures. Income tax expense is a necessary component of the Company’s expenses because the Company is required to pay cash income taxes. Amortization expense is a necessary component of the Company’s expenses because the Company uses property and equipment to generate sales. Management compensates for these limitations to the use of EBITDA by using EBITDA as only a supplementary measure of profitability. EBITDA is not used by management as an alternative to net income as an indicator of the Company’s operating performance, as an alternative to any other measure of performance in conformity with generally accepted accounting principles or as an alternative to cash flow from operating activities as a measure of liquidity. A reconciliation of EBITDA to Net income is provided within the table above. Not all companies calculate EBITDA in the same manner and EBITDA does not have a standardized meaning prescribed by Canadian GAAP. Accordingly, EBITDA, as the term is used herein, is unlikely to be comparable to EBITDA as reported by other entities.
2010 compared to 2009
Net income for the year ended December 31, 2010 was $5.9 million and included an after tax charge of $0.7 million recorded in the fourth quarter, related to the removal of the cash settlement mechanic from the Company’s stock option plan in response to income tax provisions introduced in the 2010 Canadian federal budget. After adjusting for the stock option charge, net income increased by $0.3 million (5%) over 2009, as earnings momentum increased in the second half of 2010 compared to the prior year period. Sales reached $489.6 million in 2010, an increase of $52.6 million (12%) over 2009. Approximately one-half of the increase reflected the full year contribution of sales in 2010 from the acquisition of a western Canadian oil field supply competitor on June 1, 2009 (the “Acquired Business”). The remaining increase was attributable to the 50% year over year increase in industry well completions, which tend to drive demand for oilfield products used in capital projects, partially offset by the rollover of tubular and other steel product prices experienced in 2009 that contributed to lower sales and margin performance for these products in 2010. Gross profit decreased by $1.7 million in 2010 (2%) as the impact of the increase in sales was more than offset by a reduction of 2.2% in average sales margins. Lower sales margins in 2010 reflected increased customer bid activity combined with aggressive oil field supply industry competition. SG&A costs decreased by $1.7 million in 2010 compared to 2009, offsetting the reduction in gross profit. SG&A costs were reduced in 2010 due to the absence of costs incurred in 2009 to integrate the Acquired Business. Income tax expenses in 2010 increased by $0.8 million as a result of the fourth quarter stock option charge. Net income per share (basic) was $0.34 in 2010, down 6% from 2009, consistent with the decrease in net income.
2009 compared to 2008
Net income for the year ended December 31, 2009 was $6.3 million, down $15.4 million (71%) from the year ended December 31, 2008. Sales were $437.0 million, down $110.4 million (20%) from 2008 due to decreased conventional oilfield sales offset partially by an estimated $30 million in sales (8% of 2009 oilfield sales) contributed by the Acquired Business as well as increased oil sands sales. Well completions, decreased by 55% from prior year levels, contributing to the decline in the Company’s sales in 2009. Gross profit decreased by $31.1 million (29%) from the prior year. The decrease was a result of the reduction in sales combined with lower average sales margins reflecting increased lower margin oil sands and major project sales, lower tubular product margins and increased competitive pressure. SG&A expenses decreased by $7.4 million (10%) in 2009 from the prior year as compensation, selling and marketing costs were managed to a lower level in response to the reduced oil and gas industry activity levels, partially offset by increased costs associated with the expansion of the Company’s store network resulting from the Acquired Business. Costs incurred to complete the integration of the Acquired Business were $1.5 million. Income taxes decreased by $8.1 million in 2009 compared to the prior year period due to lower pre-tax earnings. Net income per share (basic) was $0.36 for the year, a decrease of 70% from 2008, consistent with the decrease in net income.
Fourth Quarter Results
Net income for the fourth quarter of 2010 was $1.6 million, and included a $0.7 million after tax charge associated with the elimination of the stock option cash settlement mechanic. Excluding the stock option charge, net income was $2.3 million, an increase of $2.8 million over the net loss of $0.5 million in the fourth quarter of 2009. Sales were $135.6 million, an increase of $42.6 million (46%) over the fourth quarter of 2009, principally due to increased oilfield sales, driven by a 200% increase in well completions over the prior year period. Gross profit reached $20.5 million, an increase of $5.2 million (34%) over the prior year period, due to increased sales partially offset by a reduction of 1.4% in average sales margins. Compared to the annual year over year decrease in sales margins of 2.2%, fourth quarter 2010 margins began to recover as tubular and other steel product margins improved as higher cost inventory was sold during 2010 and replaced with more competitively priced product. SG&A costs increased by $2.1 million (15%) over the prior year period as people and selling costs were higher in the fourth quarter to support the increase in sales compared to the prior year period. Income tax expense increased by $1.3 million over the prior year period due to increased earnings and the stock option charge. Net income per share (basic) was $0.09 in the fourth quarter of 2010, an increase of $0.12 over the net loss of $0.03 in the fourth quarter of 2009.
A more detailed discussion of the Company’s annual results from operations is provided below:
SALES
Sales for 2010 were $489.6 million, up $52.6 million (12%) over 2009. Approximately one-half of the increase reflected the full year contribution of sales in 2010 from the acquisition of the Acquired Business in the second quarter of 2009, with the remaining increase attributable to the 50% year over year increase in industry well completions, which tend to drive demand for oilfield products used in capital projects. This was partially offset by the rollover of tubular and other steel product prices experienced in 2009 that contributed to lower sales and margin performance for these products in 2010.
Oil and gas commodity prices are a key driver of industry capital project activity as product prices directly impact the economic returns realized by oil and gas companies. The Company uses oil and gas well completions and average rig counts as industry activity measures to assess demand for oilfield equipment used in capital projects. Oil and gas well completions require the products sold by the Company to complete a well and bring production on stream and are a general indicator of energy industry activity levels. Average drilling rig counts are also used by management as a leading indicator of industry activity levels as the number of rigs in use ultimately drives well completion requirements.
The table below provides well completion, rig count and commodity price information for the last 3 years:
| | | | | | | |
As at December 31 | | Average for the years ended December 31 |
| 2010 | | 2010 | % change | 2009 | % change | 2008 |
Gas – Cdn. $/gj (AECO spot) | $3.94 | | $4.00 | 1% | $3.97 | (51%) | $8.18 |
Oil – Cdn. $/bbl (Synthetic Crude) | $84.78 | | $80.57 | 17% | $69.09 | (33%) | $103.03 |
Average rig count | 393 | | 332 | 54% | 215 | (46%) | 398 |
Well completions: | | | | | | | |
Oil | n/a | | 6,541 | 105% | 3,197 | (49%) | 6,223 |
Gas | n/a | | 5,873 | 16% | 5,068 | (59%) | 12,342 |
Total well completions | n/a | | 12,414 | 50% | 8,265 | (55%) | 18,565 |
Average statistics are shown except for well completions. Sources: Oil and Gas prices – FirstEnergy Capital Corp.; Rig count data – COADC; Well completion data – Daily Oil Bulletin |
Gas prices have been depressed in 2009 and 2010, down significantly from average prices realized in 2008 while oil prices have recovered from lows experienced during the first half of 2009. Oil and gas producers have responded to the relative change in oil and gas prices during this period by shifting their focus from gas to oil projects. Gas well completions comprised 47% of total Canadian industry well completions in 2010, down from 70% in 2008. Customers have also increased the amount of competitive bid activity used to procure the products they require in an effort to reduce their costs. The Company is addressing these industry changes by pursuing initiatives focused on improving sales quotation processes and increasing the operating flexibility and efficiency of its branch network.
The chart below depicts the relative relationship of Company sales to oil and gas prices and well completions over the last five years.
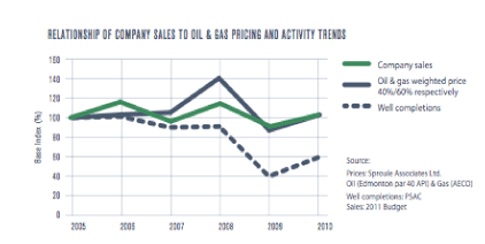
Company sales have kept pace with the relative change in oil and gas prices over the last five years and have significantly out-paced industry well completions over the same period. In 2010, the Company generated sales per industry well completion of $39,438, an increase of 49% over 2006, due to a 7% increase in the number of branch operations servicing its customer base, the build out of its product lines, and growth of its oil sands business.
| | | | | | |
End use sales demand | 2010 | 2009 | 2008 |
(in millions of Cdn. $) | $ | % | $ | % | $ | % |
Capital projects | 255.3 | 52 | 246.0 | 56 | 314.0 | 57 |
Maintenance, repair and operating supplies (MRO) | 234.3 | 48 | 191.0 | 44 | 233.4 | 43 |
Total sales | 489.6 | 100 | 437.0 | 100 | 547.4 | 100 |
Note: Capital project end use sales are defined by the Company as consisting of tubulars and 80% of pipe, flanges and fittings; and valves and accessories product sales respectively. MRO Sales are defined by the Company as consisting of pumps and production equipment, production services; general product and 20% of pipes, flanges and fittings; and valves and accessory product sales respectively.
Sales of capital project related products were $255.3 million in 2010, up $9.3 million (4%) from 2009. Capital project business for the year comprised 52% of total sales compared to 56% in 2009. The increase in capital project end use sales reflects the 50% increase in total industry well completions to 12,414 in 2010, partially offset by the rollover of tubular and other steel product prices during 2009. Industry activity decreased in 2009, particularly in the second half of the year before recovering in 2010 as the collapse in oil and gas prices experienced earlier in 2009 coupled with reduced access to capital, constrained industry capital programs. Sales of capital project related products were $246.0 million in 2009, down $68.0 million (22%) from 2008. Capital project sales as a percentage of total sales in 2009 were comparable to 2008, despite a 55% decrease in year over year total well completions as project sales to oil sands customers increased.
MRO product sales are related to overall oil and gas industry production levels and tend to be more stable than capital project sales. MRO product sales for 2010 increased by $43.3 million (23%) to $234.3 million compared to 2009 and comprised 48% of the Company’s total sales (2009 – 44%, 2008 – 43%). Higher MRO sales in 2010 were due to increased conventional oilfield activity combined with the full year sales contribution in 2010 from the Acquired Business. MRO product sales for 2009 decreased by $42.4 million (18%) to $191.0 million compared to 2008 due to reduced conventional oilfield activity partially offset by sales generated from the Acquired Business in the second half of 2009.
The Company services over 3,000 customers of which the top ten customers comprised 38% of total sales in 2010 (2009 – 46%, 2008 – 42%). The Company’s largest customer comprised less than 10% of total sales in 2010 (2009 and 2008 – one customer comprised 10% of sales). The increased customer concentration of sales in 2009 was due to the Company’s focus on alliance customer programs coupled with lower capital program activity conducted by smaller oil and gas companies due to reduced industry operating cash flows and access to capital. Improved industry access to capital in 2010 contributed to a broader distribution of sales across the Company’s customer base.
The Company distributes over 25,000 stock keeping units sourced from over 2,000 suppliers. In 2010, the top 10 suppliers comprised 41% of total cost of goods sold (2009 – 34%, 2008 – 59%) of which its largest supplier comprised 10% of cost of goods sold (2009 – one supplier comprised 12% of cost of goods sold, 2008 – two suppliers comprised 31% of cost of goods sold). Supplier concentration increased in 2010 compared to 2009 due to increased focus on centralized product procurement. Supplier concentration in 2009 compared to 2008 decreased due to the relative decline in tubular product sales.
The Company’s strategy is to grow profitability by focusing on its core western Canadian oilfield equipment service business, complemented by an increase in the product life cycle services provided to its customers, and the focus on oil sands and industrial capital project and MRO sales opportunities. Revenue results of these initiatives to date are provided below:
| | | | | | |
Sales | 2010 | 2009 | 2008 |
($millions) | $ | % | $ | % | $ | % |
Oilfield | 410.7 | 83 | 362.0 | 83 | 491.3 | 90 |
Oil sands | 61.3 | 13 | 64.5 | 15 | 39.4 | 7 |
Production services | 17.6 | 4 | 10.5 | 2 | 16.7 | 3 |
Total sales | 489.6 | 100 | 437.0 | 100 | 547.4 | 100 |
Sales of oilfield products to conventional western Canada oil and gas end use applications were $410.7 million for 2010, up $48.7 million (13%) from 2009. Approximately one-half of the increase in sales was attributable to the 50% year over year increase in industry well completions, which tend to drive demand for oilfield products. The remaining increase reflected the full year sales contribution in 2010 from the Acquired Business subsequent to its June 1, 2009 acquisition date. These increases were partially offset by the impact on sales resulting from the rollover in tubular and other steel product prices that commenced in the second quarter of 2009. Oilfield sales in 2009 decreased by $129.3 million (26%) from 2008 levels. This decrease was primarily driven by the 55% decrease in 2009 well completions compared to 2008 and the rollover of tubular prices mentioned above. Sales from the Acquired Business subsequent to the June 1, 2009 acquisition date, comprised approximately 8% of annual 2009 oilfield sales and helped mitigate the impact on sales resulting from the decline in industry activity.
