UNITED STATES
SECURITIES AND EXCHANGE COMMISSION
Washington, D.C. 20549
Form 10-K
(Mark One)
þ | ANNUAL REPORT PURSUANT TO SECTION 13 OR 15(d) OF THE SECURITIES EXCHANGE ACT OF 1934 |
For The Fiscal Year Ended December 31, 2010
OR
¨ | TRANSITION REPORT PURSUANT TO SECTION 13 OR 15(d) OF THE SECURITIES EXCHANGE ACT OF 1934 |
For the Transition Period from to
Commission File Number 001-12755
Dean Foods Company
(Exact name of Registrant as specified in its charter)

| | |
Delaware | | 75-2559681 |
(State or other jurisdiction of incorporation or organization) | | (I.R.S. Employer Identification No.) |
2711 North Haskell Avenue Suite 3400
Dallas, Texas 75204
(214) 303-3400
(Address, including zip code, and telephone number, including
area code, of Registrant’s principal executive offices)
Securities Registered Pursuant to Section 12(b) of the Act:
| | |
Title of Each Class | | Name of Each Exchange on Which Registered |
Common Stock, $.01par value | | New York Stock Exchange |
Securities Registered Pursuant to Section 12(g) of the Act: None
Indicate by check mark if the registrant is a well-known seasoned-issuer, as defined in Rule 405 of the Securities Act. Yes þ No ¨
Indicate by check mark if the registrant is not required to file reports pursuant to Section 13 or Section 15(d) of the Act. Yes ¨ No þ
Indicate by check mark whether the registrant (1) has filed all reports required to be filed by Section 13 or 15(d) of the Securities Exchange Act of 1934 during the preceding 12 months (or for such shorter period that the registrant was required to file such reports), and (2) has been subject to such filing requirements for the past 90 days. Yes þ No ¨
Indicate by check mark whether the registrant has submitted electronically and posted on its corporate Web site, if any, every Interactive Data File required to be submitted and posted pursuant to Rule 405 of Regulation S-T (§232.405 of this chapter) during the preceding 12 months (or for such shorter period that the registrant was required to submit and post such files). Yes þ No ¨
Indicate by check mark if disclosure of delinquent filers pursuant to Item 405 of Regulation S-K is not contained herein, and will not be contained, to the best of registrant’s knowledge, in definitive proxy or information statements incorporated by reference in Part III of this Form 10-K or any amendment to this Form 10-K ¨
Indicate by check mark whether the registrant is a large accelerated filer, an accelerated filer, a non-accelerated filer, or a smaller reporting company. See the definitions of “large accelerated filer,” “accelerated filer” and “smaller reporting company” in Rule 12b-2 of the Exchange Act. (Check one):
| | | | | | |
Large accelerated filer þ | | Accelerated filer ¨ | | Non-accelerated filer ¨ | | Smaller reporting company ¨ |
| | | | (Do not check if a smaller reporting company) | | |
Indicate by check mark whether the registrant is a shell company (as defined in Rule 12b-2 of the Exchange Act). Yes ¨ No þ
The aggregate market value of the registrant’s voting and non-voting common stock held by non-affiliates of the registrant at June 30, 2010, based on the $10.07 per share closing price for the registrant’s common stock on the New York Stock Exchange on June 30, 2010, was approximately $1.79 billion.
The number of shares of the registrant’s common stock outstanding as of February 18, 2011, was 183,130,138.
DOCUMENTS INCORPORATED BY REFERENCE
Portions of the registrant’s definitive Proxy Statement for its Annual Meeting of Stockholders to be held on or about May 19, 2011, which will be held within 120 days of the registrants fiscal year end, are incorporated by reference into Part III of this Form 10-K.
TABLE OF CONTENTS
Forward-Looking Statements
This Annual Report on Form 10-K (the “Form 10-K”) contains forward-looking statements within the meaning of the Private Securities Litigation Reform Act of 1995, which are subject to risks, uncertainties and assumptions that are difficult to predict. Forward-looking statements are predictions based on expectations and projections about future events, and are not statements of historical fact. Forward-looking statements include statements concerning business strategy, among other things, including anticipated trends and developments in and management plans for our business and the markets in which we operate. In some cases, you can identify these statements by forward-looking words, such as “estimate,” “expect,” “anticipate,” “project,” “plan,” “intend,” “believe,” “forecast,” “foresee,” “likely,” “may,” “should,” “goal,” “target,” “might,” “will,” “could,” “predict,” and “continue,” the negative or plural of these words and other comparable terminology. All forward-looking statements included in this Form 10-K were based upon information available to us as of the filing date of this Form 10-K, and we undertake no obligation to update any of these forward-looking statements for any reason. You should not place undue reliance on forward-looking statements. The forward-looking statements involve known and unknown risks, uncertainties and other factors that may cause our actual results, levels of activity, performance, or achievements to differ materially from those expressed or implied by these statements. These factors include the matters discussed in the section entitled “Part I — Item 1A — Risk Factors” in this Form 10-K, and elsewhere in this Form 10-K. You should carefully consider the risks and uncertainties described under these sections.
PART I
We are one of the leading food and beverage companies in the United States, as well as a global leader in branded plant-based beverages, such as soy, almond, and coconut milks, and other soy-based food products. As we continue to evaluate and seek to maximize the value of our strong brands and product offerings, we have aligned our leadership teams, operating strategies and supply chain initiatives around our two business segments: Fresh Dairy Direct-Morningstar and WhiteWave-Alpro. Fresh Dairy Direct-Morningstar is the largest processor and distributor of milk and other dairy products in the United States, with products sold under more than 50 familiar local and regional brands and a wide array of private labels. WhiteWave-Alpro markets and sells a variety of nationally branded dairy and dairy-related products, such asHorizon Organic® milk and other dairy products,The Organic Cow® organic dairy products, as well as other plant-based beverages and soy food products,International Delight® coffee creamers andLAND O LAKES® creamers and fluid dairy products, andSilk® plant-based beverages, such as soy, almond and coconut milks, and cultured soy products. WhiteWave-Alpro also offers branded soy-based beverages and food products in Europe and markets its products under theAlpro® andProvamel® brands. Additionally, with our Hero/WhiteWave joint venture we have expanded the WhiteWave product footprint beyond the dairy case to capitalize on the chilled fruit-based beverage opportunity with the introduction ofFruit2Day.
Our principal executive offices are located at 2711 North Haskell Avenue, Suite 3400, Dallas, Texas 75204. Our telephone number is (214) 303-3400. We maintain a worldwide web site atwww.deanfoods.com. We were incorporated in Delaware in 1994.
Our Reportable Segments
We have two reportable segments, Fresh Dairy Direct-Morningstar and WhiteWave-Alpro.
In the first quarter of 2010, our Chief Executive Officer, who is our chief operating decision maker, changed the way he evaluates the performance of our operations, develops strategy and allocates capital resources. As a result, beginning in the first quarter of 2010, our Morningstar operations were aligned with our Fresh Dairy
1
Direct operations so that our two reporting segments consisted of Fresh Dairy Direct-Morningstar and WhiteWave-Alpro. This change reflects the divergence between the strategies and objectives of these two segments. Our value-added branded operations at WhiteWave-Alpro added scale with the acquisition of Alpro in July 2009 and are focused on driving growth through effective marketing and innovation. Our traditional dairy operations at Fresh Dairy Direct-Morningstar are driven by a focus on cost and service leadership. We believe these revised segments have increased internal focus and offered management and investors improved visibility into the performance of the segments against their specific objectives. All segment results set forth herein have been recast to present results on a comparable basis. These changes had no impact on consolidated net sales or operating income.
During the second quarter of 2010, we committed to a plan to sell the business operations of our Rachel’s Dairy companies (“Rachel’s”), which provide organic branded dairy-based chilled yogurt, milk and related dairy products primarily in the United Kingdom. The sale of these operations was completed on August 4, 2010. The decision to sell these operations was part of our strategic growth plan and allows us to target our investments in growing our core dairy and branded businesses by divesting non-core businesses. All of our Rachel’s operations, previously reported within the WhiteWave-Alpro segment, have been reclassified as discontinued operations. See Note 2 to our Consolidated Financial Statements. Unless stated otherwise, any reference to income statement items in this Annual Report on Form 10-K refers to results from continuing operations.
In the fourth quarter of 2010, we entered into two separate agreements to sell our Mountain High and private label yogurt operations, which are part of our Fresh Dairy Direct-Morningstar segment. We expect to recognize a gain related to the sale of both of these operations. On February 1, 2011, we completed the sale of our Mountain High yogurt operations. We expect our private label operations sale to close in the first half of 2011. These operations did not meet the requirements to be accounted for as discontinued operations.
Fresh Dairy Direct-Morningstar
Fresh Dairy Direct-Morningstar manufactures, markets and distributes a wide variety of branded and private label dairy case products, including milk, creamers, ice cream, cultured dairy products, juices and teas to retailers, distributors, foodservice outlets, educational institutions and governmental entities across the United States. Fresh Dairy Direct-Morningstar is also one of the leading U.S. manufacturers of private label cultured and extended shelf life dairy products such as ice cream mix, sour and whipped cream, yogurt and cottage cheese.
Fresh Dairy Direct-Morningstar’s net sales totaled $10.2 billion in 2010, or approximately 84% of our consolidated net sales. The following charts graphically depict Fresh Dairy Direct-Morningstar’s 2010 net sales by product and customer and the volume mix of company branded versus private label products.
2
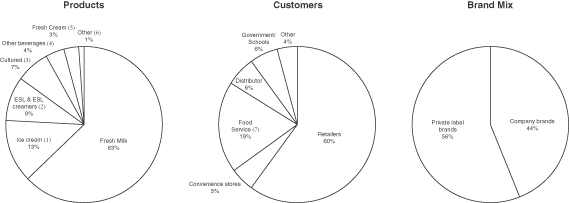
(1) | Includes ice cream, ice cream mix and ice cream novelties. |
(2) | Includes creamers and other extended shelf life (“ESL”) fluids. |
(3) | Includes yogurt, cottage cheese, sour cream and dairy-based dips. |
(4) | Includes fruit juice, fruit-flavored drinks, iced tea and water. |
(5) | Includes half-and-half and whipping cream. |
(6) | Includes items for resale such as butter, cheese, eggs and milk shakes. |
(7) | Includes restaurants, hotels and other foodservice outlets. |
Fresh Dairy Direct-Morningstar sells the majority of its products under local and regional proprietary or licensed brands. Products not sold under these brands are sold as private label. Fresh Dairy Direct-Morningstar sells its products primarily on a local or regional basis through its local and regional sales forces, although some national customer relationships are coordinated by a centralized corporate sales department. Fresh Dairy Direct-Morningstar’s largest customer is Wal-Mart, which includes its subsidiaries such as Sam’s Club, and accounted for approximately 19% of Fresh Dairy Direct-Morningstar’s net sales in 2010.
3
As of December 31, 2010, Fresh Dairy Direct-Morningstar’s local and regional proprietary and licensed brands included the following:
Alta Dena®
Arctic Splash®
Atlanta Dairies®
Barbers®
Barbe’s®
Berkeley Farms®
Broughton™
Borden® (licensed brand)
Brown Cow®
Brown’s Dairy®
Bud’s Ice Cream™
Chug®
Country Charm®
Country Churn®
Country Delite™
Country Fresh®
Country Love®
Creamland™
Dairy Fresh®
Dean’s®
Dipzz®
Fieldcrest®
Foremost® (licensed brand)
Friendship™
Gandy’s™
Garelick Farms®
Hershey’s® (licensed brand)
Hygeia®
Jilbert™
Knudsen® (licensed brand)
LAND O LAKES® (licensed brand)
Land-O-Sun & design®
Lehigh Valley Dairy Farms®
Liberty™
Louis Trauth Dairy Inc.®
Maplehurst®
Mayfield®
McArthur®
Meadow Brook®
Meadow Gold®
Mile High Ice Cream™
Model Dairy®
Mountain High®
Nature’s Pride®
Nurture®
Nutty Buddy®
Oak Farms®
Over the Moon®
Pet® (licensed brand)
Pog® (licensed brand)
Price’s™
Purity™
Reiter™
Robinson™
Saunders™
Schenkel’s All*Star™
Schepps®
Shenandoah’s Pride®
Stroh’s®
Swiss Dairy™
Swiss Premium™
Trumoo®
T.G. Lee®
Tuscan®
Turtle Tracks®
Verifine®
Viva®
Fresh Dairy Direct-Morningstar currently operates 95 manufacturing facilities in 35 states located based on customer needs and other market factors. For more information about facilities in Fresh Dairy Direct-Morningstar, see “Item 2. Properties.” Due to the perishable nature of its products, Fresh Dairy Direct-Morningstar delivers the majority of its products directly to its customers’ locations in refrigerated trucks or trailers that we own or lease. This form of delivery is called a “direct store delivery” or “DSD” system. We believe that Fresh Dairy Direct-Morningstar has one of the most extensive refrigerated DSD systems in the United States.
The primary raw material used in Fresh Dairy Direct-Morningstar products is conventional raw milk (which contains both raw milk and butterfat) that we purchase primarily from farmers’ cooperatives, as well as from independent farmers. The federal government and certain state governments set minimum prices for raw milk and butterfat on a monthly basis. Another significant raw material used by Fresh Dairy Direct-Morningstar is resin, which is a fossil fuel based product used to make plastic bottles. The price of resin is subject to fluctuations based on changes in crude oil and natural gas prices. Other raw materials and commodities used extensively by Fresh Dairy Direct-Morningstar include diesel fuel, used to operate our extensive DSD system, and juice concentrates and sweeteners used in our products. Fresh Dairy Direct-Morningstar generally increases or decreases the prices of its fluid dairy products on a monthly basis in correlation with fluctuations in the costs of raw materials, packaging supplies and delivery costs. However, in some cases, we are competitively or contractually constrained with respect to the means and/or timing of price increases, particularly for non-dairy input costs such as diesel and resin.
Fresh Dairy Direct-Morningstar has several competitors in each of our major product and geographic markets. Competition between dairy processors for shelf-space with retailers is based primarily on price, service, quality and the expected or historical sales performance of the product compared to its competitors. In some cases Fresh Dairy Direct-Morningstar pays fees to customers for shelf-space. Competition for consumer sales is
4
based on a variety of factors such as brand recognition, price, taste preference and quality. Dairy products also compete with many other beverages and nutritional products for consumer sales.
The dairy industry is a mature industry that has traditionally been characterized by slow to flat growth, low profit margins, fragmentation and lack of network optimization. According to the United States Department of Agriculture (“USDA”), per capita consumption of fluid milk continues to decline. Volume sales growth across the industry has declined recently. In this environment, price competition is particularly intense, as smaller processors seek to retain enough volume to cover their fixed costs. In addition, in this increasingly competitive environment, we have been subject to a number of competitive bidding situations in Fresh Dairy Direct-Morningstar, which has reduced our profitability on sales to several customers. In bidding situations, we are subject to the risk of losing certain customers altogether. In addition, supermarkets and food retailers have utilized competitive pricing on dairy products to drive traffic volume and influence customer loyalty, which has significantly reduced their profit margins realized on the sale of such products. This margin compression is being absorbed by both retailers and dairy processors. These industry dynamics have driven private label market share gains over branded products, which is impacting the growth and profitability of our regionally branded products. With unusually low pricing on private label gallons, our regionally branded products are exposed to significantly wider retail price gaps versus private label. Although we expect these trends to continue, we began to see price stabilization over the latter part of 2010.
In response to this dynamic and significant competitive pressure, many processors, including us, are now placing an increased emphasis on cost reduction in an effort to increase margins. We made significant progress against such initiatives in 2009 and 2010 and will continue these efforts for the next 3 to 5 years. Defined strategies for network optimization and organizational changes are in process to improve performance, and programs have been launched to reduce our total cost to serve and our selling and general and administrative costs. We are focusing on sustaining positive cash flow, net debt reduction and are reinvesting for the future in spite of the current challenging environment.
For more information on factors that could impact Fresh Dairy Direct-Morningstar, see “— Government Regulation — Milk Industry Regulation”, “Part II — Item 7. Management’s Discussion and Analysis of Financial Condition and Results of Operations — Known Trends and Uncertainties — Prices of Raw Milk and Other Inputs,” as well as Note 19 to our Consolidated Financial Statements.
WhiteWave-Alpro
WhiteWave-Alpro manufactures, develops, markets and sells a variety of nationally branded dairy and dairy-related products, such asHorizon Organicmilk and other dairy products,The Organic Cow organic dairy products, as well as other plant-based beverages, such as soy, almond, and coconut milks, and soy food products,International Delightcoffee creamers andLAND O LAKEScreamers and fluid dairy products, andSilkplant-based beverages, such as soy, almond and coconut milks, and cultured soy products. WhiteWave-Alpro also offers branded soy-based beverages and food products in Europe and markets its products under theAlproandProvamel brands. Additionally, with our Hero/WhiteWave joint venture we have expanded the WhiteWave product footprint beyond the dairy case to capitalize on the chilled fruit-based beverage opportunity withFruit2Day.
WhiteWave-Alpro’s net sales totaled $1.9 billion in 2010, or approximately 16% of our consolidated net sales. WhiteWave-Alpro sells its products to a variety of customers, including grocery stores, club stores, natural foods stores, mass merchandisers, convenience stores, drug stores and foodservice outlets. WhiteWave-Alpro sells its products primarily through its internal sales forces and independent brokers. WhiteWave-Alpro’s largest customer is Wal-Mart, which includes its subsidiaries such as Sam’s Club, accounting for approximately 16% of WhiteWave-Alpro’s net sales in 2010. Approximately 82% of WhiteWave-Alpro’s net sales are domestic.
5
The following charts graphically depict WhiteWave-Alpro’s 2010 net sales by the mix of our branded versus private label products and customer:
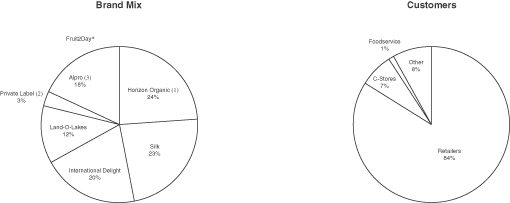
*Represents less than 1% of our total brand mix.
(1) | IncludesHorizon OrganicandThe Organic Coworganic dairy products. |
(2) | Includes private label organic milk and plant-based products. |
(3) | Includes bothAlpro andProvamel brands in Europe. |
WhiteWave-Alpro currently operates five domestic and four international manufacturing facilities. For more information about facilities in WhiteWave-Alpro, see “Item 2. Properties.” The remaining products are manufactured by third-party manufacturers under processing agreements. The majority of WhiteWave-Alpro’s products are delivered through warehouse delivery systems.
The primary raw materials used in our soy-based products include both organic soybeans and non-genetically modified (“non-GMO”) soybeans. Both organic soybeans and non-GMO soybeans are generally available from several suppliers and we are not dependent on any single supplier for these raw materials.
The primary raw material used in our organic milk-based products is organic raw milk. We currently purchase approximately 90% of our organic raw milk from a network of more than 550 family dairy farmers across the United States. The balance of our organic raw milk is sourced from two farms that we own. We generally enter into supply agreements with organic dairy farmers with typical terms of two to five years, which obligate us to purchase certain minimum quantities of organic raw milk.
The primary raw material used in our non-organic dairy products is conventional raw milk. Other raw materials used in WhiteWave-Alpro’s products include palm oil, flavorings and sweeteners. Certain of these raw materials are purchased under long-term contracts in order to better manage the supply and costs of our inputs.
WhiteWave-Alpro has several competitors in each of its product markets. Competition to obtain shelf-space with retailers for a particular product is based primarily on brand recognition and the expected or historical sales performance of the product compared to its competitors. In some cases, WhiteWave-Alpro pays fees to retailers to obtain shelf-space for a particular product. Competition for consumer sales is based on many factors, including brand recognition, price, taste preferences and quality. Consumer demand for plant-based and organic beverages and foods has grown in recent years due to growing consumer confidence in the health benefits attributable to these products, and we believe WhiteWave-Alpro has a leading position in these categories.
For more information on factors that could impact the results of WhiteWave-Alpro, see “— Government Regulation-Milk Industry Regulation,” “Part II — Item 7. Management’s Discussion and Analysis of Financial Condition and Results of Operations — Known Trends and Uncertainties — Prices of Raw Milk and Other Inputs,” as well as Note 19 to our Consolidated Financial Statements.
6
Current Business Strategy
The evolution of Dean Foods into a leading dairy processor began in the early nineties with an acquisition-focused strategy centered on creating scale to align with a consolidating customer base. Since 1993, we have completed more than 40 acquisitions of high quality dairies, dairy products and soy brands, increasing net sales from $150 million to more than $12 billion in 2010. We believe our portfolio of manufacturing and distribution assets enables us to offer regional and national branded and private label products across a variety of product categories, ranging from short shelf life (less than 20 days) to extended shelf life (45 to 60 days) to shelf stable products (6 to 12 months), to customers in a cost effective manner. We believe that Fresh Dairy Direct-Morningstar operates one of the most extensive refrigerated DSD networks in the United States, and WhiteWave-Alpro maintains significant share positions in soy-based and other plant-based beverages, organic dairy and creamers in the United States and Europe.
Our two business reporting segments, Fresh Dairy Direct-Morningstar and WhiteWave-Alpro, operate as two distinct businesses, and we have developed separate strategies to address their respective sets of business opportunities and challenges. As explained more fully below, our Fresh Dairy Direct-Morningstar strategy focuses on reducing cost and increasing profitability, while working to optimize our fluid milk production network. In contrast, we believe WhiteWave-Alpro is well positioned to build on the continuing growth of its branded businesses, and we have developed a strategy to further expand that growth while continuing to focus on cost reduction and capability building.
Fresh Dairy Direct-Morningstar
Large format gallons of milk are the core of our dairy business. Fresh Dairy Direct-Morningstar’s strategy is centered around achieving significantly lower cost per unit of product produced. To build the core business while meeting current market challenges and customer expectations, the Fresh Dairy Direct-Morningstar strategy focuses on the following:
| • | | reducing farm-to-store cost for gallons of milk in large format outlets by optimizing the efficiency of our production network; |
| • | | getting leaner across the business while improving key functional capabilities by redesigning and further streamlining certain processes, such as back office functions; |
| • | | integrating the sales teams of our Fresh Dairy Direct and Morningstar organizations to offer our key customers the breadth of our dairy portfolio and provide one face to the customer; |
| • | | driving profitable growth in winning categories by selectively exiting certain non-core categories and reinvesting in others; and |
| • | | aligning our organizational structure and mobilizing the employee base to address key initiatives while sustaining customer and profit focus. |
WhiteWave-Alpro
WhiteWave-Alpro competes in categories such as organic milk, creamers and plant-based beverages (such as soy milk and almond milk) that we believe have strong long-term growth potential due to their relative immaturity, low household penetration numbers and strong consumer interest. Within these categories, WhiteWave-Alpro brands are often category leaders. To build further growth, the WhiteWave-Alpro strategy encompasses the following:
| • | | expanding the plant-based beverage category’s scope by further expansion with products such as almond and coconut milk, and continuing to innovate behind theSilk brand; |
| • | | investing in emerging and alternative channels and expanding the geography and platform of our portfolio; |
| • | | reducing costs to increase profitability, including creation of a new, centrally-located U.S. production facility to add needed capacity and further optimize the supply chain for growth; |
7
| • | | developing commercial, marketing, innovation, customer logistics, financial management and strategic sales capabilities to enhance growth within the organization; and |
| • | | continuing to support our environment, community and employees through sustainability efforts, building organizational diversity and safeguarding the unique culture and reputation of the organization. |
Future Direction
Within these strategies, a sense of corporate responsibility remains an integral part of our efforts. As we work to improve our business, we are committed to do it in a way that is right for our employees, shareholders, consumers, retail customers and the environment. We will realize savings by reducing waste and duplication while we continue to support programs that improve our local communities.
Seasonality
Our business is affected by seasonal changes in the demand for dairy products. The demand for dairy is fairly stable through the first three quarters of the year with a marked increase in the fourth quarter. Fluid milk volumes tend to decrease in the second and third quarters of the year primarily due to the reduction in dairy consumption associated with our school business. However, this drop in volumes is offset by the increase in ice cream and ice cream mix consumption during the summer months. Sales volumes are typically higher in the fourth quarter associated with increased dairy consumption, especially fresh cream and creamers, during seasonal holidays. Because certain of our operating expenses are fixed, fluctuations in volumes and revenue from quarter to quarter may have a material effect on operating income for the respective quarters.
Intellectual Property
We are continually developing new technology and enhancing existing proprietary technology related to our dairy operations. As of December 31, 2010, 16 United States patents have been issued to us and 20 United States patent applications are pending. We primarily rely on a combination of trademarks, copyrights, trade secrets, confidentiality procedures and contractual provisions to protect our technology and other intellectual property rights. Despite these protections, it may be possible for unauthorized parties to copy, obtain or use certain portions of our proprietary technology or trademarks.
Research and Development
With our state-of-the-art research and development (“R&D”) facility, we are building our capabilities through a team of top consumer packaged goods talent across many disciplines such as product development, dairy and plant-based science, culinary and sensory science, nutrition, packaging design and engineering, and process engineering. Our R&D activities primarily consist of generating and testing new product concepts, new flavors and packaging. Our total R&D expense was $25.8 million, $25.5 million and $14.0 million for 2010, 2009 and 2008, respectively.
Developments since January 1, 2010
Amendment and Extension of Senior Secured Credit Facility and Receivables-Backed Facility — On June 30, 2010, we amended and restated our credit agreement governing our $1.5 billion 5-year senior secured revolving credit facility, our original $1.5 billion 5-year senior secured term loan A and our original $1.8 billion 7-year senior secured term loan B. The terms of the agreement were modified to extend the maturity date for a portion of the principal amount of the revolving credit facility and term loan A by two years, a portion of term loan B by two years and a portion of term loan B by three years (subject to the condition that we meet one of the required leverage, debt, cash or credit rating tests); amend the maximum permitted leverage ratio; as well as amend certain other terms, including an increase in the undrawn costs of the extended portion of the revolving
8
credit facility and the drawn costs of the extended portions of the revolving credit facility, term loan A and term loan B. Additionally, on June 30, 2010, we amended our receivables-backed facility to modify the maximum permitted leverage ratio to be consistent with the senior secured credit facility. The receivables-backed facility was also modified to extend the liquidity termination date and to amend certain other terms.
On December 9, 2010, we entered into an amendment to the credit agreement governing our senior secured credit facility. The terms of the agreement were modified to amend our maximum permitted leverage ratio and minimum permitted interest coverage ratio and to add a senior secured leverage ratio to the existing credit facility. Additionally, on December 9, 2010, we amended our receivables-backed facility to modify the maximum permitted leverage ratio and minimum interest coverage ratio and to add a senior secured leverage ratio to be consistent with the amended ratios discussed above with respect to the senior secured credit facility. The terms of our receivables purchase agreement were also modified to extend the liquidity termination date and to amend certain other terms.
Senior Notes Offering — On December 9, 2010, we agreed to sell in a private placement $400 million in aggregate principal amount of 9.75% senior notes due 2018. These notes are our senior unsecured obligations and mature on December 15, 2018 with interest payable on June 15 and December 15 of each year, commencing June 15, 2011.
On December 16, 2010, the date the senior notes were issued, we used the net proceeds of the offering to pay fees and expenses related to the December 2010 amendment to the senior secured credit facility described above and to repay a portion of our outstanding 2014 tranche A term loan borrowings.
See “Part II — Item 7. Management’s Discussion and Analysis of Financial Condition and Results of Operations — Liquidity and Capital Resources — Current Debt Obligations” below regarding our outstanding indebtedness and Note 9 to our Consolidated Financial Statements for a more complete description of the credit facility amendments, receivables-backed facility amendments and the $400 million senior notes offering.
Competitive Pressuresand Consumer Environment — As a result of the intensely competitive dairy environment, we have been subject to a number of competitive bidding situations in Fresh Dairy Direct-Morningstar, which has reduced our profitability on sales to several customers. The dairy industry has experienced widespread price renegotiations. In bidding situations, we are subject to the risk of losing certain customers altogether. In addition, supermarkets and food retailers have utilized competitive pricing on dairy products to drive traffic volume and influence customer loyalty, which has significantly reduced their profit margins realized on the sale of such products. This margin compression is being absorbed by both retailers and dairy processors, which negatively impacts our margins. Also, these industry dynamics continue to drive private label market share gains over branded products, which is impacting the growth and profitability of our regionally branded products. With unusually low pricing on private label gallons of fresh fluid milk, our regionally branded products are exposed to significantly wider retail price gaps versus private label products. Although we expect these trends to continue, we began to see price stabilization over the latter part of 2010. These margin pressures underscore the importance of our low cost strategy.
In response to this dynamic and significant competitive pressure, many processors, including us, are now placing an increased emphasis on cost reduction in an effort to increase margins. We made significant progress against such initiatives in 2009 and 2010 and intend to continue these efforts over the next three to five years. Defined strategies for network optimization and organizational changes are in process to improve performance and programs have been launched to reduce our total cost to serve and our selling and general and administrative costs. We remain focused on sustaining positive cash flow, and net debt reduction, and we are reinvesting for the future in spite of the current challenging environment for our core dairy business.
In addition to these ongoing pressures, additional challenges became more pronounced as 2010 progressed. The continued recessionary environment has resulted in a significant segment of consumers who are cutting back on purchases of even the most essential items, which has had a pronounced impact on the fluid milk category.
9
We have experienced a reduction in volumes in the industry and in our Fresh Dairy Direct-Morningstar segment. In addition, our customer base has underperformed their historical growth rates versus their peers which has negatively impacted our total volume growth. We expect this trend to continue in the near term.
Conventional Milk Environment — Conventional milk prices continued to increase throughout 2010 compared to historic lows in 2009. We expect the Class I and Class II price to increase fairly dramatically through mid-second quarter of 2011 and level off in the back half of the year. This significant increase in conventional milk prices is a result of limited supply due to production challenges coupled with strong global demand for both Class I and Class II inputs.
Divestiture of Non-core Dairy Operations — During the second quarter of 2010, we committed to a plan to sell the business operations of Rachel’s, which provides organic branded dairy-based chilled yogurt, milk and related dairy products primarily in the United Kingdom. The sale of these operations was completed on August 4, 2010. The decision to sell these operations was part of our strategic growth plan and allows us to target our investments in growing our core dairy and branded businesses by divesting non-core businesses. All of our Rachel’s operations, previously reported within the WhiteWave-Alpro segment, have been reclassified as discontinued operations. See Note 2 to our Consolidated Financial Statements.
In the fourth quarter of 2010, we entered into two separate agreements to sell our Mountain High and private label yogurt operations, which are part of our Fresh Dairy Direct-Morningstar segment. We expect to recognize a gain related to the sale of both of these operations. On February 1, 2011, we completed the sale of our Mountain High yogurt operations. We expect our private label operations sale to close in the first half of 2011. These operations did not meet the requirements to be accounted for as discontinued operations.
Management Changes — On October 8, 2010, we announced that Harrald F. Kroeker would no longer serve as President of our Fresh Dairy Direct division, effective October 6, 2010. Mr. Kroeker received benefits in accordance with our Executive Severance Pay Plan, filed as Exhibit 10.1 to our Current Report on Form 8-K filed on November 19, 2010. We also announced that Christopher Sliva was promoted to Chief Commercial Officer effective October 6, 2010. In this new role, Mr. Sliva has responsibility for directing the commercial strategy of both the Fresh Dairy Direct and Morningstar divisions’ sales and lines of business. These management changes are consistent with the recent realignment of our segments to focus on cost and service leadership within the Fresh Dairy Direct-Morningstar segment.
On November 9, 2010, we announced that Jack Callahan would resign his role as Executive Vice President and Chief Financial Officer to accept a similar position as Chief Financial Officer of another publicly traded company. We also announced that Shaun P. Mara would succeed Mr. Callahan as our Chief Financial Officer effective December 1, 2010. Mr. Mara began his employment as our Senior Vice President and Chief Accounting Officer on June 28, 2010.
On November 30, 2010, we terminated the employment of Paul T. Moskowitz, Executive Vice President, Human Resources. Mr. Moskowitz received benefits in accordance with our Executive Severance Pay Plan, filed as Exhibit 10.1 to our Current Report on Form 8-K filed on November 19, 2010.
On December 9, 2010, we announced the appointment of Scott K. Vopni as our Vice President and Chief Accounting Officer, effective December 15, 2010. Mr. Vopni had previously served as our Vice President and Corporate Controller since joining us in May of 2008.
Facility Closing and Reorganization Activities— In an effort to continue to optimize our distribution network, we closed one facility and announced the closure of another facility within Fresh Dairy Direct-Morningstar during 2010. Additionally during 2010, we incurred charges related to work force reductions under management and department realignments, and a broad-based reduction of facility and distribution personnel and peer benchmarking plans. We recorded facility closing and reorganization costs of $30.8 million in 2010. We
10
will continue to look for areas of opportunity and will likely incur additional costs related to this effort and other initiatives in the near term as we look to transform our business.
Vermont Litigation Settlement— We have reached an agreement with the plaintiffs in our previously disclosed purported class action antitrust lawsuit filed in the United States District Court for the District of Vermont to settle all claims against us in such action. Pursuant to the agreement, which is subject to court approval, we would be obligated to pay $30 million and would agree to other terms and conditions with respect to our raw milk procurement activities at certain of our processing plants located in the Northeast. These other terms and conditions are not expected to have a material impact to our results of operations. We recorded a pre-tax charge in the fourth quarter of 2010 of approximately $30 million with respect to the proposed settlement. See “Item 3. Legal Proceedings.”
Employees
As of December 31, 2010, we had the following employees:
| | | | | | | | |
| | No. of Employees | | | % of Total | |
Fresh Dairy Direct-Morningstar | | | 22,711 | | | | 88 | % |
WhiteWave-Alpro | | | 2,311 | | | | 9 | |
Corporate | | | 758 | | | | 3 | |
| | | | | | | | |
Total | | | 25,780 | | | | 100 | % |
| | | | | | | | |
Approximately 37% of Fresh Dairy Direct-Morningstar’s and 27% of WhiteWave-Alpro’s employees participate in collective bargaining agreements. We believe our relationship with our employees and these organizations is satisfactory.
Government Regulation
Food Related Regulations
As a manufacturer and distributor of food products, we are subject to a number of food-related regulations, including the Federal Food, Drug and Cosmetic Act and regulations promulgated thereunder by the U.S. Food and Drug Administration (“FDA”). This comprehensive regulatory framework governs the manufacture (including composition and ingredients), labeling, packaging and safety of food in the United States. The FDA:
| • | | regulates manufacturing practices for foods through its current good manufacturing practices regulations; |
| • | | specifies the standards of identity for certain foods, including many of the products we sell; and |
| • | | prescribes the format and content of certain information required to appear on food product labels. |
In addition, the FDA enforces the Public Health Service Act and regulations issued thereunder, which authorizes regulatory activity necessary to prevent the introduction, transmission or spread of communicable diseases. These regulations require, for example, pasteurization of milk and milk products. We are subject to numerous other federal, state and local regulations involving such matters as the licensing and registration of manufacturing facilities, enforcement by government health agencies of standards for our products, inspection of our facilities and regulation of our trade practices in connection with the sale of food products.
We use quality control laboratories in our manufacturing facilities to test raw ingredients. Product quality and freshness are essential to the successful distribution of our products. To monitor product quality at our facilities, we maintain quality control programs to test products during various processing stages. We believe our facilities and manufacturing practices are in material compliance with all government regulations applicable to our business.
11
Employee Safety Regulations
We are subject to certain safety regulations, including regulations issued pursuant to the U.S. Occupational Safety and Health Act. These regulations require us to comply with certain manufacturing safety standards to protect our employees from accidents. We believe that we are in material compliance with all employee safety regulations applicable to our business.
Environmental Regulations
We are subject to various environmental regulations. Our plants use a number of chemicals that are considered to be “extremely” hazardous substances pursuant to applicable environmental laws due to their toxicity, including ammonia, which is used extensively in our operations as a refrigerant. Such chemicals must be handled in accordance with such environmental laws. Also, on occasion, certain of our facilities discharge biodegradable wastewater into municipal waste treatment facilities in excess of levels allowed under local regulations. As a result, certain of our facilities are required to pay wastewater surcharges or to construct wastewater pretreatment facilities. To date, such wastewater surcharges have not had a material effect on our financial condition or results of operations.
We maintain above-ground and under-ground petroleum storage tanks at many of our facilities. We periodically inspect these tanks to determine whether they are in compliance with applicable regulations and, as a result of such inspections are required to make expenditures from time to time in order to ensure that these tanks remain in compliance. In addition, upon removal of the tanks, we are sometimes required to make expenditures to restore the site in accordance with applicable environmental laws. To date, such expenditures have not had a material effect on our financial condition or results of operations.
We believe that we are in material compliance with the environmental regulations applicable to our business. We do not expect the cost of our continued compliance to have a material impact on our capital expenditures, earnings, cash flows or competitive position in the foreseeable future. In addition, any asset retirement obligations are not material.
Milk Industry Regulation
The federal government establishes minimum prices that we must pay to producers in federally regulated areas for raw milk. Raw milk primarily contains raw skim milk, in addition to a small percentage of butterfat. Raw milk delivered to our facilities is tested to determine the percentage of butterfat and other milk components, and we pay our suppliers for the raw milk based on the results of these tests.
The federal government’s minimum prices vary depending on the processor’s geographic location or sales area and the type of product manufactured. Federal minimum prices change monthly. Class I butterfat and raw skim milk prices (which are the minimum prices we are required to pay for raw milk that is processed into Class I products such as fluid milk) and Class II raw milk prices (which are the prices we are required to pay for raw milk that is processed into Class II products such as cottage cheese, creams, creamers, ice cream and sour cream) for each month are announced by the federal government the immediately preceding month.
Some states have established their own rules for determining minimum prices for raw milk. In addition to the federal or state minimum prices, we also may pay producer premiums, procurement costs and other related charges that vary by location and supplier.
Organic Regulations
Our organic products are required to meet the standards set forth in the Organic Foods Production Act and the regulations adopted thereunder by the National Organic Standards Board. These regulations require strict methods of production for organic food products and limit the ability of food processors to use non-organic or
12
synthetic materials in the production of organic foods or in the raising of organic livestock. We believe that we are in material compliance with the organic regulations applicable to our business.
Minority Holdings and Other Interests
Consolidated Container Company
We own an approximately 25% non-controlling interest, on a fully diluted basis, in Consolidated Container Company (“CCC”), one of the nation’s largest manufacturers of rigid plastic containers and our largest supplier of plastic bottles and bottle components. We have owned a minority interest in CCC since July 1999 when we sold our U.S. plastic packaging operations to CCC. Vestar Capital Partners, an unaffiliated entity, controls CCC through a majority ownership interest. Pursuant to our agreements with Vestar, we control two of the eight seats on CCC’s Management Committee. We also have entered into various supply agreements with CCC through December 31, 2011, pursuant to which we have agreed to purchase certain of our requirements for plastic bottles and bottle components from CCC. We spent $314.9 million, $268.2 million and $330.3 million on products purchased from CCC during the years ended December 31, 2010, 2009 and 2008, respectively. See Note 3 to our Consolidated Financial Statements for more information on our relationship with CCC.
Hero/WhiteWave Joint Venture
In January 2008, we entered into and formed a 50/50 strategic joint venture with Hero Group (“Hero”), a producer of international fruit and infant nutrition brands, as a strategic growth platform for both companies to extend their global reach by leveraging their established innovation, technology, manufacturing and distribution capabilities over time. The joint venture, Hero/WhiteWave, LLC, which is based in Broomfield, Colorado, combines Hero’s expertise in fruit, innovation and process engineering with WhiteWave’s deep understanding of the American consumer and distribution network, as well as the go-to-market system of WhiteWave. In the second quarter of 2009, the joint venture introducedFruit2Day to grocery and club store channels in North America.
Beginning January 1, 2009, several new agreements, including a capital lease for plant assets constructed within WhiteWave’s existing facilities and operating agreements that include the assignment of day to day management responsibilities to WhiteWave, were entered into between WhiteWave and the joint venture. We determined that this, along with the increased risk created by the capital expenditures and favorable lease terms to the joint venture, as well as the benefit the new product line brings to WhiteWave’s existing customer relationships, resulted in the decision that WhiteWave was the primary beneficiary of the variable interests. As such, the financial position and the results of operations for the joint venture should be consolidated for financial reporting purposes. Accordingly, the joint venture has been consolidated as of January 1, 2009. The resulting non-controlling interest’s share in the equity of the joint venture is presented as a separate component of stockholders’ equity in the Consolidated Balance Sheets and Consolidated Statements of Stockholders’ Equity and the net loss attributable to the non-controlling interest is presented in the Consolidated Statements of Income.
During 2010 and 2009, our joint venture partner made cash contributions of $8.0 million and $12.7 million, respectively, and non-cash contributions of $0.5 million in 2009 to the joint venture. Our joint venture partner did not make any non-cash contributions in 2010. During 2010 and 2009, we made cash contributions of $8.8 million and $10.5 million, respectively, and continued non-cash contributions in the form of the capital lease for the manufacturing facility constructed at one of our existing WhiteWave plants. The joint venture has assets of $26.6 million, primarily property, plant and equipment, and liabilities of $3.5 million, which are included within the WhiteWave-Alpro segment.
Where You Can Get More Information
Our fiscal year ends on December 31. We file annual, quarterly and current reports, proxy statements and other information with the Securities and Exchange Commission.
13
You may read and copy any reports, statements or other information that we file with the Securities and Exchange Commission at the Securities and Exchange Commission’s Public Reference Room at 100 F Street, N.E., Washington D.C. 20549. You can request copies of these documents, upon payment of a duplicating fee, by writing to the Securities and Exchange Commission. Please call the Securities and Exchange Commission at 1-800-SEC-0330 for further information on the operation of the Public Reference Room.
We file our reports with the Securities and Exchange Commission electronically through the Securities and Exchange Commission’s Electronic Data Gathering, Analysis and Retrieval (“EDGAR”) system. The Securities and Exchange Commission maintains an Internet site that contains reports, proxy and information statements and other information regarding companies that file electronically with the Securities and Exchange Commission through EDGAR. The address of this Internet site ishttp://www.sec.gov.
We also make available free of charge through our website atwww.deanfoods.com our annual report on Form 10-K, quarterly reports on Form 10-Q, current reports on Form 8-K, and amendments to those reports filed or furnished pursuant to Section 13(a) or 15(d) of the Securities Exchange Act of 1934 as soon as reasonably practicable after we electronically file such material with, or furnish it to, the Securities and Exchange Commission.
Our Code of Ethics is applicable to all of our employees and directors, with the exception of our Alpro employees, who are subject to a comparable code of ethics. Our Code of Ethics is available on our corporate website atwww.deanfoods.com, together with the Corporate Governance Principles of our Board of Directors and the charters of all of the Committees of our Board of Directors. Any waivers that we may grant to our executive officers or directors under the Code of Ethics, and any amendments to our Code of Ethics, will be posted on our corporate website. If you would like hard copies of any of these documents, or of any of our filings with the Securities and Exchange Commission, write or call us at:
Dean Foods Company
2711 North Haskell Avenue, Suite 3400
Dallas, Texas 75204
(214) 303-3400
Attention: Investor Relations
Competitive Risks
Continued Discounting of Fluid Milk by Large Format Retailers, and the Continued Shift to Private Label, Has Decreased Our Operating Margins and Profitability.
Many of our customers, such as supermarkets, warehouse clubs and food distributors, have experienced industry consolidation in recent years and this consolidation is expected to continue. These consolidations have produced large, sophisticated customers with increased buying power, and have increased the significance of large-format retailers and discounters. As a result, we are increasingly dependent on key retailers, which have significant bargaining power. In addition, some of these customers are vertically integrated and have re-dedicated key shelf-space currently occupied by our regionally branded products for their private label products. Higher levels of price competition and higher resistance to price increases have had a significant impact on our business. During 2010, retailers continued the trend of discounting their prices on milk to drive value for the end consumer and to increase traffic flow, resulting in lower margins for the retailers. Retailers in turn pushed suppliers for lower prices, which has decreased our margins. In addition, the fluid milk category experienced unusually low pricing on private label milk during 2010, which widened the price gaps between private label and our regional brands. As a result, we are experiencing a continued shift from branded to private label products, which further impacts our profitability. If we are unable to structure our business to appropriately respond to the pricing demands of our customers, we may lose these customers to other processors that are willing to sell product at a
14
lower cost. Additionally, if we are not able to lower our cost structure adequately, our profitability could continue to be adversely affected by the decrease in margin.
Volume Softness in the Dairy Category Has Had a Negative Impact on Our Sales and Profits.
Industry wide volume softness across dairy product categories during much of 2010, as compared to 2009, has increased the impact of declining margins on our business. Periods of declining volumes limit the amount of price increases that we can seek to recapture. If these trends continue or accelerate, our business could be further negatively impacted. In addition, during 2010, we experienced a decline in historical volumes from some of our largest customers, which negatively impacted our sales and profitability and which will continue to have a negative impact in the future if we are not able to attract and retain a profitable customer mix.
Increased Competition With Our Nationally Branded Products and Economic Conditions Could Impede Our Growth Rate and Profit Margin.
Our national brands such asSilksoymilk,Horizon Organic, Land O Lakesand International Delight have benefited in many cases from being the first to introduce products in their categories. As plant-based, organic and coffee-enhancing products have gained in popularity with consumers, our products in these categories have attracted competitors, including private label competitors who sell their products at a lower price. In addition, our nationally branded products typically have higher marketing costs than our regionally branded or private label products, which could negatively impact the profitability of this segment of our business. In periods of economic decline, consumers tend to purchase lower-priced products, including conventional milk, coffee creamers and other private label products, which could reduce sales of our nationally branded products. The willingness of consumers to purchase our products will depend upon our ability to offer products providing the right consumer benefits at the right price. Further trade down to lower priced products could adversely affect our sales and profit margin for our nationally branded products.
Many large food and beverage companies have substantially more resources than we do, and they may be able to market their products more successfully than we can, which could cause our growth rate in certain categories to be slower than our forecast and could cause us to lose sales. Some of our nationally branded products compete intensely for consumer spend. If our nationally branded products fail to compete successfully with other branded offerings in the marketplace, our sales and profitability could be negatively impacted.
The Loss of Any of Our Largest Customers Could Negatively Impact Our Sales and Profits.
Our largest customer, Wal-Mart Stores, Inc. and its subsidiaries, including Sam’s Club, accounted for approximately 19% of consolidated net sales during 2010. During 2010, our top five customers, collectively, accounted for approximately 30% of our consolidated net sales. We do not generally enter into sales agreements with our customers, and where such agreements exist, they are generally terminable at will by the customer. The loss of any large customer for an extended length of time could negatively impact our sales and profits.
We are Subject to Competitive Bidding Situations, the Outcome of Which Could Negatively Impact Our Sales and Profits.
Many of our retail customers have become increasingly price sensitive in the current economic climate, which has intensified the competitive environment in which we operate. As a result of the intensely competitive dairy environment, we have been subject to a number of competitive bidding situations, particularly within Fresh Dairy Direct-Morningstar, which reduced our profitability on sales to several customers. We expect this trend of competitive bidding to continue. In bidding situations, we are subject to the risk of losing certain customers altogether, which could negatively impact our sales and profits.
15
Commodity Risks
Availability of and Changes in Raw Material and Other Input Costs Can Adversely Affect Us.
Our business is heavily dependent on raw materials such as conventional and organic raw milk, butterfat, diesel fuel, resin and soybeans and other commodities. In addition to our dependence on conventional and organic raw milk, Fresh Dairy Direct-Morningstar is a large consumer of diesel fuel and WhiteWave-Alpro is affected by the costs of petroleum-based products through the use of common carriers and packaging. The prices of these materials increase and decrease based on market conditions, and in some cases, governmental regulation. Weather, including the heightened impact of weather events related to climate change, also affects the availability and pricing of these inputs. Sometimes supplies of raw materials, such as resin, have been insufficient to meet demand. Volatility in the cost of our raw materials, particularly diesel fuel and other non-dairy inputs, has adversely affected our profitability as upward price changes often lag changes in costs we charge our customers. In some cases the price increases of these non-dairy inputs may exceed the price increases we are able to pass along to our customers due to contractual and other limitations. In periods of rapid movements in dairy commodities, our ability to pass-through costs is impaired due to the timing of passing through the price increases. These lags and limitations have periodically decreased our profit margins in inflationary markets. In addition, raw material cost fluctuations from year to year can cause our revenues to increase or decrease significantly compared to prior periods.
The organic dairy industry is continuing to develop in terms of consumer acceptance and market penetration, and, as a result, continues to experience significant swings in supply and demand. Industry regulation, and the costs of organic farming compared to prices paid for conventional farming can impact the supply of organic raw milk in the market. An oversupply of organic raw milk can cause significant discounting in the sale of organic packaged milk, which increases competitive pressure on our branded products and could cause our profitability to suffer. An undersupply or higher input costs can increase the costs of organic raw milk, which can cause retail price gaps between private label and branded products to expand, potentially decreasing our volumes and adversely affecting our results. The impact of retail price gaps may be compounded by the current economic environment as consumers become increasingly focused on product pricing. In addition, consumers may choose to purchase conventional milk instead of organic milk due to differences in cost, which could further decrease our volumes and results.
Capital Markets and General Economic Risks
We Have Substantial Debt and Other Financial Obligations and We May Incur Even More Debt.
We have substantial debt and other financial obligations and significant unused borrowing capacity. At December 31, 2010, we had outstanding borrowings of approximately $3.0 billion under our senior secured credit facility, of which $2.6 billion were in term loan borrowings with an additional $453.0 million in outstanding borrowings under our $1.5 billion senior secured revolving line of credit. In addition, we had $1.0 billion of face value of senior unsecured notes outstanding and nothing outstanding under our receivables-backed facility at December 31, 2010.
