EXHIBIT 99.2
AGRIUM INC.
2013
MANAGEMENT’S DISCUSSION & ANALYSIS OF
OPERATIONS AND FINANCIAL CONDITION
MANAGEMENT’S
DISCUSSION
AND ANALYSIS
FEBRUARY 21, 2014
TABLE OF CONTENTS
| | |
AGRIUM ANNUAL REPORT 2013 // MANAGEMENT’S DISCUSSION AND ANALYSIS // PAGE 23 |
This Management’s Discussion and Analysis (“MD&A”) of operations and financial condition focuses on Agrium’s long-term vision, strategy and growth opportunities as well as its historical performance for the two years ended December 31, 2013. The board of directors of Agrium (the “Board of Directors”) carries out its responsibility for review of this disclosure and, prior to publication, approves this disclosure. In reviewing this disclosure, the reader should consider the cautionary notes regarding forward-looking statements contained in this MD&A (page 90) and the Consolidated Financial Statements and related notes (pages 92 to 150).
Throughout this MD&A, unless otherwise specified, “Agrium”, “the Company”, “we”, “our”, “us” and similar expressions refer collectively to Agrium Inc. and its subsidiaries, any partnerships involving Agrium Inc. or any of its subsidiaries, its significant equity investments and Agrium Inc.’s share of its joint ventures.
The Company’s consolidated quarterly and annual financial information and its Annual Information Form for the year ended December 31, 2013 (“AIF”) are available under Agrium’s corporate profile on SEDAR (www.sedar.com). The Company’s reports are also filed with the United States (“U.S.”) Securities and Exchange Commission on EDGAR (www.sec.gov).
All dollar amounts refer to U.S. dollars, except where otherwise stated. 2013 and 2012 financial information presented and discussed in this MD&A is prepared in accordance with International Financial Reporting Standards (“IFRS”) as issued by the International Accounting Standards Board (“IASB”).
We have restated 2012 comparative figures as a result of adopting IFRS 11Joint Arrangements whereby the classification and accounting of our investment in Profertil S.A. (“Profertil”) and other joint arrangements previously accounted for using the proportionate consolidation method are accounted for using the equity method.
As a result of management intending to sell components of the Advanced Technologies business unit that were not transitioned to Wholesale. We have classified these net assets as held for sale and have classified the related results of operations (including comparative 2012 results) as discontinued.
2011 and prior years have not been restated. See notes 3 and 5 of the Notes to the Consolidated Financial Statements for further details.

FORWARD-LOOKING STATEMENTS
Certain statements and other information included in this MD&A constitute “forward-looking information” and “financial outlook” within the meaning of applicable Canadian securities legislation or “forward-looking statements” within the meaning of applicable U.S. securities legislation (collectively herein referred to as “forward-looking statements”), including the “safe harbour” provisions of provincial securities legislation and the U.S. Private Securities Litigation Reform Act of 1995, Section 21E of the U.S. Securities Exchange Act of 1934, as amended, and Section 27A of the U.S. Securities Act of 1933, as amended. Forward-looking statements are typically identified by the words “believe”, “expect”, “anticipate”, “project”, “intend”, “estimate”, “outlook”, “focus”, “potential”, “will”, “should”, “would”, “could” and other similar expressions.
Forward-looking statements in this MD&A are intended to provide Agrium shareholders and potential investors with information regarding Agrium, including management’s assessment of future financial and operational plans and outlook, and may not be appropriate for other purposes. These forward-looking statements include, but are not limited to, references to: our ability to continue
| | |
PAGE 24 // MANAGEMENT’S DISCUSSION AND ANALYSIS // AGRIUM ANNUAL REPORT 2013 |
delivering value to all of our stakeholders; our adaptability to fluctuating market conditions; disclosures made under the heading“Agricultural Crop Input Overview & 2014 Outlook”; our 2014 key corporate goals, including expansion and growth of our business and operations; our core business strategies and plans for implementing them; estimates, forecasts and statements as to management’s expectations with respect to, among other things, business, growth, demand and financial prospects, financial multiples and accretion estimates, future trends, plans and objectives; key drivers for our business and global and regional industry trends; the potential for continued growth in our two business units; estimates, forecasts and statements as to management’s expectations with respect to our expansion projects, including, among others, our Vanscoy brownfield potash expansion project, our Borger brownfield expansion project, our nitrogen facility expansion project in Egypt and our brownfield expansion and efficiency project at the Profertil nitrogen facility in Argentina, and the impact of such expansion projects on Agrium’s operations; additional brownfield opportunities and greenfield expansions under evaluation, including the potential restart of our Kenai nitrogen facility in Alaska; our agreement for the long-term supply of phosphate rock and the utility of Agrium’s newly constructed import terminal on the West Coast of Canada; expectations respecting the acquisition of the majority of Viterra Inc.’s retail Agri-products assets (the “Viterra acquisition”) (as defined herein), including, among others, with respect to the final purchase price and adjustments, anticipated benefits thereof and magnitude of synergies therefrom; reserves and resource estimates relating to Agrium’s potash operations, including mine life estimates; future capital expenditures, including sustaining capital and investing capital, and capital resources; future cash requirements and long-term obligations; our expectations respecting financing of announced projects through cash provided from operating activities, existing lines of credit and funds available from new debt or equity securities offerings; anticipated tax rates; asset retirement obligations; future crop input sales and prices; availability of raw materials; risk mitigation activities; remediation and tailings management activities; the anticipated impact of emissions legislation and the implementation of emissions reduction protocols; Agrium’s emissions and emissions management activities and anticipated compliance costs; environmental and civil liabilities, including the anticipated resolution of certain legal and regulatory proceedings and the effect of such proceedings on our business; our assumptions and critical estimates in applying accounting policies; and our recently completed and proposed future acquisitions and dispositions, including the strategic dissolution of our Advanced Technologies business unit; integration plans in respect of completed and future acquisitions, any expected synergies therefrom and benefits thereof.
These forward-looking statements are based on certain assumptions and analyses made by management in light of our experience and perception of historical trends, current conditions and expected future developments, as well as other factors believed to be appropriate in the circumstances. Readers are cautioned not to place undue reliance on the forward-looking statements as such, by their nature, are subject to various known and unknown material risks and uncertainties that may cause our actual results, performance or achievements to be materially different from any future results, performance or achievements expressed or implied by such forward-looking statements. Please refer to the discussion under the heading “Key Assumptions and Risks in Respect of Forward-Looking Statements” with respect to the material assumptions and risks associated with theforward-looking statements. Additional risks and uncertainties that may affect all forward-looking information included in this MD&A include, but are not limited to, the following:
• | | changes in general economic, market, business and weather conditions, including global agricultural supply/demand factors and crop price levels; fluctuations in global and regional supply/ demand factors impacting the crop input application season and the price of crop nutrients and raw materials/feedstock; global economic and market conditions affecting availability of credit and access to capital markets; build-up of inventories in distribution channels; and shortage of labor supply; |
• | | changes in government policies and legislation and regulation, or the interpretation, administration and enforcement thereof, in the jurisdictions in which we operate, regarding, among others, agriculture and crop input prices, safety, production processes, environment and greenhouse gas; |
• | | actions by competitors and others that include changes to industry capacity, utilization rates and product pricing; failure of customers, suppliers and counterparties to financial instruments to perform their respective obligations thereunder; potential for expansion plans to be delayed; restrictions on our ability to transport or deliver our products to markets, including potential changes to anti-trust laws, or interpretations thereof, that could negatively impact our international marketing operations through our one-third interest in Canpotex (as defined herein), the offshore marketing agency for potash produced by us in Saskatchewan and the two other major potash producers in Canada; and other uncertainties in the potash market due primarily to the break-up of the BPC (as defined herein) potash marketing organization; |
| | |
AGRIUM ANNUAL REPORT 2013 // MANAGEMENT’S DISCUSSION AND ANALYSIS // PAGE 25 |
• | | changes in margins and/or levels of supplier rebates for major crop inputs, such as crop protection products, nutrients and seed, as well as crop input prices declining below cost of inventory between the time of purchase and sales; |
• | | general operating risks associated with investment in foreign jurisdictions; the level and effectiveness of future capital expenditures; decline in performance of existing capital assets; and unfavorable fluctuations in foreign exchange and tax rates in the jurisdictions in which we operate; |
• | | future operating rates, production costs and sustaining capital of our facilities; unexpected costs from present and discontinued mining operations and/or labor disruptions; the inherent risks associated with our mining operations; inaccuracies in reserve and resource estimates; changes to timing, construction cost and performance of other parties in respect of new facilities, including the Argentine Profertil nitrogen facility; and risks associated with civil unrest in Egypt and the impact on our interest in the Egyptian Misr Fertilizers Production Company S.A.E. facility (“MOPCO”), including the risk that MOPCO may not be allowed to proceed with the completion of the new facilities; |
• | | changes in development plans for our expansion, efficiency, debottleneck and other major projects, including the potential for capital construction costs to be higher than expected or construction progress to be delayed due to various factors, including shortage of equipment and labor, the inadequate performance of other parties, risks associated with technology or inflationary pressure; |
• | | environmental, health, safety and security risks typical of those found throughout the agriculture, mining and chemical manufacturing sectors and the crop inputs supply chain, including risk of injury to employees, contractors or members of the public, and possible environmental contamination; and risks associated with the transportation, storage and use of chemicals and the security of our facilities and personnel; |
• | | integration risks that might cause anticipated synergies from our recent (including those described in this MD&A) and future acquisitions to be less than expected, including the acquired business’ actual results being different than those upon which we based our expectations, and industry factors which may affect us and the acquired business in general and thereby impact the demand for our products and services; and |
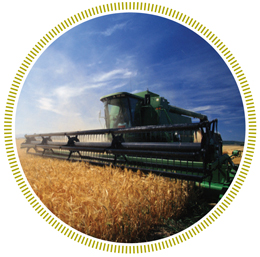
• | | various strategic risks, including our ability to effectively implement our business strategy and our risk mitigation strategies, including hedging and insurance; our ability to complete proposed acquisitions and dispositions as anticipated, including the strategic dissolution of our Advanced Technologies business unit; our ability to integrate and achieve synergies from any recent or proposed acquisitions within expected time frames; specifically, there are risks associated with the Viterra acquisition, including potential liabilities associated with the assets acquired by Agrium and the introduction of technologies in the agricultural industry that may be disruptive to our business. |
The above items and their possible impact are discussed more fully in the relevant parts of this MD&A, including the sections headed “Key Business Risks”, “Key Business Metrics” and “Enterprise Risk Management” and in our AIF. Additional information on the foregoing and other risk factors is also detailed from time to time in the reports filed by Agrium as part of our continuous disclosure on SEDAR and EDGAR.
In addition to the foregoing, all of the forward-looking statements contained in this MD&A are qualified by the cautionary statements contained herein and by stated or inherent assumptions and apply only as of the date of this MD&A. Except as required by law, Agrium disclaims any intention or obligation to update or revise any forward-looking statements as a result of new information or future events.
| | |
PAGE 26 // MANAGEMENT’S DISCUSSION AND ANALYSIS // AGRIUM ANNUAL REPORT 2013 |
EXECUTIVE SUMMARY – YIELDING RESULTS FROM OUR INTEGRATED BUSINESS
2013 IN REVIEW
Agrium’s business spans the crop input value chain, as we produce and distribute nutrients, seed and crop protection products and services to growers. We are among the largest producers of the three major crop nutrients – nitrogen, phosphate and potash – in the world and the largest global agricultural retailer. This combination of earnings streams proved itself in 2013, a year when disruptions in the global nutrient markets caused significant volatility of earnings in the fertilizer industry. Throughout this time, our Retail business unit has performed steadily, continuing to meet growers’ needs every day. North America experienced a comparatively wet and late spring in 2013, which delayed seeding and subsequently pushed the agricultural input cycle later throughout the year. Despite these challenges, crop yields were impressive across the U.S., and Canada saw a record harvest in 2013, setting expectations for strong crop input demand in 2014.
In 2013, we continued to expand our business with the acquisition of certain retail Agri-products assets from Viterra Inc. (the “Viterra acquisition”). Agrium acquired over 200 retail locations in Western Canada, and several locations in Australia. Agrium is now the largest agricultural input retailer in Canada, complementing our leading position in the U.S., Australia and South America. During the year, significant progress was made on work at the Vanscoy potash mine expansion, and Agrium continues to evaluate other growth opportunities.
Global supply and demand imbalances in the nitrogen, potash and phosphate markets led to a year of lower crop nutrient pricing. However, we believe long-term demand fundamentals are strongly in favor of Agrium’s business. Every day, the global population grows, and with it the need for more food. Agrium is, and will continue to be, a critical link in the production chain to feed the world.
The Company also significantly increased its dividend in 2013 to its current level of $3.00 per share annually. This was in addition to the implementation of our Normal Course Issuer Bid in 2013, pursuant to which we purchased 5.8 million shares at an average price of USD$86 for a total consideration of $498-million.
2013 CONSOLIDATED AND BUSINESS UNIT FINANCIAL PERFORMANCE
In 2013, Agrium’s net earnings from continuing operations were $1.1-billion, compared to $1.5-billion in 2012. Our 2013 EBITDA1 fell to $2.1-billion, from $2.6-billion in 2012. OurRetail business unitachieved EBITDA of $986-million in 2013, which includes Viterra for three months of operation, a $257-million one-time purchase gain from the Viterra acquisition and a $220-million goodwill impairment for the Retail – Australia operations. Integration costs from the Viterra acquisition in the fourth quarter of 2013 were $8-million. Excluding these three one-time items, Retail’s 2013 EBITDA was a record $957-million, compared to the previous record of $951-million reported in 2012. The increase was a result of the increasing balance across our input product lines (which can be seen in the sales growth across the seed category) and our continued focus on growth of our proprietary products (primarily Loveland Products (“Loveland”) and Dyna-Gro, which are expected to be further enhanced with the Viterra canola varieties). OurWholesale business unit achieved Adjusted EBITDA1 of $1.3-billion in 2013, compared to $1.9-billion in 2012, reflecting lower nutrient prices and lower nitrogen production volumes due to the extended outages at our Redwater and Carseland facilities. OurAgrium Advanced Technologies (“AAT”) business unit produced EBITDA of $30-million in 2013, with the impact of lower nutrient prices offsetting higher demand for Environmentally Smart Nitrogen® (“ESN”), compared to $58-million in 2012. Following a strategic review process, Agrium decided to dissolve the AAT business unit. The Agriculture business, which includes the ESN and Micronutrient products, will now be incorporated into Wholesale, and Management intends to sell the Turf and Ornamental and Direct Solutions businesses. These businesses have been reported within discontinued operations.
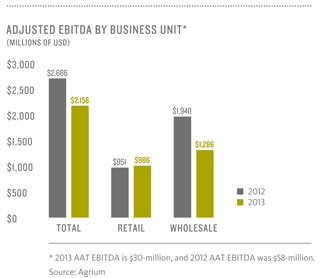
1 | Refer to Additional IFRS and Non-IFRS Financial Measures on page 83 of this MD&A. |
| | |
AGRIUM ANNUAL REPORT 2013 // MANAGEMENT’S DISCUSSION AND ANALYSIS // PAGE 27 |
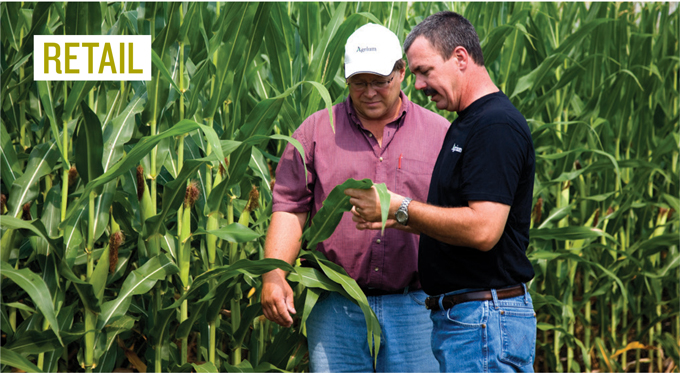
Every day, Agrium’s agricultural Retail business unit is focused on offering innovative crop input products and related services to our customers, including high-quality seed, crop nutrition, crop protection products and related agronomic and precision agriculture services. We are committed to being the leading provider of agricultural inputs and services in each of the key markets we serve. Retail is the largest global agricultural retailer, with close to 1,500 facilities spanning North America, Australia and much of South America.
Retail works directly with growers to help them maximize the productivity of their farms through the implementation of the best crop management practices, based on a thorough understanding of soils, climate conditions and crop requirements. We provide innovative technologies, products and experience, backed by a commitment to sound environmental practices. Retail also provides application services for the products we sell, offering the latest precision agriculture equipment and standards to meet growers’ needs. In Australia, Retail also provides livestock marketing and auction services.
Retail is focused on providing our customers with the products and services they need to grow the best crops possible. We do this farm by farm, one customer at a time, by leveraging our extensive expertise gained as a result of being in the business as part of Agrium or its predecessor companies for over 50 years and drawing on our global depth and reach. A core component of our Retail strategy is the focus we place on performance management, building on our strong grower relationships and the strength of our brands, including our proprietary Loveland crop protection and specialty nutrient products and Dyna-Gro seed. Serving customers in diverse markets requires a variety of marketing programs and we are able to effectively adapt to these different market conditions. We provide a complete offering of products and agronomic services in order to achieve greater market penetration and customer loyalty. Additionally, we strive to build strong relationships with leading growers in each of our markets, allowing us to grow along with our customers. We leverage the scale of our Retail business to minimize costs, grow sales of our proprietary products and adopt new technologies to more effectively serve our customers. Through all of these efforts, we are committed to protecting the environment and the health and safety of our employees, customers and the communities in which we operate.
| | |
PAGE 28 // MANAGEMENT’S DISCUSSION AND ANALYSIS // AGRIUM ANNUAL REPORT 2013 |
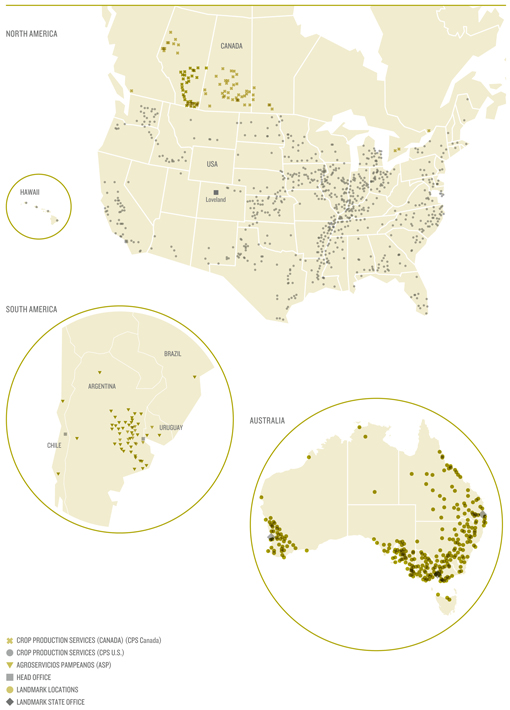
| | |
AGRIUM ANNUAL REPORT 2013 // MANAGEMENT’S DISCUSSION AND ANALYSIS // PAGE 29 |
RETAIL – KEY DEVELOPMENTS
One of the major developments in 2013 was the Viterra acquisition. This transaction closed on October 1, 2013, and provided Retail with over 200 new retail branches across Western Canada, adding to the approximately 63 retail branches owned in the region prior to the Viterra acquisition. As part of the Viterra acquisition, we also acquired distribution assets in Australia. Total annual sales from the Viterra acquisition are estimated at approximately $1.7-billion. During 2013, a purchase gain of $257-million was recognized to reflect the difference between the fair value of acquired net assets and the purchase price. The final purchase price allocation is expected to be completed in 2014. This acquisition positions Agrium as the largest agricultural retailer in Canada. We expect synergies from the Viterra acquisition of at least $15-million annually by the end of 2015, primarily from economies of scale and by increasing the distribution of our proprietary crop protection, nutrient and seed products. The Viterra acquisition is also expected to offer potential synergy opportunities for Agrium’s Wholesale business unit.
In addition to the Viterra acquisition, we also completed a number of acquisitions of smaller independent retail operations in 2013. This included 20 facilities, representing annual sales of approximately $115-million. It also included a few specialty or vertical integration opportunities. One of these was our acquisition of Echelon AG Inc. (“Echelon”). Echelon is a provider of precision agriculture services utilizing state-of-the-art satellite imagery technology in conjunction with proprietary algorithms to identify optimal application rates for nutrients, seed and other inputs. Based in Western Canada, Echelon has been operating since 2007, and has been working with Crop Production Services, Inc. (“CPS U.S.”) and Crop Production Services (Canada) Inc. (“CPS Canada”) since 2010, to provide precision agriculture services to our grower customers in Alberta, Saskatchewan, Manitoba, North Dakota and Montana.
Our Retail business continues to focus on opportunities to organically grow our earnings, by increasing the sales in our seed business in general and our proprietary seed, specialty nutrient and chemical businesses in particular. We also continue to focus on the optimization of our network of facilities through further implementation of our “hub and spoke” model, which may include strategic store closures. During 2013, we consolidated 43 facilities across our distribution channel.
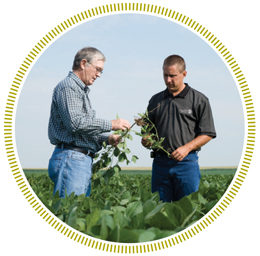
Retail’s Landmark business in Australia remains a focus for continued improvement and additional synergies in 2014. Specific key developments include the implementation of Retail’s North American Information Technology systems in Australia and the licensing of additional Loveland products and Viterra canola in Australia, which are expected to enhance margins in that region.
In the fourth quarter of 2013, we recorded the Viterra acquisition within Retail. This resulted in a $257-million purchase gain, representing the difference between the fair value of acquired net assets and the purchase price. During the quarter, we also recorded goodwill impairment in Retail – Australia of $220-million due to synergy delays and reduced expectations for sales, gross margins and long-term growth.
| | |
PAGE 30 // MANAGEMENT’S DISCUSSION AND ANALYSIS // AGRIUM ANNUAL REPORT 2013 |
RETAIL – FINANCIAL RESULTS
Retail sales reached $11.9-billion in 2013, compared to $11.5-billion in 2012, while gross profit rose to $2.6-billion from $2.5-billion in 2012. Total EBIT in 2013 was $748-million, which included the Viterra purchase gain, Viterra operating results in the fourth quarter (which included $8-million of integration costs) and the impairment of Retail – Australia goodwill. Excluding the Viterra gain and integration costs and the Landmark impairment, EBIT was $719-milllion in 2013, compared to $757-million recorded in 2012, and EBITDA (excluding the same items) reached another historical record of $957-million in 2013, compared to $951-million in 2012.
Retail’s results this year were impacted by a comparatively late start to both the spring and fall application seasons in the U.S., particularly when compared to the very early and long spring and fall application seasons experienced in 2012.
Normalized comparable store sales1, which are normalized for changes in commodity nutrient prices, increased by 5 percent in 2013, compared to an 8 percent increase in 2012. Excluding the Viterra acquisition, all other acquisitions completed by the end of 2012 and in 2013 contributed approximately $400-million in addition to the comparable store base in sales. Depreciation and amortization expenses increased to $238-million in 2013, compared to $194-million in 2012, due to the Viterra acquisition and recent smaller acquisitions. Retail’s increased sales in 2013 were offset by a corresponding increase in cost of product sold, which was $9.3-billion in 2013, compared to $9.0-billion in 2012. Total non-cash working capital was $2.1-billion at the end of 2013, which is approximately the same as the prior year. The Viterra acquisition added working capital requirements in the fourth quarter of 2013 in a relatively low sales quarter, which was offset by lower priced year-end nutrient inventory compared to 2012. As a result, average non-cash working capital as a percentage of sales was flat year-over-year at 20 percent.
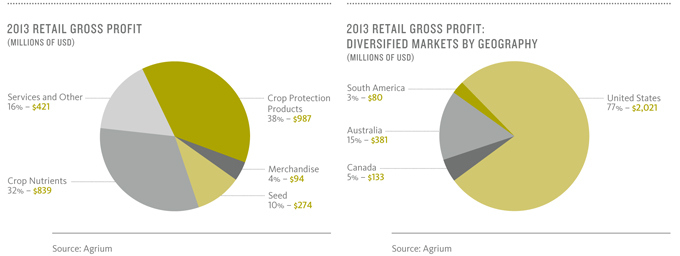
1 | Refer to Additional IFRS and Non-IFRS Financial Measures on page 83 of this MD&A. |
| | |
AGRIUM ANNUAL REPORT 2013 // MANAGEMENT’S DISCUSSION AND ANALYSIS // PAGE 31 |
RETAIL – EXPENSES
Retail selling expenses increased by 11 percent to $1.8-billion in 2013. The majority of this variance was due to operating costs associated with recent acquisitions, including integration expenses for the Viterra acquisition of $8-million in the fourth quarter of 2013, partly due to severance costs. Total selling expense as a percentage of sales was 15.5 percent in 2013, an increase from the 14.5 percent recorded in 2012. Retail’s operating coverage ratio also increased to 71 percent in 2013, up from 69 percent in 2012, primarily due to higher expenses from Viterra in the fourth quarter, which is a slower sales period for that business. In 2013, EBITDA (excluding the purchase gain of $257-million for the Viterra acquisition and the $220-million goodwill impairment of Landmark) as a percentage of sales was 8.0 percent, compared to 8.3 percent in 2012. This was partly due to the addition of Viterra’s lower EBITDA margin business in the fourth quarter of 2013.
„ RETAIL PERFORMANCE
| | | | | | | | |
| | Years ended December 31, | |
(millions of U.S. dollars, except as noted) | | 2013 | | | 2012 | |
Sales | | | 11,913 | | | | 11,479 | |
Cost of product sold | | | 9,298 | | | | 9,001 | |
Gross profit | | | 2,615 | | | | 2,478 | |
Expenses | | | | | | | | |
Selling | | | 1,847 | | | | 1,669 | |
General and administrative | | | 116 | | | | 122 | |
Earnings from associates and joint ventures | | | (9 | ) | | | (9 | ) |
Purchase gain | | | (257 | ) | | | — | |
Goodwill impairment | | | 220 | | | | — | |
Other income | | | (50 | ) | | | (61 | ) |
EBIT | | | 748 | | | | 757 | |
EBITDA | | | 986 | | | | 951 | |
EBITDA to sales(%) | | | 8.3 | | | | 8.3 | |
Operating coverage ratio(%) | | | 71 | | | | 69 | |
Comparable store sales(%) | | | (2 | ) | | | 8 | |
Normalized comparable store sales(%) | | | 5 | | | | 8 | |
Average non-cash working capital to sales(%) | | | 20 | | | | 20 | |
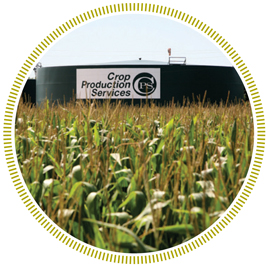
CROP NUTRIENTS: PRODUCTS AND SERVICES
Retail supplies the crop nutrients that are essential to growing healthy plants, including dry and liquid nitrogen, phosphate, potash, sulfur and micronutrients. Agrium Retail acquires crop nutrient products from a wide variety of suppliers at market prices, including purchases from Agrium Wholesale. These are typically bulk blended at Agrium Retail branches, or applied using variable rate technology or conventional equipment. Our Retail branches work closely with growers to understand their goals and customize our delivery of products, agronomic advice and product application services to help achieve these goals. Agrium Retail also delivers additional value to growers through its application services, which are provided on a fee-for-service basis. Our Retail agronomists use the 4R nutrient stewardship system to help determine the right nutrient source, applied at the right time, at the right rate and in the right place. We offer a full precision agriculture service, which we rebranded under the name “Echelon” in 2013, formerly known as Nutriscription HD. The precision agriculture service provides growers with highly sophisticated tools that help growers adjust crop inputs to better recognize the differences in yield potential within a field and thereby increase yields with more effective utilization of crop inputs. Precision agriculture technologies such as Echelon can provide significant improvements to both grower profitability and environmental protection.
| | |
PAGE 32 // MANAGEMENT’S DISCUSSION AND ANALYSIS // AGRIUM ANNUAL REPORT 2013 |
CROP NUTRIENTS: FINANCIAL RESULTS
Our crop nutrient sales were $5.0-billion in 2013, compared to $5.1-billion in 2012. The decrease was due to lower average nutrient prices offsetting higher sales volumes when compared to 2012. Average crop nutrient sales prices at the retail level were down 8 percent year-over-year due to weaker global prices for all three major nutrients: nitrogen, potash and phosphate. Total Retail nutrient sales volumes increased by 6 percent, reaching 8.6 million tonnes in 2013, compared to 8.2 million tonnes in 2012. The higher volumes were attributable to Viterra and other acquisitions in 2013 and to stronger volumes in Australia. Cost of product sold was down slightly on lower purchased nutrient prices to $4.2-billion in 2013, compared to $4.3-billion in 2012. Gross profit reached $839-million this year, compared to $821-million in 2012. Crop nutrient margins were $97 per tonne in 2013, compared to $101 per tonne in 2012. The decrease was primarily due to declining nutrient prices throughout 2013 and partly due to the higher proportion of sales in Australia and Canada, where margins tend to be lower than in the U.S. Nutrient margins in our Australian operations are lower than those in North and South America, as nutrients in this market are primarily held at port and blended by the product suppliers once Agrium arranges a sale. However, per-tonne margins in Australia showed year-over-year improvement in 2013. Total Retail gross profit as a percentage of crop nutrient sales was 16.8 percent in 2013, compared to 16.0 percent in 2012.