Sales to oil sands end use applications in 2010 were $61.3 million, down $3.2 million (5%) from 2009 as increased capital project sales were more than offset by the impact of the rollover of steel product pricing in 2010. Oil sands sales increased by $25.1 million (64%) in 2009 compared to $39.4 million for 2008 due to growth in market share. The Company continues to position its major project execution capability and Fort McMurray branch to penetrate this growing market for capital project and MRO products.
Production service sales reached $17.6 million in 2010, up $7.1 million (68%) over 2009, outpacing the 17% increase in oil prices over the same period. Production service sales in 2009 decreased $6.2 million (37%) compared to $16.7 million in 2008 as customers deferred oil production maintenance activities in response to the 33% reduction in average year over year oil prices experienced in 2009.
| | | |
Gross Profit | 2010 | 2009 | 2008 |
Gross profit(millions) | $ 75.0 | $ 76.6 | $ 107.7 |
Gross profit as a % of sales | 15.3% | 17.5% | 19.7% |
Gross profit composition by product sales category: | | | |
Tubulars | 3% | 5% | 13% |
Pipe, flanges and fittings | 28% | 31% | 31% |
Valves and accessories | 20% | 19% | 17% |
Pumps, production equipment and services | 14% | 12% | 15% |
General | 35% | 33% | 24% |
Total | 100% | 100% | 100% |
Gross profit was $75.0 million in 2010, down $1.6 million (2%) from 2009 as the 12% increase in sales was more than offset by a decrease in average gross profit margins from 17.5% in 2009 to 15.3% in 2010. Lower sales margins in 2010 reflected increased customer bid activity combined with aggressive oilfield supply industry competition. The reduction in tubular gross profit composition in 2010 compared to 2009 reflected the rollover of tubular prices and margins that commenced in the second quarter of 2009 and began to recover in the fourth quarter of 2010. The increase in general products profit composition reflects the relative increase in higher margin MRO sales in 2010 and 2009 compared to 2008. Gross profit was $76.6 million in 2009, down $31.1 million (29%) from 2008 due to the 20% decline in sales combined with a decrease in average gross profit margins from 19.7% in 2008 to 17.5% in 2009. Gross profit margins decreased in 2009 from 2008 levels due to an increase in lower margin oil sands sales, reduced tubular margins, reduced supplier rebates in 2009 due to lower purchasing levels, and increased competitive activity as industry activity declined.
SELLING, GENERAL AND ADMINISTRATIVE COSTS
| | | | | | |
| 2010 | 2009 | 2008 |
($millions) | $ | % | $ | % | $ | % |
People costs | 36.3 | 58 | 36.2 | 56 | 41.3 | 58 |
Selling costs | 6.6 | 11 | 7.5 | 12 | 10.2 | 14 |
Facility and office costs | 13.4 | 21 | 13.3 | 21 | 12.8 | 18 |
Other | 6.3 | 10 | 7.2 | 11 | 7.3 | 10 |
SG&A costs | 62.6 | 100 | 64.2 | 100 | 71.6 | 100 |
SG&A costs as % of sales | 13% | | 15% | | 13% | |
SG&A costs decreased $1.6 million (2%) in 2010 from 2009, representing 13% of sales (2009 – 15%, 2008 – 13%). The year over year improvement in SG&A costs as a percentage of sales in 2010 reflects a strong focus on cost control in 2010 and the 12% increase in sales compared to the relatively high fixed cost nature of the Company’s branch network and supporting supply chain infrastructure. Similarly, the increase in SG&A costs as a percentage of sales in 2009 compared to 2008 reflects the 20% year over year decrease in sales which outpaced the 10% reduction in costs over the same time period.
SG&A costs decreased in 2010 compared to 2009 due to lower selling costs resulting from a reduction in the number of agent operated branch locations and reduced accounts receivable bad debt expense. The absence of $1.5 million in “other costs” incurred in 2009 to integrate the Acquired Business was partially offset by a full year of costs to operate the five additional branch locations in 2010 that were added with the Acquired Business.
SG&A costs decreased in 2009 compared to 2008 by $7.4 million (10%). People costs decreased by $5.1 million from 2008 due to reduced variable compensation associated with the reduction in earnings and a net 5% decrease in the number of employees. Selling costs were down $2.7 million compared to 2008 levels due to decreased sales commissions and a reduction in bad debt expense. Facility and office costs increased $0.5 million in 2009 compared to 2008 mainly due to higher lease costs associated with the expansion of the Company’s store network in 2009 and 2008.
The Company leases 34 of its 45 branch locations as well as its corporate office in Calgary and Distribution Centre. Seven branch locations are owned and four are operated by agents. During 2010, the Company opened one new branch location and closed five locations. Customer service requirements are being provided by adjacent branch locations.
AMORTIZATION EXPENSE
Amortization expense at $2.5 million in 2010 was comparable to 2009 and 2008 levels.
INTEREST EXPENSE
Interest expense was $0.7 million in 2010, down $0.2 million and $0.3 million from 2009 and 2008 respectively, due to lower average borrowing levels and floating interest rates.
FOREIGN EXCHANGE LOSS AND OTHER
There were nominal foreign exchange gains in 2010, a marginal improvement over 2009 and 2008 performance despite significant exchange rate volatility. Gains and losses reflect the impact of exchange rate fluctuations on United States dollar denominated product purchases and net working capital liabilities.
INCOME TAX EXPENSE
The Company’s effective tax rate for 2010 was 36.8%, compared to 29.5% and 33.0% in 2009 and 2008, respectively. The increase in the 2010 effective rate reflects the write off of $0.5 million of future tax assets related to the removal of the cash settlement mechanism from the Company’s stock option plan in the fourth quarter as a result of provisions contained in the federal government’s 2010 budget which effectively eliminated the ability to deduct for tax purposes, cash payments made to settle stock option obligations. This rate impact was partially offset by a 1% year over year reduction in statutory rates. The reduction in the effective tax rate in 2009 compared to 2008 reflected a 0.5% decrease in statutory tax rates combined with the ability to deduct the cost of stock option exercises for tax purposes, enabled by the implementation of a stock option cash settlement mechanism during 2009. Substantially all of the Company’s tax provision is currently payable.
SUMMARY OF QUARTERLY FINANCIAL DATA
The selected quarterly financial data below is presented in Canadian dollars and in accordance with Canadian GAAP. This information is derived from the Company’s unaudited quarterly financial statements.
| | | | | | | | |
(in millions of Cdn. dollars except per share data) | | | | | | |
| 2009 | 2010 |
Unaudited | Q1 | Q2 | Q3 | Q4 | Q1 | Q2 | Q3 | Q4 |
Sales | $ 140.7 | $ 109.1 | $ 94.1 | $ 93.0 | $ 121.9 | $ 99.9 | $ 132.2 | $ 135.6 |
Gross profit | 26.4 | 17.5 | 17.4 | 15.3 | 19.7 | 15.6 | 19.2 | 20.5 |
Gross profit % | 18.8% | 16.0% | 18.5% | 16.5% | 16.1% | 15.6% | 14.5% | 15.1% |
EBITDA | 9.5 | 1.7 | 0.5 | 0.6 | 4.1 | 0.7 | 3.8 | 3.8 |
EBITDA as a % of sales | 6.8% | 1.6% | 0.5% | 0.6% | 3.4% | 0.7% | 2.9% | 2.8% |
Net income (loss) | 6.0 | 0.6 | 0.2 | (0.5) | 2.2 | (0.1) | 2.2 | 1.6 |
Net income (loss) as a % of sales | 4.3% | 0.5% | 0.2% | (0.5%) | 1.8% | (0.1%) | 1.7% | 1.2% |
Net income (loss) per share | | | | | | | | |
Basic | $ 0.33 | $ 0.04 | $ 0.01 | ($ 0.03) | $ 0.13 | ($ 0.01) | $ 0.12 | $ 0.09 |
Diluted | $ 0.33 | $ 0.03 | $ 0.01 | ($ 0.03) | $ 0.12 | ($ 0.01) | $ 0.12 | $ 0.09 |
Net working capital(1) | 153.2 | 137.0 | 131.1 | 136.6 | 113.9 | 111.8 | 129.0 | 125.7 |
Long term debt/Bank operating loan(1) | 40.7 | 25.8 | 21.6 | 26.8 | 1.4 | – | 14.4 | 6.4 |
Total well completions | 3,947 | 1,274 | 1,468 | 1,576 | 2,846 | 2,197 | 2,611 | 4,760 |
(1)Net working capital, bank operating loan and long term debt amounts are as at quarter end. |
The Company’s sales levels are affected by weather conditions. As warm weather returns in the spring each year, the winter’s frost comes out of the ground rendering many secondary roads incapable of supporting the weight of heavy equipment until they have dried out. In addition, many exploration and production areas in northern Canada are accessible only in the winter months when the ground is frozen. As a result, the first and fourth quarters typically represent the busiest time for oil and gas industry activity and the highest oilfield sales activity for the Company. Oilfield sales levels drop dramatically during the second quarter until such time as roads have dried and road bans have been lifted. This typically results in a significant reduction in earnings during the second quarter, as the decline in sales typically out paces the decline in SG&A costs as the majority of the Company’s SG&A costs are fixed in nature. Sales decreased in the second half of 2009 as the impact of the dramatic reduction in oil and gas industry activity during this period more than offset normal seasonal sales trends. Net working capital (defined as current assets less accounts payable and accrued liabilities, income taxes payable and other current liabilities, excluding the bank operating loan) and borrowing levels follow similar seasonal patterns as sales.
Liquidity and Capital Resources
The Company’s primary internal source of liquidity is cash flow from operating activities before changes in non-cash net working capital balances. Cash flow from operating activities and the Company’s $60.0 million revolving term credit facility are used to finance the Company’s net working capital, capital expenditures and acquisitions.
As at December 31, 2010, long term debt was $6.4 million and was comprised principally of borrowings under the Company’s revolving term credit facility. Borrowings decreased by $20.4 million from December 31, 2009 due to the Company generating $10.7 million in cash flow from operating activities, before net changes in non-cash working capital balances and a $12.8 million reduction in net working capital. This was offset by $1.3 million in capital expenditures and $1.9 million for the purchase of shares to resource stock compensation obligations and the repurchase of shares under the Company’s Normal Course Issuer Bid (“NCIB”).
As at December 31, 2009, borrowings under the Company’s bank operating loan were $26.5 million, a decrease of $8.4 million from December 31, 2008. Borrowing levels decreased due to the Company generating $10.9 million in cash flow from operating activities, before net changes in non-cash working capital balances and a $14.8 million reduction in net working capital. This was offset by $2.6 million in capital and other expenditures, $11.3 million related to the acquisition of the Acquired Business and $3.4 million for the purchase of shares to resource stock compensation obligations and the repurchase of shares under the Company’s NCIB.
Net working capital was $125.7 million at December 31, 2010, a decrease of $10.9 million from December 31, 2009. Accounts receivable at December 31, 2010 was $93.0 million, an increase of $25.5 million (38%) from December 31, 2009, due to the 46% increase in fourth quarter sales compared to the prior year period, partially offset by a 7% improvement in days sales outstanding in accounts receivable (“DSO”) in the fourth quarter of 2010 to 56 days from 60 days in the fourth quarter of 2009. DSO is calculated using average sales per day for the quarter compared to the period end customer accounts receivable balance. Inventory at December 31, 2010 was $94.8 million, down $7.8 million (8%) from December 31, 2009. Inventory turns for the fourth quarter of 2010 improved by 63% to 4.9 turns from 3.0 turns in the fourth quarter of 2009 as sales increased while inventory decreased. Inventory turns are calculated using cost of goods sold for the quarter on an annualized basis, compared to the period end inventory balance. Accounts payable and accrued liabilities at December 31, 2010 were $63.7 million, an increase of $26.7 million (70%) due to increased purchasing activity in the fourth quarter of 2010 to resource the increase in sales compared to the prior year period.
Capital expenditures in 2010 were $1.3 million, a decrease of $1.3 million (50%) and $4.3 million (77%) from 2009 and 2008 expenditures, respectively. Expenditures in 2010 were directed towards branch facility and business system expansion and maintenance. The majority of the expenditures in 2009 and 2008 were directed towards branch and Distribution Centre facility expansions. Capital expenditures in 2011 are anticipated to be in the $3.5 million to $4.5 million range and will be directed towards business system, branch facility, vehicle and operating equipment upgrades and replacements.