We have pledged substantially all of our assets (including the assets of our subsidiaries) to secure our indebtedness. Our debt level and related debt service obligations:
| • | | require us to dedicate significant cash flow to the payment of principal and interest on our debt which reduces the funds we have available for other purposes; |
| • | | may limit our flexibility in planning for or reacting to changes in our business and market conditions or funding our strategic growth plan; |
| • | | impose on us additional financial and operational restrictions; |
| • | | expose us to interest rate risk since a portion of our debt obligations are at variable rates; and |
| • | | restrict our ability to fund acquisitions. |
16
In addition, in the current economic climate, investors may be apprehensive about investing in companies such as ours that carry a substantial amount of leverage on their balance sheets, and this apprehension may adversely affect the price of our common stock.
Under our senior secured credit facility, we are required to maintain certain financial covenants, including, but not limited to, maximum senior secured leverage, maximum leverage and minimum interest coverage ratios, each as defined under and calculated in accordance with the terms of our senior credit facility and receivables-backed facility. As of December 31, 2010, our maximum permitted leverage ratio was 5.75 times consolidated funded indebtedness to consolidated EBITDA for the prior four consecutive quarters. As of December 31, 2010, our leverage ratio was 5.13 times. The maximum permitted leverage ratio under both the senior secured credit facility and the receivables facility will decline to 5.50 times as of March 31, 2012. Failure to comply with the financial covenants (as defined in our credit agreements), or any other non-financial or restrictive covenant, could create a default under our senior secured credit facility and under our receivables-backed facility. Upon a default, our lenders could accelerate the indebtedness under the facilities, foreclose against their collateral or seek other remedies, which would jeopardize our ability to continue our current operations. We may be required to amend our credit facility, refinance all or part of our existing debt, sell assets, incur additional indebtedness or raise equity. Further, based upon our actual performance levels, our senior secured leverage ratio, leverage ratio and minimum interest coverage ratio requirements or other financial covenants could limit our ability to incur additional debt, which could hinder our ability to execute our current business strategy.
Throughout 2010, significant pricing pressures from our retailer customers, as well as volume declines, decreased our operating profitability. Our ability to make scheduled payments on our debt and other financial obligations and comply with financial covenants depends on our financial and operating performance. Our financial and operating performance will continue to be subject to prevailing economic conditions and to financial, business and other factors, some of which are beyond our control.
Our ability to maintain an adequate level of liquidity in the future is dependent on our ability to renew our receivables-backed facility annually and refinance our senior secured credit facility, portions of which mature beginning in 2012. See “Part II — Item 7. Management’s Discussion and Analysis of Financial Condition and Results of Operations — Liquidity and Capital Resources — Current Obligations” below for more information. The timing, approach, and terms of any such refinancing would depend upon market conditions and management’s judgment, among other factors.
An Impairment in the Carrying Value of Goodwill Could Negatively Impact Our Consolidated Results of Operations and Net Worth.
As of December 31, 2010, we had $3.2 billion of goodwill representing approximately 40% of our total assets, of which $2.5 billion was associated with our Fresh Dairy Direct-Morningstar segment, and $0.7 billion was associated with our WhiteWave-Alpro segment. We record goodwill initially at fair value and review its fair value for impairment at least annually, as of December 1, or more frequently if impairment indicators, such as disruptions to the business, unexpected significant declines in operating performance or sustained market capitalization declines, are present. Goodwill impairment is determined using a two-step process. The first step is to identify if a potential impairment exists by comparing the fair value of a reporting unit with its carrying amount, including goodwill. If the fair value of a reporting unit exceeds its carrying amount, goodwill of the reporting unit is not considered to have a potential impairment and the second step of the impairment test is not necessary. However, if the carrying amount of a reporting unit exceeds its fair value, the second step is performed to determine if goodwill is impaired and to measure the amount of impairment loss to recognize, if any. The second step compares the implied fair value of goodwill with the carrying amount of goodwill. If the implied fair value of goodwill exceeds the carrying amount, then goodwill is not considered impaired. However, if the carrying amount of goodwill exceeds the implied fair value, an impairment loss is recognized in an amount equal to that excess.
17
In performing the first step analysis, we calculate the value of goodwill using an income approach based on the present value of future cash flows of each reporting unit, as well as a market approach that reflects market participant views we believe would exist in an exit transaction. For fiscal 2010, our analysis indicates that each of our reporting units has a fair value in excess of its carrying value and no impairment charge will be required; however, the excess of the reporting unit fair values over carrying values, specifically with respect to our Fresh Dairy Direct reporting unit, is significantly less than in prior years. We can provide no assurance that we will not have an impairment charge in future periods as a result of changes in our operating results.
In assessing the fair value of our reporting units, we make estimates and assumptions about sales, growth rates, our cost of capital and discount rates based on budgets, business plans, economic projections, anticipated future cash flows and marketplace data. There are inherent uncertainties related to these factors and management’s judgment in applying these factors and different assumptions could result in goodwill impairment charges in the future, which could be substantial. Any such impairment would result in our recognizing a non-cash charge, which may adversely affect our results of operations.
The Costs of Providing Employee Benefits Have Escalated, and Liabilities Under Certain Plans May be Triggered due to Our Actions or the Actions of Others, Which May Adversely Affect Our Profitability and Liquidity.
We sponsor various defined benefit and defined contribution retirement plans, as well as contribute to various multi-employer plans on behalf of our employees. Changes in interest rates or in the market value of plan assets could affect the funded status of our pension plans. This could cause volatility in our benefits costs and increase future funding requirements of our plans. Pension and post-retirement costs also may be significantly affected by changes in key actuarial assumptions including anticipated rates of return on plan assets and the discount rates used in determining the projected benefit obligation and annual periodic pension costs. Recent changes in federal laws require plan sponsors to eliminate, over defined time periods, the underfunded status of plans that are subject to ERISA rules and regulations. In addition, turmoil in the financial markets in 2008 brought significant declines in the fair market value of the equity and debt instruments that we hold within our defined benefit master trust to settle future defined benefit plan obligations. Our funded status as of December 31, 2010 decreased by $4.5 million from the prior year end and is still $55.6 million lower than our funded status at December 31, 2007. A significant increase in future funding requirements could have a negative impact on our results of operations, financial condition and cash flows.
Certain of our defined benefit retirement plans, as well as many of the multi-employer plans in which we participate, are less than fully funded. Network optimization activities, including facility closings, may trigger cash payments or previously unrecognized obligations under our defined benefit retirement plans or multi-employer plans in which we participate. In addition, certain actions or the financial condition of other companies which participate in multi-employer plans may create financial obligations for us, which circumstances are entirely out of our control. Future funding requirements, and related charges, associated with multi-employer plans in which we participate could have a negative impact on our results of operations, financial condition and cash flows.
The Continued Recessionary Economy May Adversely Impact Our Business and Results of Operations.
The dairy industry is sensitive to changes in general economic conditions, both nationally and locally. The continued recessionary economy has had an adverse effect on consumer spending patterns. Higher levels of unemployment, higher consumer debt levels, or other unfavorable economic factors could further adversely affect consumer demand for products we sell or distribute, which in turn adversely affects our results of operations. There can be no assurances that government responses to the economic downturn will restore consumer confidence.
18
Changes in Our Credit Ratings May Have a Negative Impact on Our Future Financing Costs or the Availability of Capital.
Some of our debt is rated by Standard & Poor’s, Moody’s, and Fitch Ratings, and there are a number of factors beyond our control with respect to these ratings. During 2010, in response to the decline in our operating results and the difficult dairy operating environment, both Standard & Poor’s and Fitch Ratings downgraded our credit ratings by one level each. Following these actions, our credit ratings continue to be considered below “investment grade” by the ratings agencies. Although the interest rate on our existing credit facilities is not affected by changes in our credit ratings, these recent ratings changes or further downgrades in our credit ratings may impair our ability to raise additional capital in the future on terms that are acceptable to us, may cause the value of our securities to decline and may have other negative implications with respect to our business. Ratings reflect only the views of the ratings agency issuing the rating, are not recommendations to buy, sell or hold our securities and may be subject to revision or withdrawal at any time by the ratings agency issuing the rating. Each rating should be evaluated independently of any other rating.
Strategic Growth Plan Risks
We May Not Realize Anticipated Benefits from Our Strategic Growth Plan or Reduce Costs as Expected.
We are implementing a strategic growth plan, which includes a number of transformational initiatives, that we believe are necessary in order to position our business for future success and growth. Our future success depends upon our ability to achieve a lower cost structure and operate efficiently in the highly competitive food and beverage industry, particularly in an environment of increased competitive activity. In order to capitalize on our cost reduction efforts, it will be necessary to make certain investments in our business, which may be limited due to capital constraints. In addition, it is critical that we have the appropriate personnel in place to continue to lead and execute our plan. Currently, operating conditions have had negative implications for overall employee compensation, which has increased the risk that we may not be able to retain qualified personnel to carry out our strategies. We continue to implement profit-enhancing initiatives that impact our supply chain and related functions. These initiatives are focused on cost-saving opportunities in procurement, distribution, conversion and network optimization. Over the next several years, these initiatives will require investments in people, systems, tools and facilities. Our future success and earnings growth depends in large part on our ability to reduce costs, improve efficiencies and better serve our customers. If we are unable to successfully implement these initiatives or fail to implement them as timely as we anticipate, we could become cost disadvantaged in the marketplace, and our competitiveness and our profitability could decrease. In addition, our failure to achieve anticipated cost savings could lead to an impairment of our goodwill.
Product, Supply Chain and Systems Risks
We Must Identify Changing Consumer Preferences and Develop and Offer Products to Meet Their Preferences.
Consumer preferences evolve over time and the success of our products depends on our ability to identify the tastes, dietary preferences and purchasing habits of consumers and to offer products that appeal to their preferences. Introduction of new products and product extensions requires significant development and marketing investment, and we may fail to realize anticipated returns on such investments due to lack of consumer acceptance of such products. Currently, we believe consumers are trending toward health and wellness beverages. Although we continue to invest in research and development in order to capitalize on this trend, there are currently several global companies with greater resources which compete with us in the health and wellness space. In addition, as consumers become increasingly aware of the environmental and social impacts of the products they purchase their preferences and purchasing decisions may change. If our products fail to meet changing consumer preferences, the return on our investment in those areas will be less than anticipated and our product strategy may not succeed.
19
We May Experience Liabilities or Harm to Our Reputation as a Result of Product Issues, Such as Product Recalls.
We sell products for human consumption, which involves a number of risks. Product contamination, spoilage or other adulteration, product misbranding or product tampering could require us to recall products. We also may be subject to liability if our products or operations violate applicable laws or regulations or in the event our products cause injury, illness or death. In addition, we advertise our products and could be the target of claims relating to false or deceptive advertising under U.S. federal and state laws, including consumer protection statutes of some states. A significant product liability or other legal judgment against us or a widespread product recall may negatively impact our profitability. Even if a product liability or consumer fraud claim is unsuccessful or is not merited, the negative publicity surrounding such assertions regarding our products or processes could materially and adversely affect our reputation and brand image, particularly in categories such as fluid milk that have strong health and wellness credentials.
Disruption of Our Supply Chain or Transportation Systems Could Adversely Affect Our Business.
Damage or disruption to our manufacturing or distribution capabilities due to weather, natural disaster, fire, terrorism, pandemic, strikes, the financial and/or operational instability of key suppliers, distributors, warehousing and transportation providers, or other reasons could impair our ability to manufacture or distribute our products. To the extent that we are unable, or it is not financially feasible, to mitigate the likelihood or potential impact of such events, or to effectively manage such events if they occur, there could be an adverse effect on our business and results of operations, and additional resources could be required to restore our supply chain. In addition, we are subject to federal motor carrier regulations, such as the Federal Motor Carrier Safety Act, with which our extensive DSD system must comply. Failure to comply with such regulations could result in our inability to deliver product to our customers in a timely manner, which could adversely affect our reputation and our results.
Our Business Operations Could be Disrupted if Our Information Technology Systems Fail to Perform Adequately.
The efficient operation of our business depends on our information technology systems. We rely on our information technology systems to effectively manage our business data, communications, supply chain, logistics, accounting and other business processes. If we do not allocate and effectively manage the resources necessary to build and sustain an appropriate technology infrastructure, our business or financial results could be negatively impacted. In addition, our information technology systems may be vulnerable to damage or interruption from circumstances beyond our control, including systems failures, security breaches, and viruses. Any such damage or interruption could have a material adverse effect on our business.
Legal and Regulatory Risks
Pending Antitrust Lawsuits May have a Material Adverse Impact on Our Business.
We are the subject of several antitrust lawsuits, the outcome of which we are unable to predict. Increased scrutiny of the dairy industry has resulted, and may continue to result, in an increase in litigation against us. Such lawsuits are expensive to defend and could cause a diversion of management’s attention. In some cases, pursuant to statute, damages recoverable by private plaintiffs may be trebled, which could result in a large judgment against us in the event we do not prevail in a trial situation. In addition to increased litigation costs, these actions could expose us to negative publicity, which might adversely affect our brands, reputation and/or customer preference for our products. In addition, mergers and acquisitions activities are subject to these antitrust and competition laws, which have impacted, and may continue to impact, our ability to pursue strategic transactions.
20
The Dairy Industry in Which We Operate Has Been Subject to Increased Government Scrutiny Which Could Have an Adverse Impact on Our Business.
We are subject to antitrust and other competition laws in the United States and in the other countries in which we operate. We cannot predict how these laws or their interpretation, administration and enforcement will impact us. Throughout 2010, the dairy industry was the subject of increased government scrutiny. In 2010, the current administration initiated a review of existing dairy policies in order to consider potential changes to those policies. This review process may result in changes to the dairy industry that we cannot anticipate and that may have a material adverse impact on our business.
Litigation or Legal Proceedings Could Expose Us to Significant Liabilities and Have a Negative Impact on Our Reputation.
We are party to various litigation claims and legal proceedings. We evaluate these litigation claims and legal proceedings to assess the likelihood of unfavorable outcomes and to estimate, if possible, the amount of potential losses. Based on these assessments and estimates, we establish reserves and/or disclose the relevant litigation claims or legal proceedings, as appropriate. These assessments and estimates are based on the information available to management at the time and involve a significant amount of management judgment. Actual outcomes or losses may differ materially from our current assessments and estimates.
Labor Disputes Could Adversely Affect Us.
As of December 31, 2010, approximately 37% of Fresh Dairy Direct-Morningstar’s and 27% of WhiteWave-Alpro’s employees participated in collective bargaining agreements. At any given time, we may face a number of union organizing drives. When we face union organizing drives, we and the union may disagree on important issues which, in turn, could possibly lead to a strike, work slowdown or other job actions at one or more of our locations. A strike, work slowdown or other labor unrest could in some cases impair our ability to supply our products to customers, which could result in reduced revenue and customer claims.
Our Business is Subject to Various Environmental Laws, Which May Increase Our Compliance Costs.
Our business operations are subject to numerous environmental and other air pollution control laws, including the federal Clean Air Act, the federal Clean Water Act, and the Comprehensive Environmental Response, Compensation and Liability Act of 1980, as amended, as well as state and local statutes. These laws and regulations cover the discharge of pollutants, wastewater, and hazardous materials into the environment. In addition, various laws and regulations addressing climate change are being considered or implemented at the federal and state levels. New legislation, as well as current federal and other state regulatory initiatives relating to these environmental matters, could require us to replace equipment, install additional pollution controls, purchase various emission allowances or curtail operations. These costs could adversely affect our results of operations and financial condition.
Changes in Laws, Regulations and Accounting Standards, Including Those of Non-US Jurisdictions, Could Have an Adverse Effect on Our Financial Results.
We are subject to federal, state, local and foreign governmental laws and regulations, including those promulgated by the United States Food and Drug Administration, the United States Department of Agriculture, the Sarbanes-Oxley Act of 2002 and numerous related regulations promulgated by the Securities and Exchange Commission and the Financial Accounting Standards Board. Changes in federal, state or local laws, or the interpretations of such laws and regulations, may negatively impact our financial results or our ability to market our products. In addition, we have operations outside of the United States which may present unique challenges and increase our exposure to the risks associated with foreign operations, including foreign currency risks and compliance with foreign rules and regulations. Any or all of these risks could adversely impact our financial results.
21
Item 1B. | Unresolved Staff Comments |
None.
Our corporate headquarters are located in leased premises at 2711 North Haskell Avenue, Suite 3400, Dallas, TX 75204. In addition, we operate more than 100 manufacturing facilities. Management believes that Dean Foods’ facilities are well maintained and are generally suitable and of sufficient capacity to support our current business operations and that the loss of any single facility would not have a material adverse effect on our operations or financial results. The following tables set forth, by business segment, our principal manufacturing facilities.
Fresh Dairy Direct-Morningstar
Fresh Dairy Direct-Morningstar currently conducts its manufacturing operations within the following 95 facilities, most of which are owned:
Homewood, Alabama(2)
Decatur, Alabama
Buena Park, California
City of Industry, California(2)
Fullerton, California
Gustine, California
Hayward, California
Riverside, California
Tulare, California
Delta, Colorado
Denver, Colorado
Englewood, Colorado
Greeley, Colorado
Newington, Connecticut
Deland, Florida
Miami, Florida
Orlando, Florida
Baxley, Georgia
Braselton, Georgia
Hilo, Hawaii
Honolulu, Hawaii
Boise, Idaho
Belvidere, Illinois
Harvard, Illinois
Huntley, Illinois
O’Fallon, Illinois
Rockford, Illinois
Decatur, Indiana
Huntington, Indiana
Rochester, Indiana
LeMars, Iowa
Louisville, Kentucky
Murray, Kentucky
Newport, Kentucky(2)
New Orleans, Louisiana
Shreveport, Louisiana
Bangor, Maine
Frederick, Maryland
Franklin, Massachusetts
Lynn, Massachusetts
Mendon, Massachusetts
Evart, Michigan
Grand Rapids, Michigan
Livonia, Michigan
Marquette, Michigan
Thief River Falls, Minnesota
White Bear Lake, Minnesota
Woodbury, Minnesota
Billings, Montana
Great Falls, Montana
North Las Vegas, Nevada
Reno, Nevada
Florence, New Jersey
Albuquerque, New Mexico
Delhi, New York
Friendship, New York
Rensselaer, New York
High Point, North Carolina
Winston-Salem, North Carolina
Bismarck, North Dakota
Tulsa, Oklahoma
Marietta, Ohio
Springfield, Ohio
Toledo, Ohio
Erie, Pennsylvania
Lansdale, Pennsylvania
Lebanon, Pennsylvania
Schuylkill Haven, Pennsylvania
Sharpsville, Pennsylvania
Spartanburg, South Carolina
Sioux Falls, South Dakota
Athens, Tennessee
Nashville, Tennessee(2)
Dallas, Texas(2)
El Paso, Texas
Houston, Texas
Lubbock, Texas
McKinney, Texas
San Antonio, Texas
Sulphur Springs, Texas(2)
Waco, Texas
Orem, Utah
Salt Lake City, Utah
Richmond, Virginia
Springfield, Virginia
Ashwaubenon, Wisconsin
Richland Center, Wisconsin
Sheboygan, Wisconsin
Waukesha, Wisconsin
The majority of Fresh Dairy Direct-Morningstar’s manufacturing facilities also serve as distribution facilities. In addition, Fresh Dairy Direct-Morningstar has numerous distribution branches located across the country, some of which are owned but most of which are leased. Fresh Dairy Direct-Morningstar’s headquarters are located within our corporate headquarters.
22
WhiteWave-Alpro
WhiteWave-Alpro currently conducts its manufacturing operations from the following 9 facilities, most of which are owned:
City of Industry, California
Jacksonville, Florida
Bridgeton, New Jersey
Cedar City, Utah
Mt. Crawford, Virginia
Wevelgem, Belgium
Issenheim, France
Landgraaf, Netherlands
Northamptonshire, United Kingdom
WhiteWave also owns two organic dairy farms located in Paul, Idaho and Kennedyville, Maryland. WhiteWave’s headquarters and our research and development facility are located in leased premises in Broomfield, Colorado. Alpro’s headquarters are located in leased premises in Gent, Belgium.
We are not party to, nor are our properties the subject of, any material pending legal proceedings, other than as set forth below:
We were named, among several defendants, in two purported class action antitrust complaints filed on July 5, 2007. The complaints were filed in the United States District Court for the Middle District of Tennessee, Columbia Division, and allege generally that we and others in the milk industry worked together to limit the price Southeastern dairy farmers are paid for their raw milk and to deny these farmers access to fluid Grade A milk processing facilities (“dairy farmer actions”). A third purported class action antitrust complaint (“retailer action”) was filed on August 9, 2007 in the United States District Court for the Eastern District of Tennessee, Greeneville Division. The complaint in the retailer action was amended on March 28, 2008. The amended complaint alleges generally that we, either acting alone or in conjunction with others in the milk industry, lessened competition in the Southeastern United States for the sale of processed fluid Grade A milk to retail outlets and other customers, and that the defendants’ conduct also artificially inflated wholesale prices for direct milk purchasers. Plaintiffs in both the dairy farmer actions and the retailer action are seeking damages for the alleged violations. If plaintiffs are successful and we are judged to have violated the antitrust laws, plaintiffs are entitled to three times the damages caused by the violations found. Four additional purported class action complaints were filed on August 27, 2007, October 3, 2007, November 15, 2007 and February 13, 2008 in the United States District Court for the Eastern District of Tennessee, Greeneville Division. The allegations in these complaints are similar to those in the dairy farmer actions.
On January 7, 2008, a United States Judicial Panel on Multidistrict Litigation transferred all of the pending cases to the Eastern District of Tennessee, Greeneville Division. On April 1, 2008, the Eastern District Court ordered the consolidation of the six dairy farmer actions, and ordered the retailer action to be administratively coordinated with the consolidated dairy farmer actions. A motion to dismiss the dairy farmer actions was denied on May 20, 2008, and an amended consolidated complaint was filed by the dairy farmer plaintiffs on June 20, 2008. A motion to dismiss the retailer action was denied on July 27, 2009. Motions for class certification were filed in both actions on May 1, 2009. The motion for class certification in the dairy farmer action was granted on September 7, 2010. A petition seeking leave to appeal that decision was filed with the Sixth Circuit on September 21, 2010 and is currently pending. The motion for class certification in the retailer action is still pending. A motion for summary judgment in the retailer action was granted in part and denied in part on August 4, 2010. Defendants filed a motion for reconsideration on September 10, 2010, and filed a supplemental motion for summary judgment as to the remaining claims on September 27, 2010. Those motions are currently pending before the court. A motion for summary judgment in the dairy farmer action was filed on July 27, 2010 and remains pending. Fact discovery and expert discovery are complete in these matters, and expert reports have been submitted. Presently, trial in the dairy farmer action is scheduled to begin in June 2011. If the Sixth Circuit grants the petition to appeal the class certification motion, we expect that the trial will be postponed. We intend to continue to vigorously defend against these lawsuits.
23
On June 29, 2009, another purported class action lawsuit was filed in the Eastern District of Tennessee, Greeneville Division, on behalf of indirect purchasers of processed fluid Grade A milk (“indirect purchaser action”). The allegations in this complaint are similar to those in the retailer action, but primarily involve state law claims. Because the allegations in this complaint substantially overlap with the allegations in the retailer action, on September 1, 2009, the Court granted the parties’ joint motion to stay all proceedings in the indirect purchaser action pending the outcome of the summary judgment motions in the retailer action.
On October 8, 2009, we were named, among several defendants, in a purported class action antitrust complaint filed in the United States District Court for the District of Vermont. The original complaint was amended on January 21, 2010, and contained allegations similar in nature to that of the dairy farmer actions (noted above), and alleges generally that we and others in the milk industry worked together to limit the price dairy farmers in the Northeastern United States are paid for their raw milk and to deny these farmers access to fluid Grade A milk processing facilities. A second similar complaint was filed by a different plaintiff on January 14, 2010. The Company has reached an agreement with the plaintiffs to settle all claims against the Company in this action. The settlement agreement is subject to court approval, and multiple motions related to the settlement agreement are currently pending before the court. There can be no assurance that the court will approve the agreement as proposed by the parties. Pursuant to the agreement the Company would be obligated to pay $30 million, and would agree to other terms and conditions with respect to its raw milk procurement activities at certain of its processing plants located in the Northeast.
On January 22, 2010, the United States Department of Justice (“DOJ”) and the States of Wisconsin, Illinois and Michigan (“Plaintiff States”) filed a civil action in the Eastern District of Wisconsin (“DOJ lawsuit”) alleging that the Company violated Section 7 of the Clayton Act when it acquired the Consumer Products Division of Foremost Farms USA on April 1, 2009 (the “acquisition”) for an aggregate purchase price of approximately $35 million. The DOJ and the Plaintiff States seek a declaration that the acquisition violates Section 7 of the Clayton Act, divestiture by the Company of all assets and interests it acquired as part of the acquisition, an order permanently enjoining the Company from further ownership and operation of the assets that were part of the acquisition, and to compel the Company to provide certain advance notification of future acquisitions involving school milk or fluid milk processing operations. A motion to partially dismiss the DOJ lawsuit was denied on April 7, 2010. This matter is currently in the fact discovery stage. The Company intends to vigorously defend against this action.
On April 28, 2009, a stockholder derivative complaint was filed purportedly on behalf of Dean Foods Company (the “Company”) in the United States District Court for the Eastern District of Tennessee, Greeneville division. The complaint names the Company’s then current directors, as well an officer of the Company, and a former director among the defendants. The complaint alleges that the officers and directors breached their fiduciary duties to the Company under Delaware law by approving the 2001 merger between the former Dean Foods Company and Suiza Foods Corporation, and allegedly participating in, or failing to prevent, a purported conspiracy to fix the price of Grade A milk. The complaint also names others in the milk industry as defendants for allegedly aiding and abetting the officers’ and directors’ breach of their fiduciary duties and names the Company as a nominal defendant. The plaintiffs are seeking, on behalf of the Company, an undisclosed amount of damages and equitable relief. On August 7, 2009, the Company and other defendants filed a motion to dismiss the complaint and a motion to transfer the case to the United States District Court for the Northern District of Texas. The defendants’ motion to transfer the case was granted on March 31, 2010. On September 14, 2010, the Court granted the motion to dismiss this matter. The plaintiffs subsequently filed an amended complaint, and the Company and the other defendants have filed a motion to dismiss the amended complaint. On January 26, 2011, the Court granted a motion to dismiss the amended complaint and entered a judgment dismissing the case with predjudice.
On January 18, 2008, our subsidiary, Kohler Mix Specialties, LLC (“Kohler”), was named as a defendant in a civil complaint filed in the Superior Court, Judicial District of Hartford. The plaintiff in the case is the Commissioner of Environmental Protection of the State of Connecticut. The complaint alleges generally that
24
Kohler improperly discharged wastewater in to the waters of the State of Connecticut, and bypassed certain wastewater treatment equipment in violation of certain Connecticut environmental regulations and Kohler’s wastewater discharge permit. The plaintiff is seeking injunctive relief and civil penalties with respect to the claims. On December 14, 2009, Kohler filed its answer to the complaint. This matter is currently in the fact discovery stage.
At this time, it is not possible for us to predict the ultimate outcome of the matters set forth above.
Other than the matters set forth above, we are party from time to time to certain claims, litigations, audits and investigations. Potential liabilities associated with the other matters referred to in this paragraph are not expected to have a material adverse impact on our financial position, results of operations or cash flows.
Other — We are in discussions with numerous states, most but not all of whom have appointed an agent to conduct an examination of our books and records to determine whether we have complied with state unclaimed property laws. In addition to seeking remittance of unclaimed property, some states may also seek interest and penalties. At this time, it is not possible for us to predict the ultimate outcome of these potential examinations.
25
PART II
Item 5. | Market for Registrant’s Common Equity, Related Stockholder Matters and Issuer Purchases of Equity Securities. |
Our common stock trades on the New York Stock Exchange under the symbol “DF.” The following table sets forth the high and low closing sales prices of our common stock as quoted on the New York Stock Exchange for the last two fiscal years. At February 18, 2011, there were 4,241 record holders of our common stock.
| | | | | | | | |
| | High | | | Low | |
2009: | | | | | | | | |
First Quarter | | $ | 21.13 | | | $ | 17.83 | |
Second Quarter | | | 20.70 | | | | 17.61 | |
Third Quarter | | | 21.92 | | | | 17.60 | |
Fourth Quarter | | | 19.65 | | | | 15.90 | |
2010: | | | | | | | | |
First Quarter | | | 18.53 | | | | 14.46 | |
Second Quarter | | | 16.89 | | | | 9.57 | |
Third Quarter | | | 12.00 | | | | 9.49 | |
Fourth Quarter | | | 10.80 | | | | 7.26 | |
We have not historically declared or paid a regular cash dividend on our common stock. We have no current plans to pay a cash dividend in the future.
See “Item 7. Management’s Discussion and Analysis of Financial Condition and Results of Operations — Liquidity and Capital Resources — Current Debt Obligations” and Note 9 to our Consolidated Financial Statements for further information regarding the terms of our senior secured credit facility, including terms restricting the payment of dividends.
Stock Repurchases — Since 1998, our Board of Directors has from time to time authorized the repurchase of our common stock up to an aggregate of $2.3 billion, excluding fees and expenses. We made no share repurchases in 2010 or 2009 and do not intend to make any repurchases for the foreseeable future. As of December 31, 2010, $218.7 million was available for repurchases under this program (excluding fees and commissions). Shares, when repurchased, are retired.
26
Item 6. | Selected Financial Data |
The following selected financial data as of and for each of the five years in the period ended December 31, 2010 has been derived from our audited Consolidated Financial Statements. The selected financial data do not purport to indicate results of operations as of any future date or for any future period. The selected financial data should be read in conjunction with our Consolidated Financial Statements and related Notes.
| | | | | | | | | | | | | | | | | | | | |
| | Year Ended December 31 | |
| | 2010 | | | 2009 | | | 2008 | | | 2007 | | | 2006 | |
| | (Dollars in thousands except share data) | |
Operating data: | | | | | | | | | | | | | | | | | | | | |
Net sales | | $ | 12,122,887 | | | $ | 11,113,782 | | | $ | 12,361,311 | | | $ | 11,731,870 | | | $ | 10,011,018 | |
Cost of sales | | | 9,116,965 | | | | 8,008,561 | | | | 9,438,593 | | | | 9,015,216 | | | | 7,290,290 | |
| | | | | | | | | | | | | | | | | | | | |
Gross profit(1) | | | 3,005,922 | | | | 3,105,221 | | | | 2,922,718 | | | | 2,716,654 | | | | 2,720,728 | |
Operating costs and expenses: | | | | | | | | | | | | | | | | | | | | |
Selling and distribution | | | 1,904,526 | | | | 1,818,833 | | | | 1,802,214 | | | | 1,708,594 | | | | 1,636,825 | |
General and administrative | | | 629,656 | | | | 623,835 | | | | 482,392 | | | | 415,694 | | | | 405,985 | |
Amortization of intangibles | | | 11,295 | | | | 9,637 | | | | 9,836 | | | | 6,744 | | | | 5,983 | |
Facility closing and reorganization costs | | | 30,761 | | | | 30,162 | | | | 22,758 | | | | 34,421 | | | | 25,116 | |
Other expense(2) | | | 30,000 | | | | — | | | | — | | | | 1,688 | | | | — | |
| | | | | | | | | | | | | | | | | | | | |
Total operating costs and expenses | | | 2,606,238 | | | | 2,482,467 | | | | 2,317,200 | | | | 2,167,141 | | | | 2,073,909 | |
| | | | | | | | | | | | | | | | | | | | |
Operating income | | | 399,684 | | | | 622,754 | | | | 605,518 | | | | 549,513 | | | | 646,819 | |
Other (income) expense: | | | | | | | | | | | | | | | | | | | | |
Interest expense(3)(6) | | | 248,301 | | | | 246,510 | | | | 308,178 | | | | 333,328 | | | | 194,630 | |
Other (income) expense, net(8) | | | 161 | | | | (4,221 | ) | | | 1,123 | | | | 5,956 | | | | 429 | |
| | | | | | | | | | | | | | | | | | | | |
Total other expense | | | 248,462 | | | | 242,289 | | | | 309,301 | | | | 339,284 | | | | 195,059 | |
| | | | | | | | | | | | | | | | | | | | |
Income from continuing operations before income taxes | | | 151,222 | | | | 380,465 | | | | 296,217 | | | | 210,229 | | | | 451,760 | |
Income taxes | | | 73,482 | | | | 151,845 | | | | 114,330 | | | | 82,862 | | | | 174,376 | |
| | | | | | | | | | | | | | | | | | | | |
Income from continuing operations | | | 77,740 | | | | 228,620 | | | | 181,887 | | | | 127,367 | | | | 277,384 | |
Gain (loss) on sale of discontinued operations, net of tax | | | 7,521 | | | | 89 | | | | (1,275 | ) | | | 608 | | | | (1,978 | ) |
Income (loss) from discontinued operations, net of tax | | | (2,505 | ) | | | (862 | ) | | | 3,158 | | | | 3,378 | | | | (49,992 | ) |
| | | | | | | | | | | | | | | | | | | | |
Net income | | | 82,756 | | | | 227,847 | | | | 183,770 | | | | 131,353 | | | | 225,414 | |
Net loss attributable to non-controlling interest | | | 8,735 | | | | 12,461 | | | | | | | | — | | | | — | |
| | | | | | | | | | | | | | | | | | | | |
Net income attributable to Dean Foods Company | | $ | 91,491 | | | $ | 240,308 | | | $ | 183,770 | | | $ | 131,353 | | | $ | 225,414 | |
| | | | | | | | | | | | | | | | | | | | |
Cash dividend paid per share | | $ | — | | | $ | — | | | $ | — | | | $ | 15.00 | | | $ | — | |
| | | | | | | | | | | | | | | | | | | | |
Basic earnings per common share: | | | | | | | | | | | | | | | | | | | | |
Net income attributable to Dean Foods Company | | $ | 0.50 | | | $ | 1.41 | | | $ | 1.23 | | | $ | 1.01 | | | $ | 1.68 | |
| | | | | | | | | | | | | | | | | | | | |
Diluted earnings per common share: | | | | | | | | | | | | | | | | | | | | |
Net income attributable to Dean Foods Company | | $ | 0.50 | | | $ | 1.38 | | | $ | 1.20 | | | $ | 0.96 | | | $ | 1.61 | |
| | | | | | | | | | | | | | | | | | | | |
Average common shares: | | | | | | | | | | | | | | | | | | | | |
Basic | | | 181,799,306 | | | | 170,986,886 | | | | 149,266,519 | | | | 130,310,811 | | | | 133,938,777 | |
| | | | | | | | | | | | | | | | | | | | |
Diluted | | | 182,861,802 | | | | 173,858,303 | | | | 153,395,746 | | | | 137,291,998 | | | | 139,762,104 | |
| | | | | | | | | | | | | | | | | | | | |
Other data: | | | | | | | | | | | | | | | | | | | | |
Ratio of earnings to fixed charges(4) | | | 1.50 | x | | | 2.26 | x | | | 1.81 | x | | | 1.55 | x | | | 2.85 | x |
| | | | | |
Balance sheet data (at end of period): | | | | | | | | | | | | | | | | | | | | |
Total assets | | $ | 7,956,667 | | | $ | 7,843,941 | | | $ | 7,040,192 | | | $ | 7,033,356 | | | $ | 6,770,173 | |
Long-term debt(5)(6) | | | 4,067,525 | | | | 4,228,979 | | | | 4,489,251 | | | | 5,272,351 | | | | 3,355,851 | |
Other long-term liabilities | | | 351,645 | | | | 393,575 | | | | 411,991 | | | | 320,181 | | | | 238,682 | |
Non-controlling interest | | | 14,543 | | | | 15,286 | | | | — | | | | — | | | | — | |
Dean Foods Company stockholders’ equity(6)(7) | | | 1,499,525 | | | | 1,351,946 | | | | 558,234 | | | | 51,267 | | | | 1,809,399 | |
27
(1) | As disclosed in Note 1 to our Consolidated Financial Statements, we include certain shipping and handling costs within selling and distribution expense. As a result, our gross profit may not be comparable to other entities that present all shipping and handling costs as a component of cost of sales. |
(2) | Results for 2010 include a charge of $30.0 million related to a class action antitrust complaint settlement (see “Part I — Item 3. Legal Proceedings” for more information regarding this charge) and 2007 includes a loss of $1.7 million relating to the sale of our tofu business. |
(3) | Results for 2010 include charges totaling $12.3 million in financing costs associated with the amendments of our senior secured credit facility on June 30, 2010 and December 9, 2010. Additionally, results for 2007 include a charge of $13.5 million to write-off financing costs related to the refinancing of our senior secured credit facility. |
(4) | For purposes of calculating the ratio of earnings to fixed charges, “earnings” represents income before income taxes plus fixed charges. “Fixed charges” consist of interest on all debt, amortization of deferred financing costs and the portion of rental expense that we believe is representative of the interest component of rent expense. |
(5) | Includes the current portion of long-term debt. |
(6) | In May 2009, we issued and sold 25.4 million shares of our common stock in a public offering. We received net proceeds of $444.7 million from the offering. The net proceeds from the offering were used to repay the $122.8 million aggregate principal amount of our subsidiary’s 6.625% senior notes due May 15, 2009, and indebtedness under our receivables-backed facility. |
| On March 5, 2008, we issued and sold 18.7 million shares of our common stock in a public offering. We received net proceeds of approximately $400 million from the offering which were used to reduce debt outstanding under the revolving portion of our senior secured credit facility. |
| On April 2, 2007, we recapitalized our balance sheet with the completion of a new $4.8 billion senior secured credit facility and the return of $1.94 billion to shareholders of record as of March 27, 2007, through a $15 per share special cash dividend. |
(7) | Effective January 1, 2007, we adopted Financial Accounting Standards related to “Accounting for Uncertainty in Income Taxes”. As a result, we recognized a $25.9 million increase in our liability for uncertain tax positions, a $20.1 million increase in deferred income tax assets, a $0.3 million decrease to additional paid-in capital, a $0.2 million decrease to goodwill and a $5.7 million decrease to retained earnings. |
| The balance at December 31, 2006 reflects a $14.8 million reduction related to the adoption of Financial Accounting Standards related to “Employers’ Accounting for Defined Benefit Pension and Other Postretirement Plans — an Amendment of FASB Statements No. 87, 88, 106, and 132(R)”. The reduction had no impact on net income. |
(8) | Results for 2009 include a gain of $4.2 million related to a Euro-based forward currency contract related to the Alpro acquisition. Results for 2007 include charges of $4.5 million for professional fees and other costs related to the second quarter special cash dividend. |
28
Item 7. | Management’s Discussion and Analysis of Financial Condition and Results of Operations |
Business Overview
We are one of the leading food and beverage companies in the United States. Fresh Dairy Direct-Morningstar is the largest processor and distributor of milk and other dairy products in the country, with products sold under more than 50 familiar local and regional brands and a wide array of private labels. WhiteWave-Alpro markets and sells a variety of nationally branded dairy and dairy-related products, such asHorizon Organicmilk and other dairy products,The Organic Cow organic dairy products, as well as other plant-based beverages and soy food products,International Delightcoffee creamers andLAND O LAKEScreamers and fluid dairy products, andSilk plant-based beverages such as soy, almond and coconut milks and cultured soy products. WhiteWave-Alpro also offers branded soy-based beverages and food products in Europe and markets its products under theAlproandProvamel brands. Additionally, with our Hero/WhiteWave joint venture we have expanded the WhiteWave product footprint beyond the dairy case to capitalize on the chilled fruit-based beverage opportunity with the introduction ofFruit2Day.
Our Reportable Segments
We have two reportable segments, Fresh Dairy Direct-Morningstar and WhiteWave-Alpro.
In the first quarter of 2010, our Chief Executive Officer, who is our chief operating decision maker, changed the way he evaluates the performance of our operations, develops strategy and allocates capital resources. As a result, beginning in the first quarter of 2010, our Morningstar operations were aligned with our Fresh Dairy Direct operations, so that our two reporting segments consisted of Fresh Dairy Direct-Morningstar and WhiteWave-Alpro. This change reflects the divergence between the strategies and objectives of these two segments. Our value-added branded operations at WhiteWave-Alpro added scale with the acquisition of Alpro in July 2009 and are focused on driving growth through effective marketing and innovation. Our traditional dairy operations at Fresh Dairy Direct-Morningstar are driven by a focus on cost and service leadership. We believe these revised segments have increased internal focus and offered management and investors improved visibility into the performance of the segments against their specific objectives. All segment results set forth herein have been recast to present results on a comparable basis. These changes had no impact on consolidated net sales or operating income.
During the second quarter of 2010, we committed to a plan to sell the business operations of Rachel’s, which provides organic branded dairy-based chilled yogurt, milk and related dairy products primarily in the United Kingdom. The sale of these operations was completed on August 4, 2010. The decision to sell these operations was part of our strategic growth plan and allows us to target our investments in growing our core dairy and branded businesses by divesting non-core operations. All Rachel’s operations, previously reported within the WhiteWave-Alpro segment, have been reclassified as discontinued operations. See Note 2 to our Consolidated Financial Statements. Unless stated otherwise, any reference to income statement items in these financial statements refers to results from continuing operations.
In the fourth quarter of 2010, we entered into two separate agreements to sell our Mountain High and private label yogurt operations, which are part of our Fresh Dairy Direct-Morningstar segment. We expect to recognize a gain related to the sale of both of these operations. On February 1, 2011, we completed the sale of our Mountain High yogurt operations. We expect our private label operations sale to close in the first half of 2011. These operations did not meet the requirements to be accounted for as discontinued operations.
Fresh Dairy Direct-Morningstar — Fresh Dairy Direct-Morningstar is our largest segment, with approximately 84% of our consolidated net sales in 2010. Fresh Dairy Direct-Morningstar manufactures, markets and distributes a wide variety of branded and private label dairy case products, including milk, ice cream, cultured dairy products, creamers, ice cream mix and other dairy products, to retailers, distributors, foodservice outlets, educational institutions and governmental entities across the United States. Due to the perishable nature
29
of its products, Fresh Dairy Direct-Morningstar delivers the majority of its products directly to its customers’ locations in refrigerated trucks or trailers that we own or lease. We believe that Fresh Dairy Direct-Morningstar has one of the most extensive refrigerated DSD systems in the United States. Fresh Dairy Direct-Morningstar sells its products primarily on a local or regional basis through its local and regional sales forces, although some national customer relationships are coordinated by a centralized corporate sales department.
The dairy industry is a mature industry that has traditionally been characterized by slow to flat growth, low profit margins fragmentation and lack of network optimization. According to the USDA, per capita consumption of fluid milk continues to decline. Volume sales growth across the industry has declined recently. The continued recessionary environment has resulted in a significant segment of consumers who are cutting back on purchases of even the most essential items, which has had a pronounced impact on the fluid milk category. We have experienced a reduction in volumes in the industry and in our Fresh Dairy Direct-Morningstar business. We expect this trend to continue in the near term.
As a result of the intensely competitive dairy environment, we have been subject to a number of competitive bidding situations in Fresh Dairy Direct-Morningstar, which has reduced our profitability on sales to several customers. In bidding situations, we are subject to the risk of losing certain customers altogether. In addition, supermarkets and food retailers have utilized competitive pricing on dairy products to drive traffic volume and influence customer loyalty, which has significantly reduced their profit margins realized on the sale of such products. This margin compression is being absorbed by both retailers and dairy processors. These industry dynamics have driven private label market share gains over branded products, which is impacting the growth and profitability of our regionally branded products. With unusually low pricing on private label gallons, our regionally branded products are exposed to significantly wider retail price gaps versus private label. Although we expect these trends to continue, we began to see price stabilization over the latter part of 2010.
In addition to these industry dynamics, we have faced challenges with our conventional milk costs as well. Conventional milk prices continued to increase throughout 2010 compared to historic lows in 2009. We expect the Class I and Class II price to increase fairly dramatically through mid-second quarter of 2011 and level off in the back half of the year. This significant increase in conventional milk prices is a result of limited supply due to production challenges coupled with strong global demand for both Class I and Class II inputs.
In response to this dynamic and significant competitive pressure, many processors, including us, are now placing an increased emphasis on cost reduction in an effort to increase margins. We made significant progress against such initiatives in 2009 and 2010 and intend to continue these efforts over the next three to five years. Defined strategies for network optimization and organizational changes are in process to improve performance and programs have been launched to reduce our total selling, general, and administrative costs. We remain focused on sustaining positive cash flow, net debt reduction and are reinvesting for the future in spite of the current challenging environment.
Fresh Dairy Direct-Morningstar has several competitors in each of our major product and geographic markets. Competition between dairy processors for shelf-space with retailers is based primarily on price, service, quality and the expected or historical sales performance of the product compared to its competitors. In some cases Fresh Dairy Direct-Morningstar pays fees to customers for shelf-space. Competition for consumer sales is based on a variety of factors such as brand recognition, price, taste preference and quality. Dairy products also compete with many other beverages and nutritional products for consumer sales.
WhiteWave-Alpro — WhiteWave-Alpro’s net sales were approximately 16% of our consolidated net sales in 2010. WhiteWave-Alpro manufactures, develops, markets and sells a variety of nationally branded dairy and dairy-related products, such asHorizon Organicmilk and other dairy products,The Organic Cow organic dairy milk,International Delightcoffee creamers andLAND O LAKEScreamers and fluid dairy products, andSilk plant based beverages including soy, almond and coconut milks and cultured soy products. WhiteWave-Alpro also offers branded soy-based beverages and food products in Europe and markets its products under theAlpro and
30
Provamel brands. Additionally, with our Hero/WhiteWave joint venture we have expanded the WhiteWave product footprint beyond the dairy case to capitalize on the chilled fruit-based beverage opportunity with the introduction ofFruit2Day. WhiteWave-Alpro sells its products to a variety of customers, including grocery stores, club stores, natural food stores, mass merchandisers, convenience stores, drug stores and foodservice outlets. WhiteWave-Alpro sells its products primarily through its internal sales force and independent brokers. The majority of the WhiteWave-Alpro products are delivered through warehouse delivery systems.
WhiteWave-Alpro has several competitors in each of its product markets. Competition to obtain shelf-space with retailers for a particular product is based primarily on brand recognition and the expected or historical sales performance of the product compared to its competitors. In some cases, WhiteWave-Alpro pays fees to retailers to obtain shelf-space for a particular product. Competition for consumer sales is based on many factors, including brand recognition, price, taste preferences and quality. Consumer demand for soy, other plant-based and organic beverages and foods has grown in recent years due to growing consumer confidence in the health benefits attributable to these products, and we believe WhiteWave-Alpro has a leading position in the these category.
Recent Developments
See “Part I — Item 1. Business — Developments Since January 1, 2010” for recent developments that have impacted our financial condition and results of operations.
Results of Operations
The following table presents certain information concerning our financial results, including information presented as a percentage of net sales.
| | | | | | | | | | | | | | | | | | | | | | | | |
| | Year Ended December 31 | |
| | 2010 | | | 2009 | | | 2008 | |
| | Dollars | | | Percent | | | Dollars | | | Percent | | | Dollars | | | Percent | |
| | (Dollars in millions) | |
Net sales | | $ | 12,122.9 | | | | 100.0 | % | | $ | 11,113.8 | | | | 100.0 | % | | $ | 12,361.3 | | | | 100.0 | % |
Cost of sales | | | 9,117.0 | | | | 75.2 | | | | 8,008.6 | | | | 72.1 | | | | 9,438.6 | | | | 76.4 | |
| | | | | | | | | | | | | | | | | | | | | | | | |
Gross profit(1) | | | 3,005.9 | | | | 24.8 | | | | 3,105.2 | | | | 27.9 | | | | 2,922.7 | | | | 23.6 | |
Operating costs and expenses: | | | | | | | | | | | | | | | | | | | | | | | | |
Selling and distribution | | | 1,904.5 | | | | 15.7 | | | | 1,818.8 | | | | 16.4 | | | | 1,802.2 | | | | 14.6 | |
General and administrative | | | 629.6 | | | | 5.2 | | | | 623.8 | | | | 5.6 | | | | 482.4 | | | | 3.9 | |
Amortization of intangibles | | | 11.3 | | | | 0.1 | | | | 9.6 | | | | 0.1 | | | | 9.8 | | | | 0.1 | |
Facility closing and reorganization costs | | | 30.8 | | | | 0.3 | | | | 30.2 | | | | 0.3 | | | | 22.8 | | | | 0.2 | |
Other expense | | | 30.0 | | | | 0.2 | | | | — | | | | — | | | | — | | | | — | |
| | | | | | | | | | | | | | | | | | | | | | | | |
Total operating costs and expenses | | | 2,606.2 | | | | 21.5 | | | | 2,482.4 | | | | 22.4 | | | | 2,317.2 | | | | 18.8 | |
| | | | | | | | | | | | | | | | | | | | | | | | |
Operating income | | $ | 399.7 | | | | 3.3 | % | | $ | 622.8 | | | | 5.5 | % | | $ | 605.5 | | | | 4.8 | % |
| | | | | | | | | | | | | | | | | | | | | | | | |
(1) | As disclosed in Note 1 to our Consolidated Financial Statements, we include certain shipping and handling costs within selling and distribution expense. As a result, our gross profit may not be comparable to other entities that present all shipping and handling costs as a component of cost of sales. |
31
Year Ended December 31, 2010 Compared to Year Ended December 31, 2009 — Consolidated Results
Net Sales — Net sales by segment are shown in the table below.
| | | | | | | | | | | | | | | | |
| | Net Sales | |
| | 2010 | | | 2009 | | | $ Increase/ (Decrease) | | | % Increase/ (Decrease) | |
| | (Dollars in millions) | |
Fresh Dairy Direct-Morningstar | | $ | 10,184.9 | | | $ | 9,480.8 | | | $ | 704.1 | | | | 7.4 | % |
WhiteWave-Alpro | | | 1,938.0 | | | | 1,633.0 | | | | 305.0 | | | | 18.7 | |
| | | | | | | | | | | | | | | | |
Total | | $ | 12,122.9 | | | $ | 11,113.8 | | | $ | 1,009.1 | | | | 9.1 | |
| | | | | | | | | | | | | | | | |
The change in net sales was due to the following:
| | | | | | | | | | | | | | | | |
| | Change in Net Sales 2010 vs. 2009 | |
| | Acquisitions | | | Volume | | | Pricing and Product Mix Changes | | | Total Increase/ (Decrease) | |
| | (Dollars in millions) | |
Fresh Dairy Direct-Morningstar | | $ | 157.7 | | | $ | (365.7 | ) | | $ | 912.1 | | | $ | 704.1 | |
WhiteWave-Alpro | | | 172.7 | | | | 106.9 | | | | 25.4 | | | | 305.0 | |
| | | | | | | | | | | | | | | | |
Total | | $ | 330.4 | | | $ | (258.8 | ) | | $ | 937.5 | | | $ | 1,009.1 | |
| | | | | | | | | | | | | | | | |
Net sales — Consolidated net sales increased $1.0 billion during 2010 compared to 2009 primarily due to the pass-through of higher commodity costs, acquisitions and an increase in sales volumes of our branded products, particularlyInternational Delight, Horizon Organic andSilk. These increases were partially offset by highly promotional retail pricing and wholesale pricing pressures, as well as lower sales volumes across all categories in our Fresh Dairy Direct-Morningstar segment.