CROP PROTECTION PRODUCTS: PRODUCTS AND SERVICES
Agrium Retail’s crop protection business markets a broad spectrum of herbicide, fungicide, insecticide and adjuvant products that help growers minimize yield losses and protect crop quality from weeds, disease and insects. Our Retail business serves as both a retailer of crop protection products and, to a lesser extent, a wholesaler to other retail operators. We are the largest independent distributor of crop protection products in the U.S. As part of our proprietary Loveland crop protection business, we own and operate five blending and formulation facilities, including major production facilities located in Greeley, Colorado; Billings, Montana; Greenville, Mississippi; Fairbury, Nebraska; Casilda, Argentina; and we have a joint venture formulation plant based in Winnipeg, Manitoba.
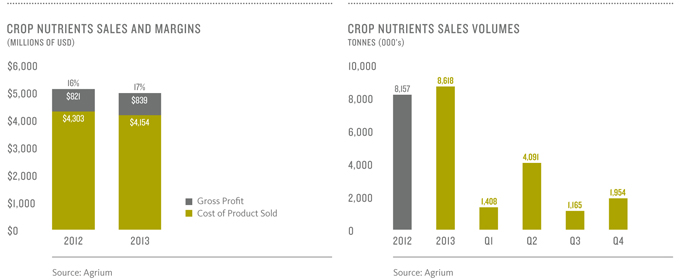
| | |
AGRIUM ANNUAL REPORT 2013 // MANAGEMENT’S DISCUSSION AND ANALYSIS // PAGE 33 |
CROP PROTECTION PRODUCTS: FINANCIAL RESULTS
The crop protection product category delivered strong results in 2013. Crop protection product sales increased to $4.2-billion in 2013, compared to $3.9-billion in 2012. The cost of crop protection product sold also increased to $3.2-billion in 2013, compared to $3.0-billion in 2012. Gross profit for crop protection products reached $987-million in 2013, compared to $928-million in 2012. The increase in sales and gross profit was attributable to both higher sales volumes and prices. Increased sales volumes were partly due to recent acquisitions. In addition, higher sales were also aided by increased demand for different types of herbicides, as some weeds have become resistant to glyphosates, and by greater demand for fungicides in 2013 due to a wetter growing season and an overall upward trend in demand for these types of products. Gross margin for crop protection products was 23.5 percent compared to 23.6 percent in 2012. In North America, our proprietary Loveland crop protection products accounted for approximately 18.2 percent of our total crop protection product sales, compared to approximately 17.6 percent in 2012, and continued to contribute margins significantly higher than other crop protection products.
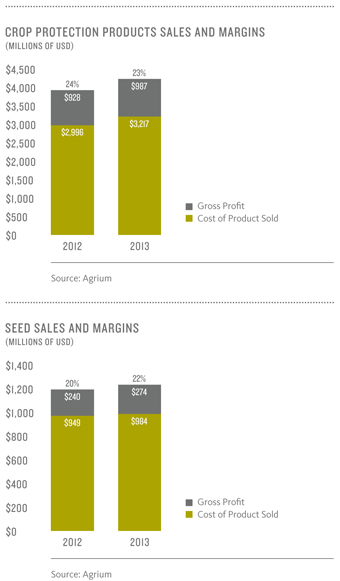
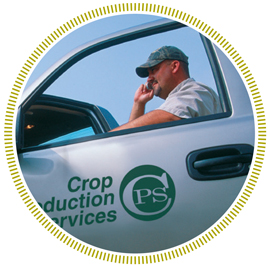
SEED: PRODUCTS AND SERVICES
Agrium Retail’s network provides seed and seed-related information to growers across key agricultural regions. We offer our own proprietary Dyna-Gro branded seed and also procure seed from top global suppliers. Our Dyna-Gro seed specialists license leading seed traits from major seed suppliers and match seed characteristics to local soil and growing conditions in order to achieve the best results for growers in each area. Increases in seed market share, combined with continued technological advances in seed genetics and our focus on delivering high-quality seed products to our customers, provide significant potential for continued strong growth in this key area of our business. The Viterra acquisition brought with it a significant seed canola research and development program. With laboratories in Saskatoon, Saskatchewan and Horsham, Australia, a vast germplasm bank and research farms in Saskatchewan, we have acquired significant plant breeding capabilities that will allow us to continue Viterra’s work in developing improved seed varieties. Viterra has developed and patented a number of proprietary seed genetics and varieties, and these proprietary product lines are expected to make up a significant portion of our seed sales in Canada.
SEED: FINANCIAL RESULTS
Seed sales reached $1.3-billion in 2013, compared to $1.2-billion in 2012. The increase in seed sales was primarily due to higher seed prices compared to 2012. The cost of product sold for seed also increased slightly to $984-million in 2013, compared to $949-million in 2012. Gross profit from seed was $274-million, compared to $240-million in 2012. Gross margin for 2013 was 21.8 percent, up from the 20.2 percent reported in 2012. In 2013, Agrium’s proprietary Dyna-Gro branded seed sales increased by 11 percent over the previous year and accounted for approximately 18.7 percent of our total North American seed sales versus 17.8 percent in 2012.
| | |
PAGE 34 // MANAGEMENT’S DISCUSSION AND ANALYSIS // AGRIUM ANNUAL REPORT 2013 |
MERCHANDISE: PRODUCTS AND SERVICES
The merchandise product category includes fencing, feed supplements, livestock-related animal health products, irrigation equipment and other products. The fuel and equipment businesses acquired from Viterra in Canada are also included in the merchandise category. This product line is a much larger component of our Australian and Canadian operations than it is for Agrium’s U.S. and South American Retail operations.
MERCHANDISE: FINANCIAL RESULTS
Merchandise sales totaled $612-million in 2013, compared to $524-million in 2012. Gross profit reached $94-million in the current year, compared to $93-million in 2012. The increases in sales and gross profit are the result of the fourth quarter merchandise earnings from Viterra and improvement in animal health and other livestock-related products in Australia in the second half of 2013. The results from Viterra’s fuel business are also included in the 2013 fourth quarter results, which had the effect of increasing sales and lowering margins as a percentage of sales. The fuel business acquired through the Viterra acquisition provides Retail with another touch-point with our grower customers.
SERVICES AND OTHER: PRODUCTS AND SERVICES
Agrium delivers value to growers and earns customer loyalty through services such as product application, soil and leaf testing and crop scouting. We maintain a large fleet of application equipment in order to ensure timely applications at optimal rates. Seed treatment is another service that we provide to growers. This service involves applying products to seeds to protect them from pests and disease. Services in our Australian operations also include providing customers with livestock marketing, as well as various insurance and real estate services.
CPS U.S. offers customers a variety of specialty services in the Western U.S. to help ensure effective crop input applications aimed at optimizing yields and minimizing input losses on the region’s high-value crops. This includes the operation of our Precision Ag Lab laboratory services and a wireless network of weather stations in the region, which supply field-specific weather data and soil moisture information to proprietary software that predicts disease and infestation. CPS provides tissue and soil sampling services aimed at optimizing yields. Our Echelon precision agriculture offering includes services such as yield data mapping, record keeping, soil fertility management, variable rate fertilizer application and variable rate seeding recommendations. Agrium’s precision agriculture service is being used on over 10 million acres of growers’ land in the U.S.
SERVICES AND OTHER: FINANCIAL RESULTS
Sales of services and other were $846-million in 2013, compared to $718-million in 2012. The increase was primarily due to stronger demand for application services in North America as a result of increased crop protection sales volumes in 2013 and the growing use of precision agriculture services by growers in North America. The addition of Viterra also contributed to the increased sales of services and other. Gross profit increased to $421-million in 2013, compared to $396-million in the previous year.
„ PRODUCT LINE PERFORMANCE
| | | | | | | | |
| | Years ended December 31, | |
(millions of U.S. dollars, except as noted) | | 2013 | | | 2012 | |
Crop nutrients | | | | | | | | |
Sales | | | 4,993 | | | | 5,124 | |
Cost of product sold | | | 4,154 | | | | 4,303 | |
Gross profit | | | 839 | | | | 821 | |
Gross profit (%) | | | 16.8 | | | | 16.0 | |
Crop protection products | | | | | | | | |
Sales | | | 4,204 | | | | 3,924 | |
Cost of product sold | | | 3,217 | | | | 2,996 | |
Gross profit | | | 987 | | | | 928 | |
Gross profit (%) | | | 23.5 | | | | 23.6 | |
Seed | | | | | | | | |
Sales | | | 1,258 | | | | 1,189 | |
Cost of product sold | | | 984 | | | | 949 | |
Gross profit | | | 274 | | | | 240 | |
Gross profit (%) | | | 21.8 | | | | 20.2 | |
Merchandise | | | | | | | | |
Sales | | | 612 | | | | 524 | |
Cost of product sold | | | 518 | | | | 431 | |
Gross profit | | | 94 | | | | 93 | |
Gross profit (%) | | | 15.4 | | | | 17.7 | |
Services and other | | | | | | | | |
Sales | | | 846 | | | | 718 | |
Cost of product sold | | | 425 | | | | 322 | |
Gross profit | | | 421 | | | | 396 | |
Gross profit (%) | | | 49.8 | | | | 55.2 | |
Total sales | | | 11,913 | | | | 11,479 | |
Total cost of product sold | | | 9,298 | | | | 9,001 | |
Total gross profit | | | 2,615 | | | | 2,478 | |
Total gross profit(%) | | | 22.0 | | | | 21.6 | |
| | |
AGRIUM ANNUAL REPORT 2013 // MANAGEMENT’S DISCUSSION AND ANALYSIS // PAGE 35 |
„ REGIONAL PERFORMANCE
| | | | | | | | | | | | | | | | |
| | 2013 | | | 2012 | |
(millions of U.S. dollars, except as noted) | | North America | | | International | | | North America | | | International | |
Sales | | | 9,329 | | | | 2,584 | | | | 8,997 | | | | 2,482 | |
Cost of product sold | | | 7,175 | | | | 2,123 | | | | 6,975 | | | | 2,026 | |
Gross profit | | | 2,154 | | | | 461 | | | | 2,022 | | | | 456 | |
Gross profit (%) | | | 23.1 | | | | 17.8 | | | | 22.5 | | | | 18.4 | |
Expenses | | | | | | | | | | | | | | | | |
Selling | | | 1,450 | | | | 397 | | | | 1,278 | | | | 391 | |
General and administrative | | | 64 | | | | 52 | | | | 58 | | | | 64 | |
Earnings from associates and joint ventures | | | (3 | ) | | | (6 | ) | | | (2 | ) | | | (7 | ) |
Purchase gain | | | (257 | ) | | | — | | | | — | | | | — | |
Goodwill impairment | | | — | | | | 220 | | | | — | | | | — | |
Other income | | | (40 | ) | | | (10 | ) | | | (31 | ) | | | (30 | ) |
EBIT | | | 940 | | | | (192 | ) | | | 719 | | | | 38 | |
EBITDA | | | 1,142 | | | | (156 | ) | | | 869 | | | | 82 | |
Sales and margins in North America increased in 2013 due to recent acquisitions and higher crop protection products sales as well as improved margins in crop nutrients and seed compared to 2012. Growth in higher margin proprietary product lines was also a significant contributor to higher gross margins in 2013. International sales and margins also increased due to increased margins per tonne in Australia and the full year results from our venture into the Brazilian market compared to 2012.
North American EBIT increased due to improved margins across the majority of the Retail product lines and to recent acquisitions. Also included in 2013 North American EBIT was a purchase gain on the Viterra acquisition of $257-million. International EBIT was lower than 2012 primarily due to a goodwill impairment charge for Retail – Australia of $220-million and challenges in the Australian livestock markets.
| | |
PAGE 36 // MANAGEMENT’S DISCUSSION AND ANALYSIS // AGRIUM ANNUAL REPORT 2013 |
RETAIL – QUARTERLY RESULTS
Our Retail business is seasonal in nature and is strongly influenced by the North American second quarter spring application and planting season. The second quarter is also important to our Landmark operations in Australia, given that significant application occurs ahead of the winter wheat seeding that generally takes place in the second quarter. This year, the U.S. experienced a late and wet spring season and the later timing also resulted in a later harvest than last year and a compressed fall nutrient application window.
Due to the significant difference in weather patterns between 2012 and 2013, we saw some sales that were in the second quarter last year move to the third quarter this year. A compressed fall season as experienced in 2013 often results in a stronger than normal spring fertilizer application season in the following year, as growers attempt to make up for lower than expected application opportunities in the previous fall.
„ RETAIL QUARTERLY RESULTS*
| | | | | | | | | | | | | | | | | | | | | | | | | | | | | | | | |
| | 2013 | | | 2012 | |
(millions of U.S. dollars, except as noted) | | Q4 | | | Q3 | | | Q2 | | | Q1 | | | Q4 | | | Q3 | | | Q2 | | | Q1 | |
Sales – North America* | | | 1,538 | | | | 1,531 | | | | 4,657 | | | | 1,587 | | | | 1,451 | | | | 1,249 | | | | 4,406 | | | | 1,873 | |
Sales – international* | | | 564 | | | | 578 | | | | 906 | | | | 552 | | | | 524 | | | | 585 | | | | 813 | | | | 578 | |
Total sales | | | 2,102 | | | | 2,109 | | | | 5,563 | | | | 2,139 | | | | 1,975 | | | | 1,834 | | | | 5,219 | | | | 2,451 | |
Cost of product sold | | | 1,516 | | | | 1,598 | | | | 4,421 | | | | 1,763 | | | | 1,466 | | | | 1,396 | | | | 4,115 | | | | 2,024 | |
Gross profit | | | 586 | | | | 511 | | | | 1,142 | | | | 376 | | | | 509 | | | | 438 | | | | 1,104 | | | | 427 | |
Gross profit (%) | | | 28 | | | | 24 | | | | 21 | | | | 18 | | | | 26 | | | | 24 | | | | 21 | | | | 17 | |
Gross profit by product | | | | | | | | | | | | | | | | | | | | | | | | | | | | | | | | |
Crop nutrients | | | 178 | | | | 116 | | | | 424 | | | | 121 | | | | 155 | | | | 111 | | | | 400 | | | | 155 | |
Crop protection products | | | 205 | | | | 248 | | | | 406 | | | | 128 | | | | 203 | | | | 202 | | | | 400 | | | | 123 | |
Seed | | | 60 | | | | 30 | | | | 140 | | | | 44 | | | | 43 | | | | 28 | | | | 125 | | | | 44 | |
Merchandise | | | 30 | | | | 19 | | | | 23 | | | | 22 | | | | 21 | | | | 17 | | | | 32 | | | | 23 | |
Services and other | | | 113 | | | | 98 | | | | 149 | | | | 61 | | | | 87 | | | | 80 | | | | 147 | | | | 82 | |
EBIT | | | 123 | | | | 91 | | | | 562 | | | | (28 | ) | | | 75 | | | | 69 | | | | 556 | | | | 57 | |
EBITDA | | | 195 | | | | 147 | | | | 619 | | | | 25 | | | | 124 | | | | 121 | | | | 605 | | | | 101 | |
| | |
| | 2013 | | | 2012 | |
(in percentages) | | Dec 31 | | | Sept 30 | | | June 30 | | | March 31 | | | Dec 31 | | | Sept 30 | | | June 30 | | | March 31 | |
Return on operating capital employed(a) | | | 17 | | | | 16 | | | | 15 | | | | 15 | | | | 18 | | | | 17 | | | | 18 | | | | 16 | |
Return on capital employed(a) | | | 9 | | | | 8 | | | | 8 | | | | 8 | | | | 9 | | | | 9 | | | | 9 | | | | 8 | |
Average non-cash working capital to sales(a) | | | 20 | | | | 20 | | | | 20 | | | | 20 | | | | 20 | | | | 20 | | | | 20 | | | | 21 | |
Operating coverage ratio(a) | | | 71 | | | | 72 | | | | 72 | | | | 72 | | | | 69 | | | | 70 | | | | 70 | | | | 72 | |
Comparable store sales(b) | | | (2 | ) | | | | | | | (3 | ) | | | | | | | 8 | | | | | | | | 15 | | | | | |
Normalized comparable store sales(b) | | | 5 | | | | | | | | 1 | | | | | | | | 8 | | | | | | | | 13 | | | | | |
(a) | These measures are based on rolling four quarters ended. |
(b) | These measures are based on 12 or six months ended. |
* | Sales by location of third-party customers |
| | |
AGRIUM ANNUAL REPORT 2013 // MANAGEMENT’S DISCUSSION AND ANALYSIS // PAGE 37 |
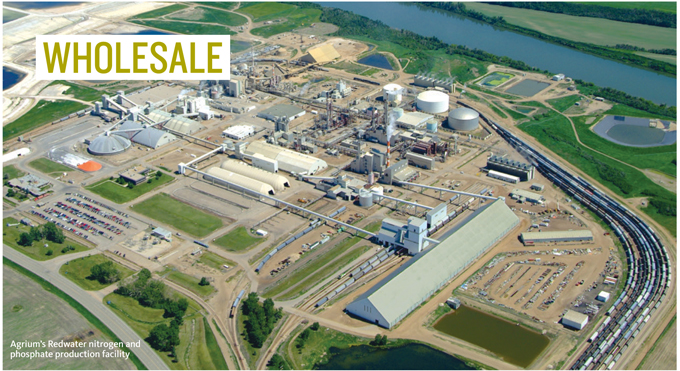
Every day, Agrium’s Wholesale business unit is focused on producing, marketing and distributing all major fertilizer products across the globe in the most efficient, safe and sustainable manner possible. We have over nine million tonnes of nutrient production capacity and significant associated distribution capability. This diverse asset mix enables us to provide the critical crop nutrients our customers need to help them optimize crop yields in order to sustain a growing world population.
Agrium Wholesale has numerous competitive advantages that drive our performance and earnings on a daily basis. The majority of our production capacity and distribution capability is located close to our key end-markets, allowing us to leverage lower freight costs and logistical synergies. These factors, combined with access to long-term, low-cost raw material inputs for the production of crop nutrients, enables us to realize some of the highest margins in North America. For nitrogen, we have access to some of the most secure and lowest cost natural gas in the world at our North American nitrogen facilities. Our potash reserves are located in Saskatchewan, Canada, representing some of the highest quality and lowest cost potash in the world. Our phosphate business benefits from a competitive cost position in sulfur, obtained as a byproduct from Canadian oil production, as well as an integrated ammonia supply from our nitrogen facilities.
| | |
PAGE 38 // MANAGEMENT’S DISCUSSION AND ANALYSIS // AGRIUM ANNUAL REPORT 2013 |
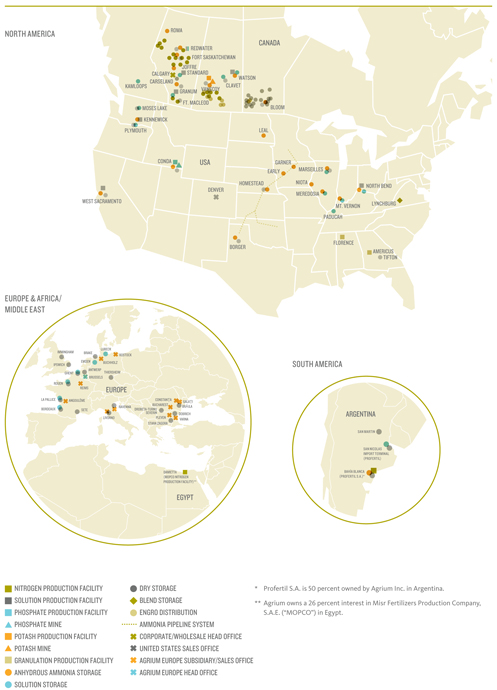
| | |
AGRIUM ANNUAL REPORT 2013 // MANAGEMENT’S DISCUSSION AND ANALYSIS // PAGE 39 |
Growers use the following three key crop nutrients to help replenish soil nutrient balance and enhance both crop yields and quality.
| | | | |
N | | P | | K |
Nitrogen | | Phosphate | | Potash |
| | Role of nutrient | | |
| | |
Improves crop growth, yield and protein levels | | Stimulates root development and flowering and encourages early crop development | | Regulates plant growth processes and helps protect crops from drought and disease |
| | Our products | | |
| | |
Ammonia, urea, urea ammonium nitrate (“UAN”) solutions, ammonium nitrate | | Monoammonium phosphate (“MAP”), superphosphoric acid (“SPA”) products | | Muriate of potash (“MOP” or “potash”) |
| | Our advantages | | |
| | |
• Overall low North American natural gas prices and a further Western Canadian AECO gas advantage relative to NYMEX; and • Facilities located near key end-markets in the Americas and Europe. | | • Competitive cost position for sulfur and ammonia; • In-market freight advantage; and • Integrated Conda rock supply. | | • World-scale, high-quality and low-cost advantage; • High historical operating rate due to integration with Retail and a balanced geographic sales mix; • Capacity expansion initiative; and • Partner in a major international marketing and logistics company (Canpotex). |
„ 2013 WHOLESALE CAPACITY, PRODUCTION AND SALES
| | | | | | | | | | | | |
(thousands of product tonnes) | | Capacity | | | Production (a) | | | Sales (b) | |
Nitrogen volumes | | | | | | | | | | | | |
North America | | | | | | | | | | | | |
Canada | | | 3,515 | | | | 2,499 | | | | 1,618 | |
U.S. | | | 1,333 | | | | 1,122 | | | | 1,774 | |
Total nitrogen | | | 4,848 | | | | 3,621 | | | | 3,392 | |
Potash volumes | | | | | | | | | | | | |
North America | | | | | | | | | | | | |
Canada | | | 2,035 | | | | 1,713 | | | | 143 | |
U.S. | | | — | | | | — | | | | 734 | |
International | | | — | | | | — | | | | 654 | |
Total potash | | | 2,035 | | | | 1,713 | | | | 1,531 | |
Phosphate volumes | | | | | | | | | | | | |
North America | | | | | | | | | | | | |
Canada | | | 660 | | | | 607 | | | | 544 | |
U.S. | | | 510 | (c) | | | 504 | | | | 482 | |
Total phosphate | | | 1,170 | (c) | | | 1,111 | | | | 1,026 | |
Ammonium sulfate and other volumes | | | | | | | | | | | | |
North America | | | | | | | | | | | | |
Canada | | | 355 | | | | 344 | | | | 278 | |
U.S. | | | 296 | | | | 228 | | | | 335 | |
Total other | | | 651 | | | | 572 | | | | 613 | |
Total produced product | | | 8,704 | | | | 7,017 | | | | 6,562 | |
Product purchased for resale volumes(d) | | | | | | | | | | | | |
North America | | | | | | | | | | | | |
U.S. | | | — | | | | — | | | | 526 | |
International | | | — | | | | — | | | | 2,161 | |
Total product purchased for resale | | | | | | | | | | | 2,687 | |
Total Wholesale | | | 8,704 | | | | 7,017 | | | | 9,249 | |
Wholesale equity accounted joint ventures: | | | | | | | | | | | | |
International nitrogen(e) | | | 635 | | | | 531 | | | | 540 | |
International product purchased for resale | | | — | | | | — | | | | 304 | |
(a) | Production, net of transfers. |
(b) | Sales represent country of sales destination, not country of production. |
(c) | SPA and Merchant Grade Phosphoric Acid (“MGA”) are reported by cargo weight. |
(d) | Purchase for resale includes sales of all the major crop nutrient products. |
(e) | Represents our 50 percent joint venture interest in the capacity of Profertil, which is accounted for using the equity method. |
| | |
PAGE 40 // MANAGEMENT’S DISCUSSION AND ANALYSIS // AGRIUM ANNUAL REPORT 2013 |
WHOLESALE – KEY DEVELOPMENTS
During 2013, Wholesale continued to progress expansion plans for potash and nitrogen, which will increase our capacity, help lower costs and grow future earnings for the Company.
Our brownfield potash expansion project at Vanscoy is on schedule for completion in the second half of 2014. The project is expected to increase our annual production capacity by one million tonnes and reduce our cash cost of production by approximately $20 per tonne by 2017, when total incremental production is fully operational. In the second half of 2014 we intend to bring the plant down for approximately 14 weeks for the final tie-in to existing production. The project is expected to exceed previous spending estimates by approximately 25 percent due to labor shortages, contractor productivity and extreme weather conditions in Saskatchewan1. Current estimates are contingent on improved contractor productivity and adherence to the current construction schedule1.
Agrium has a 50 percent interest in the Profertil nitrogen facility located in Bahia Blanca, Argentina, which currently has a total annual capacity of 1.2 million tonnes of urea and 70,000 net tonnes of merchant ammonia. A brownfield expansion and energy efficiency project is currently underway to increase the facility’s total projected annual production capacity by approximately 125,000 tonnes of urea and 10,000 net tonnes of merchant ammonia. The expansion project is designed to significantly increase gas utilization efficiency, such that no additional gas will be required to produce the additional volume, leading to significant anticipated reductions in per-tonne production costs. The expansion project is proceeding as planned and is expected to be completed in the second half of 2014.
Agrium also owns a 26 percent stake in a nitrogen facility located in Egypt, the Egyptian Misr Fertilizers Production Company S.A.E. (“MOPCO”). The 675,000 tonne urea facility has a competitive gas cost structure. An expansion project to triple the annual capacity by adding two new facilities was put on hold due to security concerns resulting from political and civil unrest. The project was over 90 percent complete when it was suspended.

The expansion project would increase production capacity to 1.95 million tonnes of urea and 150,000 net tonnes of merchant ammonia. There remains continued interest from the Egyptian government to complete the project, given the existing facility’s strong environmental and economic performance and the positive contribution the expanded facility could provide to the Egyptian economy. There was a positive development in late 2013, with the Egyptian government issuing a decree supporting the recommencement of construction and at this time MOPCO is on-site and assessing the plant condition in the anticipation of a restart of construction. However, it is too early to say whether the project will be successfully completed.
During the fourth quarter of 2013, construction was completed for Agrium’s phosphate rock import terminal at Neptune Bulk Terminals (Canada) Ltd. on the West Coast of Canada. This dedicated terminal will facilitate the handling and delivery of imported phosphate rock from Morocco for production at our facility in Redwater, Alberta. The phosphate rock supply from our mine in Kapuskasing, Ontario ceased in the second quarter of 2013, as the mine was closed due to depletion of its economic reserves.

1 | Exclusive of sustaining capital scope and owner’s costs. |
| | |
AGRIUM ANNUAL REPORT 2013 // MANAGEMENT’S DISCUSSION AND ANALYSIS // PAGE 41 |
Throughout 2013, engineering and evaluation continued on the Borger brownfield expansion project, with approval by the Board of Directors received and construction started in the first quarter of 2014. The estimated cost of the project is $720-million and it is expected to add over 600,000 tonnes of new urea capacity once complete, which is estimated to be the fourth quarter of 2015.
Agrium’s nitrogen greenfield project assessment continued in 2013 but due to the risk of cost escalation, the focus has shifted to finding a potential partner and long-term gas contract for the project.
We are also evaluating whether a restart of the Kenai, Alaska nitrogen facility might be possible in the future, given the recent additional drilling in the Alaskan Cook Inlet. The Kenai facility was shut down in October 2007 due to a lack of natural gas in the region. The critical factor in determining a potential restart would be the attainment of natural gas supply contracts at an appropriate price. The capacity of the facility is just over 900,000 tonnes of saleable nitrogen.
In December 2013, Agrium announced that after a strategic review of the AAT business unit it had decided to transfer the ESN and Micronutrient products of the Agriculture business of AAT back to the Wholesale business unit. Prior to the formation of the AAT business unit, ESN production was within Wholesale. We will look to leverage the existing manufacturing and distribution capabilities of Wholesale to deliver potential synergies. The Agriculture business of AAT will be reported in Wholesale’s results commencing in the first quarter of 2014. In note 27 of the Notes to the Consolidated Financial Statements, we have modified our segment reporting to reflect the change by including AAT’s 2012 and 2013 Agriculture business results within our Wholesale business unit.
WHOLESALE – FINANCIAL RESULTS
Sales from Wholesale operations were $4.3-billion in 2013, compared to $5.1-billion in 2012. Gross profit was $1.1-billion in 2013, compared to $1.8-billion in 2012. Wholesale EBIT was $1.0-billion in 2013, compared to $1.7-billion in 2012. Adjusted EBITDA also decreased to $1.3-billion in 2013 from $1.9-billion in 2012. The decline in sales and earnings was primarily a result of lower global nutrient prices across all three major nutrients, particularly in the second half of 2013.
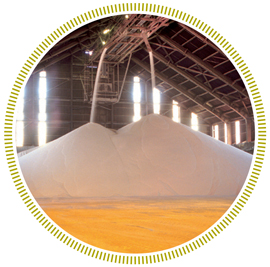
WHOLESALE – EXPENSES
Wholesale expenses were $77-million in 2013, compared to $57-million in 2012. The increase was primarily due to lower earnings from associates and joint ventures this year, as well as asset decommissioning and mine remediation costs associated with the closing of our Kapuskasing phosphate rock mine.