In July 2010, the Company entered into a $60.0 million revolving term credit facility that matures in July 2013 (the “Credit Facility”). The Credit Facility provides lower borrowing costs, improved covenant flexibility and extended repayment terms compared to the previous $60.0 million, 364 day operating credit facility. Borrowings under the Credit Facility bear interest based on floating interest rates and are secured by a general security agreement covering all assets of the Company. The maximum amount available under the Credit Facility is subject to a borrowing base formula applied to accounts receivable and inventories. The Credit Facility requires the Company to maintain the ratio of its debt to debt plus equity at less than 40%. As at December 31, 2010, this ratio was 4%. The Company must also maintain coverage of its net operating cash flow as defined in the Credit Facility agreement over interest expense for the trailing twelve month period of greater than 1.25 times. As at December 31, 2010, this ratio was 14.1 times. The Credit Facility contains certain other covenants with which the Company is in compliance. As at December 31, 2010, the Company had borrowed $6.1 million and had available undrawn borrowing capacity of $53.9 million under the Credit Facility.
CONTRACTUAL OBLIGATIONS
The following table outlines the Company’s contractual obligations for debt, lease and related obligations having initial terms in excess of one year:
| | | |
(millions of Canadian dollars) Period Due | Long term debt | Operating lease commitments | Total |
2011 | – | 6.8 | 6.8 |
2012 | 0.3 | 6.3 | 6.6 |
2013 | 6.1 | 5.5 | 11.6 |
2014 | – | 4.8 | 4.8 |
2015 | – | 4.1 | 4.1 |
thereafter | – | 21.6 | 21.6 |
| 6.4 | 49.1 | 55.5 |
Approximately 99% of operating lease obligations are related to office, warehouse, and store facility leases (2008 – 95%). Automobile, warehouse and office equipment leases comprised the remaining lease obligations. Future operating lease commitments at December 31, 2010 were $49.1 million, a $6.5 million (12%) decrease from 2009 commitments as no new significant lease obligations, or extension of existing lease obligations, were entered into during 2010. In management’s opinion, the Company’s existing working capital position combined with available borrowing capacity under its Credit Facility and cash flow from operations, are sufficient to resource its ongoing obligations.
The Company is not aware of any environmental asset retirement obligations that could have a material impact on its operation.
Market Risk
The Company’s bank operating loan bears interest based on floating Canadian interest rates. As at December 31, 2010, the Company’s average borrowing cost was 3.8% (2009 – 3.2%, 2008 – 3.2%). Based on the Company’s borrowings levels as at December 31, 2010, a change of one percent in interest rates would be expected to decrease or increase the Company’s annual net income by $0.1 million.
The Company purchases certain products priced in U.S. dollars and sells such products to its customers typically priced in Canadian dollars. As a result, fluctuations in the value of the Canadian dollar relative to the U.S. dollar can result in foreign exchange gains and losses. As at December 31, 2010, the Company had entered into contracts to purchase in 2011, U.S. $6.5 million at fixed exchange rates for the purpose of mitigating its foreign exchange exposure. The Company does not use financial instruments for speculative purposes. As at December 31, 2010, a one percent change in the Canadian dollar relative to the US dollar would be expected to have no material impact on net income.
Capital Stock
As at December 31, 2010 and 2009, the following common shares and securities convertible into common shares were outstanding:
| | |
| December 31, 2010 | December 31, 2009 |
(millions) | Shares | Shares |
Shares outstanding | 17.5 | 17.6 |
Stock options | 1.1 | 1.2 |
Share units | 0.5 | 0.4 |
Shares outstanding and issuable | 19.1 | 19.2 |
The basic weighted average number of shares outstanding in 2010 was 17.5 million, a decrease of 0.3 million shares from the prior year due principally to the purchases of shares under its NCIB and to resource share unit obligations. The diluted weighted average number of shares outstanding in 2010 was 18.0 million and was comparable to 2009, as the decrease in the basic number of common shares outstanding was offset by the dilutive effect of removing the cash settlement mechanic from the stock option program in the fourth quarter of 2010. In the future, stock option obligations will be settled with shares issued from treasury.
The Company has established an independent trust to purchase shares of the Company on the open market to resource share unit plan obligations. For the year ended December 31, 2010 there were 204,300 shares acquired by the trust at an average cost per share of $6.91. (2009 – 120,700 at an average cost per share of $5.60). As at December 31, 2010, the trust held 450,732 shares representing approximately 100% of stock unit plan obligations outstanding (December 31, 2009 – 360,576 shares representing approximately 96% of stock unit plan obligations outstanding).
During the fourth quarter of 2010, the Company discontinued the settlement of stock option obligations with cash payments in favor of issuing shares from treasury. The cash settlement mechanism was discontinued as a result of provisions contained in the federal government’s 2010 budget which effectively eliminated the ability to deduct for tax purposes, cash payments made to settle stock option obligations. An after tax charge of $0.7 million was recorded in the fourth quarter comprised of a $0.2 million stock based compensation charge and the write off of $0.5 million of future income tax asset related to stock option obligations. The mark to market current obligation of $2.1 million was transferred to Contributed Surplus on the balance sheet as a result of this change in settlement of stock option obligations. The cash settlement mechanism had been implemented during the third quarter of 2009 to enable the Company to manage its share dilution while resourcing its stock option plan on a tax efficient basis.
On December 23, 2009, the Company announced the renewal of its NCIB to purchase for cancellation through the facilities of NASDAQ, up to 880,000 common shares representing approximately 5% of its outstanding common shares. In 2010 the Company purchased 61,769 shares at a cost of $0.4 million ($6.62 per share). During 2009, the Company purchased 553,710 shares at a cost of $2.9 million ($5.17 per share) under its NCIB. On December 21, 2010, the Company announced the renewal of the NCIB, effective January 3, 2011, to purchase up to 850,000 common shares representing approximately 5% of its outstanding common shares. Shares may be purchased up to December 31, 2011.
Critical Accounting Estimates
The preparation of the consolidated financial statements requires the Company to make estimates and judgments that affect the reported amounts of assets, liabilities, revenues and expenses, and related disclosure of contingent assets and liabilities. The Company evaluates its estimates on an ongoing basis, based on historical experience and other assumptions that are believed to be reasonable under the circumstances. Actual results may differ from these estimates under different assumptions and conditions.
The Company believes the following describes the significant judgments and estimates used in the preparation of its consolidated financial statements.
ALLOWANCE FOR DOUBTFUL ACCOUNTS
The Company extends credit to customers and other parties in the normal course of business. Management regularly reviews outstanding accounts receivable and provides for estimated losses through an allowance for doubtful accounts. In evaluating the level of the established allowance, management makes judgments regarding a party’s ability to make required payments, economic events and other factors. As the financial condition of a party changes, circumstances develop or additional information becomes available, adjustments to the allowance for doubtful accounts may be required. As at December 31, 2010 and 2009, the allowance for doubtful accounts was $1.9 million and $2.3 million, respectively.
INVENTORY RESERVES
The Company has significant investments in inventory to service its customers. On a routine basis, the Company uses judgment in determining the level of write-downs required to record inventory at the lower of average cost or net realizable value. Management’s estimates are primarily influenced by market activity levels. Changes in these or other factors may result in a write-down in the carrying value of inventory. As at December 31, 2010 and December 31, 2009, the Company had recorded net realizable value reserves for inventory of $5.0 million and $6.3 million, respectively.
GOODWILL
The Company has acquired certain operations which have resulted in the recording of $20.6 million of goodwill on the balance sheets as at December 31, 2010 and 2009. In accordance with Canadian GAAP, the Company is required to perform an annual goodwill impairment evaluation. The Company evaluates goodwill impairment as at December 31 at the consolidated level as it operates through a single operating segment and cash generating unit. The impairment evaluation involves comparing the estimated fair value of the Company’s business to its carrying amount to determine if a write down to fair value is required. Fair value is estimated using future cash flow projections, discounted to their present value. Future cash flows are based on various assumptions and judgments including actual performance of the business, management’s estimates of future performance of the business, indicators of future oil and gas industry activity levels including future commodity price forecasts, and long term growth rates of 5% derived from earnings and cash flow trading multiples for comparable public energy service companies. Present value discount rate assumptions use an estimate of the Company’s weighted average cost of capital, based on the average five-year historic volatility of public energy service company share prices and benchmark interest rates. The after tax discount rate ranges from 12% to 14%. Changes in such estimates or the application of alternative assumptions could produce significantly different results. As at December 31, 2010 the estimated fair value of the Company’s business would approximate its carrying amount if the after tax discount rate were to increase by 1% to 3%, or the assumed growth rate was reduced by 1% to 3%. See “Business Outlook” for discussion of industry conditions.
FUTURE TAX ASSETS AND LIABILITIES
Future tax assets and liabilities are recognized for differences between the book value and tax value of the net assets of the Company. In providing for future taxes, management considers current tax regulations, estimates of future taxable income and available tax planning strategies. If tax regulations, operating results or the ability to implement tax planning strategies vary, adjustments to the carrying value of future tax assets and liabilities may be required. See Note 10 to the consolidated financial statements for the significant components of the future income tax assets and liabilities, and a reconciliation of the Company’s income tax provision.
Risk Factors
In addition to the information set forth elsewhere in this MD&A, the following factors should be carefully considered when evaluating CE Franklin.
Fluctuations in the overall profitability of the oil and gas industry can affect the demand for CE Franklin’s products and services and, therefore, CE Franklin’s sales, cash flows and profitability. CE Franklin’s operations are materially dependent upon the level of activity in oil and gas exploration, development and production in western Canada. Both short-term and long-term trends in oil and gas prices affect activity levels of such activity. Other factors that can impact the level of drilling, exploration and production and oil sands project activity and the overall profitability of the oil and gas industry include:
s
relatively minor changes in, or threats to, the worldwide supply of and demand for oil and natural gas;
s
the ability of the members of the Organization of Petroleum Exporting Countries (“OPEC”) to maintain price stability through voluntary production limits;
s
the level of oil production by non-OPEC countries;
s
the level of North American gas production and liquefied natural gas imports, relative to North American demand for gas;
s
the movement of the Canadian dollar relative to its U.S. counterpart (crude oil and natural gas exports are generally traded in U.S. dollars);
s
general economic and political conditions in North America and worldwide; and
s
the presence or absence of drilling incentives such as Canadian provincial royalty holidays, availability of new leases and concessions and government regulations regarding, among other things, export controls, carbon taxes, regulatory emissions reduction targets and other environmental protection measures, changes in royalty rates, taxation, price controls and availability of product transportation and refining capacity.
CE Franklin believes that any prolonged reduction in oil and gas prices or other factors that may impact the profitability of the oil and gas industry, would depress the level of exploration and production activity. This would likely result in a corresponding decline in the demand for CE Franklin’s products and services and could have a material adverse effect on CE Franklin’s sales, cash flows and profitability. There can be no assurance as to the future level of demand for CE Franklin’s products and services or future conditions in the oil and gas and oilfield supply industries.
CE Franklin operates in a highly competitive industry, which may adversely affect CE Franklin’s sales, cash flows and profitability. The Canadian oilfield supply industry in which CE Franklin operates is very competitive. The Company believes that its future profitability is partially influenced by competitive factors beyond its control, including:
s
the ability of some customers to purchase pipe, valves, flanges, fittings, production equipment, tubular products and other general oilfield supplies directly from the manufacturer rather than from the Company;
s
the ability of new brokers and distributors to enter the market;
s
price competition among existing brokers and distributors;
s
cost of goods being subject to rising or declining commodity prices, such as the price of steel, and the inability of CE Franklin to pass these price increases on to customers, or the risk CE Franklin may have higher-cost inventory during declining commodity prices resulting in a deterioration in gross profit margins.
CE Franklin and its largest competitors generally operate at low profit margins due to price competition. Price competition is due in part to customer price pressure, in addition to the major supply companies competing for the same business.
A substantial portion of the Company’s sales to customers depend on written contracts that are cancelable at any time, or are based on verbal agreements. The key factors which will determine whether a customer will continue to use the Company are pricing, service quality and availability, strategically located service centers and technical knowledge and experience. There can be no assurance that the Company’s relationships with its customers will continue, and a significant reduction or total loss of business from these customers, if not offset by increased sales to new or existing customers, could have a material adverse effect on the Company’s net income or cash flow from operations.
The loss of CE Franklin’s major suppliers could adversely affect the Company’s sales and gross profit. A portion of CE Franklin’s business are sales where product is obtained from one supplier. In the event the Company is unable to source products from its existing suppliers, then CE Franklin would need to search for alternate suppliers of these goods. There can be no assurance that suitable alternate suppliers for such goods would be found.
Significant downtime at the Company’s centralized Distribution Centre located in Edmonton, Alberta could materially impact net income and cash flow from operations. The Company operates a hub and spoke distribution model with the Distribution Centre strategically located within reasonable proximity to a majority of its vendors. The Distribution Centre acts as a supply hub for its 45 branches. Significant downtime at this facility could impact the Company’s gross profit margins, net income and cash flow from operations.