Cost of Sales — All expenses incurred to bring a product to completion are included in cost of sales, such as raw material, ingredient and packaging costs; labor costs; and plant and equipment costs. Cost of sales increased $1.1 billion, or 13.8%, in 2010 as compared to the prior year, primarily due to higher commodity prices, particularly raw milk and Class II butterfat costs, offset by lower overall volumes in Fresh Dairy Direct-Morningstar. Conventional milk prices were at historically low levels for most of 2009, with a fairly sharp increase in the fourth quarter of 2009 that continued throughout 2010. We expect the Class I and Class II price to increase fairly dramatically through mid-second quarter of 2011 and level off in the back half of the year. This significant increase in conventional milk prices is a result of limited supply due to production challenges coupled with strong global demand for both Class I and Class II inputs.
Operating Costs and Expenses — Our operating expenses increased $123.8 million, or 5.0%, during the year compared to prior year. Significant changes to operating costs and expenses include the following:
| • | | Selling and distribution costs increased $85.7 million driven by the impact of acquisitions, including $36.0 million related to Alpro, higher freight and fuel costs. In addition, WhiteWave experienced increased outside storage facility costs and related distribution costs due to capacity constraints. We expect such outside storage costs to decrease in 2011 as we realize additional capacity as a result of our capital expenditures at WhiteWave. These increases were partly offset by a decrease in our self-insurance reserve due to changes in loss development factors as a result of a continuous decline in claims and better claims management. We expect 2011 expenses related to self-insurance to increase next year. |
| • | | General and administrative costs increased $5.8 million primarily driven by the impact of acquisitions, including $24.5 million for Alpro, and higher consulting fees, offset by lower employee-related costs, largely due to decreased short term incentive compensation. We expect 2011 expenses related to short term incentive compensation to increase next year. |
32
| • | | Net facility closing and reorganization costs increased $0.6 million. See Note 16 to our Consolidated Financial Statements for further information on our facility closing and reorganization activities. |
| • | | Other expense represents a $30.0 million charge related to a pending class action antitrust settlement (see “Part I — Item 3. Legal Proceedings” for more information regarding this charge). |
Other (Income) Expense — Excluding $12.3 million in financing costs associated with the amendments of our senior secured credit facility on June 30, 2010 and December 9, 2010, interest expense decreased $10.5 million from the prior year, primarily due to lower average debt balances, lower interest rates during the first six months of 2010 and the expiration of $800 million notional amounts of fixed interest rate swap agreements in the first quarter of 2010. In 2009 we recorded a $4.2 million gain related to a Euro-based forward currency contract related to the Alpro acquisition.
We expect to see an increase in interest expense in 2011 as a result of higher average interest rates, due to the June 30, 2010 credit facility amendment and the December 16, 2010 senior notes issuance. This higher interest expense will be slightly offset by expected lower average debt balances resulting from free cash flow generation and the net proceeds from the sale of our Mountain High and private label yogurt businesses, as well as the expiration of certain of our fixed interest rate swap agreements. The sale of our Mountain High business closed February 1, 2011, and we expect to close the sale of our private label yogurt business in the first half of 2011.
Income Taxes — Income tax expense was recorded at an effective rate of 48.6% for 2010 compared to 39.9% in 2009. Our effective tax rate varies primarily based on the relative earnings of our business units. Additionally, in 2010, we identified unrecoverable deferred tax asset balances associated with errors primarily related to periods prior to 2007. Since the effects of the errors are not material to the financial results for the year ending December 31, 2010 and were not material to any individual year prior to 2010, we adjusted our deferred tax assets and recorded a non-cash income tax charge of $10.8 million in the fourth quarter of 2010. Excluding the impact of this correction, the effective tax rate for 2010 was 41.4%, which was higher than 2009 primarily as a result of lower net earnings. Our 2010 and 2009 effective tax rates were both negatively impacted by the exclusion of the tax benefit attributable to our non-controlling interest in the Hero/WhiteWave joint venture.
Year Ended December 31, 2010 Compared to Year Ended December 31, 2009 — Results by Segment
Fresh Dairy Direct-Morningstar
The key performance indicators of Fresh Dairy Direct-Morningstar are sales volumes, gross profit and operating income.
| | | | | | | | | | | | | | | | |
| | Year Ended December 31 | |
| | 2010 | | | 2009 | |
| | Dollars | | | Percent | | | Dollars | | | Percent | |
| | (Dollars in millions) | |
Net sales | | $ | 10,184.9 | | | | 100.0 | % | | $ | 9,480.8 | | | | 100.0 | % |
Cost of sales | | | 7,873.3 | | | | 77.3 | | | | 6,961.4 | | | | 73.4 | |
| | | | | | | | | | | | | | | | |
Gross profit | | | 2,311.6 | | | | 22.7 | | | | 2,519.4 | | | | 26.6 | |
Operating costs and expenses | | | 1,807.1 | | | | 17.7 | | | | 1,762.7 | | | | 18.6 | |
| | | | | | | | | | | | | | | | |
Total operating income | | $ | 504.5 | | | | 5.0 | % | | $ | 756.7 | | | | 8.0 | % |
| | | | | | | | | | | | | | | | |
Net Sales — Fresh Dairy Direct-Morningstar’s net sales increased $704.1 million, or 7.4%, during 2010 compared to the prior year, primarily due to the pass-through of higher commodity costs and the impact of acquisitions. These increases were partially offset by the impact of highly promotional retail pricing and wholesale pricing pressures, as well as overall volume declines across all product categories. Changing consumer behavior with increased pricing sensitivity and focus on value in the challenging domestic economy has driven material shifts across the retail grocery industry. Retailers began lowering their margins on milk to hit key price
33
points and demonstrate strong value to customers in an effort to keep or win market share in the challenging environment. Beginning in 2009 and throughout 2010, we experienced an increasing demand to absorb pricing concessions, which were originally absorbed by retailers. Although we expect these trends to continue, we began to see price stabilization over the latter part of 2010.
Fresh Dairy Direct-Morningstar generally increases or decreases the prices of its fluid dairy products on a monthly basis in correlation to fluctuations in the costs of raw materials, packaging supplies and delivery costs. However, in some cases, we are competitively or contractually constrained with respect to the means and/or timing of price increases. This can have a negative impact on Fresh Dairy Direct-Morningstar’s profitability. The following table sets forth the average monthly Class I “mover” and its components, as well as the average monthly Class II minimum prices for raw skim milk and butterfat for 2010 compared to 2009:
| | | | | | | | | | | | |
| | Year Ended December 31* | |
| | 2010 | | | 2009 | | | % Change | |
Class I mover(1) | | $ | 15.35 | | | $ | 11.48 | | | | 33.7 | % |
Class I raw skim milk mover(1)(2) | | | 9.26 | | | | 7.40 | | | | 25.1 | |
Class I butterfat mover(2)(3) | | | 1.83 | | | | 1.24 | | | | 47.6 | |
Class II raw skim milk minimum(1)(4) | | | 9.85 | | | | 7.09 | | | | 38.9 | |
Class II butterfat minimum(3)(4) | | | 1.86 | | | | 1.26 | | | | 47.6 | |
* | The prices noted in this table are not the prices that we actually pay. The federal order minimum prices applicable at any given location for Class I raw skim milk or Class I butterfat are based on the Class I mover prices plus a location differential. Class II prices noted in the table are federal minimum prices, applicable at all locations. Our actual cost also includes producer premiums, procurement costs and other related charges that vary by location and supplier. Please see “Part I — Item 1. Business — Government Regulation — Milk Industry Regulation” and “— Known Trends and Uncertainties — Prices of Raw Milk and Other Inputs” below for a more complete description of raw milk pricing. |
(1) | Prices are per hundredweight. |
(2) | We process Class I raw skim milk and butterfat into fluid milk products. |
(4) | We process Class II raw skim milk and butterfat into products such as cottage cheese, creams and creamers, ice cream and sour cream. |
Cost of Sales — All expenses incurred to bring a product to completion are included in cost of sales, such as raw material, ingredient and packaging costs; labor costs; and plant and equipment costs. Fresh Dairy Direct-Morningstar’s cost of sales increased $911.9 million, or 13.1%, in 2010 compared to 2009 primarily due to higher commodity prices experienced throughout the year, particularly raw milk and Class II butterfat costs, slightly offset by lower personnel costs.
Conventional milk prices continued to increase throughout 2010 compared to historic lows in 2009. We expect the Class I and Class II price to increase fairly dramatically through mid-second quarter of 2011 and level off in the back half of the year. This significant increase in conventional milk prices is a result of limited supply due to production challenges coupled with strong global demand for both Class I and Class II inputs.
Gross Profit— Fresh Dairy Direct-Morningstar’s gross margin decreased to 22.7% in 2010 from 26.6% in 2009. Gross margins trended downward due to the increasingly intense competitive environment we have experienced. In addition to the increasing demands to absorb pricing concessions, we experienced a continued shift from branded to private label products, exacerbated by weak volumes across dairy and non-dairy product offerings, further impacting profitability. Although we began to see price stabilization over the latter part of 2010, we expect these trends to continue. These margin pressures underscore the importance of our low cost strategy. We continue to focus on cost control and supply chain efficiency through cost-cutting initiatives, improved effectiveness in the pass-through of costs to our customers as well as our continued focus to drive productivity and efficiency within our operations.
34
Operating Costs and Expenses — Fresh Dairy Direct-Morningstar’s operating costs and expenses increased $44.4 million, or 2.5%, during the year compared to prior year. Significant changes to operating costs and expenses include the following:
| • | | Selling and distribution costs increased $28.2 million, primarily driven by increased fuel and freight costs. These costs were offset by a decrease in our self-insurance reserve due to changes in loss development factors as a result of a continuous decline in claims and better claims management, as well as benefits from efficiencies gained in our distribution network with route reductions and lower fuel usage. We expect 2011 expenses related to self-insurance to increase next year. |
| • | | General and administrative costs increased $15.2 million due to an increase in supply chain management and higher consulting fees, offset by lower personnel-related costs, largely due to decreased short term incentive compensation. We expect 2011 expenses related to short term incentive compensation to increase next year. |
WhiteWave-Alpro
The key performance indicators of WhiteWave-Alpro are sales volumes, net sales dollars, gross profit and operating income.
| | | | | | | | | | | | | | | | |
| | Year Ended December 31 | |
| | 2010 | | | 2009 | |
| | Dollars | | | Percent | | | Dollars | | | Percent | |
| | (Dollars in millions) | |
Net sales | | $ | 1,938.0 | | | | 100.0 | % | | $ | 1,633.0 | | | | 100.0 | % |
Cost of sales | | | 1,242.7 | | | | 64.1 | | | | 1,058.2 | | | | 64.8 | |
| | | | | | | | | | | | | | | | |
Gross profit | | | 695.3 | | | | 35.9 | | | | 574.8 | | | | 35.2 | |
Operating costs and expenses | | | 529.1 | | | | 27.3 | | | | 444.5 | | | | 27.2 | |
| | | | | | | | | | | | | | | | |
Total operating income | | $ | 166.2 | | | | 8.6 | % | | $ | 130.3 | | | | 8.0 | % |
| | | | | | | | | | | | | | | | |
Net Sales — Net sales of the WhiteWave-Alpro segment increased $305.0 million, or 18.7%, driven by the impact of our Alpro acquisition and strong volume growth in our branded products. Excluding the impact of our Alpro acquisition, net sales increased $132.3 million, or 8.1%. Sales for the creamers business, which includes bothInternational Delight andLAND O LAKES,grew low double digits compared to 2009.Horizon Organicbrand sales also grew low double digits whileSilk brand sales grew high single digits compared to the prior year.
Cost of Sales — WhiteWave-Alpro’s cost of sales increased $184.5 million, or 17.4%, in 2010 compared to the prior year. This increase was primarily driven by a $92.9 million increase due to our Alpro acquisition higher sales volumes and higher input costs.
Gross Profit— WhiteWave-Alpro’s gross profit increased to 35.9% in 2010 from 35.2% in 2009, driven by the impact of our Alpro acquisition, strong volume growth, a favorable brand mix, as well as benefits from productivity initiatives.
Operating Costs and Expenses — WhiteWave-Alpro’s operating costs and expenses increased $84.6 million, or 19.0%, during 2010 compared to 2009. Significant changes to operating costs and expenses are summarized below:
| • | | Selling and distribution costs increased $50.1 million, driven by a $36.0 million increase due to the Alpro acquisition, volume growth and higher fuel costs. In addition, WhiteWave experienced increased outside storage facility costs due to capacity constraints. We expect such costs to remain at higher levels as we work to add additional production and storage capacity. |
| • | | General and administrative costs increased $33.8 million, primarily driven by a $24.5 million increase due to our Alpro acquisition. |
35
Year Ended December 31, 2009 Compared to Year Ended December 31, 2008 — Consolidated Results
Net Sales — Net sales by segment are shown in the table below.
| | | | | | | | | | | | | | | | |
| | Net Sales | |
| | 2009 | | | 2008 | | | $ Increase/ (Decrease) | | | % Increase/ (Decrease) | |
| | (Dollars in millions) | |
Fresh Dairy Direct-Morningstar | | $ | 9,480.8 | | | $ | 10,924.4 | | | $ | (1,443.6 | ) | | | (13.2 | )% |
WhiteWave-Alpro | | | 1,633.0 | | | | 1,436.9 | | | | 196.1 | | | | 13.6 | |
| | | | | | | | | | | | | | | | |
Total | | $ | 11,113.8 | | | $ | 12,361.3 | | | $ | (1,247.5 | ) | | | (10.1 | ) |
| | | | | | | | | | | | | | | | |
The change in net sales was due to the following:
| | | | | | | | | | | | | | | | |
| | Change in Net Sales 2009 vs. 2008 | |
| | Acquisitions | | | Volume | | | Pricing and Product Mix Changes | | | Total Increase/ (Decrease) | |
| | (Dollars in millions) | |
Fresh Dairy Direct-Morningstar | | $ | 159.0 | | | $ | (61.2 | ) | | $ | (1,541.4 | ) | | $ | (1,443.6 | ) |
WhiteWave-Alpro | | | 176.4 | | | | (31.2 | ) | | | 50.9 | | | | 196.1 | |
| | | | | | | | | | | | | | | | |
Total | | $ | 335.4 | | | $ | (92.4 | ) | | $ | (1,490.5 | ) | | $ | (1,247.5 | ) |
| | | | | | | | | | | | | | | | |
Net sales decreased $1.2 billion during 2009 compared to 2008 primarily due to lower pricing in our Fresh Dairy Direct-Morningstar segment, as significantly lower commodity costs were passed through to customers. Net sales in our WhiteWave-Alpro segment increased as the Alpro acquisition more than offset the impact of the pass-through of lower commodity costs to customers and slightly lower sales volume, coupled with the exit of several business relationships.
Cost of Sales — All expenses incurred to bring a product to completion are included in cost of sales, such as raw material, ingredient and packaging costs; labor costs; and plant and equipment costs. Cost of sales decreased $1.4 billion, or 15.2%, in 2009 as compared to the prior year, primarily due to continued favorable commodity prices, particularly raw milk costs, as well as benefits from our strategic initiatives across our manufacturing network. Overall, commodity prices remained low compared to 2008 levels. Conventional milk prices were at historically low levels for most of 2009, with a fairly sharp increase in the fourth quarter of the year.
Operating Costs and Expenses — Our operating expenses increased $165.2 million, or 7.1%, during the year compared to the prior year. Significant changes to operating costs and expenses include the following:
| • | | General and administrative costs increased $141.4 million primarily driven by the impact of acquisitions and investments in the capability build-out of our supply chain, information technology and research and development functions that are foundational to our strategies; higher personnel-related costs including incentive-based compensation, share-based compensation expense and additional headcount; higher professional fees and other outside services primarily related to our strategic initiatives, as well as higher transaction-related costs. |
| • | | Selling and distribution costs increased $16.6 million driven by an increase in marketing spend, especially in the fourth quarter, on our nationally branded products at WhiteWave, higher expenses attributable to our Hero/WhiteWave joint venture and the impact of our recent Alpro acquisition, partially offset by lower fuel costs and benefits from our strategic initiatives across our distribution network. |
| • | | Net facility closing and reorganization costs increased $7.4 million. See Note 16 to our Consolidated Financial Statements for further information on our facility closing and reorganization activities. |
36
Other (Income) Expense — Interest expense decreased to $246.5 million in 2009 from $308.2 million in 2008, primarily due to lower average debt balances and lower interest rates during 2009 compared to the prior year. Additionally, in 2009, a $4.2 million gain was recognized related to a Euro-based forward currency contract related to the Alpro acquisition.
Income Taxes — Income tax expense was recorded at an effective rate of 39.9% for 2009 compared to 38.6% in 2008. Our effective tax rate varies primarily based on the relative earnings of our business units. In 2009, our effective tax rate was negatively impacted by the exclusion of the tax benefit attributable to our non-controlling interest in the Hero/WhiteWave joint venture. In 2008, our effective tax rate was positively impacted by the settlement of taxing authority examinations and the effects of state tax law changes.
Year Ended December 31, 2009 Compared to Year Ended December 31, 2008 — Results by Segment
Fresh Dairy Direct-Morningstar
The key performance indicators of Fresh Dairy Direct-Morningstar are sales volumes, gross profit and operating income.
| | | | | | | | | | | | | | | | |
| | Year Ended December 31 | |
| | 2009 | | | 2008 | |
| | Dollars | | | Percent | | | Dollars | | | Percent | |
| | (Dollars in millions) | |
Net sales | | $ | 9,480.8 | | | | 100.0 | % | | $ | 10,924.4 | | | | 100.0 | % |
Cost of sales | | | 6,961.4 | | | | 73.4 | | | | 8,480.7 | | | | 77.6 | |
| | | | | | | | | | | | | | | | |
Gross profit | | | 2,519.4 | | | | 26.6 | | | | 2,443.7 | | | | 22.4 | |
Operating costs and expenses | | | 1,762.7 | | | | 18.6 | | | | 1,762.7 | | | | 16.2 | |
| | | | | | | | | | | | | | | | |
Total operating income | | $ | 756.7 | | | | 8.0 | % | | $ | 681.0 | | | | 6.2 | % |
| | | | | | | | | | | | | | | | |
Net Sales — Fresh Dairy Direct-Morningstar’s net sales decreased 13.2% during 2009 compared to the prior year, primarily due to lower pricing as significantly lower commodity costs were passed through to customers. Recent acquisitions and solid execution drove higher fluid milk sales volumes of approximately 2.7%, which were more than offset by lower sales volumes in other products for an overall volume decline of 0.6%.
Fresh Dairy Direct-Morningstar generally increases or decreases the prices of its fluid dairy products on a monthly basis in correlation to fluctuations in the costs of raw materials, packaging supplies and delivery costs. However, in some cases, we are competitively or contractually constrained with respect to the means and/or timing of price increases. This can have a negative impact on Fresh Dairy Direct-Morningstar’s profitability. The following table sets forth the average monthly Class I “mover” and its components, as well as the average monthly Class II minimum prices for raw skim milk and butterfat for 2009 compared to 2008:
| | | | | | | | | | | | |
| | Year Ended December 31* | |
| | 2009 | | | 2008 | | | % Change | |
Class I mover(1) | | $ | 11.48 | | | $ | 18.00 | | | | (36.2 | )% |
Class I raw skim milk mover(1)(2) | | | 7.40 | | | | 12.94 | | | | (42.8 | ) |
Class I butterfat mover(2)(3) | | | 1.24 | | | | 1.57 | | | | (21.0 | ) |
Class II raw skim milk minimum(1)(4) | | | 7.09 | | | | 11.13 | | | | (36.3 | ) |
Class II butterfat minimum(3)(4) | | | 1.26 | | | | 1.57 | | | | (19.7 | ) |
* | The prices noted in this table are not the prices that we actually pay. The federal order minimum prices applicable at any given location for Class I raw skim milk or Class I butterfat are based on the Class I mover prices plus a location differential. Class II prices noted in the table are federal minimum prices, applicable at all locations. Our actual cost also includes producer premiums, procurement costs and other related charges |
37
| that vary by location and supplier. Please see “Part I — Item 1. Business — Government Regulation — Milk Industry Regulation” and “— Known Trends and Uncertainties — Prices of Raw Milk and Other Inputs” below for a more complete description of raw milk pricing. |
(1) | Prices are per hundredweight. |
(2) | We process Class I raw skim milk and butterfat into fluid milk products. |
(4) | We process Class II raw skim milk and butterfat into products such as cottage cheese, creams and creamers, ice cream and sour cream. |
Cost of Sales — All expenses incurred to bring a product to completion are included in cost of sales, such as raw material, ingredient and packaging costs; labor costs; and plant and equipment costs. Fresh Dairy Direct-Morningstar’s cost of sales decreased $1.5 billion, or 17.9%, in 2009 compared to 2008 primarily due to favorable commodity prices experienced throughout the year, particularly raw milk costs, as well as benefits from our strategic initiatives across our manufacturing network, slightly offset by higher personnel-related costs.
Gross Profit — Fresh Dairy Direct-Morningstar’s gross margin increased to 26.6% in 2009 from 22.4% in 2008. Despite an overall increase on a year-over-year basis, the gross margin trended downward as 2009 progressed driven by the increasing intense competitive environment we experienced. Changing consumer behavior with increased pricing sensitivity and focus on value in the challenging domestic economy drove material shifts across the retail grocery industry. Retailers began lowering their margins on milk to hit key price points and demonstrate strong value to customers in an effort to keep or win market share in the challenging environment. Initially, this margin compression was absorbed by retailers, but as the year progressed, we experienced an increasing demand to absorb pricing concessions. In addition, we experienced a continued shift from branded to private label products, further impacting profitability. These margin pressures underscore the importance of our low cost strategy.
Operating Costs and Expenses — Fresh Dairy Direct-Morningstar’s operating costs and expenses were relatively flat during the year compared to prior year. Distribution costs declined due to relatively lower fuel costs and strategic initiatives across our distribution network which was offset by higher professional fees primarily related to strategic initiatives, particularly supply chain and information technology, increased advertising expenses as well as higher personnel-related costs.
WhiteWave-Alpro
The key performance indicators of WhiteWave-Alpro are sales volumes, net sales dollars, gross profit and operating income.
| | | | | | | | | | | | | | | | |
| | Year Ended December 31 | |
| | 2009 | | | 2008 | |
| | Dollars | | | Percent | | | Dollars | | | Percent | |
| | (Dollars in millions) | |
Net sales | | $ | 1,633.0 | | | | 100.0 | % | | $ | 1,436.9 | | | | 100.0 | % |
Cost of sales | | | 1,058.2 | | | | 64.8 | | | | 961.1 | | | | 66.9 | |
| | | | | | | | | | | | | | | | |
Gross profit | | | 574.8 | | | | 35.2 | | | | 475.8 | | | | 33.1 | |
Operating costs and expenses | | | 444.5 | | | | 27.2 | | | | 363.3 | | | | 25.3 | |
| | | | | | | | | | | | | | | | |
Total operating income | | $ | 130.3 | | | | 8.0 | % | | $ | 112.5 | | | | 7.8 | % |
| | | | | | | | | | | | | | | | |
Net Sales — Net sales of the WhiteWave-Alpro segment increased $196.1 million, or 13.6%, driven by the impact of our Alpro acquisition and strong sales growth in our creamers business, partially offset by the impact of certain businesses exited during 2009.
38
Throughout 2009, we experienced continued softness in the organic milk category. We believe milk consumers were price sensitive to premium priced categories, including organic products due to the recessionary environment. We continue to monitor our position in the organic milk category including taking proactive steps to manage our supply in the short-term and we remain focused on maintaining our leading banded position as we balance market share considerations against profitability.
Cost of Sales — WhiteWave-Alpro’s cost of sales increased $97.1 million in 2009 compared to the prior year. This increase was primarily driven by the impact of our Alpro acquisition and continued lower commodity costs, partially offset by the impact of lower sales volumes, driven by the exited businesses, and the impact of our productivity initiatives.
Operating Costs and Expenses — WhiteWave-Alpro’s operating costs and expenses increased $81.2 million during 2009 compared to 2008, driven by the Alpro acquisition and higher marketing spending driven principally by the launch-year marketing investments related to the Hero/WhiteWave joint venture. These increases were partially offset by productivity initiatives which impacted distribution costs.
Liquidity and Capital Resources
General
We believe that our cash on hand, coupled with future cash flows from operations and other available sources of liquidity, including our amended and restated $1.5 billion 5-year senior secured revolving credit facility and our $600 million receivables-backed facility, which we expect to renew under similar 364-day terms at the end of the current term, will provide sufficient liquidity to allow us to meet our future cash requirements. Our anticipated uses of cash include capital expenditures, working capital needs, pension contributions and financial obligations. On an ongoing basis, we will evaluate and consider strategic acquisitions, divestitures, joint ventures, repurchasing shares of our common stock, as well as other transactions to create shareholder value and enhance financial performance. Such transactions may require cash expenditures or generate proceeds.
At December 31, 2010, we had $4.1 billion of outstanding debt obligations, cash-on-hand of $92.0 million and an additional $1.4 billion of combined available future borrowing capacity under our existing senior secured revolving credit facility and receivables-backed facility. Of this combined amount, based on our outstanding indebtedness and the maximum permitted leverage ratio in effect at December 31, 2010, and assuming additional borrowings were not utilized to acquire incremental EBITDA, $484.1 million was then available to finance working capital and other general corporate purposes. Based on our current expectations, we believe our liquidity and capital resources will be sufficient to operate our business. However, we may, from time to time, raise additional funds through borrowings or public or private sales of debt or equity securities. The amount, nature and timing of any borrowings or sales of debt or equity securities will depend on our operating performance and other circumstances, our then-current commitments and obligations; the amount, nature and timing of our capital requirements; any limitations imposed by our current credit arrangements; and overall market conditions.
39
Historical Cash Flow
The following table summarizes our cash flows from operating, investing and financing activities:
| | | | | | | | | | | | |
| | Year Ended December 31 | |
| | 2010 | | | 2009 | | | Change | |
| | (In thousands) | |
Net cash flows from: | | | | | | | | | | | | |
Operating activities | | $ | 525,700 | | | $ | 658,079 | | | $ | (132,379 | ) |
Investing activities | | | (293,575 | ) | | | (840,068 | ) | | | 546,493 | |
Financing activities | | | (217,692 | ) | | | 192,765 | | | | (410,457 | ) |
Discontinued operations (operating and investing) | | | 32,886 | | | | 1,950 | | | | 30,936 | |
Effect of exchange rate changes on cash and cash equivalents | | | (502 | ) | | | 808 | | | | (1,310 | ) |
| | | | | | | | | | | | |
Net increase in cash and cash equivalents | | $ | 46,817 | | | $ | 13,534 | | | $ | 33,283 | |
| | | | | | | | | | | | |
Operating Activities
Net cash provided by operating activities from continuing operations decreased in 2010 compared to 2009 mainly due to the impact of lower net earnings. In addition, fluctuations in our working capital resulted in an overall decrease in cash driven by a decrease in the source of cash from accounts receivable, which was partially offset by a reduction in the use of cash for accounts payable. During 2009, accounts receivable balances declined significantly due to the pass-through of declining commodity prices. During 2010, accounts receivable balances remained relatively stable. Additionally, income tax payments were $150.7 million lower in 2010 compared to 2009 due to accelerated tax deductions and lower earnings.
Investing Activities
Net cash used in investing activities decreased in 2010 primarily due to a decrease in cash paid for acquisitions, which was partially offset by higher payments for capital expenditures. During 2010, no cash was used for acquisitions compared to $581.2 million used in 2009, primarily for the acquisition of Alpro, as well as other smaller acquisitions. In 2010, we funded $302.0 million in capital expenditures compared to $267.7 million in 2009 primarily in connection with the capital investments under our strategy to optimize the fluid milk production network to increase profitability by reducing costs.
Financing Activities
Net cash used in financing activities increased in 2010 primarily due to debt repayments and deferred financing costs as a result of costs associated with the amendments of our senior secured credit facility. In 2009 we issued 25.4 million shares of our common stock resulting in net proceeds of $444.7 million.
40
Current Debt Obligations
Senior Secured Credit Facility — Our senior secured credit facility consists of an original combination of a $1.5 billion 5-year senior secured revolving credit facility, a $1.5 billion 5-year senior secured term loan A and a $1.8 billion 7-year senior secured term loan B. As described more fully in Note 9 to our Consolidated Financial Statements, we amended and restated the credit agreement governing our senior secured credit facility on June 30, 2010 and further amended this agreement on December 9, 2010. The terms of the agreement were modified in the aggregate as follows:
| • | | Extension of the maturity dates for certain principal amounts as summarized in the key terms table below; |
| • | | Amendment of the maximum permitted leverage ratio and minimum interest coverage ratio, and the addition of a senior secured leverage ratio (each as defined in our credit agreement) to permit minimum and maximum ratios of: |
| | | | | | | | | | | | |
For Quarters Ending During the Period | | Minimum Interest Coverage Ratio | | | Maximum Leverage Ratio | | | Maximum Senior Secured Leverage Ratio | |
Amendment effective date – December 31, 2011 | | | 2.50 | | | | 5.75 | | | | 4.25 | |
March 31, 2012 – December 31, 2012 | | | 2.75 | | | | 5.50 | | | | 3.75 | |
March 31, 2013 – June 30, 2013 | | | 3.00 | | | | 5.25 | | | | 3.50 | |
September 30, 2013 and thereafter | | | 3.00 | | | | 4.50 | | | | 3.50 | |
| • | | Amendment of certain other terms, including, but not limited to, leverage-based limitations on the payment of dividends and other restricted payments, acquisitions and prepayments of senior notes; and |
| • | | Increase in the undrawn costs of the extended portion of the revolving credit facility and the drawn costs of the extended portions of the revolving credit facility, term loan A and term loan B. |
The following table summarizes the key terms of the senior secured credit facility as of December 31, 2010:
| | | | | | | | | | |
| | Principal(2) | | Maturity Date | | Applicable Base Rate Margin(3) | | Applicable LIBOR Rate Margin(3) | | Quarterly Commitment Fee on Undrawn Amounts |
Revolving Credit Facility | | $225 million | | April 2, 2012 | | 0.00% – 0.75% | | 0.625% –1.75% | | 0.125% –0.375% |
| | $1.28 billion | | April 2, 2014 | | 1.00% – 2.25% | | 2.00% – 3.25% | | 0.375% –0.500% |
Term Loan A | | $150 million | | April 2, 2012 | | 0.00% – 0.75% | | 0.625% –1.75% | | — |
| | $695 million | | April 2, 2014 | | 1.00% – 2.25% | | 2.00% – 3.25% | | — |
Term Loan B | | $687 million | | April 2, 2014 | | 0.375% –0.75% | | 1.375% –1.75% | | — |
| | $490 million | | April 2, 2016 | | 2.00% – 2.25% | | 3.00% – 3.25% | | — |
| | $558 million | | April 2, 2017(1) | | 2.25% – 2.50% | | 3.25% – 3.50% | | — |
(1) | Subject to the condition that we meet certain leverage, debt, cash or credit rating tests following December 31, 2015. However, if at least one of these tests is not met, the maturity date will be April 2, 2016. |
(2) | Amounts for term loan A and term loan B represent outstanding principal balances as of December 31, 2010. The revolving credit facility principal amount represents the total original borrowings available to us under the facility. |
(3) | The senior secured credit facility bears interest, at our election, at the Alternative Base Rate (as defined in our credit agreement) plus a margin depending on our leverage ratio or LIBOR plus a margin depending on our leverage ratio. Interest is payable quarterly or after the end of the applicable interest period. |
41
Our credit agreement permits us to complete acquisitions that meet all of the following conditions without obtaining prior approval: (1) the acquired company is involved in the manufacture, processing and distribution of food or packaging products or any other line of business in which we were engaged as of April 2007, (2) the net cash purchase price for any single acquisition is not greater than $500 million and not greater than $100 million if our leverage ratio is greater than 4.50 times, (3) we acquire at least 51% of the acquired entity, (4) the transaction is approved by the board of directors or shareholders, as appropriate, of the target and (5) after giving effect to such acquisition on a pro-forma basis, we would have been in compliance with all financial covenants. All other acquisitions must be approved in advance by the required lenders.
The senior secured credit facility contains limitations on liens, investments and the incurrence of additional indebtedness, prohibits certain dispositions of property and restricts certain payments, including dividends. There are no restrictions on these certain payments, including dividends, when our leverage ratio is below 4.50 times. The senior secured credit facility is secured by liens on substantially all of our domestic assets including the assets of our subsidiaries, but excluding the capital stock of subsidiaries of the former Dean Foods Company (“Legacy Dean”), and the real property owned by Legacy Dean and its subsidiaries.
Under the senior secured credit facility, we are required to comply with certain financial covenants, including, but not limited to, maximum senior secured leverage, maximum leverage and minimum interest coverage ratios, each as defined under and calculated in accordance with the terms of our senior secured credit facility and our receivables-backed facility. Our leverage ratio at December 31, 2010 was 5.13 times consolidated funded indebtedness to consolidated EBITDA for the prior four consecutive quarters. The maximum permitted leverage ratio of consolidated funded indebtedness to consolidated EBITDA for the prior four consecutive quarters was 5.75 times as of December 31, 2010 and decreases periodically as summarized in the ratio table above. As described in more detail in the Amended and Restated Credit Agreement, the leverage ratio is calculated as the ratio of consolidated funded indebtedness, less restricted subsidiary cash up to $100 million, to consolidated EBITDA for the period of four consecutive fiscal quarters ended on the measurement date. Consolidated funded indebtedness is comprised of the outstanding indebtedness of the Company and certain of its subsidiaries. Consolidated EBITDA is comprised of net income plus interest expense, taxes, depreciation, amortization expense and other non-cash expenses, and add-backs resulting from acquisition related non-recurring charges of the Company and certain of its subsidiaries. In addition, the leverage ratio may include adjustments related to other charges reasonably acceptable to the administrative agent and is calculated on a pro-forma basis to give effect to any acquisitions, divestitures or relevant changes in the composition of the Company or certain of its subsidiaries.
Our interest coverage ratio at December 31, 2010 was 3.45 times consolidated EBITDA to consolidated interest expense for the prior four consecutive quarters. The minimum permitted interest coverage ratio of consolidated EBITDA to consolidated interest expense for the prior four consecutive quarters was 2.50 times as of December 31, 2010 and increases periodically as summarized in the ratio table above. This ratio is calculated as the ratio of consolidated EBITDA to consolidated interest expense for the period of four consecutive fiscal quarters ended on the measurement date. Consolidated EBITDA is comprised of net income plus interest expense, taxes, depreciation, amortization expense and other non-cash expenses, and add-backs resulting from acquisition-related non-recurring charges of the Company and certain of its subsidiaries. Consolidated EBITDA may include adjustments related to other charges reasonably acceptable to the administrative agent and is calculated on a pro-forma basis to give effect to any acquisitions, divestitures or relevant changes in the composition of the Company or certain of its subsidiaries. Consolidated interest expense is comprised of consolidated interest expense paid or payable in cash, as calculated in accordance with generally accepted accounting principles, but excluding non-cash losses from foreign exchange translations or swap agreements and third party fees and expenses related to acquisitions, investments, dispositions and the incurrence or early extinguishment of indebtedness.
Additionally, the December 9, 2010 amendment of our credit agreement resulted in the addition of a senior secured leverage ratio, as defined under and calculated in accordance with the terms of our senior secured credit facility. Our senior secured leverage ratio at December 31, 2010 was 3.80 times consolidated funded senior secured indebtedness to consolidated EBITDA for the prior four consecutive quarters. The maximum permitted
42
senior secured leverage ratio of consolidated funded senior secured indebtedness to consolidated EBITDA for the prior four consecutive quarters allowed was 4.25 times as of December 31, 2010 and decreases periodically as summarized in the leverage ratio table above. This ratio is calculated as the ratio of consolidated funded senior secured indebtedness, less restricted subsidiary cash up to $100 million, to consolidated EBITDA for the period of four consecutive fiscal quarters ended on the measurement date. Consolidated funded senior secured indebtedness is comprised of the outstanding senior secured indebtedness of the Company and certain of its subsidiaries. Consolidated EBITDA is comprised of net income plus interest expense, taxes, depreciation, amortization expense and other non-cash expenses, and add-backs resulting from acquisition related non-recurring charges of the Company and certain of its subsidiaries. In addition, the senior secured leverage ratio may include adjustments related to other charges reasonably acceptable to the administrative agent and is calculated on a pro-forma basis to give effect to any acquisitions, divestitures or relevant changes in the composition of the Company or certain of its subsidiaries.
We are currently in compliance with all financial covenants, and based on our internal projections we expect to maintain such compliance for the foreseeable future.
The credit agreement contains standard default triggers, including without limitation: failure to maintain compliance with the financial and other covenants contained in the credit agreement, default on certain of our other debt, a change in control and certain other material adverse changes in our business. The credit agreement does not contain any requirements to maintain specific credit rating levels, except as described above with respect to determining the maturity date of the 2017 tranche of term loan B.
At December 31, 2010, there were outstanding borrowings of $3.0 billion under our senior secured credit facility (compared to $3.6 billion at December 31, 2009), which consisted of $2.6 billion in term loan borrowings and $453 million under the revolver. The decrease of $563 million in our senior secured credit facility outstanding borrowings was primarily due to the prepayment of approximately $384 million in outstanding 2014 Term Loan A borrowings as a result of the Senior Notes Offering discussed in Note 9 to our Consolidated Financial Statements, quarterly payments on our term loan A and term loan B, and a lower outstanding balance on our revolver borrowings at December 31, 2010 in comparison to December 31, 2009. At December 31, 2010, there were $171.3 million of letters of credit under the revolving line that were issued but undrawn. As of February 24, 2011, $106.2 million was borrowed under our senior secured revolving credit facility.
Receivables-backed Facility — In addition to our senior secured credit facility, we also have a $600 million 364-day receivables-backed facility in which current availability is subject to a monthly borrowing base formula. This facility is scheduled to mature September 30, 2011, and we intend and expect to renew the facility at the end of the current term under similar terms currently established.
As of December 31, 2010, the receivables-backed facility had $496.5 million available, of which zero was drawn. Our average daily balance under this facility during 2010 was $175.3 million. At February 24, 2011, $339.0 million was outstanding under this facility.
Senior Notes & Capital Leases — Other indebtedness outstanding at December 31, 2010 also included $500 million face value of outstanding indebtedness under Dean Foods Company’s senior notes due 2016, $400 million face value of outstanding indebtedness under Dean Foods Company’s senior notes due 2018, $142 million face value of outstanding indebtedness under Legacy Dean’s senior notes due 2017 and $7.7 million of capital lease and other obligations.
Alpro Revolving Credit Facility — On July 2, 2009, our newly acquired subsidiary, Alpro N.V. entered into a two year multi-currency revolving credit facility for borrowings in an amount not to exceed €20 million (or its currency equivalent). In December, 2009, we reduced the facility to an amount not to exceed €10 million (or its currency equivalent) and in December 2010, we further reduced the facility to an amount not to exceed €1 million (or its currency equivalent). The facility is unsecured and is guaranteed by Dean Foods Company and
43
various Alpro N.V. subsidiaries. Use of proceeds under the facility is for working capital and other general corporate purposes of Alpro N.V. The subsidiary revolving credit facility will be available for the issuance of up to €1 million of letters of credit. No principal payments are due under the subsidiary revolving credit facility until maturity on July 2, 2011. At December 31, 2010, there were no outstanding borrowings under the facility.
Contractual Obligations and Other Long-Term Liabilities
In the normal course of business, we enter into contracts and commitments that obligate us to make payments in the future. The table below summarizes our obligations for indebtedness, purchase, lease and other contractual obligations at December 31, 2010. See Note 18 to our Consolidated Financial Statements for more detail about our lease obligations.
| | | | | | | | | | | | | | | | | | | | | | | | | | | | |
| | Payments Due by Period | |
| Total | | | 2011 | | | 2012 | | | 2013 | | | 2014 | | | 2015 | | | Thereafter | |
| | (In millions) | |
Senior secured credit facility | | $ | 3,033.5 | | | $ | 167.5 | | | $ | 290.5 | | | $ | 231.7 | | | $ | 1,337.7 | | | $ | 10.5 | | | $ | 995.6 | |
Dean Foods Company senior notes(1) | | | 900.0 | | | | — | | | | — | | | | — | | | | — | | | | — | | | | 900.0 | |
Subsidiary senior notes(1) | | | 142.0 | | | | — | | | | — | | | | — | | | | — | | | | — | | | | 142.0 | |
Capital lease obligations and other | | | 7.7 | | | | 6.7 | | | | 0.6 | | | | 0.4 | | | | — | | | | — | | | | — | |
Purchase obligations(2) | | | 1,007.3 | | | | 635.4 | | | | 175.4 | | | | 112.0 | | | | 14.8 | | | | 14.3 | | | | 55.4 | |
Operating leases | | | 502.1 | | | | 123.0 | | | | 98.2 | | | | 78.2 | | | | 62.0 | | | | 46.5 | | | | 94.2 | |
Interest payments(3) | | | 1,032.9 | | | | 242.1 | | | | 194.2 | | | | 170.9 | | | | 130.2 | | | | 118.5 | | | | 177.0 | |
Benefit payments(4) | | | 325.1 | | | | 22.3 | | | | 21.0 | | | | 21.5 | | | | 22.1 | | | | 21.3 | | | | 216.9 | |
Litigation settlement(5) | | | 30.0 | | | | 30.0 | | | | — | | | | — | | | | — | | | | — | | | | — | |
| | | | | | | | | | | | | | | | | | | | | | | | | | | | |
Total(6) | | $ | 6,980.6 | | | $ | 1,227.0 | | | $ | 779.9 | | | $ | 614.7 | | | $ | 1,566.8 | | | $ | 211.1 | | | $ | 2,581.1 | |
| | | | | | | | | | | | | | | | | | | | | | | | | | | | |
(1) | Represents face value. |
(2) | Primarily represents commitments to purchase minimum quantities of raw materials used in our production processes, including diesel fuel, soybeans and organic raw milk. We enter into these contracts from time to time to ensure a sufficient supply of raw ingredients. In addition, we have contractual obligations to purchase various services that are part of our production process. |
(3) | Includes fixed rate interest obligations, expected cash payments on our interest rate swaps based on the notional amounts of the swaps and the LIBOR forward curve at December 31, 2010 and interest on our variable rate debt based on the rates and balances in effect at December 31, 2010. Interest that may be due in the future on the variable rate portion of our senior secured credit facility and receivables-backed facility will vary based on the interest rate in effect at the time and the borrowings outstanding at the time. Future interest payments on our interest rate swaps will vary based on the interest rates in effect at each respective settlement date. Excluded from the table above are expected cash receipts related to the interest rate swaps. |
(4) | Represents expected future benefit obligations of $307.5 million and $17.6 million related to our pension plans and postretirement healthcare plans, respectively. |
(5) | Represents the agreement to settle all claims in a class action antitrust complaint reached in the fourth quarter of 2010. See Note 18 to our Consolidated Financial Statements for a summary of the agreement. |
(6) | The table above excludes our liability for uncertain tax positions of $58.2 million because the timing of any related cash payments cannot be reasonably estimated. |
Pension and Other Postretirement Benefit Obligations
We offer pension benefits through various defined benefit pension plans and also offer certain health care and life insurance benefits to eligible employees and their eligible dependents upon the retirement of such employees. Reported costs of providing non-contributory defined pension benefits and other postretirement benefits are dependent upon numerous factors, assumptions and estimates. For example, these costs are impacted
44
by actual employee demographics (including age, compensation levels and employment periods), the level of contributions made to the plan and earnings on plan assets. Pension and postretirement costs also may be significantly affected by changes in key actuarial assumptions, including anticipated rates of return on plan assets and the discount rates used in determining the projected benefit obligation and annual periodic pension costs. In 2010 and 2009, we made contributions of $10.3 million and $24.5 million, respectively, to our defined benefit pension plans.
Our pension plan assets are primarily made up of equity and fixed income investments. Changes made to the provisions of the plan may impact current and future pension costs. Fluctuations in actual equity market returns, as well as changes in general interest rates may result in increased or decreased pension costs in future periods. In accordance with Accounting Standards related to “Employers’ Accounting for Pensions,” changes in obligations associated with these factors may not be immediately recognized as pension costs on the income statement, but generally are recognized in future years over the remaining average service period of plan participants. As such, significant portions of pension costs recorded in any period may not reflect the actual level of cash benefits provided to plan participants. In 2010, we recorded non-cash pension expense of $13.0 million, of which $11.3 million was attributable to periodic expense and $1.7 million was attributable to settlements compared to a total of $21.1 million in 2009, of which $20.2 million was attributable to periodic expense and $0.9 million was attributable to settlements.
Almost 90% of our defined benefit plan obligations are frozen as to future participants or increases in accumulated benefits. Many of these obligations were acquired in prior strategic transactions. As an alternative to defined benefit plans, we offer defined contribution plans for eligible employees.
The weighted average discount rate reflects the rate at which our defined benefit plan obligations could be effectively settled. The rate, which is updated annually with the assistance of an independent actuary, uses a model that reflects rates of a hypothetical portfolio of zero-coupon, high quality corporate bonds that mirror our forecasted benefit plan payments in the future. The weighted average discount rate was decreased from 6.00% at December 31, 2009 to 5.28% at December 31, 2010, which will increase the net periodic benefit cost in 2011.
Substantially all of our qualified pension plans are consolidated into one master trust. The investments held in the master trust are managed by an established Investment Committee with assistance from independent investment advisors. In July 2009, the Investment Committee adopted a new long-term investment policy for the master trust that decreases the expected relative holdings of equity securities that targets investments in equity securities at 59% of the portfolio, fixed income at 37%, cash equivalents at 3% and other investments of 1%. At December 31, 2010, our master trust was invested as follows: investments in equity securities were at 62%; investments in fixed income were at 34%; cash equivalents were at less than 1% and other investments were at 4%. Given meaningful equity returns in the fourth quarter of 2010, these investment percentages were slightly different from the Investment Committee targets noted above, and we rebalanced our master trust investments accordingly during the first quarter of 2011 in order to be consistent with those targets.
See Notes 14 and 15 to our Consolidated Financial Statements for information regarding retirement plans and other postretirement benefits.
Other Commitments and Contingencies
On December 21, 2001, in connection with our acquisition of Legacy Dean, we purchased Dairy Farmers of America’s (“DFA”) 33.8% interest in our operations. In connection with that transaction, we issued a contingent, subordinated promissory note to DFA in the original principal amount of $40 million. DFA is a primary supplier of raw milk, and the promissory note is designed to ensure that DFA has the opportunity to continue to supply raw milk to certain of our facilities until 2021, or be paid for the loss of that business. The promissory note has a 20-year term and bears interest based on the consumer price index. Interest will not be paid in cash, but will be added to the principal amount of the note annually, up to a maximum principal amount of $96 million. We may
45
prepay the note in whole or in part at any time, without penalty. The note will only become payable if we materially breach or terminate one of our related milk supply agreements with DFA without renewal or replacement. Otherwise, the note will expire at the end of 20 years, without any obligation to pay any portion of the principal or interest. Payments we make under this note, if any, will be expensed as incurred. We have not terminated, and we have not materially breached, any of our related milk supply agreements with DFA related to the promissory note. We have previously terminated unrelated supply agreements with respect to several plants that were supplied by DFA. In connection with our goals of accelerated cost control and increased supply chain efficiency, we continue to evaluate our sources of raw milk supply.
We also have the following commitments and contingent liabilities, in addition to contingent liabilities related to ordinary course litigation, investigations and audits:
| • | | certain indemnification obligations related to businesses that we have divested; |
| • | | certain lease obligations, which require us to guarantee the minimum value of the leased asset at the end of the lease; and |
| • | | selected levels of property and casualty risks, primarily related to employee health care, workers’ compensation claims and other casualty losses. |
See Note 18 to our Consolidated Financial Statements for more information about our commitments and contingent obligations.
Future Capital Requirements
During 2011, we intend to invest a total of approximately $325 to $350 million in capital expenditures primarily for our existing manufacturing facilities and distribution capabilities under our strategy to optimize our fluid milk production network to increase profitability by reducing costs and to increase production capacity at WhiteWave-Alpro to meet demand. We expect cash interest to be approximately $246 million to $254 million based upon current debt levels and projected forward interest rates under our senior secured credit facility. Cash interest excludes amortization of deferred financing fees and bond discounts of approximately $15 million. The portion of our long-term debt due within the next 12 months totals $174.3 million. From time to time, we may repurchase our outstanding debt obligations in the open market or in privately negotiated transactions, subject to meeting certain terms and conditions as outlined in our credit agreements. We expect that cash flow from operations and borrowings under our senior secured credit facility and receivables-backed facility will be sufficient to meet our future capital requirements for the foreseeable future.
We currently have a maximum permitted senior secured leverage ratio of 4.25 times and maximum leverage ratio of 5.75 times consolidated funded indebtedness to consolidated EBITDA for the prior four consecutive quarters, each as defined under and calculated in accordance with the terms of our senior secured credit facility and our receivables-backed facility. As of December 31, 2010, the senior secured leverage ratio was 3.80 times and the leverage ratio was 5.13 times. The maximum permitted senior secured leverage ratio and leverage ratio under both the senior secured credit facility and the receivables-backed facility will decline to 3.75 times and 5.50 times, respectively, as of March 31, 2012. These reduced leverage ratio requirements could limit our ability to incur additional debt.