Earnings from associates and joint ventures in 2013 were $61-million, compared to $80-million in 2012. This decrease was primarily due to lower net earnings for our 50 percent investment in the Profertil nitrogen plant in Argentina. Profertil reported $43-million in equity earnings in 2013, compared to $76-million in 2012. The decrease was due to lower global urea prices in 2013 and lower urea production at the facility due to longer gas curtailments during cold weather this year. This was partly offset by higher equity earnings from our 26 percent interest in the MOPCO nitrogen facility. MOPCO reported $17-million in equity earnings in 2013, compared to a contribution of $2-million in 2012.
| | |
PAGE 42 // MANAGEMENT’S DISCUSSION AND ANALYSIS // AGRIUM ANNUAL REPORT 2013 |
„ WHOLESALE PERFORMANCE
| | | | | | | | |
| | Years ended December 31, | |
(millions of U.S. dollars, except as noted) | | 2013 | | | 2012 | |
Nitrogen | | | | | | | | |
Sales | | | 1,724 | | | | 2,012 | |
Gross profit | | | 672 | | | | 1,075 | |
Potash | | | | | | | | |
Sales | | | 564 | | | | 618 | |
Gross profit | | | 270 | | | | 342 | |
Phosphate | | | | | | | | |
Sales | | | 654 | | | | 797 | |
Gross profit | | | 67 | | | | 199 | |
Ammonium sulfate and other | | | | | | | | |
Sales | | | 266 | | | | 284 | |
Gross profit | | | 89 | | | | 103 | |
Product purchased for resale | | | | | | | | |
Sales | | | 1,131 | | | | 1,347 | |
Gross profit | | | 9 | | | | 31 | |
Total sales | | | 4,339 | | | | 5,058 | |
Total gross profit | | | 1,107 | | | | 1,750 | |
Expenses | | | | | | | | |
Selling | | | 39 | | | | 38 | |
General and administrative | | | 65 | | | | 42 | |
Earnings from associates and joint ventures | | | (61 | ) | | | (80 | ) |
Other expenses | | | 33 | | | | 57 | |
EBIT | | | 1,031 | | | | 1,693 | |
EBITDA | | | 1,232 | | | | 1,883 | |
EBITDA to sales(%) | | | 28.4 | | | | 37.2 | |
Adjusted EBITDA | | | 1,286 | | | | 1,940 | |
NITROGEN [N] PRODUCTS
Nitrogen represents over 60 percent of the total volume of crop nutrients used globally, and a similar proportion of our 2013 Wholesale sales of manufactured product. Nitrogen is the one crop nutrient most likely to result in an immediate adverse impact on a crop’s yield if application rates are reduced. The foundation for virtually all nitrogen products is ammonia, which can be applied directly as a fertilizer or upgraded to products such as urea, UAN solutions or ammonium nitrate.
Agrium owns and operates five major nitrogen production facilities in North America and has a 50 percent joint venture interest in Profertil’s South American nitrogen facility, along with an additional five facilities in North America that upgrade ammonia to other nitrogen products, such as UAN and nitric acid. These facilities have a combined annual nitrogen production capacity of approximately 5.5 million tonnes. MOPCO’s Egyptian nitrogen facility has a total annual production capacity of 675,000 tonnes of urea; this represents approximately 175,000 tonnes attributable to Agrium through its 26 percent equity ownership in the facility. Collectively, these global production assets place Agrium among the world’s top four publicly traded nitrogen producers.
Our extensive North American nitrogen facilities benefit from the development of long-term, low-cost, non-conventional (shale) natural gas, which has positioned North America, and Alberta in particular, among the lowest gas cost regions in the world. Furthermore, Agrium’s numerous locations and extensive distribution network facilitate the supply of these products to our core markets in Western Canada, the U.S. Pacific Northwest and the U.S. Plains, where nitrogen prices are generally higher than in the other regions of North America. Profertil’s nitrogen facility also benefits from similar in-market advantages related to its position in Argentina’s large domestic fertilizer market.
On an annual basis, approximately 75 percent of our North American nitrogen sales are directed to agricultural markets, with the remaining 25 percent sold to industrial customers. North American demand from agricultural customers is highly seasonal in nature, while industrial demand is more evenly distributed throughout the year. A high proportion of our industrial ammonia sales are priced on a gas index-plus margin basis, thereby contributing to stability in sales and earnings throughout the year. As a result, our average sales price for ammonia in a given quarter will be influenced by the relative weighting of sales to industrial customers compared to sales to the generally higher return agricultural markets. Industrial ammonia sales volumes were approximately 467,000 tonnes in 2013, compared to 495,000 tonnes in 2012.
| | |
AGRIUM ANNUAL REPORT 2013 // MANAGEMENT’S DISCUSSION AND ANALYSIS // PAGE 43 |
NITROGEN – FINANCIAL RESULTS
„ NITROGEN PERFORMANCE
| | | | | | | | |
| | Years ended December 31, | |
(millions of U.S. dollars, except as noted) | | 2013 | | | 2012 | |
Nitrogen | | | | | | | | |
Sales | | | 1,724 | | | | 2,012 | |
Cost of product sold | | | 1,052 | | | | 937 | |
Gross profit | | | 672 | | | | 1,075 | |
Tonnes sold (’000) | | | | | | | | |
Ammonia | | | 1,219 | | | | 1,188 | |
Urea | | | 1,270 | | | | 1,511 | |
Other | | | 903 | | | | 1,030 | |
Total North American tonnes sold (’000) | | | 3,392 | | | | 3,729 | |
Selling price per tonne | | | | | | | | |
Ammonia | | | 627 | | | | 627 | |
Urea | | | 490 | | | | 581 | |
Other | | | 374 | | | | 377 | |
Selling price per tonne | | | 508 | | | | 539 | |
Margin per tonne | | | 198 | | | | 288 | |
Equity accounted joint ventures: | | | | | | | | |
Nitrogen | | | | | | | | |
Sales | | | 234 | | | | 286 | |
Cost of product sold | | | 173 | | | | 166 | |
Gross profit | | | 61 | | | | 120 | |
Tonnes sold (’000) | | | 540 | | | | 556 | |
Selling price per tonne | | | 433 | | | | 514 | |
Margin per tonne | | | 113 | | | | 216 | |
Total nitrogen including equity accounted joint ventures | | | | | | | | |
Sales | | | 1,958 | | | | 2,298 | |
Cost of product sold | | | 1,225 | | | | 1,103 | |
Gross profit | | | 733 | | | | 1,195 | |
Tonnes sold (’000) | | | 3,932 | | | | 4,285 | |
Selling price per tonne | | | 498 | | | | 536 | |
Cost of product sold per tonne | | | 311 | | | | 257 | |
Margin per tonne | | | 186 | | | | 279 | |
NITROGEN GROSS PROFIT
Nitrogen gross profit was $672-million in 2013, compared to $1.1-billion in 2012. The decrease was due to lower realized sales prices and volumes. We experienced extended production outages at our Redwater and Carseland nitrogen facilities this year, which impacted our volumes and raised operating costs. Our average margins on a per tonne basis were $198 per tonne in 2013, compared to $288 per tonne in 2012.
NITROGEN PRICES
Agrium’s average realized nitrogen price was $508 per tonne in 2013, compared with $539 per tonne in 2012. Benchmark U.S. Gulf (NOLA) urea prices averaged $377 per tonne in 2013, a 26 percent decrease from $512 per tonne in 2012. Agrium’s average realized urea prices were $490 per tonne in 2013, a 16 percent reduction from 2012 levels. North American ammonia prices were also lower in 2013, with average benchmark U.S. Corn Belt ammonia prices of $692 per tonne, compared to $777 per tonne in 2012. Nitrogen prices were tempered in 2013 due to higher Chinese urea exports and a decline in crop prices.
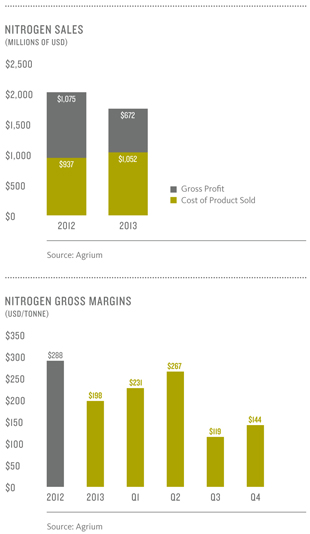
| | |
PAGE 44 // MANAGEMENT’S DISCUSSION AND ANALYSIS // AGRIUM ANNUAL REPORT 2013 |
NITROGEN PRODUCT AND GAS COST
Nitrogen cost of product sold was $1.1-billion in 2013, somewhat higher than $937-million in 2012. On a per-tonne basis, cost of product sold averaged $310 per tonne in 2013, compared with $251 per tonne in 2012. The increase in per-tonne cost of product sold was due to higher natural gas costs in 2013 and the impact of planned and unplanned production outages at our Redwater and Carseland nitrogen facilities in the second half of 2013. Production asset depreciation and amortization expense of $23 per tonne is included in cost of product sold in 2013, compared to $16 per tonne in 2012.
Gas volumes purchased in 2013 were 113 billion cubic feet, down from 120 billion cubic feet in 2012. Agrium’s gas cost represented in nitrogen cost of product sold for 2013 was $3.45 per MMBtu (overall gas cost of $3.32 per MMBtu, including the impact of realized gains on natural gas derivatives), compared to $3.07 per MMBtu in 2012 (overall gas cost of $3.38 per MMBtu, including the impact of realized losses on natural gas derivatives). Hedging gains or losses on all gas derivatives are included in other expenses and therefore not included in cost of product sold. The average U.S. benchmark (NYMEX) natural gas price for 2013 was $3.67 per MMBtu, compared to $2.80 per MMBtu in 2012. The Alberta (AECO) basis differential was a $0.60 per MMBtu discount to NYMEX in 2013, higher than the $0.40 discount per MMBtu differential in 2012.
„ NATURAL GAS PRICES:
NORTH AMERICAN INDICES AND NORTH AMERICAN AGRIUM PRICES
| | | | | | | | |
(U.S. dollars per MMBtu) | | 2013 | | | 2012 | |
NYMEX | | | 3.67 | | | | 2.80 | |
AECO | | | 3.07 | | | | 2.40 | |
Basis | | | 0.60 | | | | 0.40 | |
Wholesale | | | | | | | | |
Overall gas cost excluding realized hedging impact | | | 3.45 | | | | 3.07 | |
Realized hedging impact | | | (0.13 | ) | | | 0.31 | |
Overall gas cost(a) | | | 3.32 | | | | 3.38 | |
(a) | Weighted average gas price of all gas purchases, excluding our 50 percent share of the Profertil facility. |
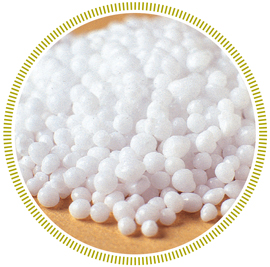
NITROGEN SALES VOLUMES AND OPERATING RATES
Nitrogen sales volumes were 3.4 million tonnes in 2013, compared to 3.7 million tonnes in 2012. The decrease in nitrogen sales volumes in 2013 primarily resulted from lost production at our Redwater and Carseland facilities in the second half of the year due to increased planned and unplanned outages. Overall North American demand for nitrogen was comparable to 2012, as planted acreage across most crops was similar to the levels attained in 2012.
Our nitrogen product category primarily consists of urea, ammonia, UAN and industrial grade ammonium nitrate. Urea is the highest volume nitrogen product sold globally, and accounted for over 40 percent of Agrium’s nitrogen capacity and 2013 production.
„ NATURAL GAS USE (BCF)
| | | | | | | | | | | | | | | | | | | | |
| | Western Canada | | | U.S. (Borger, Texas) | | | International (Profertil) | | | Potash and other | | | Total | |
2013 | | | 78 | | | | 19 | | | | 14 | | | | 2 | | | | 113 | |
2012 | | | 84 | | | | 19 | | | | 14 | | | | 3 | | | | 120 | |
| | |
AGRIUM ANNUAL REPORT 2013 // MANAGEMENT’S DISCUSSION AND ANALYSIS // PAGE 45 |
POTASH [K] PRODUCTS
Agrium is North America’s third largest producer of potash. Potash deposits are highly concentrated in only a few regions globally, with the world’s largest known potash deposits located in Saskatchewan, Canada, whose mines accounted for about 46 percent of 2013 global potash reserves. Additionally, Canada accounted for approximately 39 percent of the global potash trade in 2013. Agrium produces potash at our facility in Vanscoy, Saskatchewan and exports international sales through our interest in Canpotex. Canpotex is an industry association owned equally by the three major Canadian potash producers, tasked with marketing the portion of our produced potash that is sold outside of Canada and the U.S. Our share of Canpotex total sales was 9.3 percent in 2012, averaged 9.1 percent in 2013 and is expected to be 8.2 percent at the start of 2014. The downward trend is a result of recent capacity expansions by the other Canpotex producers. However, we anticipate our Canpotex allocation will rise back up above the 2012 figure of 9.2 percent once our major expansion project at our Vanscoy facility and associated test-run is completed in 2015.
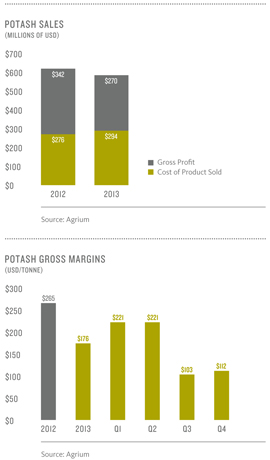
POTASH – FINANCIAL RESULTS
„ POTASH PERFORMANCE
| | | | | | | | |
| | Years ended December 31, | |
(millions of U.S. dollars, except as noted) | | 2013 | | | 2012 | |
Potash North America | | | | | | | | |
Sales | | | 369 | | | | 437 | |
Cost of product sold | | | 201 | | | | 203 | |
Gross profit | | | 168 | | | | 234 | |
Tonnes sold (’000) | | | 877 | | | | 819 | |
Selling price per tonne | | | 421 | | | | 534 | |
Margin per tonne | | | 192 | | | | 286 | |
Potash international | | | | | | | | |
Sales | | | 195 | | | | 181 | |
Cost of product sold | | | 93 | | | | 73 | |
Gross profit | | | 102 | | | | 108 | |
Tonnes sold (’000) | | | 654 | | | | 473 | |
Selling price per tonne | | | 298 | | | | 383 | |
Margin per tonne | | | 156 | | | | 228 | |
Total potash | | | | | | | | |
Sales | | | 564 | | | | 618 | |
Cost of product sold | | | 294 | | | | 276 | |
Gross profit | | | 270 | | | | 342 | |
Tonnes sold (’000) | | | 1,531 | | | | 1,292 | |
Selling price per tonne | | | 369 | | | | 479 | |
Cost of product sold per tonne | | | 193 | | | | 214 | |
Margin per tonne | | | 176 | | | | 265 | |
POTASH GROSS PROFIT
Our potash gross profit in 2013 was $270-million, compared to $342-million in 2012. The decrease in gross profit this year was due to substantially lower North American and international realized potash prices, resulting from significantly weaker global supply and demand fundamentals. Our sales volumes for both North American and international sales increased relative to 2012. This was a result of 2012 volumes and average per tonne costs being negatively impacted by the first of two major planned turnarounds as part of our ongoing brownfield expansion project at our Vanscoy mine. The benefits from the higher volumes in 2013, and the associated reduction in per tonne costs, were more than offset by lower prices. Our potash margins averaged $176 per tonne in 2013, compared to $265 per tonne in 2012.
| | |
PAGE 46 // MANAGEMENT’S DISCUSSION AND ANALYSIS // AGRIUM ANNUAL REPORT 2013 |
POTASH PRICES
North American and international sales prices for potash came under pressure in 2013 due to factors such as capacity additions by a number of key producers, weaker crop prices, weak demand from India, delays in second half Chinese supply agreements and significant market uncertainty created by the break-up of the Belarusian Potash Company (“BPC”) marketing agency in the summer of 2013. Benchmark prices in the U.S. Corn Belt trended lower throughout 2013, averaging $471 per tonne in 2013 compared to $570 per tonne in 2012 and ending the 2013 year at $405 per tonne. Our realized North American selling price declined by 21 percent to $421 per tonne in 2013, compared to $534 per tonne in 2012. Our average realized international sales price was $298 per tonne in 2013, a 22 percent decline from the $383 per tonne realized in 2012. International prices are referenced at the mine site, thereby excluding transportation costs, while North American sales are referenced at delivered prices. North American sales volumes accounted for 57 percent of total potash sales in 2013, compared to 63 percent in 2012. Agrium’s realized selling price for total potash sales was $369 per tonne in 2013, compared to $479 per tonne in 2012.
POTASH PRODUCT COST
Potash cost of product sold in 2013 was $294-million, compared to $276-million in 2012. On a per-tonne basis, the average cost of product sold in 2013 was $193 per tonne, compared to $214 per tonne in 2012. The decrease in cost of product sold per tonne relative to 2012 was attributed to higher production in 2013, resulting from an eight-week turnaround in 2012 related to the Vanscoy expansion. The decrease in cost of product sold was also driven by a slightly higher proportional shift in our sales mix towards the international market. Production asset depreciation and amortization expense of $33 per tonne is included in cost of product sold in 2013, compared to $32 per tonne in 2012.
In the second half of 2014, Agrium expects to complete a 14-week turnaround to finalize the tie-in of the one million tonne brownfield expansion project. This is anticipated to lower volumes produced and increase per-tonne production costs significantly during the second half of 2014.
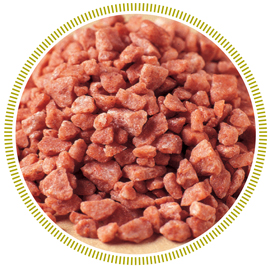
POTASH SALES VOLUMES AND OPERATING RATES
Potash sales volumes were 1.5 million tonnes in 2013, compared to 1.3 million tonnes in 2012. The increase in volumes was primarily due to higher production rates in 2013 as we undertook a planned eight-week turnaround at our Vanscoy facility in 2012. International sales were also higher in 2013 compared to the prior year as most major consumers purchased at higher volumes in the first half of the year compared to 2012. Sales of produced product into the North American market were 877,000 tonnes in 2013, an increase from 819,000 tonnes in 2012. International potash sales volumes accounted for 654,000 tonnes of product sales in 2013, which was significantly higher than the 473,000 tonnes sold in 2012, but remained below historic norms. Production volumes in 2013 were 1.7 million tonnes, compared to 1.4 million tonnes in 2012.
Our current annual production capacity of two million tonnes requires 5.9 million tonnes of feed at a grade of 24.6 percent K2O and a milling recovery rate of 85 percent. Our Technical Report1 gives an expected mine life of 46 years when considering Proven and Probable Mineral Reserves and Measured and Indicated Mineral Resources, with an additional 15 years estimated to be contained in Inferred Mineral Resources at our higher forecasted post-expansion rate. This is based on the estimate of 65.8 million tonnes of Proven Mineral Reserves (24.5 percent K2O), 15.2 million tonnes of Probable Mineral Reserves (22.7 percent K2O), 168.2 million tonnes of Measured Mineral Resources (22.7 percent K2O) and 113.0 million tonnes of Indicated Mineral Resources (24.9 percent K2O) as described in the Technical Report1. Mineral resources that are not mineral reserves do not have demonstrated economic viability.
1 | Certain scientific and technical information regarding Vanscoy Potash Operations is based on the technical report entitled “National Instrument 43-101 Technical Report on Vanscoy Potash Operations” dated February 15, 2012 (the “Technical Report”) prepared by A. Dave Mackintosh, P Geo. of ADM Consulting Limited and Erika D. Stoner of the Company, both of whom are Qualified Persons as defined in National Instrument 43-101 –Standards of Disclosure for Mineral Projects. The Technical Report has been filed with the securities regulatory authorities in each of the provinces of Canada and with the U.S. Securities and Exchange Commission. Portions of the following information are based on assumptions, qualifications and procedures that are not fully described herein. Reference should be made to the full text of the Technical Report, which is available for review on SEDAR at www.sedar.com and on EDGAR at www.sec.gov. |
| | |
AGRIUM ANNUAL REPORT 2013 // MANAGEMENT’S DISCUSSION AND ANALYSIS // PAGE 47 |
PHOSPHATE [P] PRODUCTS
Agrium is North America’s fifth largest producer of phosphate. Collectively, Agrium’s two phosphate facilities have the capacity to produce approximately 1.2 million tonnes of phosphate-based fertilizer products annually. At our facility in Conda, Idaho we produce MAP, SPA and MGA products, which are sold primarily in the Northwestern U.S. Our Redwater, Alberta facility is the only phosphate production site in Canada and produces MAP primarily for distribution in Western Canada.
Three primary raw materials are required to produce granular ammonium phosphates: phosphate rock, sulfur and ammonia. Our Conda, Idaho facility obtains rock from our Rasmussen Ridge rock mine located in the region. Our Redwater, Alberta facility previously obtained rock from our Kapuskasing, Ontario mine before its closure in the second quarter of 2013 due to depletion of economic reserves. Redwater now sources rock from Morocco in a long-term supply agreement with OCP S.A. (“OCP”). This agreement covers rock supply for the period up to 2020, with purchase prices based on a formula derived from the global price of finished phosphate products. The agreement also enables Agrium to continue benefiting from our Redwater phosphate facility’s competitive sulfur and ammonia cost positions, as well as our in-market delivered pricing advantage in Western Canada.
Our Redwater facility produces ammonia on-site and sources sulfur locally. Given the abundant supply of sulfur in the region, due to the presence of oil and gas producers, we obtain sulfur at highly favorable prices relative to global prices. Our Conda facility sources sulfur and sulfuric acid domestically, while obtaining the majority of its ammonia from our Alberta nitrogen plants. Our competitive cost position for sulfur and ammonia is a major benefit. A further competitive strength is our transportation cost advantage for local customers in Western Canada and the Western U.S. relative to the major phosphate producers based in Florida.
PHOSPHATE – FINANCIAL RESULTS
„ PHOSPHATE PERFORMANCE
| | | | | | | | |
| | Years ended December 31, | |
(millions of U.S. dollars, except as noted) | | 2013 | | | 2012 | |
Phosphate | | | | | | | | |
Sales | | | 654 | | | | 797 | |
Cost of product sold | | | 587 | | | | 598 | |
Gross profit | | | 67 | | | | 199 | |
Tonnes sold (’000) | | | 1,026 | | | | 1,095 | |
Selling price per tonne | | | 638 | | | | 728 | |
Cost of product sold per tonne | | | 573 | | | | 547 | |
Margin per tonne | | | 65 | | | | 181 | |
PHOSPHATE GROSS PROFIT
Phosphate gross profit was $67-million in 2013, compared to $199-million in 2012. The decrease was due to a combination of significantly lower realized sales prices and slightly higher cost of product. On a per-tonne basis, our phosphate margins were $65 per tonne in 2013, compared to $181 per tonne in 2012.
PHOSPHATE PRICES
Central Florida diammonium phosphate (“DAP”) prices averaged $487 per tonne in 2013, compared to $534 per tonne in 2012. Benchmark Central Florida prices began the year at approximately $557 per tonne and ended the year at approximately $380 per tonne, a decline of approximately 32 percent, as international demand for phosphates was weak during the second half of 2013. Our realized phosphate price represents a blend of phosphate products, with over 80 percent of our sales made up of MAP and the remainder being higher valued SPA and MGA. Our average realized phosphate sales price was $638 per tonne in 2013, compared to $728 per tonne in 2012. Phosphate prices are higher in Western Canada than in the Southern U.S. or U.S. Corn Belt, as pricing in this region reflects the cost of transportation associated with Western Canada’s position as a net importer of phosphates from the Southeastern U.S.

| | |
PAGE 48 // MANAGEMENT’S DISCUSSION AND ANALYSIS // AGRIUM ANNUAL REPORT 2013 |
PHOSPHATE PRODUCT COST
Phosphate cost of product sold was $587-million in 2013, compared to $598-million in 2012. The decrease was primarily attributable to slightly lower sales volumes. On a per-tonne basis, cost of product sold was $573 per tonne in 2013, compared to $547 per tonne in 2012. Throughout the first half of 2013, costs increased at the Kapuskasing mine as it approached the end of its economic reserve life. At the mid-point of 2013, we started blending in imported rock at the Redwater facility and by year-end we were fully operational with imported rock. Production asset depreciation and amortization expense of $52 per tonne is included in cost of product sold in 2013, compared to $70 per tonne in 2012. The year-over-year reduction is due to elevated depreciation expenses in 2012 due to higher asset retirement obligations at Conda in 2012 and also at Kapuskasing related to the end of mine life.
PHOSPHATE SALES VOLUMES AND OPERATING RATES
Phosphate sales volumes were 1.0 million tonnes in 2013, a slight decrease from 1.1 million tonnes in 2012. Operating rates achieved in 2013 at our Redwater facility were slightly lower than in 2012 due to longer planned and unplanned nitrogen outages impacting ammonia supply this year and transitioning to imported rock in the second half of 2013.
AMMONIUM SULFATE AND OTHER WHOLESALE PRODUCTS
Our Other Wholesale products are primarily comprised of ammonium sulfate products produced in Western Canada. Ammonium sulfate fertilizer contains both nitrogen and sulfur, resulting in one of the most effective methods of supplying sulfur to soils in an immediately available form.
Our Rainbow® Plant Food (“Rainbow”) business produces nitrogen, phosphate and potash (“NPK”) products in the Southeastern U.S. The Rainbow product line offers homogeneous distribution of NPK products, with a specific combination of nutrients contained in each granule. In contrast to the more common practice of blending different nutrient granules at a farm center, this alternative offers the advantages of reduced product segregation and a more unified distribution of nutrients. Rainbow products are produced at our facilities in Americus, Georgia and Florence, Alabama, and are often used on high-value crops such as cotton, peanuts, vegetables and tobacco, as well as having limited use on row crops.

AMMONIUM SULFATE AND OTHER WHOLESALE – FINANCIAL RESULTS
Ammonium sulfate and other gross profit was $89-million in 2013, compared to $103-million in 2012. The decrease was primarily attributable to a decrease in realized sales prices for both ammonium sulfate and our Rainbow product line.
„ AMMONIUM SULFATE AND OTHER PERFORMANCE
| | | | | | | | |
| | Years ended December 31, | |
(millions of U.S. dollars, except as noted) | | 2013 | | | 2012 | |
Ammonium sulfate and other | | | | | | | | |
Sales | | | 266 | | | | 284 | |
Cost of product sold | | | 177 | | | | 181 | |
Gross profit | | | 89 | | | | 103 | |
Tonnes sold (’000) | | | | | | | | |
Ammonium sulfate | | | 328 | | | | 327 | |
Other | | | 285 | | | | 292 | |
Total other tonnes sold (’000) | | | 613 | | | | 619 | |
Selling price per tonne | | | | | | | | |
Ammonium sulfate | | | 383 | | | | 423 | |
Cost of product sold per tonne | | | | | | | | |
Ammonium sulfate | | | 191 | | | | 203 | |
Margin per tonne | | | | | | | | |
Ammonium sulfate | | | 192 | | | | 220 | |
| | |
AGRIUM ANNUAL REPORT 2013 // MANAGEMENT’S DISCUSSION AND ANALYSIS // PAGE 49 |
PRODUCT PURCHASED FOR RESALE
In addition to selling our manufactured products, our Wholesale business unit purchases crop nutrient products from other suppliers for resale to customers in the Americas and Europe. This business enables us to leverage the value of our extensive distribution and marketing network beyond what is possible through the sale of our manufactured product alone.
Sales of product purchased for resale were $1.1-billion in 2013, compared to $1.3-billion in 2012. Total sales volumes for this business were lower at 2.7 million tonnes in 2013, compared to 2.9 million tonnes in 2012. The breakdown of sales volumes by geographic region was 2.2 million tonnes in Europe, 0.4 million tonnes in North America and 0.1 million tonnes in South America.
Gross profit from our product purchased for resale business was $9-million in 2013, compared to $31-million in 2012. Our average selling price was $421 per tonne in 2013, compared to $460 per tonne in 2012. Our average per-tonne margins were $3 per tonne in 2013, down from the $11 per tonne achieved in 2012. The decrease in gross profit was due to lower realized sales prices and margins per tonne in both North American and international markets. This was attributable to declining global prices during 2013 experienced across all fertilizer products.
WHOLESALE – DISTRIBUTION AND STORAGE
Agrium Wholesale has developed an extensive transportation, storage and warehousing network to optimize deliverability of product to our agricultural customers in the highly seasonal peak demand periods. In total, our global distribution and storage capacity amounts to over 2.5 million tonnes. We also have approximately 4,500 rail cars under long-term operating leases and use barges, pipelines and ocean vessels to transport our product. Our wholly-owned subsidiary, Agrium Europe, owns and leases over 450,000 tonnes of dry and liquid storage capacity at both port and inland sites.