Labour shortages could adversely affect the Company’s ability to service its customers. The Company faces the challenge of attracting and retaining workers to meet any increase in demand for its products and services. In a highly competitive market for employees, the Company may experience periods of high employee turnover that could result in higher training costs or reduced levels of service to customers. The Company may also experience wage inflation. These could result in increased costs or the loss of customers and market share.
During periods of high demand for products and services, the Company may experience product shortages. The frequency and duration of the shortages may impact the financial performance of the Company. Product shortages may impact profit margins or could result in the loss of customers.
The Company may experience a financial loss if inventory becomes obsolete or otherwise un-saleable. The rate of product technical innovation and the company’s ability to return un-saleable inventory to suppliers may impact financial performance.
Weather conditions could decrease the demand for CE Franklin’s products and services. CE Franklin’s financial performance is tied closely to the seasonality of drilling activity. Higher drilling activity in Canada is generally experienced in the winter months. In the spring and early summer, drilling activity slows dueto the difficulty in moving equipment during the spring thaws. To the extent that unseasonable weather conditions such as excessive rain or unusually warm winters affect the ability of CE Franklin’s customers to access their oil and gas sites, then the demand for CE Franklin’s products and services would temporarily decrease and the Company’s sales, cash flows and profitability would be adversely affected.
The Company may experience a financial loss if its significant customers fail to pay CE Franklin for its products or services. The Company’s ability to collect the proceeds from the sale of its products and services from its customers depends on the payment ability of its oil and gas customer base. A decline in oil and gas prices may increase the payment risk associated with the Company’s customers.
The Company’s major shareholder may influence the Company’s affairs. The Company’s share ownership is highly concentrated and, as a result, CE Franklin’s principal shareholder effectively controls the Company’s business. As at the date of this Form 20-F, CE Franklin’s largest shareholder, Schlumberger, owned approximately 56% of the Company’s common shares outstanding. As a result, Schlumberger has the voting power to significantly influence the Company’s policies, business and affairs and the outcome of any corporate transaction or other matter, including mergers, consolidations and the sale of all, or substantially all, of the Company’s assets.
In addition, the concentration of the Company’s ownership may have the effect of delaying, deterring or preventing a change in control that otherwise could result in a premium in the price of the Company’s common shares.
The Company relies on its revolving bank turn loan to finance its ongoing net working capital and other funding requirements. CE Franklin has a $60 million borrowing facility that matures in July 2013. While management believes that this facility will be adequate to fund its working capital requirements, there can be no assurance that additional credit will become available if required, or that an appropriate amount of credit with comparable terms and conditions will become available when the facility matures. The revolving bank term loan contains restrictive covenants which if breached by the Company, could result in a default or an event of default that could allow the lender to discontinue lending or to declare all borrowings outstanding there under to be due and payable.
If the Company is unable to successfully address potential material weakness in its internal controls, or any other control deficiencies, its ability to report its financial results on a timely and accurate basis and to comply with disclosure and other requirements may be adversely affected. The Company has complied with Section 404 of the Sarbanes-Oxley Act of 2002, and is therefore required to make an assessment of the effectiveness of its internal controls over financial reporting for that purpose. A material weakness is defined as a significant deficiency, or a combination of significant deficiencies, that results in more than a remote likelihood that a material misstatement of the annual or interim financial statements will not be prevented or detected.
CE Franklin will continue to monitor the effectiveness of these and other processes, procedures and controls and will make any further changes management determines appropriate, including to effect compliance with Section 404 of the Sarbanes-Oxley Act of 2002. The steps CE Franklin has taken and will take in the future may not remediate any potential material weakness. In addition, the Company may identify material weaknesses or other deficiencies in our internal controls in the future.
Any material weaknesses or other deficiencies in the Company’s control systems may affect its ability to comply with reporting requirements and stock exchange listing standards or cause its financial statements to contain material misstatements, which could negatively affect the market price and trading liquidity of its common stock, cause investors to lose confidence in the Company’s reported financial information, as well as subject CE Franklin to civil or criminal investigations and penalties.
Forward Looking Statements
The information in this MD&A contains “forward-looking statements” within the meaning of Section 27A of the Securities Act of 1933 and Section 21E of the Securities Exchange Act of 1934. All statements, other than statements of historical facts, that address activities, events, outcomes and other matters that CE Franklin plans, expects, intends, assumes, believes, budgets, predicts, forecasts, projects, estimates or anticipates (and other similar expressions) will, should or may occur in the future are forward-looking statements. These forward-looking statements are based on management’s current belief, based on currently available information, as to the outcome and timing of future events. When considering forward-looking statements, you should keep in mind the risk factors and other cautionary statements in this MD&A, including those under the caption “Risk factors”.
Forward-looking statements appear in a number of places and include statements with respect to, among other things:
s
forecasted oil and gas industry activity levels in 2011 and beyond;
s
planned capital expenditures and working capital and availability of capital resources to fund capital expenditures and working capital;
s
the Company’s future financial condition or results of operations and future revenues and expenses;
s
the Company’s business strategy and other plans and objectives for future operations;
s
fluctuations in worldwide prices and demand for oil and gas; and
s
fluctuations in the demand for the Company’s products and services.
Should one or more of the risks or uncertainties described above or elsewhere in this MD&A occur, or should underlying assumptions prove incorrect, the Company’s actual results and plans could differ materially from those expressed in any forward-looking statements.
All forward-looking statements expressed or implied, included in this MD&A and attributable to CE Franklin are qualified in their entirety by this cautionary statement. This cautionary statement should also be considered in connection with any subsequent written or oral forward-looking statements that CE Franklin or persons acting on its behalf might issue. CE Franklin does not undertake any obligation to update any forward-looking statements to reflect events or circumstances after the date of filing this MD&A, except as required by law.
Transition to International Financial Reporting Standards (“IFRS”)
In February 2008, the Canadian Accounting Standards Board confirmed that the basis for financial reporting by Canadian publicly accountable enterprises will change from Canadian GAAP to IFRS effective for January 1, 2011, including the preparation and reporting of one year of comparative figures. This change is part of a global shift to provide consistency in financial reporting in the global marketplace.
PROJECT STRUCTURE AND GOVERNANCE
A Steering Committee has been established to provide leadership and guidance to the project team, assist in developing accounting policy recommendations and ensure there is adequate resources and training available. Management provides status updates to the Company’s Audit Committee on a quarterly basis.
RESOURCES AND TRAINING
CE Franklin’s project team has been assembled and has developed a detailed workplan that includes training, detailed Canadian GAAP to IFRS analysis, technical research, policy recommendations and implementation. The project team completed initial training and ongoing training will continue through the project as required. The Company’s Leadership Team and the Audit Committee have also participated in IFRS awareness sessions.
IFRS PROGRESS
The project team is advanced in its assessment of the differences between Canadian GAAP and IFRS. A risk based approach was used to identify significant differences based on possible financial impact and complexity. No accounting policy differences have been identified to date that would give rise to significant differences between Canadian GAAP and IFRS. Similarly, there have been no significant information system change requirements identified in order to adopt IFRS. The project team has substantially completed its assessment of changes to financial statement presentation, disclosure and again no significant differences have been identified to this point. There are some additional disclosures required under IFRS that the company will be presenting in its first IFRS financial statements. Work is ongoing on internal controls over financial reporting that will be required to adopt IFRS. There are a number of IFRS standards in the process of being amended by the International Accounting Standards Board and are expected to continue until the transition date of January 1, 2011. The Company is actively monitoring proposed changes.
At this stage in the project, CE Franklin cannot reasonably determine the full impact that adopting IFRS would have on its financial position and future results.
Recent Accounting Pronouncements
i)
Topic 820 – Improving disclosures about fair value measurements
This statement provides amendments, to subtopic 820-10 that require new disclosures and that clarify certain existing disclosures related to fair value measurements.
The new disclosures and clarifications of existing disclosures are effective for interim and annual reporting periods beginning after December 15, 2009 except for the disclosures about purchases, sales, issuances and settlements in the roll forward activity in Level 3 fair value measurements. Those disclosures are effective for fiscal years beginning after December 15, 2010 and for interim periods within those fiscal years.
ii)
Topic 605 – Multiple-deliverable revenue arrangements
This statement provides another alternative for determining the selling price of deliverables. Eliminates the residual method of allocating arrangement consideration. Requires expanded qualitative and quantitative disclosures. Effective prospectively for revenue arrangements entered into or materially modified in years beginning on or after June 15, 2010.
iii)
Topic 810 – New Consolidation Guidance for Variable Interest Entities (“VIEs”)
The statement amends the consolidation guidance for VIEs under Fin 46(R) including (1) the elimination of the exemption for qualifying special purpose entities, (2) a new approach for determining who should consolidate a VIE, and (3) changes to when it is necessary to reassess who should consolidate a VIE. Management reviewed the application of this statement and determined that it had minimal effect on the financial statements.
Under revised CICA section 1506, “Accounting Changes” and the U.S. Securities and Exchange Commission’s (SEC) Staff Bulletin No. 74 (SAB 74), the Company is required to disclose certain information related to recently issued accounting standards. This guidance requires that when a new accounting standard has been issued but has not yet been adopted, the Company should discuss the effect that the new standard will have on the Company’s financial statements when adopted.
RECENT CANADIAN GAAP PRONOUNCEMENTS
i)
CICA 1582 – Business Combinations, CICA 1601 – Consolidated Financial Statements and CICA 1602 – Non-controlling Interests
These statements replaced CICA 1581 – Business Combinations and CICA 1600 – Consolidated Financial Statements and established a new statement for accounting for non-controlling interests. The Company believes that the early adoption of these standards will be assessed as appropriate, as the effective date is for acquisitions on/after the beginning of the first annual reporting period beginning on/after January 1, 2011.
RECENT US GAAP PRONOUNCEMENTS
Since the Company will be adopting IFRS for 2011, future US GAAP pronouncements are not applicable as a US GAAP reconciliation will no longer be required.
CONTROLS AND PROCEDURES
CE Franklin’s Chief Executive Officer and Chief Financial Officer, after evaluating the effectiveness of the Company’s disclosure controls and procedures (as defined in Exchange Act Rule 13a-15(e)) as of the end of the period covered by this Form 20-F, have concluded that, as of such date, the Company’s disclosure controls and procedures were effective.
Report of CE Franklin Management on Internal Control Over Financial Reporting: CE Franklin’s Board of Directors and management are responsible for establishing and maintaining adequate internal control over financial reporting. The Company’s internal control system was designed to provide reasonable assurance to management and Board of Directors regarding the reliability of financial reporting and the preparation and fair presentation of its published consolidated financial statements.
All internal control systems, no matter how well designed, have inherent limitations. Therefore, even those systems determined to be effective may not prevent or detect misstatements and can provide only reasonable assurance with respect to financial statement preparation and presentation. Also, projections of any evaluation of effectiveness to future periods are subject to the risk that controls may become inadequate because of changes in conditions, or that the degree of compliance with the policies or procedures may deteriorate.
Management assessed the effectiveness of the Company’s internal control over financial reporting as of December 31, 2010. In making this assessment, it used the criteria established in Internal Control—Integrated Framework issued by the Committee of Sponsoring Organizations of the Treadway Commission (COSO). Based on the Company’s assessment, management has concluded that as of December 31, 2010, CE Franklin’s internal control over financial reporting is effective based on those criteria.
Our independent registered public accounting firm, PricewaterhouseCoopers LLP, audited the effectiveness of the Company’s internal control over financial reporting as at December 31, 2010, as stated in its attestation report, which is included on pages 48 and 49 of this Annual Report.
There were no changes to the Company’s internal control over financial reporting that occurred during 2010.
Management’s Report On Internal Control Over Financial Reporting
Management of the Company is responsible for establishing and maintaining adequate internal control over financial reporting as defined in Rule 13a – 15(f) under the Securities Exchange Act of 1934. The Company’s internal control over financial reporting is designed to provide reasonable assurance regarding the reliability of financial reporting and the preparation of financial statements for external purposes in accordance with generally accepted accounting principles. A company’s internal control over financial reporting includes those policies and procedures that (1) pertain to the maintenance of records that, in reasonable detail, accurately and fairly reflect the transactions and dispositions of the assets of the company; (2) provide reasonable assurance that transactions are recorded as necessary to permit preparation of financial statements in accordance with generally accepted accounting principles, and that receipts and expenditures of the company are being made only in accordance with authorizations of management and directors of the company; and (3) provide reasonable assurance regarding prevention or timely detection of unauthorized acquisition, use, or disposition of the company’s assets that could have a material effect on the financial statements.