At December 31, 2010, $496.5 million was available under the receivables-backed facility, with $875.7 million also available under the senior secured revolving credit facility, subject to the limitations of our credit agreements. Availability under the receivables-backed facility is calculated using the current receivables balance for the seller entities, less adjustments for vendor concentration limits, reserve requirements, and other adjustments as described in the Amended and Restated Receivables Purchase Agreement. Availability under the senior secured revolving credit facility is calculated using the total commitment amount less current borrowings and issued and outstanding letters of credit. Assuming additional borrowings were not utilized to acquire incremental EBITDA, of this combined amount, $484.1 million was then available to finance working capital and other general corporate purposes. At February 24, 2011, approximately $1.3 billion was available under the
46
receivables-backed and revolving credit facilities, subject to the limitations of our credit agreement. Of this combined amount, assuming additional borrowings were not utilized to acquire incremental EBITDA, approximately $492 million was available to finance working capital and other general corporate purposes.
Known Trends and Uncertainties
Prices of Raw Milk and Other Inputs
Conventional Raw Milk and Butterfat— The primary raw material used in Fresh Dairy Direct-Morningstar’s products is conventional milk (which contains both raw milk and butterfat). The federal government and certain state governments set minimum prices for raw milk and those prices are set on a monthly basis. The regulated minimum prices differ based on how the raw milk is utilized. Raw milk processed into fluid milk is priced at the Class I price and raw milk processed into products such as cottage cheese, creams and creamers, ice cream and sour cream is priced at the Class II price. Generally, we pay the federal minimum prices for raw milk, plus certain producer premiums (or “over-order” premiums) and location differentials. We also incur other raw milk procurement costs in some locations (such as hauling, field personnel, etc.). A change in the federal minimum price does not necessarily mean an identical change in our total raw milk costs as over-order premiums may increase or decrease. This relationship is different in every region of the country and sometimes within a region based on supplier arrangements. However, in general, the overall change in our raw milk costs can be linked to the change in federal minimum prices. Because our Class II products typically have a higher fat content than that contained in raw milk, we also purchase bulk cream for use in some of our Class II products. Bulk cream is typically purchased based on a multiple of the AA butter price on the Chicago Mercantile Exchange (“CME”).
In general, Fresh Dairy Direct-Morningstar changes the prices charged for Class I dairy products on a monthly basis, as the costs of raw milk, packaging, fuel and other materials fluctuate. Prices for some Class II products are also changed monthly while others are changed from time to time as circumstances warrant. However, there can be a lag between the timing of a raw material cost increase or decrease and a corresponding price change to our customers, especially in the case of Class II butterfat because Class II butterfat prices for each month are not announced by the government until after the end of that month. Also, in some cases, primarily with respect to diesel fuel and other non-dairy inputs, we are competitively or contractually constrained with respect to the implementation of price changes. This can have a negative impact on our profitability and can cause volatility in our earnings. Our sales and operating profit margin fluctuate with the price of our raw materials and other inputs.
Conventional milk prices continued to increase throughout 2010 compared to historic lows in 2009. We expect the Class I and Class II price to increase fairly dramatically through mid-second quarter of 2011 and level off in the back half of the year. This significant increase in conventional milk prices is a result of limited supply due to production challenges coupled with strong global demand for both Class I and Class II inputs.
Organic Raw Milk — The primary raw material used in our organic milk-based products is organic raw milk. We currently purchase approximately 90% of our organic raw milk from a network of more than 550 family dairy farmers across the United States. The balance of our organic raw milk is sourced from two farms that we own. We generally enter into supply agreements with organic dairy farmers with typical terms of two to five years, which obligate us to purchase certain minimum quantities of organic raw milk. The organic dairy industry regularly experiences significant swings in supply and demand based on consumer economic factors. Retail price increases on private label products generally lag that of branded products, causing retail price gaps to expand. Such gaps can create challenges where increasing costs of food and energy drive up the cost of organic milk faster than retail prices can be increased. During 2010, we experienced increased demand for our organic products particularly ourHorizon Organic brand, and we have taken actions to meet the rising demand. We continue to monitor our position in the organic milk category including taking proactive steps to manage our supply, and we remain focused on maintaining our leading branded position as we balance market share considerations against profitability.
47
Soybeans — Historically, the primary raw material used in our soy-based products has been organic soybeans. However, in 2009, we began augmenting our current product line by offering customers and consumers soy-based products manufactured with non–Genetically Modified Organism (“non-GMO”) soybeans. The launch of these new products has shifted a substantial portion of our raw material requirements from organic to non-GMO soybeans. Both organic soybeans and non-GMO soybeans are generally available from several suppliers and we are not dependent on any single supplier for these raw materials.
Fuel and Resin Costs — Fresh Dairy Direct-Morningstar purchases diesel fuel to operate its extensive DSD system and incurs fuel surcharge expense related to the products it delivers through third-party carriers. WhiteWave-Alpro primarily relies on third-party carriers for product distribution and the transportation agreements typically adjust for movement in diesel prices. Although we may utilize forward purchase contracts and other instruments to mitigate the risks related to commodity price fluctuations, such strategies do not fully mitigate commodity price risk. Adverse movements in commodity prices over the terms of the contracts or instruments could decrease the economic benefits we derive from these strategies.
Another significant raw material we use is resin, which is a fossil fuel based product used to make plastic bottles. Fresh Dairy Direct-Morningstar purchases approximately 28 million pounds of resin and bottles per month. In 2010, we have experienced a sharp increase in the price of resin, particularly during the fourth quarter of 2010. The prices of diesel and resin are subject to fluctuations based on changes in crude oil and natural gas prices. We expect that fuel and resin costs will continue to fluctuate throughout 2011.
Competitive Environment
Supermarkets and food retailers have utilized competitive pricing on dairy products to drive traffic volume and influence customer loyalty, which has significantly reduced their profit margins realized on the sale of such products. During 2010, this margin compression was increasingly absorbed by dairy processors. Also, these industry dynamics continue to drive private label market share gains over branded products, which impacted the growth and profitability of our regionally branded products. These pressures have been exacerbated by volume declines across dairy and non-dairy product categories. Although we began to see price stabilization over the latter part of 2010, we expect these trends to continue. Margin pressures underscore the importance of our low cost strategy. We continue to focus on cost control and supply chain efficiency through cost-cutting initiatives, improved effectiveness in the pass-through of costs to our customers and our continued focus to drive productivity and efficiency within our operations.
Additionally, there has been significant consolidation in the retail grocery industry in recent years, and this trend is continuing. As our customer base consolidates, competition has intensified as we compete for the business of fewer customers. In addition, there are several large regional grocery chains that have captive dairy operations.
As a result of the intensely competitive dairy environment, we have been subject to a number of competitive bidding situations in Fresh Dairy Direct-Morningstar, which has reduced our profitability on sales to several customers. Currently, the dairy industry has experienced widespread price renegotiations. In bidding situations, we are subject to the risk of losing certain customers altogether. The loss of any of our largest customers could have a material adverse impact on our financial results. We do not generally enter into sales agreements with our customers, and where such agreements exist, they are generally terminable at will by the customer.
48
Critical Accounting Estimates
In certain circumstances, the preparation of our Consolidated Financial Statements in conformity with generally accepted accounting principles requires us to use our judgment to make certain estimates and assumptions. These estimates affect the reported amounts of assets and liabilities and disclosures of contingent assets and liabilities at the date of the Consolidated Financial Statements and the reported amounts of net sales and expenses during the reporting period. Our senior management has discussed the development and selection of these critical accounting estimates, as well as our critical accounting policies (see Note 1 to our Consolidated Financial Statements), with the Audit Committee of our Board of Directors. The following accounting estimates are the most critical to aid in fully understanding and evaluating our reported financial results, and they require our most difficult, subjective or complex judgments.
| | | | |
Estimate Description | | Judgment and/or Uncertainty | | Potential Impact if Results Differ |
| | |
Goodwill and Intangible Assets Our goodwill and intangible assets result primarily from acquisitions and primarily include trademarks with finite lives and indefinite lives and customer-related intangible assets. Perpetual trademarks and goodwill are evaluated for impairment at least annually to ensure that the carrying value is recoverable. A perpetual trademark is impaired if its book value exceeds its estimated fair value. Goodwill is evaluated for impairment if the book value of its reporting unit exceeds its estimated fair value. Amortizable intangible assets are only evaluated for impairment upon a significant change in the operating environment. If an evaluation of the undiscounted cash flows indicates impairment, the asset is written down to its estimated fair value, which is generally based on discounted future cash flows. In the fourth quarter of 2010, we completed our annual impairment testing using the methods described above and did not record an impairment charge. Our goodwill and intangible assets totaled $3.9 billion as of December 31, 2010. | | Considerable management judgment is necessary to initially value intangible assets upon acquisition and to evaluate those assets and goodwill for impairment going forward. We determine fair value using widely acceptable valuation techniques including discounted cash flows, market multiples analyses and relief from royalty analyses. Assumptions used in our valuations, such as forecasted growth rates and our cost of capital, are consistent with our internal projections and operating plans. We believe that a trademark has an indefinite life if it has a history of strong sales and cash flow performance that we expect to continue for the foreseeable future. If these perpetual trademark criteria are not met, the trademarks are amortized over their expected useful lives. Determining the expected life of a trademark requires considerable management judgment and is based on an evaluation of a number of factors including the competitive environment, trademark history and anticipated future trademark support. | | We believe that the assumptions used in valuing our intangible assets and in our impairment analysis are reasonable, but variations in any of the assumptions may result in different calculations of fair values that could result in a material impairment charge. The fair value of each of our reporting units exceeds its related carrying value by approximately $229 million or 6.4%, $367 million or 65.1%, $856 million or 80.4% and $33 million or 7.8% for Fresh Dairy Direct, Morningstar, WhiteWave and Alpro, respectively. Increasing our discount rates assumed in these analyses by 0.25% would not have resulted in an impairment charge. The terminal growth rates utilized in calculating the fair value of our reporting units (ranging from 1.8% to 3.5%) is dependent upon meeting our internal projections and operating plans, as well as other factors and assumptions. A 0.25% reduction in the terminal growth rate assumptions used could result in a material impairment charge. While the results of our testing indicate that each of our reporting units has a fair value in excess of its carrying value and no impairment charge was required, the excess of the reporting unit fair values over carrying values, specifically with |
49
| | | | |
Estimate Description | | Judgment and/or Uncertainty | | Potential Impact if Results Differ |
| | | | respect to our Fresh Dairy Direct reporting unit, is significantly less than in prior years. While testing results do not indicate an impairment charge, we can provide no assurance that we will not have an impairment charge in future periods as a result of changes in our operating results or our assumptions. |
| | |
Property, Plant and Equipment We perform impairment tests when circumstances indicate that the carrying value may not be recoverable. Indicators of impairment could include significant changes in business environment or planned closure of a facility. Our property, plant and equipment totaled $2.1 billion as of December 31, 2010. | | Considerable management judgment is necessary to evaluate the impact of operating changes and to estimate future cash flows. | | If actual results are not consistent with our estimates and assumptions used to calculate estimated future cash flows, we may be exposed to impairment losses that could be material. |
| | |
Self Insurance Accruals We retain selected levels of property and casualty risks, primarily related to employee health care, workers’ compensation claims and other casualty losses. Many of these potential losses are covered under conventional insurance programs with third-party carriers with high deductible limits. In other areas, we are self-insured with stop-loss coverages. At December 31, 2010 we recorded accrued liabilities related to these retained risks of $187.3 million, including both current and long-term liabilities. During 2010, we reduced our property and casualty insurance reserves by $20 million, primarily due to a continuous decline in claims and better claims management. | | Accrued liabilities related to these retained risks are calculated based upon loss development factors, which contemplate a number of variables including claims history and expected trends. These loss development factors are developed by us in consultation with external insurance brokers and actuaries. | | If actual results differ from our assumptions, we could be exposed to material gains or losses. A 10% change in our self-insured liabilities could affect net earnings by approximately $11.2 million. |
50
| | | | |
| | |
Employee Benefit Plans We provide a range of benefits including pension and postretirement benefits to our eligible employees and retirees. | | We record annual amounts relating to these plans, which include various actuarial assumptions, such as discount rates, assumed investment rates of return, compensation increases, employee turnover rates and health care cost trend rates. We review our actuarial assumptions on an annual basis and make modifications to the assumptions based on current rates and trends when it is deemed appropriate. The effect of the modifications is generally recorded and amortized over future periods. | | Different assumptions could result in the recognition of different amounts of expense over different periods of time. A 0.25% reduction in the assumed rate of return on plan assets or a 0.25% reduction in the discount rate would increase our annual pension expense by $0.5 million and $0.6 million, respectively. A 1% increase in assumed healthcare costs trends would increase the aggregate post retirement medical obligation by approximately $1.1 million. |
| | |
Stock Based Compensation Plans Options and RSUs We provide a number of option and other stock based compensation plans to our eligible employees. We determine the fair value of our stock option and other stock based awards at the date of grant using the Black-Scholes option pricing model. Cash Awards Linked to our Stock Price Our Cash Performance Unit (“CPU”) awards are designed to link compensation of certain executive officers and other key employees to our performance over a three-year period. The performance metric, as defined in the award, is the performance of our stock price relative to that of a peer group of companies. The range of payout under the award is between 0% and 200% and is payable in cash at the end of the performance period, which is generally three years. Due to our relative stock performance during 2010, we have no liability associated with our 2010 CPU awards. | | Option-pricing models and generally accepted valuation techniques require management to make assumptions and to apply judgment to determine the fair value of our awards. These assumptions and judgments include estimating the future volatility of our stock price, expected dividend yield, future employee turnover rates and future employee stock option exercise behaviors. Changes in these assumptions can materially affect the fair value estimate. | | If actual results are not consistent with our estimates or assumptions we may be exposed to changes in stock-based compensation expense that could be material. A 10% change in our stock-based compensation expense for the year ended December 31, 2010 would have affected net earnings by approximately $2.2 million. Additionally, remeasurements of the fair value of our CPUs as a result of fluctuations in our stock price as compared to our peers can cause variability in our results of operations. |
51
| | | | |
| | |
Income Taxes A liability for uncertain tax positions is recorded to the extent a tax position taken or expected to be taken in a tax return does not meet certain recognition or measurement criteria. A valuation allowance is recorded against a deferred tax asset if it is not more likely than not that the asset will be realized. At December 31, 2010, our liability for uncertain tax positions, including accrued interest, was $58.2 million, and our valuation allowance was $7.7 million. | | Considerable management judgment is necessary to assess the inherent uncertainties related to the interpretations of complex tax laws, regulations, and taxing authority rulings as well as to the expiration of statutes of limitations in the jurisdictions in which we operate. Additionally, several factors are considered in evaluating the realizability of our deferred tax assets, including the remaining years available for carryforward, the tax laws for the applicable jurisdictions, the future profitability of the specific business units, and tax planning strategies. | | Our judgments and estimates concerning uncertain tax positions may change as a result of evaluation of new information, such as the outcome of tax audits or changes to or further interpretations of tax laws and regulations. Our judgments and estimates concerning realizability of deferred tax assets could change if any of the evaluation factors change. If such changes take place, there is a risk that our effective tax rate could increase or decrease in any period, impacting our net earnings. |
Recent Accounting Pronouncements
Recently Adopted Accounting Pronouncements — Effective January 1, 2010, we adopted the Accounting Standards related to “Improving Disclosures about Fair Value Measurements” for the portion of this standard that is effective for interim and annual reporting periods beginning after December 15, 2009. The amendments in this standard are intended to improve the disclosures around fair value measurements. This standard requires disclosure of significant transfers in or out of Level 1 and Level 2 fair value measurements, as well as the reasons for the transfers. It also clarifies existing disclosures related to the level of disaggregation in the disclosures, as well as the required disclosures about inputs and valuation techniques. The adoption of this portion of the standard has not had a material impact on our Consolidated Financial Statements. See Note 10 to our Consolidated Financial Statements. Additionally, a portion of the standard is effective for interim and annual reporting periods beginning after December 15, 2010. This portion requires disclosure of purchases, sales, issuances and settlements in the reconciliation of Level 3 fair value measurements. This portion of the standard is not anticipated to have a material impact on our Consolidated Financial Statements.
Effective January 1, 2010, we adopted the Accounting Standards related to “Amendments to FASB Interpretation No. 46(R)”. This standard changes how a company determines when an entity that is insufficiently capitalized or is not controlled through voting (or similar rights) should be consolidated. The determination of whether a company is required to consolidate an entity is based on, among other things, an entity’s purpose and design and a company’s ability to direct the activities of the entity that most significantly impact the entity’s economic performance. The adoption of this Accounting Standard did not change our accounting for our investment in our Hero/WhiteWave joint venture. See Note 3 to our Consolidated Financial Statements.
Effective January 1, 2010, we adopted the Accounting Standards related to “Accounting for Transfer of Financial Assets”. This standard requires more disclosure of information about transfers of financial assets, including securitization transactions, and where companies have continuing exposure to the risk related to transferred financial assets. It eliminates the concept of a “qualifying special-purpose entity”, changes the requirements for derecognizing financial assets and requires special disclosures. The adoption of this Accounting Standard did not have a material impact on our Consolidated Financial Statements.
Impact of New Federal Legislation — The Patient Protection and Affordable Care Act became law on March 23, 2010, and on March 30, 2010 the Health Care and Education Reconciliation Act of 2010 became law
52
(together the “Act”). The enactment of this legislation has not had, nor is it expected to have, a material impact on our Consolidated Financial Statements.
Item 7A. | Quantitative and Qualitative Disclosures About Market Risk |
We are exposed to market risk due to commodity price, interest rate and foreign currency fluctuations. From time to time we enter into arrangements with other parties to hedge our exposure to these fluctuations.
Commodity Price Fluctuations
We are exposed to commodity price fluctuations, including milk, organic and non-GMO soybeans, butterfat, sweeteners and other commodity costs used in the manufacturing, packaging and distribution of our products, including utilities, natural gas, resin and diesel fuel. In order to secure adequate supplies of materials and bring greater stability to the cost of ingredients and their related manufacturing, packaging and distribution, we routinely enter into forward purchase contracts and other purchase arrangements with suppliers. Under the forward purchase contracts, we commit to purchasing agreed-upon quantities of ingredients and commodities at agreed-upon prices at specified future dates. The outstanding purchase commitment for these commodities at any point in time typically ranges from one month’s to one year’s anticipated requirements, depending on the ingredient or commodity. These contracts are considered normal purchases and sales. In addition to entering into forward purchase contracts, from time to time we may purchase over-the-counter contracts with our qualified banking partners or exchange-traded commodity futures contracts for raw materials that are ingredients of our products or components of such ingredients.
Our open commodity derivative contracts that qualify for hedge accounting had a notional value of $34.3 million as of December 31, 2010. These contracts resulted in net unrealized gains of $2.7 million as of December 31, 2010. At the end of 2010, the potential change in fair value of commodity derivative instruments, assuming a 10% adverse movement in the underlying commodity price, would have resulted in an unrealized net loss of $1.1 million.
Although we may utilize forward purchase contracts and other instruments to mitigate the risks related to commodity price fluctuation, such strategies do not fully mitigate commodity price risk. Adverse movements in commodity prices over the terms of the contracts or instruments could decrease the economic benefits we derive from these strategies. See Note 10 of our Consolidated Financial Statements for a description of our commodity related hedges.
Interest Rate Fluctuations
In order to reduce the volatility of earnings and cash flows that arise from changes in interest rates, we manage interest rate risk through the use of interest rate swap agreements. These swap agreements, including our forward starting swap agreements that have an effective date of March 31, 2012, provide hedges for loans under our senior secured credit facility by limiting or fixing the LIBOR interest rates specified in the senior secured credit facility until the indicated expiration dates.
We are exposed to market risk under these arrangements due to the possibility of interest rates on our senior secured credit facility falling below the rates on our interest rate derivative agreements. We believe the credit risk under these arrangements is remote since the counterparties to our interest rate derivative agreements are major financial institutions. However, if any of the counterparties to our hedging arrangements become unable to fulfill their obligation to us, we may lose the financial benefits of these arrangements.
A majority of our debt obligations are hedged at fixed rates and the remaining debt obligations are currently at variable rates. We have performed a sensitivity analysis assuming a hypothetical 10% adverse movement in
53
interest rates. As of December 31, 2010, the analysis indicated that such interest rate movement would not have a material effect on our financial position, results of operations or cash flows. However, actual gains and losses in the future may differ materially from that analysis based on changes in the timing and amount of interest rate movement and our actual exposure and hedges.
Foreign Currency Fluctuations
Historically, our international operations represented less than 1% of our sales and long-lived assets. With our acquisition of Alpro in July 2009, the relative percentage of our international sales increased slightly. Sales in foreign countries, as well as certain expenses related to those sales, are transacted in currencies other than our reporting currency, the U.S. dollar. Our foreign currency exchange rate risk is primarily limited to the Euro and the British Pound. We may, from time to time, employ derivative financial instruments to manage our exposure to fluctuations in foreign currency rates or enter into forward currency exchange contracts to hedge our net investment and intercompany payable or receivable balances in foreign operations. During 2010, we did not enter into any foreign currency related contracts.
54
Item 8. | Consolidated Financial Statements |
Our Consolidated Financial Statements for 2010 are included in this report on the following pages.
| | | | |
| | Page | |
Consolidated Balance Sheets as of December 31, 2010 and 2009 | | | F-1 | |
Consolidated Statements of Income for the years ended December 31, 2010, 2009 and 2008 | | | F-2 | |
Consolidated Statements of Stockholders’ Equity for the years ended December 31, 2010, 2009 and 2008 | | | F-3 | |
Consolidated Statements of Cash Flows for the years ended December 31, 2010, 2009 and 2008 | | | F-5 | |
Notes to Consolidated Financial Statements | | | F-6 | |
1. Summary of Significant Accounting Policies | | | F-6 | |
2. Discontinued Operations, Divestitures and Acquisitions | | | F-10 | |
3. Investment in Affiliates | | | F-12 | |
4. Inventories | | | F-13 | |
5. Property, Plant and Equipment | | | F-14 | |
6. Goodwill and Intangible Assets | | | F-14 | |
7. Accounts Payable and Accrued Expenses | | | F-16 | |
8. Income Taxes | | | F-17 | |
9. Debt | | | F-20 | |
10. Derivative Financial Instruments and Fair Value Measurement | | | F-33 | |
11. Common Stock and Share-Based Compensation | | | F-36 | |
12. Earnings per Share | | | F-40 | |
13. Other Comprehensive Income (Loss) | | | F-41 | |
14. Employee Retirement and Profit Sharing Plans | | | F-41 | |
15. Postretirement Benefits Other Than Pensions | | | F-47 | |
16. Facility Closing and Reorganization Costs | | | F-49 | |
17. Supplemental Cash Flow Information | | | F-51 | |
18. Commitments and Contingencies | | | F-51 | |
19. Segment, Geographic and Customer Information | | | F-55 | |
20. Quarterly Results of Operations (unaudited) | | | F-58 | |
Report of Independent Registered Public Accounting Firm | | | F-59 | |
55
DEAN FOODS COMPANY
CONSOLIDATED BALANCE SHEETS
| | | | | | | | |
| | December 31 | |
| | 2010 | | | 2009 | |
| | (Dollars in thousands, except share data) | |
ASSETS | | | | | | | | |
Current assets: | | | | | | | | |
Cash and cash equivalents | | $ | 92,007 | | | $ | 45,190 | �� |
Receivables, net of allowance of $15,347 and $16,888 | | | 891,019 | | | | 871,833 | |
Income tax receivable | | | 71,337 | | | | 19,434 | |
Inventories, net | | | 425,576 | | | | 436,061 | |
Deferred income taxes | | | 141,653 | | | | 154,927 | |
Prepaid expenses and other current assets | | | 77,510 | | | | 90,061 | |
Assets held for sale | | | 117,114 | | | | 30,088 | |
| | | | | | | | |
Total current assets | | | 1,816,216 | | | | 1,647,594 | |
Property, plant and equipment, net | | | 2,113,391 | | | | 2,102,253 | |
Goodwill | | | 3,179,192 | | | | 3,272,814 | |
Identifiable intangible and other assets | | | 847,868 | | | | 821,280 | |
| | | | | | | | |
Total | | $ | 7,956,667 | | | $ | 7,843,941 | |
| | | | | | | | |
LIABILITIES AND STOCKHOLDERS’ EQUITY | | | | | | | | |
Current liabilities: | | | | | | | | |
Accounts payable and accrued expenses | | $ | 1,262,876 | | | $ | 1,225,017 | |
Current portion of long-term debt | | | 174,250 | | | | 248,352 | |
Liabilities of disposal groups held for sale | | | 3,839 | | | | 9,045 | |
| | | | | | | | |
Total current liabilities | | | 1,440,965 | | | | 1,482,414 | |
Long-term debt | | | 3,893,275 | | | | 3,980,627 | |
Deferred income taxes | | | 756,714 | | | | 620,093 | |
Other long-term liabilities | | | 351,645 | | | | 393,575 | |
Commitments and contingencies (Note 18) | | | | | | | | |
Stockholders’ equity: | | | | | | | | |
Dean Foods Company stockholders’ equity: | | | | | | | | |
Preferred stock, none issued | | | — | | | | — | |
Common stock 182,255,334 and 180,854,163 shares issued and outstanding, with a par value of $0.01 per share | | | 1,823 | | | | 1,809 | |
Additional paid-in capital | | | 1,061,253 | | | | 1,025,502 | |
Retained earnings | | | 583,102 | | | | 491,611 | |
Accumulated other comprehensive loss | | | (146,653 | ) | | | (166,976 | ) |
| | | | | | | | |
Total Dean Foods Company stockholders’ equity | | | 1,499,525 | | | | 1,351,946 | |
Non-controlling Interest | | | 14,543 | | | | 15,286 | |
| | | | | | | | |
Total stockholders’ equity | | | 1,514,068 | | | | 1,367,232 | |
| | | | | | | | |
Total | | $ | 7,956,667 | | | $ | 7,843,941 | |
| | | | | | | | |
See Notes to Consolidated Financial Statements.
F-1
DEAN FOODS COMPANY
CONSOLIDATED STATEMENTS OF INCOME
| | | | | | | | | | | | |
| | Year Ended December 31 | |
| | 2010 | | | 2009 | | | 2008 | |
| | (Dollars in thousands, except share data) | |
Net sales | | $ | 12,122,887 | | | $ | 11,113,782 | | | $ | 12,361,311 | |
Cost of sales | | | 9,116,965 | | | | 8,008,561 | | | | 9,438,593 | |
| | | | | | | | | | | | |
Gross profit | | | 3,005,922 | | | | 3,105,221 | | | | 2,922,718 | |
Operating costs and expenses: | | | | | | | | | | | | |
Selling and distribution | | | 1,904,526 | | | | 1,818,833 | | | | 1,802,214 | |
General and administrative | | | 629,656 | | | | 623,835 | | | | 482,392 | |
Amortization of intangibles | | | 11,295 | | | | 9,637 | | | | 9,836 | |
Facility closing and reorganization costs | | | 30,761 | | | | 30,162 | | | | 22,758 | |
Other expense | | | 30,000 | | | | — | | | | — | |
| | | | | | | | | | | | |
Total operating costs and expenses | | | 2,606,238 | | | | 2,482,467 | | | | 2,317,200 | |
| | | | | | | | | | | | |
Operating income | | | 399,684 | | | | 622,754 | | | | 605,518 | |
Other (income) expense: | | | | | | | | | | | | |
Interest expense | | | 248,301 | | | | 246,510 | | | | 308,178 | |
Other (income) expense, net | | | 161 | | | | (4,221 | ) | | | 1,123 | |
| | | | | | | | | | | | |
Total other expense | | | 248,462 | | | | 242,289 | | | | 309,301 | |
| | | | | | | | | | | | |
Income from continuing operations before income taxes | | | 151,222 | | | | 380,465 | | | | 296,217 | |
Income taxes | | | 73,482 | | | | 151,845 | | | | 114,330 | |
| | | | | | | | | | | | |
Income from continuing operations | | | 77,740 | | | | 228,620 | | | | 181,887 | |
Gain (loss) on sale of discontinued operations, net of tax | | | 7,521 | | | | 89 | | | | (1,275 | ) |
Income (loss) from discontinued operations, net of tax | | | (2,505 | ) | | | (862 | ) | | | 3,158 | |
| | | | | | | | | | | | |
Net Income | | | 82,756 | | | | 227,847 | | | | 183,770 | |
Net loss attributable to non-controlling interest | | | 8,735 | | | | 12,461 | | | | — | |
| | | | | | | | | | | | |
Net income attributable to Dean Foods Company | | $ | 91,491 | | | $ | 240,308 | | | $ | 183,770 | |
| | | | | | | | | | | | |
Average common shares: | | | | | | | | | | | | |
Basic | | | 181,799,306 | | | | 170,986,886 | | | | 149,266,519 | |
Diluted | | | 182,861,802 | | | | 173,858,303 | | | | 153,395,746 | |
Basic earnings per common share: | | | | | | | | | | | | |
Income from continuing operations attributable to Dean Foods Company | | $ | 0.48 | | | $ | 1.41 | | | $ | 1.22 | |
Income from discontinued operations attributable to Dean Foods Company | | | 0.02 | | | | — | | | | 0.01 | |
| | | | | | | | | | | | |
Net income attributable to Dean Foods Company | | $ | 0.50 | | | $ | 1.41 | | | $ | 1.23 | |
| | | | | | | | | | | | |
Diluted earnings per common share: | | | | | | | | | | | | |
Income from continuing operations attributable to Dean Foods Company | | $ | 0.47 | | | $ | 1.39 | | | $ | 1.19 | |
Income (loss) from discontinued operations attributable to Dean Foods Company | | | 0.03 | | | | (0.01 | ) | | | 0.01 | |
| | | | | | | | | | | | |
Net income attributable to Dean Foods Company | | $ | 0.50 | | | $ | 1.38 | | | $ | 1.20 | |
| | | | | | | | | | | | |
See Notes to Consolidated Financial Statements.
F-2
DEAN FOODS COMPANY
CONSOLIDATED STATEMENTS OF STOCKHOLDERS’ EQUITY
| | | | | | | | | | | | | | | | | | | | | | | | | | | | | | | | |
| | Dean Foods Company Stockholders | | | Non- controlling Interest | | | Total Stockholders’ Equity | | | Comprehensive Income | |
| | Common Stock | | | Additional Paid-In Capital | | | Retained Earnings | | | Accumulated Other Comprehensive Income (Loss) | | | | |
| | Shares | | | Amount | | | | | | | |
| | (Dollars in thousands, except share data) | |
Balance, January 1, 2008 | | | 132,236,217 | | | $ | 1,322 | | | $ | 70,214 | | | $ | 67,533 | | | $ | (87,802 | ) | | $ | — | | | $ | 51,267 | | | | | |
Issuance of common stock, net of tax impact of share-based compensation | | | 3,100,254 | | | | 31 | | | | 27,736 | | | | — | | | | — | | | | — | | | | 27,767 | | | | | |
Share-based compensation expense | | | — | | | | — | | | | 35,180 | | | | — | | | | — | | | | — | | | | 35,180 | | | | | |
Public offering of equity securities | | | 18,700,327 | | | | 187 | | | | 399,290 | | | | — | | | | — | | | | — | | | | 399,477 | | | | | |
Net income | | | — | | | | — | | | | — | | | | 183,770 | | | | — | | | | — | | | | 183,770 | | | $ | 183,770 | |
Other comprehensive income (loss) (Note 13) | | | | | | | | | | | | | | | | | | | | | | | | | | | | | | | | |
Change in fair value of derivative instruments, net of tax benefit of $64,797 | | | — | | | | — | | | | — | | | | — | | | | (105,911 | ) | | | — | | | | (105,911 | ) | | | (105,911 | ) |
Amounts reclassified to income statement related to hedging activities, net of tax of $15,984 | | | — | | | | — | | | | — | | | | — | | | | 26,640 | | | | — | | | | 26,640 | | | | 26,640 | |
Cumulative translation adjustment | | | — | | | | — | | | | — | | | | — | | | | (8,497 | ) | | | — | | | | (8,497 | ) | | | (8,497 | ) |
Pension liability adjustment, net of tax benefit of $30,992 | | | — | | | | — | | | | — | | | | — | | | | (51,459 | ) | | | — | | | | (51,459 | ) | | | (51,459 | ) |
| | | | | | | | | | | | | | | | | | | | | | | | | | | | | | | | |
Comprehensive income | | | | | | | | | | | | | | | | | | | | | | | | | | | | | | $ | 44,543 | |
| | | | | | | | | | | | | | | | | | | | | | | | | | | | | | | | |
Balance, December 31, 2008 | | | 154,036,798 | | | $ | 1,540 | | | $ | 532,420 | | | $ | 251,303 | | | $ | (227,029 | ) | | $ | — | | | $ | 558,234 | | | | | |
Issuance of common stock, net of tax impact of share-based compensation | | | 1,412,365 | | | | 15 | | | | 9,292 | | | | — | | | | — | | | | — | | | | 9,307 | | | | | |
Share-based compensation expense | | | — | | | | — | | | | 39,371 | | | | — | | | | — | | | | — | | | | 39,371 | | | | | |
Public offering of equity securities | | | 25,405,000 | | | | 254 | | | | 444,419 | | | | — | | | | — | | | | — | | | | 444,673 | | | | | |
Fair value of non-controlling interest acquired | | | — | | | | — | | | | — | | | | — | | | | — | | | | 14,499 | | | | 14,499 | | | | | |
Capital contribution from non-controlling interest | | | — | | | | — | | | | — | | | | — | | | | — | | | | 13,248 | | | | 13,248 | | | | | |
Net loss attributable to non-controlling interest | | | — | | | | — | | | | — | | | | — | | | | — | | | | (12,461 | ) | | | (12,461 | ) | | | | |
Other comprehensive income (loss) (Note 13) | | | | | | | | | | | | | | | | | | | | | | | | | | | | | | | | |
Net income attributable to Dean Foods Company | | | — | | | | — | | | | — | | | | 240,308 | | | | — | | | | — | | | | 240,308 | | | $ | 240,308 | |
Change in fair value of derivative instruments, net of tax benefit of $13,387 | | | — | | | | — | | | | — | | | | — | | | | (22,417 | ) | | | — | | | | (22,417 | ) | | | (22,417 | ) |
Amounts reclassified to income statement related to hedging activities, net of tax of $42,466 | | | — | | | | — | | | | — | | | | — | | | | 70,772 | | | | — | | | | 70,772 | | | | 70,772 | |
Cumulative translation adjustment | | | — | | | | — | | | | — | | | | — | | | | 2,509 | | | | — | | | | 2,509 | | | | 2,509 | |
Pension liability adjustment, net of tax of $3,260 | | | — | | | | — | | | | — | | | | — | | | | 9,189 | | | | — | | | | 9,189 | | | | 9,189 | |
| | | | | | | | | | | | | | | | | | | | | | | | | | | | | | | | |
Comprehensive income | | | | | | | | | | | | | | | | | | | | | | | | | | | | | | $ | 300,361 | |
| | | | | | | | | | | | | | | | | | | | | | | | | | | | | | | | |
Balance, December 31, 2009 | | | 180,854,163 | | | $ | 1,809 | | | $ | 1,025,502 | | | $ | 491,611 | | | $ | (166,976 | ) | | $ | 15,286 | | | $ | 1,367,232 | | | | | |
F-3
DEAN FOODS COMPANY
CONSOLIDATED STATEMENTS OF STOCKHOLDERS’ EQUITY—(Continued)
| | | | | | | | | | | | | | | | | | | | | | | | | | | | | | | | |
| | Dean Foods Company Stockholders | | | Non- controlling Interest | | | Total Stockholders’ Equity | | | Comprehensive Income | |
| | Common Stock | | | Additional Paid-In Capital | | | Retained Earnings | | | Accumulated Other Comprehensive Income (Loss) | | | | |
| | Shares | | | Amount | | | | | | | |
| | (Dollars in thousands, except share data) | |
Issuance of common stock, net of tax impact of share-based compensation | | | 1,401,171 | | | | 14 | | | | (1,121 | ) | | | — | | | | — | | | | — | | | | (1,107 | ) | | | | |
Share-based compensation expense | | | — | | | | — | | | | 36,872 | | | | — | | | | — | | | | — | | | | 36,872 | | | | | |
Capital contribution from non-controlling interest | | | — | | | | — | | | | — | | | | — | | | | — | | | | 7,992 | | | | 7,992 | | | | | |
Net loss attributable to non-controlling interest | | | — | | | | — | | | | — | | | | — | | | | — | | | | (8,735 | ) | | | (8,735 | ) | | | | |
Other comprehensive income (loss) (Note 13) | | | | | | | | | | | | | | | | | | | | | | | | | | | | | | | | |
Net income attributable to Dean Foods Company | | | — | | | | — | | | | — | | | | 91,491 | | | | — | | | | — | | | | 91,491 | | | $ | 91,491 | |
Change in fair value of derivative instruments, net of tax benefit of $12,491 | | | — | | | | — | | | | — | | | | — | | | | (17,360 | ) | | | — | | | | (17,360 | ) | | | (17,360 | ) |
Amounts reclassified to income statement related to hedging activities, net of tax of $37,180 | | | — | | | | — | | | | — | | | | — | | | | 59,393 | | | | — | | | | 59,393 | | | | 59,393 | |
Cumulative translation adjustment | | | — | | | | — | | | | — | | | | — | | | | (20,707 | ) | | | — | | | | (20,707 | ) | | | (20,707 | ) |
Pension liability adjustment, net of tax benefit of $525 | | | — | | | | — | | | | — | | | | — | | | | (1,003 | ) | | | — | | | | (1,003 | ) | | | (1,003 | ) |
| | | | | | | | | | | | | | | | | | | | | | | | | | | | | | | | |
Comprehensive income attributable to Dean Foods Company | | | | | | | | | | | | | | | | | | | | | | | | | | | | | | $ | 111,814 | |
| | | | | | | | | | | | | | | | | | | | | | | | | | | | | | | | |
Balance, December 31, 2010 | | | 182,255,334 | | | $ | 1,823 | | | $ | 1,061,253 | | | $ | 583,102 | | | $ | (146,653 | ) | | $ | 14,543 | | | $ | 1,514,068 | | | | | |
| | | | | | | | | | | | | | | | | | | | | | | | | | | | | | | | |
See Notes to Consolidated Financial Statements.
F-4
DEAN FOODS COMPANY
CONSOLIDATED STATEMENTS OF CASH FLOWS
| | | | | | | | | | | | |
| | Year Ended December 31 | |
| | 2010 | | | 2009 | | | 2008 | |
| | (In thousands) | |
Cash flows from operating activities: | | | | | | | | | | | | |
Net income | | $ | 82,756 | | | $ | 227,847 | | | $ | 183,770 | |
(Income) loss from discontinued operations | | | 2,505 | | | | 862 | | | | (3,158 | ) |
(Gain) loss on sale of discontinued operations | | | (7,521 | ) | | | (89 | ) | | | 1,275 | |
Adjustments to reconcile net income to net cash provided by operating activities: | | | | | | | | | | | | |
Depreciation and amortization | | | 276,080 | | | | 253,930 | | | | 236,820 | |
Share-based compensation expense | | | 36,872 | | | | 39,371 | | | | 35,180 | |
Loss on disposition of assets and operations | | | 5,627 | | | | 12,638 | | | | 2,968 | |
Write-down of impaired assets | | | 14,186 | | | | 16,815 | | | | 20,740 | |
Write-off of financing costs | | | 3,695 | | | | — | | | | — | |
Deferred income taxes | | | 121,043 | | | | 40,352 | | | | 67,980 | |
Other | | | (1,379 | ) | | | (1,337 | ) | | | (6,380 | ) |
Changes in operating assets and liabilities, net of acquisitions: | | | | | | | | | | | | |
Receivables, net | | | (25,659 | ) | | | 57,577 | | | | 58,383 | |
Inventories | | | 4,020 | | | | (8,389 | ) | | | (4,820 | ) |
Prepaid expenses and other assets | | | 5,764 | | | | 5,393 | | | | 11,055 | |
Accounts payable and accrued expenses | | | 62,931 | | | | 59,148 | | | | 64,656 | |
Income taxes receivable/payable | | | (55,220 | ) | | | (46,039 | ) | | | 45,037 | |
| | | | | | | | | | | | |
Net cash provided by operating activities—continuing operations | | | 525,700 | | | | 658,079 | | | | 713,506 | |
Net cash provided by operating activities—discontinued operations | | | 8,765 | | | | 2,475 | | | | 3,122 | |
| | | | | | | | | | | | |
Net cash provided by operating activities | | | 534,465 | | | | 660,554 | | | | 716,628 | |
Cash flows from investing activities: | | | | | | | | | | | | |
Payments for property, plant and equipment | | | (301,974 | ) | | | (267,690 | ) | | | (256,139 | ) |
Payments for acquisitions, net of cash received | | | — | | | | (581,211 | ) | | | (95,851 | ) |
Proceeds from sale of fixed assets | | | 8,399 | | | | 8,833 | | | | 11,329 | |
| | | | | | | | | | | | |
Net cash used in investing activities—continuing operations | | | (293,575 | ) | | | (840,068 | ) | | | (340,661 | ) |
Net cash provided by (used in) investing activities—discontinued operations | | | 24,121 | | | | (525 | ) | | | (826 | ) |
| | | | | | | | | | | | |
Net cash used in investing activities | | | (269,454 | ) | | | (840,593 | ) | | | (341,487 | ) |
Cash flows from financing activities: | | | | | | | | | | | | |
Proceeds from issuance of debt | | | 400,000 | | | | — | | | | — | |
Repayment of debt | | | (514,457 | ) | | | (330,363 | ) | | | (109,987 | ) |
Proceeds from senior secured revolver | | | 4,006,680 | | | | 3,689,000 | | | | 3,298,200 | |
Payments for senior secured revolver | | | (4,068,880 | ) | | | (3,173,800 | ) | | | (3,848,500 | ) |
Proceeds from receivables-backed facility | | | 2,445,500 | | | | 1,784,728 | | | | 1,852,320 | |
Payments for receivables-backed facility | | | (2,445,500 | ) | | | (2,244,728 | ) | | | (1,992,320 | ) |
Payments of financing costs | | | (52,720 | ) | | | — | | | | — | |
Issuance of common stock | | | 3,415 | | | | 454,326 | | | | 419,663 | |
Tax savings on share-based compensation | | | 278 | | | | 894 | | | | 7,581 | |
Capital contribution from non-controlling interest | | | 7,992 | | | | 12,708 | | | | — | |
| | | | | | | | | | | | |
Net cash provided by (used in) financing activities | | | (217,692 | ) | | | 192,765 | | | | (373,043 | ) |
Effect of exchange rate changes on cash and cash equivalents | | | (502 | ) | | | 808 | | | | — | |
| | | | | | | | | | | | |
Increase in cash and cash equivalents | | | 46,817 | | | | 13,534 | | | | 2,098 | |
Cash and cash equivalents, beginning of period | | | 45,190 | | | | 31,656 | | | | 29,558 | |
| | | | | | | | | | | | |
Cash and cash equivalents, end of period | | $ | 92,007 | | | $ | 45,190 | | | $ | 31,656 | |
| | | | | | | | | | | | |
See Notes to Consolidated Financial Statements.
F-5
DEAN FOODS COMPANY
NOTES TO CONSOLIDATED FINANCIAL STATEMENTS
Years Ended December 31, 2010, 2009 and 2008
1. | SUMMARY OF SIGNIFICANT ACCOUNTING POLICIES |
Nature of Our Business — We are one of the leading food and beverage companies in the United States, as well as a global leader in branded plant-based beverages, such as soy, almond and coconut milks, and other soy-based food products. As we continue to evaluate and seek to maximize the value of our strong brands and product offerings, we have aligned our leadership teams, operating strategies and supply chain initiatives around our two lines of business: Fresh Dairy Direct-Morningstar (previously Fresh Dairy Direct) and WhiteWave-Alpro (previously WhiteWave-Morningstar). Fresh Dairy Direct-Morningstar is the largest processor and distributor of milk and other dairy products in the country, with products sold under more than 50 familiar local and regional brands and a wide array of private labels. WhiteWave-Alpro markets and sells a variety of nationally branded dairy and dairy-related products, such asHorizon Organicmilk and other dairy products,The Organic Cow organic dairy products,International Delightcoffee creamers andLAND O LAKEScreamers and fluid dairy products, andSilkplant-based beverages such as soy, almond and coconut milks and cultured soy products. WhiteWave-Alpro also offers branded soy-based beverages and food products in Europe and markets its products under theAlproandProvamel brands.
Basis of Presentation and Consolidation — Our Consolidated Financial Statements are prepared in accordance with U.S. generally accepted accounting principles (“GAAP”), and include the accounts of our wholly-owned subsidiaries, as well as those of our 50% owned joint venture between WhiteWave and Hero Group (“Hero”). The resulting non-controlling interest’s share in the equity of the joint venture is presented as a separate component of stockholders’ equity in the Consolidated Balance Sheets and Consolidated Statements of Stockholders’ Equity and the net loss attributable to the non-controlling interest is presented in the Consolidated Statements of Income. All intercompany balances and transactions are eliminated in consolidation.
Unless otherwise indicated, references in the report to “we,” “us” or “our” refer to Dean Foods Company and its subsidiaries, taken as a whole.
In the first quarter of 2010, our Chief Executive Officer, who is our chief operating decision maker, changed the way he evaluates the performance of our operations, develops strategy and allocates capital resources. As a result, beginning in the first quarter of 2010, our Morningstar operations were aligned with our Fresh Dairy Direct operations, so that our two reporting segments consisted of Fresh Dairy Direct-Morningstar and WhiteWave-Alpro. This change reflects the divergence between the strategies and objectives of these two segments. Our value-added branded operations at WhiteWave-Alpro added scale with the acquisition of Alpro in July 2009 and are focused on driving growth through effective marketing and innovation. Our traditional dairy operations at Fresh Dairy Direct-Morningstar are driven by a focus on cost and service leadership. We believe these revised segments have increased internal focus and offered management and investors improved visibility into the performance of the segments against their specific objectives. All segment results set forth herein have been recast to present results on a comparable basis. These changes had no impact on consolidated net sales or operating income.
During the second quarter of 2010, we committed to a plan to sell the business operations of our Rachel’s Dairy companies (“Rachel’s”), which provide organic branded dairy-based chilled yogurt, milk and related dairy products primarily in the United Kingdom. The sale of these operations was completed on August 4, 2010. The decision to sell these operations was part of our strategic growth plan and allows us to target our investments in growing our core dairy and branded businesses by divesting of non-core businesses. All of our Rachel’s operations, previously reported within the WhiteWave-Alpro segment, have been reclassified as discontinued operations. See Note 2. Unless stated otherwise, any reference to income statement items in these financial statements refers to results from continuing operations.
F-6
Use of Estimates — The preparation of our Consolidated Financial Statements in conformity with GAAP requires us to use our judgment to make estimates and assumptions that affect the reported amounts of assets and liabilities and disclosures of contingent assets and liabilities at the date of the Consolidated Financial Statements and the reported amounts of net sales and expenses during the reporting period. Actual results could differ from these estimates under different assumptions or conditions.
Cash Equivalents — We consider temporary investments with an original maturity of three months or less to be cash equivalents.
Inventories — Inventories are stated at the lower of cost or market. Our products are valued using the first-in, first-out method. The costs of finished goods inventories include raw materials, direct labor and indirect production and overhead costs. Reserves for obsolete or excess inventory are not material.
Property, Plant and Equipment — Property, plant and equipment are stated at acquisition cost, plus capitalized interest on borrowings during the actual construction period of major capital projects. Also included in property, plant and equipment are certain direct costs related to the implementation of computer software for internal use. Depreciation is calculated using the straight-line method typically over the following range of estimated useful lives of the assets:
| | |
Asset | | Useful Life |
Buildings | | 15 to 40 years |
Machinery and equipment | | 3 to 20 years |
Leasehold improvements | | Over the terms of the applicable lease agreements |
We perform property, plant and equipment impairment tests when circumstances indicate that the carrying value may not be recoverable. Indicators of impairment could include significant changes in business environment or planned closure of a facility. Considerable management judgment is necessary to evaluate the impact of operating changes and to estimate future cash flows. Assumptions used in our impairment evaluations include product development, volume growth and contribution margins. Leasehold improvements are amortized over the shorter of their lease term or their estimated useful lives. Expenditures for repairs and maintenance, which do not improve or extend the life of the assets, are expensed as incurred.
Intangible and Other Assets — Identifiable intangible assets, other than trademarks that have indefinite lives, are typically amortized over the following range of estimated useful lives:
| | |
Asset | | Useful Life |
Customer relationships | | 5 to 15 years |
Certain finite lived trademarks | | 5 to 15 years |
Customer supply contracts | | Over the terms of the agreements |
Noncompetition agreements | | Over the terms of the agreements |
Deferred financing costs | | Over the terms of the related debt |
In accordance with Accounting Standards related to “Goodwill and Other Intangible Assets”, we do not amortize goodwill and other intangible assets determined to have indefinite useful lives. Instead, we conduct impairment tests on our goodwill, trademarks and other intangible assets with indefinite lives annually and when circumstances indicate that the carrying value may not be recoverable. To determine whether impairment exists, we primarily utilize a discounted future cash flow analysis.