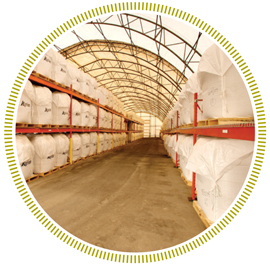
WHOLESALE – QUARTERLY RESULTS
The agricultural sector is the primary market for our Wholesale business unit, so timing of sales fluctuates based on seasonal factors. The second quarter, which coincides with the spring application season in North America, is typically Wholesale’s most important quarter from a sales volumes and EBIT perspective. The fourth quarter is also important in terms of sales volumes and EBIT, as it encompasses the fall fertilizer application season in the northern hemisphere and the spring application season in Argentina. The first quarter is generally the weakest, as application and sales volumes are light in the winter months.
| | |
PAGE 50 // MANAGEMENT’S DISCUSSION AND ANALYSIS // AGRIUM ANNUAL REPORT 2013 |
„ WHOLESALE QUARTERLY RESULTS
| | | | | | | | | | | | | | | | | | | | | | | | | | | | | | | | |
| | 2013 | | | 2012 | |
(millions of U.S. dollars, except as noted) | | Q4 | | | Q3 | | | Q2 | | | Q1 | | | Q4 | | | Q3 | | | Q2 | | | Q1 | |
Sales – external | | | 711 | | | | 665 | | | | 1,272 | | | | 964 | | | | 1,058 | | | | 886 | | | | 1,407 | | | | 1,017 | |
Sales – inter-segment | | | 252 | | | | 87 | | | | 224 | | | | 164 | | | | 215 | | | | 100 | | | | 239 | | | | 136 | |
Total sales | | | 963 | | | | 752 | | | | 1,496 | | | | 1,128 | | | | 1,273 | | | | 986 | | | | 1,646 | | | | 1,153 | |
Cost of product sold | | | 793 | | | | 629 | | | | 1,010 | | | | 800 | | | | 820 | | | | 687 | | | | 994 | | | | 807 | |
Gross profit | | | 170 | | | | 123 | | | | 486 | | | | 328 | | | | 453 | | | | 299 | | | | 652 | | | | 346 | |
Gross profit (%) | | | 18 | | | | 16 | | | | 32 | | | | 29 | | | | 36 | | | | 30 | | | | 40 | | | | 30 | |
Nitrogen | | | | | | | | | | | | | | | | | | | | | | | | | | | | | | | | |
Sales | | | 415 | | | | 286 | | | | 641 | | | | 382 | | | | 544 | | | | 424 | | | | 696 | | | | 348 | |
Cost of product sold | | | 286 | | | | 210 | | | | 347 | | | | 209 | | | | 251 | | | | 209 | | | | 284 | | | | 193 | |
Gross profit | | | 129 | | | | 76 | | | | 294 | | | | 173 | | | | 293 | | | | 215 | | | | 412 | | | | 155 | |
Tonnes sold (’000) | | | 907 | | | | 636 | | | | 1,103 | | | | 746 | | | | 966 | | | | 819 | | | | 1,216 | | | | 728 | |
Selling price (per tonne) | | | 458 | | | | 450 | | | | 582 | | | | 510 | | | | 561 | | | | 517 | | | | 574 | | | | 477 | |
Margin (per tonne) | | | 144 | | | | 119 | | | | 267 | | | | 231 | | | | 304 | | | | 262 | | | | 339 | | | | 213 | |
Potash | | | | | | | | | | | | | | | | | | | | | | | | | | | | | | | | |
Sales | | | 107 | | | | 93 | | | | 212 | | | | 152 | | | | 153 | | | | 80 | | | | 246 | | | | 139 | |
Cost of product sold | | | 68 | | | | 66 | | | | 92 | | | | 68 | | | | 74 | | | | 57 | | | | 93 | | | | 52 | |
Gross profit | | | 39 | | | | 27 | | | | 120 | | | | 84 | | | | 79 | | | | 23 | | | | 153 | | | | 87 | |
Tonnes sold (’000) | | | 344 | | | | 265 | | | | 544 | | | | 378 | | | | 341 | | | | 160 | | | | 512 | | | | 279 | |
Selling price (per tonne) | | | 313 | | | | 349 | | | | 389 | | | | 404 | | | | 449 | | | | 503 | | | | 480 | | | | 497 | |
Margin (per tonne) | | | 112 | | | | 103 | | | | 221 | | | | 221 | | | | 233 | | | | 140 | | | | 299 | | | | 313 | |
Phosphate | | | | | | | | | | | | | | | | | | | | | | | | | | | | | | | | |
Sales | | | 159 | | | | 122 | | | | 211 | | | | 162 | | | | 201 | | | | 183 | | | | 224 | | | | 189 | |
Cost of product sold | | | 163 | | | | 115 | | | | 184 | | | | 125 | | | | 154 | | | | 136 | | | | 182 | | | | 126 | |
Gross profit | | | (4 | ) | | | 7 | | | | 27 | | | | 37 | | | | 47 | | | | 47 | | | | 42 | | | | 63 | |
Tonnes sold (’000) | | | 285 | | | | 192 | | | | 317 | | | | 232 | | | | 279 | | | | 260 | | | | 313 | | | | 243 | |
Selling price (per tonne) | | | 560 | | | | 633 | | | | 667 | | | | 698 | | | | 722 | | | | 703 | | | | 713 | | | | 780 | |
Margin (per tonne) | | | (16 | ) | | | 38 | | | | 83 | | | | 161 | | | | 166 | | | | 184 | | | | 132 | | | | 260 | |
Ammonium sulfate and other | | | | | | | | | | | | | | | | | | | | | | | | | | | | | | | | |
Sales | | | 42 | | | | 41 | | | | 103 | | | | 80 | | | | 65 | | | | 45 | | | | 95 | | | | 79 | |
Cost of product sold | | | 30 | | | | 29 | | | | 66 | | | | 52 | | | | 39 | | | | 28 | | | | 65 | | | | 49 | |
Gross profit | | | 12 | | | | 12 | | | | 37 | | | | 28 | | | | 26 | | | | 17 | | | | 30 | | | | 30 | |
Tonnes sold (’000) | | | 124 | | | | 110 | | | | 213 | | | | 166 | | | | 145 | | | | 105 | | | | 203 | | | | 166 | |
Product purchased for resale | | | | | | | | | | | | | | | | | | | | | | | | | | | | | | | | |
Sales | | | 240 | | | | 210 | | | | 329 | | | | 352 | | | | 310 | | | | 254 | | | | 385 | | | | 398 | |
Cost of product sold | | | 246 | | | | 209 | | | | 321 | | | | 346 | | | | 302 | | | | 257 | | | | 370 | | | | 387 | |
Gross profit | | | (6 | ) | | | 1 | | | | 8 | | | | 6 | | | | 8 | | | | (3 | ) | | | 15 | | | | 11 | |
Tonnes sold (’000) | | | 648 | | | | 566 | | | | 710 | | | | 763 | | | | 646 | | | | 650 | | | | 806 | | | | 828 | |
Selling price (per tonne) | | | 370 | | | | 372 | | | | 462 | | | | 462 | | | | 481 | | | | 390 | | | | 476 | | | | 482 | |
Margin (per tonne) | | | (9 | ) | | | 1 | | | | 11 | | | | 8 | | | | 13 | | | | (5 | ) | | | 19 | | | | 13 | |
EBIT | | | 160 | | | | 91 | | | | 453 | | | | 327 | | | | 447 | | | | 289 | | | | 628 | | | | 329 | |
EBITDA | | | 210 | | | | 130 | | | | 517 | | | | 375 | | | | 495 | | | | 348 | | | | 677 | | | | 363 | |
Adjusted EBITDA | | | 234 | | | | 143 | | | | 525 | | | | 384 | | | | 516 | | | | 376 | | | | 686 | | | | 362 | |
| | |
AGRIUM ANNUAL REPORT 2013 // MANAGEMENT’S DISCUSSION AND ANALYSIS // PAGE 51 |
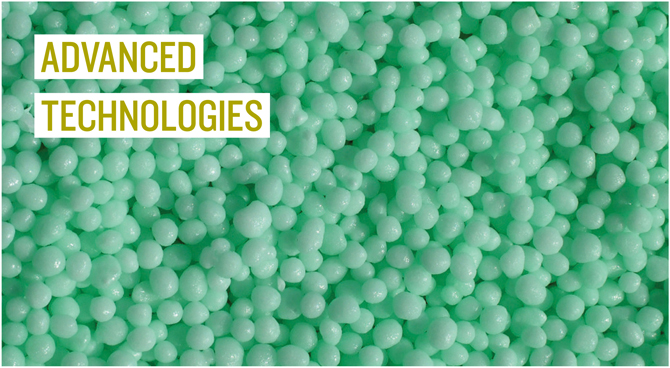
Agrium Advanced Technologies produces ESN, a leading controlled-release fertilizer product used on row crops and provides growers significant economic and environmental benefits. We also provide an array of micronutrient products.
KEY DEVELOPMENTS
After conducting a strategic review of AAT in 2013, a decision was made in December 2013 to transition the Agriculture business of AAT back to our Wholesale business unit. The Agriculture business includes ESN and Micronutrient products. Management has commenced a divestment process for the Turf and Ornamental and Direct Solutions businesses. These businesses are reported in discontinued operations. As a result, in 2013 we moved to two core business units, Wholesale and Retail. The results reported for AAT in this MD&A represent only the Agriculture business, which will be reported in Wholesale in the 2014 results; consequently these results are not directly comparable to prior years. In note 27 of the Notes to the Consolidated Financial Statements, we have modified our segment reporting to reflect the change by including AAT’s 2012 and 2013 Agriculture business results within our Wholesale business unit.
ESN is our premier polymer-coated urea product, which offers several key advantages over traditional nitrogen products. ESN has been shown to increase crop yields significantly in specific agricultural conditions compared to traditional nitrogen products, while also providing quality improvements in crops such as wheat, canola and potatoes. Additionally, ESN provides significant protection against nitrogen loss to the air and water through reduced volatilization, denitrification and leaching.
ESN sales volumes grew by approximately 20 percent in 2013 as we utilized the 136,000 tonnes of additional ESN production capacity provided by the expansion project at our New Madrid, Missouri facility that was completed in 2012. We also continued with trial testing of ESN across a wide variety of crops and countries.
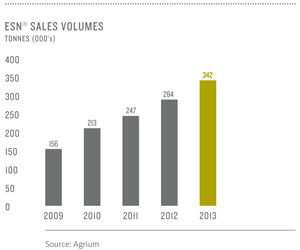
| | |
PAGE 52 // MANAGEMENT’S DISCUSSION AND ANALYSIS // AGRIUM ANNUAL REPORT 2013 |
AAT AGRICULTURE BUSINESS – FINANCIAL RESULTS
Sales in the Agriculture business were $263-million in 2013, compared to $264-million in 2012, as higher product sales volumes were offset by lower global nitrogen prices and higher urea costs. Gross profit was $35-million in 2013, compared to $67-million in 2012. EBIT was $14-million in 2013, down from $45-million in 2012. EBITDA declined to $30-million in 2013, compared to $58-million in 2012.
Sales volumes for ESN were 342,000 tonnes in 2013, up from 284,000 tonnes in 2012. This was offset by lower realized sales prices for our controlled release products and higher input costs, primarily as a result of outages at our Carseland ESN facility in the second half of 2013.
ADVANCED TECHNOLOGIES – EXPENSES
Expenses were $21-million in 2013, down from $22-million in 2012, due to cost efficiencies implemented in 2013.
„ ADVANCED TECHNOLOGIES AGRICULTURE BUSINESS FINANCIAL RESULTS
| | | | | | | | |
| | Years ended December 31, | |
(millions of U.S. dollars, except as noted) | | 2013 | | | 2012 | |
Agriculture | | | | | | | | |
Total sales | | | 263 | | | | 264 | |
Total cost of product sold | | | 228 | | | | 197 | |
Total gross profit | | | 35 | | | | 67 | |
Expenses | | | | | | | | |
Selling | | | 4 | | | | 3 | |
General and administrative | | | 16 | | | | 19 | |
Earnings from associates and joint ventures | | | 1 | | | | (2 | ) |
Other expenses | | | — | | | | 2 | |
EBIT | | | 14 | | | | 45 | |
EBITDA | | | 30 | | | | 58 | |
EBITDA to sales (%) | | | 11.4 | | | | 22.0 | |
ADVANCED TECHNOLOGIES – AGRICULTURE QUARTERLY RESULTS
ESN and Micronutrient sales are marketed to the agricultural sector and are therefore seasonal in nature. However, ESN sales are generally distributed more evenly during the year than other nitrogen products, partly due to the broader application window it affords.
„ ADVANCED TECHNOLOGIES AGRICULTURE QUARTERLY RESULTS
| | | | | | | | | | | | | | | | | | | | | | | | | | | | | | | | |
| | 2013 | | | 2012 | �� |
(millions of U.S. dollars, except as noted) | | Q4 | | | Q3 | | | Q2 | | | Q1 | | | Q4 | | | Q3 | | | Q2 | | | Q1 | |
Sales – external | | | 57 | | | | 25 | | | | 80 | | | | 57 | | | | 64 | | | | 51 | | | | 52 | | | | 32 | |
Sales – inter-segment | | | 10 | | | | 9 | | | | 18 | | | | 7 | | | | 13 | | | | 7 | | | | 21 | | | | 24 | |
Total sales | | | 67 | | | | 34 | | | | 98 | | | | 64 | | | | 77 | | | | 58 | | | | 73 | | | | 56 | |
Cost of product sold | | | 65 | | | | 33 | | | | 81 | | | | 49 | | | | 54 | | | | 40 | | | | 55 | | | | 48 | |
Gross profit | | | 2 | | | | 1 | | | | 17 | | | | 15 | | | | 23 | | | | 18 | | | | 18 | | | | 8 | |
Gross profit (%) | | | 3 | | | | 3 | | | | 17 | | | | 23 | | | | 30 | | | | 31 | | | | 25 | | | | 14 | |
EBIT | | | (1 | ) | | | (4 | ) | | | 12 | | | | 7 | | | | 15 | | | | 14 | | | | 13 | | | | 3 | |
EBITDA | | | 3 | | | | 1 | | | | 17 | | | | 9 | | | | 18 | | | | 17 | | | | 17 | | | | 6 | |
Our Other business unit is a non-operating segment comprised of corporate and administrative functions that provide support and governance to our operating business units.
The Other business unit is also used to eliminate inter-segment transactions so that each operating segment can be evaluated and managed on a stand-alone basis. The eliminations relate to purchase and sale transactions between our core Retail and Wholesale business units.
Expenses included in EBIT of our non-operating segment primarily comprise general and administrative costs at our headquarters in Calgary, Alberta, share-based payments expense and other expenses such as regulatory compliance, foreign exchange gains and losses and business development costs associated with evaluating new growth opportunities.
Other business unit EBIT was a $163-million net expense in 2013, compared to a $279-million net expense in 2012. The decrease in net expense was primarily attributable to a change in share-based payments. As our share price decreased year-over-year, we experienced a share-based payments recovery of $7-million in 2013, compared to a share-based payments expense of $108-million in 2012.
| | |
AGRIUM ANNUAL REPORT 2013 // MANAGEMENT’S DISCUSSION AND ANALYSIS // PAGE 53 |

Nutrient markets have shown some promising improvement in the first part of 2014, and we are optimistic on the outlook for the coming year. Global demand for all three nutrients is expected to increase over 2013 levels and grower fundamentals are expected to support strong crop inputs spending in 2014.
GROWERS RESPONDED TO ROBUST ECONOMIC SIGNALS AND FAVORABLE WEATHER TO PRODUCE RECORD GLOBAL GRAIN AND OILSEED CROP YIELDS IN 2013
• | | Global production of grains and oilseeds set a record of 2.9 billion tonnes, 8 percent above 2012/13 levels and 9 percent above the five-year average. |
• | | Crop prices have declined year-over-year in 2013 as a result of higher global production; however, prices and U.S. grower margins remain above historical levels. |
• | | Reduced and more stable crop prices have supported robust demand growth. The United States Department of Agriculture (“USDA”) projects that global grain demand growth will be over 4 percent in 2013/14, which would be the highest annual growth since 1978/79 and more than 1.5 percentage points above any year in the past decade, which was a period of very strong demand growth. |
• | | Chinese grain and oilseed imports have grown at an average rate of 15 percent per year over the past decade, driven in large part by Chinese pork consumption, which has more than doubled since 1992. |
• | | Analysts expect that lower corn prices and a more comfortable supply and demand balance will lead to reduced corn area in the U.S. in 2014, from 95.4 million acres in 2013 to a forecasted range of 91 to 94 million acres in 2014. This is expected to result in higher plantings of other crops such as soybeans, cotton and wheat. |
• | | In Western Canada, growers produced record crop yields, with overall crop production up 33 percent from 2012 levels and 37 percent above thefive-year average. Increased production means increased nutrient removal, which is expected to support crop nutrient demand in 2014. |
• | | U.S. corn yields in 2013 were 29 percent above 2012 levels, which is expected to result in increased nutrient removal from soils this year compared to 2013 levels. |
• | | Growers enter 2014 in a robust financial position. The USDA estimates that U.S. net farm income was a record $131-billion in 2013, 44 percent above the previous five-year average, which has put growers in a position to invest in top-quality seed, crop protection products, crop nutrients and agronomic services in 2014. |
| | |
PAGE 54 // MANAGEMENT’S DISCUSSION AND ANALYSIS // AGRIUM ANNUAL REPORT 2013 |
CROP PROTECTION PRODUCT KEY FACTORS
• | | We expect that growers will continue the trend of increased use of alternative crop protection products to combat the growing incidence of glyphosate resistant weeds. |
• | | Glyphosate selling prices are expected to remain relatively stable in 2014, following increased prices in 2013. |
• | | Continued strength in demand for fungicides, adjuvants and nutritionals (liquid micronutrients) is anticipated in 2014 assuming normal growing conditions. |
SEED MARKET KEY FACTORS
• | | Seed demand and margins are expected to continue to benefit from new trait offerings from major seed suppliers. |
• | | Among such new traits are 2,4-D and dicamba resistant seed varieties, which are expected to be available in 2015 to help address glyphosate resistant weeds. |
• | | There has been rapid growth of soybean and corn area in the Northern U.S. and Western Canada, a trend that is expected to continue as seed companies invest in shorter-season varieties. |

| | |
AGRIUM ANNUAL REPORT 2013 // MANAGEMENT’S DISCUSSION AND ANALYSIS // PAGE 55 |
NITROGEN MARKET SITUATION AND OUTLOOK
Global nitrogen markets were under downward pressure in the second half of 2013, partly due to increased Chinese urea export availability and capacity additions in Algeria and Abu Dhabi. However, global prices rebounded significantly in early 2014 and have the potential to remain firm through the spring application season in the northern hemisphere.
• | | Global nitrogen consumption increased by over 2 percent in 2013 and is projected to increase by 1.5 percent to 2 percent in 2014. |
• | | Nitrogen capacity additions have tended to be delayed over the past several years, making it difficult to project the timing of export capacity within a year. In 2014, Algeria is expected to add over 1.3 million tonnes of urea export supply, as is Saudi Arabia. Both projects are expected to commence production in the second half of the year. There are projects in India and Turkmenistan that will not provide significant export supply, but in the case of India may impact import demand, although natural gas supplies may be a restriction. China is also adding significant nitrogen capacity, although delays have been common in China in recent years. |
• | | The Chinese government announced in December 2013 that it would reduce the export tax rate during the Chinese peak demand periods. The peak demand periods run from January 1 through June 30 and November 1 through December 31. The lower export tariffs are still expected to be restrictive enough to provide some support to global urea prices during those months. |
• | | Export restrictions in certain nitrogen export markets, such as Algeria and Libya, had a significant impact on the nitrogen market in 2013 and have the potential to limit nitrogen exports from these markets again in 2014. |

• | | Ukrainian urea operating rates were reduced significantly in the third and early fourth quarters of 2013. Russia recently agreed to lower natural gas prices with the Ukraine, which will reduce the cost of production and likely lead to increased annual production and exports in 2014. |
• | | U.S. fall ammonia applications were below expected levels in 2013 due to a short fall application season. This should support demand for all nitrogen products in the spring of 2014, despite an expected reduction in U.S. corn area. |
• | | A severe winter in North America in late 2013 and early 2014 contributed to higher year-over-year natural gas prices. However, North American gas prices remain at historically low levels, particularly relative to European prices. This has resulted in the continuation of solid North American nitrogen margins, even with lower global nitrogen prices. |
| | |
PAGE 56 // MANAGEMENT’S DISCUSSION AND ANALYSIS // AGRIUM ANNUAL REPORT 2013 |
PHOSPHATE MARKET SITUATION AND OUTLOOK
• | | Global phosphate demand declined by approximately 1 percent in 2013. Global phosphate demand is projected to grow by between 2 percent and 3 percent in 2014. After a prolonged slide in phosphate prices in the second half of 2013, global phosphate prices started to firm in early 2014. |
• | | Phosphate capacity additions are expected in Jordan and Tunisia in 2014, although there is the risk that further civil unrest in Tunisia could reduce phosphate production there in 2014. Morocco is expected to increase granulation capacity in 2014. |
• | | The Indian phosphate import market is an important one globally and lower demand from India negatively impacted the phosphate market in 2013. This was a result of low North American demand after a significant increase in North American phosphate prices since 2010, exacerbated by the devaluation of the rupee in 2013. However, we believe Indian domestic inventories were drawn down in 2013, which should lead to an improvement in import demand in 2014. |
• | | The global phosphate cost curve declined slightly in 2013 due to lower sulfur and ammonia prices, which are two important raw materials used for phosphate production. However, sulfur markets firmed again in early 2014. |
• | | 2013 was a year of consolidation in the North American phosphate market, as the largest phosphate producer announced it intended to acquire the production assets of the third largest producer in North America and another producer shut down some capacity. |
• | | Brazil imported record volumes of DAP/MAP in 2013 and import demand is expected to be strong again in 2014. |
• | | China exported 4.5 million tonnes of DAP/MAP in 2013, roughly equivalent to levels in 2012. We expect Chinese exports to be between four and five million tonnes of DAP/MAP in 2014. |
POTASH SITUATION AND OUTLOOK
• | | Global potash consumption increased by less than 1 percent in 2013 but is expected to increase by a more normal 3 percent to 4 percent in 2014. |
• | | Global potash capacity is projected to increase by approximately four million product tonnes in 2014, with most of the capacity being added in Canada. |
• | | The breakup of the BPC (Russian/Belarusian) potash marketing organization was a source of significant uncertainty in potash markets in the second half of 2013, resulting in buyers globally purchasing potash on a just-in-time basis. Ownership and leadership changes at Uralkali in late 2013 and a new Chinese potash contract in January 2014 are expected to bring more stability to potash markets in 2014. |
• | | India contracted for increased volumes of potash for its 2013/14 agricultural year, but the subsequent decline in the value of the Indian rupee and uncertainty created by the BPC development resulted in delayed shipments and renegotiated pricing. |
• | | China had a robust potash import program in the first half of 2013. However, delays in a potash import supply agreement in the second half of the year led to a reduction in 2013 import levels compared to 2012. We expect that Chinese potash imports will increase in 2014. |
• | | Brazil imported a record volume of potash in 2013 and we expect Brazil to import a similar volume of potash in 2014. |
• | | North American potash applications were below expected levels in the fall of 2013 due to the late harvest and early onset of winter conditions. This is expected to support strong demand in the spring of 2014. |
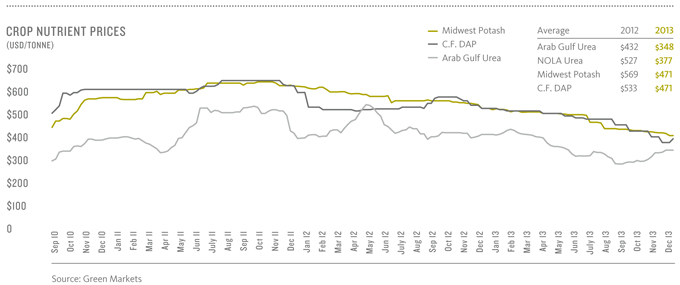
| | |
AGRIUM ANNUAL REPORT 2013 // MANAGEMENT’S DISCUSSION AND ANALYSIS // PAGE 57 |
KEY BUSINESS METRICS
Our financial results are sensitive to a number of factors that affect our operations and resulting net earnings. The following table sets out the impact of changes in some key variables on our earnings based on activity levels for the year ended December 31, 2013.
SENSITIVITIES ON 2013 SALES, MARGINS OR TONNES
„ RETAIL AND WHOLESALE SENSITIVITY IMPACT TO EBIT, NET EARNINGS AND NET EARNINGS PER DILUTED SHARE
| | | | | | | | | | | | | | | | |
(millions of U.S. dollars, except as noted) | | Change in factor | | | EBIT impact | | | Net earnings impact | | | Net earnings impact per diluted share (f) | |
Retail(a) | | | | | | | | | | | | | | | | |
Crop nutrients | | | 1.00 | % | | | 50 | | | | 37 | | | | 0.25 | |
Crop protection products | | | 1.00 | % | | | 42 | | | | 31 | | | | 0.21 | |
Seed | | | 1.00 | % | | | 13 | | | | 9 | | | | 0.06 | |
Merchandise | | | 1.00 | % | | | 6 | | | | 4 | | | | 0.03 | |
Wholesale(b) | | | | | | | | | | | | | | | | |
Nitrogen(c)(d) | | $ | 10.00 | | | | 34 | | | | 25 | | | | 0.17 | |
Potash(c)(e) | | $ | 10.00 | | | | 15 | | | | 11 | | | | 0.07 | |
Phosphate(c) | | $ | 10.00 | | | | 10 | | | | 8 | | | | 0.05 | |
Product purchased for resale(a) | | | 1.00 | % | | | 11 | | | | 8 | | | | 0.05 | |
Exchange rate from CAD to USD | | $ | 0.01 | | | | 6 | | | | 5 | | | | 0.03 | |
(a) | Change in factor is gross profit as a percentage of sales. |
(b) | Wholesale’s sensitivity to a $0.50/MMBtu change in natural gas prices is $35-million in EBIT and $27-million in net earnings. The sensitivity assumes no change to the price spread between U.S. and Alberta natural gas and excludes the impact of natural gas derivatives and industrial ammonia sales, which are on a gas index-plus margin basis. |
(c) | Change in factor is margin per metric tonne of North American Wholesale produced sales. |
(d) | Excludes the impact of natural gas sensitivity described in footnote (b) above. |
(e) | Excludes the impact of potash production tax and resource surcharge. |
(f) | Based on Agrium’s 2013 effective tax rate of 27 percent and 148 million weighted average outstanding shares. |
| | |
PAGE 58 // MANAGEMENT’S DISCUSSION AND ANALYSIS // AGRIUM ANNUAL REPORT 2013 |
MARGINS
RETAIL
Retail product margins are normally more stable than Wholesale margins, as Retail tends to be more of a cost-plus margin business than Wholesale. However, there are several factors that can influence Retail margins. For example, nutrient margins are impacted by price volatility between the time we purchase the product and the time we sell the product to the grower, as well as price volatility driven by the relative timing of our competitors’ nutrient purchases in relation to our purchases. Fluctuations in commodity prices affect the types of crops planted, resulting in different crop input needs, but more significantly affect the timing of growers’ decisions on the application levels and rates of our products. Lower crop commodity prices relative to the price of the inputs may result in growers delaying purchase and application of crop inputs that would otherwise optimize crop yields. Weather conditions can create significant fluctuations in the timing of Retail’s sales and the related margins based on the ability to plant or harvest and the associated application of inputs. Finally, crop protection and seed margins are influenced by changes in the value of chemicals and newer seed varieties from our suppliers, as well as shortages or oversupply of different products.
WHOLESALE
Nitrogen cost of product sold is affected by changes in North American natural gas prices and nitrogen prices are impacted by changes in the global nitrogen supply/demand situation. The combination of these market fluctuations impacts nitrogen production margins. Fluctuations in raw material input costs such as phosphate rock, sulfur and ammonia affect our phosphate margins. Foreign trade policies, the existence and activities of marketing agencies, and buying strategy affect global supply/demand, which also influences potash pricing and margins. Wholesale’s purchase for resale margins are impacted by price volatility of a crop nutrient between the time we purchase the product and the time we sell the product to the customer.
FOREIGN EXCHANGE
The international currency of the agribusiness industry is the U.S. dollar and, accordingly, we use the U.S. dollar as our reporting currency. We conduct business primarily in U.S. and Canadian dollars, and we also have some exposure to the Argentine peso, Australian dollar and euro. Fluctuations in these currencies could also impact our financial results.
SELECTED RETAIL AND CONSOLIDATED FINANCIAL MEASURES
„ PERFORMANCE RATIOS
| | | | | | | | | | | | | | | | | | | | | | | | |
| | 2013 | | | 2012 | |
(in percentages) | | Retail – North America * | | | Retail * | | | Consolidated Agrium | | | Retail – North America * | | | Retail * | | | Consolidated Agrium | |
Return on operating capital employed(a) | | | 28 | | | | 17 | | | | 15 | | | | 23 | | | | 18 | | | | 26 | |
Return on capital employed(a) | | | 14 | | | | 9 | | | | 11 | | | | 11 | | | | 9 | | | | 17 | |
Average non-cash working capital to sales(b) | | | N/A | | | | 20 | | | | 17 | | | | N/A | | | | 20 | | | | 16 | |
EBITDA to sales * | | | 12 | | | | 8 | | | | 13 | | | | 10 | | | | 8 | | | | 16 | |
* | Represents a non-IFRS financial measure, which does not have a standardized meaning prescribed by IFRS and therefore may not be directly comparable to similar measures presented by other issuers. See the discussion in the section “Additional IFRS and Non-IFRS Financial Measures” on page 83. |
(a) | Tax rate of 27 percent (2012 – 28 percent). |
(b) | Retail – North America average non-cash working capital to sales not disclosed. |
| | |
AGRIUM ANNUAL REPORT 2013 // MANAGEMENT’S DISCUSSION AND ANALYSIS // PAGE 59 |
CONSOLIDATED PERFORMANCE
„ SELECTED ANNUAL INFORMATION
| | | | | | | | | | | | |
(millions of U.S. dollars, except per share amounts) | | 2013 | | | 2012 | | | 2011 | |
Sales | | | 15,727 | | | | 16,024 | | | | 15,470 | |
Cost of product sold | | | 11,954 | | | | 11,716 | | | | 11,137 | |
Gross profit | | | 3,773 | | | | 4,308 | | | | 4,333 | |
Expenses | | | | | | | | | | | | |
Selling | | | 1,876 | | | | 1,697 | | | | 1,673 | |
General and administrative | | | 329 | | | | 428 | | | | 335 | |
Earnings from associates and joint ventures | | | (68 | ) | | | (91 | ) | | | (21 | ) |
Purchase gain | | | (257 | ) | | | — | | | | — | |
Goodwill impairment | | | 220 | | | | — | | | | — | |
Other expenses | | | 43 | | | | 58 | | | | 123 | |
Earnings before finance costs and income taxes | | | 1,630 | | | | 2,216 | | | | 2,223 | |
Finance costs related to long-term debt | | | 90 | | | | 89 | | | | 101 | |
Other finance costs | | | 66 | | | | 41 | | | | 59 | |
Earnings before income taxes | | | 1,474 | | | | 2,086 | | | | 2,063 | |
Income taxes | | | 394 | | | | 570 | | | | 555 | |
Net earnings from continuing operations | | | 1,080 | | | | 1,516 | | | | 1,508 | |
Net loss from discontinued operations | | | (17 | ) | | | (18 | ) | | | (133 | ) |
Net earnings | | | 1,063 | | | | 1,498 | | | | 1,375 | |
Attributable to: | | | | | | | | | | | | |
Equity holders of Agrium | | | 1,062 | | | | 1,494 | | | | 1,371 | |
Non-controlling interest | | | 1 | | | | 4 | | | | 4 | |
Total net earnings | | | 1,063 | | | | 1,498 | | | | 1,375 | |
Earnings per share attributable to equity holders of Agrium | | | | | | | | | | | | |
Basic earnings per share from continuing operations | | | 7.31 | | | | 9.67 | | | | 9.53 | |
Basic loss per share from discontinued operations | | | (0.11 | ) | | | (0.11 | ) | | | (0.84 | ) |
Basic earnings per share | | | 7.20 | | | | 9.56 | | | | 8.69 | |
Diluted earnings per share from continuing operations | | | 7.31 | | | | 9.67 | | | | 9.52 | |
Diluted loss per share from discontinued operations | | | (0.11 | ) | | | (0.12 | ) | | | (0.84 | ) |
Diluted earnings per share | | | 7.20 | | | | 9.55 | | | | 8.68 | |
Total assets | | | 15,977 | | | | 15,805 | | | | 13,140 | |
Non-current financial liabilities | | | | | | | | | | | | |
Long-term debt | | | 3,066 | | | | 2,069 | | | | 2,098 | |
Other financial liabilities | | | 24 | | | | 36 | | | | 20 | |
Derivative financial liabilities | | | — | | | | — | | | | 16 | |
Total non-current financial liabilities | | | 3,090 | | | | 2,105 | | | | 2,134 | |
Dividends declared | | | 367 | | | | 154 | | | | 44 | |
Dividends declared per share | | | 2.50 | | | | 1.00 | | | | 0.28 | |
| | |
PAGE 60 // MANAGEMENT’S DISCUSSION AND ANALYSIS // AGRIUM ANNUAL REPORT 2013 |
SALES
Consolidated sales decreased 2 percent to $15.7-billion from 2012 to 2013 due to lower Wholesale sales attributed to weaker market pricing across all commodities. Overall, Wholesale sales decreased by 14 percent. However, this was partially offset by increased Retail sales of 4 percent resulting from favorable weather conditions, which increased sales of fungicides, growth regulators and herbicides. Viterra contributed $276-million in sales during the year.