Because of its inherent limitations, internal control over financial reporting may not prevent or detect misstatements. Also, projections of any evaluation of effectiveness to future periods are subject to the risk that controls may become inadequate because of changes in conditions, or that the degree of compliance with the policies or procedures may deteriorate.
The Company’s management assessed the effectiveness of the Company’s internal control over financial reporting based on criteria established in Internal Control-Integrated Framework issued by the Committee of Sponsoring Organizations of the Treadway Commission. Based on this assessment, management concluded that the Company’s internal control over financial reporting was effective as of December 31, 2010.
The effectiveness of the Company’s internal control over financial reporting as of December 31, 2010 has been audited by PricewaterhouseCoopers LLP, the independent auditor, as stated in their report which appears on pages 48 and 49 of this Annual Report.
Michael West
Mark Schweitzer
President and Chief Executive Officer
Vice President and Chief Financial Officer
February 2, 2011
February 2, 2011
Management’s Report
The preparation and presentation of the accompanying consolidated financial statements are the responsibility of the management of the Company. The statements have been prepared in accordance with Canadian generally accepted accounting principles as described in note 1 to the consolidated financial statements. The financial information elsewhere in the annual report has been reviewed to ensure consistency with that in the consolidated financial statements.
Management acknowledges responsibility for the integrity of its financial information. Where appropriate, management has made informed judgments and estimates in accounting for transactions, which were not complete at the balance sheet date. The Company maintains disclosure controls and procedures and internal controls designed to ensure that information required to be disclosed in the consolidated financial statements and annual report is recorded, processed, summarized and reported properly. CE Franklin’s Chief Executive Officer and Chief Financial Officer evaluated the Company’s disclosure controls and procedures as at December 31, 2010 to ensure that such disclosure controls and procedures are effective. There were no significant changes in the Company’s internal controls or in other factors that could significantly affect those controls subsequent to the evaluation date.
The Board of Directors has appointed an Audit Committee that consists of three directors who are not officers or employees of the Company and have no direct or indirect material relationship with the Company. The committee meets with management and the Company’s external auditor to discuss internal control, accounting policies and financial reporting matters. The Audit Committee has reviewed the consolidated financial statements. The Board of Directors has approved the consolidated financial statements on the recommendation of the Audit Committee.
Michael West
Mark Schweitzer
President and Chief Executive Officer
Vice President and Chief Financial Officer
February 2, 2011
February 2, 2011
Independent Auditors’ Report
To the Shareholders of CE Franklin Ltd.
We have completed integrated audits of CE Franklin Ltd. and its subsidiary’s 2010, 2009, and 2008 consolidated financial statements and their internal control over financial reporting as at December 31, 2010. Our opinions, based on our audits, are presented below.
Report on the consolidated financial statements
We have audited the accompanying consolidated financial statements of CE Franklin Ltd. and its subsidiary, which comprise the consolidated balance sheets as at December 31, 2010 and December 31, 2009 and the consolidated statements of operations and comprehensive income, changes in shareholders’ equity and cash flows for each of the three years in the period ended December 31, 2010, and the related notes including a summary of significant accounting policies.
Management’s responsibility for the consolidated financial statements
Management is responsible for the preparation and fair presentation of these consolidated financial statements in accordance with Canadian generally accepted accounting principles and for such internal control as management determines is necessary to enable the preparation of consolidated financial statements that are free from material misstatement, whether due to fraud or error.
Auditor’s responsibility
Our responsibility is to express an opinion on these consolidated financial statements based on our audits. We conducted our audits in accordance with Canadian generally accepted auditing standards and the standards of the Public Company Accounting Oversight Board (United States). Those standards require that we plan and perform an audit to obtain reasonable assurance about whether the consolidated financial statements are free from material misstatement. Canadian generally accepted auditing standards require that we comply with ethical requirements.
An audit involves performing procedures to obtain audit evidence, on a test basis, about the amounts and disclosures in the consolidated financial statements. The procedures selected depend on the auditor’s judgment, including the assessment of the risks of material misstatement of the consolidated financial statements, whether due to fraud or error. In making those risk assessments, the auditor considers internal control relevant to the company’s preparation and fair presentation of the consolidated financial statements in order to design audit procedures that are appropriate in the circumstances. An audit also includes evaluating the appropriateness of accounting principles and policies used and the reasonableness of accounting estimates made by management, as well as evaluating the overall presentation of the consolidated financial statements.
We believe that the audit evidence we have obtained in our audits is sufficient and appropriate to provide a basis for our audit opinion on the consolidated financial statements.
Opinion
In our opinion, the consolidated financial statements present fairly, in all material respects, the financial position of CE Franklin Ltd. and its subsidiary as at December 31, 2010 and December 31, 2009 and the results of their operations and cash flows for each of the three years in the period ended December 31, 2010 in accordance with Canadian generally accepted accounting principles.
Report on internal control over financial reporting
We have also audited CE Franklin Ltd.’s internal control over financial reporting as at December 31, 2010, based on criteria established in Internal Control – Integrated Framework, issued by the Committee of Sponsoring Organizations of the Treadway Commission (COSO).
Management’s responsibility for internal control over financial reporting
Management is responsible for maintaining effective internal control over financial reporting and for its assessment of the effectiveness of internal control over financial reporting included in the accompanying Management’s Reports.
Auditor’s responsibility
Our responsibility is to express an opinion on the Company’s internal control over financial reporting based on our audit. We conducted our audit of internal control over financial reporting in accordance with the standards of the Public Company Accounting Oversight Board (United States). Those standards require that we plan and perform the audit to obtain reasonable assurance about whether effective internal control over financial reporting was maintained in all material respects.
An audit of internal control over financial reporting includes obtaining an understanding of internal control over financial reporting, assessing the risk that a material weakness exists, testing and evaluating the design and operating effectiveness of internal control, based on the assessed risk, and performing such other procedures as we consider necessary in the circumstances.
We believe that our audit provides a reasonable basis for our audit opinion on the Company’s internal control over financial reporting.
Definition of internal control over financial reporting
A company’s internal control over financial reporting is a process designed to provide reasonable assurance regarding the reliability of financial reporting and the preparation of financial statements for external purposes in accordance with Canadian generally accepted accounting principles. A company’s internal control over financial reporting includes those policies and procedures that (i) pertain to the maintenance of records that, in reasonable detail, accurately and fairly reflect the transactions and dispositions of the assets of the company; (ii) provide reasonable assurance that transactions are recorded as necessary to permit preparation of financial statements in accordance with Canadian generally accepted accounting principles, and that receipts and expenditures of the company are being made only in accordance with authorizations of management and directors of the company; and (iii) provide reasonable assurance regarding prevention or timely detection of unauthorized acquisition, use, or disposition of the company’s assets that could have a material effect on the financial statements.
Inherent limitations
Because of its inherent limitations, internal control over financial reporting may not prevent or detect misstatements. Also, projections of any evaluation of effectiveness to future periods are subject to the risk that controls may become inadequate because of changes in conditions or that the degree of compliance with the policies or procedures may deteriorate.
Opinion
In our opinion, CE Franklin Ltd. maintained, in all material respects, effective internal control over financial reporting as at December 31, 2010 based on criteria established in Internal Control – Integrated Framework, issued by COSO.
PricewaterhouseCoopers LLP
Chartered Accountants
Calgary, Alberta
February 2, 2011
Consolidated Balance Sheets
| | |
(in thousands of Canadian dollars) As at December 31 | 2010 | 2009 |
ASSETS | | |
Current assets | | |
Accounts receivable(note 12(b)) | 92,950 | 67,443 |
Inventories (note 3) | 94,838 | 102,669 |
Other | 1,625 | 4,960 |
| 189,413 | 175,072 |
Property and equipment (note 4) | 9,431 | 10,517 |
Goodwill | 20,570 | 20,570 |
Future income taxes(note 10) | 1,116 | 1,457 |
Other | 147 | 339 |
| 220,677 | 207,955 |
LIABILITIES | | |
Current liabilities | | |
Bank operating loan (note 6) | – | 26,549 |
Accounts payable and accrued liabilities | 63,363 | 38,489 |
Income taxes payable(note 10) | 348 | – |
| 63,711 | 65,038 |
Long term debt(note 6) | 6,430 | 290 |
| 70,141 | 65,328 |
Commitments and contingencies(note 7) | | |
SHAREHOLDERS’ EQUITY | | |
Capital stock(note 8) | 23,078 | 23,284 |
Contributed surplus | 19,716 | 17,184 |
Retained earnings | 107,742 | 102,159 |
| 150,536 | 142,627 |
| 220,677 | 207,955 |
See accompanying notes to these consolidated financial statements.
Approved by the Board:
Robert McClinton
Keith Turnbull
Director
Director
Consolidated Statements of Changes in Shareholders’ Equity
| | | | | |
| Capital Stock | | | |
(in thousands of Canadian dollars and number of shares) | Number of Shares | $ | Contributed Surplus | Retained Earnings | Shareholders’ Equity |
December 31, 2007 | 18,370 | 24,306 | 17,671 | 76,243 | 118,220 |
Stock based compensation expense (note 8 (b) and (c)) | – | – | 1,365 | – | 1,365 |
Stock options excercised (note 8 (b)) | 13 | 69 | (20) | – | 49 |
Purchase of shares in trust for Share Unit Plans(note 8 (c)) | (300) | (2,058) | – | – | (2,058) |
Shares issued from Share Unit Plan Trust(note 8 (c)) | 11 | 181 | (181) | – | – |
Net income | – | – | – | 21,747 | 21,747 |
December 31, 2008 | 18,094 | 22,498 | 18,835 | 97,990 | 139,323 |
Normal course issuer bid(note 8 (d)) | (554) | (724) | – | (2,139) | (2,863) |
Stock based compensation expense (note 8 (b) and (c)) | – | – | 1,662 | – | 1,662 |
Modification of Stock option plan(note 8 (b)) | – | – | (1,276) | – | (1,276) |
Stock options excercised(note 8 (b)) | 57 | 235 | (86) | – | 149 |
Purchase of shares in trust for Share Unit Plans(note 8 (c)) | (121) | (676) | – | – | (676) |
Shares issued from Share Unit Plan Trust(note 8 (c)) | 105 | 1,951 | (1,951) | – | – |
Net income | – | – | – | 6,308 | 6,308 |
December 31, 2009 | 17,581 | 23,284 | 17,184 | 102,159 | 142,627 |
Normal course issuer bid(note 8 (d)) | (62) | (81) | – | (328) | (409) |
Stock based compensation expense (note 8 (b) and (c)) | – | – | 1,751 | – | 1,751 |
Modification of Stock option plan(note 8(b)) | – | – | 2,075 | – | 2,075 |
Stock options excercised (note 8 (b)) | 46 | 290 | (121) | – | 169 |
Purchase of shares in trust for Share Unit Plans and settlement of Deferred Share Unit Exercise(note 8 (c)) | (204) | (1,410) | (178) | – | (1,588) |
Shares issued from Share Unit Plan Trust(note 8 (c)) | 113 | 995 | (995) | – | – |
Net income | – | – | – | 5,911 | 5,911 |
December 31, 2010 | 14,474 | 23,078 | 19,716 | 107,742 | 150,536 |
See accompanying notes to these consolidated financial statements.
Consolidated Statements of Operations and Comprehensive Income
| | | |
(in thousands of Canadian dollars except shares and per share amounts) For the years ended December 31 | 2010 | 2009 | 2008 |
Sales | 489,585 | 437,027 | 547,429 |
Cost of sales | 414,579 | 360,370 | 439,760 |
Gross profit | 75,006 | 76,657 | 107,669 |
Other expenses | | | |
Selling, general and administrative expenses | 62,554 | 64,226 | 71,587 |
Amortization | 2,465 | 2,535 | 2,367 |
Interest expense | 698 | 915 | 1,031 |
Foreign exchange (gain)/loss | (65) | 37 | 242 |
| 65,652 | 67,713 | 75,227 |
Income before income taxes | 9,354 | 8,944 | 32,442 |
Income tax expense/(recovery)(note 10) | | | |
Current | 3,102 | 2,894 | 10,474 |
Future | 341 | (258) | 221 |
| 3,443 | 2,636 | 10,695 |
Net income and comprehensive income for the year | 5,911 | 6,308 | 21,747 |
Net income per share | | | |
Basic | 0.34 | 0.36 | 1.19 |
Diluted | 0.33 | 0.35 | 1.17 |
Weighted average number of shares outstanding(000’s) | | | |
Basic | 17,499 | 17,750 | 18,255 |
Diluted(Note 8 (e)) | 18,000 | 17,953 | 18,561 |
See accompanying notes to these consolidated financial statements.