Assets Held for Sale — We classify assets as held for sale when management approves and commits to a formal plan of sale and our expectation is that the sale will be completed within one year. The carrying value of the net assets of the business held for sale are then recorded at the fair market value, less costs to sell. As of
F-7
December 31, 2010 and 2009, assets of $117.1 million and $30.1 million, respectively, related to the sale of our yogurt operations, within Fresh Dairy Direct-Morningstar, in 2010 and related to the discontinued operations of our Rachel’s business, within WhiteWave-Alpro, in 2009, were recorded within the assets held for sale line on our Consolidated Balance Sheets within and are no longer being depreciated. See Note 2. As of December 31, 2010 and 2009, assets of $2.3 million and $24.9 million, respectively, related to facilities that are closed or to be closed, were held for sale and recorded in prepaid expenses and other current assets line on our Consolidated Balance Sheets within our Fresh Dairy Direct-Morningstar segment and are no longer being depreciated. During the third quarter of 2010, we reclassified $14 million of assets designated as held for sale to assets held for use. Of this amount, $7 million related to a property that we now intend to use for additional capacity to support the growth in our WhiteWave Foods business. The remaining $7 million relates to a facility that we continue to actively market for sale but, given current market conditions, we no longer believe will be sold in the near term. These transfers did not have a material impact to our results of operations for the period ended December 31, 2010. In 2010 and 2009, we recorded a charge of $13.2 million and $16.3 million, respectively, primarily to write-down certain of the closed facility assets to their estimated fair value. These charges were recorded within facility closing and reorganization costs. See Note 16.
Foreign Currency Translation — The financial statements of our foreign subsidiaries are translated to U.S. dollars. The functional currency of our foreign subsidiaries is generally the local currency of the country. Accordingly, assets and liabilities of the foreign subsidiaries are translated to U.S. dollars at year-end exchange rates. Income and expense items are translated at the average rates prevailing during the year. Changes in exchange rates that affect cash flows and the related receivables or payables are recognized as transaction gains and losses and are recognized in the statement of income with their related operational activity. Currently, an immaterial amount of transaction gains and losses are reflected in general and administrative expense in our Consolidated Statements of Income. The cumulative translation adjustment in stockholders’ equity reflects the unrealized adjustments resulting from translating the financial statements of our foreign subsidiaries.
Share-Based Compensation — Share-based compensation expense is recognized for equity awards over the vesting period based on their grant date fair value. The fair value of option awards is estimated at the date of grant using the Black-Scholes valuation model. The fair value of restricted stock unit awards is equal to the closing price of our stock on the date of grant. Compensation expense is recognized only for equity awards expected to vest. We estimate forfeitures at the date of grant based on our historical experience and future expectations. Share-based compensation expense is included within the same financial statement caption where the recipient’s cash compensation is reported and is classified as a corporate item for segment reporting.
Sales Recognition and Accounts Receivable — Sales are recognized when persuasive evidence of an arrangement exists, the price is fixed or determinable, the product has been delivered to the customer and there is a reasonable assurance of collection of the sales proceeds. Sales are reduced by certain sales incentives, some of which are recorded by estimating expense based on our historical experience. We provide credit terms to customers generally ranging up to 30 days, perform ongoing credit evaluation of our customers and maintain allowances for potential credit losses based on our historical experience. Estimated product returns have not historically been material.
Income Taxes — All of our wholly-owned U.S. operating subsidiaries, as well as our proportional share of the operations of our unconsolidated affiliates and our consolidated joint venture, are included in our U.S. federal consolidated tax return. Our foreign subsidiaries are required to file local jurisdiction income tax returns with respect to their operations, the earnings from which are expected to be reinvested indefinitely. At December 31, 2010, no provision had been made for U.S. federal or state income tax on approximately $43.8 million of accumulated foreign earnings as they are considered to be indefinitely reinvested.
Deferred income taxes arise from temporary differences between amounts recorded in the Consolidated Financial Statements and tax bases of assets and liabilities using enacted tax rates in effect for the years in which the differences are expected to reverse. Deferred tax assets, including the benefit of net operating loss and tax credit carryforwards, are evaluated based on the guidelines for realization and are reduced by a valuation allowance if deemed necessary.
F-8
We recognize the income tax benefit from an uncertain tax position when it is more likely than not that, based on technical merits, the position will be sustained upon examination, including resolutions of any related appeals or litigation processes. We recognize accrued interest related to uncertain tax positions as a component of income tax expense, and penalties, if incurred, are recognized as a component of operating income.
Sales Incentives and Advertising Expense — We market our products through advertising and other promotional activities, including media, agency, coupons, trade shows and other promotional activities. Advertising expense is charged to income during the period incurred, except for expenses related to the development of a major commercial or media campaign which are charged to income during the period in which the advertisement or campaign is first presented by the media. Advertising expense totaled $190.7 million in 2010, $174.3 million in 2009 and $121.3 million in 2008. Additionally, prepaid advertising costs were $2.3 million and $1.5 million at December 31, 2010 and 2009, respectively. Certain customer and trade promotional programs, such as rebates, are recorded as a reduction of sales.
Shipping and Handling Fees — Our shipping and handling costs are included in both cost of sales and selling and distribution expense, depending on the nature of such costs. Shipping and handling costs included in cost of sales reflect inventory warehouse costs and product loading and handling costs. Shipping and handling costs included in selling and distribution expense consist primarily of those costs associated with moving finished products from production facilities through our distribution network, including costs associated with its distribution centers, route delivery costs and the cost of shipping products to customers through third party carriers. Shipping and handling costs that were recorded as a component of selling and distribution expense were $1.4 billion, $1.3 billion and $1.4 billion during 2010, 2009 and 2008, respectively.
Insurance Accruals — We retain selected levels of property and casualty risks, primarily related to employee health care, workers’ compensation claims and other casualty losses. Many of these potential losses are covered under conventional insurance programs with third party carriers with high deductible limits. In other areas, we are self-insured with stop-loss coverage. Accrued liabilities for incurred but not reported losses related to these retained risks are calculated based upon loss development factors which contemplate a number of factors including claims history and expected trends.
Research and Development — Our research and development activities primarily consist of generating and testing new product concepts, new flavors and packaging. Our total research and development expense was $25.8 million, $25.5 million and $14.0 million for 2010, 2009 and 2008, respectively. Research and development costs are primarily included in general and administrative expenses in our Consolidated Statements of Income.
Recently Adopted Accounting Pronouncements — Effective January 1, 2010, we adopted the Accounting Standards related to “Improving Disclosures about Fair Value Measurements” for the portion of this standard that is effective for interim and annual reporting periods beginning after December 15, 2009. The amendments in this standard are intended to improve the disclosures around fair value measurements. This standard requires disclosure of significant transfers in or out of Level 1 and Level 2 fair value measurements, as well as the reasons for the transfers. It also clarifies existing disclosures related to the level of disaggregation in the disclosures, as well as the required disclosures about inputs and valuation techniques. The adoption of this portion of the standard has not had a material impact on our Consolidated Financial Statements. See Note 10. Additionally, a portion of the standard is effective for interim and annual reporting periods beginning after December 15, 2010. This portion requires disclosure of purchases, sales, issuances and settlements in the reconciliation of Level 3 fair value measurements. This portion of the standard is not anticipated to have a material impact on our Consolidated Financial Statements.
Effective January 1, 2010, we adopted the Accounting Standards related to “Amendments to FASB Interpretation No. 46(R)”. This standard changes how a company determines when an entity that is insufficiently capitalized or is not controlled through voting (or similar rights) should be consolidated. The determination of whether the company is required to consolidate an entity is based on, among other things, an entity’s purpose and
F-9
design and a company’s ability to direct the activities of the entity that most significantly impact the entity’s economic performance. The adoption of this Accounting Standard did not change our accounting for our investment in our Hero/WhiteWave joint venture. See Note 3.
Effective January 1, 2010, we adopted the Accounting Standards related to “Accounting for Transfer of Financial Assets”. This standard requires more disclosure of information about transfers of financial assets, including securitization transactions, and where companies have continuing exposure to the risk related to transferred financial assets. It eliminates the concept of a “qualifying special-purpose entity”, changes the requirements for derecognizing financial assets and requires special disclosures. The adoption of this Accounting Standard did not have a material impact on our Consolidated Financial Statements.
Impact of New Federal Legislation — The Patient Protection and Affordable Care Act became law on March 23, 2010, and on March 30, 2010 the Health Care and Education Reconciliation Act of 2010 became law. The enactment of this legislation has not had, nor is it expected to have, a material impact on our Consolidated Financial Statements.
2. | DISCONTINUED OPERATIONS, DIVESTITURES AND ACQUISITIONS |
Discontinued Operations
During the second quarter of 2010, we committed to a plan to sell the business operations of Rachel’s, which provides organic branded dairy-based chilled yogurt, milk and related dairy products primarily in the United Kingdom. We completed the sale of our Rachel’s business on August 4, 2010 and recognized a gain of $5.7 million, net of tax. Our Rachel’s operations, previously reported within the WhiteWave-Alpro segment, have been reclassified as discontinued operations in our Consolidated Financial Statements for the twelve-month periods ended December 31, 2010, 2009 and 2008 and as of December 31, 2009.
The following is a summary of Rachel’s assets and liabilities held for sale as of December 31, 2009:
| | | | |
| | December 31, 2009 | |
| | (In thousands) | |
Assets | | | | |
Current assets | | $ | 11,514 | |
Property, plant and equipment, net | | | 6,626 | |
Goodwill, identifiable intangibles and other assets | | | 11,948 | |
| | | | |
Assets of discontinued operations held for sale | | $ | 30,088 | |
| | | | |
Liabilities | | | | |
Accounts payable and accrued expenses | | $ | 5,156 | |
Other liabilities | | | 3,889 | |
| | | | |
Liabilities of discontinued operations held for sale | | $ | 9,045 | |
| | | | |
The following is a summary of Rachel’s operating results, which are included in discontinued operations:
| | | | | | | | | | | | |
| | Year Ended December 31 | |
| | 2010 | | | 2009 | | | 2008 | |
| | (In thousands) | |
Operations: | | | | | | | | | | | | |
Net sales | | $ | 26,319 | | | $ | 44,606 | | | $ | 93,302 | |
| | | |
Income (loss) before income taxes | | | (3,783 | ) | | | (642 | ) | | | 3,460 | |
Income tax | | | 1,399 | | | | (220 | ) | | | (507 | ) |
| | | | | | | | | | | | |
Net income (loss) | | $ | (2,384 | ) | | $ | (862 | ) | | $ | 2,953 | |
| | | | | | | | | | | | |
F-10
In 2010 and 2008, we recognized expense of $121,000 and income of $205,000, respectively, related to prior discontinued operations. In 2010, 2009 and 2008, we recognized a gain of $1.8 million, a gain of $89,000 and a loss of $1.3 million, respectively, on the sale of prior discontinued operations.
Divestitures
In the fourth quarter of 2010, we entered into two separate agreements to sell our Mountain High and private label yogurt operations, which are part of our Fresh Dairy Direct-Morningstar segment. We expect to record a gain related to the sale of both of these operations. On February 1, 2011, we completed the sale of our Mountain High yogurt operations. We expect our private label operations sale to close in the first half of 2011. These operations did not meet the requirement to be accounted for as discounted operations. We intend to use the proceeds from the sale of our yogurt operations to pay down outstanding debt under our senior secured credit facility. See Note 9.
The following is a summary of our Mountain High and private label yogurt operations’ assets and liabilities held for sale as of December 31, 2010:
| | | | |
| | December 31, 2010 | |
| | (In thousands) | |
Assets | | | | |
Current assets | | $ | 8,329 | |
Property, plant and equipment, net | | | 26,346 | |
Goodwill, identifiable intangibles and other assets | | | 82,439 | |
| | | | |
Assets held for sale | | $ | 117,114 | |
| | | | |
Liabilities | | | | |
Accounts payable and accrued expenses | | $ | 3,839 | |
| | | | |
Acquisitions
Alpro — As discussed in Note 1, on July 2, 2009, we completed the acquisition of Alpro, a privately held food company based in Belgium, for an aggregate purchase price of €314.6 million ($440.3 million), after working capital adjustments, excluding transaction costs which were expensed as incurred. Alpro manufactures and sells branded soy-based beverages and food products in Europe. The acquisition of Alpro has provided opportunities to leverage the collective strengths of our combined businesses across a global soy beverages and related products category.
Assets acquired and liabilities assumed in connection with the acquisition have been recorded at their fair values. The fair values were determined by management based in part on an independent valuation of the net assets acquired, which includes intangible assets of $117.6 million. Intangible assets subject to amortization of $21.0 million are being amortized over a weighted-average period of 15 years and relate primarily to customer relationships.
The excess of the net purchase price over the fair value of the net assets acquired of $175.1 million was recorded as goodwill and represents a value attributable to an increased competitive position in the soy-based beverages and foods in Europe. The goodwill is not deductible for tax purposes.
F-11
Identifiable assets acquired and liabilities assumed are as follows:
| | | | |
| | July 2, 2009 | |
| | (In thousands) | |
Current assets | | $ | 103,050 | |
Property, plant and equipment | | | 195,477 | |
Goodwill | | | 175,100 | |
Identifiable intangible assets | | | 117,627 | |
Other long-term assets | | | 34,079 | |
Current liabilities | | | (83,654 | ) |
Other long-term liabilities | | | (101,424 | ) |
| | | | |
Net identifiable assets acquired | | $ | 440,255 | |
| | | | |
The final valuation of the assets acquired and liabilities assumed in this acquisition was completed in 2010. Alpro’s results of operations have been included in our Consolidated Statements of Income and the results of operations of our WhiteWave-Alpro segment from the date of acquisition. The pro-forma impact of the acquisition on consolidated net earnings would not have materially changed our 2009 reported net earnings.
Other acquisitions — Excluding the acquisition of the Alpro division of Vandemoortele, N.V. (“Alpro”), we completed the acquisition of several businesses during 2009 and 2008, for an aggregate purchase price of approximately $143.5 million and $95.9 million, respectively. These acquisitions were not material individually or in the aggregate, including the pro-forma impact on earnings. All of these acquisitions were funded with cash flows from operations and borrowings under our senior secured credit facility and our receivables-backed facility. The results of operations of the acquired companies are included in our Consolidated Financial Statements subsequent to their respective acquisition dates. At the acquisition date, the purchase price was allocated to assets acquired, including identifiable intangibles and liabilities assumed based on their estimated fair market values. There were no acquisitions completed during 2010.
During the year ended December 31, 2010, we recorded expenses of approximately $9.8 million in connection with the Rachel’s sale as well as other transactional activities. Of this amount, $3.6 million was recorded in discontinued operations for the year ended December 31, 2010. During the year ended December 31, 2009, we recorded expenses of approximately $31.3 million in connection with our Alpro and Fresh Dairy Direct-Morningstar acquisitions, as well as other transactional activities, which were recorded in general and administrative expenses in our Consolidated Statements of Income.
3. | INVESTMENT IN AFFILIATES |
Unconsolidated Affiliate and Related Party
Consolidated Container Company — We own an approximately 25% non-controlling interest, on a fully diluted basis, in Consolidated Container Company (“CCC”), one of the nation’s largest manufacturers of rigid plastic containers and our largest supplier of plastic bottles and bottle components. We have owned our minority interest since July 2, 1999, when we sold our U.S. plastic packaging operations to CCC. Vestar Capital Partners, an unaffiliated entity, controls CCC through a majority ownership interest. Pursuant to our agreements with Vestar, we control two of the eight seats on CCC’s Management Committee.
Since July 2, 1999, our investment in CCC has been accounted for under the equity method of accounting. During 2001, we concluded that our investment was permanently impaired so we wrote off our remaining investment. Our investment in CCC has been recorded at zero value since then and is still generating no income under the equity method of accounting. We have received no distributions from CCC since writing the investment down in 2001. As the tax basis of our investment in CCC is calculated differently than the carrying value of the investment recognized in our Consolidated Financial Statements, the sale or liquidation of our investment, the timing of which may be beyond our control, could result in a significantly disproportionate tax obligation.
F-12
We have supply agreements with CCC to purchase certain of our requirements for plastic bottles and bottle components from CCC through December 31, 2011. We spent $314.9 million, $268.2 million and $330.3 million on products purchased from CCC during the years ended December 31, 2010, 2009 and 2008, respectively. As of December 31, 2010 and 2009, we had net payables to CCC of $12.8 million and $18.7 million.
Non-controlling Interest in Consolidated Affiliate
Hero/WhiteWave Joint Venture — In January 2008, we entered into and formed a 50/50 strategic joint venture with Hero Group (“Hero”), a producer of international fruit and infant nutrition brands, as a strategic growth platform for both companies to extend their global reach by leveraging their established innovation, technology, manufacturing and distribution capabilities over time. The joint venture, Hero/WhiteWave, LLC, which is based in Broomfield, Colorado, combines Hero’s expertise in fruit, innovation and process engineering with WhiteWave’s deep understanding of the American consumer and distribution network, as well as the go-to-market system of WhiteWave. In the second quarter of 2009, the joint venture introducedFruit2Day to grocery and club store channels in North America.
Beginning January 1, 2009, several new agreements, including a capital lease for plant assets constructed within WhiteWave’s existing facilities and operating agreements that include the assignment of day to day management responsibilities to WhiteWave, were entered into between WhiteWave and the joint venture. We determined that this, along with the increased risk created by the capital expenditures and favorable lease terms to the joint venture, as well as the benefit the new product line brings to WhiteWave’s existing customer relationships, resulted in the decision that WhiteWave was the primary beneficiary of the variable interests. As such, the financial position and the results of operations for the joint venture should be consolidated for financial reporting purposes. Accordingly, the joint venture has been consolidated as of January 1, 2009. The resulting non-controlling interest’s share in the equity of the joint venture is presented as a separate component of stockholders’ equity in the Consolidated Balance Sheets and Consolidated Statements of Stockholders’ Equity and the net loss attributable to the non-controlling interest is presented in the Consolidated Statements of Income.
During 2010 and 2009, our joint venture partner made cash contributions of $8.0 million and $12.7 million, respectively, and non-cash contributions of $0.5 million in 2009 to the joint venture. Our joint venture partner did not make any non-cash contributions in 2010. During 2010 and 2009, we made cash contributions of $8.8 million and $10.5 million, respectively, and continued non-cash contributions in the form of the capital lease for the manufacturing facility constructed at one of our existing WhiteWave plants. The joint venture has assets of $26.6 million, primarily property, plant and equipment, and liabilities of $3.5 million, which are included within the WhiteWave-Alpro segment.
Inventories, net of reserves of $5.9 million at years ended December 31, 2010 and 2009, consisted of the following:
| | | | | | | | |
| | December 31 | |
| | 2010 | | | 2009 | |
| | (In thousands) | |
Raw materials and supplies | | $ | 187,176 | | | $ | 202,991 | |
Finished goods | | | 238,400 | | | | 233,070 | |
| | | | | | | | |
Total | | $ | 425,576 | | | $ | 436,061 | |
| | | | | | | | |
F-13
5. | PROPERTY, PLANT AND EQUIPMENT |
Property, plant and equipment at years ended December 31, 2010 and 2009 consisted of the following:
| | | | | | | | |
| | December 31 | |
| | 2010 | | | 2009 | |
| | (In thousands) | |
Land | | $ | 242,666 | | | $ | 231,617 | |
Buildings | | | 927,836 | | | | 921,337 | |
Leasehold improvements | | | 89,337 | | | | 67,124 | |
Machinery and equipment | | | 2,381,545 | | | | 2,287,171 | |
Construction in progress | | | 91,461 | | | | 79,924 | |
| | | | | | | | |
| | | 3,732,845 | | | | 3,587,173 | |
Less accumulated depreciation | | | (1,619,454 | ) | | | (1,484,920 | ) |
| �� | | | | | | | |
Total | | $ | 2,113,391 | | | $ | 2,102,253 | |
| | | | | | | | |
For 2010 and 2009, we capitalized $1.4 million and $1.7 million in interest related to borrowings during the construction period of major capital projects, which is included as part of the cost of the related asset. Other non-cash additions to property, plant and equipment were $13.0 million in 2010. Other non-cash additions to property, plant and equipment were not material in 2009 and 2008.
6. | GOODWILL AND INTANGIBLE ASSETS |
The changes in the carrying amount of goodwill for the years ended December 31, 2010 and 2009 are as follows:
| | | | | | | | | | | | |
| | Fresh Dairy Direct- Morningstar(1) | | | WhiteWave- Alpro(1)(2) | | | Total | |
| | (In thousands) | |
Balance at December 31, 2008 | | $ | 2,522,843 | | | $ | 540,809 | | | $ | 3,063,652 | |
Acquisitions and purchase accounting adjustments | | | 37,059 | | | | 175,041 | | | | 212,100 | |
Foreign currency translation | | | — | | | | (2,938 | ) | | | (2,938 | ) |
| | | | | | | | | | | | |
Balance at December 31, 2009 | | $ | 2,559,902 | | | $ | 712,912 | | | $ | 3,272,814 | |
Acquisitions and purchase accounting adjustments | | | (4,696 | ) | | | — | | | | (4,696 | ) |
Foreign currency translation | | | — | | | | (6,487 | ) | | | (6,487 | ) |
Goodwill transferred to assets held for sale(3) | | | (82,439 | ) | | | — | | | | (82,439 | ) |
| | | | | | | | | | | | |
Balance at December 31, 2010 | | $ | 2,472,767 | | | $ | 706,425 | | | $ | 3,179,192 | |
| | | | | | | | | | | | |
(1) | Due to changes in our reportable segments as discussed in Note 1, $336.3 million of goodwill was transferred from WhiteWave-Alpro to Fresh Dairy Direct-Morningstar in the first quarter of 2010. Amounts at December 31, 2009 and 2008 have been recast to reflect this change. |
(2) | In the third quarter of 2010, $9.9 million of goodwill within the WhiteWave-Alpro segment attributable to Rachel’s was sold. Amounts at December 31, 2009 and 2008 have been moved to assets held for sale to reflect this change. |
(3) | In the fourth quarter of 2010, we announced that we entered into agreements to sell our Mountain High and private label yogurt operations. In connection with these planned divestitures, goodwill of $82.4 million has been allocated to these operations and recorded as assets held for sale as of December 31, 2010. |
F-14
The gross carrying amount and accumulated amortization of our intangible assets other than goodwill as of December 31, 2010 and 2009 are as follows:
| | | | | | | | | | | | | | | | | | | | | | | | |
| | December 31 | |
| | 2010 | | | 2009 | |
| | Gross Carrying Amount | | | Accumulated Amortization | | | Net Carrying Amount | | | Gross Carrying Amount | | | Accumulated Amortization | | | Net Carrying Amount | |
| | (In thousands) | |
Intangible assets with indefinite lives: | | | | | | | | | | | | | | | | | | | | | | | | |
Trademarks(1)(2) | | $ | 593,387 | | | $ | — | | | $ | 593,387 | | | $ | 608,339 | | | $ | — | | | $ | 608,339 | |
Intangible assets with finite lives: | | | | | | | | | | | | | | | | | | | | | | | | |
Customer-related and other | | | 133,829 | | | | (44,622 | ) | | | 89,207 | | | | 135,993 | | | | (35,737 | ) | | | 100,256 | |
Trademarks | | | 18,614 | | | | (4,474 | ) | | | 14,140 | | | | 10,146 | | | | (1,940 | ) | | | 8,206 | |
| | | | | | | | | | | | | | | | | | | | | | | | |
Total | | $ | 745,830 | | | $ | (49,096 | ) | | $ | 696,734 | | | $ | 754,478 | | | $ | (37,677 | ) | | $ | 716,801 | |
| | | | | | | | | | | | | | | | | | | | | | | | |
(1) | A trademark with a gross carrying amount of $7.5 million was moved from indefinite lived intangible assets to finite lived intangible assets in the first quarter of 2010. The remaining decrease in the gross carrying amount of intangible assets with indefinite lives is the result of foreign currency translation adjustments. |
(2) | In the third quarter of 2010, $2.1 million of indefinite lived intangible assets attributable to Rachel’s were sold. Amounts at December 31, 2009 have been moved to assets held for sale to reflect this change. |
Amortization expense on intangible assets for the years ended December 31, 2010, 2009 and 2008 was $11.3 million, $9.6 million and $9.8 million, respectively. Estimated aggregate intangible asset amortization expense for the next five years is as follows:
| | | | |
2011 | | $ | 11.2 million | |
2012 | | | 9.9 million | |
2013 | | | 9.8 million | |
2014 | | | 9.1 million | |
2015 | | | 9.0 million | |
Our goodwill and intangible assets have resulted from acquisitions. Upon acquisition, the purchase price is first allocated to identifiable assets and liabilities, including trademarks and customer-related intangible assets, with any remaining purchase price recorded as goodwill. Goodwill and trademarks with indefinite lives are not amortized.
A trademark is recorded with an indefinite life if it has a history of strong sales and cash flow performance that we expect to continue for the foreseeable future. If these perpetual trademark criteria are not met, the trademarks are amortized over their expected useful lives. Determining the expected life of a trademark is based on a number of factors including the competitive environment, trademark history and anticipated future trademark support.
We conduct impairment tests of goodwill and intangible assets with indefinite lives annually in the fourth quarter or when circumstances arise that indicate a possible impairment might exist. If the fair value of an evaluated asset is less than its book value, an impairment charge is recorded. Our reporting units are Fresh Dairy Direct, WhiteWave, Morningstar and Alpro. We did not recognize any impairment charges related to goodwill during 2010, 2009 or 2008.
Considerable management judgment is necessary to evaluate goodwill for impairment. We determine fair value using widely acceptable valuation techniques including discounted cash flows, market multiples analyses and relief from royalty analyses. Increasing our discount rates assumed in these analyses by 0.25% would not have resulted in an impairment charge. Assumptions used in our valuations, such as forecasted growth rates and
F-15
our cost of capital, are consistent with our internal projections and operating plans. The terminal growth rates utilized in calculating the fair value of our reporting units (ranging from 1.8% to 3.5%) is also dependent upon meeting our internal projections and operating plans, as well as other factors and assumptions. A 0.25% reduction in the terminal growth rate assumptions used could result in a material impairment charge.
Based on our analysis performed in the fourth quarter of 2010, each of our reporting units tested had fair values in excess of book values by approximately $229 million or 6.4%, $367 million or 65.1%, $856 million or 80.4% and $33 million or 7.8% for Fresh Dairy Direct, Morningstar, WhiteWave and Alpro, respectively. The sum of the fair values of our reporting units was in excess of our market capitalization. We believe that the difference between the fair value and market capitalization is reasonable (in the context of assessing whether any asset impairment exists) when market-based control premiums are taken into consideration. While the results of our testing indicate that each of our reporting units has a fair value in excess of its carrying value and no impairment charge was required; the excess of the reporting unit fair values over carrying values, specifically with respect to our Fresh Dairy Direct reporting unit, is significantly less than in prior years. We can provide no assurance that we will not have an impairment charge in future periods as a result of changes in our operating results or our assumptions.
While the results of our testing indicate that each of our reporting units has a fair value in excess of its carrying value and no impairment charge was required; the excess of the reporting unit fair values over carrying values, specifically with respect to our Fresh Dairy Direct reporting unit, is significantly less than in prior years. While testing results do not indicate an impairment charge, we can provide no assurance that we will not have an impairment charge in future periods as a result of changes in our operating results.
The sum of the fair values of our reporting units was in excess of our market capitalization. We believe that the difference between the fair value and market capitalization is reasonable (in the context of assessing whether any asset impairment exists) when market-based control premiums are taken into consideration.
In 2009, we recognized an impairment charge of $0.5 million in Fresh Dairy Direct related to a perpetual trademark for a regional brand due to projected declining annualized sales volumes and profitability. This trademark was no longer deemed to have a perpetual life and therefore is amortized over its estimated remaining life. In 2008, we recognized an impairment charge of $2.3 million related to three perpetual trademarks for regional brands in Fresh Dairy Direct. The write-downs were the result of lower annualized sales volumes from certain facilities partly related to movement of production between regional brands. These trademarks were no longer deemed to have a perpetual life and are being amortized over their respective estimated remaining lives.
Amortizable intangible assets are only evaluated for impairment upon a significant change in the operating environment. If an evaluation of the undiscounted cash flows indicates impairment, the asset is written down to its estimated fair value, which is generally based on discounted future cash flows.
7. | ACCOUNTS PAYABLE AND ACCRUED EXPENSES |
Accounts payable and accrued expenses for the years ended December 31, 2010 and 2009 consisted of the following:
| | | | | | | | |
| | December 31 | |
| | 2010 | | | 2009 | |
| | (In thousands) | |
Accounts payable | | $ | 782,185 | | | $ | 699,040 | |
Payroll and benefits | | | 131,177 | | | | 176,811 | |
Health insurance, workers’ compensation and other insurance costs | | | 74,934 | | | | 83,812 | |
Current derivative liability | | | 60,326 | | | | 90,194 | |
Other accrued liabilities | | | 214,254 | | | | 175,160 | |
| | | | | | | | |
Total | | $ | 1,262,876 | | | $ | 1,225,017 | |
| | | | | | | | |
F-16
The following table presents the 2010, 2009 and 2008 provisions for income taxes:
| | | | | | | | | | | | |
| | Year Ended December 31 | |
| | 2010(1) | | | 2009(2) | | | 2008 (3) | |
| | (In thousands) | |
Federal | | $ | (48,528 | ) | | $ | 94,190 | | | $ | 39,651 | |
State | | | 1,704 | | | | 15,060 | | | | 9,605 | |
Foreign | | | 2,050 | | | | 3,295 | | | | 629 | |
Deferred income taxes | | | 118,256 | | | | 39,300 | | | | 64,445 | |
| | | | | | | | | | | | |
Total | | $ | 73,482 | | | $ | 151,845 | | | $ | 114,330 | |
| | | | | | | | | | | | |
(1) | Excludes $8.7 million in income tax benefit related to discontinued operations. |
(2) | Excludes $0.3 million in income tax benefit related to discontinued operations. |
(3) | Excludes $0.4 million in income tax benefit related to discontinued operations. |
The following table presents the 2010, 2009 and 2008 income from continuing operations before income taxes for our domestic and foreign operations:
| | | | | | | | | | | | |
| | Year Ended December 31 | |
| | 2010 | | | 2009 | | | 2008 | |
| | (In thousands) | |
United States | | $ | 127,934 | | | $ | 370,642 | | | $ | 293,107 | |
Other Countries | | | 23,288 | | | | 9,823 | | | | 3,110 | |
| | | | | | | | | | | | |
Total income from continuing operations before income taxes | | $ | 151,222 | | | $ | 380,465 | | | $ | 296,217 | |
| | | | | | | | | | | | |
The following is a reconciliation of income taxes computed at the U.S. federal statutory tax rate to income taxes reported in the Consolidated Statements of Income:
| | | | | | | | | | | | | | | | | | | | | | | | |
| | Year Ended December 31 | |
| | 2010 | | | 2009 | | | 2008 | |
| | Amount | | | Percentage | | | Amount | | | Percentage | | | Amount | | | Percentage | |
| | (In thousands, except percentages) | |
Tax expense at statutory rate | | $ | 52,928 | | | | 35.0 | % | | $ | 133,163 | | | | 35.0 | % | | $ | 103,676 | | | | 35.0 | % |
State income taxes | | | 5,855 | | | | 3.9 | | | | 14,476 | | | | 3.8 | | | | 4,422 | | | | 1.5 | |
Foreign taxes versus U.S. statutory rate | | | (4,792 | ) | | | (3.2 | ) | | | 884 | | | | 0.2 | | | | (459 | ) | | | (0.2 | ) |
Deferred tax asset adjustment | | | 10,848 | | | | 7.2 | | | | — | | | | — | | | | — | | | | — | |
Exclusion of non-controlling interest tax benefit | | | 3,057 | | | | 2.0 | | | | 4,876 | | | | 1.3 | | | | — | | | | — | |
Nondeductible compensation | | | 2,713 | | | | 1.8 | | | | 3,434 | | | | 0.9 | | | | 4,796 | | | | 1.6 | |
Corporate owned life insurance | | | (926 | ) | | | (0.6 | ) | | | (1,839 | ) | | | (0.5 | ) | | | 4,025 | | | | 1.4 | |
Audit settlements | | | (1,910 | ) | | | (1.3 | ) | | | (1,289 | ) | | | (0.3 | ) | | | (5,616 | ) | | | (1.9 | ) |
Other | | | 5,709 | | | | 3.8 | | | | (1,860 | ) | | | (0.5 | ) | | | 3,486 | | | | 1.2 | |
| | | | | | | | | | | | | | | | | | | | | | | | |
Total | | $ | 73,482 | | | | 48.6 | % | | $ | 151,845 | | | | 39.9 | % | | $ | 114,330 | | | | 38.6 | % |
| | | | | | | | | | | | | | | | | | | | | | | | |
In 2010, we identified unrecoverable deferred tax asset balances associated with errors primarily related to periods prior to 2007. Since the effects of the errors are not material to the financial results for the year ending December 31, 2010 and were not material to any individual year prior to 2010, we adjusted our deferred tax assets and recorded a non-cash income tax charge of $10.8 million.
F-17
The tax effects of temporary differences giving rise to deferred income tax assets (liabilities) were:
| | | | | | | | |
| | December 31 | |
| | 2010(1) | | | 2009(2) | |
| | (In thousands) | |
Deferred income tax assets: | | | | | | | | |
Accrued liabilities | | $ | 128,469 | | | $ | 118,756 | |
Retirement plans and postretirement benefits | | | 38,324 | | | | 52,418 | |
Share-based compensation | | | 45,091 | | | | 42,485 | |
Receivables and inventories | | | 26,218 | | | | 23,698 | |
Derivative instruments | | | 24,866 | | | | 45,880 | |
Net operating loss carryforwards | | | 28,902 | | | | 28,377 | |
State and foreign tax credits | | | 11,143 | | | | 14,244 | |
Other | | | 3,774 | | | | 6,310 | |
Valuation allowances | | | (7,660 | ) | | | (9,108 | ) |
| | | | | | | | |
| | | 299,127 | | | | 323,060 | |
| | |
Deferred income tax liabilities: | | | | | | | | |
Intangible assets | | | (550,197 | ) | | | (496,586 | ) |
Property, plant and equipment | | | (342,824 | ) | | | (268,942 | ) |
Investment in unconsolidated affiliates | | | (21,167 | ) | | | (22,698 | ) |
| | | | | | | | |
| | | (914,188 | ) | | | (788,226 | ) |
| | | | | | | | |
Net deferred income tax liability | | $ | (615,061 | ) | | $ | (465,166 | ) |
| | | | | | | | |
(1) | Includes $14.3 million of deferred tax assets related to uncertain tax positions. |
(2) | Includes $20.6 million of deferred tax assets related to uncertain tax positions. |
These net deferred income tax assets (liabilities) are classified in our Consolidated Balance Sheets as follows:
| | | | | | | | |
| | December 31 | |
| | 2010 | | | 2009 | |
| | (In thousands) | |
Current assets | | $ | 141,653 | | | $ | 154,927 | |
Noncurrent liabilities | | | (756,714 | ) | | | (620,093 | ) |
| | | | | | | | |
Total | | $ | (615,061 | ) | | $ | (465,166 | ) |
| | | | | | | | |
At December 31, 2010, we had $28.9 million of state and foreign net operating loss carryforwards and $11.1 million of state and foreign tax credits available for carryover to future years. These items are subject to certain limitations and begin to expire in 2011. A valuation allowance of $7.7 million has been established because we do not believe it is more likely than not that all of the deferred tax assets related to state and foreign net operating loss carryforwards, state credit carryforwards and foreign tax credit carryforwards will be realized prior to expiration. Our valuation allowance decreased $1.4 million in 2010 for foreign tax credits which expired, partially offset by the expected nonrealization of certain state net operating loss and credit carryforwards and certain foreign net operating loss carryforwards.
F-18
The following is a reconciliation of gross unrecognized tax benefits, including interest, recorded in our Consolidated Balance Sheets:
| | | | | | | | | | | | |
| | December 31 | |
| | 2010 | | | 2009 | | | 2008 | |
| | (In thousands) | |
Balance at beginning of year | | $ | 72,611 | | | $ | 41,400 | | | $ | 46,089 | |
Increases in tax positions for current year | | | 1,245 | | | | 5,204 | | | | 4,196 | |
Increases in tax positions for prior years | | | 7,857 | | | | 5,641 | | | | 3,387 | |
Acquired increases in tax positions for prior years | | | — | | | | 31,019 | | | | — | |
Decreases in tax positions for prior years | | | (18,295 | ) | | | (4,181 | ) | | | (10,834 | ) |
Settlement of tax matters | | | (3,884 | ) | | | (5,249 | ) | | | (400 | ) |
Lapse of applicable statutes of limitations | | | (1,369 | ) | | | (1,223 | ) | | | (1,038 | ) |
| | | | | | | | | | | | |
Balance at end of year | | $ | 58,165 | | | $ | 72,611 | | | $ | 41,400 | |
| | | | | | | | | | | | |
These unrecognized tax benefits are classified in our Consolidated Balance Sheets as follows:
| | | | | | | | | | | | |
| | December 31 | |
| | 2010 | | | 2009 | | | 2008 | |
| | (In thousands) | |
Accrued expenses | | $ | 5,620 | | | $ | 3,333 | | | $ | — | |
Other long-term liabilities | | | 52,545 | | | | 69,278 | | | | 41,400 | |
| | | | | | | | | | | | |
Total | | $ | 58,165 | | | $ | 72,611 | | | $ | 41,400 | |
| | | | | | | | | | | | |
Of the balance at December 31, 2010, $18.0 million would impact our effective tax rate, $0.2 million would be recorded in discontinued operations, and $25.7 million would be offset by tax benefits associated with potential transfer pricing adjustments, if recognized. The remaining $14.3 million represents tax positions for which the ultimate deductibility is highly certain but for which there is uncertainty about the timing of such deductibility. Due to the impact of deferred income tax accounting, the disallowance of the shorter deductibility period would not affect our effective tax rate but would accelerate payment of cash to the applicable taxing authority. We do not expect any material changes to our liability for uncertain tax positions during the next 12 months.
We recognize accrued interest related to uncertain tax positions as a component of income tax expense. Penalties, if incurred, are recognized as a component of operating income. Income tax expense for 2010, 2009 and 2008 included interest expense, net of tax of ($1.6) million, $1.1 million and $(0.6) million, respectively. Our liability for uncertain tax positions included accrued interest of $4.9 million and $8.5 million at December 31, 2010 and 2009, respectively.
As of December 31, 2010, our 2007 to 2009 tax years remain subject to examination in our major jurisdictions. The statute on our 2006 U.S. federal income tax return remains open until the first quarter of 2011. State income tax returns are generally subject to examination for a period of three to five years after filing. We have various state and foreign income tax returns in the process of examination, appeals, or settlement.
F-19
| | | | | | | | | | | | | | | | |
| | December 31 | |
| | 2010 | | | 2009 | |
| | Amount Outstanding | | | Interest Rate | | | Amount Outstanding | | | Interest Rate | |
| | (In thousands, except percentages) | |
Dean Foods Company debt obligations: | | | | | | | | | | | | | | | | |
Senior secured credit facility | | $ | 3,033,529 | | | | 2.96 | %* | | $ | 3,596,950 | | | | 1.25 | %* |
Senior notes due 2016 | | | 498,765 | | | | 7.00 | | | | 498,584 | | | | 7.00 | |
Senior notes due 2018 | | | 400,000 | | | | 9.75 | | | | — | | | | | |
| | | | | | | | | | | | | | | | |
| | | 3,932,294 | | | | | | | | 4,095,534 | | | | | |
Subsidiary debt obligations: | | | | | | | | | | | | | | | | |
Senior notes | | | 127,504 | | | | 6.90 | | | | 126,027 | | | | 6.90 | |
Receivables-backed facility | | | — | | | | — | | | | — | | | | 2.00 | |
Capital lease obligations and other | | | 7,727 | | | | | | | | 7,418 | | | | | |
Alpro revolving credit facility | | | — | | | | — | | | | — | | | | 3.41 | |
| | | | | | | | | | | | | | | | |
| | | 135,231 | | | | | | | | 133,445 | | | | | |
| | | | | | | | | | | | | | | | |
| | | 4,067,525 | | | | | | | | 4,228,979 | | | | | |
Less current portion | | | (174,250 | ) | | | | | | | (248,352 | ) | | | | |
| | | | | | | | | | | | | | | | |
Total long-term portion | | $ | 3,893,275 | | | | | | | $ | 3,980,627 | | | | | |
| | | | | | | | | | | | | | | | |
* | Represents a weighted average rate as of December 31, 2010, including applicable interest rate margins, for the senior secured revolving credit facility, term loan A and term loan B. See schedule of interest rates in effect at December 31, 2010 below. |
The scheduled maturities of long-term debt, at December 31, 2010, were as follows (in thousands):
| | | | | | | | | | | | | | | | |
| | Total | | | Term Loan A | | | Term Loan B | | | Other* | |
2011 | | $ | 174,250 | | | $ | 149,866 | | | $ | 17,674 | | | $ | 6,710 | |
2012 | | | 291,074 | | | | 204,926 | | | | 17,675 | | | | 68,473 | |
2013 | | | 232,080 | | | | 213,975 | | | | 17,675 | | | | 430 | |
2014 | | | 1,337,727 | | | | 276,384 | | | | 676,229 | | | | 385,114 | |
2015 | | | 10,535 | | | | — | | | | 10,535 | | | | — | |
Thereafter | | | 2,037,590 | | | | — | | | | 995,590 | | | | 1,042,000 | |
| | | | | | | | | | | | | | | | |
Subtotal | | | 4,083,256 | | | | 845,151 | | | | 1,735,378 | | | | 1,502,727 | |
Less discounts | | | (15,731 | ) | | | — | | | | — | | | | (15,731 | ) |
| | | | | | | | | | | | | | | | |
Total outstanding debt | | $ | 4,067,525 | | | $ | 845,151 | | | $ | 1,735,378 | | | $ | 1,486,996 | |
| | | | | | | | | | | | | | | | |
* | Includes our revolving credit facility, Dean Foods Company senior notes, subsidiary senior notes, capital lease obligations and other debt. |
Senior Secured Credit Facility — On June 30, 2010, we amended and restated the credit agreement governing our $1.5 billion 5-year senior secured revolving credit facility, our original $1.5 billion 5-year senior secured term loan A and our original $1.8 billion 7-year senior secured term loan B. We further amended this agreement on December 9, 2010. The terms of this agreement were modified in the aggregate as follows:
| • | | Extension of the maturity dates for certain principal amounts as summarized in the key terms table below; |
F-20
| • | | Amendment of the maximum permitted leverage ratio and minimum interest coverage ratio, and the addition of a senior secured leverage ratio (each as defined in our credit agreement) to permit minimum and maximum ratios of: |
| | | | | | | | | | | | |
For Quarters Ending During the Period | | Minimum Interest Coverage Ratio | | | Maximum Leverage Ratio | | | Maximum Senior Secured Leverage Ratio | |
Amendment effective date — December 31, 2011 | | | 2.50 | | | | 5.75 | | | | 4.25 | |
March 31, 2012 — December 31, 2012 | | | 2.75 | | | | 5.50 | | | | 3.75 | |
March 31, 2013 — June 30, 2013 | | | 3.00 | | | | 5.25 | | | | 3.50 | |
September 30, 2013 and thereafter | | | 3.00 | | | | 4.50 | | | | 3.50 | |
| • | | Amendment of certain other terms, including, but not limited to, leverage-based limitations on the payment of dividends and other restricted payments, acquisitions and prepayments of senior notes; and |
| • | | Increase in the undrawn costs of the extended portion of the revolving credit facility and the drawn costs of the extended portions of the revolving credit facility, term loan A and term loan B. |
The following table summarizes the key terms of the senior secured credit facility as of December 31, 2010:
| | | | | | | | | | | | |
| | Principal(2) | | | Maturity Date | | Applicable Base Rate Margin(3) | | Applicable LIBOR Rate Margin(3) | | Quarterly Commitment Fee on Undrawn Amounts |
Revolving Credit Facility | | $ | 225 million | | | April 2, 2012 | | 0.00% – 0.75% | | 0.625% – 1.75% | | 0.125% – 0.375% |
| | $ | 1.28 billion | | | April 2, 2014 | | 1.00% – 2.25% | | 2.00% – 3.25% | | 0.375% – 0.500% |
Term Loan A | | $ | 150 million | | | April 2, 2012 | | 0.00% – 0.75% | | 0.625% – 1.75% | | — |
| | $ | 695 million | | | April 2, 2014 | | 1.00% – 2.25% | | 2.00% – 3.25% | | — |
Term Loan B | | $ | 687 million | | | April 2, 2014 | | 0.375% – 0.75% | | 1.375% – 1.75% | | — |
| | $ | 490 million | | | April 2, 2016 | | 2.00% – 2.25% | | 3.00% – 3.25% | | — |
| | $ | 558 million | | | April 2, 2017(1) | | 2.25% – 2.50% | | 3.25% – 3.50% | | — |
(1) | Subject to the condition that we meet certain leverage, debt, cash or credit rating tests following December 31, 2015. However, if at least one of these tests is not met, the maturity date will be April 2, 2016. |
(2) | Amounts for term loan A and term loan B represent outstanding principal balances as of December 31, 2010. The revolving credit facility principal amount represents the total original borrowings available to us under the facility. |
(3) | The senior secured credit facility bears interest, at our election, at the Alternative Base Rate (as defined in our credit agreement) plus a margin depending on our leverage ratio or LIBOR plus a margin depending on our leverage ratio. Interest is payable quarterly or after the end of the applicable interest period. |
The senior secured revolving credit facility is available for the issuance of up to $350 million of letters of credit and up to $150 million of swing line loans. No principal payments are due on the revolving credit facility until April 2, 2012, at which time any principal borrowings on a pro rata basis related to the $225 million of non-extended revolving credit facility commitments would become payable. No principal payments are due on the remaining $1.275 billion of extended revolving credit facility commitment until April 2, 2014. The credit agreement requires mandatory principal prepayments upon the occurrence of certain asset sales (provided that such sales, in total, exceed $250 million in any fiscal year), recovery events, or as a result of exceeding certain leverage limits.
As discussed in Note 2, on February 1, 2011, we completed the sale of our Mountain High yogurt operations. We used the proceeds to pay down a portion of the outstanding 2012 tranche A term loan borrowings. We intend to use the proceeds from the sale of our private label yogurt operations, which is expected to be completed in the first half of 2011, for additional debt repayments.
F-21
Our credit agreement permits us to complete acquisitions that meet all of the following conditions without obtaining prior approval: (1) the acquired company is involved in the manufacture, processing and distribution of food or packaging products or any other line of business in which we were engaged as of April 2007, (2) the net cash purchase price for any single acquisition is not greater than $500 million and not greater than $100 million if our leverage ratio is greater than 4.50 times, (3) we acquire at least 51% of the acquired entity, (4) the transaction is approved by the board of directors or shareholders, as appropriate, of the target and (5) after giving effect to such acquisition on a pro-forma basis, we would have been in compliance with all financial covenants. All other acquisitions must be approved in advance by the required lenders.
The senior secured credit facility contains limitations on liens, investments and the incurrence of additional indebtedness, prohibits certain dispositions of property and restricts certain payments, including dividends. There are no restrictions on these certain payments, including dividends, when our leverage ratio is below 4.50 times. The senior secured credit facility is secured by liens on substantially all of our domestic assets including the assets of our subsidiaries, but excluding the capital stock of subsidiaries of the former Dean Foods Company (“Legacy Dean”), and the real property owned by Legacy Dean and its subsidiaries.
The credit agreement contains standard default triggers, including without limitation: failure to maintain compliance with the financial and other covenants contained in the credit agreement, default on certain of our other debt, a change in control and certain other material adverse changes in our business. The credit agreement does not contain any requirements to maintain specific credit rating levels, except as described above with respect to determining the maturity date for the 2017 tranche of term loan B.
We are currently in compliance with all financial covenants, and based on our internal projections we expect to maintain such compliance for the foreseeable future.
At December 31, 2010, there were outstanding borrowings of $3.0 billion under our senior secured credit facility, which consisted of $2.6 billion in term loan borrowings and $453 million drawn under the revolver. At December 31, 2010, there were $171.3 million of letters of credit under the revolving line that were issued but undrawn. As of February 24, 2011, $106.2 million was borrowed under our senior secured revolving credit facility.
We incurred financing costs of $34.2 million in connection with the completion of the amended and restated senior secured credit facility on June 30, 2010, of which $6.7 million was expensed in the second quarter of 2010. The capitalized deferred financing costs will be recorded as interest expense over the terms of their applicable instrument under the credit facility.
In connection with the December 9, 2010 amendment to our credit facility, we incurred financing costs of approximately $8.8 million, of which $1.9 million was expensed in the fourth quarter of 2010. Additionally, as a result of this amendment and reduction of principal, $3.7 million in previously deferred financing costs related to the senior secured credit facility were written off in the fourth quarter of 2010. The remaining financing costs related to the amendment were deferred and capitalized and will be recorded as interest expense over the terms of their applicable instrument under the credit facility.
Receivables-Backed Facility — We have a $600 million receivables securitization facility pursuant to which certain of our subsidiaries sell their accounts receivable to four wholly-owned entities intended to be bankruptcy-remote. The entities then transfer the receivables to third-party asset-backed commercial paper conduits sponsored by major financial institutions. The assets and liabilities of these four entities are fully reflected in our Consolidated Balance Sheets, and the securitization is treated as a borrowing for accounting purposes.
On June 30, 2010, we amended the maximum leverage ratio covenant to permit a maximum leverage ratio of 5.50 from June 30, 2010 to March 31, 2011; 5.00 from June 30, 2011 to September 30, 2012; and 4.50 from December 31, 2012 thereafter. We also amended certain other terms, including, but not limited to, changes in the maximum purchase interest percentage and loss reserve floor; as well as extending the termination date of the 364-day facility to June 29, 2011. As a result of the amendment we incurred fees of approximately $0.6 million.
F-22
On December 9, 2010, we further amended the maximum leverage ratio covenant to be consistent with the leverage ratios under our senior secured credit facility, including the addition of a senior secured leverage ratio to the agreement, as described above. Additionally, we amended certain other terms, including, but not limited to, extension of the maturity termination date of the facility to September 30, 2011; as well as changes in the maximum purchase interest percentage and loss reserve floor. As a result of this amendment, we incurred fees of approximately $0.6 million.
During 2010, we borrowed and subsequently repaid $2.5 billion under this facility with no remaining balance at December 31, 2010. The total value of receivables sold to these entities as of December 31, 2010 was $817.5 million. The receivables-backed facility bears interest at a variable rate based upon commercial paper rates plus an applicable margin. Our average daily balance under this facility during 2010 was $175.3 million. Our ability to borrow under this facility is subject to a monthly borrowing base formula. This facility had $496.5 million of availability as of December 31, 2010, based on this formula.