Consolidated sales from 2011 to 2012 increased 4 percent to $16.0-billion, largely the result of Retail sales experiencing an 11 percent increase mainly driven by an earlier spring season and extended fall application season. Increased planted acreage in 2012 led to higher volumes of crop protection products sold coupled with increased crop nutrient usage. Wholesale sales decreased by 9 percent, attributed to lower international potash demand.
GROSS PROFIT
Gross profit for the year ended December 31, 2013 was $3.8-billion, a $535-million decrease over 2012. The decrease was primarily due to Wholesale experiencing a gross profit decrease of $643-million as a result of lower realized sales prices for nitrogen and phosphate due to weaker market conditions, higher nitrogen input costs from higher natural gas prices, and lower potash margins stemming from uncertainty in the potash market due primarily to the break-up of BPC. These were partially offset by a Retail gross profit increase of $137-million as a result of increased crop protection and seed sales and the impact of a full year of earnings from acquisitions made in the second half of 2012.
SELLING EXPENSES
Selling expenses were $1.9-billion in 2013 compared to $1.7-billion in 2012. Approximately 98 percent of our selling expenses were in our Retail business unit. Selling expenses were higher in 2013 compared to 2012, driven by higher Retail sales activity coupled with costs associated with late 2012 and 2013 tuck-in acquisitions. Selling expenses of $63-million were related to the Viterra acquisition.
GENERAL AND ADMINISTRATIVE EXPENSES
General and administrative expenses decreased due to a decline in share-based payments expense, as there was a share-based payments recovery of $7-million in 2013 compared to a share-based payments expense of $108-million in 2012. The change in share-based payments expense was attributed to a decrease in share price in 2013 compared to an increase in share price in 2012. Our closing share price on the New York Stock Exchange at December 31, 2013 was $91.48, compared to $99.87 at December 31, 2012. General and administrative expenses for the years ended December 31, 2013 and 2012 were $329-million and $428-million, respectively.
„ DEPRECIATION AND AMORTIZATION
| | | | | | | | | | | | | | | | | | | | |
(millions of U.S. dollars) | | Retail | | | Wholesale | | | Advanced Technologies | | | Other | | | Total | |
2013 | | | | | | | | | | | | | | | | | | | | |
Cost of product sold | | | 5 | | | | 187 | | | | 13 | | | | — | | | | 205 | |
Selling | | | 222 | | | | — | | | | — | | | | — | | | | 222 | |
General and administrative | | | 11 | | | | 14 | | | | 3 | | | | 17 | | | | 45 | |
| | | 238 | | | | 201 | | | | 16 | | | | 17 | | | | 472 | |
2012 | | | | | | | | | | | | | | | | | | | | |
Cost of product sold | | | 7 | | | | 185 | | | | 10 | | | | — | | | | 202 | |
Selling | | | 169 | | | | — | | | | — | | | | — | | | | 169 | |
General and administrative | | | 18 | | | | 5 | | | | 3 | | | | 16 | | | | 42 | |
| | | 194 | | | | 190 | | | | 13 | | | | 16 | | | | 413 | |
Depreciation and amortization included in selling expenses was $222-million in 2013 compared to $169-million in 2012. The full amount of the increase was attributed to the Retail business unit, as Retail had a greater depreciable base as a result of recent acquisitions. Wholesale depreciation and amortization included in general and administrative increased by $9-million, caused by accelerated depreciation at our Kapuskasing mine coinciding with its closure.
EARNINGS FROM ASSOCIATES AND JOINT VENTURES
Earnings from associates and joint ventures were $68-million and $91-million in 2013 and 2012, respectively. Our earnings from associates and joint ventures decreased from the prior year as the Profertil facility faced lower global urea prices and an increase in gas supply interruptions during the year. These interruptions reduced production and tonnes available for sale and increased costs per tonne. This was partially offset by increased earnings from our MOPCO nitrogen facility as the facility was restarted in September 2012.
| | |
AGRIUM ANNUAL REPORT 2013 // MANAGEMENT’S DISCUSSION AND ANALYSIS // PAGE 61 |
PURCHASE GAIN
Upon completion of the Viterra acquisition, we recorded a purchase gain of $257-million representing the difference between the fair value of the acquired net assets and the purchase price. Refer to note 4 of the Notes to the Consolidated Financial Statements for further discussion.
GOODWILL IMPAIRMENT
A $220-million goodwill impairment was recorded in the Retail – Australia business as a result of delayed synergy realization and reduced expectations for sales, gross margins and long-term growth of Retail – Australia. Refer to note 14 of the Notes to the Consolidated Financial Statements for further discussion.
OTHER EXPENSES
„ OTHER EXPENSES BREAKDOWN
| | | | | | | | |
(millions of U.S. dollars) | | 2013 | | | 2012 | |
Realized (gain) loss on derivative financial instruments | | | (1 | ) | | | 24 | |
Unrealized gain on derivative financial instruments | | | (15 | ) | | | (17 | ) |
Interest income | | | (76 | ) | | | (91 | ) |
Foreign exchange loss | | | 43 | | | | 23 | |
Environmental remediation and asset retirement obligations | | | 7 | | | | 80 | |
Bad debt expense | | | 9 | | | | 22 | |
Potash profit and capital tax | | | 21 | | | | 16 | |
Other | | | 55 | | | | 1 | |
| | | 43 | | | | 58 | |
In 2013, there was a net gain of $16-million on net realized and unrealized derivative financial instruments compared to a net loss of $7-million in 2012. The change was primarily driven by gains in the Wholesale business unit from favorable gas and power price derivative contracts.
Interest income decreased by $15-million from 2012 to 2013 as the early spring season in 2012 shifted Retail sales to earlier in the year, resulting in more earned interest. The spring season returned to a more normal weather pattern in 2013.
Foreign exchange loss increased from $23-million in 2012 to $43-million in 2013 as there were losses incurred on draws from our global credit facility.
Environmental remediation and asset retirement obligations decreased by $73-million as there were charges in 2012 for legacy Canadian and Conda sites that did not recur in 2013.
Other expenses increased by $54-million from 2012 to 2013 due to a combination of items, including proxy defense costs of $17-million and $13-million in acquisition costs related to the Viterra acquisition.
OTHER FINANCE COSTS
Other finance costs were $66-million in 2013, compared to $41-million in 2012. The increase was due to higher interest expenses under the global credit facility borrowings and extension fees to increase the facility limits. Additionally, there was also higher interest expense on pensions in 2013.
INCOME TAXES
Our overall effective tax rate was 27 percent for both 2013 and 2012. The non-taxable purchase gain on the Viterra acquisition in Canada was largely offset by the goodwill impairment related to Retail – Australia which is not deductible for tax purposes.
The effective tax rate in Canada was 14 percent in 2013 compared to 22 percent in 2012. This was largely due to the purchase gain on the Viterra acquisition.
Changes in statutory income tax rates, the mix of earnings, tax allowances and realization of unrecognized tax assets among the jurisdictions in which we operate can impact our overall effective tax rate. Further details of the year-over-year variances in these rates for the years ended December 31, 2013 and 2012 are provided in note 8 of the Notes to the Consolidated Financial Statements.
NET LOSS FROM DISCONTINUED OPERATIONS
In December 2013, Agrium’s Board of Directors approved the plan to sell components of the Advanced Technologies business unit. The operations of the Turf and Ornamental and Direct Solutions businesses have been classified as discontinued and we recorded the assets held for sale at fair value less costs to sell, which resulted in a write-down of $60-million (see notes 5 and 14 of the Notes to the Consolidated Financial Statements for further information).
Additionally, following the settlement of litigation in December 2013, we received $75-million for an insurance claim related to a division of AWB Limited (“AWB”) that we acquired in 2010 and sold in 2011. We had not previously accrued a receivable for this claim because of the uncertainty of the outcome of the litigation. We incurred an additional $22-million of legal fees and additional settlements relating to the sold division of AWB.
| | |
PAGE 62 // MANAGEMENT’S DISCUSSION AND ANALYSIS // AGRIUM ANNUAL REPORT 2013 |
ASSETS
Total assets increased by 1 percent from 2012 to 2013. The advance to Glencore International plc (“Glencore”) initiated in the fourth quarter of 2012 was settled with cash and assets acquired in the Viterra acquisition in 2013. See the discussion in the section “Financial Condition” on page 65 for detailed analysis. From 2011 to 2012, total assets increased by 20 percent. The majority of this increase was due to the above-mentioned advance coupled with increased spending in 2012 compared to 2011 for the Vanscoy potash expansion project.
NON-CURRENT FINANCIAL LIABILITIES
Total non-current financial liabilities increased by 47 percent from 2012 to 2013. This was attributed to the issuance of $500-million of 3.5 percent debentures due June 2023 and $500-million of 4.9 percent debentures due June 2043, both in the second quarter of 2013. See the discussion in the section “Financial Condition” on page 65 for detailed analysis. Total non-current financial liabilities decreased by 1 percent from 2011 to 2012.
DIVIDENDS DECLARED
Starting in 2011 and through to 2013, a series of dividend increases were approved by the Board of Directors, as follows:
„ DIVIDEND BREAKDOWN
| | | | | | | | | | | | |
Effective date | | Dividends declared per share | | | Frequency | | | Dividends declared per share on an annualized basis | |
May 10, 2011 | | $ | 0.055 | | | | Semi-annually | | | $ | 0.11 | |
December 14, 2011 | | $ | 0.225 | | | | Semi-annually | | | $ | 0.45 | |
June 7, 2012 | | $ | 0.500 | | | | Semi-annually | | | $ | 1.00 | |
December 14, 2012 | | $ | 0.500 | | | | Quarterly | | | $ | 2.00 | |
September 23, 2013 | | $ | 0.750 | | | | Quarterly | | | $ | 3.00 | |
We declared dividends on our common shares of $367-million in 2013 and $154-million in 2012. Common share dividends paid were $334-million in 2013 and $115-million in 2012.
| | |
AGRIUM ANNUAL REPORT 2013 // MANAGEMENT’S DISCUSSION AND ANALYSIS // PAGE 63 |
QUARTERLY RESULTS OF OPERATIONS
The agricultural products business is seasonal in nature. Consequently, comparisons made on a year-over-year basis are more appropriate than quarter-over-quarter comparisons. Crop input sales are primarily concentrated in the spring and fall crop input application seasons, which are in the second quarter and fourth quarter. Crop nutrient inventories are normally accumulated leading up to each application season. Our cash collections generally occur after the application season is complete.
„ SELECTED QUARTERLY INFORMATION
| | | | | | | | | | | | | | | | | | | | | | | | | | | | | | | | |
| | 2013 | | | 2012 | |
(millions of U.S. dollars, except per share amounts) | | Q4 | | | Q3 | | | Q2 | | | Q1 | | | Q4 | | | Q3 | | | Q2 | | | Q1 | |
Sales | | | 2,867 | | | | 2,796 | | | | 6,908 | | | | 3,156 | | | | 3,093 | | | | 2,768 | | | | 6,669 | | | | 3,494 | |
Cost of product sold | | | 2,127 | | | | 2,167 | | | | 5,209 | | | | 2,451 | | | | 2,119 | | | | 2,038 | | | | 4,838 | | | | 2,721 | |
Gross profit | | | 740 | | | | 629 | | | | 1,699 | | | | 705 | | | | 974 | | | | 730 | | | | 1,831 | | | | 773 | |
Expenses | | | | | | | | | | | | | | | | | | | | | | | | | | | | | | | | |
Selling | | | 511 | | | | 423 | | | | 546 | | | | 396 | | | | 438 | | | | 375 | | | | 527 | | | | 357 | |
General and administrative | | | 116 | | | | 57 | | | | 62 | | | | 94 | | | | 49 | | | | 134 | | | | 95 | | | | 150 | |
Earnings from associates and joint ventures | | | (29 | ) | | | (11 | ) | | | (15 | ) | | | (13 | ) | | | (22 | ) | | | (35 | ) | | | (13 | ) | | | (21 | ) |
Purchase gain | | | (257 | ) | | | — | | | | — | | | | — | | | | — | | | | — | | | | — | | | | — | |
Goodwill impairment | | | 220 | | | | — | | | | — | | | | — | | | | — | | | | — | | | | — | | | | — | |
Other (income) expenses | | | (4 | ) | | | 16 | | | | 42 | | | | (11 | ) | | | (20 | ) | | | 43 | | | | 4 | | | | 31 | |
Earnings before finance costs and income taxes | | | 183 | | | | 144 | | | | 1,064 | | | | 239 | | | | 529 | | | | 213 | | | | 1,218 | | | | 256 | |
Total finance costs | | | 39 | | | | 35 | | | | 42 | | | | 40 | | | | 37 | | | | 30 | | | | 31 | | | | 32 | |
Income taxes | | | 34 | | | | 29 | | | | 278 | | | | 53 | | | | 134 | | | | 43 | | | | 328 | | | | 65 | |
Net earnings from continuing operations | | | 110 | | | | 80 | | | | 744 | | | | 146 | | | | 358 | | | | 140 | | �� | | 859 | | | | 159 | |
Net (loss) earnings from discontinued operations | | | (11 | ) | | | (4 | ) | | | 3 | | | | (5 | ) | | | (4 | ) | | | (11 | ) | | | 1 | | | | (4 | ) |
Net earnings | | | 99 | | | | 76 | | | | 747 | | | | 141 | | | | 354 | | | | 129 | | | | 860 | | | | 155 | |
Attributable to: | | | | | | | | | | | | | | | | | | | | | | | | | | | | | | | | |
Equity holders of Agrium | | | 96 | | | | 76 | | | | 749 | | | | 141 | | | | 354 | | | | 127 | | | | 860 | | | | 153 | |
Non-controlling interest | | | 3 | | | | — | | | | (2 | ) | | | — | | | | — | | | | 2 | | | | — | | | | 2 | |
Earnings per share from continuing operations attributable to equity holders of Agrium: | | | | | | | | | | | | | | | | | | | | | | | | | | | | | | | | |
Basic | | | 0.74 | | | | 0.54 | | | | 5.00 | | | | 0.98 | | | | 2.37 | | | | 0.87 | | | | 5.44 | | | | 0.99 | |
Diluted | | | 0.74 | | | | 0.54 | | | | 5.00 | | | | 0.98 | | | | 2.36 | | | | 0.87 | | | | 5.43 | | | | 0.99 | |
Earnings per share attributable to equity holders of Agrium: | | | | | | | | | | | | | | | | | | | | | | | | | | | | | | | | |
Basic | | | 0.66 | | | | 0.52 | | | | 5.02 | | | | 0.94 | | | | 2.34 | | | | 0.80 | | | | 5.44 | | | | 0.97 | |
Diluted | | | 0.66 | | | | 0.52 | | | | 5.02 | | | | 0.94 | | | | 2.34 | | | | 0.80 | | | | 5.44 | | | | 0.97 | |
EBITDA | | | 314 | | | | 250 | | | | 1,191 | | | | 347 | | | | 635 | | | | 331 | | | | 1,322 | | | | 341 | |
Adjusted EBITDA | | | 338 | | | | 263 | | | | 1,199 | | | | 356 | | | | 656 | | | | 359 | | | | 1,331 | | | | 340 | |
Dividends declared | | | 108 | | | | 110 | | | | 74 | | | | 75 | | | | 75 | | | | — | | | | 79 | | | | — | |
Dividends declared per share | | | 0.75 | | | | 0.75 | | | | 0.50 | | | | 0.50 | | | | 0.50 | | | | — | | | | 0.50 | | | | — | |
| | |
PAGE 64 // MANAGEMENT’S DISCUSSION AND ANALYSIS // AGRIUM ANNUAL REPORT 2013 |
Significant items affecting the comparability of quarterly results include the following:
2013
• | | We had record sales for a second quarter, as there was a return to more normal seasonal crop input demand compared to the second quarter of 2012, when the early spring season shifted sales typically earned in the second quarter to the first quarter of 2012; |
• | | During the fourth quarter, the Turf and Ornamental and Direct Solutions businesses of the AAT business unit were reported within discontinued operations. See the section “Net loss from discontinued operations” under “Consolidated Performance” on page 60 for additional discussion; |
• | | Also included in the fourth quarter was a purchase gain of $257-million related to the Viterra acquisition (see page 62 for further information); |
• | | Additionally, goodwill impairment of $220-million occurred in the fourth quarter in relation to delayed synergies realized and reduced expectations for sales, gross margins and long-term growth in Australia – Retail (see page 62 for further information); and |
• | | Our share-based payments expense for the first and fourth quarters was $16-million and $28-million, respectively, compared to share-based payments recovery of $30-million and $21-million, respectively, in the second and third quarters. The changes between quarters were largely driven by movements in fair value due to changes in share price. |
2012
• | | Sales were a first quarter record as there was strong demand for crop input products due to an early spring season; |
• | | We had record gross profit for a second quarter, largely attributed to higher Retail sales resulting from increased sales volumes for most of our major product lines as a result of the early spring; |
• | | Our third quarter net earnings included a charge of $66-million related to environmental remediation liabilities. Also during the quarter, we were impacted by the eight-week planned turnaround and some additional mining related challenges at the Vanscoy facility, which resulted in 54 percent lower potash sales tonnes compared to the third quarter of 2011; and |
• | | Our share-based payments expense for the first, second and third quarters of 2012 was $64-million, $9-million and $53-million, respectively, compared to a share-based payments recovery of $18-million in the fourth quarter of 2012. The changes between quarters were largely driven by movements in fair value due to changes in share price. |
FINANCIAL CONDITION
„ BALANCE SHEET ANALYSIS
| | | | | | | | | | | | |
(millions of U.S. dollars) | | 2013 | | | 2012 | | | Variance | |
Assets | | | 15,977 | | | | 15,805 | | | | 172 | |
Liabilities | | | 9,181 | | | | 8,885 | | | | 296 | |
Shareholders’ equity | | | 6,796 | | | | 6,920 | | | | (124 | ) |
| | |
AGRIUM ANNUAL REPORT 2013 // MANAGEMENT’S DISCUSSION AND ANALYSIS // PAGE 65 |
The following are changes to the financial condition of our consolidated balance sheets for the year ended December 31, 2013.
„ DETAILED BALANCE SHEET ANALYSIS
| | | | | | | | | | | | | | | | | | |
(millions of U.S. dollars, except as noted) | | December 31, 2013 | | | December 31, 2012 | | | $ Change | | | % Change | | | Explanation of the change in balance |
Assets | | | | | | | | | | | | | | | | | | |
| | | | | |
Cash and cash equivalents | | | 801 | | | | 658 | | | | 143 | | | | 22 | % | | See discussion in the section “Liquidity and Capital Resources”. |
Accounts receivable | | | 2,105 | | | | 2,224 | | | | (119 | ) | | | (5 | %) | | Lower Wholesale receivables of $156-million resulting from lower fourth quarter sales in all product lines were partially offset by increased Retail rebates receivable. |
Income taxes receivable | | | 78 | | | | 32 | | | | 46 | | | | 144 | % | | Increased due to expected refunds in Canada and the U.S. as a result of tax installments paid that were greater than taxes payable. |
Inventories | | | 3,413 | | | | 3,094 | | | | 319 | | | | 10 | % | | Retail crop protection products inventory increased in North America in 2013 by $222-million to position against future price increases. The remaining increase was due to the Viterra acquisition. |
Advance on acquisition of Viterra Inc. | | | — | | | | 1,792 | | | | (1,792 | ) | | | (100 | %) | | The Viterra acquisition was completed in 2013 and the advance was settled in full. |
Prepaid expenses and deposits | | | 805 | | | | 740 | | | | 65 | | | | 9 | % | | Prepaid seed increased in North America to lock in pricing and support growth in the business. Crop protection prepay also increased due to favorable rates. |
Other current assets | | | 104 | | | | — | | | | 104 | | | | N/A | | | Increase in marketable securities resulting from a change in the nature of investments previously classified as cash and cash equivalents. |
Assets held for sale | | | 202 | | | | — | | | | 202 | | | | N/A | | | In December 2013, Agrium’s Board of Directors approved the plan to divest the AAT Turf and Ornamental and Direct Solutions businesses. |
Property, plant and equipment | | | 4,960 | | | | 3,484 | | | | 1,476 | | | | 42 | % | | Wholesale additions increased by approximately $1-billion due to spending related to the Vanscoy potash expansion project and approximately $130-million due to nitrogen expansion projects. The remaining increase was primarily due to the Viterra acquisition of $286-million. |
Intangibles | | | 738 | | | | 636 | | | | 102 | | | | 16 | % | | The increase was primarily due to the Viterra acquisition adding $148-million of intangibles. This was offset by amortization and amounts reclassified as assets held for sale related to the AAT Turf and Ornamental and Direct Solutions businesses. |
Goodwill | | | 1,958 | | | | 2,349 | | | | (391 | ) | | | (17 | %) | | The majority of the decrease is due to goodwill impairment of $220-million recognized in 2013 for Retail – Australia in addition to the reclassification of AAT assets held for sale. Foreign exchange translation comprised the remainder of the decrease. |
Investments in associates and joint ventures | | | 639 | | | | 627 | | | | 12 | | | | 2 | % | | — |
Other assets | | | 99 | | | | 99 | | | | — | | | | — | | | — |
Deferred income tax assets | | | 75 | | | | 70 | | | | 5 | | | | 7 | % | | — |
| | |
PAGE 66 // MANAGEMENT’S DISCUSSION AND ANALYSIS // AGRIUM ANNUAL REPORT 2013 |
| | | | | | | | | | | | | | | | | | |
(millions of U.S. dollars, except as noted) | | December 31, 2013 | | | December 31, 2012 | | | $ Change | | | % Change | | | Explanation of the change in balance |
Liabilities | | | | | | | | | | | | | | | | | | |
| | | | | |
Short-term debt | | | 764 | | | | 1,314 | | | | (550 | ) | | | (42 | %) | | The decrease was due to higher short-term borrowings outstanding in 2012 relating to cash management strategies for operational needs and to fund the advance of the Viterra acquisition. |
Accounts payable | | | 3,985 | | | | 3,479 | | | | 506 | | | | 15 | % | | Increase primarily due to the Viterra acquisition, adding approximately $320-million of total accounts payable. Customer prepayments increased by $56-million. Trade payables increased by approximately $134-million which is directly related to increases in inventory. |
Income taxes payable | | | 2 | | | | 137 | | | | (135 | ) | | | (99 | %) | | Change is due to lower earnings in Canada. |
Liabilities held for sale | | | 44 | | | | — | | | | 44 | | | | N/A | | | In December 2013, Agrium’s Board of Directors approved the plan to divest the AAT Turf and Ornamental and Direct Solutions businesses. |
Long-term debt | | | 3,124 | | | | 2,587 | | | | 537 | | | | 21 | % | | Long-term debt increased as a result of the issuance of an aggregate $1-billion of debentures in May 2013. This was partially offset by the repayment of a $460-million facility. |
Post-employment benefits | | | 135 | | | | 184 | | | | (49 | ) | | | (27 | %) | | The decrease was primarily the result of an actuarial gain of approximately $45-million recorded in 2013 resulting from a revision to the discount rate. |
Other provisions | | | 538 | | | | 521 | | | | 17 | | | | 3 | % | | Increase resulting from the Viterra acquisition. |
Other liabilities | | | 59 | | | | 79 | | | | (20 | ) | | | (25 | %) | | Decrease primarily due to a reduction in the fair value of share-based payment liabilities primarily as a result of a decrease in our share price. |
Deferred income tax liabilities | | | 530 | | | | 584 | | | | (54 | ) | | | (9 | %) | | Decrease in U.S. deferred income tax liabilities offset by an increase in the Canadian deferred income tax liabilities resulting from the Viterra acquisition. |
WORKING CAPITAL
Our working capital from continuing operations, defined as current assets excluding current assets held for sale less current liabilities excluding current liabilities held for sale, at December 31, 2013 was $2.4-billion, a decrease of $599-million over December 31, 2012. See the discussion of current assets in the section “Financial Condition” on page 65 for more information on the drivers of this change in working capital from continuing operations.
„ WORKING CAPITAL BREAKDOWN
| | | | | | | | |
(millions of U.S. dollars) | | 2013 | | | 2012 | |
Current assets excluding current assets held for sale | | | 7,306 | | | | 8,540 | |
Current liabilities excluding current liabilities held for sale | | | 4,921 | | | | 5,556 | |
Working capital from continuing operations | | | 2,385 | | | | 2,984 | |
| | |
AGRIUM ANNUAL REPORT 2013 // MANAGEMENT’S DISCUSSION AND ANALYSIS // PAGE 67 |
SHAREHOLDERS’ EQUITY
Shareholders’ equity was $6.8-billion at December 31, 2013, a decrease of $124-million compared to December 31, 2012. This was primarily driven by a net increase in retained earnings of $298-million at December 31, 2013 compared to December 31, 2012, which represents the 2013 net earnings attributable to equity holders of Agrium offset by the Normal Course Issuer Bid (“NCIB”) share repurchase coupled with dividends of $367-million. The NCIB share repurchase of $498-million resulted in a reduction to share capital of $72-million and a reduction to retained earnings of $426-million. Additionally, shareholders’ equity was impacted by a $340-million foreign currency translation loss in accumulated other comprehensive loss due to the decline in the exchange rates of the Canadian and Australian dollar.
DISCONTINUED OPERATIONS
After conducting a strategic review of AAT in 2013, Agrium’s Board of Directors approved the transition of parts of the AAT business unit, consisting of our ESN and Micronutrient products, to our Wholesale business unit. Management intends to sell components of the AAT business unit that we did not transition to Wholesale. We consider that a sale by December 2014 is highly probable. We have classified assets of the operations not transferred to Wholesale as held for sale, and have classified related results of operations as discontinued. Refer to note 5 of the Notes to the Consolidated Financial Statements for further detail.
LIQUIDITY AND CAPITAL RESOURCES
Our liquidity and capital resources needs can be met through a variety of sources, including cash on hand, cash provided by operations and short-term borrowings from the issuance of commercial paper and borrowings from our credit facilities, as well as long-term debt and equity capacity from the capital markets. Depending on the nature, timing and extent of any potential acquisitions or greenfield and brownfield development opportunities, we may consider expanding existing sources of financing or accessing other sources of financing.
„ SOURCES AND USES OF CASH
| | | | | | | | |
(millions of U.S. dollars) | | 2013 | | | 2012 | |
Cash provided by operating activities | | | 1,767 | | | | 2,070 | |
Cash used in investing activities | | | (681 | ) | | | (3,302 | ) |
Cash (used in) provided by financing activities | | | (867 | ) | | | 581 | |
Effect of exchange rate changes on cash and cash equivalents | | | (24 | ) | | | 37 | |
Increase (decrease) in cash and cash equivalents from continuing operations | | | 195 | | | | (614 | ) |
Cash and cash equivalents used in discontinued operations | | | (52 | ) | | | (15 | ) |
CASH PROVIDED BY OPERATING ACTIVITIES
Cash provided by operating activities is made up of net earnings from continuing operations adjusted for items not affecting cash, interest received, interest paid, income taxes paid, dividends from associates and joint ventures and net changes in non-cash working capital.
Net earnings from continuing operations adjusted for items not affecting cash was a source of cash of $1.9-billion in 2013 and $2.6-billion in 2012. Non-cash items include depreciation and amortization, earnings from associates and joint ventures, purchase gain, goodwill impairment, share-based payments, unrealized gain on derivative financial instruments, interest income, finance costs and income taxes. The significant non-cash items include goodwill impairment of $220-million recognized in 2013 offset by the purchase gain of $257-million, a share-based payments recovery in 2013 compared to a share-based payments expense in 2012, and a decrease in income taxes in 2013.
NON-CASH WORKING CAPITAL
Our non-cash working capital levels are affected by numerous factors including: demand for our products and services, together with pre-sales of product and inventory build leading up to the spring and fall crop input application seasons; selling prices of our products and services; raw material input and other costs; and foreign exchange rates.