Consolidated Statements of Cash Flows
| | | |
(in thousands of Canadian dollars) For the years ended December 31 | 2010 | 2009 | 2008 |
Cash flows from operating activities | | | |
Net income | 5,911 | 6,308 | 21,747 |
Items not affecting cash | | | |
Amortization | 2,465 | 2,535 | 2,367 |
Future income tax expense/(recovery) | 341 | (258) | 221 |
Stock based compensation expense | 1,991 | 2,306 | 1,365 |
Other | 27 | – | 74 |
| 10,735 | 10,891 | 25,774 |
Net change in non-cash operating working capital balances(note 9) | 12,779 | 14,776 | (8,373) |
| 23,514 | 25,667 | 17,401 |
Cash flows (used in)/from financing activities | | | |
Issuance of capital stock – stock option exercises(note 8(b)) | 169 | 149 | 49 |
Purchase of capital stock through normal course issuer bid(note 8(d)) | (409) | (2,863) | – |
Purchase of capital stock in trust for share unit plans and settlement of deferred share unit exercise(note 8(c)) | (1,588) | (676) | (2,058) |
Increase in long term debt | 6,126 | – | – |
Decrease in bank operating loan | (26,549) | (8,399) | (10,231) |
| (22,251) | (11,789) | (12,240) |
Cash flows (used in)/from investing activities | | | |
Purchase of property and equipment | (1,263) | (2,592) | (5,602) |
Business combinations(note 2) | – | (11,286) | 441 |
| (1,263) | (13,878) | (5,161) |
Change in cash and cash equivalents during the year | – | – | – |
Cash and cash equivalents – beginning and end of year | – | – | – |
Cash paid during the year | | | |
Interest | 698 | 915 | 1,031 |
Income taxes | 1,725 | 7,230 | 6,594 |
See accompanying notes to these consolidated financial statements.
Notes to Consolidated Financial Statements
December 31, 2010, 2009 and 2008
(tabular amounts in thousands of Canadian dollars, except share and per share amounts)
1.
Accounting Policies
GENERALLY ACCEPTED ACCOUNTING PRINCIPLES
The consolidated financial statements of the Company have been prepared in accordance with accounting principles generally accepted in Canada (“GAAP”). These principles differ in certain respects from accounting principles generally accepted in the United States (“U.S.”). The material differences that affect the Company’s consolidated financial statements are described in note 16.
USE OF ESTIMATES
The preparation of the consolidated financial statements in conformity with generally accepted accounting principles requires management to make estimates and assumptions that affect the reported amounts of assets and liabilities and disclosure of contingent assets and liabilities at the dates of the consolidated financial statements and the reported amounts of sales and expenses during the reporting periods.
Management believes the most significant estimates and assumptions are associated with the valuation of accounts receivable, inventories, vendor rebates, future tax assets (liabilities), stock based compensation and goodwill. If the underlying estimates and assumptions, upon which the consolidated financial statements are based, change in future periods, actual amounts may differ materially from those included in the accompanying consolidated financial statements.
BASIS OF PRESENTATION
The consolidated financial statements include the accounts of the Company and its wholly owned subsidiaries. The accounting principles applied are consistent with those set out in the Company’s annual consolidated financial statements for the year ended December 31, 2009 except as noted below. All significant transactions and balances between the Company and its subsidiaries have been eliminated on consolidation. The financial statements have also been prepared on the basis that the Company will continue to operate as a going concern, which contemplates the realization of assets and the settlement of liabilities and commitments in the normal course of business.
CHANGE IN ACCOUNTING POLICIES
Canadian GAAP
There were no significant changes to Canadian GAAP in 2010 that affected the Company’s accounting policies.
US GAAP
i)
Topic 820 – Improving disclosures about fair value measurements
This statement provides amendments, to subtopic 820-10 that require new disclosures and that clarify certain existing disclosures related to fair value measurements.
The new disclosures and clarifications of existing disclosures are effective for interim and annual reporting periods beginning after December 15, 2009 except for the disclosures about purchases, sales, issuances and settlements in the roll forward activity in Level 3 fair value measurements. Those disclosures are effective for fiscal years beginning after December 15, 2010 and for interim periods within those fiscal years.
ii)
Topic 605 – Multiple-deliverable revenue arrangements
This statement provides another alternative for determining the selling price of deliverables. Eliminates the residual method of allocating arrangement consideration. Requires expanded qualitative and quantitative disclosures. Effective prospectively for revenue arrangements entered into or materially modified in years beginning on or after June 15, 2010.
iii)
Topic 810 – New Consolidation Guidance for Variable Interest Entities (“VIEs”)
The statement amends the consolidation guidance for VIEs under Fin 46(R) including (1) the elimination of the exemption for qualifying special purpose entities, (2) a new approach for determining who should consolidate a VIE, and (3) changes to when it is necessary to reassess who should consolidate a VIE. Management reviewed the application of this statement and determined that it had minimal effect on the financial statements.
Under revised CICA section 1506, “Accounting Changes” and the U.S. Securities and Exchange Commission’s (SEC) Staff Bulletin No. 74 (SAB 74), the Company is required to disclose certain information related to recently issued accounting standards. This guidance requires that when a new accounting standard has been issued but has not yet been adopted, the Company should discuss the effect that the new standard will have on the Company’s financial statements when adopted.
CASH AND CASH EQUIVALENTS
Cash and cash equivalents consists of cash on hand and investments in highly liquid instruments with maturities of 90 days or less on the date acquired.
ALLOWANCE FOR DOUBTFUL ACCOUNTS
The Company maintains an allowance for doubtful accounts to provide for receivables which may ultimately be uncollectible. Reserves are determined in light of a number of factors including customer specific conditions, economic events and the Company’s historical loss experience.
INVENTORIES
Inventories, consisting primarily of goods purchased and held for resale, are valued at the lower of average cost or net realizable value. Average cost includes the cost of bringing inventory to its present location and condition. The reversal of any write down of inventory arising from an increase in net realizable value shall be recognized as a reduction in cost of sales in the period in which the reversal occurred.
PROPERTY AND EQUIPMENT
Property and equipment are recorded at cost less related accumulated amortization. The Company provides for amortization of property and equipment using rates as follows:
| | |
Buildings | 5% to 10% | straight line |
Leasehold improvements | over the term of the lease | straight line |
Computer equipment and software | 15% to 33% | straight line |
Equipment and machinery | 10% to 100% | straight line |
Furniture and office equipment | 15% to 20% | straight line |
Automotive equipment | 30% | straight line |
GOODWILL
The Company performs an annual goodwill impairment evaluation at December 31, at the consolidated level as it operates through a single operating segment and cash generating unit. The impairment evaluation involves comparing the estimated fair value of the Company’s business to its carrying amount to determine if a write down to fair value is required. If the fair value is less than the book value, then a second test is performed to determine the amount of the impairment. The amount of the impairment is determined by deducting the fair value of the assets and liabilities from the fair value of the Company to determine the implied fair value of goodwill and comparing that amount to the book value of the goodwill. Any excess of the book value of goodwill over the implied fair value of goodwill is the impairment amount.
The fair value of the business is estimated from value in use calculations using future cash projections, discounted to their present value. The required valuation methodology and underlying financial information that is used to determine fair value, require significant judgments to be made by management. These judgments include, but are not limited to long term projections of future financial performance and the selection of appropriate discount rates used to determine the present value of estimated future cash flow and may be impacted by changes in oil and gas industry conditions. Changes in such estimates or the application of alternative assumptions could produce significantly different results.
REVENUE RECOGNITION
The Company’s revenue, which is primarily comprised of product sales, is generally subject to contractual arrangements, which specify price and general terms and conditions.
Revenue from the provision of goods is recognized when the risks and rewards of ownership of goods have been transferred to the customer and collectability has been reasonably assured. The risks and rewards of ownership of goods are deemed to have been transferred when the goods are shipped to, or picked up by, the customer.
Sales from agent operated branches are recorded as sales in the Consolidated Statement of Operations and Comprehensive Income as the Company is the primary obligor in agent operated revenue transactions.
Revenue from services is recognized when the service provided to the customer has been completed.
VENDOR REBATES
The Company enters into arrangements with certain vendors providing for inventory purchase rebates. These purchase rebates are accrued as earned and are recorded initially as a reduction in inventory with a subsequent reduction in cost of sales when the product is sold. Vendor rebates consist of volume discount incentives earned from the purchase of selected products during the year from specified vendors. These discounts are based on contractual agreements with the vendors which outline price, volume and general terms and conditions.
STOCK OPTIONS
The Company operates a stock option plan that is described in Note 8(b). During the quarter ended September 30, 2009, the Company modified its stock option plan to include a cash settlement mechanism. As a result, the Company’s stock option obligations were classified as current obligations (subject to vesting) based on the positive difference between the Company’s closing stock price at period end and the underlying option exercise price. The offset to the generation of the current liability was contributed surplus, up to the cumulative expensed Black Scholes valuation, and compensation expense for the excess of the intrinsic value over the cumulative expensed Black Scholes value. The liability was marked to market at each
period end, with any adjustment allocated to the relevant account as detailed above.
During the fourth quarter of 2010, the Company modified its stock option plan to remove the cash settlement mechanism. As a result, the Company now recognizes compensation expense based on the fair value of the options on the modification date or the grant date for new options, which is determined by using the Black-Scholes options pricing model. The fair value of the options is recognized over the vesting period of the options granted as compensation expense and an increase of contributed surplus. The amount initially recorded for the options in contributed surplus is reduced as options are exercised and is credited to capital stock.
OTHER STOCK-BASED COMPENSATION
Restricted share units (“RSU”), Performance share units (“PSU”) and Deferred share units (“DSU”) are granted entitling the participant, at the Company’s option, to receive either a common share or cash equivalent in exchange for a vested unit. For the PSU plan, the number of units granted is dependent on the Company meeting certain return on net asset (“RONA”) performance thresholds during the year of grant. The multiplier within the plan ranges from 0%-200% dependent on performance. The vesting period for RSUs and PSUs is one third per year over the three year period from the grant date. DSUs vest on the date of grant. Compensation expense related to the units granted is recognized over the vesting period based on the fair value of the units, at the date of the grant and is recorded to contributed surplus. The contributed surplus balance is reduced as the vested units are exchanged for either common shares or cash.
FOREIGN CURRENCY TRANSLATION
Monetary assets and liabilities are translated into Canadian dollars at period-end exchange rates and gains or losses from translation are recognized in the Consolidated Statements of Operations and Comprehensive Income. Sales and expenses are translated at the exchange rate prevailing on the date the transaction occurs.
FINANCIAL INSTRUMENTS
The Company measures financial instruments at estimated fair value. Financial assets are categorized as “loans and receivables”, consisting of accounts receivable. Financial liabilities are categorized as “other financial liabilities” consisting of accounts payable and accrued liabilities, bank operating loan, and long term debt.
Loans and receivables
Loans and receivables are non-derivative financial assets with fixed or determinable payments that are not quoted in an active market and with no intention of trading. They are included in current assets, except for maturities greater than 12 months after the balance sheet date, which are classified as non-current assets. Loans and receivables are included in accounts receivable and other current assets in the balance sheet.
Other financial liabilities
Other financial liabilities are financial liabilities that are not quoted on an active market and with no intention of being traded. They are included in current liabilities, except for the long term debt as it has a maturity greater than 12 months after the balance sheet date and is classified as a non-current liability.
Derivative instruments
In the normal course of business, the Company enters into foreign currency forward exchange contracts with financial institutions to fix the value of liabilities or future commitments. These foreign currency exchange contracts are not designated as hedges for accounting purposes. The values of contracts are marked to market at period end and the change in value is recognized in the Consolidated Statements of Operations and Comprehensive Income.
INCOME TAXES
The Company uses the liability method of accounting for income taxes under which future tax assets and liabilities are recognized when there are differences between the financial statement carrying amounts of existing assets and liabilities and their respective tax basis. Future tax assets and liabilities are measured using substantively enacted tax rates in effect in the period in which those temporary differences are expected to be recovered or settled. The effect on future tax assets and liabilities of a change in tax rates is recognized as part of the provision for income taxes in the period that includes the enactment date.
EARNINGS PER SHARE
Earnings per share are computed based on the weighted average basic number of shares outstanding for the period. Diluted earnings per share have been calculated using the treasury stock method, whereby diluted earnings per share are calculated as if options, RSUs, PSUs and DSUs were exercised at the beginning of the year and funds received were used to purchase the Company’s common shares on the open market at the average price for the year. From September 2009 to December 2010, stock options were recorded as a liability and settled by means of cash payment, and accordingly were not included in the diluted earnings per share calculation. In December 2010, the cash settlement mechanism for stock options was removed and the Company returned to following the treasury stock method to determine the dilution related to the stock option plan.