Dean Foods Company Senior Notes due 2018 – On December 16, 2010, in connection with the December 9, 2010 amendment to our senior secured credit facility discussed above, we issued $400 million aggregate principal amount of 9.75% senior unsecured notes. The senior notes were sold in a private placement to qualified institutional buyers and in offshore transactions, and have not been registered under the Securities Act of 1933. These notes are our senior unsecured obligations and mature on December 15, 2018 with interest payable on June 15 and December 15 of each year, commencing June 15, 2011.
In connection with the offering of the senior notes, we also entered into a registration rights agreement dated as of December 16, 2010. Under the registration rights agreement, we agreed to file with the SEC a registration statement with respect to an offer to exchange the senior notes for identical new notes (except that the new notes will not be subject to restrictions on transfer) registered under the Securities Act of 1933. Under the registration rights agreement, we may also be required to provide a shelf registration statement to cover resales of the senior notes under certain circumstances. If we fail to satisfy our obligations under the registration rights agreement, we may be required to pay special interest on the senior notes, up to a maximum amount of 1.0% per annum of the principal amount of the senior notes entitled to such registration rights then outstanding.
We incurred fees and expenses related to the senior notes offering of $9.1 million, which were capitalized during the fourth quarter of 2010 and will be amortized as interest expense over the term of the notes. We used the net proceeds from the offering to pay down a portion of the outstanding 2014 tranche A term loan borrowings under our senior secured credit facility and to pay fees and expenses related to the amendment of our credit facility, as discussed above. The indenture under which we issued the senior unsecured notes does not contain financial covenants but does contain covenants that, among other things, limit our ability to incur certain indebtedness, enter into sale-leaseback transactions and engage in mergers, consolidations and sales of all or substantially all of our assets. The outstanding balance of these notes at December 31, 2010 was $400 million.
Dean Foods Company Senior Notes due 2016 — On May 17, 2006, we issued $500 million aggregate principal amount of 7.0% senior unsecured notes. The senior unsecured notes mature on June 1, 2016 and interest is payable on June 1 and December 1 of each year, beginning December 1, 2006. The indenture under which we issued the senior unsecured notes does not contain financial covenants but does contain covenants that, among other things, limit our ability to incur certain indebtedness, enter into sale-leaseback transactions and engage in mergers, consolidations and sales of all or substantially all of our assets. The outstanding balance at December 31, 2010 was $498.8 million.
Subsidiary Senior Notes — The former Dean Foods Company (“Legacy Dean”) had certain senior notes outstanding at the time of its acquisition, of which one series ($150 million face value) remains outstanding with a maturity date of October 15, 2017. During the third quarter of 2009, we repurchased in the open market $8.0 million of these subsidiary senior notes and recognized an immaterial book loss. The balance of these outstanding notes is $127.5 million at December 31, 2010 at 6.9% interest. During the fourth quarter of 2008, we
F-23
repurchased in the open market, $77.0 million of Legacy Dean’s subsidiary senior notes that were to mature on May 15, 2009. Additionally, the net proceeds of our equity offering in May 2009 were used in part to repay the remaining balance of $122.8 million of these senior notes upon maturity.
The related indentures do not contain financial covenants but they do contain certain restrictions, including a prohibition against Legacy Dean and its subsidiaries granting liens on certain of their real property interests and a prohibition against Legacy Dean granting liens on the stock of its subsidiaries. The subsidiary senior notes are not guaranteed by Dean Foods Company or Legacy Dean’s wholly owned subsidiaries.
Capital Lease Obligations and Other — Capital lease obligations and other subsidiary debt includes various promissory notes for financing current year property and casualty insurance premiums, as well as the purchase of property, plant and equipment and capital lease obligations. The various promissory notes payable provide for interest at varying rates and are payable in monthly installments of principal and interest until maturity, when the remaining principal balances are due. Capital lease obligations represent machinery and equipment financing obligations, which are payable in monthly installments of principal and interest and are collateralized by the related assets financed. See Note 18.
Alpro Revolving Credit Facility — On July 2, 2009, our newly acquired subsidiary, Alpro N.V. entered into a two year multi-currency revolving credit facility for borrowings in an amount not to exceed €20 million (or its currency equivalent). In December of 2009, we reduced the facility to an amount not to exceed €10 million (or its currency equivalent), and in December 2010 we further reduced the facility to an amount not to exceed €1 million (or its currency equivalent). The facility is unsecured and is guaranteed by Dean Foods Company and various Alpro N.V. subsidiaries. Use of proceeds under the facility is for working capital and other general corporate purposes of Alpro N.V. The subsidiary revolving credit facility will be available for the issuance of up to €1 million of letters of credit. No principal payments are due under the subsidiary revolving credit facility until maturity on July 2, 2011. At December 31, 2010, there were no outstanding borrowings under the facility.
Interest Rate Agreements — See Note 10 for information related to interest rate swap arrangements associated with our debt.
Guarantor Information — On May 17, 2006, we issued $500 million aggregate principal amount of 7.0% senior notes due 2016, and on December 16, 2010, we issued $400 million aggregate principal amount of 9.75% senior notes due 2018. Both the 2016 and 2018 senior notes are unsecured obligations and are fully and unconditionally, joint and severally guaranteed by substantially all of our wholly-owned U.S. subsidiaries other than our receivables securitization subsidiaries.
F-24
The following condensed consolidating financial statements present the financial position, results of operations and cash flows of Dean Foods Company (“Parent”), the wholly-owned subsidiary guarantors of the 2016 and 2018 senior notes and separately the combined results of the wholly-owned subsidiaries that are not a party to the guarantees. The wholly-owned non-guarantor subsidiaries reflect foreign and certain other operations, including our Hero joint venture, in addition to our three receivables securitization subsidiaries. We do not allocate interest expense from the receivables-backed facility to the three receivables securitization subsidiaries. Therefore, the interest costs related to this facility are reflected within the guarantor financial information presented.
| | | | | | | | | | | | | | | | | | | | |
| | Condensed Consolidating Balance Sheet as of December 31, 2010 | |
| | Parent | | | Guarantor Subsidiaries | | | Non- Guarantor Subsidiaries | | | Eliminations | | | Consolidated Totals | |
| | (In thousands) | |
ASSETS | | | | | | | | | | | | | | | | | | | | |
Current assets: | | | | | | | | | | | | | | | | | | | | |
Cash and cash equivalents | | $ | 307 | | | $ | 9,750 | | | $ | 81,950 | | | $ | — | | | $ | 92,007 | |
Receivables, net | | | 353 | | | | 33,941 | | | | 856,725 | | | | — | | | | 891,019 | |
Income tax receivable | | | 71,173 | | | | — | | | | 164 | | | | — | | | | 71,337 | |
Inventories | | | — | | | | 394,862 | | | | 30,714 | | | | — | | | | 425,576 | |
Intercompany receivables | | | 193,051 | | | | 4,211,670 | | | | 13,924 | | | | (4,418,645 | ) | | | — | |
Other current assets | | | 105,345 | | | | 96,967 | | | | 16,851 | | | | — | | | | 219,163 | |
Assets held for sale | | | — | | | | 117,114 | | | | — | | | | — | | | | 117,114 | |
| | | | | | | | | | | | | | | | | | | | |
Total current assets | | | 370,229 | | | | 4,864,304 | | | | 1,000,328 | | | | (4,418,645 | ) | | | 1,816,216 | |
Property, plant and equipment, net | | | 222 | | | | 1,900,192 | | | | 212,977 | | | | — | | | | 2,113,391 | |
Goodwill | | | — | | | | 3,013,516 | | | | 165,676 | | | | — | | | | 3,179,192 | |
Identifiable intangible and other assets | | | 88,135 | | | | 616,435 | | | | 143,298 | | | | — | | | | 847,868 | |
Investment in subsidiaries | | | 9,335,787 | | | | — | | | | — | | | | (9,335,787 | ) | | | — | |
| | | | | | | | | | | | | | | | | | | | |
Total | | $ | 9,794,373 | | | $ | 10,394,447 | | | $ | 1,522,279 | | | $ | (13,754,432 | ) | | $ | 7,956,667 | |
| | | | | | | | | | | | | | | | | | | | |
LIABILITIES AND STOCKHOLDERS’ EQUITY | | | | | | | | | | | | | | | | | | | | |
Current liabilities: | | | | | | | | | | | | | | | | | | | | |
Accounts payable and accrued expenses | | $ | 168,869 | | | $ | 1,014,819 | | | $ | 79,188 | | | $ | — | | | $ | 1,262,876 | |
Intercompany payables | | | 3,568,750 | | | | 21,586 | | | | 828,309 | | | | (4,418,645 | ) | | | — | |
Current portion of long-term debt | | | 167,540 | | | | 6,454 | | | | 256 | | | | — | | | | 174,250 | |
Liabilities of disposal groups held for sale | | | — | | | | 3,839 | | | | — | | | | — | | | | 3,839 | |
| | | | | | | | | | | | | | | | | | | | |
Total current liabilities | | | 3,905,159 | | | | 1,046,698 | | | | 907,753 | | | | (4,418,645 | ) | | | 1,440,965 | |
Long-term debt | | | 3,764,754 | | | | 127,892 | | | | 629 | | | | — | | | | 3,893,275 | |
Other long-term liabilities | | | 624,935 | | | | 379,017 | | | | 104,407 | | | | — | | | | 1,108,359 | |
Dean Foods stockholders’ equity | | | 1,499,525 | | | | 8,840,840 | | | | 494,947 | | | | (9,335,787 | ) | | | 1,499,525 | |
Non-controlling interest | | | — | | | | — | | | | 14,543 | | | | — | | | | 14,543 | |
| | | | | | | | | | | | | | | | | | | | |
Total Stockholders’ equity | | | 1,499,525 | | | | 8,840,840 | | | | 509,490 | | | | (9,335,787 | ) | | | 1,514,068 | |
| | | | | | | | | | | | | | | | | | | | |
Total | | $ | 9,794,373 | | | $ | 10,394,447 | | | $ | 1,522,279 | | | $ | (13,754,432 | ) | | $ | 7,956,667 | |
| | | | | | | | | | | | | | | | | | | | |
F-25
| | | | | | | | | | | | | | | | | | | | |
| | Condensed Consolidating Balance Sheet as of December 31, 2009 | |
| | Parent | | | Guarantor Subsidiaries | | | Non- Guarantor Subsidiaries | | | Eliminations | | | Consolidated Totals | |
| | (In thousands) | |
ASSETS | | | | | | | | | | | | | | | | | | | | |
Current assets: | | | | | | | | | | | | | | | | | | | | |
Cash and cash equivalents | | $ | 9,665 | | | $ | — | | | $ | 35,525 | | | $ | — | | | $ | 45,190 | |
Receivables, net | | | 469 | | | | 35,001 | | | | 836,363 | | | | — | | | | 871,833 | |
Income tax receivable | | | 19,329 | | | | — | | | | 105 | | | | — | | | | 19,434 | |
Inventories | | | — | | | | 408,431 | | | | 27,630 | | | | — | | | | 436,061 | |
Intercompany receivables | | | 2,252,463 | | | | 5,325,673 | | | | 723,109 | | | | (8,301,245 | ) | | | — | |
Other current assets | | | 155,267 | | | | 71,277 | | | | 18,444 | | | | — | | | | 244,988 | |
Assets held for sale | | | — | | | | — | | | | 30,088 | | | | — | | | | 30,088 | |
| | | | | | | | | | | | | | | | | | | | |
Total current assets | | | 2,437,193 | | | | 5,840,382 | | | | 1,671,264 | | | | (8,301,245 | ) | | | 1,647,594 | |
Property, plant and equipment, net | | | 500 | | | | 1,868,458 | | | | 233,295 | | | | — | | | | 2,102,253 | |
Goodwill | | | — | | | | 3,100,652 | | | | 172,162 | | | | — | | | | 3,272,814 | |
Identifiable intangible and other assets | | | 50,796 | | | | 616,616 | | | | 153,868 | | | | — | | | | 821,280 | |
Investment in subsidiaries | | | 9,009,741 | | | | — | | | | — | | | | (9,009,741 | ) | | | — | |
| | | | | | | | | | | | | | | | | | | | |
Total | | $ | 11,498,230 | | | $ | 11,426,108 | | | $ | 2,230,589 | | | $ | (17,310,986 | ) | | $ | 7,843,941 | |
| | | | | | | | | | | | | | | | | | | | |
LIABILITIES AND STOCKHOLDERS’ EQUITY | | | | | | | | | | | | | | | | | | | | |
Current liabilities: | | | | | | | | | | | | | | | | | | | | |
Accounts payable and accrued expenses | | $ | 214,717 | | | $ | 930,933 | | | $ | 79,367 | | | $ | — | | | $ | 1,225,017 | |
Intercompany payables | | | 5,278,204 | | | | 1,520,421 | | | | 1,502,620 | | | | (8,301,245 | ) | | | — | |
Current portion of long-term debt | | | 243,000 | | | | 4,843 | | | | 509 | | | | — | | | | 248,352 | |
Liabilities of disposal groups held for sale | | | — | | | | — | | | | 9,045 | | | | — | | | | 9,045 | |
| | | | | | | | | | | | | | | | | | | | |
Total current liabilities | | | 5,735,921 | | | | 2,456,197 | | | | 1,591,541 | | | | (8,301,245 | ) | | | 1,482,414 | |
Long-term debt | | | 3,852,533 | | | | 127,573 | | | | 521 | | | | — | | | | 3,980,627 | |
Other long-term liabilities | | | 557,830 | | | | 345,087 | | | | 110,751 | | | | — | | | | 1,013,668 | |
Dean Foods stockholders’ equity | | | 1,351,946 | | | | 8,497,251 | | | | 512,490 | | | | (9,009,741 | ) | | | 1,351,946 | |
Non-controlling interest | | | — | | | | — | | | | 15,286 | | | | — | | | | 15,286 | |
| | | | | | | | | | | | | | | | | | | | |
Total Stockholders’ equity | | | 1,351,946 | | | | 8,497,251 | | | | 527,776 | | | | (9,009,741 | ) | | | 1,367,232 | |
| | | | | | | | | | | | | | | | | | | | |
Total | | $ | 11,498,230 | | | $ | 11,426,108 | | | $ | 2,230,589 | | | $ | (17,310,986 | ) | | $ | 7,843,941 | |
| | | | | | | | | | | | | | | | | | | | |
F-26
| | | | | | | | | | | | | | | | | | | | |
| | Condensed Consolidating Statements of Income for the Year Ended December 31, 2010 | |
| | Parent | | | Guarantor Subsidiaries | | | Non- Guarantor Subsidiaries | | | Eliminations | | | Consolidated Totals | |
| | (In thousands) | |
Net sales | | $ | — | | | $ | 11,760,772 | | | $ | 362,115 | | | $ | — | | | $ | 12,122,887 | |
Cost of sales | | | — | | | | 8,905,747 | | | | 211,218 | | | | — | | | | 9,116,965 | |
| | | | | | | | | | | | | | | | | | | | |
Gross profit | | | — | | | | 2,855,025 | | | | 150,897 | | | | — | | | | 3,005,922 | |
Selling and distribution | | | — | | | | 1,807,075 | | | | 97,451 | | | | — | | | | 1,904,526 | |
General and administrative | | | 7,924 | | | | 584,982 | | | | 48,045 | | | | — | | | | 640,951 | |
Facility closing and reorganization costs | | | — | | | | 30,761 | | | | — | | | | — | | | | 30,761 | |
Other operating expenses | | | — | | | | 30,000 | | | | — | | | | — | | | | 30,000 | |
Interest expense | | | 237,037 | | | | 10,598 | | | | 666 | | | | — | | | | 248,301 | |
Other (income) expense, net | | | (7,909 | ) | | | 8,948 | | | | (878 | ) | | | — | | | | 161 | |
Income from subsidiaries | | | (388,274 | ) | | | — | | | | — | | | | 388,274 | | | | 0 | |
| | | | | | | | | | | | | | | | | | | | |
Income (loss) from continuing operations before income taxes | | | 151,222 | | | | 382,661 | | | | 5,613 | | | | (388,274 | ) | | | 151,222 | |
Income taxes | | | 73,482 | | | | 185,947 | | | | 25 | | | | (185,972 | ) | | | 73,482 | |
| | | | | | | | | | | | | | | | | | | | |
Income (loss) from continuing operations’ | | | 77,740 | | | | 196,714 | | | | 5,588 | | | | (202,302 | ) | | | 77,740 | |
Income (loss) from discontinued operations, net of tax | | | (2,505 | ) | | | — | | | | (2,505 | ) | | | 2,505 | | | | (2,505 | ) |
Gain (loss) on sale of discontinued operations, net of tax | | | 7,521 | | | | — | | | | 7,521 | | | | (7,521 | ) | | | 7,521 | |
| | | | | | | | | | | | | | | | | | | | |
Net income (loss) | | | 82,756 | | | | 196,714 | | | | 10,604 | | | | (207,318 | ) | | | 82,756 | |
Net loss attributable to non-controlling interest | | | 8,735 | | | | — | | | | 8,735 | | | | (8,735 | ) | | | 8,735 | |
| | | | | | | | | | | | | | | | | | | | |
Net income (loss) attributable to Dean Foods Company | | $ | 91,491 | | | $ | 196,714 | | | $ | 19,339 | | | $ | (216,053 | ) | | $ | 91,491 | |
| | | | | | | | | | | | | | | | | | | | |
F-27
| | | | | | | | | | | | | | | | | | | | |
| | Condensed Consolidating Statements of Income for the Year Ended December 31, 2009 | |
| | Parent | | | Guarantor Subsidiaries | | | Non- Guarantor Subsidiaries | | | Eliminations | | | Consolidated Totals | |
| | (In thousands) | |
Net sales | | $ | — | | | $ | 10,928,250 | | | $ | 185,532 | | | $ | — | | | $ | 11,113,782 | |
Cost of sales | | | — | | | | 7,896,766 | | | | 111,795 | | | | — | | | | 8,008,561 | |
| | | | | | | | | | | | | | | | | | | | |
Gross profit | | | — | | | | 3,031,484 | | | | 73,737 | | | | — | | | | 3,105,221 | |
Selling and distribution | | | — | | | | 1,752,829 | | | | 66,004 | | | | — | | | | 1,818,833 | |
General and administrative | | | 18,287 | | | | 591,569 | | | | 23,616 | | | | — | | | | 633,472 | |
Facility closing and reorganization costs | | | — | | | | 30,162 | | | | — | | | | — | | | | 30,162 | |
Interest expense | | | 230,454 | | | | 14,912 | | | | 1,144 | | | | — | | | | 246,510 | |
Other (income) expense, net | | | (22,468 | ) | | | 19,060 | | | | (813 | ) | | | — | | | | (4,221 | ) |
Income from subsidiaries | | | (606,738 | ) | | | — | | | | — | | | | 606,738 | | | | — | |
| | | | | | | | | | | | | | | | | | | | |
Income (loss) from continuing operations before income taxes | | | 380,465 | | | | 622,952 | | | | (16,214 | ) | | | (606,738 | ) | | | 380,465 | |
Income taxes | | | 151,845 | | | | 248,622 | | | | (2,176 | ) | | | (246,446 | ) | | | 151,845 | |
| | | | | | | | | | | | | | | | | | | | |
Income (loss) from continuing operations | | | 228,620 | | | | 374,330 | | | | (14,038 | ) | | | (360,292 | ) | | | 228,620 | |
Gain on sale of discontinued operations, net of tax | | | 89 | | | | 89 | | | | — | | | | (89 | ) | | | 89 | |
Loss from discontinued operations, net of tax | | | (862 | ) | | | — | | | | (862 | ) | | | 862 | | | | (862 | ) |
| | | | | | | | | | | | | | | | | | | | |
Net income (loss) | | | 227,847 | | | | 374,419 | | | | (14,900 | ) | | | (359,519 | ) | | | 227,847 | |
Net income (loss) attributable to non-controlling interest | | | 12,461 | | | | — | | | | 12,461 | | | | (12,461 | ) | | | 12,461 | |
| | | | | | | | | | | | | | | | | | | | |
Net income (loss) attributable to Dean Foods Company | | $ | 240,308 | | | $ | 374,419 | | | $ | (2,439 | ) | | $ | (371,980 | ) | | $ | 240,308 | |
| | | | | | | | | | | | | | | | | | | | |
F-28
| | | | | | | | | | | | | | | | | | | | |
| | Condensed Consolidating Statements of Income for the Year Ended December 31, 2008 | |
| | Parent | | | Guarantor Subsidiaries | | | Non- Guarantor Subsidiaries | | | Eliminations | | | Consolidated Totals | |
| | (In thousands) | |
Net sales | | $ | — | | | $ | 12,346,026 | | | $ | 15,285 | | | $ | — | | | $ | 12,361,311 | |
Cost of sales | | | — | | | | 9,426,707 | | | | 11,886 | | | | — | | | | 9,438,593 | |
| | | | | | | | | | | | | | | | | | | | |
Gross profit | | | — | | | | 2,919,319 | | | | 3,399 | | | | — | | | | 2,922,718 | |
Selling and distribution | | | — | | | | 1,801,355 | | | | 859 | | | | — | | | | 1,802,214 | |
General and administrative | | | 1,575 | | | | 485,503 | | | | 5,150 | | | | — | | | | 492,228 | |
Facility closing and reorganization costs | | | — | | | | 22,758 | | | | — | | | | — | | | | 22,758 | |
Interest expense | | | 269,423 | | | | 37,181 | | | | 1,574 | | | | — | | | | 308,178 | |
Other (income) expense, net | | | 571 | | | | (648 | ) | | | 1,200 | | | | — | | | | 1,123 | |
Income from subsidiaries | | | (567,786 | ) | | | — | | | | — | | | | 567,786 | | | | — | |
| | | | | | | | | | | | | | | | | | | | |
Income (loss) from continuing operations before income taxes | | | 296,217 | | | | 573,170 | | | | (5,384 | ) | | | (567,786 | ) | | | 296,217 | |
Income taxes | | | 114,330 | | | | 221,225 | | | | (2,187 | ) | | | (219,038 | ) | | | 114,330 | |
| | | | | | | | | | | | | | | | | | | | |
Income (loss) from continuing operations | | | 181,887 | | | | 351,945 | | | | (3,197 | ) | | | (348,748 | ) | | | 181,887 | |
Loss on sale of discontinued operations, net of tax | | | (1,275 | ) | | | (1,275 | ) | | | — | | | | 1,275 | | | | (1,275 | ) |
Income from discontinued operations, net of tax | | | 3,158 | | | | 205 | | | | 2,953 | | | | (3,158 | ) | | | 3,158 | |
| | | | | | | | | | | | | | | | | | | | |
Net income (loss) attributable to Dean Foods Company | | $ | 183,770 | | | $ | 350,875 | | | $ | (244 | ) | | $ | (350,631 | ) | | $ | 183,770 | |
| | | | | | | | | | | | | | | | | | | | |
F-29
| | | | | | | | | | | | | | | | |
| | Condensed Consolidating Statement of Cash Flows for the Year Ended December 31, 2010 | |
| | Parent | | | Guarantor Subsidiaries | | | Non- Guarantor Subsidiaries | | | Consolidated Totals | |
| | (In thousands) | |
Net cash provided by continuing operations | | $ | 149,935 | | | $ | 380,908 | | | $ | (5,143 | ) | | $ | 525,700 | |
Net cash used in discontinued operations | | | — | | | | — | | | | 8,765 | | | | 8,765 | |
| | | | | | | | | | | | | | | | |
Net cash provided by operating activities | | | 149,935 | | | | 380,908 | | | | 3,622 | | | | 534,465 | |
Payments for property, plant and equipment | | | — | | | | (288,785 | ) | | | (13,189 | ) | | | (301,974 | ) |
Payments for acquisitions, net of cash received | | | — | | | | — | | | | — | | | | — | |
Proceeds from sale of fixed assets | | | — | | | | 8,212 | | | | 187 | | | | 8,399 | |
| | | | | | | | | | | | | | | | |
Net cash used in investing activities — continued operations | | | — | | | | (280,573 | ) | | | (13,002 | ) | | | (293,575 | ) |
Net cash provided by investing activities — discontinued operations | | | — | | | | — | | | | 24,121 | | | | 24,121 | |
| | | | | | | | | | | | | | | | |
Net cash provided by (used in) investing activities | | | — | | | | (280,573 | ) | | | 11,119 | | | | (269,454 | ) |
Proceeds from the issuance of debt | | | 400,000 | | | | — | | | | — | | | | 400,000 | |
Repayment of debt | | | (501,220 | ) | | | (13,092 | ) | | | (145 | ) | | | (514,457 | ) |
Proceeds from senior secured revolver | | | 4,006,680 | | | | — | | | | — | | | | 4,006,680 | |
Payments for senior secured revolver | | | (4,068,880 | ) | | | — | | | | — | | | | (4,068,880 | ) |
Proceeds from receivables-backed facility | | | — | | | | — | | | | 2,445,500 | | | | 2,445,500 | |
Payments for receivables-backed facility | | | — | | | | — | | | | (2,445,500 | ) | | | (2,445,500 | ) |
Payment of deferred financing costs | | | (52,720 | ) | | | — | | | | — | | | | (52,720 | ) |
Issuance of common stock | | | 3,415 | | | | — | | | | — | | | | 3,415 | |
Tax savings on share-based compensation | | | 278 | | | | — | | | | — | | | | 278 | |
Capital contribution from non-controlling interest | | | — | | | | — | | | | 7,992 | | | | 7,992 | |
Net change in intercompany balances | | | 53,154 | | | | (77,493 | ) | | | 24,339 | | | | — | |
| | | | | | | | | | | | | | | | |
Net cash provided by (used in) financing activities | | | (159,293 | ) | | | (90,585 | ) | | | 32,186 | | | | (217,692 | ) |
Effect of exchange rate changes on cash and cash equivalents | | | — | | | | — | | | | (502 | ) | | | (502 | ) |
| | | | | | | | | | | | | | | | |
Increase (decrease) in cash and cash equivalents | | | (9,358 | ) | | | 9,750 | | | | 46,425 | | | | 46,817 | |
Cash and cash equivalents, beginning of period | | | 9,665 | | | | — | | | | 35,525 | | | | 45,190 | |
| | | | | | | | | | | | | | | | |
Cash and cash equivalents, end of period | | $ | 307 | | | $ | 9,750 | | | $ | 81,950 | | | $ | 92,007 | |
| | | | | | | | | | | | | | | | |
F-30
| | | | | | | | | | | | | | | | |
| | Condensed Consolidating Statement of Cash Flows for the Year Ended December 31, 2009 | |
| | Parent | | | Guarantor Subsidiaries | | | Non- Guarantor Subsidiaries | | | Consolidated Totals | |
| | (In thousands) | |
Net cash provided by continuing operations | | $ | 194,778 | | | $ | 421,541 | | | $ | 41,760 | | | $ | 658,079 | |
Net cash provided by (used in) discontinued operations | | | — | | | | (735 | ) | | | 3,210 | | | | 2,475 | |
| | | | | | | | | | | | | | | | |
Net cash provided by operating activities | | | 194,778 | | | | 420,806 | | | | 44,970 | | | | 660,554 | |
Payments for property, plant and equipment | | | (1,220 | ) | | | (260,809 | ) | | | (5,661 | ) | | | (267,690 | ) |
Payments for acquisitions, net of cash received | | | (580,068 | ) | | | — | | | | (1,143 | ) | | | (581,211 | ) |
Proceeds from sale of fixed assets | | | — | | | | 8,833 | | | | — | | | | 8,833 | |
| | | | | | | | | | | | | | | | |
Net cash used in investing activities — continuing operations | | | (581,288 | ) | | | (251,976 | ) | | | (6,804 | ) | | | (840,068 | ) |
Net cash used in investing activities — discontinued operations | | | — | | | | — | | | | (525 | ) | | | (525 | ) |
| | | | | | | | | | | | | | | | |
Net cash used in investing activities | | | (581,288 | ) | | | (251,976 | ) | | | (7,329 | ) | | | (840,593 | ) |
Repayment of debt | | | (186,751 | ) | | | (143,612 | ) | | | — | | | | (330,363 | ) |
Proceeds from senior secured revolver | | | 3,689,000 | | | | — | | | | — | | | | 3,689,000 | |
Payments for senior secured revolver | | | (3,173,800 | ) | | | — | | | | — | | | | (3,173,800 | ) |
Proceeds from receivables-backed facility | | | — | | | | — | | | | 1,784,728 | | | | 1,784,728 | |
Payments for receivables-backed facility | | | — | | | | — | | | | (2,244,728 | ) | | | (2,244,728 | ) |
Issuance of common stock | | | 454,326 | | | | — | | | | — | | | | 454,326 | |
Tax savings on share-based compensation | | | 894 | | | | — | | | | — | | | | 894 | |
Capital contribution from non-controlling interest | | | — | | | | — | | | | 12,708 | | | | 12,708 | |
Net change in intercompany balances | | | (396,885 | ) | | | (38,770 | ) | | | 435,655 | | | | — | |
| | | | | | | | | | | | | | | | |
Net cash provided by (used in) financing activities | | | 386,784 | | | | (182,382 | ) | | | (11,637 | ) | | | 192,765 | |
Effect of exchange rate changes on cash and cash equivalents | | | — | | | | — | | | | 808 | | | | 808 | |
| | | | | | | | | | | | | | | | |
Increase (decrease) in cash and cash equivalents | | | 274 | | | | (13,552 | ) | | | 26,812 | | | | 13,534 | |
Cash and cash equivalents, beginning of period | | | 9,391 | | | | 13,552 | | | | 8,713 | | | | 31,656 | |
| | | | | | | | | | | | | | | | |
Cash and cash equivalents, end of period | | $ | 9,665 | | | $ | — | | | $ | 35,525 | | | $ | 45,190 | |
| | | | | | | | | | | | | | | | |
F-31
| | | | | | | | | | | | | | | | |
| | Condensed Consolidating Statement of Cash Flows for the Year Ended December 31, 2008 | |
| | Parent | | | Guarantor Subsidiaries | | | Non- Guarantor Subsidiaries | | | Consolidated Totals | |
| | (In thousands) | |
Net cash provided by continuing operations | | $ | 317,002 | | | $ | 336,426 | | | $ | 60,078 | | | $ | 713,506 | |
Net cash provided by (used in) discontinued operations | | | — | | | | (1,304 | ) | | | 4,426 | | | | 3,122 | |
| | | | | | | | | | | | | | | | |
Net cash provided by operating activities | | | 317,002 | | | | 335,122 | | | | 64,504 | | | | 716,628 | |
Payments for property, plant and equipment | | | (1,780 | ) | | | (249,504 | ) | | | (4,855 | ) | | | (256,139 | ) |
Payments for acquisitions, net of cash received | | | (95,851 | ) | | | — | | | | — | | | | (95,851 | ) |
Proceeds from sale of fixed assets | | | — | | | | 11,329 | | | | — | | | | 11,329 | |
| | | | | | | | | | | | | | | | |
Net cash used in investing activities — continuing operations | | | (97,631 | ) | | | (238,175 | ) | | | (4,855 | ) | | | (340,661 | ) |
Net cash used in investing activities — discontinued operations | | | — | | | | — | | | | (826 | ) | | | (826 | ) |
| | | | | | | | | | | | | | | | |
Net cash used in investing activities | | | (97,631 | ) | | | (238,175 | ) | | | (5,681 | ) | | | (341,487 | ) |
Repayment of debt | | | (18,000 | ) | | | (91,987 | ) | | | — | | | | (109,987 | ) |
Proceeds from senior secured revolver | | | 3,298,200 | | | | — | | | | — | | | | 3,298,200 | |
Payments for senior secured revolver | | | (3,848,500 | ) | | | — | | | | — | | | | (3,848,500 | ) |
Proceeds from receivables-backed facility | | | — | | | | — | | | | 1,852,320 | | | | 1,852,320 | |
Payments for receivables-backed facility | | | — | | | | — | | | | (1,992,320 | ) | | | (1,992,320 | ) |
Issuance of common stock | | | 419,663 | | | | — | | | | — | | | | 419,663 | |
Tax savings on share-based compensation | | | 7,581 | | | | — | | | | — | | | | 7,581 | |
Net change in intercompany balances | | | (69,525 | ) | | | (11,340 | ) | | | 80,865 | | | | — | |
| | | | | | | | | | | | | | | | |
Net cash used in financing activities | | | (210,581 | ) | | | (103,327 | ) | | | (59,135 | ) | | | (373,043 | ) |
| | | | | | | | | | | | | | | | |
Increase (decrease) in cash and cash equivalents | | | 8,790 | | | | (6,380 | ) | | | (312 | ) | | | 2,098 | |
Cash and cash equivalents, beginning of period | | | 601 | | | | 19,932 | | | | 9,025 | | | | 29,558 | |
| | | | | | | | | | | | | | | | |
Cash and cash equivalents, end of period | | $ | 9,391 | | | $ | 13,552 | | | $ | 8,713 | | | $ | 31,656 | |
| | | | | | | | | | | | | | | | |
F-32
10. | DERIVATIVE FINANCIAL INSTRUMENTS AND FAIR VALUE MEASUREMENTS |
Derivatives
Interest Rates — We have interest rate swap agreements in place that have been designated as cash flow hedges against variable interest rate exposure on a portion of our debt, with the objective of minimizing the impact of interest rate fluctuations and stabilizing cash flows. These swap agreements provide hedges for interest on our senior secured credit facility by fixing the LIBOR component of interest rates specified in the senior secured credit facility at the interest rates noted below until the indicated expiration dates of these interest rate swap agreements.
The following table summarizes our various interest rate agreements in effect as of December 31, 2010(1):
| | | | | | | | |
Fixed Interest Rates | | Expiration Date | | | Notional Amounts | |
| | | | | (In millions) | |
4.91%(2) | | | March 2011 — 2012 | | | $ | 1,500 | |
2.70% to 2.89%(3) | | | March 2017 | | | | 350 | |
(1) | On December 31, 2010, $450 million of notional amounts of our swap agreements expired and thus have been excluded from the table above. |
(2) | On March 31, 2010, $800 million of notional amounts of the swap agreements expired. The notional amounts of the swap agreements further decrease by $250 million on March 31, 2011 and the remaining balance on March 30, 2012. |
(3) | In August 2010, we entered into forward starting interest rate swap agreements that have an effective date of March 30, 2012. |
These swaps are recorded as an asset or liability in our Consolidated Balance Sheets at fair value, with an offset to accumulated other comprehensive income to the extent the hedge is effective. Derivative gains and losses included in other comprehensive income are reclassified into earnings as the underlying transaction occurs. Any ineffectiveness in our hedges is recorded as an adjustment to interest expense. There was no hedge ineffectiveness during 2010, 2009 or 2008.
We are exposed to market risk under these arrangements due to the possibility of interest rates on our senior secured credit facility falling below the rates on our interest rate derivative agreements. Credit risk under these arrangements is believed to be remote as the counterparties to our interest rate swap agreements are major financial institutions; however, if any of the counterparties to our hedging arrangements become unable to fulfill their obligation to us, we may lose the financial benefits of these arrangements.
Commodities — We are exposed to commodity price fluctuations, including milk, organic and non-genetically modified (“non-GMO”) soybeans, butterfat, sweeteners and other commodity costs used in the manufacturing, packaging and distribution of our products, including utilities, natural gas, resin and diesel fuel. In order to secure adequate supplies of materials and bring greater stability to the cost of ingredients and their related manufacturing, packaging and distribution, we routinely enter into forward purchase contracts and other purchase arrangements with suppliers. Under the forward purchase contracts, we commit to purchasing agreed-upon quantities of ingredients and commodities at agreed-upon prices at specified future dates. The outstanding purchase commitment for these commodities at any point in time typically ranges from one month’s to one year’s anticipated requirements, depending on the ingredient or commodity. These contracts are considered normal purchases and sales.
In addition to entering into forward purchase contracts, from time to time we may purchase over-the-counter contracts with our qualified banking partners or exchange-traded commodity futures contracts for raw materials that are ingredients of our products or components of such ingredients. Certain of the contracts offset the risk of increases in our commodity costs, and are designated as hedging instruments when appropriate. Other contracts
F-33
may be executed related to certain customer pricing arrangements. We have not designated such contracts as hedging instruments; therefore, the contracts are marked to market at each reporting period and a derivative asset or liability is recorded on our balance sheet. A summary of these open commodities contracts recorded at fair value in our Consolidated Balance Sheet at December 31, 2010 is included in the table below.
Although we may utilize forward purchase contracts and other instruments to mitigate the risks related to commodity price fluctuation, such strategies do not fully mitigate commodity price risk. Adverse movements in commodity prices over the terms of the contracts or instruments could decrease the economic benefits we derive from these strategies.
Foreign Currency — Historically, our international operations represented less than 1% of our sales and long-lived assets. With our acquisition of Alpro in July 2009, the relative percentage of our international sales has increased to approximately 3% during the year ended December 31, 2010. Sales in foreign countries, as well as certain expenses related to those sales, are transacted in currencies other than our reporting currency, the U.S. dollar. Our foreign currency exchange rate risk is primarily limited to the Euro and the British Pound. We may, from time to time, employ derivative financial instruments to manage our exposure to fluctuations in foreign currency rates or enter into forward currency exchange contracts to hedge our net investment and intercompany payable or receivable balances in foreign operations.
In June 2009, in connection with our acquisition of Alpro, we entered into a forward contract to purchase €325.0 million. The forward contract was entered into in order to hedge the impact on the purchase price resulting from foreign currency exchange rate fluctuations. The forward contract was not designated as a hedging instrument for accounting purposes. In July 2009, the acquisition closed and the foreign currency forward contract was settled. A gain of $4.2 million was recorded for the year ended December 31, 2009, within other income. No foreign currency derivatives were entered into in 2010.
As of December 31, 2010 and 2009, our derivatives recorded at fair value in our Consolidated Balance Sheets were:
| | | | | | | | | | | | | | | | |
| | Derivative Assets | | | Derivative Liabilities | |
| | December 31, 2010 | | | December 31, 2009 | | | December 31, 2010 | | | December 31, 2009 | |
| | (In thousands) | |
Derivatives designated as Hedging Instruments | | | | | | | | | | | | | | | | |
Interest rate swap contracts — current(1) | | $ | — | | | $ | — | | | $ | 59,379 | | | $ | 90,194 | |
Interest rate swap contracts — noncurrent(2) | | | 4,156 | | | | — | | | | 13,058 | | | | 42,262 | |
Commodities contracts — current(1) | | | 2,754 | | | | — | | | | — | | | | — | |
Derivatives not designated as Hedging Instruments | | | | | | | | | | | | | | | | |
Commodities contracts — current(1) | | | 1,478 | | | | — | | | | 947 | | | | — | |
| | | | | | | | | | | | | | | | |
Total derivatives | | $ | 8,388 | | | $ | — | | | $ | 73,384 | | | $ | 132,456 | |
| | | | | | | | | | | | | | | | |
(1) | Derivative assets and liabilities that have settlement dates equal to or less than 12 months from the respective balance sheet date were included in other current assets and accounts payable and accrued expenses, respectively, in our Consolidated Balance Sheets. |
(2) | Derivative assets and liabilities that have settlement dates greater than 12 months from the respective balance sheet date were included in identifiable intangible and other assets and other long-term liabilities, respectively, in our Consolidated Balance Sheets. |
F-34
Gains and losses on derivatives designated as cash flow hedges reclassified from accumulated other comprehensive income into income for the years ended December 31, 2010 and 2009 were (in thousands):
| | | | | | | | | | | | |
| | Year Ended December 31 | |
| | 2010 | | | 2009 | | | 2008 | |
Losses on interest rate swap contracts(1) | | $ | 96,573 | | | $ | 113,238 | | | $ | 42,624 | |
Losses on commodities contracts(2) | | | 6 | | | | — | | | | — | |
(1) | Recorded in interest expense in our Consolidated Statements of Income. |
(2) | Recorded in distribution expense in our Consolidated Statements of Income. |
Based on current interest rates, we estimate that approximately $59.4 million of hedging activity related to our interest rate swaps and $2.8 million of hedging activity related to our commodities contracts will be reclassified from accumulated other comprehensive income into income within the next 12 months.
Fair Value Measurements
Fair value is an exit price, representing the amount that would be received to sell an asset or paid to transfer a liability in an orderly transaction between market participants. As such, fair value is a market-based measurement that should be determined based on assumptions that market participants would use in pricing an asset or liability. As a basis for considering assumptions, we follow a three-tier fair value hierarchy, which prioritizes the inputs used in measuring fair value as follows:
| • | | Level 1 — Quoted prices for identical instruments in active markets. |
| • | | Level 2 — Quoted prices for similar instruments in active markets, quoted prices for identical or similar instruments in markets that are not active and model-derived valuations, in which all significant inputs are observable in active market. |
| • | | Level 3 — Unobservable inputs in which there is little or no market data, which require the reporting entity to develop its own assumptions. |
A summary of our derivative assets and liabilities measured at fair value on a recurring basis as of December 31, 2010 is as follows (in thousands):
| | | | | | | | | | | | | | | | |
| | Fair Value as of December 31, 2010 | | | Level 1 | | | Level 2 | | | Level 3 | |
Asset — Interest rate swap contracts | | $ | 4,156 | | | $ | — | | | $ | 4,156 | | | $ | — | |
Liability — Interest rate swap contracts | | | 72,437 | | | | — | | | | 72,437 | | | | — | |
Asset — Commodities contracts | | | 4,232 | | | | — | | | | 4,232 | | | | — | |
Liability — Commodities contracts | | | 947 | | | | — | | | | 947 | | | | — | |
A summary of our derivative liabilities measure at fair value on a recurring basis as of December 31, 2009 is as follows (in thousands):
| | | | | | | | | | | | | | | | |
| | Fair Value as of December 31, 2009 | | | Level 1 | | | Level 2 | | | Level 3 | |
Liability — Interest rate swap contracts | | $ | 132,456 | | | $ | — | | | $ | 132,456 | | | $ | — | |
Due to their near-term maturities, the carrying amounts of accounts receivable and accounts payable are considered equivalent to fair value. In addition, because the interest rates on our senior secured credit facility and certain other debt are variable, their fair values approximate their carrying values.
F-35
The fair value of our Dean Foods Company senior notes and subsidiary senior notes was determined based on quoted market prices. The following table presents the carrying value and fair value of our senior and subsidiary senior notes at December 31:
| | | | | | | | | | | | | | | | |
| | 2010 | | | 2009 | |
| | Carrying Value | | | Fair Value | | | Carrying Value | | | Fair Value | |
| | (In thousands) | |
Subsidiary senior notes | | $ | 127,504 | | | $ | 123,185 | | | $ | 126,027 | | | $ | 135,255 | |
Dean Foods Company senior notes due 2016 | | | 498,765 | | | | 458,750 | | | | 498,584 | | | | 490,000 | |
Dean Foods Company senior notes due 2018 | | | 400,000 | | | | 403,000 | | | | — | | | | — | |
We hold certain deferred compensation assets that are held at fair value. The following table presents a summary of these assets measured at fair value on a recurring basis as of December 31, 2010 (in thousands):
| | | | | | | | | | | | | | | | |
| | Total | | | Level 1 | | | Level 2 | | | Level 3 | |
Money market | | $ | 3,502 | | | $ | — | | | $ | 3,502 | | | $ | — | |
Mutual funds | | | 1,013 | | | | — | | | | 1,013 | | | | — | |
The following table presents a summary of the deferred compensation assets measured at fair value on a recurring basis as of December 31, 2009 (in thousands):
| | | | | | | | | | | | | | | | |
| | Total | | | Level 1 | | | Level 2 | | | Level 3 | |
Money market | | $ | 5,010 | | | $ | — | | | $ | 5,010 | | | $ | — | |
Mutual funds | | | 1,653 | | | | — | | | | 1,653 | | | | — | |
11. | COMMON STOCK AND SHARE-BASED COMPENSATION |
Our authorized shares of capital stock include one million shares of preferred stock and 500 million shares of common stock with a par value of $.01 per share.
Public Offerings of Equity Securities — In May 2009 and March 2008, we issued and sold 25.4 million and 18.7 million shares of our common stock in public offerings, respectively. Net proceeds from these offerings of $444.7 million and $399.5 million, respectively, were used to reduce our indebtedness under our credit agreements.
Stock Award Plans — As of December 31, 2010, we had three award plans with shares remaining available for issuance. These plans, which are our 1997 Stock Option and Restricted Stock Plan, the 1989 Dean Foods Company Stock Awards Plan (which we adopted upon completion of our acquisition of Legacy Dean) and the Dean Foods Company 2007 Stock Incentive Plan (the “2007 Plan”) provide for grants of stock options, stock units, restricted stock and other stock-based awards to employees, officers, directors and, in some cases, consultants, up to a maximum of 37.5 million, 5.7 million and 10.0 million shares, respectively. Options and other stock-based awards vest in accordance with provisions set forth in the applicable award agreements. The remaining shares available for grant under the historical plans are granted pursuant to the terms and conditions of the 2007 Plan. As of December 31, 2010, we had 5,584,003 million shares, in aggregate, available for issuance.
Under our stock award plans, we grant stock options and restricted stock units to certain employees and directors. Non-employee directors also can elect to receive their director’s fees in the form of restricted stock in lieu of cash.
Stock Options — Under the terms of our stock option plans, employees and non-employee directors may be granted options to purchase our stock at a price equal to the market price on the date the option is granted. In general, employee options vest one-third on the first anniversary of the grant date, one-third on the second anniversary of the grant date and one-third on the third anniversary of the grant date. All unvested options vest immediately upon a change of control or in certain cases upon death or qualified disability. Options granted to non-employee directors generally vest immediately.
F-36
We recognize share-based compensation expense for stock options ratably over the vesting period. The fair value of each option award is estimated on the date of grant using the Black-Scholes valuation model, using the following assumptions:
| | | | | | | | | | | | |
| | Year Ended December 31 | |
| | 2010 | | | 2009 | | | 2008 | |
Expected volatility | | | 34 | % | | | 33 | % | | | 25 | % |
Expected dividend yield | | | 0 | % | | | 0 | % | | | 0 | % |
Expected option term | | | 5 years | | | | 4.75 years | | | | 4.5 years | |
Risk-free rate of return | | | 1.26 to 2.59 | % | | | 1.65 to 2.66 | % | | | 1.71 to 3.34 | % |
The expected term of the options represents the estimated period of time until exercise and is based on historical experience of similar awards, giving consideration to contractual terms (generally 10 years), vesting schedules and expectations of future employee and director behavior. Expected stock price volatility is based on a combination of historical volatility of our stock and expectations with regard to future volatility. The risk-free rates are based on the implied yield available on U.S. Treasury zero-coupon issues with an equivalent remaining term. We have not historically declared or paid a regular cash dividend on our common stock, and we have no current plans to pay a cash dividend in the future.
The following table summarizes stock option activity during the year ended December 31, 2010:
| | | | | | | | | | | | | | | | |
| | Options | | | Weighted Average Exercise Price | | | Weighted Average Contractual Life | | | Aggregate Intrinsic Value | |
Options outstanding at January 1, 2010 | | | 22,218,381 | | | | 20.52 | | | | | | | | | |
Granted | | | 1,917,255 | | | | 13.86 | | | | | | | | | |
Forfeited and cancelled(1) | | | (1,818,725 | ) | | | 22.27 | | | | | | | | | |
Exercised | | | (793,178 | ) | | | 9.03 | | | | | | | | | |
| | | | | | | | | | | | | | | | |
Options outstanding at December 31, 2010 | | | 21,523,733 | | | $ | 20.20 | | | | 4.86 | | | $ | 222,416 | |
| | | | | | | | | | | | | | | | |
Options vested and expected to vest at December 31, 2010 | | | 21,440,736 | | | | 20.22 | | | | 4.84 | | | $ | 220,179 | |
Options exercisable at December 31, 2009 | | | 15,900,822 | | | | 19.48 | | | | | | | | | |
Options exercisable at December 31, 2010 | | | 17,209,000 | | | | 20.60 | | | | 4.00 | | | $ | 182,024 | |
(1) | Pursuant to the terms of our stock option plans, options that are forfeited or cancelled may be available for future grants. |
The following table summarizes information about options outstanding and exercisable at December 31, 2010:
| | | | | | | | | | | | | | | | | | | | |
| | Options Outstanding | | | Options Exercisable | |
Range of Exercise Prices | | Number Outstanding | | | Weighted-Average Remaining Contractual Life | | | Weighted-Average Exercise Price | | | Number Exercisable | | | Weighted-Average Exercise Price | |
$7.44 to 11.69 | | | 2,853,316 | | | | 1.81 | | | $ | 11.01 | | | | 2,546,567 | | | $ | 11.13 | |
12.36 to 14.25 | | | 2,438,641 | | | | 1.94 | | | | 14.23 | | | | 2,435,308 | | | | 14.23 | |
14.56 to 17.91 | | | 3,046,444 | | | | 5.87 | | | | 16.38 | | | | 1,707,211 | | | | 17.71 | |
18.00 to 19.98 | | | 1,942,293 | | | | 4.41 | | | | 18.54 | | | | 1,806,553 | | | | 18.53 | |
20.07 | | | 2,761,790 | | | | 7.79 | | | | 20.07 | | | | 1,067,352 | | | | 20.07 | |
20.19 to 25.37 | | | 2,905,116 | | | | 6.16 | | | | 24.79 | | | | 2,154,972 | | | | 24.75 | |
25.39 to 25.68 | | | 2,327,759 | | | | 4.61 | | | | 25.64 | | | | 2,250,611 | | | | 25.64 | |
25.81 to 30.11 | | | 2,888,445 | | | | 5.61 | | | | 29.18 | | | | 2,880,497 | | | | 29.18 | |
30.18 to 31.87 | | | 244,365 | | | | 4.61 | | | | 31.20 | | | | 244,365 | | | | 31.20 | |
31.90 | | | 115,564 | | | | 6.38 | | | | 31.90 | | | | 115,564 | | | | 31.90 | |
F-37
The following table summarizes additional information regarding our stock option activity during the years ended December 31, 2010, 2009 and 2008 (in thousands, except per share amounts):
| | | | | | | | | | | | |
| | Year Ended December 31 | |
| | 2010 | | | 2009 | | | 2008 | |
Weighted-average grant date fair value of options granted | | $ | 4.68 | | | $ | 6.26 | | | $ | 6.61 | |
Intrinsic value of options exercised | | | 2,507 | | | | 8,486 | | | | 45,806 | |
Fair value of shares vested | | | 21,972 | | | | 24,142 | | | | 24,070 | |
Stock option expense | | | 16,243 | | | | 22,288 | | | | 23,374 | |
Tax benefit related to stock option expense | | | 6,135 | | | | 8,197 | | | | 8,328 | |
During the year ended December 31, 2010, cash received from stock option exercises was $7.1 million and the total cash benefit for tax deductions to be realized for these option exercises was $1.0 million.