The net change in non-cash working capital for the year ended December 31, 2013 was a source of cash of $536-million compared to a use of cash of $138-million for the year ended December 31, 2012. The 2013 increase in cash flow from non-cash working capital, after adjusting for amounts added through acquisitions, was primarily driven by a decrease in receivables and inventories coupled with increases in payables and a lower increase in prepaid expenses and deposits.
For further discussion of working capital balance sheet account changes from December 31, 2012 to December 31, 2013, see the section “Financial Condition” on page 60.
| | |
PAGE 68 // MANAGEMENT’S DISCUSSION AND ANALYSIS // AGRIUM ANNUAL REPORT 2013 |
CASH USED IN INVESTING ACTIVITIES
Investing activities used $681-million of cash in 2013, a decrease of $2.6-billion compared to 2012.
BUSINESS ACQUISITIONS
In 2012, we advanced $1.8-billion to Glencore for the Viterra acquisition. In 2013 upon completion of the Viterra acquisition, we received cash and assets of $1.3-billion in settlement of the advance.
In 2013, we completed various acquisitions of smaller, independent retail operations for total consideration of approximately $60-million. In 2012, we completed various retail acquisitions, which included the domestic acquisitions of Ritter Crop Services and West Texas Agriplex in addition to Utilfertil in Brazil.
CAPITAL EXPENDITURES
„ CAPITAL EXPENDITURES BREAKDOWN
| | | | | | | | |
(millions of U.S. dollars) | | 2013 | | | 2012 | |
Sustaining capital | | | 591 | | | | 499 | |
Investing capital | | | 1,164 | | | | 726 | |
Total | | | 1,755 | | | | 1,225 | |
CAPITAL EXPENDITURES BY BUSINESS UNIT
„ CAPITAL EXPENDITURES BY BUSINESS UNIT
| | | | | | | | | | | | |
(millions of U.S. dollars) | | 2013 | | | 2012 | | | 2011 | |
Retail | | | 197 | | | | 186 | | | | 169 | |
Wholesale | | | 1,529 | | | | 991 | | | | 461 | |
AAT and Other | | | 29 | | | | 48 | | | | 33 | |
| | | 1,755 | | | | 1,225 | | | | 663 | |
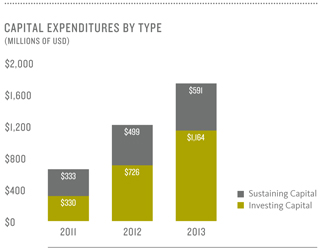
Sustaining capital includes the cost of replacements and betterments of our facilities. Our sustaining capital expenditures increased in 2013 by $92-million, largely related to sustaining projects at the Vanscoy potash facility. Retail’s sustaining capital expenditures in 2013 were $166-million.
In the prior year, we had planned for a sustaining capital program of approximately $500-million to $550-million during 2013. Our actual sustaining capital expenditures in 2013 were $591-million. The variance was primarily a result of planned 2014 sustaining expenditures being shifted into 2013 in addition to increased sustaining projects at our Vanscoy potash facility.
Investing capital typically includes a significant expansion of existing operations or new acquisitions. Our investing capital expenditures increased compared to 2012 due to expenditures related to the Vanscoy potash expansion project.
CASH (USED IN) PROVIDED BY FINANCING ACTIVITIES
Financing activities used $867-million of cash in 2013, a change of $1.5-billion compared to 2012, when financing activities provided $581-million of cash.
SHORT-TERM DEBT
Cash used in the repayment of short-term debt in 2013 was $511-million compared to cash provided by short-term debt in 2012 of $1.1-billion. The repayment of short-term debt in 2013 related to the multi-jurisdictional facility that was drawn upon for operational needs and for the 2012 advance of funds to Glencore for the Viterra acquisition.
LONG-TERM DEBT
On May 28, 2013, we issued $500-million of 3.5 percent debentures due June 1, 2023 and $500-million of 4.9 percent debentures due June 1, 2043.
On October 1, 2012, we issued $500-million of 3.15 percent debentures due October 1, 2022.
The debentures were issued under our base shelf prospectus, which permits issuance in Canada and the U.S. of common shares, preferred shares, subscription receipts, debt securities or units.
In May 2013, we repaid a $460-million floating rate bank loan. We also repaid $58-million of the South American credit facilities during 2013.
DIVIDENDS
See the discussion in the section “Consolidated Performance” on page 60 for information about our dividends.
| | |
AGRIUM ANNUAL REPORT 2013 // MANAGEMENT’S DISCUSSION AND ANALYSIS // PAGE 69 |
NORMAL COURSE ISSUER BID
In May 2013, we announced the acceptance by the Toronto Stock Exchange of our notice of intention to make an NCIB. Pursuant to the NCIB, we are authorized to make purchases of up to 5 percent, approximately 7,472,587 common shares, until May 20, 2014 through the facilities of the Toronto Stock Exchange, the New York Stock Exchange and/or alternative trading platforms, subject to compliance with applicable Canadian and U.S. rules.
During 2013, we purchased approximately 5,770,182 shares for total consideration of approximately $498-million pursuant to the NCIB.
CASH AND CASH EQUIVALENTS USED IN DISCONTINUED OPERATIONS
Cash and cash equivalents used in discontinued operations was $52-million in 2013 and $15-million in 2012. For further discussion on discontinued operations, see the section “Net loss from discontinued operations” under “Consolidated Performance” on page 60.
CASH POSITION
Our year-end cash balance was $801-million in 2013 and $658-million in 2012. The increase in cash in 2013 was primarily driven by significantly lower cash used in investing activities than in 2012. In 2012, $1.8-billion was advanced to Glencore for the Viterra acquisition. During 2013, $1.3-billion of the advance related to the Viterra acquisition was repaid to Agrium by Glencore. This was partially offset by an increase in capital expenditures and higher cash used in financing activities. Although long-term debt issued during the year was higher in 2013 compared to 2012, and the amount paid for shares repurchased during 2013 was lower than in 2012, dividends, short-term debt and long-term debt payments were all higher during 2013. Long-term debt issued in 2013 comprised of $1-billion of debentures and long-term debt issued in 2012 consisted of $500-million of debentures.
We do not hold material cash balances in currencies other than the U.S. dollar and the Canadian dollar. We do not depend on repatriation of cash from our foreign subsidiaries to meet our liquidity and capital resources needs.
DEBT INSTRUMENTS, CAPITAL MANAGEMENT AND RATINGS
DEBT INSTRUMENTS
Short-term debt consists mainly of U.S. dollar-denominated commercial paper (“CP”) issued in Canada and the U.S. as well as various bank lines of credit for our operations in Europe, South America and Australia. As of December 31, 2013, we had $503-million of commercial paper outstanding at a weighted average interest rate of 0.33 percent. For our international operations, we had credit facilities of approximately $696-million of which $261-million was outstanding at December 31, 2013, including $180-million in Europe, $50-million in South America and $31-million in Australia. We also have a $2.3-billion credit facility in North America, which expires in 2017.
Refer to note 17 of the Notes to the Consolidated Financial Statements for further information on our short-term debt and long-term debt.

| | |
PAGE 70 // MANAGEMENT’S DISCUSSION AND ANALYSIS // AGRIUM ANNUAL REPORT 2013 |
CAPITAL MANAGEMENT
Refer to note 26 of the Notes to the Consolidated Financial Statements for further information on our capital management policies.
„ MULTI-JURISDICTIONAL FACILITY COVENANTS
| | | | | | | | |
| | | Limit | | | | 2013 | |
Interest coverage ratio(a) | | ³ | 2.5 | | | | 13.5 | |
Debt to capital ratio(b) | | £ | 0.65 | | | | 0.32 | |
(a) | Calculated as the last 12 months’ net earnings from continuing operations before finance costs, income taxes, depreciation and amortization divided by interest, which includes interest on long-term debt plus other interest. |
(b) | Calculated as the sum of short-term debt and long-term debt, divided by the sum of total debt and total equity. |
These covenants were met as at December 31, 2013 and December 31, 2012.
DEBT RATINGS
The following information relating to Agrium’s credit ratings is provided as it relates to our financing costs, liquidity and operations. Specifically, credit ratings affect Agrium’s ability to obtain short-term and long-term financing and the cost of such financing. A reduction in the current rating on our debt by the rating agencies, particularly a downgrade below investment grade, or a negative change in the outlook for the Company, could adversely affect Agrium’s cost of financing and our access to sources of liquidity and capital.
„ DEBT RATINGS BREAKDOWN
| | | | | | | | | | | | | | | | |
Rating agency | | Date of affirmation | | | Long-term debt rating | | | USD commercial paper | | | Ratings outlook | |
Standard & Poor’s Ratings Services | | | November 27, 2013 | | | | BBB | | | | A-2 | | | | Stable | |
Moody’s Investors Service | | | November 27, 2013 | | | | Baa2 | | | | P-2 | | | | Stable | |
DBRS Limited | | | May 28, 2013 | | | | BBB | | | | N/A | | | | Stable | |
Refer to our 2013 AIF in the section “Item 7 – Description of Capital Structure – 7.3 Debt Ratings” for further information on our ratings, including ratings definitions.
FUTURE CASH REQUIREMENTS
CONTRACTUAL OBLIGATIONS AND OTHER COMMITMENTS
At December 31, 2013, our aggregate contractual obligations for continuing operations are as set out in the table below.
„ CONTRACTUAL AND OTHER OBLIGATIONS
| | | | | | | | | | | | | | | | | | | | |
| | Payment due by period | | | | |
(millions of U.S. dollars) | | Less than one year | | | One to three years | | | Four to five years | | | More than five years | | | Total | |
Long-term debt(a) | | | 227 | | | | 355 | | | | 436 | | | | 4,827 | | | | 5,845 | |
Operating leases | | | 262 | | | | 290 | | | | 213 | | | | 97 | | | | 862 | |
Purchase obligations | | | 752 | | | | 518 | | | | 265 | | | | 154 | | | | 1,689 | |
Asset retirement obligations(c) | | | 19 | | | | 52 | | | | 33 | | | | 371 | (b) | | | 475 | |
Environmental remediation liabilities(d) | | | 34 | | | | 82 | | | | 17 | | | | 49 | | | | 182 | |
Total | | | 1,294 | | | | 1,297 | | | | 964 | | | | 5,498 | | | | 9,053 | |
(a) | Figures include interest and principal payments and capital lease repayments. |
(b) | This figure does not include estimated asset retirement obligations related to our potash operations. See the following discussion in the section “Asset retirement obligations”. |
(c) | Represents the undiscounted, inflation-adjusted estimated cash outflows. |
(d) | Represents the undiscounted, estimated cash outflows. |
| | |
AGRIUM ANNUAL REPORT 2013 // MANAGEMENT’S DISCUSSION AND ANALYSIS // PAGE 71 |
LONG-TERM DEBT
Failure to maintain certain financial ratios in respect of our credit facilities and bank loans and other covenants in the various debt instruments may trigger early repayment provisions. See the discussion in the section “Debt Instruments, Capital Management and Ratings” on page 70.
OPERATING LEASES
Operating lease commitments consist primarily of leases for railcars and contractual commitments at distribution facilities in our Wholesale business unit, vehicles and application equipment in our Retail business unit, and office equipment and property leases throughout our operations. The commitments represent the minimum payments under each agreement.
PURCHASE OBLIGATIONS
Purchase obligations include minimum commitments for North American natural gas purchases, which include both floating rate and fixed rate contracts, and are calculated using the prevailing NYMEX forward prices for U.S. facilities and AECO forward prices for Canadian facilities at December 31, 2013.
Profertil has three long-term gas contracts denominated in U.S. dollars, expiring in 2017. These three contracts account for approximately 85 percent of Profertil’s gas requirements. YPF S.A. (“YPF”), our joint venture partner in Profertil, supplies approximately 26 percent of the gas under these contracts.
We have a power co-generation agreement for our Carseland facility that expires on December 31, 2026. The maximum commitment under this agreement is to purchase 60 megawatt-hours of power per hour through 2026. The price for the power is based on a fixed charge adjusted for inflation and a variable charge based on the cost of natural gas, which is provided to the facility for power generation.
Our phosphate rock supply agreement extends to 2020. Our minimum commitment is to purchase 800,000 tonnes in 2014 and 798,000 tonnes from 2015 to 2018, with subsequent volumes to be determined in 2016. The purchase price is based on a formula that tracks finished product pricing and key published phosphate input costs. We entered into a freight contract to import phosphate rock extending to 2018, with a total outstanding commitment of $162-million at December 31, 2013.
In addition to amounts disclosed in the preceding table, future capital expenditures include cancellable contracts for total costs of approximately: (i) potash facility expansion – $750-million to $850-million; (ii) Texas nitrogen expansion project – $22-million; and (iii) Profertil nitrogen expansion project – $48-million.
ASSET RETIREMENT OBLIGATIONS
Our mining, extraction, processing and distribution activities result in asset retirement obligations, which are part of our normal course of operations. Such retirement obligations include closure, dismantlement, site restoration or other legal or constructive obligations for termination and retirement of assets. Expenditures may occur before and after closure. We expect to incur expenditures for obligations over the next 30 years, with the exception of those for potash operations, which are expected to occur after 100 years. The timing of retirement expenditures is dependent on a number of factors such as the life and nature of the asset, legal requirements and technology. The discounted, inflation-adjusted estimated cash outflows required to settle the asset retirement obligations are estimated at $314-million at December 31, 2013.
ENVIRONMENTAL REMEDIATION LIABILITIES
We establish provisions for environmental expenditures that relate to existing conditions caused by past operations that do not contribute to current or future revenue generation. We capitalize environmental expenditures that extend the life of the property, increase its capacity or mitigate or prevent contamination from future operations. The discounted, inflation-adjusted estimated cash outflows required to settle the environmental remediation liabilities are estimated at $165-million at December 31, 2013.
FUTURE CAPITAL EXPENDITURES
SUSTAINING CAPITAL
Our sustaining capital is expected to be approximately $550-million to $600-million in 2014 due to a number of large sustaining projects planned for the year. The 2014 sustaining capital program includes the following:
• | | Reliability projects for Wholesale manufacturing facilities; |
• | | Wholesale resource development projects; |
• | | Risk management and risk reduction projects; |
• | | Planned turnaround inspection and overhaul at certain Wholesale facilities; and |
• | | Spending at our Retail operations in North and South America and Australia. |
INVESTING CAPITAL
Our investing capital program planned for 2014 includes the following:
• | | Further expenditures on the Vanscoy potash expansion project to increase annual production capacity by one million tonnes; |
• | | Debottlenecking of the Borger ammonia facility and brownfield urea expansion; and |
• | | Retail investments in efficiency opportunities. |
We anticipate that we will be able to finance the announced projects through a combination of cash provided from operating activities, existing lines of credit (see the discussion in the section “Debt Instruments, Capital Management and Ratings” on page 70 for further details) and funds available from new debt or equity securities offerings.
| | |
PAGE 72 // MANAGEMENT’S DISCUSSION AND ANALYSIS // AGRIUM ANNUAL REPORT 2013 |
BUSINESS ACQUISITIONS
We completed the Viterra acquisition on October 1, 2013. The acquired assets form part of our Retail business unit and include over 200 farm centers in Canada as well as distribution assets in Australia.
Our purchase price allocation is not final because we are continuing to obtain and verify information required to determine the deferred income taxes arising on recognition of the assets acquired and liabilities assumed. Our valuation is expected to be completed within 12 months of the acquisition date.
We have recorded a purchase gain of $257-million representing the difference between the fair value of the acquired net assets and the purchase price.
During 2013, the Retail business unit completed the acquisition of various businesses for total consideration of approximately $60-million. Refer to note 4 of the Notes to the Consolidated Financial Statements for further information on our business acquisitions.
OUTSTANDING SHARE DATA
The number and principal amount of our outstanding shares at February 21, 2014 were as follows:
„ OUTSTANDING SHARES AT FEBRUARY 21, 2014
| | | | | | | | |
| | Number of shares | | | Market value | |
Common shares | | | 144 million | | | $ | 13-billion | |
At February 21, 2014, the number of stock options outstanding (issuable assuming full conversion, where each option granted can be exercised for one common share) was approximately nil.
OFF-BALANCE SHEET ARRANGEMENTS
GUARANTEES
We are contractually obligated to reimburse Canpotex, an industry association of which we are a one-third owner, for our approximately 9 percent pro-rata share of any operating losses or other liabilities incurred. We believe that the probability of conditions arising that would trigger this guarantee is remote. Reimbursements, if any, are made from reductions of our cash receipts from Canpotex.
FINANCIAL INSTRUMENTS
RISK MANAGEMENT
In the normal course of business, our balance sheet, results of operations and cash flows are exposed to various risks. On an annual basis, the Board approves a strategic plan that takes into account the opportunities and major risks of our business and mitigating factors to reduce these risks. The Board sets upper limits on the transactional and balance sheet exposures that management can manage, and the time periods over which management is permitted to manage. Our Corporate Financial Risk Committee reviews risk management policies and procedures on an annual basis, and monitors compliance with these limits and associated exposure management activity. We manage risk in accordance with our Exposure Management Policy. The objective of the policy is to reduce volatility in cash flows and earnings.
Our derivative financial instruments and the nature of the risks to which they are, or may be, subject are set out in the following table:
„ DERIVATIVE FINANCIAL INSTRUMENTS
| | | | | | | | | | | | | | | | |
| | Risks | |
| | Currency | | | Commodity price | | | Credit | | | Liquidity | |
Foreign currency forward and option contracts | | | X | | | | | | | | X | | | | X | |
Natural gas and seed forward, swap and option contracts, nutrient swap contracts and power swap contracts | | | | | | | X | | | | X | | | | X | |
Refer to note 23 of the Notes to the Consolidated Financial Statements for further information on our financial instruments.
| | |
AGRIUM ANNUAL REPORT 2013 // MANAGEMENT’S DISCUSSION AND ANALYSIS // PAGE 73 |
ENTERPRISE RISK MANAGEMENT
WE MANAGE RISKS TO OUR ENTERPRISE
In the normal course of operations, our business activities expose us to risk. The acceptance of certain risks is both necessary and advantageous in order to achieve our growth targets and our vision. We focus on long-term results and manage related risks and uncertainties. Our risk management structure strives to ensure sound business decisions are made that balance risk and reward and drive the maximization of total shareholder return.
RISK METHODOLOGY
Through Agrium’s structured Enterprise Risk Management (“ERM”) process, senior management, business units and corporate functions seek to identify and manage risks facing our business. Once identified, risks and related mitigation strategies are evaluated, documented and reviewed on an “evergreen” basis, with a formal review and quarterly sign-off. Many of these risks cross business units and corporate functions. In these cases, the aggregate risk to Agrium is considered and an overall corporate risk is recorded. Additional mitigation strategies are developed by the senior leadership team for implementation where residual risk is considered to be unacceptably high. Residual risk represents the remaining risk after taking into account existing mitigation strategies.
The risks we identify are assigned to six categories: strategic, financial, operational, market, environmental and political.
RISK RANKING MATRIX
At Agrium, we utilize our risk matrix to assess the potential impact of risks based on the expected frequency and consequence of risk events:
• | | We assess consequence based on the potential aggregate impact of a risk event on the following three areas: (a) company reputation; (b) our financial health; and (c) the environment and the health and safety of our employees and external parties; and |
• | | Frequency represents how often a consequence related to a risk is expected to occur – it is akin to probability of loss from the risk. |
AGRIUM’S RISK MATRIX
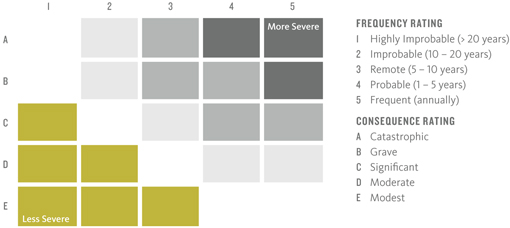
| | |
PAGE 74 // MANAGEMENT’S DISCUSSION AND ANALYSIS // AGRIUM ANNUAL REPORT 2013 |
RISK GOVERNANCE STRUCTURE
At Agrium, we believe that good risk management is critical to successful execution of strategy, and that everyone on the Agrium team has a role to play in managing risk.
BOARD OF DIRECTORS
• | | Governs risk management directly and through its committees; |
• | | Responsible for understanding the material risks of the business and the related mitigation strategies, and taking reasonable steps to ensure that management has an effective risk management process in place; and |
• | | Individual committees of the Board oversee specific risks relevant to their areas of responsibility. For example, the Audit Committee monitors the risk management process for financial risks; the Environment, Health, Safety and Security Committee monitors the process for managing environmental, health, safety and security (“EHS&S”) risks; and the Compensation Committee assesses risks in compensation programs. |
MANAGEMENT
• | | Risks that are unique to our separate strategic business units are managed by the presidents of those business units and their teams; and |
• | | Functional risks are managed by the corporate functional heads and their teams. |
CHIEF RISK OFFICER
• | | Agrium has an appointed Chief Risk Officer (“CRO”). The CRO is responsible for maintaining an effective ERM process. The CRO monitors current developments in risk management practices, drives improvements in Agrium’s risk management philosophy, program and policies, and champions development of a “best practice” risk management culture; |
• | | The CRO reports quarterly to the Board and senior management on all significant risks, including new or increased risks resulting from changes in operations or external factors; and |
• | | The CRO also formally reports to the Board of Directors annually on the ERM process and material risks. |
GOVERNANCE FUNCTIONS
• | | Agrium maintains several risk governance functions that contribute to our overall control environment, including Internal Audit, Corporate EHS&S, Legal, and the Internal Control and Disclosure Compliance team. |
KEY BUSINESS RISKS
The following is a discussion of the key business risks facing Agrium.
PRODUCT PRICE AND MARGIN
Agrium’s operating results are dependent on product prices and margins, which are in turn dependent on demand for crop inputs. Demand for crop inputs can be affected by a number of factors, including weather conditions, outlook for crop nutrient prices and farming economics, governmental policies, access of our customers to credit and build-up of inventories in distribution channels.
The majority of our Wholesale nutrient business is a commodity business with little product differentiation. Product prices are largely affected by supply and demand conditions, input costs and product prices and, therefore, resulting margins can be volatile.
Within our Wholesale business unit, we sell manufactured product as well as product we have purchased for resale. Both components of the business are subject to margin volatility.
Our Retail business unit experiences relatively stable margins, which provides stability to our annual cash flows and earnings. Nonetheless, during times of significant price volatility, margins can be affected to a certain degree by the above factors.
RAW MATERIALS
Natural gas is the principal raw material used to manufacture nitrogen and is the single largest purchased raw material for our Wholesale operation. North American natural gas prices are subject to price volatility. An increase in the price of natural gas increases our nitrogen cost of production, and may negatively impact nitrogen margins for our North American nitrogen sales. This is particularly important for our nitrogen facilities in Western Canada and Borger, Texas where we purchase gas on the open market. Higher production costs may be partially or fully reflected in higher domestic and international product prices, but these conditions do not always prevail. In addition, the price for natural gas in North America can vary significantly compared to the price for natural gas in Europe and Asia. Significantly lower natural gas prices in Europe and/or Asia would give our competitors in Europe and Asia a competitive advantage, which could, in turn, decrease international and domestic product prices to a level below what we would consider to be competitive given our input costs.
There is also a risk to the Profertil nitrogen facility concerning gas deliverability during the winter due to strains on gas distribution and residential demand in Argentina. The Argentine government has at times reduced the amount of gas available to industrial users in favor of residential users during the peak winter demand season. Profertil may also not be able to renew its long-term gas supply contracts at favorable rates or at all.
There are inherent risks associated with mining. For phosphate, there are risks associated with the variability in the quality of phosphate rock that can impact cost and production volumes. For potash mining, there is a risk of incurring water intake or flooding, as well as variability in quality, that can impact cost and production volumes.
| | |
AGRIUM ANNUAL REPORT 2013 // MANAGEMENT’S DISCUSSION AND ANALYSIS // PAGE 75 |
ENVIRONMENT, HEALTH, SAFETY AND SECURITY
We face EHS&S risks typical of those found throughout the agriculture, mining and chemical manufacturing sectors and the international fertilizer supply chain. These include the potential of physical injury to employees and contractors; possible environmental contamination and human exposure to chemical releases and accidents during manufacturing, transportation, storage and use; and the security of our personnel, products, intellectual property and physical assets domestically and overseas from intentional acts of destruction, crime, violence, terrorism, and ethnic and international conflicts. In addition, there are risks of natural disasters and risks to health, including pandemic risk.
UNPLANNED PLANT DOWNTIME
The results of our Wholesale business are dependent on the availability of our manufacturing facilities. Prolonged plant shutdown may result in a significant reduction in product that is available for sale, may affect the environment and/or the community, and may cause injury to an employee or a member of the public.
COUNTRY
We have significant operations in Canada, the U.S. and Australia. We also operate in a number of South American and European countries, and have business investments in Egypt and China. International business exposes us to a number of risks, such as uncertain economic conditions in the countries in which we do business, abrupt changes in foreign government policies and regulations, restrictions on the right to convert and repatriate currency, political risks and the possible interruption of raw material supply due to transportation issues or government imposed restrictions. We do not engage in business activities in any country that is a state sponsor of terrorism.
Construction of two new trains at the MOPCO-operated nitrogen plant in Egypt was shut down in November 2011 due to civil unrest, and as a result MOPCO may be unable to complete the planned expansion of the facility. As Agrium holds a 26 percent interest in MOPCO, failure to complete the expansion could have an adverse effect on our profitability, financial condition and results of operations.
Following its nationalization by the Argentine government, YPF, as the other 50 percent owner of the Profertil nitrogen facility, may have different business and economic interests or policy objectives under government management than it did in the past, which may be inconsistent with our interests as the 50 percent owner of that facility and which could have an adverse effect on the profitability, financial condition and results of operations of the Profertil facility. The Argentine government has imposed currency controls and regulatory measures to limit the flow of U.S. dollars out of the country. We do not depend on repatriation of cash from our foreign subsidiaries to meet our liquidity and capital resources needs.
BUSINESS ACQUISITIONS AND EXPANSIONS
There is a risk that recent acquisitions could fail to fully deliver the expected economic benefits, or we may experience integration challenges that could result in delays in achieving some or all of any anticipated synergies and require the allocation of additional resources to integrate the acquired businesses. Similarly, there is a risk that expansions of existing facilities or greenfield developments undertaken may have higher capital construction costs or be delayed or that such expansions may not generate the expected return on investment.
FOREIGN EXCHANGE
A significant shift in the value of the Canadian dollar against the U.S. dollar could impact the earnings of our Canadian operations, which earn revenues mainly in U.S. dollars and incur expenses mainly in Canadian dollars. The major impact would be to our Canadian potash and phosphate operations, on a per unit cost of product basis, as well as to our corporate overhead costs. Significant changes in the Canadian dollar can also have a direct impact on our Canadian effective income tax rate.
A significant shift in the value of the Australian dollar against the U.S. dollar could impact the reported earnings of our Australian operations, which earn revenues mainly in Australian dollars but report in U.S. dollars.
CREDIT AND LIQUIDITY
Our business is dependent on access to operating credit lines to fund our ongoing operations. Should overall credit liquidity in the markets be limited, this could impact our ability to operate under normal conditions.
COUNTERPARTY
We face the risk of loss should a counterparty be unable to fulfill its obligations with respect to accounts receivable or other contracts, including derivative financial instruments.
LEGISLATIVE RISK
We are subject to legislation, regulation and government policies in the jurisdictions in which we operate. We cannot predict how these laws, regulations or policies or their interpretation, administration and enforcement will change over time, and it is possible that future changes could negatively impact our operations, markets or cost structure.
LITIGATION RISK
Agrium, like any other business, is subject to the risk of becoming involved in disputes and litigation. Any material or costly dispute or litigation could adversely impact our consolidated financial position and results of operations. See the discussion “Litigation” in the section “Contingent Liabilities” on page 78.
| | |
PAGE 76 // MANAGEMENT’S DISCUSSION AND ANALYSIS // AGRIUM ANNUAL REPORT 2013 |
TRANSPORTATION
Reducing the delivered cost of product and ensuring reliability of product delivery to our customers are key success factors for our Wholesale marketing operations. A potential medium-term risk is the increased regulations and costs of transporting ammonia within North America given the safety risks of transporting this product.
HUMAN RESOURCES
Long-term forecasts predict a tight labor market across many areas in which we operate due to changing demographics, including the general aging of the population. A tight labor market, including the associated risks of losing key individuals and difficulty attracting and retaining qualified personnel, is a risk to the business.
WEATHER
Anomalies in regional weather patterns can have a significant and unpredictable impact on the demand for our products and services, and may also have an impact on prices. Our customers have limited windows of opportunity to complete required tasks at each stage of crop cultivation. Should adverse weather occur during these seasonal windows, we could face the possibility of reduced revenue in those seasons without the opportunity to recover until the following season. In addition, we face the significant risk of inventory carrying costs should our customers’ activities be curtailed during their normal seasons. We must manufacture product throughout the year in order to meet peak season demand, as well as react quickly to changes in expected weather patterns that affect demand.
CONTROLS AND PROCEDURES
DISCLOSURE CONTROLS AND PROCEDURES
We maintain disclosure controls and procedures designed to provide reasonable assurance that information required to be disclosed by us in our annual filings, interim filings (as these terms are defined in National Instrument 52-109, Certification of Disclosure in Issuers’ Annual and Interim Filings) and other reports filed or submitted by us under provincial and territorial securities legislation is recorded, processed, summarized and reported within the required time periods. Our Chief Executive Officer (“CEO”) and Chief Financial Officer (“CFO”), after evaluating the effectiveness of our disclosure controls and procedures as of the end of the period covered by the annual filings, being December 31, 2013, have concluded that, as of such date, our disclosure controls and procedures were effective in providing reasonable assurance that information required to be disclosed by Agrium in reports that it files or submits is (i) recorded, processed, summarized and reported within the required time periods, and (ii) accumulated and made known to management, including the CEO and CFO, to allow timely decisions regarding required disclosure.