RECENT CANADIAN GAAP PRONOUNCEMENTS
i)
CICA 1582 – Business combinations, CICA 1601 – Consolidated Financial Statements and CICA 1602 Non-controlling Interests
These sections replaced CICA 1581 – Business Combinations and CICA 1600 – Consolidated Financial Statements and established a new section for accounting for non-controlling interests. The Company believes that the early adoption of these standards will be assessed as appropriate, as the effective date is for acquisitions beginning on/after January 1, 2011.
In February 2008, the Canadian Institute of Chartered Accountants’ Accounting Standards Board confirmed that Canadian publicly accountable entities will be required to adopt International Financial Reporting Standards (“IFRS”) as promulgated by the International Accounting Standards Board in place of generally accepted accounting principles in Canada (“GAAP”) effective January 1, 2011. The Company is currently in the process of assessing those accounting policies that will be affected by the change to IFRS and the potential impact of these changes on its financial position and results of operations.
RECENT US GAAP PRONOUNCEMENTS
Since the Company will be adopting IFRS for 2011, future US GAAP pronouncements are not applicable as a US GAAP reconciliation will no longer be required.
2.
Business Combinations
On June 1, 2009, the Company acquired the net assets of a western Canadian oilfield equipment distributor, for total consideration of $11.3 million, after $0.7 million of post closing adjustments related principally to inventory reductions. Using the purchase method of accounting for acquisitions, the Company consolidated the assets from the acquisition and allocated the consideration paid as follows:
| |
Cash consideration paid | 11,286 |
Net assets acquired | |
Inventory | 10,462 |
Property, Equipment and Other | 824 |
| 11,286 |
3.
Inventories
Inventories consisting primarily of goods purchased for resale are valued at the lower of average cost and net realizable value. Inventory net realizable value reserve expense of $0.9 million (2009 – $1.2 million; 2008 – $1.4 million) was charged to cost of sales for the year ended December 31, 2010. As at December 31, 2010 and December 31, 2009, the Company had recorded inventory net realizable value reserves of $5.0 million and $6.3 million respectively.
During the year ended December 31, 2010, inventory valuation reserves of $2.2 million (2009 – $0.6 million; 2008 – $0.4 million) were drawn down for sales of related items. No reversals of previously written down inventory were recorded in the periods.
4.
Property and equipment
| | | | | | |
As at December 31 | 2010 | 2009 |
| Cost | Accumulated Amortization | Net | Cost | Accumulated Amortization | Net |
Land, buildings and leasehold improvements | 11,999 | 5,696 | 6,303 | 11,624 | 4,958 | 6,666 |
Computer equipment and software | 21,254 | 20,348 | 906 | 20,751 | 19,721 | 1,030 |
Equipment and machinery | 6,535 | 5,627 | 908 | 6,412 | 5,350 | 1,062 |
Furniture and office equipment | 3,864 | 2,859 | 1,005 | 3,822 | 2,408 | 1,414 |
Automotive equipment | 1,065 | 756 | 309 | 838 | 493 | 345 |
| 44,717 | 35,286 | 9,431 | 43,447 | 32,930 | 10,517 |
5.
Capital management
The Company’s primary source of capital is its shareholders’ equity and cash flow from operating activities before net changes in non-cash working capital balances. The Company augments these capital sources with a $60.0 million, revolving term bank credit facility (the “Credit Facility”) that is used to finance its net working capital and general corporate requirements. The Company’s capital is summarised as follows:
| | |
| December 31, 2010 | December 31, 2009 |
Shareholders’ equity | 150,536 | 142,627 |
Long term debt/Bank operating loan | 6,430 | 26,839 |
Net working capital | 125,702 | 136,583 |
Net working capital is defined as current assets less accounts payable and accrued liabilities and income taxes payable.
6.
Long term debt and bank operating loan
| | |
As at December 31 | 2010 | 2009 |
Bank operating loan | – | 26,549 |
JEN Supply debt | 290 | 290 |
Revolving term credit facility | 6,140 | – |
Long term debt | 6,430 | 290 |
In July of 2010, the Company entered into a $60.0 million revolving term Credit Facility that matures in July 2013. The Credit Facility replaced the existing $60.0 million, 364 day bank operating loan. Borrowings under the Credit Facility bear interest based on floating interest rates and are secured by a general security agreement covering all assets of the Company. The maximum amount available under the Credit Facility is subject to a borrowing base formula applied to accounts receivable and inventories. The Credit Facility requires that the Company maintains the ratio of its debt to debt plus equity at less than 40%. As at December 31, 2010, this ratio was 4% The Company must also maintain coverage of its net operating cash flow as defined in the Credit Facility agreement, over interest expense for the trailing twelve month period, at greater than 1.25 times. As at December 31, 2010, this ratio was 14.1 times. The Credit Facility contains certain other covenants, with which the Company is in compliance. As at December 31, 2010, the Company had borrowed $6,140,000 and had available undrawn borrowing capacity of $53,860,000 under the Credit Facility. In management’s opinion, the Company’s available borrowing capacity under its Credit Facility and ongoing cash flow from operations, are sufficient to resource its ongoing obligations.
The JEN Supply debt is unsecured and bears interest at the floating Canadian bank prime rate and is repayable in 2012.
7.
Commitments and Contingencies
The following table outlines the Company’s contractual obligations for debt, lease and related obligations, having initial terms in excess of one year. Obligations due over the next five years and thereafter are as follows:
| | | |
Period Due (000’s) | Long term debt (note 6) | Operating lease commitments | Total |
2011 | – | 6,836 | 6,836 |
2012 | 290 | 6,248 | 6,538 |
2013 | 6,140 | 5,480 | 11,620 |
2014 | – | 4,842 | 4,842 |
2015 | | 4,101 | 4,101 |
thereafter | – | 21,610 | 21,610 |
| 6,430 | 49,117 | 55,547 |
A)
The Company leases certain office, warehouse and store facilities and automobiles under long-term operating leases. Future operating lease commitments include commitments aggregating $5.5 million over the remaining 8 year period related to the lease of a branch location from an employee. Rental terms under the lease commitment are at market rates.
B)
The Company is involved in various lawsuits and has various contractual performance and product warranty obligations, the losses from which, if any, are not anticipated to be material to the consolidated financial statements.
8.
Capital Stock
A)
The Company has authorized an unlimited number of common shares with no par value.
B)
STOCK OPTIONS
The Board of Directors may grant options to purchase common shares to substantially all employees, officers and directors and to persons or corporations who provide management or consulting services to the Company. The exercise period and the vesting schedule after the grant date are not to exceed 10 years.
Option activity for each of the years ended December 31 was as follows:
| | | | | | |
| 2010 | 2009 | 2008 |
| Number of Options (000’s) | Weighted average exercise price per share | Number of Options (000’s) | Weighted average exercise price per share | Number of Options (000’s) | Weighted average exercise price per share |
Outstanding – beginning of year | 1,195 | 5.95 | 1,294 | 5.80 | 1,262 | 5.78 |
Granted | – | – | – | – | 75 | 6.26 |
Exercised | (86) | 4.57 | (59) | 3.05 | (13) | 3.85 |
Forfeited | (36) | 7.68 | (40) | 5.52 | (30) | 7.28 |
Outstanding – end of year | 1,073 | 6.01 | 1,195 | 5.95 | 1,294 | 5.80 |
Exercisable – end of year | 897 | 5.67 | 842 | 5.23 | 822 | 4.88 |
A summary of stock options outstanding at December 31, 2010 is set out below:
| | | | | |
| Outstanding stock options(000’s) | Exercisable stock options |
Range of Exercise price | Number | Weighted average remaining contractual life | Weighted average exercise price | Number | Weighted average exercise price |
$2.70 to $3.50 | 287 | 2.3 years | 3.05 | 287 | 3.05 |
$4.60 to $6.50 | 591 | 4.3 years | 5.94 | 473 | 5.81 |
$10.30 to $10.90 | 195 | 6.1 years | 10.56 | 137 | 10.67 |
| 1,073 | 5.0 years | 6.01 | 897 | 5.67 |
Options vest one third or one fourth per year from the date of grant. There were no options granted during the year ended December 31, 2010 and 2009. The fair value of common share options granted during the year ended December 31, 2008 were $274,000. The fair value of stock options at the grant date and plan modification dates were estimated using the Black-Scholes option-pricing model, using the following assumptions:
| | |
| 2008 Grant | 2010 Plan Modification |
Dividend yield | Nil | Nil |
Risk-free interest rate | 3.88% | 3.48% |
Expected life | 5 years | 5 years |
Expected volatility | 50% | 63.2% |
During the year ended December 31, 2009, the Company modified its stock option plan to include a cash settlement mechanism. As a result, the Company’s stock option obligations were classified as a current liability (subject to vesting) based on the positive difference between the Company’s closing stock price at period end and the underlying option exercise price. As at December 31, 2009, the Company’s accrued stock option liability was $1,918,000 representing a $642,000 increase in compensation expense, since implementation of the cash settlement mechanism, over the equity obligation of $1,276,000 previously recorded to contributed surplus using the Black Scholes valuation model. As stock option obligations were recorded as a liability on the Company’s balance sheet, stock options were not included in the calculation of the diluted number of shares outstanding (see note 8(e)).
During the fourth quarter of 2010, the Company discontinued the settlement of stock option obligations with cash payments in favour of issuing shares from treasury. At the time of this plan modification the current liabilities of $2,075,000 was transferred to contributed surplus.
Total stock option compensation expense recorded in 2010 was $723,000 (2009 – $1,358,000; 2008 – $843,000) and is included in selling, general and administrative expenses on the Consolidated Statement of Operations and Comprehensive Income.
C)
SHARE UNIT PLANS
The Company has Restricted Share Unit (“RSU), Performance Share Unit (“PSU”) and Deferred Share Unit (“DSU”) plans (collectively the “Share Unit Plans”), whereby RSUs, PSUs and DSUs are granted entitling the participant, at the Company’s option, to receive either a common share or cash equivalent in exchange for a vested unit. RSUs and PSUs are granted to the Company’s officers and employees and vest one third per year over the three year period from the date of grant. DSUs are granted to the independent members of the Company’s Board of Directors (“Board”), vest on the date of grant, and can only be redeemed when the Director resigns from the Board. For the PSU plan, which was introduced in 2009, the number of units granted is dependent on the Company meeting certain return on net asset (“RONA”) performance thresholds during the year of grant. The multiplier within the plan ranges from 0% – 200% dependent on performance. For 2010, the PSU performance adjustment was a negative reduction of 58% from target, resulting in a 77,000 unit adjustment ($284,000). (2009 – negative reduction of 66% from target, resulting in a 103,000 unit adjustment). Compensation expense related to units granted is recognized over the vesting period based on the fair value of the units at the date of the grant and is recorded to compensation expense and contributed surplus. The contributed surplus balance is reduced as the vested unit obligations are settled. For 2010, the fair value of the Share Units granted, net of thePSU performance adjustment, was $1,497,000 (2009 – $1,455,000; 2008 – $279,000) and $1,268,000 of compensation expense was recorded (2009 – $948,000; 2008 – $521,000).
Share Unit Plan activity for the year ended December 31, 2010, 2009 and 2008 was as follows:
| | | | | | | | | | | |
| 2010 | 2009 | 2008 |
| Number of Units | Number of Units | Number of Units |
| RSU | PSU | DSU | Total | RSU | PSU | DSU | Total | RSU | DSU | Total |
Outstanding at January 1 | 223 | 53 | 98 | 374 | 165 | – | 67 | 232 | 182 | 37 | 219 |
Granted | 145 | 132 | 31 | 308 | 172 | 161 | 31 | 364 | 1 | 30 | 31 |
Performance adjustment | – | (77) | – | (77) | – | (103) | – | (103) | – | – | – |
Excercised | (82) | (7) | (49) | (138) | (105) | – | – | (105) | (11) | – | (11) |
Forfeited | (13) | (4) | – | (17) | (9) | (5) | – | (14) | (7) | – | (7) |
Outstanding at December 31 | 273 | 97 | 80 | 450 | 223 | 53 | 98 | 374 | 165 | 67 | 232 |
Exercisable at December 31 | 30 | 10 | 80 | 120 | 33 | – | 98 | 131 | 73 | 67 | 140 |
The Company’s intention is to settle Share Unit Plan obligations from an independent trust established by the Company to purchase common shares of the Company on the open market. The trust is considered to be a variable interest entity and is consolidated in the Company’s financial statements with the cost of the shares held in trust reported as a reduction to capital stock. During 2010, 204,300 common shares were purchased by the trust (2009 – 120,700 common shares; 2008 – 300,095) at an average cost of $6.91 per share (2009 – $5.60 per share; 2008 – $6.86 per share). As at December 31, 2010, the trust held 450,732 shares (2009 – 360,576 shares).