At December 31, 2010, there was $13.6 million of total unrecognized stock option expense, all of which is related to nonvested awards. This compensation expense is expected to be recognized over the weighted-average remaining vesting period of 1.4 years.
Restricted Stock Units — We issue restricted stock units to certain senior employees and non-employee directors as part of our long-term incentive program. A restricted stock unit represents the right to receive one share of common stock in the future. Restricted stock units have no exercise price. Through December 31, 2008, restricted stock units granted to employees generally vest ratably over five years, subject to certain accelerated vesting provisions based primarily on our stock price, a change of control, or in certain cases upon death or qualified disability. Starting in January 2009, restricted stock units granted to employees generally vest ratably over three years, subject to certain accelerated vesting provisions based primarily on a change of control, or in certain cases upon death or qualified disability. Restricted stock units granted to non-employee directors vest ratably over three years.
The following table summarizes stock unit activity during the years ended December 31, 2010, 2009 and 2008:
| | | | | | | | | | | | |
| | Employees | | | Directors | | | Total | |
Stock units outstanding at January 1, 2008 | | | 1,140,152 | | | | 78,863 | | | | 1,219,015 | |
Stock units issued | | | 938,021 | | | | 22,950 | | | | 960,971 | |
Shares issued | | | (193,042 | ) | | | (30,132 | ) | | | (223,174 | ) |
Stock units cancelled or forfeited(1) | | | (131,901 | ) | | | — | | | | (131,901 | ) |
| | | | | | | | | | | | |
Stock units outstanding at December 31, 2008 | | | 1,753,230 | | | | 71,681 | | | | 1,824,911 | |
Stock units issued | | | 1,173,542 | | | | 36,926 | | | | 1,210,468 | |
Shares issued | | | (337,972 | ) | | | (34,284 | ) | | | (372,256 | ) |
Stock units cancelled or forfeited(1) | | | (191,660 | ) | | | (9,203 | ) | | | (200,863 | ) |
| | | | | | | | | | | | |
Stock units outstanding at December 31, 2009 | | | 2,397,140 | | | | 65,120 | | | | 2,462,260 | |
Stock units issued | | | 1,416,768 | | | | 27,009 | | | | 1,443,777 | |
Shares issued | | | (516,637 | ) | | | (21,743 | ) | | | (538,380 | ) |
Stock units cancelled or forfeited(1) | | | (648,428 | ) | | | — | | | | (648,428 | ) |
Stock units outstanding at December 31, 2010 | | | 2,648,843 | | | | 70,386 | | | | 2,719,229 | |
| | | | | | | | | | | | |
Weighted average grant date fair value | | $ | 18.49 | | | $ | 15.74 | | | $ | 18.43 | |
(1) | Pursuant to the terms of our stock unit plans, employees have the option of forfeiting stock units to cover their minimum statutory tax withholding when shares are issued. Stock units that are cancelled or forfeited may be available for future grants. |
F-38
The following table summarizes information about our stock unit grants and stock unit expense during the years ended December 31, 2010, 2009 and 2008 (in thousands, except per share amounts):
| | | | | | | | | | | | |
| | Year Ended December 31 | |
| | 2010 | | | 2009 | | | 2008 | |
Weighted-average grant date fair value of stock units granted | | $ | 18.43 | | | $ | 19.78 | | | $ | 24.91 | |
Stock unit expense | | | 20,629 | | | | 17,109 | | | | 11,806 | |
Tax benefit related to stock unit expense | | | 6,256 | | | | 5,156 | | | | 3,522 | |
At December 31, 2010, there was $32.6 million of total unrecognized stock unit expense, all of which is related to nonvested awards. This compensation expense is expected to be recognized over the weighted-average remaining vesting period of 1.8 years.
Restricted Stock — We offer our non-employee directors the option to receive their compensation for services rendered in either cash or shares of restricted stock equal to 150% of the fee amount. Shares of restricted stock vest one-third on grant, one-third on the first anniversary of grant and one-third on the second anniversary of grant. The following table summarizes restricted stock activity during the years ended December 31, 2010, 2009 and 2008:
| | | | | | | | |
| | Shares | | | Weighted- Average Grant Date Fair Value | |
Nonvested at January 1, 2008 | | | 32,033 | | | $ | 34.09 | |
Restricted shares granted | | | 53,469 | | | | 19.92 | |
Restricted shares vested | | | (37,824 | ) | | | 28.14 | |
Restricted shares forfeited | | | (1,486 | ) | | | 22.37 | |
| | | | | | | | |
Nonvested at December 31, 2008 | | | 46,192 | | | | 22.94 | |
Restricted shares granted | | | 38,405 | | | | 18.24 | |
Restricted shares vested | | | (42,882 | ) | | | 22.39 | |
Restricted shares forfeited | | | (2,369 | ) | | | 24.27 | |
| | | | | | | | |
Nonvested at December 31, 2009 | | | 39,346 | | | | 18.87 | |
Restricted shares granted | | | 77,613 | | | | 10.41 | |
Restricted shares vested | | | (52,885 | ) | | | 14.88 | |
Restricted shares forfeited | | | — | | | | — | |
| | | | | | | | |
Nonvested at December 31, 2010 | | | 64,074 | | | $ | 11.92 | |
| | | | | | | | |
Cash Performance Units— In February 2010, we began granting awards of cash performance units (“CPUs”) as part of our long-term incentive compensation program under the terms of our 2007 Stock Incentive Plan (the “2007 Plan”). The CPU awards are cash-settled awards and are designed to link compensation of certain executive officers and other key employees to our performance over a three-year period. The performance metric, as defined in the award, is the performance of our stock price relative to that of a peer group of companies. The range of payout under the award is between 0% and 200% and is payable in cash at the end of the performance period.
| | | | |
| | Units | |
Outstanding at December 31, 2009 | | | — | |
Granted | | | 12,658,001 | |
Converted/paid | | | — | |
Forfeited | | | (1,846,000 | ) |
| | | | |
Outstanding at December 31, 2010 | | | 10,812,001 | |
| | | | |
Vested at December 31, 2010 | | | — | |
| | | | |
F-39
We reversed $0.8 million of expense in the fourth quarter of 2010 due to the underperformance of the plan. We have no liability recorded related to this plan at December 31, 2010, and based on the cumulative expected returns versus that of the peer group companies, we do not expect to record any compensation expense in the future related to these awards. Our management is currently exploring other alternatives for our long-term incentive programs, as described below.
For fiscal 2011, we changed the design of our Long-Term Incentive program by adding additional forms of equity-based and cash-based long-term compensation. For employees at the Senior Vice President level and below, we instituted a deferred cash award with three-year cliff vesting. For employees at the Vice President level and below, we instituted a grant of phantom shares, which are similar to RSUs in that they are based on the price of the Company’s stock and vest ratably over a three-year period, but are cash settled based upon the value of the Company’s stock at each vesting period. For the executive officers, we retained the allocation of long-term incentive grants among stock options, RSUs and cash performance units, or CPUs, as with grants made in 2010.
Rights Plan — On February 27, 1998, our Board of Directors declared a dividend of the right to purchase one half of one common share for each outstanding share of common stock to the stockholders of record on March 18, 1998. The rights plan expired pursuant to its terms effective March 18, 2008.
Stock Repurchases — Since 1998, our Board of Directors has from time to time authorized the repurchase of our common stock up to an aggregate of $2.3 billion, excluding fees and expense. We made no share repurchases in 2010 or 2009. As of December 31, 2010, $218.7 million was available for repurchases under this program (excluding fees and commissions). Shares, when repurchased, are retired.
Basic earnings per share is based on the weighted average number of common shares outstanding during each period. Diluted earnings per share is based on the weighted average number of common shares outstanding and the effect of all dilutive common stock equivalents outstanding during each period. The following table reconciles the numerators and denominators used in the computations of both basic and diluted earnings per share (“EPS”):
| | | | | | | | | | | | |
| | Year Ended December 31, | |
| | 2010 | | | 2009 | | | 2008 | |
| | (In thousands, except share data) | |
Basic EPS computation: | | | | | | | | | | | | |
Numerator: | | | | | | | | | | | | |
Income from continuing operations | | $ | 77,740 | | | $ | 228,620 | | | $ | 181,887 | |
Net Loss attributable to non-controlling interest | | | 8,735 | | | | 12,461 | | | | — | |
| | | | | | | | | | | | |
Income from continuing operations attributable to Dean Foods Company | | $ | 86,475 | | | $ | 241,081 | | | $ | 181,887 | |
Denominator: | | | | | | | | | | | | |
Average common shares | | | 181,799,306 | | | | 170,986,886 | | | | 149,266,519 | |
Basic EPS from continuing operations attributable to Dean Foods Company | | $ | 0.48 | | | $ | 1.41 | | | $ | 1.22 | |
Diluted EPS computation: | | | | | | | | | | | | |
Numerator: | | | | | | | | | | | | |
Income from continuing operations | | $ | 77,740 | | | $ | 228,620 | | | $ | 181,887 | |
Net Loss attributable to non-controlling interest | | | 8,735 | | | | 12,461 | | | | — | |
| | | | | | | | | | | | |
Income from continuing operations attributable to Dean Foods Company | | $ | 86,475 | | | $ | 241,081 | | | $ | 181,887 | |
Denominator: | | | | | | | | | | | | |
Average common shares — basic | | | 181,799,306 | | | | 170,986,886 | | | | 149,266,519 | |
Stock option conversion(1) | | | 574,094 | | | | 2,474,227 | | | | 3,975,370 | |
Stock units(2) | | | 488,402 | | | | 397,190 | | | | 153,857 | |
| | | | | | | | | | | | |
Average common shares — diluted | | | 182,861,802 | | | | 173,858,303 | | | | 153,395,746 | |
| | | | | | | | | | | | |
Diluted EPS from continuing operations attributable to Dean Foods Company | | $ | 0.47 | | | $ | 1.39 | | | $ | 1.19 | |
(1) Anti-dilutive options excluded | | | 19,681,022 | | | | 12,846,720 | | | | 10,068,998 | |
(2) Anti-dilutive stock units excluded | | | 158,991 | | | | 57,664 | | | | 970,868 | |
F-40
13. | OTHER COMPREHENSIVE INCOME (LOSS) |
Comprehensive income (loss) comprises net income plus all other changes in equity from non-owner sources. The components of accumulated other comprehensive income (loss), as reflected in the Consolidated Statements of Stockholders’ Equity at December 31, 2010 and 2009, are as follows:
| | | | | | | | |
| | December 31 | |
| | 2010 | | | 2009 | |
| | (In thousands) | |
Cumulative translation adjustment | | $ | (24,239 | ) | | $ | (3,532 | ) |
Fair value of derivative instruments, net of tax | | | (40,100 | ) | | | (82,133 | ) |
Pension and other postretirement liability adjustment, net of tax | | | (82,314 | ) | | | (81,311 | ) |
| | | | | | | | |
Total accumulated other comprehensive income (loss) | | $ | (146,653 | ) | | $ | (166,976 | ) |
| | | | | | | | |
14. | EMPLOYEE RETIREMENT AND PROFIT SHARING PLANS |
We sponsor various defined benefit and defined contribution retirement plans, including various employee savings and profit sharing plans, and contribute to various multi-employer pension plans on behalf of our employees. Substantially all full-time union and non-union employees who have completed one or more years of service and have met other requirements pursuant to the plans are eligible to participate in one or more of these plans. On July 2, 2009, we acquired Alpro, including its defined benefit pension plans. During 2010, 2009 and 2008, our retirement and profit sharing plan expenses were as follows:
| | | | | | | | | | | | |
| | Year Ended December 31 | |
| | 2010 | | | 2009 | | | 2008 | |
| | (In thousands) | |
Defined benefit plans | | $ | 12,975 | | | $ | 21,053 | | | $ | 4,398 | |
Defined contribution plans | | | 27,182 | | | | 28,300 | | | | 23,331 | |
Multi-employer pension and certain union plans | | | 28,768 | | | | 29,604 | | | | 28,295 | |
| | | | | | | | | | | | |
Total | | $ | 68,925 | | | $ | 78,957 | | | $ | 56,024 | |
| | | | | | | | | | | | |
Defined Benefit Plans — The benefits under our defined benefit plans are based on years of service and employee compensation. Our funding policy is to contribute annually the minimum amount required under ERISA regulations plus additional amounts as we deem appropriate.
Included in accumulated other comprehensive income at December 31, 2010 and 2009 are the following amounts that have not yet been recognized in net periodic pension cost: unrecognized transition obligation of $225,000 ($138,000 net of tax) and $337,000 ($206,000 net of tax), unrecognized prior service costs of $5.6 million ($3.5 million net of tax) and $7.1 million ($4.4 million net of tax) and unrecognized actuarial losses of $124.1 million ($76.0 million net of tax) and $120.4 million ($73.7 million net of tax). The transition obligation, prior service costs, and actuarial losses included in accumulated other comprehensive income and expected to be recognized in net periodic pension cost during the year ended December 31, 2011 are $112,000 ($69,000 net of tax), $763,000 ($467,000 net of tax), and $9.0 million ($5.5 million net of tax), respectively.
F-41
The reconciliation of the beginning and ending balances of the projected benefit obligation and the fair value of plans assets for the years ended December 31, 2010 and 2009 and the funded status of the plans at December 31, 2010 and 2009 is as follows:
| | | | | | | | |
| | December 31 | |
| | 2010 | | | 2009 | |
| | (In thousands) | |
Change in benefit obligation: | | | | | | | | |
Benefit obligation at beginning of year | | $ | 294,569 | | | $ | 276,355 | |
Service cost | | | 3,699 | | | | 3,147 | |
Interest cost | | | 16,941 | | | | 16,947 | |
Plan participants’ contributions | | | 66 | | | | 48 | |
Actuarial (gain) loss | | | 16,619 | | | | 10,330 | |
Benefits paid | | | (20,822 | ) | | | (18,873 | ) |
Plan amendments | | | — | | | | — | |
Plan settlements | | | (2,914 | ) | | | (1,769 | ) |
Acquisition | | | — | | | | 8,605 | |
Exchange rate changes | | | (627 | ) | | | (221 | ) |
| | | | | | | | |
Benefit obligation at end of year | | | 307,531 | | | | 294,569 | |
Change in plan assets: | | | | | | | | |
Fair value of plan assets at beginning of year | | | 223,369 | | | | 181,027 | |
Actual return on plan assets | | | 22,240 | | | | 34,062 | |
Employer contribution | | | 10,277 | | | | 24,517 | |
Plan participants’ contributions | | | 66 | | | | 48 | |
Benefits paid | | | (20,822 | ) | | | (18,873 | ) |
Plan settlements | | | (2,914 | ) | | | (1,769 | ) |
Acquisition | | | — | | | | 4,496 | |
Exchange rate changes | | | (394 | ) | | | (139 | ) |
| | | | | | | | |
Fair value of plan assets at end of year | | | 231,822 | | | | 223,369 | |
| | | | | | | | |
Funded status at end of year | | $ | (75,709 | ) | | $ | (71,200 | ) |
| | | | | | | | |
The underfunded status of the plans of $75.7 million at December 31, 2010 is recognized in our Consolidated Balance Sheet and includes $845,000 classified as a current accrued pension liability. We do not expect any plan assets to be returned to us during the year ended December 31, 2011. We expect to contribute approximately $12.1 million to the pension plans in 2011.
A summary of our key actuarial assumptions used to determine benefit obligations as of December 31, 2010 and 2009 follows:
| | | | | | | | |
| | December 31 | |
| | 2010 | | | 2009 | |
Weighted average discount rate(1) | | | 5.28 | % | | | 6.00 | % |
Rate of compensation increase(1) | | | 4.00 | % | | | 4.00 | % |
(1) | Assumptions in this table represent the assumptions utilized for our domestic pension plans as they represented more than 90% of our total benefit obligation as of December 31, 2010 and 2009. |
F-42
A summary of our key actuarial assumptions used to determine net periodic benefit cost for 2010, 2009 and 2008 follows:
| | | | | | | | | | | | |
| | Year Ended December 31 | |
| | 2010 | | | 2009 | | | 2008 | |
Weighted average discount rate(1) | | | 6.00 | % | | | 6.32 | % | | | 6.40 | % |
Expected return on plan assets(1) | | | 7.70 | % | | | 7.70 | % | | | 8.00 | % |
Rate of compensation increase(1) | | | 4.00 | % | | | 4.00 | % | | | 4.00 | % |
(1) | Assumptions in this table represent the assumptions utilized for our domestic pension plans as they represented more than 90% of our total net periodic benefit cost during the years ended December 31, 2010, 2009 and 2008. |
| | | | | | | | | | | | |
| | Year Ended December 31 | |
| | 2010 | | | 2009 | | | 2008 | |
| | (In thousands) | |
Components of net periodic benefit cost: | | | | | | | | | | | | |
Service cost | | $ | 3,699 | | | $ | 3,147 | | | $ | 2,727 | |
Interest cost | | | 16,941 | | | | 16,947 | | | | 16,160 | |
Expected return on plan assets | | | (16,584 | ) | | | (14,017 | ) | | | (19,185 | ) |
Amortizations: | | | | | | | | | | | | |
Unrecognized transition obligation | | | 112 | | | | 112 | | | | 112 | |
Prior service cost | | | 716 | | | | 921 | | | | 890 | |
Unrecognized net loss | | | 5,594 | | | | 12,093 | | | | 2,038 | |
Effect of curtailment | | | 790 | | | | 945 | | | | — | |
Effect of settlement | | | 1,707 | | | | 905 | | | | 1,656 | |
| | | | | | | | | | | | |
Net periodic benefit cost | | $ | 12,975 | | | $ | 21,053 | | | $ | 4,398 | |
| | | | | | | | | | | | |
The overall expected long-term rate of return on plan assets is a weighted-average expectation based on the targeted and expected portfolio composition. We consider historical performance and current benchmarks to arrive at expected long-term rates of return in each asset category.
The amortization of unrecognized net loss represents the amortization of investment losses incurred. In 2010, we closed a plant in South Carolina and also carried out a broad-based workforce reduction plan within our Fresh Dairy Direct-Morningstar segment. The effect of curtailment cost in 2010 represents the recognition of net periodic pension service costs associated with these activities. In 2009, we closed a plant in Michigan. The effect of curtailment cost in 2009 represents the recognition of net periodic pension service costs associated with the closure of that plant. The effect of settlement costs in 2010, 2009 and 2008 represents the recognition of net periodic benefit cost related to pension settlements reached as a result of plant closures.
Pension plans with an accumulated benefit obligation in excess of plan assets follows:
| | | | | | | | |
| | December 31 | |
| | 2010 | | | 2009 | |
| | (In millions) | |
Projected benefit obligation | | $ | 299.6 | | | $ | 286.0 | |
Accumulated benefit obligation | | | 290.2 | | | | 283.2 | |
Fair value of plan assets | | | 226.3 | | | | 217.0 | |
The accumulated benefit obligation for all defined benefit plans was $295.0 million and $289.0 million at December 31, 2010 and 2009, respectively.
Almost 90% of our defined benefit plan obligations are frozen as to future participants or increases in accumulated benefits. Many of these obligations were acquired in prior strategic transactions. As an alternative to defined benefit plans, we offer defined contribution plans for eligible employees.
F-43
The weighted average discount rate reflects the rate at which our defined benefit plan obligations could be effectively settled. The rate, which is updated annually with the assistance of an independent actuary, uses a model that reflects rates of a hypothetical portfolio of zero-coupon, high quality corporate bonds that mirror our forecasted benefit plan payments in the future. The weighted average discount rate was decreased from 6.00% at December 31, 2009 to 5.28% at December 31, 2010, which will increase the net periodic benefit cost in 2011.
Substantially all of our qualified pension plans are consolidated into one master trust. The investments held in the master trust are managed by an established Investment Committee with assistance from independent investment advisors. On July 1, 2009, the Investment Committee adopted a new long-term investment policy for the master trust that decreases the expected relative holdings of equity securities that targets investments in equity securities at 59% of the portfolio, fixed income at 37%, cash equivalents at 3% and other investments of 1%. Policy objectives include maximizing long-term return at acceptable risk levels, diversifying among asset classes, if appropriate, and among investment managers, as well as establishing relevant risk parameters within each asset class. The investment policies permit variances from the targets within certain parameters. The investment policy prohibits investments in non-marketable or exotic securities, such as short-sale contracts; letter stock; commodities and private placements, without the Investment Committee’s prior approval. At December 31, 2010, our master trust was invested as follows: investments in equity securities were at 62%; investments in fixed income were at 34%; cash equivalents were less than 1% and other investments were at 4%. Given meaningful equity returns in the fourth quarter of 2010, these investment percentages were slightly different from the Investment Committee targets noted above, and our master trust investments were rebalanced accordingly during the first quarter of 2011 in order to be consistent with those targets. Equity securities of the plan did not include any investment in our common stock at December 31, 2010 or 2009.
Estimated pension plan benefit payments to participants for the next ten years are as follows:
| | | | |
2011 | | $ | 19.8 million | |
2012 | | | 19.2 million | |
2013 | | | 19.7 million | |
2014 | | | 20.4 million | |
2015 | | | 19.8 million | |
Next five years | | | 106.0 million | |
Fair value is an exit price, representing the amount that would be received to sell an asset or paid to transfer a liability in an orderly transaction between market participants. As such, fair value is a market-based measurement that should be determined based on assumptions that market participants would use in pricing an asset or liability. As a basis for considering assumptions, we follow a three-tier fair value hierarchy, which prioritizes the inputs used in measuring fair value of our defined benefit plans’ consolidated assets as follows:
| • | | Level 1 — Quoted prices for identical instruments in active markets. |
| • | | Level 2 — Quoted prices for similar instruments in active markets, quoted prices for identical or similar instruments in markets that are not active and model-derived valuations, in which all significant inputs are observable in active market. |
| • | | Level 3 — Unobservable inputs in which there is little or no market data, which require the reporting entity to develop its own assumptions. |
F-44
The fair values by category of inputs as of December 31, 2010 were as follows (in thousands):
| | | | | | | | | | | | | | | | |
| | Fair Value as of December 31, 2010 | | | Level 1 | | | Level 2 | | | Level 3 | |
Equity Securities: | | | | | | | | | | | | | | | | |
Common Stock | | $ | 17 | | | $ | 17 | | | $ | — | | | $ | — | |
Index Funds: | | | | | | | | | | | | | | | | |
U.S. Equities(a) | | | 114,232 | | | | — | | | | 114,232 | | | | — | |
International Equities(b) | | | 22,933 | | | | — | | | | 22,933 | | | | — | |
Equity Funds(c) | | | 5,722 | | | | — | | | | 5,722 | | | | — | |
| | | | | | | | | | | | | | | | |
Total Equity Securities | | | 142,904 | | | | 17 | | | | 142,887 | | | | — | |
Fixed Income: | | | | | | | | | | | | | | | | |
Bond Funds(d) | | | 74,322 | | | | — | | | | 74,322 | | | | — | |
Diversified Funds(e) | | | 4,353 | | | | — | | | | — | | | | 4,353 | |
| | | | | | | | | | | | | | | | |
Total Fixed Income | | | 78,675 | | | | — | | | | 74,322 | | | | 4,353 | |
Cash Equivalents: | | | | | | | | | | | | | | | | |
Short-term Investment Funds(f) | | | 1,783 | | | | — | | | | 1,783 | | | | — | |
| | | | | | | | | | | | | | | | |
Total Cash Equivalents | | | 1,783 | | | | — | | | | 1,783 | | | | — | |
Other Investments: | | | | | | | | | | | | | | | | |
Insurance Contracts(g) | | | 6,169 | | | | — | | | | — | | | | 6,169 | |
Partnerships/Joint Ventures(h) | | | 1,913 | | | | — | | | | — | | | | 1,913 | |
Insurance Reserves | | | 378 | | | | — | | | | — | | | | 378 | |
| | | | | | | | | | | | | | | | |
Total Other Investments | | | 8,460 | | | | — | | | | — | | | | 8,460 | |
| | | | | | | | | | | | | | | | |
Total | | $ | 231,822 | | | $ | 17 | | | $ | 218,992 | | | $ | 12,813 | |
| | | | | | | | | | | | | | | | |
(a) | Represents a pooled/separate account that tracks the Dow Jones U.S. Total Stock Market Index. |
(b) | Represents a pooled/separate account that tracks the MSCI EAFE Index. |
(c) | Represents a pooled/separate account comprised of approximately 90% U.S. large-cap stocks and 10% in international stocks. |
(d) | Represents a pooled/separate account which tracks the overall performance of the Barclays Capital Long Term Government/Credit Index. |
(e) | Represents a pooled/separate account investment in the General Investment Accounts of two investment managers. The accounts primarily invest in fixed income debt securities, such as high grade corporate bonds, government bonds and asset-backed securities. |
(f) | Investment is comprised of high grade money market instruments with short-term maturities and high liquidity. |
(g) | Approximately 90% of the insurance contracts are financed by employer premiums with the insurer managing the reserves as calculated using an actuarial model. The remaining 10% of the insurance contracts are financed by employer and employee contributions with the insurer managing the reserves collectively with other pension plans. |
(h) | The majority of the total partnership balance is a partnership comprised of a portfolio of two limited partnership funds that invest in public and private equity. |
F-45
The fair values by category of inputs as of December 31, 2009 were as follows (in thousands):
| | | | | | | | | | | | | | | | |
| | Fair Value as of December 31, 2009 | | | Level 1 | | | Level 2 | | | Level 3 | |
Equity Securities: | | | | | | | | | | | | | | | | |
Common Stock | | $ | 28 | | | $ | 28 | | | $ | — | | | $ | — | |
Index Funds: | | | | | | | | | | | | | | | | |
U.S. Equities(a) | | | 103,535 | | | | — | | | | 103,535 | | | | — | |
International Equities(b) | | | 21,219 | | | | — | | | | 21,219 | | | | — | |
Equity Funds(c) | | | 6,560 | | | | — | | | | 6,560 | | | | — | |
| | | | | | | | | | | | | | | | |
Total Equity Securities | | | 131,342 | | | | 28 | | | | 131,314 | | | | — | |
Fixed Income: | | | | | | | | | | | | | | | | |
Bond Funds(d) | | | 73,142 | | | | — | | | | 73,142 | | | | — | |
Diversified Funds(e) | | | 4,674 | | | | — | | | | — | | | | 4,674 | |
| | | | | | | | | | | | | | | | |
Total Fixed Income | | | 77,816 | | | | — | | | | 73,142 | | | | 4,674 | |
Cash Equivalents: | | | | | | | | | | | | | | | | |
Cash and Cash Equivalents | | | 2,000 | | | | 2,000 | | | | — | | | | — | |
Short-term Investment Funds(f) | | | 4,562 | | | | — | | | | 4,562 | | | | — | |
| | | | | | | | | | | | | | | | |
Total Cash Equivalents | | | 6,562 | | | | 2,000 | | | | 4,562 | | | | — | |
Other Investments: | | | | | | | | | | | | | | | | |
Insurance Contracts(g) | | | 5,197 | | | | — | | | | — | | | | 5,197 | |
Partnerships/Joint Ventures(h) | | | 2,092 | | | | — | | | | — | | | | 2,092 | |
Insurance Reserves | | | 360 | | | | — | | | | — | | | | 360 | |
| | | | | | | | | | | | | | | | |
Total Other Investments | | | 7,649 | | | | — | | | | — | | | | 7,649 | |
| | | | | | | | | | | | | | | | |
Total | | $ | 223,369 | | | $ | 2,028 | | | $ | 209,018 | | | $ | 12,323 | |
| | | | | | | | | | | | | | | | |
(a) | Represents a pooled/separate account that tracks the Dow Jones U.S. Total Stock Market Index. |
(b) | Represents a pooled/separate account that tracks the MSCI EAFE Index. |
(c) | Represents a pooled/separate account comprised of approximately 90% U.S. large-cap stocks and 10% in international stocks. |
(d) | Approximately 60% of investment represents a pooled/separate account that tracks the overall performance of the Barclays Capital U.S. Aggregate Bond Index. The remaining 40% represents a pooled/separate account invested in government and investment grade corporate securities. |
(e) | Represents a pooled/separate account investment in the General Investment Accounts of two investment managers. The accounts primarily invest in fixed income debt securities, such as high grade corporate bonds, government bonds and asset-backed securities. |
(f) | Investment is comprised of high grade money market instruments with short-term maturities and high liquidity. |
(g) | Approximately 90% of the insurance contracts are financed by employer premiums with the insurer managing the reserves as calculated using an actuarial model. The remaining 10% of the insurance contracts are financed by employer and employee contributions with the insurer managing the reserves collectively with other pension plans. |
(h) | The majority of the total partnership balance is a partnership comprised of a portfolio of three limited partnership funds that invest in public and private equity. |
F-46
A reconciliation of the change in the fair value measurement of the defined benefit plans’ consolidated assets using significant unobservable inputs (Level 3) during the years ended December 31, 2010 and 2009 is as follows (in thousands):
| | | | | | | | | | | | | | | | | | | | |
| | Diversified Funds | | | Insurance Contracts | | | Partnerships/ Joint Ventures | | | Insurance Reserves | | | Total | |
Balance at December 31, 2008 | | $ | 4,770 | | | $ | — | | | $ | 2,937 | | | $ | 361 | | | $ | 8,068 | |
Actual return on plan assets: | | | | | | | | | | | | | | | | | | | | |
Relating to instruments still held at reporting date | | | 58 | | | | — | | | | (845 | ) | | | (1 | ) | | | (788 | ) |
Acquisitions(1) | | | — | | | | 5,197 | | | | — | | | | — | | | | 5,197 | |
Purchases, sales and settlements (net) | | | (2,265 | ) | | | — | | | | — | | | | — | | | | (2,265 | ) |
Transfers in and/or out of Level 3 | | | 2,111 | | | | — | | | | — | | | | — | | | | 2,111 | |
| | | | | | | | | | | | | | | | | | | | |
Balance at December 31, 2009 | | $ | 4,674 | | | $ | 5,197 | | | $ | 2,092 | | | $ | 360 | | | $ | 12,323 | |
Actual return on plan assets: | | | | | | | | | | | | | | | | | | | | |
Relating to instruments still held at reporting date | | | 226 | | | | 284 | | | | (179 | ) | | | 18 | | | | 65 | |
Purchases, sales and settlements (net) | | | (3,410 | ) | | | 688 | | | | — | | | | — | | | | (3,410 | ) |
Transfers in and/or out of Level 3 | | | 2,863 | | | | — | | | | — | | | | — | | | | 3,835 | |
| | | | | | | | | | | | | | | | | | | | |
Balance at December 31, 2010 | | $ | 4,353 | | | $ | 6,169 | | | $ | 1,913 | | | $ | 378 | | | $ | 12,813 | |
| | | | | | | | | | | | | | | | | | | | |
(1) | Represents the plan assets transferred in as part of the Alpro acquisition on July 2, 2009. |
Defined Contribution Plans — Certain of our non-union personnel may elect to participate in savings and profit sharing plans sponsored by us. These plans generally provide for salary reduction contributions to the plans on behalf of the participants of between 1% and 20% of a participant’s annual compensation and provide for employer matching and profit sharing contributions as determined by our Board of Directors. In addition, certain union hourly employees are participants in company-sponsored defined contribution plans, which provide for employer contributions in various amounts ranging from $24 to $91 per pay period per participant.
Multi-Employer Pension and Certain Union Plans — Certain of our subsidiaries contribute to various multi-employer pension and certain union plans, which are administered jointly by management and union representatives and cover substantially all full-time and certain part-time union employees who are not covered by our other plans. The Multi-Employer Pension Plan Amendments Act of 1980 amended ERISA to establish funding requirements and obligations for employers participating in multi-employer plans, principally related to employer withdrawal from or termination of such plans. We could, under certain circumstances, be liable for unfunded vested benefits or other expenses of jointly administered union/management plans. At this time, we have not established any significant liabilities because withdrawal from these plans is not probable or reasonably possible.
15. | POSTRETIREMENT BENEFITS OTHER THAN PENSIONS |
Certain of our subsidiaries provide health care benefits to certain retirees who are covered under specific group contracts. As defined by the specific group contract, qualified covered associates may be eligible to receive major medical insurance with deductible and co-insurance provisions subject to certain lifetime maximums.
Included in accumulated other comprehensive income at December 31, 2010 and 2009 are the following amounts that have not yet been recognized in net periodic benefit cost: negative unrecognized prior service costs of $225,000 ($138,000 net of tax) and $291,000 ($178,000 net of tax) and unrecognized actuarial losses of $4.2 million ($2.6 million net of tax) and $4.8 million ($2.9 million net of tax), respectively. The negative prior service cost and actuarial loss included in accumulated other comprehensive income and expected to be recognized in net periodic benefit cost during the year ended December 31, 2011 is negative $66,000 ($40,000 net of tax) and $494,000 ($302,000 net of tax), respectively.
F-47
The following table sets forth the funded status of these plans:
| | | | | | | | |
| | December 31 | |
| | 2010 | | | 2009 | |
| | (In thousands) | |
Change in benefit obligation: | | | | | | | | |
Benefit obligation at beginning of year | | $ | 18,620 | | | $ | 15,736 | |
Service cost | | | 24 | | | | 51 | |
Interest cost | | | 967 | | | | 937 | |
Actuarial (gain) loss | | | (48 | ) | | | 4,367 | |
Benefits paid | | | (2,012 | ) | | | (2,197 | ) |
Plan amendments | | | — | | | | (266 | ) |
Plan curtailments | | | — | | | | (8 | ) |
| | | | | | | | |
Benefit obligation at end of year | | | 17,551 | | | | 18,620 | |
Fair value of plan assets at end of year | | | — | | | | — | |
| | | | | | | | |
Funded status | | $ | (17,551 | ) | | $ | (18,620 | ) |
| | | | | | | | |
The unfunded portion of the liability of $17.6 million at December 31, 2010 is recognized in our Consolidated Balance Sheet and includes $2.5 million classified as a current accrued postretirement liability.
A summary of our key actuarial assumptions used to determine the benefit obligation as of December 31, 2010 and 2009 follows:
| | | | | | | | |
| | December 31 | |
| | 2010 | | | 2009 | |
Healthcare inflation: | | | | | | | | |
Healthcare cost trend rate assumed for next year | | | 8.70 | % | | | 9.00 | % |
Rate to which the cost trend rate is assumed to decline (ultimate trend rate) | | | 4.50 | % | | | 4.50 | % |
Year of ultimate rate achievement | | | 2029 | | | | 2029 | |
Weighted average discount rate | | | 4.68 | % | | | 5.51 | % |
A summary of our key actuarial assumptions used to determine net periodic benefit cost follows:
| | | | | | | | | | | | |
| | Year Ended December 31 | |
| | 2010 | | | 2009 | | | 2008 | |
Healthcare inflation: | | | | | | | | | | | | |
Healthcare cost trend rate assumed for next year | | | 9.00 | % | | | 9.00 | % | | | 10.01 | % |
Rate to which the cost trend rate is assumed to decline (ultimate trend rate) | | | 4.50 | % | | | 5.40 | % | | | 5.38 | % |
Year of ultimate rate achievement | | | 2029 | | | | 2014 | | | | 2012 | |
Weighted average discount rate | | | 5.51 | % | | | 6.32 | % | | | 6.40 | % |
F-48
| | | | | | | | | | | | |
| |
| | Year Ended December 31 | |
| | 2010 | | | 2009 | | | 2008 | |
| | (In thousands) | |
Components of net periodic benefit cost: | | | | | | | | | | | | |
Service and interest cost | | $ | 991 | | | $ | 988 | | | $ | 3,319 | |
Amortizations: | | | | | | | | | | | | |
Prior service cost | | | (66 | ) | | | (333 | ) | | | (69 | ) |
Unrecognized net loss | | | 524 | | | | 1,061 | | | | 623 | |
Effect of curtailment | | | — | | | | (24 | ) | | | — | |
| | | | | | | | | | | | |
Net periodic benefit cost | | $ | 1,449 | | | $ | 1,692 | | | $ | 3,873 | |
| | | | | | | | | | | | |
Assumed health care cost trend rates have a significant effect on the amounts reported for the health care plans. A one percent change in assumed health care cost trend rates would have the following effects:
| | | | | | | | |
| | 1-Percentage- Point Increase | | | 1-Percentage- Point Decrease | |
| | (In thousands) | |
Effect on total of service and interest cost components | | $ | 69 | | | $ | (61 | ) |
Effect on postretirement obligation | | | 1,069 | | | | (956 | ) |
We expect to contribute $2.5 million to the postretirement health care plans in 2011. Estimated postretirement health care plan benefit payments for the next ten years are as follows:
| | | | |
2011 | | $ | 2.5 million | |
2012 | | | 1.8 million | |
2013 | | | 1.7 million | |
2014 | | | 1.7 million | |
2015 | | | 1.5 million | |
Next five years | | | 6.5 million | |
16. | FACILITY CLOSING AND REORGANIZATION COSTS |
Approved plans within our multi-year initiatives and related charges, are summarized as follows:
| | | | | | | | | | | | |
| | Year Ended December 31 | |
| | 2010 | | | 2009 | | | 2008 | |
| | (In thousands) | |
Closure of facilities at Fresh Dairy Direct-Morningstar(1) | | $ | 21,350 | | | $ | 30,097 | | | $ | 22,529 | |
Workforce reductions within Fresh Dairy Direct-Morningstar resulting from: | | | | | | | | | | | | |
Realignment of finance and transaction processing activities(2) | | | — | | | | 65 | | | | 229 | |
Management realignment(3) | | | 3,100 | | | | — | | | | — | |
Broad-based reduction of facility and distribution personnel(4) | | | 3,404 | | | | — | | | | — | |
Other: | | | | | | | | | | | | |
Department realignment(5) | | | 2,907 | | | | — | | | | — | |
| | | | | | | | | | | | |
Total | | $ | 30,761 | | | $ | 30,162 | | | $ | 22,758 | |
| | | | | | | | | | | | |
(1) | These charges in 2010 primarily relate to a facility closure in Florence, South Carolina, an announced facility closure in Baxley, Georgia, and efforts related to the optimization of our operations in Southern California, as well as previously announced closures. Charges in 2009 primarily relate to four facility closures in Flint, Michigan; Lincoln, Nebraska; Portsmouth, Virginia and Kingsport, Tennessee; as well as previously announced closures. Charges in 2008 primarily relate to the closure of ice cream operations in |
F-49
| Hickory, North Carolina; and the closure of facilities in Kalispell, Montana and Denver, Colorado; as well as previously announced closures in Detroit, Michigan; Union, New Jersey; Akron, Ohio; South Gate, California; and Belleville, Pennsylvania. We expect to incur additional charges related to these facility closures of $2.9 million, related to shutdown and other costs. As we continue the evaluation of our supply chain, it is likely that we will close additional facilities in the future. |
(2) | Charges relate to the centralization of certain finance and transaction processing activities from local to regional facilities. We do not expect to incur additional costs related to this initiative; however, we will continue to evaluate additional opportunities for centralization of activities, which could result in additional charges in the future. |
(3) | In 2010, we realigned management positions within our Fresh Dairy Direct-Morningstar segment to facilitate supply-chain and commercial focused functions across the segment. This resulted in the elimination of the position filled by the then President of Fresh Dairy Direct and we incurred $3.1 million of workforce reduction costs. As part of this initiative, we incurred $3.1 million of workforce reduction costs. We do not expect additional costs related to this initiative; however, we continue to evaluate opportunities to further align and integrate our Fresh Dairy Direct-Morningstar operations, which could result in additional charges in the future. |
(4) | These charges relate to a plan to reduce the workforce within our Fresh Dairy Direct-Morningstar segment impacting approximately 230 positions. Implementation began during the second quarter of 2010 and was carried out over the balance of the year. The reduction in workforce affected employees across the country and resulted from operational changes from supply chain initiatives. The workforce reduction costs related to this plan are part of an existing benefit arrangement; therefore, the full amount of expected severance benefits was accrued during the second quarter of 2010. Additional supply chain initiatives are expected to result in further broad-based reductions of facility and distribution personnel throughout 2011 and 2012. As the specifics of such initiatives are being developed, the charges expected are currently not estimable. |
(5) | In 2010, as a result of peer comparisons and our ongoing cost control initiatives, our management team approved a multi-year cost reduction plan aimed at centralization, process improvement and talent replacement, as well as business unit and functional organization redesigns. Charges relate to workforce reduction costs associated with this plan. The plan was implemented during the fourth quarter of 2010 beginning with the redesign of certain functions within human resources, legal and finance, and is ultimately expected to result in the elimination of approximately 150 to 200 positions throughout 2011 as each function reorganizes its processes in line with the peer comparisons and internally developed functional blueprints as approved by an executive operating team. As these individual plans and terminations are not yet approved, future costs are not yet estimable. |
Activity for 2010 and 2009 with respect to facility closing and reorganization costs is summarized below and includes items expensed as incurred:
| | | | | | | | | | | | | | | | | | | | | | | | | | | | |
| | Accrued Charges at December 31, 2008 | | | Charges | | | Payments | | | Accrued Charges at December 31, 2009 | | | Charges | | | Payments | | | Accrued Charges at December 31, 2010 | |
| | (In thousands) | |
Cash charges: | | | | | | | | | | | | | | | | | | | | | | | | | | | | |
Workforce reduction costs | | $ | 1,739 | | | $ | 6,950 | | | $ | (6,370 | ) | | $ | 2,319 | | | $ | 13,011 | | | $ | (11,470 | ) | | $ | 3,860 | |
Shutdown costs | | | 13 | | | | 5,288 | | | | (5,278 | ) | | | 23 | | | | 2,419 | | | | (2,426 | ) | | | 16 | |
Lease obligations after shutdown | | | — | | | | 268 | | | | (268 | ) | | | — | | | | 254 | | | | (254 | ) | | | — | |
Other | | | 14 | | | | 396 | | | | (391 | ) | | | 19 | | | | 552 | | | | (566 | ) | | | 5 | |
| | | | | | | | | | | | | | | | | | | | | | | | | | | | |
Subtotal | | $ | 1,766 | | | | 12,902 | | | $ | (12,307 | ) | | $ | 2,361 | | | | 16,236 | | | $ | (14,716 | ) | | $ | 3,881 | |
| | | | | | | | | | | | | | | | | | | | | | | | | | | | |
Noncash charges: | | | | | | | | | | | | | | | | | | | | | | | | | | | | |
Write-down of assets(1) | | | | | | | 16,315 | | | | | | | | | | | | 13,173 | | | | | | | | | |
Loss on sale of related assets | | | | | | | — | | | | | | | | | | | | 562 | | | | | | | | | |
Pension curtailment | | | | | | | 945 | | | | | | | | | | | | 790 | | | | | | | | | |
| | | | | | | | | | | | | | | | | | | | | | | | | | | | |
Total charges | | | | | | $ | 30,162 | | | | | | | | | | | $ | 30,761 | | | | | | | | | |
| | | | | | | | | | | | | | | | | | | | | | | | | | | | |
F-50
(1) | The write-down of assets relates primarily to owned buildings, land and equipment of those facilities identified for closure. The assets were tested for recoverability at the time the decision to close the facilities was more likely than not to occur. Estimates of future cash flows used to test the recoverability of the assets included the net cash flows directly associated with and that are expected to arise as a direct result of the use and eventual disposition of the assets. The inputs for the fair value calculation were based on assessment of an individual asset’s alternative use within other production facilities, evaluation of recent market data and historical liquidation sales values for similar assets. |
We are currently working through a multi-year initiative to optimize our manufacturing and distribution capabilities. This initiative will have multiple phases as we evaluate and modify historical activities surrounding purchasing, support, and decision-making infrastructure, supply chain, selling organization, brand building, and product innovation. These initiatives will require investments in people, systems, tools, and facilities. As a direct result of these initiatives, over the next several years, we will incur additional facility closing and reorganization costs including:
| • | | One-time termination benefits to employees; |
| • | | Write-down of operating assets prior to the end of their respective economic useful lives; |
| • | | Shutdown costs, including those costs necessary to prepare abandoned facilities for closure; and |
| • | | Costs incurred after shutdown, such as lease obligations or termination costs, utilities and property taxes. |
We consider several factors when evaluating a potential facility closure, including, among other things, the impact of such a closure on our customers, the impact on production, distribution and overhead costs, the investment required to complete any such closure, and the impact on future investment decisions. Some facility closures are pursued to improve our operating cost structure, while others enable us to avoid unnecessary capital expenditures, allowing us to more prudently invest our capital expenditure dollars in our production facilities and better serve our customers.
17. | SUPPLEMENTAL CASH FLOW INFORMATION |
| | | | | | | | | | | | |
| | Year Ended December 31 | |
| | 2010 | | | 2009 | | | 2008 | |
| | (In thousands) | |
Cash paid for interest and financing charges, net of capitalized interest | | $ | 233,616 | | | $ | 242,691 | | | $ | 301,795 | |
Cash paid (received) for taxes | | | 9,184 | | | | 159,840 | | | | (3,425 | ) |
18. | COMMITMENTS AND CONTINGENCIES |
Contingent Obligations Related to Divested Operations — We have divested certain businesses in prior years. In each case, we have retained certain known contingent obligations related to those businesses and/or assumed an obligation to indemnify the purchasers of the businesses for certain unknown contingent liabilities, including environmental liabilities. We believe that we have established adequate reserves which are immaterial to the financial statements for potential liabilities and indemnifications related to our divested businesses. Moreover, we do not expect any liability that we may have for these retained liabilities, or any indemnification liability, to materially exceed amounts accrued.
Contingent Obligations Related to Milk Supply Arrangements — On December 21, 2001, in connection with our acquisition of Legacy Dean, we purchased Dairy Farmers of America’s (“DFA”) 33.8% interest in our operations. In connection with that transaction, we issued a contingent, subordinated promissory note to DFA in the original principal amount of $40 million. The promissory note has a 20-year term that bears interest based on the consumer price index. Interest will not be paid in cash but will be added to the principal amount of the note
F-51
annually, up to a maximum principal amount of $96 million. We may prepay the note in whole or in part at any time, without penalty. The note will only become payable if we materially breach or terminate one of our related milk supply agreements with DFA without renewal or replacement. Otherwise, the note will expire in 2021, without any obligation to pay any portion of the principal or interest. Payments made under the note, if any, would be expensed as incurred. We have not terminated, and we have not materially breached, any of our milk supply agreements with DFA related to the promissory note. We have previously terminated unrelated supply agreements with respect to several plants that were supplied by DFA. In connection with our goals of accelerated cost control and increased supply chain efficiency, we continue to evaluate our sources of raw milk supply.
Insurance — We retain selected levels of property and casualty risks, primarily related to employee health care, workers’ compensation claims and other casualty losses. Many of these potential losses are covered under conventional insurance programs with third party carriers with high deductible limits. In other areas, we are self-insured. These deductibles are $2.0 million for casualty claims but may vary higher or lower due to insurance market conditions and risk. We believe that we have established adequate reserves to cover these claims. At December 31, 2010 and 2009, we recorded accrued liabilities related to these retained risks of $187.3 million and $206.1 million, respectively, including both current and long-term liabilities.
Lease and Purchase Obligations — We lease certain property, plant and equipment used in our operations under both capital and operating lease agreements. Such leases, which are primarily for machinery, equipment and vehicles, have lease terms ranging from one to 20 years. We did not have any material capital lease obligations as of December 31, 2010 or 2009. Certain of the operating lease agreements require the payment of additional rentals for maintenance, along with additional rentals based on miles driven or units produced. Certain leases require us to guarantee a minimum value of the leased asset at the end of the lease. Our maximum exposure under those guarantees is not a material amount. Rent expense was $158.5 million, $158.4 million and $147.3 million for 2010, 2009 and 2008, respectively.
In June 2009, we announced our intention to relocate our corporate headquarters to a leased facility in Dallas, Texas. The new facility is in close proximity to our previous headquarters. The relocation of personnel was completed during 2010. The decision to relocate the headquarters was due in part to our growth and the increased centralization of strategic, operational and functional personnel. The lease agreement for our previous headquarters facility terminated at the end of 2010. In connection with the relocation, we incurred duplicate lease expense, as well as move-related expenses in 2010. These costs were not material to our consolidated results of operations.
Future minimum payments at December 31, 2010, under non-cancelable operating leases with terms in excess of one year are summarized below (in thousands):
| | | | |
| | Operating Leases | |
| | (In thousands) | |
2011 | | $ | 122,981 | |
2012 | | | 98,170 | |
2013 | | | 78,145 | |
2014 | | | 62,002 | |
2015 | | | 46,538 | |
Thereafter | | | 94,235 | |
| | | | |
Total minimum lease payments | | $ | 502,071 | |
| | | | |
We have entered into various contracts, in the normal course of business, obligating us to purchase minimum quantities of raw materials used in our production and distribution processes, including diesel fuel, soybeans and organic raw milk. We enter into these contracts from time to time to ensure a sufficient supply of raw ingredients. In addition, we have contractual obligations to purchase various services that are part of our production process.