Our disclosure controls and procedures are designed to provide reasonable assurance of achieving their objectives and, as indicated in the preceding paragraph, the CEO and CFO believe that our disclosure controls and procedures are effective at that reasonable assurance level, although the CEO and CFO do not expect that the disclosure controls and procedures will prevent all errors or fraud. A control system, no matter how well conceived or operated, can provide only reasonable, not absolute, assurance that the objectives of the control system will be met.
INTERNAL CONTROL OVER FINANCIAL REPORTING
Management is responsible for establishing and maintaining adequate internal control over financial reporting, as defined in Rules 13(a)-15(f) and 15(d)-15(f) under the Securities Exchange Act of 1934, as amended. Internal control over financial reporting is designed to provide reasonable assurance regarding the reliability of financial reporting and preparation of financial statements for external purposes in accordance with International Financial Reporting Standards.
Under the supervision and with the participation of our management, including our CEO and CFO, we conducted an evaluation of the design and effectiveness of our internal control over financial reporting as of the end of the fiscal year covered by this report based on the framework issued by the Committee of Sponsoring Organizations of the Treadway Commission in Internal Control – Integrated Framework (1992). Based on this evaluation, the CEO and CFO concluded that as of December 31, 2013 we did maintain effective internal control over financial reporting.
The effectiveness of internal control over financial reporting as of December 31, 2013 was audited by KPMG LLP, an independent registered public accounting firm, as stated in their report, which is included in this 2013 Annual Report to Shareholders.
We completed the Viterra acquisition on October 1, 2013 as more fully described in note 4 of the Notes to the Consolidated Financial Statements. This business was excluded from management’s evaluation of the effectiveness of the Company’s internal controls over financial reporting as of December 31, 2013 due to the proximity of the acquisition to year-end. The associated net assets represent 11 percent of consolidated net assets and total revenues represent 2 percent of consolidated revenues included in Agrium’s 2013 consolidated financial statements.
| | |
AGRIUM ANNUAL REPORT 2013 // MANAGEMENT’S DISCUSSION AND ANALYSIS // PAGE 77 |
CONTINGENT LIABILITIES
LITIGATION
From time to time, we become involved in legal or administrative proceedings related to our current and acquired businesses. Such proceedings expose us to possible losses and we expect our involvement in such matters to continue in the normal conduct of our business. We regularly assess the need for accounting recognition and/or disclosure of these matters. Our assessment considers the probability of adverse judgments and the range of possible losses. We base our assessment of the probable outcome on our judgment of a number of factors, including similar past experience and history, precedents, relevant financial, scientific and other evidence of each matter, and opinions from corporate and outside counsel. Accruals are recorded when occurrence is probable and the outcome is reasonably estimable. We may not be able to make a reliable estimate of losses or the range of possible losses when claims do not specify an amount of damages sought, there are numerous plaintiffs or when a case is in its early stages. We will represent our interests vigorously in all of the proceedings in which we are involved.
Legal proceedings and environmental matters are inherently complex and, as described above, we apply significant judgment in estimating probable outcomes. As a result, there exists the potential for adjustments to liabilities and material variance between actual costs and estimates.
Information on the amounts accrued for litigation, environmental remediation and asset retirement are disclosed in note 20 of the Notes to the Consolidated Financial Statements. Our assessment of specific litigation matters at the date of issuance of this MD&A is set out below. For a discussion on Idaho Mining Properties and Manitoba Mining Properties, see the section “Environmental Contingencies” on page 79.
OIL-FOR-FOOD PROGRAMME
On June 27, 2008, the Iraqi government filed a civil lawsuit in the U.S. against AWB, a subsidiary we acquired in 2010, and 92 other parties alleging that the defendants participated in an illegal conspiracy to divert funds from the United Nations Oil-For-Food Programme (“OFFP”) escrow account. The lawsuit seeks total damages in excess of $10-billion from the defendants, jointly and severally, as well as treble damages under the U.S. Racketeer Influenced and Corrupt Organizations Act. As to AWB specifically, the lawsuit alleges that AWB unlawfully diverted more than $232-million from the OFFP escrow account. AWB and a number of other defendants filed motions to dismiss the complaint in June 2010. The court granted the motions and dismissed the lawsuit with prejudice in a decision dated February 6, 2013. The plaintiff has appealed this decision. Although we believe that the possibility of a material financial effect from this matter is remote, an adverse decision could have a material adverse effect on AWB and on Agrium’s consolidated financial position and results of operations.
ENVIRONMENTAL PROTECTION REQUIREMENTS
Agrium’s operations are subject to a variety of federal, provincial, state and local laws, regulations, licenses and permits, the purpose of which is to protect the environment. These environmental protection requirements may apply during design and construction, operation or modification, at the time of plant or mine closure, and beyond.
The environmental requirements for new projects typically focus on: baseline site conditions; ensuring that the design and equipment selection meet operating requirements; the satisfaction of permitting, pre-construction studies, discharge and other operating requirements; and the use of appropriate safeguards during construction.
Licenses, permits and approvals at operating sites are obtained in accordance with laws and regulations, which may limit or regulate: operating conditions, rates and efficiency; land, water and raw material use and management; product storage, quality and transportation; waste storage and disposal; and emissions and other discharges. Additional legal requirements may apply in circumstances where site contamination predates the current applicable regulatory framework or where there is otherwise evidence that remediation activities have not been successful in protecting the environment. These additional requirements may result in an environmental remediation liability that must be resolved.
Finally, the environmental protection requirements that may apply at the time of plant closure can be of two types: environmental remediation that did not come due or arise until operations ceased; or asset retirement obligations stipulated by contractual or constructive obligations or other legal requirements. Asset retirement obligations typically involve the removal of the asset, remediation of any contamination resulting from the use of that asset and reclamation of the land.
We record provisions under IFRS for environmental remediation and asset retirement. Provision amounts are provided in note 20 of the Notes to the Consolidated Financial Statements. If a matter does not meet the requirements for recognition as a provision under IFRS, it is classified as an environmental contingency.
| | |
PAGE 78 // MANAGEMENT’S DISCUSSION AND ANALYSIS // AGRIUM ANNUAL REPORT 2013 |
ENVIRONMENTAL CONTINGENCIES
We are responsible for environmental remediation of certain facilities and sites. Work at these sites is in various stages of environmental management; we are assessing and investigating some sites and remediating or monitoring others. New information, including changes in regulations or results of investigations by regulatory bodies, could lead to reassessment of our exposure related to these matters. In addition, we may revise our estimates of our future obligations because they are dependent on a number of uncertain factors, including the method and extent of the remediation and cost-sharing arrangements with other parties involved.
In assessing whether we would accrue a provision, at each reporting period we undertake a provision review process. Our process includes a review by in-house legal counsel in consultation with internal accounting, business unit and other technical staff to determine whether current information available to us supports our estimates of the financial effect of these matters and our related disclosures. Where appropriate, in-house legal counsel consults with external counsel as to its analysis and conclusions about the facts of each case, the status of litigation, and discussions and correspondence with third parties. We also review publicly available information for similar matters involving other companies. Our review includes previously assessed matters and an assessment as to whether any new matters require review.
Some remediation activities at our sites are subject to the U.S. Comprehensive Environmental Response, Compensation, and Liability Act (“CERCLA”), the U.S. Resource Conservation and Recovery Act (“RCRA”) and similar federal, state, provincial and local environmental laws. CERCLA provides for phases of remediation (investigation, risk assessment, remedy selection, remedial design and construction, maintenance and long-term monitoring, and closure) under regulatory oversight. Remediation activities at our sites are predominantly in the investigation phase.
For the matters described below, at the date of issuance of our 2013 Financial Statements, we determined that we could not make a reliable estimate of the amount and timing of any financial effect in excess of the amounts accrued for the ultimate resolution of these matters. Reasons for this determination include: complexity of the matters; early phases of most proceedings; lack of information on the nature and timing of future actions in the matters; dependency on the completion and findings of investigations and assessments; and the lack of specific information as to the nature, extent, timing and cost of future remediation. Until we have greater clarity as to our liability and the extent of our financial exposure, it is not practical to make a reliable estimate of the financial effect of these matters. As negotiations, discussions and assessments proceed, we may provide estimates. Events or factors that could alleviate our current inability to make reliable estimates for these matters include: further identification of allegations or demands; completion of remediation phases; a ruling by a court; or initiation of substantive settlement negotiations.
UNITED STATES ENVIRONMENTAL PROTECTION AGENCY PHOSPHATE INDUSTRY INITIATIVE
In 2003, the United States Environmental Protection Agency (“EPA”) began investigating the phosphate industry as part of its National Enforcement Initiative regarding the mineral processing industry. The purpose of the EPA’s National Enforcement Initiative is to ensure that waste resulting from mineral processing is managed in accordance with RCRA regulations. RCRA is the federal statute that governs the generation, transportation, treatment, storage and disposal of hazardous wastes. The EPA is also evaluating the industry’s compliance with certain U.S. Clean Air Act (“CAA”) programs, including Prevention of Significant Deterioration (“PSD”) and Maximum Achievable Control Technology (“MACT”), the U.S. Emergency Planning and Community Right to Know Act (“EPCRA”) and CERCLA.
In 2005, the EPA and the Idaho Department of Environmental Quality (“IDEQ”) commenced an investigation of the Conda facility to evaluate compliance with CAA, RCRA, CERCLA and relevant state law. The EPA notified Nu-West Industries, Inc. (“Nu-West”), a wholly-owned subsidiary of Agrium, of potential violations of RCRA, CAA, EPCRA and CERCLA at the Conda facility.
In 2007, the EPA issued a notice of violation (“NOV”) to Nu-West alleging certain violations of the CAA and MACT at phosphoric acid production facilities, primarily involving pollution control equipment as well as start-up, shut-down and malfunction procedures. Nu-West formally responded to the EPA allegations; however, the NOV remains open. The EPA has yet to identify any further allegations or demands.
In 2008, the EPA issued a NOV to Nu-West identifying certain alleged violations of RCRA, focusing principally on the government’s interpretation of the Bevill exemption, among other regulatory standards. Nu-West is cooperating with the government’s inquiry and is in active discussion to resolve the EPA’s allegations. Among other activities designed to assist in obtaining resolution of the EPA’s claims, in 2009, Nu-West entered into a voluntary consent order with the EPA to evaluate potential impacts on the environment from the Conda facility’s operations by means of an environmental assessment pursuant to section 3013 of RCRA. Nu-West is working cooperatively with the EPA and the IDEQ to negotiate work scopes to advance this assessment. In 2013, Nu-West continued to perform site assessment activities and we expect that the assessment will be substantially complete by 2014; however, final completion will be dependent on the results of the assessment.
| | |
AGRIUM ANNUAL REPORT 2013 // MANAGEMENT’S DISCUSSION AND ANALYSIS // PAGE 79 |
Nu-West, along with other industry members also being evaluated under the same National Enforcement Initiative, is involved in ongoing discussions with the EPA, the U.S. Department of Justice (“DOJ”) and various environmental agencies to resolve these matters. Although Agrium is uncertain as to how the matters will be resolved or if litigation will ensue, potential resolution of the government’s RCRA allegations may be by a settlement and may include requirements to pay certain penalties, which Agrium currently believes will not be material, modify certain operating practices and undertake certain capital improvement projects, and to provide financial assurance for the future closure, maintenance and monitoring costs for the phosphogypsum stack system at the Conda facility, as well as resolve the RCRA section 3013 voluntary consent order site investigation findings. Nu-West continued to negotiate the terms of settlement with the EPA and DOJ.
In 2008, the EPA further notified Nu-West that the government had commenced investigation of phosphate industry compliance with certain provisions of CERCLA and EPCRA. In March 2011, the EPA issued a NOV to Nu-West alleging violations of certain emissions reporting and related requirements under CERCLA and EPCRA. Nu-West has performed technical research in support of developing reporting protocols and had discussions with the EPA in response to these allegations. The EPA discussions with Nu-West and other industry members are ongoing.
LEGACY ENVIRONMENTAL REMEDIATION ACTIVITIES: IDAHO MINING PROPERTIES
Nu-West has performed, is performing, or in the future may perform site investigation and remediation activities at six closed phosphate mines and one mineral processing facility near Soda Springs, Idaho. These sites were mined and operated from as early as 1955 until as late as 1997. Selenium, a trace mineral essential for optimal human health, but which can be toxic at higher concentrations, was found to be leaching from reclaimed lands associated with historic phosphate mines owned, leased or operated by Nu-West or other parties. Nu-West, the U.S. government and other phosphate producers have been working diligently to identify the sources of selenium contamination, develop remedies for the closed mines and implement best practices to ensure selenium issues do not become a concern for current and new mining operations.
In 2009, Nu-West initiated a lawsuit against the U.S. government, which is the owner and lessor of four of the historic mine sites (the “Lawsuit”). The Lawsuit was brought under CERCLA to determine the U.S. government’s liability to pay for a material portion of the past and future investigation and remediation costs for those sites. In 2013, the U.S. government and Nu-West reached final settlement terms, whereby the U.S. government will: (a) pay 33 percent of past and future investigation and remediation costs; and (b) contribute, independent of its 33 percent share, all the funds remaining from the government’s recovery of approximately $16-million in a bankruptcy proceeding involving Washington Group International, a past responsible party at the historic mine sites, which remaining funds are estimated to be approximately $7-million. Nu-West has not accrued any amounts for potential recoveries from third parties. Since reaching this settlement with the U.S. government, Nu-West has executed subsequent agreements with federal and state environmental agencies under CERCLA establishing the scope of preliminary work to be conducted at the four historic mine sites. Nu-West commenced the preliminary scope of work in 2013, and it is expected to take one to three additional years to complete. Completion of the preliminary phase of work will enable Nu-West and the agencies to determine what, if any, further remediation work will be required.
LEGACY ENVIRONMENTAL REMEDIATION ACTIVITIES: MANITOBA MINING PROPERTIES
As part of the acquisition in 1996 of Viridian Inc. (“Viridian”), which is now a wholly-owned Canadian subsidiary of Agrium, we assumed certain liabilities associated with the Fox Mine Site, a closed mineral processing site near Lynn Lake, Manitoba. Viridian is currently treating water draining from the site in order to meet downstream water quality standards. Viridian has substantially completed the investigation phase of remediation and we are currently commencing remedial alternatives selection. We expect to receive approval of a remedial design within the next 36 months. For this matter, we have not disclosed information about the amount accrued for site remediation because disclosure of the information would seriously prejudice our position.
| | |
PAGE 80 // MANAGEMENT’S DISCUSSION AND ANALYSIS // AGRIUM ANNUAL REPORT 2013 |
CLIMATE CHANGE AND GREENHOUSE GAS ISSUES
Directly and indirectly, Agrium generates greenhouse gas (“GHG”) emissions through the production, distribution and use of its products. These emissions may be subject to climate change policy and regulations being developed in North America. However, these policies are developing in a unique way within the various state, provincial and federal jurisdictions.
In the province of Alberta, legislation has been enacted that applies to facilities emitting greater than 100,000 tonnes of CO2 equivalent (“CO2e”) per year. Existing facilities that exceed this threshold are required to decrease their emissions intensity by 12 percent relative to their 2003–2005 average baseline. If a company is unable to decrease its emissions intensity through increases in operational efficiency, it is still able to comply with the Alberta requirements by purchasing qualifying emission offsets from other sources in Alberta or by contributing to the Climate Change and Emissions Management Fund (“the Fund”). Historically, the contribution costs to the Fund have been set at $15 per tonne of CO2e.
Agrium has three facilities in Alberta with CO2e emissions in excess of 100,000 tonnes per year. Those facilities are Redwater Fertilizer Operations (total typical annual emissions of approximately 750,000 tonnes, excluding NH3-1 emissions, which can contribute up to approximately 420,000 tonnes of CO2e); Carseland Nitrogen Operations (total typical annual emissions of approximately 550,000 tonnes); and Fort Saskatchewan Nitrogen Operations (total typical annual emissions of approximately 550,000 tonnes), in each case depending on operating time, which is influenced by market demand and supply factors. The annual impact of this legislation on Agrium is expected to range from $1-million to $4-million a year going forward based on a valuation of $15 per tonne, depending on variations in production from year to year, which will directly impact CO2e emissions. These expected annual costs are lower than they otherwise could have been, due in part to Agrium’s implementation of various efficiency and emissions reduction projects. These projects include overall efforts to increase operational efficiency, the purchase of emission offset credits, as well as the operation of a cogeneration facility in partnership with TransCanada Energy Ltd. at Carseland that captures waste heat and produces emission offset credits. Agrium has also been involved in the development of the Nitrous Oxide Emissions Reduction Protocol (“NERP”), which is designed to generate credits for farmers who reduce their nitrous oxide (“N2O”) emissions. NERP was approved by Alberta Environment in October 2010. The implementation of NERP is expected to result in more effective farm application of nitrogen fertilizer, reduced GHG emissions at the farm level and the introduction of additional low-cost offsets to the market.
Agrium’s Canadian retail arm, Crop Production Services (Canada), has a branded service called Carbon Reduction Offset Credit for the aggregation of carbon offsets in accordance with established government regulatory protocols on GHG reduction.
Agrium will continue to take a leadership role in the fertilizer industry’s negotiations with governments on fair and equitable air emission reduction targets in an effort to achieve a pragmatic and realistic compliance system that preserves the global competitiveness of the industry. To that end, Agrium and the Canadian fertilizer industry are currently in discussions with the Government of Canada on the industry’s GHG reduction target to help meet Canada’s commitment pursuant to the Copenhagen Accord to reduce GHG emissions by 17 percent below 2005 levels by 2020. In an effort to reduce CO2e emissions, Agrium has also developed strategies to improve energy efficiency in our operations, capture and store carbon, reduce the amount of N2O emissions from our nitric acid facilities and reduce emissions in agriculture.
About 60 percent of the natural gas required to produce ammonia, the basic building block of all nitrogen fertilizer, is used to provide the necessary hydrogen for the process. Given current economically viable technologies, the CO2 emissions related to this process are fixed by the laws of chemistry and cannot be reduced. Use of the remaining natural gas may be managed through improvements in energy efficiency, which will reduce CO2 emissions. Significant early action has been implemented by the Company to achieve these improvements and the Fort Saskatchewan facility is currently being used as a demonstration project for implementing an additional energy efficiency program for our nitrogen operations. Independent government-sponsored studies estimate that a further 3 percent to 5 percent reduction in combustion emissions intensity may be theoretically attainable for the Canadian industry but will be a challenging and potentially cost prohibitive target.
Where feasible, Agrium is pursuing opportunities to capture CO2 from our nitrogen operations for enhanced oil recovery (“EOR”), industrial use or underground storage. At our Borger, Texas operation, approximately 315,000 tons of CO2 were captured in 2013 for EOR. In 2007, Agrium signed an agreement to capture CO2 emissions from our Redwater, Alberta facility for EOR, where we sell the CO2 to a third party who will manage the total project relating to the CO2 transmission and EOR. This project is scheduled to become operational in late 2015; in the prior year, the project had been planned to become operational in early 2015. The change to late 2015 was due to revised time frames issued by the builders of the Alberta Carbon Trunk Line.
Agrium also has installed N2O reduction technology at two of our three operating U.S. nitric acid plants and has plans to install N2O reduction technology at our third plant during 2015 or beyond, depending on reduction technology performance currently under evaluation.
| | |
AGRIUM ANNUAL REPORT 2013 // MANAGEMENT’S DISCUSSION AND ANALYSIS // PAGE 81 |
In addition to the stewardship initiatives at our manufacturing plants, Agrium and the fertilizer industry are also promoting efforts to reduce GHG emissions at the farm field level, where we are working with several groups to promote 4R nutrient stewardship (use of the right fertilizer source at the right time in the right rate and in the right place). Through this stewardship system, farmers are reducing field emissions of GHGs. Careful placement, timing, attention to rate and product selection (all tenets of the 4R system) can significantly reduce these common agricultural emissions.
Agrium estimates that the production stage of its operations accounts for roughly 95 percent of its overall emissions. In 2011, Agrium met its 2020 commitment to reduce North American GHG emissions intensity by 10 percent from 2005 levels. The GHG emissions intensity reduction target was met ahead of schedule, primarily through the closure of less carbon-efficient facilities and increased production at more carbon-efficient facilities. Agrium is currently considering an updated and more stringent GHG emissions intensity reduction target.
In the U.S., the EPA has recently enacted GHG emissions legislation that establishes a reporting program for emissions of CO2, methane and other GHGs, as well as a permitting program for large GHG emissions sources. While the U.S. Congress has considered various legislation to reduce or tax GHG emissions, to date it has not enacted any laws in that regard. However, if Congress undertakes comprehensive tax reform in the coming year, it is possible that such reform could include a carbon tax.
ACCOUNTING ESTIMATES
The 2013 and 2012 financial information presented and discussed in this MD&A is prepared in accordance with IFRS as issued by the IASB.
CRITICAL ACCOUNTING JUDGMENTS AND ESTIMATES
We prepare our financial statements in accordance with IFRS, which requires us to make judgments in applying accounting policies. Judgments that have the most significant effect on the amounts recognized in these financial statements are described in note 2 of the Notes to the Consolidated Financial Statements. We also make assumptions and critical estimates. Critical estimates are those which are most subject to uncertainty and have the most significant risk of resulting in a material adjustment to the carrying amounts of assets and liabilities within the next year. We base our assumptions and estimates on our historical experience, current trends and all available information that we believe is relevant at the time we prepare the financial statements. However, future events and their effects cannot be determined with certainty. Accordingly, as confirming events occur, actual results could ultimately differ from our assumptions and estimates. Such differences could be material.
Our significant accounting policies are discussed in note 28 of the Notes to the Consolidated Financial Statements. We believe that the following accounting estimates are the most critical in helping readers understand and evaluate our reported financial results. As well, they require our most difficult, subjective or complex judgments, resulting from the need to make estimates about the effects of matters that are inherently uncertain.
SIGNIFICANT JUDGMENTS
• | | Determination and group of cash generating units and impairment testing; |
• | | Deferred income tax assets. |
ASSUMPTIONS AND CRITICAL ESTIMATES
• | | Goodwill and intangible assets; |
• | | Business acquisitions – purchase price allocations. |
Refer to note 2 of the Notes to the Consolidated Financial Statements for further information on our significant judgments and assumptions and critical estimates.
ACCOUNTING STANDARDS AND POLICY CHANGES NOT YET IMPLEMENTED
Refer to note 28 of the Notes to the Consolidated Financial Statements for further information on our accounting standards and policy changes not yet implemented.
| | |
PAGE 82 // MANAGEMENT’S DISCUSSION AND ANALYSIS // AGRIUM ANNUAL REPORT 2013 |
ADDITIONAL IFRS AND NON-IFRS FINANCIAL MEASURES
Certain financial measures in this Annual Report are not prescribed by IFRS. We consider these financial measures discussed herein to provide useful information to both management and investors in measuring our financial performance and financial condition.
In general, an additional IFRS financial measure is a measure relevant to understanding a company’s financial performance that is not a minimum measure mandated by IFRS. A non-IFRS financial measure generally either excludes or includes amounts that are not excluded or included in the most directly comparable measure calculated and presented in accordance with IFRS. We consider the additional IFRS and non-IFRS financial measures discussed herein to provide useful information to both management and investors in measuring our financial performance and financial condition. Refer to the following tables for further discussion of how they are calculated and their usefulness to users including management. Non-IFRS financial measures are not recognized measures under IFRS and our method of calculation may not be directly comparable to that of other companies. These non-IFRS measures should not be considered as a substitute for, or superior to, measures of financial performance prepared in accordance with IFRS.
The following table outlines our additional IFRS financial measures, their definitions and how management assesses each measure. As the measures set out below are presented in our consolidated financial statements included in this Annual Report, they are classified as additional IFRS financial measures where they reflect consolidated Agrium, and are classified as non-IFRS financial measures where they do not reflect consolidated Agrium, including references to EBITDA when presented on an operating segment basis.
„ ADDITIONAL IFRS FINANCIAL MEASURES
| | | | |
Additional IFRS financial measures | | Definition | | Management’s assessment |
| | |
EBIT | | Earnings (loss) from continuing operations before finance costs and income taxes. | | EBIT provides a supplemental measure used by management to: (1) evaluate the effectiveness of our businesses; (2) evaluate our ability to service debt; and (3) determine resource allocations. We believe EBIT is useful to investors, securities analysts and management, as the measure allows for an evaluation of segment performance exclusive of capital structure and income taxes, both of which are not a direct result of the efficiency of each business and are generally accounted for and evaluated on a consolidated basis. |
| | |
Consolidated ROOCE (Consolidated return on operating capital employed) | | Last 12 months’ EBIT less income taxes at a tax rate of 27 percent (2012 – 28 percent) divided by rolling four quarter average operating capital employed. Operating capital employed includes non-cash working capital, property, plant and equipment, investments in associates and joint ventures, and other assets. | | Consolidated ROOCE provides a measure of our operating performance and the efficiency of our capital allocation process over the long term. We believe this metric is useful in measuring and maximizing shareholder value in a growing company. |
| | |
Consolidated ROCE (Consolidated return on capital employed) | | Last 12 months’ EBIT less income taxes at a tax rate of 27 percent (2012 – 28 percent) divided by rolling four quarter average capital employed. Capital employed includes operating capital employed, intangibles and goodwill. | | Refer to ROOCE. |
| | |
Interest coverage | | Last 12 months’ net earnings from continuing operations before finance costs, income taxes, depreciation and amortization divided by interest, which includes interest on long-term debt plus other interest. | | Multiple monitored by management as part of strategic capital management, as our revolving credit facilities require that we maintain specific interest coverage. We believe this metric is useful in assessing our ability to cover our net interest charge with our operating income. |
| | |
Net debt to net debt plus equity | | Net debt includes short-term debt and long-term debt, net of cash and cash equivalents. Equity consists of shareholders’ equity. | | Multiple monitored by management as part of strategic capital management. We believe this metric is useful to investors and other interested parties in assessing our growth capacity and future capital needs. |
| | |
AGRIUM ANNUAL REPORT 2013 // MANAGEMENT’S DISCUSSION AND ANALYSIS // PAGE 83 |
The following table outlines our non-IFRS financial measures, their definitions and usefulness, and how management assesses each measure.