D)
NORMAL COURSE ISSUER BID (“NCIB”)
On January 6, 2010, the Company announced the renewal of its NCIB to purchase for cancellation, up to 880,000 common shares through the facilities of NASDAQ, representing approximately 5% of its outstanding common shares. During the year ended December 31, 2010, the Company purchased 61,769 shares at an average cost of $6.62 per share for an aggregate cost of $409,000. (2009 – 553,710 shares purchased at an average cost of $5.17 per share for an aggregate cost of $2,863,000).
On December 21, 2010, the Company announced the renewal of the NCIB effective January 3, 2011, to purchase up to 850,000 common shares through the facilities of NASDAQ, representing approximately 5% of its outstanding common shares. Shares may be purchased up to December 31, 2011.
E)
RECONCILIATION OF WEIGHTED AVERAGE NUMBER OF DILUTED COMMON SHARES OUTSTANDING
| | | |
(thousands) | 2010 | 2009 | 2008 |
Weighted average common shares outstanding – basic | 17,499 | 17,750 | 18,255 |
Effect of Stock options | 194 | – | 101 |
Effect of Share Unit Plans | 307 | 203 | 205 |
Weighted average common shares outstanding – diluted | 18,000 | 17,953 | 18,561 |
9.
Net Change in Non-cash Working Capital Balances Related to Operations
| | | |
For the years ended December 31 | 2010 | 2009 | 2008 |
Accounts receivable | (25,479) | 33,070 | (10,997) |
Inventories | 7,831 | 27,042 | (33,138) |
Other current assets | 2,358 | 5,800 | (6,619) |
Accounts payable and accrued liabilites | 26,691 | (46,702) | 38,128 |
Income taxes payable | 1,378 | (4,434) | 4,253 |
| 12,779 | 14,776 | (8,373) |
10.
Income Taxes
A)
RECONCILIATION OF THE INCOME TAX PROVISION
The difference between the income tax provision recorded and the provision obtained by applying the combined federal and provincial statutory rates is as follows:
| | | | | | |
For the Years Ended December 31 | 2010 | % | 2009 | % | 2008 | % |
Income before income taxes | 9,354 | | 8,944 | | 32,442 | |
Income taxes calculated at statutory rates | 2,647 | 28.3 | 2,628 | 29.4 | 9,700 | 29.9 |
Non-deductible items | 104 | 1.1 | 119 | 1.3 | 164 | 0.5 |
Capital taxes | 11 | 0.1 | 19 | 0.2 | 56 | 0.2 |
Share based compensation | 712 | 7.6 | (70) | (0.8) | 735 | 2.3 |
Adjustments on filing returns and other | (31) | (0.3) | (60) | (0.7) | 40 | 0.1 |
| 3,443 | 36.8 | 2,636 | 29.4 | 10,695 | 33.0 |
As at December 31, 2010, included in current liabilities are taxes payable of $348,000. As at December 31, 2009, income taxes receivable of $1,029,000 were included in other current assets.
B)
Future income taxes reflect the net effects of temporary differences between the carrying amounts of assets and liabilities for financial reporting purposes and the amounts used for income tax purposes. Significant components of future income tax assets and liabilities are as follows:
| | |
As at December 31 | 2010 | 2009 |
Assets | | |
Property and equipment | 870 | 852 |
Share based compensation | 487 | 856 |
Other | 156 | 127 |
| 1,513 | 1,835 |
Liabilities | | |
Goodwill and other | 397 | 378 |
Net future income tax asset | 1,116 | 1,457 |
The Company believes it is more likely than not that all future income tax assets will be realized.
11.
Related Parties
Schlumberger Limited (“Schlumberger”) owns approximately 56% of the Company’s outstanding shares. The Company is the exclusive distributor in Canada of down hole pump production equipment manufactured by Wilson Supply, a division of Schlumberger. Purchase of such equipment is recorded at exchange amounts agreed to by the parties as follows:
| | | |
For the years ended December 31 | 2010 | 2009 | 2008 |
Cost of sales | 8,212 | 6,703 | 10,680 |
Inventory | 3,544 | 4,154 | 4,549 |
Accounts payable and accrued liabilities | 1,457 | 991 | 759 |
The Company pays facility rental expense to an operations manager in the capacity of landlord. These rent payments are being recorded at exchange amounts agreed to by the parties. For the year ended December 31, 2010, those costs totalled $798,000 (2009 – $765,000; 2008 – $137,000).
12.
Financial Instruments
A)
FAIR VALUES
The Company’s financial instruments recognized on the consolidated balance sheet consist of accounts receivable, accounts payable and accrued liabilities, bank operating loan and long term debt. The fair values of these financial instruments, excluding long term debt, approximate their carrying amounts due to their short-term maturity. At December 31, 2010, the fair value of the long term debt approximated its carrying value due to its floating interest rate nature and short term maturity.
B)
CREDIT RISK
A substantial portion of the Company’s accounts receivable balance is with customers within the oil and gas industry and is subject to normal industry credit risks. The Company follows a program of credit evaluations of customers and limits the amount of credit extended when deemed necessary. The aging of the trade receivable is a follows:
| | |
| December 31, 2010 | December 31, 2009 |
Current | 40,014 | 32,967 |
Less than 60 days overdue | 41,253 | 25,766 |
Greater than 60 days overdue | 5,519 | 6,398 |
Trade accounts receivable | 86,786 | 65,131 |
Other accounts receivable | 8,051 | 4,647 |
Less allowance for credit losses | (1,887) | (2,335) |
Total accounts receivable | 92,950 | 67,443 |
The Company maintains provisions for possible credit losses that are charged to selling, general and administrative expenses by performing an analysis of specific accounts. Movement of the allowance for credit losses is as follows:
| | |
| December 31, 2010 | December 31, 2009 |
Opening balance | 2,335 | 2,776 |
Write offs | (1,385) | (1,026) |
Recoveries | 952 | 440 |
Change in provision for credit losses | (15) | 145 |
Closing balance | 1,887 | 2,335 |
C)
MARKET RISK
The Company’s long term debt bears interest based on floating interest rates. As a result the Company is exposed to market risk from changes in the Canadian prime interest rate which can impact its borrowing costs. Based on the Company’s borrowings levels as at December 31, 2010, a change of one percent in interest rates would be expected to decrease or increase the Company’s annual net income by $0.1 million.
D)
RISK MANAGEMENT
From time to time the Company enters into foreign exchange forward contracts to manage its foreign exchange market risk by fixing the value of its liabilities and future commitments. The Company’s foreign exchange risk arises principally from the settlement of United States dollar dominated net working capital balances as a result of product purchases denominated in United States dollars. As at December 31, 2010 the Company had contracted to purchase US $6,515,000 (2009 – $930,000) of these level two financial instruments at fixed exchange rates with terms not exceeding eight months. The fair market value of the contracts was nominal at December 31, 2010 and 2009.
The Company purchases certain products in US dollars and sells such products to its customers typically priced in Canadian dollars, leading to accounts receivable and accounts payable balances that are subject to foreign exchange gains and losses upon translation. As a result, fluctuations in the value of the Canadian dollar relative to the US dollar can result in foreign exchange gains and losses. As at December 31, 2010, a one percent change in the Canadian dollar relative to the US dollar would be expected to not have a material impact on net income.
13.
Economic Dependency
In respect of the Company’s sales, there is no customer that comprised more than 10% of sales in 2010, (2009 and 2008 one customer comprised 10% of sales).
In respect of the Company’s purchases, 10% of the product purchased is derived from one supplier (2009 – 12%; 2008 – 27%).
14.
Group Registered Retirement Savings Plan
The Company contributes amounts based on employee salaries to a maximum of 6% and the amount deductible under the Income Tax Act, to employees registered retirement savings plans. Contributions in respect of this plan incurred and paid during the year were $765,000 (2009 – $772,000; 2008 – $683,000).
15.
Segment Reporting
The Company distributes oilfield equipment products and related services through its network of 45 branches located in western Canada to oil and gas industry customers. Accordingly, the Company has determined that it operates through a single operating segment and geographic jurisdiction.
16.
Reconciliation of Canadian and United States Generally Accepted Accounting Principles (GAAP)
These consolidated financial statements have been prepared in accordance with Canadian GAAP. The Company’s accounting policies are consistent with US GAAP with the following exceptions:
A)
STATEMENT OF OPERATIONS
There are no material differences between Canadian GAAP net income and comprehensive income and US GAAP net income and comprehensive income.
B)
STATEMENTS OF CHANGES IN SHAREHOLDERS’ EQUITY
| | | |
As at December 31 | 2010 | 2009 | 2008 |
Shareholders’ equity under Canadian GAAP | 150,536 | 142,627 | 139,323 |
Restructuring provision adjustment (i) | (324) | (324) | (324) |
Benefit of deferred tax assets applied to goodwill (ii) | (1,058) | (1,058) | (1,058) |
Shareholders’ equity under U.S. GAAP | 149,154 | 141,245 | 137,941 |
i)
The restructuring provision adjustment relates to a 1995 transaction where restructuring expenditures were recorded in the purchase equation as goodwill under Canadian GAAP but were expensed in the statement of operations for US GAAP.
ii)
In 1996, the Company realized the benefit of certain deferred tax assets on which a 100% valuation provision had been recorded in 1995. This benefit was recorded as a reduction of goodwill for US GAAP.
C)
BALANCE SHEETS
The following table indicates the restated amounts for the items in the Balance Sheets of the Company that would be affected had the consolidated financial statements been prepared in accordance with US GAAP:
| | |
As at December 31 | 2010 | 2009 |
Goodwill (b)(i) and (b)(ii) | 19,188 | 19,188 |
Retained earnings (b)(i) and (b)(ii) | 106,164 | 100,581 |
The following table indicates additional disclosure required had the consolidated financial statements been prepared in accordance with US GAAP:
| | |
As at December 31 | 2010 | 2009 |
Trade payables | 23,996 | 16,736 |
Accrued liabilities | 37,867 | 19,963 |
Accrued compensation expense | 1,500 | 1,790 |
Total accounts payable and accrued liabilities | 63,363 | 38,489 |
D)
STATEMENTS OF CASH FLOWS
Under US GAAP, the disclosure of total cash flows from operating activities prior to changes in non-cash working capital balances related to operations is not permitted.
E)
RECENT US GAAP PRONOUNCEMENTS
Since the Company will be adopting IFRS for 2011, future changes in US GAAP are not applicable as a US GAAP reconciliation will not be required.
Five Years of Financial Data
| | | | | |
(millions of Cdn $, except statistics and per share amounts) | 2010 | 2009 | 2008 | 2007 | 2006 |
Sales | 489.6 | 437.0 | 547.4 | 466.3 | 555.2 |
Gross profit | 75.0 | 76.6 | 107.7 | 84.6 | 103.5 |
% of Sales | 15.3% | 17.5% | 19.7% | 18.1% | 18.6% |
Other expenses | | | | | |
Selling, general & administrative | 62.6 | 64.2 | 71.6 | 58.1 | 63.3 |
Amortization | 2.5 | 2.5 | 2.4 | 2.8 | 2.8 |
Interest expense | 0.7 | 0.9 | 1.0 | 2.0 | 2.7 |
Other (income)/expense | (0.1) | 0.1 | 0.2 | 0.8 | 0.1 |
Total other expenses | 65.7 | 67.7 | 75.2 | 63.7 | 68.9 |
Income before income taxes | 9.3 | 8.9 | 32.4 | 20.9 | 34.6 |
Income tax expense | 3.4 | 2.6 | 10.7 | 7.3 | 11.7 |
Net income | 5.9 | 6.3 | 21.7 | 13.6 | 22.9 |
% of Sales | 1.2% | 1.4% | 4.0% | 2.9% | 4.1% |
Net income per share | | | | | |
Basic | 0.34 | 0.36 | 1.19 | 0.74 | 1.27 |
Diluted | 0.33 | 0.35 | 1.17 | 0.72 | 1.22 |
EBITDA(1) | 12.5 | 12.4 | 35.8 | 25.7 | 40.1 |
% of Sales | 2.5% | 2.8% | 6.5% | 5.5% | 7.2% |
Current assets | 189.4 | 175.1 | 229.5 | 179.5 | 187.8 |
Total assets | 220.7 | 208.0 | 261.4 | 208.7 | 205.4 |
Net working capital Current assets less trade accounts payable and accrued liabilities | 125.7 | 136.6 | 142.8 | 134.7 | 120.2 |
Total debt Bank operating loan + long term debt
| 6.4 | 26.8 | 35.5 | 45.7 | 35.4 |
Shareholders’ equity | 150.5 | 142.6 | 139.3 | 118.2 | 102.5 |
Total debt to equity Total debt / total debt plus equity | 4.0% | 15.8% | 20.3% | 27.9% | 25.7% |
Return on equity Net income / average equity | 3.9% | 4.4% | 16.9% | 12.3% | 25.6% |
(1)See Management’s Discussion and Analysis on page 27 for a detailed description of EBITDA, a non GAAP measure.