F-52
Litigation, Investigations and Audits — We are not party to, nor are our properties the subject of, any material pending legal proceedings, other than as set forth below:
We were named, among several defendants, in two purported class action antitrust complaints filed on July 5, 2007. The complaints were filed in the United States District Court for the Middle District of Tennessee, Columbia Division, and allege generally that we and others in the milk industry worked together to limit the price Southeastern dairy farmers are paid for their raw milk and to deny these farmers access to fluid Grade A milk processing facilities (“dairy farmer actions”). A third purported class action antitrust complaint (“retailer action”) was filed on August 9, 2007 in the United States District Court for the Eastern District of Tennessee, Greeneville Division. The complaint in the retailer action was amended on March 28, 2008. The amended complaint alleges generally that we, either acting alone or in conjunction with others in the milk industry, lessened competition in the Southeastern United States for the sale of processed fluid Grade A milk to retail outlets and other customers, and that the defendants’ conduct also artificially inflated wholesale prices for direct milk purchasers. Plaintiffs in both the dairy farmer actions and the retailer action are seeking damages for the alleged violations. If plaintiffs are successful and we are judged to have violated the antitrust laws, plaintiffs are entitled to three times the damages caused by the violations found. Four additional purported class action complaints were filed on August 27, 2007, October 3, 2007, November 15, 2007 and February 13, 2008 in the United States District Court for the Eastern District of Tennessee, Greeneville Division. The allegations in these complaints are similar to those in the dairy farmer actions.
On January 7, 2008, a United States Judicial Panel on Multidistrict Litigation transferred all of the pending cases to the Eastern District of Tennessee, Greeneville Division. On April 1, 2008, the Eastern District Court ordered the consolidation of the six dairy farmer actions, and ordered the retailer action to be administratively coordinated with the consolidated dairy farmer actions. A motion to dismiss the dairy farmer actions was denied on May 20, 2008, and an amended consolidated complaint was filed by the dairy farmer plaintiffs on June 20, 2008. A motion to dismiss the retailer action was denied on July 27, 2009. Motions for class certification were filed in both actions on May 1, 2009. The motion for class certification in the dairy farmer action was granted on September 7, 2010. A petition seeking leave to appeal that decision was filed with the Sixth Circuit on September 21, 2010 and is currently pending. The motion for class certification in the retailer action is still pending. A motion for summary judgment in the retailer action was granted in part and denied in part on August 4, 2010. Defendants filed a motion for reconsideration on September 10, 2010, and filed a supplemental motion for summary judgment as to the remaining claims on September 27, 2010. Those motions are currently pending before the court. A motion for summary judgment in the dairy farmer action was filed on July 27, 2010 and remains pending. Fact discovery and expert discovery are complete in these matters, and expert reports have been submitted. Presently, trial in the dairy farmer action is scheduled to begin in June 2011. If the Sixth Circuit grants the petition to appeal the class certification motion, we expect that the trial will be postponed. We intend to continue to vigorously defend against these lawsuits.
On June 29, 2009, another purported class action lawsuit was filed in the Eastern District of Tennessee, Greeneville Division, on behalf of indirect purchasers of processed fluid Grade A milk (“indirect purchaser action”). The allegations in this complaint are similar to those in the retailer action, but primarily involve state law claims. Because the allegations in this complaint substantially overlap with the allegations in the retailer action, on September 1, 2009, the Court granted the parties’ joint motion to stay all proceedings in the indirect purchaser action pending the outcome of the summary judgment motions in the retailer action.
On October 8, 2009, we were named, among several defendants, in a purported class action antitrust complaint filed in the United States District Court for the District of Vermont. The original complaint was amended on January 21, 2010, and contained allegations similar in nature to that of the dairy farmer actions (noted above), and alleges generally that we and others in the milk industry worked together to limit the price dairy farmers in the Northeastern United States are paid for their raw milk and to deny these farmers access to fluid Grade A milk processing facilities. A second similar complaint was filed by a different plaintiff on January 14, 2010. The Company has reached an agreement with the plaintiffs to settle all claims against the Company in this action. The settlement agreement is subject to court approval, and multiple motions related to the settlement agreement are
F-53
currently pending before the court. There can be no assurance that the court will approve the agreement as proposed by the parties. Pursuant to the agreement the Company would be obligated to pay $30 million, and would agree to other terms and conditions with respect to its raw milk procurement activities at certain of its processing plants located in the Northeast.
On January 22, 2010, the United States Department of Justice (“DOJ”) and the States of Wisconsin, Illinois and Michigan (“Plaintiff States”) filed a civil action in the Eastern District of Wisconsin (“DOJ lawsuit”) alleging that the Company violated Section 7 of the Clayton Act when it acquired the Consumer Products Division of Foremost Farms USA on April 1, 2009 (the “acquisition”) for an aggregate purchase price of approximately $35 million. The DOJ and the Plaintiff States seek a declaration that the acquisition violates Section 7 of the Clayton Act, divestiture by the Company of all assets and interests it acquired as part of the acquisition, an order permanently enjoining the Company from further ownership and operation of the assets that were part of the acquisition, and to compel the Company to provide certain advance notification of future acquisitions involving school milk or fluid milk processing operations. A motion to partially dismiss the DOJ lawsuit was denied on April 7, 2010. This matter is currently in the fact discovery stage. The Company intends to vigorously defend against this action.
On April 28, 2009, a stockholder derivative complaint was filed purportedly on behalf of Dean Foods Company (the “Company”) in the United States District Court for the Eastern District of Tennessee, Greeneville division. The complaint names the Company’s then current directors, as well an officer of the Company, and a former director among the defendants. The complaint alleges that the officers and directors breached their fiduciary duties to the Company under Delaware law by approving the 2001 merger between the former Dean Foods Company and Suiza Foods Corporation, and allegedly participating in, or failing to prevent, a purported conspiracy to fix the price of Grade A milk. The complaint also names others in the milk industry as defendants for allegedly aiding and abetting the officers’ and directors’ breach of their fiduciary duties and names the Company as a nominal defendant. The plaintiffs are seeking, on behalf of the Company, an undisclosed amount of damages and equitable relief. On August 7, 2009, the Company and other defendants filed a motion to dismiss the complaint and a motion to transfer the case to the United States District Court for the Northern District of Texas. The defendants’ motion to transfer the case was granted on March 31, 2010. On September 14, 2010, the Court granted the motion to dismiss this matter. The plaintiffs subsequently filed an amended complaint, and the Company and the other defendants have filed a motion to dismiss the amended complaint. On January 26, 2011, the Court granted a motion to dismiss the amended complaint and entered a judgment dismissing the case with predjudice.
On January 18, 2008, our subsidiary, Kohler Mix Specialties, LLC (“Kohler”), was named as a defendant in a civil complaint filed in the Superior Court, Judicial District of Hartford. The plaintiff in the case is the Commissioner of Environmental Protection of the State of Connecticut. The complaint alleges generally that Kohler improperly discharged wastewater in to the waters of the State of Connecticut, and bypassed certain wastewater treatment equipment in violation of certain Connecticut environmental regulations and Kohler’s wastewater discharge permit. The plaintiff is seeking injunctive relief and civil penalties with respect to the claims. On December 14, 2009, Kohler filed its answer to the complaint. This matter is currently in the fact discovery stage.
At this time, it is not possible for us to predict the ultimate outcome of the matters set forth above.
Other than the matters set forth above, we are party from time to time to certain claims, litigations, audits and investigations. Potential liabilities associated with the other matters referred to in this paragraph are not expected to have a material adverse impact on our financial position, results of operations or cash flows.
Other — We are in discussion with numerous states, most but not all of whom, have appointed an agent to conduct an examination of our books and records to determine whether we have complied with state unclaimed property laws. In addition to seeking remittance of unclaimed property, some states may also seek interest and penalties. At this time, it is not possible for us to predict the ultimate outcome of these potential examinations.
F-54
19. | SEGMENT, GEOGRAPHIC AND CUSTOMER INFORMATION |
We currently have two reportable segments: Fresh Dairy Direct-Morningstar and WhiteWave-Alpro.
In the first quarter of 2010, our Chief Executive Officer, who is our chief operating decision maker, changed the way he evaluates the performance of our operations, develops strategy and allocates capital resources. As a result, beginning in the first quarter of 2010, our Morningstar operations were aligned with our Fresh Dairy Direct operations, so that our two reporting segments consisted of Fresh Dairy Direct-Morningstar and WhiteWave-Alpro. This change reflects the divergence between the strategies and objectives of these two segments. Our value-added branded operations at WhiteWave-Alpro added scale with the acquisition of Alpro in July 2009 and are focused on driving growth through effective marketing and innovation. Our traditional dairy operations at Fresh Dairy Direct-Morningstar are driven by a focus on cost and service leadership. We believe these revised segments have increased internal focus and offered management and investors improved visibility into the performance of the segments against their specific objectives. Our historical segment disclosures have been recast to be consistent with our current presentation.
During the second quarter of 2010, we committed to a plan to sell the business operations of Rachel’s, which provide organic branded dairy-based chilled yogurt, milk and related dairy products primarily in the United Kingdom. The sale of these operations was completed on August 4, 2010. All Rachel’s operations, previously reported within the WhiteWave-Alpro segment, have been reclassified as discontinued operations. See Note 2.
Fresh Dairy Direct-Morningstar is our largest segment with 95 manufacturing facilities geographically located largely based on local and regional customer needs and other market factors. Fresh Dairy Direct-Morningstar manufactures, markets and distributes a wide variety of branded and private label dairy case products, milk, ice cream, cultured dairy products, creamers, ice cream mix and other dairy products to retailers, distributors, foodservice outlets, educational institutions and governmental entities across the United States. Our products are primarily delivered through what we believe to be one of the most extensive refrigerated DSD systems in the United States.
WhiteWave-Alpro includes the results of our Hero/WhiteWave joint venture. WhiteWave manufactures, develops, markets and sells a variety of nationally branded plant-based beverages and other soy foods, such asSilkplant based beverages such as soy, almond and coconut milks and cultured soy products, dairy and dairy-related products, such asHorizon Organicmilk and other dairy products andThe Organic Cow dairy products,and International Delightcoffee creamers andLAND O LAKES creamers. Alpro is a leading provider of branded soy-based beverages and food products in Europe and markets its products under theAlproand Provamelbrands. Additionally, with our Hero/WhiteWave joint venture we have expanded the WhiteWave product footprint beyond the dairy case to capitalize on the chilled fruit-based beverage opportunity with the introduction ofFruit2Day. WhiteWave-Alpro sells its products to a variety of customers, including grocery stores, club stores, natural foods stores, mass merchandisers, convenience stores, drug stores and foodservice outlets. The majority of the WhiteWave-Alpro products are delivered through warehouse delivery systems.
We evaluate the performance of our segments based on sales and operating income or loss before gains and losses on the sale of businesses, facility closing and reorganization costs and foreign exchange gains and losses. The reporting segments do not include an allocation of the costs related to shared services such as audit services, corporate development, human resources, strategy, tax or treasury. In addition, the expense related to share-based compensation has not been allocated to our segments and is reflected entirely within the caption “Corporate and Other”. Therefore, the measure of segment profit or loss presented below is before such items. Additionally, a portion of our WhiteWave-Alpro products are sold through our DSD network. Those sales, together with their related costs, are included in WhiteWave-Alpro for segment reporting purposes. Prior to October 2009, the results of our WhiteWave/Hero joint venture were included in Corporate and Other. Those results are now presented with our WhiteWave-Alpro operations.
F-55
The amounts in the following tables are obtained from reports used by our executive management team and do not include any allocated income taxes or management fees. There are no significant non-cash items reported in segment profit or loss other than depreciation and amortization.
| | | | | | | | | | | | |
| | Year Ended December 31 | |
| | 2010 | | | 2009 | | | 2008 | |
| | (In thousands) | |
Net sales to external customers: | | | | | | | | | | | | |
Fresh Dairy Direct-Morningstar | | $ | 10,184,904 | | | $ | 9,480,812 | | | $ | 10,924,394 | |
WhiteWave-Alpro | | | 1,937,983 | | | | 1,632,970 | | | | 1,436,917 | |
| | | | | | | | | | | | |
Total | | $ | 12,122,887 | | | $ | 11,113,782 | | | $ | 12,361,311 | |
| | | | | | | | | | | | |
Intersegment sales: | | | | | | | | | | | | |
Fresh Dairy Direct-Morningstar | | $ | 167,523 | | | $ | 143,276 | | | $ | 147,697 | |
WhiteWave-Alpro | | | 107,923 | | | | 137,997 | | | | 125,794 | |
| | | | | | | | | | | | |
Total | | $ | 275,446 | | | $ | 281,273 | | | $ | 273,491 | |
| | | | | | | | | | | | |
Operating income: | | | | | | | | | | | | |
Fresh Dairy Direct-Morningstar | | $ | 504,442 | | | $ | 756,673 | | | $ | 681,070 | |
WhiteWave-Alpro | | | 166,269 | | | | 130,268 | | | | 112,454 | |
| | | | | | | | | | | | |
Total reportable segment operating income | | | 670,711 | | | | 886,941 | | | | 793,524 | |
Corporate and Other | | | (210,266 | ) | | | (234,025 | ) | | | (165,248 | ) |
Facility closing and reorganization costs | | | (30,761 | ) | | | (30,162 | ) | | | (22,758 | ) |
Other expense | | | (30,000 | ) | | | — | | | | — | |
| | | | | | | | | | | | |
Total | | | 399,684 | | | | 622,754 | | | | 605,518 | |
Other (income) expense: | | | | | | | | | | | | |
Interest expense | | | 248,301 | | | | 246,510 | | | | 308,178 | |
Other (income) expense, net | | | 161 | | | | (4,221 | ) | | | 1,123 | |
| | | | | | | | | | | | |
Consolidated income from continuing operations before tax | | $ | 151,222 | | | $ | 380,465 | | | $ | 296,217 | |
| | | | | | | | | | | | |
Depreciation and amortization: | | | | | | | | | | | | |
Fresh Dairy Direct-Morningstar | | $ | 186,566 | | | $ | 176,257 | | | $ | 180,661 | |
WhiteWave-Alpro | | | 68,353 | | | | 58,933 | | | | 46,012 | |
Corporate and Other | | | 21,161 | | | | 18,740 | | | | 10,146 | |
| | | | | | | | | | | | |
Total | | $ | 276,080 | | | $ | 253,930 | | | $ | 236,819 | |
| | | | | | | | | | | | |
F-56
| | | | | | | | | | | | |
| | December 31 | |
| | 2010 | | | 2009 | | | 2008 | |
| | (In thousands) | |
Assets: | | | | | | | | | | | | |
Fresh Dairy Direct-Morningstar | | $ | 5,442,229 | | | $ | 5,520,813 | | | $ | 5,391,696 | |
WhiteWave-Alpro | | | 1,984,893 | | | | 1,985,619 | | | | 1,368,341 | |
Corporate | | | 412,431 | | | | 307,421 | | | | 244,351 | |
Assets Held For Sale | | | 117,114 | | | | 30,088 | | | | 35,804 | |
| | | | | | | | | | | | |
Total | | $ | 7,956,667 | | | $ | 7,843,941 | | | $ | 7,040,192 | |
| | | | | | | | | | | | |
Capital expenditures: | | | | | | | | | | | | |
Fresh Dairy Direct-Morningstar | | $ | 199,660 | | | $ | 211,599 | | | $ | 165,613 | |
WhiteWave-Alpro | | | 52,255 | | | | 35,252 | | | | 85,128 | |
Corporate and Other | | | 50,059 | | | | 20,839 | | | | 5,398 | |
| | | | | | | | | | | | |
Total | | $ | 301,974 | | | $ | 267,690 | | | $ | 256,139 | |
| | | | | | | | | | | | |
Geographic Information — Net sales and long-lived assets for domestic and foreign operations are shown in the table below.
| | | | | | | | | | | | |
| | December 31 | |
| | 2010 | | | 2009 | | | 2008 | |
| | (In thousands) | |
Net sales to external customers: | | | | | | | | | | | | |
Domestic | | $ | 11,773,644 | | | $ | 10,934,271 | | | $ | 12,346,028 | |
Foreign | | | 349,243 | | | | 179,511 | | | | 15,283 | |
Long-lived assets: | | | | | | | | | | | | |
Domestic | | $ | 5,652,676 | | | $ | 5,672,529 | | | $ | 5,540,711 | |
Foreign | | | 487,775 | | | | 523,819 | | | | — | |
During the second half of 2009 and during 2010, net sales from our foreign operations increased due to the acquisition of Alpro, which was completed in July 2009, offset by the exit of certain business relationships within our previously existing foreign operations.
Significant Customers — Our Fresh Dairy Direct-Morningstar and WhiteWave-Alpro segments each had a single customer that represented greater than 10% of their net sales. Approximately 19% of our consolidated net sales in 2010, 2009 and 2008, were to that same customer.
F-57
20. | QUARTERLY RESULTS OF OPERATIONS (unaudited) |
The following is a summary of our unaudited quarterly results of operations for 2010 and 2009.
| | | | | | | | | | | | | | | | |
| | Quarter | |
| | First | | | Second | | | Third | | | Fourth | |
| | (In thousands, except share data) | |
2010 | | | | | | | | | | | | | | | | |
Net sales | | $ | 2,961,143 | | | $ | 2,954,653 | | | $ | 3,054,130 | | | $ | 3,152,961 | |
Gross profit | | | 747,794 | | | | 751,423 | | | | 749,629 | | | | 757,076 | |
Income (loss) from continuing operations(4) | | | 39,811 | | | | 43,461 | | | | 17,177 | | | | (22,709 | ) |
Net income (loss)(1)(4) | | | 40,915 | | | | 42,852 | | | | 21,957 | | | | (22,968 | ) |
Net income (loss) attributable to Dean Foods Company(1)(4) | | | 43,152 | | | | 44,787 | | | | 24,296 | | | | (20,744 | ) |
Earnings (loss) per common share(2): | | | | | | | | | | | | | | | | |
Basic | | | 0.24 | | | | 0.25 | | | | 0.13 | | | | (0.11 | ) |
Diluted | | | 0.24 | | | | 0.25 | | | | 0.13 | | | | (0.11 | ) |
2009 | | | | | | | | | | | | | | | | |
Net sales | | $ | 2,691,473 | | | $ | 2,669,853 | | | $ | 2,762,709 | | | $ | 2,989,747 | |
Gross profit | | | 755,527 | | | | 761,650 | | | | 785,533 | | | | 802,511 | |
Income from continuing operations | | | 75,000 | | | | 63,416 | | | | 46,126 | | | | 44,078 | |
Net income(3) | | | 75,200 | | | | 62,316 | | | | 47,104 | | | | 43,227 | |
Net income attributable to Dean Foods Company(3) | | | 76,246 | | | | 64,143 | | | | 49,653 | | | | 50,266 | |
Earnings per common share(2): | | | | | | | | | | | | | | | | |
Basic | | | 0.49 | | | | 0.38 | | | | 0.28 | | | | 0.28 | |
Diluted | | | 0.48 | | | | 0.38 | | | | 0.27 | | | | 0.27 | |
(1) | The results for the first, second, third and fourth quarters of 2010 include facility closing and reorganization costs, net of tax, of $1.0 million, $4.2 million, $5.3 million and $9.3 million, respectively. |
(2) | Earnings per common share calculations for each of the quarters were based on the basic and diluted weighted average number of shares outstanding for each quarter. The sum of the quarters may not necessarily be equal to the full year earnings per common share amount. |
(3) | The results for the first, second, third and fourth quarters of 2009 include facility closing and reorganization costs, net of tax, of $5.1 million, $7.0 million, $3.9 million and $2.6 million, respectively. |
(4) | Results for 2010 include a charge of $30.0 million related to a pending class action antitrust complaint settlement and a non-cash income tax charge of $10.8 million. See Note 8 and Note 18. |
F-58
REPORT OF INDEPENDENT REGISTERED PUBLIC ACCOUNTING FIRM
To the Board of Directors and Stockholders of
Dean Foods Company
Dallas, Texas
We have audited the accompanying consolidated balance sheets of Dean Foods Company and subsidiaries (the “Company”) as of December 31, 2010 and 2009, and the related consolidated statements of income, stockholders’ equity and cash flows for each of the three years in the period ended December 31, 2010. Our audits also included the financial statement schedule listed in the Index at Item 15. These financial statements and financial statement schedule are the responsibility of the Company’s management. Our responsibility is to express an opinion on the financial statements and financial statement schedule based on our audits.
We conducted our audits in accordance with the standards of the Public Company Accounting Oversight Board (United States). Those standards require that we plan and perform the audit to obtain reasonable assurance about whether the financial statements are free of material misstatement. An audit includes examining, on a test basis, evidence supporting the amounts and disclosures in the financial statements. An audit also includes assessing the accounting principles used and significant estimates made by management, as well as evaluating the overall financial statement presentation. We believe that our audits provide a reasonable basis for our opinion.
In our opinion, such consolidated financial statements present fairly, in all material respects, the financial position of Dean Foods Company and subsidiaries as of December 31, 2010 and 2009 and the results of their operations and their cash flows for each of the three years in the period ended December 31, 2010, in conformity with accounting principles generally accepted in the United States of America. Also, in our opinion, such financial statement schedule, when considered in relation to the basic consolidated financial statements taken as a whole, presents fairly, in all material respects, the information set forth therein.
In 2009, as discussed in Note 1 to the consolidated financial statements, the Company adopted the provisions of new Accounting Standards relating to “Business Combinations”.
We have also audited, in accordance with the standards of the Public Company Accounting Oversight Board (United States), the Company’s internal control over financial reporting as of December 31, 2010, based on the criteria established in Internal Control — Integrated Framework issued by the Committee of Sponsoring Organizations of the Treadway Commission and our report dated March 1, 2011 expressed an unqualified opinion on the Company’s internal control over financial reporting.
/s/ DELOITTE & TOUCHE LLP
Dallas, Texas
March 1, 2011
F-59
Item 9. | Changes in and Disagreements with Accountants on Accounting and Financial Disclosure |
During our three most recent fiscal years, no independent accountant who was engaged as the principal accountant to audit our financial statements, nor any independent accountant who was engaged to audit a significant subsidiary and on whom our principal accountant expressed reliance in its report, has resigned or been dismissed.
Item 9A. | Controls and Procedures |
Evaluation of Disclosure Controls and Procedures
We conducted an evaluation of the effectiveness of the design and operation of our disclosure controls and procedures (as defined in Rules 13a-15(e) and 15d-15(e) of the Exchange Act, referred to herein as “Disclosure Controls”) as of the end of the period covered by this annual report. The controls evaluation was done under the supervision and with the participation of management, including our Chief Executive Officer (CEO) and Chief Financial Officer (CFO). Based upon our most recent controls evaluation, our CEO and CFO have concluded that our Disclosure Controls were effective as of December 31, 2010.
Changes in Internal Control over Financial Reporting
There have been no changes in our internal control over financial reporting (as defined in rules 13a-15(f) and 15d-15(f) under the Exchange Act) in the quarter ended December 31, 2010 that have materially affected, or are reasonably likely to materially affect, our internal control over financial reporting.
MANAGEMENT REPORT ON INTERNAL CONTROL OVER FINANCIAL REPORTING
Our management is responsible for establishing and maintaining adequate internal control over financial reporting. Our internal control system was designed to provide reasonable assurance to our management and Board of Directors regarding the preparation and fair presentation of published financial statements.
All internal control systems, no matter how well designed, have inherent limitations. Therefore, even those systems determined to be effective can provide only reasonable assurance with respect to financial statement preparation and presentation.
We have assessed the effectiveness of our internal control over financial reporting as of December 31, 2010. In making this assessment, we used the criteria established inInternal Control — Integrated Frameworkissued by the Committee of Sponsoring Organizations of the Treadway Commission (COSO). Based on our assessment we believe that, as of December 31, 2010, our internal control over financial reporting is effective based on those criteria.
Our independent auditors, Deloitte & Touche LLP, a registered public accounting firm, are appointed by the Audit Committee of our Board of Directors, subject to ratification by our stockholders. Deloitte & Touche LLP has audited and reported on the consolidated financial statements of Dean Foods Company and subsidiaries and our internal control over financial reporting. The reports of our independent auditors are contained in this annual report on Form 10-K.
Our independent registered public accounting firm has issued an audit report on our internal control over financial reporting. This report appears on page 57.
March 1, 2011
56
REPORT OF INDEPENDENT REGISTERED PUBLIC ACCOUNTING FIRM
To the Board of Directors and Stockholders of
Dean Foods Company
Dallas, Texas
We have audited the internal control over financial reporting of Dean Foods Company and subsidiaries (the “Company”) as of December 31, 2010, based on criteria established in Internal Control — Integrated Framework issued by the Committee of Sponsoring Organizations of the Treadway Commission. The Company’s management is responsible for maintaining effective internal control over financial reporting and for its assessment of the effectiveness of internal control over financial reporting, included in the accompanying Management Report on Internal Control Over Financial Reporting. Our responsibility is to express an opinion on the Company’s internal control over financial reporting based on our audit.
We conducted our audit in accordance with the standards of the Public Company Accounting Oversight Board (United States). Those standards require that we plan and perform the audit to obtain reasonable assurance about whether effective internal control over financial reporting was maintained in all material respects. Our audit included obtaining an understanding of internal control over financial reporting, assessing the risk that a material weakness exists, testing and evaluating the design and operating effectiveness of internal control based on the assessed risk, and performing such other procedures as we considered necessary in the circumstances. We believe that our audit provides a reasonable basis for our opinion.
A company’s internal control over financial reporting is a process designed by, or under the supervision of, the company’s principal executive and principal financial officers, or persons performing similar functions, and effected by the company’s board of directors, management, and other personnel to provide reasonable assurance regarding the reliability of financial reporting and the preparation of financial statements for external purposes in accordance with generally accepted accounting principles. A company’s internal control over financial reporting includes those policies and procedures that (1) pertain to the maintenance of records that, in reasonable detail, accurately and fairly reflect the transactions and dispositions of the assets of the company; (2) provide reasonable assurance that transactions are recorded as necessary to permit preparation of financial statements in accordance with generally accepted accounting principles, and that receipts and expenditures of the company are being made only in accordance with authorizations of management and directors of the company; and (3) provide reasonable assurance regarding prevention or timely detection of unauthorized acquisition, use, or disposition of the company’s assets that could have a material effect on the financial statements.
Because of the inherent limitations of internal control over financial reporting, including the possibility of collusion or improper management override of controls, material misstatements due to error or fraud may not be prevented or detected on a timely basis. Also, projections of any evaluation of the effectiveness of the internal control over financial reporting to future periods are subject to the risk that the controls may become inadequate because of changes in conditions, or that the degree of compliance with the policies or procedures may deteriorate.
In our opinion, the Company maintained, in all material respects, effective internal control over financial reporting as of December 31, 2010, based on the criteria established in Internal Control — Integrated Framework issued by the Committee of Sponsoring Organizations of the Treadway Commission.
We have also audited, in accordance with the standards of the Public Company Accounting Oversight Board (United States), the Consolidated Financial Statements and financial statement schedule as of and for the year ended December 31, 2010 of the Company and our report dated March 1, 2011 expressed an unqualified opinion on those financial statements and financial statement schedule, and included an explanatory paragraph regarding the adoption of the provisions of new Accounting Standards relating to “Business Combinations” in 2009.
/S/ DELOITTE & TOUCHE LLP
Dallas, Texas
March 1, 2011
57
Item 9B. | Other Information |
None.
PART III
Item 10. | Directors, Executive Officers and Corporate Governance |
Incorporated herein by reference to our proxy statement (to be filed) for our May 19, 2011 Annual Meeting of Stockholders.
Item 11. | Executive Compensation |
Incorporated herein by reference to our proxy statement (to be filed) for our May 19, 2011 Annual Meeting of Stockholders.
Item 12. | Security Ownership of Certain Beneficial Owners and Management and Related Stockholder Matters |
Incorporated herein by reference to our proxy statement (to be filed) for our May 19, 2011 Annual Meeting of Stockholders.
Item 13. | Certain Relationships and Related Transactions, and Director Independence |
Incorporated herein by reference to our proxy statement (to be filed) for our May 19, 2011 Annual Meeting of Stockholders.
Item 14. | Principal Accountant Fees and Services |
Incorporated herein by reference to our proxy statement (to be filed) for our May 19, 2011 Annual Meeting of Stockholders.
58
PART IV
Item 15. | Exhibits and Financial Statement Schedules |
Financial Statements
The following Consolidated Financial Statements are filed as part of this report or are incorporated herein as indicated:
| | | | |
| | Page | |
Consolidated Balance Sheets as of December 31, 2010 and 2009 | | | F-1 | |
| |
Consolidated Statements of Income for the years ended December 31, 2010, 2009 and 2008 | | | F-2 | |
| |
Consolidated Statements of Stockholders’ Equity for the years ended December 31, 2010, 2009 and 2008 | | | F-3 | |
| |
Consolidated Statements of Cash Flows for the years ended December 31, 2010, 2009 and 2008 | | | F-5 | |
| |
Notes to Consolidated Financial Statements | | | F-6 | |
| |
1. Summary of Significant Accounting Policies | | | F-6 | |
| |
2. Discontinued Operations, Divestitures and Acquisitions | | | F-10 | |
| |
3. Investment in Affiliates | | | F-12 | |
| |
4. Inventories | | | F-13 | |
| |
5. Property, Plant and Equipment | | | F-14 | |
| |
6. Goodwill and Intangible Assets | | | F-14 | |
| |
7. Accounts Payable and Accrued Expenses | | | F-16 | |
| |
8. Income Taxes | | | F-17 | |
| |
9. Debt | | | F-20 | |
| |
10. Derivative Financial Instruments and Fair Value Measurement | | | F-33 | |
| |
11. Common Stock and Share-Based Compensation | | | F-36 | |
| |
12. Earnings per Share | | | F-40 | |
| |
13. Other Comprehensive Income (Loss) | | | F-41 | |
| |
14. Employee Retirement and Profit Sharing Plans | | | F-41 | |
| |
15. Postretirement Benefits Other Than Pensions | | | F-47 | |
| |
16. Facility Closing and Reorganization Costs | | | F-49 | |
| |
17. Supplemental Cash Flow Information | | | F-51 | |
| |
18. Commitments and Contingencies | | | F-51 | |
| |
19. Segment, Geographic and Customer Information | | | F-55 | |
| |
20. Quarterly Results of Operations (unaudited) | | | F-58 | |
| |
Report of Independent Registered Public Accounting Firm | | | F-59 | |
| |
Financial Statement Schedules | | | | |
| |
Schedule II — Valuation and Qualifying Accounts | | | | |
| |
Exhibits | | | | |
| |
See Index to Exhibits. | | | | |
59
SIGNATURES
Pursuant to the requirements of Section 13 or 15(d) of the Securities Exchange Act of 1934, the registrant has duly caused this report to be signed on its behalf by the undersigned, thereunto duly authorized.
| | |
By: | | /S/ SCOTT K. VOPNI |
| | Scott K. Vopni |
| | Vice President and Chief Accounting Officer |
Dated March 1, 2011
Pursuant to the requirements of the Securities Exchange Act of 1934, this Report has been signed below by the following persons on behalf of the registrant and in the capacity and on the dates indicated.
| | | | |
Name | | Title | | Date |
| | |
/S/ GREGG L. ENGLES Gregg L. Engles | | Chief Executive Officer and Chairman of the Board | | March 1, 2011 |
| | |
/S/ SHAUN P. MARA Shaun P. Mara | | Executive Vice President and Chief Financial Officer | | March 1, 2011 |
| | |
/S/ SCOTT K. VOPNI Scott K. Vopni | | Vice President and Chief Accounting Officer | | March 1, 2011 |
| | |
/S/ TOM C. DAVIS Tom C. Davis | | Director | | March 1, 2011 |
| | |
/S/ STEPHEN L. GREEN Stephen L. Green | | Director | | March 1, 2011 |
| | |
/S/ JOSEPH S. HARDIN, JR. Joseph S. Hardin, Jr. | | Director | | March 1, 2011 |
| | |
/S/ JANET HILL Janet Hill | | Director | | March 1, 2011 |
| | |
/S/ WAYNE MAILLOUX Wayne Mailloux | | Director | | March 1, 2011 |
| | |
/S/ JOHN R. MUSE John R. Muse | | Director | | March 1, 2011 |
| | |
/S/ HECTOR M. NEVARES Hector M. Nevares | | Director | | March 1, 2011 |
| | |
/S/ JIM L. TURNER Jim L. Turner | | Director | | March 1, 2011 |
| | |
/S/ DOREEN WRIGHT Doreen Wright | | Director | | March 1, 2011 |
S-1
SCHEDULE II
DEAN FOODS COMPANY AND SUBSIDIARIES
VALUATION AND QUALIFYING ACCOUNTS
Years Ended December 31, 2010, 2009 and 2008
| | | | | | | | | | | | | | | | | | | | |
Description | | Balance at Beginning of Period | | | Charged to (Reduction in) Costs and Expenses | | | Other | | | Deductions | | | Balance at End of Period | |
| | (In thousands) | |
Year ended December 31, 2010 | | | | | | | | | | | | | | | | | | | | |
Allowance for doubtful accounts | | $ | 16,888 | | | $ | 7,956 | | | $ | (1,379 | ) | | $ | (8,118 | ) | | $ | 15,347 | |
Deferred tax asset valuation allowances | | | 9,108 | | | | (1,448 | ) | | | — | | | | — | | | | 7,660 | |
| | | | | |
Year ended December 31, 2009 | | | | | | | | | | | | | | | | | | | | |
Allowance for doubtful accounts | | | 17,429 | | | | 2,496 | | | | 1,179 | | | | (4,216 | ) | | | 16,888 | |
Deferred tax asset valuation allowances | | | 9,645 | | | | (537 | ) | | | — | | | | — | | | | 9,108 | |
| | | | | |
Year ended December 31, 2008 | | | | | | | | | | | | | | | | | | | | |
Allowance for doubtful accounts | | | 19,830 | | | | 2,280 | | | | 187 | | | | (4,868 | ) | | | 17,429 | |
Deferred tax asset valuation allowances | | | 8,695 | | | | 950 | | | | — | | | | — | | | | 9,645 | |
INDEX TO EXHIBITS
| | | | | | |
Exhibit No. | | Description | | Previously Filed as an Exhibit to and Incorporated by Reference From | | Date Filed |
| | | |
3.1 | | Amended and Restated Certificate of Incorporation | | Annual Report on Form 10-K for the year ended December 31, 2001 | | April 1, 2002 |
| | | |
3.2 | | Amended and Restated Bylaws | | Current Report on Form 8-K | | March 9, 2009 |
| | | |
4.1 | | Specimen of Common Stock Certificate | | Annual Report on Form 10-K for the year ended December 31, 2001 | | April 1, 2002 |
| | | |
4.2 | | Indenture, dated as of May 15, 2006, between us, the subsidiary guarantors listed therein and The Bank of New York Trust Company, N.A., as trustee | | Current Report on Form 8-K | | May 19, 2006 |
| | | |
4.3 | | Supplemental Indenture No. 1, dated as of May 17, 2006, between us, the subsidiary guarantors listed therein and The Bank of New York Trust Company, N.A., as trustee | | Current Report on Form 8-K | | May 19, 2006 |
| | | |
4.4 | | Supplemental Indenture No. 2, dated as of July 31, 2007, between us, the subsidiary guarantors listed therein and The Bank of New York Trust Company, N.A., as trustee | | Quarterly Report on Form 10-Q for the quarter ended September 30, 2007 | | November 9, 2007 |
| | | |
4.5 | | Supplemental Indenture No. 6, dated as of December 16, 2010, between us, the subsidiary guarantors listed therein and The Bank of New York Mellon Trust Company, N.A., as trustee | | Current Report on Form 8-K | | December 16, 2010 |
| | | |
4.6 | | Registration Rights Agreement, dated as of December 16, 2010, between us, the subsidiary guarantors listed therein and several initial purchasers listed therein | | Current Report on Form 8-K | | December 16, 2010 |
| | | |
*10.1 | | Eighth Amended and Restated 1997 Stock Option and Restricted Stock Plan | | Annual Report on Form 10-K for the year ended December 31, 2006 | | March 1, 2007 |
| | | |
*10.2 | | Third Amended and Restated 1989 Dean Foods Company Stock Awards Plan | | Annual Report on Form 10-K for the year ended December 31, 2004 | | March 16, 2005 |
| | | |
*10.3 | | Amended and Restated Executive Deferred Compensation Plan | | Annual Report on Form 10-K for the year ended December 31, 2006 | | March 1, 2007 |
| | | |
*10.4 | | Post-2004 Executive Deferred Compensation Plan | | Annual Report on Form 10-K for the year ended December 31, 2006 | | March 1, 2007 |
| | | |
*10.5 | | Revised and Restated Supplemental Executive Retirement Plan | | Annual Report on Form 10-K for the year ended December 31, 2006 | | March 1, 2007 |
| | | | | | |
Exhibit No. | | Description | | Previously Filed as an Exhibit to and Incorporated by Reference From | | Date Filed |
| | | |
*10.6 | | Amendment No. 2 to the Dean Foods Company Supplemental Executive Retirement Plan | | Annual Report on Form 10-K for the year ended December 31, 2006 | | March 1, 2007 |
| | | |
*10.7 | | Dean Foods Company Amended and Restated Executive Severance Pay Plan | | Current Report on Form 8-K | | November 19, 2010 |
| | | |
*10.8 | | Form of Amended and Restated Change in Control Agreement for our executive officers | | Quarterly Report on Form 10-Q for the quarter ended September 30, 2008 | | November 5, 2008 |
| | | |
*10.9 | | Forms of Amended and Restated Change in Control Agreements for certain other officers | | Quarterly Report on Form 10-Q for the quarter ended September 30, 2008 | | November 5, 2008 |
| | | |
*10.10 | | Dean Foods Company 2007 Stock Incentive Plan | | Quarterly Report on Form 10-Q for the quarter ended June 30, 2007 | | August 9, 2007 |
| | | |
*10.11 | | Form of Non-Qualified Stock Option Agreement under the Dean Foods Company 2007 Stock Incentive Plan | | Filed herewith | | |
| | | |
*10.12 | | Form of Restricted Stock Unit Award Agreement under the Dean Foods Company 2007 Stock Incentive Plan | | Filed herewith | | |
| | | |
*10.13 | | Form of Cash Performance Unit Agreement under the Dean Foods Company 2007 Stock Incentive Plan | | Filed herewith | | |
| | | |
*10.14 | | Form of Phantom Shares Award Agreement under the Dean Foods Company 2007 Stock Incentive Plan | | Filed herewith | | |
| | | |
*10.15 | | Form of Dean Cash Award Agreement | | Filed herewith | | |
| | | |
*10.16 | | Form of Director’s Non-Qualified Stock Option Agreement under the Dean Foods Company 2007 Stock Incentive Plan | | Filed herewith | | |
| | | |
*10.17 | | Form of Director’s Restricted Stock Unit Award Agreement under the Dean Foods Company 2007 Stock Incentive Plan | | Filed herewith | | |
| | | |
*10.18 | | Form of Director’s Master Restricted Stock Agreement under the Dean Foods Company 2007 Stock Incentive Plan | | Quarterly Report on Form 10-Q for the quarter ended June 30, 2008 | | August 8, 2008 |
| | | |
*10.19 | | Dean Foods Company Revised 2010 Short Term Incentive Compensation Plans – Business Unit President and Corporate | | Filed herewith | | |
| | | | | | |
Exhibit No. | | Description | | Previously Filed as an Exhibit to and Incorporated by Reference From | | Date Filed |
| | | |
*10.20 | | Proprietary Information, Inventions and Non-Compete Agreement between us and Joseph Scalzo dated October 7, 2005 | | Quarterly Report on Form 10-Q for the quarter ended September 30, 2005 | | November 8, 2005 |
| | | |
*10.21 | | Amendment to Employment Agreement between us and Joe Scalzo dated November 18, 2008 | | Annual Report on Form 10-K for the year ended December 31, 2008 | | February 24, 2009 |
| | | |
*10.22 | | Employment Agreement between us and Joseph Scalzo dated November 3, 2009 | | Quarterly Report on Form 10-Q for the quarter ended September 30, 2009 | | November 4, 2009 |
| | | |
*10.23 | | Employment Agreement between us and Joseph Scalzo dated August 20, 2010 | | Current Report on Form 8-K | | August 23, 2010 |
| | | |
*10.24 | | Employment Agreement between us and Jack F. Callahan dated April 27, 2006 | | Quarterly Report on Form 10-Q for the quarter ended March 31, 2006 | | May 10, 2006 |
| | | |
*10.25 | | Proprietary Information, Inventions and Non-Compete Agreement between us and Jack F. Callahan dated May 9, 2006 | | Quarterly Report on Form 10-Q for the quarter ended June 30, 2006 | | August 9, 2006 |
| | | |
*10.26 | | Amendment to Employment Agreement between us and Jack F. Callahan dated November 21, 2008 | | Annual Report on Form 10-K for the year ended December 31, 2008 | | February 24, 2009 |
| | | |
*10.27 | | Employment Agreement between us and Shaun Mara dated April 21, 2010 | | Filed Herewith | | |
| | | |
*10.28 | | Employment Agreement between us and Shaun Mara dated November 16, 2010 | | Current Report on Form 8-K | | November 19, 2010 |
| | | |
*10.29 | | Employment Agreement between us and Gregg Tanner dated November 1, 2007 | | Quarterly Report on Form 10-Q for the quarter ended September 30, 2007 | | November 9, 2007 |
| | | |
*10.30 | | Proprietary Information, Inventions and Non-Compete Agreement between us and Gregg Tanner dated November 1, 2007 | | Quarterly Report on Form 10-Q for the quarter ended September 30, 2007 | | November 9, 2007 |
| | | |
*10.31 | | Employment Agreement between us and Harrald Kroeker dated January 14, 2008 | | Annual Report on Form 10-K for the year ended December 31, 2007 | | February 28, 2008 |
| | | |
*10.32 | | Employment Agreement between us and Paul Moskowitz dated May 3, 2007 | | Quarterly Report on Form 10-Q for the quarter ended June 30, 2007 | | August 9, 2007 |
| | | |
*10.33 | | Employment Agreement between us and Greg McKelvey dated January 15, 2008 | | Annual Report on Form 10-K for the year ended December 31, 2007 | | February 28, 2008 |
| | | | | | |
Exhibit No. | | Description | | Previously Filed as an Exhibit to and Incorporated by Reference From | | Date Filed |
| | | |
*10.34 | | Employment Agreement between us and Greg McKelvey dated November 1, 2008 | | Annual Report on Form 10-K for the year ended December 31, 2008 | | February 24, 2009 |
| | | |
*10.35 | | Employment Agreement between us and Debbie Carosella dated March 14, 2007 | | Annual Report on Form 10-K for the year ended December 31, 2007 | | February 28, 2008 |
| | | |
*10.36 | | Employment Agreement between us and Steven J. Kemps dated July 8, 2008 | | Quarterly Report on Form 10-Q for the quarter ended June 30, 2008 | | August 8, 2008 |
| | | |
*10.37 | | Employment Agreement between us and Kelly Duffin-Maxwell dated April 9, 2008 | | Quarterly Report on Form 10-Q for the quarter ended March 31, 2008 | | May 12, 2008 |
| | | |
*10.38 | | Employment Agreement between us and Chris Sliva dated November 16, 2007 | | Quarterly Report on Form 10-Q for the quarter ended June 30, 2009 | | August 6, 2009 |
| | | |
*10.39 | | Employment Agreement between us and Chris Sliva dated February 15, 2010 | | Quarterly Report on Form 10-Q for the quarter ended March 31, 2010 | | May 10, 2010 |
| | | |
*10.40 | | Employment Agreement between us and Chris Sliva dated October 6, 2010 | | Quarterly Report on Form 10-Q for the quarter ended September 30, 2010 | | November 19, 2010 |
| | | |
*10.41 | | Employment Agreement between us and Blaine McPeak dated October 14, 2009 | | Annual Report on Form 10-K for the year ended December 31, 2009 | | February 25, 2010 |
| | | |
*10.42 | | Employment Agreement between us and Thomas Zanetich dated February 18, 2011 | | Filed herewith | | |
| | | |
*10.43 | | Summary of Terms of Employment Agreement (translated from Dutch) between us and Bernard Deryckere dated April 13, 2001 | | Annual Report on Form 10-K for the year ended December 31, 2009 | | February 25, 2010 |
| | | |
*10.44 | | Amendment to Employee Agreement (translated from Dutch) between us and Bernard Deryckere dated February 4, 2011 | | Filed herewith | | |
| | | |
10.45 | | Distribution Agreement between us and TreeHouse Foods dated June 27, 2005 | | Current Report on Form 8-K | | June 27, 2005 |
| | | |
10.46 | | Tax Sharing Agreement dated June 27, 2005 between us and TreeHouse Foods | | Current Report on Form 8-K | | June 27, 2005 |
| | | | | | |
Exhibit No. | | Description | | Previously Filed as an Exhibit to and Incorporated by Reference From | | Date Filed |
| | | |
10.47 | | Amendment No. 11 to Fourth Amended and Restated Receivables Purchase Agreement among certain subsidiaries of Dean Foods Company, as sellers, the Servicers, the Companies, the Financial Institutions (each as defined in the agreement) and Bank One NA, as Agent | | Current Report on Form 8-K | | November 21, 2006 |
| | | |
10.48 | | Fifth Amended and Restated Receivables Purchase Agreement, dated as of April 2, 2007 among Dairy Group Receivables L.P., Dairy Group Receivables II, L.P., WhiteWave Receivables, L.P., as Sellers; the Servicers, Companies and Financial Institutions listed therein; and JPMorgan Chase Bank, N.A., as Agent | | Current Report on Form 8-K | | April 4, 2007 |
| | | |
10.49 | | Amendment No. 3 to Fifth Amended and Restated Receivables Purchase Agreement and Limited Waiver dated March 31, 2008 | | Current Report on Form 8-K | | April 4, 2008 |
| | | |
10.50 | | Amendment No. 4 to fifth Amended and Restated Receivables Purchase Agreement dated April 4, 2008 | | Current Report on Form 8-K | | April 4, 2008 |
| | | |
10.51 | | Amendment No. 5 to Fifth Amended and Restated Receivables Purchase Agreement and Limited Waiver dated April 30, 2008 | | Current Report on Form 8-K | | May 1, 2008 |
| | | |
10.52 | | Amendment No. 7 to Fifth Amended and Restated Receivables Purchase Agreement and Reaffirmation of Performance Undertaking dated March 30, 2009 | | Current Report on Form 8-K | | April 3, 2009 |
| | | |
10.53 | | Amendment No. 9 to Fifth Amended and Restated Receivables Purchase Agreement and Reaffirmation of Performance Undertaking dated March 29, 2010 | | Current Report on Form 8-K | | March 31, 2010 |
| | | |
10.54 | | Amendment No. 10 to Fifth Amended and Restated Receivables Purchase Agreement and Reaffirmation of Performance Undertaking dated June 30, 2010 | | Current Report on Form 8-K | | July 1, 2010 |
| | | | | | |
Exhibit No. | | Description | | Previously Filed as an Exhibit to and Incorporated by Reference From | | Date Filed |
| | | |
10.55 | | Second Amended and Restated Credit Agreement, dated as of April 2, 2007, as amended and restated as of June 30, 2010, among Dean Foods Company; J.P. Morgan Securities, Inc., Banc of America Securities LLC, Wells Fargo Securities, LLC, as Lead Arrangers; JPMorgan Chase Bank, National Association, as Administrative Agent; Bank of America, N.A., as Syndication Agent; and certain other lenders that are parties thereto | | Current Report on Form 8-K | | July 1, 2010 |
| | | |
10.56 | | Amendment No. 11 to Fifth Amended and Restated Receivables Purchase Agreement and Reaffirmation of Performance Undertaking dated December 9, 2010 | | Current Report on Form 8-K | | December 9, 2010 |
| | | |
10.57 | | Amendment No. 1 to Second Amended and Restated Credit Agreement, dated as of December 9, 2010 | | Current Report on Form 8-K | | December 9, 2010 |
| | | |
12 | | Computation of Ratio of Earnings to Fixed Charges | | Filed herewith | | |
| | | |
21 | | List of Subsidiaries | | Filed herewith | | |
| | | |
23 | | Consent of Deloitte & Touche LLP | | Filed herewith | | |
| | | |
31.1 | | Certification of Chief Executive Officer pursuant to Section 302 of the Sarbanes-Oxley Act of 2002 | | Filed herewith | | |
| | | |
31.2 | | Certification of Chief Financial Officer pursuant to Section 302 of the Sarbanes-Oxley Act of 2002 | | Filed herewith | | |
| | | |
32.1 | | Certification of Chief Executive Officer pursuant to Section 906 of the Sarbanes-Oxley Act of 2002 | | Filed herewith | | |
| | | |
32.2 | | Certification of Chief Financial Officer pursuant to Section 906 of the Sarbanes-Oxley Act of 2002 | | Filed herewith | | |
| | | |
99 | | Supplemental Unaudited Financial Information for Dean Holding Company | | Filed herewith | | |
| | |
| |
101.INS | | XBRL Instance Document(1). |
| |
101.SCH | | XBRL Taxonomy Extension Schema Document(1). |
| |
101.CAL | | XBRL Taxonomy Calculation Linkbase Document(1). |
| | |
| |
101.DEF | | XBRL Taxonomy Extension Definition Linkbase Document(1). |
| |
101.LAB | | XBRL Taxonomy Label Linkbase Document(1). |
| |
101.PRE | | XBRL Taxonomy Presentation Linkbase Document(1). |
(1) | Submitted electronically herewith. |
* | This exhibit is a management or compensatory contract. |
Attached as Exhibit 101 to this report are the following materials from Dean Foods Company’s Annual Report on Form 10-K for the fiscal year ended December 31, 2010, formatted in XBRL (eXtensible Business Reporting Language): (i) the Consolidated Statements of Income for the years ended December 31, 2010, 2009 and 2008, (ii) the Consolidated Balance Sheets as of December 31, 2010 and 2009, (iii) the Consolidated Statements of Stockholders’ Equity for the years ended December 31, 2010, 2009 and 2008, (iv) the Consolidated Statements of Cash Flows for the years ended December 31, 2010, 2009 and 2008, and (v) Notes to Consolidated Financial Statements, tagged as blocks of text.
In accordance with Rule 406T of Regulation S-T, the XBRL-related information in Exhibit 101 to this Annual Report on Form 10-K is deemed not filed or part of a registration statement or prospectus for purposes of sections 11 or 12 of the Securities Act, is deemed not filed for purposes of section 18 of the Exchange Act, and otherwise is not subject to liability under these sections.