„ NON-IFRS FINANCIAL MEASURES
| | | | |
Non-IFRS financial measures | | Definition | | Management’s assessment |
| | |
EBITDA | | Earnings (loss) from continuing operations before finance costs, income taxes, depreciation and amortization. | | Refer to EBIT. This measure is also used by investors and securities analysts as a valuation metric and as an alternative to cash flow from operations. |
| | |
Adjusted EBITDA | | Earnings (loss) from continuing operations before finance costs, income taxes, depreciation and amortization and before finance costs, income taxes, depreciation and amortization of joint ventures. | | Refer to EBIT and EBITDA. Management believes that this metric provides useful comparative information on our profitability, as Adjusted EBITDA adds back finance costs, income taxes, depreciation and amortization of joint ventures. |
| | |
EBITDA to sales | | EBITDA divided by sales. | | Metric is used to measure operating performance earnings and cash flow we generate from each dollar of sales. We believe this metric is useful in providing a basis to evaluate operating profitability that is comparable from period to period. |
| | |
Retail – North America and Retail measures: return on operating capital employed; return on capital employed; average non-cash working capital to sales; and operating coverage ratio. | | These measures when calculated using information from our Retail segment are considered non-IFRS financial measures as the specific Retail components are not separately presented in our consolidated financial statements or notes to the consolidated financial statements. See definitions of ROOCE and ROCE in the preceding Additional IFRS Financial Measures table. | | Metrics are used by management to evaluate our Retail business. We believe these metrics are also useful to investors and securities analysts in evaluating operating performance of our Retail business. |
| | |
Comparable store sales | | Represents the increase or decrease in current period Retail store sales compared to the prior period. We include a location in the comparable store base once it is in operation or owned for over 12 months. If we close a store, we retain the sales of the closed location in the comparable store base if the closed location is in close geographical proximity to an existing location, unless we plan to exit the market area or are unable to economically or logistically serve it. We do not make adjustments for temporary closures, expansions or renovations of stores. | | Metric is commonly used in the retail and distribution industry. We believe this metric is useful in highlighting the performance of our existing stores by measuring the change in sales for such stores for a period over the comparable period of equivalent length. |
| | |
Normalized comparable store sales | | Comparable store sales normalized by using published NPK benchmark prices and adjusting current year prices to reflect pricing from the previous year based on our percent of NPK utilization by product. | | Refer to comparable store sales. This metric removes fluctuations created by changes in commodity prices. |
| | |
Capital expenditures – sustaining | | Cost of replacements and betterments to our facilities. | | Used to evaluate capital spending on improving existing operations and capacity. |
| | |
Capital expenditures – investing | | Significant expansion of our existing operations. | | Used to evaluate capital spending on business expansion and development. |
| | |
PAGE 84 // MANAGEMENT’S DISCUSSION AND ANALYSIS // AGRIUM ANNUAL REPORT 2013 |
RECONCILIATIONS OF ADDITIONAL IFRS AND NON-IFRS FINANCIAL MEASURES
„ RETURN ON OPERATING CAPITAL EMPLOYED AND RETURN ON CAPITAL EMPLOYED
| | | | | | | | | | | | | | | | | | | | | | | | |
| | Rolling four quarters ended December 31, 2013 | | | Rolling four quarters ended December 31, 2012 | |
(millions of U.S. dollars, except as noted) | | Retail – North America | | | Retail | | | Consolidated Agrium | | | Retail – North America | | | Retail | | | Consolidated Agrium | |
EBIT less income taxes | | | | | | | | | | | | | | | | | | | | | | | | |
EBIT | | | 940 | | | | 748 | | | | 1,630 | | | | 719 | | | | 757 | | | | 2,216 | |
Income taxes at a tax rate of 27 percent (2012 – 28 percent) | | | 254 | | | | 202 | | | | 440 | | | | 201 | | | | 212 | | | | 620 | |
| | | 686 | | | | 546 | | | | 1,190 | | | | 518 | | | | 545 | | | | 1,596 | |
Average operating capital employed | | | | | | | | | | | | | | | | | | | | | | | | |
Average non-cash working capital | | | 1,715 | | | | 2,337 | | | | 2,698 | | | | 1,642 | | | | 2,276 | | | | 2,539 | |
Average property, plant and equipment | | | 726 | | | | 852 | | | | 4,244 | | | | 593 | | | | 708 | | | | 3,029 | |
Average investments in associates and joint ventures | | | 33 | | | | 79 | | | | 631 | | | | 17 | | | | 81 | | | | 601 | |
Average other assets | | | 5 | | | | 15 | | | | 104 | | | | 5 | | | | 19 | | | | 44 | |
| | | 2,479 | | | | 3,283 | | | | 7,677 | | | | 2,257 | | | | 3,084 | | | | 6,213 | |
Return on operating capital employed (ROOCE)(%) | | | 28 | % | | | 17 | % | | | 15 | % | | | 23 | % | | | 18 | % | | | 26 | % |
Average capital employed | | | | | | | | | | | | | | | | | | | | | | | | |
Average operating capital employed | | | 2,479 | | | | 3,283 | | | | 7,677 | | | | 2,257 | | | | 3,084 | | | | 6,213 | |
Average intangibles | | | 547 | | | | 622 | | | | 660 | | | | 499 | | | | 593 | | | | 650 | |
Average goodwill | | | 1,791 | | | | 2,125 | | | | 2,206 | | | | 1,790 | | | | 2,209 | | | | 2,305 | |
| | | 4,817 | | | | 6,030 | | | | 10,543 | | | | 4,546 | | | | 5,886 | | | | 9,168 | |
Return on capital employed (ROCE)(%) | | | 14 | % | | | 9 | % | | | 11 | % | | | 11 | % | | | 9 | % | | | 17 | % |
„ ADJUSTED EBITDA AND EBITDA TO EBIT
| | | | | | | | | | | | | | | | | | | | |
(millions of U.S. dollars) | | Retail | | | Wholesale | | | Advanced Technologies | | | Other | | | Consolidated | |
2013 | | | | | | | | | | | | | | | | | | | | |
Adjusted EBITDA | | | 986 | | | | 1,286 | | | | 30 | | | | (146 | ) | | | 2,156 | |
Equity accounted joint ventures: | | | | | | | | | | | | | | | | | | | | |
Finance costs and income taxes | | | — | | | | 40 | | | | — | | | | — | | | | 40 | |
Depreciation and amortization | | | — | | | | 14 | | | | — | | | | — | | | | 14 | |
EBITDA | | | 986 | | | | 1,232 | | | | 30 | | | | (146 | ) | | | 2,102 | |
Depreciation and amortization | | | 238 | | | | 201 | | | | 16 | | | | 17 | | | | 472 | |
EBIT | | | 748 | | | | 1,031 | | | | 14 | | | | (163 | ) | | | 1,630 | |
2012 | | | | | | | | | | | | | | | | | | | | |
Adjusted EBITDA | | | 951 | | | | 1,940 | | | | 58 | | | | (263 | ) | | | 2,686 | |
Equity accounted joint ventures: | | | | | | | | | | | | | | | | | | | | |
Finance costs and income taxes | | | — | | | | 41 | | | | — | | | | — | | | | 41 | |
Depreciation and amortization | | | — | | | | 16 | | | | — | | | | — | | | | 16 | |
EBITDA | | | 951 | | | | 1,883 | | | | 58 | | | | (263 | ) | | | 2,629 | |
Depreciation and amortization | | | 194 | | | | 190 | | | | 13 | | | | 16 | | | | 413 | |
EBIT | | | 757 | | | | 1,693 | | | | 45 | | | | (279 | ) | | | 2,216 | |
„ RETAIL COMPARABLE STORE SALES AND RETAIL NORMALIZED COMPARABLE STORE SALES
| | | | | | | | |
| | Twelve months ended December 31, | |
(millions of U.S. dollars, except as noted) | | 2013 | | | 2012 | |
Retail sales from the current period comparable store base | | | 11,234 | | | | 11,182 | |
Prior year Retail sales | | | 11,479 | | | | 10,316 | |
Comparable store sales (%) | | | (2.1 | %) | | | 8.4 | % |
Current year sales normalized for NPK benchmark prices | | | 12,000 | | | | 11,147 | |
Normalized comparable store sales (%) | | | 4.5 | % | | | 8.1 | % |
| | |
AGRIUM ANNUAL REPORT 2013 // MANAGEMENT’S DISCUSSION AND ANALYSIS // PAGE 85 |
2013 FOURTH QUARTER MANAGEMENT’S DISCUSSION AND ANALYSIS
NET EARNINGS
Agrium’s 2013 fourth quarter net earnings from continuing operations were $110-million, or $0.74 diluted earnings per share from continuing operations, compared to net earnings from continuing operations of $358-million, or $2.36 diluted earnings per share from continuing operations, for the same quarter of 2012.
„ FINANCIAL OVERVIEW
| | | | | | | | | | | | | | | | |
| | Three months ended December 31, | |
(millions of U.S. dollars, except per share amounts and where noted) | | 2013 | | | 2012 | | | Change | | | % Change | |
Sales | | | 2,867 | | | | 3,093 | | | | (226 | ) | | | (7 | ) |
Gross profit | | | 740 | | | | 974 | | | | (234 | ) | | | (24 | ) |
Expenses | | | 557 | | | | 445 | | | | 112 | | | | 25 | |
Earnings from continuing operations before finance costs and income taxes | | | 183 | | | | 529 | | | | (346 | ) | | | (65 | ) |
Net earnings from continuing operations | | | 110 | | | | 358 | | | | (248 | ) | | | (69 | ) |
Net loss from discontinued operations | | | (11 | ) | | | (4 | ) | | | (7 | ) | | | 175 | |
Net earnings | | | 99 | | | | 354 | | | | (255 | ) | | | (72 | ) |
Diluted earnings per share from continuing operations | | | 0.74 | | | | 2.36 | | | | (1.62 | ) | | | (69 | ) |
Diluted loss per share from discontinued operations | | | (0.08 | ) | | | (0.02 | ) | | | (0.06 | ) | | | 300 | |
Diluted earnings per share | | | 0.66 | | | | 2.34 | | | | (1.68 | ) | | | (72 | ) |
Effective tax rate (%) | | | 24 | | | | 27 | | | | N/A | | | | (3 | ) |
SALES
Sales decreased by $226-million to $2.9-billion for the fourth quarter of 2013. Factors that affected our performance during the fourth quarter of 2013 compared to the fourth quarter of 2012 include the following:
• | | Wholesale sales decreased by 24 percent to $963-million due to lower realized sales prices across all product lines and lower nitrogen volumes; and |
• | | Retail sales increased by 6 percent to $2.1-billion largely due to Viterra which accounted for $276-million in sales during the current quarter. Crop nutrient sales decreased as colder weather impacted North American sales. |
GROSS PROFIT
Our gross profit for the fourth quarter of 2013 was $740-million, a decrease of $234-million compared to the fourth quarter of 2012. The main drivers of this variance consisted of:
• | | Wholesale’s gross profit decreased by $283-million to $170-million for the fourth quarter of 2013, compared to the fourth quarter of 2012 primarily as a result of weaker realized sales prices across all product lines and lower urea sales volumes due to outages at our Redwater and Carseland nitrogen facilities; and |
• | | Retail’s gross profit increased by $77-million to $586-million for the fourth quarter of 2013, compared to the fourth quarter of 2012 due to the inclusion of results from Viterra coupled with favorable nutrient cost positions and higher seed rebates from suppliers. |
EXPENSES
Expenses increased by $112-million for the fourth quarter of 2013 compared to the fourth quarter of 2012. This difference is primarily a result of the following items:
• | | A $220-million goodwill impairment was recorded in Retail – Australia as a result of reduced expectations for sales, gross margins and long-term growth in Retail – Australia; |
• | | An increase in Retail selling expenses of $73-million driven by increased costs associated with Viterra and other recent acquisitions (see the section “Retail” on page 87 for further discussion); and |
• | | A $46-million unfavorable change in share-based payments, with a $28-million share-based payments expense in the current quarter compared to an $18-million share-based payments recovery in the same period last year (see the section “Other” on page 89 for further discussion). |
The above increases were partially offset by a $257-million purchase gain reported in the fourth quarter of 2013. This represents the difference between the fair value of acquired net assets and the purchase price.
| | |
PAGE 86 // MANAGEMENT’S DISCUSSION AND ANALYSIS // AGRIUM ANNUAL REPORT 2013 |
The following table is a summary of our other expenses (income) for the fourth quarters of 2013 and 2012, respectively.
„ OTHER EXPENSES BREAKDOWN
| | | | | | | | |
| | Three months ended December 31, | |
(millions of U.S. dollars) | | 2013 | | | 2012 | |
Realized loss (gain) on derivative financial instruments | | | 1 | | | | (2 | ) |
Unrealized gain on derivative financial instruments | | | (1 | ) | | | — | |
Interest income | | | (25 | ) | | | (26 | ) |
Foreign exchange loss | | | 16 | | | | 9 | |
Environmental remediation and asset retirement obligations | | | 2 | | | | 2 | |
Bad debt recovery | | | (11 | ) | | | (8 | ) |
Potash profit and capital tax | | | 6 | | | | 3 | |
Other | | | 8 | | | | 2 | |
| | | (4 | ) | | | (20 | ) |
EFFECTIVE TAX RATE
The effective tax rate on continuing operations was 24 percent for the fourth quarter compared to 27 percent for the same period last year due to permanent differences between tax and accounting on the Viterra purchase gain and the Retail – Australia goodwill impairment.
BUSINESS SEGMENT PERFORMANCE
RETAIL
Retail reported record fourth quarter sales of $2.1-billion up from $2.0-billion reported in the same quarter last year. Gross profit was $586-million in the fourth quarter of 2013, a 15 percent increase from last year’s fourth quarter of $509-million. Retail reported EBITDA of $195-million, up $71-million from the fourth quarter of last year. Included in this quarter’s results is a $257-million purchase gain for the Viterra acquisition, a $220-million goodwill impairment for the Landmark business in Australia, and results from the recently acquired Viterra business (fourth quarter EBITDA loss of $12-million), which included $8-million of integration costs. Excluding these items, EBITDA would have been $166-million, the highest fourth quarter Retail EBITDA in our history. These excellent results were achieved due to increased margins for nutrients, seed and services and other product lines, which more than offset the headwinds of lower crop nutrient sales volumes (excluding Viterra volumes), lower nutrient prices and the compressed fall application season. On a full year basis, and excluding the items listed above for the fourth quarter, EBITDA reached $957-million in 2013, surpassing last year’s record $951-million.
Total crop nutrient sales were $1.1-billion this quarter, on par with the fourth quarter of 2012. Incremental sales from Viterra were offset by lower nutrient sales volumes in the U.S. in the fourth quarter, due to the shortened fall application season. Gross profit for crop nutrients was $178-million this quarter, an increase of $23-million compared to the $155-million reported in the fourth quarter of 2012. Excluding the Viterra results in the current quarter, gross profit increased by $4-million in 2013. Total crop nutrient margins as a percentage of sales were 17 percent in the fourth quarter of 2013, higher than the 14 percent reported in the same quarter last year. Although nutrient prices declined during the second half of 2013, increased prescription blend and proprietary nutrient sales resulted in higher dollar per tonne margins than 2012.
Crop protection sales were $511-million in the fourth quarter of 2013, compared to $491-million in sales in the same period last year. The increase was driven primarily by incremental sales from Viterra and higher sales of glyphosates in the quarter. Gross profit was $205-million this quarter, compared to $203-million reported in the fourth quarter of 2012. Crop protection margins as a percentage of sales were 40 percent this quarter. The 1 percent decline in margins in the fourth quarter of 2013 relative to the same period last year was due to a higher product mix of wholesale volumes, which traditionally represent lower margins than retail sales.
Seed sales were $95-million in the fourth quarter of 2013, down from the $105-million reported in the fourth quarter of last year. The reduction in North American seed sales was due to the late fall season, which particularly impacted wheat seed sales. Gross profit was $60-million this quarter, up from the $43-million reported last year. Seed margins as a percentage of sales were 63 percent in the fourth quarter of 2013, significantly higher than the 41 percent reported in the fourth quarter of 2012. The increase in gross profit and margins in the fourth quarter of 2013 is related to higher annual seed volume, which resulted in higher rebates for seed from suppliers this quarter. The continued sales growth in our proprietary Dyna-Gro branded seed versus national brand sales mix also supported higher average seed margins both in the quarter and on an annual basis. Our proprietary product line of seeds once again demonstrated solid growth in sales and gross profit for both the fourth quarter and the 2013 year, relative to the same periods last year. Proprietary seed accounted for approximately 18 percent of our total seed sales and approximately 26 percent of our seed gross profit for calendar year 2013.
| | |
AGRIUM ANNUAL REPORT 2013 // MANAGEMENT’S DISCUSSION AND ANALYSIS // PAGE 87 |
Sales of merchandise in the fourth quarter of 2013 were $228-million, compared to $132-million in the same period last year. Gross profit for this product line was $30-million this quarter, compared to $21-million reported in the fourth quarter of 2012. The increase is related to incremental earnings from Viterra and additional sales volumes of animal health and other livestock-related products in Australia.
Services and other sales were $216-million this quarter, compared to the $151-million reported in the fourth quarter of 2012. Gross profit was $113-million in the fourth quarter of 2013, compared to $87-million for the same period last year. The increases in the current quarter relate to incremental gross profit from the purchased Viterra locations and increased Australian livestock sales commissions.
Selling expenses as a percentage of sales was 24 percent in the fourth quarter of 2013 which is up marginally from the 22 percent reported in the same period last year. Retail selling expenses were $504-million for the fourth quarter, compared to $431-million in the same period last year. The majority of the variance was due to increased costs associated with Viterra operating in a traditionally slower sales period than other Retail geographies. On a full-year basis, selling expenses as a percentage of sales remained similar to 2012 at approximately 15 percent.
In the fourth quarter of 2013, we recorded the Viterra acquisition within Retail. This resulted in a $257-million purchase gain, representing the difference between the fair value of acquired net assets and the purchase price. During the quarter, we also recorded goodwill impairment in Retail – Australia of $220-million due to synergy delays and reduced expectations for sales, gross margins and long-term growth.
WHOLESALE
Wholesale’s 2013 fourth quarter sales were $963-million, down $310-million from the same quarter last year. Gross profit was $170-million this quarter, compared to $453-million in the fourth quarter of 2012. Wholesale reported EBITDA of $210-million in the fourth quarter of 2013, down from the $495-million reported in the same period last year. Wholesale’s Adjusted EBITDA was $234-million this quarter, compared to $516-million reported in the same period last year. Wholesale’s results this quarter were principally impacted by significantly lower global crop nutrient prices.
Nitrogen gross profit in the fourth quarter of 2013 was $129-million, compared to $293-million in the same quarter last year. Nitrogen sales volumes were 907,000 tonnes in the fourth quarter of 2013, down 59,000 tonnes from the same period last year. The lower sales volumes were primarily due to reduced product availability resulting from plant outages in the fourth quarter, accompanied by a shorter fall application season in the U.S. Realized sales prices for all nitrogen products were lower than the fourth quarter of 2012, with urea realized sales prices down 27 percent, or $148 per tonne year-over-year. Nitrogen cost of product sold was $314 per tonne this quarter, compared to $257 per tonne reported in the fourth quarter of 2012. The increase was due to higher North American gas prices and costs associated with outages at our Carseland and Redwater nitrogen facilities in the quarter. These outages lowered production by approximately 130,000 tonnes of nitrogen products and impacted per tonne costs, as fixed costs were spread across lower sales volumes. Our average nitrogen gross margins were $144 per tonne this quarter, compared to $304 per tonne in the same period last year.
Agrium’s average natural gas cost included in cost of product sold was $3.51/MMBtu this quarter ($3.39/MMBtu including the impact of realized gains on natural gas derivatives), compared to $3.26/ MMBtu for the same period in 2012 ($3.35/MMBtu including the impact of realized losses on natural gas derivatives). Hedging gains or losses are included in other expenses and not cost of product sold, thus are not part of the calculation of gross profit. The U.S. benchmark (NYMEX) natural gas price for the fourth quarter of 2013 was $3.63/MMBtu, compared to $3.36/MMBtu in the same quarter last year. The AECO (Alberta) basis differential was a $0.62/MMBtu discount to NYMEX in the fourth quarter of 2013, an increase from the $0.28/MMBtu discount in the fourth quarter of 2012.
Potash gross profit for the fourth quarter of 2013 was $39-million, compared to $79-million reported in the same quarter last year. The year-over-year decline was principally due to lower realized international and North American sales prices. Prices came under pressure due to weaker demand from India, delayed negotiations for second half Chinese supply contracts and uncertainty created by the breakup of BPC. International sales volumes were 89,000 tonnes this quarter, in line with 86,000 tonnes reported in the fourth quarter of last year. North American sales volumes this quarter were 255,000 tonnes, also consistent with the volumes achieved for the same period last year. Potash cost of product sold was $201 per tonne this quarter, compared to $216 per tonne reported in the fourth quarter of 2012. The decrease was due to a higher proportion of sales shipped directly to end customers compared to last year, which lowered the average freight cost. Gross margin was $112 per tonne in the fourth quarter of 2013, compared to the $233 per tonne in the same quarter of 2012. In the second half of 2014, Agrium will take an extended 14 week turnaround at our Vanscoy potash mine to tie in the one million tonne expansion project.
| | |
PAGE 88 // MANAGEMENT’S DISCUSSION AND ANALYSIS // AGRIUM ANNUAL REPORT 2013 |
Phosphate gross profit was a loss of $4-million in the fourth quarter of 2013, compared to a $47-million profit in the same quarter last year. The decrease was primarily a result of lower realized sales prices derived from weak international market conditions in the fourth quarter. Phosphate sales volumes this quarter were 285,000 tonnes, slightly higher than the 279,000 tonnes sold in the fourth quarter of 2012. Realized phosphate sales prices were $560 per tonne this quarter, a $162 per tonne decrease from the same quarter last year. Phosphate cost of product sold was $576 per tonne in the fourth quarter of 2013, a $20 per tonne increase from the same period last year. The increase was due to higher costs at both of our phosphate facilities, partially due to higher ammonia costs resulting from higher natural gas costs. The increase in costs at the Redwater facility was largely due to higher rock input costs associated with the transition to imported rock, after economic reserves of this input from our Kapuskasing, Ontario mine were depleted in the second quarter of 2013. Gross margin was a loss of $16 per tonne in the fourth quarter of 2013, compared to a positive margin of $166 per tonne in the same period in 2012.
Gross profit from ammonium sulfate and other products was $12-million this quarter, a reduction of $14-million from the same period last year. This was due to lower realized sales prices and lower customer sales resulting from limited customer storage available this quarter. Product purchased for resale gross margin was a loss of $6-million this quarter, compared to a profit of $8-million in the fourth quarter of 2012 as a result of lower North American demand and lower global sales prices for nutrients.
ADVANCED TECHNOLOGIES
After conducting a strategic review of AAT in 2013, a decision was made in December 2013 to transition the Agriculture business of AAT back into our Wholesale business unit. The Agriculture business includes ESN and Micronutrient products. Management has commenced with a divestment process of the Turf and Ornamental and Direct Solutions businesses. These businesses have been reported within discontinued operations. As a result, in 2013 we moved to two core strategic business units, Retail and Wholesale. The results reported for AAT represent only the Agriculture business that will be reported within Wholesale in the 2014 results; consequently these results are not directly comparable to prior years.
AAT reported a quarterly gross profit of $2-million in the fourth quarter of 2013, a decrease of $21-million from the $23-million reported in the same period last year. EBITDA was $3-million in the fourth quarter, a $15-million decrease from the same period last year. The lower year-over-year results were primarily due to lower than forecasted sales resulting from the later than expected fall application window and weak urea markets that impacted ESN margins.
OTHER
EBITDA for our Other non-operating business unit for the fourth quarter of 2013 was a loss of $94-million, compared to a loss of $2-million for the fourth quarter of 2012. The unfavorable change was primarily driven by:
• | | A $46-million unfavorable change in share-based payments, where there was a $28-million expense in the fourth quarter of 2013 compared to an $18-million recovery in the fourth quarter of 2012. This was largely caused by an appreciation of our share price during the fourth quarter of 2013 compared to a depreciation of our share price during the fourth quarter of 2012; |
• | | A $7-million increase in gross profit elimination for the three months ended December 31, 2013 compared to the three months ended December 31, 2012 which reflected more inter-segment inventory held in our Retail business unit not yet sold to external customers; |
• | | A $6-million unfavorable change on foreign exchange losses; and |
• | | $6-million in Viterra acquisition costs. |
BUSINESS ACQUISITIONS
See the discussion in the section “Business Acquisitions” on page 73 for further information on the Viterra acquisition.
DISCONTINUED OPERATIONS
Refer to the section “Discontinued Operations” on page 68 for further discussion on our discontinued operations during the fourth quarter.
| | |
AGRIUM ANNUAL REPORT 2013 // MANAGEMENT’S DISCUSSION AND ANALYSIS // PAGE 89 |
ADDITIONAL IFRS AND NON-IFRS FINANCIAL MEASURES
See the section “Additional IFRS and Non-IFRS Financial Measures” on page 83 for further details on our additional IFRS and non-IFRS financial measures.
The following table is a reconciliation of our fourth quarter Adjusted EBITDA and EBITDA to EBIT as determined in accordance with IFRS.
„ RECONCILIATION OF FOURTH QUARTER ADJUSTED EBITDA AND EBITDA TO EBIT
| | | | | | | | | | | | | | | | | | | | | | | | | | | | | | | | | | | | | | | | |
| | Three months ended December 31, 2013 | | | Three months ended December 31, 2012 | |
(millions of U.S. dollars) | | Retail | | | Wholesale | | | AAT | | | Other | | | Consolidated | | | Retail | | | Wholesale | | | AAT | | | Other | | | Consolidated | |
Adjusted EBITDA | | | 195 | | | | 234 | | | | 3 | | | | (94 | ) | | | 338 | | | | 124 | | | | 516 | | | | 18 | | | | (2 | ) | | | 656 | |
Equity accounted joint ventures: | | | | | | | | | | | | | | | | | | | | | | | | | | | | | | | | | | | | | | | | |
Finance costs and income taxes | | | — | | | | 19 | | | | — | | | | — | | | | 19 | | | | — | | | | 17 | | | | — | | | | — | | | | 17 | |
Depreciation and amortization | | | — | | | | 5 | | | | — | | | | — | | | | 5 | | | | — | �� | | | 4 | | | | — | | | | — | | | | 4 | |
EBITDA | | | 195 | | | | 210 | | | | 3 | | | | (94 | ) | | | 314 | | | | 124 | | | | 495 | | | | 18 | | | | (2 | ) | | | 635 | |
Depreciation and amortization | | | 72 | | | | 50 | | | | 4 | | | | 5 | | | | 131 | | | | 49 | | | | 48 | | | | 3 | | | | 6 | | | | 106 | |
EBIT | | | 123 | | | | 160 | | | | (1 | ) | | | (99 | ) | | | 183 | | | | 75 | | | | 447 | | | | 15 | | | | (8 | ) | | | 529 | |
KEY ASSUMPTIONS AND RISKS IN RESPECT OF FORWARD-LOOKING STATEMENTS
All of the forward-looking statements contained in this MD&A are qualified by the cautionary statements contained herein and by stated or inherent assumptions and apply only as of the date of this MD&A. Except as required by law, Agrium disclaims any intention or obligation to update or revise any forward-looking statements as a result of new information or future events.
The following table outlines certain significant forward-looking statements contained in this MD&A and provides the material assumptions used to develop such forward-looking statements and material risk factors that could cause actual results to differ materially from the forward-looking statements.
| | | | | | | | |
Forward-looking statements | | Material assumptions | | Material risk factors |
Remaining portion of AUD$40-million of synergies to be achieved on the Landmark acquisition (a) | | • | | Agrium’s ability to successfully integrate the business of Landmark as planned within expected time frames and costs. | | • | | Agrium’s ability to achieve enhanced purchasing efficiencies, expansion of product offerings and reduction in overhead expenses. These could be affected by industry factors impacting Agrium’s and Landmark’s businesses generally, and the demand from growers for crop inputs and related products. |
| | | | |
Incremental EBITDA of $75-million to $95-million and synergies of $15-million to $20-million to be achieved upon the Viterra acquisition by the end of 2015 (b) | | • | | Agrium’s ability to successfully integrate the retail Agri-products assets as planned within expected time frames and costs. | | • | | Agrium’s ability to achieve enhanced purchasing efficiencies, expansion of product offerings and reduction in overhead expenses. These could be affected by industry factors impacting Agrium’s business generally, and the demand from growers for crop inputs and related products. |
| | | | |
| | | | | | • | | Agrium’s ability to integrate the acquired retail Agri-products assets, including its ability to achieve efficiencies as planned. |
| | | | |
Retail’s EBITDA to reach $1.3-billion by 2015 (c) | | • | | Retail business conditions are assumed to be within normal parameters with respect to prices, margins, product availability and supplier agreements for our major products. | | • | | Agrium’s ability to integrate acquisitions, including its ability to achieve efficiencies as planned. |
| | | | |
| | • | | Agrium’s ability to identify suitable candidates for acquisitions and to negotiate acceptable terms. | | | | |
| | | | |
| | • | | Agrium’s ability to implement its standards, controls, procedures and policies at the acquired businesses to realize the expected synergies. | | | | |
| | |
PAGE 90 // MANAGEMENT’S DISCUSSION AND ANALYSIS // AGRIUM ANNUAL REPORT 2013 |
| | | | | | | | |
Forward-looking statements | | Material assumptions | | Material risk factors |
Return of 25 percent to 35 percent of free cash flow to Agrium’s shareholders through dividends (d) | | • | | Agrium’s ability, among other matters, to achieve its performance targets, complete proposed projects on time and on budget and maintain its investment grade rating. | | • | | Agrium’s ability to generate free cash flows as planned. |
| | |
2014 capital spending program (e) | | • | | We believe we will have sufficient financial resources to fund our expected capital spending program. |
| | |
| | • | | The level of sustaining and investing capital may vary significantly depending on corporate priorities as the year progresses and based on changes in the rate of inflation or engineering costs. |
| | | | |
Construction of MOPCO’s additional urea trains, including estimated capacity increase | | • | | Recommencement of the construction of two new plants in 2014. | | • | | Further delay in the construction, completion and commissioning of the project due to civil unrest in Egypt. |
| | | | |
Brownfield expansion at our Vanscoy, Saskatchewan potash mine, including estimated capacity increase and capital costs associated with the project, to be completed in the second half of 2014 | | • | | The expansion construction will be completed on schedule as planned and on budget, as revised. | | • | | Labor shortages and/or inefficiency causing schedule delays and/or cost increases. |
| | | | | • | | There can be no assurance that anticipated contributions of additional potash capacity will be realized. |
| | |
Completion of Profertil debottleneck project by 2014, including estimated capacity increase and reduction in production costs. To be completed in the third quarter of 2014 | | • | | Project will be completed on schedule as planned and on budget. This could be affected by escalation in costs and labor shortages causing schedule delays and/or cost increases. |
| | | | |
Potential brownfield opportunity at the Borger facility, including estimated completion date | | • | | Necessary permits, utilities and project approvals are secured on time. | | • | | Labor shortages and/or inefficiency causing schedule delays and/or cost increases. |
| • | | EPC resources and shop space is available to meet the project’s fast-track approach. | | • | | There can be no assurance that anticipated contributions of additional urea capacity will be realized. |
| | | | |
Ability to finance announced projects | | • | | We will be able to utilize our available credit facilities or access capital markets for additional sources of financing. | | • | | Potential inability to access or utilize our credit facilities or access capital markets. |
| | | | |
Ability to sustain projected potash production with existing reserves and resources | | • | | Potash reserves are accessible and of sufficient quality to provide the required ore for long-term production. | | • | | Flooding and/or poor ground conditions limiting access to major sections of the ore body or resulting in poor ore quality. |
| | | | |
Carbon capture and storage project progressing as planned | | • | | Start-up in late 2015. | | • | | Carbon capture and storage funding not received from Alberta government. |
| | | | |
| | | | | | • | | Upgrader projects (specifically the NorthWest Upgrader) cancelled or delayed. |
| | | | |
| | | | | | • | | Issues with engineering/procurement or construction of the facility or pipeline. |
(a) | The purpose of this particular financial outlook is to communicate our current expectation of the impact that the Landmark acquisition may have on future results of operations. Readers are cautioned that it may not be appropriate for other purposes. |
(b) | The purpose of this particular financial outlook is to communicate our current expectation of the impact that the Viterra acquisition may have on future results of operations. Readers are cautioned that it may not be appropriate for other purposes. |
(c) | The purpose of this particular financial outlook is to assist readers in understanding our expected financial results. Readers are cautioned that it may not be appropriate for other purposes. |
(d) | The purpose of this particular financial outlook is to assist readers in assessing our liquidity and capital resources. Readers are cautioned that it may not be appropriate for other purposes. |
(e) | The purpose of this particular financial outlook is to assist readers in assessing our liquidity and capital resources. Readers are cautioned that it may not be appropriate for other purposes. |
| | |
AGRIUM ANNUAL REPORT 2013 // MANAGEMENT’S DISCUSSION AND ANALYSIS // PAGE 91 |